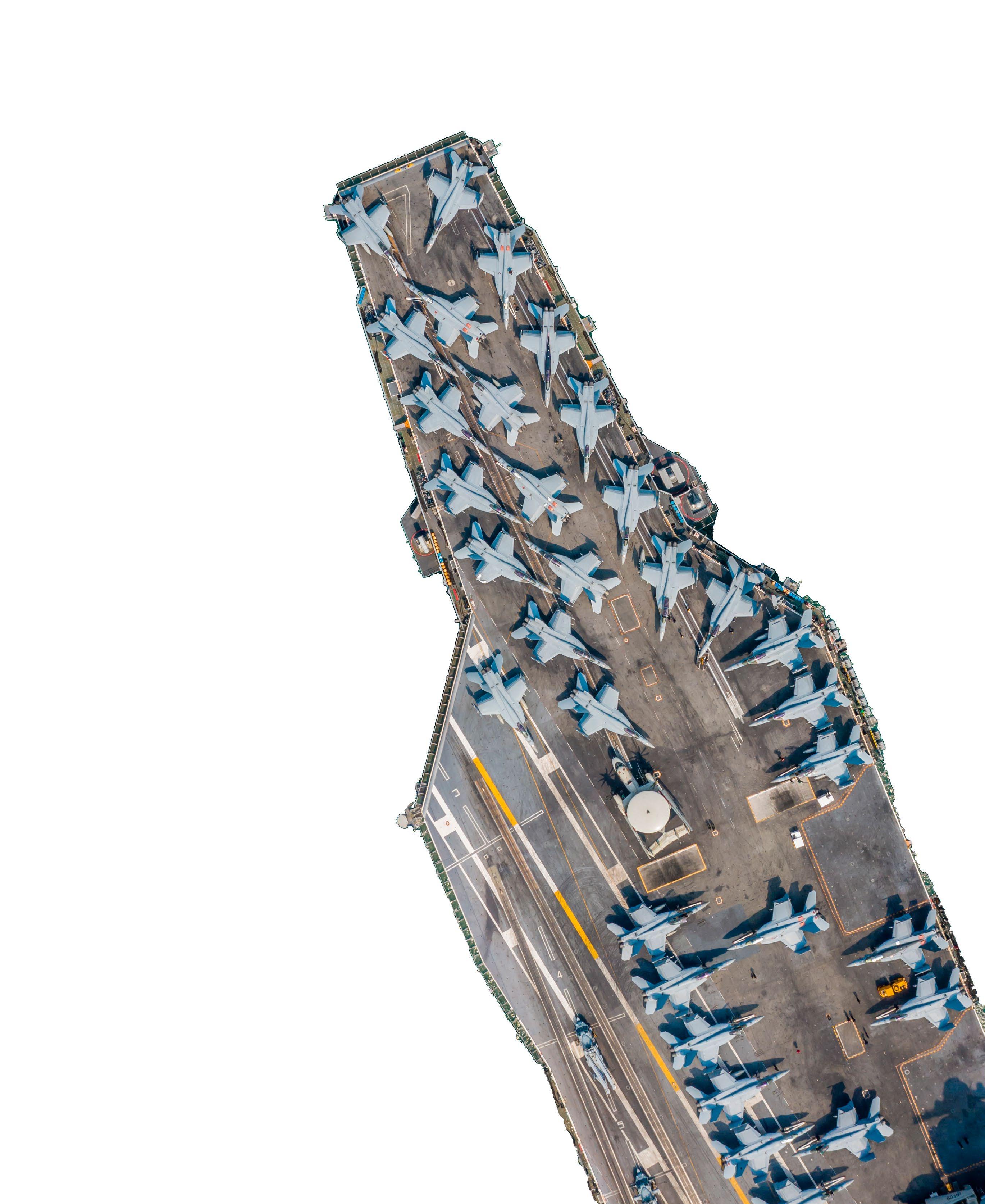
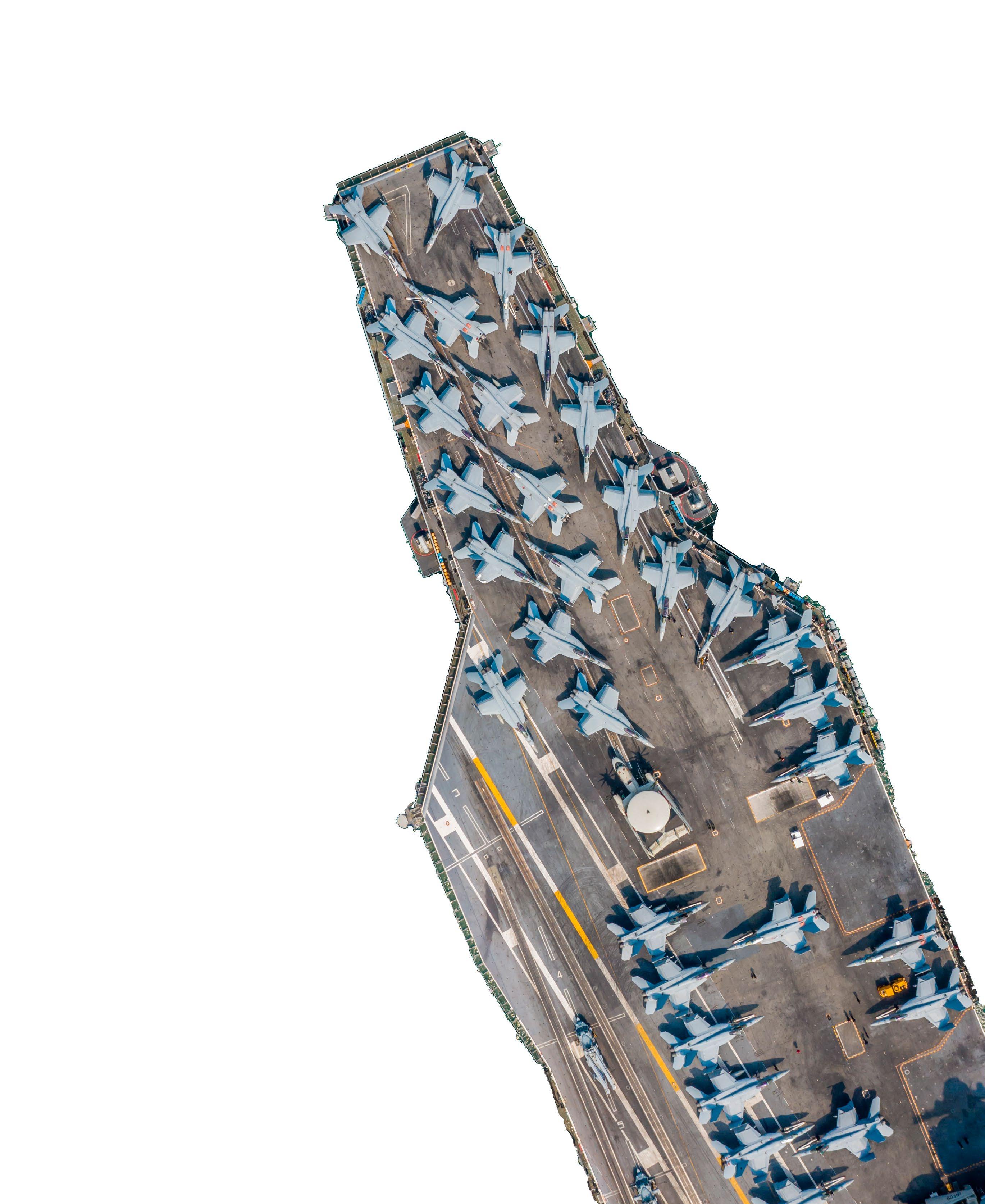
It used to skew and chatter

Now
it
This press applies up to 3,000 tons of force to form composite automobile panels. Delta’s RMC provides multi-axis position and pressure control, ensuring perfect synchronization of every moving part.

runs like a Swiss watch


Delta RMC motion controllers and graphical RMCTools software simplify complex motion design, making it smoother and more precise.
For the full case study on Wuxi LANLI Machine Tool Co. and other relevant applications, visit deltamotion.com.
Watch our training videos to see how Delta Motion can bring precision and harmony to your application.
Come see us May 12-15 in Detroit


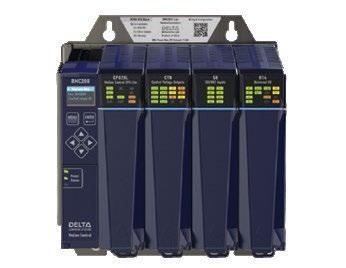


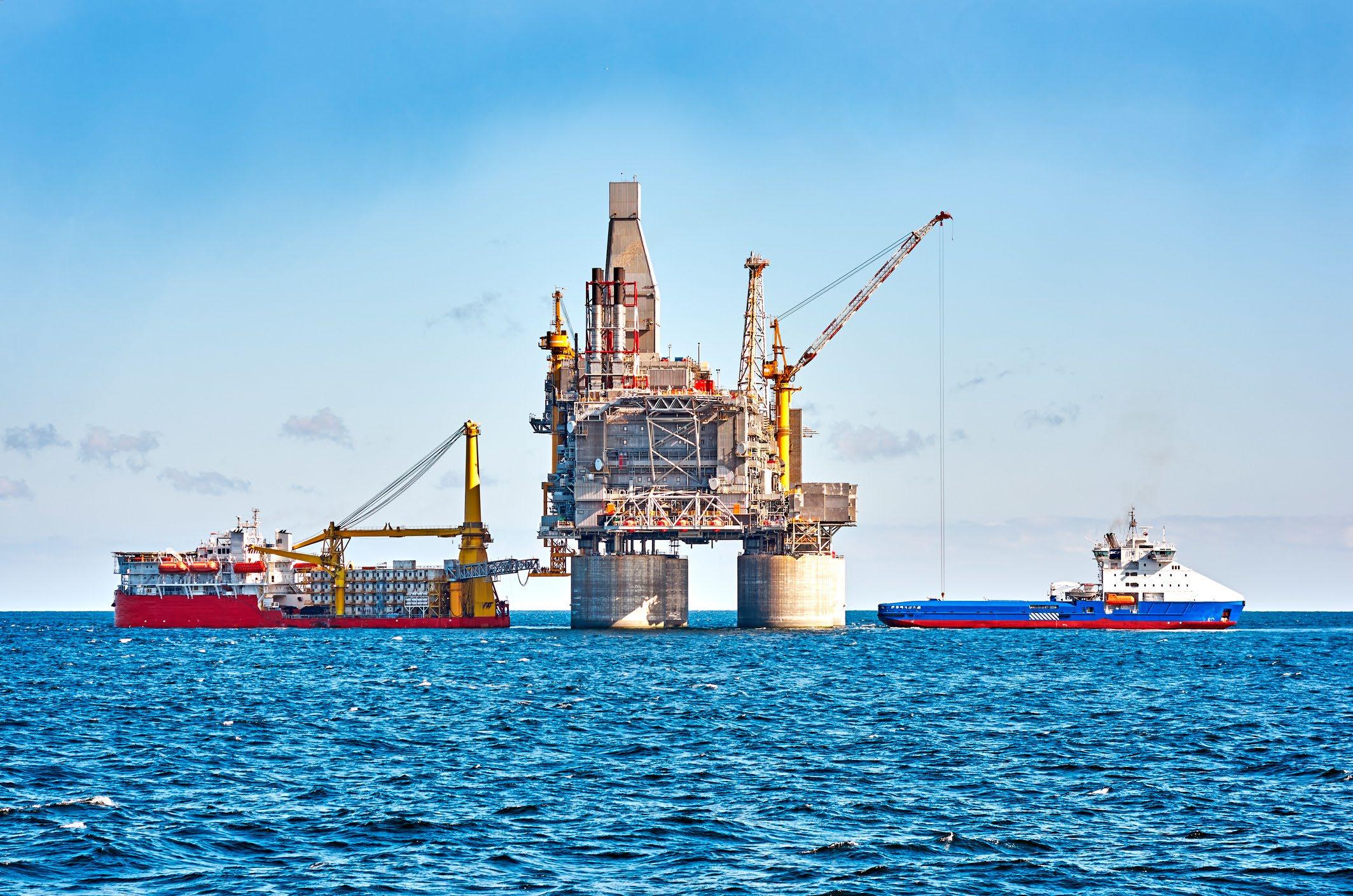
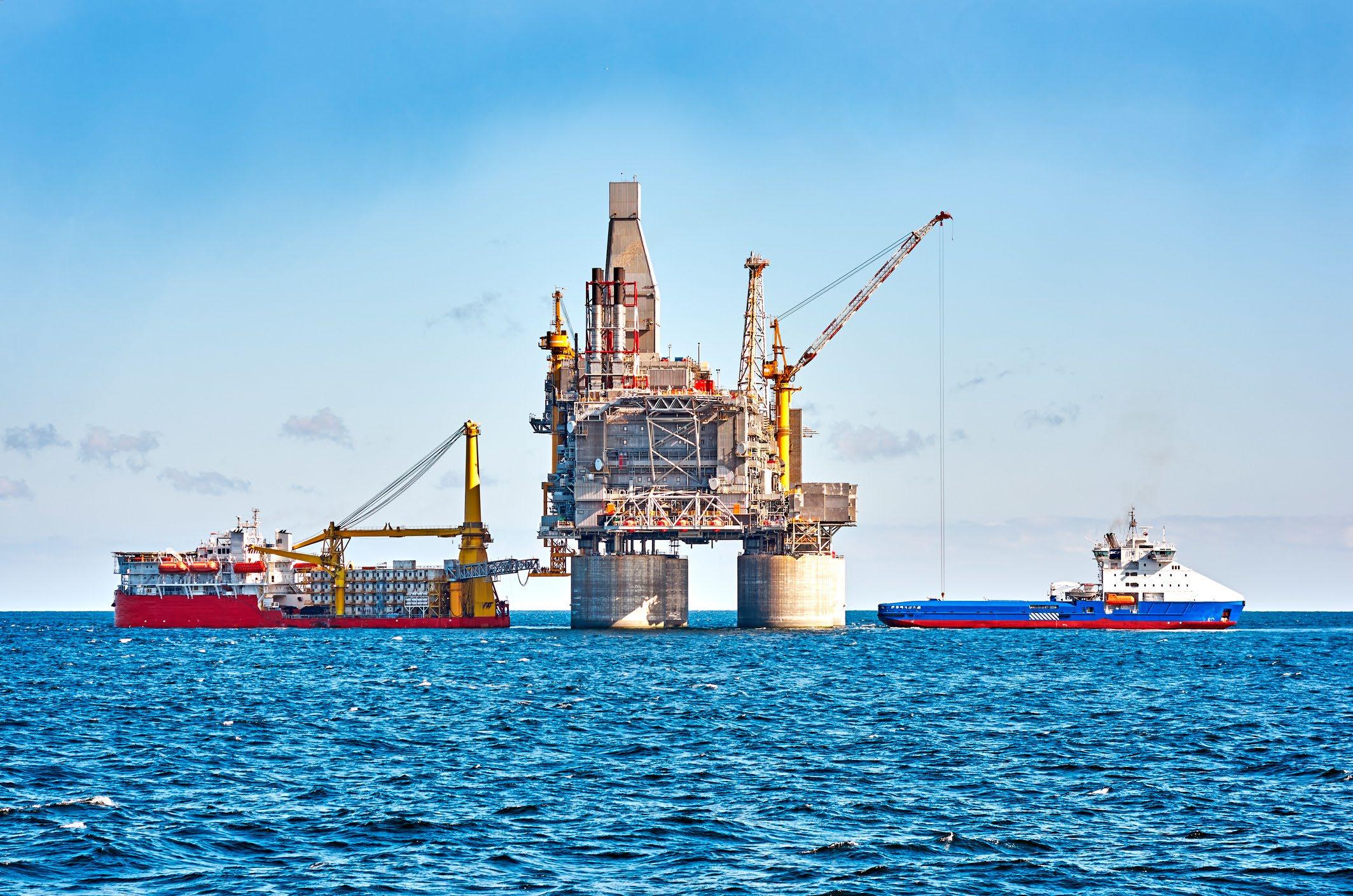

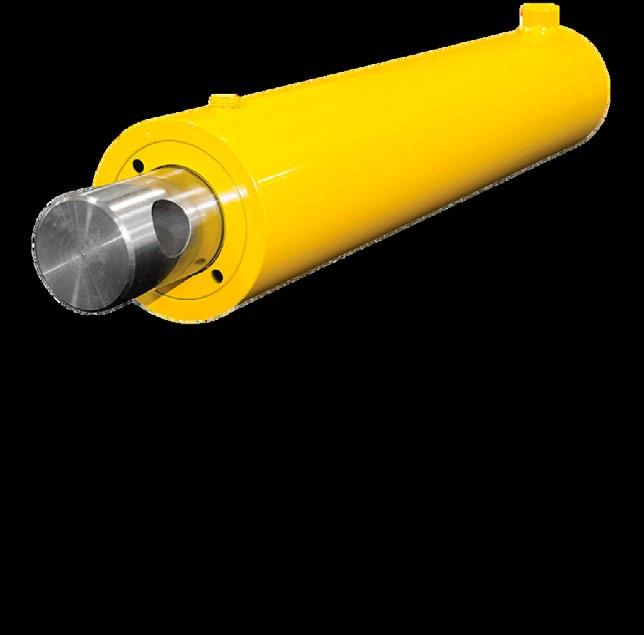
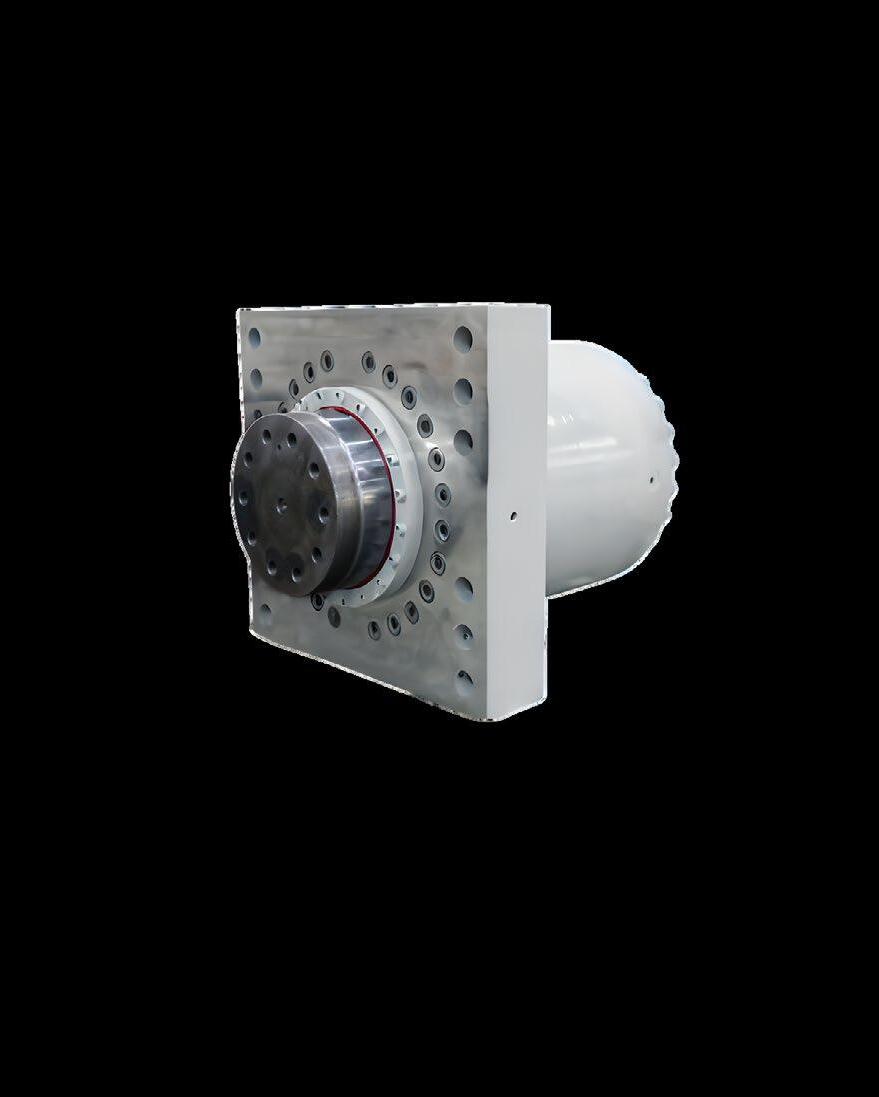
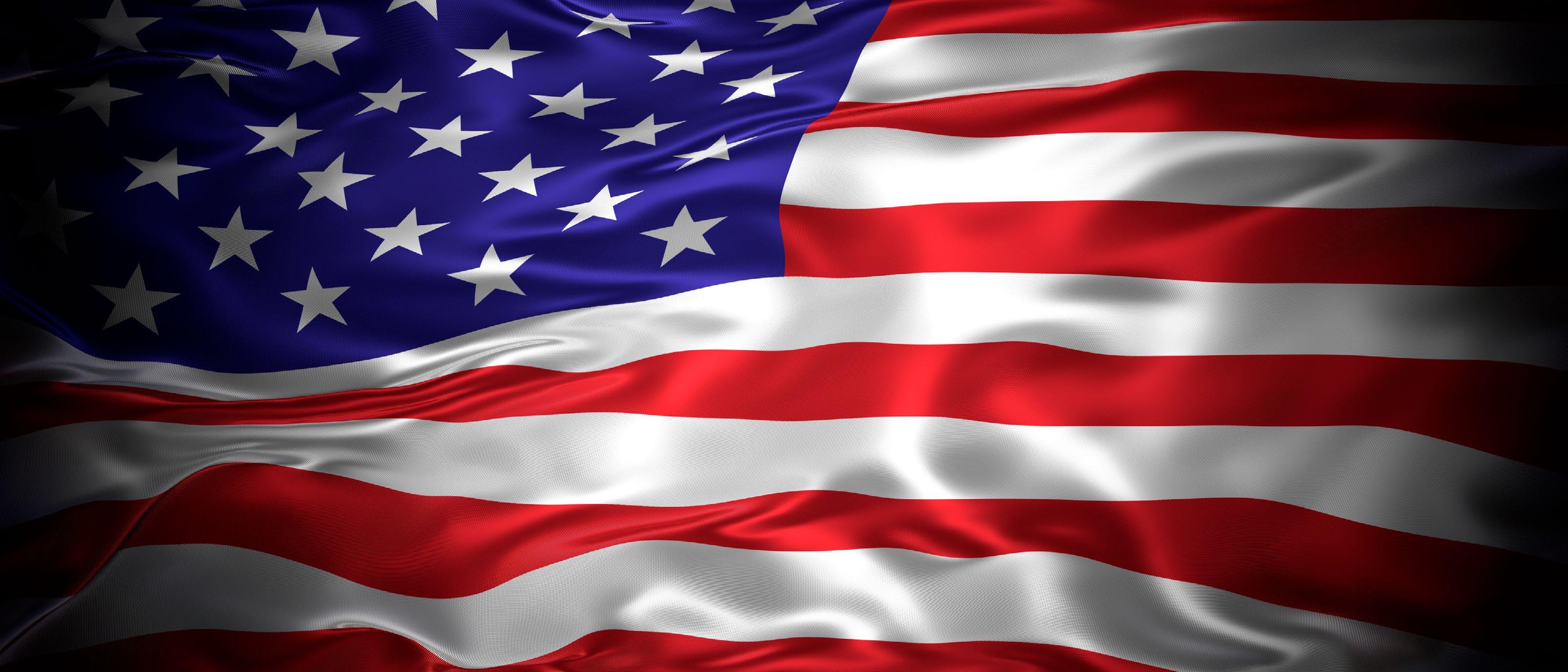
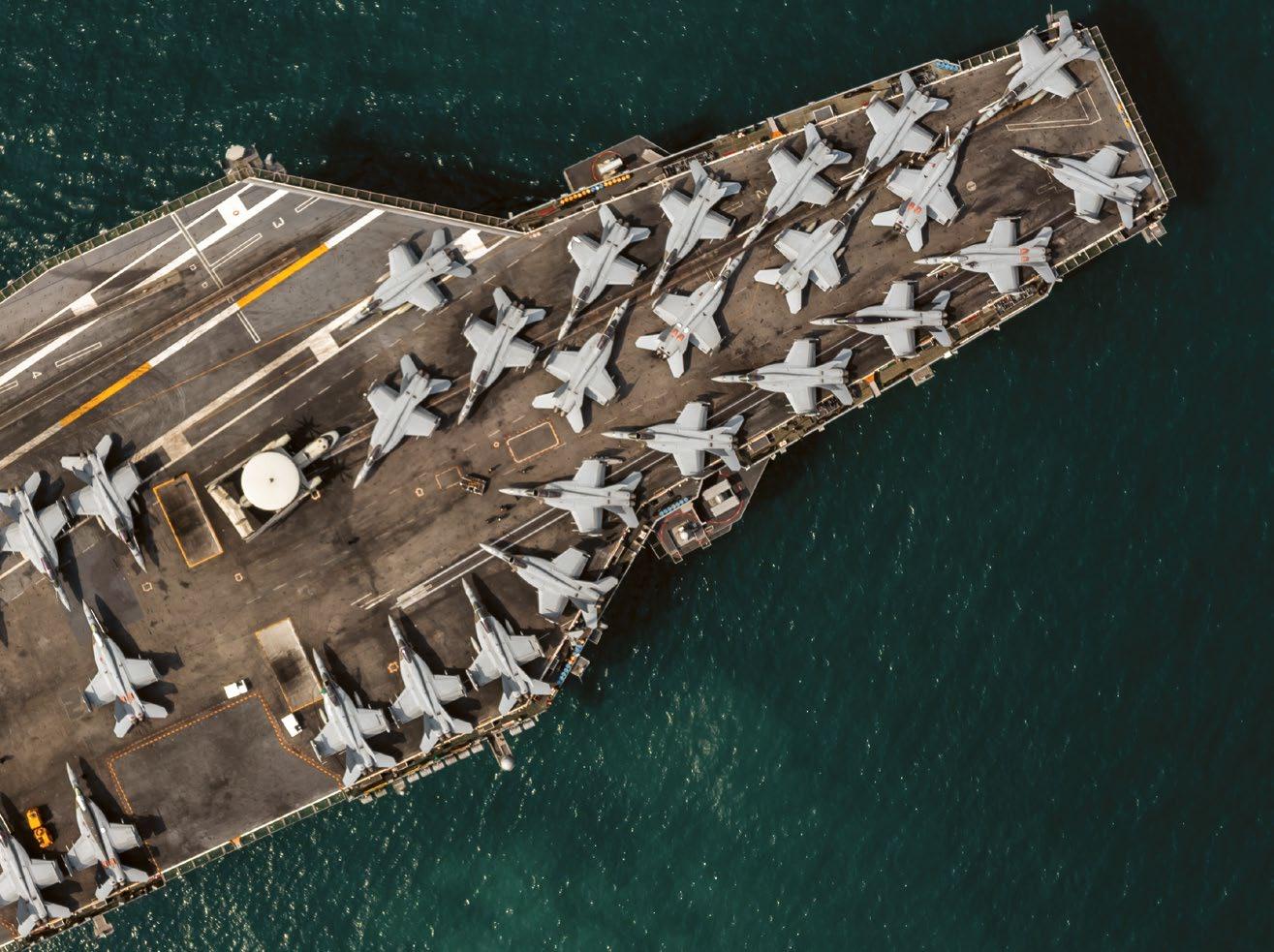


Features
Custom Hydraulic Cylinders Custom cylinders enhance system performance and reliability. 10 OTC 2025 Preview
An early look at the upcoming Offshore Technology Conference.
12 Automate 2025 Preview
Get a sneak peak of the Automate 2025 show. » TEST YOUR SKILLS 21 Understanding the Application of Accumulators
Stay sharp with this monthly lesson from the IFPS's study guide. 22 Hybrid Actuator Systems Help Bridge Gap for Plants Wanting the Robustness of Hydraulics and the Efficiency of Electrification Hybrid actuator systems revolutionize industrial motion.
Hydraulic Fittings & Hoses in Agricultural, Heavy Construction, and Civil Engineering Industries System components power machinery across industries.
COVER STORY 26 Massive Hydraulic Press Fashions Fittings For Military Ships
W&O Supply powers military-grade fittings with precision motion control.
Departments
Publisher’s Note: The information provided in this
is for informational purposes only. While all efforts have been taken to ensure the technical accuracy of the material enclosed, Fluid Power Journal is not responsible for the availability, accuracy, currency, or reliability of any information, statement, opinion, or advice contained in a third party’s material. Fluid Power Journal will not be liable for any loss or damage caused by reliance on information obtained in this publication.

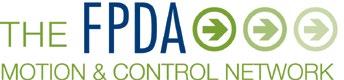

The Aging Standard
By JR (Jon) Rhodes, CFPECS, CFPAI, President of CFC Industrial Training
» WHILE
LEADING

A recent hydraulic training class that involved sizing and standards, one of the participants was frustrated with the system specifications. The participant inquired as to why the fluid power industry lacks standards compared to other industries. The math associated with sizing system attributes is riddled with the duality of imperial (U.S.) and metric measurement scales. This adds complexity to already challenging circumstances. In class, I struggled to quickly provide a meaningful answer to address these frustrations. I explained the big question as to how we’ve arrived at our present circumstance with many detailed answers.
In 1975 when I was in the 2nd grade, President Jimmy Carter appeared on my tube-type Magnavox TV and said, “The United States will convert to the metric system.” I filled up my gas tank, bought some milk, and checked my tire pressure this morning in the most imperial manner. This is not a fluid power-specific issue, as it poses a challenge for many other industries also. Prior to globalization, regional organizations developed standards specific to their global regions and industry requirements. This regionalization was prevalent in
the early days of fluid power and its effects are still wide-reaching today. Of course, there are 231 cubic inches in a gallon and 5,280 feet in a mile; how dare you pose such a question! In Europe, the U.S. customary Olde English imperial measuring systems are loathed. This seems a bit ironic, as Europeans frequently use the bar widely as their “invented” measure of pressure. (100,000 pascals = 1 bar). I’ve also seen the use of cubic decimeters (1 cubic decimeter = 1 liter). No system will ever be perfect, but the verdict is in, and the metric system is superior.
The International Standards Organization (ISO) Technical Committee 131 leads the perpetual journey for a global, unified standard for our industry. They are the preemptive organization for fluid power global standards. At last check, they had 238 developed standards and 31 new standards still under development. The National Fluid Power Association (NFPA) represents the North American market in the Technical Advisory Group (TAG), along with 16 other associations around the globe that form the governing ISO Standards Committee for fluid power. Organically, the use of U.S. customary measurements is slowly declining. ISO standards are driving new applications of fluid power systems to be purely metric. Standardization is about more than just units of measure. It drives the advancement of the industry by providing guardrails for safety and commerce.
Adhering to a single standard can greatly simplify the use of fluid power while removing
the barriers in education that help us apply products and systems. The complexities of fluid power systems are increasing as we continue to push forward. As the industry applies new devices and technology, guiding standards must accompany these technologies for standard communications and performance ratings. Applied and implemented standards for safe operation, interchangeability, and serviceability will help remove unnecessary frustrations and attract top talent into the industry. New technologies that increase efficiency and autonomy will become impossible to service and difficult to sustain without improved standardization.
At each step in the process of becoming an impressive industry, fluid power has advanced through the many organizations and associations that provide guiding standards. In the U.S., the Society of Automotive Engineers (SAE) is still an impressive, influential global institution. The fluid power industry continues to be greatly influenced by the North American market. While the argument of U.S. customary versus metric systems will most surely continue, our progress toward achieving global standardization must not be stifled. Top-down, the need for improved efficiency and safety in our industry exists. It all starts with a common set of engineering practices and compliance. It's important to remember that standards are only worthy if we adhere to them.
PUBLISHER
Innovative Designs & Publishing, Inc.
3245 Freemansburg Avenue, Palmer, PA 18045-7118
Tel: 800-730-5904 or 610-923-0380
Fax: 610-923-0390 • Email: Art@FluidPowerJournal.com www.FluidPowerJournal.com
Founders: Paul and Lisa Prass
Associate Publisher: Hannah Coursey
Editor: Lauren Schmeal
Technical Editor: Dan Helgerson, CFPAI/AJPP, CFPS, CFPECS, CFPSD, CFPMT, CFPCC
Senior Marketing Consultant: Bob McKinney
Graphic Designer: Nicholas Reeder
Accounting: Kim Kressman, Donna Bachman
Circulation Manager: Josh Shoup
INTERNATIONAL FLUID POWER SOCIETY
1930 East Marlton Pike, Suite A-2, Cherry Hill, NJ 08003-2141
Tel: 856-424-8998 • Fax: 856-424-9248
Email: AskUs@ifps.org • Web: www.ifps.org
2025 BOARD OF DIRECTORS
President: Garrett Hoisington, CFPAI, CFPS, CFPMHM
Immediate Past President: Jeff Hodges, CFPAI/AJPP, CFPMHM - Altec Industries, Inc
First Vice President: Chauntelle Baughman, CFPHSOneHydraulics, Inc.
Treasurer: Elisabeth DeBenedetto, CCFPS, GS Global Resources
Vice President Education: Daniel Fernandes, CFPS, CFPECS, Hawe Hydraulics
Vice President Membership: Brian Wheeler, CFPAI/AJPP - The Boeing Company
Vice President Certification: Bruce Bowe, CFPAI/AJPP - Altec Industries, Inc.
Vice President Marketing: Bradlee Dittmer, CFPPS - IMI Precision Engineering
DIRECTORS-AT-LARGE
Tyler Janecek, CFPHS - Engineering Systems, Inc
John Juhasz, CFPS - Kraft Fluid Systems Stephen Blazer, CFPE- Altec Industries, Inc. Brian Kenoyer, CFPS - Cemen Tech
Jeff Curlee, CFPS -Cross Mobile Hydraulics & Controls
Quest Duperron, CFPIHM, CFPCC - Coastal Hydraulics, Inc. Cary Boozer, CFPE - Motion Industries, Inc. Steven Downey, CFPAI, CFPS - Hydraulex Deepak Kadamanahalli, CFPS - CNH Industrial Kyler Craig Ridgeway, CFPHS - Bradbury Company Alex Kummer, CFPE, - National Oilwell Varco Wade Lowe, CFPS - Hydraquip Distribution, Inc.
CHIEF EXECUTIVE OFFICER (EX-OFFICIO) Donna Pollander, ACA
HONORARY DIRECTOR (EX-OFFICIO)
Ernie Parker, Hydra Tech, Inc. CFPAI/AJPP James O'Halek, CFPAI/AJPP, CFPMM, CFPMIP, CFPCCThe Boeing Company
IFPS STAFF
Chief Executive Officer: Donna Pollander, ACA
Communications Coordinator: Stephanie Coleman
Director Training/Development: Bradley (BJ) Wagner, CFPAI/AJPP
Assistant Director: Jenna Mort
Certification Logistics Manager: Kyle Pollander Bookkeeper: Diane McMahon
Instructional Designer & Layout: Chalie Clair
Fluid Power Journal (ISSN# 1073-7898) is the official publication of the International Fluid Power Society published monthly with four supplemental issues, including a Systems Integrator Directory, Off-Highway Suppliers Directory, Tech Directory, and Manufacturers Directory, by Innovative Designs & Publishing, Inc., 3245 Freemansburg Avenue, Palmer, PA 18045-7118. All Rights Reserved. Reproduction in whole or in part of any material in this publication is acceptable with credit. Publishers assume no liability for any information published. We reserve the right to accept or reject all advertising material and will not guarantee the return or safety of unsolicited art, photographs, or manuscripts.
NEW PROBLEM
Moving Flow Control Closer to the Cylinder Causes Problems
By Robert Sheaf, CFPAI/AJPP,
CFPE, CFPS, CFPECS, CFPMT, CFPMIP, CFPMMH, CFPMIH, CFPMM, CFC Industrial Training
0-24 MPa (0 - 3,500 PSI) PUMP SET AT 27.6 MPa (4,000 PSI)
0.38mm (.015" ORIFICE)
30 MPa (4,300 PSI)
METER - IN SPEED CONTROLS
95 liter (25 GAL) TANK
» A CUSTOMER HAD a system that required the vertical cylinder to accelerate at different speeds caused by different models of steel bumpers they were forming. They could adjust the cylinder's force remotely but had to climb under a table to adjust the downward speed. They found that both speed and cylinder's tonnage adjustments for the different-sized bumpers decreased their scrap.
The customer decided to fully open the meter-in flow control on the valve stack controlling the downward speed. They installed a line-mounted valve next to the pressure control to increase the operator’s convenience and safety, as well as reduce the time to convert die changes.
The counterbalance valve was located next to the valve stack and the outlet of the new flow control was plumbed directly to the cap end of the cylinder. However, they had problems with the cylinder’s downward stroke shuddering and had to adjust the counterbalance valve to eliminate the new problem.
Any idea what caused the new problem?
For the solution, see page 34.
Robert Sheaf has more than 45 years troubleshooting, training, and consulting in the fluid power field. Email rsheaf@cfcind.com or visit his website at www.cfcindustrialtraining.com. Visit fluidpowerjournal.com/figure-it-out to view previous problems.
CUSTOM
ORDERING CUSTOM HYDRAULIC CYLINDERS
By Sebastien Lajoie, Cylinder Engineering Manager, Bailey International
KEY CONSIDERATIONS
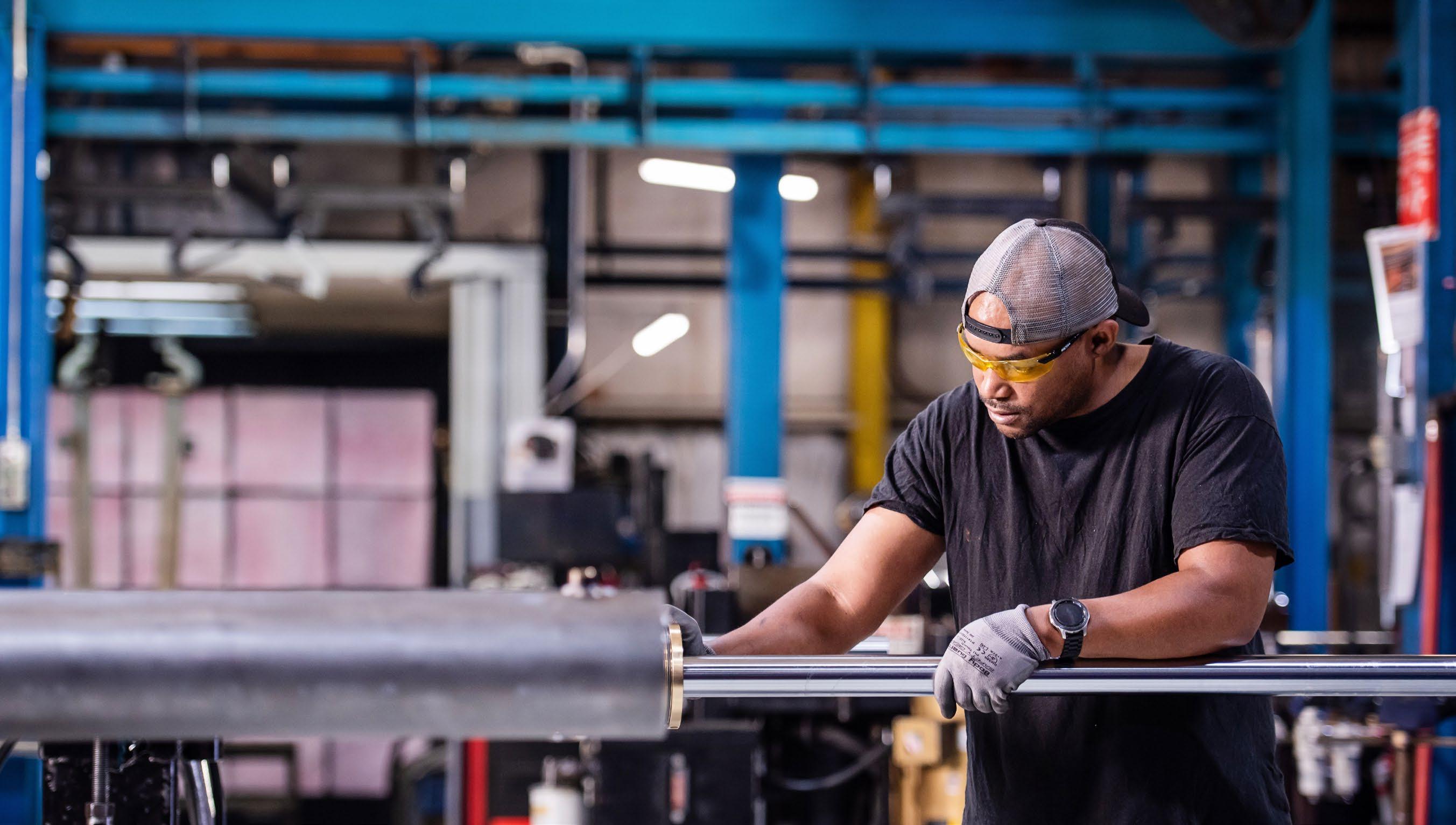
The heart of hydraulic systems lies in their ability to efficiently transfer power through the movement of fluids. This capability depends on the quality and precision of system components. Among these, custom hydraulic cylinders stand out for their ability to significantly enhance system reliability.
In the diverse world of hydraulics, adopting a one-size-fits-all approach falls short. While standard cylinders might suffice for general applications, custom hydraulic cylinders tackle specific challenges head-on and elevate system performance. By opting for custom solutions, you guarantee your hydraulic system is perfectly aligned with the unique demands of your application. This allows for improved efficiency, an extended lifespan, and lower maintenance costs.
Custom hydraulic cylinders are engineered to cater to unique operational loads and specific usage cycles, designed to thrive under challenging environmental conditions. In scenarios where installation space is at a premium, a custom cylinder can be ingeniously designed to perfectly fit the confinement. Conversely, for applications that demand high-pressure functionality, custom cylinders can be developed using robust materials and designs capable of withstanding the most rigorous conditions. These cylinders can be
equipped with special seals, coatings, or other modifications to improve durability in extreme temperatures, corrosive environments, or other harsh operational conditions.
The process of designing and manufacturing custom cylinders involves close collaboration between the client and the manufacturer. A partnership ensures that every aspect of the cylinder, from its dimensions and material selection to its sealing and mounting configurations, is optimized for the application at hand. By considering a project's specific requirements and constraints, manufacturers can deliver custom hydraulic cylinders that meet and exceed expectations, providing a competitive edge in efficiency and reliability.
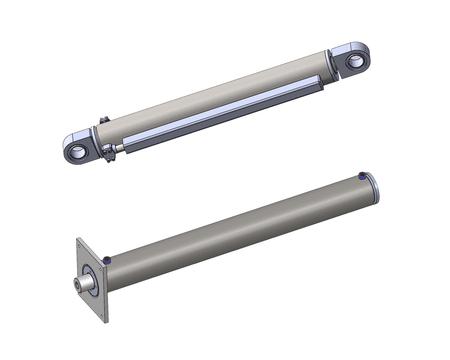
OPTIONS AND SELECTIONS
Selecting the right material significantly impacts a cylinder’s durability, resistance to environmental factors, and performance in
various applications. Among the common materials used are steel, stainless steel, and aluminum. Each offers distinct benefits and presenting certain limitations.
Steel stands out for its exceptional strength and durability, making it an excellent choice for hydraulic cylinders in heavy-duty industrial applications. A steel cylinder can withstand high pressures and harsh operational conditions. However, steel's susceptibility to corrosion is a notable drawback. This issue can be addressed through the application of protective coatings or by opting for stainless steel in environments where corrosion is a concern.
Stainless steel is renowned for its superior corrosion resistance, an attribute that makes it particularly well-suited for use in environments that are either very moist or where the cylinder might be exposed to corrosive chemicals. Stainless steel also maintains an elevated level of strength and durability. Nevertheless, these advantages come at a cost, as stainless steel is more expensive than its standard steel counterpart. This cost factor may influence the material selection process, depending on budget constraints and specific application requirements.
Aluminum, with its lighter weight, presents an advantageous option for applications that
prioritize reducing weight without significantly compromising the cylinder's integrity. Its inherent corrosion resistance further enhances its appeal, particularly in applications where environmental exposure could degrade other materials. Although aluminum may not match the sheer strength and durability offered by steel and stainless steel, its performance is more than adequate for many applications, especially those where weight considerations are paramount.
The cylinder and bore size are critical factors that must be defined to ensure the cylinder's efficacy in generating the requisite force and movement. These parameters play a pivotal role in the functionality of the cylinder in its specific application. The bore size of a cylinder directly impacts the amount of force the cylinder can exert. A larger bore size allows greater force generation, making it particularly essential in heavy-duty applications where substantial force is required. This is due to the area of the piston being larger. According to the basic principle of Force = Pressure × Area, a larger area yields a higher force output for the same pressure.
Likewise, the stroke length of a cylinder determines the distance the piston can travel
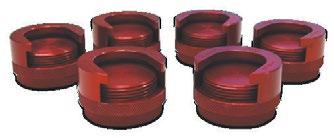
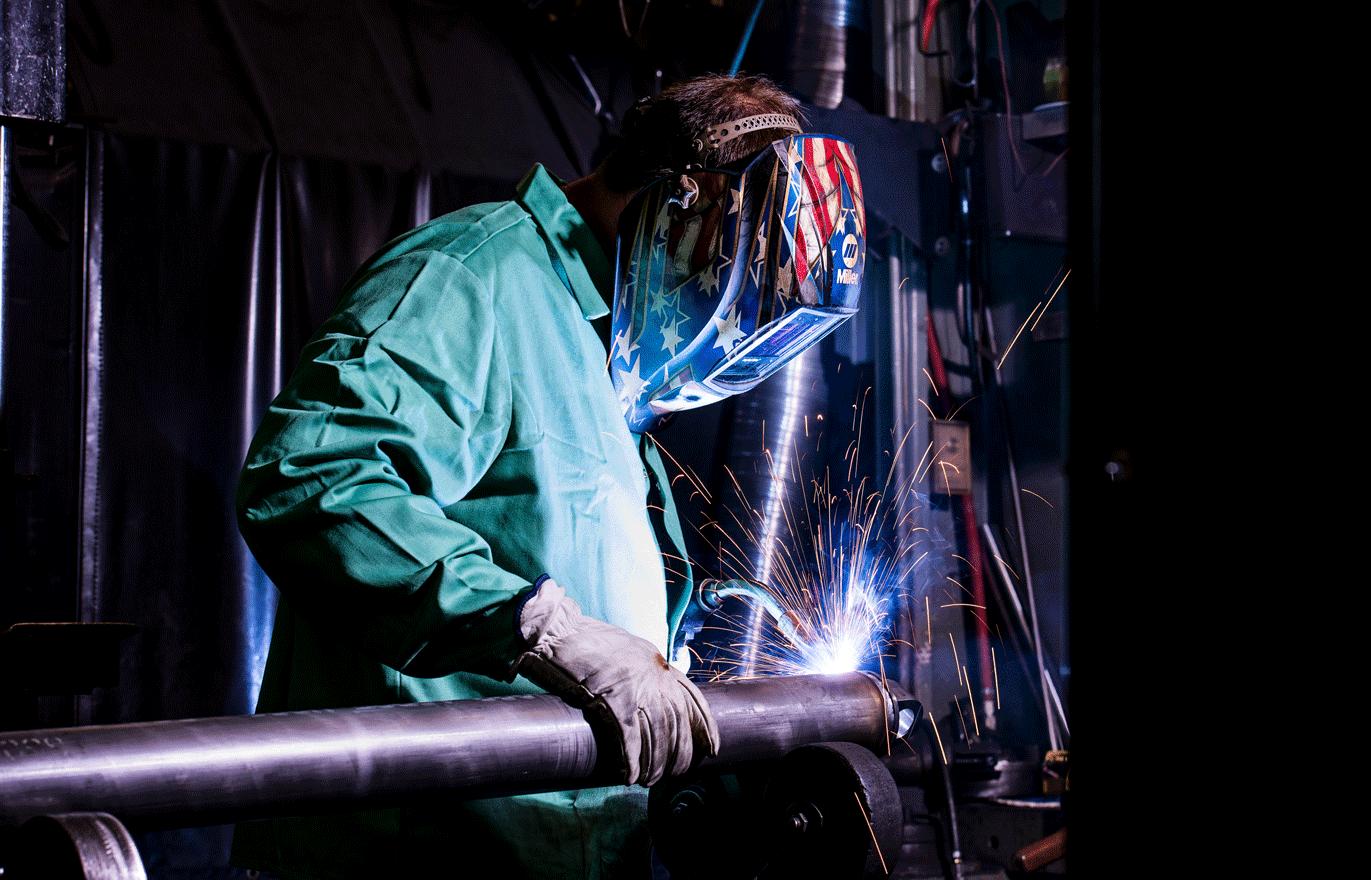
from its fully retracted position to its fully extended position. Be sure to consider the space constraints of the system to avoid choosing a stroke length too long, which could lead to an inability to install the cylinder or
CONTAMINATION CONTROL
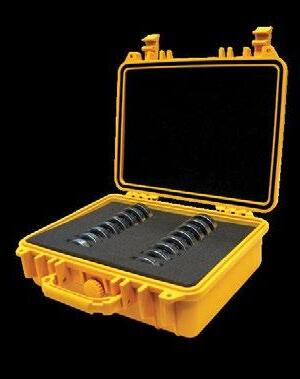
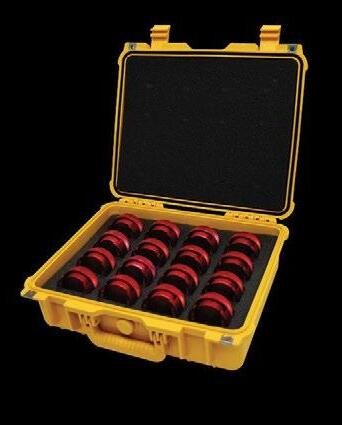

continued on page 08
Routine and scheduled maintenance of hydraulic systems are vital to getting the most out of your Hitachi Mining Excavator. While maintenance plays the largest role in the prevention of unnecessary machine downtime, it
expose the
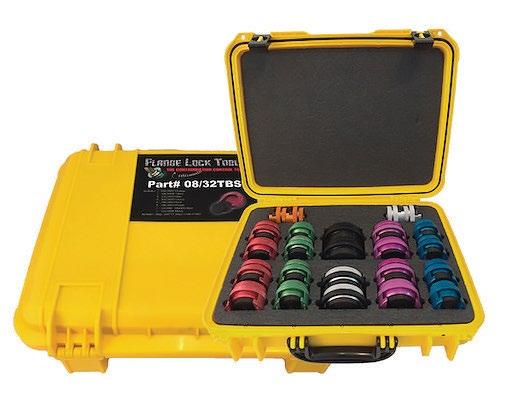
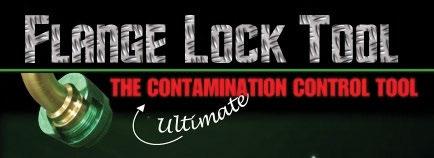
to high levels of contamination rapidly decreasing component longevity. The importance of contamination control is sometimes overlooked when performing maintenance due to incorrect practices being used.
THE FLANGELOCK™ TOOL AND CIRCUIT BLANKING CAPS
The FlangeLock™ tool and caps are the ultimate contamination control tools for protecting your hydraulic system. The FlangeLock™ allows for the simple sealing of open hydraulic flanges without tools while the caps can be bolted in place of a flange connection. Easy on, easy off, they offer a leak-proof solution to hydraulic systems and environmental cleanliness. FlangeLock™ tools and caps stop the mess.
HITACHI MAKING CONTAMINATION CONTROL EASY
Hitachi have packaged FlangeLock™ tool and caps specifically for Hitachi mining excavators. The Hitachi customised kits make sure no matter which component routine maintenance is being performed on, you will always have the exact number of FlangeLocks™* and caps to help reduce contamination.
*Note: FlangeLocks™ are not to be used under pressure
cause mechanical interference within the system. Moreover, accurate measurements and detailed specifications can help you The FlangeLock™ Tool is the ultimate contamination control tool for protecting your hydraulic systems. It allows for the simple sealing of open SAE code 61, 62 & CAT-Style hydraulic flanges without tools. Constructed from lightweight aluminum. Easy on, easy off. Offers a leakproof solution to hydraulic system and environmental cleanliness. FlangeLock™ Tools stop the mess!



avoid complications such as insufficient force generation, which could render the cylinder ineffective for its intended use, or inadequate movement range, which could limit the functionality of the system.
CONSIDERATIONS
Of course, customization extends beyond size and material. The following factors can enhance the performance and integration of the cylinder with your system:
• Mounting Options: Different applications might require specific mounting configurations, such as flange, trunnion, or clevis mounts. Custom mounting guarantees ease of installation and optimal alignment with other system components.
• Seals and Bearings: The choice of seals and bearings affects the cylinder's performance, especially in high-pressure or high-temperature environments. Customizing these
components can enhance durability and reduce the risk of leaks or failures.
• Port Configurations: Custom port configurations can simplify hydraulic system plumbing, reducing potential leak points and optimizing fluid flow.
For Procurement Managers, aligning the ordering process with strategic goals is vital to ensure timely and cost-effective delivery. It’s vital to establish clear communication channels with manufacturers to share detailed specifications and timelines. Working with a reputable supplier can streamline this process.
FUTURE TRENDS IN HYDRAULIC SYSTEM DESIGN
The field of hydraulic systems is continuously evolving, with advancements aimed at improving efficiency, sustainability, and performance. Staying on top of these trends can help engineers and designers make informed decisions when ordering custom hydraulic cylinders.
• Smart Hydraulics: Integration of sensors and IoT technology in hydraulic
cylinders is becoming more prevalent. These smart cylinders can provide real-time performance data, helping during predictive maintenance and when reducing downtime.
• Eco-Friendly Materials: There's a growing emphasis on sustainable materials and manufacturing processes. Opting for eco-friendly materials without compromising performance is an emerging trend.
• Advanced Coatings: Coatings that enhance corrosion resistance and reduce friction are advancing, contributing to longer lasting and more efficient cylinders.
Ordering custom hydraulic cylinders requires a thorough understanding of specific application needs and factors that influence cylinder performance. By focusing on material selection, size, customization options, and aligning procurement strategies, it’s a guarantee that the custom cylinders chosen will optimize system reliability.•
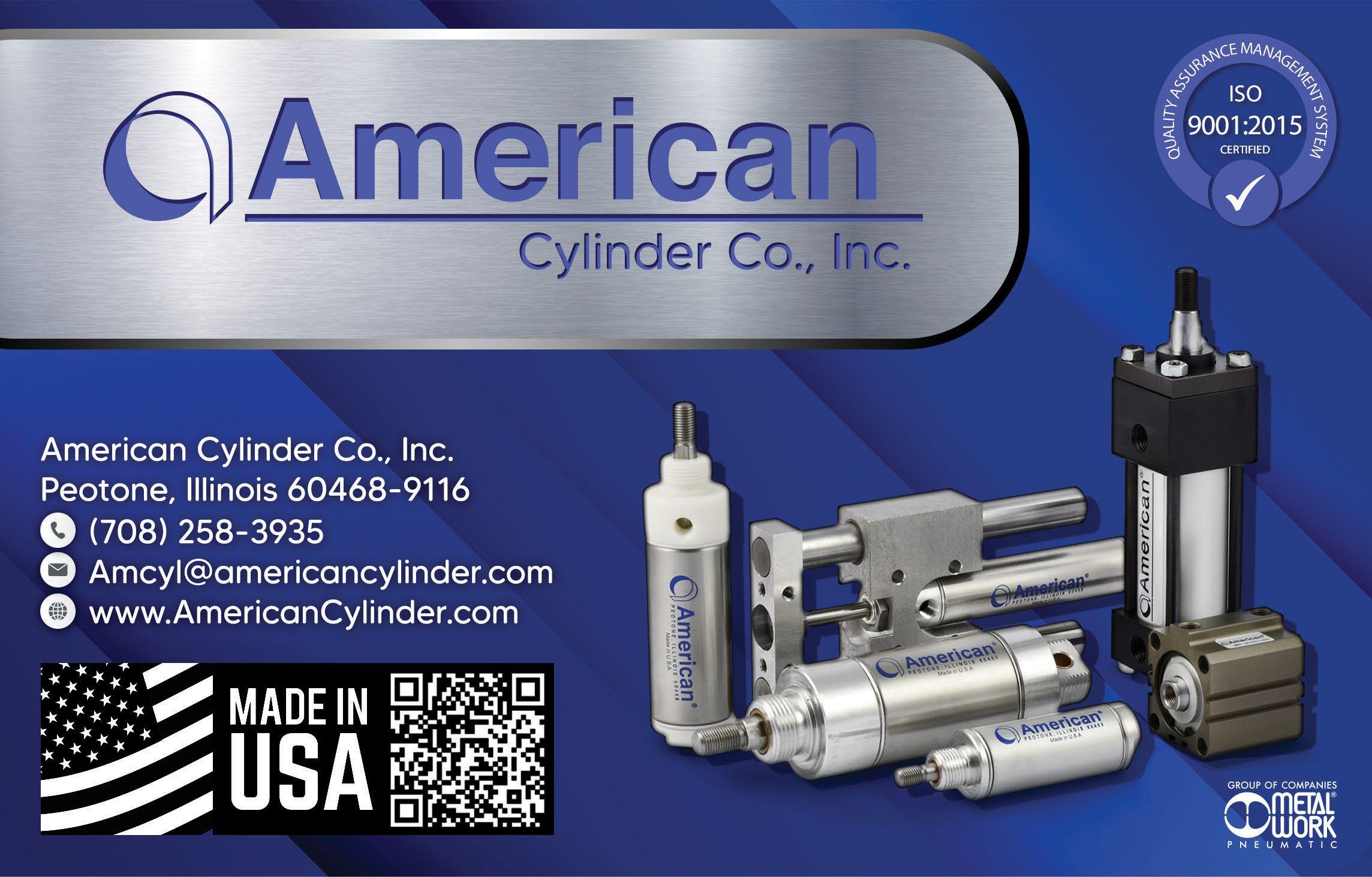
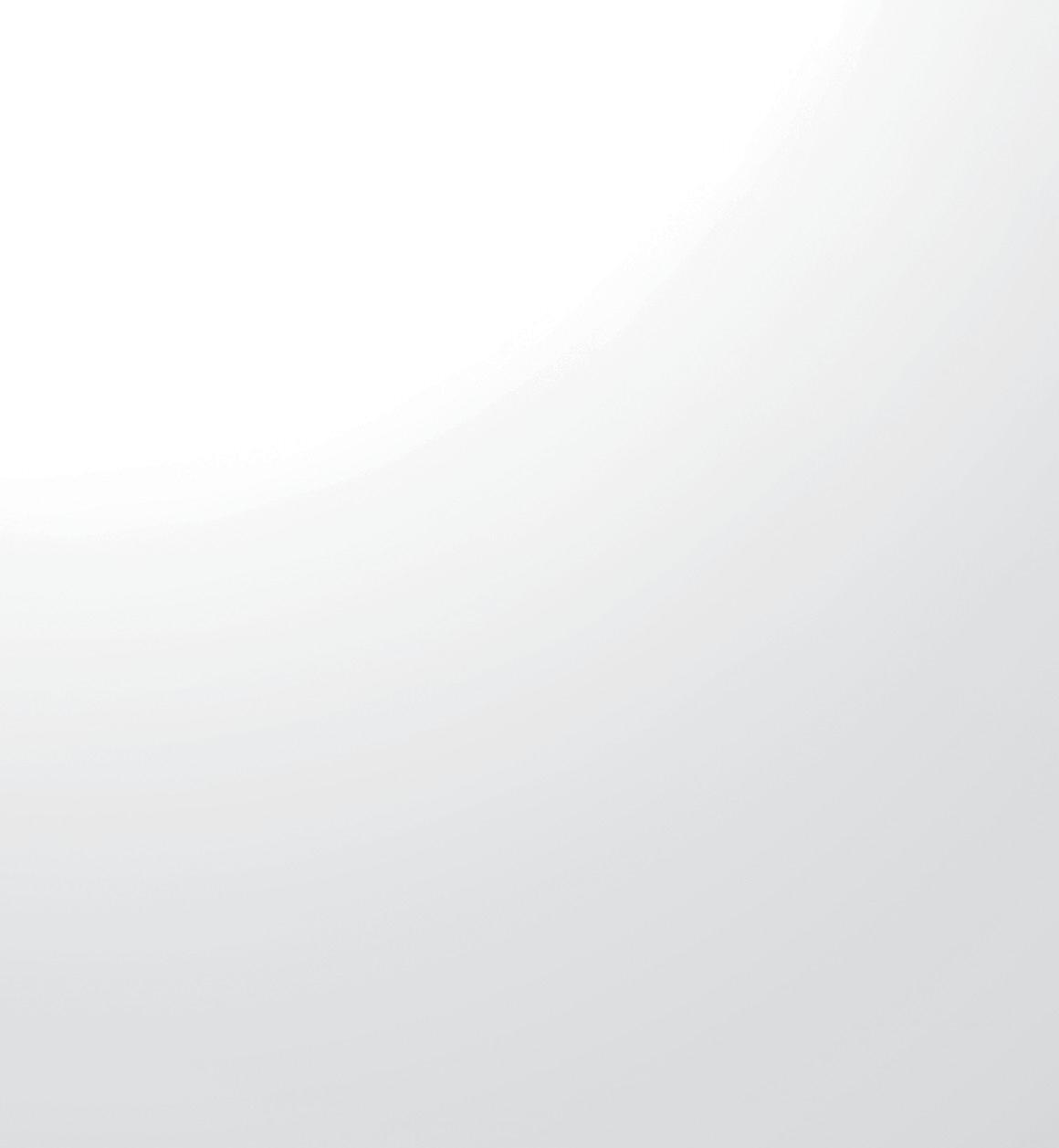
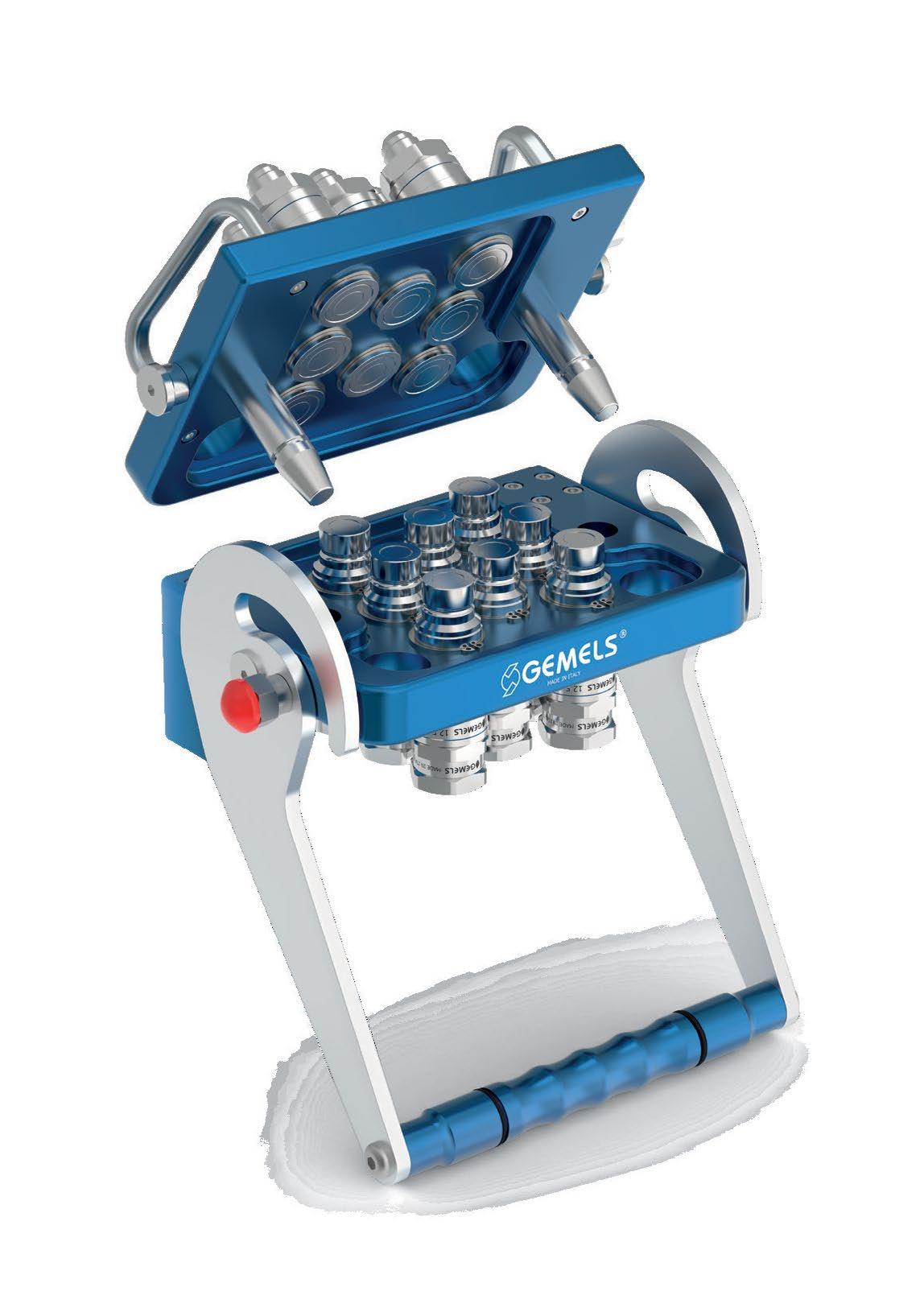


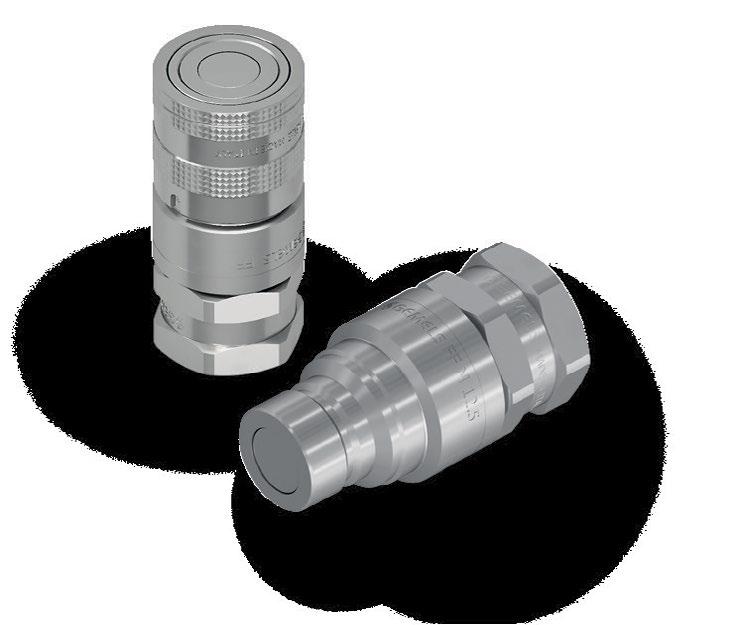
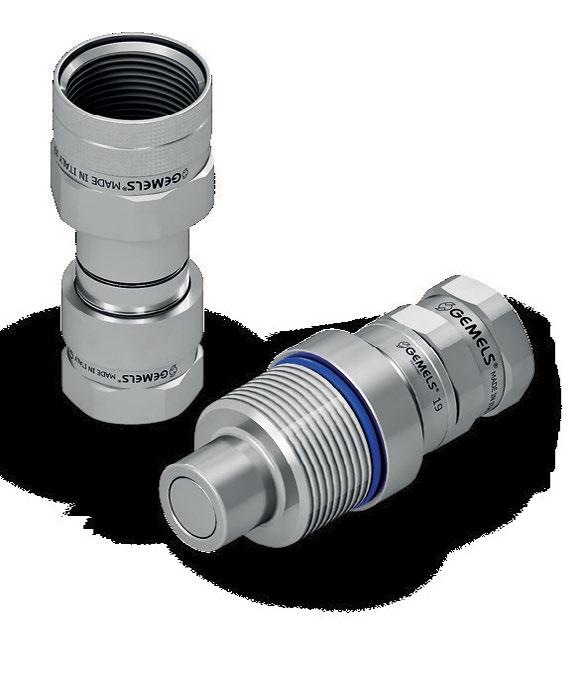
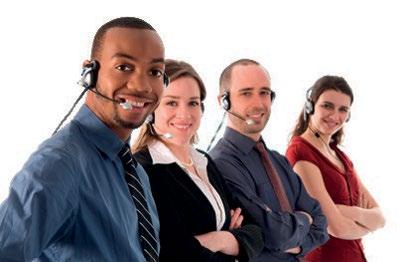


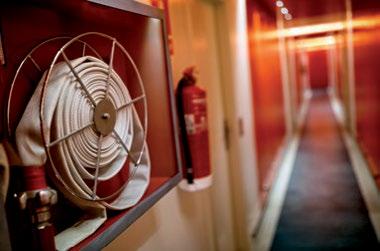
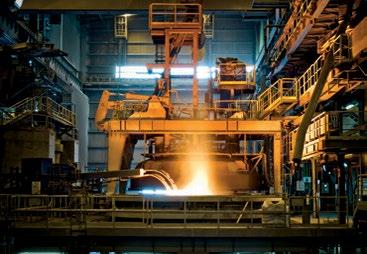
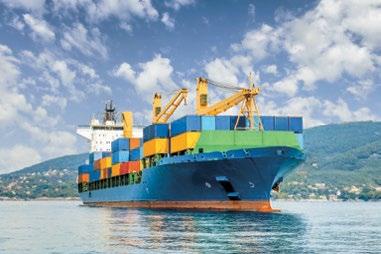
The Offshore Technology Conference (OTC) 2025, scheduled for May 5-8, 2025, in Houston, Texas, remains a key event for the fluid power industry, particularly for companies serving the oil and gas, marine, and offshore sectors. Fluid power systems play a critical role in offshore operations, providing reliable power for drilling equipment, lifting systems, and subsea applications. OTC 2025 will showcase innovations in hydraulic components, high-performance sealing technologies, and advanced pneumatic solutions designed to withstand the harshest marine environments. Industry professionals will have the opportunity to connect with experts, discover cutting-edge products, and gain insights into sustainable and efficient fluid power applications for offshore energy projects. Through technical sessions and exhibitions, OTC 2025 will provide a comprehensive view of how fluid power continues to advance offshore
TECHNICAL EXCELLENCE
Presentations and Discussions: OTC is renowned for its comprehensive technical sessions, where experts delve into diverse facets of offshore technology. Expect in-depth discussions covering exploration, drilling, production, and advancements in environmental protection within the industry.
CUTTING-EDGE EXHIBITIONS
Innovation Showcase: The conference will host a vibrant exhibition featuring the latest technologies, products, and services. Attendees can explore cutting-edge solutions and witness live demonstrations, providing invaluable insights into the future of offshore technology.
SKILLS ENHANCEMENT
Workshops and Training: Specialized workshops and training sessions will be available to enhance the skills and knowledge of professionals. These sessions aim to address industry challenges, introduce new methodologies, and ensure that participants stay at the forefront of the rapidly evolving offshore landscape.
NETWORKING OPPORTUNITIES
Industry Connections: OTC provides a conducive environment for networking, fostering connections between professionals, decision-makers, and potential collaborators. Attendees can engage in structured networking events, social gatherings, and business meetings.
KEYNOTE INSIGHTS
Industry Trends and Future Direction: Keynote speakers and panel discussions will offer strategic insights into current challenges, emerging trends, and the future trajectory
FLUID POWER EXHIBITORS AT
OTC 2025
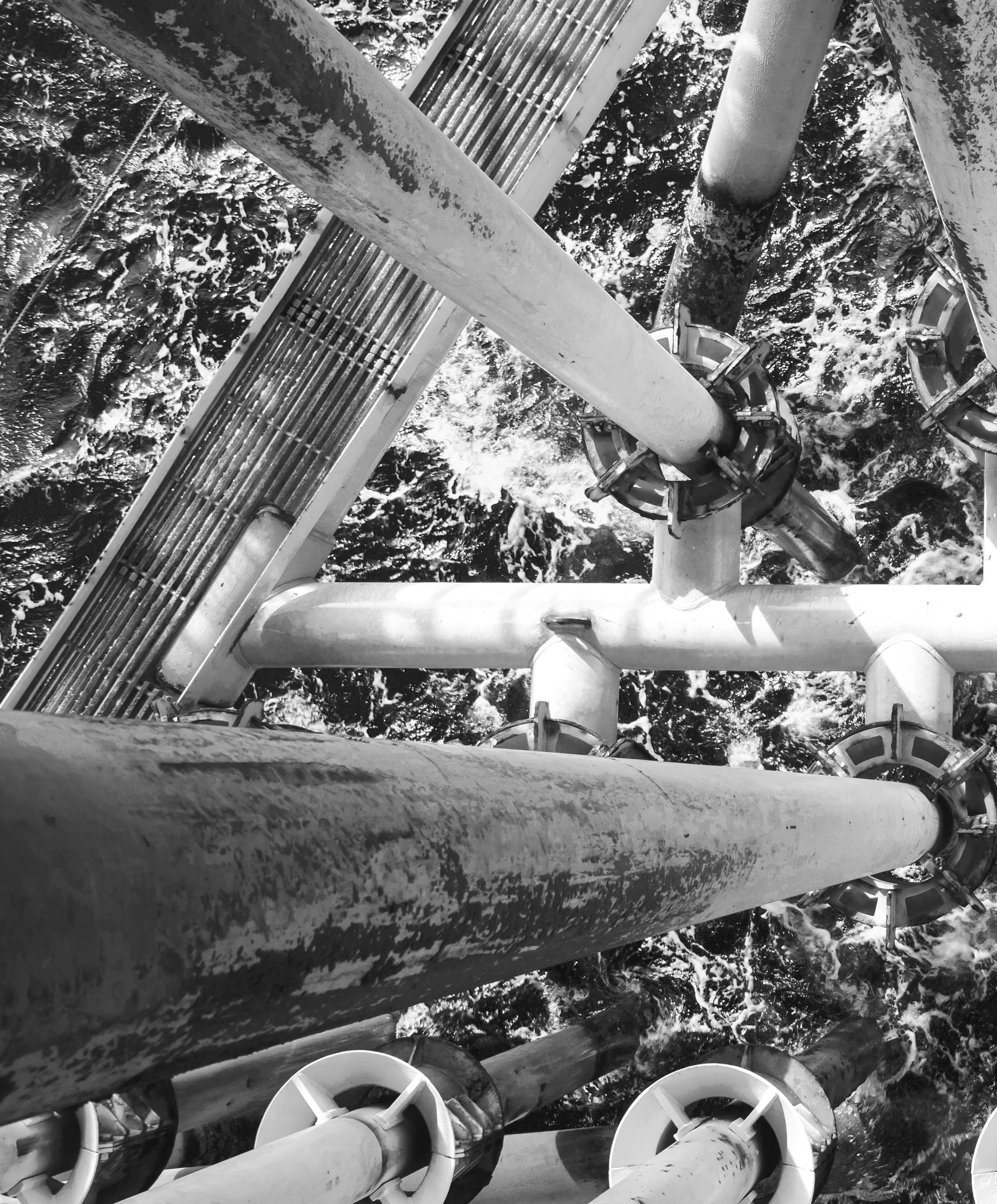
of offshore technology. This is an opportunity to gain a comprehensive understanding of the industry's direction.
GLOBAL COLLABORATION
International Perspective: OTC attracts a diverse global audience, promoting international collaboration. Participants will have the chance to explore innovations from around the world, fostering a global perspective on offshore advancements.
HOLISTIC EXPERIENCE
Experiential Learning: Beyond traditional presentations, OTC aims to provide an experiential learning environment. Attendees can expect interactive exhibits, hands-on experiences with emerging technologies, and a comprehensive overview of the offshore industry's current state.
The 2025 OTC is an immersive and enlightening experience for professionals, offering a platform to stay informed, connected, and inspired by the latest developments in technology and industry practices. •
Lubriplate’s complete line of ultra high-performance, hydraulic fluids has been designed to provide a wide range of benefits including: extended fluid change intervals, cooler operating temperatures, reduced friction and reduced downtime. Products include...
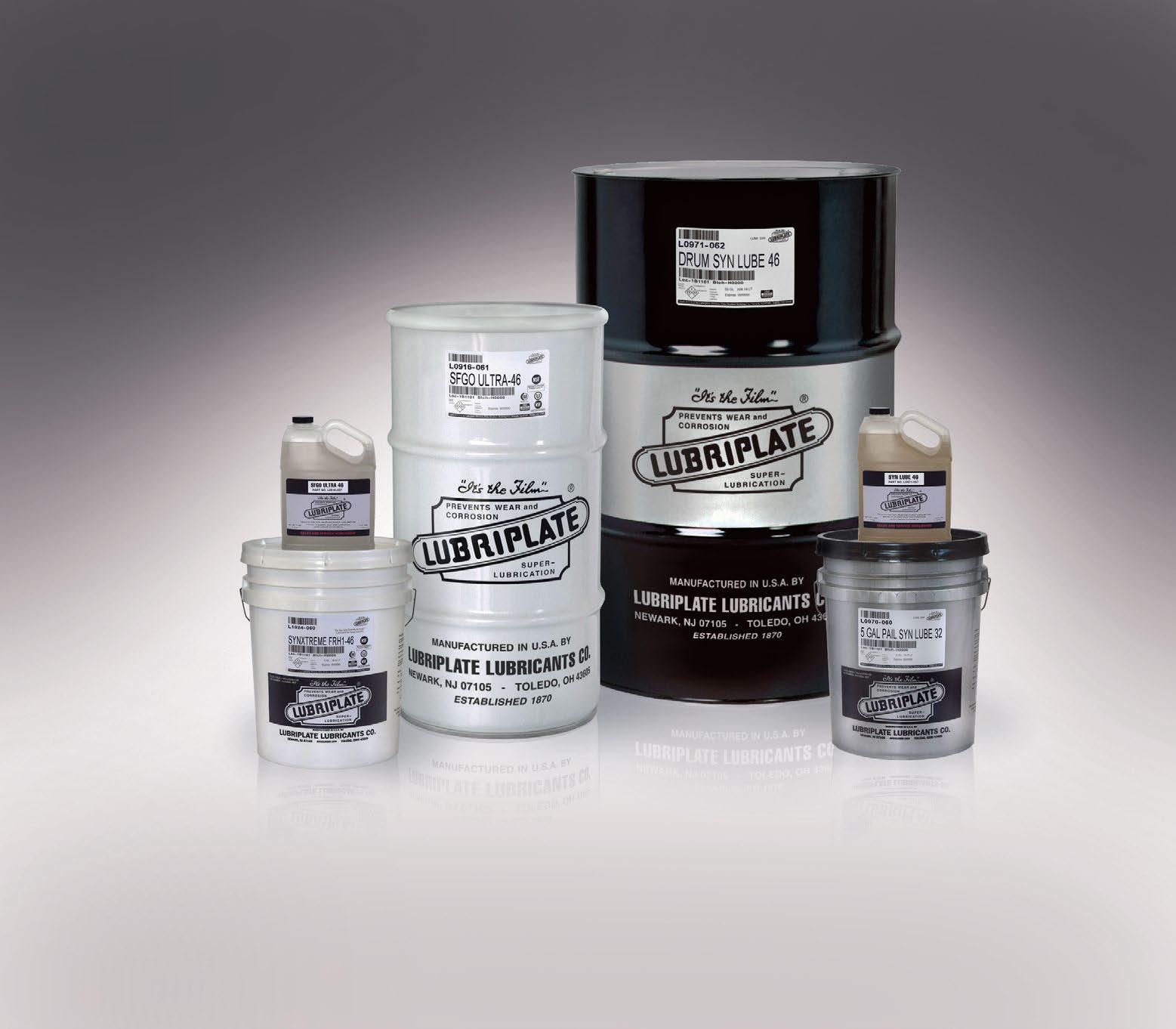
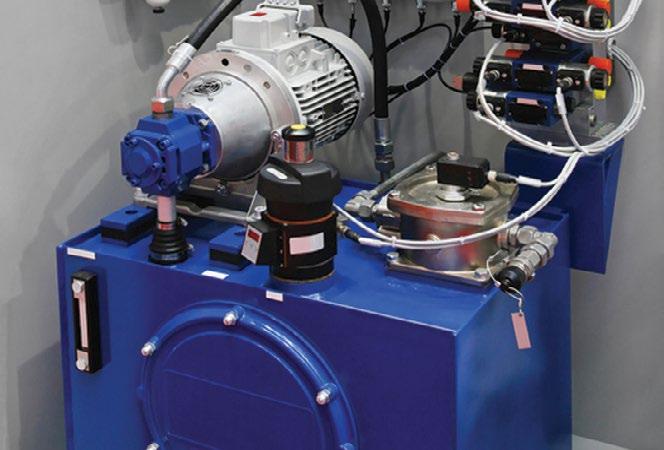
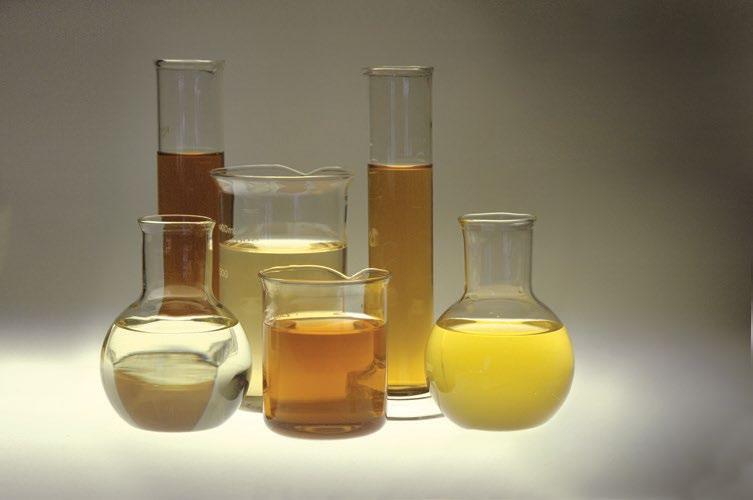
ZF SERIES HYDRAULIC FLUIDS ECO
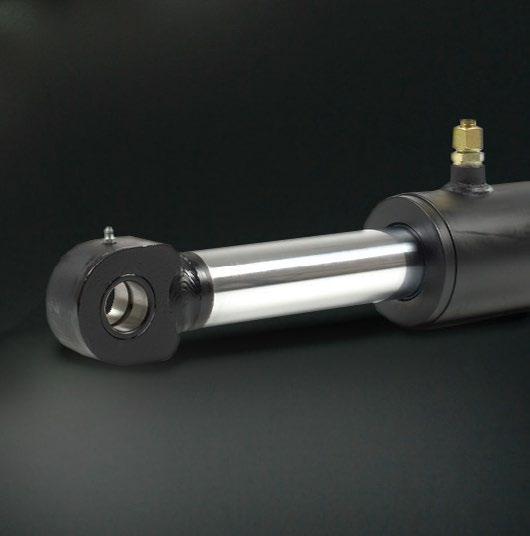
• High-Performance, 100% Synthetic, Polyalphaolefin (PAO)-Based Fluids.
• Provides extended drain intervals and excellent compatibility with seals.
• Available in ISO Viscosity Grades 32, 46 and 68.
HO SERIES HYDRAULIC OILS PETROLEUM
• Premium-Quality, Petroleum-Based Hydraulic Oils (ISO Grades 32-100).
• Anti-wear fortified to protect hydraulic system components.
• High aniline points ensure long seal life with fewer leaks.
SFGO ULTRA SERIES 7-68 NSF H1
• NSF H1 Registered and NSF ISO 21469 Certified - Food Machinery Grade.
• High Performance, 100% Synthetic Food Machinery Grade Fluids.
• Available in ISO Viscosity Grades 7, 15, 22, 32, 46 and 68.
• Fortified with Lubriplate’s proprietary anti-wear additive
SYNXTREME FRH1-46
• High-Performance, FM Approved, Fire Resistant Hydraulic Fluid.
• NSF H1 Registered and NSF ISO 21469 Certified - Food Machinery Grade.
• ECO-Friendly, Readily Biodegradable (OECD 301F).
• Fortified with Lubriplate’s proprietary anti-wear additive .
• Heavy-Duty, High-Performance, Extended Life, Hydraulic Fluids.
• ECO-Friendly - Free of zinc or silicone compounds.
• Provides long service life and extended fluid change intervals.
BIO-BASED GREEN SERIES ECO
• Vegetable-Based Oils for use in environmentally sensitive applications.
• ECO-Friendly - Ultimately Biodegradable (Pw1).
• Zinc-free additives provide exceptional anti-wear and anti-rust protection.
MARINE SAFE SERIES ECO
• For equipment operating in environmentally sensitive locations.
• Zinc-free and non-toxic to aquatic life.
• Exceeds U.S. EPA LC50 and US Fish and Wildlife requirements.
• Meets or exceeds the requirements of most hydraulic equipment
BIO-SYNXTREME HF SERIES ECO
• Advanced Synthetic Polyalkylene Glycol (PAG)-based hydraulic fluids.
• Designed for environmentally sensitive industrial and marine applications.
• Meets U.S. EPA Vessel General Permit (VGP) Requirements. Readily biodegradable.
• Does not leave a sheen on the water.

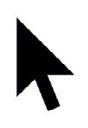
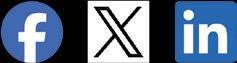

for the FLUID POWER INDUSTRY 2025
The Automate 2025 show, taking place from May 12-15, 2025, in Detroit, Michigan, will bring together leaders in robotics, automation, and advanced manufacturing, offering fluid power professionals valuable insights into the latest innovations. For the fluid power industry, the show will highlight advancements in automation technologies that integrate with hydraulic and pneumatic systems to enhance operational efficiency,
precision, and productivity. Attendees can explore how fluid power applications are evolving to meet the demands of smarter, interconnected manufacturing environments. With live demonstrations, expert panels, and networking opportunities, Automate 2025 provides a platform for fluid power professionals to learn how automation solutions can optimize performance in sectors like material handling, assembly, and industrial robotics. •
FLUID POWER EXHIBITORS AT AUTOMATE 2025
Alro
Camozzi
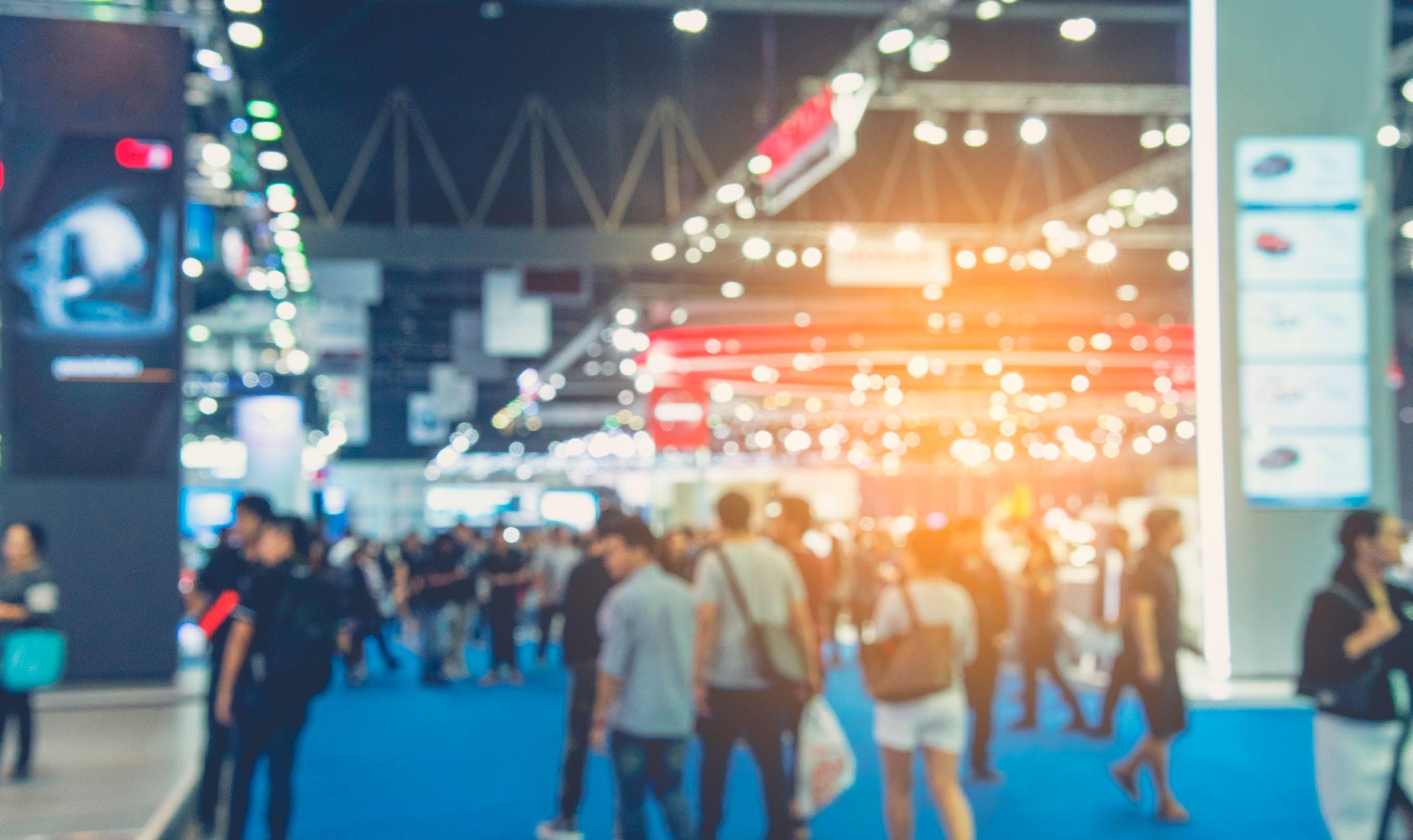
Pinnacle Systems | 127 Schmalz, Inc. | 3813 SCHUNK | 3200
SICK, Inc. | 2618
SIKO Products | 121 SMC Corporation of America | 2839 Temposonics | 6602
Tolomatic | 7004

Turck, Inc. | 6026
VacMotion | 2041
Vektek | 9116
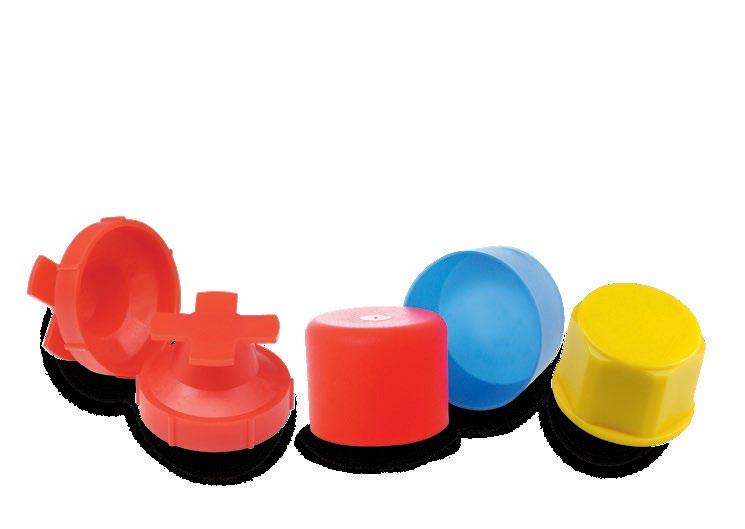
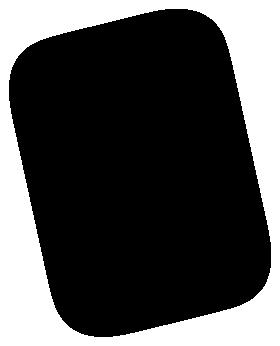

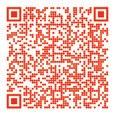

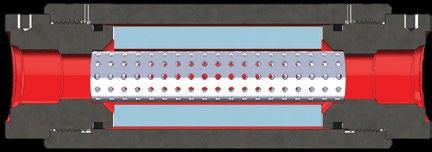

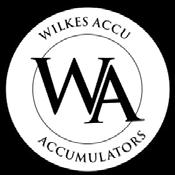
QUALITY NACOL ACCUMULATORS

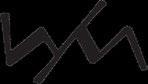
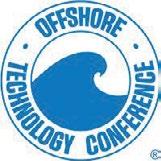

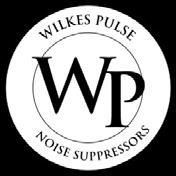
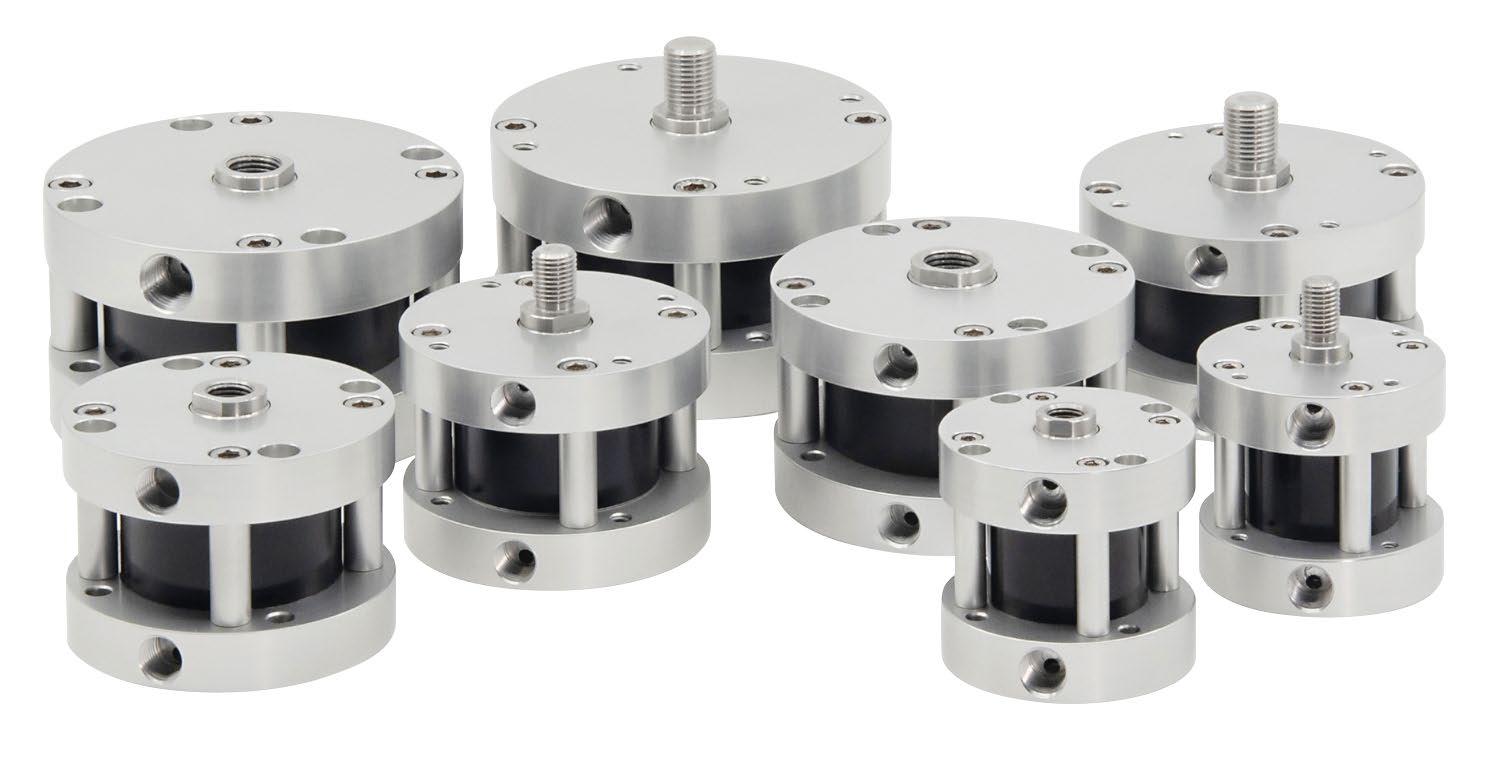

POWER THAT MOVES INDUSTRY. RELIABILITY THAT NEVER QUITS.
At Young Powertech, we build high-performance mechanical and hydraulic solutions that maximize power, efficiency, and durability in the toughest industries—farming, marine, industrial, construction, mining, and wind energy.
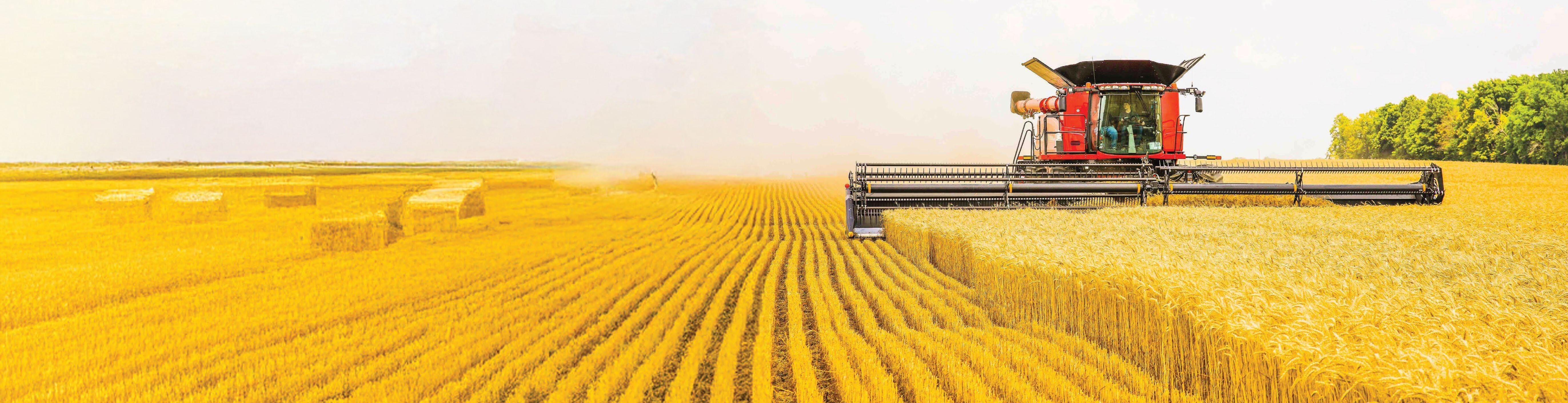
HYDRAULIC PRODUCTS
MAXIMIZE POWER, MINIMIZE DOWNTIME
High-Efficiency Hydraulic Motors
Delivering superior power, smooth operation, and longevity.
Precision Hydraulic Pumps
Engineered for optimal pressure, flow control, and performance.
Built for Demanding Industries
Keeping your systems strong, steady, and reliable.
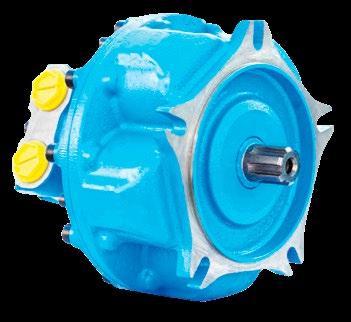
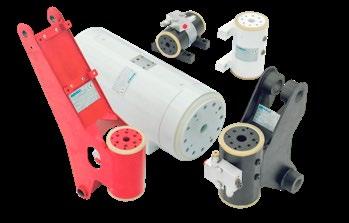
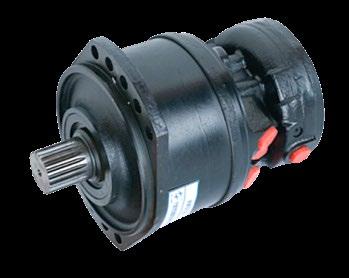

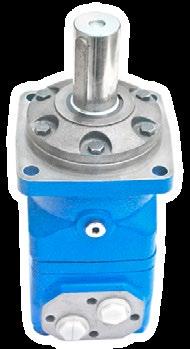

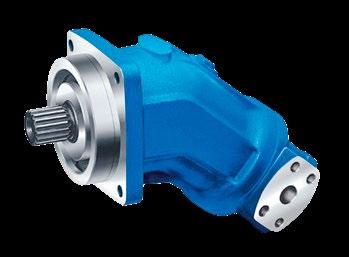
Orbital
Radial
Cam Ring
Bent Axis Gear
Helical Hydraulic Actuators
Grapple Rotators
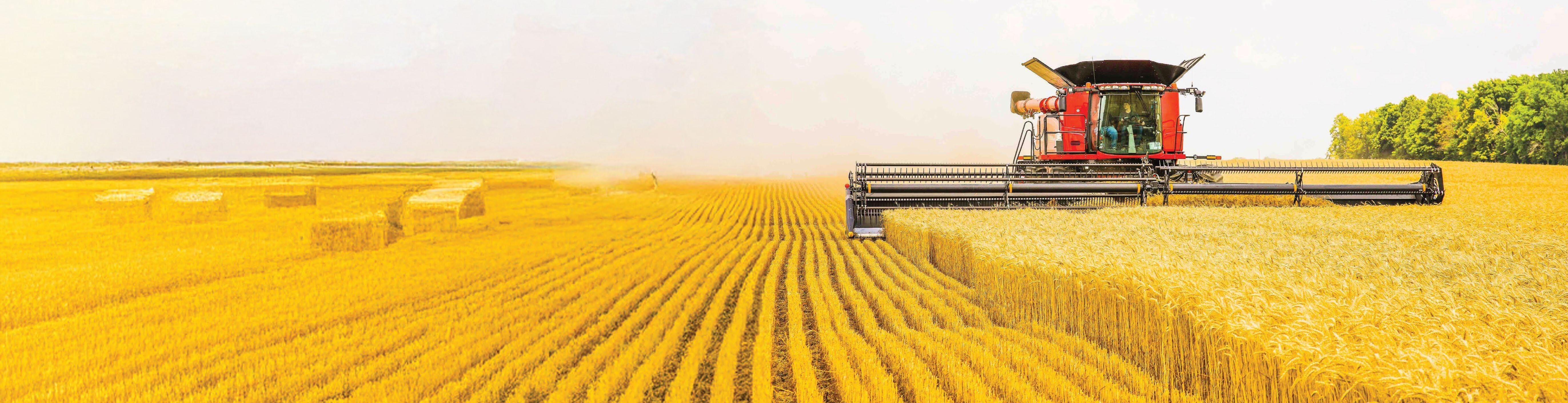
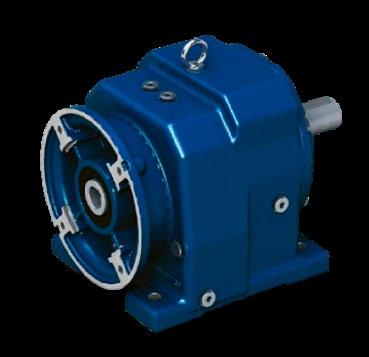

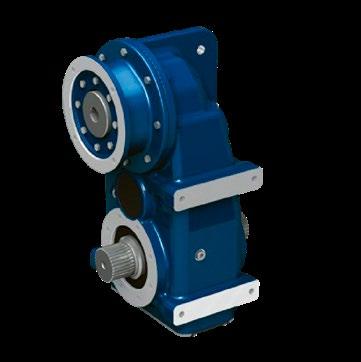
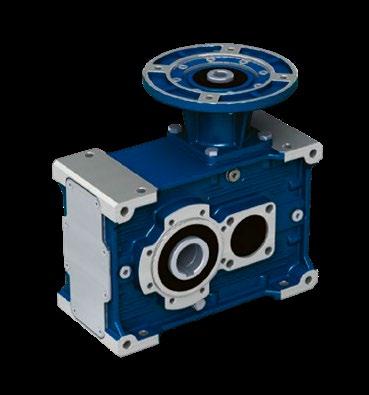
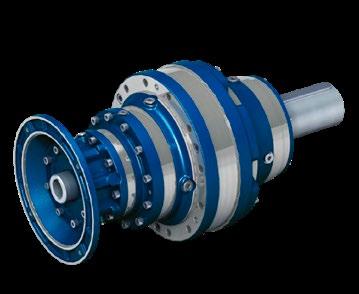
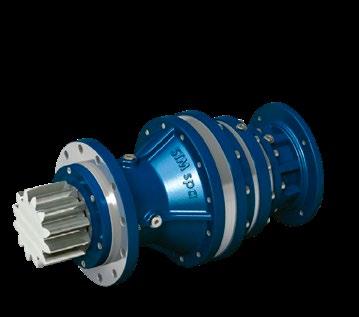
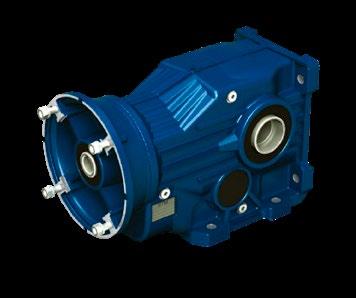
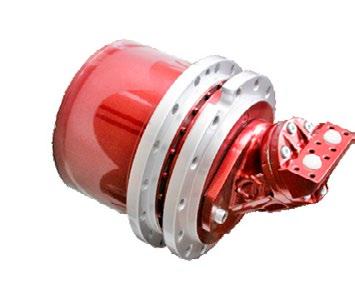
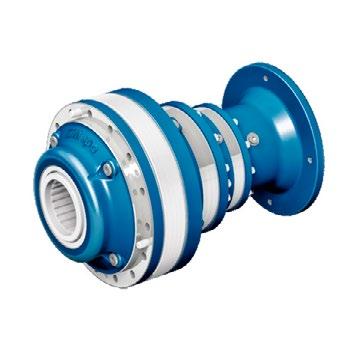
High-Performance Gearboxes
Custom Transmission Systems
Heavy-Duty Components
Designed
In-line Helical Shaft Mounting Gearboxes
Parallel and Shaft Mounting Gearboxes
Bevel Helical Gearboxes
Universal Bevel Helical Gearboxes
Gearboxes
Planetary Gearboxes
Large Size Planetary Gears Wheel and Track Drives
Fluid Power Fundamentals is Back!
» DISCOVER THE ESSENTIAL principles of fluid power with IFPS’s “Fluid Power Fundamentals” course. Designed for professionals—from customer service representatives to engineers and maintenance technicians— this virtual program explains the basics of hydraulic systems and their components. The course covers topics such as Pascal’s Law, force/ pressure/area relationships, and the dynamics of speed, flow, and power. You’ll also explore hydraulic symbology, learn about key components including pumps, various valve types, actuators, accumulators, and examine fluid conveyance, reservoirs, and contamination control per ISO 4406 standards.
Upon completion, you will receive a Certificate of Completion and the IFPS Basic Hydraulics Foundation Principles Student Workbook. With only 30 seats available, secure your spot by registering before the September 26, 2025 deadline!
The New & Improve Electronic Controls Specialist Manual
» THE IFPS IS pleased to announce the release of the newly updated Electronic Controls Specialist (ECS) Study Manual, designed to provide professionals with the most comprehensive and accessible learning experience in electronic controls for fluid power applications. Developed by industry experts, this manual has been carefully structured to ensure clarity, retention, and practical application of key concepts. What’s New in the ECS Study Manual?
• Enhanced Content – Updated material that reflects the latest advancements in electronic controls.
• Improved Graphics & Equations –Clearer visuals and refined calculations to enhance comprehension.
• Upgraded Pretests – Redesigned assessments that more effectively measure understanding and readiness for certification.
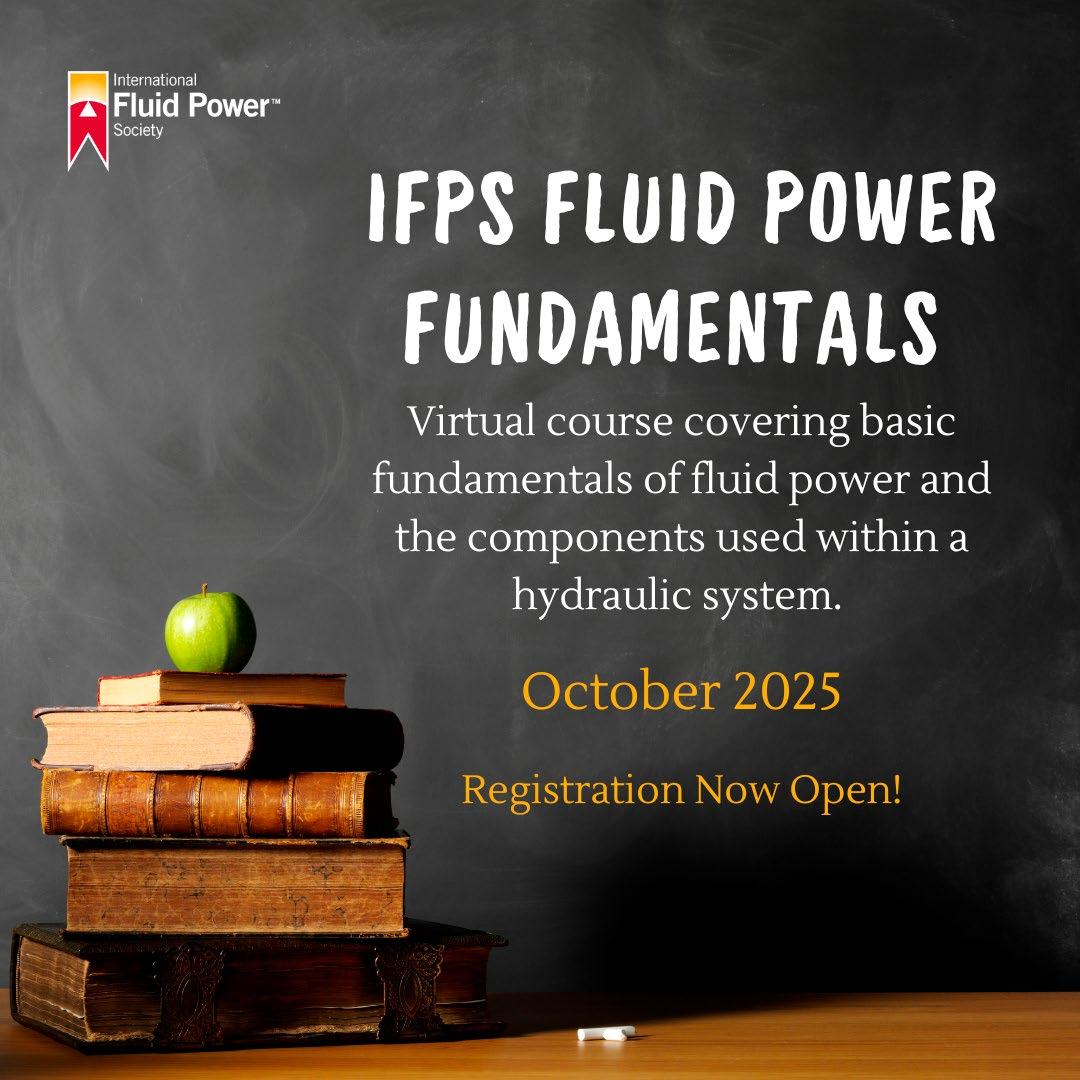
The Electronic Controls Specialist (ECS) Certification remains a recognized standard for professionals integrating electronic control systems with fluid power technology. Tailored for technicians, engineers, and sales professionals with a solid foundation in hydraulics and pneumatics, this certification evaluates expertise in fundamental fluid power concepts, electronic circuitry, sensor interfacing, PLC programming, and industrial network protocols.
Earning the ECS Certification strengthens professional credibility and creates opportunities for career advancement in system design, troubleshooting, and controls integration. Additionally, recertification every five years through a Professional Development Points system ensures specialists stay current with industry innovations, reinforcing their status as leaders in the field.
With the release of this enhanced study manual, IFPS continues to support industry professionals in achieving excellence. Secure your copy today and take the next step in mastering electronic controls!
**If you already have a printed ESC manual and have not taken the certification test, upon request, you will be shipped the upgraded ESC study guide.
Expand Your Knowledge with the IFPS Training Video & Webinar Library
» THE INTERNATIONAL FLUID Power Society (IFPS) now offers an exclusive Training Video & Webinar Library, giving IFPS members access to a wealth of industry knowledge anytime, anywhere. This new resource is designed to help professionals expand their expertise and stay up-to-date with the latest advancements in fluid power technology.
The webinars, led by industry experts, cover essential topics like electro-hydraulics, contamination control, valves, pumps, fluid power safety, and certification preparation. These in-depth sessions provide valuable insights and technical knowledge to help you grow in your career.
In addition, the technical education videos focus on hands-on learning, offering stepby-step guidance on key processes and best practices. Whether you’re looking to refine
your skills or learn something new, these videos provide practical training to enhance your efficiency in the field.
This exclusive member benefit ensures you have the tools to stay ahead in the industry. Visit today to explore the library and take advantage of these valuable educational resources!
Newly Certified Professionals
FEBRUARY 2025
CONNECTOR & CONDUCTOR
Brady Sherbahn, The Boeing Company
Brenton Lee, The Boeing Company
Casey Hoffman, The Boeing Company
David Franchuk, The Boeing Company
Eric Lektorich, The Boeing Company
Kristopher Vinson, The Boeing Company
Liam Phipps, The Boeing Company
Michael Ryan, The Boeing Company
ELECTRONIC CONTROLS SPECIALIST
Matthew Lilyquist, Altec Industries, Inc.
Richard Haas
Robert Wedepohl, Beckwood Press
Thomas Yarick, Parker
HYDRAULIC SPECIALIST
Jonathan Schmidt, Neff Press Inc.
INDUSTRIAL HYDRAULIC MECHANIC
Ashton Bright, The Boeing Company
Christian Whalen, The Boeing Company
William Staley, The Boeing Company
MOBILE HYDRAULIC MECHANIC
Andrew Berge, Altec Industries, Inc.
Brandon Rutz, AEP
Charles Giraldo, Florida Power and Light
Christopher Staiger, Duquesne Light
Daniel Murphy, Altec Industries, Inc.
Dave Tornow, Altec Industries, Inc.
David Kaminski, Duquesne Light
Jose Hernandez, Altec Industries, Inc.
Joshua Mitchell, Duquesne Light
Justin Alexander, Florida Power and Light
Kenneth Horstman, Altec Industries, Inc.
Mark Meleika, Florida Power and Light
Michael Zimmerman, Altec Industries, Inc.
Omar Dockery, Altec Industries, Inc.
Philip Isbell, Pedernales Electric
Richard Hawley, Altec Industries, Inc.
Richard Wright, Pedernales Electric
Tanner Kelley, Altec Industries, Inc.
Ted Grant, Pedernales Electric
Thomas Hill, Altec Industries, Inc.
Thomas Kissel, Duquesne Light
Tony Gera, Altec
Tyler Avocato, Entergy
Wallace Shifflett, Virginia Department of Transportation
MOBILE HYDRAULIC TECHNICIAN
Joshua Cook
PNEUMATIC SPECIALIST
Thomas Yarick, Parker
PNEUMATIC TECHNICIAN
Joshua Cook
SUPPORT ASSOCIATE
Anthony Smith, Motion Industries
Austin Bailey, SFP
Blake Cravens, SFP
Brian Wattenbarger, SFP
Chad Owens, SFP
Cory Meeks, SFP
Heather Fonte, SFP
Howard Johnson, SFP
Jarrad Peace, SFP
Jason Kirk, SFP
Johnny Morel, SFP
Joshua Neal, SFP
Justin Owens, SFP
Nick Beason, SFP
Nick Clarke, SFP
Scott Coffman, SFP
Tommy Hailey, SFP
Tommy Holder, SFP
Tyler Field, SFP

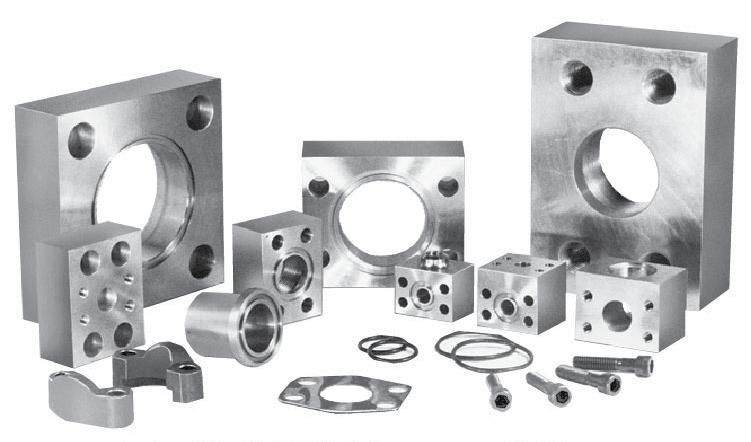
HYDR AULIC FL ANGES
PROUDLY SERVING THE INDUSTRY FOR OVER 6 5 YEARS * SAE J518


D COMPONENTS
MI 48439
800.521.7918
info@MAINmfg.com
www.MAINmfg.com/fpj
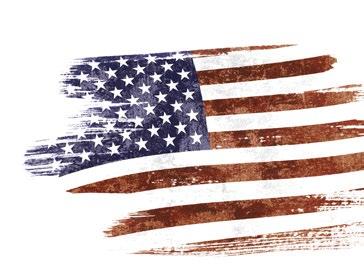
Individuals wishing to take any IFPS written certification tests can select from convenient locations across the United States and Canada. IFPS is able to offer these locations through its affiliation with the Consortium of College Testing Centers provided by National College Testing Association. Contact Kyle Pollander at Kpollander@ifps.org if you do not see a location near you. Every effort will be made to accommodate your needs.
Written Certification Test Locations
Alabama Auburn, AL Birmingham, AL Calera, AL Decatur, AL Huntsville, AL Jacksonville, AL Mobile, AL Montgomery, AL Normal, AL Tuscaloosa, AL
Alaska Anchorage, AK Fairbanks, AK
Arizona Flagstaff, AZ Glendale, AZ Mesa, AZ Phoenix, AZ Prescott, AZ Scottsdale, AZ
Sierra Vista, AZ Tempe, AZ Thatcher, AZ Tucson, AZ Yuma, AZ
Arkansas Bentonville, AR Hot Springs, AR Little Rock, AR
TENTATIVE TESTING DATES FOR ALL LOCATIONS
MAY 2025
Tuesday 5/6 • Thursday 5/22
JUNE 2025
Tuesday 6/10 • Thursday 6/26
JULY 2025
Tuesday 7/8 • Thursday 7/24
AUGUST 2025
Tuesday 7/5 • Thursday 8/21
California Aptos, CA Arcata, CA Bakersfield, CA Dixon, CA Encinitas, CA Fresno, CA Irvine, CA
Marysville, CA Riverside, CA Salinas, CA San Diego, CA San Jose, CA San Luis Obispo, CA Santa Ana, CA Santa Maria, CA Santa Rosa, CA Tustin, CA Yucaipa, CA
Colorado Aurora, CO Boulder, CO Springs, CO Denver, CO Durango, CO Ft. Collins, CO Greeley, CO Lakewood, CO Littleton, CO Pueblo, CO
Georgia Albany, GA
Athens, GA
Atlanta, GA
Carrollton, GA
Columbus, GA
Dahlonega, GA
Dublin, GA
Dunwoody, GA
Forest Park, GA
Lawrenceville, GA
Morrow, GA
Oakwood, GA
Savannah, GA
Statesboro, GA
Tifton, GA
Valdosta, GA
Hawaii Laie, HI
Idaho
Boise, ID
Coeur d ‘Alene, ID
Idaho Falls, ID
Lewiston, ID
Moscow, ID
Nampa, ID
Rexburg, ID
Twin Falls, ID
Illinois
Carbondale, IL
Carterville, IL
Champaign, IL
Decatur, IL
Edwardsville, IL
Glen Ellyn, IL
Joliet, IL
Malta, IL
Normal, IL
Peoria, IL
Schaumburg, IL
Springfield, IL
University Park, IL
Indiana
Bloomington, IN
Columbus, IN
Evansville, IN
Fort Wayne, IN
Gary, IN
Indianapolis, IN
Kokomo, IN
Lafayette, IN
Lawrenceburg, IN
Madison, IN
Muncie, IN
New Albany, IN
Richmond, IN
Sellersburg, IN
South Bend, IN
Terre Haute, IN
Iowa
Ames, IA
JOB PERFORMANCE TEST LOCATIONS
Arizona California Colorado Florida Georgia
Maine Michigan Minnesota Montana New Jersey Nova Scotia Pennsylvania Texas Washington Wyoming Western Australia
Delaware Dover, DE Georgetown, DE Newark, DE
Florida Avon Park, FL Boca Raton, FL Cocoa, FL Davie, FL
Daytona Beach, FL
Fort Pierce, FL
Ft. Myers, FL Gainesville, FL Jacksonville, FL Miami Gardens, FL Milton, FL
New Port Richey, FL Ocala, FL Orlando, FL
Panama City, FL
Pembroke Pines, FL
Pensacola, FL Plant City, FL Riviera Beach, FL Sanford, FL Tallahassee, FL
Tampa, FL
West Palm Beach, FL
Wildwood, FL
Winter Haven, FL
Maryland
Arnold, MD
Bel Air, MD
College Park, MD
Frederick, MD
Hagerstown, MD
La Plata, MD
Westminster, MD
Woodlawn, MD
Wye Mills, MD
Massachusetts
Boston, MA
Bridgewater, MA
Danvers, MA
Haverhill, MA
Holyoke, MA
Shrewsbury, MA
Michigan
Ann Arbor, MI
Big Rapids, MI
Chesterfield, MI
Dearborn, MI
Dowagiac, MI
East Lansing, MI
Flint, MI
Grand Rapids, MI
Kalamazoo, MI
Lansing, MI
Livonia, MI
Mount Pleasant, MI
Sault Ste. Marie, M
Troy, MI
University Center, MI
Warren, MI
Minnesota
Alexandria, MN
Brooklyn Park, MN
Duluth, MN
Eden Prairie, MN
Granite Falls, MN
Mankato, MN
Mississippi
Goodman, MS
Jackson, MS
Mississippi State, MS
Raymond, MS
University, MS
Missouri
Berkley, MO
Cape Girardeau, MO
Columbia, MO
Cottleville, MO
Joplin, MO
Kansas City, MO
Kirksville, MO
Park Hills, MO
Poplar Bluff, MO
Rolla, MO
Sedalia, MO
Springfield, MO
St. Joseph, MO
Cedar Rapids, IA
Iowa City, IA
Ottumwa, IA
Sioux City, IA
Waterloo, IA
Kansas
Kansas City, KS
Lawrence, KS
Manhattan, KS
Wichita, KS
Kentucky
Ashland, KY
Bowling Green, KY
Erlanger, KY
Highland Heights, KY
Louisville, KY
Morehead, KY
Louisiana
Bossier City, LA
Lafayette, LA
Monroe, LA
Natchitoches, LA
New Orleans, LA
Shreveport, LA
Thibodaux, LA
New Mexico
Albuquerque, NM
Clovis, NM
Farmington, NM
Portales, NM
Santa Fe, NM
New York
Alfred, NY
Brooklyn, NY
Buffalo, NY
Garden City, NY
New York, NY
Rochester, NY
Syracuse, NY
North Carolina
Apex, NC
Asheville, NC
Boone, NC
Charlotte, NC
China Grove, NC
Durham, NC
Fayetteville, NC
Greenville, NC
Jamestown, NC
Misenheimer, NC
Mount Airy, NC
Pembroke, NC
Raleigh, NC
Wilmington, NC
North Dakota
Bismarck, ND
Ohio
Akron, OH
Cincinnati, OH
Cleveland, OH
Columbus, OH
Fairfield, OH
Findlay, OH
Kirtland, OH
Lima, OH
Maumee, OH
Newark, OH
North Royalton, OH
Rio Grande, OH
Toledo, OH
Warren, OH
Youngstown, OH
Oklahoma Altus, OK
Bethany, OK
Edmond, OK
Norman, OK
Oklahoma City, OK
Tonkawa, OK
Tulsa, OK
Oregon Bend, OR Coos Bay, OR Eugene, OR Gresham, OR
Klamath Falls, OR
St. Louis, MO
Warrensburg, MO
Montana
Bozeman, MT
Missoula, MT
Nebraska Lincoln, NE
North Platte, NE
Omaha, NE
Nevada
Henderson, NV
Las Vegas, NV
North Las Vegas, NV
Winnemucca, NV
New Jersey
Branchburg, NJ
Cherry Hill, NJ
Lincroft, NJ
Sewell, NJ
Toms River, NJ
West Windsor, NJ
Medford, OR
Oregon City, OR
Portland, OR
White City, OR
Pennsylvania
Bloomsburg, PA Blue Bell, PA
Gettysburg, PA
Harrisburg, PA
Lancaster, PA
Newtown, PA Philadelphia, PA
Pittsburgh, PA
Wilkes-Barre, PA York, PA
South Carolina
Beaufort, SC Charleston, SC
Columbia, SC
Conway, SC
Graniteville, SC
Greenville, SC
Greenwood, SC
Orangeburg, SC
Rock Hill, SC
Spartanburg, SC
Tennessee Blountville, TN
Clarksville, TN
Collegedale, TN
Gallatin, TN
Johnson City, TN
Knoxville, TN
Memphis, TN
Morristown, TN
Murfreesboro, TN Nashville, TN
Texas
Abilene, TX
Arlington, TX
Austin, TX
Beaumont, TX
Brownsville, TX
Commerce, TX
Corpus Christi, TX
Dallas, TX
Denison, TX
El Paso, TX
Houston, TX
Huntsville, TX
Laredo, TX
Lubbock, TX
Lufkin, TX
Mesquite, TX
San Antonio, TX
Victoria, TX
Waxahachie, TX
Weatherford, TX
Wichita Falls, TX
Utah Cedar City, UT
Kaysville, UT
Logan, UT
Ogden, UT
Orem, UT
Salt Lake City, UT
Virginia
Daleville, VA
Fredericksburg, VA
Lynchburg, VA
Manassas, VA
Norfolk, VA
Roanoke, VA
Salem, VA
Staunton, VA
Suffolk, VA
Virginia Beach, VA
Wytheville, VA
Washington
Auburn, WA
Bellingham, WA
Bremerton, WA
Ellensburg, WA
Ephrata, WA
Olympia, WA
Pasco, WA
Rockingham, WA
Seattle, WA
Shoreline, WA
Spokane, WA
West Virginia Ona, WV
Wisconsin
La Crosse, WI
Milwaukee, WI
Mukwonago, WI
Wyoming Casper, WY
Laramie, WY
Torrington, WY
CANADA
Alberta Calgary, AB
Edmonton, AB
Fort McMurray, AB
Lethbridge, AB
Lloydminster, AB Olds, AB Red Deer, AB
British Columbia
Abbotsford, BC
Burnaby, BC
Castlegar, BC
Delta, BC
Kamloops, BC
Nanaimo, BC
Prince George, BC Richmond, BC Surrey, BC
Vancouver, BC Victoria, BC
Manitoba Brandon, MB
Winnipeg, MB
New Brunswick Bathurst, NB Moncton, NB
Newfoundland and Labrador
St. John’s, NL
Nova Scotia Halifax, NS
Ontario
Brockville, ON Hamilton, ON London, ON Milton, ON Mississauga, ON Niagara-on-the-Lake, ON
North Bay, ON North York, ON Ottawa, ON Toronto, ON Welland, ON Windsor, ON
Quebec
Côte Saint-Luc, QB Montreal, QB
Saskatchewan Melfort, SK
Moose Jaw, SK Nipawin, SK Prince Albert, SK Saskatoon, SK
Yukon Territory Whitehorse, YU
UNITED KINGDOM
Elgin, UK
GHAZNI Kingdom of Bahrain, GHA Thomasville, GHA
EGYPT Cairo, EG
JORDAN Amman, JOR
NEW ZEALAND Taradale, NZ
CFPAI
Certified Fluid Power Accredited Instructor
CFPAJPP
Certified Fluid Power Authorized Job Performance Proctor
CFPAJPPCC
Certified Fluid Power Authorized Job Performance Proctor Connector & Conductor
CFPE
Certified Fluid Power Engineer
CFPS
Certified Fluid Power Specialist (Must Obtain CFPHS & CFPPS)
CFPHS
Certified Fluid Power Hydraulic Specialist
CFPPS
Certified Fluid Power Pneumatic Specialist
CFPECS
Certified Fluid Power
Electronic Controls Specialist
CFPMT
Certified Fluid Power Master Technician (Must Obtain CFPIHT, CFPMHT, & CFPPT)
CFPIHT
Certified Fluid Power
Industrial Hydraulic Technician
CFPMHT
Certified Fluid Power
Mobile Hydraulic Technician
CFPPT
Certified Fluid Power Pneumatic Technician
CFPMM
Certified Fluid Power Master Mechanic
(Must Obtain CFPIHM, CFPMHM, & CFPPM)
CFPIHM
Certified Fluid Power
Industrial Hydraulic Mechanic
CFPMHM
Certified Fluid Power
Mobile Hydraulic Mechanic
CFPPM
Certified Fluid Power
Pneumatic Mechanic
CFPMIH
Certified Fluid Power
Master of Industrial Hydraulics
(Must Obtain CFPIHM, CFPIHT, & CFPCC)
CFPMMH
Certified Fluid Power
Master of Mobile Hydraulics (Must Obtain CFPMHM, CFPMHT, & CFPCC)
CFPMIP
Certified Fluid Power
Master of Industrial Pneumatics (Must Obtain CFPPM, CFPPT, & CFPCC)
CFPCC
Certified Fluid Power
Connector & Conductor
CFPSD
Fluid Power System Designer
CFPSA
Certified Fluid Power Support Associate
Tentative Certification Review Training
IFPS offers onsite review training for small groups of at least 10 persons. An IFPS accredited instructor visits your company to conduct the review. Contact kpollander@ifps.org for details of the scheduled onsite reviews listed below.
FLUID POWER SUPPORT ASSOCIATE
» CFC Industrial Training – Fairfield, Ohio | May 5–8, 2025 | December 1–4, 2025
HYDRAULIC SPECIALIST
For custom IFPS training inquiries, please contact Bj Wagner (bwagner@ifps.org)
» CFC Industrial Training – Fairfield, Ohio | May 19–23, 2025 | October 20–24, 2025
ELECTRONIC CONTROLS SPECIALIST
For custom IFPS training inquiries, please contact Bj Wagner (bwagner@ifps.org).
PNEUMATIC SPECIALIST
For custom IFPS training inquiries, please contact Bj Wagner (bwagner@ifps.org)
» CFC Industrial Training – Fairfield, Ohio | August 4–8, 2025
CONNECTOR & CONDUCTOR
For custom IFPS training inquiries, please contact Bj Wagner (bwagner@ifps.org).
» CFC Industrial Training – Fairfield, Ohio | July 15–17, 2025
MOBILE HYDRAULIC MECHANIC
For custom training IFPS inquiries, please contact Bj Wagner (bwagner@ifps.org)
Online Mobile Hydraulic Mechanic certification review for written test is offered through CFC Industrial Training. This course surveys the MHM Study Manual (6.5 hours) and every outcome to prepare you for the written test. Members may e-mail for a 20% coupon code off the list price. Test fees are not included.
» CFC Industrial Training – Fairfield, Ohio | June 23–27, 2025 | October 13–17, 2025
INDUSTRIAL HYDRAULIC MECHANIC
For custom IFPS training inquiries, please contact Bj Wagner (bwagner@ifps.org).
» CFC Industrial Training – Fairfield, Ohio | June 2–6, 2025
INDUSTRIAL HYDRAULIC TECHNICIAN
For custom IFPS training inquiries, please contact Bj Wagner (bwagner@ifps.org).
» For dates, call CFC Industrial Training at (513) 874-3225 or visit www.cfcindustrialtraining.com.
MOBILE HYDRAULIC TECHNICIAN
For custom IFPS training inquiries, please contact Bj Wagner (bwagner@ifps.org).
PNEUMATIC TECHNICIAN & PNEUMATIC MECHANIC
For custom IFPS training inquiries, please contact Bj Wagner (bwagner@ifps.org).
» For dates, call CFC Industrial Training at (513) 874-3225 or visit www.cfcindustrialtraining.com.
Optimizing Vacuum Applications A FRESH PERSPECTIVE
By Daniel Pascoe, Davasol Inc
» VACUUM TECHNOLOGY, INCLUDING pneumatics and hydraulics, offers a wide range of component choices and system integration methods. Unlike its counterparts, vacuum technology has fewer component manufacturers and resources, making informed selection and integration more complex. As a result, end-users often depend heavily on the expertise of their local distributor or supplier’s sales representatives, who may only be experts on their own firm’s brands. Let’s explore alternative approaches and often-overlooked options for optimizing vacuum applications. The goal is to provide a more effective and cost-efficient solution for the vacuum end-user.
Rethinking Replacement Parts in Vacuum Applications
When users seek vacuum components, the most common request is for direct replacements of existing parts. While this approach is straightforward, it may not always be the best option. Consider the case of a manufacturer using silicone vacuum cups to handle molded plastic components at 49°C
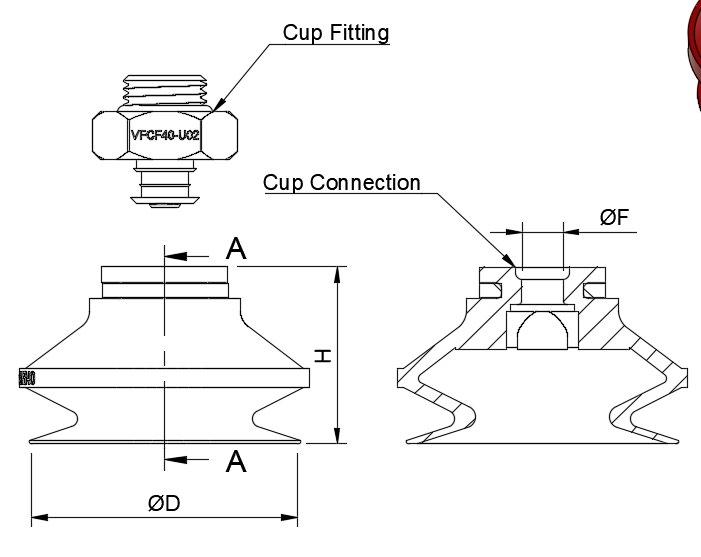
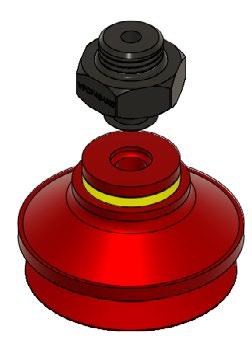
(120°F). While silicone is a common choice, other materials such as nitrile rubber (NBR) may perform just as well, offering cost savings given that NBR is less costly.
Similarly, dimensional differences between suction cups can cause hesitation in switching suppliers. If a competitor’s cup is slightly longer, (Fig 1), the user should assess whether machine stroke adjustments can accommodate the new part. If the cup connection differs from the original (dimension F), replacing the cup fitting with the new supplier’s suction cup may be a viable solution using familiar threads, such as 3 mm or 6 mm (1/8 or 1/4NPT). This occurs often at a cost offset by long-term savings and improved supply chain options.
Evaluating Vacuum Venturi and Pumps
Beyond vacuum cups, selecting the right vacuum venturi or pump requires careful consideration. If a venturi requires replacement, the easiest choice is to find an exact match. However, this is not always optimal. Factors such as mounting configurations and vacuum flow capacity should be evaluated before settling on a replacement. For instance, an existing venturi with a 500 lpm (18 cfm) airflow may have been initially oversized for the application. The reasons for this are numerous but often a “That should do it!" attitude leads from the front.
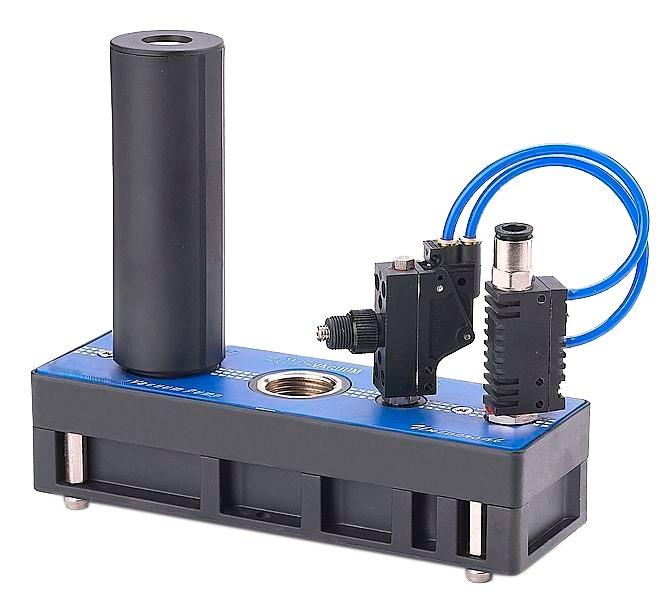
A smaller unit might reduce compressed air consumption without sacrificing machine performance. In applications requiring extended vacuum hold times, integrating an energy-saving venturi automatically shuts off the compressed air supply when a stable vacuum level is reached. This can significantly lower operational costs. Fig 2 shows this energy savings kit setup installed on a vacuum generator.
Vacuum pump selection follows similar principles. Users often request the same pump specifications they have been using for years, without considering advances in pump technology. If an 8,500 lpm (300 cfm) centralized vacuum system was installed years ago, has the production environment
changed since then? A revaluation might reveal that a smaller, more efficient pump is now a better fit.
Addressing Vacuum Control Valves and System Efficiency
Vacuum control valves are another frequently misapplied component. Many systems use pneumatic valves instead of purpose-built vacuum ones, leading to suboptimal performance. Unlike hydraulics and pneumatics industry standards for consistent sizing and functionality, vacuum components vary significantly between manufacturers. This lack of standardization underscores the importance of selecting components based on actual application needs rather than simply replacing parts with identical specifications. For instance, a vacuum system using a 5,600 lpm (200 cfm) pump does not automatically require a 5,600 lpm (200 cfm) control valve. The key consideration should be the actual vacuum flow demand of the application, not just the pump’s capacity. Understanding the system’s cycle time and flow requirements allows for smarter valve selection, improving efficiency and reliability.
Conclusion: A Smarter Approach to Vacuum Component Selection
A well-informed approach to vacuum system design can yield significant benefits in cost savings, efficiency, and long-term performance. Rather than defaulting to direct replacements, Sales Engineers and Application Specialists should focus on understanding the broader application requirements. By exploring material alternatives, adjusting system configurations, and leveraging newer technologies, businesses can improve performance and lower operating costs. While reduced upfront costs may seem appealing, the true value of a well-optimized vacuum system lies in its long-term reliability and efficiency. By taking a proactive approach to component selection, fluid power professionals can provide their customers with solutions that enhance productivity and operational sustainability.
This article is the opinion of the author, Daniel Pascoe of Davasol Inc., an industrial brand management firm. One of Davasol’s clients, Vacuforce LLC, based in Indianapolis, partners with the author on this article. Contact Daniel at dpascoe@vacuforce.com
Figure 2
Figure 1
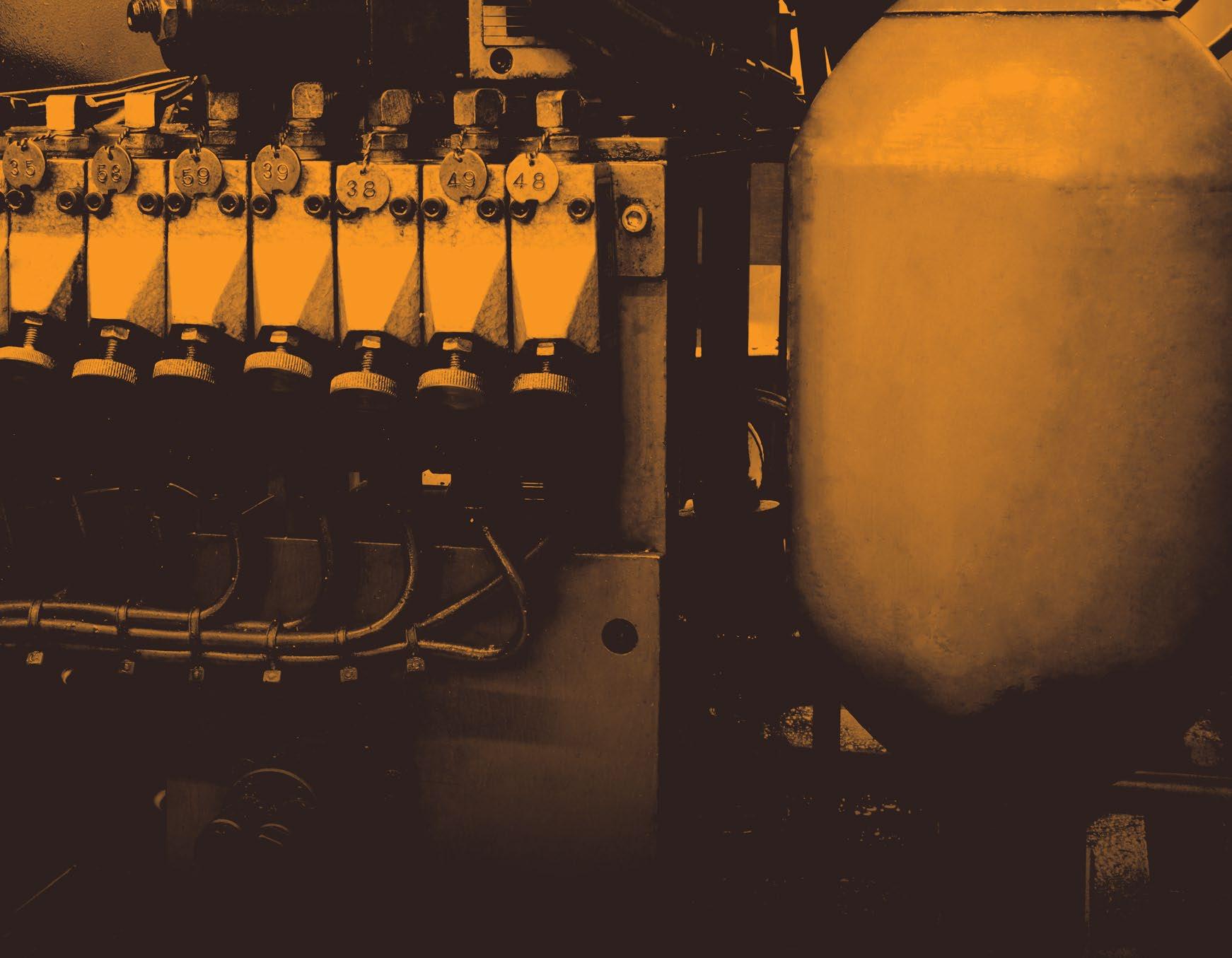
UNDERSTANDING THE APPLICATION OF ACCUMULATORS
Accumulator circuits store pressurized fluid. They are used for several purposes:
1. Maintain system pressure.
2. Absorb hydraulic shocks.
3. Supplement pump flow.
4. Provide auxiliary power.
5. Act as a barrier between dissimilar fluids.
Auxiliary power: One of the major benefits of using hydraulic accumulators is that they can store energy for later use. There are some functions that must occur, even if there is a power failure or if the
prime mover is not functional. Stored energy in an accumulator can be directed through manually operated, or DC solenoid operated valves to safely position equipment or isolate personnel from a dangerous environment. Some systems have a wide variation in loads or significant dwell time. The addition of an accumulator may allow the system designer to smooth out the power demand by providing an average flow to the system. When more flow is available than is required in a portion of the cycle, the extra volume is stored in an accumulator. When the required flow exceeds the pump flow, the accumulator will make-up the difference with the stored energy.•
TEST YOUR SKILLS
1 When servicing an accumulator and the hydraulic pressure gauge reads zero:
a. The gas may still have stored energy.
b. The nitrogen pressure will also be zero.
c. It is safe to remove the end cap.
d. Compressed air can be used to replace the nitrogen.
e. The bladder has ruptured and must be replaced.
See page 34 for the solution.
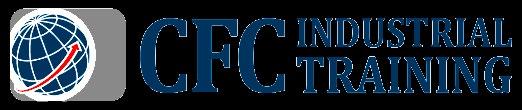
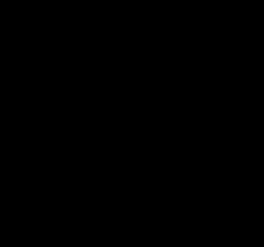
Safety tip: The accumulator must be completely discharged or blocked out of the circuit before attempting to disconnect any hydraulic lines. Never try to disassemble any
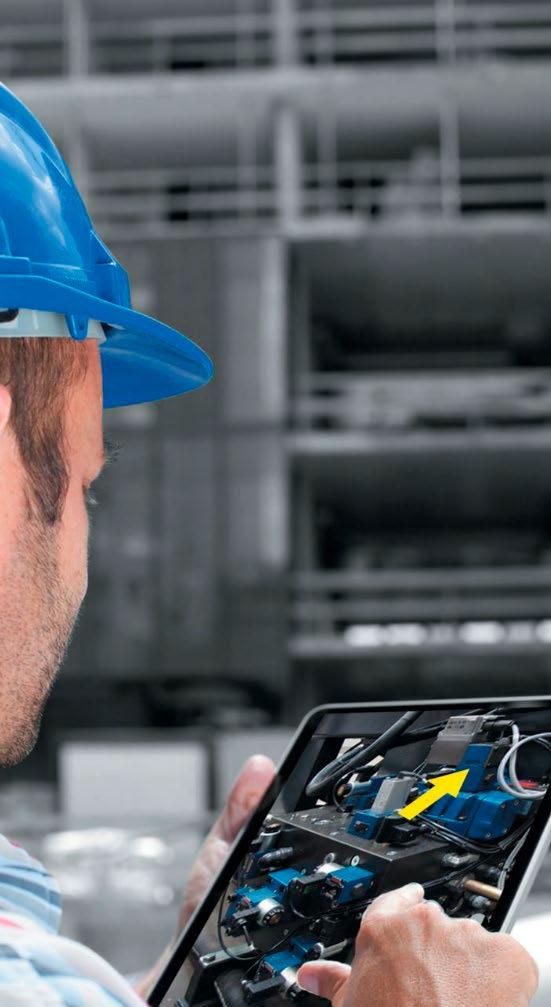
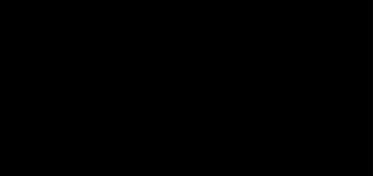

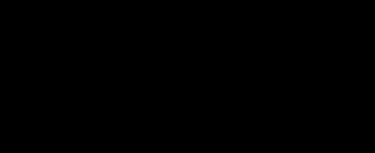
Digital Documents reverse-engineer systems cross/type components
Photo Navigation drilling down to individual components & parts
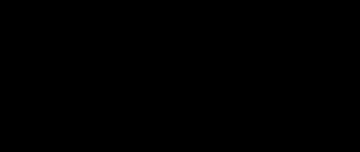
Interactive Prints illustrate machine operations & functions

Video Troubleshoot capture tribal knowledge & train on-the-job
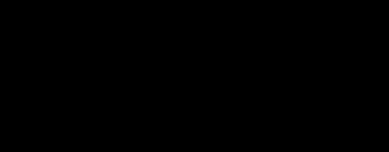
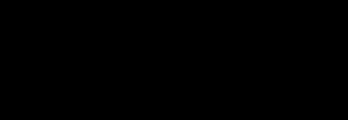
Can Work Offline on any device browser
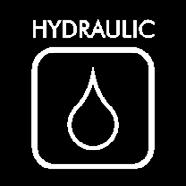
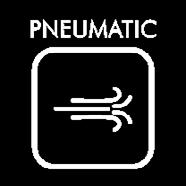
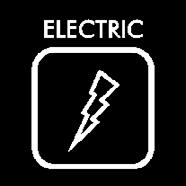
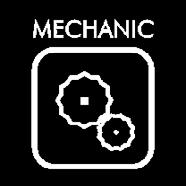
Fig. 1-46 Accumulator Circuit Operation
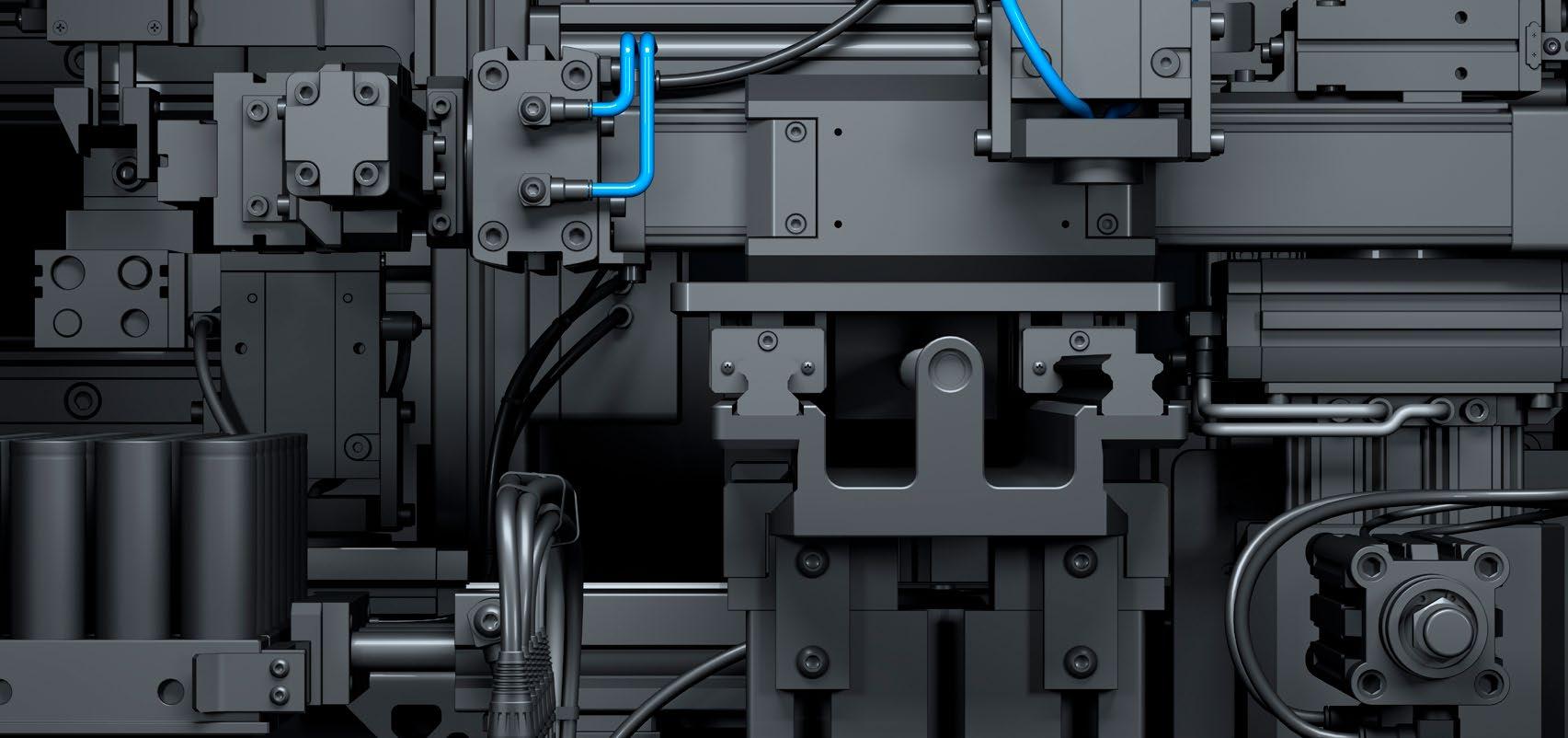
HYBRID ACTUATOR SYSTEMS HELP BRIDGE GAP FOR PLANTS WANTING THE ROBUSTNESS OF HYDRAULICS AND THE EFFICIENCY OF ELECTRIFICATION
By Bruce Besch, Alternative Motion Sales Manager, Parker Hannifin’s Cylinder and Accumulator Division
Traditional hydraulic systems have been the norm in most plants for decades. With the push to electrify and leverage greener solutions, machine builders have been exploring alternatives that combine these benefits. While it’s unlikely that manufacturing will be only electric, innovative hybrid options exist that are highly efficient, affordable, and robust.
THE HYDRAULIC APPROACH
There’s a reason that hydraulic systems have been around for so long. They represent a robust, reliable, and proven solution. They are controlled by a central power unit consisting of an induction motor, hydraulic pump, and valves to control direction, speed, and pressure. The fluid in the systems provides continuous lubrication and separates contaminants from moving parts, creating a self-cleaning, self-lubricating design. The fluid also provides dampening benefits to resist vibration and tolerate shock. The greatest benefit of hydraulics, however, is its power density. This is measured by its power-to-weight ratio. Traditional systems do have limitations. First, there are components in the system that must synchronize to achieve motion. When one component fails, it takes time to identify a failed component, and it takes the skill of an experienced hydraulics technician to fix the problem. In this era of many seasoned technicians retiring, responsibility often falls on less-experienced professionals who may not possess the knowledge needed to diagnose and remedy the problem. In addition, consolidated valve configurations in hydraulic systems create pressure loss, which consumes energy and creates heat, thus requiring the addition of a heat exchange. This makes for an inefficient design. Adding to the inefficiency is the fact that a central
hydraulic system must continuously operate, whether all functions are working or not.
Another serious concern is the potential for fluid leaks. Although hydraulics have a long-standing history of reliability, there remains the potential for fluid leaks. With numerous components requiring multiple connections, the risk of leaks is amplified. Additionally, the size of the system is another downside. Since it runs on centralized power, it requires a large motor, reservoir, and valving, taking up valuable machine space.
THE RISE OF ELECTROMECHANICAL ACTUATORS AND THEIR LIMITATIONS
Electromechanical solutions have been gaining ground in many applications due to their plug-and-play simplicity. Electromechanical actuators are typically fitted with permanent magnet alternating current (PMAC) motors. These motors have a high power-to-weight ratio and a high dynamic response. They allow for quick acceleration and can operate at a wide range of speeds, thus allowing for on-demand operation.
A screw drive is typically a ball screw or planetary roller screw with a lead that determines the travel per revolution. This serves as the prime mover. By controlling the screw speed (RPM), it’s possible to control the speed of the electromechanical actuator by varying the motor speed with a frequency converter. Since torque on the screw results in thrust, the same controller can limit amps to the motor. This restricts the motor torque passed to the screw, thus limiting the EMA thrust.
The motor runs only when power is needed, saving energy in comparison with traditional hydraulic solutions in which the motor runs continuously. Additionally, electromechanical solutions are generally quieter, and their
all-in-one modular design minimizes downtime since the entire actuator can be replaced for servicing. Despite these benefits, electromechanical actuators have a comparatively short service life and, on average, are three times the size of their hydraulic counterparts, which means more floor space. Because the systems are very rigid, they do not handle shock well. Any impact loading is passed from the nut to the screw, which means upsizing is required to handle any shock loading. Furthermore, they add a layer of complexity in programming, and cost per axis can be significant when compared to hydraulics.
THE PROMISE OF HYBRID ACTUATOR SYSTEMS
Given the shortfalls of both hydraulic and electromechanical systems, engineers have been focusing on ways to design a system that combines the benefits of both approaches without bringing along any inherent weaknesses. Doing so has opened the door to hybrid actuation systems that provide the desired speed and torque control with greater efficiency. This includes up to 80% energy savings and up to 90% space savings. Hybrid actuator systems are self-contained linear actuation systems that bring electrification and efficiency to where the work needs to be performed. This type of localized power optimizes energy consumption, increases machine performance, and reduces downtime. They look and feel like an electrical actuator yet have the power density and failsafe characteristics associated with traditional hydraulics. Hybrid actuator systems use many of the same concepts of an electromechanical system, but these systems turn a pump rather than turning a screw, using fluid transmission to move the actuator. With hybrid actuator solutions, the direction is controlled by changing the direction of the motor, speed is controlled by regulating the pump’s RPM, and thrust is managed by controlling motor torque.

The Hybrid Actuator System consolidates the entire hydraulic system into a single component integral to the actuator with all the controllability of electromechanical plus the fail-safe features and power density of a traditional hydraulic cylinder.
The result serves as an OEM machine design game-changer. This innovative approach allows engineers to strategically place actuators in locations previously deemed impractical or impossible due to electromechanical size constraints. Utilizing this method, designers can optimize machine layouts, enhancing performance and efficiency while reducing the overall footprint. This implementation of node-based hydraulics facilitates machine diagnostics and operational learning, which maximizes uptime. If maintenance is needed, the entire system can be replaced; this reduces downtime to only a few minutes. Additional advantages over a hydraulic and electromechanical approach include:
• Easier Maintenance: An all-in-one design creates a type of plug-and-play actuator that facilitates troubleshooting and is easy to install and set up.
• Superior Power in a Smaller Footprint: Since the actuator is hydraulic, it delivers three times the power density of a comparably sized electromechanical solution.
• Easy to Install and Control: Hybrid systems provide the desired control and accuracy without the use of valves.
• Energy Savings: This approach reduces pressure loss and significantly lowers wasteful energy consumption.
• Quieter Operation: Power On-Demand shortens the system's activation time, thereby reducing machine harmonics. Additionally, incorporating proportional control without relying on valves mitigates the "bang-bang" behavior commonly associated with traditional solenoid valves.
• Reduced Leak Points: A self-sealed design and fewer components means there are fewer potential leak points.
• Reduced Oil Reservoir Volumes: The size of these reservoirs is only a fraction of the size of those found in traditional hydraulic systems. These typically require less than a gallon of fluid.
• Longer Service Life: Environmental contamination is not a concern because of a sealed reservoir, which allows it to function in dirty environments. These systems offer up to 8,000 hours of maintenance-free operation.
• Greater Shock and Vibration Resistance: The fluid used is slightly compressible, so it can dampen any shock or vibration. This makes it ideal for heavy-duty applications that are too rugged for rigid electromechanical systems to handle.
• Superior Connectivity: The serial bus/ network is able to provide health and

performance feedback. The potential exists to monitor direction, speed, and thrust. Machine operating thresholds for scheduled maintenance and actuator replacement may also be assessed.
CONCLUSION
Hybrid actuation systems leverage the best of hydraulic and electromechanical solutions.
They are quickly gaining popularity in mobile and industrial applications that require the power, toughness, and resiliency of hydraulics in a smaller, smarter, and greener package. The improvements in safety and productivity made possible by advances in IoT connectivity are expected to transform numerous industries and operations dependent on linear motion.•
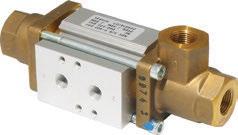

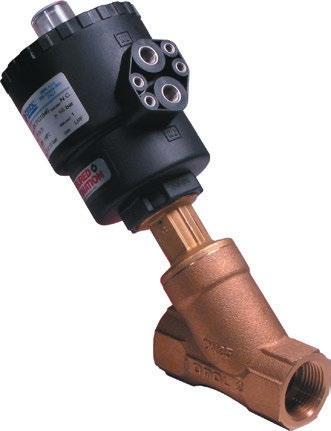
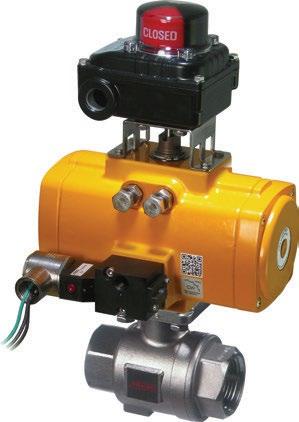

OEM’s, integrators, and factories all over the world are turning to Assured Automation’s compact on/o valves and high-cycle ball valves to improve machine reliability and increase productivity.
Localized Power vs Central Power
HYDRAULIC FITTINGS & HOSES
i n Agricultural, Heavy Construction, and Civil Engineering Industries
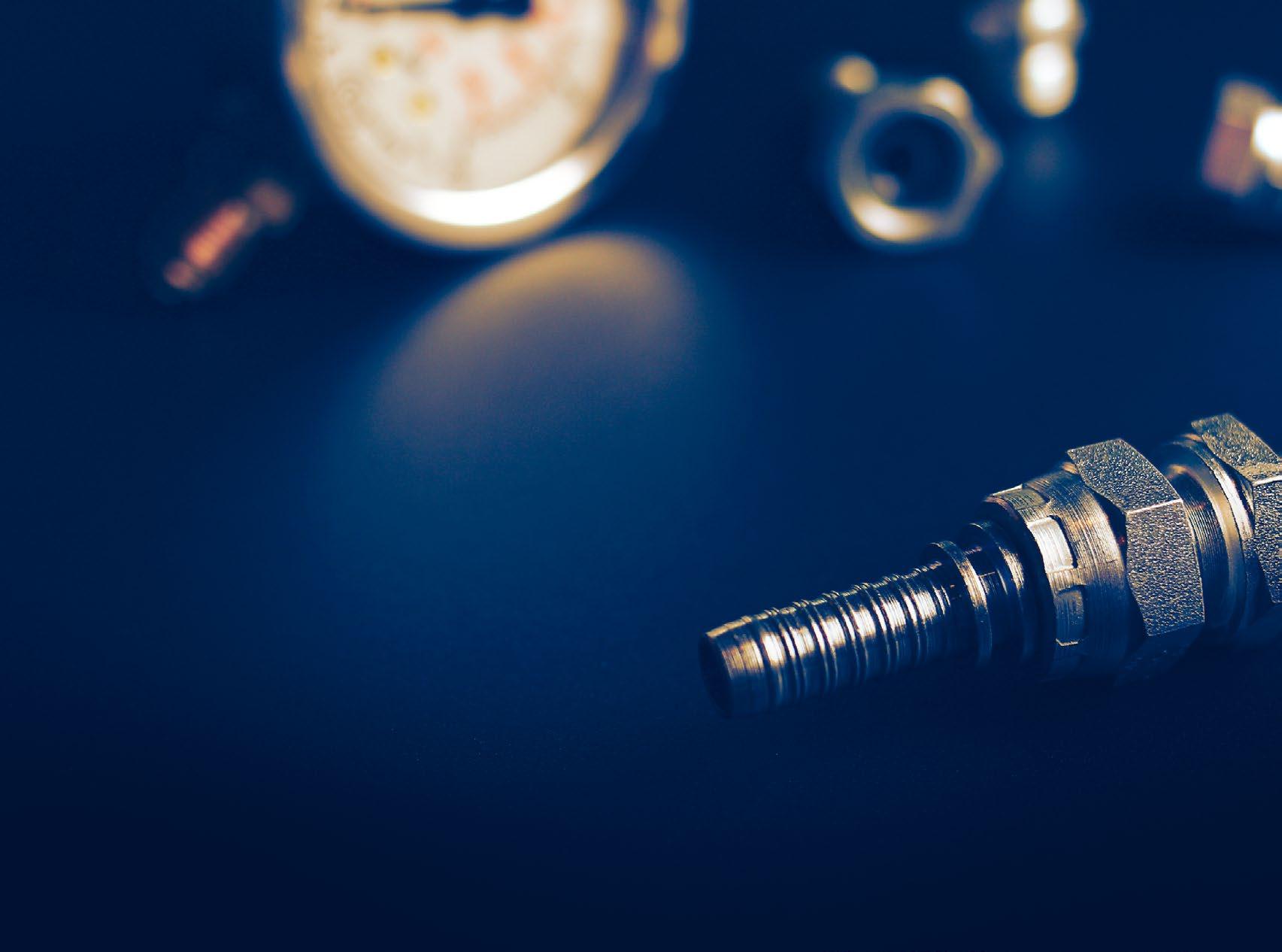
hydraulic systems rely on high-quality hoses and fittings to ensure that the fluid moves efficiently through the system, which is crucial when handling heavy loads. During harvesting, hydraulic hoses and fittings power mechanisms that help unload crops, adjust the cutting height, and rotate augers. Sprayers use hydraulic systems to control the boom arms that distribute pesticides, herbicides, and fertilizers. These systems need high-pressure hoses and fittings to deliver the necessary fluid at optimal flow rates, even under extreme pressure.
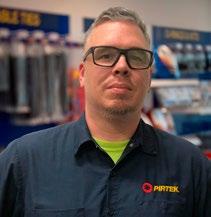
By Ryan O'Lone, Product Manager, PIRTEK USA
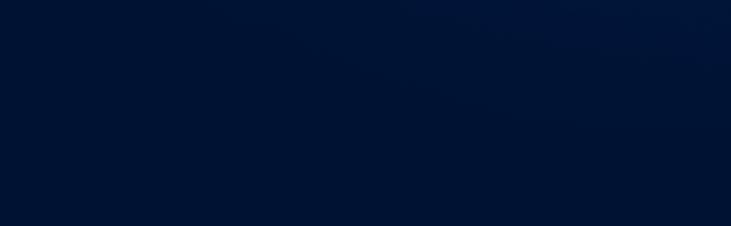
Hydraulic systems are integral to the operation of machinery and equipment across several industries, including agriculture, heavy construction, and civil engineering. Hydraulic fittings and hoses are essential components that facilitate the transfer of hydraulic fluid, which powers machines including tractors, excavators, bulldozers, and cranes. These systems rely on high-performance hoses and fittings to ensure safety, efficiency, and reliability in demanding environments. Below, we explore the role of hydraulic fittings and hoses in these industries, focusing on their types, functions, and maintenance requirements.
THE ROLE OF HYDRAULIC FITTINGS AND HOSES
At its core, a hydraulic system relies on the movement of fluids under pressure to perform work. Hydraulic hoses transport this fluid between different system components, while hydraulic fittings connect various hoses, pipes, and other components. These fittings and hoses are designed to withstand high pressure and extreme conditions, ensuring the machinery performs optimally. There are many factors to consider when choosing a hydraulic hose, including size and pressure rating. Still, it is important to consider other aspects such as the temperature ratings of the material the hose conveys and the ambient temperatures it will encounter. The hose’s resistance to
these temperatures plays a big part in the hose's life span, along with the minimum bend radius. If a hose is subjected to constant flexing while under pressure, then the makeup of the reinforcement used in the hose and its minimum bend radius must be considered to ensure a peak hose life span.
It's important to ensure that fittings are compatible with the size and type of hose used. There are published certified crimp specifications for assembling the fitting to the hose. It is also important to consider the hose’s use environment. While the most common type of hydraulic fitting is carbon steel with corrosion-resistant plating, it may be necessary to use stainless steel or another more corrosion-resistant material or plating type, depending on the environment in which the hose assembly will be used.
HYDRAULIC SYSTEMS IN AGRICULTURE
The agricultural industry relies heavily on hydraulic technology for equipment including tractors, harvesters, sprayers, and plows. The use of hydraulic systems in agriculture has greatly improved productivity by making machines more versatile and easier to operate. In agricultural machinery, hydraulic fittings and hoses help efficiently transfer fluid that powers key functions, such as lifting, steering, and controlling attachments.
Tractors are the backbone of modern agriculture. They use hydraulic systems to raise and lower implements like plows, seeders, and fertilizer spreaders. These
Agricultural hydraulic systems face unique challenges due to exposure to dirt, chemicals, and moisture, which can degrade hoses and fittings over time. These components must be resistant to wear and tear due to the harsh environments in which they operate. Regular inspection and maintenance are essential to prevent failures that can lead to costly downtime and decreased productivity.
HYDRAULIC SYSTEMS IN HEAVY CONSTRUCTION
Heavy construction equipment such as excavators, backhoes, bulldozers, and cranes depend on hydraulic systems for a wide range of functions, including lifting, digging, and moving materials. These machines work in demanding environments, often under extreme conditions, requiring hydraulic hoses and fittings that are both durable and reliable. Safety is paramount in heavy construction. Hydraulic hose failure can lead to sudden, catastrophic machine failure, posing a risk to operators and bystanders. Proper maintenance and using high-quality hoses and fittings are critical to ensuring safety and avoiding costly repairs.
Excavators and backhoes use hydraulic cylinders and motors to power the bucket, boom, and arm movements. These movements require high-pressure hydraulic fluid, and the hoses and fittings must be able to handle the force while maintaining fluid integrity. Hydraulic cranes and load lifters rely on hydraulic pumps and valves that control heavy loan hoisting and lowering. The hydraulic hoses must withstand the high-pressure fluid required to move tons of weight, while the fittings must maintain a secure seal to prevent leaks. Bulldozers and compactors utilize hydraulic systems to control blades and other attachments. As with other heavy machinery, hydraulic hoses and fittings must resist extreme pressures and harsh environments such as dust, dirt, and temperature fluctuations.
HYDRAULIC SYSTEMS IN CIVIL ENGINEERING
Civil engineering projects involve large-scale construction tasks, including road building, bridge construction, and underground utilities installation. Hydraulic systems play a vital role in these projects, with hydraulic machines used to move earth, pour concrete, and install infrastructure. Hydraulic pile drivers use powerful hydraulic systems to drive piles deep into the earth as part of foundation construction. The hoses and fittings used in these systems must endure high pressures and vibrations while maintaining their integrity over time.
Concrete pumps rely on hydraulic power to move concrete through pipelines to the construction site. These pumps require hydraulic hoses and fittings that can handle abrasive materials, high flow rates, and pressure extremes without leaking or bursting. In road construction, hydraulic systems control the movement and adjustment of rollers, pavers, and other heavy equipment. These systems often operate in harsh conditions, requiring durable hoses and fittings that are resistant to the elements.
Civil engineering projects also require robust hydraulic systems to handle the complexity and scale of construction. These projects often occur in challenging environments. As a result, the need for durable, high-quality hydraulic hoses and fittings cannot be overstated.
KEY CONSIDERATIONS FOR HYDRAULIC HOSES AND FITTINGS
In all of these industries, the performance of hydraulic systems depends heavily on the quality and design of the hoses and fittings. The following factors are critical in selecting the right components:
• Hydraulic systems in agricultural, construction, and civil engineering equipment are often exposed to high pressures. Therefore, the hoses and fittings must be rated to withstand these pressures without failure.
• Hydraulic systems in these industries can experience extreme temperatures, from freezing winter to scorching summer heat. Hydraulic hoses and fittings must be able to resist these temperature ranges without degrading.
• Equipment in these industries should be durable in rough environments, where dirt, debris, and chemicals can damage components. Hydraulic hoses and fittings must resist abrasion, corrosion, and chemical exposure.
• Hydraulic fittings come in various shapes and sizes. It’s essential to ensure that the
right fittings are chosen for the specific hydraulic system. Ill-sized fittings can lead to leaks or system failure.
• Hydraulic fluid leaks are a significant safety concern, as they can cause malfunctions or hazardous environmental spills. High-quality hydraulic hoses and fittings help ensure a secure and leak-free system.
MAINTENANCE AND INSPECTION
Regular maintenance and inspection of hydraulic systems are vital to extending the life of hoses and fittings. In all three industries, downtime due to hydraulic failure can result in significant operational delays and financial losses. Routine checks should include:
• Visual Inspections: Look for signs of wear, cracks, or leaks around hoses and fittings.
• Pressure Testing: Ensure that the hydraulic system is holding pressure correctly and that the hoses and fittings are not compromised.
• Cleaning: Equipment should be cleaned regularly to prevent the buildup of dirt and debris around hoses and other components, which can cause abrasion wear and build up, not allowing hoses to dissipate heat buildup.
• Replacement: Hoses and fittings that show signs of age and wear should be replaced immediately to avoid more extensive damage. Do not wait until a hydraulic hose has completely failed before replacing it.
CONCLUSION
Hydraulic fittings and hoses are fundamental to the operation of machinery in agriculture, heavy construction, and civil engineering. These components enable the efficient transfer of hydraulic fluid, ensuring equipment functions smoothly under tough conditions. Given the demanding nature of these industries, the quality of hydraulic hoses and fittings is paramount. Regular maintenance, proper selection, and timely replacement of worn-out parts are critical to ensuring the longevity and safety of hydraulic systems. By choosing the right components and maintaining them properly, operators can ensure that their machines ultimately contribute to the success of their operations.•

MASSIVE HYDRAULIC PRESS FASHIONS FITTINGS FOR MILITARY SHIPS
By Jason Palmer, PMP, CHPHS, Regional Sales & Applications, W&O Supply

Large military vessels require large diameter pipes and big fittings to move oil, steam, seawater, or anything else a ship might need. While conventional fittings have pressure ratings of 50 to 100 pounds per square inch (psi), these maritime fittings need to withstand pressures up to 6000 psi at diameters from 0.25 to 32 inches.
W&O Supply’s Seamless Marine Fittings Division is one of a few suppliers capable of meeting the stringent specifications for military applications. W&O Supply has over 45 years in the maritime industry, covering everything from repairing valves to supplying pipe, as well as retrofitting military and commercial vessels. The company has 18 branches dedicated to supporting marine construction, repair, and servicing on a global level.
In metalworking, a cold press is a machine tool that uses a non-heated die to shape or form metal blanks into desired shapes. It is a versatile and efficient technique used to produce a wide range of components, particularly those requiring precise dimensions
and intricate geometries. Cold presses shape fittings by bending them over a mandrel or through a closed die, which attaches to the central press’s ram. This results in stronger, more accurate fittings with greater consistency than is possible with hot presses, which can make the metal more brittle. In addition to producing better parts, cold presses also use less energy and produce less waste heat.
According to William Abbott, Director of Quality for W&O Supply, the U.S. Navy identified a supply chain weakness for such parts in 2017. There weren’t enough suppliers in the world making fittings in those size and tolerance ranges. The company sought to address the market need for such fittings; to do so, it needed a very large, highly accurate press. Such presses are not off-the-shelf purchases; each one must be custom-designed and manufactured.
W&O started small, with a 500-ton press able to handle fittings up to 10 inches as its first foray into this market. The design targeted high-strength materials and
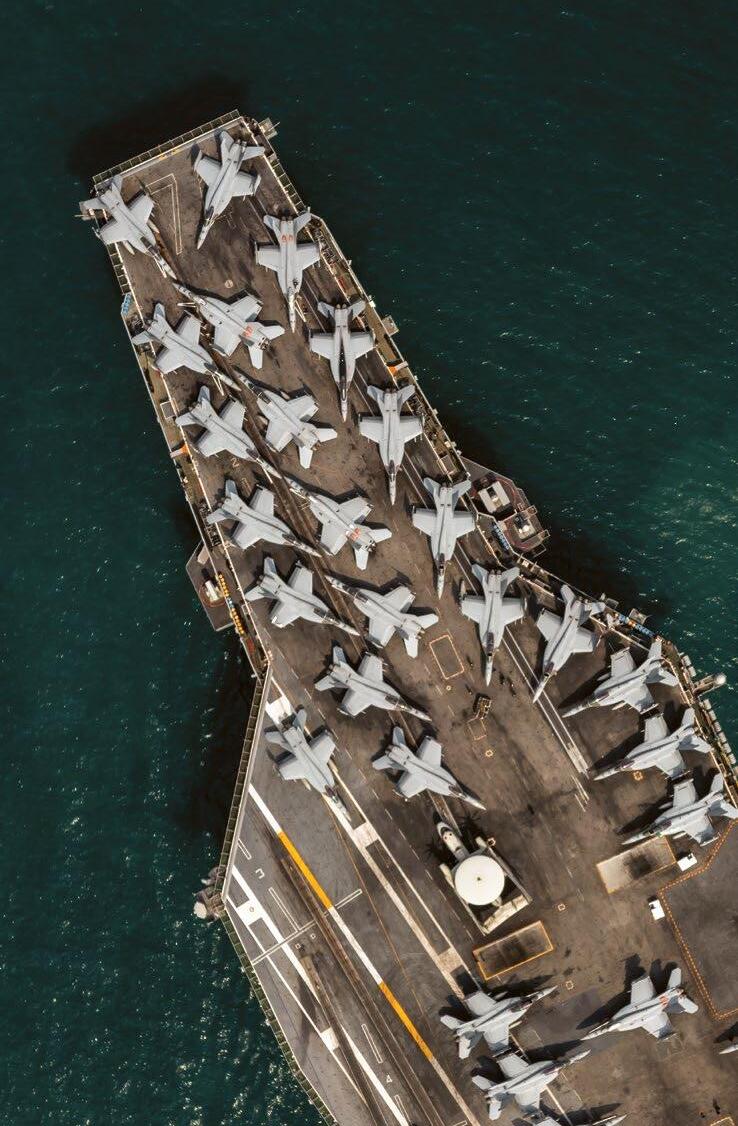
difficult-to-manufacture items. Due to its fast success, W&O significantly scaled up its next iteration. The “full-size” four-post press handles 3,000 tons or six times the pressure of its predecessor. The total force contributed by all cylinders, each of which provides up to 1.2 kilotons of energy force, is 6,000 tons. Abbott notes its capacity to support the construction of military vessels including submarines, carriers, and destroyers. He also acknowledged that fittings in the commercial world would benefit from this product as well.
OVERCOMING THE MOTION CONTROL CHALLENGE
Precision motion control is critical for these presses. Erratic control ruins part quality and causes excessive press wear. William Abbott and W&O Supply have tried a range of motion controllers in their presses over the decades. Too often, Abbott notes that motion control solutions providers claim to have the capacity to fulfill all needs. However, limitations present themselves.
Abbott suspects the solutions were never intended to provide the necessary control, and the features won’t support it. Controllers exist that provide nearly hardware-level access to fundamental components, inputs, outputs, and ADCs. However, he states that many motion controllers are “black boxes you can’t see inside of.”
Abbott had seen controllers from Delta Motion used in other successful industrial applications and reached out to Delta to assess whether its system could handle the demands of W&O’s high-pressure cold press. Given the project required processes rarely seen in hydraulic presses, Abbott was initially skeptical but quickly recognized the potential of Delta’s RMCTools software. Noting the simple interface that provided W&O the
THE WRONG VALVE WOULD RUIN THE
ENTIRE PROJECT,
AS ABBOTT HAD DISCOVERED IN OTHER IMPLEMENTATIONS.
critical details, such as valve selection. Anything controlling velocity or pressure per the demands of this project had to respond accurately and consistently under high-pressure conditions. The wrong valve would ultimately ruin the entire project, as Abbott had discovered in other implementations.
SUCCESSFUL COMMISSIONING IN RECORD TIME
All in all, the Delta integration was seamless thanks in part to the quality of Delta’s PROFINET connectivity. Abbott notes that typically 1-2 weeks is allocated to get a motion control rack up and running. With Delta and the cold press, the team started on Monday morning, had the racks communicating by midday, and cylinders moving that night.
on industrial hydraulic motion control, with solutions from 1 axis to 50 axes, and motion loop times up to 8,000 times per second or 125 μs. Delta’s history of long-term support proved critical for presses that may be used and upgraded for half a century.
W&O Supply loved Delta RMCTools for its user-friendly interface and powerful features. Delta’s programming software provides the same powerful feature set needed to optimize performance, regardless of which controller was purchased. He was amazed to find that, whether a company opts for the least or most expensive controller in Delta's lineup, RMCTools is included at no additional cost. He also admired Delta’s “old-school” approach to service—referring to Delta Motion’s emphasis on knowledgeable

access needed to fulfill a number of functions, it became very clear to Abbott that the product fulfilled all of the company’s needs.
W&O selected a Delta RMC200 motion controller equipped with an SSI interface and high-resolution analog modules, along with two digital channels. The modules were highly configurable and prevented W&O from purchasing special modules for specific widgets. Abbott happily noted W&O’s ability to now utilize SSI and analog feedback for position and velocity. He also acknowledged Delta’s distinctive, rare level of expertise pertinent to different kinds of motion.
Abbott collaborated with his hydraulic designers and Delta’s engineering team on
Integration was completed in a single day. Similarly, the normal time required for tuning the motion axes on an installation would have been a week. With Delta, it was only one more day. Abbott contrasted this experience with the 500-ton press W&O had developed earlier using a motion control system from another supplier. It didn’t work as well over four years versus what the company accomplished in two days with Delta.
BUILDING FOR THE FUTURE
Delta's RMC200 can control up to 50 axes, surpassing the application's current needs of 5 axes. Abbott had scalability in mind from the outset. W&O Supply appreciated Delta’s focus
and responsive technical support. Abbott notes that all Delta personnel were wellversed in their areas of expertise, which he attributes to a high caliber of training, paired with customer needs acumen.
Previously, W&O worked with a vendor that recently entered into the motion control arena and expressed confidence in its ability to meet W&O’s needs. After 4 years, Abbott states that the vendor’s solution does not work as well as what the company achieved in 2 days with Delta. Since commissioning this application, W&O has experienced zero failures and needs to make zero adjustments. The motion system has constantly operated since its inception and continues to perform flawlessly.•
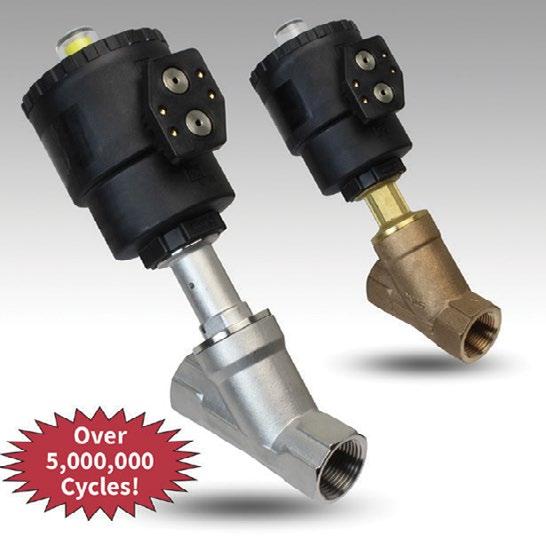
High Cycle-Life Angle Valve
2-way pneumatically actuated angle seat valves are suitable for liquids, gases, and steam. The unique design of the piston enables the plug to retract further from the flow path, ensuring the highest flow capacity. The dual packing design, and a large diameter self-aligning stem ensures the highest cycle life. 3/8” to 2” NPT & Tri-clamp. Bronze or 316SS. IN STOCK!
https://assuredautomation.com/anglevalve 800-899-0553 | sales@assuredautomation.com
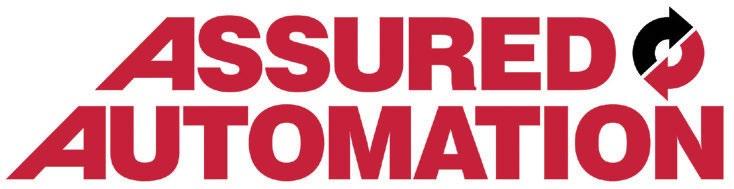
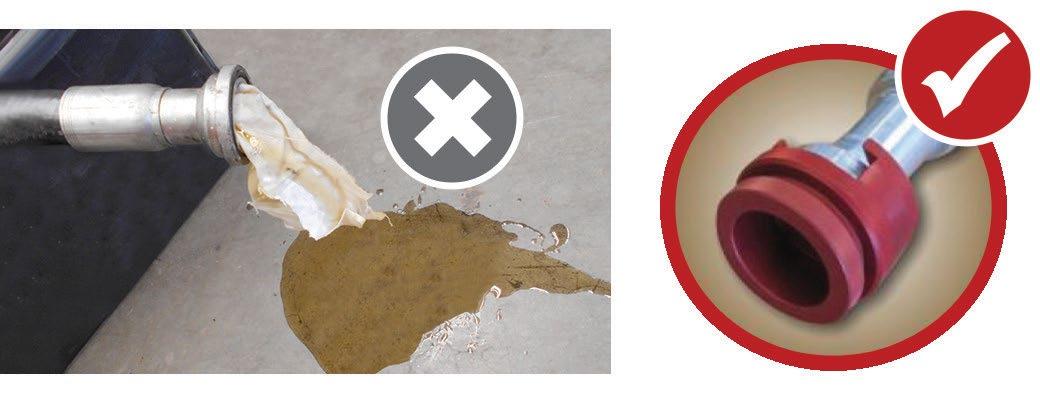
Stop The Mess!
• No tools required
• No expensive hardware needed
• No more rags stuffed into hoses
• No more messy plastic caps
• The ultimate contamination control tool
• One hand installation
• Eliminate hydraulic oil spills & clean up
• Quick installation & ease of usage
• Safe for personnel & environment
• Industry acclaimed
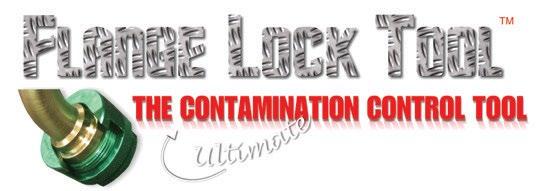
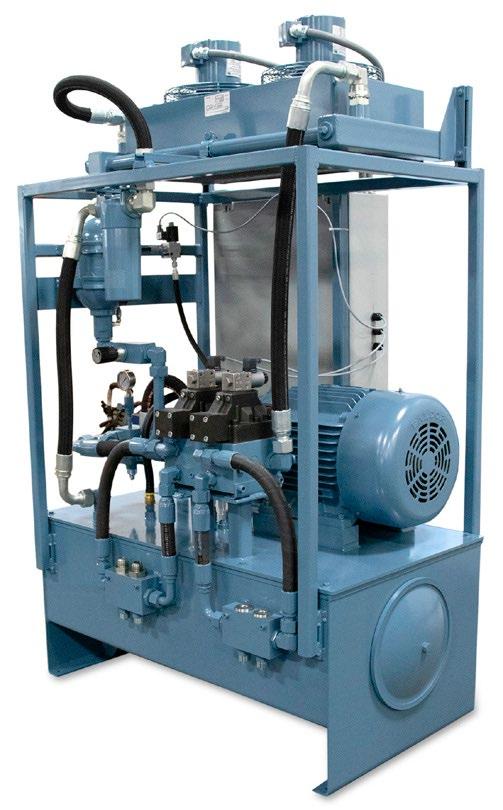

Continental Hydraulics/Hydreco
At Continental Hydraulics / Hydreco, we manufacture high-quality HPUs, pumps, motors, valves, and manifolds with short leadtime. Don’t take the risk of using substandard solutions when these products have a strong influence on machine efficiency, productivity and operating expenses. Rely on us, a premier fluid power manufacturer, and benefit from our expertise and world-leading variable frequency drive technology.
continentalhydraulics.com sales@conthyd.com

FluiDyne Fluid Power Stocks A4V Piston Pumps & Parts
FluiDyne carries a complete line of A4V piston pumps that are available in displacement of: 40, 71, 125, 180, 250. Our units are used in many different applications: agriculture, forestry machinery, construction, on-highway, commercial vehicles, offshore, marine, wind/ocean energy, automotive and more.
Controls include: DR, DRG, FR, FRG, DFR, and LR2. They are available in SAE or metric. The versatile A4V units carry the industry leading 18 month warranty. Units are fully tested, documented and guaranteed to perform 100% to the original manufacturer’s specification.
Call, email, chat…we’re ready to help!
For more information, call (203) 861-9400 or email sales@flangelock.com. www.flangelock.com

586.296.7200 • sales@fluidynefp.com • www.fluidynefp.com
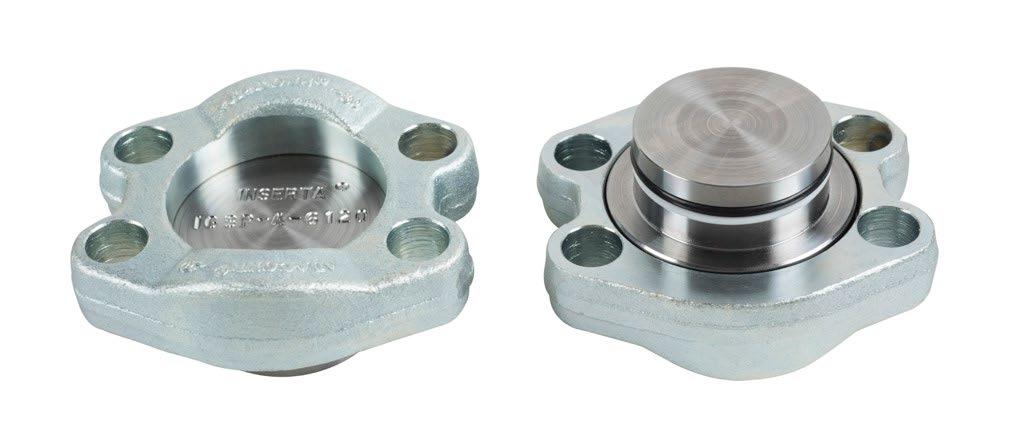
Slip-In Check Valve Retaining Assembly
Inserta® IGSP Slip-In Check Valve Retaining Assembly, Flange Type, provides an effective means to retain an Inserta® IGS Slip-In Check Valve in a 90 degree flow path application (oil inlet-axial, oil outlet-radial). These are available to retain nominal valve sizes from one inch to two inches inclusive, for flows up to 200 gpm, and pressures up to 6000 psi. Inserta® IGS Slip-In Check Valves used with a 90 degree flow path may be considered as potentially more efficient alternatives to typical thread-in cartridge check valves.
Inserta® Products
Blue Bell, PA | www.inserta.com | 215.643.0192
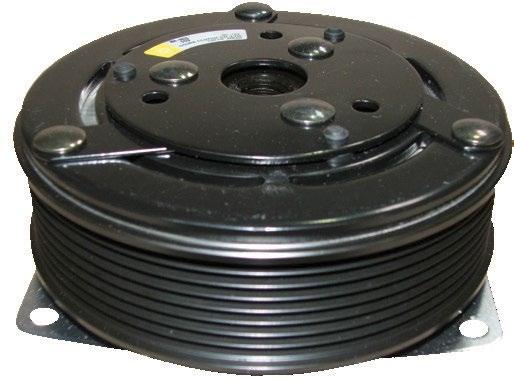
Electric Clutches for Pumps
Ogura produces a wide variety of electric clutches for mobile applications. These clutches provide simple on/off operation for a variety of pumps. Remotely engaging the pump through the clutch reduces drag on engine start-up, increases pump-life and allows multiple pumps to be used off one engine. Various belt types as well as pump shafts can be accommodated.
Watch our video on how they work: https://ogura-clutch.com/video-mobile.php
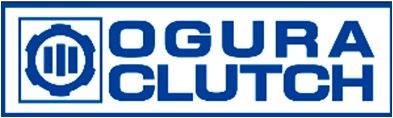
Ogura Industrial Corp.
100 Randolph Road • Somerset, New Jersey 08873
Phone: 732-271-7361 • Fax: 732-271-7580
www.ogura-clutch.com • info@ogura-clutch.com

Retaining Adapters
Inserta® 4-Bolt Retaining Adapters and Connectors provide an excellent means to retain and terminate a series of flange type modular components. They are ideally used with the Inserta® family of flange type ball valves, check valves, and modular fittings. The Adapter and Connector may be used together to sandwich modular components into an inline assembly, or the Adapter may be used alone to mount modular components onto a manifold surface. The adapters are available in Code 61 and Code 62 sizes from ½″ to 3″, with the outlet port of the same or one reducing size. Adapters that permit conversion between Code 61 and Code 62 patterns are also available.
Inserta® Products
Blue Bell, PA | www.inserta.com | 215.643.0192
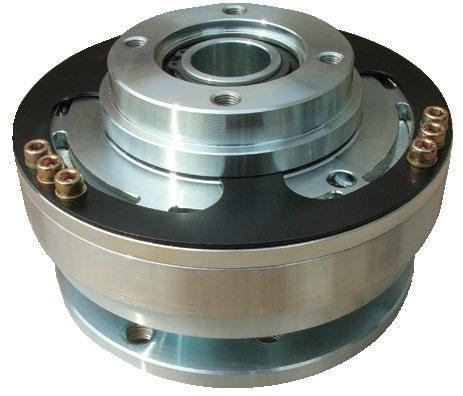
Marine Duty Electric Clutches
Ogura electromagnetic clutches provide a quick and easy engagement of a hydraulic pump, winch drives or other marine components. Available torque range is 100 pound feet to 1500 pound feet with single-face friction designs. Multiple disc units can generate torques over 8,000 pound feet. Large bearings, e-coating and a single piece bi-directional spring provide durability in harsh environments.
Watch our video on how they work: https://ogura-clutch.com/video-mobile.php
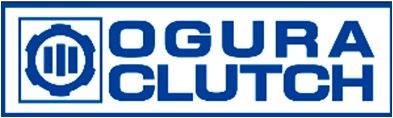
Ogura Industrial Corp.
100 Randolph Road • Somerset, New Jersey 08873
Phone: 732-271-7361 • Fax: 732-271-7580
www.ogura-clutch.com • info@ogura-clutch.com
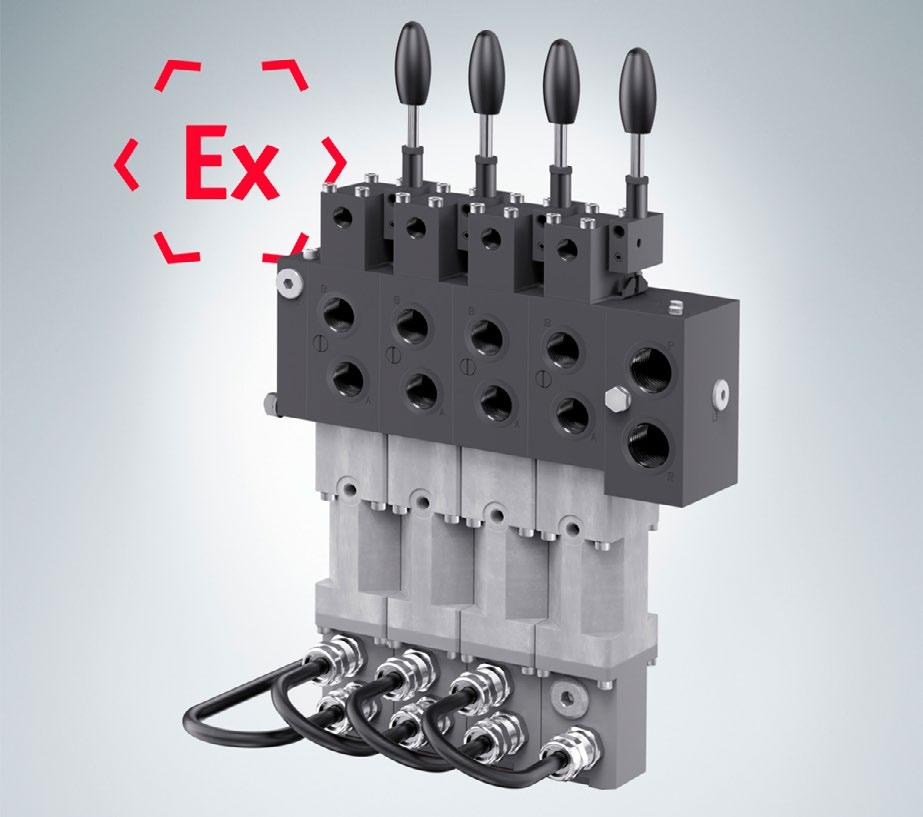
PSL-CAN is now Explosion-Proof!
HAWE’s proportional directional spool valve PSL-CAN is the ideal entry into CAN bus communication. This proven technology easily connects the valve bank into the CAN Bus along with other sensors and actuators on your machine. And now HAWE offers an explosionproof version of this valve for use in explosion hazardous areas. Benefits: Simple wiring; preset parameters; and more.
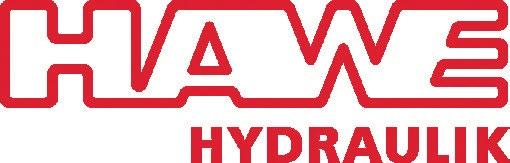
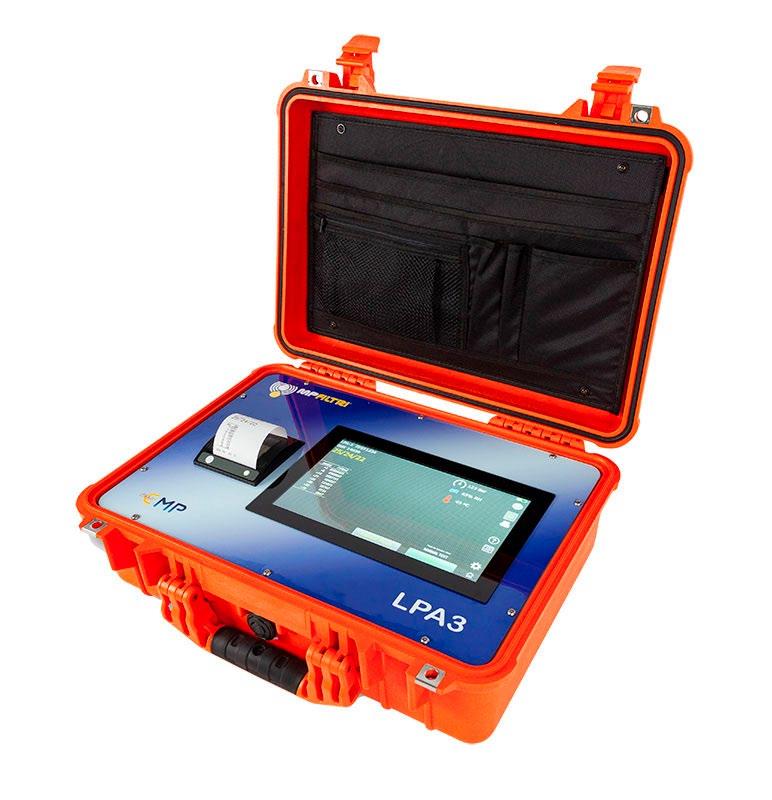
LPA3, The World’s most versatile mainstream portable contamination monitor. MP Filtri’s Contamination Monitoring Products and highperformance filtration ensure efficient, reliable machine performance dedicated to keeping your company moving forward. Condition monitoring provides real-time data and trend analysis, along with MP Filtri’s filtration protecting and extending your equipment’s life. With LPA3, reduce downtime and lower maintenance costs from anywhere. Stop contamination at the source.
mpfiltriusa.com | sales@mpfiltriusa.com | 215-529-1300
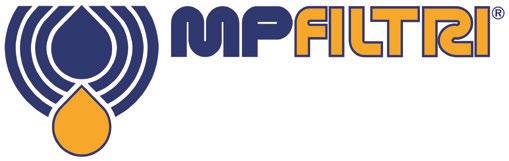
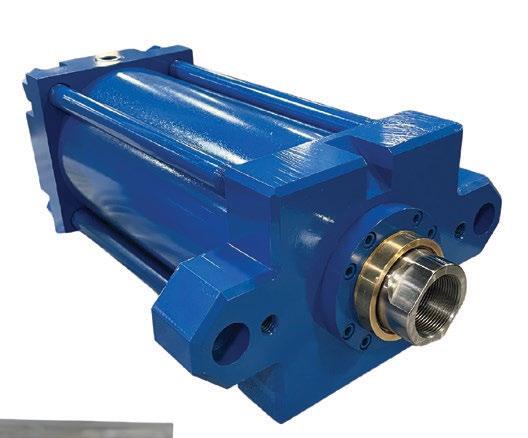
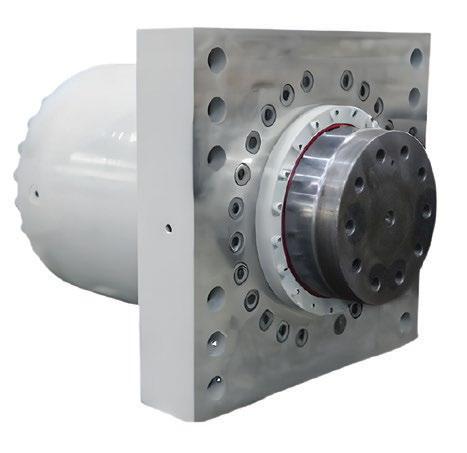
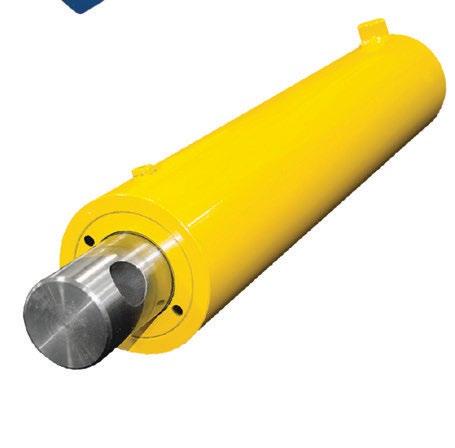
Think Yates Cylinders for ALL of your cylinder needs!
» Talk to your account rep or visit fluidpowerjournal.com/advertise

Custom Welded Cylinders: • 1.5” up to 50” bore, with strokes exceeding 300”
Heavy Duty Mill Cylinders: • 1.5” up to 50” bore, with strokes exceeding 300”
NFPA/JIC Tie Rod Cylinders: • 1.5” up to 24” bore; interchangeable with all brands
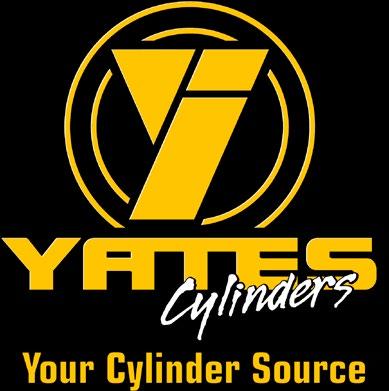
Smoother load control just got easier.
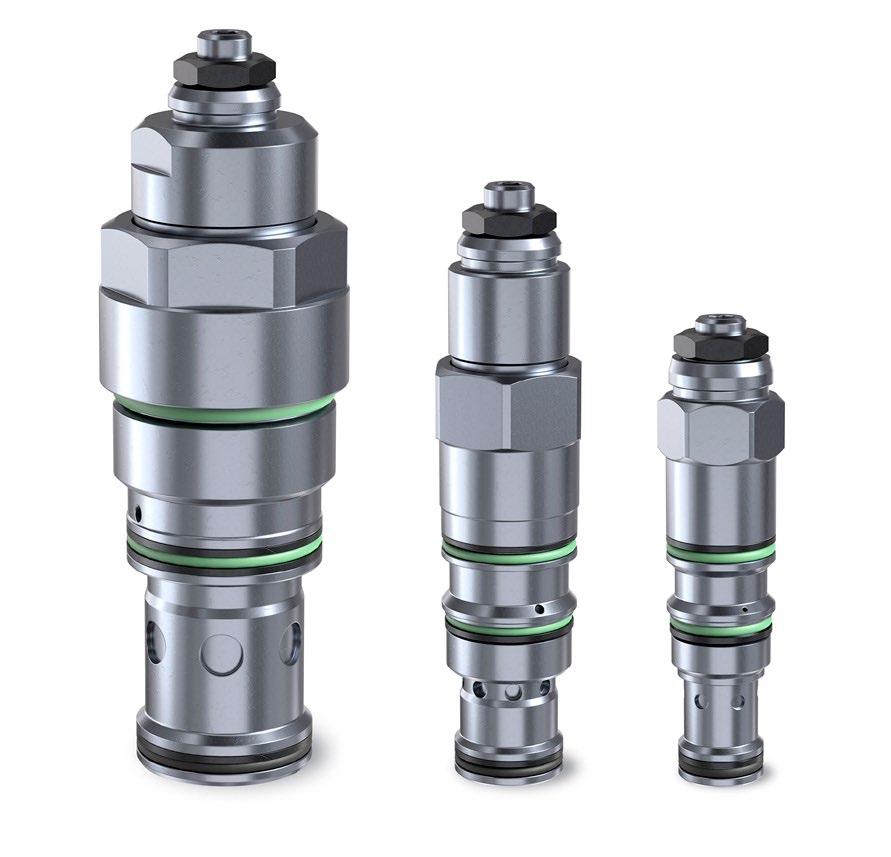
Responsive proportional control of suspended loads is essential for safe operation of mobile elevating work platforms. Bosch Rexroth
High-performance Counterbalance Valves are built for industry standard cavities, making them easily interchangeable. Precise, stable, and remarkably energy-efficient, their unique design provides exceptionally smooth load control without need for low pilot ratios.

HydraForce.com • sales-us@hydraforce.com • 847-232-6193
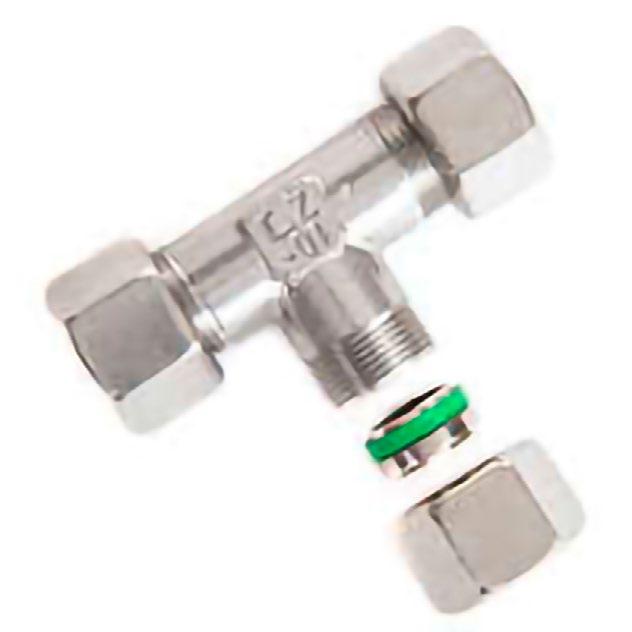
DIN Compression Fittings
At World Wide Metric, we define performance. Our DIN 2353 compression fittings, available in carbon and stainless steel, are engineered for uncompromising reliability in the most demanding fluid power systems. Available in sizes from 4mm to 42mm, our fittings are trusted worldwide to keep your world flowing.
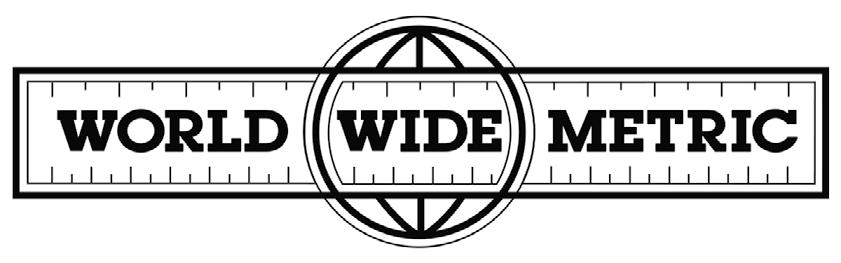
Contact them for more information www.worldwidemetric.com sales@worldwidemetric.com 732-247-2300
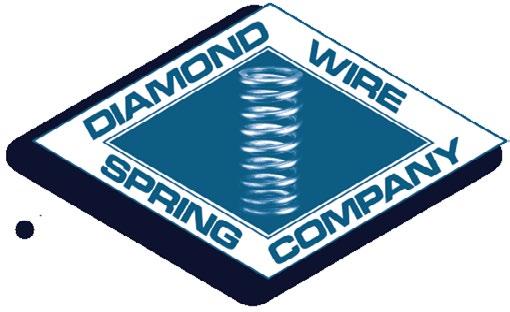
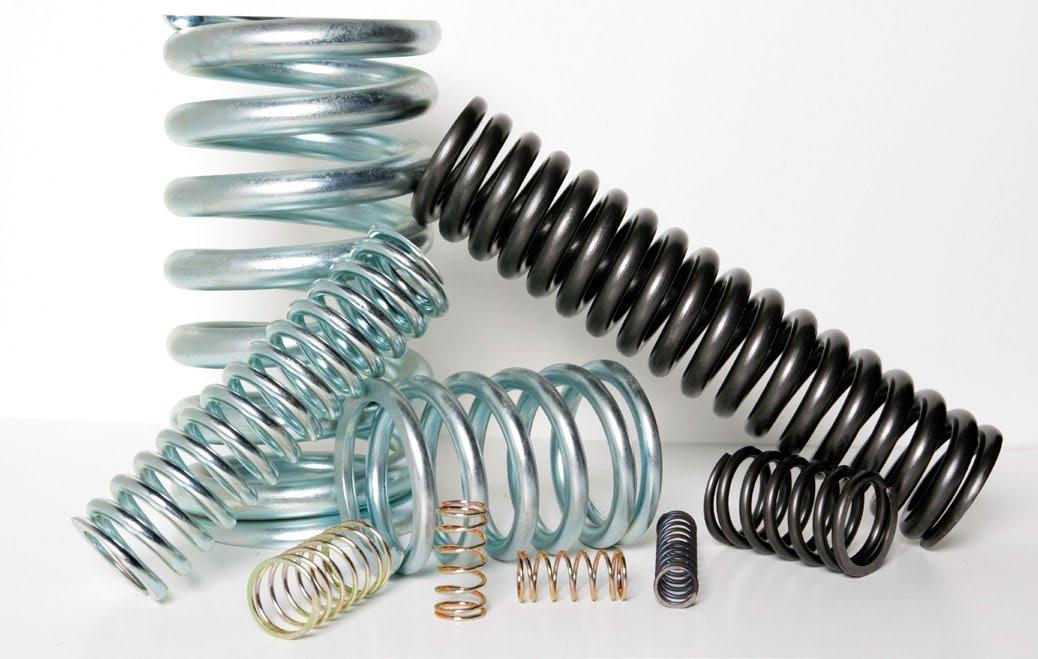
Pumps and Valves use a variety of Compression Spring sizes, depending on the application. Diamond Wire Spring has three US locations manufacturing pump and valve springs for over 85 years, we are ready to partner with your next project. Visit us at www.Diamondwire.com
Spir Star High Pressure Valves and Fittings
10,000 to 60,000 PSI Working Pressures
Manufactured in the USA, SPIR STAR valves are trusted and proven with a reputation for quality and durability.
• Needle Valves
• Ball Valves
• Check Valves
• Field Adjustable Relief Valves
1-800-890-7827 sales@spirstar.com www.spirstar.com www.spirstarvalves.com
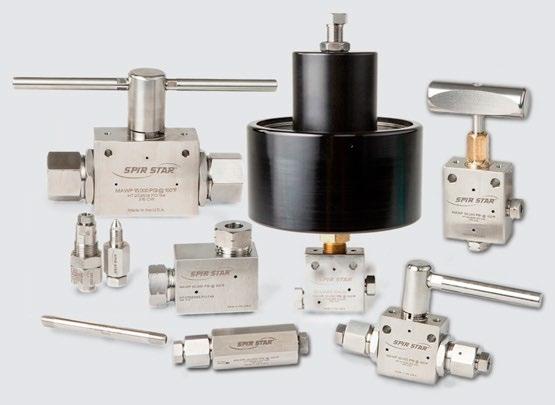
• Double Block & Bleed Valves
• Air Actuated Valves
• Non-standard Custom Valves
• Multi-Port/Valve Manifolds
• Quick Disconnects
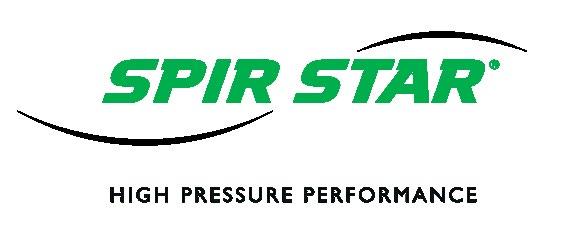
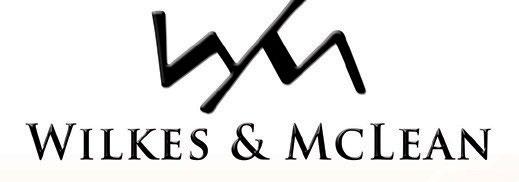
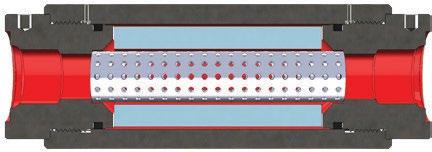
Hydraulic Noise and Shock Suppressor
Wilkes and McLean manufactures an In Line Noise and Shock Suppressor for hydraulics and is a stocking distributor of Nacol Accumulators. Our suppressors eliminate pulsations, which greatly reduces noise and vibration from applications from a few gallons up to 200 gallons. We stock all of our suppressor sizes as well as Nacol Accumulators and parts from 1/5 of a pint up to 15 gallons, in our Schaumburg, Illinois facility. 877.534.6445 | info@wilkesandmclean.com | www.wilkesandmclean.com
PRODUCT SPOTLIGHT
Protection for All Things Hydraulic, Pneumatic and Fluid Power
MOCAP manufactures an extensive range of protective closures to guard pipes, hoses, and hydraulic fittings from dirt, moisture, and damage to help maintain equipment reliability. Included are a variety of sizes and styles of Threaded and Non-Threaded plastic Caps and Plugs for Metric, NPT, BSP, JIC and SAE Threaded Connections, Ports and Fittings. These are in addition to MOCAP’s already extensive lines of lowcost Caps, Plugs, Grips, Netting, Tubing and Tapes for general Product Protection, Finishing and Masking. All of our stocked items are ready for immediate shipment and available in Box, Mini-Pack and Micro-Pack quantities. Free Samples are always available for testing purposes.
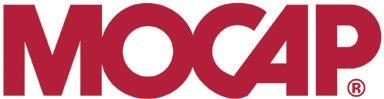
sales@mocap.com www.mocap.com
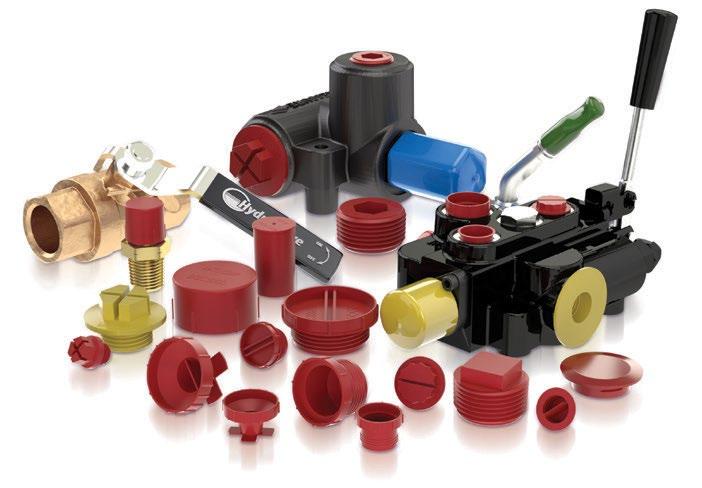



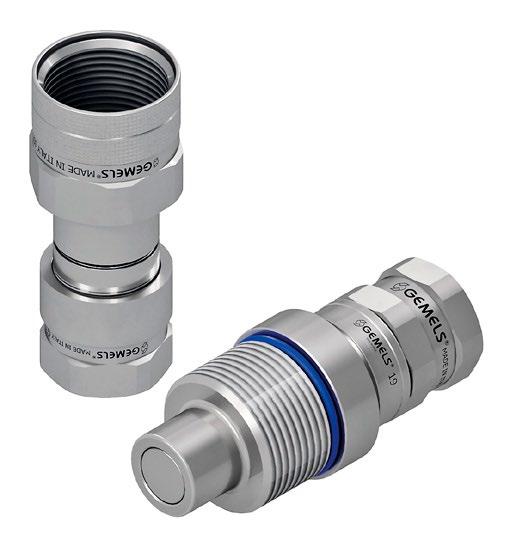
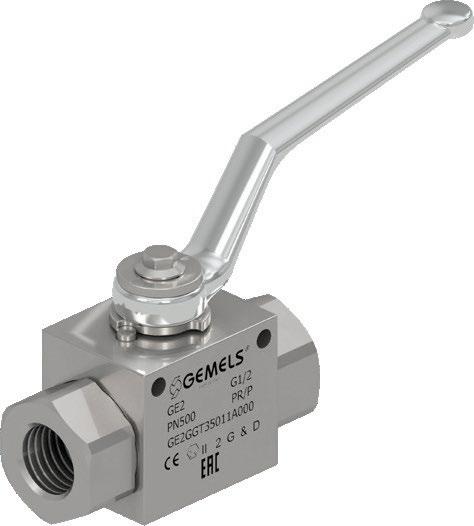
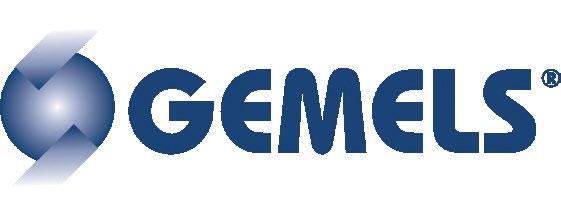
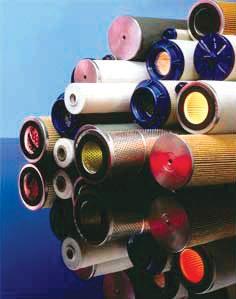
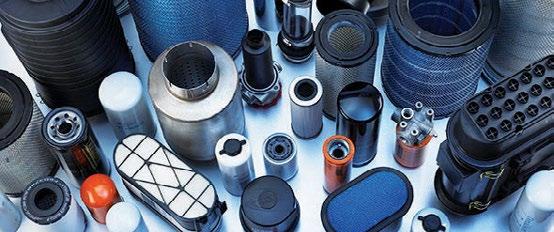

Genuine
Donaldson | Internormen-Eaton | Velcon-Parker
We're hydraulic filter experts. We've been doing it for over 30 years. We're very competitive and happy to serve your needs. If you need hydraulic filter application help, we know the right questions, and we can give you the right answers.
J/T Hydraulics & Service Co. Inc.
1108 E. Hwy 6, Suite I
Alvin, TX 77511
Phone: 713.984.9727 www.jthydraulics.com
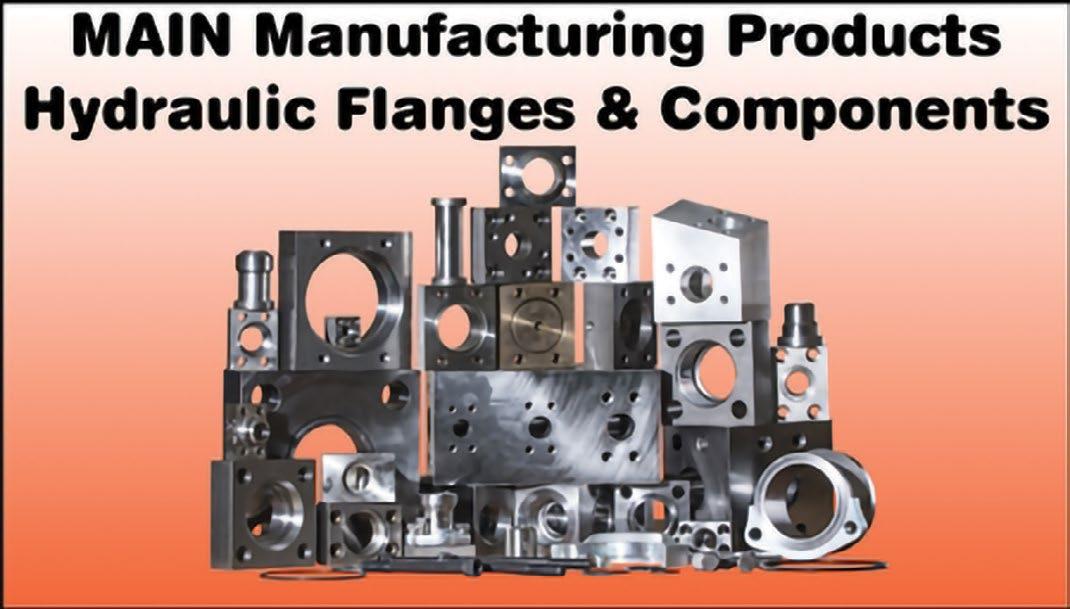
Don’t Compromise – That hydraulic flange you want may be at MAIN
MAIN stocks 10,000+ hydraulic flanges and manufactures components in 4-7 days in the USA.
SAE J518 Code 61 and J518 Code 62, JIS, DIN, ISO 6162, ISO 6164, and specials with socket-weld, buttweld, ORB, BSPP, etc.; all geometries, flange heads, flange adapters; in carbon, stainless, cupro-nickel, ductile, aluminum, etc. Sixty years’ experience plus SAE and ISO technical committee experience.
MAIN Manufacturing Products, Inc.
800.521.7918
https://mainmanufacturing.com/block-categories
COMPONENT
ES Series Miniature Electronic Valves
Spider technology is renowned worldwide for exceptional leak resistance and long life. Clippard developed, patented and perfected this spider technology. Ideal applications have exceeded 1,000,000,000 cycles with this technology which utilizes one moving part that travels a mere 0.007” during operation. This single moving part with a short stroke enables the ES series to operate with exceptional reliability.
The ES series features large cross sectional o-rings, minimal leak points, and proven poppet designs. All mounting hardware is outside of the flow path for the ES, and no internal parts are threaded during assembly to reduce the possibility of contamination. The ES has the best performance-to-price ratio for low leak valves.
The compact footprint coupled with the long life, and exceptional leak resistance make the ES line suited to improve reliability in a wide range of applications including biomedical, dental, test equipment, oxygen control, textile, packaging, pressure control, automation and portable systems.
• Over 1 billion cycles (under ideal conditions)
• 0.01 sccm leak rate
• No threads in flow path
• Fast response - 5 to 10 ms (nominal)
• Close mounting - 7/8” on center. Overall height less than 1”
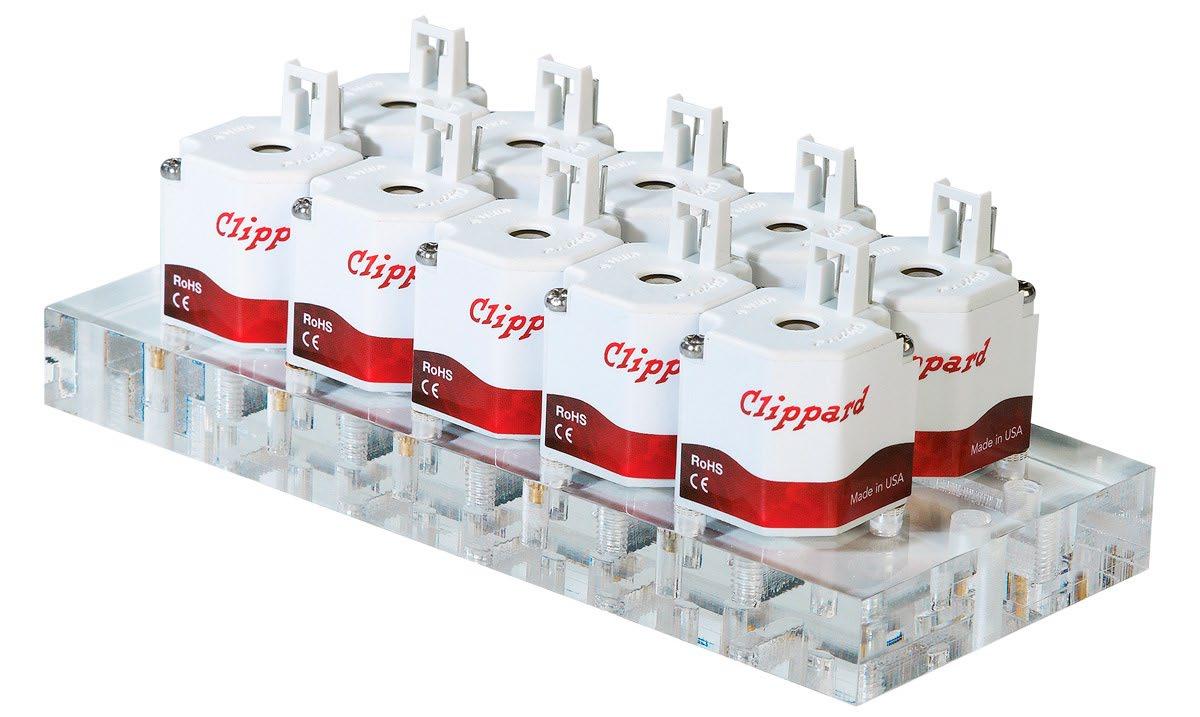
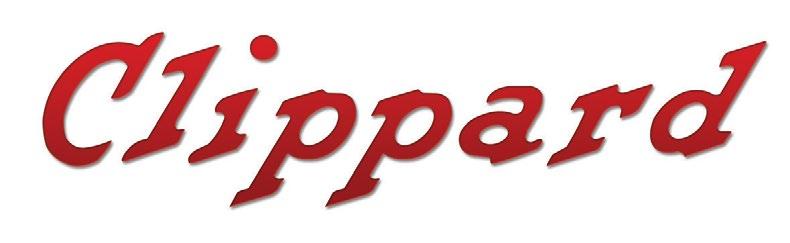
• No anaerobic sealant
• Ideal for ultra-low leak applications
• Made in USA
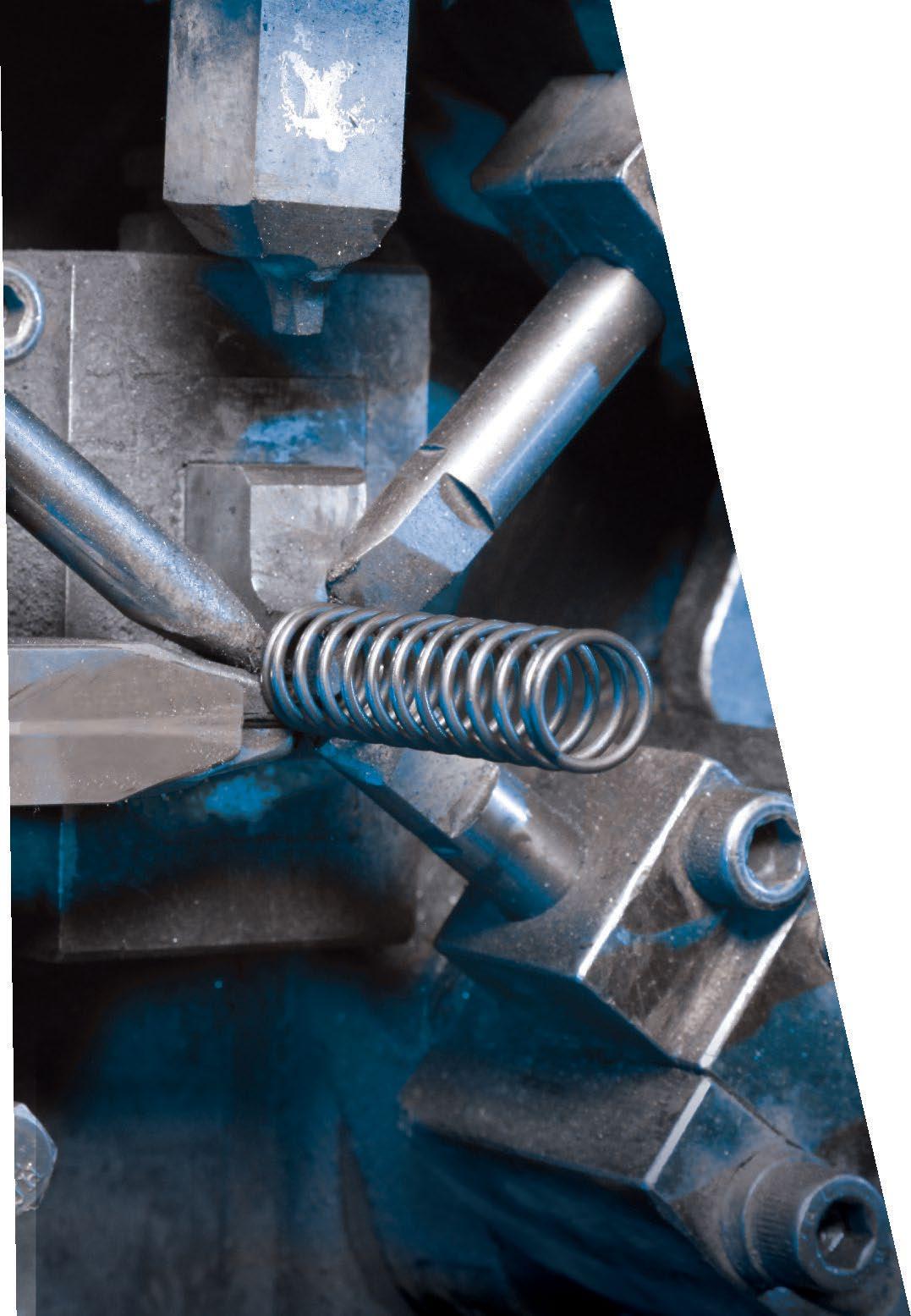

For further information on the ES Series Electronic Valves or any of Clippard’s line of precision fluid control products, visit www.clippard.com. Proudly made in the USA.


WEB MARKETPLACE
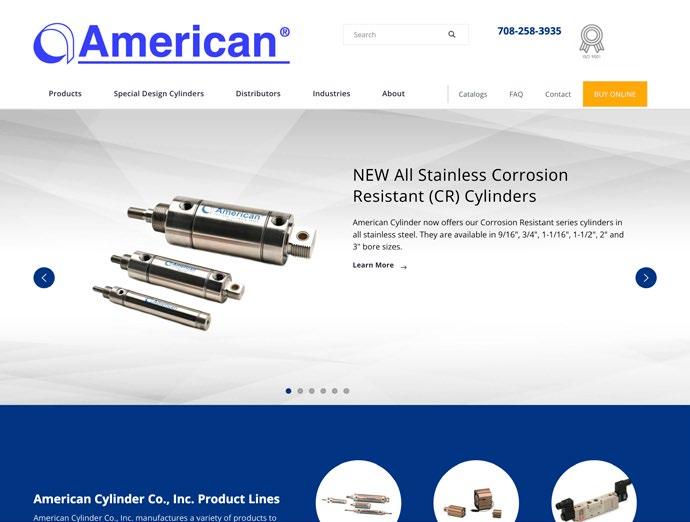
www.americancylinder.com
American Cylinder offers a variety of pneumatic cylinder products to satisfy your small bore air cylinder requirements. Choose from the Industrial Interchange Stainless Steel Series air cylinders, the Heavy Duty Aluminum 76 Series, the Magnetic Field MFC Series, the Low Profile LPC Series, the Corrosion Resistant CR Series, Tie Rod Cylinders, Three Position Cylinders, or Linear Slides. Call: 708-258-3935
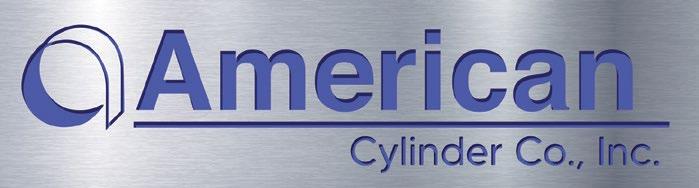
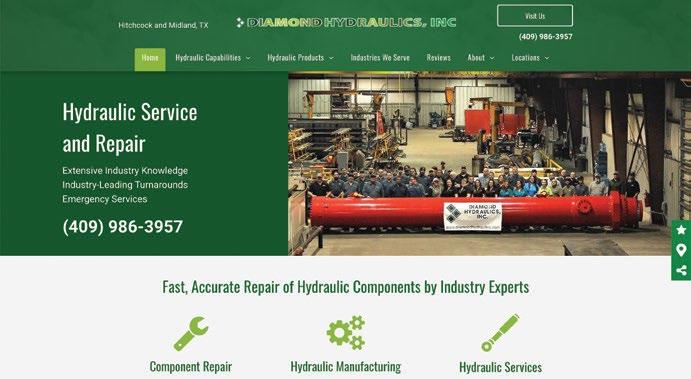
www.diamondhydraulics.com
Diamond Hydraulics is a veteran owned small business that manufactures, rebuilds, and repairs hydraulic equipment including cylinders, pumps, motors, valves, power units, and much more. We were established in 1999, and have over five decades of experience in hydraulic equipment repair.
Diamond Hydraulics provides quality workmanship, extensive industry knowledge, and fast turnaround time on repairs and replacements. All repairs are brought back up to OEM standards and tested with state-of-the-art test equipment.
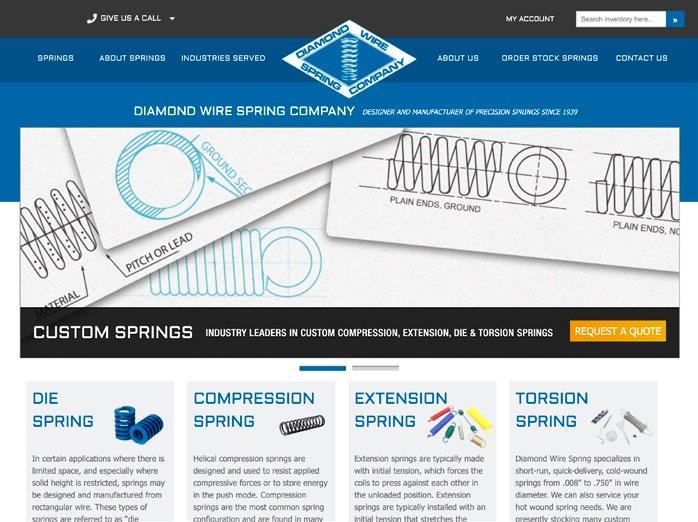
www.diamondwire.com
A family-owned designer and manufacturer of precision springs since 1939, with more than 80 years of experience, Diamond Wire Spring continues to hold fast to its founding principles of providing quality sprints with a strong emphasis on personalized customer service and satisfaction.
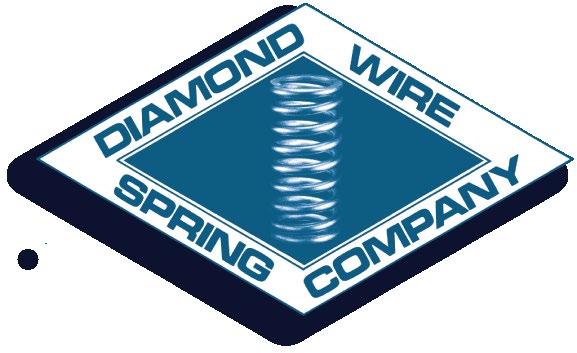
» HERE IS THE SOLUTION TO FIGURE IT OUT ON PAGE 05
When they installed a new flow control, the customer needed to replumb the external pilot line on the counterbalance valve between the new flow control and the cylinder’s cap end. The counterbalance function is focused on the cap end pressure. If it starts to drop, the counterbalance closes off just enough to keep the cylinder from speeding up faster than the meter-in flow control requires.
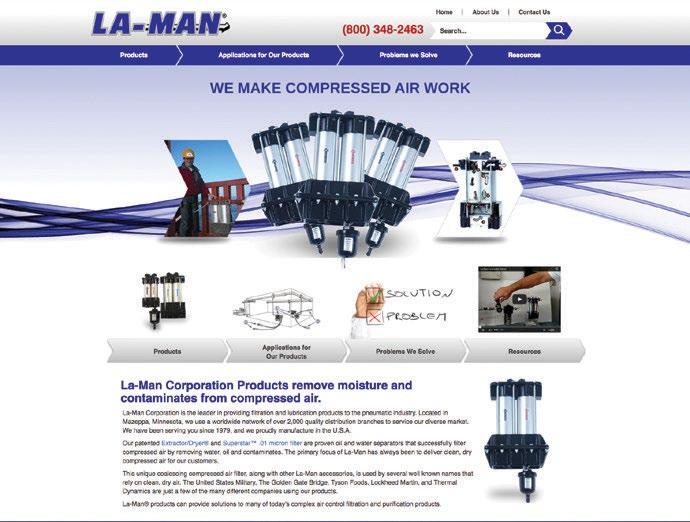
www.laman.com
W. C. Branham, Inc., 398 Troy St. River Falls, WI 54022 941-896-8000. SOLUTIONS
The correct answer to Test Your Skills on page 21 is 1A.

La-Man Corporation is a leading manufacturer of compressed air filtration products. With over 30 years of experience, we truly understand the importance of protecting valuable machinery, tools, and finished products from dirty, wet, contaminated air. La-Man’s line of products include the patented Extractor Dryer, .01 micron filter, as well as, LA-MAN-Air Breathing Systems™, SuperStar™ Membrane Dryers, and the Refrigerated Extractor/Dryer. PO BOX 328 • Mazeppa, MN 55956 800-348-2463
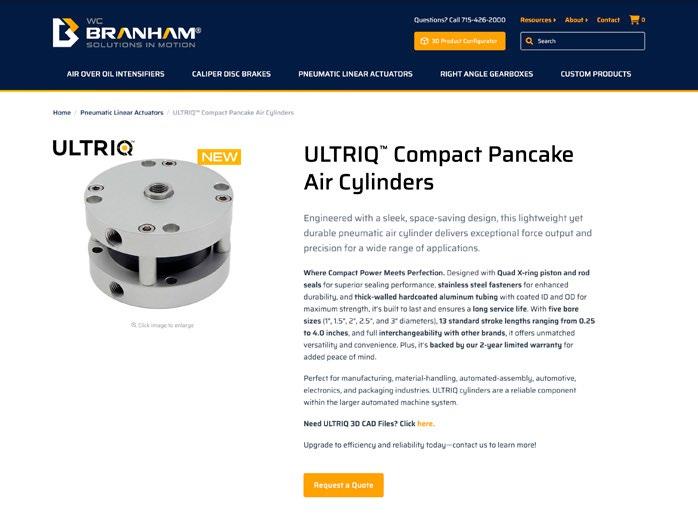
www.ultriq.com
Engineered with a sleek, space-saving design, this lightweight yet durable pneumatic air cylinder delivers exceptional force output and precision for a wide range of applications.
Perfect for manufacturing, materialhandling, automated-assembly, automotive, electronics, and packaging industries. ULTRIQ cylinders are a reliable component within the larger automated machine system.
CLASSIFIED BULLETIN









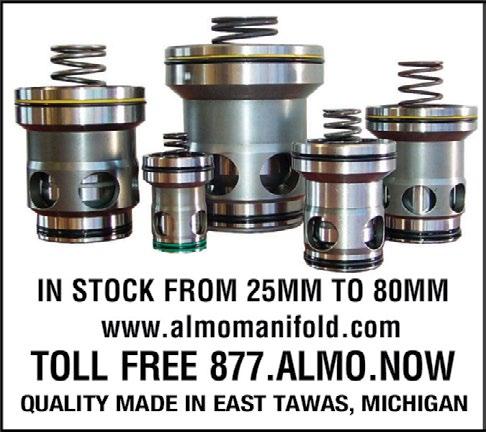

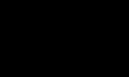




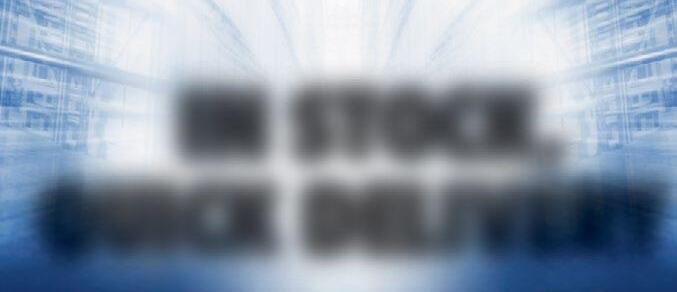
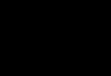







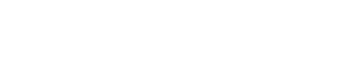
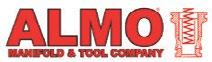
almomanifold.com

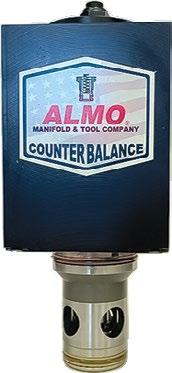

Almo Manifold
American Cylinder 8, 34
Assured Automation 23, 28
Branham, W.C. 13, 34
CFC Industrial Training 21
Web
almomanifold.com
americancylinder.com
1-800-899-0553 assuredautomation.com/fpj
715-426-2000 wcbranham.com
1-513-874-3225 cfcindustrialtraining.com
Clippard Instruments Lab Inc 33 877-245-6247 clippard.com
Continental Hydraulics/Hydreco 28
952-894-6400 continentalhydraulics.com
Delta Motion IFC 1-360-254-8688 deltamotion.com
Diamond Hydraulics 34, 36 409-986-3957 diamondhydraulics.com
Diamond Wire Spring Company 31, 33, 34
Essentra Components 13
1-800-816-5613 diamondwire.com
1-800-847-0486 essentracomponents.com
EUFMC 12 757-220-1795 eufmc.com
Flange Lock 7, 28 203-861-9400 flangelock.com
FluiDyne Fluid Power 28, 35, IBC 586-296-7200 fluidynefp.com
Gemels North America 9, 32 gemels.com
HAWE North America, Inc 30
704-509-1599 hawe.com
HydraForce 31 847-793-2300 hydraforce.com
Inserta Products 29 1-215-643-0192 inserta.com
J/T Hydraulics & Service Co 32
1-800-591-8280 jthydraulics.com
La-Man Corp 34 1-800-348-2463 laman.com
Lubriplate, Inc 11 1-800-733-4755 lubriplate.com
Main Mfg Products 17, 32, 35 1-800-521-7918 mainmfg.com
MOCAP Inc 32 1-800-633-6885
Wilkes
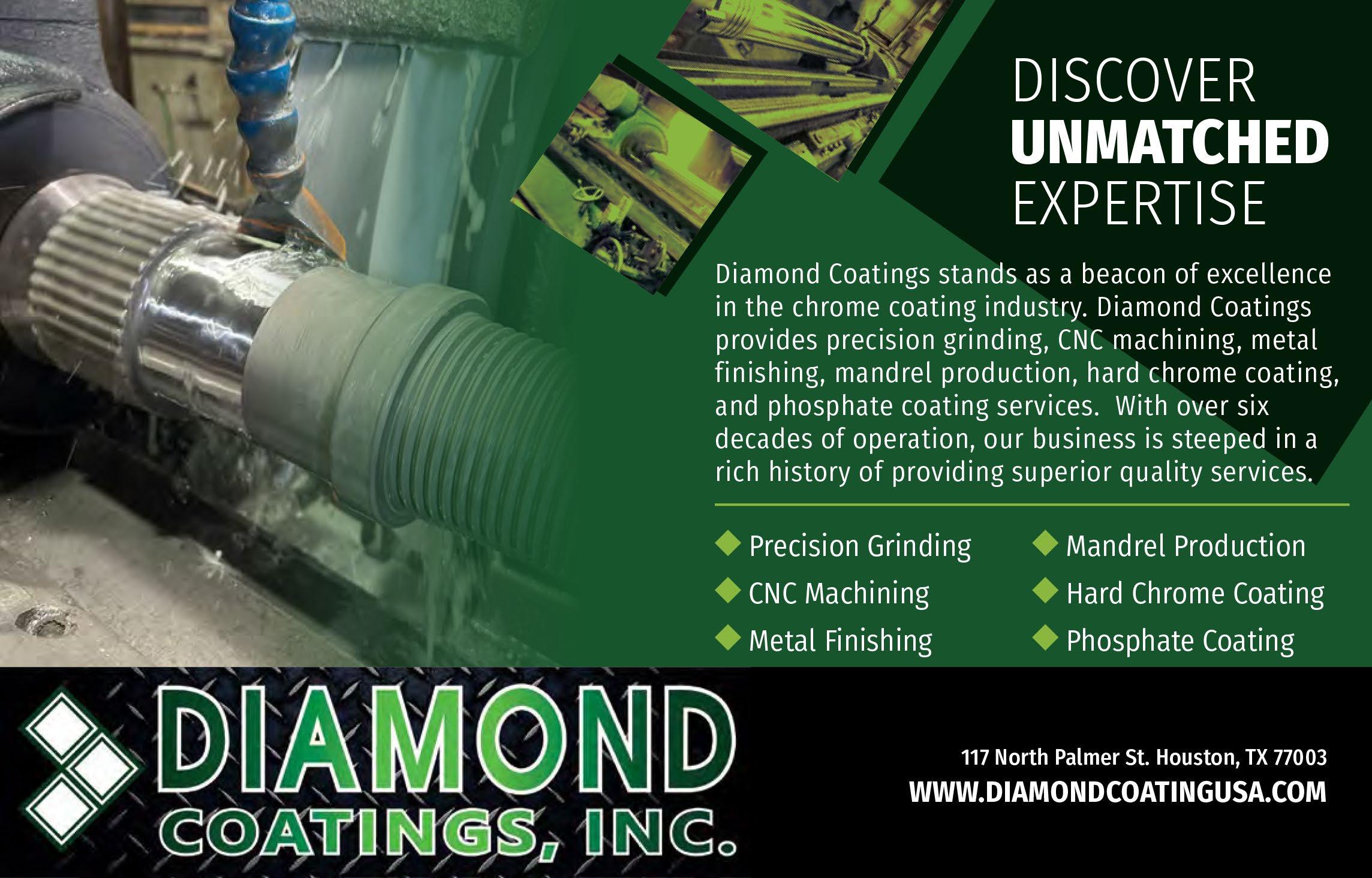
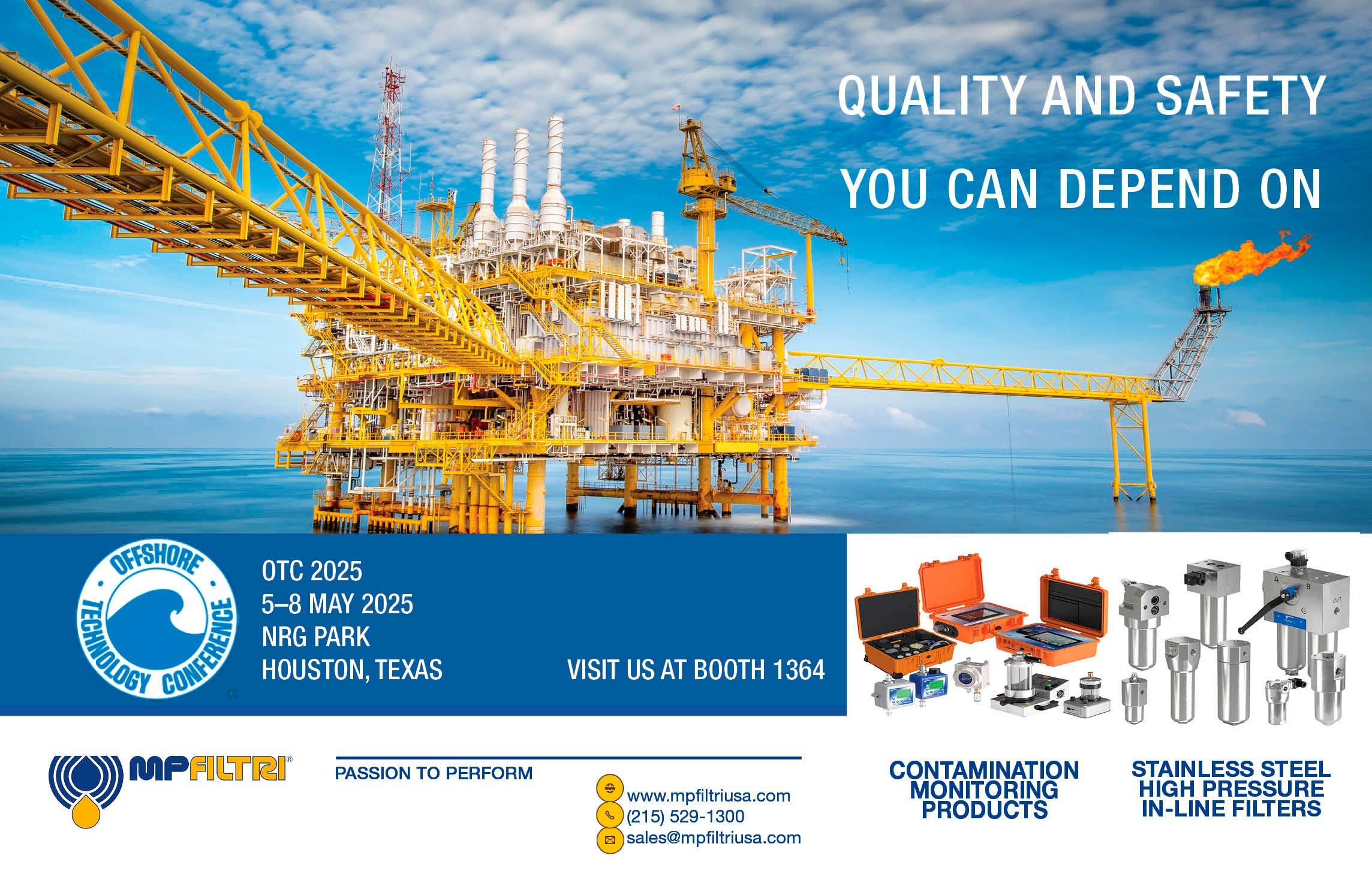
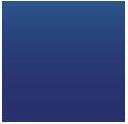
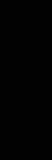
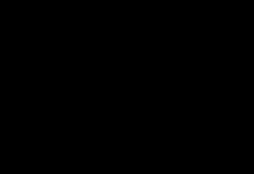
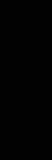








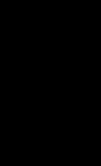
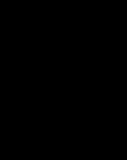


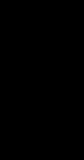
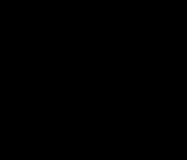
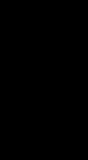

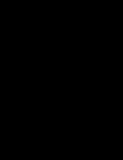
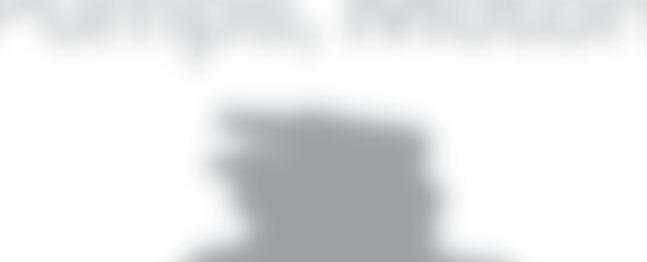
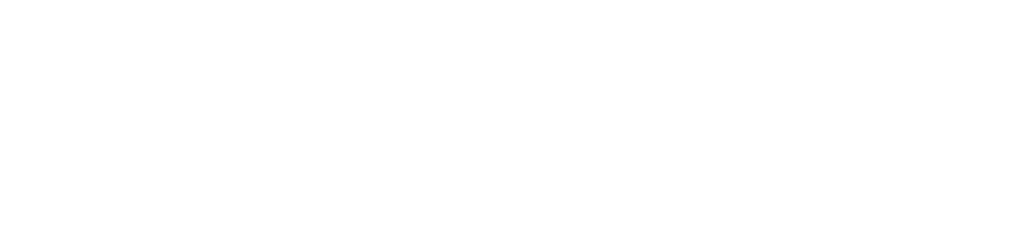

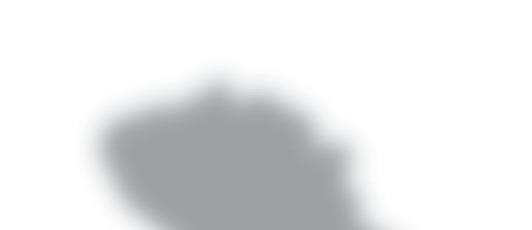
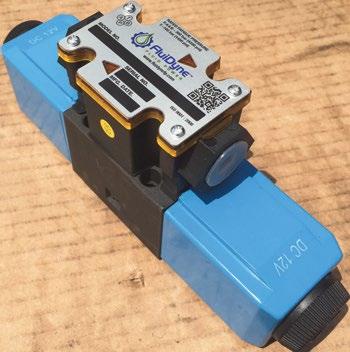
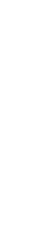





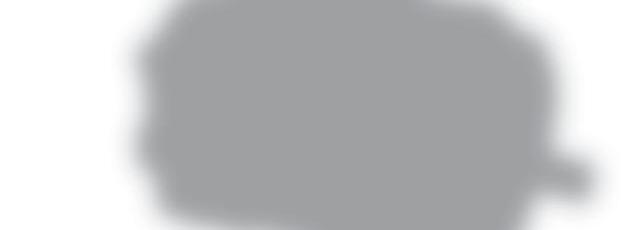

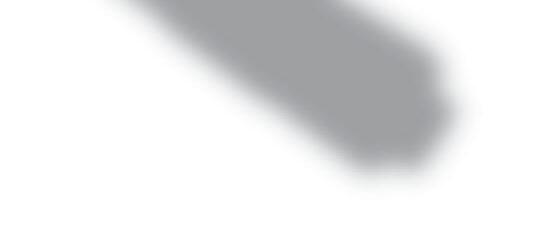
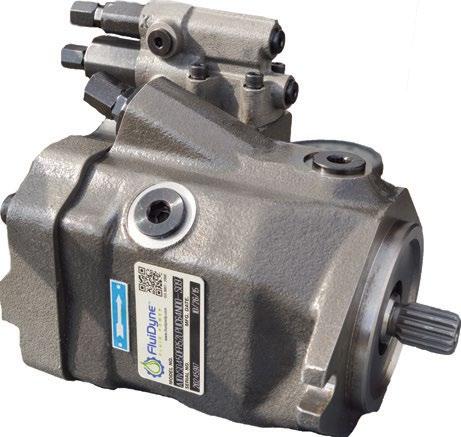
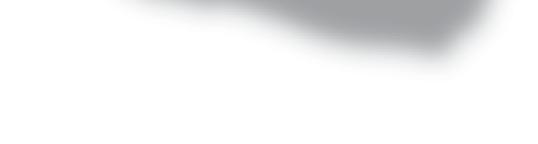


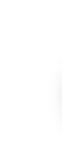
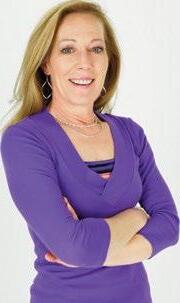

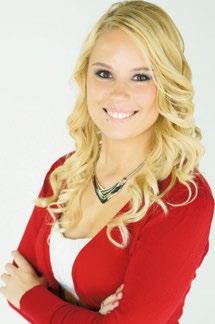
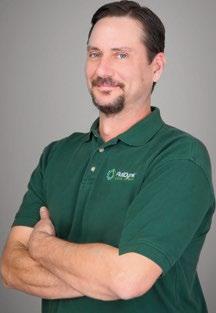


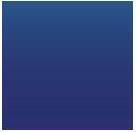


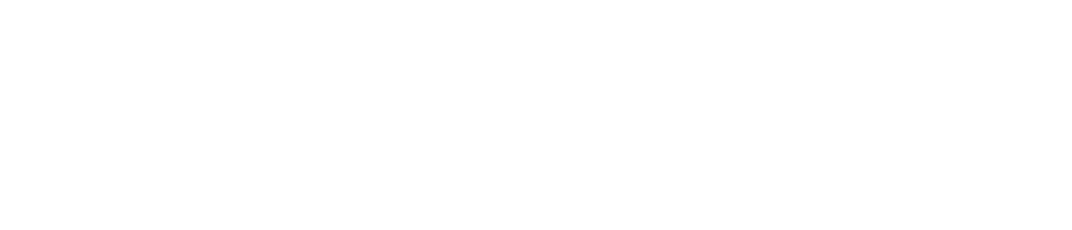

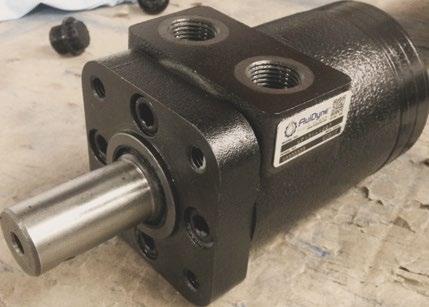
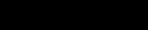

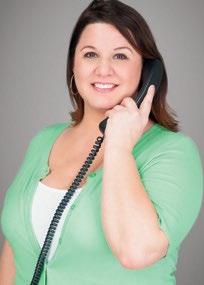







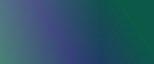
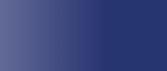
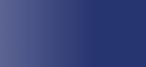



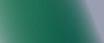





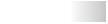

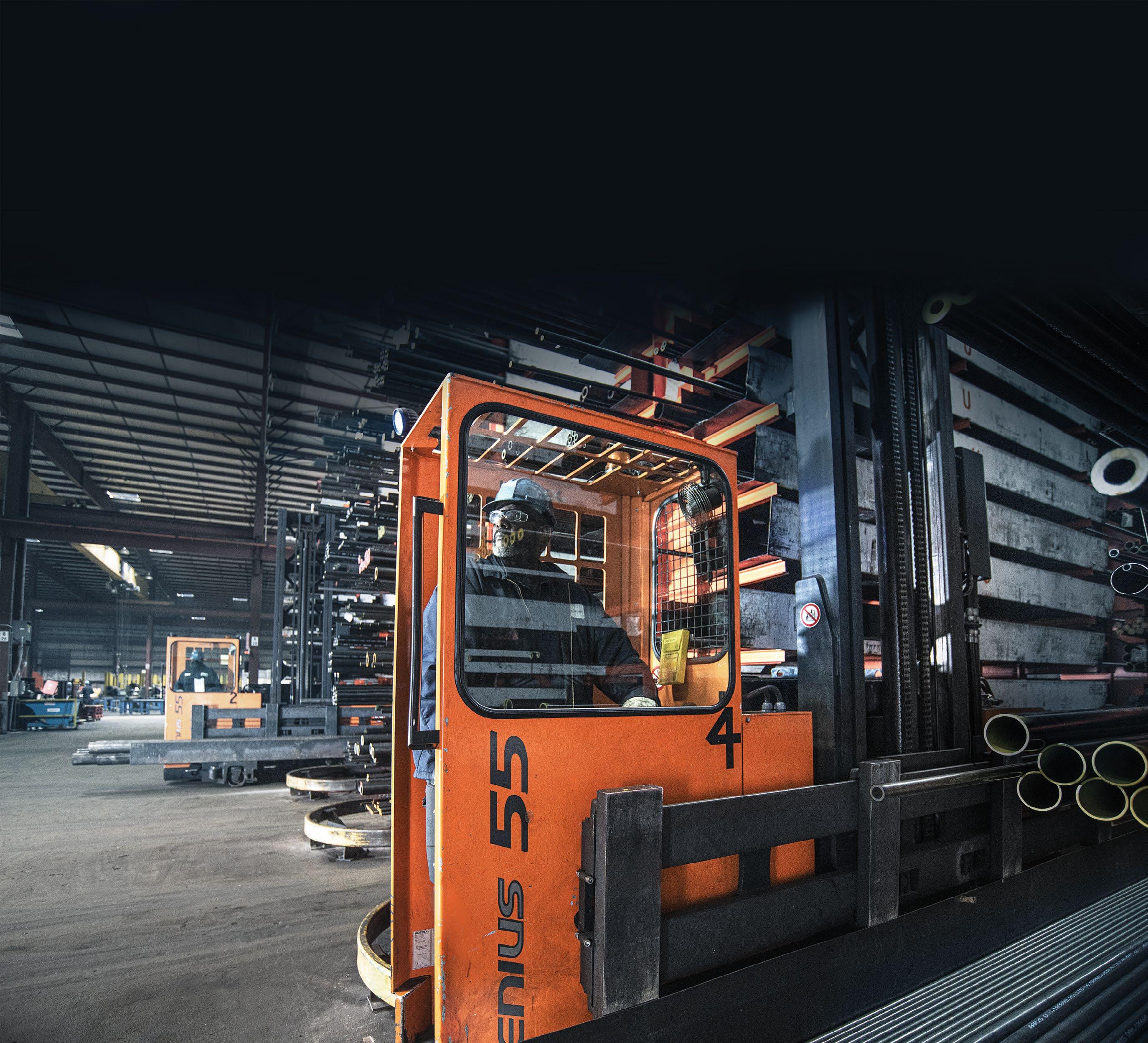
National Tube Supply’s fluid power products are precisely manufactured and expertly finished to minimize leakage and ensure longer seal life and optimum performance.
Our experienced team is always available to help customers identify the best product for their project specifications, quality requirements and bottom line. We’ll even work with you to set forecasts for JIT delivery management!
Hydraulic Fluid Line Tubing
Cylinder Barrels
Pneumatic Cylinder Tubing
Pump Barrels
Honed Steel Tubing
Chrome ID Tubing
Chrome OD Tubing
DOM Tubing
Seamless Steel Tubing
Chrome Plated Piston Rods
1045 Steel
Ductile Iron & Alloy
We have a massive inventory at your disposal with 8 locations across North America – most orders ship next day!
The Right Supply, Right On Time.