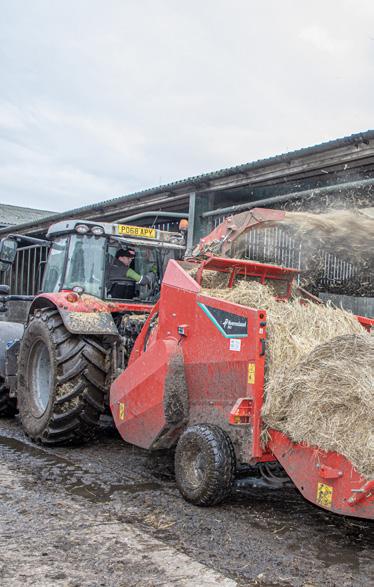
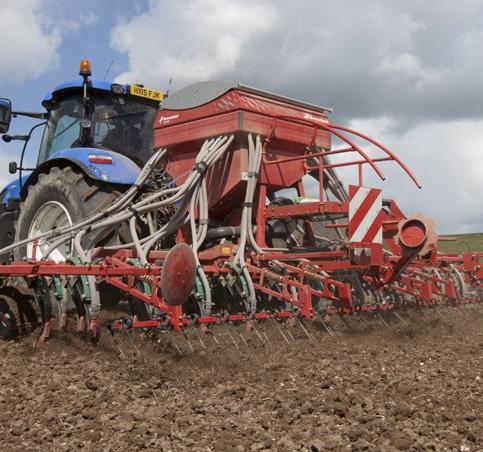
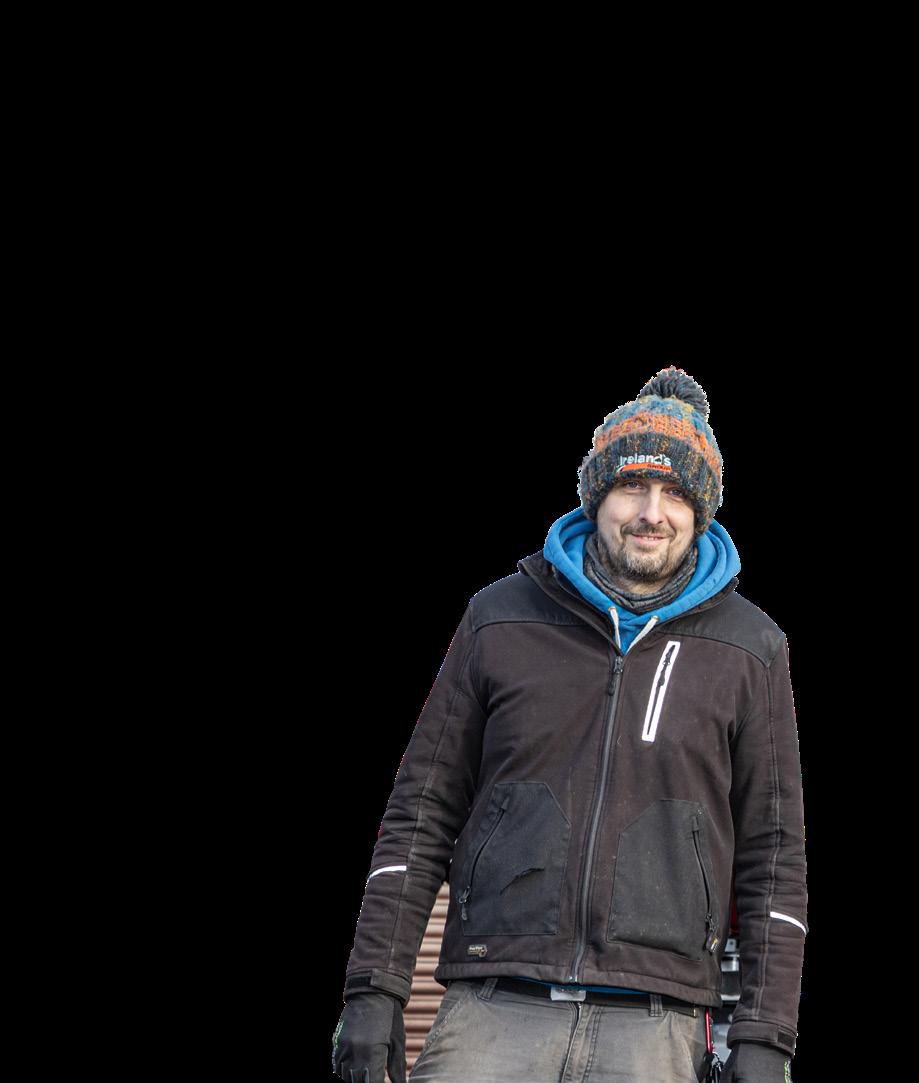
As another eventful year has drawn to a close, we find ourselves looking forward to what 2023 holds, already knowing it brings with it many more challenges.
These include the future direction of commodity and energy prices as global supply chains continue their recovery from COVID, while carefully managing the impact of the war in Ukraine.
Our industry continues to look to the government for clarity, as to how the new farm support system will be implemented, to allow farmers to formulate their longterm business plans.
Looking back on 2022, we as Kverneland have experienced another good year and we thank you for your custom. We would also like to extend our best wishes to you and your families, and hope that you’ve enjoyed a peaceful and restful Christmas.
As the New Year gets off to a cautious start, we’re looking forward to working successfully with you, our customers, and our dealer network, throughout 2023.
Cumbria-based CT Hayton Ltd is the latest dealer to join the Kverneland network. With two depots located in Kendal and Wigton, the appointment of CT Hayton extends access to the entire Kverneland machinery range across Cumbria and the Lake District.
A Case-IH dealer, the business operates with a team of four sales personnel, with 15 service technicians, and a fleet of eight mobile engineers stretching across Cumbria.
“We’re excited to be part of the Kverneland network – it brings a range of equipment that
fits very well with our existing franchises,” explained Ian Smith, CT Hayton’s general manager. “It’s great to have a broad portfolio with a strong implement brand that is instantly recognisable to our customers,” he said. “The next phase of development will be to build a purpose-built depot on a new site in Kendal, to enable our business to continue expanding.”
When it comes to loyalty and longevity, the relationship between Kverneland and family-owned dealership TNS is perhaps one that will be hard to beat. That’s because the East Anglian-based company is celebrating 50 years as a Kverneland dealer and has received a commemorative scale model Kverneland plough to celebrate the milestone.
“We are extremely pleased to have developed this long-standing relationship with TNS,” explained Joe Bell, Kverneland managing director. “It is testament to the loyalty that exists between the two companies.”
TNS managing director James Thurlow, who took over from his father John (pictured at the controls, left) said that as a family-run business TNS values the relationship it has developed with Kverneland.
Joe Bell | Managing DirectorRoyal Highland Show
22-25 June, Royal Highland Centre, Edinburgh
Groundswell
28-29 June, Lannock Manor Farm, Hertfordshire
Royal Welsh Show
24-27 July, Royal Welsh Showground, Builth Wells
UK Dairy Day
13 September, The International Centre, Telford, Shropshire
“Kv shares the same core values that we do,” he said. “Professional, caring, respect, trust and together. Our 50-year relationship is significant, and we value the commitment from Kverneland to support us and our customers.”
Dairy farms handling delicate forage or seeking an alternative to the traditional rake now have additional choices when it comes to swath production following Kverneland’s recent introduction of ROC mergers to its grass machinery line-up.
Three models were evaluated during 2022, including the front-mounted, 2.95m wide
RT380, and the trailed RT730 and RT880 models, with working widths of up to 7.7m and 8.8m respectively.
Additional models are expected for the 2023 grass season, including the RT1150 offering a working width of 11.5m.
The major appeal of the merger is its ability to gently lift and convey forage crops while preserving delicate leaves, and this gentle action is less likely to lift stones and dirt from the ground. As a result, reduced contamination preserves forage quality, and those with forage harvesters are likely to extend the working life of blades and chute liners.
ROC mergers use a 1.0m deep belt-type pickup that can throw forage either left or right, or create a central swath.
Kverneland’s IsoMatch FarmCentre fleet management and wireless telematics solution has been updated to include greater functionality, along with the ability to communicate with the universal data exchange platform, Agrirouter.
With FarmCentre, operators can use their IsoMatch Tellus PRO and Tellus GO+ universal terminals as a gateway to link Kverneland Group implements to cloud-based services. This enables real-time data exchange for sending and receiving tasks.
By adding communication to Agrirouter, implement data access is also available to those using third party terminals, improving
Trials have been taking place in the UK to determine a suitable low disturbance tine option for the ts-drill, to further build on its popularity.
“We’re seeking to expand the ts-drill’s capabilities, so it can also be used as a one-pass drill working direct into stubbles,” explains Kverneland seeding specialist Graham Owen.
The ts-drill has an enviable reputation for working in far from ideal conditions, helped by its five rows of tines that can be spaced for 12.5cm or 15cm row
widths. As a low disturbance drill, row widths are increased to 16.7cm.
“We’re looking to make the most of the drill’s tine stagger and clearance, and are currently testing a variety of tine and point options to develop its low disturbance capability in time for the 2023 season,” explains Graham.
cross-manufacturer compatibility between tractors and implements.
Among the new features of FarmCentre is a dedicated dashboard that corresponds to the implement and the task controller, simplifying evaluation of in-field performance, either with specific tasks or throughout the machine’s lifecycle.
Accuracy and precision continue to evolve for Kverneland sprayers with the development of several new features, all focused on harnessing technology.
These include SpotSpray technology, the introduction of 25cm nozzle spacings and the next generation of Boom Guide ProActive spray height control.
SpotSpray technology is an extension of variable rate application maps. While these maps have been applicable to seed drills and fertiliser spreaders with task control, the same technology can now be applied to Kverneland sprayers that are equipped with iXspray software, when combined with iXflow Air/iXflow E individual nozzle control.
SpotSpray uses prescription maps that include a zero application rate. By loading a map into the
control terminal, the sprayer controls individual nozzles through the SpotSpray software, following only the indicated areas on the map.
These could be weed spots, wet areas, non-germination areas and parts of a field with known soil problems. As a result, liquid application costs can be reduced, further protecting healthy crops from unnecessary blanket applications.
With the introduction of a 25cm nozzle spacing, lower boom heights can be achieved to further reduce spray drift to a minimum. Working at 30cm boom height instead of 50cm has been made possible with
the latest generation of Boom Guide ProActive ultrasonic boom control, which delivers greater precision and consistent boom control at higher forward speeds.
“This is my second Siloking in 12 years, and it’s been so reliable that its replacement will be identical with the addition of tub magnets,” explains Clive.
From Blaenpibydd Farm, Llanfyrnach, Pembrokeshire, Breeze Farms feeds a combination of mixes each day to its 300 head
As an ambassador for local dealer Clarke & Pulman, Amy ‘Ginge’ Wilkinson is kept busy testing kit at the 800-acre White Otter Farm near Southport, where she farms with her dad, David (pictured).
For Clive Breeze, the ability to operate a reliable and efficient feeder day in, day out, backed up by an equally reliable dealer, is why he continues to operate a Kverneland Siloking mixer wagon. Her opinions often make it onto Instagram and other social media platforms, as she provides an insight into her life on the family-run farm. Though one piece of kit she recently tested, a Kverneland 863 shredder-bedder,
proved such an improvement that it ended up being bought.
“I was very glad to try this one out, as our old Kv bedder had become a bit temperamental after 10 years of use and abuse,” explains Amy. “And over a week’s test, we saw such an improvement with the new 863, that I persuaded Dad to buy a new one.”
With around 600 head of beef to bed on a daily basis through the winter months, the Wilkinsons are kept busy. And any unwanted breakdowns mean lost time and reduced efficiency.
of pedigree dairy cows and followers. Rations can include blend, whole crop wheat, clamp and baled silage, with straw mixed in for dry cows.
“It’s all about feed quality, and the mixer wagon delivers a light, fluffy ration that’s not overmixed,” explains Clive. “While good quality forage brings us extra litres and better milk quality, having the right dry cow mix is also essential to prepare freshly calved cows for their return to milk.”
Supplied by JE Rees, the 16 cubic metre trailed Duo has proved robust, and Clive knows what to expect from the machine and his dealer.
“There’s always someone at Rees’ that answers the phone, and for me, that’s a great level of customer
service that goes beyond standard business hours,” he adds.
With silage made by contractor, Clive says trying a multi-cut system in 2021 didn’t bring the improvement in forage quality he had first hoped for.
“We took six cuts, but the forage was simply too rich for the cows,” he says. “So this last season, we ended up with a few round bales during third cut because of the very hot dry weather. And those bales proved to be a game changer in the ration.”
Clive says that having slightly longer, drier forage has improved digestibility, taking just a few extra minutes to mix.
“It’s almost haylage that we add in, and it seems to work like rocket fuel for my herd,” he says. “And now I want to have one bale available every day, to put into the ration with the clamp silage.”
“We shred around 16 round bales/ day, blowing the chopped straw into the pens, and it’s the sort of kit that you rely on – it needs to work,” she says. “We don’t feed with it – but it has to spread straw well, so we can make the most of our wheat straw.”
Amy noted that compared to the older version, this newer 863 model is a lot more powerful, with a wider spout and a more open intake to keep straw flowing through the rotor.
“The 863 is definitely a massive step up and a vast improvement all-round,” says Amy. “Our bales
are stacked outside, which means we get our fair share of wet straw to deal with.”
“And we could block the old machine quite easily with wet bales, where this one just seems to eat its way through straw without struggling,” she adds. And it’s a point that Dad David agrees with.
“It’s a far superior machine,” explains David. “This model also has a stronger six-stud axle which is better at carrying two wet round bales, plus there’s a wider, stronger spout and the ability to blow straw further, at lower revs.”
“It’s almost haylage that we add in, and it seems to work like rocket fuel for my herd.”
For Worcestershire grower Andrew Symonds, the switch to a u-drill with MD disc has doubled output and reduced operating costs, while suiting a wide mix of field conditions.
“We looked for a drill which could work in a variety of scenarios, including ploughed and pressed ground, single-pass cultivated and also direct drilling into stubbles, without any cultivations,” explains Andrew Symonds, who farms 860 acres from Lincomb Farms, Stourporton-Severn.
The arable area includes a rotation of winter wheat and barley, winter cover crops and spring barley, with an extended rotation provided by a vegetable grower who uses around one third of the farm to produce a range of irrigated crops including squash, salad onions, peas and beans. The diversity of crops and the variability of post-harvest soil conditions has recently prompted a rethink with drilling.
“I had been using a 3m power harrow drill combination with my Fendt 724,” he explains. The outfit could handle most conditions, but the trade-off was a lack of direct drilling capability, plus a high fuel burn and a relatively slow output.”
Supplied by TH White’s Stourport branch, the ex-demonstration 6m u-drill arrived on farm in autumn 2021, with a specification that includes wheel track eradicators, pre-emergence markers,
tramlining kit and GPS-controlled half-width shut-off.
As Lincomb Farms already uses a Kverneland fertiliser spreader and Vicon sprayer, Mr Symonds’ two Fendt tractors already had the ISOBUS-compatible IsoMatch Tellus dual-screen terminal installed. This avoided investing in a further terminal, and ensured plug-and-play compatibility.
Andrew Symonds’ u-drill comprises a front set of press wheels followed by two gangs of the wavy edged MD discs, followed by a second row of pneumatic press wheels and finally the disc coulters. Surface levelling and finishing is achieved with a conventional harrow at the rear.
The MD discs are placed vertically and each moves a narrow band of soil – typically 30-50mm – ahead of each disc coulter. This is important for Andrew, as it reduces both the draft required and the volume of soil moved, lending itself to a one-pass, direct drilling approach when the right surface conditions are achieved.
“The u-drill gives me double the work rate, going up from three to six metres compared to the power harrow it replaced, but my tractor has been using the same,
and sometimes less, fuel,” says Andrew. “With hydraulic fan drive, there is no pto and the tractor is running at between 1,500 and 1,700rpm.”
The grain-only seed tank holds 4,350 litres – enough for two tonnes of seed – and feeding 36 coulters, it creates a 16.7cm row width. When planting cover crops or oilseed rape at a wider spacing, distribution head outlets are blanked-off to suit.
Seed depth control and disc pressure can be managed from
either the IsoMatch Tellus PRO terminal or the tractor screen, allowing on-the-move adjustment of the drill’s sections, without the need to stop to add or remove ram stops, as working conditions change.
“I’m very pleased with the operational flexibility provided by the u-drill,” he says. “And the MD disc is definitely the right approach for my soils.
I’m very pleased with the operational flexibility provided by the u-drill
Seedbed quality and cultural control are among the key reasons why Barrington Park Estate continues to plough the lion’s share of its combinable crop acreage.
The organic 5,000-acre farm located in the Cotswolds, Gloucestershire, turns over almost 3,000 acres/year using a pair of six-furrow Kverneland semimounted ploughs, as it makes the most of clean and level seedbeds, to give its cereals the best possible start.
“As an organic farm, the plough will always be an integral part of our cultivations strategy,” explains foreman James Francis. “We have recently extended our rotation to seven years by including peas and beans, and with two-year red and white clover leys, our preference is to plough the grass in preparation for a first cereal.”
Barrington Park Estate has recently upgraded to a 6300S, replacing
one of its two PB100 models through Chandlers Farm Equipment. Specification includes hydraulic front furrow and press arm, with bolt-on reversible points favoured over knock-on points.
Operators favour the single, central skimmer adjustment and the revised headstock design that enables tighter headland turns to be made.
“We’ve had Kv ploughs for over 20 years, and it’s well-built kit that does a great job,” he says.
“Though it helps when you have two very good ploughmen who also compete in matches. The finish they achieve is superb and when they follow each other in the same field, you can’t
Reflecting on yield taken from 180 acres of grain maize established using a six-row Kultistrip followed by a sixrow Optima V, Somerset grower Andy Longman believes the technique holds a lot of potential. “During this year’s exceptionally dry growing season, where crop stress was high, our yields were no different to those who established maize by ploughing and power harrowing,” explains Andy. “From a productivity viewpoint, the work we’re now covering in 30 minutes used to take 90 minutes for example, so we’re clocking up fewer hours and burning a lot less diesel. See issue 42. It’s encouraging to know that our processes have enabled us to trim establishment costs, without suffering a yield penalty,” he adds. “It’s a positive step forward.”
differentiate the finish from either plough.”
James adds that on the thinly soiled Cotswold brash, the farm ploughs at 5-6in deep pulling furrow widths of 14 or 16in, depending on surface conditions and field location. Auto-reset is essential given the stony brash, and the switch to number 28 bodies suits 650 tyres in-furrow. Both ploughs are used with furrow presses during summer, but any winter ploughing is left open rather than pressed, which does provide a little extra output.
“Using Fendt 724’s, each plough covers 30-40 acres/day when pressing, helped with 1,800kg on the front linkage and up to 600kg in each rear wheel. It’s a very
flexible solution for all field work,” he says. “Our soft Cotswold stone isn’t abrasive, so a set of points can last a season.”
“We’ve had Kv ploughs for over 20 years, and it’s wellbuilt kit that does a great job”
As silage making processes continue to evolve, so too does the type of equipment required to get the job done quickly and efficiently.
That’s the findings of north Wales contractor Andrew Kippax, based at Wigfair Hall, St Asaph, who has recently added a 53100MT butterfly mower conditioner to his fleet.
“With many customers choosing to take more frequent cuts of lighter grass crops, we’ve found that more mowing capacity is needed to keep enough grass in front of our 580hp forager,” explains Andrew. “There was a time when you could mow 150 acres/day and that would be enough – now we need to be capable of mowing up to 250 acres/day when dealing with much lighter crops.”
While he continues to run a 6m front/rear combination using a 3632FT and a 3332MT, the extra fire-power from the 53100MT Vario affords a 9.8-10.2m mowing width. Supplied by Mona Tractors, the butterfly outfit uses two 3.6m beds, in combination with a front-mounted 3632FT.
“With the ability to put up to five mower beds on the ground, I can hit spot work rates of 28 acres/ hour,” he says. “Though we continue to operate with modest power – a John Deere 6195R is all that’s required to operate the triple.”
His logic is simple – make full use of tractor power and keep forward
speeds under control to achieve a high quality of cut. It’s a philosophy that avoids shaking operators and equipment to pieces.
“Speed is not the key,” he adds. “Matching kit to tractors is far more important. And everything just works so much smoother, and the mowers leave a superior finish.”
“Ground contour following is superb with the Race Car
suspension, and the Vario frame lets us tweak the butterfly mowers to suit slopes or flat ground,” he adds. “Stubble heights are consistent, and silage quality is maintained.”
“We’ve been really impressed with the quality of cut from all our Kverneland mowers,” he says. “And genuine Kv blades still cut well when they’re almost worn out.”
Reflecting on a decade of successful and reliable use of GEOSPREAD technology, father and son team Peter and Mat Grant, pictured, believe it’s the only way to accurately spread solid fertiliser.
“We bought an Exacta TL GEOSPREAD from Irelands Farm Machinery in spring 2020 to maintain reliability and keep our kit up-to-date,” explains Mat Grant. “This time, we had the very latest dual screen Tellus PRO terminal which has more processing power for variable rates.”
From the 1,050-acre Highfield Farm near Cadwell in Lincolnshire,
GB Grant’s previous GEOSPREAD model had applied over 2.5 million kilos of product, equating to over 4,500 bags of fertiliser. All with impressive accuracy and efficiency.
“We just couldn’t fault our old spreader,” explains Mat. “Auto start-stop and auto section control were always accurate, and the spreader’s reference sensor
compensated for all our in-field slopes and steeper gradients.”
Mat says that 319 tonnes were applied to over 5,400 acres during 2022, representing a fertiliser value of £95,436.
“This is a reminder that you can’t afford to overlap when applying fertiliser,” he adds. “And the last 10 years of using GEOSPREAD has reinforced that.”
Where tramlines had been at 20m, the farm has gone wider this year with a move to 28m. “We have confidence in the spreader’s ability to easily work at this wider setting,” he says. “It coincided with a cost-effective widening of our sprayer’s boom, so we can now get over the sprays and fertiliser workloads with greater timeliness and efficiency.”
Specification changes have been few. A set of storage wheels have been bought to avoid pallets, and a ladder has been added to the side of the hopper.
“When we start spreading at 28m in spring, the extra output will bring better timeliness,” he says. “Spreading wider avoids the need to go faster – at 12kph, we’ll be comfortably on top of the job.”
While logistics and productivity will be much improved this season from the new sprayer’s wider boom and larger tank, he admits there is much to learn as the farm takes its first step on the precision farming ladder.
“I’m excited but nervous at the same time,” says Roger. “Until now, we’ve been applying blanket rates across the farm with an old sprayer and no technology – now we’ve gone all-in with auto start-stop and section control,
with the long-term aim of using variable rate application maps.”
“There is a lot to learn, but it doesn’t all have to be understood in one season,” he adds. “And there’s plenty of specialist help on-hand to guide us on our way.”
The farm’s new iXtrack T4 was supplied by C&O Tractors. It brings a 36m boom and 4,600-litre tank to replace a 3,000-litre, 24m trailed model that had given decent service for the farm. Having moved away from outdoor pig activities, a wider boom was the first option on the wish-list for more output, now that seedbed remediation after pigs is no longer required.
“We didn’t expect to jump straight to 36m, but having seen the boom stability during a demonstration, it was the logical thing to do,” says Roger. “So now I’m starting with the basics, so I can get to understand the new sprayer before advancing into the technology.”
“We’re in a transitional year, with early drilled crops sown on 24m tramlines, and later drilled crops
at 36m,” he says. “So this is a season to learn and understand, to set field boundaries and get under the skin of the sprayer.”
“On tank size alone, I’m already much more efficient,” he says. “Where our largest fields required two loads, I can now cover them in one. When we make full use of auto start-stop and reduce overlaps, we’re really going to make a positive impact on crop canopies and yields, while saving money.”
In the cab of his MF 7722 Dyna VT are an IsoMatch Grip multifunction programmable joystick and an IsoMatch Tellus PRO dual screen terminal – the latter can also be utilised with the farm’s 6m ts-drill.
“There’s a lot of information at my fingertips, and having time in the cab button-bashing will give me a greater understanding of the technology before I put it all into practice,” he says. “I really like the convenience of auto-fill, and the simplicity of iXclean Pro one-touch cleaning. But having a clear suction filter is a stroke of genius.”
“There’s plenty of specialist help on-hand to guide us on our way.”