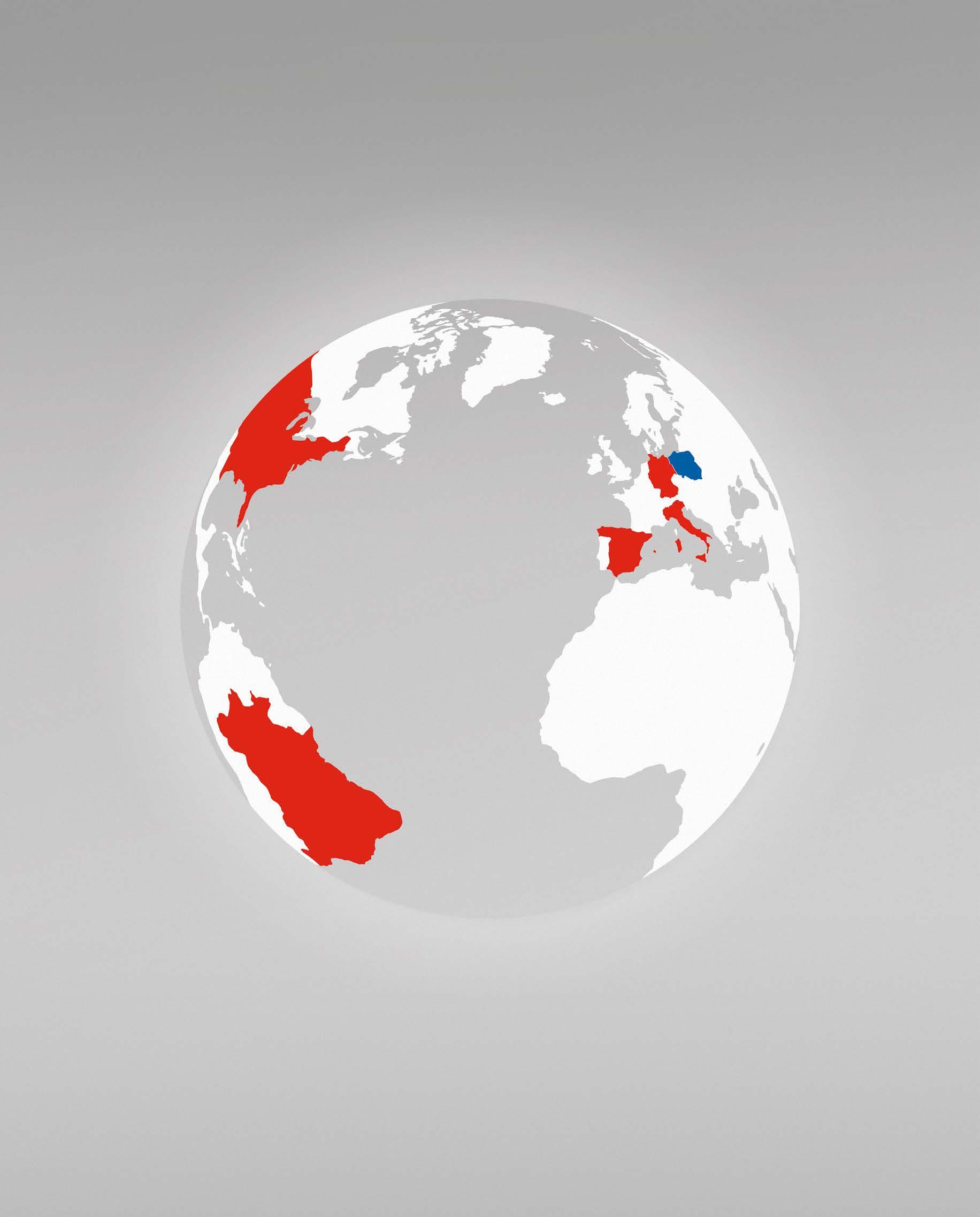
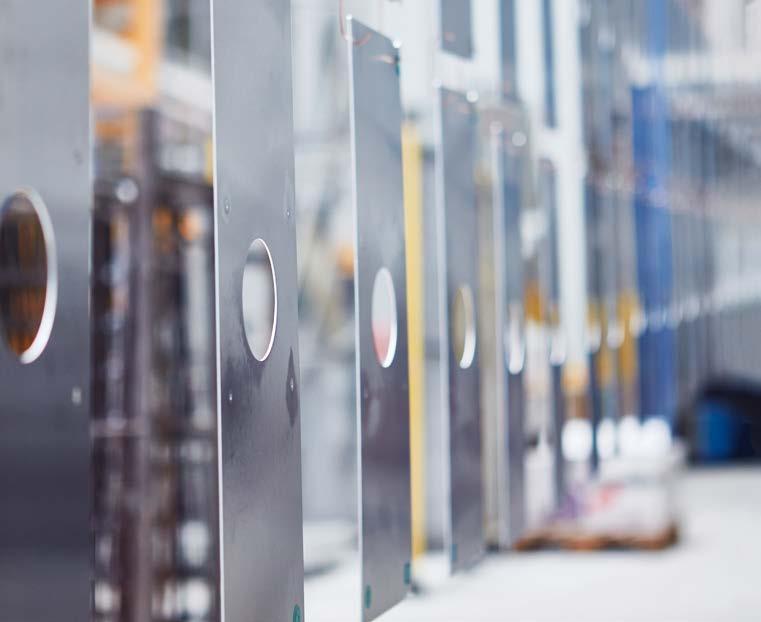
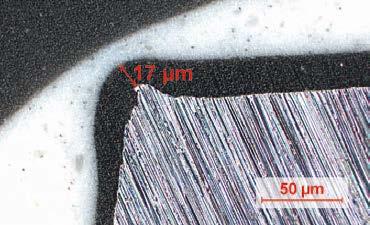
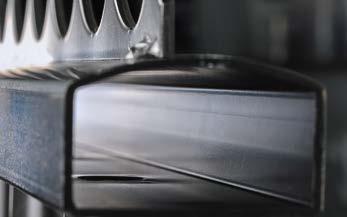
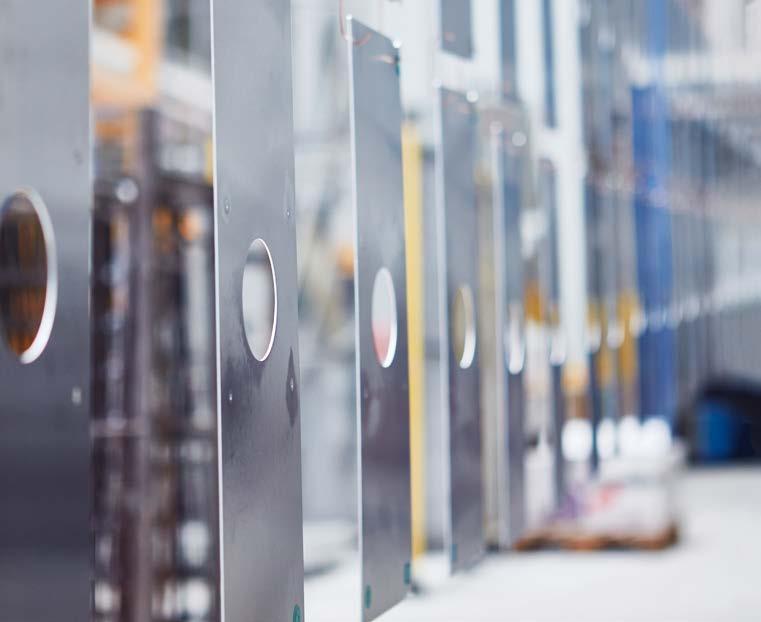
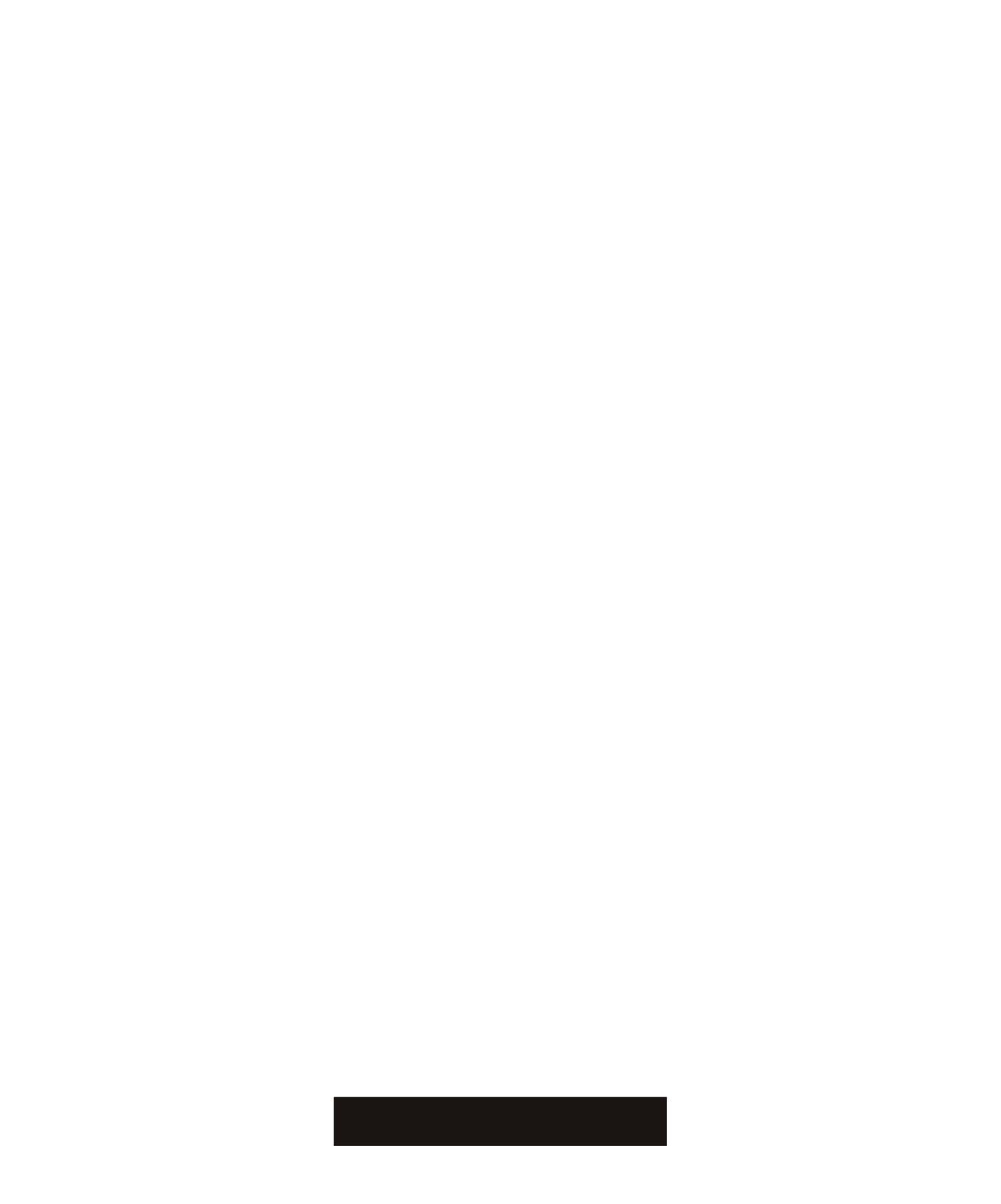
Following the positive response last last time and thanks to the increasing international interest in the event, Scandinavian Coating will once again be organized in Denmark. We welcome back all professionals from the surface treatment industry to Copenhagen 2023!
Scandinavian Coating has established itself as the premier meeting place and exhibition for the entire surface treatment industry in Scandinavia. Over the years the event has become more international with participants from 15 countries. The exhibition with some 80 exhibitors shows the very latest product news and all sorts of equipment and services needed for the treatment of wood, plastic and metal.
Apart from the highly important exhibition, Scandinavian Coating offers a high quality two-day conference program with educational and interesting seminars that reflects the latest developments in the industry.
Kolzer ® MK34” the new era of vacuum coating machines.
PVD 2.0 technology allows extremely dense and homogeneous decorative/ technical coatings, with reduced production times, positions the new PVD at maximum performance technical and aesthetic and offer sustainable technology with extremely low production costs.
Quality, 70 years of manufacturing experience, assistance 24/7, make Kolzer ® your ideal partner.
How much is the market actually willing to innovate?
On the one hand, it is true that investments have never been as numerous and substantial as they have been in recent years, not least because of the numerous incentives given by virtually all European governments for business digitalisation.
Yet the doubt is legitimate, especially after perceiving discouragement in numerous companies, beneath the enthusiasm for a market demand that has been strong for two years now and is going to remain strong for at least the first half of 2023, despite rumours of an impending crisis.
The observations we gathered during our traditional end-of-year meetings with some of the players in the surface treatment industry can be traced back to two trends: a lack of attention to what is new – as in, truly new – on the market, due to excessive focus on achieving the lowest possible price; and a lack of willingness to assess any proposed solutions on a technical bases and in detail, due to superficiality often leading one to trust any claim without verifying it before investing.
The first trend is frightening: if the market is not interested in testing or even inquiring about innovative products that are the result of careful and continuous research and development, the companies that do such research, investing high percentages of their turnover, will sooner or later stop doing so, discouraged by too little demand for their solutions’ potential.
The second trend is certainly the result of a lack of industrial culture in this sector but, at the same time, I think it can also be traced to the fact that, in general, people’s attention threshold is getting lower and lower. For most of us, everyday life has become an endless scrolling of pages, images, and brief information, for which neither great concentration nor much time is required.
Paradoxically, this attitude is also reflected in work activities. Abandoning a webinar after only a few minutes of listening or refusing to read the clauses of a contract because they are too long is behaviour that is considered (fortunately by very few) almost justified by lack of time.
My wish for this new year is that end users, especially those working in strategic industries such as the metal architecture and design ones – to which this issue is dedicated and which impact many aspects of social life, from urban planning to landscaping, from sustainability to the liveability of spaces, up to aesthetics – stop focusing on the here and now, but rather go back to having a more far-reaching vision, to being curious and ready to experiment, and to showing a more attentive and structured approach to new proposals.
Only in this way will we be able to nurture innovation, breathe life into research, support and reward companies that offer refined products and services, and above all contribute to the growth of the sector.
For our part, we start this new year by welcoming ipcm’s first US client, a confirmation of our interest and willingness to invest in expanding in that market, as a means of promotion not only for European companies in the Unites States, but also for American companies in their own market.
Alessia Venturi Editor-in-chief Direttore ResponsabileThe Coating Additives business line of Evonik has developed a new multifunctional polymer additive for powder coating formulations: TEGO® Powder Aid D01 makes the formulation easier to disperse during extrusion by promoting pigment wetting and effectively reducing melt viscosity.
The lower melt viscosity also leads to better degassing, which aids flow and levelling as the formulation cures and prevents pinholes in the coating. Thus, the new additive optimises gloss development and ensures better DOI (Distinctness of Image) on the coating surface.
Another plus point of TEGO® Powder Aid D01 is its particularly versatile applicability in formulations with inorganic fillers and pigments, along with organic pigments including carbon black.
“Our new product thus offers a wide range of benefits for formulators who desire one multifunctional additive for various powder coating systems,” has stated Maximilian Morin, head of the Industrial & Transportation Coatings market segment.
“TEGO® Powder Aid D01 generates a large effect in small amounts and acts as a synergist with other additives.”
TEGO® Powder Aid D01 also plays to its strengths in HAA curing systems for powder coatings with water being formed as a byproduct.
“The challenge during crosslinking is, that the water needs to escape from the system. This can result in pinholes or small craters in the film,” has explained Bernhard Resch, Scientist in Market Segment Industrial & Transportation Coatings.
To avoid this, the low melt viscosity is particularly important: homogenisation of the ingredients and levelling of the surface is improved. “TEGO® Powder Aid D01 prevents pinholes by increasing the degassing threshold and enables the application of thicker coating films,” has added Resch. Powder coatings containing TEGO® Powder Aid D01 also show comparable resistance to weathering, making this additive suitable for use in exterior applications. So-called overbake yellowing, even at elevated temperatures, is manageable. The new additive imparts these positive properties
to powder coating formulations without containing surface-active waxes. As a result, overcoating is also possible without any problems.
“TEGO® Powder Aid D01 is a new addition to the additive portfolio from Evonik´s Coating Additives Business Line, intended to be extruded into powder coating formulations,” has concluded Resch. For further information: www.coating-additives.com
The automatic plastic sorting systems in recycling plants work with NIR sensors that do not always correctly identify certain colorants such as conventional silver shades. ECKART has then developed NIR Silver, a pigment solution that is tailored to the needs of automatic sorting.
NIR spectroscopy uses the wavelength signature of specific polymers to distinguish between them. NIR Silver optimally reflects these specific wavelengths and thus supports the sorting of plastics. The pigments are easy to process in all conventional plastics and provide impressive silver metallic effects. Particularly effective in
combination with post-consumer resins, NIR Silver offers the packaging industry an interesting opportunity to further strengthen its efforts regarding sustainability.
With NIR Silver, ECKART provides the industry with another pigment solution on how to best reduce its environmental footprint – an additional building block in the growing sustainability portfolio of the effect pigment manufacturer.
For further information: www.eckart.net
Vibrating with vim and vigour, a shade rooted in nature descending from the red family demonstrating a new signal of strength.
Pantone’s Color of The Year, Viva Magenta 18-1750, vibrates with vim and vigour. It is a shade rooted in nature descending from the red family and expressive of a new signal of strength. Viva Magenta is brave and fearless, and a pulsating colour whose exuberance promotes a joyous and optimistic celebration, writing a new narrative. This year’s Color of The Year is powerful and empowering. It is a new animated red that revels in pure joy, encouraging experimentation and self-expression without restraint, an electrifying, and a boundaryless shade that is manifesting as a stand-out
statement. PANTONE 18-1750 Viva Magenta welcomes anyone and everyone with the same verve for life and rebellious spirit.
It is a colour that is audacious, full of wit and inclusive of all.
Tapping into the experimental spirit of Viva Magenta, Pantone explores the dynamic between Artificial Intelligence and human creativity to create “The Magentaverse” available to the public for the first time.
PANTONE 18-1750 Viva Magenta writes a new narrative. Brave and fearless, a pulsating colour whose exuberance promotes optimism and joy. Powerful and empowering,
it is an animated red that encourages experimentation and self-expression without restraint; an electrifying, boundaryless shade that is manifestly “out there” and is a stand-out statement. Audacious, witty and inclusive of all, PANTONE 18-1750 Viva Magenta welcomes anyone and everyone with the same rebellious spirit.
A nuanced crimson red tone that presents a balance between warm and cool, PANTONE 18-1750 Viva Magenta is also a hybrid colour, one that comfortably straddles the physical and virtual, evocative of our multi-dimensional world. Assertive but not aggressive, it is a carmine red that does not boldly dominate but instead takes a “fist in a velvet glove” approach. Exuding dynamism, PANTONE 18-1750 Viva Magenta is a transformative red tone capable of driving design to create a more positive future.
“In this age of technology, we look to draw inspiration from nature and what is real. PANTONE 18-1750 Viva Magenta descends from the red family, and is inspired by the red of cochineal, one of the most precious dyes belonging to the natural dye family as well as one of the strongest and brightest the world has known. Rooted in the primordial, PANTONE 18-1750 Viva Magenta reconnects us to original matter. Invoking the forces of nature, PANTONE 18-1750 Viva Magenta galvanizes our spirit, helping us to build our inner strength,” has explained Leatrice Eiseman, the executive director of Pantone Color Institute.
For further information: www.pantone.com
KANSAI HELIOS has expanded its portfolio of powder and liquid coatings thanks to two strategic acquisitions.
KANSAI HELIOS has announced that it has signed a share purchase agreement to acquire CWS Lackfabrik GmbH, a manufacturer of powder coatings and liquid and solid synthetic resins headquartered in Düren (Germany). After the fulfilment of closing conditions, it will become the new owner of CWS and its subsidiaries in Germany, U.S.A, Denmark and Poland. In addition, the company also acquired the Railway Coatings business of Becker Industrie SAS, establishing KANSAI HELIOS France SAS. The asset purchase agreement was signed on December 9th, 2022. After completion of closing conditions, KANSAI HELIOS will acquire all business assets of
Beckers in the Railway Coatings segment, such as recipes and railway homologations and customer database (excluding customers from India and China).
KANSAI HELIOS develops, manufactures and distributes industrial coatings solutions, chemicals for bleaching and cleaning, materials for sticking and sealing, high-quality resins, architectural paints and refinishing coatings.
With these agreements, the company is significantly expanding its strategic position in the powder coating segment, gaining additional know-how and distribution channels, as well as an increased production
and storage capacity that will further strengthen its presence in Europe.
Founded in 1864, CWS is a family-owned company with around 250 employees specialised in the development, production and marketing of technically sophisticated and customised powder coatings, with a turnover of around €100 million and a production volume of approx. 18,000 tons of powder coatings. “This acquisition is a milestone in line with the ESG and growth strategy of KANSAI HELIOS. With CWS we have found a perfect complement and extension of our own competences, in powder coatings and synthetic resins as well as the existing liquid coating business, which strengthens our system supplier strategy, because we not only share the same philosophy, but also the same values. I am convinced that this step will lead us from good to great,” has stated Bastian Krauss, the executive director of the KANSAI HELIOS Group.
The Beckers Group provides, among other products, a wide range of industrial coatings designed to protect railway vehicles and ensure cost-efficiency, long life durability, quality and environmental protection. In addition to the proven solvent-borne range, the company also offers a full waterborne range. Those product range and technologies will be transferred to KANSAI HELIOS and integrated to the existing portfolio.
“For KANSAI HELIOS the Railway Coatings development and production has always been of great importance and we have achieved a strong market position in recent years, being the largest producer of Railway Coatings in Europe with important brands such as Wefa, Rembrandtin and Helios. Since quality, efficiency, and the broad range of colour shades, but also highly advanced system solutions have been convincing rail vehicle manufacturers in more than 40 countries worldwide for decades, this purchase rounds off the field perfectly. This business acquisition is a further step of KANSAI HELIOS in the Railway Coatings segment, following our most recent asset acquisition and establishment of KANSAI HELIOS Wefa in Essen, Germany,” has added Jost. “The Beckers Railway Coatings team is excellent and we are delighted that they have chosen the KANSAI HELIOS team to continue to serve their valued existing and new customers in France and around the world.”
For further information: www.kansai-helios.eu
Turn key solutions for industrial wastewater treatment
Design and manufacturing of plants and chemicals for industrial wastewater treatment
Chemical-physical plants
Sludge treatment and compactor systems
Ion exchange demineralization systems and reverse osmosis systems
Oil separators
Filtering systems
Batch type systems
Flotation units
Chemicals and spare parts for water treatment
Technical service, support and maintenance of wastewater treatment plants
Anew production capability that will enable AkzoNobel Powder Coatings to locally produce and deliver bonded metallic powder coatings to customers in North Africa is now available in its manufacturing facility in Egypt. The increased demand for bonded products is being driven by the huge development in construction and growth in domestic appliance manufacturing in the region. AkzoNobel’s advanced bonding techniques can significantly improve the lustre and finish of its premium special effect metallic powder coatings to deliver a uniform metallic finish with even greater colour consistency and performance. “Customers can now order from a range of stunning colours and textures that are always on trend with the confidence that comes with working with a global partner who understands the critical importance of local presence, and faster delivery,” has stated Sanal Limoncuoğlu,
the commercial director for South and East Europe of AkzoNobel Powder Coatings. Limoncuoğlu has also added that he is pleased that the introduction of the new bonding line fulfils a long-held ambition: “Significantly expanding our local production capabilities and the speed with which we can deliver bonded metallic products to our customers in the region, is just one of the ways we’re growing within the market and helping our customers stay out in front. Partnership is at the heart of everything we do. We exist because of and for our customers. We have listened to what our customers need, and with new colours, shades and metallic finishes, we can help them on a journey to a new world of possible.”
For further information: www.akzonobel.com
Plasmatreat GmbH from Steinhagen was demonstrating its innovative Openair-Plasma processes at the world’s leading trade fair for the plastics and rubber industry in October. In addition to its main booth I65 in Hall 11, the company was also represented in the VDMA Circular Economy Forum. At both booths, the world market leader for atmospheric plasma technology and various partners was demonstrating, among other things, how the quality of components produced by 3D printing can be significantly improved by plasma treatment, while at the same time reducing the carbon footprint of the manufacturing company.
Product samples, tools, products in small batches, individualised items, spare parts and more can be produced in a very short time using 3D printing. This makes additive manufacturing a technology in demand, e.g., to counteract supply bottlenecks. Surface treatment with plasma can significantly improve the quality of the result.
Post-processing of 3D-printed components
Plasmatreat has demonstrated the cell4_Plasmatreat automation solution developed together with KUKA and the Openair-Plasma treatment using the example of a dashboard printed in 3D technology.
Benchmarks are set by the icon-based programming of partner FPT Robotics GmbH, which enables simple and fast commissioning, as well as program changes, without the operator having to have special robotics knowledge. The parts were produced by 3D printing specialist thinkTEC using HP Multi Jet Fusion technology, which uses a powder bed process. The individual parts are then subsequently bonded with adhesives from the manufacturer DreiBond GmbH, selectively coated with PlasmaPlus and individually digitally printed.
At the booth, visitors expected live how the CO2-neutral OpenairPlasma process significantly improves the product properties of 3D-printed components as well as process efficiency: activating the surface with Openair-Plasma allows environmentally friendly printing and painting without resorting to conventional flame treatment or chemical pretreatment. The long-term durability of inks and coatings can also be further increased by a supplementary PlasmaPlus coating. When bonding products from the 3D printer, the use of plasma technology also replaces the use of chemical adhesion promoters (primers) and achieves long-term stable bonds - even when originally incompatible materials are used. Users thus benefit from an expanded choice of materials. “3D printing alone is not enough. A strong network of manufacturers and companies that master the upstream and downstream processes is key to the breakthrough of this revolutionary technology in the industry. Plasmatreat is taking a step ahead here and shows that solutions can be implemented quickly and sustainably,” says Frank Petrolli, VP Strategic Market Development at Plasmatreat.
When plasma with its high energy level comes into contact with materials, it changes the surface properties, e.g., from hydrophobic to hydrophilic. Fine cleaning of metal and glass, for example, with Openair-Plasma from Plasmatreat gently and safely removes dust, grease, release agents and additives from surfaces. In the case of plastics, in addition to cleaning, an increase in surface energy is brought about by so-called activation through the introduction of hydroxyl groups into the plastic surface. In both cases, an optimized wettability of the substrate surface can be achieved and the adhesion ability significantly increased. In this way, long-term stable adhesion of adhesives and coatings is achieved. With Plasmatreat’s PlasmaPlus technology, the application (deposition) of nanocoatings can additionally produce specifically functionalized surfaces with defined properties, e.g., an adhesion promoter layer.
Opening photo: An automotive dashboard pre-treated with Openair-Plasma.
Following the acquisition of the CISART brand and know-how, C.I.E. can now offer a complete range of engineering and chemical solutions for the aluminium surface treatment sector.
C.I.E. Srl, a leading company in the supply of water treatments for metal finishing processes, is continuing its expansion in the aluminium sector. Recently, it has acquired the brand and know-how of long-standing engineering company CISART, a leader in the design of anodising and coating plants for aluminium, with approximately 200 plants built in Italy and around the world since its foundation in 1972.
The resulting “Anodising and Coating Plants” division will be headed by Claudio Cittadini, the former General Manager of the CISART GROUP as well as a skilled designer and expert technologist known and respected throughout the world of aluminium finishing.
“The acquisition of CISART,” states C.IE. General Manager Franco Falcone, “enables our parent company CIE-MST Chemicals to provide its customers with comprehensive engineering and chemical solutions for their anodising and painting processes, from water treatment systems to process chemicals. One group, one team, one global service for all aluminium oxidisers and coaters in Italy, Europe, and the world.”
Since 1980, C.I.E. (Compagnia Italiana Ecologia) has been specialising in the treatment of water from the cleaning, etching, and painting stations of metal finishing lines (CRS, HDG, EG, aluminium, and alloys). It has already installed more than 500 plants in Italy and the rest of the world (Western Europe, Eastern Europe, Middle East, America, and Australia). C.I.E.’s systems are already successfully operating in all metal finishing fields:
• steel production;
• cold forming;
• automotive;
• household appliances;
• aluminium extrusion;
• aluminium cans;
• coil coating;
• general aluminium processing lines.
For further information: www.cieeng.com
rotoli, pannelli e celle in fibra di vetro celle filtranti per alte temperature rotoli e pannelli in fibra sintetica accumulatore vernice “Columbus” filtri “Andreae” cartucce filtranti filtri assoluti applicazioni speciali
rolls, panels and cells of glass fiber
filtering cells for high temperatures
rolls and panels of synthetic fiber paint accumulator “Columbus” “Andreae” filters filtering cartridges absolute filters special application
distributori esclusivi per l’Italia
massima efficienza massimo accumulo di vernice massima durata
=
minori costi di smaltimento
minori costi di manutenzione
L’esclusivo design alveolare permette di trattenere quantità di overspray notevolmente superiori rispetto ai filtri oggi in commercio
www.defil.it
Hammonds, the Fitted Furniture Company, which manufactures and retails high quality tailored storage solutions upgraded panel coating line with Graco equipment.
Hammonds, the Fitted Furniture Company, based in Leicestershire (United Kingdom), design, manufacture and retail tailored fitted storage solutions nationwide. Through their website customers can arrange for a designer to visit customers home and design a tailored storage solution to meet their storage needs, whether that’s through fitted wardrobes in the bedroom, office solutions in study or storage for the lounge, they’ve got a solution to maximise space throughout the home. They offer a wide range of both vinyl and painted furniture.
Hammonds is renowned for producing quality furniture and opened their painted factory in 2016, a first for the company. Over the years they’ve worked extensively on their painted facility constantly looking
to improve their manufacturing technics to the benefit of both the customer and the business.
Hammonds automated paint plant utilises flat line multi spray gun coating systems to apply Ultra Violet light curing 2-component paint to wooden components. It wanted to improve on its existing process of manually weighing and mixing the 2-component paint which is then supplied to the spray guns from a single pump through a hopper or “hot potting” in a bid to reduce wastage, improve quality and consistency as well as efficiencies which would allow them to increase production capacity.
In an attempt to find a solution, Hammonds contacted Graco and asked for some assistance. Dave Blurton of Graco visited site to see in person the situation and advise what solutions Graco could offer. After the initial meeting an authorised Graco distributor Fluid Technologies Ltd
located in the Midlands were introduced to Hammonds. Martin Cresswell and Steve Smith from Fluidtec, provided a solution incorporating Graco Promix 2KS Electronic Mixing System and Merkur Supply Pumps. Graco’s Promix 2KS Electronic Mixing System is a tried and tested, reliable, accurate system for the on ratio mixing of 2-component paints. The system is ideal for a wide range of solvent-borne, water-borne and high-solids materials including in this case UV curing paint. The Promix 2KS was installed using the non-contact Coriolis flow meter for the UV curing base paint, this meter has no moving parts in contact with the material.
The simple integration into the automated spraying system made possible with the EasyKey controls of the Promix 2KS. Graco’s Merkur Pneumatic High Pressure Supply Pumps were used to supply the paints, hardener and flushing materials to the Promix 2KS at the pressure and volume required for multiple spray guns on the automatic flat line spraying machine.
The hardener utilised the Merkur Bellows Pump featuring a fully enclosed piston packing, this eliminates problems with the moisture curing hardener drying on the piston rod causing leaks.
Fluid Technologies Ltd installed one Promix 2KS, four Merkur and one Merkur Bellows pumps and the necessary supply lines on a skid frame assembly for quick installation. The new paint system was installed and commissioned together with re-instating the Air Assist function of the existing spray guns on the flat line machine. Hammonds are very pleased with their new paint supply and mixing system. “The Graco Promix 2KS system gives the mix ratio accuracy we need for our application, saving on time and waste. This has allowed us to increase production and improve product quality by improving paint laydown on the component and paint performance for our customers. We also saw an improved application by being able to use the Air Assisted Airless spray guns as they should be,” explains Steve Fitter Paint and Finishing Operations Manager. “With the Promix 2KS controlling the cleaning cycle for the mixed material means we use the minimum flushing material every time”.
For further information: www.graco.com
Researchers have discovered a new catalyst technology that converts renewable materials such as trees and corn into the key chemicals for paints and coatings.
Ateam led by University of Minnesota Twin Cities researchers has recently invented a ground-breaking new catalyst technology that converts renewable materials such as trees and corn into the key chemicals, acrylic acid and acrylates used in paints, coatings and superabsorbent polymers. The new catalyst technology is also highly efficient, which means lower costs for the manufacturing renewable chemicals. The research team was supported by the U.S. National Science Foundation through the NSF Center for Sustainable Polymers, a multi-university collaborative team with the mission to transform how plastics are made, unmade and remade through innovative research.
The new catalyst formulation converts lactic acid-based chemicals derived from corn to acrylic acid and acrylates with the highest yield achieved to date. The technology exhibits substantially higher performance when benchmarked against other classes of leading catalysts. The public is most familiar with acrylic acid and associated acrylates through its uses in everyday items from paints and coatings to sticky adhesives to superabsorbent materials used in diapers. These chemicals and materials have been made for the last century from fossil fuels. But in the last few decades, the corn industry has been growing to expand beyond food and livestock feed to manufacturing useful chemicals. One such corn-derived chemical is sustainable lactic acid, a key ingredient in the manufacturing of renewable and compostable plastic used in many everyday applications.
Lactic acid can also be converted to acrylic acid and acrylates using catalysts. However, until this new catalyst discovery, traditional catalysts were very inefficient achieving low yields and making the overall process too expensive.
“Our new catalyst formulation discovery achieves the highest yield to date of acrylic acid from lactic acid,” said Paul Dauenhauer, professor in the University of Minnesota Department of Chemical Engineering and Materials Science. “We benchmarked the performance of our new catalyst to all prior catalysts, and the performance far exceeds previous examples.”
The new catalyst formulation substantially reduces the cost of manufacturing renewable acrylic acid and acrylates from corn by
improving yield and reducing waste. For the first time, this could reduce the price of renewable acrylic acid below fossil-derived chemicals. The economic opportunity generated by the new catalyst is being pursued by Lakril Technologies, a startup company that aims to manufacture low-cost renewable acrylic acid and acrylates. By licensing the catalyst technology from the University of Minnesota, Lakril Technologies will develop the technology beyond the laboratory.
“Chemical manufacturing has relied on a class of catalysts called ‘zeolites’ for half a century,” said Dr. Chris Nicholas, CEO of Lakril Technologies. “Because the new catalyst discovery is based on a zeolite formulation already available at scale, our new process to make acrylic acid and acrylates will achieve low cost with low risk.”
At the University of Minnesota, the research team plans to continue their basic research on catalyst design to understand the fundamental aspects of the chemistry with financial support from the Center for Sustainable Polymers headquartered at the University of Minnesota. “This is a wonderful example of how addressing important basic research questions that are at the heart of fundamental catalysis can lead to innovative new processes that have true technological promise,” said Marc Hillmyer, director of the Center for Sustainable Polymers and a professor in the University of Minnesota Department of Chemistry. “A grand challenge in the Center for Sustainable Polymers is the efficient and sustainable conversion of biomass to polymer ingredients, and this work represents a groundbreaking solution to that challenge that will have lasting impact.”
Lakril Technologies, located in Chicago, already has received $1.4 million in pre-seed financing to scale the process. The Iowa Corn Growers Association led the financing with participation from the Kentucky Corn Growers Association along with grants from the Minnesota Corn Research and Promotion Council, Indiana Corn Marketing Council, Corn Marketing Council of Michigan, along with Small Business Innovation Research (SBIR) awards from both the U.S. Department of Agriculture and the U.S. Department of Energy.
For further information: www.specialchem.com
©
CPCA will hold its 110th annual conference in Niagara-on-the-Lake on 25th and 26th May 2023.
CPCA – the Canadian Paint and Coatings Association – has recently announced that its annual conference and AGM will be held at the Queen’s Landing hotel in Niagara-on-the-Lake from 25th to 16th May 2023.
The 110th conference of the association will describe the latest developments in the local paints and coatings industry, as well as provide a meeting place for all professionals and experts involved. Besides a brief introduction by the Board and Committee Chairs explaining the work of the association over the past year, the event will focus on the evolving nature of the industry, the opportunities and challenges ahead and how the industry can continue to provide essential products for a wide range of end use customers. In addition to several speakers, the conference will also welcome students from several Canadian universities presenting research posters.
Finally, the most important contributors will be honoured during the traditional Chair Awards Dinner at the Château des Charmes winery and vineyard.
“The coatings industry has become a leader in advancing more sustainable products, which continues to help reduce the environmental footprint of many end users. The attendees can expect excellent networking opportunities, engaging discussions and an evening of fine dining and entertainment,” has stated Gary LeRoux, the president and CEO of CPCA.
The Early-Bird registration is now open, allowing to save 20% until 20th March. The rate for CPCA members is $1,080 CDN, while for the nonmembers is $1,320 CDN.
For further information: www.canpaint.com
Brandt had already many years of experience in liquid and powder coating of metal components. However, the demand for coating sensitive substrates is steadily increasing, so it decided to rely on the flexible electrostatic M-Line powder coating system from J. Wagner GmbH.
Brandt has been active in professional industrial coating for 50 years and is today one of the leading contract coaters in Denmark. The company employs around 100 people at its headquarters in Varde, Denmark. To be able to respond to the most diverse customer requirements, Brandt covers the entire technology spectrum - from manual coating to highly automated coating systems with liquid and powder paint. Customers include manufacturers from the wood and furniture, metal, construction and plastics industries.
Brandt already has many years of experience in liquid and powder coating of metal components. However, the demand for coating
sensitive substrates is steadily increasing. These include organic and mineral materials (e.g. wood based materials or plastics), fibre cement panels and a variety of hybrid material composites. They are processed, for example, into MDF kitchen fronts or window frames. Many of these materials have no or only very low electrical conductivity and are sometimes very temperature-sensitive.
Government environmental regulations and VOC guidelines in liquid coating are becoming increasingly restrictive. Therefore, Brandt was looking for a sustainable powder coating solution that can also be applied to sensitive substrates - materials that are traditionally liquid coated.
Besides the smaller ecological footprint, another advantage of powder
coating is the significant saving of resources. The surfaces are seamlessly coated, scratch-resistant and extremely durable.
After a careful analysis with corresponding application trials, experienced specialists from WAGNER (Ursin Huwiler, Mats Rapp, Niels Ole Larsen, Janus Wemmelund), TRIAB (a Scandinavian system house provider of powder ovens) and selected powder coating manufacturers developed a flexible system concept that was installed at Brandt at the end of 2021.
With the electrostatic M-Line powder coating system, Brandt, as one of the first companies in the Scandinavian region, can also offer powder coating for non-metallic substrates. Non-conductive, temperature-sensitive materials such as plastics and even inhomogeneous natural materials such as wood are powder-coated with high efficiency in a material-friendly manner. To achieve this, the coating system can process highly reactive low-temperature powders and UV powders in addition to conventional metal powders. The M-Line system comprises ideally matched components which ensure that different powder coatings can be applied with a high
degree of efficiency, even on non-conductive materials. A core element here are the suction pipes arranged laterally along the coating booth on both sides, which minimize the air flow in the coating zone. WAGNER Field Controllers improve the grounding of electrically low-conductive workpieces, optimize the coating thickness distribution and prevent the so-called picture frame effect. The special geometry of the piping and monocyclone reduces the pressure loss in the system and the risk of powder deposits. This so-called Energy Efficiency Package (EEP) from WAGNER reduces powder friction during recovery, which generates less heat energy.
This enables gentle recirculation of the highly reactive low-temperature powder. Brandt uses the SuperCenter EVO powder center with Twin Sonic Sieve to control the complete system technology, including automatic guns and movement units. Powder feeding and color change processes are automated and very reliable. Preheating and melting processes take place in infrared ovens (IR). Curing is then carried out using either electric infrared (IR) or ultraviolet (UV) technology in the TRIAB “Speedoven UV”. A precise interplay of infrared radiation, convection air and ultraviolet radiation makes it possible to completely cure extremely temperature-sensitive substrates already at below 120°C and within 2-3 minutes.
Brandt can achieve savings in many areas: With the Energy Efficiency Package, the coating system requires up to 40% less energy than comparable systems, as a smaller fan motor is sufficient to generate the same extraction volume in the coating booth. Brandt was able to significantly improve its environmental footprint with the new powder system. Moreover, in contrast to liquid coating, no solvents are used. Thanks to the recycling of overspray powder, an enormous amount of material is saved. With the robust 1-layer powder technology, which does not require any intermediate sanding, Brandt also significantly reduces manual processes. Compared to liquid coating, the throughput time per workpiece can be significantly reduced: About one minute of preheating, another minute of powder coating, about five minutes of curing in the oven followed by 20 minutes of cooling - in total, the throughput time for one circulating layer is only around 30 minutes. For Brandt, the system offers completely new possibilities: Thanks to the very flexible overall concept, the contract coater can now successfully process a wide range of non-metallic objects and materials and can respond more flexibly to customer requests.
For further information: www.wagner-group.com
Dear Joe,
We currently use a “Midnight Black” wrinkle powder coating supplied by a major powder producer. Can a second touchup coat be applied after first coat has cured? The first coat is being applied over cleaned HRPO (hot-rolled, pickled and oiled) steel. The second touchup coat does not adhere to the first coat and flakes off easily. Any comments, suggestions?
Loyd Fields Austin, TexasDear Loyd, Recoating wrinkle finishes can be a headache. This product is epoxy based which makes the task even more difficult. Your best option is to scuff sand the entire surface to be recoated, blow it off, then solvent wipe with acetone or MEK. This should provide the adhesion you need. Using a polyester-based wrinkle is another option. These are not as hard as the epoxy wrinkle which should make recoating somewhat easier. However, the polyester wrinkles are more sensitive to substrate surface defects and pre-treatment streaking. HRPO steel can sometimes exhibit imperfections that will probably interfere with the development of a polyester wrinkle finish. I would try the scuff sanding followed by solvent wiping. If this doesn’t work, you may be relegated to stripping the defective parts, cleaning them and powder coating a virgin surface. Good luck with sorting this out.
Best Regards, Joe
Thanking you in advance,
Dear Ali, I am aware of two methods used to determine powder density. Both are covered in detail in ASTM D5965 - 02(2007) Standard Test Methods for Specific Gravity of Coating Powders. One uses the volume displacement of the powder into a fluid (kerosene or hexane) with a known density. The weight of the powder is known so the relationship between weight and volume can then be calculated.
Powder Specific Gravity = Weight of Powder (grams) / (Final Volume – Original Volume (millilitres))
This method involves introducing the fluid into a graduated cylinder. The volume and weight of the fluid is recorded. Next a given weight of powder is mixed into the fluid and the displaced volume is determined. It is essential that you eliminate all air pockets in the mixture to obtain a reasonably accurate measurement. Please be aware that this method doesn’t easily account for the surface porosity common with most powder coatings and typically results is a lower than true specific gravity. Nevertheless, it can be used as a decent tool to compare powders.
A much more accurate method is based on the Ideal Gas Law and utilizes a gas pyncometer instrument which measures volume of a known weight of powder by gas displacement. These are relatively expensive instruments and are available from a number of commercial instrument suppliers. Each instrument is slightly different; some measure volume, others can measure volume and density. You would have to consult the specific procedure provided by the instrument manufacturer to successfully measure specific gravity of powders.
I recommend you use the simpler fluid method but always run a control sample of know specific gravity along with your samples to be evaluated. I hope that this helps.
Best Regards, Joe
Dear Joe, Is there any method, equation or software program to calculate powder density?
Ali Baluli Saudi Arabia
Hi Joe, I have a cleaner/phosphate that is supposed to treat magnesium but how should it be handled as far as dry-off and cure temps? I tried a couple of parts this morning, with a low gloss clear coat and they came out looking like desert storm camouflage. This was cured for 12 minutes at 180 °C.
New Jersey
Dear Bryan, Thanks for the question. Magnesium alloys are a tricky substrate to powder coat unless you know how to do it. Most magnesium fabricated products are cast resulting in a certain degree of porosity on its surface. Cleaning the substrate is a great idea however the cleaners, pre-treatment and rinses can remain harbored in the pores. Indeed, even without cleaning air resides in the pores. As the powder melts and flows the cleaners and air escape from the pores. Most powders are curing at this point and can’t recover or reseal the holes caused by the volatiles. The result is pinholes, low gloss and unsightly surface disruptions. My advice is to continue cleaning as you are but run the parts through a relatively high temperature dry-off before you apply the powder coating. It’s preferable to coat the parts very soon after the dry-off, even while they are still warm so they don’t re-absorb ambient moisture. As for dry-off temperature, 200⁰C for 10 minutes is a good place to start. You should also be aware that many powder suppliers offer product lines that are better suited for porous substrates such as magnesium. It may be best to use one of these with a well-controlled dry-off process. Good luck. Joe © Kevin Biller
10X magnification of wrinkle powder coating surface. Wrinkle finish powders require sanding to smooth the surface when recoating.In winter, face masks can lead to fogged glasses. Here, the left lens (right from the reader’s perspective) has the new antifogging nanocoating. The other lens is uncoated.
Researchers in the group led by ETH Professors Dimos Poulikakos and Thomas Schutzius point out that their coating is fabricated with methods which are used extensively in manufacturing. In a cleanroom and using vapor deposition under vacuum, minute amounts of gold are deposited onto the surface.
ETH Zurich has applied for a patent on the coating.
Absorbing a large proportion of infrared radiation
What is special about the new coating is that it absorbs solar radiation selectively. Half of the energy contained in sunlight resides in the infrared spectrum, the other half in the visible light and UV radiation spectrum. “Our coating absorbs a large proportion of the infrared radiation, which causes it to heat up – by up to 8 degrees Celsius,” explains ETH doctoral student Iwan Hächler, who was a driving force behind the development. It absorbs only a
minor fraction of the radiation in the visible range, which is the reason why the coating is transparent.
The new coating takes an approach that differs from conventional antifogging methods. Traditionally, surfaces are coated with water-attracting (hydrophilic) molecules, which results in an even spread of condensation. This is how antifog sprays work. But the new method instead heats the surface, thus preventing humidity-induced condensation from forming there in the
first place. It is the same principle as is used for a car’s rear window. But, as Hächler points out, electric heating is inefficient and energy wasteful. In contrast, the new coating is heated passively and requires, during daytime, no additional energy source.
Thinner, pliable and more efficient Poulikakos, Schutzius and their teams have been working on passively heated surface coatings for several years. Three years ago, the scientists published their first research paper on a gold coating that prevented transparent surfaces from fogging up (see previous ETH News article). The coating they have now presented has many benefits over the first: It is made up of a single gold nanolayer and is significantly thinner, which makes it more transparent as well as pliable. Further, it is also more transparent and efficient because it absorbs infrared light more selectively.
Gold might be expensive, but the researchers emphasise that their coating requires so little that the material costs remain low. The coating comprises minuscule, extremely thin clusters of gold sandwiched between two ultrathin layers of titanium oxide, an electrically insulating material. Due to their refractive properties, these two outer
layers increase the efficacy of the heating effect. Moreover, the top layer of titanium oxide acts as finish that protects the gold layer from wear. This whole “sandwich” is just 10 nanometres thick. By way of comparison, a common gold leaf is twelve times thicker.
The individual gold clusters touch each other minimally, which is what allows the gold layer to just start conducting electricity. So, in the absence of sunlight, it would still be possible to use electricity to heat the coating.
The researchers will now develop the coating further for other applications. In the process, they will investigate whether other metals work just as well as gold. In addition to eyewear and windshields, this antifogging method could be used wherever objects must be both heated and transparent – such as windows, mirrors or optical sensors.
There is no need to fear, however, that this would cause a car or a building to heat up more in the summer.
ETH doctoral student Hächler explains: “The pane coating absorbs infrared rays from the sun, which specifically heats the pane and prevents the radiation from reaching the inside of the car or building. As a result, the interior heats up even less than it would without the coating.”
Alessia Venturi, ipcm®
Aluminium and beyond. In the solar awning sector, especially when it comes to covering rather large spaces, using both steel and aluminium allows combining structural lightness and strength. The offer of Sprech Srl (Martano, Lecce, Italy), a company specialising in the conception, design, planning, and industrialisation of outdoor solutions, is geared towards this goal, with a particular focus on open-air public areas. Recently, the success of Sprech’s industrial philosophy has called for the installation of a new powder coating plant capable of providing the company with the finishing quality and operational flexibility required to cope with its increased production volumes. Euroimpianti has thus developed a highly efficient, automatic plant solution in collaboration with Futura Convogliatori Aerei and Wagner Italia.
Sprech was established over forty years ago based on an idea of its current Managing Director Pasquale Rescio, who decided to combine his passion and experience in the steel and textile awning field to start a firm whose core competence was the design of tensile structures. Today, Sprech is a family business led by its founder and his children, assisted by a highly qualified technical and professional team. The solid technological know-how acquired and constantly fine-tuned over the years allows it to offer spot-on solutions for every market need: modular covers, pergolas, gazebos, dehors, and tensile structures for commercial or residential use, with a particular focus on public spaces and coastal environments. All Sprech products are designed to improve their users’ quality of life and foster a balanced relationship with the environment. All of its solutions can be adapted to any landscape and requirement, for both public and private use. Functionality, aesthetic refinement, and environmental sustainability are the principles that guide the design of these products. “A team of architects and engineers as well as a large research & development staff enables us to launch an average of five new products every year, striving to reach performance degrees that always exceed market demands,” states Lucia Rescio, one of the founder’s daughters. “Sprech also owns a foundation that sponsors the biennial event Agora Design, which offers a rich programme of exhibitions, lectures, and thematic workshops, including a competition for the prototyping of new structures that provides an opportunity for designers to make themselves known.”
“My father Pasquale was the first to patent a pagoda-shaped outdoor cover, which is a structure with four steel poles stretching a PVC sheet,” adds Rescio. “Over the years, our business’ evolution has led Sprech to become a leader in Italy in the field of steel canopies for exteriors. We then incorporated all the technology necessary for the production of aluminium bioclimatic pergolas. Today, our main target market is Europe, with a 40% export share, which also includes small shares in North Africa and the Middle East. Our strength remains the manufacturing of large-sized outdoor coverings: thanks to the expertise and experience gained in metalworking, Sprech is the only company in this sector able to cover large areas with a minimum of uprights. In this design and production context, the coating process is clearly a delicate and strategic phase, as it provides the structures with their final appearance, allows customising the proposed solutions, and guarantees excellent outdoor durability of finishes. “The powder coating plant that Euroimpianti designed by integrating Wagner’s latest application technology and a reliable Futura Convogliatori Aerei conveyor represents the end of a production line that starts from the profile cutting station and reaches directly the finishing one,” explains Alessandra Ripa, the Marketing Manager of Sprech.
“It also enables us to coat both hot-dip galvanised steel and aluminium with equal quality and durability results in compliance with the Qualicoat guidelines.”
From top:
- The loading bay of the horizontal coating plant for aluminium and steel profiles and sheets supplied by Euroimpianti (Valeggio sul Mincio, Verona, Italy).
- The pre-treatment cell tunnel.
- The inside of the spray pre-treatment tunnel.
As can be seen from the type of workpieces hanging from the load bars, Sprech paints a wide range of parts in very different sizes.
At Sprech, raw materials (extrusions and sheet metal) of the highest quality, state-of-the-art technology, and last-generation machinery form the basis of a fully vertically integrated production process guaranteeing certified products and high quality standards. The entire manufacturing cycle is handled in-house: site surveys, design, rendering, prototyping, production, and supervision of assembly on site. “Sprech’s production activities are divided into two business lines, one related to steel and one to aluminium, and they take place in four plants built within a radius of 15 km from Martano, where our headquarters and showroom are located,” indicates Lucia Rescio. “One site performs metalwork operations, from laser cutting to robotic welding. Another one is devoted to the processing of PVC for fabrics. The headquarters in Martano deals with aluminium processing, powder finishing, packaging, and shipping. Finally, we have a woodworking factory for manufacturing the wood components required for some custom projects.” In fact, flexibility in the production of the different components allows each part to be adapted to the specific needs of each end customer, offering extremely functional solutions that do not sacrifice aesthetics. Sprech’s flagship products include canopies, which combine the strength of steel or aluminium load-bearing structures with the flexibility and lightness of textile materials; gazebos capable of meeting all the needs of the public and private sector; tensile structures and marquees for fitting out large areas; and the pergolas from the QBox line, the ideal solution for creating continuity between indoor and outdoor environments, with steel uprights for covering large areas or minimal aluminium uprights for covering small spaces. “With such a variety of products and very often working on customised projects, the manual
The application area, with a focus on the switches of the power&free conveyor supplied by Futura Convogliatori Aerei (Robecco Pavese, Pavia, Italy), which create the storage buffers needed to guarantee the flexibility of the system.
powder coating plant in use until last year could no longer meet our quality requirements nor our constantly increasing production volumes,” notes Lucia Rescio. “In 2021, therefore, we started working on the project for a new coating system, which we wanted to be automatic and very flexible, as well as able to process both steel and aluminium since it had to treat all Sprech’s metal components. “We assessed several painting plant manufacturers and engineering firms: Euroimpianti presented us with the best performing turnkey solution, in terms of both coating quality and plant sturdiness. The system is indeed both robust and flexible, and the fact that it is equipped with a power&free conveyor – for which we chose to rely on the know-how of Futura Convogliatori Aerei – allows working to order without any loss of productivity. At Sprech, we coat not only our products’ profiles, but their entire structures complete with accessories, coupling plates, and other components. Our customers can choose from the forty colours in our catalogue, five of which are exclusive to Sprech, at no extra charge or select a customised tint, for which we guarantee a lead time of no more than ten to fifteen days from ordering.”
The new coating plant designed, built, and installed by Euroimpianti was part of an investment in Industry 4.0. It is equipped with Wagner application technology and Futura Convogliatori Aerei power&free conveyor. “The combination of technologies and expertise brought into play by these partners has enabled the creation of a “smart” coating plant that guarantees maximum quality and functionality. It consists
of high-tech machinery with automatic control even of the individual components’ maintenance process: overhead conveyor, pre-treatment tunnel, drying and curing ovens, and powder application booths. Speed and quality are guaranteed for every order. Moreover, the whole system is optimised for energy saving,” says Alessandra Ripa. Futura’s electronic power&free overhead conveyor has a capacity of 1000 kg per load bar. The spray pre-treatment tunnel for galvanised steel and aluminium is made of stainless steel and is equipped with automatic doors to contain the heat in all hot-temperature phases, i.e. cleaning, drying, and curing, with a view to energy saving. The pre-treatment cycle includes ten stages in specific and separate cells for aluminium or galvanised steel. It starts with profile degreasing, deoxidising, acid degreasing, and rinsing with mains water to remove metal residues. It then continues with an additional rinse and the application of the nanotechnology surface conversion product based on titanium salts, which guarantees a corrosion resistance value of over 1,000 hours in compliance with the ISO 9227 standard. After pre-treatment, the conveyor takes the load bars to the drying oven at 150 °C, followed by a visual check by the quality officers in order to verify the correct and uniform treatment of parts. Once they have left the drying oven, the load bars are sorted between the two Wagner booths in order to
optimise the process. One booth is automated and equipped with a “smart” gauge reader capable of detecting the size and shape of workpieces in order to correctly trigger the eight automatic guns, which move closer or further away depending on part geometry. This booth includes a manual post-finishing platform to avoid even the smallest imperfections and a SuperCenter EVO powder centre for quick and reliable colour changes through highly automated, contamination-free operations. Equipped with sensors for data acquisition, this powder management unit sends the user statistics on various production data, such as powder consumption. “Within one working day, we are able to change fifteen to twenty different colours in just 6 minutes and with one operator,” emphasises Lucia Rescio. “Although it is a very quick colour change, it guarantees effective cleaning. Since the start-up of this plant, we have already recorded significant powder savings, thanks to a 90% overspray recovery rate.” The second booth is manual and it is used for primer application, should the customer require a two-coat finishing cycle, or for painting small batches or with nonstandard colours.
After coating, the parts are transported to the curing oven, where they dwell for about 25 minutes at 180 °C, depending on the type of paint applied. Then, they are placed in a cooling area before proceeding to the packaging area prior to shipping to customers.
Every single phase of the coating process is monitored through Industry 4.0-oriented management software for greater manufacturing efficiency. All the machines that make up the plant are interconnected, have preventive and predictive maintenance functions, and track all the working parameters of every batch loaded onto the conveyor. “Considering the parameters of efficiency, coating quality, and production flexibility, we can say we are extremely pleased with the choice of installing this system and especially with the selection of the technical partners that collaborated on its implementation,” states Sprech founder Pasquale Rescio. “The new coating plant is an integral part of the evolution process that Sprech is pursuing to put customer satisfaction at the heart of all its production stages.”
From top:
- The Wagner SuperCenter EVO powder management unit.
- The SuperCenter’s paint feeding system.
- Antonio Cimenes, the sales representative of Euroimpianti, Wagner, and Pulverit for the Puglia region, with Lucia Rescio from Sprech.
Alessia Venturi, ipcm®
Pramaor Srl (Taibon Agordino, Belluno, Italy) designs and manufactures titanium spectacles under the brand name Blackfin®. It recently collaborated with Water Energy (San Pietro in Casale, Bologna, Italy), a company specialising in the treatment of waste water from water-curtain coating booths, which built and installed a system enabling the efficient separation of paint overspray accumulated in the booths’ water tanks and the consequent optimisation of the eyewear production process, while also reducing maintenance costs.
The Italian eyewear sector has always been distinguished by one important feature: design. This is particularly true for the province of Belluno, on one of the most beautiful mountain ranges in the world, the Dolomitic Alps. It all began here in the 1960s with Luxottica, which specialised in the creation of metal spectacle frames and from which numerous satellite companies in the eyewear sector gradually emerged. One of these is Pramaor Srl, owner of the trademark Blackfin®. It was 1971 when Maria Luisa Pramaor, then the eighteenth Luxottica employee, asked Cavaliere Leonardo Del Vecchio if she could open her own workshop to independently manage certain eyewear production stages. This would have gone on to become a company called Pramaor Srl, the owner of the trademark Blackfin®, now known all over the world.In the 1980s, when frames were made of common metal and acetate, it would not have occurred to anyone to use titanium. However, in 1990, Primo Del Din and his wife Maria Pramaor started working with this material to stand out from the competition. They sent their technical managers to Japan, set up a small department devoted to this metal, and began to build up the know-how that is still key to manufacturing each Blackfin® titanium frame today. This brand has since become synonymous with glasses built entirely in titanium and 100% made in Italy.
Every Blackfin® pair of glasses starts out as a concept, then it becomes a sketch, and it finally turns into a prototype. In between, there are technical trials, colour matching tests, and continuous adjustments, up until the creation of a marvellous object in terms of both technique and aesthetics. This is why the coating stage is so important for Pramaor, as it is strategic in guaranteeing the aesthetic excellence of its products, which are exceptional in terms of raw materials and design, but also of production processes.
As a leading company that is constantly evolving and striving for the best quality, Pramaor recently installed a treatment system for the water coming from the overspray collection curtains of the six liquid coating booths that make up its finishing department. After a thorough assessment of different technologies, the company selected Water Energy Srl as a partner for the installation of this plant for water treatment, a very important step in guaranteeing not only the efficiency of coating systems but also the perfect quality of finishes, since water curtains are responsible for the cleanliness of the air circulating in the booths.
From top:
- The precision sandblasting of frames.
- The six water-curtain manual coating booths supplied by Ultratech Srl.
- A detail of the paint spraying operation. Behind the frame, you can see the booth’s water curtain, perfectly clean thanks to the treatment system installed by Water Energy Srl.
In addition to its most reliable and proven technologies, Water Energy integrated the plant with an innovative system for collecting paint-contaminated water through the “fountain effect”. Each of the six identical application booths is equipped with an overflow system that make the contaminated liquid coming from the water curtains flow into one collection tank located behind the row of booths. A single pump draws the paint-contaminated water from this tank, sending it to the purification system, while the individual booths’ pumps draw clean water from the bottom of their related water tanks, recirculating it to the vertical overspray collection curtains.
Each Blackfin® frame is made only in Japanese titanium, whereas the workmanship is entirely Italian. The manufacturing process follows several steps: it starts with the acquisition of the raw material, namely titanium plates, from which eyewear temples and front frames are cut. The surfaces are then cleaned in a pickling bath to remove titanium oxide and subjected to several welding and milling phases. After assembly of the temples, the frames are cleaned again with a hard rubber wheel to remove all residual weld marks and harmonise their surfaces. Only for some models, some areas are then polished with a soft cloth wheel. This is followed by masking by applying a protective gel in order to prepare the frames for sandblasting, which is carried out with micro-splinters of glassy materials that roughen their surfaces to improve the adhesion of the paint film. In preparation for coating, the frames also undergo a treatment cycle in vacuum cleaning machines using solvents. Finally, the frames are coated by means of six water-curtain coating booths, located inside a clean room to guarantee the highest quality of the circulating air and thus minimise the risk of contamination of the treated products. At that point, they are ready for the final process phases and, after the last quality check, they can be sent to opticians around the world.
The major investment made by Pramaor in an ancillary phase of its coating process, namely the treatment of the water flowing from the overspray collection curtains of its application booths, is proof of the importance it
The tank for collecting contaminated water, which cascades here from the top of each booth by overflow.
places on air quality. Indeed, good water quality in these curtains is essential to maintain a high overspray capture rate and thus keep booth air clean.
Water Energy built and installed a customised system particularly aimed at solving a critical issue encountered by Pramaor during its eyewear coating phase: the presence of paint residues in the booths’ water collection tanks, which over time clogged nozzles and filters and compromised the frames’ surface quality.
Water Energy’s plant is a SKIMMERFLOT device with a capacity of 8000 litres/hour, an automatic flotation system for sludge removal, which manages the proportional dosing of flocculation products (also known as flocculants, chemical substances that favour the separation of paint from water) in the six booths’ water tanks as well as the continuous-flow removal of paint sludge from their water curtains. Sludge removal takes place through the separation of paint by flotation: floating the paint sludge directly into the booth’s water tank means that the pump recirculating the water to the nozzles can draw clean liquid, while the paint-contaminated liquid overflows
The
The
from the top of the booth and cascades into the collection tank that feeds the SKIMMERFLOT system. As a result, the recirculated water in the booths’ vertical curtains and nozzles is 99% paint-free. In addition to this, the automation of the cleaning process of the overspray water curtain collection tanks keeps the nozzles clean, thus guaranteeing proper cleaning of air, which would otherwise remain polluted with paint and soil the filters above the nozzles and those protecting the recirculation units.
Prior to the installation of Water Energy’s automatic system, the sludge removal and product dosing operations were done manually, leading to two problems. The first related to what is called “denaturation fluctuation”, which occurs when the amount of denaturant, namely the product used for eliminating paint stickiness, is not constant but rather fluctuates, i.e. sometimes it is too much and sometimes too little. The second problem related to the manual sludge removal process itself, as over time paint could precipitate to the bottom of the tank and the recirculation pump could thus pick up old paint residues, recirculating them back into the booth and clogging the nozzles, making them unable to adequately clean the airflow. This dirt could also clog the back-booth filters located above the nozzles, reducing the booth’s draught and creating additional overspray that risked contaminating both the eyewear frames to be painted and those already painted. Finally, in order to recover most energy, namely heat since the work takes place around 20/22 °C, the operators had to properly clean the air that was not intended for direct emission, but directed into the heat exchangers.
The adoption of Water Energy’s automatic system to treat a booth water flow rate of 8,000 litres/hour enabled Pramaor to achieve the following results:
high degree of water cleanliness in the coating booths;
complete separation of paint overspray;
reduction of the booths’ maintenance costs;
increase in the concentration of paint sludge, which is now drained and disposed of in special containers;
reduction of booth water disposal to an annual frequency.
In order to implement the customer’s trust, an increasing number of companies decides to certify their systems and products in compliance with high quality standards. Starting from the end of the 1970s, GSB International defines these standards of quality for the area of aluminium and steel coating throughout Europe.
As 1977 dawned, powder coating was making its way into the construction sector. As it is common with new technologies, there were still some start-up difficulties at the beginning of the implementation. The first complaints were observed in the window and facade industry.
In the process, cases of damage can become extremely costly. Although a coating typically only accounts for a low single-digit percentage of the cost of an aluminium facade, however, if there is a quality defect in this respect, in the worst-case scenario an entire facade must be dismantled and recoated.
If this is the case, it can result in bankruptcy for the coating company. But not only that. The building owners can also be negatively affected by the situation, because delays can occur on the construction site or - should the defect appear after the building has been put into operation - the use can be affected.
Consequently, at the end of the 1970s, it was necessary to establish a quality assurance system. So, a few companies joined forces to draft the first GSB Quality Regulations. One thing was certain. Regardless of the rules manifested in the Quality Regulations, concerning parameters, factory production control, etc., an incentive had to be created so that the regulations would be adhered to at any time and the quality control would be reliable.
There was only one way to ensure reliable implementation of the Quality Regulations. Thus, there was no way around having unannounced company inspections. This means that the coating companies must be prepared for the possibility of an inspection at any given time. In order to permanently hold one of the coveted GSB Quality Seals, the Quality Regulations must therefore be continuously fulfilled. For the coating companies, too, this is an advantage, because they are externally encouraged to ensure quality and to document the quality assurance process. In this way, there is no temptation to let quality control fall behind in the stressful daily business.
Unannounced tests and strict quality criteria are of great importance, but they must also be trustworthy in order to be accepted by the market. For this reason, GSB inspections are carried out by independent accredited testing institutes. This way, quality monitoring by neutral third parties is always guaranteed.
This does not rely on just one testing institute. Several institutes test for GSB. At first glance, one might think that several accredited testing institutes, which test according to specified norms
and standards, would also come up with the same test results - for instance, in the weathering tests for which the test sheets are drawn within the scope of the company inspections. But this is a misconception.
This topic can be well explained by means of corrosion tests. There are tolerances in the international and European standards of the tests (humidity, concentrations, etc). So, it is possible that testing institute A comes to a different result than testing institute B if they operate at opposite ends of the tolerances.
Consequently, the laboratories must also be compared with each other. It is common practice to conduct round robin tests. In this process, identical sets of samples are sent to the different institutes and it is checked whether the they come to comparable results. In this way, the independent accredited testing institutes are checked again by the GSB itself.
During the regular process of updating the Quality Regulations, it became clear relatively quickly that coating powders and liquid paints have a major influence on the quality of the coatings. Thus, quality assurance was extended to the coating materials and it was manifested in the Quality Regulations that GSB-certified coating companies must also use GSBcertified coating materials. In the approval process for the coating materials, test sheets are coated with the coating materials in accordance with the GSB Quality Regulations and subjected to a wide range of laboratory tests. The heart of the test, however, is the outdoor weathering. The test sheets are stored in an outdoor weathering facility in Florida.
After 1, 3, 5 or 10 years of ageing, the coating materials must meet a residual gloss of at least 50 % and colour distances within specified tolerances. If the preceding laboratory tests are also positive, the coating materials are certified with the muchappreciated quality seal, which also displays the UV resistance in years. Furthermore, the quality of the coating materials is continuously checked - thus test sheets are constantly sent to Florida for outdoor weathering.
Great care is also taken to ensure that the right incentives are in place to maintain quality when
taking samples for the prolongation tests. Thus, whenever possible, the samples for the tests of the coating materials are taken at the coating companies within the framework of the company inspections and not at the material manufacturers. In this way, the material manufacturers do not know from which batch the samples are taken.
At the end of the 1990s, the use of chromiumor chromium-VI-free pre-treatment chemicals emerged and quickly expanded in the market as a result of the REACh regulation, which is much talked about today. Almost all GSB-certified coating companies now use chromium- or chromium-VI-free pre-treatment chemicals when coating aluminium. This type of so-called alternative pre-treatment chemicals requires mandatory approval when used by GSB-certified coating companies. Only in this case the chemical receives the approval. The quality of the approved pre-treatment chemicals is continuously checked. Samples are also taken in this case. In the case of these prolongation tests, this is done at the coating companies where the chemicals are in use. A wide variety of laboratory tests is carried out – for example, the acetic acid salt spray test and the filiform corrosion test. But before a chemical receives its approval, it has to pass the initial tests. For this, the same laboratory tests take place as in the prolongation test. In addition, outdoor weathering is carried out as part of the approval test. This takes place in Hoek van Holland in a highly corrosive environment characterised by a combination of sea and industrial climate. The exposure to weathering lasts for 3 years. After 5 and 10 years, the samples are re-evaluated to gather empirical values.
This is an excellent point to draw a bridge
to the continuous evolution of the Quality Regulations, as the experience gained over decades is of immense value. In addition to this accumulated experience, the knowledge of the people who subject the Quality Regulations to a continuous improvement process is the guarantor of regulations that are always oriented towards practice. The group of people who continuously develop the Quality Regulations consists of two quality committees - one for the coating of aluminium
and one for the coating of steel and galvanised steel. In the quality committees themselves, the practical relevance could hardly be more direct, because the committees are made up of delegates from the membership. They are elected every 4 years at the general assembly and always develop the Quality Regulations above the standards. Following the democratic principle of the GSB, all member companies vote on the amendments of the Quality Regulations every two years within the framework of the General Assembly.
The art of quality assurance is to keep the Quality Regulations constantly up to date and, above all, practical. The GSB Quality Assurance System offers THE standard of the architecture industry in this respect. The mere fact that the Quality Regulations cover many norms and standards gives GSB-certified coating companies an enormous competitive advantage, as they cover several standards at the same time through certification.
The Quality Regulations are always developed further using the latest versions of the corresponding standards and guidelines. Practical relevance is the top priority. It is continuously discussed whether the measuring and testing methods are practiceoriented. If there are new testing methods, they are tested and compared with the current methods. This pursuit of perfect quality has established the GSB Quality Assurance as a permanent fixture in the market for exterior coatings in architecture and industry.
The interest in the GSB is so great that even in times of staff shortages and tightly scheduled working days, young professionals from the membership get involved in the Young GSB Working Group and contribute their valuable input. In doing so, the members of the working group work independently on a wide variety of projects and also bring their input directly to the board and the quality committees.
AMS - Architectural & Metal Systems Ltd is Ireland’s only independently owned manufacturer of extruded aluminium profiles. AMS can offer a complete, turnkey solution for all aluminium products and service requirements. Beside fabrication, powder coating, and wood effect finishes, since last June AMS is also capable of providing anodizing in different colours, from light bronze to black. The anodizing line was provided by the Italian SAT, which supplied a comprehensive system that includes a user-friendly software, a conveyor technology made by four different bridge cranes to ensure production flexibility and a high throughput of the line, up to a waste water treatment system.
According to many different industry reports, the Irish aluminium market skyrocketed in 2021, with a significant expansion in consumption as well.
AMS - Architectural & Metal Systems Ltd – Ireland’s only independently owned manufacturer of extruded aluminium profiles – was established in Cork, in 1990, by Chris Martin, President, Pat O’Hara, CEO, and the late Dave Rawlings, Technical Director. AMS can offer a complete, turnkey solution for all aluminium products and service requirements. It specialises in aluminium extrusion, powder coating and sheet metal fabrication as wells as providing many other services from its vast 450,000 sq. ft. (about 42.000 sqm) facility with 275 employees. The company’s business divisions include standard engineering products, architectural glazing systems, curtain walling, a bespoke aluminium design & extrusions service, and providing a wide range of thermally efficient aluminium windows, door and other commercial systems to various industries globally.
Two extrusion presses and a state-of-the-art powder coating, wood
finish and fabrication facility bring products from conception to project delivery all under one roof. AMS can offer consistency in service, quality, colour and complete traceability maintaining and ensuring quality standards such as ISO 9001, 14001 and 50001. Because the company has total control over all the processes from start to finish, it is able to offer its customers the best possible service to enable them to react to tight deadlines. In June last year, AMS started a new anodizing line to round up its offer of aluminium finishes and provide its customers with the most complete finishing service. For this project, it relied on the know-how and design skills of the Italian engineering company SAT, specialised in the supply of various kind of finishing systems for the aluminium industry.
Opening photo: General view of the anodizing line supplied by SAT. AMS new anodizing line supplied by SAT has an electro-colouring tank with the possibility to get a variety of colours, such as: champagne, bronze, brown, and black (here below).
The loading area.
Focus on investments in technology and know-how
AMS understands the value of innovation, keeping ahead of the latest trends and technologies. Investments in research and development have greatly contributed to the growth of the company, which is very proud of its numerous innovative and patented products which include window, door and curtain wall systems.
“With over 180 dynamic and resourceful employees, we pride ourselves in supplying to the marketplace a professional, unrivalled high-quality service”, Chris Martin, President at AMS, states. “We have an experienced sales and design team who offer help and assistance to companies and architectural practices to bring their concepts to fruition. Our in-house capability further complements this system for the design and production of bespoke profiles tailored to suit modern and pioneering designs. These profiles come in an extensive range of colours and finishes, including our in-house wood-imitation finishes. Last but not least, we are proud to announce that we have just concluded the start-up of an anodizing line for which we have chosen an Italian engineering company, SAT in Verona. “We are the only extrusion company in Ireland. We put in our first press – a seven-inch press – in mid 2000s we have added a second press inch since then and we plan to put in a third press,” Pat O’Hara – AMS Chief Executive Officer, tells. “We moved to Little Island in 2001 and that’s when we started manufacturing and started powder coating. We put in a second powder coating line and eventually - as our business grew- we ordered a vertical paint line that was installed in 2008 and it’s been running very well since then. It’s been our dream, really, for many years to put in an anodizing line. When we started anodizing in the middle of May this year, we put through some scrap sections and they came up so well I couldn’t believe it. And within, I’d say, the next day we went into production. All this thanks to
SAT excellent design and manufacturing capabilities, to the user-friendly software developed by SAT to run the line and last but not least to the training sessions offered to our staff”. Today, we boast processes that are nowhere else offered in the island and the anodizing plant is the last piece of the jigsaw for AMS”.
The design of the line foresees three anodizing tanks, each equipped with a rectifier of 15.000A (for a total size of the plant of 45.000A). SAT provided also one electro-colouring tank equipped with a transformer of 8000A, with the possibility to get the variety of tonality as: champagne/bronze/brown/black. The line is equipped with a third bridge crane; these are special bridge cranes able to handle two anodic bars at the same time and have a device on board to adjust the distance between the two anodic bars.
To eliminate the drop of productivity due to the return in counter-flow of the empty bars along the tanks line, SAT designed an extra crane with special design, operating at a higher level than the other bridge cranes. Kevin Crowley, Plant Manager at AMS, goes on describing the anodizing line: “We have a control room run by one operator, the controller operator, who basically loads the program or the recipe. We have a loading area with six operators and an unloading area with two. The anodizing line stages are: degreasing, rinsing, E6 etching which is our strong aggressive etching, E0 etching which is a lighter etching for small hollow sections or for smaller profiles that have any channels. Then the process features a neutralization tank, a desmut tank (which is a stripping of any residual smut after the etching). Finally, we have the anodizing tanks themselves: we have the option of a colour tank of tin sulfate or straight to a hot seal tank of 98°C. The bronze colours that we are getting are very consistent.
As an example, we have just done a job with 1100 profiles and you probably couldn’t tell the difference between the start and the end of the process. The lack of difference in colour has been unbelievable!
Another important feature to underline about this anodizing line is the software in support of the installation: it is very intuitive; we were trained by the SAT team on how to use the software and I learned how to run the line very quickly. After using it for some weeks, the software is probably a lot simpler than I was expecting it to be.” “One of the main challenges we faced when designing the new line was the available footprint in the building” Andrea Trevisan –SAT Chief Executive Officer adds. “Outside these walls you literally have the seaside so we had to find innovative solutions to install the line within this perimeter. Each jig is loaded with two bars and the distance between these two anodic bars can be increased or decreased based on the stage where the jig is located. The line foresees three bridge cranes that are used to move the jigs through the process. But it is also equipped with a fourth bridge crane that is used to bring jigs back to the loading area in order not to affect the productivity of the line with a counter flow movement. As SAT, we supplied the complete system including the rectifiers, the bridge cranes and an effluent treatment plant. The important thing for SAT was to provide AMS with a complete solution and I think this is exactly what we did in the end”.
“At AMS we have invested heavily in state-of-the-art extrusion facilities so, as well as extruding our own profiles, we can offer design and extrusion of aluminium profiles to third parties, not only to the façade industry, but to any industry where aluminium extrusions are being used. Imagine the flexibility of being able to have an extrusion that was previously not in stock, available the next day,” Pat O’Hara enthuses. “Having the full control of the extrusion process inhouse allows us to extrude profiles of non-standard lengths to reduce optimised wastage for large contracts. The extrusion plant has brought AMS into various new markets e.g., aerospace, engineering, renewable energies, transportation to mention a few. It has also generated important export opportunities to many other markets in Europe including the UK and the USA.
We can produce over 16,000 tonnes of extrusion per annum on our two extrusion presses. Once the metal has been extruded the aluminium alloy is heat treated for strength. Once aging is complete, it can then be made available to the customer, or indeed, go into another process within the same building e.g. powder coating, wood-effect finishes, thermal break, sheet metal fabrication or, thanks to SAT new installation, anodizing”.
AMS has capabilities, through its vertical and horizontal powder coating lines, to paint extruded profiles of all shapes and sizes inhouse.
“The benefit of having an inhouse painting service means we can offer consistency in colour, quality and efficient lead times,” Chris Martin adds. “Our vertical paint line has the ability to paint over 4000 profiles up to 7.3 m in length in a shift, which is a huge improvement over the industry standard. It can perform a colour change in only 4 minutes, making it the most efficient method of powder coating aluminium profile systems. Our horizontal paint line is devoted to painting aluminium sheets and flashings, as well as section profiles with lengths up to 7.0 m and bespoke pieces. This service has proven very beneficial to many customers as both profiles and pressings can be painted in the one facility. The powder coating process of both lines is Qualicoatapproved and performs an 8-stage chrome-free pre-treatment. We stock a wide range of standard RAL colours to suit our customers’ specific powder coating requirement and we rely on different powder coatings suppliers, among which Tiger, IGP, Syntha Pulvin, AkzoNobel and Axalta.
“With over 20 years’ experience in this field, we have the dedication and knowledge to cater for all our customers’ requirements. We pride ourselves in the production of quality fabricated profiles and pressings and we ensure customers’ needs and delivery times are at the forefront of operation. The installation of an anodizing line early last year is the fulfilment of a dream and the icing on the cake for our services,” Chris Martin concludes.
At the ZAK World of Facades Conference, that took place on 24th November 2022 in Hanoi (Vietnam), AkzoNobel Powder Coatings presented its innovations in the field of sustainability, durability and metallic colours.
The innovations in the field of sustainability, durability and metallic colours of Interpon powder coatings for architects and specifiers have been the key themes surrounding the presence of AkzoNobel Powder Coatings at the ZAK World of Façade, a conference that took place in Hanoi (Vietnam) on 24th November 2022.
Hanna Nguyen, the County Sales Manager of AkzoNobel Powder Coatings who is a business leader and expert in the infrastructure and construction industry, covered the life cycle of powder coatings and how its durability can support sustainability during the ‘Powder Coating Technology for the Built Environment’ session.
In addition, she also discussed the latest colours and design collections for facades, as well as the high-quality special effect metallic finishes for both interior and exterior achieved with the breakthrough bonding technology AkzoNobel.
Finally, she presented a second powder coating plant now fast becoming operational in North Vietnam, to serve the expanding needs of the local market.
Among the new products showed there was also the Anodic range, which has the stunning look of anodized aluminium but with a minimal environmental impact.
The range is available in a wide range of colours and makes the ideal alternative to
anodized aluminium for windows and facades. For example, Interpon D2000 Anodic III finish delivers superior colour and gloss retention and better colour consistency. Also shown for the first time was the Interpon Futura range.
Featuring a superdurable performance supported by a 25-year warranty, the Futura range boasts 50 beautiful on-trend colours designed to help feel closer to natural environment, safe in the knowledge that our creations and our world are now better protected.
As with the Anodic powder coatings, metallic colours within the Interpon Futura range are possible thanks to AkzoNobel’s unique bonding technology.
This means the metallic pigments are chemically bonded (as opposed to mechanically blended) to the base powder, to give far greater lustre, consistency, and performance.
Maximilien Schreder, Regional Commercial Director South Asia for AkzoNobel Powder Coatings, has explained the importance of innovation: “Our customers expect innovation not only in the products we create, but also in the processes we deliver. With our superb range of metallic effect powder coatings, supported by our investment in new facilities and new manufacturing technology, we are excited about sharing our expertise with customers at the ZAK World of Facades.” ZAK World of Facades also provided an opportunity for AkzoNobel to showcase Wild Wonder – Interpon’s newly announced Color of the Year 2023. It is one in a palette of eight new colours inspired by nature within the Interpon Futura range.
For further information: www.interpon.com
AUTOMOTIVE APPLIANCES HEATING SYSTEM ALUMINIUM SYSTEMExperience and technology: this is the winning combination that has allowed Italian powder coating contractor GPS to design and build a new plant with a handling system supplied by CM Automazione that is efficient, has a high application performance, and is geared towards making the work environment as clean, healthy, and comfortable as possible for operators.
Plant design is a very complex intellectual process blending indepth knowledge of mechanical engineering and production management. The further combination of these two elements with passion and long-standing experience can then give rise to uncommon and essentially unique results – in this case, a powder coating plant in which a coater’s experience, its attention to the environment, consumption, and working comfort, and the latest technologies developed by its suppliers have led to the creation of a truly original solution. At the same time, the perfect integration of the plant with a handling system specifically designed for the special needs of this coating contractor has further improved its entire production process.
GPS specialises in powder coating of components for the HVAC, agricultural, and heavy metalwork sectors.
©
Guido Borella, the owner and sole director of GPS Srl (Bagnoli di Sopra, Padua, Italy), a company specialising in powder coating of components for the metalwork and heavy industry sectors, has always worked in the field of surface treatments, first in an important carpentry company as manager of the powder coating department and, now, as owner of GPS Srl and MICOLOR Srl.
“In 2002, I founded GPS Srl together with a partner, who later withdrew from the company. Over the last twenty years, the business has grown a lot, going from six to forty employees and acquiring another powder coating company, MICOLOR Srl.” Currently, GPS extends over a total covered area of 7,000 m2, which includes a 2,000 m2-wide hall and a new 5,000 m2-wide building housing a second coating line, installed in August 2022 to cope with increasingly frequent production peaks. The project for this new plant had started a year earlier: “I developed it myself,” confirms Borella, “together with a long-standing company from the Italian coating world, Peron Group (Officine Munari). Its integration with the part handling system featuring a one-rail conveyor provided by CM Automazione Srl (Giussano, Monza e Brianza, Italy), then, was a key step for introducing a number of technical measures that improved the flexibility and speed of our coating cycle.”
Full service and attention to detail: the cornerstones of GPS
A part of the new hall is still being completed. “The new coating line became fully operational within a short time, but we still have to finish setting up the 3000 m2 warehouse area. In the open area adjacent to it, we are going to build a canopy for unloading and loading materials to optimise the traffic of trucks bringing them in and picking them up and, in the near future, we are also going to add a new cataphoresis department to offer a complete service to our customers, which operate mainly in the HVAC, agricultural, and heavy metalwork sectors. In order to provide a galvanising service when required in addition to powder coating, we currently rely on specialist Mita (Conselve, Padua). Once galvanised, the parts reach our warehouse, where they are thoroughly cleaned to remove any impurities and/or oxidation traces remaining on the zinc film and thus improve the adhesion of the powder layer to be applied subsequently.” Such attention to detail and a team of qualified employees has enabled this firm to establish itself in the northern and central Italian market and become a trusted partner for some of the most important firms in the air conditioning and agricultural industries. “We strive to meet the high quality standards imposed not only by the ISO 9001, ISO 14001 and
45001 standards, but also by the approval processes of the multinational companies that contact us, so that we can present ourselves as a very promising choice for anyone in need of an effective service in the field of industrial painting.”
The coating cycle is similar in both GPS’ lines: pre-treatment with phosphodegreasing and passivation, drying, automatic powder coating with manual pre and post-finishing operations, oven curing, quality control, and final shipment. “What does change is the size of the treated components: in the older plant, we handle small to medium-sized parts with dimension of 3.5 x 2 x 1.10 m and a maximum weight of 300 kg, while, in the new one, they can reach a size of 4 x 2.20 x 1.10 m and a weight of 400 kg. In MICOLOR we handle the largest pieces with
dimensions of 7 x 2.5 x 1.25 and a maximum weight of 700 kg. The other difference relates to process management and control documents (hardcopy in the former and digital in the latter), whereas tracking is done by QR code scanning in both cases.” The size of the new plant is also bigger: “Whereas the first hall is 2,000 m2 wide, in the new one this is the area occupied by the coating line alone.”
The
“Every company in this sector knows the importance of selecting the right strategic devices during the design phase: one of them is certainly the conveyor,” notes Borella. “It is the core of the line and the element that determines its timing and, in some respects, its performance degree. I
From top left clockwise:
- The control PLC’s display with the layout of the new plant.
- The entrance to the pre-treatment tunnel.
- The Morris X458 overhead conveyor is equipped with 806 two-axle trolleys.
- Top view of the one-rail conveyor installed by CM Automazione.
therefore decided to rely on CM Automazione, which proved to be an ideal partner especially in terms of the availability and flexibility with which it complied with our project, the promptness with which it solved some initial problems, and the high quality/ price ratio of its system. Compared with our old plant, the length of the chain is more than double (from 150 to 330 metres), including a 70 metre-long pre-treatment tunnel with a bend corner. My design envisaged a 4-inch chain and a maximum load capacity of 200 kg per trolley, with a continuous flow operation. One of the most complex aspects, however, was precisely the movement of 4 metre-long parts through the bend corner of the pre-treatment tunnel. Together with Peron Group, we studied all possible solutions in detail and asked the company to create a system with such wide bends that it was possible to hang a 4 metre-long and 1.10 metre-wide workpiece at any point on the load bar while maintaining a distance of no more than 1 metre from its ends.
“Another special feature of the conveyor’s layout that I particularly insisted on was the construction of three uphill segments: one The pitch between the hooks is 409.6 mm and the chain speed is 2.5 m/min.
With over 50 ZLD plants installed all over the world, CIE is a leader company in Zero Liquid Discharge for metal finishing industry www.cieeng.com - info@cieeng.com
in the loading area, one in front of the drying oven, and one in the unloading area. I was aware that this could have posed a problem in a one-rail conveyor, due to the risk of a component hooked at two points of a load bar (e.g. a panel wider than 1.5 m) becoming unhooked. However, we also solved this critical issue by finding the right slope value and optimising the descent phase in the unloading area – where, if there is a defect, the component must be manipulated and sent for retouching. Moreover, in cooperation with CM Automazione, we developed a special system for locking the load bars so that they cannot tilt beyond a certain threshold during ascent. In the case of workpieces hooked at two points, this also helps prevent detachment from hooks.”
The one-rail overhead conveyor installed in GPS’s new hall is a Morris X458 system equipped with 806 two-axle trolleys. The pitch between the hooks is 409.6 mm, the chain speed is 2.5 m/min, and the motor power is 0.75 kW x2. “I was very doubtful about one component: the chain tensioner, which has no springs,” confesses Borella. “I had never seen any like it and wondered how, without this technical element, it could be possible to prevent any chain elongation due to the expansion of the iron reaching high temperatures in the oven. Actually, the chain has such a tension degree that the risk of expansion is nullified. This also allows performing maintenance only once a year. “Our partnership with CM Automazione was also very fruitful in terms of attentive advice and respected delivery times. Finally, we were not sure we could find a supplier capable of solving all the critical issues of a pioneering project that had not been devised by its own technical department and that had never been realised before, but CM Automazione did so with proficiency and professionalism, actually even optimising some aspects.”
After manual loading, the parts are hung on the conveyor that leads them to the pre-treatment tunnel, made of AISI 304 and 316 stainless steel. Here, phosphodegreasing with chemicals supplied by Kendell, now part of the BASF Group, is followed by two rinses with mains water, a rinse with demineralised water, passivation, and a last rinse with demineralised water. The components then enter the drying oven. “We designed the new pre-treatment plant in such a way that, should the need arise to replace the baths, we can only replace the first ones and not all of them as is the case with our old plant, while keeping the parameters of the others unchanged and with constant values. In addition, one of the technical aspects that I personally wanted and that I had already tried first-hand on our old plant was the presence of tank doors on both sides of the pre-treatment tunnel. Cleaning and maintenance of the structure is easier and without the risk of the operator getting dirty. I also chose to install the electric pumps above the tanks and not on the ground as is usually the case, so that the collectors do not draw from the bottom, but from a height of 1.5 m above the
ground. In this way, the nozzles always remain clean and the noise of the pumps during operation is greatly reduced.”
Colour change: the “pit stop” of a coating process After drying in the air stream oven, the parts are taken to the coating booth. “The new system is equipped with a dense phase powder booth from the Silver Booth series installed by Siver Srl, the exclusive dealer of Nordson systems for Italy. The manufacturer had guaranteed five-minute colour change operations; however, since I have been doing this for over twenty years, I trained my operators and managed to reduce this time to just one minute. The secret is to consider this delicate step in the painting process as a car pit stop. As the conveyor is of the one-rail type, we can carry out a colour change in the time between the passage of one load bar and the next: in this way, we do not have to stop the chain, we avoid leaving parts waiting in the pre-treatment tunnel with all the risks and consequences that this entails, and we optimise production times. In addition to our standard daily checks, at the customers’ request, we mark the coated batch using special plates, which undergo the same process
of the material and, at the end of the treatment, are tested to guarantee the suitability of the coating.” Afterwards, the parts reach the curing oven consisting of two combustion chambers; at its exit, a conveyor chain extension allows for thorough quality control of each hanging workpiece.
“We have an operator specifically assigned to this operation only, because accurate quality control results cannot be achieved if the same person also has the task of unloading the part from the line,” emphasises Borella. Once they have passed inspection, the parts are packed and labelled according to the RAL code required by the customer and taken to the warehouse before final shipment.
The company’s future in the hands of young people
In addition to plans for the completion and improvement of its production structure, Guido Borella has clear ideas about what the future of his company should be: “I am trying to create a team of young people with a few bright stars, including production manager and my daughter Gaia, in charge of our customers’ certification and approval procedures. I hope to leave a solid and promising company in their hands, capable of maintaining the high quality level for which it is recognised in the market today. I put all my experience in the project for our new coating plant, but this would have never been enough on its own: the combination with the state-of-the-art systems developed by our suppliers, in particular the conveyor, was the winning mix that enabled us to obtain an efficient, flexible, fast, and high-performance line as well as a suitable and comfortable environment for all those who work there.”
Dürr developed a new generation of pneumatic vertical piston pumps that increases process reliability and requires less maintenance: EcoPump2 VP is designed for several media and can be used in many fields such as mechanical engineering, metal working and the furniture industry.
Dürr has developed a new generation of pneumatic vertical piston pumps that increases process reliability yet requires much less maintenance.
The EcoPump2 VP is designed for various media typically found in industry and can be used in many fields such as mechanical engineering, metal working and woodworking, as well as in the furniture industry. The new pump only needs one seal for most applications, which is also much quicker and easier to change than on the predecessor model. The fluid parts can be disconnected from the air motor with conventional tools via a quick coupling. The new air motor can be operated without any oil. This significantly reduces the maintenance required, including in comparison with the competition. A further benefit is that the contactless changeover valves used to regulate the air motor changeover guarantee higher process reliability. Using quick-exhaust valves cuts changeover times, reduces pulsations, and increases performance.
With five different versions of the EcoPump2 VP covering a pressure range from 22 to 306 bar, the pump is suitable for applying paints, highviscosity materials, and adhesives to furniture, steel constructions, and
many more materials. It can also handle acidic hardeners commonly used in the 2K process in the North American market without any difficulty.
The first feedback from customers has been consistently positive. The pump is quieter, it pulsates less, and takes less time to clean than the predecessor model.
The Dürr Group is one of the world’s leading mechanical and plant engineering firms with extensive expertise in automation and digitalisation/Industry 4.0. Its products, systems and services enable highly efficient and resource-saving manufacturing processes in different industries. The Dürr Group supplies sectors like the automotive industry, mechanical engineering, chemical, pharmaceutical and medical technology industries.
The company has around 18,100 employees and 120 business locations in 33 countries.
For further information: www.dürr.com
From 21st to 23rd March 2023 in Stuttgart, the German company Dörken will present its high-performance corrosion protection solutions during Fastener Fair Global.
The German company Dörken Coatings GmbH & Co. KG, an international manufacturer specialised in high-performance corrosion protection solutions, has announced that it will showcase its latest technologies and innovations in the area of premium surface protection during Fastener Fair Global 2023, the 9th international exhibition dedicated to the fastener and fixing industry that will take place from 21st to 23rd March at the Messe Stuttgart. Taking place every two years in Stuttgart (Germany), Fastener Fair Global is an international event that brings together manufacturers, wholesalers, distributors and suppliers. The event covers all areas of the fastener and fixing industry and provides real insight into industry trends and key information about the latest developments in the sector. It is then an excellent opportunity to exchange knowledge and ideas, keep up to date with the latest innovations and network with professionals worldwide.
Consequently, Christos Tselebidis – the sales vice-president for the Industrial Coatings division of Dörken – and the Key Account Manager Martin Juros will welcome distributors, suppliers, engineers and other industry professionals at booth 1056 to better discuss how to protect their important assets and products.
For further information: www.doerken.com
Kynar Aquatec® of Arkema was used in the protective clearcoat applied on the Artemis 1 Space Launch System.
Arkema has proudly announced that it has been selected to protect NASA’s iconic logo on the Artemis 1 Space Launch System (SLS). The innovative coating is powered by Arkema’s Kynar Aquatec® PVDF latex and provides extreme durability to keep NASA’s red “worm” logo on the solid rocket boosters intact while soaring to space.
The historic Artemis 1 SLS lifted off from Kennedy Space Center in Florida on 26th November 2022. It has sent the Orion spacecraft approximately 1.3 million miles, orbiting the Moon and returning to Earth on 11th December. The SLS boosters featuring NASA’s red logo are the largest, most powerful solid propellant boosters ever built for flight. Watch the video.
The waterborne clearcoat protecting the logo was created by Arkema’s partner, Acrymax® Technologies Inc. Kynar Aquatec® PVDF latex enabled Acrymax® Technologies to design a water-based protective coating with exceptional durability in low VOC, air-dry systems.
“We work hand-in-hand with partners like Acrymax® Technologies to create custom solutions. Their ability to extend this partnership to NASA and develop a formulation strong enough to withstand the intensity of the most powerful rocket in the world is spectacular in many ways,” has explained Paul Lavallee, the global market manager of Kynar® Coatings at Arkema. “Kynar Aquatec® PVDF latex is really unique in that it delivers such world-leading performance in a user-friendly fashion. No baking or post-treatment is required.”
In 2021, bicycle manufacturer Sport Mechanical Workshop (Timisoara, Romania) opened an important bicycle factory in cooperation with French multinational company Decathlon. VISA Impianti (Triuggio, Monza Brianza, Italy) was among the protagonists of this ambitious project with the supply of a new powder coating line.
Romania occupies second place on the podium of the main bike producers in Europe, only surpassed by Portugal and followed by Italy. This is what emerges from the latest report published by Eurostat1. Indeed, what has been defined as one of the largest bike factories in Europe was recently inaugurated in Romania, specifically in Timisoara. The protagonist of this ambitious project was Sport Mechanical Workshop. SMW was established in 2016 by three associates with solid experience in the bicycle industry and a deep understanding of their sole partner: Decathlon, the French multinational company specialising in the sale of sports goods.
“We are Laszlo Nyaradi, the owner of ALLCOLORS, a coating contractor based in Tirgu Mures (Romania) that painted the bicycles marketed by Decathlon up until the opening of SMW; Francesco Russo, a former Decathlon executive; and Vittorio Olagnero, the owner of Telai Olagnero, an Italian company specialising in the production of bicycles also on behalf of Decathlon itself,” explains Russo.
“The idea to found SMW stemmed from our willingness to assemble and paint bicycles on behalf of Decathlon while supplying it with these products within a reasonable geographic distance to limit the costs, logistical problems, and pollution related to the transport of goods. SMW is located in a very strategic area that enables Decathlon to cover the whole of European territory: it already had a partner in the Iberian Peninsula and one in Italy, and now SMW allows is to also cover Eastern Europe.”
This is how, in 2021, what has been defined as one of the largest bicycle factories in Europe came into being. It occupies a total area of around 25,000 m² and it will soon produce and paint up to 2 million bicycles each year.
As for painting, SMW decided to rely on VISA Impianti, which supplied a fully automated, green powder coating plant that integrates the technologies of several leading Italian manufacturers: Futura Convogliatori Aerei (Robecco Pavese, Pavia), Ecoteam (Scandicci, Florence), Ciroldi (Ganaceto, Modena), Wagner Italia (Valmadrera, Lecco), and Chemetall (Giussano, Monza e Brianza).
The production and coating cycle Sport Mechanical Workshop manufactures a wide range of bicycles mainly in aluminium and steel: from 14’’ children’s bikes up to the most complex and structured e-bikes. “Decathlon’s catalogue includes a huge range of bicycles. SMW does not produce this entire portfolio for the time being, but our factory was conceived to be able to manufacture the entire range of bikes marketed by Decathlon in the near future.”
SMW’s production phase begins directly with the surface preparation and coating operations. “The customer provides us with all the required components, including tyres, frame components, and other parts. We store them in our 10,000 m2-wide warehouse and then take care of coating the frames, assembling the wheels, and preparing the products to be sent back to the customer.”
The coating cycle starts with the pre-treatment phase, which includes the following stages:
• Pre-degreasing
• Degreasing
• 2 rinses with mains water
• 1 rinse with demineralised water
• Nanotechnology passivation
• 1 rinse with demineralised water.
From top:
SMW assembles and paints a wide range of bicycles mainly in aluminium and steel. A section of the paint shop.
The components at the entrance to the pre-treatment tunnel.
Pre-treatment is performed with chemicals developed by Chemetall. It is followed by a blow-off and drying phase. The frame is then transported by means of a power&free conveyor to one of the two coating booths for the application of powder products. “Depending on the colour to be applied, the operator chooses which of the two booths to use for each product. This optimises timing and reduces the time needed for colour changes. Both booths, of the Wagner SuperCenter Evo type, are air-conditioned and located inside a clean room,” explains VISA Impianti owner Paolo Massari. “As far as paint application is concerned, we exclusively use polyester powders. We cooperate mainly with two suppliers, Adapta Color and Tiger Coatings. After powder application, the components enter the curing oven for about 24 minutes at 180 °C and finally reach the cooling tunnel”, states Nyaradi.
One of the manufacturing steps that truly enable to customise each bicycle is the application of stickers and decals. Therefore, SMW’s plant is designed to perform two alternative processes:
• The frame is unloaded, stickers are applied, and then the frame is reloaded onto the conveyor for the application of a second layer of clear coat.
• The frame is unloaded only after colour, clear coat, and sticker application.
The takt-time is 37-40 minutes per load bar.
“The difference between these two processes lies in the type of decals that the project requires. Some stickers need to be applied before coating, others between colour and clear coat application, and others, such as phosphorescent stickers, in the final stage after clear coat,” explains Nyaradi. “This step posed a significant technical challenge in terms of system design, because we required the greatest possible flexibility to be able to handle all these peculiarities efficiently. At the same time, in addition to flexibility, we were also looking for a plant that guaranteed high productivity. With VISA Impianti, we have obtained both benefits,” states Laszlo Nyaradi.
“The coating plant was conceived to work in three shifts, although we currently work in two shifts with around 70-80 operators. As many employees work on the assembly lines,” explains Russo.
The plant was designed not only to ensure high flexibility and productivity, but also to meet all SMW’s sustainability and energy-saving requirements. “Our factory is equipped with some significant green technologies, including a photovoltaic system on its roof. At SMW, we are very aware of environmental issues. As a consequence, it was of paramount importance that our coating system was also in line with our corporate values,” notes Francesco Russo. “The plant does not discharge water but rather treats it with two evaporators in order to recirculate it. Ecoteam also installed a water purification unit.”
“Moreover, the system boasts a heat recovery unit that uses the fumes generated by the curing oven to heat the drying one. However, there remains a significant amount of residual heat, which can be recovered in future to heat the factory as much as possible. The paint stripping oven, supplied by Ciroldi, is also prearranged for the installation of a heat recovery unit to obtain even more energy,” discloses Massari.
“Our long-term goal is to recover as much heat as possible to heat our entire 10,000 m2-wide warehouse. This will guarantee a very important benefit in terms not only of environmental protection, but also of reduction of energy-related costs.”
The coating plant and the entire production department were also designed to meet the Industry 4.0 requirements. “Through our ERP software, we are able to control every data and parameter of each production and painting stage, thus achieving a high degree of traceability. Within our paint shop, we even have an automated powder storage warehouse,” says Nyaradi.
Energy costs are through the roof right now. A higher hanging density is often the most efficient way to both save energy and drastically lower the total coating cost.
Find out how much you can save on your coating line at ccc.hangon.com
The valuable collaboration with VISA Impianti “For this project, VISA took care of the supply of every plant component, collaborating with numerous leading Italian companies: the conveyor was provided by Futura Convogliatori Aerei, the zero liquid discharge and duplex demineralisation plant was designed by ECOTEAM SpA, and the hook paint stripping oven was supplied by Ciroldi SpA.”
“We opened our paint shop at the beginning of 2022 and we have only been using it at full capacity for a little over six months. However, our collaboration with VISA Impianti had already started in 2015. I own a contract coating company located approximately 300 km away from Timisoara, which painted bikes on behalf of Decathlon prior to the foundation of SMW. This is where we installed the first plant supplied by VISA, which enabled the treatment of around 750,000 frames per year, as well as three other lines for coating aluminium profiles,” states Nyaradi. “Since then, for us VISA Impianti has become a point of reference for everything painting. The powder coating line in Timisoara
is therefore the fourth plant we have designed together and we are already planning to install a further one.”
“VISA Impianti will definitely be part of SMW’s future, as we plan to install another new system, this time for liquid coating, at our Timisoara site,” adds Laszlo Nyaradi. The opportunity to expand the factory’s capacity and production area will also be assessed in the years to come. “Currently, our company has a production capacity of about 1.5 million units, depending on the type of bikes produced, but our plant was developed to be able to treat around 2 million frames per year. For 2023, we expect an increase of 4-5%; in general, it will be an important year for the bike market. We are therefore going to be ready for any increase in sales during the current year. Finally, we have an additional 15,000 m2 available to expand our production facility even further, according to future needs,” says Nyaradi.
The right partner in the green transition
AVIN Srl is a company specialising in the design, construction, revamping and installation of surface treatment plants, from cataphoresis to powder and liquid spraying or immersion painting, as well as cleaning and air treatment systems.
AVIN does not only design, manufacture, and install systems based on innovative concepts, but it can also convert already existing machines into new, more advanced, state-of-the-art plants geared towards reaching maximum efficiency and meeting each customer’s needs and objectives. “The experience gained to date
enables us to build high-tech, energy-efficient coating and cataphoresis systems,” states Morgan Infanti, the General Manager of AVIN. “All our plants are digitised, perfectly in line with the requirements of Industry 4.0. We also offer the remote activation of our tele-assistance service to allow direct intervention by our technical support team.”
AVIN has also developed specifically high-performance electroplating cells and ultrafiltration membranes for ultrafiltration and cataphoresis plants. “From design of the smallest detail to performance and functionality checks, our technical staff offers a high level of flexibility and reliability, with the utmost attention paid to even the most complex requirements of our customers. One of our latest product innovations are the electroplating cells of the AUF65 and AUFL80 with extruded membranes series for cataphoresis and anaphoresis tanks, which we have developed with a view to energy savings, penetration power, ease of operation and maintenance, and longer service life combined with high performances.”
“In electrophoretic coating (cataphoresis and anaphoresis), ultrafiltration membranes are used to recover drag-out paint and to manage the bath’s chemical and physical parameters. The entire range of membranes developed by AVIN is specifically designed to achieve the highest performance level during the process. AVIN is thus able to respond to the most particular market requirements with different types
of products: tubular, hollow and compact, or single-module membranes for microfiltration, ultrafiltration, nanofiltration, and reverse osmosis processes.”
The new AUF membranes are obtained by extrusion and they are therefore free of bonding or welding areas. Their simple and economical design reduces resource consumption. Their self-supporting disposable plastic housing elements facilitate quick installation and removal and they are ideal for rinsing or recovering anodic and cathodic paint solids. The membrane, based on polyvinyl fluoride (PVDF) chemistry, provides a robust and reliable solution in the harsh conditions of the electroplating process.
“To help our customers cut energy costs, which are increasingly weighing on all companies’ budgets,” adds Infanti, “we have studied these new extruded tubular dialysis cells that are more energy efficient than flat membranes, thanks to their lower energy absorption and high penetrating power at a given voltage (12% to 18-20% higher). Furthermore, the AUF extruded self-supporting membranes do not
need to have an anode assembled with PVC grids as is the case with flat membranes and they do not require internal or external support. Finally, thanks to their special construction method, they can expand freely from the dry to the wet state.”
The AUF anodes allow the anolyte to circulate under pressure (250 l/h at 0.3 bar and up to 1000 l/h at 0.6 bar); its requirements range from 3 to 5 l/h/Ampere/ m2. “These characteristics guarantee greater process safety, eliminating the risk of leaks and reducing paint sedimentation thanks to the fact that the membranes are extruded and waterproof. Indeed, their special design eliminates the risk of the anolyte/catholyte escaping from the cell into the tank. Furthermore, in the event of the rupture of a membrane, the circulation under pressure of the anolyte prevents the risk of the “siphon” effect. Finally, in the event of bacterial contamination, the AUF anodes can be cleaned and completely emptied via a screw cap at the bottom of the membrane itself.”
Other peculiarities of these dialysis cells are their ability to expand without any internal or external constraints and their roughness-free surface that does not retain paint.
“Also in terms of maintenance, the main objective was to simplify the work of operators,” notes Infanti. “It is indeed possible to dry an AUF cell after cleaning its surface with demineralised or mains water, leaving the anolyte/catholyte circulation at a lower flow rate during maintenance. The AUF membranes’ surfaces can also be brushed with a Scotch-Brite product to remove any traces of settled and/or dried paint. The anodes weigh only 15 kg each for an active membrane length of about 2.1 m, so moving or replacing them requires no special lifting equipment and only one operator, while maintenance requires a maximum of two people. Removal of the AUF anode is made easier by the PVC plastic ring nut on the top of the cell.”
The smooth surface of the AUF membranes prevents the formation of wrinkles or cracks that cause them to become clogged with paint pigments.
“Our experience confirms that the AUF anodes guarantee correct functionality even after three years of operation. Their service life can be extended by rotating the electrode through 90° over time (every
four to six months). This is why AVIN guarantees its AUF membranes for twelve months (excluding the electrode)”.
Technical data for AUF65 tubular cells
• Type of membrane:
- PVDF with ionic resins
- Extruded (weld-free)
- Extruded membrane surface: Ø 65.3 mm -> 0.2 m² active/meter
- Membrane thickness: 2.95 mm
- Electrical resistance: 175 Ohm/cm²
- Ion exchange: 1.37 - 1.72 meq/g (dry)
- No water permeability
- pH resistance: 1 - 12
- Maximum pressure: 0.8 bar
• Electrodes:
- Materials: AISI 316 L, 316 Ti (extruded, weld-free)
- Diameter: 48.3 mm x 2.77 mm
- Surface: 0.153 m²/m
- Maximum allowed intensity: 60 A/m²
- Operating pressure: min. 0.2 bar, max. 1 bar
• Anolyte/Catholyte: - Flowrate: 3 to 8 l/h/Amp/m²
• Cell size: - Customisable.
Technical data for AUFL80 tubular cells
• Type of membrane:
- PVDF with ionic resins + Divinylbenzene
- Extruded (weld-free)
- Extruded membrane surface: Ø 65.3 mm -> 0.2 m² active/meter
- Membrane thickness: 2.95 mm
- Electrical resistance: 175 Ohm/cm²
- Ion exchange: 1.37 - 1.72 meq/g (dry)
- No water permeability
- pH resistance: 1 - 12
- Maximum pressure: 0.8 bar
• Electrodes:
- Materials: AISI 316 L, 316 Ti (extruded, weld-free)
- Diameter: 60.3 mm x 2.77 mm
- Surface: 0.191 m²/m
- Maximum allowed intensity: 60 A/m²
- Operating pressure: min. 0.2 bar, max. 1 bar.
The new AUF-80-PLUS membrane
In August 2022, AVIN launched a new model of ultrafiltration membranes on the market: the new AUF-80-PLUS series. “The new development technologies introduced in our production cycle have
with a complete service that includes system design manufacturing, installation, technical support and chemicals
RESIN DEMINERALIZATION SYSTEMS REMEDIATION OF CONTAMINATED SITES BIOLOGICAL SYSTEMS BATCH TREATMENTS PHYSICAL-CHEMICAL SYSTEMS ADSORPTION FILTRATION REVERSE OSMOSIS MEMBRANE SYSTEMS EVAPORATORS BIOGAS BIOMASS SYSTEMS OIL SEPARATORS DESANDERS DESALINATION SYSTEMS PYROCHAR
Via Torricelli, 79 - Z.I. Fossatone 40059 MEDICINA (BO) - tel. (+39) 051 856263 info@hydroitalia.com - www.hydroitalia.com
enabled us to conceive a higher-performance filter cloth, which guarantees a 15% greater total filter surface area and an overall higher yield compared with our AUF80 membrane described above, which averages 22-25% of ultrafiltrate produced,” says Infanti. “With this product, we wanted to stabilise and maximise the durability of the membranes and the performance level of the new cataphoretic/anaphoretic coating technologies currently on the market.” The new AUF80-PLUS membranes do not require any plant modifications and fit the IN-OUT head components of the previous versions. The technical features of these new membranes are as follows:
• recirculation flow rate: 12/20 m³/h
• operating pressure: 3.0-4.1 bar
• maximum inlet pressure: 4.4 bar
• minimum outlet pressure: 1.0 bar
• maximum operating temperature (production): 50 °C (EDP temperature)
• maximum operating temperature (cleaning): 50 °C (max. 30 minutes)
• minimum storage temperature: 5 °C
• prefiltration: 50 µ
• membrane surface area: 30.6 m2
• weight: 29.5 kg
• pH: 2÷10.
“At a time when the cost of energy resources is rising dramatically, it is important for a company like AVIN to contribute to reducing consumption, helping its customers by all possible means. The tools we have at our disposal to do this are our expertise and experience and a vision of the future that can no longer disregard cost assessments, not only at the time of the commercial contact for the purchase/sale of our systems, but also in terms of operation, maintenance, and durability of the installed devices,” concludes Infanti.
Using products that allow working at 25 °C instead of 50 °C guarantees significant energy savings, which translate into lower costs and reduced greenhouse gas emissions. Moreover, as well as reducing energy costs, operating at lower temperatures also provides numerous other technical advantages, including reduced consumption of water or process liquids (at low temperatures, evaporation losses are minimised), less downtime after routine maintenance (no time is lost in heating the working solution), fewer fouling problems, reduced equipment wear, and a healthier working environment (no steam is generated in the room where the plant is located). These are all the
reasons why we believe that such innovations can provide end users with significant economic and technical advantages. Therefore, below is a brief description of our products for lowtemperature application.
Condorcoat EC 930 Condorcoat EC 930 is a nanotechnology passivating agent for the surface conversion of ferrous materials, galvanised iron, and aluminium. The formulations of our Condorcoat EC 900 series can be used to replace outdated pre-treatment processes such as phosphodegreasing,
zinc phosphating, and tricationic or heavy iron conversion.In particular, Condorcoat EC 930 replaces phosphodegreasing treatments and guarantees higher cost effectiveness. Its working temperature is particularly low, between 20 and 30 °C.
The product is formulated to combine a strong degreasing action with the surface conversion of the substrate.
The nano-coating layer that is created on the treated metal surface is characterised as follows:
• compact, hard, and resistant;
• uniform, consistent, and watertight;
• mineral;
• protective.
Its typical thickness, around 40 nm, is extremely reduced – it is more than 10 times thinner than conventional amorphous phosphates.
Condorcoat EC 930 has a low environmental impact thanks to the absence of phosphates and toxic metal compounds, it guarantees low energy consumption, it has negligible impact in terms of COD, and it emits no VOCs.
The use of Condorcoat EC 930 brings important economic and application benefits, including as follows:
• lower operating temperatures (20-30 °C lower than in traditional cycles);
• no sludge production;
• less equipment maintenance required;
• longer service life of the bath;
• lower water consumption;
• more compact systems.
Condorcoat EC 930 can also be used in a one-stage degreasing/surface conversion process, as it is enriched with surfactants that guarantee the perfect removal of oils and greases commonly found on raw parts. It is preferably diluted with demineralised water and it can be used by either spraying or dipping.
The workpieces’ treatment must be followed by a rinse with demineralised water. Pre-treatment with Condorcoat EC 930 is compatible with all painting processes.
Condorine SG 515 BT
Condorine SG 515 BT is a low-temperature alkaline degreaser, suitable for ferrous metals and galvanised steel.
Its balanced combination of surfactants and selected raw materials guarantees high degreasing power and thorough cleaning of parts, even at moderate temperatures. Its special composition prevents foaming even when operating at low temperatures in spray systems.
Sequestering agents keep the iron in solution, thus minimising sludge formation.
The special feature of Condorine SG 515 BT is its effectiveness already at 20-30 °C, which is 20-25 °C lower than that required by conventional products.
It is highly appreciated by several large metalworking and industrial painting companies, which have already been using it successfully for years.
Condorine SG 576 N
It is a multi-metal passivating degreaser for highpressure applications. Suitable for use on any metal and material (ferrous alloys, aluminium alloys, copper alloys, plastics), this neutral degreaser is used for both intermediate treatment stages in one-tank plants and high-pressure operations (e.g. highpressure deburring). It is additivated with special corrosion inhibitors that protect the treated parts against atmospheric corrosion. It is non-foaming and can be used at low temperatures.
Condorine SG 576 N is therefore a very versatile product that can be employed in many different applications.
Condorfos K 12 L
Condorfos K 12 L is a liquid phosphodegreaser suitable for ferrous components. It is an easy-to-use, highly concentrated formulation, active from 20 °C. Given the optimal pH of its working conditions, it does not require neutralisation. It allows amorphous ferric phosphate salts to deposit on surfaces, preparing them for the subsequent coating process.
If it is unavoidable to work at low temperatures (below 40 °C), Condorfos K 12 L can still perform its degreasing and passivating action, preserving the parts against flash rusting after drying.
It can be used by dipping or spraying even in suitably
equipped open spaces, with low-pressure nozzles or, better still, with high-pressure washers, on large workpieces or heavy metalwork structures that are difficult to treat in tank or tunnel systems. Finishing can be done with traditional, water-based, or powder coatings. Condorfos K 12 L can also be used in “dry in place – no rinse” mode if the treated parts have no particular stagnation areas: in such cases, it is possible to simply allow the workpieces to dry before painting, without any rinsing.
It is a universal multi-metal paint stripper suitable for ferrous metals, light alloys, galvanised steel, aluminium, etc.
Even at room temperature, this paint stripper removes solvent-based, water-based, and powder coatings (epoxy, polyurethane, polyvinyl, etc.) from any metal without having to resort to formulations containing chlorinated solvents. If left to act for the necessary time, it even attacks and removes paint layers with a considerable thickness, up to several millimetres, also working at room temperature, i.e. 40-50 °C lower than conventional formulations.
Moreover, it guarantees as follows:
• it contains no solvents that are harmful by inhalation;
• it has a limited odour;
• it does not contain methylene chloride, phenols, or other particularly hazardous solvents;
• it is not classified as flammable;
• it can be removed by simply washing with water;
• the containers used can be made of common iron;
• the treated iron parts do not rust after cleaning.
The SVA 583 paint stripper is already successfully used by several major aluminium finishing companies to restore profiles for repainting. When paint stripping aluminium, it is essential that the product is kept anhydrous.
It is a neutral pickling agent suitable for ferrous metals, galvanised steel, and aluminium.
Condorite 796 N is recommended for metal deoxidisation even at low temperatures: it has strong deoxidising properties and it is capable of removing surface oxides or mineral residues from components. Typical applications are as follows: removal of thermal oxides after laser cutting or welding; treatment of heavy rust/calamine layers; removal of scales and insoluble salts found in hard water. Its balanced composition and near-neutral pH value preserve the substrates against attack, concentrating the action on the contaminants to be removed. This inherent ability not to corrode the treated parts allows for considerable variability and flexibility of working parameters.
Condorite 796 N is also active at room temperature and it can be additivated with suitable degreasing additives. This enables to perform pickling and degreasing in one operation, even at low temperatures. The product is odourless and it does not emit harmful fumes. It is not classified as dangerous under the provisions of the Regulation (EC) No. 1272/2008 (CLP) and subsequent amendments.
Economic developments and industrial needs have often collided with and sometimes upset the delicate ecological balance. The challenge is to turn this conflict into a possible alliance. CONDOROIL’s research laboratories and technicians have been focusing on the increasingly important issues relating to the future of our planet. Our company is convinced that there will soon no longer be any room for highenvironmental impact technologies and that only environmentally friendly production processes are going to be implemented in the near future. With this in mind, we believe that investing time and resources in optimising such processes means investing in the future. The products we have briefly described stem precisely from this vision. CONDOROIL’s technical service is at the customers’ complete disposal for laboratory tests and demonstrations, allowing them to assess the effectiveness of its proposed solutions before their application in-line without any obligation.
4 0
Y e a r s o f A d v a n c e d S o l u t i o n s f o r M e t a l S u r f a c e s T r e a t m e n t
4 0 y e a r s o f t a r g e t e d g o a l s , p r e c i s e c h o i c e s a n d c o n t i n u o u s e ff o r t d e v e l o p i n g h i g h l y p e r f o r m i n g a n d i n n o v a t i v e p r o d u c t s F o r E u r o p o l v e r i t h i s anniversary represents only the first step in the taken direction Today the main challenge is to plan the future with a constantly evolving growth s t r a t e g y a n d g r e a t c a r e a n d s e n s i t i v i t y t o t h e e c o l o g i c a l - e n v i r o n m e n t a l c o n t e x t Z a n o l o C d A0 3 2 2
EUROPOLVERI S.p.A. - Sandrigo (VI) Italy - Ph. +39.0444.750643 - Fax +39.0444.750653
FILIALI/Branch Office: Cernusco sul Naviglio (MI) Ph +39 02 92148001 - Erbusco (BS) Ph +39 030 7704158
Only by combining technical expertise, knowledge of the industry and existing technologies, and proven experience is it possible to position oneself in the market as a one-stop-shop partner for all things painting equipment.
Total Finishing Systems, a division of Total Finishing Solutions (Riverside, California, USA), is part of a family of companies created to provide businesses in North America with a single point of contact that they can rely on for their coating systems, from design to installation and after-sales. We interviewed Total Finishing Solutions president Ty T. Crowder to find out more about his company’s history and current challenges.
Three business units to offer an all-round service: how did the Total Finishing family come about?
The Total Finishing family was founded as a group of companies aiming at bringing together the skills, knowledge, and resources needed to devise, design, and maintain finishing and painting plants and equipment for the general industry. It indeed includes three business units:
• Total Finishing Solutions is the first branch of the company and it specialises in the supply of spray booths, UV and IR ovens, abrasive blasting equipment, and industrial automation solutions such as flatlines reciprocators and coating robots, with the latter being built by our partners VD Finishing Solutions, Lesta, and ABB Robotics. Our solutions group has also has been introducing Powercarts, which are battery operated autonomous carts to many finishing lines. This has been extremely useful in the door, window, and furniture coating markets.
• Total Finishing Systems was established recently for the design and integration of complex, high-quality painting systems. It supplies customised powder and liquid coating plants mainly for the automotive (Tier 1 and Tier 2), aerospace, and defence industries.
• Total Finishing Supplies is the division devoted to the supply of all consumable materials and equipment necessary to maintain the operation and efficiency of plants. We have an e-commerce platform for the sale of spray guns, paint pumps, spray booth components, and so on, supplied by the partners we work with, such as Carlise FT, Wagner, Anest Iwata, and SATA Engineering. Our team of experts supports the digital shopping experience via chat.
Having these three divisions enables us to present ourselves on the market as a one-stop-shop partner that assists its customers at all stages, from the identification of the most suitable solution to aftersales services.
At the same time, our synergies and close partnerships with numerous market leaders allow us to offer proven, high-quality technologies.
It is well known that the powder sector is still rather marginal on the American continent, compared with the liquid paint market. What is your approach to powder coating?
Total Finishing Systems specialises in the design, manufacture, and assembly of turnkey systems for both powder and liquid coating operations. The type of painting process required is not a discriminating factor for us: our offer is based solely on the requirements of our customers. We propose and advise them on the most suitable and profitable investment possible based on their application processes and the sector in which they operate. For example, we recently proposed a cataphoresis system (E-Coat) for a manufacturer of bed frames that needed to dip coat its components, rather than a powder system. Why? Because it was the best ROI for the customers investment.
Total Finishing Systems is always looking for new and profitable collaborations and synergies with other companies. Entering into exclusive agreements means being able to offer increasingly innovative, cutting-edge systems, processes, and technological solutions.
In this framework, we have recently forged new partnerships with leading firms in the surface treatment sector. In November, we announced an exclusive agreement with SFB AG, a leading manufacturer of horizontal (flatline) powder coating systems, which will enable us to provide the industry with new options for powder coating that were previously unavailable in the US market. In particular, the combination of the expertise of Total Finishing Systems and SFB has led to the development of a unique, fully automated powder coating plant that is going to especially benefit firms needing to treat small components.
www.eco-techno.it sales@eco-techno.it
A flat conveyor belt handles the workpieces, which are powder-coated on one side, cured, and then turned and painted on the other side. In addition, an innovative transport and suction system allows recycling of the powder and requires no hooks or racks, meaning there is nothing to clean or burn off. The process also allows for perfect single sided painting of parts with no masking. Another partnership we are very proud of is the one with Erzinger, a Brazilian manufacturer of equipment for surface treatments, pre-treatment operations, electrostatic powder application, and cataphoresis (E-Coat). We have been designing and have now sold several systems together with them, to be built and installed over the current year. Erzinger will also help us set up and open our new laboratory for North America, which will deal with both powder and liquid coating equipment, housing and analysing the latest innovations
From top left clockwise:
- Powercarts are extremely useful in the door, window, and furniture coating markets.
- A detail of the flatline powder coating system developed together with SFB.
- A flat conveyor belt handles the workpieces, which are powder-coated on one side, cured, and then turned and painted on the other side.
and technologies presented by leading manufacturers of plant components.
Is Europe part of your future plans?
Currently, we do not consider Europe as a commercial target area. Our extensive sales network covers the United States, Canada, and Mexico. However, Europe is a very fertile ground for leading surface treatment technologies and companies. Our goal is therefore to scour the market in order to learn about the major technological trends and be the first to bring these innovations to North America, thus offering our customers up-to-date, state-of-the-art products and processes.
Total Finishing Systems is going to present its new projects in the next issues of ipcm_International Paint&Coating Magazine.
ww w .infr a g a s . c o m
For a well-known contract coater of decorative components for the automotive and electrical user interface industries, Venjakob Maschinenbau developed an automatic coating solution that can coat both flat and curved 2.5D components in one spray booth. Another special feature of the system is that UV coatings can also be processed by means of a UV robot.
The 40-meter finishing line for plastic parts has been given the nickname “all-rounder” by the contract coater. Whether flat or curved, UV, water or solvent-based coating, everything passes through here at a constant speed via the pallet conveyor system also developed by Venjakob. With brilliant results.
The curves are controlled precisely Durable, resistant to scratches, light and weathering effects – the requirements for the contract coater for coating quality of decorative high-gloss surfaces are strict. Equal coating thicknesses at every point of the component as well as uniform curing for the UV coatings used.
How do you get this precision work done on 2.5D components?
Gert große Deters, General Industry and Automotive Business Unit Manager at Venjakob, explains: “We went through intelligent control in this case. We adapted the spray jet parameters of the spray guns to the part geometry and stored them in the control system. At the machine infeed, a sensor measures the geometry of the workpiece and automatically generates the spray jet parameters that we previously defined in test runs.”
A coating system that uses UV coating systems in addition to wet coatings must take their special features into account during processing. For this reason, the conveyor system of the coating line was designed to avoid carryover and contamination by the UV coating material as far as possible. For cleaning during the painting process, a water-wash spray mist extraction system and a paint sludge separator for the contaminated booth water are used. The cleaning of organic solvents in the exhaust air is carried out by an exhaust air purification system developed by Venjakob Umwelttechnik.
The special feature of this system is the robot with UV lamp. It is used
for hardening edges and curves of complex 2.5D components within seconds and was positioned directly in front of the 6-level dryer. In the higher-level controller, it is possible to select whether the robot is used with the UV unit or not.
Pallet conveyor guarantees uniform flow of goods The entire system is designed for fast throughput times. The pallet conveyor moves the components in a horizontal position at a constant speed through all system components. The flash-off and drying sections are matched to this conveying speed
so that the desired treatment and holding times are achieved. The maximum conveying speed is two meters per minute. The process steps include pre-treatment with CO2 cleaning, ionization and flame treatment, painting, curing if necessary, and the drying process. The 6-level dryer used, five of which are heated, manages to dry the components completely in 30 minutes. Afterwards, they can be processed directly or transported through the system again for another coating layer.
For further information: www.venjakob.com
Fastrip ISP is a stripping machine featuring a horizontal tank above which the rail runs for the in-line handling of hooks and frames intended for electrostatic coating processes. These are immersed and flow into the stripping bath for a variable time of approximately 2 minutes. After leaving the chemical bath while still hanging onto the chain, they result perfectly clean and ready to be used in a new coating cycle. ALIT offers the complete paint stripping solution: tank and chemical paint stripping product with high performance and low environmental impact.
From bucket seats and vehicle accessories to power distribution boxes and rotor blades, the triumphant march of glass-fibre and carbon fibre-reinforced plastics has continued unabated for decades and their applications keep increasing.
The main reason for this success are the many advantages of these glass-fibre and carbon-fibre reinforced composites: They are very light, extremely durable, water, heat and cold-resistant and they can be pressed into just about any shape. FreiLacke, the German Black Forest-based coatings manufacturer, now not only offers diverse coating materials for the surfaces of parts but also the components for their manufacture.
One example is the new CM powder technology. Due to a special two-stage principle, this innovative composite powder resin system stands out against conventional resin systems for composite plastics in that it can be melted on without starting the hardening process. That allows them to be processed into so-called PrePregs with complete waterproofing. “As a coatings manufacturer, we have all raw materials on site and can use them to develop new solutions”, explains Heiko Blattert, FreiLacke’s head of development of PG Composites.
The powder-resin system contains no ingredients that have to be declared and it is free from solvents as well as any harmful carcinogenic substances, which makes storage and transportation much easier. It is
available in various colours and reaction speeds and is highly compatible with various fibres, filling materials, inserts and core materials. Among the applications for the new CM powder resins are the rotor blades of wind turbines. The best part of it: This also allows the blades to be manufactured in a single piece. The previously required bonding process of two individual parts is no longer required, which also eliminates a critical predetermined breaking point.
Rotor blades spin with top speeds of 300 kilometres per hour or more. The aerodynamic profile at its front edges plays an important role because it contributes significantly to the effectiveness of the turbine. These front edges are especially prone to erosion: Environmental influences, such as rain, snow, hail, sand, UV radiation as well as severe temperature and moisture fluctuation, can sharply accelerate this erosion. In the case of offshore turbines, the humidity and salinity they are exposed to can add further strains.
A high-performance edge protection coating, which is also referred to as leading edge protection (LEP), is essential.
FreiLacke already has multiple leading edge protection systems available for its customers in the wind energy sector. “It will only work well if it is matched specifically to the substrate or the coating materials below it”, emphasises Heiko Blattert. That is why FreiLacke is offering the complete product range for the coating of
rotor blades completely from a single source. In addition, FreiLacke also offers and uses proven coating system structures for the production of the concrete towers of wind turbines. These systems can also be transferred to other industrial concrete coating applications and are already being used successfully in these areas.
The company keeps a series of coating solutions for composite materials ready – ranging from colour pastes and fillers to gel coats and top coats. The family-owned business offers them for spreading or spraying on the basis of PU/PUR or unsaturated polyester resins. The gel coats and top coats are coloured coatings that can be applied directly into tools and moulds and provide moulded parts with long-term protection against moisture, UV radiation and impact damage. After it has been manufactured and demoulded, the component is already fully coated. When comparing the PU/PUR coatings to the UP materials, the light fastness and fastness to weathering of the former is much higher.
FreiLacke have also succeeded in significantly reducing the percentage of styrene in the UP gel coats as the substance is deemed hazardous to health and problematic to the environment.
“Using an alternative monomer, we have manufactured a reduced styrene gel coat that delivers even better results than conventional systems in terms of weather resistance and shelf life”, declares the head of development.
Powder InMould Coating (PIMC)
FreiLacke also offers an exceptional coating expertise when it comes to other composites, such as the sheet moulding compound (SMC), i.e. plateshaped, dough-like moulding materials made from thermosetting reaction resins and glass fibres. In a single-step production process, electrostatically charged powder coatings that are based on UP resins are applied onto the hot mould. During the hot-pressing process the coating creates a chemical compound with the material. This compound is scratch-resistant, and also extremely resistant against chemicals, graffiti and UV radiation, which is particularly important for outdoor uses. The
cycle time is only extended by the duration of the powder coating application and, depending on the component, takes about a minute. After pressing, the finished, coated component can be demoulded. The typical fibre marking is completely levelled out by the PIMC process, the parts are given a highly resistant and very homogeneous surface.
Powder InMould Coating (PIMC) offers a wide range of colours since nearly all RAL colours can be used. That means there is no limit when it comes to the colour range of the components. The material is free from solvents, hazardous substances or carcinogenic raw materials.
“As an alternative, we developed a liquid coating system that can be injected into the closed mould during the production of the component”, explains Blattert, the head of development. It features very short pressing times as well as high resistances in terms of light fastness and fastness to weathering. The component is ready when using “finished casting” or can simply be coated later on. This also allows applications at the exterior of cars, he emphasises.
FreiLacke has long-established itself as a specialist for coating systems and has now gone a step further: with the CM power resins, customers have the option of directly receiving the materials as well as a comprehensive consultation when it comes to the project development and production of the components. And they can count on the expertise of the coating experts from the Black Forest. Many companies, especially those in the automotive and commercial vehicles sectors, in mechanical engineering, the industrial sector in general and in construction are already counting on FreiLacke composites.
Heiko Blattert believes that a cornerstone of this success is the close cooperation with the customers: “Ever since our early days, we have been convinced that true quality of service is only possible if problems and tasks have also been viewed from the customer’s perspective, and are fully understood as a result” said the head of development. “We do not merely support them all the way to series production, but even beyond that across the entire cycle”.
Over the past twenty years, RKT has supplied more than 4,000 DDF powder pumps in various models worldwide as replacements for Venturi injectors. Based on our experience, most old DDF2 and DDF2-DP pumps do operate smoothly and efficiently. However, the greater yield and benefits guaranteed by the DDF pumps only become truly apparent when customers and operators understand that they are different in nature from traditional Venturi injectors and recognise that their operating principles are not the same. In fact, over time, some of these customers have suggested we implemented a few improvements to our DDF pumps for different reasons. They all basically boiled down to the fact that DDF pumps are “more difficult to control” than the Venturi injectors. This is why we developed the new DDF4 powder pump. RKT began to analyse the different causes behind these customer suggestions already about ten years ago and, as a result, decided to develop the DDF4 pumps. The research study carried out found that the fact that powder is transported “at a high density” in DDF-type pumps aggravated the issues reported. The negative impact of these factors has therefore been overcome and reduced with the development of the new DDF4 pumps. Indeed, the main difference between the DDF2 and DDF4 models lies in design. In the latter, powder is sucked into the powder chambers from the sides instead of from the bottom of the two cylinders. Higher vacuum, better powder flow consistency, improved powder management, long-term reliability, higher performance, and the ability to spray 8 g/min of powder without gushes nor blockages are only some of the improvements guaranteed by the DDF4 units.
The DDF4 pumps work best with the 600 series guns. In order to achieve good operating results, in general, these dense-flow pumps require applicators with greater operating and maintenance capabilities.
The DDF4 pumps are managed through small individual control units with one PLC for each pump. This results in greater system reliability and ease of adaptation of programmes, should they need to be modified. All changes are made via an HMI screen.
The DDF4 pumps are housed in the lower section of a control cabinet, while the PLC control units are located in the central section. Each individual PLC manages the functions of a DDF4 pump. Powder feeding is controlled through the piston speed adjustment.
The upper part of the control cabinet houses the PLC Master unit. This makes both maintenance and operation easier.
In the GCU-S600 electrostatic control module, it is possible to set the gun’s parameters, which are saved in the PLC of each pump/gun. The HMI screen allows selecting the programme number, the powder spray rate, and DDF4 pump’s flow rate. As showed in the diagram, these parameters are then sent to the corresponding pump. The operating principle is similar to that of DDF2 pumps, but with technologically updated systems. The Micro Powder Center (MPC-5Mk2) guarantees high performance levels for fast, high-quality colour changes with the DDF4 dense phase pumps; it is particularly useful for plants performing more than ten colour change operations per shift.
The most frequent faults experienced by the DDF2 pumps, i.e. the generation before DDF4, are as follows:
• inconsistent powder flow;
• clogging of powder discharge tubes;
• contamination of vacuum control valves, leading to inconsistent powder delivery;
• with some types of powder, colour contamination caused by insufficient compressed air pressure for cleaning.
The causes of these problems are linked to two main factors:
• Powder quality: formulations containing a high percentage of particles smaller than 32 microns result in higher absorption of water from the air and, in general, greater chance of clogging. Formulations with a sticky nature can create small lumps, resulting in an uneven, poor-quality flow.
• Operating environment: DDF pumps can also operate in high-humidity and hot climates, and lumps may easily form if powders are not stored properly. Poor compressed air quality, e.g. contaminated with oil and water, makes it very difficult to transport dense powders. Although less severe with Venturi devices, this is a prevalent problem in many plants. Hot compressed air may not only cause clumps of powder to clog the tubes, but, in extreme cases, also dissolve the powder around pistons inside the pumps.
The DDF4 pumps’ design includes the following improved features: • improved seal and vacuum control to ensure reliable long-term
performance, especially when working with powders with poor particle size distribution;
• improved power feeding, internal movement, and powder discharge. The introduction of fluidised air in the lower part of the powder chamber has significantly improved the flow of powder out of the chamber, a crucial aspect when using coating systems with reduced thicknesses. In addition, the horizontal powder inlet allows for much smoother entry of the powder into the chamber;
• better consistency and uniformity of the powder flow. Thanks to a special pulsed air unit, the dense powder flows evenly from the pump to the guns. This is particularly useful when using powders with diversified particle size distribution;
• improved pump control. The installation of a single, more userfriendly, and reliable control mechanism enables DDF pumps to adapt to different types of powder;
• reduced downtime and pump operating costs. The removal of the
Y-tube in the DDF4 pump design has not only eliminated the cost of this component, but also significantly reduced the possibility of powder clogging in the tubes;
• improved design. The DDF4 powder pumps’ greater ease of use has significantly reduced their initial set-up time, but also maintenance downtime.
At the same time, some optimisation work should also be carried out by each customer to solve other issues, such as the presence of hot and contaminated compressed air.
For the delivery of high-density, low-speed powder coatings to be truly effective, compressed air must be dry, clean, and cool (>22 °C):
• Air humidity: 1.3 g/m3 (maximum)
• Oil content in the air: 0.1 g/m2 (maximum).
Gabriele Lazzari, ipcm® ipcm® Academy, which has been active for over ten years in the education of surface treatment professionals, has updated its programme for the training of new Industrial Surface Finishing Process Technologists.
ipcm® Academy, the training division of eos Mktg&Communication, the publisher of the ipcm® magazines, has presented the 2023 programme of its training course dedicated to the role of Industrial Surface Finishing Process Technologist, recently included in Lombardy’s Regional Framework of Professional Standards (QRSP).
It is still possible to obtain a 5% discount, when registering for either the complete course or some individual thematic days by 28 February 2023.
The quality and durability of a coating are closely related to the correct handling of its related surface finishing processes. “The causes of premature degradation of a coating can be traced back to various finishing issues such as, for example, the use of defective materials, inadequate technical specifications, a process that is not suited to
guaranteeing the expected durability, or even the improper use of the part. At the same time, all the players involved in the development and management of the finishing process, as well as in the final use of the component, may be responsible for its premature deterioration: designers, paint manufacturers, applicators, inspectors, maintainers, and users,” explains Paolo Rami, the ipcm® Academy director of studies and an expert in the design and approval of anti-corrosion systems as well as in the analysis of specific problems and defects in painting processes, also awarded a Merit for Labour.
Why undertake a training course Knowledge and careful control of the entire finishing process can therefore avoid or at least limit damages resulting from premature degradation of coatings.
or click the code to browse the 2023 training programme
“As there is no school for industrial painting and finishing technicians, our sector has suffered from a lack of qualified personnel for many years. At the same time, the new technologies and constantly changing regulations make it necessary to keep up-to-date professionally.
This is why, more than ten years ago, we inaugurated this course together with Paolo Rami and other industry experts, aimed at training all-round professionals capable of organising and managing production and process approval activities, defining protection and finishing processes, and performing requirement and technical reviews,” says Paola Giraldo, founder of ipcm® Academy. “We have already delivered over a thousand hours of theoretical and practical training, involving more than 150 companies. That is clear proof that the industry needs this.”
The training course for Industrial Surface Finishing Process Technologists is for as follows:
• coating operators;
• paint shop managers;
• technical sales employees at paint manufacturers;
• quality control managers;
• unemployed people;
• adult workers seeking vocational specialisation.
This year, as usual, the training consists of two sessions of 100 hours each: one is taking place from March 30 to June 15 and the other from September 21 to November 16. Each session consists of 12 days in total and it includes a theoretical part, in which specific topics are presented in depth, and a practical part with demonstrations and tests for quality control, through the use of professional tools and the control of samples, with the direct interaction of participants.
Upon completion, the trainees can sit the final exam, at the end of which, if successful, they are going to receive the Industrial Surface Finishing Process Technologist certificate valid at both the national and European levels.
In order to promote versatile training that is really close to the needs of individual participants, the courses are going to take place in hybrid mode, i.e. both in the classroom, at Innovhub’s headquarters in Milan, and online.
Revolutionary precision in automatic application brings efficiency to product customization. Dürr’s solution EcoPaintJet applies sharpedged paint lines on surfaces, pushing the limits for efficient and resource-saving coating: No overspray, no more masking of your product. www.verind.it
The exam sheet to become Industrial Surface Finishing Process Technologist.
Practical analysis of samples during the lecture dedicated to coil coating.
2023 lesson calendar
• Corrosion: 30 March / 21 September
• Pre-treatment: 13 April / 28 September
• Water treatment and purification: 20 April / 29 September
• Application of powder coatings: 4 May / 5 October
• Application of liquid paint: 11 May / 12 October
• Plastic painting: 12 May / 13 October
• Controls: 17 May / 18 October
• Control methods, tools, and practical tests: 18 May / 19 October
• ACET test and visit to Innovhub labs: 19 May / 20 October
• Plants and equipment: 25 May / 26 October
• Failure analysis: 8 June / 9 November
• Documentation, process control, and management of investments and practical activities: 14 and 15 June / 15 and 16 November
• Coil coating: 22 June / 23 November
This edition of the ipcm® Academy course also includes two topics that are not mandatory parts of the complete course. Since the first session of 2022, our course has been including a training day focusing on the painting of plastics, a subject that is now very relevant in the field of surface coatings. This additional lesson provides an overview of the market and an in-depth look at the currently available thermoplastic and thermosetting coatings, coating cycles, main suppliers, equipment characteristics, cleaning operations, pretreatment, application, and curing processes, environmental impact, controls, and plant solutions.
A lecture has also been added about continuous-flow coil coating, an advanced surface finishing process used for various metal substrates such as steel and aluminium, with an output of several million square metres per year. The process is presented in all its details, from the definition of the product in terms of
metal quality and the pre-treatment operations required to the type of paint to be used. In addition, a visit to the control laboratories offers the opportunity to see the characteristics of paint products first-hand and analyse different types of finished products.
In addition to attending the entire training course, this year too ipcm® Academy offers a further option: enrolling in individual thematic days, after which a certificate of attendance is issued.
ipcm® Academy can also organise customised courses to be held at the premises of interested companies with particular needs for the professional training of their staff.
Thanks to its collaboration with ASP Mazzini, accredited by the Lombardy Region for the provision of training and orientation services located in Cinisello Balsamo (Milan), the training courses offered by ipcm® Academy can count on various financing options:
• Training vouchers made available by the Lombardy Region and activated directly by companies;
•Training financed by the endowment system of the Lombardy Region for unemployed or redundant persons;
• Interprofessional funds, through company membership and participation in company and intercompany training plans.
For further information: https://ipcmacademy.com or send an e-mail to: corsi@ipcm.it
“He who works with his hands is a labourer. He who works with his hands and his head is a craftsman. He who works with his hands and his head and his heart is an artist.”
Saint Francis of AssisiFor over three years now, our magazine has been investigating the relationship between the surface treatment industry and art. Last December, ipcm® and eos Mktg&Communication, the publishing house of our magazines, had the opportunity to play an active role in a high-profile art exhibition for the first time, becoming its sponsor: “Poesia Geometrica: l’arte come atto vitale” (i.e. “Geometric Poetry: art as a vital act”).
Held from 3 to 24 December 2022, then extended until 31st December, in the old parish church of Urago Mella (Brescia, Italy), this solo show brought together the works realised from 2020 to 2022 by Giovanni Lamberti, AKA Le Rond, already the protagonist of several articles published on these pages1. Aimed at reflecting this Brescia-based artist’s aesthetic development over the last two years, the exhibition was part of the broad range of events connected to the appointment of BresciaBergamo as Italy’s Capital of Culture for 2023.
One of the reasons why Le Rond’s artistic world is so fascinating can be traced right in the works on display in this exhibition, characterised by the perfect balance between “concrete and exact forms, with a clear geometric and rational imprinting” – as Giovanna Galli stated in the critical comment she wrote for the show’s catalogue2 – and by the willingness to communicate through colour, “double knotted to the works’ purely aesthetic content, but also emotional and playful, thus promoting interpretative freedom within an unavoidable relational dimension.” Such a dimension was made even more evocative by the location chosen for this solo exhibition: a restored 17th-century parish church, in which Lamberti’s works were perfectly integrated through their balance between shapes and colours.
1 https://www.ipcm.it/en/open/ipcm/2020/61/148-150.aspx
https://www.ipcm.it/en/open/ipcm/2021/68/142-144.aspx
https://www.ipcm.it/en/open/ipcm/2022/76/116-118.aspx
2 “Giovanni Lamberti: poesia geometrica, l’arte come atto vitale – opere e progetti 2020-2022”, Intese Grafiche Srl, November 2022.
Throughout his production, Le Rond has always had a predilection for wood and metal (iron). For this exhibition, the artist transformed wood recovered from marble quarries in the surrounding area into artistic objects, emphasising his deep connection both with his roots and with this material, which lends itself to various poetic interpretations, be it raw or treated and painted. On the other hand, metal, which evokes the craftsmanship and the industrial processes that can be observed in a foundry, had a double value in this solo show: in addition to being the constituent material of most of the works on display, it was also chosen for the exhibition’s display supports. Indeed, with the exception of the largest ones (about 2 m), which were placed on the ground, all the works of art presented were positioned on special “suspended” modular metal
structures in harmony with each other, designed by architect Stevan Tesic from Studio Di_archon_ass, the curator of the exhibition’s set up.
One of the most significant pictorial elements of Le Rond’s artistic research is colour, as Galli pointed out in her critical comment: “[…] the most solid pictorial foundation of his research is colour, almost always highlighted through monochromatic choices, which were previously restricted to primary colours but are now open to a wider range.” The artist uses this element to enhance shapes, surfaces, and volumes and to bring out “spaces, perspectives, movement, environments, and interaction within a precise vision of art as a vital act that implies a continuous exchange of stimuli and responses, of actions and reactions, of rules and exceptions.”
In one of his last interviews, Lamberti emphasised that for him art is “a means of building the world, through the creation of sculptural works that look out at us every day, reminding us of the beauty and work of the human being as a builder.”3
With the works on show in this solo exhibition, Le Rond was able to 3 https://www.ipcm.it/en/open/ipcm/2022/76/116-118.aspx
go beyond the simple juxtaposition of geometries and colours and to provoke visitors by playing with his interpretative skills, while keeping his gaze focused not only on the origins of his chosen materials, but also on his surrounding environment. The continuous cross references between ancient and modern, craft and industry, art and play, and perfection and imperfection of forms make his artistic research increasingly immersed in a poetic and surprising vision of the world.
For further information: www.lerond.it © ipcm © ipcm
One of the works in the solo exhibition “Geometric Poetry: art as a vital act” by Le Rond.
One of the most significant elements of Le Rond’s artistic research is colour.
LR is one of the exhibited works made of recycled wood from marble quarries and coated with water-based impregnating agent.
UCIF – Italian Surface Treatment Equipment Manufacturers’ Association Milan, Italy info@ucif.net
Especially at this time of year, when beginning to draw up our plans for the future, we all tend to compare past and present and try to learn from our experience in order to improve ourselves or, at least, not to make the same mistakes again. Time, understood as the past, leaves indelible traces in our lives. This applies to every human being, regardless of their characteristics, let alone their job or social background. Despite seemingly too philosophical, this concept is actually applicable to our lives on a daily basis, albeit in an abstract way (memories, teachings, the “hard knocks” of life...). However, there is one particular manufacturing field that deals with the “marks of time” to ensure that they are as few as possible or even to prevent them at all. It is the finishing sector.
Treating a surface is not just about giving it a colour or making it less rough. It means lending it a longer life, prolonging the freshness of a product while also improving its aesthetics and often its functionality. The best example of this are cars. When we buy a new car, we can choose its colour and the related paint, but it is actually not just about the “coating”: the body is first pre-treated to prevent future damages and colour fading over time. How many adverse phenomena will that car experience? Rain, hail, summer heat... In the course of its service life, it will be subjected to temperature fluctuations of up to 40-50 °C (at least in Italy) and its body, suitably pre-treated and processed, will have
to ensure that its external conditions are maintained over the years, if not decades. This does not apply only to cars, but also, in general, to products subjected to industrial processes that involve surface treatments such as shot blasting or vibratory finishing. The finishing sector, whose manufacturers are represented in Italy by the UCIF association, is therefore driven by a focus not simply on coatings, but rather on performance and durability. In terms of industrial activities, this requires a lot of effort in research and development both of materials and chemicals, a commitment to increasingly improve pretreatments, and above all the ability to analyse and understand each finished product’s intended environment, since external conditions are going to be the main cause of changes in its properties (exterior characteristics and durability). Anti-corrosion research alone is crucial to guarantee product durability. Just think, for example, of train carriages spending most of their service lives outdoors, subjected to atmospheric agents of all kinds.
However, time is not only a cause of indelible traces, but also a source of experience that enriches today’s knowledge. UCIF is well aware of this, as it turns 50 in 2023, with a series of events already being planned to celebrate. Because we can always learn from time and never stop improving ourselves.
After the success of the last edition, the Polish trade fair dedicated to corrosion protection technologies and surface treatments will come back for four days.
EXPO-SURFACE, the most important exhibition dedicated to corrosion protection technologies and surface treatments in Central and Eastern Europe, has proudly announced that it is growing: as a matter of fact, the 2023 edition will last four days – from 28th to 31st March 2023 at Targi Kielce in Poland.
As part of the series of industrial exhibitions held under the STOM banner, EXPO-SURFACE has become a permanent point in many calendars belonging to industry experts. The event has proven hugely popular: even the harsh pandemic time did not diminish the expo cycle’s importance. The 2022 expo brought together 500 exhibitors who used all 7 exhibition halls. Dozens of companies from Poland, Italy, Germany, Greece and several other countries presented their offering at EXPO-SURFACE.
Visitors were able to hear guests speaking in many different languages and virtually all corners of the world were represented. The three expo days of 2022 welcomed almost 10,000 industry visitors so, according to the exhibitors’ suggestions, the management of the Kielce exhibition and congress centre resolved to extend the duration
of the exhibition for this year. EXPO-SURFACE 2023 will offer a wide scope of products and services, meeting the expectations of surface protection specialist. The products and services showcased will range to include technologies and devices for protective coatings applications, equipment for cleaning and preparing surfaces, specialist chemicals, varnishing, enamelling and plastic coating equipment, equipment for chemical and thermal surface treatment, laser and plasma technologies for surface coating, devices for thermal spraying, special surface treatment systems, measuring and control devices and research equipment. In addition, the event will also host service providers, research organisations and industry institutions presenting new solutions for anti-corrosion insulation and innovative materials. EXPO-SURFACE is complemented and enhanced with the events organised by the “Industrial Varnishing” portal, which offer a valuable substantive and practical dose of knowledge
For further information: www. expo-surface.com
After four years, the European Coatings Show will once again support the international dialogue among experts from the paints and coatings sector from 28th to 30th March 2023 in Nuremberg (Germany).
From 28th to 30th March 2023, the coatings community will reunite at the Exhibition Centre Nuremberg (Germany) for the European Coatings Show.
Finally, the trade fair will once again provide a platform for industry stakeholders for whom making business contacts, face-to-face encounters and networking are indispensable. Whether their focus is on paints, printing inks, laboratory, production testing, measuring equipment, adhesives or construction chemicals,
trade visitors can look forward to specialised suppliers from all around the world and a very extensive range of products. As the gathering place for the coatings industry, the event will present ground-breaking trends and allow visitors to find out about the latest formulations, process and equipment technology and reap the benefits of exchanging experiences with like-minded professionals. As a matter of fact, the exhibition will provide plenty of input about key topical issues like the shortage of raw materials and their rising costs.
In addition, with more than 140 presentations, the semi-parallel European Coatings Show Conference on 27th and 28th March will offer intensive knowledge transfer, as high-calibre speakers will once again offer interesting insights into a wide range of topics.
The opening keynote will be by Wijnand Bruinsma from Akzo Nobel on the topic: “The role of paints and coatings in a sustainable future.” One other session is devoted to the results of The Decoat Project, an international research partnership funded by the EU which is developing a solution to facilitate the use of textiles and plastic components with (multilayer) coatings according to the closed loop recycling principle.
The nine pre-conference tutorials on the Sunday, 26th March – conducted by renowned experts – will quickly bring newcomers to the field up to speed with the state-of-the-art and offer a good preparation for actively participating in the subsequent conference.
Following an intensive first day at the European Coatings Show Conference, the after-work reception offers additional scope for personal dialogue. In a relaxed atmosphere, participants can chat to the speakers
and build up their network with other experts from the coatings industry.
The European Coatings Show 2023 will occupy a total of eight exhibition halls, six of which will be dedicated to raw materials for paints, printing inks and adhesives, construction chemical precursors and associated services.The Start-up Area in Hall 2 allows start-ups and young companies from Germany and other countries to present their services and product innovations to the professional audience at reduced rates. Additional presentations in the exhibitor forum in Hall 3 will provide further insights into the start-up scene of the paints and coatings sector. Furthermore, this area will allow to share expertise in more than 140 product presentations combined into 24 sessions.
Finally, Hall 4 will put the spotlight on laboratory and production technology, testing and measuring systems, application technology, environmental protection and occupational safety.
For further information: www.european-coatings-show.com
The event held in Atlanta has witnessed an increase in attendance, exhibitors and show floor size.
FABTECH 2022, North America’s largest metal forming, fabricating, welding and finishing event, made its return to Atlanta and welcomed attendees from around the world for three days of ground-breaking innovations, inspiring keynote presentations and solution-based education sessions for the global metal fabrication community.
From November 8-10, nearly 30,000 attendees – an increase of 22.6% over the 2021 event –from 70 countries and all 50 states gathered at the Georgia World Congress Center to meet with world-class suppliers, conduct product evaluations, network with peers and find the tools to improve productivity and increase profits. Four expansive exhibit halls covering 610,000+ square feet of exhibit space featured nearly 1,200 exhibitors, including 150 making their debut at FABTECH, all highlighting the emerging trends and technologies influencing the future of manufacturing.
“Thank you to everyone who joined us in Atlanta to make FABTECH 2022 a complete success,” said John Catalano, SME senior director US events and strategic partnerships, FABTECH. “FABTECH was nearly back to pre-pandemic attendance numbers and saw increases across the board over 2021 with more attendees, more exhibitors and a bigger show floor. Year after year, FABTECH continues to be our industry’s leading event by providing the latest insights and trends, attracting key decision makers and buyers, and showcasing the most innovative technologies shaping the future of manufacturing.”
The energy at FABTECH 2022 was high, and sales activity was strong each day on the busy exhibit floor. The show floor was 19.5% larger than in 2021 and welcomed over 30% more exhibitors. Attendees explored eight technology
pavilions covering four halls that focused on 3D/Additive Manufacturing, Forming & Fabricating, Finishing, METALFORM, Tube/Pipe, Robotics and Industrial Automation, Welding and Welding Automation. FABTECH also saw the return of many exhibitors to its welding pavilion, which featured approximately 350 companies, including industry leaders Lincoln Electric, IPG Photonics, FANUC America Corp, OTC DAIHEN Inc, Path Robotics, and Miller Electric Mfg LLC.
“FABTECH 2022 was the most effective tradeshow we’ve exhibited at in close to a decade! Not only the volume of traffic, but the quality of the attendees exceeded our expectations and we’re looking forward to replicating that success in 2023 in Chicago,” said Josh Dixon, COO at Beckwood Press Company.
“Abagy Robotic Systems participated for the first time in the FABTECH expo and conference, and we were really impressed with the quality of attendees and the level of organization. We had a great response from hundreds of manufacturers and have already booked our booth space for the next show in Chicago”, said Kate Degai, CMO at Abagy Robotic Systems.
FABTECH featured an inspiring line-up of special events, including keynote presentations and FABx Tech Talks that addressed the emerging trends, innovations and challenges impacting the industry today. Attendees walked away with insights into today’s pressing topics— from cutting-edge technology and the latest manufacturing processes to building successful businesses and rethinking leadership, change management, and risk. Speakers included Brad Keselowski, owner of Keselowski Advanced
Manufacturing and NASCAR champion, and Jake Wood, executive chairman of Team Rubicon and founder/CEO of Groundswell. The FABx Tech Talks featured speakers Gillen Young, chief architect of IIOT Solutions at AT&T, Richard Boyd, CEO of Tanjo AI; and Bryce Austin, CEO of TCE Strategy, with a special appearance from Bill Carlton, owner/mastermind of Ekstensive Metal Worlds. Additional special events included: The daily Leadership Exchange Panels included groups of subject matter experts who will discuss the next phase of advanced manufacturing, how innovation is key to outperforming the competition, tactics for cultivating the next generation of manufacturing talent and how to protect your company from a cyber security threat. Wednesday’s sold-out Women of FABTECH breakfast featured three inspiring leaders in manufacturing—Shelly Foland, CEO of Softies, Holly Gotfredson, president of American Metalcraft, Inc./Finishing Dynamics; and Lisa Winton, CEO and co-owner of Winton Machine—who covered manufacturing trends, marketing strategies and real-world examples of their experiences as women leaders. During Thursday’s State of the Industry session, Omar Nashashibi,
founding partner of The Franklin Partnership, provided a post-election analysis and the impact of the results on tariffs, taxes, trade negations, regulations, and workforce training. He also offered an overview of the priorities for the upcoming session and a 2023 outlook for the manufacturing industry.
FABTECH 2022 also offered over 150 carefully curated education sessions led by industry thought leaders and subject matter experts. The program spanned 16 technology tracks with sessions focused on automation, smart manufacturing, welding, cutting, lasers, workforce development, business management strategies and more.
“This was my first time attending FABTECH and I was very impressed by the quality of information shared by the presenters during the conference sessions. I look forward to attending FABTECH again in the future,” said Rebeca Hernandez, a mechanical engineer at Republic Manufacturing. FABTECH 2023 is set to take place on September 11-14 in Chicago, with registration expected to open in the spring of 2023.
For further information: www.fabtechexpo.com
Eos Mktg&Communication srl www.eosmarketing.it - info@eosmarketing.it www.myipcm.com - info@ipcm.it
Redazione - Sede Legale: Via Pietro Mascagni, 8 - 20811 - Cesano Maderno (MB) - Italy Tel. +39.0362.503215 - Fax. +39.0362.1794768
Prof. Massimiliano Bestetti: Department of Chemistry, Material and Chemical Engineering, Politecnico of Milan –Section of Applied Chemistry and Physics
Prof. Paolo Gronchi: Department of Chemistry, Material and Chemical Engineering, Politecnico of Milan –Chemical Engineering Section
Kevin Biller: ChemQuest Powder Coating Research
EDITOR IN CHIEF / DIRETTORE RESPONSABILE
ALESSIA VENTURI venturi@ipcm.it
EDITORIAL DIRECTOR / DIRETTORE EDITORIALE
FRANCESCO STUCCHI stucchi@ipcm.it
EDITORIAL OFFICE / REDAZIONE
PAOLA GIRALDO giraldo@ipcm.it
MONICA FUMAGALLI fumagalli@ipcm.it
NICOLE KRAUS kraus@ipcm.it
MATTEO SOTTI sotti@ipcm.it
BARBARA PENNATI pennati@ipcm.it
ILARIA PAOLOMELO paolomelo@ipcm.it GABRIELE LAZZARI redazione@ipcm.it
EDITORIAL OFFICE AND GRAPHICS
ELISABETTA VENTURI grafico@ipcm.it
MEDIA SALES
FRANCESCO STUCCHI stucchi@ipcm.it
BARBARA PENNATI pennati@ipcm.it
ILARIA PAOLOMELO paolomelo@ipcm.it
NICOLE KRAUS kraus@ipcm.it
SVEN KRAUS sven.kraus@ipcm.it
CLAUS GÖRLICH goerlich@ipcm.it
This magazine is wrapped with a biodegradable and compostable film. Questa rivista è confezionata con un film biodegradabile e compostabile.
ELISABETTA VENTURI grafico@ipcm.it
PRINT/ STAMPA ROTOLITO SPA info@rotolito.com
Prof. Stefano Rossi: Material Engineering and Industrial Technologies, University of Trento - Product Design
Dr. Fulvio Zocco: Environment and quality
SUBSCRIPTION SERVICE - SERVIZIO ABBONAMENTI: Sale only on subscription - Vendita solo su abbonamento E.mail info@ipcm.it Subscription Rates 2023 - Tariffe Abbonamento 2023:
Annual subscription print + digital: EMEA 110,00 € (postage included)
Rest of world 350,00 € (fast airmail shipping included)
Abbonamento annuale cartaceo + digitale: EMEA 110,00 € (spese postali incluse)
Resto del mondo 350,00 € (spedizione via aerea inclusa)
Single copy: 15,00 € EMEA (postage included) - Rest of world (postage excluded)
Back issues: 30,00 € EMEA (postage included) - Rest of world (postage excluded)
Fascicolo singolo: 15,00 € EMEA (spese postali incluse) - resto del mondo (spese postali escluse)
Arretrati: 30,00 € EMEA (spese postali incluse) - resto del mondo (spese postali escluse)
Subscriptions can be made by bank transfer to the following account: Eos Mktg&Communication Srl IBAN IT97F0844033270000000084801 - SWIFT CODE CRCBIT22 or via payment online at: www.myipcm.com
Gli abbonamenti possono essere sottoscritti versando il relativo importo a mezzo b/b IBAN IT97F0844033270000000084801 intestato a eos Mktg&Communication Srl oppure con carta di credito direttamente dal sito www.myipcm.com L’Iva sugli abbonamenti, nonchè sulla vendita di singole copie è assolta ai sensi dell’art.74 comma 1 lett. C DPR 633/72, DM 29/12/1989.
Registrazione al Tribunale di Monza N° 1970 del 10 Dicembre 2009Eos Mktg&Communication srl è iscritta nel Registro degli Operatori di Comunicazione con il numero 19244
POSTE ITALIANE S.P.A. – SPEDIZIONE IN ABBONAMENTO POSTALE –D.L. 353/2003 (CONV. IN L. 27/02/2004 N.46) ART. 1, COMMA 1 LOM/MI/4351
It is forbidden to reproduce articles and illustrations of “ipcm®” without authorization and without mentioning the source. The ideas expressed by the authors do not commit nor magazine nor eos Mktg&Communication S.r.l and responsibility for what is published is the authors themselves.
È vietata la riproduzione di articoli e illustrazioni di “ipcm®” senza autorizzazione e senza citarne la fonte. Le idee espresse dagli autori non impegnano nè la rivista nè eos Mktg&Communication S.r.l e la responsabilità di quanto viene pubblicato rimane degli autori stessi.