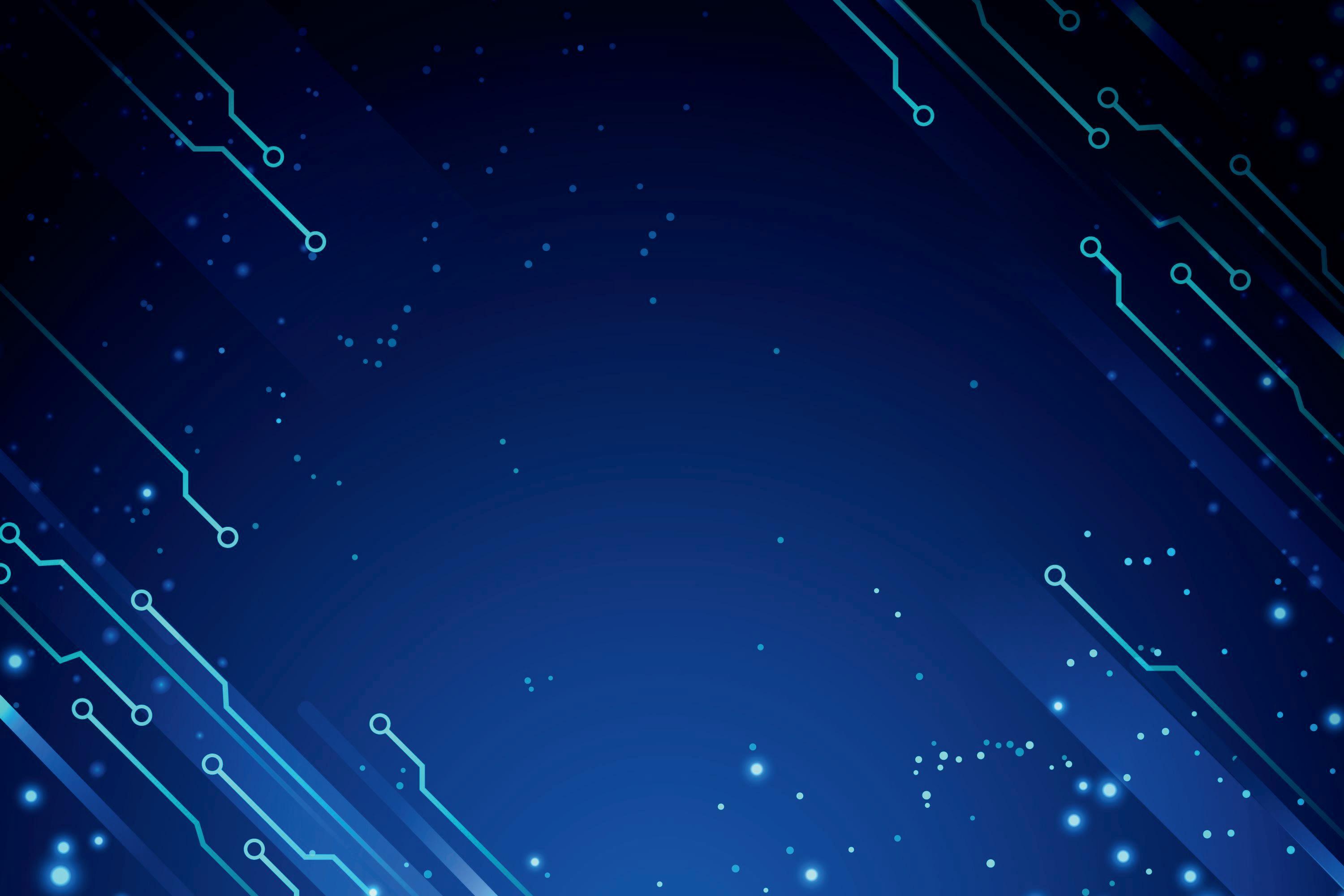

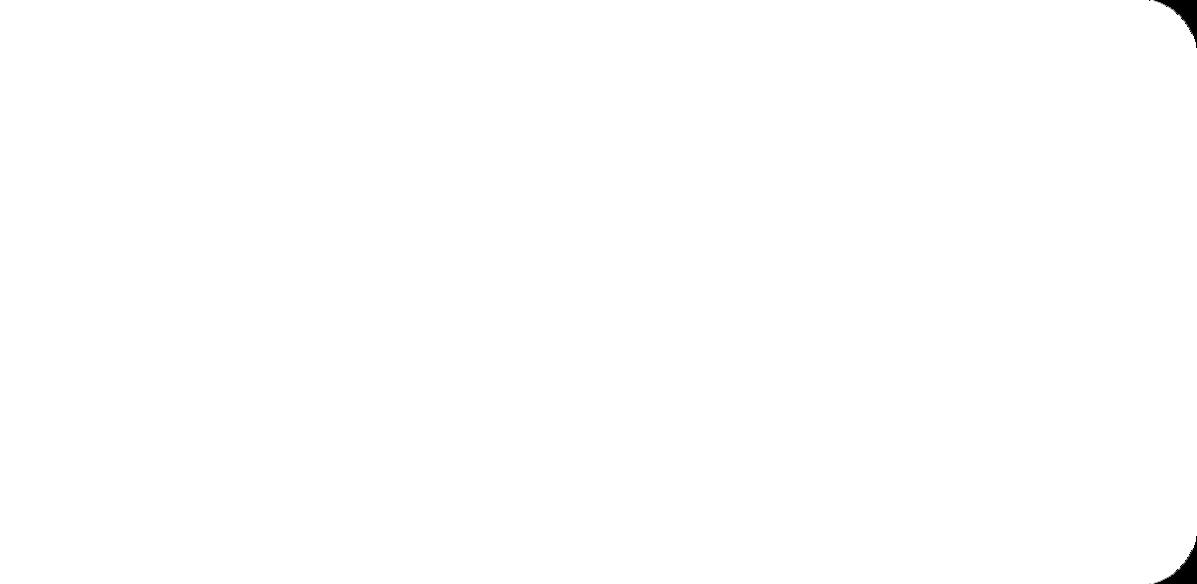
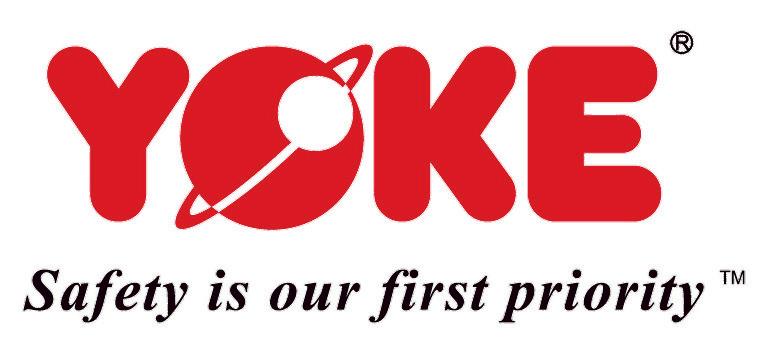
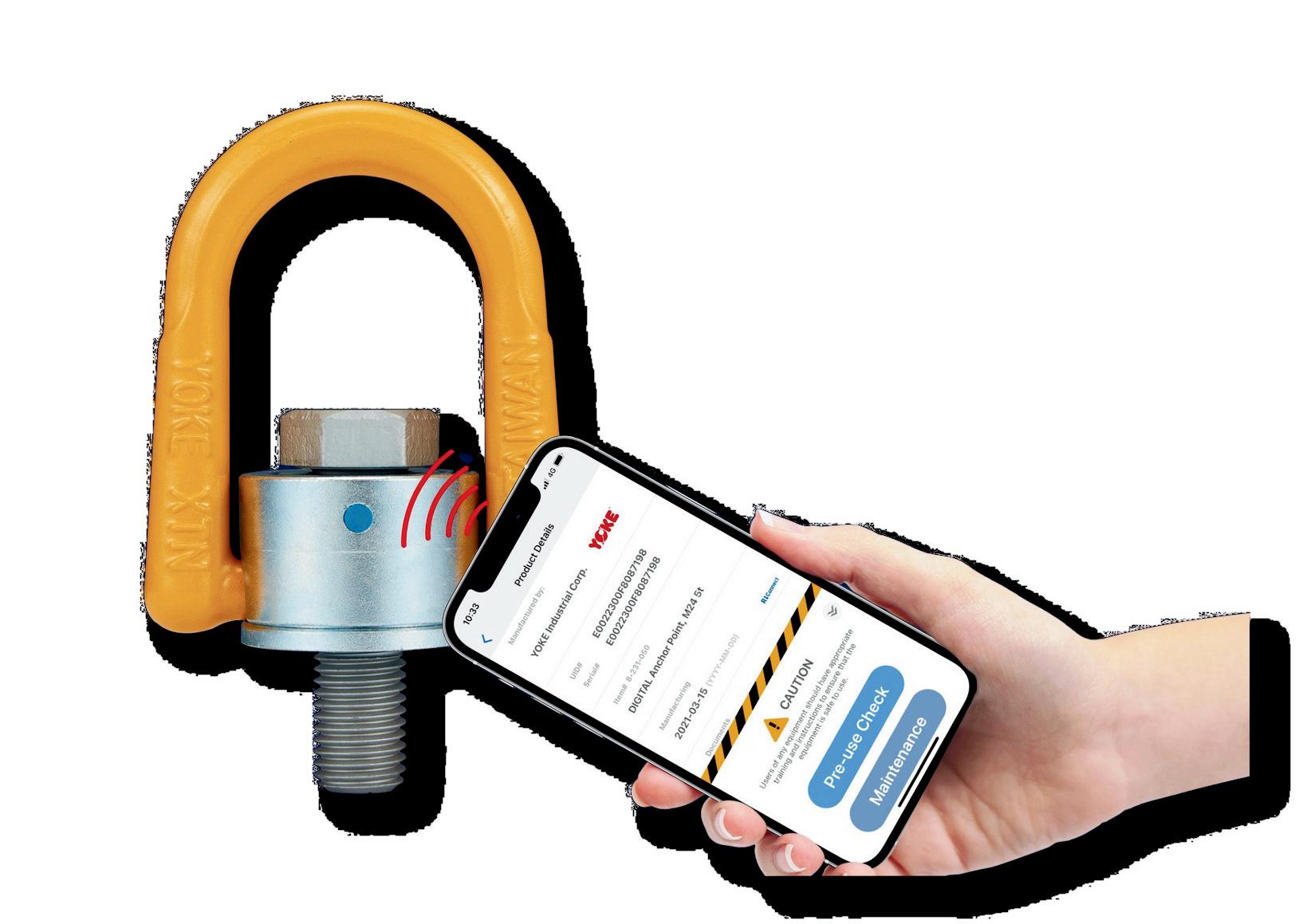
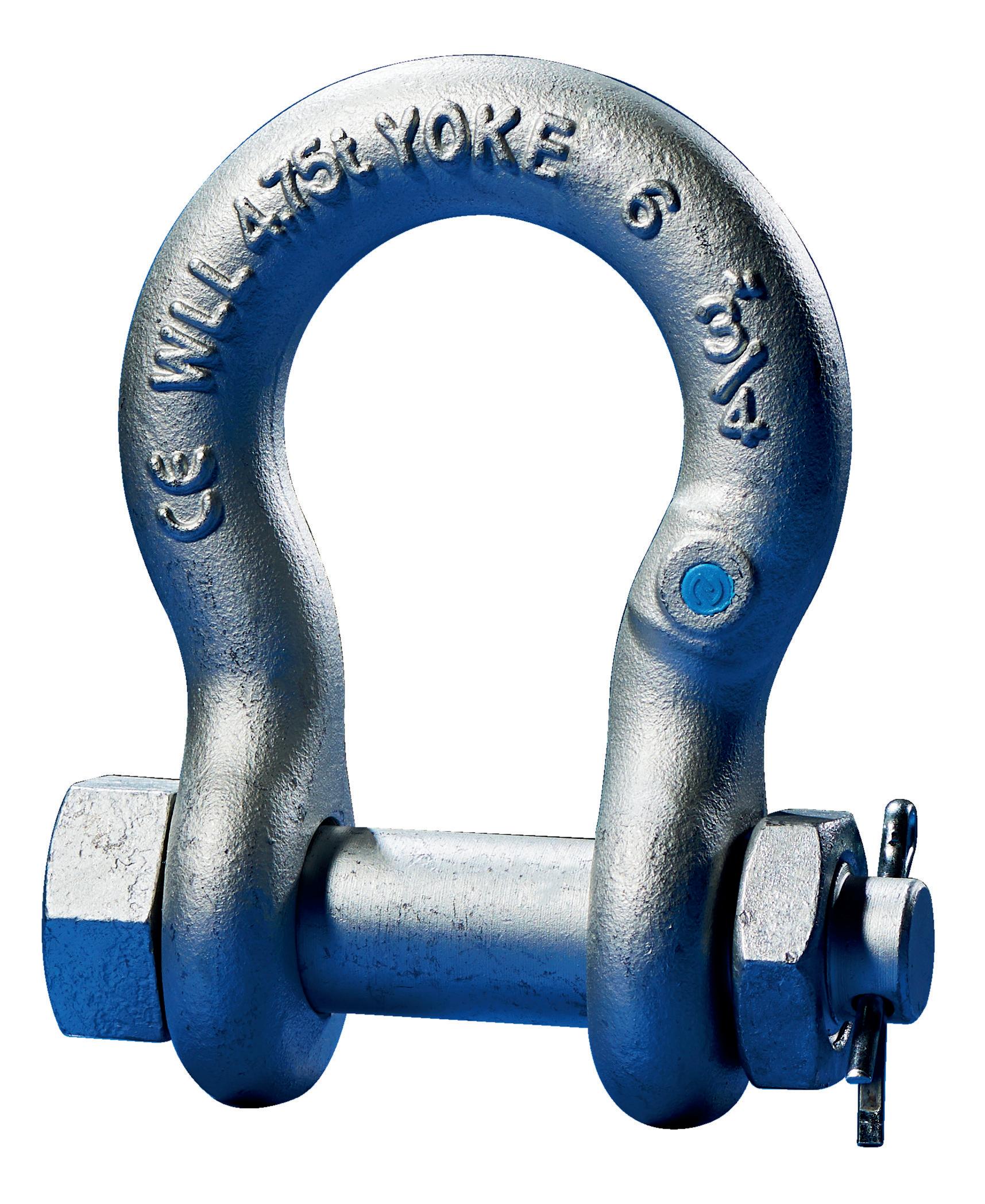
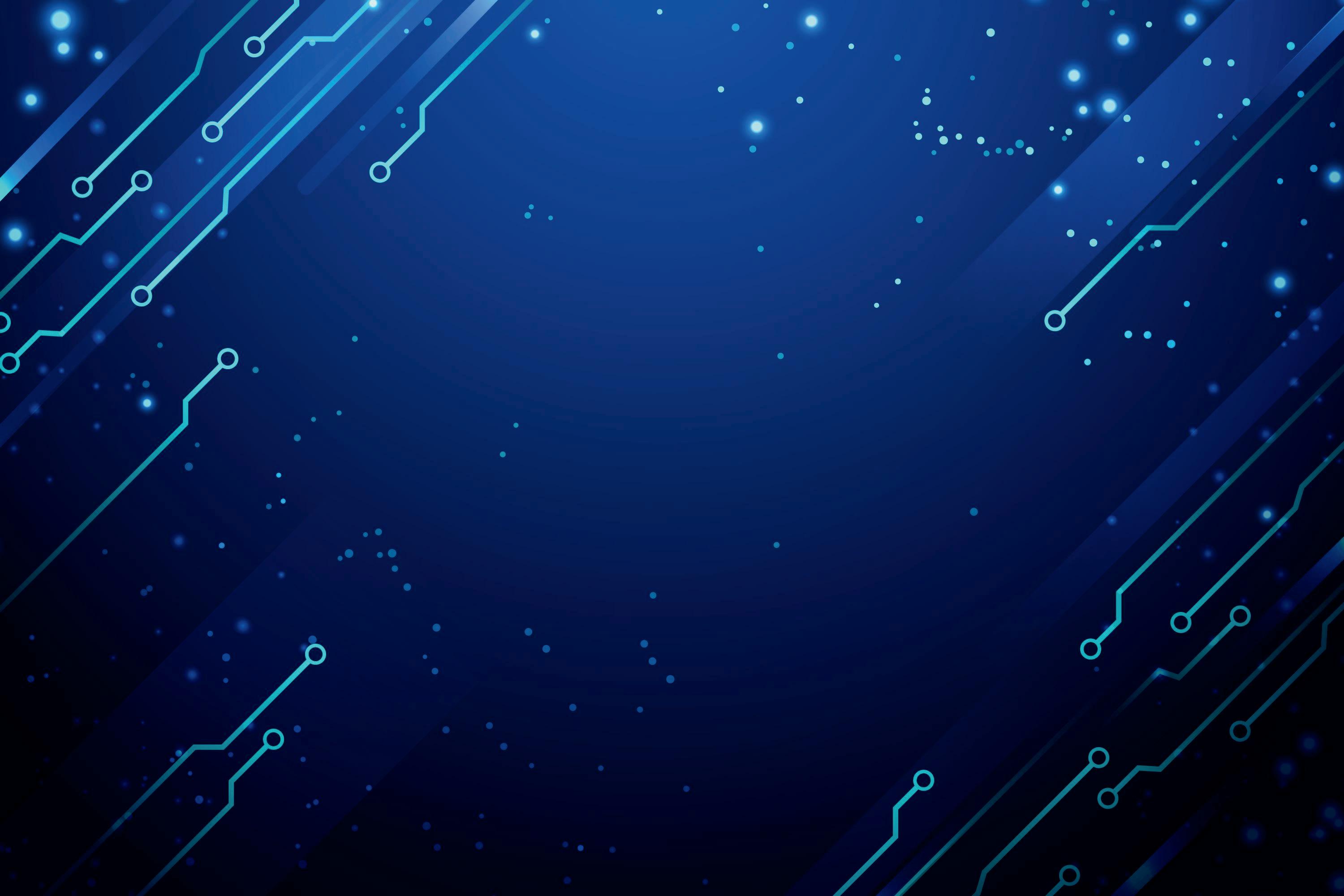
Lifting Africa’s annual Lifting Awards celebrate the outstanding achievements and innovations in the lifting industry, recognising excellence across various categories. These awards aim to highlight the significant contributions of individuals and companies that have set new benchmarks in safety, sustainability, innovation and technical expertise. By acknowledging these exemplary efforts, the Lifting Awards inspire continued growth and development within the industry, fostering a culture of excellence and advancement.
Apprentice / Technician of the Year Award
Excellence in Engineering
Excellence in People Development
Environment Award
Industry Leader Award
Innovation in Service Award
Innovation Award (Manufacturer Product
Innovation of the Year)
Project of the Year
Rising Star Award
Safety and Training Award
Services to the Lifting Industry / Lifetime
Achievement Award
www.liftingawards.co.za
A bifocal modernisation strategy, implemented in 2011, is ongoing at YOKE Industrial Corp.’s pioneering industrial lifting equipment manufacturing facility.
Production at YOKE Industrial Corp. started in 1997.
A lot has changed since, as we’ll explore. What hasn’t, is that there are long-term career opportunities in an everevolving manufacturing environment.
YOKE’s approx. 56,000 square-metre facility produces a staggering 20 million pieces per year. The smart factory is built on 71 automation systems with 108 robotic arms; it is an automated fleet of state-of-the-art Fanuc equipment, that represents approx. US$30m worth of investment. In October 2024, for example, the total time of robotics operation topped 5,176 hours.
Importantly, the factory, located in Taiwan, also employs 500 employees, while human workforce numbers globally are on a steady upward trajectory.
As Steven Hong, the company’s president, says, “We aim to achieve regional business services through the expansion of expatriate staff.”
It’s been nearly 14 years since Hong took what was an unprecedented step at the time, into the world of robotics, with a two-tiered belief that still endures today:
1. A fast in-and-out operational mindset.
2. The companies that can solve handling and fast inventory management in the future will be the winners.
The first automated function was related to stacking finished products onto pallets — and it is still performing the same task today.
With the benefits evident, automated storage and lineside storage systems were soon installed, and they were joined by unmanned automated guided vehicles (AGVs).
Automated optical inspection (AOI) and automatic measurement systems were later installed for inspecting and measuring items during production processes.
Automated systems for personnel assembly, and more loading / unloading technology were all added over the years that followed, principally to improve product quality and stabilise production quantity. Even today, a dedicated department is constantly evaluating and designing future smart factory installations.
“The pace of automation implementation will never stop,” says Hong, “And many people are discussing the feasibility of introducing automation into various processes every day.” Despite such a wholesale commitment to robotics and automation, YOKE staff numbers have not decreased.
“On the contrary,” says Hong. “Because of the expansion in production capacity, we have continued to add staff. However, the criteria for recruitment has changed, due to modifications in production and management models.” The overall operation serves as proof that humans and robots are most efficient together. The automation systems introduced by YOKE are aimed at stabilising product quality, reducing reliance on personnel, and enhancing the value of employees.
While production efficiency may not necessarily always improve, as robots are difficult to fully replace human hands, the benefits are clear:
• Stable quality
• Stable production volume
• Enhanced employee value
Exposure to new technological systems enables employees to operate complex equipment and manage multiple machines. This transition from monotonous tasks, such as loading and unloading, to operating machinery enhances the value of their work. Creating a dynamic, fast-paced, technology-driven environment, also engages a younger demographic of recruits.
Many roles are directly related to automated processes; professionals are responsible for the design of moulds and fixtures, while personnel are involved in project evaluation for automation implementation.
“The smart factory environment does appeal to younger people,” says Hong. “The younger generation is more inclined to engage with new technologies and automation systems. This kind of working environment also offers opportunities for learning new skills and challenging themselves, which attracts more talent to join us.”
Any business looking to introduce automated systems must continue to value the human workforce. One of YOKE’s many strategies is a company-wide suggestion and improvement project, which has been in place since 2021. All employees, regardless of role or hierarchy, are invited to submit proposals each month on topics such as reducing production costs; improving quality; enhancing efficiency; process improvements; eliminating
waste; enhancing workplace safety; energy-saving; etc.
Hong explained, “Department heads form a proposal review committee, and they select the top three proposals each month for rewards. Award-winning cases are announced to encourage all employees to follow suit. Everyone in YOKE can use this platform to raise any issues or suggestions related to production or environmental improvements.”
Climb to the summit
As YOKE’s fleet of robots has grown — from those stacking finished products onto pallets to AOI and everything in between — so too has the prevalence of the Fanuc logo, the iconic badge of the Japanese robotics company. Fanuc is one of the largest industrial robot manufacturers in the world, holding approximately 30% of the global market share. It is located at the foot of Mount Fuji in Japan, with over 5,000 robotic arms in use at its facility.
Hong says, “YOKE believes in the compounding effect of strong partnerships, and trusts that Fanuc can provide appropriate solutions for each manufacturing process as we implement automation. We are committed to advancing manufacturing by integrating both automation and digitalisation. We believe digitalisation is essential for improving efficiency, product quality, and staying competitive in the future. By implementing smart sensors, cloud-based platforms, and data analytics, we can optimise production processes and make data-driven decisions. While not claiming to be the sole leader, we strive to be at the forefront of this digital and automation transformation in the industry.”
YOKE’s growth, through robotics and ongoing personnel recruitment, is an example to follow for other manufacturing businesses, in lifting and other sectors.
YOKE Industrial Corp, info@mail.yoke.net, www.yoke.net
been happening behind the scenes at LEEASA. Many new ideas, many ways to improve how LEEASA functions have been put on the table and explored.
As many members were informed in the last edition, Gert Oosthuizen was appointed as the associations Business Development Manager. Gert has shaped into this role perfectly with big plans and a lot of energy to ensure the continuity of LEEASA and the profession as a whole.
We look forward to our annual conference at The KITE exhibition, which will take place in July and the conference aligned with the Lifting Awards which will take place in August. We are also looking to explore ensuring we reach other provinces in South Africa and are able offer conferences to all of our members around South Africa.
LEEASA also encourages persons interested in CPD training, to compile the content and intellectual property and then registering for CPD certification on the courses. The industry really needs this training in order to ensure the continuity of the profession.
A reminder of how dire the situation is, at present we estimate there are just over 640 active LMI’s. This number illustrates the state of the industry, with more upskilling and training needed for existing or old staff.
LEEASA is exploring innovative ways to train and asses new potential LMI’s. This is a long road but we believe our concept will not only assist potential LMI’s with their training but also potentially assist ECSA when it comes to practical examinations.
LEEASA encourages all members to join our social pages and Whatsapp group to stay up to date with the latest developments. This includes LInkedin and Facebook.
We have not yet held our regular meeting with The Department of Employment and Labour (DEL) and ECSA, however this has been requested by LEEASA, as to ensure we can align with the DEL and present our new proposed plans.
Mr. Aaldrik Graham Kiewiet
Mr. Akeal Ramraj
Mr. Alan Victor Botha
Mr. Alfa Janes Grouws
Mr. Amogelang Gilbert Mmusi
Mr. Amos Tulela
Mr. Andre van der Merwe
Mr. Andrew John Ferguson
Mr. Andries Aucamp
Mr. Andries Gordon
Mr. Andries Josias Agenbag
Mr. Arnoul Spitsbaard
Mr. Ashley Mark Davis
In the coming weeks LEEASA members will receive insightful information on a regular basis, which includes safety bulletins and informative videos. If you are a member and have not been added to the group, please contact Desire´on admin@leeasa.co.za.
LEEASA’s membership is definitely growing – we see this through our membership renewal and new members that have signed on. We encourage all members to pay their membership. The membership fees enable LEEASA to do more for our members.
Finally we would like to wish all members well for the remainder of 2025. If there is anything LEEASA can assist with – please contact Desire´ on admin@leeasa.co.za and we will ensure you are assisted by one of our team members.
Chairman: Kyle Graham: kyle@leeasa.co.za
Vice Chair: Ashley Davis: ashley@leeasa.co.za
Ordinary Members: Francois Weideman: francoisw@leeasa.co.za
Roger Day: roger@leeasa.co.za
Katiso Mogaki: katiso@leeasa.co.za
Carlos Marques: carlos@leeasa.co.za
Association Development Manager: Gert Oosthuizen: gert@leeasa.co.za
Administration: Desiré Davis: admin@leeasa.co.za
Marketing and Design: Xané Roestroff: production@leeasa.co.za
Feel free to reach out to the council members if the need requires.
Yours in SAFE LIFTING, Kyle Graham and the rest of the LEEASA team
Mr. Barend Andreas Lubbe
Mr. Bartholomeus Jakobus Erasmus
Mr. Bekezela Abel Ndlovu
Mr. Carel Gustavus Potgieter
Mr. Carel Hendrik Ferreira
Mr. Challe Andre Bonhamme
Mr. Charl van Heerden Strauss
Mr. Charles Casgoigne
Mr. Christiaan Ernst Gerhard Schutte
Mr. Christiaan Hendrik Van Wyk
Mr. Christo Van Eyk
Mr. Christo van Huyssteen
Mr. Clifford Mubvuta
Mr. Coenraad Hendrik Heunis
Mr. Collin Kubayi
Mr. Cornelis Henry Cyrus Spamers
Mr. Cornelius Frederick van der Nest
Mr. Cornelius Johannes van der Walt
Mr. Cyril Raymond Laredo
Mr. Damien Oscar Stephen
Mr. Daniel Ntatenyane Mangwegape
Mr. Darrin Ian Cass
Mr. David Henry Cooks
Mr. Dean Edwin White
Mr. Dean Eppel
Mr. Deon Bonthuyzen
Mr. Desmond Errol Lloyd
Mr. Dewald Schutte
Mr. Diederik Arnoldus Dahms
Mr. Dirk Johannes Christoffel Geldenhuys
Mr. Donavon Hugh Spamers
Mr. Drean Johannes Kotze
Mr. Dwayne Partridge
Mr. Edius Topera Mashamba
Mr. Edward Hall
Mr. Edward Kruger
Mr. Emile de Koning
Mr. Ernest Khanyile
Mr. Ettiene Pollard
Mr. Eugene Terence Redelinghuys
Mr. Evans Farai Chabata
Mr. Ferdinand Pieterse
Mr. Francois Dewald Blignaut
Mr. Francois Frederikus Le Grange
Mr. Francois Weideman
Mr. Frederek Gerhardus Opperman
Mr. Frederick Johannes Jacobus Fourie
Mr. Frederik Wilhelm Stonehouse
Mr. Fungai Vumbunu
Mr. Garth Vincent Barnes
Mr. Gavin Rayson
Mr. George Khehla Kuhlase
Mr. Gert Vos
Mr. Given Nyathi
Mr. Glenton William Rebello
Mr. Happy Tafara Tati
Mr. Harris Naidoo
Mr. Hendrick Rapule Mahuma
Mr. Hendrik de Jong
Mr. Hendrik de Kock
Mr. Hermanus Barend Dahms
Mr. Ian O’Hara
Mr. Isaac Thupaakgosi Leshotho
Mr. Israel Mooketsi
Mr. Jacobus (Jacques) Mare
Mr. Jacobus Rudolph Kruger
Mr. Jacques Jonker
Mr. Jaen Pienaar
Mr. Jan Frederick van Niekerk
Mr. Jan Louis Venter
Mr. Janus Jacobus Van Biljon
Mr. Jason Brett Mulder
Mr. Jeen-Pierre Groenewald
Mr. Jetro Mzwandile Ngwenya
Mr. Joao Carlos de Freitas Marques
Mr. Johan Frederick Herselman
Mr. Joseph Johannes van Huyssteen
Mr. Joseph Mabaso
Mr. Juan Breitebach
Mr. Justin Henry Brown
Mr. Karel Johannes Francois Du Toit
Mr. Kebareng Daniel Molausi
Mr. Kevin Clive Reckas
Mr. Kevin Keith Godfrey
Mr. Khathutshelo John Phalandwa
Mr. Kobus Van Tonder
Mr. Kyle Graham
Mr. Kyle Streak
Mr. Leon Johan Snyders
Mr. Pieter Albert Schoeman
Mr. Pieter Andries Engelbrecht
Mr. Pieter Eduard Kriel
Mr. Ralph Errol Shamrock
Mr. Randy Mmoto Makeke
Mr. Raphael Letsema Shobane
Mr. Reino Schutte
Mr. Richard James Don Donaldson
Mr. Richard Leonard Albrecht
Mr. Rishi Mungroo
Mr. Robert Du Toit
Mr. Rodger Wayne van wyk
Mr. Johan Michiel van Wyk
Mr. Johan Smith
Mr. Johann du Plessis
Mr. Johannes (Jaco) van Biljon
Mr. Johannes Gideon Kruger
Mr. Johannes Hendrik Snyder
Mr. Johannes Jurgens Marais
Mr. Johannes Roos
Mr. John Carsten Allers
Mr. John George Smith
Mr. Jonathan Rapetsoa
Mr. Rodney Bassingthwaighte
Mr. Paulus Stephanus Marais
Mr. Peter Abraham du Toit
Mr. Peter Jacobus Nel
Mr. Petrus Abraham Bester
Mr. Petrus Lafras Fritz
Mr. Phata Simon Mailula
Mr. Philip John Lourens
Mr. Philip Viviers
Mr. Philippus Stefanus Kruger
Mr. Phillip Demetrius Kemp
Mr. Phiwayinkosi Manazi Biyela
Mr. Rudzani Collins Masiagwala
Mr. Sarel Petrus Jacobus Dreyer
Mr. Schalk Willem Johannes Burger
Mr. Shimane Martin Diutlwileng
Mr. Stephen Andrew McGregor
Mr. Tshisamphiri Moses Mukoma
Mr. Victor Manuel Batista Ferreira
Mr. Weddington Chimbane Moyo
Mr. Werner Hermann Schroer
Mr. Willem Abram (Bossie) Prinsloo
Mr. William Henry Pepler
Mr. William Peter Park
Mr. Wisdom Nhlakanipho Mkhomazi
Mr. Wynand Byleveldt
Mr. Yogandren Soobramoney
Mr. Zenzele Siphamandla Ntshakala
Mrs. Ruwaida Mahomed
Mrs. Sandile Wyeth Mzimela
Ms. Naom Thobile Milanzi
“These records are up to date at the time of going to print”
Productivity is key in the world of logistics, warehouse operations and supply chain management. Managing a forklift fleet effectively can enhance a company’s operational effectiveness, boosting productivity, safety and profitability.
Today, telematics technology has transformed forklift fleet management, providing businesses with real-time data and insights that allow for better decisionmaking and greater control over their warehouse operations.
Stephen Mostert, National Technical Manager at CFAO Equipment, says Toyota Material Handling was the first company in the industry to introduce I_Site, its proprietary telematics technology, as standard equipment on electric forklifts in 2008. “Today, the business operates over 200,000 connected forklifts internationally, delivering valuable data and insights to enhance efficiency and optimise operations.”
He outlines the benefits of using telematics technology in pursuit of more efficient operations.
Improve productivity
Productivity directly translates
to profitability in warehouse operations. Telematics technology enables businesses to monitor the real-time performance and usage of each forklift, tracking key metrics such as operating hours, load weight, idle time, fork position and even details on battery health. This data is then transmitted to fleet managers through detailed reports, providing them with a clear view of each forklift’s performance. By identifying underperforming equipment or potential breakdown risks, fleet managers can take proactive steps, such as scheduling maintenance or redistributing workloads to other forklifts.
Telematics technology helps companies identify inefficiencies by tracking forklift usage. For instance, if the data shows certain forklifts are idling for extended periods, fleet managers can investigate
the cause and make necessary adjustments to optimise operations.
Whether the issue stems from poorly optimised routes, lack of coordination between warehouse workers or overworked equipment, the ability to pinpoint these inefficiencies through telematics empowers businesses to make data-driven decisions, enhancing workflow and minimising operational delays.
A critical advantage of telematics technology in forklift fleet management is its ability to improve safety. Forklifts are powerful machines that can pose significant risks in busy warehouse environments, especially, when not operated properly.
Telematics allows fleet managers to track crucial safety data, including forklift speed on impact,
the frequency of sudden stops, impacts and sharp turns. In cases of repeated safety violations, fleet managers can take corrective action, such as retraining operators or introducing stricter safety measures.
Telematics technology simplifies scalability. As operations expand and more forklifts are added to their fleets, managing an expanded number of vehicles can become increasingly complex and timeconsuming.
With telematics, fleet managers can easily oversee a larger fleet from a single dashboard, providing a comprehensive view of performance across multiple locations or warehouses.
This makes it easier to scale operations while ensuring that all forklifts continue to operate at peak efficiency.
On the flip side, Mostert notes that telematic data can also reveal when operations have an excess of forklifts. “With telematics insights, we can conduct site surveys to determine if customers have too many drivers or pieces of equipment, and whether a forklift should be replaced with a reach truck or another type of machinery.”
Track forklifts
Telematics technology enables fleet managers to continuously track the location of each forklift.
In large warehouses or distribution centres, forklifts can often be misplaced, and operators may
struggle to find the right equipment when needed. With GPS-enabled telematics systems, fleet managers can ensure that forklifts are in the correct locations, minimising time spent searching for equipment and optimising the flow of goods within the facility.
“Forklifts are always on the radar with telematics. For example, during the unrest in KwaZulu-Natal in 2021, we were able to track and remotely disable connected forklifts to prevent them from being removed from our customers’ premises,” notes Mostert.
Check operator credentials
Just as drivers are not permitted to travel on South African roads without a license, forklift operators cannot operate a forklift without a legitimate licence.
Government can shut down operations if drivers are involved in accidents resulting in serious injuries or fatalities, and do not have licenses.
Mostert says one of the standout features of Toyota’s I_Site is its ability to lock out operators who have not completed their on-screen safety checklists or renewed their licenses.
“Every operator has a unique pin code that they enter every time they use a forklift. As part of the initial onboarding process, the operator’s license is verified and its expiration date is entered into the system.”
“I_Site then prompts fleet managers three months ahead of time when a driver’s licence is close to expiring.
If the licence is not renewed in time, the operator is locked out of the system. Fleet managers cannot alter an operator’s status on I_Site unless they have proof of the renewed licence.”
The I_Site edge
I_Site is unique in the market: it’s a Toyota-built system and carries a 12-month or 2,000-hour warrantee. It forms part of the DNA of Toyota’s material handling equipment and data is transmitted wirelessly to onboard data handling units (DHU), something that other systems are unable to do.
This allows for 24/7 live communication for each forklift, enabling managers to monitor all machines remotely.
The system provides automated daily, weekly or monthly reports, along with warnings that allow them to troubleshoot issues in realtime.
It also allows them to send messages to forklift operators, alerting them to issues or providing operational instructions.
Mostert emphasises that for businesses relying on forklift fleets to maintain smooth operations, telematics is no longer a luxury.
“As businesses continue to face pressure to improve efficiency and reduce operational costs, telematics technology is a necessity for gaining the competitive edge.”
CFAO Equipment SA, +27 (0) 11 571 0200, info@cfaoequipment.co.za, www.cfaoequipment.co.za
Goscor Lift Trucks (GLT), a leader in materials handling solutions, proudly celebrates its decade-long partnership with Crusader Logistics, a trailblazer in supply chain solutions.
This collaboration exemplifies a shared commitment to innovation, reliability, and customer satisfaction, underscoring GLT’s position as a trusted partner in the logistics sector.
Crusader Logistics first partnered with GLT nearly ten years ago, drawn by GLT’s competitive pricing and specialised expertise in narrowaisle material handling equipment (MHE), such as Bendi forklifts. Over the years, this relationship has evolved into a strategic alliance, with Crusader naming GLT as their preferred MHE contractor. Today, Crusader operates a fleet of 55 GLT machines across its national facilities, including counterbalance forklifts, reach trucks, very narrow aisle machines, and power pallet trucks.
Stuart Roos, Managing Director of Crusader Logistics, highlights the significance of this partnership, “GLT has consistently demonstrated their understanding of our operational needs. Their ability to deliver innovative solutions, such as narrow-aisle applications, has been instrumental in optimising our warehouse space and revolutionising our racking configurations.” Roos believes GLT’s
solutions are integral to Crusader’s success in demanding logistics environments. From supporting narrow-aisle operations to standard ride-ons, he asserts GLT’s equipment enhances efficiency and ensures seamless materials handling. “Their robust aftermarket support, group servicing to minimise downtime, and shortterm rental (STR) capabilities address critical challenges faced by warehouse operators,” he states.
National Warehousing Executive at Crusader Logistics, Myen Naidoo, emphasises the importance of uptime in the logistics industry, stating “our business relies on fully operational equipment to meet daily KPIs and service levels. GLT’s commitment to minimising downtime and maintaining competitive pricing has helped us achieve operational excellence.”
Crusader Logistics has referred GLT to several partner warehouses, underscoring their trust in GLT’s products and services. Roos affirms this trust, by stating “we’re confident that we have chosen an ideal business partner who truly understands our needs. GLT’s consistent service and innovative approach make them an invaluable
ally in our operations.” Reflecting on the partnership, GLT’s Patrick Barber, Director of Business Development, believes, “Crusader Logistics’ trust in GLT over the past decade is a testament to our shared values and dedication to excellence. We’re proud to provide solutions that empower their operations and look forward to many more years of collaboration.”
The success of the partnership between Crusader Logistics and GLT highlights the power of trust and collaboration in business. Over the past decade, GLT has consistently demonstrated its commitment to understanding the unique needs of Crusader Logistics, ensuring that their operations run smoothly and efficiently. As both companies continue to grow, GLT will remain a trusted partner, providing the ongoing support and innovative solutions necessary for Crusader’s continued success. This enduring partnership reflects the shared values of reliability, excellence, and dedication to meeting customer needs.
Goscor Access Solutions, +27 (0 11 393 6437, accesssolutions@goscor.co.za, www.goscoraccesssolutions.co.za
Manufacturing and Modification of Cranes
Erection, Servicing & Load Testing of Cranes
Sling Inspection
Designing of Electrical Panels
Factory Maintenance
Supply, Installation of Standard & Specialized
Radio Control Systems
Hiring of Mobile Cranes and Load Test Weights
A Service That Meets The Requirements of Our Clients
Provide Well Managed, Trained and Motivated Personnel
Meeting any Regulatory and Statutory Requirements
Applicable to Our Business
The Development and Maintenance of a QUALITY SYSTEM
Designed to Ensure Continuous Improvement and Meeting
The Requirements of CertX SA ISO 9001 : 2015
SkyJacks, a trusted leader in access, lifting, and handling solutions, has penned an exclusive distribution agreement with Atlas Lifting and Rigging (ALR) across Southern Africa.
The strategic partnership, formalised late last year, enables SkyJacks to distribute an extensive range of ALR chain hoists, lever hoists, and heavy-duty trolleys.
These solutions are designed to meet the stringent demands of sectors such as mining, engineering, and construction. With stock now readily available, businesses can enhance their operational safety, productivity, and cost-efficiency.
Uncompromising safety and durability
ALR products meet SANS 1594 and SANS 1636 safety standards, ensuring they perform reliably even in tough conditions. Their chain hoists offer precise and secure lifting for heavy loads, especially in areas without easy access to power.
Lever hoists are ideal for pulling, lifting, and positioning tasks in demanding environments. And with capacities ranging from 0.5T to 20T, ALR’s heavy-duty trolleys adapt easily to I-Beams, H-Beams, A-Frames, and various track systems, giving businesses the flexibility they need
A commitment to quality and performance
According to Alistair Bennett, Managing Director at SkyJacks, this partnership reflects the company’s dedication to delivering high-quality lifting solutions tailored to the region’s specific needs.
“Being the exclusive distributor of ALR products in Southern Africa is evidence of SkyJacks’ commitment to providing industries
such as mining, construction, and engineering with premium, timetested lifting gear. This relationship not only brings greater operational effectiveness and safety but also ensures our customers have access to unparalleled local assistance, training, and servicing throughout the product lifecycle.”
Product lineup and applications
ALR lifting solutions are suited to a number of applications. These include:
• Chain blocks: Designed for vertical lifting in confined spaces, available in both Premium and Industrial ranges with capacities from 0.5T to 20T.
• Lever hoists: Compact and lightweight, ideal for pulling, lifting, and positioning loads in heavy-duty applications, with capacities ranging from 0.8T to 9T.
• Heavy-duty trolleys: Available in Plain and Geared options, enabling smooth movement of hoists along beams in workshops, warehouses, and construction sites.
Key benefits of ALR products
SkyJacks’ distribution of ALR
products brings several key advantages to businesses:
• Strength and durability: Upgraded alloy steel side plates, welded pinion shafts, and caged roller bearings ensure long-lasting performance.
• Enhanced safety: Overload protection, traceable manufacturing codes, and structural integrity exceeding four times the workload limit.
• Reliability: Zinc flake coating for superior corrosion resistance, a Weston-Style twin ratchet brake system, and an easy hook replacement design for extended maintenance intervals.
• Regulatory compliance: Meets stringent SANS safety standards, reducing accident risks and ensuring adherence to legal and safety requirements.
• Advanced safety features: Dual pawl Weston brake, enclosed mechanisms, and optional overload protection.
• User-friendly design: Lightweight yet robust construction for ease of use and manoeuvrability. The new lever handle grip features an ergonomic non-slip hilt at the base that guards against losing grip. Additionally, the redesigned handle allows for maximum power and lower headroom, making it ideal for jobs in restricted spaces.
• High load capacity: Reducing the need for multiple lifts, increasing efficiency, and minimising downtime.
Competitive pricing for costeffective solutions
ALR products provide a costeffective option without
compromising performance or safety. Large-volume OEM production, advanced manufacturing techniques, and gearing optimisation allow ALR to provide high-quality lifting equipment at competitive prices. This makes it possible for companies to spend money on high-quality lifting solutions while being cost-effective.
Expanding distribution for greater accessibility
In order to provide availability across Southern Africa, SkyJacks is leveraging its extensive distribution network. Strategically located regional warehouses ensure timely delivery, enabling businesses to procure products at the point of requirement. The company is also expanding its network of authorised resellers across SADC countries to enhance product availability in strategic markets. SkyJacks is also making investments in online platforms to enable customers to easily view product information, quotations, and buying facilities, making procurement simpler.
Future growth and industry leadership
In the future, SkyJacks will continue to enhance and grow the ALR product line to meet evolving market demands. Future initiatives involve developing and implementing comprehensive training programmes to help customers effectively use and maintain the products and enhancing customer service delivery to assist clients throughout their product lifespan. “Through addressing these priority areas,
SkyJacks will establish ALR as the Southern African standard for lifting and rigging solutions,” Bennett goes on to add.
Industry-leading inspection and testing services
Beyond product distribution, SkyJacks provides comprehensive inspection and testing services.
As a registered Lifting Machinery Entity (LME) with the Department of Employment and Labour, the company offers testing for multiple equipment categories, including chain blocks and lever hoists.
SkyJacks’ Core Inspection System enhances efficiency by offering:
• Automated load test certificates, registers, and compliance reminders.
• Consistent inspections and realtime data capture.
• Online access to certificates and compliance documents.
• A paperless workflow for seamless regulatory adherence.
With an unwavering commitment to safety, reliability, and industryleading solutions, SkyJacks is wellpositioned to drive innovation and efficiency in Southern Africa’s lifting and rigging business.
SkyJacks, +27 (0) 82 300 6537, Alistair.bennett@skyjacks.co.za, www.skyjacks.co.za
Manitowoc is pleased to unveil its latest rough-terrain crane at bauma 2025: the Grove GRT550, manufactured at the Niella Tanaro factory in Italy. The GRT550 succeeds the Grove RT550E, continuing its legacy with the longest boom in its class.
Additionally, the GRT550 boasts enhanced load charts and a variety of new features. The GRT550’s fivesection boom with TWIN-LOCK® and MEGAFORM® retains the 39 m reach, with a 49 m tip height possible with the 8 m offsettable swingaway extension.
Maximum capacity is 50 t and there are overall load chart improvements over the RT550. The GRT550 also offers an impressive line pull of up to 5,552 kg – an increase from the 5,100 kg offered by the RT550E.
In addition, it requires less line, speeding rigging time, and enabling a maximum line speed of 155 m/ min (an improvement of 43 m/min).
Even with these performance improvements, the new crane remains lightweight, with a GVW below 29 t allowing for road transport across Europe without permitting. I
ts compact 6.9 m-long, 2.55 m-wide
carrier enhances transport and jobsite setup, with the new Site Steering mode simplifying handling.
An updated outrigger system boosts stability and performance, with smart monitoring of the singlestage outrigger beams contributing to a generous 6 m spread.
The MAXbase™ variable-position outrigger system boosts 360° load capacities and offers more flexibility for congested jobsites.
A new, more comfortable cab with high-capacity HVAC has also been adopted. Visibility has improved – particularly to the boom – and there’s a three-camera system available as an option.
Operators will appreciate the improved setup, which includes an adjustable heated seat with armrest-mounted joystick controls and the new 12 in CCS 1+ touchscreen display.
Power comes from a proven and
reliable Cummins QSB6.7 engine which has an ECO mode for even higher fuel efficiency. “Retaining features such as remote-mounted filters and centrally located service points shows just how technicianfriendly the GRT550 is,” said Daniele Montanaro, product manager for rough-terrain cranes, Manitowoc.
“And we’ve added advanced service and diagnostics features such as the Grove CONNECT™ fleet management system and our On Crane Service Interface (oCSI).”
“All are designed to make the technician’s job much easier, while uptime reaches new highs – exactly what owners are seeking in a powerful RT crane that’s capable of tackling all general handling and maintenance jobs.”
Crane Load Technology, +27 (0) 11 323 9600, sales@craneloadtech.co.za, www.cltcranes.com
Raubex Building, a leading South African construction company, has taken delivery of a new Potain MCT 185 topless tower crane to support the construction of a key housing project in South Africa. The new development is set for completion in November 2026.
The Potain MCT 185, configured with its full 65 m jib and erected at a height of 36 m, will be on-site for approximately 13 months. It boasts a maximum capacity of 8 t and can lift 1.5 t at its full jib end. The crane’s efficient design ensures quick and easy assembly with minimized dimensions and weight.
Hugo van Zyl, plant manager at Raubex Building, said the productive performance of the crane plus the excellent local
support from Potain dealer Crane and Hoist Equipment make the MCT 185 a perfect choice for the job.
“We wanted a cost-effective, reliable, and productive crane, so opted for the Potain MCT 185. But it’s the aftersales service that truly sets this crane apart. We’ve worked with Crane and Hoist Equipment on previous projects, and the company’s commitment to reliable support has always exceeded our expectations. Knowing we
can count on the expertise and responsiveness of Crane and Hoist Equipment gives us confidence that this crane will keep performing at its best long into the future, helping us meet deadlines while maintaining high construction standards.”
Crane & Hoist Equipment SA, +27 (0) 83 424 2658, info@che-sa.co.za, www.che-sa.co.za
Tadano introduces the CC 78.1250-1, the next generation of a 1250-ton capacity lattice boom crawler crane in its lineup. Building on the proven performance of its predecessor, the CC 68.1250-1, this newest model incorporates significant advancements in performance, safety, efficiency, and transportability.
Designed to meet the evolving demands of heavy lifting applications, including the growing wind power sector, the CC 78.12501 achieves a maximum hook height of 224,5 meters when it is equipped with a 15-meter fixed jib. In this configuration it can lift an outstanding 140 tonnes.
To improve its stiffness, the width of the base crane was increased to 3.5 meters. Furthermore, the two available crawler shoe widths – 2.0 meters and 2.4 meters – can accommodate varying ground pressure requirements.
“The CC 78.1250-1 represents a significant step forward in Tadano’s crawler crane development,” says Andreas Hofmann, Executive Vice President of Research & Development. “Customer feedback played a crucial role in its design, ensuring that this crane delivers not only superior lifting capacity but also transport-optimized
components and efficient assembly sequences.”
Tadano’s CC 78.1250-1 is designed to offer multiple redundancies maximizing uptime and enhancing safety. The crane features a dual-engine arrangement with an optimized hydraulic system, allowing for single-engine operation at reduced speeds. Flexible userfriendly interfaces and an optional dual CAN BUS system contribute to increased reliability and operational flexibility. Additionally, the optional auxiliary power unit enables cab systems, HVAC, and lighting to operate using a compact 17kW diesel engine, reducing fuel consumption and emissions during standby operation.
Tadano prioritizes safety, and the CC 78.1250-1 offers multiple features designed to enhance operator confidence and job site security. The crane is equipped with the Tadano Fall Protection System and incorporates protective access to the superstructure and the undercarriage including improved handrails, catwalks, and access ladders.
IRIZAR HOOKS: ELEVATING STANDARDS IN THE GLOBAL CRANE INDUSTRY
The cab design provides an expanded field of view, while an array of cameras and mirrors help the operator see the hoist drums and other blind spots around the crane.
For job sites with uneven terrain, an optional Pedestal Crane (PC) kit replaces the crawlers on the undercarriage with outriggers enabling precise leveling at three different outrigger bases – 12m x 12m, 14m x 14m, and 16m x 16m – offering compatibility with existing foundations. This capability enhances setup efficiency while reducing both time and environmental impact.
The CC 78.1250-1 features the IC-1 control system, which is standard on all Tadano crawler cranes and well accepted by operators. The IC-1 also gives the operator realtime ground pressures on the rigging aids when erecting long boom systems.
This system boosts efficiency with intuitive controls and precise configurations and provides
essential information for safe and efficient operations. The crane’s twin Mercedes-Benz engines are compatible with HVO fuel, reducing CO₂ emissions without sacrificing performance. Additionally, Tadano’s IC-1 Remote telematics solution enables real-time diagnostics and remote troubleshooting, minimizing downtime and optimizing fleet management.
The CC 78.1250-1 has been designed for ease of transport, which includes accessible lifting points on components to make the assembly safe and efficient.
Manufactured in Zweibrücken, a center of excellence for mobile cranes, the crane adheres to worldclass safety standards and utilizes high-quality components from established partners. In our everchanging industry, Tadano remains committed to delivering lifting solutions that combine reliability, efficiency, and sustainability –ensuring customers can invest with confidence.
Tadano, philippe.bisch@tadano.com, www.tadano.com
HEAVY DUTY CHALLENGES. FORGED SOLUTIONS.
Irizar Forge specializes in premium heavy-duty forged components for cranes (overhead, gantry, tower, crawler) up to 5000T SWL. Since 1923, industries like steel, mining, nuclear, hydro and construction have trusted our expertly forged hooks and blocks for reliable performance. When the job demands the best, choose Irizar Forge.
Combilift, the global leader in innovative material handling, unveiled its pioneering Self-Propelled Inloader ‘COMBi-SPI’ at Bauma 2025. This highly anticipated launch marks a significant milestone in the transport of high loads, such as precast concrete, wall panels or glass A-frames, within production facilities and yard environments.
Revolutionising High-Load Transport
Development of the COMBiSPI began in April 2022, driven by the need for an efficient, manoeuvrable, and cost-effective alternative to expensive trailers and trucks.
The objective was clear: to create a versatile solution capable of handling 30-tonne loads on industry standard Inloader Pallets with superior visibility, agility, and ease of operation.
The collaboration with Spaansen, a specialist in precast concrete, influenced the design through to the final stages.
Early prototypes focused on reducing overall length and width and enhancing manoeuvrability for working in busy production facilities.
However, the project took a significant turn when Spaansen opted for a fully electric model middevelopment. This shift required a complete redesign to integrate the electric wheel motors as well as fit the interchangeable batteries into the legs of the machine.
Advanced Features for Unmatched Performance
• Side-Facing Cab: Provides operators with a clear view of both the load and direction of travel, ensuring enhanced safety and precision.
• Sliding Load Supports: Adjustable supports along the chassis to accommodate various load lengths and heights during travel.
• Pivoting Front Dual-Wheel Configuration: Eliminates the need for suspension, optimises stability and gives a tighter turning circle.
• 300mm Ground Clearance: Designed for both concrete and gravel yards, offering reliability across diverse work environments.
• Power Options: Available in Electric (with interchangeable battery system), Diesel, and LPG, catering to different operational needs.
• Large Solid Tires for durability and yard maintenance.
• Compact Yet Powerful: The short chassis enhances load support, maintains a low centre of gravity and offers more manoeuvrability, especially while operating within production facilities.
Industry-Changing Efficiency
With unmatched manoeuvrability and faster operational speed, the Self-Propelled Inloader transforms yard-based logistics by eliminating the reliance on multiple trailers and shunters, significantly enhancing efficiency and reducing operational costs for businesses handling oversized, high loads.
“This project showcases Combilift’s commitment to innovation and customer-driven design,” said Josh Moffett - Heavy Equipment Manager at Combilift. “We’ve leveraged decades of expertise in specialised transport machinery to develop a state-of-the-art solution that meets the evolving needs of the concrete and glass industries.”
The Self-Propelled Inloader is now on display at Bauma 2025 at stand FS.1003/4. Attendees are invited to experience this revolutionary solution firsthand and discover how it redefines material handling for high-load applications
Introducing the Konecranes D-eries electric chain hoist: Where advanced features are standard
Konecranes has launched the new Konecranes D-Series electric chain hoist, designed to meet the demands of industries that require high-performance lifting equipment.
With its robust construction, advanced safety features and compact design, the Konecranes D-Series is engineered to prioritise safety, boost productivity and deliver long-term reliability across a wide variety of industrial applications.
Initially available in the EMEA region, with global availability and additional options planned for release through 2026, the Konecranes D-Series offers lifting capacities ranging from 80 kg to 5,000 kg across seven frame sizes. Its design delivers optimal performance even in challenging environments and where space is limited, supporting industries such as manufacturing, automotive and process operations.
“The Konecranes D-Series reduces downtime with its modular design and low-maintenance components, enabling proactive maintenance that saves time and lowers costs. Designed for seamless integration with Konecranes equipment — including KBK workstation lifting systems, jib cranes and overhead cranes — it provides a flexible and efficient solution for a wide range of industrial applications. Starting in March 2025, we will also offer pre-configured quick-ship hoists with standard features, pendants and trolleys available directly from stock for fast delivery,” says Klaus Möllmann, Senior Manager, LLE Product Sales and Offer Support, EMEA.
Key Features of the Konecranes D-Series electric chain hoist include:
• Advanced safety features: Includes a slipping clutch with speed monitoring for automatic safe stops, 24V contactor control and operating limit switches for enhanced safety.
• Quick and easy installation: Featuring a height-
adjustable control pendant, “plug & lift” and “plug & drive” electric connections, ensuring easy installation and user-friendly operation.
• Wide temperature range: Reliable operation from -20°C to +45°C with the ability to perform at up to 60°C (or even more), ensuring adaptability in various working conditions.
• Low maintenance: The gearbox, slipping clutch and brake are maintenance-free for up to 10 years (in oneshift-operation), minimizing downtime and reducing lifecycle costs.
• Versatile suspension bracket: The flexible suspension system allows easy integration into trolleys and includes several options to meet customer needs.
• Compact design: Even with its advanced features, the Konecranes D-Series maintains a compact form factor, making it ideal for operations in tight spaces.
• Status display for easy service: The 7-digit status display is visible from the outside and shows you real-time information such as operating time, status, warnings and errors.
Ian Grobler, Sales Manager for Konecranes South Africa said “Technology that increases safety compliance whether it be regulatory or operator focused is an important component of the Konecranes offering in South Africa.”
“We are pleased to announce that the new Konecranes D-Series electric chain hoist incorporates advanced safety features like operating limit switches, a slipping clutch with speed monitoring for automatic safe stops and 24V contactor control, which help reduce the risk of accidents and unexpected downtime. Additionally, the hoist offers accurate load positioning and controlled lifting for reliable, efficient operations. The global recognition that Konecranes has for safety first, is more than justified with this new D-Series electric chain hoist”.
The ergonomic pendant control, standard with the hoist, provides smooth and comfortable load handling. Konecranes also offers an ergonomic single-handed operation with a Manulift control unit for loads up to 500 kg.
The Manulift control unit enables operators to efficiently manage the chain hoist and guide the load using only one hand, enhancing load handling efficiency. Suitable for both right-hand and left-hand operation, the Manulift can be easily customized for various tasks with a variety of load handling attachments developed to meet the specific requirements of different industries. Optional radio control systems are also available for enhanced flexibility, further helping to improve both safety and productivity.
Environmental impact considered throughout the hoist’s lifecycle
As is standard with all Konecranes material handling equipment, environmental sustainability aspects have been considered during the design and production process of the Konecranes D-Series electric chain hoist.
The hoist has been developed applying the Konecranes Design for Environment (DfE) concept principles that focus on minimizing environmental impact by emphasizing repairability, durability, material selection and energy efficiency.
Manufactured at the Konecranes factory in Wetter, Germany, the hoist is produced using 100% renewable electricity.
Its modular design allows for easy maintenance of individual components, while key parts, such as the gearbox, slipping clutch and brake, are maintenance-free for up to 10 years, reducing the need for replacements and minimizing downtime. Primarily made from recyclable metals like steel, aluminum and cast iron, the hoist is engineered with sustainability in mind.
Additionally, its packaging is made from fully renewable and recyclable materials, reinforcing Konecranes’ commitment to environmental sustainability throughout the product’s lifecycle.
A strong focus on customers, commitment to business growth, and continuous improvement make Konecranes a material handling industry leader.
This is underpinned by investments in digitalisation and technology, as well as efforts to make material flows more efficient with solutions that decarbonise the economy and advance circularity and safety.
Konecranes, +27 (0 11 898 3500, info.za@konecranes.com, www.konecranes.com
Vacuum lifters are increasingly becoming indispensable tools in various industries, from manufacturing and construction to logistics and warehousing. These devices utilize suction to lift and move heavy or bulky materials efficiently and safely, reducing the physical strain on workers and increasing productivity.
As industries evolve and demand for automation and efficiency grows, understanding the function and benefits of vacuum lifters is essential.
vacuum lifters work
At the core of a vacuum lifter is a simple yet effective mechanism: it creates a vacuum between the lifter and the object to be lifted. This is typically achieved using a vacuum pump that removes air from the lifter’s pad, creating a pressure differential. When the pressure inside the lifter is lower than that of the surrounding atmosphere, the atmospheric pressure holds the object firmly against the lifter pad.
These devices can be equipped with various types of pads—rubber, foam, or specialized materials—to accommodate different surfaces, from smooth glass and metal to rough concrete. Some vacuum lifters even have the capability to adjust suction levels based on the weight and type of material, enhancing their versatility.
Benefits of vacuum lifters
• Improved Safety: One of the primary advantages of vacuum lifters is the significant reduction in workplace injuries. Manual lifting of heavy objects often leads to musculoskeletal injuries, which are a common concern in industries that require heavy lifting. By
automating the lifting process, vacuum lifters minimize physical strain on workers, contributing to a safer work environment.
• Enhanced Efficiency: Vacuum lifters can dramatically speed up material handling processes. Unlike traditional lifting methods, which often require multiple personnel to maneuver heavy objects, a single operator can efficiently use a vacuum lifter to move items quickly and accurately. This not only saves time but also optimizes labor resources, allowing workers to focus on other important tasks.
• Versatility: Vacuum lifters are adaptable to a wide range of materials and shapes. They can handle everything from flat panels and glass sheets to irregularly shaped objects. This versatility makes them suitable for various applications across multiple industries, including construction, manufacturing, and logistics.
• Reduced Damage to Materials: The gentle lifting action of vacuum lifters minimizes the risk of damage to sensitive materials. For instance, when handling glass or delicate surfaces, traditional lifting methods can lead to scratches or breakages. Vacuum lifters provide a secure grip without exerting pressure that could compromise the integrity of the materials.
They can be integrated into robotic systems for precise and efficient material handling, further enhancing productivity and accuracy.
Vacuum lifters are utilized in various sectors:
• Manufacturing: In factories, vacuum lifters are used for assembly line processes, enabling the quick and safe movement of components, such as metal sheets or glass panels.
• Construction: They are essential in lifting heavy building materials, including concrete blocks and prefabricated components, thus speeding up construction projects.
• Integration with Automation: As industries increasingly adopt automation, vacuum lifters have found a significant role in automated systems.
• Logistics and Warehousing: In distribution centers, vacuum lifters streamline the handling of packages and pallets, improving workflow and reducing the time needed for sorting and shipping.
• Food Industry: Specialized vacuum lifters are designed to handle food products safely, ensuring compliance with hygiene standards while enhancing efficiency in food processing and packaging.
Air & Vacuum Technologies, +27 (0) 11 318 3241, info@vactech.co.za, www.vactech.co.za
Becker Mining SA’s Kito RX electric wire rope hoists - launched in Africa two years ago - play a critical role in many industries, including mining, construction, shipbuilding, food, beverage and pharmaceutical processing, manufacturing and general industry, as well as in chemical and petrochemical plants and the wind power sector.
“The addition of Kito electric wire rope hoists to our extensive range of Kito manual and electric chain hoists and lever hoists has been a great success,” explains Rick Jacobs, Senior General Manager (SGM)
for Consumables, Becker Mining South Africa – distributors of the Kito range in Africa since 1986. “Our customers rely on dependable and safe lifting equipment, supported by the assurance of stringent
quality specifications, as well as a reliable support service.
“Kito RX electric wire rope hoists have been developed with a robust design and advanced technology for dependable operation and extended service life in tough conditions. Typical applications are in production plants, plant engineering, production lines and workshops, as well as shipbuilding and general maintenance procedures.
“These flexible hoists are adaptable for use in conjunction with existing cranes and machinery and all components are easily accessible for ease of maintenance.”
Technical features
The Kito RX range, with lifting capacities between 1 000 kg and 50 000 kg, is available from Becker Mining in units with two or four rope strands, reeving 2/1, 4/1 and 4/2. These hoists have lifting speeds from 1.5 m/min to 12 m/min, with the option of single-speed,
two-speed and frequency-control.
Features include 380 – 440 V / 50 –60 Hz / 3 phases, Insulation Class: IP 55 (standard) or IP 66 (optional) and a control voltage of 42 V, 110 V, 24 V, 48 V or 230 V (optional).
These hoists are powered by a three-phase asynchronous motor or the option of a sliding anchor motor. A planetary gearbox ensures optimum power transmission between the hoist motor and rope drum.
For enhanced safety, an electromagnetic disc brake acts directly on the rotor shaft for effective braking force.
Electronic overload protection, with two adjustable levels, offers protection to the hoist and all its components from overloading (Performance Level C). There is also integrated overheating protection for the motor.
A notable design feature includes the rope guide which consists of two parts - the guide ring and tension spring.
The tension spring ensures that the rope lies correctly in the drum groove, while the guide ring always maintains the rope in the correct position, preventing it from coming off the drum groove. By moving the guide ring along the drum, limit switches are activated for the highest and lowest hook positions.
The double-girder trolley is equipped with double-flange wheels, all with high-quality ball bearings.
This construction, where driven wheels are connected directly to the self-braking gear motor, ensures efficient power transmission
the trolley rail. This design also ensures extended service life, reduced wear and low maintenance requirements.
Trolley construction comprises a standard headroom monorail design that enables the hoist to operate directly under and parallel with, the crane or runway beam.
The hoist is directly connected to the trolley and all components are easily accessible for ease of maintenance.
Hoists available in the Kito RX range include a foot mounted hoist without a trolley, designed for lifting capacities from 1 000 kg to 50 000 kg and a hoist with a standard headroom monorail trolley, for capacities from 1 000 kg to 32 000 kg. Double girder trolleys are suitable for capacities from 1 000 kg up to 32 000 kg, either supported or suspended, version S2-S4. This range is available only in supported execution, for capacities from 20 000 kg up to 25 000 kg, two rope falls and for capacities from 40 000 kg to 50 000 kg, four rope falls.
Units are also supplied as a double hoist, with capacities up to 100 000 kg. The low headroom monorail hoist trolley is designed for capacities from 1 000 kg to 16 000 kg.
Various features have been developed to suit specific application requirements. These include radio remote control, customised painting and festoon cable systems.
Users can also choose load spectrum monitoring and synchronisation, load display, summation and measurement and
Becker Mining also supplies a full range of Kito accessories to enhance the performance of Kito hoists.
These components include universal trolleys, available in plain or hand-geared configurations, to provide smooth, precise and easy traversing and positioning.
To ensure hoists are in pristine condition and always operate effectively, specialists recommend that equipment is tested regularly at Becker Mining SA’s workshops, or any certified repair centre.
The company, which is committed to the highest standards in quality and safety, offers technical advisory, repair, test and backup services throughout Africa.
A specialised consulting, training and support facility ensures the optimum efficiency of a wide range of equipment and total safety for workers.
Becker Mining’s critical solutions also comprise high-performance, fit-for-purpose energy distribution, automation and communication, as well as transportation and roof support systems.
Included in the range are intrinsically safe (IS) and flameproof underground electrical reticulation products, as well as fluid transfer, rigging, rope attachment, steel arch tunnel support and chairlift solutions. An important feature of all Becker Mining systems is they are designed to facilitate future upgrades.
Becker Mining, +27 (0) 11 617 6300, info@za.becker-mining.com,
Being able to get instant, real-time and portable detection of wire rope flaws can make a significant difference for operational teams as it allows them to quickly address an issue before it escalates and requires more expensive and time-consuming maintenance.
Lubrication Engineers (LE) South Africa’s Managing Director Colin Ford says that he has seen a number of significant technological advancements and tools entering the market that help wire rope operators detect and resolve problems faster. “Portable inspection equipment for steel wire ropes makes it easier to see what’s happening because maintenance teams can move them around to different ropes across a plant or mine and get a detailed read of the state of their equipment,” says Ford.
In addition, this allows teams to track particular stress points in their machinery and do regular checks for issues.
LE is a regional agent for the TST FDSys.P Flaw Detection System. Tools like the TST use magnetic inductive sensing technology and magnetic flux leakage (MFL) wire rope inspection techniques. Ford is one of South Africa’s foremost experts on the use of MFL for wire ropes. He explains that the technology uses magnetic fields and complex computerised systems to determine the state of a wire rope, right from the centre of the strands to the outer layers of the rope.
Inspections can be done faster and the information will be more accurate. “These tools allow for high-speed, accurate, user-friendly inspections,” says Ford.
The TST is able to perform a 100% accurate non-destructive inspection of wire ropes with diameters ranging from 6 to 70mm. Common issues that a system like the TST can detect include broken wires, corrosion, pitting, abrasion and fatigue.
The TST Portable Wire Rope Tester can inspect upwards of 5 m/s (or as limited for safe operation). It offers >90% repeatability of quantitative detection for flaws, and 100% accuracy of severe flaw signals. It picks up both flaws, such as internal broken wires and fatigue, as well as external flaws, such as broken wire, abrasion and corrosion.
Pairing inspection with correct lubrication
For the most effective approach to wire rope maintenance, regular and accurate inspections with tools like the TST need to be paired with correct lubrication. Using automated lubricant application systems and the correct type of lubricants for wire ropes are also
crucial. Products such as LE’s Wirelife® Almasol® Coating Grease 452 can penetrate right to the core of a rope when applied using something like a Viper lubricator. Ford explains that a Viper is a collar with seals that is strapped down and held in place so that a rope can move through it.
Environmental benefit
Inspections of wire ropes at sites with mine hoisters, cranes, elevators, cableways, power grids, suspended bridges and drilling platforms also have a long-term environmental benefit as knowing about, and then dealing with, issues early on can extend the life a wire rope and reduce the need for them to be prematurely replaced. Extending the life of a wire rope has a knock-on environmental benefit, as does using the right high-quality lubricant during the rope’s lifespan. Both of these reduce waste and make sure that the maximum value is extracted from a rope; and reducing waste is key for realising environmental benefits.
Lubrication Engineers, +27 (0) 11 464 1735, gavin@lubricationengineers.co.za, www.lubricationengineers.co.za
WireCo®, a global leader in wire and synthetic ropes, unveiled a new crane hoist rope at Bauma Munich, showcasing its latest technical innovation.
WireCo’s CASAR LAZERLIFT is transforming the industry with its specialized hoist rope, engineered for large telescopic, crawler, and high-capacity tower cranes.
In demanding overhead crane operations, safety and reliability are paramount. Both the crane and its hoist rope must withstand extreme conditions while delivering consistent performance. WireCo’s hoist ropes are engineered to provide the optimal balance of cost and performance, meeting the unique requirements of crane manufacturers and operators.
“The Lazerlift hoist rope represents our latest breakthrough in rope design, and one that we expect will follow in the footsteps of our other well-known crane ropes,” said
Johannes Weirich, WireCo’s Chief Engineer for Crane Ropes. “We have met crane operator needs with a rope that has superior spooling behavior along with a superior MBF (Minimum Breaking Force).”
Lazerlift redefines durability, delivering an extended service life proven in both test bench trials and real-world crane operations. Engineered to endure extreme radial stress while maintaining superior breaking strength, it stands as the premier choice for heavylifting applications. With Lazerlift, lifting technology is stronger, longer-lasting, and more efficient than ever.
“As wind turbines grow taller and lifting demands intensify, so do the pressures on hoist ropes. Lazerlift is
designed to tackle these challenges head-on, offering exceptional strength, longevity, and resilience. With its advanced engineering, Lazerlift minimizes downtime and maintenance, ensuring operators stay ahead in a competitive industry”, said, David Rowatt, PhD, PE, SVP Global Steel Engineering, WireCo.
Visitors to the Bauma show can come by WireCo’s Stand C4.2.15 to see the Lazerlift product in person, along with other new crane rope products from the company including Boomfit, a boom rope application, and Durascend, a rope for tower crane operators.
WIRECO Germany GmbH, csg@wireco.com, www.wireco.com
iTek Drives has received an order to build motor control panels for a mine in Uganda. They will ship together with variable frequency drives and replacement electric motors, allowing a complete refit of the hoist, longtravel and cross travel on one of the mine’s cranes.
iTek Drives sales director, Ryan Bisnath, said that the order follows several similar deliveries of control panels to Zimbabwe, for borehole pump and mine pump motors.
“We are expanding our reach into Africa south of the Sahara,” Bisnath said.
“Whereas we’ve been shipping drives for fan, pump, compressor and lifting equipment applications for several years, we are now supplying the control panels as well.”
Clarifying the different terminology, Bisnath explained that the drive for a motor provides it with voltage and current as demanded by the control panel, which is itself the link between operator and machine. The panel comprises an arrangement of resistors, chokes and other electrical components which, working together with the drive (also known as a variable frequency drive, or inverter), allows fine adjustment of a motor’s speed, direction, acceleration, deceleration and torque. This can also improve the efficiency of the
application, including reduced energy consumption. Based in Johannesburg, iTek Drives has been a leading African distributor of British-manufactured Invertek Drives’ ‘Optidrive’ variable frequency drives since 2016, supporting them with a full range of service and training facilities from its headquarters in Raceway Industrial Park, Germiston.
iTek expanded its product range last year to include the supply of resistors and chokes. Motor control panels are the most recent addition to the product range.
“We source resistors and chokes from reputable manufacturers, so in addition to drives we can also supply the necessary control panel components, or we can supply these without the drive. We can also design and assemble the complete control panel,” Bisnath said. Bisnath explained that control panel assembly is currently sub-contracted to a qualified, independent manufacturer.
“This arrangement with the subcontractor will continue until
our Germiston workshop has been sufficiently developed for formal authorisation by Invertek, allowing our own technicians to take over panel-building,” he said.
Bisnath said that Optidrive is gaining market share in Africa because of a competitive pricing strategy that delivers product at a price up to 25 percent lower than the market average.
“Full Optidrive service certification will be important for our expansion programme. It will complement it,” Bisnath added.
“Until then, working with our external assembly partner, we can supply the customer with the drive itself, or just the resistor, or just the choke, or – ultimately – the optimised, turnkey solution of drive and control panel assembled and ready to plug in and go to work,”
Bisnath concluded.
iTek Drives, +27 (0 62 301 0478, ryan.bisnath@itekdrives.com, www.itekdrives.com
Bobcat is presenting several new developments at LogiMAT 2025 as part of a comprehensive display of the company’s material handling product lines, including diesel, LPG and electric forklifts, reach trucks and warehouse equipment such as pallet trucks and stackers.
Bobcat is showing three new developments in the range including:
• New lithium batteries
• New warehouse equipment range (Class 3)
• New series of lithium 3-wheel counterbalance forklifts
Introducing Bobcat Lithium (Li-ION) Batteries
At LogiMAT 2025, Bobcat is announcing the upcoming launch of the company’s new Li-ION battery range, available in various capacity options. This reliable, high-quality battery technology has
been developed by Bobcat and will be installed in each series. With a lifespan 2–3 times longer than leadacid batteries – plus fast, efficient charging – lithium battery power can ensure that work can be kept flowing more flexibly. Moreover, with a 5-year/10,000 hour warranty and seamless forklift integration, Bobcat’s lithium batteries deliver lasting value for any application.
Key specifications include:
• 400 and 600 Ah available for each voltage
• Integrated with truck CANBUS, no need for a separate display
• Cell chemistry: LiFePO4 (LFP) = Lithium iron (ferro) phosphate
• Heat management system applied
• Monitoring and diagnostics app available
New Bobcat Li-ION Chargers
The battery range is complemented by new Li-ION Chargers from Bobcat. The chargers are optimised for quick and reliable charging, ensuring equipment is powered and running efficiently.
Where the customer needs a rapid stand-alone charger, Bobcat Li-ION Chargers provide the flexibility and performance to keep operations running smoothly.
New Warehouse Equipment (Class 3)
Bobcat is updating its warehouse equipment portfolio with three new product series. In addition, the company’s current LSM12N-7 and BSL12/16N-7 stackers are now available in initial lift versions. The new warehouse products will also be available with Li-ION batteries from production.
New warehouse product series:
• BPM16/20N-7: pedestrian powered pallet trucks: 1.6 & 2 t capacity
• BPR20/25N-7: powered pallet trucks with platform: 2 & 2.5 t capacity
• BSR12/16N-7: powered platform stacker trucks: 1.2 & 1.6 t capacity
• BSR16N-7i: powered platform stacker truck with initial lift: 1.6 t capacity
The new BPM16/20N-7 pallet trucks are the perfect match for all kinds of applications in and around SMEs, manufacturing and warehousing. The long tiller arm provides optimal, highly ergonomic operation.
It requires less effort, and the operator maintains an optimal distance from the truck. Top-quality components, robust construction, a travel speed up to 6 km/h, and simplified maintenance make the pallet trucks in this series reliable partners for every task.
The BPR20/25N-7 powered platform pallet trucks feature a travel speed of up to 8 km/h, ensuring the trucks are built for optimal horizontal transportation over extended distances.
Equipped with Electric Power Steering (EPS), these trucks offer ergonomic and safe operation.
The suspension flip-down platform minimizes body vibrations, and the sideways protective arms provide additional stability and protect the operator during turns.
In walking operation mode, the platform and arms are folded compactly within the truck’s outline, conserving space. The 1.2 and 1.6 t capacity BSR12/16N-7
powered platform stacker trucks are designed for high efficiency, excelling in storage and picking operations involving heavy weights.
The ergonomic, suspension flipdown platform – paired with protective arms – greatly enhances operational efficiency.
These trucks are capable of reaching lift heights up to 5.5 m and they are also perfect for tasks over extended distances.
Thanks to the robust 8 mm metal skirt, strong chassis, durable mast and metal battery cover – along with premium components from leading suppliers – these models lower service costs and ensure constant readiness for professional use.
The EPS system, coupled with the proportional lifting function, enables smooth and effortless stacking operations.
Bobcat’s First Li-ION 3-wheel Forklifts
The company is introducing the BNT series, Bobcat’s first Li-ION 3-wheel forklifts, designed for light to medium-duty applications. These models — B16NT, B18NT and B20NT — offer a cost-effective, eco-friendly solution tailored to the growing electric forklift market. The new range extends Bobcat’s electric counterbalanced line-up.
Manoeuvrability is the key aspect in the design of these forklifts, making them ideal for use in tight environments. Despite their compact size, these forklifts boast an ergonomic design that ensures large leg room and exceptional operating comfort for the operator. Setting a new standard in confined space material handling, these
forklifts provide a smooth ride and high stability in every job.
Three different load capacity models are available:
• B16NT – 1.6 t load capacity at 500 mm
• B18NT – 1.8 t load capacity at 500 mm
• B20NT – 2.0 t load capacity at 500 mm
Key Highlights
• Dual Drive: equipped with 4.5 kW dual-drive motors to boost productivity
• Maintenance-free 51.2V 300 Ah Li-ION (LFP) battery and 150A charger (380V)
• Comfortable dimensions: designed for compact environments, while still offering comfortable spacious dimensions for the operator.
Bobcat, www.bobcat.com
RiConnect API Key bypasses user interface, enhances security. A new Application Programming Interface (API) Key allows external systems to securely connect to and interact with RiConnect Inc.’s platform programmatically, without needing to go through the user interface.
It is a central component of the company’s cloud-based Software as a Service (SaaS) offering.
Each API Key is unique to a specific integration, typically issued per user, system, or organisation, depending on the use case.
This ensures that only authorised users or systems can access the API, with each key being traceable and individually manageable for security purposes.
Administrators can create, revoke, or refresh API Keys to ensure ongoing security.
Each key is logged for audit purposes, providing traceability for integration activities.
RiConnect is committed to simplifying and digitalising processes.
It is renowned for improving compliance and traceability for equipment management, with ongoing digitalisation being a key priority.
A typical user of RiConnect services — and the API Key — is likely to be an organisation that operates in a demanding sector or large-scale enterprise.
Within these entities, the user is likely to fall into one of two categories:
1. IT teams or developers who want to integrate RiConnect data with other business systems or tools.
2. Users conducting training or testing with RiConnect via the API — for example, in sandbox environments or during onboarding exercises.
Secure access
Rob Whitehurst-Maiden, sales manager at RiConnect, said: “The API Key is designed to provide secure access for integrating RiConnect with third-party systems, applications, or internal tools, enhancing authentication and security. Each API Key is uniquely generated to ensure secure and controlled access. It must be included in the request header for authentication, reducing the risk of unauthorised access. The key enables automated data exchange, streamlining processes, including equipment status updates; compliance and inspection data synchronisation; and integration with internal dashboards, ERP [enterprise resource planning] systems, or third-party tools.”
Importantly, the API Key supports RESTful APIs, enabling seamless real-time data updates and custom automation. As Whitehurst-Maiden explained, RESTful APIs, often referred to as representational state transfer, are a standard type of web API that work over hypertext transfer protocol (HTTP). They’re widely used because they’re simple, stateless, and easy to apply across systems.
For example, a RESTful API allows an external system to ‘ask’ RiConnect, ‘What’s the current status of this equipment?’, or ‘Please create a new inspection order’ — all programmatically. The API Key integrates seamlessly with RiConnect’s Compliance Management System, upheld by the cornerstones of Compliance, Traceability, Status, and Net Zero. CTSN, as it is better known, has been embraced in all corners of the world, supported by RiConnect’s subsidiaries in the UK and US; and partners located in the Middle East, Hong Kong, Iceland, Malaysia, Singapore, and Taiwan.
RiConnect UK Limited, maiden@riconnect.tech, www.riconnect.tech
Truck mounted bin lifting equipment has played a critical role in South Africa’s domestic waste collection system since the introduction of the 240-litre wheelie bin in the early 1990s.
The equipment is installed onto the rear of waste compactor trucks, enabling the bins to be lifted high enough to deposit refuse into the trucks’ hoppers.
Sonia Pretorius, National Sales Manager for 600SA, a division of CFAO Equipment, says not all bin
lifting equipment is equal. “There are several factors that waste management operations need to consider before investing in bin lifting equipment – with the right choice ensuring greater productivity and better-preserved wheelie bins.”
600SA has partnered with a local
manufacturer of bin lifters for over a decade. The equipment is fitted onto 600SA’s range of Orakçi refuse compactors, allowing operators of a truck to lift an average of 1,400 bins a day, translating to about 7,000 bins in a five-day week. Pretorius says 600SA chose to partner with the local manufacturer because its product is specifically tailored for the South Africa market.
“Not only does it accommodate the specifications of our wheelie bins, but it is also more durable than most of the imported equipment available.”
The equipment was designed by a qualified submarine engineer who conducted extensive research into South Africa’s waste management needs.
He created a bin lifter that incorporated superior quality materials and actuators, replacing traditional cylinders and producing equipment with a trouble-free, 30year lifespan, if properly used and maintained.
Pretorius notes that some of 600SA’s competitors have begun to import bin lifters to reduce costs.
“While this might be more cost effective in the short-term, it has long-term consequences for their operations.”
“This is because the equipment is not always produced with the same robust material as the local equipment and has not been specifically designed to handle SA bins.”
Bin lifting equipment that is not designed for local refuse bins often clamps them incorrectly, causing cracks and damage.
With every bin costing the country around R500 (and citizens about R1,000 when purchased from retailers), this can become a costly and counter-productive exercise.
Some municipalities have collected so many damaged bins that they are compelled to auction them off to recyclers for conversion into other plastic products. Pretorius warns that if bin lifter equipment is not fitted properly, it can negatively
impact the bottom lines of waste management companies. “Fitting a bin lifter needs to be conducted by a qualified and accredited technician.”
“Following an intensive training and assessment process, as well as adherence to basic hydraulic principles, we (600SA) were given the greenlight to fit locally manufactured bin lifters ourselves.”
She points out that investing in locally manufactured bin lifters is not only a proudly South African choice, but also ensures that if something goes wrong, parts are easily accessible and don’t require imports. This results in both time and cost savings.
“Additionally, one of the major advantages of the locally produced bin lifters is the actuator.”
“They are amongst the best in the world and have been tested and refined over several years, making them highly effective and longer lasting than any other actuator on the market.” Notably, South Africa’s metropoles have started
implementing a tagging system, where bins are assigned with unique identifiers that can be read by Radio-Frequency Identification (RFID) systems on collection vehicles.
The local manufacturer’s latest bin lifting equipment already incorporates the RFID technology, enabling bin identification.
This is an advantage, as many other suppliers would need to retrofit their equipment with RFID technology, at an additional cost.
Pretorius says waste management companies need to weigh up the pros and cons of the various bin lifters on the market carefully before investing in equipment.
“Making a smart choice up-front will ensure they have the most durable, powerful and effective bin lifting equipment for the long term.”
Imagine a world where every intricate detail, no matter how small, is meticulously crafted to perfection. Welcome to the realm of precision engineering—a field that combines unmatched expertise and skilled craftsmanship to create solutions that drive industries forward.
Our Purpose and future
At Precision Engineering & Solutions (PES), our mission is to provide tailored engineering solutions with exceptional quality, ensuring that our clients receive the highest standards of service. By leveraging innovative technologies and extensive industry expertise, we help businesses enhance efficiency and performance. Our commitment is to build longterm partnerships based on trust, reliability, and innovation, driving progress and creating a sustainable impact in the engineering sector.
What services do we provide?
• Welding: Our expert welders adhere to AWS D1.1 standards, ensuring precision and durability in structural welding, pipeline fabrication, and custom metalwork.
• Lifting Equipment: We supply, certify, and inspect lifting equipment. As an LME-registered provider, we ensure compliance with safety regulations for cranes, hoists, and rigging systems.
• Civil Engineering: We offer construction maintenance services, including foundation reinforcement, ensuring high-quality, lasting results.
• Manufacturing: We specialize in custom steel fabrication, machining, and assembly, producing highquality components tailored to client specifications.
• Conveyor Belt Maintenance: Our team excels in belt splicing, repairs, and labour hire, minimizing downtime and optimizing material handling efficiency.
• Hydraulic Division: We supply, repair, and refurbish hydraulic pumps, cylinders, and control systems, offering diagnostic services and tailored solutions.
• Pneumatic Division: We
provide industrial automation and compressed air solutions, including air filtration and pressure regulation, ensuring seamless operations.
• PPE (Personal Protective Equipment): We supply highquality PPE, including fire-resistant clothing, safety harnesses, and respiratory protection, prioritizing workforce safety.
• Load Testing: Our experts certify machinery, cranes, and hoists, ensuring compliance with safety regulations through rigorous load evaluations.
Herlang Division
At PES, our Herlang division specializes in equipment servicing, maintenance, and repairs, maximizing reliability and performance.
We offer emergency breakdown assistance and preventative maintenance plans to keep operations running smoothly.
Precision Engineering & Solutions, +27 (0) 13 170 5019, admin@pesolutions.co.za, ppe@pesolutions.co.za
With over 35 years in the heavy lifting industry, RGM Cranes excels in manufacturing and supplying overhead cranes and gantries across Africa. Understanding the unique needs of various industries, we design, install, and maintain overhead cranes, gantries, and lifting equipment for optimal safety and efficient productivity. Our crane inspections and testing meet SANS 10375:2018 standards, ensuring top safety measures.
We maintain over R30 million in stockholding, enabling quick turnaround times and efficient service. Additionally, our advanced crane monitoring and crane asset management systems showcase RGM Cranes’ significant leap forward in crane technology. This cloud-based platform provides real-time monitoring and comprehensive asset management capabilities. Users can track crane performance, schedule maintenance, and access critical data remotely. Our advanced crane monitoring system streamlines crane operations and maintenance, guaranteeing peak performance and reliability.
Vanguard have recently unveiled a new specialist wind blade shunt trailer within the South African market. The trailers, are capable of receiving and transporting wind blades from vessels to laydown areas in either top or tail orientation and are already operational.
The trailers were commissioned by Vanguard in order to overcome client and industry challenges, by delivering the first wind blades to have ever been transported through the Port of Richards Bay.
Due to the standard top-to-tail orientation of wind blade shipping, components such as wind blades have often been delivered to specific port locations that are capable of either double handling each component that arrives in the incorrect orientation or that has extensive space to complete various shunt manoeuvres prior to arriving in laydown areas. Vanguard have now brought a cost-effective solution to the market to overcome these challenges and provide increased efficiencies across port
services sector. These innovative trailers are capable of receiving wind blades in either orientation and delivering the cargo to designated laydown areas, across tight quayside locations and with minimal disruption to the port.
The trailers have been designed with a drawbar at either end for efficient shunting purposes and can accommodate extensive wind blade overhangs when loaded in the reverse orientation. This allows the transport arrangement to proceed to laydown areas in much tighter spaces, without having to undergo extensive ground work or street furniture removal. The trailers can be mobilised at site/quayside using bespoke beams to allow for specific length configurations, with
the first project having required the receiving and transportation of wind blades measuring 90.646m long.
The first ongoing project includes the receiving and transportation of 75 wind blades from the Port of Richards Bay to a laydown area outside the port, before being transshipped to Vanguards Scheuerle RBTS (Rotor Blade Transportation System) trailers and transported to a site approximately 500km away.
“Vanguard have provided consultancy from the initial concept, right through to the design and manufacturing of the trailers and it’s been great to see them in action and working so efficiently. Despite the challenging restrictions at the Port, the team have been able to efficiently receive and transport over 15 blades a day to the laydown area, regardless of the orientation.” Laura Hodgkinson, Senior Manager.
Vanguard, +27 (0) 11 616 1800, info@vanguardheavylift.com, www.vanguardheavylift.com
Manitou Southern Africa (Pty) Ltd, a subsidiary of Manitou Group, is pleased to announce the appointment of South Gear Co. (SGC) as the new authorised dealer for its GEHL brand of telehandlers, skid steer loaders and backhoe loaders.
SGC will be responsible for sales, service, and support of GEHL equipment in the Southern Africa region, commencing on March 1, 2025. SGC will work in a close relationship with Manitou Southern Africa.
This strategic partnership combines the strength and innovation of the GEHL brand with SGC’s commitment to providing exceptional customer service. Customers can expect a seamless transition and continued access to GEHL’s high-quality equipment, backed by SGC’s expertise.
SGC, while a newly formed company, is built on a foundation of extensive experience in the construction and agricultural equipment industry. Led by Gavin Leask and Quintin Vorster, formerly of Manitou SA, the team possesses in-depth knowledge of GEHL equipment, making them perfectly suited to support the brand. Their expertise ensures customers will receive knowledgeable guidance in selecting the right GEHL
equipment for their needs, along with dedicated support to maximise performance.
“I’m excited about the prospect of working closely with Gavin and Quintin, who both have the necessary expertise and experience in our product range,” said Darren Hall, Managing Director of Manitou SA. “I am confident that SGC will be successful in developing and promoting the GEHL product range across Southern Africa.”
“SGC is excited to represent GEHL, marking the beginning of an exciting new chapter for GEHL in South Africa,” said Gavin Leask, CEO of SGC. This strategic move allows SGC to be disruptive in the local market by offering world-class products that meet the diverse needs of industries and our customers. SGC is committed to delivering customer-centric solutions that go beyond just equipment, focusing on providing exceptional service and tailored support to ensure maximum value and satisfaction. With this, we aim to revolutionise
the market, empowering customers with the highest quality machinery and unmatched reliability and solutions.”
The GEHL brand is synonymous with quality, reliability, and innovation. GEHL equipment is designed to meet the demands of today’s construction and agricultural professionals, offering a wide range of solutions for various applications. With SGC as the new dealer, customers can expect the same high level of performance and durability they have come to expect from GEHL, along with enhanced customer service and support.
Manitou SA and SGC are committed to ensuring a smooth transition for existing GEHL customers. SGC will honour all existing warranties and service agreements, and customers can continue to rely on the same trusted GEHL equipment they have come to depend on.
Manitou Group, +27 (0) 10 601 3000, info.msa@manitou-group.com, www.manitou.com
Tele Radio has its latest step into the future with its next-generation product line: PAQ. This new line of solutions seeks to enhance flexibility, safety, and user experience in the industrial workplace like never before.
The first product of the line, the SupraPAQ TH76 together with the new R30 receiver, are now available throughout the Tele Radio network with the rest of the line coming later in the year. The PAQ line seeks to address the ever-changing needs of the industrial workplace, which always holds the stringiest safety requirements.
Support and device monitoring are key for maintaining smooth operations. The new line comes with a dedicated smartphone companion app that completely changes the way users interact with Tele Radio remote controls.
The FieldManagerä app enables operators to view device information easily, such as online manual and settings. The app can also be used to manage the device’s settings and installed plug-ins. For future releases of the app more features will come to further simplify operations, allowing for wireless firmware updates, full data synchronization, and remote support from Tele Radio technicians.
Enhanced Safety
Security remains paramount in industrial remote-control systems, and the new platform is all ready to
meet upcoming safety regulations. While maintaining the critical emergency stop functionality, the system introduces additional safety features that create multiple layers of protection for operators and equipment alike.
Each of the remote control’s functions – radio communications, plugins, security – is assigned its own processor unit. This creates a natural barrier between the different compartments and prevents mutual interference. As a result, individual customer software can never affect a remote control’s vital “organs.”
RFID tags for permission management is another prominent feature for enhanced safety, ensuring only certified users operate the most dangerous parts of the machine from a position that ensures optimal operation.
On top of these new safety features the devices’ stop function is PLe, CAT4, SIL3 certified, ensuring optimal working safety in risky conditions.
PAQ brings with it the possibility of integrating custom plug-ins to the remote controls. By building the platform in the programing language C, it allows users to tailor
the experience to their specific needs.
In future releases, to enhance flexibility of operations, the transmitters will be able to be run at the 433 MHz and 915 MHz frequency transmissions in addition to the globally accepted 2.4 GHz; will come with a rechargeable 2000mAh battery with a temperature sensor; and feature 48V charging for faster charging and extended runtime.
These also give the PAQ line the possibility of integrating to most existing applications using Tele Radio products, in short, PAQ can match the features of existing Tele Radio systems already in operation. Thus, inventory management, scalability, hardware replacement becomes easier and more costeffective.
The PAQ line is Tele Radio’s latest step into a future powered by technology. Through these innovations, the company continues to deliver reliable products to ensure the safest solutions for users and long-lasting partnerships with their clients.
Radio AB, info@tele-radio.com, www.tele-radio.com
LEEASA
T: +27 (0) 64 507 6857
E: admin@leeasa.co.za
W: www.leeasa.co.za
Condra Cranes
T: +27 (0) 11 776 6000
E: sales@condra.co.za
W: www.condra.co.za
Elephant Lifting Equipment
T: +27 (0)12 661 6105
E: info@elephantlifting.co.za
W: www.elephantlifting.co.za
Johnson Crane Hire
T: +27 (0) 11 455 9222
E: PeterY@jch.co.za
W: www.jch.co.za
Liebherr Africa
T: +27 (0) 11 365 2000
E: info.laf@liebherr.com
W: www.liebherr.com
Bell Equipment Southern Africa
T: +27 (0) 11 928 9846
E: susanmy@bell.co.za
W: www.bellequipment.com
Bobcat
W: https://www.bobcat.com/mea/en/ industry/material-handling
www.bobcat.com
Goscor Lift Trucks
T: +27 (0) 11 230 2600
E: lifttrucks@goscor.co.za
W: www.goscorlifttrucks.co.za
Jungheinrich
T: +27 (0) 10 596 8460
E: info@jungheinrich.co.za
W: www.jungheinrich.co.za
H&H Specialized Services
T: +27 (0) 82 446 2899
E: werner@h-hss.co.za
W: www.h-hss.co.za
Morris Material Handling SA
T: +27 (0) 11 748 1000
F: +27 (0) 11 748 1093
E: sales@morris.co.za
W: www.morris.co.za
H&H Specialized Services
T: +27 (0) 82 446 2899
E: werner@h-hss.co.za
W: www.h-hss.co.za
Elephant Lifting Equipment
T: +27 (0)12 661 6105
E: info@elephantlifting.co.za
W: www.elephantlifting.co.za
Yale Lifting Solutions
T: +27 (0) 11 794 2910
F: +27 (0) 11 794 3560
E: crm@yalelift.co.za
W: www.yale.co.za
Yale Lifting Solutions
T: +27 (0) 11 794 2910
F: +27 (0) 11 794 3560
E: crm@yalelift.co.za
W: www.cmco.com
GregBev Enterprise
C: +27 (0) 82 854 5143
C: +27 (0) 72 395 4342
T: +27 (0) 53 285 0842
E: admin@gregbev.co.za
W: www.gregbev.co.za
H&H Specialized Services
T: +27 (0) 82 446 2899
E: werner@h-hss.co.za
W: www.h-hss.co.za
Kiloton
T: +27 (0) 861 707 707
E: sales@kiloton.co.za
W: www.kiloton.co.za
YOKE Industrial Corp
E: info@mail.yoke.net
W: www.yoke.net
Yale Lifting Solutions
T: +27 (0) 11 794 2910
F: +27 (0) 11 794 3560
E: crm@yalelift.co.za
W: www.cmco.com
Industrial Power
T: +27 (0) 11 966 2400
E: soniap@cfaoequipment.co.za
E: imtiaza@cfaoequipment.co.za
W: www.cfaoequipment.co.za/600sa/
IY Safety & Inspections
T: +27 (0) 82 773 7019
C: +27 (0) 82 956 3176
E: bianca@iysafetyinspection.co.za
Morris Material Handling SA
T: +27 (0) 11 748 1000
F: +27 (0) 11 748 1093
E: sales@morris.co.za
W: www.morris.co.za
Precision Engineering & Solutions
T: +27 (0) 13 170 5019
E: admin@pesolutions.co.za
E: ppe@pesolutions.co.za
W: www.iysafetyinspection.com LOAD TESTING AND RE-CERTIFICATION
3 60 5 Services
T: +27 (0) 72 207 7443
T: +27 (0) 64 687 7270
E: sales@3605services.co.za
W: www.3605services.co.za
Cranecor Africa
T: +27 (0) 10 446 5790
E: info@cranecor.co.za
W: www.cranecor.co.za
GregBev Enterprise
C: +27 (0) 82 854 5143
C: +27 (0) 72 395 4342
T: +27 (0) 53 285 0842
E: admin@gregbev.co.za
W: www.gregbev.co.za
IY Safety & Inspections
T: +27 (0) 82 773 7019
C: +27 (0) 82 956 3176
E: bianca@iysafetyinspection.co.za
W: www.iysafetyinspection.com
H&H Specialized Services
T: +27 (0) 82 446 2899
E: werner@h-hss.co.za
W: www.h-hss.co.za
Margisia Lifting Solutions
T: +27 (0) 14 763 1849
C: +27 (0) 83 992 2222
E: info@margisia.co.za
W: www.margisia.co.za
Shosholoza Consulting
T: +27 (0) 14 495 1994
C: +27 (0) 79 391 2990
E: info@shosholoza.africa
W: www.shosholoza.africa
Yale Lifting Solutions
T: +27 (0) 11 794 2910
F: +27 (0) 11 794 3560
E: crm@yalelift.co.za
W: www.cmco.com
J Express Crane Services
T: +27 (0) 11 864 8402
M: +27 (0) 83 425 5535
F: +27 (0) 11 864 8408
E: jexpress@telkomsa.net
Kiloton
T: +27 (0) 861 707 707
E: sales@kiloton.co.za
W: www.kiloton.co.za
Kempston Controls
T: +27 (0) 140 776 2888
E: holyhead@kempstoncontrols.co.uk
W: www.kempstoncontrols.co.uk
Cranecor Africa
T: +27 (0) 10 446 5790
E: info@cranecor.co.za
W: www.cranecor.co.za
Morris Material Handling SA
T: +27 (0) 11 748 1000
F: +27 (0) 11 748 1093
E: sales@morris.co.za
W: www.morris.co.za
FB Cranes
T: +27 (0) 11 902 3271
E: info@fbcranes.co.za
W: www.fbcranes.co.za
HP Cranes Consulting
T: +27 (0) 11 740-9725/28/33
F: +27 (0) 11 740 8416
E: admin1@hpcranes.co.za
W: www.hpcranes.co.za
IY Safety & Inspections
T: +27 (0) 82 773 7019
C: +27 (0) 82 956 3176
E: bianca@iysafetyinspection.co.za
W: www.iysafetyinspection.com
CSIR
T: +27 (0) 79 887 2218
E: mininglabs@csir.co.za
W: www.csir.co.za/mechanical -and-rope-testing-laboratory
T: +27 (0) 84 506 1209
E: ndt@chimaera.co.za
W: www.chimaera.co.za
By Carpel SRL - Italy
T: + 39 (0) 39 532 0952
F: + 39 (0) 39 532 0825
E: info@bycarpel.it W: www.bycarpel.it
Condra Cranes
T: +27 (0) 11 776 6000
E: sales@condra.co.za
W: www.condra.co.za
J Express Crane Services
T: +27 (0) 11 864 8402
M: +27 (0) 83 425 5535
F: +27 (0) 11 864 8408
E: jexpress@telkomsa.net
Kempston Controls
T: +27 (0) 140 776 2888
E: holyhead@kempstoncontrols.co.uk
W: www.kempstoncontrols.co.uk
KL Cranes and Lifting Equipment
T: +267 397 4853
C: +267 71344438
E: annelieze@klcranesbot.com W: www.klcranesbot.com
Morris Material Handling SA
T: +27 (0) 11 748 1000
F: +27 (0) 11 748 1093
E: sales@morris.co.za
W: www.morris.co.za
V & S Automation/Cranes
T: +27 (0) 10 442 7478
C: +27 (0) 82 787 2343
E: victor@vsautomation.co.za
W: www.vandsautomation-cranes.co.za
RACKING &
ACROW
T: +27 (0) 11 824 1527
E: info@acrow.co.za
W: www.acrow.co.za
Lifting Placements
C: +27 (0) 61 063 1687
E: info@liftingplacements.co.za
W: www.liftingplacements.co.za
Kempston Controls
T: +27 (0) 140 776 2888
E: holyhead@kempstoncontrols.co.uk
W: www.kempstoncontrols.co.uk
Giovenzana International
T: +31(0) 20 441 3576
E: giovenzana@giovenzana.com
W: www.giovenzana.com
Kiloton
T: +27 (0) 861 707 707
E: sales@kiloton.co.za
W: www.kiloton.co.za
H&H Specialized Services
T: +27 (0) 82 446 2899
E: werner@h-hss.co.za
W: www.h-hss.co.za
SOFTWARE
RiConnect
E: info@mail.yoke.net
W: www.yoke.net
CB Lifting
T: +27 (0) 22 719 1437
E: info@cblifting.co.za
W: www.cblifting.co.za
Haggie
T: +27 (0) 11 601 8400
E: Johannesburgsales@haggie.co.za
W: www.haggiedistribution.co.za
Umholi
T: +27 (0) 11 914 2210/11
F: +27 (0) 11 914 2209
E: umholi@umholi.co.za
W: www.umholi.co.za
Combi Lift
T: +27 (0) 11 900 8010
E: victor@solutions-4u.co.za
W: www.combilift.co.za
Sky Cranes
T: +27 (0) 83 648 3901
E: jacques@skycranesafrica.co.za
W: www.skycranesafrica.co.za
LMI Academy
T: +27 (0) 11 475 5876
E: info@lmi-academy.co.za
Kanu Equipment South Africa (Pty) Ltd
T: +27 (0) 11 826 6710
E: fransv@kanuequipment.com
W: www.kanuequipment.com
Manitou
T: +27 (0) 10 601 3000
E: info.msa@manitou-group.com
W: www.manitou.com
Liebherr Africa
T: +27 (0) 11 365 2000
E: info.laf@liebherr.com
W: www.liebherr.com
W: www.lmi-academy.co.za
MCLS Training
T: +27 (0) 82 506 5899
T: +27 (0) 73 089 0624
E: sinky@mclstraining.co.za
W: www.mclstraining.co.za
Phakamisa Safety Consultants
T: +27 (0) 11 462 9620/1
F: +27 (0) 11 462 9620
E: potto@icon.co.za
W: www.phakamisasafety.co.za
Crane Clinic
T: +27 (0) 11 902 7379
E: reception@craneclinic.co.za
W: www.craneclinic.co.za
Herlang Enterprises
T: +27 (0) 13 170 5019
E: admin@herlang.co.za
Palfinger Africa
T: +27 (0) 11 608 3670/1/2/3/4
E: sales@palfingerafrica.co.za
W: www.palfinger.co.za
Dymot Engineering
T: +27 (0) 11 970 1920
F: +27 (0) 11 970 1979
E: pa@dymot.co.za
W: www.dymot.co.za