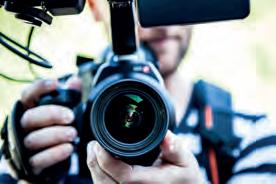
5 minute read
INTERVIEW – Siemens
IM
Insight Series VIDEO INTERVIEWS
Advertisement
Conducted in numerous global locations by Editor Dan Gleeson and Editorial Director Paul Moore, these interviews are unique collaborations by IM and the world’s leading mining technology suppliers, getting the lowdown from the key people involved in development and design

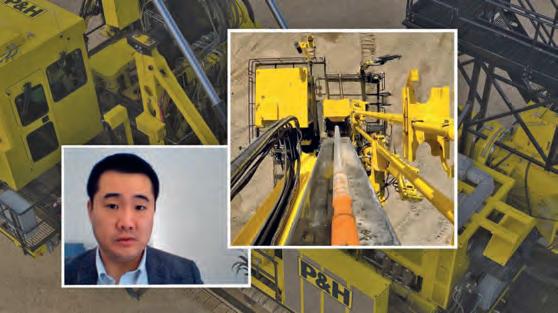
THE P&H 77XR – COMBINING DRILL POWER WITH FLEXIBILITY
An interview with Sergio Li, Product Manager – Rotary Drills, Komatsu Mining
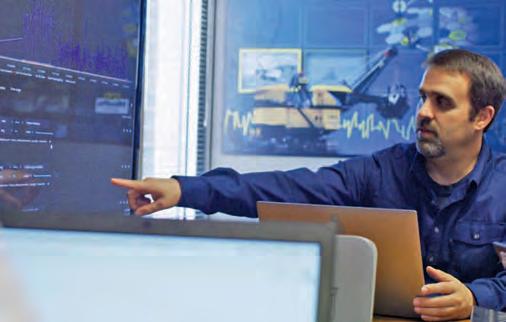
DATA DRIVEN DYNAMIC MINING
An interview with Jason Knuth, Senior Manager –Data Solutions, Komatsu Mining
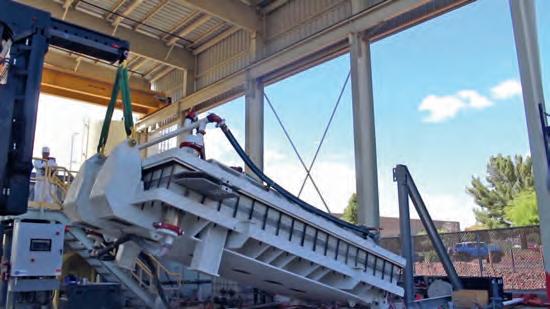
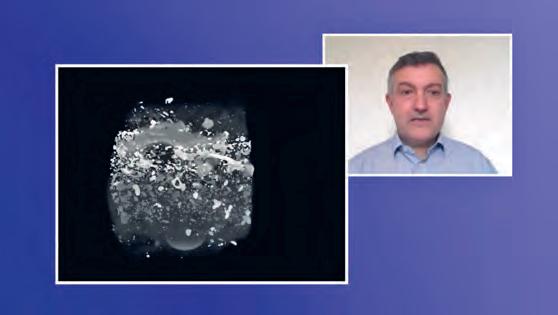
MINING’S SUSTAINABLE FUTURE
An interview with Thomas Schulz, Group CEO, FLSmidth
THE POWER OF OREBODY KNOWLEDGE
An interview with Eddy Hill, – Natural Resources and Metals, ZEISS Microscopy
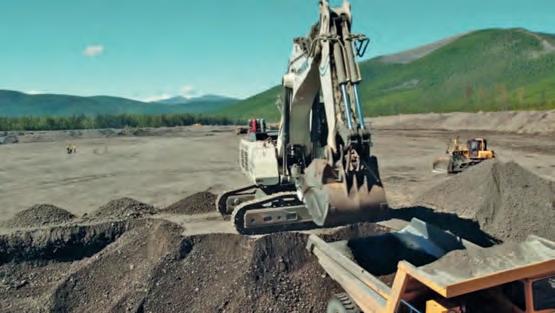
LOAD & HAUL’S NEXT LEVEL
An interview with Burkhard Richthammer, Managing Director Design and Engineering and Joerg Lukowski, Vice President, Sales & Marketing, Liebherr Mining-Equipment Colmar
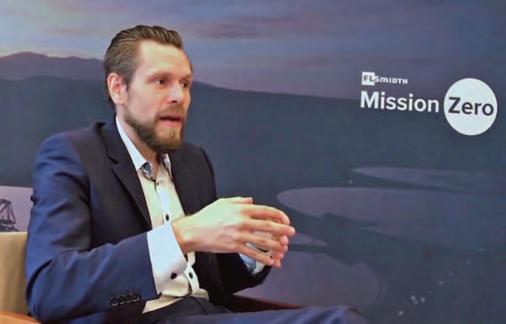
DIGITAL IS THE REAL DEAL
An interview with Mikko Tepponen, Chief Digital Officer, FLSmidth
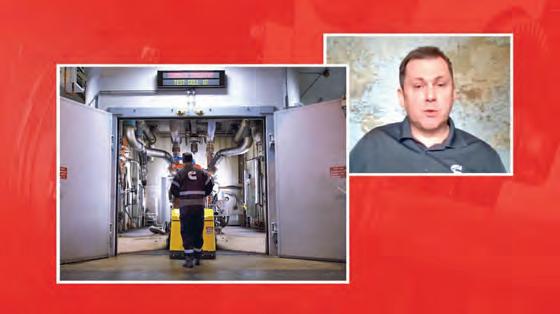
POWERING A SUSTAINABLE MINING FUTURE
An interview with Sean Lynas, Director Mining OEM Business, Cummins, and Robert Schaefer, Director Growth & Innovation, Cummins
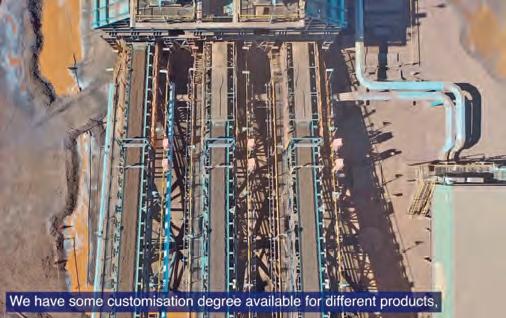
MINING’S NEXT GENERATION CRUSHING SOLUTION
An interview with Mike Grey, Chief Executive, Mining Services, Mineral Resources Ltd, & Guillaume Lambert, Vice President, Crushing,Metso Outotec
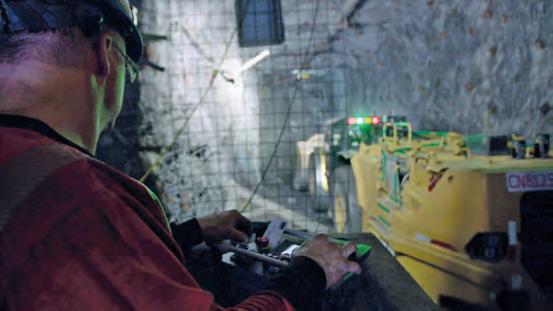
GETTING SMARTER UNDERGROUND
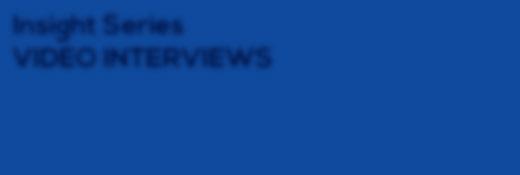
An interview with Robert Droogleever, GM Underground Mining, Caterpillar, and Randy Schoepke, Commercial Manager for Underground Technology, Caterpillar
IM
Insight Series VIDEO INTERVIEWS
If you are interested in working with us on an IM Insight Series video interview please contact Editorial Director Paul Moore at paul@im-mining.com or Editor Dan Gleeson at daniel@im-mining.com for rates and more information
Setting the standards in mining

Powering some of the world’s largest mining conveyors, grinding mills, hoists and trolley assist truck fleets, Siemens has an enviable reference list and depth of experience. Paul Moore spoke to Christian Dirscherl, VP for Mining, Excavation and Transport about its multiple market successes and continued potential going forward
Q Starting with large conveyors with gearless drives, Siemens has a unique set of application examples – can you give a brief overview and thoughts on how you have been able to achieve this depth of experience?
A Our list of gearless drive installations for large overland and underground conveyors continues to grow including a number of the world’s leading copper mines: Antapaccay, Las Bambas, Escondida OGP1, Quellaveco, Oyu Tolgoi, Cuajone plus a copper mine in Tibet, China. Quellaveco, Oyu Tolgoi and the project in Tibet are all still in the installation and commissioning phase. In terms of contract wins – the continuity Siemens conveyor GCD in place at Cuajone copper mine, Peru
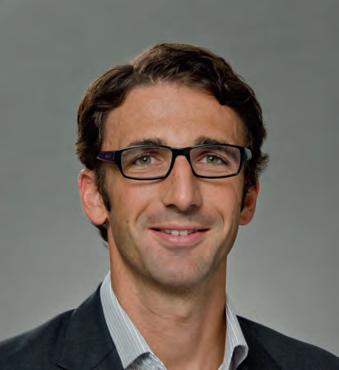
of our major orders – seven world class gearless driven conveyor projects in less than ten years –has been a factor. Plus we have continued to set records both for the power of the systems –
Cuajone and the mentioned copper mine in Tibet are both 2 x 6,000 kW and Oyu Tolgoi is 8 x 5,500 kW – and the climatic extremes – the minesite in Tibet at over 5,000 m altitude. Plus, it has involved many of the world’s top tier miners with very exacting performance and safety standards – Rio Tinto, Glencore, MMG, Southern Copper (Grupo Mexico) and BHP. Also I would mention the continuity in our team –many of the same experienced Siemens people have worked on several of the projects together. And having a series of projects has allowed us to make continuous improvements in areas like cooling, leading to greater standardisation of our solution. Another relatively recent change that will allow us to grow this market further is that before we worked exclusively with thyssenkrupp and while our close relationship with them continues, we are now in a position to work with any major conveyor system OEM or contractor and in fact are already doing so.
Q Has the pandemic had any effects?
A There have been some difficulties and delays as would be expected due to COVID-19 – there is a lot of specific expertise involved in these types of mining infrastructure projects so travel restrictions have had an impact – near the start of the pandemic, as an example, Mongolia had imposed a 25-day quarantine. Plus there are often restrictions on travelling between regions within the same country and on top of that many mines have restricted access to contractors and suppliers. Currently, for Oyu Tolgoi we are providing services remotely while at Quellaveco we have teams onsite. The pandemic has also slowed activity in terms of new feasibility/prefeasibility studies though with the current high price of copper there are several major projects now on the horizon.
Q As an example can you highlight the scope of the Quellaveco project?
A The new thyssenkrupp conveyor at Anglo American’s Quellaveco advanced development copper mine in Peru will transport 127,500 t/d of ROM copper ore to the stockpile adjacent to the copper concentrator. The conveyor will get from one valley to another through a 3.2 km long tunnel. Our input includes twin 5.5 MW gearless drives operating at a design tonnage of almost
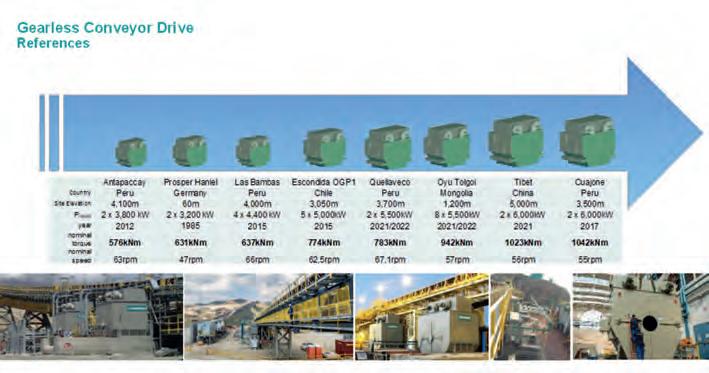
Siemens has a unique set of gearless conveyor drive references unmatched in the industry