
8 minute read
HIGH PROFILE – Sedna
Autonomy’s boots on the ground Sedna autonomous implementation team on the ground at Roy Hill mine, Western Australia. From left to right, Kurt Crossman, Jordan Oxborrow and Jacques Dijzel
Seldom are the specialist integrators that really get autonomous mining projects working on the ground talked about – but they play a crucial role. Paul Moore caught up with Darryl Mitchell, Sedna CEO
Advertisement
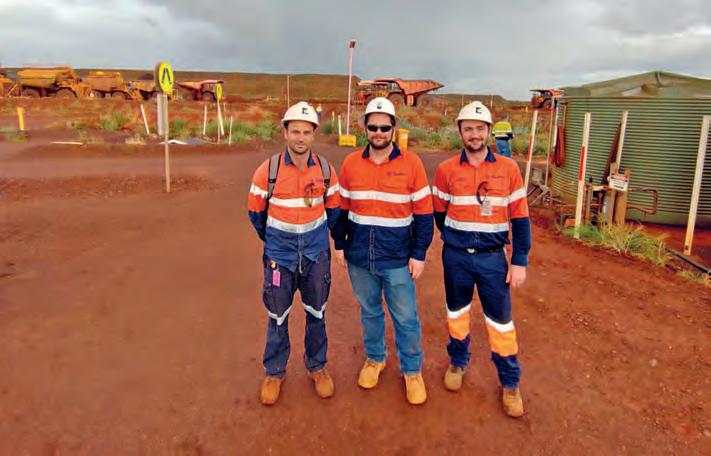
Q Are you system integrators or installers and where do you fit into the market versus others?
A We are all at once autonomous mining system integrators, troubleshooters, trainers and facilitators. A lot of Sedna’s work is with Epiroc, FLANDERS and ASI – which is dominated by autonomy retrofit to blasthole drills and mining trucks. Others in the market are also involved in retrofits but are dealing mainly with “new” autonomous machines working closely with equipment OEMs in a more productised approach. Examples include Autonomo and Mining Technicians Group Australia (MTGA) who between them have handled many of the big AHS and autonomous drilling projects in Australia, particularly since the early days. While we overlap with them to some extent, given that we are mainly retrofit focused, I would say among our strengths is coming up with innovative solutions to engineering, operational & technology problems.
Q On the ground with autonomy retrofit, what are the main challenges you help mines face?
A Number one is definitely networks. Autonomous systems have a big reliance on communications. Often it is the first time that that the comms team onsite have been tested due to the new demands being placed on the network – they are going from being largely a support function, ie maintaining systems, to becoming an integral part of the mining process. The other challenge we see relates to mine planning and surveying as there is a lot that must be put in place on that side of things for an autonomy project to be successful. AHS in particular is a lot less flexible in regard to mine planning versus conventional manned operations. All this is not meant in a negative sense – it is just part of the process that mines must go through on their autonomy journey, so change management plays a key role. I like to think of AHS as being like a process plant – and these mining companies already have people running processing plants facing very similar problems with similar procedures to mitigate risks.
Q Can you describe the IT and comms challenges in more depth – is it related to use of legacy systems?
A The fact is that the comms requirement for AHS is much more demanding than anything that has been done before in terms of its criticality. Fleet Management Systems, usually the main customer of in pit networks, are far more tolerant to comms failures and dead zones than AHS. In the event of a total comms failure a FMS continues to run and add value – with autonomy, comms reliability makes a difference to real time productivity. Autonomy can be achieved with WiFI, wireless mesh or LTE – what matters more is planning and maintenance of the network, and that the comms people have a seat at the top table in terms of mine planning and operations. Often IT and the inpit mining teams have not worked so closely before – now they really have to.
Q Given all this, what role does Sedna play in this mix?
A All of these autonomy projects have an operational readiness phase where we try to get the key decision makers to understand the technology properly, ie this is the system you bought, and this is how it works. Then we work on how to get through the main hurdles to make it work well on site, plus understanding the safety and productivity risks and how to manage those risks. There is starting to be a lot of knowledge of how autonomous systems work in general – but this does not always relate to the specifics of how the particular system being implemented actually works. Incorrect assumptions can be made. We also need to identify for that particular mine what the unique mining challenges are and translate those into system requirements, so that our partners such as ASI can work through them and come up with solutions where needed. After the operational readiness phase there is usually some kind of limited production phase, which will be when the first trucks will be retrofitted. We will sometimes get involved with designing the integration of the drive by wire system, but this is more a part of ASI’s role than ours. Often this is the first time a particular model or variant of truck will have been retrofitted so there tends to be some backwards and forwards work to get the drive by wire element working well. We support our client ASI with a raft of data and testing to help get this done. Everything on top of this layer is relatively standard.
Q Does it get easier after each project or is it always like starting over again?
A It has been getting easier from a technology and project implementation point of view! Autonomy is also getting more common. The challenge is now to keep up with timelines and new projects. We remain a fairly small company but in terms of the experience and skills of our people on the ground we very much hold our own against anyone else. This is the real challenge now – there is only a handful of people with meaningful project experience in autonomy project implementation and as demand grows exponentially, this needs to change.
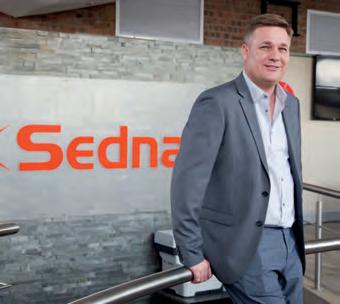
Q Are you predicting a lot more interest in retrofit as a solution such as from Tier 2 miners, contractors and others?
A There is a significant strategic advantage for a miner to remain autonomous from a single OEM,
so I think the retrofit market will continue to grow to allow miners to leverage existing fleets and to allow them to continue to leverage mixed fleets. The future also has to include a higher level of interoperability. I see in the future equipment rolling off assembly lines “autonomous ready” for drive by wire and able to operate in fleets with other OEM autonomous ready machines. Also that traffic management and FMS platforms going forward should be able to “slot in” different autonomous machines - not just one type.
Q Do you remain involved with autonomy projects you have started or at some point are you able to walk away? Has the typical project changed?
A We become less involved – moving from the project implementation to ongoing support with a smaller team. But generally we have maintained some level of continued involvement. A focus at Sedna is further developing our suite of training products to facilitate bringing engineers and technicians up to speed – for us this is strategic as it allows both for our continued growth and for customers to be as independent as they would like to be. Remember this retrofit market is relatively new – our two largest projects, Roy Hill iron ore mine in Australia and Ferrexpo Yeristovo iron ore mine in Ukraine are both in advanced implementation but are not yet full production fleets. The production trials phase of these projects has gotten quicker thanks both to our partner’s technology evolution and experience combined with our experience and learnings – that’s also why we are still in this business. We don’t get as many queries now about a few trucks in a trial to see how it performs – today the customer is saying we are going to do this, here are the KPIs and it will culminate in the full fleet. Now we are seeing about 6-8 months of operational readiness phase followed by first machines moving fairly quickly to full fleet. But the approach depends on the conversation between ASI and the customer – ASI has several potential routes to get to that point. It could include a partial installation on all the haul trucks to allow for some period of mixed manned and autonomy operation. Whatever way you skin it, you can’t afford to stop production for six months to phase it in, it must be concurrent with normal operations.
MINExpo 2021 „German Pavillion“ Booth No 5210
Q The market is really taking off and things are changing on the corporate side. Where does Sedna go from here?
A Today we fill a big niche in a small market. We expect the market to grow and there to be some consolidation, such as ASI’s partnership with Epiroc, which will bring greater scale to the retrofit market. For Sedna, we see our role as facilitating Sedna team with the first Ferrexpo haul truck fitted with ASI autonomous technology
scalability, by empowering end users and installers through knowledge transfer and training. We don’t see the future of Sedna as involving hundreds of people, rather a core group of technical people who are able to partner closely with customers to ensure their success. As the market evolves, we are seeking out new technologies and approaches to unlock productivity. For example – we recently signed a channel partner agreement with Nokia – Sedna going forward will market, distribute and service Nokia’s DAC private wireless and digital enabler platform. IM
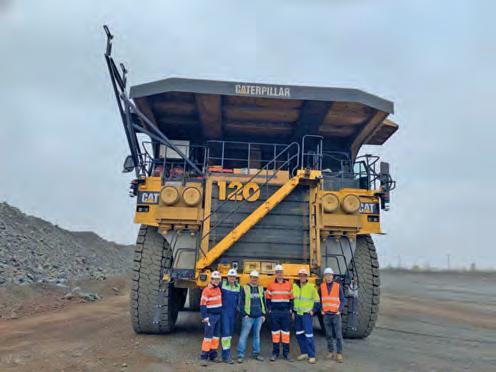
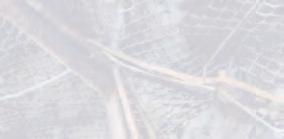
Power Grader
Paus North America Inc. Tel.: +1 (775) 293-8050 Mail: sales@paus-na.com visit us on www.paus-na.com
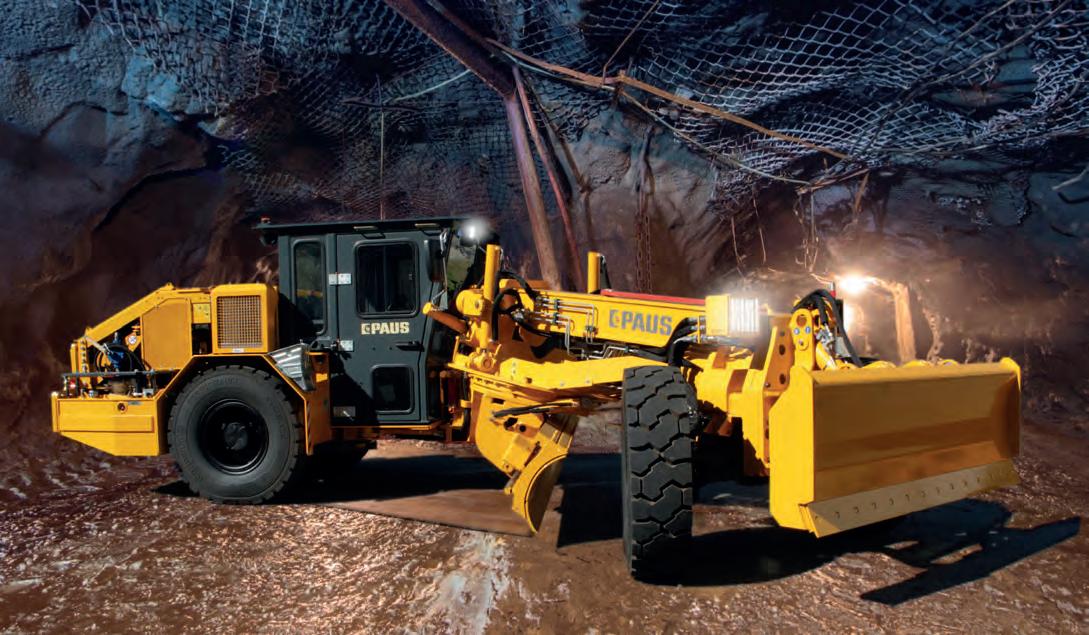