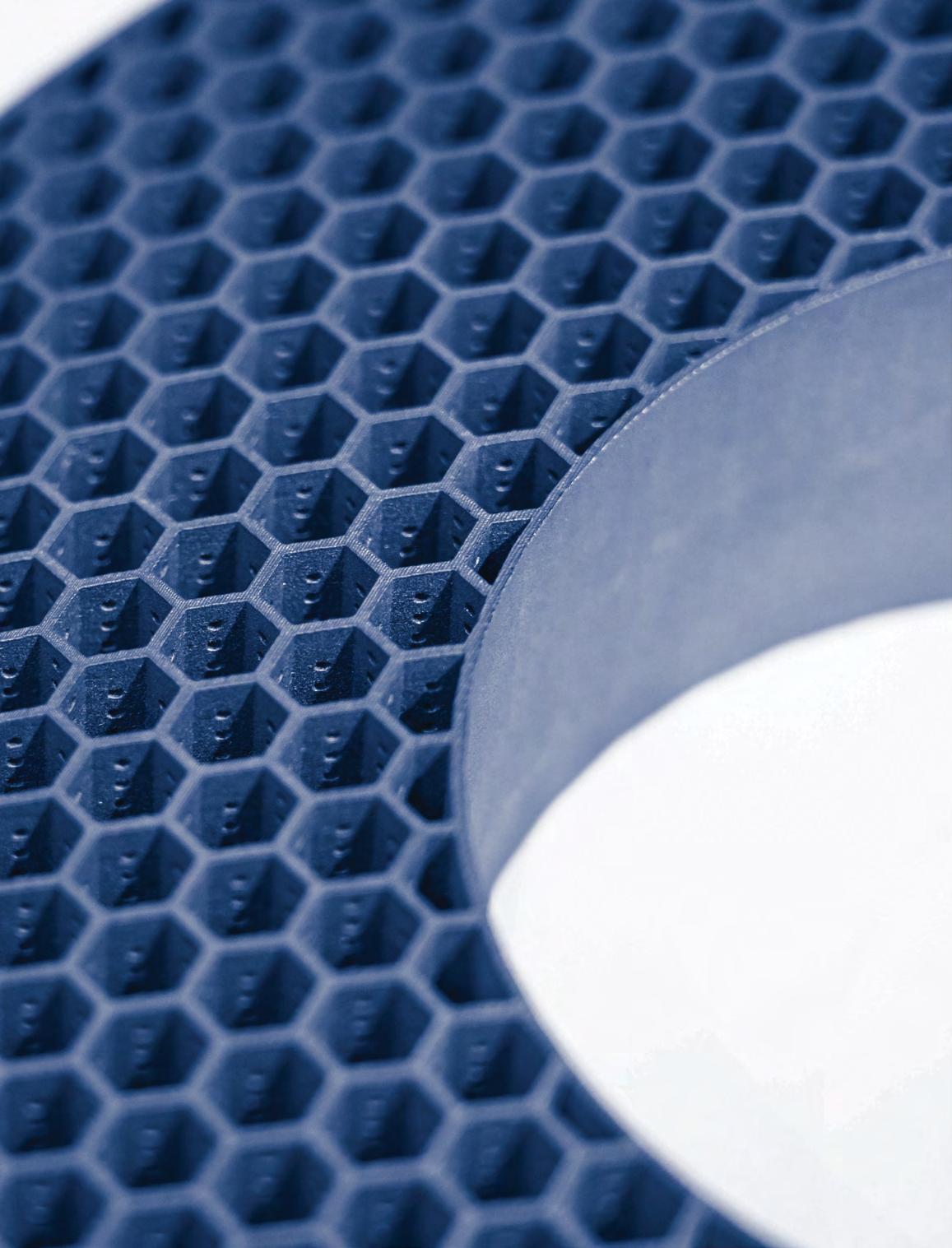
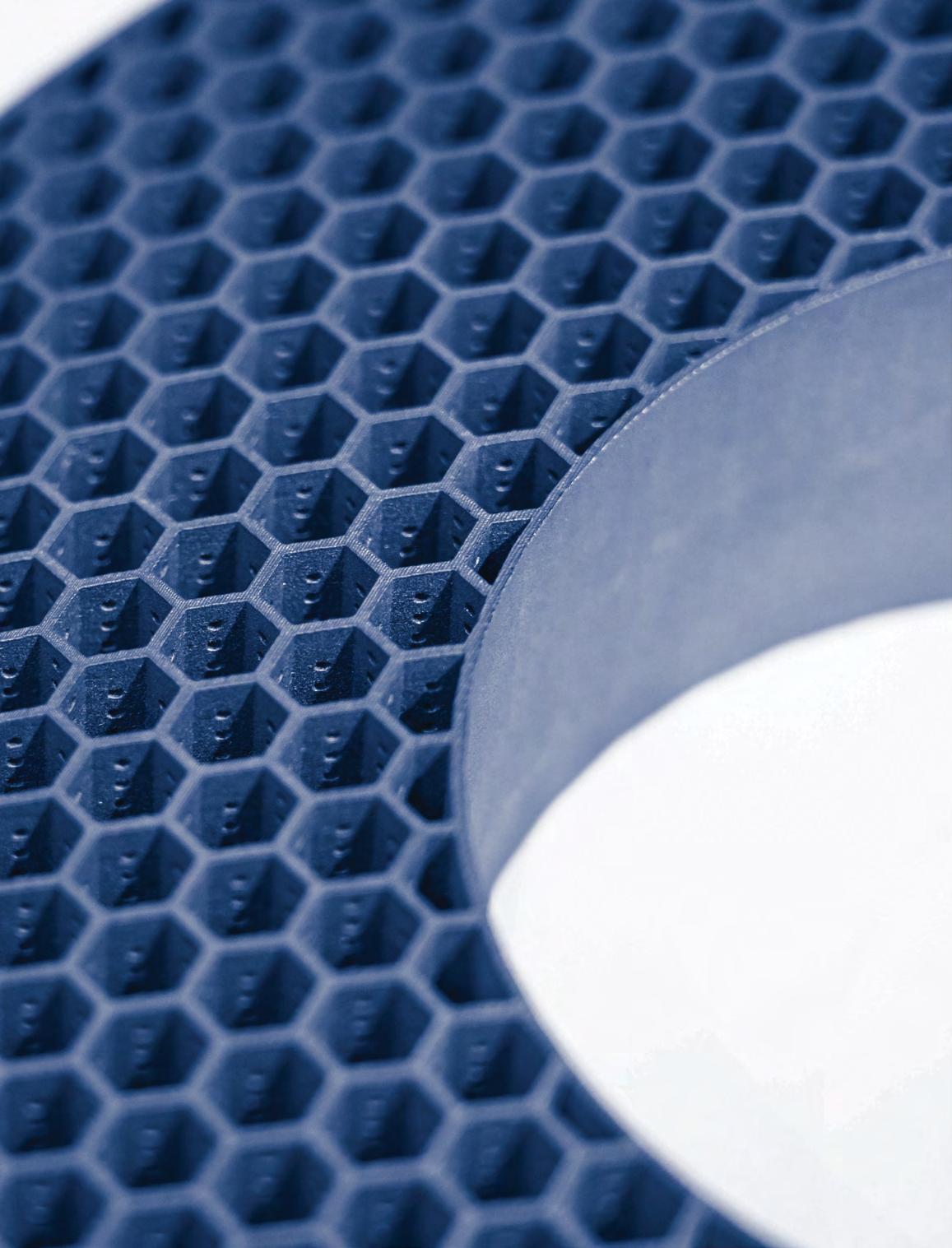
ACCESS AND ENGAGEMENT AT YOUR FINGERTIPS
MAKE CONNECTIONS, TAP INTO COMMUNITY
The Member Portal is an online platform that empowers members to connect one-on-one, maximize engagement opportunities, and provide the ability to manage and maintain membership accounts on demand.
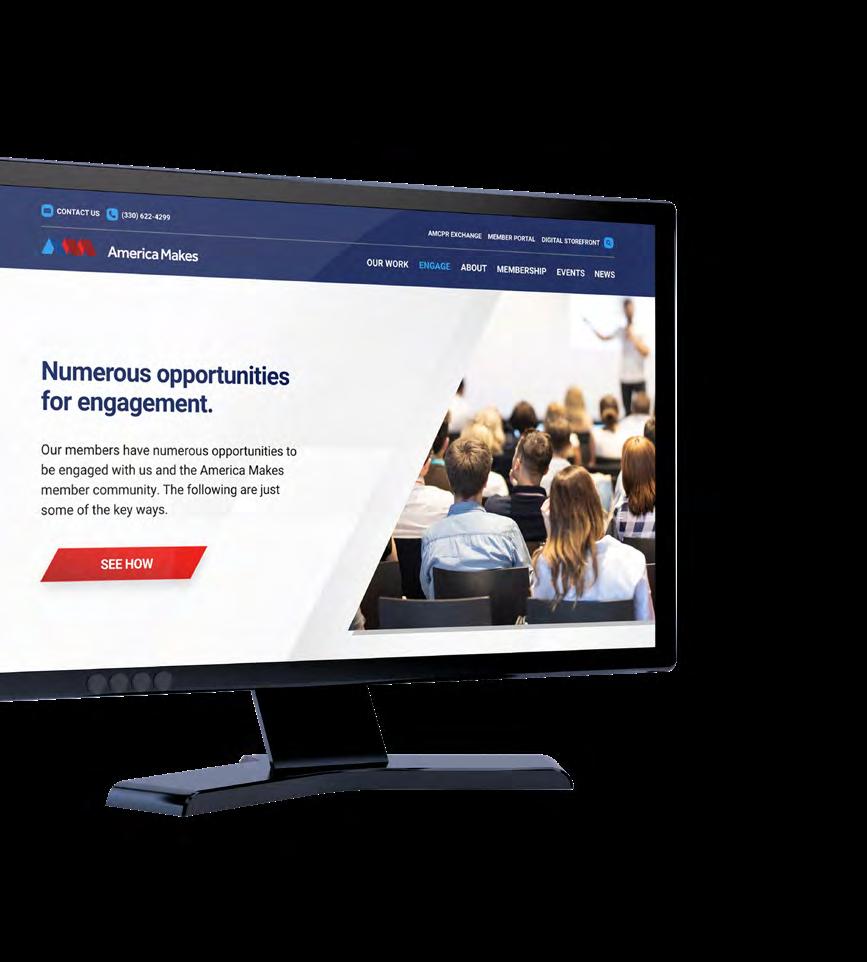
➡ America Makes “Member Portal” members.americamakes.us
STAY UPDATED
The Digest newsletter is a key source for communicating to our members, consisting of announcements, events, opportunities, and more.
GAIN ACCESS TO PROJECTS, PORTFOLIOS AND INTELLECTUAL ASSETS
The Digital Storefront is a product lifecycle management (PLM) platform that members can access to get member-exclusive information, including project deliverables and data related to all projects within our portfolio, including 15 project calls, more than 350 requirements and upwards of 500 deliverables.
➡ America Makes “Digital Storefront” americamakes.us/digital-storefront
➡ America Makes “Digest” americamakes.us/join-mailing-list SHARE
EXPERIENCE, ASK FOR INSIGHT
Forum for America Makes and its members to communicate, collaborate, discuss, and share information regarding additive manufacturing.
➡ America Makes “MembersExclusive” LinkedIn Group linkedin.com/groups/8617286
Getting “AMPED” Up Workforce development is the key to additive manufacturing climbing the “Best Sellers List” of U.S. manufacturing.

Additive Manufacturing: State of the U.S. Ecosystem Envisioning and strategizing AM as the fulcrum for a resilient, environmentally sustainable, and distributed manufacturing network.

America Makes 2022 Strategic Objectives

Here’s What You May Have Missed
opportunities, priorities and challenges that came out of recent America Makes engagements.
Windows of Opportunity Industry specifc opportunities for additive manufacturing alloy development.
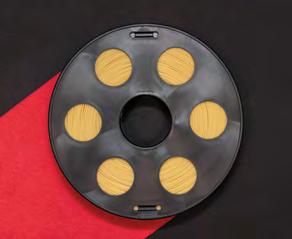
Increasing Sustainability Through AM Production While politics and the public push manufacturers to make products more sustainably, additive manufacturing is making sustainable business practices more proftable.
Data as Fuel How the AMNOW program is helping companies successfully leverage manufacturing process data for a digitally connected supply chain.
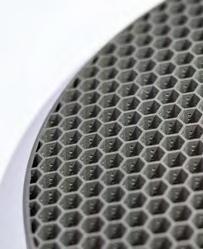
A Decade of Impact
BY JOHN WILCZYNSKI | EXECUTIVE DIRECTOR, AMERICA MAKES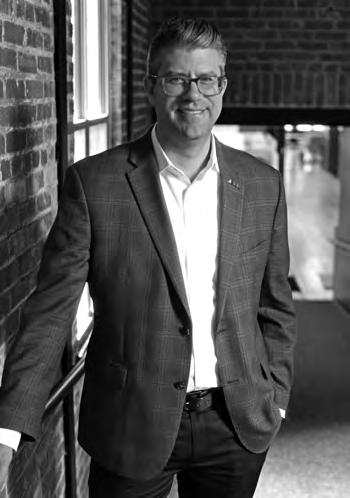
This is an exciting time to be part of America Makes as we continue to further strengthen and build upon our successful collaborative model.
Over the last decade, our mission has remained unchanged. We have worked to adjust to the needs of our growing membership and stakeholders to achieve results and to ensure the competitiveness, national security, and resiliency of the United States. We are grateful for their partnership.
The idea of “managing our mission” and amplifying projects and member successes is shifting to the forefront as we look to inform, educate, and inspire the next generation of additive manufacturing innovators and workforce. The key areas of advancing research and technology, maturing the manufacturing ecosystem, and developing the workforce (present and future), bring this premise into focus – with our membership at the nucleus.
We are proud to present our 2nd edition of LAYERS, which features articles about how
we are moving the needle forward with the latest AM technology trends and research opportunities, by engaging our membership, and through a new Additive Manufacturing Portal for Education (AMPED).
But there is much more, including a piece on the AMNOW program, which supports Army readiness and its supplier development and outreach successes (read the story on page 46).
Keeping on track with amplifying our successes, America Makes recently launched a new video series called “Where Are They Now?” Almost two years in the making due to the pandemic, the series features America Makes members, past projects, and stakeholders contributing to the growing impact of AM. The long-term success and continued performance of the projects featured in the series amplify the Institute’s mission and how our membership can work collaboratively to achieve the vision of accelerating the adoption of AM and our nation’s global manufacturing competitiveness. On page 60 we highlight “ULTEM 9085” as Tracey Albers, RP+M President and CEO, o ers an overview of the project’s evolution and the collaboration that made it possible. We encourage you to view the video (to accompany this feature) located at americamakes. us/where-are-they-now
LAYERS stems from knowledge, research, and collaboration. This is the work that de nes — and sometimes helps to re ne — the strategic direction of the Institute. We appreciate your unyielding support and engagement, and we look forward to sharing many more successes!
This second annual edition of Layers invites you to join us as we refect on engagement, measure milestones, and celebrate collective success.
BETTER TOGETHER
America Makes plays a vital institutional role in coordinating pre-competitive collaboration.
Additive manufacturing (AM) has been in development in the U.S. for decades, with industries such as the Aerospace and Defense sector having early adopters invest in and develop the technology to enable the rst novel products and applications made possible by AM. When metal AM technologies, for example, demonstrated the ability to transition into production, the industry saw continued replication in the R&D space across initial stakeholders who needed to mature the technology for their applications. This internal development delivered innovative processes and products; however, it did not address the ecosystem required to advance and adopt AM in the U.S. at scale, nor did it optimize acceleration through coordinated planning and investment at the industry level.
This is where I continue to see America Makes as a vital institute in the U.S., enabling this coordination and collaboration in the challenging – and rapidly changing – TRL 4-7 space required to move AM into the products around us. Rather than companies developing the technology individually, teams are innovating together, learning together, and strengthening our nation’s manufacturing capability while developing technologies that can be shared and adopted by other companies. This pre-competitive collaboration is accomplished through coordinated roadmap development, focused research projects, workforce development and education, and a central, coordinating body working with partners and organizations in the creation of critical industry standards.
This is an exciting time for additive manufacturing and for America Makes, as 2022 marked the Institute’s 10th anniversary. In that time, AM has realized steady growth in production and novel applications thanks to America Makes, all of which have resulted in a mindset shift from “How do I use AM?” to “How do I scale AM?” In this next chapter for America Makes, I see a focus on maturing the broader AM ecosystem to achieve the scale necessary to support growing demand and to look holistically at what’s coming in AM as we consider the needs of our members.
I am honored to serve as the Chair of the Executive Committee, and excited to support the America Makes journey to becoming the AM innovation hub while continuing to establish the U.S. as a global AM leader. The Executive Committee serves as the core strategic advisory group, ensuring appropriate strategy, policy, and advocacy are in place. The committee comprises leaders in AM across academia, industry (both small and large), and government, to ensure all voices are heard and incorporated into the Institute’s plans. I look forward to working with America Makes leadership to build upon past success and continue to support the mission of accelerating the adoption of AM and the nation’s global manufacturing competitiveness. The newly elected Executive Committee is here to serve America Makes over the next two years. Please do not hesitate to reach out and let us know if we can assist in any way.

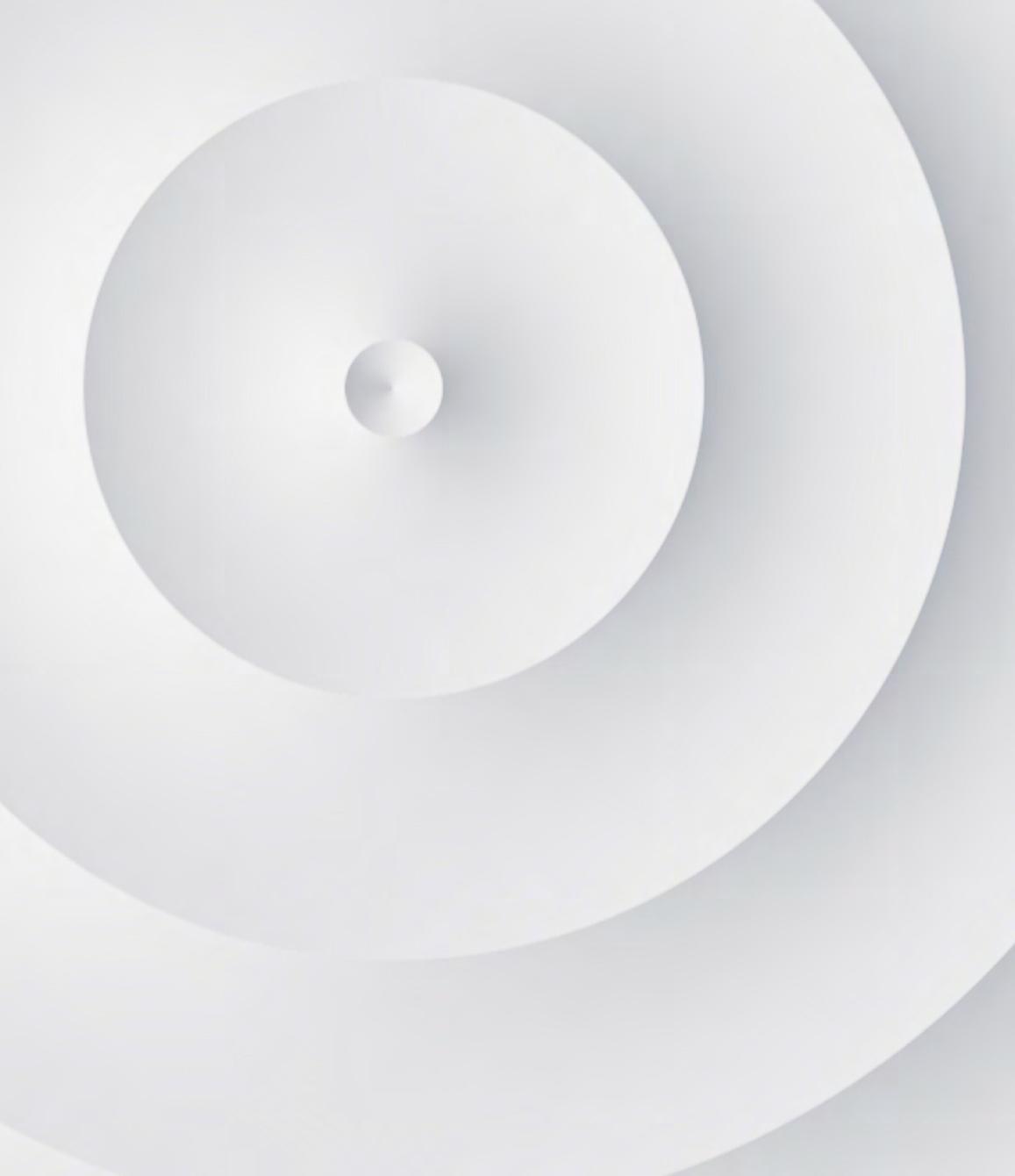
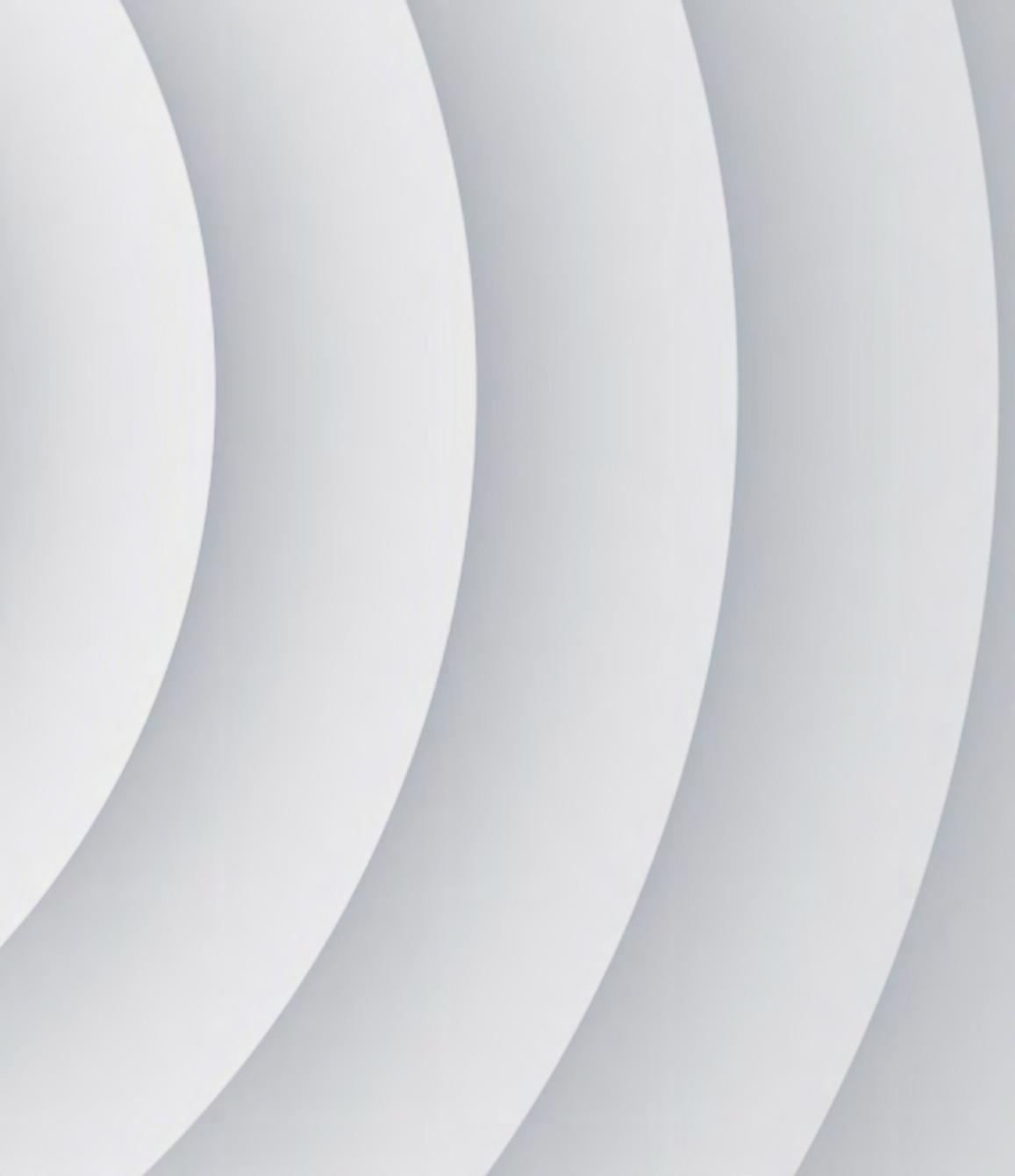
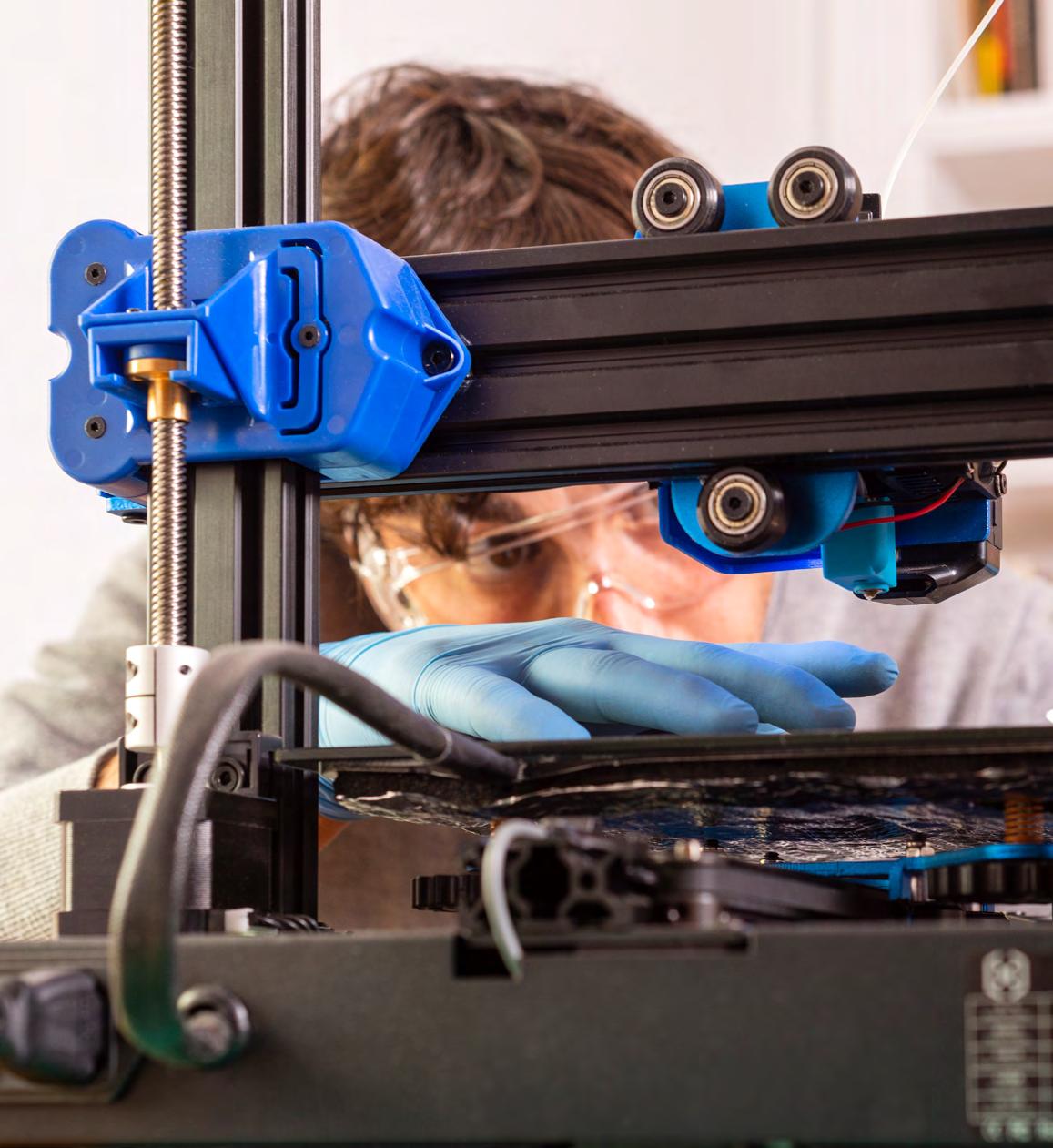
Getting “AMPED” Up
BY JOSH CRAMER | DIRECTOR OF EDUCATION AND WORKFORCE DEVELOPMENT, AMERICA MAKESManufacturing has taken a journey from low-tech high labor to high-tech low labor, which has increased automation, e ciency, and capabilities. Additive manufacturing (AM) is a rapidly growing industry. Many industries utilize AM technologies, including aerospace, medical, automotive, and energy.
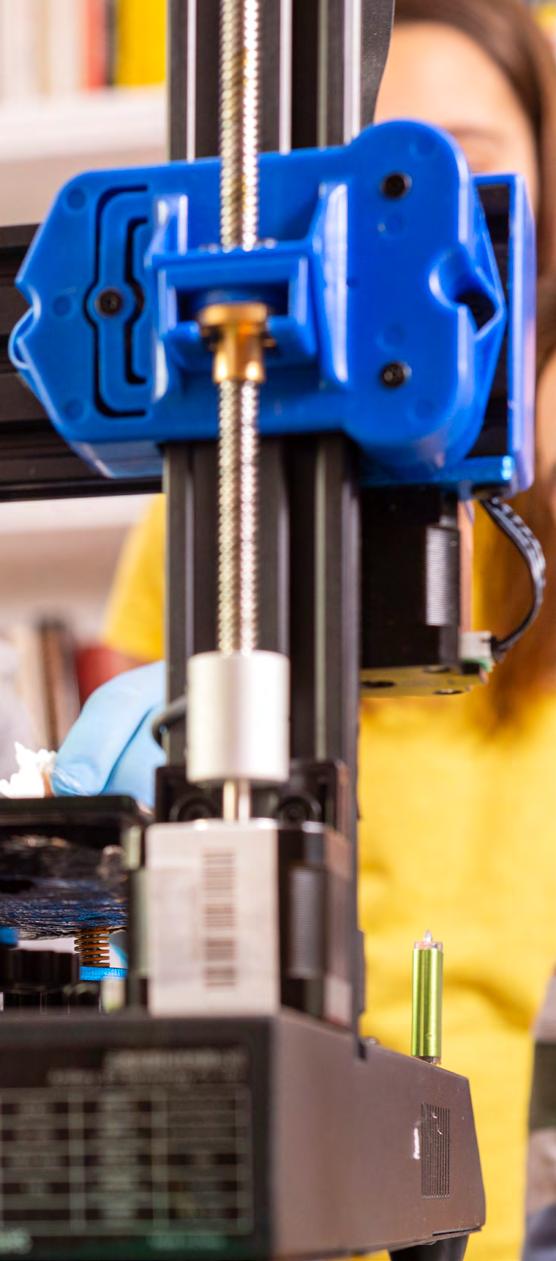
A recent Boston Consulting Group study noted the possibility of up to 1 million manufacturing jobs by reshored production and rising exports by 2025. The National Association of Manufacturers (NAM) also reports that 4.6 million manufacturing jobs will be needed in the next decade. Quali ed candidates will require training to ll positions in industries that utilize AM technologies and have access to educational pathways. Strong skillsets and knowledge within the STEM disciplines are vital to this success.
COMEBACK OF DOMESTIC MANUFACTURING = RISING NEED FOR TALENT
According to recent America Makes project studies, within the additive industry alone, there are approximately 50,000 openings across the nation that continue to remain un lled. Local small and medium manufacturers (SMM) struggle to maintain competitiveness due to a lack of capable and aligned talent from their regional talent pool. This problem is ampli ed through the investment in technology
Workforce development is the key to additive manufacturing climbing the “Best Sellers List” of U.S. manufacturing.
•
•
CELEBRATING SUCCESS
Linking Training Opportunities
JOY GOCKEL, PH.D.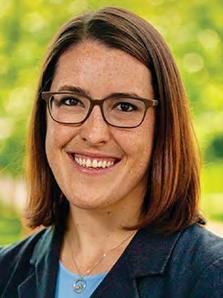
•
America Makes EWD Subject Matter ExpertParticipating in several initiatives within the EWD portfolio at America Makes is a great opportunity to discuss the overall AM body of knowledge and determine what concepts are best across a wide variety of levels of education.
I am excited to begin participating in the steering committee for the new AMPED project. This project is building critical linkages to training opportunities for the many job roles in AM, greatly impacting the AM ecosystem.
We are looking forward to collaborating with America Makes on upcoming outreach projects at the Colorado School of Mines, such as our NSF Interdisciplinary Additive Manufacturing Research Experiences for Teachers Site. Leveraging the many great EWD existing resources will allow us to focus our projects on building new tools and expanding the pipeline for a highly skilled workforce poised to strengthen the U.S. additive manufacturing industry.
The EWD efforts are a great example of what America Makes does best — bringing the academic, industry, and government communities together to solve big challenges.
fueling a comeback in domestic manufacturing. Therefore, the growth of manufacturing jobs and the need for those jobs will continue to grow further. Data shows an additional 1 3 million jobs from 2010 to 2019 could have been added, according to the Department of Labor.
Manufacturers in the U.S. have shown that they are willing to move from talent-drought areas to talentrich ones by nearly 74%, according to the Boston Consulting Groups study. A more signi cant threat to our domestic competitiveness is that 17% of companies were willing to move production away from the U.S. to access skilled workers. Manufacturers must have access to quali ed talent and, more specically, talent pipelines, assets, and resources to maintain and grow.
America Makes is a dedicated national collaborator in education and workforce development (EWD). The Institute’s mission is rooted in our nation’s competitiveness in manufacturing superiority for national security. One of the most critical threats to that mission is available human capital. Though a “renewable” resource here in the United States, manufacturers are lacking the mass of available talent and probably more so the “right” talent. There continues to be a mismatch in the industry due to several factors. The factors include new technologies, miscommunications, and myths about their adoption.
EVOLVING INDUSTRY, EVOLVING NEEDS
Today’s manufacturing roles are very di erent from those of the past. Job titles, descriptions, knowledge, skills, and abilities di er. Another missing component is the integration of the validation of technical and soft skills through industry-recognized credentials. Showing direct links to employers who value speci c credentials and those institutions and organizations that o er them is a part of building successful pathways. One of the most signi cant critical issues is the awareness vacuum that includes misperceptions of the industry, quali cations, and opportunities these careers possess and provide. America Makes has a
dedicated team laser-focused on the work of EWD but also a militia that has banded together to tackle the problem across what we call the “K through Grey” talent stream.
Nearly four years ago, the Institute reinvigorated its dedication to the EWD space. A new strategy was created and realized to build on a solid foundation from the past and carve some new trail into the future with the members, partners, and stakeholders aligned to ensure we have a strong talent stream for AM. The team has since collaborated with many local, state, and national partners to scale up from two projects to 21 projects and initiatives.
The portfolio has grown in scale and exponentially in reach and impact. The geographic spread of the Institute has never been more diverse than now, reaching participants in 49 of 50 states, including 14 focused regions. The expanded learning population must include all facets of the talent stream to respond to the warning call. From early learners through the K-12 sector to community colleges and postsecondary schools, to reskilling and upskilling our workforce and remaining dedicated to our Department of Defense (DoD) war ghters and industrial defense ecosystems, our reach is broad.
EXPONENTIAL REACH
The goal must be to get to the widest part of our talent funnel to inspire and build awareness and educate on clear pathways into validated and rigorous learning programs that meet every learner – where they learn, and how they learn. Being dedicated to a vast talent funnel also means that the team focuses on underrepresented groups and underserved regions across the nation to ensure that every learner can visualize and see themselves in our industry.
These pathways are built to the voice of need by industry and defense, a core keystone in our EWD mission. America Makes EWD engages nearly four dozen subject matter experts from industry and defense to guarantee that content is rooted in the AM body of knowledge (AMBoK) and to rigorous standards for every level of learning. This learning must also allow
Inspiring Across Generations
TRAVIS MAYBERRY•
Additive Manufacturing Technical Lead, Raytheon Missiles and Defense
•
America Make EWD Advisory Group Chair
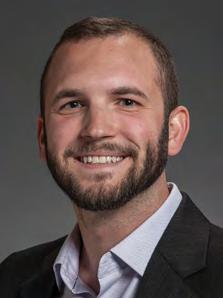
•
America Makes EWD Subject Matter Expert
When I frst joined the EWD program, I was focused on how we could steer the training resources that America Makes and industry partners have developed over the past 10 years into common training content for use by industry primes like my company, Raytheon. However, when EWD Director Josh Cramer asked me to get involved with the NOCTI content development for high school students, I realized the larger vision was to reach down into the primary education system to get students interested in “making,” which is not only great for AM but also supports the industry in general.
Exposure to manufacturing at younger ages prepares the next generation to better understand what it takes to “make” and opens them to careers in advanced manufacturing. This will diffuse up to the Raytheon’s of the world and our customers in due time and may prove to be one of the most important efforts for the promotion and general awareness of AM technology currently underway.
Although generating interest and skills at the K-12 level is primary, awareness and inspiration in the general industrial population and among mainstream adults must also be a focus to allow the industry to onboard more of an incumbent workforce. We are actively working on both facets, and I am excited to reap what has been sewn over the next decades.
participants to receive industry-recognized credentialing in which the members of America Makes play a critical role. The Institute now has a foundation for a credential pathway validated through our membership and the continued growth within the EWD roadmap.
America Makes remains a close ally with various federal partners such as the DoD and the National Institute of Standards and Technology (NIST) o ces. The portfolio also has engagements across several state-led e orts, including some philanthropic and industry-funded projects. As the institutes build sustainability for the future, the continuation of maintaining a detailed national EWD roadmap will be a constant. The need to ensure the industry remains e cient to reduce redundancies in education and workforce training becomes even more critical.
begin to check out the available assets.
The DoD and its Department of Manufacturing Technology Program stepped up over the last year to support the build-out of the pilot demonstration of the new portal. This essential collaboration further enriched engagement between America Makes EWD and the Joint Additive Manufacturing Working Group’s EWD Stakeholder Committee (JAMWG EWD).
AMNation:
[ā·'em·nā·shən] noun
a systematic approach to scaling promised practices of the EWD portfolio through members and partners to gain a broader reach and impact.
AMPED solves a critical requirement to execute a library of deep and rich assets from industry and defense in a digital catalog that is easy to access and navigate. A linchpin of this program also includes mapping and aligning core competencies within the AM industry.
AMNation – REALIZING SCALABILITY
A cornerstone of the reinvigorated strategy that is now coming into focus is AMNation. AMNation is a systematic approach to scaling promised practices of the EWD portfolio through our members and partners to gain a broader reach and impact. The team continues to build out components that will support and engage AMNation, such as the AMNation Pipeline Portal, the up-and-coming AMJobs site, and an ongoing e ort referred to as the Additive Manufacturing Portal for Education (AMPED).
Before “AMPED” was AMPED, this concept had been part of the America Makes EWD strategy as the Institute needed a “card catalog” and “best seller” list of all the “books” or education and workforce development assets in the EWD library. This new crowd that we call AMNation is now holding “library cards” and is ready to
Competencies detailed as knowledge, skills, and abilities (KSA) will be aligned to the AMBoK built and validated by both America Makes members and the industry. This work will leverage a variety of foundational work also done in collaboration with the JAMWG EWD Stakeholder Council and workshop materials executed during the AMMO Workshop – Additive Manufacturing Maintenance and Operations.
Resources include the initial identi cation of core job roles and functions along with initial KSA mapping across both industry and defense. Job role identi cation and standardization and KSA work will assist those seeking to enter the industry in understanding pathways aligned with interests and strengths.
PATHWAYS FOR SEEKERS
A core function of AMPED is building pathways for those seekers into training assets across America Makes, the DoD enterprise, and the industry on how and where to obtain those skillsets for that desired job role. The project will also seek to include America Makes’ work in the credentialling sector, aligning industry-recognized credentials tied and aligned to the
assets to educate seekers. AMPED will provide a demonstration of the technology, work, and platform.
Over the next year, this team is focusing on up to 14 critical and mass need job roles in AM. Of those down selected roles, the team will be looking to align and showcase capabilities of the portals matching functionality with at least one training asset within America Makes, the DoD enterprise, academia, or across the industrial base.
Lastly, under this project, the America Makes team will be furthering the development of the microlearning pathway in cap-stoning four new modules dedicated to the defense and industry leadership within AM. These new micro-learning modules will share a home with the other micro-learning modules in middle school, high school, and adults within our AMNation Pipeline Portal. The AMNation Pipeline Portal a ords the Institute a dedicated home easily accessible and scaled within the industry, academia, and defense.
FOSTERING A DIVERSE TALENT STREAM
In celebrating our 10th anniversary in 2022, America Makes recognizes the importance of driving to ensure that we can link the rm foundation of the past with the innovation of the future. The Institute has a dedication to providing that the nation accomplishes superior manufacturing capabilities supported by robust human capital. A diverse talent stream that inspires is essential. Inclusivity for people from all walks of life and circumstances is paramount to having a diverse and healthy talent stream. Manufacturing, now in the 4th industrial revolution, is rooted in ine ciencies, and the Institute shares that across the EWD sectors. Thus, AMPED’s core mission is to provide a new platform that brings an accessible “card catalog” of the assets aligned to de ned job roles and competencies of those roles.
It will take us all, AMNation. Let’s go!
To learn more or get involved, reach out to Josh Cramer, Director of Education and Workforce Development, at josh.cramer@ncdmm.org.
CELEBRATING SUCCESS
Mastering a New Domain
LAWRENCE A. BINEK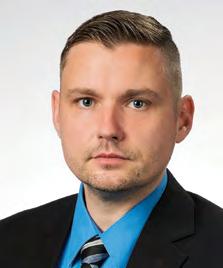
•
•
•
America Makes EWD Subject Matter Expert
Additive Manufacturing is a dynamic technology, constantly evolving. This new tool signifcantly expands the design space and we’re constantly pushing the boundaries.
Students are starting their AM journey at home or in middle school and the America Makes EWD training structure aligns them toward what is needed in industry. Raytheon Technologies has been working with America Makes on curriculum development and helping build out the additive talent pipeline. We are training a new workforce and retraining an existing workforce in a highly accelerated technology and very often we need to decalcify traditional design thinking to harness the value proposition of AM. Through the America Makes EWD initiatives, I’ve had the opportunity to collaborate with industry and academia to build inclusive and holistic training material for youth and adults. It has been enlightening to see new modalities of learning enabled by digital technology. Through this work, we can communicate industry-specifc standards and practices that accelerate the readiness of the learner. Engaging with EWD is critical in keeping up with the rapid advances in technology, which in turn ensures a current and profcient workforce. Simply put, AM is a new domain that we need to master. We have the digital and machine tools and what we really need is to harness the imagination and energy of a workforce eager to learn. This is how we get there.
Senior Principal Engineer, Pratt & Whitney Operations America Makes EWD Advisory Group MemberAdditive Manufacturing: State of the U.S. Ecosystem
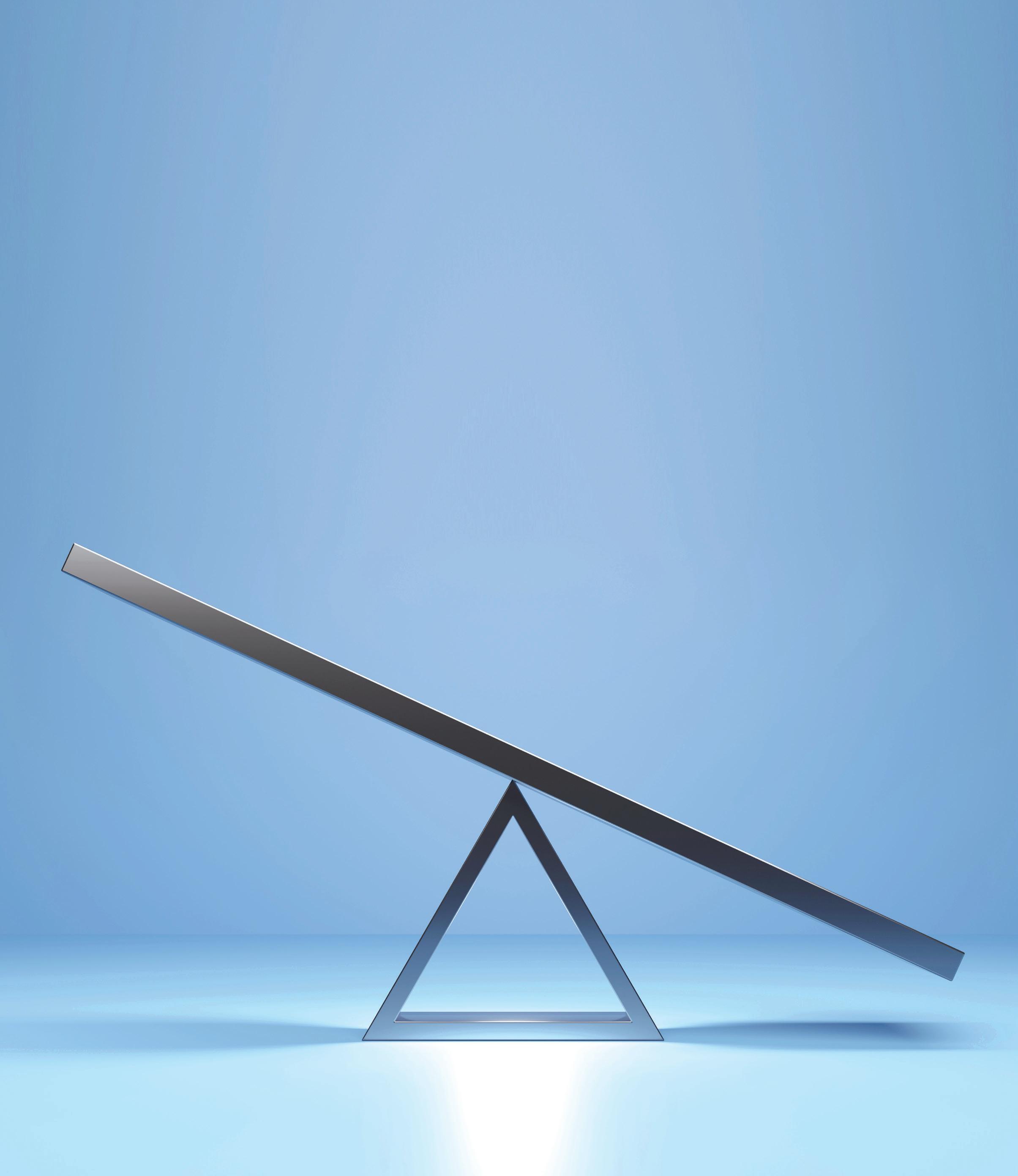
Envisioning
BY KIMBERLY GIBSON | ECOSYSTEM DIRECTOR, AMERICA MAKESWe stand at the edge of something that we have spent the last decade nurturing. Our mutual mission is accelerating the adoption of additive manufacturing (AM) technologies across industry sectors in our nation and in our world. In service to that mission, we have developed roadmap technology platforms with new materials to solve problems that are too large for any one of us. We have seen equipment speeds increase, and post-processing and inspection technologies improve. We have discussed standards and quali cations to use AM processes in complex systems. We have crafted training and education curricula to uplevel the current workforce and stimulate the imagination of our younger generation so that AM design thinking is endemic to the way they will approach future design. We have endured a pandemic that thrust AM technology into the forefront and demonstrated, in real time, how AM can support complex and far- ung supply chains.
We have come so far – and throughout, we have collaborated with one another, in earnest, to advance our collective understanding of what is possible so that additive technologies may take their place alongside traditional manufacturing. Yet, there is so much more to do.
Our world is much changed. Commercial space
exploration and NASA Gateway Projects bring forth the notion that we are closer to becoming an o -planet species. Shifting geopolitical landscapes and earthbound realities like double-digit in ationary pressures and increased weather-related disasters must factor into our plans as they create urgency to rethink global supply chains and the future deployment of resources. Unprecedented investment to support modernizing and digitizing American manufacturing is underway via a series of congressional bills including the CHIPS and Science Act and the In ation Reduction Act. These dollars are once-in-a-generation investments and we must act decisively to align around a shared vision, an industrial policy for our nation.
ECOSYSTEM ADVISORY GROUP: MANAGING THE MISSION
America Makes is launching an advisory group to guide and support the direction of the AM ecosystem. The old and time-consuming linear research transfer process is insu cient for the digital age. Instead, technology transfer must be done via ecosystems — focused on the vivid interplay of know-how among partners, in the cone of trust from science and integrators to end users. The bulk of this work happens in proximity within regions, and in the zoom era, communities of practice have never
been more relevant. The early focus of the group will be on design and vetting AM Applications Accelerators, data analysis of AM business ecosystems, understanding research needed to demonstrate AM’s potential to support greater environmental sustainability, and weighing in on national and state public policies needed to support the AM industry. The Ecosystem Advisory Group will also explore the implementation of diversity, equity, inclusion, and access (DEIA) within the AM community.
THE APPROACH: COMMON QUALIFICATIONS
The industrialization of AM requires a dedicated focus on critical items such as equipment speeds,
reliability and repeatability, post-processing, and inspection technologies. This will occur within specific industry sectors, such as engine systems and parts subassemblies, given unique complexities and proprietary knowledge. The call for a common set of qualifications is underway. At MMX 2022 , separate roundtables for large and small businesses highlighted a significant need to address qualifications. The complexity and costs associated with current methods to qualify materials, parts and systems was cited as a key impediment to AM adoption across the ecosystem. Look for more activity on this topic in 2023
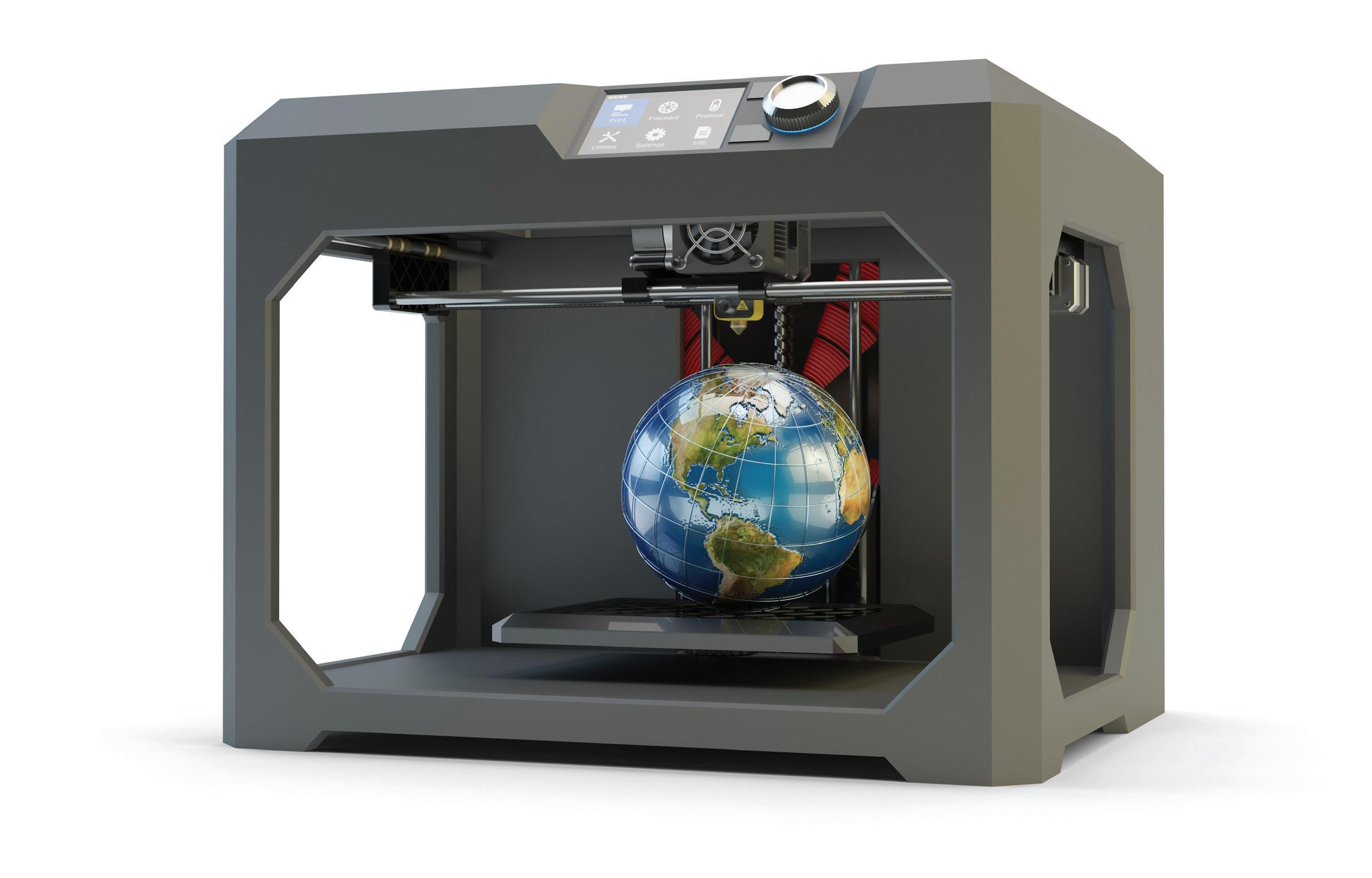
DATA ANALYSIS
The AM industry is moving fast. It is indeed di cult to make decisions without a deeper understanding of trends and patterns. America Makes has partnered with the Association for Manufacturing Technology (AMT) to bring the AM industry in line with traditional manufacturing to collect economic data and aggregate it as an industry. The combined e ort of
NATIONAL AND STATE POLICIES
In the U.S. and abroad, we have what some have called an implementation crisis – essentially focusing on laws to prevent what we don’t want vs. creating what we do. The network of Manufacturing Innovation Institutes represents a grand vision. Over the past decade, we have applied first design principles to go from “Can it be done?” to “Can it be designed for manufacturability?” For the more mature technologies, we are at the stage where the industry needs to address which laws, protocols, and standards need modification to enable the greater use of AM.
Likewise, we need to consider where AM introduces unacceptable levels of risk. As an industry, we are ready to find our collective voice on policy matters. In collaboration with the Additive Manufacturing Coalition, America Makes will sponsor forums on important policy topics for the industry aligned with key priorities.
two trusted third parties to provide regular updates on what is happening in the AM economy and ensure a variety of players — large and small — are captured in the analysis. The rst step is a pilot survey of users and providers to benchmark the data in early 2023 with quarterly updates moving forward. The objective is a regular quantitative look at the AM industry with insights that can help guide policy and investment.
The challenge before us is to take all the individual pieces, the mature ideas and the applications successes, the demonstrations, and the good business models and advance coherent pathways to success within. To move forward and create a true industrial ecosystem with AM as a fulcrum for a resilient, environmentally sustainable, and distributed manufacturing network that leverages the strengths of places, of industry and honors the diversity of our American citizenship to support
next-generation economy.
“The challenge before us is to take all the individual pieces, the mature ideas and the applications’ successes, the demonstrations, and the good business models and advance coherent pathways to success within. To move forward and create a true industrial ecosystem with AM as a fulcrum for a resilient, environmentally sustainable, and distributed manufacturing network that leverages the strengths of places, of industry and honors the diversity of our American citizenship to support next-generation economy.”
America Makes 2022 Strategic Objectives
BY BRANDON D. RIBIC, PH.D. | TECHNOLOGY DIRECTOR, AMERICA MAKES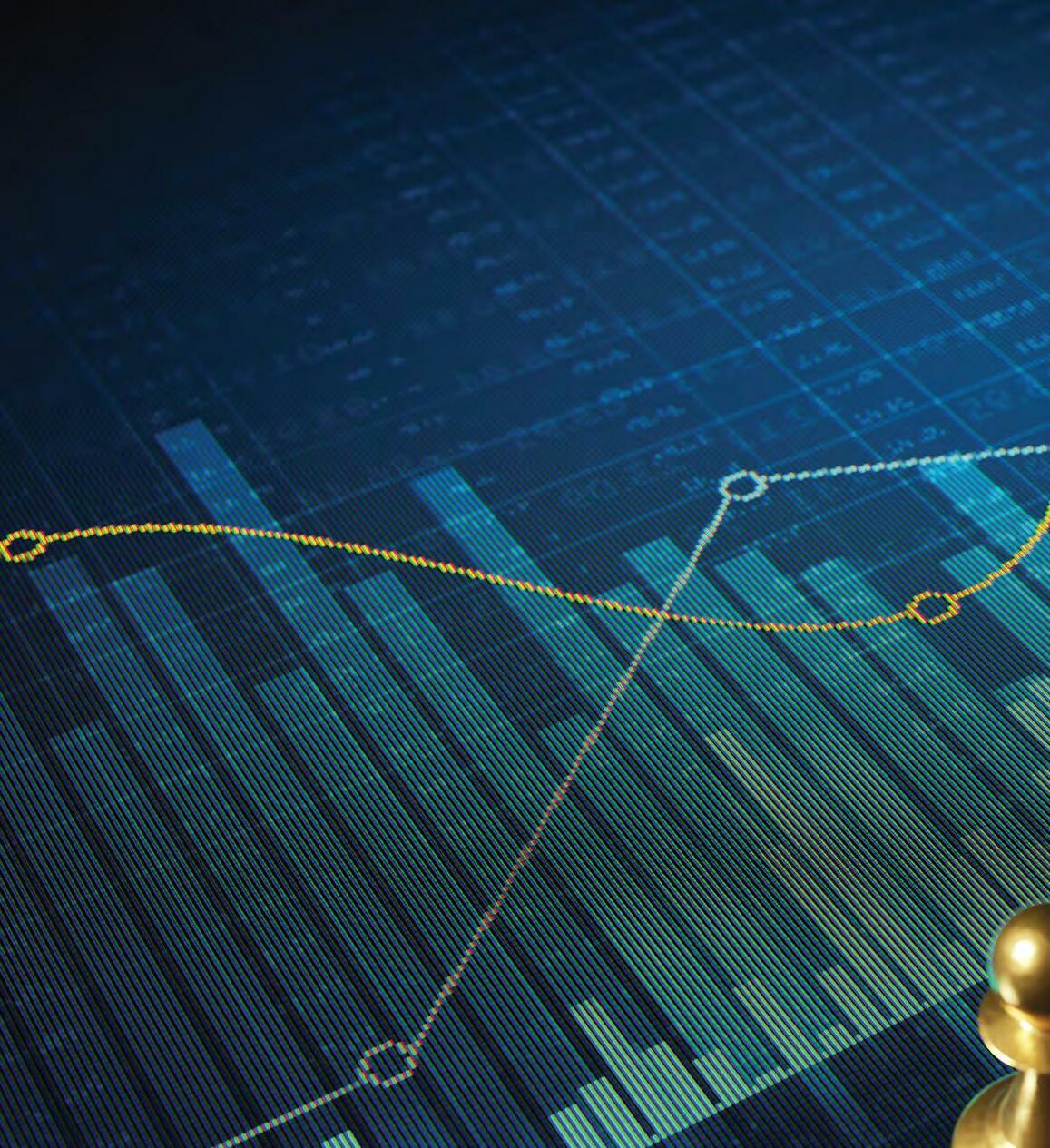
These strategic objectives are the product of America Makes membership input and workshops executed in the Summer of 2021 and Spring of 2022. Workshop discussions focused on each of the ve America Makes AM Technology Roadmap swimlanes (design, material, process, value chain, and AM genome). Participants were asked to outline needs and prioritize those needs according to a timeline where substantial progress can be made within 2 years (now term), 3-4 years (near term), or more than 4 years (long term). The following strategic objectives are the results of those e orts.
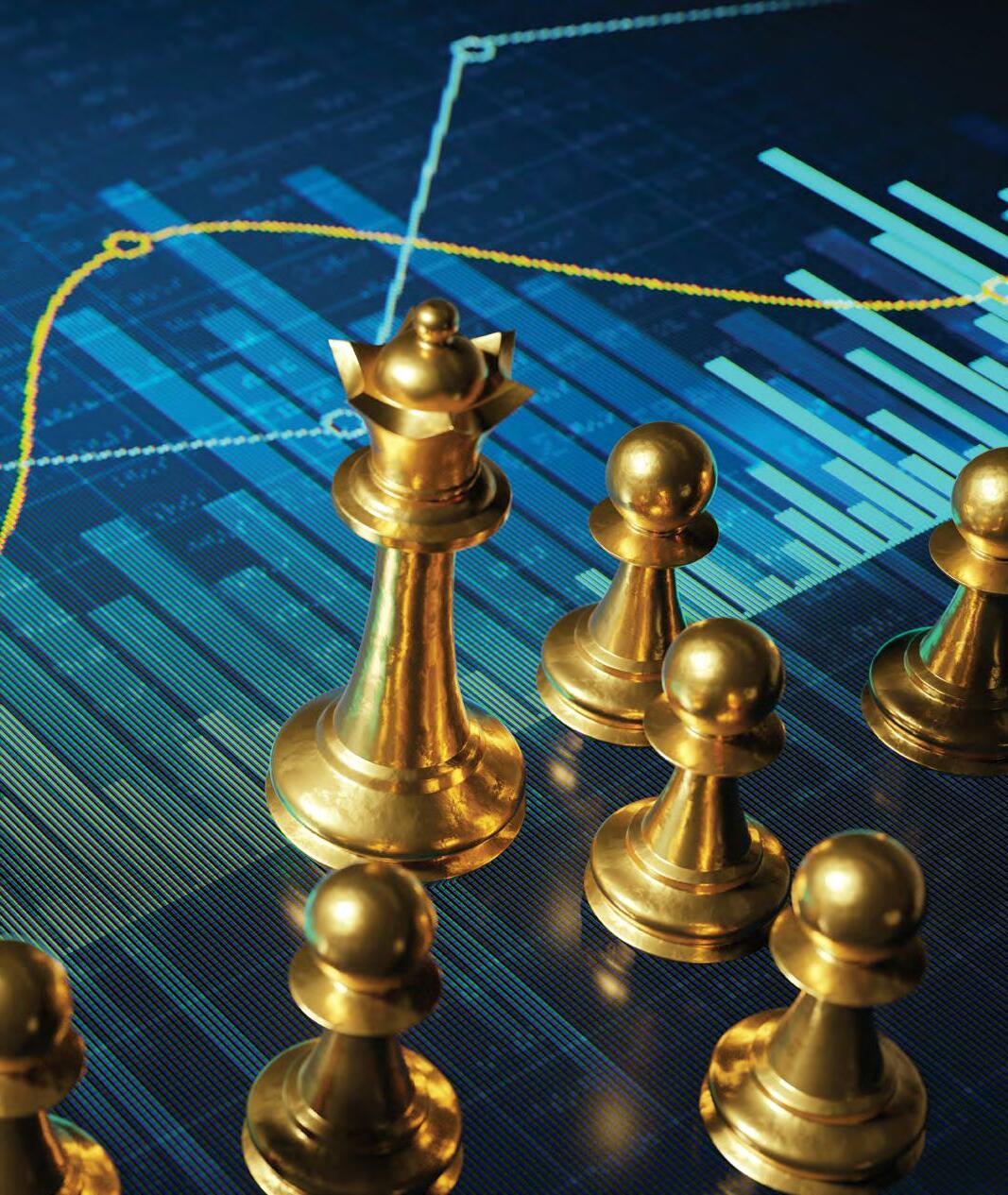
DESIGN
Now-term objectives:
• Practices, knowledge, and tools that improve design for inspection and inspect-ability
• Design tools that accelerate qualifcation and certifcation for thermal management and light-weighting
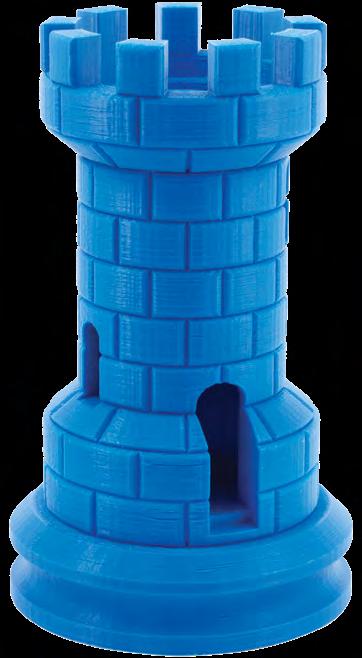
• Design of lattice to solid body or other interfaces for improved heat transfer, load, and robust manufacturability
Near-term objectives:
• Maturation of generative design tools
• Understanding failure and dynamic loading of topology optimized structures
• Design allowances that consider manufacturing variance and quantify damage tolerance
• Validation of model-based generative design tools/methods for fight-critical applications
Long-term objectives:
• Design for post-processing
• Precompetitive best practices, documentation of key process variables, establishing essential process variable limits and quantifying key performance parameters for life limited applications
• Design methods that include multi-physics and multi-objective approaches
MATERIAL
Now-term objectives:
• Powder reuse effects for both powder bed fusion and directed energy deposition
• Standard test methods for data deliverables
• Vendor sources to obtain and develop new materials
• Repairability of additively manufactured parts
• Opportunities for testing of material samples outside of projects
Near-term objectives:
• Reduce testing costs for part and process qualifcation
• Thermal treatments of binder jetting materials
• Materials for civil engineering and public projects (e.g. roads, cities, etc.)
Long-term objectives:
• Use of recycled materials
• Graded materials for improved corrosion resistance
VALUE CHAIN
Now-term objectives:
• Cost and value of in-situ process monitoring capabilities for various AM processes
• Extent of physical understanding attained by in-situ process monitoring
• Process verifcation – machines are performing within tolerances
• Affordability and limits of various post-process inspection or ex-situ inspection methodologies
• Qualifcation framework to leverage ex-situ inspection to cover gaps from in-situ inspection
• Capability assessments of various ex-situ inspection methodologies
• Qualifcation requirement drafting and validation for repairs
Near-term objectives:
• Verifcation – modeled vs. as-produced
• Advancements in sensor technology to interrogate material quality
• Improved data fusion of in-situ inspection with ex-situ inspection results
• Best practices guidance for leveraging ex-situ inspection in conjunction with in-situ inspection
Long-term objectives:
• Leveraging in-situ monitoring to quantify AM product performance/life
• Integration of product model-based defnition and model-based inspection with in-situ inspection
PROCESS
Now-term objectives:
• Easier operation (sensor calibration, machine health monitoring, standardized defect generation, etc.)
• Processes that are better, faster, and less costly (reduce stress, less post-processing, larger and smaller scale, etc.)
• Repairs using additive manufacturing processes
Near-term objectives:
• Better integration with multiple AM and other digital manufacturing functions
• Closed loop control related to monitoring, data management, visualization, etc.
• Expanded diversity of materials printed into individual parts
Long-term objectives:
• Smart, autonomous processes
• Printing processes for more increasingly exotic materials (materials not currently available)
AM GENOME
Now-term objectives:
• Findable, accessible, interoperable, and reusable AM data
• ICME tool to simulate metal evolution
• High throughput experiments
• Prediction of inherent defects in Ti64, IN718 and IN625
• Multi-scale molten pool model from micron to mm scale for non-ferrous alloys
Near-term objectives:
• Standard thermally relevant LCF, HCF coupons
• Correlate thermal features to microstructure
• Microstructure to material property model after heat treatment
• Physics-based thermal models
Long-term objectives:
• How to qualify models
Here’s What
You May Have Missed
Since the beginning of 2021, America Makes has been an instrumental player in nearly 70 different engagements. From workshops to conferences, we’ve gathered diverse voices from all industry sectors and parts of the country. Here’s a rundown of some of the key opportunities, priorities, and challenges that came out of those events.

America Makes is a orded the privilege to serve as a coordinator and collaborator in the AM community. Since January of 2021, the Institute has or will participate in approximately 70 discrete engagements (workshops, symposia, presentations, and teleconferences) outlining trends, gaps, and interests for AM technology maturation. Individuals throughout industry, government, academia, national labs, and non-pro t organizations come together to share perspectives that serve to re ne the strategic direction of the Institute. Here’s a summary of ndings from a selection of those gatherings. Have something to add to the conversation? We want your input. Email me at brandon.ribic@ncdmm.org or reach out to Todd Spurgeon at todd.spurgeon@ncdmm.org.
AMMO Additive Manufacturing (AM) Workshops
Held in both 2021 and 2022, the Additive Manufacturing for Maintenance Operations (AMMO) AM Workshop addresses key issues necessary for Department of Defense (DoD)-wide adoption of additive manufacturing. The forum offers an opportunity for government, industry, academia, and nonprofts to collaborate on issues that pertain to leveraging AM capabilities, and then promote the discovery and sharing of solutions that support the implementation of AM throughout the DoD and its partners.
2021 AND 2022 BREAKOUT SESSIONS:
• Research and Development to Advance AM Qualifcation and Certifcation
• Cybersecurity
• Common AM Data Package Approach (JAMA)
• Education and AM Workforce Development
• AM Standards – Defense Industry Priorities and Addressing R&D Gaps
• Integrated AM Network Response – How Industry and Government Can Work Together to Respond to Urgent and Important Needs
• AM Decision Making – Business Case Analysis for AM in the Defense Industry
• DoD Standardization Prioritization
• Cybersecurity (wargame) Hack-a-Thon and Improving AM in Small and Medium Manufacturers
• Manufacturing Crisis Response
• Additive Manufacturing Portal for Education (AMPED)
• Agile Inspection and Testing
NOTE: The 2021 AMPED session was focused on understanding critical roles, competencies, training resources, and knowledge to accelerate adoption of AM. The 2022 JAMA breakout was a feedback session on the data package model, designed to achieve exportability, modularity, adaptability, and expansive acquisition. More information about the outcomes of these sessions are available at gbm.media/AMPED and gbm.media/AMMO
2021 AMMO BREAKOUT GROUPS
R&D to Advance AM Qualifcation and Certifcation
Prioritized near-term (2 years) gaps:
• Materials data for dynamic applications including process-structure-property relationships (fatigue data, effects of defects, design/material allowables)
• Improved inspection throughput and techniques
• Machine calibration (validated tools, methods, and techniques)
• ICME tools
• Distortion prediction
• Residual stress measurement (validated tools, methods, and techniques)
• In-situ monitoring and data registration with inspection data
Prioritized long-term (5+ years) gaps:
• Valid ICME methods for qualifcation, including dynamic property (fatigue life) prediction
• AM equipment equivalency for qualifcation and vendorto-vendor validation
• AM material-specifc acceptance criteria
• AM system designs that promote reliability and repeatability (includes sensing technologies)
• Use of industry standards compared to proprietary standards/specifcations to enable vendor certifcation and approval
Cybersecurity (2021 & 2022)
Top fve needs identifed included making security more invisible and unobtrusive; making key security properties or controls “built in;” AM machine manufacturers providing secure machine environments; developing case studies of where security improvements paid off in ways that matter to manufacturers; and keeping the security posture up to date (limiting vulnerabilities).
Education and AM Workforce Development
The breakout session included the delivery of an AM training course and outlined opportunities for additional focus within the education and workforce development domain including safety training and disposal chains.
AM Standards – Defense Industry Priorities and Addressing Research and Development Gaps
The top 10 priority gaps included the following:
• AM part classifcation system for consistent qualifcation standards
• Machine qualifcation
• Contents of a technical data package (TDP)
• Harmonizing of AM qualifcation and certifcation (Q&C) terminology
• Design allowables
• Machine calibration and preventative maintenance
• Material properties
• Recycle and reuse of materials
• AM process-specifc metal powder specifcations
• Design of test coupons
Integrated AM Network Response
Educational gaps identifed for times of crisis include AM design; AM quality systems; AM technology and methods; AM post-processing; and AM materials. Other noteworthy needs and opportunities for development include enablers for distributed manufacturing supply networks; monitoring software for order production and fulfllment; digital iterative design collaboration spaces; and integration of digital thread including regulatory, quality management systems, and an associated approved supplier database.
AM Decision Making – Business Case Analysis for AM in the Defense Industry
Opportunities for development include mathematical frameworks for objective evaluation of business case (AM compared to AM or traditional); objective, quantitative evaluation of business case (cost avoidance or savings) for non-DoD applications; and standardized approaches for costing and business case analysis.
AMMO BREAKOUT GROUPS
DoD Standardization Prioritization
Top fve priority gaps included machine qualifcation; AM part classifcation system for consistent qualifcation standards; contents of an AM TDP; recycle and reuse of materials; and material properties and design allowables. Other noteworthy needs and gaps included understanding acquisition realities in circumstances of a crisis and how such conditions promote or diminish AM utility; re-qualifcation; cost of material and design allowable generation; and going beyond laser powder bed fusion AM processes.
Manufacturing Crisis Response
Several opportunities were identifed from the efforts of the breakout group including:
• Tools and practices to expand AM operational profciency
• New business and operating models for the acquisition of AM data
• Enabling AM at forward-operating locations
Agile Inspection and Testing
The breakout group defned agile inspection and testing as, “versatile and adaptable solutions that leverage technology to accelerate observed understanding and decision making to enhance warfghter readiness.” Considering the successful development, validation, and integration of these technologies into manufacturing operations, participants outlined short-term benefts (1 to 3 years), including supply chain resilience; cost saving (lead time reduction, reduce expediting cost, overhead cost/non-recurring/capital); National Technology Industrial Base (NTIB); and adoption of diagnostic testing. Longer term benefts (3 to 5 years) include accelerating the adoption of AM cost savings; shorter schedules (lead times, readiness, testing); and attritable parts on exquisite platforms.
Some challenges and opportunities to foster the maturation and use of agile inspection and testing include:
• Damage and durability tolerance/effects of defects
• Known variability of AM process (material state/performance)
• Material design bias
• Risk-based design
• Lack of standards and specifcation
• Documented certifcation: equipment, parts, people, process
• PoD/QA plan
• Current NDI/NDT/NDE technology
• Manpower/labor to perform testing
• Manufacturing limitations
• Processing sensitives
• Lack of technical data
• Big data utility/management
• Fabrication size constraints
• In-situ processing monitoring trust
• Data completeness/pedigree for qualifed AM parts
• Inherent uniqueness of AM parts
• Workforce competency
• Vetted multi-scale testing methods
• Relevant standard test methods
• Adoption of new test methods
On the other hand, enabling activities that can address these challenges and opportunities include rapid inspection technologies; available probability of detection data; effects of defects analysis; data sharing to accelerate expansive supply chain learning; a standardized technical data package for certifcates of conformance; policy advancements that foster distributed manufacturing operations; equivalency and testing methods; materials and process standards; and accreditation programs and workforce training.
RAPID INNOVATION CALL TOPICS
The following is a list of concepts submitted for the 2021 Rapid Innovation Call:
• Development and demonstration of an AM data ecosystem with insight into the fndability, accessibility, interoperability, and reusability of AM data
• Demonstration of AM methods to produce high-temperature steel dies
• Demonstration of Internet of Things (IoT) to produce an AM component and correlate with relevant product/system performance metric
• Process development and documentation of processstructure-property relationships for laser powder bed fusion of refractory alloys
• Demonstration of utilizing multiple inspection (non-destructive and destructive) techniques to assess sensitivity and probability of detection for relevant AM product geometries/materials
• Demonstrate improvements relevant to the design of lightweight structures using powder bed fusion
• Demonstrate feasibility, repeatability, and performance of fused flament fabrication for the repair of thermoplastic components/products
• Demonstrate methods for real-time correction of AM process-induced defects using hybrid AM
• Develop a method to characterize transient effects which impact emission spectra relevant to process monitoring technologies for molten pool temperature measurements during AM of reactive materials
• Development and demonstration of an AM process to produce solid composite electrolytes
• Demonstration of factors relevant to qualifcation of Directed Energy Deposition (DED) for the repair of copper alloys
• Identifcation and demonstration of novel acquisition and reconstruction procedures for x-ray CT (rapid inspection)
• Conduct a study of various types of MPEAs such as transition metal, refractory metal, lightweight, brasses and bronzes, and potential others for structural, high temperature, and other functional applications
• Delivery of an actionable plan for the development of an effective AM data hub
• Accelerate the commercialization of serial polymeric production parts by the creation of a lattice design toolkit
• Investigate the effect of build interruptions on the microstructure of laser powder bed fusion product relevant geometries
• Document AM process capability to successfully and reliably produce polymer heat exchangers
• Complete ICME prediction and test validation of recycled powder parts and provide the foundation for virtual ICME recycled powder engineering
• Develop and pilot introductory professional development digital badges for 3D printing instructors
• Development of effective multi-up printing for microelectronics
• Develop and demonstrate an approach for identifability of AM parts and secure tracking from initial print to end of life
• Leverage nanocomposite design and process optimization for fused flament fabrication to attain the required properties by optimizing materials composition and process parameters simultaneously with machine learning
• Conduct a hackathon to identify and document legacy models or experimental data for materials processing that were reported in the older literature (e.g., from the 1950s onwards) to fnd new ways to cross-check and address potential gaps among the state-of-the-art approaches, particularly process-structure-property relationships
• Provide the America Makes membership and the wider community with a framework for how different applications should be integrated along the digital value chain
• Demonstrate and validate Cold Spray (supersonic particle deposition) of Al and/or Al alloys as a costeffective, environmentally acceptable technology to provide surface protection and a repair/rebuild methodology to a variety of Mg alloy components
• Demonstrate a simple, low-cost instrument, and an associated sampling/testing method, that can determine the degree of similarity between two powders within minutes
• Capture the needs of the DoD AM community to inform the DoD in establishing a framework for AM Data Management
• Develop a technical report summarizing the key technical considerations, criteria, and application guidance for the use of AM Part Family’s concept to enable a more effective Q&C process of AM parts that would beneft both the industry and regulators
The following is a list of concepts submitted for the 2022 Rapid Innovation Call:
• Evaluation of one or more alloys to look at the impact of additive manufacturing on the resultant casting for all the following: 3D printed sand, 3D printed ceramic molds, additive manufacturing evaporative casting

• Development and testing of an LPBF AM friendly, highly oxidation resistant, high operating temperature nickel superalloy
• Identify, analyze, and demonstrate methods for various in-situ, ex-situ measurement techniques and AM processes
• Select and produce aluminum wire for DED AM from commercially available casting alloys and demonstrate utility to produce casting replacements
• Repair-by-design for a notional high-temperature nickel superalloy component in need of a deposition repair to restore geometry and service material properties while avoiding cracking, etc.
• AM ceramic tooling for casting applications – yield, quality, cost
• Experimental investigation of factors that promote variation in thermal history, microstructure, and critical to quality
properties (mechanical, physical, etc.) for different component geometries for DED AM processes
• Develop and demonstrate approaches for the design of pre-compensated geometries and/or sintering support strategies that provide controlled distortion to the fnal desired shape for testing for binder jet technologies
• Leverage the DoD’s activities to establish new vehicle system categories of airworthiness like attritable and exquisite, and to apply those concepts to guide implementation of additively manufactured systems, subsystems, components, and hardware
• Quantify the effects of common defects in additively manufactured components with the goal of setting quantitative inspection criteria
• Develop a standard method for rotating drum powder characterization that better represents critical-to-quality properties for AM processes
RAPID INNOVATION CALL TOPICS, continued
• AI/ML approaches to address AM process transferability across machine make/model
• Evaluate and document feedstock characteristics necessary to accelerate the maturation and available data necessary for AM machine qualifcation
• Fusion, sintering, and adhesion can play a critical role in the consolidation of AM materials, regardless of the AM process technology. Machine controls and the resulting process physics are interrelated and hence this topic looks to make quantitative information pertaining to sensitivities, measurement methods, etc., available to the membership
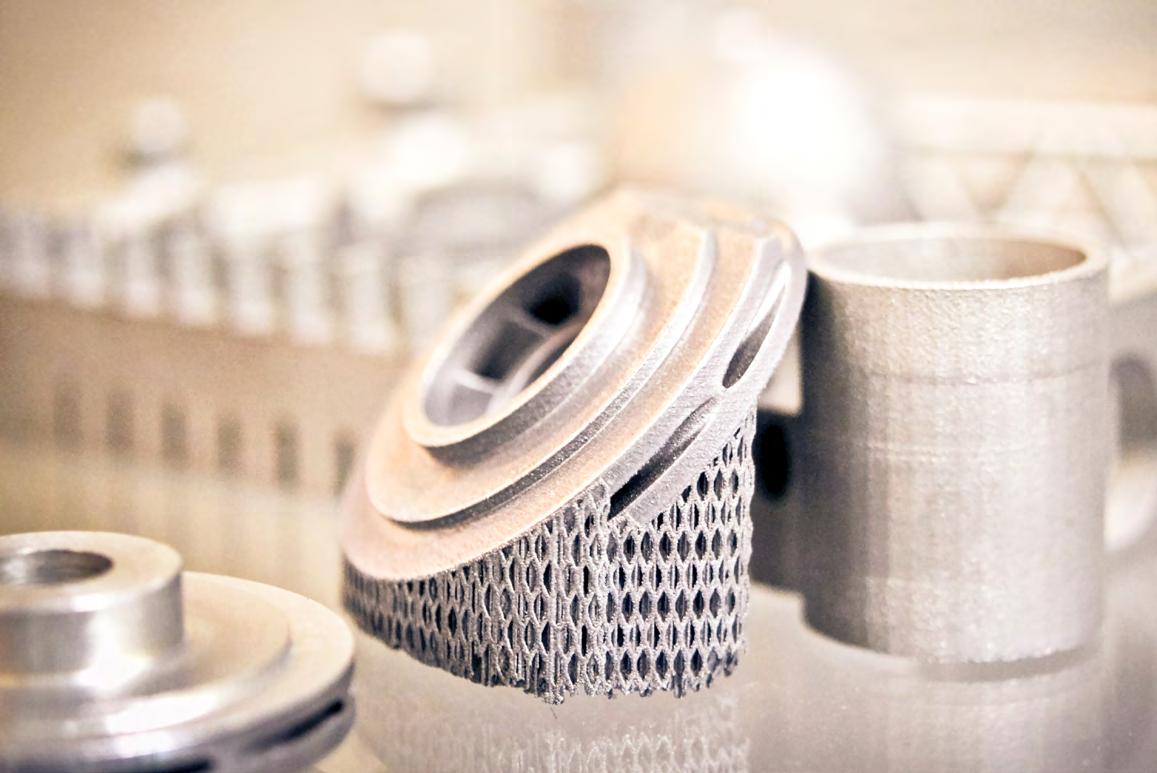
• Develop a method to characterize effects that are driven by variation in part geometry and establish a range of geometric features which exhibit a known nominal and
tolerance within a certain confdence interval based upon the product of multiple builds
• Quantify one or more AM process and/or equipment attributes, and their nominal operating ranges to establish AM machine qualifcation framework guidance and data which will accelerate the development of standard protocols, data models, supply chain readiness, etc.
• Identify a system, subsystem, process, or phenomena to evaluate for an AM process that exhibits a signifcant correlation with AM material/product quality and establish a statistically signifcant understanding of how to measure and characterize this factor in an industrially viable manner and execute a cost analysis
• Execute analysis of qualifcation and certifcation metrics, methods, tools, and techniques necessary for legacy manufacturing methods and designs for electronics applications and outline unique factors that those in the AM community may need to consider as these technologies continue to advance
• Identify and analyze methods to measure or characterize metal powder feedstocks undergoing reuse cycles in an industrially relevant manner to understand the correlation between metrics and critical to product/material quality factors such as microstructure, geometry and tolerancing, surface fnish, and physical/mechanical properties
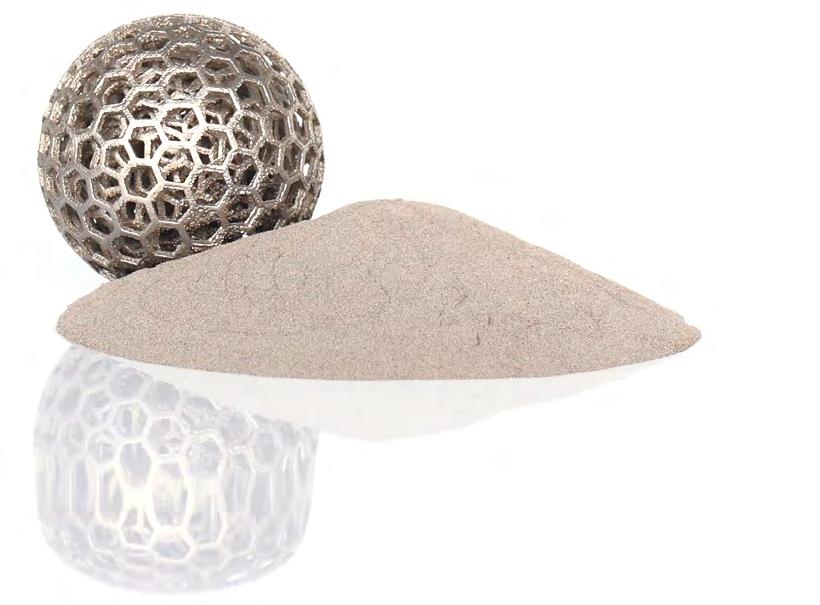
• Identify and analyze methods to measure or characterize polymer feedstocks undergoing reuse cycles in an industrially relevant manner to understand the correlation between metrics and critical to product/material quality factors such as microstructure, geometry and tolerancing, surface fnish, and physical/mechanical properties
• Develop a method to characterize and calibrate an AM process for a single material along with the associated data retention protocols which will signifcantly beneft those in the AM modeling and monitoring community
• Execute a survey of high potential in-situ process monitoring sensors, methods, and tools for two to three AM processes or material types (metal, polymer, composite, ceramic) and complete a cost-beneft analysis that considers quality, productivity, operational costs, recurring and non-recurring costs, and quantifes cost benefts or conditions which show viability for AM process monitoring
• Develop and deliver an AM for medical device production quality control training
• Execute a critical review of published AM standards which outlines the content, operational guidance, considerations, and opportunities for strategic research which will foster the identifcation and prioritization of R&D for the purpose of obtaining fundamental data to support the development of AM equipment qualifcation protocols and specifcations
• Execute an effort to demonstrate methods, tools, and practices to produce a sub-QMP (see NASA-STD-6030)
• Address design for part family, part families for processes other than PBF, part families for procurement, and develop case studies
ASTM ICAM 2021
The ASTM ICAM brought together the international AM community in fall of 2021 in Anaheim, CA. The event provided a range of AM discussions and focus areas spanning several industry sectors including healthcare, energy, aerospace, defense, and automotive. Common themes and opportunities for research and development identifed as a result of America Makes participation in the event include the following:
• Equivalency, standard methods to quantify AM process and material critical to quality metrics, diminishing machine-specifc sources of variation
• Powder safety
• Machine-to-machine variation driven by process and feedstock factors
• Standard methods to qualify materials and processes applicable to various AM modalities and material types (metal, ceramic, polymer, composite)
• Driving ability to enable AM in forward deployed operating environments which offer access to energy, data, and engineering support
• Fostering tools, methods, and techniques which allow for an objective assessment of AM design and technology selection in comparison to other manufacturing methods
• Enabling expansive understanding of the utility of AM and diminishing reliance on point design solutions so AM can become a more common design tool
• Qualifcation and validation of AM products
• Standard methods and protocols for qualifcation of materials and processes
• Design tools and methods which incorporate mutimaterial, multi-performance, multi-process objectives
• Integration, validation, and quantifcation of the value proposition of the digital thread for AM
• Education for the design community
• Cybersecurity
• Factors that enable AM to thrive as a data for purchase (data as a service) distributed manufacturing technology
• Leveraging multiple AM modalities to enable step change in product design (embedded sensors)
• Qualifcation of AM products for NACE qualifed applications
• Coating and surface engineering for AM products
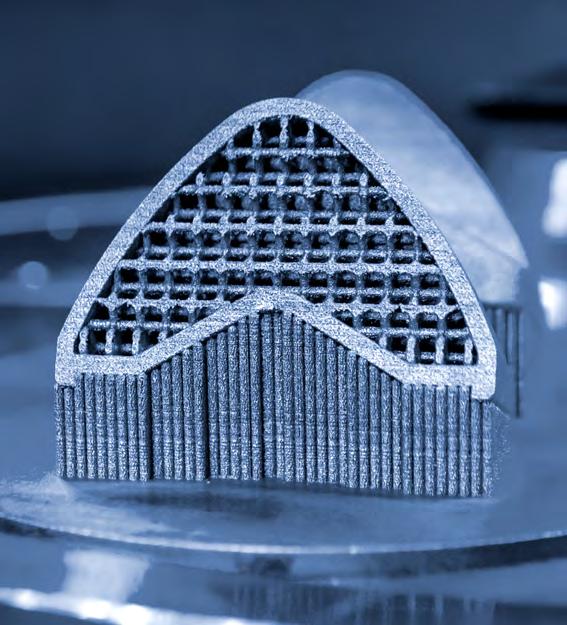
• Predictability of AM materials and products for wear and corrosion
• Post-processing including HIP and heat treatment
• NDE data integration with design data
• Effects of defects analysis
• Calibration and maintenance of AM equipment
• Qualifcation and certifcation for AM repairs
• Sustainability and life cycle assessments for AM products
• Alloy development
• Powder reuse, characterization, control, and operational management
• Addressing subsequent instances of establishing qualifed material processes at a lower cost, with less time and testing – the process can require 30 to 120+ days to execute depending upon complexity
• Part family approaches to AM qualifcation
• Limiting reliance on NDE using in-situ process monitoring
RAPID+TCT 2021 and 2022
RAPID+TCT was held in Chicago in 2021 and in Detroit in 2022. Conversations from the event outlined the latest advancements in AM technologies. Perspectives of the AM community were shared through presentations and panel discussions summarizing the industrialization of AM technologies. Some of the themes and opportunities for R&D identifed as a result of America Makes participation in the event included:
• AM equipment considerations such as calibration
• Material considerations such as AM material fracture mechanics; AM of refractory alloys; process and material modeling; feedstock production — capability, capacity, costs; material development — the compatibility of feedstock materials with AM processes; predictability of AM material quality and performance

• Application considerations such as large-scale AM; AM for repair applications; AM for wax printing and casting applications; AM for point-of-care and forward-operating locations; AM for the production of patient-specifc care; AM for the production of tooling and spares applications, along with manufacturing aids and product testing jigs/ fxtures; AM for gap-bridging manufacturing
• Sustainability and the reuse and recycling of AM feedstocks
• Design considerations such as generative design for AM components; design for inspectability
• Business considerations such as tools and methods for objective analysis of AM business cases; cybersecurity; workforce training
• Policy and standards considerations such as policies and acquisition models for AM data as a service; addressing the lack of heritage data (in comparison to other manufacturing methods) for AM materials and processes; AM standards; qualifcation and certifcation; reducing challenges with DfAM and promoting familiarity with DfAM within design and manufacturing communities
• Scalability of AM — product size, production rates, quality controls, cost, economic viability; demonstration, validation, and analysis of utility for AM digital thread
• In-situ process monitoring
• Post-processing
Overarching Consensus
There is a clear desire within the AM community to evaluate the conditional utility of AM technologies. Utility is known to be infuenced by the intended application, AM manufacturing capability limits, material performance, manufacturing workfow productivity, and cost. The observations presented indicate persistent demand for quantitative evidence to objectively explore the performance and cost of AM. These efforts will require rigor to enable AM product entry to service (qualifcation
and certifcation) through examining materials, processes, and manufacturing operations practices. The strategic objectives of the Institute (see page 18) are in line with the AM industry, and there appears to be overarching consensus in the essential components needed to enable AM adoption across variousindustries including aerospace, medical, energy, automotive, and defense.
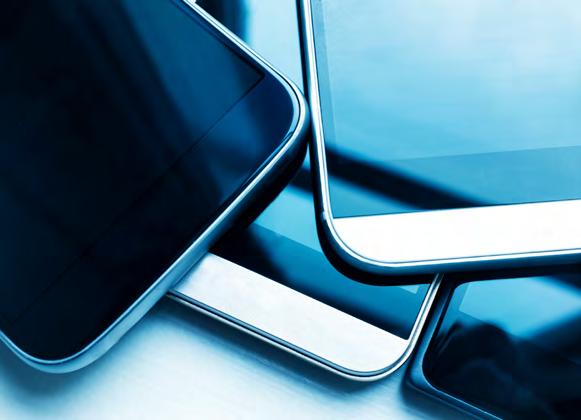

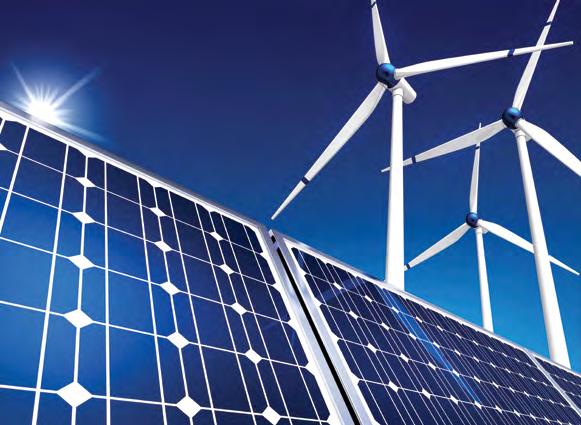
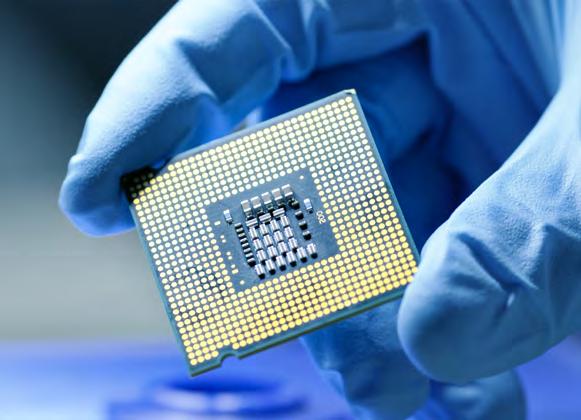
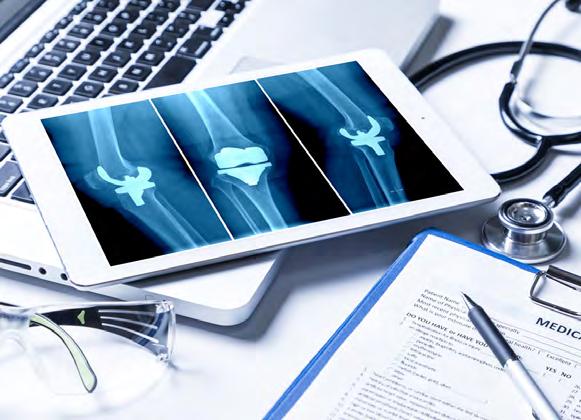

Modi cation of legacy alloys or development of entirely new alloys for additive manufacturing (AM) o ers a range of potential bene ts including improved product performance, increased yield and productivity, and reduced post-processing costs. However, development and quali cation through existing trusted approaches is subject to risk — cost
product designs for a range of industries including defense, aerospace, medical, automotive, and others.
“Given the current state of the domestic AM supply chain and the U.S. government’s interest in expansively using AM technologies for various capability needs, identifying investment opportunities that will accelerate AM alloy development and qualification while bolstering domestic manufacturing competitiveness is timely and warranted.”
and time to market can jeopardize adoption within the production bill of materials or fail to meet ROI criteria.
BOLSTERING MANUFACTURING COMPETITIVENESS
There are numerous opportunities for developing and validating new tools, techniques, and methods to accelerate alloy development for AM processes. Enabling more rapid and cost-e ective means to qualify and certify alloys would enhance domestic manufacturing competitiveness as well as foster broader industrialization of AM materials and
Given the current state of the domestic AM supply chain and the U.S. government’s interest in expansively using AM technologies for various capability needs, identifying investment opportunities that will accelerate AM alloy development and quali cation while bolstering domestic manufacturing competitiveness is timely and warranted. To ensure development e orts of the domestic supply chain are aligned to the needs of government, America Makes conducted an AM Alloy Development Workshop to address techno-economic risks and challenges through collaborative research and development identi ed by the U.S. AM supply chain.
IDENTIFY, STRATEGIZE, PRIORITIZE
The workshop explored factors in uencing AM materials quali cation, certi cation, and commercialization. This included application-speci c bene ts, value chain cost drivers, and technology gaps that complicate the development and commercialization of entirely new or modi ed legacy metal alloys. America Makes gathered a cross-section of the
domestic AM supply chain and scienti c community from industry, academia, government, and national labs to identify and prioritize strategic opportunities for investment that will advance the nation’s ability to e ectively develop AM metal alloys and strengthen U.S. AM competitiveness.
What follows is a summary of industry-speci c opportunities and associated bene ts for AM alloy development for aerospace, energy (including nuclear), electronics, medical, and automotive industries gathered from the 2021 America Makes AM Alloy Development Workshop.
ENERGY (INCLUDING NUCLEAR)
TABLE 2 is a summary of energy applications identifed and the associated benefts, challenges, and alloy development opportunities.
APPLICATIONS BENEFITS CHALLENGES
Gearing
• Applicable to multiple industries
• Performance & durability
• Topological design
Heat exchangers
• Density
• Geometry & tolerancing
• Corrosion resistance
• As-built surface roughness
• Scalability • Material & AM process compatibility
• Post-processing
• Availability of feedstock
• Commercially available AM equipment
• Inspection
• Post-processing
• Productivity (build rate)
Turbine blades; Combustors; Vanes; Mixers and nozzles
Reactors
ASSOCIATED ALLOY DEV. OPPORTUNITIES
• High hardenability steels
• Gradient materials
• Aluminum alloys
• Copper alloys
• Maraging steels
Pressure Manifolds
Hydrogen engines/power systems
ELECTRONICS
• Efciency
• Monolithic structure & lower cost
• Use temperature
• Geometry & tolerancing
• Durability & performance
• Feedstock costs & reuse
• Qualifcation
• Powder production (capability & capacity)
• Powder reuse, recycling, & material form factors
• Material & AM process compatibility • Inspection
• High entropy alloys
• Refractory alloys
• Nickel alloys
New Alloy Modifed Alloy
• Titanium aluminides
• Ease of integration & repair
• Wear resistance
• System efciency
• As-built surface roughness
• Thermal fatigue resistance
• Criticality
• Oxidation & corrosion resistance
• Use temperature
• Oxidation resistance
• Durability & performance
• Manufacturability & repeatability
• Product criticality
• Efcient test techniques & methods
• Post-processing • Long heat treatment times • Alloy addition/modifcation costs
• Hf additions present risks
• Material costs require low volume material test capability
• Print process optimization costly & time-consuming
• Material & AM process compatibility
• Manufacturability & repeatability
• Feedstock production capability & capacity & form
• Post-processing
• Durability & performance
• Specifc strength • Density
• Component weight
• Efciency • Criticality
• Durability & performance
• Geometry & tolerancing
• Product criticality • Powder reuse, recycling, & material form factors • Feedstock production capability & capacity & form
• Post-processing
• Product criticality
• Efcient test techniques & methods
• Liquid oxygen compatible, high strength alloys
• Nickel alloys
• Zirconium alloys
• Refractory alloys
• High entropy alloys
• Titanium aluminides
• Aluminum alloys
• Stainless steels • Steel alloys
TABLE 3 is a summary of electronic applications identifed and the associated benefts, challenges, and alloy development opportunities.
APPLICATIONS BENEFITS
• Motors/rotor bars/ stators
• Leads & lead frames
• Electrically conductive structure/ conformal electronics
• Terminals & traces
• Integrated sensors Batteries
CHALLENGES
ASSOCIATED ALLOY DEV. OPPORTUNITIES
• Efciency
• Sustainability & environmental benefts
• Reduce fossil fuel consumption
• Performance & durability
• Noise reduction & low observable feature benefts
• Use temperature
• Thermo-physical properties (conductivity)
• Geometry & tolerancing
• Manufacturability & repeatability
• Material & AM process compatibility
• Powder reuse, recycling, & material form factors
• Feedstock production capability & capacity & form
• Aluminum alloys
• Copper alloys
• Covetic alloys
• Steel alloys
• High entropy alloys
• Productivity (high volume production)
• Product criticality
• Feedstock & precursor materials availability
• Postprocessing
• Surface roughness sensitivity
MEDICAL
TABLE 4 is a summary of medical applications identifed and the associated benefts, challenges, and alloy development opportunities.
APPLICATIONS BENEFITS
Bioresorbable implants
Robotic surgical devices
Antimicrobial instruments
Arthroplasty replacement
Orthopedic omplants
• Density
• Durability & performance
• Geometry & tolerancing
• Biocompatibility
• Corrosion resistance
• As-built surface roughness
• Geometry & tolerancing
• Durability & performance
• Repairability
CHALLENGES
• Manufacturability & repeatability
• Material & AM process compatibility
• Scaling from coupons to parts
• FDA approval cost & time
• Post-processing
• Mechanical & physical property optimization for function & biocompatibility
ASSOCIATED
ALLOY
DEV. OPPORTUNITIES
• Magnesium alloys
• Bulk metallic glasses
• High entropy alloys
• Coated titanium alloys
• Density
• Scaling from coupons to parts
• Inspection
• Material & AM process compatibility
• Efcient test techniques & methods
• Manufacturability & repeatability
AUTOMOTIVE
APPLICATIONS BENEFITS CHALLENGES
Brake rotors
Steering knuckles
Piston heads and cylinders
Heat exchangers
• Durability and performance
• Oxidation and wear resistance
• Use temperature
• Geometry and tolerancing
• Productivity • Manufacturability and repeatability
• Titanium alloys
• Titanium metal matrix composites
• Titanium alloys
• Titanium alloys
• Coated titanium alloys
TABLE 5 is a summary of automotive applications identifed and the associated benefts, challenges, and alloy development opportunities.
ASSOCIATED ALLOY DEV. OPPORTUNITIES
• Cast iron alloys
• Material and AM process compatibility • Powder reuse, recycling, and material form factors • Feedstock production capability and capacity and form
• Ductile iron
• Aluminum alloys
Bearings
Electric motors
• As-built surface roughness
• Geometry and tolerancing • Corrosion resistance
• Inspection • Post-processing • Productivity (build rate)
• Feedstock costs and reuse
• Aluminum alloys
• Copper alloys
• Efciency
• Monolithic structure and lower cost
• Durability and performance
• Oxidation and wear resistance
• Use temperature
• Geometry and tolerancing
• Qualifcation
• Productivity • Manufacturability and repeatability
• Material and AM process compatibility
• Powder reuse, recycling, and material form factors • Feedstock production capability and capacity and form
• Criticality
• Manufacturability and repeatability
• Maraging steels
• High entropy alloys
• Steel alloys
• Efciency
• Sustainability and environmental benefts
• Reduce fossil fuel consumption
• Performance and durability
• Noise reduction and low observable feature benefts
• Material and AM process compatibility
• Powder reuse, recycling, and material form factors
• Aluminum alloys
• Copper alloys
• Thermo-physical properties (conductivity)
• Use temperature
• Geometry and tolerancing
• Feedstock production capability and capacity and form
• Product criticality
• Productivity (high volume production)
• Feedstock and precursor materials availability
• Post-processing
• Surface roughness sensitivity
• Steel alloys
• Covetic alloys
• High entropy alloys
OBSTACLES AHEAD
While not extensively explored during the workshop, it is acknowledged that the adoption of novel alloys will eventually encounter various political, economic, and social challenges. Examples may include:
• Demand estimation (forecasting), variability, and associated or dedicated manufacturing capacity
• Maintenance and prevalence of manufacturing capability
• Workforce dynamics and providence of subject matter expertise
• Economic, trade, and supply chain dynamics that affect the availability and cost of precursor materials
• Supplier/customer relationships
• Cultural perceptions for collaborative alloy development
• Risk or emergence of competing alternative material solutions (performance and cost)
• Design and regulatory authority acceptance of risks with novel materials adoption, qualifcation, and certifcation
• Design authority aversions to initiating alloy development
• Rate of TRL/MRL progression to meet insertion opportunity timelines, requirements, and associated costs
• Factors infuencing alloy production yield, repeatability, and associated cost dynamics throughout the development cycle
With the acceleration of AM alloy development, qualifcation, and certifcation, some of the economic and social challenges may begin to be addressed.
MARKET DEMAND, CHALLENGES, AND FUTURE OUTLOOK
The workshop outlined various application-speci c bene ts and alloy development, quali cation, and certi cation challenges. Clear demand exists for the development of refractory, nickel, aluminum, titanium, covetic, and hydrogen-resistant alloys. Common bene ts include improvements in product durability, performance, reliability, temperature capability, energy e ciency, patient standard of care, and system cost. Common challenges included manufacturability, repeatability, AM process compatibility, feedstock reuse and recycling, material form factors, feedstock production capacity and capability, post-processing, and quali cation costs and methods. The impact of the identi ed alloy development opportunities o ers improvement in domestic manufacturing capacity and capability, product performance, domestic manufacturing
competitiveness, expanded application capability, and application e ciency improvements.
Additive manufacturing o ers the opportunity for rapid exploration of process and material microstructure relationships which are key to the e cient scaling of novel materials. Understanding of post-processing e ects is needed. Furthermore, validation of e cient test methods for quantifying material and product performance is also important to AM alloy development. Material and process model development and validation should accompany these e orts. It can be anticipated that these e orts will lead to improvements and expanded utility for di erent modeling tools and analytical approaches for material development, quali cation, and certi cation. A broad spectrum of organizations, expertise, and skills will be necessary to successfully deliver solutions for these alloy development needs.

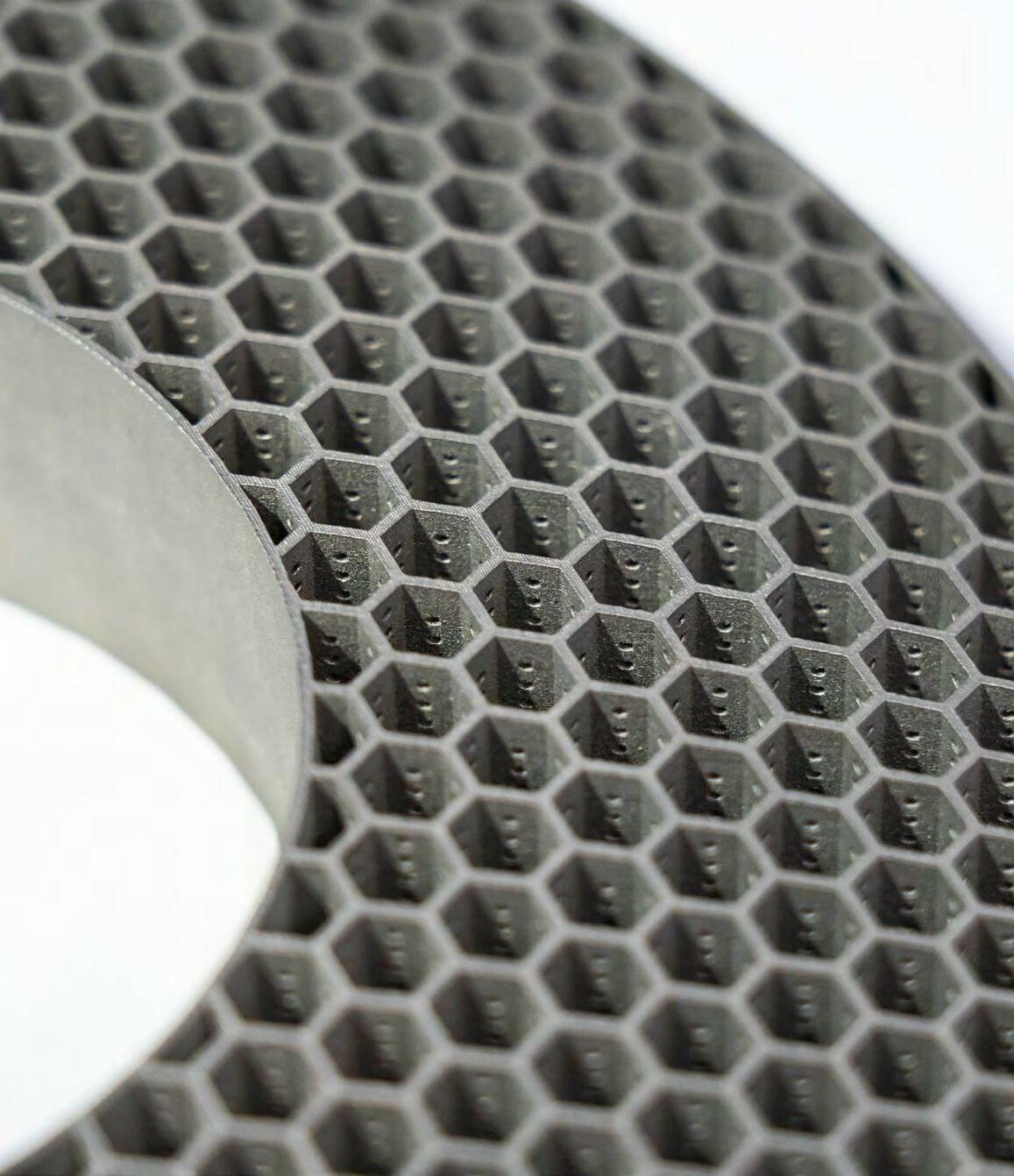
Increasing Sustainability Through AM Production
While politics and the public push manufacturers to make products more sustainably, additive manufacturing is making sustainable business practices more proftable.
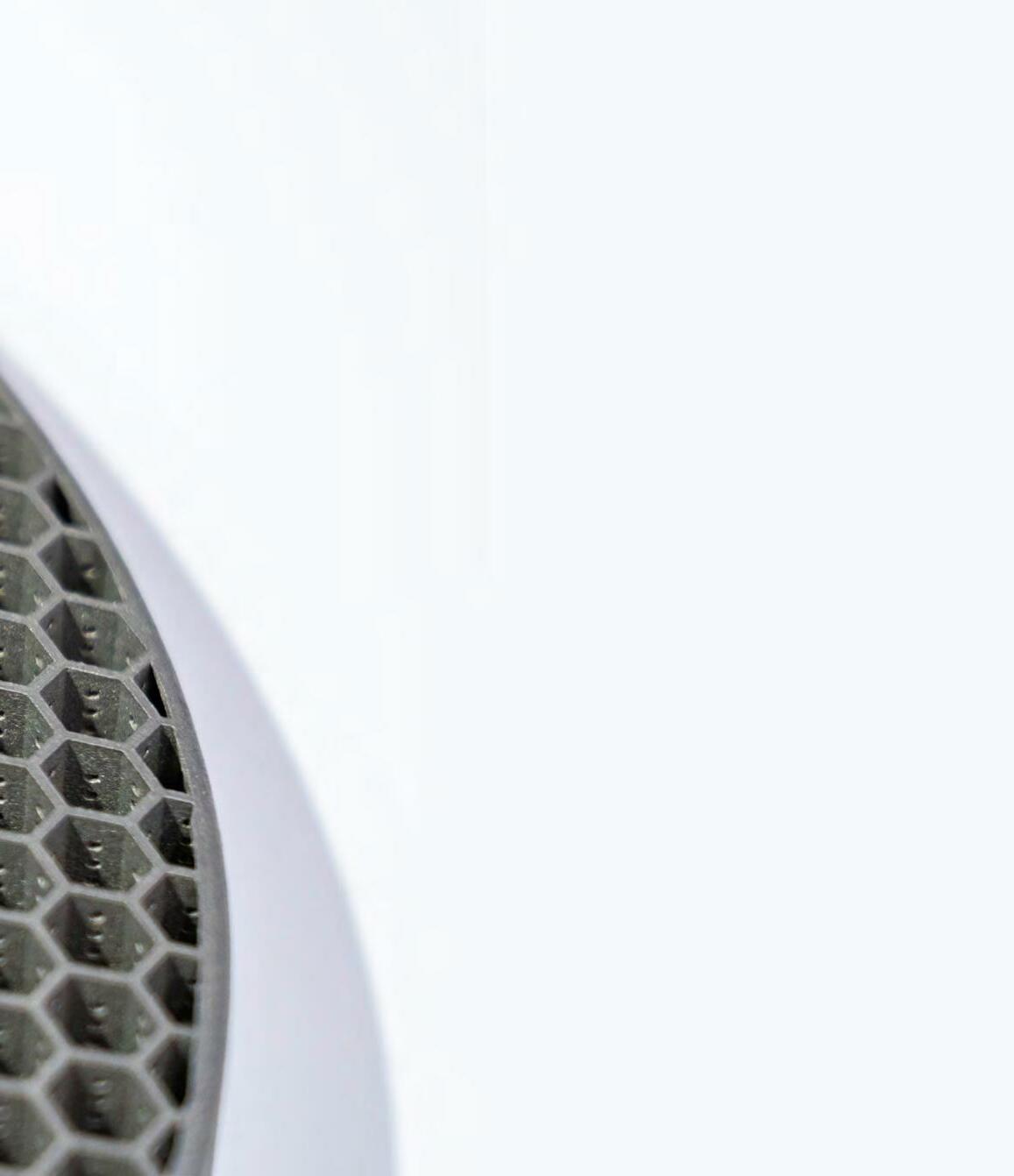
Additive manufacturing (AM) is a major force in remaking fractured supply chains to ensure greater e ciency and resilience with respect to energy, waste streams and transportation. The technology promises new methods of distributed manufacturing at the point of need, reclaiming and reusing feedstocks including metals, polymers, resins and old additive parts, as well as lightweighting through advanced e cient designs.
The time is now for a dedicated e ort to establish a baseline for scientically measuring AM processes and the ability of AM to sustainably support reshoring and the economic security of U.S. supply chains. This could be accomplished by examining AM material recovery paradigms for critical feedstocks and exploring traceability regimes for secure part production as well as speci c life cycle analysis approaches.
The potential result? AM sustainment and resilience metrics, design guides for material recovery and new research on reuse and reclamation of feedstocks.
CASE STUDY: AM as a Sustainability Driver
MELISSA ORME, PH.D. | VICE PRESIDENT, BOEING ADDITIVE MANUFACTURINGAdditive manufacturing (AM), when examined across the end-to-end value stream, is a positive sustainability driver. The Boeing Co. is committed to reducing the ve impact categories of total energy consumption, global emissions, solid waste to land ll, total hazardous material use, and water consumption. We have recently demonstrated that AM aligns to these goals.
We can separate AM sustainability opportunities in two components: 1) in the end to end fabrication process; and 2) in the fabricated part performance. In the rst category, AM provides opportunities to drive positive sustainability trades through: reduced material usage, material recycling, printing at point of use, elimination of parts (and the associated processes and transportation), and simulation guided
Figure 1: Life Cycle Assessment Results
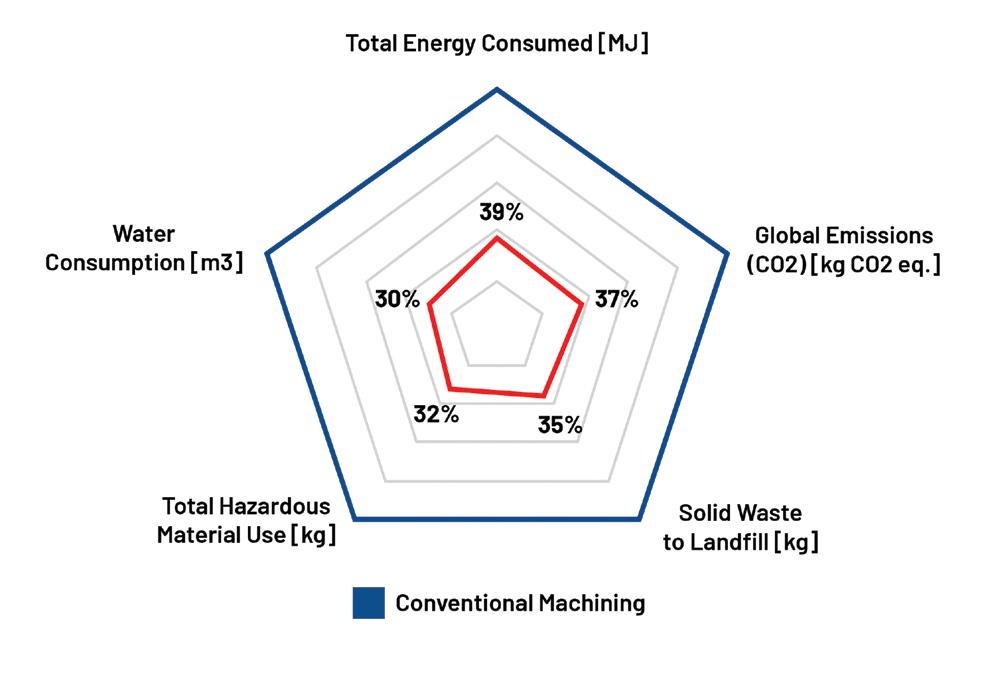
builds to eliminate energy wasting physical iterations. In the second category, and speci cally in Aerospace and Defense, AM has the ability to optimize and lightweight the part, and more importantly to reduce the volumetric footprint of strategic components so that the vehicle in which it is incorporated can become lighter and more streamlined, resulting in less drag, ultimately consuming less energy in operation.
Boeing Additive Manufacturing has recently completed a Life Cycle Assessment (LCA) of a part that was converted from traditional manufacturing process to an Additive process. Having manufacturing data from each process helped provide an understanding of sustainability opportunities. The part considered is
the Ti-wire aft galley tting that has been in production since 2017 and pictured below in Figure 2
The results of the LCA are shown in Figure 1, where the blue line indicates the values for the traditional fabrication process and the orange line is the result of the AM fabrication process. Hence, it can be seen that there are signi cant reductions in the ve impact categories of total energy consumption, global emissions, solid waste to land ll, hazardous material use and water consumption.
It should be noted that the sustainability gains for the AM component were largely driven by the reduced material extraction and conversion and machining operations. These gains outweighed the added need for stress relief, increased energy
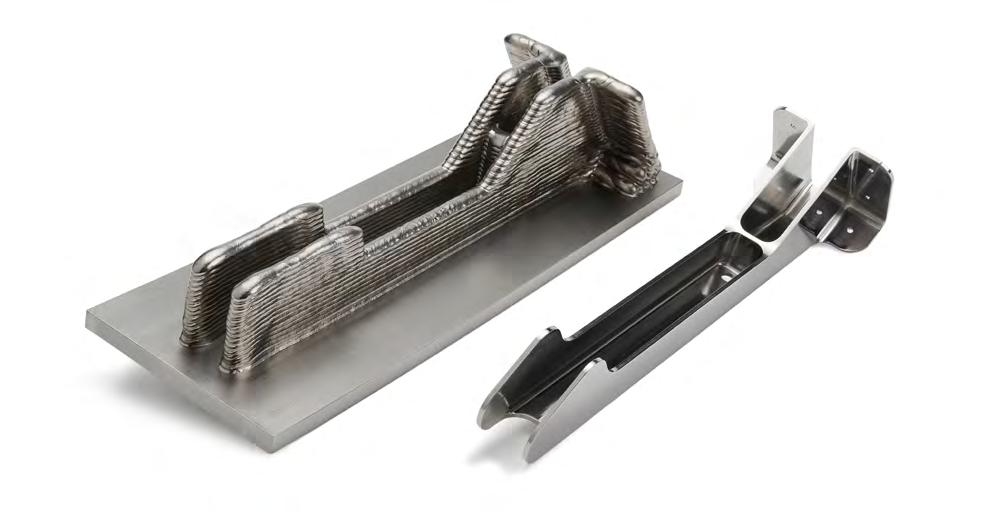
consumption during the AM manufacturing process, and argon shielding gas.
Boeing is currently working to examine more LCA cases, including the powder bed AM process and both metal and polymer material systems. It should be noted, that not all LCA studies are expected to have the positive outcome as indicated in this example. For example conventional sheet-metal parts converted to AM will likely consume more energy and will not exhibit positive sustainability trades. Coincidentally, parts that do not exhibit positive sustainability trades are often the same parts that do not possess positive business cases for AM. Hence, AM is not the answer to every part but when selected strategically will have a positive business case as well as a positive sustainability trade.
Figure 2: Ti-wire aft galley ftting
SUSTAINABILITY
In our conversations on sustainability the topics have centered on three core fronts — lifecycle assessment, reduction of waste in manufacturing, and recycling of feedstocks. Key needs include:
• RECLAMATION and REUSE of AM materials, including metals and polymers, powders and resins
• RESEARCH to understand performance post recycling
• METRICS to track throughout supply chain
• LEADERSHIP from industry and government
• LOGISTICS beneft of fexible feedstock logistics tradeoffs
SUSTAINMENT
Much of America’s domestic manufacturing prowess aligns to high end, mixed volume production. Manufacturing at the pace of need is sought after across industry. America Makes members are exploring designing and qualifying an AM part for conventionally outsourced components so they can more easily deal with the early life ramp up, manage future supply chain risks, and deal with later life sustainment for their products. AM offers a solution to the expense and waster of warehousing entire catalogues of parts.
RESHORING
Capabilities tested and proven out through the AMNOW program (see page 46) have been important in strengthening the ability of the domestic supply chain to deal with intermittent demand signals and address those unexpected manufacturing needs. Covid and the logistical hurdles that followed, caused many industries to reassess exporting manufacturing work to China, citing reliability as well as intellectual property concerns. Many found that the simplifed supply chain provided by reshoring through leveraging AM as bridge manufacturing, revealed a path forward to the modern "microfactory," - a domestic distributed collection of small businesses that could support larger industries.
A conversation with America Makes Additive Manufacturing Project Engineer Todd Spurgeon
What is AM’s role in creating a sustainable manufacturing environment?
Additive interacts with sustainability in a lot of di erent ways. On the one hand, there’s the more e cient use of material. For example, when you are cutting a part out of a blank, you can only cut it into only so many parts using subtractive methods and depending on the part, you could have as much as 60% or 70% wasted material, whereas with AM whatever doesn’t get sintered into the part gets reused.
You also have to consider the increased exibility you have with raw stock. If you have a bit of bar stock or some metal blanks, you can only cut those pieces into so many di erent parts. The geometry of the raw material simply limits your capabilities. With powder, wire, or other forms of additive stock, you don’t have to nd the right shape or size of raw material. You just load in the powder and make the part.
A lot of people, when they think of sustainability, just think of the immediate e ects. But if you have to rush order a certain size of bar stock, that’s increasing the amount of time it takes to produce the part, increasing emissions from the truck that has to deliver it, and putting additional strain on a supply chain that has been shaky.
Sustainability is not just about waste, but rather how reliable a process is over the long term, and the exibility that AM a ords manufacturers is going to greatly improve long-term reliability.
How recyclable is the powder after completing an AM build? And what about non-powder materials like flament or wire?
AM material is very recyclable, especially compared to machined material. In fact, you often can just lter the leftover powder to remove sintered pieces, remove
contaminants and then reuse it. With subtractive manufacturing, even under the best circumstances you must separate the material, clean it, remove contaminants, and then process it in essentially the same way it was initially forged. Every one of those recycling steps is energy intensive, and you still may not recover all the material.
With regards to lament, there have been a lot of advances recently. There are processes for melting used lament and combining it with virgin material to make usable lament. It can actually be done quite easily. And the capture e ciency of metal wire feed is actually very high. If the process is well-designed, you can have as much as 99% e ciency. Now, you may have to overbuild and then machine down, but the e ciency of that compared to a billet is still far and away better, as are the lead times.
In fact, quick-turning forgings using a wire feedstock to get the needed shape, then use a forging die to attain the necessary forged properties is starting to become more popular.
Are there any other ways AM is improving sustainability?
One of the big ways is reshoring. Some companies that have been producing overseas have run into these enormous supply chain issues over the past two years and are looking at how to bring production closer to home, and AM is one of the keys.
The U.S. is an early adopter of AM production, and with that comes a massive knowledge base of manufacturers who are experienced with AM. These people can take advantage of the exibility of AM to quickly take on new jobs. You can implement a production line with nothing but your printers and the CAD le, so turnaround can be extremely fast compared to subtractive processes.

This means that jobs that were being ful lled overseas are now being done here, which cuts out shipping through foreign countries, export duties, the cost of shipping over water, and transportation costs within the U.S. At every step, this reduces carbon emissions and costs for the part buyer.
THE AM ECOSYSTEM NEEDS YOUR INPUT
Over the past year, America Makes has seen increasing interest in understanding the quantitative impacts that AM can have on sustainability - from meeting corporate ESG targets to new research on practical use of reclaimed materials. How important is this effort to you?
Get in touch with the America Makes team and share your suggestions: Email Kimberly.Gibson@ncdmm.org or Todd.Spurgeon@ncdmm.org
Data as Fuel
How the AMNOW program is helping companies successfully leverage manufacturing process data for a digitally connected supply chain and forward-looking organizational evolution.
BY ASHLEY TOTIN | SENIOR PROJECT ENGINEER, AMERICA MAKES & JOE VERANESE | VICE PRESIDENT & CHIEF INFORMATION OFFICER, NCDMM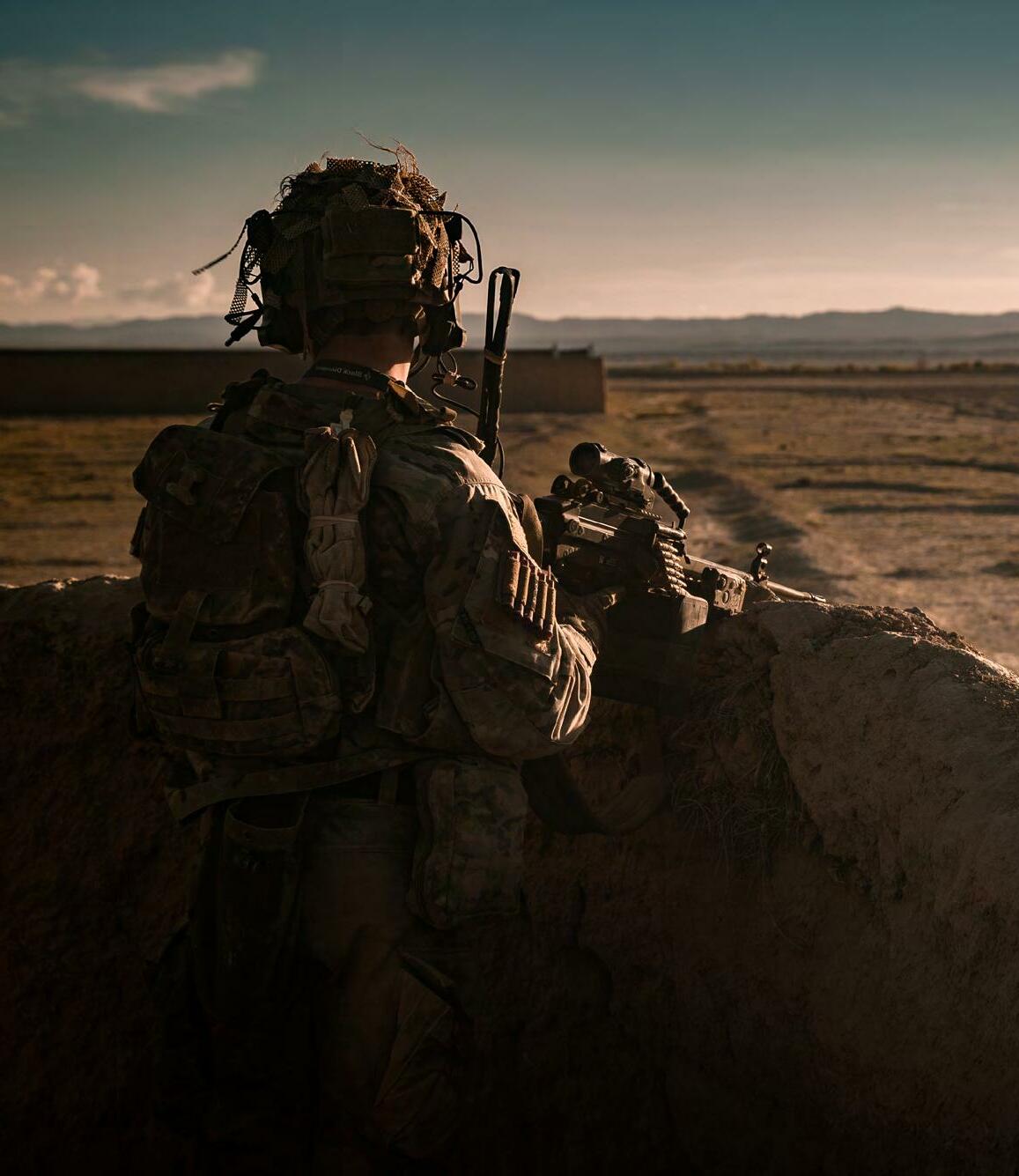
Today’s manufacturing world continues to grow and diversify, and individuals within the industry are working to expand its horizon. Organizations looking to improve productivity, reduce cost, or build a better mouse trap are turning to Smart Manufacturing or Industry 4 0 as a potential way to reach these goals.
What is at the heart of most Smart Manufacturing techniques? Data. In Smart Manufacturing, data is the power and the fuel that allows an organization to reach its goal. The AMNOW program was designed to demonstrate the value of a digitally connected supply chain and the ability to mine data from the manufacturing process.
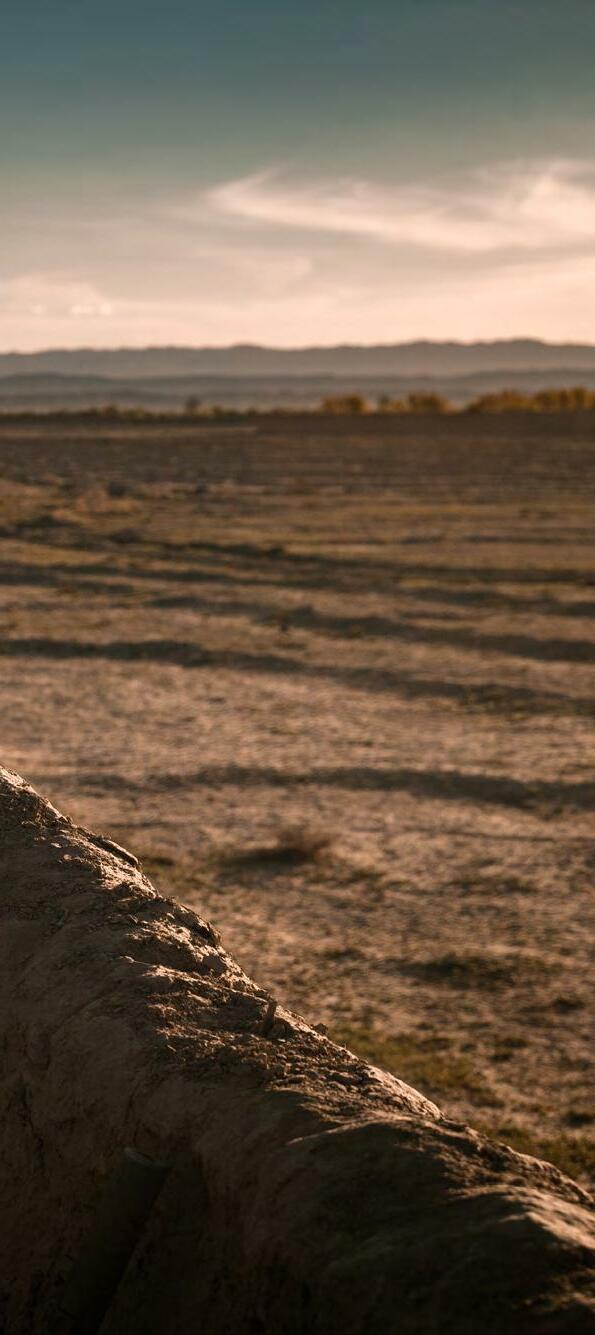
This e ort provides value to both the manufacturer and the customer. For the manufacturer, the availability of process information in real time opens the door for all the goodness expected from Smart Manufacturing. For the customer, having access to the manufacturing process data allows for greater con dence that the part being manufactured will perform as expected.
It is anticipated that an organization that can collect and provide manufacturing process data as a deliverable, along with hardware, will have a signicant market advantage over its competitors. The AMNOW program strove to interact directly with the supply chain, helping each organization understand the power of data and what data was already within their reach. The next step was to walk with them into
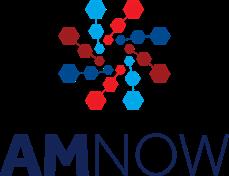
the realm of Smart Manufacturing. The team accomplished this by providing each supplier access to an IIoT device designed to gather manufacturing process data from across their production environment. Simple speeds and feeds we regathered but also so much more. Power usage, environment, vibration, chatter, moisture, process temperature, and anything else that had the potential to a ect outcomes could be monitored in real time. Once the data was gathered, the supplier could store the data for interrogation later or deliver that same data as part of the deliverable package to the customer.
The observation prior to AMNOW was that most suppliers thought they were gathering information on their processes, but that activity was sporadically maintained at best, if at all. Their information was either incomplete or was kept by a single team member who then became a single point of failure. There was minimal ability to store and analyze the data to use that knowledge to drive e ciencies within the systems. Data must be gathered, but additionally must be made reusable to provide any real value.
The collection of data has one more important bene t to an organization that was demonstrated within the AMNOW program. Data is a catalyst that can be used to justify change and challenge the notion that “This is the way we have always done it.” This challenge can be di cult to overcome especially when young
engineers/operators are brought into a manufacturing environment. New ideas and a fresh perspective can be supported with hard data to drive transformation even within the most steadfast processes.
After the program had demonstrated the ability to gather data on processes, the next step was to validate how that data could be used to drive better operational e ciencies. Several suppliers that participated within the AMNOW program were quickly able to leverage the information collected to make simple changes that immediately paid dividends. One supplier discovered that the simple act of staggering the retooling to two production lines provided an immediate 15% cost savings. Another organization realized the value of remotely monitoring small liquid bath temperatures in lieu of positioning an operator within the room during the process. Still another organization found value in monitoring the weight of a tube lling station remotely and providing that information to the operator. This allowed the operator to adjust the line as needed to ensure accurate and consistent lling of product thus reducing waste and downtime.
Monitoring machines externally is only one way the AMNOW program gathered data. Additive and
SUPPORTING ARMY READINESS
Advanced Manufacturing machines produce and collect a mountain of process data automatically. The AMNOW program sought to tap into that data store onboard the machines and deliver it to the operator in real time. This required building interfaces between the IIoT edge device and the machine controller. For some machines, the process was as simple as enabling a protocol. Others required the installation of an interface by the OEM. As with all systems, some were more mature than others.
Part of the AMNOW program mission was to drive this need back toward the OEM community and push for advancements in the interfaces. Success is measured in results. For the AMNOW program, it was important that success experiences were gathered to demonstrate the value of the approach. This story of the value of data within the manufacturing process is one best told by those who lived it. Told by those who had their beliefs in their internal process challenged. And once challenged, their organization exercised in a way that allowed them to realize the operational e ciencies that may have been alluding them. Manufacturing process data must be gathered but equally important is that data must be transformed into operational knowledge and made reusable.
Through a robust digital additive manufacturing supply chain
The AMNOW program was launched in 2019 with a mission to establish and demonstrate a robust capable digital manufacturing supply chain to support Army readiness. Executing that mission required elevating the capabilities of the supply chain; elevating additive manufacturing (AM) processes as a reliable technology; visualizing the supply chain back to the Army; and capturing production data as a contract deliverable.
As the program progressed, many suppliers have been engaged to make that mission a success.
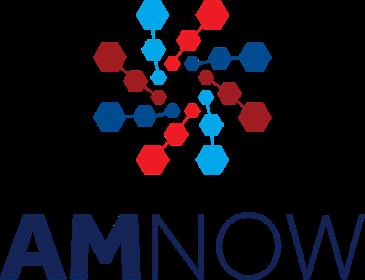
ATI, a $4.1 billion global specialty materials company, has a strong vertically integrated supply chain that can produce alloys, shapes, fnished components that withstand the ultimate extremes in temperature, corrosion, and stress. This unique capability is the result of a corporate history that dates back beyond the dawn of the space age, the jet age, or the industrial age — all the way back, in fact, to the American Revolution.
Combining ATI’s AM technology offering with precision traditional manufacturing and machining made them well suited as an early supplier partner for AMNOW.
ATI has been part of the AMNOW program since September 2020. During that time, they have engaged in 10 projects and delivered more than 220 parts.
Because of their participation, ATI has realized several key benefts.
1. Expanding Connections
AMNOW provided ATI with the opportunity to engage with new post-processors and other supply chain members. This expanded supplier network provides ATI increased fexibility to meet customer needs going forward.
2. Elevating Marketing
ATI has been able to use their participation in AMNOW to promote their capabilities to support DoD needs.
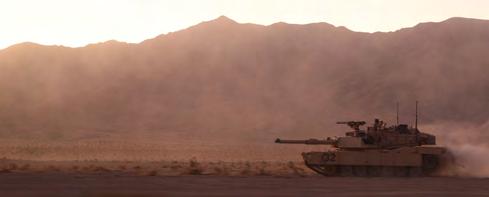
3. Enhanced Data Collection
The AMNOW program provided an IoT device to enable automated collection of required process data. ATI’s experience using the device has promoted interest in how this data can be leveraged internally for better process control and performance. The result of this is an expected increase in efciency and a decrease in overall production costs.
PENN UNITED TECHNOLOGIES, INC.
An employee-owned company, Penn United Technologies, Inc. was founded in 1971 as a small tool-and-die shop near Saxonburg, PA. They have grown from a one-service shop into a high-tech manufacturing operation with more than 700 employee owners offering a wide variety of manufacturing solutions.
Combining Penn United’s AM technology offering with precision traditional manufacturing and machining made them well suited as an early supplier partner for AMNOW.
Penn United has been part of the AMNOW program since February 2020. During that time, they have engaged in nine projects and delivered more than 320 parts.
Because of their involvement, Penn United has obtained several key benefts.
1. Expanding Material Capabilities
Penn United has expanded its material capabilities with two additional aluminum and Inconel alloys, materials they had not used prior to involvement in AMNOW. The experience has also paved the way for expanding into titanium.
2. Elevating the AM Process
Penn United had a robust internal additive parameter development process in place before they were involved in AMNOW. Through AMNOW project execution, they were able to demonstrate and further validate that process.
3. Enhanced Data Collection
The AMNOW program requires process data to be collected as part of a digital deliverable and the program provided an IoT device that enabled automated data collection. Using this device to efciently capture data has helped Penn United better understand their AM process, and support improvements in their ability to prevent or correct process issues.
ATI atimaterials.com pennunited.comPRODUCT EVALUATION SYSTEMS, INC.
Product Evaluation Systems, Inc. (PES) is an independent full-service testing laboratory. Their Latrobe, Pennsylvania, laboratory houses mechanical, chemical, and nondestructive testing facilities, as well as a metallurgical lab and machine shop. With this suite of capabilities, PES is providing its customers with a full-spectrum of testing services and solutions, as well as cost and time-saving advantages.
PES was considered well suited as an early supplier partner for AMNOW because of their technical staff and their more than 40 years of materials testing experience.
PES has been part of the AMNOW program since August 2019, having participated in the pilot supplier assessment process. Since that time, they have completed more than 2,300 coupon tests in support of both the Participant Integration and Demonstration Projects.
pes-testing.com
Because of their participation, PES has realized several key benefts.
1. Expanding Exposure
AMNOW provided PES the opportunity to establish new customer-based relations through a publicized article that showcased their testing services on parts that underwent an exemplary U.S. Army hardware fight test operation.
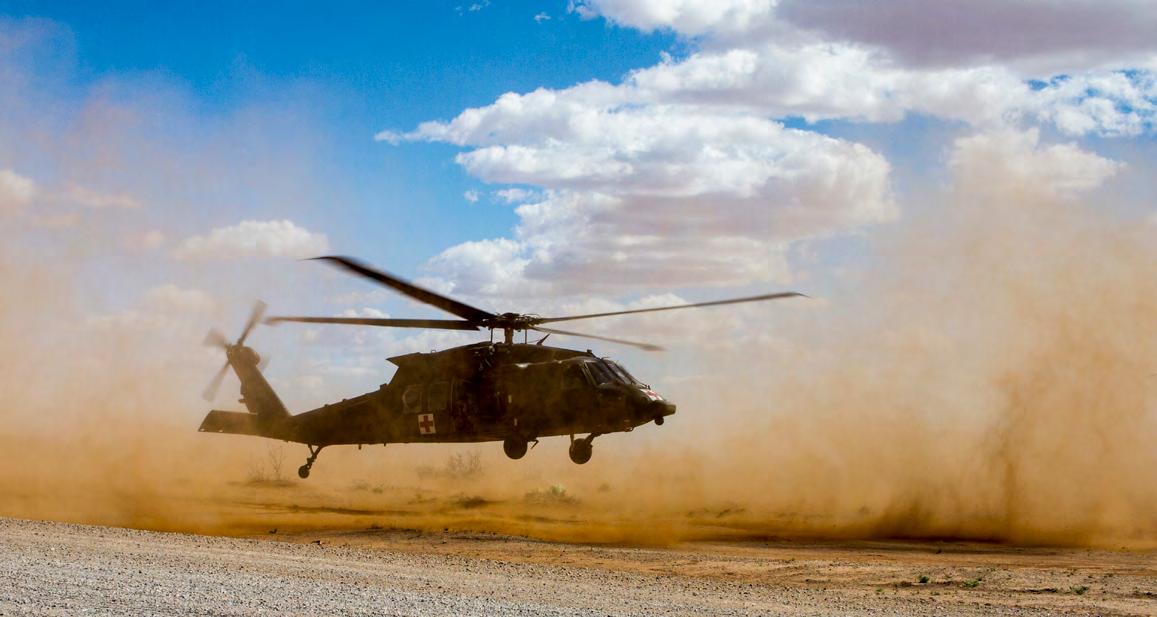
2. Elevating Best Practices
While adhering to program requirements for effective data handling, PES was introduced to more efcient data management processes and methods. They have been incorporating these practices to improve their business offerings.
3. Enhanced Operations
Participation enabled PES to expand from their traditional services by exercising their full suite of capabilities within a single project. This full-scope execution also provided more in-depth exposure of AM part testing to their staff.
VISTA AST
An educational curriculum, equipment, and support service provider, with a team composed of 10 individuals, Vista AST designs and manufactures fused-flament desktop 3D printers and related technologies specifcally for education and workforce development use. They have developed a proprietary software application that creates a virtual collaborative learning environment, allowing remote operation of digitally controlled equipment and real-time technical support.
Combining Vista AST’s AM technology offering with experienced support services made them well suited as an early supplier partner for AMNOW. Additionally, Vista AST’s afliated company, AST2, is a certifed 8a contractor providing services exclusively to the U.S. Government.
Vista AST has been part of the AMNOW program since March 2020. During that time, they have contributed to the frst AMNOW Demonstration Project which fully implemented the digital thread.
Because of their participation, Vista AST has realized several key benefts.
1. Expanding Connections
AMNOW provided Vista AST with the opportunity to establish new relations with a testing and research facility. This expanded supplier network provides Vista AST increased fexibility to meet customer needs going forward.
2.
Elevating Material Capabilities
Vista AST broadened and optimized its material capabilities with an additional polymer that had not previously been used prior to involvement in AMNOW. This also led to increased capability regarding the reporting of raw material specifcations.
3. Accelerated Process Improvements
Participation in the AMNOW program has improved Vista’s print quality processes. This includes elevated understanding of material characteristics with quality control standards for future commercial clients and projects.
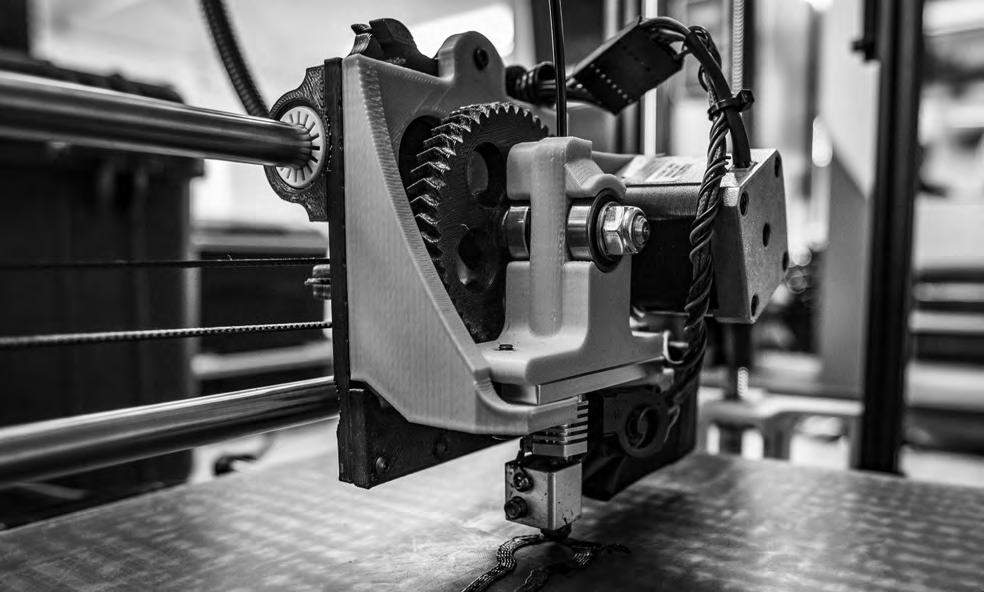
CELEBRATING OUR 2022 AMBASSADORS
Recognizing
As the additive manufacturing industry realized increased momentum this year, America Makes was proud to announce its newest Class of Ambassadors at the 2022 Members Meeting and Exchange (MMX) held August 16 - 18 at the Covelli Centre in Youngstown, OH.
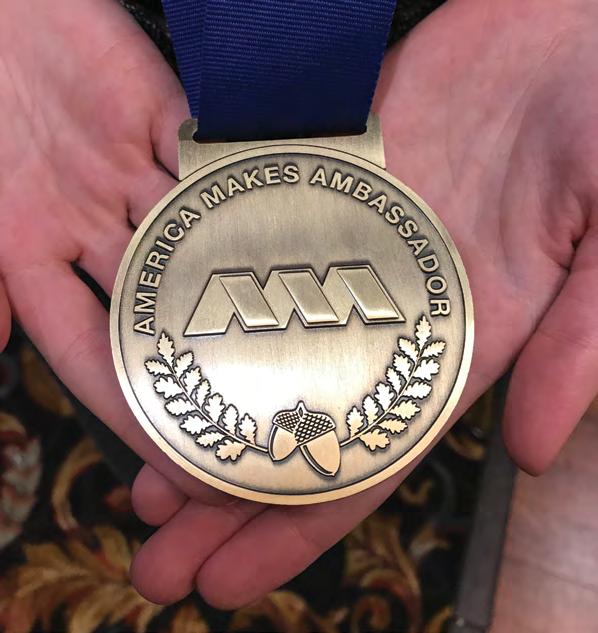
The Ambassador Program, launched in 2017, recognizes individuals who continually demonstrate outstanding dedication to advancing America Makes and its mission.
The 2022 class represents a cross-section of the industry whose work helped further advance additive technology and demonstrated the resilience of the additive manufacturing community. These champions also represent the progress made in additive manufacturing technology, ecosystem and workforce development.
Also during the MMX event, Dennis Butcher, Ph.D., was presented with the 2022 America Makes Distinguished Collaborator Award. Dr. Butcher is the Lead in Additive Manufacturing Composites for Limited Life Aircraft Structures at the Air Force Research Laboratory, Wright-Patterson AFB. Established in 2014, this award recognizes individuals or organizations with an exceptional commitment and dedication to advancing additive manufacturing technology, practices, and innovation in the manufacturing industry. Awardees are honored for cultivating e ective collaborative relationships with academia, government, and industry and contributing to the mission of America Makes.
Thank you, ambassadors, for your contribution and commitment.
THE VALUE OF ENGAGEMENT
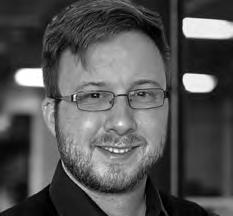
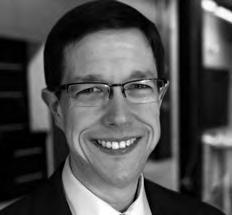
How workshop and working group participation led to funded topics for the 2022 Open Project Call.
One of the rst questions members often ask in their America Makes journey is how to get engaged. As new members begin to learn the range and variety of engagement opportunities, they can nd themselves overwhelmed and frequently ask for assistance to understand what aligns best with their needs and strategic interests. There are occasions when members want to explore how they can share their interests and needs in order to in uence the future direction of the Institute, especially when there seems to be a disconnect or misalignment. The following is a real-world example of how members have shared their passion and in uenced the future strategic interests of the Institute while creating opportunities for funded activity, which matters most to them.
CHARTING THE AM TECHNOLOGY ROADMAP
The 2022 Open Project Call journey started in the Spring of 2021 when America Makes and the Roadmap Advisory Group (RMAG) initiated e orts to coordinate and host a series of workshops determined to update the America Makes AM Technology Roadmap. The preliminary plan was that three roadmap swimlanes would develop and host workshops to gather feedback and input from the membership at the August 2021 Technical Review & Exchange (TRX) at The Ohio State
University. The Design, Material, and AM Genome swimlanes were selected to go rst since those working groups were prepared to leverage workshop participant support. The remaining two roadmap swimlanes were to host workshops in the fall of 2021 at the Members Meeting & Exchange (MMX). Unfortunately, the MMX was forced to pivot to a virtual event format, and fall workshops were delayed until the Spring of 2022 at the TRX hosted at Utah Advanced Materials and Manufacturing Initiative (UAMMI).
TAKING A CRITICAL APPROACH
Before any of the workshops occurred, America Makes members gathered on a bi-weekly basis in their respective working groups to review components of the AM Technology Roadmap. The purpose was to identify areas that may be obsolete, redundant, or would bene t from updating at the upcoming workshop. Everything was deemed within scope for the review including swimlanes, critical technology
BRANDON D. RIBIC, PH.D. Technology Director, America Makeselements (CTE), and requirements. It was important that the Institute ensure that the roadmap is an accurate depiction of the needs of the membership and re ects the current state of AM technologies. The goal of the workshops was to deliver a full update of the AM Technology Roadmap and a time-phased series of strategic objectives for the Institute. The timephased, strategic objectives became a vital component to prioritizing topics in the 2022 Open Project Call.
Each working group brought its own unique perspectives and needs to the workshop. These perspectives were integrated into the approach, outcomes, and discussions which spawned from each workshop. For example, the Design working group desired to have a greater focus on transitioning a pre-competitive baseline knowledge and best practices. Hence, the working group elected to gather feedback on their newly updated charter and CTE.
Recognizing that not every member is available to participate in the working groups, o ering an opportunity for a cross-section of the membership to provide input, feedback, and guidance on the charter (scope and objectives) and CTE of each working group was a critical component. Workshop participants were led through a series of exercises to gather input and needs. Subsequent exercises asked participants to identify a time when they deemed a substantial solution could be delivered to address the identi ed need or topic.
Finally, all participants were asked to vote on which of the topics and needs identi ed were most important to them. The outcomes of the workshop provided a breadth of information for the RMAG to establish a series of time phased, strategic objectives for each swimlane, as well as a wealth of content, which would result in nalization of the updated roadmap.
IDENTIFYING PRIORITIES
By May of 2022, the RMAG was tasked with identifying and prioritizing topics for the 2022 Open Project Call. The workshop data and working group discussions had yielded the necessary information to promptly assess topics and needs which exhibited the appropriate priority and characteristics to produce
substantial progress through a relatively short period of performance e ort. The Design working group attained a consensus amongst its membership that surface nishing for complex structures as a means to increase performance seemed to be a key aspect of several of the inputs obtained from the workshop exercise. The input received during the workshop identi ed the importance of the following:
• Surface nishing for heat exchangers
• Improved fatigue life of generative structures
• Guides for coatings and powder removal in the heat exchanger domain
By early July 2022, all the working groups had provided topics and guidance on technical scope requirements that would best serve the priorities within each of the topics shared. The topics delivered by each working group for the 2022 Open Project Call included:
• DESIGN – Design Best Practices and Surface Finishing in Complex Thermal Management Applications
• MATERIAL – Material E ects on Fatigue Properties
• PROCESS – Rapid Tooling Using a Novel AM Process Chain
• VALUE CHAIN – Demonstration of Combined Methods/ Frameworks of In-Situ Inspection, Ex-Situ Inspection, and Process Monitoring to Ensure Quality of Parts and AM Processes
• AM GENOME – Characterization of Transient Phenomena Impacting In-situ Molten Pool Temperature Measurement for AM of Reactive Metals
At present, working groups continue to meet as they nalize revisions, whch are anticipated to conclude by the close of 2022. But this does not mean the chance to introduce new considerations has expired. These e orts are ongoing processes, so there is time to get involved. We are in the course of planning workshops for 2023 and beyond. As always, if there is something that may be missing from the roadmap, please reach out and let us know. Please visit the Membership Portal to join a working group, connect with working group members, or to get more involved.
OPPORTUNITIES IN CASTING AND FORGING
Identifying opportunities, challenges, and gaps for Additive Manufacturing research and development.
Development of additive manufacturing (AM) technologies for casting and forging applications has been investigated for more than 10 years. AM has demonstrated viability for spares production and supply chain gap bridging manufacturing for casting applications. The e orts of the AM community have led to various point solutions (quali ed AM products for a single part number, often from a single serial number AM machine) for a limited number of applications in production today.
Some of the most noteworthy applications to date have been in the case of defense and sustainment applications. AM components for forging applications are less prevalent or often prohibited due to the criticality of these applications. The need remains for expansive understanding and data to address gaps and challenges that foster AM to complement or augment casting and forging operations, as well as to accelerate certi cation of AM parts for select casting and forging applications. Addressing these gaps and challenges will cultivate exploration of the unique design and material characteristics of AM which can address application geometric, integration, and performance requirements.
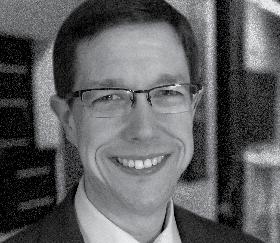
Much like other manufacturing technologies, additive manufacturing o ers conditional utility. Factors that may in uence the utility of AM include:
• Current limits to AM capabilities
• AM process productivity rates
• Application criticality and operating environment
• Demand volumes and timelines
• Costs
These factors demonstrate that successful transition is not dependent upon quality and technological feasibility alone. Cost, productivity, and time-dependent economic viability must also be considered. In addition, it is important to regularly assess the utility of manufacturing technologies, especially in the case of maturing technologies such as additive manufacturing, in order to maintain research and development targets are aligned with appropriate transition opportunities and goals.
In 2016, America Makes initiated a three-phase e ort called Maturation of Advanced Manufacturing for Low-Cost Sustainment (MAMLS). The e ort was quali cation-focused and generated material and product-speci c data including:
• AM process and post-process development
• Material characterization and test data
• Product scale demonstrations and proof testing
• Material and product inspection data
Forging applications were not in the scope of the e ort. In addition, large-scale AM technologies were not extensively explored. The program showed potential for further analysis of AM technologies to augment manufacturing operations and demonstrated utility for AM to produce casting tooling. Opportunities exist for further analysis of AM product certi cation, which was not a primary focus of the program. Motivations and opportunities for strategic AM research and development relevant to casting and forging manufacturing and applications are summarized.
MOTIVATIONS FOR AM FOR CASTING MANUFACTURING AND APPLICATIONS
In the case casting applications, approaches exist to quantitatively verify and validate AM product quality, but there are opportunities for improved e ciency. Requali cation is also a known challenge for AM processes. The long-term success of AM operations and supply chain depends on the ability to readily certify products. R&D to further understand certi cation and airworthiness of AM components for casting applications are necessary.
AM technologies are known to o er bene ts for low-rate, high-mix casting production. A preliminary investigation was executed with the MAMLS program. The design limits and performance of these products manufactured using AM technologies need further evaluation. AM o ers bene ts not only for tooling design but also exhibits opportunities to augment productivity rates in upstream or downstream operations from the casting process. The ability to augment work ows and limit risks of downstream bottlenecks should be explored. To date, the majority of work has focused on aluminum casting applications. There remains a need for demonstration of nickel and titanium alloy castings.
AM FOR FORGING APPLICATIONS
It is known that AM exhibits signi cant bene t if it can be reliably utilized for safety of ight applications. Qualifying AM products for forging applications represents a signi cant challenge due to performance and criticality requirements. Limiting AM product performance debits in comparison to a wrought material can be di cult and cost prohibitive. The need exists for data and understanding to assess how AM technologies scale for forging applications from both a quality and cost perspective. The development of large-scale AM technologies in the last ve years o ers opportunities to explore the limits of these manufacturing capabilities and demonstrate how these technologies may bene t AM for forging applications. The quality, performance, productivity, and costs associated with these materials and processes are not well understood and warrant further investigation.
FUTURE RESEARCH OPPORTUNITIES
Given the opportunities and gaps summarized and to support the maturation of AM technologies for the bene t of casting and forging manufacturing and applications, the following areas of future research and development are proposed:
• AM for casting and forging manufacturing and applications strategic road mapping.
• Certi cation of AM products for casting applications that address application-relevant performance, probability of detection, and costs.
• Demonstration of the utility of AM technologies for advanced casting design to augment casting operations, productivity, and cost.
• Demonstration and characterization of AM technologies for casting tooling for nickel and titanium alloys.
• Demonstration of AM for forging applications to assess reliability, design trade-o s, and cost.
• Evaluation of large-scale AM processes for forging applications to demonstration design guides, material mechanical and physical properties, processing capabilities, and cost.
We Asked. You Answered.
America Makes turns member feedback into actionable program enhancements.
BY TIFFANY WESTBAY | MEMBERSHIP DIRECTOR & OPERATIONS DEPUTY DIRECTOR2022 MEMBERSHIP SURVEY - AMERICA MAKES OPERATIONS
FEEDBACK RESPONSE
As America Makes continues to evolve, more transparent communication regarding the direction and focus of the Institute is needed.
America Makes is currently analyzing its membership model. Our top priority is to work in tandem with members to generate a revised model that will ensure America Makes is strategically focused and able to meet membership needs.
The Digital Storefront could beneft from greater ease of navigation, as well as improved visualization of data from single projects and the consolidation of data from multiple related projects.
@Program cost share is very generous; however, there is an increased desire to allow cost share to be claimed for hours spent on employee engagement (i.e. working group engagement).
America Makes is actively working on a complete redesign of the existing Digital Storefront. The new system will be appealing, modern, easier to use, and offer data more intuitively. We are also incorporating new features such as the ability to add data, dynamic reporting, and integration with our membership portal.
America Makes offers cost share credits under the @Program to make reporting uncomplicated. However, members also have the option to report cost share based on time dedicated to a non-project activity and are encouraged to fully track their activities and submit itemized cost share reports.
Consider hosting events in conjunction with other major conferences or near centers of additive manufacturing or technology centers.
America Makes events are scheduled two years in advance. Following each event, information is gathered from members through a post-event survey, which includes suggestions on future event locations. Due to an increased interest in hosting events, America Makes is considering a membership vote on future venues.
America Makes is de ned by the voice of our membership and we understand the criticality of hearing the needs of our members and responding with actions. From July 1-31, 2022, America Makes o ered its annual Membership Satisfaction Survey, allowing us the opportunity to capture feedback and suggestions relating to the institute and the additive ecosystem. Several key
takeaways realized from the survey results are being utilized to improve processes and steer program strategies that will ultimately enhance the bene ts to our valued members.
With 234 members surveyed and 162 total responses received, the following is a breakdown of the top takeaways and how America Makes is responding with real action.
2022 MEMBERSHIP SURVEY - AMERICA MAKES PILLARS
FEEDBACK RESPONSE
America Makes should incentivize companies who transition AM technologies outside of the membership and encourage companies to share material data for the Digital Storefront.
There is a need for additional material development for demanding environmental conditions such as space fight and automotive. America Makes should introduce projects to establish material dataset developments and defects characterization.
America Makes has an ongoing request for members to share impact stories. These feature stories allow us to promote our members’ technological advancements. America Makes is working on a solution to inventory and integrate a wide array of AM / 3DP information to be housed in the Digital Storefront
America Makes and government partners are in complete agreement! Evidence of this consensus can be found within recent America Makes project calls such as GAMAT - August 2022 - America Makes. Stay current with future project calls at America Makes Open Project Calls - America Makes.
Exploring detailed market research is key among members. Monitoring dollars spent on material and hardware, and changes in market size can signal a demand that infers greater willingness to more closely evaluate AM, ultimately leading to the utilization and advancement of AM technologies and solutions.
America Makes has committed to expanding the AM ecosystem by providing access to accurate supply market research and services. One way America Makes plans to accomplish this is through the recently announced partnership with The Association for Manufacturing Technology.
There is a heightened interest in how members can access, deploy, and scale America Makes education and workforce development (EWD) assets.
America Makes offers a comprehensive library of EWD resources available to the membership. Members are encouraged to connect with the EWD team or learn how to obtain access at americamakes.us/amnation
WHERE ARE THEY NOW?
The Birth of a Material All-Star
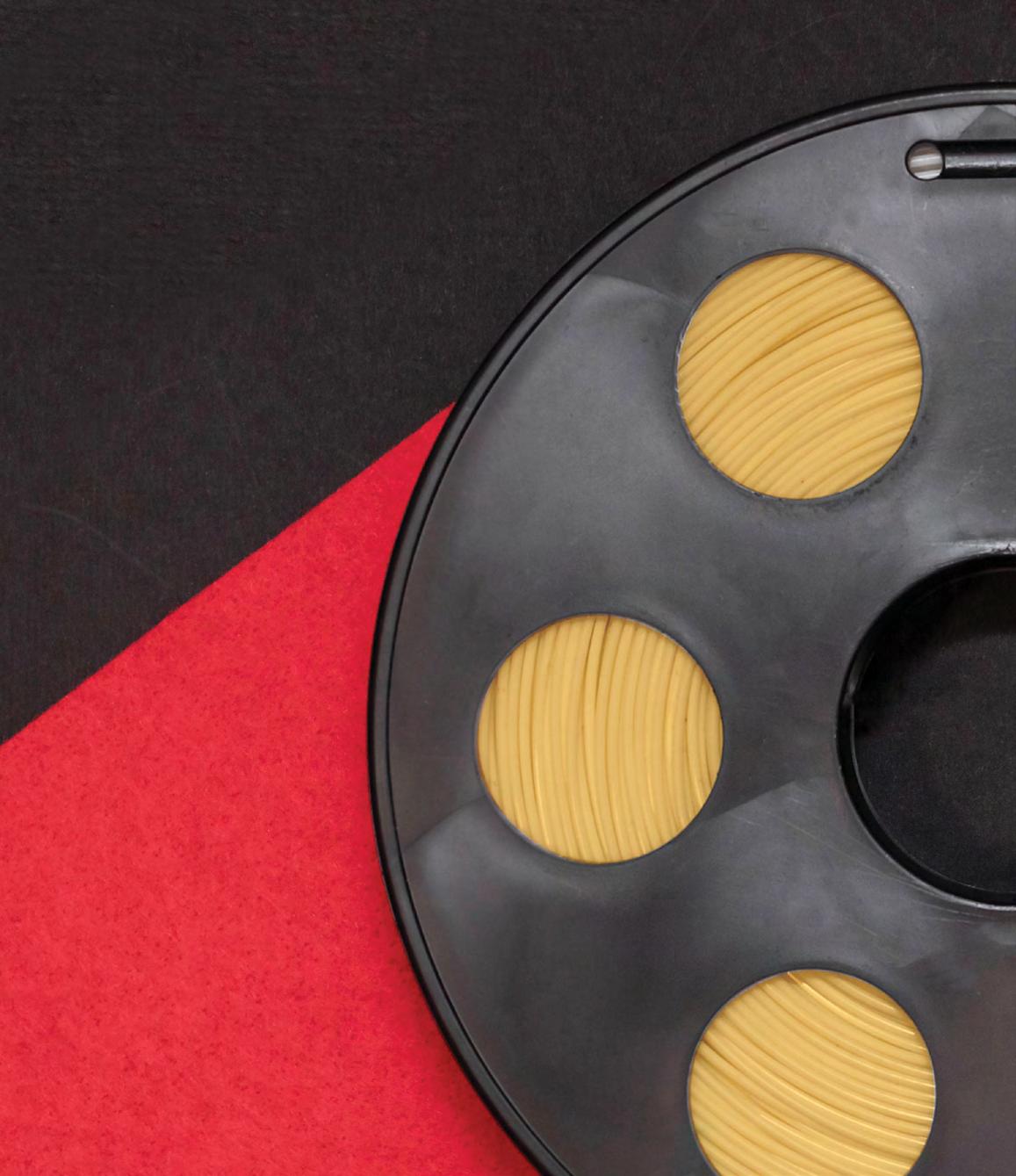
Since the onset of the ULTEM 9085 project, the dataset generated under America Makes has fostered signifcant utility.
BY DAWN MARZANO | COMMUNICATIONS MANAGER, AMERICA MAKESULTEM 9085 is a high-performance thermoplastic that is strong, lightweight, and ame resistant. This material is ideal for use in aerospace, automotive, medical, and other industrial applications where a high-strength, heat-resistant thermoplastic material is needed. It is one of the very few high-performance thermoplastics available for Fused Depositing Modeling (FDM), permitting engineers to 3D-print advanced functional prototypes and parts.
Establishing a complete database of material properties to further enable use in various commercial and government applications was critical yet challenging because such a database did not exist. However, the dataset was a necessity to meet a minimum requirement for the deployment of an additively manufactured solution in a production environment. The good news is that project participants, led by Rapid Prototype and Manufacturing (rp+m), based out of
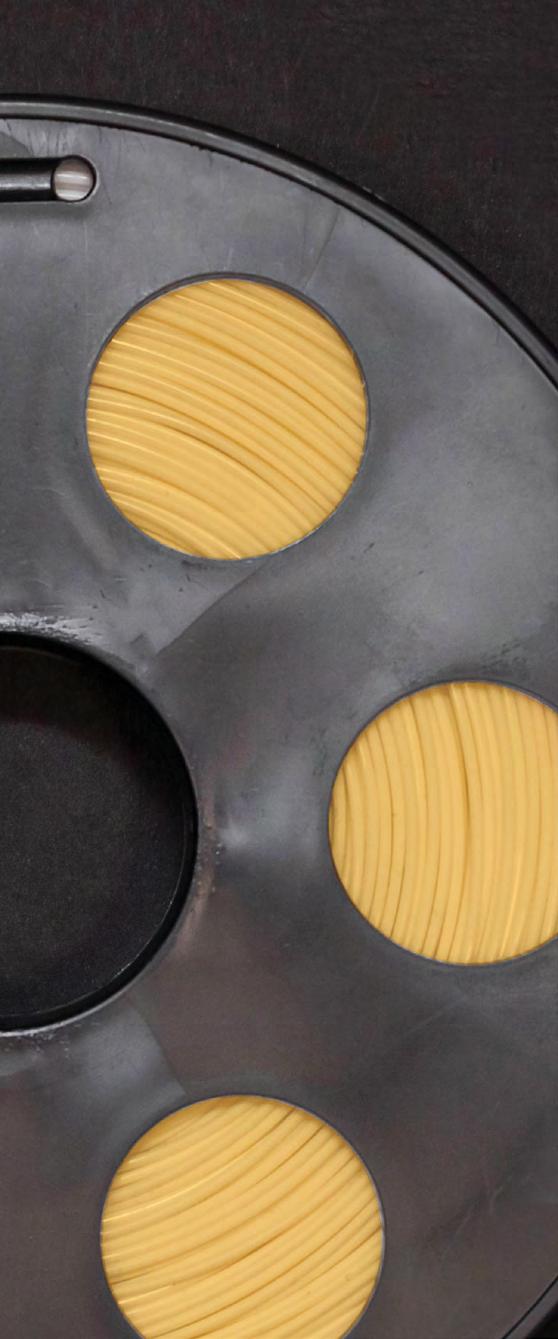
Avon, OH, were able to build upon results from a rst-round study to expand and create a supplementary, standalone dataset that addressed concerns and aws. The project, which concluded in 2018, o ered this dataset to America Makes’ members and government partners to enable broad dissemination of the collective knowledge for future part design. A further objective was to allow industry members to use their design-allowable methodologies for statistical data
analysis, thereby creating a well-utilized and broadly applicable dataset that would produce a framework for future materials and processes.
“This project was critical foundationally for additive manufacturing because the technology was originally built around prototyping and what the market is saying is that we need more than prototyping – we need production,” according to Tracey Albers, President and CEO of rp+m. And, in the world of manufacturing, production means repeatability.
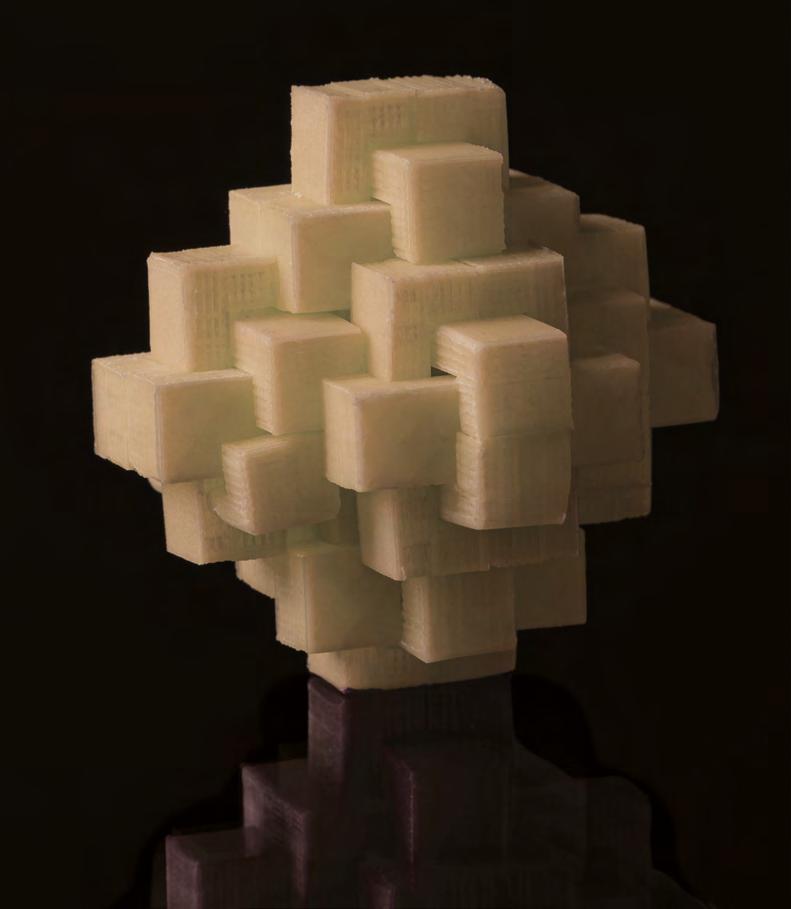
Albers explained that the drivers for the Ultem 9085 project were focused on repeatability. To take machines that were generally built to do something one time and then control that process so that time after time the machines produce the exact same outcome.
Once the team performed FDM machine process control evaluation and generated documentation, they also developed process parameters (resulting in a published process speci cation) that included machine setup, calibration, and maintenance. A framework for the quali cation of materials according to the process speci cation was also developed.
Reproducible material properties were con rmed across a well-recognized and accepted methodology for the quali cation of aerospace-grade manufacturing. This con rmation was enabled through the
americamakes.us/where-are-they-now
creation of a complete test matrix, including detail on test conditions, coupon quantities, process parameters, material traceability, and coupon management. Thus, solving a repeatability problem that historically had no solution.
What does this all mean? Thanks to the diligence and collaboration of private and public participants (rp+m, Stratasys, Lockheed Martin, Wichita State University - National Institute for Aviation Research and National Center for Advanced Material Performance, U.S. Department of Defense, Federal Aviation Administration) the list of accomplishments resulting from the dataset associated with the ULTEM 9085 project continues to widen its reach outside of the aerospace industry, which was the original target.
The project followed procedures of the National Institute of Aviation Research’s (NIAR) National Center for Advanced Materials and Process (NCAMP) to generate a baseline set of quali cation data in accor-
or polyetheretherketone (PEEK), industries are just coming around to the vast scope in which this material can be utilized. For example, the automotive industry is using ULTEM 9085 as an alternative to steel and aluminum because of its high strength-to-weight ratio. This thermoplastic solution is found in transmission components, sensors, and thermostat housings to name a few. ULTEM 9085 is also used to make ventilation system components, cable ducts, and seemingly insigni cant items such as hinges and door handles. Consumers encounter many of these items daily yet rarely give them a second thought.
As a direct result of the dataset, Albers stated that rp+m is now working with several aerospace and defense OEMs, which is not typically part of their customer base. “For us, this has meant real business opportunities that have transformed the way we work on a daily basis,” she noted. “This is a totally di erent space now. The applications require more than prototyping. What we have demonstrated is that the ability to control means the ability to trust what comes out of the machine. When you’re talking about moving into the aerospace and defense community, that is a must.”
dance with industry-standard methods used for statistical reduction, including, and complying with the Composite Materials Handbook for Polymer Matrix Composites (CMH-17).
ULTEM 9085 is currently considered an all-star material for aerospace, civil aircraft, and automobile manufacturing. And, due to its overall strength, reduced manufacturing costs, and production time compared to plastic alternatives such as polyaryletherketone (PAEK)
The project’s success has proven that by coupling the right materials with the right application and manufacturing processes, it is possible to produce reliable parts that are strong, lightweight, compliant, and cost-e cient. Above all, they can be used across a variety of industries.
Albers said she not only considered the functionality of the team a huge success, but also the cohesiveness of the project’s funding. “I am convinced that none of the science and data would have been generated without a funding entity like America Makes pulling it all together,” she concluded.
Thanks to the diligence and collaboration of participants the list of accomplishments resulting from the dataset associated with the ULTEM 9085 project continues to widen its reach outside of the aerospace industry.
Simply put, AM is a new domain that we need to master. We have the digital and machine tools and what we really need is to harness the imagination and energy of a workforce eager to learn.
This is how we get there.
— LAWRENCE A. BINEK | SENIOR PRINCIPAL ENGINEER, PRATT & WHITNEY OPERATIONS | AMERICA MAKES EWD ADVISORY GROUP MEMBER & SUBJECT MATTER EXPERTOPPORTUNITIES, EVENTS, PROJECTS
Your membership makes you a part of the additive manufacturing ecosystem. Your engagement makes you a part of the evolution. americamakes.us/engage