Icebug AB social report
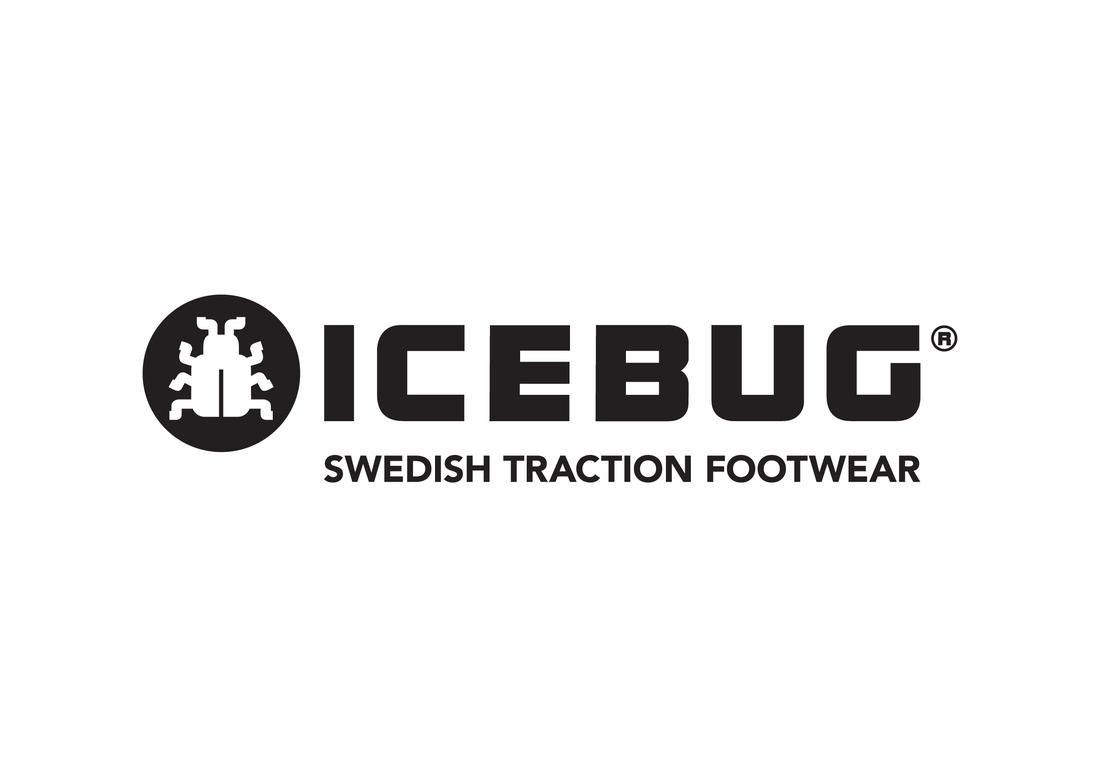
Reporting period: Financial year March 2022 – February 2023

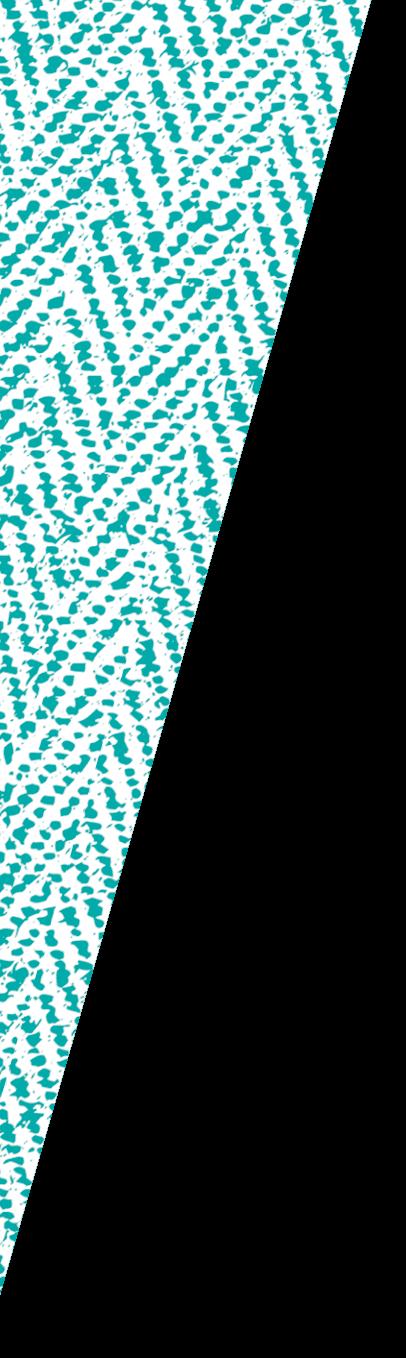
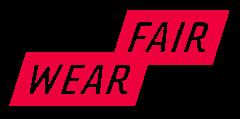
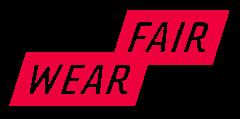
Reporting period: Financial year March 2022 – February 2023
Icebug AB is a Sweden based outdoor footwear brand with HQ based in Jonsered, outside of Göteborg in south west of Sweden. Overall management, product development, sales, product logistics and customer service is done from the HQ. The value flow Teams follow the Collection work (Assortment, Development and production, Preorder, Sales channels & Logistics, Growth engine, Sales, Customer relations) and are also integrated in each others work through roundabouts where value flow deliveries are made and responsibility is handed over between the teams. In the center you see the Management, Work at Icebug, Finance, Tech and Sustainability that is integrated in all of sible in the everyday work.
offices in Germany and USA. The shoe assembly production is made in four assembly factories in Vietnam and China, the shoe mid- and outsoles are made by two main suppliers (Yi Chang and Michelin) and different materials are supplied from many materials suppliers. Icebug’s sourcing partner and co-owner Vanbestco, Taiwan, supports in the sourcing
Social Report March 2022 – February 2023
process as well as quality control including chemicals testing. Please see below value chain chart showing Icebug’s value chain structure. The light green boxes are the material suppliers chosen by the assembly factories (light blue) or Vanbestco (purple). The dark green boxes are nominated suppliers that Icebug choses to get more sustainable materials.
The past year we at Icebug have been focusing on the Fairwear audits of the assembly factories, and the follow up of these audits according to the Fairwear requirements with support of the Corrective Action Plans (CAP). During one year, starting with the external Sumation audit of Fulgentsun in November 2021, 100 % of our assembly factories conducted Fairwear approved social audits. During the financial year 2022-23 three of our four factories were audited by Fairwear Icebug initiated the audit of Great Process in Vietnam, Icebug’s main assembly supplier, and the two other audits were initiated by other brands and shared between brands.
To follow up on the audits has been a good learning process and we are grateful that we could cooperate with some other brands sourcing in the same factories and with longer experience of Fairwear membership. As a small company with limited resources, auditing all factories and doing the follow up work, was challenging and it would probably have been too much if Icebug would have had to do it by our won, , so the fact that we collaborated with other brands was crucial to make this
Social Report March 2022 – February 2023
happen during such a short time. We still have many actions to follow up during the year to come and will continue to learn and make regular improvements of the labor conditions as well as in our way of working together with our suppliers in this area. We will strive to get a closer involvement from the workers in the audit follow up.
Icebug Development & Production Team has visited the two factories in the Ho Chi Minh area twice (September and December 2022) to follow up the CAPs on site We had valuable discussions with the factory management about on-site findings and proposals from their side how to solve these issues.
In September 2022, Icebug took part in our first Brand performance check, for year 2021-22. As this year was highly influenced by Covid, we did not have much sharp field activities to report but more of an introduction year to the Fairwear working methods. Icebug was ranked as a “Good” company. See the result here: https://api.fairwear.org/wp-content/uploads/2022/11/BPC-Icebug-AB-2022.pdf
In February 2023, Icebug received the first complaint from Fairwear helpdesk , which was solved with the factory management in collaboration with another brand in same factory Icebug discovered that we need to appoint clear responsibility for complaints as it will always be urgent to solve.
By the end of the financial year, we started to do the HRDD risk assessment according to the new guidelines from Fairwear. The Fairwear audit findings for Icebug’s Vietnamese suppliers are well in line with the general finding of Fairwear Vietnam country report. Summarizing the risk assessment, Icebug has identified the following risks as most prioritized to follow up in Vietnam for the next year in order to prevent and remediate risks.
• Freedom of association and collective bargaining
• Reasonable working hours (overtime)
• Payment of a living wage
• Gender based discrimination
• Safety issues in the factories need regular follow up
For the Ironsteel factory in China we did not go deeply into the risk analysis Ironsteel produced less than 2 % of Icebugs total FOB in 2022/23, 251 000 USD, and we don’t have any plans for future shoe production in China. If placing a new order, the risk analysis will be thoroughly done. The Overshoe/ Floorsaver production is also moved to Taiwan and Vietnam.
We also made a Responsible Business Conduct Policy, that is more detailed than the former Code of conduct regarding the process of risk assessment, preventing and stopping harm, tracking and validating the progress and the reporting in risks and progress. Icebug choose to replace the former Code of Conduct with the Responsible Business Conduct Policy, as we want to limit the number of policy documents and simplify for our suppliers and partners to get an overview of what we demand and expect from them.
See https://issuu.com/icebug/docs/icebug_ab_responsible_business_conduct_policy_2302
“There are many ways to approach why improving labour conditions is so important to Icebug and what we want the company to do. Our vision is to be a changemaker for a society where people can thrive on a planet in balance. That our products are made in a fair and just way is an obvious part of that. On the governance side, our owners’ directives specifically names people involved in our supply chain as stake holders, meaning that their interest always needs to be factored in when running the company. We strive to use our business as a force for good and taken responsibility for the people that we influence is simply the right thing do.” David Ekelund, co-founder and co-CEO ICEBUG.
All purchase decisions have some level of risk that needs to be mitigated. Icebug considers and evaluate certain social and environmental risks before every purchase decision. In addition to the sourcing strategy for new assembly factories we also have a special procedure regarding all new materials that are evaluated to consider potential risks. We are also aligned with several certification bodies with labour conditions as part of their scope: Leather Working Group (LWG), Bluesign, Forest Stewardship Council (FSC), B corps and Fairwear
By the end of 2022 Icebug started to follow a more structured Human Rights Due diligence process with the steps described below. We first established a Responsible Business Conduct policy, see https://icebug.com/sustainability/workersconditions that describes our commitment to responsible business, how we implement that to prevent and mitigate risks and what we expect all suppliers to follow and support.
The Responsible Business Conduct Policy is approved by Icebug’s top management and concerns all of Icebug’s employees. For the suppliers it will mainly be the Development & Production team and the Vanbestco team that manage sourcing and follow up Fairwear audits, but it’s also on the agenda for top management meetings. The Sustainability manager is responsible for developing and updating Fairwear policies and educate the rest of the organization.
Step 2: Conducting a scoping exercise, risk assessment and informing workers and suppliers
Icebug’s Human Rights Due Diligence risk assessment of the supply chain describes the risks at country, sector, factory and product level and is updated yearly (or more often when new supplier conditions require an update) by the Development & Production team. It is reviewed by the management and form the basis for the next year Fairwear work plan and what we will focus on to prevent risks.
Gender inequality is a high risk in the textile and garment supply chains in the countries where Icebug has the main production. Therefore, Icebug includes a “gender lens” throughout the work.
From the initial period of Fairwear membership, based on country reports, audits and audit follow-up, the following risks are identified as prioritized on a general level:
• Freedom of association and collective bargaining
• Reasonable working hours (overtime)
• Payment of a living wage
• Gender issues such as lack of lactation room, work conditions for pregnant women, inequal payment for parents
• Site specific safety issues as chemicals, safety passage, storage, PPE
Based on the outcomes of the risk assessment (step 2 of the HRDD process) Icebug determines a risk profile and prioritise follow up actions. This is done in the Fairwear work plan on a general level. On a facility level, depending on the factory’s risk profile, Icebug formulates a plan to implement the corresponding improvement or prevention programmes, including a timeline and capacity estimation. Gender, social dialogue and freedom of association should be included in the follow-up actions.
The eight elements of Fairwear’s code of labour practices, with special focus on the identified risks and on gender issues, are monitored by:
• Fairwear audits of Tier one factories (producing Icebugs labelled goods) – minimum every third year.
• Yearly risk assessment of Icebug suppliers, based on Fairwear audits, external audits and regular factory visits and sourcing dialogue.
• Special follow up on pilot projects and Fairwear trainings on various topics.
• The Fairwear social report summarizes the years’ actions and results.
Icebug is reporting the sustainability performance in the supply chain in the yearly Impact report. The Fairwear system (Fairforce, Brand performance check, audits and Corrective action plans CAPs) provides a framework for tracking implementation and validate the progress made.
Icebug is developing a set of social indicators that will be added to the impact report, where workers and suppliers will play an integral role in monitoring progress against goals
Icebug’s annual Impact Report is available on our website, displaying our targets and the yearly sustainability progress, https://icebug.com/impact-report The Brand Performance Check made annually by Fair Wear Foundation is available at https://api.fairwear.org/wpcontent/uploads/2022/11/BPC-Icebug-AB-2022.pdf, where the result of our social sustainability performance is shown, including the areas which need improvements. Our yearly Social Report is displayed here https://icebug.com/sustainability/workersconditions
Icebug buy the ready made shoes FOB from four assembly factories. The sourcing of materials, key parts as midsoles and outsoles and the quality control of ready products is made in close cooperation with Icebug’s sourcing partner and co-owner Vanbestco, Taiwan, see value chain chart above.
The sourcing strategy forms the framework for the outsourced supply chain of the Icebug brand. It is the basis for the development of all responsible purchasing practices that are crucial to reach a good level of the elements in Fairwears Code of Labour Practices (CoLP).
The basis for Icebug’s sourcing strategy is long-term cooperation with suppliers where mutual trust is created through a practice of treating each other as equal partners – Icebug doesn’t have supplier contracts with penalties. We then collaborate to raise the sustainability level of the supply chain. Since the start of the company in 2001, Icebug’s owners have searched for suppliers sharing the same values as Icebug and that are open to develop and improve Changing business conditions and product portfolio as well as different rates of organizational development, sometimes leads to changes in which suppliers Icebug works with, but our aim is to always work long term. Icebug presently doesn’t have any supplier that we haven’t worked with for at least seven years (for Fulgentsun we changed the factory from Fulgentsun Cambodia to Fulgentsun Vietnam in 2020 but it’s part of the same company group with same top management). Since 2015 when Icebug started to work with sustainability in a more structured way, we have asked our suppliers to source materials with lower resource use and negative impact (recycled, biobased, low impact processes, climate smart etc). This field is developing fast and there is a value in the Icebug development working proactively in this part of the sourcing. Being identified as a sustainability leader in the footwear industry, Icebug is now adays often approached by material innovators. So for new materials and processes, the Icebug team frequently nominates suppliers of high sustainability standard (see dark green boxes in the supply chain chart).
The social conditions are integrated in the sourcing strategy. Icebug’s former Code of conduct was replaced in March 2023 with the more detailed Responsible Business Conduct policy, see https://icebug.com/sustainability/workersconditions that we expect all suppliers to meet In Icebug’s concept “Follow the footprints” we display the ecological footprint and show the product journeys supply chain for all shoe styles, see example: https://m.trustrace.com/product/Icebug/en/Eide-WoolBiosole/product-journey. In this end customer communication we aim to include more information about social conditions in the supply chain and start to do so with the assembly factories during 2023/24. The plan is to get and display social data from suppliers in Tier 1-3.
In the Vanbestco sourcing team 15 persons support Icebugs sourcing, and their leader is member in Icebug’s Development & Production Team securing regular contact and feedback both ways. The team from Taiwan visit the factories regularly to carry out quality controls and check production. In addition, an Icebug-employed sourcing expert and quality controller in China conducts regular on-site inspections at the factories. The production team in Sweden has frequent exchanges with them.
Icebug’s Development & Production Team, responsible for sourcing, has 8 members: 5 HQ team members of Designers, Product engineers and the Sustainability manager who is placed in this team
to closely follow both ecological and social sustainability issues of the sourcing. The team has 3 Asian team members – the sourcing manager of Vanbestco, a sourcing expert, an Icebug employed sourcing expert and quality controller. The development & Production Team leader together with the Preorder Team leader decide which manufacturers will get orders of different styles. The decisions are based on formal criteria such as technical capacity, margins, tooling investment, compliance with labour standards, sustainability and quality.
The price level of Icebug’s products is medium to high, and we aim to sell at full price and don’t do Black Friday or in-season sales to drive consumption with aggressive pricing. The price reflects the quality of the products and is also a strategy to be able to make durable, high quality shoes with high sustainability content (durable, low climate impact with high content of recycled and biobased materials that are manufactured in low impact processes from responsibly sourced raw materials). This also includes social responsibility for workers in the supply chain, and to cover living wages for all workers.
Further corner stones in the sourcing strategy are:
- Having a concentrated supplier base so that Icebug can be an important customer
- Avoid dependence of high-risk areas and the two which has most practical implications for our operations:
- Planning production to avoid causing excessive overtime
- Paying prices that allows for paying a living wage
A responsible production planning starts with a deep understanding of the supply chain partners capacity and respecting lead times. Based on Icebug’s forecast, the supply chain partners provide a production plan with allocation of quantity in different periods, with a corresponding order placing plan that Icebug then follow. Icebug has deliberately set up the business model in a way that enables us to spread production over a longer period: No fashion or single season styles or colorways. A high degree of carry over styles that last for many years enable long-term planning and to avoid campaign prices thus keep the margins up. Safeguarding the value of the products is also a mechanism that enables us to pay correct purchase price – FOB prices paid by Icebug should always allow to pay living wages throughout the supply chain.
Suppliers are regularly visited by the Development & Production team before placing the order to understand the setup of the production locations and ensure there are no apparent human rights violations. Some of the details that are up-dated and evaluated on a season to season basis are:
• Quantities per country / supplier / style / season
• The factory capacity and how to plan production to avoid excessive over-time
• Ratio sampling vs. bulk production
• Supplier matrix per product
• Supply chain mapping (partners per supply chain step)
• Internal analysis (key success factors, strategic success position, strengths and weaknesses, key performance indicators)
• External analysis (market trends, industry benchmarks, opportunities and risks)
• Tracking and validation of social progress are included in the sourcing dialogue between member brands and suppliers.
Based upon these parameters Icebug take decision on whether to place orders, how to prevent and mitigate risks, and what remediation steps may be necessary.
Upon the start of a new business relationship (before first order is placed) Icebug needs to gain a basic level of insight into the human rights situation at a potential factory to inform sourcing decisions. As a Fairwear member Icebug commits to:
• Raise awareness of the workers and the management on human rights
• Stress the importance of gender-representative social dialogue (with democratically elected worker representatives)
• Assess whether there is an effective operational-level grievance mechanism established through social dialogue with workers
• Establish the Fair Wear helpline as a safety net
• If the supplier is in a new country, update the HRDD risk assessment at country level
The production cycle and planning has so far been based around two seasons per year, SpringSummer and Fall-Winter where the development starts about 2 years before the season and the first forecasts to factories are made 9-10 months before the start of the deliveries for the season. Icebug places the orders in a window of 9-6 months before the products are made available to customers, the order placing period for the highest volume season fall/winter, is spread out over a period of nearly six months – this is to make use of factories’ production space both before and after the peak season.
From 2021 there is less focus on seasons and more successive launching of products when the value offers are ready for market. Icebug sells increasingly more from own webshop allowing launching of new styles to be more flexible. However the big majority of Icebug’s production volumes are and will continue to be carry over products that are produced for many years. Icebug make efforts to make clear plans and involve the manufacturer as early as possible to support good manufacturing planning allowing reasonable hours of work and avoiding overtime peaks. We do not produce ad-hoc or spontaneous customer requests.
The sourcing agent Vanbestco and our employee in Asia are in close contact with the assembly factories and have regular dialogue about the sourcing process, sampling process and production planning, so that the production plan will grow in a communication between the manufacturer and Icebugs Preorder and Development team. Icebug partially nominates materials and buys outsoles and midsoles directly from the suppliers. Nevertheless, Icebug always buys ready-made footwear (FOB) from its four main suppliers.
There has been no selection of new assembly factories last year, neither any terminated Icebug supplier relationship. However there is currently no new order planned for 2023/24 from the Chinese factory Ironsteel, due to a combination of market and sustainability factors, which means that we do not have any plans at present for future production in China
A new outsourcing factory for stitching, Wei Jie, has been proposed by GTP in Vietnam, and prepared for orders in 2023/24 (no order was made last financial year 2022/23). Initial visits with health and safety check have been performed. Wei jie has been informed about Fairwear Code of labor practice and posted the Fairwear worker sheet on the wall.
When selecting a new assembly factory or other key supplier for Icebug, Icebug look for partners and the following criteria apply:
• Long term strategy matching and aligned business vision
• Quality references and technology processes (membranes, other critical moments)
• Development capabilities
• Openness and organizational support
• Sustainability maturity level: basic sustainability in place or a long way to go? (available external social audit reports, certifications done (FSC, Ökotex, other), climate data)
• Commitment to Code of labour practice, See also above in Sourcing strategy & Pricing As a Fairwear member Icebug commits to:….)
• Low carbon energy source
• Location – evaluation of country risks and logistics
• Price level
Three Fairwear audits were conducted in Icebug’s assembly factories last year: Haksan and Great Process in the Ho Chi Mihn area of Vietnam and Ironsteel in Guangdong, China. As Fulgentsun in the Hanoi rural area in Vietnam was audited by Sumations the precedent year (June 2021 -Jan 2022), it means that 100 % of Icebugs assembly factories have been audited within one year. The findings of these audits are described below for each factory.
For Ironsteel one finding was of a very serious nature: rubber materials were stocked in the floor under a dormitory, creating a serious safety risk of fire. However it was soon clarified that the dormitory was not used during the concerned period, and it’s followed up regularly by local safety authorities This matter will be thoroughly checked before any new Icebug orders of safety shoes will be considered (no orders are planned for 2023/24).
There was no single finding in any of the other factories that made us question whether we shall continue sourcing from them. All the CAP findings (including the fire risk mentioned above) were of the nature that we can discuss with the management and solve together, and that will be part of the continuous improvement.
For one Vietnam factory, that did not experience Fairwear audits before and where no other brand is a Fairwear member, the management was quite overwhelmed with the detailed requirements. They also felt that it was not really a dialogue as they had expected (after our initial description of the Fairwear method) but only focus on negative points. So they were a bit disappointed with the method and approach and we had a hard time motivating for the next steps. It’s understandable as Icebug is
Social Report March 2022
February 2023
demanding a lot from the suppliers, not only about labor conditions. Icebug initiates several pilot projects within other sustainability areas such as FSC certification, solar energy project and we ask for detailed BOM lists and energy calculations in order to calculate climate footprint. Even if Icebug wishes to follow the Fairwear recommended time tables for the CAP and actions taken, we see that we need to take the factories total work load into concern, and make adapted schemes for them.
Icebug is a small company with limited resources (app. one full time sustainability person covering both environmental and social issues) and we must admit that it became a bit too intense to do all factory audits so tightly and it was a challenge to follow up all CAPs in time and still also do other burning sustainability tasks. So the fact that we collaborated with other brands was crucial to make this happen during this short time (big thanks to these brands!) And we needed to leave some issues in the CAPs on the To do-list to solve for next year.
Evaluations of new material suppliers (Tier 2, not included in the Fairwear scope) are regularly ongoing. The selection process is made with clear sustainability criteria regarding material properties and responsible raw material sourcing. Working conditions are often part of sustainable sourcing certifications such as Forest Stewardship council (FSC) for the natural rubber in outsoles and leather Working Group for leather. However, there is need for more clear criteria of material suppliers social conditions. This will be the next level of Icebug’s risk assessment after covering all Tier 1 factories.
In a coherent monitoring system the different monitoring activities provides understanding of the risks and opportunities within the supply chain. During the last year Icebug, has undertaken the following actions to monitor and remediate problems in Icebug’s supply chain:
• For Great Process (Fairwear audit April 2022) there are no other Fairwear brands. We initiated the Fairwear audit and prepared the factory management of Fairwear requirements and the audit process
• For Ironsteel (Audit May 2022) and Haksan (Audit July 2022) other brands initiated the audits and we responded on the invitations to join and share the planned audits German company Fond of took lead in the CAP follow up of Haksan and we had several meetings discussing the CAP and also informed each other about factory visits
• Icebug Development & Production Team has visited the two factories in the Ho Chi Mihn area twice (September and December 2022) to follow up the CAPs on site. We had valuable discussions with the factory management about on-site findings and proposals from their side how to solve these issues.
• We also continued the CAP follow up of Fulgentsun that was audited by Sumations in January 2022, where Salewa had the lead and informed us about the progress There was some confusion regarding the different Fulgentsun sites in the Hanoi area, that has been solved by creating a new site 35172 Fulgentsun in Fairforce It has no effect on Icebug’s factual data or evaluations, as Icebug had the correct match between FGS site and audit all the time.
• Together with Fond of we arranged a WEP Basic (workplace education program) training at Haksan in November 2022.
During 2023/24, Icebug plans to continue the follow up and remediation of the recently conducted Fairwear audits and the external audit at Fulgentsun. We plan to visit all Vietnam factories for deeper knowledge about the challenges and also try to get more engagement from the workers in the follow up work of the audits. We will identify need for training of manufacturers and their employees about the Code of Labour Practices. We also plan to restart the suppliers self-assessments by the Worldy FEM Facility environmental module (former Higg tools) where several aspects are connected to labor conditions, such as waste handling and chemicals In that way we may address those issues in a more preventive way, by addressing them in the product specifications and chemical test programs.
Icebug has the following suppliers in Vietnam, based on ruling factory list:
• Haksan, Assembly factory Ho Chi Mihn area (Collaboration with brand Fond Of)
• Great Process, Assembly factory Ho Chi Mihn area
• Fulgentsun, Assembly factory, Hanoi area (Collaboration with brand Salewa)
• Wei Sheng, insole factory
• Wei Jie shoes, external producer (Great Process) – no production in 2022/23
The recent audits of Icebug’s suppliers (Fulgentsun, 2019 external audit, /Great Process Fairwear audit april 2022 / Haksan Fairwear audit July 2022) show that all three Vietnamese factories have challenges regarding reasonable working hours and use of excessive overtime. They had a wage level representing an average of 87 – 144 % of the Anker living wage reference so the challenge is to reach 100 % for all factories and for all employees in the factories (not only average). The workers knowledge about freedom of association varied (depending on how long the brands had been
member of Fairwear and if they got education) but all has still substantial improvements to make in this matter.
Several cases of gender-based discrimination was pointed at, as lack of lactation room, childcare allowance was paid only to women, and pregnant women did not get easier tasks or shorter work hours as required by law.
There are also some findings regarding safe and healthy working conditions – concerning chemicals handling and smell of glue at workplaces. The details of the audit follow ups are dealt with in meetings with all suppliers using the CAP (Corrective action plan), for two factories the follow up is done together with other Fairwear brands.
The audit findings for Icebug’s Vietnamese suppliers are well in line with the general finding of Fairwear country report for Vietnam Summarizing the above, Icebug has identified the following risks as most prioritized to follow up in Vietnam for the next year in order to prevent and remediate risks.
• Freedom of association and collective bargaining
• Reasonable working hours (overtime)
• Payment of a living wage
• Gender based discrimination
• Safety issues in the factories need regular follow up
Regarding the living wage, Icebug short term aim is that all workers in all our Tier1 factories shall get paid at least the living wage referred to by the Anker method, see https://www.globallivingwage.org./countries/vietnam. We then compare the audits wage per month with Bonus without overtime (bonus is regular part of salary) with the Anker reference living wage level in the concerned area. The audit results show that all factories are close, as the average wage of our Vietnam factories are 87% - 144 % of the Anker living wage (only one factory is below 100 % for the average). So high priority during 2023/24 is to work with the factories to make a clear plan so that all workers shall reach this level.
GTP represents 26 % of Icebug’s FOB, and is the most prioritized factory as long term partner, and also the only that is not supplying other Fairwear member brands The estimated leverage in GTP is
25 %. A Fairwear audit was made in April 2022 and the results showed that GTP average salary was 1o0 % of the Anker living wage (315 USD per month). However, it also indicates that the wages are in some cases, for some groups of workers, lower than the living wage, and Icebug will follow up on this issue closely.
Some findings in the CAP have been solved by the management and checked during Icebug’s visits autumn 2022, such as posting required Fairwear document, providing anti-fatigue mats for standing workers, installed ventilation for glueing stations, providing better storage and safety labelling in LPG storage, better washing and eyewash facilities at chemical storage. Other issues found by the auditor are still under discussion with the factory management, and will be followed up in each Icebug visit and by our local sourcing partners There is a challenge to reduce excessive overtime. The factory has no democratically elected workers' representatives, and the workers are not aware of the Unions. Therefor Icebug plan to initiate a WEP training
Icebug buys 23 % of our FOB from Haksan and have an estimated leverage of 5 %. Latest external social audit by another Fairwear member brand was made in August 2019 and a Fairwear audit was made in July 2022.
The Fairwear audit results in 2022 showed that Haksan average salary was 87 % of the Anker living wage (272 USD per month). The lowest wage was 85% and the highest 94% of the Anker reference so here we see a need for a general wage raise for most of the workers. We have started the discussion to break down the costs into labor costs (cost per minute) so that we can link the labor costs more correctly to the purchase costs, and we also aim to do a pilot project in this area.
Both Icebug and Fond of offered Covid support to Haksan during 2021/22, however they did not accept Icebug’s support, and Icebug is also a small customer in this factory. However it came up as a remark in the audit that there was still a small gap to cover the minimum wage during the Covid lockdown periods. This was discussed in the follow up, calculations were adjusted and Fond of paid the remaining amount
Haksan did a very good job in taking fast action and solve the issues that came up
Some issues are still unsolved and are under discussion with the Haksan management The union is not independent because the Chairperson is a part of the management team. Next election is end of June 2023. Total working time per week are regularly above 60 hours
In February 2023 Fairwear received a complaint from a worker that was dismissed after coming back late form the Chinese new year. See Complaints handling below.
Icebug bought 45 % of our FOB from Fulgentsun in 2022/23 and have an estimated leverage of 2 %. Latest external social audit by Sumations was conducted in September 2021 (June -January), with complementary interviews in April 2022. It was initiated by Salewa/Jack Wolfskin (also Fairwear member brands) and latest Fairwear was done audit in March 2019. The audit is verified by Fairwear but stated as NOT count for monitoring threshold, however it’s unclear to us why it does not count as we did not get this information until the audit was moved to the new Fairwear platform.
Icebug’s review of salary level (based on Sumations external audit in september 2021, initiated by Salewa/Jack Wolfskin ) shows that Fulgentsun is paying above living wage for all workers, the average wage was 144 % referring to the Anker living wage reference in rural area zone 4 Lowest salary at Fulgentsun was 252 USD while living wage in rural area zone 4 is 195 USD for a typical family according to Anker method. Fulgentsun paid average wage including overtime 280 USD per month by the audit date
In November 2022, the Fulgentsun sustainability management participated in a Fairwear training about labor costing and Fair price application.
The most important findings in the CAP from 2021 Sumations audit was that FWF complain procedure is not included in the worker training, too long probation period for some workers, excessive overtime and health checks did not cover all occupational related risks. Salewa/Jack Wolfskin took lead in the follow up of the audit and we have exchanged information between brands sourcing at Fulgentsun. The open points of the CAP are and will be further followed up
Icebug has the following Tier 1 suppliers in China, based on ruling factory list:
• Dongguan Qiaomai Shoes Co – Ironsteel assembly factory, Dongguan region
• Quingdao Upall CO, Icetubes, Shandong region
• Dongguan Daojiao Zhanhui Shoe Materials Factory – Yi Chang, Overshoe, Guangdong area.
• Brandon - Ningbo Danunion International Trading, Zhejiang province, Harness accessory.
Icebug also sources some materials from China: in total 30 materials in Trustrace (our traceability platform) are produced in China and approximately 10 of them are nominated suppliers or suppliers where HQ has been involved in sourcing process: Hempfortex, Tiong Liong, Feiteng, Fullxin, BOA, Michelin, Gore (Cosmo).
The audit findings for Icebug’s Chinese footwear supplier are well in line with the general finding of Fairwear that the most challenging issues at our Chinese suppliers are:
• freedom of association and collective bargaining
• reasonable working hours (overtime)
• wage levels must be of high concern even if the single audit showed a reasonable level
• Safety issues in the factories need regular follow up
• Gender based discrimination
The country risk of forced labor was not mentioned as a finding or risk in the supplier audit.
Summarizing the above, Icebug has identified that China represents a high general human rights risk that is too high to motivate to seek NEW Chinese suppliers. Icebug’s key Tier 2 supplier Yi Chang recently moved the outsole production from China and Icebug has no plan for future shoe production in China.
Ironsteel / Dongguan Qiaomai Shoes, Guangdong region, China
Ironsteel only produces safety shoes for Icebug, that are certified according to EN ISO 20345 S3. Icebug buy less than 2 % of our FOB from Ironsteel, 251 000 USD during 2022/23, and has a leverage of less than 1 %. The recent Fairwear audit (May 2022) of Icebug’s Chinese supplier Ironsteel show that this factory has the same challenges as in Vietnam regarding reasonable working hours and use of excessive overtime. The wage level represents on average 135 % of the Anker living wage reference, however far below the Asian floor wage. The lowest paid worker also reached the Anker level.
30 % of the workers were unaware of the GS Code of labour practice (posted in factory) and the workers knowledge about freedom of association was low as the factory is not unionized. A Workplace Education Programme (WEP) was performed in 2021.
There are also findings regarding safe and healthy working conditions – concerning fire risk due to storing rubber below a dormitory (that was not used at that period), the factory needed to strengthen its fire safety management and chemical safety, machinery safety and PPE. The details of the audit follow ups are dealt with in collaboration with Engelbert Strauss, in mail conversations using the CAP (Corrective action plan).
External production is finished goods which are bought by member from other brands for resale in a retail or wholesale (web) shop owned by the member. Members generally have limited influence over the sourcing behaviour of external brands. However, Fair Wear believes it is important for members that have a retail or wholesale arm to at least know if the brands they resell are members of Fair Wear or a similar organisation, and in which countries those brands produce goods.
Icebug do not yet conduct monitoring activities at suppliers of ‘external production’. However we do collect the signed Fairwear questionnaire and ask suppliers to post the Fairwear worker sheet to inform about the Code of labor practice also for external production.
Icebug’s production of insoles and accessories was purchased from the following suppliers 2022/23:
• Wei Sheng CO, Ben cat, Vietnam. Insoles (FOB: 645 000 USD)
• Cansocks AB, West Sweden. Socks (FOB: 40 000 USD)
• Brandon/Ningbo Danunion International Trading, China. Harness (FOB: 8 400 USD)
• Qingdao Upall CO, Shandong, China. Icetubes (FOB: 42 80 USD)
The total cost for purchased accessories is representing 4% of total FOB.
In February 2023 Icebug received the first complaint via Fairwear helpdesk relating to Living wage; Legally binding employment relationship. The complainant was a worker at Haksan in Vietnam who was dismissed after coming back late form the Chinese New Year due to transport problems. In collaboration with Fond of we asked for explanations from the factory management The complainant met the Human Resources officer who said they were dismissed due to being absent for
Social Report March 2022
February 2023
five days and will have no payment (no remaining salary) nor provide a dismissal decision. They want Fair Wear to help them obtain their remaining salary (salary for January 2023) and dismissal decision to apply for the unemployment allowance, which the social insurance agency pays. The factory delivered the salary on 16th of February and the required documents were delivered 12th of March
To make sure workers at Icebug’s suppliers are aware of the Fair Wear complaint mechanism, we have asked the factories to post information sheet about Fairwear well visible to the workers. There is a Fairwear contact phone number, encouraging to report any complaint and with promise to treat it confidentially: “Fair Wear will always treat your complaint confidentially”.
Icebug needs to appoint clear responsibility for handling Complaints as it will always be urgent to solve. We will appoint two persons who can deal with complaints and make sure someone is available also during holidays.
The following activities were undertaken to inform and train the Icebug staff, in HQ Sweden and at sales offices in Germany and US, about Fair Wear membership:
• Presentations of Fairwear membership and planned activities at Sales kick off meetings for SS23 (May 2022) and FW23 (October 2022)
• Fairwear and working conditions in supply chain are included in Icebugs sustainability base education, for all employees, and in sustainability team workshops, latest was held 221024.
• Presentation to “All of Icebug” of salary levels in Icebugs supply chain, March 2022
• Presentation of Fairwear and Icebugs membership in Workbooks (sell in Collection cathalogue) from seasons SS22 and all coming seasons.
The following activities were undertaken to inform and train the sales agents of Icebug about Fairwear:
• Presentations of Fairwear membership and planned activities at Sales kick off meetings for SS23 (May 2022) and FW23 (October 2022)
• Presentation of Fairwear and Icebugs membership in Workbooks (sell in Collection cathalogue) from seasons SS22 and coming seasons.
The past year Icebug and Fond of initiated a WEP basic training for Haksan, Vietnam that was
Icebug will keep track of progress on the implementation of the Code of Labour practices by following up on social indicators and report yearly progress about these in Icebug’s sustainability impact report. Some will also be displayed in the Product Journey in Follow the footprint, see example. Initially for assembly factories and then for material suppliers (Tier 2) and raw material suppliers (Tier 3). We still have a work to do to define those indicators, some early ideas are:
Supplier level, display some of them in Follow the footprint product journey:
• Average wage, % of the relevant living wage for that area (above 100 % is acceptable).
Social Report March 2022 – February 2023
• % of workers that get on or above living wage level (should be 100 %).
• % of woman workers
• % of workers that got training in Code of labor practices
• Complies to X of 8 CoLP practices (1-8), confirmed by Fairwear audit/external social audit
• If not compliance, areas to improve: name relevant issue of 1-8 in CoLP
• Latest Fairwear audit/external social audit of the factory: YYMMDD
• Has democratically elected worker representatives in Union and CBA
We welcome feedback and ideas to social indicators.
The past year Icebug made a yearly impact report where we describe overall sustainability targets action and progress, including social issues, https://icebug.com/impact-report see pages 46-47
Fairwear is mentioned on icebugs web page: https://icebug.com/sustainability/workersconditions Fairwear and to commit to Code of labor practices is also an important part of “our promise”
https://icebug.se/ourpromises
We did several posts in social media on our engagement in Fair Wear. Our Instagram and Linkedin channels have approximately 30.000 followers.
Also, Fair Wear was mentioned in newsletters with approximately 60.000 subscribers.
We don’t always mention Fair Wear by name, but fair working conditions is one of the recurring themes of our brand communication.
During the reporting period, Icebug has increasingly started to address the views of stakeholders and what sustainability impact the company’s activity has on different stakeholders, including nature as one stakeholder. Icebug partly uses “stakeholder capitalism” as a framework for the sustainability reporting
Icebug engages several stakeholder groups both in Europe and in production countries to raise various key topics/concerns through stakeholder engagement Icebug is member of FSC Sweden – a certification of sustainable forestry that has labor condition requirements in the standard and will affect the labour conditions in the supply chain of FSC certified materials that we use (so far natural rubber and carton) Social issues are a big part of the holistic sustainability B corps certification where Icebug was approved as a B corps during 2022, see https://www.bcorporation.net/en-us/find-a-bcorp/company/icebug-ab/ Icebug is also member of 1 % of the Planet where we support sustainability NGO’s and organisations working for inclusion, as Inclusive Business Sweden and Hej Främling!
We did use the Fair Wear stakeholder resources such as country studies to do the HRDD risk assessment and also to generally get better knowledge on Vietnams and Chinas labor conditions.
Icebug has put increased focus on inclusiveness in different ways.
Inclusive business in the supply chain: Icebug initiated a sourcing project with Inclusive business Sweden and FSC international, aiming at enabling small rubber farmer cooperatives in Thailand to connect their supply of FSC certified rubber with the demand side in the footwear industry. The FSC certification includes social working conditions and the project aims to enforce the farmers to stay independent compared to working for big rubber plantations.
Inclusive design and marketing: Icebug also focus more on inclusive design and marketing to target a more diverse group of customers in our marketing, feeling welcoming for all and make sure we are a driver towards no discrimination of any kind (gender, rase, age, sexuality, disability or other).
Inner development Goals: Icebug is doing a pilot project for all employees where we explore the so called Inner development Goals, and how our inner development can help us act more aligned with what will be required to face/solve the sustainability challenges of our time.
https://www.innerdevelopmentgoals.org/