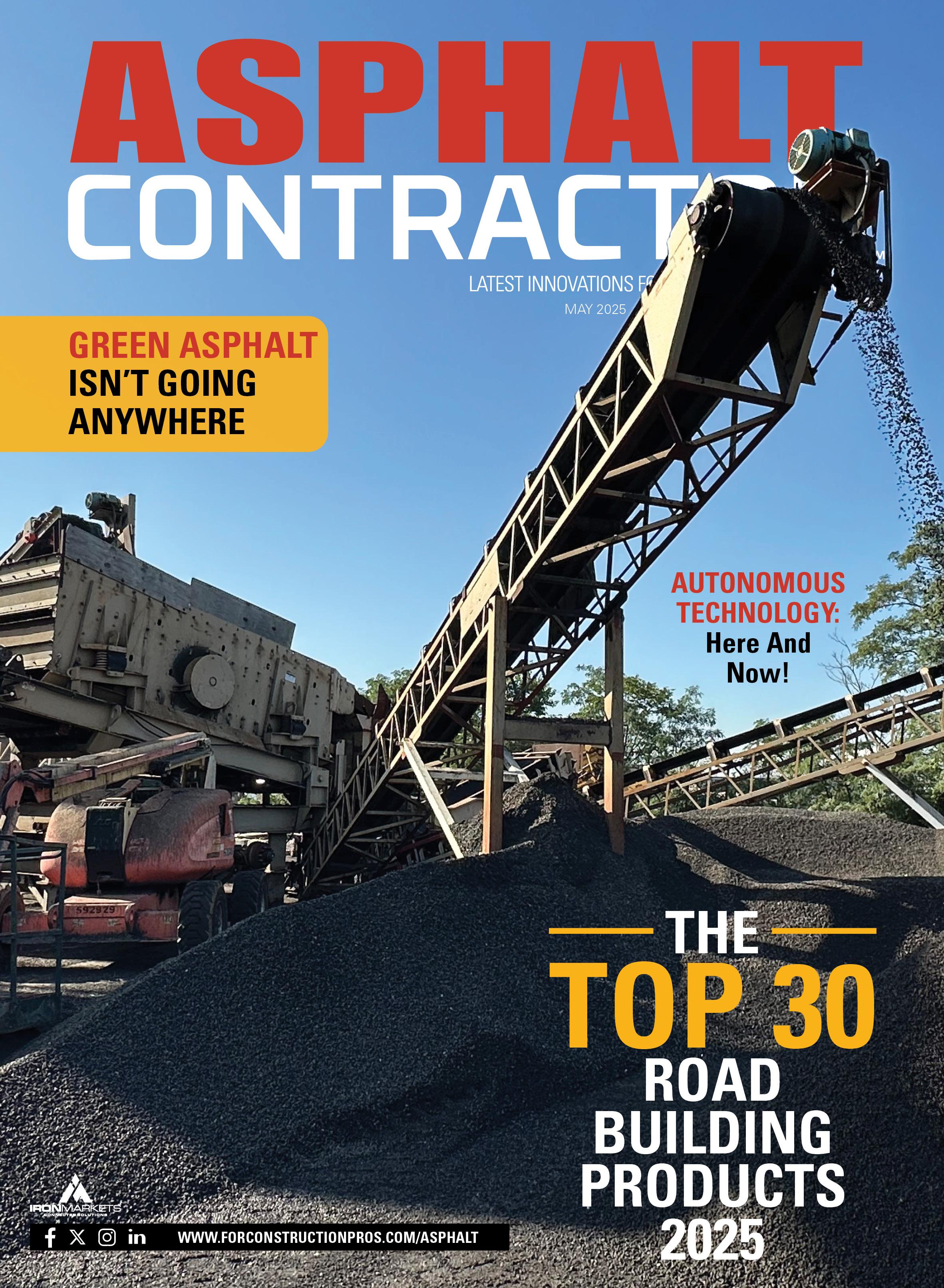
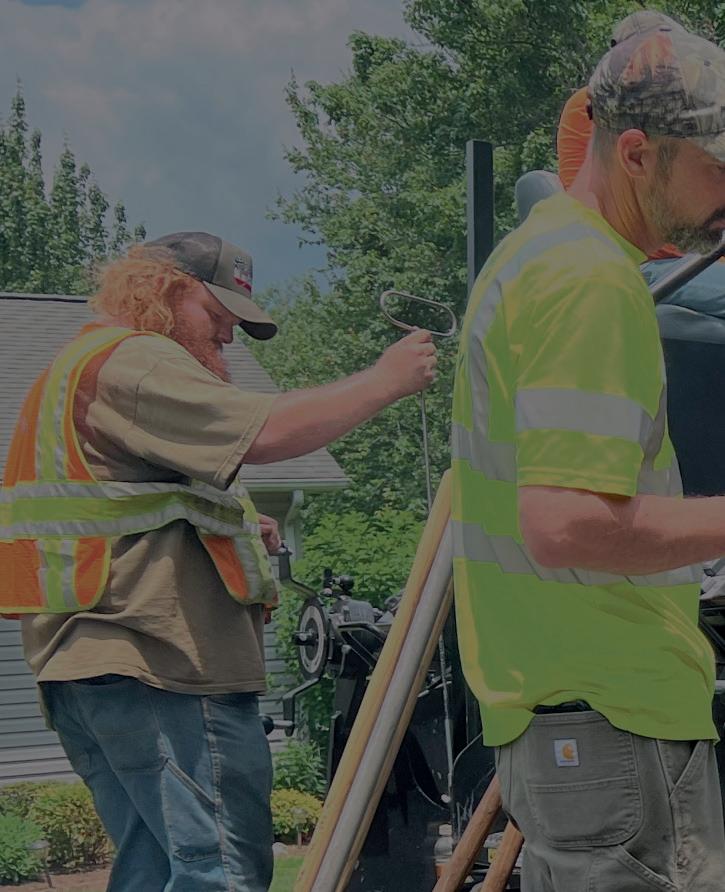
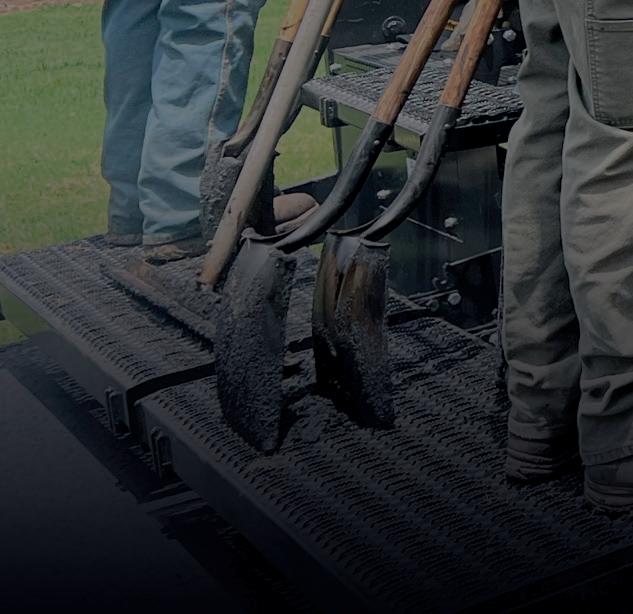
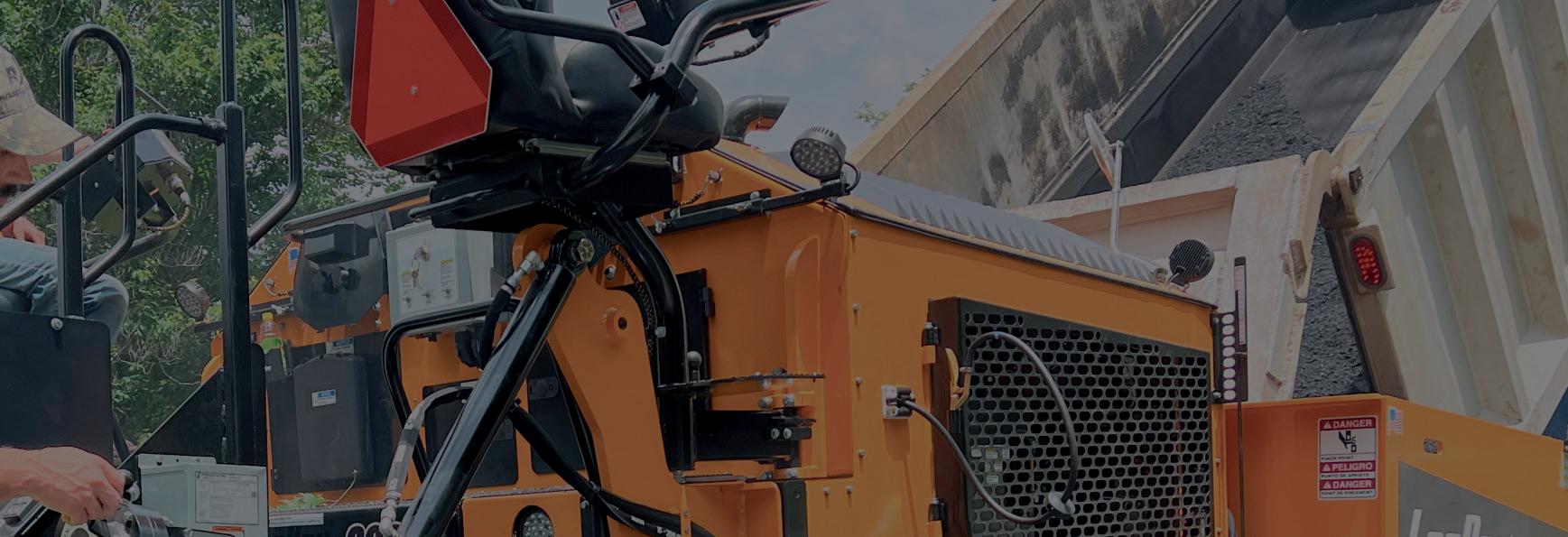


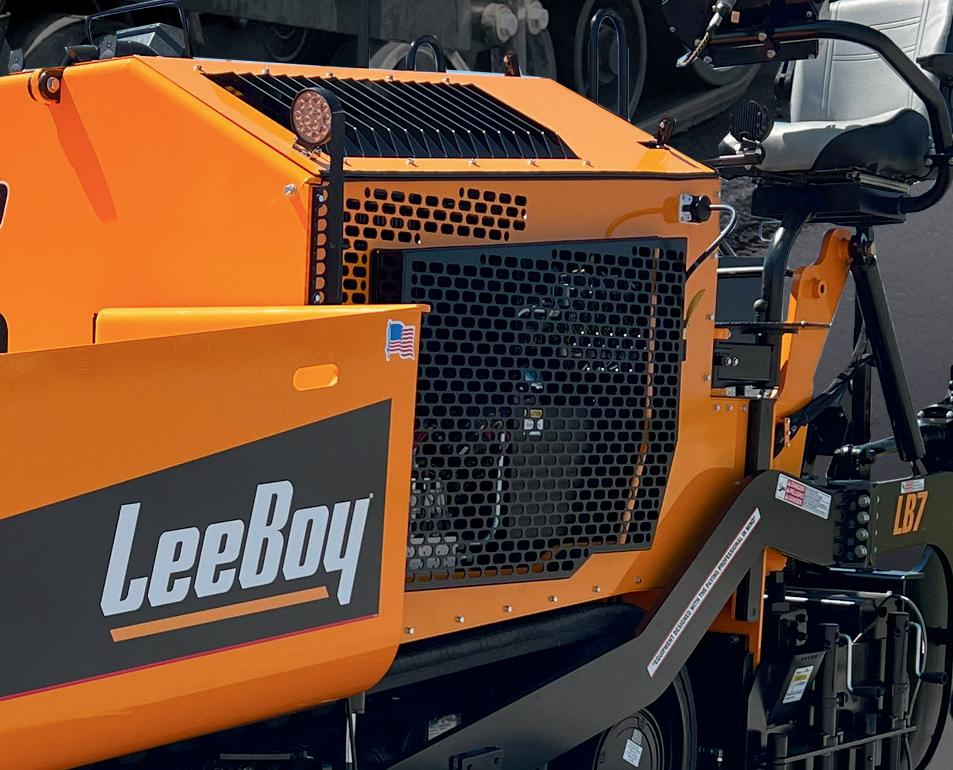



ONE ROAD AT A TIME ONE ROAD AT A TIME
The 8680 Asphalt Paver delivers high production capacity while maintaining a compact and maneuverable footprint meeting the ne of heavy commercial and main-line contractors alike.
210 hp (157 kW) Kubota Tier 4 Final Diesel Engine
needs
Weight: 33,600 lbs. with LB5 Screed; 36,000 lbs. with LB7 Screed
Paving Widths Variable Up To 15’ 6”
High Speed Smooth Rubber Tracks
Actuator Driven Hood Lift to Aid in Maintenance
Inside developments from the Trimble Dimensions 2024 and a look at tomorrow’s equipment tech integrations.
Benefits of Rubber Modified Asphalt
How can this sustainable product, created from recycled used tires, directly impact your business and your customers?
The best new and innovative products for the asphalt and road building industry.
Governments, trade organizations, construction companies, and industry groups have to work together to ensure we successfully attract groups who have historically been more hesitant to consider a career in construction into the industry.
Understanding the importance of pavers and how they are used to not only optimize smoothness, but also build long-lasting roads.
Asphalt Contractor (ISSN 1055-9205, USPS 0020-688): is published ten times per year: January, February, March/April, May, June/July, August, September, October, November, December by IRONMARKETS, 201 N. Main St. Ste 350, Fort Atkinson, Wisconsin 53538. Periodicals postage paid at Fort Atkinson, Wisconsin and additional entry offices.
POSTMASTER: Please send change of address to ASPHALT CONTRACTOR, 201 N. Main St. Ste. 350, Fort Atkinson, WI 53538. Printed in the U.S.A.
SUBSCRIPTION POLICY: Individual subscriptions are available without charge only in the USA. The Publisher reserves the right to reject nonqualifying subscribers. One-year subscription to nonqualifying individuals: U.S. $45.00, Canada & Mexico $65.00,
The editor of Asphalt Contractor magazine, Brandon Noel, steps way out of his comfort zone and into a giant concrete pour. The crew at Ace Avant in North Carolina put him through the paces of any rookie’s first day on the job
Watch the video at: https://asph.link/nc9joi9g
Everything new, cool, and cutting edge at the World of Asphalt trade show in St. Louis, IL! New tech, new equipment, and some really important updates to the industry’s most reliable manufacturers.
Read more at: https://asph.link/ po15p74u
Smart Compact Pro makes a decisive contribution to extending the service life of road surfaces and reduces construction and renovation costs as well as potential additional expenditures at the contractor’s expense.
Read more at: https://asph. link/40bmeh19
Debuting at bauma 2025, the Dynapac SD25 and XD25 Highway Paver series will feature the new integrated interface for auto-steering and screed edge control from Leica, aimed at enhancing the precision and efficiency of asphalt paving operations.
Read more at: https://asph. link/81mn9ezs
25 Products to Prime Your Plans for Roadbuilding
Equipment Today’s roadbuilding roundup brings together some of construction’s recent releases designed to drive productivity on your next project, including compactors, concrete equipment and accessories, pavers, rollers and more.
Read more at: https://asph.link/ hj032lsl
Signup for the Roadbuilding Update, a free bi-monthly newsletter for the most up-to-date DOT, FHWA, asphalt, and other industry news
Astec paves the way for sustainable, innovative asphalt plants. The new IntelliPac Moisture System is a revolutionary solution that integrates seamlessly with Astec control systems. This provides unparalleled, real-time visibility into virgin aggregate moisture content. IntelliPac empowers operators to optimize mix design, minimize energy consumption, and reduce environmental impact. With Astec, you get superior asphalt production – better for the environment, better for your business.
Brandon Noel, Editor
Those who don’t know their history, are doomed to repeat it.
On March 10, 2025, the U.S. Transportation Secretary Sean P. Duffy rescinded certain memos issued by the Biden Administration which added guidelines to federal infrastructure project spending. These guidelines included special considerations for so-called “social justice” issues, environmental concerns, and equityfirst design.
It was another step in the Trump Administration’s efforts to dismantle the infrastructure legacy of the Biden era. Love him or hate him, President Biden passed historic legislation to rebuild America’s infrastructure and manufacturing strength through the IIJA.
The press release sent from the Transportation Secretary’s office said that these policies had, “no basis in statute,” and in that description alone it may be technically correct, however, it falls flat in its overall intent.
Make no mistake, before the Biden memo’s were issued, infrastructure spending was
political. Where a road gets built has always been based in a political ideology. During the great expansion of the national interstate system post-World War Two, many tens of thousands of people were displaced from their homes in the name of progress, but the demographic make up of the displaced signals clearly what political ideology was behind the wheel.
In the decades since, an overwhelming amount of research has proven that the decisions made during that time caused irreparable harm, not only to the communities that were razed to make room for highways, but to the very economic fabric of those cities. As we entered the new century, progress in this area was beginning to be made. The mistakes of the past were starting to be undone.
During the crafting of the Inflation Reduction Act (IRA), there was initially $20 billion earmarked for projects set to restore some of these communities nationwide, strengthening cities once more. When the bill eventually passed, it was knocked down to only $1 billion, but still it was progress.
The fact of the matter is this: reverting to the status quo of the 20th century is a political choice. It’s a political choice that says we would prefer not to learn from the past, but to continue on, blind to our predecessors’ mistakes, ensuring more will suffer the consequences, and passing the buck forward to some unknown future generation to fix.
See you on the road.
EDITORIAL
Editor Brandon Noel bnoel@iron.markets
Content Director, Marketing Services Jessica Lombardo jlombardo@iron.markets
AUDIENCE
Audience Development Director Angela Franks
PRODUCTION
Senior Production Manager Cindy Rusch crusch@iron.markets
Art Director April Van Etten
ADVERTISING/SALES
Brand Director Amy Schwandt aschwandt@iron.markets
Brand Manager Megan Perleberg mperleberg@iron.markets
Sales Representative Sean Dunphy sdunphy@iron.markets
Sales Representative Kris Flitcroft kflitcroft@iron.markets
IRONMARKETS
Chief Executive Officer Ron Spink
Chief Revenue Officer Amy Schwandt VP, Finance Greta Teter VP, Operations & IT Nick Raether VP, Demand Generation & Education Jim Bagan
Corporate Director of Sales Jason DeSarle
Brand Director, Construction, OEM & IRONPROS .....................................................Sean Dunphy
Content Director Marina Mayer Director, Online & Marketing Services Bethany Chambers Director, Event Content & Programming........ Jess Lombardo
CIRCULATION & SUBSCRIPTIONS
201 N. Main St. Ste. 350, Fort Atkinson, WI 53538 (877) 201-3915 | Fax: (847)-291-4816
circ.asphaltcontractor@omeda.com
LIST RENTAL
Sr. Account Manager Bart Piccirillo | Data Axle (518) 339 4511 | bart.piccirillo@infogroup.com
REPRINT SERVICES
Brand Manager Megan Perleberg mperleberg@iron.markets | (800) 538-5544
Published and copyrighted 2025 by IRONMARKETS. All rights reserved. No part of this publication may be reproduced or transmitted in any form or by any means, electronic or mechanical, including photocopy, recording, or any information storage or retrieval system, without written permission from the publisher.
Kathy Wells, Editor-in-Chief,
Trimble’s off-site location provided a glimpse into the future of autonomy on the jobsite, featuring prototypes of an autonomous excavator and compactor.
IRONMARKETS
Inside developments from the Trimble
Dimensions 2024 and a look at tomorrow’s equipment tech integrations
supporting industry professionals’ desire to better understand the future, especially with regard to technology applications in the real world of construction.
TThe 2024 theme “New, Next, Now” focused on the company’s vision for the future, including expanding connected capabilities, technology integrations, new collaborations and partnerships, and a wealth of cutting-edge technologies, all pointed toward its goal of advancing the construction industry.
rimble Dimensions 2024, held Nov. 11-13, 2024, in Las Vegas, Nevada, is an annual conference organized by software, hardware and services company Trimble, bringing together professionals across the geospatial, construction, agriculture and transportation industries. The three-day event featured keynote presentations, hands-on training, networking opportunities and exhibits showcasing the latest innovations and solutions in technology and software. Every other year, the conference also features a sizeable off-site setup for equipment operation and technology in the field.
Alongside a busy schedule of events throughout the conference, Trimble made several major announcements, including news about the extension of its longstanding joint venture (JV) with Caterpillar, the introduction of Trimble’s Siteworks Machine Guidance Module for compact track loaders, and more.
With a record-breaking 7,000 registrants and more than 800 educational sessions, the event is aimed at
The Trimble/Caterpillar JV expansion is aimed at enhancing interoperability, innovation and adoption in construction technology. According to executives, key drivers include growth, market acceleration, and technology advancements. The
partnership, which is now in its fourth iteration, focuses on seamless integration across different systems and workflows, enabling customers to use products across various infrastructure. Trimble notes, “Innovations like the chassismount system and automated excavation have improved efficiency and accuracy. The new agreement also includes a distribution model to extend Trimble’s technology reach and a 3D grade-ready factory option for Caterpillar machines, offering flexibility in activation and ownership. The goal is to support both skilled and non-skilled operators, with a focus on future-proofing technology and maintaining customer preferences.”
Trimble and its executives welcomed discussion about the future of AI and autonomy throughout the conference. “Our institutional view on autonomy is it’s a series of progressive automation, “ said Trimble President CEO Rob Painter. “We’re not institutional believers that we’re going to wake up one day and have Level 5 autonomy — by the way,
Our UL asphalt tanks have properly sized normal and emergency venting as standard.
All structural attachments are OSHA approved and are af xed to our tanks per code.
All tanks are tested to UL142 Section 42.2.1a 10th Edition.
All weld joints are per UL142 standards.
Your asphalt tanks will be properly labeled and registered with UL142.
machine control guidance is emerging at Level 1 and Level 2,” he said. Painter pointed out that the company, which has been developing IoT and autonomy and AI solutions for decades, recognizes that not every task on a jobsite is fit to become completed autonomously.
doing, to us, we see it as the brain.”
For example, at the off-site, Trimble showcased an autonomous compactor. “The compactor,” said Painter, “is a logical workflow to automate. You could have a lead-and-follow concept, or you could fully automate it. We’ve got beta customers who are using it.” The technology, which is not yet available to the market but is currently in testing stages, is just one such task. According to Painter, “We’ll look at workflows like trenching applications, linear trenching application, we would see that as one.” Painter says the company is working backward, pinpointing customer problems and opportunities, and working to drive efficiency, which in turn becomes the path toward autonomy.
According to Painter, a fully autonomous world is possible at a point further down the road. “I just think it’ll be further than what prognosticators will tell us,” he said. “That autonomous side of that autonomous equipment, it needs a brain. What work are you going to do? How are the machines all coordinating? When are you going to refuel? When are you going to recharge? You need a work plan. And so all the things that we’re
Ian Welch, director of engineering, autonomous solutions at Trimble, notes that one of the company’s bigger focuses today is how it can get more machine control onto more machine types. At its off-site location, Trimble showcased several autonomous solutions that are not yet available to the open market, including an autonomous excavator and compactor. Trimble’s goal moving forward is to bring more types of assistive technologies to operators. “How do we take some of that learning and technology and spin it off into actual products we can use today?” said Welch. “One example is steering control for autonomy. We took that steering control we put it as a product called auto steer in compactors, and it’s also in earth moving equipment, bulldozers or dozers. So that helps that basically better utilize that equipment to get a higher return, both with more accuracy and more efficiency.” At the end of the day, says Welch, the idea is provide solutions that help contractors run their businesses better. “we go back to the compactor example, right? So, pretty basic machine. That’s fair, but how do you do exactly what you need to do, and no more, no less. So we’re working on software that allows you to plan exactly where that machine should go to give you perfect overlap. So like in road construction, you know, if you’re looking at either rolling out the dirt or rolling out the asphalt, minimize the overlap so the machine can do exactly what you need, and no more, no less. Then it moves on to the next thing. So you get more, you can optimize the use of that team doesn’t still on,”
five more years, the next year, I think we’re probably it’s, I think what we will see is simple machines like either asphalt rollers or compactors. We’ll see them get automated first. And I would, I would guess that probably in the next 10 years, potentially, the big hurdle to clear is we can make the machine do the work. We can figure that out. We can do that. We can provide that value to an autonomous machine, or to a machine that has a person sitting in the cab. We get value today, the quantum leap is going from person in the cab to no person in the cab because we have all these sensors, perception sensors, cameras, LiDAR, radars, all those things, and they work, but they have to, have to be guaranteed to work in a functionally safe manner. And that is the quantum leap that we can’t quite get past. And I don’t think there are no regulations or standards that say if you do these things, you’re good, right? So the industry is trying to catch up and figure out, what does that look like.”
When it comes to the future of autonomy, Welch says we are well on our way, although the path is more complicated than one might think. “so I always look at automotive leading indicator,” said Welch. “And like, how long we’ve been San Antonio’s not automotive, right? It’s always been five years, and the next year,
Geoffrey Kirk, product manager, autonomy and assist, at Trimble – comments on 10 years possibly being the timeline for fully autonomous jobsites, noting that Trimble is investing in solutions to help make its products better in the future autonomy, “We are on a journey to autonomy, and what we are doing is taking the things that we learn from making a machine fully autonomous, such as [an] excavator, and we’re going to leverage that information and those learnings to make assistive products available sooner,” Kirk said.
The Warthog robot is being tested to autonomously move around, stop, scan and provide progress updates and data to field operations.
So when you think about making a machine fully autonomous, it means you have to understand fully what that workflow is. And so once we understand, in this example, pipe, a change in for pipe, we can take that and we can make a work order. We can take that understanding and make it more directly applicable into the manual machine we are showing fully autonomous here, but there’s a person nearby with the right control. So what’s on here in the pipeline application with these two stages is excavation, and then you may use a pipe layer, or often you’re using excavator. So we’re using remote control for those non grade related tasks
Weiler Material Transfer Vehicles lead the way with proven innovations to provide the lowest cost per ton of operation.
Innovative and reliable operator friendly features such as paver hopper management system with distance to paver, storage hopper management and auto chain tensioning.
Clam shell doors and full width drop down floors provide unmatched access for cleanout and maintenance.
Variable speed elevator and conveyors meet production requirements while minimizing wear.
The multiple, incremental improvements to the 4th generation of chains, sprockets and augers are retrofittable to all machines and provide increased wear life.
to make it simple and easy for that person, so you don’t need to do the hand signals to the operator to tell them where to move the bucket so you can attach it, because you have control where you need the thick cycle is fully autonomous from a Trimble standpoint, we want to help you run your site better, so interacting with the geospatial model, the design, so we can optimize what you’re doing. That’s a key part for us. So remote control is something we did as part of that process. We think remote control is a niche product long term, and as long as you have one operator to one machine, you’re not getting those scaling effects. So that’s why you’ll have a fully autonomous machine. You’ll notice we have a mixed fleet. We have support compactors, excavators, and over time, we’ll add more machines to the autonomous place. And again, we are learning from these autonomous flows and optimizations so that we can make things better generally today, because autonomy is still a decent distance out, the excavator is also a good example of not everything can be done autonomously. So the autonomous system is built on top of Trimble earthworks that allows us so when you can’t do something autonomously, you have those assistive features of triple earthworks. We also have this dozer here that’s not autonomous at all, that’s showing that mix site. We believe autonomy is a journey, and you can’t do every task. Not every machine will be autonomous. In the compaction workflow we have material comes in, we spread it, and then we compact it. Spreading is done by that dozer operator. They are there. They could look after the machine. It can be safe. And today that those are operators telling the compact operator what to do anyway. So we’re just taking out steps in that flow, making it easier. And you tell us what you want to do, and we will work out the best way of doing it. So if you think about compaction, you give us an area, and you say, what speed, what overlap, and how many passes you want? And we will do that. So we’ll create an optimal path plan, and we’ll go do that task for you. Same for that change, you
• Better — Autonomous solutions will lead to better operational insights on what’s happening and what machines are doing on your jobsites.
• Safer — Emerging technologies are being designed and added to enhance safety and many are already in use on jobsites today.
• Faster — Working with more accuracy and precision delivers more projects on time with less rework: With autonomy, what was designed is exactly what was built.
• Cheaper — The potential for savings stretch across different corners of the construction environment: time, budget, labor, gauging percent of improvement in all these areas, etc.
• Greener — Anytime we can do a task faster with less fuel, that’s not only good for your pocketbook, but it’s also good for the environment.
say, I need it to be four foot deep. We’ll drive to the start of the change, and we’ll optimally do that again. The technology that optimizations is available. We’re showing it on the bow mag down there, which is has a safety operator in it. So part of the thing that we’ve been finding with people is they want the quality improvements they want, the production improvements that comes with these fully automated systems, but they’re not ready for autonomy. So we will be bringing out these assistive systems in whatever place
the customer wants, right and whatever level of autonomy they’re ready for. And regulatory Europe and Australia, for example, are a lot harder. So we’ll be able to bring those improvements in productivity out in those markets sooner by doing the assistance.”
But before we reach a fully autonomous future, Welch says there are some priorities earmarked for Trimble along the way. “So we at Trimble, we look at autonomy as a test bed to learn and try new things and then spin those technologies out into products,” said Welch. “So the journey to get there will be more automation, more automation, more automation, and eventually we’ll get to a point where we will have automated all these tasks, the maturity of the perception system software will have gotten to a point, and we’ll come together and be ready for a fully autonomous thing. So our approach is, how do we provide value to people sitting in the machine to do their adopted.”
On the topic of adoption, Welch notes there are two camps. “You see one camp is, we’re all in, we love it, and the other is, I can do it better than the machine,” said Welch.
Moving forward, says, Welch, “AI and autonomy is a focus, I will say, for autonomy, it’s not so much about the autonomous machine that will sell, but all the value that we get along the way, and yet, AI is very, very big to Trimble right now. How can we make even small improvements? If I get a five to 10% improvement by using AI, that’s real money. People care about that, which will create more investment in it.”
According to Welch, safety is a huge challenge, especially on the jobsite. I think getting the right sensors on the machines right. There’s a lot of sensors built into the machines, and they’re great, but we also need so not just the sensors to detect people, but you can imagine you’re digging a trench. Okay, while you’re digging it, some of them chill, might fall in the trench. You have to be able to detect that as they don’t
gotta do one more pass just to clean that trench up as you go. Or sensors that can basically look it up, stockpile material, send that to say, a dozer, and say, what’s the optimum way to push this pile around and spread it around? Yeah. So I think I’m most excited about those sensors becoming part of the ecosystem to even solve problems if you put in the cab.”
Alongside that concern, Welch says, once adoption is underway is “number one will be, how do I know it’s doing the right thing...and so it takes a lot of getting people showing them, bring it to their site, give a demo, get them comfortable with them, or get them comfortable with it. I think there’ll be that trust issue I don’t trust. And then again, on the safety side, the same thing, again, right? Like, well, how do we know that’s where we need regulatory people that say we’ve proven through engineering controls and practices that it is, in fact, safe. And they go, Okay, you’re good, I’m good, right? But it’s gonna be it’s interesting. But again, if we can take some of that technology and slowly introduce it to contractors and operators, over time, they will naturally get more comfortable with it. So by the time it’s a fully autonomous thing, they go, oh yeah, yeah. We know all the other stuff. Yeah. Good with it, yeah. Trust it well.”
And when cost and other concerns are a barrier, Trimble has a plan to overcome. Welch says, “so we were focused really on an integrated platform. So earthworks has, there are a lot of sensors, a lot of capabilities in earthworks that we could leverage to do other things. So how can we leverage that platform, even to the point of using it to do different things, right? So more automation or as a platform, excuse me, that others could integrate with so if we have a sensor expert that does people detection, how do we make it easy to integrate that in your first platform and give value to our customers? We kind of lower that barrier entry, where not everything has to be done by Trimble. We don’t have to sell every piece that goes on your machine. Instead, how do we create an ecosystem that gives you value and that might be inviting other people into that ecosystem stuff?
According to Welch, it will take a long time to replace operators, especially skilled operators. “And so I actually like to flip the conversation. Say, what can we learn from skilled operators? Because we’re not going to stick and punch some keys on a keyboard and figure it out in 10 minutes. This is a journey to get there. So how can we partner with what is the best way to do this operation? OR operation? Or, why do you do it this way? Or what can you teach us about it? So we actually want to work with them to figure out how to do it is. It’ll be a long time before we’re placed field operators, According to Welch, one of the things that he’s most excited about when it comes to autonomation is the optimization of tasks on a site. “Yes, we have autonomy, and yes, we will get [to a fully autonomous future] eventually, but what can we accomplish along the way? And I think that is optimizing the things that people do every day,” he said. “It seems pretty simple, but if we can make you 2%, 3%, 5% better, that’s a real improvement.”
Read More eqtoday.co/24dimensions
By Brandon Noel, Editor
This is where the rubber meets the road, literally! Modified asphalt binder is a great way to boost the quality and longevity of your mix.
How can this sustainable product, created from recycled used tires, directly impact your business and your customers? Here are five ways that you can see immediate results.
There is an ever present, near constant need to find new and more sustainable answers for the asphalt and paving industry. Advances with reclaimed asphalt pavement allow for old roads and surfaces to be milled up and returned to plants, treated and then reincorporated along with virgin aggregates. That is one solution, and a valuable resource. It does have some drawbacks if you are a smaller
contractor who may not have access to the sophisticated sorting required for maximum recycling, or if your primary service needs don’t usually call for its use altogether.
An alternative sustainable product is seeing large gains and new growth with new investments into ecologically green markets. Rubber modified asphalt (RMA) is made from used and reclaimed tires, broken down, cleaned, and then ground into “crumb rubber”. It isn’t treated to undergo any sort of chemical changes, it’s just the same rubber. It has seen wide adoption and success in municipalities and areas across thirty-two different states.
Here are some of the primary benefits reported from its use, as researched by the Recycled Rubber Coalition.
This benefit doesn’t directly impact the contractor, but it is still a relevant factor as the industry continues to push towards a carbon net zero and more sustainable future. Over 300 million used rubber tires are created each year in the United States alone, and close a billion or more globally. As recently as 5 years ago, approximately 96% of these used tires were being recaptured and recycled. The most recent data shows, however, that things are trending in the wrong direction. Current data reveals that only about 76% of used tires are getting reused and kept out of landfills or illegal dumping situations. Rubber modified asphalt (RMA) is one of the best secondary uses available for tire recapture and recycling.
Whether you’re repaving a driveway, a shopping mall parking lot, or even a
stretch of interstate--everyone is looking for ways to reduce material budgets and lower the overhead on their production. Utilizing RMA in to varying degrees in your asphalt mix has shown to reduce overall project costs between 10% and 40%. Those are significant savings on any project and for any contractor, no matter how big or small they are. For example, on a fifteen mile stretch of road in Bend, OR, the project reported that costs per mile were $70,000 cheaper than with a traditional asphalt resurface.
In addition to the price tag, every client you do a job for cares about how long the pavement surface is going to hold up. How long will it keep its integrity and its esthetic quality before climate, weather, erosion, traffic and other variable conditions start to break it down. The integration of RMA usage within the asphalt mixes has been shown to extend the average overall lifespan of surfaces by 10%. How is this measured?
There was a study conducted by Recycled Rubber Coalition on asphalt pavement that incorporated RMA in Australia, a part of the world that regularly experiences scenarios of prolonged extreme temperatures. The results
found that internal thermal aging was slowed by 50% versus non-RMA surfaces. That’s a massive factor when talking with customers about the value of the product they are investing in. However, it was also shown to be more resistant to extreme cold temperatures, as documented in the upper peninsula of Michigan by county engineers.
There are, also, several direct benefits and added value to the drivers who will use the RMA surfaces.
• Skid Resistance
• Reduced Tire Wear
• Better Ride Quality (due to smoother contact with surface features)
• Lower Incidence of Damage to Automobiles
• Reduced Road Noise (Up to 10 decibels)
Due to the fact that RMA is more resistant to potholing, cracking and other damages to its surface, the need for frequent maintenance is reduced by up to 20%, as reported by the State of Alabama who utilized the product instead of a tradition, all-asphalt mix. Without having to regularly seek out sealing, patching and other repair
There are many state and federal DOT specs that require a modified asphalt binder for their roadway systems.
works, clients can rest assured that their investment is well-made, first of all. And secondly, they won’t have to be as concerned about shelling out thousands more from their already tight budgets to fix the work you’ve done.
For more information about RMA, it’s uses, the science behind it, as well as how you can incorporate it into your business visit: https://recycledrubbercoalition.org
By Brandon Noel, Editor
innovative
Each year, manufacturers release hundreds of new products into our industry. Sometimes they are small improvements on a longstanding, popular design, and, other times, they’re launching a whole new innovation into the asphalt space. This list comprises some of the very best products available on the market today, as chosen by our editorial team at Asphalt Contractor magazine. The 2025 Top 30 products have a little bit of everything from rollers and pavers, new software platforms, dirt work tools, and even a concrete mixing truck! Road builders need every possible tool in the toolbox to get the job done.
The SD2500CS high-density paver is powered by a Cummins QSB 6.7 watercooled, turbo-diesel, Tier 4 Interimcertified engine rated for 200 hp at 2,200 rpm.
• “Infinitely variable eco mode” produces less noise and decreases fuel consumption
• Choice of high-density tamping bar screeds
• Vario screeds offer an 8-ft. minimum and 32-ft. maximum work width
• Can be outfitted with VarioSpeed drive option with automated load sensing
• Hydraulic push rollers minimize impact from the truck during asphalt delivery
• Operator’s platform can slide hydraulically from one side to the other
The Quasar 360 patented unique latch and slide assembly comes in at only 16 lbs. and is the brightest, lightest and strongest on the market at the 300 Watt classification. It’s one push to rapidly deploy and another to de-latch the balloon has made it the simplest to set up. Robotically welded, nickel-plated latch and slide are built with rust protection for many years of service. The top and bottom assemblies are anodized billet aluminum to ensure the strength. This design was made to withstand the rigors of heavy construction and outdoor elements. Easy to fabricate mounts for different applications with no set screws to fail. Portable Lighting Solutions is one of the only balloon light manufacturers to offer a screw in, consumer replaceable LED bulb.
Cemen Tech has introduced the CD2, the next generation in its line of computerized models. This fully automated addition to the C Series lineup features a split bin with individual compartments to transport and blend various supplementary cementing materials (SCMs). The mixer is equipped to handle fly ash, a component mandated by Department of Transportation (DOT) standards and municipalities. The CD2 combines Cemen Tech’s volumetric mixing technology with a new SCM dual bin, enabling real-time mixing of individual ingredients at various proportions. A dual bin design doubles the amount of mixes this unit can produce.
The company’s newest system for eradicating odor-causing emissions produced as a byproduct during hot-mix asphalt production. Invisible emissions from plants — specifically, the odor-causing volatile organic compounds (VOCs) that reside in hot asphalt storage tanks — can create a number of challenges for producers, ranging from regulatory requirements to overt opposition from neighbors. When the X-VOCS technology is coupled with the company’s Blue Smoke Control system, emissions from hot-mix plants can be reduced to nearly zero, providing owners with the means to achieve the highest level of environmental stewardship. Implementation of this technology has been proven to virtually end calls from nearby neighbors regarding odor and visual emissions. Similar to X-VOCS, the Blue Smoke Control system is retrofittable with few plant modifications. The X-VOCS System features proprietary carbon absorption technology designed to filter and remove up to 99 percent of odors and VOCs, such as Hydrogen Sulfide (H2S), from tanks X-VOCS incorporates a five-stage filtration system. In the first three stages, a series of filters remove more than 95 percent of targeted particulates down to 0.3 microns. In the final two stages, carbon filtration beds remove remaining odors and volatiles.
The 8680 delivers high production capacity while maintaining a compact and maneuverable footprint meeting the needs of heavy commercial and main-line contractors alike. As your daily productivity demands increase the 8680 doesn’t struggle with the load, but powers ahead with its class leading 210 hp Kubota engine. Features high speed smooth rubber tracks with oscillating bogeys, a 4-speed drive system, power tunnel shields, and height adjustable augers. Dual swing out consoles with intuitive icon-based keypads deliver productivity without the learning curve.
Introducing the new E-Z Grader skid-steer attachment which boasts a built-in roller compactor, retractable ripper shanks, and deployable wings for superior performance. The attachment is designed for seamless compatibility with all top skid-steer brands. The E-Z Grader is a multifaceted attachment designed to deliver precise grading across a wide range of projects with the ability to grade in both 2D and 3D. This tool is perfect for various applications, including warehouses, parking lots, and athletic fields.
At the core is the EZ-OP PRO —a contractor-focused control system designed for simplicity, precision, and full visibility. With real-time material monitoring and responsive production controls, operators can dial in performance and keep quality locked in from start to finish.
The fixed aggregate gate ensures consistent material flow and application accuracy, eliminating constant adjustments and keeping crews moving.
And now, telematics come standard. With remote access to machine health, productivity stats, and usage data, you're equipped with the insights to manage jobs smarter and maximize uptime.
This dual facing heavy equipment dash camera is fully integrated with TennaCANbus, which allows it to deliver ECU data alongside video telematics. The TennaCAM 2.0 Heavy Equipment is intended for use within the closed cabin of a piece of heavy construction equipment. Paired with a monitor and additional auxiliary cameras around the sides and rear of the machine, this product provides footage and live visibility around the operation and surrounding area of heavy equipment on active jobsites. The intent is for contractors to see how well the operator is performing, enabling them with a view of the jobsite from the cab to reduce blind spots; all while seeing the machine’s real-time telematics data.
More than 55 years of material and equipment innovation has positioned SealMaster as an
Feed capacities up to 350 t/h, a large feed hopper, screening surface of 5.4 m² and wide main discharge conveyor. The speed of all conveyor belts is adjustable. A wide setting range of the screen casing angle promotes high screening capacity. The selection of screening media also contributes to performance. Whether finger decks for clayey excavated earth or square mesh for classifying decorative grit – from a large selection of screen media, the screen decks of the MOBISCREEN MSS 502(i) EVO can be covered to match the required application.
With hydraulically adjustable width ranging from 8-to-14 feet via a wireless remote control, the Broom Box ensures precise coverage. Its quick-release broom heads facilitate easy replacement, while the high-lift attachment enables self-loading onto trailers, minimizing downtime.
Equipped with a box that contains emulsion, the Broom Box eliminates run-off against curbs or road edges, reducing mess and ensuring environmental compliance. Its hinged design automatically flexes on crowned roads, while the firm attachment to the distributor prevents drifting on sloped surfaces.
The Broom Box features a self-contained electric over hydraulic control system, eliminating the need for external power sources. Its cordless controller offers freedom of movement and ease of operation. Additionally, three variable broom types cater to different surface conditions, ensuring optimal performance in various environments. Designed for convenience and longevity, the Broom Box includes a storage stand to extend the life of brooms between production days and during transportation, preventing brooms from matting when not in use. With its positive height adjustment and poly head brooms for extended life, the Broom Box is engineered for durability and efficiency, making it a great solution for road maintenance professionals.
Designed to support operator safety and sealing operations. Powered by a 27-hp electric start gasoline engine, the machine features a single piece drum design with cutouts on each side of the housing for access. The R3 is equipped with a 6-gal. fuel tank and dual-stage air cleaners. Features include:
• Belly-bar Hands-Free Emergency Shutdown: Supports operator safety.
• Kohler Engine: Provides performance with low maintenance.
• Quick Stop II Anti-Kickback System: Stops backward travel when handles are released.
• Integrated Depth Gauge: Displays depth gauge.
• Large Tilt-Up Shroud: Allows bit access.
• Electronic Clutch provides a way to disengage cutting drum without powering down machine.
Material Supply with Ticket Accounting was meticulously designed to enhance the efficiency and effectiveness of raw material supply management for contractors, delivering significant benefits that drive operational success.
Material Supply addresses critical challenges faced by asphalt contractors, including high transport costs and inefficient material flow management. By automating raw material supply processes, it not only reduces transport expenses but also streamlines the entire supply chain, ensuring that contractors have timely access to the materials they need.
One of the standout features of Material Supply is its centralized view of raw materials inventory, which empowers contractors to make informed decisions based on real-time data. With Ticket Accounting, the digitization of all raw materials delivery receipts and the automation of invoice reconciliation simplify administrative tasks, allowing teams to focus on core operations rather than paperwork. This unique combination of features supports seamless operations, optimizes planning, and strengthens supplier relationships.
In a competitive industry where efficiency is paramount, Material Supply stands out as a game-changer, providing asphalt contractors with the tools they need to succeed and thrive. Its innovative approach to material supply management not only solves existing problems but also sets a new standard for excellence in the field.
The 12-ton machine becomes the largest model in the Volvo soil compaction portfolio with an 84-in. smooth-drum and operating weight of 26,565 lbs. Active DPF regeneration eliminates material build-up, reducing emissions. The center joint provides +/-35 degrees of articulation and +/-12 degrees of drum oscillation for stable and flexible performance over rough terrain. Because the drum is in constant contact with the ground, compaction is smooth and uniform. The additional static weight on the drum frame facilitates the ability to negotiate 35% slopes for gradeability.
Powered by 48.9 hp, 3 cyl. engines, the CT380/430 are built to handle rigorous daily use. Their operating weights strike a balance between easy transport and heavy-duty performance. Features:
• Dual-drum widths of 51 in. (CT380) and 55 in. (CT430) deliver centrifugal forces of up to 13,800 lbs. and 14,600 lbs. per drum
• Maximum travel speeds of 6.2 mph, enabling efficient movement
• With a ±34-degree steering angle and ±13-degree oscillation angle, the rollers navigate tight turns and uneven terrain
• Adjustable seats, intuitive controls, and visibility reduce fatigue
Available in 6- and 9-ton payload configurations, the first site dumper to feature a rotating cab, taking operator safety to a new level with maximum visibility in all directions, and eliminating the need to twist and turn for visibility of the travel path and jobsite. The Revotruck 6 features a 13,288-lb. payload with a total operating weight of 13,040 pounds. For heavier-duty applications, the Revotruck 9 provides a 19,842-lb. payload with a 14,473-lb. operating weight. Each variant is equipped with a hydrostatic transmission top speed of 17.4 mph to quickly navigate jobsites. Operators can rotate the cab 225 degrees with the touch of a button, allowing them to maintain their vision and focus on the job, while also staying aware of any surrounding obstacles. This sets it apart from other site dumpers on the market that offer limited visibility. The cab rotation and swivel of the bed from left-to-right increases efficiency by eliminating the need to reposition the machine when going from loading to dumping.
The KX040-5 introduces a redesigned hydraulic system, a spacious and quiet cab, and tech features that now come on standard models. Powered by a 40.3-hp Kubota diesel engine, a digging depth of 11 ft., 2.3 in., and a bucket breakout force of 9,397 lbs.,it can tackle the toughest tasks on the jobsite. The improved hydraulic system utilizes engine horsepower to its fullest extent allowing flow rate to be increased for performance while using a hydraulic attachment and operating other functions simultaneously. The load-sensing hydraulics deliver smooth and efficient operation, allowing operators to travel and multitask effortlessly, improving jobsite productivity. There are three dozer blade options available— straight, angle, and 6-in-1. A spacious and comfortable cab provides operators with an expanded glass area for better visibility, and the removed roof window slash bars provide clear visibility of the bucket during loading and dumping. Its slim and quiet interior features expanded head and foot space over the previous model.
Astec Industries announced the launch of the SiteLine operator environmental awareness camera system for its cold planers. Key Features:
• The SiteLine system provides a custom panoramic view of mobile equipment, starting with the cold planer products.
• Advanced image processing stitches multiple camera feeds together, creating a natural and uninterrupted view for the operator - helping to identify and avoid potential hazards.
• Improved situational awareness allows operators to work more efficiently and confidently, leading to faster project completion times.
• Ability to tap any one of the camera screens to zoom in and get a close-up look at a specific area of the machine, then return to bird’s eye view.
A high-production, rubber track paver that excels on airports runways, interstates, highways, and other large jobsites. Its high travel speed, flotation, and traction deliver superb mobility. Features:
• Exclusive 70 kW integrated generator delivers fast, reliable screed heating and is designed for long life by the same team that developed the D7E electric drive dozer
• Fast heating screed leads to more daily production, heating time in 15 minutes
• Mobil-trac undercarriage design delivers excellent traction, good flotation, and fast travel that helps lead to increased production
• Exclusive air flow design improves operating conditions for the crew and keeps components cooler for lasting durability
• Versatile screed designs deliver excellent ride, density, and mat texture while providing superior adjustment; available with front-mount extenders, rear-mount extenders, or tamper-bar systems
• Tow-point design utilizes exclusive linkage for optimal screed flotation
In collaboration with Q Point, the digitalization experts, Ammann offers an integrated solution that improves the efficiency, transparency, and sustainability of the entire asphalt-related process. The Connected Worksite brings together all the puzzle pieces to create one coordinated workflow. This advanced communication streamlines each phase of roadbuilding and ultimately brings operational efficiency and cost savings. The accessible technology can be utilised for the entirety of a project, or during specific phases:
• Construction planning and order management
• Planning and production at the asphalt plant
• Loading and delivery of materials
• Paving and compaction
• Thorough documentation
ASPHALT
Bio-based Trick Shot Sustainable Products
Asphalt SOLVENT AND CLEANER has been specifically developed as an EPA allowed alternative for the asphalt production, paving, and maintenance industries. Trick Shot is a high-performance product that dissolves bitumen, tar, oil, and tack from paving machinery, equipment, and tools. Trick Shot melts asphalt products with ease without harsh chemicals. It does not release harmful fumes, is non-flammable, safe for contact with skin, and is even registered NSF-H1 food safe making it extremely worker friendly.
The new Echelon Mode addresses the unique challenges of echelon rolling, a common technique used in highwayclass paving.
• Millimeter-wave radar or 3D LiDAR to detect potential collisions with personnel or equipment, warn the operator progressively, and automatically brake to prevent accidents if needed.
• Echelon Mode allows two SAKAI SW884 (79”) or SW994 (84”) asphalt rollers, equipped with Guardman, to operate in close proximity without generating false alarms but still protecting against collisions.
• Enables closer, more efficient echelon formation, maximizing productivity
InsigniaLS combines loading, KPI, reporting, security, and ticketing all in one package. The all-new user interface allows the user to customize the features that are directly visible. Themes allow the operator to choose what color scheme is best for the viewing environment. Live ticket view allows the operator to see the ticket as it is created so ticket errors and reprints are corrected before they are needed. Data integration is a priority whether it be to the Insignia Cloud suite or to a remote database at the main office - replication speeds are routinely under 10s. Third party integrations are a breeze for the system - sample integrations include Apex, Broadloop, Haulhub, and Viewpoint.
✔ Micro Surfacing ✔ Slurry Seal ✔ Asphalt Emulsion ✔ Asphalt Rubber ✔ Modified Asphalt ✔ Hot Boxes & Patch Trucks
Trucks
The W73's hydrostatic drive, with 2-speed motor and 2-speed gearbox, delivers 350fpm (106 mpm) working speed and 12 mph(19 km/hr) transport speed. A 3.5 yd3 (2.6 m3) hopper means fewer truck exchanges during the workday. The 30” (762 mm) wide belt and 800 fpm (242 mpm) belt speed provides quick placement of materials to either side of the machine. The hydraulically adjustable dump hopper accommodates varying trucks. 25” (635 mm) tall strike-off tools widen from1’ (.3 m) to 14’ (4.2 m) and are capable of placing material up to 12” (305 mm) above and below grade. Multiple tool sizes, plus hydraulically adjustable tools, ensure precise strike-off and can be set to exact grade and slope specifications. All controls are on a single panel within easy reach of the operator. Sliding control console enhances operator ease of use, enabling both left-and-right side access to all machine controls. The operator is back from the dump hopper and toward the outer edge of the machine.
A state-of-the-art pavement profiling system designed for use in stop-and-go traffic conditions. Ensuring highly accurate road profile measurements. This innovative high-speed profiler is ideal for urban environments, construction zones, and areas with frequent intersections. Equipped with advanced laser technology and precision GPS, the 8300 delivers real-time data. The Ames 8300 Stop & Go Profiler enhances efficiency by eliminating the need for road closures and ensuring high-quality pavement assessments in complex traffic environments. Designed to improve workflow and accuracy, this profiler helps contractors meet smoothness specifications, reduce rework, and optimize project timelines. Its unique ability to function in variable traffic conditions makes it an essential too.
Offers a unique way to both measure and draw irregular job sites, quickly and precisely. As it walks the site, Moasure automatically captures:
• Perimeter
• Area
• Volume
• Surface area
• Elevation changes
Enables site managers to significantly simplify the planning of an upcoming road construction project, monitor the ongoing paving process in real-time and, quickly take corrective action, enabling even better paving quality in road construction, fulfilling the requirements of QSBW 4.0 and QAA 4.0.
• Calculate the mix requirements
• Communicate with the mixing plant
• Calculate the truck scheduling
• Pass on process changes directly
• Intuitive, integrated construction site planning in one program
• Preparation of all paving parameters on the basis of site pre-measurements
• Provision of complete construction sequence planning with highly efficient scheduling
• Reliable material and cost planning
• Easy generation of invoices, overall analysis, and reports
As the app is capturing measurements, it simultaneously draws a 2D and 3D diagram on the user’s smartphone or tablet. Exclusively with Moasure 2 PRO, users can also access Layout Mode, designed to help locate and mark points based on a set of predefined coordinates without the need for GPS, Wi-Fi, line of sight, or even an extra pair of hands – only using a Bluetooth connection between the device and app. By moving the device from one point to another, users can measure complex and irregular shapes even across challenging terrain where elevation changes are typical. The intuitive app interface allows users to refine measurements, add annotations, and inspect data at their leisure, including an organized filing system they can refer back to at any time. In the app, construction professionals can export their drawings to CAD, as a PDF or CSV file.
Some key new features include:
• Labeling and ignoring data points while measuring
• Color-coded layers for easier identification
• An intuitive Area Calculator to automatically determine net areas between multiple layers within diagrams
• A refreshed app interface with a clean, professional color scheme
• New scaled grid and scale marker options in 2D modes
• 3D Contour View
While the HD+ 120i V-VIO 12 t tandem roller features a vibrating roller drum (50 Hz or 3,000 vpm) at the front and a VIO drum at the rear, the HD+ 120i VIO-2 HF provides additional application options with two VIO drums. An automatic control feature on the HD+ 120i VIO-2 HF keeps the front drum (in relation to the direction of travel) always working in vibration mode, while oscillation or static compaction is used on the rear drum. The HD+ 120i VIO-2 HF has also been designed as a high-frequency machine (HF), offering a vibration frequency of 67 Hz or 4,020 vpm (front and rear). Both models are powered by a 115 kW (154 hp) Deutz engine. The tandem rollers also have the ability to switch between vibration and oscillation or, in the case of the HD+ 120i VIO-2 HF, combine two vibration and oscillation drums together, removing the need to switch machines or deploy an additional machine and another operator on the construction site.
Trimble DA2 GNSS Smart Antenna is available worldwide for civil and building construction applications through Trimble’s subscription program. Combined with Trimble Siteworks or Trimble FieldLink Software, the DA2 can perform a variety of construction surveying tasks and site supervision for both civil and building construction. For civil contractors, this includes pole-mount for checking, truck-mount for site supervision and ATV-mount for progress monitoring, volume calculations, site topos, verifying as-builts, road centerlines and more. For building contractors, this includes underground utility layout, building foundation set out, construction quality assurance and more. The DA2 leverages the Trimble ProPoint GNSS engine for GNSS yield and positioning accuracy when operating near trees and buildings. The Bluetooth-enabled DA2 works with a range of Trimble data collectors depending on the desired use, including the Trimble TSC7 and TSC5 Controllers and Trimble T7, T10x and T100 Tablets. The optional Trimble EM940 Empower Module adds local base station corrections.
The EX 8845 features an 88-in.drum diameter and 45-ft. drum length. These counterflow plants can produce up to 425 TPH and handle up to 50% RAP. Like all EX Series plants, the EX 8845 features singledrum counterflow technology, providing the longest aggregates drying and mixing times in the industry to ensure consistent, quality asphalt, meeting all federal and state specifications. Counterflow technology captures residual gases and reintroduces them back to the combustion zone, virtually eliminating blue smoke and hydrocarbon emissions to meet strict environmental regulations.
Stockpile Reports is an Enterprise SaaS platform that helps customers eliminate write-offs in bulk materials using an automated, scalable, controlled process to achieve accurate inventory in financial statements. Stockpiles are digitized using imagery from phones, drones, and installed cameras using automated data integrations. Stockpile Reports’ image processing is powered by EveryPoint, an intelligent software service that continuously replicates real-world assets.
• Reduce Inventory Variances: Stop relying on inaccurate perpetual inventory systems. Measure your entire site in minutes and get realtime physical inventory counts.
• Eliminate Unplanned Downtime: Not sure if you have enough material on hand to keep your operations going through the weekend? Get a quick spot check on your inventory to ensure you have enough.
• Verify 3rd Party Deliveries: Keep your vendors honest by measuring your stockpiles at the time of delivery, ensuring you get what you paid for.
• Optimize Bidding Accuracy: Accurately measure pre-crushed material to base bids on real data, reducing the risk of overbidding or underbidding for more competitive, profitable projects.
• Keep Projects on Track: Ensure projects stay on schedule by taking daily measurements, helping to determine if they will finish in time for the next job.
• Enhance Production Transparency for Timely Payments: Provide clients with daily output measurements to enhance transparency and ensure timely pay
By Brandon Noel, Editor
Green Asphalt’s Jim McMurray discusses their groundbreaking one-hundred percent recycled asphalt technology, challenging industry skepticism and paving the way for more sustainable road construction.
Ifirst wrote about Green Asphalt two years ago, and things were a lot different in 2023. If you compare where the industry and the country were then to where things stand at present, it’s a very different environment that we are all operating in.
Two years ago, the IIJA and the IRA were humming along, and slowly steering the asphalt, road building, and general construction towards a more sustainable future. Recent changes in leadership have already stalled, reversed course, and, in some cases, outright cancelled funding dedicated to the transition.
In the midst of all this upheaval and uncertainty, Green Asphalt continues to spread their vision, and they’ve made some big strides since I last saw them. At World of Asphalt 2025, we had the chance to catch up with Jim McMurray, head of National Business Development for Green Asphalt, and talk about all that’s changed for them in the last two years.
Brandon Noel: A lot has changed since we last spoke at your plant in New York! Back then, we talked about struggling
to get in front of producers and contractors, but last year during the NAPA Mid-Year conference [Green Asphalt] gave tours to attendees. Now that you’ve had some increased face time with larger players in the industry, what has the reception been like?
Jim McMurray: So, let’s go back in time, first. We gage the perception of us by looking back ten years, and ten years ago, people were laughing at us and said that one-hundred percent RAP is impossible. Well, they’re not laughing at us anymore, and I know that doesn’t sound like a lot, but for us, it means a lot. People are coming to the booth now, and they know who we are. Our brand and our recognition, has gone through the roof. People are coming from all over the world to see us at these events.
Noel: When people hear about it for the first time, I don’t think the question they first think of is whether they would use it or not. It’s usually: “Is this for real?” When you face that, how do you talk to that person?
McMurray: They usually approach us very skeptically. They don’t believe it, at first. You know, the national average for RAP is twenty-one percent. We’re all talking about net-zero, zero emissions, lowering emissions, and green infrastructure, so how are we still at twenty percent RAP? We’re still tying one hand behind our backs.
Noel: How do you engage a conversation with producers?
McMurray: That’s one of the first things we ask: How much RAP are you running? And some people are higher. Some people are trying fifty percent in some of their commercial mixes, and we like to hear that, because they’re less skeptical. But a lot of guys are doing zero RAP. If they’re doing airport work or Port Authority work, doing State work, they’re stuck around whatever their state cap is.
Noel: I think that the other difficultly is the contractors, the pavers, right? You know, if you can win over the producers, that’s one half of the battle.
But they’re not the customer, though. The producers are beholden to the people that are gonna buy the asphalt from them.
McMurray: Our technology is a tough sell because the agencies aren’t ready for it. Let’s say you owned a plant, and you want to do this. Who are you going to sell it to? Are you going to try to convince every one of your customers to use a product that no one’s ever used before?
That last questions McMurray asked is ironic, since that is exactly the task that Green Asphalt had before them when they set out into the industry.
Noel: The biggest thing that I run up against when I talk about your onehundred percent RAP to contractors, is they immediately just say, “It’s gonna be a shit-mix.” They just write it off immediately, and before they can even hear the arguments in favor of it. How do you overcome that kind of stonewalling?
McMurray: (Laughing) Well, everyone knows, you can make a “shit-mix,” and you can have shitty lay down whether you use one-hundred percent RAP or virgin mix. The proof is in the pudding. We’re working with New York State right now, and they’ve given us a goal post,
it’s very similar to balance mix design. It’s called a PEM spec, performance engineered mix. They said, if you want to be taken seriously, you have to meet this spec and we’ll talk. We’ve been working on that diligently for the last eighteen months. We did a couple test runs. We’re doing another two tests in April, and
New York State will send down inspectors, and they sample it and they test it side-by-side with our guys. They want to see us succeed.
Noel: It’s good to know that the people who are championing net-zeros and championing efficiencies are actually working with you, and not just
USDA Certified Biobased
– Tested at 96% bio-based
No Petroleum Distillates, Near Zero VOC’s (EPA 24)
High Flash Point
– Non-flammable in liquid form
Foodsafe (NSF-H1 Reg), Non-toxic (OECD 201, 202, 203), Biodegradable (OECD 301B, ASTM D5864), VGA/EAL, CA Prop 65
Competitive Bulk Pricing
Recyclable Containers
machinery, equipment, and tools. TSAS&C® melts asphalt products with ease without harsh chemicals. It does not release harmful fumes, is non-flammable, safe for contact with skin, and is even registered NSF-H1 food safe making it extremely worker friendly.
Safely Remove Asphalt from Skin – Non-irritating formula
throwing down arbitrary roadblocks. But what about in other states?
McMurray: Let’s say we meet someone in Massachusetts who’s interested in one-hundred percent RAP. We will reach out to Massachusetts DOT to set up a meeting. We’re not trying to get anything approved, yet. We just want to talk about what we’re doing. What are your concerns? Have you ever heard of one-hundred percent RAP? What are your limits? What are your biggest worries? For some of them it’s performance, because no one’s ever done it before. How do you know where your millings are coming from? Do you test them? Do you separate them? They are all great questions! And it helps us know what information to provide, and then we’ll also join that state asphalt association, just to get to know other members and not be an outsider. Obviously, it’s a process, and we’re not a huge staff, so we can’t do all 50 states at once.
One huge opportunity that Green Asphalt had last year was the mid-year conference which was held nearby in Brooklyn, NY, last June. As part of the
conference, NAPA offered a guided tour of their plant and operations so that members could see for themselves just what they’re up to.
Noel: I wondered if you had an anecdote from your presentation and the tour you did at the mid-year. In your mind, was that a successful event? Do you feel like you got to win there?
McMurray: I think we went above and beyond, and we actually made mix. We had a spreader and a truck there, and had a paving crew put down one-hunred feet of asphalt and gave people shovels. It was really good, because you can talk about it all you want, but we had people who were shoveling asphalt and looking at it and saying, “There’s no way this is one-hundred percent RAP,” and that was a win, that felt like a real win. Did we sell a conversion that day? No, but are we are we one step closer we onehundred percent are.”
•
•
•
•
•
Governments, trade organizations, construction companies, and industry groups have to work together to ensure we successfully attract groups who have historically been more hesitant to consider a career in construction into the industry.
The construction industry is grappling with an unprecedented labor crisis. Despite construction spending being at an all-time high, the U.S. labor force is currently missing over half a million workers needed to build essential housing and upgrade our nation’s infrastructure. This shortage is exacerbated by an aging workforce and a lack of new entrants into the industry, particularly from underrepresented groups such as women.
Today, women make up a mere 11% of the construction industry. When it comes to skilled trades, this number plummets by almost three times: women represent just 4% of the US workforce.
Women constitute over half of the U.S. population: there is an immense, untapped potential to mitigate the labor crisis by actively recruiting more women into the construction industry.
This shift would not only address the workforce gap but also offer women across the country access to higher
@Chalermphon - adobe.stock.com
wages. Construction has the highest industry average hourly earnings for workers without a bachelor’s degree and is among the top in gender pay equity.
This article covers the nationwide initiatives paving the way, as well as the most effective strategies construction companies can implement to attract more women into the industry. The faster we can multiply these, the faster we’ll solve the labor crisis we’re facing.
There are inspiring initiatives being run all over the U.S. by groups ranging from trade associations to local governments.
Groups such as Chicago Women in Trades offer free training programs with robust curriculums that prepare women to build careers in the manufacturing, welding, and metalworking trades.
National organizations such as the National Association of Women in Construction run leadership academies and scholarship programs to help remove barriers to women entering and
If companies can put their female employees at the forefront of these efforts, women will more easily see themselves in the open roles.
progressing in the construction industry.
In Maine, Governor Mills signed an Executive Order to improve the recruitment, training, and retention of women in Maine’s construction industry. In California, the Los Angeles metro launched a website dedicated to giving women information about joining apprenticeship readiness training programs. In Arizona, the Arizona Builders Alliance runs a Women in Leadership program to support continued advancement in leadership.
Now, it is our collective responsibility to ensure we increase the number of these initiatives.
The most impactful strategies for companies to pursue.
Across the 500+ trade contractors we work with, these strategies have proven most effective in attracting more women into the construction industry:
Run targeted online recruitment campaigns that are focused on highlighting the opportunities available across the industry. Showcase successful women within construction companies, share their career progression stories, and emphasize the range of jobs available across field and office teams.
In general, recruitment efforts at many construction companies suffer when potential employees can’t see that the industry is for them. This can be because it seems outdated, or simply because they don’t see people like them in the roles they’d be hired into. The more companies can show candidates that they’ll use modern tools, learn transferable skills, and solve challenging and rewarding problems, the more successful their recruiting efforts. If companies can put their female employees at the forefront of these efforts, women will more easily see themselves in the open roles.
Form partnerships with high schools, vocational schools, and universities to increase the exposure to careers in construction. Offering scholarships, internships, and apprenticeships specifically for women, as well as hosting targeted workshops and career fairs, are powerful ways to expand the candidate pool.
Following the CHIPS Women in Construction Framework, create pathways such as training investments, apprentice utilization goals, and apprenticeship readiness programs. Offering increased technical, leadership, and safety training can help position the construction industry as being more proactive in investing in women.
➍
Provide on-site childcare, flexible working hours, and robust antiharassment policies to create a more
welcoming environment. Other initiatives we’ve seen work well include creating mentorship programs where experienced female employees mentor new recruits, as well as promoting gender diversity in leadership positions.
In May, the U.S. Department of Commerce launched the “Million Women in Construction Community Pledge” to encourage leading construction companies to demonstrate ongoing commitment to increasing women’s access to training, jobs, and leadership opportunities.
Signing a pledge is just the beginning, but it’s an important step in making the entire company aware that fixing the gender ratio in construction is something that matters.
Leading companies including Suffolk Construction, Power Design, Gilbane Building Company, and Turner Construction have already signed the pledge and begun running targeted recruitment, training, and mentorship programs for women.
The U.S. is on the verge of a major transformation. We’re reshoring manufacturing so we can make our supply chains more resilient. We’re electrifying
Offering scholarships, internships, and apprenticeships specifically for women, as well as hosting targeted workshops and career fairs, are powerful ways to expand the candidate pool.
our infrastructure so we don’t have to rely as much on fossil fuels. We’re upgrading our grid system so we can handle increased demand for electricity. We’re building more homes to reduce our 1.5 million home deficit. We’re building data centers to power innovation and advancements in AI which are needed for us to maintain our global leadership position.
The timely completion of all of these is crucial, and it requires more workers. Taking the electrical industry as an example: current forecasts show we’ll need over 80,000 more electricians entering the industry per year over the next 10 years to keep up with expected demand.
This moment in time requires us to invest heavily in developing our workforce. Governments, trade organizations, construction companies and industry groups have to work together to ensure we successfully attract groups who have historically been more hesitant to consider a career in construction into the industry. The biggest of those groups is women.
By empowering women to enter and grow within the construction industry, we’ll unlock a tremendously powerful force in helping us build more, faster.
Maria Davidson is the CEO and founder of Kojo. Visit usekojo.com.
by Maria Davidson is the CEO and founder of Kojo.
Understanding the importance of pavers and how they are used to not only optimize smoothness, but also build long-lasting roads
What’s one everyday necessity almost everyone takes for granted? Smooth roads and highway systems. Cody Wagner, roadbuilding technologies product manager at RDO Equipment Co., says, “You never notice when you’re driving on a well-maintained road, but you’ll be sure to notice when it’s not.”
Uneven slopes, potholes or deteriorated asphalt increase wear and tear on your vehicle, and you’ll be in for a noisy ride. In recent years, many, including the federal government, have recognized the need to invest in restoring roads because of their age, heavy use from
increased traffic volume, inadequate maintenance over time and the impact of weather conditions.
As I’ve transitioned to lead RDO Equipment Co.’s business across 12 states, I’ve connected with Original Equipment Manufacturers (OEMs), pavers and roadbuilders as they partner to gear up for what may be the busiest year yet. And according to many, these roadbuilding projects are long overdue.
American roadbuilders began building our interstate highway system in the 1950s. Back then, they couldn’t have known that drivers would enjoy the quality of these roads for more than 70
years. In fact, the Texas Department of Transportation (DOT) reports that its oldest highway, the Gulf Freeway, I-45, first opened in 1951. The road is slated for an extended lifespan, too, as late last year, Texas’ DOT celebrated the groundbreaking of the I-45 infrastructure project, designed to expand roadway capacity, reduce congestion, improve safety and enhance mobility.
These “mega infrastructure” projects, like Texas’ I-45, are made possible by the Infrastructure Investment and Jobs Act (IIJA), community support and technological advancements in roadbuilding equipment.
As we look forward to the first half of the year, we are cautiously optimistic that these IIJA funds will continue to trickle down to meet the demand to revitalize our roads and highways.
While we can’t predict the forthcoming actions of a new administration, we can pave the way to the future by following roadbuilding fundamentals to improve something that many of us rely on every day.
Most drivers don’t notice when pavers achieve accurate compaction for optimal smoothness, but when ride quality deteriorates, it is sure to be a topic of conversation at the diner.
“Ride quality is how comfortable
riding down the road is,” Wagner said. “It’s about the surface being even, without unnecessary bumps or ruts.”
Uneven roads cause more friction and impact on both vehicles and the road itself, leading to the need for more repairs and all the time, money, materials and emissions associated with doing the work again. Wagner explains that smoother roads reduce vehicle wear and tear and are safer, too.
“When a roadway has unintended varying slopes, a driver is more at risk during certain weather conditions like ice or fog,” Wagner said. “When roadbuilders focus on improving ride quality during every pavement pass, they ensure we all can arrive quickly and safely at our destination.”
With the ability to connect machines to Fleet Management Software like John Deere Operations Center™, roadbuilders can track specific data points, like GPS (Global Position System) location or production hours, to share with direct stakeholders.
Wagner, who has worked for more than
eight years in paving quality control partnering with state and county municipalities, explains that these entities will highlight areas that require attention.
“After the state, county or city selects certain roadways for repair, they will determine if it’s a complete rebuild or resurfacing project,” Wagner explains. “Roadbuilders use GPS equipment, like Topcon positioning systems, to mark these areas.”
Before any asphalt removal, resurfacing or paving begins, the contractor and subcontractor will analyze the GPS-marked areas and determine the intended depths based on the current roadway’s changing slopes. Then, the roadbuilding team will use the data they’ve collected from surveying to develop a digital model with their milling operators.
“Once the team has a digital plan, they’ll spray paint to mark intended slopes and depths,” Wagner said. “After milling, the team will survey the road to determine if they need to do a leveling pass to fill in spots before paving to ensure optimal compaction.”
RDO’s Telematics Support Manager
Roadbuilders use surveying equipment like Topcon Positioning systems to record varying slopes quickly.
Larry Herman Jr. explains that tracking a paver’s location optimizes the roadbuilding site when many stakeholders require real-time info, like the length and depth of paved passes.
Ultimately, any roadbuilding team will monitor the paver’s grade closely, continuously monitoring thickness to achieve the road’s appropriate density
for its environment.
The roadbuilding team determines the road’s density based on the soil and weather conditions of their community. To achieve the density, roadbuilders compact the soil, aggregate or asphalt to remove air voids.
“Optimal compaction while paving is the base of any smooth roadway,” Wagner said.
Wagner explains that without proper compaction, roads will be more susceptible to cracking and other forms of distress.
“Proper compaction cannot be achieved when the paving mix reduces in temperature due to environmental factors like air or ground temperatures,” Wagner said. “When the mix loses heat, and its temperature cools, the mix will be ‘hard to stick,’ become brittle and will not have the structure or binding that occurs from compacting at an accurate temp.”
To ensure a smoother profile, several
roadbuilding teams in states like Minnesota use Topcon’s RD-M1 Scanner and partner with RDO. The RD-M1 Scanner is a LIDAR (Light and Detection and Ranging) scanner fitted to the back of the truck. A Department of Transportation (DOT) team member drives the roadway to record imperfections and roughness.
“We then load this data into a mill equipped with 3D milling technology and software, using GPS and LPS (local positioning system) to guide the mill,” Wagner said. “After milling, we use these same data points, plus the grade information from the scan, so the paving team will have the machine data and control info to pave a smoother profile.”
Paving and milling crews are among the earliest adopters of roadbuilding technology. Crews used strings to
guide machines in building straight roads, but since the integration of telematics, OEMs have developed machine control technology. Wirtgen’s AutoPilot system eliminates the need for strings and uses satellite navigation. With the AutoPilot system, roadbuilders can pave complex geometric shapes like curves.
Most roadbuilding crews use an autopilot system so project managers can program depths for operators. Often, a foreman and project manager will review data points automatically collected at the end of the day to check if the paver has completed the planned path. Roadbuilders who partner with RDO work with our telematics and connected support teams to learn best practices for making data-informed decisions.
“We can track whether machines are working or idle, which helps fleet managers allocate resources. We can also monitor fuel usage, machine speed and engine data,” Herman Jr. said. “We can focus on the entire job site to partner with a roadbuilder to effectively manage projects and to plan for future roadbuilding bids.”
As we gear up for the next phase of infrastructure development, roadbuilders can follow the same fundamentals that roadbuilders established nearly a century ago. Since the IIJA passed in 2021, government funds have covered planning costs to assess various roadbuilding projects’ scopes. In the coming months, we should expect roadbuilders to have the necessary info and funds to procure the latest equipment or technological solutions. With this information, roadbuilders can partner with a trusted dealer to precisely pave smooth roads to last for decades.
by Dennis Howard is senior vice president of Roadbuilding and Minerals at RDO Equipment Co.
Asset maintenance is one of the biggest cost centers in fleet. Having clear performance benchmarks can help rental fleets determine if, where, and how their current strategies could be improved.
It’s no secret that fleet costs have been on the rise over the past several years, with inflation, emissions regulations, and supply chain issues playing a prominent role in those increases. In a 2024 fleet benchmarking report, data showed the median rental and leasing sector’s cost per mile was $0.60 — the third highest among 12 industries — though fuel spend and distance traveled in this sector were among the lowest. Because fuel and maintenance are the two highest cost centers for fleets, and because the rental and leasing sector’s fuel spend is on the lower side, the sector’s higher cost per mile could be attributed to maintenance and repair spend. “The National Private Truck Council’s (NPTC) Benchmarking Survey Report 2024, which was released on Aug. 22, found that among private fleets, overall equipment and maintenance costs per mile increased 76 percent since 2020,” according to Penske. Though the new administration is already making moves to help slow inflation and reduce the cost of doing business, the results aren’t the sort that happen overnight. Early to mid 2025 costs will likely change little, but toward the latter half of the year, we could start to see some downward movement in various business and fleet costs.
While it’s hard to plan for all budgetary challenges that might come your way, you can more easily allocate funds where they’re needed most — or where you see the greatest fluctuation in spend — through benchmarking. Rental fleets can also use benchmarking to assess maintenance effectiveness, compare their performance against industry standards, and make strategic operational improvements.
➊ Identify Where You’re At Before making any big changes, it’s important to first establish a baseline for the metrics you’re tracking — or going to track. These can be things like preventive maintenance (PM) compliance rates, inspection completion rates and failed inspection item trends, service expenses, downtime, cost per mile, and so on. All this data works together to create a clearer picture of the fleet’s health and performance, as well as the cost versus value of assets so you can determine optimal replacement windows.
➋ Determine and Prioritize Goals
Benchmarking allows you to compare your operation to the industry standard, like those outlined in benchmarking reports, or you can benchmark against yourself to measure the success of any changes you make. Before you make any changes, though, you’ll want to define specific goals based on the results of your baseline, such as:
• Reducing unscheduled downtime
• Improving service workflows
• Optimizing inventory
• Graduating from reactive to proactive — and even predictive — maintenance practices
Regardless what your goals are,
defining them is only the first step. From there, prioritize your goals to help ensure that improvement efforts are focused, measurable, and manageable. In short, don’t start by biting off more than you can chew.
➌ Develop an Action Plan
Alright, you’ve got your baseline, and your goals are defined and prioritized; now it’s time for an action plan. Let’s say your priority goal is to reduce unscheduled downtime. You’ll need to first find the cause or causes of the problem, which can include things like:
• Pencil-whipping inspections (or poor inspection completion rates)
• Poor PM compliance
• Harsh driving
• Recurring mechanical issues
• Shop-related downtime due to understaffing, high workloads, or replacement parts delays Targeting these issues one at a time can help you implement subtle but effective process changes that you can build on over time without getting overwhelmed by either data or change management. You can use digital fleet solutions like a fleet optimization platform to corral all your fleet data in one place to easily see trends in metrics related to your priority goal. You can use digital inspections with set requirements that include photos, documents, or comments to reduce pencil-whipping and improve inspection compliance rates, for instance. Likewise, digital
work orders with estimated versus actual time to repair and status updates can shed light on where shop delays might be occurring.
This is the point where benchmarking against your baseline really comes into play by enabling you to track your progress over time. Measuring key performance indicators (KPIs), such as cost per mile, downtime rates, and the impact of maintenance process changes on overall fleet efficiency allows you to see what adjustments have worked, what hasn’t, and what still needs a bit of fine tuning. Adjustments should be made as needed based on real-time data, but don’t be afraid to scrap a change that’s had a negative impact. It’s also important to set expectations after changing a process to allow a sort of buffer zone between implementation and payoff so stakeholders aren’t expecting a 15 percent cost reduction in one day.
The key to benchmarking is data, and not just any data, but useful data. Many fleets are already using fleet management tools for data collection, including telematics and fleet maintenance software. Some fleets are even opting for a fleet optimization platform to consolidate fleet, finance, and business data through integrations. Pairing telematics with an optimization platform enables easier remote maintenance management; you can track and monitor asset issues and assess the severity of those issues no matter where vehicles or equipment may be.
Using fleet solutions doesn’t just make benchmarking easier, it provides a level of data visibility and automation that can improve maintenance workflows. All the data mentioned above — and more — is accessible in real-time and displayed visually on a customizable dashboard so you can focus on the metrics most important to
meeting the fleet’s goals.
Digital inspections provide failed item alerts from which you can create an issue and attach it to an existing or new work order. You can receive DTC fault alerts in real time and take a snapshot of related sensor data, which can also be attached to existing or new work orders, speeding up issue diagnosis. You can include priority statuses on digital work orders to ensure the most critical issues are addressed in a timely manner. You can also use fleet solutions to optimize your inventory based on usage trends and set re-order thresholds; parts assigned to work orders are automatically removed from your inventory in the system.
Using fleet solutions as a benchmarking tool to help guide maintenance decisions can help rental fleets reduce costs and downtime and stay competitive within the industry. by Rachael Plant is a senior content marketing specialist for Fleetio.
DECEMBER 3 - 5, 2025
LOCATED AT THE OPAL SOL | CLEARWATER, FLORIDA
Leadership isn’t about one person—it’s about rising together. At IGNITE 2025, discover strategies to navigate uncertainty, inspire your team, and drive success. Step up, lead boldly, and shape the future of your company.
Astec revolutionized the paving industry with the introduction of the Shuttle Buggy, and now the SB-3000 sets a new standard in material transfer vehicles. Effortless maintenance, unmatched performance, and four steering modes for ultimate agility keep paving seamless. Experience groundbreaking innovation with the patented Ground Crew Control Station for the ultimate user experience and protection. The SB-3000 isn’t a machine, it’s a revolution in material transfer, built on Astec’s legacy of industry firsts.