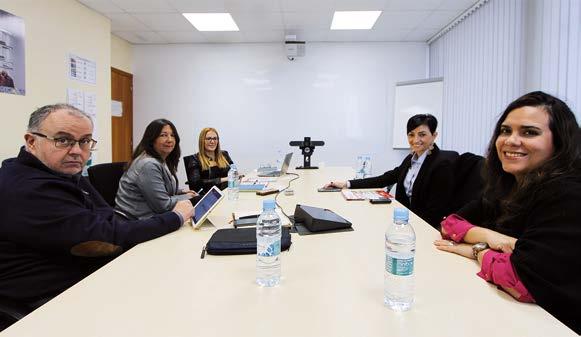
26 minute read
APUESTA POR LA TECNOLOG Í A FOCO NA TECNOLOGIA
AkzoNobel ha estandarizado 1600-1700 colores que siempre están disponibles en sus 6 almacenes europeos. El programa RTS nace de la necesidad de estandarizar un surtido de colores que había alcanzado una complejidad imposible de manejar, con matices sutiles incluso dentro del mismo RAL, por ejemplo, consumidos por dos empresas de aplicación diferentes. Este programa nos permite mantener una respuesta técnica puntual y ofrecer un suministro rápido a nuestros clientes”.
“La oferta RTS se basa en un estudio de la demanda del mercado que se realiza diversas veces al año e incluye los colores RAL más populares a nivel europeo, así como todos los colores propios de AkzoNobel en las distintas colecciones y calidades”, explica Nanet Tamayo. “Naturalmente, si un cliente compra volúmenes significativos de un producto desarrollado exclusivamente para él, también mantenemos este producto en almacén, en el centro de almacenamiento europeo más cercano a su establecimiento”.
“Installux tiene su propia carta de colores RAL con diferentes acabados – algunos suministrados por AkzoNobel – incluyendo los colores de alta rotación. De todas formas, cualquier cliente puede pedirnos un color o un producto de acabado final especial, o venir con su propia referencia de pintura, y nosotros estamos siempre listos para satisfacer su petición”, interviene Susana Bózquez. “Si, hasta hace 20 años, se pintaba cada día con un cierto color y, para despachar un pedido de ese mismo color pero que llegaba en un día diferente había que esperar a la semana siguiente, actualmente nuestra línea de recubrimiento realiza hasta 20 cambios de color al día, con una cabina de aplicación dedicada solo a los blancos y la otra dedicada a todos los demás colores”.
Las ventajas técnicas de una colaboración de 20 años
“La estrecha e ininterrumpida colaboración con AkzoNobel dura desde el año 2001, año en que esta fábrica fue adquirida por el Grupo Installux”, continúa explicando Montse Martos. “A lo largo de los años esta relación ha crecido y se ha mantenido. Me gustaría destacar la gran capacidad técnica de AkzoNobel: conocen perfectamente nuestra instalación y consiguen aportar una solución rápida a cualquier problema. Esta es solo una de las ventajas de trabajar con AkzoNobel. Otra es la rapidez de respuesta a la hora de proporcionar un color especial o incluso para desarrollarlo. “Cuando hablamos de acabado superficial, pensamos en nuestras ventanas, en nuestras puertas, en todos nuestros productos: la europeus. O programa RTS nasceu da necessidade de padronizar uma gama de cores que atingia dimensões incontroláveis, com nuances mínimas entre um mesmo RAL, utilizadas, por exemplo, por duas empresas de aplicação diferentes, para nos permitir manter uma resposta técnica eficiente e o rápido abastecimento dos nossos clientes".
“A oferta RTS baseia-se em estudo da demanda do mercado, que se realiza várias vezes ao ano, e inclui as cores RAL mais solicitadas a nível europeu, além de todas as cores próprias da AkzoNobel nas várias coleções e qualidades” explica Nanet Tamayo.
“Além disso, se um cliente compra grandes volumes de um produto desenvolvido exclusivamente para ele, também mantemos esse produto no depósito, no centro de armazenamento europeu mais próximo de sua sede”.
“A Installlux oferece um catálogo de cores RAL própria, com diversos acabamentos; alguns dos quais são fornecidos pela AkzoNobel, que inclui cores de alta rotação. Entretanto, qualquer cliente pode nos solicitar uma cor ou acabamento especial ou apresentar sua própria referência de tinta e nós estamos prontos para satisfazê-lo” explica Susana Bózquez. “Se até 20 anos atrás se pintava cada dia uma cor diferente e, para atender um pedido daquela mesma cor que chegava no outro dia, era preciso esperar até a semana seguinte, hoje a nossa linha de pintura realiza até 20 mudanças de cor por dia, com uma cabine de aplicação específica apenas para os brancos e outra dedicada às demais cores”.
As vantagens técnicas de uma colaboração de 20 anos “A estreita e contínua relação de colaboração com a AkzoNobel dura desde 2001, ano em que esta fábrica foi comprada pelo grupo Installux” explica Montse Martos. “Com o passar dos anos, esse relacionamento se desenvolveu e se manteve. Gostaria de destacar a grande capacidade técnica da AkzoNobel: eles conhecem perfeitamente a nossa fábrica e conseguem fornecer uma solução rápida para qualquer problema. Esta é apenas uma das vantagens de trabalhar com a AkzoNobel. Outra é a rapidez de resposta para fornecer uma cor especial ou mesmo desenvolvê-la.
De izquierda de la mesa a la derecha: Vicente Herrero Asensio de AkzoNobel, Montse Martos y Susana Bózquez de IES, Alessia Venturi de ipcm®, Nanet Tamayo Durango de AkzoNobel.
Da esquerda da mesa para a direita: Vicente Herrero Asensio da AkzoNobel, Montse Martos e Susana Bózquez da IES, Alessia Venturi da ipcm® e Nanet Tamayo Durango da AkzoNobel.
“Quando falamos de acabamento superficial, pensamos nas nossas janelas e portas, em todos os nossos produtos: para a IES a importancia del acabado no es simplemente una cuestión estética para IES: también es una cuestión de protección, de vida del aluminio. Akzo nos ha ayudado desde nuestros inicios a conocer de primera mano las calidades que cada producto puede ofrecer. En IES tenemos algo muy claro: ofrecemos servicio” declara Susana Bózquez. “Evidentemente también asesoramos a nuestros clientes, pero el resultado final es ofrecer lo que necesitan. Actualmente con Akzo trabajamos con recubrimientos de Clase I y Clase II. El abanico de acabados es enorme: brillo, mate, texturados, metalizados, moteados, imitación al anodizado. Akzo dispone de un servicio técnico excelente, con disponibilidad absoluta y predisposición siempre que hemos tenido algún problema o alguna duda. Anualmente nos auditan en la aplicación de la Clase I y II. Recibimos formaciones internas realizadas por su departamento de marketing. Trabajar con Akzo nos ofrece la posibilidad de estar siempre a la última con respecto a la pintura en polvo y sus aplicaciones”.
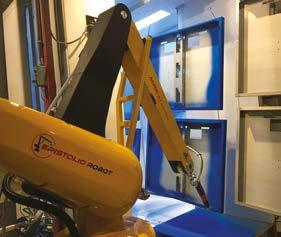
Conclusiones
Después de todos estos años de experiencia en el mundo del lacado en polvo, IES ha podido garantizar su calidad mediante las certificaciones (QualicoatSeaside, Qualimarine QM-069 y Qualilaquage QL-034). Además, cuenta con la certificación ISO 9001 e ISO 14001-Gestión Ambiental. “IES está totalmente comprometido con nuestro medio ambiente y participa activamente en el proceso de economía circular del aluminio. Podrán descubrir todo lo comentado a través de nuestra web, le invitamos a seguirnos en Linkedin donde estamos al día con respecto al aluminio y sus acabados. Para ello, contamos con la agencia Ipanema que nos ayuda en nuestra transformación digital” concluye Susana Bózquez. “Gracias también a AkzoNobel por su entrega profesional y su cercanía. Confiamos que nuestra relación cliente-proveedor, perdurará en el tiempo”.
importância do acabamento não é só uma questão estética, é também uma questão de proteção, da vida útil do alumínio. A Akzo nos ajudou desde o início a conhecer em primeira mão as qualidades que cada produto pode oferecer. Na IES uma coisa é muito clara: oferecemos um serviço” declara Susana Bósquez. “Claro que também oferecemos consultoria aos nossos clientes, mas o resultado final é oferecer o que eles precisam. Atualmente, com a Akzo trabalhamos com tintas Classe I e Classe II. A gama de acabamentos é enorme: brilhantes, foscos, texturizados, metálicos, salpicados, símil anodizados. A AkzoNobel possui um excelente atendimento técnico, com absoluta disponibilidade e presteza sempre que temos algum problema ou dúvida. Somos auditados anualmente para aplicação das Classes I e II. Recebemos treinamento interno realizado por seu departamento de marketing. Trabalhar com a Akzo nos permite estar sempre atualizados em relação à pintura a pó e suas aplicações”.
Conclusão
Após todos estes anos de experiência no mundo da pintura a pó, a IES consegue garantir a sua qualidade através das certificações Qualicoat - Seaside, Qualimarine QM-069 e Qualilaquage QL-034. Além disso, é certificada ISO 9001 e ISO 14001Gestão Ambiental.
“A IES está totalmente comprometida com o meio ambiente e participa ativamente do processo de economia circular do alumínio. Através do nosso site é possível saber de tudo o que é discutido. No Linkedin é possível acompanhar todas as nossas novidades sobre o alumínio e seus acabamentos. Para isso, temos a agência Ipanema que ajuda na nossa transformação digital”, conclui Susana Bósquez. “Agradecemos também à AkzoNobel por sua dedicação profissional e proximidade. Acreditamos que nosso relacionamento cliente/fornecedor será muito duradouro”.
El Groupe Installux: 100 años de historia
El ADN de la carpintería
La empresa Installux es heredera de casi cien años de tradición carpintera y ebanista. Fue en 1923 cuando Alfred Ollier fundó su empresa de carpintería en la calle Baraban de Lyon (Francia). Como carpintero artesano, muy pronto situó los valores humanos en el centro de la filosofía de su empresa. Aunque las actividades de la empresa se amplían gradualmente, la proximidad al cliente sigue siendo prioritaria en cualquier circunstancia.
Si el aluminio es la clave, los carpinteros están en el centro
En 1963, ante la evolución de las técnicas de construcción y renovación de edificios, las empresas Ollier se abren a la utilización de nuevos materiales. Ese año se creó una actividad de aluminio bajo la marca Installux. Tanto para los trabajos en madera como en aluminio, la empresa Ollier desarrolla su posición de fabricante de productos propios. A partir de entonces, el objetivo del fabricante de productos Installux ya no era fabricar carpintería, sino suministrar productos de calidad a artesanos y fabricantes que, gracias a ellos, podían desarrollar soluciones técnicas originales y personalizadas.
En 1987, la empresa Ollier pasa a manos de sus empleados y se centra en las soluciones de aluminio. Christian Canty es nombrado Presidente y Director General. Este fue el comienzo de un gran periodo de crecimiento para Installux. La década siguiente fue especialmente fructífera para la empresa de Rhône-Alpes, que experimentó un desarrollo tanto nacional como internacional.
Extender los conocimientos técnicos a todos los eslabones de la cadena de valor
En la década de 1990, la empresa experimentó una importante expansión de sus actividades con la adquisición de las empresas Tiaso y Roche en Francia, la creación de redes de artesanos en Francia, la creación de una filial Installux Gulf en Bahréin en 1997.
Desde principios de los años 2000, Installux ha seguido consolidando su actividad de integración de Sofadi, experto en soluciones de equipamiento de tiendas. Esto ha permitido a la empresa con sede en Saint-Bonnet-de-Mure (Francia) ampliar aún más su presencia en el sector del acabado de edificios.
Installux integra el negocio de lacado con la adquisición de FAC. Fundada en 1989, France Alu Color está especializada en el recubrimiento en polvo de chapas y perfiles de aluminio.
Installux invierte de nuevo en su filial FAC ampliando la planta industrial y equipándola con una nueva línea de lacado vertical de alto rendimiento.
La crisis de 2008 afecta al principal proveedor de Installux para la extrusión de perfiles de aluminio: Metales. Su responsable cierra su planta de extrusión de Santa Perpètua de Mogoda. La explotación de este centro es una oportunidad para Installux de asegurar sus suministros de aluminio. El reinicio de la unidad, iniciado en 2010, da lugar a la creación de Installux Extrusion Services (IES).
Centrarse en IES: uno de los pilares industriales del Grupo
Installux sigue invirtiendo en IES con la adquisición de la planta de Parets del Vallès en 2014.
En 2018 Christian Canty, tras más de 30 años al frente del Grupo Installux, cede el testigo a su hijo. Christophe Canty es nombrado director general del Grupo Installux.
En 2019 IES aumenta su capacidad de producción con la integración de una nueva prensa de 2000 toneladas aumento así su capacidad de producción.
Installux no deja de invertir en IES. Esta vez con la adquisición – en 2020 – de la nave en el polígono industrial de Santa Oliva (Tarragona). La nave dispone de una línea de lacado vertical con 2 cabinas, que lleva trabajando desde 2008. Han sido muchas las inversiones realizadas en esta línea, ello a supuesto un salto cualitativo sustancial. La unidad de producción de extrusión situada en Santa Perpetua se traslada y la prensa se instala en el nuevo emplazamiento de IES (Santa Oliva-Tarragona), directamente conectada a la línea de lacado vertical. La planta también está equipada con un centro de mecanizados CNC 5 ejes, sierras de corte, líneas de ensamblaje y líneas de embalajes especiales.
O DNA da carpintaria
Grupo Installux: 100 anos de história
A empresa Installux é herdeira de quase 100 anos de tradição nos setores de carpintaria e marcenaria. De fato, foi em 1923 que Alfred Ollier fundou sua empresa de carpintaria na Rue Baraban, em Lyon, França. Como carpinteiro artesanal, desde cedo colocou os valores humanos no centro da filosofia da sua empresa e, embora o negócio estivesse se expandindo gradualmente, a proximidade com o cliente manteve-se uma prioridade em todas as circunstâncias.
Se o alumínio é a chave, os carpinteiros são o centro
Em 1963, diante da evolução das técnicas de construção e reestruturação de edifícios, as empresas Ollier se abriram ao uso de novos materiais: foi o ano da criação do departamento de alumínio com a marca Installux. Tanto para o processamento de madeira, quanto do alumínio, a empresa Ollier desenvolveu a função de fabricante de seus próprios produtos. Desde então, o objetivo do fabricante Installux deixou de ser a produção de carpintaria e passou a ser o fornecimento de artigos de qualidade para artesãos e produtores que, com esses produtos poderiam desenvolver soluções técnicas originais e personalizadas. Em 1987, a Ollier passou para as mãos de seus funcionários e se concentrou em soluções de alumínio. Christian Canty foi nomeado presidente e diretor executivo da empresa. Para a Installux, este foi o início de um grande período de crescimento. A década seguinte foi particularmente lucrativa para a empresa de Rhône-Alpes, que passou por um desenvolvimento nacional e internacional.
Estender o conhecimento técnico para todos os elos da cadeia de valor
Na década de 1990, a empresa passou por uma expansão significativa de suas atividades, com a compra das empresas Tiaso e Roche, na França, a criação de redes de artesãos, também na França, e o estabelecimento da filial Installux Gulf, no Bahrein, em 1997. Desde o início dos anos 2000, a Installux continuou a consolidar suas atividades de integração da Sofadi, especialista em soluções de equipamentos para lojas. Isso permitiu que a empresa de Saint-Bonnet-de-Mure (França) expandisse ainda mais sua presença no setor de acabamento de edifícios.
A Installux integrou a atividade de pintura com a compra da FAC (France Alu Color). Fundada em 1989, a empresa era especializada na pintura a pó de chapas e perfis de alumínio.
A Installux investiu ainda mais na filial FAC, ampliando a fábrica e introduzindo uma nova linha de pintura vertical de alta performance.
A crise de 2008 afetou o principal fornecedor da Installux para a extrusão de perfis de alumínio: a Metales. O seu proprietário fechou a fábrica de extrusão de Santa Perpètua de Mogoda.
O aproveitamento deste centro foi uma oportunidade para a Installux garantir o seu abastecimento de alumínio. A reabertura do departamento, iniciada em 2010, levou à criação da Installux Extrusion Services (IES).
Foco na IES: um dos pilares industriais do grupo
A Installux continuou a investir na IES com a compra da fábrica de Parets del Vallès, em 2014.
Em 2018, Christian Canty, agora com mais de 30 anos à frente do grupo Installux, passou o bastão ao filho: Christophe Canty foi nomeado diretor executivo do grupo Installux.
Em 2019 a IES aumentou a sua capacidade de produção com a integração de uma nova prensa de 2000 toneladas.
A Installux nunca parou de investir na IES. Desta vez, com a aquisição, em 2020, de um galpão na zona industrial de Santa Oliva, Tarragona, que dispõe de uma linha de pintura vertical com duas cabines, em funcionamento desde 2008. Muitos investimentos foram feitos nesta linha, que representaram um salto de qualidade muito importante.
A fábrica de extrusão localizada em Santa Perpetua foi então transferida e a prensa instalada na nova sede da IES, em Santa Oliva, Tarragona, conectada diretamente à linha de pintura vertical. A fábrica também está equipada com um centro de processamento CNC de cinco eixos, com serras e linhas especiais de montagem e embalagem.
Bombas DDF4 de Spray SA
Ramseier Koatings Technology – Spray S.A. han desarrollado la nueva bomba DDF4 como mejora a la bomba DDF2.
Durante los últimos 20 años, se han suministrado más de 4000 unidades de bombas para polvo DDF de diferentes modelos de RKT en todo el mundo, suplantando al Venturi. Según la experiencia, la mayoría de las bombas DDF2 y DDF2-DP más antiguas pueden funcionar de manera consistente y eficaz, pero el rendimiento superior y los beneficios que aportan las bombas DDF normalmente se manifiestan cuando el cliente / los operarios entienden que las bombas DDF son de naturaleza diferente a los venturies convencionales y se debe entender que su concepto y operatividad no son lo mismo. Sin embargo, algunos de dichos clientes, por diferentes motivos, han sugerido mejoras a las bombas DDF. En esencia, todo se reduce a que “las bombas DDF eran más difíciles de controlar” que los venturies. Por ello se ha desarrollado la nueva bomba para polvo DDF4. Desde hace unos 10 años RKT comenzó a investigar las diferentes causas a las sugerencias de los clientes y optaron como resultado desarrollar la nueva bomba DDF4. A partir de la investigación efectuada, se descubrió que el hecho de que el polvo en una bomba tipo DDF se transporte en forma de ‘alta densidad’ agravaba y aumentaba los problemas. Por ello, al desarrollar la nueva bomba DDF4, se ha superado y reducido la influencia negativa de estos condicionantes. La diferencia básica está en el diseño de la DDF4 vs la DDF2. El polvo ahora se succiona hacia las cámaras de polvo desde los lados en lugar de desde la parte inferior de los dos cilindros. Todas las ventajas de la DDF4, como por ejemplo el mejor vacío obteniendo un flujo de polvo más consistente y constante, su mejor manejo del polvo y fiabilidad a largo plazo, su rendimiento y su capacidad de pulverizar 8 gr/min de polvo sin borbotones ni oclusiones, son algunas de las mejoras efectuadas.
Las bombas DDF4 funcionan mejor con las pistolas de la Serie 600, sin embargo, para tener buenos resultados operativos, estas
Bombas DDF4, da Spray SA
A Ramseier Koatings Technology e a Spray S.A. desenvolveram a nova bomba DDF4 para melhorar a bomba DDF2.
Nos últimos 20 anos, mais de 4.000 unidades de bombas para pó DDF de vários modelos foram fornecidas pela RKT em todo o mundo, substituindo os Venturi. Com base na experiência, a maior parte das bombas DDF2 e DDF2-DP mais antigas podem operar de forma uniforme e eficiente. No entanto, a maior eficiência e os benefícios das bombas DDF são percebidos quando o cliente/operador entende que essas bombas são diferentes dos Venturi tradicionais, portanto, deve-se entender que o conceito e o funcionamento não são os mesmos. Apesar disso, alguns desses clientes, por vários motivos, sugeriram melhorias nas bombas DDF. Tudo se resume no fato que “as bombas DDF eram mais difíceis de controlar” do que os Venturi. É por isso que a nova bomba para pó DDF4 foi desenvolvida.
Já há cerca de 10 anos, a RKT começou a analisar as causas por trás desses pedidos dos clientes e, assim, decidiu desenvolver as bombas DDF4. Das pesquisas realizadas, verificou-se que os problemas aumentavam e se agravavam pelo fato que o pó, na bomba tipo DDF, era transportado em forma de ‘alta densidade’. Por isso, com o desenvolvimento da nova bomba DDF4, o impacto negativo destes fatores foi superado e reduzido”.
A principal diferença está no design da bomba DDF4, em relação à bomba DDF2. O pó agora é aspirado para dentro das câmaras de pó pelos lados, e não pelo fundo dos dois cilindros.
Todas as vantagens da DDF4, como, por exemplo, o melhor vácuo, obtendo um fluxo de pó mais consistente e constante, o melhor gerenciamento do pó e a confiabilidade a longo prazo, o desempenho e capacidade de pulverizar 8 g/min de pó sem bolhas nem oclusões, são algumas das melhorias realizadas.
As bombas DDF4 funcionam melhor com as pistolas da série 600; no entanto, para obter bons resultados operacionais, bombas de flujo denso requieren operarios con mayores habilidades operativas y de mantenimiento de las mismas.

Bombas DDF4 en un sistema electrostático automático
Las bombas DDF4 se controlan en pequeñas unidades individuales, disponiendo de un PLC para cada bomba. Ello implica más confianza en el sistema y facilidad para actualizar el programa, si es preciso modificarlo en el futuro. Toda modificación se realiza a través de una pantalla HMI. Las bombas DDF4 están alojadas en la sección inferior de un cuadro de control y los PLC de control para cada bomba están ubicados en la sección central. Cada PLC individual controla las funciones de las DDF4. El ajuste de la velocidad de los pistones de las bombas DDF4 controla el suministro de polvo. La sección superior del cuadro de control alberga la unidad de PLC Master. Esto hace que el mantenimiento y la operación sean muy fáciles de usar. Desde el módulo de control electrostático GCU-S600 fijamos los parámetros de la pistola, los cuales se almacenarán en el PLC por bomba/pistola y desde la pantalla HMI se podrá seleccionar la bomba, el número de programa, el caudal de polvo de pulverización y caudal polvo bomba DDF4. Tal y como indica el esquema dichos parámetros serán enviados a la bomba correspondiente. La operativa es similar a DDF2 pero con sistemas actualizados técnicamente.
El Micro Powder Center (MPC-5Mk2) ofrece un alto rendimiento para un cambio rápido de color de alta calidad con bombas de densos DDF4. El MPC-5Mk2 es muy útil para quellas instalaciones que deban cambiar de color más de 10 veces por turno de trabajo.
Anomalías de las DDF2
Las anomalías más frecuentes de las bombas DDF2, o sea la generación antecedente a las DDF4, son:
• Flujo de polvo inconsistente.
• Obstrucción de los tubos de descarga de polvo.
• Contaminación de las válvulas de control de vacío que conlleva a un suministro de polvo inconsistente.
• En ciertos tipos de polvo puede haber contaminación del color debido a una presión de aire comprimido insuficiente para la limpieza.
Las causas de estos problemas están relacionados a dos factores principales:
• La calidad de polvo. Formulaciones que contienen un alto porcentaje de partículas por debajo de 32 micras dará como resultado una mayor absorción de agua del aire y en general mayor facilidad de crear grumos. Formulaciones con características pegajosas pueden crear pequeños grumos, y como resultado obteniéndose un flujo no homogéneo y de mala calidad.
• Entorno operativo: Las bombas DDF funcionan tanto en entornos essas bombas a alto fluxo denso requerem operadores com mais habilidades operacionais e capacidade de manutenção das mesmas.
Bombas DDF4 em um sistema eletrostático automático
As bombas DDF4 são controladas em pequenas unidades, com um PLC para cada bomba. Isso resulta em mais segurança no sistema e facilidade de atualização do programa, caso seja necessário modificá-lo no futuro. Todas as modificações são feitas através de uma tela HMI. As bombas DDF4 estão alojadas na parte inferior, enquanto os PLCs de controle para cada bomba estão localizados na parte central. Cada PLC controla as funções das DDF4. A regulação da velocidade dos pistões controla a alimentação do pó. A parte superior do painel de controle abriga o PLC Master. Isto simplifica tanto a manutenção, quanto a operação.
No módulo de controle eletrostático GCU-S600 configuramos os parâmetros da pistola, que serão armazenados no PLC por bomba/ pistola e, na tela HMI, será possível selecionar a bomba, o número do programa, o fluxo de pó para pulverização e a taxa de fluxo de pó da bomba DDF4. Conforme mostra o diagrama, esses parâmetros serão enviados para a bomba correspondente. O funcionamento é semelhante ao da DDF2, mas com sistemas atualizados tecnicamente. O Micro Powder Center (MPC-5Mk2) oferece alto desempenho para mudanças rápidas de cor de alta qualidade com bombas de fase densa DDF4. O MPC-5Mk2 é muito útil para sistemas onde as mudanças de cor devem ser feitas mais de 10 vezes por turno de trabalho.
Anomalias das bombas DDF2
As anomalias mais frequentes das bombas DDF2, ou seja, da geração anterior à DDF4, são:
• Fluxo de pó inconsistente;
• Obstrução dos tubos de descarga de pó.
• Contaminação das válvulas de controle de vácuo, que causa uma distribuição inconsistente do pó
• Com alguns tipos de pó pode haver contaminação da cor, devido a uma pressão insuficiente de ar comprimido para a limpeza.
As causas desses problemas estão relacionadas a dois fatores principais:
• A qualidade do pó: formulações com alto percentual de partículas menores que 32 mícron resultarão em maior absorção de água do ar e, em geral, maior facilidade na formação de grumos. Formulações pegajosas podem criar pequenos grumos, resultando em um fluxo não homogêneo e de baixa qualidade.
• Ambiente operacional: as bombas DDF operam tanto em ambientes com alta umidade, quanto em climas quentes e, se o pó não for
Avances Avan Os
de alta humedad como en climas cálidos y si el polvo no se almacena correctamente, se pueden formar grumos con facilidad. Una mala calidad del aire comprimido, por ejemplo con aceite y agua, hará que el polvo denso sea muy difícil de transportar. Este problema es menos grave en los venturies, aunque prevalece en diversas instalaciones. Un aire comprimido caliente podría resultar no sólo en grumos de polvo obstruyendo los tubos de polvo, sino que en casos extremos el polvo se derretiría alrededor de los pistones dentro de las bombas.
Objetivos de mejoras de la bombas DDF4
El diseño de la bomba DDF4 incorpora las siguientes mejoras: armazenado corretamente, é fácil que se formem grumos. A baixa qualidade do ar comprimido, por exemplo com óleo e água, irá dificultar muito o transporte do pó denso. Este problema é menos grave nos Venturi, embora seja prevalente em muitas fábricas. O ar comprimido quente pode causar não só grumos de pó que entopem os tubos, mas, em casos extremos, o pó pode derreter ao redor dos pistões dentro das bombas.
• Mejor sellado y control de vacío de la bomba. Para garantizar un rendimiento fiable a largo plazo de la bomba DDF4, especialmente cuando trabaja con polvos con una mala distribución del tamaño de las partículas.
• Mejor diseño de la alimentación, movimiento interno y descarga del polvo. La introducción de aire fluidizado en la parte inferior de la cámara de polvo ha mejorado en gran medida el flujo de salida de polvo de la cámara y esto es especialmente esencial cuando se utiliza polvo com micrajes reducidos. Además, la entrada de polvo horizontal permite una entrega mucho más suave de polvo en la cámara de polvo.
• Mejor consistencia y uniformidad del flujo de polvo. Gracias a la adaptación de una unidad especial de aire pulsado el polvo denso fluye uniformemente desde la bomba hasta las pistolas. Esto es particularmente útil cuando se usan polvos con una distribución de partículas de diversos tamaños.
Objetivos do aperfeiçoamento das bombas DDF4
O design da bomba DDF4 incorpora as seguintes melhorias:
• Melhor vedação e controle de vácuo da bomba, para garantir um desempenho seguro a longo prazo, especialmente ao trabalhar com pós com má distribuição granulométrica;
• Melhor design da alimentação, movimento interno e descarga de pó. A introdução de ar fluidizado na parte inferior da câmara de pó melhorou significativamente o escoamento do mesmo para fora da câmara, aspecto fundamental quando se utilizam pós com espessuras reduzidas. Além disso, a entrada horizontal do pó permite um fornecimento muito mais suave do pó na câmara de pó;
• Melhor consistência e uniformidade do fluxo de pó. Graças à introdução de uma unidade especial de ar pulsado, o pó denso flui uniformemente da bomba para as pistolas. Isto é muito útil quando se usam pós com distribuição de partículas de várias dimensões;
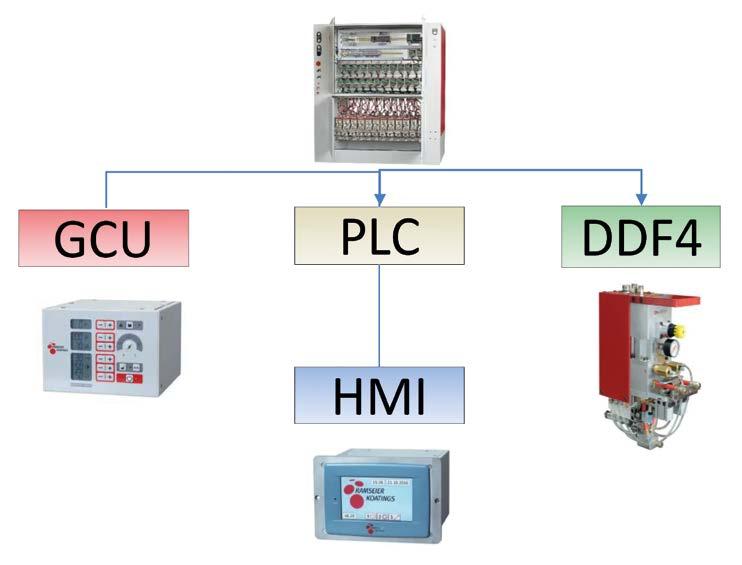
• Mejor control de la bomba. Instalación de un único mecanismo de control más fácil de usar y repetible para las bombas DDF para así adaptarse a los diferentes tipos de polvo.
• Reducción del tiempo de inactividad y el coste operativo de las bombas. La eliminación del uso del tubo en “Y” en el diseño de la bomba de polvo DDF4 no solo ha reducido el coste de este componente, sino que también ha reducido en gran medida la posibilidad de que el polvo se obstruya en los tubos de polvo.
• Mejor diseño. Un diseño más fácil de usar ha reducido en gran medida el tiempo de configuración inicial de las bombas de polvo DDF4 y también su tiempo de inactividad por mantenimiento.
Conclusiones
No obstante las mejoras también deben crearse por parte del cliente, que deberá mejorar otros factores como el aire comprimido sucio y caliente. Para que los sistemas de recubrimientos en polvo de alta densidad y baja velocidad sean realmente efectivos, la calidad del aire comprimido debe ser seca, limpia y fría ( >22 °C):
• Humedad en el aire – 1,3 gr/m3 (máx)
• Contenido de aceite en el aire – 0,1 gr/m2 (máx).
Tu aliado para procesos químicos verdes
• Melhor controle da bomba. Instalação de um mecanismo de controle único, mais intuitivo e repetível para as bombas DDF, para se adaptar a diferentes tipos de pó;
• Redução do tempo de inatividade e dos custos operacionais das bombas. A eliminação do uso do tubo a“Y” na estrutura da bomba DDF4 não só reduziu o custo desse componente, mas também reduziu bastante a possibilidade de entupimento dos tubos com o pó;
• Design melhorado. O novo desenho reduziu significativamente o tempo de configuração inicial das bombas para pó DDF4, além de reduzir também as paradas para manutenção.
Conclusão
As medidas de otimização, entretanto, também devem ser criadas pelo cliente, que terá que melhorar outros fatores, como o ar comprimido quente e contaminado. Para que a aplicação de revestimentos em pó de alta densidade e baixa velocidade seja realmente eficaz, o ar comprimido de qualidade deve ser seco, limpo e frio (>22°C):
• Umidade do ar – 1,3 g/m³ (máximo)
• Teor de óleo no ar – 0,1 g/m² (máximo).
Nuestros productos químicos revolucionarios están diseñados para tener un impacto medioambiental muy limitado, reducir el consumo de recursos y para una mayor simplicidad operativa.
Con las tecnologías de Chemtec puedes reemplazar fosfatado de hierro y zinc:
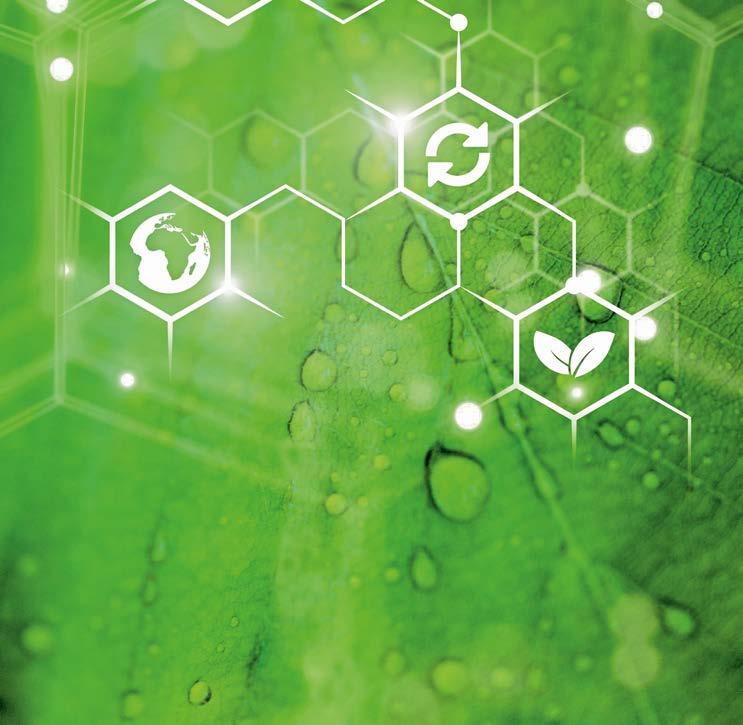
PRONORTEC tratamiento de superficies multi-metal
TORAN 3® proceso de pre-tratamiento multi-metal
Sistemas anticorrosivos Adapta Rustproof System® de última generación vs ISO 12944:2018 CX
El sistema anticorrosivo Adapta Rustproof System®, que se sometió a varios procesos de prueba con respecto a la norma ISO 12944:2018 CX, es muy recomendable en entornos extremadamente corrosivos, como edificios e instalaciones costeras.
Sistemas anticorrosivos de última geração Adapta Rustproof System® vs ISO 12944:2018 CX
O sistema anticorrosivo Adapta Rustproof System®, que passou por diversos processos de teste de acordo com a norma ISO 12944:2018 CX, é altamente recomendado em ambientes extremamente corrosivos, como edifícios e instalações costeiras.
Los repetitivos ciclos de exposición intentan simular la exposición a climas extremos de las estructuras offshore.
Os ciclos de pintura anticorrosiva simulam a exposição a climas extremos das estruturas offshore.
El fenómeno de la corrosión constituye un problema de primer orden a nivel mundial, tanto por los problemas de seguridad laboral asociados como por las pérdidas económicas que anualmente genera.
En los países más desarrollados el coste de la corrosión anual se ha estimado en un 3,1% del PIB, es por ello que las instituciones y las comunidades científicas estén destinando esfuerzos y recursos al análisis y prevención de este fenómeno.
En este sentido, Adapta ha considerado muy interesante el testar sus sistemas anticorrosivos de última generación en relación a la ISO 12944:2018 CX, pues entendemos que el comité técnico que ha desarrollado esta norma ha incorporado una componente realmente interesante; el estrés del recubrimiento ante los cambios atmosféricos y de temperatura.
La norma ISO 12944:2018 CX para pinturas y barnices “Requisitos de funcionamiento para los sistemas de recubrimiento para la protección de estructuras Offshore y estructuras asociadas", prevé un total de 4.200 horas de exposición del recubrimiento divididas en 25 ciclos. Cada ciclo se divide en las siguientes etapas (Fig. 1):
• 72 horas de exposición UV y condensación según la norma UNE EN ISO 16474-3:2014, alternando el envejecimiento artificial de 4 horas de UV a 60 ± 3º C y 4 horas de condensación a 50 ± 3º C. Lámparas Tipo 1ª (UVA340);
• 72 horas de exposición a la niebla salina según UNE-EN-ISO 9227:2012;
• 24 horas de exposición a baja temperatura, -20 ± 2º C. Esto totaliza al finalizar los 25 ciclos el siguiente número de horas de exposición en cada una de las diferentes etapas:
• 1800 horas de QUV 340;
• 1800 horas de Cámara de Niebla Salina;
• 600 horas a - 20ºC.
Ofenômeno da corrosão é um problema primordial em todo o mundo, tanto pelas questões de segurança de trabalho associadas, quanto pelas perdas econômicas que gera atualmente.
Nos países desenvolvidos, o custo anual da corrosão foi estimado em 3,1% do PIB, e por isso as instituições e comunidades científicas estão destinando esforços e recursos para a análise e prevenção desse fenômeno.
Levando isso em consideração, a Adapta considerou essa forma de pesquisa muito interessante para testar os seus modernos sistemas de revestimento anticorrosivo em relação à ISO 12944:2018 CX , porque o comitê técnico responsável pelo desenvolvimento desta norma incorporou um componente realmente importante: o estresse do revestimento diante das mudanças climáticas e de temperatura.
A norma ISO 12944:2018 CX para tintas e vernizes, “Requisitos funcionais para os sistemas de revestimento para a proteção de estruturas offshore e estruturas associadas”, prevê um total de 4200 horas de exposição do revestimento subdivididas em 25 ciclos. Cada ciclo é dividido nas seguintes etapas (fig. 1):
• 72 horas de exposição aos raios UV e condensação de acordo com a norma UNE EN ISO 16474-3: 2014, alternando o envelhecimento artificial de 4 horas de UV a 60 ± 3°C e 4 horas de condensação a 50 ± 3°C. Lâmpadas do tipo 1ª (UVA340);
• 72 horas de exposição à névoa salina de acordo com a UNE-EN-ISO 9227: 2012;
• 24 horas de exposição a baixa temperatura, -20 ± 2°C. Ao fim dos 25 ciclos é totalizado o seguinte número de horas de exposição, em cada uma das várias fases:
• 1800 horas de QUV 340;
• 1800 horas de câmara de névoa salina;
• 600 horas a -20°C.
Avances Avan Os
Antes de dar comienzo a los ciclos se realiza una incisión de 50 mm. sobre el recubrimiento con una anchura de 2 mm. Los repetitivos ciclos de exposición intentan simular la exposición a climas extremos de las estructuras offshore, es decir, estructuras expuestas al medio marino o sumergidas en agua de mar o agua salobre. Las estructuras offshore pueden ser flotantes o fijadas al fondo marino, siendo las más representativas, las plataformas petrolíferas y las de extracción de gases, muy abundantes en el Mar del Norte y el Mar de Noruega.
Adapta ha seleccionado para los ensayos dos tipos de sustratos preparados según NORSOK Standard M-501 (Surface preparation and protective coating - Edition 6, February 2012): acero galvanizado (Fig. 2) y aluminio (Fig. 3). Ambos sustratos han recibido, previo a la pintura, un tratamiento de superficie nanotecnológico exento de fosfatos. Los estándares NORSOK están basados en normas reconocidas internacionalmente e incorporan aquellos requisitos adicionales que se consideran necesarios para satisfacer las elevadas exigencias de la industria petrolera noruega. Recoge los requisitos para la selección de materiales de revestimiento, preparación de la superficie, procedimientos de aplicación e inspección de revestimientos protectores que se aplicarán durante la construcción e instalación de estructuras offshore.
Antes do início dos ciclos é realizada uma incisão de 50 mm no revestimento, com uma largura de 2 mm.
Os ciclos de exposição repetidos tentam simular a exposição a climas extremos das estruturas offshore, ou seja, estruturas expostas ao ambiente marinho ou submersos na água do mar ou água salobra. As estruturas offshore podem ser flutuantes ou fixadas ao fundo do mar; dessas, as mais representativas são as plataformas de petróleo e para a extração de gás, muito comuns no Mar do Norte e no Mar da Noruega.
Para o teste a Adapta selecionou dois tipos de substratos, preparados de acordo com o padrão NORSOK M-501 (Surface preparation and protective coating - Edition 6, February 2012): aço galvanizado (fig. 2) e alumínio (fig. 3). Ambos os substratos receberam, antes da pintura, um tratamento de superfície nanotecnológico isento de fosfatos. Os padrões NORSOK são baseados em normas internacionalmente reconhecidas e incorporam os requisitos adicionais que são considerados necessários para satisfazer as exigências rigorosas da indústria petrolífera norueguesa. Coletam os requisitos para a seleção de materiais de revestimento, preparação de superfície, procedimentos de aplicação e inspeção de revestimentos de proteção que serão aplicados durante a construção e instalação de estruturas offshore.
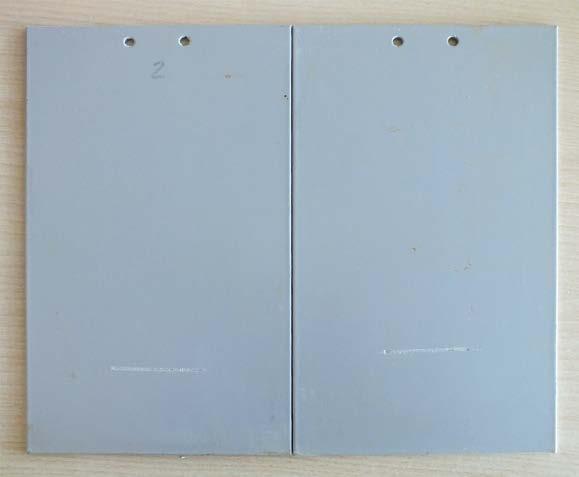

El recubrimiento anticorrosivo aplicado consiste en un sistema de recubrimiento a dos manos. La primera capa la compone una imprimación Adapta ROC, RB-7708 y la segunda un metalizado en calidad superdurable (Adapta SDS), el DX-9006-XW.
En ambos sistemas el espesor total de ambas capas se encuentra entre 140 y 180 micras, siendo este espesor muy inferior al mínimo solicitado (>225 micras) que es el requerido en sistemas basados en pinturas liquidas.
Esto aporta también una reducción de costes y de procesos en comparación a estos sistemas líquidos.
Los ensayos se han realizado en los laboratorios acreditados de Tecnalia Research & Innovation donde posteriormente se procedió a la evaluación de defectos según la UNE-EN-ISO 4628, la adhesión según la UNE-EN-ISO 4624 y la adhesión por tracción según la UNE-EN-ISO 4624. siendo todos los resultados satisfactorios. Por lo que el uso del sistema anticorrosivo Adapta Rustproof System® es altamente recomendado en ambientes extremadamente corrosivos, como por ejemplo en las edificaciones e instalaciones costeras.
O revestimento anticorrosivo aplicado consiste em um sistema de revestimento em duas demãos. A primeira camada é constituída por um primer Adapta ROC, RB-7708, e a segunda é um metalizado de qualidade super durável (Adapta SDS), o DX-9006-XW. Nos dois sistemas, a espessura total de ambas as camadas é entre 140 e 180 micron, sendo esta espessura muito inferior ao parâmetro mínimo de referência (>225 micron), necessária para sistemas baseados em tintas líquidas. Isto também proporciona uma redução de custos e de processos, em relação a estes sistemas líquidos. Os testes foram realizados nos laboratórios credenciados da Tecnalia Research & Innovation, onde, posteriormente, procedeuse à avaliação de defeitos de acordo com a UNE-EN-ISO 4628, a adesão de acordo com a UNE-EN-ISO 14624 e a resistência à tração de acordo com a UNE-EN-ISO 4624, e todos os resultados foram satisfatórios. Por esta razão, a utilização do sistema anticorrosão Adapta Rustproof System® é altamente recomendável para ambientes extremamente corrosivos como, por exemplo, edifícios e instalações costeiras.