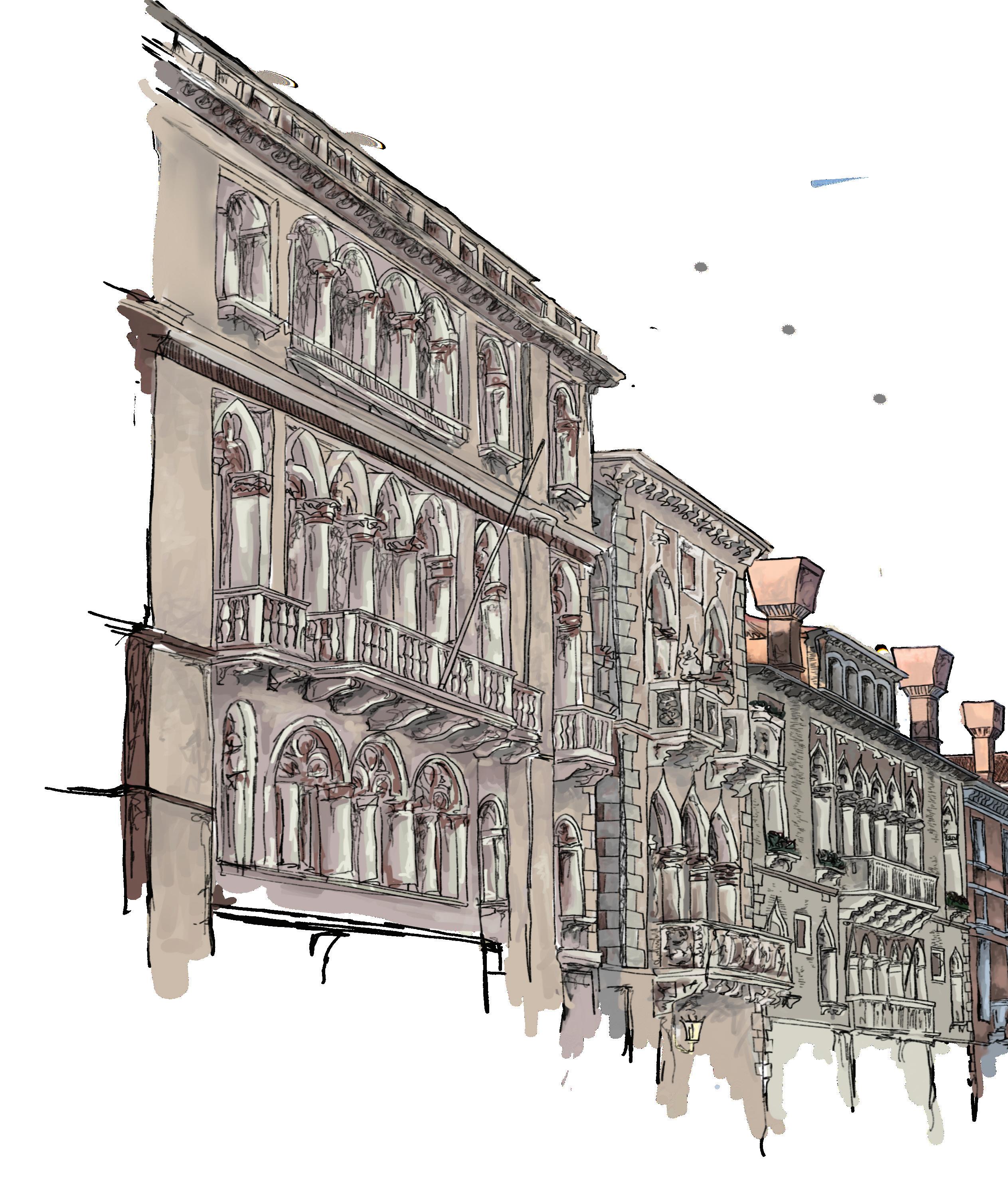
31 minute read
Material Sustainability: How To Provide The Same With Less?
Illustration by Isabel Chau
Katrina Cheng
“Plastic accounts for about 1% of the UK’s carbon dioxide emissions, and plastic bags make up 1% of plastic use.” Julian M Allwood, Professor of Engineering at the University of Cambridge, once said. In fact, “even if all plastic bags were scrapped and their substitutes were carbon neutral…we would only be addressing 0.01% of the UK’s carbon footprint”.
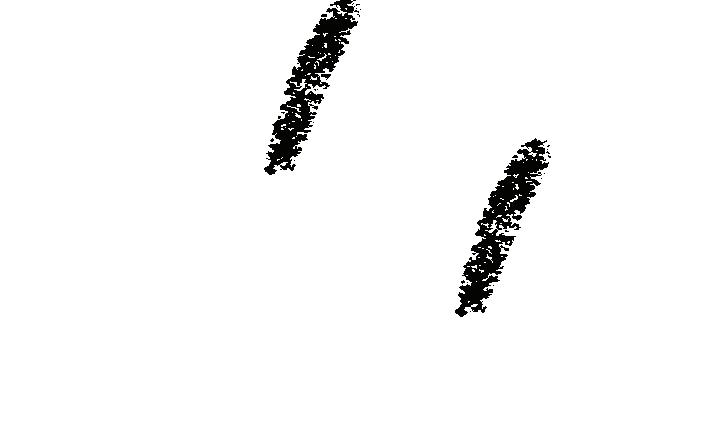
To truly reduce carbon emissions and find the solution, we need to start focusing on scale and identifying areas that can actually make a significant difference. Out of the total global carbon emission, 64% are energy-related, of which 35% are from the industry, 31% are from buildings, and 27% are from transport. Climate scientists tell us that we have to cut our gas emissions to zero by 2050 and that we are not even close to this goal. Environmental impacts of material production and processing are becoming increasingly impossible to ignore and one of our biggest opportunities for change comes from material efficiency - essentially, providing the same with less. Steel is 100% recyclable once it is produced as it has a theoretically endless life cycle. Here is the cycle simplified: iron ore is mined, melted then manufactured, the consumer orders the required steel for its required purpose (transport, buildings, appliances) and the steel enters its ‘use’ phase. Once the steel is exhausted, it is recycled through melting or used as steel scrap where the whole cycle repeats. To address material sustainability regarding the whole cycle, we can target the two areas with the most significant gain and which save as much as 75% of energy: material design and material reuse.
one. MATERIAL DESIGN

“At least 25% of liquid steel and 40% of liquid aluminium never get made into products,” Allwood states. For simplicity, materials in the industry are manufactured into regular shapes and sizes, which are then cut into smaller pieces according to the appliance needed. Unfortunately, by doing so, there are metals in perfect condition that are left unused when cutting and processing. In reality, the metal scrap formed is more of a habit rather than a necessity. If manufacturers started using all metals manufactured to maximum efficiency, we could cut carbon emissions by 7% in the aluminium industry and a further 16% in the steel industry. In this section of the paper, we will explore different ways of saving materials through different designs; we will also explore reasons why good-quality steel and aluminium remain unused and start introducing potential solutions to achieve maximum efficiency.
1. YIELD LOSSES
Imagine this scenario: you are making cookies for your afternoon tea party. You roll out the cookie dough into a rectangular block and bring out your circular shaped cookie cutter. You fit as many circles onto the dough until there is no more extra space. Then you would usually take the leftover dough, roll it out, and repeat this process until you use up all the dough. With your freshly baked cookies and drinks prepared, your tea party begins. In the construction industry, we call the process used by the cookie-cutter as ‘blanking’. Sadly, in the material industry, we cannot very easily roll the leftover dough out again and repeat procedures. Instead, the leftover dough, known as metal ‘scrap’, will simply not be part of the final component and will need to be recycled under an energyintensive melting process, further contributing to the greenhouse gas effect. In a later section titled ‘Material Reuse’, we will explore how such scrap in good condition and without surface corrosion can be trimmed and processed to be part of a new application - a process that sounds very ideal, yet is only done on a very small scale.
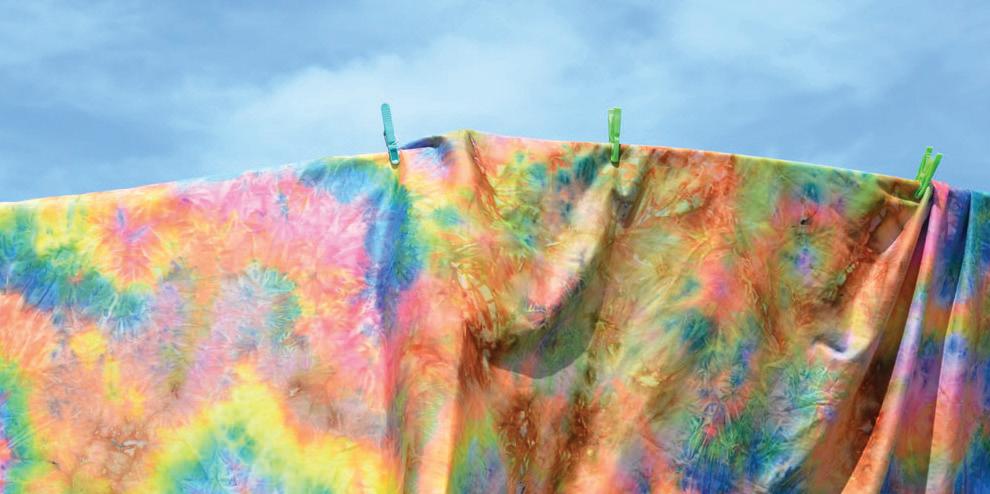
Reasons for yield loss
Despite very few customers actually wanting the shape they purchase, the reason that the steel and aluminium industry continues to manufacture fixed sizes is due to economic reasons and manufacturing simplicity. For instance, because aircraft wings are thinner at the tip than the centre, a perfectly uniformed plate will need to be wedged into the shape of the airfoil. Also, can makers, similar to cookie-making, want circular disks of aluminium sheets to make the cans. However, they receive perfectly rectangular sheets from which they blank circles and send the leftover scrap for remelting. Poor tessellation will cause us to scrap 26% of all liquid steel and 41% of all liquid aluminium; this is recycled and melted in an energy-intensive process, once again contributing to the total global carbon footprint. Imagine pieces of scrap that might never end up in any components or applications but are forever part of a permanent energy-demanding cycle! Liquids solidify from the outer surface into the inner surface, and for liquid metals with complex compositions, the whole composition of the remaining liquid changes. As a result, the head and tail of each aluminium cast are removed by scalping. After casting, most steel and aluminium are rolled out, which has a significant throughput in the middle of each coil or place, forcing the head and tail of any rolled material to be cut off. At the same time, the cracked edges formed during rolling are also trimmed. This will already contribute to around 25% of all yield losses in steel and a further 40% of all yield losses in aluminium. Additionally, although most sheets are supplied flat, their final product is not flat in use. This requires the common process of ‘deep drawing’, which is forming and moulding the flat sheet into shape. If a sheet is formed without gripping its edges, a cup, for instance, will be very shallow and tear. Similarly, if edges are not restrained, the edges will wrinkle. Deep drawing allows the gripping of the edges to prevent wrinkling and tearing. A very clever and efficient process at that; however, it requires about 25mm to be trimmed from each finished part - leading to a further yield loss of about 15%.
Potential solutions to reduce yield losses
Designers of metal components are largely unaware of the implications of their geometric choices, but they could employ potential designs with tessellating or nearly tessellating shapes. Let’s take a look at the clothing and textiles industry. They face a similar challenge for fabric, and have now developed sophisticated computer algorithms to maximise clothing yield from rolls of fabric. In fact, many cut out the fabric with fast laser cutters to further optimise blanking patterns. Speaking technically, if we had a large variety of shapes, the chance of finding small pieces to fit in between larger ones is higher, increasing the yield. Yet at present, the blanking processes used in cutting parts from metal are designed to cut one piece from the coil then move forward to cut the same shape again along the coil, giving very little opportunity for tessellation. Similar to the textile industry, laser cutting for metal is occurring; however, the process is relatively slow, making it very difficult to completely translate fabric cutting into metal sheets.

Many exciting manufacturing technologies are under development, and the whole field of 3D printing has attracted a lot of attention. The 3D printing machine can essentially make shapes and objects programmed into it. For example, the aerospace industry is looking at making complex parts of titanium using this new technology. 3D printing follows a process known as ‘selective laser melting’ where the powder of the material is placed under a scanning laser that then draws the pattern of the product, melting and bonding the powder. This process repeats until all layers are formed. 3D printing has its drawbacks, however: only powdered metals are usable, which is formed by energy-intensive processes of spraying and freezing, lasers are energy-demanding, printing rate is slow and surfaces and small corners can be of bad quality.
Over-specification
The cost of steel is lower compared to the cost of labour in developed countries, so it is generally cheaper to save the cost of labour than to save materials. During construction, designers do not ever want a lack of materials to be a concern or a problem since when everything is in excess, the risk of a material problem is lower. In general, the main driver of overspecification is conservatism. Designers often over-specify the amount of steel in a building by 30-40% even though they rarely have been required to use this surplus; they are concerned that clients will change the specification of their buildings at a late stage, so they factor and build in extra capacity ‘just in case’ any plans change. In a case where clients ask for lightweight, efficient buildings, designers know exactly what to do and can lead to a saving of 50% of the material used. This suggests that over-specifying is not a technical challenge and may even reduce the overall cost, but will only occur through conscientious clients requesting it. After the analysis of 23 buildings in London, a report found that on average only 50% of the steel in their beams was utilised in meeting the standards, suggesting that if we met Eurocode requirements rather than exceeding it, we can cut emissions from commercial buildings by 80%.

2. ADAPTED DESIGNS
Structural optimisation is a discipline dealing with the optimal design of load-carrying mechanical structures to minimise the total weight of the structure subject. Apart from aerospace applications where every extra mass makes a big difference, optimisation is rare and is usually only limited to small moving parts.
Beams
Figure 1 shows a simple point load supported by an arm some distance from a wall. It can represent a crane or a balcony. To make sure the arm won’t break, we need to ensure it is strong enough by designing for stiffness rather than strength. The arm from Figure 1 has a uniform load spread, so it is most likely to break at the wall. For a stronger arm that won’t break at the wall, we want it deeper near the wall and shallower near the tip. This brings us to Figure 2, a more optimised design in which the depth of the arm varies, giving the arm a high stiffness at the tip. Already, Figure 2 is lighter than Figure 1 by 16% and has reduced metal use. However, both the first and second beam would fail when a load is applied. The Figure 2 beam’s failure will start at the upper and lower surfaces. Logically, it makes sense to have more material on the upper and lower surfaces and make the middle thinner. This theory brings us to Figure 3, in which the cross-section of the beam looks like a capital “I”. This is the standard form in which structural steel is used. I-beams are made by rolling with specially shaped rollers with the same cross-section along their length due to manufacturing convenience. If we compare Figure 1’s design with a standard I-beam with constant crosssection, 54% of the mass is saved; if we then compare Figure 1’s design with Figure 3’s variable I-beam, there is another 85% reduction in mass. As loading increases, the required deflection must decrease, and to do so, the cross-sectional area must increase. We should aim to reduce the required loads and increase allowed deflections - an application already being used in the industry.

1.

2.
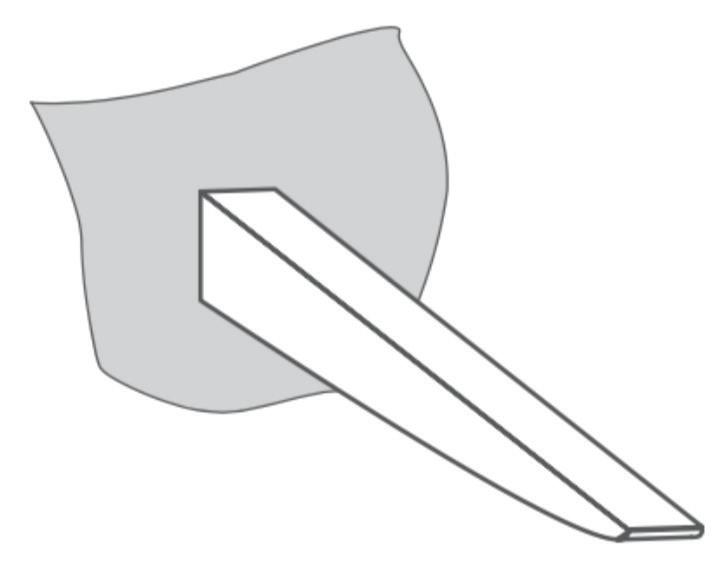
3 .
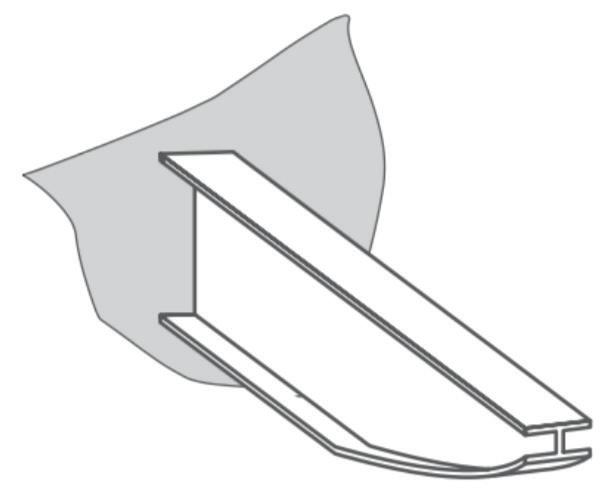
Standard universal I-beams are the key components of steel-framed buildings. They are designed for bending stiffness and used as horizontal beams to support floors and roofs; they are manufactured in a standardised set of geometries and listed by steel producers. Within the list, their geometry is constant; a constant cross-section is chosen for ease of manufacture, so it is not perfectly efficient. However, once again, clients will often over-specify ‘just in case’, which may be quite wasteful knowing that the office is already strong enough to hold a swimming pool on each floor. Over-specification occurs in construction because of a process called rationalisation. A young civil engineer would choose to design a building according to standard codes and choose the optimum beams; however, when an older and more experienced engineer reviews the design, he or she will reduce the number of different beam sections required. This decision simplifies the job for building contractors because of the lower cost of steel compared to the cost of labour in developed countries.
Steel reinforcing concrete
In an exploration of beams in construction, there are obvious and significant opportunities to reduce metal use, but they are not currently taken because of the higher relative costs of labour. The example used here would be steel-reinforcing bars, commonly known as rebars. They are extensively used to provide structural reinforcement for concrete. Concrete is made of ceramic and other aggregates, making them strong in compression but weak in tension. On the other hand, steel rebars have properties opposite to those of concrete - strong in tension, but weak in compression - and, thus, are added to provide tensile strength to concrete. Since rebar designs are often constrained by strength rather than stiffness, the selection of a stronger steel type to make the rebar would mean less material is needed to provide the same tensile strength. So if stronger steel were selected to Photo by Isabel Chau make the rebar, mass required could already be reused. There is a degree of rationalisation in the selection and in the layout of reinforcing steel since bars of the same diameter and same spacing are used across large areas to simplify detailing, identification, laying and checking. This adds 15-30% more reinforcing steel than is strictly required to meet codes. Moreover, there is a different issue with the over-specification of loads with rebars. Unfortunately, even if the building as a whole is designed without over-specification, designers and contractors would still make choices making excess rebar. This is because the simplicity and speed in laying out rebar in simple geometries at a single spacing and with as little different bar diameters as possible reduce the risk of mistakes and make inspections easier. On a more positive note, modern computer control systems such as Qube can design meshes with varying lengths, spacing and diameters. They minimise over-specification with an advanced finite element approach for designing and detailing reinforcement using the Bamtec prefabricated rolled reinforcement carpet system. These carpets typically comprise of smaller diameter bars which are placed at a reduced spacing to achieve the same reinforcement area required by design. These rolled carpets are robotically manufactured and read from detailed drawings. These complex bar sequences significantly reduce the degree of rationalisation without any loss of stiffness. Each bar is spot welded to thin gauge steel straps during manufacture and can quickly and easily roll out when transported to the construction site. Although it is not necessarily what is happening in practice, Qube’s approach is an attractive example of intelligent innovations that can lead to material savings. It is estimated that if size and placement optimisation is carried out to its maximum, we could reduce 15% of global rebar production.
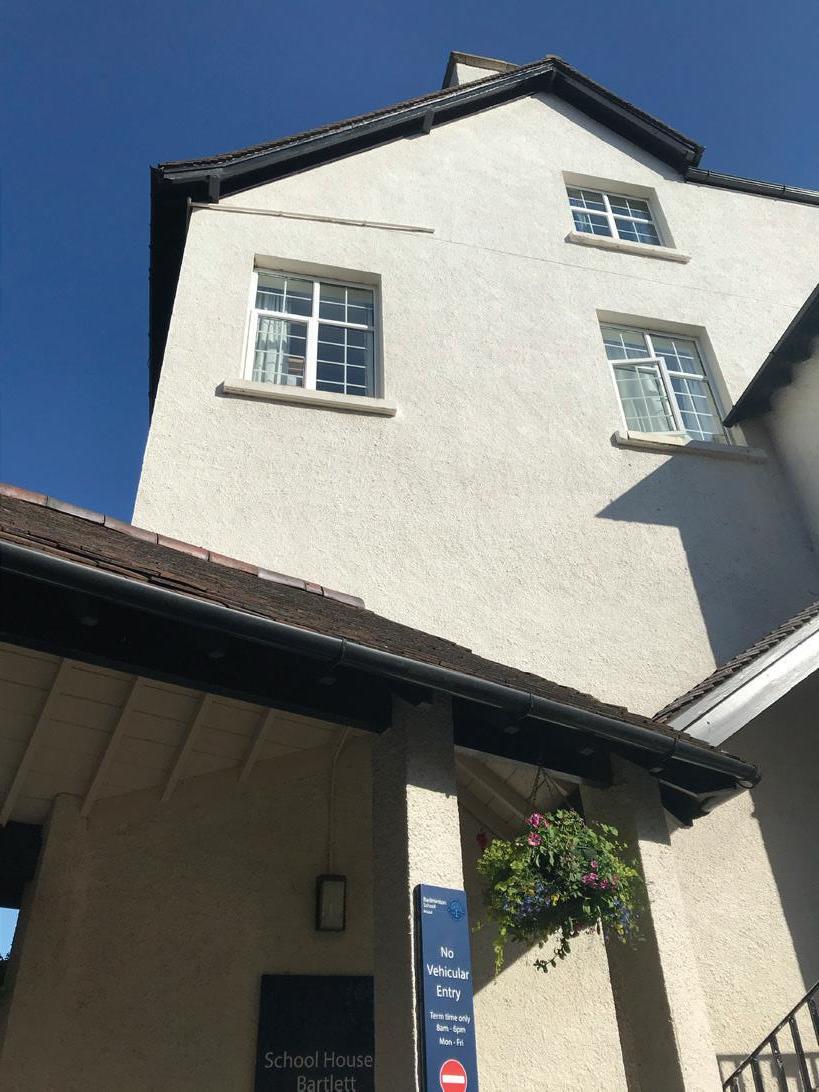
Topology
Topology optimisation takes a 3D design and literally removes material from it to achieve the most efficient design. There is no concern about aesthetics, traditional approaches, and any other usual design constraints. We start with a very regular finite element analysis, FEM, of mesh occupying design space where the initial analysis will show the stress distribution and efficiency throughout this design space. The optimiser will remove the elements not under so much stress and with little strain energy. As the areas are removed, the overall structure is analysed and checked to observe any changes. The topology optimisation of structures has proven to be a valuable tool for the identification of best concepts in the early phases of the design process. Topology optimisation wonderfully embodies the definition of material sustainability and is entirely adapted into modern technology. It is widely used in the lightweight design of structures in the automotive and aerospace industry, as well as civil, material, and bio-engineering with the aim of further expansion into other industries. In the beginning, the design variables are selected, and limitations of these variables and system performance factors such as stress and buckling are defined. By changing variable values, we can test to see how different changes can give the best combination among the design space. Design variables, size, and properties of materials are selected to be optimal. Topology optimisation helps to achieve efficient designs within a small time interval. With the help of FEM software, we can check designs for range, different loads and conditions and design and manufacturing constraints. Nowadays, we can use drawing software in forming different topologies and alter old designs to produce new alternative ones in virtual environments.
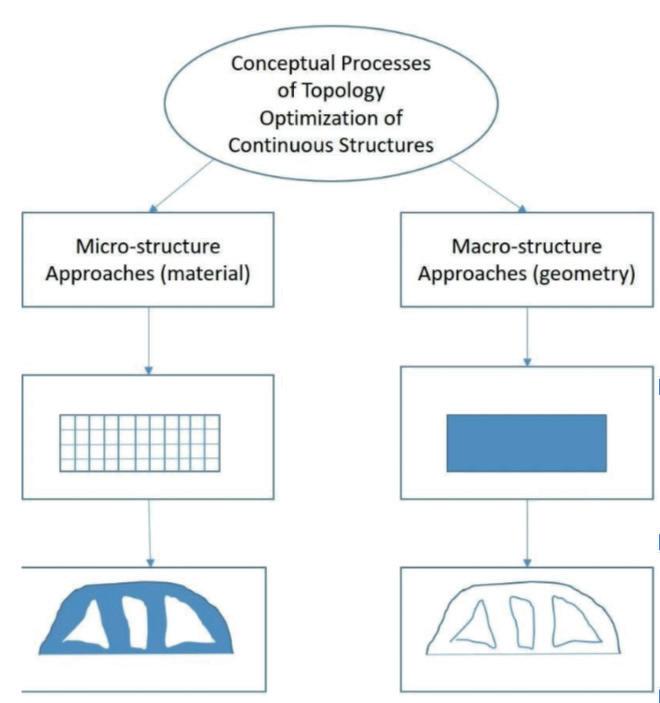
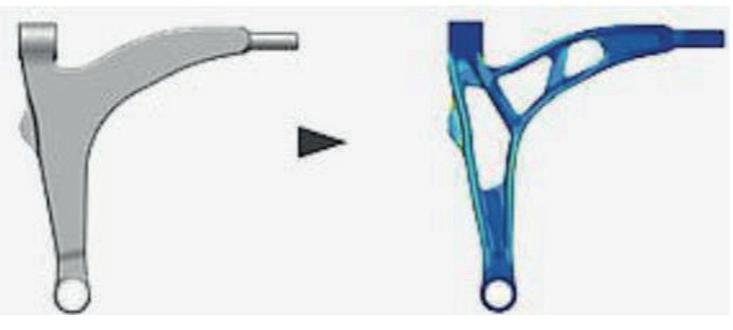
Conclusion
By using less metal in designs for all steel and aluminium, we could potentially use 30% less metal than we do at present, with no change in the level of material service provided, simply by optimising product designs and controlling loads they experience. In fact, it can lead to a 30% reduction in all emissions associated with steel and aluminium production. The consequence of this saving would actually lead to a greater reduction in emissions than estimated due to three co-benefits demonstrated with moving articles: 1. In any moving application, lighter vehicles use less fuel. If we stopped compensating for weight saving by introducing new luxury features, we would have reduced emissions even more than our estimate. 2. Lighter weight products have improved performance. Lighter cars accelerate, brake and turn better and lighter shipping containers can be lifted more rapidly. 3. One lighter component leads to another lighter component. The weight of the structure of oil rigs below its surface depends on the weight of the topsides, and the decreased weight of trains lead to reduced rail wear. In general, there are different motivations for and against metal conservation in different industries. It is not only the size that benefits or the weight saving that motivates change but also other factors of costs and the preferences of customers.
two. MATERIAL REUSE
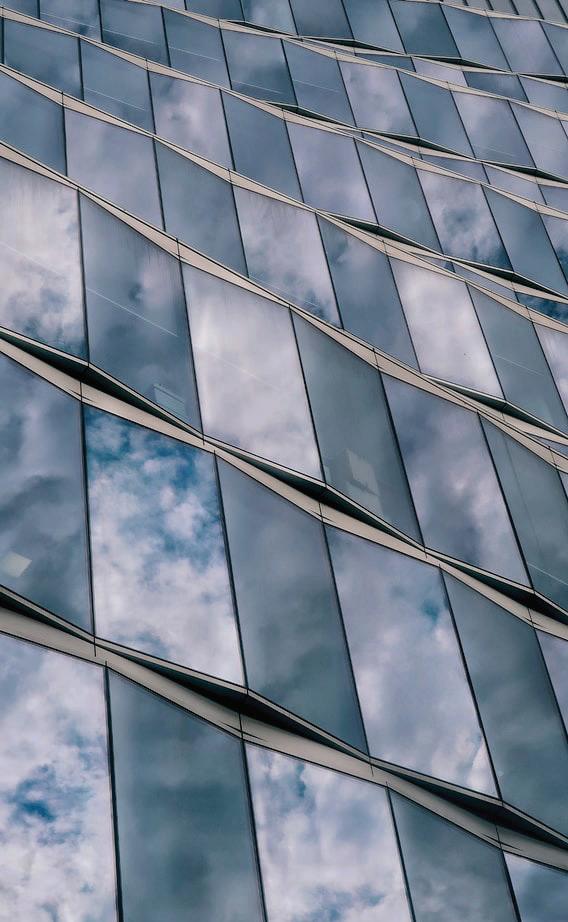
1. MANUFACTURING SCRAP
Currently, 35% of the world’s steel is made from scrap, and the rest is from newly mined ore. Metal scrap is essentially the leftover product of manufacturing and consumption, such as parts of vehicles, building supplies and surplus materials, which are then put to use and returned to the cycle again. Using metal scrap can save energy. Making liquid steel from steel scrap requires one-third of the energy needed to make the same steel from ore, emitting less than one-quarter of the carbon dioxide emissions. However, scrap recycling involves melting with a temperature of around 1500 degrees Celsius, adding to the energy required. Overall, steel-making accounts for 9% of global carbon dioxide emissions, of which 1% is directly from steel scrap melting. Now looking at aluminium, one-third of the world’s aluminium is made from scrap. Since producing liquid aluminium from scrap needs around 20 times less energy than from ore, recycling aluminium is much more attractive and in demand. Recycling both steel and aluminium may seem like a very energy-efficient process compared to the energy needed from making new metal from ore, thus increasing recycling rates in the metal industry. However, considering that global metal demand will almost double over the next 40 years, the total energy required and the carbon footprint from scrap recycling will be very significant. Is there an alternative? Albeit on a small scale, metal reuse without melting is already possible. By making the right design choices, looking into emerging technologies, and adopting more collaboration between different sectors, limitations of metal reuse can be surpassed and metal reuse can be deployed on a large scale.
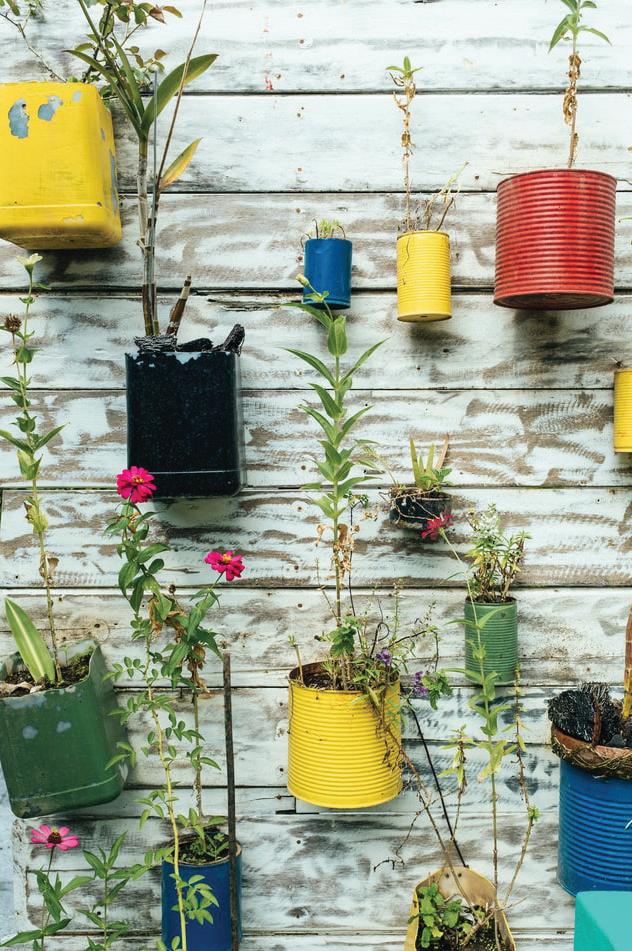
Right design choices
Without standardisation, disassembly is expensive, unless products are designed with disassembly in mind. For instance, to reuse components, we want to find components that can easily separate from parent products, without an overall effect on others, with just superficial change or simple trimming. Moreover, structures are built upon the premise of certified elements and well-executed fabrication and erection, along with marked standard specifications. Engineers, without the pressure of time, look favourably upon reusing steel and will most definitely enjoy an interesting challenge. Most of them would have no problem using reused steel; however, the steel would have to be certified with the required properties and pass a controlled supply chain process. This will not only reassure the engineers but also gain a client’s confidence. Hence, reuse of construction materials would only be adopted by engineers and clients if the material properties are known. A way of doing so is at regular intervals; we can mark and regulate different steel sections with information to determine steel size, grade and quality, removing the need to test and certify the steel at the end of its life. The 1990s saw a shift from manual labour to mechanised demolition methods, further driven by governmental pressure to reduce health and safety risks and by commercial pressure for time-saving. Demolition machines badly deform steel, which is not a problem for metals that are recycled through melting, but it is a major barrier to reuse without melting. Yet site owners have a strong preference towards demolition in deconstruction due to its speed and ease. The consequence of this preference is that even when a building can be deconstructed, contractors will still opt for deconstruction, giving their reason as time. However, when we look at the timeline, many derelict buildings are left for quite some time after planning decisions are made and before any action starts. By changing the sequence of decisions and effectively using this time for deconstruction instead of demolition, deconstruction can easily become the next norm. Moreover, whether it is demolition or deconstruction, contractors rarely own large stockyards that can hold large amounts of secondary steel, so they need to find a buyer or storage site before they start their job for the materials to be claimed immediately afterwards. Nonetheless, the economic value of scrap is fairly low, creating a low-profit margin and discouraging any incentive to find ways to reclaim steel for reuse - a cycle that will repeat itself if we don’t add other factors.
Unfortunately, our world has other incentives not to be eco-friendly. Most manufacturers do not see scrap as part of their core business resulting in production lines designed without considering the value of scrap. Larger blanking skeletons are chopped into small pieces for ease of handling and to prevent disruption to overall construction, instead of considering factors such as where to cut to minimise scrap produced. For instance, the aerospace industry places a high priority on the weight of materials, meaning 90% of highquality aluminium is turned into chips. They will sell swarf with alloys mixed for a price of around 1% of what they paid for, yet swarf can be up to 90% of their output. Looking on the bright side, Abbey Steel, a family run business, buys steel obtained from a diverse range of UK manufacturing industries and resells the processed sustainable steel back into the industry. Industries consume large amounts of steel, leading to the production of waste material, a byproduct of this process. These waste materials cannot be used in any of the processes and are destined to be recycled through smelting. Abbey Steel steps in and reclaims the steel to be trimmed and put back into the supply chain - “reused not recycled”. By doing so, the only energy required is for transportation and reprocessing of the steel, already reducing carbon dioxide emissions to 2.3 tonnes of CO 2 per tonne of metal. Abbey Steel - the world’s first green brand of sustainably sourced steel - has been created to showcase a prime steel byproduct sourced from multi-industry applications. This environmentally-friendly inspiration would be able to grow its business further if people were more willing to segregate more cut-outs for sale, especially to have car manufacturers hand over scrap.
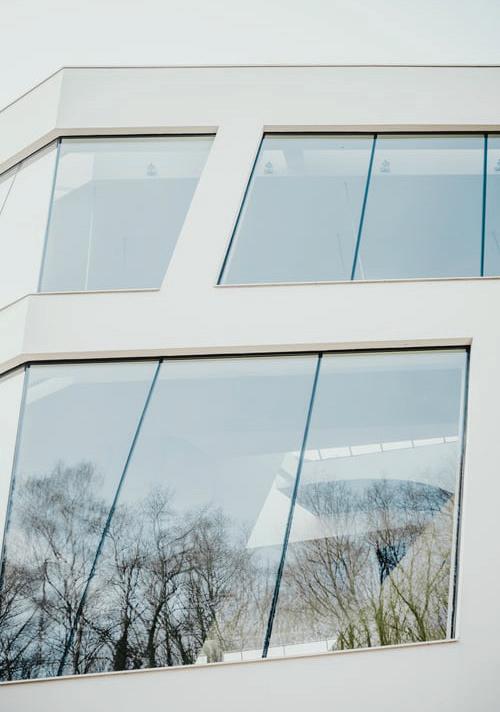
Photo by Isabel Chau

Emerging innovative technologies
New creations such as solid bonding can bond aluminium chips into solid material without any melting, potentially replacing recycling by melting. Solid bonding is welding without addition of a brazing filler at a temperature below a metal’s melting point. To begin with, clean chips of a single alloy are compressed under high pressure and at a temperature of 450-500 degrees celsius. The high pressure and extension cause surface oxide layers to crack, revealing reactive aluminium metal which can be welded into a solid product. The oxide remains on the interface, but as an applied strain stretches the material, clean metal becomes exposed. Entrapped air oxidises some of the exposed metal and, provided the strains are great enough, clean metal will be extruded through cracks in the oxide. Solid bonded chips require 100 times less energy than the manufacture of primary aluminium, reducing carbon dioxide emissions by 96%. Although the solid bonded material shows a reduction of around 10% in ultimate tensile strength and 15% in ductility, further development can potentially reduce these differences. Overall, the surface quality and bonding of the bar pieces were very good. At the same time, many applications, including aluminium window frames, do not actually demand the full strength and full ductility of aluminium, meaning sustainable solid bonded material can be used here instead. If more trials succeed, the technology of solid bonding could soon be seen in the market - reusing 100kt of aluminium scrap would avoid up to 750kt of carbon dioxide emissions.
Adopting collaboration between different sectors
The lack of trust between sectors about the quality of steel can be a central problem and deter them from steel reuse. Very few will consider reused steel if it costs more or takes more time. However, some delays can be tolerated if the costs are lowered, or on the other hand, one may decide to pay more to speed up the program. After surveying many, there is a common perception that reusing steel is difficult, and there is an overall scepticism over steel reuse across the supply chain. The considerable difference between the perception of barriers and the experienced barriers indicates the lack of communication across the supply chain. To list, fabricators are prevented from steel reuse due to the lack of the certification of the steel and the fact that the practice is uncommon; stockists have business models that will not allow long-term steel storage and there is no large cheap storage land, making it not economically viable. Demolition contractors also face the lack of a reliable market for reused steel, and structural engineers are pressed for time. On the contrary, architects, main contractors and structural engineers are protected by this costly structure as they would simply charge higher costs to clients. Nonetheless, green projects do happen if there is a motivation to preserve a valued heritage or if reused elements serve a decorative purpose. Successful steel reuse projects are the result of a willing client and a tightly integrated team that perhaps is responsible for both design and rebuilding. For example, when the owner of the new building also owned the previous building (or has a strong relationship with the previous owner) or when the main contractor is the designer, any legal uncertainty is eliminated. When there is an opportunity for reuse, there are few obstacles to forming a practical plan. Still, there are limitations: structural design usually assumes elements will be fabricated as required, and this might not be the case with reused elements as desired sizes or lengths may not be available, and there would need to be substantial changes to plan. Moreover, there is an old and new perception to reused steel where clients feel that reused steel is inferior and thus refuse to accept reused steel. People can be very stubborn at times and refuse to accept new practices - once again where development of trust and communication is needed. Let us be reminded that if just one sector in the supply chain is unwilling to adopt reused steel, the project cannot and will not go ahead. Building trust can take time, and if the different sectors have not worked together, they will rely on common practice and industry norms, meaning steel reuse becomes unlikely. To overcome this, fabricators can be involved in projects from the start and will have more time to prepare for any uncommon operations. Indeed, as suggested by Allwood and Cullen, steel reuse can play an important part of a global strategy for the efficient use of materials as the carbon and energy embodied in structural frames can represent up to 20–30% of the assumed 50-year lifetime carbon footprint of a building. “Steel reuse can play an important part of a global strategy for the efficient use of materials as the carbon and energy embodied in structural frames can represent up to 20–30% of the assumed 50-year lifetime carbon footprint of a building.” “Steel reuse is a potentially excellent strategy and general guidance about the reuse process is available. Nonetheless, widespread reuse does not seem to occur.”
2. LONGER LIFE PRODUCTS
Most demand for products in developed economies isn’t to expand the overall stock but to replace existing items. For instance, we destroy 33% more fridges every year than we make cars. This suggests the need to modify products and develop adaptable designs.
Reasons for replacing goods: 1. Degraded failure - the product can no longer be used. For example when clothes are worn out or when metal surfaces are damaged. 2. Inferior failure - the user has changed, meaning the original product is no longer valuable to existing customers. For example, clothing no longer fits or a two-seater car cannot fit a newborn baby. 3. Unwanted failure - the product still functions but is not valued by its current owner. For example, the latest fashion or styling has changed or new legislations are introduced.

For degraded components, we can intervene through design changes, possible restoration to original speciation, or condition monitoring and maintenance for better prediction of when a component needs replacement or restoration. In fact, all of these practices are already in use; however, it should be applied at a larger scale and more widely. Construction quality measures how a particular work meets the demanded requirements of that project. Durability is a quantifiable indicator informing us of the extent to which a material maintains its original requirements. Evidently, the greater the material durability, the lower the time and resources required to maintain it becomes.
In the case of some assets, it is assumed that through their service life they shall receive proper maintenance. However, in the construction industry, this is not the case and buildings are not catered for maintenance. With some exceptions, for example, an oil rig placed in the North Sea has a guaranteed service life. Buildings are rarely demolished due to a performance failure but instead, their value to owners or tenants has declined, classifying them as unsuitable or unwanted. Same goes with cars; the second-hand car industry is big and growing, not because the car cannot function anymore, but because the first owner wants it replaced due to personal and social reasons. Moreover, electric cables could technically last for years, but due to population growth and those who are hungry for the latest technology, older cables must transmit power beyond the original design load, making it unsuitable. We usually discard our fridge because it is a few millimetres short of lubricants in small bearings in fridge compressors. However, replacing compressors can be labour-intensive as they are designed to be sealed and not replaced. As we are aiming to reduce metal demand, we must start identifying the areas likely to fail and start designing the products so that there is a simple and common means to replace the failed parts only. Due to the imminent danger related to environmental issues and growing public awareness, governments around the world have been forced to implement stricter environmental policies that have successfully driven some changes. Undoubtedly, these force organisations to play a greater role in recycling activities, regardless of costs. Regarding metal sustainability, in developing and underdeveloped countries, 1-2% of the population makes a living by picking recyclable waste to sell - an area not often looked at with much significance. In fact, the efficiency of waste collection is so high that hardly any metal will go to the landfill. Although much of today’s waste-picking activities remain unregulated or non-formalised, international organisations have been working to formalise and organise these waste-pickers. The importance of a comprehensive policy framework to address the issue of recycling activities and metal recycling, in particular, can not only enhance employment opportunities but also promote a cleaner environment.
CONCLUSION
In this article, we have explored ways of addressing material sustainability divided into two sections: material design and material reuse. Under ‘Material Design’, we discovered the reason for materials not being used to their full potential: manufacturing simplicity and overspecification. Regarding the reasons explored, we consider potential solutions to maximise material usage, including adapted engineering designs and newly invented technologies. Then moving onto the second method of achieving material efficiency, titled ‘Material Reuse’, we learnt about the metal recycling processes and what limits the lack of material recycling in the construction industry. We also investigated how just by extending the product’s life expectancy, we can achieve a large decrease in carbon emissions. To conclude, there are many ingenious and innovative ways to reduce material usage, but whether or not they are adopted depends heavily on many other factors. In the future, material demand, especially metals, will only ever increase. We not only need to start researching ways to meet these demands but also need conscientious people to carry out the plans and think for the betterment of society. Regarding the reduction of global carbon footprints, material sustainability has much potential. As scientists, engineers, and conservationists, we need to find ways to overcome the many limitations material sustainability has brought and will bring to us and, on top of that, pave new paths for the generations to come.

Bibliography
Abbey, Tony. “What Is Topology Optimization and Why Is It Useful?” PTC, PTC, 27 July 2020, www.ptc. com/en/blogs/cad/what-is-topologyoptimization.
“Absolute Zero.” UK FIRES, ukfires. org/absolute-zero/.
Admin, Abbeysteel. Abbeysteel™ and Shearing Co Ltd - Steel Stockholder and Supplier of Cut Steel Blanks, www. abbey-steel.co.uk/welcome/.
Allwood, Julian M., et al. Sustainable Materials: with Both Eyes Open. UIT Cambridge, 2012.
“Beam and Truss Bridges.” Bright Hub Engineering, 8 Mar. 2010, www. brighthubengineering.com/structuralengineering/65884-construction-ofbeam-and-truss-bridges/.
Buildsum. (2014, May 03). Why use reinforcement in Concrete. Retrieved December 03, 2020, from https://www. youtube.com/watch?v=vuZcPTp51Zk
Burj Khalifa: Tallest Building in the World- Mega Structures National Geographic. (2016, August 04). Retrieved December 03, 2020, from https://www.youtube.com/ watch?v=xsVUsk82Qtw
Collins, D., Says, A., & Azam. (2019, November 29). Stiffness and deflection: Mechanical properties of materials. Retrieved December 03, 2020, from https://www.linearmotiontips.com/ mechanical-properties-of-materialsstiffness-and-deflection/
Cooper, Daniel R., and Julian M. Allwood. “The Influence of Deformation Conditions in Solid-State Aluminium Welding Processes on the Resulting Weld Strength.” Journal of Materials Processing Technology, vol. 214, no. 11, 2014, pp. 2576–2592., doi:10.1016/j.jmatprotec.2014.04.018.
Dunant, Cyrille F., et al. “Options to Make Steel Reuse Profitable: An Analysis of Cost and Risk Distribution across the UK Construction Value Chain.” Journal of Cleaner Production, Elsevier, 15 Feb. 2018, www. sciencedirect.com/science/article/pii/ S0959652618304542.
Gaille, Louise. “13 Beam Bridge Pros and Cons.” Vittana.org, 19 Mar. 2018, vittana.org/13-beam-bridge-pros-andcons.
Miller, Brandon. “14 Truss Bridges Advantages and Disadvantages.” Green Garage, 27 Mar. 2019, greengarageblog. org/14-truss-bridges-advantages-anddisadvantages.
WorldEconomicForum. (2016, February 19). Self-healing concrete for lowcarbon infrastructure | Abir AlTabbaa. Retrieved December 03, 2020, from https://www.youtube.com/ watch?v=8QXVwU82wrw
Sergent, Fran. “Material Demand Reduction in Buildings.” The Use Less Group, 8 Apr. 2019, www.uselessgroup. org/research/buildings.
Yellishetty, Mohan, et al. “Environmental Life-Cycle Comparisons of Steel Production and Recycling: Sustainability Issues, Problems and Prospects.” Environmental Science & Policy, vol. 14, no. 6, 2011, pp. 650–663., doi:10.1016/j.envsci.2011.04.008.
Biology and Chemistry
