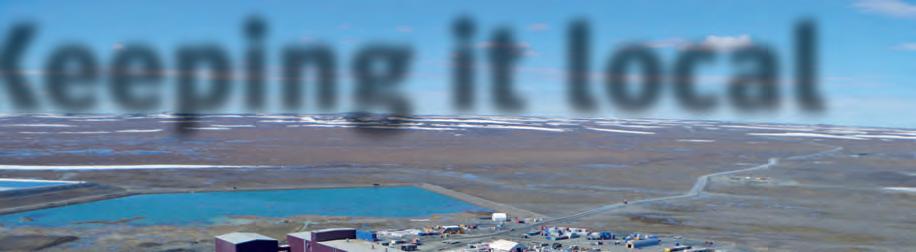
18 minute read
REMOTE MINING SERVICES
Keeping it local
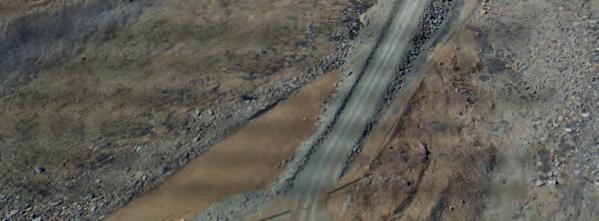
Advertisement

As border closures and COVID-19-related restrictions took hold over the last year, on-site suppliers of key services have risen to the fore. Dan Gleeson reports on initiatives and contract wins from some of the sector’s integral industry contractors
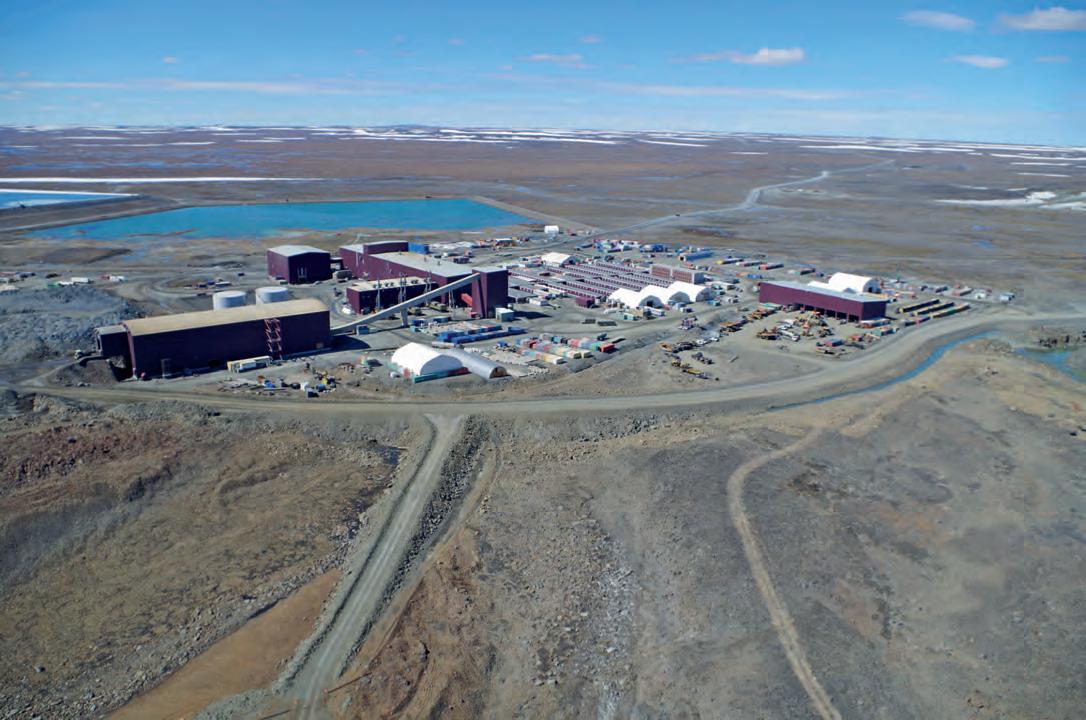
As COVID-19 hit, the importance of critical service suppliers at remote mine sites became obvious.
The fly-in fly-out restrictions and shutdown of supply chains made it harder than ever to get equipment, personnel and supplies into the operations that needed it.
This flexed the muscles of remote service suppliers – testing established supply chains and logistics networks – but, in the face of these issues, they continued to deliver.
At the same time as they continued to get key supplies in, they ensured the virus did not get out and spread.
Many contractors were called on to instil a rigorous cleaning regime, social distancing procedures and adaptable dining options to ensure COVID-19 could not spread exponentially in remote camp sites or into local communities.
Sundeep Singh, BHP’s Group Procurement Officer, paid tribute to these service suppliers during the IMARC Online event late last year.
“Once it was clear COVID-19 would present a significant challenge to our operations, our first priority was to keep people safe,” he told attendees. “We were quick to enforce strict social distancing and hygiene protocols.
“For the supply chain, we triggered the traditional responses such as seeking alternative sources of supply for things like hygiene products. We managed our inventory levels for critical spares for our mobile and fixed plant, we even stepped up data analytics for supply chain transparency – however, none of this alone gave us our resilience.”
Singh said it was the support of BHP’s supply chain that ensured the company kept operating and generating employment, taxes, royalties and dividends in this time of crisis.
“Over this past year, it is with your support that BHP’s global supply chain adapted quickly to respond to the crisis,” he said to the company's suppliers. “Partnering enabled us to react swiftly and confidently in these times. It has allowed our supply chain to rapidly repair with preferential treatment, re-route through joint collaboration and re-invent for new value.”
He provided some examples, in the process referencing UK-headquartered Compass Group.
Compass provides facilities management support for BHP’s operations across Australia, which was critical during COVID-19, according to Singh. This included everything from providing hygiene supplies, to the safe movement and accommodation of people.
Within this contract, Compass was providing more than just the basics during COVID, as Singh explained.
“Partnership led Compass through this time, and through this difficult year, to build a facility in Perth, known as…‘The Academy’. ‘The Academy’ includes a training kitchen, juice and barista training stations, simulation accommodation rooms.”
The benefit of ‘The Academy’ was two-fold, according to Singh.
“Our BHP residents benefit from the higher standards and the skills of the Compass staff to manage this new COVID normal,” he said. “Compass benefits via improved customer satisfaction, but also the ability to train their people more broadly for roles outside of BHP. We now have continued safe flow of people and a better experience for our workforce on site.”
Compass Group Australia Managing Director, Shelley Roberts, referenced the importance of such training in her own presentation at IMARC Online.
She also highlighted how the company works with indigenous groups at mine sites to help clients achieve their ESG goals, as well as share some of mining’s benefits with local communities.
Roberts, during the event, said the service supplier was building sustainability practices into its supply chain and, where possible, employing indigenous workers and subcontracting indigenous businesses.
Compass provides workplace support for every aspect of daily community life in largescale accommodation centres – including meals, accommodation, beds, laundry – and has a diverse mining and resources industry workforce in Australia.
Close to 10% of its contingent are Aboriginal and Torres Strait Islands employees, while it has
In July 2020, Sodexo was engaged to provide facility and food services at CRI's copper-nickel mining camp in Nunavik, Canada (credit: Canadian Royalties Inc)
Colluli is located in the Danakil Depression region of Eritrea, around 230 km by road southeast of the Port of Massawa (credit: Danakali)
close to 50 indigenous suppliers in its supply chain, Roberts said.
In Australia, it has successfully integrated more indigenous representation into its camps in Port Hedland and Onslow, but Roberts was keen to emphasise that there was no ‘cookie cutter’ exercise to replicating this at every site in Australia.
“A process of discovery is required in every community,” she said. “It is essential to get a strong sense of the local community first. By doing so, it is possible to identify the best opportunities to make an impact and achieve a positive outcome for the local community.”
This sees the company carry out in-depth research into the community in which it might become a part of before offering up guarantees to the client and community at hand.
The same due diligence is employed to ensure more of its procurement comes from local suppliers.
“What we have learnt about making local procurement successful is we often need to support capability building in key corporate processes like food safety and other compliance requirements,” she said. “That effort is really worthwhile and creates life-changing community benefit.”
Another service provide that has successfully incorporated indigenous groups into its local offering is France-headquartered Sodexo.
Sodexo Canada recently partnered with its Inuit partner, Nuvu, to successfully mobilise a comprehensive integrated facility and food service to Canadian Royalties Inc’s (CRI) copper and nickel mine base camp in Nunavik, the most northern region of Quebec, Canada.
The company has been providing food and facilities management services in Canada for over 40 years. It has a focus on enhancing safety, work process and well-being, exemplified by a recent decision to partner with Bureau Veritas on introducing a hygiene verification label for Sodexo procedures and services to support business reopening amid COVID-19.
At a national level, Sodexo Canada counts more than 80 Indigenous suppliers to deliver local goods in the remote camps it is serving, from Nunavut to the North territories.
Like Compass Group, the company ensures its partners meet its standards through on-the-job training and coaching to get the “right engagement in the process and ensure that the process is in place for the continuity of our business relationship”, Pierre-Henry Arsapin, District Manager Energy & Resources at Sodexo Canada, said.
Arsapin added: “Food safety is, of course, our utmost priority and it is our responsibility to make sure that our partners are following the protocols we put in place to ensure a safe work environment.”
In July 2020, Sodexo was engaged to provide facility and food services at CRI’s mining camp in addition to supplying the necessary PPE considering the evolving global COVID-19 pandemic. Due to weather as well as the mine’s location and operational needs, Sodexo’s mobilisation required the sourcing and delivery of the nine-month supply of food and provisions in a six-week timeframe while managing the transition of essential hospitality services to ensure the health and safety of all employees.
Sodexo and Nuvu successfully established a team to secure a reliable supply chain. Together, they leveraged Sodexo’s international experience and Nuvu’s local expertise to apply innovative methods and cultivate meaningful relationships with the community to deliver results, Sodexo said.
During the mobilisation, mine operations went uninterrupted, with Sodexo sourcing and distributing all supplies through its Canadian supply chain network. It involved the sourcing of provisions for three meals per day over 279 days and the delivery of 102 containers.
In addition, Sodexo was managing accommodation, concierge and logistics for the home-to-home journey experience of more than 450 base camp employees and CRI collaborators.
The company explained: “Our team coordinated efforts across our global company and with our local partners to deliver provisions safely and on schedule. Sodexo sourced cleaning and disinfectant products to ensure pandemic health and safety protocols could be followed at the base camp. At destination, the team was responsible for unloading the containers, transferring goods to trucks for transport to the base camp. The unloading required the team to use special insulated blankets to ensure provisions didn’t freeze.”
The company was able to exceed the project’s environmental targets through “responsible sourcing”. This included providing milk in recyclable containers.
Erwin Joosten, Senior Vice President, Energy & Resources, said: “At Sodexo, sustainability is one of our key pillars. I’m proud of our supply team who collaborated with local partners to think outside of the box in order to ensure we were able to meet and exceed our environmental goals for this project.”
Sodexo said its work with CRI went beyond supplying provisions, with the company transitioning some of its existing employees to the base camp and, through its partnership with Nuvu, welcoming new employees from the surrounding Inuit community.
Joosten added: “Our relationships with Inuit communities are true partnerships that are mutually beneficial. Our work boosts the education, health and overall wellness of the communities we serve. At the same time, with the support of Nuvu, we have been able to leverage Inuit talent to help us deliver our services.”
Sodexo also hired a special COVID-19 team, in charge of distributing cabarets, glasses and utensils, as well as cleaning high touch surfaces on an hourly basis. These measures were taken to ensure a safe working environment for everyone, it said.
Sodexo Canada, having applied the ‘hygiene verification label’ and leveraged standard operating procedures for COVID-19 developed operating all over the globe, has ended up being viewed as a “strategic business partner” as opposed to a subcontractor, according to Arsapin.
This has seen existing clients and prospects request specific “Pandemic Protocol” on top of the company’s core offering.
Arsapin explained: “What we call a business continuity plan used to be an ‘annex’, but now it’s part of the core offer, and is a requirement to
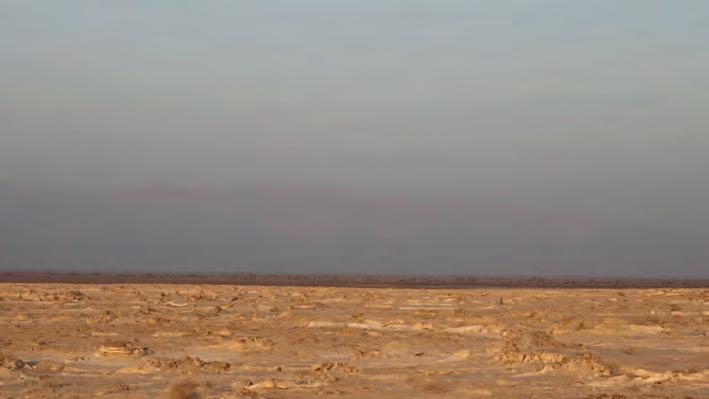
be detailed and supported by specific documentation and protocols known and updated by the management on site.”
The company’s use of mobile app services, contactless payment systems and safe selfservicing with “smart fridges”, among other initiatives, has helped its growing reputation, he said.
“Within a year, we were able to bring the quality of living on the sites we take care of to the next level,” he said. “Having one global leader to carry all the core services not related to the mining business helps our clients to focus their energy where it should be and create the perfect synergy with their main provider: us.”
Building ESG into its offering
UAE and UK-based RA International says its reputation as an ESG and sustainability provider is supporting commercial companies like miners in delivering their own sustainability objectives.
This will be put to the test in Eritrea where the company has been named preferred contractor for the supply of accommodation, support services and other infrastructure buildings at the Colluli sulphate of potash project development as part of a contract worth more than $20 million.
RA specialises in building, operating and maintaining facilities in remote and challenging conditions across Africa, providing services for various industries including mining.
It recently concluded contract negotiations with Danakali Ltd, a 50:50 owner with the Eritrean National Mining Corporation of Colluli Mining Share Company, the entity holding Colluli, for the construction of camp accommodation for 1,200 personnel, administration and service facilities, as well as the provision of integrated facilities management services (such as catering, cleaning, laundry, pest and vector control, grounds keeping and waste management) at the project.
The camp accommodation has been designed to accommodate 600 personnel during the production phase with the flexibility to accommodate 1,200 during construction, according to RA International.
The plant administration and services facilities will incorporate administration offices, medical clinic, warehouses and workshops.
The construction works are to be phased, with the first of three phases commencing upon receiving the necessary approvals and subsequent phases commencing as CMSC funding is available, RA International said. Construction activities are anticipated to be completed within a year, with the operating contract commencing immediately, postconstruction.
On top of this contract, the company, in March, said it was in advanced discussions to secure a significant contract in connection with a new mining project in North Africa.
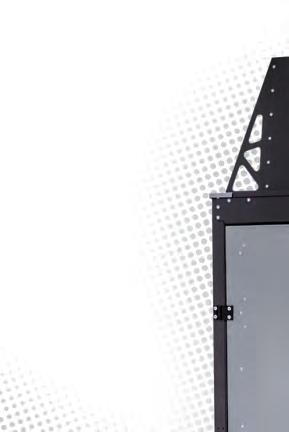
Remote communications
Specialised ICT and communications provider, Aqura Technologies, has ensured many remote mining sites have access to these all-importance services during the COVID-19-affected period.
Western Australia’s iron ore sector has been a particularly fruitful area for the Veris Ltd subsidiary, with Aqura capturing business with BHP, Roy Hill and Fortescue Metals Group in the last year or so.
The company’s ‘opex as a service’ model has been key to adding much of this new business to its portfolio.
In July 2020, Aqura signed a multi-year service contract with BHP’s Western Australia Iron Ore (WAIO) business unit that will see it provide managed support for all in-room communications and entertainment system services across the miner’s accommodation villages in the Pilbara.
The company added to this remit in August 2021 with a contract that would see Aqura upgrade and extend the technology and communications infrastructure at a range of BHP WAIO accommodation sites surrounding the township of Newman, also in the Pilbara. The scope of work involved the design, procurement and construction of new point-to-point microwave, DOCSIS and fibre-optic infrastructure to enable upgrades of in-room Wi-Fi for a number of
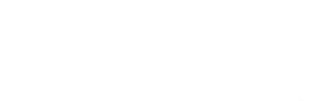

MINE MINExpo xpo
South Hall, booth South Hall, booth 26139 26139
THE NEW METHOD FOR GREASE DISCHARGE
The one of a kind discharging solution for lubricants in mining and steel industry
STURDY & STRONG
• For heavy-duty work environments • Twists and squeezes with great force, residue levels down to 2%
SAFE & SEALED
• Grease kept clean from dust, particles and moisture • Discharge mechanism behind safety doors
265 or 240 gal. container
www.fluid-bag.com
Aqura Technologies CEO, Travis Young, says mine site accommodation network investments fundamentally support and enhance the positive wellbeing for fly-in fly-out staff who are away from home for extended periods and need reliable infrastructure to support connections to family and friends
accommodation sites, Veris said.
Later that month, it then secured a new agreement to provide Managed Services Support for BHP WAIO accommodation village entertainment networks across nine sites.
This will see Aqura’s in-house team will provide managed support services for village entertainment network and Wi-Fi access across BHP WAIO village accommodation rooms and public areas as part of this agreement.
This latest contract award leverages the internal investment undertaken by Aqura over recent periods to develop leading-edge Content Access Networks As a Service solutions, it said. “These provide capability to generate multi-year managed services frameworks with clients across a range of sectors while delivering best of breed user experiences replicating their at-home experience in a remote setting,” Aqura explained.
Young said the engagement was a significant recognition of Aqura’s capability and skills in the delivery and efficient operation of large-scale networks and further solidifies the company’s strategic transition to a product and servicebased business.
“This engagement continues a highly successful relationship supporting BHP’s Inroom Communications and Entertainment Solution (IRCES), which saw Aqura upgrade over 12,000 rooms to provide high-quality connectivity access for their workers when they are away from home,” he said.
“We are proud to continue supporting BHP who have further shown their commitment to local businesses with this three-year engagement to ensure the IRCES network continues to deliver reliable and cost-effective access for many years to come.”
In February 2021, meanwhile, the company was awarded A$1.1 million ($849,165) in works to undertake an upgrade of the in-situ accommodation network at Fortescue Metals Group’s Kangi 1,850 room village in the Pilbara.
The scope of the Kangi village engagement was to design and deliver physical upgrades to the GPON network to ensure a high level of reliability of services to village guests, it said. The enhancement of the existing infrastructure, using Aqura’s specialist technical expertise, will establish an extremely robust platform for the delivery of entertainment services and wellbeing programs to the large workforce accommodated at the site, the company explained.
Aqura was expected to have completed the scope of works by now.
“The new contract adds to Aqura’s strong track record in delivering high-performance Content Access Network (CAN) solutions for clients such as BHP, Newmont, OZ Minerals and Abra Mining,” Veris said of the FMG contract. “Aqura’s expertise in the delivery of CAN solutions has delivered enhanced user experiences in over 16,000 accommodation rooms completed to date.”
Aqura Technologies CEO, Travis Young, added: “We are very mindful of the benefits of this type of investment, which fundamentally supports and enhances the positive wellbeing for fly-in fly-out staff who are away from home for extended periods and need reliable infrastructure to support connections to family and friends.”
Improving connectivity was also behind Roy Hill’s decision to contract Aqura for support in designing, installing and commissioning the first phase of a new high-performance private LTE network for its operations in the Pilbara. It followed similar projects for Rio Tinto and OZ Minerals.
The scope of the Roy Hill engagement includes providing services for the first phase of a private 4G LTE network for large-scale mining operations, encompassing design, engineering, site installation and commissioning.
Aqura’s first phase works were expected to be completed last month.
Just last month, Aqura was awarded a grant from the Australian Government under the 5G Innovation Initiative to, it says, augment the organisation’s own development work to address the challenge of delivering underground 5G LTE.
The grant is an important step to overcome the technical and commercial barriers associated with operating next-generation broadband wireless networks in sub-surface environments, according to Aqura.
The 5G Innovation Initiative grant will complement investment already made by Aqura to deliver technical architectures, commercial model development and installation of a live Private 5G LTE network in an operating mine. The project leverages a lot of learnings from a 2017 project where Aqura successfully delivered Private 4G LTE in an underground mine in the Kalgoorlie region of Western Australia, Aqura said.
The focus of the program is to fast-track the enablement of applications and processes that are being adopted in surface operations so underground operators can realise the benefits of enhanced environmental, safety and productivity outcomes that advanced wireless communications can deliver, it added.

Alliance takes flight
Despite the issues getting personnel into and out of remote mine sites during the pandemic, many mining companies have pledged to continue operating fly-in fly-out operations in Australia, among other locations.
Alliance Aviation Services has been a beneficiary of this, recently securing several air charter service agreements across the country.
Alliance specialises in offering transportation by air of its mining and energy customers’ employees and contractors to and from remote locations.
The company, in April, announced a two-year extension of its air charter services agreement with BHP’s Western Australia Iron Ore division.
This extension, Alliance said, was further evidence of its reputation of outstanding customer retention, solidifying a relationship that started with the first flight for BHP’s Western Australia Iron Ore division in 2009.
The announcement came only six months after agreeing a three-year contract extension (with two 12-month extension options) with the
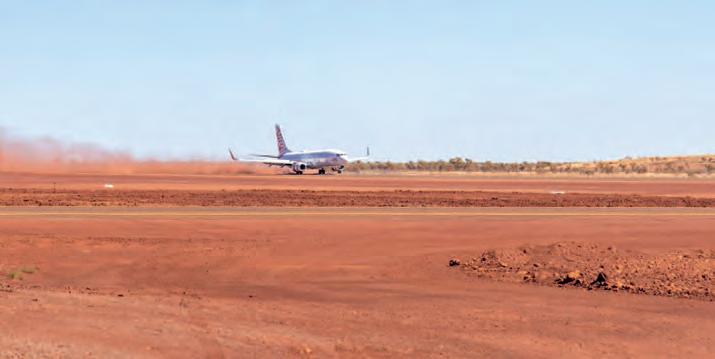
major miner for charter services into the Olympic Dam mine site operations, in South Australia, as well as scheduled services supporting the local community of Roxby Downs.
The contract, building on 14 years of serving Olympic Dam and the Roxby Downs community, will see the introduction of Fokker 100 jet aircraft, a 100-passenger seat aircraft, into Olympic Dam Airport, coinciding with significant upgrades at the airport.
The introduction of larger capacity aircraft will provide ongoing savings to both Alliance and BHP Olympic Dam, provide the miner with greater scalability for future growth plans and ensure greater comfort for all passengers, Alliance said.
Alliance’s Chief Executive Officer, Lee Schofield, added: “Passengers will enjoy a smoother, quieter and, more importantly, quicker flight between Adelaide and Roxby Downs with a reduction of 20 minutes, or 25%.”
In January, meanwhile, Alliance, executed a contract extension with Newmont to continue chartering flights for the miner to the Granites Mine Site in the Northern Territory of Australia from bases in Perth, Darwin and Brisbane.
The three-year agreement servicing Newmont’s Tanami mine, one of the most remote in Australia, extended the contract with the miner until 2024.
Schofield said of this award: “Air charter services to Newmont’s mine site have increased over the last nine years and it is the only site in Australia where we fly into from three different states/territories.”
It was a Virgin Australia-branded plane that became the first to hit the runway of Western Australia’s newest airport in November last year.
The new Gudai-Darri airport, owned by Rio Tinto and situated some 35 km northwest of the Yandicoogina mine, can accept a range of different aircraft including Boeing 737s, A320s, F100s and King Airs. The airport was built to handle more than 600 workers in a day at peak operating times, according to Rio.
The airport is delivering significant benefits in terms of minimising employee interaction with vehicles and driving, as well as helping to manage employee fatigue thanks to a significant reduction in travel time from an alternate regional airport, Rio said upon the facility opening. As well as servicing Rio’s newest iron ore mine, it will also provide a safer landing option for the company’s long-standing partner, the Royal Flying Doctor Service.
The full construction and design of the airport was completed by local partners Primero Group, NRW Holdings, Worley and GHD, together with NRW sub-contractors Colas, Fulton Hogan, TEC services, Brookdale Contractors, Bennco and Karlka Fencewright. IM
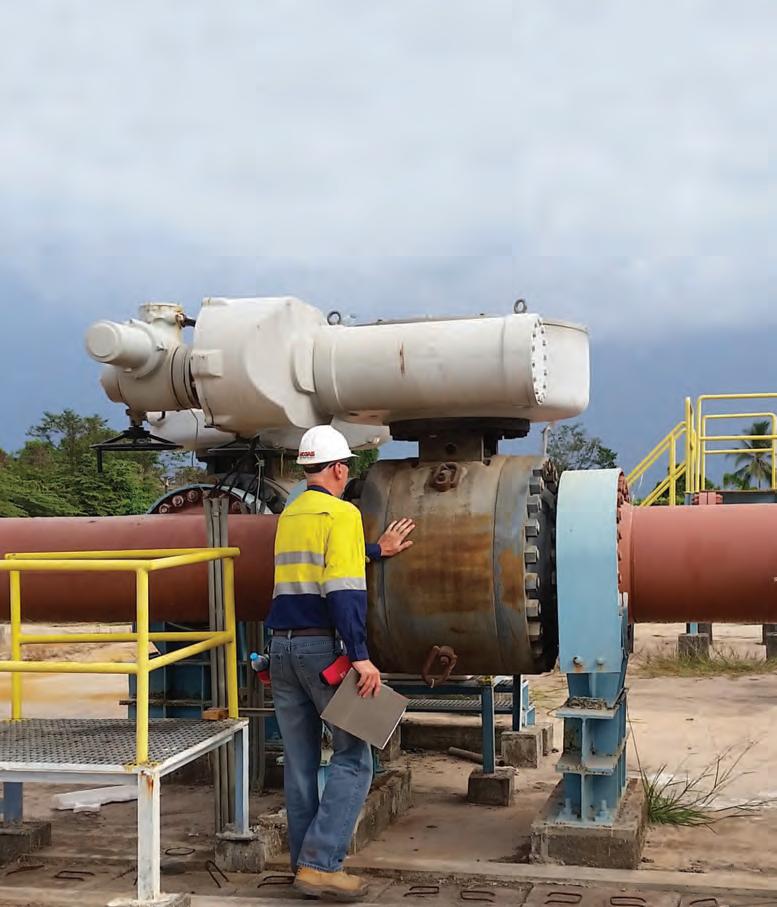
Gudai-Darri airport in Western Australia has been designed to handle more than 600 workers in a day at peak operating times, according to Rio Tinto (credit: Rio Tinto)