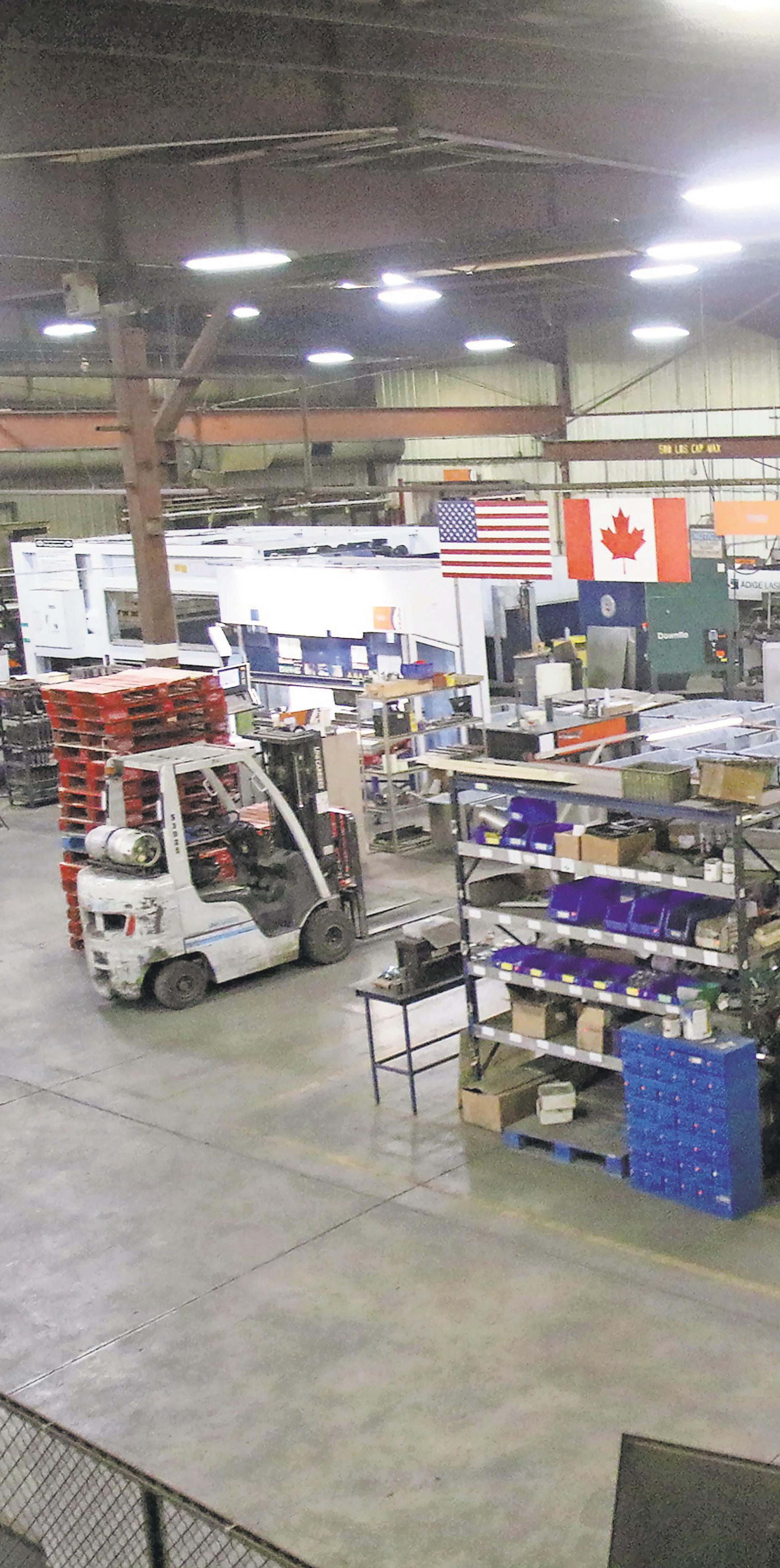
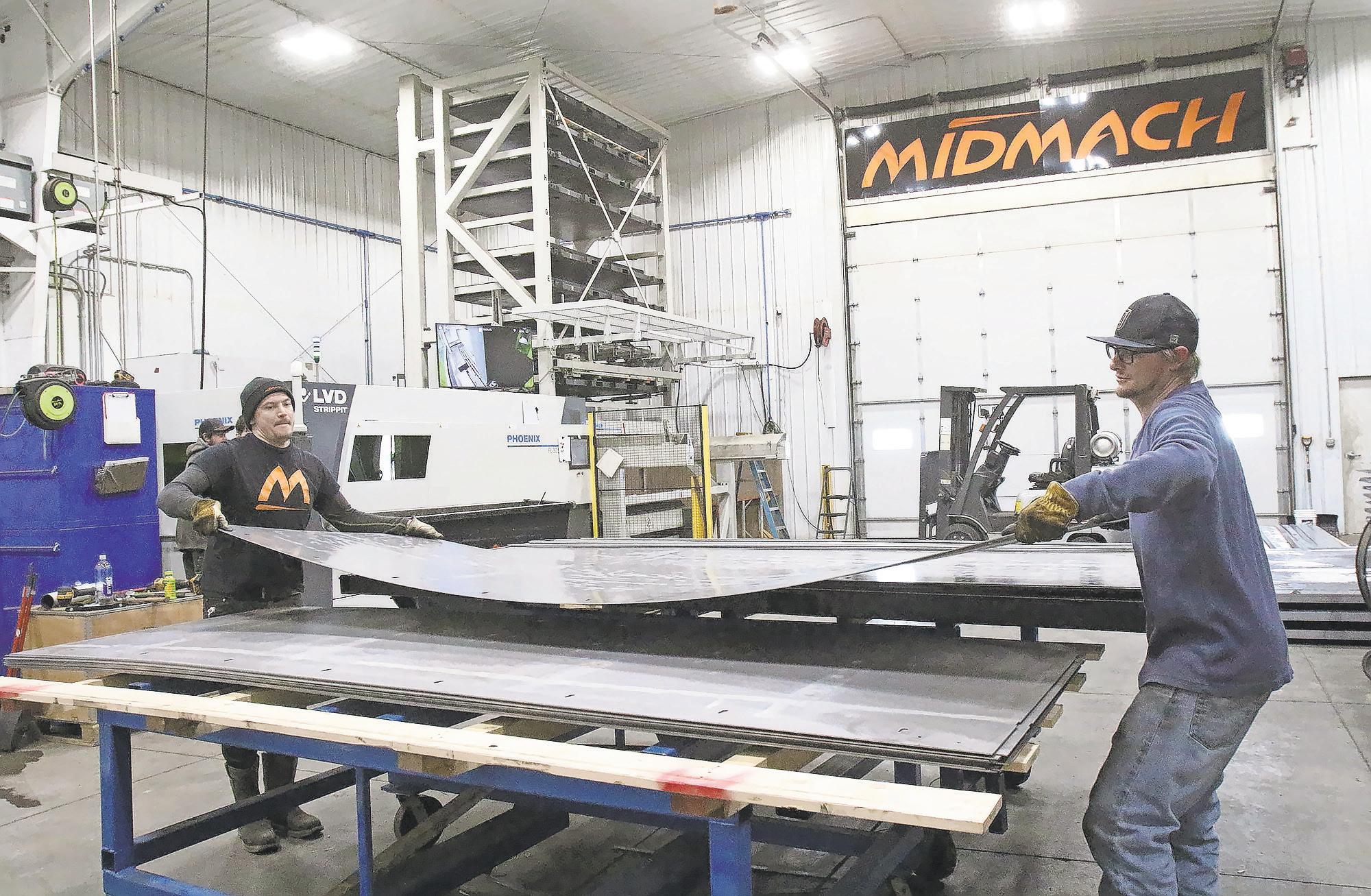
By Keith Norman For The Jamestown Sun
JAMESTOWN — Flat piec-
es of metal arrive at the shop of Midmach and, through a process of cutting, bending and welding, leave as completed buildings used by the oil industry to house equipment,
according to Casey Veil, vice president of the company.
The company’s fabrication and manufacturing work is about evenly split between agricultural components and oil and gas field equipment.
“Primarily we manufacture different types of agricultural
products and for the oil and gas industry,” he said. “We make a broad range of ag products under contract for other companies.”
Those products flow through the fabrication process at Midmach without Veil or the staff knowing the final product
their component is destined for. Each component is built to the specifications supplied by the company that will do the assembly. Veil said that none of the agricultural components they fabricate could be identified by the equipment user.
“Almost 100% goes outside the Jamestown area,” he said.
The company’s oil and gas field products are also shipped around the nation.
“We are national in scope,” Veil said. “We have a good mix
MIDMACH: Page A3
split up between North Dakota, South Dakota, Texas, Wyoming and Illinois.”
These products include a variety of products including stairs and catwalks around oil storage tanks and the small buildings used at oil and gas facilities.
Veil said they build the shell of the building with all parts welded together to produce a watertight enclosure that is then powder coated to prevent rust.
Powder coating involves spraying a powder on the parts which adhere due to a static electrical charge. The part is then baked in an industrial oven at 450 degrees to form a durable finish.
The buildings are then shipped to another company that fits out the interior for use to house electrical components at an oil facility.
“We’ve built hundreds of these buildings for the oil field,” Veil said.
The buildings don’t carry the Midmach logo or name but are common in oil production facilities around the country.
“We work with the customers to understand the scope of the project then design and build,” Veil said. “An example would be the catwalks and stairways to access an oil tank farm.”
Each tank farm has different dimensions and requirements, but Midmach works to utilize components such as stair or catwalk sections it already has designed to reduce costs for the project. Any necessary engineering and design work is done in-house to prepare the final product.
- Casey Veil, vice president, Midmach
Most items fabricated at Midmach are built to order with little inventory of finished products at its facilities. The company employs more than 30 people and is actively looking for a couple of additional workers.
“We are willing to train people that want to learn and work,” Veil said. “There is not much we can’t teach them if they want to learn and work.”
“Lots of high-tech equipment,” Veil said. “Probably some of the most technically advanced equipment used in manufacturing in Jamestown.”
While the equipment improves accuracy and efficiency, it is not the
Most equipment used at Midmach has some sort of computer technology to assist in the machine work and fabrication.
most critical part of the process.
“Good people are still the most important part of the business,” Veil
said. “We could immediately hire three or four but then we’d max out the facility.” Midmach looks to
address that problem later this year.
“We have a building expansion planned in 2023,” Veil said. Plans call for a 24,000-square-foot expansion at its facility in Jamestown. The facility will include manufacturing and office space for the growing company.
What is currently known as Midmach started as Midwestern Machine back in 1977.
“In 2014, we rebranded to sound less like a machine shop,” Veil said. Veil said the company managed to keep all of its employees through the COVID-19 pandemic.
“Kept virtually all of them even though we had no work,” he said.
By Kathy Steiner
The Jamestown Sun
JAMESTOWN — Scot
Loyd and his wife, Candy, moved to Jamestown in August, after he accepted a job as assistant professor of communication at the University of Jamestown.
The Loyds didn’t know anybody in Jamestown when they arrived from their previous state of Oklahoma.
But that changed through the Welcome to Jamestown Program offered by the Jamestown Area Chamber of Commerce. Two chamber ambassadors, Shirley Jackson and Jordan Padilla, came to Loyd’s office at the university bearing a “Welcome Home” floor mat and offers from chamber member businesses.
“And they were just very friendly and welcoming,” Loyd said.
Loyd said like anyone who moves to a new community, he wondered how he was going to make connections and get to know people. He said he felt more connected to Jamestown after the ambassadors visited his office.
“The idea that you have people going out of their way to make others feel welcome, coming into the community, I thought that they both represented the community very well,” he said.
Emily Bivens, executive director of the chamber, said the Welcome to Jamestown Program launched in 2022 as a way to help integrate new residents into the community and increase retention.
“Last year was the first full year of this and we were able to welcome 20 new residents through the program,” she said.
Bivens said the ambassador committee of the chamber worked on the Welcome to Jamestown Program. The ambassadors are what Bivens calls the “PR arm of the chamber,” about 30 volunteer members who attend ribbon cuttings and groundbreakings, for example.
“They help spread the good word of what the chamber does and what the chamber can do for businesses,” she said.
The Welcome to Jamestown Program is available to chamber member businesses. A chamber member business that hires a new employee reaches out to the chamber. An ambassador then schedules a time to meet with the employee, bringing a “Welcome home Jamestown, ND” floor mat and a “Welcome to Jamestown” membership card. The card is used to identify the person as a new resident who may take advantage of a variety of offers that are available from participating chamber businesses. Those offers range from a free one-year membership to The Arts Center to two movie passes or discounts on memberships or other items. There are currently 16 “welcoming gifts” from chamber member businesses, a number that Bivens noted has grown since the program launched.
Loyd said he and his wife used those offers to learn more about the community, trying out restaurants and going to the movie.
“Otherwise, we might have just gotten in the car because we’re new and driven to Bismarck or Fargo but because we had those incentives, we had those
WELCOME: Page A5
opportunities to experience local businesses,” he said. “It gave us an opportunity to stay here and discover what opportunities and availabilities were where that we may not have done otherwise.”
The only cost to the chamber member businesses providing the offer is what they offer, Bivens noted. The person receiving the incentives through the program, which are good for a year, must be a Jamestown resident of fewer than four months who is currently employed with an active chamber member.
The Welcome to Jamestown Program made so much of an impression on Loyd that only weeks later, he became a chamber ambassador too. Now he’s attending events in the community such as ribbon cuttings and recognizing people through ambassador activities.
“It’s been rewarding,” he said. “It’s given me opportunities to meet people in the community. It’s given me opportunities to be aware of businesses that are both
Last year was the first full year of this and we were able to welcome 20 new residents through the program.
- Emily Bivens, executive director, Jamestown
Commerce
Area Chamber of
new that are coming to the community and … established businesses that are expanding, and it gave me opportunities and insights into the community that maybe I wouldn’t have had otherwise.”
Loyd said he feels it’s important to give something back to the community to make it a better place and recalled going with the ambassadors to recognize a Walmart employee for good work.
“I think if we do those kinds of things in the communities in which we live that it accumulates and over time it just makes the place better,” he said. “We can choose to look at the world negatively or positively and there’s a lot
of negative things going on so it’s good to have avenues to celebrate the positives.”
Chamber businesses looking to welcome a new employee through the program may go to the chamber website at jamestownchamber.com and click on the Welcome to Jamestown link at the bottom of the page and provide the necessary information.
“I just encourage people that haven’t had the opportunity or haven’t availed themselves of the opportunity to get involved in their community that they are out there and the chamber and the ambassadors provide a wonderful opportunity to do so,” Loyd said.
ksteiner@jamestownsun.com | (701) 952-8449
fabrication.
From Page A3
“We came out the other side and have been busier than ever.”
Coming out of the pandemic, materials were difficult to acquire but that also seems to have improved, Veil said.
“Right now our main hurdle is employees,” Veil said.
About 90% of the products produced by Midmach leave the facilities on the company’s own trucks.
“Most of our products ship as quickly as they are completed,” Veil said. Jamestown’s geographic location at the crossroads of U.S. High-
way 281 and Interstate 94 is beneficial for shipping agriculture and oil field products, Veil said.
“We are centrally located among the ag manufacturers we market to,” he said. “And we are just far enough away from the oil field that we aren’t competing for employees but close enough to be attractive to them as a manufacturer.”
Corry Shevlin, CEO of the Jamestown/Stutsman Development Corp., said companies like Midmach are important to the community.
“As primary-sector companies, they bring more wealth to the area,” he said. “They provide jobs but they also bring in wealth
from all over the country.”
The wealth comes in the form of the value of the products sold outside the area entering the local economy as wages paid to local employees. It puts new money in circulation in the Jamestown economy, Shevlin said. And Veil said those employees are good at their jobs.
“It is a great place to work,” he said. “We have a lot of long-time employees and offer good benefits.”
And they produce a good product.
“Our employees are proud of the products they make,” Veil said. Midmach can be reached at www.Midmach.com.
We believe abig part of learning is living. Yes, your GPA matters. But agreat GPA, backed by avibrant campus life –where
By Kathy Steiner
The Jamestown Sun JAMESTOWN – Three primary reasons helped bring Cavendish Farms to Jamestown, said Matt Pederson, director of operations for Cavendish’s Jamestown plant.
“North Dakota has soil that is rich, black and nutrient-packed, and the region is one of the most productive in the United States delivering great potato yields,” he said. People and partnerships also played roles in bringing the French fry producer here.
Pederson praised the Midwest work ethic for providing “a great team that works together for the best possible outcomes” and said the local farms and farming partners use cutting-edge and innovative technology with environmental
stewardship to cultivate “the healthiest, most delicious potatoes possible” that helps Cavendish deliver premium quality French fries to its customers.
Cavendish Farms is a family-owned company that started more
than 40 years ago in the Canadian province of Prince Edward Island. It produces frozen potato products and appetizers for the North American and international food industry, supplying customers in the retail, restaurant and institutional sectors. According to its website, Cavendish Farms is the fourth-largest processor of frozen potato products in North America.
“At Cavendish Farms, we pride ourselves on
CAVENDISH: Page A7
From Page A6
high-quality products, exceeding our customers’ needs, and strong relationships with growers in our communities,” Pederson said. “There are three pillars (family, farm and food) that form the foundation of our brand and who we are.”
Cavendish Farms sells its products in over 30 countries, Pederson said.
“It’s important to maintain relationships on a global scale to continue to have a market for our great-tasting French fries,” he said.
The company, which has grown significantly since opening, Pederson said, operates four potato processing plants. In addition to the Jamestown plant, there are three in Canada, two
located on Prince Edward Island and one in Alberta. It also operates a fifth plant specializing in appetizers in Ontario, Canada.
“We are committed to investing in the business and acquiring state-of-the-art technology,” Pederson said.
Cavendish Farms Jamestown requires 14,000 acres of irrigated potato crops annually, Pederson said. The majority of raw potatoes for the plant — 85% — come from North Dakota and Minnesota.
“We are proud to partner with 15 farmers in the area to deliver great-tasting frozen potato products to our customers,” he said. “We are looking for potatoes that are long Russet-type varieties and are always evaluating new potato varieties that use less inputs, have a smaller carbon footprint and have better disease resistance than traditional varieties.”
He said to get the best French fries, they are looking for potatoes with a certain gravity (solids), size, color and shape.
“They also need to have internal and external defect resistance and have good storability and disease resistance,” he said.
Cavendish works to stay innovative with its products through its culture of innovation driven by the changing dynamics of the marketplace, Pederson said.
“We’ve forged a strategic partnership with Holland College’s Culinary Institute of Canada to create the Cavendish Culinary Creation Center,” he said. “Our team of food experts uses its know-how to transform food trends into crowd-pleasing flavors and innovative new foods.”
PARTNERS: Page A9
-
By Keith Norman
For The Jamestown Sun
JAMESTOWN — Rolls of flat steel weighing tons arrive at the Sunward Steel Buildings plants in Jamestown, according to Doug Hicks, technical manager for the company.
Ready-to-assemble steel buildings under the WedgCor brand leave the plant.
Hicks estimated 80,000 buildings have been shipped around the world although primarily to locations in the continental U.S. The company’s products are also certified for sale in Canada, Alaska and Hawaii.
“Our biggest sales point is quality,” he said.
Amy Wirth is the company CEO and works out of its Denver office.
“There are a lot of things done right here,” she said. “Our existence has always been to fulfill the customer’s dreams and goals.”
Good employees help the company meet those goals.
“We’ve always taken into consideration our employee’s best interest,” Wirth said. “… we wouldn’t be where we are without the employees. They are our inspiration to be a better company.”
Sunward currently employs about 75 people at its Jamestown locations. It also has administrative headquarters in Denver and another manufacturing plant in Walterboro, South Carolina.
The plant in South Carolina also produces steel buildings but under the Rockford brand name. Building orders placed with Sunward in the eastern part of the U.S. are fulfilled by Rockford and orders from the western part of the country are fulfilled by WedgCor out of Jamestown.
The WedgCor brand has a long history in Jamestown, according
to Shawn Gould, chief operating officer for Sunward out of its Denver office.
“It has a tremendous legacy,” he said. “Quite a large employer in Jamestown.”
The company started its growth when acquired by Danton Wirth more than 50 years ago, Hicks said.
Danton Wirth was a private pilot and sometimes landed his plane on gravel roads or fields near farms when making a sales call back in those early days.
“Within five years they expanded into the old “Rollohome” plant and increased our plant size to 150,000 square feet,” he said.
The company grew to about 500 employees in the 1990s. Production at the factory included three shifts producing steel buildings for sale around the world.
The company added a trucking division that could deliver its products to the customers.
That segment of Sunward no longer operates.
The ups and downs of the economy reduced the number of workers in Jamestown to 35 people in 2010 and the company has been rebuilding ever since.
The large market area WedgCor reaches is an asset to the company’s sustainability and to the community, according to Corry Shevlin, CEO of the Jamestown/Stutsman Development Corp.
“WedgCor adds value to the raw materials,” he said. “They have a lot bigger service area that adds health and stability to the company. That helps sustain the community.”
Physically, WedgCor is one of the largest manufacturing facilities in Jamestown with about 400,000 square feet under roofs.
That is roughly 10 acres used for manufacturing and storage in the community.
The prospects for the
company are positive looking into the future, Gould said.
“The industry (metal buildings) is extremely large and continuing to grow,” he said. “Sunward has seen growth as well with year-over-year double-digit growth.”
While the industry is growing, the types of metal buildings sold change over time.
“We haven’t sold any schools or shopping malls for a while,” Hicks said. “The biggest increase seems to be in barndominiums. Metal structures that are designed to serve as a house and have other uses.”
Other popular types of buildings have been rental storage facilities and airplane hangars. One airplane hangar project was a connected series of buildings about one-half mile long.
No matter what the structure, it is individually designed to meet all applicable local building codes and then built to order. This includes reviewing the required snow-load capacity for roofs, the ability to stand through high winds and the overall structural stability in earthquake-prone areas.
The company also reacts to changes in the customer’s needs with many new agricultural buildings having higher roofs and bigger doors to accommodate larger farm equipment.
WedgCor fabricates the frame, walls, roof and trim but purchases windows, insulation and doors. It takes roughly six to 10 weeks from the time the order is placed until the fabricated building materials are shipped to the desired location.
Buildings are available in panel-arch designs, buildings with a continuous curve to the walls and roof, and straightwall structures. Both can be modified to fit the customer’s needs. With growth and a
strong future, the company continues to invest in equipment and workforce in Jamestown, Gould said. The company has been
rebuilding its labor force and doubled the number of workers in Jamestown in the past five years.
“We are always looking for employees,”
Gould said. “Overall, it is difficult to find employees aligned with the company’s mission and vision.”
The biggest increase seems to be in barndominiums. Metal structures that are designed to serve as a house and have other uses.
- Doug Hicks, technical manager, Sunward Steel Buildings
From Page A8
The company’s mission is shared with new hires.
“We want to grow sustainability,” Gould said.
One of the ways WedgCor is growing is through a cooperative work agreement with the James Valley Career
From Page A7
Cavendish Farms has also partnered with North Dakota State University for the past 20 years including hiring many interns in its operations. For the last 10 years, Cavendish Farms has also worked directly with potato agronomist Andy Robinson and collaborated on research initiatives that are important for the potato industry, its partner growers and its business, Pederson said. “The research is critical in ensuring the sustainability of the potato industry in North Dakota and Minnesota,” he said. Jamestown workforce
and Technology Center. “The students get some work experience,” said Darby Heinert, assistant director at the Career and Technology Center. “They work side by side with the professionals.”
Heinert said the number of students participating in the program is growing.
“It is much more than giving them some work experience,” he
said. “We are trying to show they can have a good career right in Jamestown.”
Amy Wirth said bringing another generation of local workers to WedgCor would be a positive for the company.
“North Dakotans are hard-working, dedicated people,” she said.
“These are the people we’ve counted on in our 50 years in Jamestown.”
Cavendish Farms employs 210 people in the Jamestown plant and currently has openings in raw procurement, production, shipping and maintenance. Cavendish Farms also offers opportunities for career advancement within the organization, Pederson said.
“Cavendish Farms is a family company with an engaging culture rooted in our values,” he said. “We take pride in our people and support them.”
He said Cavendish Farms has an industry-leading employee incentive program, 401K with a company match up to 5%, and continually reviews and adjusts its rates of pay to ensure it remains competitive.
“We provide unri-
Cavendish Farms announced its purchase of the former AVIKO USA plant in Jamestown in November of 2001, according to a Jamestown Sun story in 2001 on the purchase.
valed benefit plans for our employees and their families, most of which start the first of the month after hire … ,” he said.
Those include medical, prescription, dental and vision coverage, flex spending accounts, life and supplemental insurance, long-term disability insurance and paid time off with carryover, he said.
“Our other industry-leading benefits include internal growth opportunities, paid breaks, uniform and shoe allowance, referral bonuses, and relocation assistance,” he said.
He said Cavendish Farms is committed to the communities where its employees live and work. For more information, visit https://us.cavendishfarms.com/. ksteiner@jamestownsun.com | (701) 952-8449
is a third-party metal manufacturer.
We’ve powered our communities for more than a century. And we’ll keep providing the reliable, low-cost electricity you depend on. Power and people you can count on
By Kathy Steiner
The Jamestown Sun
JAMESTOWN – Champ Industries USA has about 30 employees at its Jamestown location and hopes to be at 50 employees by the end of the year, says President and General Manager Kevin Medwick.
“We’re investing in Jamestown and we’re really hoping that we’re able to find the folks that want to grow with us,” he said. “That’s our main challenge, is finding people to do work in the skilled trades.”
Champ Industries USA is a third-party metal manufacturer supplying tier 1 original equipment manufacturers (OEMs), Medwick said.
“We support all the tier 1 manufacturers in North America,” he said.
A tier 1 company supplies a product to the market, he said.
“We’re a North American company so we have customers in Colorado, we have customers in Nebraska, Saskatchewan, Manitoba, North Dakota, South Dakota, Minnesota,” Medwick said.
Champ Industries USA provides sheet metal and tube weldments used by other companies in their products. A weldment is a part created from smaller components that are welded together.
Ideally, Medick said, they are looking for customers that want parts to be laser cut, formed, welded and painted.
“Typically our customers are either transportation, agriculture or construction,” Medwick said.
He said those customers are two types: customers that aren’t large enough so they don’t have the
type of equipment that
Champ Industries USA has, and customers that are getting too large and don’t have enough of the equipment or people to do it themselves.
The types of products they make include bracketry, battery boxes and suspension parts.
“You name it, if it’s made out of metal on a tractor or on a bulldozer or on a bus, then we may make it or we’ve looked at making it in the past,” Medwick said.
Champ Industries was founded in the 1950s in Winnipeg, where its plant there now employs 100 people, Medwick said. The Jamestown location opened in 2005.
CHAMP: Page B2
“The laws started to change in the (United) States as far as how manufacturing was performed when the ‘Buy American’ laws were brought into place,” he said. “So a lot of our customers now needed us to be able to provide U.S. content and thus Jamestown was born.”
Large sheets of steel, aluminum or stainless steel are loaded into the laser machine, where they are quickly cut for a specific job.
“It really all depends on the type of material and the thickness of the material,” Medwick said, “but you’re looking at a part every 3 seconds to every 15 seconds.”
Depending on the job, said Shannon Scholz,
production manager at Champ Industries USA, pieces cut by the laser may then move to another machine called the brake where they are “broke” (bent) into the needed product shape.
“A lot of stuff that gets cut comes through the brake,” Scholz said.
The factory/plant recently added a tube laser machine at the Jamestown plant that uses the same technology as the flat sheet laser machine but instead will
cut tube, Medwick said. It’s expected to be in use around the end of March and will provide another component to Champ Industries’ production.
“Typically the weldments that we do have two different types of materials in them,” Medwick said. “They have flat sheet (metal) that we cut and break into parts and they have tube (metal) that we cut and weld into the weldments. So instead
of paying other companies to cut the tube for us, we can now cut the tube for ourselves which opens a whole bunch of different doors. In North Dakota, we’re not aware of anybody else right now that’s offering laser cutting, welding and powder coating all out of the same facility when it comes to tube, so that’s why the investment was made.”
The company has also added laser welding technology, anoth-
er investment in the Jamestown plant, Medwick said.
There are multiple jobs occurring at the same time in the plant and they vary according to the individual company’s needs.
“Typically, I would say at any given time there’s 30 to 50 jobs on the go …,” Medwick said.
He said the equipment is only running at about
PLANT: Page B3
50 percent capacity right now. He said sales are expected to grow and they are looking at multiple avenues to find workers.
Medwick noted that Champ Industries USA’s need for workers is similar to other companies.
“Everybody is struggling to find people so our customers typically, what they’ll do, is they’ll transition their people out of the types of things that we do into assembly and completion roles and farm this type of work out to other companies that are being a little bit more successful finding people,” he said. “That’s where the majority of our growth is coming from. You can tie that back to supply chain issues that everybody in North America has been having for the last three years. …”
Champ Industries USA has three shifts for employees and is currently looking for welders and people to operate machinery.
“On the welding side, we’d like to see some type of education, even if it’s just through the
high school or through the technical colleges,” Medwick said. “We are willing to train from scratch, though. On the machine side, … all we’re looking for are people with mechanical aptitude. So maybe they worked for dad in the garage for a year when they were a kid or they like to play in their own garage, take things apart and put them back together. That’s really all we’re looking for. We’re 100 percent willing to train specific on our equipment.”
Medwick said the workforce at the Jamestown plant is “diverse,” noting there are people with many years of employment as well as those who have fewer years with the company.
“Once people are here and get to know the company, they tend to stay,” he said.
He said the company’s benefit package and overall remuneration are “very competitive.”
“Our culture is very much family oriented,” he added. “… We’re very willing to work with people to make sure their schedules match their bus schedules for their children and all that different kind of stuff. People work to support their family,
they don’t support their family so they can work … so that’s very important to us.”
For more information, visit https://champmetalfabrication.ca/ home.
ksteiner@jamestownsun.com | (701) 952-8449
- Kevin Medwick, president and general manager, Champ Industries
By Keith Norman For The Jamestown Sun
JAMESTOWN — The labor force is defined as the civilian population over the age of 16 that is working or actively seeking work, said Danica Chaput, workforce cen-
ter manager at Job Service North Dakota in Jamestown. For example, it does not include inmates in the Stutsman County Correctional Center or the James River Correctional Center or people who are retired, students or otherwise not
looking for employment. It is a number that has been declining in Stutsman County. The most recent labor force number for Stutsman County is 10,295 people, Chaput said. Looking back to 2012, for
example, the labor force in Stutsman County was 10,362. In 2002, it was 11,673 people.
Expanding the territory to the nine-county area that includes Barnes, Dickey, Foster, Griggs, LaMoure, Logan, McIn-
WITH
tosh, Stutsman and Wells, the labor force was 30,808 in 2002 and is now 26,358. The population of the nine-county area declined from 61,274 in 2000 to a 2020 population of 57,349.
WORKFORCE: Page B9
By Keith Norman
For The Jamestown Sun
JAMESTOWN — While most people think of outdoor billboards when they think of Newman Signs, the company does much more, according to Kari Newman Ness, CEO of the company. Along with digital and printed outdoor signs, the company manu -
factures traffic signs, installs residential and commercial fencing, prints advertising and decor items and operates a transportation safety division that provides signage and other services in road construction zones. The billboard, fencing and roadway safety divisions all offer products and services
in North Dakota and regionally across the Northern Plains. The traffic signs and printed products are sold nationally with travelers having a chance to see a Newman-manufactured traffic sign in every state but Hawaii. Billboards were the first product of Newman Signs and are still the company’s most visible
product although the technology is changing.
“We are always converting static to digital billboards,” Newman Ness said. “Right now we have 63 digital billboards mostly in North Dakota.”
Digital billboards use computer technology to display messages on a large scale visible to passing traffic. The
messages change every few seconds offering viewers a variety of information as they travel.
While the technology of digital billboards is most visible, it is the process of making traffic signs currently getting an upgrade in technology, Newman Ness said.
“I’m still struck by
how labor intensive it is to make a traffic sign,” she said. “Digital printing of traffic signs has helped a lot but we can do more.”
The new equipment is not intended to reduce the workforce but rather allow the company to do more with the available staff. The company
NEWMAN: Page B8
By Masaki Ova The Jamestown Sun
JAMESTOWN – Applied Digital Corp.’s next-generation data centers are being built to support the growing high-performance computing industry, according to Regina Ingel, chief marketing officer. Applied Digital has facilities near Jamestown and Ellendale. The 100-megawatt facility about 7 miles north of Jamestown became operational in 2022. Applied Digital announced on March 7 that the 180-megawatt facility in Ellendale has been energized. The total contracted capacity for Applied Digital is nearly 500 megawatts. Applied Digital, which is headquartered in Dallas, is also constructing a 5-megawatt facility next to its 100-megawatt hosting facility north of Jamestown. The plan is for the new facility to host more traditional high-performance computing applications such as natural language processing, machine learning and other high-performance computing applications developments. The 5-megawatt facility is planned for energization in the first quarter of 2023. Applied Digital, formerly Applied Blockchain Inc., designs, develops and operates next-generation data centers across North America to provide digital infrastructure solutions to the rapidly-growing high-performance computing (HPC) industry, according to its website. Customers of Applied Digital include BITMAIN and Marathon Digital Holdings.
Applied Digital Corp.’s facility located about 7 miles of
Digital. She said the cool climate was a big factor in deciding to construct facilities in the state.
“We have customers that come in and they effectively rent, energize space from us,” Ingel said. “So we receive their equipment, we set it up, we plug it in and then we run it, but we don’t mine any cryptocurrency. We don’t own the Bitcoin mining equipment, so that has not changed.”
Applied Digital changed its name from Applied Blockchain to more accurately reflect its services and broader business offerings to serve customers that require large computing-powered applications, according to a news release on its website.
“We felt it fitting to remove Blockchain from the name because really we are more than a onetrick pony,” Ingel said. Ingel said North Dakota is good for Applied
Being in North Dakota allows the company to save money on installing air-conditioning units and electricity, said Nick Phillips, executive vice president of hosting operations and public affairs.
“Some people also do evaporative cooling which means they use water and they spray water into the air and it evaporates which causes cooling,” he said.
“We also don’t have to do that. So we don’t use water or electricity like we would have to in Arizona, for example.”
Philips said North Dakota is one of the more stringent electrical jurisdictions in the U.S.
“It’s positive because we end up having to build to a very high standard from an electrical standpoint for what we do,” he said. “From a regulatory standpoint,
North Dakota has been great. There’s been a lot of folks in the state who have been very excited to work with us and help us get permitted and deal with all the vari-
ous issues that happen to come up.”
New Jamestown facility
The 5-megawatt facility will be designed and purposely built for graphics processing units and will be separate from the company’s other buildings. It is Applied Digital’s first HPC hosting facility.
The 16,382-square-foot building is designed to provide ultra-low-cost and high-efficiency infrastructure for HPC.
My parents chose Jamestown largely because of its location and never regretted their
- Kari Newman Ness, CEO, Newman Signs
is also looking for new employees.
“Even if we were more technology focused, it’s the people here that keep things moving,” Newman Ness said. “I cannot see a scenario when that will not be the case for Newman Signs.”
Newman Ness said that holds true even in a changing job market.
“Employees can be choosy,” she said. “It is very challenging right now for everyone who is hiring.”
That makes retain-
ing existing workers important.
“We have a few employees who have been at Newman Signs for over 45 years,” she said. “We also have many long-term employees who have been with us 20- or 30-plus years. I cannot overstate the importance and value they bring to Newman Signs.”
Workers and prospective employees bring a wide variety of skills to the job, Newman Ness said. Workers in the manufacturing segments of the business are often trained on the job while other areas require some experience or education.
“Experience is helpful,” Newman Ness said. “It helps us accomplish our goals and, of course, helps the employee move within the company.”
While many individual employees of Newman Signs support the charities of their choice, company-wide efforts include an annual food drive in November and a Christmas message placed across the front of the building during the holiday season.
“I will say there is plenty of need in the Jamestown community and we hope we are doing our share,” Newman Ness said. Workers at Newman
Signs utilize a wide variety of raw materials depending on the product. The company builds its own billboard structures which require steel of varying dimensions. The static or printed signs are made from vinyl which is printed at the company’s plant in Jamestown.
“Billboards are no longer painted by hand which would take one person days,” Newman Ness said. “Now they are printed on a large printer in about an hour.”
Traffic signs are made
from sheet aluminum and reflective sheeting while the traffic safety division works with road cones and barrels.
The print division utilizes vinyl, Plexiglass, canvas and other materials to produce its products.
Newman Signs began operations in Jamestown in June 1956 and currently employs 126 people.
“Jamestown has never been a detriment to us,” Newman Ness said. “We’ve always been able to find employees. Jamestown has just
been home. We’ve been able to do everything we wanted to do here.”
Harold Newman started the company by hand-painting signs and moved his young family to Jamestown when he graduated college.
“My parents chose Jamestown largely because of its location and never regretted their choice,” Newman Ness said. “… this is an attractive city with much to offer. The only disadvantage, right now, is the lack of workforce. This isn’t specific to Jamestown.”
on there.”
Once the 5-megawatt facility is complete, the project is expected to move to a pilot program with 300 graphics processing units with the initial customer launch expected in the first quarter of 2023, according to a news release on its website. Full-scale operations are expected out of the facility shortly after. The first customer is expected to primarily use the capacity for machine learning.
A 5-megawatt facility that hosts HPC applications is quite large, Phillips said. He said there are very few facilities of that type in the U.S. The equipment for
From Page B4
However, the Stutsman County population grew from 21,908 in 2000 to 22,623 in 2020.
With a declining population, the challenge has been to recruit workers from outside the region, according to Katie Ralston Howe, director of the Workforce Team at the North Dakota Department of Commerce.
Howe said people consider factors such as affordable housing, child care, the potential for the spouse or other family members and schools when contemplating relocating to a new area.
“The North Dakota population grew in the last decade,” Howe said. “We have to do both, bring people to the state and keep people from leaving North Dakota.”
The Department of Commerce has operated the “Find the Good Life” promotion as a talent attraction promotion for the entire state. It has also empowered local and regional groups to operate their own incentives through grant funding.
mining cryptocurrency and blockchain uses application-specific integrated circuits, he said. For mining, he said the application-specific integrated circuits are purposely built for blockchain and validating transactions.
Phillips said the machines in the 5-megawatt facility will be used for different purposes and HPC involves graphics processing units.
“High-performance compute has what’s called GPUs so they are like graphic cards for playing video games so they are really good at doing math,” Phillips said. “They can be used for different things, so they can be used for machine learning, artificial intelligence, neu-
ral networks and you name it. There are dozens of different types of applications.”
An application such as ChatGPT – an artificial intelligence chatbot developed by OpenAI – finds data that is available, feeds it to a computer system like what Applied Digital has and learns from what it reads, he said.
“In the case of ChatGPT, they had it learn from millions of articles out there,” he said. “Now when you ask it a question, … it kind of knows how to answer questions by having read a lot of text out there. … If you wanted to ask a question or have something write for you or interact with a person in some way, all these types of HPC apps can be run
He said HPC can be used for medical, gene or protein sequencing, drug discovery or other online artificial intelligence systems. He said Tesla’s self-driving cars use some sort of artificial intelligence that learns about video of people crossing a street or a vehicle that is turning to keep individuals safe.
“All those types of systems have to use computer systems that do artificial intelligence or machine learning or other things,” he said.
Recruiting employees
Ingel said Applied Digital has 37 employees in North Dakota and a large portion work in Jamestown. She said Ellendale
is not completely hired yet.
“The pool of individuals who have any background and experience in this particular industry because it’s so niche, it’s very small,” she said.
She said Applied Digital has created an internal training program with an expectation that any incoming employee will need training. She said the company is all about promoting internally.
“We are looking for entry-level positions and we will train you because in our company (at) these facilities, there is absolutely a track in place where you can just keep growing and building your career internally with us,” she said.
Phillips said it has been challenging to hire
people for the Ellendale location.
“We have a lot of open positions and they are entry-level positions and we do all the training,” he said. “We have a very robust in-house training program available for folks who would like to apply for our entry-level positions in Ellendale.”
Ingel said working with Applied Digital is being at the forefront of the new era of technology that is emerging.
“Our team is putting the digital infrastructure for these applications of the future in place and that’s pretty exciting,” she said.
For more information on Applied Digital, visit applieddigital.com.
mova@jamestownsun.com | (701) 952-8454
“We want to stabilize child care,” she said. “… this is helping them hire staff, maybe pay some benefits. Hire and retain people.”
The intent is with more child care facilities, it will be easier to recruit workers for other jobs in the region.
Chaput said on average, child care workers earn about $12 per hour in Stutsman County. This is lower than the statewide average for work of that type and lower than fast food and retail jobs in the Jamestown area.
In Stutsman County, the number of job openings exceeds the number of job seekers by more than 2 to 1, Chaput said.
“As of March 8, we had 535 openings listed,” she said. “That is probably understated in the retail and service sector.”
Employers in the food industry and retail often list a single opening and then hire multiple people depending on the number of qualified applicants.
Stutsman County currently has 225 people listed as unemployed
“It allows the community to decide the greatest need,” Howe said. In the Stutsman County area, officials determined child care as the greatest need. South Central Dakota Regional Council will administer a $1 million grant for the next year, according to Traci Redland, director of the SCDRC.
but most of them are construction and farm workers who are seasonally unemployed and planning to return to their former employer in the spring.
Wages have also increased in Stutsman County and the region, according to statistics from the North Dakota Labor Department.
In 1990, the average annual wage in the region was $14,676.
Workers in Stutsman County had the highest wages with a $16,744 average.
By 2010, the region’s average wage climbed to $31,870 and Foster County offered the highest average wage in the region at $35,932.
The increase in wages in the region between 1990 and 2010 amounted to 61.7% and exceeded the statewide increase in wages for the same period of 54.3%.
Recruiting workers can be a challenge even with increasing wages, Chaput said.
“People just exiting the justice system or the military could be good sources for workers willing to relocate,” she said.
And high school and college graduates this spring should also find good chances in the job market.
“There are so many opportunities for them,” Chaput said. This is especially true
of March 8, we had 535
Danica
for students who took part in internships or cooperative work experi-
By Masaki Ova The Jamestown Sun
JAMESTOWN — From a focus on building bomb racks in 1970 in Jamestown, Collins Aerospace has been manufacturing cargo systems and working with every airline that flies a widebody aircraft today.
“We have product support people that work with all these airlines, support them, make sure they got the equipment they need, the spares they need,” said Craig Olin, director of business development for cargo systems at Collins. “We literally touch every corner of the world with our employees, with our product.”
Collin Aerospace started as a Western Gear location in 1970 in Jamestown and focused on building items for the military. In 1977, it began producing cargo components for a Boeing 747 freighter.
“That expanded over the years as we got into more and more cargo businesses and fewer military businesses,” Olin said.
He said Collins Aerospace in Jamestown deals specifically with cargo-handling systems. The cargo systems help quickly move cargo through the main and lower decks of an aircraft, according to its website.
Collins Aerospace is one of the four major business areas of a merger between United Technologies Corp. and Raytheon Co. The merger in 2020 between United Technologies and Raytheon Co. formed Raytheon Technologies Corp. In 1996, the aerospace company began working on cargo systems for a main deck of a Boeing 747 freighter that has very large cargo capability. In 2011 or 2012, the company, known as UTC Aerospace Systems at that time, won a contract to build cargo systems for CH-47 Chinook helicopters, Olin said.
“Since then, we’ve also started work on other
military cargo systems,” he said. “ … We’ve had a rich history here for 50 years.”
The Jamestown location has three plants in different locations. Plant 1 is the main facility where the production team, management and support functions are located.
A 20,000-square-foot addition is being con-
structed and will be attached to the main section of the plant. The Jamestown expansion includes space for new state-of-the-art chemical processing and paint lines designed to maximize operational efficiency, improve site ergonomics and provide customers with expedited delivery schedules. The
chemical processing line will grow to include eight to 10 additional tanks, expanding the internal parts processing capabilities of the facility.
Plant 2 is close to Jamestown Regional Airport and is where Collins’ engineering group is located and tests items.
Plant 4 is located in the same building as Job Ser-
vice North Dakota and is where new product introduction happens.
Jamestown is a good location for Collins because it’s located in the central-northern U.S., said Charles O’Neil, general manager of cargo systems for Collins Aerospace He said Jamestown has a lot of good, hard-working people.
The cargo systems include ball-transfer units, power-drive units, control systems, freighter-common turntables, centerline restraints, bumpers, unicaster panels, door sill assemblies and rollout stops, according to Collins’ website. The website says the components work together to convey and secure cargo within an aircraft for fast and easy loading and unloading.
“Our system powers these containers in on power-drive units and then drives them down the tube of the aircraft where they are locked in place,” Olin said. “It’s very complicated. It’s a lot of software, a lot of electrical, mechanical.”
By Masaki Ova
The Jamestown Sun
JAMESTOWN – Prima-
ry-sector businesses are important for a healthy community and create many secondary jobs,
which creates wealth within the state and the community, according to Corry Shevlin, CEO of the Jamestown/Stutsman Development Corp. Shevlin said the state definition to get certified as
a primary-sector employer by the North Dakota Department of Commerce is bringing in 75% of its revenue from outside of the state. He said bringing in that much revenue from outside the state builds
wealth for the state and the community.
“As those companies … thrive and bring in money, it’s only better for the community and better for the state, and value creation is what we are
after,” he said. A primary-sector business is an individual, corporation or limited liability company, partnership or association that is
certified by the state Department of Commerce’s Division of Economic Development and Finance which through the employment of knowledge or labor adds value to a product, process, or service which results in the creation of new wealth, according to the commerce department’s website.
Value is added, for example, when a farmer can sell a bushel of corn but if it can be refined into a few different products, Shevlin said.
“That’s when you start to see a significant difference in your community’s makeup and how those jobs pay and the opportunities that those companies are able to provide for the citizens,” he said. “When you are moving through that process of further refining or value adding to any product, there are additional opportunities that come up throughout that process additionally.”
A majority of the larger manufacturing companies in the area are primary-sector certified, he said. Getting certified as a primary-sector employer unlocks additional incentives such as getting funds from PACE, the New Jobs Training Fund, Automation Tax Credit, Seed Capital Investment Tax Credit, Sales Tax Exemption on Computer and Telecommunications Equipment or the research expense credit, the commerce department’s website says.
“Those programs are important for the healthiness of the community,” Shevlin said.
He said primary-sector companies that add value and jobs are the exact type of employer that JSDC wants to see come to the community.
“They relocate, start here, they are the kind of companies that we want to see thrive,” he said. “Obviously we want to see all our companies thrive but the primary-sector job growth and the value add is
invaluable for a community.”
By adding value to products, businesses are able to offer higher-paying jobs and it creates more jobs in the secondary sector which in turn creates more in the tertiary sector. Shevlin said employees are needed for the primary-sector businesses, which also need suppliers that employ other individuals.
“You bring in families for those jobs. You need jobs for spouses, schools for kids to go to and all things that are associated with that,” Shevlin said. “Part of a healthy community is having those types of jobs.”
Wages for primary-sector employees can range
anywhere from the lower to higher ends of the pay scale depending on the position, he said. But the benefit is the opportunities in the secondary and tertiary markets where more indirect or induced jobs are created even though they might not pay as high as a primary-sector employee.
“There is a whole list of additional indirect jobs that come that aren’t direct employees of whatever specific company that is,” Shevlin said.
He said all businesses are important in the community and all employees in the area need places to shop.
Shevlin said the JSDC primarily targets primary-sector job development but it also
provides funding to retail and commercial companies.
“We understand that to have a community, you need all of the things,” he said. “You can’t just have one or the other.”
The JSDC also invested in land in the Jamestown area to create business parks where the infrastructure is developed. The developed land is made available to companies that are either looking to relocate or expand their operations.
“We’ve had a lot of success with the land development model and I think it’s an appropriate thing that works for our community,” he said. He said the JSDC looks to recoup the funds that were
invested for acquiring and developing the land so it is cost effective for businesses looking to move into the business parks.
“We want the companies that are in Jamestown and Stutsman County to be as healthy as possible,” Shevlin said. “For us there is value in paying additional taxes, providing employment opportunities for the constituents here, those kind of added benefits we see as what our return is.”
The Spiritwood Energy Park Association’s industrial park near Spiritwood has been targeted for manufacturers of value-added agricultural products, Shevlin said. With development of business parks, the JSDC staff has to identify what is unique that can be offered to companies to locate there.
“You have to make it advantageous,” he said. There’s a reason that they want to be here whether that’s a cost savings or you provide for the Spiritwood Energy Park, it’s a specific utility that isn’t available in other places. So identifying what your unique advantages are and then kind of capitalizing on those advantages and then obviously doing that in a cost-effective way is important also.”
For example, the SEPA industrial park having rail for trains and being close to Interstate 94 is advantageous to companies that locate there, Shevlin said. He said waste steam that is produced from Great River Energy’s Spiritwood Station can be used by other industrial uses that locate there. Midwest AgEnergy’s Dakota Spirit biorefinery utilizes the steam from Spiritwood Station for ethanol production, he noted. Green Bison Soy Processing, which is being constructed in the SEPA industrial park, plans to utilize the steam as well.
“There’s not too many places that couple those things together that have unit train service and access to steam heat everywhere,” he said.
mova@jamestownsun.com | (701) 952-8454
By Kathy Steiner
The Jamestown Sun
JAMESTOWN – When
Jerry Waagen began his part-time job in August as the work-based learning coordinator at James Valley Career and Technology Center, he expected to have about 15 students sign up for the program.
There were 25.
This semester, a record number of Jamestown students — 38 — are participating in a workbased learning experience, and Waagen hopes to continue that trend with students and employers.
“Basically, what we’re taking is the knowledge that the students are getting in the classroom and putting it into the workplace experience,” he said.
Jack Biloweth is one of those students. He moved to Jamestown last year and was interested in machinist work.
Now the senior at Jamestown High School is using his education to learn and acquire more skills at Dan Poland Machine in Jamestown.
Work-based learning — also known as cooperative work experience — offers a way for students to try career areas that they’re interested in before going on to college and learning a certain field is not for them.
“That’s the basic premise of the whole program,” Waagen said.
The goal is to create a relationship between students, businesses and schools that benefits all to meet employ-
ment needs now and in the future, according to information on the program.
“There’s a number of reasons why co-ops are so valuable,” said Darby Heinert, assistant director of the Career and Technology Center. “First
of all, it gives a student an opportunity to network with an employer. And so they get to work at a progressive company in Stutsman County.”
For the employer, there’s the possibility of finding a future employee, he said.
Heinert said they want to keep students in Stutsman County, noting they can find good jobs here instead of moving elsewhere.
“We try to promote these as much as we can because we’re trying to keep our talent, our kids, our skills local,” he said.
“... We have a depleted workforce and we’re doing our very best to help industry and to collaborate with industry to build a more sustainable workforce here.”
Students need to be enrolled or have previously taken a career and technical education course and have at least 1 credit in the program area, Waagen said. Courses related to work-based learning experiences include
STUDENTS: Page C5
Participating businesses in work-based learning experiences
Anne Carlsen
Ben Tompkins Farm
Brown’s Farms
Building Blocks Child Development
Butler Machinery
Child in Our Hands
Cornerstone Nutrition
Creative Journey
Dakota Cabins
Dan Poland Machine
Dr. Dawn’s Pet Shop
Edgewood Senior Living
Heartland HVAC
Interstate Engineering
Jamestown Plumbing and Heating
Jamestown Regional Medical Center
Menards
Messner Construction
Northwest Tires
Rock of Ages
St. John’s Academy
Scott’s Electric
SMP Health - Ave Maria
Southwood Veterinary Clinic
Sunward Steel Buildings
TMT Farms
Triump Inc.
21st Century After School Program
Two Rivers Activity Center
From Page C4
child development, auto collision, auto technology, construction, health careers, small animal care, nutrition and food preparation. If approved for a cooperative work experience, students can earn half a credit for 75 hours of work or 1 credit for 150 hours in a semester.
“They’re working,”
Heinert said. “This is not shadowing. They’re actually working with the equipment at these places. They’re contributing. In most cases, these are paid positions. These companies are paying our kids to work. So it’s a win-win. The kid gets paid and earns credit at the same time. They get to work with equipment that we probably won’t have at the Career and Tech (Center) depending on the experience.”
As the work-based learning coordinator, Waagen connects with businesses to provide experiences for students interested in specific areas of work. This semester, there are 29 employers participating from a range of career fields.
“It’s so varied which is part of the fun of the program as well,” Waagen said. “The employers, when I connect with the new employers, most of them are very receptive and happy to have our students come there.”
Waagen said students are evaluated at the end of the work experience on job-related items from
their quality and quantity of work to attendance/ punctuality, appropriate dress, attitude, dependability and relations with coworkers, among other criteria. There are also specific competencies that are job specific that the employers help select, he said.
For businesses, students in a cooperative work experience can help them during a time when workers are desperately needed.
“They’re trying to find employees,” Waagen said. “I think that’s partially what this workbased learning program is about. Hopefully, we can help fill some of that gap. It doesn’t matter what field it is, almost any position in the city is looking to be filled. We
have students that are helping as direct professional support people … we have a CNA, we have a student working in HVAC. You name it, I mean, we can kind of do that.”
Bill Ringuette, machinist at Dan Poland Machine, which fabricates parts and repairs broken parts, said Biloweth’s education was a key fit for his cooperative work experience.
“Jack actually has a fairly extensive knowledge already of machining,” Ringuette said. “We have a number of machines that are computer controlled, so he’s programming those computers to make the parts from the machine. It’s basically a robotic machine for cutting metal.”
Biloweth said he took
precision machine and tool before moving to Jamestown.
“I used to live in Pennsylvania and when I was there I went to two years of a tech school during my sophomore and junior year,” Biloweth said. Biloweth says he can see himself staying in Jamestown and working in a place like Dan Poland Machine.
“I enjoy this kind of work,” he said. “I’ve always liked making things and this basically allows me to make things professionally. Prior to my taking a class at my tech school back in Pennsylvania, I didn’t know what machining was, but ever since I found it, I love it.”
WORK: Page C8
•
•
•
•
•
•
•
•
•
•
•
•
•
•
•
•
By Keith Norman For The Jamestown Sun
JAMESTOWN — The newest manufacturing operation in Jamestown is growing rapidly, according to Meghan Bintz, general manager of Shocker Hitch LLC. The Jamestown operation is an expansion from the original Shocker Hitch Co., which has been producing equipment for connecting trailers of all types to vehicles for more than 20 years at Arthur, North Dakota.
“We have 33 employees between the two locations,” Bintz said. “It is about evenly split between Arthur and Jamestown.”
The Jamestown crew has worked in the new Jamestown location since late February. The building had previously been the home of RealTruck.com and most recently Infinity Builders.
The Shocker Hitch company builds specialized hitches that increase the
comfort and safety of people towing trailers with their vehicles.
“Anything you need for towing, we make it,” said Curtiss Heidebrink, purchasing and procurement specialist for the company. What makes the Shocker Hitch unique is its ability to cushion the shocks and jerks that occur when the vehicle and trailer encounter bumps in the road. The shock absorbing capacity is provided by air bladders that can be adjusted to accommodate the specific weight of the trailer and load in any circumstance.
SHOCKER: Page C7
“The advantage is that these hitches take out 60% to 90% of the road shock,” Heidebrink said. “It makes for safer and smoother towing.”
Robert Sagen developed the hitches and founded the company at Arthur. When he retired, the company was purchased by Scott Bintz and part of the operations were moved to Jamestown. At this time, bumper-pull hitches are manufactured in Jamestown while fifth-wheel and gooseneck trailer hitches continue to be manufactured at Arthur. All are marketed under the Shocker Hitch brand.
“We build them from a wide range of raw materials,” Heidebrink said. “A lot of flat pieces and tubing, all raw steel.”
The components are welded together and assembled at the Jamestown Shocker Hitch plant. Future expansions include adding a powder coating system to apply high-quality paint to the products which are available in red and two shades of black.
Customer service and sales personnel also work out of the Jamestown office. The crew is settling in for what is the busiest season in the trailer hitch and accessory industry.
“It is seasonal,” Heidebrink said. “When the snow is gone, people will start to think about pulling campers, boats and other trailers.”
Most of their sales come from word-of-mouth and advertising videos offered through social media, Meghan Bintz said.
To meet the increased demand, the company has transitioned from building each hitch when it is ordered to creating an inventory of products.
“We are working on shipping the same day the order is placed,” Heidebrink said.
They are also working on developing a lighter hitch made of aluminum, Bintz said.
Other goals of the company include continual improvements to its products, improved customer service and increasing efficiency, she said.
The advantage is that these hitches take out 60% to 90% of the road shock. It makes for safer and smoother towing.
- Curtiss Heidebrink, purchasing and procurement specialist, Shocker Hitch
Shocker Hitch is also looking to grow its workforce.
“We try to make it as fun as possible,” Bintz said.
“We take people’s skills into account and let them work at what they are good at.”
They are currently looking to hire welders, assemblers
and customer service workers. Welders have an opportunity to work a three-day weekend shift putting in 36 hours while being paid for 40 hours.
Prospective workers have an opportunity to join a new company in Jamestown.
“Our current employees are happy to get into the company at the ground floor,” Bintz said. “It is an exciting environment to be in.”
Heidebrink said the company builds quality products with a one-year warranty included with all of its prod-
ucts. Interested customers can also learn more about the products through social media. The company offers a wide variety of hitch configurations to fit most needs.
“We don’t have an outlet here at the plant in Jamestown,” Bintz said. “Our sales are by e-commerce and through a network of dealers in the United States, Australia and Canada.”
One of its dealers is James Kota Inc., a trailer dealership on the west side of Jamestown.
“They have a good display of our products,” Bintz said. More information is available at www.ShockerHitch. com.
We’recommitted toprovidingthe cutting-edgetechnologyyouneedto poweryourbusinessandconnectto theworld. Standingouttoyour customersmeansprovidinga professional experience, andno matter howsmall your businessyou shouldhaveaccesstothesame servicesandprofessional functionalityofa bigcompany.
Whetheryour businessisnew orold, bigorsmall,our local experts areat your service so you’realways up, alwaysconnected. We knowall businesses don’t run8-5,whichis whywe’vegot your back 24/7. Let’s work together to buildapowerful networkthat won’tletyou down.
We try to promote these as much as we can because we’re trying to keep our talent, our kids, our skills local.
- Darby Heinert, assistant director, James Valley Career and Technology Center
At Two Rivers Activity Center, Blair Arbuckle is also in a cooperative work experience.
“Blair’s position is basically directly related to our guest services department,” said Boya Quichocho, facility manager. “She does help run our point of sale systems, she deals with customer relations and just overall monitoring the building and greeting guests when they come in.”
Arbuckle said she can usually be found at the TRAC front desk and she’s learned there’s a lot that goes on behind the scenes. She said she’s leaning toward a career in the physical therapy area or overall health and wellness in general.
“I think getting out to experience what you’re interested in is a really good idea and it helps lead you into a direction of what you want to do as a career,” Arbuckle, a senior, said of her work experience.
“I really enjoy it. I also do some job shadowing up at JRMC (Jamestown Regional Medical Center) in the PT (physical therapy) department. … I love going up there, honestly.”
Quichocho said this is the first year that TRAC has participated in the work-based learning
program, and employees work to train the students and teach them the skills they need to be successful, not only there but with their next employer or college.
“From our experience, it’s been great, even with the few that we’ve had,” he said. “ … they’ve been great to work with and I feel like they’ve learned as well as us.”
Heinert noted that a
number of businesses go on to sponsor students in college; the students will then return to work for that company.
“Auto technology, diesel technology is maybe our most active field right now,” Heinert said. “The lion’s share that are in automotive technology ... they will build a sponsorship with a local agency like John Deere, Valley Plains (Equip-
ment), they’ll work with Butler (Machinery), they could work with Titan (Machinery),” he said. “All these companies sponsor our kids (in college).”
Sponsorships vary from employer to employer and can be set up how they want, Heinert said. It may be assistance with college costs up front or after training is completed over a period of time while working for the employer. It could be help with paying for tools, for example, in exchange for working for the employer for a specific time. If the student ends the agreement before planned, the student would pay the employer back a specific amount.
“The kid has a job waiting for them right after college,” Heinert said. “We’re keeping our home talent right here in Jamestown and they leave college with minimal student loan debt so it just makes sense to do it.”
Biloweth says he’s enjoyed his work experience and has learned a lot at Dan Poland Machine.
“They’ve been all very helpful, especially Bill (Ringuette), whenever I have any questions he’s always ready to answer them,” he said.
Ringuette said he thinks it’s key to the success of the experience that the students want to learn or have some type of idea it’s what they want to do. He noted people are needed in many fields and when someone shows an interest in it and excels at it, it makes sense to provide the experience.
“A lot of the older machinists are retiring and there’s nobody to replace them and when somebody’s young and has some enthusiasm for it, you’ve got to run with it,” he said. “I think it’s a good thing, I really do. I think it’s something we need to do.”
Quichocho says he wants to continue providing work-based learning experiences at TRAC.
“They’re right across the street so it kind of makes sense that they could do their work experience here,” he said.
“And we do have needs in many departments, so
hopefully, we can provide opportunities for a variety of students’ needs or wants.”
Heinert said local businesses have been “incredibly supportive” of the center’s programs.
“I think they see the value in it, they recognize the power of CTE, they recognize how important it is and how CTE supports so many industries not only to Jamestown but North Dakota,” he said. “They recognize the benefit of a kid getting some great handson experience with their company. It’s a way to pay it forward, if you will. It’s also a way for them to get a very good employee down the road.
“I’m also excited to see what’s next,” he added.
“We have 38 kids placed (this semester) and that’s for a part-time workbased learning coordinator. Where’s the ceiling? What does that look like? And I don’t know what that is.”
For more information on the program, contact Waagen at 252-8841.
ksteiner@jamestownsun.com | (701) 952-8449
The cargo systems are contoured to match any type of aircraft. The powered control system can move and rotate palletized containers through the lower or main decks of an aircraft.
Olin said sometimes an aircraft will be filled with nothing but iPhones. He said sometimes aircraft are transporting race cars or horses.
He also said aircraft had to transport the coronavirus vaccines around the world as fast as possible. He said the vaccines had to be kept at a certain frozen temperature and time was limited to keep dry ice around them.
“We felt like we were able to help support (during the pandemic) in some sense,” he said.
Aircraft can carry cargo on the lower deck with passengers on an upper deck. There are also aircraft that carry just cargo on the lower and upper decks.
O’Neil said items ordered through E-commerce companies such as Amazon are sometimes shipped from overseas.
“The cargo systems that are designed, qualified and manufactured out of Jamestown are what they are being carried on,” he said. “A lot of those Amazon packages, not all of them, but a good chunk of them have been on a cargo system out of Jamestown.”
Collins also produces a cargo on/off loading system for the CH-47 Chinook helicopters for the U.S. Army, Olin said. In flight, the system can convert from a flat floor when troops are transported to a cargo floor with rollers in 12 minutes, he said.
“They had a problem because if they were going to carry people, they wanted a flat floor, so nobody would trip over anything, but if they wanted to carry cargo, then they wanted to be able to have rollers and locks,” he said.
Developing its products can take anywhere from 18 months up to five years, O’Neil said. He said a lot of engineering work goes into designing a cargo system because each aircraft is different.
He said Collins either develops a product that it wants to bring to the market or original manufacturers approach the company with ideas or solutions for an aircraft. Then the development work begins.
“We go into prototyping. We then go into builds, alignment with the customers on the expectations and those
requirements,” O’Neil said. “Then we go through qualifications effort where we make sure we meet those requirements or specifications of the customer. Then we test it to make sure that that works. Then it goes onto an aircraft for flying and then it’s tested at the aircraft level, and then becomes a system that is available to support the aircraft.”
Olin said a lot of time is spent on research and development to bring a next-generation cargo system to market.
“There’s a lot of companies out there, Amazon, that now fly their own aircraft that are looking for semi-autonomous, autonomous-type systems,” he said. “I think you will see the cargo industry is going to evolve in the future. … It’s going to be an ever-changing industry for the near future, and we want to stay at the forefront of that.”
Olin said there are now companies such as Natilus that are developing unmanned cargo aircraft.
“They should be flying within a couple of years, and we are working very closely with Natilus on cargo systems for them,” he said.
Employees and workforce
Olin said the employees at the Jamestown location are key.
“I think they are probably the best in the aerospace industry,” he said. “There is nothing that you can’t ask of them that they aren’t successful at.”
Collins employs 320 employees at its main facility and another 96 at the other two locations in Jamestown, O’Neil said.
“We expect to continue to grow this year in the range of about 40 employees for the cargo industry and the growth that we have,” he said.
He said Collins is looking to fill entry-level positions with assembly work, machinists and electrical, mechanical, stress, certification and software engineers.
O’Neil said Collins has employees who started as an hourly material handler and worked their way into sales, traveling all over the world to see all the airlines that want the company’s products.
“They built their career with the company, and there are several employees that have that opportunity,” he said. “We also have people who have been doing the same job for 20-plus years and are tickled to death to continue to do so. The nice thing about Collins Aerospace is once you get in the door, the destination is what you want it to be whether
that is to stay in cargo or even outside of cargo within the Collins Aerospace or Raytheon Technologies company.”
Collins offers benefits such as medical, dental and vision insurance, 401(k) with company match and tuition reimbursement among others.
O’Neil said the tuition reimbursement program is “phenomenal” and he is currently working on his master’s degree while the company pays for a part of that.
Olin said Collins works closely with the James Valley Career and Technology Center for machinists in training. He said the company supports any STEM activities it can find. He said Collins also works closely with many colleges, including the University of North Dakota, North Dakota State University and the University of Jamestown.
“(We’re) trying to reach in and get as many of these people interested in Jamestown and cargo as possible. It’s a strong co-op program, intern program,” he said.
O’Neil said a lack of housing is an issue in Jamestown.
“We need a community that wants to grow so that there are places for them, for all of these employees to come in and raise their families,” he said. “The jobs are there, wonderful career, a wonderful company to join, great opportunities, but we need to make sure when I go and recruit
either from within our company, our wonderful universities here or around the globe, they
Careeropportunitiesareavailableinclinicalandnursing professions,facilit yservicesanddirectsuppor tpositions.
Joinourteamand receive:
•Competitivebenefitspackage
•Tuition reimbursement
•Recruitmentbonuses
•Internshipstostar tyourcareer
We also partnerwithDakotaCollege at Bottineaunursing programwithclassestaught onourcampus.
Over the course of more than three decades, Alpha Opportunities Inc. has been serving the community of Jamestown by catering to the needs of children and adults living with developmental disabilities. At this time, Alpha Opportunities Inc. operates a day program in addition to having one residential group home, two ICF group homes and residential habilitation services.
Over the course of its existence, Alpha Opportunities Inc. has gone through a number of organizational changes and expanded the range of services it provides to the people it supports.
The organization is currently embarking on a journey to success, it said. This incorporates empowering people supported and staff to create a positive environment for them.
The day program has
Contributed / Alpha Opportunities
started a comprehensive revision in light of this fresh approach to achieving success.
The community rallied behind the idea, and after a vote involving people supported and staff, the day center got its new name, and renovation work began. This project was able to get off the ground because of the generous contributions made by members of the community. The centerpiece of this makeover is a sensory room that is completely outfitted and designed
to accommodate people supported while also assisting them in developing and engaging their senses. Those who struggle with sensory processing issues can especially benefit from having a space like this one, which can bring them a sense of peace, focus and comfort.
Alpha Opportunities has also begun new initiatives with the goal of educating and including
the people it serves in the day-to-day activities of life. As a result of all the recent changes and the expansion of Alpha Opportunities, there are now many employment options available, ranging from those involving direct support people to positions in management. Visit the website at alphaopportunities. org to view all of the open positions.
By Kathy Steiner
The Jamestown Sun JAMESTOWN –
Increased demand for children’s programming at The Arts Center is the main reason behind a $2 million capital campaign announced in early March, said Mindi Schmitz, executive director.
“We have waiting lists for every Arts After School class and so we need more classroom space,” she said.
The nonprofit Jamestown Fine Arts Association, which has operated The Arts Center for almost 60 years, will use funds from the “Raising the Bar for the Arts” campaign to purchase the former Wonder Bar building next door and convert it into a multi-purpose arts space. Although the campaign theme is a play on words for
the building purchase, it also reflects the need to “raise the bar” for the arts in Jamestown, Schmitz said.
“All of the visits that we’ve had to community leaders (about the project) are very positive,” Schmitz said. “‘... We know that art matters and this is a place where they can do it. Our cornerstone program here is Arts After School and we hate turning kids away.”
More than $860,000 has already been raised and the campaign is expected to be complete by May 1, Schmitz said.
Construction will begin May 2, and a grand opening on the project is planned in July 2024.
The project includes providing more classrooms and bathrooms, a gallery/commons, multipurpose outdoor area, studios and a living/work space upstairs, where regional or national art-
A
pieces sold,” she said. “I never would have been able to do that if I didn’t have the support from all of the people that work at The Arts Center, and I don’t think I could be where I am today without them.”
Schmitz noted The Arts Center offers a scholarship program to help children who need financial assistance to attend Arts After School. Out of the 17 children attending, five are doing so through the scholarship program.
ists may stay when they come to Jamestown.
The current classroom in the existing Arts Center will become a culinary kitchen for classes.
Closing the gap
While Arts After School programming has grown, there are still needs that have not yet been met, Schmitz said. The project
will help close that gap.
“We’re going to expand kids’ programming to include middle school and younger grades because right now we’re just 3 through 6th grade,” she said.
In the 2021-22 school year, 12 to 15 students could attend Arts After School, with 30 sessions that school year. After
the renovation, they expect to serve 56 students per school year.
Caroline Stoterau said she’s been going to Arts After School since the second grade. The nowfifth grader said the teachers have helped her improve her art.
“I just put my art in the annual show for the first time and all of my
ksteiner@jamestownsun.com | (701) 952-8449 Contributed / The Arts Center
“And that’s what it’s all about,” she said. “That means five kids who couldn’t go got scholarships to attend programming.”
There are naming opportunities with the capital campaign. For more information, contact The Arts Center at 251-2496.
By Keith Norman For The Jamestown Sun
JAMESTOWN — One of the people in Jamestown impatiently waiting for spring weather is Jeff Romsdal, owner and general manager of Central Sales, which plans to start construction on its new building this spring.
“Going to be happening as soon as we get rid of this white stuff,” he said, referring to the snow on the ground. “We’ll be going from about 15,500 square feet to more than 29,000 square feet.”
Romsdal said the expansion is intended to better accommodate its line of Melroe Bobcats as well as improve sales and service for all of its products.
For example, the new shop area will have a higher roof and ceiling, accommodating newer combines that are too tall to fit easily into the current shop.
The move will also put the dealership closer to
Jamestown and make it more visible in the community. Currently, Central Sales is located 2 miles south of town on U.S. Highway 281. The planned location is on the frontage road between Menards and the Jamestown Regional Medical Center in southwest Jamestown.
“We are a destination for our customers now,” Romsdal said. “A little out of sight and out of mind for the farmers who don’t drive by us.”
Romsdal said the dealership could move to its new location by this fall or the spring of 2024, depending on several variables including the weather.
The dealership includes the Bobcat and AGCO lines of equipment.
John
Central Sales Inc., of Jamestown, has a top-skilled staff of technicians in the service department and carries a large inventory of accessories and parts for products. The business will expand its facility with a new building project scheduled to begin in the spring.
“AGCO includes the Massey Ferguson, White planters and Gleaner combines,” Romsdal said. “Our dealership in Casselton handles the Versatile equipment so we have access to that as well.” Central Sales began operations in 1974 and is
M.
These five managers at Cash Wise Foods in Jamestown have 100 years of combined work experience in the business. From left: Laura Hust, baker manager, 36 years; Kristen Hoggarth, assistant dairy/frozen foods manager, 10 1/2 years; Paul Stroh, dairy/frozen foods manager, 36 years; Krista Kruize, deli manager, 10 1/2 years; and Sarah O’Heron, store director, 7 1/2 years. Visit www.cashwise.com to learn more about Cash Wise.
family owned. Originally, it sold Allis-Chalmers equipment but has expanded and changed
its product offerings over the years as the agricultural equipment industry has changed.
By Masaki Ova
The Jamestown Sun
JAMESTOWN – Collins Aerospace has made some huge investments into the main facility in Jamestown which shows the company is growing, according to Bill Seekins, facilities and operations excellence manager.
Collins is currently constructing a 20,000-square-foot addition that will be complete around September, Seekins said. The next step is to put in the process line in the beginning of 2024, which will take about two years.
“Then once we get the process line up and running, then we will demo and remodel the old process line and put the new paint line in,” he said. “It’s a multiyear project. We will wrap it up probably in early ’27.”
Starting in 2027, Collins plans to start replacing older machines, which is about a 10-year project.
“A lot of money is going into this facility the last few years and going forward as well,” Seekins said.
Collins also improved its office area at the main facility which helps employee morale and the teaming aspects of working together, Seekins said. The upstairs of the main facility has been remodeled and is now a more
efficient working environment.
He said more office spaces and conference rooms were added as well as electronic standup desks. Camera systems were also installed in most conference rooms so remote and on-site employees can meet virtually.
“We still have the separation, still have the taller cubicles in the area,” Seekins said. “We’ve got the offices that have their own heat, got their own whiteboard, every office has got a TV in it to share with the people that they meet with.”
The HVAC and air conditioning systems were redone which improved the airflow and temperature control.
“It’s obviously a lot of investment,” said Rod Johnson, operations manager. “We are doing that because the business is doing incredibly well. … The demand for air cargo just continues to go up, up, up every year.”
Employee recruitment and retention
Collins is growing and more opportunities for current and future employees will become available within the company, Seekins said.
“Just the career growth alone in this company is just going to be tremendous,”
he said. “If somebody is looking for career growth in Jamestown, North Dakota, this is the place to be. I don’t think there is any other facility within Stutsman County that is growing like this.”
Collins currently has around 450 employees, Seekins said.
“We are going well over 500,” he said. “That just this year alone.”
Collins will be hiring for many positions including assemblers, inspectors, machinists and engineers.
“We will continue to hire for years to come,” Johnson said.
He said Collins is looking to hire about 40 hourly employees and around 15 to 20 salaried employees. Collins has openings for part-time positions as well.
“I think you are going to see similar levels in the next three to five years,” he said. He said the company is growing and there are also people who might retire.
He said Collins has a “super competitive” benefits package that includes health, dental and vision insurance and 401(k) with company match among others. He said new employees start with three weeks of vacation time and get 12 paid holidays a year.
Johnson said Collins has an employee schol-
“Farming has changed so much in 50 years,” Romsdal said, referring to the years Central Sales has operated. “It was small grains and a lot of cow-calf operations. Now it’s corn and soybeans. We’ve gone from levers and mechanical operations to high-tech electronics.”
Central Sales is also looking to change with the times.
Romsdal said the new facility will help Central Sales continue to provide service for all equipment. It will also allow Central Sales to expand from its current workforce of 15 to about 21 workers.
“We have a great team,” he said. “… without the passion from our people, it would be difficult to look at investing in a new location.”
Central Sales can be reached at 252-7030 or www.CentralSalesInc. com.
A new structure is going up at Applied Digital north of
Corp. designs, builds and operates next-generation
centers across North America to provide digital infrastructure solutions to the growing high-performance computing industry. For more information on Applied Digital, visit applieddigital. com.
has made investments into
and more opportunities for current and future employees will be available
the company, according to Bill Seekins, facilities and operations
ar program where the company pays for tuition and books and gives employees three hours per week of their work time that can be used to study while getting paid. He said employees who use the program don’t need to study in the field in which they work.
“You could be an assembler and you could have the company pay for schooling to be an engineer, for example,” he said.
Seekins said several employees have gone through the program and received college degrees from all over the U.S.
“The company has a vision that education is good,” he said. “It develops people. It makes you better.”
Collins is also hiring remote and hybrid employees. Seekins said the hybrid positions allow employees to work two or three days a week
at home and the remainder of the week on site.
“Overall we’ve got a lot of flexibility in some of the positions on how we work with different groups of people,” he said.
Johnson said Collins will train employees as well, including factory positions such as assemblers, dispatchers and painters.
“We actually have a machinist-in-training program we are going to kick off here,” he said. “ … We are setting up apprenticeships with the North Dakota State College of Science in Wahpeton.”
Seekins said Collins has many long-term employees because of the company’s business culture and how they treat their workers. He said the company has a good mix of tenured employees.
“We have a pretty good culture here that I think everybody enjoys work-
ing for the company,” he said. “We take care of our people.”
Johnson said kids in the area don’t have to go too far outside of Jamestown to find a good career.
“If they like North Dakota, there’s a lot of opportunities here for them,” he said.
Seekins said Collins draws employees from outside of Jamestown, including Fargo, Medina and Cleveland among other locations.
“I think overall we have a pretty good working relationship with the community, and I think it’s mutually based because we care about our workers very deeply,” he said. “It’s more of a family culture than a corporate culture here I think.”
For more information about Collins Aerospace, visit www.collinsaerospace.com.
Auto
and More
cars and oil and gas
By Keith Norman For The Jamestown Sun
JAMESTOWN —
The largest auto showroom in Jamestown is also one of the community’s largest displays of community and automotive memorabilia, according to Dale Lende, owner of Dale’s Auto Mall and More.
The building, previously the Safari Lanes bowling alley, offers 18,000 square feet of space where up to 20 classic cars and 40 utility terrain vehicles and all-terrain vehicles are displayed.
“It is complete indoor shopping,” Lende said. “There is not another place like this in North Dakota.”
Dales Auto Mall handles the Massimo and Aodes lines of ATV and UTVs. The vehicles can handle a number of transportation and hauling needs on the farm or ranch.
“The uniqueness is these are assembled in America,” Lende said. “They have a better
warranty and complete service here, and people can save thousands over some other brands.”
The Auto Mall is the largest dealership in the U.S. for the Massimo and Aodes brands.
While there are more ATVs and UTVs on the showroom floor, it is the classic cars that catch the most attention.
“We buy, sell and consign classic cars,” Lende said. “I’ve always liked classic cars.”
Along with sales of vehicles, the Auto Mall also offers complete service for small and large engines under the same room. Even with all those services, it might just be the memorabilia on the walls that attract the most attention.
“People usually only get to see this kind of stuff only on ‘American Pickers,’” Lende said. “People like to bring in their families just to look around.”
Lende has operated service stations and other automotive-related businesses in James-
town since 1978 and some of the items were gathered by him from his businesses. Other items go back to the 1930s and reflect the automotive and petroleum industries.
Some items are icons from Jamestown’s past including the sign from the Blockbuster franchise that operated on First Avenue in years gone by.
And a mannequin changing into a Superman costume in a phone booth is an interesting piece of American pop culture.
Lende said he is currently looking for three or four additional employees to work in sales and service at the Auto Mall. Future plans include expanding sales into late-model vehicles and probably hanging a few more pieces of memorabilia on the wall.
Dale’s Auto Mall and More is located next to the Paradiso Restaurant on the south side of Jamestown. Its website is www.dalesautomall.com.
operation. Hofmann Trucking has more than 300 employees at its locations
By Keith Norman For The
JAMESTOWN —
Hofmann Trucking has expanded a great deal since its founding 24 years ago, according to Curt Waldie, CEO and one of the original founding partners.
“We started on July 1, 1999,” he said. “Myself and Larry Hoffmann were partners and we had three people working for us.”
The company has grown to more than 150 employees with offices in Tioga and Fargo, North Dakota, Douglas, Wyoming, and its corporate headquarters, which has always been in Jamestown.
“We started with a little office in the Orlady Building,” Waldie said.
After the Orlady Building (on First Avenue) burned, the company moved to the Meidinger Square building and has now operated for seven years on the west edge of Jamestown in the former Wiest Truck Line building.
The company has seen growth in all of its divisions including overthe-road trucking and its maintenance shop, where it services trucks and trailers. The company continues to recruit qualified workers for all its divisions.
“We are seeing growth all across the industry but we are particularly expanding what we call our pneumatic division,” Waldie said.
Trucks hauling bulk food materials like sugar and flour make up the pneumatic division. The trailers are specially constructed to prevent exposure of the materials to the outside air and elements while being transported.
Waldie credits a number of factors for the company’s growth over the past 24 years.
“A large group of employees has grown with us over the years,” he said. “We have a great team.” The majority of the
staff has worked for the company for at least five years and between 20% and 30% have at least 15 years of experience working for Hofmann Trucking, Waldie said.
Location is another factor in the company’s success.
“The I-94 and U.S. Highway 281 corridors are important,” he said. “There are a lot of trucking and transportation companies in Jamestown.” And Hofmann Trucking is proud to be a part of the Jamestown community and aids and sponsors a variety of community events throughout the year.
“We are thankful to be part of Jamestown,” Waldie said. “Jamestown has been our hometown the entire life of the company and we are glad to be part of the community.”
Hofmann Trucking can be reached at www. HofmannTrucking.com.
By Masaki Ova The Jamestown Sun
JAMESTOWN — Now in its 64th year, West End Hide, Fur and Metal Co. Inc. is one of the last larger family-owned larger scrap metal processing facilities in North Dakota, according to Jeff Oster, co-owner with his brother, Mike.
“We do our best to give good service, good pricing, and with our improvements over the last five to 10 years, it’s making things that much easier for the customers and better for us as a company,” Jeff Oster said.
West End accepts iron, cast iron, copper, brass, aluminum, lead, car bodies, aluminum cans and batteries, according to its website. West End does not do anything with cattle hide, deer skins or furs but continues to do scrap metal recycling and distributing new steel, aluminum and stainless and struc-
tural products.
“It’s fun and challenging to concentrate on what we are doing now,” he said. “Every day is different. It’s a challenge and I like challenges.”
West End has been changing its image. A sign on its building has the slogan “Scrap With Us.” Improvements include getting machinery such as material handler cranes, a Sierra stationary shear and a mobile shear.
“It’s just bigger machines that help us process material faster,” Oster said. He said a digital scale helps get the semitrailers in and out faster. He said West End is trying to be more customer and operator friendly.
He said the yard is getting cleaned up because of the influx of material West End will get during the spring.
Oster said West End is short about three to four employees because the
company has expanded its operations in the yard. West End originally started on 13 acres of land at its location and has grown to 35 acres to expand its recycling operations to the south.
He said West End has a good core of employees. He said the employees “work hard but have fun.”
“The biggest thing is team effort around here,” he said. He added that team effort allows West End to accomplish a lot of work.
Oster said West End offers good benefits and salaries are always increasing.
“I think as a company, the owners are good to the employees,” he said.
He said Jamestown is a good supportive community for West End and the company supports the community too.
For more information about West End, visit westendonline.net.
mova@jamestownsun.com | (701) 952-8454
By Kathy Steiner
The Jamestown Sun
JAMESTOWN – Even-
tide Jamestown Senior
Living Apartments is not only a place to live but also to make connections with others, said Jackson Johnsrud, executive director, Eventide Jamestown.
“We have a really tight-knit group of individuals (living) in there,” he said. “Even if we’re not having an activity going on we still have individuals that are hanging out, sitting around the table. They could be grabbing a meal together, playing cards or just visiting. I think that’s really unique and you’re not going to find that at a bigger location.”
Eventide Jamestown
Senior Living Apart-
ments opened in 2017.
There are 43 one- and two-bedroom apart -
ments and a guest suite that is available to visitors.
Residents can live in their apartment independently or with services, and services can be added at any time as needed, Johnsrud noted. If an apartment tenant needs rehabilitation care after a surgery, for example, that person can stay in the transitional care unit in the care center and then return to the apartment. If a higher level of care or memory care is eventually needed, an apartment resident can be served in the care center.
Johnsrud says there are experienced staff working at the apartments, noting some have been with Eventide for quite a few years.
“They’re extremely passionate about what they do and what Eventide stands for and they
work for those tenants in that building,” he said.
A continental breakfast is served each day, and lunch and dinner are available, all in the dining area. The apartments also have full kitchens. Meals and weekly housekeeping services are included in the rent.
Johnsrud said the restaurant-style dining area is where most people have their meals.
“I know that is one of many of our tenants’ favorite things about the facility,” he said. “... It’s just such a cool little area for tenants to be able to hang out together, get meals together, and our cook and the rest of our kitchen staff do a fantastic job in there providing homelike meals as well.”
Residents can be as active or social as they choose. There is a monthly activity calendar and holiday celebra-
By Kathy Steiner The Jamestown Sun
JAMESTOWN – Lifestyle Appliance & Entertainment Center has been in business since 1977, and owners Colin and Toni Wegenast say they have loyal customers and dedicated employees.
“We wouldn’t be here without them,” said Toni. “We have a lot of repeat customers and a lot of word-of-mouth references, and those are a big deal to us and very appreciated.” Colin echoed that.
“We super appreciate our customers and our employees and the Jamestown and surrounding communities for supporting us all these years,” Colin said.
Lifestyle Appliance & Entertainment Center carries larger kitchen appliances including fridges, stoves, microwaves and dishwashers, along with washers and dryers. They also sell Big Green Egg grills, mattresses and hot tubs along with the chemicals and supplies for them.
Before the coronavirus pandemic, the business had cookouts in the parking lot featuring food made on the Big Green Egg grill, and Toni says people should watch for information on those returning in the spring.
“The Big Green Egg is something that you can try to explain to somebody what the flavor of it is but it’s so different than anything else out there …,” Toni said.
She said most of their sales from Big Green Eggs come from people who have tasted food made on them and want one for their own. The Green Egg
We have a lot of repeat customers and a lot of word-of-mouth references, and those are a big deal to us and very appreciated.
- Toni Wegenast, co-owner, Lifestyle Appliance & Entertainment Center
uses natural lump charcoal.
Colin said the supply chain issues related to the coronavirus pandemic have eased in the last six months. During the pandemic, it was challenging to get appliances and parts, Toni said.
“It’s been a struggle the last number of years to get product in a timely fashion,” Colin added. “We’re finally getting back to where instead of a few months, it’s just a few weeks usually to get most stuff. “ Colin said manufacturers are again offering sales on some products, which they can pass along to their customers.
Lifestyle Appliance & Entertainment Center also carries Amazing Rest mattresses.
“The mattresses are a very well-built product, made in America, reasonably priced,” Colin said. They are displayed in another area of the warehouse, so people wouldn’t see them on the showroom floor.
Lifestyle Appliance &
among the most popular activities for tenants at
professional instructor provides
Entertainment Center has a third-generation family member now, Colin said, with their son, Noah, working in sales.
The business has also grown from three to four full-time service technicians, Toni said. There are 10 total employees at the business including Toni and Colin.
“We encourage our employees to get involved in the community as well and we give back to the community as much as we can,” Toni said. “We’re both pretty involved in the community and we encourage our employees to be also.”
Lifestyle Appliance & Entertainment Center provides sales and service in just over a 60-mile radius of Jamestown.
“The service after the sale is still huge from us,” Toni said. “We don’t sell anything that we can’t service.”
For more information, call 252-8111 or visit https://www.lifestyleappliance.com/. ksteiner@jamestownsun.com | (701) 952-8449
tions. There’s an exercise room and exercise classes are available. A theater room provides a movie-type screen and popcorn machine that are popular when viewing films.
One of the most popular monthly activities is the canvas painting class taught by an instructor, Johnsrud said.
“It’s really incredible
what she’s (the instructor) able to do,” he said.
“Even with individuals that don’t really have much for artistic experience, she’s able to get them to do outstanding things … in these canvas painting classes.”
Eventide Jamestown Senior Living Apartments has open positions and opportunities for student loan reimbursement. Learn more at
https://eventide.org.
In development is a program called Eventide University, where they are looking for people in the community to come in and give some type of presentation to residents. Topics could be about almost anything, Johnsrud says.
ksteiner@jamestownsun.com | (701) 952-8449
at Jamestown
Medical Center in Jamestown. For more information, visit www.essentiahealth.org.
John M. Steiner / The Jamestown Sun
The Posthouse is conveniently located in the heart of downtown Jamestown near a library, grocery store, pharmacy and some great eateries. The Posthouse is part of MetroPlains Management.
John M. Steiner / The Jamestown Sun
Kelly Stoudt, sales manager, is part of the fourth generation of the family-operated R.M. Stoudt Inc. in Jamestown.
By Keith Norman For The Jamestown Sun
JAMESTOWN — R.M. Stoudt is beginning the transition to offer more electric vehicles in 2023, according to Kelly Stoudt, sales manager for the dealership.
“This year Ford wants us to go in the direction of electric infrastructure,” he said. “We are planning on becoming a “Model E” dealer and already offer the Ford Lightning.”
Ford’s Model E is the division of the company dedicated to electric vehicles. The Ford Lightning is a half-ton all-electric pickup truck.
“Casey (Casey Stoudt, owner of the dealership) has been driving one for 6,000 miles and loves it,” Kelly Stoudt said.
The Ford Mustang Mach E is also an electric vehicle. Both the Lightning and the Mustang Mach E are in high demand and it can take a year or more to fill an order, he said.
“Ford is all in with electric cars,” Kelly Stoudt said, “but as realists, we
probably won’t see them as mainstream in North Dakota for years.”
At some point, half our technicians will work on internal combustion and half electric.
On the corporate level, Ford is building new factories to manufacture electric vehicles and the batteries needed for them to operate. On a local level, the first steps will probably be a charging station which could be constructed in the next 12 months, Kelly Stoudt said.
“These will be level three chargers which will charge way faster than the others that are out there,” he said. Casey Stoudt anticipates the transition will take years.
“The interesting part is it will be a whole new era of service,” he said. “We have a whole generation of people with expertise in internal combustion engines. Now we will transition to electric. At some point, half our technicians will work on internal combustion and half electric.”
By Keith Norman For The Jamestown Sun JAMESTOWN —
Repairing construction and farm equipment with specialty or out-of-inventory parts is the specialty at Dan Poland Machine in Jamestown.
“If you break it, we’ll make it,” said Brett Poland, owner of the company. “Some people can’t find the parts they need. Sometimes it’s just not available. We also repair and rebuild hydraulic cylinders and make hoses. All to fit the customer’s needs.”
The company employs 12 people with the ability to determine what is wrong with a piece of equipment and make the parts necessary to get it back operational.
“Our people have the skills and knowledge and dedication it takes to repair things that are non-functioning,” Poland said. “They have to have an eye to see what it takes to make something that doesn’t work to work again.”
Poland said he is currently looking for a couple more employees that
fit that description.
“Our employees are an extraordinarily valuable part of the business,” he said. “We have self-motivated people who see what needs to be done and then get dirty and get it done.”
Dan Poland Machine also operates a “millwright” division that assembles and provides service to on-farm and commercial grain-handling equipment such as grain elevators, grain bin auger systems, and catwalks. This operation includes two cranes that work on a variety of projects in the region.
Poland said the company’s Jamestown location puts it in the heart of its agricultural and construction business.
“We are right between Fargo and Bismarck and cover quite an area,” he said, “but we know our customers well.”
Dan Poland Machine was originally part of Enzminger Builders which was founded in 1985. The machine shop operation became a separate operation in 2000 with Dan and Vicki
Poland as owners.
In 2021, Brett Poland bought the operation from his parents.
“We offer welding, CNC machine work, fabrication and repairs,” he said. “We do some manufacturing but repair is the main thing for us.”
They also offer retail sales of equipment including power-takeoff equipment, hydraulic equipment and electrical generators through a showroom at the front of the shop.
“We probably have the biggest selection of PTO equipment in the tristate area,” Poland said. Poland said most equipment needing repairs is brought to the shop on the west edge of Jamestown adjacent to Interstate 94.
“We do make service calls once or twice a month,” he said. “Of course, all of the millwright work done on elevators or grain bin systems has to be done on-site.”
Dan Poland Machine can be reached at 2529353 or www.danpolandmachine.com.
When that point will occur is still unknown, according to Clint Boom, general manager at the dealership.
“There are many benefits to the internal combustion engine and to the electric,” he said. “We’ll be a dealer for both for the foreseeable future.”
R.M. Stoudt intends to keep its traditions of service within the community going even as it transitions to new technology and vehicles, Kelly Stoudt said.
“The Running of the Pink is really huge for us and growing year after year,” he said. “The event has raised over $200,000 over the years.”
This year will mark the 15th anniversary of the annual event and is scheduled for June 4 at the dealership in south Jamestown. All proceeds of the event are used for local breast and cervical cancer screenings.
More information about R.M. Stoudt and the Running of the Pink is available at www.stoudtford.com.
By Katie Ringer The Jamestown Sun
JAMESTOWN — Ashley Cole always had an eye for home design.
So why not turn it into a career?
Cole and her husband, Anders, own Jamestown’s Home Design Center. When the couple purchased the business in 2019, there were three separate locations — the showroom on Main Street, Valley Flooring in Valley City and Jamestown Creek Cabinetry.
Since signing the papers four years ago, Cole has helped grow the business to offer more services and options for those in the market for an update to their home or business.
“We took all of the flooring out of our Main Street location and put it down at our (Valley Flooring) location by Jetstream,” Cole said. “So when you go into
that store, that is strictly flooring whether that be hard surface or carpet. It was just kind of taking over the showroom.”
For everything else besides flooring, the Main Street location is the place to be for anyone who has a hankering for a home design project.
“If you want to come in and simply browse decor, because you want to refresh your space, you can do that,” Cole said. “Or if you are doing a remodel project, we have all the materials needed for that — if you are doing cabinetry, countertops, you can get light fixtures in here, window treatments, decorative hardware, paint, tile — you name it. We get told a lot that we have very unique items in here.”
The couple added a paint line and furniture and has expanded window treatment selections.
While customers are encouraged to browse and purchase the decor offered at the Main Street location, Cole said most of the company’s business comes via the home design process.
“If they want a kitchen redone, they come into us and we would go out to their home, measure up the space, figure out things they are wanting — things they like about their space, things they dislike about their space — and then we have a design program that we put all of that into,” Cole said. “We show them different layout concepts and then from there we would help them pick out the cabinets, countertops — everything they would need to do that project.”
She said some people like to be involved in the electrical or plumbing aspects of a project, but if they don’t want to be involved, Home Design
Center can line up all of the disciplines for the project.
“We can do product only as well,” she said. “Every situation is just a little bit different.”
Cole said the Home Design Center team typically services Jamestown, Valley City and
surrounding rural areas like Cooperstown, Carrington, Edgeley and Gackle-Streeter.
“We have different options to fit different budgets,” Cole said. “We can help with the project from start to finish.
For more information, visit www.homedesignnd.com.
kringer@jamestownsun.com |
We have our own install crew, we can help get the products for the entire project. We’re kind of a one-stop shop. We can do anything from the studs in.”
@KaitlynRinger on Twitter
By Kathy Steiner
The Jamestown Sun
JAMESTOWN — Three
University of Jamestown employees are key to students’ experience on campus, said Dustin Jensen, dean of students/ vice president for student affairs. They are Ryder Weischedel, Gabe Martinez and Sara Robinson.
Weischedel is the director of strength, conditioning and campus wellness. Also on his staff are assistant director Emily Sosa and graduate assistant Tayler Cullen.
“We write comprehensive athletic performance programs for all the (600-plus) student-athletes on campus so they have training basically year-round that they follow …,” Weischedel said.
The training is not only to enhance athletic performance but to reduce the risk of injury by being stronger, more powerful athletes, Weischedel said.
The university also offers exercise classes to students, faculty and staff, he said, primarily contracting with Two Rivers Activity Center and other businesses to
help provide them.
“A majority of our clientele, obviously, are student-athletes, that makes up the majority of our campus,” Weischedel said, “but just keeping everyone fit and healthy on campus is not only good physically but mentally as well.”
Martinez, director of residence life and public safety, oversees about 35 undergraduate and six professional staff. He noted 85% of students live on campus, and there are nine residence halls including apartment buildings.
“What it really comes
down to is education and outreach,” Martinez said. “Not only in residence life, how do we get our students to learn, to live, to grow and to develop but also on the public safety side, what education outreach do we put out to ensure that students can stay informed about their personal safety and can make choices about how to stay safe for them.”
Martinez said he’s focusing on how to bring UJ’s mission, values and education plan into the residence halls, preparing them for living outside of the university
setting while they are on campus. That education comes through trained
resident assistants, he said.
Robinson began working at UJ in 2020, initially on UJ’s response to the coronavirus pandemic including as a consultant for the National Association of Intercollegiate Athletics to oversee its protocols for national championships.
“It was such a privilege to be part of something bigger than just UJ, to be able to have an impact on students across the nation,” she said.
Now, as director of student engagement, she collaborates with a team of students to bring opportunities to Jamestown for students that they wouldn’t have oth-
erwise, such as entertainment and planning ways for them to engage and make connections on campus.
Robinson also oversees UJ’s mental health and counseling center.
“UJ is really a place that we care about our students and that is always at the heart of what we do,” she said.
“Every decision that we make as a team, everything that kind of comes down the line, every conflict that we’re faced with, our team of student affairs – our number one question that we always fall back to is what is best for students.”
ksteiner@jamestownsun.com |
(701) 952-8449
By Kathy Steiner
The Jamestown Sun
JAMESTOWN – Matt Perkins, owner of the Medicine Shoppe, grew up playing baseball in Jamestown.
He got involved with the baseball program again about four years ago when his own kids started playing. And that was when he was reminded that it wasn’t too different from his youth.
“Those fields (at McElroy Park) haven’t changed down there, I think, for six decades, at least any meaningful improvements,” Perkins said.
Perkins noted there had been previous efforts to improve the ball fields that hit some type of roadblock. About a year and half ago, he and four other dads decided something needed to get done.
“... we were having troubles getting people
to come and play us,” Perkins said. “It’s very difficult for us to host tournaments, to bring people to town for baseball.”
With the help of a donor’s seed money for project design and renderings, a project to renovate the fields at McElroy Park took shape.
The three-phase project will renovate the youth complex and Jack Brown Stadium and include a youth tee ball field, Babe Ruth field, two Cal Ripken fields (one with a turf infield) and a restroom and concessions building. The effort includes working to name a field after Tom Gould, Perkins said. Partnering in the project are Jamestown Parks and Recreation, Jamestown Area Youth Baseball Association, Outlaw Fastpitch Softball, Blue Jays and University of Jamestown. Perkins, who is presi-
dent of Jamestown Area Youth Baseball and has taken the lead on the project, said he and his wife, Molly, and the Medicine Shoppe have financially supported the project.
“Community involvement to me is really important,” he said. “.. If we have the ability to help out baseball or choir or band or whoever the group is in the community that’s looking to help with fundraising, we certainly try
to do that or help with projects. That’s like a core belief of what we have here. And I think there’s lots of people in the community that are like that as well. We’ve found a lot of success so far with the baseball project and just going around various businesses in town and those groups realizing that it’s something that should be done.”
More than $2.3 million has been raised for the almost $3.9 mil-
lion first-phase project including grants, he said.
“It’s been really, I would say, quite humbling and just really quite amazing to see all of the support for what we’re trying to do,” Perkins said.
Perkins noted the community has not only been generous with the field project but The Arts Center and Anne Carlsen capital campaigns as well. For Perkins, the projects are about making Jamestown a more
enjoyable place to live and attracting young people to move here.
“Those sort of things I think are what a young person like myself that has young kids, a young family, looks for when you’re looking at a community and how it is to live in that community …,” he said.
He encourages people able to contribute financially to support any of the efforts.
ksteiner@jamestownsun.com | (701) 952-8449
By Kathy Steiner
The Jamestown Sun
JAMESTOWN – The Jamestown Area Chamber of Commerce works to help businesses retain employees, says Mike Delfs, president of the board of directors.
Delfs, who is also president and CEO of Jamestown Regional Medical Center, says all businesses in Jamestown are struggling to some degree with workforce, whether it’s recruiting or retaining employees. He said most have focused on recruiting.
“So we’ve thrown money at the problem, we’ve given wages that three years ago none of us would have ever dreamt of giving, we’ve given sign-on bonuses in some cases, etc.,” he said. “The problem, though, is that we all kind of do the same
things to get people in the doors. It’s what do you do to keep them inside.”
Engagement and fulfillment are key to retention, he said, and the chamber helps by offering what he calls “developmental programs,” such as learning a practical skill related to a job or expanded duties or other information.
Those have ranged from a Microsoft Excel course to a presentation on visa programs to get workers here.
“The strength of the chamber program to me is really about that,” Delfs said. “It’s about offering development opportunities so that people stay as opposed to go find a new job.”
He said people who have options tend to be “much happier people in terms of being employ-
ees and good team members and providing really great customer service.”
While the chamber has offered educational programs for years, Delf said programs have become “far more focused” in the last several years based upon business needs and feedback from employees and employers.
The chamber board has played a role, he said.
“The board is a great resource because everyone on the board either works in a business, manages a business or owns a business so that’s a great to group to start with, to say ‘what are your struggles with recruiting and retaining,’ and then we also do that through committees as well,” he said, such as Young Professionals of Jamestown.
“We ask those ques-
Your focus needs to be on once you have an employee, how do you retain them, how do you make sure that they’re happy in their job, that they’re a good team member, that they’re finding fulfillment.
- Mike Delfs, president, Jamestown Area Chamber of Commerce Board of Directors
tions,” Delfs said. “‘What do you need to continue to be successful? What do you need to stay here in Jamestown.’”
They also work with programs at the high school and college level, he said.
Delfs said everyone gets caught up in trying to fill openings and he believes that’s the wrong approach.
“Your focus needs to be on once you have an employee, how do you retain them, how do you make sure that they’re happy in their job, that they’re a good team member, that they’re finding fulfillment,” he said. “These programs really are a bridge to be able to do that. I would say that the chamber has responded to the hardest part about employment right now which is retention.”
ksteiner@jamestownsun.com | (701) 952-8449
Joinusasweengineerthesolutions oftomorrow
Newchallengesneedfreshideas. CollinsAerospace overcomeshurdles,breaksbarriersandachievesnew levelsofinnovationthroughworkforce reskilling programsandspecializedtraining. Weofferthe opportunityto growandthriveinyourcareer, nomatterhow fasttechnologyischanging.
VisitourCareerspageat collinsaerospace.com
By Masaki Ova The Jamestown Sun JAMESTOWN
– The Jamestown/Stutsman Development Corp. has launched programs in the last couple of years to help solve the workforce shortage.
The JSDC launched its Intern Reimbursement Program in 2021 to help increase the number of local internships and assist Stutsman County employers in workforce recruitment and retention. The JSDC received the 21st Century Workforce Award in October during the Main Street ND Summit for the innovation and forward thinking in addressing its community’s workforce shortage.
Corry Shevlin, CEO of JSDC, said the program has been successful. He said a majority of the students who participated in the program stayed in the community afterward.
“Our goal is to try and create those relationships between potential college
students coming in and getting familiar with our community and how it operates,” he said. The Internship Reimbursement Program is designed to increase the number of local internships and assist employ-
ers in Stutsman County in workforce recruitment and retention, according to the JSDC’s program guidelines. The program contributes up to $3,500 to reimburse employers that hire university/college students to assist
in the payroll costs. The program is open to students from technical colleges.
The program requires Stutsman County employers to pay interns at least $15 per hour. There are three funding
rounds — one for summer interns, another for the fall semester and one for the spring semester — for the Internship Reimbursement Program.
The JSDC recently launched the Daycare Expansion Assistance Program that helps new child care startups and existing remodeling projects increase capacity. Shevlin said the JSDC understands that day care is an important piece to help find solutions to help address the workforce shortage.
If reliable day care is available for everybody, more individuals are available in the workforce, he said. He said the day care availability is important and that’s what the program is hoping to improve.
Shevlin said the JSDC will review the Daycare Expansion Assistance Program at the end of the year.
“If there are changes that need to be made or if we find that there is not a need, we will move in
a different direction but I think we will find that there is,” he said. The pilot program is a 1-to-1 match and cannot exceed $10,000 in matching funds, according to JSDC’s guidelines and terms and conditions. The funds can be used for fixtures, furniture, equipment and construction-related costs.
Approval will be required prior to the start date of the project. All receipts must be submitted before reimbursement.
The project must be a licensed child care facility or be in the process of getting licensed through the state of North Dakota. Providers who receive funding must remain in operation for a minimum of two years from the application date, and failure to do so will result in a prorated return of grant dollars to the JSDC. For more information about JSDC, visit www. growingjamestown.com. mova@jamestownsun.com | (701) 952-8454
By Masaki Ova
The Jamestown Sun
JAMESTOWN — The North Dakota Sports Hall of Fame will hold its induction ceremony this year in November.
The induction ceremony is usually held in June or July, but one of the inductees won’t be available until November, said Dave Greenwood, president of the North Dakota Sports Hall of Fame Board of Directors. The plan was then made to move the induction ceremony to November for just this year.
The inductees have not been announced. Previous inductees into the North Dakota Sports Hall of Fame include Phil Jackson, Roger Maris, Lute Olson, Darin Erstad, Phil Hansen, Virgil Hill, Jim Kleinsasser, Ricky Helling and Travis Hafner, among others.
The North Dakota Sports Hall of Fame is located inside the Jamestown Civic Center.
The purpose of the North Dakota Sports Hall
of Fame is to honor and recognize individuals who have played a major role in the growth and development of sports in the state and to further promote sports and sportsmanship by honoring those who have made outstanding contributions in sports, according to its website. The North Dakota Sports Hall of Fame was established by the North Dakota Legislature in 1989. North Dakota Sports Hall of Fame inductees receive the Cliff Cushman Award. Cushman, a hurdler in track at the University of Kansas, was named the 1960 North Dakota Athlete of the Year. He won a silver medal in the 400-meter hurdles in the 1960 Olympics. His dream of winning a gold medal at the 1964 Olympics came to an end after he stumbled over a hurdle at the final U.S. Olympic trial meet in Los Angeles but wrote a letter of inspiration to the Grand Forks Herald asking young people in
his hometown to not feel sorry for him and to set goals for themselves.
Greenwood said the North Dakota Sports Hall of Fame is always interested in more nominations for inductions.
“There is always somebody out there that is deserving and should be looked at,” he said.
He said a committee of about 12 to 14 people look through the nominations and vote for three to four to be inducted. If a nomination does not get enough votes to be inducted, the committee does not eliminate any of the past nominations. The committee can vote on the past nominations again in future years.
The Civic Center also houses other organizations’ halls of fame such as for amateur baseball and basketball, fishing and bowling, among others. For more information about the North Dakota Sports Hall of Fame, visit ndsportshalloffame.com.
mova@jamestownsun.com | (701) 952-8454
Center.
By Kathy Steiner
The Jamestown Sun
JAMESTOWN – Wheth-
er people are beginning their career or looking to revitalize retirement, the North Dakota State Hospital provides opportunities for them to do so.
And the flexibility, support and tuition reimbursement availability in those individual journeys make a difference, employees say.
Kim Matroni
Kim Matroni is the director of inpatient services at the hospital.
She started working as a CNA in 2007 with no CNA certification and received her training at the hospital, she said. At the time she started working, she had a four-year psychology degree.
“There’s not a lot you can do with a four-year psych degree and so I figured instead of working elsewhere in town, I would come someplace where I could use the degree knowledge and get some experience to be able to build my resume,” she said.
Matroni worked in the admission unit for about 3 ½ years and returned to school twice, getting her master’s degree in psychology, and later a master’s in clinical mental health. She currently oversees the treatment and rehabilitative services for inpatient clients.
“All of my psych experience has been here at the State Hospital working in various roles and I think without the support of the leadership that was in place during each of those transition points in my hospital career, I wouldn’t have had the opportunities that I have been afforded,” Matroni said.
She said people who are willing to do the work can find many opportunities for growth in their employment at the State Hospital.
Barb Mickelson Barb Mickelson, a nurse practitioner, said retirement wasn’t really what she thought it was going to be.
“I found myself always thinking, am I retired or just unemployed?” she said.
So she began working at the hospital six months ago and said it’s worked out “very well.”
“I feel a sense of purpose, I can offer to who I consider a marginalized population my experience and my medical experience,” she said.
Mickelson works two days a week.
“I’m very flexible as is the institution,” she said. “If something doesn’t work for me, I can switch. If something doesn’t work for my colleagues, they switch with me. So it’s very flexible.”
Mickelson works in what’s called the consult clinic, which deals with medical issues, she said. She said after 48 years in her field, what she likes about working at the State Hospital is that she still has much to learn and people are willing to help her.
“I feel so appreciated and valued here and that just makes it so much easier to come to work each day and really enjoy that,” she said.
She said she thinks for other retirees, working at the hospital could fill a need for them too.
“... You can only clean so much when you’re at home (in retirement) … and when you come here you use all the experience and the knowledge you’ve learned over the years and apply it,” she said.
Andrea Christianson
Andrea Christianson, director of social services at the hospital, had a bachelor’s degree when she started working at the hospital as a social worker in 2014. She, like Matroni, returned to school and earned a
master’s in social work in 2017.
“The hospital picked up 80 percent of my tuition for my master’s program, which was immensely helpful,” she said. “It helped me a lot. Because I honestly don’t think I would have gone back if I didn’t have help.”
She noted she was able to do her internship for her master’s program at the hospital.
“I know I’ve had a couple employees that have done it as well and have done tuition reimbursement who are very grateful for it as well,” she said. “My thought is, if I’m already in the field and I can further my education, that’s great, and if I can get help paying for it, also another benefit. The hospital’s been very flexible, they were very flexible when it came to doing my internship, being able to find aspects of my current job that I wasn’t doing that I could apply to a master’s level internship.”
Misty Miller
Misty Miller received
CNA training at the hospital when she began working there as a temporary employee in 2018 after moving to Jamestown that year with her husband, Joshua, and family. She soon was working in a full-time CNA position.
In 2020, they began offering a licensed practical nursing program at the hospital through Dakota College at Bottineau.
“I wasn’t sure about it but one of our physician’s assistant, Linda Regan, she pushed me and pushed me,” Miller said. “She said, ‘You need to do this. You will be an amazing nurse. You have to do it.’ So I broke down and applied for the program and I graduated with my LPN in 11 months.”
Miller went on to earn an associate RN degree and became a registered nurse in 2022. She is currently attending Minot State University for her Bachelor of Science in Nursing and is
expected to finish in July.
Miller said she has used the tuition reimbursement program throughout, which has helped because she couldn’t pick up extra shifts every week during school and with her family. She said the hospital was flexible with her hours, working with her school schedule.
“The staff are amazing. Everyone is there for you,” she said.
Abby Newman Abby Newman was a student at the University of Jamestown working on her Master of Science in Clinical Counseling when she came to the hospital in late 2021 to complete her practicum requirement.
“I sought out the State Hospital, I thought it would be a good opportunity, a good learning experience,” Newman said. “... and in that experience, I really quickly realized that I hadn’t had much exposure to an inpatient setting personally and pro-
fessionally.”
She said she hadn’t really seen herself as a counselor in an inpatient setting before coming there.
“It was invaluable experience and I really really enjoyed the State Hospital and the work I could do as a counselor in an inpatient setting,” Newman said. Newman and Matroni, her supervisor, discussed Newman returning to do her internship and working at the hospital, which she did. She became a full-time employee in early 2022 and completed her internship after that.
“When you’re looking at working full time and being a full-time student and having to complete 600 internship hours on top of that, I was at that point kind of wondering how I was going to keep up with it all,” Newman said.
She is now a fulltime licensed associate professional counselor employed at the hospital as a human relations counselor and says one of the things she has enjoyed is the opportunity to be on a clinical treatment team for clients.
The North Dakota State Hospital offers an 80% tuition reimbursement to qualified employees. To qualify, the degree must support the employee’s role within the organization, be approved by its leadership team and fall within state-identified parameters.
The University of Jamestown also offers NDSH employees a 10% reduction on tuition.
For more information on careers, visit www. hhs.nd.gov ksteiner@jamestownsun.com | (701) 952-8449
By Masaki Ova
The Jamestown Sun
JAMESTOWN — Wil-
helm Chevrolet Buick GMC has made an investment to keep the Buick franchise at the auto dealership in Jamestown, according to Rod Wilhelm, co-owner of Wilhelm Chevrolet Buick GMC.
“We decided to keep the Buick because we’ve already invested in GMC and Chevrolet,” Wilhelm said. ”We like the Buick franchise. There’s some good products and we are going to stay with it.”
He said many Buick franchise dealers took a buyout from General Motors for several reasons including the investment and Buick will also all be electric by 2030.
Tim Schulz, new car manager, said General Motors has six electric vehicles coming out from between now and 2024. Electric vehicles coming out include the GMC Hummer EV pickup and SUV and the Chevrolet Blazer EV this spring, the Chevrolet Equinox EV and the Chevrolet Silverado EV this fall and the Sierra EV Denali Edition 1 in spring 2024.
In addition, the Chevrolet Corvette E-Ray is available to order as well. The Corvette E-Ray will have an electric allwheel-drive system that works with its engine, standard all-season tires and magnetic selective ride control, according to Chevrolet’s website.
He said the Corvette E-Ray is a gasbased vehicle, but it comes with a 1.9-kilowatt-hour lithium-ion battery that powers the front wheels. The battery is self-charging.
Schulz said customers can make reservations to get the electric vehicles. He said customers can go to chevrolet. com or gmc.com and get on the waiting list for an electric vehicle by making a $100 deposit. Customers can pick their auto dealership, and Wilhelm Chevrolet Buick GMC will receive a notification of the reserved electric vehicle.
“As of right now, most of these are already presold and sold out,” he said. “There is a waiting list for the customers. The reservation tells you what year the reservation is.”
He said the Chevrolet Bolt EV and EUV (electric utility vehicle) are available right now.
Schulz said Wilhelm Chevrolet Buick GMC is planning to install a dual-charging station this year.
Certified preowned vehicles
As a GM dealership, Wilhelm Chevrolet Buick GMC can certify any 2018 or newer preowned
vehicle, Schulz said. A 12-month or 12,000-mile bumperto-bumper limited warranty is fully transferable with no deductible in addition to any remaining original factory bumperto-bumper warranty, the dealership’s website says. Certified preowned vehicles also can get a powertrain limited warranty for up to six years or 100,000 miles from the vehicle’s original in-service date, and no deductible for warrantable repairs that are required as a result of defects due to material and/or workmanship to the powertrain components.
Super Cruise
The Super Cruise driver assistance technology is available for the Bolt EUV, 2024 Blazer EV, 2024 Equinox EV and 2024 Silverado EV along with other current models. Super Cruise is a hands-free driver assistance technology for compatible roads, according to Chevrolet’s website.
Schulz said the technology has safety features to slowly pull the vehicle over to the roadside if someone is having a medical issue or texting.
Supporting the community
The dealership holds the annual Don Wilhelm Car Show & 5K Run/ Walk for Huntington’s Disease. This year’s 12th annual event will be held on Sept. 23. The event is held in memory of Dan Wilhelm, the brother of Rod and Jeff Wilhelm and Lisa Wilhelm-Lindberg, who died of Huntington’s disease.
Rod Wilhelm said the event has raised more than $200,000 for Huntington’s Disease Society of America’s Northern Plains Chapter.
“It’s been growing and hopefully it’s helped,” he said.
Steve “Skovy” Jaskoviak, business manager, said the car show expects anywhere from 100 to 200 vehicles. This year the car show is a North Dakota Street Rod Association pick site, and participants will come from North Dakota, South Dakota, Minnesota and even Canada, he said.
“This year is going to be one of the bigger shows here around with that NDSRA pick site,” he said. “There are only six pick sites a year and we are one of them.”
Car show entrants also receive plaques and have an opportunity to win trophies and cash for certain categories.
Wilhelm said 1,500 raffle tickets will be sold at $20 each with the grand prize being a 2007 Saturn Sky Red Line. Second place will receive an orange
The business is a supporter of Giving Hearts Day, Toys for Tots, local schools, car-seat checks and other various local events and clubs and does the Fill the Silverado Campaign for James River Humane Society.
A GMC Hummer EV allwheel-drive bike will be donated for the University of Jamestown Dine and Bid auction. It also has an annual blowout for new and used vehicles.
ment, uniforms and training, employee discounts, encouragement and support for community involvement and advancement opportunities.
Wilhelm said the dealership has been in business for over 60 years and has an open door to interview potential employees.
-
Schwinn Krate bicycle, and the third-, fourthand fifth-place prizes will receive $500, $300 and $250, respectively. Proceeds from the raffle support the Huntington’s Disease Society of America. Wilhelm also said the business donates to Stutsman County 4-H because members help sell raffle tickets.
A color run was added to the 5K Run/ Walk for Huntington’s Disease, which helped increase participation, said Stephanie Johnson, marketing and advertising coordinator who also serves on the board for Huntington’s Disease Society of America’s Northern Plains Chapter.
The event also includes a live auction and burgers and brats for a freewill donation that goes to Huntington’s Disease Society of America’s Northern Plains Chapter.
The dealership is a sponsor of area golf tournaments, Jimmie Booster Club, Spiritwood Lake Jam, Miss
Rodeo of North Dakota and the Heartland Scholarship Program.
Employee recruitment and retention
The business offers benefits and perks to employees such as health and dental insurance, health savings account, life insurance, vacation, retire-
He said scholarships are available through the North Dakota Auto Dealers Association. He also said the business allows students to job shadow where they can spend time with a service technician or others.
For more information about Wilhelm Chevrolet Buick GMC, visit www.donwilhelm.com.
mova@jamestownsun.com | (701) 952-8454
By Keith Norman For The Jamestown Sun
JAMESTOWN —
Enzminger Steel’s new building is about six months old and offers 13,500 square feet of storage for components for steel buildings and grain bins and a few antiques, according to Dennis Enzminger, president of the company.
“Mostly we offer grain storage and grain handling equipment,” he said. “Mostly on-farm storage.”
Duane Enzminger began selling steel buildings and grain bins in 1974. Originally, it also owned Dan Poland Machine which spun off into its own operation, although Enzminger Steel and Dan Poland Machine continue to operate side by side on the west edge of Jamestown.
Dennis Enzminger began working in the business in 1996 and bought out his brother in 2007. With more than 25 years of experience in steel buildings, he has seen many changes in the industry in central North Dakota.
“Growing corn has been the biggest change,” he said.
A crop of corn has about three times the volume compared to wheat and other small grains that
had been the principal crop previously.
“It increased our storage demand,” Enzminger said.
Much of the corn crop is stored on the farm after the fall harvest and can be delivered under contract to ethanol facilities or commercial elevators through the winter, he said.
Enzminger Steel offers equipment such as belt conveyors and augers to make handling the grain easier. Stair systems and ladders also make loading and unloading materials easier and safer.
Another aspect of grain storage is maintaining the quality of what is kept in the bins.
“Drying and ventilation equipment is an important part of our business,” Enzminger said.
But worker safety is more a matter of procedures than the equipment in and around the grain bin.
“Just don’t go in the bin, ever,” Enzminger said.
Another change in grain storage in the last 30 years has been the size of the bins.
“We started out putting 5,000-bushel bins on the farms,” he said. “Now, we build them as large as 300,000 bushels.”
Enzminger said farmers should monitor farm programs for low-inter-
John M. Steiner / The Jamestown
Enzminger Steel LLC, formerly Enzminger Builders, has been in the grain bin business for more than 40 years. Whether you are interested in a single bin project or a multi-bin project the staff, has the knowledge and experience to assist you. From left: Dennis Enzminger, president; Larry Berg, maintenance; Adam Gaiser, dryer tech/sales; Sheri Guthmiller, office manager (foreground); and MaKenna Prigge, sales/graphic designer.
est loans or other incentives to build on-farm grain storage and notes he does have a supply of bins ready for construction this summer.
“We work with sub-
contractors for the summer building projects,” he said. “For farm bins, we are usually in and out of the place in two days.”
Enzminger Steel
employs five people. People interested in grain bins and accessories can stop at the shop at 8040 36th St. SE, in Jamestown and see displays of grain bin acces-
sories and take a look at the antique tractor and wagons on display above the office area. Online, information can be viewed at www. Enzmingersteel.com.
By Kathy Steiner
The Jamestown Sun
JAMESTOWN – Matt Perkins, owner of the Medicine Shoppe, grew up playing baseball in Jamestown.
He got involved with the baseball program again about four years ago when his own kids started playing. And that was when he was reminded that it wasn’t too different from his youth.
“Those fields (at McElroy Park) haven’t changed down there, I think, for six decades, at least any meaningful improvements,” Perkins said.
Perkins noted there had been previous efforts to improve the ball fields that hit some type of roadblock. About a year and half ago, he and four other dads decided something needed to get done.
“... we were having troubles getting people to
come and play us,” Perkins said. “It’s very difficult for us to host tournaments, to bring people to town for baseball.”
With Perkins taking the lead and the help of a donor’s seed money for project design and renderings, the project to renovate the fields at McElroy Park took shape.
The three-phase project will renovate the youth complex and Jack Brown Stadium and include a youth tee ball field, Babe Ruth field, two Cal Ripken fields (one with a turf infield) and a restroom and concessions building. The effort includes working to name a field after Tom Gould, Perkins said.
Partnering in the project are Jamestown Parks and Recreation, Jamestown Area Youth Baseball Association, Outlaw Fastpitch Softball,
Blue Jays and University of Jamestown. Perkins, who is president of Jamestown Area Youth Baseball, said he and his wife, Molly, and the Medicine Shoppe have financially supported the project.
“Community involvement to me is really important,” he said. “... If we have the ability to help out baseball or choir or band or whoever the group is in the community that’s looking to help with fundraising, we certainly try to do that or help with projects. That’s like a core belief of what we have here. And I think there’s lots of people in the community that are like that as well. We’ve found a lot of success so far with the baseball project and just going around various businesses in town and those groups realizing that it’s
Contributed / Jamestown Parks and Recreation
Matt Perkins, the owner of Medicine Shoppe and president of Jamestown Area Youth Baseball, says projects like the plan to renovate fields at McElroy Park help make the community better for residents and attractive to young families. Perkins, seen here coaching kids in tee ball, says it’s been getting more difficult to host tournaments because of the need to make improvements.
... If we have the ability to help out baseball or choir or band or whoever the group is in the community that’s looking to help with fundraising, we can certainly try to do that or help with projects.
- Matt Perkins, owner, Medicine Shoppe
something that should be done.”
More than $2.3 million has been raised for the almost $3.9 million firstphase project including grants, he said.
“It’s been really, I would say, quite humbling and just really quite amazing to see all of the support for what we’re trying to do,” Perkins said.
Perkins noted the community has not only been generous with the field project but The Arts Center and Anne Carlsen capital campaigns as well.
For Perkins, the projects are about making Jamestown a more enjoyable place to live and attracting young people to move here.
“Those sort of things I think are what a young
person like myself that has young kids, a young family, looks for when you’re looking at a community and how it is to live in that community …,” he said. He encourages people able to contribute financially to support any of the efforts.
ksteiner@jamestownsun.com | (701) 952-8449
By Kathy Steiner
The Jamestown Sun
JAMESTOWN —
Jamestown Parks and Recreation will gather input from the community and conduct in-depth planning to determine what the community wants in the future, said Amy Walters, executive director.
“What does the community want Parks and Recreation to be droing and to be prioritizing and investing in so that we can maintain a vibrant and healthy community, whether it’s our facilities or programs, whether it’s continuing things or starting new,” Walters said.
Having a healthy, vibrant community keeps people and the workforce in the community, she noted, and Jamestown Parks and Recreation plays a large role in that.
“We’re really looking to go through a comprehensive process of gathering information from the community and then in turn putting together a strategic plan,” Walter said.
Also planned is an assessment of existing facilities and formulating long-term plans for maintenance of those as well as how that fits with any growth.
“How do we contin-
ue to maintain what we already have or look to grow or look to add to what we can provide to the community,” Walters said.
To facilitate the process, Jamestown Parks and Rec will seek an outside organization through a request for qualifications (bid process) with experience in that type of work and knowledge of parks and recreation in general, Walters said. The process will include aspects such as surveys, community meetings and targeted focus group meetings with specific stakeholder groups.
“... then that organization would look to filter that information, compare it with like-size communities and standards within parks and recreation so that we can get a good snapshot of where our strengths are and our opportunities for growth, or opportunities for improvement,” Walters said.
She said they expect to have that organization lined up by June, with work expected to continue in the summer and fall before a plan is formulated.
Input from people in the community will be key, she said.
“I really want them to engage in the pro-
cess,” Walters said.
“Oftentimes as a staff, we think we know what the community wants or would like but we can only go off the information that we have, and so I really encourage people to participate in the process. … If they‘ve had experiences when they’ve either lived in other communities or traveled to other places, we want to know what those are so that we could potentially move forward with those ideas.”
She said the intent would be to take the information learned from the community and compare it to benchmarks within the parks and recreation industry and then put forward a plan to move forward in Jamestown Parks and Recreation.
She noted more than likely they will be looking at a five- to 10-year plan and community engagement will continue to be important.
“While we’ll develop a five- to 10-year plan, we know things happen and changes come about so we will want to kind of begin to create that standard of … soliciting the input from the community to continue to evolve,” she said.
ksteiner@jamestownsun.com | (701) 952-8449
By Kathy Steiner
The Jamestown Sun
JAMESTOWN — RE/ MAX is marking a milestone this year with 50 years in business dealing with varying markets, said Beth Keller, broker/owner of RE/ MAX Now Jamestown and Valley City.
That experience gives RE/MAX Now’s agents the education and the platform to move forward in confidence with clients and customers, she said.
RE/MAX has grown globally since it launched in 1973 and is now in 110 countries with 145,000 agents worldwide.
“In the United States, we were voted the number one-trusted real estate company,” Keller said.
RE/MAX Now agents say they are provided resources and support to knowledgeably assist their clients and customers.
“RE/MAX has so many resources for us to use,” said Sally Domke, who has been at the Jamestown location for six years. “Tons of internet resources. They’ve got marketing. They’ve got advertising, they’ve got education, so you don’t have to reinvent the wheel when you become a RE/ MAX agent. You have a ton of resources behind you.” She said it’s important to have a well-known franchise behind agents to support them.
“Having one behind you allows a Realtor to start their own business but you’ve got all the brand resources behind you,” she said. “You’ve got the name, you’ve got the international recognition …”
She also noted the annual RE/MAX convention, held recently in Las Vegas, provides a way for agents to grow in their career.
“They have so many opportunities for us to learn, to be excited about us, motivate us and that’s not something you’re going to get if you’re just your own little mom-andpop business,” Domke said.
RE/MAX’s resources were important to Alicia Wanzek, who has been
at the RE/MAX Now Jamestown office for two years.
“When it came to deciding where I wanted to hang my real estate license, I wanted to be with a company that had the experience and the proven success of RE/MAX,” she said.
That was echoed by Tim Perkins, who has been at RE/MAX Now for five years.
“It means that I am backed by the top real estate brand in the industry and always have the best resource and technology to support my business and allows us to give our clients the best experience possible,” he said.
“I am very thankful and blessed to be a part of the RE/MAX team,” he added. “The leadership and the colleagues we have here locally and at headquarters are first class. They provide us with tremendous amounts of resources to make our business successful and always allowing us to stay ahead of our competitors.”
The RE/MAX Now Jamestown and Valley City agents say they want to make the experience the best it can be for the clients and customers that they assist.
“... my passion is just helping people,” said Nichole Rahn Klundt, an agent with three
years at the Jamestown location.
“I want to help people with the process in every step of the process because anytime you’re buying or selling there’s a lot of stress, there’s a lot of emotion and I just want to make people feel comfortable. … I want to get it done to the best of my abilities and make everybody happy at the end of the day. I want them to have a good experience.”
“I just believe that every successful real estate transaction has a strong foundation of trust,” Wanzek added. “RE/MAX prides itself on having the number one-trusted agents in the U.S. for our clients who are having to make the largest investments of their lives, knowing that you can trust the agent you have representing you and trust that they have your best interests at heart is huge.”
“I really enjoy helping buyers with one of their biggest purchases of their lifetime and sellers moving on to the next chapter of their life,” Perkins said.
“It’s rewarding to me to help clients through this process and see their excitement.”
He also likes to see how properties transform over the years,” he said.
The market Keller said there’s currently a housing market shortage in Jamestown and Valley City.
“Even though the interest rates are a little bit higher at this point which was meant to slow down the buying of homes, we still are about 1,500 short between Stutsman County and Barnes County,” she said.
She said the demand remains for housing and the market is strong for
people who want to sell.
“So as we are going forward, obviously, we know that we’re possibly facing a recession and our inflation is higher and our interest rates are higher,” she noted.
But RE/MAX Now Jamestown and Valley City has 50 years of RE/ MAX experience with varying markets behind it, she said.
“They give me the confidence with their past experience and their education to move forward with customers and clients so they are confident in what we’re doing,” she said. “And
that was really what the (recent RE/MAX) convention was about. They just really paved the way for us to be a stronger company for the future ahead.”
At RE/MAX Now Jamestown and Valley City, the agents are also Realtors, members of the National Association of Realtors who operate under a code of ethics.
James Jensen is the associate broker/owner for RE/MAX Now Jamestown and Valley City. He is located in Valley City.
To learn more, visit www.findrealtynow.com
ksteiner@jamestownsun.com | (701) 952-8449
4-Stroke, 1500# Roller Trailer, Load Guides, Extra Seat, Fuel Tank, Cover, Fuel Tank Hider, Fire Extinguisher, 2 Bank Charger, Minn Kota 55PD BT 54”, Humminbird Helix 5 GPS, (Black color) Regular Price $26,999
New 2023 Lund 1600 Fury Tiller Mercury 40EL- HPT 4-Stroke, 1500# Roller Trailer, Load Guides, Extra Seat, Fuel Tank Hider, Fire Extinguisher, 6.6 Gallon Fuel Tank, Hider, Cover, 2 Bank Charger, Minn Kota 55PD BT 54”, Humminbird Helix 5 GPS, (Gunmetal color) Regular Price $24,999
New 2023 Lund 1650 Angler SS Mercury 50ELPT 4-Stroke, Roller Trailer, Spare Tire, Load Guides, Extra Seat, Tilt Steering, Seat Slider, Fire Extinguisher, Kicker Stereo, Auto Bilge, 3 Bank Charger, Cover, 24V Plug, Minn Kota 70PD BT 60”, Helix 7 GPS (All Red Boat) Regular Price $31,699
New 2023 Lund 1650 Rebel XL Mercury 90ELPT Roller Trailer, Lundguard, Analog Gauges, Spare, Load Guides, Extra Seat, Tilt Steering w/Slider, Fire Extinguisher, kicker stereo, Auto Bilge, 24V Upgrade (Arctic White) Regular Price $33,499
By Keith Norman For The Jamestown Sun
JAMESTOWN — Central Valley Health District marks 50 years of service to Jamestown and Stutsman County this year with the same focus it has always had.
“Disease prevention is what public health has always been about,” said Robin Iszler, former unit administrator of the district. “It still is.”
Central Valley came about in 1973 when the positions of Jamestown city nurse and Stutsman County nurse were merged into a single department. In 1977, the district expanded to offer services in Logan County, which it continues.
With its long history, Kara Falk, current unit administrator of the district, said it is important for the community to understand the services it provides.
“We offer a lot of nursing services,” she said. “Community nursing, medicine setup, school nursing, school screening and environmental health programs like pool inspections and inspections of body art operations.”
Another key aspect of public health is emergency preparedness, according to Frank Balak, regional emergency preparedness and response coordinator at the district.
He said the planning done by public health became obvious during the recent coronavirus pandemic.
“The things we did in COVID were planned for well in advance,” Balak said. “COVID may be over but we are preparing for the next thing that may come down the line.” Preparations are not limited to diseases.
“We take an all-hazard approach,” he said.
“We prepare for natural and man-made problems. Everything from flooding, virus outbreaks, even hazardous materials.”
Balak said that emergency preparedness services are provided for an eight-county area in south-central North Dakota and provide a connection between local first responders and community care providers and the state agen-
cies also involved with emergency service.
For a flooding situation, for example, the district compiles lists of locations of people who might need specialized assistance if flooding occurs or roads are washed out.
“We prepare evacuation plans and other any other preparedness for flooding,” Balak said. “We assess the needs all across the region.”
Falk said that planning continued through the coronavirus pandemic although it was less noticeable to the public.
“Right now we are trying to figure out our new normal after the COVID focus,” she said.
Iszler described working at Central Valley Health through COVID19 as “intense.”
Falk said the coronavirus pandemic made public health in general more visible in the community and across the nation.
“They had evidence of what we do,” she said. “We saw a community appreciation of what we do.”
Through the pandemic, Central Valley Health continued to provide its full list of services in the community.
Those services are provided by 24 employees.
Public health employees are eligible for retirement and health insurance benefits through the state of North Dakota, Iszler said. Other benefits are determined by the Central Valley board, she said.
“We survey the employees every year,” Iszler said. “We find out from the employees what they want. If it is reasonable and doable, we consider implementing it.”
This has created a “family friendly” workplace, she said.
“Maybe we can’t pay as much as some employees,” Iszler said, “but we try to offer attractive benefits.”
Most of the positions at Central Valley are funded through grants.
“There is a risk we would have to lay off people if a grant ends,” Iszler said. “That hasn’t happened often and things have been steady since the 1990s.”
Currently, Central Valley Health District is not recruiting any additional employees.
Those workers continue to provide health services to the public of Stutsman and Logan counties.
“We make sure we have the supplies, organization and infrastructure that is needed whatever happens,” Balak said. “It goes unnoticed until there is a need.”
And they continue to provide more immediate services such as car seat safety, family planning, injury prevention, substance use prevention, Women, Infants and Children program, Women’s Way and vaccinations and immunizations in the community, Falk said.
Programs under the injury prevention category include school sports physicals and safe cribs for children.
The Women’s Way program provides pap smears and mammograms for women who can not afford the screening tests.
The Women, Infants and Children program provides nutritious foods for pregnant, breastfeeding women and young children in need.
Substance use programs address alcohol, tobacco and illegal substance use in the community and can include assistance in quitting tobacco use or preventing opioid overdoses.
The car seat safety program inspects car seats and provides assistance for those with questions about the installation and use of car seats for children under 8 years of age.
All of the programs offered by Central Valley Health are designed to meet the needs of the community, Falk said.
Those needs really haven’t changed over history and will probably gain importance over the next 50 years, Falk said.
“Health promotion and disease prevention are what public health has always been about,” Falk said. “It always will be.”
information about Central Valley Health District is available at www.CentralValleyHealth.org.