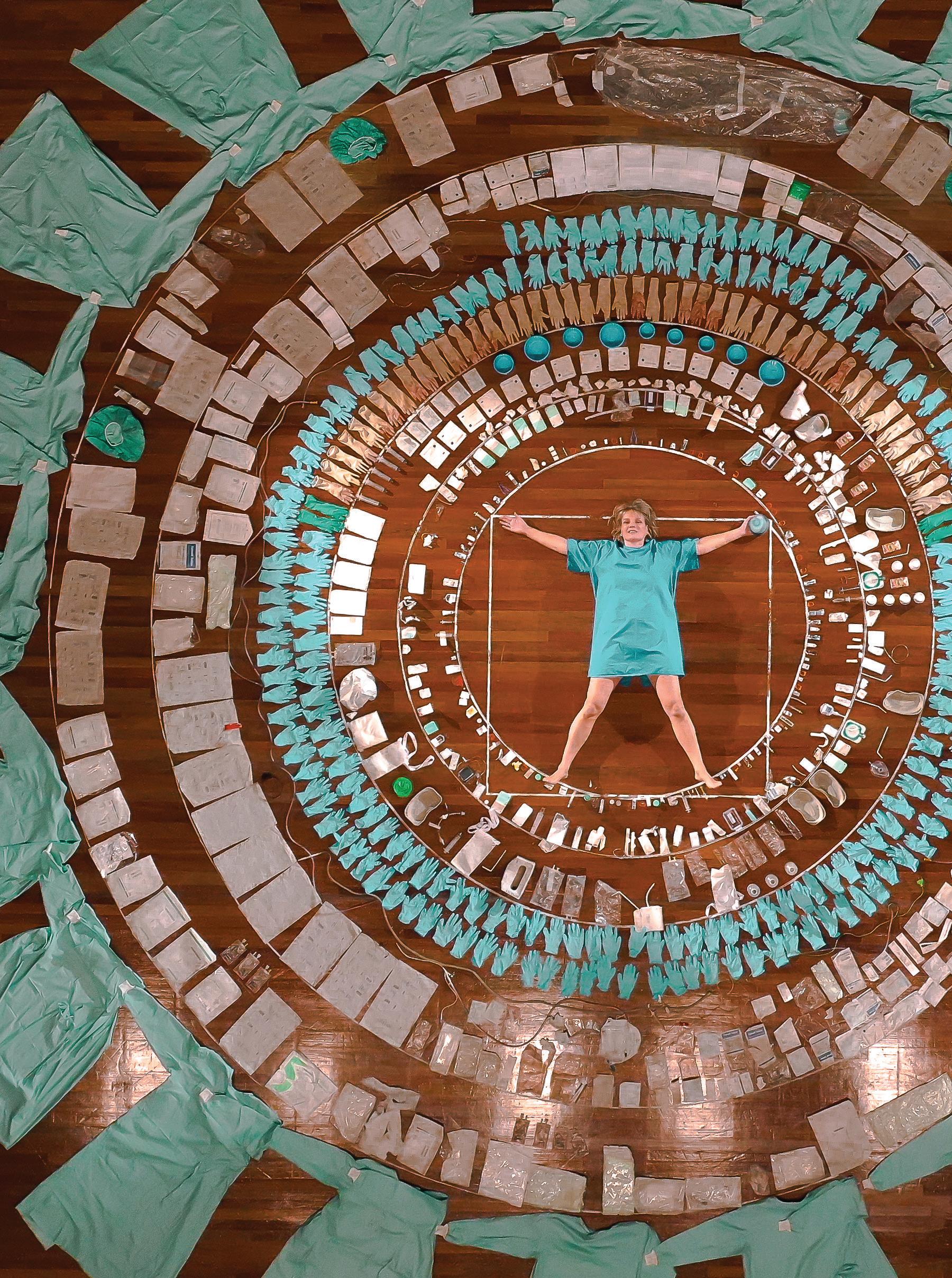
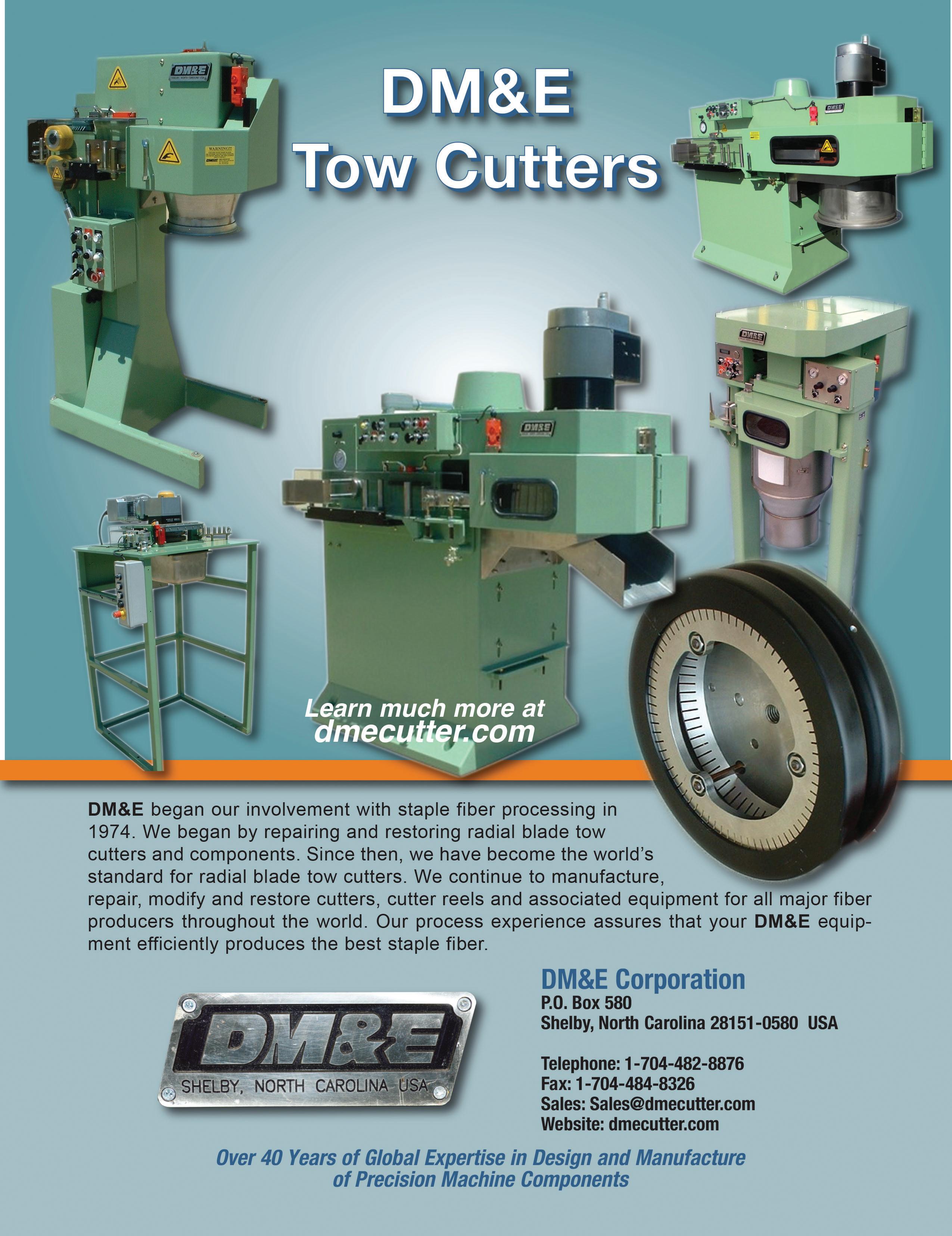
VacuFil is a PET recycling line with direct feed to your spinning line or pelletizer. Developed by real spinning experts and equipped with the Visco+ unit for the requested IV-boost and homogenous melt VacuFil ensures the exact melt quality you need – reliable and reproducible!
IV-increase up to 30%
IV-homogeneity
Compact size
Spinnability POY, DTY, FDY, BCF
Patent pending
14
View short film at https://youtu.be/w28M7wjIr6E
Koijck says: “My goal with this film was to create a movement within the medical and surgical industry, considering the waste it produces. The film has reached over one million views worldwide! You see me laying in the middle of an incredible amount of waste from just one surgery, my surgery. In 2019, I was diagnosed with breast cancer, which required removal of my entire left breast. After a successful recovery, I had another surgery to give me an entire new breast made from my own bodily materials.
I am so grateful for the chance to feel beautiful again, but during this process I discovered that 60% of the surgery materials used are disposable. I asked the doctors to collect all of the materials used for my operation. I was in shock to receive six bags full of plastic waste from this one operation.
14 10 20
Reducing Fugitive Microplastic Pollution – Q&A with Andrea Ferris
By Caryn Smith, Chief Content Officer &The Green Factor Grows at INDEX™23
Publisher, IFJ
Power in the Punch – DILO Launches
New MicroPunch Needling
By Caryn Smith, Chief Content Officer & Publisher, IFJ
Industrial Advantages to 3D Printing
By Adrian Wilson, IFJ International Correspondent
Textile Solutions for Medical Devices
By Geoff Fisher, European Editor, IFJ
Textile Recycling: State of Play
By Marie O’Mahony
34 38
Advances in Bio-Based Fibers
By Jason Chen, IFJ International Correspondent
Potential in Bio-Based Fibers & Yarns
By Chris Plotz
SHOW PREVIEW: Dornbirn
6
Make Good Choices
By Caryn Smith, Chief Content Officer & Publisher, IFJ
Tech Spotlight
Nefab’s GreenCalc™ Tool
Tech Notes
New Technology Briefs
Tech Talk
Advancements in Advanced Textiles Sector
By Dr. Seshadri Ramkumar, Ph.D., Texas Tech University
Movers & Shakers
26 24 COLUMNS & DEPARTMENTS 7 46 24 30
Industry News and Notes
We are making the best synthetic textile facilities through the power of Korea in global competition
Applications
Multi Filament Line(PA, PET, PP, Bi-Component)
- High Speed Spinning(POY, FDY, SDY)
- Micro Fiber Spinning
- Bi-Component Conjugate Spinning
Staple Fiber Line
• Industrial Yarn
• Textile Yarn
• Sewing Yarn
• Carbon Fiber
• Lyocell
• Aramid Fiber
• Acrylic Fiber
• Spandex Yarn
International Fiber Journal is actively seeking contributed technical articles from qualified industry professionals and those allied to the fiber industry. If you would like to pitch an article for publication in IFJ , please contact Caryn Smith at csmith@inda.org
Annual textile yearbook covering natural and manmade fibers, feedstocks, nonwovens, trade data, 20 country profiles and a wealth of further information helping to conduct business.
In addition, major associations and industry experts provide their views on the markets.
Publication: May 2023
https://thefiberyear.com/ info@thefiberyear.com
RESEARCH, INNOVATION & SCIENCE FOR ENGINEERED FABRICS CONFERENCE
September 26-27, 2023 Raleigh, North Carolina
RISE® is at the forefront of sustainable technologies and global innovations. Scientific leaders will deliver thought-provoking research and intelligence. Next-gen materials and applications will shape near- AND long-term product strategies. New solutions will help transform supply chains and legacy processes.
RISE® is designed for these functional areas…
Technology Scoutwing Product Managers
Senior Scientists Business Developers Development Engineers
Innovation connects with real-world applications.What’s possible becomes what’s next at RISE®.
Questions or for more Information: Please Contact the Registrar, Email: registrar@inda.org Telephone: +1 919 459 3724 Web: riseconf.net, inda.org
positions. They are the blue-chip – large, wellestablished, and financially-sound with excellent reputations. I wonder if these qualities alone will be enough going forward?
Wraising kids and empowering employees, the best thing you can hope for is that they do the right thing. The right thing is usually determined by the culture of a home or office, as well as standards of a community or nation. Many times I have said to my kids, “Make good choices!” They knew what I meant! And, it works in the workplace, too, usually emphasized around employee review time.
Companies make choices too, from product offerings to marketing campaigns to responses to emerging ideas to technology. What happens as a business or corporation makes a choice? It depends. Sometimes nothing, and yet sometimes, everything. Just Google “boycotts” to remind yourself of news that has not faired well for people and brands. Unfortunately for some, the result of a choice wasn’t known until public sentiment starts chattering.
In his book, How: Why How We Do Anything Means Everything ... in Business (and in Life), Dov Seidman says, “Great companies and leaders today know that their reputational capital is as valuable to their success as their physical capital.” In fact, the global online reputation management services market size was valued at 199.14 million in U.S. dollars in 2021 and is expected to reach 440.11 million by 2027.
One survey shows that 87% of consumers read online reviews. Nearly 94% say that a negative online review has convinced them to avoid a business. I use them when searching for businesses or products.
The impact of a company’s choices on both sides, buyer and seller, influences and upholds all transactional relationships, whether they are vendors or direct to consumer.
There are industry legacy companies who have large marketshare and hold dominant
As I have visited in industry expositions this year, I have talked with emerging companies offering new choices, many of them are sustainability-driven. Most say their concept was driven by the current gaps in the marketplace. So they developed it, like CiCLO® CEO Andrea Ferris, whom I interview on page 10.
Companies in the Medical and Surgical space, with stories on pages 14 and 26, also are working their way through varying change.
The new consumer is calling for more than a product. They want: Sustainability. Transparency. Equity. Brands that align with them personally. They want it affordably and with ease of access. No longer is a consumer adapting to transactional exchanges the way a company wants to do them. They want a company to adapt to them. McKinsey & Company says, “Seventy-one percent of consumers expect companies to deliver personalized interactions. And seventy-six percent get frustrated when this doesn’t happen.”
TheWorldCounts.com estimates that the size of the consumer class is expected to increase to 5.6 billion people in 2030 meaning that almost 4 billion people more than in 2010 will have the resources to buy products and services beyond their basic needs. I would assume many will want customized buying experiences ... and supply chain transparency.
One Deloitte study says, “The coming decade will see an exponential surge in personal choice and an accelerated shift from a traditional supply-driven model to one that is demand-driven.” Many new companies are entering this space, with subscription services.
I don’t have any answers. It will be interesting to see how it all comes about.
Caryn Smith Chief Content Officer & Publisher, INDA Media, IFJGUIDE Joan Oakley CHINA Zhang Xiaohua
EUROPE & INDIA Sabine Dussey ITALY Ferruccio & Filippo Silvera UNITED STATES Frank Strazzulla
ADVISORY BOARD
DAVID ALLEN Fiber Processing Development Engineer, Cotton, Inc.
MICHAEL GOLDMAN President, TSG Finishing LLC
International Fiber Journal is published by INDA Media, the b2b publishing arm of INDA, Association of the Nonwoven Fabrics Industry. +1.919.459.3700 info@inda.media | www.inda.media
INTERNATIONAL FIBER JOURNAL (ISSN: 1049801x) is published bi-monthly by INDA, Association of the Nonwoven Fabrics Industry. Subscription price is $125 per year for non-U.S. subscribers. Periodicals postage paid at Charlotte, NC, and additional mailing offices. POSTMASTER: Please send address changes to International Fiber Journal PO Box 158 Cedar Rapids IA 52406-0158 USA.
MISSION
International Fiber Journal covers fiber-related trends and material science developments and how they impact the supply chain from raw material to end use. IFJ provides thoughtful insights and perspectives to global producers, users and business leaders who need to know about what’s next in fibers, filaments and processing solutions.
“In any moment of decision, the best thing you can do is the right thing. The worst thing you can do is nothing.”
– Theodore Roosevelt hen
efab, a leading global industrial packaging and logistics services company is seeking to put its imprint on carbon emission with its advanced digital tool for identifying CO2 eq emissions and cost savings in supply chains. By analyzing the total lifecycle of packaging solutions, GreenCalc™ supports the global demand for optimizing transport efficiency and driving sustainable supply chains.
“Since its introduction, GreenCalc™ has helped thousands of businesses understand their packaging impact, lower their environmental footprint and total costs and driven improvements to create savings in line with various sustainability goals,” said Oliver de Guitaut, EVP Technology and Portfolio, Nefab Group.
Reducing the materials and resources needed to design and ship packaging is one of the proven ways businesses can generate savings while minimizing their environmental footprint. GreenCalc™ is a perfect tool for that as it identifies potential CO 2 eq and cost savings of a packaging solution using Life Cycle Analysis (LCA). As a result, the tool looks at the total lifecycle of packaging from the cradle to the grave, calculating the environmental impact for the production, transport, and end-of-life phases.
The tool allows Nefab to gather data about existing packaging and logistics flow. By measuring the emissions, waste, returnability, and different types of materials in all flows, Nefab can ensure that optimal conditions are met during packaging shipment. Through its dedicated Scope 3 GAIA dashboard, GreenCalc™ allows the customer to access their packaging and logistics environmental
impact baseline but also monitor the impact of the improvement initiatives.
Since 2021, Nefab completed over 3000 GreenCalc™ analyses, assisting its customers in reducing, on average, 31% tons of CO 2 eq emissions over the entire life cycle of the packaging, including its production, transportation, and end-of-life. For example, by designing a packaging solution that enables the product to be stacked during transportation, Nefab’s customers were able to increase the load per truck, resulting in approximately 20% financial savings per year, in addition to CO2 eq savings. In fact, the latest version of GreenCalc™ can evaluate over 44 different packaging materials which allows to model almost any type of solution.
“Through a collaborative approach and together with our customers, our long-term ambition is to reduce supply chain emissions worldwide by 10 million tons by 2030,” summarized Olivier de Guitaut.
Nefab saves environmental and financial resources by optimizing supply chains, by innovating together with customers to create
smarter packaging and logistics solutions while always respecting people and high ethical standards. This contributes to a better tomorrow for our customers, for society and for the environment.
With more than 70 years of experience combined with competence and presence in more than 35 countries, the company offers global solutions and local service worldwide to companies in industries such as Telecom, Datacom, Energy, Automotive, Healthcare, Aerospace, and Lithium Batteries. Nefab Group has over 4,500 employees spread across 35 countries, with a yearly turnover of nearly 10 BSEK.
• GreenCalc™ is Life Cycle Analysis (LCA) tool that tracks and quantifies all financial and environmental data, related to packaging and logistics in customers’ supply chains.
• Since 2021, Nefab has completed over 3000 GreenCalc™ analyses, assisting its customers in reducing, on average, 31% of CO2 eq equivalent emissions and achieving 20% financial savings. www.nefab.com
For details on how to submit your company’s technology for consideration as a “Technology Spotlight” in IFJ, contact Ken Norberg at ken@ifj.com or +1 202.682.2022.
Lenzing Group, a leading global producer of wood-based specialty fibers, has introduced a new approach that covers yarn pre-treatment and knitting technique to achieve aesthetics that resemble the washdown effects of traditional dyeing in ready-to-wear and knit garments.
To address the pollution caused by dyeing and finishing in the textile industry, the new approach will significantly reduce environmental impact and is ideal for use on pre-treated fabrics and yarns made with TENCEL™ Lyocell fibers. The approach also complements the wet-processing and production facilities of fabric mills, bringing added benefits for value chain partners.
In traditional dyeing, multiple washes using a significant amount of water, energy, dyes and chemicals may be required to achieve a desig-
nated shade of color. With the new approach, only one round of dyeing is required, reducing water, energy and chemical usage by up to 50%, 40% and 90%, respectively.
With the new approach’s direct application to TENCEL™ Lyocell fibers or TENCEL™ Lyocell with REFIBRA™ technology, different shades of color, wash-down or fade-out effects can be customized. This makes it ideal to produce ready-to-wear, knit apparel and denim-looking garments in various color shades.
www.lenzing.com
The KARL MAYER GROUP, the Südwolle Group and another player in the natural fibers sector have joined forces in a project to explore the possibilities of merino wool for warp knitting technology. The project was triggered by the increasing market demand for textiles made from sustainable and environmentally friendly materials. The cooperation was to develop innovative fabrics from renewable raw materials for use in underwear and functional sportswear. The focus of the work was on the use of wool as a material with excellent comfort properties and the look and feel of lightweight single jersey goods. The natural fiber fabric qualities are not typical for warp knitting processing, so the challenges during the project work were diverse.
Regarding the choice of material, the product development team of Südwolle Group recommended the Hidalgo yarn from their product portfolio. The yarn was created using the in-house developed Betaspun technology, in which a filament was twisted around a merino core. When natural fibers such as wool, cotton or silk are combined with sustainable fibers such as biodegradable polyamide as the filament, the spinning process can create durable, lightweight yarns that disintegrate completely without residue after use. The yarns made from the two components also have good running properties for use in warp knitting.
The Hidalgo yarn, which is made from merino wool, was processed on a warp knitting machine using a carefully thought-out lapping selection to produce a light, soft fabric which, above all, retains its shape. The textile specialists at KARL MAYER had experimented with two different single bar fabric qualities beforehand and had thus adopted a new approach for jersey machines.
The first results are promising, showing good running properties and excellent fabric quality, according to the development team. Now more trials are needed to perfect the technique. Development partners are needed, including fabric producers, brands, and garment manufacturers, with whom the fabric qualities, machine equipment and orientation to the end applications can be refined.
The KARL MAYER GROUP and the Südwolle Group are also unanimous in their desire to push the boundaries of what is possible with merino wool and knitting technology and to develop exciting new solutions for the textile industry through further project work. www.karlmayer.com
Circular Polymers by Ascend, a market-leading recycler of postconsumer carpet, announced the launch of Cerene™, a line of recycled polymers and materials made from the company’s proprietary carpet reclaiming technology. Cerene is available as polyamide 6 and 66, PET, polypropylene and calcium carbonate as a consistent, sustainable feedstock for many applications, including molding and compounding.
Ascend Performance Materials, a fully integrated producer of durable high-performance materials and the majority owner of Circular Polymers by Ascend, is known for its innovations in nylon 6,6. Cerene will continue that legacy with offerings in nylon 6,6 while also bringing to market recycled polymers such as nylon 6, PET and PP.
“Customers around the globe are seeking consistent and reliable post-consumer recycled materials,” said Maria Field, business director of Circular Polymers by Ascend. “Cerene is mechanically recycled using a process that minimizes our carbon footprint and environmental impact.”
For more than 50 years, Fi-Tech has successfully worked with manufacturers of machines and key techical components used in the production of:
Our customers trust us to provide the best quality and rely on our commitment to their needs when exploring new opportunities to grow and to improve their manufacturing businesses.
Equally, our suppliers highly value the service, dedication, and access to the markets we provide.
sive physical sampling, a version of the UltraView, VisionView, is available with an internal monitor to enable physical samples to be compared with their digital versions, if required.
For non-contact color measurement and digital imaging, VeriVide’s DigiEye collects and processes data that can be communicated and shared instantly.
www.verivide.com
Reports abound on the issue of textile materials and waste and the implications for the environment. Most companies serving the industry have research and development teams attached to tackling their part in the bigger environmental picture.
This is essentially what led Andrea Ferris and her team to invent CiCLO® technology, which enables polyester and nylon fibers to eventually biodegrade if they unintentionally end up polluting the environment. Inspired by a crisis of conscience as long-time workwear industry professionals, in 2012 the team set out to create a better polyester for their own clients, and then realized it was too beneficial to the environment to keep it from the textiles industry at large.
Over 60% of today’s textiles are made with synthetic fibers1: from clothing and carpets to pillows and towels, and more. These synthetic fibers – largely polyester and nylon – are plastics which, when fugitive in the environment, can remain indefinitely because they are not inherently biodegradable.
Considering that an average household generates approximately 44 pounds of dust a year, 13 of which consists of
microfibers from synthetic clothing 2 , carpets and furniture – the environmental impacts to the Earth can be staggering. In addition to dust, tiny fibers are shed from almost all fabrics during manufacture, use and care. Studies show that microplastics (i.e., particles <1 mm)3,4 present in the marine environment may fall into the optimal range of prey size for a wide range of marine organisms5 and can jeopardize different levels of biological organization,6 thus representing a potential threat to the conservation of biodiversity and ecosystem function.
After understanding more about the impact of polyester on the planet, they set out to reduce the environmental impact of the workwear they designed and supplied to major brands, and eventually created a whole new company to support commercialization of the technology. While these innovators are generally known as the “CiCLO® team” because the CiCLO® brand has grown to be so well recognized, Intrinsic Advanced Materials (IAM) is the company established in 2018 to scale it. IAM is a joint venture between Intrinsic Textiles Group, a Silicon Valley startup that spun out of a workwear company, and Parkdale Advanced Materials, the innovative fibers and yarns division of Parkdale, Inc., the world leader in the manufacture of spun yarns.
Gaining attention, we caught up with Co-Founder and Co-Inventor, Andrea Ferris, who also serves as CEO of IAM, to discuss the current status of CiCLO’s technology.
International Fiber Journal: Explain the origins of CiCLO® technology.
Andrea Ferris: It’s actually a neat story. The idea for CiCLO® – which didn’t have a name when we first had the idea – emerged over a decade ago in 2012. I was working for a uniforms and branded merchandise company owned by my now business partners, Alan McIntosh and Wayne Beasley, where we offered everything from the design to manufacturing to delivery to customer. It was around that time when research began to emerge on the shedding factor of textiles. The uniforms industry is heavy in polyester, due to its great performance attributes, affordability and availability. Almost all fabrics shed to some extent, and with polyester being plastic, it is shedding plastic into the environment. Once tiny fibers are fugitive in the environment, they cannot be recaptured. This was concerning to us.
We researched to see if there was an off-the-shelf fix for this problem, but came up empty handed. However, we learned a lot about the science behind biodegradable plastics on our journey, and set out to invent a tailored biodegradable solution specifically for textiles; a technology that allows polyester to maintain the durability and performance characteristics that we choose it for, but that enables it to eventually biodegrade like natural fibers when it winds up in the environment. Sounded really easy at the time! We hired our Chief Scientist and got to work.
After CiCLO® polyester fully biodegraded in a 3.5 year third party lab study (versus only 6% for conventional polyester), we recognized we’d invented something important for the earth and were compelled to make it available beyond our own clients. We created the CiCLO brand for our newly discovered sustainable textile technology, and spun off a separate company to commercialize it.
Because we initially developed it for our own use, we knew which boxes to check
in research and development. The end products had to maintain performance and durability. Spinning efficiency had to remain high. Dye processes had to remain unchanged. Chemistry had to be 100% safe for those handling it, and those wearing it. The technology had to last the life of a garment and never wash off.
Yet, the end products shouldn’t persist forever in the environment like conventional polyester.
IFJ: How have you seen the view of microplastics change through the years?
Ferris: In 2012, there was emerging news about the shedding of textiles being identified as a source of microplastic pollution in the form of little fibers, commonly referred to as microfibers. Now, there are textbooks dedicated to the topic of microfiber pollution and more research and news published practically daily. Research shows that synthetic fibers shed from textiles are the #1 form of microplastic pollution
in all environments across the globe. Synthetic microfibers account for 35% of the microplastics found in the oceans. Government agencies like the EPA and NOAA, state legislators, NGOs, brands and manufacturers are all researching this massive problem and seeking solutions.
In 2018, The Ellen MacArthur Foundation published The Circular Fibres Initiative, a comprehensive report that calls out many problems within the textiles industry, including pollution caused by synthetic textiles. The authors estimate that the amount of synthetic microfibers entering the oceans annually is equivalent in weight to 50 billion plastic bottles. These very small fibers and hard to see, but they are everywhere and cannot be recaptured once they’re in the environment.
Research shows that synthetic fibers that shed from textiles are the #1 microplastic source in all environments across the globe.
IFJ: Tell us more details about the progression from idea to spinning off a new company.
Ferris: When we started the journey in 2012, we didn’t even know the ‘ins and outs’ of how fiber was made or what conditions were required for materials to biodegrade. We had to learn everything from scratch, which was fun and insightful! We visited compost facilities, landfills, waste water treatment plants and biodegradation testing labs. We hired landfill and marine plastic pollution experts. We wanted to understand the realistic best-case solutions to create biodegradable polyester by considering pollution and end-of-life problems.
In 2016, Intrinsic Textiles Group was spun out of the workwear company, and the technology was launched under the brand name CiCLO® in the summer of 2017. It was also around that time when we met our now joint venture partner, Parkdale Advanced Materials,
the innovative fibers and yarns division of Parkdale, Inc., the world leader in the manufacture of spun yarns. Our joint venture creates a wonderful balance of stability and agility. We have this stellar combined team of resources, including R&D, brand protections, marketing, PR, manufacturing, fulfillment, customer service and business development … it is a fantastic partnership.
Ferris: CiCLO® translates to “cycle” and we chose the word for our brand because CiCLO technology is part of the circular economy. It was very important for us –as we were creating this technology to help plastic biodegrade – that the brand name didn’t imply it fits into the current linear “take-make-waste” economy, or the idea that because it is biodegradable it’s intended to be disposable. The intent of CiCLO technology is to apply it to durable textiles where the use of plastics
like polyester and nylon are necessary, and for those products to be utilized for a long time, hopefully recycled someday, then eventually return to basic natural elements when they end up in the environment.
IFJ: What would you like to see people do with these products when they are done with them, like say, a pair of jeans?
Ferris: Repair, reuse, hand down or recycle! We hope to eventually see an infrastructure in place for all textiles to be recycled. CiCLO® polyester and nylon can be mechanically or chemically recycled, just like conventional synthetics.
IFJ: What kind of R&D for biodegradability took place in development of CiCLO®?
Ferris: To test for biodegradability, we contracted with third-party labs around the world, including Intertek and Bureau Veritas, who use internationally recognized ASTM and ISO Test Methods designed to study the biodegradability of plastics in various environments. We compare CiCLO® polyester versus a comparable conventional polyester. The tests are based on “all things equal.”
At what rates do these two things biodegrade if they wind up in the same environmental conditions? We choose Test methods that measure the rate and extent of biodegradation in environments where synthetic microfibers are prolific pollutants, including landfill conditions, soil, waste water treatment plant sludge and natural sea water.
Microfibers shed from textiles are transient, so it makes sense to test in various environments. For instance, shedding during home laundering is one major pathway that is well established. From a washing machine, they move onto wastewater treatment plants. Studies show that 65% up to 99% of synthetic microfibers can get trapped in wastewater treatment plant sludge. Sludge is often used for landfill cover or as a soil amendment. And since the ocean is downhill from everywhere, huge amounts of synthetic microfibers are polluting the ocean.
IFJ: How many iterations of your formula did you develop before the final one? And how does it now get into the marketplace?
Ferris: During our R&D iterations, we looked at about 15 different formulations, looking for active ingredients that could compound well together, that are safe once compounded into our final product, could spin efficiently, and allow the finished fibers to biodegrade at greatly accelerate rates. We looked at the all these different formulations side-by-side to decide on which are best, based on their performance in various environments, and narrowed it down to our final chemistries. CiCLO® technology is patented around the globe.
We sell the CiCLO® chemistry to our global network of CiCLO® Certified Manufacturers of polyester and nylon fiber and yarn manufacturers. They add CiCLO to conventional or recycled polyester and nylon during melt extrusion.
IFJ: How do you help your customers and brands understand their best use of CiCLO®?
Ferris: We are highly engaged with end brands to help them understand how the product works, how it’s added, safety and efficacy. We regularly advise on the best supply chain partners to get CiCLO® into their products, and help with any testing required. It’s also important for retailers and brands to understand how to market products using CiCLO® fibers to end consumers, so we offer responsible
marketing guidelines and our marketing team works closely with customers to support them in whatever capacity is necessary.
As of today, at least 50-60 brands have products with CiCLO® fibers for sale at retail. In development, we are working with hundreds of interested manufacturers and brands.
IFJ: What markets you’re working in?
Ferris: The CiCLO® brand and solution is specific to the textiles industry, and includes everything from apparel, accessories, home textiles, medical textiles, filtration, fiber fill, geotextiles and more. Consider anywhere that polyester and nylon are being used … those are the markets we’re working in today.
IFJ: What is your vision and mission for the company now?
Ferris: The mission for CiCLO® technology is to make the greatest possible contribution towards mitigating synthetic microfiber pollution in the environment. Our vision for the future is that all synthetics will utilize CiCLO® technology.
There’s no excuse for not using CiCLO® technology to manage the unavoidable microplastic pollution caused by synthetic textiles. As a company, IAM is working on sustainable solutions for other sectors beyond textiles, but nothing I can share with you today. You can expect more smart products commercialized in the near future.
IFJ: Do you see the textile industry adopting a circular economy anytime soon?
Ferris: Over the last several years we have met with hundreds of brands, and I’ve yet to come across a brand who doesn’t want to do better than they’re doing today. The textiles industry is moving towards much better days and implementing good solutions. The fact is that for sustainable materials to be adopted, there must be the business case behind it. We could come up with better materials all day long, but if they’re not available globally and affordable, they’re not going to be adopted. As technology and materials inventors, we see it as our job to make products that meet these requirements and can be easily implemented.
IFJ: Do you have any final comments?
Ferris: I hope people understand that microplastic pollution is not just a waste issue. It’s tied into climate change and is a hazard to human health. There is research emerging about how microplastics in the oceans are inhibiting the ocean from doing its job of sequestering carbon from the atmosphere. So all of these combined add up to a very complex problem that is going to require many solutions.
CiCLO® technology is one of these solutions, and we’ve made it easy for manufacturers and brands to adopt.
Over the last several years we have met with hundreds of brands, and I’ve yet to come across a brand who doesn’t want to do better than they’re doing today. The textiles industry is moving towards much better days and implementing good solutions.1. Source: The Good Trade; 2. Source: Sourcing Journal; 3. Hartmann, N. B. et al. Are we speaking the same language? Recommendations for a definition and categorization framework for plastic debris. Environ. Sci. Technol. 53, 1039–1047 (2019); 4. Browne, M. A. et al. Linking effects of anthropogenic debris to ecological impacts. Proc. R. Soc. B. 282, 20142929 (2015); 5. Wright, S. L., Thompson, R. C. & Galloway, T. S. The physical impacts of microplastics on marine tr: a review. Environ. Pollut. 178, 483–492 (2013); 6. Galloway, T. S., Cole, M. & Lewis, C. Interactions of microplastic debris throughout the marine ecosystem. Nat. Ecol. Evol. 1, 0116 (2017).
The international nonwovens community came together in droves, excited to, once again, be in Geneva for April’s INDEX™23. The event showcases a massive global presence, with 610 exhibitors from 43 countries showcasing products throughout 50,000 m² of gross exhibition space. The number of attendees increased from 2,021 to 12,017 representing over 100 countries. The energy of the event was felt all over the two-tiered show floor.
“We are here to do business, but the nonwovens industry showed me that our supply chain is also one big family,” said Murat Dogru, EDANA’s General Manager. “It was a real pleasure to see the industry reunited once again in person to exchange, smile, negotiate, network, debate, and much more as we addressed challenges and discussed innovations.”
“It has been heartwarming to see so many representatives from the younger
generations who feed the industry’s need in terms of new ideas, sustainable solutions, and business architecture,” added Pieter Meijer, Chairman of the INDEX™ Advisory Board.
Discussions with exhibitors uncovered the massive investments in green initiatives that will bring nonwoven producers more options in the future to meet sustainability goals being imposed on the industry – both internally and externally.
The most in-depth discussion centered around medical nonwovens, which was highlighted as a massive source of waste, with single use items the biggest culprit. Berry Global’s Robert Garcia, application and product development director, EMEIA hygiene and healthcare, defined the acute COVID-driven problem with statistics. Between 2019 and 2020, the overall increase in global import volume
of nonwoven medical went from .86 M tons to 1.1 M tons. Berry Global identified that recycling solutions for medical waste were the best option to reduce CO2, based a six-month study of PPE products. For instance, they discovered that by using reusable gowns, CO2 could be reduced by 17%, and by recycling gowns, 35%. In the process of seeking recyclability in 2020,
they encountered huge obstacles to green initiatives, including lack of infrastructure, legislative support and users’ behavior in efforts to recycle facemasks in 2020 within the company.
“Recycling is the way. We tried to recycle as producers, and we couldn’t. There were no solution providers. Only in the U.K. were we able to collect used facemasks,” Garcia said. “Another way must be possible. Survival of the planet and the industry is possible if we all get engaged and share a vision. Vision with passion moves the world forward.”
The company created collaborated on a project with Mölnlycke, a global medical solutions company with corporate headquarters in Gothenburg, Sweden, to collect and recycle scrubs. It was based on collection/melting, re-pelletization, and molding being the circular ambitions, and yielded positive results.
As of July 2023, Berry is now working with Deaconess Midtown Hospital and
Algaeing demonstrated live experiments to illustrate the biodegradability of their product offerings, algae-made threads and dyes. Right, shows how plants can thrive through products left to decay in a natural setting. Far left, algae used for product-making.
Nexus Circular to initiate circular collaboration that restores sterile, pre-surgery plastic packaging and unused fabrics to productive use. Deaconess Midtown Hospital’s Surgical Center is collecting around 500 pounds per week – 350 bags – of clean, used plastics from the hospital’s surgical suite, pharmaceutical, laboratory, and warehouse and are diverted from landfills.
Strategic sourcing manager Pontus Lindstedt at Mölnlycke discussed the company’s sustainability efforts. He noted that if healthcare was a country, it would be the fifth largest CO2 emitter, and said, “Our company is very dependent on this industry to decarbonize our business,” calling for sustainable healthcare options. “We want to see more supply chain transparency to get more data.”
SABIC’s Jelena Bozovic-Vukic, MDTS, market developer and technical service engineer, made a push for safer chemistry designed for recycling in polymer production. She highlighted circular renewable polymers– contributing to a bio-based economy, and certified circular polymers – contributing to waste management. Both options reduce fossil feedstock dependency and improve CO2 levels. SABIC’s vision for the future is that plastic should never end up in the environment, landfill or oceans and instead is reused and remade into new products. TRUCIRCLE™ is SABIC’s vision that requires a total transformation of the value chain, with a closed loop for plastics using circular and renewable products, as well as mechanical recycling and ultimately design for recyclability.
Rounding out the conversation, David Scheeres, director, Thermal Compaction Group Ltd. presented on Sterimelt. This
mechanical process turns a disposal cost into a revenue, according to Scheeres. “Our innovative and sustainable technologies re-engineer single-use disposable non-woven (SMS) polypropylene products such as sterilization wrap, patient transfer sheets, scrubs, gowns, drapes and even face masks into a recovered resource, thus enabling what was a single use disposable plastic to become a multiuse plastic by reintroducing it back into the supply chain as new products, diverting single-use plastics away from incineration and or landfill.”
Walking the Expo, one could witness the focus on green technology dominating the show floor. International Fiber Journal talked to some to see what they are offering to the marketplace.
Algaeing – Building upon their algaebased dye formulation that is 100% biodegradable and offers inherently stunning tones, the company is now in the fiber space with threads made from algae and cellulose, and hued with Algadye 3.0 dye. The company shows plants growing through textiles that simulated discarded waste, to illustrate the biodegradability of the product.
Stora Enso – NaturaFluff Eco is a new product from the company that can be utilized in hygiene products like baby and feminine care, adult incontinence, and air-laid nonwovens. NaturaFluff Eco only differs from traditional fluff pulp in two ways: color and carbon footprint. It is an oxygen delignified fluff pulp. To produce it, there is bleaching of the pulp. Instead, it is treated with oxygen to remove the lignin. As a result, this fluff pulp is of a warm natural beige color and has a roughly 30% lower carbon footprint in comparison to traditional fluff pulp, but its performance isn’t altered. It also benefits from FSC® and PEFC™ chain-of-custody certified products from sustainably managed forests.
Fiberpartner® – The winner of an INDEX® Raw Materials or Components Innovation Award for BicoBio, a future proof biocomponent fibre which has a core sheath construction developed from sustainable materials with low carbon footprint. The component was designed to biodegrade in soil and water. The bio-based PE is produced from sugar cane, with a negative carbon footprint. The Recycled PET is GRS certified, and PrimaLoft® Bio™ is a cutting-edge technology that enables polyester and fabric fibres to biodegrade in the environment. BicoBio fibres can be processed in a variety of nonwoven technologies, such as airthrough, thermo-
bonded, carded and airlaid. The core mission is to fix polyester, and the technology is a break-through innovation that has the potential to change the polyester industry.
To test production, ANDRITZ has tried the biodegradable* PET 1,4 den spunlace nonwoven fiber on their carded and Jetlace hydro-entanglement process. Production trials were done on the ANDRITZ Perfojet pilot line in Montbonnot, France. The company produced nonwoven spunlace fabrics from 35 to 50 gsm, with 100% PET PrimaLoft® Bio™ fiber. As a result, the fibers are confirmed processing by the ANDRITZ spunlace systems as other standard PET fibers.
NatureWorks – The company touts their low-carbon alternative to petrochemicalbased plastics and fibers, called Ingeo 6500D – a biopolymer, made from renewable bio-based feedstocks that makes the products we use every day safer and more sustainable. Ingeo 6500D has a wide range of applications including extrusion and thermoforming, injection molding, films and cards, fibers and nonwovens, and 3D printing. Delivering enhanced fluid management for hygiene applications, it boasts improved tensile strength and up to a 40% increase in softness that offers a better performing spunbond nonwoven that minimizes converting challenges while providing a 62% smaller carbon footprint.
“Building on our expertise in bio-based nonwovens, we developed a product that, based on our rigorous testing, can improve the softness of spunbound nonwovens by 40% over nonwovens made with generic PLA,” says Robert Green, vice president of performance polymers, at NatureWorks. “The tensile strength of the new Ingeo solution offers improved processing for converters while offering efficient low basis weight fabric production on the latest generation of spunbond equipment. We are looking forward to collaborating with the supply chain as we continue the development of this new Ingeo solution in nonwoven applications including diapers and wipes.”
Akinal – BioFlush® is the company’s multi-purpose hygiene cleaning product suitable for different uses. The company markets the 100% flushable and biodegradable nonwoven for use as baby wet wipes or wet toilet paper. It produces BioFlush® from 100% natural raw materials and uses no chemicals. It has CTP Laboratory Certification and meets the EDAN and INDA guidelines.
Pulp for feminine care, baby diapers and adult incontinence products is how the company provides environmental benefits to nonwovens customers. The thinner product profiles allow manufacturers to compress cores to create higher density, thinner products without sacrificing softness and flexibility. Fiber is sourced from southern coastal pine forests that are responsibly managed and certified. Golden Isles CO® fluff pulps are made from a coarse, bulky, long fiber and are used in a variety of absorbent applications – offering optimum fluid retention, liquid distribution (wicking), and pad integrity. This is especially important with thinner products and with the use of super-absorbent polymers. Supply chain savings include smaller packages and the potential for increased package counts.
Sparkle – Making a splash for their biobased Sparkle sanitary pads, the company is now developing Sugar Fluff,™ a woodfree, sustainable, and cost-effective fluff designed for absorbent hygiene products, and made from bagasse fibers – dry pulpy fibrous material that remains after crushing sugarcane. The company says it is high performing, as well as circular, including the bonus that no extra land is required to grow bagasse fibers as fibers are readily available from the sugar industry.
OrganoClick – The nonwovens industry is dependent on binders used to improve the mechanical properties of nonwoven and technical textiles, and common binders are mainly made of fossil plastic polymers such as ethyl vinyl acetate (EVA) and acrylates. OrganoClick has developed the 100% biobased binder OC-BioBinder™ which is based on biopolymers from residual streams in the food industry such as orange peel, shrimp shells and wheat bran. With the help of these bio-binders, nonwoven and technical textiles can become 100% biodegradable, non-toxic and 100% compostable. The bio-based and biodegradable binders are adapted for several different nonwovens and specialty papers such as airlaid, wetlaid, spunlace, spunbond, carded, and drylaid. The binders are available in varying degrees of softness, (Tg), with different degrees of dry and wet strength, and that are hydrophilic or hydrophobic. They also offer binders that improve fire protection. They offer other bio-brands, such as the biocomposite OrganoComp – also 100% biodegradable, renewable, toxin-free and made from residual streams in the food industry.
Business unit manager of Biocomposites, Dan Blomstrand talks to an INDEX attendee in their busy booth. Below is the chart of OC Binders and their qualities. Caryn Smith
Open to products that were made commercially available by January 31, 2023, and selected by a jury of experienced industry peers, EDANA’s INDEX™ Awards for “Excellence in the nonwovens and related industries” are the highest accolade for distinction in the nonwovens value chain. Here are the winners for 2023:
1. Nonwoven roll goods
WINNER: Suominen – HYDRASPUN® Circula Nonwoven
HYDRASPUN® Circula is one the first nonwovens on the market to be produced with recycled paper and virgin cellulosic fibres. It is challenging to use a waste source as a raw material in nonwovens due to high quality and hygiene requirements, which makes
HYDRASPUN® Circula stand out as a successful example of innovation.
2. Finished products made from, or incorporating nonwovens
WINNER: Henkel – Smart Adult Care
Smart Adult Care transforms a conventional diaper into a smart, connected medical device. This is a vital step into the future of patient-centered care and smart hygiene services. Equipped with a lightweight, flexible printed sensor and reusable pod, the diaper enables remote monitoring of moisture, movement, and temperature. It was developed in cooperation with Henkel’s IoT partner Smartz AG.
3. Raw materials or components (e.g., fibre, binder, polymer, tape), of special relevance to the nonwovens industry and related converted products
WINNER: Fiberpartner – BicoBio
A future proof bicomponent fibre core sheath construction, developed from materials with a low carbon footprint, this component was designed to biodegrade in the environments where most plastics eventually find themselves: landfills and ocean water.
• The bio-based PE is produced from sugar cane and has a negative carbon footprint.
• The Recycled PET is GRS certified.
• PrimaLoft® Bio™ an additive technology that enables polyester and fabric fibres to biodegrade in the environment.
4. Innovation in machinery of special relevance to the nonwovens industry WINNER: Curt G. Joa, Inc. – ESC-8™ JOA’s ESC-8™ Electronic Size Change unit offers a previously unavailable push-button product changeover technology. It uses numerous methods and processes that are truly unique to inline product changeover and flexibility. As one example, each absorbent insert carriage within the ESC-8™ unit is controlled and cammed independently leading to unparalleled process flexibility and user control.
5. Sustainable Product WINNER: Sparkle Innovations –SugaFluff™
Made from bagasse fibres, SugaFluff™ offers a wood-free, sustainable, costeffective, high performing and truly circular alternative source of fluff pulp for absorbent hygiene products. No extra land is required to grow bagasse fibres for SugaFluff,™ as sugarcane bagasse is an abundantly available by-product of the sugar industry.
Suzano – The company’s core product, Eucafluff® is the world’s first eucalyptus fluff and is a renewable-source raw material with a smaller carbon footprint, while simultaneously providing end consumers with a more efficient product that offers greater well-being. It is an innovative product designed for disposable sanitary absorbent products and other personal hygiene items, such as baby diapers, adult incontinence products, pet pads and for use in hospital supplies. As a sustainable solution from a renewable source, it offers companies the benefits of the lower carbon footprint.
Bast Fibre Technologies Inc. – The natural hemp fibre sero™ is designed as Bast Fibre’s product that meets the rigorous technical standards required by commercial fabric manufacturing, including hygiene applications. It is a plug-and-play replacement for synthetic fibre, made from a highly efficient renewable agricultural crop that is one of the best natural sources of fibre. sero™ natural hemp fibre enables manufacturers to create consumer products with a circular, soil-to-soil lifecycle. Beyond plant based, sero™ is intact plant fibre, ideal for creating next-generation sustainable consumer products. It has the qualities of being natural, strong, clean and bright, soft and absorbent, with the environmental benefits of true sustainability, zero plastic, forest friendly, and 100% compostable.
UPM – Lignin is a 100% bio-based substance that can be found in the cell walls of all plants and especially trees. UPM BioPiva™ lignin is a versatile natural polymer, verifiably non-toxic and responsible sourced raw material. Lignin plays an important role in the natural carbon cycle by binding atmospheric carbon dioxide and serving as a long-term carbon storage. The goal is to transform the sustainability performance of products and help radically improve manufacturers CO₂ footprint. UPM BioPiva™ 100 is a purified, kraft softwood lignin that can be used in various applications. It is a non-toxic product from renewable sources. UPM BioPiva™ 100 can be used to replace and to reduce the usage of fossil-based materials without compromising the performance.
Lenzing — The environmentally-sound offerings from Lenzing are numerous, and under continual advancement. The company has dedicated its resources to making the most of wood-based fiber solutions, while also leading the way in corporate environmental sustainability measures. Tencel™, EcoVero™ and Veocel™ provide non-woven manufacturers with options. EcoVero™ viscose fibers have a lower environmental impact than generic viscose, according to Higg MSI. Veocel™ Lyocell fibers are the latest generation of fibers with botanic origin which combine advanced performance, comfort and sustainability for everyday consumer needs. Unique physical properties lead to their high-tenacity profile in both dry and wet states, efficient absorbency and gentleness to skin for multiple hygiene applications.
n news off the ITMA 2023 expo floor, the DILO Group –Engineering for Nonwovens unveiled new groundbreaking MicroPunch Needling for Lightweight technology that solves a significant problem in manufacturing of lightweight nonwoven materials. “We have come to this launch with an advanced economic and environmental solution,” said CEO Johann-Philipp Dilo during the launch. “MicroPunch overcomes hydroentanglement issues, saves money on energy, water, and waste is low.” IFJ caught up with company CEO Johann-Philipp Dilo to get more details to this amazing development, and how the industry can utilize the technology.
IFJ: Explain the core problem this tech solves for the industry?
Johann-Philipp Dilo: After two decades of development work Dilo now offers the MicroPunch technology to enlarge the range of applications of needled products into the low weight sectors. Here staple fiber nonwovens are mainly offered as hygiene or medical products like wipes for personal care or single-use garment, operation covers, etc. However, also many technical applications for nonwovens exist in the lower weight range and even the garment and bedding applications could profit from nonwoven material which is produced at high production rates and low energy consumption. So far, this has been dominated by products typically water entangled. This high-speed process is currently considered ideal for such fine fleeces consisting of fine fibers below 1 dtex up to about 3.3 dtex having weights of ca. 30 up to 100 g/m². Needling, on the other hand, has been ideal more in the upper weight range above ca. 100 g/m² and going as high as several kilograms/m², normally with coarser fiber. Due to the enormous range
of textile parameters, like fiber material, fiber fineness, staple length, crimp and surface features together with machine parameters like stitching density, depth of penetration, needle fineness etc., the number of parameter combinations is immense and makes needling adaptable to a very large number of different products and their applications. The hydroentan-
gling process, however, has many limitations in that weights above 100 g/m² are normally excluded as are fibers above 6.7 dtex fineness. From that perspective, hydroentangling addressed foremost the low weight range with fine fiber for hygiene and medical products with the exceptions in some technical fields, coating substrate and roofing material. Given that situation, it was only natural to study the market for such hygiene products with their share of total nonwoven production. Wipes for personal care, industrial and domestic applications cover almost 30 % of all staple fiber drylaid nonwovens.
At the same time the amount of energy necessary per kilogram of nonwoven material is very high within the hydroentangling process. A lot of electrical power is required to reach a high water pressure forming the water jets, to vacuum the material, get water out of the fleece, pump the water through filtration systems and also gas to dry the material when leaving the water jet area.
Additionally of concern is the amount of water consumed through the drying process and the wastewater. This is a considerable amount which is of particular concern when water resources are shrinking. The high energy consumption is responsible for a large part of the total costs.
Considering all costs, the costs of the fibers which leave the system as a nonrecyclable filter cake is again to be accounted for. Also, the edgetrim material typically strongly consolidated is difficult to reopen and to recycle. All in all, the described shortcomings of water entangling motivate for an alternative which has been found in MicroPunch intensive needling. A much smaller amount of electrical energy is needed for this process, no water is consumed, no gas-heated drying applied and fibre consumption is reduced. Cost comparisons have shown energy savings in a region of ca. 75 %. Overall cost savings are possible between 25 and 50% depending on the weight of the material. As a conclusion, the problems MicroPunch can solve for the industry are a tremendous reduction of energy consumption, water consumption and fiber waste. This is reflected by an overall cost reduction per kilogram of manufactured material.
IFJ: Can you tell us how it was developed?
Dilo: MicroPunch is an advanced and modified intensive needling method which was developed by Dilo around 2005, at the time using a needle density of 20,000 per meter per board, applying fine barb needles. This has given good results for lightweight material with a high abrasion resistance, good drape and softness for liquid absorption, generally apt for hygiene and medical applications. The economics at the time, however, with
the necessity to invest in a total of six needlelooms per line where not convincing enough.
MicroPunch is applying a large number of needles with up to 45,000 needles per meter per board in three needlelooms of four boards each which has made necessary a solution to equip the needles in a board more economically. This was solved by the invention of our needle module X22 with 22 needles in one module which can be mounted in cassettes of a so-called container board at only 15 minutes per meter per board. Together these have defined the ingredients for a breakthrough in the economics of the new intensive needling method “MicroPunch”.
IFJ: Is anyone using the tech now?
Dilo: Since this technology is brand new and presented to the public for the first time at ITMA 2023 in Milan, marketing of this whole technology has only just started, yet already created a lot of interest in many sectors like hygiene, medical, technical, garment, upholstery and automotive.
IFJ: What segments is it best suited for?
Dilo: It is best suited for a weight range of 30 to 120 g/m² and therefore applicable in the sectors as described above with a focus on wipes for personal care, cosmetic pads, household and industrial use.
IFJ: How does it work with other Dilo solutions?
Dilo: Dilo is a specialist for complete needling lines. Therefore, a MicroPunch line is offered including fiber preparation with bale opening, blending, fine opening, dosing and air systems engineering for dedusting and pneumatic conveying of fiber flocks to the individual machines. Furthermore, preferably random cards are applicable in order to have a fiber orientation not only in running direction but also in cross direction. This is preferred to allow needles to catch fiber from various directions into the stitching channel in order to consolidate the fleece. After the card the needling units
The ratio of power and energy needed to produce 1 kilogram of material is uniquely low. The number of application sectors is extremely high.Top: A view inside the DILO machinery, where one million MicroPunch needles are at work. Right: A Closeup of the needles. Far right: A view of some MicroPunched fabric. DILO
for pre-needling and finish-needling follow either directly after the card exit or when a crosslapper is integrated after a drafting frame. It may result in products with an MD:CD strength ratio of 1. This is a positive feature for many applications. After the needling station the end of line units for winding, longitudinal and cross cutting are added together with packaging or palletizing for roll good.
IFJ: Any other unique details that are interesting for readers to know?
Dilo: Historically, needling as a technology to consolidate staple fiber fleece was not among the so-called modern technologies to attract a whole lot of public awareness or esteem. For many years, it was almost considered as outdated, slow and old-fashioned. Yet, the machine builders have developed this technology which was invented in England in the 19th century to a modern state-of-the-art industrial
manufacturing technology for nonwovens which has proven to be highly productive, cost-efficient and energy-efficient. The ratio of power and energy needed to produce 1 kilogram of material is uniquely low. The number of application sectors is extremely high at the same time. The needling technology has dominated many nonwoven
sectors particularly those at medium to high weights. The MicroPunch approach to penetrate also the low weight area cannot only be considered to reduce the energy consumption but also be viewed as a strategic tool to take a share of the low weight sector and thus provide a sound basis for a positive future of needling in general.
atureWorks is continuously expanding its portfolio of Ingeo polylactic acid (PLA) materials which includes well-established grades for fibers and nonwovens, extrusion and injection molding, and increasingly those for 3D printing.
Monofilaments made with Ingeo PLA have notable 3D printing characteristics such as precise detail, good adhesion to build plates with no heating needed, less warping or curling and low odor. This makes them suitable for many different types of printers and for a broad range of printing applications.
A special composite grade of Ingeo was required, however, for a somewhat ambitious project undertaken by the University of Maine Advanced Structures and Composites Center (ASCC) last year – the first 3D-printed house made entirely with biobased materials.
BioHome3D was developed with funding from the U.S. Department of Energy’s Hub and Spoke program between UMaine and Oak Ridge National Laboratory.
The 600-square-foot prototype features 3D-printed floors, walls and roof which are fully recyclable and highly insulated with 100% wood insulation and customizable R-values. Construction waste was nearly eliminated due to the precision of the printing process.
“Many technologies are being developed to 3D print homes, but unlike BioHome3D, most are printed using concrete,” said ASCC director Habib Dagher. “However, only the concrete walls are printed on top of a conventionally cast
concrete foundation. Traditional wood framing or wood trusses are used to complete the roof. Unlike the existing technologies, the entire BioHome3D was printed, including the floors, walls and roof. The biomaterials used are 100% recyclable, so our great-grandchildren can fully recycle BioHome3D.”
“Our interest was in making 3D printing greener and using more renewable materials to decrease the carbon footprint and we were introduced to NatureWorks through our partners who have previously used PLA in a demonstration project for the printing of a pavilion,” explained Susan MacKay, ASCC senior R&D program manager. “PLA is known to print really well and it’s used worldwide in desktop printing in filament form, but when you get to large-scale additive manufacturing there are some issues.
“While we liked the renewability of PLA we incorporated wood fillers wood flour, nanocellulose and pulp with the PLA to create new types of composite materials to improve the impact and tensile strength. We were struggling with the traditional PLA because it’s semicrystalline, which causes a lot of shrinkage and some distortion.”
“The testing we did showed that compared to the normal semicrystalline PLA, this material worked similarly in terms of mechanical properties but printed better at such a scale,” added Doug Gardner of the Advanced Engineered Wood Composites Center at UMaine. “Having an amorphous polymer lends itself to processing by large scale 3D printing, with less dimensional stress during the laying down of the part and the cooling that occurs during this manufacturing. Most significantly we have used a totally 100% sustainable material that also sequesters carbon.”
The U.S. is experiencing a crisis-level shortage of affordable housing. The National Low Income Housing Coalition reports that nationally, there is a need for more than seven million affordable housing units. In Maine alone, the deficit is 20,000 housing units and growing each year, according to the Maine Affordable Housing Coalition. Nearly 60% of low-income renters in Maine spend more than half of their income on housing.
The BioHome3D technology is designed to address these issues and less time is required for on-site building and fitting up the home due to the use of automated manufacturing and off-site production. Printing using abundant, renewable, locally sourced wood fiber feedstock reduces dependence on a constrained supply chain.
Using the advanced manufacturing processes and materials developed at UMaine, future low-income homes can be customized to meet a homeowner’s space, energy efficiency and aesthetic preferences. Importantly, as the manufacturing technology and materials production are scaled up, homebuyers can expect faster delivery schedules.
The prototype home is currently sited on a foundation outside ASCC, equipped with sensors for thermal, environmental and structural monitoring to test how BioHome3D performs. Researchers expect to use the data collected to improve future designs.
BioHome3D was printed in four modules, then moved to the site and assembled in half a day. Electricity was running within two hours with only one electrician needed on site.
UMaine is no stranger to such largescale projects – in 2019 it received no less than three Guinness World Records
for the world’s largest prototype polymer 3D printer, the largest solid 3D-printed object, and the largest 3D-printed boat.
From the macro to the micro – advanced materials produced using Stratasys J850 TechStyle 3D printers feature in the interior of the new Peugeot Inception concept electric vehicle – achieving a level of resolution that would not have been possible with traditional embellishment methods.
The Inception has a minimalistic cockpit devised by design director Matthias Hossann to support the car’s aim of reinventing the driver experience. Immersive seats covered with a velvet made from 100% recycled polyester extend to the floor and feature 3D patterns created with the Stratasys 3D printing technology.
“At Peugeot, we always like to combine function with aesthetics,” said Maud Rondot, of the Advanced Design team at Peugeot. “Our objective with the Inception’s seating area was to modernize the velvet material used and compartmentalize the design by extending it to also serve as a visually impactful floor mat.”
Where the floor area space would typically need to be treated with a protective overlay, the Inception concept leverages direct-to-textile 3D printing to deliver a
unique combination of functionality, texture and aesthetics which would not have been achievable with other technologies.
“Although we have access to relatively flat designs with current embellishment methods, it is not possible to build thickness and height,” said Rondot. “It is thanks to 3DFashion technology that we could 3D print directly onto the flexible material. Often, there is a delta between what we imagine and what we can obtain, so it was quite magical to see our idea arrive precisely as envisaged and with a remarkable quality of execution.”
The team selected a metallic shade for the velvet, which is designed to play with light before using the printer to create the semi-transparent ‘micro-architectures’.
“Instead of covering the whole stretch of material, it was really advantageous that we could leave the velvet visible,” Rondot said. “3D printing allowed us to modify and reprint the files very easily, but also important is its durability and efficiency – as a technology it doesn’t require molds, which is revolutionary in terms of industrialization.”
niversities and research institutes in Europe are among the world leaders in developing medical textiles – fiberbased materials used in healthcare applications such as prevention, care and hygiene. These include dressings, prostheses, surgical sutures, healthcare apparel and barrier fabrics, as well as hygiene applications such as diapers, menstrual pads and surgical wipes.
As implantable medical devices, medical textiles have many diverse applications. They can be used as flexible scaffolds or structures for tissue in-growth and implant integration, conduits or barriers for blood flow, and as a means to join materials and secure implants in the body.
They are also used for tissue reinforcement and wound support, joint support and retrieving blood clots or preventing or reducing plaque debris in neurovascular applications.
Recent research in Europe demonstrates how medical textiles are an emerging interdisciplinary field in which con-
ventional textile technologies, such as weaving, knitting, braiding and embroidery, are combining with other scientific fields, such as chemistry, medical and biomedical technology, pharmaceuticals and electrical engineering.
A nanocellulose wound dressing that can reveal early signs of infection without interfering with the healing process has been developed by Swedish researchers at Linköping University, in collaboration with colleagues from Örebro and Luleå Universities.
The dressing is made of tight mesh nanocellulose, which provides a barrier to bacteria and other microbes. At the same time, the material lets gases and liquid through, which is important for wound healing. Once applied, the dressing is designed to stay on during the entire healing process. Should the wound become infected, the dressing will show a color shift. Non-infected wounds have a pH of
about 5.5. When an infection occurs, the wound becomes increasingly alkaline and may have a pH of 8 or higher, as bacteria in the wound change their surroundings to fit their optimal growth environment. An elevated pH in the wound can be detected long before any pus, soreness or redness, which are the most common signs of infection.
To make the wound dressing show the elevated pH, the researchers used bromthymol blue (BTB), a dye that changes color from yellow to blue when the pH exceeds 7. For BTB to be used in the dressing without being compromised, it was loaded onto a silica material with pores only a few nanometers in size. The silica material could then be combined with the dressing material without compromising the nanocellulose. The result is a wound dressing that turns blue when there is an infection.
Wound infections are often treated with antibiotics that spread throughout the body. But if the infection is detected at an early stage, local treatment of the
wound may suffice, so the researchers are also developing antimicrobial substances based on lipopeptides that kill all types of bacteria.
Also in Sweden, research has been conducted at the University of Borås, to develop more resource-efficient methods for producing functional textiles using digital ink-jet printing.
The doctoral thesis of Ph.D. student Tuser Biswas involved fabrics printed with enzymes, which could be used in medical textiles with antimicrobial properties or to measure biological or chemical reactions. While developing a good enzyme ink was not easy, he was able to show how a printed enzyme could bind another enzyme to the surface of a fabric.
Although the activity of the enzymes decreased by 20–30% after printing, the results are still promising for future applications. The work has also provided new knowledge on many fundamental questions about printing biomaterials on fabric.
Biswas hopes that continued research in textile technology can provide alternatives to the use of antibiotics, which has resulted in increasing antibiotic resistance worldwide.
“Instead of treating the patient with a course of antibiotics, one can act preventively and more effectively by damaging the bacteria on the surface where they start to grow,” he said.
“In a wound dressing, for example, nanoparticle-based antimicrobials can reduce growth effectively. It is possible as nanoparticles can interact better with the bacterial membrane and reach the target more easily than conventional antimicrobials.”
Last year, Stockholm, Sweden-based SHL Healthcare established a textile center of excellence in Borås to extend and streamline support for early project phases in collaboration with customers.
The facility is strategically situated inside the Textile Fashion Center and adjacent to a cluster of industry organizations such as Science Park Borås, Smart Textile,
the Swedish School of Textiles and the University of Borås.
This will allow SHL Healthcare to easily access technology, engineering and textile materials that can optimize product innovations and sustainability.
In Germany, researchers at RWTH Aachen University have developed a novel technology for the treatment of hollow organ tumors, which achieved second place in the RWTH Innovation Award.
A hollow organ tumor is responsible for one in four deaths from cancer and can-
not usually be removed surgically. It is only possible to open the hollow organ for a short time using a stent. However, the tumor can grow back and penetrate the hollow organ through the stent.
The technology, developed by Dr. Ioana Slabu from the Institute of Applied Medical Technology and Benedict Bauer from the Institut für Textiltechnik at RWTH Aachen University, involves a polymer stent that has magnetic nanoparticles embedded in its fibers.
When electromagnetic fields are applied, the nanoparticles provide a controlled heating of the stent material and thus of the tumor. Because the tumor reacts more sensitively to heat than healthy tissue, it is destroyed, and the hollow organ remains open.
According to the researchers, the stent can be used to treat tumors in various hollow organs, such as in the bile duct or the esophagus, and also has the potential to treat tumors in other parts of the body, such as the prostate, stomach, intestine or bladder, or for cardiovascular diseases.
The treatment of nerve injuries with the aid of nerve guidance conduits has led to the desired regenerative success in some, but by no means all, cases. Now, a research team from the Medical University of Vienna (MedUni Vienna), Austria, and the UK’s University of Oxford has used silk as a promising material for repairing severed nerves.
In their experiments with silk from silkworms and spiders, the scientists also gained new insights into the effects of silk on neuronal healing processes, which could significantly advance therapeutic
options in peripheral nerve reconstruction.
In the search for improved therapeutic options for nerve injuries, the team led by Professor Christine Radtke, head of MedUni Vienna’s Department of Plastic, Reconstructive and Aesthetic Surgery, in collaboration with researchers from Oxford, produced nerve conduits from two different types of silk: silk from silkworms was used for the tubes, while silk from spiders was used to fill them.
The function of these conduits was investigated in an animal model. Their experiments showed that the severed nerves adapted to the novel silk nerve guidance conduits and grew along the silk threads over the defect distance until the severed nerve endings were successfully reconnected.
Researchers at the Fraunhofer Institute for Silicate Research ISC and the Fraunhofer Institute for Toxicology and Experimental Medicine ITEM in Germany have developed a bioresorbable membrane for the treatment of both large
external and internal wounds. The membrane is said to support wound healing and biodegrades completely in the body to a natural substance.
The novel membrane is based on a fiber fleece developed at Fraunhofer ISC, which has been approved as a medical device to support the regeneration of chronic wounds such as diabetic foot ulcers. During the healing process, the material dissolves completely within six to eight weeks.
Using an electrospinning method, the researchers have now managed to reduce the 50-µm fiber diameter by a factor of more than 50, resulting in fibers with diameters of less than 1 µm, which has made it possible to spin a Renacer silica gel sol into an open-meshed silica gel membrane consisting of fibers with a diameter of about 1 µm (in some cases, the diameters achieved were as small as 100 nm).
Using a confocal microscope, it was shown that the small-meshed membrane exhibits a barrier function, which prevents the passage of connective tissue cells for a period of at least seven days
Experiments showed that the severed nerves adapted to the novel silk nerve guidance conduits and grew along the silk threads over the defect distance until the severed nerve endings were reconnected.Electrospun Renacer membrane (5 x 5 cm). Fraunhofer ISC The wound dressing developed by Swedish researchers is made of tight mesh nanocellulose, preventing bacteria and other microbes from getting in. At the same time, the material lets gases and liquid through. Olov Planthaber
without interfering with cell proliferation. In addition, the membrane is resorbable, is not cytotoxic or genotoxic, and thus causes no direct damage to tissue or DNA. In addition, drugs can be encapsulated into the matrix of the silica gel fibers to be released during material resorption.
At Fraunhofer ISC, the GlioGel project is testing whether the Renacer material platform can be used as a depot for active substances in the treatment of brain tumors.
Researchers at the UK’s University of Birmingham have demonstrated that silver retains antimicrobial activity longer when impregnated into bioactive glass, and they have shown how this combination can deliver more long-lasting antimicrobial wound protection than conventional alternatives.
Bioactive glasses are a unique class of synthetic biomaterials made from silicone and have been used for many years in bone grafting.
Meanwhile, silver has long been known to prevent or reduce the growth of biofilms (communities of bacteria) in open wounds, and silver-based treatments are increasingly popular as they are effective against many antibiotic-resistant strains of bacteria.
These antimicrobial properties depend on silver remaining in an ionic form so it can penetrate bacterial cell walls and disrupt their life cycle. However, the silver ions or nanoparticles in wound dressings are prone to transforming to silver sulfide or silver chloride, which can reduce antimicrobial activity and hinder the success of treatment.
The researchers investigated the effects of bioactive glass doped with ionic silver on biofilms formed by Pseudomonas aeruginosa, a multi-drug resistant bacterium that easily forms biofilms and is a common cause of infection in chronic wounds.
The study showed that specific preparation, storage and application techniques can minimize the transformation of silver ions to silver chloride and so retain antimicrobial activity.
Women at risk of pregnancy loss who need a specialist surgical procedure could benefit from a single-stranded suture thread to reduce the risk of infection, according to results from the C-STICH clinical trial conducted by the University of Birmingham.
The trial involved more than 2,000 expectant mothers in the UK who needed a cerclage, a procedure in which a purse string suture is placed around the cervix during their pregnancy. Women were randomly allocated to have the surgical procedure performed using either a singlestranded thread or a braided thread.
The researchers evaluated whether there would be any difference in miscarriage or stillbirth, owing to an increased risk of infection, from using a braided suture thread. The team found that the mothers treated with single-stranded threads had no differences in pregnancy loss or preterm birth and reported fewer instances of infection and sepsis.
Dr. Vicky Hodgetts-Morton, National Institute for Health and Care Research clinical lecturer in obstetrics at the University of Birmingham and Birmingham Women’s Hospital, said: “The C-STICH trial results did show an increased risk of infections in labor and around the time of delivery with braided threads and this supported our hypothesis that a singlestranded thread could reduce the risk of infection developing during the pregnancy.”
However, the study also highlighted that while single-stranded suture threads led to better outcomes around infection, clinicians mentioned that such sutures were subjectively more difficult to remove and more often required surgery to help remove them under a general anesthetic.
Geoff Fisher is the European editor of International Fiber Journal, editor of Medical Textiles and a director of UK-based Textile Media Services, a B2B publisher of news and market reports on transport textiles, medical textiles, smart materials and emerging markets. He has more than 35 years of experience covering fibers and technical textiles. He can be contacted at gfisher@ textilemedia.com or +44 1603 308158.
The April launch of a new report “Textile Recycling: State of Play,” was directed not just at the textile industry but at potential investors. I spoke with report author Brett Mathews, textile and apparel industry writer, influencer and disruptor, also publisher and editor of Apparel Insider magazine that has long focused on sustainability. Never one to hold back on saying it how he sees it, I began by asking why a report on just one aspect of circularity, and why recycling?
Marie O’Mahony: First Brett, congratulations on a really insightful report! In Apparel Insider you write about all aspects of circularity, so why did you decide to focus on recycling for this report?
Brett Mathews: We chose recycling because this is the issue we are asked about the most. In the past few years various consultants have approached us to ask for our thoughts on textile recycling, prospects for this segment etc. So, the initial plan was to produce a kind of investor guide to textile recycling so we could point them to this publication. Then as we looked into this, it became harder to produce just a small briefing. We wanted to produce something coherent which would give ALL industry stakeholders an idea about where we are right now with recycling, with a focus on novel recycling technologies.
MO: The main emphasis of the report is on chemical rather than mechanical recycling processes driven by industry stakeholder interest. You describe how less than 1% of recycled clothing is being recycled using chemical processes and point to Spinnova’s mechanical recycling process as clean and environmentally benign. Do you agree with stakeholder emphasis on chemical recycling?
BM: I think there is room for both chemical and mechanical. We focused on chemical as that seems to be where much of the interest is in terms of investment. The theory goes that chemical recycling offers the potential to recycle some clothing which mechanical recycling cannot. But, of course, there are caveats to that which we explore in the report. It’s worth noting that mechanical recycling is by far the most popular and it’s been happening for decades, very successfully. India and Pakistan are huge secondary markets for mechanical textile recycling and it’s a really important part of the value chain. So, I think that it would be a mistake to get carried away with the chemical textile recycling being the ‘be all and end all,’ it’s not, and there is still a huge part to play for traditional mechanical recycling. There are some big players in this area. Recover in Bangladesh is taking off-cuts from the production process and mechanically recycling it. They are working with brands such as Tillys in the
U.S., on their sustainable RSQ capsule collection that contains a minimum of 20% low-impact recycled cotton fiber according to Recover. The benefit of chemical recycling is that it offers a way of recycling more difficult fibers such as the blends so that it is a more ambitious way of doing things.
MO: Some fiber and yarn spinners have spoken of the technical challenges in using recycled content, such as short fibers, nep content and the fineness that can be achieved. Do you see evidence of the two industries working together to overcome this?
BM: Not in any major way. Fashion has talked for years about designing for circularity. But apart from a few pilots and one-off initiatives I haven’t seen much evidence of this. Plus, the market is now being flooded with ultra-cheap clothing from the likes of Shein, Boohoo which is mainly polyester and more difficult to recycle than ever. On the quality of recycled fibers, people that I have spoken with have said that they are actually pretty good and it’s quite difficult to tell the difference between these and virgin fibers. We’ve seen C&A designing fully circular denim jeans but this is going back three or four years and I’m not sure there has been much follow up on that. There’s quite a few that have worked with the Ellen MacArthur Foundation that have put out guidelines on circularity, including some specifically relating to jeans. A few brands have done small pilot productions but it’s all a bit ad hoc and no one has really scaled this work which perhaps tells its own story.
MO: Elastane you cite as a big issue of course, do you see more sustainable stretch fibers such as the Roica Eco-Smart range or Cotton Inc.’s stretchable cotton as offering a good alternative?
BM: Potentially yes. Without checking, I am guessing these fibers will come at a premium over conventional elastane. This being the case, they will remain niche. Fashion brands are ultra-sensitive on price, especially in the fast fashion space. Luxury brands might be more willing to absorb this premium as their margins are greater. In 2019, Cotton Inc. developed a 100% cotton elasticated fabric called Natural Stretch, that uses a special mechanical manufacturing process to provide stretch. According to the company’s website there are only a small number of licensed suppliers, all bar one in Asia and none in North America. I’m not sure how successful it has been, I don’t know of any brands using it, so it looks like it is not getting any significant market traction.
MO: Declining qualities of feedstock is proving challenging for chemical recyclers. Fast fashion is not going away any time soon so are you seeing any innovative work-around for the quality problem?
BM: Not really. As mentioned previously, we have seen pilots and one-off lines but in the main the business model remains the same. There is a real disconnect on this issue in terms of what brands say on circularity and recycling and the clothing they produce. It is hard to over emphasize also the impact of brands such as Shein and Temu. They are a huge threat to the legacy of fast fashion players such as H&M, Primark etc. There is a genuine danger these new ultra-fast fashion brands will lead the industry in a fresh race to the bottom, including on quality issue.
MO: You have mentioned the Ellen MacArthur Foundation a few times, and I get the sense that you are seeing a lot of exciting initiatives coming through the foundation but not actually scaling up.
BM: A lot of what the foundation is suggesting or asking brands to do is idealistic, it would cost more money in theory to do. So, they have come up with these design guidelines and various other initiatives, but it’s all a little bit pie in the sky. A lot of brands have signed up and there is a lot of funding, but in terms of practical impacts on the ground I can’t see what’s happened on the ground,
so I do wonder what they are actually achieving for the industry. My question to them is that having been operational for more than ten years, can they tell us something tangible that they have done, apart from a catalogue of reports, to make the industry better and more circular?
MO: When you interviewed Afry about the biggest problem to scaling chemical recycling, they pointed to five key challenges. Can you tell us what these are and whether you agree with their analysis?
BM: These challenges are technical, regulatory, financial, market pull and supply chain management/logistics. I pretty much agree with all of these! What has to be remembered is that these five challenges have to come together all at once. Not all the technologies are commercialization-ready yet, and while that is happening all the funding streams have to be kept in place and it’s going to be several years before they make any money, making it a nervy thing. Afry is pretty impressive, they take pilot ideas and help them to scale. They were very open about the financial side and what became clear is the huge amount of money that is needed to take projects from a pilot phase to full commercialization – we are talking tens of millions of Euros or dollars. Who is going to fund this? It needs someone with deep pockets really.
MO: Textile collection and sorting for recycling is seen as a significant bottleneck, how is this being done at present, and do you see a role for technologies such as smart labelling?
BM: Sorting is carried out in various ways depending on the location. Often local authorities are involved and these work in unison with charities and private sector partners such as Bank & Vogue and Value Village. Bank & Vogue do some brilliant work, and they are front leaders in how this kind of work can be done. Some countries are more progressive than others on this, however, expect the EU countries to take a lead given the ambitions of the EU Textile Strategy.
I’m not so sure about smart labeling. Like sorting technology, it has been talked about for years but there has been limited progress. Why is this? Is it because of cost (it usually is)? Even in Germany, where wages are among the highest in Europe, they are still doing most sorting by hand as using technology solutions is prohibitively expensive.
It is probably worth noting that sorting technologies are not cutting edge. The technology is not ultra-sophisticated. So, given that sorting has been a requirement for used clothing for decades, why has no major recycling adopted it at scale prior to now? The RFID technology has been around for the best part of a decade and if it’s been around for so long why is it not being used more widely? I’m guessing it comes down to cost.
MO: The focus of your report is the apparel industry, do you see progress being made by the mainstream fashion industry in designing for recycling?
BM: Not to any significant, coordinated degree. The industry is fragmented on this issue, with brands all doing their own thing, putting out occasional lines
based on the Ellan MacArthur circularity principles, for instance.
The problem brands face is they are trying to balance competing in an intense price war, on the one hand, with becoming more sustainable on the other. Something has to give at some point. Better made clothing which is more easily recycled costs more and it would be a brave brand that fully committed to this route in the current environment.
It’s a bit like talk of slow fashion and degrowth. Which brand would dare to make the first move on this? And what would shareholders think?
MO: In the UK only 23% of clothing and textiles were collected for reuse or recycling, in the U.S. it is 14% but France is managing to achieve 61%. What is needed here, is it about political will and regulations, or is it about finding a business model that shows profit?
BM: Probably a bit of both. France has led the way on this. It was the first country in Europe to bring in Extended Producer Responsibility laws for textiles and there has certainly been a lot of political will there on environmental issues.
I also get the feeling young consumers in countries such as France and also Germany are more sustainably minded than, say, the U.S. and UK.
Of course, the business model has to
show profit. In the UK, I know recyclers have faced huge financial challenges in recent years, with the price of used clothing having sunk to new lows. Much of this comes back to fast fashion, and too much of it flooding the market.
MO: Extended Producer Responsibility (EPRs) for textiles have been adopted by a small number of countries fairly recently. Are you seeing any results yet on how they are getting on particularly around the issue of clothing returns, identifying where the EPR lies and enforcing it?
BM: I think it is still early days on this. Much depends on what the levy is set at for EPR. I understand it is pretty low in France, too low to make much of a difference many believe. But it is a start. Australia has just introduced a kind of voluntary EPR for clothing. This will become mandatory next year if not enough brands sign up. But again, many think the levy is too low. I think it is around 4 percent that is applied to the manufacturer. I’m not sure how enforceable this is given the complex global nature of the supply chains. Reshoring would make this a lot easier to enforce.
MO: In Part V of the report you offer guidance and recommendations first for Investors, then for fashion brands. Most of
the investors mentioned in the report have been fashion brands, what other types of investors do you see entering this space?
BM: Great question. We seem to have seen a growth in the number of investment funds with ‘climate’ or ‘green’ in their name. The talk is that fund managers will increasingly have a focus on sustainable investments moving forwards and, to this end, one could argue that novel textile recycling is a good fit.
But any fund manager will want to see a profit or evidence of a potential profit. They won’t just back these technologies because it seems like the right thing to do. Although we don’t say it directly in the report, some of the solutions would appear to be a better bet than others as things stand. Also bear in mind a hard-nosed investor will ask tough questions and want clear projections on growth, profit, etc. They will want to look right under the bonnet. Other potential investors include philanthropic foundations. Also, might some public sector bodies such as local authorities look to establish publicprivate partnerships with some of these recyclers? I would not rule this out.
MO: You said at the beginning of this interview that the report was prompted by a desire to reach investment fund managers. Are you seeing any invest at present, also do you see any single advance that would lift the barrier to investment?
BM: Investors I see as those with green funds, ESG investors and those that have ‘climate’ in the name, but they would need to see a return on their investment. To give the HIGG Index as an example. Eighteen months ago, they got $50 million investment, and I guess the difference with the HIGG Index is that it is an existing business model that is known to be working and bringing in lots of revenue and even for them it’s not easy to get this kind of investment. So, I would guess these new technologies are chasing this kind of money but it will be more challenging for them to get this kind of investment because a lot of them are not viable yet. Much of what we are seeing is something
very new and it could take years for these companies to get up to scale and that is a challenge. Where you see lots of garments being produced already that makes a difference. If I was an investor I would want to see some clothing that they have made already, otherwise it is just on paper and theoretical. However, companies like Renewcell have tweaked an existing technology so they are getting up and running and I could see them becoming profitable in the next two to three years.
MO: Most of the innovations mentioned in the report come from Europe and North America, can you suggest why this might be and do you see any signs of change ahead?
BM: This is arguably because these are two huge markets for clothing. And the media in these parts of the world has been very loud and vocal on sustainability issues and awareness raising. In terms of this changing, I anticipate some big developments from China. There are dozens of papers on the internet around textile recycling research by Chinese universities. They are a real dark horse here. When China commits to something in business, there tends to be no half measures and if Chinese solutions regarding textile recycling were to be developed they would likely get government funding.
MO: Final question. What would be the one thing that you like the fiber and yarn industry reader to take away from your report?
BM: I would hope the report is a useful guide to the current state of play in this segment, just as the title says. We tried to make it practical and easy to read and offer some genuine insight based on many hours of research and conversations.
“Textile Recycling: State of Play” (2023) is published by Apparel Insider priced £595 (760) and available from https://apparelinsider.com/briefing/textilerecycling-state-of-play/.
Dr. Marie O’Mahony is an industry consultant, author and academic. She the author of several books on advanced and smart textiles published by Thames and Hudson. www.linkedin.com/in/marie-omahony-94776836
A Primer on the Sustainable Golden Ticket
By Jason ChenBio-based fibers are the fiber industry’s response to the world’s calls for sustainability. However, the term “biobased fiber” is often used loosely. In a broad definition, bio-based fibers include any fibers derived of biological origins, which can be divided into three major types: bio-based natural fibers (e.g., wool, cotton, hemp, flax, jute); regenerated fibers (e.g., cellulose, protein, chitosan); and bio-based synthetic fibers (e.g., polylactic acid). But some definitions may exclude one of these three major types –for example, bio-based synthetic fibers are often excluded because they are chemically modified.
Moreover, each major type could have different definitions. For example, some organizations define regenerated fibers as regenerated cellulose fibers (e.g.,
viscose, modal, lyocell), while some other definitions may also include cellulose-like regenerated fibers (e.g., soybean protein fibers, chitosan fibers) and even modified cellulose fibers (e.g., acetate fiber).
On the other hand, the terms biobased and biodegradable are often confused or used interchangeably. These two classes, however, are not necessarily mutually inclusive – bio-based fibers are not necessarily biodegradable and vice versa. Briefly speaking, all natural fibers and regenerated fibers are biodegradable, but bio-based synthetic fibers could be biodegradable (e.g., polylactic acid) or non-biodegradable (e.g., bio-based polytrimethylene terephthalate).
This article will provide an overview on the advances of markets and technologies for some of the most prominent biobased fibers.
Natural fibers include three product types based on their origins: mineral-, animal-, and plant-based. Animal fibers and plant fibers are bio-based, but mineral fibers (e.g., asbestos) are not. Animal-based natural fibers include animal hair (e.g., wool, cashmere, camel) and cocoon (silk), while plant-based fibers include seed (e.g., cotton), bast (e.g., hemp, jute, flax, ramie), and leaf (e.g., pineapple).
The use of natural fibers began before recorded history. Today the bio-based natural textile fiber market is dominated by cotton with nearly 90% market share, followed by wool, bast and leaf fibers, and silk.
Cotton alone accounts for nearly one fourth of the global textile fiber production. The International Cotton Advisory Committee (ICAC) estimated the global
cotton output was 24.55 million metric tons in 2022-2023, down from 25.18 million metric tons in 2021-2022. However, the future of cotton cultivation is inhibited by problems such as extensive land use, vast amounts of water consumption, and significant use of pesticides and fertilizers. The fiber industry’s answers to these problems include growing organic cotton or bast and leaf fibers that uses less land, water, pesticides, and fertilizers.
Growing organic cotton has made some progress in recent years. According to Textile Exchange, 342,265 metric tons of organic cotton fibers were produced in 2020/21, up 37% from the 2019/20 level, accounting for 1.4% of all cotton grown. However, the overall cotton production is still slow, projected to grow only 1.5% per year to reach 28 million metric tons by 2030, according to the Organization for Economic Cooperation and Development (OECD).
On the other hand, some of the bast and leaf fibers have unique properties and advantages such as being stronger and more resilient, which allow them to be used in a wide range of end applications and create a substantial market size. However, bast and leaf fibers also have disadvantages such as being more difficult to process or spin, more expensive, or less comfortable compared to cotton, which impair their competitiveness against other popular fibers. In addition, the production of bast and leaf fibers also rely heavily on weather, prices, farmers’ economic incentives, and other factors. All these factors reduce the potential of bast and leaf fibers’ contribution to natu-
ral fibers’ growth. According to the Food and Agriculture Organization (FAO), total flax fiber and tow production reached an all-time high of approximately 1.5 million metric tons (including both textile and non-textile applications) in 2005 and an all-time low of 0.49 million metric tons in 2011. The average annual growth was only 0.4% from 1961 to 2021.
Cellulose fibers have a history of more than 160 years. Rayon, developed in 1846 to replace silk, is the world’s first cellulose fiber, and also the first manmade fiber. Cellulose fibers are made from natural cellulose sources, such as cotton pulp and wood pulp, by dissolving them in chemicals and reforming them into fibers. Cellulose, which is part of all major plants, is bio-based and biodegradable, and its degradation does not cause any microplastic particles. Therefore, producers of cellulose fibers are positioning themselves for sustainability claims, which boosted a growth of more than 5% per year in recent years.
However, there are also some hurdles that impede the further growth of cellulose fibers. For example, the raw materials of cellulose fibers rely heavily on wood and cotton, but cotton production stagnates and the cellulose yield from wood is low. On the other hand, there are lack of cradle-to-cradle life cycle analyses that prove the benefits of cellulose – in fact, the standard process for cellulose production may involve washing and bleaching with chlorine, or other chemicals which exacerbate pollutants.
Currently, researchers are finding new solutions to tackle these problems. Manufacturers have done life cycle analyses based on innovated technologies that produce sustainable benefits – for example, energy-efficient processes for cleanly separating cellulose from lignin and hemicellulose, or close-loop recycling systems to separate and reuse water, gas, and chemicals in the manufacturing process.
On the raw material side, cellulose is also found in straws, bagasse, bamboo, the cell walls of green algae, and the membranes of most fungi. New technologies allow these materials to be used to replace wood and cotton in cellulose fiber production. An example is the China-based Qingdao Yuanhai New Material Technology launched the world’s first commercialized alginate fiber plant in 2019, with an annual capacity of 5,000 metric tons. Their alginate fibers are used for nonwoven, garments, medical applications, etc.
Cellulose-like fibers are also developed to reduce the consumption of wood and cotton. Chitosan fibers and protein fibers are among these examples. Chitosan is a chemically cellulose-like biopolymer, which is processed from chitin, the world’s second largest natural polymer only after cellulose in terms of annual production volume. Chitosan fibers are bio-based, biodegradable, non-toxic, and biocompatible. However, they also have limitations such as poor mechanical and thermal strength. Currently, several companies have built chitosan fiber production facilities at scales of hundreds of metric tons annually.
Bio-based synthetic fibers are produced by chemically or biologically synthesizing renewable organic materials. Polylactic acid (PLA) was the first bio-based synthetic fiber, first synthesized more than 150 years ago. But it was not commercialized until the late 1980s and early 1990s when DuPont and Cargill explored applications for lactic acid, lactide and PLA. Cargill first produced PLA in a 6,000 metric tons per year plant in 1994 and developed a continuous process for high-purity lactide production based on reactive distillation.
Currently the global bio-based synthetic fiber market is dominated by polytrimethylene terephthalate (PTT) fibers, polylactic acid (PLA) fibers, polyethylene terephthalate (PET) fibers, and polyamide (PA) fibers. But polybutylene succinate (PBS) fibers, polyhydroxyalkanoates (PHAs) fibers, and several others also show promise. PLA, PBS, PHAs are biodegradable, while PTT, PA, and PET nonbiodegradable.
Based on the projections from European Bioplastics e.V. and other sources, biobased synthetic fibers could have a strong growth of around 25% per year from 2022 through 2027. But they had a market size of only 200,000 to 300,000 metric tons by 2022, much smaller than regenerated fibers (above 7.5 million metric tons) and bio-based natural textile fibers (approximately 27 million metric tons). Based on the above information and analysis,
rough estimates can be made that the global fiber industry could produce approximately 3 million metric tons more regenerated fibers, 2 million metric tons more bio-based natural fibers, and 0.5 million tons more bio-based synthetic fibers in 2027 than in 2022.
PLA is derived from agricultural products with monomers that can be produced by microbial fermentation. It is well suited for melt spinning into fibers. Compared with the solvent process used for synthetic cellulosic fibers, the melt spinning process is less expensive and produces better properties. PLA fibers are nontoxic and fully biodegradable, reverting to their basic constituents: carbon dioxide (CO2) and water.
European Bioplastics e.V. forecasts that the global capacity of PLA polymers will have a compound annual growth rate (CAGR) of 39% from 460,000 metric tons in 2022 to 2.38 million metric tons in 2027 as a result of a series of large-scale new facilities built in Asia, North America, and Europe. Approximately 10% of the capacity, or 50,000 metric tons per year, was for fiber application in 2022. Historically, the fiber segment grew a little slower than the whole PLA market, and if this trend continues, PLA fibers could grow at a CAGR of 30%-35% from 2022 to 2027 and
reach a capacity between 186,000 and 224,000 metric tons per year.
Unmodified PLA has several limitations such as brittleness, especially below 45ºF, and low heat distortion temperatures (HDTs). Strong market perspective has driven innovations for PLA modification, mainly through three routes: chemical modification, physical modification, and compatibilizer modification.
Chemical modification methods include block copolymerization, graft copolymerization, cross-linking, and chain extension for improving the tensile strength, tensile modulus, thermal stability, and biocompatibility of PLA fibers. Physical modification uses thermoplastics (e.g., poly ether-ether ketone), biodegradable resins (e.g., polycaprolactone), elastomers, rubbers, nano-particles, block polymers, graft polymers, or other fibers to improve the tensile strength, tensile modulus, thermal stability, crystallinity, biodegradability, biocompatibility, and elongation at break. Compatibilizers (e.g., PBS and ethylene glycol methacrylate) are used to improve the tenacity of PLA fibers.
In addition to the above three modification methods, technological innovations for PLA fibers also focus on the following segments: the technologies of fermentation, separation, and purification for PLA raw material, lactic acid;
the green dyeing technologies for PLA fibers and yarns; the design for industryscale melt-spinning facilities; and additional properties to PLA fibers such as flame retardance and antibacterial performance.
Polyhydroxyalkanoates (PHAs) and Polybutylene Succinate (PBS) Fibers
PHAs are biodegradable in soil and aquatic environments. The most prominent commercially available PHAs are polyhydroxybutyrate (PHB) and polyhydroxybutyrate hydroxyvalerate (PHBV). Currently, the U.S.-based Danimer Scientific and companies in China, Germany, Italy, and Brazil are key suppliers to PHAs.
Danimer Scientific estimated the PHA market could have a potential of 230 million metric tons per year. However, today the PHA industry is still in its infancy, with a global capacity of around 50,000 metric tons per year. Moreover, fiber accounts for only a fraction of PHAs applications. In 2022, the world’s total production of PHAs fibers was less than 1,000 metric tons.
PHBV fibers are biocompatible and biodegradable, which make them ideal materials for making medical textiles. Currently, the China-based Tianan is the largest PHBV supplier. However, PHBV fibers have several limitations such as brittleness, poor thermal stability, and being difficult to process. Currently, researchers are using block copolymerization, graft copolymerization, physical modification, and other methods to solve these problems.
PHB, the simplest PHA with properties similar to polypropylene (PP), is produced by bacteria that process glucose or starch. The Germany-based Biomer extruded their resin into multifilament fibers for woven surgical patches.
On the other hand, PBS is a bio-based polyester with similar properties to PET. It
has excellent mechanical and biodegradable properties and good thermal stability and is easy to process, which allow it to be used in a wide range of end applications ranging from food packages to hygiene products. Currently, the commercialization for PBS fiber is still in the early stage. However, it is a promising product worthy of note for the following decade.
The non-degradable bio-based synthetic fiber market is dominated by bio-based PTT fibers, followed by bio-based PA fibers and PET fibers. While the expansion for bio-based PTT fiber and PET fiber stagnates, the main driver for the capacity growth is bio-based PA fiber.
Today, the bio-based PA market is dominated by petrochemical giants such as BASF, DuPont, and Arkema. In 2007, BASF introduced Ultramid Balance nylon 6/10 which is based on approximately 60% sebacic acid, a material derived from castor oil. In 2009, DuPont introduced the Zytel product family which includes nylon 10/10 and nylon 6/10 along with their copolymers and their alloys with other polymers. DuPont’s nylon 10/10 contains 100% sebacic acid content while its nylon 6/10 contains 63%. China’s Cathey joined the competition in 2021 with an annual capacity of 100,000 metric tons of PA56, which is based on 45% renewable sources.
Currently the global production capacity for bio-based PA resins was more than 200 million metric tons if measured at the level of their bio-based content. Around 40 thousand metric tons are used for fiber production. Based on the current expansion plans, the global capacity of bio-based PA fibers is very likely to exceed 100,000 metric tons per year by 2027.
On the other hand, PTT is linear aromatic polyester made from 1, 3-propane-
diol (PDO). The bio-based edition of PTT was first commercialized by DuPont when the company launched Sorona, a PTT fiber based on bio-based 1, 3-PDO made through fermenting biomass sugars and glucoses.
Currently, bio-based PTT fiber is the largest bio-based synthetic fiber, with a capacity of over 200,000 metric tons a year. On the other hand, bio-based PET is mostly used for plastic bottles, and only a little more than 10,000 metric tons go to fiber production. Key manufacturers of bio-based PTT include the U.S.-based DuPont, and the China-based Shenghong and Glory.
Fiber manufacturers are currently pushing the use of bio-based PTT in highend garments, home textiles, and industrial textiles. PTT provides good stretch recovery, softness and dyeability to garments, as well as excellent resilience, wearability, dyeability, static resistance, and chemical resistance to home textiles and industrial textiles.
Today, there is an overcapacity in the bio-based PTT and bio-based PET resin industries. Therefore, there is no largescale bio-based PTT and bio-based PET resin projects planned for the next few years, though their fiber applications could still have significant growth in the same period.
Jason Chen is an international correspondent for International Fiber Journal . He is a leading journalist covering the fiber industry in Asia and a senior analyst who has published more than 50 books and reports for polymers, composites, and other advanced materials and technologies. He can be reached at jasonchen200501@ hotmail.com
Fiber manufacturers are currently pushing the use of bio-based PTT in high-end garments, home textiles, and industrial textiles.fiber sliver, pre-yarn. MINIFibers
The global textile industry involves the production, processing, and distribution of various fibers, fabrics, and finished textile products. It encompasses a wide range of activities, including fiber cultivation, spinning, weaving, knitting, dyeing, printing, and garment manufacturing. Unfortunately, the textile industry has been associated with several environmental challenges and impacts throughout its value chain.
The industry is increasingly recognizing the need for sustainable practices and materials to mitigate its environmental impact. Sustainable textiles encompass various approaches, including the use of bio-based fibers, recycled fibers, eco-friendly dyeing processes, and circular economy principles. Bio-based fibers and yarns, are promising solutions by utilizing renewable resources and reducing reliance on fossil fuels.
Bio-based fibers and yarns are materials that are derived from renewable plants, animals, or mineral sources, as opposed to fibers that come from petroleum-based sources. These materials are becoming increasingly popular in the textile industry because they are more sustainable and eco-friendlier than manmade materials. What was old is now new again. Bio-based fibers can be spun into yarns that can then be used to make a wide range of textile products, such as clothing, bedding, and towels.
Plant-based biomass sources include cotton, flax, hemp, bamboo, jute, and sisal. These fibers are obtained from the stems, leaves, or seeds of plants. Plantbased fibers are widely used in the textile industry and are known for their comfort, breathability, and versatility. Animal-based fibers are obtained primarily through shearing, combing, or collecting
naturally shed fibers. Examples include wool from sheep, cashmere from goats, silk from silkworms, and angora from rabbits. Animal-based fibers are valued for their insulation properties, softness, and luxurious feel. Microorganisms, such as bacteria and fungi, can be engineered to produce bio-based fibers through fermentation processes. Microbial fermentation offers the potential to create novel and sustainable fibers with customizable properties.
The extraction and processing methods for bio-based fibers depend on the biomass source and the desired characteristics of the fibers. Some common methods include:
Mechanically separating fibers from the plant or animal matrix through processes such as retting, decortication, ginning, or carding. These methods mechanically remove non-fiber components
and align the fibers for further processing. Chemical methods use solvents or chemical treatments to dissolve or break down non-fiber components, allowing the extraction of pure fibers. Examples include the use of alkali solutions for processing plant-based fibers like bamboo or wood pulp for cellulose fibers. Enzymatic processes utilize enzymes to break down non-fiber components selectively. Enzymes can be used to treat plant-based fibers like hemp or bamboo, facilitating the separation of fibers from other plant constituents. Advances in biotechnology have enabled the development of genetically modified microorganisms capable of producing specific fibers. Through fermentation processes, these microorganisms can synthesize fibers directly, bypassing the need for extraction from biomass sources.
Fiber formation techniques play a crucial role in determining the final properties and characteristics of the bio-based fibers, such as strength, diameter, length, and surface texture. Once the fibers are extracted or synthesized, they undergo fiber formation techniques to transform them into usable forms for textile applications.
Spinning is the most common technique for forming fibers. It involves drawing out the extracted fibers into continuous filaments and twisting them to enhance strength and cohesion. Spinning methods can vary depending on the fiber type, including ring spinning, open-end spinning, and air jet spinning. Extrusion is a technique used for synthetic bio-based fibers. It involves melting or dissolving the biopolymer and extruding it through spinnerets to form continuous filaments. The extruded filaments are then solidified, often through cooling or chemical processes, to create the fibers. Wet spinning is a process used to produce regenerated cellulose fibers, such as viscose and lyocell. It involves dissolving the cellulose in a solvent and extruding it into a coagulation bath, where the solvent is removed, and the cellulose solidifies into fibers.
The adoption of bio-based fibers and yarns in textile production brings multiple environmental benefits, including
the conservation of resources, reduction in greenhouse gas emissions, and the potential for a more circular and sustainable textile economy. Biomass sources for bio-based fibers often sequester carbon dioxide during growth, helping to offset emissions and mitigate climate change impacts. By embracing these fibers, the industry can move towards a more sustainable and responsible approach to meet the growing demand for textiles.
While bio-based fibers offer numerous benefits, there are also challenges and limitations that need to be addressed. Some key considerations include supply chain and related scalability issues, technical limitations and durability and performance concerns.
The production of bio-based fibers relies on a complex supply chain involving sourcing, cultivation, extraction, and processing of biomass sources. Scaling up the production of bio-based fibers to meet the demand of the textile industry can be challenging. Issues such as inconsistent quality, limited availability of biomass sources, and the need for infrastructure development pose hurdles to achieving large-scale production, widespread adoption of bio-based fibers.
The production processes for bio-based fibers often require specialized technologies and equipment, which may be limited in availability or require further
development. Technological advancements are necessary to improve the efficiency, quality, and cost-effectiveness of bio-based fiber production. Additionally, the cost of bio-based fibers can be higher compared to conventional fibers due to factors such as limited economies of scale, processing complexities, and availability of raw materials. Addressing these limitations is crucial to make bio-based fibers more accessible and competitive in the market.
Bio-based fibers may face challenges related to durability, strength, and performance compared to conventional synthetic fibers. Achieving the desired performance characteristics, such as
tensile strength, abrasion resistance, and colorfastness, while maintaining the sustainable attributes of bio-based fibers requires ongoing research and development. Improvements in fiber processing techniques, fiber modifications, and blending with other fibers can help enhance the performance and durability of bio-based fibers.
Overcoming these challenges and limitations requires investments in research and development, technological innovation, sustainable sourcing practices, and infrastructure development are essential to drive the growth and adoption of biobased fibers in the textile industry. By addressing these challenges, the industry can unlock the full potential of bio-based fibers and contribute to a more sustainable and responsible future.
Bio-based fibers have significant market opportunities and economic potential, driven by the growing demand for sustainable textiles, evolving consumer preferences, and the potential for new business models. As sustainability becomes a central focus in the textile industry, bio-based fibers have the potential to
capture a larger market share and meet the demand for sustainable textiles. The market for bio-based fibers is driven by trends such as “green” and “clean” fashion, circular economy principles, and a desire for transparency in supply chains. The adoption of bio-based fibers can stimulate the development of new business models and value chains in the textile industry. From sourcing biomass materials to fiber production, processing, and distribution, bio-based fibers offer opportunities for innovation and collaboration across the value chain.
In order maximize the benefits of biobased fibers, advancements in fiber extraction and processing technologies, improvement in fiber properties and performance, expansion of biomass feedstock options, and collaboration between academia, industry, and policymakers are key areas for focus. Additionally, research should prioritize life cycle assessments (LCAs) and sustainability certifications to provide transparent information about the environmental impacts and benefits of bio-based fibers. These assessments can inform decision-making processes,
guide the development of best practices, and enable the adoption of standardized sustainability metrics.
The adoption and utilization of biobased fibers and yarns presents a pathway towards a more sustainable and responsible textile industry. By addressing the challenges, driving research and development, and providing policy support, the industry can accelerate the transition towards a more environmentally conscious and economically viable future in the textile sector. At MiniFIBERS we continue to work with our partners to bring responsibly sourced and sensible natural, bio-based, recycled, upcycled and second life fibers to the market. We continue to innovate our processes to provide what our customers need to be competitive and meet their circularity goals.
Chris Plotz is the Director of Technical and Business Development at MiniFIBERS Inc.in Johnson City TN. Plotz is a business leader with 25 years of technical product and business development in a number of industries. He is responsible for leading and supporting all segments of growth of MiniFIBERS markets including C.A.S.E., nonwovens, composites and textiles of both synthetic and natural fibers. He can be reached at cplotz@ minifibers.com or +1 423 616 2171.
While biobased fibers offer numerous benefits, there are also challenges and limitations that need to be addressed.MINIFibers By Seshadri Ramkumar, Ph.D.
Seshadri Ramkumar, Ph.D., is professor of nonwovens and advanced materials at Texas Tech University. He is a member of Technical Advisory Board at INDA, Association of the Nonwoven Fabrics Industry. He was the immediate past chair of the Nonwovens Engineers & Technologists (NET) Division of TAPPI, and he publishes a column called TexSnips. He can be reached at s.ramkumar@ttu.edu.
ince COVID-19, manufacturing is receiving much needed attention as part of nations’ goals to have a good supply of life-saving materials, reviving their economy and generating highly skilled jobs. Funds have been budgeted in national budgets for infrastructure projects, defense materials, major R&D projects, and enhanced defense procurement. In all these initiatives, different forms and types of research and development in fibrous substrates is involved. In these advanced fiber-based materials, aesthetics and fashion take back seats, while high performance and functional aspects occupy the front seats. There is opportunity and necessity for stakeholders in the sector to be involved in engaged outreach about the industry to the general public, policymakers, and end users.
Our industry needs to be proactive in research and development in areas related to sustainability, functional fibers, environmentally friendly chemicals, recyclability and reusability aspects. The advanced textile sector has to align itself with the United Nations’ sustainability goals in terms of the use of earth-friendly materials, reducing energy usage, adapting reuse and recycle strategies, etc.
In the case of hygiene, medical, forensic and some defense applications, textile products are predominantly single-use in nature. The technical textiles industry has to pay attention in developing cost-effective single-use and semi-durable products which are less dependent on petroleum-based sources and promote cost-effective disposal methods. More importantly, genuine and positive information about the usefulness and advantages of using advanced textile products has to be relayed to the end-users and the public. In this regard, efforts undertaken by the Cary-based Association of the Nonwoven Fabrics Industry, INDA, in formulating flushability standards and engaging with the public and broader press has to be recognized. The industry should focus on timely R&D which can result in need-based products. This needs engagement with government agencies and academia.
Agile and advanced manufacturing such as 3D printing are areas that offer growth potential. Particularly, polymer-based medical textiles and implants can be developed using 3D printing. “3D printed patient specific implantable and nonimplantable devices are becoming more sustainable with the reduction in cost of production, more adoption of the technology by the surgeons due to its advantages and introduction of more costeffective 3D printable materials with the required biomechanical and physiological properties,” stated Dr. Jayanthi Parthasarathy, Manager of 3D Printing, Nationwide Children’s Hospital, Columbus, OH.
In the realm of functional chemicals, research is needed, states Ganesh Srinivasan, CEO of Bengaluru,
Efforts undertaken by the Association of the Nonwoven Fabrics Industry, INDA, in formulating flushability standards and engaging with the public and broader press has to be recognized. The industry should focus on timely R&D which can result in need-based products.
India-based Resil Chemicals. “For instance, the market requires long-lasting fluorine-free water repellents and flame retardants that can resist more than 30 washes. It is necessary to use low-toxic fire retardants that can provide fire protection while minimizing physiological heat stress,” added Srinivasan.
Given the need to develop products that can have a balance between cost and functionality, the industry needs to be creative in utilizing resources. One strategy is to have a symbiotic relationship with academia and research organizations. Particularly for advanced textile products, science and technology need to be borrowed from different disciplines such as chemistry, physics, biotechnology and materials science. The functional textiles industry needs the support of organic chemistry, analytical science, surface physics, coating science, etc. to develop multifunctional properties. For example, nonwoven wipes, which are intended for wiping away toxic chemicals, need support of chemistry and physics disciplines for characterization involving FTIR, Gas Chromatography, etc. Research laboratories focusing on fiber science and manufacturing need to work with chemistry departments to speed up innovations and move ideas to commercialization. In fast moving and hot fields such as the development and replace-
ment of regulated chemicals, large collaborative projects involving multiple laboratories from different countries will be beneficial. For example, the industry has worked at warp speeds to find suitable alternatives for PFAS (Per- and polyfluoroalkyl substances). Several national governments due to forthcoming regulations are interested in funding such projects.
Research in functional textiles is of interest to federal agencies in advanced nations such as the U.S. Department of Defense. A major initiative is underway with the support of U.S. DoD called Advanced Functional Fabrics of America, centered at Massachusetts Institute of Technology. Advanced sustainable manufacturing and recycling initiatives also receive much needed support such as The REMADE Institute which is a division of Sustainable Manufacturing Innovation Alliance Corporation.
Given the heightened awareness among policy makers to boot the manufacturing sector, focusing on sustainability and enhancing workforce skills, are some areas that can receive good support. The advanced textile sector can avail many large-scale funding opportunities and move towards its next phase. Innovation is the way forward!
In the ever-evolving landscape of the fiber industry, the Dornbirn GFC Global Fibre Congress has emerged as the beacon of innovation and collaboration. As the world’s leading innovation congress in “everything fibers,” the event has become the annual pilgrimage for professionals and experts from all corners of the globe. With its focus on generating new ideas and breakthroughs, the 62nd Dornbirn GFC is set to take place from September 13-15, 2023, at the Kulturhaus in Dornbirn, Austria.
The annual event brings together the entire fiber industry, encompassing key stakeholders from fiber production to textile manufacturing, brands, and retail. The congress prides itself on connecting the entire textile value chain, fostering partnerships, and presenting sustainable innovations. A lineup of 125 lectures awaits participants, promising insights into the latest research and development breakthroughs and their practical applications.
The congress opens with plenary lectures that set the tone for the event’s innovative spirit. Stephan Sielaff, CEO of Lenzing AG, will delve into “Circularity: The New Business Model,” offering a cuttingedge perspective on the industry’s future. Furthermore, Dirk Vantyghem, CEO of EURATEX, will provide an overview of the “EU Sustainable Textiles Strategy” and its global impact, paving the way for a more sustainable and eco-friendly future.
Giuseppe Gherzi, CEO of Gherzi Textil Organisation AG, will explore the prospects and challenges that lie ahead in the “2030 – a New Textile World Order” presentation. By analyzing the evolving global textile industry, Gherzi will shed light on the emerging opportunities and transformations that await the sector in the coming decade.
A notable addition to the congress is Verbund AG, a prominent energy pro-
vider. Rudolf Zauner, Innovation Director, will present “Energy innovations – the Key to Climate Neutrality,” highlighting the crucial role of the fiber and textile industry in achieving climate goals. This presentation underscores the industry’s commitment to sustainability and its significant impact on the environment.
The Dornbirn GFC emphasizes sustainability and circular economy as central themes. To further this mission, the congress collaborates with RWTH Aachen University to offer a series of lectures focusing on sustainable innovations in the fiber industry. Topics include automation and digitalization for textile sorting, length-preserving tearing for highquality yarn production, and the use of shape memory fibers in 4D textiles, among others.
In addition to the main congress, the 3rd Innovation Days, organized in cooperation with FashionForGood and PWC, provide a platform for more than 20 innovators. These innovators will present their ideas, which range from light-curing processes for stretch textiles to quantification methods for recycled fibers in fabrics and yarns. The Innovation Days are a testament to the industry’s commitment to pushing the boundaries of sustainable fiber technology.
The Dornbirn GFC acknowledges contributions to the field of fiber research and development through various awards. Lenzing AG’s “Young Scientist Award” recognizes young researchers’ exceptional work with a prize of €5,000, fostering further innovation and technological progress. Moreover, the Paul Schlack Prize, awarded by the European Man-Made Fibres Association (CIRFS), celebrates R&D excellence, encouraging collaboration between academia and industry.
The Dornbirn GFC 2023 encompasses four key topics driving the future of the fiber industry. These include fiber innovation and biomaterials; sustainability and circular economy practices; nonwovens and technical textiles; and advancements in apparel and sports textiles. The congress explores these topics to inspire positive change and transformation within the industry.
The 62nd Dornbirn GFC Global Fibre Congress promises to be a platform of exciting discussions, path-breaking ideas, and groundbreaking innovations, cementing its position as the preeminent event in the fiber industry. As professionals, experts, and thought leaders gather in Dornbirn, Austria, the stage is set for a transformative journey towards a sustainable and prosperous future for fibers.
Market-leading innovations from over 350 exhibitors from 30 countries combined with thousands of attendees gathered for Techtextil North America and Texprocess Americas in Atlanta, held at the Georgia World Congress Center in May 2023.
The Techtextil Symposium was wellattended, highlighting functional fabrics, circular economy, medical textiles, aerospace and defense applications and nonwovens. Tech Zone Talks were presented by exhibitors, and the Tech Zone talks were mini-sessions on specific niches like ChatGPT and Design, PFAS, Circular Polyment, Biocatalytic textiles, and more.
Focusing on two key Techtextil symposium discussions, the advancements and solutions to tackle textile’s welldocumented environmental challenges were on aplenty from platforms and show floor presentations, spilling over into exhibitor booth discussions.
In Innovative Fibers for a Circular Economy, reducing plastic consumption was a high priority during one opening session for Techtextil North America. Diana Wyman of ATTCC moderated a panel that included Sonja Salmon, Ph.D., associate professor of textile engineering, chemistry and science, North Carolina State University; Harrie Schoots, consultant for Fibers52; and Andrea Ferris, CEO, Intrinsic Advanced Materials.
With expertise in bio-based textile materials and processes, Professor Salmon focused her comments on her research, Enzymatic Conversion of Cellulosic Textiles for Recycling.1 The project resulted in the successful separation of cotton from polyester in blended fabric. “We can separate all of the cotton out of a cottonpolyester blend, meaning now we have clean polyester that can be recycled,” said Salmon. “In a landfill, the polyester is not going to degrade, and the cotton
might take several months or more to break down. Using our method, we can separate the cotton from polyester in less than 48 hours.”
Harrie Schoots discussed his work with Fiber52, a company focused on sustainable dye solutions for cotton. “There is a lot of talk today about recycling fibers which is good, we need to do more of this,” he said, focusing his discussion on cotton fiber as a go-to fiber with enhancements. “A lot of water is being used in today’s cotton scour and bleach process and dyeing and finishing. Fiber52™ comfort cotton brings a patent-pending technology that minimizes the use of resources at this phase.” The technology allows textile manufacturers to continue using the same machinery, but replace harsh chemicals with inexpensive bioproducts, and achieve the same quality results. There is also savings on heat, energy, water, and time.
Intrinsic Advanced Materials CEO Andrea Ferris discussed the company’s advancement to eliminate micro plastics. “CiCLO® is biodegradable technology aimed to reduce the impacts of fugitive synthetic microfiber pollution in the oceans,” she said. “Our seas are truly
sick. Biodegradability of plastic doesn’t always make sense, such as small single use straws, etc., but there are times when biodegradability is essential. We have an upstream solution that balances durability and sustainability.” CiCLO® technology is a sustainable textiles ingredient in the form of an additive that is combined with polyester and nylon during melt extrusion at the very beginning of the fiber-making process. When CiCLO®-enhanced fibers end up in environments where biodegradation can occur naturally, microbes are attracted to the fibers and can mineralize them at rates comparable to natural fibers, such as wool. (Read more about this in our interview of Ferris on page 10.)
Delving into Nonwovens Advancements, the session was moderated by Behnam Pourdeyhimi, executive director of the Nonwovens Institute, with expert panelists Charles Vaillant, CTO/CDO, Mann+Hummel Group; Bryan Haynes, Ph.D., Technical Director Global Non-
wovens, Kimberly Clark; and Jeff Strahan, Ph.D., Sustainability and Compliance, Milliken & Company.
Charles Vaillant led the discussion with vehicle filtration. Filtration support is a challenge of today’s society with the increases in air quality and regulations, notes Vaillant. “They are tightening the regs on what is acceptable for humans. Pollutants need to be reduced. Europe and North America have the cleanest air in the world, but other countries are not so good. Ultra-fine particles are numerous, invisible, and dangerous – the lungs are not capable to deal with them and they end up in bloodstream. Mann+Hummel is focusing efforts on Smart Cabin Air Filter systems, where sensors to determine the air quality inside and around the vehicle. This leads to a lasting improvement in air quality, while at the same time reducing energy consumption. They are utilizing HEPA filtration of ultrafine particles (<0,1 µm), combined with sensors that continuously control the system and monitor the air quality, making for cleaner and safer cabin air. “The traffic jam is where you need protection,” Vaillant notes. Moving towards EV filtration, M+H’s Intelligent FreciousSmart cabin air filter system provides clean air and simultaneously reduces power consumption, something the company says is a perfect concept for electric vehicles.
Brian Haynes provided a historical perspective of plastics and textile pollution. How big is this, he asked? “First disposal product was invented in 1950s. We have spent the last 70 years producing 20 trillion pounds of plastic, enough to fill 8,000 football stadiums.” Why should we care? “We eat one credit card of plastic each week. It is everywhere.” He noted that if we continue, by 2040 plastic pollution is estimated to increase 300% by 2040. “It is an industry wake-up call,” he said, that requires a very strong industry response and aggressive plans to deal with plastics. He suggests that companies look for partnerships for innovation pathways.
At Kimberly-Clark, “By 2030, we want to achieve 50% reduction in our plastic use. Eventually, we want to get to circularity with packaging, product, and waste man-
Shining a light on the industry’s cutting-edge advancements, the Innovation Awards 2023 revealed the front-runners of innovative textile technologies. “We are happy to bring the Innovation Awards to the U.S. editions of Techtextil North America & Texprocess Americas which will enable and encourage new market developments and is a testament to the ingenuity and vision of the brands participating at these shows,” says Kristy Meade, Vice President of Technical Textiles & Technology Shows for Messe Frankfurt, Inc. The awardwinning developments were presented to:
New Concept Winner: Henderson Sewing Machine Co. Inc. and Matsuya R & D For the development of “The Intelligent Robot Sewing Machine with Digital Image Processing System”
New Technology Winner: SPEC and Svegea of Sweden for the development of “SVEGEA EC-450XF”
New Application Winner: Pathfinder Cutting Technology for the Development of “FabricPro: Revolutionizing Fabric Spreading with Innovative Safety Features and Improved Operator Ergonomics”
New Product Winner: Stratasys for the development of “Stratasys J850™ TechStyle™ direct-to-textile 3D printer”
agement systems. There is no silver bullet, it will take all the above,” he notes. Labeling it “coopetition,” he believes it is going to take a combined effort to address this in the years to come, with emphasis on bio-based feedstocks, recycling, composting pathways, and other combined efforts.
“All companies here at Techtextil will be required to have science-based targets in two years,” shared Jeff Strahan in his discussion. Net zero by 2050 goals are covered in the Paris Agreement, where the EU and 194 states, totaling over 98% of anthropogenic emissions, have ratified or acceded to the agreement. Interestingly, Science Based Targets (SBTi) is a
New Approaches on Sustainability & Circular Economy Winner: Henderson Sewing Machine Co. Inc. & Twine Solutions Ltd for the development of “Thread Digital Dyeing System TS-1800”
New Technologies on Sustainability & Recycling Winner: Dürkopp Adler GmbH for the development of “M-TYPE DELTA e-con”
New Technology & Digitalization winner: SEDDI For the development of “SEDDI Textura: Real Fabrics Digitized Brilliantly with AI”
nonprofit that manages the net-zero data global data and regularly adds companies to their list at sciencebasedtargets.org, in blockchain style, on Scope 1 (direct fuel usage), 2 (indirect GHG emissions), and 3 (indirect emissions from downstream and upstream operations) stages of compliance. Milliken and Company is one of the first 50 companies to have verified net-zero targets by SBTi and is well on their way to meeting the 2050 goal. To date, they are on track to meet company Scope 1 and 2 greenhouse gas emissions goals (50.4% by 2030), and Scope 3 goals (30% reduction by 2030), which include supply chain partners.
1https://www.sciencedirect.com/science/article/pii/S2666916123000117?via%3Dihub
INDA, the Association of the Nonwoven Fabrics Industry, announced that registration and tabletop exhibit reservations are open for the ninth edition of Hygienix™, November 13-16, New Orleans, Louisiana. More than 450 absorbent hygiene and personal care professionals from around the world will gather for four days of networking, presentations, and business opportunities.
The theme for this year’s Hygienix is “Shaping the Future of Absorbent Hygiene.” The event will focus on the market’s continued growth with presentations on sustainability, technology advancements, disruptive small brands, and market data and trends. Hygienix will also offer a workshop on absorbent hygiene systems led by Jim Robinson, Absorbent Hygiene Insights, LLC, Monday, November 13th. The full Hygienix program will be announced at a later date.
INDA is also introducing a new element for Hygienix – pre-conference webinars. Carlos Richer, principal, Diaper Testing International, will present insights and trends in diaper design in the U.S. market and Heidi Beatty, CEO, Crown Abbey, LLC, will share her expertise in the absorbent hygiene sector.
More than 50 companies will showcase their innovations and technologies during the evening tabletop exhibits and receptions. Participants will be able to discuss their needs with technical leaders and source better solutions for their products, Nov. 14-15.
Nominations are being accepted through August 7th for the Hygienix Innovation Award™. Three finalists will be selected to present their absorbent hygiene products on Tuesday, November 14th to hundreds of senior-level professionals. The winner of the award will be
announced at the end of the event, Thursday, November 16th.
Last year’s award recipient was Pads on a Roll™ by Egal Pads. “Participating in the Hygienix conference (and winning the award) was an incredible opportunity for Egal on so many fronts,” said Penelope Finnie, CEO, Egal Pads, Inc. “First, it was amazing to get such incredible validation of our product from those who have literally seen it all. As a newcomer to the industry, it was an incredible opportunity to learn from so many veterans. The connections that were created have really helped move us forward. I credit winning the award with providing much of that momentum,” Finnie continued. www.hygienix.org
Kelheim Fibres: Change in Management Team
After nearly 30 years with the company, Matthew North, Commercial Director at renowned viscose specialty fiber manufacturer Kelheim Fibres, retired July 1, 2023. Throughout his long and successful career, he has played a significant role in transforming Kelheim Fibres from a supplier of standard fibers to the European textile industry into a supplier of predominantly customized specialty fibers for the hygiene, specialty paper, and textile industries.
Craig Barker, CEO of Kelheim Fibres, said, “On behalf of the entire team, I would like to express our gratitude to Matthew for his outstanding work over the past decades. His wealth of experience, calm nature, and British humor will be greatly missed. We wish him all the best for his exciting new chapter in life. At the same time, we wish Mark von der Becke and Dr. Marina CrnojaCosic much success in the new responsibilities they have now assumed.”
Mark von der Becke will assume the position of sales director and become part of the management team at Kelheim Fibres. The 48-year-old brings extensive experience in sales, marketing, and key account management. He has held various leadership positions in companies such as Hoechst, Clariant, and DS Smith in Germany, Switzerland, and China. He is known for successfully developing and implementing strategy and change programs.
Dr. Marina Crnoja-Cosic, who has been serving as director of new business development and a member of the management team at Kelheim Fibres since 2020, will take on the responsibility for marketing and communications. She has already proven herself as a dedicated and competent leader and will now drive the further development of the marketing strategy and communication with customers and partners. www.kelheim-fibres.com
Several members of Congress recently introduced the PFAS Alternatives Act. The bipartisan bill would support the development of next-generation safety materials for firefighter turnout gear that are free of perand polyfluoroalkyl substances (PFAS).
Globe Manufacturing Company, one of several U.S. companies that makes structural turnout gear for firefighters, supports the PFAS Alternatives Act because it will help the industry meet firefighters’ call for PFAS-free gear. msasafety.com
THE SHARP CUT TO MORE EFFICIENCY. HIGH PERFORMANCE BLADES AND STATE-OF-THE-ART-COATING FOR SUPERIOR CUTTING RESULTS IN STAPLE FIBERS.
100% MADE IN SOLINGEN · GERMANY!
TSG Finishing LLC recently announced the strategic expansion of its chemical compound sales. The move brings more than a century’s worth of specialized chemical and coating knowledge directly to its clients.
With a deep understanding of synthetic latex polymers such as acrylic, SBR, vinyl, polyurethane, and many more, TSG Finishing integrates raw materials from a wide range of manufacturers to create custom formulations. Their expertise extends to C6 and C0 DWR’s, flame retardants, and antimicrobials, as well as a host of non-standard products such as liquid absorption and stiffeners.
Said CEO Brian Rosenstein: “Our expansion into chemical compound sales underscores our commitment to fostering scientific rigor, innovation, and technical excellence within our clientele’s coating processes. Our custom formulations and compounds are meticulously crafted to meet each client’s unique needs.” www.tsgfinishing.com
PUBLISHER Driven By Design LLC advertising@inda.media • +1 239.225.6137
Sabine Dussey
GERMANY, FRANCE, AUSTRIA, SWITZERLAND, SCANDANAVIA, BENELUX sabine.dussey@dussey.de • +49 2129.348390
Joan Oakley BUYER’S GUIDE & CLASSIFIED ADS
joakley@inda.media • +1 248.347.3486
Ferruccio Silvera & Filippo Silvera ITALY & SPAIN info@silvera.it • +39 02.284.6716
Frank Strazzulla UNITED STATES +1 949.459.1767 • franks@tmsmedia.net
Zhang Xiaohua CHINA ifj_china@126.com • +86 13522898423
ADVERTISING COORDINATOR VICKIE SMEAD vsmead@inda.org • +1 919 459 3700 x 3720
Lenzing has partnered with Neutrogena to transition the production of its market-leading makeup removal wipes to 100% Veocel plant-based fibers. The new wipes utilize Veocel branded fibers made with renewable wood from sustainably managed and certified forests. The makeup removal wipes can be composted at home in 35 days, eliminating waste which ends up in a landfill.
Conventional makeup removal wipes are popular because of how convenient they are – users simply wipe off makeup after a long day. However, popular makeup removal wipes mostly contain polyester, polypropylene, and rayon, making them unable to decompose. Their one-time usage means they are sent to landfills or many people flush them down the toilet, clogging the sewer system or leaking microplastics into waterways.
The goal of this new partnership is to develop a product that has moved on from synthetic materials to an entirely cellulose-based solution. These new Neutrogena makeup removal wipes are described as ultra-soft, while also retaining the same effective cleaning function of its predecessors, with oil-based technology and micelle-infused water.
www.neutrogena.com
Milliken & Company, a diversified global manufacturer with a portfolio of textile, specialty chemical, floor covering and healthcare innovations, named Patrick Keese as its executive vice president and president of Milliken’s Floor Covering Business. Effective July 25, Keese will lead Milliken’s international floor covering operation, spanning four continents and 290 product collections.
Most recently serving as SVP and general manager of Altium Packaging, Keese has background in international business leadership. At Altium, he led more than 1,300 employees at 30 locations to produce plastic and packaging components.
Prior to this, Keese worked for Sonoco Products Company, a global provider of consumer packaging, industrial products, protective packaging and healthcare packaging solutions based in Hartsville, S.C. He holds a Bachelor of Science in industrial management and marketing from Clemson University, as well as certifications in various executive development programs at Columbia University and the Rensselaer Hartford Graduate Center. www.milliken.com
PET/PBT/PBAT/PBS/PTT/PLA/PETG/PC/PA6/PA66..
POLYMER: Physics / Chemistry
BDO/EG/MeOH/Heat recovery and comprehensive u�liza�on
HP
Hydrogen Peroxide, H2O2
R&D
Own R&D Center and pilot plant
Project EPC Contrac�ng (Turn-key)
Manufacturing of Cri�cal Equipment
POLYTEX is a professional chemical engineering company and technology supplier integra�ng R&D, engineering, equipment manufacturing, procurement and EPC management services. From technology licensing, project planning, equipment manufacturing and engineering design, procurement and construc�on management, as well as start-up and opera�on services, Polytex provides diversified services and one-stop solu�ons to customers all over the world.
Corp: 5th Floor, No.20 Wenchang Mid Rd. Yangzhou, Jiangsu, PRC.
Head: No.1, Private Industrial Park, Yuetang, Yizheng, Jiangsu, PRC.
Tel: +86-514-85553618; +86-514-87859276
Mail: market@polytex.cc; polytex@vip.sohu.com
Website: www.polytex.cc
24/7 Technical Support & Service
Bo�le grade, Tex�le grade, Film grade PET chips will be launched soon. Our own factory capacity in phase-1st will reach up to 1260 tons per day.
China Sales:
Mr Sun Mob: +86-133 1990 0139; Email: sg_sun@e-plastmer.com
Mr Cao Mob: +86-181 5290 1436; Email: cao@e-plastmer.com
Ms Pu Mob: +86-185 0992 5214; Email: pu@e-plastmer.com
Russia and Central Asia Sales:
Mr Li Mob: +86-189 5105 3772; Email: �ger@e-plastmer.com
Mr Gao Mob: +86-138 5159 0251; Email: gaocx@e-plastmer.com
Mr Dos Mob: +86-135 1991 0418; Email: dos@e-plastmer.com
Other markets:
Ms Emma Mob: +86-158 9939 1075; Email: emma@e-plastmer.com