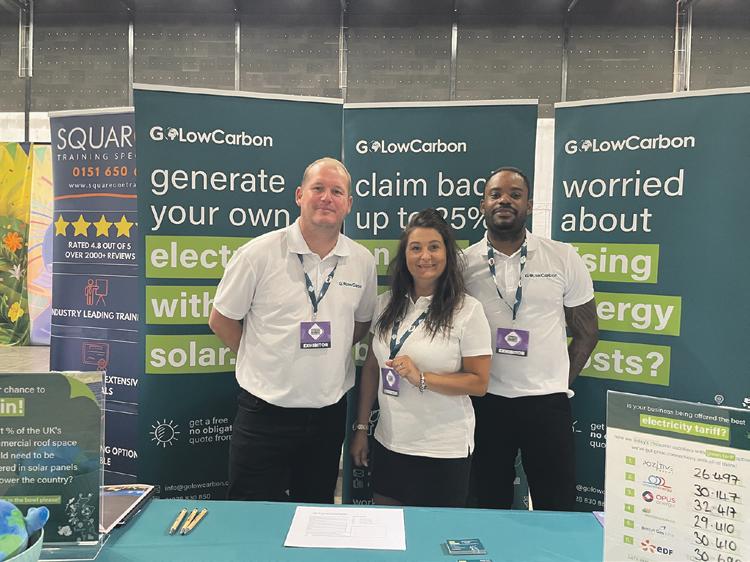
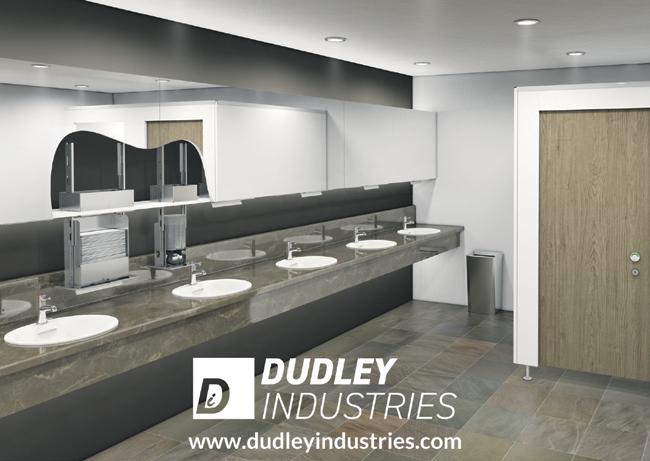
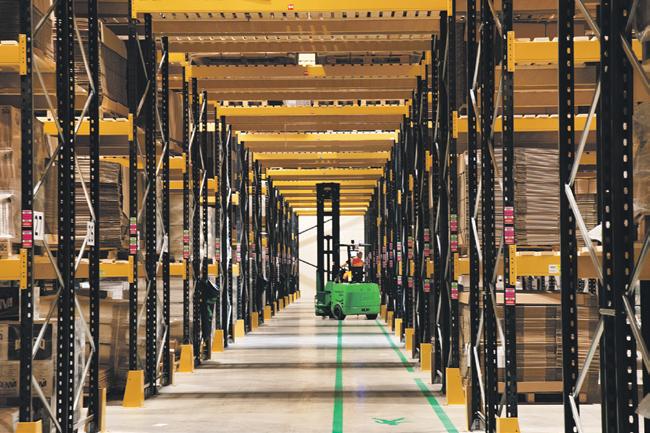
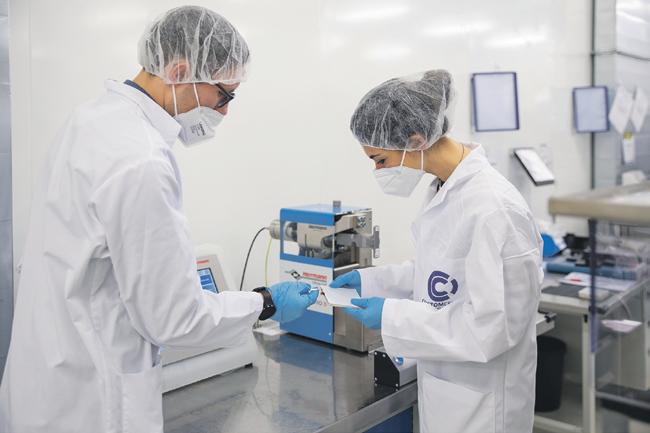
The all-new lone worker Safety Watch is the first lone worker device that is able to communicate via Wi-Fi.
The watch, which is 2G/3G/4G ready and uses Bluetooth Technology is ideal for those who work alone or remotely on site in complex buildings, where signal can be poor or non-existent, or when locating people in an emergency could take a long time. The powerful and technically advanced device allows lone workers to answer and receive calls over Wi-Fi or cell. Designed with safety in mind, the watch can raise alarms by detecting no movement, a fall or raise an alarm through the SOS button, which can be directed straight to our alarm receiving centre.
For added pinpoint location accuracy the Safety Watch can be used in conjunction with Bluetooth Beacons, which can be
customised to floor level or room and is managed within our lone worker management portal, The OWL.
For more information on the Safety Watch or products that can be used for complex locations please visit www. lonealert.co.uk/lone-worker-devices/ lone-worker-safety-watch/
high-resolution printing up to 34mm made possible with the Integra PP Razr 34
Where there is a need to print larger text, graphics or barcodes onto primary or secondary packaging without compromising on quality, thermal transfer (TTO) has usually been the go-to technology – it’s clean, crisp and offers great adhesion to most porous and nonporous surfaces, providing the correct ribbon has been selected.
However, the new Integra PP Razr 34 from Rotech can guarantee excellent resolution printing up to 34mm high, creating a seamless, consistent print on the majority of packaging types.
A need to reduce waste In today’s day and age, manufacturers are increasingly feeling the pressure to review their processes and look for ways that they can be made greener, and less wasteful. Coding and marking is no exception.
While TTO is a well-established, reliable coding technology that will remain unchallenged for some applications i.e. printing entire ingredients declarations, cartridge-based alternatives, such as thermal inkjet (TIJ) and Piezo are very capable of matching the quality of print produced by thermal transfer, but with much less waste produced. There are no ribbons to contend with, just the ink needed to produce the desired format. These drop on demand printers are also a lot more compact, making them more energy-efficient and easier to integrate onto existing lines.
Such a system is the new Integra PP Razr 34. The impressive Piezo system is capable of printing excellent quality prints – up to 900dpi – at high speeds (up to 150m/min at 300dpi).
Printing up to 34mm high, the Razr eliminates the unwanted stitching of text and graphics from multiple printheads. The ink used offers excellent adhesion and resistance, making it ideal for printing onto shiny, non-porous surfaces, such as plastic or film.
Other advantages of the system include its increased uptime in comparison to TTO and continuous inkjet (CIJ) – it starts up and shuts down instantaneously and the bleeding of the ink system and changing of the cartridge can be done without stopping production.
Ideal for replacing labels
The Integra PP Razr 34 is also proving a popular solution for direct printing onto packaging where labels would have previously been used. The razor-sharp print ensures that the codes remain readable by scanners – a crucial factor for those operation in logistics, where the shipping boxes need to be fully traced throughout their lifecycle.
To further ensure reliability, the Razr has two separate nozzle channels that can be controlled individually. This means that if one fails, the other ensures that the print quality remains consistent.
www.rotechmachines.com
and utilisation of all ball valve operation. The team took onboard all of the technical requirements, used existing and proven valve technology and materials to create the perfect solution to this problem. It’s often said, that when engineers creatively let off steam, it usually results in some of the most amazing solutions, and this has been no exception.
On completion of initial trials, the 2” DBB valves are to be installed on other UK and overseas processing plants.
For more information on how Oliver Twinsafe can custom-design valves for
processing plant using the very best in valve design and technology,
"We are thrilled to unveil our redesigned website and introduce our new web address to our valued customers, some of whom have been with us long enough to recall when we traded as ESL, and who will hopefully appreciate a return to our roots" said Roy Simmons, Director at ESG. Sam Awolesi, Chief Executive Officer at ESG says "By simplifying our website and narrowing our services, we can better serve our customers, focus our expertise and deliver the highest level of quality, on which our reputation has built all these years.”
To celebrate the launch of the new website, ESG is offering an exclusive limited time promotion for first time customers looking to use either their Safety Data Sheet authoring or checking services. Interested individuals can visit www.esldatasheets.com
StopTite is renowned for its heavyweight thread locking, retaining, gasketing and sealing products for mechanical assemblies. All products are manufactured and shipped from the UK and if you’re looking for industrial strength adhesives: the 006 and 007 products can bond metal and other compound applications.
The new drip-it oilers are part of the new eco-range from StopTite. Design-engineered for the sustainable era, with no moving parts or power required, all parts are recyclable, making this the most environmentally-friendly purchase you will make this year. Drip-it oil reservoirs are comprised of recyclable high-impact plastic, with no compromise on functionality, these systems can contend with the majority of industrial requirements, from farming, mining, steel works, robotics, wind power to rail.
Only the highest-quality valves are used, to give optimal flow control and Drip-it will limit stretch to chains, reduce friction, component weathering and corrosion. The expert design means no more reduced downtime, maintaining streamlined machinery.
The Drip-it Gravity oiler can be utilised as a single drip feeder or as a multi-drip or brush application, using the balanced adjustable valves. Ideal for lubricating all sizes of chains, with three easy adjustable outlets, two governed by the side links and one to the centre roller, giving full reach to chains and sprockets.
Available in two sizes: 2Lt or 5Lt, you will receive a straightforward self-install kit to get you started in no time.
To purchase your Drip-it today, see the website below:
T 01584 874220 sales@stoptite.co.uk www.stoptite.co.uk/drip-it-gravity-chain-slide-oilers
andheld fibre laser welding technology is new to the UK welding industry, offering excellent welding performance, improving production efficiency and reducing operational costs. Up to 4 times faster than traditional welding methods, it offers high precision and neat welding seams on various materials. The Weld Star – Max Photonics system advanced air-cooling with self-adaptive fans ensures long-term stability and a neat, compact design. It is lightweight and ergonomically designed welding torch offers comfort and manoeuvrability to the user at only 680 grams and guarantees multiple safety precautions for welding operations.
A full colour 7-inch graphical user interface with synergic set up and the possibility to save up to 32 stored jobs offers easy set up and high repeatability to the user. Shooting mode offers controllable
and repeatable tack welding and single sided spot welding, whilst pulse mode offers aesthetically pleasing welds similar to that of traditional TIG welding methods.
Quick training times with the laser process gives employers the opportunity to up-skill workers and increase production.Laser safety is a big factor with this process being a Class 4 appliance. As such, it is imperative that the guidance is followed and this equipment is operated within a suitably approved class 4 enclosure. Wilkinson Star can offer a full package solution in compliance with EN 608254. Machines come with a 2 year warranty and torches a 12 month warranty.
www.wilkinsonstar247.com/laser-welding
Available through Wilkinson Star’s authorised network of distributors
Whad to be integrated into the setup.
Rainer Hönle, the founding owner, CEO and head of development at DELTA LOGIC, stated: “Continuous development of ACCONAGLink within this partnership-based development has been strongly promoted through both continuously upcoming new challenges faced by the products and those put forward by customers.”
For more information, see below.
www.deltalogic.de
www.deltalogic.de/products/software/accon-aglink www.winccoa.com/news/detail/simatic-wincc-oa-iot-suite.html
Drainage engineers from Lanes Group plc are carrying out important annual maintenance work for a Derbyshire council to ensure public spaces can be used and enjoyed by businesses, residents and visitors.
They have been working through a three-week programme of surface drainage asset cleaning for Erewash Borough Council at dozens of locations in towns and villages across the local
authority area.
The planned preventative maintenance (PPM) work is carried out every year across public spaces and facilities owned and managed by the borough council, including shopping precincts, leisure centres and car parks.
Critical drainage assets
Drainage engineers from the Lanes Derby depot are carrying out the work.
Lanes Area Development Manager Chris Norbury said: “We’re very pleased to have been awarded this project through competitive tender to support Erewash Borough Council’s asset maintenance programme.
“We’re using our jet vac tankers to clean a range of different drainage assets at 41 locations right across the borough, including slot drains, road drains, surface water gullies and silt traps.
“The drainage systems our teams are working on serve the busiest urban areas in the borough. They are critical for commercial activity and transport, so it’s vital they’re maintained to a high standard.”
Lanes is the largest independent wastewater and drainage maintenance specialist in the UK. The Derby depot is one of more than 40 depots and service delivery hubs the company operates.
Asset condition checks
Its teams are carrying out the work for the borough council during May and June, with much of it being done at weekends and during night shifts to minimise disruption for residents, businesses and road users.
Towns and villages they are working in include Ilkeston, Long Eaton, Sandiacre, and Breaston.
Key sites include the marketplaces in Ilkeston and Long Eaton, and associated public car parks.
Where asset condition issues are encountered – for example, if there appears to be a difficult blockage – the borough council can authorise Lanes to carry out a CCTV drainage survey to establish their cause.
Chris Norbury said: “As Erewash borough council has an established PPM programme, these drainage assets are well looked after, so the risk of serious blockages or of drains being damaged is reduced.
“However, as Lanes is the UK’s largest independent drainage specialist, if a problem is identified, whatever the size, complexity and urgency, we have the expertise, experience, and capacity to deal with it.”
Flood risk increase
Climate change is making the importance of drainage maintenance work like this more important than ever. Rainfall is becoming more volatile, with heavier downpours more probably throughout the year.
This can put extra strain on drainage systems, resulting in temporary pooling of water disrupting roads, pedestrian areas, and car parks. At worst, it can contribute to serious local flooding, causing damage to business premises and homes.
www.lanesfordrains.co.uk
The 2023 annual Instrumentation, Analysis & Testing Exhibition took place at the iconic Silverstone Race Circuit on the 16 May, following its recordbreaking year last year. Organised by the Engineering Integrity Society, it was the perfect opportunity for engineers to network and look for potential new partners and distributors from across aerospace, automotive, motorsport, rail, off-highway, power gen and civil engineering.
With more than 60 exhibitors showcasing the latest advancements across testing and analysis technologies, this year’s theme was on: “Test & Measurement: the road to visualisation.” Industry experts were treated to a showcasing of the new WMC300FR hybrid 3-wheeled motorcycle, from White Motorcycle Concept’s Ltd, currently being trialled by the emergency services across the country.
This year’s seminars included the latest R&D innovations in the motorcycle industry, such as powertrain technologies, virtual testing in vehicle development: x-in-the-loop integrated accelerated development environments and digital image correlation (DIC) for pyroshock testing in rail space.
Exhibitors gained knowledge of the latest trends in testing and analysis, across multiple technology cross-overs.
The date for the 2024 Instrumentation, Analysis & Testing Exhibition will be confirmed soon on the website below:
www.e-i-s.org.uk
Using cutting edge laser sources and interferometry, Optomet Laser Doppler Vibrometers enable the non-contact measurement of vibration over a range of several orders of magnitude, from atomic dimensions all the way to large buildings.
The duration of product development processes from concept to series production is getting shorter and shorter. This is particularly the case in the automotive industry, where the switch to electromobility is accelerating change. New components and the use of lightweight construction require extensive vibration analysis.
Even though the mechanical properties of components and entire component groups are increasingly and more precisely examined by numerical simulations, experimental measurements of physical objects are still required to validate these calculations. Non-contact measurement techniques such as laser vibrometry have the advantage that they do not influence the vibrations of the components and deliver excellent results in a very short time with little effort.
The superior signal quality of the Optomet infrared technology produces the best possible measurement results even on poorly reflective surfaces. This makes the devices suitable for measuring any component, regardless of its material or optical reflectivity. Discover the ease of use and powerful measurement capabilities that drastically reduce development time.
Acoustic Camera UK Ltd has been distributing German made SoundCams from CAE software und systems GmbH across the UK market, since 2019. With more than 30 years’ acoustic engineering expertise, CAE are the leading global acoustic camera supplier.
For acoustic experts across the industry, the SOUNDCAM’s (3rd generation.) Bionic: The MODULAR Acoustic Camera, released in 2021, is a game-changer. With advanced built-in specifications, it offers superior sound imaging properties. The soundcam quickly pinpoints noise sources on screen, and is already extensively used in reducing EV powertrain and motor noise.
The internal battery measures continuously for three and a half hours, with a handy optional IP45 water-resistant option also available. Once the case is opened, measurements start within five minutes and with user-friendly, touch-screen software, the portable application covers an impressive audible frequency range from 20Hz to 24kHz.
With a choice of four different microphone arm sizes: XS, S, M or L, each comprised of 112 magnetically-attached microphones, users can locate sound sources over the entire audible frequency range.
The live beamforming at a phenomenal rate of 100 frames per second and the additional Noise Inspector post-processing
Optomet has the longest experience of any manufacture, especially when it comes to constructing Infrared-LaserScanning-Vibrometers. Let us convince you of our expertise!
Contact details:
Optomet GmbH
Pfungstädter Straße 92 64297 Darmstadt
T +49 (0) 6151 3843 260
sales@optomet.de www.optomet.com
ISince
With
software provides a comprehensive range of state-of-the-art analysis algorithms.
Our high-frequency specialist model, the SoundCam ULTRA, will locate sources up to 100kHz making it perfect for finding air and gas leaks, even in noisy factory environments. It also includes a thermal imaging camera.
To find out more today, see the website below:
T +44 (0) 2476 98 2424
office@soundcam.uk
https://www.acoustic-camera-uk.com/products/
bionic-modular/
Metalitest provides high quality materials testing machines and material inspection/ analysis hardware & software to a wide range of industries including aerospace, automotive, metals, construction, energy, textiles and medical.
An experienced team with the expertise to provide bespoke solutions for individual applications. With a core focus on sample preparation, image analysis and materials testing of metals, plastics, composites. And a specialist team taking care of material specific testing machines for concrete, cement, paper and rope, amongst others.
The Birmingham based company was a top exhibitor at The Instrumentation, Analysis and Testing Expo at the Silverstone Race Circuit on 16 May 2023. The Expo is regarded as the leading annual event for the latest, innovative testing and analysis technologies, with the Metalitest team on hand to discuss expert materials testing/analysis with interested delegates.
Metalitest’s innovative product portfolio includes:
Relyence UK Limited was at this year’s Engineering Integrity Society’s Instrumentation, Analysis & Testing Exhibition, which was according to Simon Brailsford: Relyence’s Professional Services Manager, “highly successful for two reasonswe spoke to influencers directly about our software and we gauged which direction the industry is moving in, feeding directly back to our in-house developers.”
The globally renowned analysis software is developed by Relyence Corporation in the USA, with Relyence UK Limited part of the global support network. Relyence’s Quality & Reliability Management Suite offers state-of-the-art, cloud-integrated FMEA, FRACAS, Fault Tree and Reliability Prediction Software analysis software. Project Managers can access reliability data at the touch of a button from tablets, smartphones or
office computers, without any timeconsuming client installs.
Providing a world-class reliability & quality analysis software, Relyence provides flawless integration between existing FMEAs, FRACAS analyses and Fault Trees, with cutting-edge Reliability Predictions, Maintainability Analysis, Weibull and Accelerated Life Testing (ALT).
“Our intuitive, customised, configurable software works across all industries from aerospace, automotive, oil & gas, rail to civil engineeringproviding next-level reliability and risk reduction. We have been resolving pain points
impact, tensile, compression, bending, fatigue, static, dynamic and creep configuration testing, whereas the advanced analysis systems streamline complex microscopy and characterisation tasks.
Metalitest are now UKAS accredited to calibrate materials testing machines in accordance with ISO and ASTM standards for force (tension and compression), displacement, speed, extensometers, impact (Charpy and Izod) and creep. Additionally they offer a unique calibration service for strain alignment, resolving the issues in measuring strain alignment at numerous angles at the same time.
To find out more, see the website below:
T +44 (0) 121 7512112 sales@metalitest.com
www.metalitest.com
In this issue of Industry Update, we are proud to announce Go Low Carbon as our carbon reduction solutions Company of the Month.
Since the signing of the historic Paris Agreement in 2015, The Intergovernmental Panel on Climate Change (IPCC) has continued to warn about catastrophic global warming levels beyond 1.5°C. The UK Government has in turn, laid down the gauntlet with its 2050 net-zero target, with businesses now looking to actively reduce their carbon footprint.
Go Low Carbon is the joint brainchild of Ryan Park and Islam Pearson: set up in 2016, to support businesses towards a net-zero status, through practical, sustainable advice and solutions. With the head office in Cumbria, the company
acts as an independent utility consultancy to SME’s and larger companies, through satellite BDM’s in Liverpool, North Wales, Glasgow and Suffolk.
With an overarching focus on carbon reduction, this cuttingedge company works on a three-pronged service approach: green energy brokering, industrial/commercial solar PV installation and detailed carbon reduction implementation via audit. But as Ryan Park, CEO points out they are more than just energy brokers,
“We’re pleased to say that we’ve just completed a major solar PV installation for a large food production company in the North of England, its output is 756.5kWp and consists of 1780 on-roof panels. The emissions saved per year are equivalent to a standard family car driving 664,500 miles and over the lifespan of the system, the customer will save approximately £4,593,000 in electricity costs.
We're currently in our 2nd growth phase of solar in the UK and we're supporting businesses through a volatile time for business expense: we're also providing the solutions to the all-important sustainability credential questions on tenders and in the eyes of suppliers and customers.
For those concerned about up-front costs, we've expanded our PPA offering, whereby we're able to install a commercial solar PV system at zero cost to the client: the solar panels remain our property but we're still able to sell the electricity to the client at around a 30% discount.”
Companies are still under the common misconception that reducing carbon footprint will be costly and may reduce productivity. Go Low Carbon helps companies navigate the confusing world of energy tariffs, whilst presenting solutions to mitigate further taxes, such as the Climate Change Levy.
“We work steadfastly with clients across manufacturing, engineering, agriculture, leisure, healthcare: in fact, any business seeking to reduce their energy expenditure from a financial and a carbon perspective.
We offer expertise, value, education, holistic customer journeys & consistent support during and after. We stay true
to our values: our ultimate goal is to enable businesses to become more sustainable and environmentally friendly: saving them money is an attractive bi-product. The results of our work make your business more attractive in the eyes of every audience, your supply chain, prospective clients, existing customers, even job-applicants and your homegrown staffing base,” continues Ryan.
With many businesses operating with labour skill shortages, many simply don’t have the time or knowledge needed to carry out internal carbon audits or to look for cheaper, greener energy suppliers. The expert, independent consultants at Go Low Carbon can offer bespoke turnkey auditing provisions, designed to reduce carbon emissions. The solutions are bite-sized, data-driven, and certified by Go Low Carbon's Carbon Conscious or Carbon Neutral watermarks offsetting any fears around greenwash
labelling. Their work seeks to enable business leader to make informed decisions about their carbon reduction journey.
With direct access to over 30 energy providers, consultants can calculate current energy usage and suggest cheaper, greener energy tariffs. By combining water, gas and electricity provision, the team can negotiate better rates on your behalf, with estimated savings of up to 40%.
If you’re looking for an independent energy consultant who can help you reduce your carbon footprint while saving money today, talk to Go Low Carbon today:
T 01228 830850
info@golowcarbon.co.uk
www.golowcarbon.co.uk
Leading land-based and environment skills charity Lantra has taken on the challenge to help attract new talent, and retain existing expertise in the sector, with the launch of its NEW website.
Using their own resources to re-establish their position as a trusted source for career information across a wide range of land-based industries, the new Lantra website, with its extensive careers content, is set to be just the first in a series of focused activities.
The new website is simple and aims to help visitors navigate easily by answering three key questions…
t What jobs could I do, and what do they involve?
t What training, qualifications, and experience will I need?
t Where can I get the training and qualifications I need?
The new website lists details of more than 250 job roles across 12 industries and includes a selection of videos and case studies from real employees, explaining what each job involves, how they got into their current role and why they love it.
Lantra’s website also highlights the amazing new technologies and innovative working practices that are springing up in many industries, whether it be GPS and drones, or robotics and precision farming. All of which require higher levels
of technical skills as well as the ability to understand data, solve complex problems and lead increasingly diverse teams.
Lantra’s recently appointed Chair of Trustees, David Llewelyn commented:
“Lantra’s new website is designed to provide an easily accessible tool for people to explore their career options and training pathways.
“This is a significant development and will enable us to give people the information they need, literally at their fingertips. We know that the land-based sector is a great place to work with hundreds of varied roles, but its sheer scale has meant finding ‘joined up’ information all in one place has been a challenge.
“We’re confident the new website will provide convenient, relevant and accessible information for people wanting to start a career in the great outdoors, and for those already working in the sector who want to progress their career to the next level.”
All job roles on the new website are linked to a range of relevant qualifications and training. These can be university or college qualifications, apprenticeships, vocational short-courses, or e-learning. The new website already has more than 2,500 courses listed so people can find out more including where and when they
are available.
As a not-for-profit organisation, with a long history of supporting landbased industries, Lantra is uniquely placed to provide objective information on careers opportunities and associated training and, whilst the provision of careers advice is not part of their remit, they are confident the wealth of information provided will help signpost individuals on a career path, whatever their interests or aspirations.
Dawne Middleton, National Trust Gardener, Croome, Worcester, said: “Getting the necessary training and RHS qualifications required lots of hard work and lots of studying. Sometimes finding out who was the right person to contact, or which was the most appropriate qualification wasn’t straightforward, so Lantra’s new website resource would’ve been invaluable.
“As part of my development, I also had the opportunity to teach some younger college students and I’m confident people in their position will also value the information on the new website.”
The new website can be viewed here www.lantra.co.uk.
For more information contact marketing@lantra.co.uk or call 02476 696 996
Interface Force Measurement Solutions (Interface) is a UK company specialising in the supply and distribution of high-quality sensors and associated electronics and displays for a wide variety of industries. Working previously with clients such as Airbus, BAE Systems, and Formula One Teams, we spoke with Tony Rokins, Business Development & Pressure Mapping Specialist, who explained some of the companies well known products.
“Our product portfolio is applicable to many industries.
For instance, we are well known for our high-quality pressure mapping systems that are used by many of our automotive and motorsport customers.
Our sensors deliver highly accurate, repeatable measurements and many of our load cells are used by calibration houses as calibration reference devices. Our high-quality, yet competitively priced 3 and 6 axis load
cells are used for many R&D, renewable energy and robotic applications.”
In terms of recent developments, Tony continued, “Being responsive to our customer’s needs and being able to offer a high-quality product with strong product knowledge at a competitive price with the best possible lead times is our number one priority. Last year we launched our range of G-Series Load Cells. The range comprises of miniature and small sensors for industrial applications, with capacities starting from just 4.5N Newton up to 200kN with metric threads.
These are high-performance devices but aimed at more cost-conscious applications. This is a new market for us, but we have already had increasing interest.
We also launched our brand-new e-commerce website on the 1st of April for the G-Series that showcases Interface load cells at competitive prices with all the convenience purchasing online offers,” stated Tony.
The new e-commerce website offers G-Series load cells on short lead times with next business day delivery for small quantities. Following its successful launch in 2021, it has become an increasingly popular product range for students, industrial engineers, OEMs and anyone requiring a small form force sensor offering accuracy, repeatability and Interface quality.
In the future, Interface is keen to continue its growth trajectory for 2022. Tony mentioned, “we are also working on new, wireless force and vibration sensors for remote monitoring in systems such as luggage carousels. One more area we are pushing for growth is with XSensor’s pressure mapping systems, particularly in the Hi-speed systems designed for high-speed impact or crash testing and tire foot-print research. These systems are capable of capturing data up to 2,500 frames per second. The tire sensor can be driven over at speeds of up to 140kph. I believe this is a unique capability we can bring to the industry.”
As the company looks to continue strengthening its position with its customers in its more traditional markets of aerospace, automotive, motorsport, Universities and alternative energy research, it will be attending some expos over the next 12 months and be readily on hand to discuss any questions you may have about force, torque, pressure mapping or pressure, level & temperature measurement.
Visit us at Advanced Engineering 1st & 2nd November 2023 Stand P172 also at the NEC, Birmingham.
Contact T 01344 776666 info@interface.uk.com www.interfaceforce.co.uk
Dudley Industries, a British washroom equipment manufacturer, has introduced new additions to its 'Classic Behind-the-Mirror' range: pull-down soap and paper towel dispensers. These units, designed to fit bespoke cabinetry, include a touch-free 2-litre soap dispenser and a large capacity paper towel dispenser. They are installed behind a mirror or panel.
The distinctive feature of these new products is their 'pull down' mechanism, which facilitates easy replenishment. The units are equipped with lockable sliding cartridges that drop down below the cabinet, allowing convenient access to the soap and paper towel containers. After refilling, the cartridges can be raised back and securely locked, protecting the consumables from tampering.
Unlike many other cabinet systems, which require the front-facing mirror to be opened outward like a door, these dispensers offer a different approach. Installation of the dispensers is straightforward. A hole needs to be cut into the cabinet's base, and the dispenser is then inserted and securely fastened. Dudley Industries provides the necessary technical data and installation guide with each order.
Manufactured at Dudley Industries' production facility in Lytham, Lancashire, the products in the ‘pull down’ range come with a 10-year warranty. Detailed specifications for the new Behind-the-Mirror dispensers can be found on NBS Source and bimobject.com.
www.dudleyindustries.com
Curtiss-Wright Surface Technologies, Everlube® Coating Products have partnered with BioCote® to expand their fluoropolymer coating product range to create Fluregiene 200 : an antimicrobial coating that is ideally suited for many surfaces and environments.
Based on existing Everlube® coating technology, the new Fluregiene 200™ is a unique fluoropolymer coating that offers low friction, easy-clean properties combined with superb chemical and abrasion resistance. With a view to improving hygiene standards, Everlube® Coatings have integrated BioCote® antimicrobial technology to protect the coating from microbes such as bacteria, mould and fungi. Benefits of applying antimicrobial technology into the Fluregiene 200™ include:
Anti-fouling
t Low COF Surface coating (0.08 – 0.2 static)
t Corrosion resistance and excellent chemical resistance
t Excellent chip and abrasion resistance
t Reduces and prevents build-up of contaminates
t Excellent flexibility
t Dirt and debris less likely to attach to the surface
Microbial & bacteria growth inhibitor
t Using patented BioCote® antimicrobial technology against microbial growth
t Inhibits and reduces microbial growth on protected coating
t Protects treated surfaces against bad odours, staining and material degradation
Easy clean and reduced cleaning intervals
t Provides continual microbial reduction on coating
t High PTFE content allows easy wipe down and cleaning
t Provides more hygienic and cleanable surface than brushed or finished steels
Applicable to a wide range of parts and components such as door handles, elevator buttons, airport seating and gym equipment, the Fluregiene 200™ will be highly beneficial for these surfaces. BioCote® also has real-life data to support the application of this antimicrobial technology in environments such as health care, transport, education, public areas and much more.
For more information on Fluregiene 200™ and Everlube® Coating Products, please contact our coatings team on:
T +44 (0)1386 421444 info@cwst.co.uk www.cwst.co.uk
In
Plasmatreat
Plasmatreat is an award-winning surface specialist and globally renowned supplier for atmospheric plasma technology, with added expertise in low pressure plasma processes. Established in 1995 in Steinhagen, Germany, the company was the brainchild of current CEO: Christian Buske.
With over 150 patents worldwide and production sites in Germany, Chin and the USA, the company has grown exponentially to house 167 subsidiaries worldwide and stateof-the-art technology centres across 11 countries. Supplying to a wide range of industries from automotive, life sciences, electronics, appliances, packaging, transportation, textiles and renewable energy, this company offers industry gold-standard plasma technology.
With an impressive annual turnover of €56M in 2021, the company now boasts world-ranking customers including: Volkswagen, Miele and Rohde & Schwarz and is the full-system supplier to Bosch.
Plasmatreat UK Ltd is in Grove Business Park in Wantage, Oxfordshire and is a fully owned subsidiary of Plasmatreat GmbH. We spoke to Andrew Nixon: Technical Sales Consultant, to find out more,
“Our main role of the company is providing a voc-free surface treatment technology of various substrates prior to bonding, coating (painting) using Openair-Plasma® Our cutting-edge technology allows customers to forgo using more traditional solvent based cleaners or primers, and flame treatment and instead invest in sustainable, reliable, cost-effective plasma technology.
We have a fully functional application lab here in our UK office, where customers can trial Openair-Plasma®. For larger projects where a 6-axis robot maybe required, the customer can send parts to our state-of-the-art International Technology Centre in Germany for testing.
Our latest development is called Plasmaplus®, which allows customers to coat a nano coating onto the surface, to enhance bonding on difficult substrates such as glass, stainless steel, or composite materials.”
Plasmaplus® provides inline and optimised corrosion protection and can be used across a wide range of applications from: battery housing, street lighting, and fuel cell. It can even print onto challenging materials, with its one-step digital printing mechanism, which considerably improves adhesion and moisture-resistance of UV inks across challenging materials.
The Wantage-based team can provide a bespoke consultation with each individual application, to ensure the plasma technology can meet the specification and desired outcome.
Once the green light is given, customers will receive full, comprehensive training on the equipment during the rental period, with access to 24/7 technical support for troubleshooting.
“We are continuing to expand our plasma technology across the globe, with a recently added Swedish subsidiary to cover the Nordic countries. For UK interested parties, we will be hosting some ‘open house’ networking events at our premises, to enable customers to meet like-minded companies across specific industries.
Come and see us in person at Interplas: 26-28 September:
NEC) and the Advanced Engineering Show (1-2 November: NEC) to find out more about how we can help your industry,” concludes Andrew.
+44 7761 004099 www.plasmatreat.co.uk
Award-winning
science, surfactants, cleaning & Detergents (homecare and personal care), CMPs, container closure and battery/electronics.
With a long illustrious heritage from Nordic lab tech companies, Biolin evolved from a succession of mergers from different product brands, such as: QSense, Attension and KSV NIMA. The company headquarters are in Gothenburg, Sweden, with a R&D focused production facility in Espoo, Finland. Biolin Scientific supports a large distribution partner network around the world with direct sales in UK & China.
In the 1990’s, pioneering scientists from Chalmers University of Technology in Sweden created the first commercial QCMD instrument.
We spoke to Dr Usha Devi: Regional Sales Manager UK & Ireland to find out more about this trailblazing company,
“Our instrumentation is a highly suitable platform for label free, nanoscale tracking of interactions and thin film deposition at surfaces and interfaces in real time. Typical processes are for example: adsorption, desorption, binding/release, building up/ degradation, crosslinking, swelling/collapse to name a few. With this acoustic wave technique, you are able to measure molecules in the range of an Angstrom (Å) to one micro/ micrometre (µm). These molecules may be surfactans, lipids, dendrimers, Protein, DNA, Micelles, Antibodies, Polymers, Nanoparticles, liposomes and cells amongst others.’’
QSense® is our world-leading, premium QCM-D solution for nanoscale tracking of interactions at surfaces and interfaces. It provides unique, reproducible, in-depth data with high productivity and useability. QCM-D allows you to also track the viscoelastic properties of the layer of interest, which aids understanding of in-depth interaction analysis, especially for high-impact publications within academy.
Attension® is the second largest brand in optical and force tensiometers offering a broad range of high-end instruments. With its intuitive user interface, modern design, and all-inclusive software, it is easy to operate with high flexibility and unrivalled automation options.
KSV NIMA provides instruments and measurement solutions for the fabrication and characterization of advanced organised thin films with controlled packing density. The most common applications include for example: depositing highly controlled nanoparticle coatings and studying biological lipid membranes.”
The newest product, QSense Omni, is the next-generation premium QCM-D instrument. QSense Omni gives you enhanced, sharper QCM-D data and a seamless journey in the lab.
The QCM-D instrument: QSense® Omni won a Red Dot Product Design Award this year. The annual Red Dot awards recognise international distinctions in the design field and is known affectionally as the Oscars of design. Biolin is no stranger to
the Red Dot awards, with the Theta Flex optical measuring instrument winning ‘the best of the best’ award back in 2020.
The Nordic Powerhouse has seen some recent changes this year, with the new CEO appointment of Karin Fisher during the third quarter of 2023, ready to drive the company forward. With the growing industry recognition of newly launched QCM-D instrument, Biolin are hoping to attract new customers across academia and industry.
For further information, see the website below:
T 0161 436 9700 www.biolinscientific.com
The inaugural Environmental Services & Solutions Expo (ESS) will take place at the NEC, Birmingham from the 13-14 September 2023. ESS has evolved from the previously celebrated exhibitions: RWM (Resource & Waste Management), Letsrecycle Live. Contamination & Geotech Expo and Flood Expo.
This is the first year that the four shows will now unite under one roof: RWM (Resource & Waste Management Expo), EFD (Energy, Fuels & Decarbonisation Expo), FWM (Flood & Water Management Expo) and CLR (Contamination & Land Remediation Expo). Billed as showcasing 360 degrees of the environmental
sectors, it is focused on the latest developments across the circular economy, net-zero emission, sustainability and biodiversity conservation.
The pivotal forward-thinking Expo is expected to attract over 800 exhibitors, over 18,000 visitors, from over 47 countries. It collectively brings together the brightest minds from the environmental sectors, to network, collaborate and share visions of a more sustainable future, from professionals across the supply chain, council representatives, to business strategists.
Speakers and exhibitors will focus on the following pertinent
topics: resource scarcity, plastic pollution, waste reduction, decarbonisation, carbon capture, hydrogen technologies, water scarcity, flood/drought cycles, brownfield regeneration, biodiversity protection, plus many more topics.
Find out more from the website: www.ess-expo.co.uk
Japanese knotweed is known for being hard to identify and requiring a special license to clear it from site, and this year enquiries for our specialist control services have gone through the roof! We suspect this is due to a much wetter spring and hotter weather beginning earlier in the year, boosting invasive plant growth.
And there are many other Invasive Non-Native Species (INNS) that cause £millions worth of damage to businesses every year. Plants such as the highly toxic Giant hogweed or the problematic Himalayan balsam are also on our hitlist, and ground contaminated with non-licensed asbestos is a growing issue as more UK brownfield sites are being developed.
Finding knotweed onsite, the biggest issue is the immediate effect - it puts projects on hold until the infestation is either controlled or completely removed.
We help by providing identification, survey, treatment, excavation, and removal services. Japanese Knotweed Ltd is the largest knotweed specialist in the UK, we’ve been in the industry since 2010. Environment Controls (part of JKL) provides the same services for other invasive plants and controlled removal of asbestos-contaminated soils.
Come and see us at the ESS Expo - Stand CT-F44 www.Japaneseknotweed.co.uk
T 0333 2414 413 contact@knotweed.co.uk
SAVECO Environmental Limited is a member of the globally operating WAMGROUP –market leaders in bulk materials handling since 1968.
SAVECO provides state-of-the-art solutions to customers in the United Kingdom and in the Republic of Ireland, providing a comprehensive product range of machines and equipment designed for effluent pre-treatment and sludge treatment in both municipal and industrial wastewater treatment plants, as well as livestock farming and biogas plants.
Delivering innovative, market-oriented, and industrially manufactured products, SAVECO has a proven track record of success – working on major projects with Tier 1 & 2 Contractors as well as leading water utilities.
SAVECO is determined to supply the most comprehensive range of equipment available to deliver a one-stop solution to its customers.
SAVECO assures customers in any place in the world the highest possible quality product and service at a fair price.
T +44 (0)1684 29 91 04
sales@saveco-water.co.uk
www.saveco-water.co.uk
Stand: CT-H62
Sustainable energy and waste experts, Tidy Planet Ltd, will be exhibiting at this year’s RWM (NEC) at Stand R-F290.
Tidy Planet Energy, along with its partners, Sugimat, QToploader, Glosfume and Turboden are set to showcase a range of decentralised RDF and SRF energy from waste plants.
Tidy Planet Energy is the Energy division of Tidy Planet Ltd alongside Tidy Planet Waste. Both headquartered in Macclesfield, Cheshire, the company has a diverse customer network spanning the entire globe.
As the UK’s exclusive distribution partner of Valencia-based Sugimat’s industrial waste-toenergy boilers, it brings its innovative technologies to the UK market.
With boiler sizes from 300kW to 50MW for hot water, steam and thermal oil, the comprehensive
CThis year, RWM forms part of a larger event called the Environmental Services & Solutions Expo (ESS), which, as the name implies, is why this event has always been a highlight of CPL’s annual events calendar.
In previous years, CPL has exhibited one of its large Clean-Flo® mobile carbon filters on their stand and they are planning to do the same at this year’s event. Having a seven-metre tall piece of equipment on the stand is certainly a great talking point – usually starting with “how did you get it in here?” – and also has the advantage of making the stand easy to find from anywhere inside the Hall.
Trange meets the needs of most customers.
Partnering with industry leaders across the world, Tidy Planet Energy offers a range of efficiency-led solutions for the UK’s waste processors, including biomass and solid waste boilers, and small waste incineration plants (SWIP), which offer maximum waste throughput and energy recovery.
To find out more, visit www.energy.tidyplanet. co.uk or email hello@tidyplanet.co.uk
So, if you are planning to visit the RWM/ESS 2023 expo at the NEC from 13-14 September, and would like to find out more about liquid and gas phase purification with activated carbon, then you can visit CPL on Stand R-F320.
For more information, see below.
T 01942 824 240 info@activated-carbon.com www.activated-carbon.com
CPalfinger stand or browse through our selection of trailers at our Stand: Y5.
www.colsontrailers.co.uk
info@colsontrailers.co.uk
T 01773 424 210
Products you can trust, Experience you can rely on
For over 23 years QM Environmental International is a supplier of bioaugmentation and bioremediation products in Europe. Our products are used in municipal and industrial wastewater treatment plants, in bioremediation projects, in sewer networks reducing FOG and H2S and many other applications. The products we offer are:
t MicroCat bioaugmentation products for wastewater treatment, bioremediation, FOG removal in drains, traps and sewers, composting and odour control
t EOS Substrates for anaerobic bioremediation of chlorinated hydrocarbons, perchlorate, chromate, explosives, acid mine drainage
t CoBupHMg for pH adjustment in acidic aquifers
t EOx and EAS for bioremediation of petroleum hydrocarbons
t BAC9 microbial cultures for chlorinated hydrocarbons (PCE, TCE, DC, VC), chlorinated ethanes and methanes, BTEX, petroleum hydrocarbons, PAH's, 1,4-dioxane
t QMZviER zero valent iron formulations for PRB construction, soil mixing or injection
t MicroAktiv agricultural bioformulations for livestock,
arable & greenhouse farming and aquaculture.
QM Environmental International will be exhibiting during the Contamination & Land Remediation Expo at the NEC in Birmingham. Come and meet us on 13 & 14 September, stand no. WM-G72, and learn how our products can assist you in creating a cleaner environment.
T +31 858 768 862 info@qmes.nl www.qmes.eu
BOur team can provide a full range of services from routine works, and service checks to full rebuilds. Where remote access is available, we can dial in to offer diagnostics to potentially provide instant solutions.
The Water Utility sector is a growing part of our business, and we now offer a range of on-plant inspections of ageing Anaerobic Digester assets, to offer a structured and tailored analysis of required refurbishments and enhancements to ensure statutory compliance and maximum the plants efficiency.
Lime dosing of both treated and untreated effluent from wastewater plants is a specialist function of our experienced team. Using the resources of our own Parent company's (Singleton Birch) lime production and proven automated dosing technology, we work together with the Water Utilities engineers to develop both "off the shelf" and "bespoke" solutions.
RCP Systems specialises in the consulting, sales, installation, and servicing of recycling systems, of which it has been supplying and maintain for 45 years. Through the use of Macpresse Baling Presses, RCP Systems offers an optimal and environmentally friendly solution to your recycling requirements.
MACPRESSE balers are available in a wide variety of sizes and models. What they all have in common is the consistent quality of production, equipment with the latest microprocessor controls and a long service life. Producing heavy, dense bales with an energy efficient design, ensures low operational costs and maximum returns for a variety of materials such as paper and cardboard, plastics, MSW, RDF as well as aluminium and tin cans.
We look forward to welcoming you to the RWM Exhibition Stand R-N110
For all your recycling machinery requirements contact us on:
T +44 743 7004 247
www.swiss-recycling-solutions.com
john.dooley@rcp-systems.org
Total Safety UK are a leading provider of industrial safety solutions for the waste-to-energy sector. We are committed to providing the highest level of protection for personnel and facilities in this rapidly growing industry.
analysis through the BioLab and the Bioresources services team and provide liquid and powder lime dosing for a range of applications.
Birch Solutions also provides a range of Parts and Service Support packages tailored to suit the requirements of your individual site. We are the preferred UK supplier for many key parts suppliers, giving you instant access to the parts and maintenance you need, to ensure you minimise any downtime. This service includes full site audits and experts on hand to provide advice. Access to a full UK parts store, import parts from OEMs and rapid response with 24 hours call out, enables our qualified teams to install key equipment and provide support when you need it most.
Our support and expertise encompass all elements of your AD plant, including the service and maintenance your CHP.
To learn more about how Birch Solutions can help you, contact our expert team today by emailing parts@ birchsolutions.co.uk or calling 01652 686060. You can also visit our website at www.birchsolutions.co.uk and find us on LinkedIn, Facebook and Twitter to follow our journey and hopefully assist you with yours!
www.linkedin.com/company/birch-solutions-uk-ltd/ www.facebook.com/birchsolutionsuk
Birch Solutions (@BirchSolution)/Twitter
Stand number R-K280
As the waste-to-energy sector continues to evolve, ensuring safety throughout the entire process is of paramount importance.
Total Safety UK recognises this need and offers a comprehensive range of services for waste-to-energy facilities.
Our services include:
1. Specialised Safety Personnel: Highly trained and experienced safety professionals who are adept at handling the unique challenges of the waste-to-energy sector.
2. Gas Detection Services: Advanced gas detection systems and expert technicians to monitor and detect potentially hazardous gases in real-time, ensuring prompt response and mitigation.
3. Breathing Air Solutions: State-of-the-art breathing air equipment and systems to protect workers from harmful airborne contaminants.
4. Safety Critical Solutions: Tailored safety solutions to address critical areas of operation, including fall protection, confined space management, and more.
5. Training: With a range of accreditations, we offer customised and bespoke training courses relating to industrial safety.
During RWM we will be showcasing our unique, innovative Centralised Confined Space Monitoring System. We look forward to welcoming you on our stand.
www.totalsafety.com
K Pallets Ltd, one of
We like to showcase industrial best practice and, in this issue, Industry Update recommends UNISIG for its leading global machinery manufacturing specialism in deep hole drilling.
UNISIG is a world-leading American producer of deep hole drilling machines, supplying to everyone from smaller bespoke companies to large original equipment manufacturers (OEM). As leading experts, UNISIG has the expertise to provide precision-driven machinery for every job, with its complete deep hole drilling solution from machinery, tools to automation.
Since its inception in 1981, UNISIG has built up an enviable position in the industry with its unrivalled production of gun drilling and deep hole drilling machines. In 1995, it was acquired by Entrust Manufacturing Technologies and moved to the Milwaukee headquarters.
With a dominant installation presence across the world: Europe, Asia and America, UNISIG has a strong customer base across the aerospace, automotive, energy, firearms, hydraulic cylinders, military and medical sectors.
UNISIG has the design engineering expertise to design and develop machinery for other deep hole procedures from: BTA, gun drilling, counterboring/reaming, pull boring, trepanning, skiving and roller burnishing, bottle boring, bottom forming and many more.
Boring and Trepanning Association (BTA) drilling has been revolutionised by UNISIG’s high powered B-series, allowing precision drilling of 25mm to 500mm, up to 20m deep, perfect for the vast majority of BTA drilling applications. For rigid, deep hole drilling, the larger swing B-series has a powerful drive, with state-of-theart smart controls, giving high usability with unlimited capability.
Philipp Steimle, Sales and Service manager for Europe talked us through planned developments for the next 12 months,
“As we have seen a lot of disrupted supply channels, our company is expanding its own manufacturing department. The recently installed Kellenberger CNC grinding machine will allow us to finish all the drilling spindles in-house. The next eight weeks will see us installing a laser cutting machine and a CNC – press
brake as well as welding stations, so that we can do all the guarding and coolant reservoirs in-house to avoid delays in our machine building.
“One of our latest developments was the UNE6 series for medical instrument drilling. With machines that feature two independent drilling units on one machine bed and a robot work piece loading and even an automatic tool changer, this was a game changer for the medical industry. The product was a big hit in the market and we have struggled to build them fast enough! We are investing in more in-house production rather than external third parties, to keep on top of our orders.”
In 2019, the Milwaukee facility at global headquarters was already expanded by over 100,000sqft, hugely expanding production capabilities. The recent CNC grinding machine addition will certainly propel production further. With all the production facility
currently upgrading, The UNISIG Tech Centre in Milwaukee has continued pressing forward with testing and innovative design engineering. If a customer needs a custom-built drilling machine, the expert team of engineers can design a prototype quickly, to specific requirements.
UNISIG ships machinery and parts quickly across the world, offering routine servicing and repairs both remotely and on-site. Installation can be carried out anywhere across the world, by the expert team of inhouse engineers.
The UNISIG website has the full machinery range, with high-resolution photos and full specification capability, including hole depth (in mm.)
Best Practice Recommends UNISIG for its expert, highquality machinery in the deep hole drilling industry, with its decades’ long commitment to innovation and customer service.
The UNISIG team will be showcasing its innovative, AI-driven machinery capability at EMO Hannover: the world’s leading trade fair for production technology from the 18- 23 September.
The team will be happy to answer enquiries from across all sectors. For more information on UNISIG, see the website:www.unisig.com
In this issue of Industry Update, we are delighted to announce Virus Shield Biosciences Limited as our microbial health & hygiene specialist Company of the Month.
Since the advent of the SARS-CoV-2 (COVID-19) global pandemic, the world has opened its eyes to optimised infection control. To combat serious infections such as C. diff and MRSA in operating theatres and intensive care units (ICU), everyday disinfectants just don’t provide the strength that’s needed. However, Virus Shield Disinfectant with a 99.9999% efficiency rate, kills pathogens within 30 seconds, solving these issues. Virus Shield Biosciences Limited’s patented technology not only destroys microbials but removes biofilm, meaning recolonisation takes significantly longer.
“Our products kill the microbes within 30 seconds by destroying the cell wall which prevents the creation of harmful superbugs,” explains CEO Craig Shaw.
Virus Shield Biosciences Limited had grown exponentially since its inception over three years ago, to become a truly global company with offices and distributors in the UK, USA, Africa, South America, Europe, Latin America and newcomer, Asia by the end of this year.
“We’ve already successfully eradicated Avian Influenza in several large poultry farms in Latin America and just completed a six-month efficacy testing to supply to the NHS, using our robust products on A&E wards and operating theatres, in the battle against deadly C-DIFF and MRSA and other viruses.”
This pioneering company was initially set up to treat microbial infection in livestock, mainly cattle. With an esteemed background in biosciences, Craig, together with his wife Jill, designed, patented and produced highly efficient, environmentally-friendly infection control products for dairy farmers. This has significantly reduced their vet visits, antibiotic
use and cell count. Although this is the niche area that the company is best known for, it has now moved into many other market sectors.
“Our company works across the whole biosciences field: animal health, plant science, human health, soil sciences, air quality, through to mould/mildew control. From mould spores in Florida housing, working with the National Association of Funeral Directors on sensitive care of the deceased, to prolonging the shelf life of perishable fruit, we are focussed primarily on the sustainable and environmentally-friendly removal of harmful bacteria.”
Two of the biggest challenges facing fruit producers around the world are bacterial infection, caused by climate change, and delayed shipping which increases mould and bacterial growth on the produce and leads to loss of revenue due to spoilage.
“South African mangoes would normally arrive on supermarket aisles within 28 days, but they are now taking 2-3 months, due to delayed shipping times. If the shipping containers are treated, using a small gas diffuser which is loaded with the produce at the time of shipping, this prevents mould and bacteria from destroying the produce during these long delays. It can potentially increase the shelf life of the produce to between 4 – 8 weeks depending on the type of produce. This is game changing technology for anyone in the shipping and logistics industry. Vineyards, olive groves and other crops are now suffering from a variety of infections. By periodically dosing our products into the irrigation system, it is absorbed with the nutrients in to the plant, thereby destroying the harmful bacteria and its biofilm. We have recently been working with French vineyards to protect precious grapes and Cypriot/Greek olive farmers from the catastrophic Olive Knot, that destroys
Alongside European fruit and vegetable produce, the company has just signed an exclusive deal with Mole Valley Farmers, to distribute products to 75% of dairy farmers across the UK.
“Our customers are distributors, with an existing large market share. Working in partnership with Mole Valley Farmers, we will be supporting our British dairy industry which has been hit by funding cuts, higher energy bills and staff shortages. Not only that, but our products are 100% sustainable: our cardboard packaging can be recycled, contains no phosphates and is easy to store, reducing carbon footprint significantly.”
To find out more about this truly pioneering company, visit the website today:
T +44 1225 983710 www.vsbiosciences.com
Inow employs over 100 staff members, which is a remarkable milestone for a medium-sized family company.
The company is now looking forward to celebrating its 30th
anniversary next year and to reflect on how far SPEKTRA has come over the years. We spoke to Audrey Stein: Business Development & Marketing Manager at SPEKTRA to find out more about this dynamic company,
“One of our esteemed cofounders, Dr Holger Nicklich retired in December 2022 and his son, Martin Nicklich, previous co-director since 2013 has now become General Manger in his father’s place.
For the 30th anniversary in 2024, we are preparing a SPEKTRA roadshow and probably some pop-up events throughout the year.
During 2023, we have focussed on working with the automotive and aerospace industries in particular. We have worked in crash testing since our inception and can offer state-of-the-art testing, calibration and characterisation of sensors. This can include everything from: proximity, yaw rate and angular rate sensors, accelerometers, shock loggers, digital vibration transducers, to surface microphones, speedometers.”
Exhibiting at Automotive Testing Expo Europe 2023, the expert team showcased truly innovative solutions across the industry. This was further consolidated by Product Manager: Michael Mende giving a well-received presentation on sensor calibration challenges and how the CS Q-LEAP™ calibration system can
remedy these challenges, at the June European Test and Telemetry Conference in Toulouse, France.
The CS Q- LEAP™ system is hailed as a trailblazer in sensor calibration, with a truly future-proof solution design for the digital sensor age. Perfect for analogue and digital sensors, it offers flexible software adaptability to new DUT types and is fully traceable to PTB and other national metrology institutes.
Springpack Ltd celebrates relocation to a state-of-the-art warehouse and office facility, reinforcing commitment
Springpack, a renowned provider of packaging solutions, is excited to announce its successful transition to a new warehouse and office facility.
This strategic move not only marks a significant milestone in Springpack's growth but also reflects the company's unwavering dedication to sustainability, workplace well-being, and delivering cutting-edge packaging solutions to its valued customers.
The new 90,000Square foot facility, which is located on a 6-acre site, showcases Springpack's commitment to providing
an exceptional inventory management experience. Equipped with 18,500 storage locations, which are managed by the latest system in Warehouse Management technology, the warehouse ensures efficient storage and distribution of a wide range of packaging products. The addition of 10,000 square feet of mezzanine space enhances Springpack's ability to offer innovative products to the market, bolstering its comprehensive packaging solutions portfolio.
One of Springpack's core objectives with the new warehouse is to provide increased convenience and flexibility to its
customers. To achieve this, Springpack now offers the option to stock hold customers' bespoke packaging products. By availing this service, customers can create call-off orders, effectively reducing stress on their own warehouses and significantly improving operational efficiency. This offering strengthens Springpack's commitment to being a trusted partner, providing endto-end solutions that meet the unique needs of every customer.
In addition to the state-of-the-art warehouse, Springpack has carefully designed its new office space to prioritise workplace well-being. Understanding that a conducive work environment directly impacts employee satisfaction and productivity, the offices are thoughtfully crafted with innovative design elements. Spacious and ergonomic workstations, collaborative areas, and dedicated breakout spaces foster communication and creativity. Employee well-being is paramount to Springpack ensuring a positive and energising atmosphere, which is why an advanced inhouse gym facility has been produced, including showers.
"Sustainability lies at the heart of our business values, and this relocation exemplifies our commitment to making ecoconscious choices," said Jerry Francis, CEO of Springpack.
"We are proud to have sustained our carbon-neutral status and continue to seek new ways to minimise our environmental impact. Our new facility not only enables us to offer a wider range of innovative packaging solutions but also reaffirms our dedication to workplace well-being and our customers' success."
In line with its sustainability mission, Springpack offers a range of eco-friendly packaging brands that cater to diverse requirements. Among them are Armour Wrap, the revolutionary nano machine film, designed for exceptional performance and reduced waste. Postal Plus, a dedicated range of e-commerce products, ensures safe and secure shipping in the digital age. Additionally, SimplyECO delivers packaging solutions that seamlessly combine performance with sustainability, contributing to a greener future.
As part of its relentless commitment to sustainability, Springpack has successfully maintained its carbon-neutral status. Through ongoing initiatives and responsible practices, the company strives to minimise its carbon footprint and actively contribute to global environmental preservation efforts.
With the completion of this relocation, Springpack is well-positioned to elevate its service offerings to new heights. The expanded warehouse capacity, sustainable focus, and emphasis on workplace well-being underscore Springpack's commitment to delivering innovative, ecofriendly packaging solutions while exceeding customer expectations.
For more information about Springpack and its comprehensive range of sustainable packaging solutions, please visit springpack.co.uk or email enquiries@springpack.co.uk
Increase control of your sign and labelling costs, and add a new level of flexibility and performance to all your product and process labelling.
In-house saves time and money
Bringing sign and label production in-house is an increasing benefit to manufacturing, MRO and the process industry. All the original considerations that put companies off of this have been removed by technology. Just in time labelling keeps material stock to a minimum and allows enormous flexibility and customisation benefits to companies.
Ease of use and great value for money
The new Rebo SMS R1 system is designed to be easy – not only for the specialist designers or graphically trained – anyone can design and create in minutes. Using the very latest touch screen technology it tells the user what to do, step by step. The ideal tool to achieve in-house product labelling in up to 14 colours and – remarkably – in any shape you can imagine. It is fast and easy to use – and runs with almost all the currently popular software being used to day. As a desktop product, the SMS R1 is compact and unobtrusive in any environment, accessible to everyone and fully networkable.
Label stock holding is a thing of the past – as the SMS R1 uses one width of material and effectively cuts the dimensions required – so no stocks of multiple label sizes is needed and there are none of the typical proofing delays and economies of scale issues you have with an outside label printing company.
One product does almost everything
The range of materials the SMS R1 can print and cut is extensive, so high performance labelling is easy – with high temperature, low temperature, high durability and specialist materials always available for the most demanding environments. We offer, among others, glow in the dark, reflective, hologram security, ten and five year outdoor vinyl, metallised polyesters, unique long life polyesters, Hi-Viz and the range increases as customers create new applications.
and green
The material range on offer also includes fully recyclable material that contains no environmentally damaging solvents, plasticisers and is fully REACH compliant.
Benefits all industries
Currently the SMS R1 is actively being used to produce: LO/TO labelling and tags, maintenance labelling, Health and Safety, cable and wire marking, pipe identification, tank and valve identification. part of product labelling, Shutdown/Turnaround labelling, prototype labelling, plant and equipment labelling.
We have continued interest from the petrochemical industry, manufacturing, construction and Installation. HVAC, MRO, logistics, material handling and the alternative energy markets.
A
The SMS R1 can easily deliver small labels in long runs of over ten meters, mixed label sizes and styles and also can cut in batches – all designed to make production easy and practical. From the smallest component labels up to large equipment labels – the SMS R1 is purpose built.
Create and print what you want, when you want it
Where some components or instruments need to be designed for unique applications – lower volumes and bespoke content are the greatest challenges – these disappear with the SMS R1, which can produce ‘one-offs’ and smaller batches of labels on-demand.
Perfect for creating high quality, professional label sets for prototypes and for specialist, low volume production runs.
Available Internationally
Rebo has established distribution in the UK, Europe, Asia and the Middle East. Our network is constantly increasing.
Find out more about how the SMS R1 can add value to your manufacturing through cost savings and greater flexibility.
T +31 35 601 69 41 clinton@rebo.nl www.rebo.nl/en/sms-r1-multicolour-printer/
Introducing the newest innovation in Multi-Sensor alarms from Aico, the Ei3030 Multi-Sensor Fire and Carbon Monoxide (CO) alarm. The flagship alarm in Aico’s technologically advanced 3000 Series, the Ei3030 combines individual Optical, Heat and CO sensors, for the ultimate fire and CO response.
Aico continues to evolve its offering to provide products that align with its customers’ requirements while maintaining the simplicity that Installers love.
The Ei3030 multi-sensor Fire and CO specifications include:
t Fire Response - The device contains a Thermistor Heat Sensor and high-performance Optical Sensor that intelligently work together, but will also operate independently.
t CO Response - The proven electrochemical CO Sensor provides an accurate CO response. The CO response is in line with BS EN 50291-1:2018.
t Visual Indicators - The Ei3030 has visual Fire and CO indicators. The relevant indicator flashes depending on what has triggered the alarm.
t Kitemarks – This device holds Kitemarks for British Standards BS EN 14604:2005, BS 5446-2:2003 and BS EN 50291-1:2018.
Michael Wright, Product Development Manager at Aico comments, “The Ei3030 continues Aico’s pioneering development of MultiSensor Fire and CO alarms for domestic properties by offering both Multi-Sensor fire detection and CO detection from one alarm. This
maximises coverage whilst making installation simpler and easier. The alarm sits alongside the Ei3028 Multi-Sensor Heat and CO alarm, meaning users can achieve combined fire and CO coverage for all areas of the home from our flagship 3000 Series”
The Ei3030 also has a range of additional benefits, including built-in dust compensation technology. The unique self-monitoring dust compensation mechanism reduces the risk of false alarms. The optical sensor chamber continually self-monitors minute changes in dust levels, automatically recalibrating the alarm’s trigger point when necessary to reduce false alarms. The Ei3030 can also be fitted in any room where both Fire and CO protection is required (excluding the kitchen) meaning coverage can be provided with fewer alarms.
Like all alarms in the 3000 series, the Ei3030 utilises an easi-fit base, is mains powered, has a 10-year rechargeable lithium cell backup, and is compatible with other Aico mains-powered units. The device is also compatible with the Ei3000MRF Module for wireless interconnection and data extraction via the Ei1000G Gateway.
The Ei3030 also includes Aico’s award-winning AudioLINK+ technology, making it simple to gain data directly from the alarm head via the AudioLINK+ app, reporting on information such as alarm activations, sensor status and record of testing.
To learn more about the Ei3030, please visit: https://www.aico.co.uk/product ei3030-multi-sensor-fire-and-carbon-monoxide-alarm/
Healthcare organizations are seeking solutions to treat patients in home care settings to reduce the burden on traditional healthcare facilities. While this approach improves patient comfort and convenience, it can be difficult to manage compared to a controlled clinical setting where care is administered by trained medical professionals. When a home medical device manufacturer approached industrial heating technology manufacturer Watlow, for a thermal solution for its home hemodialysis device, Watlow delivered an innovative solution that not only met requirements for size and safety, but also improved the overall system.
According to the National Kidney Federation, around 30,000 people are on hemodialysis in the UK. Hemodialysis is the procedure where blood is cleaned using a dialysis machine with a filter acting as an artificial kidney.
In-home care allows for more frequent treatment, improving patient outcomes while reducing the
overall cost of therapy. In the medical device market, this trend has been a double-edged sword. On one hand, it has increased the demand for certain medical devices. On the other, it has led to greater scrutiny of devices and increasingly stringent safety standards. Measures used to increase safety precautions are often at odds with the need to make home care devices smaller and more portable than those used in a clinical setting.
While at home medical devices are improving comfort and convenience for patients, a number of regulations arise regarding safety. Specifically, IEC 60601-1-11 outlines safety requirements for medical devices intended for use in home care settings. Manufacturers must identify the specific product safety risks associated with using their equipment in a non-clinical environment. To achieve certification, manufacturers must mitigate those risks through appropriate product design, in addition to clear user instructions and training.
An important consideration for any automated
medical device is electrical safety. In the design of these machines, some features are considered MOPs (Means of Protection). Medical devices need two or more MOPs to reduce the risk of electrocution. Traditionally, MOPs have been added to devices with a trained third-party operator in mind (usually in an in-patient setting), in addition to MOPPs (Means of Patient Protection).
A clinical setting allows MOPPs that are not usually present in a home setting, since the patient is now also the operator. Manufacturers must include those MOPPs in the medical device itself, which creates some additional design challenges. In a home care setting, higher levels of patient safety are required than in a clinical setting.
This is largely down to the absence of device training and the risks surrounding voltage and outlets. In a hospital, the electrical outlets are guaranteed to have appropriate voltage, be effectively grounded and tested and certified as safe. But these guarantees cannot be made for a patient’s home. As a result, MOPPs must provide much more protection, as the safety requirements for home care devices will be that much more stringent, and the clinical assumptions about operator health and training cannot be assured. In this case, responsibility for ensuring safe operation shifts to the device manufacturer.
Home hemodialysis machines include a final challenge — fluids must be kept at body temperature to prevent thermal shock. Higher temperatures are also needed to disinfect the machine itself. Unsurprisingly, the heating requirements of these medical devices greatly influence both the size and the electrical requirements of the machine. Heating fluid on
demand requires a fair amount of power, increasing the possibility of current leakage, and the risk to patients.
Mitigating those risks is possible with more traditional technology, but that technology adds to both the bulk and cost of medical devices. This is where innovation in thermal solutions, including heaters, sensors, temperature controllers, power controllers and supporting software working together as an integrated system, can make a difference. Watlow’s engineers used knowledge of the full system standards and system level requirements to help the customer create an optimized system architecture for its home hemodialysis device. This featured a FLUENT in-line heater with a ceramic substrate tube and polymer fittings to create an entirely non-metal surface.
The FLUENT heater addresses efficiency and electrical safety concerns with a size and weight footprint that is smaller than legacy solutions. In addition, using thermal spray, the heater makes use of its entire surface to produce heat, which optimizes heat transfer and temperature uniformity.
The goal of Watlow’s customer was to design a home hemodialysis device that met all safety guidelines while being portable and convenient for patient use. Using a systems approach helped Watlow to navigate the engineering tradeoffs between size and safety without compromise, to produce a safe device with a small footprint.
Watlow has extensive experience understanding how to meet the required trade-offs and develop a design suitable for many applications. Visit the website to find out more watlow.com
Lanes Group plc has launched a new national highways drainage surveying service backed by a dedicated data processing centre and advanced asset laser scanning technology.
It means the company can provide clients with a safer, faster and more comprehensive highways drainage surveying service, integrated with its unrivalled cleaning, repair and rehabilitation services.
One of the first major projects Lanes has supported with the new service has been A66 Northern Trans-Pennine, a scheme to improve the A66 between the M6 in Penrith and the A1(M) at Scotch Corner.
Faster and safer
Lanes Head of Highways Ben Forsyth said: “Developing our own in-house highways data capture and processing capability allows Lanes to deliver a faster, more agile, and safer surveying service for clients.
“This can be coordinated with our drainage cleaning, repair and rehabilitation teams to give highway contractors and National Highways the best possible integrated drainage service.”
Lanes can now deliver a broad range of highway survey services with in-house teams, including CCTV, GPS, full HADDMS and asset conditions surveys.
It has also invested in the latest chamber laser scanning technology, so assets can be surveyed more safety and faster than ever before, with no need for confined space entry.
Portable scanner
The CleverScan inspection system is highly portable, fast and accurate. It creates a flat scan and a dense point cloud image of chambers up to 10
metres deep that can be merged into CAD and 3D applications. Using CleverScan, Lanes teams can carry out more than 30 chamber surveys per shift, twice as many as conventional methods. The laser scanner is lightweight and can be operated away from a vehicle.
Data is added directly to National Highways shape files which are then sent via the cloud to a new dedicated highways drainage survey processing centre in Manchester.
Its qualified and experienced highways drainage data technicians then compile reports precisely in line with client needs.
The service meets National Highways targets for updating HADDMS, while providing detailed interim survey reports for client engineers.
Lanes has proved the value of its new in-house service while working on the A66 scheme which is being progressed by contractors in a National Highways regional delivery partnership.
End-to-end service
Between January and March 2023, drainage engineers from the Lanes Newcastle depot completed 40 night shifts, working on the eastern section of the planned upgrade route.
A team of Lanes drainage engineers from Preston and Manchester were due to begin a similar programme of works on a stretch of the A66 in Cumbria.
All Lanes personnel hold the National Highways Passport and receive thorough in-house training on the new surveying systems.
Lanes Contract Manager Andrew Lindsay said: “Combining the latest data capture technology like, CleverScan, with cloud data transfer and
When it comes to the safety of workers out in the field, we are the people to contact when it comes to emergency safety showers and eye wash stations. It isn’t just about the end product. We will recommend and advise you on the best safety shower solution to suit your requirement. As there is no one-fits-all approach we have the flexibility to adapt or modify our units in our manufacturing facility in Great Britain.
Our range of emergency products and equipment offer protection against serious injury and are all built to exceed ANSI/EN safety standards.
Whilst we hope there is never the need for your safety showers to be used, having one is imperative on site should be working around harmful substances.
Our goal is to create essential pieces of equipment that become the standard in every laboratory and facility that uses harmful substances.
Are you properly prepared in case of an emergency?
Aqua Safety Showers can keep your workers safe with our wide range of products and units available. For a bespoke quotation or free site survey, please get in touch with our dedicated sales team today.
T +44 (0) 1942 318096
Email: sales@aqua-safety.com
Facebook: www.facebook.com/ aquasafetyshowers
Linked In: www.linkedin.com/company/ aqua-safety-showers-international-ltd
You Tube: www.youtube.com/channel/ UC2IeWZzOlQDOrQiWVGYtYRw
centralised processing is a game-changer for our clients.
“We can give them more tailored reports that are more accurate and delivered faster than ever before. Then, if remedial work is needed, we have all the assets and skills needed as well.
“It’s an end-to-end service that maximises operational effectiveness, sustainability – through multitasking and use of digital technologies – and value, through efficiencies created by service integration.”
www.lanesfordrains.co.uk
Wuppertal, 13 June 2023.
The Schmersal Group has expanded its range of optoelectronic protective devices with a series of safety light curtains/grids in Ex design. The new EX-SLC/ SLG440 series is designed in the ignition protection types EX d (gas atmospheres), EX t (dust atmospheres) and EX op is (optical radiation) and is thus especially suitable for access protection of potentially explosive areas in industrial production - namely for zones 1 and 21.
There is an elevated risk of explosion in many areas of manufacturing, such as in the chemicals industry, in refineries or paint shops where flammable coatings are being used. In industries that process bulk materials, such as in the animal feed or recycling industries, as well as in sawmills and plants that process cereals and grains, there is a risk of dust explosion and the occasional formation of a potentially explosive dust cloud during normal operation.
Schmersal has developed the SLC/SLG440 safety light curtain/grids in Ex version precisely for these applications. These devices can be installed in potentially explosive gaseous and dusty atmospheres of zones 1/21 and 2/22, category 2GD and are used to protect hazardous areas and machine access. When one or more of the beams is interrupted, hazardous movements are brought to a halt.
The series is ATEX certified and further certification – IECEx, INMETRO and CCC Ex – are due to follow. The sensor system is accommodated in a protective enclosure made from non-breakable glass.
Ex-SLC440 safety light curtains for finger, hand and body detection are available in versions with a resolution of 14 and 30 mm as well as ranges of between 0.3 and 20 m. Ex-SLG440 safety light curtains are suitable for access control to hazardous areas.
The waterproof and dustproof devices achieve IP66 and IP67 protection class and also have the capability to be used outside.
www.schmersal.co.uk
Engineers at Lanes Group plc have completed a sensitive project to install a new drainage pipe beneath one of London’s largest cemeteries.
They carried out investigations and planned the installation of the 50-metre-long concrete pipe beneath Hither Green Cemetery in Lewisham, south London.
The 50-metre-long concrete pipe was needed to connect track drains along the South Eastern Main Line to a Thames Water surface water culvert.
Protecting graves
The original 300mm diameter clay pipe serving the track drains had collapsed. Early investigations showed a new pipe had to follow a different route to minimise the risk of graves being disturbed.
Network Rail commissioned Lanes Professional Services and sister company UKDN Waterflow (LG) to work together on the project.
Their task was to carry out a study to establish how best to restore the drainage and then to support a specialist contractor as it installed the new pipe using a trenchless solution called auger boring.
Increased diameter
Head of Lanes Professional Services Andrew McQueen said: “The original pipe was thought to be over 100 years old and the cemetery had developed significantly since it was put in.
“This meant there was a risk of graves being disturbed if a new pipe was installed along the same line.
“Our surveying work identified the best line for the new pipe to take through a less intensively used section of the cemetery nearby.
“The route then took the new pipe back towards the Thames Water culvert, which also runs through the cemetery.
“Its diameter was increased by 50 per cent to ensure it had the capacity needed to cope with the volumes of surface water being generated, not least because climate change is making weather patterns more volatile.”
New chambers
The Lanes team carried out three different investigations – a topographic survey, a ground penetration survey and a buried services survey – to establish the optimum route and depth of the pipe.
A specialist contractor then carried out the auger boring installation, a trenchless solution that does not need extensive ground excavation.
Four new large access chambers were also created above the drainage pipe – two on the railway line, one where the pipe turned under the cemetery, and the other above the culvert – to support effective maintenance.
Serious disruption
Andrew McQueen said: “This was a project with clear sensitivities, and we worked closely with the cemetery management team to ensure the new drainage was located correctly.
“It was important for the pipe to be replaced to allow
water from track drains to be channelled away from the railway line.
“Without it, the track bed could become waterlogged and could flood during periods of heavy rain, which would have caused seriously disruption to train services.”
Gothic chapel
Lanes Professional Services provides a wide range of engineering services, including design and consultancy, drainage and hydraulics surveys, laser profiling, and aerial drone (UAV) surveys.
Hither Green Cemetery opened as Lee Cemetery in 1873 and, in its early years, expanded to take in adjacent farmland. It now covers 37 acres.
The cemetery has two gothic chapels and war graves from both the First World War and the Second World War.
www.lanesfordrains.co.uk
Mould making isn’t easy. There are many intricate challenges that include: highly complex geometry with 2D and 3D features, managing a wide range of part sizes, and short lead times on small quantities and new designs with no room for error. Compounding these challenges is the pressure to keep up
with the rapid pace of demand and technology.
But there’s a way to overcome those obstacles: Do better work with technology designed specifically for complex mould making.
Our USC-M series Milling and Drilling
Centres allow you to drill faster and mill better with a single machine and fewer setups. These Milling and Drilling Centres meet the challenges of milling and gundrilling all types of metals with either a single universal combination spindle or dedicated milling and drilling spindles. Utilising high performance spindles that provide exceptional rigidity
and power transmission, these machines deliver high-torque milling capability for aggressive metal removal and shorter cycle times. Additionally, 5-axis positioning enables mould manufacturers to tackle complex geometries with exacting precision in a single setup.
Many manufacturers claim to provide milling and drilling in a single machine, but the truth is those hybrid machines neither mill nor drill well enough to make a significant difference in either operation. In effect, one process is an afterthought of the other. Our USC-M series, however, was designed from the beginning to be a single machine with superior milling and drilling performance and accuracy. State-ofthe-art milling technology is embedded into a machine that has the power, thrust, speed and process monitoring competitors thought would be difficult to attain, or simply not possible.
In addition to superior quality and accuracy, the pay-off for single setup milling and drilling is efficiency and an improved bottom line. Mould makers cut delivery times to their customers with faster setups and production along with reduced overall labor costs. Once they move away from mould making operations with two machines, most of our customers find they can’t afford to manufacture without a USCM-series Milling and Drilling Centre.
The benefits of milling better and drilling faster with USC-M series machines do not stop at the spindle. There are intangible benefits as well. UNISIG USC-M series Milling and Drilling Centres allow mould manufacturers to approach their work differently and explore different approaches to mould making. With the entire manufacturing process streamlined, customers find their engineers and design teams enjoy more freedom and flexibility with the expanded capabilities. Finishing and assembly are faster because the design is more efficient, and manufacturers can do things effortlessly that were a struggle previously.
Ultimately, it’s about setting the bar high and keeping it there. UNISIG sets a standard looked up to by the competition. It’s a state-of-the-art mindset that takes mould finishing to a new level with a machine that allows you to mill better and drill faster.
www.unisig.com
In this issue of Industry Update, we are delighted to select Customcells as our lithium-ion battery cells manufacturer Company of the Month.
The first mock-up of lithium-ion batteries started back in the 1970’s, when English chemist, Stanley Whittingham started experimenting with titanium disulfide and lithium metal. Further research in the 1980’s pioneered the elimination of lithium metal but it wasn’t until the 1990’s when the first commercial cells were actively produced.
Following concerns about the safety of lithium metal batteries, researchers started to focus development on lithium-ion batteries, in accordance with strict safety measures. Lithium-ion batteries are rechargeable, with an exceptionally high energy density and lower self-discharge rate, meaning they have a shelf life from 10-12 years. The popularity of lithium-ion batteries has grown as they continue to power laptops, mobile phones, hybrid/electric cars to emergency medical and navigational equipment and are now the most rechargeable batteries across the world.
Customcells is a renowned, globally leading DIN EN ISO 9001-certified company in the field of lithium-ion battery cell development, from individual prototypes to medium-series volumes. As previously mentioned, Lithium-ion batteries are now the most used rechargeable batteries across the world, with graphite routinely used as the anode material. Graphite is chosen for its long-life cycle and its ability to create a stable, solid electrolyte interphase (SEI) layer, thereby protecting the anode further from reactions with the electrolyte. Customcells however, are now leading the charge for alternative anode materials, such as silicon, with its superior lithium storage ion capacity, with the resident R&D team working on teething issues such as volume expansion during the charging/discharging cycle.
Working with industries as diverse as aerospace, automotive, maritime to medical, Customcells holds considerable expertise in the battery cell area, from materials, cells, to battery modules and systems. Priding itself on offering a twofold service: comprehensive portfolio of products and expert consulting services for energy storage concepts and process technology, the company has earnt its place as a leading global
manufacturer and consultant.
However, the company goes above and beyond by also facilitating workshops and seminars for industry professionals on in-house lithium-ion batteries and its applications. The resident research & development department keeps abreast of cutting-edge material technology in the battery industry. Furthermore, Customcells provides a full licensing service, where new technologies re developed and scaled for various lithiumion battery cell applications on behalf of customers.
Customcells was founded in 2012 by Leopold König and Torge Thönnessen, as an offshoot from the Fraunhofer Institute for Silicon Technology (ISIT). During his time at ISIT, Leopold worked on electromobility at the Development Department for lithium-polymer cells. Electromobility is the current sustainability focus of the automotive industry, as it pertains to electric vehicles and its charging infrastructure. Torge also holds an extensive background in electromobility, battery cell development, product development and process analysis/optimisation and together, this dynamic duo have spearheaded traction across the electromobility sector.
The remit of the founding site in Itzehoe (Germany, Schleswig-Holstein) is the development of battery cells and the evolution of production of prototype production to series maturity. Meanwhile the second newer site in Tuebingen (Germany, Baden- Wuerttemberg) operates one of Europe’s most modern cell production lines, offering customers series production of lithium-ion pouch cells for aviation at the highest technological level. Moreover, utilising the latest in automation technology, ensures that moisture is kept out of production, as contact between the workers and materials is minimised. This substantially reduces the ‘air drying process,’ making the process more substantial and reduce carbon footprint.
We spoke to Dr Dirk Abendroth, CEO of the Customcells Group, to find out more about the unique customer benefits of premium products from Customcells.
“We provide specialised energy storage solutions, spanning across the aviation, automotive, maritime, and medical sectors and offer unique benefits to our clients through our ability to produce energy storage systems for extreme conditions.
We understand our clients' unique needs and have access to 14 industrialised electrode technologies and over 250 raw materials, which enables us to produce highly customised battery cells according to our customers' applications.
Our technology has already demonstrated its success in real-world applications. There have been more than 600 satisfied customers as part of more than 1,400 projects. Furthermore, we serve as the battery cell supplier for well-known companies operating in the aviation industry, a sector with enormous future potential.
Together with several partners, Customcells, is working on a smart battery factory. In a leadership role, Customcells has initiated the collaborative project TwinTRACE, which unites industry and research partners. The primary objective of this endeavour is to establish highly efficient production processes through the implementation of a digital twin. Through TwinTRACE, the project partners are elevating the standards of battery cell production by enhancing quality and traceability, positioning themselves as world leaders in this domain. Additionally, they are setting benchmarks for intelligent digitization within the industry.”
In addition to the exciting cutting-edge TwinTRACE project, Customcells has recently strengthened its top management and recruited a number of highly respected managers from well-known companies such as Continental, Rimac, BMW, Magna and Kion. This move is aimed at accelerating the company's global growth, through optimising internal organisational processes. At the end of 2022, Customcells successfully secured EUR 60 million in Series A financing, to continue its future endeavours in this trailblazing area.
“Being at the forefront of innovation, our company is dedicated to establishing the benchmarks for the future of battery cell technology. Our focus lies in developing highperformance battery cells that aim to carve out a new premium segment in the worldwide market. This segment will be defined by remarkable energy and power density, setting new standards in the industry.
Furthermore, with the expansion of our site in Itzehoe,
we aim to offer even more comprehensive support across all areas of process development. As part of our growth strategy, we are also actively exploring potential expansion into additional locations, including the United States.
Customcells is 'powered by people' – and has been for almost ten years. Our business is driven by the ideas of our employees. As such, we are always looking for talented individuals who share our values and are eager to contribute to our mission, inviting them to join our team,” concludes Dirk Abendroth
For further information, see the websites below:
T +49 4821- 1339200
contact@customcells.org
www.customcells.org
www.medium.com/master-of-batteries