On the brink of 50 years in business, Forel’s customary enthusiasm to participate at this biennial event is once again ignited, recognising that Glasstec is the premier international event for the glass industry.
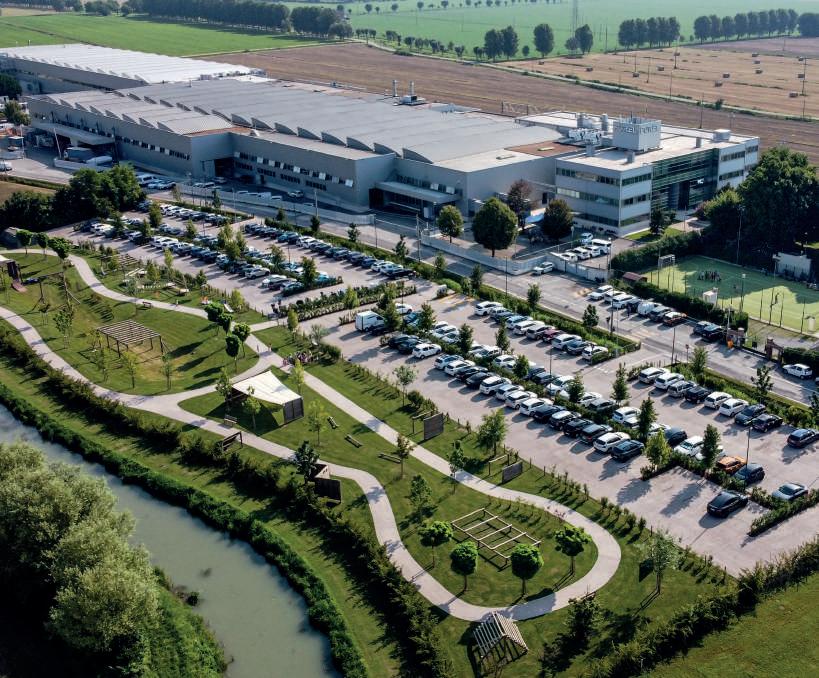
On the brink of 50 years in business, Forel’s customary enthusiasm to participate at this biennial event is once again ignited, recognising that Glasstec is the premier international event for the glass industry.
With a large, dedicated booth, Forel arrives at the fair with the industry advanced technologies designed to optimize efficiency and precision for the insulating and flat glass processing markets.
Prominent among the innovations is a new solution to enhance thermoplastic processing to enable extrusion thicknesses to over 20 millimetres, this will ensure improved versatility, range and quality for glass manufacturers, further consolidating Forel’s innovative leadership in this market. Also on display at the booth are other technologies such as, the new grinding machine with automatic tool changer, the new seaming / arrissing machine with combined rough edge grinding, and a profile bender with the very latest upgrades
Game Changers: Buffer with Thermoplastic Frame Alignment Station
New Solutions: Seaming combined with Rough Edge Grinding
Focus: GlassBuild America and our triplethin IGU journey begins
Production Buffer expanded with countermeasure option
Unveiled for the first time at Glasstec 2024, is our latest (patented) invention that enables the extrusion of thermoplastic profiles for IGU’s with a spacer width greater than 20 mm. This is a significant milestone and a result of months of R&D and now expands our thermoplastic range further, enabling production manufacturers greater scope in their offers to their market.
How did we get there?
Let’s take a step back to 2022, the year our R&D team embarked on their ambitious quest to improve the performance of thermoplastic spacer, a system distinguished for perfect processability with undisputed quality and durability. By thoroughly understanding the critical issues that existed, we identified key areas that presented room for development: the extrusion process, pressing and manufacturing technique
This dynamic device is a result of our concerted and coordinated R&D effort: today we have optimized it to enhance the application process of thermoplastic.
The production control Buffer is a revolutionary innovative solution, strategically placed between the thermoplastic applicator and the coupling press. This module has the task of consolidating newly extruded thermoplastic profile, making it far more thermally stable and compact. In this way, faster and safer coupling can be achieved.
As of this year, and thanks to the new exclusive countermeasure option (international patent pending), it is possible to optimize the process further in the case of profile widths over 20 mm and up to 25 mm, correcting the extruded material back to the optimal geometric position removing any deformation.
Corrects the extruded material back to optimum geometric position.
A common characteristic with thermoplastic profiles exceeding a width greater than 20 mm is for the material to become misaligned with respect to its horizontal flatness relative to the perpendicular glass pane (it tends to sag). While the material is hot it’s not possible to rectify this phenomenon with any consistent accurate result and therefore, processing the glass through the buffer allows for the material to consolidate.
Before the IGU transits to the coupling press, +20 mm wide spacer frames are restored to the correct horizontal plane to ensure correct flat positioning perpendicular to the glass. The panel with the extruded thermoplastic profile on it passes through the realignment station allowing the dynamic rollers to reposition any deformation, effectively resetting the gravitational forces exerted on the material.
AUTOMATION AND BEYOND
Integrated logistics that frees production from constraints.
An extremely useful solution for both flexible spacer (fewer changes due to thickness) and thermoplastic spacer (reduced risk of glass sheer due to profile deformation).
Frees production from production constraints
Does not deform Warehouses thermoplastic IGU’s glass panels with catalysed sealants 1 2 3 4
Reduces interruptions due to spacer width changes of flexible profile
Patented supports are applied beneath the panel post sealing
Panels move automatically to the automatic warehouse.
Upon exiting sealing, the sorting system for the automatic unloading of completed IGU’s allows for the newly sealed panels to be stored automatically within the warehouse. Sorting by individual ID optimizes batches by recalling all the associated items within the warehouse assigned to the final dispatch.
It’s a step toward total automation because no manual intervention is employed to offload and sort postproduction IGU’s. After the sealing phase, patented supports are positioned underneath the insulating glass panel to allow it to move directly to the automatic warehouse completely upright in a 90-degree vertical position, without the risk of any deformation and for accurate completion of the catalysation stage.
Grinding and Seaming
Grinding machine with automatic tool changer
The new automatic cone and tool change functionality of Forel’s EM grinding machine is a complement to the vertical edge processing machine
Thanks to the 8-position magazine, it is possible to quickly and automatically manage the exchange of preprepared tool cones, optimizing set-up time, increasing output productivity and flexibility. This solution is particularly suitable for glass factories working with high volumes of glass with frequent job changes.
Processing different types and thickness of glass with various processes is a reality and where necessary the need to continuously alternate job orders, the automatic tool cone
changer delivers unquestionable increases to production efficiency and output of the line.
The magazine, available for models with a vertical axis of 2500 mm and up, is positioned to the rear of the machine; the individual cones that hold a grinding wheel pack of 75 mm allow for the front coupling flange to manage the tool changeover. The operator displays the service window, where the wheel pack compositions are automatically loaded and, following
COMBINED SEAMING AND ROUGH EDGE GRINDING FOR IMPROVED VERSATILITY
the preset job sequence, as per Industry 4.0 requirements, the various processes are activated automatically.
This functionality is enhanced when the grinding machine with automatic changeover is included in automated logistics systems (Sorting System) where the constant presence of an operator is not needed, except for supervision and oversight.
Seaming machine with coarse edge grinding
The growing market demand for a solution that can combine rough edge grinding jobs with glass edge seaming, our R&D team responded with a redesigned EG machine that now makes it multifunctional. This innovative machine combines seaming / arrissing and rough edge grinding in a single process, optimizing production time while delivering the highest quality results. With larger spindles and increased stroke, the new EG with a 70 mm wheel pack for various configurations (V, trapezoidal, flat)
can perform precise and uniformed seaming, preparing the glass for downstream processing. Rough edge grinding is performed with flat diamond encrusted grinding wheel (with the entry operating head) along with seaming that utilises both operating heads.
The presence of special idle rollers ensures optimal support for the glass sheet during the process, compensating for differences in stock removal at the bottom of the sheet.
Enhancements focus on user interface customization, measurement accuracy, and the introduction of automated profile reverse function.
Profile bending is a fundamental process in insulating glass production that uses rigid box spacer but in recent years, demands for precision, speed and flexibility have increased significantly. In response to these demands, new hardware devices and software upgrades have been developed that have helped to innovate this part of the production process.
Considering some of the key points of our upgrades we can find a new graphic interface, which has been simplified to make it easier for operators to interact with the system: the possibility of customizing
the interface, viewing historic work files and monitoring the consumption of materials used, increases the efficiency and traceability of the entire process. Related to that aspect, is the possibility to manage inventory levels within the profile warehouse, a useful function in operational business management.
The management of files and panels with different spacer widths has been optimized to speed up processing times. At a mechanical component level, we point out the introduction of the automated profile reverse function (which can be
activated when the size of the spacer bar being processed is greater than 1200 mm) combined with greater accuracy in bar measurement and a reduction to the minimum bend radius for more accurate results.
Also to be considered is the improved thermoregulation function: additional resistance to the vice has improved thermal control, ensuring better bending quality of bendable plastic profiles combined with reduced cycle times.
“Forel is never satisfied with the status quo. Our mission is to push beyond the boundaries and constantly improve what we offer our customers as solutions that make a tangible difference. With our new thermoplastic spacer system, we have overcome existing challenges, providing the market with a tool that can redefine insulating glass manufacturing standards.”
RICCARDO VIANELLO Forel CEO and Vice President
ARTIGIANVETRO
Headquarters
San Severino Marche, ITALY
“We aim to achieve a superior finished product because we are aware that, in order to live in a comfortable environment, it is necessary to have clear carefully crafted glass and windows in one’s home.” – Daniele Marcantonelli, co-founder of Artigianvetro.
Established in 1985 as a small artisan workshop, Artigianvetro established its roots from Graziano Marcantonelli’s and his passion for working with glass by hand. With a workbench and few tools, he laid the foundations of a business destined to grow rapidly.
A few years later his younger brother Daniele joined him, thus strengthening the team and consolidating the company.
With increasing orders and a desire to perfect machining techniques, the business growth began, which saw the workshop expand, reaching the point where building new headquarters was required.
For the real leap in quality in the insulating glass sector, we have only to wait a few years: in the mid-1990s, with the introduction of the first automatic cutting benches, washing machine and first Forel flatbed coupling press, investments are made to automate as much of the production possible, guaranteeing ever greater precision and quality. Rapid
but controlled growth that rewards the courage and foresight of the Marcantonelli brothers in anticipating the future and investing in cutting-edge technology.
The relationship and collaboration with Forel increase over the following years, thanks to the introduction of other automatic machinery such as the profile bender, desiccant filler, edging machine and sealing robot that, when combined with the washing machine and coupling press, converted the insulating glass production line to fully automatic.
In 2012, following a new location change, Artigianvetro decided to invest again in innovation together with Forel. In fact, a new insulating glass line is installed with two important innovations: vertical edge grinding machine and automatic flexible spacer applicator, among the first plants to do so in Italy.
With the entry of Nicola Marcantonelli (Graziano’s son and current Production Manager) into the company, the step change that leads to the incorporation
of Industry 4.0 is achieved delivering increased fluidity within the production processes.
In 2017 the new Forel system for advanced logistics was introduced into the San Severino Marche glass factory: the Sorting System
This system makes it possible to significantly increase work in progress, production efficiency, operator safety, while optimising the level of industrial automation.
Connecting the various production processes thanks to the systems modular and flexible design maximises the available space and manufacturing control.
And so, we come to the most recent installation, we are in 2023, Artigianvetro is now ready for Jumbo size manufacturing.
“The decision to invest in a new Jumbo Line matured during 2022, following analysis of market trends that indicated a growing demand for larger glazing and faster delivery times. After a careful study phase with Forel, a long-standing partner known for its ability to innovate, we looked at several options to expand our production capacity.” - Nicola explains. ”Considering the companies forward thinking and growth philosophy, the decision for a new Jumbo line was dictated by the desire to take another step
forward and to offer our customers a larger size product that we were unable to produce before.”
In detail, the implementation of a High Tech Jumbo IGU line, containing a flexible T-Shape spacer applicator and a SR HT automatic sealing robot combined with unique non-stop double-bracket dosing system for two products (polyurethane and structural silicone), has enabled Artigianvetro to improve greater efficiency and consistent repeatability even more. The SR HT’s technology ensures that the sealant is always cantered within the cavity. Its innovative “Special Inset” system automatically ensures normal, partial and retracted sealing on the same double-glazed unit whether the glass panes are aligned or offset.
Looking to the future, new frontiers of exploration in the field of glass processing are clear at Artigianvetro: technological innovations, environmental sustainability
and the relationship between customization and flexibility. The idea is to continue to invest in new technologies that can improve the efficiency and quality of machining processes, gradually including the support of artificial intelligence and data analysis with the goal of optimizing results.
“Ensuring production meets with our customers’ needs”
Nicola Marcantonelli, Artigianvetro
“Forel is a long-standing partner for us, known for its ability to innovate.”
An increasing focus will be placed on environmental sustainability by developing technologies and processes that reduce the environmental impact of IG processing, such as reducing energy consumption and adopting environmentally sustainable production practices. In this regard, the Sorting System has enabled the company to better manage glass waste, anticipating the cutting of defective pieces to avoid subsequent downtime during insulating glass production.
Ultimately, tailor-made production must be supported by the ability to propose innovative solutions, pandering to limitations and putting the human relationship of collaboration at the centre for each project. It is precisely that human relationship that has marked the bond between the two companies, based on mutual trust and the sharing of common values such as innovation and sustainability, that is the solid foundation on which to build
new ambitious projects and investment opportunities.
Artigianvetro is a story of growth and expansion that has rewarded ingenuity, transforming a small village business into a leading industrial frontrunner on the national scene. With the ability to differentiate production between residential and commercial insulating glass, capable of producing large sizes and thicknesses too. An industrial vanguard that remains with an artisan soul. “And the soul is very important, it is fundamental “ - as Daniele Marcantonelli points out.
“We aim to obtain a superior finished product because we know that, in order to live in a comfortable environment, it is necessary to have in one’s home glazing that approaches perfection and produced with the utmost care” - concludes Daniele.
The partnership with Forel has certainly been a turning point for Artigianvetro, allowing the company to introduce
cutting-edge technologies and optimize its production processes. Thanks to this partnership, Artigianvetro looks to the future with optimism, ready to face new challenges and seize the opportunities offered by a constantly evolving market. The goal is to consolidate its leading position in the area, continuing to invest in order to offer its customers products and services of the highest quality
The GlassBuild America trade show has recently concluded, and this year’s event, held under the wonderful Dallas sun, was again a fantastic success.
We would like to thank all our supporters and visitors to the Forel booth, where we once again demonstrated our most advanced technology live.
We chose to present our High-Speed line for insulating glass in combination with the innovative process solution of triplethin glass combining flexible warm edge spacer and a thin 1mm centre pane in just 45 seconds: providing the advantages of improved thermal and energy-saving performance with the same weight and size as a double-glazed unit.
The first major advantage is the reduced units thickness compared to that of a standard triple glazed unit. This reduced dimension makes it possible to use existing window frame systems found in both new build and the replacement / renovation window sector.
The second advantage is realised in production by reducing the sealing time since our triple thin production method doesn’t require two separate applications of sealant. This new production technique positions the smaller thinner lite centred between the two thicker outer lites. Once the flexible spacer has been applied and the unit fully coupled the inner pane is centred equally between the two outer panes effectively creating a single cavity to seal, significantly reducing time.
Finally, the comparatively light weight of a triple thin unit requires no upgrade to existing window hardware, positively impacting the management of costs while adding benefits such as quality, price, and overall thermal performance.
1
2
3
During the summer, the entire Forel family gathered for a memorable evening at Villa Claudia Augusta in Treviso. More than 500 participants, including team members, partners, and families, shared moments of joy and fun. During the event, we recognised the long service of some of our employees with special awards
In addition, the evening was further celebrated with live music, dancing, children’s entertainment and our traditional moment of cutting the cake. These moments reinforce our commitment to prosperity and passion for family. Thank you all for making this night unforgettable!
From May to July, Forel hosted Demo Days, which were a great success. These events allowed us to showcase our flagship machines, such as the High-Tech Jumbo Line with thermoplastic applicator and the HighSpeed line for residential glazing. We continue to create opportunities to share our expertise, technology and innovation with you.
Forel recently expanded its manufacturing headquarters with the addition of a new hall, a strategic step to support continued growth and optimize production capacity, further strengthening our commitment to customers and innovation.
9,000 square meters of new area is the footprint of the new expansion. Photovoltaic panels with a total capacity of 700 KWp have been installed to the entire roof contributing to the overall sustainability of the new area.
WE BUILD RELATIONSHIPS FROM ALL OVER THE WORLD
Sincere thanks to all who participated in the exhibitions in China, Brazil, Mexico, Saudi Arabia, UAE and America. Cultivating strong global contacts is essential to our development and allows us to build lasting relationships around the world.
We are proud of the success our summer camps bring, dedicated to the children of Forel employees. These opportunities provide fun, security and personal growth for the children that attend, while simultaneously supporting parents work life balance during school vacations. We believe in a positive, family-oriented work environment that is critical to the well-being of all our employees.
VETECO 5 Nov - 8 Nov
Madrid, Spain
EURASIA GLASS 16 Nov - 19 Nov Istanbul, Turkey
G24 AWARDS 29 Nov (Forel UK Finalist) London, UK
GLASSTECH ASIA 11 Dec - 13 Dec Ho Chi Minh City, Vietnam
CHINA GLASS 26 May - 29 May 2025 Beijing, China
VITRUM 16 Sep - 19 Sep 2025 Milan, Italy