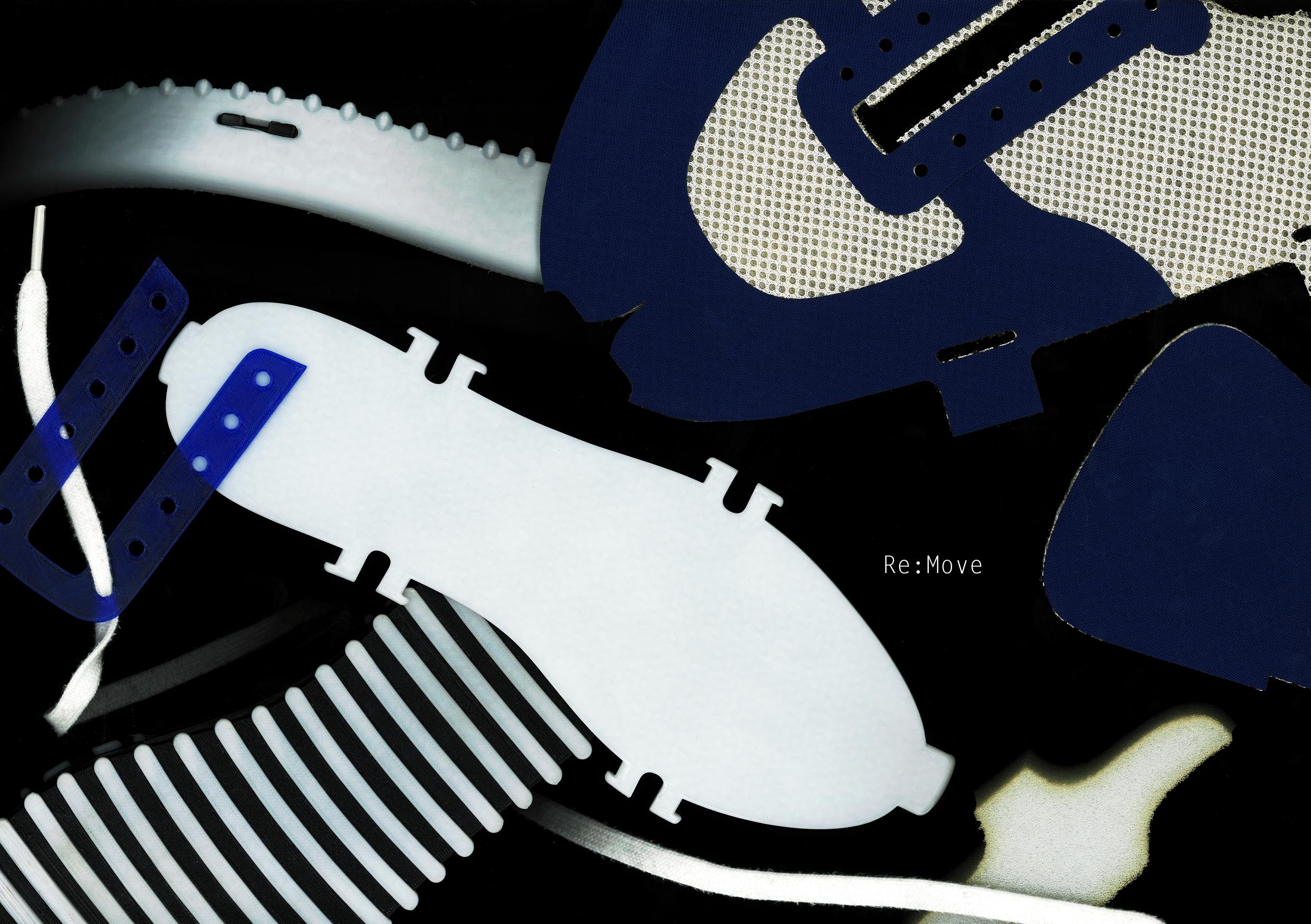
Dokumentation
HSLU D.F.K.
OBJEKTDESIGN
BACHELOR 2025
DOKUMENTATION
AN: OD KLASSE MY MOM MY GF
ANDREAS SAXER
THAI HUA
MENTORAT: ANDREAS SAXER
VERA SACCHETTI
LEA SCHMIDT
URS LANDI
Abstract
Die Schuhindustrie ist heute geprägt von kurzlebigen Modellen, klebstoffbasierten Fertigungsweisen und schwer trennbaren Materialkombinationen – ein System, das Reparatur und Recycling nahezu unmöglich macht. Der zunehmende Konsum verschärft dieses Problem zusätzlich: Schuhe werden oft gekauft, bevor die alten verbraucht sind, und landen schnell im Müll, obwohl sie kaum recyclebar sind.
Angesichts wachsender Müllberge und eines globalen Überkonsums von Schuhen entwickelt dieses Projekt
ein modulares Gegenmodell: Re:Move stellt konventionelle Macharten infrage, indem Sohle und Schaft mechanisch miteinander verbunden sind – ganz ohne Klebstoff. Die einzelnen Komponenten bestehen aus sortenreinen Monomaterialien und lassen sich dank eines Stecksystems nicht nur einfach austauschen, sondern auch vollständig recyclen. Das Ergebnis ist ein zirkuläres System, das materialbewusstes
Design, Reparierbarkeit und ressourcenschonenden Konsum miteinander verbindet.
Schriftliche Arbeit
Welche Faktoren haben im Laufe der Zeit das Konsumverhalten gegenüber Schuhen beeinflusst und geprägt?
- Geschichtliche Analyse des Konsums
- Analyse des Konsums heute + Umfrage
- Ein Blick auf die Industrie
= Früher wurde Sorge getragen und repariert.
Heute wird zu viel produziert und sehr viel konsumiert.
- Fallbeispiele von Marken mit konsumbewussten Aspekten:
Reparaturfreundlich, nachhaltige Produktion / Material
Eine Lösung = modulares Schuhsystem
Ein modulares Schuhsystem beschreibt einen Aufbau, bei
dem der Schuh aus separaten, funktional verbundenen Einzelteilen besteht – typischerweise Sohle, Schaft und Innenschuh – sowie einem Verbindungssystem, das die Komponenten zusammenhält. Ergänzt wird dieses durch eine Schnürung oder Bindung, die den Schuh am Fuss fixiert. Durch diesen Aufbau kann vollständig auf Klebstoffe oder irreversible Verbindungen verzichtet werden. Die einzelnen Teile lassen sich unabhängig voneinander austauschen, reparieren oder individuell anpassen.
Schnürung/Bindung
Schaft
Verbindungssystem
Laufsohle Innensohle
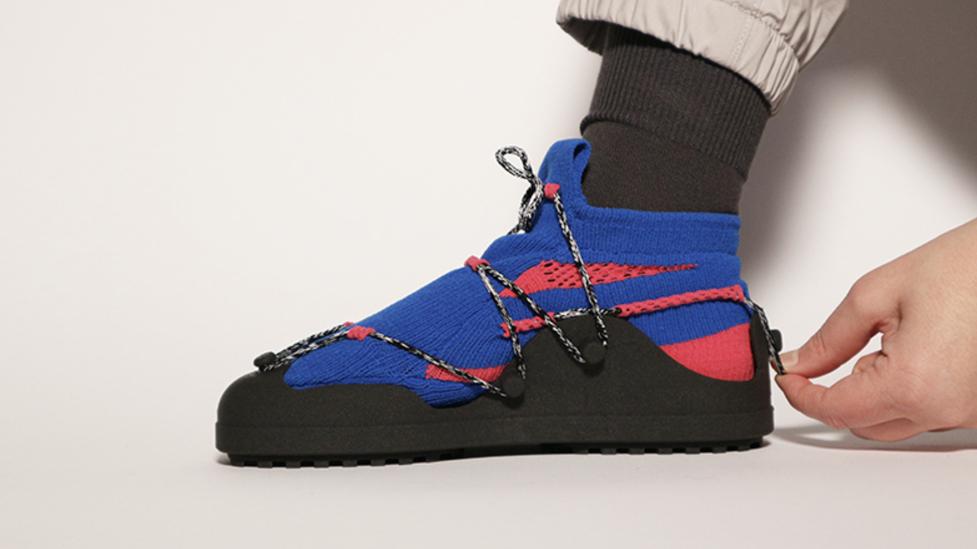
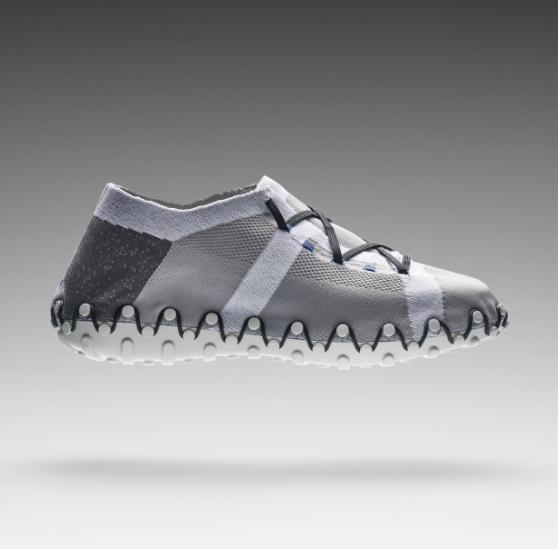



Viele bereits existierende modulare Schuhkonzepte werden von aussen durch Schnürungen oder sichtbaren Verbindungen zusammengehalten, was sie deutlich als modular erkennbar machen. Mein
Ziel ist es, ein System zu entwickeln, bei dem die Verbindung der Einzelteile aus dem Inneren des Schuhs funktioniert. Auf diese Weise würde der Schuh optisch wie ein herkömmlicher Schuh wirken, jedoch modular und funktional trennbar bleiben.
Designprozess
1. Schritt: Design des Systems (Machart)
- Entwicklung der Grundkonstruktion
- Verbindung zwischen Schaft, Zwischensohle und Sohle
- Definition der mechanischen Verbindung
2. Schritt: Design der Optik der Einzelteile / Prototypisieren
- Entwicklung eines Kollektionsgedankens
- Material- und Farbauswahl
- Gestaltung und Umsetzung erster Modelle
3. Schritt: Testen & Adaptieren
- Überprüfen von Passform, Ergonomie und Funktionalität
- Nutzerfreundlichkeit und Handhabung bewerten
4. Schritt: Potenzielle Materialien für industrielle Fertigungsmethoden
- Fokus auf Monomaterialien
- Recyclingfähigkeit
- Übertragbarkeit auf industrielle Prozesse
5. Schritt: Evaluation und Ausblick
- Analyse der Stärken und Schwächen
- Bewertung des modularen Verbindungssystems
- Potenzial für Variationen
- Weiterentwicklung und Zukunftsfähigkeit
ERSTE IDEE

Durch die Modularität eines funktionierenden Systems
können verschiedene Schäfte mit derselben Sohle oder potenziell auch anderen Sohlen kombiniert werden.
Somit werden unterschiedliche Varianten innerhalb eines Baukastensystems ermöglicht.
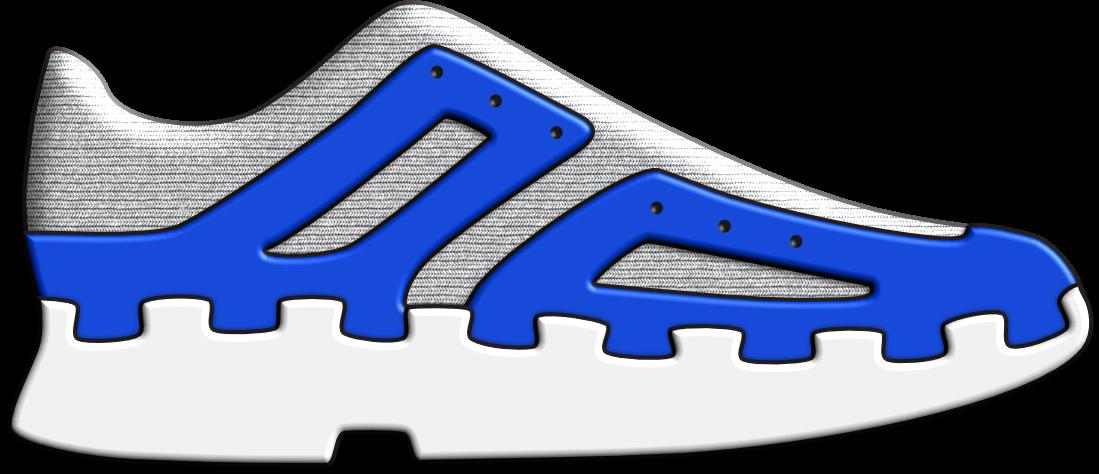
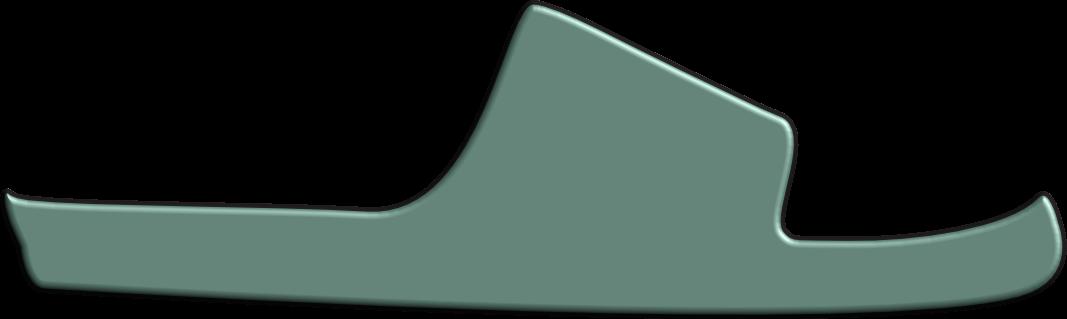

MODULAR SYSTEM IDEAS
Wie kann ein solches System konkret aufgebaut sein?
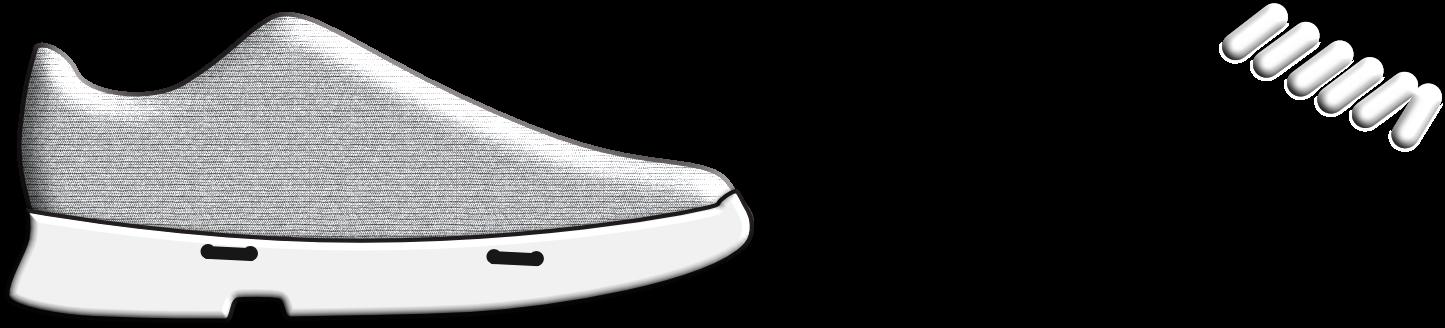
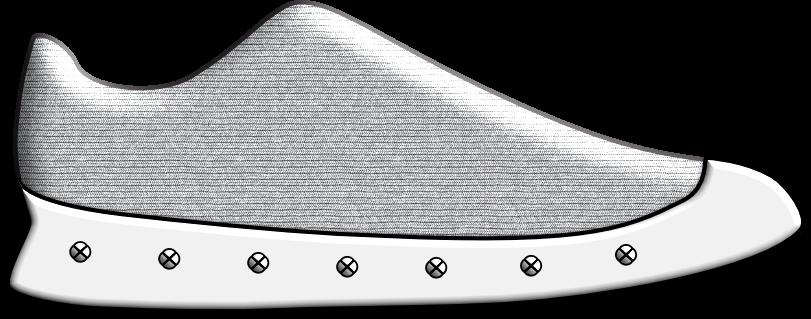
- Etwa durch eine Art Stecksystem, bei dem Sohle und Schaft mechanisch verbunden werden und zusätzliche Elemente von aussen angebracht werden können.
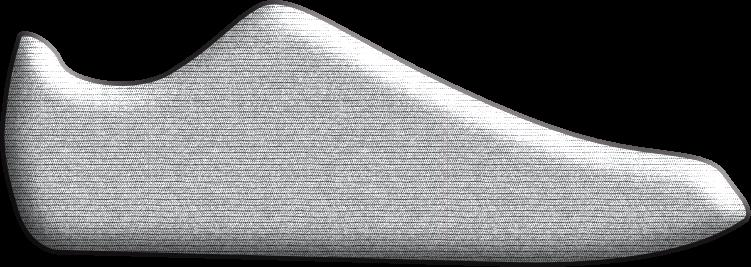
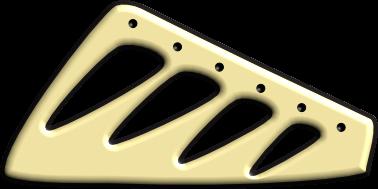

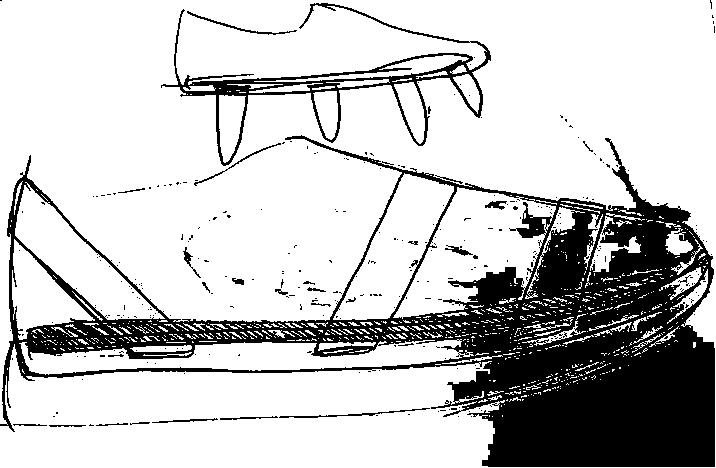
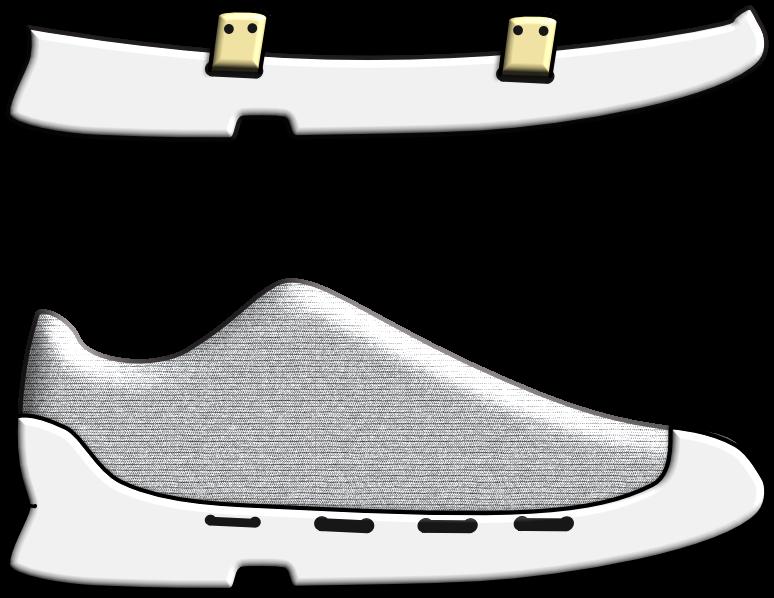
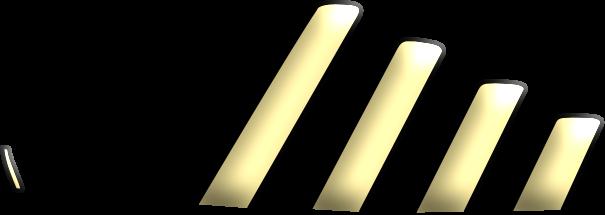
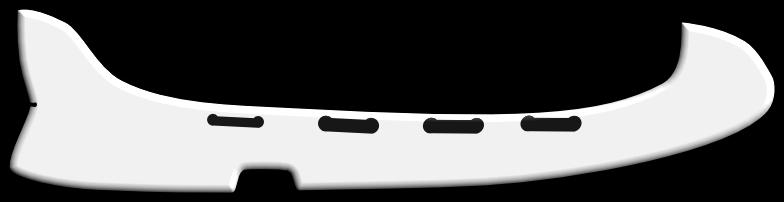
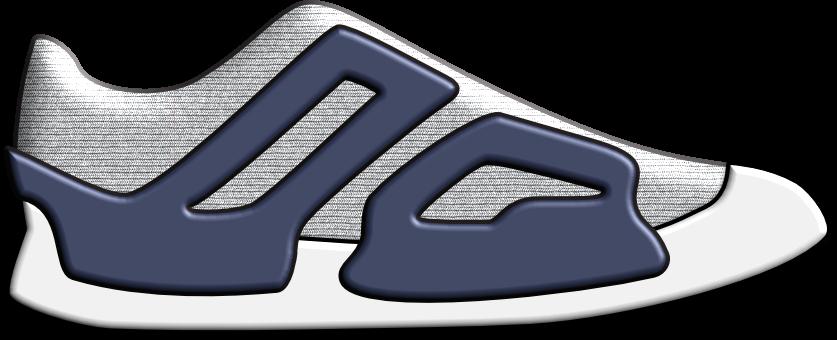
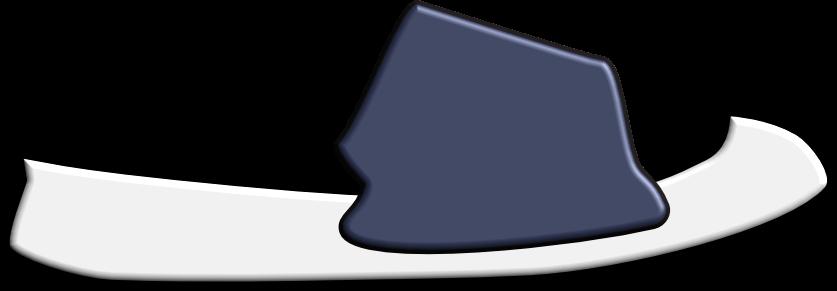
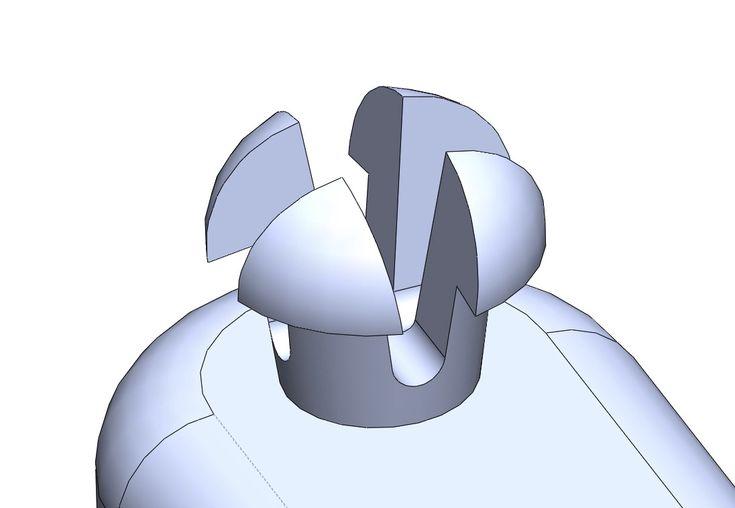
Die erste Sohlen- und Systemidee wurde mit dem CAD Programm Rhino entwickelt und im 3D-Druckverfahren umgesetzt. Für den Umriss diente eine einfache Einlegesohle in meinem Schuh. Dafür kam TPU (Thermoplastisches Polyurethan) zum Einsatz – ein elastisches und zugleich robustes Material, das auch in der industriellen Schuhproduktion häufig für Sohlen verwendet wird. Hier würde der Schaft als Socke unter die Zwischensohle ragen und die seitlichen Riemen der Zwischensohle durch den Schaft und Sohle gehen. Die Riemen würden hier als Möglichkeit dienen, Schaft und Schnürteile anzubringen.
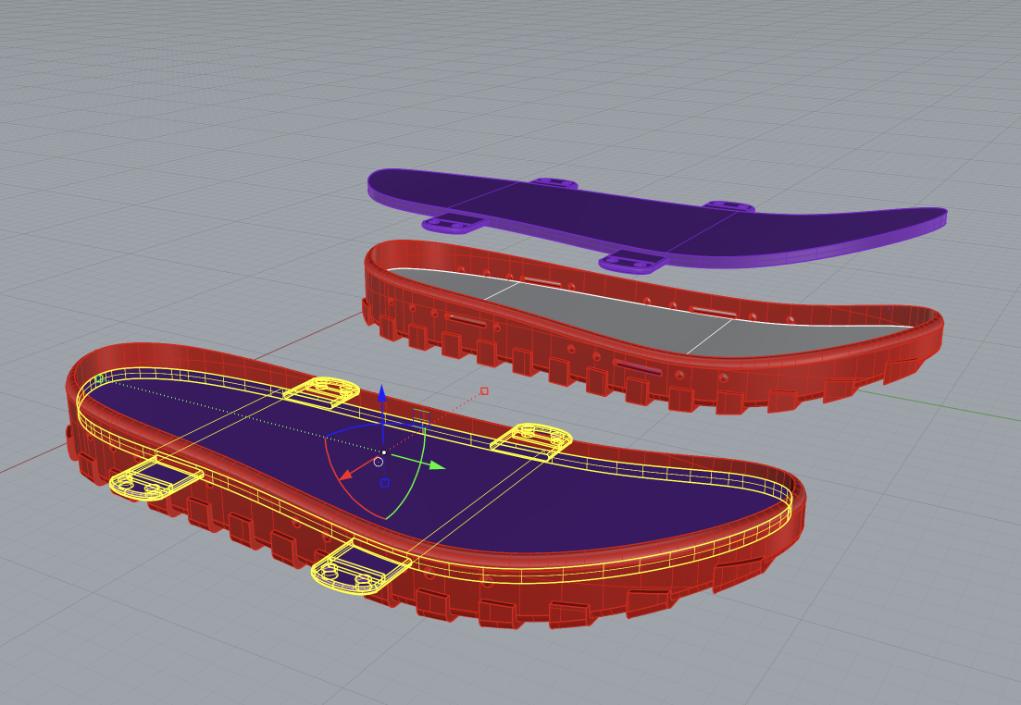
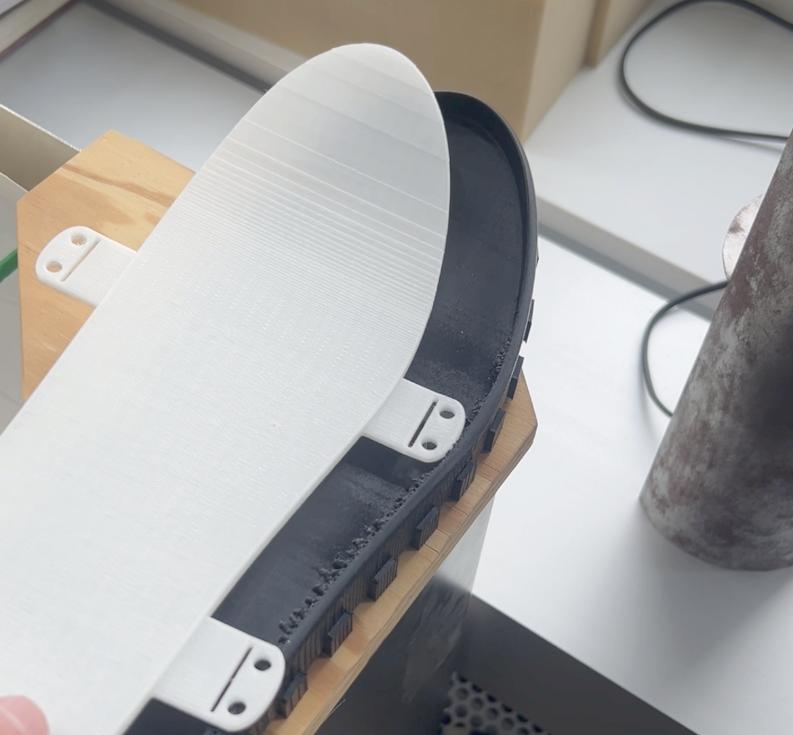
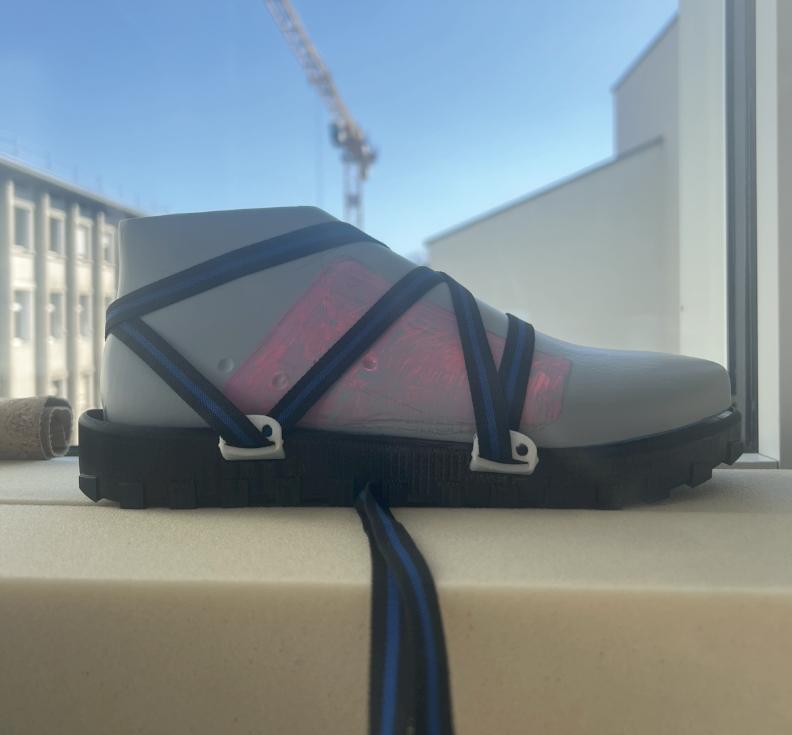
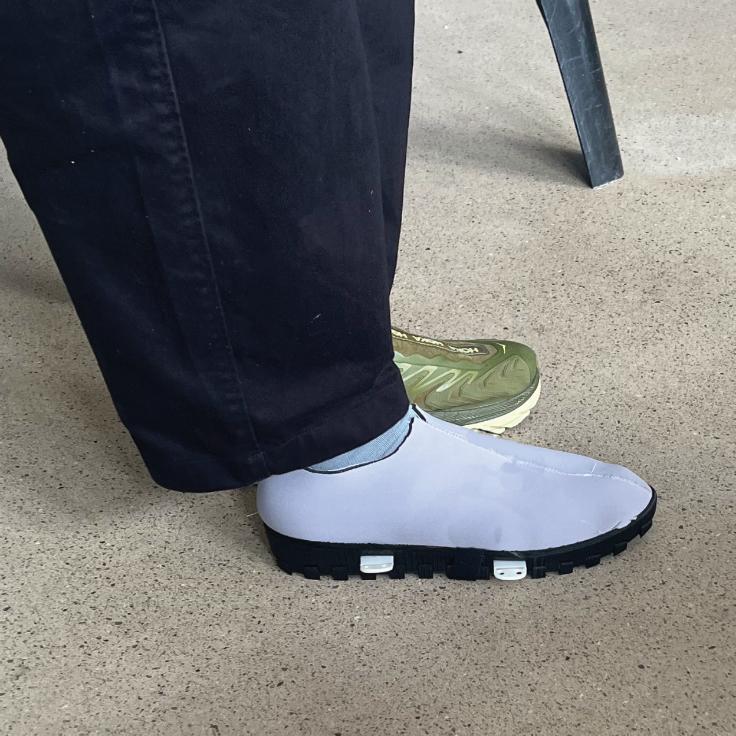
3D Strick?
Ich besuchte Herrn Urs Landi in seinem Atelier in Turgi (AG), um die Möglichkeit zu besprechen, einen Sockenschaft mittels 3DStricktechnologie herzustellen. Dabei zeigte sich, dass seine Produktion in Materialwahl und Schnitt stark eingeschränkt war, da nur ein bestehendes Strickprogramm einer anderen Schuhmarke zur Verfügung stand. Eine Umsetzung wäre grundsätzlich möglich gewesen, jedoch wäre die Integration der Aussparungen für das Stecksystem nur schwer realisierbar gewesen und hätte viel Entwicklungsaufwand gefordert.

Urs Landi bot alternativ die Möglichkeit an, flächige Strickteile im 3D-Strickverfahren herzustellen, die ich anschliessend in die gewünschten Schnittformen auslasern würde. Dadurch wäre eine grössere gestalterische Freiheit bei der Formgebung möglich gewesen, allerdings mit zusätzlichem Arbeitsaufwand und Unklarheiten in der Weiterverarbeitung.
Ich entschloss mich, den Schuh auf klassische Weise zu konstruieren und ein eigenes System zu entwickeln, um den Schaft mit dem Stecksystem zu verbinden.
Ziel war es, eine individuelle Lösung zu finden, die unabhängig von externen
Produktionen funktioniert und sich passgenau in das modulare Gesamtsystem mit den mir vorhandenen Mitteln integrieren lässt.
Daraufhin nahm ich Kontakt mit dem Forschungsteam von Mono.Loop.Poly auf, um eine mögliche Kooperation anzustossen. Im Rahmen des Austauschs erklärten sie sich bereit, mich darüber zu informieren, welche Standards und Voraussetzungen erfüllt sein müssten, damit ein Polyester-Schaft recyclingfähig ist. Bis jetzt gäbe es aber noch keine Schuhprojekte im Mono.Loop.Poly - Konzept.
Mono.Loop.Poly ist ein von InnoSuisse gefördertes Forschungsprojekt der Hochschule Luzern (Design, Film und Kunst). Deren Ziel ist es, einen lokalen geschlossenen „Textil-zu-Textil“-Kreislauf für Polyester zu etablieren, damit bei Sportbekleidung frisches Polyester vermieden werden kann. Dafür wurden Standards entwickelt, welche sicherstellen sollen, dass fertige Produkte als Ganzes chemisch recyclebar sind.
Gemäss den im Rahmen des Projekts definierten Standards gilt ein Produkt dann als recyclingfähig, wenn es zu mindestens 95% aus Polyester besteht – unabhängig davon, ob es sich dabei um unterschiedliche Polyesterarten oder um weiche bzw. harte Materialien handelt. Diese Vorgabe bildet die Grundlage für die chemische Rückführung im angestrebten Textil-zu-Textil-Kreislauf.
Quelle: https://www.hslu.ch/de-ch/hochschule-luzern/forschung/projekte/detail/?pid=6528
Sketch the Steck-System
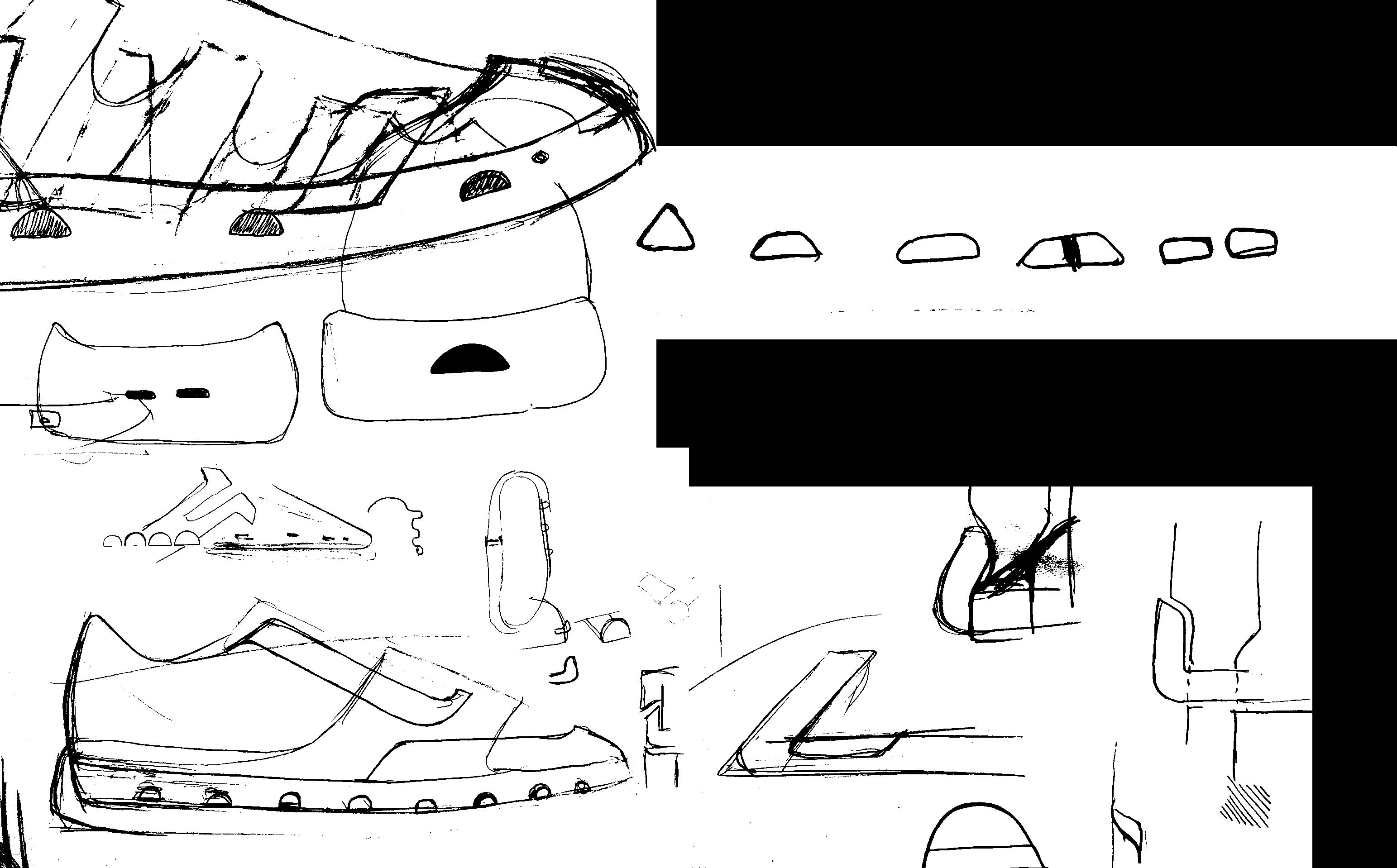

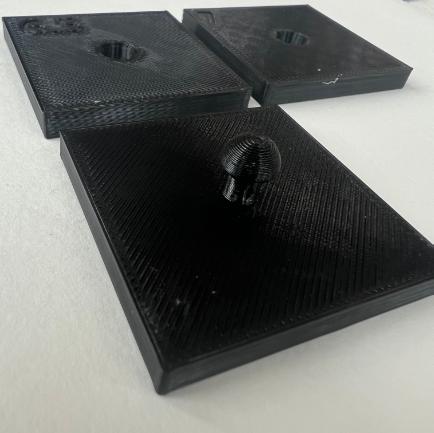
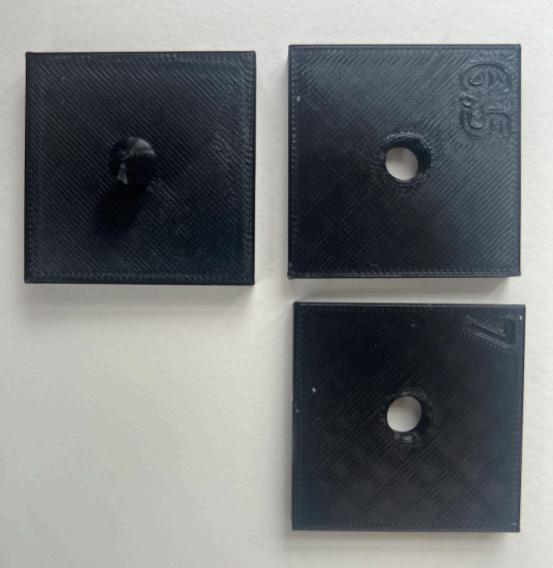
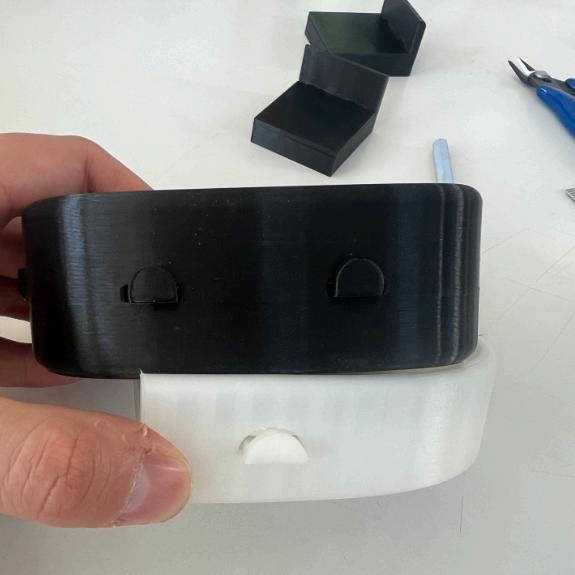
Es wurden verschiedene Ansätze für ein Stecksystem erprobt, um eine stabile und gleichzeitig lösbare Verbindung zwischen Sohle und Schaft zu ermöglichen. Dabei wurden unterschiedliche mechanische Verbindungen getestet – etwa Haken- und Rastmechanismen, um herauszufinden, welche Varianten sich am besten für den Einsatz am Schuh eignen und wie sich diese in den Materialeigenschaften von TPU umsetzen lassen. Es kristallisierte sich ein Favorit unter den Mechanismen.
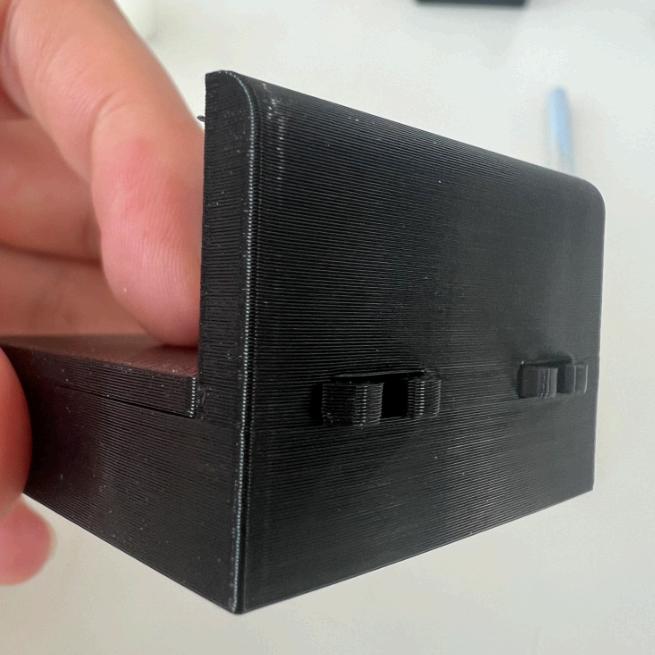
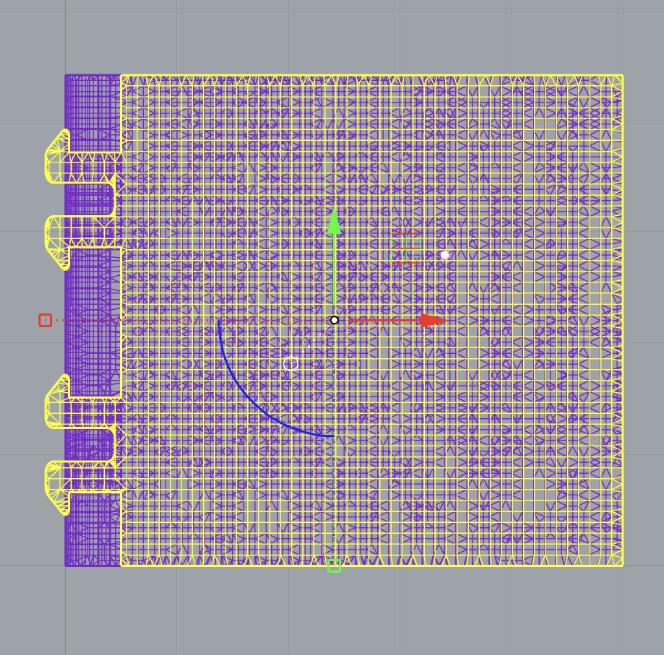
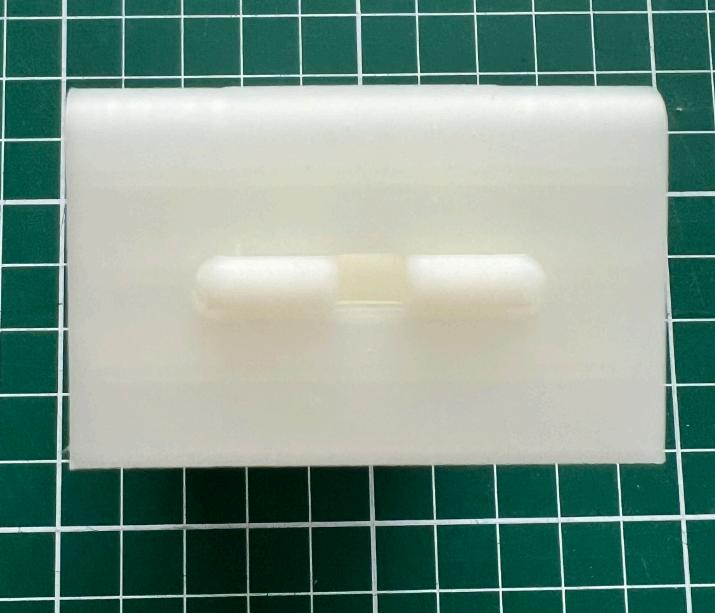
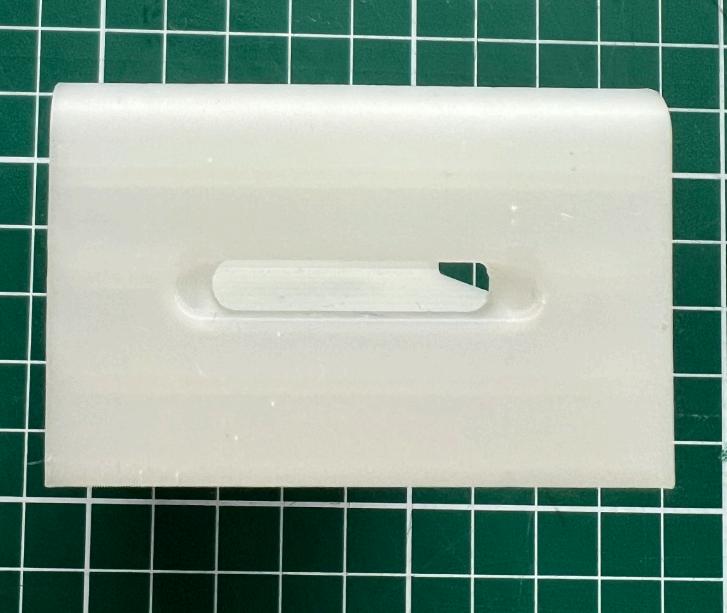
Das passende Stecksystem wurde weiter entwickelt und davon Proben angefertigt, um zu testen, wie sich das Einrasten verhält. In einem weiteren Schritt wurden verschiedene Füllgrade beim 3D-Druck eingesetzt, um die Flexibilität und das Nachgiebigkeitsverhalten des Materials gezielt zu beeinflussen und die optimale Balance zwischen Halt und Handhabung zu finden. Hier wurde TPU mit Shore-Härte A85 verwendet, was etwas weicher ist als das bereits verwendete schwarze TPU mit Shore- Härte A95.

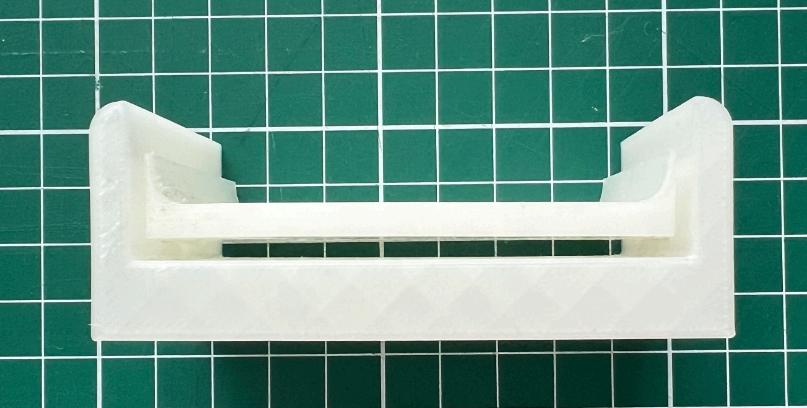
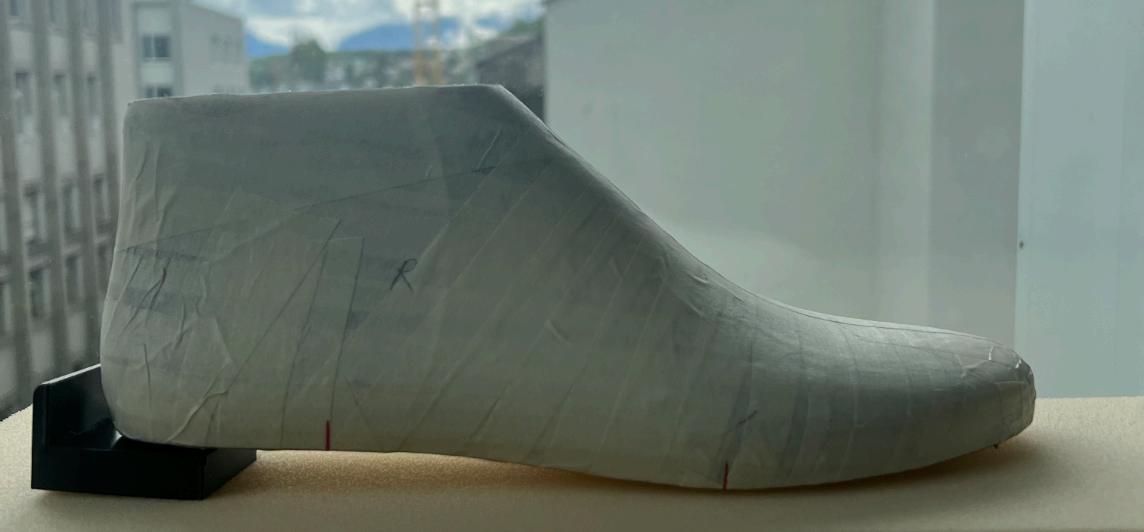
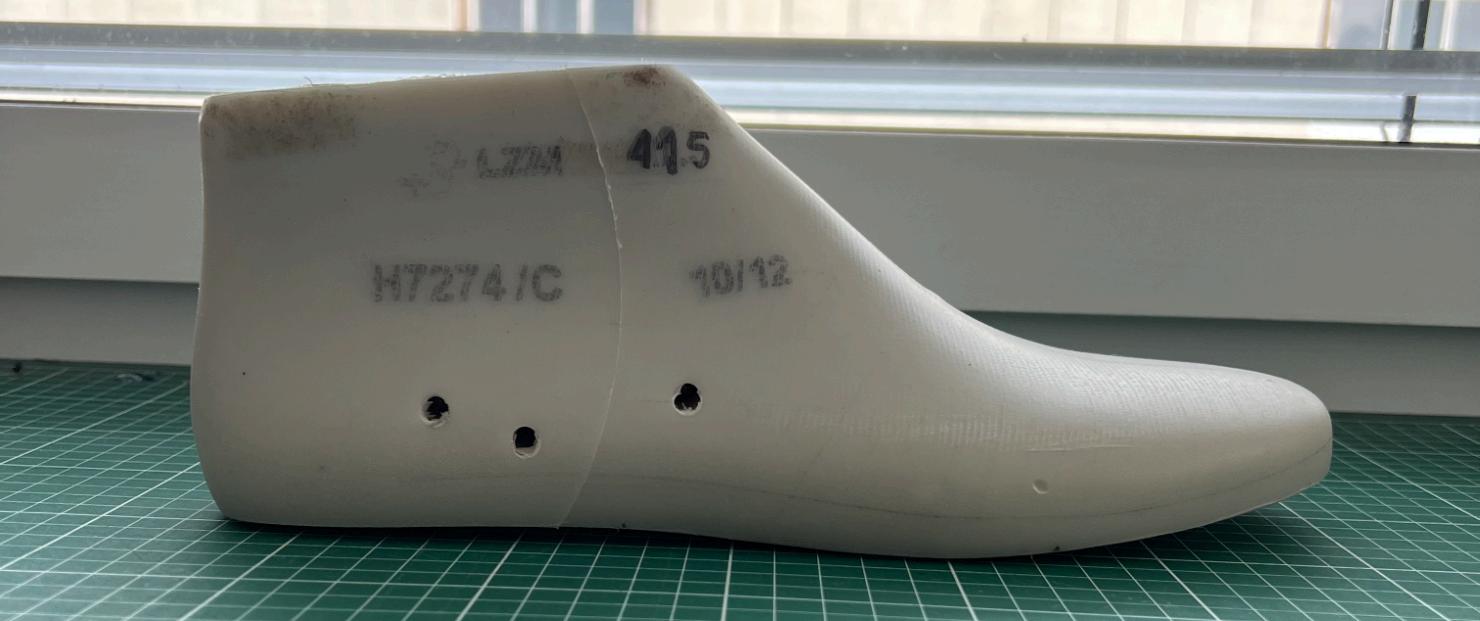
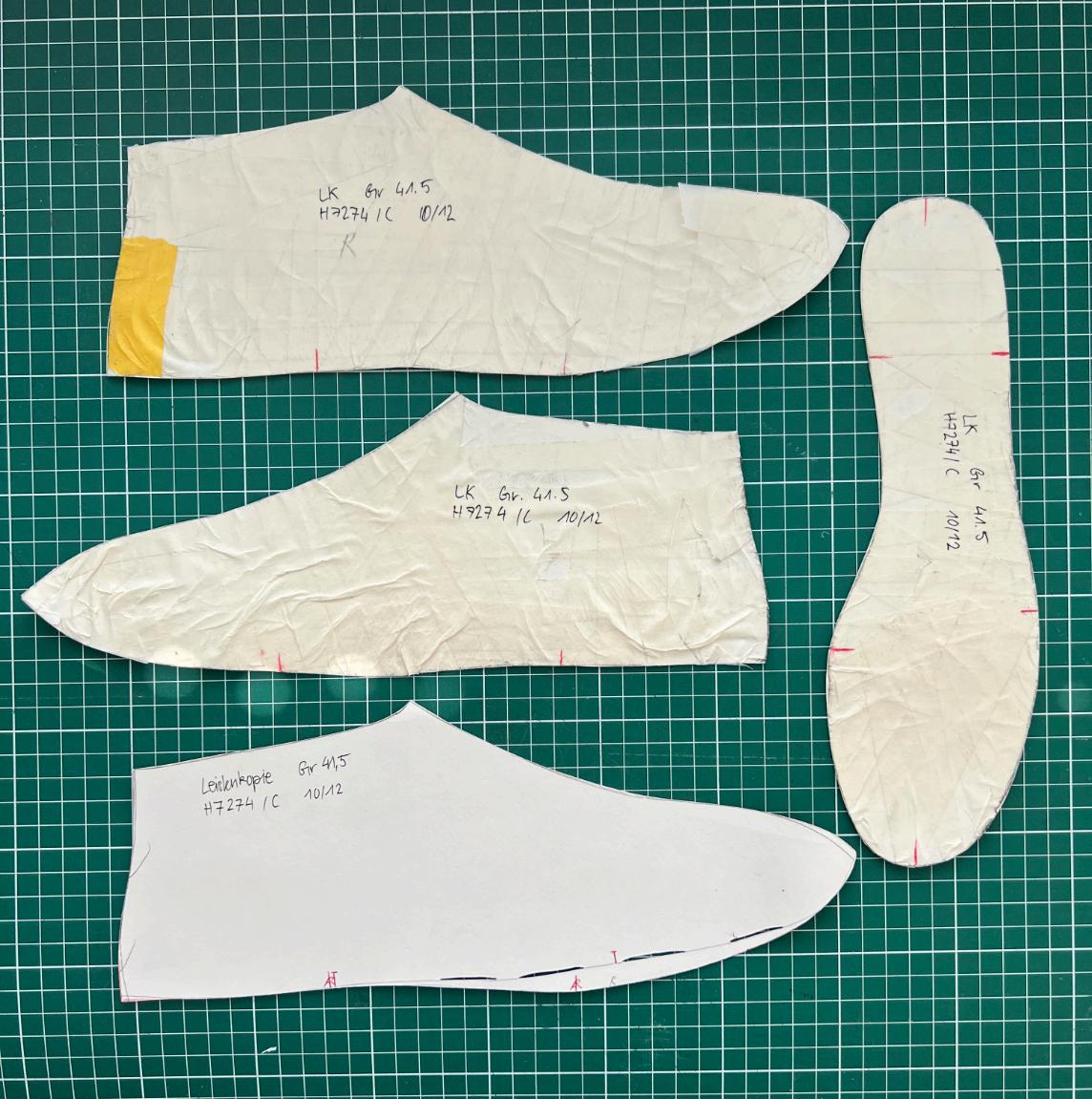
Es wurde eine Leistenkopie angefertigt – also eine 2D Nachbildung eines bestehenden Schuhleistens, der als formgebende Grundlage für die Entwicklung des Schuhs dient. Der Leisten bestimmt die Passform, das Volumen und die Proportionen des Schuhs. In diesem Fall wurde die Kopie auf Basis eines Sneaker-Leistens erstellt, der sich bereits in meinem Besitz befand und aus meiner früheren Ausbildung als Schuhmodelleur stammt. Diese Vorlage diente als Ausgangspunkt für die Entwicklung des modularen Schuhsystems.
Eine erste Probesohle mit integriertem Stecksystem wurde 3D gedruckt, um die Funktionalität und Passgenauigkeit der Verbindung zu testen. Dabei stand im Fokus, wie sich das mechanische System in das Sohlenmaterial TPU integrieren lässt und welche Anforderungen an Form und Flexibilität erfüllt werden müssen.
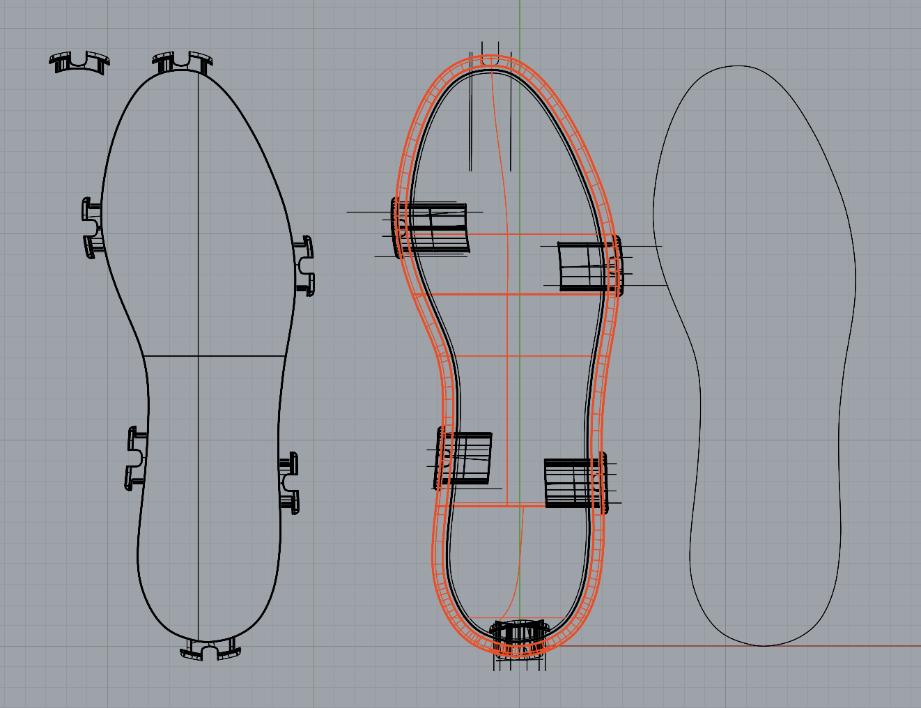
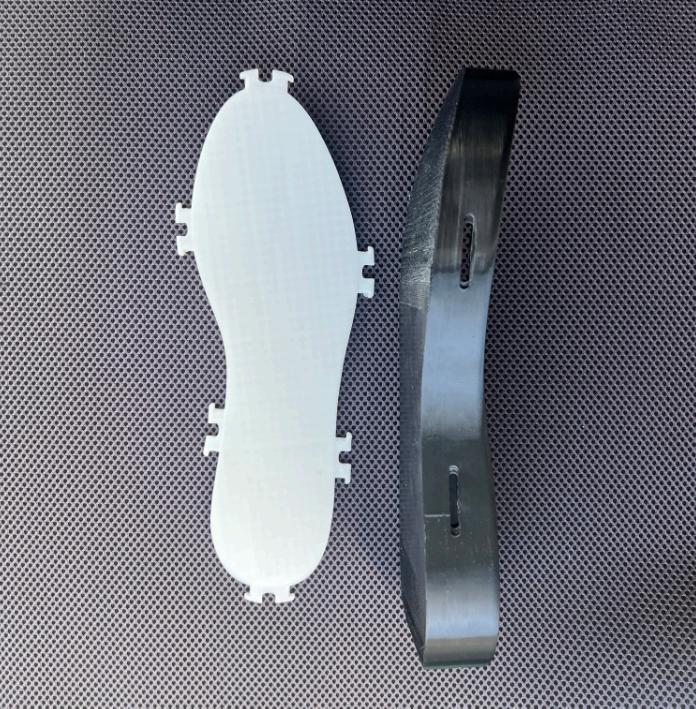
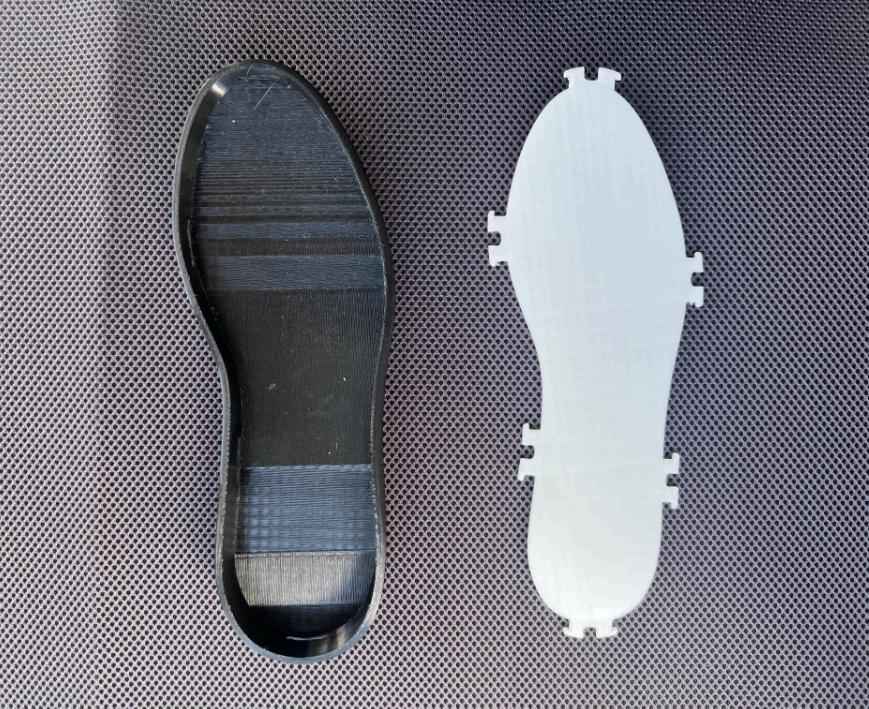
Die Sohle wurde mit einem 2mm Versatz zur Zwischensohle gedruckt, um zwischen diesen beiden Ebenen einen Sockenschaft einführen zu können. Durch diesen Abstand entsteht ein schmaler Zwischenraum, der als Aufnahme für den Schaft dient und so eine stabile Verbindung innerhalb des modularen Systems ermöglicht.
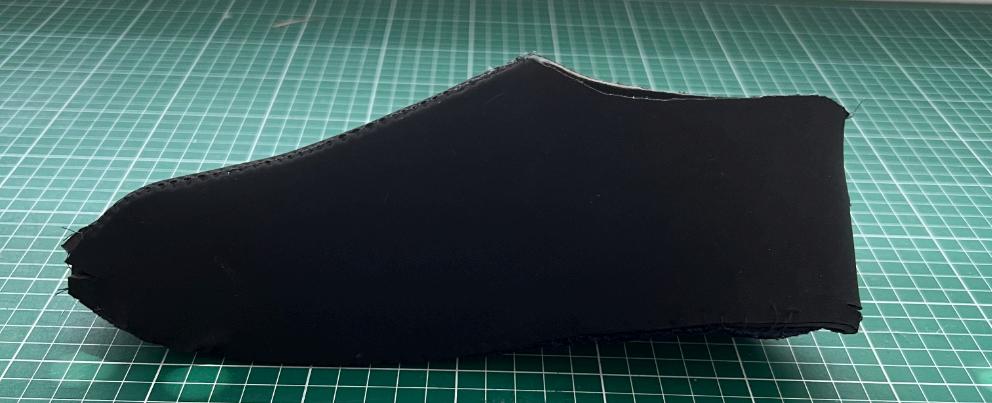

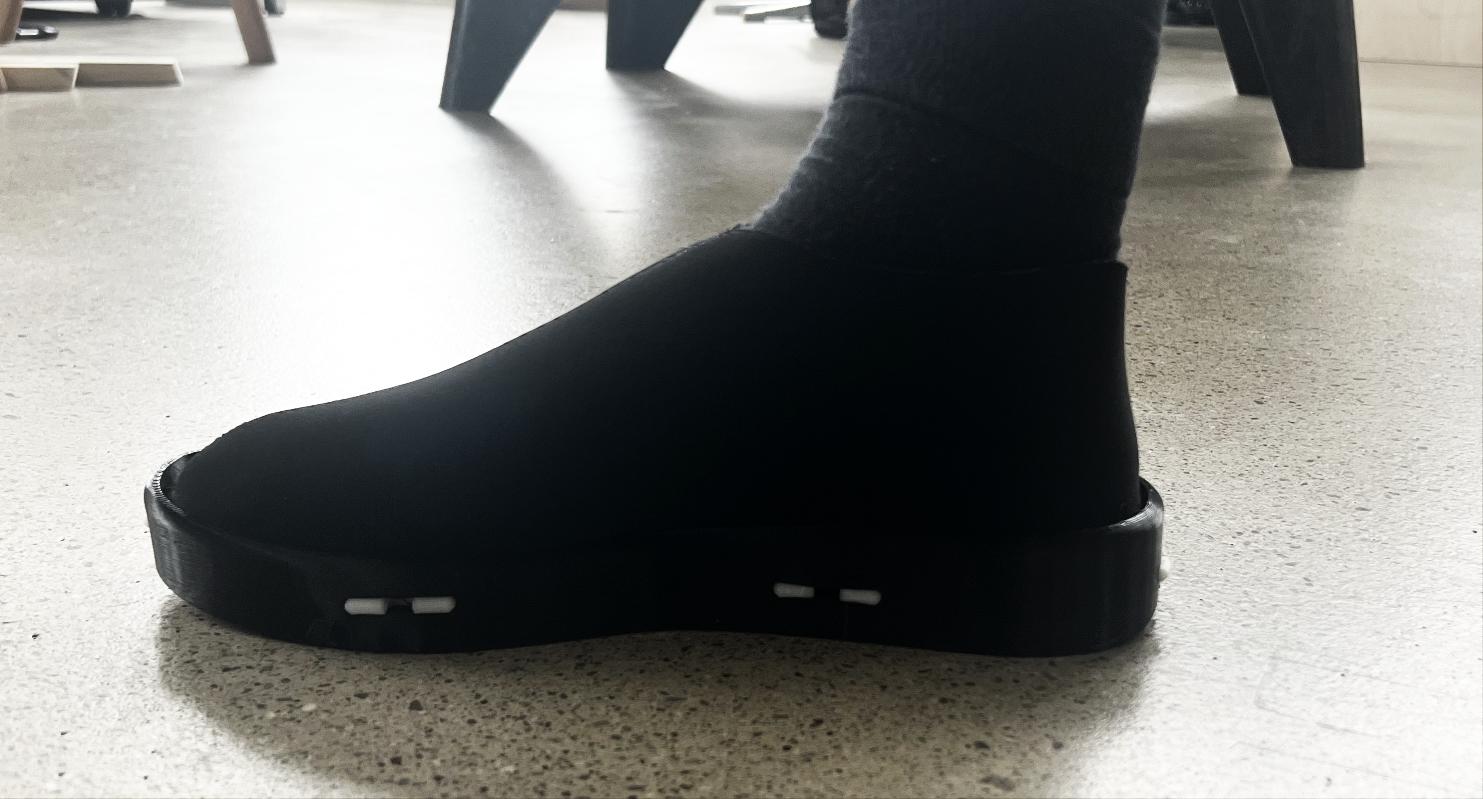
Die Probesohle mit dem integrierten Stecksystem zeigte in ersten
Tests eine funktionierende Verbindung und hielt den aus drei Teilen bestehenden Sockenschaft aus Neoprenstoff zuverlässig in Position.
Das System erwies sich als stabil und gleichzeitig flexibel genug, um den Schaft sicher einzufassen und zu halten, sowie damit zu laufen.
Auf der Grundlage der abgenommenen Leistenkopie wurde mit Hilfe eines Konstruktionsheftes auf klassische Weise von Hand ein Grundmodell erstellt. Dieses wurde anschliessend in Rhino digitalisiert und weiter modelliert. So sind das Grundmodell und alle Einzelteile flexibel anpassbar und können direkt aus Rhino für den Einsatz mit dem Lasercutter in Illustrator aufbereitet werden.
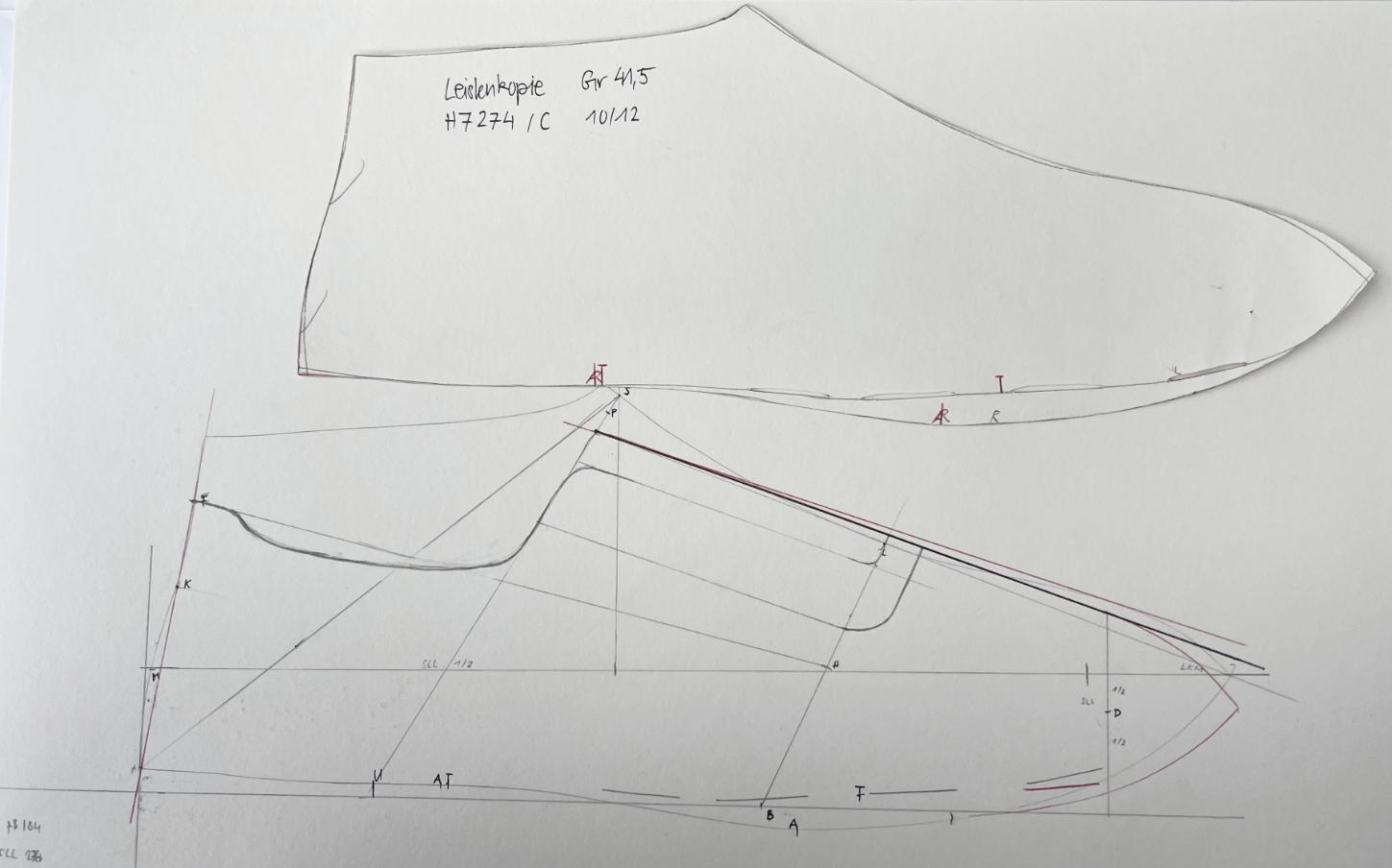
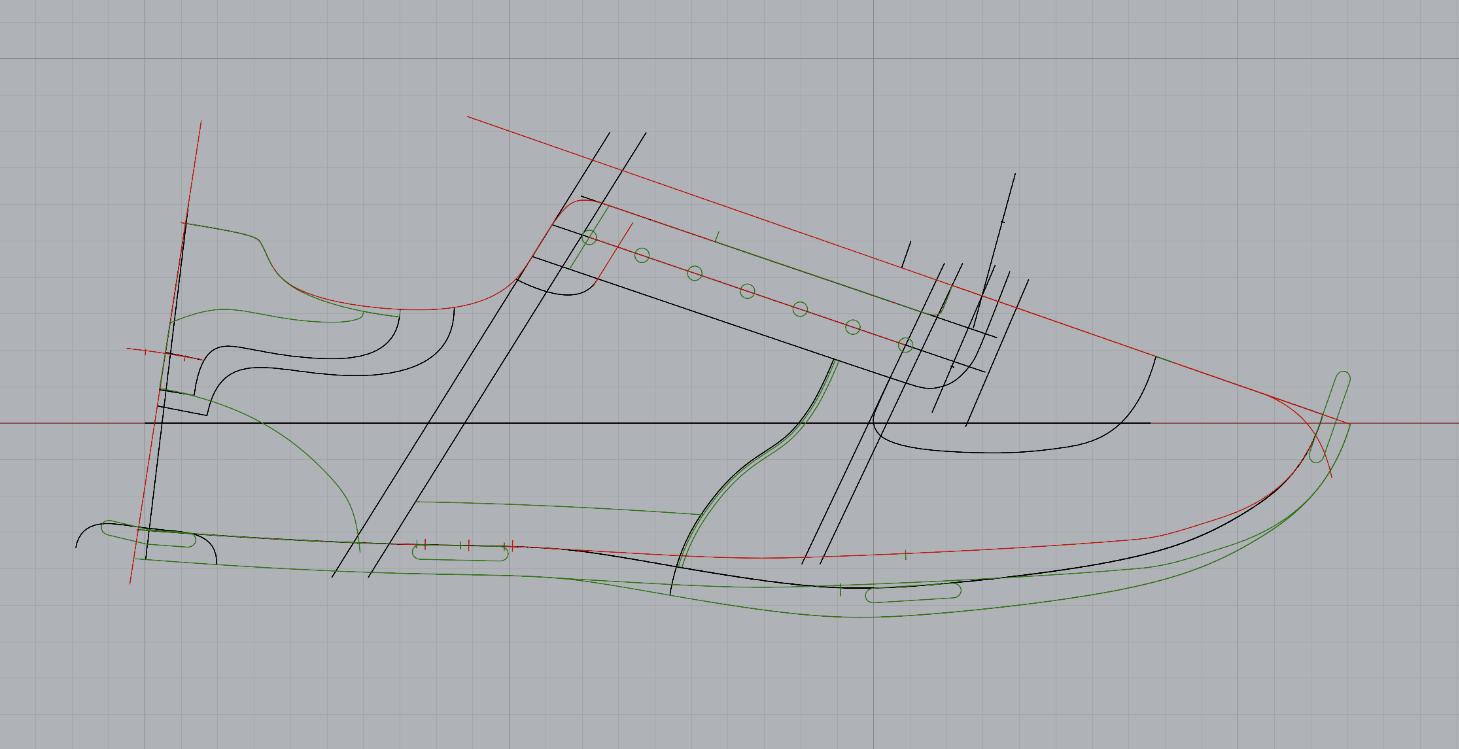
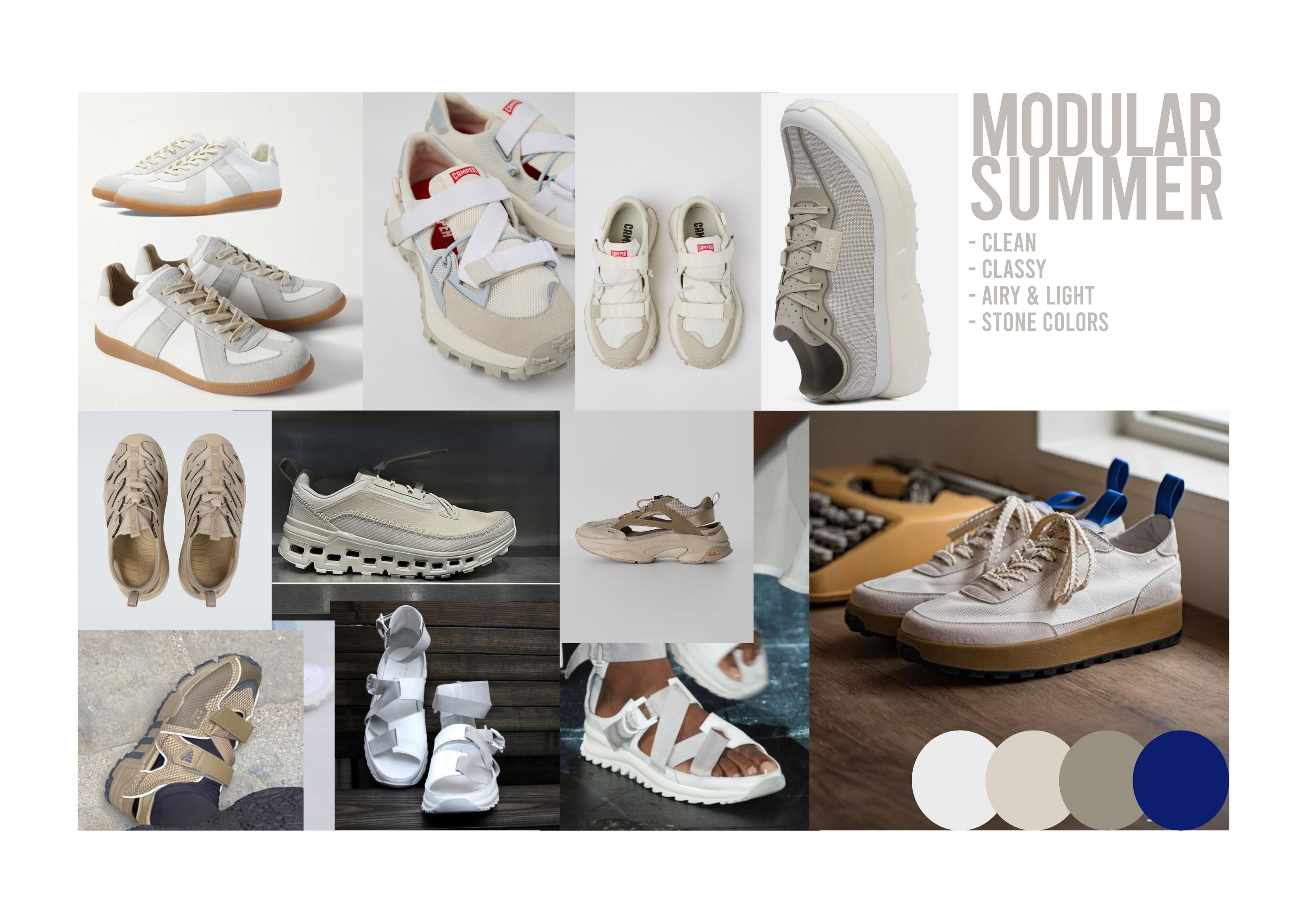
Mood- und Inspirationsboard
Im Austausch mit Joel Hügli von Mono.Loop.Poly erhielt ich
Empfehlungen zu verschiedenen Webseiten, die eine gute und vertrauenswürdige Auswahl an reinen Polyesterstoffen anbieten. Auf Basis meines Moodboards und der ersten
Modellidee eines klassischen Sneakers, wählte ich gezielt unterschiedliche Materialien aus: von stabileren, etwas steiferen Stoffen bis hin zu 3D-Mesh-Gewirken, wie sie häufig
in der Sneaker-Herstellung verwendet werden. Ergänzend dazu wurden auch ein Veloursleder-Imitat für Futter-Optionen, sowie Vliese für potenzielle Zwischenfutter zur Erprobung verschiedener Materialkombinationen eingekauft.
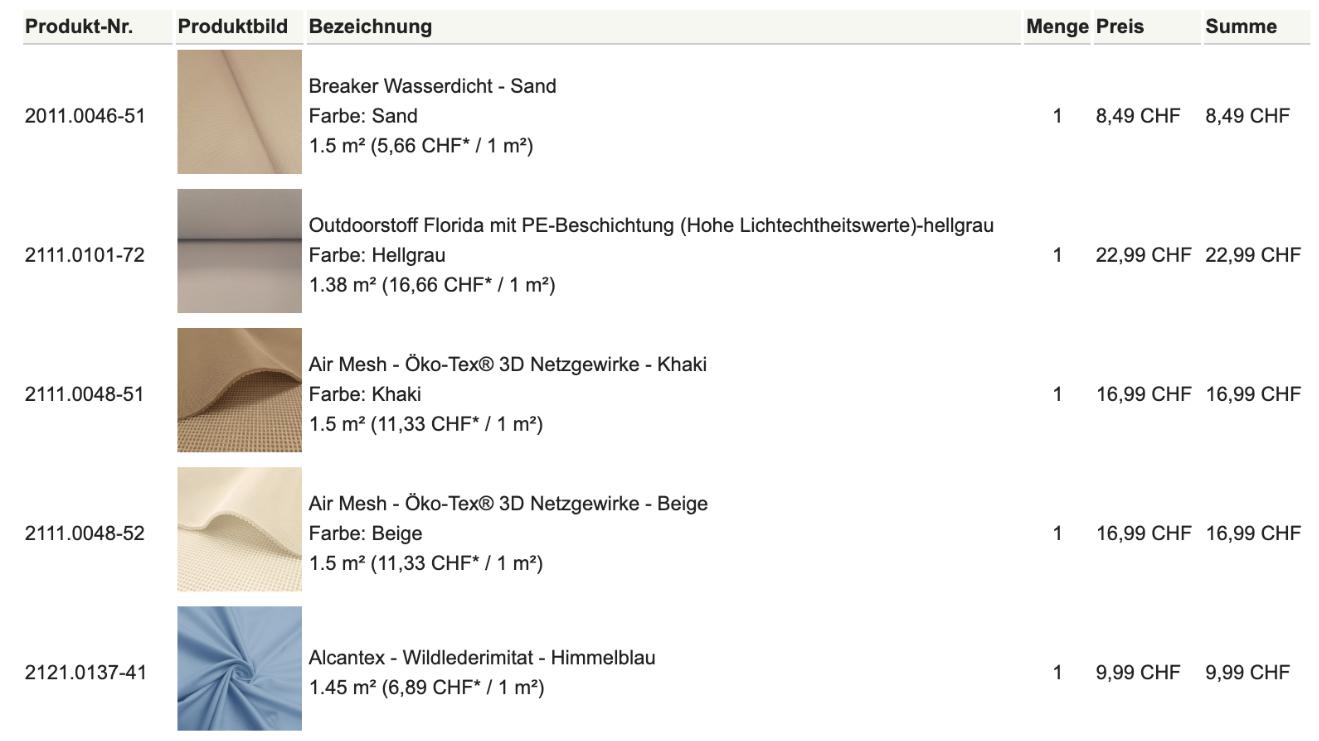

https://www.aktivstoffe.ch
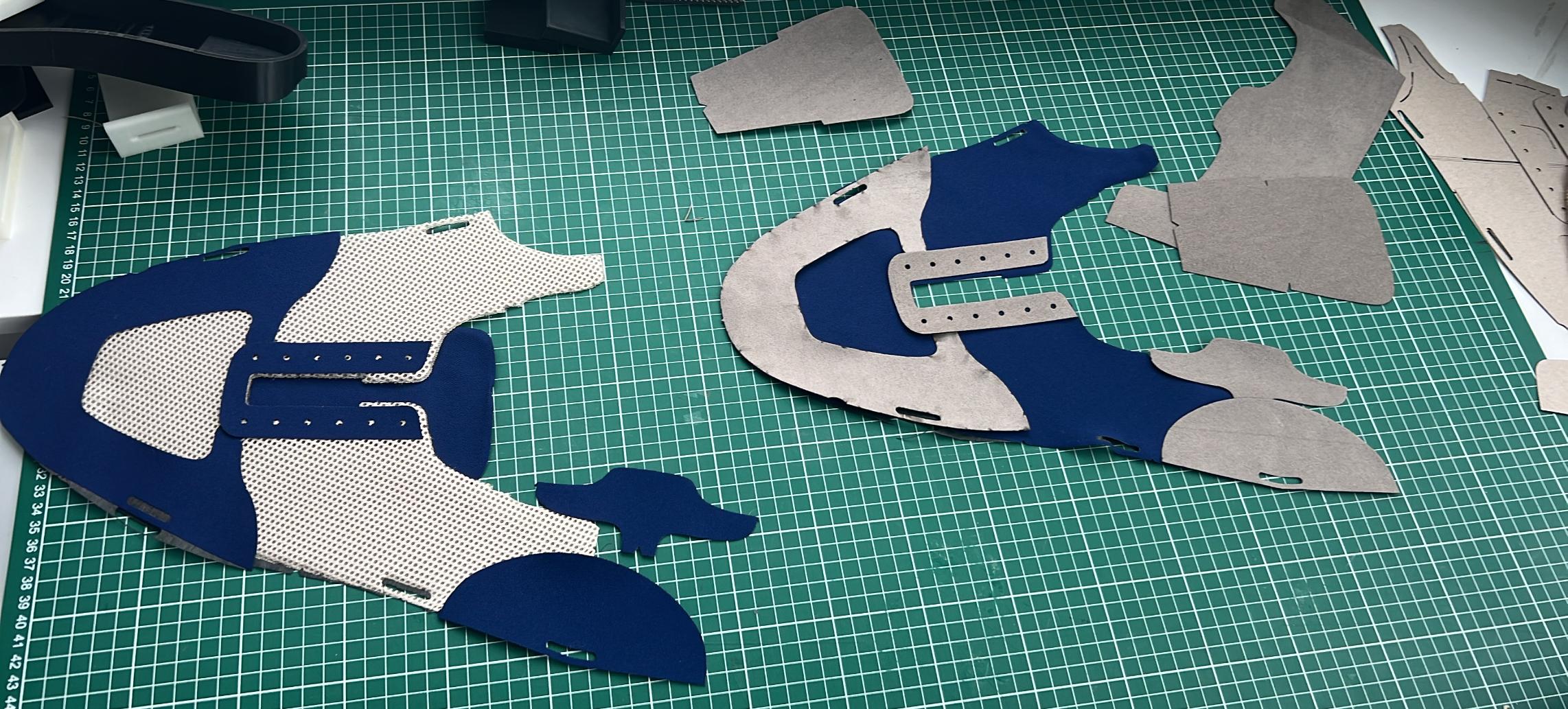
Aus der Materialauswahl wurden die einzelnen Schnittteile mit dem Lasercutter ausgeschnitten und anschliessend zu Modellen zusammengelegt. So konnten unterschiedliche Material- und Farbkombinationen direkt miteinander verglichen und hinsichtlich ihrer Wirkung, Haptik und Eignung bewertet werden. Auf dieser Grundlage wurde eine gezielte Auswahl für die weiteren Entwicklungsschritte getroffen. Es zeigte sich, dass das 3D-Mesh-Gewirke besonders gut als Hauptmaterial für den Schaftkörper (Body) geeignet ist, da es flexibel, atmungsaktiv und optisch sportlich wirkt. Der blau gewebte Polyesterstoff erwies sich hingegen als ideal für funktionale und optisch akzentuierende Elemente wie das Schnürteil sowie die Vorder- und Hinterkappen.
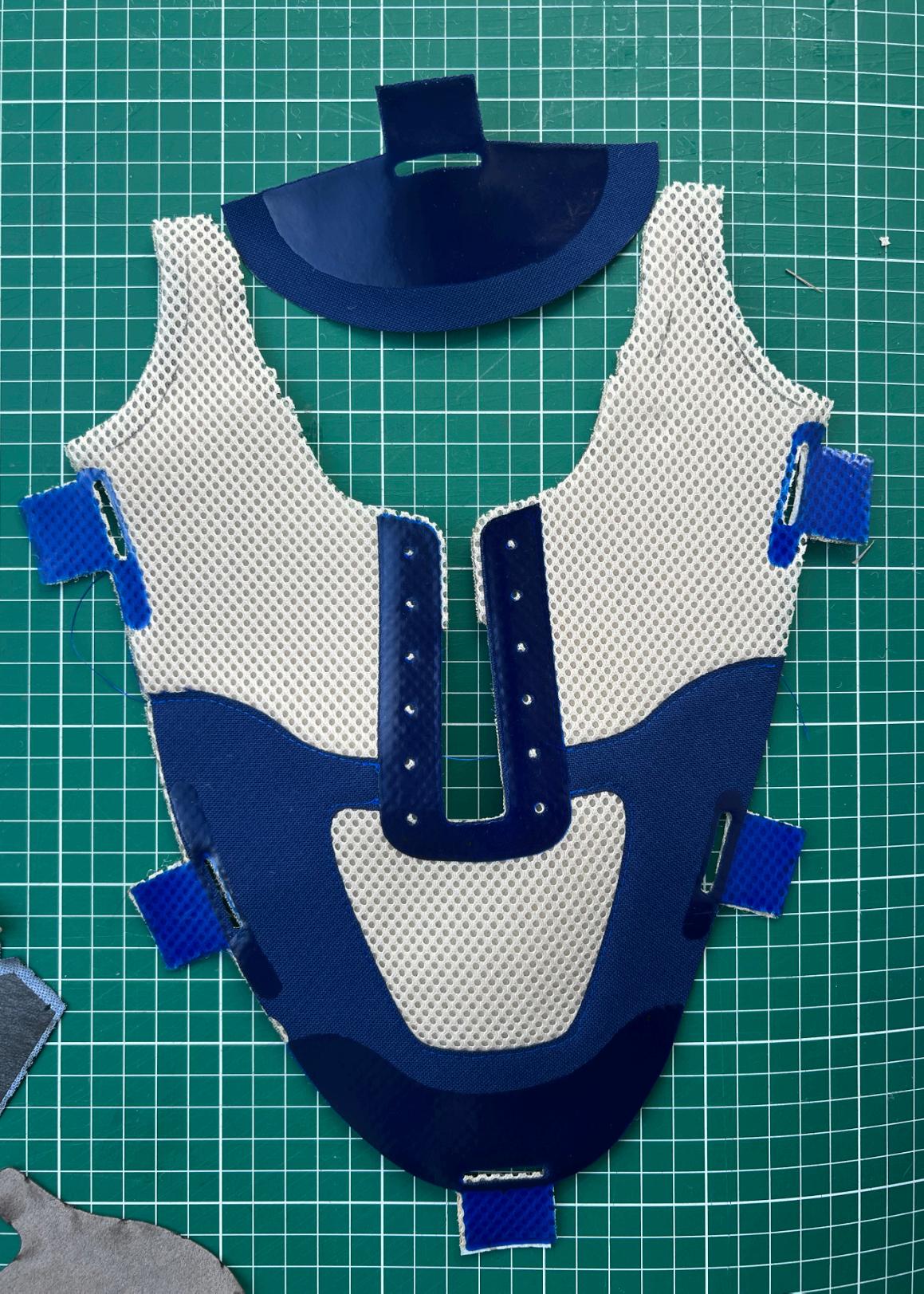
Ein erster Probeschaft wurde genäht. Für die modulare Konstruktion und die dafür notwendigen Öffnungen, durch welche die Sohlenkonstruktionsriemen des Stecksystems geführt werden, kamen Verstärkungsteile aus PETG zum Einsatz, die im 3D-Druckverfahren hergestellt wurden. Da auch PETG ein Polyester ist, lässt es sich im Sinne des Mono.Loop.Poly-Prozesses recyclen und entspricht den Anforderungen eines sortenreinen Materialaufbaus. Die Verstärkungsteile wurden mithilfe einer Heatpress-Maschine thermisch mit dem Schaftmaterial verbunden und fixiert.
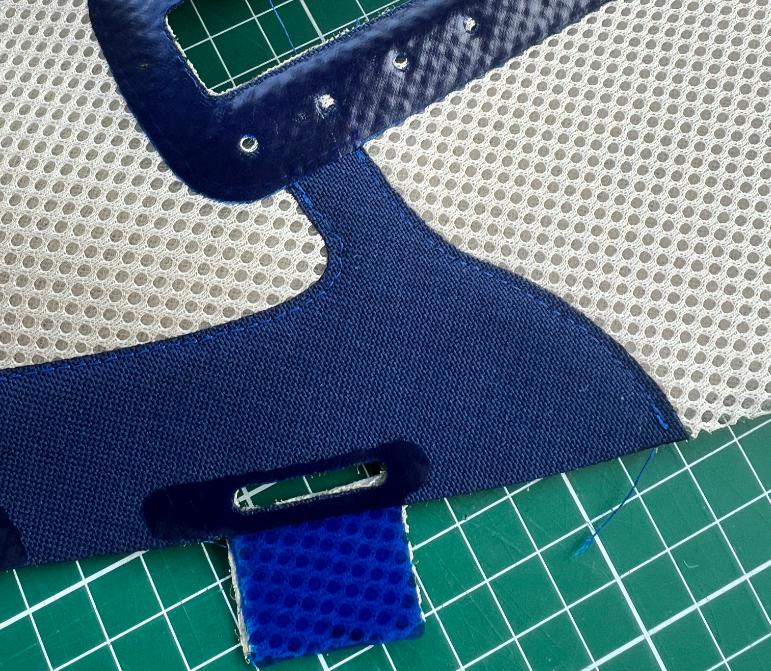
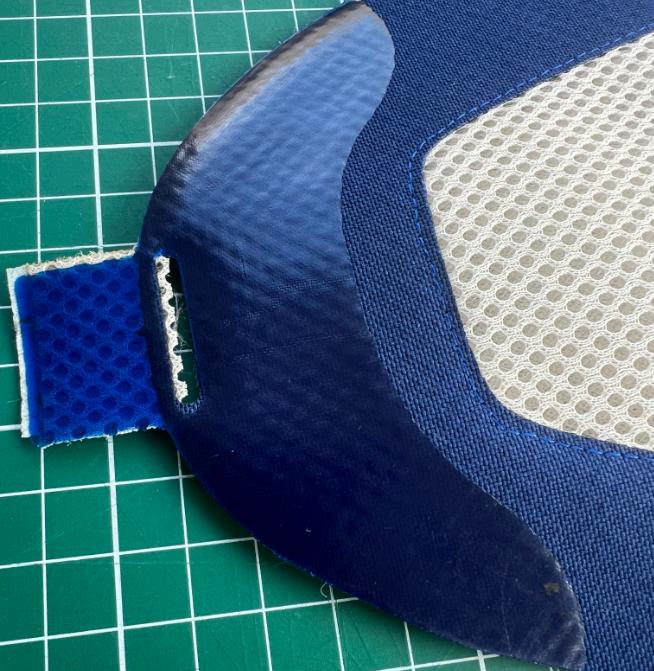
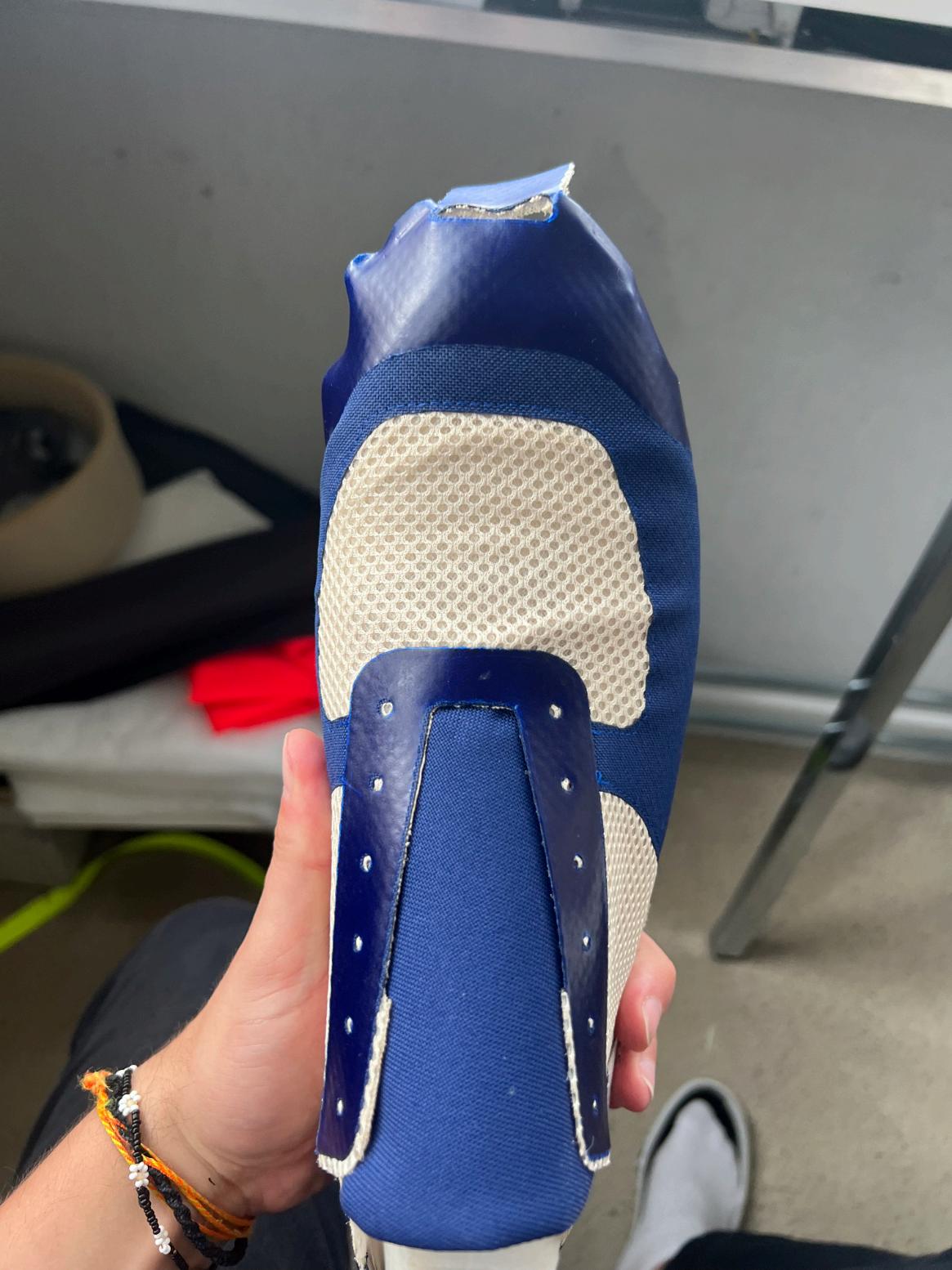
Da die Wölbung bzw. Krümmung des Schafts – insbesondere im Bereich von Spitze und Ferse – im digitalen Modell nicht berücksichtigt wurde, entwickelte ich die Idee, auch die Spitze mit einem PETG-Teil zu verstärken und dieses mithilfe von Hitze an den Leisten anzupassen. Ziel war es, durch thermische Verformung die gewünschte Form zu erzielen. In der Umsetzung zeigte sich jedoch, dass sich das PETG-Teil, trotz Verschmelzung mit dem Obermaterial mittels Heatpress, nicht ausreichend an die Rundung der Leistenform anpassen liess. Diese Methode erwies sich somit als ungeeignet.
Aufgrund der Problematik bezüglich der Kappenform entschied ich mich, die Kappen für Ferse und Vorderfuss direkt in der Leistenform zu drucken, und zwar als 3D-gedruckte PETGTeile. Diese wurden auf Rhino anhand eines 3DScans des Leistens konstruiert. Die erste Version passte jedoch noch nicht exakt und musste angepasst und überarbeitet werden, bis die Form und Passung stimmten. Die Kappen sind so konstruiert, dass sie unter die Zwischensohle ragen und dadurch zusätzlich zur
Stabilität und Fixierung innerhalb des modularen Systems beitragen.

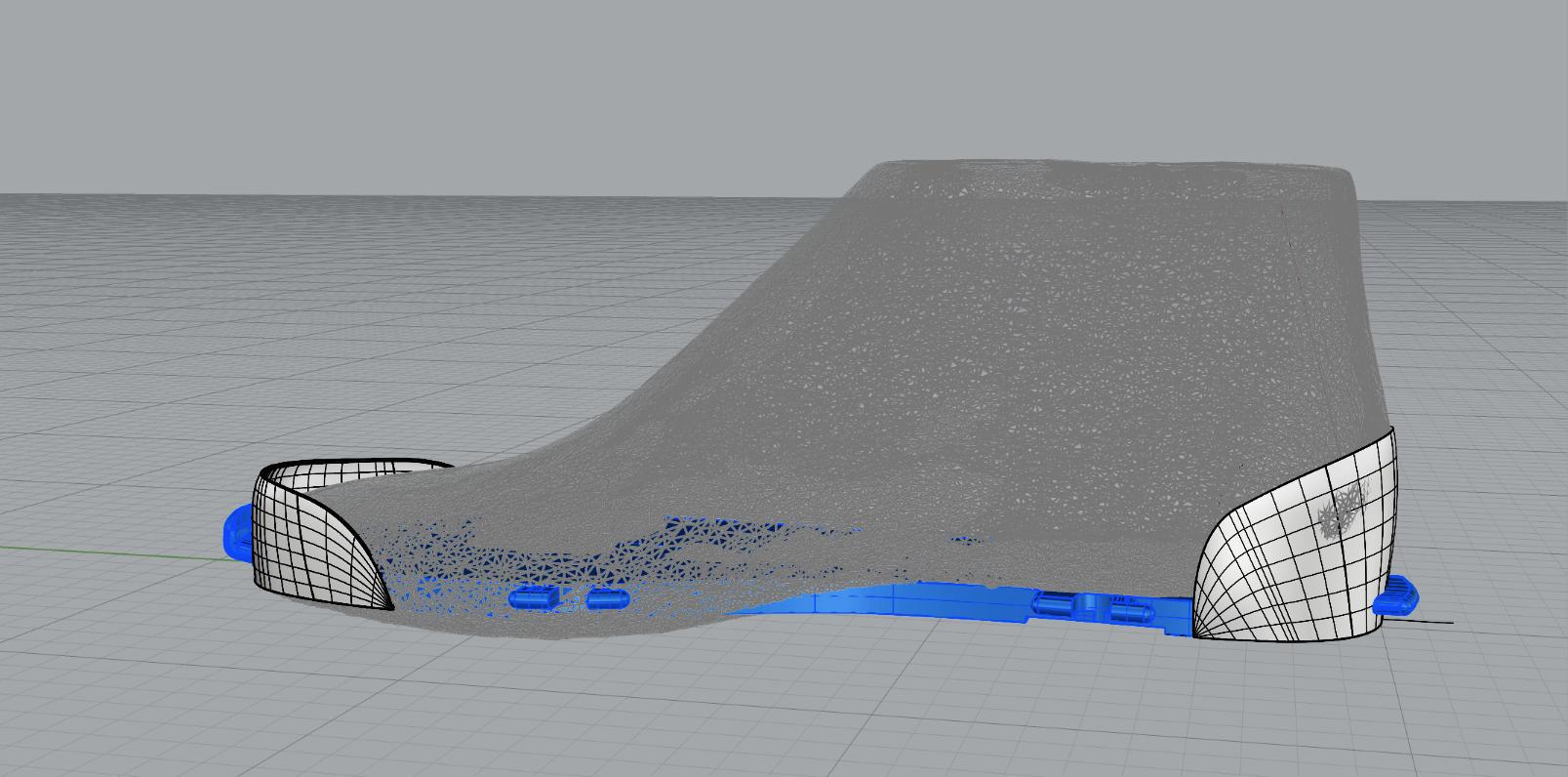
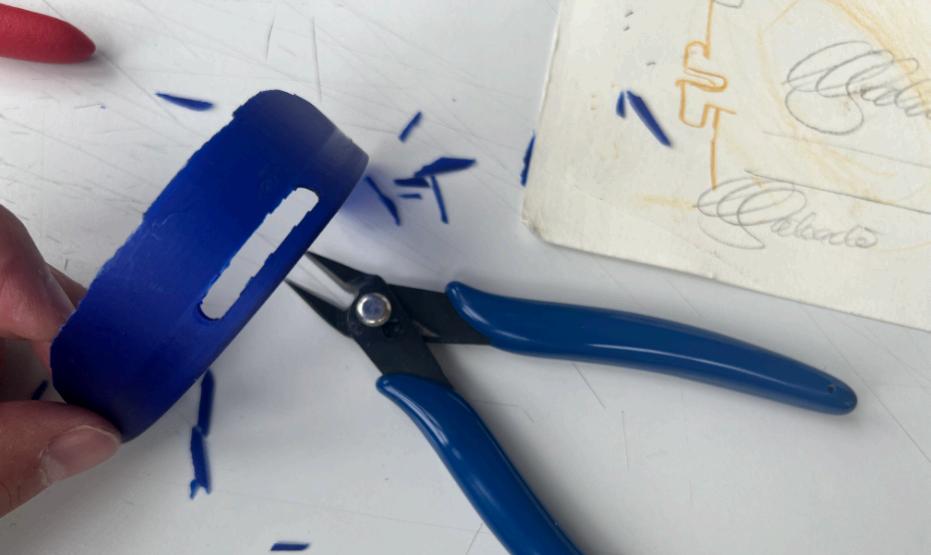
Auch die Sohle wurde überarbeitet und neu konstruiert. Dabei wurde am oberen Rand eine Abdichtungslippe im Design integriert, die über den Schaft greift. Diese soll mögliche Zwischenräume zwischen Sohle und Schaft verhindern und so für einen sauberen Abschluss sowie verbesserten Halt im modularen Aufbau sorgen.
Beim Sohlen-Design wurde ein Profil integriert, dessen Form sich an der Rundung des Stecksystems orientiert. Hier handelte es sich zunächst um eine Probe des Designs, welche noch nicht in Originalgrösse gedruckt werden konnte, da dies nur mit dem PRUSA XL in Echtgrösse möglich wäre.
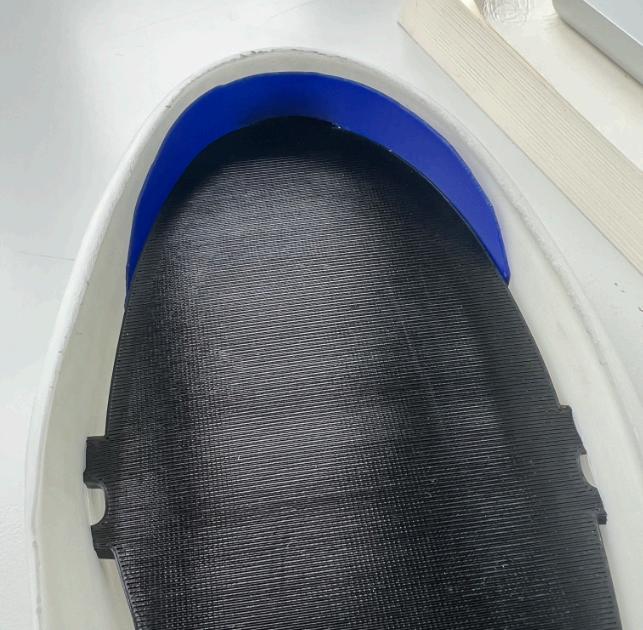
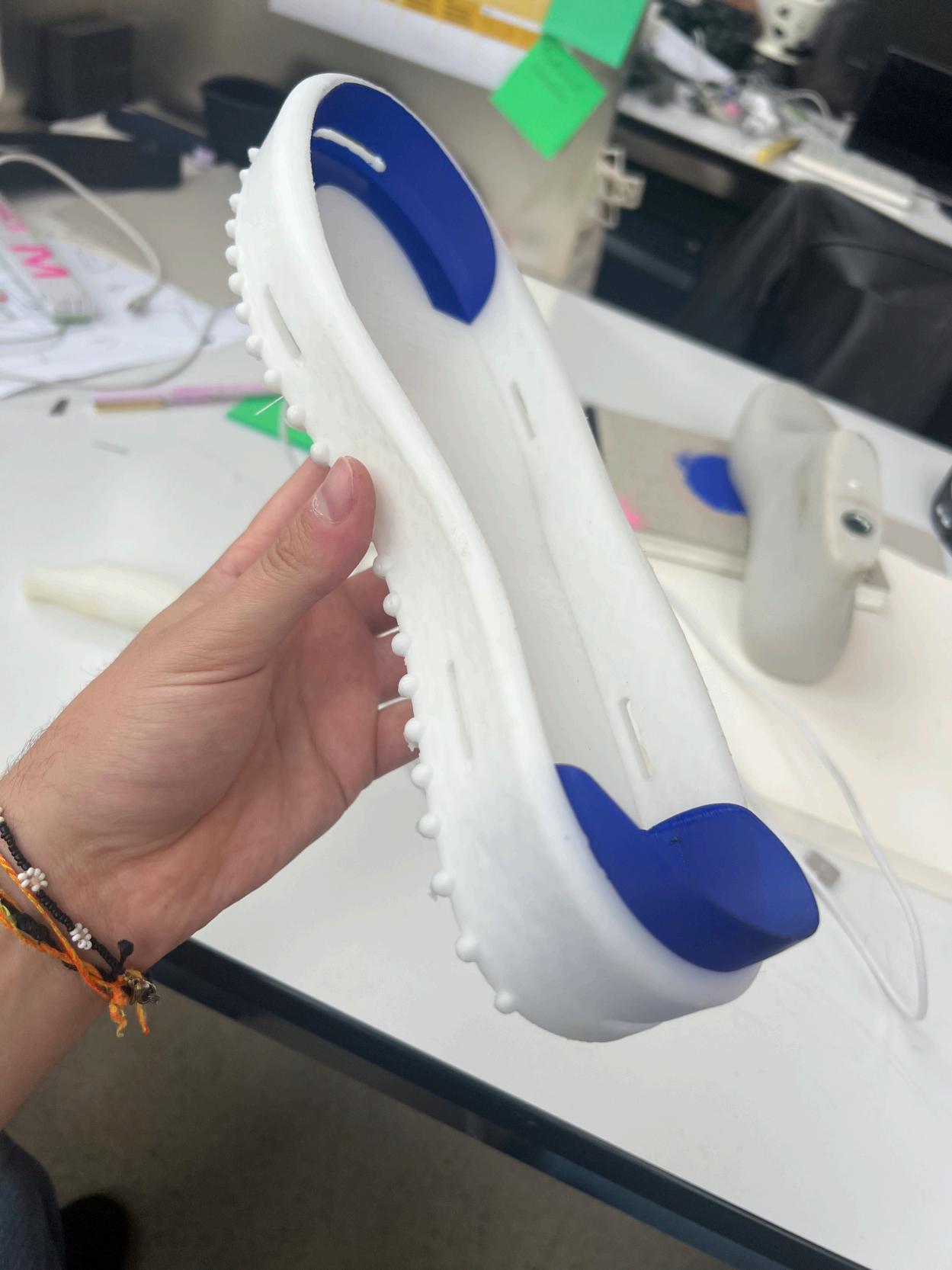
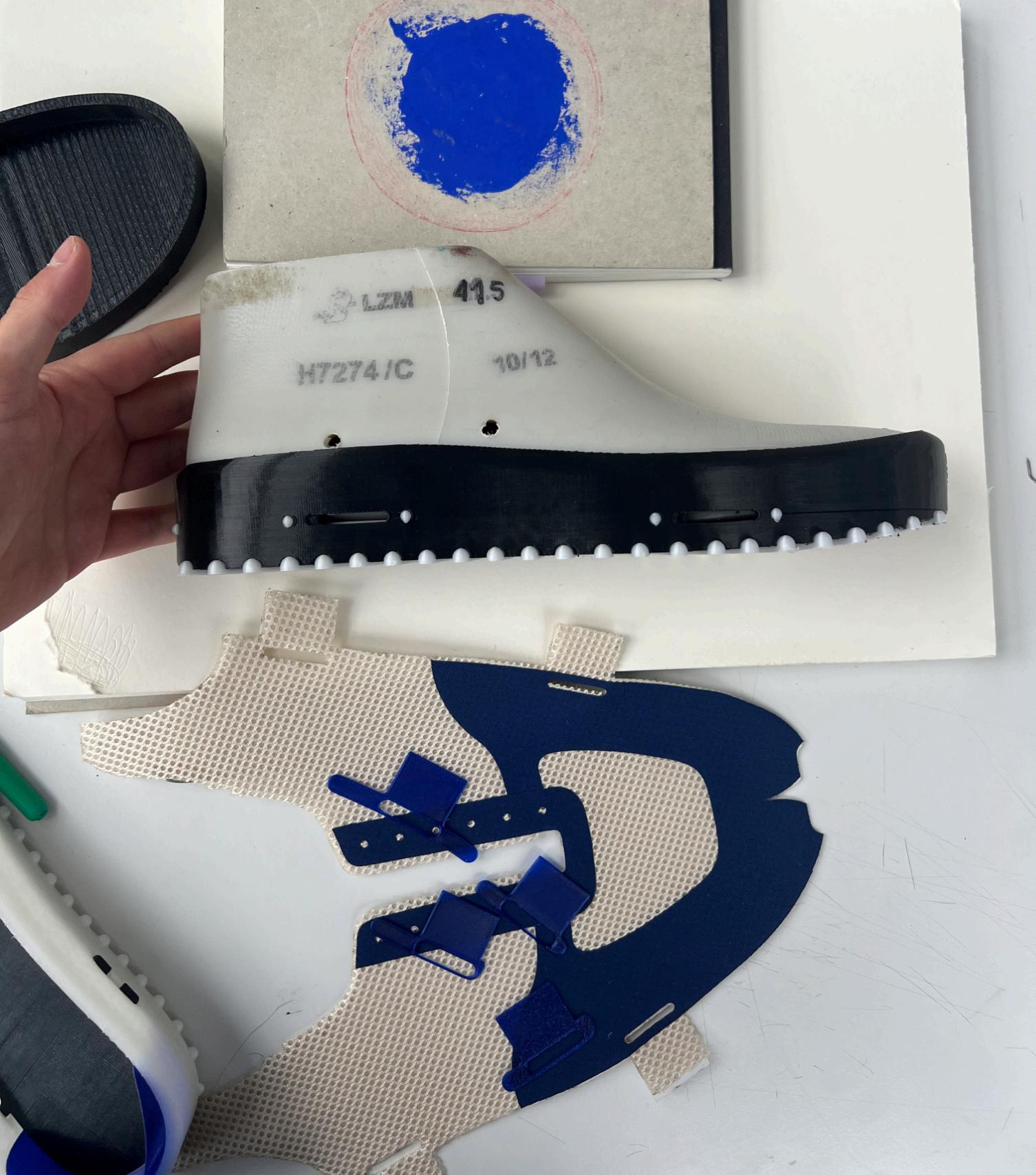
Mit dem Prusa XL konnte die Sohle in tatsächlicher Grösse und mit zwei Filamentfarben gedruckt werden. Dadurch war es möglich, sowohl funktionale als auch gestalterische Aspekte der Sohle präzise umzusetzen.
Als nächstes wurden die Komponenten zusammen gefügt und getestet.
Der Schaft wurde genäht und gemeinsam mit der gedruckten Sohle zum ersten vollständigen Prototypen des modularen Schuhsystems zusammengefügt.
Es zeigte sich an mehreren Stellen Optimierungsbedarf. Der Schaftschnitt musste in bestimmten Bereichen angepasst werden, ebenso die Abdichtungslippe an der Sohle, die nicht optimal auflag und einen deutlichen Zwischenraum bildete.
Auch der Verschlussmechanismus der Zwischensohle erwies sich als zu umständlich und sollte benutzerfreundlicher gestaltet werden. Das Profil der Sohle entsprach gestalterisch noch nicht meinen Vorstellungen. Auch die Höhe des Einschlupfs, die Position und Form des Schnürteils sowie die Rundung der Vorderkappe wurden als verbesserungswürdig erkannt. Diese Erkenntnisse flossen direkt in die Weiterentwicklung des Designs ein.
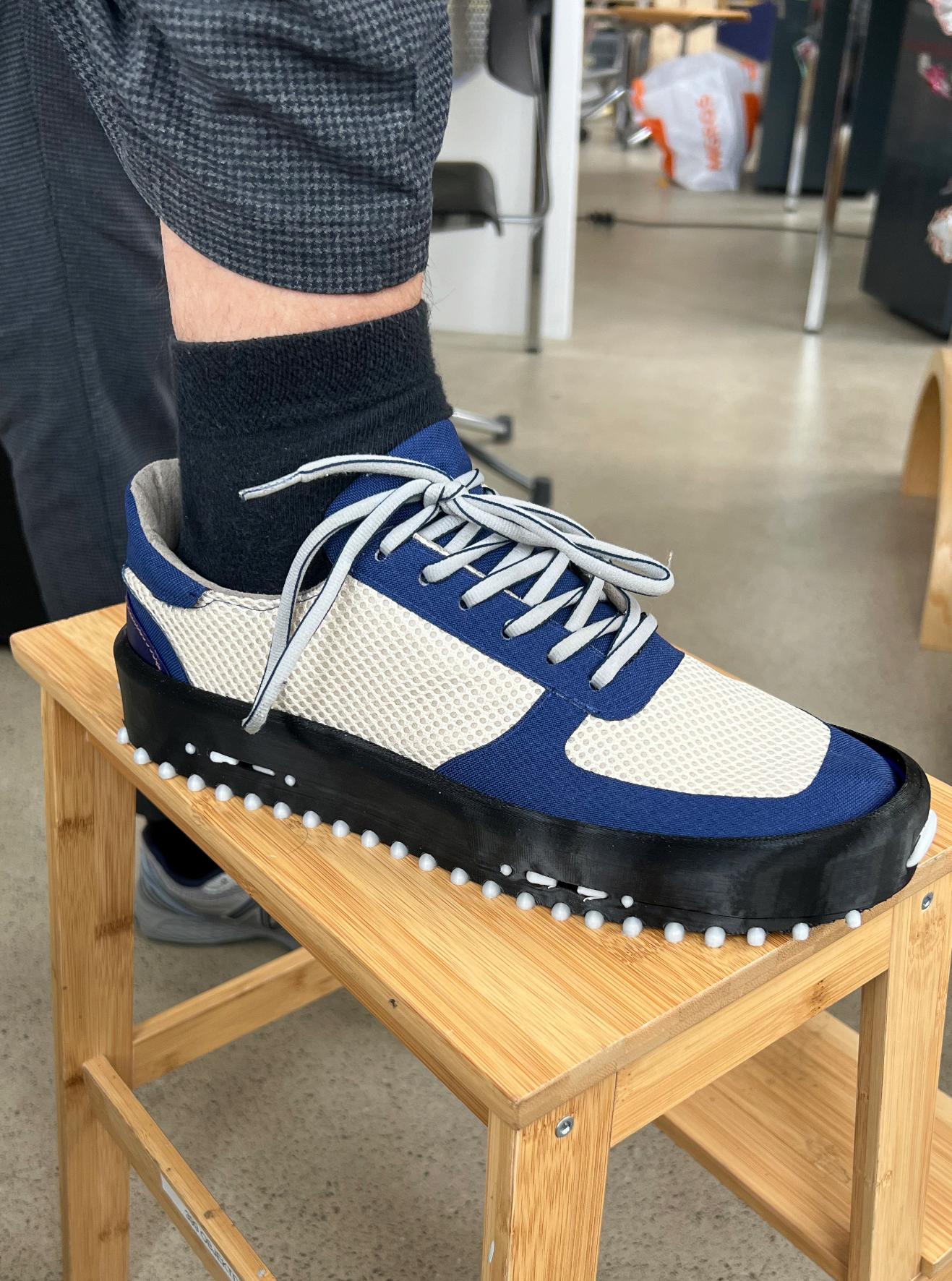
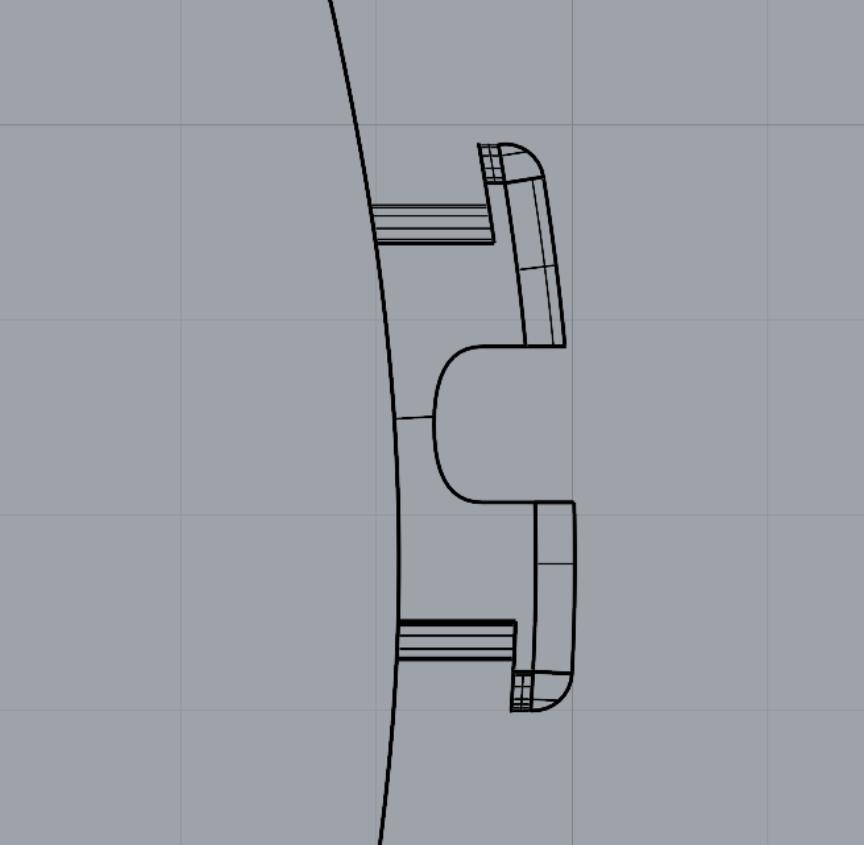
Die Form des Verschluss- bzw. Einrastmechanismus wurde im Zuge der Weiterentwicklung von einer symmetrischen zu einer asymmetrischen Variante überarbeitet. Statt beidseitig einzurasten, greift nach Überarbeitung nur eine Seite aktiv in das Gegenstück ein, während die andere bündig und satt am Rand anliegt. Diese Anpassung vereinfacht die Handhabung und sorgt dennoch für einen sicheren Halt im System.
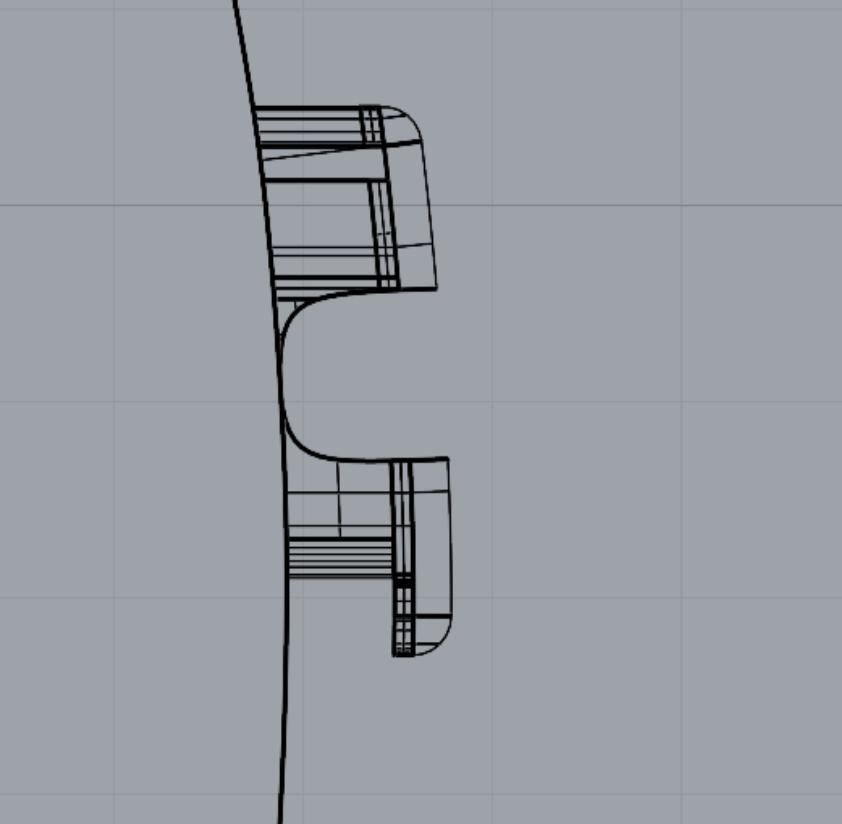
Auf der Suche nach geeigneten TPU-Filamenten in passenden
Farben stiess ich auf Filaflex Foamy TPU – ein Material, das speziell für die Herstellung von Schuhsohlen und Einlegesohlen entwickelt wurde. Ich wählte zwei Farben aus, Beige bzw „Nude“ und Blau, die gestalterisch gut zum Modell passen sollten. Beim Auspacken der Filamente zeigte sich jedoch, dass der Farbton „Nude“ nicht dem Onlinebild entsprach und nicht optimal mit dem restlichen Farbkonzept harmonierte. Als Alternative bestellte ich zusätzlich ein weisses Filament, das jedoch nicht rechtzeitig geliefert wurde. Daher entschied ich mich, den Prototyp dennoch mit dem Nude-Filament umzusetzen. Glücklicherweise verändert sich das Filament durch den Temperatureinfluss des 3D-Drucks etwas im Farbton.
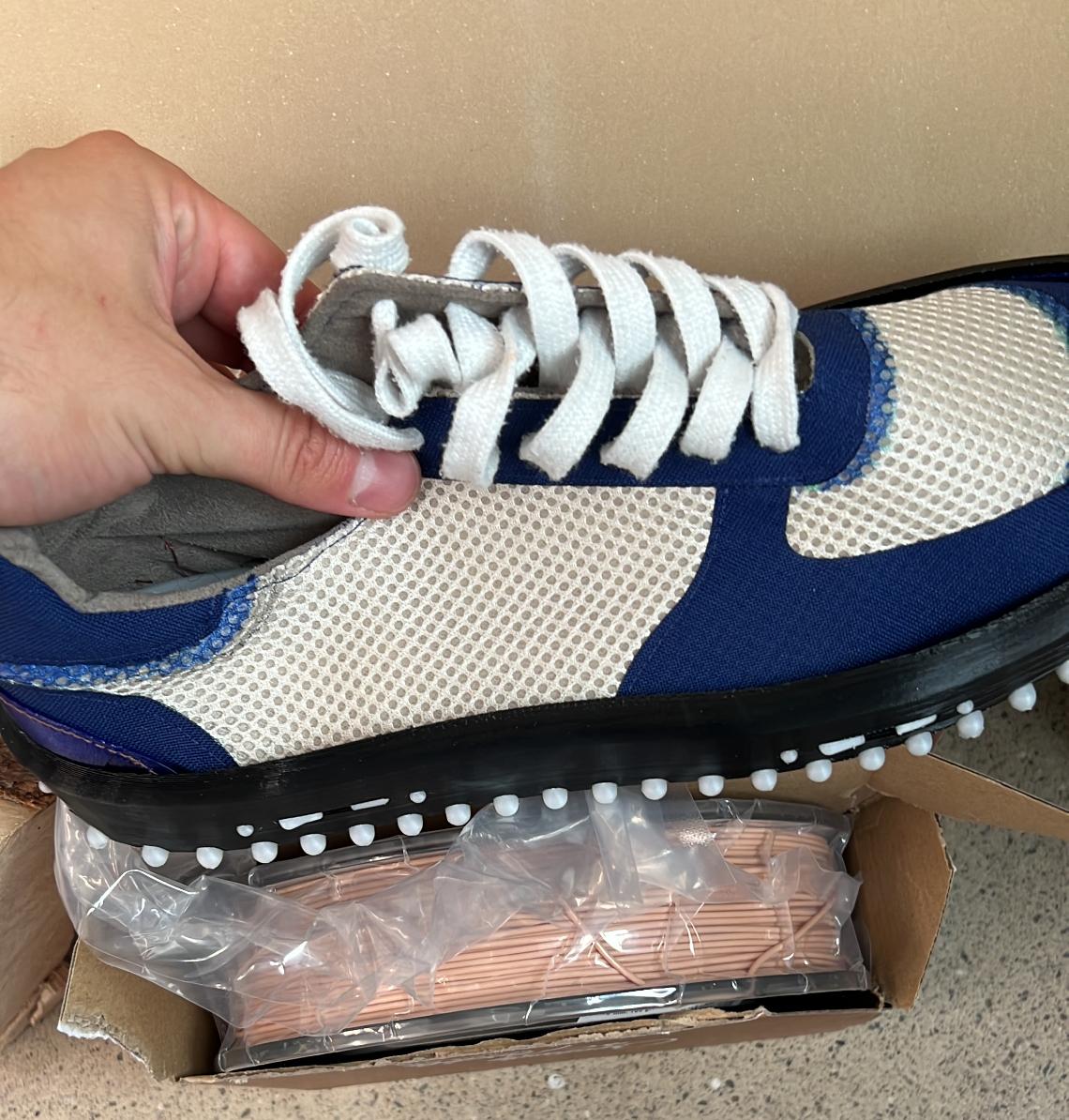
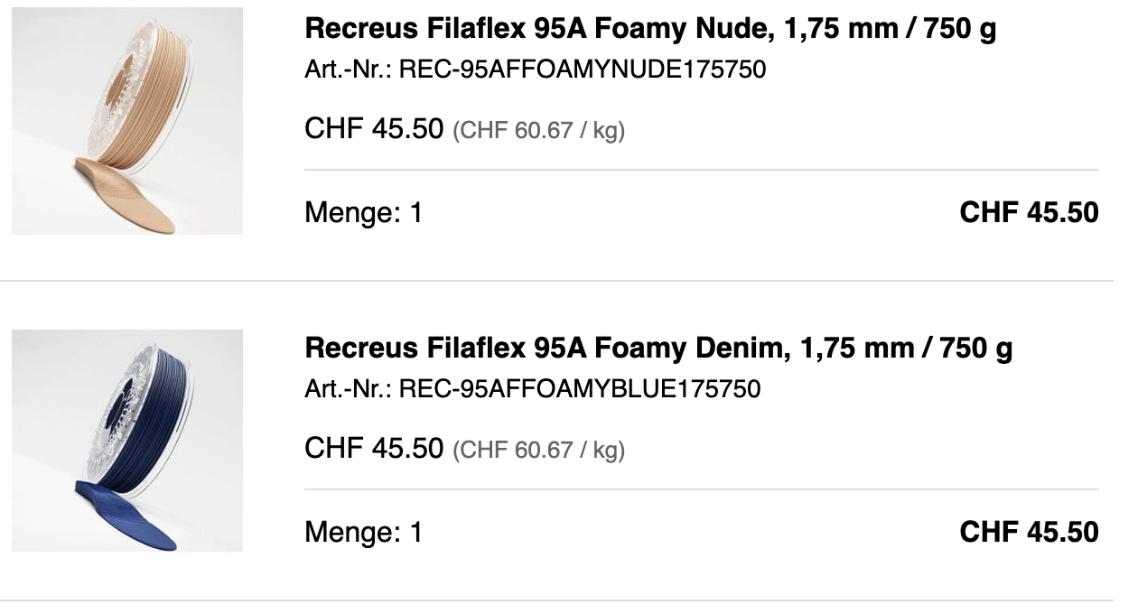
Der erste Druckversuch mit dem neuen Filaflex Foamy
TPU-Filament missglückte, da es andere Anforderungen an die Druckparameter stellte als das zuvor verwendete TPU. Diese Unterschiede betrafen unter anderem die notwendige Materialvorbereitung und die spezifischen Einstellungen im Druckprozess. Das Filament muss trocken sein, da es stark hygroskopisch ist und Feuchtigkeit zu Druckfehlern führen kann.
Zudem mussten die Extrusionstemperatur zwischen 245–
255°C sein, der Filamentfluss zwischen 60–100%, (je nach gewünschter Weichheit), die Druckgeschwindigkeit
(20–40 mm/s) sowie Retract-Einstellungen (ca. 2,5–6mm
Retraction bei 35–50 mm/s) angepasst werden. Nach entsprechender Anpassung dieser Parameter konnte der Druck erfolgreich durchgeführt werden.
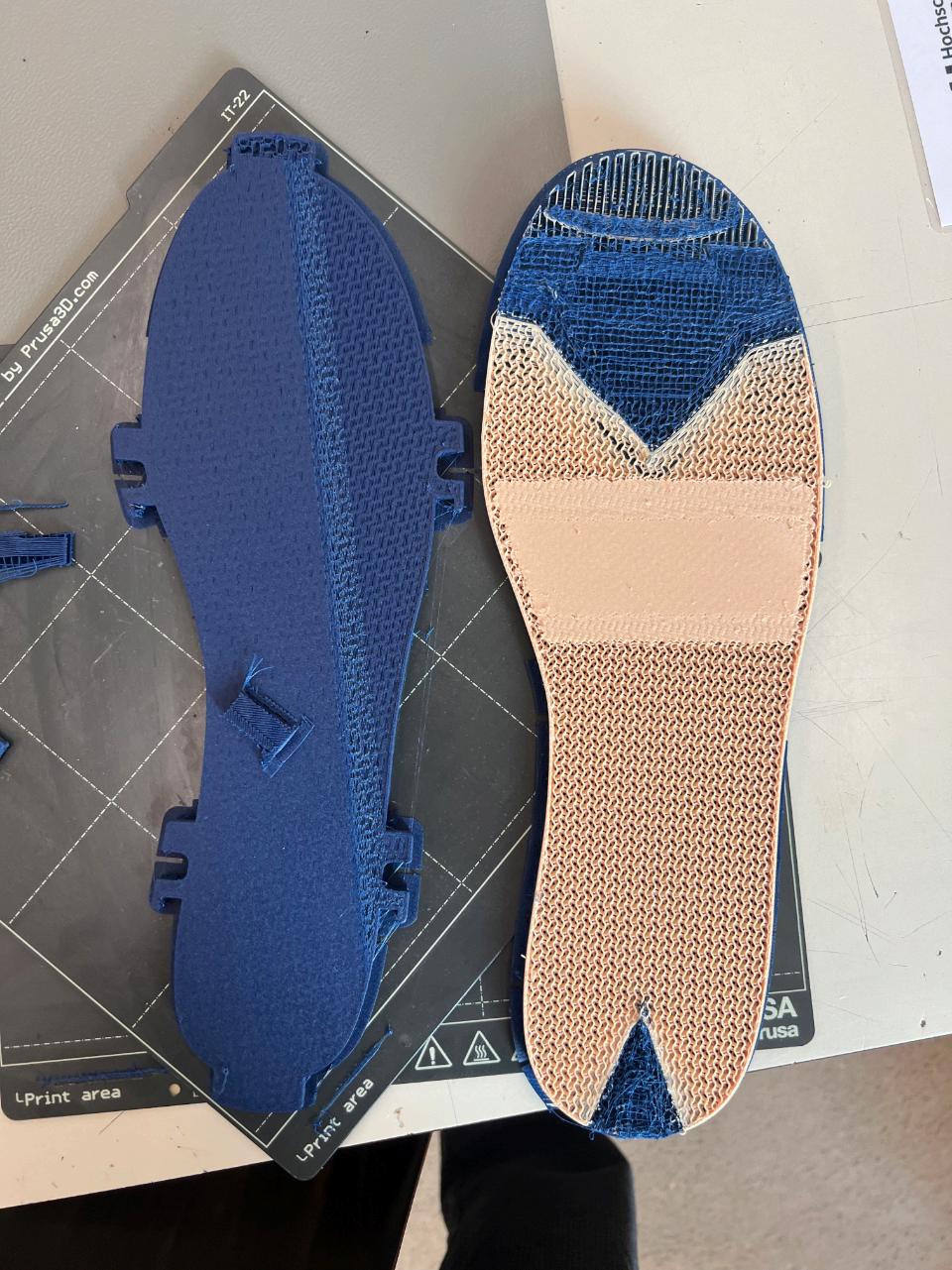

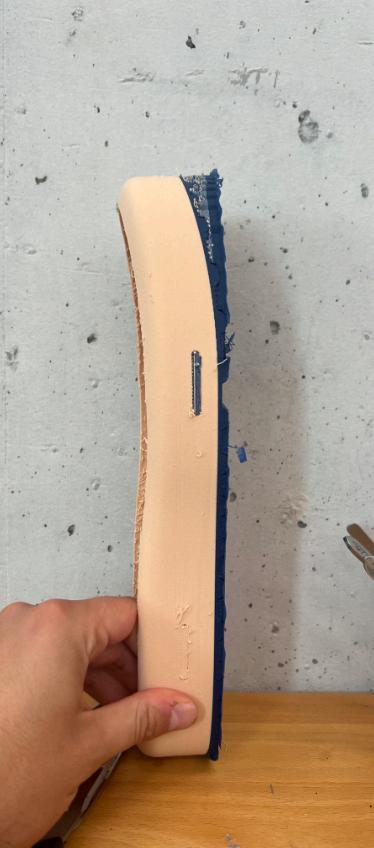
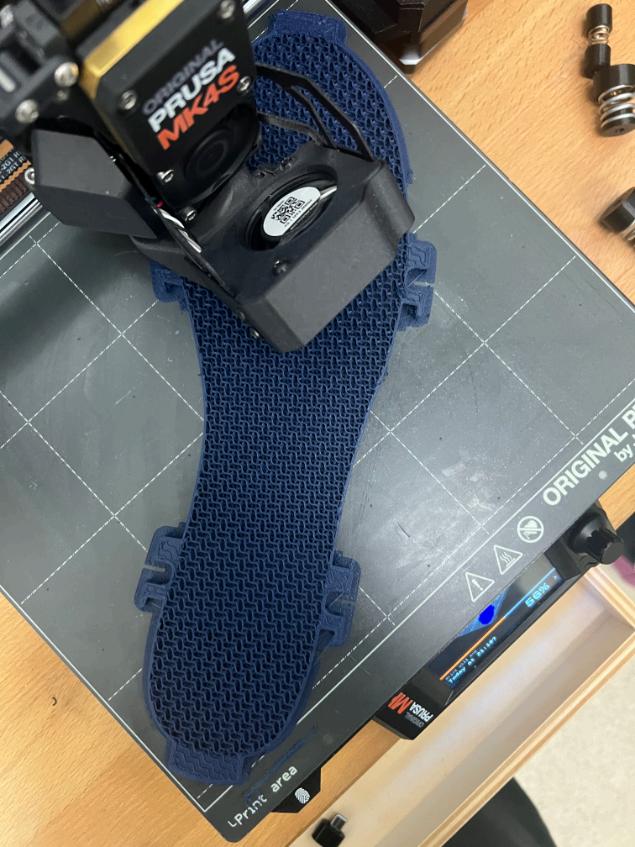
Der nächste Druck verlief erfolgreich. Nach dem Entfernen der Stützstrukturen konnte die Sohle mit dem neu angepassten, fertig genähten Schaft und der Zwischensohle zusammengefügt werden. Damit war ein weiterer Prototyp im modularen System funktionsfähig montiert und bereit für erste Tests hinsichtlich Passform, Halt und Gesamtwirkung.
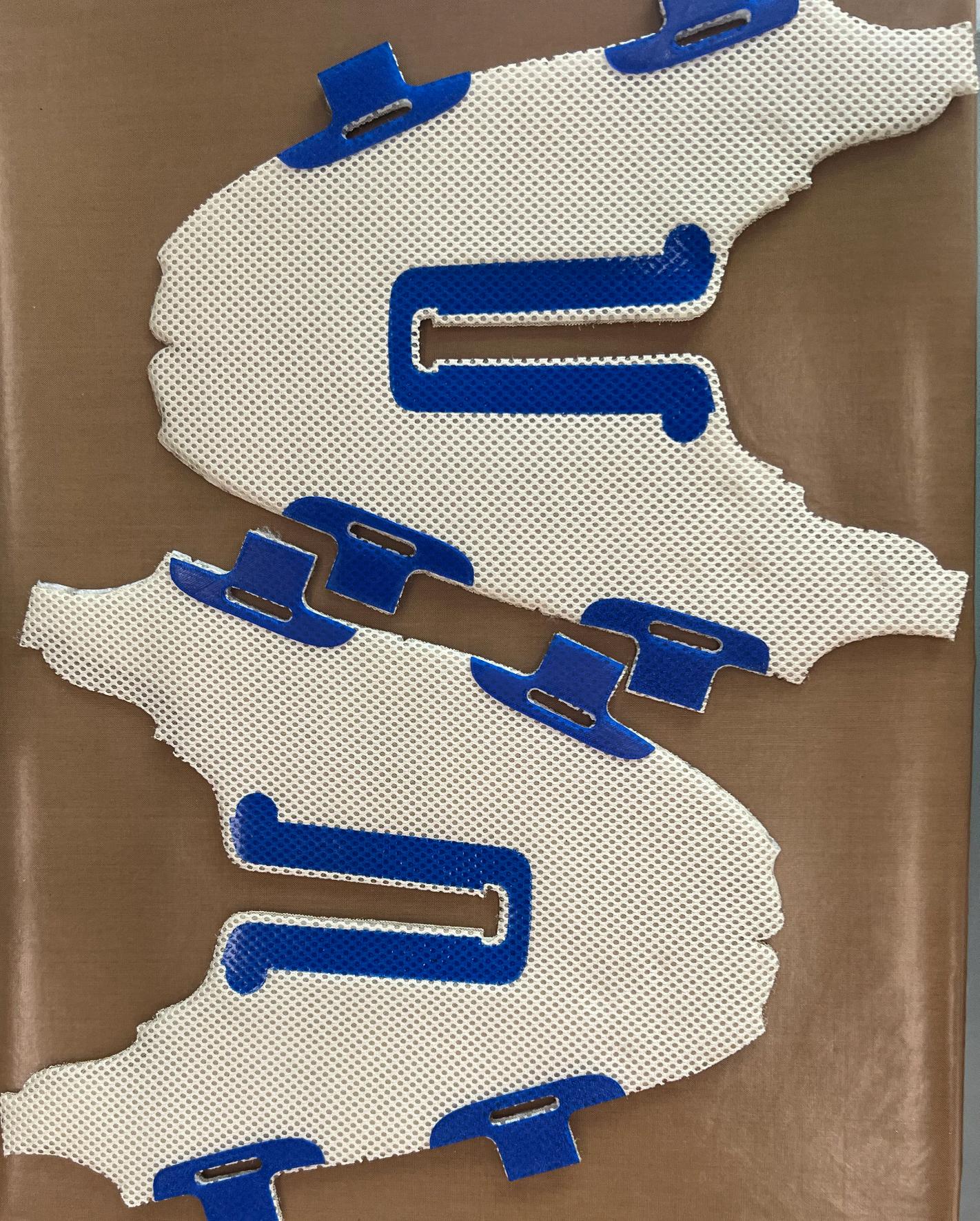
In der verbesserten Version des Schafts wurde auch das Schnürteil mit einem 3D-gedruckten Verstärkungsteil aus PETG versehen, um die Schnürung stabiler und langlebiger zu gestalten. Die Verstärkungsteile wurden mittels Heatpress direkt auf den Schaftkörper (Body) aufgebracht. Zudem wurden die Verstärkungen rund um die Konstruktionsöffnungen für die Halteriemen vergrössert und breiter ausgeführt, um eine verbesserte Belastbarkeit im modularen System zu gewährleisten.
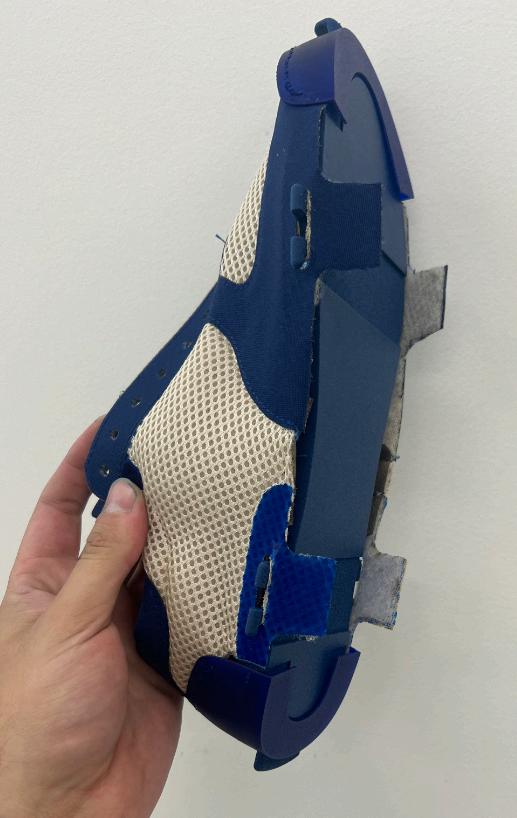
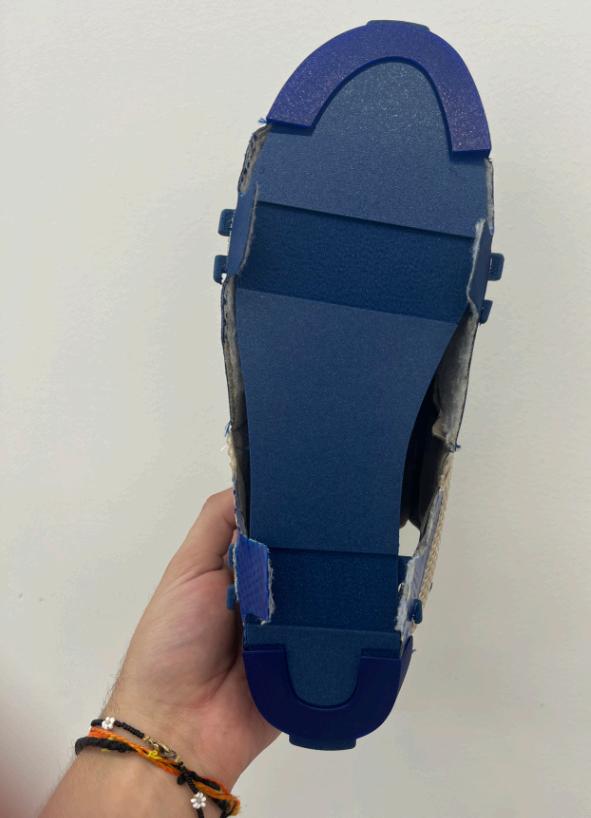
Der überarbeitete Schaft in Kombination mit der neu konstruierten Zwischensohle, passt nun präzise in die Aussparungen für die Haltebänder sowie für die Kappen. Diese Anpassungen ermöglichen eine passgenauere Verbindung der Komponenten und verbessern die Funktionalität und Stabilität innerhalb des modularen Systems.


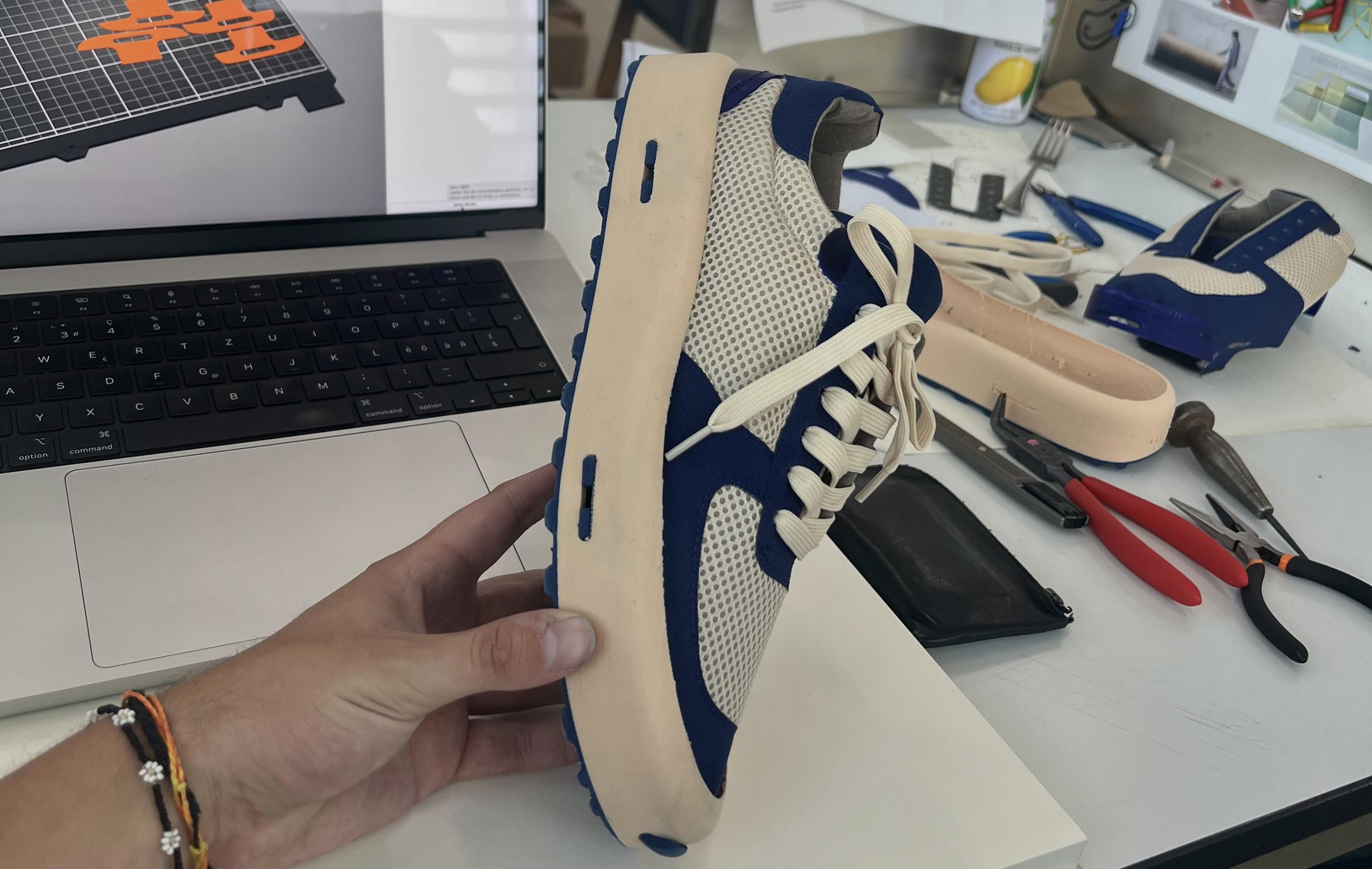
Die anfängliche Idee für den zweiten Schuhtyp war, eine Art Loafer-Sneaker zu entwickeln – ein Modell ohne klassische Schnürung, das Komfort und sportliche Ästhetik vereint. Auch dieses Konzept sollte auf dem modularen System basieren und eine alternative zum ersten Modell bieten.
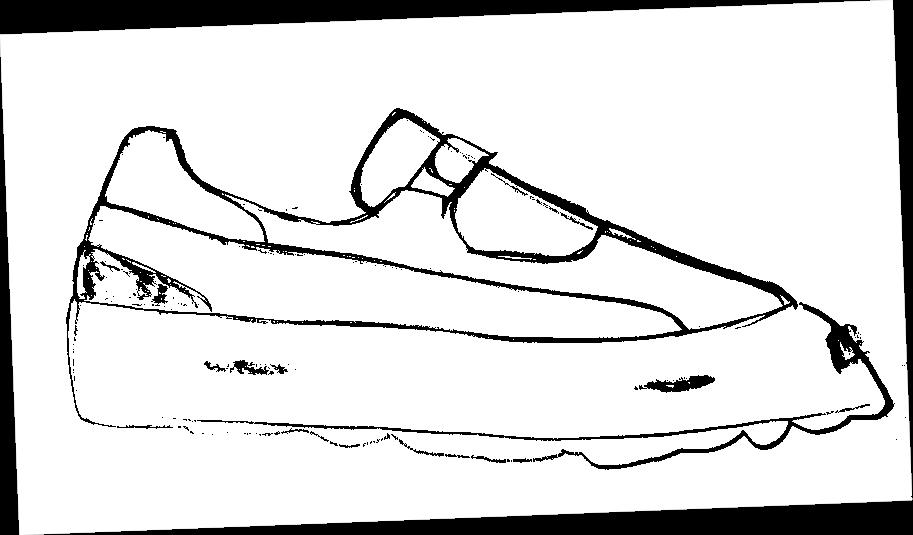
Aufgrund des zeitlichen Rahmens und der potenziellen technischen
Herausforderungen entschied ich mich jedoch, das Risiko eines unfertigen
Prototyps zu vermeiden. Stattdessen wählte ich eine einfachere Umsetzung
in Form einer offenen Sandale, angelehnt an den klassischen BirkenstockSchnitt. Diese Variante verwendet nur vier der sechs Steckriemen – ohne
Riemen an Spitze und Ferse – und wurde bewusst so simpel wie möglich gestaltet, um das System in reduzierter Form weiter zu testen und das
Potenzial aufzuzeigen.

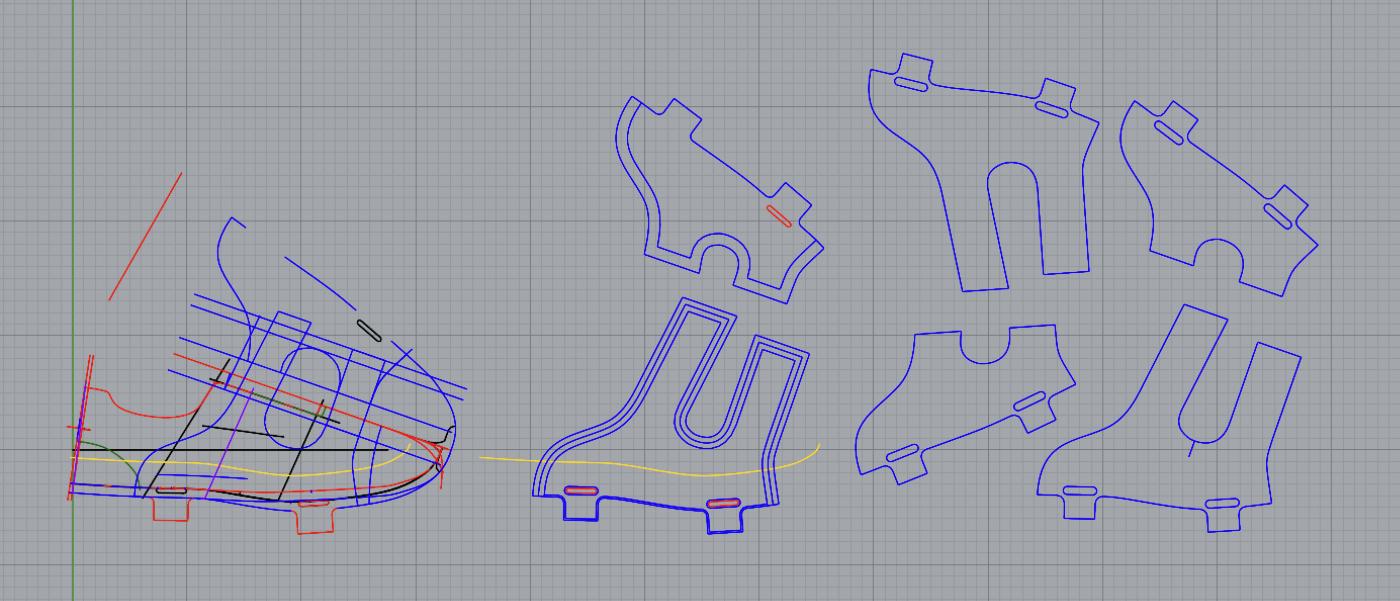

Mithilfe des bisherigen Grundmodells entwickelte ich ein vereinfachtes Sandalen-Modell in Anlehnung an den Birkenstock-Schnitt. Die Schnittteile sollten aus 3DMesh-Material mithilfe des Lasercutters ausgeschnitten werden. Diese Teile wurden mit jeweils 5 Millimetern Zugabe aufgebaut um diese gestürzt zu verarbeiten.
Bei den ersten Probeteilen wirkten jedoch die Riemen, die über den Fuss verlaufen und mit Klettverschluss gehalten werden, als zu schmal und instabil. Für die nächste Version sollten diese Riemen daher breiter und robuster gestaltet werden, um besseren Halt, Tragekomfort und eine stimmigere Proportion im Gesamtbild der Sandale zu erreichen.
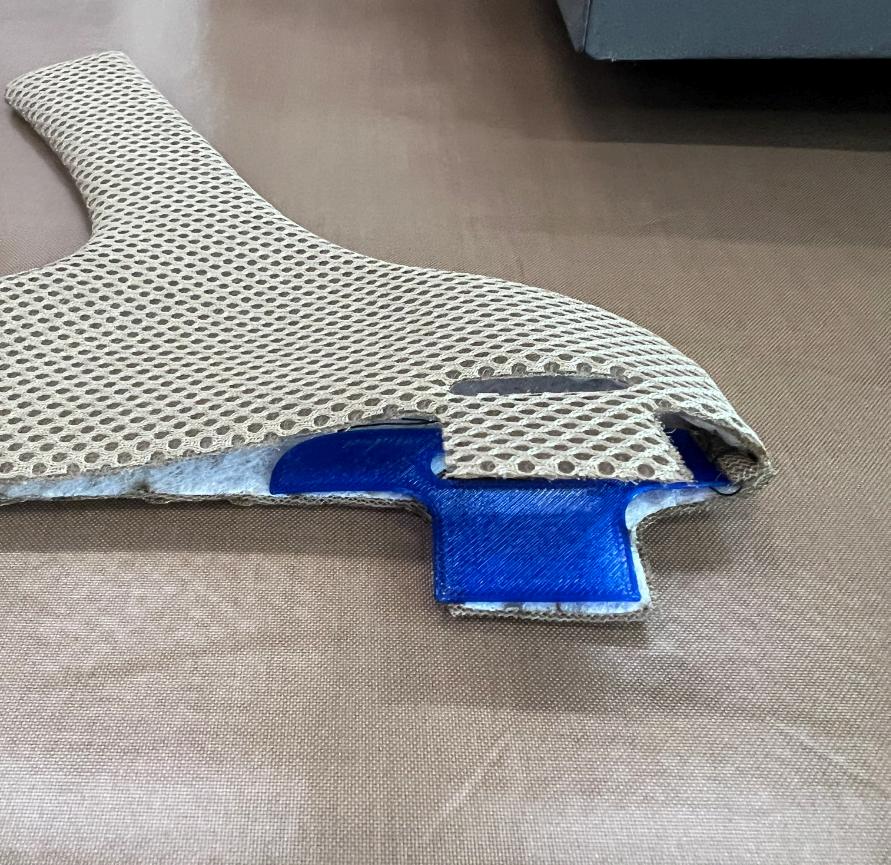
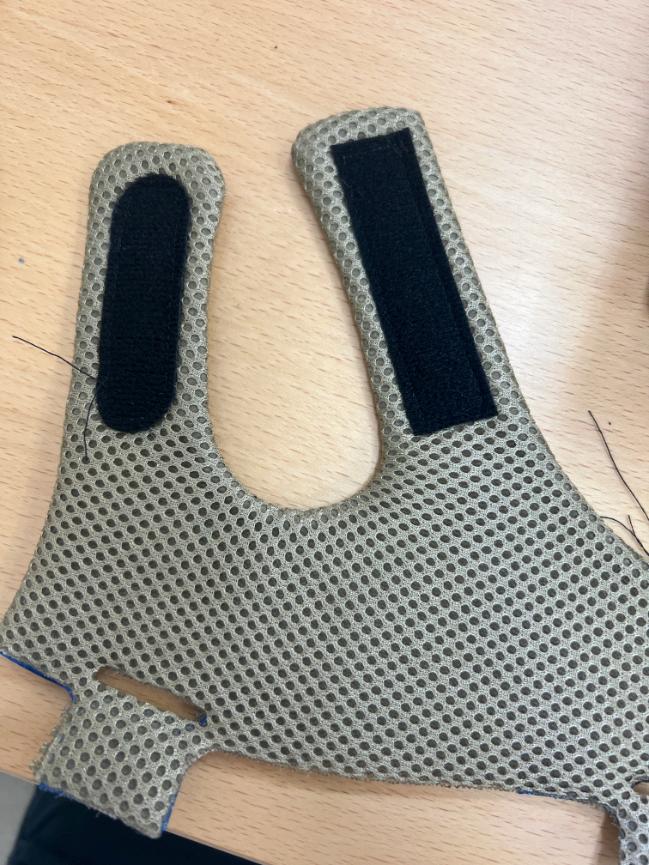
Beim angepassten Oberteil wurden – wie bereits beim Sneaker-Modell – an den Aussparungen für die Steckriemen 3Dgedruckte Verstärkungsteile aus PETG eingesetzt. Diese wurden mithilfe der Heatpress in das Material eingebügelt, um die Bereiche stabil zu fixieren und die Haltbarkeit der Riemendurchführungen im modularen System zu gewährleisten.
Der erste Sandalen-Prototyp diente als Grundlage zur Beurteilung von Passform und Riemenlängen. Dabei zeigte sich, dass die Neigung der über den Fuss verlaufenden Klettverschlussriemen noch nicht optimal war.
Für einen besseren Sitz und Halt sollte dies angepasst werden und auch die inneren Reimen verlängert werden.
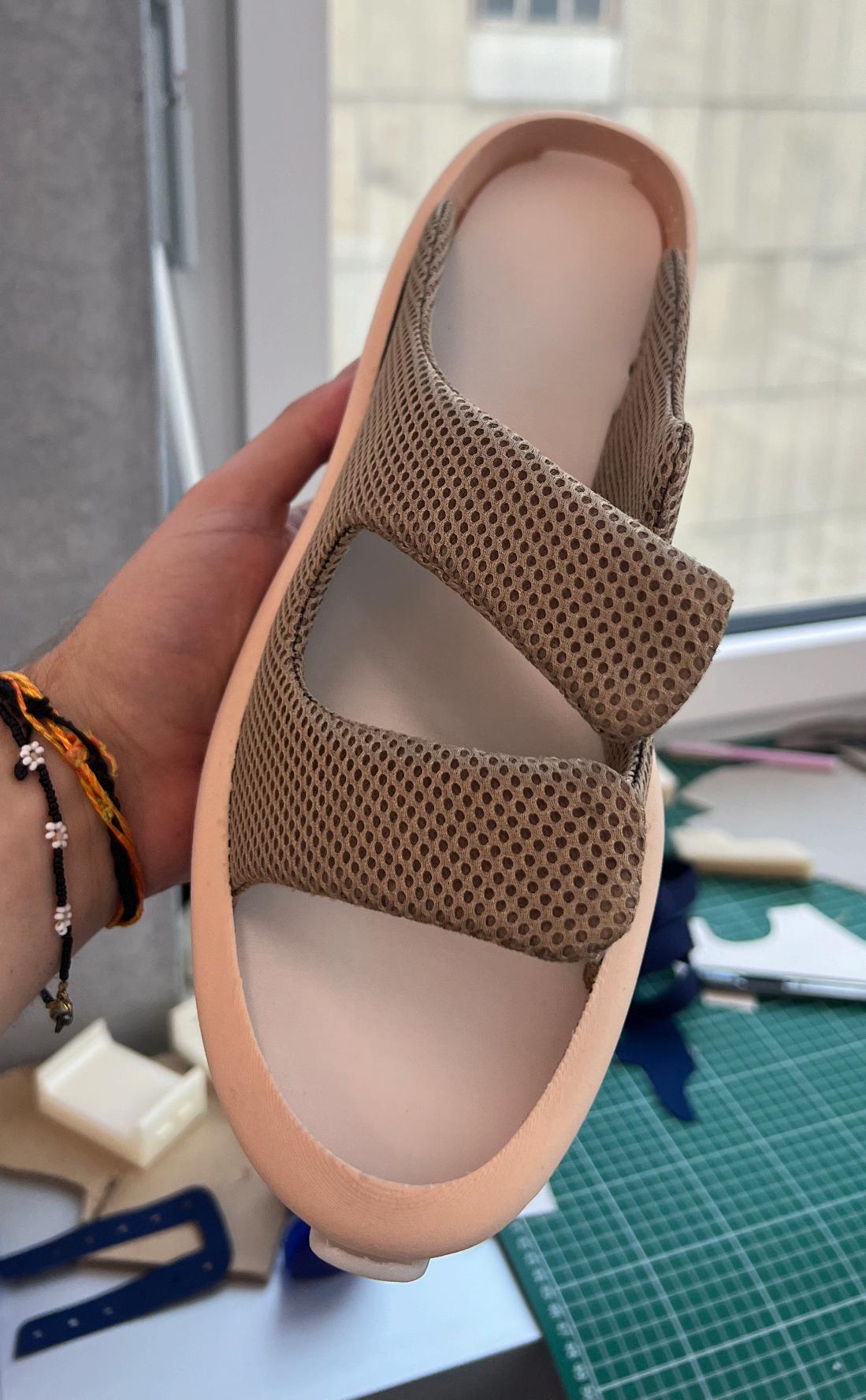

Da mir die ursprüngliche Farbe des Materials für die Sandale nicht zusagte, entschied ich mich, das MeshGewirke aus dem vorhandenen Restmaterial mit einem speziellen Polyester-Färbemittel in einem dunklen Blau einzufärben. So konnte das Material nicht nur farblich besser ins Gestaltungskonzept eingebunden, sondern gleichzeitig auch ressourcenschonend weiterverwendet werden.
Die Zuschnitt-Teile wurden passgenau im Laserprogramm angeordnet, um das vorhandene
Restmaterial möglichst effizient zu nutzen und um sicherzustellen, dass alle benötigten
Teile auf die Fläche passten. Gleichzeitig
blieb genug Reserve, um im Fall unsauber ausgeschnittener Teile 1-2 Komponenten nachschneiden zu können.
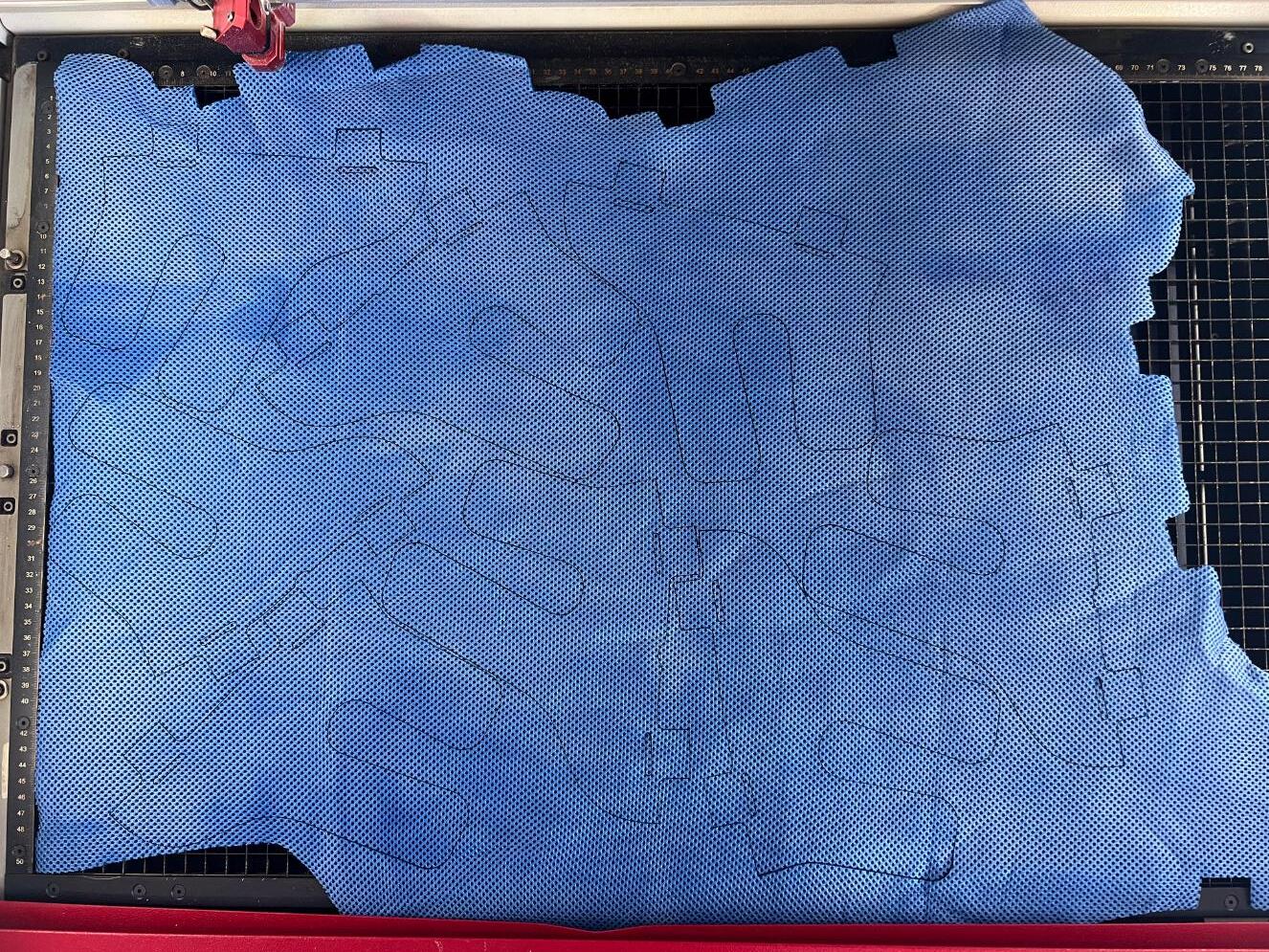
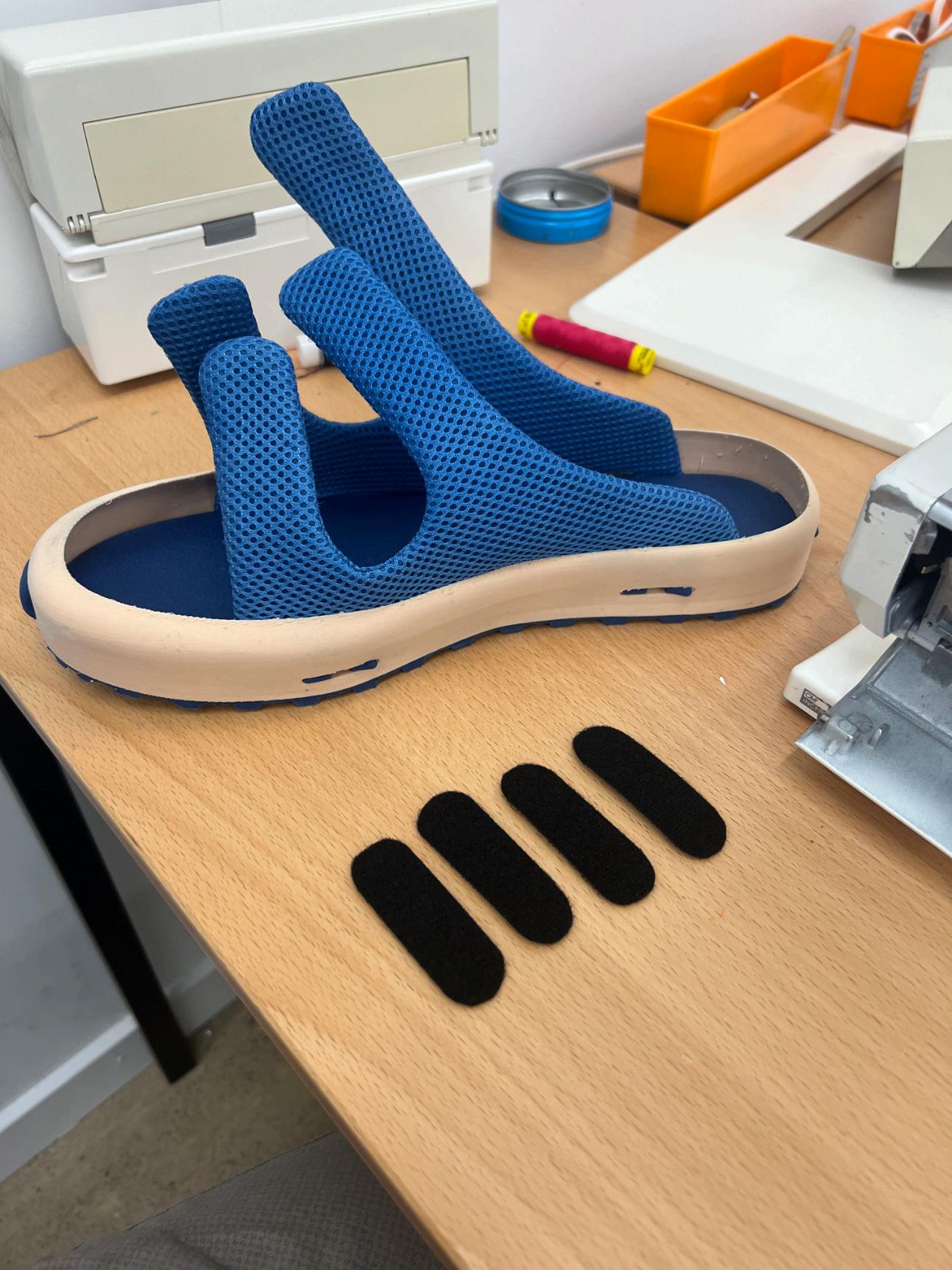
Nach dem Zusammennähen und Verstürzen der Teile wurden diese sorgfältig gebügelt. So konnten die Stürzkanten sauber gefaltet und eine präzise Kantenführung erzielt werden. Anschliessend wurden die Klettverschlüsse in der passenden Grösse zugeschnitten, an den Enden abgerundet und schliesslich aufgenäht.
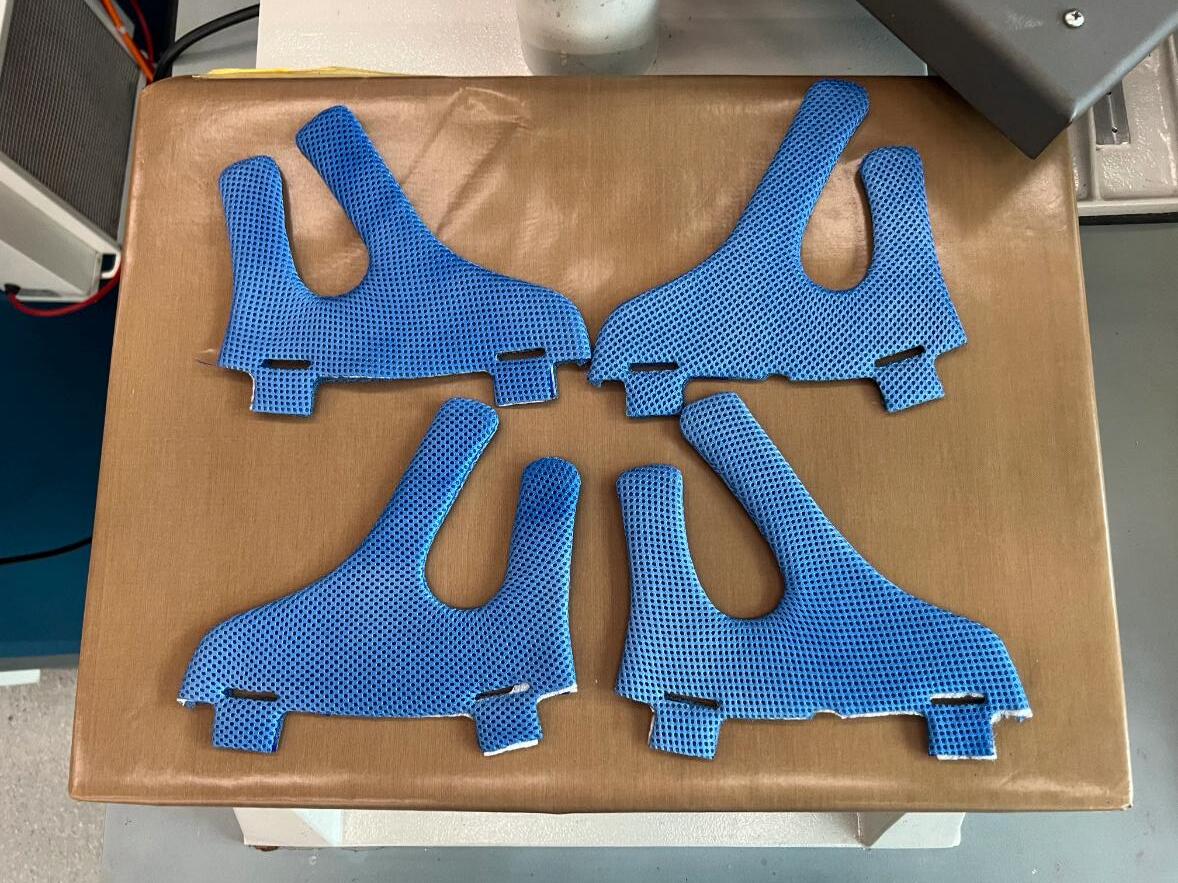
Die untere Konstruktion wurde mit den vorbereiteten Bändern vernäht. Das Sandalen-Oberteil war damit bereit für die abschliessende Verbindung mit der Sohle. So konnten alle Komponenten des modularen Sandalen-Modells funktional zusammengefügt werden.
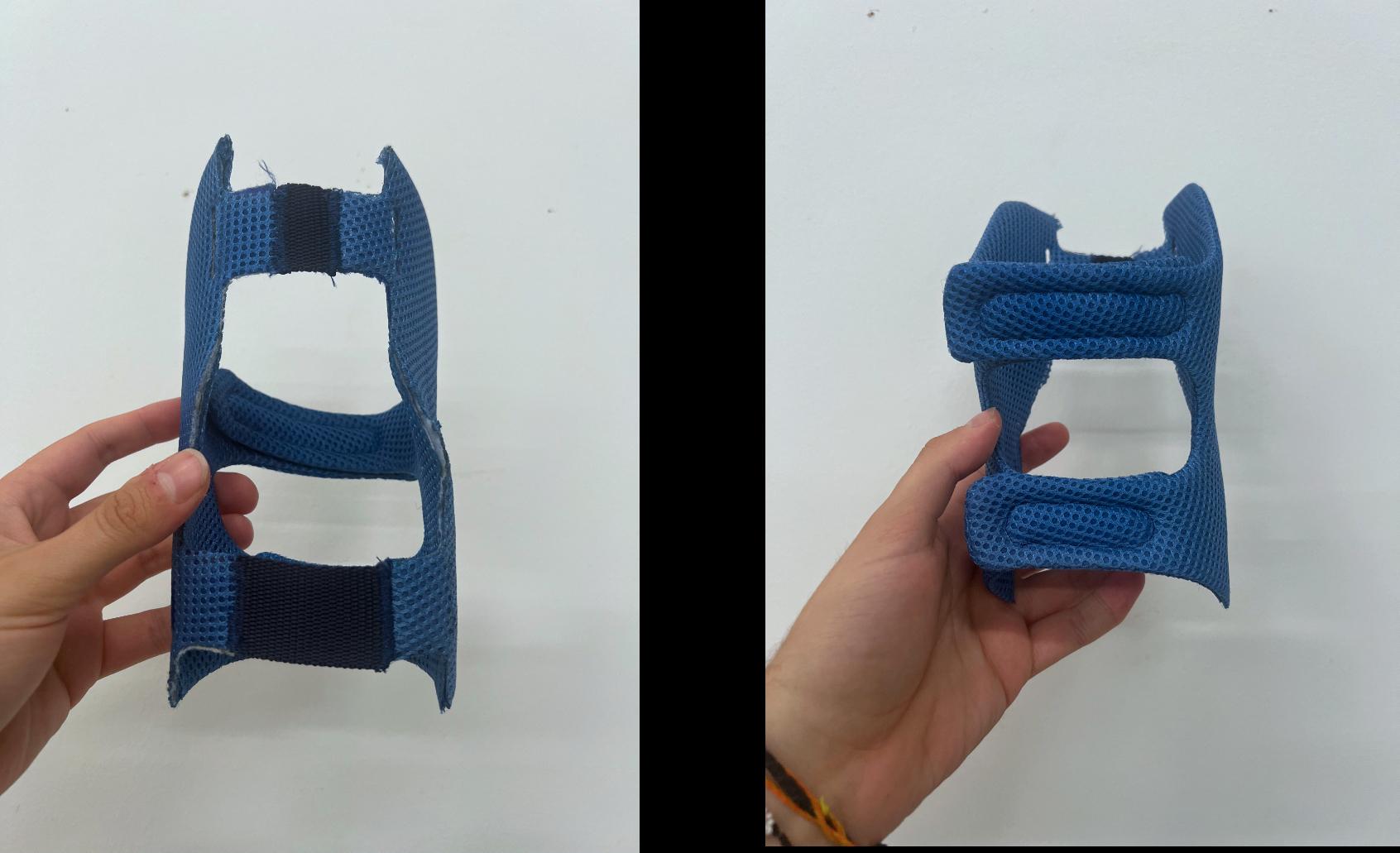
Material und Potenzial für Industrie
Für eine zukünftige Weiterentwicklung des modularen Systems könnten alternative Materialien eingesetzt werden, die noch stärker auf Nachhaltigkeit und Kreislauffähigkeit ausgerichtet sind. Im
Sohlenbereich wären biobasierte oder biologisch abbaubare Materialien wie z.B. algenbasierte TPUAlternativen, Naturkautschuk-Mischungen oder recyclebare EVA-Compounds denkbar. Besonders spannend wäre die Zusammenarbeit mit dem Schweizer Unternehmen Kuori, das an einem biologisch abbaubaren Sohlenmaterial auf pflanzlicher Basis forscht und bereits erste filamentfähige Materialien entwickelt hat. Für den Schaftbereich bieten sich reine Polyestertextilien, mechanisch recycelte PET-Garne sowie monomaterial gestrickte Oberteile an, die leichter zu trennen und sortenrein recyclebar sind.
Entscheidend bleibt dabei die Trennbarkeit und Materialreinheit, um ein funktionierendes zirkuläres System zu gewährleisten.
Evaluation und Ausblick
Ich bin mit dem Ergebnis des Projekts sehr zufrieden. In meinen Augen zeigt es deutlich das Potenzial, das in einem modularen Schuhsystem steckt. Die Grundidee der Modularität konnte funktional umgesetzt und in einem realen Prototyp erfolgreich erprobt werden – der Proof of Concept wurde damit erbracht. Die Möglichkeit, verschiedene Schaftvarianten und Sohlenformen zu kombinieren, eröffnet nicht nur gestalterische Freiräume, sondern auch neue
Ansätze für einen bewussteren und ressourcenschonenderen Konsum. Optimierungspotenzial besteht bei technischen
Details wie dem Verschlusssystem, der Abdichtungslippe und der Vorder- und Hinterkappe.
Re:Move legt somit eine tragfähige Grundlage für weitere Entwicklungen im Bereich nachhaltiger, modularer
Schuhkonzepte – mit Perspektiven auf Serienfertigung, Individualisierung und einem zirkulären Produktsystem. Das System erweist sich als zukunftstauglich und bietet eine solide Grundlage für Weiterentwicklungen.

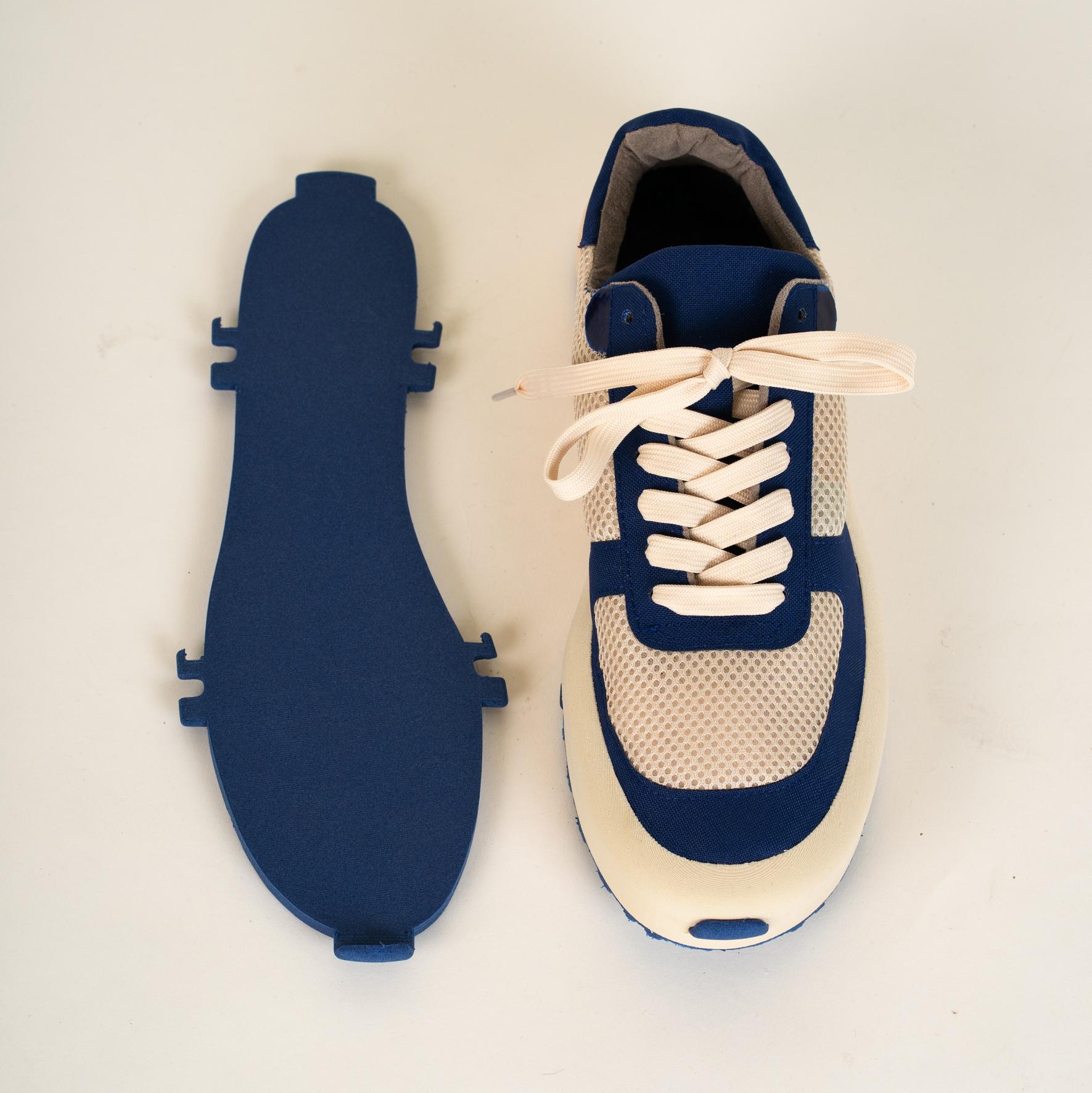


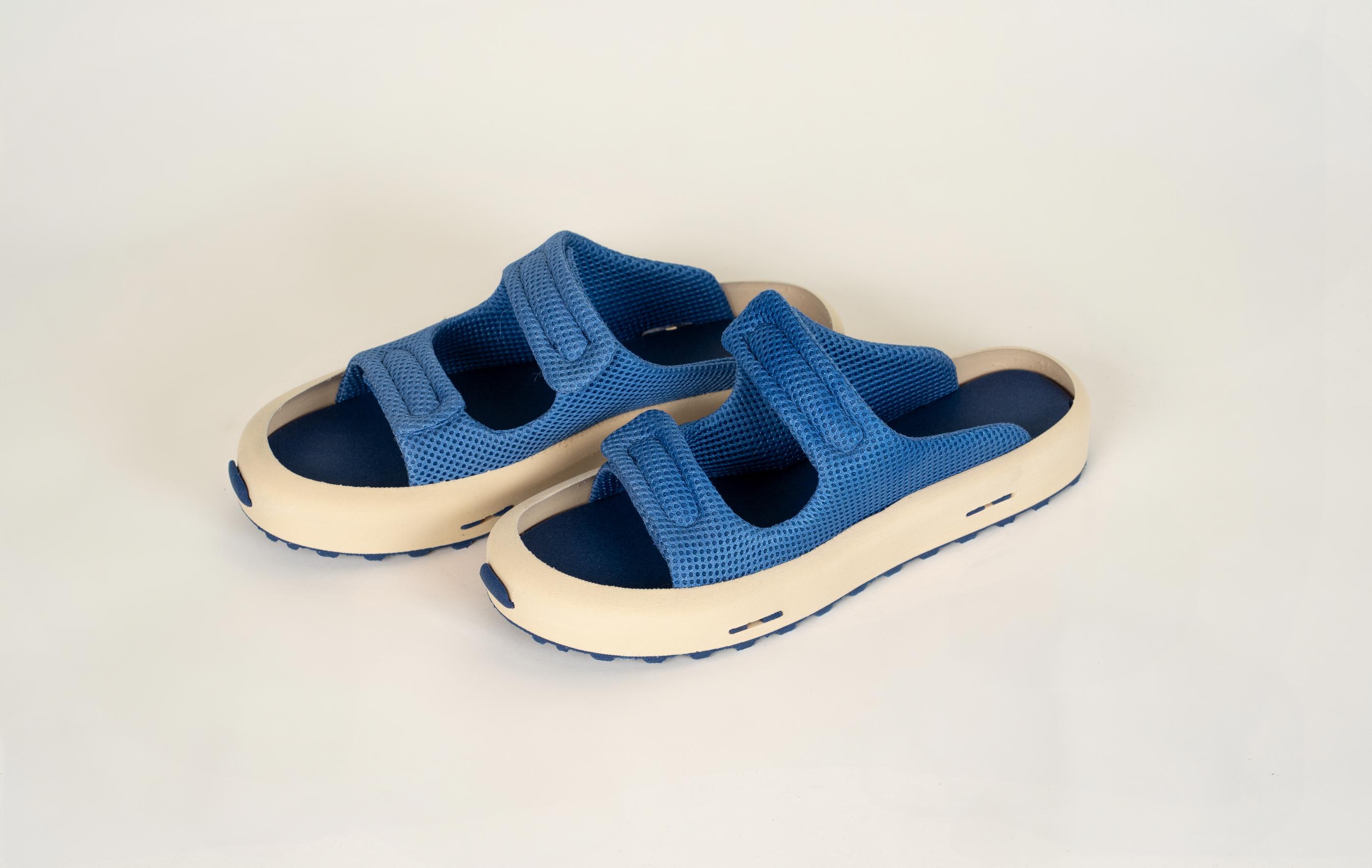
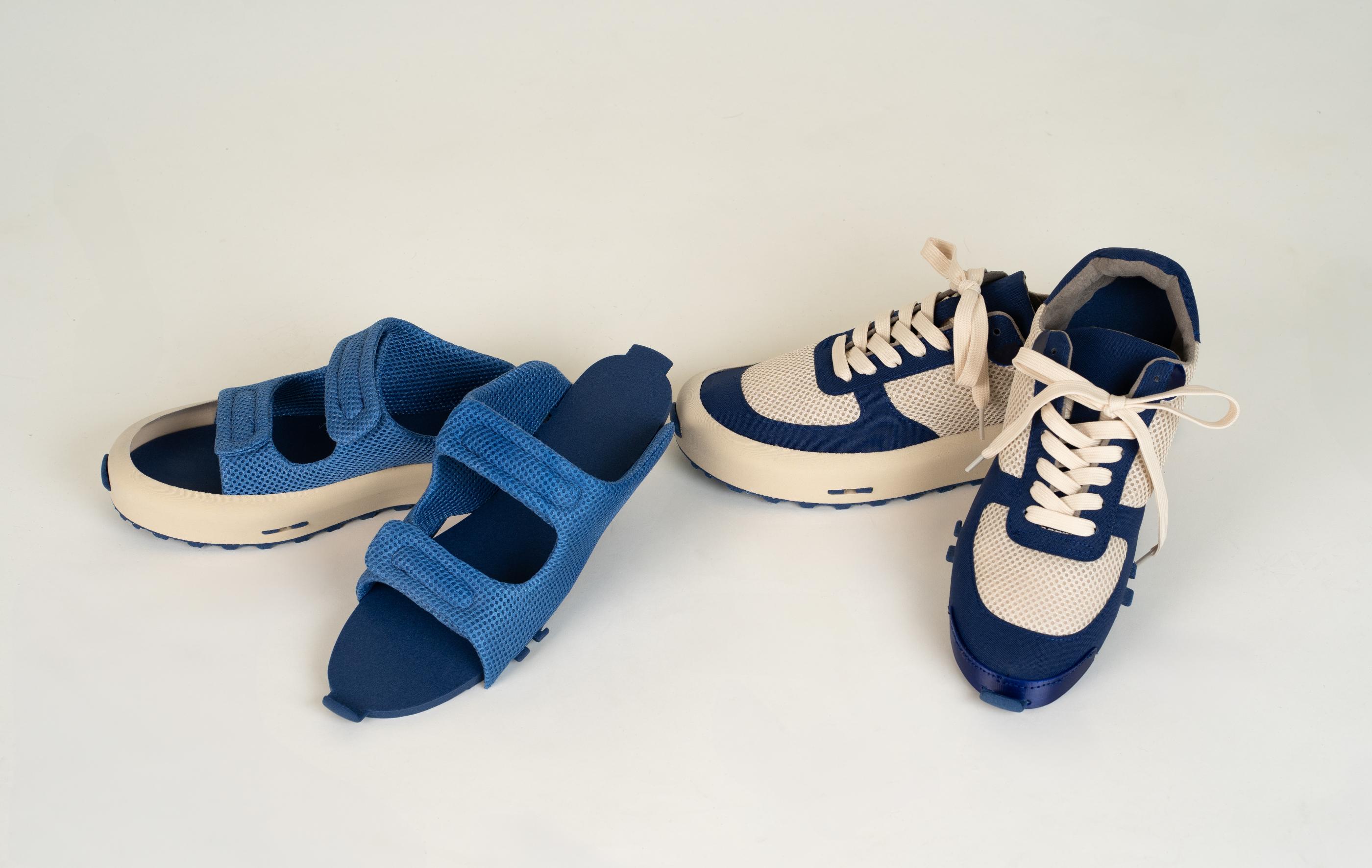
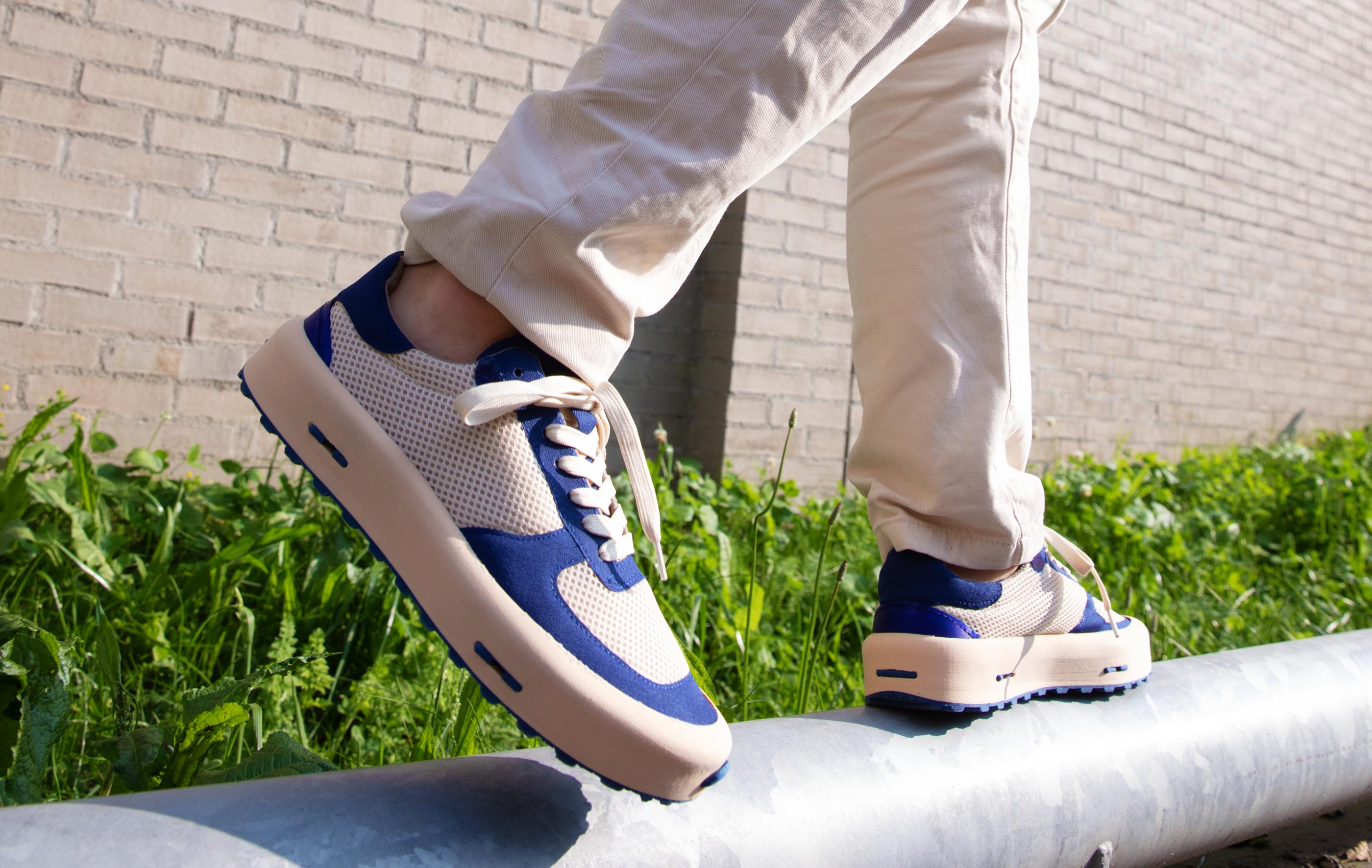
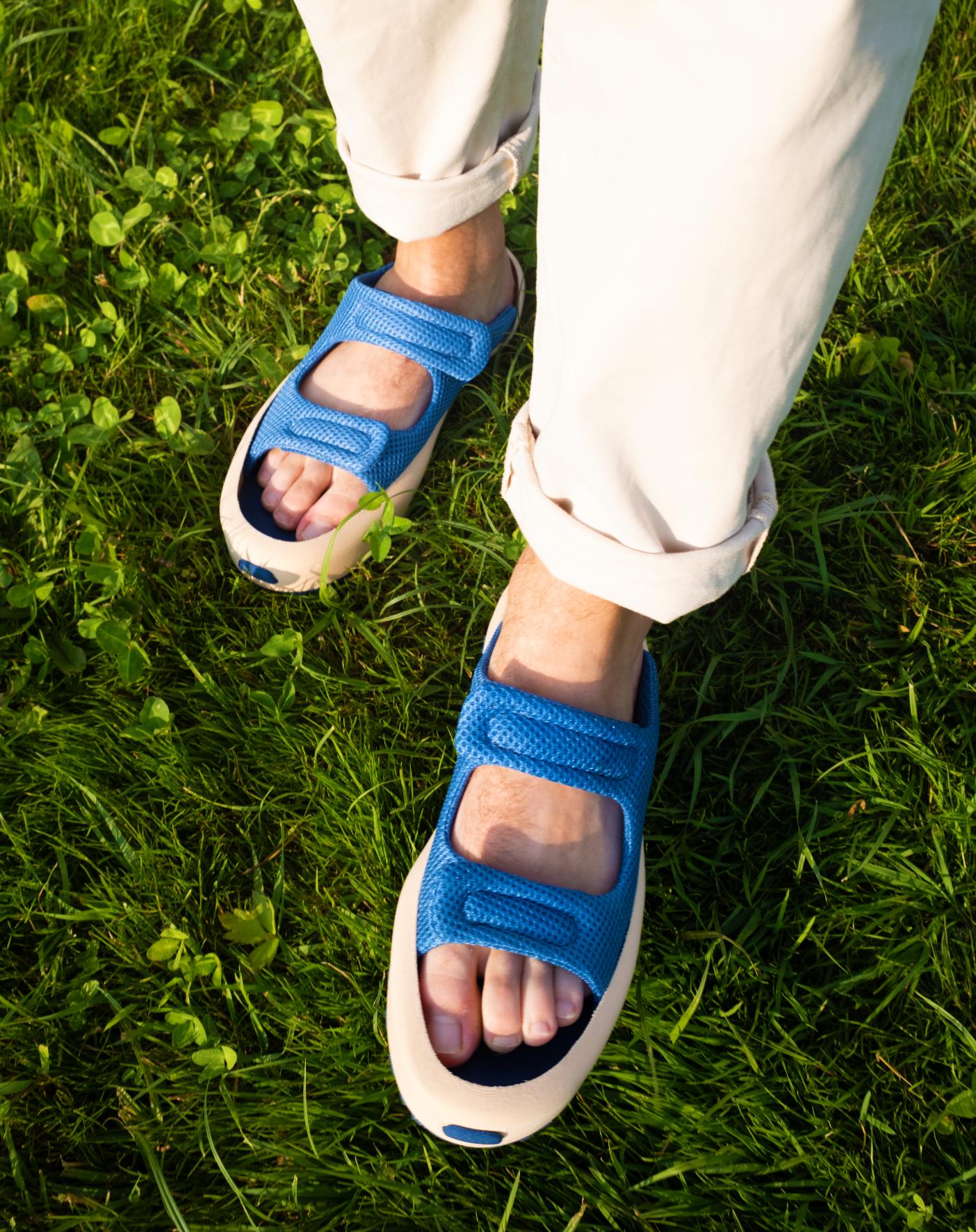