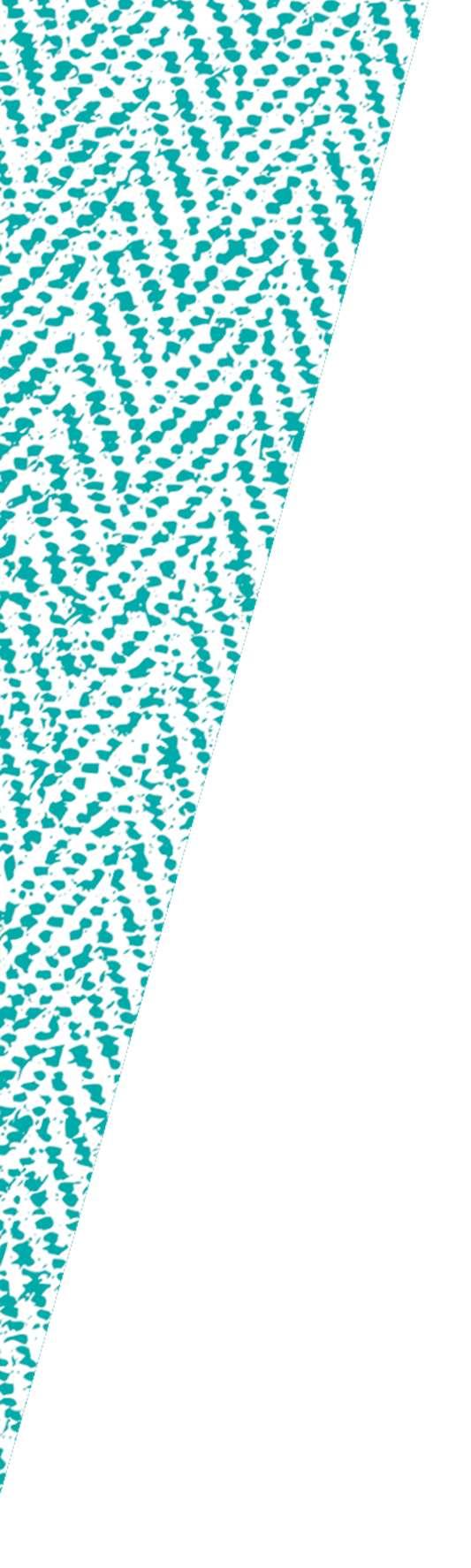
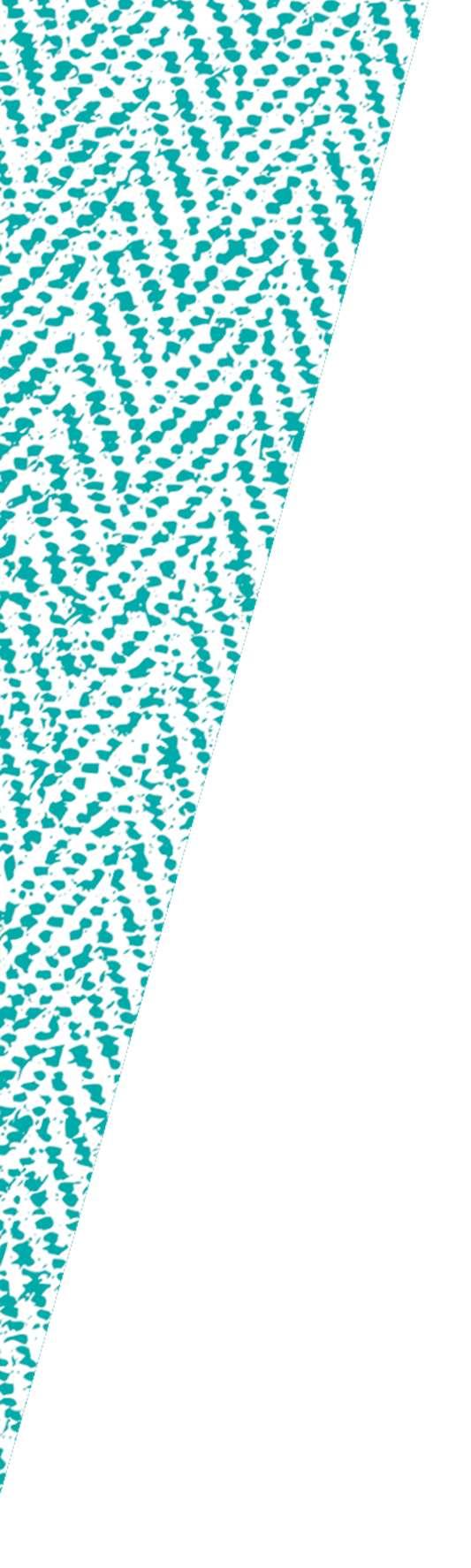
IcebugABsocialreport
Reportingperiod:FinancialyearMarch2023–February2024
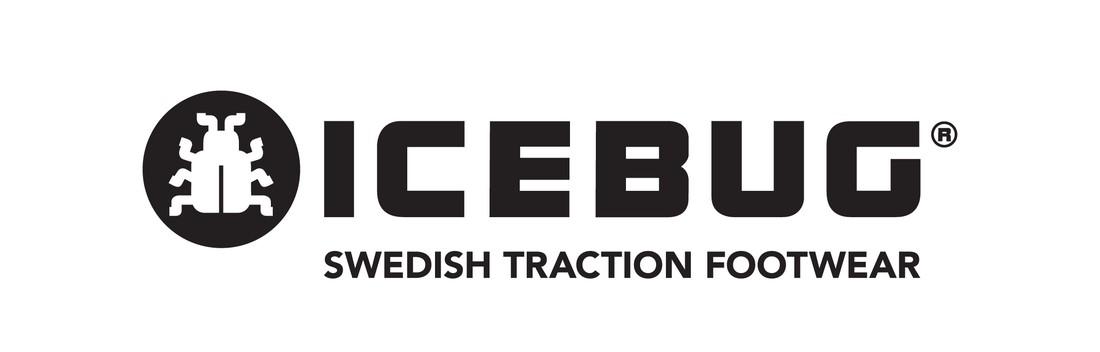

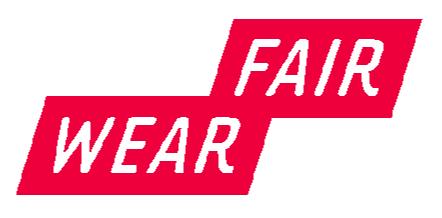
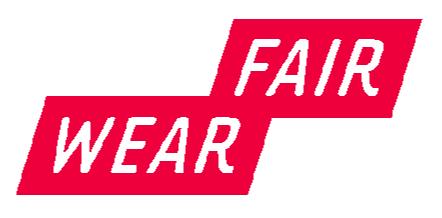
Icebug AB social report
Organisational chart
Icebug AB is a Sweden based outdoor footwear brand with HQ based in Jonsered, outside of Göteborg in southwest of Sweden. Overall management, product development, sales, product logistics and customer service are done from the HQ. The value flow Teams follow the Collection work (Assortment, Development and production, Preorder, Sell through and Inventory management (STIM), Growth engine, Sales, Customer relations and Retail, and are also integrated in each other’s work through roundabouts where value flow deliveries are made, and responsibility is handed over between the teams. In the center you see the Management, Work at Icebug, Finance, Tech and Sustainability that is integrated in all of Icebug’s work. The organizational chart is well visible on the office wall.
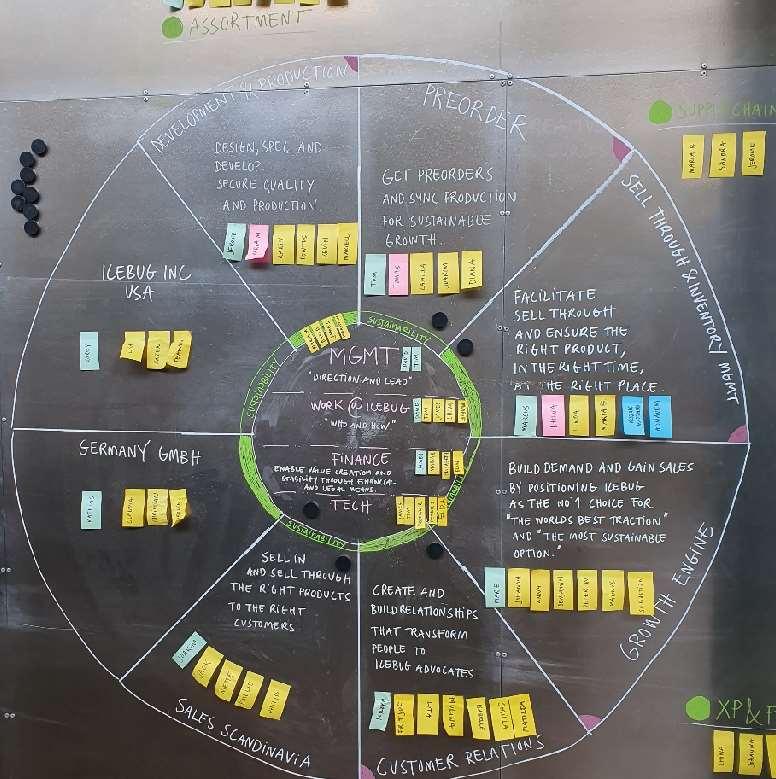
Icebug also has sales and marketing offices in Germany and USA. The shoe assembly production is made in four assembly factories in Vietnam and China, the shoe mid- and outsoles are made by two main suppliers (Yi Chang and Michelin) and different materials are supplied from many materials suppliers. Icebug’s sourcing partner and co-owner Vanbestco, Taiwan, supports in the sourcing
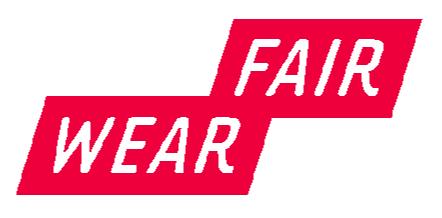
processaswellasqualitycontrolincludingchemicalstesting.Pleaseseebelowvaluechainchart showingIcebug’svaluechainstructure(specificsuppliersmightchange).Thelightgreenboxesare thematerialsupplierschosenbytheassemblyfactories(lightblue)orVanbestco(purple).Thedark greenboxesarenominatedsuppliersthatIcebugnominatetogetmoresustainablematerials.
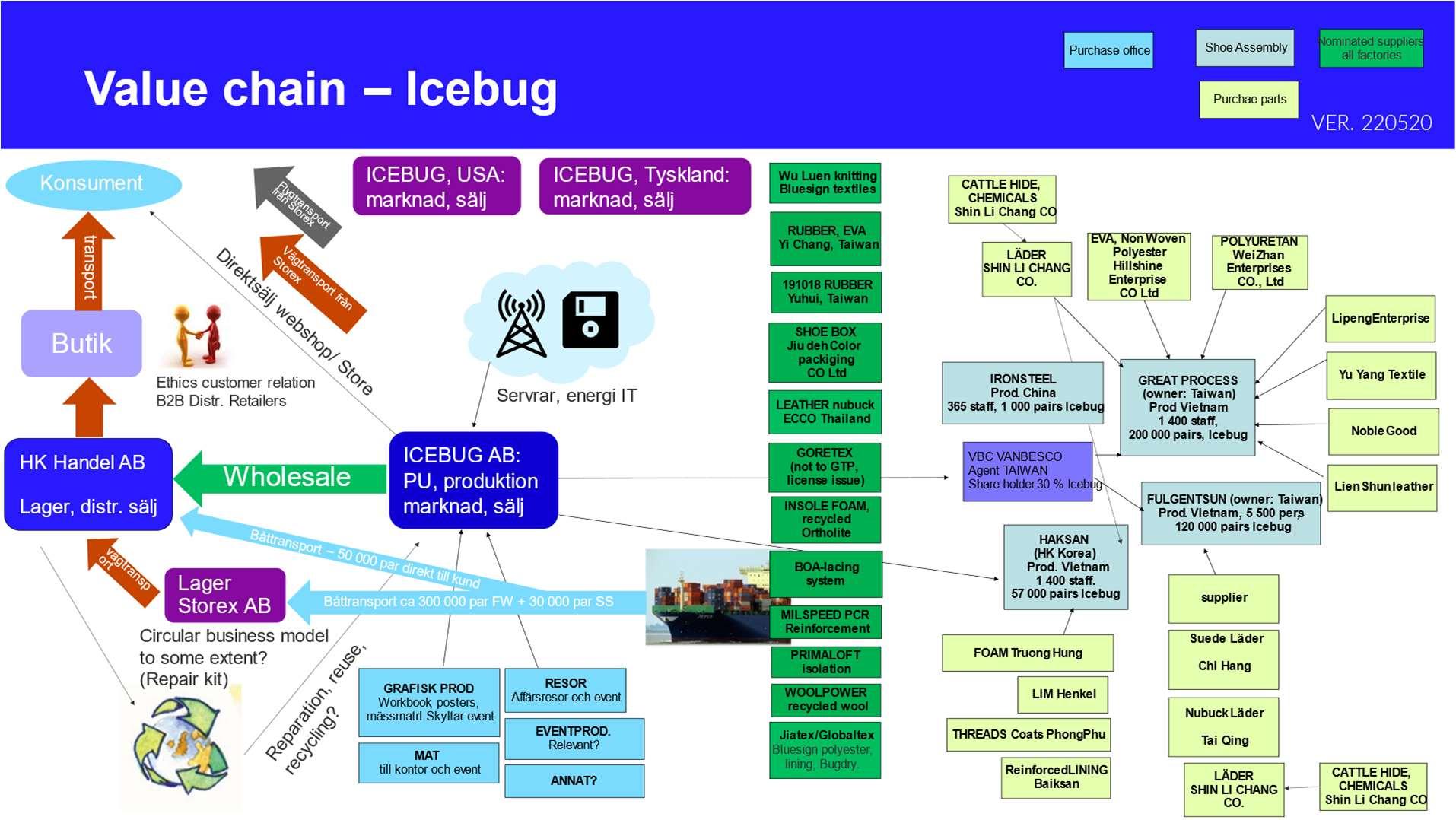
Summary:Goals&Achievements2023-24
ThepastyearweatIcebughavebeenfocusingondeepeningtheriskscopingandriskassessmentin oursupplychainaswellasgettingadeeperunderstandingoftherootcausesofactualharmsorclear risksofthefactories.Wealsofocusonbuildingupmoresystematicroutinesandprocessesfor preventionandremediationofharms.ThecontinuedfollowupoftheperformedFairWearauditsof theassemblyfactoriesin2022,withsupportoftheCorrectiveActionPlans(CAP),hasalsobeen importantassomeofthefindingshavetakensometimetosolveorimprove.During2022threeout ofthreefootwearassemblyfactorieswereauditedbyFairWearorFairWearapprovedexternalaudit, atpresentcovering95%oftheFOBvalue,therestbeingaccessoryproducts.Wehavestopped sourcingsafetyshoesinChina.Bothforcommercialreasonsandtoconsolidatethesupplierbaseand lowerthehumanrightrisk(asChinahashighriskofforcedlabor).
Doingfollowupoftheauditshasbeenagoodlearningprocessandwearegratefulthatwecould cooperatewithsomeotherbrandssourcinginthesamefactoriesandwithlongerexperienceofFair
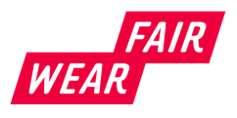
Wear membership. We still have some actions to follow up during the year to come, especially in one factory that do not have other Fair Wear brands. We can clearly see the difference in how brand collaboration facilitates to make regular improvements of the labor conditions.
During the past year, we strived to get closer engagement from workers’ representatives in the workers’ conditions improvements in audit follow up and during our visits in the factories. We have met the workers representatives in all assembly factories and hope to develop those relationships so we can get to the next level of social dialogue between workers and managements.
Icebug Development & Production HQ Team has visited the two assembly factories in the Ho Chi Minh area three times in the past year (June 2023, November 2023 and March 2024) and the factory in Hanoi area was visited in November 2023. We had valuable discussions with the factory management about on-site findings and their solving of the issues, documented in each CAP. All practical health and safety findings from the social audits are now solved for all three assembly factories, except for the lack of legally required short breaks that has not been provided at one factory, despite several discussions and showing examples of how it works well in other shoe factories.
We also visited the Fulgentsun factory Fujian Sunshine in China in November 2023 and March 2024, as well as a midsole Tier 2 supplier. In addition to the HQ team visits our China based sourcing expert and quality controller visits the factories approximately once a month.
In general, a need for strengthening the social dialogue between workers and managements remains, including strengthening of awareness regarding gender-based discrimination. It’s also important to keep the current low level of extensive overtime (also due to low order volumes during the past year) and to make sure that ALL workers get a living wage, not only that the average wage of a factory is above the living wage. It’s also important to always follow up on the totality of the eight labor aspects in a structured way, based on the current risk level, from risk assessment that are updated on an annual basis.
Living wages The shoe assembly factories (representing 95 % of Icebug FOB) average wages were found to be at a fairly decent level for the first estimate, as a baseline for improvement. In the Fair Wear audits in 2021-22 two of three shoe assembly factories average wage was on 100 % or above the Anker reference for the relevant region in Vietnam, and the third factories average wage was on 87 % of the Anker reference for region 1, Ho Chi Minh City. During this year we reached out to four
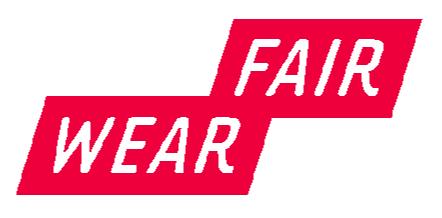
other brands in this factory to make joint effort to establish the correct Living wage reference. We aim to verify if region 1 is the correct Anker reference (as factories are located in Bihn Duong province which should have lower cost of living than neighbouring Ho Chi Minh City) and to raise the wages up to living wage level or at least find a way for Icebug and other brands to pay our share of living wages. These brands showed interest already before Covid and finally we could get together to start a Living wage project. See more under payment of living wage in “System for monitoring and remediation”.
In June 2023, Icebug took part in our second Brand performance check, for year 2022-23. As our first year as Fair Wear member 2021/22 was highly influenced by Covid, it was difficult to do factory visits or audits. During the second year 2022/23 we were able to do audits on 95 % of Icebugs FOB and also do practical follow up of audit results for all our assembly factories. However, this year Fair Wear changed the BPC criteria to align better with the OECD Human rights Due diligence HRDD process, demanding a more theoretical approach with risk scoping and evaluation of risks. As Icebug focused a lot on the practical follow up of factory audits and conditions, we missed out on some indicators regarding documenting the root causes and t0 implement a robust and systematic prevention programme. We also did not fully do the Fair Wear onboarding process for an accessory supplier as those (small) orders were not yet well coordinated within the company. Icebug was ranked as a “Needs improvement” company. See the result here: https://api.Fair Wear.org/wpcontent/uploads/2023/09/BPC-Icebug-AB-2023.pdf Icebug was expected to mitigate the root causes of excessive overtime as well as to assess and respond to root causes for wages that are lower than living wages in production locations. The member did not follow up on the requirements. The member brand has scored insufficient on some repeated non‐compliance indicators.
Of course we are not happy with this result. However at Icebug, we do believe in a pragmatic and practical approach to most tasks that we stand before, and it felt natural for us to first focus on the practical improvements of the factories in the short term. The past year we have digged deeper into risk scoping and discussed root causes with our suppliers to be able to avoid harm and improve the workers conditions in the long term. In practical terms, we know the root causes of excessive overtime and are actively working to mitigate those and have done for a long time. This mainly involves taking active measures in planning production windows well in advance, only take finished products to production, spreading out production and deliveries to avoid seasonal peaks and not enforcing penalties for delayed deliveries.
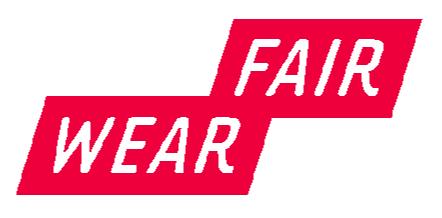
During the past year, Icebug did not receive any complaint from Fair Wear helpdesk. We have appointed clear responsibility for the complaints procedure as those will always be urgent to solve.
The HRDD risk scoping has been updated according to the Fair Wear HRDD process (see details in risk scoping report). The Fair Wear audit findings for Icebug’s Vietnamese suppliers are well in line with the general finding of Fair Wear Vietnam country report. Summarizing the risk scoping, Icebug has identified the following risks as most prioritized to follow up in Vietnam for the next year in order to prevent and remediate risks.
Freedom of association and collective bargaining
Reasonable working hours (overtime)
Payment of a living wage
Gender-based discrimination
Safety issues in the factories needing regular follow up
The suppliers of accessory products (together less than 5 % of Icebugs FOB) will be prioritized during 2024/25 to get a clearer picture of the risks in these productions. We did get external audit reports for Indonesian cap supplier and did investigations of Swedish accessory suppliers. We might not travel to visit all accessory suppliers (for climate reasons). However we aim to visit all Vietnamese and Swedish suppliers.
We stopped the production of safety shoes in the Ironsteel factory in China and the Overshoe/ Floorsaver production was moved to Taiwan and Vietnam. However, as we still have a small outsorced accessory production in China and also some material sourcing, we have done a more thorough risk scoping for China.
We have updated the Responsible Business Conduct Policy (RBC Policy), and presented it in meetings with the assembly factories in November 2023. It describes the process of risk assessment, preventing and stopping harm, tracking and validating the progress and the reporting in risks and progress. The Responsible Business Conduct Policy, gives our suppliers and partners an overview of what we demand and expect from them.
See https://Icebug.com/sustainability/reports#fair-wear-foundation-reports
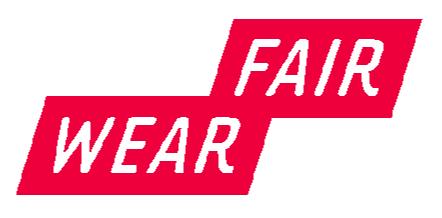
“There are many ways to approach why improving labor conditions is so important to Icebug and what we want the company to do. Our vision is to be a changemaker for a society where people can thrive on a planet in balance. That our products are made in a fair and just way is an obvious part of that. On the governance side, our owners’ directives specifically names people involved in our supply chain as stake holders, meaning that their interest always needs to be factored in when running the company. We strive to use our business as a force for good and taking responsibility for the people that we influence is simply the right thing do.” David Ekelund, co-founder and co-CEO ICEBUG.
Sourcing strategy
HUMAN RIGHTS DUE DILIGENCE
All purchase decisions have some level of risk that needs to be mitigated. Icebug considers and evaluates certain social and environmental risks before every purchase decision. In addition to the sourcing strategy for new assembly factories we also have a special procedure regarding all new materials that are evaluated to consider potential risks. We are also aligned with several certification bodies with labor conditions as part of their scope: Leather Working Group (LWG), Bluesign, Forest Stewardship Council (FSC), B corps and Fair Wear.
By the end of 2022 Icebug started to follow Fair Wear’s structured Human Rights Due diligence process with the steps described below.
Step
1: Embed HRDD in policy & management systems
We first established a Responsible Business Conduct policy that describes our commitment to responsible business, how we implement that to prevent and mitigate risks and what we expect all suppliers to follow and support. The Responsible Business Conduct Policy (Icebugs version of an HRDD policy) is approved by Icebug’s top management and concerns all of Icebug’s employees. For the suppliers it will mainly be the Development & Production team and the Vanbestco team that manage sourcing and follow up Fair Wear audits, but it’s also on the agenda for top management meetings. The Sustainability manager is responsible for developing and up-dating Fair Wear policies and educate the rest of the organization. The RBC policy includes a clause on outsourcing that also covers potential homeworking – however homeworking is not used or relevant in Icebugs supply chain where all production moments are depending on machines and coordinated production lines.
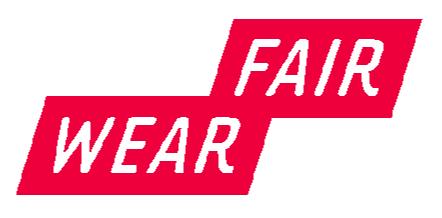
Step 2: Conducting a scoping exercise, risk assessment and informing workers and suppliers
To identify actual and potential harms, Icebug did a Human Rights Due Diligence risk scoping of the supply chain that describes the risks at country (Vietnam, China, Sweden, Taiwan and Indonesia for the past year), sector, factory and product level. It is updated yearly (or more often when new supplier conditions require an update) by the Development & Production team. It is reviewed by the management and form the basis for the next year Fair Wear work plan and what we will focus on to prevent risks.
Gender inequality is a high risk in the textile and garment supply chains in the countries where Icebug has the main production. Therefore, Icebug includes a “gender lens” throughout the work.
From the initial period of Fair Wear membership, based on country reports risk scoping and the risk assessments in the audits, audit follow-up and stakeholder meetings, the following risks are identified in the footwear assembly as prioritized on a general level:
Freedom of association and collective bargaining
Reasonable working hours (overtime)
Payment of a living wage
Gender issues such as lack of lactation room, work conditions for pregnant women, inequal payment for parents
Site specific safety issues as chemicals, safety passage, storage, PPE
Step 3: Stopping harm, prioritising and implementing prevention and mitigation
Based on the outcomes of the risk scoping and assessments (step 2 of the HRDD process) Icebug determines a risk profile and prioritise follow up actions. This is done in the Fair Wear work plan on a general level. On a facility level, depending on the factory’s risk profile, Icebug formulates an action plan to implement the corresponding improvement or prevention programmes, including a timeline and capacity estimation. Gender, social dialogue and freedom of association are included in the follow-up actions.
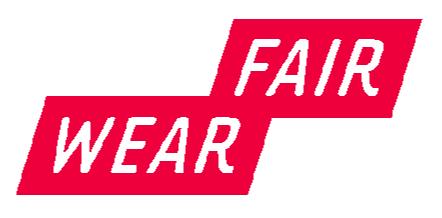
Step4:TrackingandvalidatingonprogressmadeintheImplementationandPrevention Programmes
TheeightelementsofFairWear’scodeoflaborpractices,withspecialfocusontheidentifiedrisksare monitoredby:
FairWearauditsofTieronefactories(producingIcebugslabelledgoods)–app.everythird year.
YearlyriskassessmentofIcebugsuppliers,basedonFairWearaudits,externalauditsand regularfactoryvisitsandsourcingdialogue.
SpecialfollowuponpilotprojectsandFairWeartrainingsonvarioustopics.
TheFairWearsocialreportsummarizestheyears’actionsandresults.
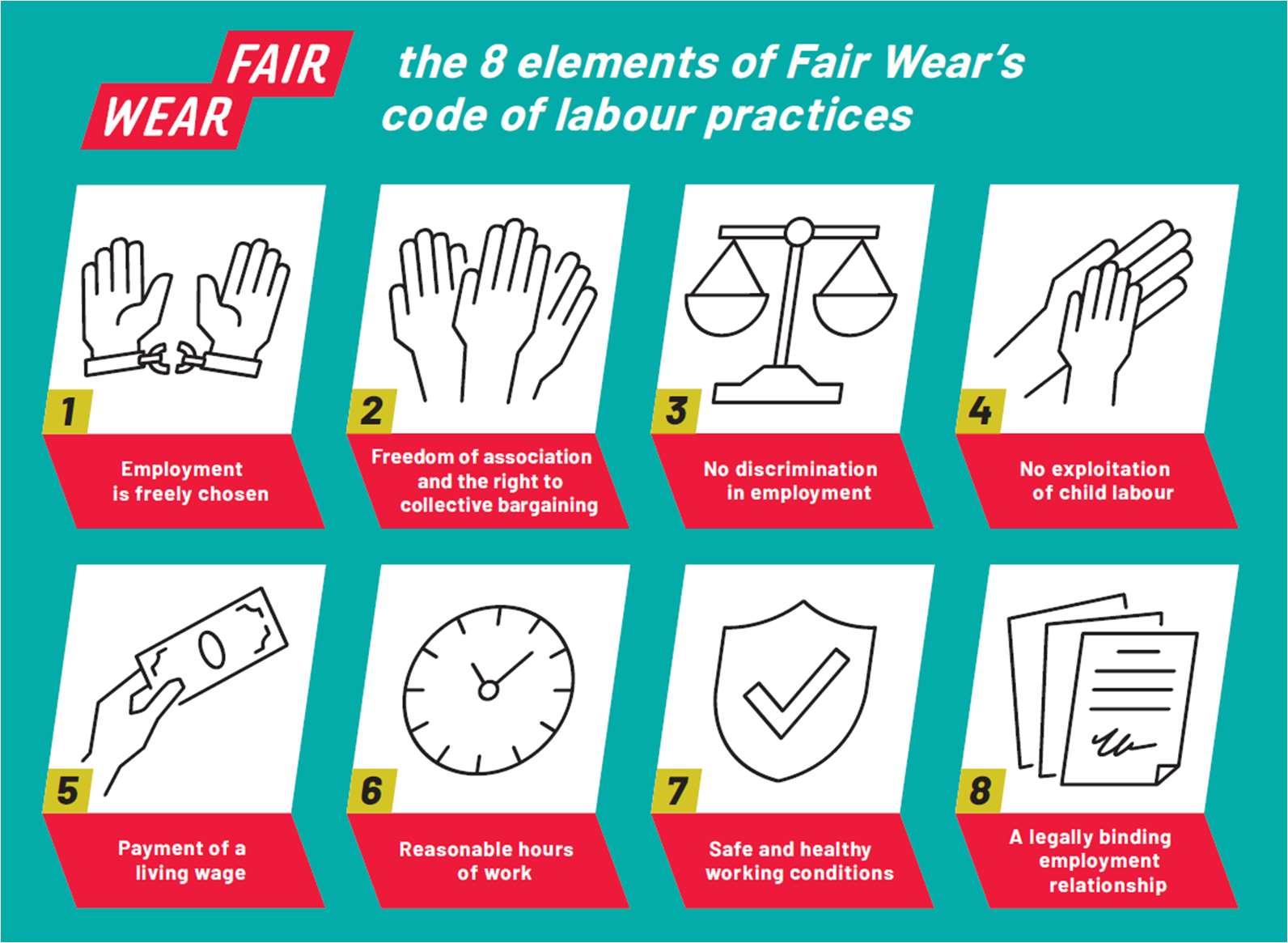
Step5:Publiclyreportingonrisksandprogress
IcebugisreportingthesustainabilityperformanceinthesupplychainintheyearlyImpactreport.The FairWearplatform,Brandperformancecheck,trainings,stakeholdermeetings,auditsandCorrective actionplansCAPsprovideaframeworkfortrackingimplementationandvalidatetheprogressmade. Icebugaimtodevelopasetofsocialindicatorsthatwillbeaddedtotheimpactreport,whereworkers andsupplierswillplayanintegralroleinmonitoringprogressagainstgoals.
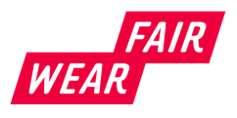
Icebug’s annual Impact Report is available on our website, displaying our targets and the yearly sustainability progress, https://Icebug.com/sustainability/reports#Icebug-impact-reports. The Brand Performance Check made annually by Fair Wear Foundation is available at https://Icebug.com/sustainability/reports#fair-wear-foundation-reports where the result of our social sustainability performance is shown, including the areas which need improvements. Here you will also find Icebugs yearly Social Report.
Step 6: Provide for or co-operate in remediation
Step 6 focuses on remediation of actual harm. Brands are expected to provide for or cooperate in the remediation of adverse impacts where they have caused or contributed to that adverse impact. When a brand has not caused or contributed to an adverse impact but is still directly linked, it is required to influence its supplier to prevent or mitigate the impact and provide remedy. If a brand identifies a potential harm (e.g. a risk which is not yet an adverse impact), the brand should seek to prevent and mitigate the risk from occurring under Step 3. An example is the living wage where Icebug is linked to the gap to payment of living wage, even if we did not directly cause the gap having a very small leverage. In this case we seek collaboration with other stakeholders/brands to influence the supplier so that we can 1) get a common picture of wins for all parties and 2) mitigate by creating an open attitude about labor cost and living wage estimate (without disturbing competition rules) that all brands and the supplier can benefit from in price calculations to strive for living wage for all workers
SOURCING STRATEGY & PRICING
Icebug buy the ready-made shoes FOB from three assembly factories in Vietnam. The sourcing of materials, key parts as midsoles and outsoles and the quality control of ready products is made in close cooperation with Icebug’s sourcing partner and co-owner Vanbestco, Taiwan, see value chain chart above. The accessory branded products in smaller volumes are bought from various suppliers depending on the product need and technical requirement. We see a need to consolidate our regular supplier base to also include these small volume purchases, in order to minimize both risk and resourses needed for the sourcing. This is an ongoing process.
The sourcing strategy forms the framework for the outsourced supply chain of the Icebug brand. It is the basis for the development of all responsible purchasing practices that are crucial to reach a good level of the elements in Fair Wears Code of Labor Practices (CoLP).
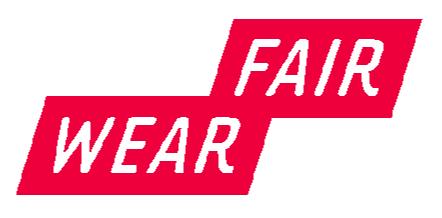
The basis for Icebug’s sourcing strategy is long-term cooperation with suppliers where mutual trust is created through a practice of treating each other as equal partners – Icebug doesn’t have supplier contracts with penalties. We then collaborate to raise the sustainability level of the supply chain. Since the start of the company in 2001, Icebug’s owners have searched for suppliers sharing the same values as Icebug and that are open to develop and improve Changing business conditions and product portfolio as well as different rates of organizational development, sometimes leads to changes in which suppliers Icebug works with, but our aim is to always work long term. Icebug presently doesn’t have any supplier that we haven’t worked with for at least eight years (for Fulgentsun we changed the factory from Fulgentsun Cambodia to Fulgentsun Vietnam in 2020 but it’s part of the same company group with same top management). Since 2015 when Icebug started to work with sustainability in a more structured way, we have asked our suppliers to source materials with lower resource use and less negative impact (recycled, biobased, low impact processes, less harmful chemicals, climate smart etc). This field is developing fast and there is a value in the Icebug development working proactively in this part of the sourcing. Being identified as a sustainability leader in the footwear industry, Icebug is nowadays often approached by material innovators. For new materials and processes, the Icebug team frequently nominates suppliers of high sustainability standard (see dark green boxes in the supply chain chart).
The social conditions are integrated in the sourcing strategy. Icebug’s former Code of conduct was replaced in March 2023 with the more detailed Responsible Business Conduct policy, see https://Icebug.com/sustainability/reports#fair-wear-foundation-reports that we expect all suppliers to meet. In Icebug’s concept “Follow the footprints” we display the ecological footprint and show the product journeys supply chain for all shoe styles, see example: https://Icebug.com/footprints In this end customer facing communication we aim to include more information about social conditions in the supply chain. The plan is to get and display social data from suppliers in Tier 1-3.
In the Vanbestco sourcing team 15 persons support Icebugs sourcing, and their leader is member in Icebug’s Development & Production Team securing regular contact and feedback both ways. The team from Taiwan visits the factories regularly to carry out quality controls and check production. In addition, an Icebug-employed sourcing expert and quality controller in China conducts regular on-site inspections at the factories. The production team in Sweden has frequent exchanges with them.
Icebug’s Development & Production Team, responsible for sourcing, has eight members: five HQ team members of Designers, Product engineers and the Sustainability manager who is placed in this team to closely follow both ecological and social sustainability issues of the sourcing. The team has
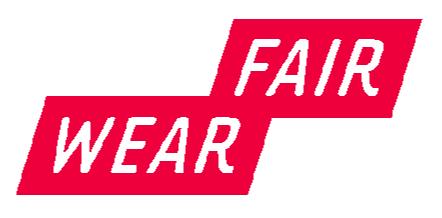
three Asian team members – the sourcing manager of Vanbestco, a sourcing expert, an Icebug employed sourcing expert and quality controller. The Development & Production Team leader together with the Preorder Team leader decide which manufacturers will get orders of different styles. The decisions are based on formal criteria such as technical capacity, margins, tooling investment, compliance with labor standards, sustainability and quality.
The price level of Icebug’s products is medium to high, and we aim to sell at full price and don’t do Black Friday or in-season sales to drive consumption with aggressive pricing. The price reflects the quality of the products and is also part of the strategy, to be able to make durable, high-quality shoes with high sustainability content (durable, low climate impact with high content of recycled and biobased materials that are manufactured in low impact processes from responsibly sourced raw materials). This also includes social responsibility for workers in the supply chain, and covering living wages for all workers.
Further corner stones in the sourcing strategy are:
- Having a concentrated supplier base so that Icebug can be an important customer
- Avoid dependence of human rights high-risk areas, with a preference for sourcing countries where workers can freely form or join a trade union and bargain collectively.
- Planning production to avoid causing excessive overtime
- Paying prices that allows for paying a living wage
A responsible production planning starts with a deep understanding of the supply chain partners’ capacity and respecting lead times. Based on Icebug’s forecast, the supply chain partners provide a production plan with allocation of quantity in different periods, with a corresponding order placing plan that Icebug then follows. Icebug has deliberately set up the business model in a way that enables us to spread production over a longer period: No fashion or single season styles or colorways. A high degree of carry over styles that last for many years enable long-term planning and avoiding campaign prices thus keeps the margins up. Safeguarding the value of the products is also a mechanism that enables us to pay correct purchase price – FOB prices paid by Icebug should always allow to pay living wages throughout the supply chain.
Suppliers are regularly visited by the Development & Production team before placing the order to understand the setup of the production locations and ensure there are no apparent human rights violations. Some of the details that are up-dated and evaluated on a season to season basis are:
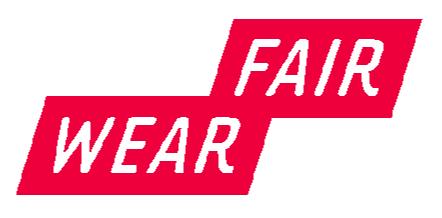
Quantities per country / supplier / style / season
The factory capacity and how to plan production to avoid excessive overtime
Ratio sampling vs. bulk production
Supplier matrix per product
Supply chain mapping (partners per supply chain step)
Internal analysis (key success factors, strategic success position, strengths and weaknesses, key performance indicators)
External analysis (market trends, industry benchmarks, opportunities and risks)
Tracking and validation of social progress are included in the sourcing dialogue between member brands and suppliers.
Based upon these parameters Icebug takes decision on whether to place orders, how to prevent and mitigate risks, and what remediation steps may be necessary.
Upon the start of a new business relationship (before first order is placed) Icebug needs to gain a basic level of insight into the human rights situation at a potential factory to inform sourcing decisions. As a Fair Wear member Icebug commits to:
Raise awareness of the workers and the management on human rights.
Stress the importance of gender-representative social dialogue (with democratically elected worker representatives).
Assess whether there is an effective operational-level grievance mechanism established through social dialogue with workers.
Establish the Fair Wear helpline as a safety net.
If the supplier is in a new country, update the HRDD risk assessment at country level.
PRODUCTION CYCLE
The production cycle and planning has so far been based around two seasons per year, Spring/Summer and Fall/Winter. The development starts about 2 years before the season. The first forecasts are sent to factories 9-10 months before the start of the deliveries for the season. The forecasts are then adjusted on a monthly basis, maintaining a long planning horizon for the factory. Icebug places the orders in a window of 9-6 months before the products are made available to customers. The delivery window for the highest volume season, fall/winter, is spread out over a
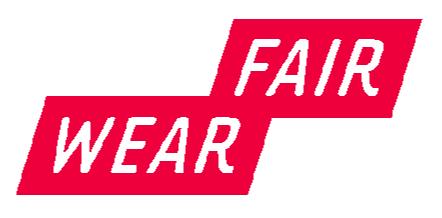
period of nearly six months, with a good balance of quantity during each month – this is to respect factories’ production capacity, and to best use the space both before and after the peak season. This is supported by the large majority of Icebug’s production volumes being carry over products that are kept in the line and produced for many years. Icebug makes efforts to make clear plans and involve the manufacturer as early as possible to support good manufacturing planning allowing reasonable hours of work and avoiding overtime peaks. We do not produce ad-hoc or spontaneous customer requests.
The sourcing agent Vanbestco and our employee in Asia are in close contact with the assembly factories and have regular dialogue about the sourcing process, sampling process and production planning, so that the production plan will grow in a communication between the manufacturer and Icebug’s Preorder and Development team. Icebug partially nominates materials and buys outsoles and midsoles directly from the suppliers. Nevertheless, Icebug always buys ready-made footwear (FOB) from its three main suppliers.
FACTORY RELATIONS
There has been no addition of new assembly factories last year, however we are doing Fair Wear onboarding processes discussion with accessory suppliers for caps (PT Capglobal Industry, Indonesia), care products (Smellwell AB, Sweden) and promotional clothes (Paper street clothing company, Sweden) for production 2024/25.
A new outsourcing factory for stitching, Wei Jie, was proposed by GTP in Vietnam late 2022, and prepared for orders in 2023/24. Wei Jie is published in the Fair Wear platform as related factory to Great Process.
Three accessory suppliers of caps (23/24), harness and Icetubes (buff) (22/23) did only get one Icebug order. There was no new order of safety shoes 2023/24 from the Chinese factory Ironsteel, due to a combination of market and human rights risk factors, and we do not have any plans for future shoe production in China.
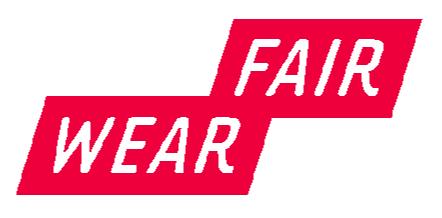
However we still have accessory production of 500 pairs of Pocket Gaiter in Fulgentsuns Chinese factory Fujian Sunshine. This production started in 2020, before Icebug became a member of Fair Wear, and was included in the Fulgentsun Vietnam production as an outsourcing partner. When we recently made internal training about the Fair Wear onboarding process, it raised the awareness about importance of small accessory volumes and also about the outsourcing clause in Icebugs RBC policy. As soon as this came into focus we did the Fair Wear onboarding process, and got the last social external audit from Fujian Sunshine. As FGS China has same owner as FGS Vietnam and also has other Fair Wear members as customers we already knew that they have a decent labor standard, and this has been confirmed in the (late) onboarding process. We have also visited this factory many times as they assist Icebug in product development.
When selecting a new assembly factory or other key supplier for Icebug, Icebug look for partners and the following criteria apply:
Long term strategy matching and aligned business vision
Quality references and technology processes (membranes, other critical moments)
Development capabilities
Openness and organizational support
Sustainability maturity level: basic sustainability in place or a long way to go? (available external social audit reports, certifications done (FSC, Ökotex, other), climate data)
Commitment to Code of labor practice, See also above in Sourcing strategy & Pricing As a Fair Wear member Icebug commits to:….)
Low carbon energy source
Location – evaluation of country risks and logistics
Price level
MONITORING ACTIVITIES AND SOURCING DECISIONS
Three Fair Wear audits were conducted in Icebug’s assembly factories during 2022: Haksan and Great Process in the Ho Chi Mihn area of Vietnam and Ironsteel in Guangdong, China. As Fulgentsun in the Hanoi rural area in Vietnam was audited by Sumations the precedent year (June 2021 -Jan 2022), it means that 100 % of Icebugs assembly factories were audited within one year, and 95 % of the FOB purchase 2023/24 has been audited during our membership period. The accessory FOB is 5 %
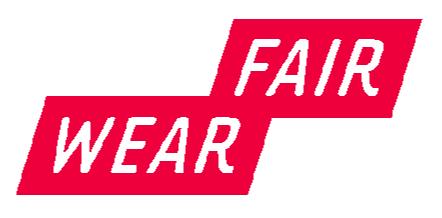
of the total FOB. The findings of these audits, and the remediation of harm that was done as a follow-up, are described below for each factory where Icebug did assembly in 2023/24.
There was no single finding in any of the factories that made us question whether we shall continue sourcing from them. All the findings in audits and in our visits were of the nature that we can discuss with the management and solve them together, and that will be part of the continuous improvement.
For one Vietnam factory, that did not experience Fair Wear audits before and where no other brand is a Fair Wear member, the management was quite overwhelmed with the detailed requirements and they experienced a negative attitude from the auditors. Since the audit in 2022 we have been following up closely with this factory management but had a hard time motivating for the next steps especially regarding social dialogue and training. It’s understandable as Icebug is demanding a lot from the suppliers, not only about labor conditions. Icebug initiates several pilot projects within other sustainability areas such as FSC certification, solar energy project and we ask for detailed BOM lists and energy calculations in order to calculate climate footprint. Even if Icebug wishes to follow the Fair Wear recommended timetables for the CAP and actions taken, we see that we need to take the factories total workload into concern and make adapted schemes for them. With that said we also make it clear when progress is too slow from the factory’s side regarding social dialogue and necessary trainings and that we expect factory partners to have an ambitious development agenda, both when it comes to social and environmental issues.
The fact that we collaborate with other brands was and is crucial to do the follow up of the audit findings and CAPs for 100 % of the assembly factories during this short time (big thanks to these brands!). The past year we continued the needed CAPs follow up but also focused more on finding root causes and do deeper risk evaluations.
Evaluations of new material suppliers (Tier 2, not included in the Fair Wear scope) are regularly ongoing. The selection process is made with clear sustainability criteria regarding material properties and responsible raw material sourcing. Working conditions are often part of sustainable sourcing certifications such as Forest Stewardship council (FSC) for the natural rubber in outsoles and leather Working Group for leather. However, there is need for clearer criteria of material suppliers’ social conditions. This will be the next level of Icebug’s risk assessment after covering all Tier 1 factories.
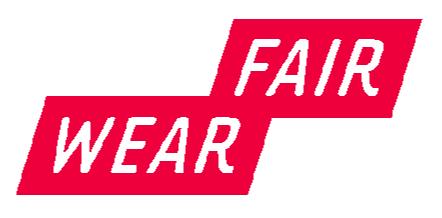
System for monitoring and remediation
In a coherent monitoring system, the different monitoring activities give understanding of the risks and opportunities within the supply chain. During the last year Icebug has undertaken the following actions to monitor and remediate problems in Icebug’s supply chain:
In addition to regular visits by Icebug’s employed QC, the HQ part of Icebug’s Development & Production Team has visited the two factories in the Ho Chi Mihn area twice during the financial year (June 2023, November 2023) and also in March 2024, and the factory in Hanoi area in November 2023 to follow up the CAPs on site, discuss social dialogue, overtime and living wages. We had factory tours for CAP follow-up and valuable discussions with the factory management and the workers representants at all three factories. We also visited accessory producers Yi Chang in November 23 and March 24 and insole producer in March 24, as well as some key material suppliers of Suede leather, outsoles and midsoles.
During 2023/24, Icebug met the workers representants of the assembly suppliers and hope to develop a closer engagement with them to strive for a deepened social dialogue between workers and management. We have identified need for training of some manufacturers and their employees about the Code of Labor Practices. We did a try to restart the suppliers’ self-assessments by the Higg FLSM facililty social labor module however this was not fully delivered during 2023/24 (or delivered with low data quality) and we’ll continue to encourage this as a good way of doing a yearly selfassessment between the external audits.
FACTORIES IN VIETNAM
Icebug has the following Tier 1 suppliers in Vietnam, based on ruling factory list 2023/24:
Haksan, Assembly factory, Bihn Duong, Ho Chi Mihn area (Collaboration with brand Fond Of)
Great Process, Assembly factory, Bihn Duong, Ho Chi Mihn area
o Wei Jie shoes, external producer for Great Process – stitching uppers.
Fulgentsun, Assembly factory, rural Hanoi area (Collaboration with brand Salewa)
o (Fujian Sunshine, China, external production of 500 pairs of Pocket Gaiter)
Wei Sheng, insole factory, Bihn Duong, Ho Chi Mihn area.
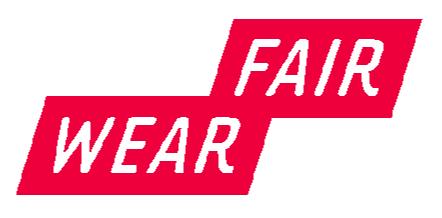
The findings of potential and actual harm by audits (Fulgentsun, 2019 external audit /Great Process Fair Wear audit april 2022 / Haksan Fair Wear audit July 2022) and factory visits for Icebug’s Vietnamese suppliers are well in line with the general risk estimates of Fair Wear country report for Vietnam.
Icebug has identified the following risks as most prioritized to follow up in Vietnam in order to raise the level to prevent future harm and to remediate actual harms that will still arise.
Freedom of association and collective bargaining
Reasonable working hours (overtime)
Payment of a living wage
Gender based discrimination
Health and Safety condition in the factories needing regular follow up
Below we describe the prioritized risk areas, the status and root causes that needs to be addressed, first per risk area (element of code of labor practice) and after that per facility. More detailed evaluation of probability and severity of potential harms are described in the risk assessment matrix (see excel files Factory risk assessments), for each factory.
Freedom of association and collective bargaining
The workers knowledge about freedom of association varied (depending on how long the brands had been member of Fair Wear and if they got education) but all has still substantial improvements to make in this matter. It was interesting to discuss the root cause with Fulgentsun Hanoi where they mentioned that some brands have zero tolerance for negative comments from workers about the facility in Social Media. The management sense a lack of trust from workers side as it is quite difficult to get workers to post suggestions and feedback, even if the idea box is situated in a place where it’s easier to do this anonymously. They also feel that workers more easily complaint in the social media than to bring it up directly with the management. Other management concerns in other Vietnam facility is that too much social dialogue would raise workers expectations to such degree that there would be risk for more strikes. The Vietnamese legislation about social dialogue is also complex and we needed guidance from Fair Wear country manager to find correct answers for some legal requirements. During last year Icebug have met the workers representatives of all assembly factories, however they often only speak Vietnamese or limited English so it’s difficult to get a discussion with them that is not “controlled” by the management.
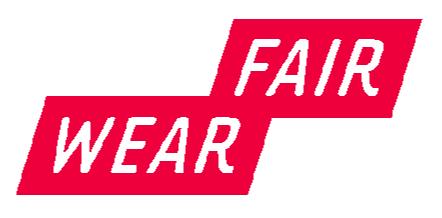
As a summary the social dialogue, engagement from workers and effective grievance mechanism still needs improvement in all factories. We did not find any direct harm to workers but believe that the risk for potential harm is still medium in general, and there is a need for more education of both management and workers.
Reasonable working hours
The audits of Icebug’s suppliers show that all three Vietnamese assembly factories and the insole producer Wei Sheng have challenges regarding reasonable working hours and use of excessive overtime. However, the past year the facilities did not report excessive overtime, thanks to production planning but also due to the lower order volumes this year where they needed to cut down on production lines. The factory managements told that some workers want to work more overtime to earn more. One factory was even afraid to lose workers to neighbour factories where workers knew they could get more overtime - this was the factory with the lowest wage level. In addition to sourcing practices and production planning, the excessive overtime issue is also clearly connected to the wage issue: if the factory pays a living wage or higher there will probably be less demand from workers for working overtime.
As a summary there is a moderate risk of excessive overtime at present, however this can change fast with rising demand, so in addition to continued good purchase planning, the issue needs to be regularly followed up with the suppliers.
Payment of living wage
Regarding the living wage, Icebug’s target is that all workers in all our Tier1 factories (not only the average) shall get paid at least the living wage referred to by the Anker method, see https://www.globallivingwage.org./countries/vietnam. We then compare the audits wage per month including bonus but without overtime (bonus is regular part of salary) with the Anker reference living wage level in the concerned area. The Vietnam assembly factories had a wage level representing an average of 87 – 144 % of the Anker living wage reference, according to the social audits 2021-22. However, with the recently updated Anker living wage references in Vietnam the proportions have changed. The latest wage update from the two factories in Ho Chi Mihn area (Binh Duong) shoew average wages corresponding to 86-91 % of the Anker reference, and for the factory based in rural area close to Hanoi it’s 116 %, so over the Anker living wage. We will revise again after the expected salary raise this summer 2024 when government will increase minimum wage with 6%, and several factories have reported plans to do the same increase.
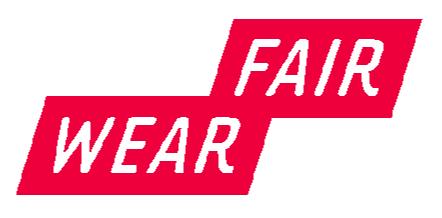
As soon as we get a robust local cost reference we will also verify the correct Anker reference for living wage for the area where our factories are situated, and see how big the gap will be to pay a living wage to all workers.
In the 2022 comparison only one factory paid average wage below the Anker living wage (13 % below) and is still lowest also in the updated comparison. In this factory Icebug initiated a living wage project with 3-4 other brands (see also page 6) to raise the living wage level at that factory. We have introduced the Fair price App and we have also examined ways to get more accurate local estimates of living wage as this has been an argument from the factory management against the living wage concept (they find the reference to be far higher than the cost level in their area). We aim to spread the learnings from this project to all Tier 1 factories we work with. So far the project needs further anchoring both with the brands’ managements and the management of the factory. The latter expressed the following concerns:
Brands often ask for reduced price, and suppliers doubt they will pay extra to close the gap to living wage.
The supplier can’t share the margins/profit, as its sensitive information and unstable (Note: they don’t have to share this within the Fair Price App or the LW project).
Supplier cannot control margin for materials from nominated suppliers, and Icebug uses much nominated material (80-90% nominated materials acc. to factory).
They don’t see big difference in their salary compared to other in industrial area: some pay by productivity and some work more overtime
Want a new LW comparison after salary increase 6 % July-24, will costs increase as well?
Level playing field: Korea owner group prefer to keep same condition in all facilities, would be easier if other Korean factories (working for big brands like Nike) implement this as well.
As a summary there is a clear risk of workers in Vietnam inc. Icebugs facilities being paid less than a living wage, leading to a stressful situation for these families. Living wages will continue to be the first priority to address for Icebug. It has proven more complex than we thought to get a full overview, but we need to establish a clear plan and speed up action to at least make sure to pay our fair share of a living wage where there is a gap.
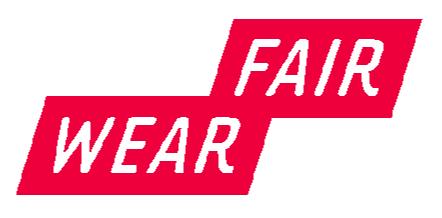
Gender based discrimination
The audit findings regarding gender-based discrimination were all solved eventually, such as lack of lactation room, childcare allowance only paid to women, and pregnant women did not get easier tasks or shorter work hours as required by law. However, we need to have a constant eye on gender-based discrimination in various ways and keep vigilant that the managements are aware of the importance of gender equality and willing to do trainings and raise awareness among management staff and workers. There was a lack of understanding of some issues from some managements, leading to interesting discussions and exposing a need for training about gender conditions as part of the social dialogue. There is a risk of potential harm and we should contribute to lower that risk by training.
Health and Safety condition in the factories
The findings regarding safe and healthy working conditions – concerning chemicals handling and smell of glue at workplaces, better ergonomics for both standing and sitting worker etc. have all been solved during the past year (what did remain since last year), with the exception of difficulties to provide short breaks in one of the factories. There is however a constant risk for new harms, however much lower with a higher awareness and good routines in place. These health and safety issues need regular reminders and good routines from staff and workers, and from the brands to do regular health and safety checks during visits. For two of Icebug’s assembly facilities the regular follow up is done together with other Fair Wear brands, which makes it easier to keep up a good level. Icebug will strengthen the routine to do either a detailed CAP follow up or a health and safety check, both with factory tours, at least once a year for all Tier 1 factories. Last year this has been done for all assembly factories, for the insole factory and for the new outsole/midsole (Tier 2) factory in Vietnam that will produce accessory Floorsaver next year. There is in general a constant low risk for harm (as the assembly factories take health and safety seriously), but if these harms arise they can have severe consequences, so the regular follow up and training of staff is crucial.
Assembly factory Great Process, GTP, Binh Duong
GTP represents 57 % of Icebug’s FOB and is the most prioritized factory as long-term partner, and also the only that is not supplying other Fair Wear member brands The estimated leverage in GTP is 21 %. We did continued CAP follow up of remaining findings and had several discussions with factory management about how to increase the social dialogue and do trainings. All practical findings in the factory were eventually solved, except for the finding that Short breaks are not provided as required by laws and regulated in factory's labor regulations. In addition to this, there are concerns from the management making it difficult to reach the next level of social dialogue.
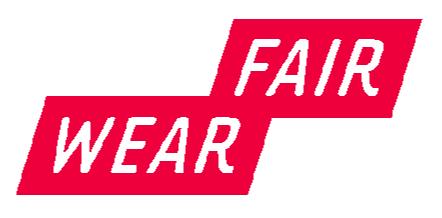
The Fair Wear audit in April 2022 showed that GTP average salary was 1o0 % of the Anker living wage (315 USD per month). Comparing January 2024 wages with the updated Anker reference 2023 showed that GTP average salary is now 91 % of the Anker reference. We will follow up again after the wage increase in July 2024, and hopefully apply findings from Haksan living wage projects as the two factories are in the same area with same cost level.
Icebug visited GTP in June and November 2023 and in March 2024. There has been a challenge to reduce excessive overtime, however at present this is not found to be a problem due to good planning and low order volumes. A concern that remains is to improve the social dialogue between workers and management. Icebug have repeatedly proposed to do a work place training in social dialogue. The management has turned down to do Fair Wear trainings and Icebug have found and proposed other alternatives as well. The management also have refused to provide short breaks as this will disturb the production. Icebug will need to show clear examples of other shoes factories, and how this can be done in a good way.
Wei Jie, GTP outsourcing - stitching uppers, Ho Chi Mihn area
62 300 pair uppers were stitched in Wei Jie, with order value 43 000 Euro, representing 0,5 % of Icebugs total FOB and with a leverage of 35 %. Wei Jie has been informed about Fair Wear Code of labor practice and posted the Fair Wear worker sheet on the wall. Initial visits with health and safety check were performed by Great Process and reported to Icebug in February 2022. In first GTP Health and Safety check they found need for improvements regarding emergency lights, emergency exits, standing work ergonomy. All findings were efficiently improved and reported with pictures.
Haksan (Viina), Ho Chi Mihn area
Icebug buys 24 % of our FOB from Haksan and have an estimated leverage of 5 %. Latest Fair Wear audit was made in July 2022 shared by German company Fond of and Icebug. All practical findings in the factory were solved very efficiently, and the main topic now is how to achieve payment of living wage to all the workers, as this factory pays lower wages than the other in the same area. A living wage pilot project have been started in collaboration between 4-5 brands sourcing from this factory and we presented a possible project plan to the Haksan management and sustainability team in Icebugs visit in March 2024. Icebug also visited Haksan in June and November 2023.
The Fair Wear audit results in 2022 showed that Haksan average salary was 87 % of the Anker living wage (272 USD per month). The updated wage data and higher Anker reference in 2023 lead to even
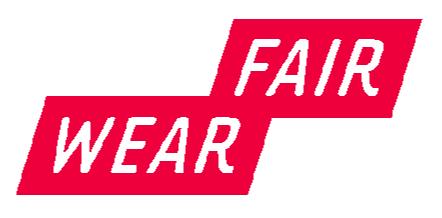
bigger gap to the living wage reference, now at 76 (lowest paid worker) to 86% for average paid, so we see a need for a general wage raise for most of the workers. The living wage project (see more above) aims to break down the costs into labor costs (cost per minute) so that we can link the labor costs more correctly to the purchase costs.
Fulgentsun, Hanoi region (rural area)
Icebug bought 14 % of our FOB from Fulgentsun in 2023/24 and have an estimated leverage of 1,2 %.
Latest external social audit by Sumations was conducted September 2021 to April 2022. It was initiated by Salewa/Jack Wolfskin (also Fair Wear member brands).
In November 2023 Icebug visited Fulgentsun Hanoi (Icebugs site is 35172 Fulgentsun). All practical findings in the factory have been solved efficiently. The main topic now is how to create trust between the management and workers to get a more engaged social dialogue, and also to achieve payment of living wage to all the workers. Even if their average wage was clearly above the living wage reference in last audit, Fulgentsun management is interested in the living wage project.
Icebug’s review of salary level in 2022 shows that Fulgentsun is paying above living wage for all workers, the average wage was 144 % referring to the Anker living wage reference in rural area zone 4. With updated Anker reference November 2023 and latest wage from Fulgentsun data the current average wage is still over the Anker reference, while the lowest paid worker gets 97% of the living wage. To be followed up after expected general wage raise in Vietnam this summer.
Wei Sheng insole producer, Ho Chi Mihn area
The insoles production last year represents 4 % of Icebugs total FOB with leverage 0,1 %.
An external social audit was done by Intertek in August 2023, resulting in overall facility score 90 % which is regarded as good (average country score 83%). All Health and safety findings were solved efficiently and other main findings were excessive overtime, which needs regular follow-up. Intertek found the average wage level to be high 11,1 mill. VND, however in the visit in March 24 Icebug was told it is 8 mill VND so we need to look closer at this and compare it with the Anker living wage.
Icebug visited Wei Sheng in Match 2024 and did a Health and Safety check with satisfying result. The manager told that the overtime is at present within the regulated hours (max. 12 h per week and 30 h OT per month), however workers would prefer more overtime.
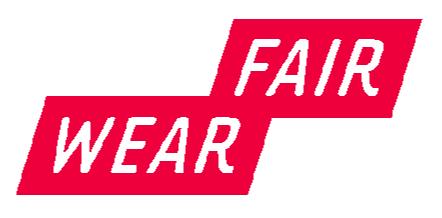
Yi Sing midsole and outsole producer, Ho Chi Mihn area
Yi Sing is a new facility of the Yi Chang group, established during last fiscal year. During 2023/24 Yi Sing was a Tier 2 supplier (not in the Fair Wear factory list) of midsoles and outsoles and in 2024/25 the Overshoe/Floorsaver branded accessory will be produced by Yi Sing.
Icebug visited Yi Sing in November 2023 and March 2024 and did a health and safety assessment with overall satisfying result. The average wage is app. 8 mill VND and lowest paid worker 6 mill VND, which we will follow up closer regarding living wages.
FACTORIES IN CHINA
Icebug has only a small production of 500 Pocket gaiters (accessories) in China, produced by: Fujian Sunshine Ltd. - Pocket Gaiter accessory, Fujian, China as outsourcing production for Fulgentsun Vietnam, and the pocket gaiters have been included in the bigger Fulgentsun Vietnam order. FGS China has same owner as FGS Vietnam and also has other Fair Wear members as customers. The Gaiters represent 0,05 % of total FOB with leverage 0,03%.
The VF brand made the latest external social SLCP audit in april 2023, showing that moderate issues were identified in: • Insufficient social insurance coverage • Insufficient machine safety management practice. The resulting designation was set at Accepted - SLCP. All remaining issues were solved before summer 2023. Icebug HQ staff have visited this factory both in November 2023 (sustainability manager doing a factory tour checking Health and safety issues but not in a formal assessment) and in March 2024 (product development). When Icebug Fair Wear responsible person became aware of this outsourcing there were already orders made for 2024/25, and the plan is to move the pocket gaiter production to Fulgentsun Vietnam for FW25.
Icebug also sources materials from China: in total 30 materials in Trustrace (our traceability platform) are produced in China and approximately 10 of them are nominated suppliers or suppliers where HQ has been involved in sourcing process: Hempfortex, Tiong Liong, Feiteng, Fullxin, BOA, Michelin, Gore (Cosmo) and Guosheng midsole.
Stopped buying safety shoes from Ironsteel / Dongguan Qiaomai Shoes, China
Ironsteel produced safety shoes for Icebug, certified according to EN ISO 20345 S3. Icebug bought less than 2 % of our FOB from Ironsteel (251 000 USD during 2022/23) and had a leverage of less than
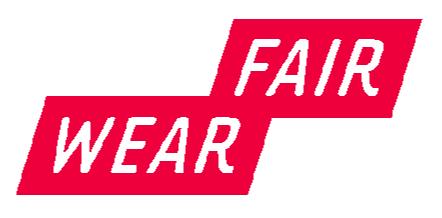
1 %. For several reasons Icebug decided to stop producing safety shoes - commercial reasons and sustainability reasons; the safety shoes had less sustainability features that Icebugs other styles and also higher human rights risk. As Icebug had very low leverage in this factory we did not follow a specific exit plan as we don’t estimate our small share to have a substantial influence on the workers conditions
Risk evaluation in China
The audit findings for Icebug’s previous Chinese footwear supplier Ironsteel were in the same areas as the findings of the Vietnam audits. However in addition to the mentioned prioritized areas above (FOA, Overtime, wages, health and safety issues and gender based discrimination) the country risk of forced labor must be specially considered when producing in China. The Fairwear Webinar in January 2024 about the specific risk of Uyghur and minority Forced Labor in China focused on how widespread this problem is and how difficult it can be to discover.
Icebug has identified that China represents a general human rights risk that is too high to motivate to seek NEW Chinese suppliers. Icebug’s key Tier 2 key supplier Yi Chang recently moved the outsole production from China to Vietnam and Icebug has no plan for future shoe production in China.
Stopped buying safety shoes from Ironsteel / Dongguan Qiaomai Shoes, China
Ironsteel produced safety shoes for Icebug, certified according to EN ISO 20345 S3. Icebug bought less than 2 % of our FOB from Ironsteel (251 000 USD during 2022/23) and had a leverage of less than 1 %. For several reasons Icebug decided to stop producing safety shoes - commercial reasons and sustainability reasons; the safety shoes had less sustainability features that Icebugs other styles and also higher human rights risk. As Icebug had very low leverage in this factory we did not follow a specific exit plan as we don’t estimate our small share to have a substantial influence on the workers conditions.
ACCESSORY FACTORIES IN SWEDEN, TAIWAN AND INDONESIA
Except for Vietnam and China production, Icebug’s production of insoles and accessories was purchased from the following suppliers during 2023/24:
Topiku LLC, caps, Indonesia via US agent (0,1 % of total FOB and estimated 2 % leverage)
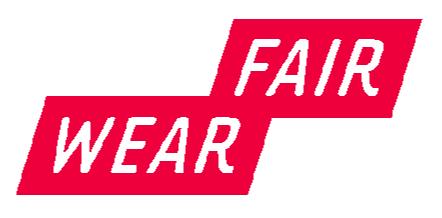
Topiku has B Corp Certification , scoring high on Community and Supply chain poverty part of their business model. They have the Supplier code of Conduct, Code of Ethics, and Modern alleviation as Slavery Policy available on their website https://www.topiku.co/impacthttps://www.topiku.co/impact
However we did not get any audit report of the Indonesian production site. Shortly after Topiku was onboarded it was clear from commercial side that we would not make reorders, so no further assessments of follow up was conducted from Icebug.
Yi
Chang,
Taiwan,
Floorsaver/overshoe (1 % of total FOB with leverage 2 %)
Icebug HQ staff visited Yi Chang factory in Vietnam in November 2023 and met the owner several times during visits in his new Vietnam factory Yi Sing (see above). No regular health and safety check was done in the Taiwan factory, however no serious findings during factory tours, and the production of Overshoe/Floorsaver is already moved to Vietnam for next year to consolidate the sole production.
Two swedish suppliers and one Indonesian supplier were onboarded for production during 2024/25 and Cansocks was already in the factory list:
Cansocks AB: Branded socks since 2021/22 (less than 1% of FOB, 2 % leverage).
Smellwell AB: Branded Shoe care products for webshop sale.
Paper street clothing company/NoPalmtree: Branded second hand T-shirts
PT Cap Global industry international, Indonesia via agent DoGree Caps, Italy.
Further information about these suppliers will follow in next social report.
Complaints handling
In February 2023 Icebug received the first complaint via Fair Wear helpdesk relating to Living wage; Legally binding employment relationship. The complainant was a worker at Haksan in Vietnam who was dismissed after coming back late form the Chinese New Year due to transport problems. In collaboration with Fond of we asked for explanations from the factory management and the complaint was solved by the parties reaching a settlement agreement. The past year we did not receive any complaints.
To make sure workers at Icebug’s suppliers are aware of the Fair Wear complaint mechanism, we have asked the factories to post information sheet about Fair Wear well visible to the workers. There
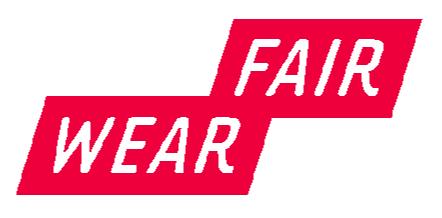
is a Fair Wear contact phone number, encouraging to report any complaint and with promise to treat it confidentially: “Fair Wear will always treat your complaint confidentially”.
It’s crucial to appoint clear responsibility for handling Complaints as it will always be urgent to solve. Icebug have appointed two persons who can deal with complaints and make sure someone is available also during holidays.
Training and capacity building
ACTIVITIES TO INFORM STAFF MEMBERS
The following activities were undertaken to inform and train the Icebug staff, in HQ Sweden and at sales offices in Germany and US, about Fair Wear membership:
Presentations of Fair Wear code of labor practice and planned activities at Sales kick off meetings for SS24 (May 2023) and SS25 (May24)
Fair Wear and working conditions in supply chain are included in Icebugs sustainability base education, for all employees, and in sustainability team workshops, 230421 and 240315.
Presentation of Fair Wear and Icebugs membership in Workbook sales material from seasons SS22 and all coming seasons.
Presentations of details in the Responsible Business Conduct Policy for Vanbestco team in Taiwan November 2023.
Icebug training Fair Wear Onboarding process, 240308, Onboarding process with sourcing agent VBC, relevant sourcing teams of Icebug including webshop product and accessories where we needed higher awareness about the requirements for even small volumes of branded products.
ACTIVITIES TO INFORM AGENTS
The following activities were undertaken to inform and train the sales agents of Icebug about Fair Wear:
Presentations of Fair Wear code of labor practice and planned activities at Sales kick off meetings for SS24 (May 2023) and SS25 (May24)
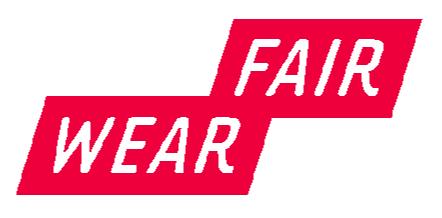
Presentation of Fair Wear and Icebugs membership in Workbooks (sell in Collection cathalogue) from seasons SS22 and coming seasons.
ACTIVITIES TO INFORM MANUFACTURERS AND WORKERS
Icebug have met workers representants in factory visits at each assembly factory, and also at Wei Sheng insole supplier. In the meetings we presented the Responsible Business Conduct Policy in detail and what we expect from the suppliers, and what they can expect from us.
In all factory visits we checked that the workers sheet, with the eight elements of the code of labor practice, was still posted in a visible way. Some places it had become sun bleached and the factory replaced it with a new workers sheet.
Icebug have not arranged any specific training at facilities during last year. We have repeatedly proposed different levels of social dialogue training with one assembly factory but without success so far, even when Icebug offered to pay the training. We will continue to promote this essential topic.
Haksan sustainability team participated in a BSCI training including discussions about living wage and how to calculate living wage based on local living costs, that they shared with Icebug. A proposal for the local Bihn Duong region was presented that Icebug showed to Living wage expert Do Quynh Chi from Research Center for Employment Relations (ERC). However, she found that the proposed living wage was too low, and proposed to show us the correct method for gathering living cost data.
Information management
Icebug will keep track of progress on the implementation of the Code of Labor practices by following up on social indicators and report yearly progress about these in Icebug’s sustainability impact report. Some will also be displayed via the Follow the Footprint QR code where we display all suppliers under “Product journey” https://Icebug.com/footprints. Initially for assembly factories and then for
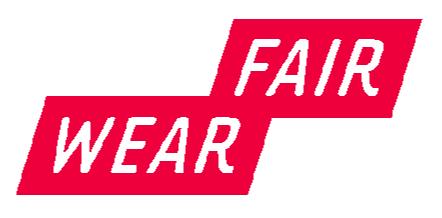
material suppliers (Tier 2) and raw material suppliers (Tier 3). We still have a work to do to define those indicators, some early ideas are:
Supplier level, display some of them in Follow the footprint product journey:
Average wage, % of the relevant living wage for that area (above 100 % is acceptable).
% of workers that get on or above living wage level (should be 100 %).
% of woman workers
% of workers that got training in Code of labor practices
Complies to X of 8 CoLP practices (1-8), confirmed by Fair Wear audit/external social audit
If not compliance, areas to improve: name relevant issue of 1-8 in CoLP
Latest Fair Wear audit/external social audit of the factory: YYMMDD
Has democratically elected worker representatives in Union and CBA
We welcome feedback and ideas to social indicators.
Transparency & communication
Icebug makes a yearly impact report where we describe overall sustainability targets action and progress, including social issues, https://Icebug.com/sustainability/reports#Icebug-impact-reports see pages 34-37. Fair Wear is mentioned on Icebugs web page: https://Icebug.com/sustainability/reports#fair-wear-foundation-reports
Fair Wear and to commit to Code of labor practices is also an important part of “our promise” https://Icebug.com/sustainability/our-promise#wages
We sometimes posts in social media on our engagement in Fair Wear. Our Instagram and Linkedin channels have approximately 40.000 followers and so have the Facebook account. Icebugs newsletter have approximately 60.000 subscribers.
We don’t always mention Fair Wear by name, but fair working conditions is one of the recurring themes of our brand communication.
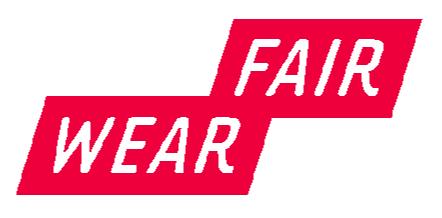
Stakeholder engagement
Icebug has increasingly started to address the views of stakeholders and what impact the company’s activity has on different stakeholders. The directive from the owners clearly points out nature and society as stakeholders prioritized over the shareholders, specifically mentioned stakeholders are also employees and suppliers. It is understood that employees of suppliers is also an important stakeholder, direct and as a part of society https://Icebug.com/explore-Icebug/owner-s-directives
Stakeholder meetings
During the year Icebug has sought deeper knowledge about relevant labor conditions through input from various stakeholders, like Fairwear meetings on specific topics, other brands both Fair Wear members and non members sourcing in “our” factories. We approached labor experts in NGO and research organisations in Vietnam. We often seek collaboration to share experience and develop.
We use the Fair Wear stakeholder resources such as country studies to do the HRDD risk scoping and also to generally get better knowledge on labor conditions in diffrerent countries. The Fairwear Webinar in January 2024 “Uyghur and minority Forced Labor in China” gave valuable insights into how widespread the forced labor problem is and how difficult it can be to discover. Icebug will look closer into this when sourcing materials, especially labor intensive fibers like hemp farming. At present Icebug don’t use hemp but we’ll stay vigilant if redoing hemp sourcing.
In March 2024 Icebugs sustainability manager met Fair Wears Vietnam country manager Duong Thi Viet Anh in Hanoi and by her recommendation she also met with labor expert Ann Dinh at the Center for Development and Integration (CDI Vietnam) and researcher Do Quynh Chi from Research Center for Employment Relations (ERC), all in Hanoi. The meetings gave valuable insights:
Fair Wear gave detailed answers about the Vietnam legislation laws regarding CAP findings where the local union did not give clear answers, and the same questions kept coming back in the CAP follow up meetings without clear direction: regulated short breaks and the requirements about workers representation in the social dialogue with the employer.
CDI developed the WE CHECK app, with the consultation with experts (on labor and occupational health), lawyers, MSI (FW, Electronics Watch, RBA, ...), and workers. The aim is to inform workers about labors rights, get workers complaints regularly, and encourage workers to do self- assessment twice a year. CDI analyze data, develops report and share to
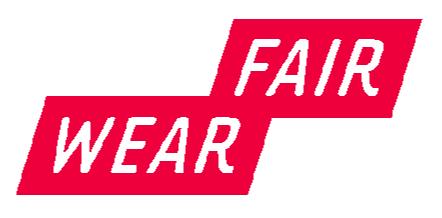
relevant stakeholders. CDI have presented this to Fair Wear in order to use in factories while keeping the independence of the app and safety of workers, a delicate balance. Icebug will follow up on this development and potential use of the app in our factories.
CDI, in collaboration with ERC, is conducting research to gain a better understanding of human rights due diligence in the apparel sector in Vietnam. For this research, they conducted in-depth interview with Icebug as a brand sourcing from Viet Nam.
The ERC researcher is expert of Anker living wage calculation methodology that has been part of ongoing revising of the Anker references in Vietnam. She gave her view on a proposed BSCI estimate for Bihn Duong that she found clearly too low, and offer to explain ERCs living wage tool kit for Icebug and other fellow brands, to make a Binh Duong estimate.
Both CDI and ERC offers social trainings to workers and managements, that we consider.
Icebug engages with several stakeholder groups both in Europe and in production countries to raise various key topics/concerns through stakeholder engagement. Icebug is member of Forest Stewardship Council, FSC Sweden – a certification of sustainable forestry that has labor condition requirements in the standard and will affect the labor conditions in the supply chain of FSC certified materials that we use (so far Icebug has certified natural rubber and carton).
Social issues are a big part of the holistic sustainability B corps certification where Icebug was approved as a B corps in 2022, see https://www.bcorporation.net/en-us/find-a-bcorp/company/Icebug-ab/. Icebug is also member of 1 % of the Planet where we support sustainability NGO’s and organisations working for inclusion, as Inclusive Business Sweden, Hej Främling! and Build Up Nepal, building climate smart earth quake restistent homes in Nepal.
Corporate Social Responsibility
Icebug has put increased focus on inclusiveness in different ways. Icebug
Inclusive business in the supply chain: Icebug initiated a sourcing project with Inclusive business Sweden and FSC international, aiming at enabling small rubber farmer cooperatives in Thailand to connect their supply of FSC certified rubber with the demand side in the footwear industry. The FSC certification includes social working conditions and the project aims to enforce the farmers to stay independent compared to working for big rubber plantations.
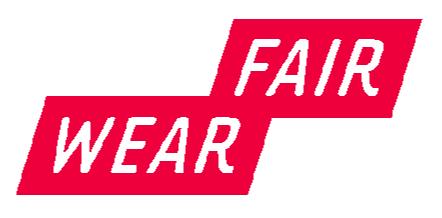
Inclusive design and marketing: Icebug also focus more on inclusive design and marketing to target a more diverse group of customers in our marketing, feeling welcoming for all and make sure we are a driver towards no discrimination of any kind (gender, rase, age, sexuality, disability or other).
Inner development Goals: During 2022 to spring 2024, Icebug has been doing a pilot project for all employees where we explore the so called Inner development Goals, and how our inner development can help us act more aligned with what will be required to face/solve the sustainability challenges of our time. https://www.innerdevelopmentgoals.org/
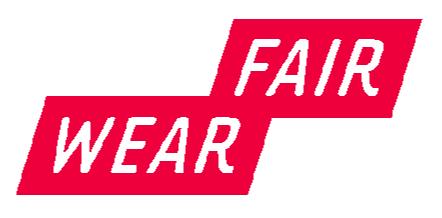