ARCHITECTURAL PORTFOLIO VOL 2 KIT YEUNG. CHAN PROFESSIONAL2017-2022 WORK Vol 2

All the Drawings in this portfolio are used for reference only. This portfolio illustrates the selected works during my employment at PWP Architects & HOP Architects from 2017 to present.
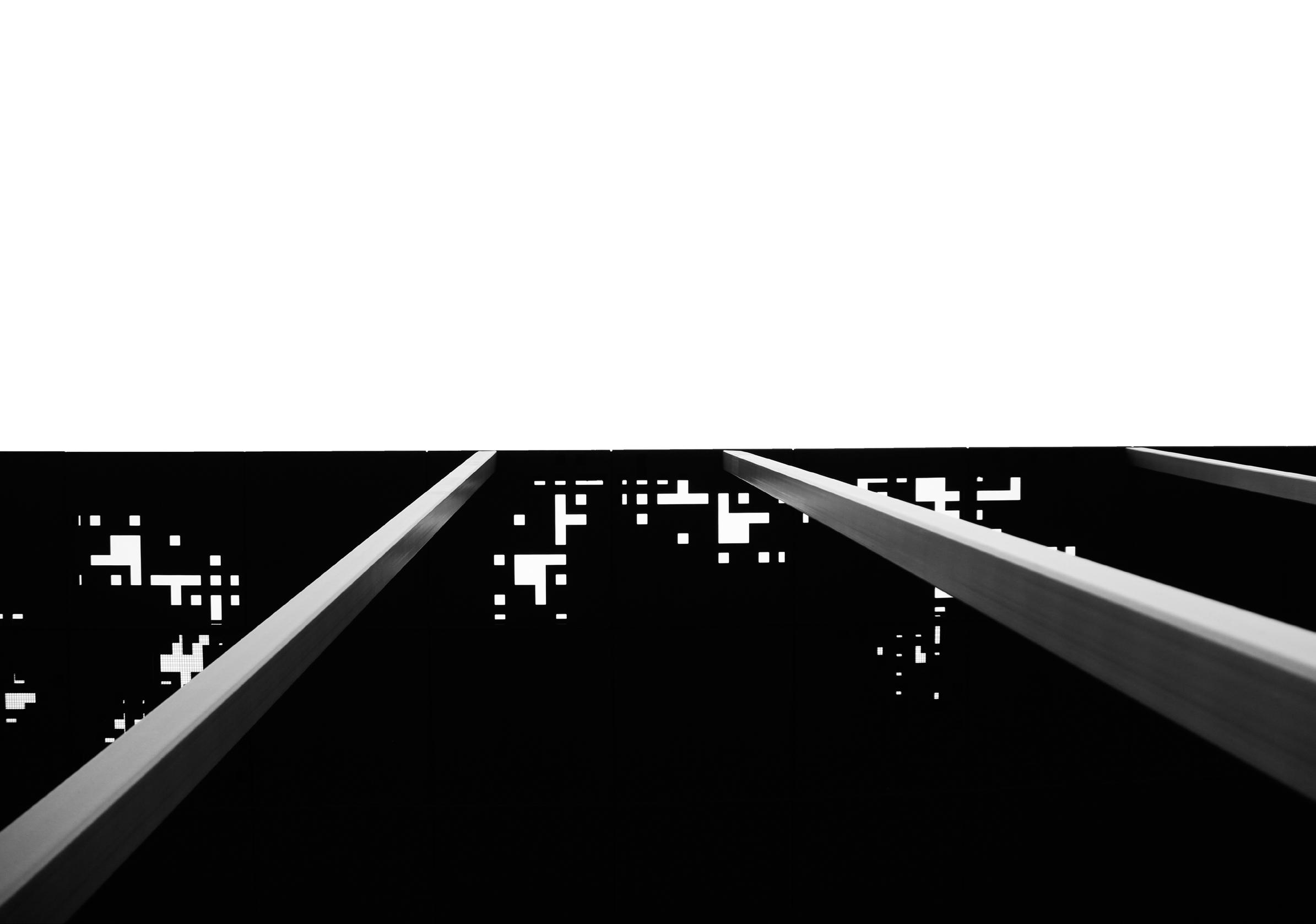
CONTENT PWP ARCHITECTS LTD 2017-2020 QUEENS HOTEL MIDDLE PARK WAY HIGH PEAK CARE HOME SOUTHSEA SKATEPARK BORROW FOUNDATION AVENUE COTTAGE SOUTHSEA, HAMPSHIRE HAVANT, BOSHAM,WATERLOOVILLE,SOUTHSEA,SOUTHAMPTON,HAMPSHIREHAMPSHIREHAMPSHIREHAMPSHIREWESTSUSSEX 3
HTTPS://VIMEO.COM/328459269
QUEENS HOTEL SOUTHSEA, HAMPSHIRE CLIENT : THE QUEENS HOTEL APPOINTMENT : 2017 STAGE: PLANNING Project brief : Renovation and extenion works to the existing hotel building -including:Conversion of basement to form hotel spa (consist of 100m2 of new build extension), re-use of remaining basement as supper club, re-use retail / cafe unit on Osborne Road frontage. - General renovation of the whole hotel. - Remodelling of existing 4th floor accommodation to reinstate further hotel -rooms.Creation of new upper floor containing 6no. residential dwellings (706m2) in double mansard with key roof features. Please click on the link below to watch a sample animation fly through rendered in twinmotion. [Individual] [ArchiCAD + Cinerender + Photoshop ] 4
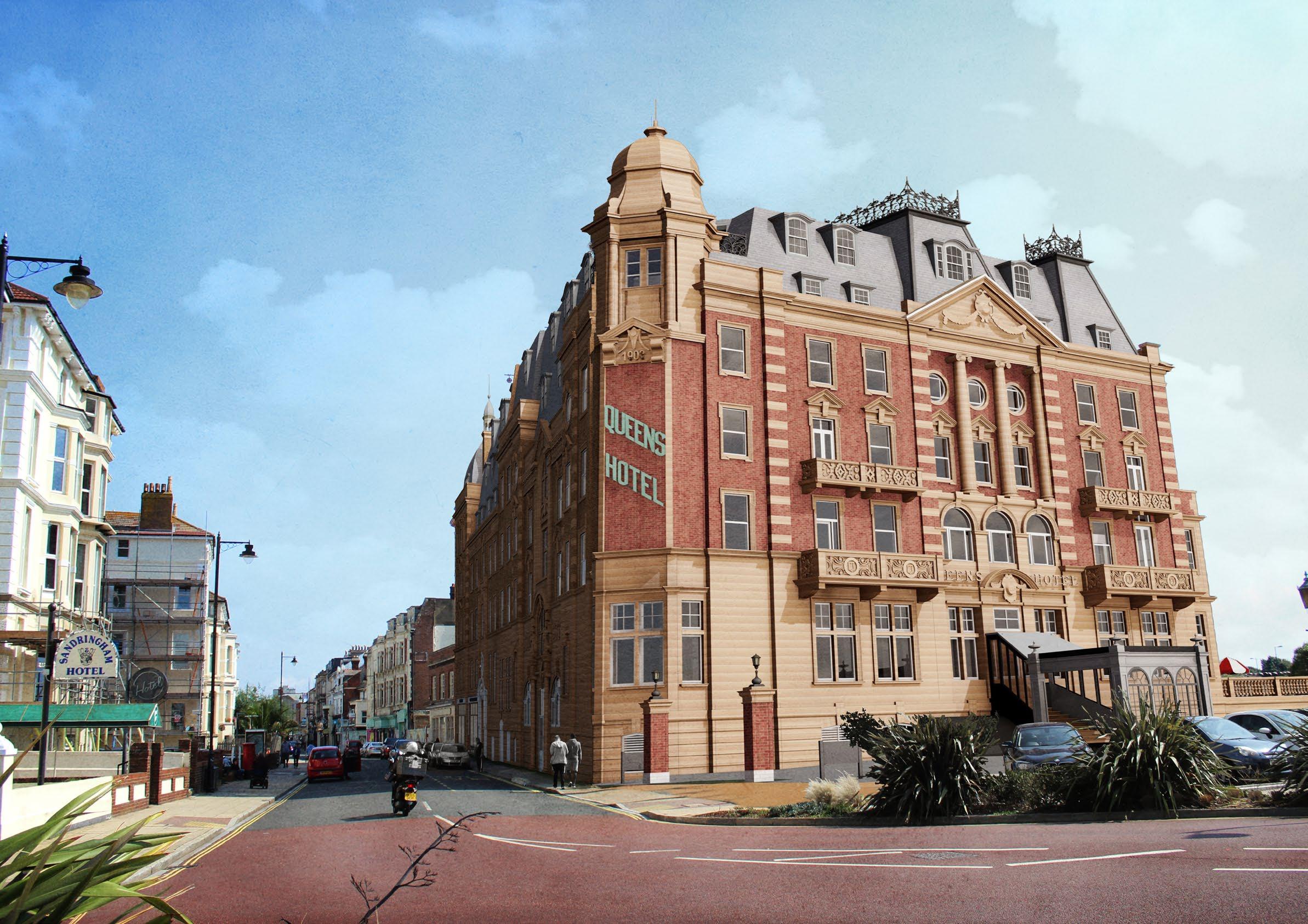
FEMALE CHANGING ROOM: (26 7m2) 4 Shower 1 Toilet 13X2 Locker unit 2+1 Changing room MALE CHANGING ROOM (16 4m2) 2 Shower 1 Toilet 1 Urinal 11X2 Locker unit 1 Changing room FAMILY & ACCESSIBLE WC SHOWER: (7 4m2) STEAM ROOM: (11 2m2) - To serve approximately 11 people SAUNA ROOM (13 9m2 - To serve approximately 13 people PED + MANICURE: (14 4m2) - 2 Pedicure + 2 Manicure MUD ROOM: (9 6m2) 2 Bath TREATMENT ROOM : 1 Two bed treatment room 2 Single bed treatment room with shower 2 Single bed treatment room RELAX ROOM: (16 6m2) 4 Recliner seat GYM: 26 8m2) 1 Weight bench 1 Pec Dec 1 Pull up machine 2 Sit up bench 1 Dumbbell bench 2 Treadmill STUDIO: (24 1m2 10 Spinning bike OR 6 Yoga space THERAPY POOL : (86 7m2) Pool (34.9m2) Lounger seats STORAGE: (14 1m2) LAUNDRY: 22 7M2) Air extraction outlet location Potential air extraction outlet location B 23.05.19 KC Laundry room revised C 05.09.19 KC Issue to Queens & M&E
[Individual]New single storey rear extension to form a new spa area [ArchiCAD] 5 QUEENS HOTEL PROPOSED BASEMENT PLAN N Queens Hotel Remodelling 2 Osborne Road Southsea 61 South Street Havant Hampshire PO9 BZ 023 9248 2494 023 9248 1152 design@pwp architects com w www pwp architects com revisions & notes status drawing name project Planning Application Proposed Basement Plan- Proposal 1 FP IC ic ic Lift Shaft Exit to outside StairstoHotelGroundFloor External Courtyard Fish Under stairs Gas Liftpipe Mechanism Water tank Blocked Boiler DH 2 04 DH 2 04 04 DH 2 04 DH 2 04 DH 02 DH 32 Tank Tosub basement to g ound IC Ramp Fuse boxes Bath to ground floor cupboard UP Room inaccessible to ground floor Fire Escape to Open Air For er Kitchen For er Nightclub Store Rooms Workshop Beer Cellar Cellar Boiler Room Male WCs Unused Area Unused Area Unused Area 16 Buzz Bar LadiesGent Li Store Rooms Store Rooms Bin Store Store UP F C 66 C 09 00 C 43 F 71 C 17 F C 48 C H 43 F 47 C 42 F C 99 C H 70 C 1 43 H 1 48 C 93 H 45 F 05 C 28 C 1 46 C H 1 44 F 29 C 37 C 1 29 C H 1 37 F C 51 C H 37 C 77 H 13 F C 53 C H 30 F 53 C H 1 30 H 1 17 F C 47 C 42 C 0 96 H 19 F C 46 C H 31 C 1 46 C H 1 31 C 1 34 C H 2 02 F C 34 C H 02 C 34 C H 02 C 34 C H 02 C 1 46 C H 1 90 F 46 C 90 F C 46 C H 90 C 1 46 H 90 UP UP UP DH 2 27 DH 55 DH 2 02 DH 07 DH 07 DH 2 08 DH 2 07 DH 2 01 DH 1 91 DH 01 DH 2 01 DH 09 DH 2 00 DH 00 DH 1 96 DH 27 DH 99 1 99 DH 2 06 DH 90 DH 2 03 DH 1 DH 99 DH 1 99 DH 2 01 DH 2 07 DH 09 DH 99 DH 2 18 DH 00 DH 1 32 DH 06 DH 2 18 DH 98 DH 2 06 DH 2 14 DH 08 DH 1 83 DH 34 DH 1 87 DH 2 02 DH 96 DH 1 96 DH DH 1 17 DH 96 DH 97 DH 1 98 DH 2 25 DH 1 94 DH 15 DH 2 23 DH 2 DH 07 DH 2 09 DH 00 DH 2 00 DH 01 2 04 DH DH 2 DH09 2 14 DH 2 00 DH 2 15 DH 99 DH 2 10 DH 2 11 DH 2 12 DH 09 DH 1 71 DH 2 11 Conference lobby ic Access to pool plant room Window to be reinstated to receive daylight the basement Window to be toreinstated receive daylight in basementthe Secondary access to pool plant room Demolish existing stage New structural opening Therapy Pool Treatment Room 2 Alter ative Ent ance Foyer for both Guests and Residents Treat ent Room 3 Treat ent Room 5 1 2m deep Upright seating Lounger seating x Waterfall High pressure waterfall shower Standing Pool Plant Ped + Manicure (dual nction Conference suite ent ance St eet Level Osbor Road) Cloakroom Accessible WC Female MaleToilet Toilet Bar Conference Lobby Main Conference Room Conference Room Storage Patisserie Patisserie Patisserie Kitchen Patisserie Kitchen Hotel Kitchen Walk in Fridge Accessible WC ToSub basement Fire Exit Fire Exit Fire Exit Fire Exit Staircase Groundto o Treat ent Room F C H 1 51 F 77 C 17 02 F H 1 90 H UP people 2000x2000 Aqualinesaunas 6-8 people 2500x3000 Tylohelo Window to be reinstated to daylightreceive in the basement Existing window opening to be blocked up Existing window opening to be blocked up Cupboard abovespace the mud plant area Female Changing Spa Entrance Reception Treatment Room 1 Relax Room Lobby Male Changing Laundr store Sauna Treat ent Room 4 Mud Room Gy Steam Mud Plant Family Accessible Shower WC Pool Plant St dio Steam Plant Fire Exit Fire Door FD60 Treat ent Room A 22.05.19 KC Revised following from meeting s comments
SPA PROPOSAL 1 KEY: Existing Wall to be demolished to create opening Existing Wall Proposed Wall
Proposed External Wall Floor: (u-value = 0 13) - 10mm wall tile - 5mm tile adhesive, - 12mm tile board (cement base), - 190mm Inner blockwork, - 90mm Kingspan K106 insulation, - 10mm Residual cavity - 100mm Outer blockwork - 90mm Terracotta block *. *Unglazed Terrcotta to be coated for protection against water based stains oil and grease
Proposed Pool Wall: - 5mm floor or wall tile - 25mm render too pool specialist, - 150mm reinforced water proof concrete, - 80mm Celotex GA4000 insulation - 1200G Damp Proof Membrane
Brick Service void Service void / backfill with concrete Stainless steel glass balustrade side fixed to the base of the terracotta balustrade Bespoke terracotta moulding piece Terracotta balustrade base Terracotta toprail Foundation to SE s design
Terracotta
The Pool Specialist will construct the hydro pool structure in concrete to BS EN1992 3 2006 The Specialist also allows for finishing the hydro pool with mosaic tiles supplied by the client
[Individual] 6 QUEENS HOTEL SPA EXTENSION SECTION [ArchiCAD]
Proposed Ground Floor: (u value = 0 09) - 10mm floor tile - 5mm bedding mortar - 65mm sand cement screed - 500G polythene separating layer - 160mm Kingspan K103 floor insulation - 1200G Damp Proof Membrane - 150mm In situ concrete slab - Sand blinding, - Hardcore Drainage grille insert Overflow channel to pool specialist s detail
Proposed Roof Terrace: (u-value = <0 09) - 22mm Paving slab - 5mm bedding mortar, - 65mm sand/cement screed to slope) - Separation layer, - Bitumen sheet - 30mm Kingspan GG300 floor insulation - 50mm Kingspan GG300 floor insulation - 100mm Kingspan OPTIM R insulation, - Protection layer - 500G separation layer - 200mm In situ concrete In situ concrete downstand beam To SE s design)
Cornicecladding
N Queens Hotel Remodelling 2 Osborne Road Southsea 61 South Street Havant Hampshire PO9 BZ 023 9248 2494 023 9248 1152 design@pwp architects com w www pwp architects com revisions & notes 100mm 0@A1 Note All dimensions to be checked on site by the contractor before fabrication and erection Figured dimensions to be taken in preference to scaled dimensions This drawing is the copyright of the architects and must not be reproduced or used without their express consent except for the purposes of a planning application Electronic issue of this drawing to be confirmed by paper hard copy only drawingrev No Project No status date scale drawn drawing name project Planning Application December 2017 SAB 52921 20 @A1 1412 Section3 Spa extension 250 2,607 250 2,607 250 2,617 1,100
moulding Existing foundation extact depth to be confirmed KEY: Where areas highlighted in pink contractor should exclude it in their works
[Teamwork] 7 QUEENS HOTEL SPA EXTENSION ELEVATION [ArchiCAD]
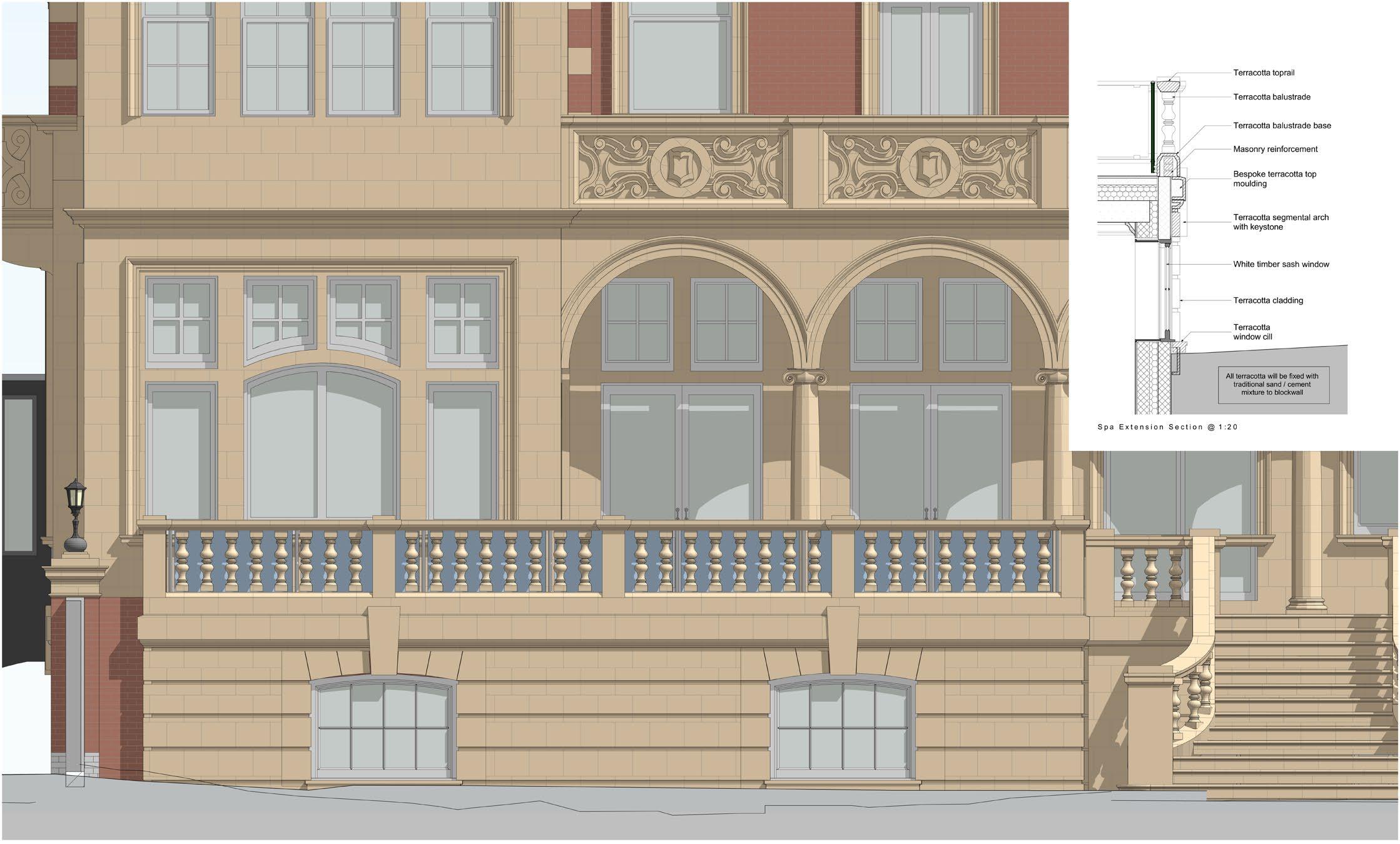
N Queens Hotel Remodelling 2 Osborne Road Southsea 61 South Street Havant Hampshire PO9 BZ 023 9248 2494 023 9248 1152 design@pwp architects com w www pwp architects com revisions & notes 100mm 0@A1 drawingrev No Project No status date scale drawn drawing name project Planning Application October 2019 KC 52921 100 @A1 1216 E Proposed Fifth Floor Plan F Dry Riser Master Bedroom Double Bedroom Living Dining Shower room Ensuite Shower Master Bedroom Double Bedrom Bathroom Ensuite Bathroom Kitchen Living Living Master Bedroom Double Bedroom Bathroom Ensuite Shower Master Bedroom Kitchen DiningLiving Double Bedroom Double Bedroom Bathroom Living Kitchen Dining Emergency exit Master Bedroom Ensuite Shower Master Bedroom Ensuite Shower Double DiningBedroom Living Kitchen Fire Fighting Staircase Kitchen Roof Access Staircase Roof Access Staircase Dining Ex er al Staircase Light ell Light ell Li Li Shower Bathroom Ensuite Shower Flat Roof Flat Flat 4 Flat 5 Flat 6 Kitchen Flat Flat 3 Dining Ter ace Ter ace Ter ace Ter ace Ter ace Ter ace Ter ace 20.02.18 KC Issued for Comments A 20.02.18 KC Issued for Comments D 11.10.19 LFM Planning Application B 20.02.18 KC Issued for Comments C 20.02.18 KC Issued for Comments Proposed 5 th Floor Plan @ 1 : 100 E 04.02.20 KC Terraces added to the north elevation flat 5 mansard wall reviesd to 55degree pitch [Teamwork] 8 QUEENS HOTEL PROPOSED NEW 5TH FLOOR The new storey will provide 6 new service apartments above the existing hotel [ArchiCAD]
[Teamwork] 9 QUEENS HOTEL EXISTING SOUTH ELEVATION [ArchiCAD]
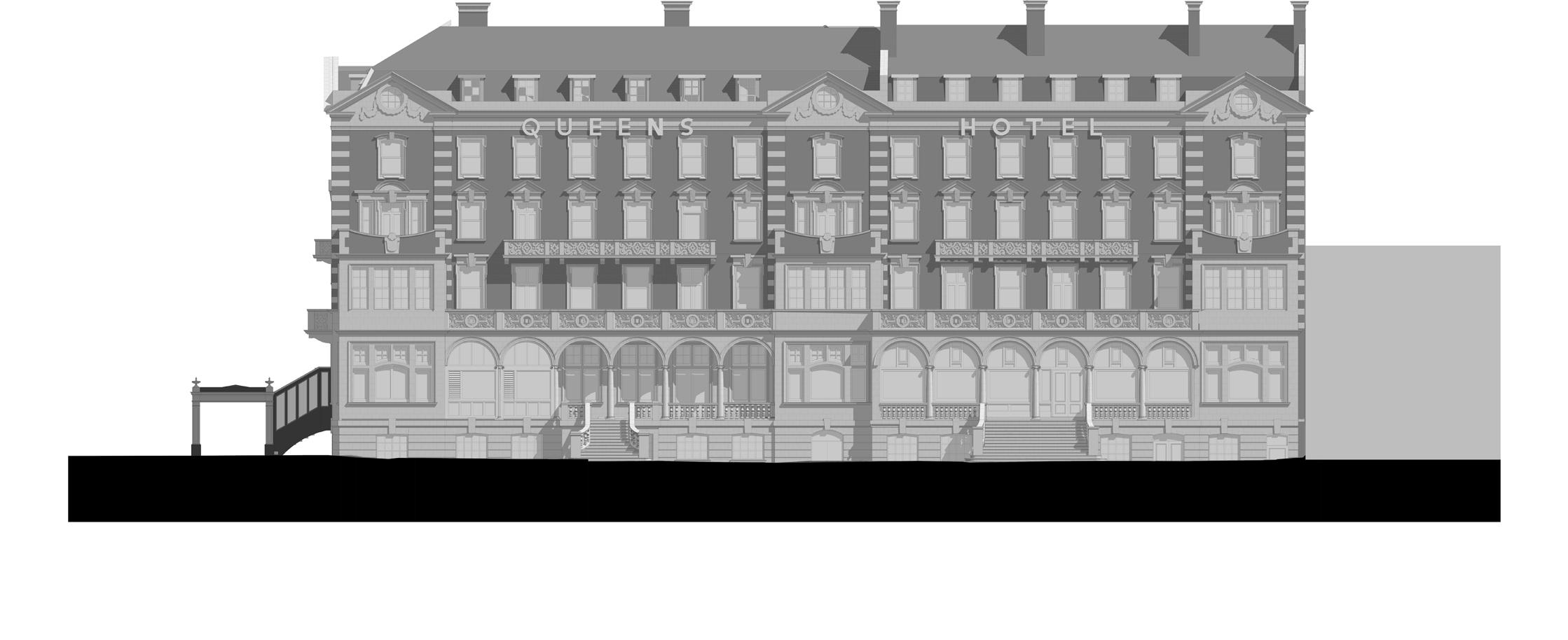
10 [Teamwork]QUEENS HOTEL EXISTING NORTH ELEVATION [ArchiCAD]
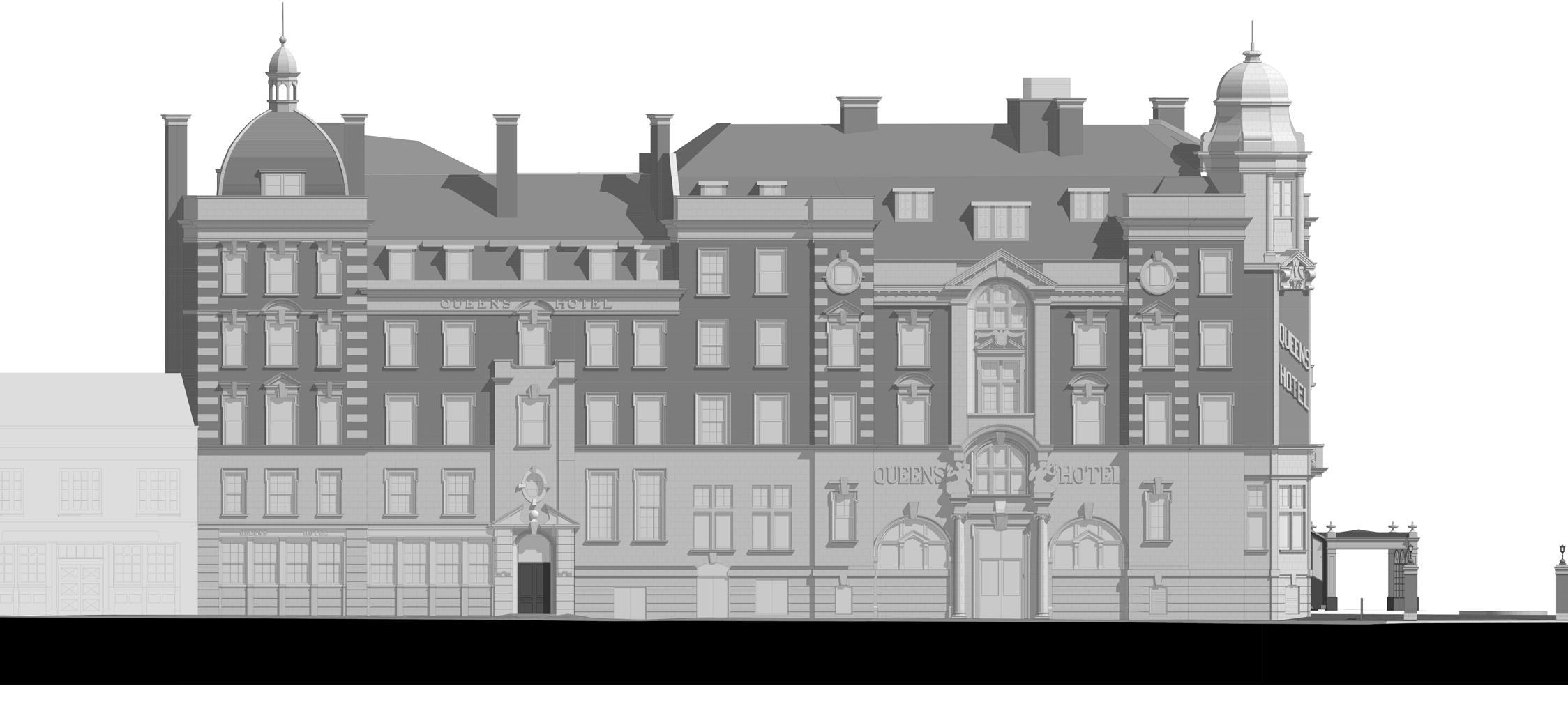
11 QUEENS HOTEL PROPOSED SOUTH ELEVATION [ArchiCAD][Teamwork]

12 [Teamwork]QUEENS HOTEL PROPOSED NORTH ELEVATION [ArchiCAD]
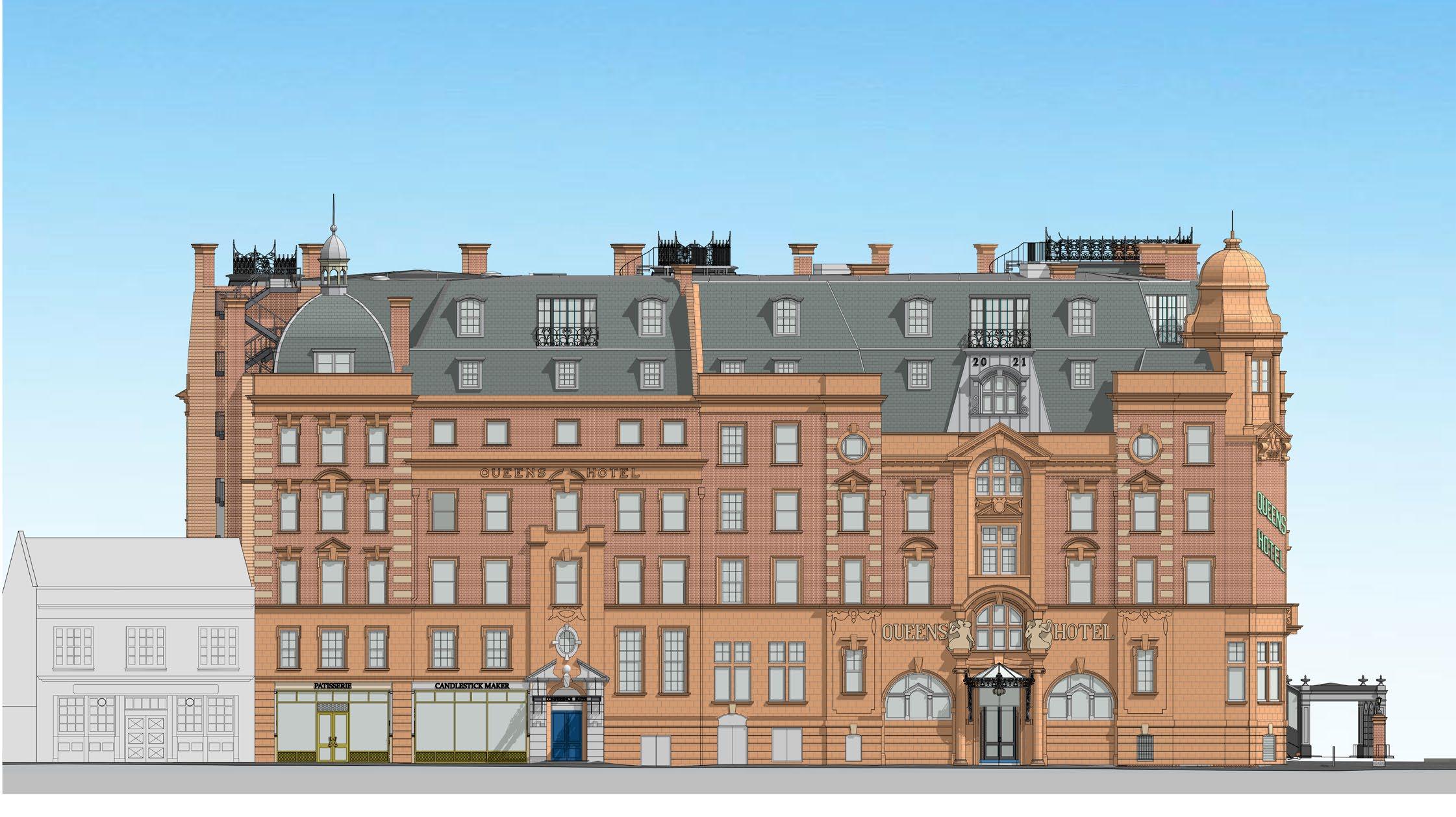
[Individual] 13Entrance & Garden QUEENS HOTEL PROPOSED 3D VISUAL [ArchiCAD + Cinerender + Photoshop]
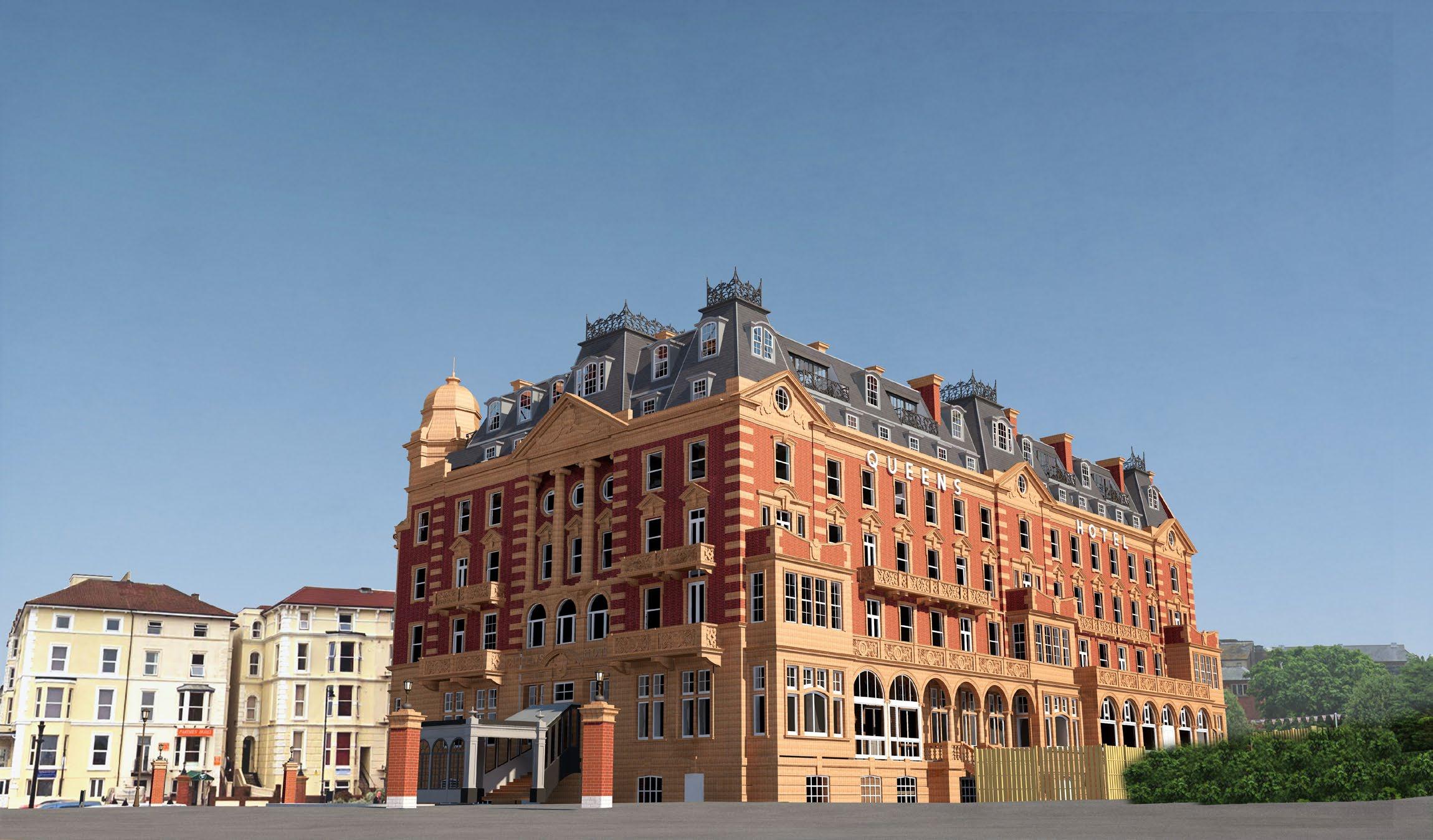
QUEENS HOTEL PROPOSED MANSARD ELEVATION + 3D VISUAL WITH CONTEXT [Individual][ArchiCAD]
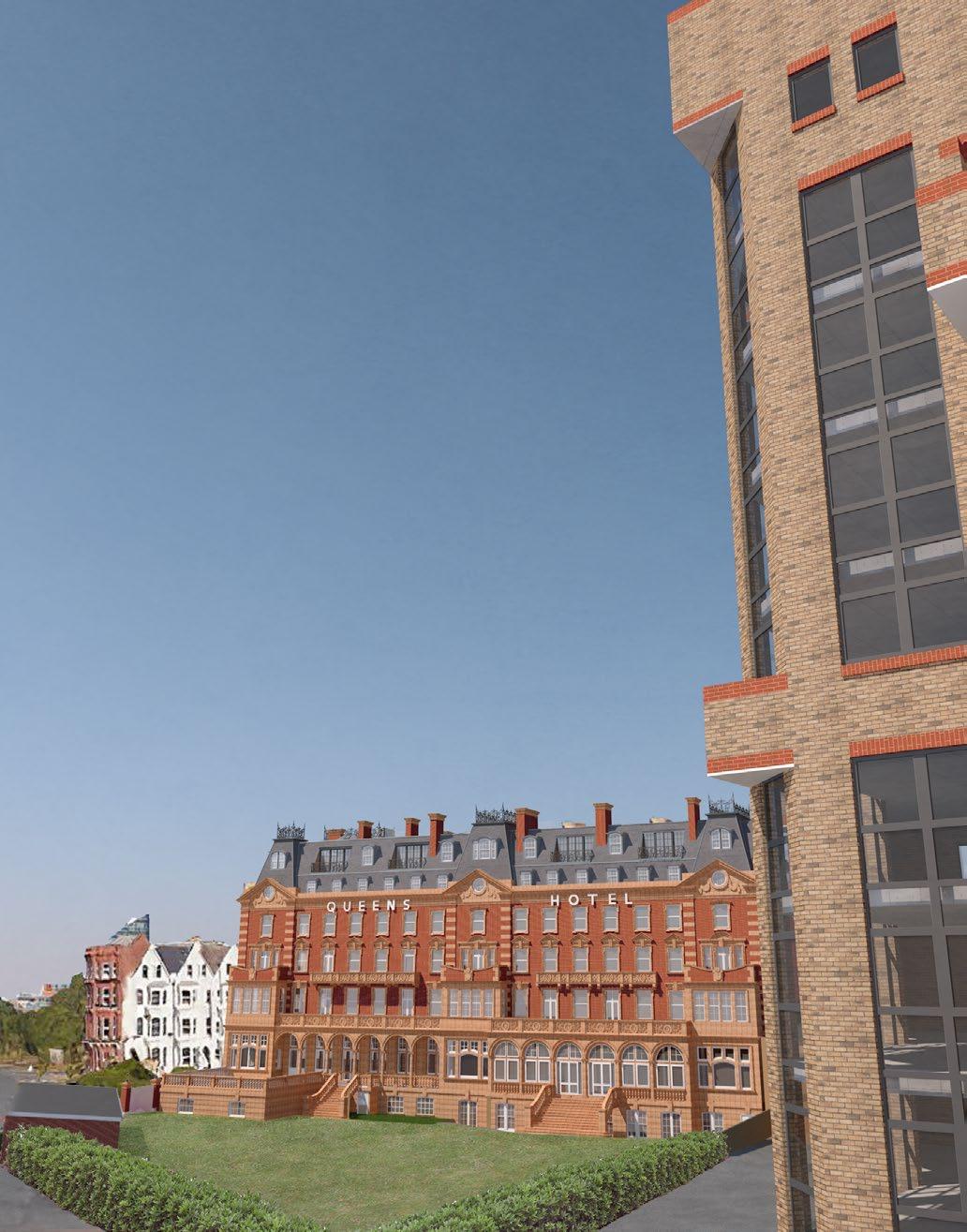
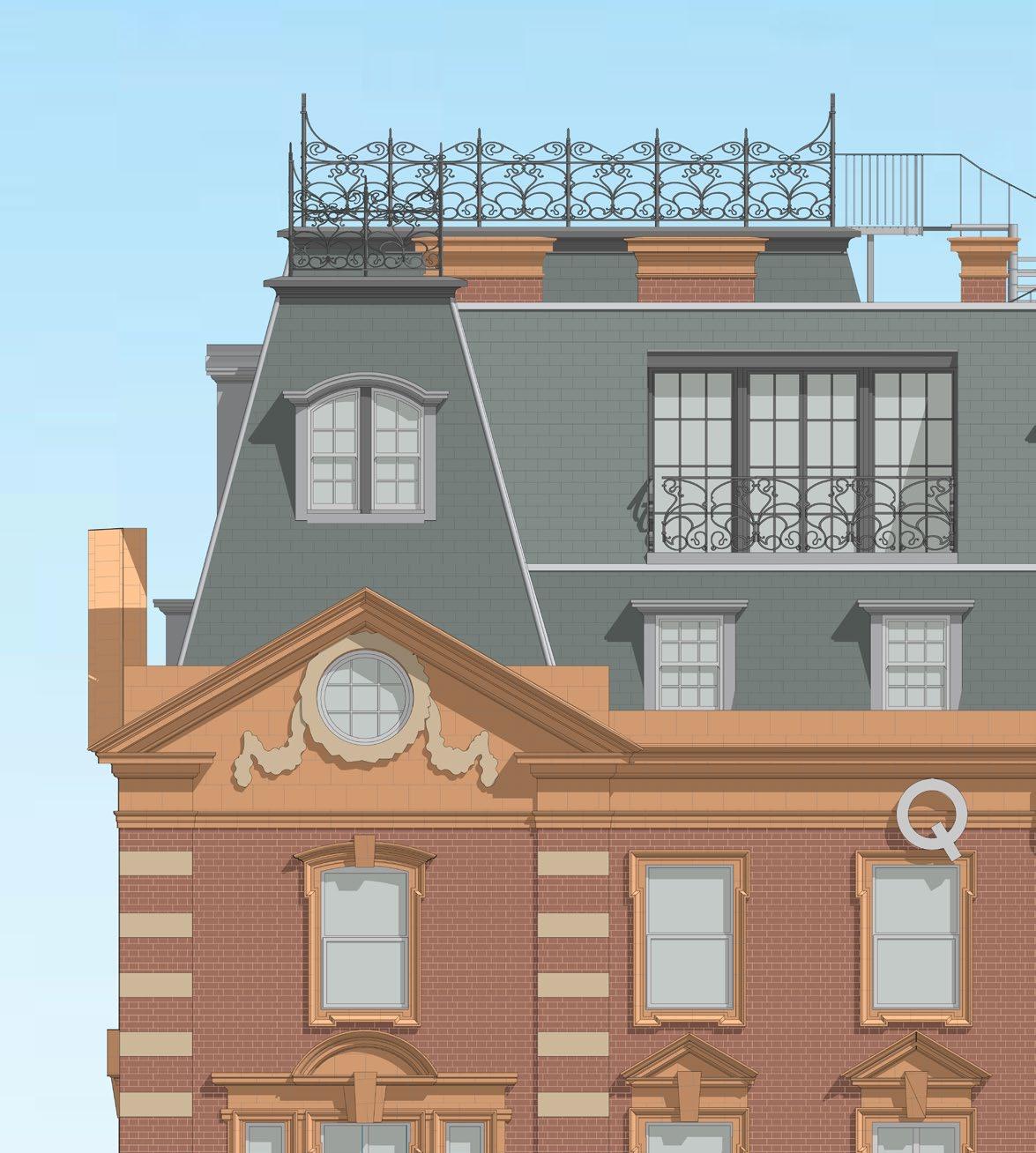
N Queens Hotel Remodelling 2 Osborne Road Southsea revisions & notes project DH 2 29 BH 3 98 BH 3 78 DH 2 DH38 1 93 DH 2 40 DH 2 40 Sky DOWN DH 1 98 DH 1 97 DH 1 98 DH 1 99 DH 1 99 DH 1 98 Sky DH 1 98 DH 1 99 BH 3 55 BH 3 98 BH 3 98 3 bay toilet cabin Disable toilet cabin Hired Container Prosecco Bar Size 6m x 2 6 x 2 44m 3 bay toilet cabin Food service size 6x2 6x2 44m Prosecco Bar size 6x2 6x2 44m Temporary Stage Temporary Bar McCathy & Stone Site boundary RetainedLand Boundary QUEENS HOTEL PROPOSED OUTDOOR GARDEN PLAN (FOR SUMMER EVENT) [Individual][ArchiCAD]
N revisions & notes drawing name project Queens Hotel Remodelling 2 Osborne Road Southsea Retained Garden Layout Perspective Retained Garden Layout Perspective 3 bay toilet cabin ( x 2 ) Disable toilet cabin Food service bar container Prosecco bar container Temporary s tage Temporary bar QUEENS HOTEL PROPOSED OUTDOOR GARDEN 3D VISUAL [Individual][ArchiCAD]
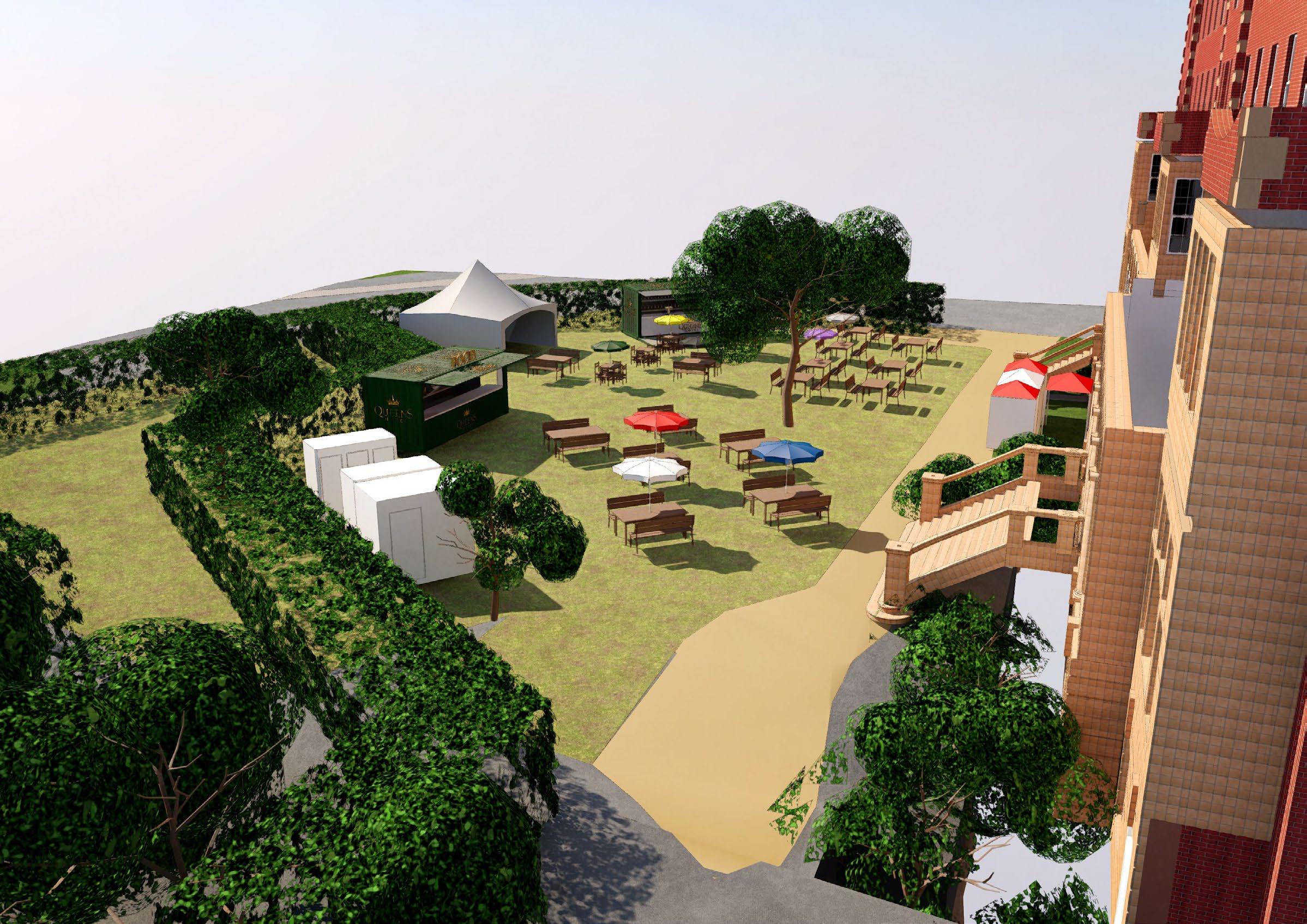
This is a design showing the conversion of a standard cargo container into a food catering bar , with the upper half of the front panel functions as a shelter when it is opened The deep green colour is chosen to reduce the visual impact in the garden setting . The gold painted Queen ' s logo for branding with a removable signage on top
QUEENS HOTEL PROPOSED CONTAINER DESIGN FOR SUMMER EVENT [Individual] [ArchiCAD + Cinerender]
design@pwp architects com w www pwp architects com Projectdrawing date scale 52921 0 95 1 1 16 1:1 67 1001 December 2017 Food Bar Container Example
.
Removable signage Front panel & solar shading
Container closed Container in operation
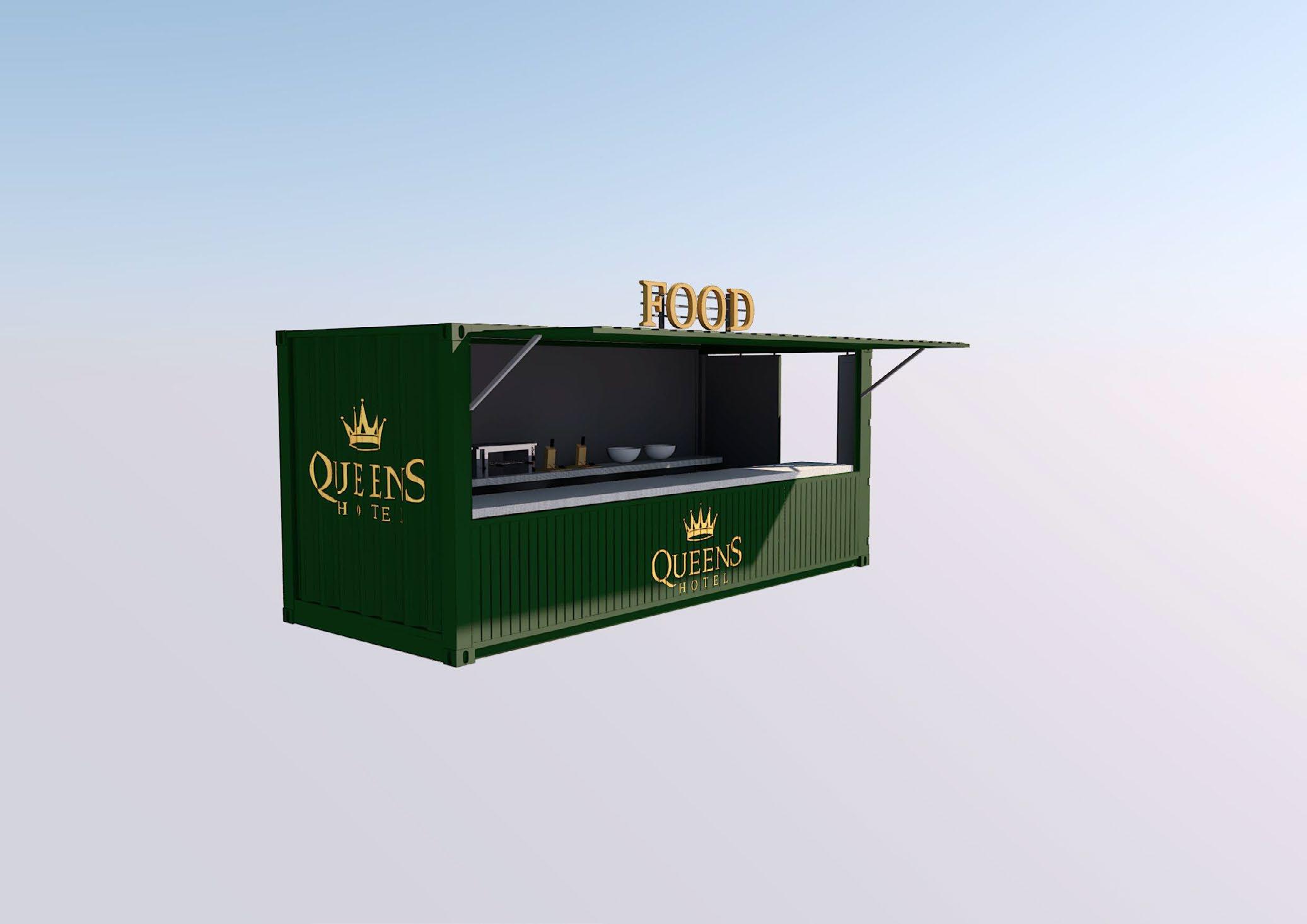


removable
Hampshire PO9 1BZ 2494 023 9248 1152 com w www pwp architects com drawingrev No 1000 Prosecco Bar Container Example
Removable signage Front panel Solar Container closed
. QUEENS HOTEL PROPOSED CONTAINER DESIGN FOR SUMMER EVENT [Individual] [ArchiCAD + Cinerender]
. The
. The
This is a design showing conversion of a standard cargo container into a bar , with the front panel functions as a deck for the bar when it is opened deep green colour is chosen to reduce the visual impact in the garden setting gold painted Queen ' s logo for branding with a signage on top
the
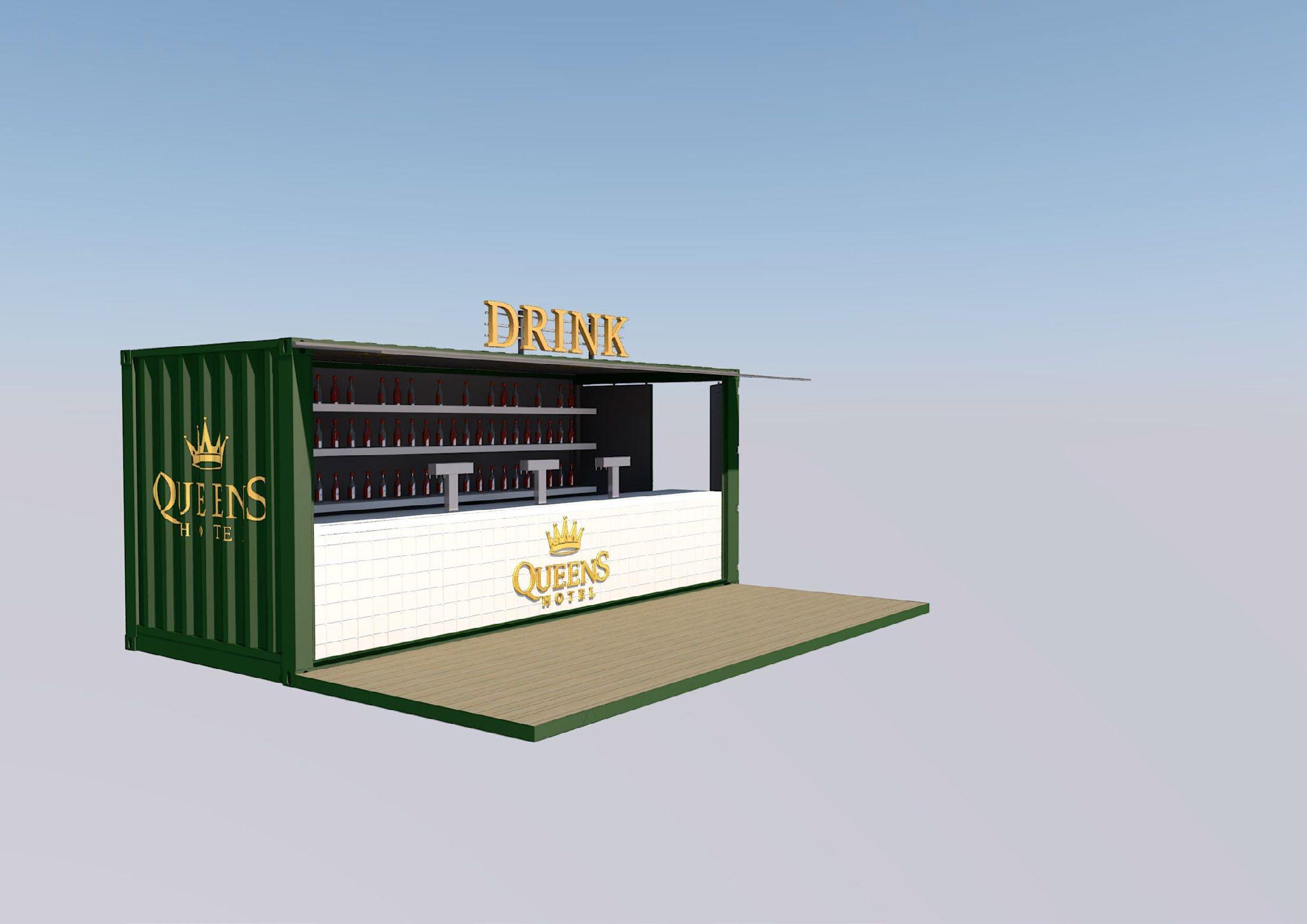

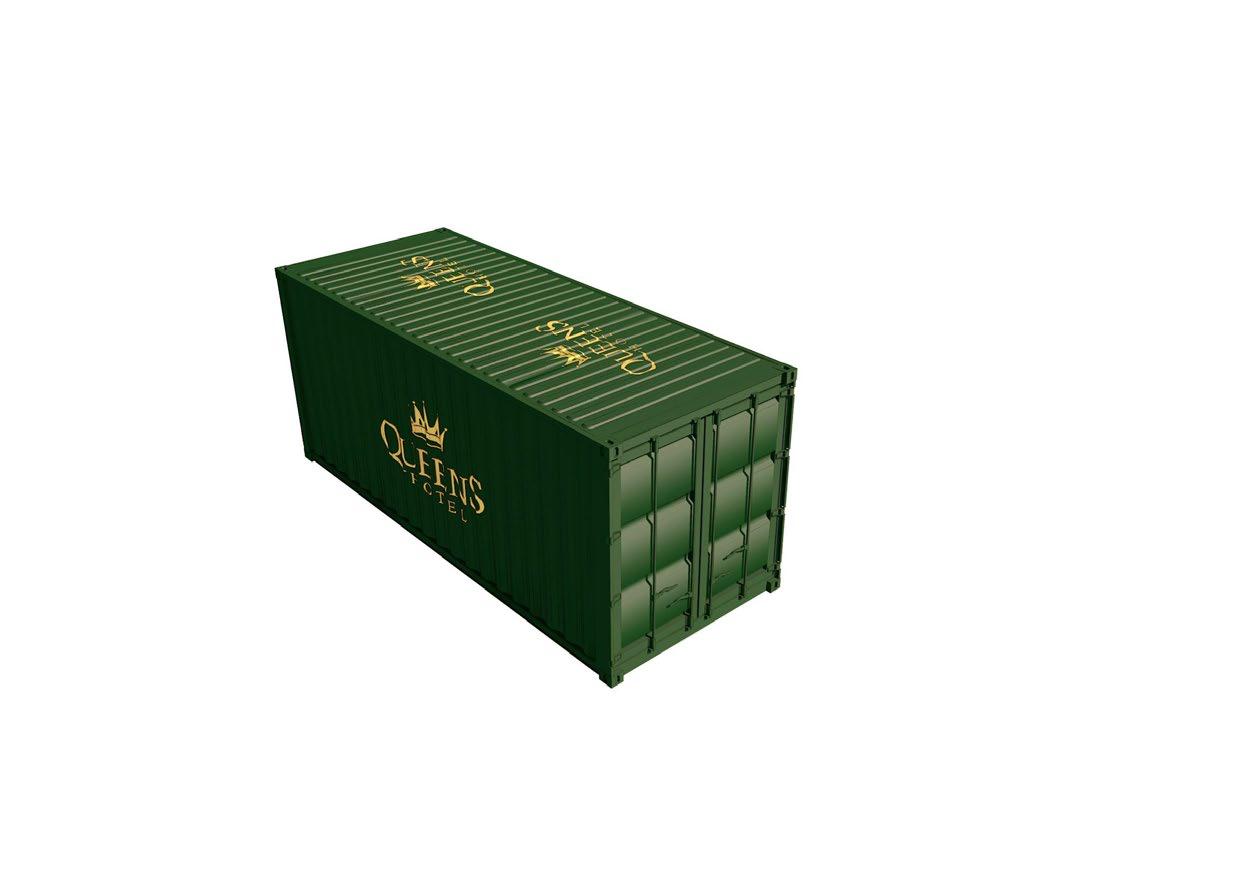
N Queens Hotel Remodelling 2 Osborne Road Southsea revisions & notes drawing project Details of Entrance 1,680mm 511mm 651mm Alter ative Ent ance Foyer for both Guests and Residents 2,005mm 225mm 3,418mm 1,709mm 1,709mm 1,444mm 871mm R2=777mm R3=1,153mm R1=1,062mm 683mm 256mm 42mm 515mm 90mm 730mm Roof glazing Primary canopy ring Secondary ring Lead flashing CL R1 Radius 2231mm R3 Radius 1768mm R2 Radius 1121mm A A 512 137 268 192 40 40 66 40 86 Elevation @ 1 : 20 Plan @ 1 : 20 Section @ 1 : 20 Primary Ring Profile Section @ 1 : 5 QUEENS HOTEL PROPOSED SIDE ENTRANCE CANOPY DESIGN [Individual][ArchiCAD]
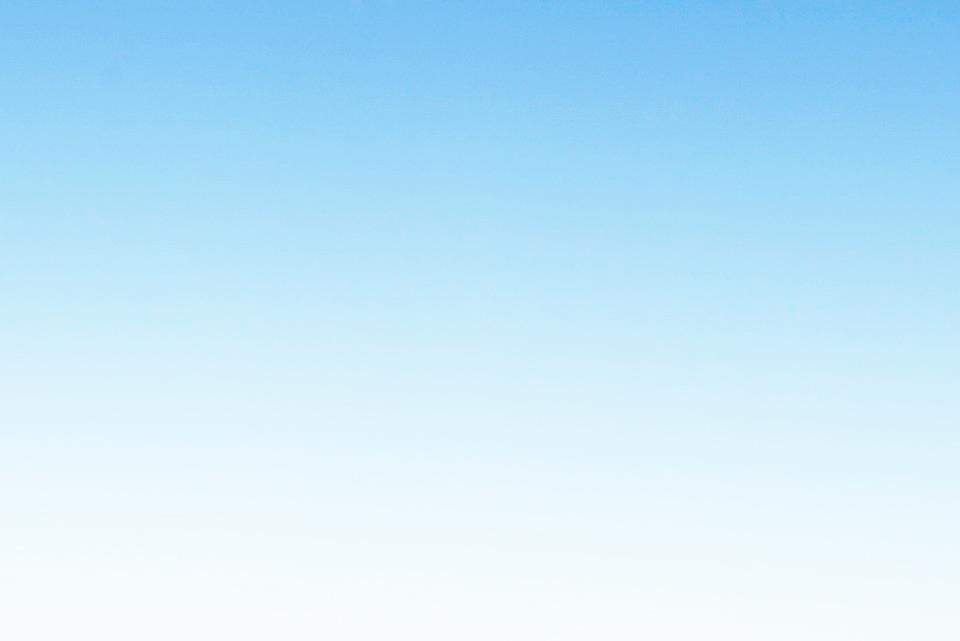
N Queens Hotel Remodelling 2 Osborne Road Southsea 61 South Street Havant Hampshire PO9 BZ 023 9248 2494 023 9248 1152 revisions & notes status drawing name project PRELIMINARY Details of Entrance Canopy B 606mm 317mm 924mm 3,457mm 83mm 2,197mm 5882,281mm588mm 6917 317 123 18 58 200 41 19 56 2022 Elevation @ 1 : 20 Plan @ 1 : 20 Section @ 1 : 20 Profile Section @ 1 : 2 QUEENS HOTEL PROPOSED SIDE ENTRANCE CANOPY DESIGNS [ArchiCAD][Individual]
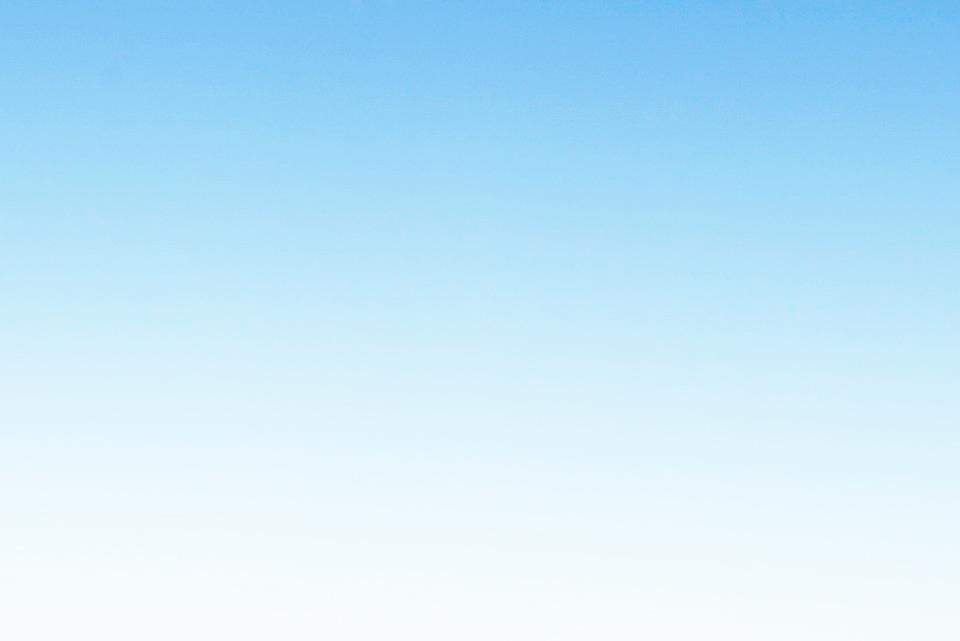
QUEENS HOTEL PROPOSED SIDE ENTRANCE CANOPY DESIGNS [Individual]
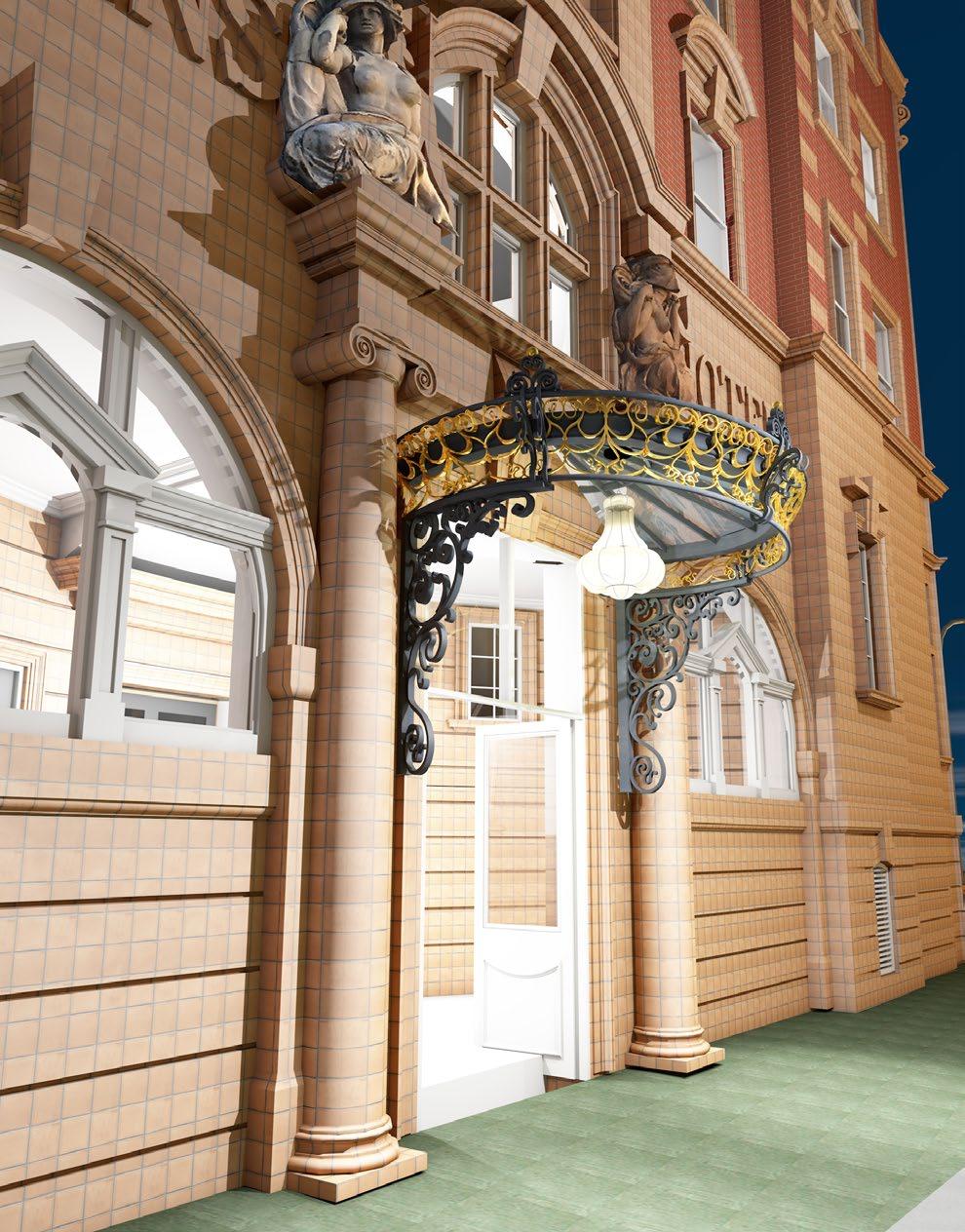
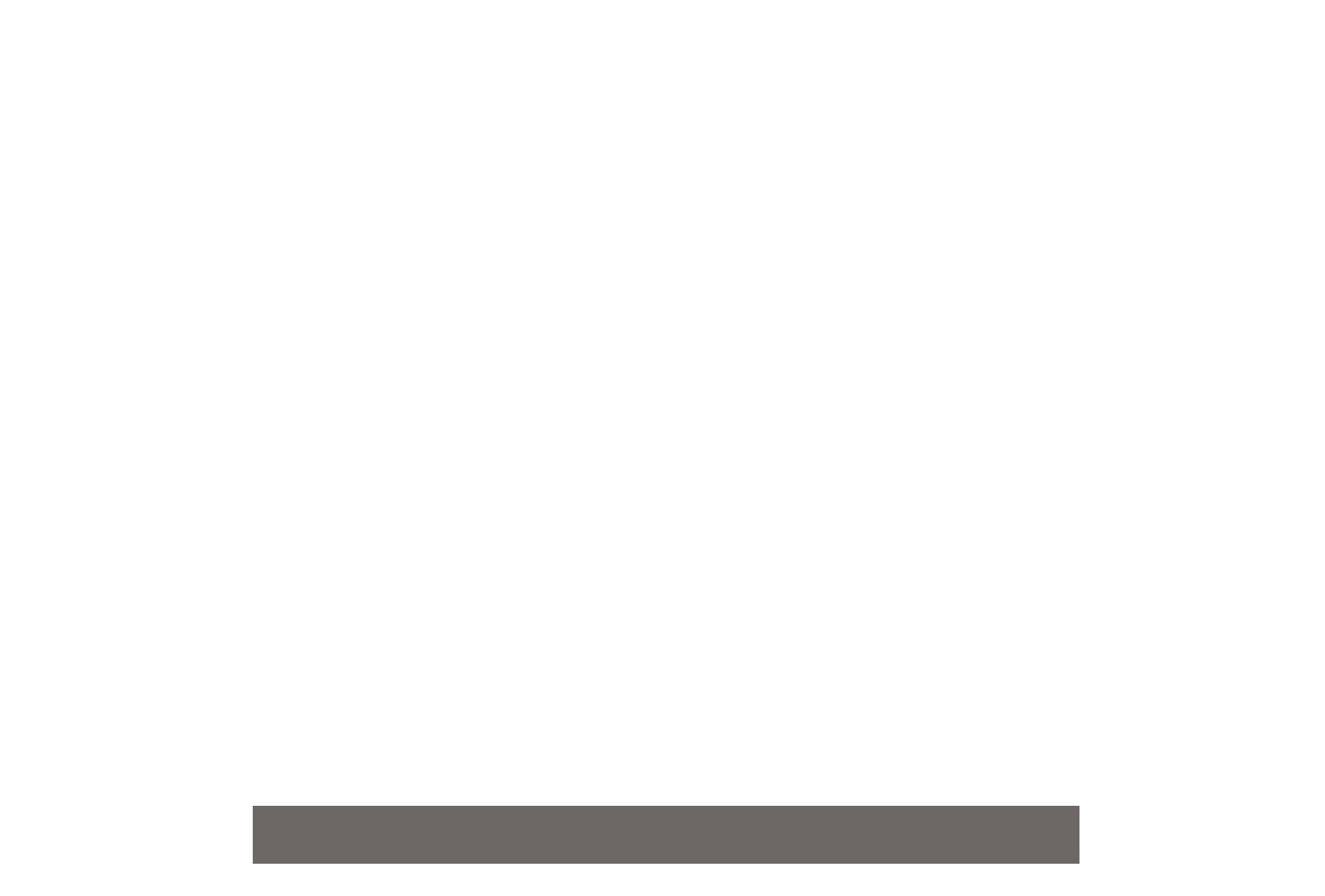
QUEENS HOTEL PROPOSED 3D VISUAL AT THE SIDE ENTRANCE [Individual] [ArchiCAD + Cinerender + Photoshop]
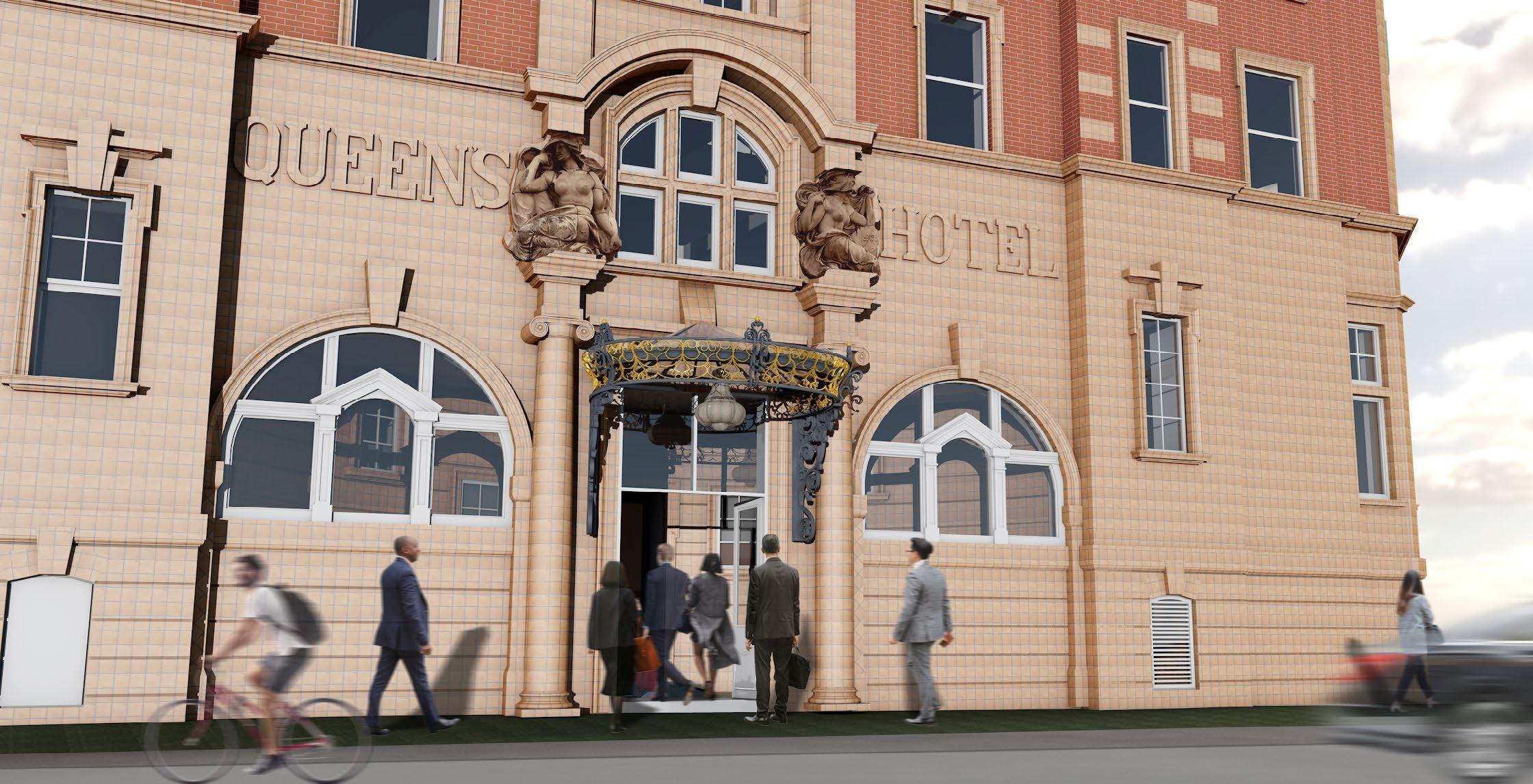
QUEENS HOTEL PROPOSED NIGHT 3D VISUAL AT THE SIDE ENTRANCES [Individual] [ArchiCAD + Cinerender + Photoshop]
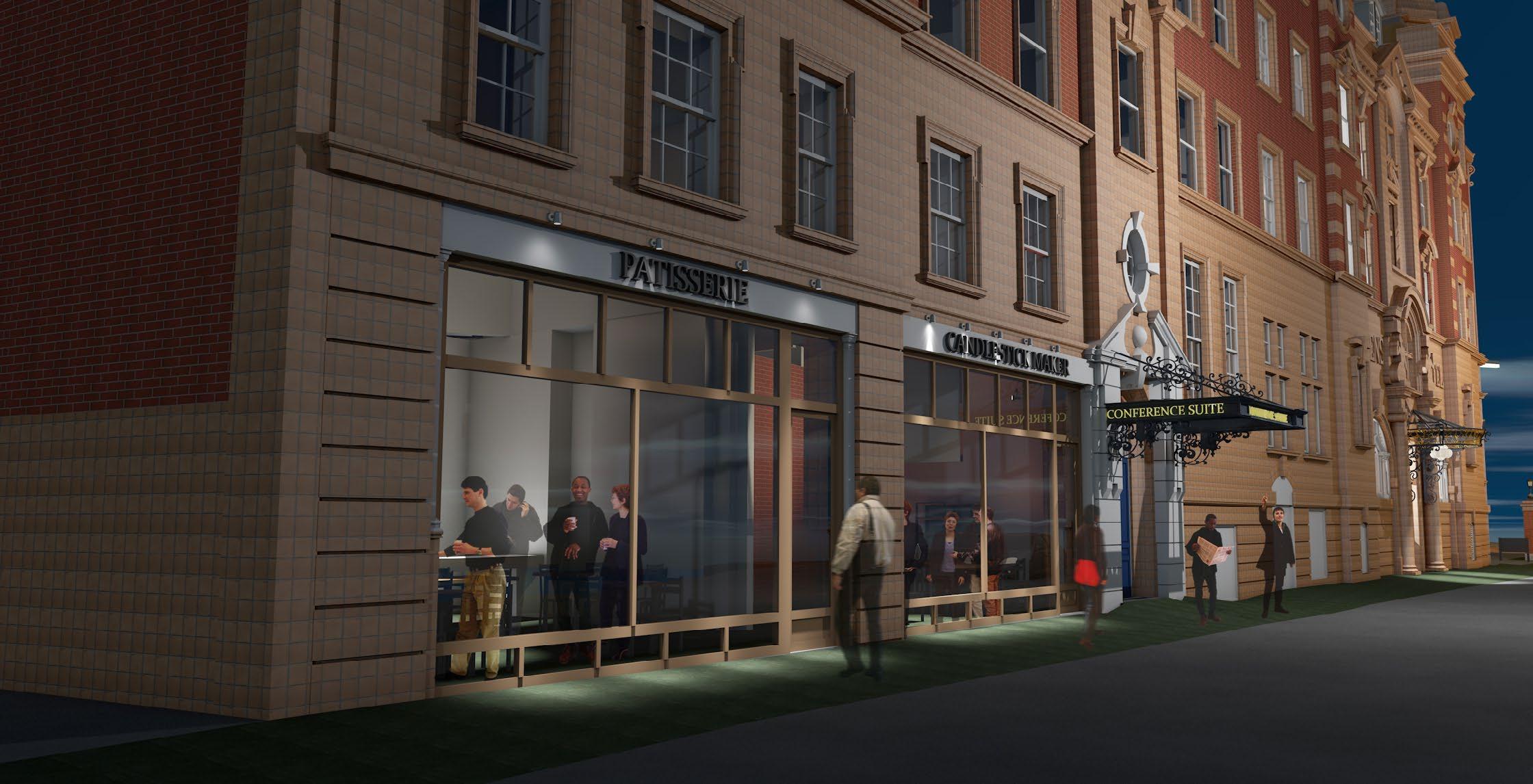
24 MIDDLE PARK WAY HAVANT, HAMPSHIRE CLIENT : PRIVATE CLIENT APPOINTMENT : 2017 STAGE: PLANNING Project brief : Demolition of 8no. existing garages and construction of a 2 storey dwelling to provide 4no. 1 bed flat located at the corner of a service road in Leigh Park, Havnt. [Individual] [ArchiCAD + Cinerender + Photoshop ]
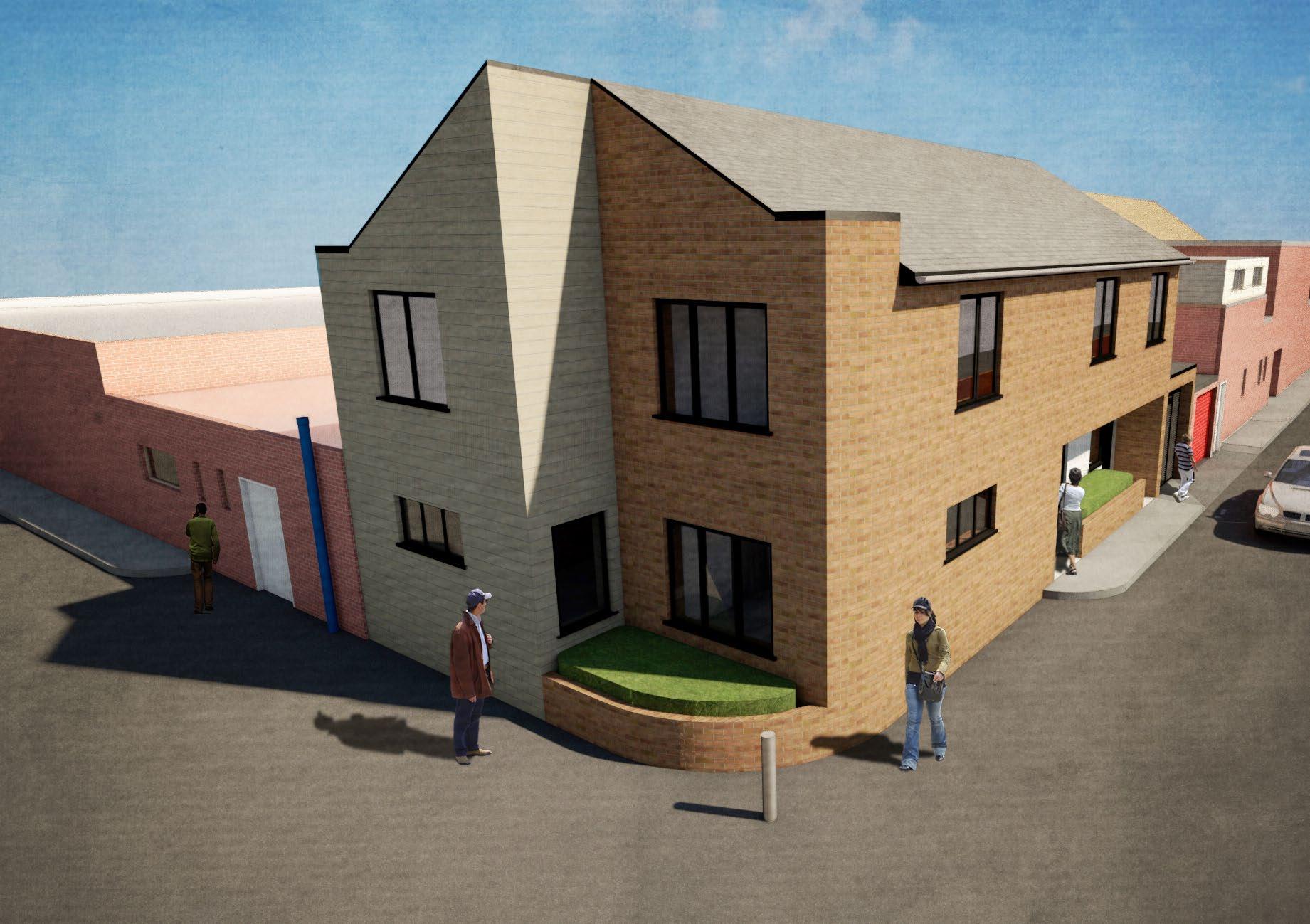
With Defensible Space
Ground floor window is protected by defensible space.
1800 mm - 27/11/17 KC Issued for comment
Recessed space for flat entrances
Without Defensible Space
High level ground floor window to prevent stranger from over looking, increase privacy for ground floor occupants
MIDDLE PARK WAY DESIGN STRATEGY 1 25 [Individual][ArchiCAD] 61 South Street Havant Hampshire PO9 1BZ 023 9248 2494 023 9248 status1152 drawing name project PRELIMINARY Ahmed Ali Garage Conversion Middle Park Way Havant Design strategy 1
Brick wall barrier to create defensible zone Vegetation within the barrier
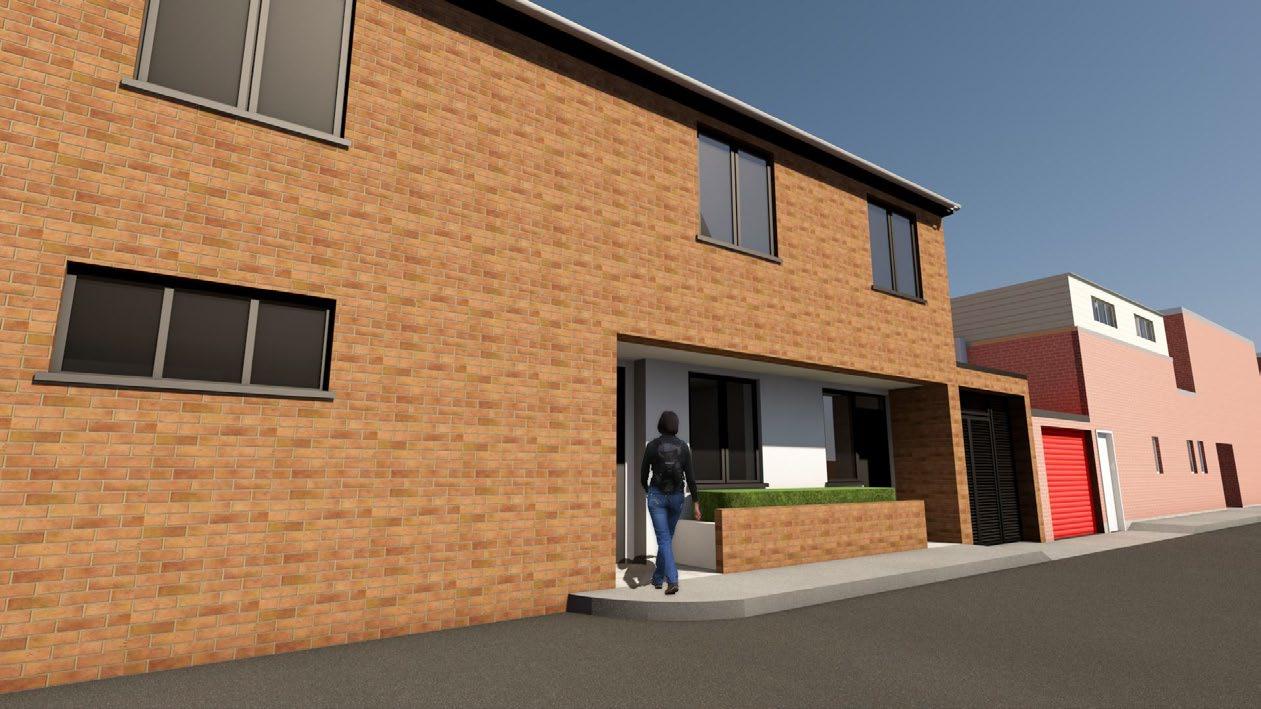

26 Ahmed Ali Garage Conversion Middle Park Way Havant 61 South Street Havant Hampshire PO9 1BZ 023 9248 2494 023 9248 1152 e design@pwp architects com w www pwp architects com revisions & notes 100mm 0@A2 Note All dimensions to be checked on site by the contractor before fabrication and erection Figured dimensions to be taken in preference to scaled dimensions This drawing is the copyright of the architects and must not be reproduced or used without their express consent except for the purposes of a planning application Electronic issue of this drawing to be confirmed by paper hard copy only drawingrev No Project No status date scale drawn drawing name project 5493 * PRELIMINARY November 2017 KC 1 5 24 1 100 1001 Design strategy 2 11 12 13 14 17 Service Road Service Road Unpaved Fence line Fence line The Co operative The Best one Fence line Proposed pavement extension Area to be cleared of debris and rubbish Ground to be leveled and block paved ( Concrete Surface ) N Existing garage ( corner of the site ) Proposed Plan ( Filleted building corner ) Building corner filleted to create buffer zone to prevent hazard from large vehicle turning Refuse Vehicle Footprint of the proposed building Refuse Vehicle Turningcurvature The photo is showing the damages caused by vehicle bashing to the corner of the exisitng garage from vehicle turning Bollard to protect the building being damaged by vehicle turning KEY : 27/11/17 KC Issued for comment MIDDLE PARK WAY DESIGN STRATEGY 2 [Individual][ArchiCAD]
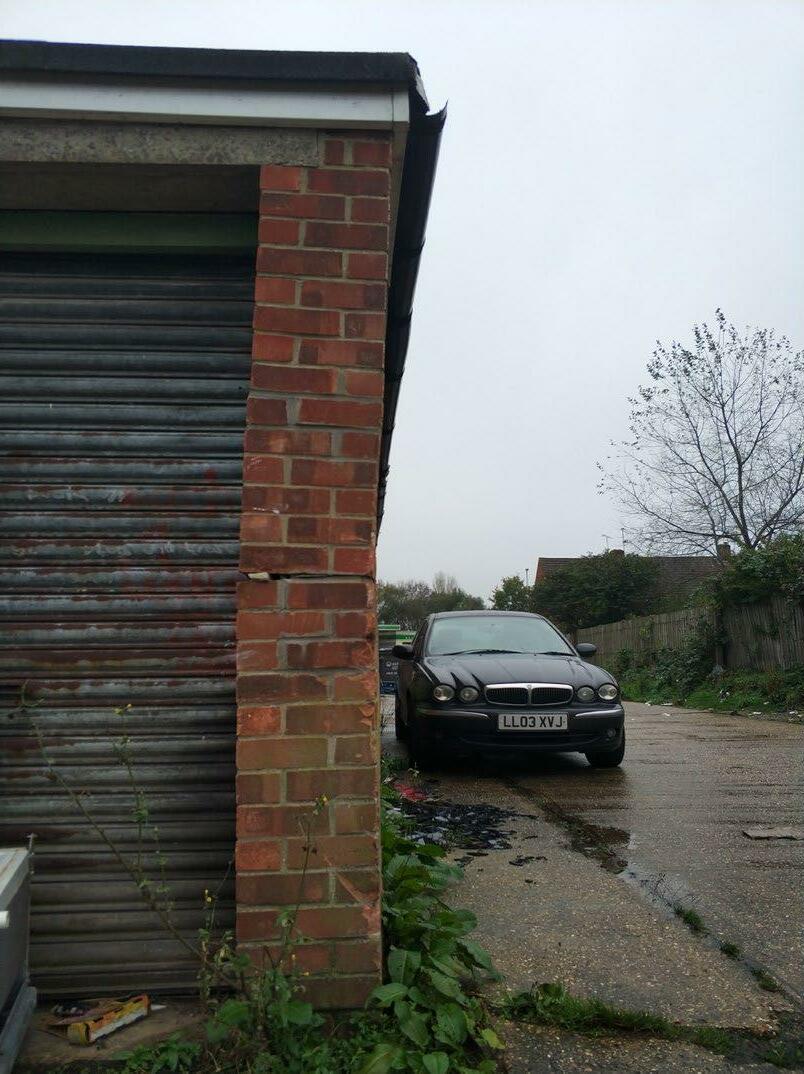
27 Ahmed Ali Garage Conversion Middle Park Way Havant 61 South Street Havant Hampshire PO9 1BZ 023 9248 2494 023 9248 1152 e design@pwp architects com w www pwp architects com revisions & notes 100mm 0@A2 drawingrev No Project No status date scale drawn drawing name project 5493 * PRELIMINARY November 2017 KC 1:100 1 2 55 1002 Design strategy 3 10 11 12 13 14 15 16 17 Existing Pavement Service Road Service Road Unpaved Unpaved Existing Pavement Fence line Fence line The Co operative The Best one Fence line Ladbrokes The Co operative Fence line Proposed pavement extension Area to be cleared of debris and rubbish Ground to be leveled and block paved ( Concrete Surface ) N 27/11/17 KC Issued for comment Road - Danger from moving vehicle Recessed entrance - Safe zone for entering or exiting, and function as a defensible space Entry / Exit to flat s) Bollard The proposed pavement will provide a safe access path for the occupants to enter the building, as well as discourage vehicle from parking and driving near the entrance KEY : Recessed entrance & Proposed pavement extension ( Occupants safety from vehicle ) Proposed pavement extension Separation between the service road and the building entrance MIDDLE PARK WAY DESIGN STRATEGY 3 [Individual][ArchiCAD]

revisions & notes project R Kitchen Care Home Development High Peak Rownhams Lane Rownhams 10 11 12 13 14 15 16 WD 016 1 275 1 135 WD 015 1 275 1 135 WD 014 1 910275 WD 011 1 275 1 135 WD 010 1 625275 ED 006 WHD 1 810x2 100 WD 024 1 650275 WD 004 1 650275 WD 005 275 135 WD 008 1 275 1 135 WD 023 275 135 WD 022 1 275 1 135 WD 021 2 075 1 135 ED 001 WHD 810x2 250 ID 009 WHD 922 x 2 023 FR FD 30 S ID 012 WHD 922 2 023 FR FD 30 S WD 006 625745 WD 007 625745 ID 017 WHD 1 760x2 023 FR FD30S ID 018 WHD 1 456x 023 FR FD30S ID 014 WHD 456 1 173 FR FD30S ID 032 WHD 760 2 023 FR FD30S ID 033 WHD 1 760 2 023 FR FD30S ID 010 WHD 922 2 023 FR a ID 020 WHD 922 x 2 023 FR FD 30 S ED 005 WHD 1 135 2 110 ID 023 WHD 922 2 023 FR FD30S ID 026 WHD 456 2 023 FR FD30S ID 021 WHD 922 2 023 FR FD30S ID 007 WHD 922x2 023 FR n ID 008 WHD 922 2 023 FR FD30S WD 003 1 275 1 135 WD 001 1 275 1 135 WD 002 275 135 ID 002 WHD 922 x 2 023 FR FD 30 S ID 011 WHD 922 2 023 FR a WD 020 2 075 1 241 WD 017 2 075 1 241 WD 018 2 075 1 241 WD 019 2 075 1 241 ID 027 WHD 1 456 2 023 FR FD 30 S ID 030 WHD 922 2 023 FR FD30S ID 004 WHD 922x2 023 FR n a ID 003 WHD 922 2 023 FR FD30S ID 001 WHD 922x2 023 FR n a ID 013 WHD 922 2 023 FR FD30S ID 016 WHD 922 2 023 FR FD 30 S ID 029 WHD 922 2 023 FR FD30S ID 031 WHD 922x2 023 FR FD30S ID 005 WHD 922x2 023 FR FD30S ID 006 WHD 922x 023 FR n a ID 025 WHD 922 2 023 FR FD30S ID 024 WHD 922x2 023 FR FD30S ID 022 WHD 922x2 023 FR FD30S ID 028 WHD 922 2 023 FR FD30S ID 019 WHD 922 x 2 023 FR FD 30 S ID 015 WHD 922x2 023 FR FD30S ED 002 WHD 1 135 2 565 A A 8 8 800 ENSUITE ENSUITE ENSUITE 432 73 m RETAIN POSITION OF EXISTING BRICK WALL FORMING RAISED BED 63 18 62 76 62 46 62 50 62 50 TIMBER BIN ENCLOSURE RECYCLING BIN RECYCLING BIN BIKE STORAGE 1500mm Diameter Wheelchair turning SVP Bedroom 01 A 12 52 m2 Bedroom 02 A 13 49 m2 Bedroom 03 A 12 98 m2 Bedroom 04 A 13 48 m2 Bedroom 05 A 13 37 m Bedroom 06 A 13 37 m2 Assist Bathroom 01 A 8 62 m Circulation 01 Communal Louge Dining Room A 105 50 m Reception A 15 20 m Staircase 01 Lounge Conservatory A 38 19 m2 Staircase 02 Quiet lounge A 26 05 m2 Kitchen A 34 72 m Circulation 02 Laundry A 7 62 m2 Plant 01 A 7 96 m Plant 02 A 1 46 m2 Disable Toilet 1 2 3 4 5 6 7 8 9 10 11 12 13 14 15 16 WD 013 275 135 WD 012 275 135 ED 007 WHD 1 135 2 110 J J K K H H G G D D C C B B F F E E 1 1 3 3 2 2 4 4 5 5 6 6 7 7 N 28 HIGH PEAK CARE HOME PROPOSED GORUND FLOOR PLAN SOUTHAMPTON, HAMPSHIRE CLIENT : PRIVATE CLIENT APPOINTMENT : 2018 WORK STAGE: BUILDING REG & TENDER Project brief : Demolition of existing residential property at High Peak and construction of 2.5 storey nursing home comprising 40 bedrooms with associated car parking, landscaping and refuse storage. [Individual][ArchiCAD]
29 HIGH PEAK CARE HOME PROPOSED FIRST FLOOR PLAN [Individual][ArchiCAD] 61 South Street Havant Hampshire PO9 1BZ 023 9248 2494 023 9248 1152 e design@pwp architects com w www pwp architects com revisions & notes 100mm 0@A1 Note All dimensions to be checked on site by the contractor before fabrication and erection Figured dimensions to be taken in preference to scaled dimensions This drawing is the copyright of the architects and must not be reproduced or used without their express consent except for the purposes of a planning application Electronic issue of this drawing to be confirmed by paper hard copy only drawingrev No Project No status date scale drawn drawing name project Building Regulation May 2018 KC 46701 50 1221 WIP Proposed First Floor Plan R Kitchen Care Home Development High Peak Rownhams Lane Rownhams 7 8 9 10 11 12 13 14 15 16 18 19 20 21 22 23 24 25 26 27 18 19 20 21 22 23 24 WD 104 1 275 1 135 WD 128 275 135 WD 124 1 275 1 135 WD 112 500750 WD 122 1 275 1 135 WD 123 1 275 1 135 WD 110 1 500 600 ID 101 WHD 922x2 023 FR FD30S WD 109 1 900275 ID 112 WHD 922x2 023 FR FD30S ID 133 WHD 922 2 023 FR FD30S ID 108 WHD 922 2 023 FR FD30S ID 111 WHD 922x2 023 FR FD30S ID 130 WHD 922x 023 FR FD30S ID 117 WHD 922 2 023 FR FD30S WD 111 1 600500 ID 113 WHD 922x2 023 FR n a WD 106 1 WD600275 108 1 275 600 WD 107 1 275 600 ID 120 WHD 922x2 023 FR FD30S ID 121 WHD 922x2 023 FR FD30S ID 124 WHD 922x2 023 FR FD30S ID 125 WHD 922x2 023 FR FD30S WD 116 1 275 1 135 WD 115 1 275 1 135 WD 114 1 275 1 135 WD 113 1 275 1 135 WD 117 1 275 1 135 ID 119 WHD 922x 023 FR a ID 122 WHD 922x 023 FR a ID 123 WHD 922x 023 FR a ID 126 WHD 922x2 023 FR n ID 100 WHD 922x 023 FR a ID 134 WHD 922x2 023 FR n WD 101 1 275 1 135 ID 118 WHD 1 304 2 023 FR n a ID 103 WHD 922x2 023 FR n ID 107 WHD 922 2 023 FR n a ID 110 WHD 922x 023 FR n WD 129 1 650275 WD 103 1 650275 WD 102 275 135 WD 100 275 135ID 141 WHD 1 304 x 2 023 FR FD 30 S ID 140 WHD 1 304 x 2 023 FR FD 30 S ID 102 WHD 922 2 023 FR FD30S ID 106 WHD 922 2 023 FR a WD 105 275 135 WD 125 1 275 1 135 WD 127 1 275 1 135 WD 126 625745 ID 109 WHD 922x2 023 FR n WD 119 625745 WD 120 625745 WD 118 1 910275 WD 121 1 275 1 135 ID 138 WHD 922 2 023 FR FD30S ID 116 WHD 922x2 023 FR FD30S ID 127 WHD 734x2 023 FR FD30 ID 128 WHD 922 2 023 FR FD30S ID 114 WHD 922 2 023 FR FD30S ID 131 WHD 922 x 2 023 FR n a ID 129 WHD 922 x 2 023 FR ID 104 WHD 922 2 023 FR FD30S ID 115 WHD 922 2 023 FR n a ID 142 WHD 922 2 023 FR FD30S ID 105 WHD 922x 023 FR a ID 136 WHD 922 2 023 FR FD30S ID 139 WHD 922 2 023 FR FD30S ID 135 WHD 922x2 023 FR FD30S ID 132 WHD 922x 023 FR FD30S ID 137 WHD 922x2 023 FR n a ID 143 WHD 922 2 023 FR a ID 144 WHD 922 2 023 FR FD30S A A 8 8 800 3 60 m ENSUITE ENSUITE ENSUITE ENSUITE ENSUITE ENSUITE ENSUITE ENSUITE ENSUITE ENSUITE ENSUITE ENSUITE ENSUITE SVP ENSUITEENSUITE NURSE S STATION SERVICE CORE 1500mm Diameter Wheelchair turning 1500mm Diameter Wheelchair turning SERVICE RISER CPD SERVICE RISER Lift core internal 2450 1700mm Bedroom 12 A: 13 37 m Bedroom 11 A 13 37 m Bedroom 10 A 13 48 m2 Bedroom 09 A 12 96 m2 Bedroom 08 A 13 49 m Bedroom 07 A 12 52 m Bedroom 23 A 14 07 m2 Bedroom 22 A 13 93 m Bedroom 21 A 13 95 m2 Bedroom 20 A 13 64 m2 Bedroom 19 A 13 03 m Bedroom 18 A 12 71 m Bedroom 17 A 13 02 m2 Bedroom 16 A 13 02 m2 Bedroom 15 A 13 02 m Bedroom 14 A 13 88 m Bedroom 13 A 14 35 m Staircase 02 Staircase 01 Circulation Circulation3 4 Circulation 5 Assisted Bathroom 03 A: 9 87 m Assisted Bathroom 02 A: 10 28 m 12 13 14 15 16 J J K K I I H H G G D D C C B B F F E E 1 1 3 3 2 2 4 4 5 5 6 6 7 7 N WIP For comment

30 61 South Street Havant Hampshire PO9 1BZ 023 9248 2494 023 9248 1152 e design@pwp architects com w www pwp architects com revisions & notes 100mm 0@A1 Note All dimensions to be checked on site by the contractor before fabrication and erection Figured dimensions to be taken in preference to scaled dimensions This drawing is the copyright of the architects and must not be reproduced or used without their express consent except for the purposes of a planning application Electronic issue of this drawing to be confirmed by paper hard copy only drawingrev No Project No status date scale drawn drawing name project Building Regulation May 2018 KC 46701 50 1:100 1222 WIP Proposed Second Floor Plan R Kitchen Care Home Development High Peak Rownhams Lane Rownhams ASSISTED BATHROOM 10 13 m2 ASSISTED BATHROOM 9 40 m 18 19 20 21 22 23 24 25 26 27 28 29 30 31 32 33 18 19 20 21 22 23 24 25 26 27 28 29 30 31 32 33 WD 210 1 600500 ID 204 WHD 922 2 023 FR FD30S WD 208 1 900275 ID 218 WHD 694 2 023 FR FD30S WD 205 1 600275 WD 207 1 275 600 WD 206 1 275 600 ID 219 WHD 922x 023 FR n a ID 222 WHD 922x 023 FR n a ID 223 WHD 922x 023 FR n a ID 203 WHD 922 2 023 FR n a WD 200 275 135 ID 207 WHD 922x2 023 FR FD30S ID 234 WHD 922x2 023 FR n WD 202 275 135 ID 201 WHD 922x2 023 FR FD30S ID 242 WHD 922 2 023 FR FD30S WD 222 1 275 1 135 WD 224 1 275 1 135 WD 223 625745 ID 230 WHD 922 2 023 FR FD30S ID 225 WHD 922x2 023 FR FD30S ID 224 WHD 922x2 023 FR FD30S ID 221 WHD 922x2 023 FR FD30S ID 220 WHD 922x 023 FR FD30S ID 202 WHD 922 2 023 FR FD30S ID 200 WHD 922x2 023 FR n ID 210 WHD 922 2 023 FR a ID 209 WHD 922 2 023 FR a ID 206 WHD 922 2 023 FR n a WD 219 1 275 1 135 ID 229 WHD 922x 023 FR n ID 214 WHD 922x 023 FR FD30S ID 216 WHD 922 2 023 FR FD30S ID 233 WHD 922 2 023 FR FD30S ID 238 WHD 922x2 023 FR FD30S ID 212 WHD 922x2 023 FR FD30S ID 217 WHD 922 2 023 FR FD30S ID 227 WHD 734x2 023 FR FD30S ID 228 WHD 922x2 023 FR FD30S ID 215 WHD 922x2 023 FR n a ID 213 WHD 922 2 023 FR a ID 231 WHD 922 2 023 FR a ID 211 WHD 922x 023 FR FD30S ID 208 WHD 922x 023 FR FD30S WD 204 910895 WD 203 910895 ID 205 WHD 922 2 023 FR n a ID 240 WHD 694x2 023 FR FD30S ID 241 WHD 1 378 x 2 023 FR FD 30 S ID 243 WHD 922x2 023 FR n ID 237 WHD 922 2 023 FR n a ID 226 WHD 922x2 023 FR n a WD 217 625595 WD 218 625595 WD 216 625595 WD 201 1 275 1 135 ID 236 WHD 922x2 023 FR FD30S ID 232 WHD 922x2 023 FR FD30S ID 235 WHD 922 2 023 FR FD30S ID 244 WHD 922 2 023 FR FD30S ID 239 WHD 922x2 023 FR n A A 8 8 3 57 m 400 43 m ESCAPE STAIR ENSUITE ENSUITE ENSUITE ENSUITE ENSUITE ENSUITE ENSUITE ENSUITE ENSUITE ENSUITE ENSUITE ENSUITE ENSUITE ENSUITE NURSE S STATION SERVICE CORE 1500mm Diameter Wheelchair turning 1500mm Diameter Wheelchair turning SERVICE RISER CPD SERVICERISER ENSUITE Lift core internal 2450 1700mm Bedroom 24 A 12 10 m Bedroom 25 A: 13 42 m Bedroom 26 A 12 87 m2 Bedroom 27 A 13 35 m Bedroom 28 A 12 16 m2 Bedroom 29 A 12 15 m Bedroom 30 A 14 62 m2 Bedroom 31 A: 14 17 m Bedroom 32 A 12 65 m2 Bedroom 33 A 12 63 m2 Bedroom 34 A 12 65 m Bedroom 35 A 12 12 m2 Bedroom 36 A 13 98 m2 Bedroom 37 A: 12 02 m Bedroom 38 A 12 68 m2 Bedroom 39 A 12 68 m2 Bedroom 40 A: 13 16 m Circulation 6 Staircase 02 Staircase 01 Circulation 7 Circulation 8 J J K K I I H H G G D D C C B B F F E E 1 1 3 3 2 2 4 4 5 5 6 6 7 7 WD 209 1 500 WD600 211 1 275 1 135 WD 212 1 275 1 135 WD 213 1 275 1 135 WD 214 1 275 1 135 WD 215 1 275 1 135 WD 221 1 275 1 135 WD 220 1 275 1 135 N WIP For comment HIGH PEAK CARE HOME PROPOSED SECOND FLOOR PLAN [Individual][ArchiCAD]
31 61 South Street Havant Hampshire PO9 1BZ 023 9248 2494 023 9248 1152 e design@pwp architects com w www pwp architects com revisions & notes 100mm 0@A1 Note All dimensions to be checked on site by the contractor before fabrication and erection Figured dimensions to be taken in preference to scaled dimensions This drawing is the copyright of the architects and must not be reproduced or used without their express consent except for the purposes of a planning application Electronic issue of this drawing to be confirmed by paper hard copy only drawingrev No Project No status date scale drawn drawing name project Building Regulation May 2018 KC 46701 50 1223 WIP Proposed Roof Plan R Kitchen Care Home Development High Peak Rownhams Lane Rownhams A A 8 8 J J K K I I H H G G D D C C B B F F E E 1 1 3 3 2 2 4 4 5 5 6 6 7 7 N WIP For comment HIGH PEAK CARE HOME PROPOSED ROOF PLAN [Individual][ArchiCAD]
32 61 South Street Havant Hampshire PO9 1BZ 023 9248 2494 023 9248 1152 e design@pwp architects com w www pwp architects com revisions & notes 100mm 0@A1 Note All dimensions to be checked on site by the contractor before fabrication and erection Figured dimensions to be taken in preference to scaled dimensions This drawing is the copyright of the architects and must not be reproduced or used without their express consent except for the purposes of a planning application Electronic issue of this drawing to be confirmed by paper hard copy only drawingrev No Project No status date scale drawn drawing name project Building Regulation May 2018 KC 46701 100 1300 WIP Proposed Elevations R Kitchen Care Home Development High Peak Rownhams Lane Rownhams K K J J H H G G F F E E D D C C B B WD 024 WD 022 WD 021 WD 015 WD 014 SW 006 WD WD122 129 WD WD123 125 WD 127 WD 126 WD WD119 120 WD 121 WD 118 WD 223 WD 219 WD WD217 218 WD 216 WD 221 WD 220 WD 020 WD WD017WD018 019 B B C C D D E E F F G G H H J J K K WD 004 WD WD006 007 WD SW010 021 109 WD 111 SW 011 103 WD 210 WD 204 WD 203 ED 002 8 8 7 7 6 6 3 3 2 2 003 001 WD 104 WD WD128 101 WD 202 WD 201 WD 200 RL 002 1 1 3 3 4 4 5 5 6 6 WD WD008 013 WD 012 116 115 113 105 N 1300 NORTH ELEVATION 1 100 1300 SOUTH ELEVATION 1:100 1300 EAST ELEVATION 1 100 1300 WEST ELEVATION 1:100 A 30 06 2017 Issued to WYG for comment B 11 07 2017 Issued to WYG following changes C 21 07 2017 Issued to WYG following changes D 08 08 2017 Issued to WYG E 07 12 2017 Amendments following pre application F 14 12 2017 Amendments to dormer windows & landscape changes G 20 12 2017 Material Amendment H 01 02 2018 Kitchen & Laundry extract added HIGH PEAK CARE HOME PROPOSED ELEVATIONS [Individual][ArchiCAD]
33 revisions & notes drawing name project Proposed Sections 1 R Kitchen Care Home Development High Peak Rownhams Lane, Rownhams 876 5 4 3 2 1 2,250 640 2,250 640 2,250 8 2,659 231 2,659 231 2,400 490 2,400 490 2,400 15 +72,159 +68,705 +65,815 +62,925 +71,929 +67,441 +64,551 Beam and block floor construction Foundation TBC by structure engineer Telescopic underfloor void ventilator Hollow core floor slab with resilient layer and screed on top underdrawn with MF concealed suspened ceiling
Facing brick and blockwork wall with insulated cavity u value = 0 26) Rainwater down pipe EPDM flat roof with 190mm insulation over rafters u value = 0 18)
White rendered wall on timber frame system with insulation u value = 0 26) TBC by structure engineer Kitchen extraction system
Concrete hollow slab floor with resilient layer and screed on top underdrawn with MF concealed suspened ceiling EPDM flat roof with 190mm insulation over rafters u value = 0 18 Facing brick and blockwork wall with insulated cavity u value = 0 26)
Pitched slate roof with 210mm insulation over and in between rafters (u value = 0 18 In situ concrete staircase Bulkhead for service pipes Hollow core floor slab with resilient layer underdrawn with Quick Lock Grid lay in ceiling Communal Lounge Dinning Room Assisted Bathroom 03 Assisted Bathroom 05 Bedroom 20 Bedroom Escape37 Staircase 02 2nd Floor Corridor 1st Floor Corridor Storage 1 2 5 6 7 8 10 11 12 13 14 15 16 17 18 19 20 21 22 23 24 25 26 27 28 29 30 31 32 87654321 +71,505 +68,705 +65,815 +62,925 +64,551 +67,260 Beam and block floor construction Foundation TBC by structure engineer Telescopic underfloor void ventilator
Pitched slate roof with 210mm insulation over and in between rafters u value = 0 18 In situ concrete staircase Concrete hollow floor slab with resilient layer underdrawn with Quick Lock Grid lay in ceiling Bedroom Assisted23 Bathroom 02 Assisted Bathroom 01 PlantReception E Storage Corridor Escape staircase 01 1st Floor Corridor 2nd Floor Corridor Assisted Bathroom 04 Bedroom 40 Bedroom 29 Bedroom 29 Bedroom 06 2 3 4 5 6 8 9 10 11 12 13 14 15 16 17 18 19 20 21 22 23 24 25 26 27 28 29 30 31 32 S 11 Building Section 1 50
N
S 06 Building Section 1 50 HIGH PEAK CARE HOME PROPOSED SECTIONS [Individual][ArchiCAD]
34 N 61 South Street Havant Hampshire PO9 1BZ revisions & notes drawing name project *Drawing name* R Kitchen Care Home development High Peak, Rownhams Lane Rownhams ID ID 001 ID 002 ID 003 ID 004 ID 005 ID 006 ID 007 ID 008 ID 009 ID 010 ID 011 ID 012 ID 013 ID 014 ID 015 ID 016 Home Story Ground Floor Ground Floor Ground Floor Ground Floor Ground Floor Ground Floor Ground Floor Ground Floor Ground Floor Ground Floor Ground Floor Ground Floor Ground Floor Ground Floor Ground Floor Ground Floor Quantity 1 1 1 1 1 1 1 1 1 1 1 1 1 1 1 1 Front View 922 2 023 922 2 023 922 2 023 922 2 023 922 2 023 922 2 023 922 2 023 922 2 023 922 2 023 922 2 023 922 2 023 922 2 023 922 2 023 456 1 173 922 2 023 922 2 023 Leaf Dimension 838×1,981 838×1,981 838×1 981 838×1 981 838×1 981 838×1 981 838×1 981 838×1,981 838×1,981 838×1 981 838×1 981 838×1 981 838×1 981 1,372×1 131 838×1 981 838×1 981 Wallhole Dimensi 922×2 023 922×2 023 922×2 023 922×2 023 922×2 023 922×2 023 922×2 023 922×2 023 922×2 023 922×2 023 922×2 023 922×2 023 922×2 023 1 456×1 173 922×2 023 922×2 023 2D Plan 922 922 922 922 922 922 922 922 922 922 922 922 922 1 456 922 922 Leaf Thickness 44 44 44 44 44 44 44 44 44 44 44 44 44 44 44 44 Fire Rating n/a FD30S FD30S n/a FD30S n a n a FD30S FD30S n/a n a FD30S FD30S FD30S FD30S FD30S Wall Thickness 0 12 0 22 0 22 0 12 0 22 0 12 0 12 0 22 0 22 0 12 0 12 0 22 0 22 0 22 0 22 0 22 Signage 1 2 3 4 5 6 Fire Door Keep Shut Store Keep Locked Shut Dining Room Fire Door Keep Shut Door Closer Hold Open Device NBS Clause L20 L20 L20 L20 L20 L20 L20 L20 L20 L20 L20 L20 L20 L20 L20 L20 Finish Ash Veneer Ash Veneer Ash Veneer Ash Veneer Ash Veneer Ash Veneer Ash Veneer Ash Veneer Ash Veneer Ash Veneer Ash Veneer Ash Veneer Painted finish Painted finish Painted finish Painted finish Lockset No Lock Sashlock masterkey 1 Sashlock masterkey 1 No Lock Sashlock masterkey 1 No Lock No Lock Sashlock - masterkey 1 Sashlock masterkey 1 No Lock No Lock Sashlock - masterkey 1 No Lock Sashlock - masterkey 2 No Lock No Lock Handle Lever Handle SS Lever Handle (SS Lever Handle (SS) Lever Handle (SS) Lever Handle (SS) Lever Handle (SS) Lever Handle (SS) Lever Handle SS) Lever Handle (SS Lever Handle (SS) Lever Handle (SS) Lever Handle SS) Push Plate and Pull Handle Lever Handle SS) Push Plate and Pull Handle Push Plate and Pull Handle ID 017 ID 018 ID 019 ID 020 ID 021 ID 022 ID 023 ID 024 ID 025 ID 026 ID 027 ID 028 ID 029 ID 030 Ground Floor Ground Floor Ground Floor Ground Floor Ground Floor Ground Floor Ground Floor Ground Floor Ground Floor Ground Floor Ground Floor Ground Floor Ground Floor Ground Floor 1 1 1 1 1 1 1 1 1 1 1 1 1 1 1 760 2 023 1 456 2 023 922 2 023 922 2 023 922 2 023 922 2 023 922 2 023 922 2 023 922 2 023 1 456 2 023 1 456 2 023 922 2 023 922 2 023 922 2 023 1,676×1 981 1 372×1 981 838×1 981 838×1 981 838×1 981 838×1,981 838×1 981 838×1 981 838×1 981 1 372×1,981 1,372×1,981 838×1 981 838×1,981 838×1 981 1,760×2 023 1 456×2 023 922×2 023 922×2 023 922×2 023 922×2,023 922×2 023 922×2 023 922×2 023 1 456×2,023 1,456×2,023 922×2 023 922×2,023 922×2 023 1 760 1 456 922 922 922 922 922 922 922 1 456 1 456 922 922 922 44 44 44 44 44 44 44 44 44 44 44 44 44 44 FD30S FD30S FD30S FD30S FD30S FD30S FD30S FD30S FD30S FD30S FD30S FD30S FD30S FD30S 0 22 0 22 0 13 0 13 0 22 0 13 0 13 0 13 0 13 0 22 0 22 0 12 0 22 0 22 Store Keep Locked Shut Fire Door Keep Shut Laundry Plant Room Laundry 3 Kitchen Staff Only Kitchen Staff Only Plant Room Bathroom L20 L20 L20 L20 L20 L20 L20 L20 L20 L20 L20 L20 L20 L20 Painted finish Painted finish Painted finish Painted finish Painted finish Painted finish Painted finish Painted finish Painted finish Painted finish Painted finish Painted finish Painted finish Painted finish No lock Sashlock - masterkey 2 No Lock No Lock Keypad No lock Keypad Sashlock - masterkey 3 No lock No lock No lock Sashlock - Masterkey3 No Lock WC thumb turn & Indicator Push Plate and Pull Handle Lever Handle (SS) Push Plate and Pull Handle Lever Handle (SS) Push Plate and Pull Handle Lever Handle SS Push Plate and Pull Handle Lever Handle (SS) Lever Handle (SS) Push Plate and Pull Handle Push Plate and Pull Handle Lever Handle (SS) Push Plate and Pull Handle Lever Handle (SS ID Home Story Quantity Front View Leaf Dimension Wallhole Dimensi 2D Plan Leaf Thickness Fire Rating Wall Thickness Signage Door Closer Hold Open Device NBS Clause Finish Lockset Handle HIGH PEAK CARE HOME EXAMPLE OF DOOR SCHEDULE [Individual][ArchiCAD]
35 N 61 South Street Havant Hampshire PO9 1BZ 023 9248 2494 023 9248 1152 design@pwp architects com w www pwp architects com revisions & notes 100mm 0@A3 Note All dimensions to be checked on site by the contractor before fabrication and erection Figured dimensions to be taken in preference to scaled dimensions This drawing is the copyright of the architects and must not be reproduced or used without their express consent except for the purposes of a planning application Electronic issue of this drawing to be confirmed by paper hard copy only drawingrev No Project No status date scale drawn drawing name project Building Regulation *Drawing name* KC 46701 1 50 1 2 WIP May 2018 R Kitchen Care Home development High Peak, Rownhams Lane Rownhams ID Home Story Quantity Front View 2D Plan Wallhole Dimension Window sill height Window head height Wall Thickness U value Accessories Finish Hinges Lockset Ventilation ID Home Story Quantity Front View 2D Plan Wallhole Dimension Window sill height Window head height Wall Thickness U value Accessories Finish Hinges Lockset Ventilation WD - 104 WD 105 WD 106 WD - 107 WD - 108 WD - 109 WD - 110 WD - 111 WD - 112 WD - 113 WD 114 WD 115 WD - 116 WD - 117 First Floor First Floor First Floor First Floor First Floor First Floor First Floor First Floor First Floor First Floor First Floor First Floor First Floor First Floor 1 1 1 1 1 1 1 1 1 1 1 1 1 1 1 135 1 275 135 1 275 600 1 275 600 1 275 600 1 275 900 1 275 600 600 500 500 750 135 1 275 135 1 275 135 1 275 1 135 1 275 1 135 1 275 135 1 135 600 600 600 900 600 600 500 1 135 1 135 1 135 1 135 1 135 1 135×1 275 1 135×1 275 600×1 275 600×1,275 600×1,275 900×1,275 600×1 500 600×1 500 500×750 1,135×1 275 1,135×1 275 1,135×1,275 1 135×1,275 1 135×1,275 800 800 800 800 800 800 600 600 1 200 800 800 800 800 800 2,075 2 075 2 075 2 075 2 075 2 075 2,100 2,100 1,950 2 075 2 075 2 075 2 075 2 075 0 34 0 34 0 35 0 35 0 35 0 35 0 34 0 34 0 34 0 34 0 34 0 34 0 34 0 34 1 4 W/m2K 1 4 W/m2K 1 4 W m2K 1 4 W m2K 1 4 W m2K 1 4 W m2K 1 4 W m2K 1 4 W/m2K 1 4 W/m2K 1 4 W/m2K 1 4 W m2K 1 4 W m2K 1 4 W m2K 1 4 W m2K Security window restrictor Security window restrictor Security window restrictor Security window restrictor Security window restrictor Security window restrictor Security window restrictor Security window restrictor Security window restrictor Security window restrictor Security window restrictor Security window restrictor Security window restrictor Security window restrictor uPVC White uPVC White uPVC White uPVC White uPVC White uPVC White uPVC White uPVC White uPVC White uPVC White uPVC White uPVC White uPVC White uPVC White Standard Friction Hinges Standard Friction Hinges Standard Friction Hinges Standard Friction Hinges Standard Friction Hinges Standard Friction Hinges Standard Friction Hinges Standard Friction Hinges Standard Friction Hinges Standard Friction Hinges Standard Friction Hinges Standard Friction Hinges Standard Friction Hinges Standard Friction Hinges Espagnolette Espagnolette Espagnolette Espagnolette Espagnolette Espagnolette Espagnolette Espagnolette Espagnolette Espagnolette Espagnolette Espagnolette Espagnolette Espagnolette Trickle Vent Trickle Vent Trickle Vent Trickle Vent Trickle Vent Trickle Vent Trickle Vent Trickle Vent Trickle Vent Trickle Vent Trickle Vent Trickle Vent Trickle Vent Trickle Vent WD - 118 WD - 119 WD 120 WD - 121 WD - 122 WD - 123 WD - 124 WD - 125 WD 126 WD 127 WD 128 WD - 129 WD - 200 WD - 201 First Floor First Floor First Floor First Floor First Floor First Floor First Floor First Floor First Floor First Floor First Floor First Floor Second Floor Second Floor 1 1 1 1 1 1 1 1 1 1 1 1 1 1 910 1 275 625 745 625 745 135 1 275 1 135 1 275 1 135 1 275 1 135 1 275 1 135 1 275 625 745 135 1 275 135 1 275 650 1 275 1 135 1 275 1 135 1 275 910 625 625 1 135 1 135 1 135 1 135 135 625 1 135 1 135 650 1 135 1 135 910×1 275 625×745 625×745 1,135×1,275 1,135×1,275 1 135×1,275 1 135×1 275 1 135×1 275 625×745 1,135×1 275 1,135×1 275 650×1,275 1 135×1,275 1 135×1,275 800 1 200 1 200 800 800 800 800 800 1 200 800 800 800 800 800 2,075 1 945 1 945 2 075 2 075 2 075 2,075 2,075 1,945 2 075 2 075 2 075 2 075 2 075 0 34 0 34 0 34 0 24 0 35 0 35 0 34 0 24 0 34 0 34 0 34 0 35 0 35 0 25 1 4 W/m2K 1 4 W/m2K 1 4 W m2K 1 4 W m2K 1 4 W m2K 1 4 W m2K 1 4 W m2K 1 4 W/m2K 1 4 W/m2K 1 4 W/m2K 1 4 W m2K 1 4 W m2K 1 4 W m2K 1 4 W m2K Security window restrictor Security window restrictor Security window restrictor Security window restrictor Security window restrictor Security window restrictor Security window restrictor Security window restrictor Security window restrictor Security window restrictor Security window restrictor Security window restrictor Security window restrictor Security window restrictor uPVC White uPVC White uPVC White uPVC White uPVC White uPVC White uPVC White uPVC White uPVC White uPVC White uPVC White uPVC White uPVC White uPVC White Standard Friction Hinges Standard Friction Hinges Standard Friction Hinges Standard Friction Hinges Standard Friction Hinges Standard Friction Hinges Standard Friction Hinges Standard Friction Hinges Standard Friction Hinges Standard Friction Hinges Standard Friction Hinges Standard Friction Hinges Standard Friction Hinges Standard Friction Hinges Espagnolette Espagnolette Espagnolette Espagnolette Espagnolette Espagnolette Espagnolette Espagnolette Espagnolette Espagnolette Espagnolette Espagnolette Espagnolette Espagnolette Trickle Vent Trickle Vent Trickle Vent Trickle Vent Trickle Vent Trickle Vent Trickle Vent Trickle Vent Trickle Vent Trickle Vent Trickle Vent Trickle Vent Trickle Vent Trickle Vent All windows to be fitted with key operated window restrictors with a master key to all All windows to be outward opening and to be restricted to maximum opening width of 100mm (NBS clause L10 xxx) HIGH PEAK CARE HOME EXAMPLE OF WINDOW SCHEDULE [Individual][ArchiCAD]
[Individual] 36 17m Mast Ring 17m Mast Ring 12m Mast Ring 12m Mast Ring 12m Mast Ring 12m Mast Ring Lower Mast Ring 12m Higher Mast Ring 17m Lower Mast Ring 12m Mast Mast Mast 0 7m Eave level 12m Lower mast ring level 17m Higher mast ring level Skate Park Plan @ 1 200 Skate Park Elevation @ 1 : 200 17m Mast Ring 17m Mast Ring 12m Mast Ring 12m Mast Ring 12m Mast Ring 12m Mast Ring Lower Mast Ring - 12m Higher Mast Ring 17m Lower Mast Ring 12m Mast Mast Mast 0 7m Eave level 12m Lower mast ring level) 17m Higher mast ring level) Skate Park Plan @ 1 : 200 Skate Park Elevation @ 1 : 200 SOUTHSEA SKATEPARK PROPOSED OUTLINE DESIGN SOUTHSEA, HAMPSHIRE CLIENT : PRIVATE CLIENT APPOINTMENT : 2019 STAGE: PRELIMINARY Project brief : A quick outline design a for skatepark shelter. [ArchiCAD]
[Individual] 37 BORROW FOUNDATION CONCEPT DESIGN WATERLOOVILLE, HAMPSHIRE CLIENT : BORROW FONDATION APPOINTMENT : 2019 STAGE: CONCEPT DESIGN Project brief : Provide concept design for a new Borrow Foundation centre. [Sketchup + Photoshop]

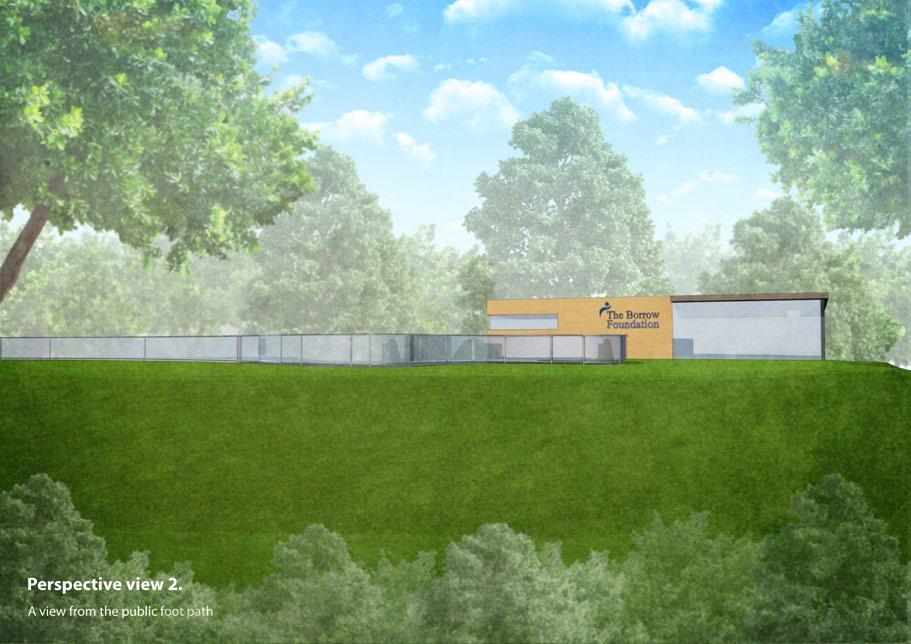

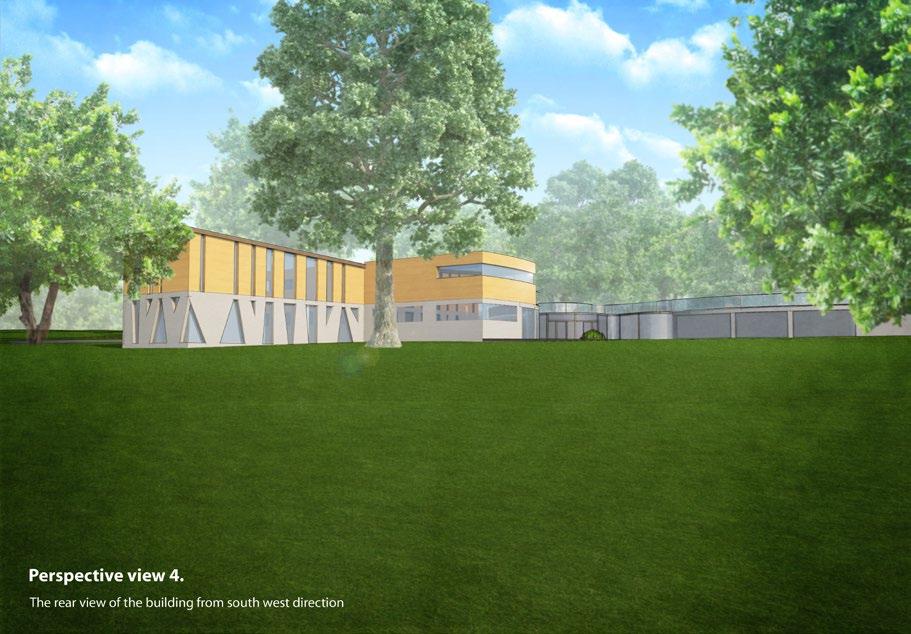
[Individual] 38 revisions & notes project A G Developments Chaswood Nursery Main Road Estrella Garage Estrella House Nursery Track Farm Hopper Cockleberry Pond Nursing Home Kings Lodge LB 5 Kabin MAIN ROAD 5 Estrella House OaklandsCockleberry 1 Farm Hopper 4 Cockleberry The (Nursing Home) Kings Lodge LB Estrella 3 The Kabin Far Close N -: KC 03 0 2020 Issued for outline application Proposed Block Plan @ 1 500 N revisions & notes drawing project A G Developments Chaswood Nursery Main Road Chidham -: KC 03 07 2020 Issued for outline application Proposed Visual South AVENUE COTTAGE PRE APP DRAWINGS BOSHAM, WEST SUSSEX CLIENT : PRIVATE DEVELOPER APPOINTMENT : 2020 STAGE: PRE APPLICATION PLANNING Project brief : Preparation a set of drawing for a residential scheme in plot with planning constraints. [ArchiCAD]
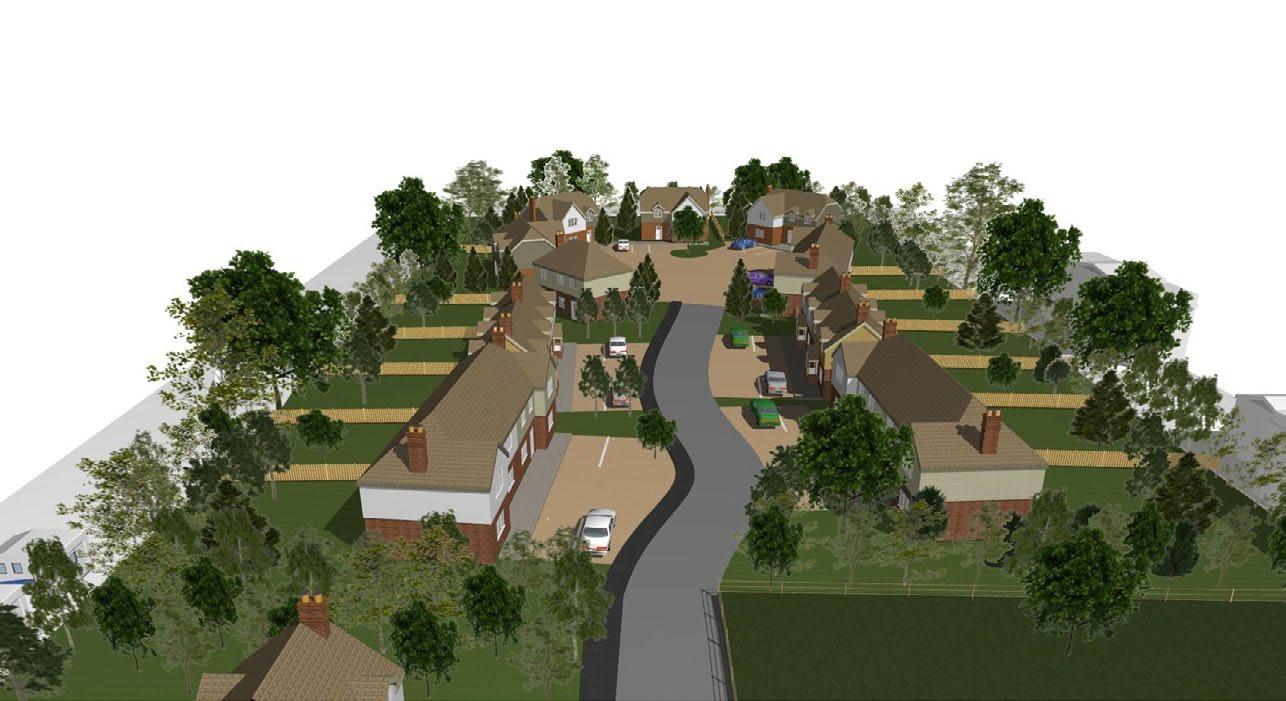
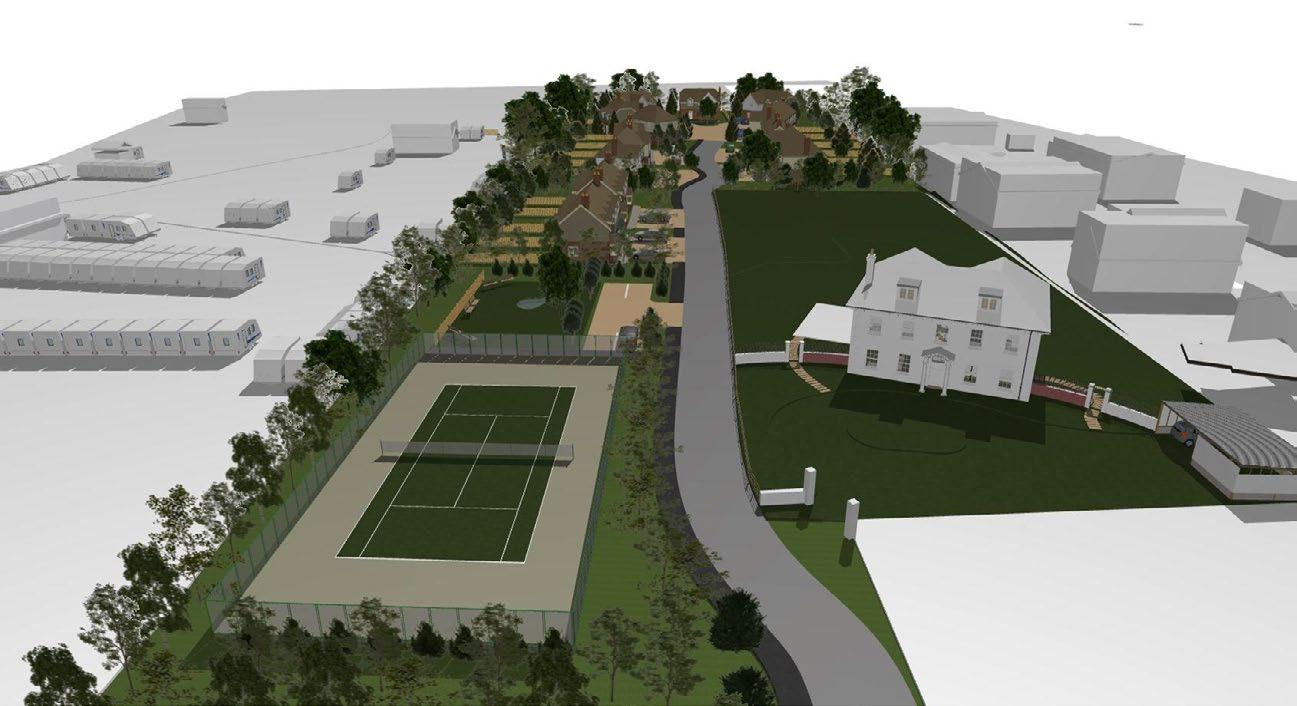
[Individual] 39 N A G Developments Chaswood Nursery Main Road Chidham revisions & notes drawing name project Site boundary Site boundary Site boundary Site boundary Site boundary Site boundary SiteSite boundary Site boundary Site boundary Site boundary -: KC 03 07 2020 Issued for outline application Proposed elevation D @ 1 : 500 Proposed elevation (long) Proposed Elevation A @ 1 : 500 Proposed Elevation B @ 1 : 500 Proposed Proposed@ Elevation A 2 @ 1 : 500 Proposed Elevation B 2 @ 1 : 500 N 61 South Street Havant Hampshire PO9 BZ 023 9248 2494 023 9248 1152 design@pwp architects com pwp architects com revisions notes 100mm 0@A1 Note All dimensions to be checked on site by the contractor before fabrication and erection Figured dimensions to be taken in preference to scaled dimensions This drawing is the copyright of the architects and must not be reproduced or used without their express consent except for the purposes of planning application Electronic issue of this drawing to be confirmed by paper hard copy only drawing No Project No status date scale drawn drawing project June 2020 KC 5443 A G Developments Chaswood Nursery Main Road Chidham 1 500@A Outline Application KC 03 7 2020 Issued for outline application Proposed Visual South Proposed Visuals NA 1000 AVENUE COTTAGE PRE APP DRAWINGS [ArchiCAD]






































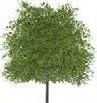
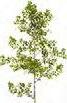

































































































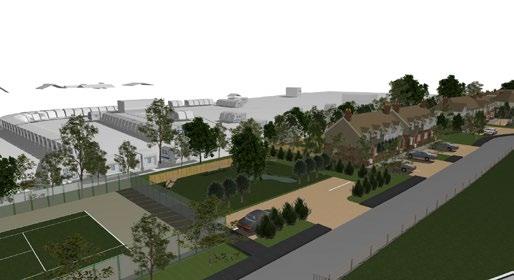
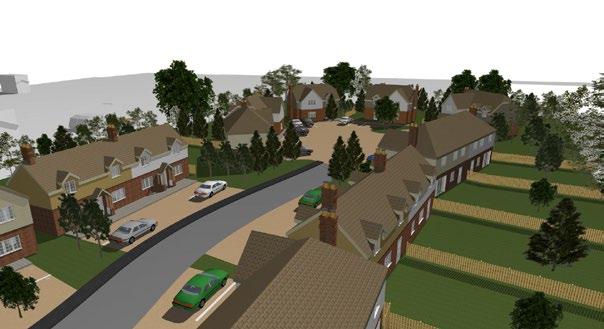
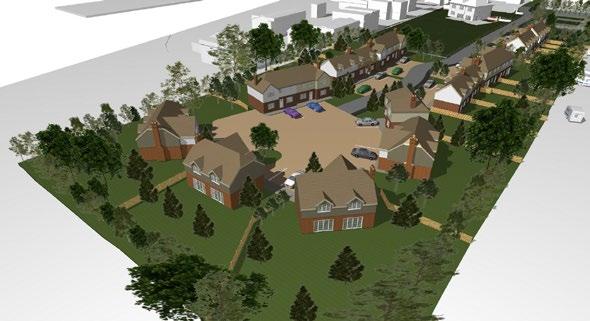
40 CONTENT HOP ARCHITECTS LTD 2020-PRESENT 5-7 STATION ROAD CROFT ALDWICKROADROADSINAH LANE SEA BOARHUNTFRONT LANE 5 CLAUSENTUM ROAD 7 CLAUSENTUM ROAD PINE SHORTHEATHROAD ROAD HAYLING ISLAND, HAMPSHIRE SELSEY, WEST SUSSEX BOGNOR REGIS, WEST SUSSEXHAYLING ISLAND, HAMPSHIRE HAYLING ISLAND, HAMPSHIRE FAREHAM, FARNHAM,CHANDLER’WINCHESTER,WINCHESTER,HAMPSHIREHAMPSHIREHAMPSHIREFORD,HAMPSHIRESURREY
[Individual] 41 5 - 7 STATION ROAD HAYLING ISLAND, HAMPSHIRE CLIENT : PRIVATE DEVELOPER APPOINTMENT : 2019 STAGE: BUILDING REGULATION - CONSTRUCTION Project brief : Demolition of existing dwelling and business units and construction of a 2/3 storey building to provide 19 flats and 2 commerical units with vehicle and cycle parking and a bin store. [ArchiCAD + Cinerender + Photoshop]

6.7m
Fire Stopping for any penetration throught compartment Floor: 1. All ventilation ducts pass throught compartmentation will require a fire damper fitting.
From dry riser outlet to the further point the floor plan 44.5m Two way communication system to an outside monitoring service (24/7) KEY Compartment Wall (60mins Fire Resistance)
2. For large opening where mutliple service pentrations at pre cast concrete plank, a layer of 50mm Rockwool Shuttering Batt* at the bottom and infill with 100mm Rockwool Firestop Compound*. 3. For any plastic pipe (up to 200mm outer diameter) pentrations through Shuttering Batt with Firestop Compound* or Concrete Plank floor, the pipes should be wraped with Rockwool FirePro Intumescent Pipe Wraps CE*. 4. For any non-combustible pipes, please use 15x15mm fillet of Rockwool FirePro Acoustic Intumescent Sealant 5. For any cable trays, please use Rockwool FirePro Mutli-Cable Firestop*.
Point Emergency
(Emergency Lighting to BS 5266-1 standard)
Smoke
3.6m 3.9m 5.8m 8.6m 2.7m KEY 30 mins Fire Resistant Door Self Closing Device FD30 FD60 60 mins Fire Resistant Door SC W CO Fire Extinguisher (Water) Fire Extinguisher (Water) Fire
8P Passenger Lift Status: Draft Building Regulation Issued to: Client Drawn by: KC Date: 09.04.21 Scale: 1:100 Drg.No: HOPA-B-1021-D Drawing: Fire Strategy Proposed First Floor Job Title 123/SR/DL HOP Architects Ltd Southsea, Hampshire 07427 080 777 Company reg. AmendmentsDate by NOT FOR CONSTRUCTION b Added AOV and service riser KC21.01.22 Notes added to AOV KC23.02.22 d FireKC22.03.22 Alarm Notes added Telecom and evacuation chair added Actuator note added Fire hose distance added Section DD Proposed First Floor Plan @ 1:100 [Individual]
Protected Corridor Wall (30mins Fire Resistance) Escape distance Fire Main outlet to the further point on the plan (fire hose distance) FD20 (Fire Alarm to BS 5839-6 standard) (Fire Alarm to LD2 Category)
Point Iluminated Directional Exit Box E Fire Exit Sign Fire Exit Directional Sign V.P Vision Panel E E E S H H S SS H H S COW COW FD60 SC FD60 SC V.P FD60 SC FD60 FD60SC SC FD60 SC V.P FD60 SC V.P FD60 SC FD20 FD20 FD20 FD20FD20 FD20 FD20FD20 FD20 FD60 SC FD20 FD20 FD20 FD60 SC FD60 SC FD20 FD20 FD20FD20 FD20 FD20 FD20 FD20 FD20 FD20 FD20 E S S S
Point
Fire Stopping at blockwork cavity between compartmentation: 1. Rockwool SP 60 Firestop system to be installed at cavity junctions between compartmentation. Or use equivalent approved product by Building Control.
Point Fire Alarm Audible Warning Device H S Heat
Fire Main Outlet Cabinet (Dry Riser) E Dry Riser to be approved by Fire BrigadeRequire total free Require total free area of 1.5m2 FD60 SC WD128 2500x1050mm Automatic window openers for smoke ventilation (approx. 1.0m2 free area) 910x1050mm Automatic window openers ventilation (approx. area) 910x1050mm Automatic window openers ventilation (approx. area)
5-7 STATION ROAD EXAMPLE OF FIRE STRATEGY PLAN 42 [Vectorwork]
3B. If gaps exceed 15mm around the aperture and the sleeve or blockwork, the gap should be filled with Rockwool Acoustic Intumescent Sealant*. 4. For any non-combustible pipes, please use 15x15mm fillet of Rockwool FirePro Acoustic Intumescent Sealant 5. For any cable trays, please use Rockwool FirePro Mutli-Cable Firestop*. Steelwork Fire Protection: 1. All steelwork should not be exposed (except the external steelwork). 2. All enclosed steelworks should be enclosed by a layer of 15mm Fireline plasterboard or two layer of Gyproc plasterboard which achieve a minimum of 30mins fire resistant.
3.5m 13.3m3m 2.8m 6.4m 3.2m 4.5m Alarm Call Detector Detector Lighting Lighting Iluminated Lighting
11m 3m
Emergency
Fire Stopping for any penetration throught compartment wall: 1. All ventilation ducts pass throught compartmentation will require a fire damper fitting. 2. For large opening where mutliple service pentrations at blockwork wall, Rockwool FirePro 50mm Ablative Coated Batt* to be installed. (up to 2 hours fire resistance) 3A. For any plastic pipe (up to 160mm outer diameter) pentrations through Ablative Coat Batt* or blockwork, the pipes should be wraped with Rockwool FirePro Insulated Fire Sleeve* 15-160mm outer diameter).
WD130 2500x1050mm Automatic window openers for smoke ventilation (approx. 1.0m2 free area) An actuator to be retrofitted to a standard uPVC window. (Building Control to confirm suitability) * * * ** 900x1400 Emergency evacuation chair Two-way telecommunication system From dry riser outlet to the further point on the floor plan 44.5m
Exit Box Emergency
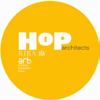
[Individual]5-7 STATION ROAD EXAMPLE OF INTERNAL SETTING OUT PLAN FOR EACH FLAT 43 Status: Building Regulations Issued to: Building Control Drawn by: KC Date: 09.04.21 Scale: 1:50 @ A3 Drg.No: HOPA-B-1052-D Job Title 123/SR/DL HOP Architects Ltd Southsea, Hampshire 07427 080 777 Company reg. 12021383 AmendmentsDate by Proposed Ground Floor Apartment 04 Issue to Acontractor KC 21/04/22 Bath Changed to BShower LMW 04/05/22 Lintel information added Dims changed to no decimal point. C KC26/05/22 SVP Dadded KC 06/06/22 1. 2. 3. 4. 5. 6. 7. 8. WD009 1200x1200mm WD010 1200x1200mm WD008 910x900mm ED010 Door2400x2100mm Window1200x2100(600x2100)x2 3575 215 3959 100 1852 2173 100 1699 100 586 878 862 193 1320 339 862 322 862 195861 100 685 100 685 100 Apartment No.4 226 1320 260 359 1320 273 303 938 2718 100 913 710 76 3575 215 2759 215 2936 162 786 1225 ID009 FD60S 838x1981 mm ID010 (Leaf) 686x1981mm ID013 Sliding Door (Leaf) 1220x1981mm ID011 FD20 (Leaf) 762x1981 mm ID012 (Leaf) 610x1981 mm ID014 FD20 (Leaf) 762x1981 mm ID015 FD20 Double Door (Leaf) 1220x1981mm ID016 Sliding Door (Leaf) 1220x1981mm ID017 FD20 (Leaf) 762x198 1mm SB100 Length 1350mm (Inner Leaf) DC200 Length 1200mm SB100HD Length 1200mm SB100HD Length 4050mm SB100HD Length 1200mm SB100 Length 1650mm SB100 Length 1650mm UB 203x102x23 (B87) (Outer Leaf) Internal Door Frame Thickness to be confirmed, therefore S/O for internal door is only indicative. AmendmentsDate by [Vectorwork]
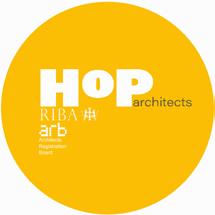
Proposed External Wall Build-Up Paint finish tbc by client 3-5mm skim coat 15mm Thistle Browning Plaster or 12.5mm Plasterboard on Dabs 100mm lightweight Blockwork 115mm EcoTherm Eco-Cavity Full Fill 10mm clear residual cavity 102.5mm brick To achieve a U-value: 0.15 W/m2·K Downpipe to be enclosed in Aluminium boxing to match the eave colour and material. (Please refer to the detail plan above)
First
3-5mm skim
Void below staircase could be used as storage for commercial unit below
and
To
board From
Proposed Internal Wall Build-Up Lightweight Blockwork 10-15mm plaster dabs 12.5mm Gyproc Plasterboard 3-5mm skim coat Paint finish tbc by client Detail AA01 Bedroom 9.5m2 Hall 6.9m Bathroom 3.6m Loft Section A-A 1:20 Hall Void Proposed First Floor Build-Up: Floor finish (tbc by client) 5mm Flooring underlay OR DRITA 25 matting, 70mm Fibre reinforced screed, Regupol 4515 acoustic layer, 150mm CBS Precast hollow core concrete plank, 100mm Mineral wool insulation within cavity, BG CasoLine MF suspended ceiling system (300mm cavity), 2x12.5mm Gyproc Plasterboard coat (paint finish tbc by client) (24kg/m3) Ground Floor Build-Up Fibre reinforced screed Vapour (500 Gauge Polythene Sheet) EcoTherm Eco-Versal 1200 gauge polythene DPM Beam Block Floor with 100mm deep dense block infill (A strip of 20mm thick insulation should placed vertically around the floor slab to prevent cold bridging. Structural engineer to size beams for floor) achieve a U-value: 0.13 W/m2·K Ground Floor SSL bottom of timber ridge Ground Floor SSL to Building Regulations Issued to: Client Drawn by: LMW Date: 02.10.20 Scale: 1:20 & 1:50 Drg.No: HOPA-B-1100-K Proposed Section A-A B-B Job Title 123/SR/DL HOP Architects Ltd Company 12021383 by Issued02.10.20 for client checking LMW Roof11.08.21 and floor changed KC floor spec KC25.11.21 10.12.21
150mm
to
From
Proposed Party Wall Build-Up 3-5mm Skim coat and paint finish, 12.5 Gyproc plasterboard, 15mm plaster dabs, 100mm Dense aggregate block, 75mm Clear cavity, 100mm Dense aggregate block, 15mm plaster dabs, 12.5mm Gyproc plasterboard, 3-5mm Skim coat and paint finish. (Party wall detail tbc by acoustician prior to construction)
Facing
updated
All
checked
Proposed Ceiling Building Up: Roof void 150mm stone mineral wool
[Individual]5-7 STATION ROAD EXAMPLE OF A SECTION [Vectorwork] 44
Drawing:
F1 F3 F5 F6
AmendmentsDate
Proposed Roof Build-Up Roof void Vapour control layer 50 x 250mm C24 timber Roof Trusses at max. 600mm centres 250mm Ecotherm Eco-Versal insulation fill fill within rafters Breather membrane 25mm Treated battens 18mm Marine plywood deck Single ply membrane (fully adhered) with standing seam profile To achieve a U-value: 0.14 W/m2·K Paving Car Park build-Up 80mm deep Aquaflow blocks installed to manufacturers spec 50mm thick 5mm nominal size clean stone SC 2000 Geotextile membrane to manufacturers details 300mm compacted sub-base 5-20mm aggregate (No fines) SC Intergrid to manufacturer details 200mm compacted sub-base 10-63mm aggragate (No fines) SC impermeable membrane to manufacturers details Sub-Grade Commercial Unit 60m ACO HexDrain Brickslot Channel with black plastic slotted grating Detail AA03
75mm
in between joists 200x50mm C24 Timber bottom chord, 2x 12.5mm Fireline Plasterboard 3-5mm skim coat Paint finish tbc by client Detail AA04 Detail AA05 Detail AA02 Pavement Level: 7.143* SSL: 7.293* Gradient of 1501:15 Landing level: 7.293* 3405 mm SSL to SSL 2851 mm (Subject to change) SSL to Ceiing Note: Proposed floor build-up above hollowcore plank to Vale Southern Construction Ltd's specification. Cowan Consultancy (Structural Engineer) drawings showing truss roof detail. Hop Architects to Liaise with with client and structural engineer about preferred roof system 3181 mm SSL to Top of steels / Bottom of Hollowcore planks 5672 (from Ground SSL) Top of timber wall plate 200x50mm C24 Timber joists 250x50mm250x50mmC24Rafters C24Rafters Position of joint in tie chord neededd with 200x300 nail plate each side of truss (min.20) 3.8mm ⌀ 30 nails in each side of each nail plate. 5885 (from Ground SSL) Bottom of bottom chord 300x50mm Timber ridge board (SE to confirm) 6564 (from Ground SSL) Top of timber wall plate 2480 mm SSL to bottom of bottom chord 200x50mm C24 Timber joist Concrete Padstone Timber plate fixed to purlin Rafters birdsmouthed over and fixed with truss clip Seeat cut on rafter and fixed to wall plate with truss clip 203 x 203 UC52 203 x 203 UC52 7388 9179 Proposed
Rainwater Enclosure Detail (Plan) 1:5 brickwork Aluminium Cladding 18mm Marine plywood (Provide gaps between boards to allow ventilation) 100x50mm Treated studs 100mm Rainwater downpipe 100mm dense blockwork below DPC level (min. 150mm concrete slab to form support for the blockworks) 363 295 118 350 Issue for construction KC 06.12.21 Floor SSL revised KC Dimension added KC25.01.22 level dimensions to be double on site KC15.07.22 structure updated KC03.08.22
Roof
top of padstone / bottom of steel 2537 2537 CL CL Status:
Control Layer

Proposed Roof Build-Up Roof void Vapour control layer 50 250mm C24 timber Roof Trusses at max. 600mm centres 250mm Ecotherm Eco-Versal insulation fill fill within rafters Breather membrane 25mm Treated battens 18mm Marine plywood deck Single ply membrane (fully adhered) with standing seam profile To achieve a U-value: 0.14 W/m2·K
Matching roofing membrane on 18mm marine plywood as soffit (around the whole projecting dormer) 3 no. 150x50mm C24 Timber joists 3 no. 150x50mm Timber studs
Continuous of roofing membrane at the valley 330.5 25mm Treated batten (Provide openings at each batten to allow horizontal ventilation) 600 3 no. 150x50mm C24 Timber joists Joist hangers 3 No. 150x50mm C24 Timber studs (*to be joist hung therefore notch will be required for fixing) Joist hanger 2 no. 150x50mm C24 Timber joists in between double rafters. (To be joist hung) 25+12.5mm Insulated plasterboard 3 no. 150x50mm C24 Timber joists in between double rafters (fixed with Truss clip to projecting 3.No 150x50mmm C24)
Matching roofing membrane on 18mm marine plywood (including all the inner faces)
Timber wallplate level Pitched roof 2 no. 250x50mm C24 Rafters 2 no. 150x50mm Timber studs (to be joist hung between 3No. 150x50mm project timber) Bottom chord 2 no. 200x50mm C24 M12 Bolt (through double rafters, double bottom chords and 3No. 150x50mm C24)
Section A-A(3) 1:20 Detail AA05 Detail AA06 Issue for
Proposed External Wall Build-Up Paint finish tbc by client 3-5mm skim coat 15mm Thistle Browning Plaster or 12.5mm Plasterboard on Dabs 100mm lightweight Blockwork 115mm EcoTherm Eco-Cavity Full Fill 10mm clear residual cavity 102.5mm brick To achieve a U-value: 0.15 W/m2·K
1No. M12 bolt (bolting the 3No. 150x50mm project timber with the 3.No 150x50mm vertical timber together) 1No. M12 bolt (bolting the 3No. 150x50mm project timber with the 3.No 150x50mm vertical timber together)
Bottom chords timber to be joist hung to 2no. 150x50mm C24 cross member Pitched roof rafters in between dormer to be seat cut and fixing over the 3no. 150x50mm cross member Lap joint and M12 bolt fixing 2 no. 150x50mm Timber studs (to be joist hung between 3No. 150x50mm project timber) Lap joint and M12 bolt fixing construction KC 06.12.21
Status: Building Regulations Issued to: Client Drawn by: LMW Date: 25.07.22 Scale: 1:20 1:10 Drg.No: HOPA-B-1105-B
Drawing: Proposed Section A-A (3) (Dormer detail) Job Title 123/SR/DL AmendmentsDate by F1 F3
Proposed First Floor Build-Up: Floor finish (tbc by client) 5mm Flooring underlay OR DRITA 25 matting, 70mm Fibre reinforced screed, Regupol 4515 acoustic layer, 150mm CBS Precast hollow core concrete plank, 100mm Mineral wool insulation within cavity, BG CasoLine MF suspended ceiling system (300mm cavity), 2x12.5mm Gyproc Plasterboard 3-5mm skim coat (paint finish tbc by client) Proposed Ceiling Building Up: Roof void 150mm stone mineral wool (24kg/m3) in between joists 200x50mm C24 Timber bottom chord, 2x 12.5mm Fireline Plasterboard 3-5mm skim coat Paint finish tbc by client SSL: 7.293* Gradient of 1501:15 Landing level: 7.293* 3405 mm SSL to SSL 2851 mm (Subject to change) SSL to Ceiing
updated [Individual]5-7 STATION ROAD SECTION DETAIL (DORMER WINDOW) [Vectorwork] 45
Cowan Consultancy (Structural Engineer) to confirm dormer structural design. 3181 SSL to Top of steels Bottom of Hollowcore planks 100x50mm C24 Timber joists 250x50mmC24Rafters 5885 (from Ground SSL) Bottom of bottom chord 203 x 203 UC52 2480 mm SSL to bottom of bottom chord 945 mm SSL to S/O 1510 mm Detail AA06 100x50mm C24 Timber joists Window height: 1510mm 25mm Treated timber packer 200x50mm C24 Timber Bottom Chord (to be joist hung to the bottom 2 No. 150x50mm C24 Timber cross member between the dormer 250x50mm C24 Timber Rafters with fully filled Ecotherm PIR insulation. 2no. M12 Bolt Matching roofing membrane on 18mm marine plywood (at a fall) Matching roofing membrane on 18mm marine plywood as soffit 100x50mm C24 Timber wallplate fixed with resin anchor M10 bolt @ 400mm c/c to the second brick from the sill. 22mm window board Matching roofing membrane on 18mm marine plywood as soffit Matching roofing membrane on 18mm marine plywood Waterpoof membrane
Commercial Unit 60m ACO HexDrain Brickslot Channel with black plastic slotted grating Detail AA05 Proposed Internal Wall Build-Up Lightweight Blockwork 10-15mm plaster dabs 12.5mm Gyproc Plasterboard 3-5mm skim coat Paint finish tbc by client Bedroom 9.5m Loft

Drawing: Proposed Detail AA03 Job Title 123/SR/DL AmendmentsDate a c b by Eave's10.11.21 material revised KC 18mm Marine plywood Vapour control layer 2 on. 12.5mm Fireline plasterboard 3-5mm Skim coat and paint finish
250mm Ecotherm Eco-Versal insulation fill fill within rafters Timber rafter to SE's specification (50 x 250mm C24 timber Rafters at 400mm centres) PVC standing seam Cavity closer 25mm Treated battens 125x50mm Timber post to be bolted to rafters (Full fill within Ecotherm Eco-Versal insulation in between timbers)
Single ply membrane (mechanically fixed)
100x50mm Treated timber joist to be bolted to Timber post 18mm Marine plywood 102.5mm Facing brickwork min. 100mm Aluminium Fasica Lining Treated timber fillet Code 4 lead flashing to form edge strip Aluminium Soffit Lining Treated timber firrings 295
Timber wallplate 100mm Medium dense blockwork 115mm Ecotherm Eco-cavity Full Fill with 10mm residual cavity 12.5mm Gyproc wallboard plasterboard 15mm dot and dab 3-5mm Skim coat and paint finish
[Individual]5-7 STATION ROAD SECTION DETAIL (EAVE GUTTER) [Vectorwork] 46
Breather membrane Box gutter formed in Code 4 lead Code 4 lead flashing to form edge strip Insect mesh (2mm maximum weave)
Status: Building Regulations Issued to: Client Drawn by: KC Date: 27.09.21 Scale: 1:5@A2 Drg.No: HOPA-B-1307-A
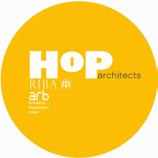
Note: Proposed floor build-up above hollowcore plank to Vale Southern Construction Ltd's specification.
Proposed External Wall Build-Up Paint finish tbc by client 3-5mm skim coat 15mm Thistle Browning Plaster or 12.5mm Plasterboard on Dabs 100mm lightweight Blockwork 115mm EcoTherm Eco-Cavity Full Fill 100mm Dense block (1.13 W/mK) 10mm Base Coat 10mm K-Rend SILICONE THIN COAT (TC) To achieve a U-value: 0.15 W/m2·K
2 no. 150x50mm C24 Timber joists in between dormer Juliet balcony railing (exact specification to be confirmed)
Single ply membrane on 18mm Marine plywood as fasica and soffit Waterproofing membrane around the gutter 2 no. M12 Bolt 220x50mmm C24 Timber stud 2 no. M12 Bolt 25mm Treated timber packer 3 no. 150x50mmm C24 Timber joists 100x50mm Simpson angle bracket at each side of the 220x50mm C24 timber stud 443x50mm C24 Timber wallplate (timber to be cut in sections if the required size is not available)
[Individual]5-7 STATION ROAD SECTION DETAIL (DORMER DOOR) [Vectorwork] 47
Closed Gutter channel Single ply membrane on 18mm Marine plywood Treatedd timber firrings Single ply membrane on 18mm Marine plywood Double timber rafters and 3 no. 150x50mm C24 timber joist to be bolted together 25mm Treated batten (Provide openings at each batten to allow horizontal ventilation)
443 Simpson angle bracket fixed to hollow core plank and timber wallplate 2 no. 150x50mm C24 Timber joist Closed Gutter channel Single ply membrane on 18mm Marine plywood Treated timber firrings Single ply membrane on 18mm Marine plywood 2 no. Timber rafter 250x50mm C24 100x50mm C24 Timber frame 220x50mm C24 Timber stud 3 no. Timber joist 250x50mm C24 2 no. M12 Bolt (Double timber rafters and 3 no. 150x50mm C24 timber joist to be bolted together) Create a notch at the 3 no. 150x50mm timber joist for the 220x50mm timber stud to be bolted together 2No. Simpson angle bracket at each side 100x50mm Timber rafters to be seat cut and fixed over the 2 no. 150x50mm timber joist 1500 Section 1:20 Detail DD1 1:10 Detail DD2 1:10
Proposed Roof Build-Up (Upper) Paint finish tbc by client 3-5mm skim coat 2x12.5mm Fireline plasterboard 50 x 150mm C24 timber Joists 44 x 220mm C24 timber Rafters at 400mm centres 18mm Plywood deck Self sealing Vapour Control Layer 180mm Ecotherm Eco-Torch insulation Single ply membrane (mechanically fixed) with standing seam profile To achieve a U-value: 0.13 W/m2·K
Proposed Roof Build-Up (Lower) Paint finish tbc by client 3-5mm skim coat 12.5mm Gypsum plasterboard 25mm Service battens Vapour control layer 50 x 250mm C24 timber Rafters at 400mm centres 250mm Ecotherm Eco-Versal insulation fill fill within rafters Breather membrane 25mm Treated battens 18mm Marine plywood deck Single ply membrane (fully adhered) with standing seam profile To achieve a U-value: 0.14 W/m2·K Laid to falls Detail DD04 Proposed First Floor Build-Up: Floor finish (tbc by client) 5mm Flooring underlay OR DRITA 25 matting, 70mm Fibre reinforced screed, Regupol 4515 acoustic layer, 150mm CBS Precast hollow core concrete plank, BG CasoLine MF suspended ceiling system (300mm cavity), 2x12.5mm Gyproc Plasterboard 3-5mm skim coat (paint finish tbc by client)
Status: Building Regulations Issued to: Client Drawn by: LMW Date: 02.10.20 Scale: 1:20 1:5 Drg.No: HOPA-B-1106 Drawing: Proposed Section D-D (2) Job Title 123/SR/DL HOP Architects Ltd by
D-D(2)

RIW sheetseal 226x300mm wide Double drain (Drainage board which protects the membrane during backfilling operations and also promotes drainage of water away from the structure) Blockwork should be sound with joints flush pointed or 'bagged out' with Cementfill or similar before the membrane is applied. Open textured surfaces should be sealed with Cementfill FC or a sand/cement slurry to provide a suitable surface.
TOC: 6.093 (As Built Level) 140mm 7.3N Dense aggregate blockwork (TBC by Engineer) 140mm 7.3N Dense aggregate blockwork (TBC by Engineer) 215mm (Laid Flat) 7.3N Dense aggregate blockwork RIW Sheetseal 226 or Flexiseal Pro (one coat) 1. 2. 3. 4. 5. As built concrete foundation 450mm deep Beam and block floor system 215mm (Laid Flat) 7.3N Dense aggregate blockwork Damp proof membrane (1200 gauge) Vapour control layer (600 gauge) 100mm Blockwork, Flexiseal Pro Primer, Flexiseal Pro (two coats). RIW sheetseal 226x300mm wide 1100 Fibre reinforced screed Concrete slab (GEN1)
surfaces should be sealed with Cementfill FC or a sand/cement slurry to provide a suitable surface. TOC: 6.093 (As Built 100Level) 450 100mm 7.3N Dense aggregate blockwork 215mm (Laid Flat) 7.3N Dense aggregate blockwork RIW Sheetseal 226 or Flexiseal Pro (one coat) Status: Building Regulations Issued to: Client Drawn by: KC Date: 02.10.20 Scale: 1:10 @A1 Drg.No: HOPA-B-1113-C Drawing: Proposed Section Lift pit Job Title 123/SR/DL HOP Architects Ltd Southsea, Hampshire Company reg. AmendmentsDate by 9. 10. 11. 12. 13. 14. 15. 16. 17. 1. 2. 3. 4. 5. 6. 7. 8. 8. 1650 1800 1930 2115 Proposed Section 1:10 B-B Proposed Section 1:10 A-A Proposed Lift Floor Plan 1:10 External Tanking Detail by RIW Reference Diagram RIW Flexiseal Pro Tanking System. Please follow the manufacturer's installation instruction. [Individual]5-7 STATION ROAD LIFT PITCH SECTION (TANKING) [Vectorwork]
Double drain (Drainage board which protects the membrane during backfilling operations and also promotes drainage of water away from the structure) SSL: 7.293* TOC: 6.463* 450 200 155 75 150 As built dimension 1800 Blockwork should be sound with joints flush pointed or 'bagged out' with Cementfill or similar before the membrane is applied. Open textured
As Built Concrete Foundation Beam and block floor system Damp proof membrane (1200 gauge) Vapour control layer (600 gauge) 1100 Fibre reinforced screed Concrete slab (GEN1)
SSL: 7.293* 100 As Built Dimension 1650 450 215mm (Laid Flat) 7.3N Dense aggregate blockwork 100mm Blockwork, RIW Flexiseal Pro Primer, RIW Flexiseal Pro (two coats).
48 1. 2. 3. 4.

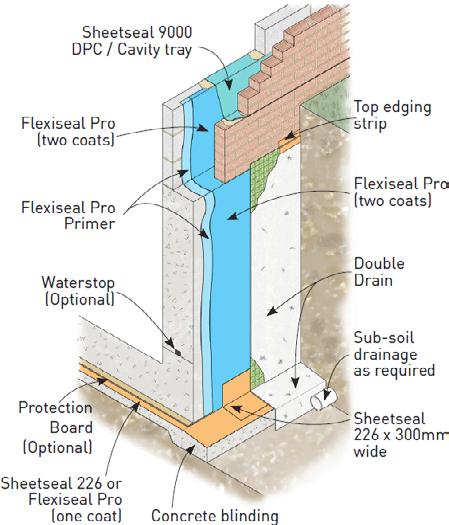
100mm Dense concrete blockwork Proposed Section FF (Boundary Trench Treatment) (Cutting Through Timber Panel) @1:5 A1 Detail revised to RIW's detail KC 25/04/22
Weepholes
New concrete footing for timber post SSL 75 150 150
49 Status: Building Regulations Issued to: Client Drawn by: KC Date: 27.09.21 Scale: 1:5@A1 Drg.No: HOPA-B-1348-A
Proposed External Ground Level For 5-7 Station Road External Ground Level For The Adjacent Site (Car Park & Public Toilet ) (Level TBC on site) 100mm Land Drain (discharges to car park area, Engineer to confirm suitability)
RIW Sheetseal 9000 min. 150mm Approx.250 mm TBC on site Approx.325.7mm TBC on site Approx.350 TBC on site 7.143* 7.293* RIW DPM Blue across main floor area (finishes over a required) min. 150mm RIW sheetseal 9000 DPC wrapped around end of floor units RIW Seal Tape RIW Protection Board (used with RIW LAC) RIW LAC Pea Shingle Gravel
100mm Dense concrete blockwork 100 125 100 SSL 75 150 150
Drawing: Proposed Section FF (Boundary Trench Treatment) Job Title 123/SR/DL HOP Architects Ltd Southsea, Hampshire 07427 080 777 Company reg. 12021383 AmendmentsDate by
New timber panel Proposed External Ground Level For 5-7 Station Road External Ground Level For The Adjacent Site (Car Park & Public Toilet ) (Level TBC on site) Pea Shingle / Gravel Approx.325.7mm TBC on site min. 150mm Approx.350 TBC on site 7.293* 7.143* RIW sheetseal 226 (Top edge must be adequately supported) RIW Sheetseal 9000 RIW DPM Blue across main floor area (finishes over a required) RIW sheetseal 9000 DPC wrapped around end of floor units RIW Seal Tape RIW Protection Board (used with RIW LAC) RIW LAC 100mm Land Drain (discharges to car park area, Engineer to confirm suitability)
[Individual]5-7 STATION ROAD BOUNDARY TREATMENT SECTION (TANKING) [Vectorwork]
Proposed Section FF (Boundary Trench Treatment) (Cutting Through Timber Post) @1:5 A1 100 125 100 RIW sheetseal 226 (Top edge must be adequately supported)

Hollowcore planks to be cut to allow for 152X152X37 to be fixed into top flange of 203X203X46 with 4No. M16 bolts UC 203X203X46 fixed between 2No. 152X152X37 steel posts
10mm Profiled curved ledger welded to the underside (All hot zinc sprayed with sealer topcoat) (Width to be confirmed)
10mm bottom plate with 4No. M16 bolts resin anchored into existing foundations (as confirmed by engineer)
UC 254x254x132 (All hot zinc sprayed with sealer topcoat bolted to the columns at each end) (Curved)
With 10mm base plate top and bottom with 4no. M16 anchors per post)
10mm Profiled curved ledger welded to the underside (All hot zinc sprayed with sealer topcoat) (Width to be confirmed)
UC 254x254x132 (Curved) (All hot zinc sprayed with sealer topcoat bolted to the columns at each end) 3734.9 74 150 2681 74 150 2681
UC 152x152x37
UC 203X203X46 fixed between 2No. 152X152X37 steel posts UC 203X203X46 fixed between 2No. 152X152X37 steel posts
UC 152x152x37 With 10mm base plate top and bottom with 4no. M16 anchors per post)
UC 254x254x132 (Curved) (All hot zinc sprayed with sealer topcoat bolted to the columns at each end)
TOC: 6.463* Ground Floor SSL: 7.293* 2905 2905 Status: Building Regulations Issued to: Contractor Drawn by: KC Date: 02.10.20 Scale: 1:20 Drg.No: HOPA-B-1352 (B) Drawing: Proposed Curved Steel Section Job Title 123/SR/DL HOP Architects Ltd Hampshire 07427 080 777 AmendmentsDate by Design plate plate added, TOC Foundation level revised UC 254x254x132 Dimension: Arc Length approx. 4852mm *outside face & Radius approx. 3002mm *outside face (All hot zinc sprayed with sealer topcoat bolted to the columns at each end) (Curved) UC 203X203X46 Dimension: approx. (L) 4265mm *depending on connection detail. (Straight, Primed, resin anchored to the underside of the planks with M10 resin anchors at 500mm c/c into the planks above.)
10mm Profiled curved ledger welded to the underside (All hot zinc sprayed with sealer topcoat) (Width to be confirmed)
[Individual]5-7 STATION ROAD CURVED STEEL SECTION [Vectorwork]
25mm Farrat Acoustic Plate (Specification to be confirmed by Farrat) 25 10 1010 10 695 10mm Farrat TBK Structural Thermal Break (To be confirmed)
Ground, First & Second Floor Plan @1:25 Apartment 1 , 6 & 14 Curved Steel Section @1:25 Section 50
Hollowcore planks to be cut to allow for 152X152X37 to be fixed into top flange of 203X203X46 with 4No. M16 bolts
UC 152x152x37 With 10mm base plate top and bottom with 4no. M16 anchors per post) 203.2 10 4115.7 10 10203.2 2644.3 10 10203.2 2517.8 10 25 10 25mm Farrat Acoustic Plate (Specification to be confirmed by Farrat)
UC 152x152x37 (Primed Resin anchored at base with 4no. M12 anchors per post) UC 152x152x37 (Primed , Resin anchored at base with 4no. M12 anchors per post)

1x Milano Barq Shower Enclosure with Hinged Return Panel. (W 300mm x L 1400mm)
Genesis 15mm white aluminium straight edge tile tirm around edges 1400 Wall tile starting point. 175 2884 430 Status: Building Reg Issued to: Client Drawn by: KC Date: 21.07.22 Scale: 1:25@A2 Drg.No: HOPA-B-1400 Bathroom Layout Type 1A Job Title 123/SR/DL HOP Architects Ltd Southsea, Hampshire Company 12021383 AmendmentsDate by Internal wall build-up (top): 215mm blockwork, 13mm Thistle universal one coat plaster, 2mm Thistle multi-finish skim coat, Moisture resistance paint finish.
1x Milano Amara Modern Mono Basin Mixer Tap (brushed copper)
Internal wall build-up (top): 100mm blockwork, 13mm Thistle universal one coat plaster, 2mm Thistle multi-finish skim coat, Moisture resistance paint finish. Top of cistern boxing: Timber studs, 18mm OSB3 board, RIW Tilesure waterproofing & decoupling membrane, 6mm tile adhesive, 9mm Calacatta wall tile. Genesis 15mm white aluminium straight edge tile trim around the edges Geberit duofix WC frame with Sigma concealed cistern. (W500mm x D80mm x H1140mm) 1252 2061 175 200 1140 Orchard contemporary back to wall toilet with soft close seat. Milano artle dual fuel anthracite straight heated towel rail. (W600mm x H1200mm)
1733 CL Milano aston light grey traditional vanity unit with basin. Geberit sigma 01 matt chrome dual flush plate. (246x164mm) 460 200 Wall Tile: Calacatta White Matt 600x300x9mm Wall Tile grout thickness: 3mm (colour to be confirmed) Wall Tile Layout: 50% offset. (Full height tiling to shower area and half height tiling to other walls)
1x Milano Aston Light Grey Traditional Vanity Unit with Basin. (W 615mmx D 400mm x H 840mm)
1650 Wall tile starting point 8 75 Milano amara thermostatic shower with shower head and hand shower (brushed copper)
1x Demister Mirror (700x500mm)
51 [Individual]5-7 STATION ROAD BATHROOM LAYOUT [Vectorwork]
1x Orchard Contemporary back to wall toilet with soft close seat. (W 355mm x D 560mm x H 385mm)
1x Milano Artle dual fuel Anthracite Straight heated towel rail. W600 x H1200mm A DCB Elevation A@1:25 Elevation C@1:25 Floor Plan@1:25 Elevation D@1:25 Elevation B@1:25 TYPE 1A Apartment no. 1 & 6
Internal wall build-up (bottom/wet room): 100mm blockwork, 175x50mm timber studs @ 400mm c/c, 12.5mm moisture resistance gypsum plasterboard, RIW FWM (flexible wall membrane) with FWM primer, 6mm tile adhesive, 9mm Calacatta white matt wall tile. CL 600 3488 1212 4 full wall tiles Wall tile starting point Milano aston light grey traditional vanity unit with basin. Milano amara modern mono basin mixer tap (brushed copper) Demister mirror (700x500mm)
Genesis 15mm white aluminium straight edge tile tirm around edges Internal wall build-up (bottom): 215mm blockwork, 13mm Thistle universal one coat plaster, 2mm thistle mutli-finish skim coat, RIW FWM flexible wall membrane) with FWM primer, 6mm tile adhesive, 9mm Calacatta white matt wall tile.
1100 (from FFL) Themostatic 2100valve (from FFL) Shower head 75 8 374 CL From FFL to centre of tapping Milano barq shower enclosure with hinged return panel. 1000 (from SSL) Wall tile starting point. 394 CL Internal wall build-up: 100mm blockwork, 8mm sand/cement render with scratch finish, 75x50mm timber stud at 400mm c/c, 12.5mm moisture resistance gypsum plasterboard, RIW FWM flexible wall membrane) with FWM primer, 6mm tile adhesive, 9mm Calacatta white matt wall tile. Wall tile starting point. 816 CL 200 CL Sanitaryware Schedule
Internal wall build-up (bottom/wet room): 215mm blockwork, 13mm Thistle universal one coat plaster, 2mm thistle mutli-finish skim coat, RIW FWM ( flexible wall membrane) with FWM primer, 6mm tile adhesive, 9mm Calacatta white matt wall tile. 1212 4 full wall tiles 1809 3 full wall tiles
Genesis 15mm white aluminium straight edge tile trim around the edges Wall Tile: Calacatta White Matt 600x300x9mm Wall Tile grout thickness: 3mm (colour to be confirmed) Wall Tile Layout: 50% offset. (Full height tiling to shower area and half height tiling to other walls) Internal wall build-up (top): 215mm blockwork, 13mm Thistle universal one coat plaster, 2mm Thistle multi-finish skim coat, Moisture resistance paint finish.
1x Milano Amara Thermostatic Shower with Shower Head and Hand Shower (brushed copper)
1x Geberit Sigma 01 matt chrome dual flush plate. (246x164mm) 1x Impey slim + shower tray waste
1x Geberit DuoFix WC Frame with Sigma Concealed Cistern. Product no. 111.799.00.1 (W 500mm x D 80mm x H 1140mm)
460 458 CL CL 374 358 75 632 100 175 2061 1252 215 CL 708 100 2251 430 CL 786 125 393 CL Floor tile starting point 75 739 8 Floor Tile: B&W XL black semi polished rectified 600x600x9mm Floor Tile grout thickness: 5mm (colour to be confirmed) Floor Tile Layout: 50% offset. Floor Tile: B&W XL black semi polished rectified 600x600x9mm Floor Tile grout thickness: 5mm (colour to be confirmed) Floor Tile Layout: 50% offset. Floor tiles slope to drain
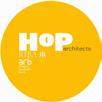
Fibre reinforced screed Status: Building Reg Issued to: Contractor Drawn by: KC Date: 21.07.22 Scale: 1:10 / 5 @A3 Drg.No: HOPA-B-1421 Typical Wetroom Shower Waste Section & Detail 2 Job Title 123/SR/DL HOP Architects Ltd Southsea, Hampshire 07427 080 777 Company reg. 12021383 AmendmentsDate a c b by Typical Wetroom Shower Waste Section@1:10
Gradient: 12mm fall per meter
Thermostatic valve 1200 SVP CL
Internal Floor build-up (Wet Room): 9mm B&W star XL black semi polished rectified floor tile, 10mm tile adhesive, 2mm RIW tilesure waterproofing and decoupling membrane, 70mm Fibre reinforced 1100screed. (From FFL)
100 150 1079 CL Floor Tile: B&W XL black semi polished rectified 600x600x9mm Floor Tile grout thickness: 5mm (colour to be confirmed) Floor Tile Layout: 50% offset.
Floor tile starts to slope at this point
Gradient: 12mm fall per meter 40mm shower waste pipe CCL Wetrooms Hi-Build Latex (TBC)
100 150 CL 40mm shower waste pipe Studs will vary Timber studs to centre of shower waste RIW reinforcing tape around the edges RIW FWM (Flexible Wall Membrane) 12.5mm Moisture resistance plasterboard 6mm Wall tile adhesive 9mm Calacatta white matt wall tile
Wetrooms Design shower waste H+M Snake 50mm CCL wetrooms Hi-Build Latex Screed (TBC)
Wetrooms sDesign linear drain Wiper 500mm Premium Pure 83 9mm B&W star XL black semi polished rectified floor tile 10mm tile adhesive RIW Tilesafe membrane CCL wetrooms MWF tapered board (TBC)
[Individual]5-7 STATION ROAD LEVEL THRESHOLD SHOWER WASTE DETAIL [Vectorwork]
Reference image (Wetrooms sDesign linear drain Wiper 500mm Premium Pure)
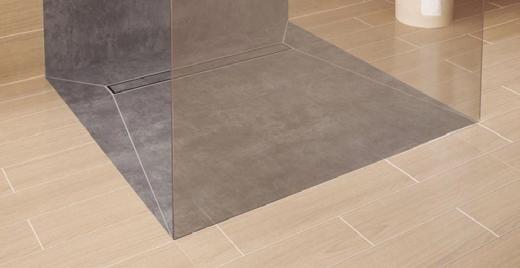
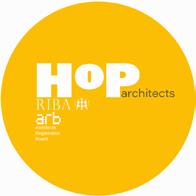
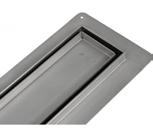
Minimmum frame overlap to be 30mm 15mm dot and dab with continous ribbon of adhesive around all openings, along the top and bottom of the wall, and at internal and external corners. 12.5mm Gyproc plasterboard with 5mm skim coat and paint finish 102.5mm Facing Brick Kommerling C70 Gold Window Frame Profile Apply flexible sealant to all interfaces between the brickwork and the window frame 65.5 70 192 102.5 125 100 Weep hole
[Individual]5-7 STATION ROAD TYPICAL WINDOW HEADER DETAIL [Vectorwork]
NOT FOR CONSTRUCTION Status: Building Regulations Issued to: Client Drawn by: KC Date: 27.09.21 Scale: 1:5@A2 Drg.No: HOPA-B-1310
Drawing: Proposed Detail EE01 Job Title 123/SR/DL HOP Architects Ltd Southsea, Hampshire 07427 080 777 Company reg. 12021383 AmendmentsDate a c b by
Apply flexible sealant to all interfaces between the plasterboard and the window frame
Proposed Typical Window Head Detail J-17 @1:2 A2 33
Fully insulated lintel without a base plate 100mm Inner leaf blockwork
Status: Building Regulations Issued to: Client Drawn by: KC Date: 27.09.21 Scale: 1:5@A2 Drg.No: HOPA-B-1310 Drawing: Proposed Detail EE01 Job Title 123/SR/DL HOP Architects Ltd Southsea, Hampshire 07427 080 777 Company reg. 12021383 AmendmentsDate a c b by Proposed Typical Bi-Folding Door Cill Detail J-20 @1:2 A2 31 100mm Outer leaf blockwork Minimmum frame overlap to be 30mm SMART VISO 1000 Bi-Folding Door Frame 101.2 125.3 102.5 150 195.5 70 62.3 Install a proprietary cavity closer having a path of minimum thermal resistancec path through the closer of not less than 0.45W/m2k Apply flexible sealant to all interfaces between the brickwork and the window frame Flexible sealant should be applied to the junction between the cavity closer and door frame Floor finish DPM Beam and Block Floor system Ensure wall insulation is installed at least 150mm below the top of floor insulation Channel drain [Individual]5-7 STATION ROAD TYPICAL SLIDING DOOR THRESHOLD DETAIL [Vectorwork]
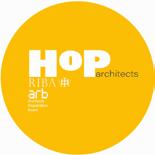
Half landing level (w/o floor finish) Floor SSL (w/o floor finish) 1537.9 Pre-cast concrete staircase Pitch: 34° Staircase structural support TBC by staircase manufacturer Staircase structural support TBC by staircase manufacturer 1000 1537.9 2280.1
BE
1st
Half landing level (w/o floor finish) Staircase structural support TBC by staircase manufacturer 2nd Floor SSL (w/o floor finish) Floor to Floor (SSL) 2905 Floor to Floor (SSL)
8. 1. 2. 3. 4. 5. 6. 7. 9. 10. 11. 12. 13. 17. 14. 15. 16. 8. 18. 19. 20. 21. 22. 23. 24. 25. 26. 27. 31. 28. 29. 30. 25. 24. 32. Ceiling Level Top of screed Top of Beam and Block Floor 1196.2 170.9 225 1367.1
Floor23.12.21 to Floor Dims
lift dims KC
revision LMW
2905
17.16.15.14.13.12.11.10.9. 1. 2. 3. 4. 5. 6. 7. 8. 8. 1650 1140 3930 Blockwork to Blockwork 1164.4 shortest point 2000 Ground Floor First Floor 2436.6 2186.6 365 1140 Dry Riser Outlet 1218.7 longest dim 1750 1000 1930 1000 215 1800 100 140 1650 140 1. 2. 3. 170.9 Riser 250 Going 25 Nosing TBC by staircase manufacturer Proposed Ground Floor Plan 1:20 Proposed Section 1:20 Proposed Detail Section 1:5 Proposed First Floor Plan 1:20 17.16.15.14.30.29.28.27.26. 18. 19 20. 21. 22. 23. 24. 25. 25. 1650 1140 3930 Blockwork to Blockwork 1164.4 shortest point 2000 Second Floor 2436.6 2186.6 365 1140 Dry Riser Outlet 1218.7 longest dim 1750 1000 1930 1000 First Floor 215 1800 100 140 1650 140 ALL PRECAST STAIRCASE JUNCTION
Drawing:
Stainless steel handrail (316 grade) 42.4mm tubular rails Straight end Supported by concealed stainless steel wall brackets 1367.1 966 116 Timber stud wall: Staircase void, 150mm mineral wool insulation filled within and over the studs, 100x50mm Timber frame, 2 layers of soundbloc 12.5mm Gyproc soundblc plasterboard, 5mm Skim coat and paint finish. Ceiling lining: Precast Concrete plank for staircase landing, 50mm void, 150mm Mineral wool insulation filled within void and timber joists, 100x50mm Timber joists, 2 layers of soundbloc 12.5mm Gyproc soundblc plasterboard, 5mm Skim coat and paint finish. DETAILS TO DESIGNED BY STAIRCASE SUPPLIER AND CONFIRM BY STRUCUTRAL ENGINEER. updated LMW Status: Building Regulations Issued to: Client Drawn by: KC Scale: 1:20 & 1:5 @A0 Drg.No: HOPA-B-1112-D Proposed Section Staircase 3 Job Title 123/SR/DL Revised16.03.22 General08.02.22 Lining
[Individual]5-7 STATION ROAD STAIRCASE 03 DRAWING [Vectorwork]
SINAH LANE HAYLING ISLAND, HAMPSHIRE CLIENT : PRIVATE CLIENT APPOINTMENT : 2020 WORK STAGE: CONCEPT DESIGN TO BUILDING REGULATION Project brief : Construction of a single storey rear extension and one new pitched roof dormer at the front elevation. [Individual] [Sketchup + Blender rendering + Photoshop]

W003 Aluminium Framed Double Glazed Unit 400 1263mm S/O W004 Aluminium Framed Double Glazed Unit 400 1263mm S/O W005 Aluminium Framed Double Glazed Unit 1000 1357mm S/O W006 Aluminium Framed Double Glazed Unit 1050x 1357mm S/O W007 Aluminium Framed Double Glazed Unit 1050 x 1357mm S/O W008 Aluminium Framed Double Glazed Unit 1050 1357mm S/O W009 Aluminium Framed Double Glazed Unit 1000 x 1357mm S/OW010 Aluminium Framed Double Glazed Unit 2024 1357mm S/O W011 Double Glazed Unit 1000 1000mm S/O W012 Aluminium Framed Double Glazed Unit W013 Double Glazed Unit 400 x 1500mm S/O W014 Aluminium Framed Double Glazed Unit 1200 1200mm S/O W015 Aluminium Framed Double Glazed Unit 1810x 1200mm S/O D002 Aluminium External Bi-flod Door Steel Beam 3043 2100mm D003 Aluminium External Bi-Fold Door Steel Beam 3043 2100mm
P3
To soakaway system (Stormwater) 5m away from any building. Existing manhole to be blocked (Assume no connection to neighbour's building) Invert level: 457mm below ground level Gully SVP SVP RWP RWP B21 (T1) Steel Beam B22 (T6) Steel Beam 203x133UB30 SVP 786 D001 Internal Door S/O 1500 x 2100mm D002 Internal Door D003 Internal Door S/O 1500 2100mm
B16 Catnic CG90/100 Steel Lintel To SE's specification B17 Catnic CG90/100 Steel Lintel To SE's specification B19 Catnic CG90/100 Steel Lintel To SE's specification P2 90x90x0.5 SHS 1500 826 827 2869 1200834 2020 B18 Box Lintel To SE's 862specification 1200 6085 460 6858 1000 826 Render on existing brickwork Render on existing brickwork 786 1800 Trench foundation to SE's design and specification B20 Catnic CNX90/100 Box Lintel To SE's specification
Internal Wall 5mm plaster and paint finish, 12.5mm Gyproc Plasterboard, 15mm dot and dab, 100mm medium dense blockwork, 15mm dot and dab, 12.5mm Gyproc Plasterboard 5mm plaster and paint finish. (Change to moisture resistant plasterboard to wet areas)
Proposed Plans Main House Job Title 075/DSSL AmendmentsDate by
D004 Internal Door S/O 826 x 2100mm D005 Internal Door S/O 856 2100mm D006 S/O 786 2100mm D007 Internal Door S/O 786 Internal2100mm Door S/O 786 2100mm D009 Internal Door S/O 786 x 2100mm D010 Internal Door S/O 834 2100mm D011 Internal Door S/O 1200 2100mm D012 S/O 1800 2100mm Internal Door S/O 862 2100mm B23 (T7) Steel Beam 203x133UB30 B24 (T3) Steel Beam B25 (T4) Steel Beam 203x203UC86 B26 (T6) Steel 203x133UB30 90x90x0.5 90x90x0.5 SHS P5 90x90x0.5 SHS P6 90x90x0.5 SHS P7 90x90x0.5 SHS P8 90x90x0.5 SHS 90x90x0.5 SHS P10 90x90x0.5 SHS Padstone P11 90x90x0.5 SHS SE to revise the steelwork at the (TBC)
External Wall (Render) Render system, 100mm Outer blockwork, 50mm Cavity, 50mm Ecotherm Eco-Cavity insulation 100mm Medium dense blockwork, 15mm Dot and dab, 12.5mm Gypsum wallboard plasterboard, 5mm plaster and paint finish. U-value = 0.27W/m2k B2 Catnic CG90/100 Steel Lintel To SE's specification 1700 B5 Catnic CNX90/100 Box Lintel To SE's specification B4 To SE's specification B7 Box Lintel To SE's specification B6 Catnic CNX90/100 Box Lintel To SE's specification B8 Catnic CNX90/100 To SE's specification B9 Catnic CNX90/100 Box Lintel To SE's specification B10 Catnic CG90/100 Steel Lintel specification B11 Steel Beam To SE's specification
P9
All existing internal wall to be re plaster and re paint
SHS P4
D003 Aluminium External Door Steel Lintel D004 Aluminium External Door Steel Lintel 2035 2100mmW016 Aluminium Framed Double Glazed Unit 417x 1200mm S/O W017 Aluminium Framed Double Glazed Unit 417x 1200mm S/O External Wall (Facing Brick) 102.5mm Facing Brick, 50mm Cavity, 50mm Ecotherm Eco-Cavity insulation 100mm Medium dense blockwork, 15mm Dot and dab, 12.5mm Gypsum wallboard plasterboard, 5mm plaster and paint finish. U-value 0.27W/m2k B9 To SE's specification
Status: Building Reg Issued to: HBC Drawn by: KC Date: 08.02.21 Scale: 1:100 @ A1 Drg.No: HOPA-004-BC
Carbon Monoxide Detector Combined Heat and Smoke Detector (Mains Fed w/battery back-up) 13 A Double socket Double dimmer switch to internal lights Receased LED light fixture Below Ground Surface Water Drainage Below Ground Soil Waste Drainage Pendant light fixture KEY 63mm Rain Water Pipe 100mm Soil Vent Pipe Exterior Motion Sensitive Light Lighting Circuitry D001 Aluminium External Door Steel Lintel 900 2100mm W002 Aluminium Framed Double Glazed Unit 2025 1315mm S/O W001 Aluminium Framed Double Glazed Unit 1533 1315mm S/O
P1 90x90x0.5 SHS B1 Steel Beam To SE's specification 2941 1500 Catnic CNX90/100 Box Lintel To SE's specification
Proposed manole (foul) Existing manole (foul) Existing manole (foul) Existing Garage Existing manole (foul) Invert level: 379mm below ground level Proposed manole (foul) Invert level: 758mm below ground level
Proposed Ground Floor Plan @ 1:50 Proposed First Floor Plan @ 1:50 Section SectionA B SINAH LANE PROPOSED GROUND AND FIRST FLOOR PLAN [Individual] [Sketchup + Blender rendering + Photoshop] [vectorwork]
B17 Steel Beam To SE's specification B12 Catnic CG90/100 Steel Lintel specification B13 Catnic CG90/100 Steel Lintel specification B14 Catnic CG90/100 Steel Lintel To SE's specification B15 Catnic CG90/100 Steel Lintel To SE's specification
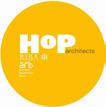
Existing first floor FFL Dwarf Wall: Roof space (Vented), 120mm EcoTherm Eco-Versal between and timber studs, 100x50mm Timber stud, 25mm Service batten, 37.5mm Insulated plasterboard, 5mm plaster and paint finish. U-value 0.19W/m2k Pitched Roof upgrade: Existing Roof tiles, Existing Treated batten, (Replace if required) Existing waterproofing membrane, 50mm ventilation space, Upgrade Timber rafter to 150x50mm Timber rafter (SE to confirm), New 100mm EcoTherm Eco-Versal partially filled between rafters, Vapour control layer, 62.5mm Insulated plasterboard, 5mm plaster and paint finish. U-value 0.17W/m2k Roof Space (vented) Dormer Pitched Roof: Matching Roof tiles, 25mm Treated batten, Breather membrane, 150x50mm Timber rafter (SE to confirm), 120mm EcoTherm Eco-Versal partially filled between rafters, Vapour control layer, 25mm Service batten, 37.5mm Insulated plasterboard, 5mm plaster and paint finish. U-value 0.18W/m2k Existing External Wall All exposed brickwork render to be dot and dabbed with plasterboard 50 2254 50 Existing Roof Existing soffit ventilation Provide ventilation at soffit Code Lead flashing (min. 150mm above)
Provide ventilation at ridge Existing Trench foundation New Trench foundation to SE's Existingdetails Trench foundation 25mm perimeter strip insulation 2345 Existing ceiling level (Highest point)
Minimum of 150mm ventilated void below beam and block floor
Proposed Section A @ 1:20
Existing ground floor New Ground Floor: Floor finishes to client's choice, 50mm Liquid Screed, Vapour control layer 110mm Ecotherm Eco-Versal insulation, Damp proof membrane. Beam & block with 100mm deep dense block infill Min 150mm ventilated void below beam & block U-value 0.15W/m2k CLIENT TO CONFIRM IF FLOOR WILL HAVE UNDERFLOOR HEATING & IF QUICK DRYING SCREED IS REQUIRED
SINAH LANE PROPOSED SECTION
Rend Silicone FT K1 White Colour (To be confirmed) 16mm 1 coat (2 passes) Outer leaf medium dense blockwork 50mm Cavity 50mm Ecotherm Eco-cavity insulation 68mm Rainwater downpipe Rainwater hopper 12.5mm Gyproc plasterboard dot and dabbed on blockwall Rainwater chute formed with 18mm marine plywood and dressed in code 4 leadowrk Aluminimum parapet capping 25mm Treated batten (vented)
To provide min. of 25mm ventilation at parapet (Use Glidevale FV250 Fascia Ventilator or similar) Ventilation between proposed flat roof and existing pitched roof
5mm plaster and paint finish Timber joist to SE's design and specification (50mm ventilation space) 18mm Plywood OSB 150mm Ecotherm Eco-Torch insulation Single ply membrane Vapour control layer Treated timber wedge Inner leaf medium dense blockwork Rainwater down pipe fixing bracket 25mm Treated batten (vented) 25+12.5mm Insulated plasterboard with 5mm skim coat 50x50mm treated batten (To provide ventilation between joists) Glidevale FV250 Fascia Ventilator similar (To provide min. of 25mm ventilation) Roof tiles to match existing 25mm Treated vertical batten for ventilation 18mm Marine plywood Timber rafter to SE's design and specification 37.5mm Insulated plasterboard 25mm Ventilation mesh Timber beam size (to be confirmed by SE) Timber beam lintel over the window (to be confirmed by SE) 25mm Treated batten 25mm Treated counter batten 25mm vertical service batten Vapour control layer 120mm Ecotherm Eco-Versal insulation between timber studs Timber studs to SE's design and specification 18mm Marine plywood Breather membrane 25mm Treated vertical batten 9mm Marine plywood White uPVC fascia board White uPVC soffit board with vent Ladder frame Code Standing Seam lead sheet Section Detail (Parapet) @ Section1:5 Detail ( Front Dormer Pitched Roof Junction) @ 1:5 AND JUNCTION
DETAILS [vectorwork][Individual]
Status: Building Reg Issued to: HBC Drawn by: KC Date: 08.02.21 Scale: 1:100 @ A1 Drg.No: HOPA-005-BC-C Proposed Section Main House Job Title 075/DSSL HOP Architects Ltd Company reg.
AmendmentsDate by KC updated Ground Floor and flat roof revised KC 30.07.21
Retained existing ridge board Dormer Wall Horizontal composite cladding, 25mm Treated vertical batten, Breather membrane, 18mm Marine plywood, 100mm EcoTherm Eco-Versal fullfill between timber studs, 100x50mm Existing timber stud, 25mm Service batten, 37.5mm Insulated plasterboard, 5mm plaster and paint finish. U-value 0.18W/m2k Existing dwarf wall New timber stud wall sit direct below the ridge board for additional support Code Lead flashing (min. 150mm above) Provision for tile vent for ventilation into the main roof. (Subject to Building Control approval) 300mm Rockwool roll insulation Roof void (vented) Fasica board
Existing External Wall Flat Roof (cold vented): Single ply membrane, 18mm Marine plywood, Treated timber firrings, 50x50mm Treated batten, 220 50mm Timber joist (SE to confirm), 150mm Ecotherm Eco-Versal insulation between joists, Vapour control layer, 25+12.5mm Insulated plaserboard, 5mm plaster and paint finish. U-value = 0.16W/m2k External Wall (Render) Render system, 100mm Medium dense blockwork, 50mm Cavity, 50mm Ecotherm Eco-Cavity insulation 100mm Medium dense blockwork, 15mm Dot and dab, 12.5mm Gypsum wallboard plasterboard, 5mm plaster and paint finish. U-value 0.27W/m2k Flat Roof (vented): Roofing membrane, 18mm Marine plywood, Treated timber firring, 100mm Existing timber joists with 50mm air gap, 50mm Ecotherm Eco-Versal partially filling between joist (50mm ventilation) Vapour Control layer, 82.5mm Insulated plasterboard, 5mm plaster and paint finish. U-value 0.18W/m2k Existing Floor upgrade: Final finishes to client's choice, 18mm T G floor board, New 200x50mm Timber joist fixed against the existing ceiling joists, New 100mm APR 1200 insulation, 15mm Dot and dab, 12.5mm Gypsum wallboard plasterboard, 5mm plaster and paint finish.

SINAH LANE PROPOSED 3D VISUAL [Individual] [Sketchup + Blender rendering + Photoshop]

PROPOSED FIRST FLOOR PLAN @ 1:100 1st Floor Ceiling Level Raised Floor Level 1st Floor FFL Ground Floor FFL Externa Deck Level PROPOSED GROUND FLOOR PLAN @ 1:100 Bedroom Study Bathroom Utility Living Room Kitchen & Dining a existing 2 storey house with a flat roof.
PROPOSED FIRST FLOOR PLAN @ 1:100
[Individual] [vectorwork + sketchup]
Status: Issued to: Drawn by: Date Various@ A1 Drg.No. HOPA-011-P New Outline Proposal A Job Title HOP Architects Southsea, Company Amendments
EAST ELEVATION (Proposed) 1:100 SOUTH ELEVATION (Proposed) 1:100 WEST ELEVATION (Proposed) 1:100 NORTH ELEVATION (Proposed) 1:100
Bedroom Dressing Room Bedroom Bathroom Living Room Sunken Seats +600mm-+0 ChimneyDining wall -+0 -+0 +600mm Study Room Vertical timber Verticallouvres timber louvres
1st Floor Ceiling Level Raised Floor Level 1st Floor FFL Ground Floor FFL Externa Deck Level PROPOSED GROUND FLOOR PLAN @ 1:100 Proposed Perperstive Proposed(Courtyard) Perperstive (Frontage) Proposed Perperstive (Street) EAST ELEVATION (Proposed) 1:100 SOUTH ELEVATION (Proposed) 1:100 WEST ELEVATION (Proposed) 1:100 NORTH ELEVATION (Proposed) 1:100
1st Floor Ceiling Level Raised Floor Level 1st Floor FFL Ground Floor FFL Externa Deck Level PROPOSED GROUND FLOOR PLAN @ 1:100 Bedroom Study Bathroom Utility Living Room Kitchen & Dining Proposed Perperstive Proposed(Courtyard) Perperstive (Frontage)
Various@
Proposed Perperstive
PROPOSED FIRST FLOOR PLAN @ 1:100
Proposed Perperstive Proposed(Courtyard) Perperstive (Frontage) SEA FRONT PROPOSED OPTION A (TIMBER CLADDING) HAYLING ISLAND, HAMPSHIRE CLIENT : PRIVATE CLIENT APPOINTMENT : 2021 WORK STAGE: PLANNING Project brief : proposed first floor front extension and minor internal alterations for
Status: Issued to: Drawn by: Date Various@ A1 Drg.No. HOPA-011-P New Outline Design Proposal A Job Title 115/SFMG HOP Architects Ltd Southsea, Hampshire Company 12021383 AmendmentsDate by KC Client LA Design 11.05.2022 EAST ELEVATION (Proposed) 1:100 NORTH ELEVATION (Proposed) 1:100 PROPOSED FIRST FLOOR PLAN @ 1:1001:100 (Courtyard) A1 New Outline Design Proposal A Job Title 115/SFMG AmendmentsDate by EAST ELEVATION (Proposed) 1:100 SOUTH ELEVATION (Proposed) 1:100 WEST ELEVATION (Proposed) 1:100 NORTH ELEVATION (Proposed) 1:100 Bedroom Dressing Room Bedroom Bathroom Living Room Sunken Seats +600mm-+0 ChimneyDining wall -+0 -+0 +600mm Study Room Vertical timber louvres Vertical timber louvres Vertical timber louvres
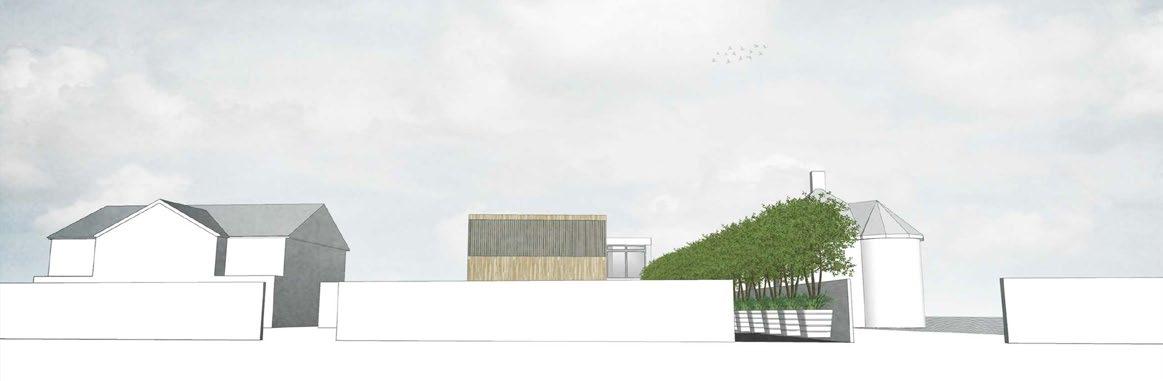
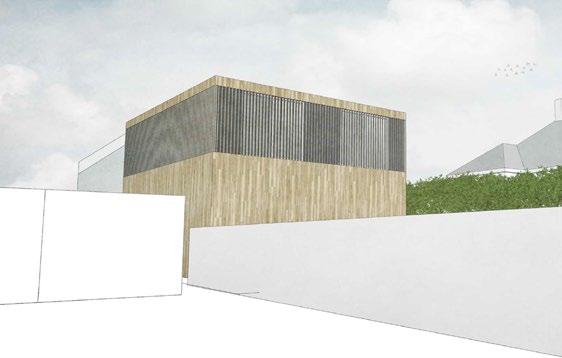
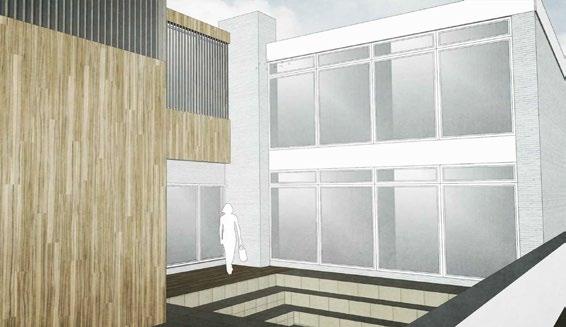






















































Status: Issued to: Drawn by: Date Various@ A1 Drg.No. HOPA-012-P New Outline Proposal B Job Title HOP Architects Southsea, Hampshire 07712 516265 Company reg. Amendments a b EAST ELEVATION (Proposed) 1:100 SOUTH ELEVATION (Proposed) 1:100 (Proposed) 1:100 NORTH ELEVATION (Proposed) 1:100 1st Floor Ceiling Level Raised Floor Level 1st Floor FFL Ground Floor FFL Externa Deck Level Proposed Perperstive (Courtyard) Proposed Perperstive (Frontage) Proposed Perperstive (Side) Proposed Perperstive (Side) EAST ELEVATION (Proposed) 1:100 SOUTH WEST ELEVATION (Proposed) 1:100 NORTH ELEVATION (Proposed) 1:100 Bedroom Dressing Room Bedroom Bathroom Living Room Seats +600mm-+0 ChimneyDining wall -+0 -+0 +600mm Study Room Corten Panel Corten Panel Corner Windows PROPOSED FIRST FLOOR PLAN @ PROPOSED1:100 GROUND FLOOR PLAN @ 1:100 Study Bathroom Utility Living Room Kitchen & Dining Proposed Perperstive (Courtyard) Proposed Perperstive (Frontage) Status: Issued to: Drawn by: Date Various@ A1 Drg.No. HOPA-012-P New Outline Design Proposal B Job Title 115/SFMG AmendmentsDate a b by KC Client / LA Design 11.05.2022 EAST ELEVATION (Proposed) 1:100 Proposed Perperstive (Frontage) Proposed Perperstive (Side) Status: Issued to: Drawn by: Date Various@ A1 Drg.No. HOPA-012-P New Outline Design Proposal B Job Title 115/SFMG HOP Architects Ltd AmendmentsDate by KC Client LA Design 11.05.2022 EAST ELEVATION (Proposed) 1:100 SOUTH ELEVATION (Proposed) 1:100 WEST ELEVATION (Proposed) 1:100 NORTH ELEVATION (Proposed) 1:100 Bedroom Dressing Room Bedroom Bathroom Living Room Sunken Seats +600mm-+0 ChimneyDining wall -+0 -+0 +600mm Study Room Corten Panel Corten Panel Corten Panel Corner Windows Corner Windows PROPOSED FIRST FLOOR PLAN @ 1:100 1st Floor Ceiling Level Raised Floor Level 1st Floor FFL Ground Floor FFL Externa Deck Level PROPOSED GROUND FLOOR PLAN @ 1:100 Bedroom Study Bathroom Utility Living Room Kitchen & Dining Proposed Perperstive (Courtyard) Proposed Perperstive (Frontage) Proposed Perperstive (Side) Proposed Perperstive (Side) SEA FRONT PROPOSED OPTION B (CORTEN PANEL) [Individual] [vectorwork + sketchup]
























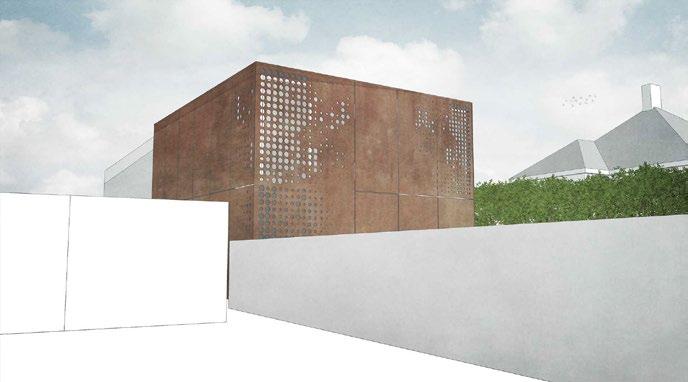













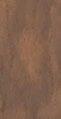
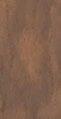



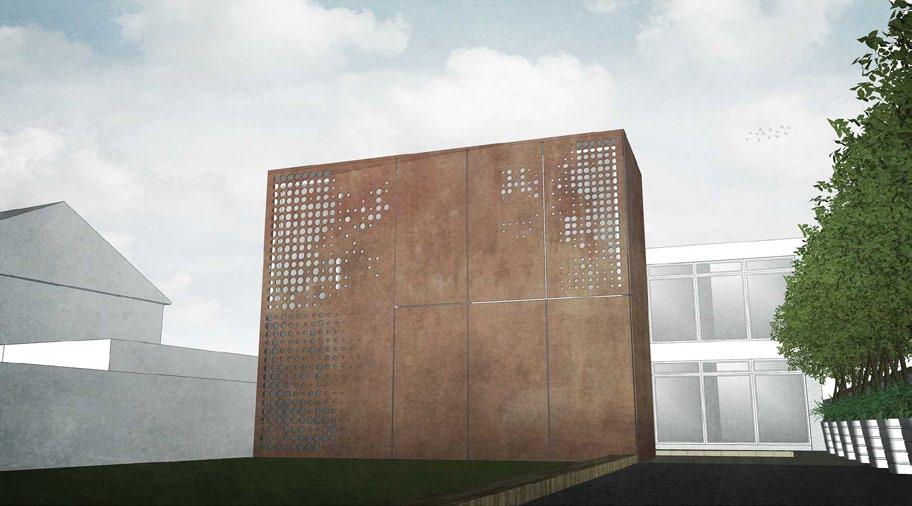

























































Proposed Kitchen Visuals Job Title 017 SC/RSP AmendmentsDate by Option A Layout Option B Layout Utility Room Utility Room SCOTT CLOSE EASTLEIGH, HAMPSHIRE CLIENT : PRIVATE CLIENT APPOINTMENT : 2021 WORK STAGE: PLANNING Project brief : provide otions for the new kitchen and dining room layout. [Individual][Sketchup]

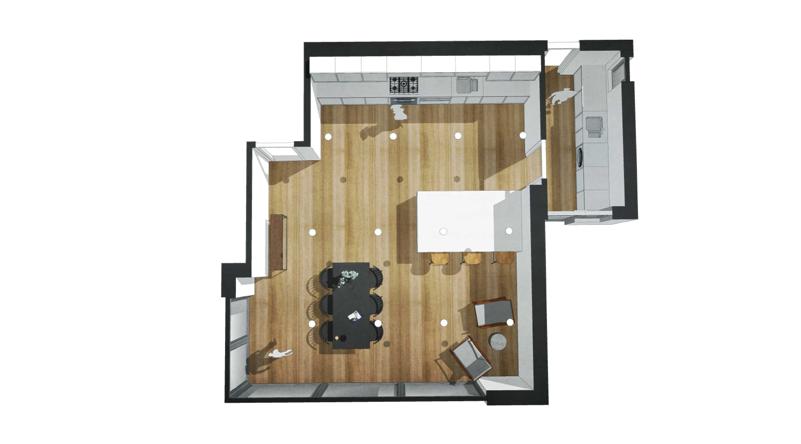
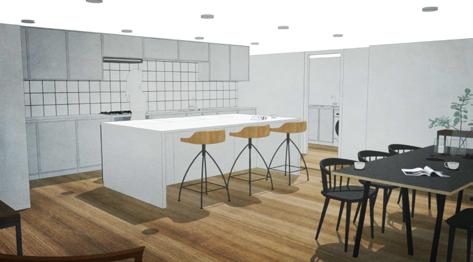

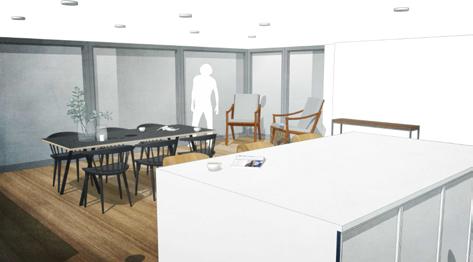
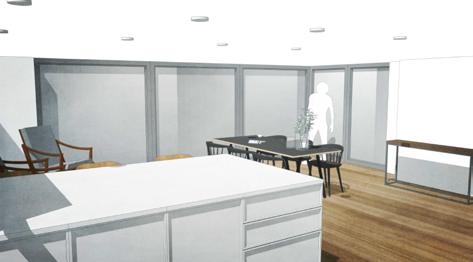
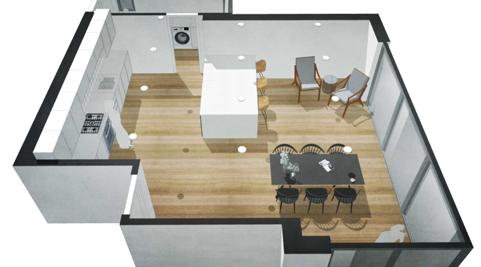
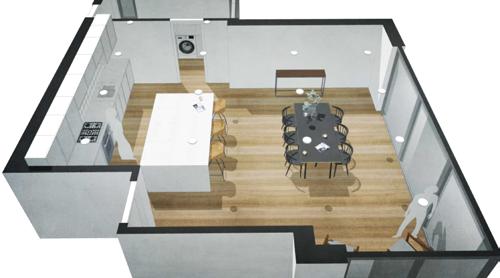
BOARHUNT LANE NEW BUILD DWELLING -NIGHT VISUAL FAREHAM, HAMPSHIRE [Individual] [Sketchup + Blender render + Photoshop]
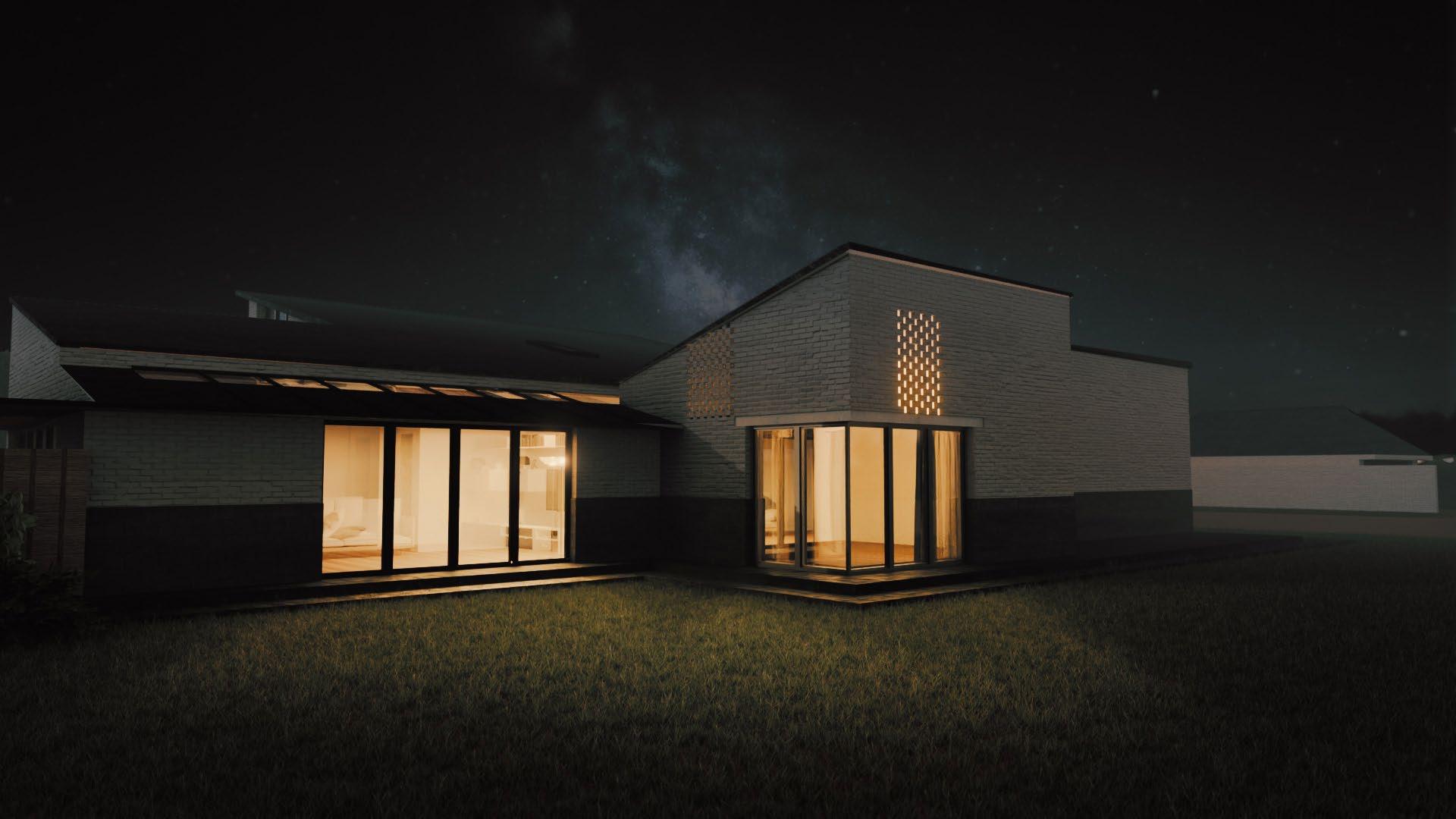
BOARHUNT LANE NEW BUILD DWELLING -DAY VISUAL FAREHAM, HAMPSHIRE [Individual] [Sketchup + Blender render + Photoshop]
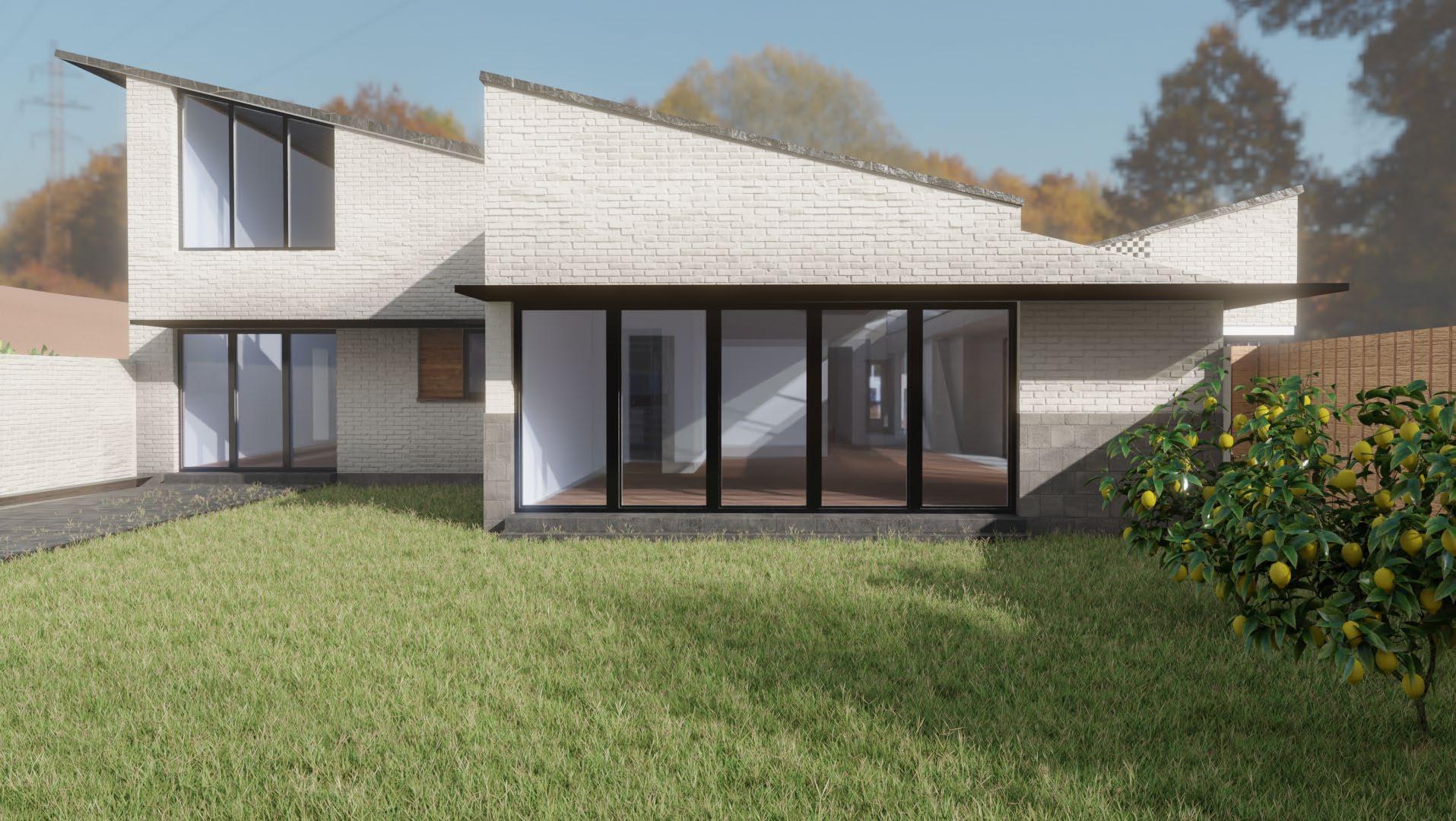
DINING ROOM KITCHEN LIVING ROOM HALL W.C BATHROOM OFFICE MASTER BEDROOM HALL Proposed Ground Floor Plan 1:100 Proposed First Floor Plan 1:100 Example of similar metal cladding Example of similar sliding doors Example of internal rooflight option Proposed Rear Elevation 1:100 Proposed Side Elevation 1:100 Proposed Side Elevation 1:100 Proposed Front Elevation 1:100 Proposed Sketch Elevation (NTS) Status: Issued to: Drawn by: Date Scale: As Shown @ A2 Drg.No: Drawing: Job Title 130/ No.5 /CR/BM HOP Architects Ltd Southsea, Hampshire 07712 516265 Company 12021383 AmendmentsDate by Proposed Plans & Elevations LMW Client Preliminary 28.07.22 HOPA-P-004 OPTION A [Individual] [Vectorwork + Sketchup]WINCHESTER, HAMPSHIRE CLIENT : PRIVATE CLIENT APPOINTMENT : 2022 WORK STAGE: PLANNING Project brief : provide otions for the side extension to an existing 2 storey house. DINING ROOM KITCHEN LIVING ROOM HALL W.C BATHROOM OFFICE MASTER BEDROOM HALL Proposed Ground Floor Plan 1:100 Proposed First Floor Plan 1:100 Example of similar vertical and horizontal brick stack bond Example of similar sliding doors Example of internal rooflight option Proposed Rear Elevation 1:100 Proposed Side Elevation 1:100 Proposed Side Elevation 1:100 Proposed Front Elevation 1:100 Proposed Sketch Elevation (NTS) Status: Issued to: Drawn by: Date Scale: As Shown @ A2 Drg.No: Drawing: Job Title 130/ No.5 /CR/BM HOP Architects Ltd Southsea, Hampshire Company reg. 12021383 AmendmentsDate by Proposed Plans & Elevations LMW Client Preliminary 28.07.22 HOPA-P-006 OPTION C 5 CLAUSENTUM ROAD SIDE EXTENSION IDEAS
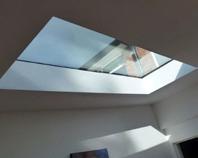
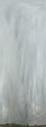
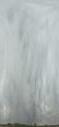
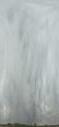
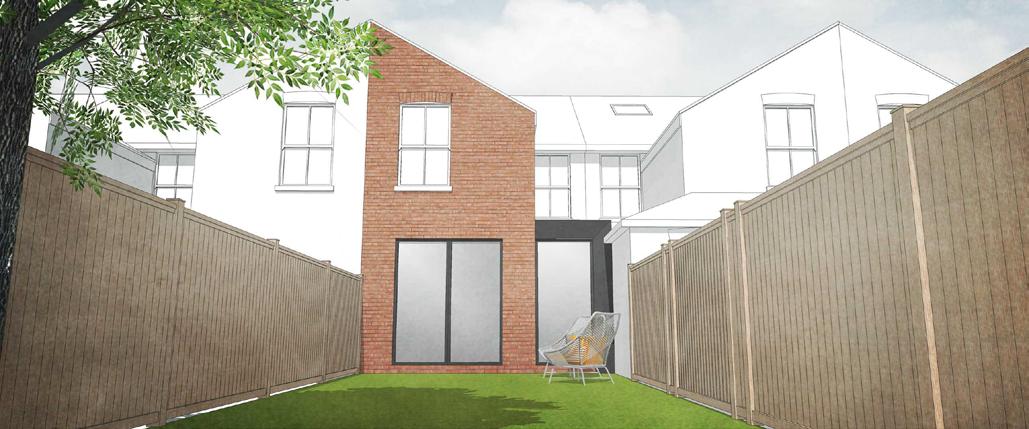
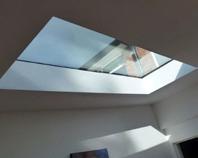
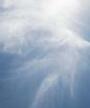
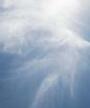

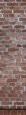
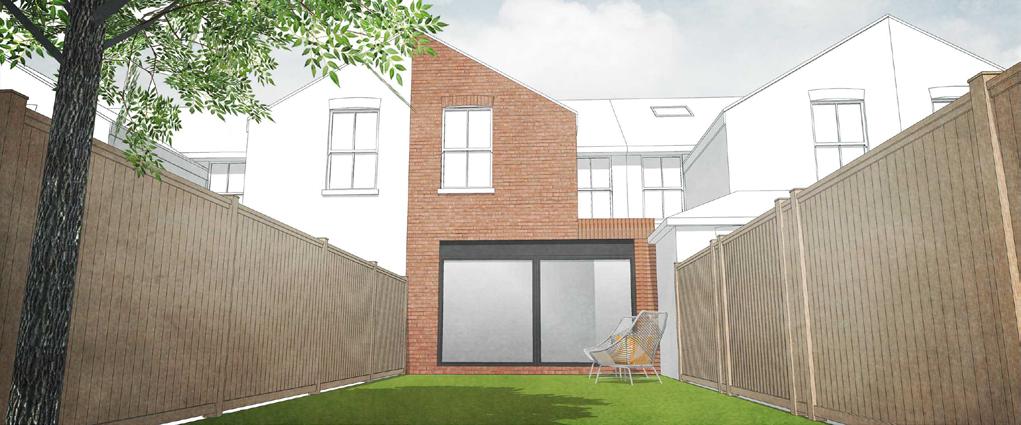
DINING ROOM KITCHEN LIVING ROOM HALL W.C BATHROOM OFFICE MASTER BEDROOM HALL Proposed Ground Floor Plan 1:100 Proposed First Floor Plan 1:100 Example of similar metal cladding Example of similar bi-folding doors Example of internal rooflight option Proposed Rear Elevation 1:100 Proposed Side Elevation 1:100 Proposed Side Elevation 1:100 Proposed Front Elevation 1:100 Proposed Sketch Elevation (NTS) Status: Issued to: Drawn by: Date Scale: As Shown @ A2 Drg.No: Drawing: Job Title 130/ No.5 /CR/BM HOP Architects Ltd Southsea, Hampshire Company 12021383 AmendmentsDate a b by Proposed Plans & Elevations LMW Client Preliminary 28.07.22 HOPA-P-007 OPTION D DINING ROOM KITCHEN LIVING ROOM HALL W.C BATHROOM OFFICE MASTER BEDROOM HALL Proposed Ground Floor Plan 1:100 Proposed First Floor Plan 1:100 Example of internal rooflight option Proposed Rear Elevation 1:100 Proposed Side Elevation 1:100 Proposed Side Elevation 1:100 Proposed Front Elevation 1:100 Proposed Sketch Elevation (NTS) Status: Issued to: Drawn by: Date Scale: As Shown @ A2 Drg.No: Drawing: Job Title 130/ No.5 /CR/BM HOP Architects Ltd Southsea, Hampshire Company 12021383 AmendmentsDate a c b by Proposed Plans & Elevations LMW Client Preliminary 28.07.22 HOPA-P-008 OPTION E Example of similar vertical and horizontal brick stack bond Example of similar sliding doors [Individual] [Vectorwork + Sketchup] 5 CLAUSENTUM ROAD SIDE EXTENSION IDEAS
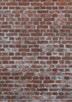

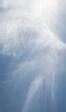
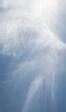
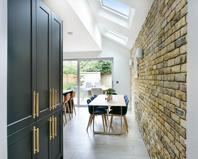
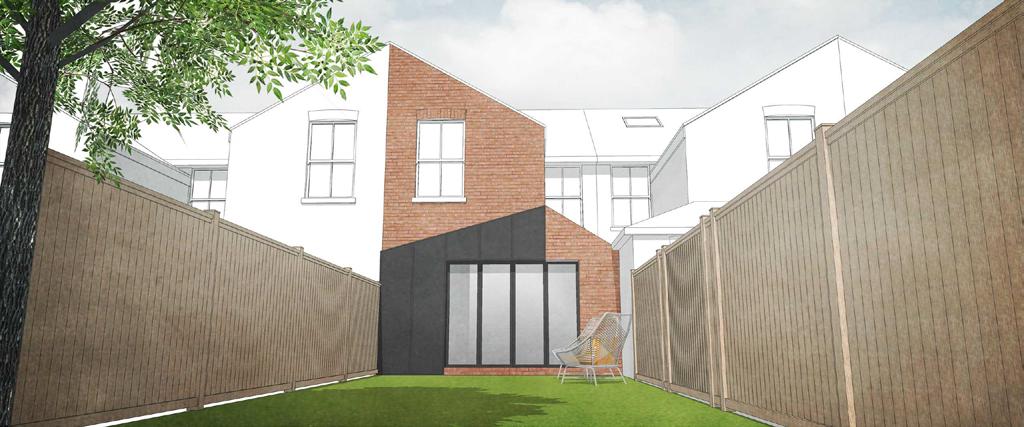


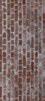
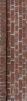
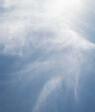
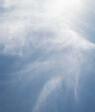
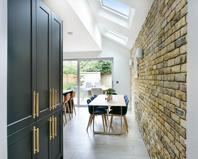
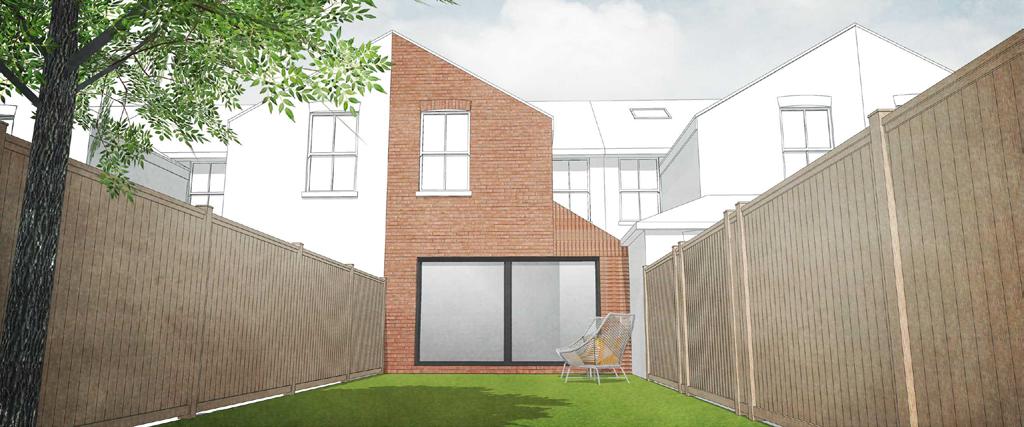
Doubled rafters to rooflight Openings Doubled rafters to rooflight Openings Doubled rafters to rooflight Openings Steel Lintel Catnic CG90/100 (SE to confirm)
Proposed Timber Double Stud Infill existing window opening: 3-5 Skim coat and paint finish, 12.5mm Gypsum plasteboard, 100 x 50mm Timber studs @400mm c/c, 50mm Isover APR 1200 insulation filled within studs, 100 x 50mm Timber studs @400mm c/c, 18mm plywood boarding to be fixed to studs 12.5mm Gypsum plasteboard, 3-5 Skim coat and paint finish, W003 Approx. existing (Exact site) Contractor to allow for a Y bend connection in this location to get pipe work around proposed foundation.
RL001 Glazing Vision Pitchglazed Fixed Roof Window 800 x 850mm (Internal Visible Opening) W001 Approx. 891 1710mm Re-use existing window from the existing kitchen side window (exact dimensions to be confirmed site) ED001
Status: Building Reg Issued to: Client Drawn by: KC Date: 01.08.22 Scale: 1:20 1:100 @ A1 Drg.No: HOPA-004-BC Drawing: Proposed Ground Floor Plan & Elevations Job Title 129/CR/J HOP Architects Ltd Southsea, Hampshire Company reg. AmendmentsDate by 1247.5 440 891 2513 Steel Lintel Catnic CG90/100 (SE to confirm) Steel Lintel Catnic CG90/100 Spanning 1355mm to SE specification
Doubled rafters to rooflight Openings
WC extraction to provide min. 15 l/s of extraction rate. (Ducting to be route to existing chinmey and up to roof level, and terminate at roof soffit. Hob extraction to provide min. 30 l/s of extraction rate. (Location of hob to be confirmed, ducting to be routed directly up to proposed pitched roof and terminate with mushroom cowl vent
FOUNDATION LINE FOUNDATION LINE
New foul drain at 1:80 87mm uPVC Rainwater downpipe 1No. 203 x 203 UC46 (SE to confirm) 1No. 203 x 203 UC46 (SE to confirm)
BASIN 400.7 1028 354
Existing Party Wall
New 450mm x 650mm Manhole to(location be confirmed on site) New 450mm 650mm Manhole (location to be confirmed on site) New soakaway system to be placed min. 5m away from any building
Proposed Timber Stud Infill: 3-5 Skim coat and paint finish, 12.5mm Gypsum plasteboard, 150 50mm Timber studs @400mm c/c, 18mm plywood boarding to be fixed to studs 50mm Isover APR 1200 insulation filled within studs, Existing masonry wall. Concrete Padstone to structural engineers specification
Proposed External Wall (Side): 102.5mm Facing brick to match existing, 10mm Clear residual cavity, 90mm Kooltherm K106 Cavity Board insulation, 100mm Inner leaf medium dense blockwork, 38mm Timber battens, 12.5mm Gypsum plasterboard, 3-5mm Skim coat and paint finish. U-value: 0.17 W/m2k
Boundary Line New stormwater drain at 1:80 WC 411.2
Insert vertical DPC into existing brickwork Vertical DPC & Furfix wall extension system to be used where new masonry abuts existing wall RL002 Glazing Vision Pitchglazed Fixed Roof Window 800 850mm (Internal Visible Opening)
1No. 203 x 203 UC45 located within new cavity wall and fixed into new foundation. Fixing detail to structural engineers specification Min. 25mm insulation between the steel column and the outer leaf brickwork WM Existing manhole to be removed and existing connect to be re-routed to the new manhole W002 Approx. 1028 x 1350mm Re use existing window from the lounge (Exact dimensions to be confirmed on site)
Proposed Internal Timber Stud Wall: 3-5 Skim coat and paint finish, 12.5mm Gypsum plasteboard*, 100x50mm Timber studs @400mm c/c, 50mm Isover APR 1200 insulation filled within studs, 12.5mm Gypsum plasterboard*, 3-5mm Skim coat and paint finish. *Change to moisture resistant gypsum plasterboard in wet areas.
Proposed Pitched Roof: Slate roof tiles, 25mm Treated batten, 38mm Treated counter battens, Breather membrane, 200x50 C24 @ 600// c/c (SE to confirm), 200mm Kingspan Kooltherm K107 insulation fully filled within rafters, Vapour control layer, 12.5mm Gypsum plasterboard, 3-5mm Skim coat and paint finish. U-value: 0.16 W/m2k
Existng internal masonry wall
Boundary Line New foul drain at 1:80 Proposed External Wall (Side): 102.5mm Facing brick to match existing, 10mm Clear residual cavity, 90mm Kooltherm K106 Cavity Board insulation, 100mm Inner leaf medium dense blockwork, 38mm Timber battens, 12.5mm Gypsum plasterboard, 3-5mm Skim coat and paint finish. U-value: 0.17 W/m2k New position for SVP (from 1st floor bathroom)
SINK Proposed Internal Timber Stud Wall: 3-5 Skim coat and paint finish, 12.5mm Gypsum plasteboard*, 150x50mm Timber studs @400mm c/c, 12.5mm Gypsum plasterboard, 3-5mm Skim coat and paint finish.
Proposed Flat Roof (Warm Roof): Single ply membrane, 18mm Marine plywood deck, 120mm Kingspan Thermaroof TR27 insulation, Vapour control layer, 18mm plywood deck, Timber firrings to create fall (1:80), 150x50 C24 @ 600// c/c (SE to confirm), 12.5mm Gypsum plasterboard, 3-5mm Skim coat and paint finish. U-value: 0.18 W/m2k Proposed Party Wall: 100mm Outer leaf medium dense blockwork, 10mm Clear residual cavity, 90mm Kooltherm K106 Cavity Board insulation, 100mm Inner leaf medium dense blockwork, 75x50mm Timber studs @ 400mm c/c, 12.5mm Gypsum plasterboard, 3-5mm Skim coat and paint finish. U-value: 0.17 W/m2k 1No. 203 203 UC45 located within new cavity wall and fixed into new foundation. Fixing detail to structural engineers specification
FOUNDATION LINE Contractor to carefully remove the existing window and re install it at the proposed rear elevation Assumed existing masonry wall is non load bearing. (To be confirmed on site)
ID001 345 x 1981mm (Leaf) Hardwood Timber Internal Door Proposed Front Elevation 1:100 Proposed Side Elevation 1:100 Proposed Side Elevation Proposed1:100 Rear Elevation 1:100 (Showing proposed extension Clausentum Road 22/01009/HOU)
TAP USBUSB Carbon Monoxide Detector Combined Heat and Smoke Detector (Mains Fed w/battery back-up) 13 Double socket (450mm above FFL) Switch to internal lights Recessed LED light fixture Below Ground Surface Water Drainage Drainage Pendant light fixture 63mm Rain Water Pipe 90mm Soil Vent Pipe Exterior Light Wall Lights Lighting Circuitry TV Key Heat HDetector Radiator LED Strip Lighting 13 Double socket (Min 1200 from FFL) Switch to internal lights 13 Double socket (Above Worktop) 13 Double socket (With USB) Outdoor Tap PROPOSED GROUND FLOOR PLAN @1:20 PROPOSED GROUND FLOOR PLAN @1:50 (showing electric layout) Section AA Section CC Section CC Section BB Section BB [Vectorwork][Individual]WINCHESTER, HAMPSHIRE CLIENT : PRIVATE CLIENT APPOINTMENT : 2021 WORK STAGE: BUILDING REGULATIONS Project brief : provide otions for the front and side extension to an existing 2 storey house. 7 CLAUSENTUM ROAD PROPOSED GROUND FLOOR PLAN
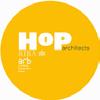



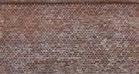
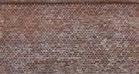
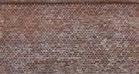
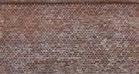
Proposed Flat Roof (Warm Roof): Single ply membrane, 18mm Marine plywood deck, 120mm Kingspan Thermaroof TR27 insulation, Vapour control layer, 18mm plywood deck, Timber firrings to create fall (1:80), 150x50 C24 @ 400mm c/c (SE to confirm), Void, 100x50mm Timber frame to form ceiling structure, 12.5mm Gypsum plasterboard, 3-5mm Skim coat and paint finish.
Lean mix concrete cavity fill 225mm below DPC 600mm 400mm GEN Concrete foundation to depth of 1000mm below EGL (to be approved by in site inspection) leaf 100mm Inner & outer leaf 7.3N Blockwork Backfilled with concrete to min 225mm, DPC to 150mm Min above EGL lapped to DPM 25mm Perimeter strip insulation around the edges 120mm Kingspan Thermaroof TR27 insulation Existing masonry outer leaf with one layer of 12.5mm gyproc plasterboard and 3-5mm skim coat. Contractor to allow for decoration (paint spec tbc by client) 203 203 UC46 with 8mm plate to carry masonry above. Steel to structural engineers specification Steel to receive 1 coat of intumenscent paint to provide minimum of 1 hour fire resistance
Code
uPVC half round gutter 89mm Rainwater downpipe Brick soldier course Upgrade to existing ceiling: Existing floorboard, Existing Timber floor joists, New 100mm mineral wool insulation between existing floor joists, New battens fixed to existing joists, (adjust to suit the new steel beam) New 12.5mm Gypsum plasterboard, New 3-5mm Skim coat and paint finish. Existing first floor window
Existing timber floor to be removed and void below to be back filled with well compacted MOT Type 1. Existing floor void depth unknown Contractor to refer to proposed ground floor build-up for new floor build-up information for details
Proposed Pitched Roof: Slate roof tiles, 25mm Treated batten, 38mm Treated counter battens, Breather membrane, 200x50 C24 @ 400mm c/c (SE to confirm), 200mm Kingspan Kooltherm K107 insulation fully filled within rafters, Vapour control layer, 12.5mm Gypsum plasterboard, 3-5mm Skim coat and paint finish. U-value: 0.16 W/m2k
Proposed Foundation: 600mm 400mm GEN Concrete foundation to a depth of 1000mm below EGL (to be approved by in site inspection) 2 x leaf 100mm Inner & outer leaf 7.3N Blockwork Backfilled with concrete to min 225mm, DPC to 150mm Min above EGL lapped to DPM
Contractor to ensure existing telecopic floor vents are adequate Existing external cavity wall
Assumed existing foundation Depth and Spec unknown Upgrade existing timber floor: Floor finish to client's choice, New 18mm T&G chipboard floorboard, Existing Timber floor joists, Remove existing floor insulation and change to 125mm Kingspan Kooltherm K103 insulation, 25mm Treated battens to support new insulation, Existing void (vented) U-value: 0.19 W/m2k Existing timber first floor
Proposed2110 Ground Floor: Floor finish to client's choice, 75mm Fibre reinforced screed, Polypipe underfloor heating system (15mm pipe), Vapour control layer, 70mm Kingspan Kooltherm K103 insulation board, 150mm Concrete slab, Damp proof membrane, Sand blinding, Hardcore. U-value: 0.19 W/m2k
Existing single leaf masonry wall Downstand steel beam final finish to be confirmed by client Existing FFL
Drawing: Proposed Section AA Job Title 129/CR/J HOP Architects Ltd Company Amendments by RoofPitchto 22
38mm treated counter battens Breather membrane 25mm treated timber batten Slate roof tiles 200mm Kingspan Kooltherm K107 insulation fully filled within rafters Vapour control layer 12.5mm gypsum plasterboard with 5mm skim coat and paint finish. 2No. bolts to connect flat roof joists to rafter. Bolts to be sized to structural engineer specification 200mm 50mm C24 @ 600mm c/c (SE to confirm) 150mm x 50mm C24 @ 400mm c/c (SE to confirm) & Timber firrings above to create fall Code lead flashing (150mm above roof level) min. 150mm Lead flashing Single ply membrane trim overlapping lead
Proposed Flat Roof (Warm Roof): Single ply membrane, 18mm Marine plywood deck, 120mm Kingspan Thermaroof TR27 insulation, Vapour control layer, 18mm plywood deck, Timber firrings to create fall (1:80), 150x50 C24 @ 400mm c/c (SE to confirm), 12.5mm Gypsum plasterboard, 3-5mm Skim coat and paint finish. U-value: 0.18 W/m2k Code lead flashing (min.150mm above flat roof)
Existing external wall to be demolished
Proposed Timber Stud Infill: 3-5 Skim coat and paint finish, 12.5mm Gypsum plasteboard, 150 50mm Timber studs @400mm c/c, 18mm plywood boarding to be fixed to studs 50mm Isover APR 1200 insulation filled within studs, Existing masonry wall. 100mm medium dense blockwork 9mm uPVC soffit and fascia board (colour TBC) 12.5mm gyproc plasterboard with 5mm skim coat & paint finish 89mm Rainwater downpipe Steel Lintel Catnic CG90/100 (SE to confirm specification) Arched brick header course 15mm dot and dab 100x50mm Timber wallplate uPVC half round gutter Breather membrane 1247.5mm x 2100mm Timber Framed doors 75mm Fibre reinforced screed with Polypipe underfloor heating system (15mm pipe) Vapour control layer 70mm Kingspan Kooltherm K103 insulation board 150mm in-situ concrete slab Damp Proof Membrane Sand blinding and Compacted hardcore French door sill to client's choice Damp Proof Course (150mm above ground level) 102.5mm Facing brick 100mm outer leaf dense blockwork (below DPC) 90mm Kooltherm K106 Cavity Board insulation 100mm inner leaf dense blockwork (below DPC)
Vapour control layer 18mm marine plywood deck Single ply membrane 18mm marine plywood deck Timber packers to be tied into web of steel to allow for down stand beam to be the same width as the wall above. 203 203 UC46 to sit over 203 203 UC 46 below
flashing PROPOSED SECTION AA @ 1:20 DETAIL A1 @ 1:5 DETAIL A2 @ DETAIL1:5 A3 @ 1:5 DETAIL A3 DETAIL A2 DETAIL A1 [Vectorwork][Individual]7 CLAUSENTUM ROAD PROPOSED SECTION AND DETAILS
U-value: 0.18 W/m2k
Status: Building Reg Issued to: Client Drawn by: KC Date: 01.08.22 Scale: 1:20 1:100 @ A1 Drg.No: HOPA-005-BC
New External to achieve an overall u-value of 1.8 W/m2k
Assumed existing foundation Depth and Spec unknown Assumed existing foundation Depth and Spec unknown Existing ground bearing slab to be broken out and contractor to allow for proposed new ground floor build-up Contractor to refer to proposed ground floor build-up for new floor build-up information for details

Proposed Foundation: 600mm sq GEN 2 Concrete foundation to depth of 1000mm below EGL (to be approved by in site inspection) x leaf 100mm Inner & Uoter leaf 7.3N Blockwork Backfilled with concrete to min 225mm, DPC to 150mm Min above EGL lapped to DPM
Proposed Ground Floor: Floor finish to client's choice, 75mm Fibre reinforced screed, Polypipe underfloor heating system (15mm pipe), Vapour control layer, 70mm Kingspan Kooltherm K103 insulation board, Damp proof membrance, 150mm Concrete slab, Sand blinding, Hardcore. U-value: 0.19 W/m2k
1No. 203 x 203 UC46 with top plate (SE to confirm) 1No. 203 x 203 UC46 with top plate (SE to confirm)
Proposed External Wall: 102.5mm Facing brick to match existing, 10mm Clear residual cavity, 90mm Kooltherm K106 Cavity Board insulation, 100mm Inner leaf medium dense blockwork, 15mm dot and dab adhesive, 12.5mm Gypsum plasterboard, 3-5mm Skim coat and paint finish. U-value: 0.17 W/m2k 1No. 203 203 UC46 with top plate (SE to confirm)
Proposed Flat Roof (Warm Roof): Single ply membrane, 18mm Marine plywood deck, 120mm Kingspan Thermaroof TR27 insulation, Vapour control layer, 18mm plywood deck, Timber firrings to create fall (1:80), 150x50 C24 @ 600// c/c (SE to confirm), Void, 100x50mm Timber frame to form ceiling structure, 12.5mm Gypsum plasterboard, 3-5mm Skim coat and paint finish. U-value: 0.18 W/m2k 100X100 Black uPVC square gutter Proposed External Wall: 102.5mm Facing brick to match existing, 10mm Clear residual cavity, 90mm Kooltherm K106 Cavity Board insulation, 100mm Inner leaf medium dense blockwork, 15mm dot and dab adhesive, 12.5mm Gypsum plasterboard, 3-5mm Skim coat and paint finish. U-value: 0.17 W/m2k Proposed Party Wall: 100mm Medium dense blockwork, 10mm Clear residual cavity, 90mm Kooltherm K106 Cavity Board insulation, 100mm Inner leaf medium dense blockwork, 100x50mm Timber studs @ 400mm c/c, 12.5mm Gypsum plasterboard, 3-5mm Skim coat and paint finish. U-value: 0.17 W/m2k Detail to be confirmed with No. 6 RoofPitchto23
1:5 DETAIL C2 [Vectorwork][Individual]7 CLAUSENTUM ROAD PROPOSED SECTION AND DETAILS
DETAIL
Drawing: Proposed Section BB & CC Job Title 129/CR/J HOP Architects Ltd AmendmentsDate
DETAIL
Steel beam to Steel column connection detail SE's design and specification Steel beam to Steel column connection detail SE's design and specification
Vapour control layer Insulation Timber packer 12.5 Gyproc plasterboard with 5mm skim coat and paint finish
Status: Building Reg Issued to: Client Drawn by: KC Date: 01.08.22 Scale: 1:20 1:100 @ A1 Drg.No: HOPA-006-BC
Proposed Ground Floor: Floor finish to client's choice, 75mm Fibre reinforced screed, Polypipe underfloor heating system (15mm pipe), Vapour control layer, 70mm Kingspan Kooltherm K103 insulation board, Damp proof membrance, 150mm Concrete slab, Sand blinding, Hardcore. U-value: 0.19 W/m2k
Proposed Pitched Roof: Slate roof tiles, 25mm Treated batten, 38mm Treated counter battens, Breather membrane, 200x50 C24 @ 600// c/c (SE to confirm), 200mm Kingspan Kooltherm K107 insulation fully filled within rafters, Vapour control layer, 12.5mm Gypsum plasterboard, 3-5mm Skim coat and paint finish. U-value: 0.16 W/m2k
Slate roof tiles Code Lead flashing Retrofit cavity tray Head tiliting fillet Head structural trimmers Insulation Timber packer Vapour control layer 25+12.5mm Insulated plasterboard 100x50mm Timber plate (fixing detail to SE's specification) 203x203 UC46 (SE to confirm specification) Top steel plate to SE's specification 12.5mm Gyproc plasterboard with dot and dab Existing facing brick Single ply membrane Single ply memrbane trim Code lead flashing trim overlapped by single membrane trim Vapour control layer Doubled timber joists at junction 100x50mm Timber wallplate fixed to doubled joists (SE to confirm design) 25+12.5mm Insulated plasterboard Rafters with birdsmouth joint to timber wallplate Breather membrane 75mm Fibre reinforced screed with Polypipe underfloor heating system (15mm pipe) Vapour control layer 70mm Kingspan Kooltherm K103 insulation board 150mm in-situ concrete slab Damp Proof Membrane Sand blinding and Compacted hardcore Damp Proof Course (150mm above ground level) 102.5mm Facing brick 100mm outer leaf dense blockwork (below DPC) 90mm Kooltherm K106 Cavity Board insulation 100mm inner leaf dense blockwork (below DPC) Lean mix concrete cavity fill 225mm below DPC 600mm 400mm GEN Concrete foundation to depth of 1000mm below EGL (to be approved by in site inspection) leaf 100mm Inner & outer leaf 7.3N Blockwork Backfilled with concrete to min 225mm, DPC to 150mm Min above EGL lapped to DPM 25mm Perimeter strip insulation around the edges B1 @ 1:5 DETAIL C1 SECTION BB @ 1:20 SECTION CC @ 1:20 DETAIL B1 DETAIL B2 DETAIL B2 @ 1:5 DETAIL C2 @ 1:5 C1 @
Proposed Foundation: 600mm sq GEN Concrete foundation to depth of 1000mm below EGL (to be approved by in site inspection) leaf 100mm Inner Uoter leaf 7.3N Blockwork Backfilled with concrete to min 225mm, DPC to 150mm Min above EGL lapped to DPM
Glazing Vision Pitchglaze fixed rooflight 100x100mm Square gutter Waterproofing membrane Breather membrane Cill code 4 lead flashing Cavity closer 102.5mm Facing brick 100x50mm Timber wallplate Sunken cill trimmers (supporting the pitchglaze) Timber firrings to provide fall to gutter 25+12.5mm Insulated plasterboard with 5mm skim coat and paint finish

Job Title Scale Drawn by Status Date Rev Note By Date A B C Drawing Ref East8 Elevation N Proposed Ground Floor Plan @ 1:100 Proposed First Floor Plan @ 1 100 100 @A1 HOPA P 003 Proposed Drawing KC 126 62 Pine Road XX Preliminary 06 06 2022 Plans Eleva & Visuals OHall / Workshop Snug Bedroom Piano Room Bathroom Kitchen Living Room Dining Room Bedroom Cpd Landing Bathroom Bedroom Walk in Wardrobe Bedroom Walk in Wa drobe En suite OPTION A Pergolas Proposed Rear Perspec Proposed Rear Perspec Proposed Front Eleva (North) @ Proposed1:100 Rear Eleva (South) @ 1 100 Proposed Side Eleva (East) @ 1 Proposed100 Side Eleva (West @ 1 100 PINE ROAD PROPOSAL A CHANDLER’S FORD, HAMPSHIRE CLIENT : PRIVATE CLIENT APPOINTMENT : 2022 WORK STAGE: PLANNING Project brief : construction of two storey rear extension and a single storey rear extension. [Individual] [ArchiCAD + Cinerender + Photoshop]
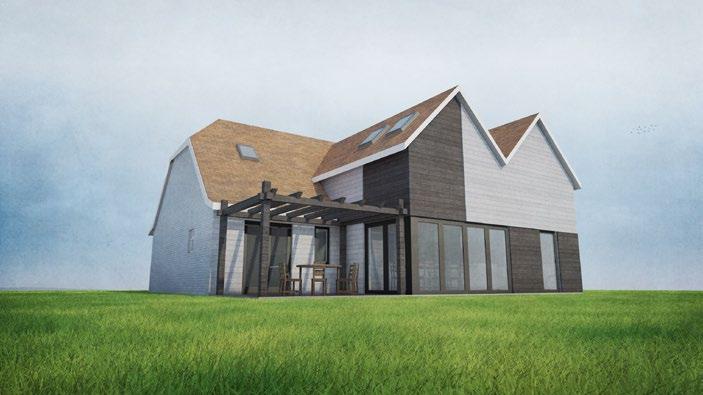
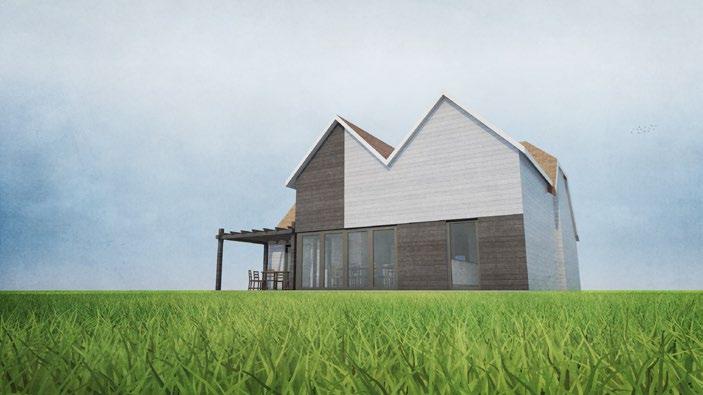
Job Title Scale Drawn by: Status Date Rev Note A B C Drawing Ref 12 13 210 N Proposed Ground Floor Plan @ 1:100 Proposed First Floor Plan @ 1 100 1 100 @A1 HOPA P 004 Proposed Drawing KC 126 / 62 Pine Road Preliminary 06 06 2022 Plans Eleva OHall Workshop Snug Bedroom Piano Bathroom Kitchen Living Room Dining Room Bedroom Cpd Landing Bathroom Bedroom Bedroom Walk in Wa drobe Store OPTION B Proposed Rear Perspec Cpd U Room Cpd Proposed Rear Perspec Proposed Front Eleva (North) @ 1 Proposed100 Rear Eleva South) @ 1:100 Proposed Side Eleva (East) @ 1 Proposed100 Side Eleva West) @ 1 100 PINE ROAD PROPOSAL B [Individual] [ArchiCAD + Cinerender + Photoshop]
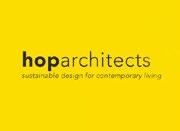
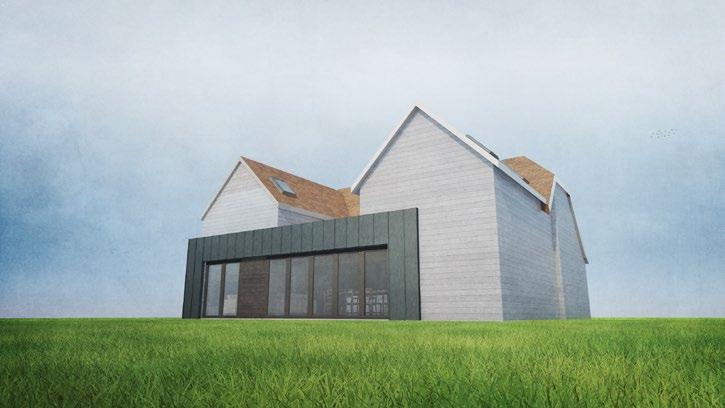
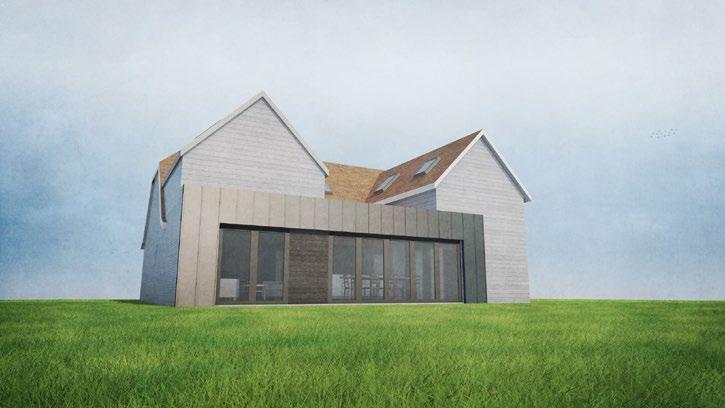
SHORTHEATH ROAD 3D VISUAL FARNHAM, SURREY CLIENT : PRIVATE CLIENT APPOINTMENT : 2022 WORK STAGE: PLANNING Project brief : construction of single storey rear extension to an 2 storey existing house. [Individual] [Sketchup + Blender render + Photoshop]
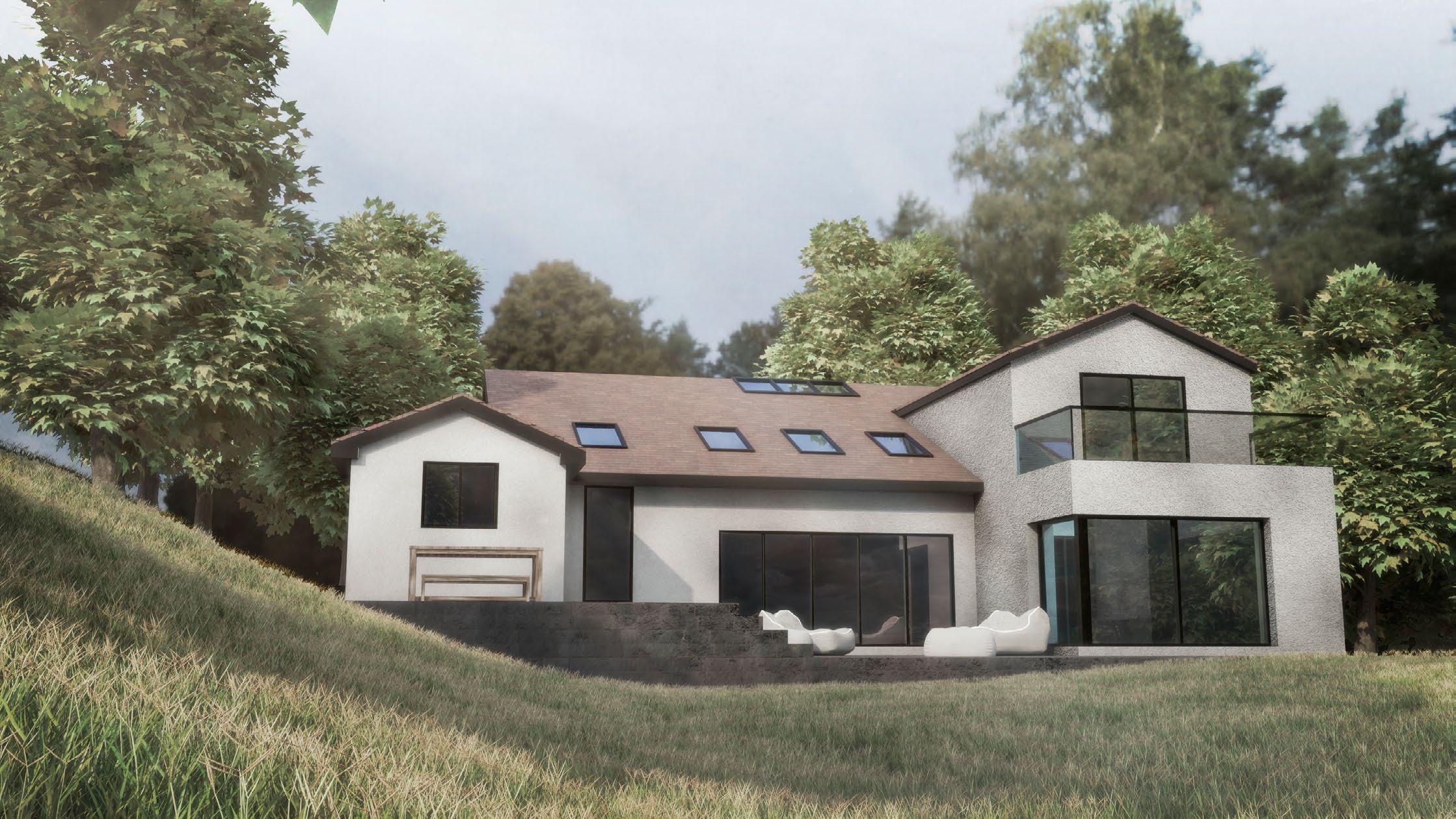
SHORTHEATH ROAD 3D VISUAL [Individual] [Sketchup + Blender render + Photoshop]
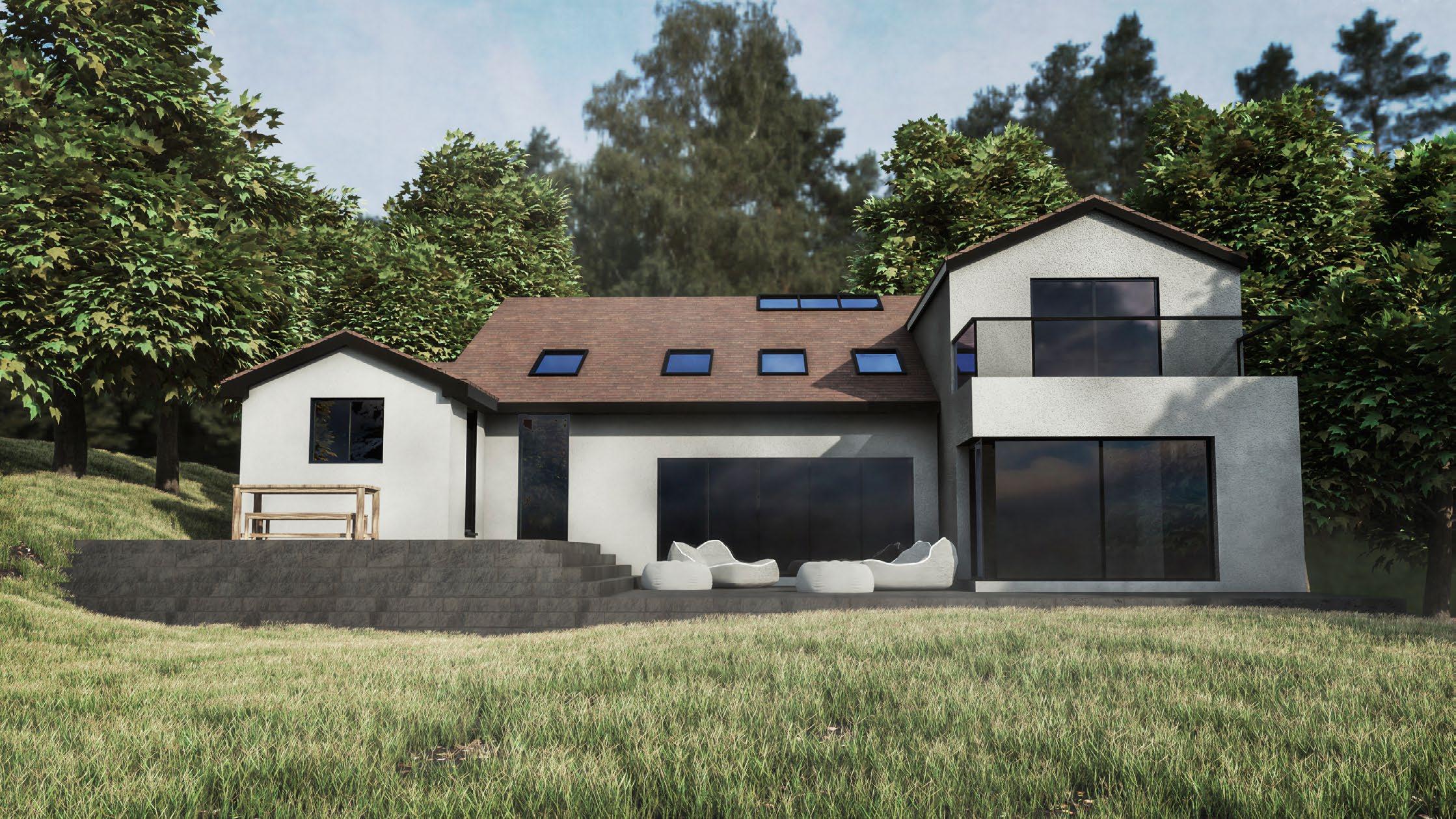
First Floor Plan (Loft) 1:50
Duty
Proposed
[Vectorwork][Individual]
Proposed Dwarf Wall: Loft (vented), 100mm Timber stud with 70mm Ecotherm Eco-Versal in between, 25+12.5mm Insulated plasterboard, Skim coat to finish. U value = 0.27 W/m2k RL005 Velux Top hung skylight (Slate Grey) (WxH) 940 980mm RL006 Velux Top hung skylight (Slate Grey) (WxH) 940 980mm R1 T5 T6 4488 2273 781 1885 TBC by client 4065 4281 150150
Sanitary pipework to be in accordance with Approved Document H1, Section 1. Discharge stack to be 100mm diameter PVC reducing to 75mm diameter (above highest branch) to terminate a minimum of 900mm above any opening within 3m, horizontally from the stack, with preformed roof tile profile thro vent. Access eye to be provided at first floor level. 75mm deep seal traps to basin, sink, bath and shower, 50mm deep seal trap to WC, 32mm waste to basin. 40mm waste to sink, bath and shower. Minimum diameter of common branch pipe to be 50mm and a gradient of 18mm to 45mm per metre. All traps to be removable or to be fitted with cleaning eye. Where access for cleaning discharge pipes cannot be provided by removing traps, then rodding points are to be included. Excessive length waste pipes to be increased in accordance with Approved document H diagram and or fitted with air admittance type anti-vac traps. Foul and rainwater drainage to be in accordance with Approved Document H1, Section and H3, Section 2. Rainwater goods (gutters, down pipes and fixings) in accordance with Approved Document H3, Section 1.All foul drainage is to be connected to existing mains foul sewer. All pipes to be 100mm dia UPVC with fully flexible joints to BSEN 13398-1 2010 laid to falls to Local Authority approval generally 1:80 and to suit site levels. All drains to be tested after installation to Local Authority approval. Drains to be laid in minimum 150mm pea shingle surround with selected backfill. Where drains pass through walls, an opening is to be formed to give at least 50mm clearance all around pipe and the opening masked with rigid sheet material to prevent the ingress of fill or vermin. Provide lintels over openings as required. All drainage to Local Authority approval and to be tested prior to backfilling and again after backfilling. All new foul drainage to connect into existing drainage runs with all falls to be designed by contractor. New SVP to be sound insulated. All sanitary fittings to have 75mm deep seal traps. All in accordance with the requirements of Part H of Schedule One of the Building Regulations and BS EN 12056-2:2000.Surface water drainage runs to be 100mm dia. UPVC with fully flexible joints to BS 4660 laid to falls between 1:80 & 1:40 to suit site levels. All drains to be tested after installation to Local Authority approval. Drains to be laid in min. 150mm pea gravel surround with selected backfill. All rainwater from new works to drain via gutter system into downpipes connecting into existing underground drainage runs. existing rainwater is drained to soakaways, main contractor to provide 100mm underground uPVC pipework connected to existing soakaway.
Proposed External Wall (Timber frame with render finish): K-Rend Silicone TC15 render system 2: 1.5mm K Rend Silicone TC15 render (white fine texture), K Rend TC Primer, 4-6mm K Rend HP12 Base, 1mm K Rend Alkali Resistant mesh, 12.5mm Knauf Aquapanel Exterior Cement Board, 25mm Treated batten, Breather membrane, 12mm Promat Supalux board 9mm OSB 3 board, 150mm Timber stud with fullfill Ecotherm Eco-Versal insulation, Vapour control layer, 9mm OSB 3 board, 25mm Service batten, 12.5mm Wallboard plasterboard, Skim coat to finish. U value= 0.23W/m2k & 30mins fire resistant on both side Proposed Internal Timber Stud Wall 12.5mm Wallboard plasterboard* with skim coat finish to both side, 100mm Timber stud with 65mm APR 1200 insulation.
Section C Section D Heat Detector Smoke Detector Proposed Ground Floor Plan 1:50
Proposed infill between Brick Pier: Existing blockwork, Vertical damp proof membrane over the existng wall, 100x50mm timber stud with 70mm Ecotherm insulation, 18mm plywood, 12.5mm gyproc plasterboard, Skim coat to finish. U value = 0.29 W/m2k Upgrade to Existing brick pier Existing brickwork, Vertical DPM, 25mm Vertical batten, 70+12.5mm insulated plasterboard (with 18mm plywood in kitchen area) Proposed SVP Existing external cavity wall
Drawings are to be checked prior to commencement of building work and any problems are to be brought up at this time. Hop Architects Ltd accepts no responsiblity after work commences. Both approval notices for planning and building regulations are to be checked prior to building for any conditions. Any existing structure that is going to be affected by this development is to be checked for suitability prior to work commencing. All drawings to be used in conjunction with SE calculations and drawings. Doors and Windows area does not exceed 25% of new floor area in addition to the area of any windows or doors which, as result of the extension works, no longer exist or are no longer exposed. Combined method U value of 1.6 W/m2K All windows to be glazed with safety glazing and fitted in accordance with manufacturers instructions. Cavity trays and closures to be fitted to all appropriate vertical and horizontal breaks and openings. No trees of significance within 35m of proposal. Background Ventilation and Intermittent Extraction provided by Manually controlled trickle vents to all new windows and checked on existing windows 1.7m above Floor level to provide suitable background ventilation; Openable window area of 1/10 of internal floor area for rapid purge ventilation of min. 1.73 sqm,
AmendmentsDate by Proposed Plans New details added KC 01.06 Internal door revised KC 14.06 Internal door revised KC 14.06
GLAZING Glazing within 800mm of floor level in windows generally, and within 1500mm of floor level in doors and windows within 300mm of doors, are to be safety glazed to comply with Building Reguation part K. All external doors are to have a toughened inner and laminated outer pane to the sealed double glazed units. Glazing to all windows adjacent to these doors are to the same. Fire alarm system Fire alarm system to be installled complying to BS 5839-6: Grade F2; all smoke and heat detector to be wireless interlinked; main powered with backup 9v battery (replaceable); sound pressure level 85 dBA. Project brief : construction of single storey front and rear extension, and a loft conversion with a flat roof dormer at the rear.
Proposed extractor unit to achieve 15 l/s extraction rate in bathroom. Ventilation duct to be diverted into the loft space and terminate at eave soffit. Existing manhole 68mm uPVC RWP
Proposed Dormer Wall (Side): Render on cement board, 25mm Treated batten, Breather membrane, 18mm OSB Board, Timber frame to SE's specification with 120mm Ecotherm Eco-Versal insulation, Vapour control layer, 25mm Service batten, 12.5mm insulated plasterboard, Skim coat to finish. U value = 0.22 W/m2k Bedroom 3 Ensuite Loft storage (vented) UP UP RL001 Flat roof skylight (Slate Grey) 1500 1500mm RL002 Flat roof skylight (Slate Grey) 1500 x 1500mm RL003 Flat roof skylight (Slate Grey) 1500 x 1500mm RL004 Flat roof skylight (Slate Grey) 1500 x 1500mm ED003 Aluminium Framed Double Glazed Double Door (WxH) 2254 1650mm 2m First Floor Head Height 1.5m Juliette balcony Carbon Monoxide Detector Combined Heat and Smoke Detector (Mains Fed w/battery back-up) 13 A Double socket Switch to internal lights Receased LED light fixture Below Ground Surface Water Drainage Below Ground Soil Waste Drainage Pendant light fixture KEY 63mm Rain Water Pipe 90mm Soil Vent Pipe Exterior Motion Sensitive Light
Existing Cavity Wall upgrade: Existing facing brick, Existing Cavity Existing inner blockwork, 15mm dot and dab, 60+12.5mm insulated plasterboard, Skim coat to finish. U value = 0.27 W/m2k
Proposed internal blockwall: 11+2mm plaster on both side with skim coat finish, 100mm medium dense blockwork.
Proposed internal blockwall (cavity): -12.5mm Wallboard plasterboard with skim coat finish on both side, 15mm Adhesive dot and dab, 100mm medium dense blockwork. Cavity to match existing, 100mm medium dense blockwork, Vertical DPM to be installed to existing brickwork Padstone/Engineering Brick to support lintel or beam. (To SE's specification) Section AA Section B Replace all existing uPVC window with aluminium framed window Soakaway system to be at least 5m away form the building. The roof areas which will be discharged into the soakaway system are as follow: Proposed Flat roof dormer: approx. 16.2m2 Existing Pitched roof (excluding dormer): approx. 22.1m2 Proposed Flat roof over the new extension: approx. 52.9m2 Total = approx. 91.2m2 Crate system: 91.2m2 x(50/3000) = 1.5m3 Minimum of 1.5m3 of crate soakaway system Hallway WC Utility LoungeRoom Dining Room Kitchen Provision to strip back and render to the existing external render finish. Bathroom Bedroom 01 Bedroom 02 Proposed extractor unit to achieve 30l/s extraction rate in kitchen. Cpd Proposed SVP to be wrapped with 25mm techwrap insulation. Terminate in the loft area with Air Admittance Valve. Proposed SVP with rodding access Proposed patio Underfloor Heating to 7.3 sqm Underfloor Heating to new areas to 69.25 sqm Proposed rooflights to achieve an overall u value of 1.6w/m2k 3000 3363 19014771043 630 W004 Aluminium Framed Double Glazed Unit (WxH) 1990 1307mm W002 Aluminium Framed Double Glazed Unit (WxH) 1990 990mm W001 Composite Framed Double Glazed Panel (WxH) 630 x 2100mm W003 Aluminium Framed Double Glazed Unit (WxH) 1290 x 1307mm Provision for Cassette gas fire 110 Upstand to Sink 110 Upstand to DW Picture window with Microchip pet door intergrated Bi-fold window's cill to be leveled with the kitchen counter top 110 Upstand to WM 110 Upstand to TD W006 Aluminium Framed Double Glazed Bi-Fold Window 3160 x 1100mm W005 Aluminium Framed Double Glazed Panel (with pet door) 910 x 2100mm ED001 Composite Framed Composite Door (WxH) 848x 2100mm ED002 Aluminium Framed Bi-fold Door (WxH) 3949x 2100mm RL001 Flat roof skylight (Slate Grey) 1500 1500mm RL002 Flat roof skylight (Slate Grey) 1500 x 1500mm RL003 Flat roof skylight (Slate Grey) 1500 1500mm RL004 Flat roof skylight (Slate Grey) 1500 x 1500mm Eccentric Foundation at boundary line Upgrade to Existing brick pier Existing brickwork, Vertical DPM, 25mm Vertical batten, 70+12.5mm insulated plasterboard 150x50mm timber stud 240780 3940 810 2436 1550 2570 443 1276 920 750 T1 T2 T3 Heavy HeavyLintel Cavity Lintel timber flat roof joist 150x50mm C24 at 400mm c/c 2435 2460
Duty Cavity
Proposed External Wall: (Blockwork with render finish) K-rend LW1 render system: 16-20mm one coat coverage (white), 100mm Medium dense blockwork, 100mm cavity with 90mm Ecotherm Eco-Cavity Full Fill insulation with 10mm residual cavity, 100mm Medium dense blockwork, -Vapour control layer, -15mm Adhesiv dot and dab, 12.5mm Wallboard plasterboard, Skim coat to finish. U value = 0.19 W/m2k Proposed rooflights to achieve an overall u value of 1.6w/m2k Proposed composite entrance door with side glazing panel to achieve an overall u value of 1.8W/m2k Existing chimney Steel beam T1 203x203UC46 fixed to T2 with angle cleat with 2no. M16 in each leg Timber joist to SE's specification Timber staircase closed tread closed stringer 198mm rise -240mm going -750mm wide -13 risers New timber floor joist 150x50mm C24 at 350mm c/c
1301394925123160903
Central Heating circuit to primarily remain as existing unless noted otherwise and be extended into new areas. Hot and cold water supply, to be designed and installed by contractors Plumber. Boiler to be installed by contractor. Heating system (other than boiler installations) to be designed and installed by contractor All installation work to be carried out by qualified operatives. In locations where moisture is present or may occur, use corrosion resistant fittings/fixings and avoid contact between dissimilar metals by use of suitable washers, etc. All equipment, pipework, components, valves, etc. to be fully accessible for maintenance, repair or replacement. Wall mounted pipe runs must not be buried in plaster or behind dry lining. Installation to be fitted with vents at high points and draining taps at low points to facilitate purging and draining.Where pipe runs in solid floors are unavoidable, they should be in access ducts with removable covers. Pipe routes within floors should be indelibly marked and noted on the flooring surface. Surface mounting of pipework is only acceptable with client approval. The heating and hot water system needs to be fully commissioned to ensure they are operating at maximum efficiency and that all controls work as indicated. The person whom carries out the commissioning must provide certificate confirming it has been carried out properly to both the client and the Building Control Officer. for all lead work to be in code 5 lead unless specified otherwise. To be in accordance with the LDA & LSA handbooks and recommendations. Allow for installing Code lead flashing dressed down over roof covering. Allow for coating all exposed lead work with patination oil on completion. Allow for all flashings as required in association with Velux Windows. 1:80 Fall 1:80 Fall
*Change to moisture resistance plasterboard at wet areas. Proposed External Wall (Boundary Line): Vertical DPM on existing brickwall, Void, Breather membrane, 18mm OSB 3 board, 100x50mm timber stud Void, 150x50mm timber stud (To SE's spec) with 120mm Ecotherm Eco-Versal insulation, Vapour control layer, 18mm plywood, 12.5mm Wallboard plasterboard, Skim coat to finish. U value = 0.23 W/m2k Proposed External Wall (Timber frame with timber cladding Facking brick): 102.5mm Facing brick, OR Horizontal timber cladding (To client's choice) 25mm Treated batten, Breather membrane, 18mm OSB 3 Board, Timber frame to SE's specification with 120mm Ecotherm Eco-Versal insulation, Vapour control layer, 25mm Service batten, 12.5mm Wallboard plasterboard, Skim coat to finish. U value= <0.23W/m2k Brick pier on both ends
Proposed Dormer Wall (front): Render on cement board, 25mm Treated batten, Breather membrane, 18mm OSB Board, Timber frame to SE's specification with 120mm Ecotherm Eco-Versal insulation, Vapour control layer, 45mm Service batten, 25+12.5mm insulated plasterboard, (to prevent steel beam cold bridging) Skim coat to finish. U value = 0.22 W/m2k 3510 3456 TBC by client 588 100 890 940 4810 940 865 Centre to proposed window below Centre to proposed window below CL CL Smoke Detector 750 Terminate in the loft area with Air Admittance Valve. 686mm leaf door 180 degree door swing: Jamb detail to be confirmed Door leaf and return dimensions to be confirmed
T4 P1 P2
CROFT ROAD PROPOSED PLANS SELSEY, WEST SUSSEX CLIENT : PRIVATE CLIENT APPOINTMENT : 2021 WORK STAGE: CONSTRUCTION
Status: Building Regulation Issued to: Client/LA Drawn by: KC Date: 18.11.20 Scale: 1:50 @ A1 Drg.No: ADS-004-BC-K
New
These drawings are to be used in conjunction with the structural engineer's calculations. All measurements and dimensions to be checked on site by contractors before work commences. All new steel lintels measued and installed with 150mm minimum over each end of opening. Existing Lintels and foundations subject to additional loading shall be exposed to determine their adequacy. Allow for all steelwork to be accordance with Structural Engineer's drawings and specifications. Steelwork to have minimum 100mm end bearing on concrete padstones as sized. All steel work to be shot-blast to SA2.5 after fabrication and painted with coat high build zinc phosphate (min DFT 125 microns). Steelwork in cavity walls to be painted with an additional coat of M.I.O. Steel levelling shims to be used as required and to be dry grouted upon installation. All in accordance with Structural Engineer's Specification. Provide insulated lintels in accordance with Structural Engineers details appropriate for spans and loads supported with suitable end bearings as specified by the lintel manufacturer with proprietary cross cavity trays over. Generally: Structural timber to be strength class C16 & C24, unless indicated otherwise. All structural and external timbers to be vacuum pressure impregnated with preservative to BS8417:2011 A12014. All sizes to be in accordance with Structural Engineers design/details on drawings. All cut timber to have cut ends treated. NB. Moisture content to comply with current TRADA Requirements. Allow for boxing of all exposed internal SVPs and waste pipes with 1no. layer of 15mm Gyproc Wallboard on s/w 50 x 50mm frame with access panels where required. Voids to be filled with acoustic mineral wool. Allow for new softwood architrave to new doors to match existing elsewhere in house. Allow for new timber window boards to new windows. Allow to supply and fit new Velux in sizes shown on drawings. Internal finish TBC with client.
Existing window to be blocked up with lightweight blockwork, and apply matching render finish externally and dot and dab plasterboard internally.
Utility room will require extractor ventilation rate of 30 l/s. Proposed extractor unit to achieve 8 l/s extraction rate in WC. Duct to terminate above the flat roof with a roof cap.
Existing Cavity Wall upgrade: Existing facing brick, Existing Cavity Existing inner blockwork, 15mm dot and dab, 60+12.5mm insulated plasterboard, Skim coat to finish. U value = 0.27 W/m2k Proposed extractor unit to achieve 15 l/s extraction rate in Bathroom. Ventilation duct to be terminate at the gable end Proposed rooflight to achieve an overall u value of 1.6w/m2k Proposed Internal Timber Stud Wall 12.5mm Wallboard plasterboard* with skim coat finish to both side, 100mm Timber stud with 65mm APR 1200 insulation. *Change to moisture resistance plasterboard at wet areas.
New staircase between ground floor to first floor to be of maximum pitch pitch of 42 degrees. Going to be a minimum of 220mm and Risers to be maximum of 220mm. Steps may have open risers if they have overlapping treads to a minimum of 16mm and the steps are constructed so that a 100mm diameter sphere cannot pass through open risers. Staircase to have clear unobstructed headroom of 2000mm over staircase. Where there is not enough space to achieve 2000mm headroom a reduced headroom of 1900mm to the centre of the flight and 1800mm to the lowest section will be acceptable. Handrail to be positioned 900mm above pitch line and 1000mm above floor line. IF the staircase is 1000mm or wider handrail to each side should be provided. Provide dedicated low energy light fittings with luminous efficacy of at least 40 lumens per circuit watt to achieve 100% of all light fittings to all new rooms. External lighting to have sensor to give automatic switch off during daylight hours Energy Efficient Lighting outlets to be fitted so they only take lamps having a Luminous efficacy greater than 40 Lumens per circuit-watt. These drawings are indicative only, electrical sub-contractor to design and specify new electrical installation that extends the existing system to suit the remodelling of the ground floor and extensions. N.B Client to approve electrical layout before installation and contractor to submit sample fittings for Client/ Architect approval before commencing installation. Allow for Builder's work in connection with Electrical Installation. All socket plates and light switches to be MK Logic plus white. Client to confirm prior to installation. Allow for supply and fitting of all recessed downlights. Samples of lights to be provided to client for approval.
Building Regulation Job Title 072/JLCR ADS Architectural Design Services (UK) Ltd Southsea, Hampshire 07712 516265
Proposed Ground Floor (Beam and Block): Final floor finish (To client's choice) 65mm Fibre reinforced screed, Vapour control layer, 70mm Ecotherm Eco-Versal insulation, Damp proof membrane, Beam and Block system to SE's specification, Min. 150mm void for ventilation U value 0.21 W/m2k Existing timber floor (vented) To be confirmed on site Existing airbrick Existing foundation Ensure sufficient ventilation between the existing void and the new void. Provision for additional airbrick for air flow. Proposed airbrick with telescopic vent
Aluminium wall coping with ventilation
Proposed Thermal Upgrade to Existing Pitched Roof: Existing roof tile, Existing treated batten, Existing roofing felt, 175x50mm C16 timber rafters to fixed against existing rafters at 400cc, New 120mm Ecotherm Eco-Versal filled within existing rafter (50mm void), Vapour control layer, 30+12.5mm Insulated plasterboard, Skim coat to finish. U value = 0.18W/m2k Proposed foundation to SE's specification Leave opening at intervals to allow air flow 2232 Assumed insulation within cavity (TBC) 2415 existing floor to ceiling heigh Ridge Beam with 15mm flange plate to sit on the underside of the existing ridge board 203x203UC60 min. 150 Code 4 lead flashing 25+12.5mm insulated plasterboard below steel beam 2337 Ventilation required at junction min. 75mm overlap 3510 CL 2035 25+12.5mm insulated plasterboard around the ridge beam
Steel beam T1 203x203UC46 fixed to T2 with angle cleat with 2no. M16 in each leg Existing Cavity Wall Existing Pitch roof
CROFT ROAD PROPOSED SECTION AND DETAILS [Vectorwork][Individual]
Proposed Flat Roof (Cold Roof): GRP roofing system, 22mm T&G OSB 3 board, Timber firring strip to create slope (1:80 fall), 150x50mm C24 Timber joist at 400 cc, -100mm Ecotherm Eco-Versal insulation between joists (Vented), -Vapour control layer, 50+12.5mm Insulated plasterboard, Skim coat to finish. U value 0.18 W/m2k
Proposed External Wall: (Blockwork with render finish) K-rend LW1 render system: 16-20mm one coat coverage (white), 100mm Medium dense blockwork, 100mm cavity with 90mm Ecotherm Eco-Cavity Full Fill insulation with 10mm residual cavity, 100mm Medium dense blockwork, -Vapour control layer, -15mm Adhesiv dot and dab, 12.5mm Wallboard plasterboard, Skim coat to finish. U value = 0.19 W/m2k
Existing wall line Existing rafter to be birdsmouth (max half depth) 2100 SSL to S/O 1100 Existing soffit vent Status: Building Regulation Issued to: Client/LA Drawn by: KC Date: 13.11.20 Scale: 1:20 @ A1 Drg.No: ADS-005-BC-F Building Regulation Job Title 072/JLCR ADS Architectural Design Services (UK) Ltd Southsea, AmendmentsDate by Proposed Section AA Proposed Section AA 1:20 Dormer revised KC 30.03 Roof pitch revised KC 16.04 New ridge beam design KC 06.05 Proposed Detail A1 1:5 Aluminium wall coping Treated firring 25mm Treated battens Air gap 25mm Fasica ventilators Or equivalent 25mm continuous opening for air flow Fitted with insect mesh at the opening. 25mm Treated battens Air gap 18mm OSB 3 board 50mm air gap between timber joists 18 25 100 15020 285
Top of the new timber joists to match the top of existing timber joists Proposed First Floor: Floor finish to client's choice, 22mm T&G chipboard flooring, -100mm APR 1200 insulation in between joists, 175x50mm C16 fixed against existing joists at 400 CC, 12.5mm Wallboard ceiling plasterboard, SKim coat to finish.
50mm air gap between timber joists Code 4 leading flashing 25mm Fasica ventilators Or equivalent 25mm continuous opening for air flow Fitted with insect mesh at the opening. 25mm Treated vertical battens Air gap 18mm marine plywood Timber fillet Code 4 leading flashing Proposed Detail A4 1:5 50mm air gap between timber joists Render carrier board Insect mesh at the opening. 25mm Treated vertical battens Air gap 18mm marine plywood Aluminium edge trim Timber firring Proposed Detail A2 1:5 Existing ridge board Drill 50mm holes at the existing ridge board for air flow 18mm marine plywood Half round ridge tile Timber battens 50mm air gap between timber joists Klober Roll-Fix (Dry ridge kit) Ventilates to BS5250 GRP to lap over the ridge Existingbatten roofing felt Existing roofing felt stop short 30mm before the apex New details added KC 01.06 Proposed Detail A3 1:5
Proposed beam and block system to be supported on the existing outer leaf blockwork/brickwork. (SE to confirm)
Proposed Flat Roof (Cold Roof): GRP roofing system, 22mm T&G OSB 3 board, Timber firring strip to create slope (1:80 fall), 150x50mm C24 Timber joist -100mm Ecotherm Eco-Versal insulation between joists (Vented), -Vapour control layer, 50+12.5mm Insulated plasterboard, Skim coat to finish. U value = 0.18 W/m2k R1 T1
Smart Visofold 1000 DV14, Standard outer frame, No cill FFL 30 65 150 100 52 31 82 Fibre reinforced screed with underfloor heating Floor insulation Floor Block Floor Beam 9mm Vitacer iWood Porcelain Tile (150x900mm) 3mm Ditra Matting 15mm Bedding (adjust to make level threshold to door frame) AS BUILT DPC LEVEL (TOP OF SCREED) AS BUILT BOTTOM OF LINTEL TOP S/O 2105 AS BUILT S/O 22 2127 DOOR S/O NEW DPC LEVEL 52 31 Smart Visofold 1000 DV14, Standard outer frame, No cill 82 20mm Quartz worktop 150 870 SSL to bottom of worktop Crown Imperial Rimano Carcase Dimenions Base: 720x555mm (870mm including leg) 838 SSL to S/O 20 AS BUILT DPC LEVEL (TOP OF SCREED) 1125 AS BUILT S/O 1000 AS BUILT SSL TO BOTTOM OF S/O AS BUILT BOTTOM OF LINTEL TOP S/O AS BUILT BOTTOM S/O 162 1287 WINDOW S/O Proposed Threshold Detail (Bi-fold Window) @ 1:5 Proposed Threshold Detail (Bi-fold Door) 1:5 Status: Building Reg Issued to: Client/LA Drawn by: KC Date: 13.11.20 Scale: 1:5 @ A1 Drg.No: ADS-012-BC-A Building Regulation Job Title 072/JLCR ADS Architectural Design Services (UK) Ltd Southsea, Hampshire 07712 516265 AmendmentsDate by Proposed Threshold details As built added KC 06.09 CROFT ROAD PROPOSED SECTIONS [Vectorwork][Individual]
Proposed foundation to SE's specification Trench block Paving slab Timber cladding soffit Proposed External Wall Horizontal timber cladding (To client's choice) 25mm Treated batten, Breather membrane, 18mm OSB 3 Board, Timber frame to SE's specification with 120mm Ecotherm Eco-Versal insulation, Vapour control layer, 25mm Service batten, 12.5mm Wallboard plasterboard, Skim coat to finish. U value= 0.23W/m2k K-Rend Silicone TC15 render system 2: 1.5mm K Rend Silicone TC15 render (white fine texture), K Rend TC Primer, 4-6mm K Rend HP12 Base, 1mm K Rend Alkali Resistant mesh, 12.5mm Knauf Aquapanel Exterior Cement Board. Rectangular hopper 68mm uPVC RWP Aluminium edge flashing Create opening for ventilation Through wall outlet for surface water discharge Proposed soldier course facing brick 2337
Blockwork
CROFT ROAD PROPOSED SECTION AND DETAILS [Vectorwork][Individual]
AmendmentsDate by
Proposed External Wall: (Blockwork with render finish) K-rend LW1 render system: 16-20mm one coat coverage (white), 100mm Medium dense blockwork, 100mm cavity with 90mm Ecotherm Eco-Cavity Full Fill insulation with 10mm residual cavity, 100mm Medium dense blockwork, -Vapour control layer, -15mm Adhesiv dot and dab, 12.5mm Wallboard plasterboard, Skim coat to finish. U value = 0.19 W/m2k
Proposed External Wall: (Blockwork with vertical timber cladding) Vertical timber cladding, 25mm Treated batten, 25mm Treated counter batten, 100mm Medium dense blockwork, -Vapour control layer, -15mm Adhesiv dot and dab, 12.5mm Wallboard plasterboard, Skim coat to finish. U value = 0.19 W/m2k Aluminium wall coping with vent Proposed foundation to SE's specification Vertical brickwork
Proposed Ground Floor (Beam and Block): Final floor finish (To client's choice) 65mm Fibre reinforced screed, Vapour control layer, 70mm Ecotherm Eco-Versal insulation, Damp proof membrane, Beam and Block system to SE's specification, Min. 150mm void for ventilation U value = 0.21 W/m2k
Timber wall plate sits below top of of joists by 50mm for ventilation 1100 S/O 1000 SSL to S/O Proposed Section B 1:20
Proposed airbrick with telescopic vent Flat roof timber canopy to be fixed with joist hanger
Proposed Flat Roof (Cold Roof): GRP roofing system, 22mm T&G OSB 3 board, Timber firring strip to create slope (1:80 fall), 150x50mm C24 Timber joist at 400 cc, -100mm Ecotherm Eco-Versal insulation between joists (Vented), -Vapour control layer, 50+12.5mm Insulated plasterboard, Skim coat to finish. U value = 0.19 W/m2k 56 Min. 50mm of timber firrings at this for ventilation T3 3no. 50x150 C24 fixed to T4 with joist hanger
New beam and block KC 16.04 Ceiling height revised KC 06.05 50mm air gap between timber joists Insect mesh at the opening. 25mm Treated vertical battens Air gap 22mm T&G OSB board Timber firring Aluminium edge trim Render on render carrier board Make opening for air flow 18mm OSB 3 board GRP roof Proposed Detail B1 1:5 New details added KC 01.06
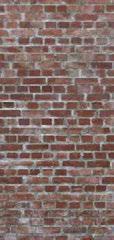

Existing Timber Fence 100x100mm Timber post Existing Timber Fence Post 2 no. 150x50mm Timber Joist 150x50mm Timber 110
Timber cladding soffit to client's choice (TBC) Aluminium drip edge trim Drainage gap Proposed Section Detail 1:5
724Joist
Status: Building Regulation Issued to: Client/LA Drawn by: KC Date: 07.09.21 Scale: 1:20 @ A2 Drg.No: ADS-012-BC Building Regulation Job Title 072/JLCR ADS Architectural Design Services (UK) Ltd Southsea, Hampshire 07712 516265
CROFT ROAD PROPOSED FRONT PORCH DRAWING [Vectorwork][Individual]
AmendmentsDate by Proposed Porch d h
100x100 Timber post Timber cladding soffit to client's choice (TBC) Render carrier board with matching render system 400x400 mm Proposed Section BB 1:20
Timber wall plate to be fixed with resin anchor Timber wall plate to be fixed into the as built timber frame Proposed Ground Floor Plan 1:20 100x100 Timber post Canopy build-up: GRP roofing, 18mm Marine Plywood, Treated timber firrings (1:80 gradient), 150x50mm Timber Joists @400 c/c, Timber Cladding to client's choice. Render carrier board with matching render system Code 4 lead flashing 150mm above canopy 400x400 mm 1:80 fall
Proposed Section AA 1:20 Section AA Section BB 100x100 Timber post Render system Render carrier board 2 no. 150x50mm Timber Joists Treated timber firrings 18mm Marine plywood deck GRP roofing
Existing pipe Pipe Invert level at the end point: 545mm from Existing DPC
This section of pipe will run below the block, between the beam (Runs parallel with the floor beams)
This section of pipe will run below the block, below the beam 2295 670 782 220 Distance: Distance:2303mm 6358mm Existing pipe Pipe Invert level at the end point: 545mm from Existing DPC Existing manhole Invert level: 648mm from Existing DPC Built brick and block 45.00°wall45.00°Distance:1757mm This section of pipe will run below the block, below the beam
Proposed Section LAYOUT
Proposed Ground Floor Existing DPC level SVP SVPA B 648 545 Existing manhole Existing pipe 2303 Y connection to SVP B 6344 End of existing pipe to SVP A 1in40 Fall Existing pipe 782 290 Floor build up 65mm fibre reinforced screed, 70mm Ecotherm floor insulation, -155mm beam and block, (100mm block & 155mm beam) 1757 Y connection to existing pipe Y connection point (45degree) 23
CROFT ROAD PROPOSED DRAINAGE
Existing manhole Invert level: 648mm from Existing DPC Built brick and block wall SVP A (Original proposed) SVP B (Alternative) 45.00°45.00°Distance:1757mm
This section of pipe will run below the block, below the beam
[Vectorwork][Individual]
Proposed Ground Floor 6344 2295 670 782 220 Distance: Distance:2303mm 6358mm
This section of pipe will run below the block, between the beam (Runs parallel with the floor beams)
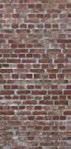

ALDWICK ROAD PHOTOREALISTIC CARD MODEL RENDER [Individual] [Sketchup + Blender render]BOGNOR REGIS, WEST SUSSEX
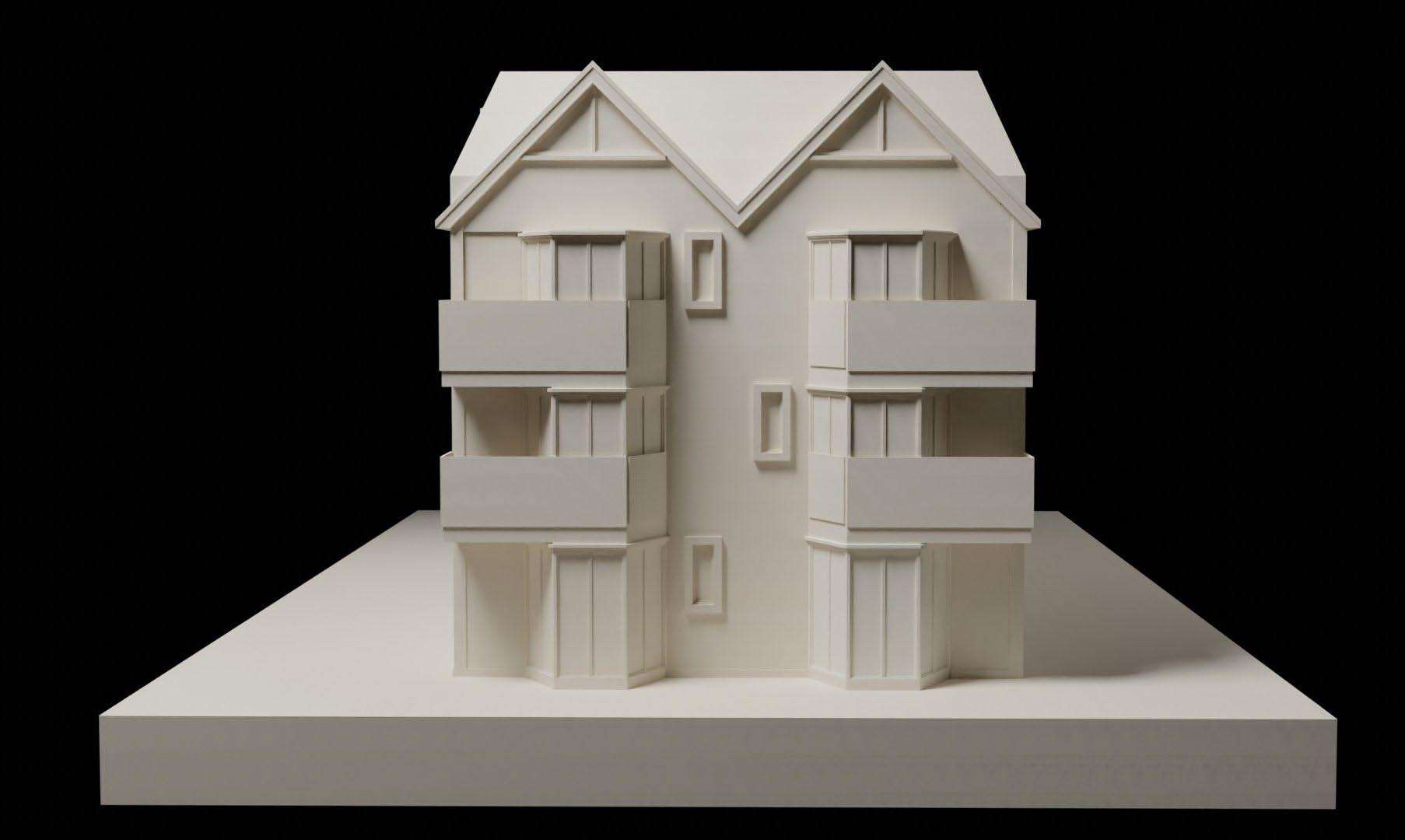
ALDWICK ROAD PHOTOREALISTIC CARD MODEL RENDER [Individual] [Sketchup + Blender render]BOGNOR REGIS, WEST SUSSEX
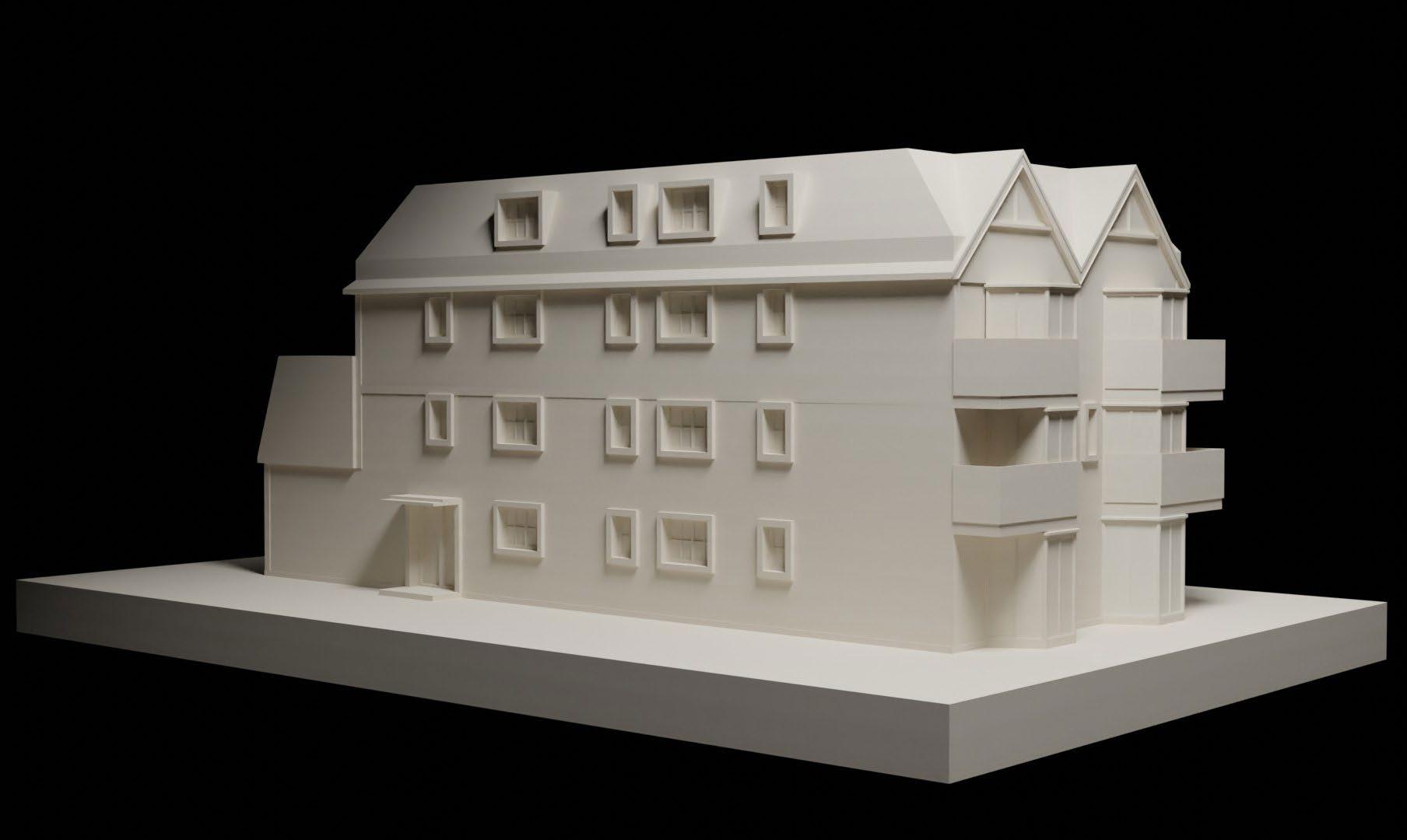
ALDWICK ROAD PHOTOREALISTIC CARD MODEL RENDER [Individual] [Sketchup + Blender render]BOGNOR REGIS, WEST SUSSEX
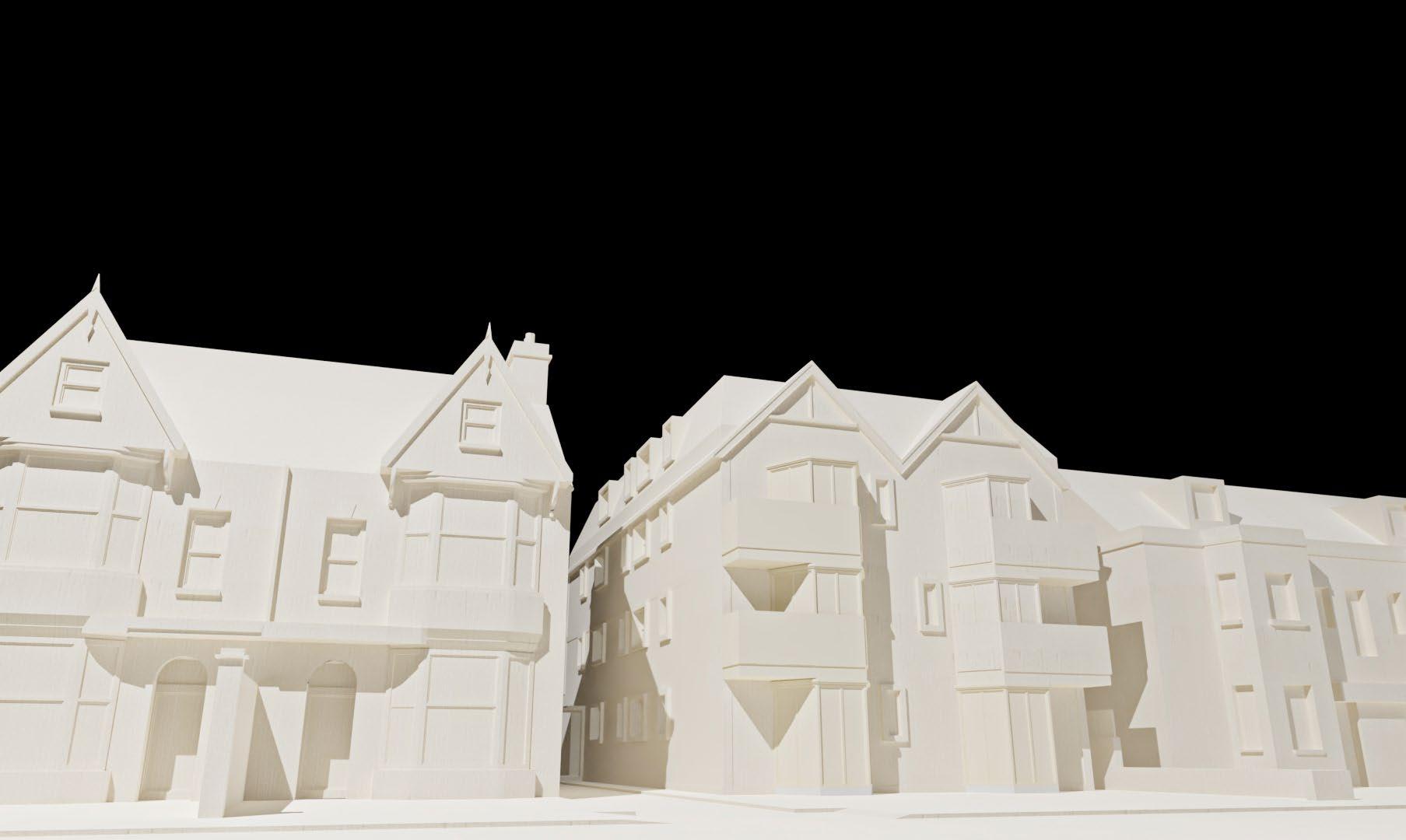
ALDWICK ROAD VISUAL [Individual] [Sketchup + Blender render + Photoshop]BOGNOR REGIS, WEST SUSSEX
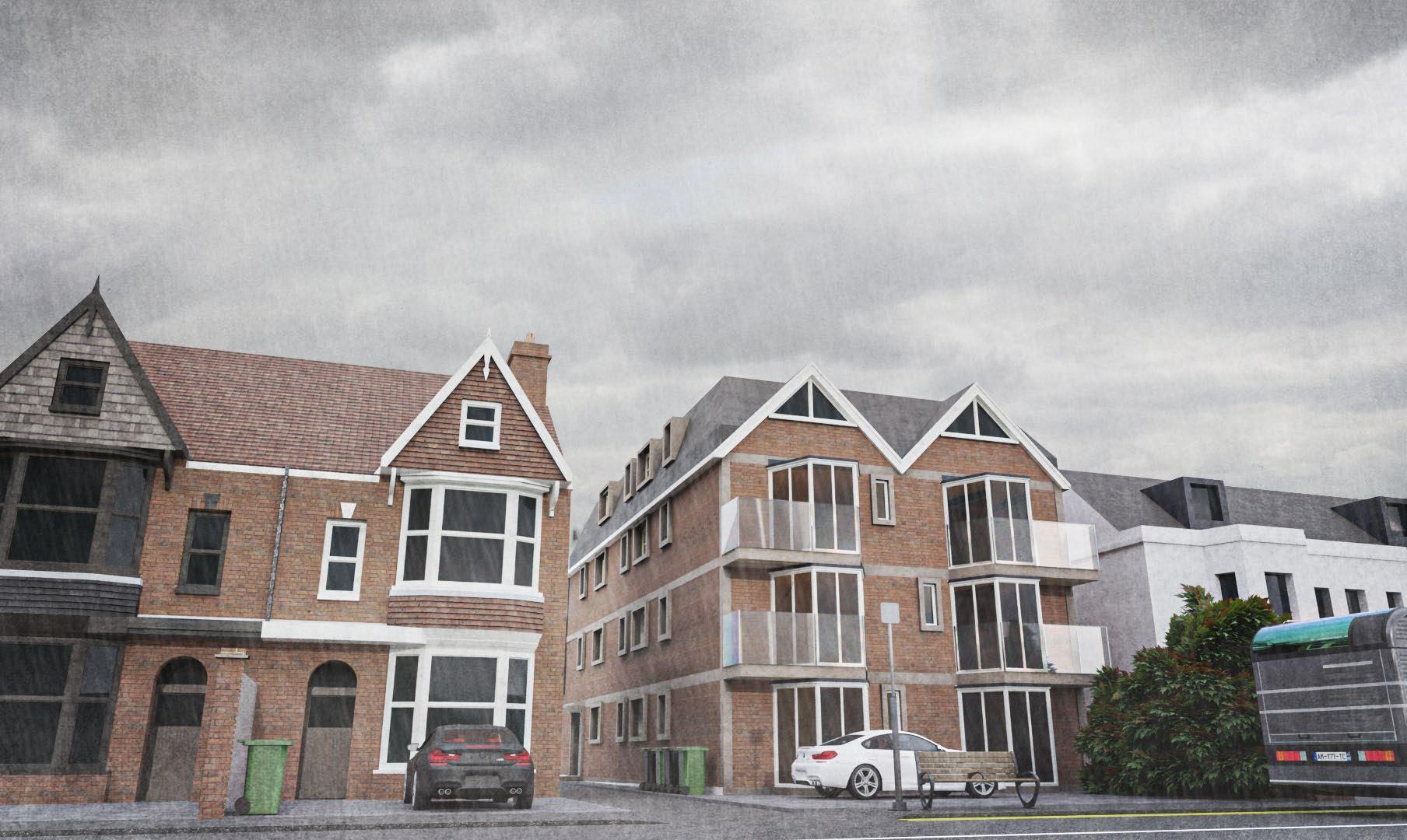
