Fredericia’s Sustainability Commitment
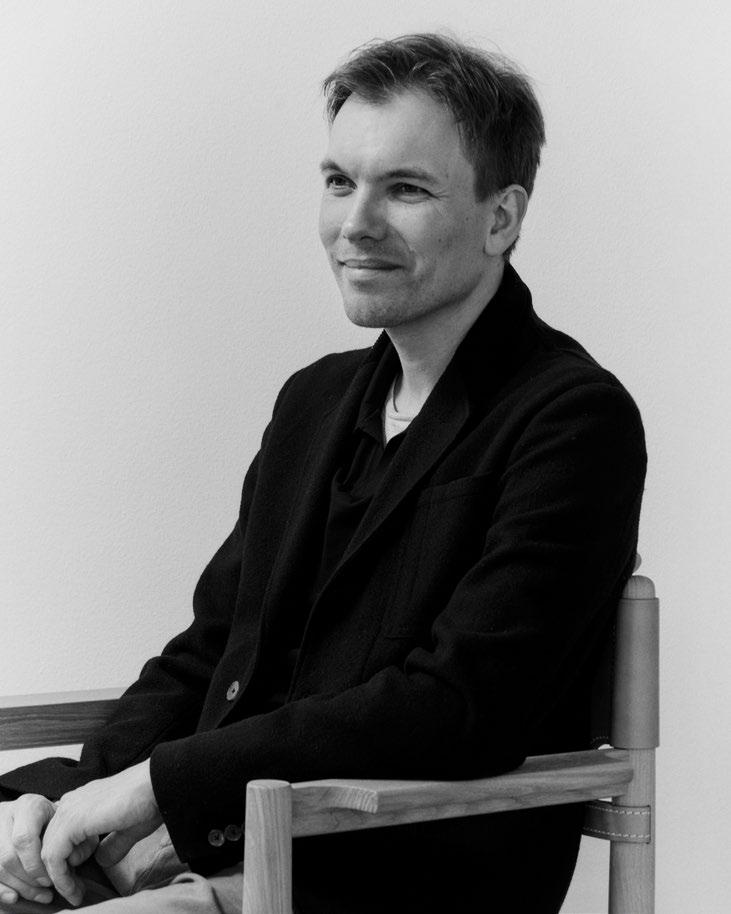
At Fredericia, sustainability is not just a trend but a core principle that has defined our company for over a century. As a third-generation leader of this family-owned business, I am proud to continue our legacy of responsible craftsmanship, ensuring that the values instilled by my grandfather, Andreas Graversen, remain relevant in a modern context. His vision was clear: to create furniture designed to last for generations, crafted with integrity, and built with a deep respect for both people and the planet.
Our commitment to sustainability is reflected in a series of ambitious initiatives aimed at minimising our environmental impact and fostering social responsibility:
∙ focuses on achieving carbon neutrality, eliminating production waste, and implementing green facility management.
∙ ensures full traceability of raw materials, the exclusion of harmful substances, and sourcing under renewable conditions.
∙ integrates life cycle analyses, spare parts accessibility, and circular business models such as refurbishment and resale programmes.
Craft & Community strengthens traditional craftsmanship, supports local communities, and provides meaningful work opportunities.
Democracy Made upholds fair labour practices across our supply chain, ensuring sound working conditions and financial security for workers.
These initiatives, which align with our B Corp certification, go beyond compliance— they shape a future where responsibility and innovation coexist. Sustainability is not just about meeting standards; it is about setting new ones. Through collaboration, innovation, and an unwavering dedication to our core values, Fredericia Furniture is committed to shaping a future where design and responsibility go hand in hand.
Rasmus Graversen CEO, Fredericia Furniture A/S
Fredericia’s commitment to sustainability permeates every aspect of our operations. As a family-owned and independent company, our decisions reflect the fundamental values ingrained in Fredericia’s sense of responsibility.
We put our values into action and proudly embrace the B Corp movement, striving to build a more inclusive and sustainable economy. Our commitment goes beyond profit, aiming to positively impact workers, communities, customers, and the planet. We take pride in enabling sustainable customer choices and obtaining the B Corp certification is crucial in our ongoing efforts for a better future
By working with Fredericia, you become part of a trusted global community that sees business as a force for good, advocating for corporate responsibility and driving positive social and environmental change.
Why is being a B Corp important to Fredericia?
As a B Corp, Fredericia is genuinely committed to creating tangible environmental and societal benefits.
Our holistic approach to sustainability integrates B Lab’s key parameters into our framework, providing transparency for partners and customers. We excel in several areas, such as conscious consumption, diversity in the workplace, extended warranty schemes, and active community engagement.
Publication of annual sustainability report. Full business transparency – from roadmap and impact to money streams. Employee representatives on the board.
∙ ISO 14001 certified to continually improve environmental performance.
∙ Enriching teams with diverse strengths and ages spanning from 20 to 70 years.
∙ Management team representing four age groups.
∙ Offering a 25-year warranty on our most iconic designs by Wegner, Mogensen, and Volther.
∙ Our customer satisfaction evaluations show a Net Promoter Score (NPS) of 91%, compared to the industry benchmark of 77%.
∙ Prioritising raw materials that are safe and toxic free making them harmless for human health.
Creating an inclusive society engaging with the local community through protective workshops.
Local production in our Danish upholstery workshop ensures the transfer of craft expertise across generations.
∙ Prioritising production and suppliers within Europe to minimise transportation and maximise transparency.
∙ Working systematiccally towards carbon neutrality in 2035.
∙ Circularity as design focus ensuring durable, reusable, repairable and recyclable products.
∙ Comprehensive evaluation from raw material to disposal for a holistic and genuine environmental footprint.
Since its founding in 1911, Fredericia has been built on a deep-rooted commitment to craftsmanship, quality, and timeless design. But our story is also one of family and visionary entrepreneurship. In 1955, Andreas Graversen took over the company, bringing with him a passion for design excellence and an unwavering belief in durability, honesty, and human empathy. One of his most defining contributions was his close collaboration with designer Børge Mogensen, whose functional and enduring approach to furniture design shaped Fredericia’s identity and established a lasting design legacy.
Under Graversen’s leadership, Fredericia became renowned for its commitment to quality and durable materials, ensuring that every piece was built to endure—both aesthetically and structurally. This philosophy of longevity has always been at the heart of what we do and remains the foundation of our approach to sustainability today.
Now, as a family-owned company in its third generation, we continue to honour these values while adapting to new sustainability demands. We are evolving our practices to meet the challenges of the future, ensuring that our heritage of craftsmanship and responsible design remains relevant for generations to come.
“It is of great importance that the things we purchase and live with, do not need to be changed but instead grow old with dignity and charm”
– Andreas Graversen, CEO for Fredericia, 1955 – 1995
“At Fredericia we strive for clarity, good materials, human empathy and above all strength, both in design and in our business.”
– Andreas Graversen, CEO for Fredericia, 1955 – 1995
In 2024, we celebrated the 100th anniversary of Andreas Graversen, and his four principles for design and business remain a guiding force as we address today’s environmental and social challenges.
Graversen believed that every component in a design should have a clear role. Today, this principle translates into circular design practices, ensuring clean material streams that support recyclability and long-term sustainability.
∙ Just as Graversen personally selected woods from German forests, we demand full traceability of our materials, requiring FSC™ certification or comparable documentation to uphold responsible sourcing.
∙ Graversen insisted that furniture should bring joy to people, knowing that cherished pieces are well cared for. We build on this philosophy by ensuring our production benefits not only individuals but also society, fostering ethical and fair manufacturing.
Strength
He demanded that only well-made furniture be produced, believing that durability ensures longevity. Today, we take this further by rigorously testing for public use, offering extended warranties, and designing for both functional and aesthetic longevity.
By staying true to these principles while adapting them to modern challenges, we ensure that Fredericia’s commitment to quality, responsibility, and sustainability continues to define our future.
Fredericia creates Scandinavian design that encourages human well-being wherever people live, work and connect.
We strive to continue our heritage of purposeful and sustainable design.
Crafted to last.
Since 2022 Fredericia has been a signatory of the UN Global Compact. We annually reaffirm our support for the Ten Principles of the United Nations Global Compact in the areas of Human Rights, Labour, Environment, and Anti-Corruption.
In our annual Communication on Progress, we disclose our continuous efforts to integrate the Ten Principles into our business strategy, culture, and daily operations, and contribute to United Nations goals, particularly the Sustainable Development Goals.
Goal 12 Responsible consumption and production. Learn more in our Circular by design initiatives (p.41)
Goal 13 Climate Action, managed from our Operation Zero initiatives (p.25)
Goal 15 Life on land. This SDG relates to our traceability efforts through our Soil to seat initiatives. (p.33)
In 2024, many of our ESG efforts have started to translate into measurable numbers in our KPIs.
Most notably:
∙ We continue to reduce our CO2e emissions in Scope 1 and 2, which have decreased by nearly 14%.
∙ Electrification projects are planned that could achieve a 72% reduction compared to the 2023 baseline. This includes the electrification of vehicles and the conversion from gas boilers to heat pumps in Svendborg, positioning Fredericia well ahead of its 2030 target.
∙ We have almost reached our 2025 target for waste reduction (98% of KPI), which means we have set an even more ambitious goal for further improvement in 2025.
We have exeeded our target on FSC-certified wood in our assortment, with 77% of items sold (compared to 75% target). Likewise, for product certification, we outperfoemred our 2025 target of 40% of items sold, achieving 48% in 2024.
Lastly, we have made significant progress in implementing our supplier code of conduct, with 97% of our suppliers now committed signatories – exceeding our 2025 target of 95%.
Areas of improvement include the implementation of FSC-certified packaging, where we achieved only a two-percentage point in 2024 compared to 2023.
The KPIs follow the traditional ESG reporting framework.
Scope 2
Scope 3 upstream
Scope 3 downstream
Energy consumption
Renewable energy
FSC certification in wood based assortment
FSC certification in packaging
Product certification in assortment
Product life cycle assesment screening
Full time employees
Gender, diversity, Executive management (C-suite)
Gender, diversity, workforce
Average seniority
Students & Trainees
Sickness absence
Gender, diversity, Board of Directors
Supplier Code of Conduct
European suppliers
Supplier average time of collaboration
B
As a manufacturing company with its own production facilities, Fredericia has direct control over a large portion of our manufacturing footprint, as well as the local comminutes surrounding our two plants in Denmark.
Our initiatives aimed at managing this environmental footprint are grouped under the headline Operation Zero:
∙ Zero Carbon – working towards Co2e emission neutrality by 2035 (scope 1 & 2)
∙ Zero Waste - Eliminating production waste through recycling practices and innovative production design
∙ Green building and facility management –Implementing sustainable building and operational practices.
Many of the initiatives under Operation Zero are managed internally by our Operations department, and our environmental practices are certified under the ISO 14001 standard.
Emissions from stationary equipment and vehicles:
∙ Vehicle consumption has decreased by 19% from 2023 to 2024.
∙ Natural gas consumption has decreased by 8% from 2023 to 2024.
Overall, Scope 1 has decreased by 13.9%:
∙ Vehicle consumption has contributed to a reduction of 17.93 tons of CO2 (9% total reduction)
∙ Natural gas consumption has contributed to a reduction of 5.42 tons of CO2 (2.7% total reduction).
The decrease in vehicle emissions is due to fewer company cars in circulation and slightly reduced usage of those in operation. In the coming years, we expect further reduction in CO2 emissions by converting our vehicle fleet from fossil-fueled cars to electric vehicles. The potential reduction is 38%
A part of the reduction in natural gas consumption can be attributed to natural fluctuations in heating demand, as there were fewer heating degree days in 2024 compared to 2023. However, this only explains about half of the variation. The remaining is due to a reorganisation of our production layout, improving efficiency and reducing door openings.
A 34% reduction in CO2 emissions can be achieved by replacing our factory gas boiler with a heat pump.
Emissions from purchased energy (electricity, district heating, etc.)
Electricity consumption in our location in Fredericia has decreased by 18% in 2024. A new ventilation system installed in the summer of 2024 has contributed to this reduction. At the same time, a reorganisation of our office spaces has improved energy efficiency in our HQ office.
Our goal is a 60% reduction in Scope 1 & 2 emissions by 2025, aiming to get as close as possible to 100% by 2035.
On our path to net zero, we are committed to full electrification by 2035, with an expected 98% reduction relative to 2023, acknowledging that the remaining 2% accounts for electricity still derived from fossil sources. We recognise that achieving 0% emissions by 2035 is unlikely based on traditional energy flows alone. Therefore, we are committed to exploring new solutions to account for the remaining 2%.
Our original target was set for a 35% reduction from 2021.
2021: 110.9 tonnes
2024: 73.3 tonnes – a total reduction of 33.9%, including 4.4% in the past year
This means we are almost at our waste reduction target! Most of our waste is recyclable, and there is no hazardous waste. However, there is still potential to minimise waste by apadpting our product design and production processes to generate less waste in the first place.
Breathing new life into textile waste
Together with the Danish design studio Sheworks Atelier, we have created an upholstery option made from textile leftovers. Challenging the way you choose upholstery - crafted from leftover scraps, each colour tone and texture might vary. Nevertheless, we have created an aesthetically appealing design product that will appear as a whole unity when put together.
With Ribbon, we use textile leftovers from our furniture production in Denmark and turn them into bespoke design products while minimising the environmental impact. Together with Sheworks Atelier, we have created a unique textile especially developed for use on the Søborg Chair by Børge Mogensen.
Who is Sheworks Atelier?
Sheworks Atelier, a Danish textile design studio founded by Martha Von Guenther and Solveig Berg Søndergaard, specialises in circular design by repurposing textiles into customised design products with a strong emphasis on aesthetics. Additionally, they have a significant social mission: Employing women on the outskirts of the labour market and providing training in their Kolding studio.
Reducing the CO2e footprint by 50%
By opting for Ribbon textile, the overall environmental impact of the Søborg Chair is significantly reduced, dropping its carbon footprint up to 50%.
A traditional Mogensen Søborg Chair (model 3062) upholstered in Hallingdal fabric is estimated to have a carbon footprint of 80 kg CO2e, whereas using Ribbon instead reduces it to 40 kg CO2e. While upcycling or repurposing textiles already has positive effects on the environment, especially in decreasing chemical and water usage in the textile industry, discovering that it can result in a reduction of up to 50% in CO2e emissions is a game changer.
From our quality standards requiring consistency in raw material quality to our sustainable practices, a fully traceable material source is fundamental to our environmental approach. A pure product, with clarity in its content declaration, allows us to systematically reduce the materials used in our production.
Our initiatives aimed at managing this environmental footprint are collected under the headline Soil to seat:
∙ Full traceability on raw materials, from leather to wood.
∙ Ensuring all raw material inputs are Red List-free and produced under renewable conditions.
∙ Source reduction - finding alternatives to environmentally harmful industry standards, including toxic agents such as Chrome 6 and carbon-heavy oilbased products.
∙ Environmental product certifications.
Our Soil to seat initiatives are driven by our procurement and product development departments.
Fredericia is working systematically to comply with the EU Deforestation Regulation (EUDR). We are committed to ensuring that all wood and relevant raw materials used in our products are sourced legally and are free from deforestation after. We work closely with our suppliers to guarantee transparency and sustainability throughout our value chain.
The FSC standard is being gradually implemented, with the goal of full compliance across all products by 2030. Implementing FSC also involves working with our smaller sub-suppliers to provide the chain of custody documentation required for certification . In 2024, these efforts have resulted in a significant increase in our FSC spend share, rising from 58% to 77%.
Fredericia is an FSC-certified company under the FSC™ license number: FSC™ C151292
Certified traceability & replanting in wood-based Assortment (FSC)
FSC share of packaging (paper)
There has been a small step forward, but a significant leap is still required in 2025.
Fredericia was among the first companies to join the movement towards leather traceability. In 2023, we successfully expanded our certified leather collection, ensuring full traceability across our entire range.
This achievement is not only the result of carefully selecting our sources but also of close collaboration with our suppliers to drive real transformation in the industry. As a result of our efforts, we are now able to offer full traceability for even more of our leather collections.
At present, there are no comprehensive benchmarks for measuring a company’s environmental impact or assessing individual products. Therefore, we rely on multiple third-party certifications to demonstrate and reinforce our commitment to sustainability.
In the early stages of product development, we challenge ourselves to make more sustainable choices, such as using raw materials from sustainable sources and meeting the high standards of third-party product certifications. Currently, Fredericia has chosen to use the following material and product certifications.
Material certifications
Product certifications
Product certifications in the assortment
Our target for 2024 was set at 40%, and we reached 48%. The significant jump from 2023 shows how the timing of incoming certifications can create a leap in the progress.
Based on the success in implementing the certifications in 2024, we have decided to increase our target, raising the bar towards 2030 from 65% to 85%.
Our original credo considers how a product ages with beauty and adheres to the demands this places on the purity of materials, the honesty of construction, and ultimately, design integrity. Today, we are extending this line of thought towards building a circular business model, as well as ensuring the highest standards of circularity in our new product development and product reengineering.
Our initiatives aimed at reducing this environmental footprint are collected under the headline Circular by Design:
∙ Life Cycle Assesments (LCA) on our entire product range.
∙ Commitment to durability with extended warranties.
∙ Customer accessibility to spare parts, maintenance and recycling instructions.
∙ Circular business model innovation with our refurbishment, resell, and take-back programme Fredericia Circular.
∙ Product reengineering and new product development, ensuring the separation of heterogeneous materials, interchangeable components, and/or restoration-ready product design.
Our Circular by Design initiatives are driven by our procurement, product development, sales, and logistics department.
As part of our sustainability strategy at Fredericia, we have introduced Environmental Product Sheets (EPS) for our core product range, developed in compliance with ISO 14021 self-declared environmental claims. These sheets are designed to quantify the environmental impact of our products during manufacturing.
The Life Cycle Assessments (LCA) are conducted using a tool provided by the Danish company Målbar, which generates valuable insights through a single metric: CO2e. CO2e represents the combined warming impact of various greenhouse gases, including carbon dioxide, methane, and nitrous oxide. By converting the warming effects of these gases into a single equivalent metric-based on their global warming potential (standardised ratios), CO2e provides a comprehensive measurement of a product’s total environmental impact over a set period.
This data informs decisions about material selection, production techniques, and future manufacturing locations. It also establishes a clear baseline for our products, enabling us to identify areas for potential improvement.
Through the development of EPS for our core range, we are increasing internal knowledge about the environmental impact of different materials. This empowers our Product Development team to make more conscious and sustainable choices. By integrating the Life Cycle Assessment tool into the early stages of product development, we can better evaluate and minimise the environmental footprint of new designs.
The calculations in our assessments are based on an average. (The climate footprint report is calculated according to EUs rules for Product Environmental Footprint (PEF)).
The charts describe the materials used in the product.
Detailed climate footprint assessment - co2e
The Climate footprint assessment is verified by Målbar April 18th, 2023
Disposal: At Fredericia Furniture, we recommend our customers to handle our products with care when the product have served its use. We emphasis therefore that spare parts are reused/recycled when possible and/or products repaired with thought of the future. Sort the spare parts according to your country’s regulations.
Use phase: This is the longest phase of the life cycle. During the use phase of our products, a limited environmental impact occurs.
Transport: Includes the transport between Fredericia’s suppliers and the transport to Fredericia.
Packaging: Includes all packaging material.
Production: This phase includes both the manu-facturing of components but also the assembly of finished goods.
Production waste: Includes the waste that is generated during the different production processes that is needed to manufacture the product.
Cover: Expresses the environmental impact that the cover has if the product consists of it.
Upholstery: Expresses the environmental impact that the cover has if the product consists of it.
Surface treatment: Showcases the total environmental impact that the product has concerning surface treatments.
Materials: Includes the extraction of materials, and the benefit of recycled content is considered.
Carbon storage: Carbon credit for bio carbon is automatically subtracted in the calculation.
J39 Mogensen Chair 21 kg CO2e
Lynderup Chair 40 kg CO2e
Plan barstool Fully Upholstered 70 kg CO2e
Pato 4 leg Chair 20 kg CO2e
Lynderup Chair Seat Upholstered 55 kg CO2e
Yksi Armchair 44 kg CO2e
Pato 4 leg Chair fully upholstered 34 kg CO2e
Plan Chair Wooden Seat 38 kg CO2e
Chair 17 kg CO2e
Sledge Chair 24 kg CO2e
Plan Chair Seat Upholstered 46 kg CO2e
Armchair 23 kg CO2e
Spine Wood Base Chair
35 kg CO2e
Spine Wood Base Chair
55 kg CO2e
Plan Chair Fully
Upholstered
50 kg CO2e
48 kg CO2e
Eyes Swivel Chair
260 kg CO2e
Spine Wood Base
Barstool
65 kg CO2e
Plan barstool Wooden Seat
65 kg CO2e
Spine Wood Base Stool
46 kg CO2e
Plan barstool Seat
Upholstered
65 kg CO2e
1060 kg CO2e
To demonstrate our commitment to producing above-average quality, Fredericia offers an extended standard warranty on our products. The extended warranty applies to products purchased after 1st January 2023.
The 25-year warranty is available on the following flagship models:
∙ The Spanish Chair
∙ OX Chair and Queen Chair
∙ Corona Chair
∙ BM 22 Collection
A 10-year warranty is provided on sofas.
A 7-year warranty is offered on armchairs, chairs, tables, coffee tables, and smaller pieces of furniture under our Complements collection (e.g., side tables).
A 2-year warranty applies to lamps and accessories, including vases and loose spare parts.
Fredericia offers an extended warranty against production and construction defects. This warranty covers faults present at the time of purchase or those that arise due to flaws inherent at the time of purchase. The warranty period is calculated from the date of the original invoice.
During the applicable warranty period, Fredericia will, at its sole discretion, either repair, replace, or issue a credit note for the defective product, part, or component.
At Fredericia, we design for longevity. Every new product is built to last, crafted from durable materials, and designed to age beautifully. Our deep knowledge of timeless craftsmanship informs strict standards for quality and durability, ensuring our furniture remains relevant for generations.
We have set strict principles for our new product design. We want our furniture to be designed for disassembly, allowing easy separation of materials for recycling or refurbishment. This approach ensures that spare parts and repair options remain accessible for much longer, extending product lifespans, reducing waste, and supporting a circular economy.
By balancing aesthetics, durability, and sustainability, we create furniture that stands the test of time —built to last, circular by design, and ready for restoration.
∙ Timeless design
∙ Durable materials with a long lifespan
∙ Crafted to last
∙ Easy disassembly for improved circularity and simplified repair of broken parts
∙ Increased use of recycled materials
∙ Replacement of harmful substances with safer alternatives
Following our Circular by Design principle, Pioneer Stool offers exceptional design flexibility while maintaining a minimal footprint in terms of fabric use. The interchangeable cover and foam part can be separated from the base, allowing for design updates over time without the need to remake all components of the chair. Fredericia offers a take-back programme for any used components, enabling their use in fully recycled models –minimising waste while preserving product value with minimal material input.
The design challenge of Gomo Chair was to create an organic and characterful shape while ensuring interchangeable upholstery. By utilising two different 2D curvatures within a single shape, this has been achieved while maintaining precise contron over the form. Additionally, the design eliminates the need for glue or special backing on the fabric, significantly reducing chemical use in production. Avoiding glue between the fabric and foam component not only minimises chemical usage but also enhances freedom of choice in fabric selection.
With the reintroduction of the Mogensen 21 Series in 2023, we have updated the original construction to ensure that customers can replace parts and each material component can be separated for maintenance and potential modifications.
The following furniture in the Fredericia Collection adheres to our Circular by Design principles. For customers requiring replacement parts, a selection of our products is designed to allow specific components to be replaced, thereby extending the overall lifespan of the furniture.
Below are key products designed with disassembly and repairability in mind:
Lynderup Chair
Selected Pato models
Spanish Collection – leather replacement
Canvas Chair – textile replacement
Piloti tables
Tableau tables
Selected Søborg models
Gomo Collection – textile replacement
Plan Collection
∙ Pioneer Collection
∙ Pato
∙ BM shaker tables
∙ Insula
To further safeguard our furniture, we use foam shapes in our packaging. Currently, this material is virgin, although some foam is reused within our operations. Over the next year, we will explore options to replace this foam with recycled alternatives or other, more sustainable materials. We will also implement a take-back scheme for our standard wooden boxes to improve recycling and reuse.
In 2023, Fredericia introduced Fredericia Circular, a new business unit focused on refurbishment rather than new production. Beyond providing new furniture for large public projects, we now offer services that extend furniture the lifespan and reduce environmental impact.
Our Refurb Division includes:
Furniture Refurbishment: We refurbish and refresh stackable chairs, upholstered pieces, and more, offering modern updates and a new warranty to ensure quality.
∙ Buyback and Reselling: We buy back used furniture for renovation or recycling in new projects, optimising resources and reducing waste.
∙ Repurposing Solutions: We are intensifying our collaboration with Sheworks Atelier and creating a separate workflow in our factory. The goal is to eliminate waste from high-carbon-intensity and high-valuable fabric and leather offcuts from our own production – see more under our Operation Zero initiative.
Fredericia’s best-selling chair throughout our history is the Trinidad Chair by Nanna Ditzel, which is now included in the Fredericia Circular scheme.
Within our Fredericia Circular model, we can increase the recycled content of each chair sold for a project from 21% in a new chair (primarily from highly processed recycled steel used for the base) to 94% recycled content – with the remaining 6% consisting of new lacquer, rivets, and screws.
Reduced environmental footprint compared to buying new
New Trinidad Chair
Refurbished Trinidad Chair
Before Trinidad Chair
Cherry, upholstered in Alcantara
Production year 2002
Typical chair from the start of the 2000s in Cherry Surface and upholstery can be damaged. At tough use, the outer rivets can lose some tightness.
After Trinidad Chair
Black with black lacquer Refurbished 2024
The original chrome surface on this chair has been given a new powder coat and is now in mint condition. Plastic spacers are changed to new ones.
The Customer delivers used chairs and recieves refurbished chairs ready to use
Customer Fredericia Furniture A/S Treldevej 183 7000 Fredericia Denmark
STEP 1 – Deliever funiture
The customer delievers furniture at Fredericia Furniture at their own cost.
Plant
After Trinidad Chair Black with black leather seat Refurbished 2024
STEP 3 – Delivery of refurbished furniture
Customer receive refurbished products (DDP) packaged as new. The product get a renewed 7-year warranty
STEP 2 – Refurbishment
Fredericia dissasembles and ship parts to refurbishment:
∙ New Laquer
∙ New wagner glides
∙ New mounting rivets and stacking spacers
∙ Possibly new upholstery
In Oslo’s Skøyen district, within a former mechanical workshop, the staff restaurant at Hoffsveien 1E has been reimagined as a vibrant, multi-functional dining space.
Housed in a Storebrand office building, the canteen serves employees from the surrounding offices, offering a café at the entrance and a larger dining area with seating for up to 300 people. Designed by IARK, the first-floor restaurant operates as a daily canteen while also adapting to host larger events.
With no existing canteen, every piece of furniture was carefully selected to suit the space, including iconic designs such as Nanna Ditzel’s Trinidad Chair and Børge Mogensen’s J39 Chair. Reflecting a strong commitment to sustainability, 55% of the furniture—comprising 176 of these chairs—was sourced second-hand, lending the space a unique and timeless character. This thoughtful selection seamlessly blends functionality with enduring design, perfectly complementing the canteen’s concept. By merging heritage architecture with sustainable design, the space fosters an inviting and dynamic environment that encourages relaxation and collaboration.
As we stand firmly by the integrity and originality of design, the preservation of traditional crafting methods is fundamental to our ability to produce high-quality furniture. This commitment is deeply rooted in our local communities, where we value long-term relationships that enable skills to be developed and passed on to future generations. As an extension of our recognition of the human and cultural significance of traditional craftsmanship, we are also proud to occasionally provide meaningful work opportunities for individuals with disabilities.
Our initiatives aimed at fostering this craftsmanship and community engagement fall under the Craft & Community programme, which includes:
∙ Maintaining craftsmanship skills through training and education programmes
∙ Sustaining supplier relationships and supporting local production
∙ Partnering with local social enterprises to provide meaningful employment for disadvantaged individuals
∙ Supporting community-driven charities
Our Craft & Community initiatives are led by our operations, procurement, and executive management teams.
Our commitment to craft traditions was at the heart of our Crafting the Present exhibition at 3daysofdesign in June 2024, where our entire company - from production to marketing - came together to showcase the processes, people, and passion behind our furniture.
Curated by designer Maria Bruun, the exhibition reexamined iconic pieces such as Hans J. Wegner’s Ox Chair and Børge Mogensen’s Spanish Chair, demonstrating how they have evolved with modern manufacturing techniques and environmental standards. Visitors had the opportunity to witness live demonstrations from our Svendborg upholstery workshop team alongside artisans from our long-standing partners at Tärnsjö Garveri, offering an intimate insight into the meticulous work that defines craft culture.
Our local production facilities are of great importance to us, and we take pride in honouring our history of local expertise and consistent quality. The name Fredericia reflects the city where the company was founded, and to this day, we maintain local production facilities for selected designs in both Fredericia and Svendborg. These facilities employ some of the finest craftsmen in furniture production and upholstery while also providing opportunities for students and trainees to contribute to our ongoing development and innovation.
A strong foundation for quality and sustainability
Long-standing supplier relationships play a crucial role in ensuring quality, innovation, and sustainability. These collaborations drive the development of sustainable materials, foster local value creation, and promote responsible consumption practices. By maintaining close partnerships with our key suppliers, we strengthen our ability to innovate while ensuring long-term stability and responsible production practices across our supply chain.
In 2024, we revised our calculation method to more accurately reflect long-term supplier relationships, including those established before our current ERP system was implemented. Previously, our data only extended back to 2007, and all suppliers were weighed equally. The new approach focuses on our 40 largest suppliers, calculating an average collaboration time based on this selection. The start date is set as June 30 of the respective year, with the reporting date as December 31, 2024.
While our products have traditionally been our core focus, we now recognise that a great customer experience goes beyond high-quality products—it’s about delivering value at every touchpoint. As part of improving our commercial excellence and providing value to our customers, we are systematically working to streamline access to product information, enhance customer care, and strengthen partnerships with key dealers and architects.
By acting on feedback and enhancing our sustainability efforts, our goal is to ensure that every interaction is seamless and inspiring.
“I know, as a fact, that our furniture serves our costumers well”
– Andreas Graversen, CEO for Fredericia, 1955 – 1995
To track our standing with customers, we conduct a biannual customer experience survey – the first of which was conducted in 2023 and is shared in this report for the first time.
Our latest survey confirms that our efforts are recognised. With a Net Promoter Score (NPS) of 84% promoters, it’s clear that our customers appreciate the quality and timeless design of our products, as well as the dedication of our team. Product quality remains the primary driver of positive feedback, reinforcing our strong reputation in the industry.
However, we also see opportunities for improvement. While our customer experience performance is strong in contract relations, there is room for growth in the residential market. Additionally, although we rank within the top 25% in differentiation, our position as a premium brand demands an even stronger value proposition beyond timeless quality. Customers have expressed a desire for a deeper relationship with us, indicating that we must shift from being seen as merely supplier to fostering closer collaboration and engagement.
Moving forward, we will enhance feedback collection, improve data quality, and ensure better alignment with customer needs. We will also strengthen our partnerships with dealers, helping us build stronger, long-term relationships and continue delivering exceptional experiences to our customers. Our aim is not only to maintain our position but to evolve and grow in ways that truly add value to those who choose Fredericia.
Data was collected from June 15th to August 12th 2023.
In designing furniture that prioritises human empathy, functionality, and user-friendliness, we believe that all production should be carried out under fair and responsible working conditions, regardless of country of origin. The fundamental democratic freedoms of everyone involved in our supply chain must be respected, and we are committed to upholding the highest standards of working conditions.
Our initiatives aimed at this fundamental ethical baseline are gathered under the headline Democracy Made, which includes:
∙ Ensuring our entire supply chain adheres to our comprehensive Code of Conduct, covering both workers’ rights and environmental management.
∙ Upholding our principle of a European production footprint.
∙ Committing to the financial security of our workers through fair salary distribution, compensated internships, and career development programmes.
∙ Continuously monitoring and improving our workplace through regular employee assessments.
Our Democracy Made initiatives are led by our procurement and executive management teams.
When evaluating our collaborations, we use a 360-degree evaluation scorecard. Based on the sustainable Triple Bottom Line sustainability theory, this scorecard ensures that our suppliers meet our ethical and operational standards. The key criteria we assess include quality, manufacturing facilities, environmental commitment, and management practices.
The implementation of this scorecard is ongoing, gradually expanding to cover a wider selection of suppliers.
The Code of Conduct is the foundation of a trustworthy partnership between Fredericia and our suppliers. Through the ongoing implementation of a Code of Conduct and a sustainable supplier selection process, we ensure that our suppliers meet essential standards related to human rights and environmental responsibility.
Our objective is to ensure that all Fredericia suppliers comply with the Universal Declaration of Human Rights, the UN Conventions on the Rights of the Child, and the local legislation of the countries where the production takes place. Additionally, all suppliers must adhere to the Ten Principles of the UN Global Compact.
To clearly define our expectations, we have formulated a Code of Conduct outlining the social responsibility requirements for our suppliers. Fredericia is comitted to upholding these principles, and we expect our suppliers to do the same.
The cost spend distribution describes the country of origin of Fredericia’s inbound supply chain purchases The data includes both parts for assembly our crafting at Fredericia’s own production plants, as well as finished products from subcontractors.
The product country of origin describes the point of most value creation, and as such it can include both a assembly, finishing or total production.
*Misc includes sale of spare parts, samples, catalouges and other marginal products, and the country of origin distribution of this category is assesed to be equal to the inbound cost spend distribution
As a family-owned company, Fredericia is able to look beyond the next fiscal year and make long-term investments that support our purpose-driven mission. A strong governance structure determines the rights and responsibilities within the organisation, with decision-making rules set by the company’s board of directors. Our employee association is set up as an independent branch of the organisation and creates social arrangements supported by the company.
Our mission and corporate values
∙ Our board structure, including employee representation on board of directors
∙ Transparency of ownership structure and value creation distribution
∙
9,2 years
Average seniority
Every sofa, every chair, every detail tells a story—not just through its design, but through the hands that have crafted it. Behind the elegant shapes and carefully chosen materials lie hours of dedicated craftsmanship, expert technique, and the continuation of proud traditions. One such master of the craft is our colleague, Birthe Mona Jensen.
For more than four decades, she has been at the heart of the upholstery workshop in Svendborg, Denmark, transforming raw textiles and wooden frames into iconic designs that now grace homes and public spaces worldwide. For Birthe, upholstery is not just a skill—but a lifelong passion. Every stitch and every adjustment are a testament to years of refinement and the pursuit of perfection.
Here, Birthe shares her journey — a life dedicated to mastering the unique art of upholstery:
“In 1984, at 18, I began working in upholstery—almost by chance. My husband worked in furniture production in Svendborg, and through him, I was offered the opportunity to do an internship. That internship quickly became full-time as I discovered my passion for creating something from scratch. Most people don’t realise just how much work goes into making a single piece of furniture—the craftsmanship, the precision, the sheer number of steps—from cutting leather and textiles to glueing, stitching, and assembling. Every stage is a challenge, but it’s also what makes the process so rewarding.
The first piece I worked on was the EJ50 sofa, with its moulded cushions in a sandcoloured fabric. I remember thinking, “I’ll never learn how to upholster something like this.” But with time, the skills settled into my hands, becoming second nature.
Of all the pieces I’ve worked on over the years, the Corona Chair by Poul M. Volther remains my most incredible pride. Even now, I love working on it. It’s always a challenge—whether upholstered in fabric or leather, each material behaves differently, requiring a unique approach. That complexity is what makes it so fascinating.
Another favourite of mine is the EJ315 sofa by Erik Ole Jørgensen. With its intricate button details and, at times, striped fabric, it requires absolute precision. It’s a demanding piece, but that’s precisely what makes it enjoyable—no two days are the same.
After 40 years, these techniques have become deeply ingrained in me. It’s only when I’m training new upholsterers that I truly realise the complexity of the craft. There are many layers and techniques; everything must be perfected through repetition. For example, upholstering a Corona Chair in leather takes at least six months to master. I’m the only one who can do it at a certain speed—a few others can make it, but they take three or four times longer.
My work is wonderfully varied. I touch nearly every piece we produce, from Børge Mogensen’s Søborg Chair to his sofas. That variety keeps my work exciting—every piece requires different techniques, ensuring that no two projects are ever the same.
My record is 41 Corona Chairs and 19 Corona Ottomans in just three weeks. After such an intense stretch, I always appreciate switching to other designs. That flexibility is something I truly value in the workshop. Even on holiday, I find my fingers itching to return to work. That’s just how it is—I’m incredibly fortunate to have turned my passion into a career, mastering a craft I take great pride in.”
Distribution by gender
Management team – Line managers
Contact
Headquarter
Fredericia Furniture A/S Treldevej 183 7000 Fredericia Denmark +45 7592 3344
info@fredericia.com @fredericiafurniture fredericia.com
Showrooms
Copenhagen Løvstræde 1, 4th & 5th floor 1152 Copenhagen
London
Unit 4, Compton Courtyard 40 Compton Street London, EC1V 0BD
Oslo
Drammensveien 120 N-0277 Oslo