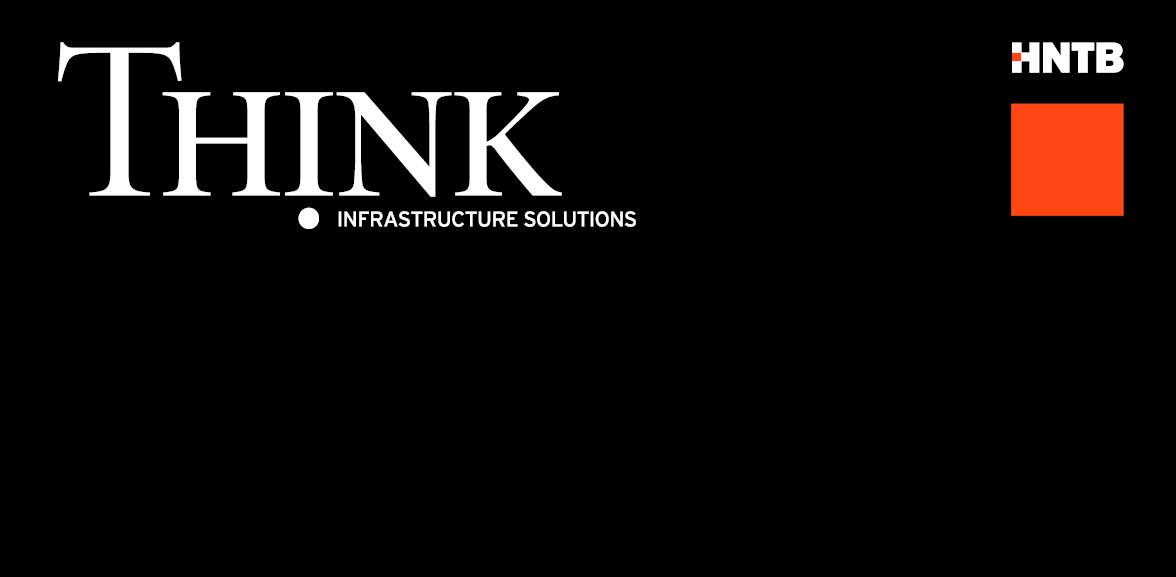
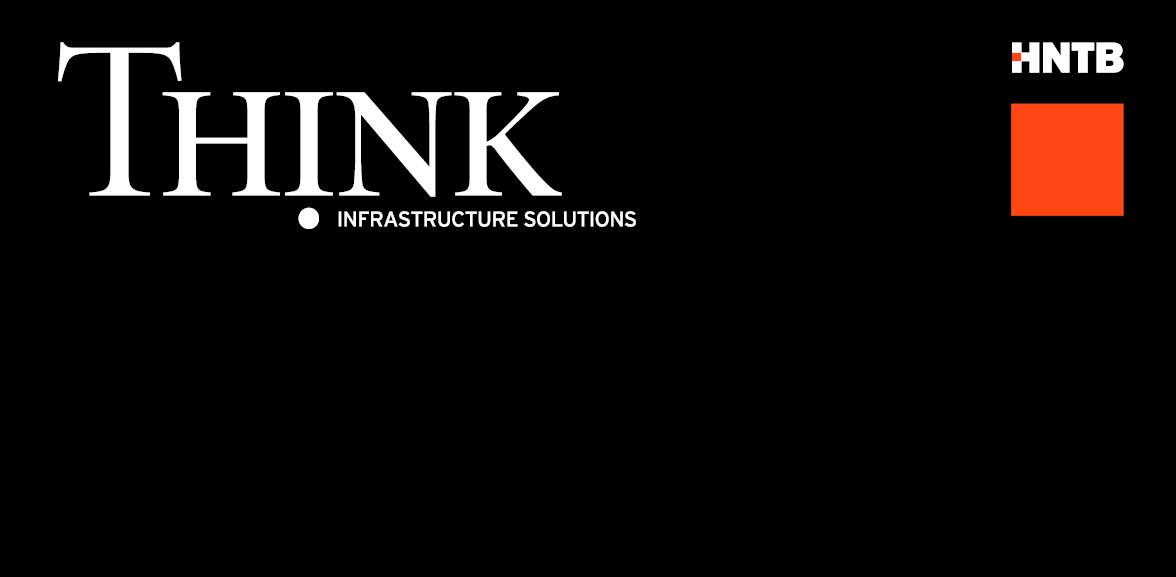
Best practices in deploying an enterprise asset management system
A
case study on an Agile project management approach to system integration and implementation
In 2021, the Southeastern Pennsylvania Transportation Authority (SEPTA) decided to deploy a digital enterprise asset management (EAM) solution to serve as the core system and tool for the agency’s maintenance and capital planning operations.
SEPTA has invested in the EAM solution and its implementation as a core strategy in its efforts to plan, optimize, execute and track the necessary activities, priorities, skills, materials, tools and information associated with its immense asset portfolio. This is core to SEPTA’s asset management program which is focused on prioritizing investments in the context of limited funding realities.

Deploying an agency-wide EAM for a 60-year-old organization that has 290 active stations, 196 routes, more than 450 miles of track (Figure 1) and around 900 end users of the system was a complex challenge. This challenge required a well-planned approach to reach successful adoption and continued utilization for maintenance, as well as aid in capital planning and forecasting for the agency.
To successfully implement the EAM system, SEPTA and HNTB developed a plan and established a team with the goal to ensure program adoptability and value creation. The team focused on these key elements when deploying the EAM:
Simplicity and Structure
The program implementation team applied simple, user-led workflows backed by an organized systems engineering framework as a pilot for a specific user group within the agency. To do this, they first developed an iterative and modular implementation approach which included a combination of typical Agile methodology steps and custom processes as noted in Figure 2.
Additionally, the team created tailored communication plans among segmented user groups to ensure information and results were being shared in a timely manner as well as address current requirements from the user groups as they evolved during the iteration phase.
By following these steps, the system was able to integrate seamlessly with existing enterprise asset inventories and the team was able to quickly implement a viable EAM platform with a minimum viable product (MVP) that proved this new system will not only provide tremendous business value, but also will evolve and grow with SEPTA as the agency and its asset portfolio develops and changes.
Value-Driven Agile Project Management
The implementation of the system needed to be iterative and flexible to meet the demands of operations and maintenance departments. The team selected the Agile methodology because it allows the implementation team to work with structure, rigor and transparency, which enable flexibility and faster decision making. For the implementation team, this process can produce productivity gains and increase quality, speed and the overall user experience.
In SEPTA’s case, the Agile process was centered around five core elements of delivery:
1. Plan around asset classes with mature, inventory data and build platform features as they are ready.
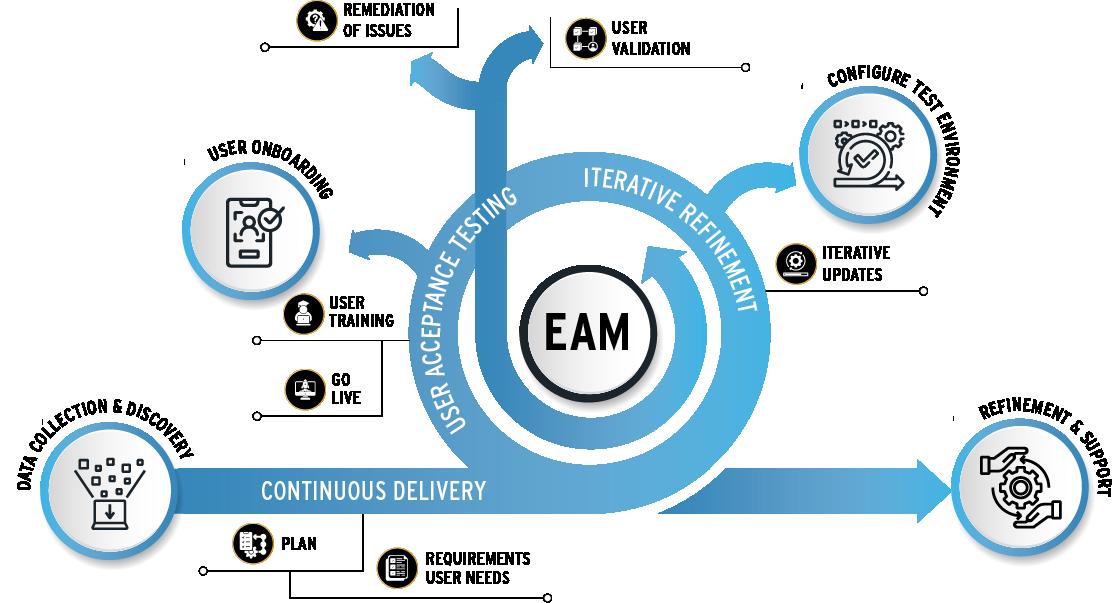
2. Focus on stakeholder engagement and valuedriven delivery.
3. Achieve MVP status quickly, allowing for continuous integration and iterative product releases.
4. Develop capacity and resource planning according to stakeholder requirements.
5. Capture function changes that occur during interactions and continuous improvement cycles and add them to the documentation process.
Focus on Program Acceptance and Usage
User acceptance is a critical milestone for any technology or software integration. For SEPTA’s EAM platform to be embraced, it must be used daily by the agency’s 900 users. The key to ensuring this acceptance was collaborative communication.
The following steps were taken to ensure collaboration wasn’t just continuous but foundational to the successful delivery of the program.
• Establish a key stakeholders’ user group.
• Create a communication process.
• Organize with detailed documentation.
Stakeholder User Group
It was important that the EAM deployment plan was introduced to the daily users of this tool early-on to achieve open communication on usability and acceptance. Engineering managers, maintenance managers and technicians made up the users’ stakeholder group for the EAM deployment because they were identified as the daily users of the tool.
With the Agile approach, the stakeholder group was engaged in several communication formats, which are as follows:
• Identifying stakeholder needs through a brainstorming workshop,
• Creating a user story for each user group based on needs assessment; and,
• Iterating within user groups during the design phase.
One of the successes the implementation team achieved was making the process relevant and relatable for stakeholders in terms of their responsibilities in the organization and their role in process development and how they will use the technology This purposeful approach to achieve stakeholder enga gement was crucial to gaining end user trust and gathering the most effective requirements around system expectations from the ultimate business users.
Communication Process
Intentional continuous communications with the stakeholders’ user groups were critical for effective progress, and for consistent improvements to what was implemented. This two-way communication among stakeholders took place in various ways (e.g. task reviews, status meetings, etc.), which allowed for quick action and rapid response time for improvements in data inventory, process changes and form edits for inspections. This type of communication creates trust among the user groups and empowers stakeholders to feel ownership in the EAM, which is the basis for user acceptance and stakeholder ownership.
An example of this occurred when configuring inspection forms in the system. The implementation team developed quick proof-of-concepts of the inspection form to demonstrate how forms will appear in the EAM. This was shared with stakeholders to showcase how this improvement allows them to quickly visualize what their forms will look like in the system and ensured that change requests could be made before investing the time to officially configure the system.
Detailed Documentation
One of the benefits to implementing an EAM is migrating to a digital platform, which creates a paperless experience that removes manually intensive work; however, digital only works when there is organized documentation of the efforts. Designing a detailed documentation process is not only great for record keeping and creating efficiencies and order, but it also is great for training and empowering users by creating a
system that has tools that are easily accessible and user-friendly. Detailed information about how each asset is configured in the system was maintained in a ‘‘wiki’’ to ensure that all project stakeholders could reference the same shared source of truth about what was in the system.
For SEPTA, a key to adoption for the most complex business units used the power of location. The implementation team determined the most complex asset classes such as track or bridges required a GIS-powered linear referencing system to be built and integrated into the EAM system to create a simple, user-friendly way to locate assets. By integrating interactive maps into the solution, the team avoided having to create complicated naming and labeling conventions for assets that often have conflicting names within the business units. The spatial location method of finding and identifying assets became the common denominator while also simplifying the user experience. This was a simple process update that supported user adoption.
Software Integration Strategy
For implementation success at SEPTA, it was important to lead a software integration strategy with a plan and process first and not let a specific vendor platform drive the process. This allows the team to focus on the program’s objectives, while also assessing the current technology stack so to avoid duplicating other tools’ functionality When possible, the team utilized existing tools and features. Equally important, the implementation effort built organizational capacity and longevity within SEPTA with a focus on long-term sustainability of the EAM platform.
Through a simple and structured approach, open communications and organizational efficiencies, the team discovered how valuable the EAM system is to the agency’s effort to modernize its system through business process improvements and a digital transformation. This resulted in a smooth enterprise-wide transition and acceptance.
About the Authors:
Jeff Siegel, GISP DirectorHNTB
Digital Transformation Solutions
jsiegel@hntb.com
Jeff is a senior vice president and director of digital transformation solutions at HNTB. Jeff has more than 30 years of experience implementing digital and data management solutions for transportation agencies. He uses data-driven initiatives to assist clients in developing more equitable, resilient and sustainable infrastructure in their communities.
Cody Barrett, GISP Project Manager IIHNTB
Digital Transformation Solutions cbarrett@hntb.com
Cody is project manager at HNTB and specializes in enterprise technology deployment and implementation. He has 18 years of experience working with enterprise asset manage ment systems and geospatial solutions. His technical skills and expertise include data analytics, geospatial technologies, web and app development, data management and governance, business systems integration and cloud systems implementations.
Laura ZaleSenior Director of Capital Program Support Southeastern Pennsylvania Transportation Authority lzale@septa.org
Laura’s experience includes developing an asset management program, coordinating construction projects with Amtrak and public relations support for SEPTA’s ‘‘Building the SEPTA Future’’ program Laura is the principal author of SEPTA's Transit Asset Management Plan. In her current role, she often collaborates with transit agency peers to advance the practice of asset management and serves on several national asset management committees. She is the Chair of APTA's State of Good Repair Working Group and a Co-Chair of APTA's Performance Based Planning Committee.
HNTB Corporation is an employee-owned infrastructure solutions firm serving public and private owners and contractors. With more than a century of service, HNTB understands the life cycle of infrastructure and addresses clients’ most complex technical, financial and operational challenges. Professionals nationwide deliver a full range of infrastructure-related services, including award-winning planning, design, program management and construction management. For more information, visit www.hntb.com.
© 2024 HNTB Companies. All rights reserved. Reproduction in whole or in part without written permission is prohibited.