
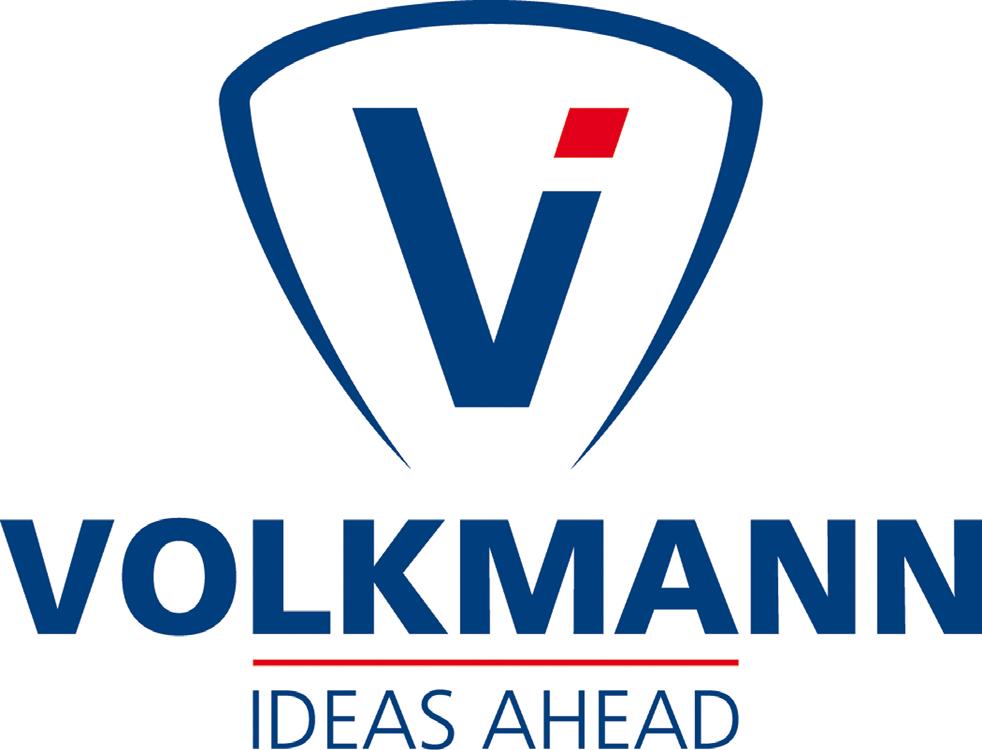
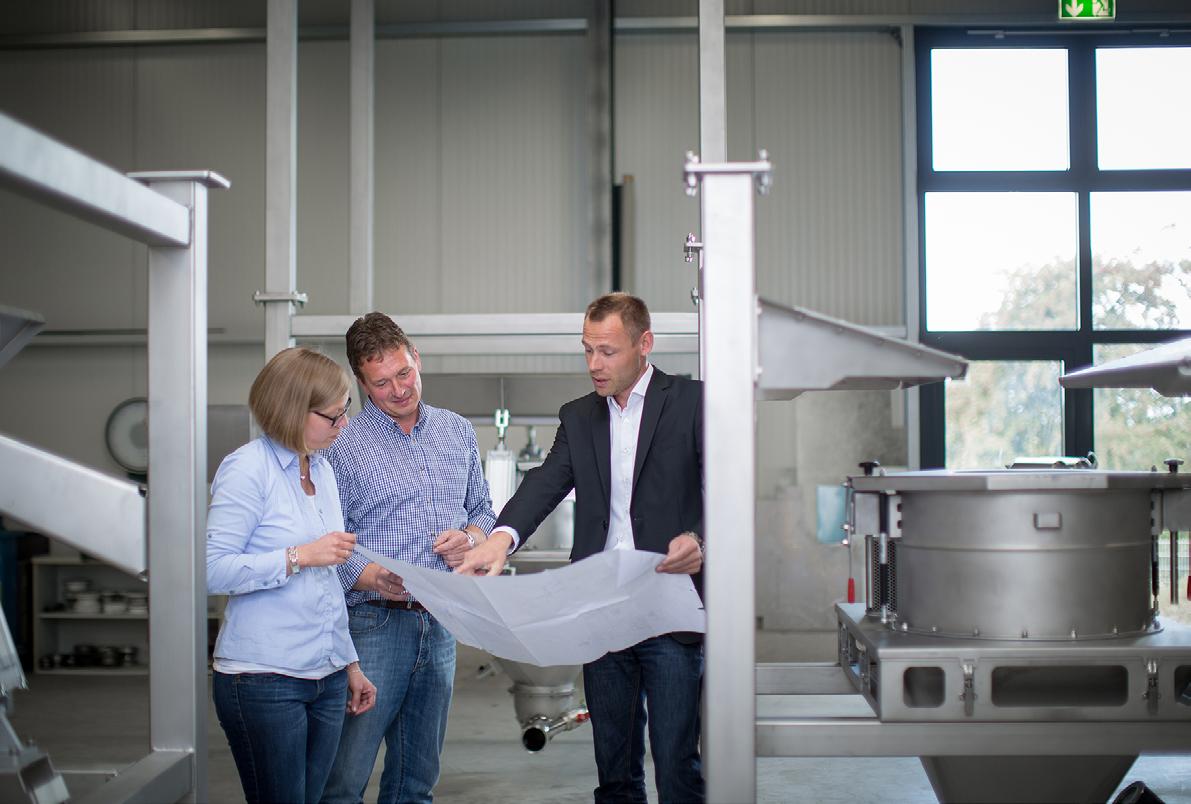

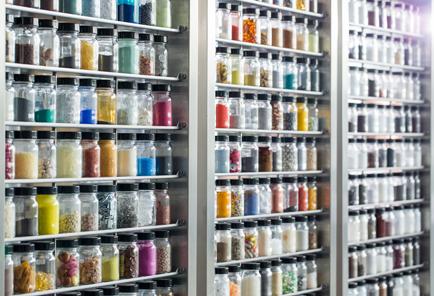
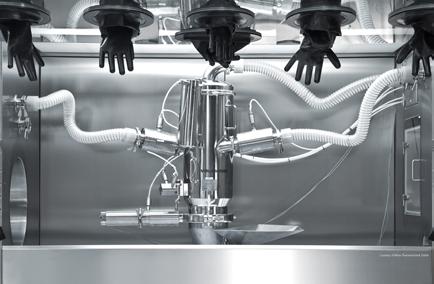
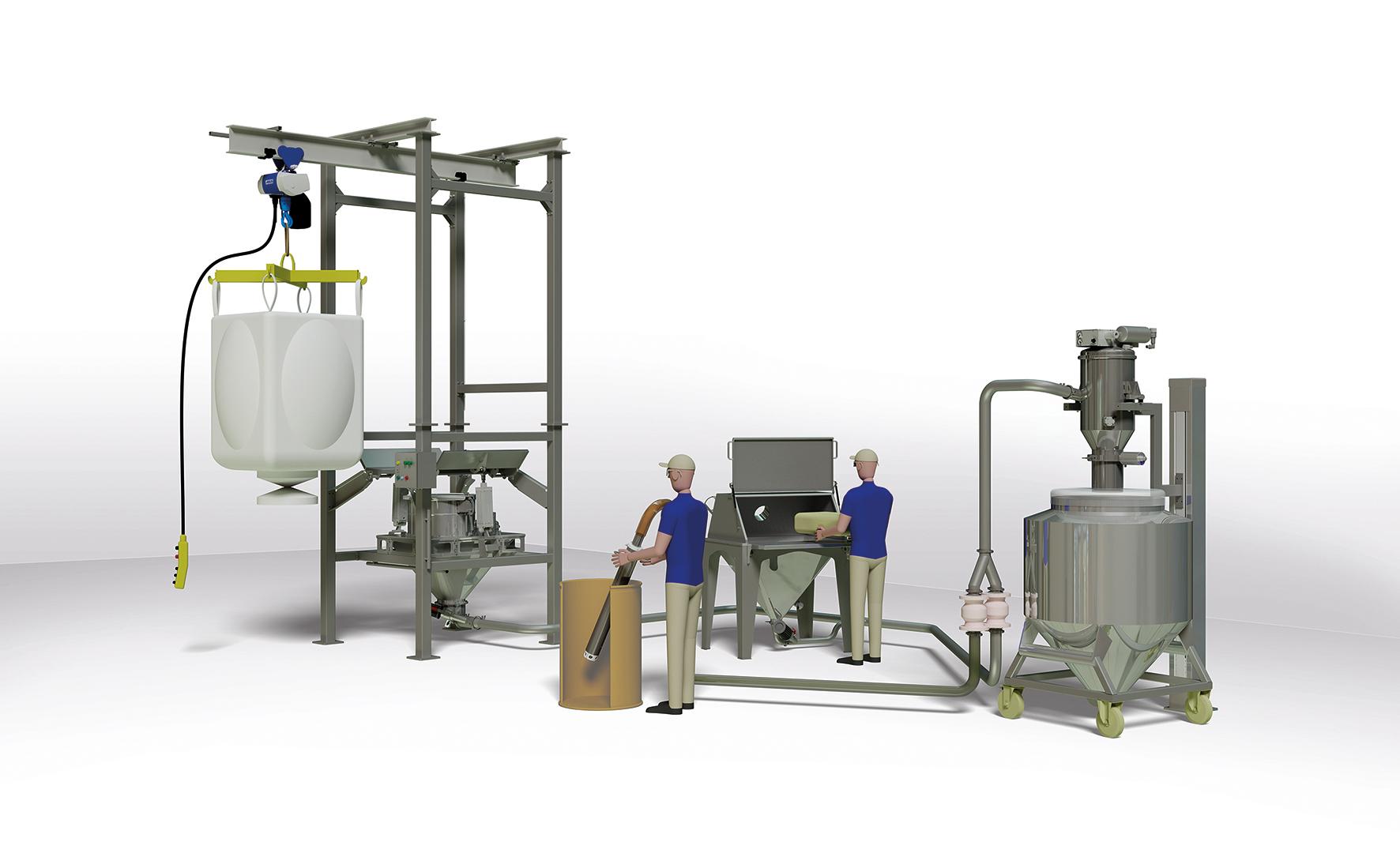
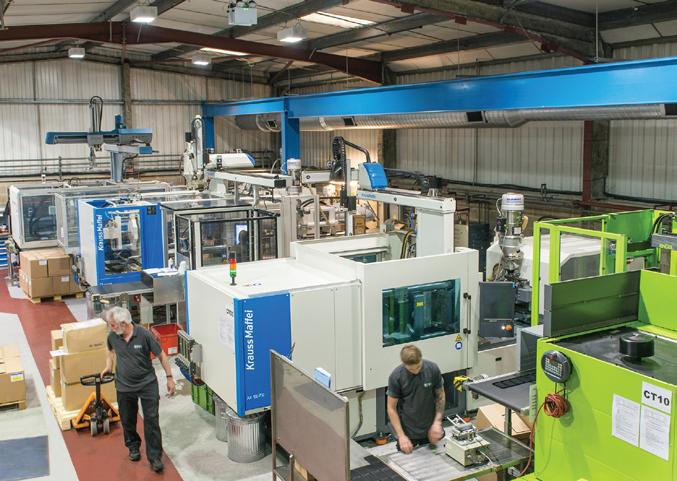
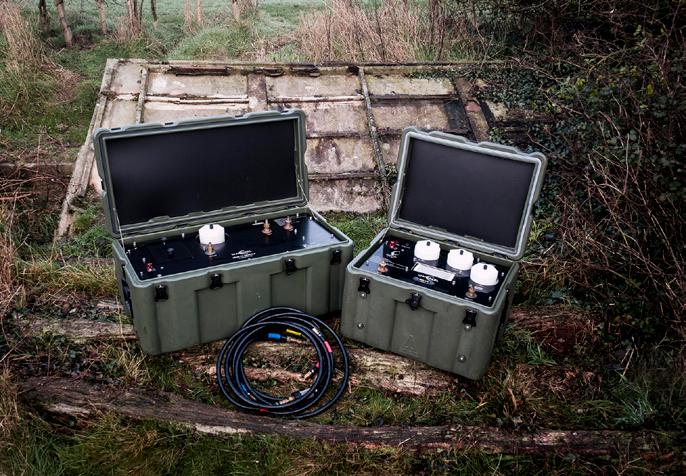

This year, Suurmond celebrates its 50th anniversary! Mr W. Suurmond founded his company in Nunspeet on the 21st December 1973 and started operating in 1974 with the commercialisation of custom designed gear pumps.
Over the years, Suurmond has opened three more offices and vastly expanded its portfolio. The company has developed into a process industry specialist with customers such as Shell, Akzo Nobel and DSM, as well as innovative start-ups. Today, gear pumps still play a key role and are increasingly used as a part of complete (dosing) systems. These systems are developed in close co-operation with the customer, Suurmond sales engineers and the company’s partners.
Suurmond’s approach is always centred around finding the best solution for the
desired process boasting a high level of technical expertise and a commitment to the highest quality standards.
Suurmond is also celebrating 20 years active in the UK and have recently moved to a larger facility in Evesham in Worcestershire allowing the UK team to better support UK based clients.
Suurmond take pride in finding and developing simple solutions to complex problems. Its work involves contributing to solutions for plastic recycling, developing new materials, and improving product quality.
Suurmond would like to welcome its clients from the UK and the Netherlands at its exhibition stands at CHEMUK (Birmingham) and WOTS (Utrecht).
T +44 (0)1386 423756 info.uk@suurmond.com www.suurmond.co.uk
Electric vehicles are a decisive factor in reducing CO2 emissions in road traffic. They store the energy required for propulsion in batteries and an electric motor converts it into motion. In contrast to combustion engines, no fossil fuels are required. If the batteries are charged with electricity from renewable energy sources, they even have a completely CO2-free energy balance. Today, lithiumion batteries are used almost exclusively as accumulators. Vacuum technology is indispensable for their production.
Tracer gas leak detection ensures quality
The proper functioning, quality and safety of lithium-ion batteries, which are used as accumulators in impermeability to external influences such as moisture ingress. For this reason, leak detection systems are used in battery production to check the batteries.
Pfeiffer Vacuum supplies the necessary vacuum solutions from a single source.
One of the world’s leading battery manufacturers for the automotive industry is currently using test gas leak detection systems from Zeltwanger Leak testing & Automation GmbH, which are equipped with complete solutions from Pfeiffer Vacuum. The systems must meet stringent requirements. The decisive factors here are achieving the required cycle time and high reproducibility of the battery cell test.
Enabled by Pfeiffer Vacuum technology, even the smallest leaks can be quantified and localized with the help of Zeltwanger’s testing systems. This makes it possible to quickly eliminate leaks in a downstream production step.
Changes to geometries and improvements to production methods and processes can be initiated based on the results obtained. This leads to quality improvements, increases the yield and reduces manufacturing and testing costs.
+49 6441 802 0
T
www.pfeiffer-vacuum.com
Industry Update covers a range of activities in the UK market – from publishing to training, from exhibitions to general updates. Our aim is to reach genuine buyers within the UK. With exciting and insightful updates in the UK industries, Industry Update covers a huge range of marketing possibilities and provides a fantastic service with cost-effective prices to promote your products and services.
Sponsored by
Hertfordshire based engineering company, Magog Industries continue to develop it’s range of bimetallic alloy hardened grades and coatings, working closely with established UK and European based coating specialists. Plastics recycling is growing within the industry with many moulders increasingly recycling in-house.
However, where recycled material needs to be bought in, problems can arise where material contain abrasive elements that pose a challenge in processing. For example, added fibres used to reinforce the moulded product can now be as high as 50%. Certain PE and some grades of bio-degradable polymers such as PVOH (Polyvinyl Alcohol) can attack the screw surface over time.
At Magog Industries, Director and General Manager, John Allsop is leading the drive in developing and presenting solutions, “We’ve been focussing on looking at
measures, particularly surface treatment for abrasion and potential corrosion to increase resilience and longevity specifically in ceramic and chrome seal coatings for demanding applications such as blown film extrusion.” John explained, “By working closely with our customers, we continue to innovate and develop our products to ensure latest solutions are available to meet the most demanding process applications.”
“For example, the recycling and reprocessing market has grown in recent years for both new and refurbished screws and barrels for the company. Regrind material can bring its own challenges but are successfully met thanks to many years of expertise within our design, engineering and production teams.”
For more information, please contact Magog Industries by email: enquiries@magog.co.uk, call: 01920 465201 or visit: www.magog.co.uk
In this issue of Industry Update, we are pleased to feature Plastic Products International as our Plastics Technology and Tooling Company of the Month
For over 50 years, PPi has met the requirements of the world’s largest global Automotive and Medical brands such as Volkswagen, Glaxo Smithline, Aston Martin, and Bentley Motors. However, its extensive expertise of tooling ranges also means that its services also stretch across Point of Sale, Telecommunications, Electrics and White Goods.
From sole traders through to multi-national organisations, Plastic Products International (PPi) has been providing complete turnkey solutions to companies that require tooling, plastic products and assemblies of the very highest quality. PPi will always work in an ethical, enthusiastic and professional manner.
The company has grown steadily over its lifetime and still remains in family ownership.
PPi has a programme of continual reinvestment that helps them to provide customers with excellent levels of quality and service.
From full end-to-end services including in-house design, toolmaking, injection moulding and inspection, its traditional values combined with cutting edge technology enables them to provide customers with the innovative solutions they need in a timely and precise manner. PPi are IATF TS16949 and ISO 9001.
PPi’s toolmakers are highly skilled and experienced and an integral part of the company. PPi has been designing and making mould tools since 1968. Its mould tools are designed and manufactured using state of the art software. Ensuring absolute speed and precision, PPI has invested in Röders high speed milling machinery to offer unsurpassed levels of speed and accuracy.
PPi also has over 25 years of experience of working with its World Class Chinese partners that help to produce tools with a full UK guarantee.
PPi provide dedicated on-site office space for its customers that is fully air-conditioned with connectivity to LAN, Wi-Fi, Telephone and presentation facilities, PPi allows customers to work on-site and maintain their busy schedules whilst overseeing trials and tool manufacture.
Reverse Engineering, 3D Rendering & Visualisation, and Moldflow are all in-house services that are provided by PPi.
Having been in business for over 50 years; PPi has a vast understanding of its client’s needs and have built its business model on ensuring that these are recognised. The MD not only designed and developed their quality systems – he took it upon himself to become a fully trained and qualified automotive VDA auditor! Everyone at PPI works together to create an ultimate solution that best suits the client’s needs.
For more information, please see below:
T 01279 445041
admin@ppiuk.net
https://www.ppiuk.net
Volkmann supports customers in solving their conveying tasks, from the idea right up to the finished plant. This is our strength. We act responsibly and pay particular attention to the perfect interaction between our and other systems applied in the process. Our expertise in consulting and design, together with the high quality of manufacture and flexibility within the company, offer the best recipe for the success of a project as well as for the satisfaction of the users, thanks to equipment and plants that can be operated simply and safely.
During the planning or improvement of process and filling-lines, the question occurs of how to optimise the material flow. Nowadays, the product flow downstream of packaging units is highly automised, however, the supply side often shows weakness. Volkmann have a loading
system, which combines the advanced Multijector®Vacuum Conveyors with a level-controlled buffer hopper.
With this transfer unit, first the respective powders, granules and other bulk materials to be packed are safely transported by vacuum and it is then used to supply the packaging and filling process on demand. The result is an interactive, enclosed transfer system, which is also suitable for pellets, capsules or tablets. This conveying method has considerable advantages over conventional, old fashioned, manual or mechanical transport technologies. Apart from supplying packaging lines, Vacuum Conveyors safely load mixers, tablet-presses or any other kind of process equipment or vessels (containers, silos etc.) (figure 1).
Conveyable bulk materials even include difficult and sensitive powders. The cyclic vacuum-plug-flow conveying set up usually results in no product separation or
segregation. When introducing small amounts of powders into the system either manual suction lances or feeding hoppers are used. For larger quantities bag rip & tip stations or big-bag unloading devices are more common. In addition, the available ATEX certificates for all Multijector®-Vacuum-Conveyors make them the perfect choice for potential EX areas (powders and gasses) and with that they are unique in the European market.
Nearly any type of bulk-materials, ranging from A for Activated Carbon to Z for Zeolithe, are conveyable with vacuum.
T +49 2921 96040
mail@volkmann.info
https://uk.volkmann.info
As surgical instrument manufacturers pursue greater throughput while facing increased labor costs, automating the medical instrument manufacturing process has become a necessity. However, integrating automation into the gundrilling process for drilling deep holes in extremely precise surgical instruments in lights-out operation is a major engineering challenge requiring more than simply pairing a robot with a deep-hole drilling machine.
The right machine, tools and process must all come together to create small holes with extreme precision in difficult-to-machine materials such as titanium and surgical stainless steel. More importantly, the entire system must flow from a unified concept where the whole is greater than the sum of its parts.
To meet these challenges, UNISIG developed its UNE6-2i750-CR dual independent spindle gundrilling machine. The UNE6-2i is capable of gundrilling hole diameters ranging from 0.8–6mm in part lengths measuring up to 30 inches with depth-to-diameter ratios from 20:1 to more than 100:1. The machine has a maximum combined drilling speed of 28,000rpm and a 3,000psi (207) bar programmable flow-based coolant system with dedicated pumps for each spindle to ensure precise coolant pressure control.
Automating hundreds of cycles of precision manufacturing, however, is not possible unless the overall operation is considered from the outset. Surgical instrument manufacturing is a sequential process: parts
must be loaded into the machine in a particular way for specific operations that happen in a specific order.
Workpiece length, shape and configuration determine where it is gripped by the robot when loaded into a machine, moved from spindle to spindle for drilling, residual cutting fluid removed, and returned to the pallet. Where a part is gripped impacts where it is clamped for drilling to ensure accuracy. Every variable along the process chain must be considered and accounted for, and the calculus is detailed and complicated.
Then there are unique customer needs and requirements. The equipment and process must accommodate a variety of part families and hundreds of parts to increase runtime and efficiency. Operators must be able to change over part types and programming without calling in an automation specialist, and the entire process must be controlled from a central interface. Add to the mix that everything must be packaged in as small a footprint as possible, and the scope of the engineering challenge comes into focus.
UNISIG’s approach to solving these problems, however, results in targeted automation that enhances the existing benefits of gundrilling, ensuring a solid foundation for reliable process-wide automation.
At its core, the automated UNE6-2i is a purpose-built machine with automation embedded in its design, not added as an afterthought. Flexibility and adaptability are maximized by a harmonious, interdependent mechanical, software and operational planning scheme.
To meet size constraints, a 6-axis robot was embedded in the machine with a pallet system on the backside of the machine, allowing easy operator access from the front to setup the machine without compromising ergonomics. The configuration enables quick setup changes between prototype and proving operations and full production runs.
The robot automatically repositions the workpiece from the front of the first spindle into the rear of the second spindle without operator input. The process of drilling a part from both ends in a single-piece flow is unique to UNISIG. Workpieces with enlarged features on one side are loaded from the rear of the collet, solving a common problem in gundrilling medical surgical instruments with full automation.
Further information on all machines and the complete UNISIG machine program is available at: www.unisig.com or follow the company on LinkedIn and Twitter (@UNISIG).
Illegal copies can be dangerous AND costly. Knockoff products can be inferior, and misapplications can be dangerous to humans and animals. At a minimum, using unverified copies can lead to double work correcting misapplications, doubling the cost. Using original systems for dispensing 2-component materials from certified manufacturers ensures greater economy and dispensing safety for people and the environment. medmix’s strict quality controls, detailed know-how, and supporting consulting service are important for professionals.
Today, Mixpac mixing systems cover the entire industry of 2-component adhesives and sealants. Years of development and co-operation with material
manufacturers and their customers in the industrial and DIY sectors allows medmix to boast top of class reliability at optimum prices. Copies can never achieve medmix’s high level of reliability because they are not developed to be compatible with an entire system. Every misapplication due to cheap copies can lead to high repair and correction costs. Cheap also means no guarantees – all misapplication costs are borne by the customer.
Cheap copies can lead to cheap seals and bonds – these are accidents waiting to happen. medmix focuses on maximum safety for people, animals, and the environment.
medmix invests millions in the development of its products to ensure safe and economic use. Long-time investments in mixer system technology allow for economically viable 2-component adhesive/sealant systems. From the dispenser to the mixer, genuine Mixpac products provide a best-inclass total system for application of 2-component adhesives and sealants.
Buying cheap copies risks damage to users and the reputation of the entire industry. Accordingly, medmix invests heavily to protect and educate the market to successfully detect and deny risky, cheap copies.
Recently, medmix prosecuted distributors of a large shipment of illegal copies of the well-known Quadro™ brand mixers. These dangerous copies of agricultural sector mixers, used in hoof care, can cause great damage. Every misapplication results in unrecoverable money lost to the farmer.
Customers and users can trust that medmix Switzerland AG will continue to defend their rights, their health, and their economic safety.
T +41 41 723 73 00
communications@medmix.com www.medmix.swiss
For over 40 years, we’ve helped our customers achieve success in deep hole drilling, providing them with the machines, automation and support they need to be competitive and profitable.
We have found that the initial energy we and our customers spend at the beginning of a quoting process pays off throughout the entire project, from inception to installation. We take a systemized approach not only during this critical phase but also throughout the entire sales process. This ensures there are no surprises and that our customers know exactly what they can expect when starting discussions with UNISIG about their gundrilling and deep hole drilling needs.
This is our approach at UNISIG:
1) We listen to our customers, ask questions and understand what they need
This may seem obvious, but often the temptation is there to just skip to a quote because we think we know what is needed after a brief discussion. Sometimes that is true, when the application is straightforward and familiar, or it is something we have a packaged solution for. We always try to make the quoting process quick and efficient, but there are times when the application deserves a more in-depth conversation. Our salespeople and engineers listen very carefully and often pick up on small details – a specific tolerance, material condition, process requirement or a future need for flexibility – that may change our recommendations.
2) We first identify a standard solution from our product line that can be applied at the lowest cost and shortest delivery possible
At UNISIG, our product development mindset is to systemize solutions from our experience in many different industries, make them automation ready and embed application flexibility whenever possible. We invest millions of dollars annually in our product line and related spare parts, giving us a strong starting point for new applications. Our standard product line encompasses much more than machines, including standard automation, workholding, accessories and tooling that we can offer as part of the solution.
3) If a standard solution isn’t available, we consider a customized solution and we stand behind it UNISIG is very good at building customized machines, and we do so often. Once we and our customers agree that a special solution is needed, we move forward with a great deal of confidence and experience. We start by evaluating how we might approach the design using standard modules
The new Menzel Elektromotoren headquarters on the outskirts of Berlin is now fully functional and operational. All works were completed on time and on budget – a remarkable feat of co-ordination between all trades and partner companies. The move has been completed, with the relocation of the large stock of motors and accessories. Menzel maintains one of the largest warehouses for large electric motors in Europe, which ensures short-term delivery capability at all times. Production and administration has also moved into the new building. Operations officially commenced on January 2nd 2024. CEO Mathis Menzel is looking forward to the future for this venture, “This move will ring in a new era in the history of our family business. The new plant is tailored to our requirements in every detail: generously proportioned logistics and production areas, continuous crane accessibility with an 80-ton lifting capacity – that will enable us to achieve streamlined production processes, to schedule and complete customer projects even more flexibly and reliably, and it will properly set us up for the future as the international headquarters of our group.”
Menzel is a medium-sized manufacturer and worldwide supplier of three-phase asynchronous motors with squirrel cage or slipring rotors up to 15MW and, in special versions, up to 25MW. In addition to standard motors with excellent performance properties, the manufacturer specializes in customer-specific and tailored drive solutions.
Photo construction diary for the new plant: https://www. menzel-motors.com/article/ photo-report-new-electric-motor-plant
T +49 30 349 922-0
info@menzel-motors.com www.menzel-motors.com
or proven concepts, thus eliminating long debug cycles and/or high costs. Then we use our mechanical and electrical engineering disciplines to virtually test the new machine before we build it.
4) If a commodity solution is readily available, we recommend that rather than upsell a machine the customer doesn’t need
We build machines that can gundrill or BTA drill deep holes that are impossible to drill on machining centers. Even if it may be possible to drill some deep holes on a CNC machining center, our machines have the power, speed, dimensional accuracy, spindle density, coolant systems and process control that will improve productivity, tool life and reliability. Typically, though, when a customer comes to UNISIG with a specific part need, at that point they’ve most likely already struggled with a conventional machine and realized that a deephole drilling machine is obviously the way to go.
Please visit: www.unisig.com, email: info@unisig.de or contact us on: +49 (0)7125 9687590.
Innovative design, rigorous testing and high precision engineering are why Oliver Hydcovalves are the most trusted valves for Hydrogen and Carbon Capture applications.
The range has grown rapidly to include instrumentation, Double Block and Bleed, Pipeline, and Subsea Gate Valves. Shown here is the 1” Hydraulic Gate Valve with manual override, DBB with 20mm bore, 3” Flange, and the ½” Hydraulic Gate Valve equipped with Remote Operated Vehicle bucket capability.
These valves, showcased for their diverse features, are en route for deployment in Carbon Capture (CC) injection applications.
For information on how Oliver Hydcovalves can provide Hydrogen and Carbon Capture valve solutions for your green renewable energy project, telephone: +44 (0)1565 632636 or visit our website at: www.valves.co.uk
It is imperative that engineers can operate valves in a plant or system manually if there is a fault, where power is not available or which hasn’t yet been wiredup or have been recently decommissioned and the power subsequently removed.
How is that possible?
The Solenoid Valve Operating Magnet from Fridgenius is the solution.
Its compact design and high usability application has already been widely praised by engineers across the HVAC industry. It is designed like a cotton reel and when placed on a solenoid valve (with coil removed), it causes the armature to open and close.
It is a time saver!
It can be used effortlessly to recover refrigerant from a plant which has already been decommissioned and power removed. In urgent emergencies, when the solenoid valve
coil fails, it is a lifesaver by keeping the system functioning, until a replacement coil is sourced and installed.
The Solenoid Valve Operating Magnet is available in four sizes: 10mm, 15mm and 18mm and 20mm. This can be customised to a colour of your choice, with bespoke company logo printing available.
Where can I buy the Solenoid Valve Operating Magnet? Fridgenius is a successful family run business, with a firm network of national and international distributors supplying the Solenoid Valve Operating Magnets. They are suitable for usage in refrigeration, air-conditioning, water, oil and gas installations. T +44 (0)2381 550189 enquiries@fridgenius.com www.fridgenius.com
Oliver Twinsafe is to supply Double Block and Bleed pipeline valves for use on Monoethylene glycol (MEG) injection pump systems. MEG is a widely used hydrate inhibitor designed to reduce the risk of hydrate formation in pipelines that could cause blockages.
The order includes a batch of 2 1/16” API 6A 5,000psi Double Block and Bleed valves in A182 F55 Super Duplex material that have been dynamically tested to meet the requirements of API 6A PSL level 3. In addition, the valve designs were pre-qualified to API 6A PR2 Appendix F, which involves multiple cycle
testing at low, ambient and high temperature with zero leakage allowed across the valve seats throughout these cycles.
A number of Oliver instrumentation valves have also been ordered, taking the total number of valves supplied for this offshore project overall to over 300 with more valves in the pipeline.
For information on how Oliver Twinsafe can provide pipeline valve solutions for your project, telephone: +44 (0)1565 632636 or visit our website at: www.valves.co.uk
Oliver Valvetek’s unique approach to Subsea valve design and manufacturing is exemplary and world-leading. They partner with one of the leading Subsea Tree and Subsea Distribution Units manufacturers in the world and is supplying valves to the Exxon Mobil Guyana Futures field.
For the past 5 years, Oliver Valvetek has provided more than 3,000 pieces of ½” 10,000psi rated Subsea Trunnion style Ball Valves for the full field development. Due to changes in production, control system requirements, and an operation pressure increase, Exxon Mobil also required a 15,000psi rated valve.
Oliver Valvetek successfully qualified a valve to API6A PR2F and API17D 3rd Ed and included specialist testing and materials that were specific to the pressure and process media application.
For more information on Subsea valves, contact Oliver Valvetek on: +44 (0)1565 632636, email: sales@valves.co.uk or visit: www.valves.co.uk
CP Cases is your go-to source for rugged protection and innovative solutions. Today, we want to talk about something close to our heart – ruggedised satellite communication equipment cases and why they are indispensable in today’s world.
Unveiling the vital link
In an era defined by connectivity, whether it is for remote work, expeditions, or emergency response, satellite communication equipment is the unsung hero that keeps you linked with the rest of the world. But for this hero to shine, it needs a trusty sidekick – ruggedised cases. Let’s explore why they are essential:
1. Unmatched durability
Our ruggedised cases and racks are built to withstand the harshest conditions. Whether it’s extreme temperatures, rough handling, or the unpredictable outdoors, they provide unparalleled protection. Think of them as the guardians of your precious communication gear.
Example: The CP Cases Amazon Rack
Our Amazon Rack is a prime example of rugged reliability. It offers a robust solution to safeguard your satellite communication equipment in any environment, ensuring it operates flawlessly when you need it the most.
2. Reliability reinvented
Imagine being in a remote location with no room for equipment failure. Rugged cases offer a shield of reliability, ensuring that your satellite gear consistently performs, regardless of the surroundings. This reliability can be a gamechanger in critical situations.
Example: The CP Cases ERack
Our ERack is a testament to innovation. It combines rugged durability with a lightweight design, making it perfect for the transportation and storage of satellite equipment. It’s the partner you can always rely on.
3. Unburdened peace of mind
Peace of mind is invaluable when you are
working or exploring in demanding environments. Ruggedised cases provide you with the confidence to concentrate on your tasks, knowing that your communication equipment is securely protected.
Example: The CP Cases Rugged Textiles
Our Rugged Textiles is designed for satellite communication applications, ensuring your equipment is safe and sound during transit. It’s the epitome of peace of mind for satellite communication professionals.
4. Versatile protection
Just as we have a deep appreciation for diverse and multifunctional equipment, we understand the importance of versatility in equipment protection. Rugged cases accommodate various satellite communication devices, from BGAN terminals to satellite phones.
Example: The CP Cases Airship
Our Airship is your all-in-one solution, designed to protect and transport a range of satellite communication equipment with custom foam that fits like a glove. Its versatility ensures that your gear remains in top-notch condition.
5. Equipment lifespan extension
Satellite communication equipment doesn’t come cheap, and replacing it is a hassle you would rather avoid. Ruggedised cases aren’t just protectors; they are equipment life extenders, offering significant cost savings in the long run.
Example: The CP Cases SatRack
Our SatRack is engineered for maximum protection and shock resistance. It is the guardian of your satellite equipment, ensuring it stays operational for years to come.
In a world where staying connected is essential, ruggedised satellite communication equipment cases play a pivotal role. They exemplify resilience and adaptability.
So, whether you are an intrepid explorer, a dedicated field worker, or simply someone who values top-notch gear, remember that ruggedised cases are the enablers of uninterrupted communication. They’re your key to staying connected in the most challenging environments.
Stay connected, stay rugged, and explore the world with confidence, knowing that CP Cases has your back.
T +44 (0)20 8568 1881 info@cpcases.com https://cpcases.com
Process heating is vital in hydrocarbon processing. While conventional methods involve burning fossil fuels, an increasing number of plants are transitioning to electric process heaters. One of the key advantages of this shift is the capability to achieve highly precise control over both the heating element surface temperature and the power consumption of the system. This level of control now extends to predictive control, made achievable through actionable insights derived from data. In this article, Chelsea Hogard, engineering team leader at thermal systems provider Watlow (pictured), explores the role that data plays in predictive maintenance.
Electrification
use heat exchangers in processes that are conducive to coking and fouling. Fouled heaters can contaminate or disrupt processing, and must be cleaned and/or replaced when issues arise.
The right data, in real time
Process heating is a significant source of energy use and greenhouse gas emissions in the industrial sector, and so replacing fossil-fuel based heaters with electric ones running on green energy should yield significant progress towards decarbonisation goals. Adopting solutions for the first time will naturally bring about questions for process end user engineers regarding process variation, network loads, as well as component failure. Modern data collection technology, along with sophisticated data analysis, can monitor processes and allow these kinds of questions to be answered in real time.
Common challenges
Petrochemical refining operations often
Having accurate data concerning the operation and health of systems and components is crucial in reducing the risks associated with new technology. For example, identifying temperature fluctuations in a process can serve as an early indication of potential coking or fouling, which could lead to maintenance issues in the future. By enabling process end users to recognise patterns of drift that signal impending problems, unplanned downtime can be averted through timely planned maintenance cycles.
To learn more about WATCONNECT integrated with Data Insights, please visit: www.watlow.com
Like all industries, pressure to decarbonise is imminent. And glass manufacturing is no exception, with the objective to attain carbon neutrality by 2050. Not only does decarbonisation benefit wider industry and society, but when done correctly, also provides efficiency and cost benefits. In this article, Mikael Le Guern, Global Glass Business Development Manager at Eurotherm, a company acquired by industrial technology company Watlow, explains how installing power boxes close to furnace electrodes can help glassmakers improve energy efficiency and reduce costs, compared to traditional power system designs.
emissions, particularly by increasing electrical boosting.
As a result of pressure to decarbonise, we are seeing more requirements to significantly increase electrical boosting for facilities all over the world. Certainly, for large glass production companies, their total CO2 emissions are the aggregate emissions of all their plants and facilities globally.
With furnace campaigns lasting between ten and 18 years before the next rebuild or cold repair and with only a few upcoming greenfield projects, the opportunities for these companies to implement carbonreducing solutions are limited. Currently, whenever a repair is due, many glass companies are already considering their options to reduce greenhouse gas (GHG)
The other movement happening in the marketplace is that all types of glass producers are looking into these issues. Years ago, the size of the furnaces and type of glass made it possible to implement small to medium size electrical boosting, on average between two and five megawatts (MW). Now, not only has the required size of electrical boosting systems grown from a few megawatts (MW) to over 10MW and beyond, but this trend is happening across most types of glass production, including float glass furnaces.
To learn more about Eurotherm and its solutions for glass manufacturing, please visit: www.eurotherm.com. To learn more about Watlow’s thermal solutions, please head to: www.watlow.com
In this issue of Industry Update, we are pleased to feature HEIDENHAIN (G.B.) Limited as our Measurement, Control, and Drive System Technology Company of the Month.
HEIDENHAIN is a high-tech company that has been pioneering in measurement, control, and drive system technology for more than 130 years. HEIDENHAIN products often lay the groundwork for technological advances in the most innovative global industries, including semiconductors, electronics, machine tools, and production equipment automation for the factories of tomorrow.
Founded in Berlin in 1889, this pioneering company for measurement and control technology looks back on a long tradition. HEIDENHAIN, located in Traunreut in southern Bavaria, now offers products and solutions for industries such as machine tools, automation, electronics, robotics, elevators, and medical technology.
HEIDENHAIN has an established network of 30 subsidiaries and 40 distributors worldwide. HEIDENHAIN (G.B.) Limited, a wholly owned subsidiary of DR.
JOHANNES HEIDENHAIN GmbH was founded in 1969 and is based in Burgess Hill, West Sussex, and is responsible for the UK and Ireland territories.
Research and development are part of HEIDENHAIN’s DNA, with a double-digit percentage of its revenues devoted to the continual development of its advanced technologies. Its market leading technologies incorporate reliability, repeatability, and accuracy at its core.
Daniel Johnson, MD HEIDENHAIN GB commented on some recently launched products for the UK market, “For 2024, HEIDENHAIN is launching our new control ‘the TNC7’ into the UK machine tool market, along with our new generation of feedback encoders with built in vibration sensors for predictive maintenance. Our new control addresses many modern machining shop problems faced by our users such as the total cost of ownership over the machine lifespan. The TNC7 control has been developed to reduce setup times through graphically assisted probing of the work piece and fixtures. We have advanced the technology of linear scales by reducing and/or eliminating the need for air purge without compromising on signal quality and reliability. Improvements in the machines cutting performance through optimised contour milling, reducing tool wear and milling times. Enhanced dynamic collision monitoring and in process monitoring without additional
sensors vastly reduces the chances of downtime due to collisions or tool breakages.”
“Furthermore, our latest generation of rotary feedback encoders have additional sensors built in such as temperature or vibration, utilising our EnDat protocol to transmit the data allowing production lines to manage alerts before they become production stoppages.”
In support of these new products, HEIDENHAIN is increasing its support for customers in the UK by bringing on board service and training partners in the UK and Ireland, as well as adding additional facilities in Burgess Hill that will also include a full 5 axis milling machine to enhance customer training and application support.
In rapidly changing technological landscapes, adaptability is key. HEIDENHAIN GB is poised to adapt to the latest UK market trends, regulatory changes and technological advancements swiftly, ensuring to remain competitive in its industry. Understanding and addressing customer needs is crucial for success. “We measure success by seeing our customers succeed, breading long lasting relationships built on trust and industrial products,” added Daniel.
For more information, please see below: T 01444 238550
sales@heidenhain.co.uk
https://www.heidenhain.co.uk
Bradshaw is the official UK distributor for Goupil, all-electric, zero-emission light commercial road and utility vehicles.
Goupil was founded in 1996 and quickly established itself as a leading manufacturer of electric utility vehicles and a pioneer in sustainable transportation solutions.
The Goupil G2 and G4 models perfectly balance sustainable, environmental, and economic functionality in an electric light commercial vehicle. With their innovative design, they are specifically tailored to meet the diverse needs of industrial and commercial operations.
Goupil electric vehicles offer a multitude of benefits that make them a compelling choice. Not only do they contribute to a cleaner and greener environment by producing zero emissions, but they also provide efficient and cost-effective transportation solutions. With their compact size and manoeuvrability, Goupil vehicles are perfect for navigating urban areas and tight spaces with ease. Additionally, their low maintenance requirements and long battery life ensure reliable and hassle-free operation. These qualities, combined with their versatility and customisable features, make Goupil electric vehicles an ideal option for various industries, including
logistics, delivery services, and municipal operations.
Environmentally friendly
Using electricity rather than fossil fuels, Electric vehicles produce zero tailpipe emissions, helping combat climate change and improving air quality.
Regenerative braking contributes significantly to environmental conservation by enhancing the energy efficiency of electric vehicles. Unlike traditional braking systems, which dissipate kinetic energy as heat, regenerative braking systems capture and reuse this energy. The regenerative braking systems on a Goupil Electric vehicle reduce wear and tear on the tyres and reduce tyre and brake dust pollution.
Silent operation
The Electric Goupil is better suited to stop-start operations compared to diesel vehicles. Diesel particulate filters (DPFs), designed to capture and store exhaust soot to reduce emissions, can pose problems. If not regularly and sufficiently heated, these filters can become clogged, leading to expensive maintenance and repair costs.
Electric vehicles offer a significant advantage in reducing noise pollution, providing a tranquil and enjoyable environment. These near-silent vehicles enable operations during evening and early morning hours without causing disturbances to the local community.
Economic benefits
Electric vehicles are incredibly efficient, enabling lower operating costs over time than traditional internal combustion vehicles. Operating electric vehicles can save money on both fuel and maintenance expenses. This is especially beneficial for businesses that operate a fleet of vehicles, as they can see significant savings over time.
No special charging infrastructure required
Charging a Goupil G4 is a straightforward process; equipped with a single-phase onboard charger, the Goupil’s plug into any 230V/13A domestic socket, negating the need for any additional electric charger installation.
The Goupil G4’s compact size and manoeuvrability make them ideally suited for urban environments, where space is premium and navigating crowded streets can be challenging.
www.bradshawev.com
CHEMUK 2024 is the UK’s largest annual chemical, laboratory and process industries exhibition. It’s back at the NEC Birmingham from 15th-16th May 2024, with over 500 exhibitors, 150 speakers and split across four show zones: Chemicals Supply Show zone, Chemicals Management Show zone, Process & Chemical Engineering Show zone and the Chemical Laboratory Show zone.
With specialist exhibitors showcasing brands and services across laboratory, process and plant engineering and supply chain functions, it is the trade event of the year for the industry. This year’s exhibitors will be bringing the latest offerings from chemicals, raw materials & ingredients, process and plant engineering, chemical operations & logistics, laboratory equipment & services, HSE and other related services.
The CHEMUK Conference offers a leading programme of expert keynote speakers, panel discussions and features hot topics impacting the chemical industries, such as: UK REACH, Bioprocessing, Energy Management, Sustainability, Digitalisation, AI, The Hydrogen Economy, Formulation, Pharma Focus and much more. Keynote speaker Thomas Birk, Managing Director of BASF plc will be discussing ‘Why we need a consistent approach to circularity in the Chemical industry’ and Vivi Hollertt, Chief Sustainability & Communications Officer for Nouryon will be looking at ‘For a greener and cleaner future.’
The Chemicals Supply Show has exhibitors covering the following specialist topics: Agrochemicals, Fuels, Oils & Lubricants, HI & I Cleaning products/Biocidal, Paints/Inks/Adhesives/Sealants/Coatings & Treatments/ Construction, Water & Waste treatment, Polymers/ Elastomers and much more.
The Process & Chemical Engineering Show has exhibitors from the following areas: Chemical Metering & Dosing, Gaskets & Sealing, Pipes, Hoses & Couplings, Pumps, Valves & Flow Solutions, Energy/Nuclear, Oil & Gas, Pharmaceutical Process Industries, Water/Waste and much more.
The Chemical Management Show has exhibitors from: Associations/Industry Bodies/Media, Business Operations, Health & Safety/Environmental Protection/Waste Management, Logistics & Transportation, Packaging & Labelling and much more.
The Chemicals Management Show has exhibitors from: Benchtop & Pilot-scale equipment, Lab Process Engineering, Control & Automation, Chemical analysis, Characterisation, Sampling, Testing, Measurement & QA/QC services, Chromatography, Formulation and much more.
In this issue of Industry Update, we have featured one of our predicted Top Exhibitors for CHEMUK 2024: Suurmond UK, see page 20 in this issue.
Suurmond UK has been designing, manufacturing and delivering sustainable solutions since 1974, directly to the processing industry with dedicated product portfolios for:
t Fluid Handling: (Pulseless gear pumps and pump systems, dosing systems, sensors and transducers.)
t Polymer Handling: Pulseless polymer gear pumps, filtration systems, control systems, sensors and transducers.
t R&D: Glass reactor systems
If you’re looking for complete solutions for pulseless flow in the processing industry, Suurmond UK offers premium rotary positive displacement pumps for innovative, modular solutions. The pumps can be customised for specific applications, with a view to the fluid’s chemical properties, operating temperatures and viscosity.
Here at Industry Update, we would also like to highlight some other exhibitors, including AVAL: a supplier of ATEXapproved low pressure and vacuum equipment in The Process & Chemical Engineering Show. This includes: flame arresters, regulators and control valves, tank gas blanketing valves and pilot-operated vent valves.
If you’re looking for leading pumps, valves and flow solutions, AVAL is the sole distributor for Cashco, Kaye MacDonald, Sensiflo and Valve Concepts equipment, and additionally is the exclusive UK agent for Lupi conservation vents and flame arresters since 1988. With customer service in mind, AVAL offers a Field Services program that provides bespoke maintenance programmes for individual applications.
A second exhibitor in The Process & Chemical Engineering Show that we would like to highlight is Jacquet Weston Engineering: A leader in the customised design and manufacturing of process plant and ancillary equipment for the surface finishing industry. With a state-of-the-art purpose built factory, the dedicated team can design, manufacture, assemble and dry-run process plants, including large ones.
CHEMUK 2023 had a staggering 3,956 attendees over the two-day event, which was a 41% leap in visitors. The professional backgrounds of visitors were wide and included: broad chemicals, chemical products and chemical-user industries, with many coming from the UK, Ireland, Europe, China, Israel and the USA. The reviews from last year were overwhelming positive with one commenter: Section Head for Concept Life Sciences stating it was like,’ ‘Disney for Chemists!’
To find out more about CHEMUK 2024, the exhibitor list and visitor demographics, please see the website below: https://www.chemicalukexpo.com
CHEMUK 2024 is fast approaching and Apex Pumps, manufacturers of high specification centrifugal pumps, is primed to present its wide range of centrifugal pumps for industry, building services, aquaculture, petrochemical plant and the entire chemical industry.
For its third year running, Apex Pumps will be based at Stand: F34 in the Process & Plant Engineering Show Zone. Managing Director, Andrew Simpson will be at the show along with his team to increase brand visibility, generate leads and showcase its innovations that include such products as ISF/ISFC Pumps, API 610 Pumps, and TVL Pumps that have all been meticulously designed and built here in Britain for the most demanding applications.
Apex Pumps put quality at the heart of every pump made being certified to ISO 9001 since 2001 and ISO 9001-2015 by Advanced Certification. Apex Pumps is also an active member of the British Pump Manufacturers Association (BPMA), and plays an integral role in influencing the future of the pump industry.
Apex Pumps’ booth will be engaging, full of informative material and knowledgeable staff members. Don’t miss out on a fantastic opportunity to talk all things pumps!
For more information, please see below: T 0117 907 7555 sales@apexpumps.com www.apexpumps.com
For over 35 years, Apex Pumps has offered the broadest ranges of centrifugal pumps in the UK. Based at its own site in Bristol where all its products are designed and built, Apex Pumps has earned an enviable reputation for the quality and endurance of its products.
THE NEXT STAGE OF ENERGYEFFICIENT TEMPERATURE CONTROL
We are LAUDA – the world market leader for precise temperatures. Our temperature control devices and systems are at the heart of important applications and hence make a contribution to a better future.
Don’t just take our word for it – visit our website or give us a call today to learn more about how we are your perfect laboratory partner.
Visit www.lauda-technology.co.uk
Email info@lauda-technology.co.uk or telephone +44 (0)1780 243118
BASA is the umbrella organisation for UK and Irish adhesives and sealants manufacturers and focusses on technical and legislative aspects and on promoting awareness of the industry and technology by providing guidance on technical and compliance issues to members via a library of documents on the website.
We are the voice of the adhesives and sealants industry and an information source for manufacturers and suppliers. We lobby on behalf of members and liaise with Government on legislation, keeping Members well informed of UK, EU and International proposals and initiatives.
With the growing concerns around the environment and using sustainable products and raw materials, BASA is dedicated to helping its members minimise harmful chemical usage and educate the public on the industry’s drive for safer products. BASA members
work hard to formulate innovative products that positively contribute to the sustainability agenda whilst maintaining performance and durability.
BASA will be available at stand Q90 and hopes to continue to reach more potential members, looking at ways to support its manufacturers post Brexit and help them to navigate potential new legislation and trade rules.
Contact Lorna Williams, Chief Executive Officer, T +44 (0)330 223 3290 lorna@basa.uk.com www.basa.uk.com
We are LAUDA – the world market leader for precise temperatures. Our temperature control devices and systems are at the heart of important applications and hence make a contribution to a better future. As a full-service provider, we guarantee the optimum temperature in research, production and quality control. We are the reliable partner for hydrogen, chemical, pharmaceuticals, biotech, semiconductors and medical technology. With competent advice and innovative solutions, we have been inspiring our customer every day for over 65 years – worldwide.
Puridest will provide ultra-pure, low-gas, sterile and pyrogen-free distillate. All of our products set impressive standards with their compact design, userfriendliness and performance.
Our Hydro Water Baths boast reliability whilst being virtually maintenance free, and are built for continuous operation in the laboratory. A further reliable partner for applications in the lab is our Varioshake Shaker; extremely userfriendly, robust and durable. The LAUDA
Don’t just take our word for it – visit our website or give us a call today to learn more about how we are your perfect laboratory partner: T +44 (0)1780 243118 info@lauda-technology.co.uk www.lauda-technology.co.uk
Blue Frog Scientific is one of our predicted Top Exhibitors for CHEMUK 2024, returning to the NEC Birmingham from 15th-16th May. CHEMUK is the country’s largest annual chemical, laboratory and process industries exhibition.
Exhibiting in the Chemicals Management Show, the team from Blue Frog Scientific will be showcasing its marketleading scientific and regulatory affairs service for the chemicals, biocides, plant protection products, human pharmaceuticals, and veterinary medicines sectors.
With locations across the UK and France, the expert team of consultants and associates provide exemplary support for regulatory compliance with hot topics such as: current and emerging PFAS regulations and endocrine disrupter assessment.
Understanding the impact of emerging PFAS regulations, such as the EU universal PFAS restriction proposal, is crucial for future substance and product compliance. Do your products contain PFAS? Are the PFAS likely to be restricted? How will the UK regulate PFAS? There is uncertainty around this varied group of substances due to their perceived risks to human health and the environment and the impact of future regulations on many potentially critical uses.
Blue Frog Scientific can support companies ensure compliance with the developing PFAS regulations and regulatory compliance of alternatives.
Want to know more?
Talk to Blue Frog Scientific at CHEMUK 2024 on Stand D94. *PFAS – Per and Poly-Fluoroalkyl substances.
T +44 (0)1313 747422 info@bluefrogscientific.com www.bluefrogscientific.com
Suurmond supplies solutions to optimise your process and improve the quality of your end-product.
We design, manufacture, and deliver sustainable solutions for the processing industry with dedicated portfolios for:
t Fluid Handling: Pulseless gear pumps and pump systems, dosing systems, sensors & transducers
t Polymer Handling: Pulseless polymer gear pumps, filtration systems, control systems, sensors & transducers
t Research and Development: Glass reactor systems
Dedicated solutions since 1974!
And always with low cost-of-ownership and sustainability in mind.
Leading brand’s rotary positive displacement pumps offer highly innovative and modular solutions for processing industry production. These pumps are tailored to fit your specific application, taking into consideration
the fluid’s chemical properties, operating temperature, pressure, and viscosity. Even for tough conditions!
Our custom solutions guarantee optimized production processes and product quality, while delivering a long service-life and low cost of ownership.
Come see visit us at CHEMUK on Stand K30.
T +44 (0)1386 423756 info.uk@suurmond.com www.suurmond.co.uk
SAMSON Controls Ltd is a global leader in Process Automation and Valve Technology, serving as the UK subsidiary of SAMSON GROUP, a larger network consisting of over 60 subsidiaries and 17 production sites across the world. Manufacturing a diverse range of control valves including globe, ball, butterfly, PTFE/PFA lined, and ceramics.
SAMSON Controls Ltd has served the UK process industry since 1958 and has earned its reputation as a reliable partner. The company’s comprehensive product portfolio encompasses various valve types designed to provide precise control and optimal performance across diverse applications. We can support our customers, with technical support through our expert technical sales engineers, service and troubleshoot control valve issues through our service engineering team, whether it be on the customer’s site or remotely, assemble and test with certification, and offer training.
pushing the boundaries of valve technology to address emerging challenges and opportunities. Utilising our decades of experience and technical knowledge, the company continues to set the standard for reliability, performance, and customer satisfaction in process automation.
SAMSON Controls Ltd will exhibit at CHEMUK2024 at Stand K52.
In an ever-evolving industrial landscape, SAMSON Controls Ltd remains at the forefront of innovation, continuously
T +44 (0)1737 766391 sales-uk@samsongroup.com https://uk.samsongroup.com/en
As a worldwide leader in dosing technology, sera Technology is a system provider of high-quality products and services for the dosing and feeding of chemicals and fluids. With 75 years of experience, sera Technology is renowned for its excellent customer service and leading German engineering, offering some of the most robust pumps available on the market.
The PolyLine from sera is a series of simple, flexible as well as economical and highperformance systems for preparing polymers. The systems are equipped with precise flow measurement for solution preparation and
level measurement to ensure efficient and economical operation of the systems.
The PolyLine is available in three different variants, each for use with liquid, powder polymer or as a variant for both polymer forms and we are now welcoming the new, smaller version – The PolyLine Flow Compact. With a footprint of 120 by 80 centimeters, it fits exactly on a Euro pallet. This means that it is not only cheaper to transport but can also be placed more easily at the customer’s site and finds its place in every room and every application.
www.sera-web.com
Ever just thought... MAKE MY LIFE EASIER, so I can live the (good) life that I want?
We have complete, reliable quality labelling solutions, with ultra-flexible options. Our software makes life easy. We take care of the processes, so you enjoy the results.
We are proud to see our work in use in homes, businesses and commercial environments. We keep people safe, we organise, we create order and clarity, we add beauty, and we add tangible value.
We genuinely enjoy making people’s lives a little less stressful by going the extra mile.
Our labels, your world.
Contact T 0800 805020
hello@avery.co.uk
https://www.avery.co.uk
Facebook https://www.facebook.com/ averyinuk
Instagram https://www.instagram. com/ukavery
Twitter https://twitter.com/ukavery Linkedin www.linkedin.com/company/ avery-uk
Pintrest www.pinterest.co.uk/ukavery Youtube www.youtube.com/AveryUK
Avery is proud to have over 80 years of experience, providing innovative materials and FREE marketleading Design & Print software for our customers to create professional and customised stickers and labels.
Upload a design and have your labels, stickers, cards and much more professionally printed, cut and shipped directly to you from our UK production site. Avery provides total choice, from designs printed by us to choosing blank labels in any material, size, shape and quantity, with the goal of making life easier for our customers.
The Health & Safety Event is the UK’s largest, strategic gathering of technology, services and products under one-roof to promote safer workplace practices. This year’s two-day event is back at the NEC Birmingham from 30th April-2nd May 2024 and covers the whole supply chain across safety and security of personnel, property and assets. The event is co-located with The Workplace Event, The Security Event, The Fire Safety Event, Professional Officer Security Live and National Cyber Security Show.
Across cutting-edge brands, practical demonstrations, and the best keynote speakers from across the industry, it is the best event for networking, brand awareness, new product launches and the latest best practice guideline and regulations.
The Health & Safety Event attracts a record number of health & safety buyers, proactively looking for the best products and solutions on the market, making it an optimised place to boost sales, pitch new products and network with decisionmakers and influencers.
Last year’s event attracted over 11,000 visitors from a wide range of backgrounds including: agricultural, building and construction, central/local Government, engineering, food processing, healthcare, hospitality, manufacturing, through to media and publishing, mining, offshore, pharmaceutical, transportation and many more. With a 24% year-on-year growth in visitors, this year’s event is expected to attract even more visitors.
This is the calendar trade event to build sales pipelines and showcase industry expertise to a captive audience of health & safety professionals. With 77% of delegates holding purchasing power or influence and 58% working for a company with over 100 employees, this is the definitive event to be an exhibitor.
The exhibitors cover the A-Z of health & safety and come from a wide background including: asbestos control, COSHH, driver safety, drug & alcohol testing, lone & vulnerable
working, noise control, PPE, risk assessments, slip & trip prevention, working at height and much, much more.
If it ain’t broken, don’t fix it and The Health & Safety Event organisers stick to what works but will also take risks and try new things. Back for 2024 is the Start-Up Street: exhibitors viewed as game-changers and movers n’ shakers. From cutting-edge innovation to risk management, these are the companies to get to know. One of the Start-Up Street exhibitors is airbliss+® – a Dutch PPE company specialising in the toughest working environments, such as confined spaces and lone working. With its next-level protective equipment, the company is focused on reducing accidents in the workplace through breathing/respiratory prevention measures, driver safety, head protection and cutting-edge health & safety software.
campaign to offer a feature in the Driver Safety Zone. This will help inform H&S professionals about best practice across driver safety and work-related road risk. Industry Update has featured the brilliant work of Driving for Better Business before in previous issues and we are delighted to see this take centre stage for such an important topic.
The Health & Safety Executive (HSE) will be exhibiting at this year’s event, as well as running presentations in The Keynote Theatre and Knowledge Hub. The hot topics this year will be: work-related stress, musculoskeletal disorders, noise and vibration (including hearing loss) and asbestos.
Shoebox is another Start-Up Street exhibitor, focused this time on solutions for hearing health professionals across the industry. The unique software-based audiometers are optimised for boothless testing, alongside mobile, in-clinic, tele-audiology solutions and online hearing screens. Perfect for the latest occupational and wellbeing solutions in the audiology sector.
The best trade shows have the best conference line-ups and The Health & Safety Event 2024 is no exception. Leading, expert keynote speakers will be giving talks and leading workshops across four designated conference spaces: Keynote Theatre, Practical Safety Theatre, The Knowledge Exchange and Lone Worker Safety Live. These programmes will guide you through the latest IOSH and HSE regulations, compliance-safety, solutions for complex H&S scenarios and how to support lone workers.
This year, The Health & Safety Event 2024 is collaborating with the National Highways Driving for Better Business
One of our predicted Top Exhibitors is HydePark Environmental, who are industry experts in spill control. Providing solutions for spill response equipment, absorbents, spill containment, bunded storage and leak control, the expert team can provide a comprehensive package for effective spill control for safer workplaces.
Established over 13 years ago, HydePark Environmental has over 3,500 lines, with solutions across environmental/waste management, hazardous material storage and handling, manual/ material handling, PPE, slip and trip prevention and a unique brand of in-house absorbents called HUG. The HUG range includes: heavyweight rolls, pads, absorbent cushions, top mats, chemical absorbent socks and much more. Turn to page 28 to read more.
To find out more about exhibiting, key note speakers and everything health & safety related, please see the website below:
https://www.healthandsafetyevent.com
Regatta Professional, a leader in performance workwear, is thrilled to announce its participation in the upcoming Health and Safety Show, where it will proudly showcase a range of cutting-edge workwear and highvisibility garments, and give you the chance to win a Virgin Experience Day!
Born from the UK’s biggest outdoor clothing brand, Regatta Professional has the trusted expertise to kit out your workforce. Through unrivalled product knowledge and a passion for the great outdoors. Regatta Professional make it their job to provide style, protection and comfort. It’s clothing that works since 1981.
Highlighting the show is their popular Tactical Hi-Vis Bomber – a gamechanger for building sites. Boasting ID Reflection technology, this bomber ensures safety from all angles. As well as safety protection, the jacket offers weather resilience with waterproof and breathable Isotex 10000 fabric. It’s complemented by a windproof fabric design and Thermoguard insulation, and adheres to a variety of safety standards.
Visit Regatta Professional at Stand 4/K12 for an exclusive look at their leading collection and stand a chance to win a Virgin Experience Day with every order placed.
For more information, please call: +44 (0)161 749 1333 or email: professional@regatta.com.
From rising levels of noise pollution in urban areas to concerns over air quality, these issues have a profound impact on the well-being of citizens and the sustainability of industries. To address these challenges, the field of environmental monitoring has emerged as a critical sector within the broader technology and engineering landscape.
Environmental monitoring solutions encompass a range of sophisticated technologies and data-driven approaches aimed at tracking and mitigating environmental factors. This includes monitoring noise levels in cities, assessing air quality in industrial zones, and measuring vibrations caused by construction activities. Such monitoring is not only essential for regulatory compliance but also for the overall quality of life and safety of individuals living and working in these environments.
In this context, companies like Cirrus Research play a pivotal role by developing innovative and reliable monitoring solutions. These solutions provide real-time data, enabling businesses and government authorities to make informed decisions to improve the environment and safeguard health. Cirrus Research’s
mission revolves around creating innovative solutions that enhance the way we monitor and manage noise and other environmental impacts. They have not only revolutionised the field of noise monitoring but also expanded their expertise in air quality, vibration, and more.
Cirrus Research’s cloud-based monitoring solutions, Quantum Indoor and Quantum Outdoor, have had a profound impact on businesses and communities across the UK. By providing real-time data on noise, air quality, and vibrations, they empower businesses and local authorities to make informed decisions. This datadriven approach not only ensures compliance but also fosters healthier, quieter, and more sustainable living and working environments.
These cloud-based monitoring solutions have not only changed the way we perceive data but have also transformed the way we live and work in the UK.
See us at Stand 4/K92.
Find out more at: https://www.cirrusresearch. co.uk/blog/2023/11/ quantum-award-of-excellence
See us at Stand 4/K92
At Betafit, our mission is clear: to be the single safety solution that revolutionises the standard of Personal Protective Equipment (PPE) above the neck.
Betafit is one brand that you can trust with consistent quality and comfort across all categories, with a focus on products that are made to fit together, offering optimum safety and reducing wearer discomfort. Our Betafit Academy provides training, videos, bespoke education and courses to improve end user safety through knowledge.
We have extensive customer service and support with bespoke resources for every customer, next day service and quarterly programmes aimed at increasing awareness and reducing accidents.
With innovation at the core of what we do, there is lots to discover from Betafit.
Come and visit us at HALL 4 – F120.
Totectors, the pioneers in safety footwear in the United Kingdom, reveal the latest addition to the family, the Williams boot, set to revolutionise the safety footwear landscape. Created for the modern tradesperson, Williams blends style, safety, and comfort, signalling a new era in the safety footwear industry.
In a world where function often outweighs fashion, Totectors is flipping the script by marrying practicality with style. Rhys, the UK representative for Totectors, emphasises, “Our message is ‘KEEP YOUR LOOK.’ We don’t want our customers to compromise on style. We’re reaching out to the younger consumer by offering safe, functional, and comfortable footwear that mirrors their weekend style.”
featuring arch support, heel cradles, and Kevlar-built midsoles. It also achieves the highest SR slip resistance rating and S7 certification for comprehensive protection.
Addressing the prevalent issue of slipping accidents on construction sites, the Williams boot meets the new SR slip rating, ensuring stability even on lubricated surfaces. Its outsole is engineered to tread confidently across different terrains, while a ladder grip system enhances safety.
The Betafit Range Includes Eyewear, Hearing Protection, Respiratory Protection and Head Protection, which includes our new range of helmets.
Contact T 08455 444000 sales@betafit.com www.betafit.com
The Clarino upper lining stands out, offering 30% greater strength than traditional leather while being more abrasion-resistant and lighter. Tested against the latest acid protection standards, it guarantees durability and safety in demanding work settings. Its design prioritises safety,
Join Totectors at The Health and Safety Event, NEC Birmingham, April 30th-May 2nd, 2024, stand 4/H90. Swing by the Totectors stand for a chance to explore our latest offerings, engage in daily competitions, and snag some exciting giveaways.
T 0031 (0)20 225 9090 www.internationalbg.com
The Health & Safety Event is the UK’s largest gathering of anyone responsible for running a safe and efficient workplace. While delegates may come to hear about new personal protective equipment and safe lifting devices, this is where they can also learn about their biggest work-place risk – driving for work.
Over the three days, in the Driver Safety Theatre, Driving for Better Business will help health and safety professionals understand the common weaknesses of many organisations whose employees use vehicles for their job and, most importantly, how to create a ‘good practice’ driving for work policy. This is a vital tool for achieving legal compliance, building a safe driving culture, and setting out the standards expected of drivers.
Each day is centred on a Mock Trial – an eye-opening walkthrough of a serious road incident that results in the company’s safety management systems coming under scrutiny, and highlighting key areas where employers fail to meet their obligations.
Driving for Better Business will then demonstrate a brand-new online resource that employers can use for free to write, review and communicate a goodpractice driving for work policy to their workforce.
“This is a major event for us,” says Simon Turner, Campaigns Manager for Driving for Better Business.
“Last year, the Mock Trial was a massive draw for visitors, with many commenting that they would like their senior team to have the same experience so they could understand the risks and weaknesses in their driver management culture and to recognise that legal
responsibility for driver safety sits at the top of the company in the same way that any other occupational health and safety issue does. In response to that, we’re running the mock trial on each of the three days of the show with a different follow-on session each day covering driving for work policy, legal compliance and internal incident investigation.”
“In addition, we are launching a free, clear and practical toolkit to help organisations create a robust policy, adapt it to their own company profile and get critical alerts when official guidance or legislation changes that could affect the policy.”
The Driver Safety Theatre features a three-day programme packed with presentations from driver safety leaders and legal experts including:
t Prof Tim Marsh, Managing Director at Anker Marsh
t Kanwal Kanda, Head of Transport at the Health and Safety Executive
t Charlotte Le Maire, a specialist criminal and regulatory lawyer and barrister
t Mel Clarke, Health, Safety and Wellbeing Director at National Highways
t John Wilkinson, Driver Safety and Performance Manager for Northern Powergrid
t Duncan McNicol, Head of Risk and Compliance at CBES Ltd
t Pete Rushmer, Managing Director at Flagship Partners
t Dr Lisa Dorn, Associate Professor of Driver Behaviour at Cranfield University and Founder and Director at PsyDrive
t Prof. Clare Anderson, Professor of sleep and
circadian science at Birmingham University
t Karl Wilshaw, Fleet Director at Travis Perkins
t Kate Walker, Managing Director of the Diabetes Safety Organisation
t Anne-Marie Penny, DfBB Programme Manager for National Highways
t Tavid Dobson, Road Safety Lead at Rail Safety & Standards Board
t Dai Fussell, Head of Compliance for the UK Civil Service
t Andrew Drewary, Managing Director of Road Safety Smart, multi-award-winning road safety specialist in collision/incident investigation
The theatre is part of the wider Driver Safety Zone where Driving for Better Business is also bringing together a range of expert partners to give guidance to event visitors on how to manage driver safety effectively. RED Driver Training, IAM RoadSmart, Flagship Partners, CheckedSafe, Randox and Drivetech will all be exhibiting in the Driver Safety Zone.
Driving for Better Business is a free to access
National Highways programme to help employers reduce work-related road risk, protecting staff who drive or ride for work, and others who they may share the road with.
support@drivingforbetterbusiness.com
https://www.drivingforbetterbusiness.com
On a day that started out just like any other, Bob Adams, a van driver very similar to many of those that work for you, begins his day’s work schedule. Some very common examples of poor driver safety management align and result in a serious incident involving a cyclist – but was it the driver’s fault or what is the employers? We examine what went wrong, why it went wrong, and what a subsequent investigation and prosecution could look like. More importantly, we look at what companies should be doing to avoid a similar scenario happening to them.
A common piece of feedback from last year’s mock trial was ‘That was such a good presentation – I wish my directors had been here to see that!’ This year, we’re running a mock
trial at 10:30 on each of the three days. This is an excellent chance to get your directors to understand full scope of work-related road risk and to ask questions of our legal experts.
The Mock Trial is presented by Simon Turner, Campaign manager for Driving for Better Business and Charlotte
Le Maire of LMP Legal. Charlotte is a specialist criminal and regulatory lawyer and barrister. She is frequently instructed to provide critical advice in the immediate aftermath of a serious or fatal incident. She is recognised nationally as a leader in the field of Fleet Risk and is regularly invited by corporates, insurers, brokers and fleet risk charities to provide training in relation to road safety matters, as well as providing practical solutions to criminal and regulatory challenges.
The Driving for Better Business team will be launching a brand new, online tool that employers can use for free to write, review and communicate a goodpractice driving for work policy to their workforce. Having a policy is a legal requirement, as is keeping it up to date, and communicating it effectively to drivers. This new resource is free to access and will allow you to:
t Access a driving for work policy template and checklist
to make sure you’ve got everything covered,
t Create a policy document that meets legal and compliance standards;
t Get email alerts for any changes in guidance or legislation that could affect your policy;
t Receive an annual reminder to review your policy, along with any changes that may be required since the last review.
Impact Technical Services is making its debut appearance at The Health & Safety Event at the NEC, Birmingham from April 30th – May 2nd.
Impact has been providing comprehensive LEV testing and extraction system design and installation for over 30 years and throughout this time has continued to increase its level of service and competency to place itself head and shoulders above its competitors.
Ensuring a high level of competency and reliability for its customers has always been a high priority, but over recent years, Impact has responded to the increasingly stringent requirements of the HSE by developing its nationwide team of technicians by extending their training to include further LEV qualifications with the British Occupational Hygiene Society (BOHS).
urging visitors attending The Health & Safety Event to visit their stand (Hall 4 Stand K142) to discuss their requirements and to ensure they are protecting workers in compliance with COSHH regulations.
As an industry leader, Impact is perfectly placed to provide industry professionals with the information and support they require to operate safely where a hazardous substance is used, or airborne contaminants are present. They are
We are excited to announce the newest addition to our line of workwear: the ROOTS Arcbuster range. This new collection embodies our continuous commitment to innovation and quality, offering advanced protection for those facing the hazards of arc flashes. With the Arcbuster range, we reinforce our promise as more than just a manufacturer; we are your dedicated partner in protection, ensuring that every garment offers unparalleled safety and comfort.
We understand the constant risk of electric arc flashes in sectors like utilities, power generation, and more, crafting garments that compromise on nothing. Our team is driven to innovate, producing protective clothing that leads in comfort, quality, and safety.
conditions with unmatched protective gear.
Deeply familiar with the diverse hazards across industrial, petrochemical, rail, and other sectors, we tailor our designs from the start to meet specific needs, ensuring no detail is overlooked. ROOTS is committed to safeguarding those who wear our products against hazardous
Our focus on continuous innovation and quality underlines our role as more than a manufacturer – we’re a dedicated partner in protection, offering garments that provide unparalleled safety and comfort.
Please see us at Stand: 4/D112.
T +31 (0)10
2 955 955
info@roots-original.com
www.roots-original.com
Contact
T +44 (0)116 244 8855 sales@impactairsystems.com https://impactairsystems.com
Hyde Park Environmental was back at The Health & Safety Event at the NEC in Birmingham from the 25th-27th April 2023 to showcase its leading range of spill control products and they caught everyone’s eye with their bright green footwear, bright blue container and yellow mobile absorbent station.
The Health & Safety Event is the leading expo for safe workplace solutions and innovations across the country and the team from Hyde Park Environmental were on hand to discuss everything Spill-related from: storage, containment, bunding, absorbents and Spill Response Training.
Established over 13 years ago, the company has locations in Antrim and Stafford and prides itself on creating a brighter future through environmental safety for industry at large.
With over 3,500 lines, the spillage experts offer solutions across environmental/waste management, hazardous material storage and handling, manual/material handling, PPE, slip and trip prevention and a unique brand of in-house absorbents called HUG. The HUG range includes: heavyweight rolls, pads, absorbent cushions, top mats, chemical absorbent socks and much more.
In addition to a growing product range, the expert team offer free site surveys and consultation, free samples (‘test before you buy’), appointed account managers for tailored service, on-site stock replenishment and same day dispatch/next day delivery for a quick turnaround.
To view the full range, please see the website below:
https://hydepark-environmental.com
Since the company was established in 2020, its mission has been to bring change to the end-user experience in selecting and buying industrial gloves, gauntlets and sleeves (PPE). As the designer and manufacturer of such an innovative range of quality industrial hand protection that is available for all industrial applications, Manosun is breaking the mould of traditional offerings with a core range of hand protection that are safe and the perfect fit for anyone that requires PPE.
“We believe our services outweigh that of any competitor because as well as our core-range of products, Manosun offers a quick turnaround product development process where we evaluate the enduser’s processes and tweak/develop a more fit for purpose product. As well as our FOC site-survey to enhance any risk assessment, we also add volume to any work operating procedure,” stated Steven Patterson, Country Manager UK & Europe.
Manosun breaks its products down into three category’s that ensure excellence, longevity and value for money. Each product is made to the highest ‘Quality’ meaning only the best quality materials and yarns are used to ensure a long-life product that can be used over again without wear or tear, and that also give comfort to all users. ‘Service’ – Manosun prides itself on its quick turnaround service whether than be
an order process, sample request, or site survey. Lastly, ‘Value,’ Manosun believe that not only does the cost-in use value matter but also its business values too. “We work closely with our distributors and end-users to nurture them in a partnership arrangement that supports each other’s enterprise,” added Steven.
Manosun’s current portfolio consists of a large range of hand protection products where it works with all end-users including globally known brands such as Nissan, JDR Cables, and SUEZ. Also part of its service, Manosun will survey any work environment, advise on the correct level of hand protection needed or if needed, and will even develop a brand-new product to the exact requirements of the customer.
For the past 12 months, Manosun has been concentrating on the growth and awareness of the brand. It’s initial approach to 2023 was to increase the awareness its products and dedicated a quarterly plan that would see them employ two new field sales persons in Q1. The first started on May 22nd and the second will start in the following six months.
From there, the plan is to keep moving in an upwards trajectory for the rest of 2023 and beyond. “Moving
A manufacturer and designer of industrial safety products
• Manosun was created during the 2020 global pandemic when industry took an all-time low in productivity
• Located in South Tyneside, the co-creator of the brand has over 16 years of industrial product development and 15 years within manufacturing including Health & Safety
• Our aim is to target the huge UK manufacturing sectors as well as power generation and conservation and offer a quality service, product and development ability, not all solutions can be found off the shelf
• We work with your traditional distribution supply chain so no need to work outside of any contractual obligations, your are free to develop and select your PPE requirements
• Manosun Ltd is also a member of the BSiF a sign and seal of quality and products that fulfil all UK and EU requirements of test and design.
Talk to Manosun for all of your hand protection needs.
Tel: 0191 300 8699
Email: admin@manosun.co.uk
Web: www.manosun.co.uk
forward, we will continue to grow our range of products. In 2023, we launched the Manosun BASIC range (not yet on the website). This is a range of gloves that contain rPET created from recycled materials (Plastic) to make industrial Polyester, each pair of gloves contains on average 36% recycled materials. Having a commitment to excellence means everything to Manosun, which is why we work with the BSiF as well as local networking and support groups NEAA (North East Automotive Alliance) and the AMF (Advanced Manufacturing Forum) to learn and adopt Best Working Practise from local industry as well as National and European requirements as a PPE provider/manufacturer currently instructed by the BSiF.”
Contact Steven Patterson: T +44 (0)7468 904409 steven.patterson@manosun.co.uk www.manosun.co.uk
www.facebook.com/manosun
www.linkedin.com/manosun
The Schmersal Group continues to expand its range of products for safe area monitoring: the company is now selling the UAM-05LP safety laser scanner from Japanese manufacturer Hokuyo in Europe, beginning with markets in Germany, France, Austria and Switzerland. The safety scanner is characterised by its extremely compact design and low weight, as well as its flexible integration options and high safety standards. This helps it to ensure maximum personal protection in logistics, manufacturing and the process industry.
Contactless protective devices, such as laser scanners, offer many benefits in the implementation of safety requirements. In contrast to guard fences and guard doors, there is no manual opening and closing requirement, and they do not impede materials transport. In addition, they also enable a clearer view of machinery and processes.
The UAM safety laser scanner handles presence control on stationary machinery and robot systems, with the UAM’s sensor utilising infrared beams to scan the environment and detect the entry of people and objects into the safety zone. This also allows the Hokuyo UAM
to achieve a wide range: with a detection range of up to 270°, a safety clearance of up to 5m and a warning detection area of 20m, the laser scanner can be used in various machinery safety applications.
The laser scanner can be easily configured for a wide range of uses and also has the ability to monitor two hazardous areas at the same time, e.g. two adjacent robots. Each of the two safety zones switches its own OSSD output.
Furthermore, the safety laser scanner is also able to undertake access control as well as arm and hand protection for safety-critical areas in work zones, e.g. as part of insertion and assembly workflows.
Another advantage of the Hokuyo laser scanner is its encoder input: with the help of encoders, the speed and direction of travel of automated guided vehicles (AGVs) are transferred to the laser scanner, so that the safety zones can be dynamically adjusted to stop the AGV in case of danger. The Hokuyo UAM-05LP is suitable for use in machinery safety applications up to PL d, Cat. 3 in accordance with EN ISO 13849 and SIL 2 in accordance with IEC 61508.
Contact Steve Watkins, Marketing Manager, T 01684 571987 swatkins@schmersal.com www.schmersal.co.uk
DCON Safety Consultants Limited offers leading health and safety consultancy and construction statute advice services. The company prioritises and specialises in the highest levels of informed and intelligent advice, senior project resource allocation and compliance assurance. Informed by industry expertise, DCON Safety Consultants Limited knows that every project has potential risks, no matter what its potential benefits, so its team of highly experienced construction professionals helps to ensure clients’ statutory conformity.
Upon gaining understanding of the specific needs, goals and desires of each client and their project, DCON Safety Consultants Limited is dedicated to implementing a design and construction management plan that will meet or exceed these requirements. And, DCON Safety Consultants Limited ensures that there is honesty, integrity, trust and professionalism underpinning every project.
Moreover, the company’s services are centred on three delivery principles:
t Maximising Quality: The company implements proven health, safety and wellbeing strategies to help clients achieve high quality and cost-effective work commensurate with the design of their projects.
t Minimising Risk: The company effectively manages design and delivery risk on projects to match each client’s desired risk level profile.
t Managing Compliance: The company relies on its extensive background working on a wide variety of projects to assist clients in developing, monitoring and maintaining compliance performance.
This excellent service would not be possible without the leadership of Diarmuid Condon, a construction industry leader who brings unique perspectives to encourage,
support and mentor the abilities of his colleagues. As a construction professional with a surveying background and experience spanning two decades, Diarmuid is emblematic of DCON Safety Consultants Limited’s commitment to providing outstanding services to clients.
Diarmuid has contributed his invaluable expertise to over 400 projects over 20 years, with a client list including public sector departments, corporate owners, real estate developers, main contractors, design professionals and infrastructural bodies. With this incredible portfolio, Diarmuid is helping DCON Safety Consultants Limited to become a leader in health and safety consultancy across the construction industry.
Key to DCON Safety Consultants Limited’s services is working as a Project Supervisor for the Design Process and CDM Advisor in various sectors across the Irish construction market. No project is too simple or too complex for the company’s construction safety consultants, all of whom are construction professionals with an average of 20 years’ experience in the built environment. The ability to
maximise this knowledge and skillset means DCON Safety Consultants Limited can generate distinctive and innovative ideas from traditional PSDP service inputs and outputs.
DCON Safety Consultants Limited also provides its main contractor clients with intelligent, practical, and reasonable physical site safety advice to support compliance and good practice adherence. Behavioural safety outcomes inform how the company approaches each solution with the contractor and their supply chain, identifying opportunities for improvement.
To complement this, DCON Safety Consultants Limited can also help with clients’ health and safety strategy. Its holistic and integrated approach can help unlock substantial benefits for clients by providing a structured, objective and SMART framework for full optimisation through the creation of an environment that embraces health, safety and wellbeing.
This means DCON Safety Consultants Limited helps clients to improve their health, safety and environmental performance; enhance staff satisfaction thanks to improved performance; improve risk management and corporate governance with a clear audit trail; gain confidence from long-term planning, better sustainability and performance; and improve overall corporate reputation, including greater staff satisfaction and a more efficient procurement and supply chain.
If you are interested in finding out more information on DCON Safety Consultants Limited’s full range of excellent services, head to the website or get in touch directly using the contact details below.
T +353 (0)1 611 1556
diarmuid.condon@dconsafety.com www.dconsafety.com
We prioritise and specialise in the highest levels of informed & intelligent advice, senior project resource allocation and compliance assurance. We know that every project with potential benefits also has potential risks with the art of planning centring on the co-ordination of these two zones of uncertainty. Our team of highly experienced construction professionals consistently ensures each client’s best interest and statutory conformity.
Schmersal is set to launch four new electromechanical safety switches with separate actuator: the AZ215/AZ216 and AZ315/AZ316 switches handle safety guard position monitoring of sideways or rotating guard doors. Their stand-out feature is the rotating actuator head made from die-cast zinc, which can be easily rotated in 90° increments before installation. This allows the head to be approached from the side from four different directions, as well as from above. With this versatile approach position and possibility of combination with different actuators, the AZ series offers maximum flexibility in installation, as well as a range of universal usage options to the user. The designer can use the AZ switch both for right-hand and left-hand design on rotating and sliding guard doors.
The plastic or metal switch housing is consistent in design and size with the PS 215/216 and PS 315/316 series position switches, giving the AZ switches an equally compact design and easy integration into the surrounding construction. The small AZ215 and AZ216 switches are consistent with standard EN 50047, while the larger AZ315 and AZ316 switches satisfy standard EN 50041.
In addition to the standard version with M20 cable entry and connection terminals, versions with 4 or 8-pin M12 connector are also available, depending on the number of contacts. With the in-built 8-pin connector, AZ switches can be connected to the SFB Safety Fieldbox. Device versions with three contacts in a wide range of combinations can also assume a signalling role in addition
to their safety function. The connection terminals on the switch elements, which are rotated by 45°, enable quick and easy wiring.
T +44 (0)1684 571980 uksupport@schmersal.com www.schmersal.co.uk
Maintaining a safety shower is crucial for ensuring its optimal performance and effectiveness during emergency situations. Here are several reasons why maintaining a safety shower is essential:
1) Reliable Emergency Response
Regular maintenance ensures that the safety shower is in proper working condition and ready to be used when needed. By conducting routine inspections and maintenance activities such as testing water flow, checking water temperature, adjusting controls, and inspecting valves, any potential issues or malfunctions can be identified and addressed promptly, ensuring that the safety shower will function reliably during an emergency.
2) Employee Safety
The primary purpose of a safety shower is to provide immediate decontamination in case of exposure to hazardous substances. Regular maintenance helps ensure that the safety shower delivers the appropriate water flow rate, temperature, and coverage necessary for effective decontamination.
3) Compliance with Regulations
Safety showers are often subject to regulatory requirements and standards that specify their maintenance and inspection. By adhering to these regulations, organizations demonstrate their commitment to compliance and workplace safety.
4) Extended Lifespan
Proper maintenance and care can significantly extend the lifespan of a safety shower. By promptly addressing any
issues, replacing worn-out components, and conducting regular cleaning, you can prevent major breakdowns and costly repairs.
5) Reputation and Employee confidence
Demonstrating a commitment to maintaining safety showers indicates a strong safety culture within an organization. Regular maintenance instils employee confidence in the workplace safety measures and shows that their wellbeing is a top priority.
Conclusion
Maintaining a safety shower is essential for its reliable performance, employee safety, regulatory compliance, and overall operational readiness. Regular maintenance and inspections help identify and address any issues promptly, ensuring that the safety shower is always ready for use during emergencies.
For more information on service and maintenance, please contact Aqua Safety Showers on: +44 (0)1942 318096 or sales@aqua-safety.com
The UK’s number one Fire Safety Event is soon to hit the NEC in Birmingham on the 30th April–2nd May 2024 and you do not want to miss it!
FSE is the UK’s fastest growing and biggest Fire Safety Event that brings together the entire UK fire and safety community to continually achieve and maintain the very highest standards of fire safety management.
Since the event was launched back in 2016, FSE has rapidly grown, attracting annual numbers in the hundreds of leading manufacturers and service providers. FSE is a leading advocate for fire safety education, training, and intelligence. With a mission to empower individuals and communities to prevent and mitigate the impact of fires, FSE provides comprehensive resources, programs, insight and support to promote a safer environment for all.
The 2024 event looks nothing short of fantastic and is aimed at supporting industry practitioners, professionals and organisations in achieving and maintaining the very highest standards of fire safety management.
There are some huge benefits to attending FSE 2024. Gain CPD points and hear from leading industry experts including government officials, lawyers and manufacturers. Expect over 10,000 of the latest fire protection and
prevention products and solutions right at your fingertips, and receive partial advice whilst having the chance to experience live demonstrations of the latest fire safety products.
This event is designed to bring together professionals and the general public to address issues surrounding fire safety and mitigation strategies. For the VIPs, The Fire Safety Leaders Summit is an exclusive summit that will offer highlevel strategic content for senior leaders within the health and safety industry.
Connect + Live returns for another year which is a hosted meeting programme that includes digital and on-site activities. This will be a great opportunity to join peers and meet other industry friends and professionals. The Networking Café will also be open on day 1 & 2 from 16:00–18:00 and day 3 from 13:00–14:30.
Opening times
Tuesday 30th April 2024 10:00–16:30
Wednesday 1st May 2024 10:00–16:30
Thursday 2nd May 2024 10:00–15:30
Get your tickets today and be part of the UK’s number one fire safety event, the perfect platform to launch new products, solutions, and services.
https://www.firesafetyevent.com
Made for fire safety professionals, facilities and health and safety teams, Firehub was created with the customer in mind.
Firehub allows the assessors to complete the reports on-site. The questions, based on PAS-79 methodology, and have a range of pre-loaded responses make completing reports quick and easy. Photos can be uploaded immediately, and it will work offline.
Each customer has a unique customer login that will give them access to a clear dashboard where they can view and download their completed reports. The significant findings from their sites will be listed on their login dashboard which clients can use as a to-do list.
The unique management level
of the app means that facilities teams, site managers, health and safety teams can have oversite across all their properties and will be able to address their improvements at all sites.
Creator, Matt Spivey says, “We want the app to be easy to use which is why personalisation is key. The questions and pre-populated responses are all editable. Personalisation, flexibility and bespoke questions and responses are all achievable with Firehub.”
Firehub is available now on iOS and Android. It is free to download, and the first report is free. See them at Stand A38 at The Fire Safety Event.
T 0800 142 2772
info@firehub.co.uk
https://firehub.co.uk
CH Materials supply a wide range of specialist technical materials and products to the Passive Fire Protection market. This includes various grades of intumescent materials for manufacture of fire stopping devices. We also supply specialist thermal protection tapes and accessories for fire rated door, glazing and ducting applications.
We are excited to announce the launch of the Flamro range of structural passive fire protection products in the UK and Ireland.
For over 30 years, Flamro have developed, tested and manufactured structural preventative fire protection products for cable and pipe penetration seals, linear joint seals, cable protection and ducting with the aim of protecting life and property. With the focus on the fire protection industry in the UK and Ireland, we feel this is an excellent time to offer a new and innovative range of fully tested and certified products, systems, and solutions to the market.
CHM is part of the SVT Group with a range of passive fire protection products for the Construction, Rail, Air and Marine transportation as well as industry leading knowledge in fire protection for battery safety.
Please see us at Stand 5/Ah.
T 01524 406088
www.chmaterials.com
Coventry-based The Big Ink Tank installed the VeloBlade Nexus 2516 in January and has already seen a significant improvement in production
Large-format printing business The Big Ink Tank has invested in a new VeloBlade Nexus 2516 wide-format digital die cutting solution from Soyang Hardware, saying it plans to use the machine to expand its service offering and win new customers.
Based in Coventry, The Big Ink Tank offers a range of print services, specialising in exhibition graphics and large-format work for galleries and museums. The printer works with a number of high-profile clients including Peugeot and the Royal Shakespeare Company, as well as major local customers such as Coventry Building Society and Coventry University.
While already having an expansive service offering and customer base, The Big Ink Tank is always on the lookout for new opportunities and ways it can deliver more for clients. This thought process was a key part in its decision to invest in the VeloBlade Nexus 2516, a specialist machine manufactured by Vivid Laminating Technologies and distributed by Soyang Hardware.
One of four machines in the VeloBlade Nexus range, the 2516 is a wide-format digital die cutter with a bed size of 2,500mm x 1,600mm. Combined with a CNC router, the system enables users to work with stocks up to 25mm in thickness such as Dibond, MDF and acrylic.
Purchased in December 2023 and installed just a few weeks later in January 2024, the VeloBlade Nexus has become an integral part of the production setup at The Big Ink Tank. Working alongside other machinery, the cutter has already been put to work on a range of applications, with its innovative automation capabilities making life much easier for staff.
“The VeloBlade Nexus fits in with our existing workflow by allowing files for cutting, routing and creasing to be automatically uploaded with minimal
input from our team,” The Big Ink Tank’s founder, Ty Power, said. “We are really benefitting from the speed of the machine; we no longer have to change the tools as they are automatic.”
“The quality of the cutting is also excellent, while the fact that the vacuum keeps the cuts so clean results in a huge time saving. We are still learning about new processes that we can then launch into the market.”
With this in mind, Ty said the focus for The Big Ink Tank is on how it can use the new machine to expand its offering and serve customers in new markets. This, Ty said, will involve speaking with its clients and working with specialist staff at both Soyang and Vivid Laminating Technologies to ensure the company gets the most out of the new device.
“Soyang is a long-term supplier for us; they are a great company to work with and really knowledgeable,”
Written by Ella Faulkner, Internal SalesTy said. “Vivid are also very interested in looking after you as a customer. So far, the training and interaction has been excellent.”
“We are keen to demo the machine to our existing customers showing them all the new materials and options we can offer. It will open up more varied work and hopefully win us new customers.”
“We are really excited by all the new product types we can offer and getting to learn what we can do with the machine.”
Contact T +44 (0)161 765 3400 sales@soyang.co.uk https://soyang.co.uk
Springpack, a leading provider of packaging solutions, understands the importance of operational efficiency and reliability in today’s fast-paced business environment. In order to uphold their commitment to excellence, Springpacks offers comprehensive operational audits tailored to the unique needs of their clients. These audits serve as invaluable tools for businesses seeking to optimise their operations, streamline processes, and enhance overall performance.
What is a Springpacks Operational Audit?
A Springpacks Operational Audit is a thorough assessment of a company’s packaging operations, designed to identify areas of improvement and opportunities for optimisation. Conducted by seasoned professionals with extensive industry experience, these audits delve deep into every aspect of the supply chain, from warehousing and inventory management to transportation and distribution.
Key components of a Springpacks Operational Audit:
1) Process evaluation: Springpacks experts meticulously examine existing processes and workflows to identify inefficiencies, bottlenecks, and areas of redundancy. By assessing the flow of goods and information within the supply chain, they pinpoint opportunities for streamlining and optimisation.
2) Technology assessment: Modern logistics relies heavily on technology, and Springpacks audits include a comprehensive evaluation of the technological infrastructure supporting operations. This encompasses everything from inventory management systems and transportation management software to warehouse automation solutions. Recommendations may be provided for upgrades or enhancements to maximise efficiency and accuracy.
3) Cost efficiency: Cost optimisation is a central focus of Springpacks Operational Audits. By analysing expenses across the supply chain, from procurement and storage to transportation and labour, they identify opportunities for cost reduction without compromising quality or service levels.
4) Compliance and sustainability: In an era of increasing regulatory scrutiny and growing environmental awareness, compliance and sustainability have become integral aspects of logistics operations. Springpacks evaluates adherence to relevant regulations and industry standards, as well as opportunities for implementing sustainable practices that benefit both the environment and the bottom line.
Why book a Springpacks Operational Audit?
1) Maximise efficiency: In today’s competitive landscape, efficiency is key to success. By booking a Springpacks Operational Audit, businesses can identify and eliminate inefficiencies in their supply chain, resulting in cost savings, faster delivery times, and improved customer satisfaction.
2) Stay ahead of the curve: The logistics industry is constantly evolving, with new technologies, regulations, and market trends emerging regularly. By undergoing regular operational audits, businesses can stay ahead of the curve, adapting their
operations to meet changing demands and maintain a competitive edge.
3) Ensure reliability: Reliability is paramount in logistics, where delays or disruptions can have far-reaching consequences. Springpacks Operational Audits help businesses identify and mitigate risks, ensuring the reliability and resilience of their supply chain even in the face of unforeseen challenges.
4) Optimise costs: Cost optimisation is a perennial concern for businesses of all sizes. By identifying inefficiencies and implementing cost-saving measures, Springpacks Operational Audits enable businesses to achieve maximum cost efficiency without sacrificing quality or service levels.
5) Enhance customer satisfaction: A well-optimised supply chain translates to faster delivery times, accurate order fulfilment, and overall better service for customers. By booking a Springpacks Operational Audit, businesses can enhance customer satisfaction and loyalty, ultimately driving growth and profitability.
In conclusion, Springpacks Operational Audits are indispensable tools for businesses seeking to optimise their packaging operations, improve efficiency, and ensure reliability in an increasingly complex and competitive business environment.
Simply visit: springpack.co.uk/operational-packagingaudits or scan the QR code and book your free operation packaging audit.
The sign and display business only installed the new VeloBlade Nexus 2516 in early January but has already seen a marked improvement in production.
Signage and display specialist Signs & Labels
Hereford has invested in a new VeloBlade Nexus 2516 from Soyang Hardware Ltd., revealing how it plans to use the machine to expand its business into new and profitable markets.
Based just outside Hereford town centre, Signs & Labels Hereford is a family-run business that has been serving the market for more than 23 years. Offering signage, print and vehicle graphics, the company is led by Director Ross Hughes, whose father and sister also work within the business.
With the company having experienced an increase in demand for its services, it opted to upgrade its cutting equipment. Signs & Labels Hereford had been running the same cutter
attention to detail in making everything as straightforward as possible for their customers. We placed the order within days of seeing the machine at the showroom.”
Signs & Labels Hereford purchased the machine in December, and it was installed at the company’s Hereford site in early January. Ross Hughes said despite the cutter having only been in place a short time, the business has already seen a significant improvement in production.
for 16 years, but as this required manual operation, the company sought out a machine with faster running speeds and automation features.
After researching the market, Signs & Labels Hereford quickly identified Vivid Laminating Technologies’ VeloBlade Nexus 2516 as the ideal solution. Distributed by Soyang Hardware Ltd in the UK and Ireland, the VeloBlade Nexus 2516 is a wide-format digital die cutter with a bed size of 2,500mm x 1,600mm.
“I had seen the machine a lot on LinkedIn and always thought it looked like the ideal piece of kit for our business,” Ross Hughes said. “Once I started looking and spoke to Vivid’s Lewis Evans, the price point for the specification stood out from other machines and further solidified my interest in the machine.”
“After speaking to Lewis during an online demo and at the showroom, I was really impressed by the customer service and
“The VeloBlade is already making production faster,” Ross Hughes said. “The automation of barcode reading means there are fewer touch points. Also, as it is so simple to use, we have been able to train up numerous members of staff on the machine; we don’t have to wait for specific team members to become available to operate it.”
Looking ahead, Ross Hughes is confident that the new VeloBlade will allow Signs & Labels Hereford to expand its offering and move into new markets, picking out bespoke packaging as one area of interest.
“I think the machine will impact us immensely,” Ross Hughes said. “It will allow us to keep up with and surpass the ever-demanding issue of lead times and take us onto the next level regarding speed and quality.”
“It gives us more scope to take on more of our current work as well as looking at expanding into other markets.”
ST-2163 Nightstar Onyx is a flexible hybrid material and has been developed for use in UV, Latex and dye sublimation printers. It is ideally suited for applications such as retail backdrops, exhibitions graphics and pop-up display systems
Soyang Europe, the leading manufacturer and distributor of digitally printable wide-format and superwide-format media and surface coverings, and – through its acquisition of Josero – a supplier of leading edge wide and superwide-format print production hardware, is delighted to announce the launch of ST-2163 Nightstar Onyx polyester blockout display fabric.
A 100% warp-knitted blockout fabric, ST-2163 Nightstar Onyx is a flexible hybrid material. It has been developed for use in UV, Latex and dye sublimation printers and is available in widths of up to 5.05m. The new material features a black back that offers users full opacity, opening up its use in a range of projects.
Customers will benefit from brilliant colours and high ink fastness, while the material’s high stability and soft feel make it the ideal solution for use in high-impact applications such
as retail backdrops, exhibitions graphics and pop-up display systems.
ST-2163 Nightstar Onyx also offers users a more sustainable option than other materials available on the market as it is both PVC and phthalate-free.
“Soyang Europe is committed to developing new and exciting products that not only guarantee high-quality output to our customers, but also offer them a competitive edge in what is a busy market,” says Mark Mashiter, Managing Director of Soyang Europe.
“Given the incredible flexibility, high print quality and stand-out environmental credentials of ST-2163 Nightstar Onyx, our latest solution fits these criteria to a tee.”
T +44 (0)161 765 3400
sales@soyang.co.uk
www.soyang.co.uk
The new single-use Quattroflow® Microdosing QB2-SD Pump operates entirely differently from the legacy line of Quattroflow products. Using the principle of positive displacement with a rotary action, the lightweight QB2-SD gently transfers fixed cavities of liquid of 25μl with a maximum flow rate of 2.7L/hr around a rotor from inlet to outlet. This provides high levels of accuracy without the need for additional sensors that are typically combined with peristaltic pumps. The pumps also generate a high vacuum capability and handle high viscosities.
The system allows easy and rapid changeovers since the single-use pumps simply click in and out of a motor drive, which is especially convenient when wearing full PPE.
The QB2-SD Microdosing Pump can be gamma irradiated up to 50kGy with USP <88> Class VI certified materials, making it an ideal solution for handling biologics, including cells, proteins, mAbs, etc.
Approved Biopharma Certifications
t Particulate Testing (Sub-visible testing per USP 788)
t Microbial Ingress
t Endotoxin (USP 85)
t Bioburden (ISO 11737-1)
Also available from PSG Biotech, Quattroflow is a plug-and-play drive device called Q-Drive-Alpha. The device is intuitively easy to use and can allow commercial use of the pumps in laboratories and similar environments.
Features & Benefits
t Single-use: Rapid changeovers with no cross-contamination
t Lightweight, compact design: Saving valuable space
t Dosing with a minimum flow rate of 75μl/s (at 1rps): For precision microdosing
t Suitable for single transfer of cells with low shear: Protecting product integrity
t Self-priming, high vacuum capabilities: For
Wetted Materials MBS, HDPE, SIL
Connector Sizing
Longevity
positioning flexibility & higher product recovery
t Bi-directional pumping: Avoids drips during filling
t Gamma compatible: Up to 1 x 50kGy
t USP <88> Class VI certified materials: Ensuring biocompatibility
Technical Specifications
Using the principle of positive displacement with a rotary action, the QB2-SD has a 6mm rotor that carries three cavities of fluid, each with a volume of 25μl. This lightweight, in-line pump features hose-
Hose barb for pump inlet and outlet. For use with 2mm ID flexible tubing
5L @ 5rps (Up to 3L @10rps)
barbed connectors, making it easy to attach tubing to the inlet and outlet. A stepper or DC motor drives the pump at a maximum operating speed of 10rps. The QB2-SD simply clicks in and out of the motor drive in seconds, making it quick and easy to swap fluids without cross-contamination. It is bi-directional, high-vacuum, and self-priming with a low dead volume.
Contact
https://www.psgdover.com
https://www.quantex-arc.com
2023 was a year of anniversaries for CPL/ Puragen Activated Carbons. Back in the summer, they celebrated 10 years of spent carbon reactivation at their Immingham facility, the site later being awarded a prestigious Green Apple environmental award as well as its ISO45001 accreditation for health & safety.
2023 also represented a significant milestone for another important area of the business, namely the rental of Clean-Flo® mobile carbon filters, which began 20 years ago. CPL had been selling carbon filters prior to this date, but 2003 was when they designed a genuinely portable unit and began the transition into a true ‘carbon & service’ business.
Mobile carbon filters offer a number of operational and financial benefits over fixed filter installations:
t No CAPEX for the customer, only OPEX – supplied on a rental basis;
t Modular, flexible arrangement – can add or remove filters as the situation demands;
t ‘Lead & lag’ or parallel layout possible for multiple filters, to optimise treatment flow;
t Simple Plug & play operation – no on-site carbon handling;
t All-in-one transportation and adsorption unit;
t Also ideal for trialling alternative activated carbons,
or for periods of plant maintenance when a fixed filtration system is unavailable.
The first rental filter was a 2m3 VOCSorber® unit, supplied to a chemicals manufacturing site in West Yorkshire that is still a customer to this day!
CPL’s mobile filter rental business grew organically in the early years but really took off in 2013, when they started recycling spent carbons and were able to supply their service via the company’s REACT-Sys process, offering a circular solution that was pioneering in the industry.
The next major change was in 2018, when they acquired the manufacturing facility in Chesterfield, now called CPL Icon, which gave the company an in-house manufacturing and engineering capability.
The previous year, 2017, saw the launch of what was (at the time) the largest mobile carbon filter on the market, the
The High Power Picosecond Pulse Laser series
FPYL-Q-PS delivers peak power up to 100W, with a pulse width of <10ps, and operates at a repetition rate of 1MHz. It offers wavelengths at 266nm (1-8W), 355nm (1-50W), 532nm (1-80W), and 1,064nm (1-100W), within a repetition frequency range of 400kHz to 2MHz. Its power stability is less than 3% (with an optional <1%), and pulse-topulse stability is under 2%, both measured in rms over four hours. The laser produces a high-quality beam (M2<1.2) with a diameter of ~3mm and divergence <1mrad, ensuring excellent
VOCSorber 30, designed primarily for demanding landfill gas (LFG) purification applications. The fleet was further augmented a few years later with an even larger unit, the High Flow HF20V VOCSorber®, standing 8m tall, designed for major odour control and VOC abatement projects, for example at waste handling facilities or food production sites.
If you would like to find out more about their range of mobile carbons filters, for both gas phase (VOCSorber®) and liquid phase (AquaSorber®) purification applications, please visit their website: https://activated-carbon.com/mobile-carbon-filters
collimation.
are a compatible power supply for 100-240V and a water chiller. These lasers are particularly effective for micro-material processing, suitable for applications in flexible and brittle materials processing, OLEDs, glass & ceramic cutting and drilling, and the semiconductor industry.
T +49 (0)6172
27978-0
sales@frlaserco.com
www.frlaserco.com
St Andrews Links Trust has appointed sustainable water and purification experts Bluewater as its Official Hydration Supplier to provide a nextgeneration drinking water solution for golfers and visitors to the Home of Golf.
The pioneering agreement will see Bluewater, a global leader in sustainable water purification & beverage solutions, provide purified drinking water across the St Andrews Links estate through its innovative refill stations, supporting a commitment for the removal of single-use plastic bottles from the Trust’s facilities.
The stations utilise the Swedish company's advanced SuperiorOsmosis
treatment process, which removes more than 99% of known contaminants from water, to provide locally purified and chilled drinking water at the point of consumption.
The refill stations will initially be installed in both the Old Pavilion next to the first tee of the iconic Old Course and at the Halfway House serving the Old, New, and Jubilee Courses with further installations at the Links Clubhouse, Golf Academy, and Castle Course Clubhouse.
Each unit will provide free-of-charge refills of chilled and purified water.
The units also feature high-bright digital TV screens to communicate key information to visitors concerning wider sustainability initiatives across the world-renowned venue.
For more information, visit: www.bluewatergroup.com, or call David Noble on +44 (0)7785 302694 or email: david.noble@bluewatergroup.com.
Welding engineers all over the world associate the name Fronius with innovative welding technology. Above all, the innovators are known for providing high-performance, high-tech welding systems. The name Fronius is also associated with revolutionary welding processes such as Cold Metal Transfer (CMT), intelligent seam detection sensors such as WireSense, and the brand new DynamicWire wirefeeder. However, there is little awareness across all industries that Fronius Welding Automation supplies automated welding systems from a single source.
There is a long tradition of plant construction at Fronius. Take, for example, the longitudinal seam welding system from 1979 for welding sheet metal sections made of steel. Today, more than 3,500 installed systems are in use across 45 different countries with over 2,000 active customers.
Since the invention of the ‘cold’ MAG welding process, Cold Metal Transfer (CMT), Fronius has continuously achieved technological leadership in many welding related areas, resulting in state of the art mechanised and automated welding systems. Advanced power source technology stabilises the arc and ensures perfect welding results. Modern monitoring sensors optimise guidance of the welding torch and compensate for component tolerances. Last but not least, smart data documentation systems assist in perfecting the welding process.
Collaborative systems, intelligent sensor technology, software solutions for data management and offline programming including welding simulation open up profitable welding opportunities for metal processing companies starting with a single batch. That is why Fronius robotic welding cells prove profitable not only for large companies, but also for small and medium sized enterprises.
The specific requirements for the welding technology are analysed together with the customer. This is followed by the creation of an individual solution. To do this, Fronius has an extensive construction kit of standardised components at its disposal. Starting with the feasibility study and continuing with planning, engineering, manufacturing and start up, the sale of welding systems is handled as a project. During this time, customers have one main point of contact: the project manager. He or she takes care of the entire project process and acts as the interface between the customer and all the Fronius sections involved. In doing so, the project manager ensures that processes run smoothly, co-operation is effective and projects are successfully completed.
Almost every project starts with a feasibility study, which determines the entire engineering process. It forms the basis for a solution that is tailored both in terms of technical and commercial viability. The integration of welding technology into the kinematic elements depends on the following factors: component conditions, process accuracy and profitability. Welding Automation sources specialised components such as robots, sensors, clamping systems and shelving systems from qualified co-operation partners.
Fronius provides and relies on software solutions that enable a high degree of control and optimal interaction between all system components. Pathfinder provides all customers with an offline programming and simulation solution that significantly increases the profitability of welding systems. WeldCube is programmed for the evaluation of welding data. The innovative software seamlessly records welding data, makes welds reproducible without any limitations and supports users in identifying optimisation potential and maintenance intervals.
Fronius Welding Automation is there to help its customers wherever they are in the world: providing support with everything from planning to feasibility studies, welding tests, commissioning, user training, remote maintenance, calibration, predictive maintenance and on-site maintenance work.
It offers one range for all industries comprising mechanised welding systems, robotic welding cells and overlay welding systems (cladding systems).
T 01908 512300 info-uk@fronius.com www.fronius.co.uk
Gold & Wassall Hinges has established itself at the forefront of the industry since its inception over 200 years ago. With its manufacturing facilities situated in Tamworth in Staffordshire, Gold & Wassall provides an impressive range of services for design, production and manufacture of hinges, all produced in house and distributed throughout the whole of the UK. Boasting an enviable reputation within the industry, the company has positioned itself firmly as the UK’s number one manufacturer of hinges.
Gold & Wassall has provided its services to various customers throughout its years in operation and serviced customers from construction to engineering companies. With a proven track record of quality, reliability and durability, Gold & Wassall ensures it maintains complete control over the design and high quality of its goods.
We asked Scott Bareham Sales and Marketing Manager at Gold & Wassall what makes the company stand out and how would he describe its services.
“All our hinges are manufactured in house, in our purpose-built facility in Tamworth, Staffordshire. We have been manufacturing hinges for over 200 years using a mixture of tried and trusted methods along with modern technology. Our offer of a bespoke hinge service enables us to manufacture any hinge for any application, and as we have over 200 years’ experience, we are greatly knowledgeable in what we do. Our services portray the highest quality ensuring each product goes through a rigorous testing procedure and receives the upmost attention to detail. We pride ourselves
on or customer service and treat every customer fairly and with respect.”
In keeping with the company’s goal of providing unrivalled customer service, Gold & Wassall also provides an abundance of finishing options for its customers. The company is dedicated to providing not only durable, high-quality hinges, but also to understanding the importance of an aesthetically pleasing, customised design. In light of this, the company is able to customise colour, add branding and create a smooth premium finish to all products. Gold & Wassall Hinges’ array of finishing options are the perfect complement for its hinges to create a smooth premium finished look.
Going into 2024, Gold & Wassall is proud to announce the launch of its brand-new website.
“The new website has been a long-term project. Initially, the website needed updating for technological and security reasons, however we thought it would be a good idea to give everything a freshen up. As well as detailing all of the usual information, we have also now made it possible to download CAD drawings and 3D models of each hinge. Furthermore, we have introduced our new "Hinge Finder" which allows the user to narrow down suitable hinges based on their required dimensions. This will help customers utilise our full range of hinges, showing hinges that they might not have found or considered previously,” added Scott.
On the website you will find their complete range of hinges from continuous/piano hinges, butt and backflap hinges and standard, to heavy duty and bespoke made to order hinges. Using the
company’s automatic section which contains eight lines of automated machines, Gold & Wassall is able to make hinges quicker and to almost any length. The company also maintains the specialist tooling for these machines which can complete multiple operations in each press.
Please note: Gold & Wassall is the only hinge company whose hinges are UK made and all of Gold & Wassall Hinges’ stock is available for immediate dispatch.
As a new year begins, we asked Scott what in store for the company in 2024 and beyond.
“In 2024 we hope to continue to strengthen following the pandemic and period of economic uncertainty. We are also looking to expand on our growing relationships with overseas customers as well as further grow our UK customer base.”
For more information, please see below:
T 01827 63391
sales@goldwassallhinges.co.uk
www.goldwassallhinges.co.uk
SEMOTA is a hardware and software solution with a web-based application that enables the remote monitoring of any load cell, force, torque or pressure sensor, using our Wi-Fi enabled hardware.
SEMOTA Continuous Remote Monitoring provides dynamic dashboard views of your events, analysis and device control. Information can be captured and stored for review and in depth analysis. Linkage to common messaging systems deliver live alerts for device management. Tailor and build applications to suit your needs and devices. Read more below, then complete the form and we’ll arrange a demonstration.
THREE YEARS STORAGE
Whether your data is needed every day or every few seconds, SEMOTA is optimised to receive, compute, and return millions of data points across the globe.
LIVE DASHBOARDS
Using SEMOTA point-and-click application development tools, create real-time dashboards to analyse data and control devices. Visualize data with SEMOTA stock graphs, charts, tables, indicators, maps, metrics, and control widgets or develop your own
using the HTML canvas and your own code. Share your data through public links, or by embedding dashboards into custom web applications.
EVENTS ENGINE
Add conditional and complex business logic to your hardware with triggered webhooks for M2M communication, and SMS, Email, Telegram, and Slack alerts to keep operators on-the-ball and informed.
SYNTHETIC VARIABLES
Transform raw data into insights with Synthetic Variables that compute complex math formulas and statistical expressions.
USER MANAGEMENT
With SEMOTA cloud software, you can build applications to best fit the operator’s needs. SEMOTA administrators can configure permissions and restrictions to any end user or operator who interacts with dashboards, devices, and/or events. Need a user to be able to oversee multiple organisations?
Not a problem. You can optionally add more users or organisations to your account and we can configure your users to best suit your application.
T 01344 776666 info@interface.uk.com www.interfaceforce.co.uk
Interface Force Measurement Solutions (Interface) is a UK company specialising in the supply and distribution of high-quality sensors and associated electronics and displays for a wide variety of industries. Working previously with clients such as Airbus, BAE Systems, and Formula One Teams, we spoke with Tony Rokins, Business Development & Pressure Mapping Specialist, who explained some of the companies well known products.
“Our product portfolio is applicable to many industries. For instance, we are well known for our high-quality pressure mapping systems that are used by many of our automotive and motorsport customers. Our sensors deliver highly accurate, repeatable measurements and many of our load
cells are used by calibration houses as calibration reference devices. Our high-quality, yet competitively priced 3 and 6 axis load cells are used for many R&D, renewable energy and robotic applications.”
In terms of recent developments, Tony continued, “Being responsive to our customer’s needs and being able to offer a high-quality product with strong product knowledge at a competitive price with the best possible lead times is our number one priority. Last year we launched our range of G-Series Load Cells. The range comprises of miniature and small sensors for industrial applications, with capacities starting from just 4.5N Newton up to 200kN with metric threads. These are high-performance devices but aimed at more cost-conscious applications. This is a new market for us, but we have already had increasing interest. We also launched our brand-new e-commerce website on the 1st of April for the G-Series that showcases Interface load cells at competitive prices with all the convenience purchasing online offers,” stated Tony.
The new e-commerce website offers G-Series load cells on short lead times with next business day delivery for small quantities. Following its successful launch in 2021, it has become an increasingly popular product range for students, industrial engineers, OEMs and anyone requiring a small form force sensor offering accuracy, repeatability and Interface quality.
In the future, Interface is keen to continue its growth trajectory for 2022. Tony mentioned, “we are also working on new, wireless force and vibration sensors for remote monitoring in systems such as luggage carousels. One more area we are pushing for growth is with XSensor’s pressure mapping systems, particularly in the Hi-speed systems designed for high-speed impact or crash testing and tire foot-print research. These systems are capable of capturing data up to 2,500 frames per second. The tire sensor can be driven over at speeds of up to 140kph. I believe this is a unique capability we can bring to the industry.”
As the company looks to continue strengthening its position with its customers in its more traditional markets of aerospace, automotive, motorsport, Universities and alternative energy research, it will be attending some expos over the next 12 months and be readily on hand to discuss any questions you may have about force, torque, pressure mapping or pressure, level & temperature measurement.
For more information, please see below:
T 01344 776666
info@interface.uk.com
www.interfaceforce.co.uk