


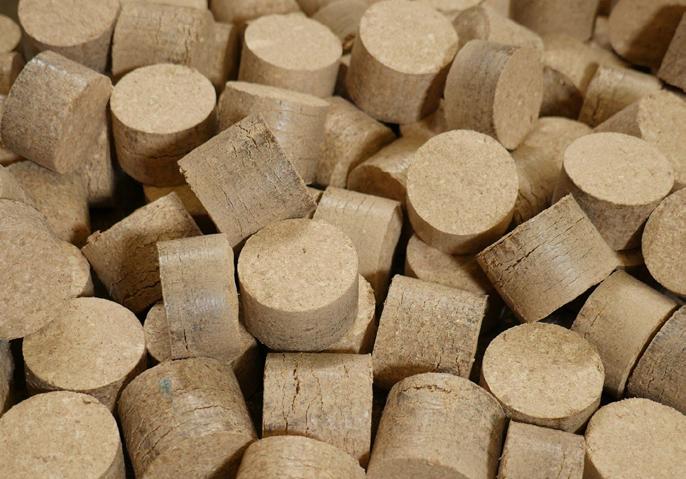

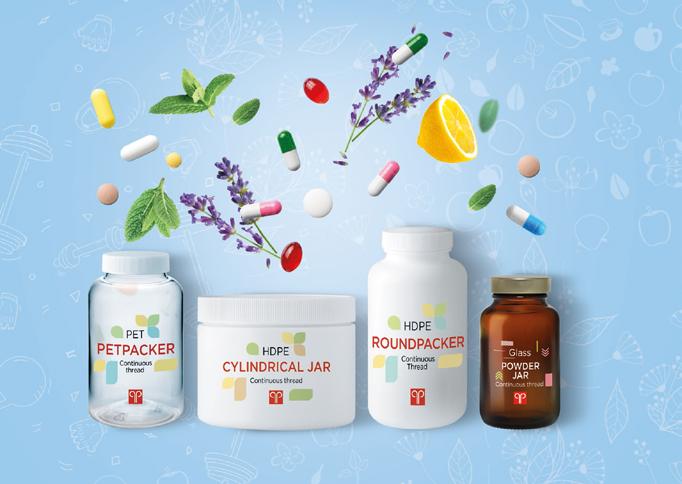
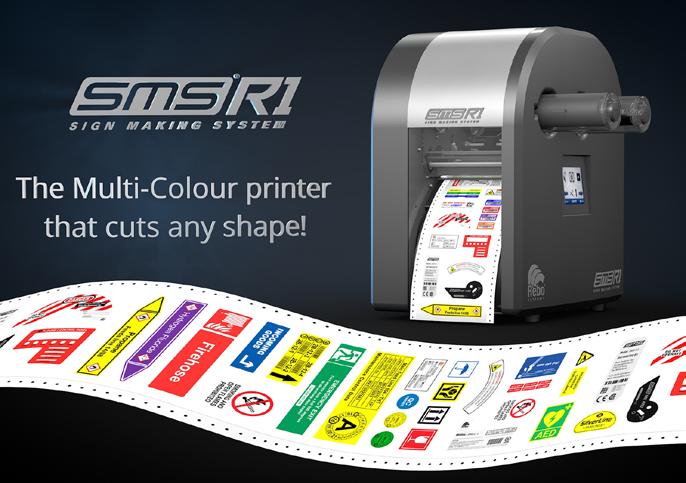
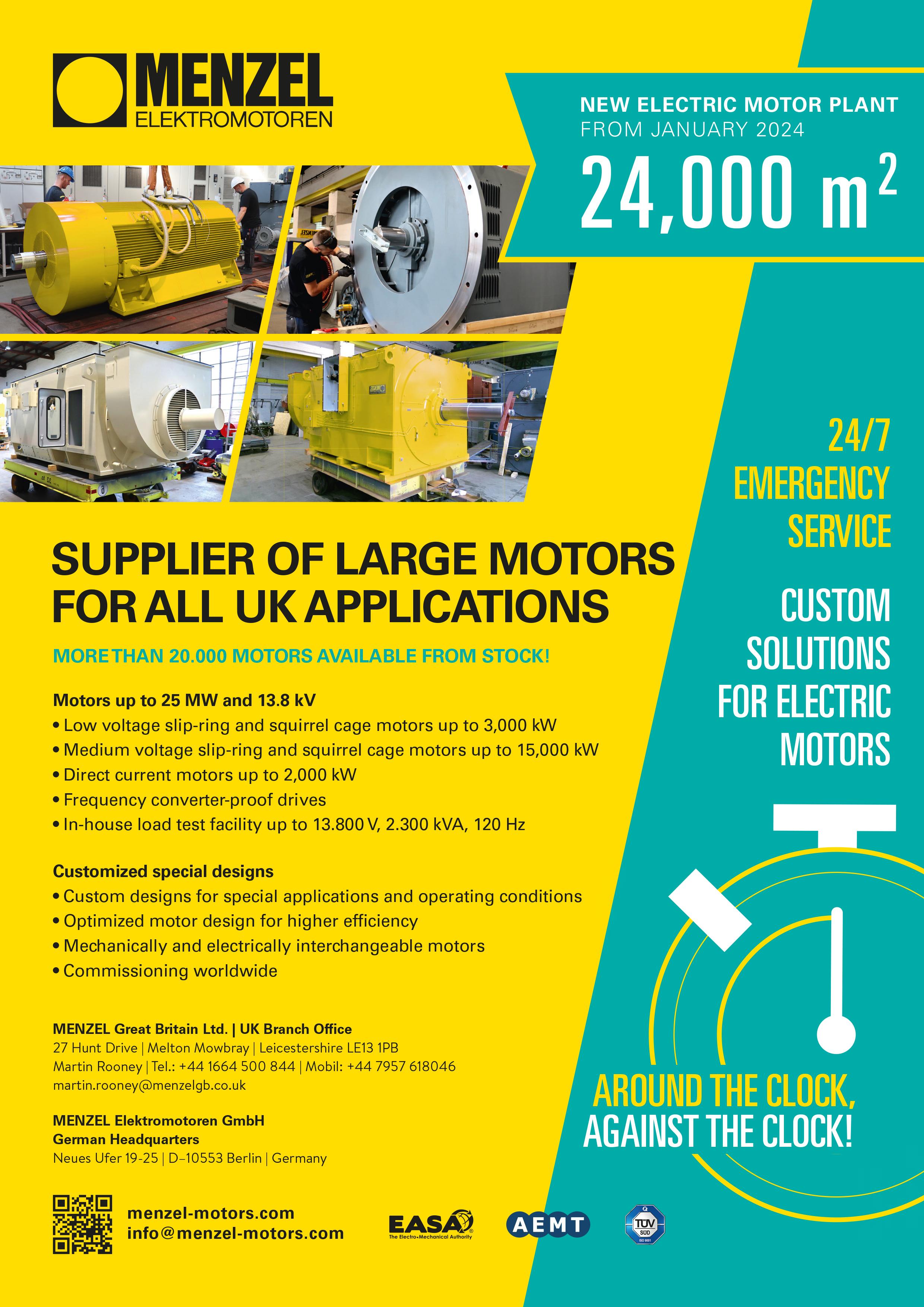
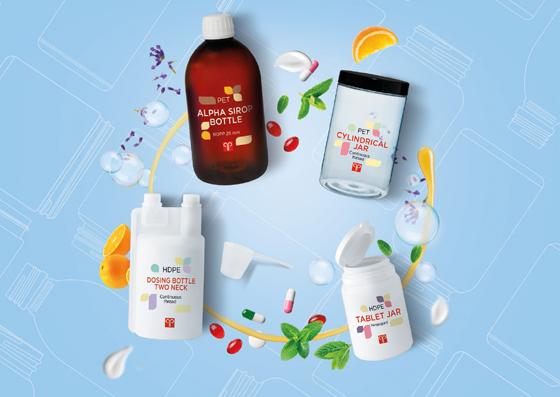
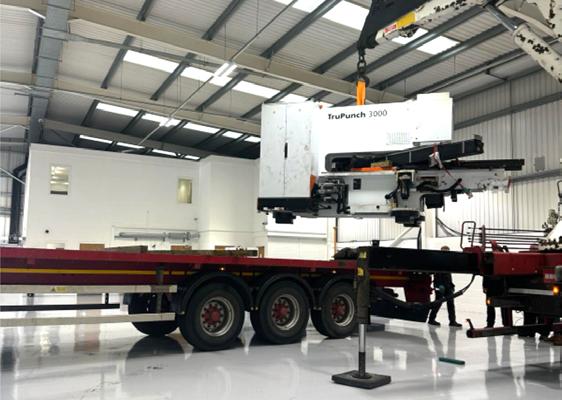
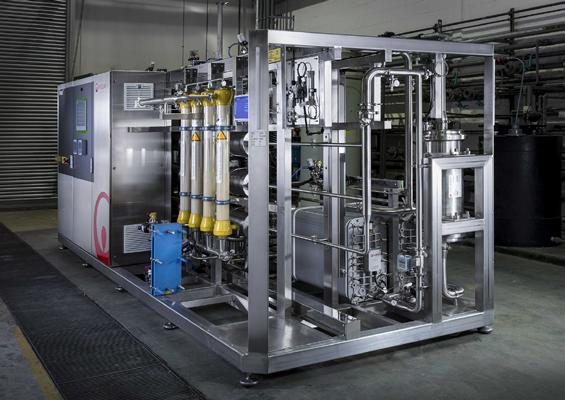
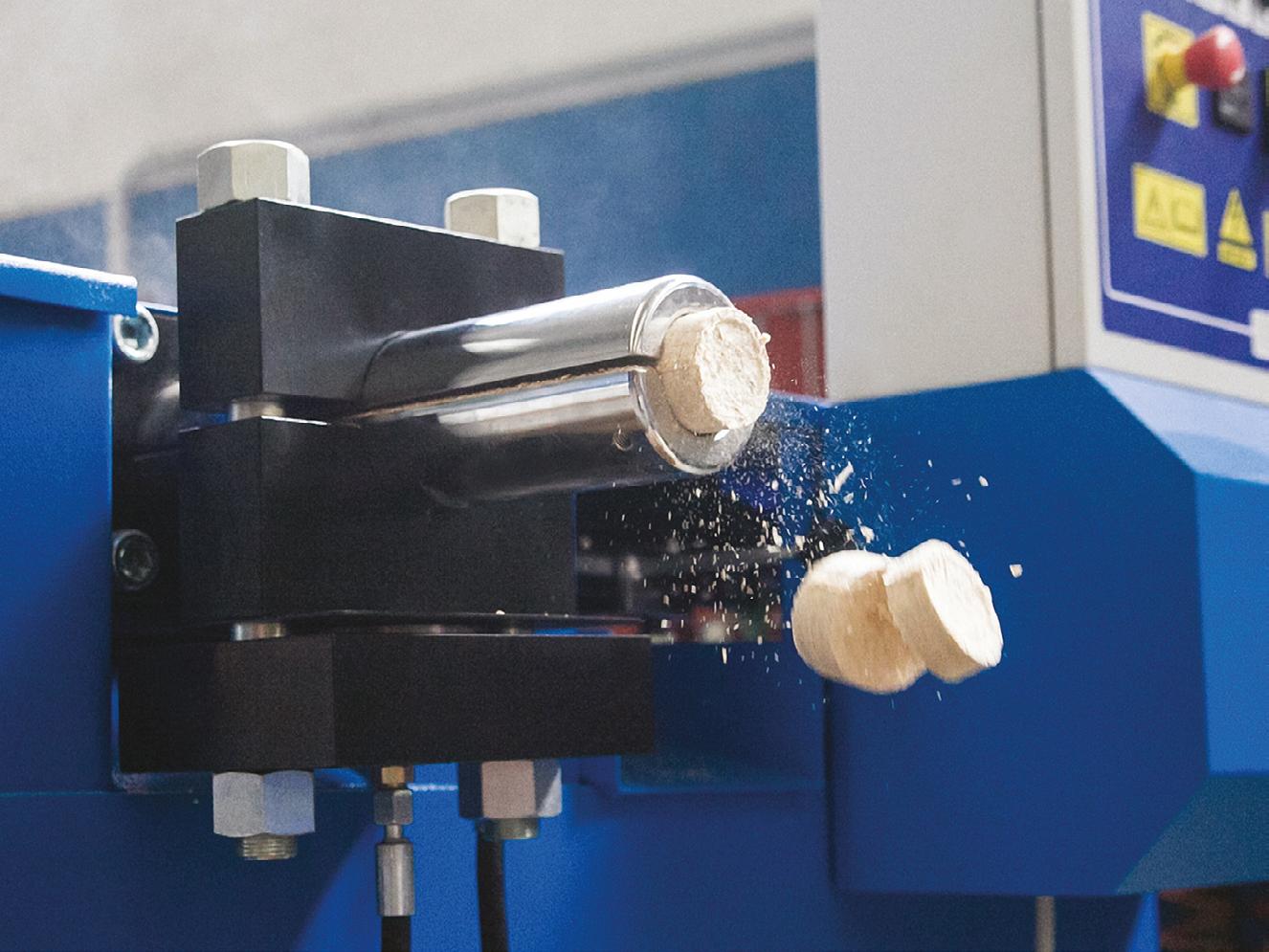
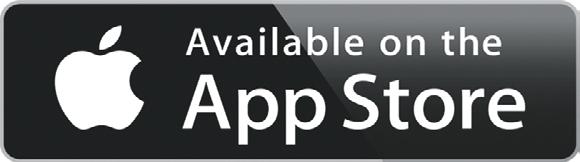
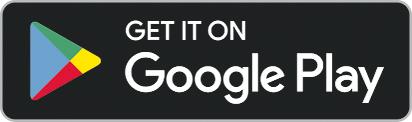
One of the technical highlights at ACHEMA 2024 was KSB Group’s new 3D-printed containment shroud for mag-drive pumps of the Magnochem type series. Named MagnoProtect, the component offers the same safety as a double-walled containment shroud – without the latter’s disadvantages of heating up strongly and having high eddy current losses.
While providing comparable safety, the overall efficiencies of the new mag-drive designs clearly exceed those of canned motor pumps. Designed with a structure of channels, the new containment shroud offers a second, redundant, static safety barrier preventing leakage of the fluid handled.
A pressure transmitter monitors the vacuum
By provisioning preventative maintenance programmes in good time, plant operators avoid costly downtimes. This is all the more important for non-standard configurations. An Argentinian steel mill operator commissioned Menzel Elektromotoren to build a special motor based on an existing motor having the type of construction IM 7311.
In order to future-proof and since this is a considerable investment, the old, still operational motor is to be stored as backup. Therefore, the new machine must replicate it in every detail, although, due to modern design techniques, Menzel implemented a performance increase at the customer’s request.
The new slip ring motor provides a nominal torque of 43,245Nm at 6,600V rated voltage and 1,345kW rated power. The format is unusual: at a total weight of 21.9 tons, the rotor alone weighs full 10.4 tons. Various accessories were installed, including HALL effect current transformers to measure the rotor current, customer-specified accelerometers on the bearings, and a level sensor for the electrolyte in the starter.
The motor features IP23 protection and IC 01 cooling (open-circuit ventilation). It has to withstand ambient temperatures up to 45°C in the rolling mill. The German, family-run company counts special motors among its core business and also designed the starter in such a way that it caters for the new motor and the original one equally.
Before shipping, the motor underwent a complete type test with additional tests according to customer specifications, including partial discharge and dissipation factor measurement (tan δ). Menzel will also handle the mill drive commissioning, which the operator will schedule to suit production planning.
More information about customised motors: www.menzel-motors.com/modification
generated, which is present during normal operation in the channels of the containment shroud. If the monitored pressure rises to atmospheric pressure, the outer containment shell is leaking. If the pressure rises above the ambient pressure, the inner containment
shell is damaged. The containment shroud design is characterised by high mechanical strength and good wear properties. It has been optimised to minimise heat losses and eddy currents.
Converting a standardised chemical pump with mechanical seal to a magnetic drive is easier and more cost-efficient than retrofitting it with a canned motor. The geometry and dimensions of the new containment shroud are integrated in the modular system of Magnochem, allowing metallic or ceramic containment shrouds to be replaced easily. This enables operators to upgrade older pump sets that are still in service without difficulty.
www.ksb.com/en-gb
PETER HIRT GmbH is expanding its product range of IO-Link touch probes. In addition to the T100 and T500 models, the smaller T200 and T070 series are now also available. As well as being used for high-precision tactile measurement tasks, IO-Link touch probes are suitable for a wide range of other applications. It is not only the simple digital integration that is impressive – the fact that the sensor and cable can be separated at the measuring point also significantly reduces the installation effort.
Thanks to over 30 years of experience in the manufacture of high-precision ball bearings, the IO-Link touch probes in the T series are characterised by precision, robustness and durability. The large number of models and a wide range of accessories enable the simple realisation of numerous measuring tasks. Additional models
Given how quickly technology is developing, machinery safety is now a crucial component of occupational health and safety, and it will only get more so in the future. This calls for systems where safety features may be easily created and added to the application.
The samos PRO COMPACT starter kit from Wieland Electric fills this need. It includes the safety control device, an SD card, a network and USB cable, and the samos PLAN safety software. This enables straightforward customisation of safety features without complex programming and efficient use of a powerful control system in small spaces.
Maximum security in the smallest space
The primary module, which has 16 safe inputs and outputs and is only 45 millimetres wide, combines flexibility and safety in one device. The compact design saves space in both the control cabinet and the storage area. At the same time, the samos PRO COMPACT supports up to 12 digital I/O modules.
and customised measuring systems can be quickly implemented as IO-Link variants thanks to the
PETER HIRT GmbH has been a manufacturer of precision linear ball bearings, measurement technology and precision mechanics for over 30 years. The portfolio includes standard products as well as OEM products and assemblies. Thanks to its agile size, the owner-managed company is committed to quality and flexibility. By specialising in small and medium series, customers benefit from stable product quality and product life cycles of several decades.
T +41 44 251 24 39 info@peterhirt.com www.peterhirt.com
Integrated Ethernet protocols enable connectivity to a standard controller or a user interface. In addition to the Ethernet interface, the safety controller has mini-USB and SD card ports. This allows the machine to be programmed flexibly. At the same time, software may be readily copied or exchanged. This greatly accelerates commissioning and reduces machine downtime. The starter kit also includes a network cable and a USB cord. This guarantees that the devices communicate effortlessly and data is transferred efficiently. The application software is easily stored using the supplied SD card.
Contact www.wieland-electric.com
Briquette Recycling Machinery Company of the Month
In this issue of Industry Update, we are delighted to showcase A&G Toseland Ltd as our Briquette Recycling Machinery Company of the Month
Briquette Press Machines compress raw materials like wood shavings, chips and dust into small log shaped carbon-neutral fuel sources and have grown in popularity since The Clean Air Strategy 2019 announcement. This introduced the subsequent banning of the burning and sale of wet wood from 2021, impacting many companies nationwide.
The Italian recycling company, POR Micucci Systems, appointed UK-based A & G Toseland as their exclusive distributor and re-seller of briquetting and shredding machinery across UK and Irish markets. These machines are ideally designed for small to medium sized companies to convert wood waste into a saleable product or useable internal fuel resource.
and packaging sector and are looking to repurpose wood or dust or make it more handable for waste management,” explains
The POR Micucci briquetting machines are built to high Italian engineering specifications, using superior components and assembly processing. In line with Industry 5.0 and the circular economy, they are designed for longevity, with minimised maintenance and downtime. All machines include: level sensors, inspection doors with viewing panels, remote controlled electric panels, superior oil quantity and quality, adjustable vices to maximise pressure and variable control of the loading drawer, to suit compatibility with a range of materials.
A & G Toseland Ltd was established in 1992 by founding director George Toseland. The familyowned business is based in Kettering and supplies an extensive range of industry-leading POR Micucci machines. Renowned across the recycling sector, they are exceptionally cost-effective and precision-designed to convert dust and other loose materials into a valuable resource, negating the need for landfill. To date, over 400 machines have been sold across UK and Ireland, signalling a clear growth trajectory in this area.
“We have installed a briquetting machine for demonstration purposes at our Kettering facility, new customers always welcome to trial materials for potential fuel sources or waste stream management. We work with wood-fuelled power stations that repurpose dust into a fuel source to power the station. Many of our customers come from the wood industry or print
The range of machines includes the following models:
t Junior
t A6
t A6 plus t Standard
t A100N t Oscar Plus Super Oscar
“We provide a fully comprehensive sales and aftercare programme to all our customers. From initial inquiry to site surveys and consultations, we offer full installation from our skilled engineers, with training and handling and maintenance throughout the machine’s lifespan. Our product range is designed to suit all budgets and capabilities and we are more than happy to advise on the correct one for different material. If you’re looking to
increase the value of your wate, reduce the costs of disposal, logistics, handling and storage costs, in line with The Clear Air Strategy to improve air quality in your workplace, talk to us today.”
Covert your expensive waste stream into extra revenue today.
Visit A & G Toseland Ltd at RWM (ESS) 2025: 17th18th September, NEC, Birmingham (Stand RS-H91). See the POR Micucci machines on display and talk to the team.
T 01536 414401
M 07837 632080 bertie@briquettetech.com www.briquettetech.com
The countdown is officially on! Packaging Innovations & Empack 2025 will open its doors at the NEC Birmingham on 12 and 13 February 2025, uniting the brightest minds and the most advanced technologies from the packaging industry. The UK’s flagship packaging exhibition has rapidly established itself as a vital gathering for professionals eager to delve into the future of packaging.
As the premier event for the entire packaging supply chain, Packaging Innovations & Empack 2025 offers a unique opportunity to connect, collaborate, and innovate. With over 430 exhibitors and more than 7,000 visitors expected, attendees will gain exclusive access to the latest trends and technologies in packaging design, materials, machinery, and sustainability.
Naomi Stewart, Marketing Manager at Easyfairs UK, emphasises the event’s significance, “As 2025 approaches, businesses face growing pressure to meet sustainability targets. Packaging Innovations & Empack provides the ideal platform for collaborative initiatives to navigate upcoming opportunities.”
From smart packaging and food service innovations to the latest sustainable solutions, the event will showcase the future of packaging across various industries. Dedicated zones will spotlight key growth areas, including Food Service, Label & Print, and Smart Packaging.
Exhibitors will engage with a rich pool of prospects from top brands and sectors, including food and beverage, fast-moving consumer goods (FMCG), pharmaceuticals, beauty, and e-commerce. Companies like Autajon Packaging, Simply Cartons, FlexPET BV, Coveris UK, and AstroNova® will present their attention-grabbing latest innovations.
Prestigious attendees will include renowned UK brands Waitrose, PZ Cussons, Diageo, Sainsbury’s, and Amazon, making this a vital platform for networking and discovering cuttingedge solutions. Exhibitors like OPRL, Taghleef, Sun Branding, Elopak, and Hazel 4D will showcase to attendees innovative packaging approaches that drive growth and sustainability.
The event sees the return of the Future Trailblazer Awards spotlighting the industry’s most promising talent, while the Packaging Start-Up Awards, sponsored by Ocado Retail, celebrate packaging’s groundbreaking start-ups. The Innovation Gallery will also showcase exceptional projects from the past year.
Secure your free visitor pass today and experience the future of packaging firsthand. Connect with industry leaders, discover the latest innovations, and attend the 50+ speaker conference programme packed with expert insights. From sustainability to cutting-edge technologies, Packaging Innovations & Empack 2025 promises to inspire and drive the industry’s future.
www.packagingbirmingham.com
Founded in 2002, Reflex is one of the UK’s largest manufacturers of labels and packaging solutions, trusted by leading global brands in the food, beverage, pharmaceutical, health & beauty and household product sectors. From the outset we valued sustainability and had a goal to be “the world’s most sustainable packaging company”, which is still at the heart of all global operations.
Operating from 24 sites in 7 countries, we proudly offer our customers a comprehensive end-to-end solution – from the initial design concept and prototyping to a diverse range of labels and packaging solutions including selfadhesive, plain labels, linerless labels, premium labels, cartonboard and flexible packaging right through to protective packaging solutions and printing systems and software.
What sets Reflex apart:
As a privately-owned company, Reflex is driven by a commitment to innovation and stays at the forefront of technology. Continuous investment in cutting-edge technology allows us to respond rapidly to emerging trends and tailor solutions to unique customer needs.
Serious about sustainability Sustainability is at the heart of our mission. Proudly carbon neutral since 2019, Reflex is now officially certified by Carbon Neutral Britain™, affirming our deep commitment to reducing environmental impact and advancing sustainable practices across our global operations.
Multi-award-winning
We are consistently recognised for our technical excellence and environmental
AtPolly Packaging and Polly POS we’re all about supporting you for every step of your products journey.
Our Packaging division are a one stop solution for all your warehousing and transit packaging needs, from labels & boxes through to 30% PIR plastics we’ve got you covered.
Our Point of Sale division offers expert guidance on getting your product off the shelves and into your customers hands!
Whether you’re looking for support back of house or front of store, the Polly team ensures that every step aligns with your brand’s goals and values.
Want to see how we bring it all together? Join Us at the Packaging Innovations Exhibition in Birmingham in February. Come visit us at our Stand T30 to experience the unique Polly ‘touch’ firsthand and have some fun in the process. Let's put the personality back into packaging.
Get in touch: enquiries@pollypackaging.co.uk hello@pollypos.co.uk
achievements by respected industry and product sector awards. In 2024 we have received twenty-four awards celebrating our accomplishments, with recognition from renowned organisations including FIAuk, FlexoTech, FTA Europe, Foodservice Packaging Association (FPA), UK Packaging Awards, Pentawards, and The Grocer, with multiple awards highlighting our technical achievements and sustainability efforts.
Reflex stands out in the industry not only for our extensive capabilities and comprehensive packaging solutions but also for our commitment to a sustainable future, supporting the needs of our clients and the planet. In 2024 alone, we achieved eight awards specifically for our sustainable operations and sustainable packaging innovations.
Visit us at Packaging Innovations 2025
We warmly invite you to visit us at Packaging Innovations 2025, where we’ll showcase our latest advancements in labels and packaging solutions. Join us at Stand D74 to explore our innovations firsthand.
marketing@reflexlabels.co.uk www.thereflexgroup.co.uk
Fudge Printers of Liverpool is one of the UK’s largest independent family run business that has accumulated over 50 years experience in the printing trade.
Our range of bespoke equipment allows for the decoration of different shaped objects using a variety of printing methods, ranging from screen printing, hot foiling and tampo pad printing.
We can print on:
t Bottles
t Jars
t Tablet containers
t Pots & tubs
t Tubes
t Closures
We deal direct with a variety of industry sectors from cosmetics, pharmaceutical and food to a variety of private and industrial sectors and are proud to have developed a close relationship with the NHS, providing a high quality printing service.
In a consumer-driven environment distinctive high quality packaging is vital, using our knowledge and experience we will advise and help you
achieve the perfect printing solution where quality and style will help you stand out in the crowd.
Our full range of services:
t Screen printing
t Tampo pad printing
t Hot foiling
t Design & origination
t Spray coating
t Product sourcing
Find us at the NEC on 12-13 February (Stand S84), or contact us today:
T 0151 298 9080
info@fudgecosmetics.co.uk
www.fudgecosmetics.co.uk www.instagram.com/ fudgeprinting_uk
Pont Packaging Ltd will be bringing its mission for customised sustainable solutions to Packaging Innovations 2025, 12th-13th February 2025 at the NEC Birmingham. As a European leader in sustainable packaging, Pont will be showcasing a wide range of progressive packaging to support brands in their journey towards greener solutions.
On a bright and beautiful stand, Pont Packaging will share its latest sustainable developments, focusing on its growing range of recyclable, reusable, and resource-efficient options.
All these creations from Pont reflect its commitment
to offering solutions that meet both consumer demand for greener products, and help businesses reduce their carbon footprint. New advances in materials, including biobased PE, recycled PET, recycled HDPE, glass, and carbon black free packaging, will give visitors a comprehensive look at how sustainability can be seamlessly integrated into their operations.
Pont Packaging’s mission has always been to provide the best possible solutions for its customers, with sustainability at its heart. By embracing renewable materials and championing sustainable solutions, Pont’s green packaging initiatives empower companies to innovate and lead, driving meaningful change towards an ecofriendlier future. Its range of environmentally responsible products keeps growing, always striving for sustainability without compromising on quality or performance.
“We believe that the future of packaging is green, and we are excited to share our latest sustainable solutions with visitors at Packaging Innovations,” said Kirsty Mumford, Commercial Director at Pont Ltd. “Our team has been working tirelessly to develop packaging options that offer the same durability and functionality,
The Navigator Company will exhibit at Packaging Innovations, at the NEC in Birmingham, 12th to 13th February 2025. The UK’s essential annual event drives business and innovation across the whole packaging journey.
By showcasing its packaging range –gKRAFT, the company aims to present its solution to the plastic crisis: a kraft paper alternative that accelerates the transition to the use of natural, sustainable, recyclable, and biodegradable fibres.
Making the most use of its extensive knowledge of the advantages of Eucalyptus globulus fibres, The Navigator Company introduced gKRAFT with three sub-brands: FLEX, BAG and BOX, covering a wide range of business needs.
With the use of virgin fibres, this highquality packaging solution offers an extra smooth finish and superior printing quality. It is also a safer and more hygienic option compared to recycled paper, which can contain harmful quantities of chemicals. However, even among its virgin fibre peers, gKRAFT has a competitive edge, as it enables more recycling cycles whilst using less wood volume per tonne of paper.
All in all, gKRAFT is a valuable asset for brands wanting to show their consumers a clear commitment to the environment.
while also supporting the transition to a more circular economy. We look forward to connecting with our partners and customers to discuss how we can shape the future together.”
Visit Pont Packaging at the show
Visitors to the Packaging Innovations show will have the opportunity to see first-hand how Pont Packaging’s products are setting new standards for sustainability. From adopting sustainable materials to exploring innovative ways to enhance the environmental performance of your packaging, Pont’s team is here to inspire and support your journey toward eco-friendly solutions.
Come and say hello at Stand P30, Hall 3A, and explore the future of green packaging to see how our innovations can benefit your business.
For more information, visit: www.ponteurope.com/green-packaging
Robinson the manufacturer specialising in value-added custom packaging – will be showcasing its new plastic and paperboard range of products.
Robinson specialises in custom packaging with technical and valueadded solutions for food and consumer product hygiene, safety, protection, and convenience, going above and beyond to create a sustainable future for their people and the planet.
product, and the unique reusable branded drinks cups for www.stackcup.co.uk
Scan the QR code to register for the event and then visit The Navigator Company’s booth at Stand J79 and learn more about gKRAFT solutions.
T 01372 728282
The company has seen massive growth in a wide range of innovative new products in 2024 with more for 2025 showcasing its agility in creating packaging solutions to fit the individual and challenging needs of its customers from initial concept to market.
On the stand are two new products including Putty Party – www. puttypals.co.uk – a perfect collaboration that led to the creation of the perfect jar for the fun sensory
Angela Doyle, Business Development Manager, says, “We are really looking forward to meeting people on the stand as we have so many new and exciting products to show them. It has been an amazingly successful year for Robinson and our everresponsive team provide enthusiasm alongside hands on collaboration to provide an agile, quick and best solution for such a wide range of products.”
The expanding portfolio has been even further enhanced with the addition of 2 new Nissei machines with more on the way!
Come see us on Stand H34.
Contact: Angela Doyle, Business Development Manager M 07557 641180
angelad@robinsonpackaging.com www.robinsonpackaging.com
12th & 13th February 2025
NEC Birmingham, Hall 3A, Stand P30
Join us at Packaging Innovations 2025 and discover the future of sustainable packaging!
Pont Packaging Ltd is excited to announce our participation in this year’s Packaging Innovations event. As a European leader in sustainable packaging solutions, we’re thrilled to showcase our latest innovations designed to help brands embrace eco-friendly practices and reduce their environmental impact.
Pioneering packaging for a greener tomorrow
At Pont Packaging, sustainability is at the heart of everything we do. Our mission is to deliver the best possible solutions while prioritising our planet. That’s why we’re expanding our range of recyclable, reusable, and resource-efficient packaging options. At the show, we’ll highlight our cuttingedge advancements in:
• Biobased PE – Renewable materials for a reduced carbon footprint
• Recycled PET & HDPE – Maximizing the value of recyclable plastics
• Glass – The original sustainable packaging –in clear & amber glass
• Carbon Black Free Packaging – A cleaner, easier-to-recycle choice for your brand
See how our sustainable packaging solutions can transform your business!
Why visit Pont Packaging at the show?
• Exclusive Product Showcases – Get a sneak peek at our latest eco-friendly packaging solutions
• In-Depth Insights – Learn how to reduce plastic usage, embrace renewable materials, and improve your packaging’s environmental impact
• Live Demonstrations – See our innovative materials and designs in action
• Expert Advice – Meet our dedicated team, ready to help your brand transition to greener, more sustainable packaging options
Don’t miss out on the opportunity to collaborate “Our team has been working tirelessly to develop packaging options that offer the same durability and functionality, while also supporting the transition to a more circular economy,” says Kirsty Mumford, Commercial Director at Pont Ltd.
Let’s shape a sustainable future together! Find us at Stand P30 in Hall 3A
We can’t wait to meet you at the show! Visit our stand for:
• Live Product Demonstrations
• Expert Consultations
• Exclusive Giveaways & More!
Mark your calendars, pack your bags, and get ready to explore the latest in sustainable packaging!
For more details on our green innovations, visit our website: www.ponteurope.com/green-packaging
Together, let’s make packaging greener and better for our planet. See you there!
The sustainability journey requires genuine transformation, not just policy changes. The UK’s evolution from basic environmental awareness of carbon emissions in the 1980s to today’s net-zero goals shows how systematic change is possible, though challenging. While initiatives like the Green Claims Code, plastics tax and Extended Producer Responsibility schemes are promising, their effectiveness depends on unified commitment from businesses, governments, and consumers.
The packaging industry is central to this revolution, with sustainability now a necessity rather than an option. Success requires fundamental changes to how we design, produce, and dispose of packaging materials. Through granular data collection consistent accurate and transparent carbon reporting using authentic third parties, businesses can identify inefficiencies, reduce waste, and optimise processes – delivering both environmental and financial benefits. This dual impact of sustainability initiatives proves that protecting the planet and protecting profits aren't mutually exclusive.
Looking toward the 2050 net-zero target, the packaging industry must reimagine possibilities rather than maintain current practices. For forward-thinking businesses, this presents an opportunity to lead market change and shape a sustainable future while reducing operational costs. The challenge isn’t about whether sustainable packaging is possible –it’s about having the determination to make it happen.
Come see us on Stand B60. T 0115 697 5500 www.benchmark-consulting.co.uk
Save time in your operation while enhancing the security of your products with Carlton Packaging’s award-winning Rapilock Pro!
As e-commerce evolves, so does the demand for secure and cost-effective packaging. This 100% recyclable, gluefree and tape-free e-commerce box is designed for unmatched tamper-evidence, providing peace of mind to both you and your customers. Through its overlapping layers at the seams and self-locking feature, Rapilock Pro provides the ultimate security for your products during handling and transit, as items cannot be tampered with without compromising the box.
manufacturing stage, and the smaller blank size means lower material costs without sacrificing box strength. Whether you’re shipping high-value items or simply looking for a smarter, more efficient way to package your products, the Rapilock Pro is the solution you’ve been waiting for.
Make sure you stop by Stand D80 at Packaging Innovations for your complimentary sample!
Rapilock Pro isn’t just about security, it also saves time in your operation. Its glue-free design reduces production costs by removing an entire
Beyondly, a Yorkshire-based, B Corp environmental compliance scheme and sustainability consultancy, is excited to showcase its datadriven environmental solutions at the Packaging Innovations & Empack event in Birmingham from 12th to 13th February 2025.
Beyondly share their knowledge with businesses to help them become more confident about their environmental choices; from meeting compliance obligations, excelling in managing environmental data, and the achieving sustainability expectations of stakeholders, and beyond.
Visitors at Packaging Innovations & Empack 2025 can find Beyondly at Stand C74, where their team of experts will be available to discuss the latest challenges and opportunities in Extended Producer Responsibility (EPR) for Packaging. In an ever-changing environmental landscape, the complexities of compliance can be daunting. Beyondly’s innovative data, compliance and sustainability offerings are designed to magic
away your EPR challenges, ensuring compliance with confidence, providing you with the tools and knowledge to navigate the complex requirements around packaging EPR.
Beyondly’s team of sustainability experts help organisations improve the recyclability of their packaging, to prepare for EPR and minimise the impact of the increased costs EPR presents for large packaging producers. Beyondly’s relationships with OPRL and Recoup enhance this service by supporting the process of determining the recyclability of consumer packaging for products. Combining these insights, with our team’s industry expertise, Beyondly has the ability to advise why an item is less recyclable and what can be done to modify the packaging.
Changes to packaging takes time, so Beyondly urge businesses to take action now.
“We are thrilled to be part of Packaging Innovations
T +44 (0)1908 277181 info@carltonpackaging.com www.carltonpackaging.com
& Empack 2025. This event provides a platform for us to connect with packaging producers, share our expertise, and demonstrate how our innovative data solutions can help businesses tackle their EPR challenges effectively. Our goal is to empower companies to excel in the world of environmental data, benefitting both their operations and the environment,” said James Marchant, Packaging Data & Workflow Leader from Beyondly.
Attendees will have the opportunity to engage in discussions on the latest trends and developments in environmental compliance, and learn how Beyondly’s bespoke solutions can be tailored to meet their specific needs.
For more information about Beyondly and its packaging compliance services, visit their website HERE, or contact their team by emailing: solutions@beyond.ly or calling 01756 794951.
The 2024 Environmental Services and Solutions Expo (ESS) took place at the NEC, Birmingham from 11-12 September 2024. Featuring five co-located expos that make up the ESS Expo family – Resource & Waste Management Expo (RWM), Energy, Fuels & Decarbonisation Expo (EFD), Water Resource Management Expo (WRM), Air Pollution Control Expo (APC), and Contamination & Land Remediation Expo (CLR) – the event drew thousands of industry experts, suppliers, and thought leaders under one roof. A true highlight of the environmental services calendar, ESS 2024 delivered cutting-edge innovations, insightful panels, and invaluable networking opportunities across two jam-packed days at the
NEC, Birmingham.
Enabling Net Zero: Re-use shops at HWRCs
SUEZ UK led a fascinating panel discussing consumer attitudes towards reuse shops at household waste and recycling centres (HWRCs). Their research showed that 95% of people were satisfied with their local reuse shop, highlighting the importance of public awareness and the need for visually appealing shops. Anna Scott from Keep Britain Tidy, who worked alongside SUEZ UK on the research, emphasised the role these shops play in reducing waste and promoting sustainability.
If you missed out, mark your calendars for next year – the 2025 ESS Expo promises to build on this year’s success with even more innovation & leadership across the environmental services spectrum, and takes place on 10-11 September 2025. This is our pick of the best exhibitors from this year’s show, listed here in alphabetical order: Environmental Combustion Technologies. Further details can be found on this page.
www.ess-expo.co.uk
Maintaining a safety shower is crucial for ensuring its optimal performance and effectiveness during emergency situations. Here are several reasons why maintaining a safety shower is essential:
1) Reliable Emergency Response
Regular maintenance ensures that the safety shower is in proper working condition and ready to be used when needed. By conducting routine inspections and maintenance activities such as testing water flow, checking water temperature, adjusting controls, and inspecting valves, any potential issues or malfunctions can be identified and addressed promptly, ensuring that the safety shower will function reliably during an emergency.
2) Employee Safety
The primary purpose of a safety shower is to provide immediate decontamination in case of exposure to hazardous substances. Regular maintenance helps ensure that the safety shower delivers the appropriate water flow rate, temperature, and coverage necessary for effective decontamination.
3) Compliance with Regulations
Safety showers are often subject to regulatory requirements and standards that specify their maintenance and inspection. By adhering to these regulations, organizations demonstrate their commitment to compliance and workplace safety.
4) Extended Lifespan
Proper maintenance and care can significantly extend the lifespan of a
safety shower. By promptly addressing any issues, replacing worn-out components, and conducting regular cleaning, you can prevent major breakdowns & costly repairs.
5) Reputation and Employee confidence
Demonstrating a commitment to maintaining safety showers indicates a strong safety culture within an organization. Regular maintenance instils employee confidence in the workplace safety measures and shows that their wellbeing is a top priority.
Maintaining a safety shower is essential for its reliable performance, employee safety, regulatory compliance, and overall operational readiness. Regular maintenance and inspections help identify and address any issues promptly, ensuring that the safety shower is always ready for use during emergencies.
For more information on service and maintenance, please contact Aqua Safety Showers on: +44 (0)1942 318096 or sales@aqua-safety.com
The pet and human cremation, waste incineration, and energy-from-waste industries are experiencing significant advancements as sustainability and environmental considerations take center stage. With growing concerns around waste management and energy efficiency, these sectors are prioritising cleaner, more efficient solutions that reduce environmental impact while meeting regulatory requirements.
In the cremation industry, both pet and human cremation services are increasingly adopting technologies that lower emissions and improve energy efficiency. This shift is driven by a demand for more eco-friendly practices that respect both the environment and the sensitivities of clients. Similarly, waste incineration and energy-from-waste facilities are playing a crucial role in the circular economy, turning waste into energy while reducing landfill dependency and lowering greenhouse gas emissions.
Environmental Combustion Technologies (ECT) supports these critical industries by delivering custom engineering solutions that optimise incineration processes and improve energy recovery. Our expertise in designing and manufacturing high-quality systems has made us a trusted partner for clients in these sectors. From improving cremation efficiency to enhancing waste-
to-energy capabilities, ECT continues to innovate, helping our clients meet their operational goals while contributing to a more sustainable future.
As these industries evolve, ECT remains at the forefront, delivering tailored solutions to support environmental responsibility.
T +44 (0)161 337 4488 sales@ec-technologies.co.uk www.ec-technologies.co.uk
With the SMS-R1 – you can now produce technical labels in-house in all sizes and shapes – because equipment has curves and recesses – in highly durable materials and in any quantity you need – in minutes. For manufacturing, health and safety even part of product labelling can now be produced on-demand, fully customised in shape, quantity and in colour.
Complete with all the necessary technical and safety pictograms, the SMS-R1 can ensure all your equipment meets current Health and Safety norms and has clear and concise operating information, maintenance information and service information.
Anything from a small component label up to highly visible labels with 95mm high text
is possible from just one system.
Our large range of materials include high strength adhesives, high visibility, temperature resistant, chemical resistant & metalized polyesters – ideal for serial plates.
Keeping equipment clearly labelled avoids damage, accidents and reduces maintenance.
Seeing is believing. Rebo have distribution in the UK and in Europe.
T +31 (0)35 601 6941 info@rebosystems.com www.rebosystems.com
Magog Industries are long established UK designers, manufacturers and suppliers of processing, mixing and conveying screws and barrels. Based in Hertfordshire, the company operate across the UK, Ireland and Europe.
Coatings and materials available are designed to enhance longer life and greater wear resistance in for increasingly demanding processing using recycled material.
“We constantly strive to offer solutions from optimal design to reduce wear to offering a wide range of surface technologies,” explained Michael Bate, General Manager.
“We design everything in-house but also work closely with specialist partners to
meet our customers’ specific processing and production requirements. Our three core competencies run through everything we do: process experience, manufacturing expertise and engineering excellence.”
Enhanced coatings include: Thin Dense Chrome (TDC) to enhance wear with low friction and is FDA Approved for food process environments. Ceramic Seal coatings reduce porosity and increase plating/coating life 4 to 10 times longer in corrosive environments, HVOF (High Velocity Oxygen Fuel) provides a crackfree 98% density with hardness of 62 to 72 HRC. This scratch-resistant tungsten carbide coating has gained much interest among plastics moulders.
Magog also specialise in refurbishment of pre-used parts which extends the life of screws and barrels by re-honing, partial re-line of barrel bores and hard welded re-build of screw flights in bimetallic alloy as standard. This provides a cost-effective option and ensure lower operating cost.
For more information, contact Magog Industries: T 01920 465201 enquiries@magog.co.uk www.magog.co.uk
Curtiss-Wright Surface Technologies (CWST) provides high quality surface treatments which will improve the life and performance of critical components through its global network of over 70 operating divisions and specialist onsite teams.
Our surface treatments have been successfully used by OEMs in major industries such as aerospace, automotive, oil & gas and power generation for many years.
We are only too aware of the logistical challenges and costs faced by our customers and so we can offer a ‘One Stop Shop’ solution providing a wide range of surface treatments including Controlled Shot and Laser Shock Peening, bespoke and trade Coating Applications, Thermal Spray Coatings and Parylene Coatings for metal, alloy, plastic and electronic components as well as Analytical Services.
We offer our customers a single source solution and point of contact
for all their surface treatments, supporting their requirements through our global network of over 70 worldwide facilities and on-site field teams, improving and reducing turnaround times and costs.
We are specialists in protecting components from common failures and reducing maintenance costs for key industries such as aerospace, oil and gas, automotive, medical and general industrial markets.
T +44 (0)1635 279621 eurosales@cwst.com www.cwst.co.uk
Machinery Supplies UK Ltd is a supplier of new and used sheet metal machinery, service spares consumables and accessories. Established in 2020, though still a new company, owner Andy Naylor brings a wealth of experience spanning over 35 years. The resident expert team of machine operators, software engineers and electronic & hydraulic engineers are on hand to help match customers with the right machinery and parts, even if they aren’t in stock.
With a focus on premium customer service, Machinery Supplies UK offers a 24/7 Support Network for customers around the country and prides itself on its ‘can do’ winning attitude.
“I have been working with sheet metal machinery since I left school in the mid-1980s and now we sell the machines I used to operate. With a truly international outlook, we have sold machinery to the USA, Taiwan, Europe as well as all over the UK. The latest cutting-edge laser welding machinery is coming from China and I travel there regularly to meet with these high-end manufacturers,” explained Andy.
Machinery Supplies UK provides the following new and used machinery and solutions to customers both in stock and on-site available for demonstration without team of experts:
t Fiber Laser cutting machines
t CNC Punching Machines
t Press Brakes
t Used Machinery
t Material storage solutions
t Deburring equipment
t Laser cleaning equipment
t Fiber laser welding
t Laser parts and maintenance
t Laser accessories
Fiber Lasers are widely used across industrial environments for a range of actions from marking, welding, cutting, cleaning, drilling, and much more and are renowned for advanced-precision. Furthermore, many companies appreciate the smaller carbon footprint, low maintenance and operating costs of Fiber Lasers. The engineers at Machinery Supplies UK offer support across most makes of Fiber Lasers and currently have the following two machines for sale:
t NEW compact 3M x 1.5M 3kW Fiber Laser – Manual pullout table complete with chiller, extraction filtration system, with Maxphotonics laser source. Full price: £59,000: including installation and warranty.
t NEW 3M x 1.5M 6kW Fiber Laser – Changeover table, chiller, extraction filter, with Raycus laser source. Full price: £119,000: including installation and warranty.
There is also a selection of used laser machines available of various kw and size ranges with chiller, extraction, software and fully installed package. This is a great addition to the circular economy, for those looking to invest in second-hand, reconditioned machinery, as part of sustainable best practice.
Machinery Supplies UK goes further than other suppliers by offering additional services such as Laser Slat Cleaners: designed to reduce part scratching and keep extraction flowing, part and parcel of laser bed longevity. This includes the 240v/415v models for varying kW laser powered machinery. Furthermore, the Rhino Parter Hammer is renowned for making the removal of tabbed laser cut parts much easier, using a handy automation impact vibration to break the tabs.
The wide selection of Press Brakes include makes such as Amada, Trumpf and Bystronic from small compact to large tonnage and bed sizes, all fully checked tested, serviced and prepared and comes with a full warranty. The team can provide tooling at an extra cost and all machinery is installed on-site, with full training given to operators. These press brakes can bend thick materials across various applications from construction, automotive, aerospace, agriculture to oil and gas.
TRUMPF is widely considered to be the pinnacle of German machinery manufacturing across the entire machine tool, laser and electronics sectors. Regarded as a world-leader in machine tools for flexible sheet metal processing, the TRUMPF CNC Punching Machines are in high demand across the UK and further afield. The expert engineering team at Machinery Supplies UK provide an extensive range of TRUMPF accessories from cartridges, multitools, collars, die adaptors and expert advice as well as spares and consumables.
“Our DEBURRING machines also offer exceptional value, adding the final finish and touch to the laser cut parts. From simple deburring to re-graining, our process of materials solutions are available to fit customer requirements.
“We are forever liaising with our NEW equipment suppliers in order to bring only the premium UK market high quality sheet metal working equipment, couple with our faultless aftersales support.
“Our new state of the art East Yorkshire showroom will be opening later this year, when we will invite new and existing customers from across the industry. Watch this space!” added Andy.
For more information, please email: info@ukmachinery.uk or visit: www.ukmachinery.uk
Built-in factory presets for welding and cleaning reduce learning curves, new welders can be trained within the hour and experienced welders realise an immediate increase to productivity. Highly Productive
High-speed welding that is 4x faster than TIG, with simple material preparation and minimal post-finishing, plus wobble head and wire feed options for consistent high-quality results.
Easily weld and clean thick, thin and reflective metals with low heat input from < .040” (1.0mm) up to 1/4” (6.35mm) with minimal part distortion, improved visual appearance and increased overall part quality. T. 07743 989565 E. info@ukmachinery.uk
Boasting over four decades of experience and rooted in Sheffield’s rich steel heritage, Charles Day Steels is thrilled to introduce their latest cutting-edge machinery acquisition – a new sheet metal bender. This state-of-the-art machine is engineered to cater to a wide spectrum of bending requirements with unparalleled efficiency and quality; emphasising Charles Day Steels’ ongoing investment strategy and commitment to advancing their bending and sheet metal pressing services.
Charles Day Steels reinforces its position as a leader in the metal processing industry, catering to a diverse range of client needs with precision and flexibility.
Effective
Building on a foundation of excellence and innovation, Charles Day Steels’ latest in a long line of machine investments underscores their commitment to providing customers with cutting-edge solutions. This strategic move not only improves their in-house capabilities but also broadens the range of services available to their clientele. Boasting a tonnage of 320 tons and a bending length capacity of 4,300mm, this newest investment marks a significant upgrade over previous capabilities; allowing them to accommodate larger and thicker materials, and expand their service offerings to include more complex and demanding projects. With this investment,
Renowned for its unparalleled precision and flexibility, this machine investment is a gamechanger in the industry, equipped with dynamic crowning and Pressure-Reference technology to ensure the highest repetition accuracy and consistent quality across all projects. Its modular machine concept, coupled with a broad power spectrum, allows for the optimal configuration for specific sheet metal work, significantly enhancing production efficiency and flexibility.
For more information about Charles Day Steels and their services, or to inquire about how the Bystronic Xpert Pro 320/4300 Press Brake can benefit your next project, please click here to get in touch today.
Contact T 0114 242 0101 sales@lasercutting.co.uk www.lasercutting.co.uk
CNC Solutions Ltd have developed and patented a new concept hybrid 5 axis Metal Additive Mill-Turn. Using a 3-axis bed mill format with a 2-axis trunnion table to manipulate the workpiece in 5-axis around fixed position spindle, turning turret & WAAM additive head stations. Controlled by the powerful Siemens – Sinumerik One – CNC & a bespoke tool probing system from Renishaw.
The machine is designed to manufacture components in excess of 800mm diameter or 600mm cube, using inverted workpiece horizontal milling spindle configuration for efficient swarf clearing, the hybrid process allows near net shape metal deposition for minimal material removal and wastage, saving raw material and tooling costs.
The machine has proved to be as capable as expected. We are currently working on producing test pieces and looking to move to the
next stage with:
t R&D projects of real-world products to trial manufacture.
t Funded R&D projects investigating ways to manufacture new products that can’t be machined from billet.
t Placement of the prototype machine in an R&D or manufacturing facility.
t A machine tool OEM or partner to help develop the concept further and take this new and innovative machine design to market.
www.effectivecncsolutions.co.uk
Independent Access Sales (IAS) supplies a leading range of platforms: including spider platforms, truckmounted access to push arounds, for all home, business or site needs. Established in 2020, this Huntingdon-based mini powerhouse has grown exponentially, with dynamic partnerships to help reach new customers across the construction, cleaning facilities, arborists and many more. To date, the team has sold over £2 million worth of Spider machines over the last two and a half years, proving that IAS is indeed a heavyweight distributor.
IAS exhibited at this year’s APF Show from the 19-21 September at the Ragley Estate, Warwickshire. The APF is a highly respected biennial event for the whole forestry, woodland, arbicoulture, firewood, fencing, tree and timber sectors. IAS brought the marketleading Easylift Spider Platforms and SOCAGE truckmounted platforms to the show.
For new customers that need some initial consultancy, Richard offers expert-led advice and value-added extras like full servicing across the range for existing customers. In a fast-moving world, it’s hard to keep on top of inspection paperwork, so
it’s handy that IAS reminds customers when the sixmonth inspections are due. The in-house team arrange certifications, making sure platforms meet industry compliance regulations, leaving you to focus on the jobs at hand. With access to a large stock of components: repairs and maintenance are easily scheduled too.
The company has a loyal customer base, who appreciate Richard’s built-in industry knowledge, not just of the industry-leading product range but of everchanging health & safety compliance.
The addition of the SOCAGE truck line has been highly popular with customers and the company will be
adding new lines shortly. The SOCAGE 20T can carry a large load up to 230kg, making this trade mounted platform ideal for the most challenging work at height. The SOCAGE 21DJ can work at a maximum height of 20.3m across all industrial and urban applications.
For arborists or specialist cleaners at height, the Easylift srl Piattaforme Aeree R360 has a turret rotation of 360°, coupled with a working height of 35.4m. It is an ideal platform for working with heritage or historical buildings with limited space. The R260 model has a maximum height of 26m, with an outreach of 13.5m. This is the ideal choice for maintenance & installation jobs.
IAS has set new standards for the access platform market. Scale new heights today with Easylift Spider Platforms and SOCAGE trucks from IAS: the experts with the best aftersales service in the business.
M 07483 246878 enquiries@iasales.co.uk www.iasales.co.uk
Training carried out by Allan Russell (3M) covering cold applied 11kV, 33kV and 72kV joints and terminations giving Gary Barnett (Training and Technical Manager) and Cable Services the status of an authorised 3M trainer.
If you wish to discuss your training requirements, please email us on: training@cabletrainingservices.co.uk or contact Gary direct on 07939 510938.
Hansford Sensors is a leading global manufacturer of industrial vibration monitoring equipment. We design, develop and manufacture a range of high-performance industrial accelerometers, vibration sensors, 4-20mA transmitters, cable assemblies, industrial enclosures and ancillary equipment. These products can be used in a wide range of industries including petrochemical, metal, paper & recycling.
Visit hansfordsensors.com, contact 0845 680 1957 or email sales@hansfordsensors.com
Maintec is the longest standing exhibition for the predictive maintenance, reliability and asset management industry, and Chris Hansford, Managing Director of Hansford Sensors Ltd, has been attending the show for almost 40 years.
As a globally recognised leader in industrial vibration monitoring, Hansford Sensors designs & manufactures a broad range of high-performance equipment. Its offerings include accelerometers, vibration sensors, 4-20mA transmitters, cable assemblies, and industrial enclosures. At Maintec 2024, Hansford Sensors highlighted key products like its Accelerometer Power Supply Modules and Vibration Sensors, showcasing its commitment to delivering reliable solutions for industrial applications.
As well as Vibration Systems and Switches, Hansford Sensors also offer a range of accessories for vibration monitoring that include DIN rail mounted monitoring and protection modules, vibration switches and charge amplifiers.
Vibration monitoring products are crucial in industry because they help detect early signs of machinery malfunction, such as misalignment, imbalance, or bearing failures. Hansford Sensors systems are ideal to support various outputs like AC acceleration and velocity, ensuring versatility in usage. Its products are designed for robustness with IP ratings suitable for harsh environments, making them ideal for industries such as manufacturing, power, and mining.
What’s more, Hansford Sensors also provide an online calculator designed to simplify your vibration analysis. From an input of acceleration, velocity or displacement the Vibration Calculator converts the amplitude and frequency into a range of engineering units to optimise analytical performance.
For more information on all products, or to use the calculator, please see below: T 0845 680 1957 sales@hansfordsensors.com https://hansfordsensors.com
Veolia Water Technologies has recently supplied a new ORION unit for Parker Hannifin’s Bioscience Filtration Facility in Birtley. Building on a successful existing relationship, the new 20,000 L/hr unit replaced an older, custom-built ORION™ and has enabled the customer to increase production, reduce risk, be more sustainable and ultimately increase profitability.
The Parker Bioscience Filtration Facility in Birtley County Durham – part of Parker Hannifin, the global leader in motion and control technologies – produces a range of filtration and separation products used in pharmaceutical and high purity critical applications. Purified Water plays an important role in production as all manufactured products must be thoroughly flushed, cleaned and validated before they can be sent to customers. As a result, the facility requires large volumes of water that consistently complies to US Pharmacopeia’s (USP) water for injection (WFI) specification.
“Veolia Water Technologies was a logical choice because we already have a solid and wellestablished relationship with them and we know the technology delivers,” commented Nathan Ryder, Facilities & Maintenance Manager at Parker Hannifin. “What’s more, we were impressed by the technology and its efficient use of resources. This enables us to better serve our customers by increasing production, while reducing our water and energy consumption.”
Veolia Water Technologies’ ORION™ system is a reliable and proven purified water technology
that combines softening, reverse osmosis (RO), continuous electrodeionisation (CEDI) and ultrafiltration in one package. Capable of delivering large volumes of treated water suitable for a range of processes, the technology boasts a high water recovery rate and low energy consumption, which suits costumers conscious of their environmental impact.
Furthermore, the new ORION™ installed at Birtley reliably delivers cold WFI at a rate of 20,000 L/hr. This allows Parker Hannifin to meet its ambition of increased production, flexibly adapting output to demand.
“The project was a big undertaking,” added Nathan. “It required the construction of a new building to house the ORION™ as well as new control panels for our four ring mains that feed the factory.”
Veolia Water Technologies had to closely coordinate its work onsite in order to replace the old control system that had managed the facility’s four water
storage and distribution ring mains. To achieve this without the need for downtime, the team focused on upgrading one of the original ring mains first as this was not capable of being sanitised with Ozone.
At the same time, the original central control system had to be upgraded due to obsolescence of critical components, and to incorporate major changes to the functionality of Parker Hannifin’s storage and distribution systems. All of this work was carried out whilst ensuring Parker Hannifin’s operations were not impeded.
Stefan Sadnani, Business Development Manager at Veolia Water Technologies, commented, “It was great to be able to work closely with Nathan and the team to make this project a success. The existing service contract on the old ORION™ unit has meant that we have built up a great understanding of the site and its needs over the years and this put us in a great position to deliver the expanded capacity that Parker Hannifin requires.”
To find out more about Veolia Water Technologies’ range of water treatment solutions for pharmaceutical applications go to: www.veoliawatertechnologies.co.uk or, for more information about Parker Hannifin, please visit: www.parker.com
Tennant Company, a world leader in the design, manufacture, and supply of industrial cleaning machines, recently unveiled the full specification and capabilities of the X4 ROVR, its first purpose-built autonomous floor cleaning machine and fourth robotic scrubber in its product line. Engineered from the ground up for autonomous operation and powered by the next generation BrainOS® Robotics Platform from autonomous technology partner Brain Corp, the X4 ROVR robotic scrubber delivers unparalleled cleaning performance and adaptability across numerous commercial environments, including retail, warehousing, distribution centres, education, as well as multiple Building Service Contractor (BSC) applications where optimised productivity is crucial to success.
Its state-of-the-art computer vision technology and compact dimensions gives the X4 ROVR the ability to intelligently navigate into small, narrow and congested spaces.
“The new X4 ROVR robotic scrubber has been meticulously developed to help cleaning teams free up bandwidth and, as a result, improve their efficiency. It aims to empower businesses to deploy autonomous cleaning that requires minimal human interaction,
truly freeing up employees for higher value tasks,” said Dave Huml, President and CEO of Tennant Company. “With Brain Corp’s nextgeneration software powering a step-change in navigation capabilities, our design team focused on delivering a robotic cleaning machine with improved manoeuvrability, durability, reliability and productivity –delivering customers a significantly faster return on investment.”
to transform how cleaning teams operate, making their work more efficient and reliable than ever before.”
Purpose built with productivity in mind, the X4 ROVR autonomous floor scrubber features a dual disk scrub path, a high-performance vacuum system, and sophisticated technology that adapts seamlessly to various hard floor environments. It is equipped with a 10 gallon solution tank and delivers an impressive cleaning productivity rate of up to 20,000ft² on a single full tank. It is also supported by a Lithium-ion battery that powers up to two and a half hours of continuous cleaning when fully charged.
David Pinn, CEO of Brain Corp, remarked, “The X4 ROVR autonomous floor scrubber is a prime example of the innovation unlocked in the partnership between Tennant and Brain Corp. Our shared vision for the future of autonomous cleaning has led to an offering that sets a new benchmark for robotic cleaning performance. The X4 ROVR comes with the tools and services needed
Users of the X4 ROVR robotic scrubber can stay connected to their autonomous cleaning operations using BrainOS® Ops Management Tools, including the BrainOS® Mobile app, BrainOS® Email Reports and BrainOS® Portal. This suite of tools empowers a digital approach to monitoring, reporting, and enhancing cleaning performance with transparent proof-of-work insights for operations. Tennant will also leverage its customer success team to support robots throughout their lifetime – with the aim of making each, a reliable, valued member of a customer’s cleaning programme.
“The X4 ROVR robot is more than just a cleaning machine,” Huml continued. “It’s a chance for our customers to adopt leading innovation, to refocus your cleaning teams on higher-value, higher-priority tasks, and to improve the efficiency, productivity and profitability of your entire operation.”
The new Tennant X4 ROVR robotic scrubber is available to order immediately. To learn more and view specification details, please visit: www.tennantco.com or contact the team at: tennantuksales@tennantco.com or call: 01604 583191.
Bradshaw EV, which since 1976 has grown to become the UK’s leading supplier and manufacturer of electric utility vehicles, is set to exhibit its increasingly popular Goupil range at Fleet & Mobility Live on Stand C30
Bradshaw EV has been at the forefront of the sweeping shift towards electric vehicles over the past four decades, with the rising popularity of its all-electric Goupil range within the private and public sector being a personal testament to this seismic change.
Also on display is the new Goupil G4 Refuse Collection Vehicle (RCV), which is expertly designed for satellite operations, efficient discharging of waste into larger collection vehicles, streamlining waste collection rounds, and reducing overall time on the streets. Equipped with an aluminium body and a robust bin lift system, Bradshaw’s G4 RCV offers a sustainable and efficient alternative to traditional refuse collection methods.
Each vehicle within the range also comes with the added benefit of being able to be charged via a typical 3-pin plug socket, removing the need for investment into expensive charging infrastructure.
Ramsy Labassi, Marketing Manager at Bradshaw Electric Vehicles, commented, “We’re excited to be showcasing our Goupil range at Fleet & Mobility Live, an event that highlights the challenges fleets face today and the innovative solutions available to overcome them.
“Our Goupil range has grown in popularity in recent years, as organisations across the public and private sectors look to integrate reliable, zero-emission options within their fleets to assist in driving forward their sustainability plans, without compromising on operational efficiency.
As organisations across the UK look to drive down emissions and integrate zero-emission vehicles into their fleets, the Goupil vehicles now feature across a wide range of industries, including last-mile, waste management, and site maintenance.
Versatile in their design, the Goupil vehicles can be equipped with lead acid or lithium batteries and can each be tailored directly to the customer’s requirements – which is furthermore complemented through their newly formed relationship with vehicle conversion and racking specialists, Bott – who fitted out a G4 Box Van with a state-of-the-art racking system, dubbed the Vario3.
The G4 road vehicles on offer include pick-ups, vans and waste collectors, all designed to transport people and equipment for a variety of different applications. With an operational range of 101 miles and maximum speed of 31mph, the G4s can be equipped with an array of body types to cater to the customer’s specific requirements and feature a safe and secure cabin as well as both left and right hand drive options.
“The Goupils’ versatility and ability to be customised for specific tasks has made it a popular choice across a wide variety of sectors from facilities and site management to waste collection and we’re very much looking forward to showcasing their advantages to visitors at the show.”
T 01780 782621 enquiries@bradshawev.com www.bradshawev.com
Packaging materials and pallet splinters can generate a lot of dirt and debris, something that is unavoidable in warehousing and logistics environments, but controlling them is critical for safety and productivity. Jamie Harris (pictured below), head of Industrial for Tennant UK, offers his advice in this area.
“Tennant floor cleaning machines not only keep surfaces clean and safe, they also protect your employees and the environment they work in.”
Research* has shown that typical slip and fall injuries cost employers around £36,800, approximately 150 million workdays are missed each year due to poor indoor air quality and the related health issues it causes, and that mechanised cleaning machines can help decrease 52% of airborne dust and 40% of bacteria found within the building.
“There are Tennant machines to clean every area of your facility,” says Jamie, “from the front office to the loading docks. We place the highest priority on worker safety as evidenced in our ergonomic designs, easy-to-use controls,
outstanding visibility, and sturdy construction. Our innovative technologies improve cleaning performance, reduce the total cost to clean, and protect health and safety.”
Jamie continues, “The innovative technologies available on our cleaning machines such as industry leading down pressures, improve cleaning performance, reduce the total cost to clean, and protect health and safety through reduced chemical usage and improved air quality, and with our range of robotic scrubber dryers working alongside your current cleaning team, cleaning has now become even more efficient as staff can
focus on other high-priority tasks while the robot gets on with cleaning the larger floor areas.”
“Tennant machines tackle every cleaning need at your site with powerful sweeping and scrubbing plus optimal dust control. Tyre marks left by vehicles can be easily removed with our highly effective scrubber-dryers where safety is enhanced by all-round visibility, overhead guards and fast, effective water pick-up.”
Book a FREE on-site demonstration and see for yourself.
With an in-depth knowledge of the warehousing and logistics sector, Tennant UK can offer you benefits that are tailored to your facilities’ unique needs.
See Tennant cleaning machines in action inside your facility before you decide to purchase (or rent) with a free, no-obligation demonstration at a site of your choice, allowing your team to see how they would work in their real-world environment.
T 01604 583191
tennantuksales@tennantco.com www.tennantco.com
*Source: Tennant flyer ‘Why Mechanised Cleaning 2021’
The Emergency Services Show and The Emergency Tech Show was held from 18-19 September 2024, welcoming thousands of visitors for two days of innovation, insights and learning as 500+ exhibitors showing 10,000+ products shared how they are preparing the emergency services for every response.
With over 16,000 visitors expected to come through the doors of Halls 4 and 5 of the NEC in Birmingham, this year’s show was bigger and better than before. The organisers were committed to showcasing solutions and content that help responders from across all parts of the emergency services deal with the challenges of an ever changing world.
The Sustainability Stage sponsored by YPO was new this year and recognised that climate change impacts need to be addressed, with experts talking about wildfire response and adapting to working in extreme temperatures. All content on the five stages of this year’s show was CPD-accredited by the partner CPDme so that visitors could demonstrate their own commitment to learning and take that back and share with their own organisations.
With the challenges and demands faced by emergency services evolving constantly, the show provided invaluable insights, networking opportunities and access to the latest advancements in equipment and training. Whether attendees were firefighters, paramedics, police officers or emergency planners, the show offered something for everyone involved in the vital work of saving lives and protecting communities.
Since 2012, FalTech GPS has been a leading specialist in GPS repeater technology supplying and installing GPS repeater systems to hundreds of police, fire, and ambulance stations nationwide.
These systems address the critical issues of weak indoor GPS signals which are often blocked by building structures, leaving devices inside unable to achieve a GPS fix. For emergency services, this lack of reliable GPS connectivity can lead to delays in call-outs, with potentially catastrophic consequences.
FalTech’s fully Ofcom-licensed GPS repeater technology provides a solution by relaying GPS signals indoors, ensuring uninterrupted signal reception. A standard repeater kit includes a rooftop GPS antenna, an antenna mount, coaxial cable, and an indoor GPS repeater unit, with bespoke solutions available for larger coverage areas. The company also offers a survey and test/demo installation service for new customers.
Let’s illustrate how this works for emergency services in turn.
When indoors, the mobile data terminal (MDT) in an appliance does not receive a GPS signal due to the blocking effect of the building structure. Crucially, when the appliance leaves the building there can be a signal acquisition delay of several minutes as the MDT re-establishes a positional fix. The repeater system ensures that navigation equipment is always ‘live locked’ to the GPS satellite service. Navigation systems are ready to go instantly and will transmit accurate location data to the control centre at all times.
Attendees enjoyed an extensive exhibition showcasing a wide range of products and services from leading suppliers in the industry. From firefighting apparatus and medical equipment to communications systems and personal protective gear, the exhibition floor was a hub of activity, providing attendees with handson demonstrations and the chance to discuss their specific needs with knowledgeable experts.
Visitors saw new product launches across the show floors and in a new feature for 2024, the Emergency Services Times sponsored Networking Cafe included a live video broadcast space called the Supplier Sessions. It’s another way that the organisers were innovating to provide exclusive insights into the products that are solving the challenges faced by the sector.
The Emergency Services Show returns next year to Birmingham’s NEC from 17-18 September 2025. This is our pick of the best exhibitors from this year’s London event, listed here in alphabetical order: Faltech GPS, Platelet Dispatch, Ring Automotive & SADS. Further details can be found on this page and the next. www.emergencyuk.com
When officers are inside a building, their handportable radios will not be able to receive a GPS signal due to the blocking effect of the building structure. A GPS repeater ensures that all devices are ‘locked on’ to the signal while indoors. When officers leave the building, there is no satellite acquisition
delay, and the radio will automatically transmit real-time, accurate data to the command-andcontrol centre. This ensures response times are quick and accurate, using the correct navigational information: saving lives once more.
When ambulances are parked at the station, they can’t receive a GPS signal, resulting in on-board navigation systems losing their positional fix. Upon exit, this results in a GPS signal acquisition delay of several minutes, causing potentially lifethreatening delays when navigating to an incident. Again, a GPS repeater prevents such delays by providing ‘live’ GPS signal inside the station at all times.
www.gps-repeaters.com
Ring Carnation showcased its product and services offering at the Emergency Services Show 2024. The vehicle conversion specialist has been the market-leading supplier of switching systems with the emergency services since 1995, with genisys™ remaining the controller of choice, providing power management and intelligent switch control.
The genisys™ family of modules includes ECUs; Output Modules; a wide range of user interfaces, including Keypads and Touch Screens; CAN Bus interface modules and Protocol Converters for third party system integration. The genisys™ system manages the numerous applications within the vehicle to ensure power is optimally maintained and provides safer working vehicles for the fleet manager and work force.
Configurable keypads enable a bespoke set of functions especially for emergency vehicle fleets, to assist when responding to incidents.
The RSU-60 Wireless Switching Power Hub was on display, which can help reduce
installation time by up to 35%. The Power Hub provides up to eight output ports with a total rating of 60A, providing ease of connection for ancillary electrical items.
Ring Carnation also carries an extensive range of hazard, work, and interior lighting as well as power supply/management
products to transform vehicles into mobile work units. Ring Carnation are ‘experts in power on the move’. Contact us today to discuss your automotive power management and control needs.
carnationsales@ringautomotive.com www.ringcarnation.com
Platelet Dispatch is a leading dispatch system for emergency couriers, with a focus on medical supplies and blood and was one of our Top Exhibitors at the recent Emergency Services Show 2024 at the NEC from 18-19 September.
Theo Cranmore: Director of platelet.app was on hand to discuss the groundbreaking Platelet Dispatch with visitors from across the emergency services sector.
Platelet Dispatch offers industry-leading benefits for all users:
t Customised dashboards for controllers and riders alike: dashboard provides an easy, quick view of all rider jobs.
t Easy-usability – at a touch of a button, users can view, edit and share job details. The in-built directory of locations and items provides quick choices, with added inventory for ease and convenience and
consignments can be prioritised for seamless flow of operations.
t Still works in areas with poor network coverage: offline capability when you need it the most.
t Updates dashboard with job status changes, giving live accurate readings
t Handy record of all consignment history: with date filters pinpointing the search.
If you work in urgent delivery, search and rescue and emergency response and would like to know more, contact the team directly on: T +44 (0)141 674 7548 info@platelet.app www.platelet.app