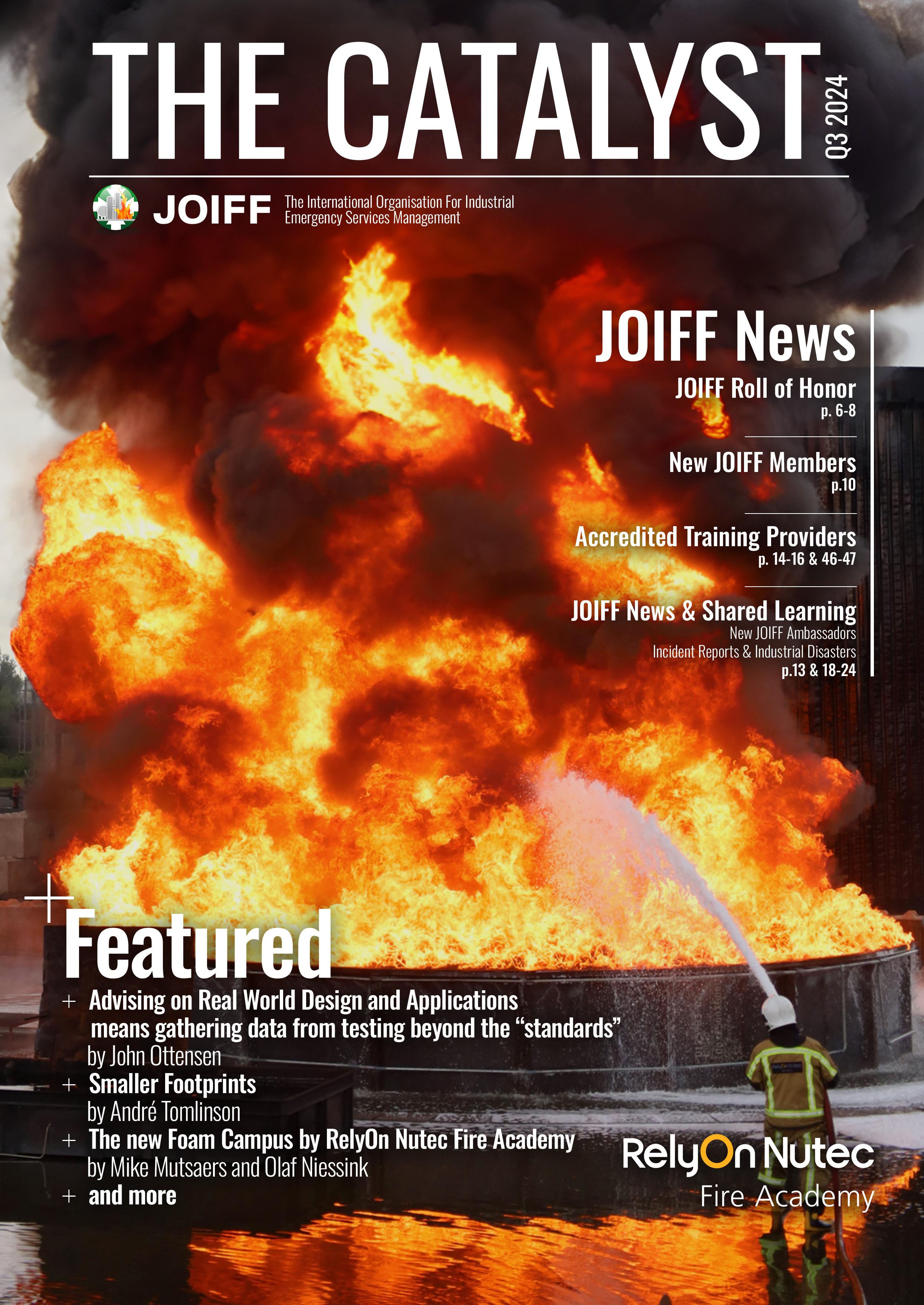
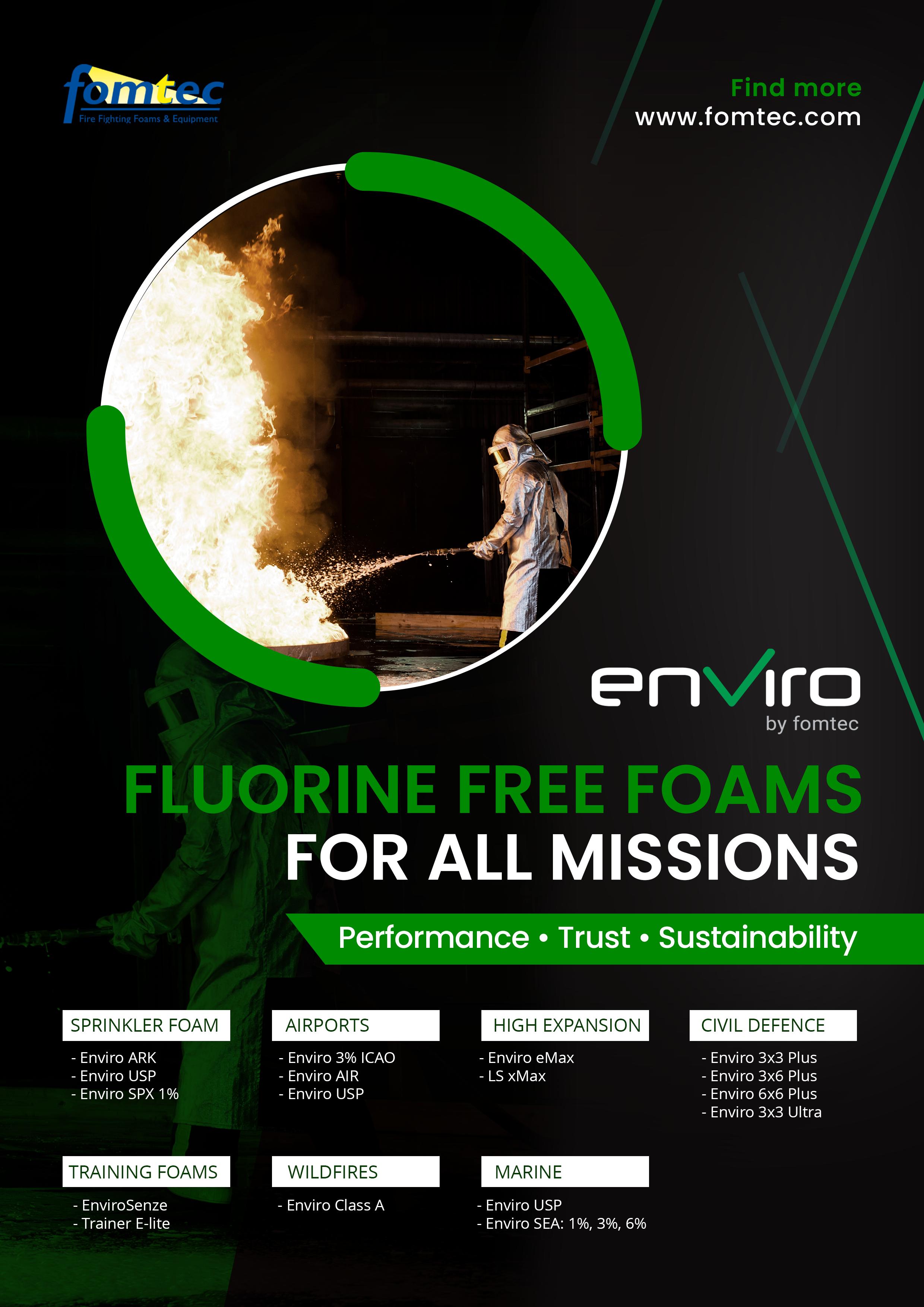
JOIFF, the International Organisation for Industrial Emergency Services Management is a not-for-profit organisation dedicated to developing the knowledge, skills and understanding of personnel who work in and/or who are required to provide emergency response to incidents In Industry, primarily High Hazard Industry, with the aim of ensuring That risks in Industry are mitigated and managed safely.
The 4 pillars of JOIFF aiming to support its Membership in preventing and/or mitigating hazardous incidents in Industry are: Shared Learning – improving risk awareness amongst JOIFF Members; Accredited Training – enhancing operational preparedness in emergency response and crisis management; Technical Advisory Group – raising the quality of safety standards in the working environment of High Hazard Industry and Professional Affiliation – networking and access to professionals who have similar challenges in their work through Conferences and other events and the prestige of being a member of a globally recognised organisation of emergency response.
Full Members of JOIFF are organisations which are high hazard industries and/or have nominated personnel as emergency responders/hazard management team members who provide cover to such organisations. Commercial Members of JOIFF are organisations that provide goods and services to organisations in the High Hazard Industry.
JOIFF welcomes enquiries for Membershipplease contact the JOIFF Secretariat for more information.
JOIFF CLG is registered in Ireland. Registration number 362542. Address as secretariat.
JOIFF is the registered Business Name of JOIFF CLG.
The Catalyst is the Official magazine of JOIFF, The International Organisation for Industrial Emergency Services Management. The Catalyst is published Quarterly – in January, April, July & October each year. The JOIFF Catalyst magazine is distributed to all JOIFF members and member organisations worldwide. The Catalyst magazine is published by ENM Media on Behalf of JOIFF.
Publisher & Advertising Sales:
Paul Budgen
Tel: + 44 (0) 1305 831 768
Email: pbudgen@edicogroup.net
Design & Production: Christelle Sakr
Tel: +44 (0) 1305 831 768
Email: christelle@edicogroup.net
Welcome to new and existing members of JOIFF to this quarter’s edition of the Catalyst e-magazine. Our aim is to bring you high-quality articles on relevant technical issues and current and new developments in Emergency Services Management. I would like to thank all those who have contributed articles and a big thank you to our advertisers for your valued support, we cannot do all this without you. Thanks also to our publishers ENM.
These are exciting times for JOIFF as we strive to build upon the 4 established pillars that are the foundation of the organisation. We are striving to extend our outreach to existing members, and we are actively reaching out to potential new members around the globe, via our JOIFF Ambassadors. Please take some time to check out the JOIFF website. I hope you are finding it much easier to navigate to find the wealth of information available within the Members’ area, particularly recent incidents, and incidents of note.
Shared learning is one of the critical 4 pillars of JOIFF. We hope that the JOIFF website and our regular email circulations will deliver the information you need, and as always, we would appreciate your feedback in furthering JOIFF’s basic principles in keeping our people safe.
For myself and fellow directors, we are focused on supporting JOIFF Technical Training centres offering JOIFF Accredited courses. Please can I ask you to engage with our Accredited Training Providers and explore the full range of JOIFF accredited courses they offer and again, please provide any feedback that you may have, particularly in advancing courses designed to meet the new and increasing challenges in terms of loss prevention and emergency response.
Finally, I would like to draw your attention to forthcoming events in September and November that we hope you can support. We have arranged a great list of speakers covering a full range of topics that we are sure will be of interest to you. There will be plenty of time built into the schedule to meet industry subject matter experts, friends and the all-important networking opportunities.
The JOIFF Seminar to be held at the National Maritime College of Ireland (MNCI) will be held in Ringaskiddy, Cork on 3rd/4th September, then the Foam Summit and Exhibition to be held in London on 12th and 13th November. We hope to arrange more webinars, please can anyone or an organisation bring forward a topic that would be of interest to our membership, we will help to facilitate the event with you.
Please remember, we are all stronger together and with your support and continued engagement, we can build an even stronger JOIFF community for the benefit of all - above all, knowledge is key in an uncertain world.
So, please enjoy this edition of the Catalyst, and I repeat, if you would like to get involved or contribute to JOIFF in any way, then please reach out to us.
Kevin Deveson MJOIFF, GIFireE
Chairman of JOIFF
Email: kevin@joiff.com
Please visit www.joiff.com
Post-nominal qualifications of a person, provide recognition as a professional, demonstrating commitment to professional standards, integrity, ethics and continuous professional development.
During Q 2 2024, the following persons were awarded JOIFF post-nominal qualifications:
The following persons successfully completed the programme and were awarded the post nominals Dip.JOIFF:
Abdullah Al Alawi • Dip JOIFF
Unity Fire and Safety Services LLC
Oman
Al Julandi Badar Al Qarni • Dip JOIFF
Unity Fire and Safety Services LLC
Oman
Khormor LPG Plant, Crescent Petroleum, Kurdistan Region of Iraq
In 2013 Dara joined the Khormor Fire department of Crescent Petroleum/Dana Gas at the Khormor Gas Plant in Kurdistan, Iraq and is currently HSE technician team leader. On successful completion of the JOIFF Accredited Technician programme and receipt of the JOIFF Post Nominals Tech.JOIFF Dara said:
“WhenIjoinedthefiredepartment,Iwasthrilledtostartlearningaboutfireservicefollowing the NFPA 1001 standard level 1. I continued my journey by completing NFPA 1001 level 2 and further certifications such as NFPA 1002 pump operator, fire officer, rope rescue level 1, air bag vehicles extrication, fire instructor, SCBA training, fire extinguisher, working at height, and confined space training. During my time as a Fire Fighter in Khormor, I had the opportunity to act as a Fire Captain in the absence of the designated officers.
I am grateful for the opportunity to expand my knowledge and experience through the JOIFF technician course, and I would like to express my gratitude to Darren Kirby for his dedication to the Khormor fire team. I am passionate about learning and honing new skills”.
Khormor LPG Plant, Crescent Petroleum, Kurdistan Region of Iraq
In 2019, Zana joined the Khormor Fire Department of Crescent Petroleum/Dana Gas at the Khormor Gas Plant in Kurdistan, Iraq. On successful completion of the JOIFF Accredited Technician programme and receipt of the JOIFF Post Nominals Tech.JOIFF Zana said:
“Since I joined Crescent Petroleum as a firefighter I have continuously expanded my knowledge and skills through daily experience, studying NFPA standards with my chief, and learning from my seniors.
My dedication to my career led me to the position of ERT Team Leader, where I now lead emergency response teams, teach, and guide new firefighters. To support my career, I have studied NEBOSH IGC and NEBOSH Process Safety Management, which has equipped me with the knowledge to understand and manage process risks effectively. I deliver various training programs, including working at heights, confined spaces, fire extinguishers, SCBA and fire hydrant awareness training. Additionally, I develop emergency preparedness plans, such as rescue plans for working at heights and confined space activities.
The JOIFF training has been instrumental in helping me organize and consolidate my knowledge and experience, ultimately bringing out the best in me”.
Khormor LPG Plant, Crescent Petroleum, Kurdistan Region of Iraq
Halo is Emergency Response Team Supervisor and dedicated Emergency Response and Technical Rescue Specialist within the Health, Safety and Environmental (HSE) Department of Crescent Petroleum/Dana Gas at the Khormor Gas Plant in Kurdistan, Iraq. On successful completion of the JOIFF Accredited Leadership 1 (Team Leader) programme and receipt of the JOIFF Post Nominals JOIFF.ERTL, Halo said:
“I have a demonstrable record of success, with over 14 years in the Oil & Gas industry. I am a self-starter with proven experience in developing, managing, and leading teams in challenging circumstances.
Thanks to JOIFF for a great and very fruitful course. I have benefited a lot and gained new technical knowledge that will assist me in developing proactive preventive and protection measures in my line of work as Emergency Response Supervisor.
I recommend JOIFF courses for those who work in the line of Emergency Services and Firefighting if they wish to take their career to the next level and are eager to preserve and protect people, property, and the environment.”
Khormor LPG Plant, Crescent Petroleum, Kurdistan Region of Iraq
With over 11 years of expertise in emergency services encompassing incident management, firefighting, confined space rescue, RTC, low/high angle rope rescue, medical first response and Hazmat material handling, Nabaz currently holds the position of ERT Supervisor (Fire Chief) at Crescent Petroleum/ Dana Gas at the Khormor Gas Plant in Kurdistan, Iraq. On successful completion of the JOIFF Accredited Leadership 1 (Team Leader) programme and receipt of the JOIFF Post Nominals JOIFF.ERTL, Nabaz said:
“Prior to joining JOIFF, I led my team in training adhering to NFPA standards, despite the absence of formal recognition for the training. I am delighted to have become a part of JOIFF and successfully completed their leadership course. This has equipped me with a strong foundation and the necessary support from JOIFF to effectively lead emergency situations and ERT training, I would like to express my gratitude, particularly to my assessor, Darren Kirby”.
Security Fire and Safety Officer, United Nations Peacekeeping Operations, MONUSCO - Security Section Kinshasa, Onatra MONUSCO Fire Station, Democratic Republic of the Congo
Renato successfully completed the JOIFF Diploma in October 2022 and immediately started to study the JOIFF Technician which he successfully completed in November 2023. He followed this by registering for the JOIFF Accredited Leadership 1 programme (Team Leader) which he successfully completed in February 2024 and became the first person to awarded the Postnominal JOIFF.ERTL. He then immediately started working on the JOIFF Accredited Leadership 2 Officer programme which he successfully completed on April 2024. On gaining the award and being the first person to receive the post nominals JOIFF ERO, Renato commented:
“I am writing to express my gratitude for the opportunity to complete the Leadership 2 course at JOIFF. The experience and knowledge gained during this course have been invaluable in enhancing my leadership skills and professional development. Throughout the duration of the Leadership 2 course, I have acquired a deeper understanding of effectiveleadershipstrategies,communicationtechniques,anddecision-makingprocesses.The course content was comprehensive and well-structured, providing me with practical insights that I can apply in my role.
I am confident that the skills and competencies acquired through the Leadership
2 course will positively impact my performance as a leader and contribute to the success of my team and organization. I look forward to implementing the knowledge gained and continuing to grow as a leader in the field of fire service.
Once again, thank you for the opportunity to participate in the Leadership 2 course at JOIFF . I am grateful for the experience and look forward to applying the learnings in my professional endeavors”.
The Directors of JOIFF extend congratulations to all those in the JOIFF Roll of Honour.
During April, May and June 2024, the JOIFF Board of Directors were pleased to welcome the following new Members:
DETKA Oktató Ltd • Debrecen, Hungary
represented by Lívia Borbély, Marketing and PR Manager and Martin Juhász, Sales Manager. DETKA specialises in training mostly for ARFF services and they also provide industrial fire and emergency medical service, and a wide range of other activities including training of airport support staff, workshop organizations, fire protection, counseling etc.
In the DETKA training centre, they operate an Airbus A350-900, an Airbus A320-200 and a Eurocopter EC135 “live-fire” simulators which are the same size as the original ones in all aspects. They also have a two-storey SCBA confidence maze and they provide training with VR simulation equipment.
Fire Protection Association of Southern Africa
represented by Marius Atterbury, Chief Executive Officer, Christine van der Westhuizen, Audit, Risk, Compliance & Office Manager, Kyle Jordaan, Head of Technical and Kennedy Sefadi - Insurance Projects Manager. The Fire Protection Association of Southern Africa was established in 1973 as a non-profit technical advisory and training organisation and operates mainly on a membership basis. Today the role of the FPASA covers fire safety Education, Information, Advice, Consultancy and Training (Fire College).
The Fire College is a professional training centre dedicated to assist in the reduction of life and property losses in the Southern African region. It provides training on request of FPASA members and non-members alike, and in addition provides standard training programmes to suit the broad spectrum of industrial, commerce, institutional and local authority requirements. The Library offers a range of fire safety management consulting services to members and clients as well a short-term insurer specific services as part of the FPASA’s Insurer Fire Impact Reduction Strategy (InFIReS) initiative.
Process Decontamination Systems Ltd • Nantwich,
represented by Matt Calveley, Senior Business Development Manager. ProDecon® is a leading provider of turnkey chemical cleaning services working across all industry sectors to support their clients most complex challenges. ProDecon® has partnered with Tetra Tech to leverage a combination unparalleled PFAS expertise together with extensive experience in implementing robust decontamination services to the emergency services sector. Through continued development of their procedures, application and analytical methods, the team developed a cost-effective, market leading PFAS decontamination solution. Their mobile solution has successfully decontaminated PFAS from a wide range of foam systems including tanks, jetties, fire engines and boats, using bespoke solutions to lower transition costs whilst ensuring minimal downtime of critical infrastructure.
represented by Einar Johannesson, Business and Operations Manager, Keith Ellis Training Manager, Lee Mitchell, Lead Emergency Response and Prakash Murugesan, QA/QC Lead. Established in 2001, Qatar International Safety Centre (QISC) is dedicated to providing comprehensive training solutions aligned with various accreditation standards and tailored to meet the unique needs of each client. Encompassing Major Emergency Management, their capabilities ensure organizations are equipped to effectively respond to a diverse range of emergency scenarios. Furthermore, their services extend to Fire Prevention, Health and Safety, Marine and Survival, and Road Safety training, addressing crucial aspects of safety preparedness.
Beyond training, QISC offers Specialist Manpower Supply, HSE Consultancy, and Equipment Supply, delivering holistic support to enhance safety performance and ensure regulatory compliance.
Following a recent audit, JOIFF is proud to welcome Qatar International Safety Centre as a JOIFF Accredited Training Provider – see picture in this edition of The Catalyst.
The Directors look forward to the involvement of our new and existing Members in the continuing development of JOIFF.
Three simple steps to a smooth fluorine free foam transition
We will support you through your transition to fluorine free foams.
Our simple three-step approach puts customers in control to meet the new environmental regulatory requirements based on your timescales and budgets.
Angus Fire’s deep technical expertise and world-wide reputation is trusted by global organisations operating in high hazard environments.
Our full range of fluorine free firefighting foam products and equipment is matched by our expert consultation and support.
We are your trusted fluorine free foam transition partner.
Find out more at angusfire.co.uk/f3t Or email
f3t@angusfire.co.uk
With the Transition to Fluorine Free foam now a fact for the majority of the Global High hazard Industry due to Environmental legislation and Supply Chain concerns.
The JOIFF International Foam Summit 2024 aims to provide provide clarity on all aspects on the process of Foam Transition.
The Challenges of Transition to SFFF • Proportioning & Hardware • Foam Transition End User • Case Studies • Standards & Testing • Decontamination • Performance of SFFF • Regulatory Updates from all major markets
In addition to the Conference presentations from Subject Matter Experts from around the world, we will also be providing a platform for suppliers to meet and discuss the transition to SFFF.
The JOIFF International Foam Summit 2024 also provides a unique opportunity to meet, discuss and learn from Peers and Foam Transition Experts in person.
If you are involved with foam transition now or are involved in programmes to transition to SFFF in the next few years, this is a must-attend event to get the facts and meet the experts.
The JOIFF Directors are proud to announce that they have appointed the following staunch member supporters of JOIFF as Ambassadors to represent and promote JOIFF in the following Regions:
During Q2 2024, successful JOIFF accreditation audits were carried out for:
Kft. • Hungary
FER Team being presented with their JOIFF certificate of accreditation
Left to right: András János Polka, Lead technician; Botond Czenki, Managing Director; István Szabó, Fire-fighting, Rescue & Service Leader (COO); Péter Halmos, Lead of fire-fighting & rescue
HSSL Safety Systems Limited • Trinidad and Tobago
HHSL Team being presented with their JOIFF certificate of accreditation
Left to right: Satesh Ramjass –General Manager; Holly Ann Duncan – Emergency Response Co-ordinator; Gerry Johnson – JOIFF Auditor; C. Agna Da Costa Vieira – Director/ Administration; Anthony VierraManaging Director; Sue-Anna Seetal – Quality and Compliance Co-ordinator; Kevin Deveson – JOIFF Auditor.
Kiwi Resource Protection Company Ltd. • Thailand
Kiwi Resource Protection Team with their JOIFF certificate of accreditation
Left to Right: Akarinth Addison, Sales & Marketing Manager – Firefighter; Yuthaphan Saesong – Service Technician / Firefighter; Pakawat Pomsaka – Service team lead / Firefighter; Siamrit Supavakul – International Training Manager / Senior instructor; Pongsakorn Leknawin – ER Team Lead / Senior instructor; Steve Fraser – Managing Director; Sakda Raemwanith – General Manager / Firefighter / Instructor; Pankorn Ratchaneweli – Fire engineer / Firefighter; Kiattisak Srijunhat – Thailand/Laos/Myanmar Training manager / Senior instructor; Sommai Khamda - Service Technician / Firefighter; Adian Hebblethwaite – Service manager / Firefighter.
Presentation of certificate of accreditation.
Lee Christie, Fire & Safety Leader, Prax Lindsey Oil Refinery, Gerry Johnson JOIFF Auditor
Qatar International Safety Centre Team with their JOIFF certificate of accreditation
Left to right: Lee Mitchell, Lead Emergency Response, Prakash Murugesan, QA/QC Lead, Gerry Johnson, JOIFF Auditor, Einar Johannesson, Business and Operations Manager, Mark Feldman, JOIFF Auditor, Keith Ellis, Training Manager.
Kiwi Resource Protection (KRP) is an internationally recognized emergency management and emergency response company located in Rayong in the heart of Thailand’s Oil, Gas, chemical and manufacturing hub. We have been providing emergency management, response, preparation, recovery, and equipment maintenance services to the industrial and commercial sectors in the Aisa Pacific region since 1995.
Led by Managing Director Steve Fraser and company General Manager Sakda Raemwanith, our team comprise of both permanent and contracted local and international staff who are highly experienced and well regarded in all hazard’s crisis management, emergency management and hands on emergency response and maintenance services for oil and gas manufacturing facilities, storage tanks, well control, oil spill, opencast and underground mining, wind turbines, marine, aviation, and specialist rescue.
Our Thailand based equipment service team are certified to inspect and maintain some of the world’s most wellknown manufacturers equipment and are a critical part of our emergency response team. Our workshop and mobile service facilities are fitted out with equipment to provide a full range of services from hydrostatic testing, extinguisher refilling, hose pressor testing, and calibration services for breathing air equipment and breath alcohol detection devices.
Becoming a JOIFF accredited training provider has opened new opportunities for KRP. Our existing and new customers, who are typically ISO certified companies have taken on the JOIFF accreditation training courses/programs with open arms. As one customer recently said:
Having KRP now JOIFF accredited has given us and our customer peace of mind that we have contracted the best company in the region to provide training to our staff that is current, safe, and quality controlled.
Contact information is available at www.kiwirp.com and if you have any questions about KRP’s JOIFF accredited training courses/programs, please don’t hesitate to drop us an email or give Steve a call at Office: +66 38 016 743
Mobile : + 66 99 0030 873
KRP is a partner company of Dynamic International who have offices in Thailand, China, Dubai, Libya, and Canada. www.der-int.com.
This shared learning event will look at aspects of High Hazard Emergency Management currently affecting Ireland.
This Summit provides a unique opportunity to meet and discuss these important matters with senior professionals from the Irish High Hazard Industries. All Irish COMAH and Seveso regulated organisations plus Ports, Airports and Regional Fire Departments will be invited to attend. We will have subject matter experts from Ireland and international experts presenting.
or scan QR code
JOIFF’s regular Shared Learning Global Incident Reports to Members are available on the JOIFF Website. Below is a list of just some of the incidents that took place during Q1 and Q2.
• Workers evacuate factory due to fire in chemical factory.
• Gas pipeline rupture at aging offshore platform off Victorian.
• Major fire at Paranagua Port.
CAMBODIA
• 20 killed many injured in ammunition explosion.
• Toxic smoke spreads when fire occurs tanks of crude oil in Manville.
• Engine room fire in cargo ship in St Lawrence river.
• 9 killed 46 injured following explosions at a military ammunition depot.
• 8 killed in dust explosion in Changzhou City.
• 10 killed in accident at a coal mine in Henan province.
• 2 killed, 4 injured following chemical plant blast in Ningxia region.
• Fire incident in Oil Refinery in Northern France.
• 1 person critically injured in blast in oil products factory in the port of Sete.
• 2 injured, 5 missing in fire outbreak in offshore platform
• 10 killed, 64 injured in explosion at chemical factory in city near Mumbai.
• 6 killed in fire in chemical plant in Jaipur.
• 4 injured in fire Oil Refinery in Khargone.
• 7 injured in factory explosion in Delhi.
• Significant fire at oil refinery in Balikapan.
• Major fire in chemical factory in Thane.
• 1 killed 3 injured in fire in Refinery in Bandar Abaas.
• 3 injured in incident at oil refinery in Duhok, Northern Iraq.
• 3 killed, 5 injured in explosion in hydroelectric plant south of Bologna.
• 1 person sustained burns in fire at Idemitsu refinery.
• Major fire at refinery in Erbil.
KUWAIT
• Fire in Al Zour refinery.
MEXICO
• 1 killed, 2 injured in fire on offshore platform in Gulf of Mexico.
MONGOLIA
• 6 killed 14 injured when truck carrying LNG collides with a car.
• 6 killed 4 injured in fire inside a coal mine.
KUWAIT
• 14 injured when fire breaks out at Al Shuala refinery
• Fire in Dangote refinery, Africa’s newest and largest refinery.
• 3 killed, 77 injured in massive blast in Oyo.
• Fire near Gbaran Gas facility extinguished.
• Fire at Oil Refinery in Mongstad extinguished.
• Gas leak prompts evacuation of majorLNG facility in Hammerfest.
• Fire on Statfjord A oil and gas platform in the north Sea.
PAKISTAN
• 11 killed in due to suffocation in coal mine in Quetta.
• Fire in Oil Refinery in Tuapse in the Krasnodar region.
• Explosion at gas terminal in St Petersburgh.
• Major fire in gas pipeline in Siberia.
• 9 injured in Chemical Plant explosion in Shakhty.
• 10 injured when Boeing 737 skidded off runway near Dakar.
• 5 killed due to toxic gas poisoning in sewage treatment plant at Casteldaccia.
• 2 killed 3 injured in factory due to exploding batteries.
• 7 crew members lost at sea when tanker overturned off coats of Japan.
• 2 killed, more injured as a result of hydrogen sulphide gas leak In SalamanCA.
• 4 killed, 13 injured, 19 unaccounted for at massive blaze in residential buildings.
• Fire consumes the Khartoum Oil Refinery, firefighting supplies exhausted.
• 13 killed in explosion in sugar factory in Morogoro region.
• Blaze consumes Phetchaburi storage factory.
• 1 killed 4 injured in explosion/fire aboard an oil tanker moored on Mae Klong river.
• 19 killed in explosion at a fireworks factory in Suphan Buri.
• 160 injured in explosion and ammonia release in Con Buri province.
• 1 killed in explosion in Rayong.
• 35 injured in fire due to gas leakage during refilling cylinders in gas depot.
• Resident instructed to shelter-in-place after chemical incident in Wales.
• Tata Chemicals fined over £1 million after contractors’ fatal accident in 2016.
• Multiple explosions at chemical plant in Mold Wales.
• Explosion at BAE Systems factory in Monmouthshire South Wales.
• Fire erupts and continues for 4 days at battery recycling plant in Scotland.
• Evacuations due to Nitric Acid leak from railcar in Georgia.
• 1 killed when chemical tanker explodes in California.
• 1 killed with severe burns following chemical fire in Chattanooga.
• 9 firefighters injured in LNG gas truck explosion in Wilmington.
• 3 dead, 9 injured when hangar under construction in Idaho collapsed.
• Injury caused by explosion at biodiesel waste facility in Ohio.
• 2 injured at incident in Refinery in Borger, Texas.
• 6 killed, bridge collapses in ship collision in Baltimore.
• 3 killed, 1 injured in fire from oil and gas well in Burleson County, Texas.
• 3 injured when tanker transporting sodium hydroxide explodes in Macedonia Ohio.
• 2 injured in fire in Refinery in Cardon.
Can disasters caused by Industry be prevented ? Many could, if information is made more freely available to allow management to learn from and act on the mistakes of others who have had the experience of similar previous disasters. Industry, Insurance and Risk Management companies all need to ask themselves if they are doing enough to educate Industry on lessons learnt. Action from lessons learnt can unquestionably reduce the number of repeat incidents and when they do occur, with knowledge gained, those attending can more effectively and competently deal with them to reduce potential loss.
“ Those who fail to learn from history are condemned to repeat it.
Winston Churchill, paraphrased the statement by George Santayana, Spanish philosopher.
VdS approval in progress
As part of the VdS approval process, fire tests with various fuels were completed successfully. vaPUREx® FXS AR 3/3 F-0 #2365 is a fluorine-free, alcohol-resistant foam agent for use in critical risk areas where polar liquids (e.g. alcohols, ketones, organic acids etc.) or non-polar hydrocarbons (diesel, kerosene, gasoline etc.) are produced, processed, transferred, transported or stored.
Information on the causes of any incidents and actions taken is not readily available at the time of an incident being reported and when the reports of incidents are eventually completed, they tend to have restricted or abridged circulation rather than being made available to those in similar organisations with similar risks. The Catalyst researches and provides reports on some of the major industrial incidents that have taken place in past years in the hope that this may stir people to action so that future incidents and subsequent unnecessary losses can be prevented.
R.M. Palmer Company, LLC, Pennsylvania, USA, has been crafting seasonal chocolate novelties since 1948 and today is one of the largest confectionery manufacturers in North America. During the afternoon of 24th March 2023, workers detected the smell of natural gas and reported this to their supervisor, who informed them that a decision to evacuate would have to be
made by more senior management. So the employees then returned to work. Half an hour later, the explosion took place.
The explosion contained so much force that it destroyed one building, damaged the main building and physically moved one of the buildings back by four feet. After the explosion, the still leaking gas
began to further fuel the ensuing fires causing further damage.
Seven people were killed and eight people were reported to have been sent to Reading Hospital to be treated for their injuries. The next day, one person was pulled out of the rubble and later reported that she and her colleagues had alerted their supervisor half an hour prior to the eventual explosion, but their pleas fell on deaf ears.
The Occupational Safety and Health Administration (OSHA) opened an investigation and issued the Company with 8 citations, 3 classified as “Serious” and 5 classified as “Other than Serious”, for violations of the Occupational Safety and Health Act of 1970 totalling US dollars $ 44,483.00 against the Company. The Citations were as a result of:
1. Serious: The employer did not furnish employment and a place of employment which were free from recognised hazards that were causing or likely to cause death or serious harm to employees from explosion hazards. On the day of the incident, the employer failed to evacuate workers during a natural gas leak inside the building resulting in an explosion causing multiple fatalities.
2. Serious: Each exit was not clearly
visible and marked by a sign reading "Exit": On or about the day of the incident, a door leading to the street was not marked with a sign identifying it as an exit. The nearest signed exit was in excess of 100 feet from the room requiring employees to pass by where the hazardous materials were stored.
3. Serious: Flexible cords were not used in continuous lengths without splice or tap: On or about the day of the incident, the flexible cords were spliced into the heat tape that was being used to warm the chocolate pipes between buildings 1 and 2, the splices were done in such a manner that the outer insulation was not maintained to prevent contact with internal wiring.
4. Other than serious: Employer did not complete an OSHA 301 Incident Report form, or an equivalent form, for each recordable injury or illness.
5. Other than serious: Each recordable injury or illness was not
entered on the OSHA 300 Log within seven (7) calendar days of receiving information that a recordable injury or illness has occurred.
6. Other than serious: The employer did not provide an authorised government representative the records within the four business hours.
7. Other than serious: The building owner, facility owner, or employer did not exercise due diligence in complying with the requirements to inform employers and employees about the presence and location of asbestoscontaining material and presumed asbestos containing material.
8. Other than serious: Employees were not provided with effective information and training on hazardous chemicals in their work area at the time of their initial assignment and whenever a new hazard that the employees had not been previously trained about was introduced into their work area.
On July 27, 2005, a major fire struck Mumbai High North offshore complex, located approximately 100km (62mi) off Mumbai, India. The accident was the consequence of a collision between a support vessel and the production platform.
The Mumbai, India, High oil field North complex (MHN), operated by the Oil & Natural Gas Corporation of India (ONGC), consisted of four bridge-linked platforms at approximately 100 kms from the shore. The complex imported well fluids from 11 unmanned wellheads and exported oil and gas to shore. At the
time of the accident, it was the monsoon season.
The multi-purpose support vessel (MSV) was supporting diving operations elsewhere in the field. A cook onboard the MSV got injured having sliced off the tips of two of his fingers and medical evacuation to shore was deemed necessary. The rough seas would make a helicopter landing unsafe and the offshore installation manager (OIM) received a request for the transfer of the injured person, the transfer to be accomplished using a man-riding basket lifted from one of the platform cranes. As the crane on the sheltered side of the platform was inoperable, the transfer
had to be made by the crane on the windward side of the platform which would make the MSV approach more complicated.
Under very difficult conditions, the transfer of the injured person was completed, however the strong swell subsequently pushed the MSV against the platform severing one or more gas export risers, which had been installed outside the jacket structure footprint. The risers were protected by structural guards, but these had been designed only for collision from smaller offshore supply vessels. The gas release immediately ignited, resulting in a massive jet fire which engulfed the MSV and spread to further risers, which lacked fire protection, and
eventually engulfed all the production platform. Within two hours from the fire onset, MHN collapsed into the sea.
A diving support vessel (DSV) was in the field at the time and was among the first providing assistance to the emergency operations. The DSV started firefighting operations and the Indian Navy, ONGC, and various supply boats also participated in the emergency and rescue operations. Several crew members of the complex sought safety by jumping directly to the sea. Rescued persons were transferred to supply boats for passage to Mumbai. Rescue helicopters remained unavailable due to weather conditions.
22 persons were killed, the whole complex was a total loss and production from the field was impacted for years. Six divers who were in a saturation chamber on the MSV were rescued 36 hours after the shipboard fire was extinguished. The DSV was handed over to tugboats for towing to shore, however she sank four days after the fire.
Inadequate design of riser locations. Failure to apply inherently safe design principles.
Inadequate procedures.
Impaired judgement by the master of the support vessel and offshore installation manager in extreme conditions.
No official investigation report has been issued publicly by either the Indian authorities or ONGC. Subsequent to the disaster, however, the Indian government empowered its Oil Industry Safety Directorate (OISD) with stronger capacities of action to promote safety in the local offshore oil and gas industry and counter poor safety practices, including in particular the mandate for the regulation of offshore safety.
India set up a regulatory body to provide oversight of offshore oil and gas production.
Risers may require subsea isolation valves to limit the consequences of any riser damage below topsides emergency shut down valves.
Riser fire protection should include fire resistant insulation and deluge systems.
Risers should be protected against collision.
Risers should be located away from platform cargo loading zones.
Minimum separation between production and accommodation platforms should be determined by fire and explosion modelling.
Hyperbaric evacuation points should be provided for divers.
Risers are Safety critical elements and should be subjected to independent risk assessment.
Could any of these incidents have been prevented ? What do you think ?
by John Ottesen
In this article Fomtec’s John Ottesen talks about why Fomtec is committed to pushing the boundaries of performance with their Enviro SFFF’s, and elaborates on why the data gathered from more than 3,000 fire tests (to date) is critical to the advice that Fomtec is able to give to their business partners and clients embarking on the transition away from PFAS containing firefighting foams.
Senior R & D Chemist used to say in their presentations and training programs that "The role of the R&D Chemist is to develop foam concentrates to pass a test." At first glance, this may seem peculiar because we’d assume the goal is to develop an effective firefighting agent. However, these objectives are not mutually exclusive. The purpose of testing is to determine the effectiveness of a foam concentrate as a firefighting agent, or more precisely, to gauge its level of effectiveness. Essentially, the function of any test is to measure the performance of the foam concentrate. Since fire performance testing needs to be repeatable, cost-effective, and controllable, the main question with any test protocol is its scalability to realworld scenarios. For example, does a 4.5 m² test pan accurately reflect a fullsurface fire on a 120 m storage tank?
Ideally, we would test each application under real-world conditions, but this is not
representative of the application. Test procedures are typically devised by standards committees or industry stakeholders. Given the diversity of applications, several different test procedures exist. Common ones for Class B foams include UL 162, FM 5130, and EN 1568, which are geographically specific, and ICAO, IMO 1312, LASTFIRE, and US MIL SPEC, which are more application-specific. This variety can leave end users wondering why there is no consensus among the creators of these test standards.
Test fires are relatively small and are typically conducted with application densities set above the critical application density but below what design standards define as design densities. The difference between test density and design density constitutes our safety margin. But what variables are these safety margins meant to cover?
Variables to consider include the type of fuel being used and the ambient conditions during the test. Water quality can also significantly impact test results, as can the ageing of the foam concentrate over time. The type of discharge device employed is another critical factor, as well as the physical differences between the test pan and a real-world fire scenario. There can be notable differences in the foam qualities achieved during testing versus those in actual conditions. Additionally, compatibility with dry chemicals and other agents must be assessed, and
the technique used by the operator can influence the outcomes.
Safety margins for PFAS-containing foam concentrates are supported by over 50 years of experience and data. Design standards such as NFPA 11 and EN 13565-2 incorporate these safety margins within their application design. As we transition to SFFF (Synthetic Fluorine-Free Foams), different approaches to performance testing are emerging from various authorities such as UL, FM, ICAO, and EN, alongside a new US Mil Spec for fluorine-free foam.
To ensure test standards are both repeatable and relevant to the intended mission, it is crucial to explore beyond standard testing to determine performance limits and gather data to support recommendations.
From when we first started using foam we had to address the issue of water miscible and water immiscible fuels which lead to foams suitable for hydrocarbon fuels and what became known as “alcohol resistant” foams which could be used on both water immiscible and water miscible fuels. This remains the case with SFFF’s although typical formulations from most manufacturers are alcohol resistant type .
Beyond the type of foam we have used reference fuels to represent groups of chemicals i.e. Heptane for “hydrocarbons”, Acetone for “ketones” and IPA for “alcohols”. In the latest version of FM 5130 for SFFF, FM has based on the flash point and vapour pressure relative to heptane, and also
for fuel blends – such as gasoline. Fomtec totally supports this approach and to date has tested with Jet A-1, Hexane, Hexane blends, Plant based hydrocarbons, and different gasoline blends.
With the water miscible fuels the situation is even more complicated because of the sheer number of different chemicals. Again it is totally impractical to test every chemical because of the numbers but also because of life safety issues with some chemicals. Fomtec experienced the difficulties early on when we looked at performance with MEK and Ethyl Acetate as both these chemicals are what we at Fomtec describe as “foam destroyers”.
MEK was the catalyst for Fomtec to initiate another data driven project. Over a two-year period Fomtec tested more than 200 chemicals in a laboratory environment where the comparison data relative to physiochemical characteristics has allowed Fomtec to develop an analytical modelling tool that looks at gel creation and foam destruction.
This data was then compared to the data available for fire test results to verify the correlation to fire performance. The tool now allows Fomtec to review a client’s fuels and predict the performance of the Enviro foams without having to fire test.
We have proven a high reliability with the tool but still some fuels fall outside the prediction range and we then still need to resort to the lab scale testing that was used to develop the tool.
Foam Qualities (FQ) of Expansion Ratio and 25% drain time have always had an impact on the fire performance of a firefighting foam, and now that with an SFFF we are totally reliant on the foam blanket to suppress and extinguish knowledge of the range of foam qualities that will achieve the mission is critical data. The issue with single point data as achieved with the EN 1568-3 and -4 testing is that we have fire performance data for one test nozzle, at a set pressure and flow rate generating one expansion ration and 25% drain time point. Even with the proposed update of this test standard the current draft / discussion documents ONLY address Expansion Ratio variation which we feel is a missed opportunity !
Fomtec believes that the approach from UL and FM for topside type II and type III testing is more appropriate as the foam qualities used for testing are required to match those achieved with real world discharge devices. Many have observed and commented on the different test densities applied with SFFF’s compared to AFFF’s, but it should be noted that application density and application duration with SFFF’s is the same as non film forming fluorinated foams such as FP !
UL has also made a further change with SFFF’s and that now listing with type II devices such as foam chambers and foam makers MUST be carried out as a separate test to the type III direct application test used for hose and monitor nozzles.
Foam that is fire tested with various foam qualities captured from real world discharge devices during testing at minimum and maximum flows and inlet pressures, take this critical variable out of the equation and turn it in to a KNOWN VARIABLE that the SAFETY MARGIN does not need to account for.
Similarly the SAFETY MARGINS applied by some designs standards cannot compensate for a complete lack of data related to foam qualities and non aspirating discharge devices.
Whilst many of the variables that impact the performance and safety margins can be tested within the standard fire performance tests by using different fuels, water, foam qualities, discharge devices (foam-water sprinklers) correlation to mission specific requirements and always evaluating the correlation between the standard tests to much larger real world are important data necessary for the transition away from PFAS containing foams.
Fomtec believes as an industry we all have a responsibility to test to obtain the data and at Fomtec we are increasing the resource of time and money that we allocate to such testing. Over the last 12 months this testing has included:
Testing our Enviro USP with standard sprinklers at approximately 14m height on Jet Fuels to verify application density as ALL hangers are higher than the approximate 4.5m test height under UL.
Setting up a 12 head test grid and pan in association with GESIP and LASTFIRE to test aspirated heads in a loading rack fire with 3,000 litres of gasoline and application density of 0.16 gpm/ft2 (6.5 lpm/m2).
and a simulated full surface tank fire with an over the top type III application method on gasoline.
Testing Enviro foams on the 13m diameter test pan at IRIS in Beaumont, Texas at both 0.08 gpm/ft2 and then at NFPA 11 minimum recommended application rate of 0.16 gpm/ft2
It’s a mantra for us at Fomtec but we have a continuing responsibility to the industry to provide accurate information and this requires data from meaningful test programmes. The Enviro Programme hit 3,000 fire tests a few weeks ago and we will continue to commit the resource to add data going forward so that we verify that the Safety Margins remain valid and achievable in the real world !
This article was presented to you by:
John Ottesen info@fomtec.com
Participation with LASTFIRE to test Enviro USP for large fires with handlines Fomtec CEO
Responsible use of C6 Fluorine Chemistry and to providing its products to firefighting foam manufacturers.
As high hazard, flammable liquid emergencies are occurring world-wide, a recap is needed:
C6 AFFFs and AR-AFFFs remain the highest performing firefighting products for flammable liquids.
C6 Foam Concentrates are required for critical uses and major fire events.
C6 Foam Concentrates are proven and e ective with decades of successful extinguishments.
C6 Foam Concentrates should not be used for testing or training. In cases of fire events or accidental release, C6 Foam Concentrate run-o should be controlled and captured. Refer to Dynax SDSs for region specific product use and disposal information.
Universal EU PFAS ban proposal does not cover PFAS in Firefighting Foams.
The proposal for PFAS in Firefighting Foam includes a 10 year derogation for Seveso III sites.
by André Tomlinson
In this instalment we will be looking at smaller sized appliances.
Colloquially trailers have been referred to as “the poor man’s fire truck.” Trailers offers a range of benefits including that they are inexpensive, resilient as any prime mover with the right tow connections and horsepower can move them plus they are always available – no flat batteries or service downtime, and, there is practically not a functionality that goes on a truck chassis that cannot be replicated on a trailer.
Trailers can be categorized as either Tow Bar or Gooseneck types. Tow Bar
trailers typically carry smaller payloads but free up the tow vehicle to perform other duties. Goosenecks can carry more payload but typically the 5th wheel hitch on the tow vehicle’s load body floor limits the use of the prime mover for other duties. Note though that gooseneck trailers can also be towed by truck heads.
What goes onto a trailer and design of the superstructure is only limited by the creativity of the specification originators and design teams. One example of such creativeness that translated into reality is the Kobra trailer, design and built by Bristol Vehicle Manufacturing out of Abu Dhabi. The challenge placed by the oil company was to create an industrial pumper equivalency on a trailer, i.e. carry all the facilities and “just add water.” The
response to the challenge was a gooseneck based trailer with three master streams (one fixed, two demountable that can act as ground monitors). The trailer collectively flows 11,000 l/min. All the monitors have swap out nozzles that makes them Hydrochem, or then triple-medium, capable. The trailer is also fitted with two water/foam cross-lays and one water/foam/Hydrochem cross-lay. Two 1,000-litre totes with 1x3 AR-AFFF forms the foam supply while a 226 kg Gorilla dry chemical skid provides the dry agent for Hydro-chem attacks. For water supply to the remote monitors as well as to pick up water from hydrants or 3rd party pumpers, the vehicle is fitted with a hose bed carrying 120 m of 152 mm supply line. As the trailer was expected to operate in areas with high heat radiation it is fitted with a self-defence water deluge system.
The virtues of high-pressure fog is well known to the firefighting fraternity and has been with us since the 70’s. The last two decades has seen the ascendency of Ultra-high Pressure (UHP) technology. First harnessed as a cutting tool punching holes through steel and concrete walls to reach fires in enclosed spaces, UHP has since graduated to become a fully-fledged all-round firefighting solution.
UHP streams are characterised by droplet sizes of 64 microns maximising the surface area of the stream and increasing its “hang time” or then the availability of the water drop for heat conversion. UHP streams produce fire knockdown through massive latent heat absorption within seconds. While only flowing a humble 75 l/min it is at 100 Bar, UHP highly economical as approximately 90% of the available water is absorbed compared to conventional spray droplets that optimally sees only 20% being utilised. UHP can extend the available water supply by 500%. UHP also produces excellent Class A and B foam.
Traditionally the use of UHP was limited to compartment fires. As this technology has gained traction in industry it has found more and more applications including spill fires, transportation events, interior structural fires (beyond the compartment), ARFF events, ship-board and wildland fires, to name a few. UHP has also been mooted as a more suitable stream to combat EV battery fires while the cutting tools have been considered for interior fires in boilers, crackers and reactors.
One of the pathfinders in the UHP sector is PyroHMA out of Florida (USA). They offer a wide range of UHP models including HyLo systems that offer both UHP flows and conventional low-pressure flows at 1,130 l/min, with or without Class A and B foam facilities, all from one device. UHP units can be provided either as self-contained
skids or as built-in modules integrated into pumpers or ARFF appliances. Built-in units have the option to run off the vehicles PTO.
One of the secrets of PyroHMA’s success is their PyroBlitz nozzle with a UHP stream that has a full adjustable patterns. This appeals to firefighters as it approaches the versatility of traditional adjustable pattern pistol-grip nozzles. PyroHMA has retained the Pyrolance cutting tool, now
called the LTAC, but offers it as an add on device carried in a case. More recently PyroHMA have evolved from providing skids only to now building light pumpers, RIV’s and brush pumpers. For the ARFF and wildland industry they now offer a UHP capable bumper turret that provides an impressive 25-meter reach as well as bumper-mounted ground sweep nozzles allowing brush units to straddle the fire line.
The Battler Quick Attack Truck flowing 22,700 l/min (Source: Williams Fire and Hazard Control).
Quick Attack Vehicles have been popular with refineries in North America for some time now. They are typically spartan vehicles and carry either one or two manual or remote controlled monitors flowing 11,000 l/min or lower. That is until a refinery in Kuwait challenged the market to
produce a Quick Attack producing 45,000 l/min of water and foam flow.
Williams Fire & Hazard Control out of Port Arthur, Texas (USA) responded to the challenge by mounting their venerable Battler monitor on a Ford F-550 chassis.
The monitor is remote controlled (wirelessand via a control panel) and has a flow range of 15,000 to 45,000 l/min. The monitor has an integrated design with manifold and ballast tank built as a skid that mounts directly to the chassis. For additional
Already in service for 20-years their latest iteration, the LFAV Generation 6, went into service in 2022.
Though on a small footprint and crewed by just three firefighters this vehicle punches well above its weight containing a number of force multipliers.
Traditionally the vehicle was crewed by four but has kicked one crew member off in the latest generation in favour of a robot, the 3R itself in its 3rd generation.
On the firefighting end the Rhino is equipped with a 1,892 l/min Darley CAFS pump, 2,650 l/min Elkhart remote controlled monitor, two 25 kg CAFS trollies and a fire blanket.
H y t r a n s f o r i n d u s t r i a l s a f e t y : H y t r a n s f o r i n d u s t r i a l s a f e t y :
G u a r a n t e e o f G u a r a n t e e o f h i g h v o l u m e & l o n g d i s t a n c e h i g h v o l u m e & l o n g d i s t a n c e
m o b i l e w a t e r t r a n s p o r t
m o b i l e w a t e r t r a n s p o r t
C a n d e a l w i t h t h e l a r g e s t i n d u s t r i a l f i r e s
C a n d e a l w i t h t h e l a r g e s t i n d u s t r i a l f i r e s
a n d w o r s t c a s e s c e n a r i o s a n d w o r s t c a s e s c e n a r i o s
II n t e g r a t e d f l u o r - f r e e f o a m s n t e g r a t e d f l u o r - f r e e f o a m s
V e r y e a s y t o d e p l o y w i t h m i n i m u m e f f o r t
V e r y e a s y t o d e p l o y w i t h m i n i m u m e f f o r t
3 5 + 3 5 + y e a r s p r o v e n p e r f o r m a n c e w o r l d w i d e y e a r s p r o v e n p e r f o r m a n c e w o r l d w i d e
R e l i a b l e e m e r g e n c y r e l i e f f o r i n d u s t r i a l f i r e s
by Hunter's Deconology®
Firefighting, an inherently perilous profession, demands stringent measures to ensure the safety and health of those who place their lives on the line. With the World Health Organisation (WHO) classifying firefighting as a cancer-causing profession, the need for advanced protective measures has never been more critical. Hunter, a leader in professional clothing and PPE management, has risen to this challenge with its groundbreaking Deconology® technology—ushering in a new era of protection for firefighters in the UK and Ireland.
Hunter's Deconology® represents the pinnacle of PPE decontamination technology, utilising Liquid Carbon Dioxide (LCO2) combined with environmentally friendly additives cleanliness and decontamination.
Traditional water-based washing methods have proven ineffective removing only 15-40% of harmful toxins from PPE. In stark contrast, the LCO2+ process ensures a 99% reduction in contaminants, effectively safeguarding firefighters from prolonged exposure to carcinogens such as benzene, formaldehyde, and dioxins. This will assist in combatting long latency diseases and help improve firefighters future health outcomes.
Deconology®’s LCO2+ technology stands as the sole provider of such advanced decontamination in the UK and Ireland, setting a new benchmark to help improve firefighter future health outcomes.
Key benefits of this innovative technology include:
1. Exceptional Cleaning Efficiency:
99% Toxin Removal: Deconology®’s LCO2+ system
significantly outperforms traditional water-based methods, ensuring almost complete elimination of harmful substances from PPE.
Comprehensive Penetration:
The LCO2+ process penetrates all layers of PPE, including the waterproof membrane, capturing toxins at a molecular level and providing a thorough clean beyond the outer shell.
Extended Life Span: The gentle, non-aggressive nature of LCO2+ cleaning extends the life of PPE, offering substantial financial savings by reducing the frequency of replacements.
Rapid Turnaround: With no drying time required, the LCO2+ process ensures a quick turnaround, enhancing operational resilience and efficiency for fire services.
3. Environmental Sustainability:
Waterless Solution: Deconology®’s process uses no water, significantly reducing environmental impact and energy consumption compared to traditional cleaning methods.
Re-capture and Reuse: Any CO2 used in the decontamination cycle is filtered and recaptured for subsequent use, underscoring the eco-friendly nature of the technology.
4. Advanced Technological Integration:
HunterCARE® and HunterPAC®:
These award-winning managed service technology platforms provide comprehensive tracking and maintenance of PPE, ensuring visibility and confidence in the safety measures implemented.
AI Sizing Technology: Ensures precise fitting of PPE, further enhancing safety and comfort for firefighters.
The occupational hazards faced by firefighters extend beyond the immediate dangers of fire and smoke.
Prolonged exposure to toxic residues on PPE has been linked to a higher incidence of cancer and other long latency diseases among firefighters.
Deconology® addresses this critical issue head-on, significantly reducing the risk of long latency diseases by ensuring PPE is free from harmful contaminants. By adopting Deconology®’s LCO2+ decontamination service, fire services can provide a safer working environment for their personnel.
This innovative technology not only protects the health of firefighters but also helps to mitigate the risk of litigation associated with occupational illnesses. Moreover, healthier firefighters mean fewer absences due to illness, enhancing
the overall operational efficiency of fire services.
Hunter's unwavering commitment to health & safety innovation has been recognised with numerous industry awards, including the British Safety Industry Federation’s (BSIF) Safety Solutions Award and accolades from the Professional Clothing Industry Association Worldwide (PCIAW). These honours underscore Hunter’s position as a leader in firefighter PPE care and maintenance.
With a rich history dating back to 1936, Hunter has continuously evolved to meet the changing needs of its customers.
Today, the company’s focus on sustainability, technological advancement, and user-centric solutions positions it at the forefront of the industry.
The exclusive partnership with the world’s leading LCO2+ system manufacturer further cements Hunter’s role in delivering cutting-edge decontamination technology to the UK and Ireland.
Hunter’s Deconology® LCO2+ decontamination technology represents a monumental leap forward in the protection of firefighters health.
By virtually eliminating harmful toxins from PPE, extending the lifespan of gear, and providing a sustainable, ecofriendly solution, Deconology® sets a new standard in occupational health & safety.
As the only provider of LCO2+ decontamination services in the UK and Ireland, Hunter is uniquely positioned to make a profound impact on the health and safety of firefighters. Through its innovative approach and unwavering commitment to excellence, Hunter continues to safeguard those
who protect society, ensuring a safer, healthier future for all.
Hunter exists to protect those on whom society depends, and with Deconology, they reaffirm their commitment to pioneering the best solutions in firefighter safety.
For further information and to explore how Hunter’s Deconology® can benefit your fire service, visit Hunter Apparel Solutions website or contact them directly:
028 7126 2542 www.hunterapparelsolutions.com
From tank farms to fuel loading racks, we’ve got you covered.
To safeguard oil, gas and chemical operations, ANSUL® non-fluorinated foam concentrates from Johnson Controls are the proven choice in fire protection:
• ANSUL THUNDERSTORM® WNF33A 3x3 AR-SFFF
Provides demonstrated effective suppression for fuel in-depth tank fires
• ANSUL NFF-331 3x3 AR-SFFF
Delivers superior sprinkler foam suppression for Class B polar solvent and hydrocarbon fuel fires
• ANSUL UL201 3x3 AR-SFFF
Offers effective suppression for Class B fixed systems and spill fire response
Check out our full portfolio of world-renowned, field-tested, UL listed and EN rated ANSUL fire protection products, all backed by unmatched technical support and customer service.
Learn more about ANSUL NFF foam concentrates
by Nick Barker
As a global leader in the fire suppression business, a week does not go by when we do not receive calls from major corporations asking if their legacy fixed foam systems are compatible with our next generation Fluorine Free Foam (F3) concentrates.
The simple answer is yes, HOWEVER, the first thing to understand is F3 concentrates are rarely a drop in replacement. A complete fixed foam system assessment (hardware, operating parameters of the hardware and fuel of concern) must take place prior to starting any conversion. Based on the current foam system review and assessment, with some potential modifications, a legacy fixed foam system can be successfully converted to a F3 system.
Our company’s global reach has enabled successful conversions of over 500 hundred (and still counting) fixed foam systems around the world for leading chemical, oil and gas, aviation, pharmaceutical and consumer goods companies.
A few decisions are required before you begin
First, you must select the F3
concentrate. The foam system hardware must be calibrated around the F3 concentrate performance capabilities. Not all F3 concentrates are created
equal, look for respected third party certifications such as UL, ICAO, FM, EN, LASTfire to support any foam supplier’s claims.
Our Respondol brand of fluorine free foam have been tested and proven effective with these various listed third party certifications. Global leading oil & gas and chemical companies have successfully replaced their legacy foams with our Respondol foam concentrate in their fixed and mobile response foam systems.
Moreover, ask yourself the following: What fuel of concern is the foam concentrate listed with?
Will the foam concentrate perform well on both hydrocarbon and polar solvent fires?
Does the foam concentrate work effectively with fresh, brackish and seawater?
Which specific polar solvents has the foam concentrate been tested or listed with? Which discharge devices have been tested?
Lastly, what raw materials are used in the foam formulation since they could become an environmental concern down the road?
We always recommend you select a foam with the GreenScreen environmental certification. GreenScreen certification helps protect the end customer from selecting F3 concentrates that may contain chemicals of concern.
The conversion process
Every fixed foam system will require a complete foam system assessment.
This should already be standard practice anytime a foam concentrate type is changed in a fixed system. The legacy system in question may have been designed years ago, utilising a different foam concentrate type, and will likely require some adjustments to its hardware and flow operating parameters as a result. This usually requires a qualified technician to review each individual foam system, to confirm the current foam concentrate type, foam hardware and system operating parameters as well as the fuel(s) being stored.
The key to a successful conversion relies on understanding how to balance the various components of the existing fixed foam system. It is a balancing act between the hazard type and size, foam type, its percentage concentration, proportioner capabilities, discharge device, type II or III (direct) application, flow rate, operating pressure, discharge rate and duration. For example, changing the foam system pressure (to achieve the desired foam quality) would require increasing the discharge rate, which would decrease the discharge time and require a larger foam concentrate storage tank. These required system changes should all be finalised and confirmed prior to any work on site starting. Angus Fire has developed and executed a proven, detailed conversion process to ensure timely and successful conversions.
Once the assessment is complete, the foam supplier and end user should present the conversion plan to the local Authority Having Jurisdiction (AHJ). The AHJ approval and sign-off are important points and help avoid any concerns after the completion of any F3 conversion process. The end-user will need to
provide documentation to the AHJ, supporting the efficacy of the converted fixed foam system and evidencing that it will continue to function properly with the new F3 concentrate. The foam concentrate supplier should be capable of providing the required documentation for the local AHJ to obtain approval and gain acceptance of the fixed foam fire suppression system.
The key is to use a qualified foam supplier capable and experienced in offering a full service to aid in a successful conversion. Angus Fire is a foam supplier with global resources capable of providing qualified technicians for on-site or remote foam system assessment, engineering / design support, fire testing facilities and experienced commissioning support, not to mention the market leading qualified F3 concentrates. With some pre-planning, and using our proven step-by-step process, a successful conversion can be accomplished in a relatively short amount of time with limited disruption to daily operations.
Nick Barker general.enquiries@angusuk.co.uk This article was presented to you by:
by Mike Mutsaers and Olaf Niessink
Across the world, the foam transition is now in full swing and many organizations have already begun this transition. Along the way, organizations are finding that this transition goes far beyond simply replacing foam concentrate with fluorinefree foam concentrate and there are many technical aspects on top of foam performance and capability that need to be addressed. The Management of Change (MOC) procedure is an indispensable tool to go through this process to ensure Foam Assurance. In recent years many performance based tests have been performed by foam suppliers and (company) fire departments, however there are still gaps to close and for the end user these performance based tests are the most important link in the foam transition. Will the new generation foams work on their products within their operating environment? In short, the foam transition is a challenging process with many failure mechanisms.
Over the past months RelyOn Nutec Fire Academy received several questions from fire departments and foam manufacturers about the foam transition and performance based foam testing. In order to be able to answer these questions and serve the market as well as possible, we have developed the RelyOn Nutec Foam Campus.
The new fluorine-free concentrates require a different approach to application technique and tactics. Being dynamic during your foam deployment is crucial and needs much more emphasis than with the old fluorinated foam concentrates. Proper application technique using the various application techniques available is essential for successful extinguishment. Achieving 90% knockdown is more difficult due to the flow properties of fluorine-free extinguishing foams. Therefore, the speed of achieving 90% knockdown has become even more important. This requires a different deployment strategy for good result to take advantage of the fluorine-free extinguishing foam characteristics.
Our Foam Campus offers advanced live fire training objects and specialized foam training programs. We have translated lessons learned in the foam transition journey into new objects and implemented improvements to existing objects.
In the Foam Campus, the focus is on the application of the new fluorine-free foam types and we have developed two new objects: the 80m² tank and the
low lying 9 m diameter storage tank. Furthermore, we have made minor adjustments to our live fire simulators units to ensure the correct application
techniques are trained. This is all in addition to the existing much used simulators such as the foam laboratory, the miniature tank storage farm, the high 9m tank and the 120M2 tank bund.
The 80m² simulator is a rectangular tray 20 x 4 meters. The tray is equipped with plates (ramps) to perform the rollon technique correctly, and by using vertical plates we can create both upwind and downwind areas where the foam can be applied indirectly onto the burning liquid. This forces trainees to apply dynamic application techniques and experience the heat loading when foam is applied on the short- and long side of the simulator. There are various objects placed in the tray to obstruct the flow path of the foam and challenge fire fighters in applying foam in the most efficient way.
The 9-meter diameter low lying storage tank is specially designed for studying and demonstrating various aspects of foam behavior. The round surface of the tank allows us to observe in detail how the extinguishing foam spreads and behaves under various conditions and this tank provides a unique opportunity to evaluate the effectiveness of different foams and application techniques.
The fire simulators have a wide range of capabilities, from basic training to larger advanced performance-based foam testing. Participants can learn how to properly apply foam utilizing the various strategies and techniques in a realistic environment. For advanced users, the tank provides the ability to conduct in-depth tests and examine specific foam issues to establish a benchmark.
The versatility of the Foam Campus makes it a valuable tool for foam suppliers to investigate various foamrelated issues, and it offers end users the opportunity to prepare even better for liquid pool and full surface tank fires.
mmutsaers@nl.relyonnutec.com
by Onur Özutku
LPG is a very important need in our lives and an easily accessible energy source that makes people's lives easier. Even if LPG provides a lot to our lives, we should not forget how dangerous it is. LPG should be protected from fire very well in its storage and during the transfer to our usage area. Gas fire Safety is very important especially in LPG storage tanks and we should protect to LPG plants and terminals with precautions and barriers. Since the mass of LPG stored is massive, it can lead to very big accidents. In this article, I explain the important of LPG tanks fire safety, fire managenent and finally bleve (explained with past accident). Anatomy of bleve is the worst scenario that may occur in case of fire, and I will explain how to prevent the Bleve phenomenon from happening.
Developing technology and rising living standards have made energy one of our most important needs. In this context, Liquid Petroleum Gas (LPG), one of the important energy sources, has been among our most basic needs in today's conditions. LPG, which with all areas of our lives, consumes both as cylinder gas and autogas (Figure 1).
LPG consists of a mixture of butane and propane gases. LPG is produced by processing petroleum in refineries or from natural gas deposits. But it is stored under pressure and in liquid form . LPG, which is liquefied for transportation and storage, is consumed in the gas phase.
It has flammable and combustible properties. It is very slightly soluble in water.
It is colorless and odorless. For this reason, it is odorised with mercaptans or sulfur compounds so that it can be detected in case of gas leakage. The presence of 2% to 9% in the air is sufficient mixing ratio for the risk of explosion. For this reason, both storage and transfer should be done
with strict safety codes, rules.
In the filling facilities and terminals (Figure 2), LPG is stored in liquefied form under pressure in specially designed cylindrical and spherical tanks. LPG is stored in tanks in three ways as propane, butane or mix. Propane has highest vapor pressure and propane storage tanks are designed to resistant higher pressures.
A typical Spherical LPG tank can be built from 1000 m3 to 5000 m3 volume and has multiple nozzles and connection points. The valve opens and closes in the liquid form, gas phase inlets and the drain lines. For this reason, these areas are critical zones for operational safety. Past disasters have shown us how important these areas are important, even during drainage operation.
Safety valves are used to protect the tank from explosion when the LPG tanks vapor pressure increase above the design pressure without any reasons. The selection of safety valves should be made according to engineering calculations and API standard and should be tested by expert inspectors at least once every five years. Safety valves are the silent guards of the tanks and are the most important safety equipment on the tank. (Figure 3)
a. Leakage prevent system; There should be zero tolerance for leakage in LPG storage tanks. All inlet and outlet nozzles of the tanks should be equipped with remotely operable emergency shutoff valves in case of LPG leaks or any emergencies that may happen in tanks or pipelines. Thanks to this emergency shut-off system, the loss of control of LPG leading it to spread out of the tank is prevented in case of emergency. It is recommended to test this emengency shut-off system regularly.
In addition, attention should be attention to zones where LPG can be collected in case of leakage, such as storm drain and sewers around LPG tanks. (Figure 4)
b. Firefighting Systems in LPG tanks; The most important active fire protection system in LPG tanks is the sprinkler systems on the spherical LPG tank. All important details are written on the NFPA 58 and API 2510&API2510A, For example: How many liters of water should be applied per square meter of the tank shells per minute, how much water reserve you should have for firefighting, fire pump flow rates etc. Fire fighting systems should be designed in accordance with this standard, otherwise it is impossible to win this dangerous war.
Emergency action plan in LPG Tank fires; The first action to do in LPG tank fire time is to stop the source of the burning LPG, otherwise it is not possible
to extinguish LPG fires.
In this type fires, emergency shut-off valves play a most important role. If the source of the LPG leak in fire is stop and the LPG in the pipeline runs out , the fire will continue some time but the fire will stop when the LPG runs out.In the meantime, if the fire zone is wetted with the many water, unwanted senario may not occur. Because, fire intensity will decrease as LPG and oxygen in the amount air will decrease due to the evaporation of water . LPG fires can occur as jet fire (Figure 5), UVCE and BLEVE. Of course, the worst of these three fires can be BLEVE. Terminals and facilities should plan the largest portion of fire fighting plan with barriers that can prevent BLEVE.
c. Bleve; The phenomenon known as Boiling Liquid Expanding Vapor Explosion BLEVE (Figure 6) is when the liquid in a tank reaches a temperature well above its boiling point, rupturing the tank it is in. If we talk about how it can happen, in fire conditions, high temperature exposure of the tank shell, the liquid LPG in the tank will heat up and increase the internal vapor pressure and Tank shell temperature increase causes a decrease in the strength of the tank shell metal.
High internal pressure and the decrease in the strength of the steel will cause a rupture in the tank in a short time.
At the end of all these scenarios, BLEVE will happen. In the event of fire, the events will develop as followed, first of all, the tank shell will heat up with the effect of the direct flames. The heat on the tank shell will be transferred
to liquid LPG, since the pressure of LPG with increasing temperature will increase, when the pressure in the tank reaches the opening pressure of the safety valves, the safety valves will be opened and the vapor of LPG will be discharged to the atmosphere.
Therefore, the pressure in the tank will decrease again. The liquid in the tank will evaporate quickly again because fire is continuing to spread and then the safety valve will open again. In this cycle, the vaporized LPG will cool the tank shell as well as inside the tank, but if you can not stop the transfer of heat to the tank shell, it will increase the internal pressure of the tank again, You can stop heat transfer to tank in two ways, first one fire should extinguish or you should cool the tank shell with enough water. When the level of liquid that can cool the tank by evaporation decreases or run out.
The flames will heat the dry portion (parts above the liquid level) inside the tank very quickly, and the rupture in the the tank shell and will result in BLEVE. The first way to prevent BLEVE in the event of a fire should be to cut off the LPG source of the burning fire.
During this period, the burning tank and adjacent tanks should be cooled with enough water. This cooling will gain time to prevent BLEVE and fight fire. (Figure 7)
The steel strength of the tank cooling with water will not decrease and will prevent the increase in the pressure inside the tank.Also, the main rule that should not be forgotten is the fire fighting with water in amount accordance with the standards for each square meter of the tank surface and enough cooling. Especially cooling the areas on the tank shell that are not in contact with liquid LPG is very important.
At the time of fire, the liquid level in the tank should be known and monitored (Figure 8). Since the liquid LPG will evaporate rapidly when the safety valves are opened, the liquid level will appear as a thin line on the tank shell, it will not be difficult to see the level in the tank in daylight conditions.
However, in night conditions or when there is a lot of smoke, it will not be possible to see the level in the tank from the outside. For this reason firefighting will be more difficult. In cases where the tank surface is not sufficiently water cooled, the time for BLEVE is running out. Knowing this situation, you should fight the fire.
d. The method of injecting water; When a leak occurs in the tank, especially in the nozzle flange gasket, weld seam or valve body, the LPG leak cannot be stoped by emergency shut-off valves. In such cases, it will be necessary to flood the tank. When water is injected into the tank, since water will down to the bottom of the tank due to the density difference and the LPG will be displaced upwards. With this operation, the LPG leak will be replaced by a water leak(Figure 9).
Thus, the LPG leak will be replaced by a water leak. LPG leakage will be end.
While designing such a system, should be attention, the water pressure should be higher than the vapor pressure of the LPG inside the tank. Also a check valve should definitely be used in the water injection lines.
Otherwise, LPG can flow to water line and the situation may become more dangerous. As a result, with this method, LPG leakage can be prevented and stopped when water is injected into the tank. It is one of the most basic barriers that can prevent BLEVE.
1.4 January 4, 1966 Feyzin Refinery
Bleve
a. What went wrong?
During the 6AM to 2PM shift at the refinery, operators were required to take a routine sample and dreyn from each of the LPG storage tanks. The operator, due to the fact that he had only a single valve spanner, opened the valves in the incorrect order. This caused the release of a small amount of water and a small amount of LPG when he opened the lower valve. This prompted the operator to close the valve and then reopen it,
leading to only a few drops emerging. The upper valve was then opened fully.
This led to a very powerful jet of LPG to rush out.
This release splashed up from the drain and gave frost burns to the operator on the face and forearm. As he recoiled from the flow, the operator partly pulled off the valve handle. The other operator, losing sight of the first operator, turnedon the water supply to the sprays fitted to the sphere and, with the operator, attempted to reposition the valve handle and shut the valve.
They failed to do so. In addition, there was no remote operable emergency shut-off valve in the LPG drainage line, and there was no excessive flow valve on the line. As a result, a big fire started.
The LPG fire continued because they could not cut the source of the LPG leak. One more mistake was added to these mistakes and they did not cooling with water the burning tank because they believed that the safety valve alone could protect the tank and only needed cooled with water the neighboring tanks.
However, BLEVE occurred in the first tank caused by fire. Not long after, other five tanks exploded. As a result of this disaster, 18 people died, 81 people were injured and 5 spherical LPG tanks exploded(Figure 10). The possibility of such disasters should be talked with risk assessment at the installation stage and the design of the tanks should be done correctly and the operation instructions should be explained to the operators with routine training. Past accidents are a very good guide to future safe days.
This accident has shown us that drainage operations should be provided with correct procedures and good designs.
I find the most fundamental deficiency in this regard in valve selection. It is recommended to use a deadman valve in this type of sampling and drainage operations.Also Interlock systems that will prevent the opening of both valves at the same time will also be an important barrier in preventing such accidents. Last, remotely controllable emergency shut-off valves should be at all inlet and outlet connections of the tanks, include dreyn line.
This article was presented to you by:
I was born in Ankara,Turkey in 1987, I have been living in Turkey/Hatay for many years.IgraduatedfromAkdenizUniversity in 2010 as a Mechanical Engineer, and in 2012 I completed my master's degree in heat transfer & fluid mechanics at Mustafa Kemal University. I have been working as a mechanical engineer in the sector for 13 years. I worked in the field of production and manufacturing for the first 3 years of my profession, and then for 2 years, I worked in project-based maintenance-repair and capacity increase works in Oil&LPG terminals. I have been working at Milangaz for the last 8 years. I have been working as LPG Operations Engineer for 5 years and as LPG Terminal Manager for 3 years.
Sources: API Natural Gas Liquids and Liquefied Petroleum Gas Emergency Response Guide RT 1 – Risque industriel » Mémento du maire et des élus locaux (mementodumaire.net) API 2510 A, https://prezi.com/188aqzh9wppw/feyzin-disaster/
by Stephen M Washington
Delivering a high-capacity direct inject foam proportioning system for the demanding industrial sector is crucial. Waterous AQUIS ULTRAFLOW provides the necessary flow rates to empower industrial firefighters when they need it most.
What sets Waterous AQUIS ULTRAFLOW apart is its exceptional pumping capability. The Waterous CRU-2 pump with inducer can deliver 4000 GPM (15000 L/min) from draft and over 6000 GPM (22,700 L/min) with a pressurized intake, all while simultaneously injecting a choice between 160/300/500 GPM (606/1135/1893 L/min) of foam concentrate in any of up to sixteen (16) discharges. Operators have direct control via a user-friendly 8-inch or 15-inch Waterous Tellurus Digital Control Panel. The system itself can be updated remotely, and for troubleshooting, customers can securely access the system or allow a servicing agent or Waterous to diagnose any potential issues locally via a secure Wi-Fi connection. Additionally, ULTRAFLOW boasts GPS position tracking, enabling coordinated deployment and positioning of apparatus during major industrial firefighting incidents.
Waterous ULTRAFLOW Tellurus Digital Control Panel Shown on Aerial Apparatus. Controls all foam discharges from single device.
Up to sixteen (16) discharges can be controlled by the Waterous ULTRAFLOW Tellurus Digital Control Panel.
160/300/500GPM (606/1135/1893 L/min) of foam concentrate in any of up to sixteen (16) discharges.
ULTRAFLOW allows the ability to never run out of foam and can flow, refill, transfer foam simultaneously.
Highly readable display under all lighting
Rugged iPad-like touchscreen
Gloved operation in water spray environment
High resolution, full-color graphics
Dynamic user interface capability
Large storage capacity for applications and data
High reliability military-grade operating system with integrated state-of-the-art security.
Sealed ruggedized design for operation in fire service.
Tested to military and European standards
Flexible vehicle connectivity options
Secure wireless connectivity
Supports multiple wireless data connection points
Wide range robust power supply designed for in-vehicle applications.
Furthermore, with a one-hundred-foot ladder fully extended, an aerial can throw concentrate/water solution over 400 feet (122 meters) from the apparatus. This extended throw range with high flow rate is becoming increasingly important for industrial firefighters to maintain a crucial application rate of the new aqueous film-forming foams (AFFF). These non-fluorinated AFFF firefighting concentrates require much higher application rates than the older fluorinated concentrates. With up to sixteen (16) discharges, ULTRAFLOW provides large-scale capacity and coverage for any industrial firefighting incident.
With a 100’ (30 meter) ladder fully extended, concentrate/water solution can be thrown over 400 feet (122 meters).
In a testament to its effectiveness, the La Chevron Refinery in El Segundo, California, recently invested in a cutting-edge industrial aerial fire truck equipped with both a Waterous fire pump and an AQUIS ULTRAFLOW direct injection industrial foam system. This integration of advanced systems into a single truck empowers industrial facilities like La Chevron to tackle large-scale incidents with confidence. The collaboration between Waterous and the apparatus builders has resulted in a truly remarkable piece of firefighting equipment, specifically tailored to address the unique challenges faced by refineries, such as flammable liquids and confined spaces.
With the ULTRAFLOW industrial system, Waterous is on the cutting edge with the best industrial fire suppression technology available to extinguish even the largest fires.
Kenbri Fire Fighting is your full service provider for PFAS Cleaning & Treatment solutions.
We combine our advisory services with extensive technical knowledge. Through our strong partnerships we can assist you from A to Z in the transition to fluorine free firefighting foam.
• Advice
• Cleaning solutions
• Fluorine free firefighting foam
• Technical engineering
• Service & maintenance
3T TRAINING
Aberdeen, Scotland
trainingservices.training@3tglobal.com www.3tglobal.com
EDDISTONE CONSULTING LTD
Heathersage, United Kingdom
+ 44 (0)1433 659 800
opportunities@eddistone.com www.nationalresponseacademy.co.uk
+44(0)330 202 0569 www.eddistone.com
Middlesbrough, United Kingdom
FALCK FIRE SERVICES UK falckfireservices@falck.com www.falck.com
+ 44 1 642 212301
Gloucestershire, United Kingdom
FIRE SERVICE COLLEGE www.fireservicecollege.ac.uk
+ 44 1608 650 831
Pacific Avenue, Pt. Lisas Industrial. Estate, COUVA Trinidad , W.I.
HHSL SAFETY SYSTEMS LIMITED & THE HUMMINGBIRD GROUP hhslservices@hhslsafety.com www.thehummingbirdgroup.net
Malta
+ 356 2165 8281/2
+ 356 9998 5211
INTERNATIONAL SAFETY TRAINING COLLEGE enquiries@istcollege.com.mt www.istcollege.com.mt
INTERNATIONAL TRAINING CENTRE
Sfax, Tunisia
Tel: +21697037456
Fax: +21671656170
Ezzeddine.kacem@itc-tunisia.net
Abu Dhabi, UAE, P O Box: 32330
JAHEZIYA: TAWAZUN SAFETY, SECURITY, DISASTER MANAGEMENT CITY inquiry@jaheziya.ae
Tel: +971 2 4928500
Fax: +971 2 4928501
www.jaheziya.ae
Ringaskiddy, Cork, Ireland
NATIONAL MARITIME COLLEGE OF IRELAND reception@nmci.ie
+ 353 433 5600
NATIONAL CHEMICAL EMERGENCY CENTRE
Oxfordshire, United Kingdom
support@thehazmatacademy.co.uk www.thehazmatacademy.co.uk
NEWCASTLE INTERNATIONAL AIRPORT
Woolsington,NewcastleUpon-Tyne,NE138BZ
+ 44 191 – 2143337
trainingacademy@newcastleinternational.co.uk www.newcastleairport.com/training-academy
Qatar
+974 44501223
QATAR INTERNATIONAL SAFETY CENTRE (QISC) training@madinagulf.com www.qisc.net
RELYON NUTEC FIRE ACADEMY
Rotterdam, The Netherlands
+31 181 376 666
fireacademy@nl.relyonnutec.com
SASOL EMERGENCY MANAGEMENT TRAINING ACADEMY
Secunda, South Africa
+ 27 17 610 6016
isabel.dejongh@sasol.com
Darlington, United Kingdom
+44 (0)1325 333317
SERCO INTERNATIONAL FIRE TRAINING CENTRE bookings@iftc.co.uk www.iftcentre.com
Aberdeen International Airport, Dyce, Aberdeen AB21 7OU, Scotland
+ 44 1224 348523
THE FIRE TRAINING GROUP enquiries@thefiretraininggroup.co.uk
IzmirRefinery,TÜRKİYE
TURKISH PETROLEUM REFINERIES CORPORATION izmiryanginegitim@tupras.com.tr
+90 232 498 55 55
YASSINE MARINE SERVICES YMS TRAINING CENTRE
Sfax, Tunisia
+216 36 408 290
yms.training@y.marineservices.com
Our international courses:
• Advanced Industrial Firefighting
5-day training – Rotterdam (The Netherlands) (JOIFF-accredited)
• Fire Team Leader
5-day training – Rotterdam (The Netherlands) (JOIFF-accredited)
• Foam School 2025
4-day event - Vernon (France) (JOIFF-accredited)