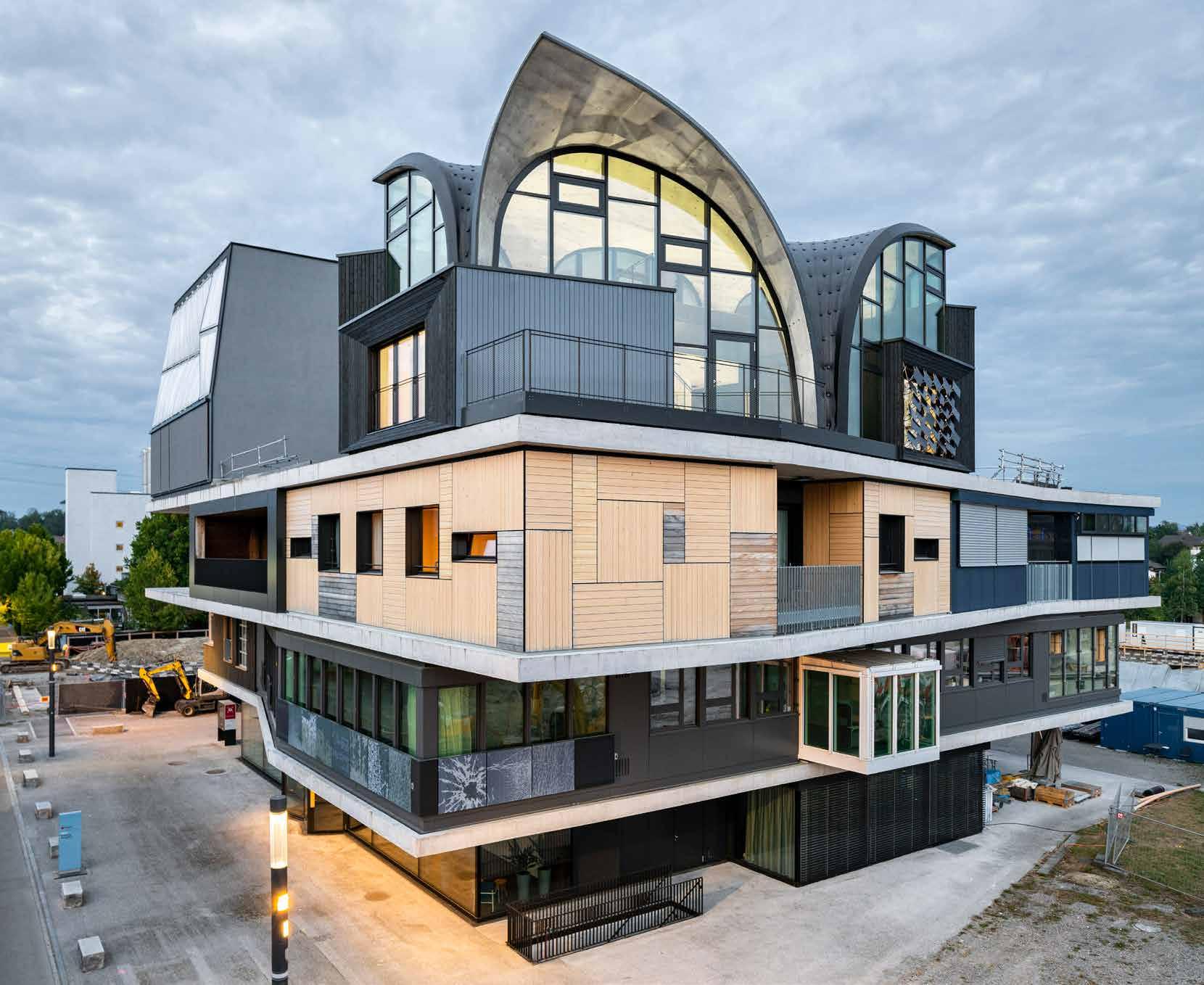
5 minute read
HiLo opened
from IM20215EN
The HiLo unit sits on the top platform of the NEST (Photo: Roman Keller)
HiLo, the latest addition to Empa and Eawag’s NEST research building in Duebendorf, Switzerland officially opened on October 6. The innovative unit illustrates nearly a decade of formative ETH Zurich research in architecture and sustainable technologies.
Advertisement
NEST is the modular research and innovation building of Empa and Eawag. At NEST, new technologies, materials and systems are tested, researched, further developed and validated under real conditions. Close cooperation with partners from research, industry and the public sector ensures that innovative construction and energy technologies are put onto the market faster. HiLo stands for ‘high performance - low emissions’. The unit allows researchers to test how the construction and operation of buildings can be designed to be as energy- and resource-efficient as possible. HiLo combines ancient building principles with futuristic construction methods: doubly curved concrete roof and novel, lightweight funicular floor system was inspired by construction methods of the past, and planned and built using state-of-the-art computational design and fabrication techniques. In the new unit, a team of scientists led by Philippe Block, Professor of Architecture and Structures, and Arno Schlueter, Professor of Architecture and Building Systems together with industrial partners explored how lightweight structures and efficient construction methods can be
A tensioned cable net was used as the primary structure of the formwork of the doubly curved HiLo roof (Photo: ETH Zurich, Block Research Group/ Juney Lee)
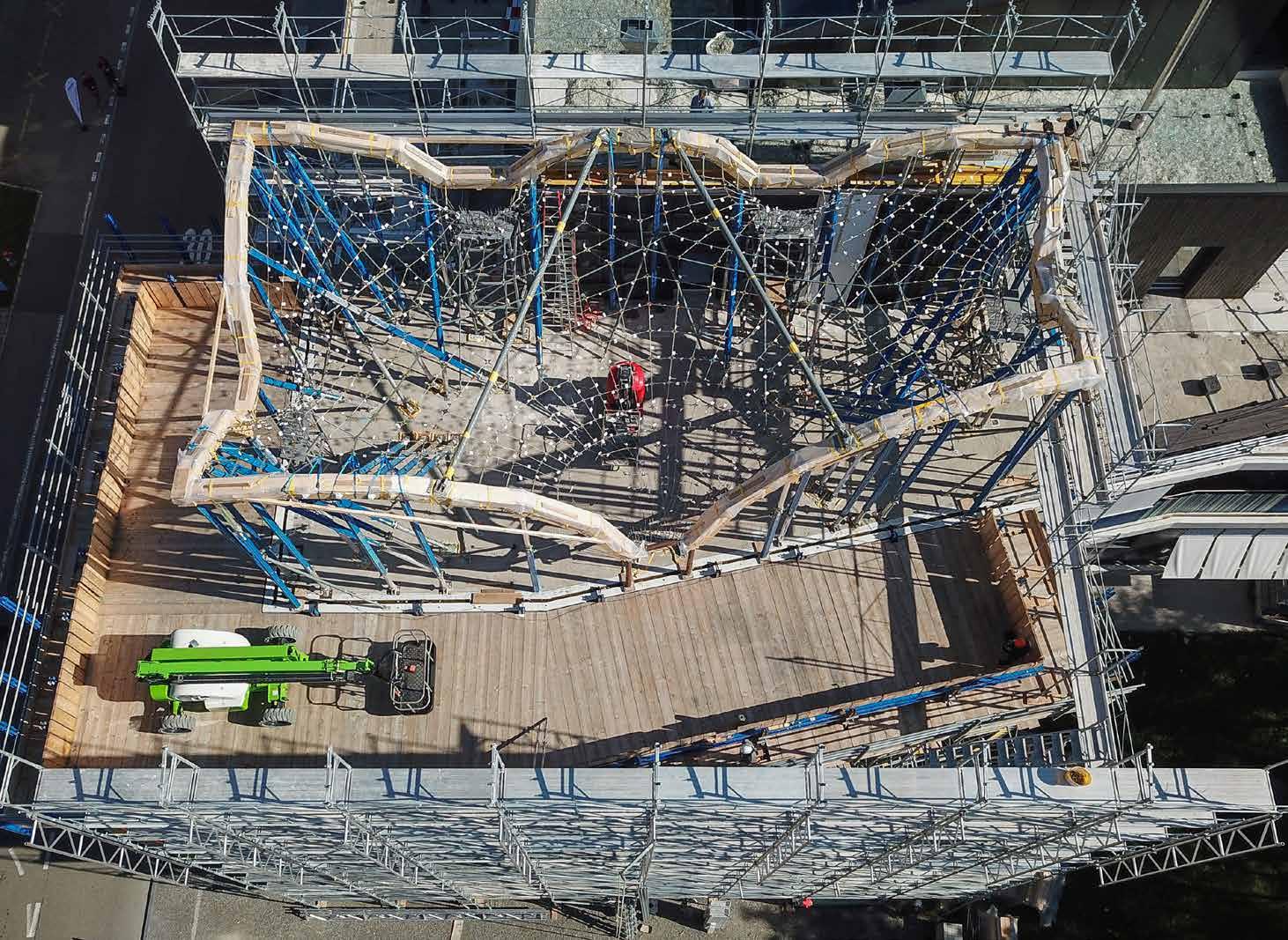
combined with intelligent and adaptive building systems to reduce both embodied and operational emissions in the construction and building industry.
Flexible formwork
The roof of the HiLo unit derives its load-bearing capacity from a strongly curved geometry in combination with a concrete sandwich structure, made of two thin layers of reinforced concrete, connected by a grid of concrete ribs and steel anchors.
In order to save large amounts of formwork material, the roof was built with a flexible formwork consisting of a tensioned cable net and textile fabric. In the construction of double-curved structures, complex and single-use wooden or EPS formwork are often used. Instead, the HiLo roof was made using a huge, reusable scaffolding structure, within which a network of steel cables was stretched. This steel net supported a (polymeric) textile layer, which in turn was covered by textile reinforcement. This created a kind of mold onto which the concrete was sprayed. The cable net was designed to take on the desired shape under the weight of the wet concrete, thanks to a calculation method developed by the Block Research Group and their collaborators in the Swiss National Centre of Competence (NCCR) in Digital Fabrication. The
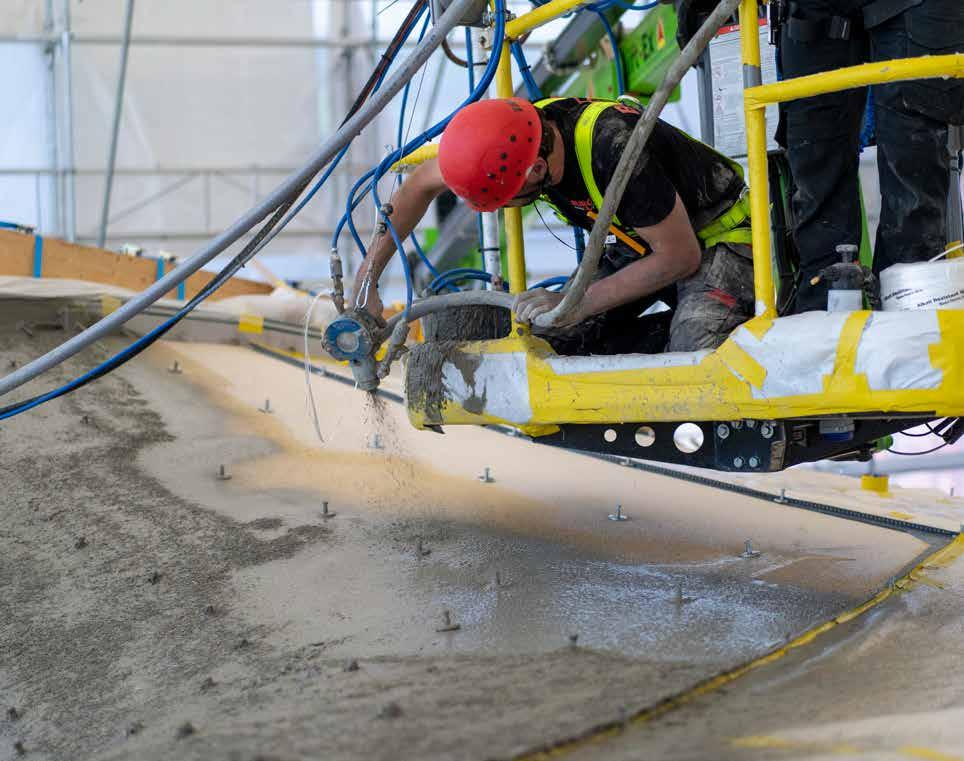
The first layer of concrete is sprayed onto the textile formwork (Photo: ETH Zurich, Block Research Group/Juney Lee)
algorithms ensure that the forces are distributed correctly between the individual steel cables and the roof assumes the intended shape precisely.
Less material
For the mezzanine floors of the twostorey unit, the researchers primarily aimed to use as little material as possible in the structure itself. By using a ribstiffened funicular shell instead of a flat plate, HiLo’s lightweight funicular system uses over 70 percent less material than conventional floor slabs in reinforced concrete. Furthermore, digital production methods allowed the integration of ventilation, cooling, and low temperature heating systems into the floor structure for an even greater reduction in materials and volume.
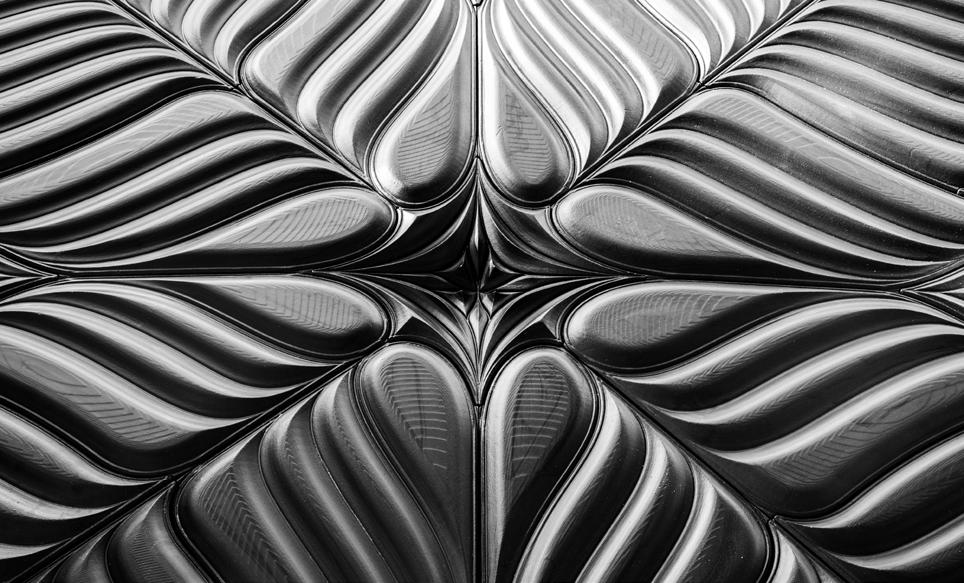
Indoor climate regulation
The HiLo unit is also equipped with an adaptive solar façade developed by Schlueter’s group. It consists of 30 photovoltaic modules that can be aligned with the sun. The flexible modules can also be used to control how sunlight enters the room in order to passively heat it or reduce cooling requirements. The adaptive solar façade is one of a series of innovative building technology components designed for efficient indoor climate regulation. During operation, the researchers consistently optimised the interplay of the individual technologies using machine learning and considering the users, in order to investigate how comfortable indoor conditions can be achieved with as little energy and emissions as possible.
Empa>
Virtual tour>
The 3D-printed formwork for the rib-stiffened funicular floor on the east side (Photo: ETH Zurich, Digital Building Technologies/Andrei Jipa)

How long can fibre reinforced polymer sustain concrete structures?
Fibre reinforced polymer coatings (FRP) are an affordable way to externally strengthen concrete structures. But how long does the protection last? Now, researchers from Korea and the USA conduct a 13-year long experiment to find out. In the FRP-strengthening of concrete, glass or carbon fibre reinforced polymer (GFRP or CFRP) composites are bonded onto concrete using an epoxy adhesive. These sheets provide additional support and strengthen the concrete structures by protecting them from harsh environmental conditions, such as high moisture levels and temperatures. But the problem is, these same environmental conditions can potentially degrade the concrete-FRP bond as well, causing the FRP protection system to fail prematurely. A research team from the Korea Maritime and Ocean University (KMOU), led by prof. Jaeha Lee of civil engineering, tested both CFRP and GFRP systems under various indoor and outdoor environmental conditions for change in a parameter called the debond onset strain. This is a measure of the deformation that occurs before failure. They found that environmental conditions had a significant impact on bond behaviour. At the end of thirteen years, larger reductions in debond strains were observed in outdoor beams than indoor beams. Further, the bond behaviour varied between materials: changes in debond strain were negligible in indoor CFRP beams, while in indoor GFRP beams, there was a notable decrease. The researchers expect their findings could ultimately help to cost-effectively minimize the risk of collapse or damage to existing structures.
More at KMOU>
The findings were recently published in Composites Part B: Engineering, titled ‘Durability assessment of FRP-concrete bond after sustained load for up to thirteen years’. DOI: https://doi.org/10.1016/j.compositesb.2021.109180
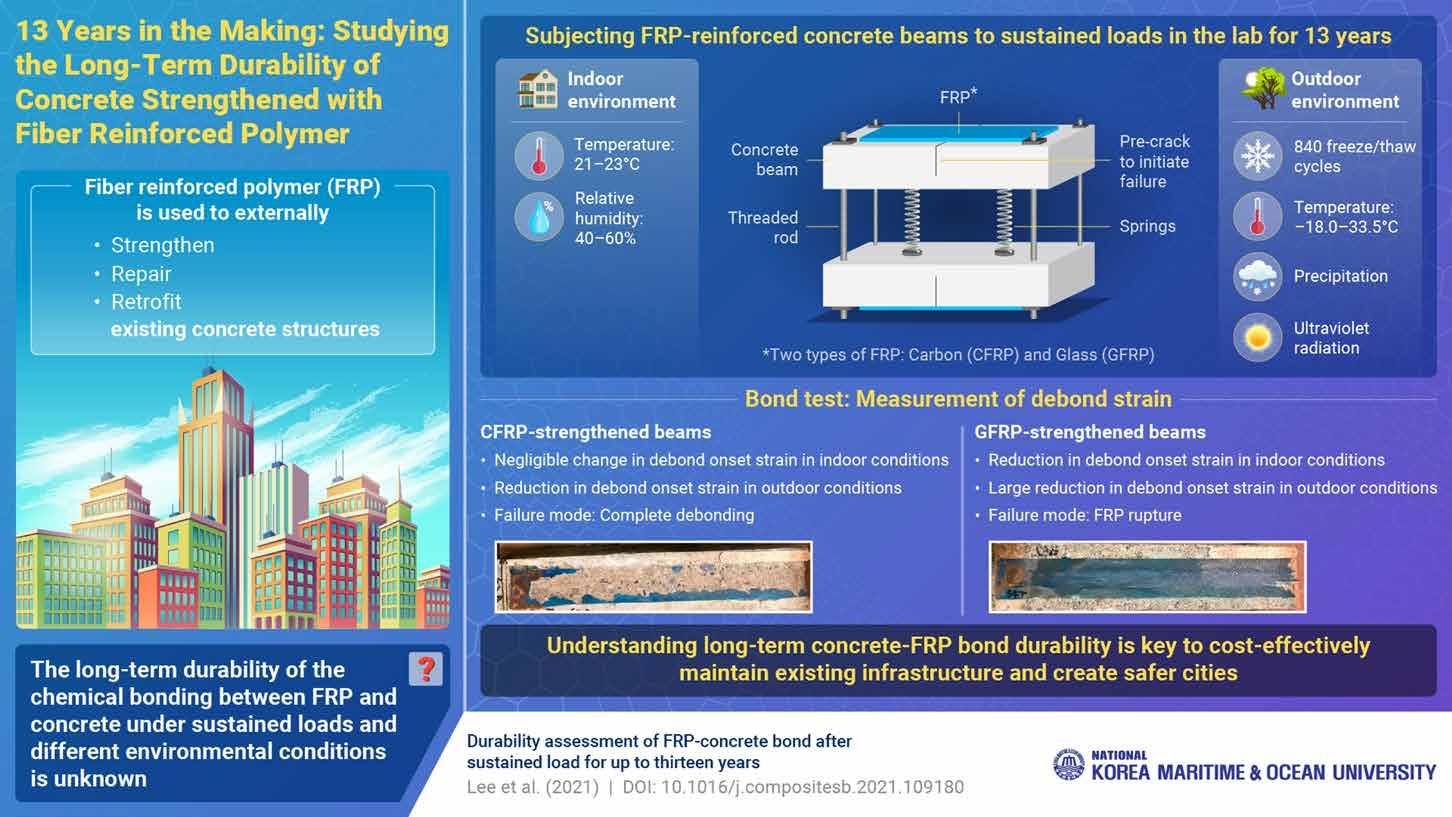