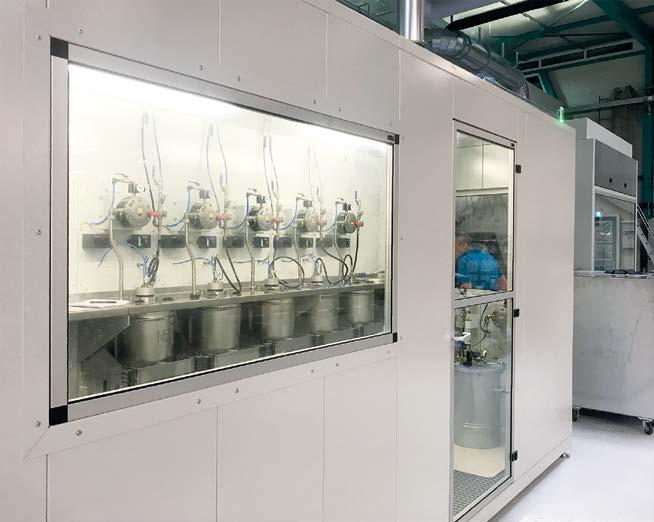
5 minute read
INNOVATION: PRESENT&FUTURE
INNOVATIONS: PRESENT&FUTURE
SPECIAL ISSUE ON ACE & OFF ROAD VEHICLES
Kornelius Berg
VENJAKOB Maschinenbau GmbH & Co.KG - Rheda-Wiedenbrück, Germania kberg@venjakob.de
La verniciatura completamente automatica nella produzione in serie è ormai parte della quotidianità di molte aziende. La produzione su commissione, invece, è una realtà diversa, poiché i lotti piccoli e la variabilità dei manufatti da verniciare generano sfide importanti in termini di automazione dei sistemi. Qui di seguito la descrizione di un sistema sviluppato da Venjakob che permette la verniciatura completamente automatica e di lotti=1 di componenti per ingranaggi complessi.
Imanufatti da verniciare sono componenti lavorati e pre-lavati per ingranaggi planetari e angolari in acciaio e alluminio. La gamma comprende 15 diversi tipi di ingranaggi di diverse dimensioni, con diametri esterni tra 50 e 350 mm, lunghezza da 40 a 420 mm e peso tra 0,5 e 30 kg. La superficie esterna dei componenti richiede la verniciatura.
Controlli e componenti meccanici cruciali
“In questo caso la sfida era progettare l'impianto per lotti fino a 1, adattandolo automaticamente ai diversi componenti”, spiega Kornelius Berg di Venjakob, che ha gestito il progetto. “Ognuno di questi componenti ha il proprio programma dedicato nel sistema di controllo dell’impianto. Essi sono differenziati per diametro, lunghezza, geometria, parametri di verniciatura e colore. Una volta identificato il componente, il sistema seleziona il programma di verniciatura corrispondente e completa automaticamente la configurazione ad esso associata”, prosegue Kornelius Berg descrivendo il processo.
© Venjakob © Venjakob
Sistema completamente automatico e compatto per la verniciatura di componenti per ingranaggi complessi (a sinistra) e alimentazione vernice con tecnologia 2K integrata per 4 cicli cromatici differenti.
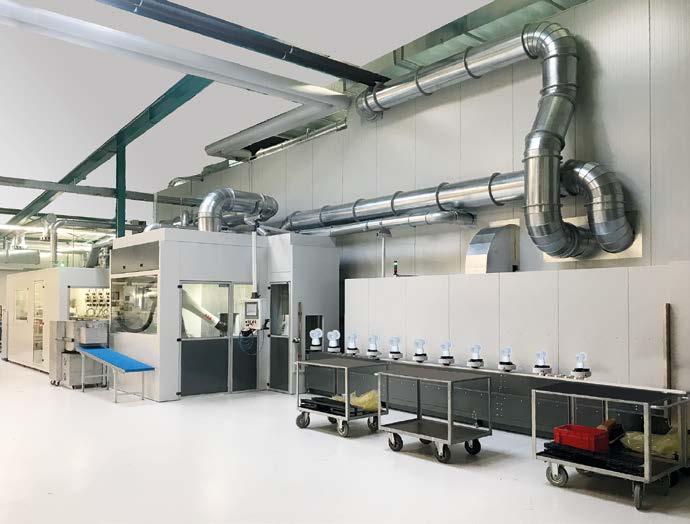
Le uniche operazioni manuali sono il carico e lo scarico. Per ogni richiesta è disponibile un numero adatto di portapezzi, sui quali l’operatore può posizionare i componenti con una mascheratura nelle aree che non devono essere verniciate. Non è necessario posizionare i componenti in un modo specifico. “Tutto doveva diventare veloce e semplice. In risposta a questa richiesta del cliente abbiamo implementato dei meccanismi di sicurezza adatti”, spiega Berg. Dopo il posizionamento l’operatore scansiona il codice a barre del manufatto, il sistema di controllo attiva il programma di verniciatura associato che, premendo un bottone, si avvia. Dopo l’avvio il sistema di controllo individua automaticamente la posizione del componente sul portapezzi. Ciò significa che possono essere individuati dei componenti posizionati in modo sbagliato. Durante questo processo il sistema controlla anche che i dati associati al codice a barre corrispondano alle dimensioni del componente. Nel caso non corrispondano, il sistema passa immediatamente in modalità malfunzionamento e segnala l’errore. Se invece le informazioni del codice a barre sono corrette, i manufatti passano alla verniciatura grazie a un convogliatore e in modalità temporizzata.
Risultati di verniciatura con una qualità elevata ed uniforme
Dopo il rilevamento della posizione i componenti sono trasportati nella cabina di verniciatura chiusa, che contiene il robot. Per garantire che una grande varietà di componenti (con o senza flange di connessione) e che componenti a rotazione simmetrica e asimmetrica siano verniciati in modo completamente automatico con la pistola, il robot è stato dotato di “programmi master”. Questi sono attivati in base al componente, tenendo conto di diversi parametri. Come descritto in precedenza, i parametri sono trasferiti al sistema di controllo quando il codice a barre viene scansionato presso la stazione di carico. Ciò significa che durante la verniciatura parametri come la velocità di spruzzatura o l’angolatura della pistola sono automaticamente adattati a dimensioni e geometria del componente. Un altro importante fattore per ottenere risultati ottimali costanti è l’aerazione continua della cabina. Il flusso d’aria controllato garantisce che temperatura e umidità siano adatte al processo di verniciatura per tutto l’anno.
Soluzioni per un ridotto consumo di materiale
Il sistema è progettato per più prodotti vernicianti. Gli ingegneri di Venjakob hanno utilizzato più approcci per mantenere il più basso possibile il consumo di materiale. Il sistema di alimentazione della vernice è posizionato direttamente vicino alla cabina, in un’altra cabina chiusa con aspirazione e scarico a circuito chiuso. Poiché il sistema vernicia componenti di dimensioni diverse è possibile caricare, per esempio, un solo portapezzi su due. Per questa ragione un’unità di scansione controlla se il mandrino è vuoto o meno durante l’ingresso in
towards the future
SOLUZIONI ROBOTIZZATE DI
ROBOTIC PAINTING SOLUTIONS VERNICIATURA
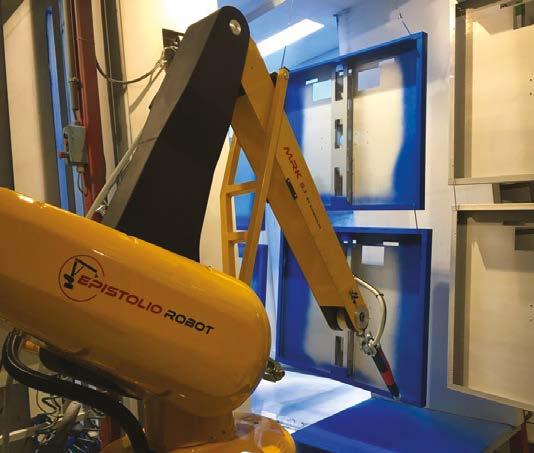
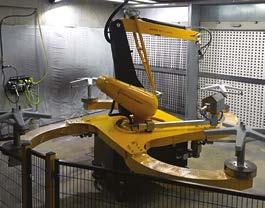

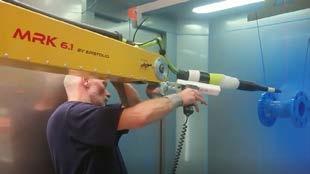
Epistolio Srl.
Via Piemonte 120 21100 Varese (VA) ITALY Ph: +39 0332 212692 Fax: +39 0332 223666 info@epistolio.com www.epistolio.it
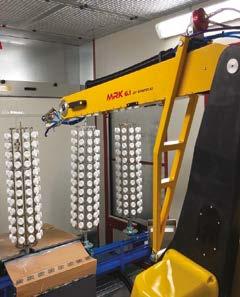
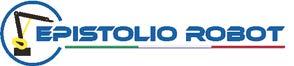
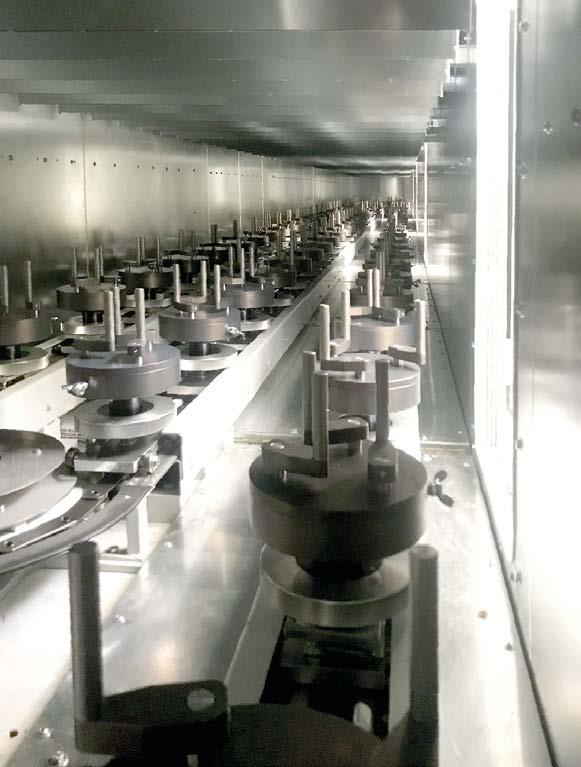
© Venjakob
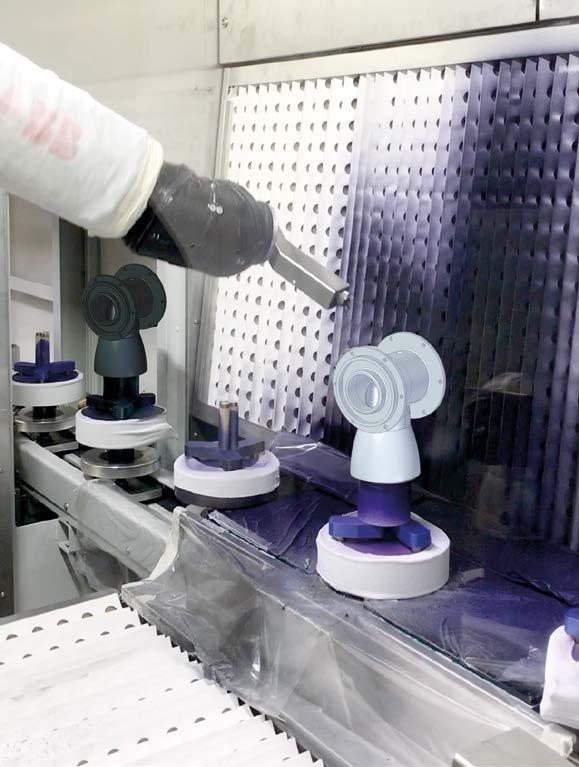
Vista interna della cabina di verniciatura robotizzata e climatizzata.
© Venjakob
Vista della zona di essiccazione con temperatura regolabile tra 50 e 90 °C.
cabina. Se il mandrino è vuoto il processo viene messo in pausa. L’utilizzo del robot consente una spruzzatura mirata, che riduce l’overspray. Qualsiasi overspray è in ogni caso raccolto dal sistema di filtrazione e può essere riutilizzato.
Pulizia automatica delle bilancelle
Dopo la verniciatura i componenti passano alla stazione di rimozione delle bilancelle. Questa utilizza un sistema ad asse orizzontale e verticale con pinze per rimuovere le bilancelle applicate nell’area di carico e le trasporta alla stazione di lavaggio. Il lavaggio prevedere tre fasi: lavaggio alcalino, risciacquo con acqua, asciugatura ad aria calda. Quindi un trasportatore riporta le bilancelle all’area di carico, dove possono essere riutilizzate.
Rimozione possibile prima dell’asciugatura
Le ultime zone cruciali per un buon risultato di verniciatura sono il tunnel di appassimento e il forno di asciugatura a getto d’aria. A monte della zona di appassimento è stato creato un punto di prelievo per i casi in cui un componente verniciato non richieda il passaggio nel forno di asciugatura. In questo punto i manufatti pesanti possono essere rimossi con un carroponte. In caso contrario, i componenti sui mandrini sono trasportati prima nel tunnel di appassimento e poi in quello di asciugatura a getto. In questa sezione il rivestimento è asciugato mediante ventilatori a ricircolo d’aria. La temperatura è sempre regolabile e l’umidità dell’aria mantenuta a un livello costante. Dopo l’asciugatura i componenti vengono trasportati al tunnel di raffreddamento e riportati alla zona di carico/ scarico.
Un balzo in avanti
Se prima la verniciatura era manuale e su 3 turni, la linea automatica robotizzata con trasportatore a mandrino ottiene lo stesso rendimento su 2 turni, riducendo sia il costo della manodopera sia dei prodotti vernicianti, assicurando al contempo una qualità elevata e costante. “Il passaggio da manuale a completamente automatico rappresenta un balzo in avanti”, conclude Kornelius Berg.
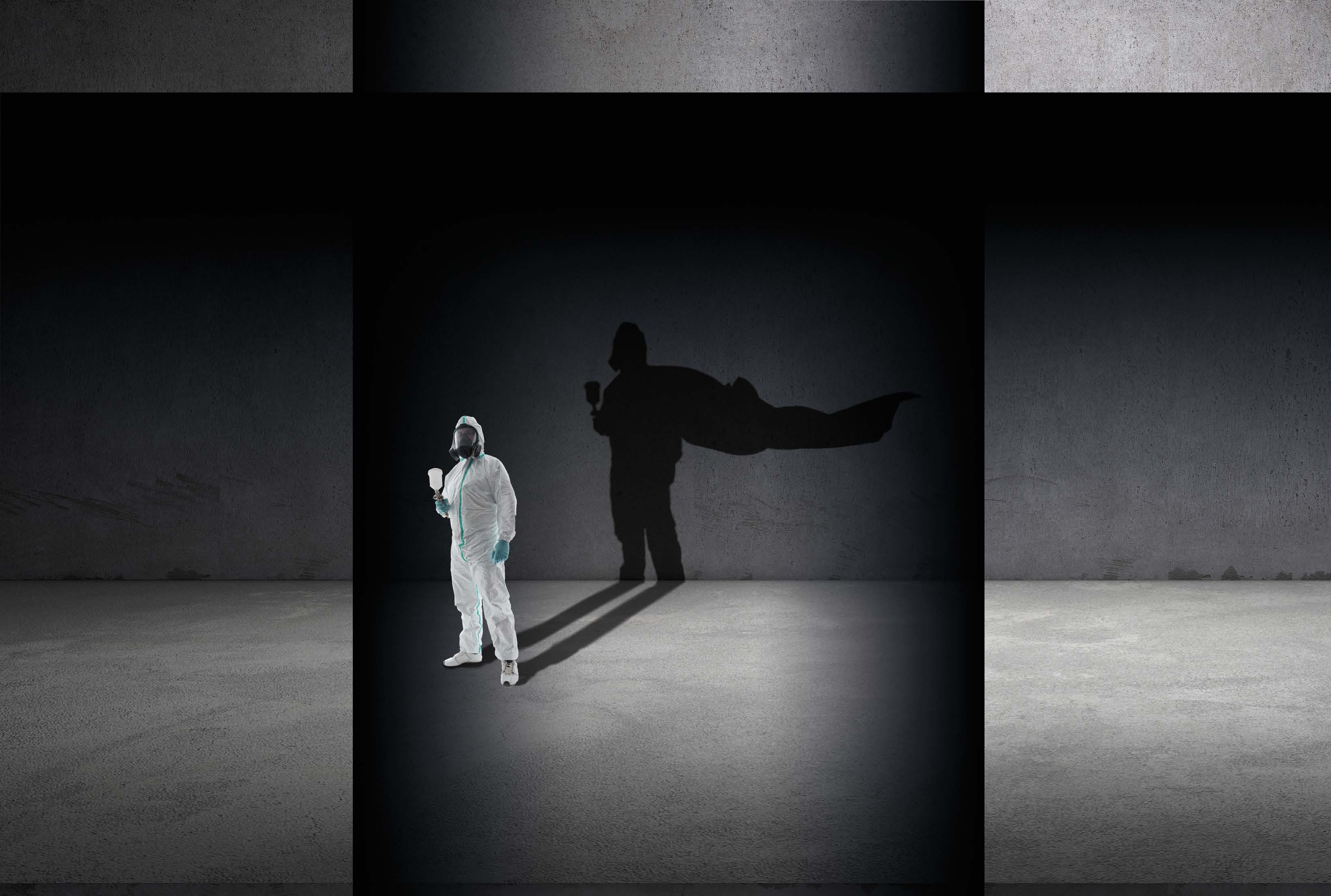