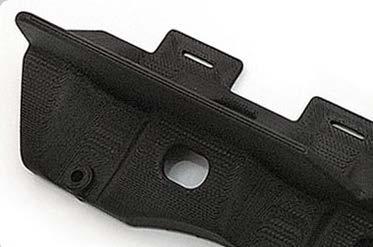
3 minute read
3.1 Fused deposition modeling (FDM
Fused deposition modeling of FDM is momenteel de meest gebruikte techniek. Zowel voor professioneel gebruik als voor hobby toepassingen is dit een zeer toegankelijke printtechniek.
In 2009 verliep het laatste patent op deze printtechniek, waardoor de technologie beschikbaar kwam voor commercieel gebruik. Sindsdien is de markt van printers die met FDM werken enorm geboomd. De 3D printers worden goedkoper en zijn in allerhande bouwpakketten beschikbaar, wat de thuisgebruiker de mogelijkheid geeft om een eigen printer aan te kopen.
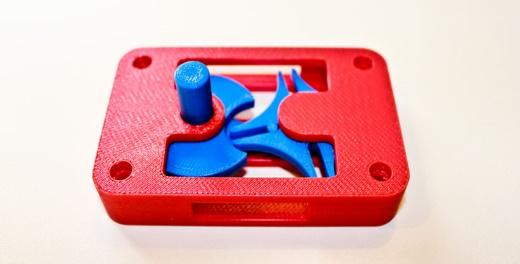
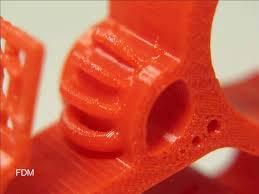
Figuur 3-3 : Voorbeelden FDM printen
FDM kent heel wat verschillende toepassingen. Zowel afzonderlijke onderdelen als hele assemblies kunnen in één keer geprint worden. Gezien de goede eigenschappen van het eindresultaat is deze techniek zowel geschikt voor visuele- als functionele modellen. Om een voldoende stevig product te bekomen moet het product minimum een wanddikte van 2 mm hebben.
Veel gebuikte synoniemen zijn:
• Material extrusion • FFF Fused Filament Fabrication • FDM Fused Deposition Modeling • PJP Plastic Jet Printing • CFF Composite Filament Fabrication
3.1.1 Techniek
Het basismateriaal voor deze techniek is filament of draad van thermoplastische kunststoffen. Deze zijn meestal beschikbaar op rol en voeden de printer continu.
In de extrusiekop wordt het materiaal door verhitting plastisch gemaakt. Hierna wordt het door een verplaatsbare printkop geperst en door de spuitmond (hot-end) in een dunne draad op het printbed neergelegd. Afhankelijk van de kunststof wordt het printbed verwarmd of wordt het materiaal direct gekoeld aan de hand van ventilatoren op de printkop. Bij sommige kunststoffen, zoals bijvoorbeeld ABS, wordt de hele kamer rond het printbed op temperatuur gehouden.
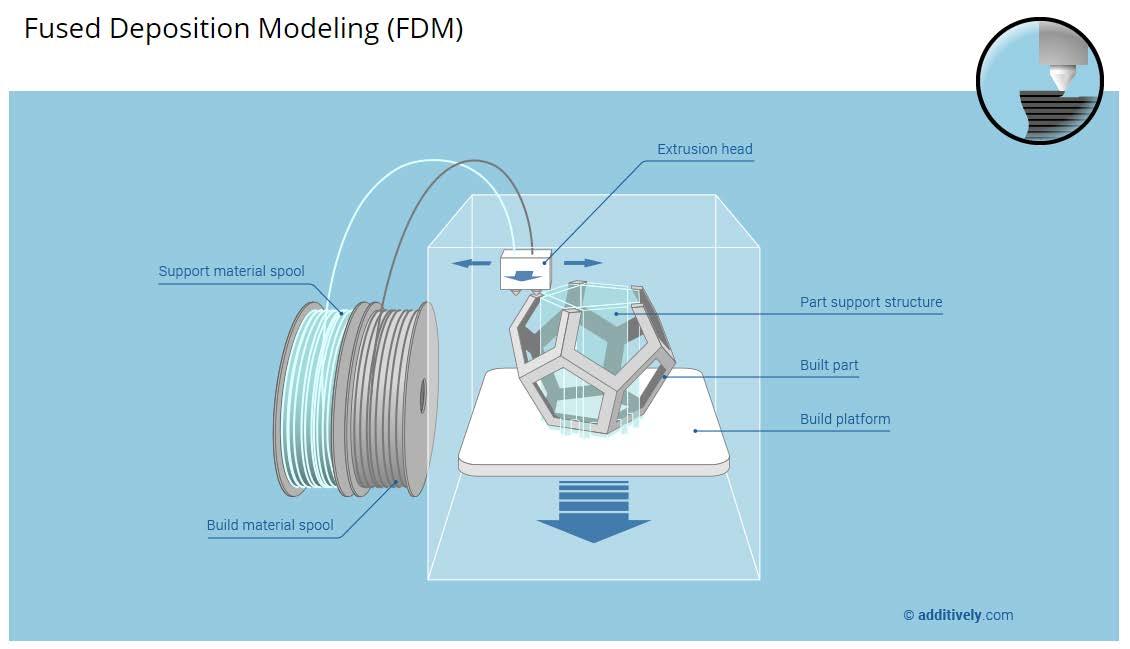
Figuur 3-4 : Fused deposition modeling (FDM) (Additively, sd)
Laag per laag wordt op deze manier opgebouwd. Afhankelijk van het type printer, is het de printkop die omhoog beweegt of het printbed dat naar beneden verschuift.
FDM 3D-printers kunnen gebruik maken van één of meerdere extruders. Met meerdere extruders kunnen verschillende materialen tegelijk geprint worden; zo kunnen kleuren gecombineerd worden of kan tegelijkertijd hoofdmateriaal en supportmateriaal geprint worden.
Supportmateriaal is nodig op plaatsen waar het product zichzelf onvoldoende ondersteund. Dit kan zowel binnenin als aan de buitenkant van het product. Na het printen wordt dit suppormateriaal weg gekraakt of aan de hand van een oplosmiddel opgelost.
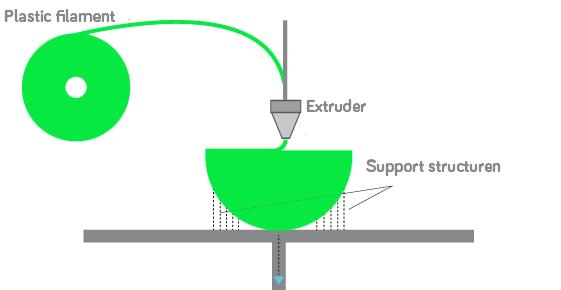
Figuur 3-5 : Support materiaal (Alles over 3D printen, 2016)
Afhankelijk van de toepassing wordt het product volledig vol geprint of wordt de binnenkant opgebouwd uit een inwendige structuur zoals bijvoorbeeld een honingraatstructuur.
Vooral bij visuele toepassingen is het niet noodzakelijk dat het product binnenin volledig dicht opgebouwd is. Het model binnenin opvullen met een grofmazige of fijnmazige structuur, spaart zowel materiaal als tijd.

Figuur 3-6 : Inwendige structuur
Afhankelijk van het gewenste eindresutaat wordt het geprinte model achteraf nabewerkt.
• overtollig materiaal weggeknippen of wegsnijden • het model opschuren • het model lakken, waterdicht maken
3.1.2 Voor- en nadelen
Elk proces heeft zijn voor- en nadelen. Hieronder volgt een korte opsomming.
Voordelen
• Goedkoopste techniek • Eenvoudig • Onderhoudsvriendelijk proces • Complexe vormen mogelijk • Zowel visuele als functionele prints mogelijk • Weinig arbeidsintensief • Redelijk nauwkeurig • Assemblies kunnen in 1 keer geprint worden • Grote open source community: RepRap
Nadelen
• Beperkte afmetingen (afmetingen machine) • Ruw oppervlak • Anisotropie • Traag proces • Support materiaal moet verwijderd worden - Manueel - Oplosmiddel
3.1.3 Materialen
• Thermoplasten • ABS - Verschillende kleuren - Gebruikt in legoblokjes, behuizingen, … - Behoudt mechanische eigenschappen
• PLA
- Polymelkzuur (thermoplastische polymeer) - Lichaamsvriendelijk
• PC • Nylon