
15 minute read
CASE STUDY
The effectiveness of sodium bicarbonate cleaning for the perfect removal of chips and neat vegetable oil from precision metal parts
MMP Torneria produces about 50 million turned components per year. In 2020, despite the difficulties due to the pandemic, it implemented a project to revamp its facility and thus improve the traceability of its processes, provide high quality products, and reduce its environmental impact. Thanks to a partnership with STS Italy, specialising in tailor-made cleaning solutions, it made its cleaning department healthier and safer, while increasing productivity and optimising results.
Swarf is one of the most critical elements resulting from metalremoval machining processes, such as turning. With this technique, lathes transmit rotary motion to mechanical components, the speed of which is determined by the hardness of their material and the required precision degree. The function of the cutting tool is to remove the machining allowance, which results in the formation of chips. A few measures can be implemented, such as placing a wedge-edged plate between the insert and the clamping bracket, which bends the chips and, finally, breaks and removes them as the bending forces increase. However, some residues may remain on the surface of the machined metal parts and these can decisively affect any subsequent production steps. Therefore, the search for cleaning solutions to eliminate swarf and machining oil is one of the most frequent items in the investment plans of turning companies.
MMP Torneria (San Lorenzo in Campo,
Pesaro Urbino, Italy) specialises in the turning of small metal parts. It was born eleven years ago from a long-standing local firm in the sector, and it found its “soul” in Attilio Rotatori, now its CEO. “Over a few years,” he confirms, “we have gone from producing almost exclusively small metal parts for major national distributors to manufacturing turned components directly for leading manufacturers in the European hydraulics and automotive sectors, particularly in Germany. Thanks to this evolution of our core business, we have been able to grow and establish ourselves in a highly competitive market. However, we have also started facing increasingly stringent specifications for the cleaning quality of our components and, at the same time, feeling the need to adapt our operations to the numerous environmental requirements that are becoming increasingly important in the manufacturing industry. We therefore decided to replace the two solvent plants we had been using since 2010 with a new machine from the Aquaroll series, designed and supplied by STS Italy (Ravenna).”
The factory’s “green” revamping
The choice of the new cleaning plant, which went into operation in December 2020, was only a part of a factory modernisation plan that included the integration of new machining systems and the construction of a new, high-performance optical metrology laboratory. “Competition is high in our area,”
Components turned by MMP Torneria. I componenti torniti da MMP Torneria.
© ipcm
L’efficacia del lavaggio con bicarbonato per la perfetta rimozione di trucioli e olio intero vegetale dalle minuterie metalliche di precisione
MMP Torneria produce circa 50 milioni di componenti torniti all’anno. Nel 2020, nonostante le difficoltà della pandemia, ha messo in atto un progetto di revamping della propria struttura per migliorare la tracciabilità dei processi, la garanzia di qualità dei propri prodotti e ridurre l’impatto ambientale. Grazie alla partnership con STS Italy, azienda specializzata nello studio di soluzioni di lavaggio personalizzate, ha reso il reparto di lavaggio più salubre e sicuro, aumentandone la produttività e ottimizzandone i risultati di pulizia.
Il truciolo è uno degli elementi più critici risultanti dalle lavorazioni meccaniche per asportazione di metallo, come la tornitura. Il tornio imprime un moto rotatorio al componente meccanico, la cui velocità è determinata dalla durezza del materiale e dal grado di precisione richiesto. La funzione dell’utensile da taglio è quella di rimuovere il sovrametallo, da cui deriva la formazione del truciolo. In tornitura, nonostante l’introduzione di alcuni accorgimenti, come la frapposizione tra l’inserto e la staffa di serraggio di una piastrina con spigolo cuneiforme, che provoca prima l’incurvamento e, poi, con l’aumento delle forze di flessione, la rottura e la dispersione del truciolo, la permanenza dei residui sulla superficie delle minuterie metalliche lavorate può inficiare in modo decisivo le fasi produttive successive. La ricerca di soluzioni di lavaggio mirate all’eliminazione del truciolo, e dell’olio di lavorazione, è una delle voci che ricorrono maggiormente nei piani di investimento delle tornerie.
MMP Torneria, con sede a San Lorenzo in
Campo (in provincia di Pesaro Urbino), è specializzata nella lavorazione di minuterie metalliche tornite. Nata 11 anni fa a partire da una storica società locale del settore, ha trovato in Attilio Rotatori, oggi Amministratore Delegato dell’azienda, l’anima della propria impresa. “In pochi anni” conferma “siamo passati da una produzione dedicata quasi esclusivamente a minuterie metalliche per i più importanti distributori nazionali a realizzare componenti torniti direttamente per i principali produttori dei settori dell’oleodinamica e dell’automotive europei, tedeschi in particolare. Grazie a questa evoluzione del nostro core business, se da un lato abbiamo potuto crescere e affermarci in un mercato fortemente competitivo, dall’altro abbiamo incontrato richieste sempre più stringenti relative alle tolleranze nella qualità del lavaggio dei componenti e abbiamo contemporaneamente rilevato l’esigenza interna di adeguare le nostre lavorazioni ai requisiti ambientali che stanno prendendo sempre più piede nell’industria manifatturiera. Abbiamo quindi deciso di sostituire i due impianti a solvente che utilizzavamo dal 2010 con una nuova macchina della serie Aquaroll, progettata e fornita dalla società STS Italy di Ravenna”.
Il revamping in ottica green dello stabilimento
La scelta del nuovo impianto di lavaggio, entrato in funzione a dicembre 2020, è rientrata in un piano di ammodernamento
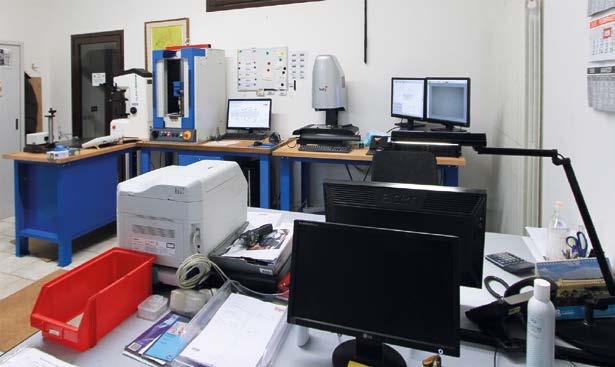
From top to bottom: - The company’s plant equipment consists of 45 automatic lathes. - The new optical metrology laboratory. - A stage in the metrological analysis of a turned part. Dall’alto al basso: - Il parco macchine è costituito da 45 torni automatici. - Il nuovo laboratorio di metrologia ottica. - Una fase dell’analisi metrologica di un pezzo tornito.
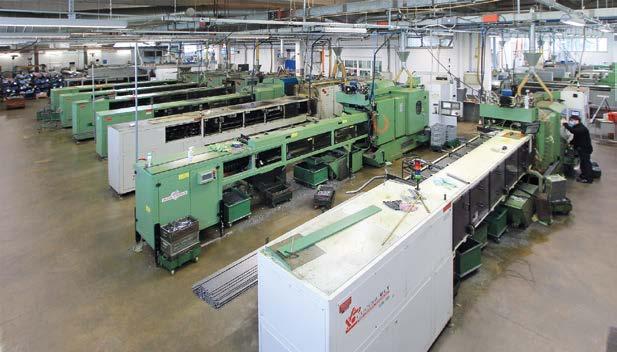
© ipcm notes Rotatori. “The need to distinguish ourselves from other companies in the sector has led us to improve our products in terms of both quality control and durability assurance. We implemented a system 4.0 with which we are now able to track all data related to our manufacturing process, from the metal casting from which a part’s material was made to the operator who handled it: every piece of data is gathered and recorded and, therefore, every stage is potentially traceable. Combined with our new laboratory, equipped with micron measurement devices that enable us to approve the finished parts with hundredth tolerances, this has given us an enviable competitive advantage.” As well as requiring a quality certification for turned components, this company’s customers are showing an increasingly binding focus on compliance with environmental regulations. “For years now, we have been striving to reduce the environmental impact of our production flow, with a daily commitment to finding the best sustainability solutions and caring for the health of our employees. For example, we undertook research to find out which oils and solvents were best to use within our departments to ensure a safe
© ipcm
© ipcm della fabbrica che ha incluso l’integrazione di nuove macchine di lavorazione meccanica e la realizzazione di un nuovo laboratorio di metrologia ottica ad alte prestazioni. “A livello territoriale la concorrenza è elevata” – continua Rotatori. “La necessità di differenziarci dalle altre aziende del settore ci ha spinto a migliorare il prodotto sia in termini di controllo della qualità, sia in termini di garanzia di durata. Abbiamo quindi deciso di introdurre un sistema 4.0 con cui oggi ci è possibile tracciare tutti i dati relativi al processo di lavorazione, dalla colata di metallo da cui è stato ricavato il materiale del pezzo fino all’operatore che l’ha preso in carico: ogni dato è rilevato e registrato e, quindi, ogni fase potenzialmente rintracciabile. Questo aspetto, unito al nuovo laboratorio dotato di dispositivi per le misurazioni al micron che ci consentono di approvare il pezzo finito con tolleranze al centesimo, ha dato a MMP un vantaggio competitivo invidiabile”. I committenti dell’azienda marchigiana, oltre a richiedere la certificazione di qualità dei componenti torniti, dimostrano un’attenzione sempre più vincolante al rispetto delle normative ambientali. “Ormai da anni la nostra società concentra i propri sforzi per ridurre l’impatto ambientale delle proprie produzioni, con un impegno quotidiano rivolto alla ricerca delle soluzioni di sostenibilità migliori e con una cura specifica della salute dei nostri addetti. Abbiamo avviato una ricerca per capire quali fossero gli oli e i solventi migliori da utilizzare all’interno dei reparti per garantire
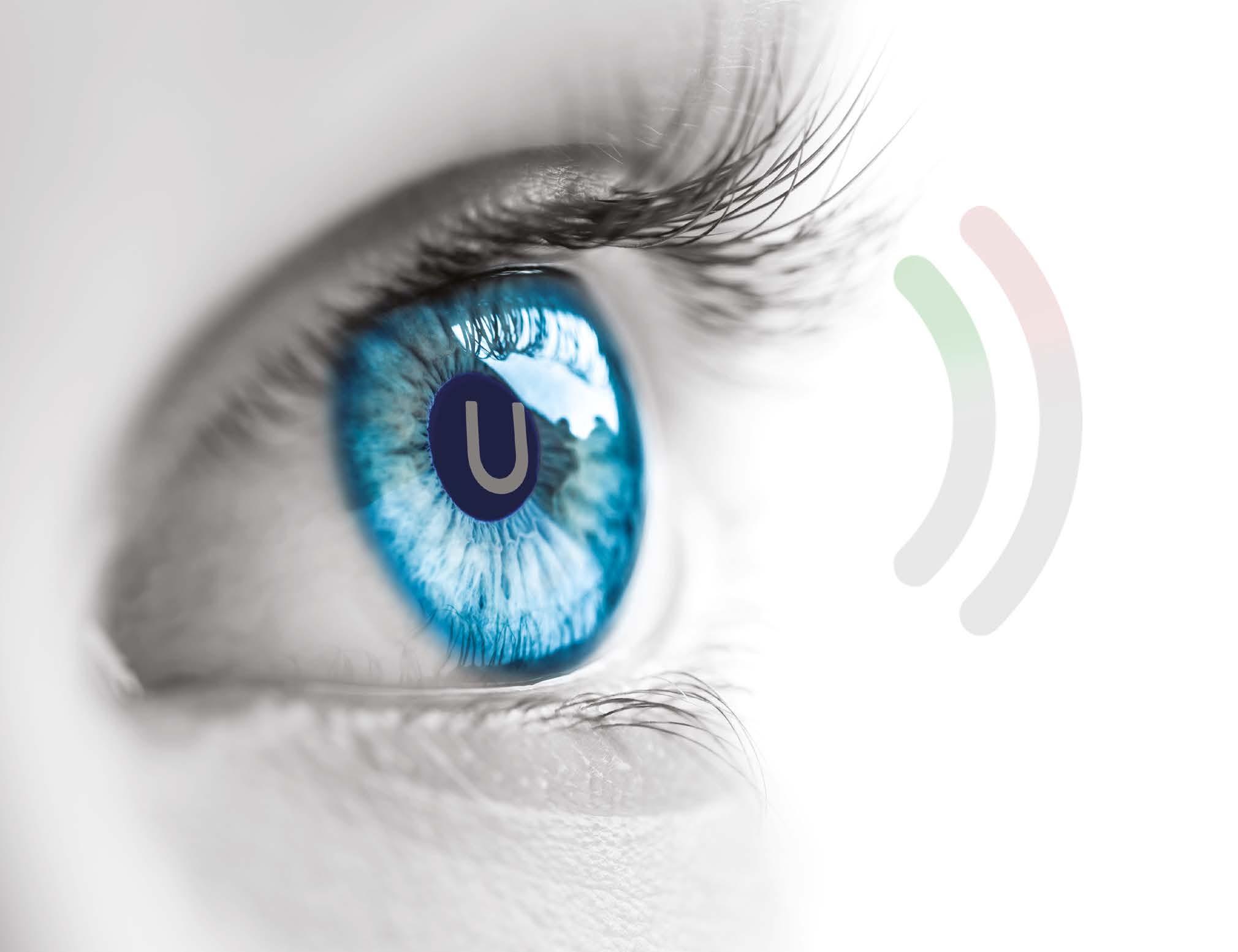
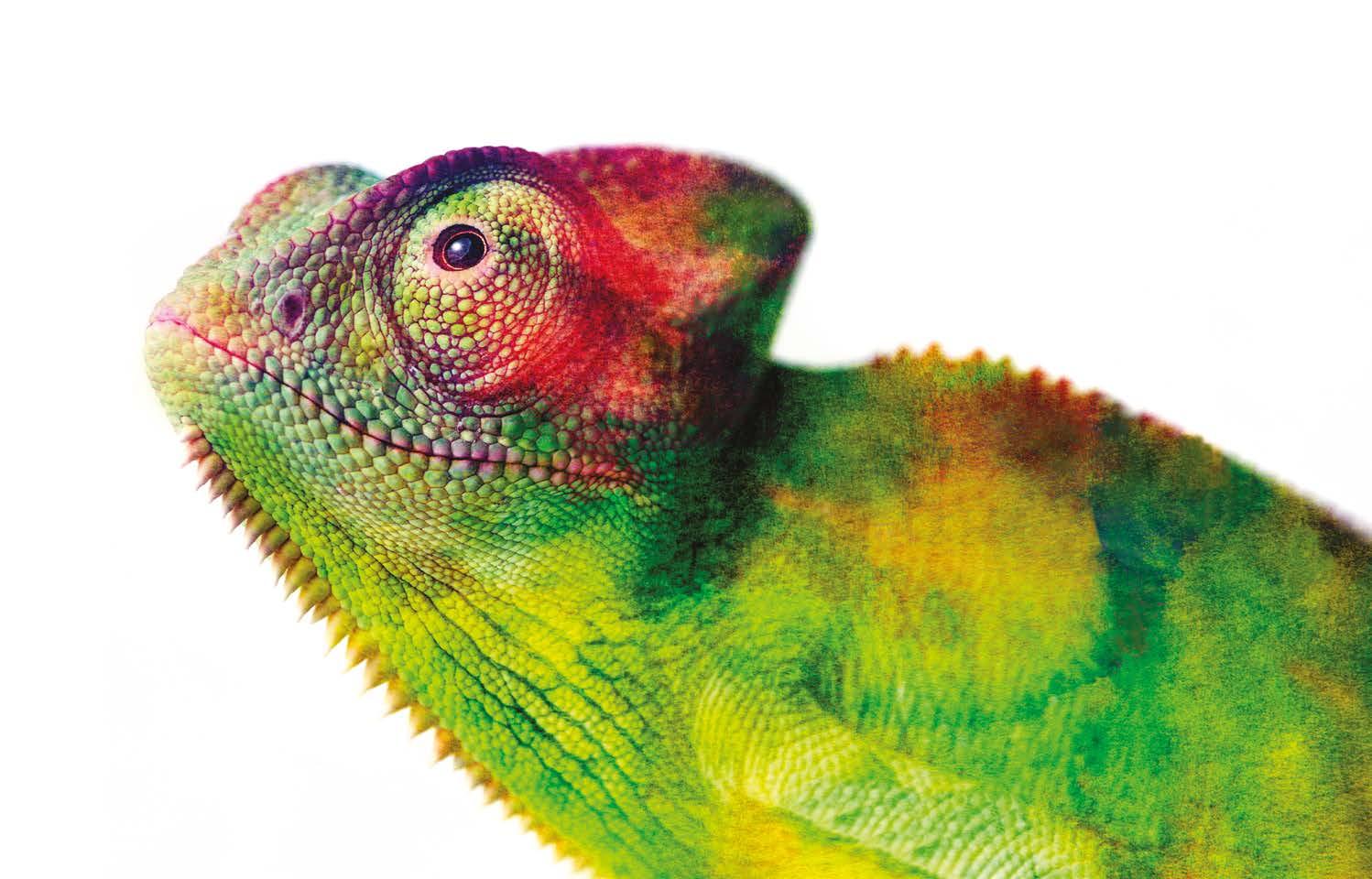
© ipcm
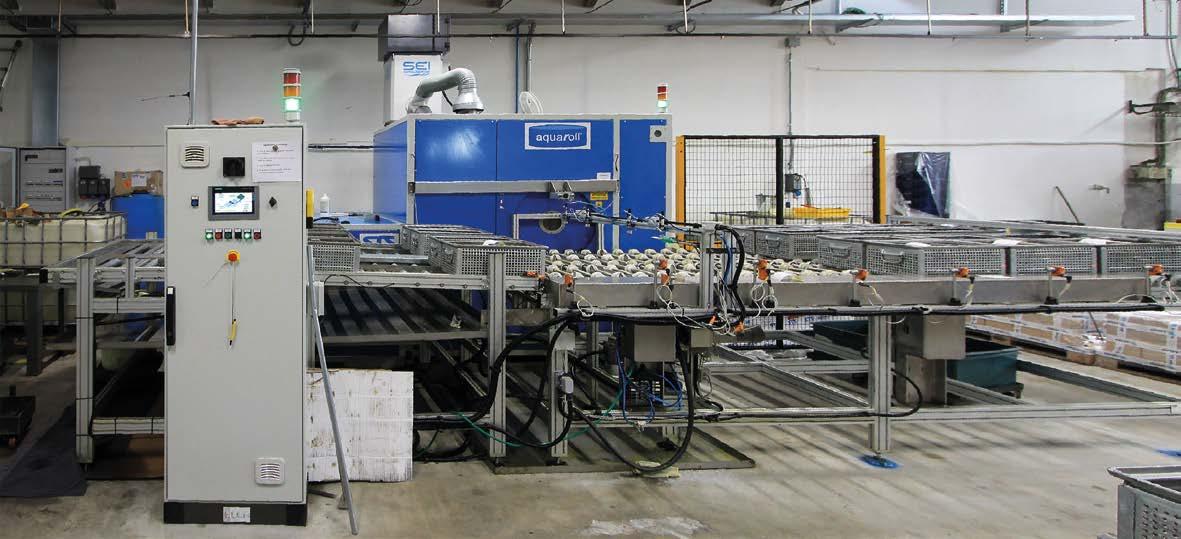
The cleaning plant from the Aquaroll EE40 series.
working environment. As a result, all the oils used on our lathes are now of vegetable origin and no longer mineral, so that the presence of carcinogenic substances in the mixtures is dramatically reduced. Moreover, all solvents used are ester-based, but with a hazard statement of less than H302, while the most commonly available products are classified into the H304 class. A further measure was to reduce the amount of liquids vaporised in our department, where compressed air is often used to clean tools or finished parts. We created special closed hoods that enable the extraction system to eliminate fumes and substance particles not only inside the machines but also in the whole working environment. Finally, MMP Torneria carries out six-monthly air analyses. The results obtained guarantee an environment where all hazard indicators are up to ten times lower than legal limits.”
The new cleaning plant
Such environmental vocation drove the MMP Torneria to opt for an uncommon cleaning solution in the industry. “The choice of a machine using the combined action of a bicarbonate-based detergent and ultrasound in a vacuum environment,” states Rotatori, “is not common in our sector, where solvent or modified alcohol solutions predominate. However, the cleaning technology offered by STS Italy immediately convinced us: we analysed its operation at other plants using this solution and visited the company’s premises in Ravenna to assess the system’s constructional features. Now, I can
L’impianto di lavaggio della serie Aquaroll EE40.
un ambiente di lavoro sicuro per la salute. Oggi tutti gli oli dei torni sono di origine vegetale e non più minerale, in modo da ridurre drasticamente la presenza di sostanze cancerogene all’interno delle miscele. Inoltre, tutti i solventi utilizzati sono a base estere, ma con un indice di pericolosità inferiore a H302, mentre i prodotti più comuni reperibili sono in classe H304. Un ulteriore accorgimento apportato è stato finalizzato alla riduzione dei liquidi vaporizzati in reparto, dove è sovente l’utilizzo dell’aria compressa per la pulizia degli utensili o dei pezzi finiti: abbiamo creato apposite cappe chiuse che permettono al sistema di aspirazione di eliminare i fumi o le particelle di queste sostanze non solo all’interno della macchina ma anche nell’ambiente di lavoro esterno. MMP Torneria, infine, effettua semestralmente le analisi dell’aria. I risultati garantiscono un ambiente dove tutti gli indicatori di pericolo sono fino a 10 volte inferiori ai limiti massimi previsti dalla legge”.
Il nuovo impianto di lavaggio
La vocazione ambientale ha spinto la direzione di MMP Torneria a preferire una soluzione di lavaggio non comune per il settore. “La scelta di una macchina che utilizzi l’azione combinata di un detergente a base di bicarbonato e ultrasuoni in ambiente sottovuoto – conferma Rotatori - non è frequente in un settore come il nostro dove prevalgono soluzioni a solvente o ad alcool modificato. La tecnologia di lavaggio proposta da STS Italy, tuttavia, ci ha convinto subito: abbiamo analizzato il suo funzionamento presso altri stabilimenti che utilizzavano questa soluzione e abbiamo visitato la sede dell’azienda a Ravenna per valutare le
say that there is no doubt about it: this was a winning choice.” “We supplied MMP Torneria with a one-chamber cleaning system Aquaroll EE40, featuring a capacity of 4 baskets with a dimension of 400 x 300 x 200 mm,” explains STS Italy General Manager, Ciro Poggioli. “The machine is equipped with an automatic loading and unloading system and a motorised roller conveyor featuring stop slats and inductive sensors for optical recognition of the basket barcode, associated with the correct cleaning program. The cleaning cycle is as follows: loading, ultrasonic cleaning, hydrokinetic cleaning with a clockwise and anti-clockwise tilting movement with automated load balancing, rinsing, and passivation. The pre-set program automatically activates or excludes each phase according to the type of turned component.” The need to treat components with very different shapes and characteristics was one of the main difficulties design-wise. “The workpieces are placed in bulk in the baskets, with a maximum capacity of 25 kg; each basket contains components with different shapes. This is why, in order to obtain high quality cleaning results with such an automatic system, STS Italy’s engineers have paid attention to every detail. MMP Torneria treats different materials, such as aluminium, carbon steel, stainless steel, and brass, by using different machines and processes: therefore, each cleaning cycle has to be tailor-made. Precisely due to the diversity of materials processed, moreover, another critical issue was the high amount of swarf remaining in the machine after cleaning. We therefore modified caratteristiche costruttive dell’impianto. Oggi posso dire che non ci sono dubbi: la nostra scelta è risultata vincente”. “Abbiamo fornito a MMP Torneria un impianto di lavaggio monocamera Aquaroll EE40 con capacità di 4 cesti di dimensioni pari a 400 x 300 x 200 mm” – spiega Ciro Poggioli, General Manager di STS Italy. “La macchina è attrezzata con un sistema di carico e scarico automatico e una rulliera motorizzata dotata di tagliole di fermo e di sensori induttivi per il riconoscimento ottico del codice a barre del cesto associato al corretto programma di lavaggio. Il ciclo di lavaggio è il seguente: carico, lavaggio con ultrasuoni, lavaggio idrocinetico che prevede movimento basculante sia in senso orario sia antiorario con bilanciamento del carico automatizzato, risciacquo e passivazione. Il programma preimpostato attiva o esclude ciascuna fase automaticamente in base alla tipologia del componente tornito”. Nella fase di progettazione dell’impianto, l’esigenza di lavare componenti con geometrie e peculiarità molto diverse tra loro ha rappresentato una delle principali difficoltà. “I pezzi sono posizionati alla rinfusa in cesti con portata massima di 25 kg. Ogni cesto contiene manufatti di diversa conformazione e, per ottenere un elevato grado qualitativo di pulizia del pezzo con un sistema automatico, i tecnici di STS Italy hanno studiato con precisione ogni minimo dettaglio. MMP lavora manufatti di materiali diversi, come alluminio, acciaio al carbonio, acciaio inox e ottone, con macchine e processi diversi, per cui ogni ciclo di lavaggio deve essere studiato ad hoc. Proprio a causa della diversità dei materiali trattati, un’altra criticità è stata riscontrata nell’elevata quantità di truciolo che restava all’interno della macchina dopo il lavaggio. Abbiamo quindi
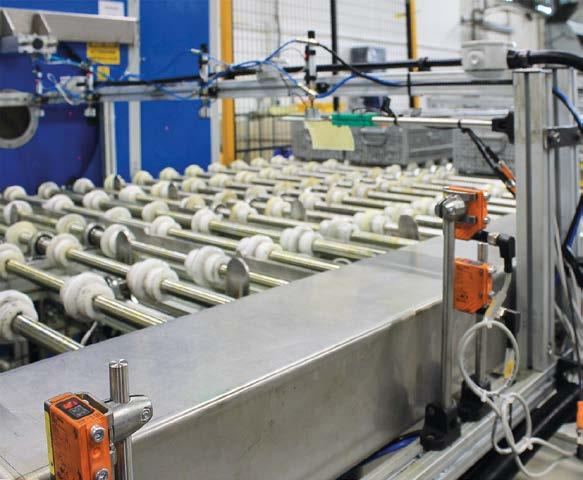
Each of the four baskets has a size of 400 x 300 x 200 mm. I 4 cesti hanno ciascuno dimensioni pari a 400 x 300 x 200 mm.
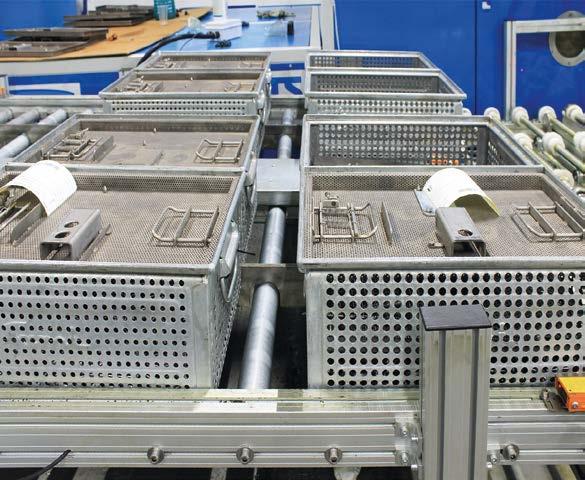
© ipcm © ipcm
The motorised roller conveyor is equipped with stop slats for blocking the baskets. La rulliera motorizzata dotata di tagliole di fermo per il blocco dei cesti.
the machine so that, at the end of the drying phase, a spray nozzle placed on a sensor can enter the system, detect the amount of residual swarf, and remove it.”
The advantages of STS Italy’s cleaning solution
“MMP Torneria produces 50 million parts per year, that is, around 200,000 per day,” indicates Rotatori. “Thanks to our new cleaning system, with cycles of 15 minutes maximum, we can now double our productivity. We work on three shifts, and the automatic system developed by STS Italy can be programmed to continue to work at night even without supervision. In this way, the following morning, our operators can find the baskets ready to be taken to the laboratory for quality control and weighing and then directly to the assembly department. The integration of the cleaning software into the company’s 4.0 system enables us to certify the cleaning phases as well, as we are able, for instance, to determine that a component has been cleaned at a precise temperature. Another important step in determining and guaranteeing our parts’ compliance with our customers’ specifications. “A further advantage is the effectiveness of bicarbonate in removing even the smallest residual particles from surfaces. Sodium bicarbonate is particularly effective in removing the new synthetic vegetable oil that we have implemented in our operations, as well as functional to avoid any product dragging in the tanks,” says Rotatori. “The combined action of the bicarbonate cleaning system, modificato la macchina in modo che, al termine della fase di asciugatura, un ugello di spruzzatura posizionato su un sensore sia in grado di entrare nell’impianto, rilevare la quantità di truciolo residuo ed eliminarlo”.
I vantaggi della soluzione di lavaggio di STS Italy
“MMP Torneria produce 50 milioni di pezzi all’anno, circa 200 mila al giorno” - afferma Rotatori. “Grazie al nuovo impianto di lavaggio che prevede cicli di massimo 15 min, potremmo raddoppiare la nostra produttività. Lavoriamo su 3 turni e il sistema automatico studiato da STS Italy ci permette di programmare la macchina in modo che continui a lavorare di notte anche senza presidio e che al mattino seguente gli operatori possano trovare i cesti già pronti per essere condotti al laboratorio per il controllo qualità e la pesatura e poi direttamente al reparto di assemblaggio. L’integrazione del software di lavaggio nel sistema 4.0 dell’azienda ci permette di certificare anche le fasi di lavaggio, per cui, per esempio, siamo in grado di determinare che quel componente è stato lavato ad una temperatura precisa. Un altro tassello importante per determinare e assicurare la conformità del pezzo ai capitolati dei nostri clienti”. Un ulteriore vantaggio è determinato dall’efficacia del bicarbonato in grado di rimuovere anche le più piccole particelle residuali rimaste sulla superficie”. “Il bicarbonato risulta molto efficace per la rimozione del nuovo olio sintetico vegetale che abbiamo introdotto nelle nostre lavorazioni e funzionale per evitare il trascinamento del prodotto nelle vasche” – prosegue Rotatori. “L’azione combinata del sistema di lavaggio con
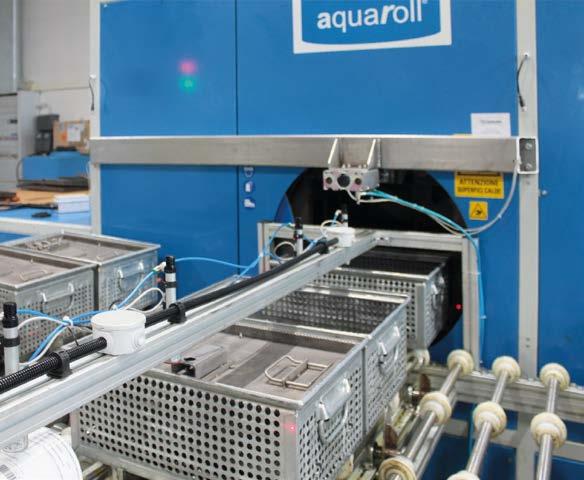
© ipcm
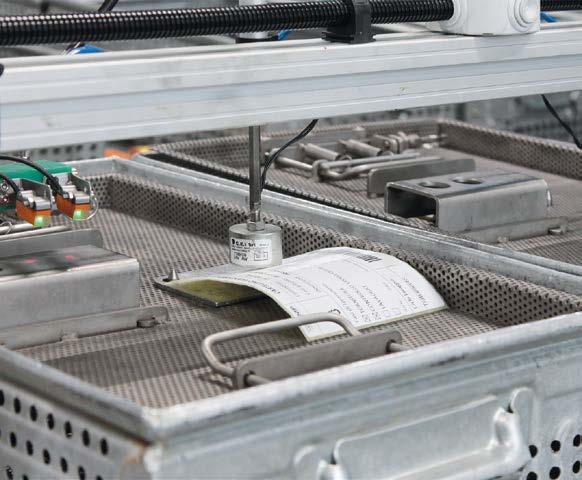
The sensors recognise the barcode associated with each basket. I sensori leggono il codice a barre abbinato a ciascun cesto.
© ipcm
Baskets entering the cleaning chamber. L’ingresso dei cesti nella monocamera di lavaggio.