FORKLIFTGUIDE®ISTER
LIFTING AFRICA’S
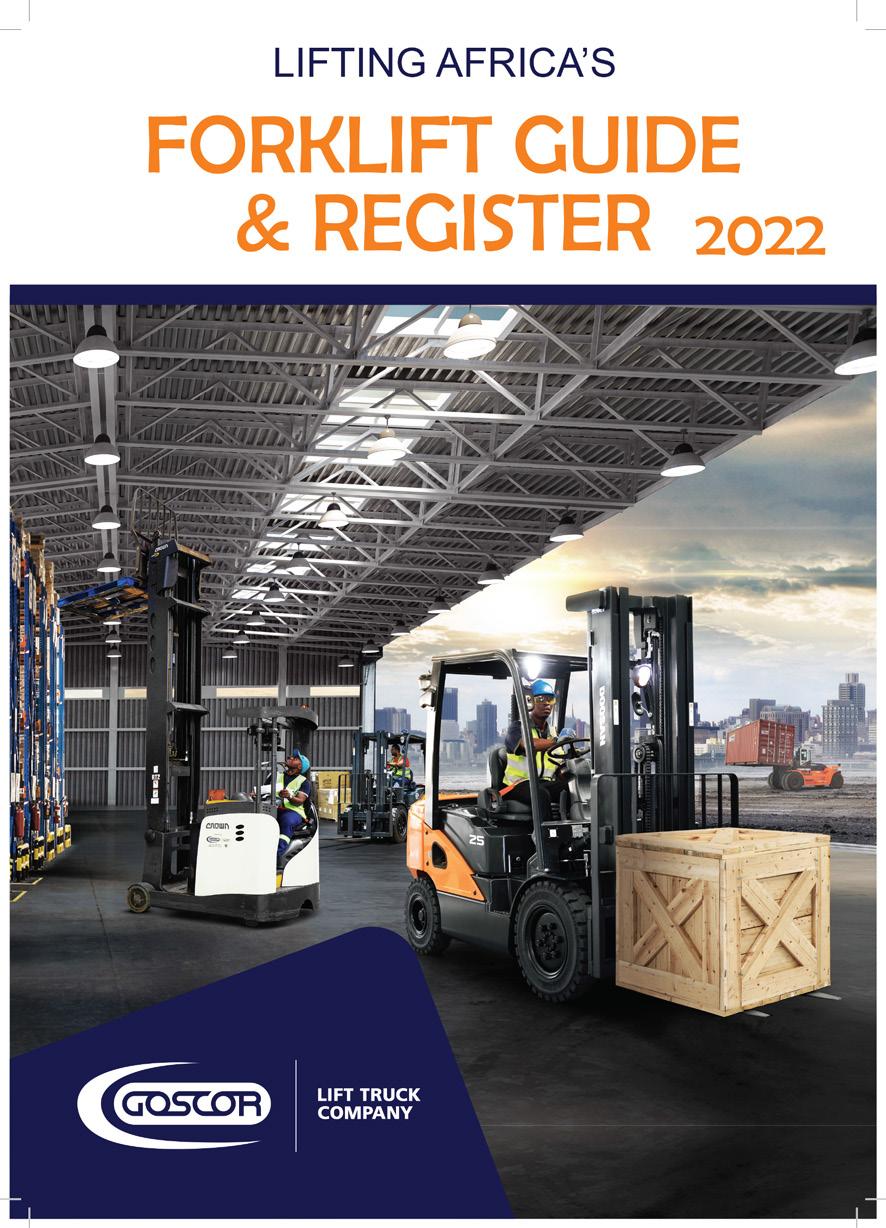

Lifting Africa - Forklift Guide & Register 3 Copyright © 2022 Lifting Africa All rights reserved No part of this publication may be reproduced or transmitted in any form or by any means, electronic or mechanical, including photocopying, recording or by any information storage and retrieval system, without permission in writing from the publisher.
Cell: +27 83 281 5761
Web: LEEASAwww.liftingafrica.co.zawww.leeasa.co.za,admin@leeasa.co.za
RACKINGMaintenance GUIDE The Do’s and Don’ts of Racking 10 Shelving safety tips to keep your warehouse FORKLIFTcompliantg REGISTER Pre-OperationalINTRODUCTION Check List 6 Monthly Inspection List Annual Performance Test Results Deviation Detected And Corrective Actions
The cost-benefit of the gas forklift
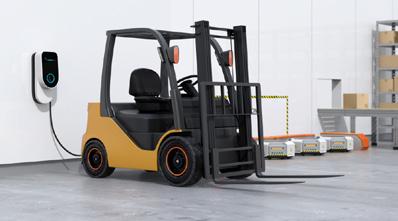
How to get your forklift license
Email: surita@liftingafrica.co.za
Maintenance contract benefits
GLTC – your total material solutions provider
Types of forklifts
FORKLIFT GUIDE
LIFTING
Inspections and Load testing
Managing editor: Surita Marx
Basic forklift hand signals
Should you buy r rent a forklift
AFRICA
Do’s and Don’ts on a forklift
When to repair or replace your forklift
Occupational Health And Safety Act, 1993 Driven Machinery Regulations, 2015 Operating a forklift safely Warehouse safety tips
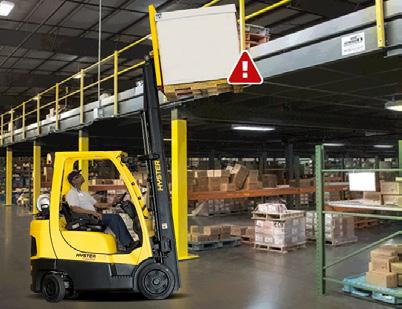
Why do forklifts weigh so much?
How to test battery capacity
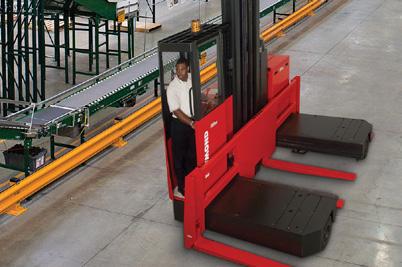
GLTC – your total material solutions provider
Goscor Lift Truck Company (GLTC) has been supplying the materials handling equipment market with world-class products since 1984. In partnership with its leading global principals, the company continually strives to be at the forefront of the technological innovations in the materials handling space, thus providing local customers with the latest solutions that speak to their exact needs.
paid to the quality and long-term utility as each component receives the necessary attention to increase the lifetime.
CSM: GLTC believes it is the only company in the country offering a solution that sits between lithium-ion and leadacid – copper stretched metal (CSM).
In these challenging economic times, the company is cognisant of the fact that it is sometimes difficult for MHE users to buy new and there are some industries that do not necessarily need MHE on a high utilisation basis.
Therefore, GLTC has made the refurbishment route a viable alternative by establishing a dedicated Rebuild Centre in March 2017, which is purely focused on refurbishing ex-long term rental units. All refurbishments – spanning across all the forklift brands in the stable – are completed in-house by experienced technicians and close attention is
Another factor that reaffirms GLTC’s one-stop shop approach is the fact that it is part of the larger Goscor Group of Companies, which comprises a variety of other solutions for the end user, ranging from cleaning equipment to earthmoving equipment and power products, to name a few. The Group has its own finance division in place to offer tailor-made financial solutions to customers.
Why GLTC?
Turnkey solutions
Like most things in today’s world, purchasing materials handling equipment (MHE) is becoming more complex. In a tough economic environment, investing in MHE can be a stressful endeavour as it ties up capital for long periods of time, and the longer the period, the greater the uncertainty and risk involved. Consequently, it must be done correctly the first time, as mistakes are not easily Inrectified.thedecision-making process, one of the critical considerations should be the ability to source all the end user’s MHE needs from a single supplier. Having to purchase equipment that drives your business from different suppliers and being serviced by all the different dealers can be time-consuming and costly. Working with an established supplier means you will have access to reliable support, as well as the parts and equipment you depend on for maximum uptime.
This is exactly GLTC’s value proposition. By virtue of being the sole distributor of several internationally renowned, complementary forklift brands such as Bendi, Crown, Doosan and DEC, as well as Battery and Energy Storage Solutions, the company is a renowned MHE supplier that can address any problem statement optimally and service end users’ needs across board. Bear in mind that in a typical warehouse, not one piece of equipment can do the complete solution, so with GLTC’s multiple brands, one has a 360-degree turnkey solution from one supplier.
Lead-acid: Lead-acid batteries have existed for more than 100 years, but they should not be dismissed as outdated technology. These batteries still remain relevant in some of the tasks. For example, anyone using their forklift in a single-shift operation, has plenty of time to charge or change batteries and is not afraid of regular maintenance, will still be able to work well with conventional lead-acid batteries for some time. The batteries have a long track record of being robust and reliable, and still remain the main battery of choice in the industry.
GLTC’s turnkey solutions approach means that it can offer customers the flexibility they need, by offering options such as outright purchase, short and long-term rental, as well as maintenance plans. This is complemented by its nationwide forklift sales, service, rentals and equipment spares through a comprehensive dealer network.
This solution has been well received in bottling applications and manufacturing environments. It is ideally suited for multi-shift applications with one battery through fast and opportunity charging, as well as seasonal business with high activity peaks. Apart from electric solutions, GLTC was one of the first MHE suppliers in the local market to
Bespoke energy solutions
In line with the industry’s focus on environmental stewardship, GLTC has for years been offering bespoke energy solutions for materials handling equipment, including lithium-ion, lead-acid and copper stretched metal Lithium-ion:(CSM). The company has been testing this technology for more than two years on some sites. A key differentiator for GLTC is that its lithium-ion offering is customer- and Theapplication-specific.companyoffers both imported and locally manufactured alternatives. The two options are for normal ambient applications such as manufacturing plants and warehousing, as well as low ambient, cold room environments where productivity is principal.
4 Lifting Africa - Forklift Safety Guide & Registration4 Lifting Africa - Forklift Guide & Register
However, infrastructure alone is not enough to influence speed of service, especially in today’s information age. The use of newer technologies, such as fleet management solutions, are helping ease maintenance issues.
As today’s tough operating and economic conditions continue to squeeze already constrained bottom lines, MHE owners are well aware that maximising uptime is the basis upon which they can keep their businesses healthy and growing.
Registration 5
Speed is such an important factor that is sought in every aspect of GLTC’s service strategy. To drive this point home, the company has set itself a target to respond within 2-4 hours within a radius of 100 km.
Lifting Africa - Forklift Safety Guide &
Goscor Lift Truck Company, +27 (0) 10 594 4339, www.lifttrucks@goscor.co.za,goscorlifttrucks.co.za
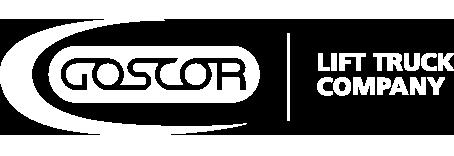
offer lift trucks powered by EU Tier 3 engines. The early transition, well ahead of any form of legislation, was purely informed by the company’s mission to play a leading role in minimising its impact on the environment through lower greenhouse gas emissions. Additionally, the development concept of EU Tier 3 engines has always pursued lower fuel consumption, better performance, reliability and durability than the previous engine generations.
Rapid development in machine technology, particularly the use of electronic controls and remote monitoring systems, have opened up new avenues of fleet monitoring and remote troubleshooting.
It is thus no surprise that today every fleet owner of capital equipment expects maximum equipment uptime.
To be able to adhere to such stringent response times across the length and breadth of South Africa, requires Goscor Lift Truck Company to have the infrastructure that allows them to respond to any service needs timeously.
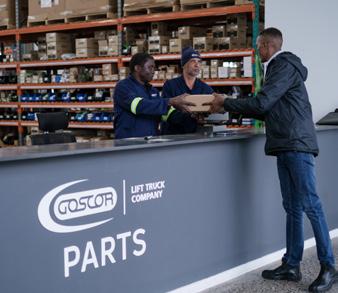
If managed correctly, GLTC’s fleet management system can cut on unnecessary costs. This technology is able to measure many different operational areas/functions on the lift truck and can be set to accommodates exact customer needs.
Speed of service
Lifting Africa - Forklift Guide &
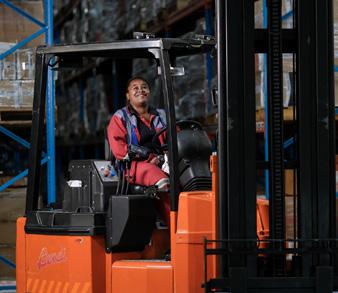
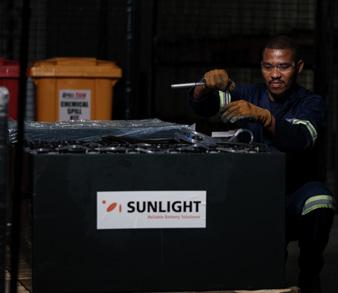
Register 5
To increase and maximise production efficiency, one must choose equipment from a supplier with the highest reliability; that does not compromise on service, to ensure that equipment runs at peak performance.
Maintenance alone is not the whole story when it comes to uptime and the consistent improvement to the bottom line. In today’s superfast modern age, a supplier’s efficiency is not only based on the provision of spare parts and fulfilment of maintenance contracts but is largely measured on how fast the service is.
The strategic national footprint of branches in Gauteng, Durban, Pietermaritzburg, East London, Port Elizabeth, Cape Town, Nelspruit, Bloemfontein, Polokwane as well as the Garden Route, complemented by a strong network of dealers in the outlying areas, allow GLTC to meet its stringent response times.

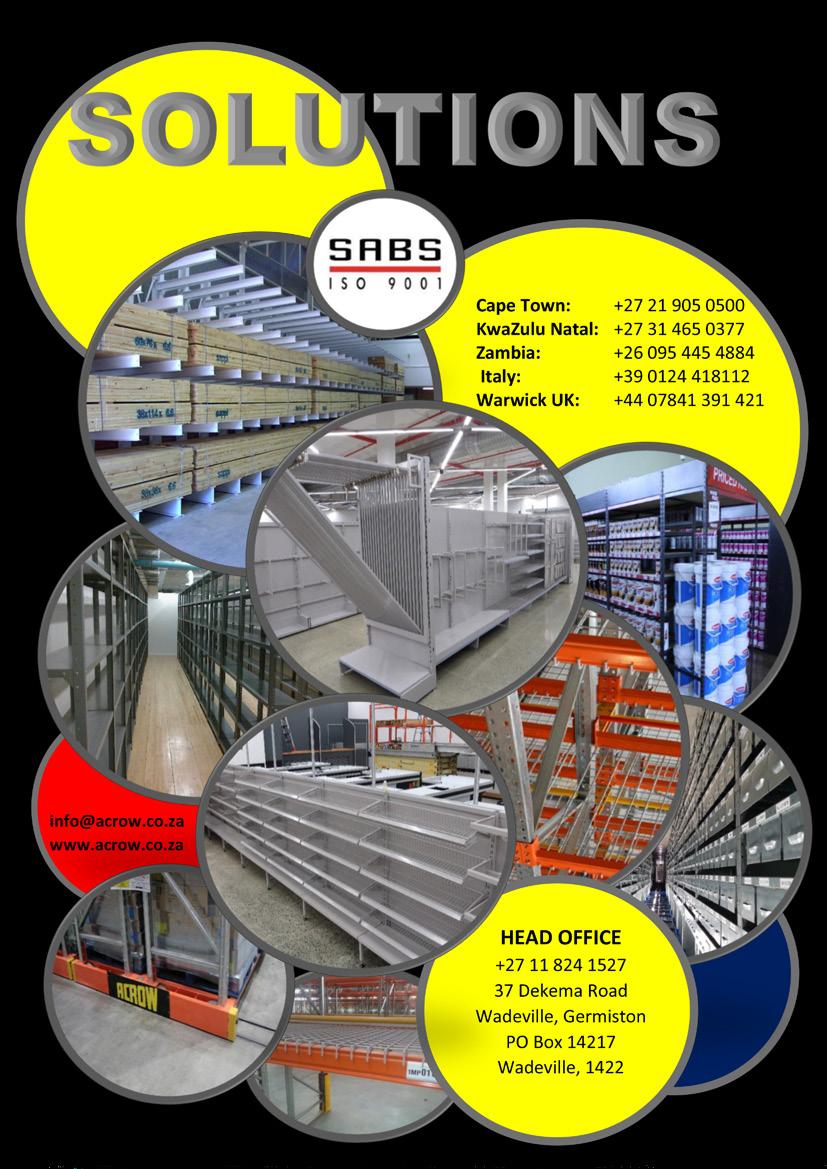
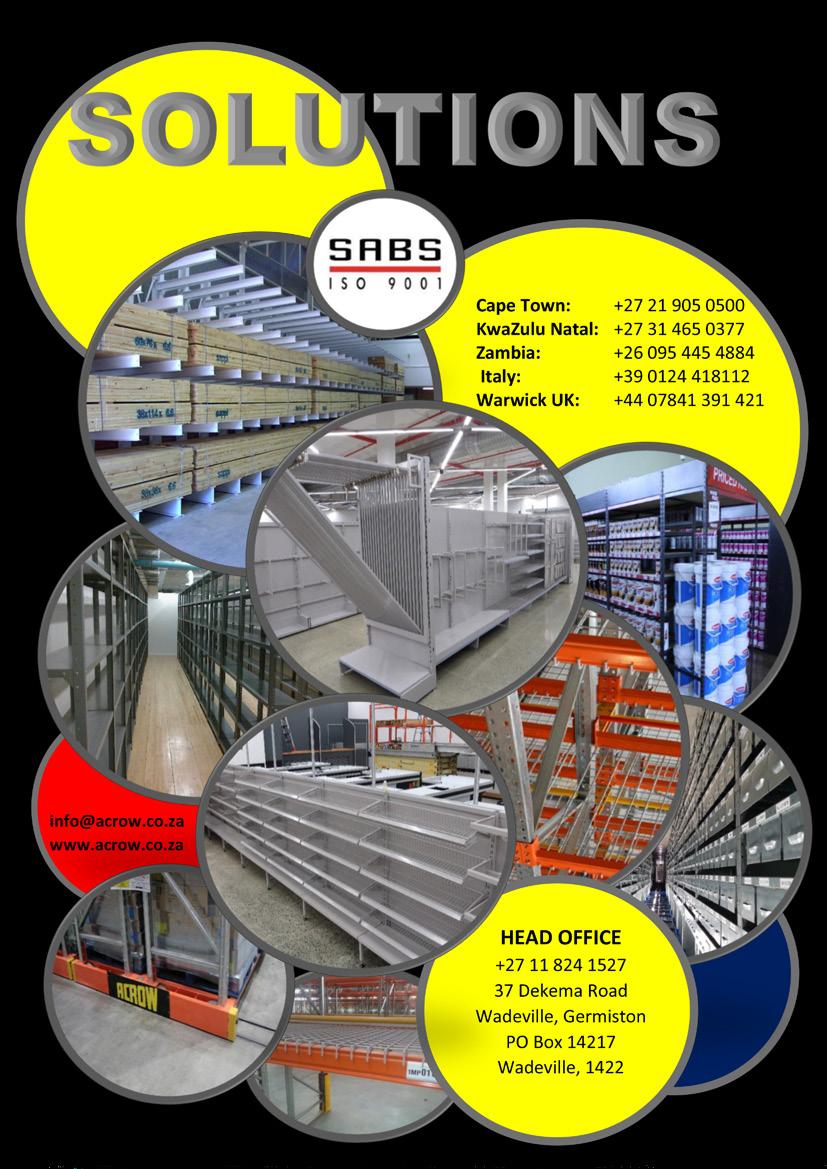
“chief inspector” means the officer designated under Section 27 as chief inspector, and includes any officer as chief inspector; “competent person” means a person who has in respect of the work or task to be performed, the required knowledge, training and experience and, where applicable, qualifications, specific to that work or task. Provided that where appropriate qualifications and training are registered in terms of the provisions of the National Qualification Framework Act, 2008 (Act No. 67 of 2008), those qualifications and that training must be regarded as the required qualifications and training: and (b) is familiar with the Act and with the applicable regulations made under the Act:
All Forklifts require regular checking and testing at routine Theintervals.result must be entered in a register and logbook designed for this purpose.
Definitions
(a) a vehicle designed solely for the purpose of lifting or towing another vehicle;
“ECSA” Engineering Council of SA “inspector” means a person designated under Section28: “LMI Certificate” means a certificate issued by ECSA confirming the competency of the LMI
“LMI Scope letter” means a letter issued by ECSA confirming a LMI scope that he is allowed to load test to “lift truck” means a mobile lifting machine, but does not include –
(b) a mobile earth-moving machine; or
This Forklift Guide and Register includes detailed task descriptions, maintenance, inspection and load testing of the work and provision for control by the responsible person.
“lifting machinery inspector” means a person who is employed by a Lifting Machinery Entity and who is registered by the Engineering Council of South Africa in terms of the Engineering Profession Act, 2000 (Act No. 46 of 2000);
Lifting Africa - Forklift Guide & Register INTRODUCTION

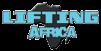
“non-integrated work platform” means a basket or cage attached for use in conjunction with lift trucks to elevate persons so they can work at a height but that does not control the lift height of the platform or move the truck “safe working load” means the mass load applicable to a piece of equipment or system as determined by a competent person taking into account the environment and operating conditions; “training provider” means a training provider for lifting machinery operators approved and registered by the chief inspector in terms of regulation 20
Definitions 1. In these Regulations, “the Act” means the Occupational Health and Safety Act, 1993 (Act No. 85 of 1993), and any word or expression to which a meaning has been assigned in the Act shall have the meaning so assigned, and, unless the context otherwise indicates
The contractor, employer, user or manager should adhere to the legal requirements regarding the safe use of forklifts as set out in the Occupational Health and Safety Act and Mine Health and Safety Act.
This is a statutory requirement. The Inspections must include all working parts of the forklift to be thoroughly examined and subjected to a performance test, as prescribed by the standard to which the forklift was manufactured and, or the standard incorporated, which is SANS 10388 – “The inspection and testing of lift trucks”, by a person who has knowledge and experience of the erection and maintenance of the type of lifting machine involved or similar machine.
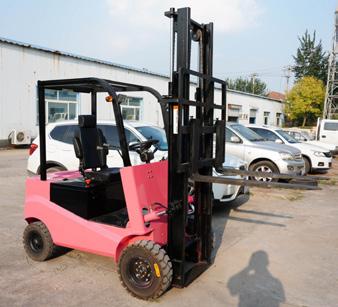
“SETA” means Sector Education and Training Authority
(c) a vehicle designed solely for the removal of a waste bin; “lifting machinery entity” means a legal entity approved and registered by the chief inspector in terms of regulation 19;
Occupational Health And Safety Act, 1993 Driven Machinery Regulations, 2015
“Lifting Machine” means a power driven machine that is designed and constructed for the purpose of raising or lowering a load or moving it in suspension, but does not include an elevator, escalator or hand powered lifting device.
This license is referred to as a certificate of competence and must be issued by a training provider that is accredited by the Transport SETA approved for the purpose, by the chief inspector. The training provider must be in possession of a valid approval certificate signed by the chief inspector.
As per DMR 18 subsection (11).
of Lift Trucks must ensure all personnel that operate the lift truck are specifically trained for the particular type of lift truck. The operators must have a valid license, as set out by the national code of practice. License codes vary according to the type of lift truck.
The Lift Truck is required to undergo a thorough examination by a COMPETENT person, at intervals not exceeding 6 months, as per the Occupational Health and Safety Act 85 of 1993, Driven Machinery Regulations, 2015, sub-section (6).
a) Non-integrated working platforms (personnel cage) must be inspected prior to every use by the responsible person.
Any non-integrated work platforms (personnel cage) should comply with SANS 583. This standard specifies the requirements for non-integrated work platforms (cradles) occasionally used on lift trucks to elevate persons performing specific tasks of short duration and where it is not practicable to use specially designed devices. The platforms are not to be used for production activities. No user shall permit any person to be moved by or supported with a lift truck, unless the lift truck is fitted with a lifting cradle (personnel cage) and is approved an inspector from The Department of Employment and Labour.
Mandatory Statutory requirements
Note:
Lifting Africa - Forklift Guide & Register INTRODUCTION
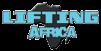
a) DMR 18 sub-section 5 refers to 110% of safe working load being applied. This must only be applied to equipment that does not have a prescribed SANS standard. SANS 10388 is the prescribed standard for lift trucks and 110% overload MUST NOT be applied, as SANS 10388 does not permit the overloading of lift trucks, unless under exceptional circumstances and in the presence of an expert b)engineer.AnLMI is not a professionally registered engineer otherwise known as a PR-ENG.
Every user of lift trucks that are leased is required at all times to keep on their premises a register in which the user is required to keep records of the latest applicable inspection and performance test, as per DMR 18 subsection (5) and (6), and service records not older than 12 months. The owner or lessor of the leased forklifts shall keep and maintain full service history records on their premises for at least 10 years. This is as per DMR 18 subsection (7 b), note (b) and SANS 10388 (9) “Reports and
EveryRecords”.user
Every user shall ensure that the Lifting Machinery Entity and Lifting Machinery Inspectors, appointed to undertake the inspection and performance test of any lift truck is
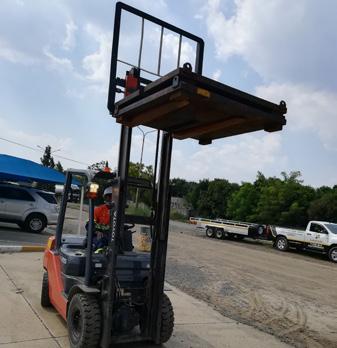
b) Non-integrated working platforms (personnel cage) shall be inspected by competent person in intervals not exceeding 6 months that will issue documentation confirming the safe use of the non-integrated working c)platforms.Non-integrated
Every user of lift trucks is required to keep on their premises a register in which the user shall record the results and full particulars of any examination and performance test referred to in DMR 18 sub-regulations (5) and (6). The User is also required to keep records of any modifications or repairs to such lift trucks. The user shall ensure that the registers are available at request for inspection by the inspector. This is as per DMR sub-section (7a) and SANS 10388 (8) “Alterations, modifications and major repairs”.
working platforms that do not comply with this standard should be withdrawn from service. As sumarized by LEEASA

The Lift Truck is required to undergo a thorough examination and performance test by an ECSA Registered LMI, at intervals not exceeding 12 months, as per the Occupational Health and Safety Act 85 of 1993, Driven Machinery Regulations, 2015, sub-section (5). This must be carried out in accordance with the manufacturer’s standard and the prescribed incorporated standard, which is SANS 10388, “The inspection and testing of lift trucks”.
Note
competent to undertake such work and has the scope of “Lift Trucks” or “Fork Lifts” on their scope of competence issued by the Department of Employment and Labour for the Lifting Machinery Entity and ECSA for the Lifting Machinery Inspector. The Onus falls on the owner/user to ensure this is met at all times. If the entity or inspector does not have the scope of competence, the certification issued will be considered null and void. Should an incident occur the owner/user would be placed with unnecessary liability and will be seen as non-compliant. Refer to LEEASA LME and LMI Vetting Guide – available in soft copy on www.leeasa.co.za. This will guide you in the vetting of service providers. For lift trucks utilising a lifting cradle (personnel cage) to carry personnel requires all operators to be certified to operate the lift truck with certification for the lifting cradle (personnel cage), as per the national code of practice, prescribed by the Occupational Health and Safety Act 85 of 1993.
• Whilst operating a forklift you must pay attention and follow any work site rules and guidelines.
Avoid hazards
Lifting Africa - Forklift Guide & Register

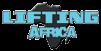
• Steer clear of any bumps or uneven ground surfaces along with slippery conditions.
• Ensure hydraulic oil has warmed up. Consider the surrounding environment
FORKLIFTS SAFETY
• The work wear must be reasonably fitted as any loose clothing can get caught on machinery.
Operate at a safe speed
• Steer clear of loose ground objects which could cause loss of control over the equipment or a load to move around.
Examine Equipment before use
• Be aware of the height of the load, mast and overhead guard of the forklift when entering or exiting buildings.
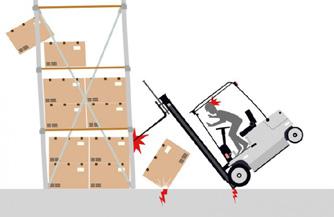
• Do not operate on bridge plates, unless they can support the weight of the forklift and load.
• Individuals who have been trained properly and contain a license to operate the equipment should only do operating forklifts.
• Don’t operate/hold any of the controls when your hands have grease on them; it may cause them to slide off and cause an accident.
Appropriate clothing must be worn
• Never proceed past the speed limit.
• Check for any overhead objects before lifting or stacking loads.
Operating new forklifts with latest safety features such as a seatbelt interlockers, overload lockout and speed controls can greatly increase operator and nearby pedestrian safety, whilst also reducing stock and capital equipment damage.
• If there are any noted damages or problems management should be notified and the forklift should not be operated if it needs to be repaired.
• Operators must do a routine check of the equipment before driving them. Some things you should check for any faults are brakes, steering, controls, warning devices, mast and tyres.
• Keep a safe distance from other trucks in case they move in an unpredictable manner.
• Make sure that you always have enough space to stop safely.
Starting up the forklift
• For safety purposes, it’s important for the operator to make use of the steps and hand grabs to seat themselves correctly in the forklift.
• Take corners and any turns slowly to minimise risk of •tipping.Make any changes in direction or any stops gradually and slowly.
• Check the loads carefully before moving them for stability and damage.
• It needs to be ensured that operators wear the appropriate safety work wear; usually consisting of a hard hat, safety shoes and hi-visibility jackets.
• Be careful when operating a forklift near the edge of a loading dock or ramp – the forklift can fall over the edge –keep a safe distance from the edge.
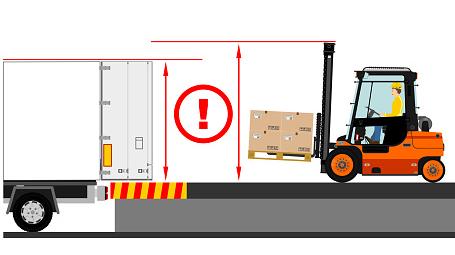
• Always consider the ‘journey’s end’ of a load before picking it up. A convenient position of a load from pick up may not be convenient for stacking.
Operators must be qualified
• Use the horn when closing in on a corner or doorway/ entrance and around people to alert pedestrians or other forklift operators of your whereabouts to avoid any unnecessary collision.
• Hydraulic oil needs warm up.
Ensure your load is stable and secure
Operating a forklift safely
• The operator must only drive the equipment in the machinery’s designated roadways.
• Observe all signs, especially those on maximum permitted floor loadings and clearance heights.
• The operator should not start the forklift until they are correctly seated with their safety belt fastened and all parts of their body are safely inside the confines of the operators cabin or the forklift.
• It is important to ensure that the load is tilted back with the forks sitting low whilst transporting in order to increase truck stability.
• Before starting the forklift it’s important to ensure all the equipment’s controls are in reach and the seat position and mirrors are adjusted to the operator’s needs.
• Do not lift a load with one fork. Use pallets and skids that can withstand the weight of the load.
• Make sure loads are correctly stacked and positioned across both forks.
• It is important to make sure you can see the racking clearly in which you are positioning your load.
Ensure the load is evenly distributed
• Do not lift or move a load unless both forks are fully under the load.
• Do not load or unload goods or turn whilst on a ramp.
• Do not authorise anyone to stand or walk under the load or forklift machinery – The load can fall causing injury or death.
When the shift ends
FORKLIFTS SAFETY
• Fully lower the forks to the floor and apply the park brake.
Ensure the forklift is not over-loaded
• If visibility is poor do not continue driving; in some circumstances, you may need a lookout helper to assist you.
• Do not use the tip of the forks as a lever to raise a heavy load.
• Know the capacity of your forklift and any attachments being used and never exceed this capacity.
Refuelling
• After use ensure the forklift is parked in a designated or authorised area.
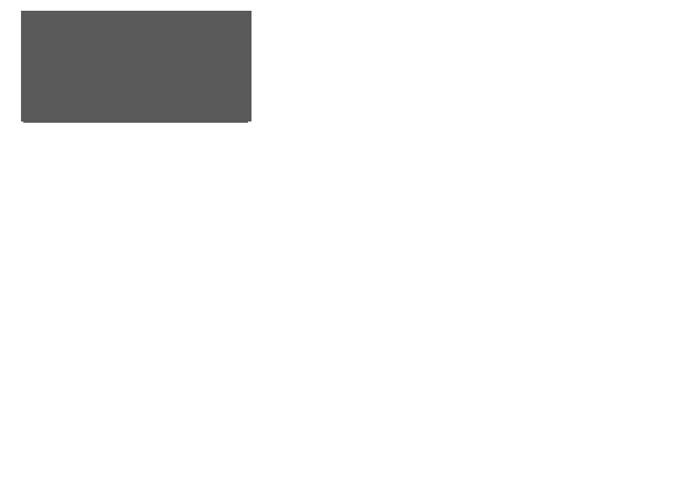
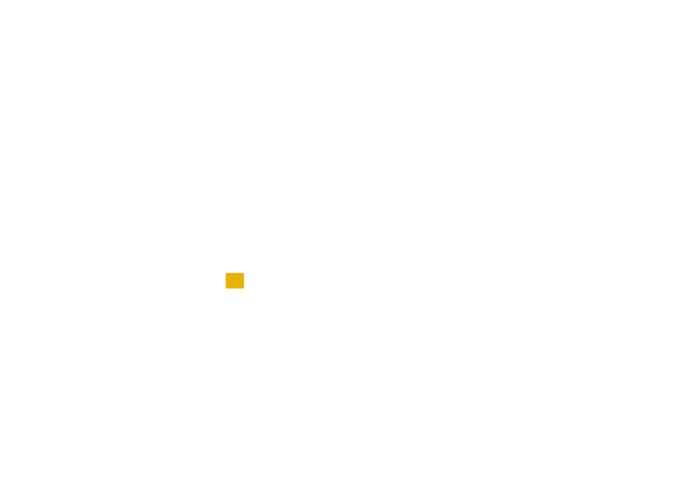
• Switch off the forklift.
• When driving up ramps’ move in a forward direction and down ramps in reverse, especially while carrying loads.
• Do not leave a forklift running whilst unattended
• Turn the forklift “off” and remove the key.
Keep clear of the mast
• An overload can cause the rear tyres to be raised off the ground and may cause the forklift to tip over.
• Do not lift or move loads that are not safe or stable.
Lifting Africa - Forklift Guide & Register

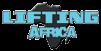
• Operate the forklift in reverse when it improves visibility; except when moving up ramps.
• For IC engine forklifts, no open flame or sparks are permitted, and refuelling should take place in a wellventilated area.
Driving on Ramps
Make sure you have clear visibility
• Stack the load on the pallet or skid safely and correctly.
• Keep hands and feet clear of the cross members of the mast – Serious injury can be caused if the mast is lowered while your hand is on it.
• Use securing measures such as ropes or bindings if required.
• Do not push a load with the tip of the forks.
• Do not use damaged, deformed or decayed pallets for holding loads.
Forklifts are for carrying loads only
• A forklift should only be refuelled or battery is charged at specially designated locations.
• If a person has to be lifted, use only a securely attached work platform and cage and follow the appropriate operating instructions.
Gear up
• Installing anti-slip flooring
Learn what the most common forklift accidents are, and what the most important warehouse safety tips are to prevent injuries and fatalities below.
Personal protective equipment can make all the difference when it comes to performing a task safely. Safety gloves, hard hats, reflective tape and other attire should be worn at all times..
For larger spills, notify your supervisor. For those areas near truck loading docks, weather can pose unique safety challenges. A slick or wet loading surface is the cause of many warehouse accidents. Assigning dedicated cleaning tasks to each employee can help keep everyone invested in maintaining a safe working environment.
Does your warehouse have easy-to-read exit signs? This is a frequently overlooked factor, but simply knowing where to exit the warehouse is a matter of life or death during a fire. Should a warehouse evacuation be necessary, you’ll want your team to know where to head well in advance of an emergency.
• Posting speed limits
Pedestrian accidents
The Most Common Warehouse Forklift Accidents
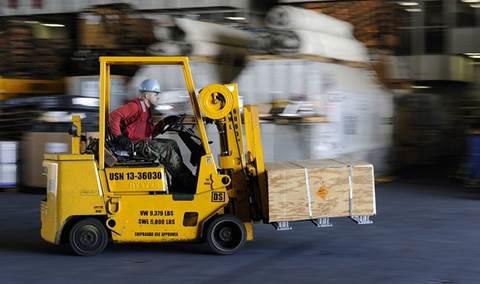
Forklift falls and crush injuries
Crush forklift injuries often happen when a forklift tips over and the driver tries to leap free of the vehicle. The Number One rule for reacting to an overturning forklift is to remain inside and keep all parts of the body under the protective canopy. This is against human nature and needs
Overturning
Lifting Africa - Forklift Guide & Register

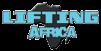
When proper warehouse safety practices are ignored, accidents involving forklifts are all too common and can cause serious injuries and deaths. Here are a few of the most common kinds of forklift accidents – and how to prevent them from happening in your warehouse:
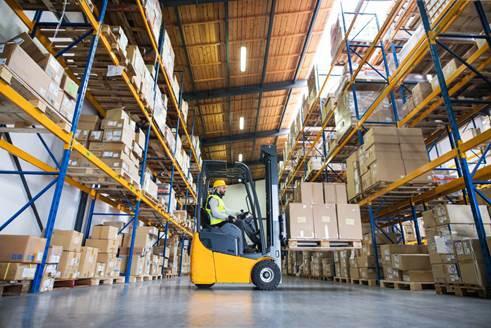
Define hazard zones
A clean workplace is a safer workplace, and that certainly applies to warehouses. If you notice a spill in the aisle, clean it up immediately.
Have an exit plan
The importance of warehouse organisation is often overlooked when it comes to creating a safe work environment. For certain areas in your warehouse, it’s a good idea to keep non-essential employees from entering. Deploy yellow caution tape, orange cones or even extra personnel to ensure special procedures, heavy loads and other uncommon tasks can be performed without distraction.
• Minimizing the opportunities for sharp turns
The best way to avoid forklifts coming into contact with pedestrians is to arrange the work area in such a way that the two populations are isolated from each other. A further protective measure is to insist that all pedestrians, employees, visitors, vendors, contractors, etc., wear a reflective high-visibility vest while on the floor where forklifts are operating.
The top warehouse safety tips
to be reinforced by keeping seat belts fastened, training and constant reinforcement in the form of signs in the workplace.
While proper training is important for fostering a safe place to work, it’s also crucial to adhere to common-sense warehouse safety tips. When used together, forklift training and a comprehensive safety plan is your best bet against preventing workplace calamities.
Keep it clean
FORKLIFT SAFETY
Tipping over a forklift is probably the single most catastrophic event that can happen to a powered industrial truck. It may occur when travelling on steep slopes, driving over slippery surfaces, being unevenly or heavily loaded, travelling too fast, especially around corners, moving a load at a dangerous height, crossing uneven ground or going over curbs or uneven steps. While these are mostly behavioural issues that can be corrected by proper training, overturning may be prevented by taking measures in the warehouse such as:
Warehouse safety tips
Follow a maintenance schedule
When it comes to warehouse safety, personal responsibility is everything. Leave nothing to chance and implement your own safety plan that’s above and beyond normal requirements. Ensure each shift has properly trained emergency response personnel available. Offer CPR training. Put extra first aid kits throughout the warehouse. Preventative action is great, but what happens when something goes wrong? As the only saying goes, “Hope for the best, prepare for the worst.” Of course, the best way to take safety matters into your own hands is to get forklift certified and maintain your certification every three years.
Check your racks & shelves
Long shifts, overtime, covering for someone who called off – there are many times when an extra 15 minutes turns into 2 hours out in the warehouse.
Take matters into your own hands
FORKLIFT
Invest in education for your workplace
Even if it’s “just a little job,” no forklift action should be undertaken by someone who isn’t properly instructed and trained. The deadly risks vastly outweigh any minor convenience you might gain from having an untrained colleague help you out.
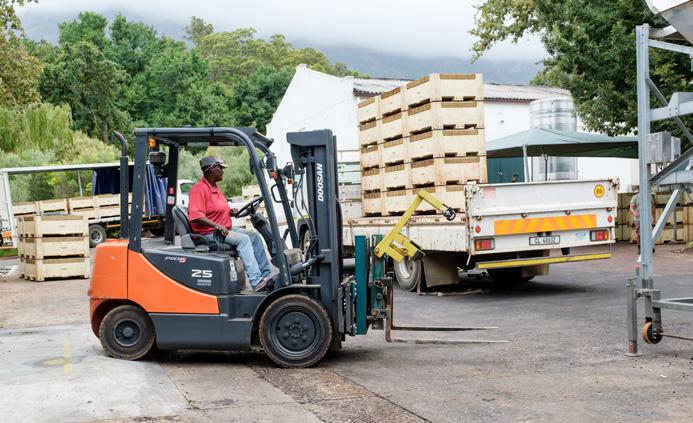
SAFETY
Remember, warehouse safety isn’t all about forklifts all the time. Your cargo and goods need a stable, safe place for storage. This means that your racks and shelves should meet & exceed load standards. Ensure your forklift operators aren’t overloading the maximum capacity requirements – if they are, big problems could be headed your way.
Keep a rigorous maintenance program for all of your equipment – forklifts, pallet jacks and more. Many workplace accidents are caused by faulty, defective forklifts. With regular maintenance a part of your daily plan, safety will naturally take care of itself. It’s amazing what you can accomplish with just a few minutes of dedicated maintenance tasks each day.
Lifting Africa - Forklift Guide & Register

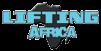
After the daily grind, make sure your floors are clean for the next shift. Fork-mounted brooms are a great idea in this regard. A clean sweep will help the next group of workers enjoy a clean, safer workspace. All spills and hazardous obstacles should be cleared immediately This is a good idea for warehouses, dock areas, shipyards and other areas where forklifts and industrial equipment are active.
All clean hands on deck
Remember to break
Limit forklift operation to only fully trained personnel
While there is no foolproof way on how to keep your warehouse safe, all of the common causes of forklift fatalities can be remedied by modifying the conduct of everyone on the shop floor. Even the most carefully laidout warehouse is no match for the fallibility of the human.
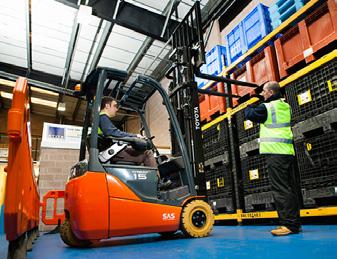
Carriage Carriage wear, stoppers, cracks & excessive play etc
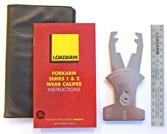
Hoist Cylinders Leaking, uneven lift, bleeding back etc.
Hoses Leaks etc.
• Fork Arms
• Engine
• Cooling systems
Data Plate No plate, wrong specs, info not legible etc.
Chains Stretched, parts missing, side wear etc.
Lifting Africa - Forklift Guide & Register
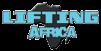
Lights Not working, broken etc.
Some of the most common causes for failure during testing:
• Manufacturers data plate
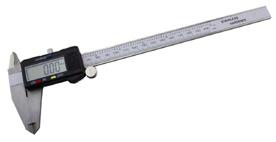
• The inspector is required to undertake a thorough examination of the lift truck, as per SANS 10388, and shall this be performed according SANS 10388, prior to the commencement of testing. The findings of the inspector shall be documented in English. The inspector shall have the correct measuring equipment such as, but not limited to; forklift chain gauge, fork calliper, laser or tape measure, vernier.
• Braking systems – wear and functions
ITEM NON COMPLIANCE - REFERENCE SANS10388
The Lift Truck is required to undergo a thorough examination and performance test by a ECSA Registered LMI, in intervals not exceeding 12 months, as per the Occupational Health and Safety Act 85 of 1993, Driven Machinery Regulations, 2015, sub-section (5). This must be carried out in accordance with the manufacturers’ standard and the prescribed incorporated standard, which is SANS 10388, “The inspection and testing of lift trucks”.
• General Structure
• There are two types of testing that shall take place in accordance with SANS 10388:
Load backrest No load backrest, broken, loose, cracked etc.
• Tyres – wear of tyres
a) For further information refer to SANS 10388.
Safety Devices Not working, bypassed etc.
Every user of lift trucks is required to keep on their premises a register in which the user shall record the results and full particulars of any examination and performance test referred to in DMR 18 sub-regulations (5) and (6). The User is also required to keep records of any modifications or repairs to such lift trucks. The user shall ensure that the register are available at request for inspection by the inspector. This is as per DMR sub-section (7 a).
• Hydraulic System
The Occupational Health & Safety Act, Act 85 of 1993, Driven Machinery Regulation requires that:
The Lift Truck is required to undergo a thorough examination by a COMPETENT person, in intervals not exceeding 6 months, as per the Occupational Health and Safety Act 85 of 1993, Driven Machinery Regulations, 2015, sub-section (6).
Forks Heel wear, cracks, straightness, wrong capacity etc.
Inspections and Annual Testing of Lift Trucks
When appointing a service provider to undertake work to certify lift trucks it is essential that you understand the following, of what is required of an inspector. Here are some points to be cognitive of:
Parking Brake Not holding
• Safety decals
Every user of lift trucks that are leased, are required at all times to keep on their premises a register in which the user is required to keep records of the latest applicable performance test, as per DMR 18 subsection (5), and service records not older than 12 months. The owner or lessor of the leased shall keep and maintain full service history records on their premises for at least 10 years. This is as per DMR 18 subsection (7 b) and note (b).
1. Functional Test – This test shall be performed without any load. The lift trucks shall be tested through all its functions, through full working range. This is to test that the machine is able to function through its full working range and all of its functions.
INSPECTION & LOAD TESTING
• Load chart
• Safety Systems and devices
Every company or owner of lifting machinery has a lawful obligation to have their lifting machinery load tested annually and inspected 6 monthly.
LEEASA’s LME and LMI Vetting guide, available on soft copy from www.leeasa.co.za.

• Traction Systems
• Emergency devices and equipment
• Chains
What is being checked during a lift truck inspection?
Note
• The LMI performing the load test must be accredited by ECSA with the correct scope to undertake the work. You can refer to LEEASA’s LME and LMI Vetting guide, available on soft copy from www.leeasa.co.za.
Checklist to ensure the legality of your inspections and load test:
• Steering system
Mast Channels Cracked, worn, bent etc.
Tyres Worn, cracked through limit ring, chunking etc.
Inspections and Load testing
• The service provider, which is appointed, and is accredited with the Department of Employment and Labour as a Lifting Machine Entity (LME) and must have the relevant scopes to undertake the work. You can refer to
Horn Not working
A static pull test is not an acceptable means of testing as the method does not comply with SANS 10388 and does not enable to the inspector to test the machine’s stability, natural creep, nor the ability of the lift truck to sustain its rated capacity through the full working range, as per the load chart of the lift truck.
Lifting Africa - Forklift Guide & Register

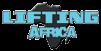
2. The natural creep (natural drop in lift cylinder) when under load.
3. The ability of the lift truck to sustain the rated capacity (SWL or WWL), through the full working range, as per the load chart of the lift truck.
This will include, but not be limited to; full extension of the mast, side shift, attachment, brake, mobility and signalling device.
• The load is being simulated by pulling an anchor point, counterweight or off the mast itself. Once the natural
The method is incorrect and applied by utilising slings and a load cell to simulate a “load”.
Note: The Static Test is not referring to a static pull test. A static pull test is when the lift truck is “tested” using slings and a load cell. The use of a static pull does not comply to SANS 10388, as it is not sufficient to evaluate the lift trucks compliance, as required.
• Stability can not be assessed when the lift truck is being pulled against itself on the mast or counterweight. When pulling an anchor point in the ground, natural creep will occur and once again the inspector will be unable to assess the stability of the lift truck.
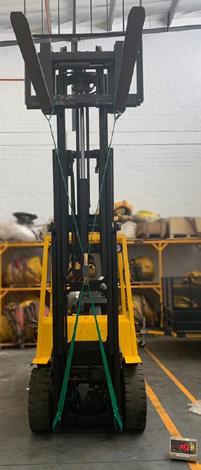
• The inspector is unable to assess the ability of the lift truck to sustain its rated capacity, through the full working range as per the load chart, as the load is simulated with slings that are different lengths, taking into account full working range requires the load to be lifted from the lowest point to the highest point, according to the load chart. While maintaining a standard load centre, which will be according to the manufacturers’ specification and visible on the data plate of the machine. The load must be applied from the bottom to the top of the working range of the lift truck. This is not possible using slings and a load cell.
Why is this method found in the industry?
A performance test must be conducted in such a way that every component of the forklift is placed under stress in order to determine the serviceability and safety of the forklift and its components.
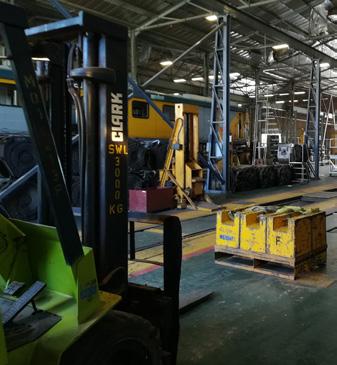
In the event of any incidents and accidents occurring within the workplace and the respective forklift being without a valid forklift load test certificate, this could land you as a person or entity into serious trouble for non-compliance with OHSA and the Driven Machinery regulations.
Why is a static pull test incorrect?
Note: The static test refers to the lift truck being stationary – in other words no movement of the lift truck wheels while the truck is being load tested.
• The reason this method is used which is incorrect is because it is cheaper to transport load cells and slings than test weights.
2. Static Test – This is referring to the performance testing of the lift truck.
• The entity undergoing the testing of lift trucks does not have test weights or the correct equipment.
Why we cannot evaluate this with the static pull method is because of the following:
INSPECTION & LOAD TESTING
The correct method of performance testing (load testing) a forklift is to utilise dynamic test weights that enable the lift truck to be assessed as per SANS 10388. Test weights are the only acceptable means of testing a forklift. This will enable to the inspector to assess the machine’s stability, natural creep and ability of the lift truck to sustain full rated capacity through full working range, as per the load chart.
creep of the machine occurs, which is allowed and must be measured according to the manufactures specifications, the tension on slings will reduce and the natural creep will not be able to be measured, as the force will be reduced.
This could mean being held liable, upon conviction, for a financial penalty or imprisonment for up to 12 months, as per DMR 18 sub-section 22. As sumarized by LEEASA
1. The stability of the lift truck.
The inspector must evaluate the lift trucks performance while under load, according to SANS 10388 criteria, which means use of test weights, which are referred to as a dynamic test load or test weights, to evaluate the lift truck for the following;
Basic forklift hand signals every operator should know
Travelling towards me
According to SANS 10296 the requirements for hand signals are:
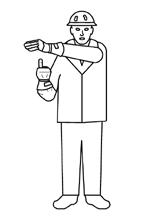
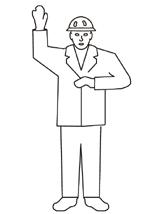
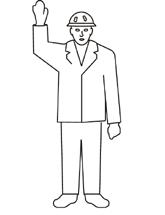
3. Non-specific one-arm signals shall be acceptable using either arm (left or right indication is a specific signal); 4. The signaler shall 1) Have a clear view of the load or equipment; 2) Be clearly visible to the operator, and 3) Be in a safe position, 5. Only one person shall give signals to the operator. The only exception to this shall be the 6. The emergency stop signal; 7. Where applicable a combination of signals may be combined and used;
FORKLIFTS SIGNALS
Operations start
Cease operations

Raise slowly
Lower slowly
Use lowering signal with one hand with the other palm motionless below facing the hand that gives the signal.
Keep both arms at the sides of the body with the forearms held vertically, both hands open, palms facing forwards. Repeatedly move the forearms up and down.
Raise both arms above the head, with the hands open and the palms facing forwards.
Every year, forklifts will get into a workplace accident. Hand signals for forklift operators play a key role in workplace safety.
Forklift signals let operators communicate with spotters while moving heavy loads. In loud, cramped environments, these signals ensure clear communication with anyone behind the wheel of a forklift.
Raise one arm above the head, with the hand open and the palm facing forwards. Hold the other arm horizontally in front of the chest, with the hand open and the palm facing downwards.
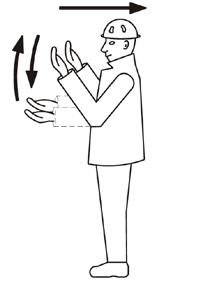
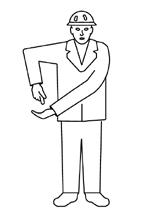
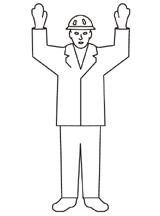
Hold the hands horizontally at waist level, with the hands open and the palms facing downwards. Repeatedly move the arms horizontally towards and away from each other.
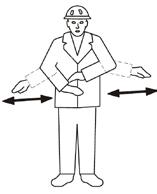
1. Only signals illustrated in this standard shall be used; 2. Misunderstanding should be avoided with clear and concise signals
Raise one arm above the head, with the hand open and the palm facing forwards.
Use raising signal with one hand and other palm motionless on top of the hand that gives the signal.
Emergency stop
Stop
Indicating vertical distance
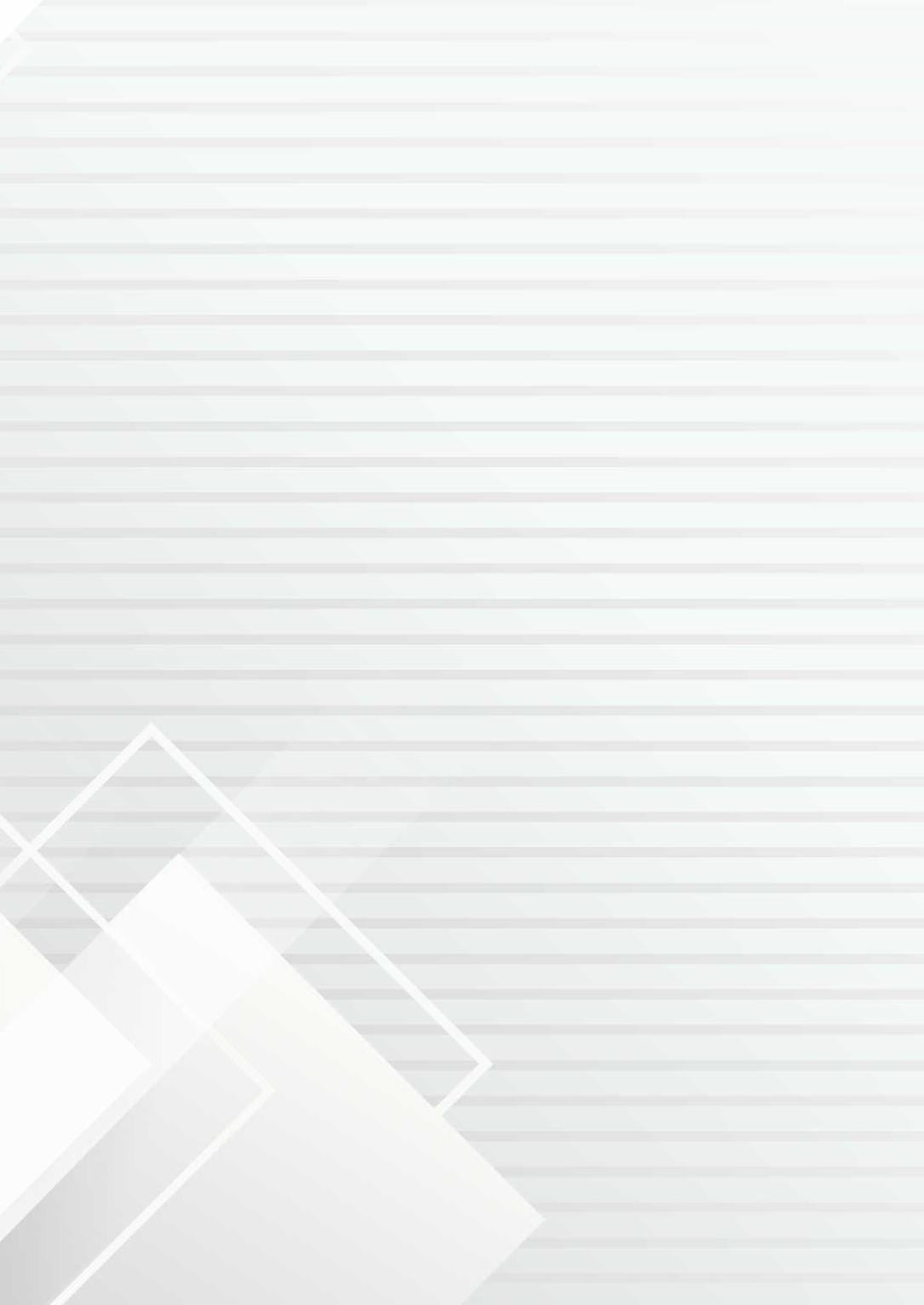
Keep both arms extended in front of the body, one above the other with palms facing each other.
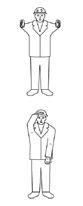
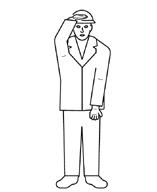
Keep one arm extended horizontally with the thumb down.
Travelling away from me
Extend one arm downwards but away from the body, with the hand closed and the index finger pointing downwards. Make small flat circles with the forearm.
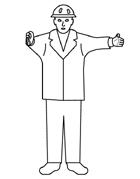
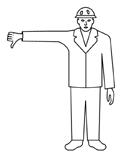
Turn over Keep both arms extended forward, parallel and horizontally, and turn 90 in the direction of turn over.
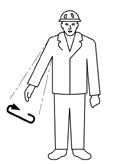
Lowering of forks
Keep one arm extended horizontally with the thumb up.
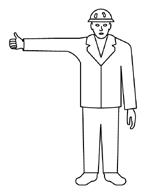
Inching or dead slow Rub palms in a circular motion against each other. After this signal, any other applicable hand signals shall apply.
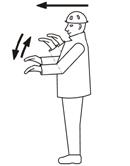
Indicatingdistancehorizontal
Lower the load at a steady rate
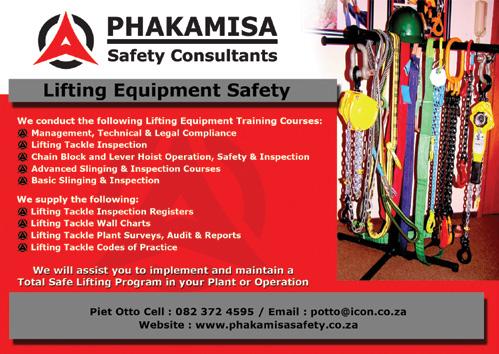
Keep both arms at the sides of the body with the forearms held horizontally to the front, both hands open, and the palms facing upwards. Repeatedly move the forearms up and down between the horizontal and the vertical positions.
Raising of forks
Keep both arms extended horizontally in front of the body with palms facing each other.
FORKLIFTS SIGNALS
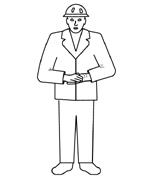
Forklift training school
• Stacking materials at the specified locations safely.
The best forklift schools are accredited and recognized by TETA/CETA to provide forklift safety training.
• Pre-shift inspections and any maintenance the operator will be required to perform
After the training, the school assesses you to determine whether you are competent.
You will get a forklift license after the training that allows you to operate the machine. Forklift training and certification take 1-2 weeks.
Forklift license renewal
• How to safely operate a fork truck on different surface conditions, ramps, and slopes
How to get your forklift license
Basically any training program should cover:
• Reporting any damages that may occur while they is driving the forklift.
• How to work safely around pedestrians in the workplace Hands-on training and evaluation
But if you’re new to forklifts, you probably have a lot of questions:
• How to refuel (internal combustion trucks) and/or charge batteries (electric trucks)
the training in one of the accredited skills development providers. You should apply for the 242974 SAQA Unit Standard titled “Operate counter-balanced lift truck” or the 244365 SAQA Unit Standard titled “Lift and move material and equipment by means of a forklift”.
“Formal instruction” simply means classroom teaching.
By the end of the forklift operator training course, you should be able to operate a counter-balanced lift truck safely, conduct pre and post inspections, and handle the loading and storage of freight.
• Carry raw materials to the manufacturing facility and deliver finished products to assigned distribution areas
Forklift driver job descriptions
This portion of training must consist of “demonstrations performed by the trainer and practical exercises performed by the trainee” In other words, you must be shown how to actually operate a forklift and also be observed doing so.
• What do I need to study?
• Formal instruction
A forklift is a lifting truck that uses forks or other attachments for transporting goods over short distances. It is used for loading and offloading.
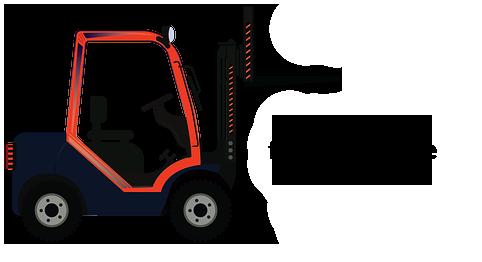
• How to operate the different types of truck the operator will be using (instructions, safety precautions, limitations, etc.)
• Moving or stacking different products or materials within the factory
• Forklift capacity, stability, steering, maneuvering, and visibility
• How do I get certified?
• Certification Formal instruction
Do you need a driver's license to operate a forklift?
Lifting Africa - Forklift Guide & Register FORKLIFTS

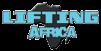
A forklift license expires after two years in South Africa and can be renewed in a day. You might be required to drive a forklift during the reassessment.
This process is called recertification. Your ID, old forklift license, and certificate are required when renewing your license.
Most forklift driver job descriptions contain the following tasks:
It can consist of a “lecture, discussion, interactive computer learning, video, and/or written material” But the instruction must also cover certain topics to be considered comprehensive.
• The dangers of operating in confined/hazardous spaces and the necessary precautions drivers should take when doing so
• How forklift attachments work
Certification
To become a forklift certified driver, you should attend
While it might seem like it, the reality is that a forklift operator license is entirely separate from a driver's license. That means that you can have one without having the other.
If you’re looking to get your forklift license, now is a great time. The number of forklift driver jobs is escalating due to the increasing usage of counterbalance forklift trucks in the manufacturing and warehousing industries.
• Perform pre usechecks to assure the working capability of the forklift
You can apply for a course at a forklift training school to acquire an operator’s license and certificate.
• Loading or offloading items from trucks
In order to get your forklift operator’s license, you must receive:
• Hands-on training and evaluation
• How to construct, transport, stack, and unstack loads
• How do I become a forklift operator?
EAZI DOES IT. Contact us for all your Work-at-Height and Material Handling Solutions. Need a full solution provider, for all your light industrial requirements? www.eazi.co.za | www.eaziafrica.com | South Africa +27 86 100 3294 Mozambique +258 87 211 5809 Namibia +264 81 166 6031 Zambia +27 79 490 0775 Zimbabwe +263 78 722 8781










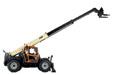



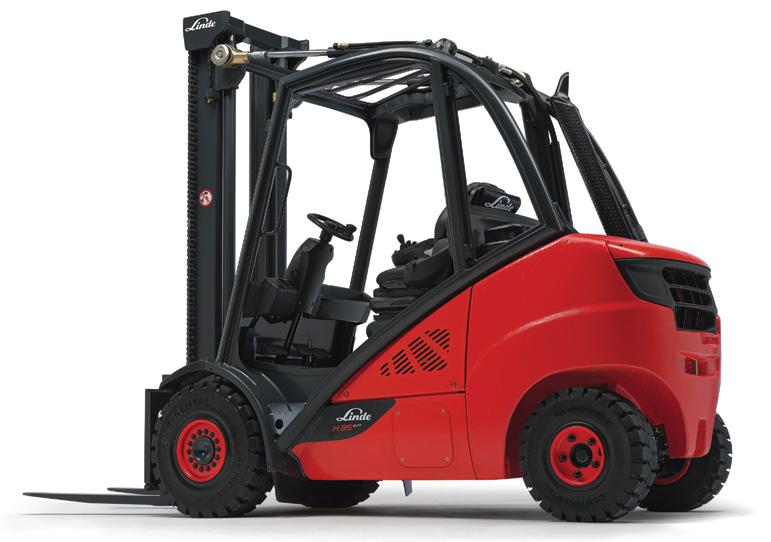
You will be required to meet a higher initial cost that may be difficult to budget. You may find it also difficult to pay for the forklift all at once.
Maintenance cost
Should you buy or rent a forklift
Lifting Africa - Forklift Guide & Register

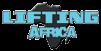
The answer to this question will make it clear if you need to buy or rent a forklift. However, there is a number of other variables that should be considered before you rent/buy Theseforklift.factors
Your own employees will also have a better opportunity of mastering it since it is at their disposal any time.
Getting stuck with an outdated model
FORKLIFTS
You are solely responsible for all maintenance cost, and this can be high depending on the mechanical issues at hand. You could end up burdened with a broken forklift that you cannot sell or return.
Tax Incentives
SARS allows you to fully deduct the cost of some of the newly purchased machinery in the first year. If your forklift fails to meet the threshold, you may file for depreciation deduction for it.
Does your forklift warranty cover repairs? Keep an eye to know for how long it is covered.
The higher initial cost may make it impossible to buy the model you want and may force you to buy a lower-cost option.
You do not need to wait for the forklift rental company to address mechanical problems or need permission to make modifications. Since you are the owner, you can sell the forklift once you are done with it, giving you an opportunity to recover some of the initial cost.
Higher Initial Cost
If your business is experiencing a decline in business or rapid growth, you can easily remove or add a forklift rental from your fleet.
Since you own the forklift, you are free to use it at any time without any obligations. With a rental, you are generally billed on the number of hours you us the lift.
What happens when a forklift becomes technologically obsolete? You will be forced to buy a new forklift long before you had budgeted for.
Pros of renting a Flexibilityforklift
Cons of buying a forklift
Renting a forklift gives your business significant flexibility with its operations.
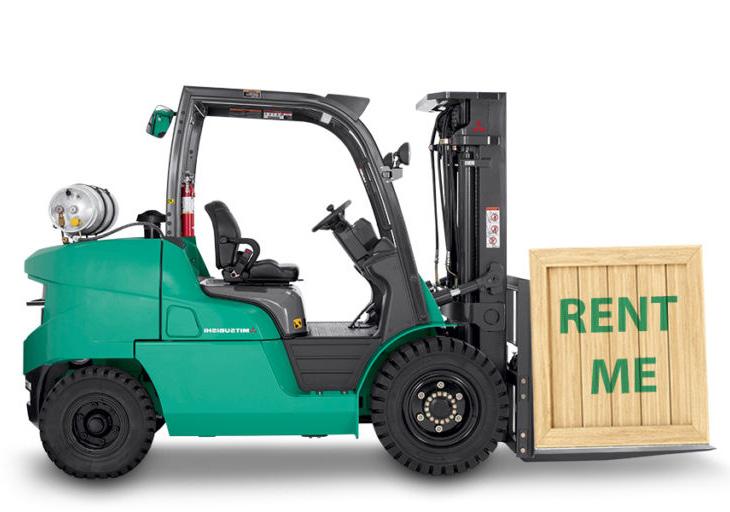
There are pros and cons for buying and renting. It’s a business individual needs and operations that determine if you should rent or buy.
No Usage Limits
Even though ownership is probably the biggest advantage to purchasing a forklift, it can also be the main disadvantage. If you buy a high-tech forklift, you run the risk that the machine may become technologically obsolete down the road.
Once the sale is complete, you will own the forklift, so you can make any modifications necessary. Maintenance is your sole responsibility, which means you have to ensure problems are fixed immediately.
How many forklifts do you run in a day?
Pros of buying a forklift Ownership
include evaluating your financial capabilities, and cost of renting v/s ownership among other factors. With all these different variables, it’s best to understand the pros and cons to help you decide which is better for your business needs.
Therefore, it is advisable to buy your forklift if your business’s location is a challenge.
Have you considered the location of your company before deciding to rent? If you don’t have a rental provider near you, you may incur huge transportation costs for delivering and picking up the forklift.
Considered alone, any of the above pros or cons could be the determinant factor in your decision.
Improved productivity
compared to buying a forklift.
Where is your business located?
Predictable monthly spending
Cons of Renting a Forklift
High monthly cost
FORKLIFTS
Renting a forklift is likely to have a high monthly cost
Renting helps your business benefit from the high performance of newer technologies without incurring the cost of buying it.
Renting allows for regular equipment replacement. This means you have a chance to use newer models of forklifts. Your employees will enjoy the safety and productivity benefits associated with newer models.
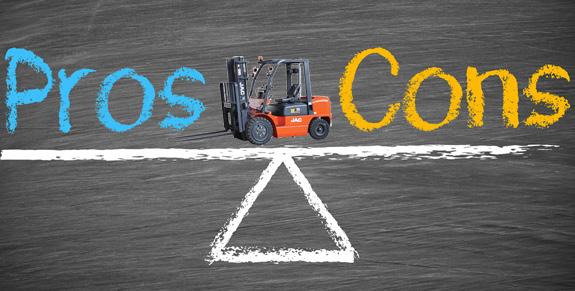
Fully understand every Pro and Con before renting a forklift
A forklift’s rental company usually supplies the most common types of forklifts. What happens if you have a specialised need? You will have to buy a forklift.
Some rental companies specify the maximum usage hours. What happens if you exceed a maximum number of hours allowed? Violation is likely to attract penalties.
That means, for instance, comparing the relative cost to your business needs or your potential maintenance services might outweigh the cost of your location (or vice versa).
If your business is new, you do not have to incur the high cost of buying forklifts. This flexibility makes it easy to scale your business and offers you room to make adjustments.
It doesn’t cater to specialised needs
However, you should take each pro and con into consideration and fully understand each before renting a forklift or buying.
Regular equipment replacement
Test new equipment
There are allowable hours of usage
Most rental programs have frequent replacement schedules aimed at reducing the average age of their client’s fleet. This gives you an opportunity to have relatively new fleet, hence reducing downtime and boosting the likelihood of peak efficiency.
Whatever your decision, just ensure you have a committed forklift rental partner who will make your rental experience more beneficial. Are you looking for products and service for material handling?
If your needs change at any given point in time, you can easily request for a different type of forklift.
Lower initial costs
Lifting Africa - Forklift Guide & Register

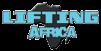
Some rental companies include the cost of forklift maintenance as part of the monthly rental fee. This is known as the maintenance package. What is the benefit of buying a maintenance package? It makes it easy for you to budget since you do not have to deal with any unpleasant surprises from forklift breakdown.
By utilizing a rental program, you can test new models without having the obligation to buying it. After the rent term, you can decide whether to buy your own or rent it once more.
The rental company charges for their equipment since they incur the cost of repairs and depreciation. They have to account for all these expenses and that is why the monthly fee of renting forklift is usually higher.
Operating safely
Why do forklifts weigh so much?
Any discussion of the basics of forklift trucks would be incomplete without a discussion of the centre of gravity and the stability triangle. One of the hardest things for lift truck operators to learn during training is how to maintain their centre of gravity within their stability triangle.
As the center of gravity for the load moves forward, the lifting capacity for the forklift decreases. The stated capacity of a forklift only applies to the load center indicated on the data plate. If the load is not centred at the specified position, the forklift's capacity will be reduced.
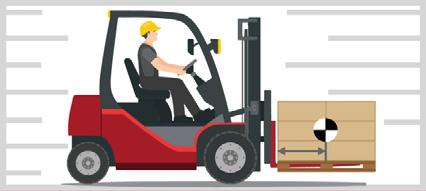
The Forklift's Centre
According to experts, overturns are the most common type of forklift accident, accounting for 24 percent of such accidents.
A forklift has a three-point suspension system. The points are found over both of the two load (front) wheels and midway between the rear wheels. When imaginary lines are drawn to connect them, what's known as the stability triangle is formed. The operator must ensure that the center of gravity of th e combined forklift and load remains within the stability triangle to guard against tipping over.
Factors such as heavy and/or unbalanced loads, driving on sloping or uneven terrain, or turning with elevated loads can result in the centre of gravity moving outside of the triangle. The result can be catastrophic.
The Load Centre
While travelling empty on a ramp, your forks should always point downhill. When carrying a load, your forks should always point toward the top of the ramp, so the load will not fall off. If a forklift starts to tip over while you are operating it, do not try to jump clear of the machine. Experts recommend staying in the cabin of the vehicle and leaning away from the direction, you're falling. Grip the wheel tightly and brace your feet.
How center of gravity is affected by the weight of a forklift, and its load:
The lift truck also has a centre of gravity, which shifts once the truck picks up a load. When the load is lifted, the centre of gravity moves forward. Care must be taken to maintain the centre of gravity within the stability triangle of the forklift by not lifting more than the maximum allowable given the load centre.
engine or another non-symmetrical item, care must be taken to estimate the center of gravity. Likewise, a large load may have a load center much farther out than 60 cm. The data plate located on your lift truck will tell you what your maximum lifting capacity is given a stated load centre and load height. If your load centre is farther out than the load centre for maximum lift capacity for your forklift, then your maximum lifting capacity is reduced, potentially dramatically.
When working, stability can be best maintained by keeping loads low to the ground and travelling with caution when turning, stopping, and starting. Also, be sure to wear your seatbelt. One area of particular concern is on ramps, slopes, or otherwise uneven terrain. Never raise a load or turn on an uneven surface. In such cases, your centre of gravity will quickly move outside of the stability triangle.
The main reason a forklift is so heavy is that it includes an internal counterweight. This is necessary in order to keep a forklift from tipping over when in use. It helps to maintain forklift balance and a stable center of gravity.
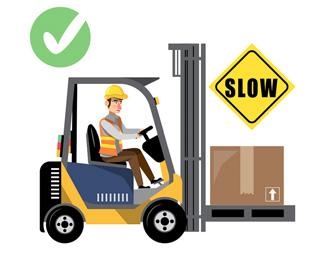
It's crucial to pay attention not only to the centre of gravity of the load you are lifting but especially to the combined centre of gravity: that of the lift truck and the load it is picking up.
Let’s start by looking at the centre of gravity of the load, which is known as the load centre. For a uniform load, such as palletized goods or a bale of material, this can be easily determined. For example, for a uniform load on a 1,2 m-long pallet, the load centre is at 60 cm, which is a common load centre for many smaller-capacity forklifts. When a load is uncentered, however, such as with an
Lifting Africa - Forklift Guide & Register FORKLIFTS WEIGHT
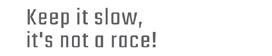

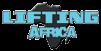
Bell1650 Tel: +27 (0)11 928 9700 • E-mail: sales@bellequipment.com • Web: www.bellequipment.com Bringing you the winning combination of premium products and a great distribution network. Wanting to reach new heights? CONSTRUCTION Choice of mast heights, attachments and carriage types so you can adapt the machine to your needs ROUGHFORKLIFTTERRAIN A powerful package loaded with versatile features to set new standards of efficiency and productivity SKID STEER The best features of a mobile crane, wheel loader and a forklift in one efficient package TELEHANDLER
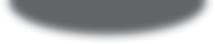

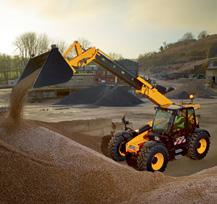
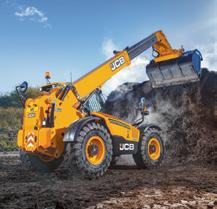
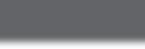
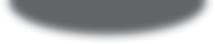

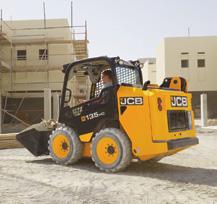
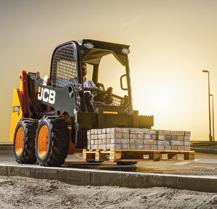
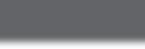
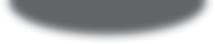

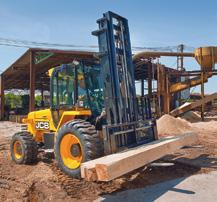

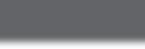
All forklifts including attachments & special equipment
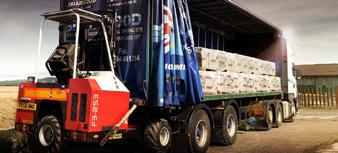
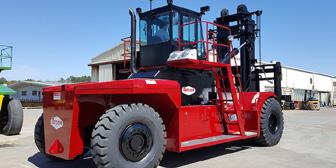
Large lift trucks
As per national code of practice
Counterbalance Forklift
Truck-mounted forklift
The truck mounted forklift is a very versatile forklift. It is mounted on the back of a truck and can be carried to the worksite and dismounted there to unload the product right at the site making it unnecessary for the customer to have a forklift at the construction site. Handy for deliveries, this lift truck offers flexibility and portability for on- and offloading on site. It’s “piggy-backed” on the rear of any truck or trailer combination.
Lifting Africa - Forklift Guide & Register

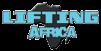
There are two main variations of counterbalance forklifts:
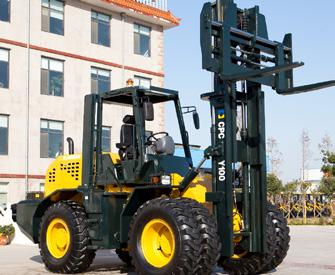
Rough Terrain Forklift Also known as a straight mast forklift, the rough terrain forklift is designed specifically for outdoor job sites. These trucks have sturdy pneumatic tires that are oversized and threaded, giving them better balance and stability to safely transport materials on rocky ground. These rugged machines are designed to be driven over uneven and rocky surfaces, while still transporting a heavy load. Due to size, tyres, and weight capacity, a rough terrain lift is primarily used outdoors.
TYPES OF FORKLIFTS
Pallet truck
2. Battery electric counter balance forklifts
The term counter balance forklift is derived from the design of the unit where the forklift has a heavy counterweight that off-sets the weight of the load being carried on the tyres out in front.
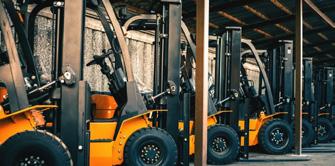
Types of forklifts
Without the counterbalance forklifts would become extremely unbalanced when picking up heavy loads with a heightened risk of the unit tipping forwards or over with the extra weight of the load on the tynes.
As the name suggests, large forklift trucks are a subsection of forklifts that are far larger in scale than their compact cousins. Typically powered by diesel, these large-scale machines are built explicitly for shifting larger loads in larger workspaces. These trucks are available in capacities ranging from 5 000 to 60 000kg. They are commonly used for container handling and very heavy loads. Types of trucks in this category include Counterbalanced FLTs, Reach stackers; and Straddle carriers.
1. Combustion engine counter balance forklifts
A pallet truck (also known as a Walkie, Walkie-rider or Rider motorised truck, pump truck or pallet jack) is a wheeled trolley designed to lift and transport pallets. The truck's tapered forks slot underneath the pallet and the pump handle can then be used to raise and lower the load. Pallet trucks are commonly seen in warehouses, stockrooms, and other environments where wooden pallets are frequently used. There are many different types of pallet truck available to suit all sorts of different requirements.
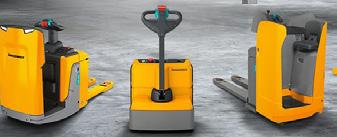
All Rough Terrain Forklift trucks
In combustion forklifts, the counterbalance is integrated to the rear of the unit, whilst battery electric forklifts are counterbalanced through the additional weight of the batteries installed into the unit.
Pedestrian controlled lift trucks
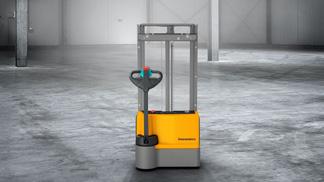
The main advantage of reach trucks is that they are very efficient in small spaces, are commonly available and are relatively simple to use.
These forklifts are very common in warehouses and factories. They are designed to be a highly efficient method of storage as they operate in narrow isles.
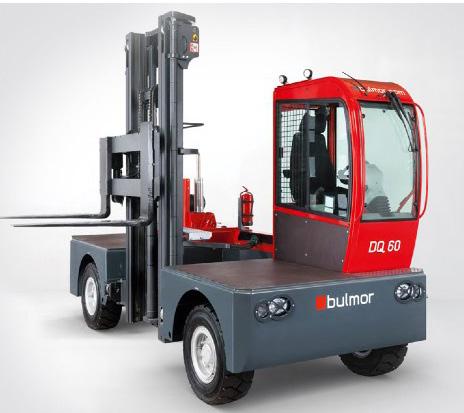

To provide quality services with an outstanding level of customer service through committed and well motivated staff To earn the trust of both our stakeholders and customers To provide solutions which are created in terms of our operational involvement in an understanding of the industry To have the required skills expertise and knowledge by employing the right people and partners To acquire technologies to fast track our total solution offering where needed To make the client s needs and wants core to our V I S I O N : M I S S I O N : C O M P A N Y P R O F I L E 2 0 1 8 D E S C R I P T I O N W W W B L U E D O T L I F T I N G C O Z A B L U E D O T L I F T I N G L O A D , B R A K E & N D T E S T I N G ( P T Y ) L T D Blue Dot s Inspection and Load test scope of Lifting machinery includes: Lifting Tackle Chain Block and Lever Hoists Overhead and gantry cranes Lift trucks Mobile Cranes Mobile elevated working platforms Tail lifters O N E S T O P S E R V I C E I M P R O V E D T U R N A R O U N D T I M E F L E X I B I L I T Y C O N S I S T E N C Y I N P R O C E S S E S Registered as a (Lifting Machinery Entity) LME The team has more than 30 years experience in customer support and business management and We provide accurate and timely test results in accordance with SANS standards We guarantee Customer satisfaction (2017/103862/07) V I S I O N : M I S S I O N : B L U E D O T L I F T I N G L O A D Blue Dot’s Inspection and Load test scope of Lifting machinery includes: Lifting Tackle Chain Block and Lever Hoists Overhead and gantry cranes Lift trucks Mobile Cranes Mobile elevated working platforms Tail lifters O N E S T O P S E R V I C E I M P R O V E D T U R N A R O U N D T I M E F L E X I B I L I T Y C O N S I S T E N C Y I N P R O C E S S E S Providing quality services with an outstanding level of customer service through committed and well motivated staff. Earning the trust of both our stakeholders and customers. Lifting Tackle Chain Block and Lever Hoists Overhead and gantry cranes Mobile Cranes Lift trucks Tail lifters Blue Dot’s Inspection and Load test scope of Lifting-machinery includes: All our testing is done in accordance with the relevant SANS Standards by our certified LMI`s 062 629 2016 / 086 225 3786 / www.bluedotlifting.co.zainfo@bluedotlifting.co.za
A pedestrian-controlled lift truck (low-lift platform truck, elevating truck) contains a platform which is supported pivotably via a base frame inner toothed racks and outer toothed racks. This is arranged on both sides below the base frame and is connected via pinion shafts and cranks. A first motor drive is controlled in such a manner that the inner toothed racks and the outer toothed racks are moved in an opposed direction in order to execute a step-up or step-down movement. A pendulum and two micro switches control a second motor drive in order to move a balancing rod in any direction so that the platform is always held in a horizontally balanced manner when the pedestrian-controlled lift truck is moving up or down steps.
TYPES OF FORKLIFTS
Side loader forklifts are powerful industrial trucks that lift loads from the side, so they are well suited to carry wide or long loads. Narrow aisles, which may be a problem for regular forklift trucks, can be easily navigated through in a side loader.
Lifting Africa - Forklift Guide & Register



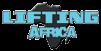
Side loaders
They come in handy when long loads need to be transportedsuch as pipes, and lengths of timber.
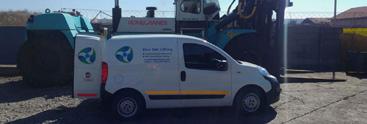
A reach truck is a narrow-aisle, right-angle stacking truck designed for unit load handling with rack interface. These lift trucks are meant to operate in narrow aisles and are best for storing and retrieving pallets in racks. They are engineered with two outer legs that help distribute the load weight, and a single set of wheels in the back.
Reach trucks
Diesel side loaders are often used in rough terrain whereas the electric powered models are used indoors on smooth surfaces.
A gas forklift is equipment that has its own driving force, through the operation of its engine. This, in turn, is activated by the chemical reaction that occurs between a substance and a gas (oxygen), that is, by combustion. The combustion forklift can have several applications. As it is a strong machine that remains efficient, even in different terrains and temperatures. It is recommended to use in open places, such as carriers and warehouses, for safety reasons. Despite the recommendation to be used outdoors, it emits much fewer pollutants and risks than a diesel forklift, for example. As long as there is ventilation, it is possible to operate this machine in places where there is less ventilation, in a safe way.
Resistance:
A big advantage of the gas forklift is that it has enough strength to move very heavy loads without losing speed and balance. The strength of the gas forklift is greater than that of other types of forklifts. Some models of combustion forklifts are capable of supporting up to seven tons.
Lifting Africa - Forklift Guide & Register GAS FORKLIFTS

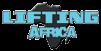
Speed:
The gas forklift reaches a higher speed than other types of forklifts such as diesel powered or electric. Speed, in this case, can be a great ally, because, as a large amount of displacement can be done per day, the operation saves a lot of time in its entirety.
The gas forklift has more power than other types of forklifts, which makes it possible for them to move easily on any type of terrain.
Greater Potency:
Move heavier loads:
It can be used in practically all types of terrain and is resistant to climatic variations and adversities. The costeffectiveness of any type of forklift depends solely on the use you make of it. The gas forklift allows possibilities that other forklifts. Do not, due to its agility and high lifting capacity. Evaluate whether this type of forklift is worth it for you and your company. Keep reading!
The cost-benefit of the gas forklift
These forklift models, being strong and quite powerful, are much more resistant to adverse conditions that may arise during use. Setbacks, with rain, mud, cold, humidity and other types of weather possibilities are not a problem for a gas powered forklift.
A combustion forklift can easily use terrain with slopes, very rough, with mud and other changes due to the climate.
Lifting capacity:
Another very interesting feature, which makes people opt for the gas forklift, is the lifting capacity. This forklift potentially lifts loads up to 6 meters high. This makes many companies prefer or specifically need a gas powered forklift.
What is a gas forklift?
The range of possibilities for using a gas forklift is very wide, as it is stronger. More powerful and faster compared to other types of forklifts.
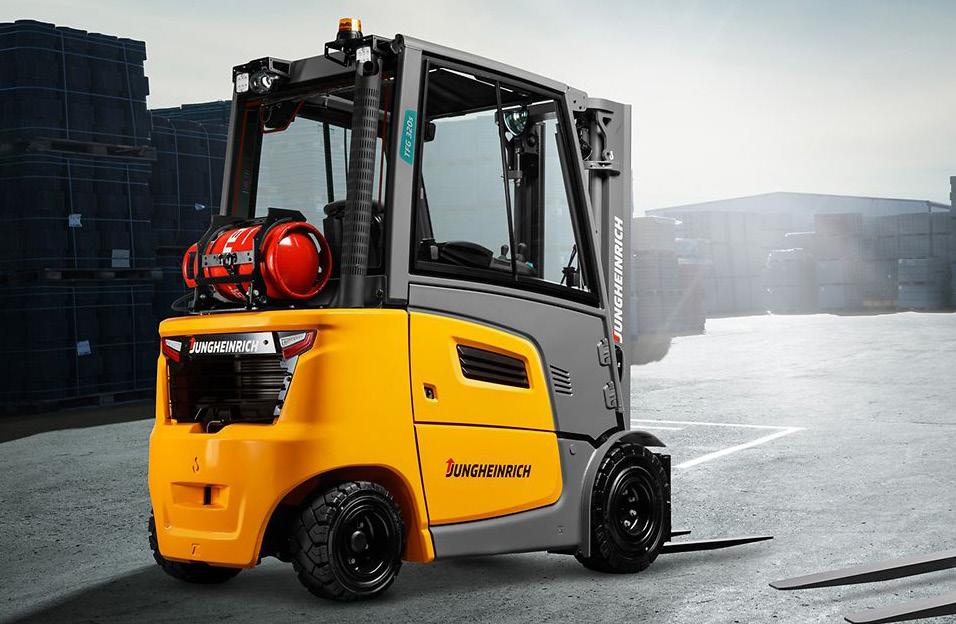
Forklifts, like most things, can decline over time with regular use. When it comes to forklifts, the purchase price is not the only cost to consider. The cost of ownership of your forklift can be affected by fuel, maintenance, labour, electricity and incorrect use of the material handling equipment.
Oils, tires, water and safety items like seatbelt, rating plate, and mirrors should be checked before every shift to ensure top performance of your forklift and safety of your employees.
lift motor, it could mean your lift truck is not being used correctly. A more appropriate piece of equipment, like a pallet truck or pallet jack, could be used in its place.


Also, be sure your industrial forklift batteries are watered after five to ten charges depending on the age of the battery.
Maintenance contract benefits


For optimal performance, it’s important to take care of the forklifts in your fleet.
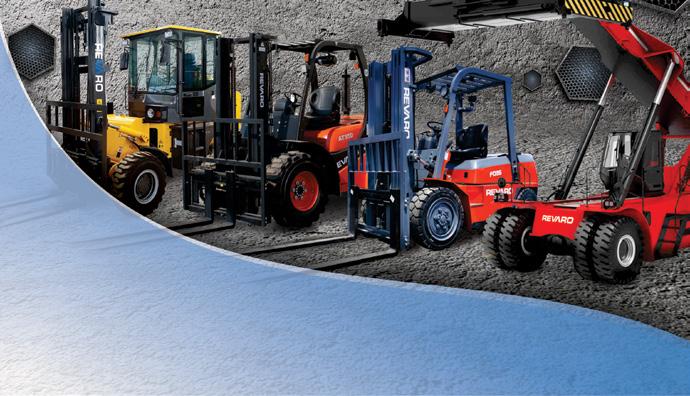
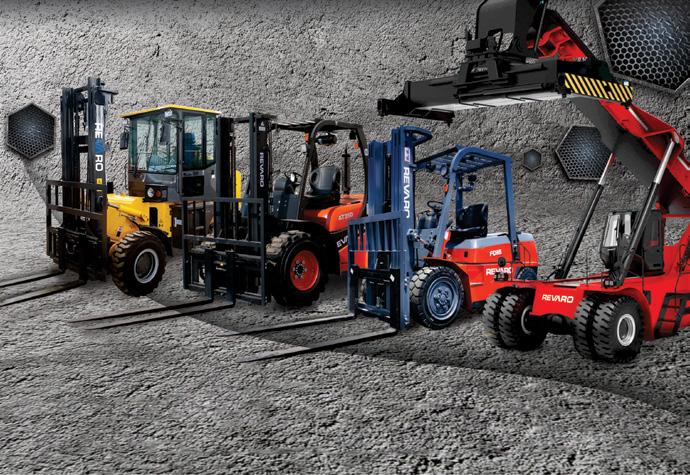
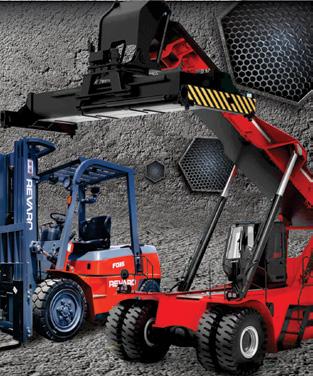
If you are not sure of what voltage the battery is, count the cells and multiply that number by two.

















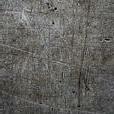
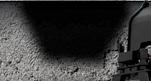



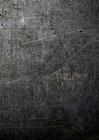
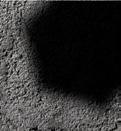
DMR18 requires that every forklift operator perform a pre-operation inspection prior to their shift to make sure everything is working properly.
Lifting Africa - Forklift Guide & Register MAINTENANCE

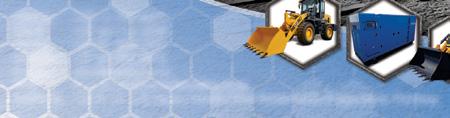
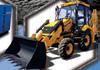



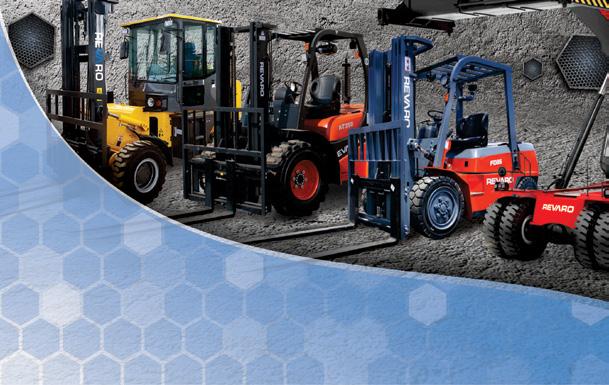

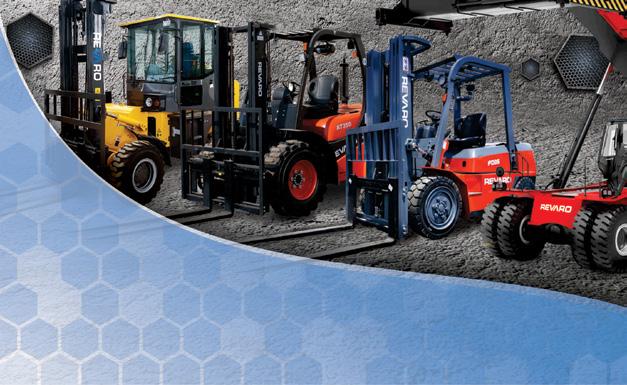
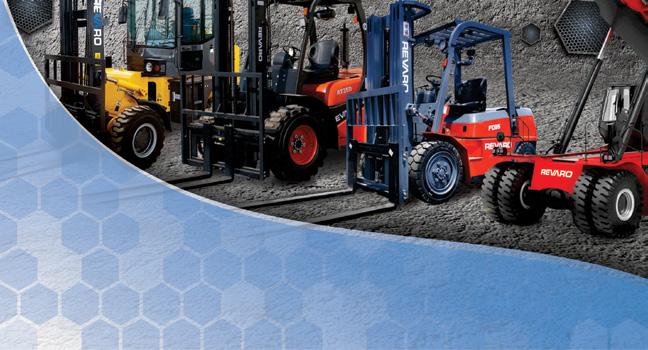
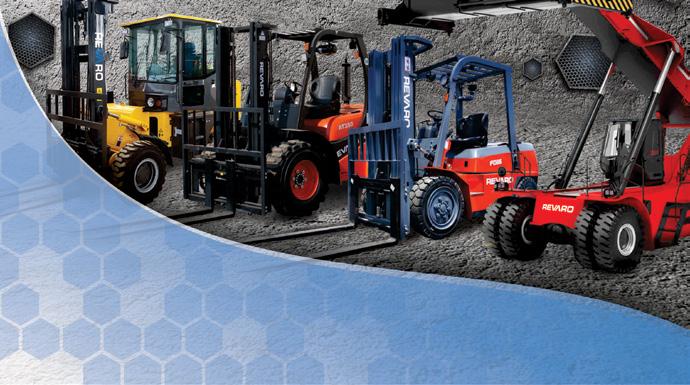

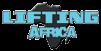
Be sure you are using the correct equipment for the task at hand. You can use data to measure this. Turn on your forklift and take a look at the hour meters.
If the drive motors have considerably more hours than the













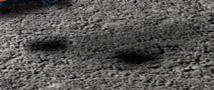
A forklift can do a lot of damage to a building, warehouse racking, the operator and or other people if the forklift driver is not fully competent on how to operate a forklift Forproperly.thisreason, it is important to properly train all warehouse employees that operate forklifts. This training will not only allow the driver to get familiar with the equipment, it will also teach them what to look for when the truck is not operating in prime condition.
Damaged batteries, forklifts or injuries can result from improper battery handling. A mistake that often happens is mismatching the voltage size of battery to the charger.
Train your forklift operators
Complete your daily checks




Pay attention to application of your equipment


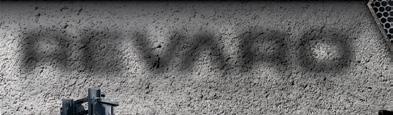
If your material handling warehouse runs on electric forklifts, it is important to take care of your batteries.

The easiest way to ensure this is by adding a scheduled preventative maintenance plan to your forklift fleet to make sure your forklifts are in prime working condition. Over time, this preventative maintenance will save you from money lost from downtime and costly major repairs.
Make sure your batteries and chargers are taken care of if you run electric forklifts
Prevent expensive repairs with a forklift maintenance




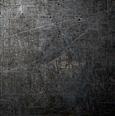
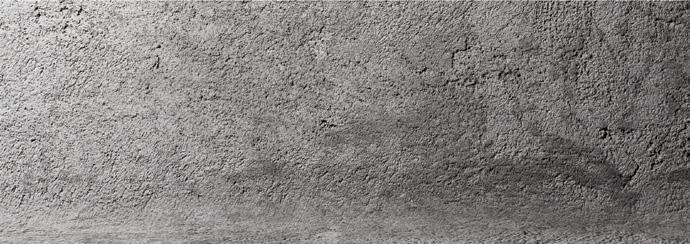
In order to accurately test the capacity of your forklift battery, it’s important to use a battery monitoring device with the right capabilities. It is a compact and wireless electronic device that attaches right to your industrial battery to provide real-time diagnostics on battery capacity, including:
Keeping your motion power equipment fully operational is essential for ongoing warehouse operations. However, your equipment can’t function properly without a wellmaintained forklift battery. A battery test makes it possible to identify weak cells, faulty intercell connectors, and other red flags that indicate repairs are needed before the battery stops working entirely.
If you don’t prioritise battery maintenance, it can result in decreased productivity for your entire warehouse. Think about it—if you have to keep stopping operations to switch out underperforming batteries, it results in extra downtime. This ultimately reduces the amount of time your forklifts are actually able to move cargo, which is what generates value for your business.
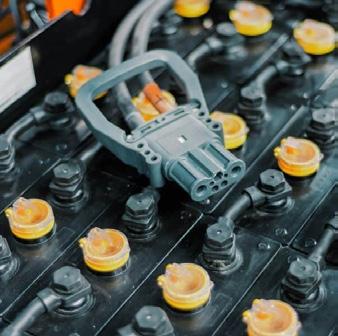
What is battery capacity?
How to test battery capacity
Lifting Africa - Forklift Guide & Register BATTERY

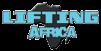
When you purchase a brand new battery, it will come with a battery rating that identifies its capacity. But, because cells age, that rating will no longer be accurate once the battery has been used more than a few times. So, to get an accurate idea of your battery’s true current capacity, you must perform routine capacity tests.
Performing routine battery maintenance is the key to keeping your batteries, and therefore your equipment, running as they should be. Battery capacity testing should be an essential part of that care plan. So, here are the basics of why testing battery capacity is so important and how it can be done!
• Electrolyte and water levels;
• Total discharge time.
This data can then be downloaded to any PC or laptop quickly and with ease. You can even consolidate data into various reports so you can analyze your entire battery fleet at one time. This can help you identify patterns in your battery usage. Plus, it reports battery faults and warnings that could easily be missed manually.
A battery’s capacity is essentially a measure of the energy it can store. When conducting a battery capacity test, you're examining the battery's ability to deliver a “specified amount of current at a constant rate to a specified end voltage for a specified time.”
To have smooth operations in your warehouse, your motive power equipment must be fully operational at all times. As the power behind your equipment, your batteries must also be operating at optimal efficiency.
• Battery voltage, current, and temperature;
Why is it important to test battery capacity?
How to test battery capacity for your forklift

Battery capacity testing helps you avoid this wasteful downtime by helping you determine where your industrial battery is on its predictable life curve. This way, you’ll know when it is about time to replace a battery. This way, you can acquire new batteries proactively before the old ones stop functioning during use and completely halt your operations Overall, battery capacity testing helps you maximize forklift battery performance so you can get the full useful life out of your industrial batteries.
• Number of charge cycles; and
EQUIPMENT THAT DOES IT ALL | GROUND-BREAKING | | EXCAVATING | | COMPACTING | | CRUSHING | | SCREENING | | LIFTING | | HANDLING | Headsales@kemach.co.zaOffice:0118266710Contactus:www.kemach.co.za
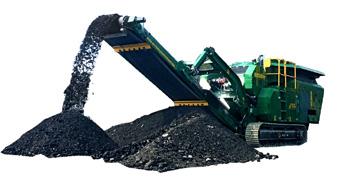

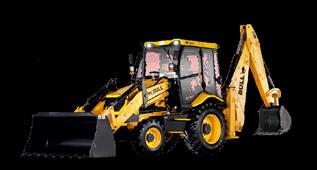
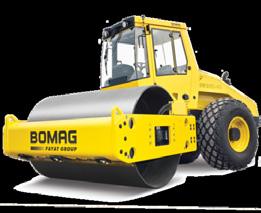
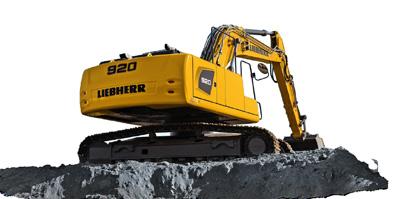
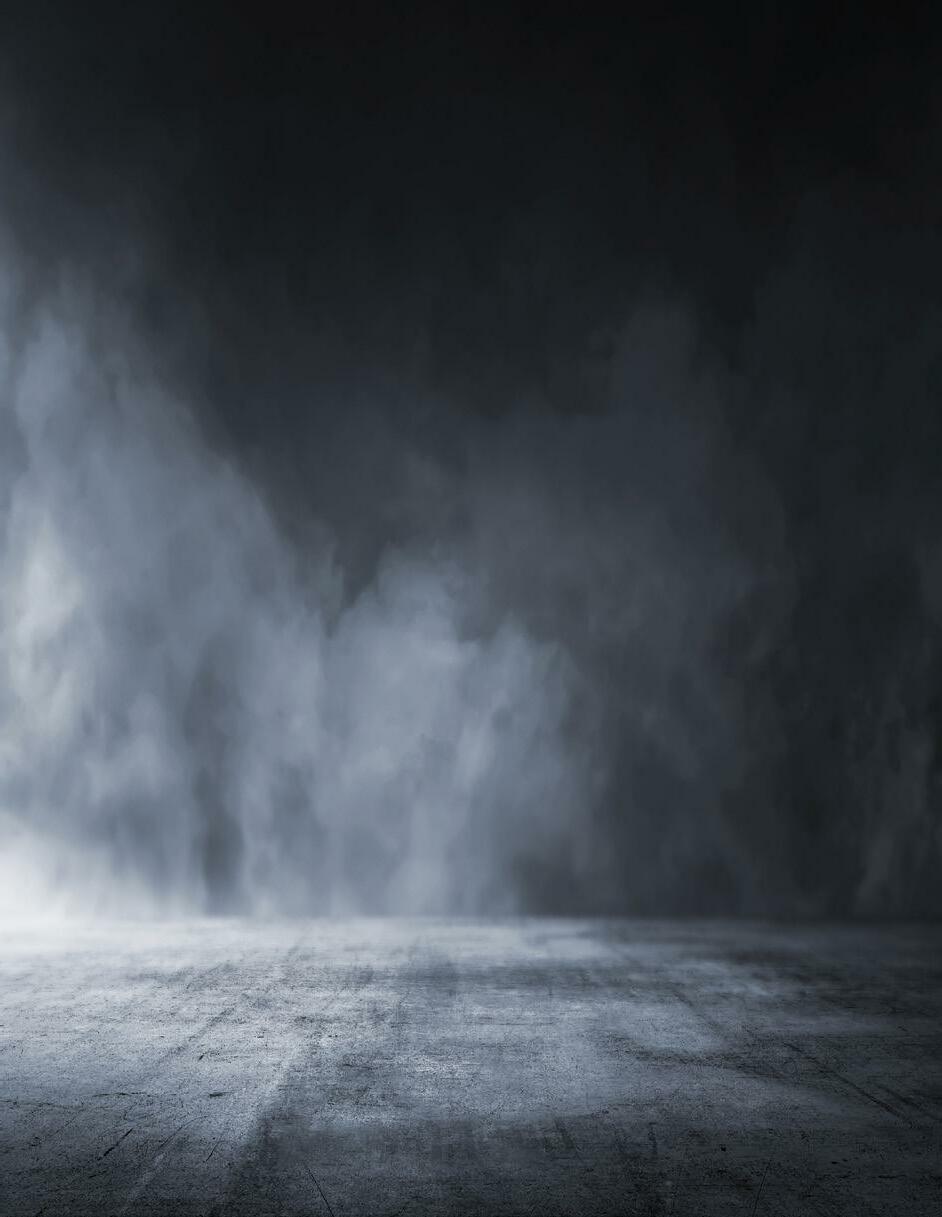
Safe forklift driving is all about what to keep your eye on –and also, specific things to avoid.
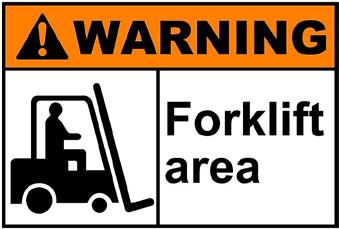
Forklift safety do’s: tips & tricks for drivers
Do’s and Don’ts on a forklift
Do wear a seatbelt. Buckle up any time you use a lift. Because, if you fail to do so, you risk falling out of a lift, particularly if you are using the lift on bumpy terrain.
Doabove.get a feel for your surroundings. If you’re working in a new area, take a quick inventory of blind spots, entries & exits, pedestrian walkways and more. The great unknown is never a good place to operate a forklift.
When it comes to forklift safety, there are many things that lift operators should do day after day, such as:
Workplace safety depends on a combination of factors. Attentive supervision helps. So does comprehensive training, with a keen eye toward DMR 18 rules & regulations. But at the end of the day, safety is ultimately determined by each individual.
Do travel with a load at axle height. By keeping the load at axle height, a forklift operator can minimise the risk of an accident.
One of the most important parts of safe forklift operation is training. Without proper instruction, operating powered industrial trucks (forklifts, pallet jacks, man lifts, etc.) is a dangerous undertaking. Accidents and injuries are bound to happen without a comprehensive training program in place
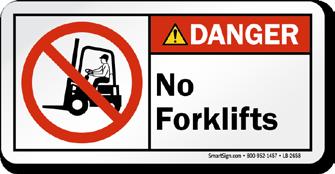
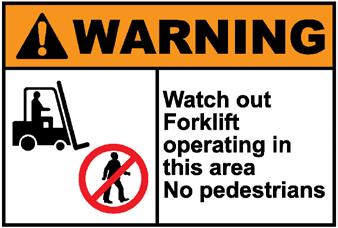
Lifting Africa - Forklift Guide & Register

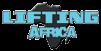
Don’t exceed a lift’s rated capacity. Weigh a load before you use a lift to raise or lower it. Under no circumstances should a load exceed the lift’s rated capacity; otherwise, if the load is too heavy, it may cause a forklift to tip over.
Do ensure forklift load is secure, especially on inclines and other tricky surfaces. If you operate forklift outside, pay attention to the terrain conditions, especially when it’s raining or snowing.
Forklift safety don’ts: what not to do on a forklift
Now that you have a good idea of forklift do’s, it’s time to learn about some forklift don’ts.
Do use three points of contact when getting on or off a forklift. Use two hands and one foot or one hand and two feet as you climb up or down a lift. In addition, you should always face the lift any time you enter or exit.
MAINTENANCE
Don’t carry or raise loads while the lift is moving. Only raise or lower loads when a forklift is stopped. Also, loads should never be raised or lowered while a forklift is turning.
Do follow your company’s safety guidelines. Established policies & procedures are in place for a reason. They work. Do take your scheduled break. Fatigue is another big factor in workplace mishaps. Tired forklift drivers are more dangerous forklift drivers. It’s all about avoiding distractions and keeping focus – see “correct clothing”
And that means forklift drivers should act in the best interests of total job safety. Sure, performance matters, but safety is the most important part of day-to-day forklift driving.
Do carry loads with the lift’s forks tilted back. Forklifts are top-heavy, so you need to ensure that the lift’s forks are approximately 15 – 25cm above the ground to avoid potential ground hazards.
What to do – and what not to do on a forklift
Do wear the correct clothing. If you’re driving outdoors in the winter, hats, gloves & extra layers always help. Don’t think you can brave the cold or harsh elements – a distracted forklift driver is more susceptible to accidents!
Don’t use a forklift if it does comply with operational standards. Use an inspection checklist to verify the quality of a forklift and ensure that it meets DMR18 standards. If a
Don’tscenarios.bea
Don’t leave a forklift unattended. Remember, anyone can access an unattended forklift, which can lead to an accident.
If you’re serious about safety, take charge of the situation. Form a safety committee. Sign up for training. Be proactive!
MAINTENANCE Complete intralogistics from a single source. This is how we move industries. We develop, produce and sell new trucks and are also involved in the logistics system and mail-order business. In addition, services. Add to this a comprehensive range of financial services, and you can see that we represent a one-stop shop covering the entire product life cycle. info@jungheinrich.co.za | 010 596 8460 www.jungheinrich.co.za
protocol for the renewal certificate. Don’t ignore spills, poor lighting and other hazards.
And speaking of lists, keeping a well-documented checklist of forklift maintenance activities is a great way to ensure all safety checks are accounted for! Don’t forget your forklift certification renewal. If you’re training credentials are about to expire, make sure you go through the correct
Don’t skip forklift maintenance. Many accidents are the direct cause of poorly maintained lifts.
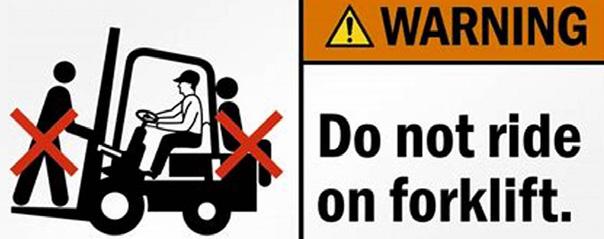
Don’t think everything’s a one-man job. Sometimes, having a spotter or “eyes in the back of your head” can help avoid accidents. The buddy system works! Many accidents have been caused by not using a spotter or other driver to help with heavy loads, blind spots, and other dangerous
Safe drivers always alert their co-workers and supervisors to potential pitfalls.
forklift is not up to code, the lift should be taken out of use until it is repaired.
follower. Proper safety requires leadership –the willingness to speak out when you think something’s wrong, and also going the extra mile.
Lifting Africa - Forklift Guide & Register


Loose hoses, bald tires, non-working safety signals and more – when talking about forklift do’s and don’ts, maintenance should be at the top of your list.
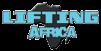
• When the tyre is worn down to the safety line
MAINTENANCE
Lifting Africa - Forklift Guide & Register

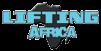
machines in many work environments. They perform a variety of jobs that can make a warehouse or other job site more efficient and productive. Yet, they also cost a lot to buy and maintain, and most don’t have a very long service life. That’s why the decision to repair or replace a forklift is so important.
• Type of forklift. Electric forklifts tend to last longer than those powered by gas, diesel, or propane. They have fewer moving parts to wear out and need fewer repairs.
can still do the job. It ends when no amount of repairs can keep it going. The economic life is the time for which it makes economic sense to maintain the forklift. This ends when it costs more to repair the forklift than to purchase a new one.
• The average use of a forklift is around 2,000 hours per year. More use than that will require more frequent maintenance and repairs. Forklifts that work longer shifts will wear out sooner.
The average lifespan of a forklift is around 10,000 to 12,000 hours. This comes to about seven years of daily use. Some high-end forklifts have a lifespan of 20,000 hours or more. Many factors can affect how long a truck lasts before needing forklift replacement. These include:
Many companies use planned forklift replacement. This involves replacing a truck when it reaches a certain age, regardless of its condition. This approach takes the guesswork out of repair versus forklift replacement decisions. It makes it easier to budget for the cost of buying or leasing a new truck. It also improves performance and safety by having new and efficient forklifts. The downside to this approach is that you may get rid of trucks that still have several years of service life left in them.
Worn forklift wheels and tires present a real safety hazard. They should always be replaced rather than repaired. It’s time for forklift wheel replacement when you spot any of these signs:
Timely maintenance will help ensure your forklifts have a long service life. Using forklift replacement parts can also help. Parts most often replaced tend to be engine components. For example, oil and air filters, chains, and spark plugs. Other parts can be replaced as well, ranging from driver seats to tires, forks, batteries, and more.
Forklifts actually have two types of lifespans – economic and useful. The useful life is the amount of time the forklift
Planned forklift replacement
Forklift replacement parts
One common forklift replacement part is the driver’s seat. When seats get worn out they become uncomfortable to the driver. This can cause distractions that lead to accidents. Forklift seats are hard to repair unless the damage is minor. Forklift replacement seats are often the better choice because they improve productivity and safety. Some forklift replacement seats come with built-in safety switches to make sure drivers put on their seat belts before starting a job.
If an old truck is in good condition and can likely provide two or three more years of use, repairing it may be the better option. After a certain point, older machines will start having performance problems, higher operating costs, and other expenses.
Forklift replacement: the lifespan of the truck
Forklift wheel replacement
When to repair or replace your Forkliftsforkliftareimportant
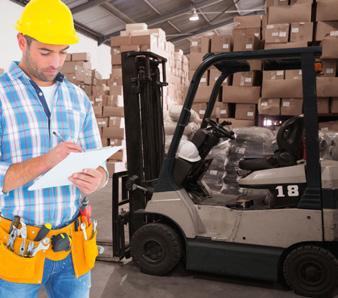
It would seem the best time to replace a forklift is when it reaches the end of its operational life. But this isn’t always the case.
• The tyre has damage in the form of chunking, tearing or cracking
Most of the time, it is more cost-effective to repair rather than replace. But sooner or later trucks will wear out. That’s when forklift replacement becomes a safety issue as well as an economic one.
• Flat spots on the tyre
• Work application. Forklifts used in rough terrain or harsh environments are exposed to more wear and tear. This results in a shorter lifespan. Frequent accidents can also cause excess wear, which can shorten the life of a truck.
• This is the biggest factor in the lifespan of a forklift. Nothing will extend the life of a truck more than regularly scheduled maintenance.
Forklift replacement seats
• Less than 2cm from the lettering on the tyres to the top of the tires
• The fork blade shows signs of wear.
There are different types of forklift tyres. When making a forklift wheel replacement, be sure to get the correct type for your truck. Never have different types of tyres on a forklift.
• Surface cracks.
Look for these signs when inspecting the safety attachments:
• Abrasions; blisters; nicks; cracks; cuts; hardness, or color changes.
• There is a difference in height.
• Reduced repair costs from less frequent equipment breakdowns.
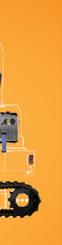
• Directional signals and brake lights do not light up.
• Increased life expectancy of forklifts and other equipment.
• Improved use of in-shop maintenance personnel with less emergency work.
• Less downtime with equipment that is being repaired with scheduled inspections.
Forklift repairs
Your sound judgment combined with regular checks will ultimately determine when your forklift needs to be repaired and replaced
• Additional areas to inspect on a forklift before operating include:
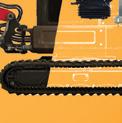

• Make sure the fuel tank is secure, the valve opens, and check the fuel level.
• Seat belts and similar restraints are torn.
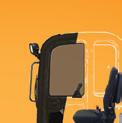
Lifting Africa - Forklift Guide & Register MAINTENANCE WWW.TVH.COM/CONSTRUCTIONCOUNTLESSPARTSONESCAN TVH PARTS HOLDING NV Brabantstraat 15 • 8790 Waregem • Belgium T +32 56 43 42 11 • F +32 56 43 44 88 • info@tvh.com • www.tvh.com LiftingAfrica_ADVE_032022.indd 1 23/03/2022 14:46

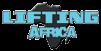
• Twisting or kinking–make sure there is enough slack to allow for length changes under pressure.
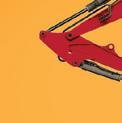
• Look for these signs when inspecting hoses that need repair:
Here are a few of the many benefits you can experience with preventative maintenance:
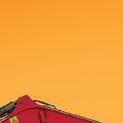
• Increased control of spare parts inventory and reduced parts usage.

• Reduced number of injuries and fatalities.
• Make sure the fuel tank is not dented in any area.
• The radiator’s coolant levels and for leaks.
• The positioning lock isn’t in working order.
• Fewer costs are given to premature purchases of new equipment.
• Warning lights do not flash.
• The fork angle from the blade to the shank is not straight.
• Contact with other hoses or metal parts.
• Mirrors are broken.
• The blade or shank isn’t straight.
• Leaks—look for puddles of fluid around the equipment, low fluid levels in the reservoir, or greasy/dirty hoses.
Forklift repairs are easier and less costly when they are performed as soon as the damage is noticed. The best way to do that is with daily inspections. When checking the forks, if you see any of these signs, they need to be repaired or replaced:
• Close proximity to a high heat source.
• Make sure the overhead guard isn’t damaged.
• Efficient production.
• The fork marking is not readable

• The air cleaner indicator—clean or change it as needed.
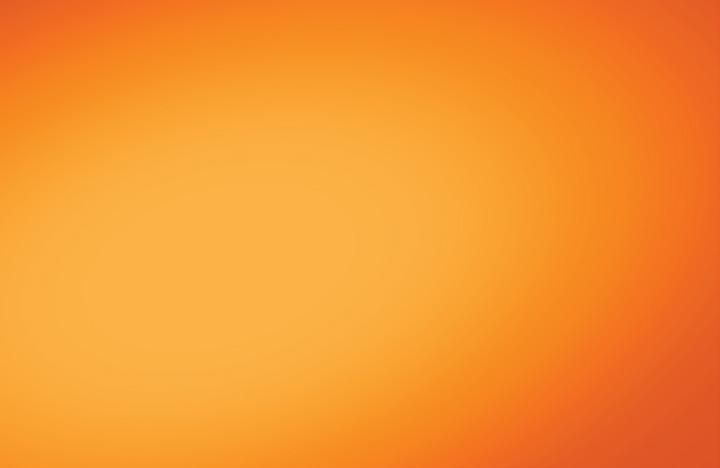
Fuel:
• There is wear on the fork hooks.
Once you’ve finished performing these maintenance checks, you may wonder if they are truly worth it.
• Horns and backup alarms do not sound when the forklift •moves/reverses.Thefireextinguisher has expired—the seal on the neck has weakened.
• Check the hydraulic tank’s oil level for any leaks.
Every year nearly 100 workers are killed and 20,000 are seriously injured in forklift mishaps.
• Uses a forklift that is not safe due to malfunctioning, or missing parts.
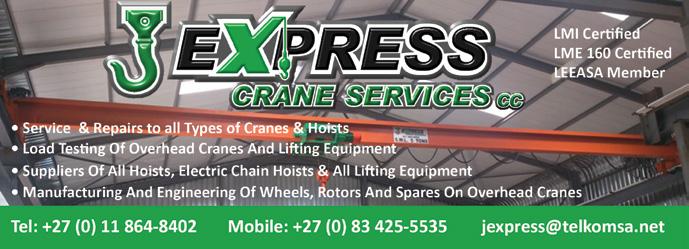
Lifting Africa - Forklift Guide & Register

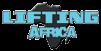
• Has not been trained in the principles of physics that allows a forklift to lift heavy loads
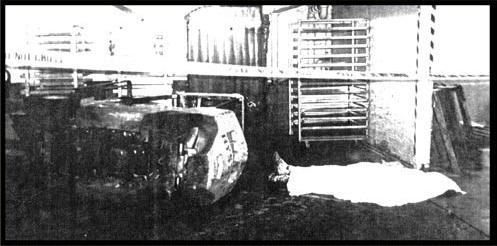
• Is not familiar with how a particular forklift operates,
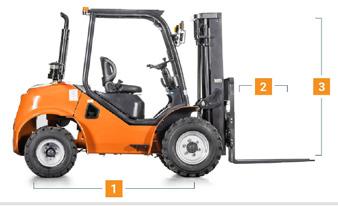
• Operates the forklift carelessly
Using a tool such as a forklift, cart or hand truck instead of lifting and carrying items by hand can reduce the risk that you will suffer a back injury.
A forklift is a powerful tool that allows one person to precisely lift and place large heavy loads
According to the National Traumatic Occupational Fatalities (NTOF) Surveillance System, 1530 workers died from forklift related accidents between 1980 and 2001.
However, there is great risk of injury or death when a forklift operator:
The top four types of incidents as a percent of the total forklift related deaths are:
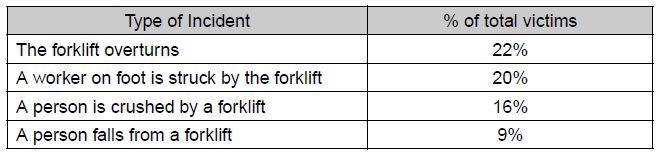
A forklift operator was struck and killed by the overhead guard when he attempted to jump as the forklift overturned.
MAINTENANCE
Tel: 011 023 5448 | info@optimasolutions.co.za Specialists in Warehouse Racking Maintenence


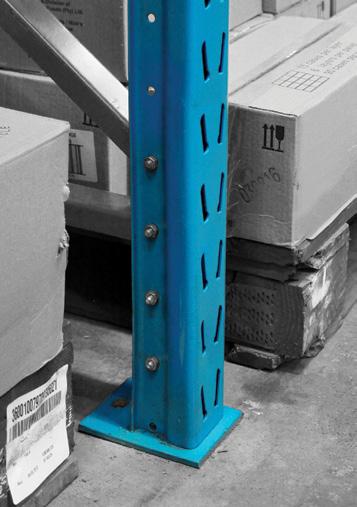


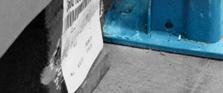
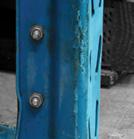
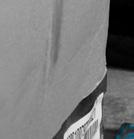
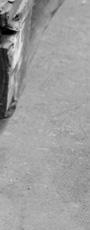


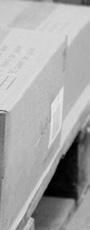
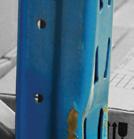
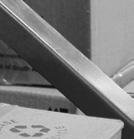



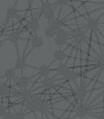
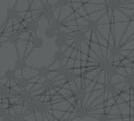
• Install guard rails. Guard rails can save a company money and keep employees safe by protecting the most vulnerable, high traffic areas around pallet racking. Corner uprights are particularly in danger of collision with lifts; having guard rails eliminates that risk. Whether a company chooses removable guard rails, or the permanent, double barred type depends on their environment.
• Do not “cheap out” with a pallet racking system. Pallet racking is a significant safety concern in a warehouse as there can be cumbersome items sitting high above the heads of workers. If racking becomes overloaded because poor quality racking cannot handle the load given, it will break. Also, if a business bought drive-in racking to save on costs, then had to switch to a FIFO (first in, first out) model instead, it would cost them unnecessary time and money to replace.
Here are several do’s and don’ts to consider when it comes to pallet racking systems: Pallet Racking Systems: What to Do
• The number one consideration for choosing a pallet racking system is size. Not the size of the system, but the total floor space and vertical space the warehouse has to accommodate a pallet racking system. There are several pallet racking systems available:
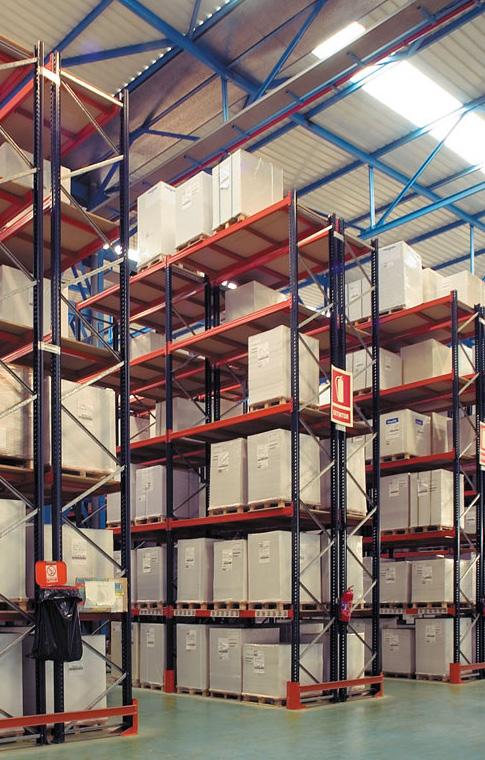
• Do not buy just what you need. Flexibility for a growing business is critical, and only buying just enough racking for current need is a mistake. Buying enough racking to suit only current needs could pose problems in the future. For instance, there could be compatibility issues between the racking systems if there is a significant period between the purchases.
Conclusion
The Do’s and Don’ts of Racking
When it comes to installing and maintaining a pallet racking system in a warehouse, there are a host of critical factors to understand to ensure safety and promote efficiency. An adequate understanding of what a pallet racking can and cannot do will not only eliminate accidents but can also save a business time and money.
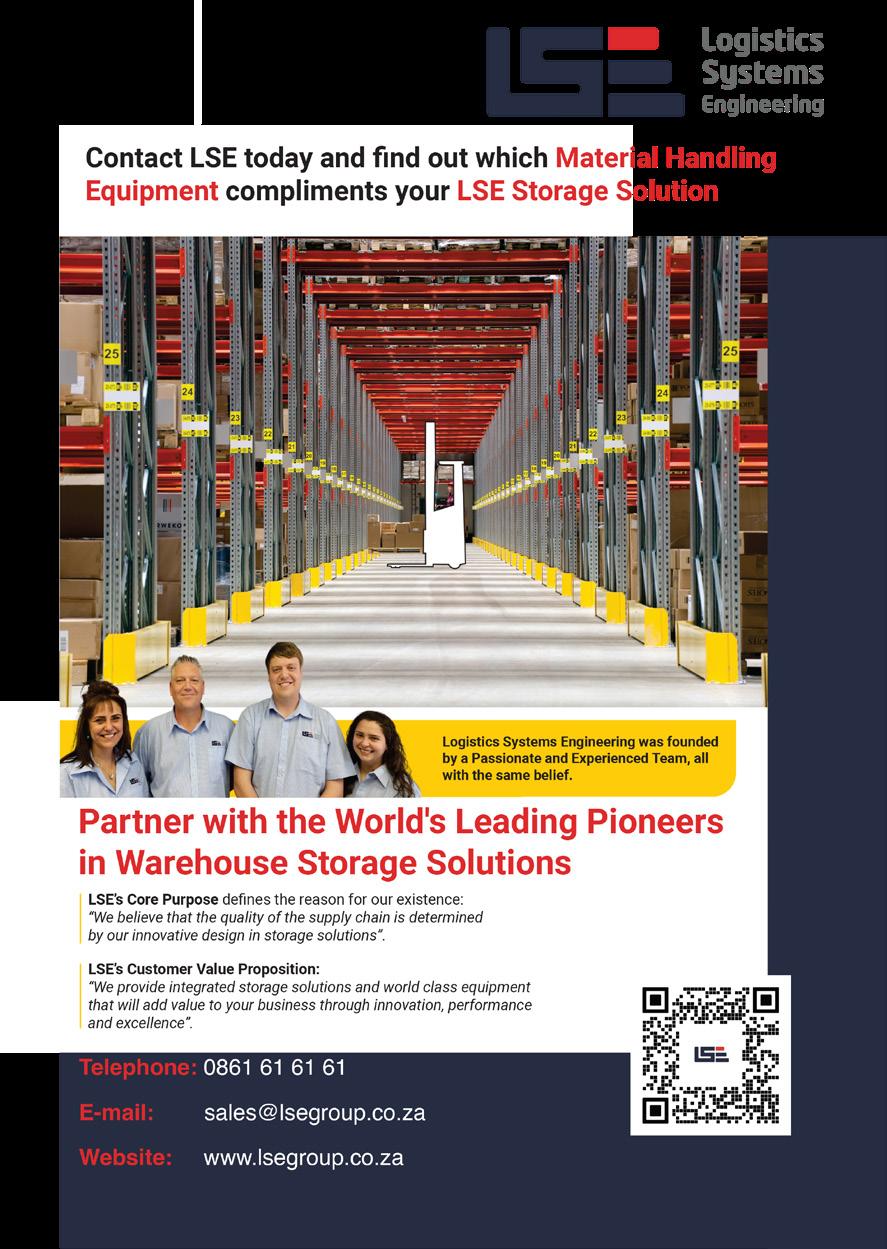
Safety is the most crucial aspect to consider when purchasing and maintaining a pallet racking system. Regardless of the type of system a business chooses to invest in, regular maintenance and understanding the capabilities of each type of system are important.
• Structural pallet racks use bolts to lock beams into place onto the uprights. Structural racking is for heavier loads, or if the chance of damage is to the racks is higher.
As well, failing to understand the cost of maintenance or what to do if the system is damaged could result in money loss or unsafe working conditions.
• Develop a procedure for identifying, reporting, and fixing damaged systems. Pallet Racks can deal with hundreds of thousands of pounds, so any dent, missing bolt or unsecured rack must be repaired immediately. As with any business, the safety of employees is paramount. Having a clear, concise procedure for reporting rack damage is imperative. All employees should be clear on those procedures, and they should be continually emphasized.
• Do not write off used pallet racking for the warehouse. Used pallet racking can be an excellent choice for a new business with limited capital looking for an effective racking system. On the other hand, if you want to upgrade your existing pallet racking, you can sell your old racking. Whether or not you buy or sell used pallet racking, it is a viable option for keeping costs down without sacrificing safety or efficiency
Pallet racking systems may seem simple, but the variety of material they hold and space they occupy raises important concerns.
Warehouse size, load types, and the type of racking system itself should all be thoroughly considered.
PALLET RACKING
• Selective pallet racks are the most common type of warehouse pallet racking. These racks have beams that slide into place using a teardrop-shaped opening in the uprights. Fast and easy to install, and accessible from both sides of the aisle, this racking type is versatile.
• Drive in racking is also for smaller spaces and/or delicate or perishable loads. These pallet racks are a last in, first out design, so space optimization is key as they can be placed against walls.
Pallet Racking Systems: What Not to Do
Lifting Africa - Forklift Guide & Register

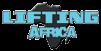
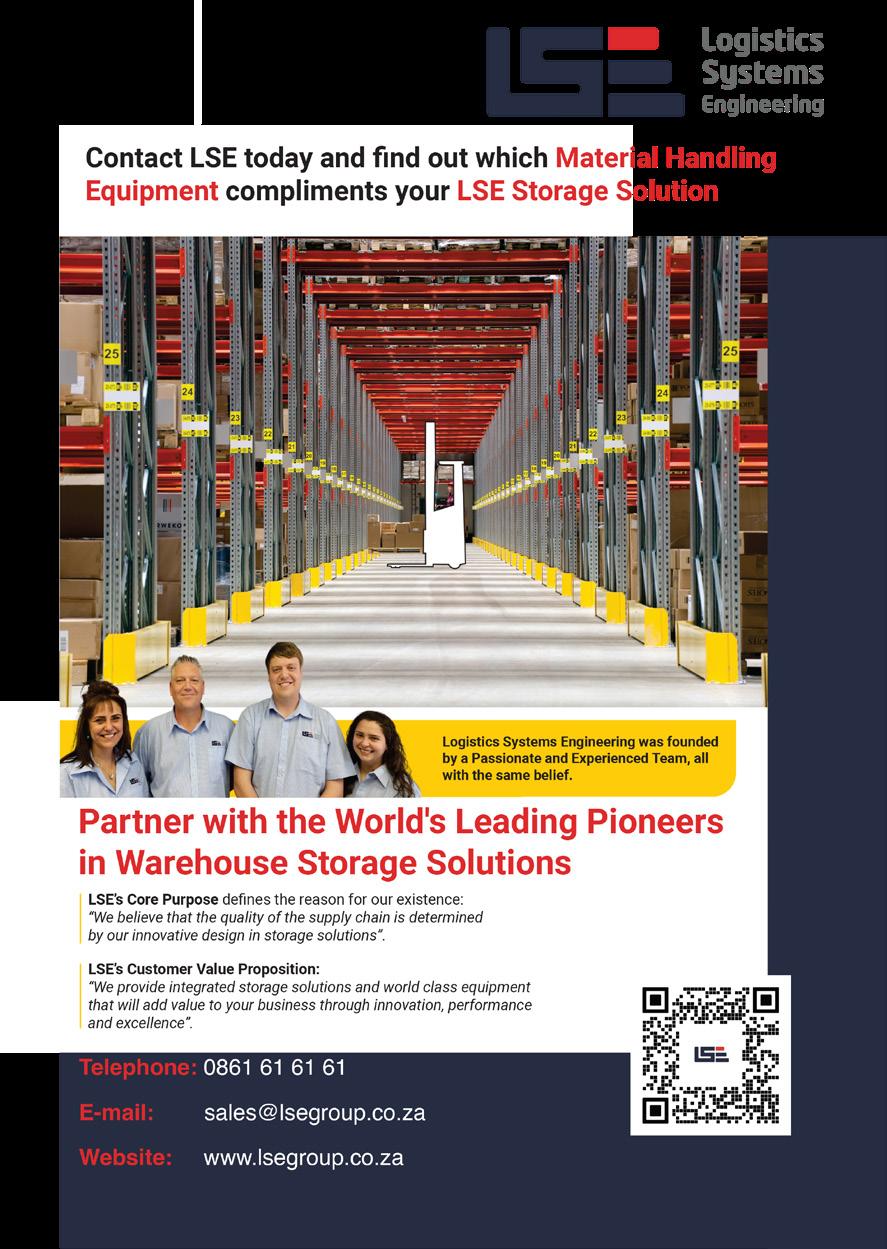
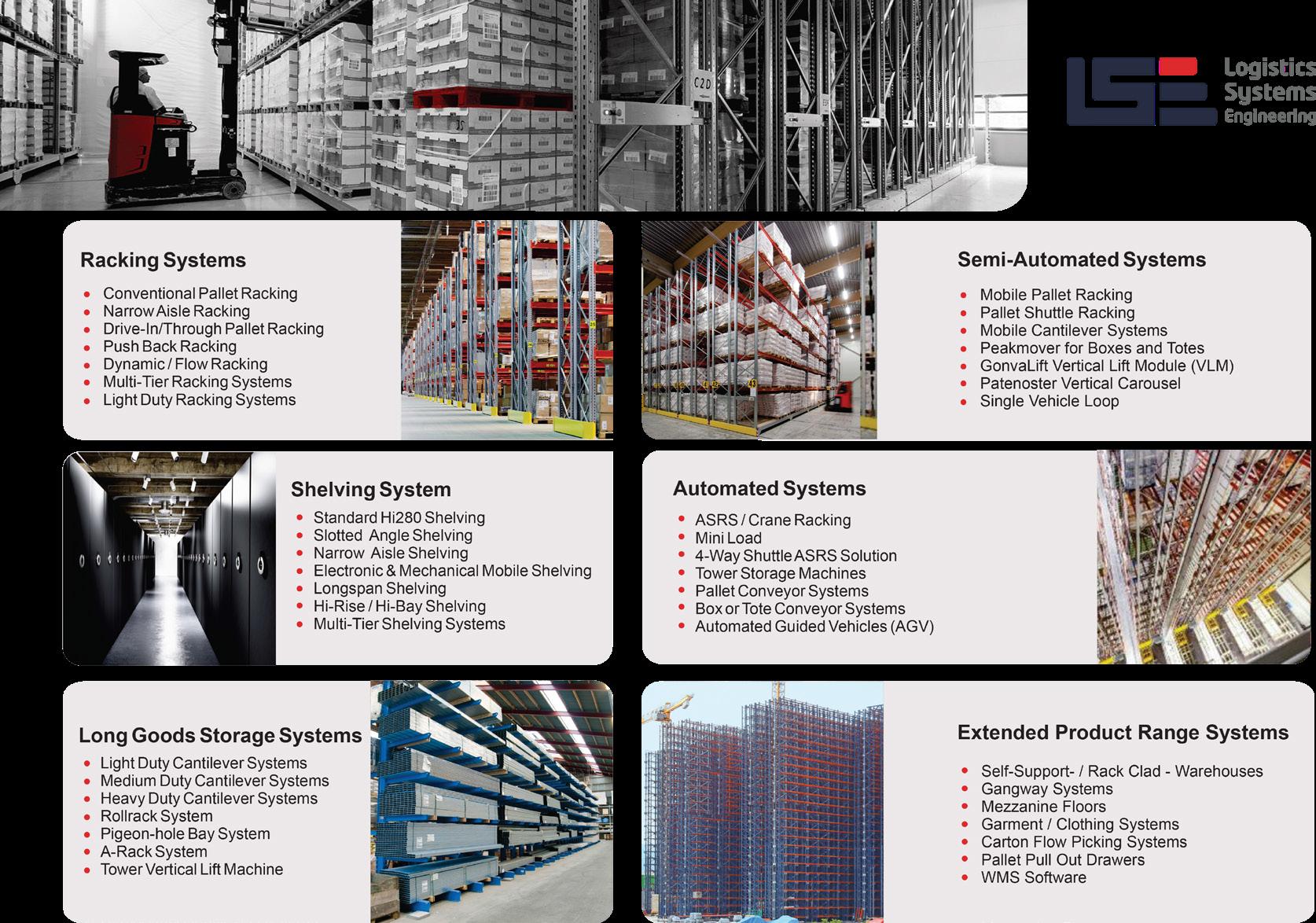
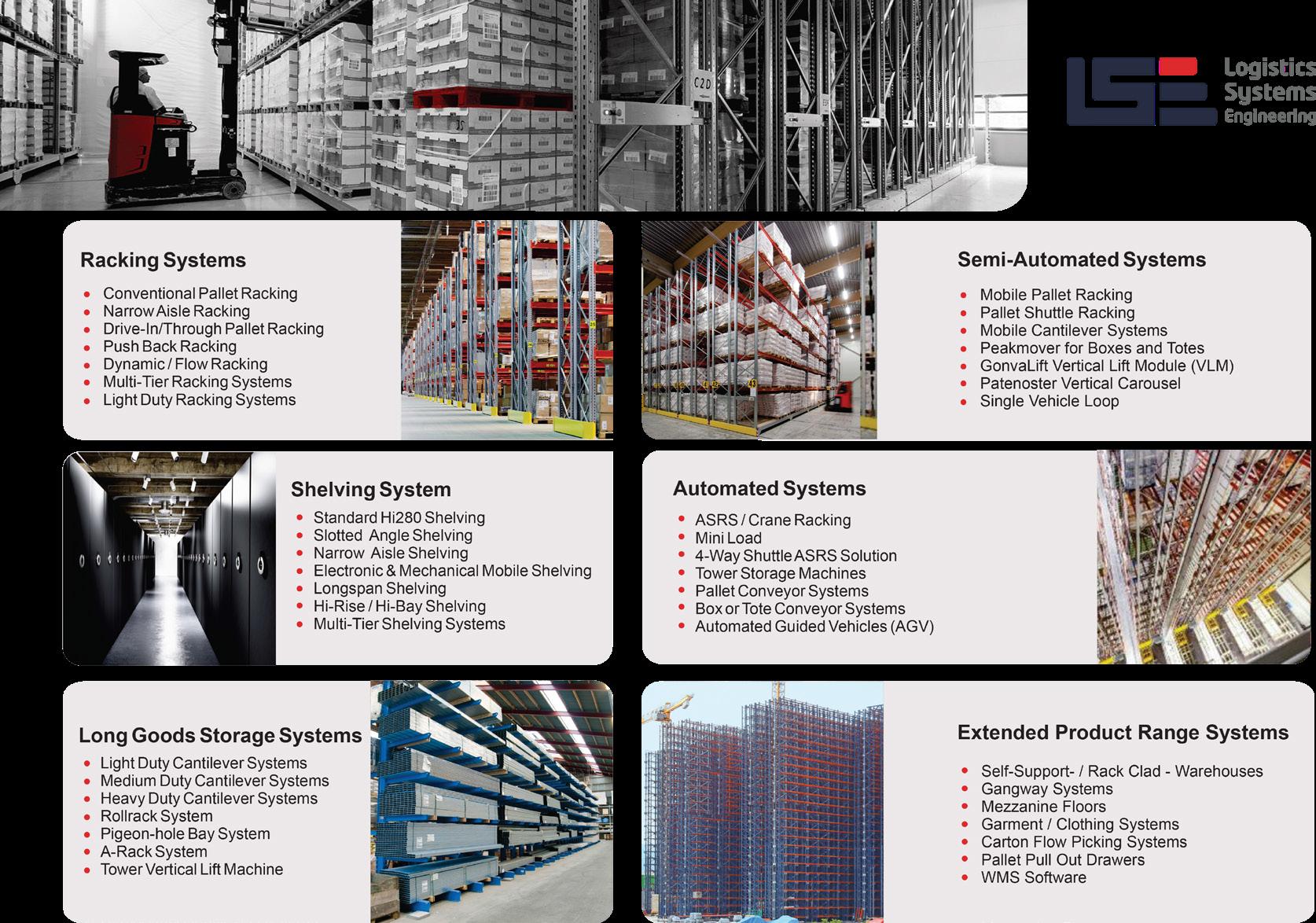
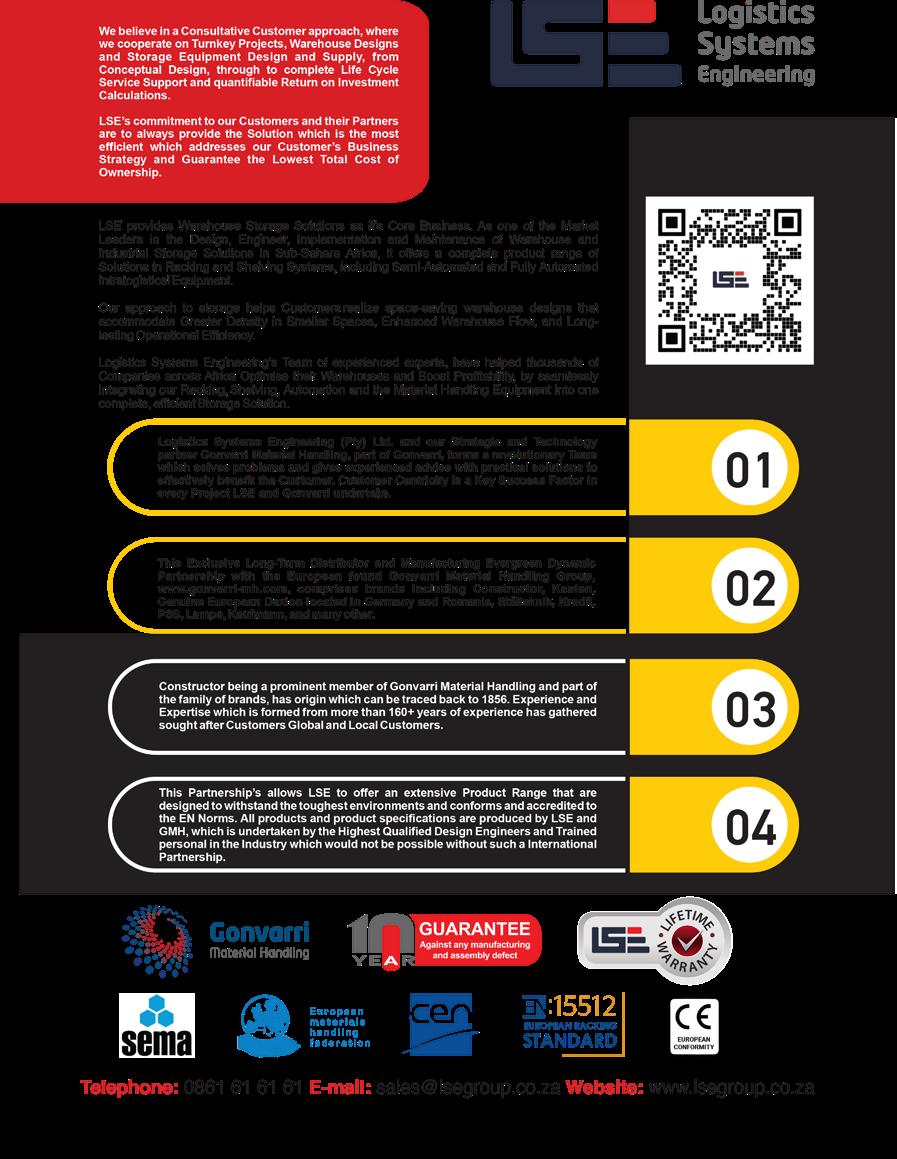
Since you can’t always control your employees’ actions, the best way to prevent accidents is to make your infrastructure as safe as possible.
Lifting Africa - Forklift Guide & Register

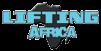
The industry standard for maximum freestanding shelf height is 4.5m. However, outside of this experts are vague about specifics for shelving safety.
The heaviest items should be placed at the bottom of the unit for added security. Storing lightweight goods on upper tiers reduces the risk of injury or product damage if items come loose.
If a facility uses high shelving units, they should be bolted to each other, to the floor, and a wall if possible. Tiers shall be stacked in a height-to-depth ratio of 6:1 or lower. Securing shelving with insufficient depth can cause an imbalance, creating dangers when loading and unloading. Materials shall not create a hazard. If goods are stored out of reach of employees, workers should be provided with the necessary handling equipment for easy access.
However, training employees is still critical since there is no way to make a warehouse or factory completely hazardfree. In addition to following requirements, businesses must proactively protect shelving from damage and monitor any signs of wear and tear or leaning that occur over time.
The weight of stored materials must not exceed safety limits.It’s also recommended that clearly marking storage equipment with safe load capacities to minimize the risk of employee error. It is easy to forget a shelf’s load limitation, especially in facilities that process high volumes of different goods.
Similar-sized products do not necessarily weigh the same, so warehouse management must prioritize warehouse layout and labeling to ensure safe and efficient product flow.
Although it’s crucial to ensure your facility has adequate pallet racking systems, shelving, and material handling equipment, keeping workers safe should be the main priority.
Warehouse accidents can result in serious employee injuries, inventory loss, and costly delays in operations. Accidents often result in a visit from the DoEL (Department of Employment and Labour)
The business can face hefty fines and follow-up visits if the facility doesn’t meet DoEL regulations. Even if the accident wasn’t management’s fault, the paperwork and resulting lost time can be burdensome and adversely impact your bottom line.
Install Height-Appropriate Shelving
Warehouses are the logistical hubs of any storage-based business, forming an integral part of the supply chain with quality equipment and efficient inventory management.
To minimize the risk of a shelving collapse or falling inventory, install shelving that falls inside the industry standards. In manual handling facilities, storage companies should use shelves at a medium height, allowing pickers to access items without reaching or stretching at an unsafe angle.
Shelving is available in various styles, sizes, and materials. For industrial applications, heavy-gauge steel is a great option. It is strong, durable, and corrosion resistant, providing years of reliable service in harsh warehouse environments.
Steel shelving typically has a higher load capacity than other materials, offering space efficiency in small facilities. Opting for high-quality steel shelving helps ensure your
Choose the Right Load Capacity
height, and with sufficient safety accessories to prevent Otherwise,accidents. a warehouse can be cited for failing to provide a safe working environment for its workers.
SAFETY
10 Shelving safety tips to keep your warehouse compliant
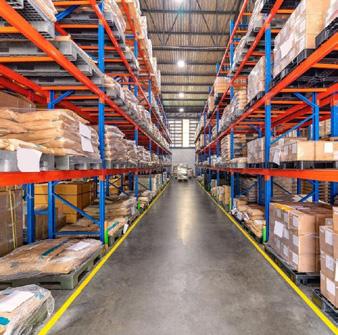
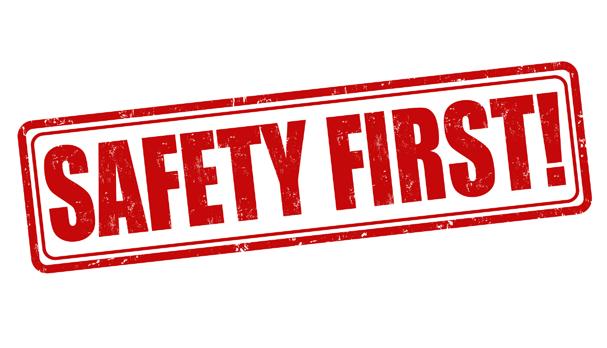
Warehouse organisations can be held responsible for an accident if they fail to do their due diligence to protect their employees. Essentially, this means all storage areas and equipment must be installed appropriately, at a safe
Industrial shelving is labeled with a specific load capacity, helping users identify the weight and volume of goods each unit is capable of supporting.
The extra large displays, enabling fast and accurate identification of goods. The matte finish is durable and allows your items to be quickly scanned using a barcode reader.
SHELVING
Opt for High-Quality Shelving Materials
Once all the necessary equipment and safety protocols are in place, it’s important to conduct regular inspections to ensure safe operations are continued.
Continuous Staff Training
Use Wire Cages and Guardrails
Industrial shelving units are made from high-quality steel. They come with complete high load-bearing shelves, some with a maximum weight capacity of 500kg.
The main causes of racking collapses are; Inadequate design; Incorrect Overloadinginstallation;atpallet locations;
Even employees who don’t regularly lift and load pallets require training on basic safety procedures regarding shelving zones.
An improper installation may also mean that the unit can’t support the maximum load capacity, making regular use extremely dangerous.
Lifting Africa - Forklift Guide & Register

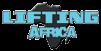
Some goods are potentially hazardous if they are involved in a forklift accident. Flammable and fragile materials should be kept quarantined and mustn’t be handled with a forklift. This includes aerosols, as a punctured aerosol could cause significant damage or even breathing problems for nearby workers.
There is several free warehouse safety training programs
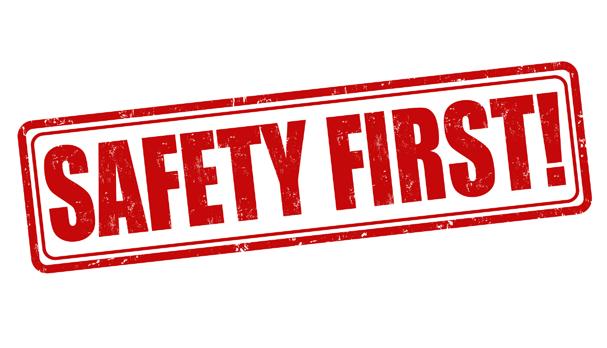
MechanicalDamage
for workers available. These courses teach a range of safety procedures and cover the necessary topics to prepare workers for workplace hazards.
Professional Installation
A stand guard ribbed rails are made from 10-gauge, hightensile steel with durable sleeves that are welded to the posts. These guards feature a drop-in, lift-out design, offering ample protection against machinery.
All employees should undergo general safety procedures and protocol refresher training once a year.
Employers should never allow untrained employees to operate a forklift. Training for other equipment, such as handcarts, should also be thorough.
handling equipment (MHE) impacts; Supporting floor failure; Environmental or chemical deterioration; Change of configuration away from that for which the racking was designed; Poor weight distribution on pallets, or pallet failure.
SHELVING SAFETY
A key advantage of these units is their versatility. They assemble without nuts, bolts, or clips so they can easily be set up, taken down, and reconfigured. This doesn’t require cross braces for support, providing direct access to goods from all sides. These units are a perfect option for facilities that handle a variety of product.
An authorized third-party professional has the necessary equipment and experience to determine the structural integrity of shelving units and whether they have degraded over the year. If any safety issues arise, they can be quickly addressed to avoidan investigation by the DoEL
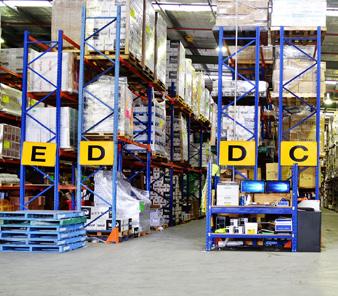
Warehouse safety training equips employees with the knowledge and requirements to operate in a fast-paced, industrial environment and to correctly handle potentially hazardous scenarios.
This can help protect the shelving and other critical infrastructure from damage caused by forklifts or machinery. While guardrails require an initial up-front cost, they can prevent thousands of dollars in damages and lost man-hours caused by damage to shelving units.
Consider using wire cages to keep these items away from reach and erect fenced-off storage areas for forklift-free zones. You can also use flammable goods cabinets to keep flammable gas and other hazardous warehouse supplies separate from regular use shelves.
Conduct Regular Inspections
Sometimes fragile goods still need to be stored in tiers or inside pallets, making them difficult to move without machinery. In this case, consider creating safety barriers using guardrails.
Daily visual inspections help managers identify obvious signs of damage or wear, while more thorough checks on a weekly and monthly basis can detect more serious issues. All warehouse and storage facilities should be professionally inspected once per year.
For shelving to perform as it should, it must be properly installed. Poorly installed equipment is a safety hazard and may collapse or sag under duress.
equipment has adequate storage capacity for all items. Its durability limits damage, making it safer to use
Warehouse managers should consider putting all employees through a basic training program to help with year-round compliance.
These units are available at heights ranging from 1m to 12 3.5m ensuring they fall into industry standard regulations.
Hiring a professional to install your warehouse equipment properly improves the facility’s overall safety, reduces the risk of shelving collapse, and helps your warehouse to be safe.
They can be secured further with floor mounting hardware.
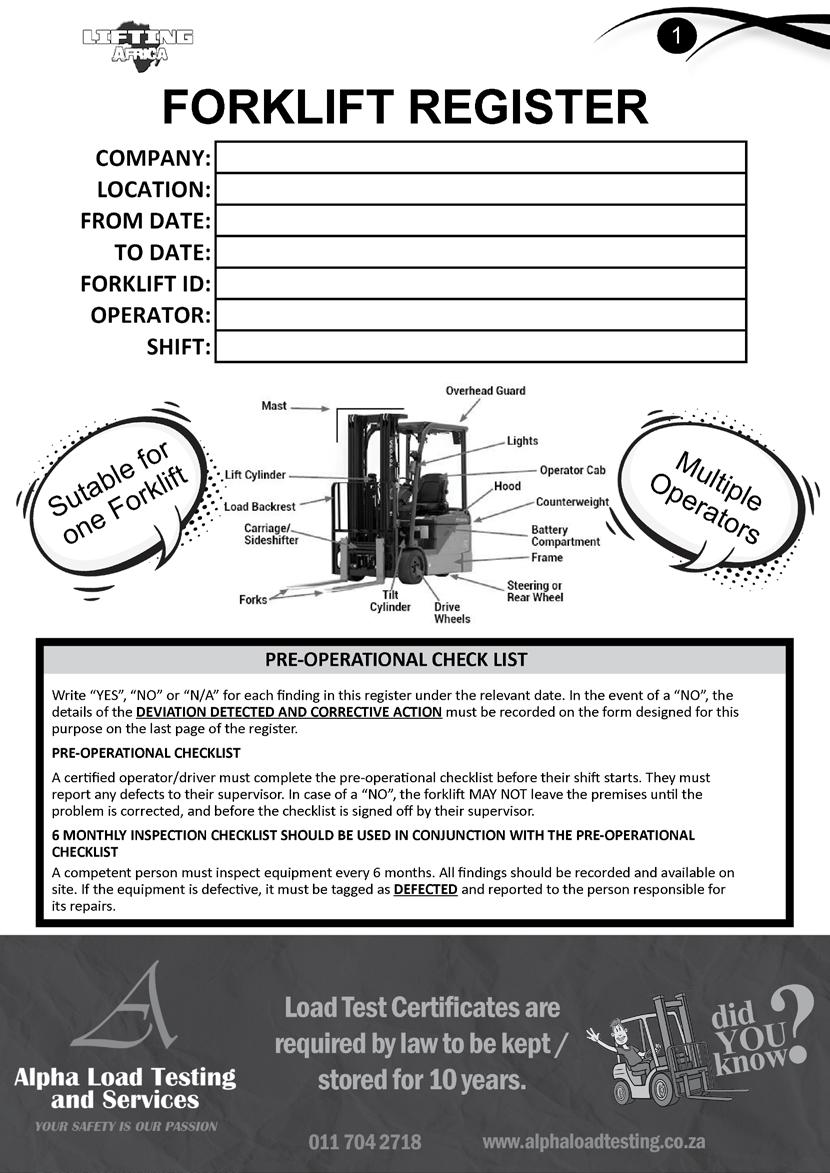
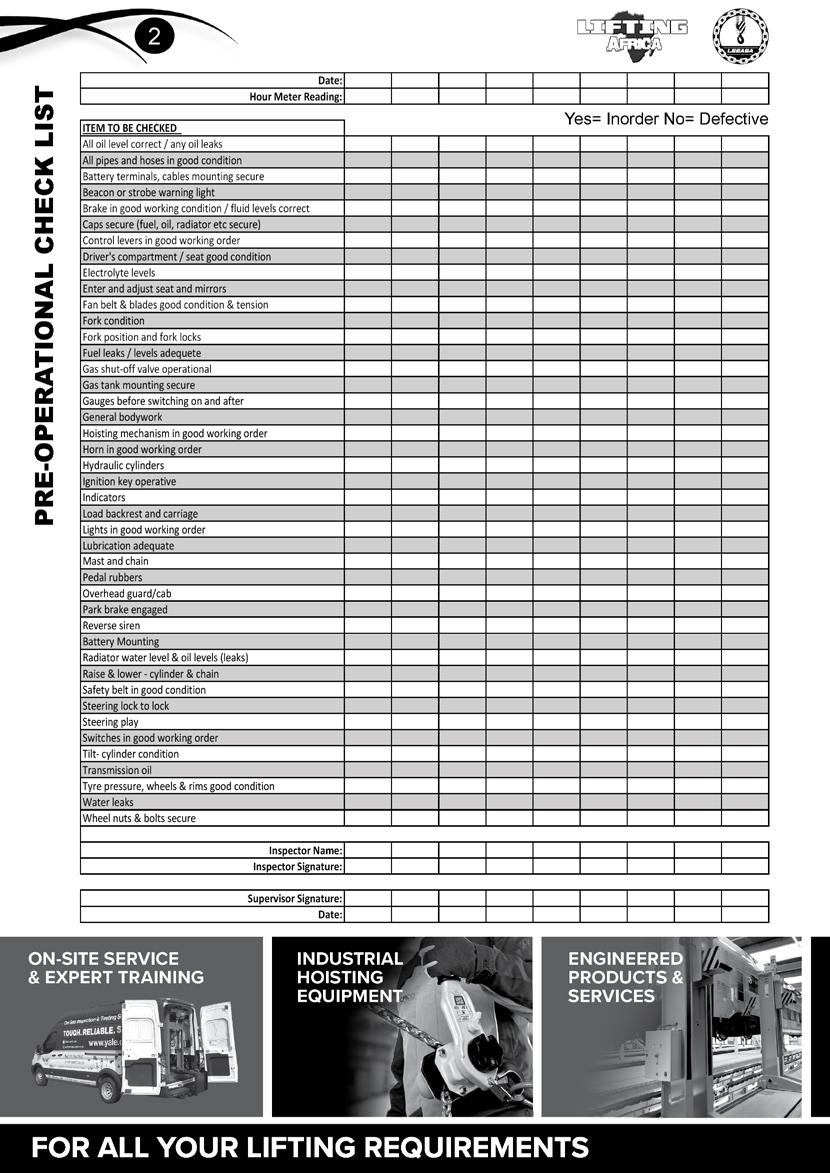
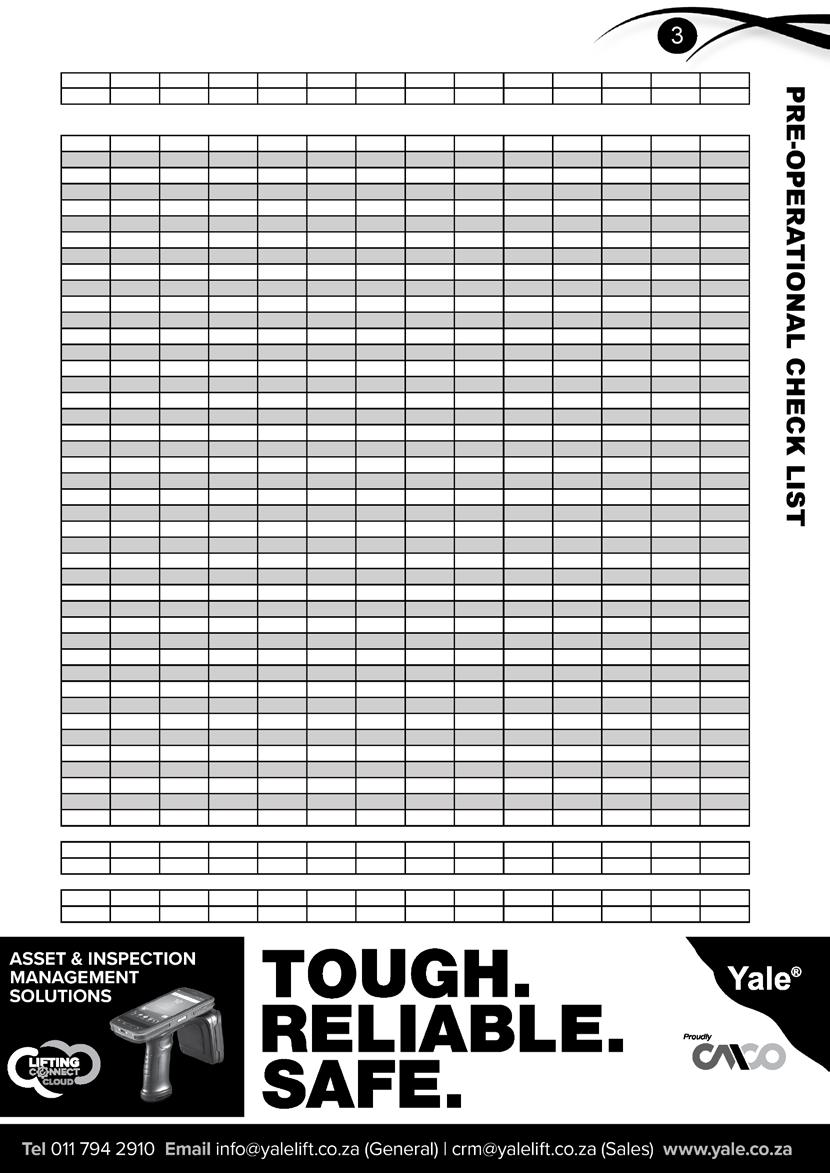

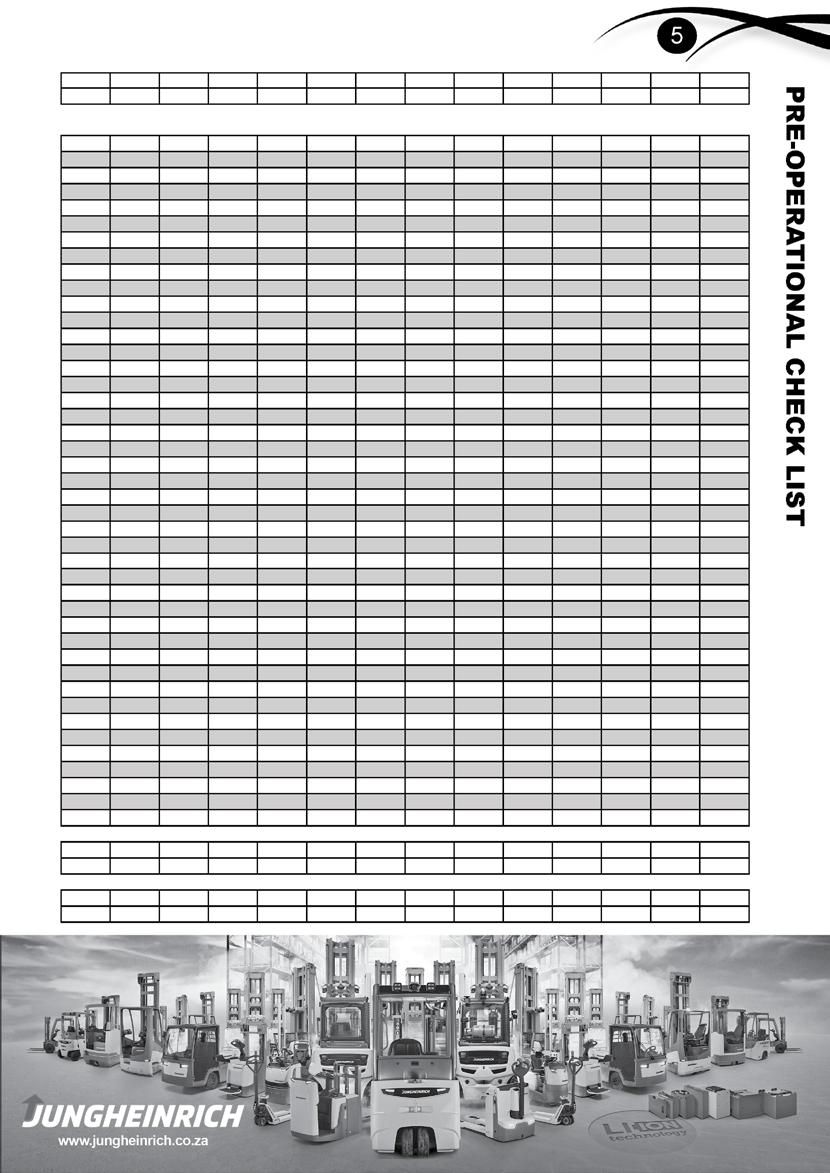
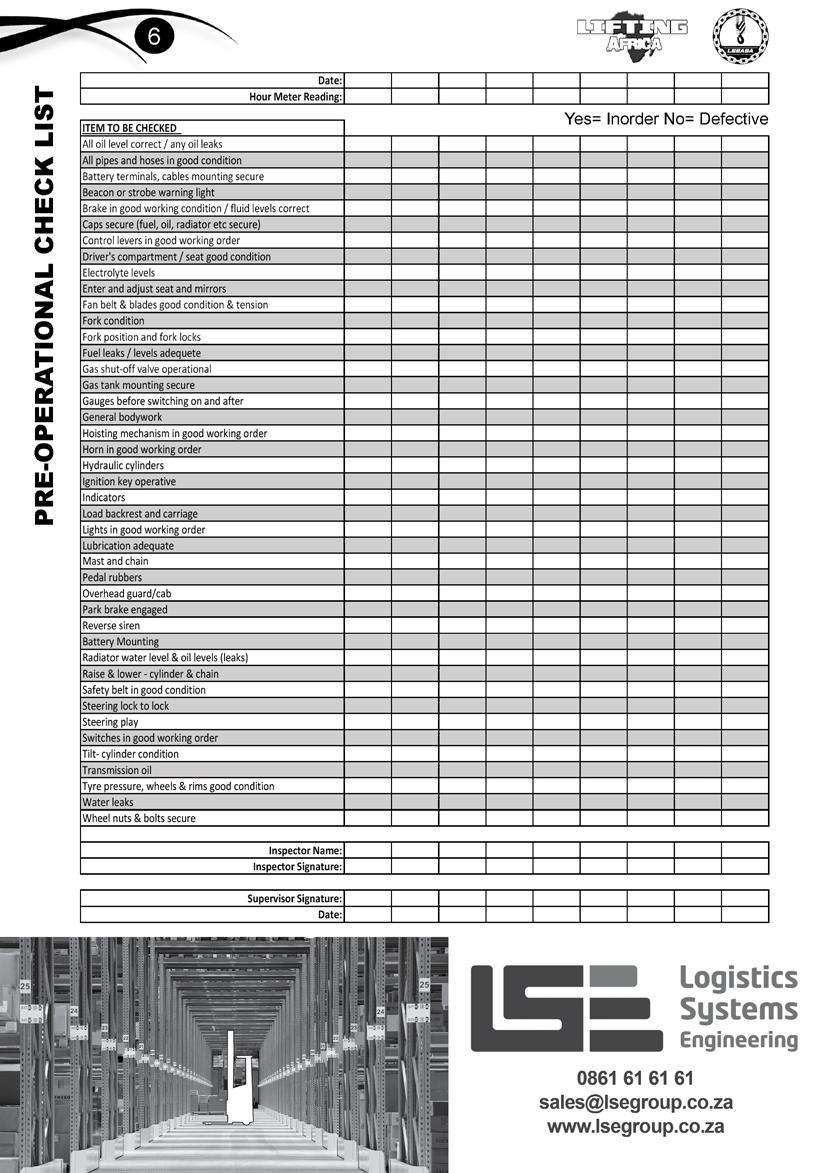
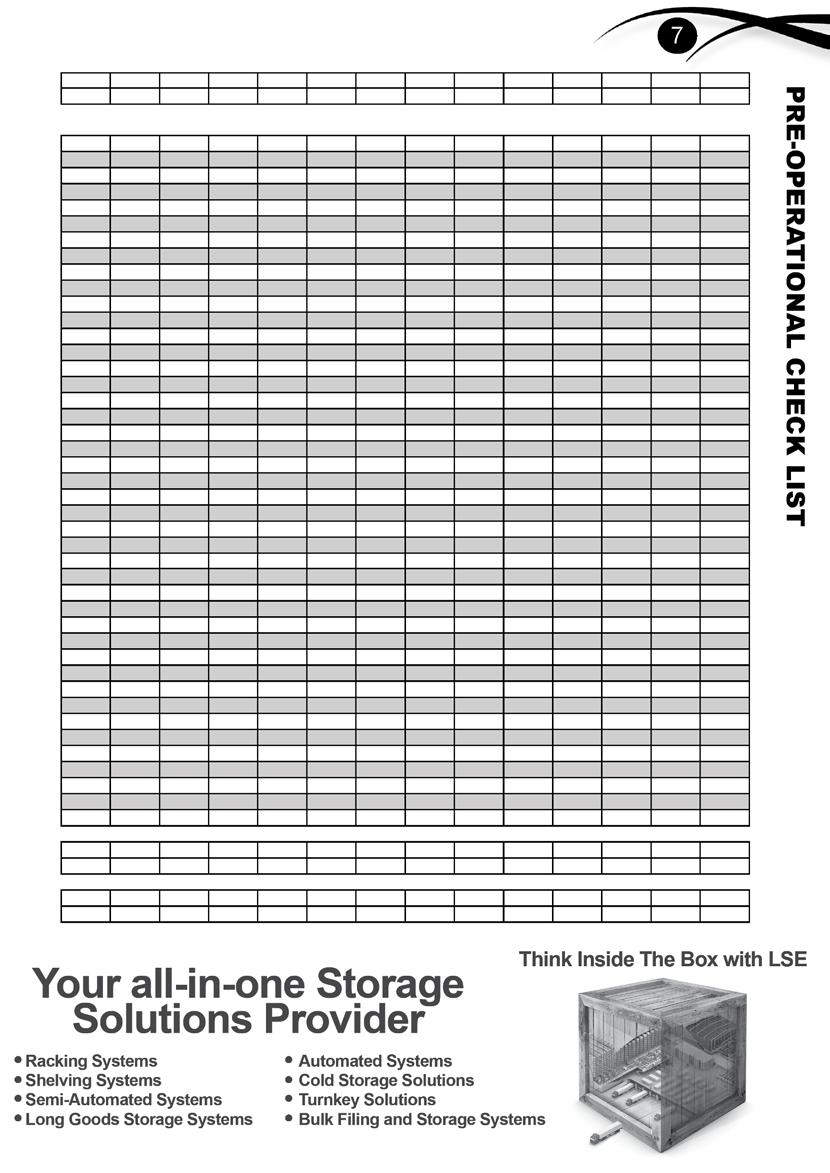
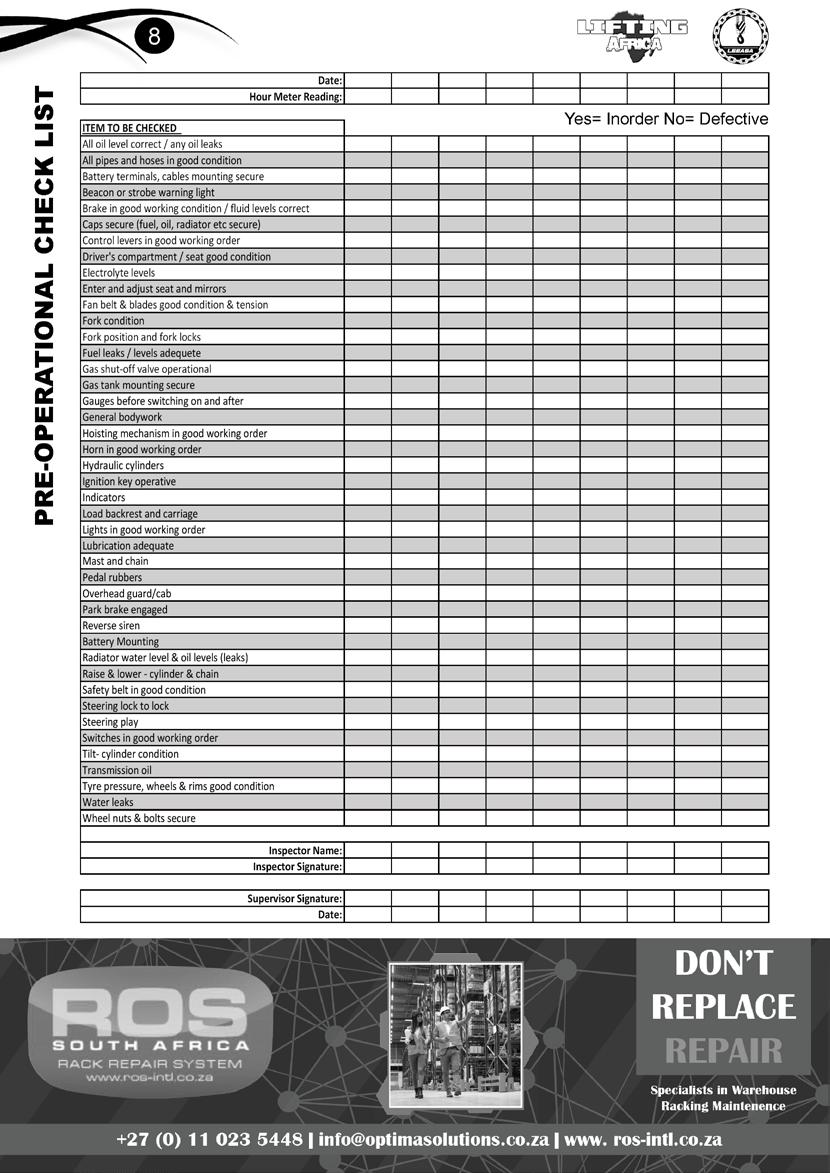
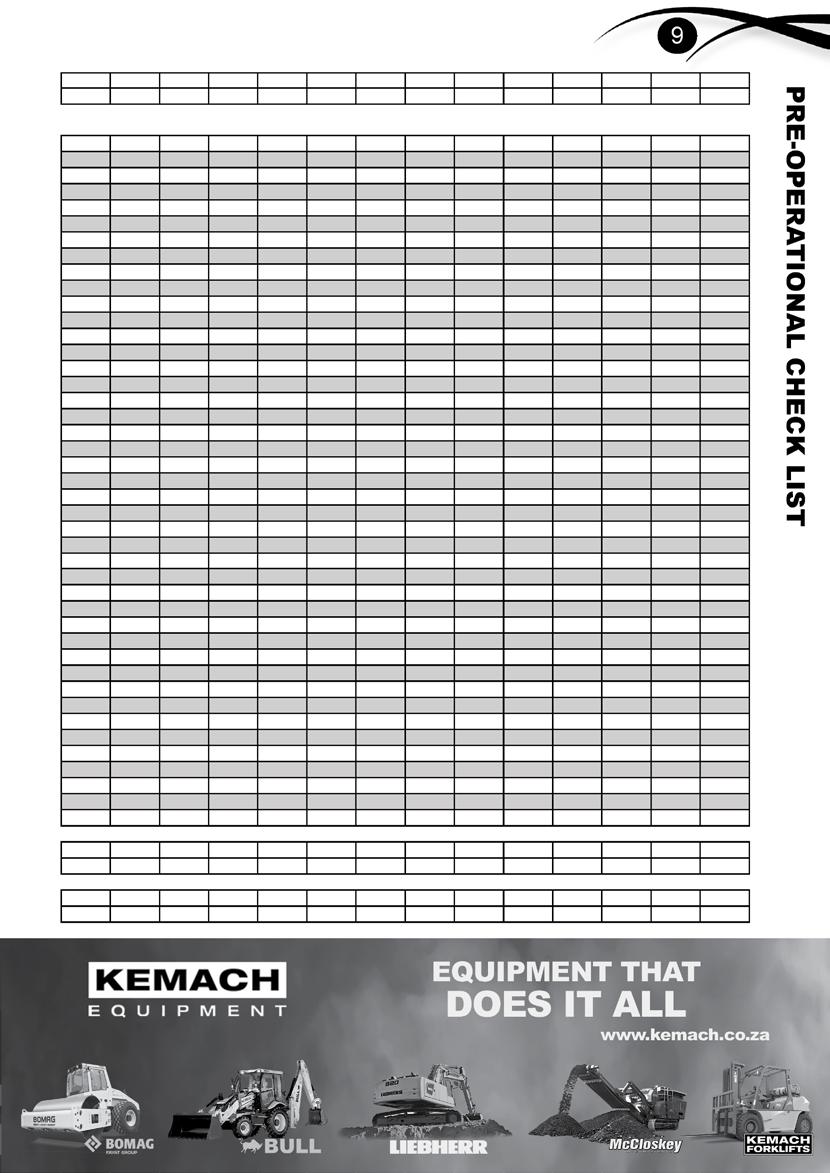
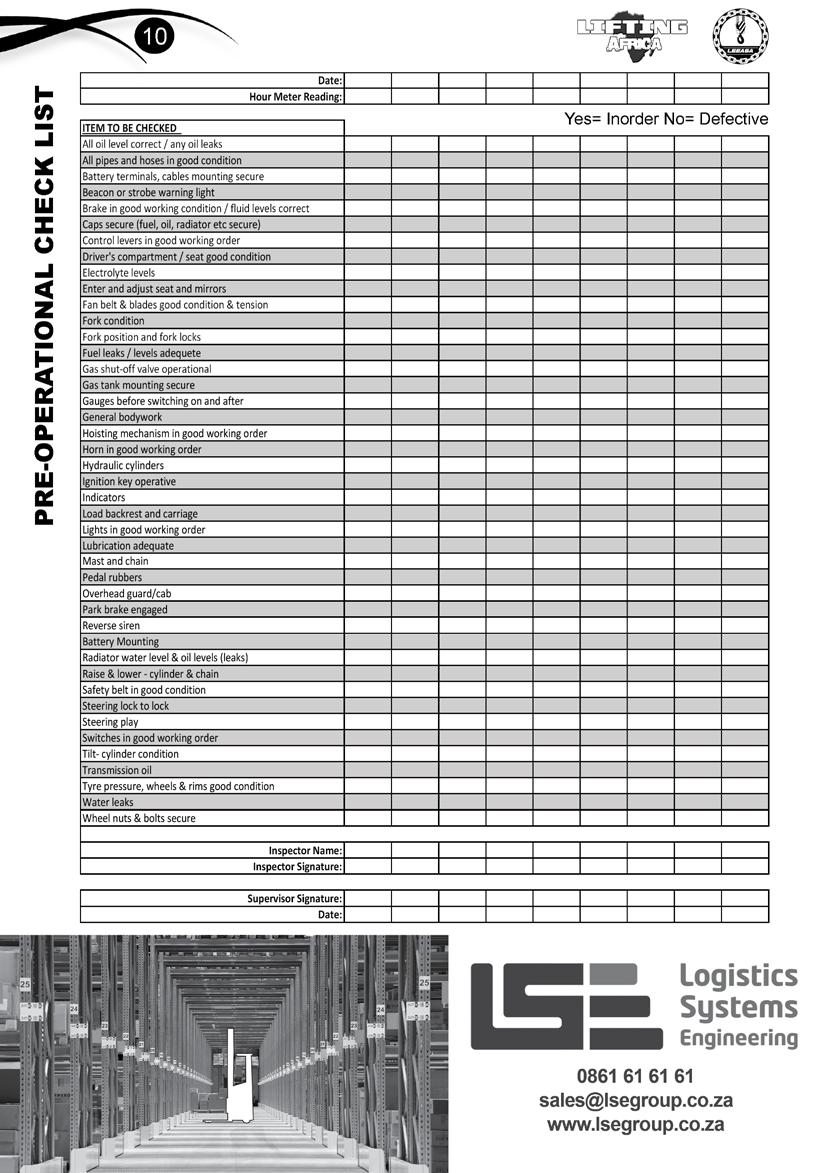
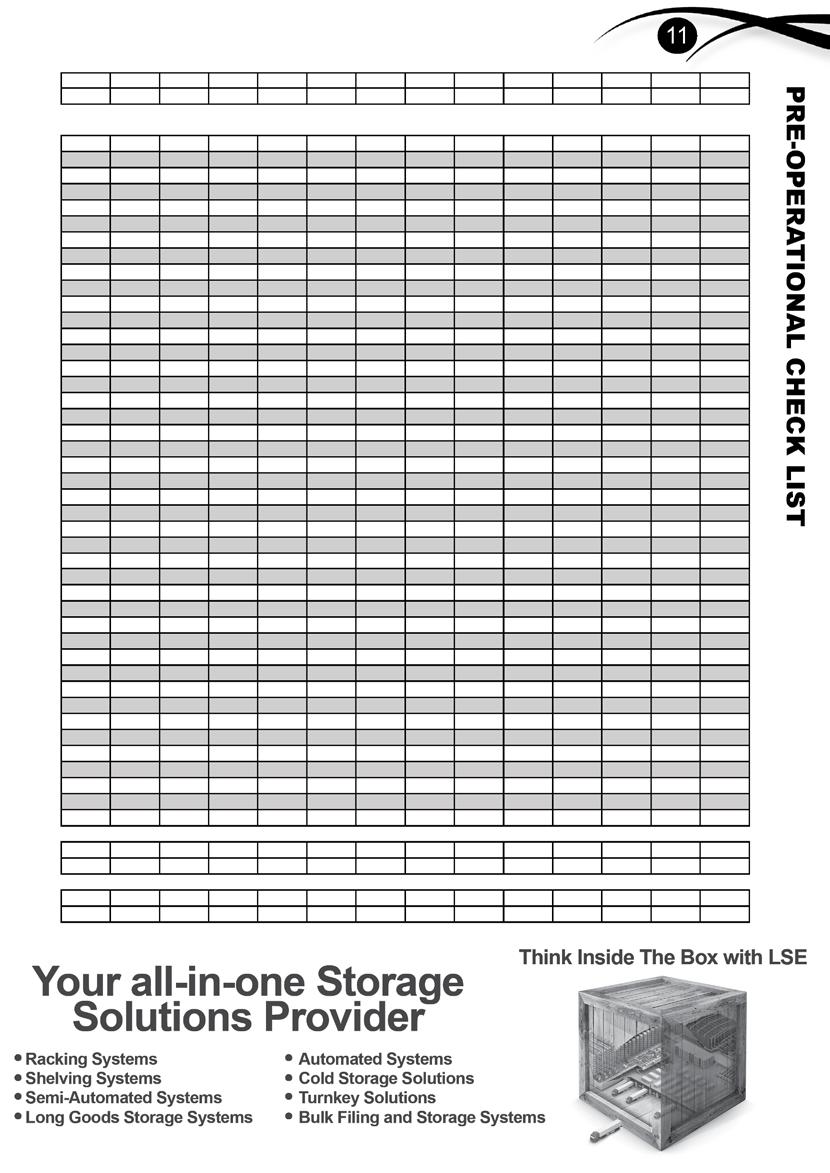
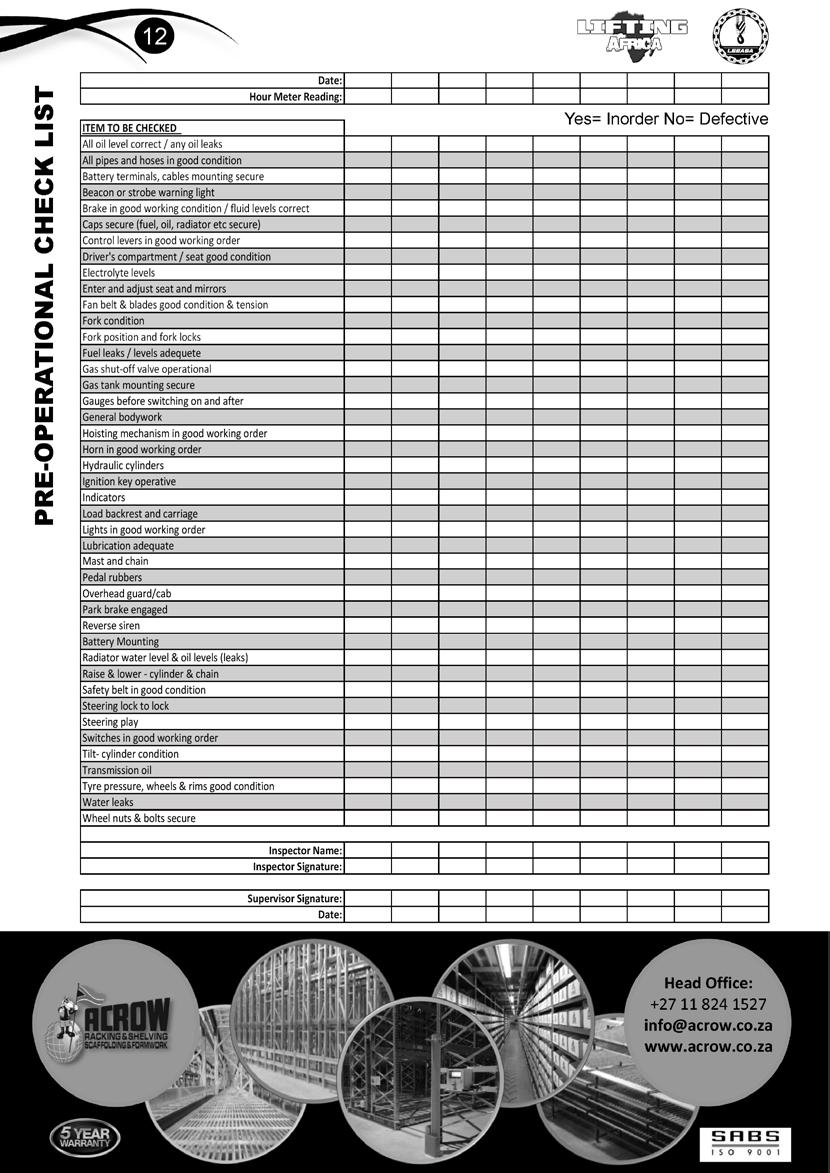
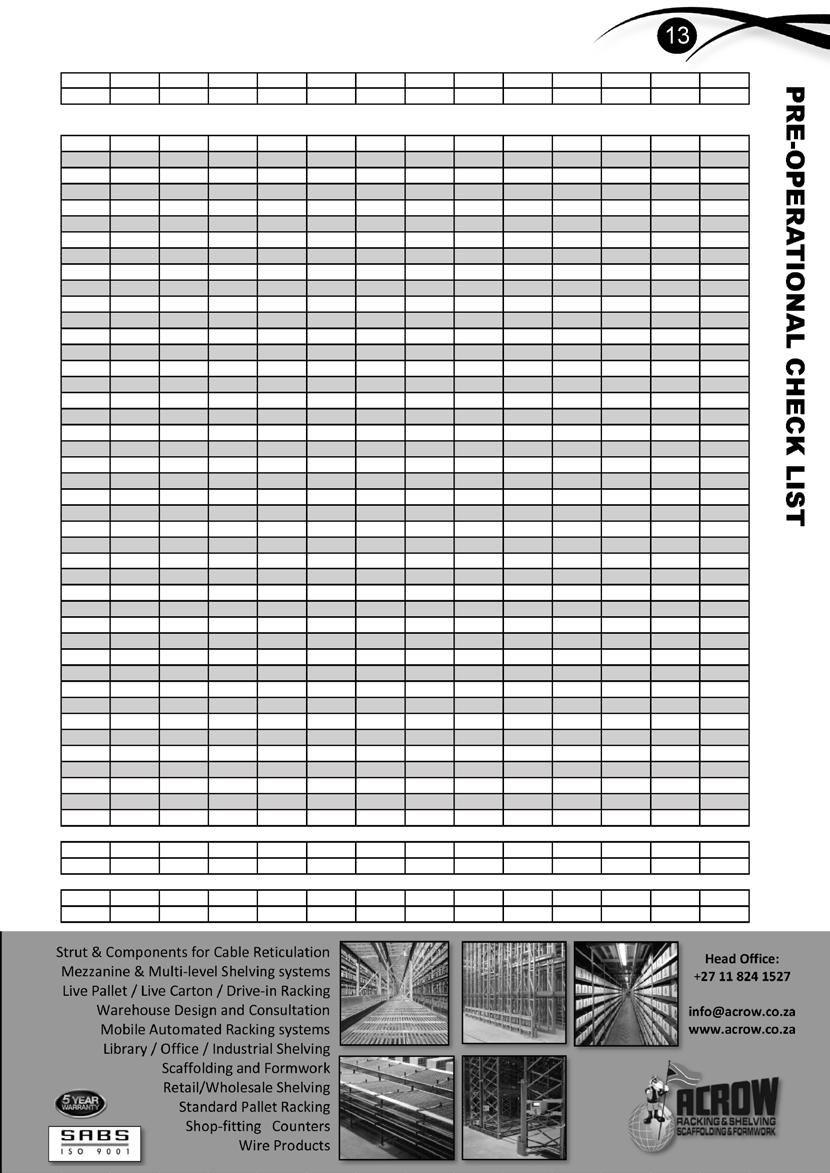
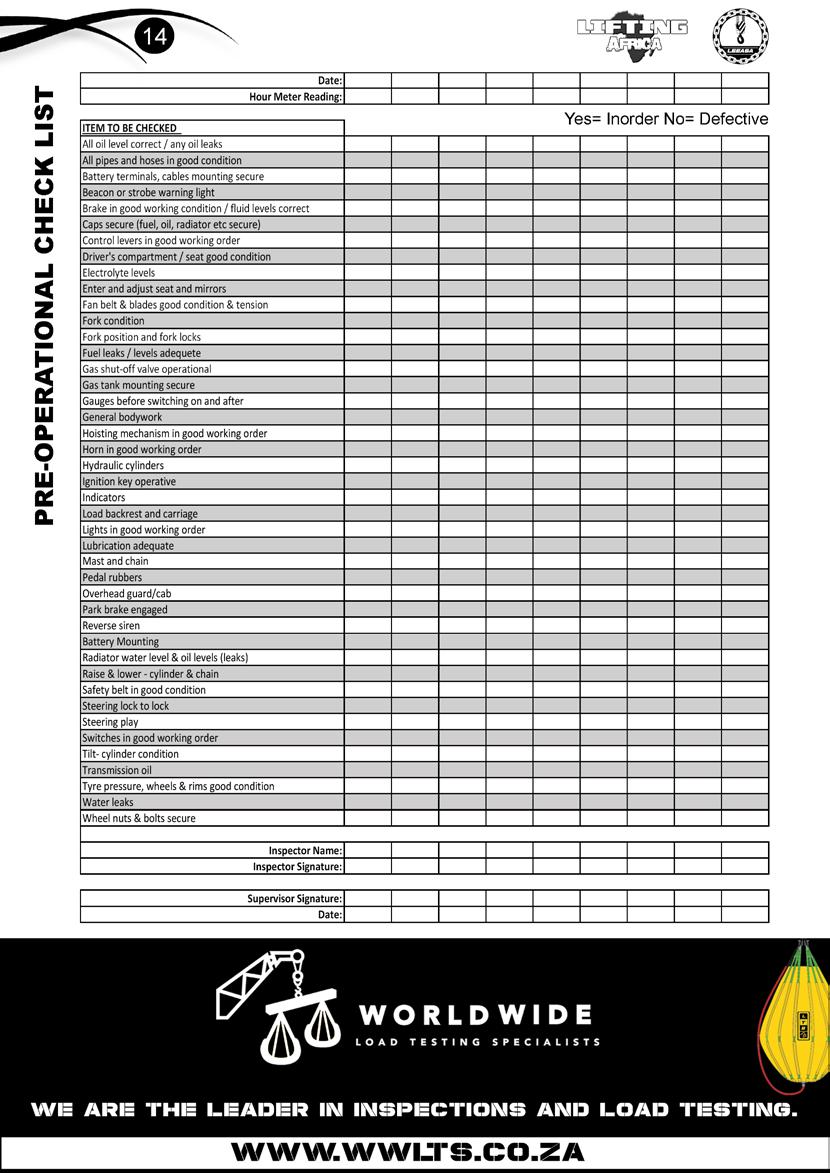
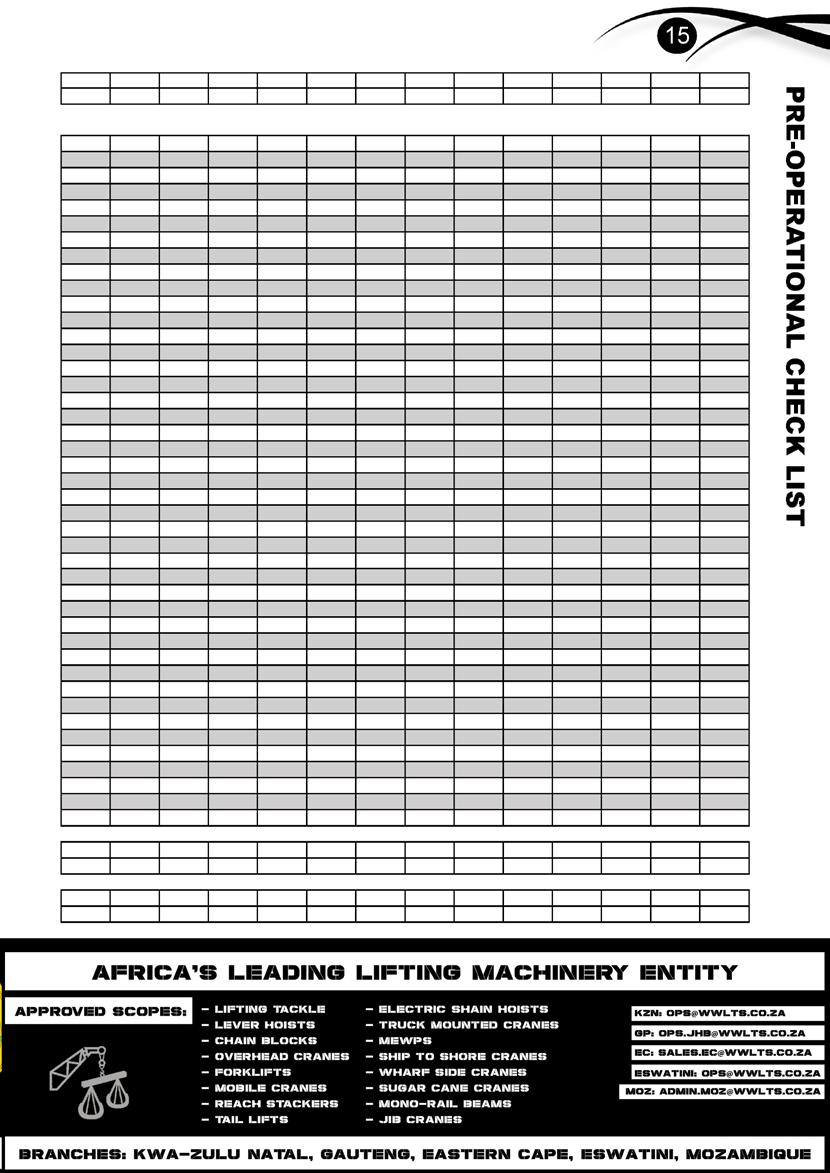
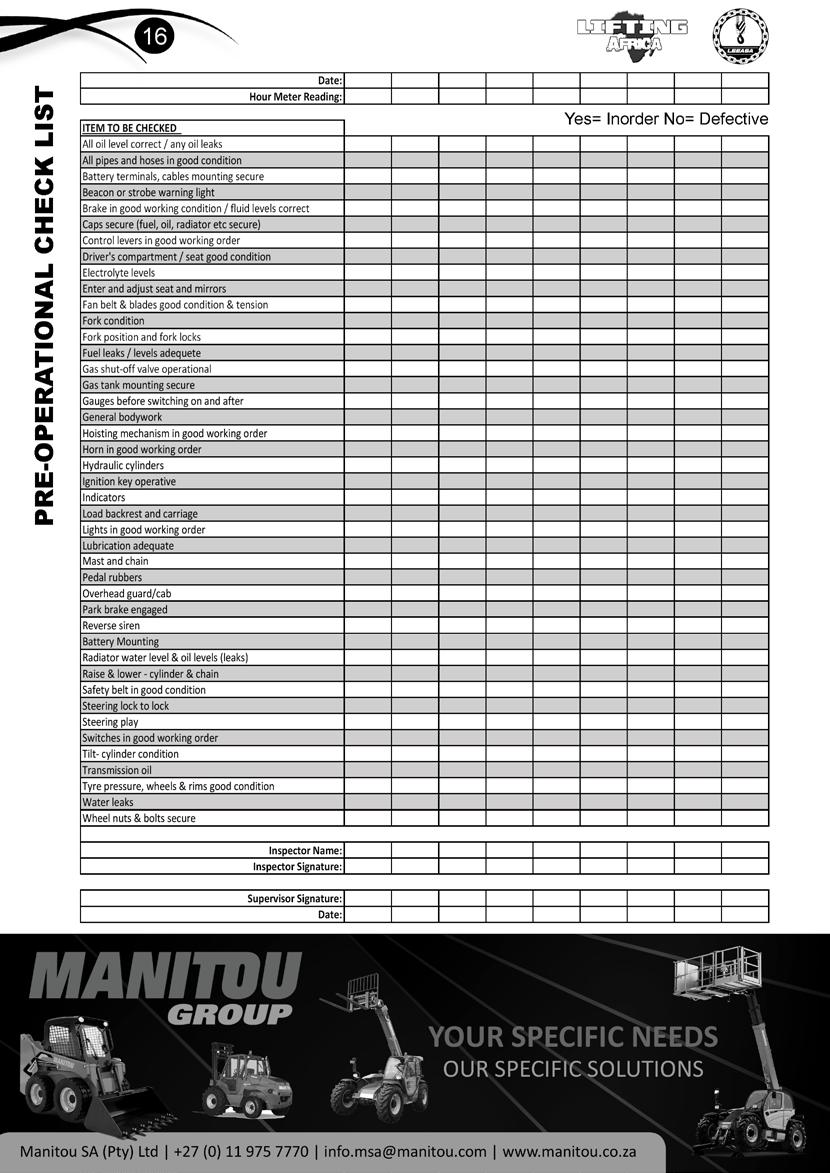

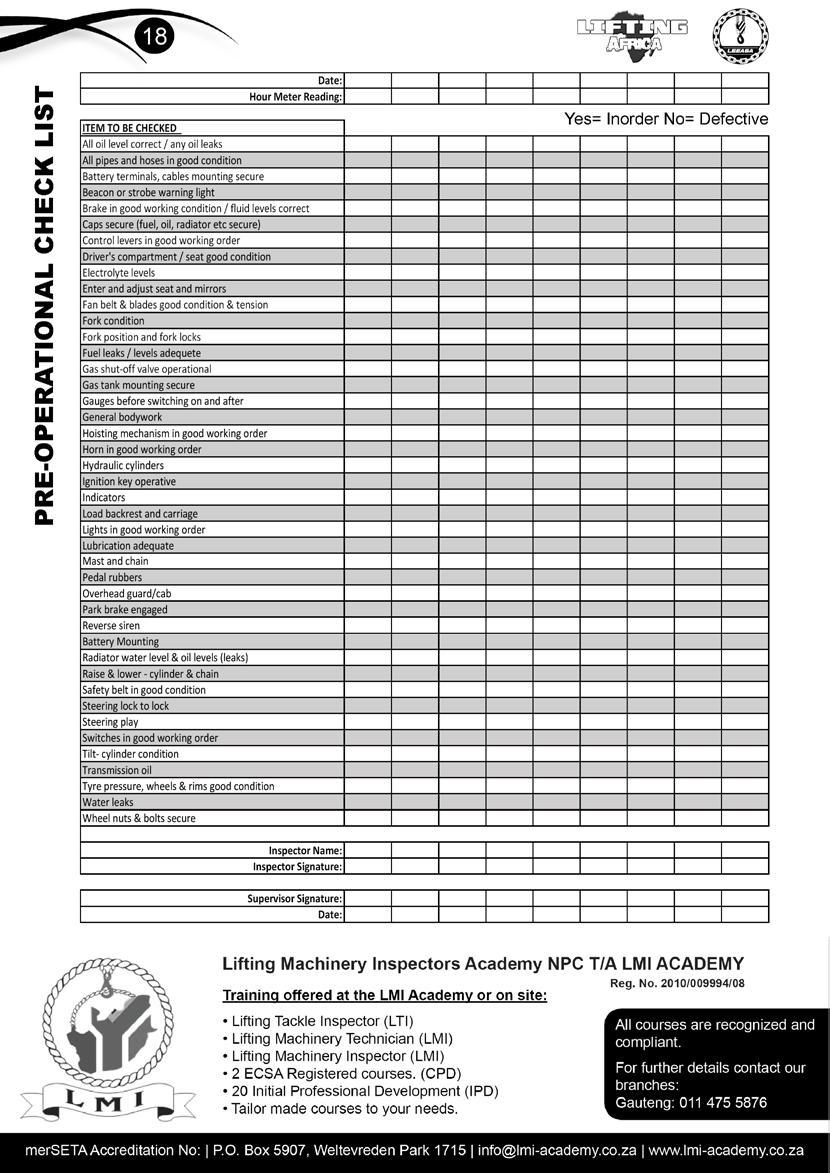
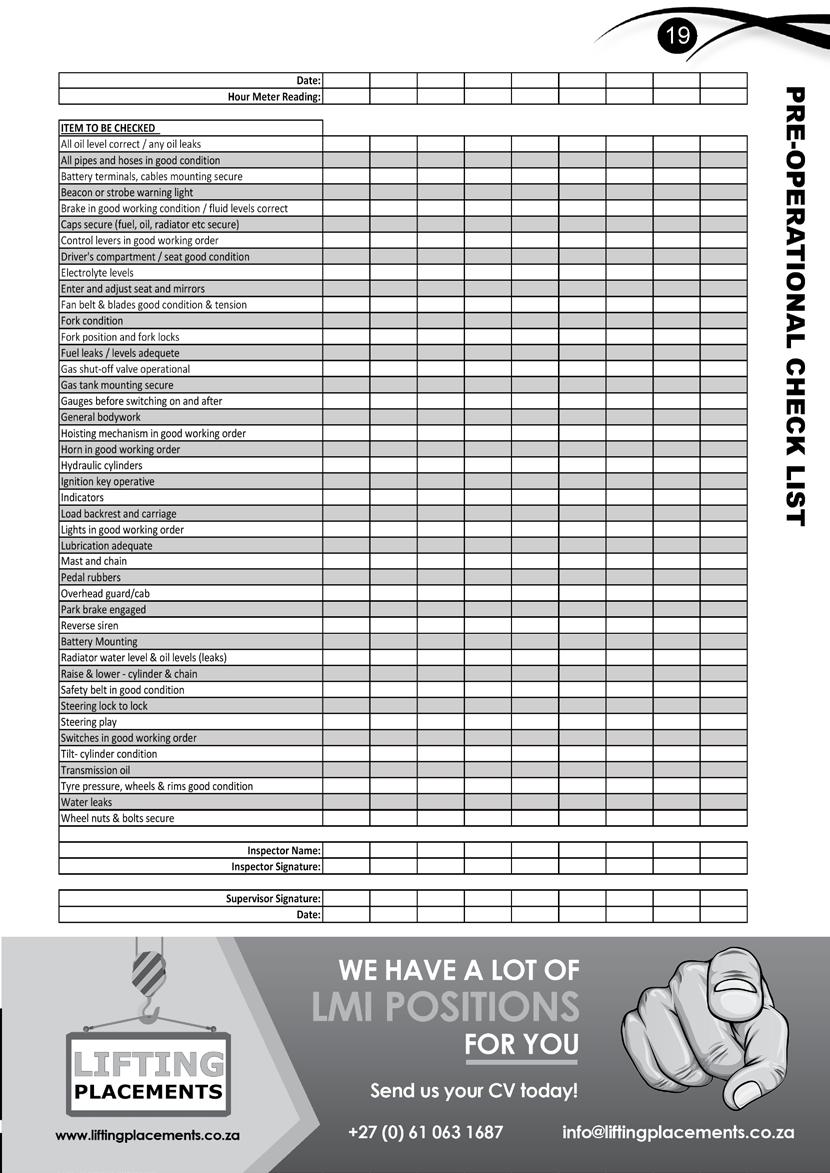
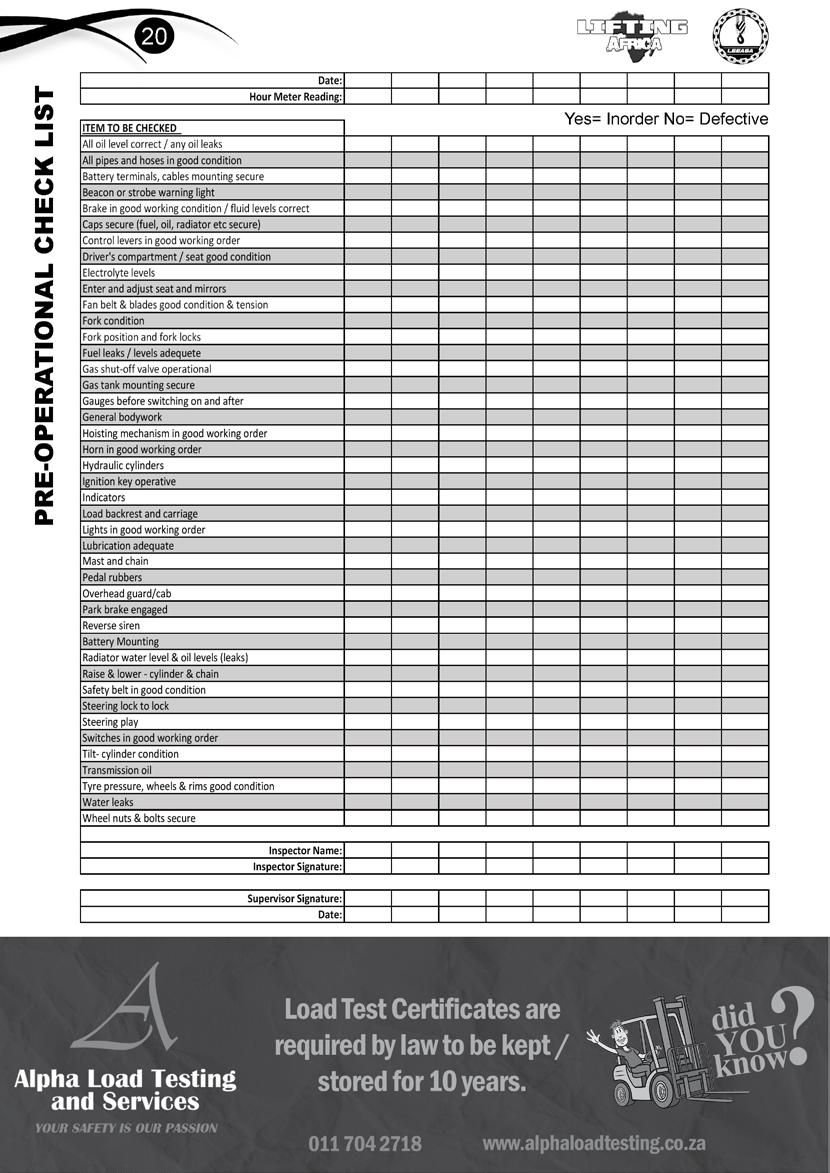
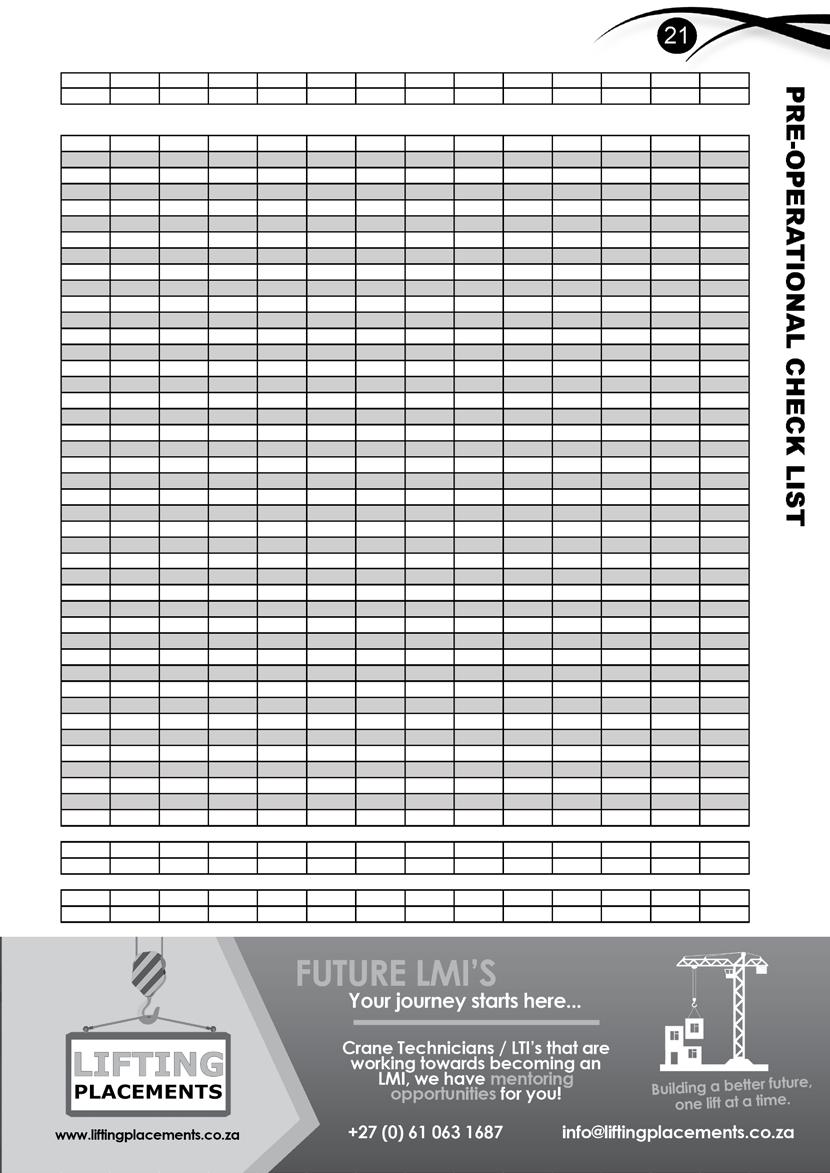
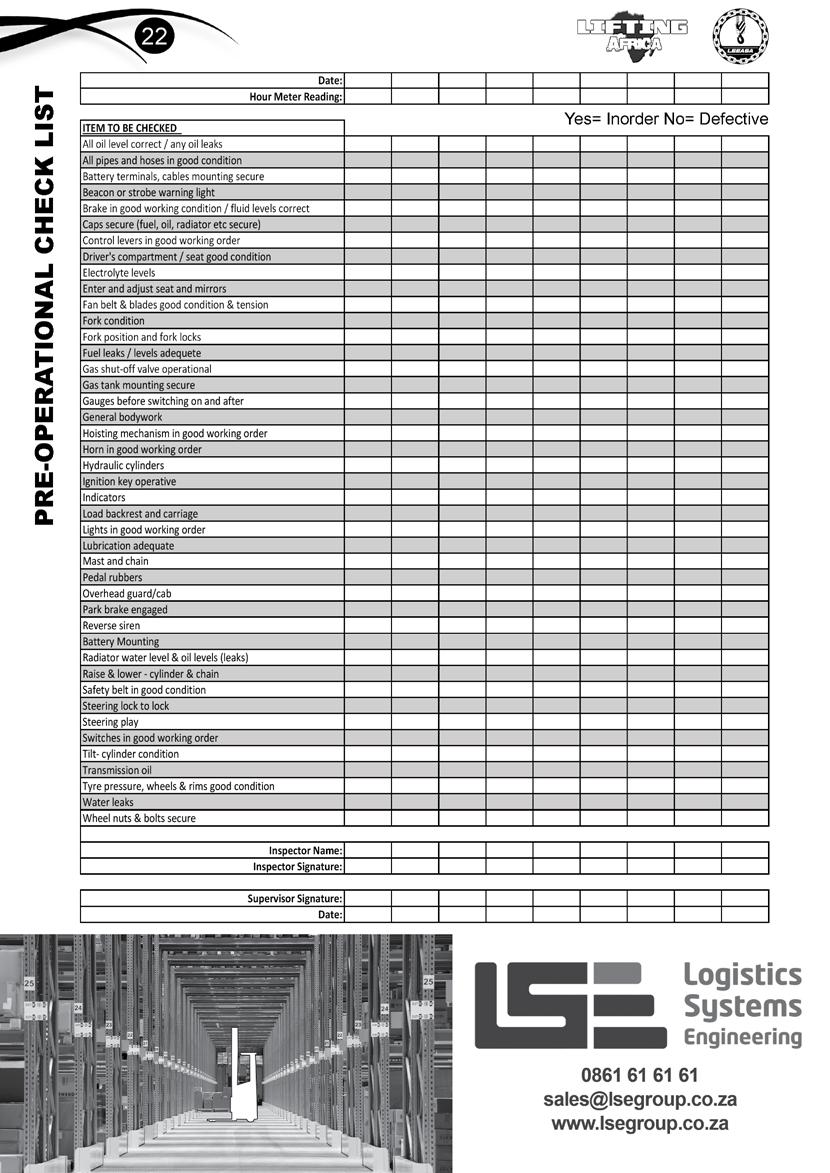
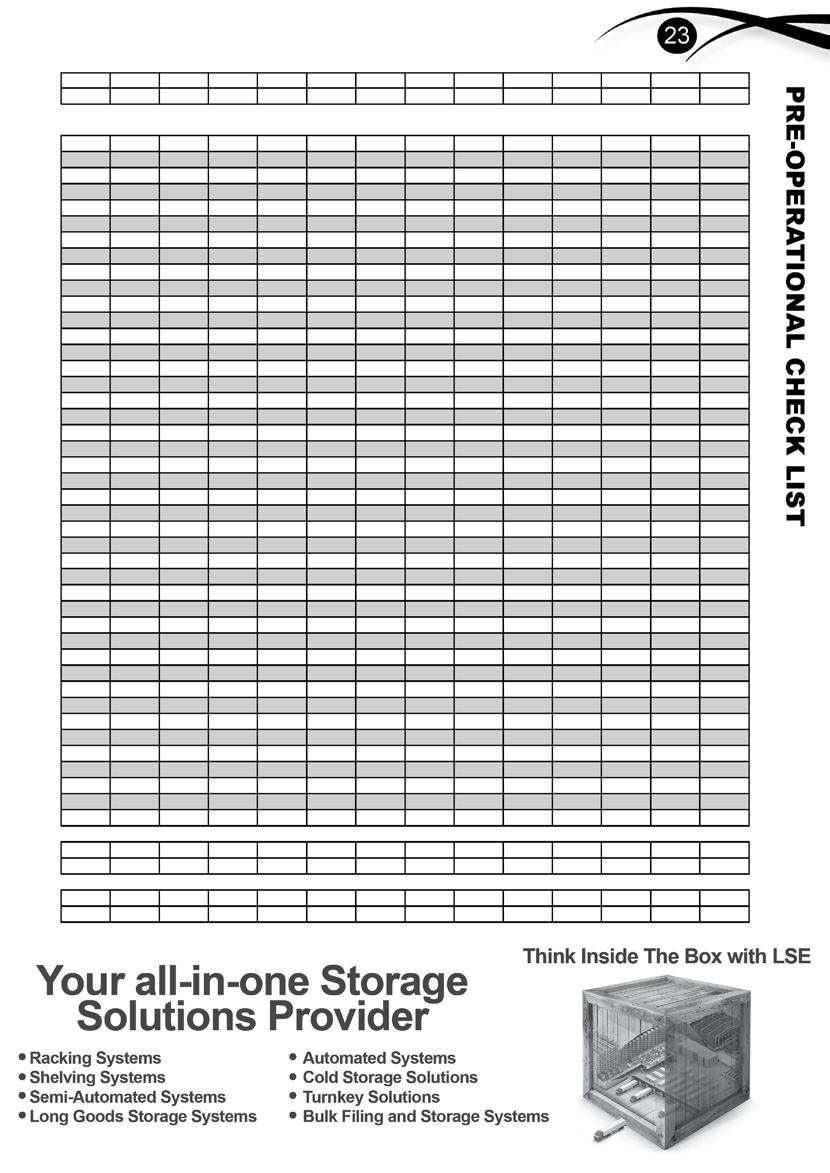
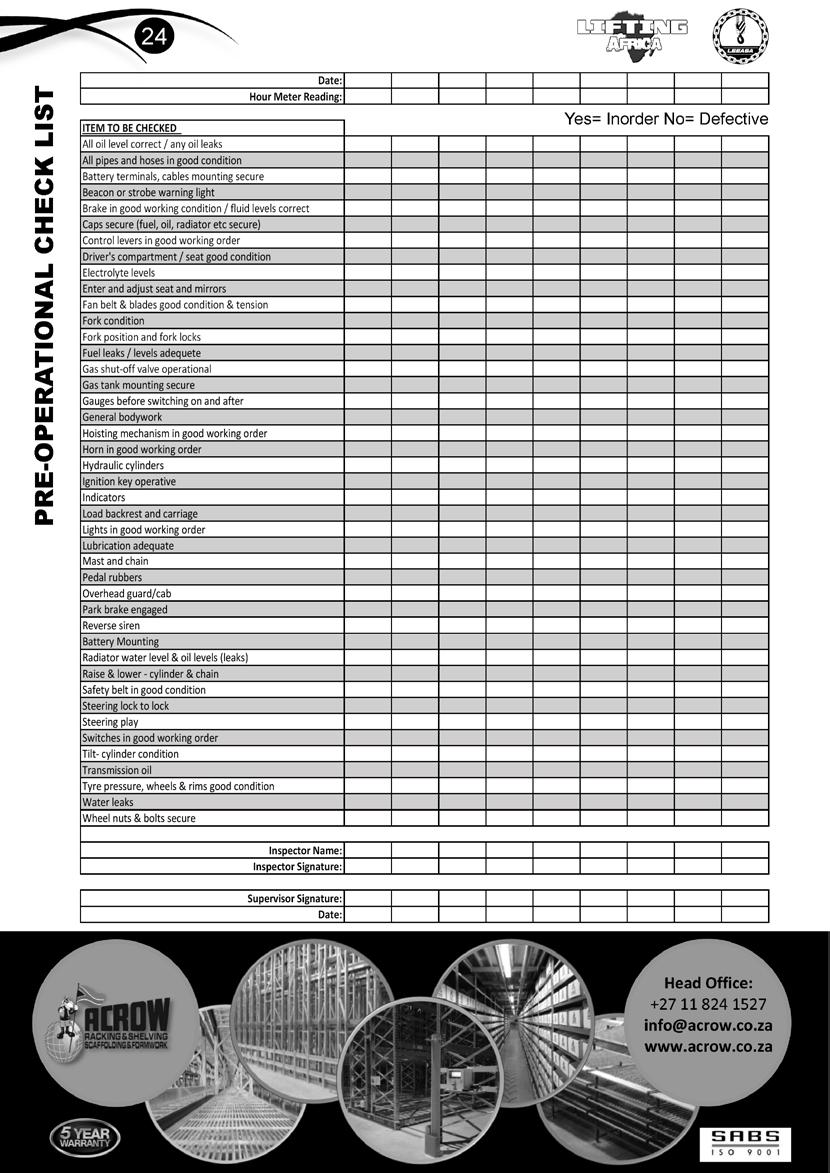

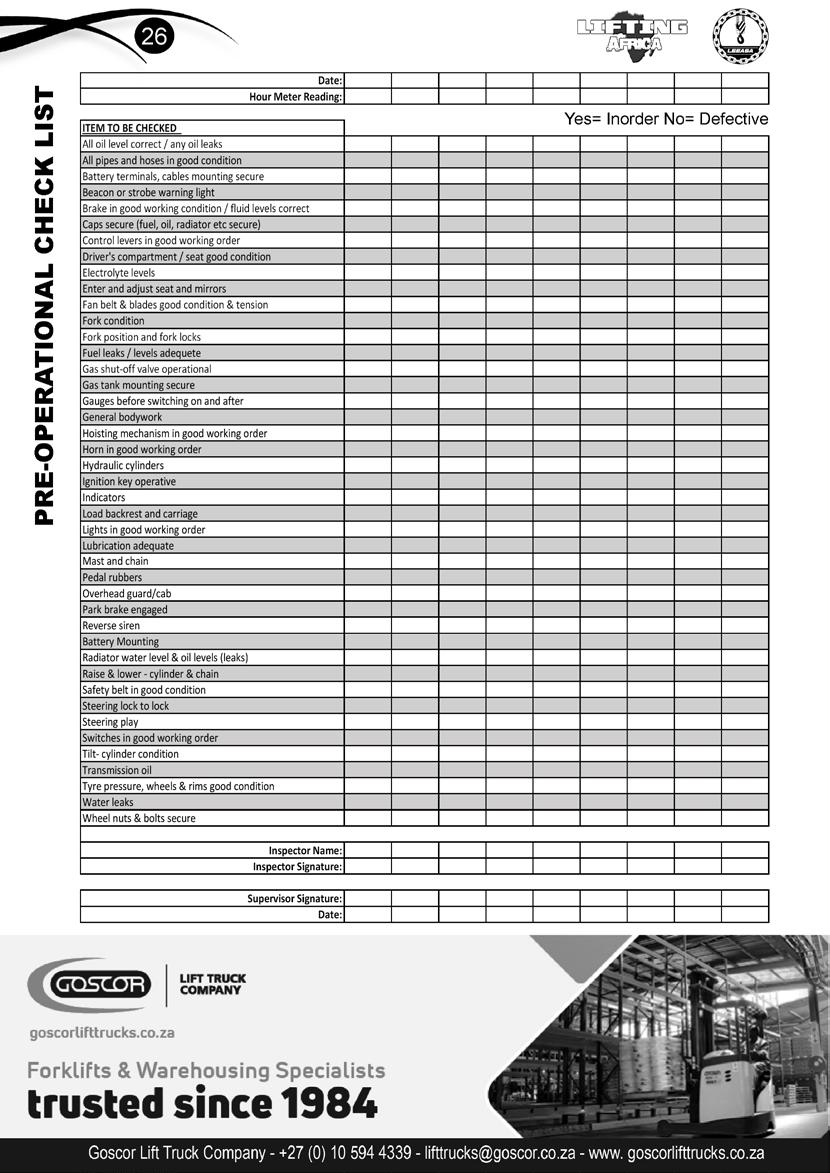
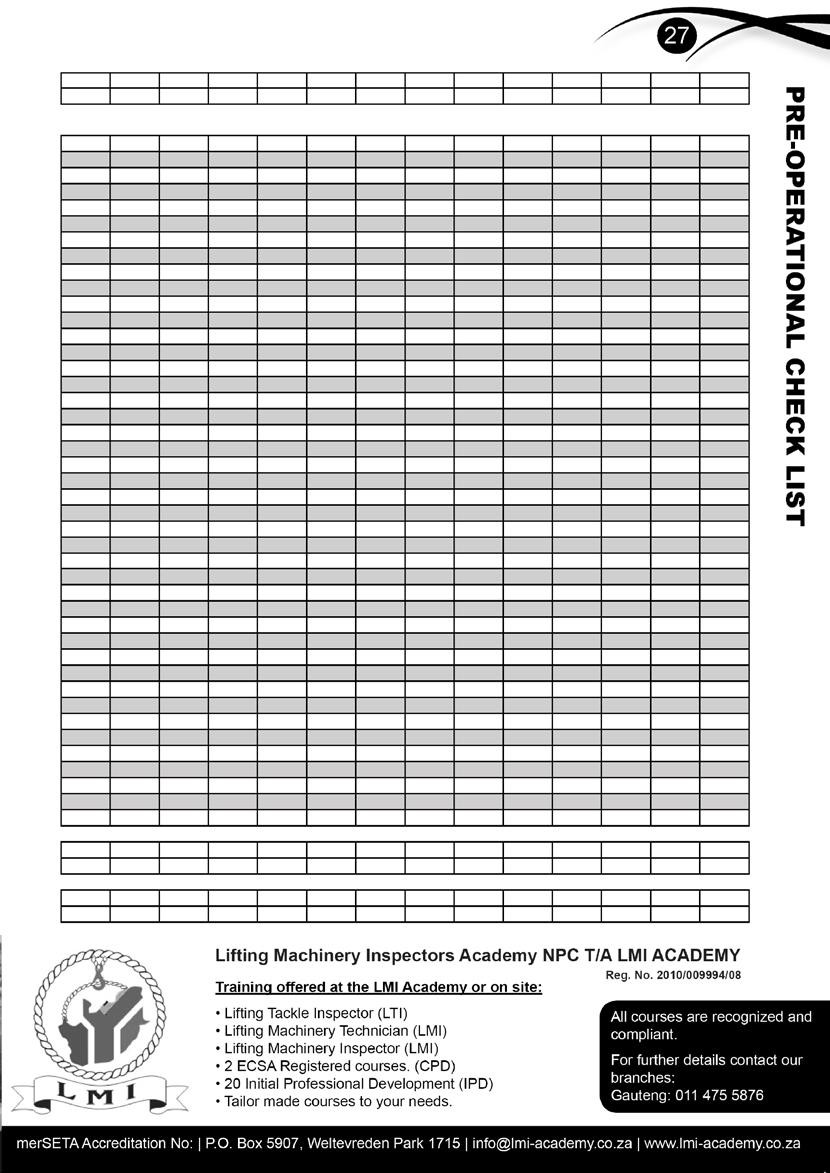


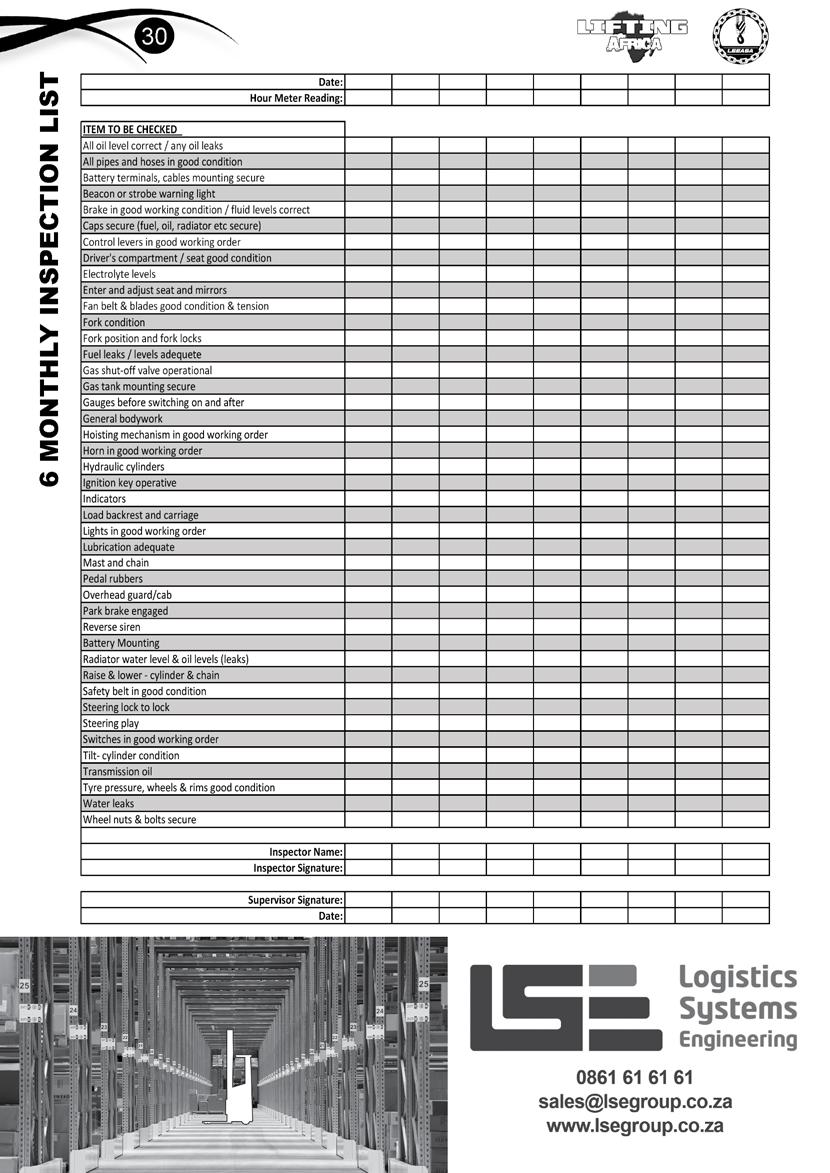
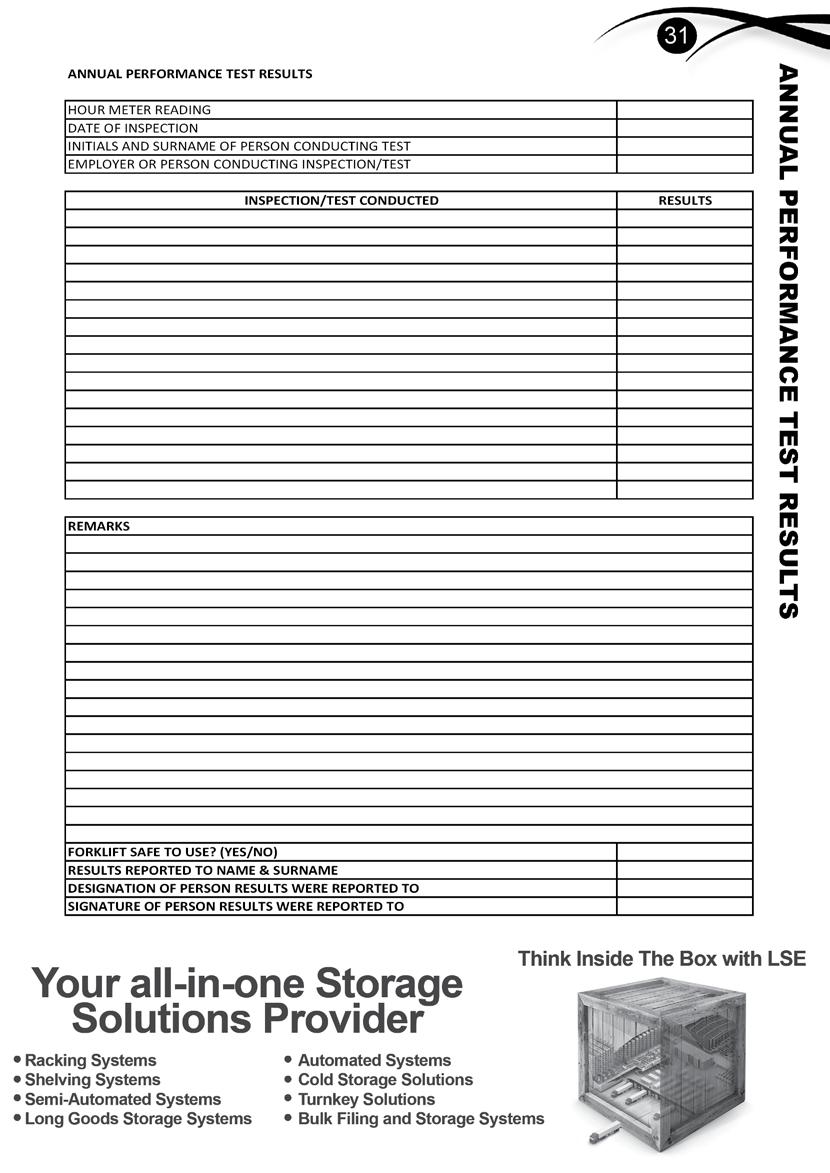
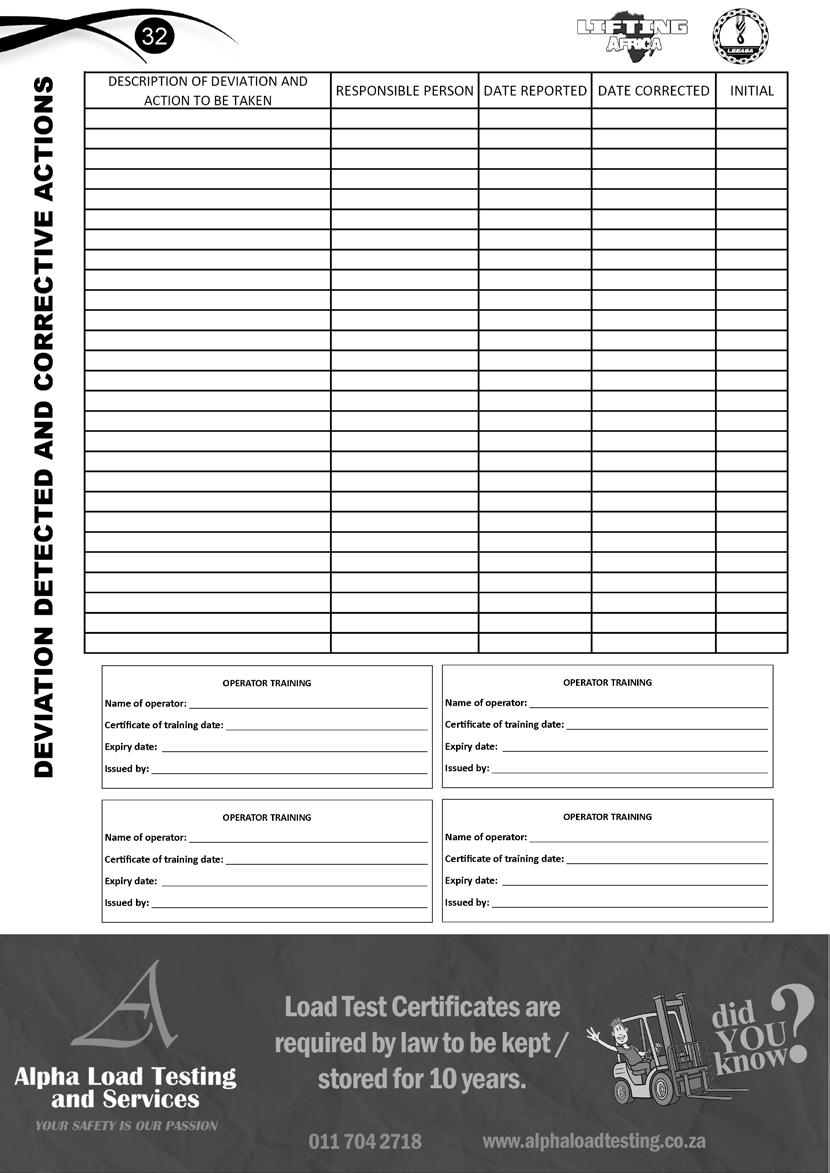
Combi-SC Complete independence when moving containers & oversized loads • Up to 100,000 kg capacity • Works in narrow aisles • Eliminate waiting trailers • Full load ground to trailer loading • Low ground pressure fully loaded • Low running & maintenance costs • Optional remote control • Telescopic function - ideal for low doorways COMBi i F T L I F T I N G I N N O V A T I O N Shamrock.co.za 010 593 4342 Combilift, world leaders in providing material handling solutions, offer a full range of innovative products including 4-Way Forklifts, Pedestrian Stackers and Straddle Carriers. Combilift products are designed to handle long and oversized loads better than anyone else, guaranteeing considerable improvements in space utilization and safety. With capacities ranging from 1000 kg to 100,000 kg, it’s a safe choice to go with Combilift. Find out more at Material Handling Solutions for Your Industry
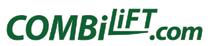
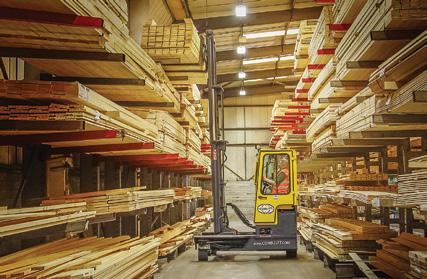
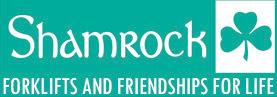
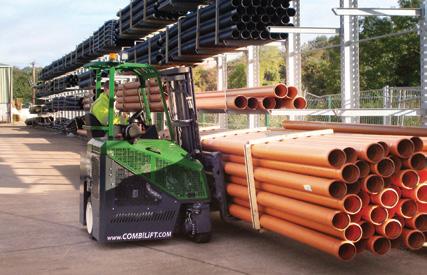
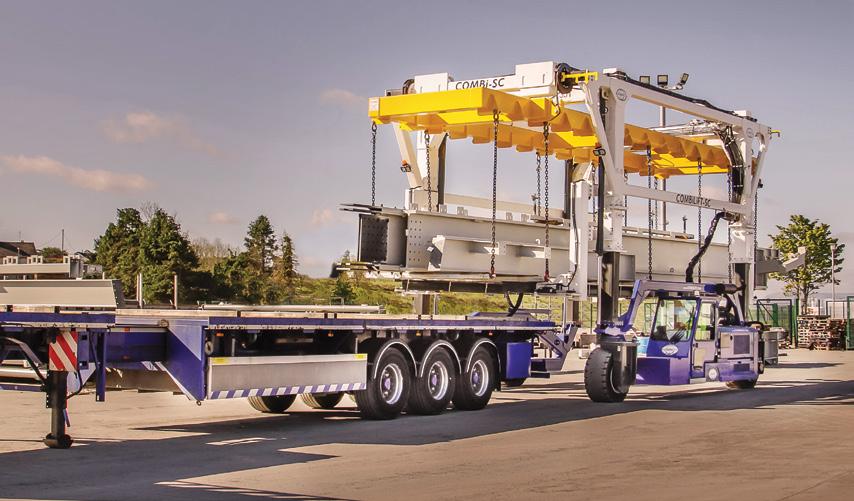
Logistics Systems Engineering’ s Team of experienced experts, have helped thousands of Companies across Africa Optimise their Warehouses and Boost Profitability, by seamlessly integrating our Racking, Shelving, Automation and the Material Handling Equipment into one complete, efficient Storage Solution.
Your all-in-one Storage Solutions Provider
Get the solution your warehouse needs to achieve optimum business efficiency
LSE provide Warehouse Storage Solutions as it’s Core Business. As one of the Market Leaders in the Design, Engineer, Implementation and Maintenance of Warehouse and Industrial Storage Solutions in Sub‑Sahara Africa, it offers a complete product range of Solutions in Racking and Shelving Systems, including Semi‑Automated and Fully Automated Intralogistical Equipment.
Our range of intralogistical equipment and solutions includes: Racking Systems Shelving Systems Long Goods Storage Systems Semi‑Automated Systems Automated Systems Cold Storage Solutions Bulk Filing and Storage Systems Turnkey Solutions
Telephone: 0861 61 61 61 E-mail: sales@lsegroup.co.za Website: www.lsegroup.co.za
Think Inside The Box with LSE
Contact us today to unpack your warehouse potential!
Our approach to storage helps Customers realize space‑ saving warehouse designs that accommodate Greater Density in Smaller Spaces, Enhanced Warehouse Flow, and Long‑lasting Operational Efficiency
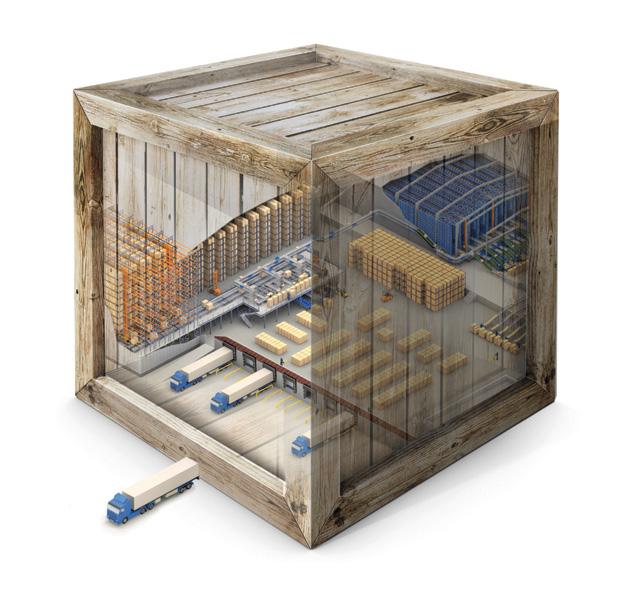