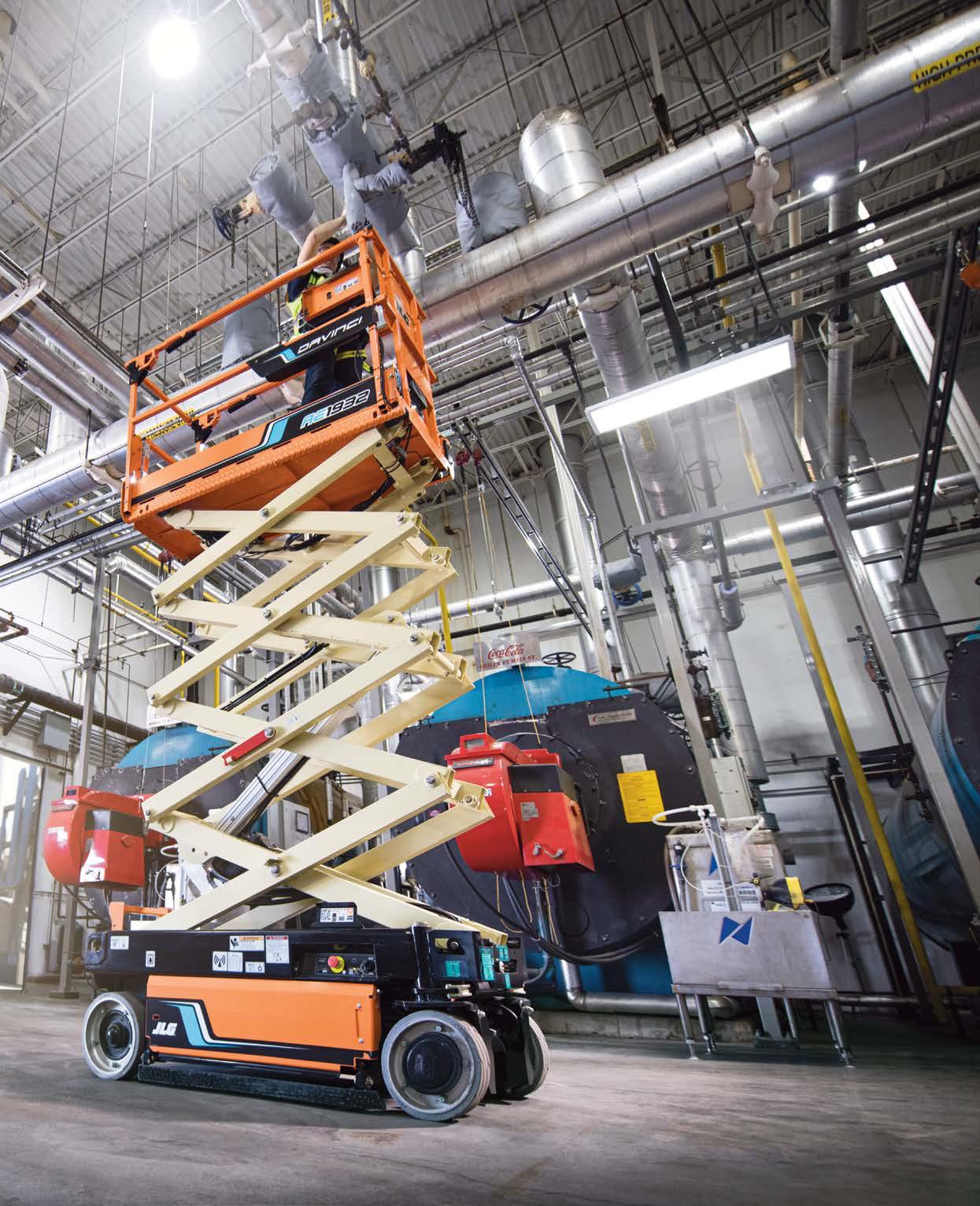



Dear clients and business partners, welcome to the latest edition of JLG Insight.
With time fast winding down towards Christmas and the holiday season, this edition of Insight provides a great opportunity to offer a heart-felt thank-you to all our loyal customers for their continued support. While the challenges of the last two years are easing, operating conditions have not yet returned to normal, so we are appreciative of your ongoing understanding and patience.
It’s also pertinent to acknowledge the great work of the broader JLG team during this period – they’ve adapted and remained resilient in order to deliver the best solutions and service for our customers in light of the circumstances. Fortunately, we believe the worst of the supply chain and general inventory issues are now well behind us, and should continue easing from early 2023 onwards.
These constraints aside, 2022 was an extremely positive year for JLG on all other fonts, with several all-new models launched along with the continued evolution of the broader range. Among the product highlights was the release of four new ERT and four new Diesel Rough Terrain Scissor Lifts and the new X26JP and X33JP Compact Crawler Booms.
In this edition, you will also read about the new DaVinci™ AE1932, the industry’s first fully electric Scissor Lift –it’s completely electric with no hydraulic components and makes a fantastic addition to the JLG product line-up. And the good news is that the new model introductions will continue in the year ahead with new boom lifts set for introduction, as well as the wider availability of hybrid technologies.
This year we also increased our company’s safety and wellbeing program through the wider introduction of our ‘Safety 365’ initiative. Safety 365 takes a proactive approach to safety and was developed to better engage with JLG team members as well as with our customers, contractors, partners, and suppliers. There’s a full overview of the program within this edition.
On the business front, we’re extremely optimistic about the year ahead. Along with supply chain pressures further easing, major infrastructure projects have been slated for commencement across Australia and New Zealand in the coming months; this bodes well for our business, for many of our customers and more broadly for the wider economy.
Please enjoy this edition, and on behalf of JLG Australia and New Zealand, I wish you a very safe festive season, we thank you for your business and all the best for the year ahead.
Scott Daly General Manager - Australia & New Zealand
JLG’s new DaVinci™ AE1932, the industry’s first fully electric scissor lift is now available for Australia and New Zealand, offering new technologies that will increase efficiency and convenience for operators, while also reducing total cost of ownership.
With full electric operation, the AE1932 Electric Scissor Lift has no hydraulic components, eliminating the risk of oil leaks, which makes the machine ideal for use in sensitive areas such as food production facilities, clean rooms, medical buildings or on carpeted floors.
The new JLG AE1932 Electric Scissor Lift also features the latest electric drivetrain technology, including AC drive motors for zero emission power and low draw, meaning more work can be achieved on a single charge. Further extending run time on these units is an innovative energy recovery system that uses gravity to recapture power as the platform descends.
Such is the AE1932’s low rate of power consumption that only a single 24V Lithium-Ion battery is required on the unit. The battery also provides Zero Performance Degradation, which maintains performance and productivity even as the battery depletes.
When recharging is needed, a full charge can be achieved in under 4 hours, and for greater convenience and runtime, opportunity charging is also possible without damaging the battery –fast 30-minute lunch break charges will lead to hours of additional productivity. Additionally, the AE1932 features a 5-minute quick charge function that allows 30 metres of driving and provides enough torque for the scissor lift to be loaded onto a truck or trailer for transportation.
Along with the environmental, efficiency and low maintenance benefits, the AE1932 offers a generous 5.8 metre elevated platform height and platform capacity of 275kg, providing ample accommodation for work crews (two occupants indoors and one outdoors) and
their tools. A high efficiency steering system with zero inside turning radius and 6.4 km/h lowered drive speed also makes the machine more maneuverable. For added productivity, the AE1932 can also be driven at 0.8 km/h in the elevated platform position, with the machine’s industry-exclusive progressive elevated drive speed system adapting the drive speed depending on the platform height.
Preparing the AE1932 for work is also faster, its QuikFold rails unfold in a fraction of the time of standard machines, while fully raising and lowering the platform takes just 24 and 26 seconds respectively. Positioning the AE1932 is also more efficient thanks to independent wheel motor control which also reduces tyre wear and limits damage to sensitive flooring.
Operators control the new machine via the platform control box, while the JLG Mobile Control app also allows users to drive, steer and load the stowed DaVinci from a distance using their smartphone.
Although JLG’s new DaVinci™ Series Scissor Lift is virtually maintenance free, in the unlikely event of an issue, operators or technicians can perform diagnostics using the exclusive DaVinciGO™ app through a smartphone or tablet. This technology provides software updates, machine configuration and calibration – the app even allows the machine to be connected remotely to a JLG service centre.
With an expected battery life of 10 years, JLG’s new DaVinci™ AE1932 all-electric scissor lift delivers low total cost of ownership benefits, and for addition owner peace of mind, is backed by the extensive JLG Ground Support network.
The JLG
more, with the launch
Plus Compact Crawler Boom
The new X33J Plus offers a market-leading work envelope including 17.20 m up-and-over height and 16.5 m of horizontal working outreach. With below-grade capabilities, the X33JP is suitable for both above and below level work and is highly manoeuvrable to fit through double doorways, for hassle free movement between outdoor and indoor work zones.
Equipped as standard with a Bi-Energy system, choose between operating a diesel engine or Lithium-ion electrical system that doesn’t produce emissions.
FEATURES:
Articulated boom design for maximum working envelope
Unrestricted 230kg platform capacity
New jib with over/under and rotating platform
Powered track extension with non-marking rubber tracks
SkyGuard and forklift pockets fitted as standard
Reduced setup time with auto-levelling outriggers with variable placement
Small footprint for ease of transport and operation in weight restricted areas
Working Height
Working Outreach
South Australia is a diverse state in terms of the industries it accommodates. As well as servicing the usual sectors including rental fleets, warehousing, logistics and civil construction, JLG’s Adelaide branch customers extend much further afield – viticulture, agriculture, manufacturing and mining are also important markets.
This means that for JLG’s 14-strong South Australian team, there’s never a dull day. Working from a spacious facility that offers customers sales, service and parts capabilities, the Adelaide branch based in the suburb of Green Fields, includes five workshop bays that allow its five technicians to handle multiple machines in each bay.
These in-house servicing capabilities are supported by four field technicians who travel the breadth of the state undertaking scheduled and unscheduled maintenance work on customer machines. Additionally, Green Fields is responsible for coordinating the Northern Territory region.
Other benefits of the site include a large outside stock area for new and used equipment, a small internal display space for feature machines, generous parts warehousing and modern offices.
Heading up the South Australian branch is Manager, Danny Clark-Tosic, who has worked with JLG for five years, but also boasts a further 15 years’ experience within the broader industry.
Danny said that as well as providing JLG customers with quality facilities to handle their needs, a convenient location and ample parking, another important contributor to the success of JLG in South Australia and the Northern Territory, was the high caliber of the team.
“We’re extremely fortunate to have a dedicated and knowledgeable team in our South Australian operations,” Danny said.
“A good portion of our members have been with JLG for between seven and ten years. This is great for the customer both from a knowledge perspective, but also because of the strong relationships that we’ve developed with these clients. It also shows that JLG is a great place to work.”
While a full range of JLG equipment is available from the Adelaide branch, Danny said that the JLG ES and R Series electric scissor lifts were its most popular models.
JLG’s South Australian branch may be one of the company’s smaller volume outlets, but it still has a big job to do.
“The smaller electric scissor lift ranges are versatile and very well regarded with our local customers,” he said.
“Our clients also love our scissor lift trailers – the fact that we have Australian-made products such as these trailers and the lighting towers available, is really appreciated and supported by the customers.”
Recently the Green Fields site has made the transition to LED lighting to reduce energy consumption, and other minor upgrades are scheduled at the location in the coming months to further improve the efficiency, functionality and appearance of the branch for customers and employees.
We’re extremely fortunate to have a dedicated and knowledgeable team in our South Australian operations.
Used equipment is an important contributor to the JLG business, especially during recent years, where tight supply chains have resulted in reduced availability of some new equipment – we learn more from JLG used Equipment Sales Manager – Aus/NZ, Stephen Heffernan.
There’s no question that everyone enjoys putting a new piece of access equipment to work within their operation, but sometimes it may not be an ideal solution. Owners of smaller businesses may not be able to justify the outlay, especially if it’s their first piece of equipment and they don’t know if it will be utilised sufficiently. In such situations, a quality used model could be a better answer for them.
Of course, in the last two or so years, used equipment has also been extremely appealing to buyers, making up for reduced availability of new machines due to supply chain issues and manufacturing interruptions caused by pandemic restrictions.
These are operating conditions that have kept Stephen extremely busy, sourcing quality used equipment for JLG’s customer base. He’s been part of the JLG team for over 12 years now, working in various sales, support and operations roles before being appointed to his current position in 2019.
“One of the key aspects of my role is to develop and maintain relationships with auction houses, brokers, used equipment traders and rental companies, and to continuously seek opportunities for the purchase and trade-in of suitable used equipment,” he said.
“I really enjoy the thrill that comes with sourcing and purchasing machines and the subsequent satisfaction of securing the sale of these machines while successfully meeting our clients’ needs.”
A rush on quality used equipment from JLG has had a flow-on affect to other areas of the company’s business in Australia and New Zealand, according to Stephen.
“While the demand for used equipment has been particularly strong because of the supply constraints affecting new machine supply, this has influenced our workshop workloads preparing the used equipment for checks and recertification before sale,” Stephen said.
“Until the situation balances out, we’re overcoming these circumstances by moving machines between various JLG locations to get the work done as efficiently as possible as slots become available.”
As well as the sourcing and acquiring machines, another important component of his role is to develop new sales prospects for used equipment in Australia and New Zealand, as well as liaising with existing clients and distributors to further grow sales and profitability.
Away from work, Stephen enjoys watching Rugby Union (which he also used to play when younger), and is also a ‘petrol head’, owning a classic HR Holden and some modern Aussie muscle in the form of a Gen F R8 HSV.
Keep the contents of your platform secure and the platform area tidy and free from tripping hazards with a Heavy Duty Pipe Rack from JLG. These highly versatile racks have adjustable mounting clamps and are rated to be used by a large number of JLG models.
Ease of installation
Adjustable mounting clamps
Transferable between platforms
Removable when not in use
Ideal for plumbing, electrical and sprinkler
4045R, R4045, RT3369, ERT3369, 3369LE, M3369LE, RT4069, ERT4069, 4069LE, M4069LE, RT 4769, ERT4769
RT2669, ERT2669, 260MRT, RT3394, 330LRT, 3394RT, RT4395, 430LRT, 4394RT, RT5394, 530LRT
The JLG Handheld Analyser is a compact, lightweight tool that allows the user to search for fault codes, enable/disable machine options, and adjust machine parameters, if needed, for service repairs.
The JLG PC Analyser is an alternative tool accessed via computer. The PC Analyser also functions as a “LogLifter” which records all the information which are viewable into the analyser menu to a text file.
To use:
Download the machine analyser software from Online Express and register your details
Open the software and connect your PC/Laptop via the usb port to the analyser port of the ground control box or platform control box
The screen is similar to that of the Handheld Analyser
Click the buttons on the screen to navigate through the menus
To use as a “LogLifter” click ‘Export” within the software, save the file, select as ‘text’ and select “operator root” or “current location” depending on access level parameters.
Once complete the software program can be closed
Having a strong awareness of safety is a core value at JLG Industries, and over the past 12 months our safety efforts have been boosted by several exciting initiatives that have been introduced under JLG’s new ‘Safety 365’ initiative.
Safety 365 is part of a broader global JLG program that we have adjusted to suit our requirements in Australia and New Zealand. It’s an initiative that takes a more proactive approach to safety and is designed to engage not only with JLG team members, but more broadly externally, including with our customers, contractors, partners, and suppliers.
Helping to introduce the program to our local market, was JLG National HSEQ Manager, Matt Farrington. Having joined JLG in 2008 as State Manager for SA & NT, Matt transitioned to his current role in 2015, keen for a new challenge and the chance to lead JLG’s safety efforts.
“Striving for safe workplaces has always been a strong interest of mine, and since I’ve been involved in my current role, it’s been extremely satisfying to watch JLG’s safety systems expand and evolve to where they now are,” Matt said.
365: We need to focus on safety today, and everyday –365 days a year.
Safety: The safety of our team members is at the heart of everything we do, therefore ‘Safety’ is at the centre of the logo. Arrow: The arrow represents the action-orientated approach we need to take towards safety. Circle: This represents our continuous improvement approach. Six safety basics: The tail end of the arrow includes six dashes highlighting the following safety basics:
Matt said that the principles of the program could relate to a broad range of work scenarios.
“The principles of Safety 365 can be applied in all environments in which JLG team members may find themselves working, not only within JLG facilities. As an example, the Take 5 approach which forms part of the Stop & Think safety basics list, must be used by technicians operating in the field, or even if a JLG representative is visiting the facilities of a prospective customer,” he said.
Take 5 encourages JLG team members to undertake a risk assessment of their location, where they should consider if there are any potential risks associated with the task they need to perform. They should then identify the potential concern, asses the level of risk involved, implement measures to eliminate or minimise the likelihood of occurrence, and then continue to monitor the situation and environment.
Safety 365 also sees JLG managers regularly meet to discuss any safety incidents that may have occurred either locally or across other regions or departments; this increases awareness of incidents and allows preventative measures to be put in place to minimise the chance of similar incidents occurring in other locations.
introduced, Safety 365 has been well received by JLG employees
occurrence of safety incidents have been trending downwards.
said that to build safe workplaces and champion a safe work culture,
safety message must be embraced by all.
share,”
New Control Box Common Scissor Lift Layout incl USB Port
Steel Platform and Rails with Self closing, Self locking Gate
545 kg Platform Capacity at full height both Indoors (2 x person) and outdoors (1 x person)
Inbuilt Variable Tilt Technology with Height Indicator on Upper Control Box
MDI at Ground Controls for onboard diagnostics and troubleshooting
Electric Front Wheel Drive and Front Wheel Steer provides a Zero Inside Turning Radius
Active Pot hole Protection