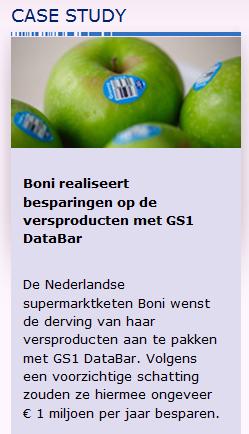
6 minute read
markt
1.3.3 Case 1.3: MOBA produceert eiersorteer- en verpakkingsmachines voor een wereldwijde markt.
Bron : Visser, H.M. en Van Goor, A.R. (2019) Werken met logistiek, p176.
De historie van Moba begint in 1947. De heer J.H. Mosterd start in een schuurtje te Barneveld met het repareren van eiersorteermachines. Daarna wordt een eigen machine gebouwd voor de eier- en pluimvee-industrie. Vijftien jaar later, in 1962, krijgen de eerste –baanbrekende – ideeën vorm om van de bestaande handpakkers volautomatische eiersorteermachines te maken. In 1970 brengt Moba de eerste machine die automatisch sorteert en verpakt op de markt.
Daarna volgen nieuwe ontwikkelingen elkaar snel op. Zoals de ‘balans’ : het gebruik ervan als weegschaal én als transportmiddel bezorgt Moba wereldfaam.
De methodes die worden ontwikkeld voor individuele eierbehandeling – de ‘Gentle Touch’ –worden het handelsmerk van Moba.
Door het overlijden van de stichter in 1971 is er geen opvolger. Holding Barneveld BV wordt overgenomen door Thyssen-Bornemisza op 01 januari 1982. Eerst volgen er roerige tijden. Tot twee keer toe zijn er in de jaren tachtig ontslagrondes geweest. Daarna werd het bedrijf stabieler. Moba werd wereldmarkleider op het gebied van eiersorteermachines. Het is nog steeds gevestigd in Barneveld en op deze locatie vindt verkoop, ontwikkeling, ontwerp en productie van de machines plaats. Bij het bedrijf werken ongeveer 250 medewerkers en de omzet ligt in de buurt van 60 miljoen euro. De meest geavanceerde productiemachines hebben een productiecapaciteit van 180 000 eieren per uur. Die kosten dan wel meer dan een miljoen euro.
De fabricage vond oorspronkelijk plaats in een werkplaats achter het woonhuis van de heer Mosterd. Met de groei van het bedrijf werd het gebouw stap voor stap uitgebreid. Steeds weer barste het bedrijf uit zijn jasje. In de jaren negentig ontstond zo een aan elkaar gegroeide situatie van allerlei afdelingen. Het bedrijf had gekozen voor een functionele indeling. Dit wil zeggen dat de productieafdelingen zich hadden gespecialiseerd in aparte bewerkingen. Zo was er een ontvangstafdeling, een zagerij, een draaierij, een lasserij, het magazijn en een samenbouw.
Het bedrijf was een van de eerste klanten van Baan MRP software voor bedrijfsbesturing (nu Infor). De software werd ‘as is’ ingevoerd. Dat betekende dat de MRP software leidend was in de bedrijfsaansturing. Het werd letterlijk en figuurlijk een papieren winkel. Voor elke opdracht moest een bon gemaakt worden. Zo gingen de producten van afdeling naar afdeling. Het magazijn was daarin de spil. Daar werkten wel dertig mensen om de stroom op gang te houden. De onderdelen werden in de fabriek in batches gemaakt. Het geheel was door de material requirement planning gestuurd op een push methode. En dan te weten dat het aantal verschillende onderdelen wel opliep tot boven de 25000. Op die manier is het te begrijpen hoe complex de aansturing was. Hierdoor ontstonden grote voorraden. Het magazijn was 4200 m2 in omvang. De doorlooptijden voor het maken van een machine liep op tot meer dan zestien weken. Daarnaast bleek er veel incourant te zijn.
De ommekeer kwam in 2000. Toen werd het hele proces geanalyseerd. Met behulp van een door studenten uitgevoerde ABC-analyse kwam aan het licht wat snel en wat traag lopende
onderdelen waren. Waar mogelijk werden incourante voorraden uit het proces afgevoerd. Tevens werd het proces gestroomlijnd. De functionele processen werden omgezet naar een flowgewijze manier van produceren.
In de onderdelenfabricage werden autonome groepen gecreëerd. In plaats van het los verwerken van opdrachten in batches, op basis van prognose, werd er machine voor machine gefabriceerd. Zo maakten de werknemers zelf handige transportkarren. Daarop werden de benodigde onderdelen voor een bepaalde order bij elkaar gehouden. Zo konden er tientallen onderdelen in één keer worden gemaakt. Hiertoe moesten de stuklijsten worden aangepast. Dat scheelde enorm in doorlooptijd. De negen weken voor onderdelenaanmaak konden teruggebracht worden naar één week. De onderdelen hoefden nu ook niet meer door het magazijn heen. Per opdracht voor een gehele kar was nog maar één document nodig. De scheelde wel 80 % in het papiergebruik.
Voor de snellopende en regelmatige verbruikte 3000 onderdelen werd de bevoorrading vanuit het magazijn verplaatst naar de werkplaats. De montagemedewerker bewaakte zo zijn of haar eigen voorraad. Dat gebeurde met behulp van een tweebakkensysteem, ook wel two bin genoemd. Zodra er één bak leeg is, wordt het seintje gegeven om een nieuwe bak te brengen. Een klein kaartje op de bak, de zogenoemde kanban, was voldoende voor de stuurinformatie.
De actieve onderdelen liggen nu als kanban voorraad op de werkvloer. Doordat de medewerker precies ziet hoe de voorraad verloopt en vroegtijdig actie neemt om zelf te bestellen door de barcode te scannen, komen tekorten nauwelijks meer voor. Door deze pullaansturing zakte ook de gemiddelde voorraad sterk. Het centrale magazijn kon teruggebracht worden naar 1.700 vierkante meter. Dat komt neer op 60 procent minder ruimtegebruik.
De tevredenheid van de medewerkers nam door de verbeterde service sterk toe. De irritatie over tekorten liep sterk terug. Nog beter was de winst voor de klant, want de doorlooptijd van het totale proces liep terug tot de helft van de oorspronkelijke zestien weken. Financieel gezien leverde dit verbeteringsproces Moba geen windeieren op. Het bedrijf belevert inmiddels 70 procent van de wereldmarkt.
Vragen :
1. Verklaar het begrip ‘incourante voorraad’.
2. Op welke manier bestuurde Moba eerst ? En na 2000 ? Licht beide bestuursvormen toe voor deze case, en verklaar waarom de laatste het meest geschikt is voor dit bedrijf.
3. Dit project kan terecht beschouwd worden als een win-win situatie voor alle partijen. Welke partijen winnen ? Bespreek.
4. Duid de begrippen aan die te maken hebben met logistiek en leg ze uit aan de hand van de tekst.
1.3.4. Case 1.4: Boni realiseert besparingen op de versproducten met GS1 DataBar
http://www.gs1belu.org/nl/boni-realiseert-besparingen-op-de-versproducten-met-gs1-databar
Met de GS1 DataBar krijgt Boni veel beter inzicht in derving en daardoor kan de kwaliteit van het versaanbod worden verhoogd. Dit gaat dan vooral over producten met een korte houdbaarheidsdatum zoals vlees, gesneden groenten en vis.
Inzicht in houdbaarheid
Boni houdt de houdbaarheidstermijn in de winkels nu handmatig bij. Als de houdbaarheidsdatum nadert dan wordt er een kortingsticker geplakt op het product. Dit is arbeidsintensief maar ook fraudegevoelig aangezien deze stickers gemakkelijk op een ander product geplakt kunnen worden zonder dat dit kan worden gecontroleerd.
Met de GS1 DataBar kan naast het artikelnummer (of GTIN – Global Trade Item Number) ook aanvullende informatie zoals houdbaarheidsdatum worden weergegeven. Voor Boni biedt het de mogelijkheid om te bepalen hoeveel artikelen met welke houdbaarheidsdatum er op het schap staan en met één druk op de knop is te zien welke producten er morgen over de houdbaarheidsdatum heen zijn en waar de dreigende houdbaarheidsdata zich bevinden. Met de GS1 DataBar hoeft Boni de houdbaarheidsdatum dus niet meer handmatig bij te houden en kan er bij de kassa automatisch worden afgeprijsd op bepaalde houdbaarheidsdata.
Sturen op houdbaarheid
Voor de hele markt betekent de GS1 DataBar dat de houdbaarheidsdatum kan worden bijgehouden en worden gemeten van bij binnenkomst van een product tot de verkoop ervan. De gegevens van de doorlooptijd van een product kunnen op elk gewenste tijd worden geprojecteerd op de aanwezige houdbaarheidsdatum van dat product. Zo kan bij ontvangst of het verlaten van het distributiecentrum al worden berekend of het betreffende product met de juiste houdbaarheidsdatum de klant bereikt. Mochten er producten toch vernietigd worden omwille van de houdbaarheidsdatum, dan is het te traceren waar het in de keten is misgegaan. Boni en haar versleveranciers kunnen de keten zo heel gericht sturen en de derving van versproducten aanzienlijk reduceren.