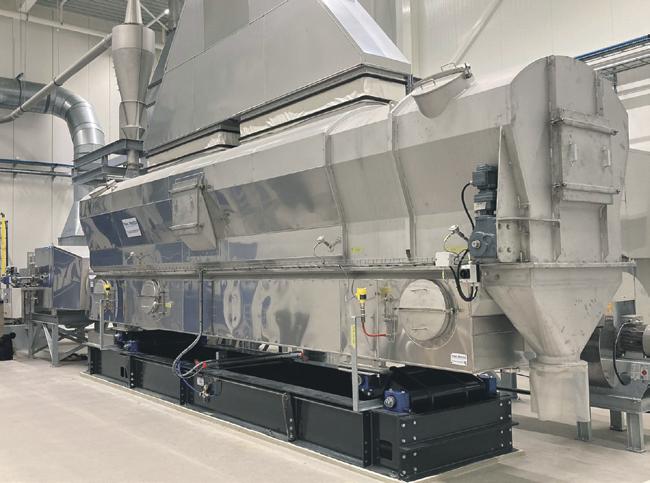
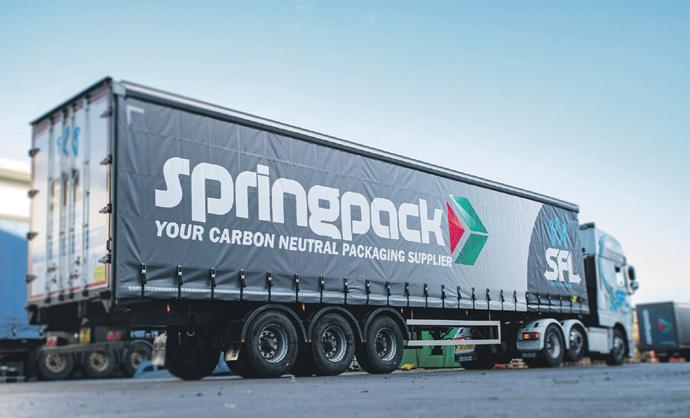

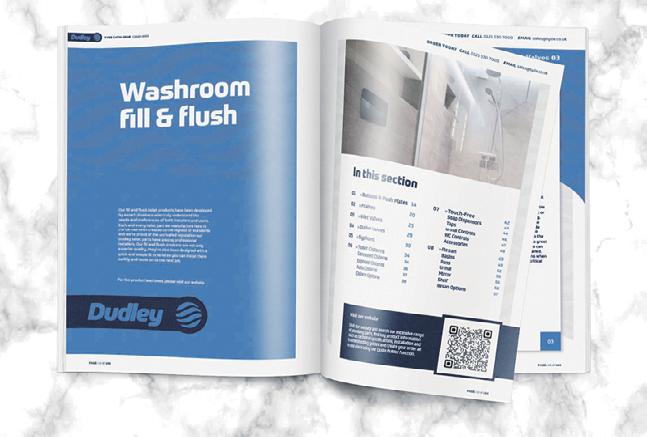
Bringing the industry together once again, CHEMUK 2023 is set to return on the 10 – 11th May 2023 in Hall 1 at the NEC in Birmingham.
This year the show will be presenting over 400 specialist exhibitors and over 150 expert speakers that will be split between three major show zones: Chemical Industries Supply Chain; Chemical, Process & Plant Engineering; and NEW for 2023 CHEMLAB –Laboratory & Innovation.
Brand new this year, the CHEMLAB Show will showcase specialist laboratory chemicals and chemical equipment suppliers supporting Research & Development, Analysis, Process Design & Development, Scale-Up, and Quality Testing within the Chemical & Chemical Product Industries. CHEMLAB will invite laboratory professionals from across the chemical industries involved in a number of sectors such as Formulation Development, Reaction Process Analysis,
Regulatory / EHS support, and many more.
The Chemical, Process & Plant Engineering show zone will be dedicated to Process Engineering Technology, Plant Engineering Solutions, Control & Instrumentation, Asset Management, and many more. This zone will be a great chance to meet specialist suppliers of Process Engineering and Chemical Plant & Asset Technology and Services, and is supported by IChemE, GAMBICA, BPMA and BVAA.
CHEMUK 2023 will host a number of exhibitors from a broad range of industries including Logistics, Operations & Fulfilment, Digital & Automation, Business Services – Skills, HR, Finance, Laboratory, R&D, Analytical Chemistry & Process Scale-up and many more.
Visitor registration is now open for CHEMUK 2023
www.chemicalukexpo.com
Siga Filtration works with engineers and users to design, improve and replace
The unit has been designed with only a few parts to allow for quick maintenance on site. Stainless Steel material of construction makes the F-SF-TW units ideal for aggressive chemical applications. A hygienic version is also available for food use. It can be challenging to correctly identify the source of contamination but our transfer line filters allow users to capture dirt at source and discuss remedial measures with suppliers and tanker companies. F-SF-TW units are capable of high flow rates in a small footprint.
For more information, see below. T +44 (0) 1276 583 046 enquiries@sigafiltration.co.uk
SPIROL has knowledge and expertise to help customers determine what pins are best for your application…
There are two types of Slotted Spring Pins that the company manufactures: SPIROL Standard Slotted Pins and ISO 8752 Slotted Pins.
Oliver
Business Development Manager for the Middle East region, Haridas
SPIROL Standard Slotted Pins offer significant advantages as compared to ISO 8752 Slotted Pins, which were originally designed to function as Dowel Bushings.
Dowel Bushings are used in conjunction
with bolts and isolate bolt threads from shear planes.
Conversely, SPIROL Standard Slotted Spring Pins were designed to perform one of the following pinning functions without the addition of any other fastener: hinge, alignment, retention, stop, or hub/shaft connection.
While both SPIROL Standard Slotted Spring Pins and ISO 8752 Slotted Pins can be effective in an assembly, SPIROL Standard Slotted Spring Pins are easier to install and
superior in form, fit, and function.
Whilst both pins are of great quality and a high standard, the SPIROL Standard Slotted Spring Pins have a few extra advantages that make this product an asset to any assembly.
SPIROL’s application engineers will work alongside your design to make sure that you are using the most effective and efficient fastening solutions in your product.
www.spirol.com
Sizing an ECLISSE pocket door system starts with understanding the thickness of studwork into which it is being installed.
UK delivers water treatment solution to gin distillery
Veolia Water Technologies UK (VWT UK) recently supplied a water treatment solution to optimise the operational processes at a large-scale gin distillery. By adding its Hydrex™ 4301 water treatment chemical via a single dosing pump, VWT UK successfully removed excessive levels of residual free chlorine from the feedwater to improve the efficiency of the water conditioning units and prevent damage to the water softeners.
One of the oldest distilleries in the world, producing a significant percentage of the UK’s gin, the company uses a set of water conditioning units to process approximately 30m3/hr of raw water.
However, since moving location, the distillery suffered from an uncontrolled deterioration of the ion exchange resin beds inside these units. While this issue did not affect product quality from the site, it resulted in increased CAPEX to maintain the required levels of gin production. This was due to excessive levels of residual free chlorine, approximately 0.89 mg/l, in the facility’s feedwater.
Therefore, the distillery decided to work with a water treatment specialist that could help to reduce the presence of residual free chlorine in the feedwater to approximately 0.2 mg/l, a level that would not damage the distillery’s water softeners. It was also crucial that the solution was installed efficiently to resolve the issues as quickly as possible.
Following a competitive bid, the company selected water treatment specialist VWT UK. VWT UK had previously carried out periodic servicing of the distillery’s water softeners and reverse osmosis (RO) systems, so the two companies had a good rapport.
To effectively treat the residual free chlorine for removal from the facility’s feedwater, VWT UK supplied its Hydrex™ 4301 – a water treatment chemical that is specifically formulated for RO systems with polyamide membranes that can be affected by chlorine.
As it was vital that the issue could be resolved with minimal operator input, VWT UK installed a single dosing pump with flexible dosing pipework and an intermediate bulk container (IBC) bundstand. The dosing pump was then connected via a 110v lead and socket to transmit a signal to stop and start dosing depending upon whether the water feed pump was active. This ensured that the Hydrex™ 4301 chemical was only dosed when required.
Thanks to the water treatment solution, the distillery has now been able to reduce the level of residual free chlorine in its feedwater to <0.2 mg/l and prolong the life of the components in the water softeners. This eliminated the need to bring in demineralised water with the use of road tankers, a process that had been required when the resin beds had failed previously.
The company has also been able to accurately baseline its facility output and plan its day-to-day operations more effectively, resulting in reduced unplanned spend and CAPEX while maintaining the same levels of gin production.
“I was delighted to provide a simple and effective solution to one of my local businesses. The dosing system is still going strong after being in operation for over 12 months. The site is very happy with the extremely low usage of Hydrex™ 4301, which is even lower than originally estimated,” commented Brian Jones, Business Development Manager (North and West) at Veolia Water Technologies UK.
For more information on Veolia Water Technologies UK and its range of solutions, including its range of Hydrex™ water treatment chemicals, visit: www.veoliawatertechnologies.co.uk.
The highly anticipated Utility Week Live 2023 is just around the corner on the 16-17 May. Over 3,000 pan utility professionals are priming themselves to descend on the NEC in Birmingham for a two-day Expo that gives access to the latest innovations, insight and solutions to collaborate, lead and deliver.
Known as the UK’s only pan-utility exhibition that’s FREE to attend, the Expo is a great way to gain inspiration and fresh ideas from sector leaders and
Leading provider of compliance, technical and safety training, Develop Training is inviting Utility Week Live attendees to visit its stall F2, where experts from the company will be on hand to discuss the premium training services it can provide to an individual or a company.
CompEx, also part of the JTL Group, is the international scheme for competency validation and certification of personnel who work in explosive atmospheres and will also be available on the stand to discuss how we can help you or your business.
Training experts from a number of fields within Develop Training will be available at the stand during 16th – 17th May to answer queries about the benefits of training and upskilling a workforce as well as provide information about Develop Training’s courses and centres.
With courses including training for confined spaces as well as broad packages for work in gas, water, the utilities sector, building services engineering and more, Develop Training can answer both bespoke training needs and standardised industry requirements.
Develop Training delegates include some of the UK's largest and best-known organisations from the utilities and construction, defence, healthcare, facilities management, and telecommunication sectors.
Operating from a network of centres that cover eight key regions in the UK including: Scotland, the Southeast, the Midlands, Southwest, East Anglia and Yorkshire. Develop Training also delivers virtual and on-site training packages.
For more information about Develop Training, visit:
www.developtraining.co.uk
transformational companies from across the industry.
Utility Week Live 2023 will be hosting a Challenge Programme that will cover most of the critical challenges facing businesses today. Such topics will include Asset Management, Water 2023, Decarbonisation – delivering net zero, new approaches to capital delivery, Optimising workforce and field operations, and much more.
Hosted from the Keynote Stage, The Keynote Programme: The new world order, will focus on building resilience in a time of challenge with discussions around how utilities can prove themselves resilient to the interlocking challenges of climate change, shifting societal expectations and technological complexities.
Some more unmissable show features include NEW! House of the Future, Spring Water Innovation Zone, EIC
Innovation Zone, and Isle’s Innovation Zone.
If you’re interested in making new connections, discovering innovation and having the chance to solve critical challenges whilst taking away practical advice, then save your seat today by booking below.
For more information, see below.
www.utilityweeklive.co.uk
Webster Technologies has come a long way since the 1960’s designing, developing and manufacturing heavy duty equipment for the coal mining industry. It was here that we brought much needed innovation becoming the first to use hydraulic technology for cutting.
The closure of the coal mines in the late 80’s brought some challenging times for the company. Ian Webster turned this into an opportunity
to reach out to other sectors, designing and developing equipment for the construction and tunnelling industries.
In 2000 Webster Technologies was formed and one of Ian Webster’s most successful designs is the Rockwheel. Now an industry standard, the hydraulic excavator mounted attachment (also referred to as rotary cutters or transverse cutting units) is used extensively in the UK and around the world on high profile projects for demolition,
tunnelling, trenching and a range of other applications such as soil mixing which we are now looking to advance in and put our own stamp on.
The business has grown from strength to strength, and boasts the largest rental fleet of Webster Rockwheels in the UK. Our ethos of innovation and continuous improvement led to developments of the original Rockwheel design which continues to be one of the most technically advanced on the market.
As a designer of our own products we know what it takes to turn an idea into a reality. We are passionate about what we do and thrive on tackling even the most complex design challenges. Our team has experience in designing and developing solutions for projects including sub-sea mining, salt mining in Canada, Micro and Narrow Trenching and more. We are also Proud Authorised Dealers in UK and Northern Ireland to the Infrastructure Industry covering road planning, road milling and road stabilising, foundation drilling, chain and wheel trenchers, agriculture, and recycling.
Being recognised for our latest innovation, we received the prestigious World Demolition Award, The ROCKHIT, which challenges conventional design concepts resulting in environmental and sustainable benefits including fuel savings, increased productivity and improved operator/driver health and safety conditions. Described as ground breaking and a massive step forward for innovation in the Hydraulic Hammer market, we are embarking on the final developmental stages towards product launch. We are looking to engage with UK manufacturers who are interested in being part of this exciting journey.
For futher information, see visit www.webstertechnologies.co.uk
APlympton based precision engineering company pulled back from the brink of collapse just 5 years ago has recorded another strong year of growth. PTG Precision Engineers Limited were weeks away from going under and laying off all their employees when local Plymouth businessman, David Rowe, bought the business and transformed its future.
Rowe, owner of one of the largest engineering companies in the area, Applied Automation (UK) Ltd, felt strongly that losing PTG with its level of engineering knowledge and skills and with almost 40 years of trading was unthinkable. “As a machine builder I also knew they would be a great asset to my core engineering business and following the acquisition, which gave them financial stability, I appointed Mike Stevens,
one of my senior managers at Applied Automation as their Managing Director. Since the acquisition in 2017, the company’s performance, despite the many challenges including covid and the increasing skills shortage within the industry, has been remarkable. PTG has truly risen like a phoenix from the ashes”, he said.
Under Mike Stevens guidance the company has retained IS09001 accreditation and is currently working towards ISO45001 (Health and Safety) and have significant knowledge, experience and the skills required to work in the nuclear sector along with the necessary inspection facility.
Over the past two years, PTG have invested in new machinery and are also able to offer specialist services which are in short supply in the South West of England, such as cylindrical grinding.
Mike Stevens is justly proud of the company’s customer retention rate, “It is exceptionally high and probably down to the fact that we really like to work closely with our customers. This ethos and working practice have helped us generate new business from some very prestigious customers, such as Leonardo Helicopters (previously Westland),” he said.
Stevens went on to explain that in his view probably the biggest current challenge the industry and the company face is attracting
young people to become precision engineers.
“We work with local colleges and training companies and want to take on a couple of apprentices now. But, whilst many students consider a career in engineering, for some reason hands-on precision engineering seems to miss out”, he said. “For that reason, we’re now taking on people that are currently working in the engineering sector, such as setter operators for example, and we provide the upskilling and training to give them the
skills and experience PTG will need in the future”.
With 2023 plans to expand their existing services in the Workholding, Nuclear and Aerospace sectors, where their expertise and experience makes them stand out from the crowd, the future is looking very positive for PTG.
www.ptgltd.co.uk
Foften pick up on small details – a specific tolerance, material condition, process requirement or a future need for flexibility – that may change our recommendations. When it makes sense, our experienced sales team or engineers will visit a customer to see what is needed firsthand. Whether a site visit or just a virtual meeting, this initial investment of time to clarify the need saves the customer money and
provides them a truly valuable solution.
2. We first identify a standard solution from our product line that can be applied at the lowest cost and shortest delivery possible.
At UNISIG, our product development mindset is to systemise solutions from our experience in many different industries, make them automation ready and embed application flexibility whenever possible. We invest millions of dollars annually in our product line and related spare parts, giving us a strong starting point for new applications. Our standard product line encompasses much more than machines, including standard automation, workholding, accessories and tooling that we can offer as part of the solution.
Once we have identified a standard machine as a starting point, our engineers seek out smart, practical ways to meet the customer’s application needs. The goal is to innovate within the machining operation planning, work holding or automation, as opposed to engineering a completely special solution without first exhausting opportunities to solve problems with standard products.
For our customers, this approach provides them a reliable, standard machine that can be used for many years and that has the built-in flexibility for easy re-tooling to adapt to future needs. For us, initially working within the boundaries of our catalogue cultivates new ideas that can then be applied to improve our standard products as well as help us direct future research and development budgets.
3. If a standard solution isn’t available, we consider a customised solution and we stand behind it.
UNISIG is very good at building customised machines, and we do so often. Once we and our customers agree that a special solution is needed, we move forward with a great deal of confidence and experience. We start by evaluating how we might approach the design using standard modules or proven concepts, thus eliminating long debug cycles and/or high costs. Then we use our mechanical and electrical engineering disciplines to virtually test the new machine before we build it.
One of the key reasons our customers are confident moving forward with a UNISIG custom machine is that they know we will stand behind it and that we have substantial capabilities to ensure it always exceeds their production expectations. We approach these special projects with the mindset that a custom machine will be used for decades in production, which is why we provide the same documentation and long-term technical support for all our machines whether standard or custom.
4. If a commodity solution is readily available, we recommend that rather than upsell a machine the customer doesn’t need.
We build machines that can gundrill or BTA drill deep holes that are impossible to drill on machining centres. Even if it may be possible to drill some deep holes on a CNC machining centre, our machines have the power, speed, dimensional accuracy, spindle density, coolant systems and process control that will improve productivity, tool life and reliability.
Typically, though, when a customer comes to UNISIG with a specific part need, at that point they’ve most likely already struggled with a conventional machine and realised that a deep hole drilling machine is obviously the way to go.
However, our team knows how to identify whether or not an application would truly benefit from a UNISIG solution. When it wouldn’t, we will suggest viable alternatives. It’s not that we don’t want to sell a machine. But the fact is that our experience has shown that at some point the alternative-solution direction becomes obvious, and we want to make that apparent early on in the process so as to avoid wasting a lot of our customer’s time.
Our customers expect the best from us, and we believe that our proven process ensures we never disappoint. Our goal is to leverage our core values to serve our customers as best we can and build strong, productive relationships for years to come.
Please contact us at:
www.unisig.com
As surgical instrument manufacturers pursue greater throughput while facing increased labor costs, automating the medical instrument manufacturing process has become a necessity. However, integrating automation into the gundrilling process for drilling deep holes in extremely precise surgical instruments in lightsout operation is a major engineering challenge requiring more than simply pairing a robot with a deep-hole drilling machine.
The right machine, tools and process must all come together to create small holes with extreme precision in difficult-to-machine materials such as titanium and surgical stainless steel. More importantly, the entire system must flow from a unified concept where the whole is greater than the sum of its parts.
To meet these challenges, UNISIG developed its UNE6-2i-750-CR dual independent spindle gundrilling machine. The UNE6-2i is capable of gundrilling hole diameters ranging from 0.8 – 6 mm in part lengths measuring up to 30 inches with depth-to-diameter ratios from 20:1 to more than 100:1. The machine has a maximum combined drilling speed of 28,000 rpm and a 3,000 psi (207) bar programmable flow-based coolant system with dedicated pumps for each spindle to ensure precise coolant pressure control.
Automating hundreds of cycles of precision manufacturing, however, is not possible unless the overall operation is considered from the outset. Surgical instrument manufacturing is a sequential process: parts must be loaded into the machine in a particular way for specific operations that happen in a specific order.
Workpiece length, shape and configuration determine where it is gripped by the robot when loaded into a machine, moved from spindle to spindle for drilling, residual cutting fluid removed, and returned to the pallet. Where a part is gripped impacts where it is clamped for drilling to ensure accuracy. Every variable along the process chain must be considered and accounted for, and the calculus is detailed and complicated.
Then there are unique customer needs and requirements. The equipment and process must accommodate a variety of part families and hundreds of parts to increase runtime and efficiency. Operators must be able to change over part types and programming without calling in an automation specialist, and the entire process must be controlled from a central interface. Add to the mix that everything must be packaged in as small a footprint as possible, and the scope of the engineering challenge comes into focus.
UNISIG’s approach to solving these problems, however, results in targeted automation that enhances the existing benefits of gundrilling, ensuring a solid foundation for reliable process-wide automation.
At its core, the automated UNE6-2i is a purpose-built machine with automation embedded in its design, not added as an afterthought. Flexibility and adaptability are maximized by a harmonious, interdependent mechanical, software and operational planning scheme.
To meet size constraints, a 6-axis robot was embedded in the machine with a pallet system on the backside of the machine, allowing easy operator access from the front to setup the machine without compromising ergonomics. The configuration enables quick setup changes between prototype and proving operations and full production runs.
The robot automatically repositions the workpiece from the front of the first spindle into the rear of the second
spindle without operator input. The process of drilling a part from both ends in a single-piece flow is unique to UNISIG. Workpieces with enlarged features on one side are loaded from the rear of the collet, solving a common problem in gundrilling medical surgical instruments with full automation.
Control of the UNE6-2i and a computer are consolidated into the Human Machine Interface (HMI), a menudriven touch screen system for easy, intuitive operation. Training and operator engagement with the system is significantly reduced due to user-friendly UNISIG controller menus and prompts.
UNISIG’s comprehensive and integrated approach to automating medical part manufacturing is a vison that sets it apart in the industry. It’s more than drilling the impossible hole. It’s a commitment to understanding and to the research that drives continuous improvement and innovation for automated part production at its full potential.
Further information on all machines and the complete UNISIG machine program is available at: www.unisig.com or follow the company on LinkedIn and Twitter (@UNISIG).
You will also meet us at the EMO 2023 show in Hannover, Germany, from 18.–23. September.
Hygiene equipment application specialists H&M Disinfection Systems Ltd and specialist hygiene solution provider Christeyns Food Hygiene have today announced the signing of a strategic partnership.
Christeyns Food Hygiene, (CFH), based in Warrington and H&M Disinfection Systems Ltd of Northwich are both industry leaders with over 30 years of experience in their respective fields. Having worked together for three decades, this strategic alliance will allow the two companies to provide a turn-key solution to the food, dairy and beverage industries for effective cleaning and disinfection operations.
The current CFH engineering offering for the optimisation of water, energy consumption, dosing, time and labour will be strengthened, combining both chemical and engineering expertise including a complete equipment portfolio, CIP sets, Washdown Systems, Bulk tanks and bespoke engineering. This unique full-service package will include maintenance and periodic safety inspections.
“We are delighted to confirm this formal alliance with H&M Disinfection. The excellent equipment, control systems and reliable pump-sets they manufacture, combined with formulations created by Christeyns Food Hygiene will ensure our customers can rely not only on the chemistry, but also on the application equipment,” commented CFH Operations Director, Andy Bethel.
For over 30 years Christeyns Food Hygiene has produced effective formulations of detergents and disinfectants for all application in the food, dairy and beverage industries with customers from across a range of household consumer brands and suppliers to the UK’s food retailers. As part of Belgium parent company, Christeyns NV, they are able to draw on international support and expertise as required.
Since 1989 H&M Disinfection Ltd have built a reputation for providing high quality, bespoke hygiene application equipment which is the corner-stone of many customer’s food safety management systems. Their “CIP in a box” solution, where a temporary or stand-in CIP set is required to cover breakdowns or scheduled system maintenance, is one example of their innovative solutions.
Stephen Hall from H&M Disinfection: “This partnership cements our long-term relationship enabling us to better service customers from both companies, with high quality formulations and the equipment to reliably and safety apply them to achieve a hygienic manufacturing unit.” www.christeyns.com
The worlds first smart, simple and low-height industrial floor cleaning robot sweeper machine.
Short-staffed or looking for a more cost-effective cleaning option for your site? The K900 is a fully autonomous vacuum-sweeper solution that has been built from the ground up to perform in industrial environments.
With advanced SLAM (Simultaneous Localization and Mapping) navigation and 3D environmental perception, the K900 not only chooses the most efficient way
to clean, but also reacts to a constantly changing environment along with reporting a heat map of the area cleaned to ensure maximum coverage.
Low-height racking or hard-to-clean spaces? No problem, thanks to a super low 35cm design and radio control option for operated use. When it comes to automated cleaning in industrial environments, the K900 is truly superior in design, technology and performance.
For more information, see below.
T 01789 415695 www.crescentindustrial.co.uk
range used not only for problem solving tasks but strategically listed in the earliest phases of project tendering.
We spoke to P&M Pumps Director, Andrew Parr to find out more about this dynamic company,
“We are suppliers of specialist pumps and systems, mainly for the Municipal wastewater and renewable energy sectors but also, the food industry, prisons, hospitals, restaurants, holiday campsanywhere that feeds into a main system and spends too much time unblocking and repairing pumps.
We specialise in supplying pumps for difficult applications where frequent blockages occur, using the Vaughan range of Chopper pumps.
Together with Vaughan Co we also design and supply Rotamix pumped tank mixing systems where the Vaughan chopper pump is always the heart of the system.”
With the advent of severe weather battling the UK, and due to unprecedented climate change, many waste water companies have to deal with excess debris and rag in the systems. Having access to the correct type of pump gives companies a head-start on reducing blockages and downtime. The Vaughan Chopper Pump gives uninterrupted service, even in the toughest of conditions.
The Vaughan Chopper Pump has many patented features, allowing it to handle even the toughest of slurries, sludges in effluent and process streams. The Vaughan cartridge-style mechanical seal is superior to single-spring seals and is designed to complement the heavy duty chopping components built in to handle solids around the seal which are reduced in size by patented rear pump out vanes. The solids entering the suction are chopped by sharp , curved impeller vanes, forming a smooth slicing effect, allowing the reconditioned slurry to be pumped through quickly and efficiently. Any fibrous debris at the pump inlet centre is sliced by the patented cutter nut. Furthermore, there is an option to install the Vaughan disintegrator tool which is designed to reduce larger solids (where fibrous material is not present), preventing suction blockage.
The Vaughan Chopper Pump has such a strong, reputation, that it is the only pump solution for the most arduous jobs. P&M pumps are going from strength-to-strength, providing excellent customer service for Municipal wastewater and renewable energy sectors across the UK and Ireland, as Andrew shares,
“Like everyone we have seen an impact on the costs involved with sourcing and transporting goods since the COVID- pandemic but have seen business levels return to pre-pandemic levels. We have had to slightly adjust lead times temporarily, but we previously managed our UK inventory to ensure we always served our customers well and continue to outperform our competitors in providing new pumps, spare parts and service.
We are looking to take the company forward for another thirty years by undertaking recruitment of younger members for our team to benefit from the combined experience from an existing work force of around 120 years working with pumps and process systems.
For more information, see below:
T 01487830123 sales@pumpmix.co.uk www.pumpmix.co.uk
In this issue of Industry Update we are proud to announce TEMA Process B.V. as our fluid bed systems design manufacturer Company of the Month.
A Fluid bed dryer is essentially precision-driven process equipment, designed to remove moisture content through fluidisation: translating from a solid state to a fluid component. These revolutionary dryers have a relatively quick drying time, compared to more conventional freeze or vacuum drying. With overall low investment and maintenance outlays, they allow for large-scale production and requires considerably lower air temperatures than spray drying.
TEMA Process B.V. is a relatively new dynamic, Dutch company, specialising in the detailed design and manufacturing of fluid bed systems for the drying of chemicals, minerals, salt, food, recycling, biomass and feed sectors. The innovative TEMA fluid bed is extremely versatile: in addition to drying, it can be routinely applied in cooling, puffing, roasting, torrefaction, blanching, stripping, in spice and herb sterilisation, pasteurisation and calcining.
In 2017, this dynamic company relocated to Wapenveld, Gelderland, in the Eastern Netherlands to a purpose-built 18.000 m2 engineering production facility, equipped with passive heating and cooling installations. This has enhanced further manufacturing capacity of the fluid bed dryers, coolers and other equipment.
TEMA Process B.V. is part of a larger conglomerate including: Hein Lehmann, Siebtechnik, Steinhaus and the Multotec Group. The group has grown steadily over 90 years, across an incredible 45 companies worldwide.
TEMA Process is able to offer bespoke, customised solutions for the production industry. We caught up with Mark Kragting: Sales Manager to find out more about this rapidly expanding company,
“TEMA Process BV was founded by Henk Dijkman, Managing Director in 2009. We manufacture TEMA fluid beds for the process industry but with a difference: ours has a shaking mechanism on the fluid bed.”
Showcasing its dynamic design expertise at World Biogas Expo 2022, TEMA Process unveiled its own sustainability contribution through waste stream conversions to granulated fertilisers.
The TEMA Process fluid bed system can convert waste streams from anaerobic digestion (AD) plants into a granulated fertiliser. With a rich organic content, alongside high levels of Nitrogen, Potassium and Phosphor, this is a fertiliser that farmers and soil will love. This innovative method of producing a natural fertiliser from waste stream, shows the simplicity required to reduce carbon footprint in agricultural farming. TEMA Process has had extensive design manufacturing experience across the organic fertiliser sector: using manure, digestates, biomass, food waste and insect frass. The TEMA Process dryer has drying results of <10% water and pelletisation.
TEMA Process is hugely committed to research and development, through its state-of-the-art testing facilities. Expert staff are always looking determining which is the right technology for particular adaptions, through meticulous experiments.
For further details, please see the details below:
T +31 88 5225800
sales@temaprocess.com
info@temaprocess.com
www.temaprocess.com
Astaggering 28% of the greenhouse gases produced worldwide come from the energy used to power, heat and cool buildings. Facing the real possibility of a global emergency, changes need to be made to conserve and protect the environment.
With sustainability high on the agenda, tenants and landlords are now turning to solar power to cut emissions and greenhouse gases. Solar PV panel systems also have the potential for payback in as little as 7-8 years due to the rising cost of energy, which is a great incentive to make the switch.
Prior to the commencement of any commercial solar PV installation, you should consider the condition of your metal roof. It is crucial that the remaining life cycle of the roof aligns with the expected life cycle of the solar PV system. A decision would need to be made regarding the replacement, repair or refurbishment of the roof after 10 years of its lifecycle.
Refurbishment with the correct products is the most sustainable option due to the amount of embodied carbon that can be saved. Did you know that refurbishing a metal roof using Sharmans roof refurbishment systems incurs 5x less embodied carbon than a standard roof replacement?
Whilst replacing the roof may make your building more energy efficient, there are a number of other factors for you to consider. Raw materials must be sustainably sourced, manufactured and shipped to the site, all of which add to the project's carbon footprint.
This would also apply to the oversheeting process, as it requires the use of new metal and does not provide any protection against the life cycle. Your roof will still go through the process of breakdown which in turn results in more disruption, additional cost and potentially adds to the carbon footprint rather than reducing it.
Patch repairs are generally not the most effective or sustainable way to bring the roof back up to standard. They may seem appealing in the form of minimal cost and low disruption, but there is the possibility of recurring issues with the roof, leading to future upheaval.
Choosing roof refurbishment over repair or replacement offers the same guaranteed lifespan, but at a fraction of the cost. Not to mention the environmental benefits it carries as no new metal is required, significantly reducing the amount of embodied carbon produced.
The best option for refurbishing metal roof sheets is applying silicone coating products. These products address the issues of metal roof fabric degradation and cut edge corrosion, therefore extending the life cycle of your metal roof by up to 25 years.
Sharmans market leading roof coating systems, Delcote® and Seamsil®, are used to bring your roof back up to standard.
An advanced metal roof coating system, Delcote® provides a 25 year product guarantee and is designed to extend the life and sustainability of any commercial metal roof.
The cut edge corrosion system, Seamsil® is backed by an industry leading 15 year product guarantee and is precisely engineered to prevent cut edge corrosion.
If you are amongst those that prioritise reducing their carbon footprint and energy costs through solar PV installations, you should opt for roof refurbishment when looking to bring your roof back to standard. Please contact Sharmans for more information on our roof refurbishment systems.
T 01298 812371
info@hdsharman.co.uk
www.hdsharman.co.uk
lliance Disposables have recently entered into a partnership with GreenTeck Global to offer their AquaTeck SC100 system to industry.
The AquaTeck SC100 system uses ordinary tap water, fed through a standard water softener and food-grade salt, to produce up to two litres of non-toxic solution every minute.
Cleaning bottles can then be refilled on-site with a chemicalfree all-purpose sanitising solution that can be applied directly to surfaces, mops, buckets and even industrial-floor cleaners. Once finished, the solution can be safely tipped away; a
process which has the added benefits of helping keep drains clean.
The environmentally-friendly system maximises the effective cleaning properties of hypochlorous acid (HOCL) – a naturally occurring steriliser – and eliminates the need for added detergents. As the most powerful natural disinfectant available, HOCL destroys 99.99% of all bacteria, pathogens, and viruses as well as destroying odours and is approximately 80 times more effective than bleach and passes EN1276 & EN14476. Delivers the highest levels of cleanliness via a sustainable sanitising solution that is non-allergenic and safe
for skin, as well as the environment through reduced carbon footprint & significantly reduces plastic wate.
For more information on the AquaTeck SC100 and to discuss with one of our local reps email us on hello@ allianceonline.co.uk or call us on 01270 252 333.
In this issue of Industry Update, we are proud to announce the British Institute of Cleaning Science (BICSc) as our membership cleaning educational Company of the Month.
The British Institute of Cleaning Science (BICSc) is the UK’s largest, independent, educational cleaning body, with over 55,000 Individual and Corporate Members in the UK and abroad. Established over 60 years ago by Eric Hill to give the cleaning industry a voice; BICSc has been an active agent in raising the professional profile of cleaning operatives everywhere.
The COVID-19 pandemic suddenly propelled the importance of quality hygiene control, primarily in hospitals but also across the retail, supermarkets, hospitality and catering sectors and educational establishments. Suddenly, cleaning operatives were essential ‘key workers:’ (although this was never formally acknowledged!), keeping the nation safe – although arguably
this all-too-often invisible workforce has always provided a vital, key service. During lockdown, BICSc focussed on research and development innovation, developing its online Virtual Training Suite for members around the globe.
Once cleaning operatives have completed the Licence to Practice (LTP) assessment, they can work their way through the other detailed courses offered in The Cleaning Professional’s Skills Suite (CPSS.) The base units cover vital skills such as dust control mop sweeping and damp mopping. The additional units include buffing hard floors – vital in office spaces and increasingly more hospitals – leading to specialist units such as bodily fluids/sharp objects. The healthcare version of the CPSS units align with the NHS National Standards of Healthcare Cleanliness 2021, offering quality assurance to cleaning operatives in the healthcare sector.
BICSc is an independent, professional body primarily focused
on raising contemporary standards of cleaning education, driving best practice at all times. With a head office in Northampton, members can complete courses at the inhouse training suite, or online via the virtual training suite, in addition to the training team delivering courses at customer sites across the UK and abroad, offering optimal convenience.
We chatted with Neil Spencer-Cook, Chief Operating Officer, and cleaning extraordinaire to find out more about this important company.
“We are a membership organisation that strives to bring recognition of the vital role cleaning operatives play in everyone's day-to-day life.
“With a range of both practical and theoretical qualifications available, BICSc has something to help further the career of every cleaning professional – from entry-level, through to supervisor level, and up to an employer with your own business tendering for cleaning contracts.”
Neil Spencer-Cook is a well-respected authority in the cleaning industry and was a keynote speaker at this year’s Cleaning Show at ExCeL, London. One of the keyways to increase cleaning workflow efficiency is to adhere to an inspection audit system that has clearly defined acceptable/unacceptable levels of
cleanliness between cleaning tasks and after cleaning tasks, helping maintain streamlined cleaning procedures.
To help organise these cleaning inspections, BICSc has launched the new Cleaning and Hygiene Audit App – perfect for highlighting processes, paperwork, policies, cleaning equipment standards, all encompassed within the cleaning inspection framework. The app can be downloaded onto Apple/Android smartphones and provides a handy, portable system on the go. BICSc offers free online training courses on this digital innovation on this indispensable app. Furthermore, it is a perfect SMART tool for the sustainable age: eliminating unnecessary reams of paperwork in a one-stop app.
For over 60 years, BICSc has galvanised the cleaning operative profession, offering state-of-the-art training to its members and therefore increased morale, fewer workplace accidents and standardised best practice. Neil Spencer-Cook outlines future plans going forward: “In addition to our new Cleaning and Hygiene Audit App, we are enhancing our virtual training, introducing rolled skills, and we are trying to increase our spread by making more inroads into the consumer market. We have also started to work towards training for the Domestic Cleaning Market.”
For further information, see the website below:
T +44 (0) 1604 678710 info@bics.org.uk www.bics.org.uk
Following
Springpack is a leading packaging company, focussed on the UK manufacturing industry and its latest range of e-commerce related products include the launch of Postal Plus. This range includes: eco-friendly mailing bags, expandable envelopes, and returnable postal boxes.
Established in 1975 by current General Manger Laurence Francis, the company has grown extensively to offer complete packaging solutions, packing equipment and packaging audits.
Situated in the heart of Worcester, the packaging experts can supply protective packaging for fragile goods, cartons and cases, strapping, tapes and adhesives, polythene products, packing room equipment and janitorial products. All the packaging products are carefully handpicked with over 45 years of industrial and transit packaging intricate knowledge.
The demand for Springpack’s packaging solutions have substantially increased across a diverse range of sectors, as Simon Rees, Head of Marketing explains,
“Springpack offer a wide range of stocked products including Pallet Wrap, Packing Tape, Void Fill, Cardboard Boxes and Packaging Automation Solutions.
Springpack's target customer base is larger-scale customers such as fulfilment companies, however we service customer across the Midlands, across multiple sectors from manufacturing and assembly to aviation.”
Due to increased demand, Springpack are soon moving to a state-of-the-art 79,000 sq. Ft warehouse and office facilities.
“With a two-tiered mezzanine floor and conveyor system: the new site will allow us to offer a much deeper range of products and the unique ability to stock hold
The
Bringing the industry together once again, CHEMUK 2023 is set to return on the 10 – 11th May 2023 in Hall 1 at the NEC in Birmingham.
This year the show will be presenting over 400 specialist exhibitors and over
For over 60 years, Drallim Industries Ltd has served the Aerospace, Industrial & Utility sectors with its innovative, technology-driven British engineering.
Achieving a global presence, Drallim is a leading innovator in technology, providing engineering skills, manufactured equipment, and custombuilt systems. The Industrial Division was born out of the innovative Rotary Selector Valve.
Originally designed and built in 1958 and still very much sort after and used to this day. Using the same footprints, we can offer longevity,
integrity and a robust product that will last for many years to come.
We have continually manufactured and executed a diverse range of products that include electrical, pneumatic & hydraulic control panels, mechanical cables and control rods, specialist test equipment, alongside running a general electro-mechanical/mechatronic contract design manufacture and test service. If you have a problem, we can solve it.
We’re excited to be exhibiting (again) at the free to attend CHEMUKEXPO 2023 with the
focus being on our Rotary Selector Valve and showcasing it’s diversity and applications. A unique valve with Multiple configurations for a multitude of applications. You will find us at Stand J8 on the 10-11 May 2023 at the NEC, Birmingham.
We very much looking forward to welcoming all visitors, so come along to Stand J8 to see the products and meet the team.
T 01424 205140 sales@drallim.com www.drallim.com
Rupture disc for particularly high temperatures and leak-tightness requirements
TThe
PowTechnology is your ideal partner for digital transformation! We deliver IIoT solutions globally, with a deep understanding of the Industrial Internet of Things, backed up by 30 years demonstrable expertise & practical experience in instrumentation & digitalisation, ISO9001 and ISO27001 accreditation.
We offer proprietary IoT devices and platform, IIoT solution design, manufacture, comprehensive testing and installation.
PowTechnology helps customers remotely monitor, collate and interpret data on their critical processes . on temperature, pressure,
flow, level, vibration, humidity, CO2, proximity, distance, colour, movement and more.
Metron Intelligence, our versatile suite of IIoT technologies integrates GSM/GPRS, Sigfox, LoRa, RS232, RS485, Ethernet, Wi-Fi, CAN, MODBUS & IO-Link to our MetronView platform and from there creating reports, alarms and integrating data to other portals via an API.
PowTechnology IIoT digital transformation solutions make processes smarter, enabling our customers to get data flowing rapidly as a first step towards their digital transformation and then supporting them through to an international estate of connected assets.
Turn data into knowledge!
Whether you need utility monitoring, condition monitoring of machinery to maximise uptime and productivity, or reliable remote monitoring of environmental factors to ensure best practice, compliance and safety. please talk to us!
Stand Number: C54
For more information, see below.
M +44 1827 310 666
sales@PowTechnology.com
www.PowTechnology.com
PowTechnology Ltd, 12 Ninian Park, Tamworth, B77 5ES, UK
Assentech reduced the GWP of a 12” breather vent from 161 tonnes to 185kg
Assentech has been developing techniques to measure and reduce emissions from tank farms for over a decade. The key is keeping volatile compounds inside the tanks but allowing them to breathe when required such as filling/emptying and fluctuations in temperature. At all other times a breather valve should remain closed with minimal leakage.
These valves have immense flow capacity so if not functioning or set correctly can leak hundreds of tons of invisible GWP emissions along with company profits into the atmosphere.
“We have a deep understanding of how breather vents work and how to optimise their performance. As they are modulating pressure relief devices they can begin to open from as low as 75% of their set point. As many digesters run at 90% design pressure this overlap represents a large potential for mis-applied devices to leak excessively at standard operating pressures,” says Cox.
Two international standards ISO28300 and API2000 specify maximum leak rates for all production vents, ie. 0.014m³/h for vents up to 6”. The shame is that only 2 out of the 20 worldwide manufacturers test to this standard.
Unfortunately, the majority of breather valves that are installed at facilities do not seal and will allow huge volumes of vapour to release into the atmosphere. We are the only company which has the technology, knowledge and service capability to keep you safe, compliant and profitable.
See us on Stand F26 at CHEM UK T +44 (0)1726 844707 info@assentech.co.uk www.assentech.co.uk
At TW Metals, peace of mind is assured with our dedicated-to-service, experienced and knowledgeable team with over 100 years of industry know-how.
TW Metals is proud to partner with customers from the Oil & Gas, Chemical Processing, Heat Treatment, Hydrogen, and Commercial Industries to deliver high-performance, quality metals and processing where and when needed.
TW Metals provides clients access to a complete range of materials, including Nickel Alloys, Stainless Steel, Duplex, Titanium and Aluminum in Tube, Bar, Sheet Plate, Pipe and Fittings.
Our processing capabilities include cut-to-size programs, material testing, deburring, laser cutting, waterjet cutting, PVC sheet coating and more.
To discover TW Metals’ full range of highperformance metals and supply chain solutions, meet the team at CHEMUK this May on stand B10.
RAS Ltd is an independent firm of risk experts, specialising in major accident hazards. Capabilities include hazard identification, risk assessment, ALARP demonstration and emergency response planning. We are founded on a set of simple principles: recruit the best people in the industry, only work in our areas of expertise, and work with our clients, not for them. We work with a number of leading companies in the oil and gas, and specialist chemical sectors, helping them to manage safety, environmental and business risks. Our core aim is to support a safer, smarter and sustainable approach to risk management.
It’s an approach that sees us working on some of the most influential and novel projects in the industry. One of our key strengths is the range of backgrounds and expertise our specialists have. This deliberate diversity enables us to develop effective solutions to risk management in any situation.
We’re proudly independent, with freedom to do what’s right for our clients without being slowed down by corporate structures and consultancy models. That’s not to say that we don’t have our own methodology and risk models – we do – but we approach every single project differently, and don’t provide uniform services ‘off the shelf’.
Stand K11
T 01244 674 612
www.ras.ltd.uk
enquiries@ras.ltd.uk
There are documented safety issues around medium-voltage process heaters; now considered the popular alternative to gasfired heaters for larger application utilisation. Arc flash events are rare but carry potentially deadly consequences. The new usage of larger medium-voltage process heaters in hydrocarbon processing have raised a few safety eyebrows.
Flash mitigation features are a key consideration to offset safety risks and prevent serious injuries.
The risks posed by arc flash
Thankfully, arc flash events are rare: estimated at 3,500 globally every year but their capacity for serious injury, damage and death must never be underestimated.
The propensity for arc flash events increases when corrosive or conductive dust unexpectedly or negligently builds-up, causing a sudden short circuit. Other causes include pest infestations and even accidentally dropped industrial tools.
Equipment operating at higher voltages (above 600 volts) naturally carries more risk for potential arc flash, whereas those functioning at below 400 volts, will not cause large arch flash events.
Mitigating the risks of arc flash are an essential part of risk assessments, to protect workers and workplaces. Global concerns about carbon emissions, have led many companies to find practical solutions for decarbonisation, such as replacing gas-fired heaters with larger electrical heaters.
Furthermore, many applications are now assembling large megawatt heaters, connected to multiple panels. This necessitates an engineered solution scenario: isolating the arc flash section and thereby isolating the faults from the main breaker/ feeder, to avoid fire and fatalities.
Reducing the effects of an arc flash event
There are three essential strategies to negate the impact of potential arc flashes across industrial equipment:
1. Reduce the available fault current
2. Expand the distance from the potential source of an event
3. Decrease event duration (how long the arc primarily exists)
If money were not object, all three strategies would offer optimal safety but sadly, project costs can make this impractical to implement.
However, the third point has the largest impact on the total energy released and is the most effective way to reduce potential arc flash hazards.
In the debated safety dichotomy between arc-resistant cabinets and arc mitigation technologies: the mitigation technologies are generally considered more cost-effective and ultimately carry a higher safety return.
Therefore, implementing safety mitigation technologies into medium voltage process heater designs, is considered industrial best practice.
Fool proof Arc Flash Mitigation Technologies
Arc flash mitigation technologies work on the premise of reducing the energy of the event itself, by purposefully limiting its duration. This smart technology pre-empts the flash, simultaneously tripping the circuit in question, thus averting further damage. The technology either sensing the current arc mitigation (current) or the optical arc mitigation (light).
In the latter approach, the arc light is detected and a signal is sent to a protective relay, instantly tripping the breaker autonomously. This has the huge advantageous approach of detecting the arc at its infancy, thus rendering the duration to minimum levels, with the total energy produced dramatically downsized.
Current arc mitigation solutions
Current arc mitigation uses transducers to detect arc-inducing current increases. However, if the transducers are incorrectly sized, they are incapable of proactively shutting down the system or clearing the event in a timely fashion.
The optical arc mitigation technology has the sizeable advantage of reducing clearing time and arc energy release by 50%, compared to current transducers.
Safety comes first
The Watlow® POWERSAFE™ system: designed for medium voltage process heaters, allows for sensors to be placed in the thermal controller, SCR node and/or single contactor node: all protected by a feeder/breaker.
An astonishing 12 heaters can collectively operate from a single feeder/breaker, whilst each individual heater is monitored by a hub/ switching circuit node. In the event that the sensors detect an arc flash across any compartment: the feeder/braker will instantly close the line-up, thereby further minimising any arc damage.
Semiconductor fabrication creates a number of waste gases, which can be corrosive, pyrophoric and potentially explosive. Often, diluting these gases with nitrogen (N2) is an early step in the abatement process to make sure the gases stay below the lower explosive limit (LEL) or reduce corrosive effects. However, the use of nitrogen can cause condensation and deposits, as well as leak out of the system. Here, Rob Johnston end user business unit director at industrial electric heater manufacturer Watlow, explains how this can be prevented.
Abating hazardous gases
One way to abate hazardous gases in process exhaust streams is to dilute them using a less harmless gas. In semiconductor fabrication, nitrogen gas is often used because it is readily available and effective at diluting more hazardous gases prior to other abatement steps.
A good example of this solution can be seen with potentially explosive gases, such as hydrogenated gases. These gases have an explosive range, a specific range of gas concentrations where explosion is likely to occur. Gas concentrations must be kept below the lower explosive limit (LEL), which is the minimum concentration of gas needed to reach this explosive range. But mixing with nitrogen lowers the ratio, making the gas too lean to pose an explosion risk.
That said, when introducing a new gas into the exhaust stream, condensation can cause issues by creating deposits in the system. This eventually creates clogging, leading to unplanned downtime. The addition of nitrogen poses a dilemma, forcing plants to choose potential line shutdown in order to ensure safety — a trade-off no one wants to make.
An alternative solution
If adding room-temperature nitrogen into a waste stream causes condensation problems, heating the nitrogen can be a sufficient remedy. However, getting nitrogen to temperature has proven to be a tricky engineering problem.
One of the biggest issues is with nitrogen leaks. Introducing a heater into the system can potentially create another place where nitrogen can leak, meaning that not all the nitrogen gets into the waste stream for abatement. If the leak is severe enough, the hazardous gases will not be diluted enough to ensure safety. This means that a potentially explosive gas might still be well within its explosive range.
There is limited space that can be taken up within an existing an abatement system, which limits the number of components, controllers and wires that can be added to the system, especially in multi-chamber setups.
The no-leak last resort
meaning that semiconductor manufacturers no longer need to tradeoff between safety concerns and possible downtime caused by the need to flush clogged exhaust systems.
To overcome these challenges, a compact, no-leak heater design can ensure the reliability of exhaust abatement systems in semiconductor fabrication. For instance, Watlow’s FLUENT® in-line heater is designed to allow movement of a fluid or gas over the heater surface without any loss of the fluid or gas through the outer shell.
A no-leak design not only includes a seamless stainless steel outer protection tube, but it also has the heating
A first step in the abatement of waste gases in semiconductor fabrication should be dilution with nitrogen gas. However, engineers must consider the issues that can arise and consider opting for a solution that covers all potential issues associated with nitrogen heating. In this case, a design that is modelled around eliminating leakage can prevent clogging and downtime.
For more information about the FLUENT® heater, go to www.watlow.com
Companies don’t buy an uninterruptible power supply (UPS), they buy a guarantee of clean, continuous power for their critical load. So, what type UPS should a professional organisation buy and how much should they spend?
Single v parallel UPS
Availability is a key consideration in today’s on demand world and much is written about increasing system availability and resilience through the use of parallel redundant UPS. It is true that parallel redundant UPS, and in particular modular UPS, deliver the highest availability (Centiel’s CumulusPower’s class leading availability is currently “9 nines” or 99.9999999%), however, not every application requires such very high availability and for these organisations, a single free standing UPS like Centiel’s PremiumTower is a simple cost-effective solution.
A vast number of stand-alone UPS are available and a Google search on “uninterruptible power supply” will show a bewildering number of products to choose from but beware of “cheap”. Would you buy the cheapest parachute?
Buy cheap, buy twice
Cheap UPS are cheap because they are old technology and use cheap components.
A well-made, well specified and well-maintained UPS will have a typical useful working life of over 10 years. It will be permanently installed into the
building’s electrical infrastructure and will be an operational challenge to repair or replace.
Cheap components like capacitors and fans have a useful working life of 3-4 years whereas higher quality components will last 8-10 years. Cheap batteries, with a design life of 5 years, have a typical useful working life of 3-4 years at 20°C whereas 10 year design life batteries will typically last 8 years at 20°C.
It is expensive to replace capacitors, fans & batteries every 3-4 years rather than every 8-10 years.
Total Cost of Ownership (TCO)
All costs, not just purchase price, must be considered when installing a UPS. The two most important UPS running costs are energy efficiency and maintenance.
UPS operate 24 hours/day, 365 days/year and an inefficient UPS wastes expensive energy and creates heat that must be cooled. If a 100kW UPS is only 1% less efficient than the most efficient UPS system it is wasting 1kWH every hour. At 50.897p/kWH (accurate at the time of writing) this UPS is wasting £4,458p/a, or £44,585 over a 10 year useful working life. Saving c.£1,000 when purchasing an inefficient 100kW UPS is a very expensive mistake.
UPS systems must be properly maintained to remain both efficient and reliable, so maintenance costs are an important consideration. Beware of third-party companies offering “cheap” UPS maintenance. They are cheaper because they do not fully product train their engineers, keep stocks of components or keep their technical documents updated. Failing to properly maintain a UPS causes massive disruption to an organisation’s operations when the UPS fails to work when needed. Would you allow an untrained person to pack your parachute?
Summary
In today’s economic climate, cost reduction is a key consideration but considering purchase price in isolation could prove to be an expensive mistake.
Over a UPS’s working life it will be cheaper to purchase a latest technology, high quality UPS with very high operating efficiency and an excellent, cost effective maintenance regime than to purchase a cheap alternative that lacks these benefits.
Don’t get buyer’s remorse. Work with a manufacturer like Centiel with a reputation for high quality, leading edge technology products, listen to their advice and consider all costs, not just the initial purchase price.
Centiel manufactures and supplies UPS to some of the world’s leading institutions and their comprehensive product range contains class leading free standing and true modular UPS. For more information about Centiel’s range of UPS solutions please see: www.centiel.co.uk
The upcoming 2023 Health & Safety Event will be held at the NEC, Birmingham from 25- 27 April. It is the quintessential event dedicated to improving health & safety and security of employees, workplaces and assets.
As the UK’s largest comprehensive Expo, it is conveniently co-located with five other leading sector events, over an impressive 20,000sqm area.
The five co-located sectors are: fire safety event, security event, professional security office event, workplace event and national cyber security show. With representatives from areas
such as asbestos control, environmental waste, occupational health and wellbeing, lone working, slip & trip prevention, PPE, cutting-edge cyber security technology, security officer training, fire safety solutions and workplace best practice: it is the unmissable health & safety event of the year.
Last year’s event has over 8,000 visitors, from sectors as diverse as agricultural, emergency services, food processing, manufacturing, retail and mining.
The event gives huge, direct brand exposure to delegates: 79%
of which have purchasing power or influence and 87% are at managerial or at senior level responsibility. The co-location with the other sectors creates a synergy for exhibitors and visitors alike, across all aspects of health & safety, making the three days fruitful for networking and purchasing power.
The Health & Safety 2023 Event runs from: 25- 27 April, Hall 4, NEC, Birmingham.
www.healthandsafetyevent.com/co-located-events www.healthandsafetyevent.com
working. From initial assessment and advisory services we propose dust control solutions, including constant
and programmes of training in understanding dust and dust management, appropriate to the levels of personal responsibility.
We are using HSE2023 to launch the new MAXVAC AQM Supervisor platform for real-time air quality management in the workplace. Like a pair of ears listening out for discrepancies and non-conformances in air quality across the workplace, It brings data to life with real time graphic visualisation, raising alerts and alarms when limits are breached, when filters are blocked, when airflows are compromised and when potential hazards are looming.
HSE2023 is running for 3 days over 25-27 April 2023 and we welcome you to come over to booth 3A/2 for a chat. Check out www.healthandsafetyevent. com/exhibitors/airflo-dynamics or email sales@airflodynamics.com and we'll send you details and your personal invite.
The optrel swiss air respiratory protection system enables wearers to breathe in air of exceptional quality, similar to that found in the Swiss Alps.
The TH3 respiratory protection system features a ventilated half mask that creates a breathing space around the wearer's mouth and nose, reducing breathing resistance through positive pressure. swiss air is self-sufficient and compatible
Marlowe Software, Risk and Compliance offers integrated platforms to enhance visibility, increase productivity and reduce risk. We drive client growth and unlock asset potential by the services offered from our three brands: William Martin Compliance, Elogbooks and Barbour EHS.
William Martin creates next generation building compliance by fusing clever consultancy with cuttingedge technology. Whatever your sector and wherever you are, we give you the support you need to keep compliant, strong, and successful.
Elogbooks enables our clients to maximise their buildings' performance by providing support around the clock. With our team of experienced problem solvers and our unrivalled platform, you gain full control of your facilities' performance.
Barbour EHS provides a simplified, all-in-one solution to help your organisation remain compliant. Our service brings you regional legislation and guidance from over 800 trusted industry sources, plus a wealth of exclusive supporting content including legislation summaries, legal register templates, how-to guides, model policies and editable training tools.
For further information go to www.marlowe-src.com or visit us on Stand 3/F52
Global Facilities are excited to be exhibiting at the prestigious Fire Safety Show at the NEC in Birmingham this April. The team will be on stand 3A/E60, discussing our fully comprehensive Fire Safety services, while serving drinks and showcasing our freshly launched website.
In 2021, there were a staggering 280 fire-related fatalities in the UK. Our aim is to drastically reduce this number by informing and educating customers, and delivering end-to-end fire safety services that protect people. Our expert team can carry out in-depth inspections and service plans, through to installation and maintenance of essential
equipment, such as alarms and fire doors.
We’ll talk to attendees about the recently updated Fire Door Regulations, which state that fire doors should be checked more regularly and the importance of them emphasised to residents.
Come and see us between 25-27 April on stand 3A/E60,
Regarding workers' safety, some workplaces are more dangerous than others. Companies have a duty to ensure that every employee returns home safely at the end of every day, even in emergency situations.
Protecting human life and health is fundamental to our operations at Dräger. Our range of safety equipment has been developed to detect a hazard, protect against a range of hazards and if necessary, escape from that hazard.
Protection. Detection. Dräger
Visit our website at www.draeger.com for more information or email marketing.uk@draeger.com
The 2023 Safety & Health Expo will be back at the ExCeL, London from 16-18 May as the UK’s largest health & safety event. It is the perfect arena for showcasing new products, maximising brand exposure and increasing ROI, through the latest sales pipelines projects.
The Safety & Health Expo is conveniently co-located with three leading other events: facilities management, fire safety (FIREX), and security (IFSEC), providing a streamlined experience for exhibitors and delegates.
The Safety & Health Expo will look at
pressing solutions around site safety, hazardous material management through to the perils of lone working. There are IFSEC representations from integrated security systems: including SMART buildings, cloud security and surveillance. The Facilities Show showcases the latest PPE workwear and e-learning training and FIREX will be focussing on pressing concerns, such as fire safety legislations on single staircases in high-rise buildings.
Previous exhibitors and visitors have praised the collaborative approach, enjoying the vast opportunities to network with a diverse range of professionals from construction, local government facilities services to
With a staggering 23,000 visitors and over 600 exhibitors, it is the perfect opportunity to meet senior heads of departments, directors and owners. With one in four attendees having an annual combined purchasing power of £1 million, this is the best event for increasing ROI and benefitting from cohesive networking opportunities.
The 2023 Safety & Health Expo will be at the ExCeL, London from 16-18 May.
www.safety-health-expo.co.uk
Tmore safely, so why not come and visit us at the Safety & Health Expo 2023 in Excel, London on May 16th-18th on stand SH.1452 and see for yourself.
You can watch a full demo of the Compliance Genie and have a chance to win a brand-new tablet on our Whack-A-Bee!
www.be-safetech.com/features
I
ACognitica AI is leading this transformation. Utilizing cuttingedge AI and machine learning technologies, we have developed breakthrough products to solve complex industrial safety problems. Our solutions represent a revolutionary step forward in enhancing industrial safety and reducing the risk of accidents that lead to injuries and even fatalities.
Cognitica AI products are capable of recognizing and preventing various types of safety hazards. They can recognize human presence in blind spots of industrial material handling vehicles (like forklifts), absence of PPEs, fire breakouts and unauthorized personnel, and many other.
One of our biggest strengths is the versatility of our products, enabling tailoring them to our customers' needs. The possibilities for the use cases they can solve are endless. With our advanced AI and ML capabilities, imagination is the only limitation to the capabilities our products.
Our products can be applied to ensure safety around industrial mobile equipment, large stationary machines, hazardous spaces,
and other safety considerations.
Cognitica AI's solutions are a giant leap ahead of other products in the market. Cognitica AI is revolutionizing industrial safety!
Stall at the London Health and Safety fair: SH1239
Contact M +358-400-887122 jukka.ahvonen@cognitica.ai
Be aware of rodent issues, before they become business problems
PestSense introduces a radically new approach to risk-based digital pest management for facilities managers
PestSense is excited to preview its new software platform and Predictor 10 smart rodent station, which uniquely provide insights into the nature & scale of rodent activity to enable pre-emptive actions to be taken.
Our ‘IPM 2.0’ approach minimises environmental impact, as the PestSense system monitors non-toxic bait consumption and can thus assess the extent of rodent activity. An optimal mix of non-toxic and chemical based pest management can therefore be employed, with toxicity only introduced for limited periods to clear up infestations.
This new risk-based approach to digital pest management for facilities managers is designed to provide greater insights and proactively minimise customers’ risk exposure. The PestSense system monitors 24x7 and enables pest management efforts to be more effectively targeted and cost effective, whilst providing evidence of cause & effect for audited facilities. Pest management can at last be integrated
alongside other digitised building services.
Please visit us at Stand FM.4671 to learn more or attend our Smart Buildings Theatre session: May 16th 2023, 15.20–15.40, Digital Pest Management: The Future of Rodent Infestation Control.
PestSense Pty Ltd
7 Bell Yard, London, WC2A 2JR T +44 20 8638 7131
We all hear about car, van and truck crashes every day. But vehicles don’t crash. People crash. they just happen to be in a car, van or truck at the time. If you employ or manage those people then you have legal compliance responsibilities to ensure any work activities that involve driving are properly managed so they don’t put your drivers or other road users at risk.
Driving for Better Business is a completely free programme helping employers reduce work-related road risk and improve operational efficiency. We do this by sharing guidance on compliance requirements, case studies of good practice, and the business benefits from good driver management that include improved performance, greater efficiency and important cost control.
At this year’s Safety and Health Expo, Campaign Manager Simon Turner will be presenting in the OSH Operational Excellence Theatre at 14:55. Simon’s presentation brings important new insight into the management of driver safety and will look at:
Refreshment Systems Ltd is a wellestablished vending machine business based in the heart of Yorkshire, serving customers throughout the UK since 1967. With over 50 years of experience in the industry, they offer innovative technology and solutions to meet the unique needs of every customer.
The company provides a wide range of flexible options to suit their clients' requirements, from simple vending machines to more complex systems, all equipped with the latest technology, including touch screen displays and cashless payment options.
Their innovative remote monitoring system ensures that machines are always fully stocked and running smoothly, making them easy and convenient to use.
RSL is committed to providing excellent customer service, with a team of experts always available to offer advice and support, ensuring that vending machines are always running smoothly and providing customers with the refreshments they need. The company also offers a range of other
t What is distracting our drivers on the road?
t A quick recap of a safety manager’s legal responsibilities
t How to identify important gaps in driver safety management
t New free resources to help with driver communication
Safety & Health Expo: Stand SH1670
Contact Details: www.drivingforbetterbusiness.com admin@drivingforbetterbusiness.com
refreshment solutions, including water coolers, 24/7 Hot Food Machines, and Coffee Machines, ensuring that they have a solution that is perfect for every client.
Overall, RSL is a reliable and experienced vending machine business that offers innovative technology and flexible solutions, combined with excellent customer service.
Their 50 years of experience in the industry ensures that they have the expertise to provide solutions that meet the unique needs of every customer. Contact them today to find out more about their services.
www.refreshmentsystems.co.uk
Dustcontrol UK will be exhibiting a range of its construction dust extractors and factory-fitted centralised dust extraction units at Safety & Health Expo 2023.
Exhibiting at stand SH2650, the Dustcontrol team will be showcasing and demonstrating its industrial H Class dust extractors including the DC 1800, DC 2900, and DC Tromb 400, in addition to its range of air cleaners.
The DC Tromb 400 is Dustcontrol’s most powerful single-phase dust extractor, having been designed to meet modern safety requirements and work in conjunction with tools that have become ever more efficient on today’s construction sites.
The powerful DC 2900 range will also be on display, which can be used for industrial vacuuming or on-tool dust extraction. Its suction casings make it particularly effective for dustcreating activities.
The company, based in Milton Keynes, has more than 50 years of experience in developing cyclone based portable dust extractors and centralised
vacuum systems to fit client requirements in the manufacturing, engineering, food processing, construction, and demolition industries. They are experts in problem solving with a high technical capability of capturing dust at its source, then containing and transporting it to a convenient discharge solution.
For further information on Dustcontrol UK's products, please call 01327 858001, or email sales@dustcontrol.co.uk.
Alternatively, for further information on Dustcontrol UK, visit www.dustcontrol.uk.
Vismo will be on stand SH1474 at the Safety & Health Expo 2023. Visit Vismo and learn more about our award-winning technology, and the benefits to your business and lone workers.
Vismo will demonstrate its mass notification feature that allows employers to notify all lone workers, or a specific group or individual, to provide safety guidance about a nearby risk. No matter the location, Vismo actively or passively tracks employees’ location and understands their risk status. A discreet alert can be activated by lone or other workers - via a panic button in the Vismo Locate & Protect App on their smartphone to notify their employer of an incident or risk 24/7.
By implementing Vismo’s technology, organisations will have an effective communication plan that works if an emergency happens, ensuring business continuity is maintained. And employees gain peace of mind knowing they can be contacted in an emergency and immediate assistance will be provided.
We will demonstrate handheld satellite devices, ideal for locations across the UK that have little or no
mobile coverage. All devices fully integrate into the Vismo platform.
For more information, see below.
www.vismo.com
T +44 (0) 194 616666 enquiries@vismo.com
The UK has introduced new environmental regulations called the Medium Combustion Plant Directive (MCPD) and the Industrial Emissions Directive (IED) to reduce air pollution and improve air quality.
The MCPD applies to combustion plants with a thermal input of 1-50 MW, setting limits on emissions of nitrogen oxides, sulfur dioxide, and dust. The IED covers a range of industrial activities, including tank storage, and sets limits on emissions of nitrogen oxides, sulfur dioxide, particulate matter, and volatile organic compounds. Operators must use best available techniques to prevent and reduce emissions and establish a reporting framework to demonstrate adherence.
Well-maintained tank storage facilities do not suffer product loss, environmental enforcement notices, litigation claims, criminal prosecution, unplanned outages, tank corrosion and the associated bad press. Furthermore, the quality of stored product remains at a premium, resulting in minimal production issues and product quality does not decline.
Tank breather valves are critical safety devices that are often overlooked on tank storage facilities. Designed to maintain safe and equal pressure in a storage tank unit even when it is being filled or under sudden changes in ambient temperature and will also prevent media leakage to the atmosphere.
These valves must be designed, manufactured and certified to the International Standard API2000. This level of certification will demonstrate use of the best available techniques to protect you, your facility and the environment.
According to this standard every production valve must achieve at least 75% of the set pressure with a fixed minimal air feed flow rate defined in Table 10. It must also demonstrate control of the required pressure setting. A certificate that connects the individual valve serial number with the valve functional performance is essential for demonstrating competence and integrity.
Demonstrating best practice with management of aging assets is essential for both the environment and your facility.
t Traceability of individual assets
t Definition of specific maintenance tasks and test objectives
t Service frequency
t Asset suitability for intended use
t Familiarisation of the applicable International Standards
t Competence of maintenance personnel
t Suitability of Test equipment including calibration accuracy
t Certification detail and accuracy with reference to relevant International Standard (from new and at service)
Following this guidance will reduce emissions from poor venting, improve site operating efficiency, save money on emission loss, prevent site downtime, protect staff from inhaling potentially hazardous media and protect the environment. As well as evidencing compliance, duty of care and best
A recent case study demonstrated that replacement of cheap, untested leaking valves were replaced with quality leak tight models. The Environment agency were delighted to find leak rates were reduced from the equivalent of 200 double decker buses to less than 20% of one bus. A saving of over £8300 in lost gas per year. The cost of the replacement valve was £6500 so a payback was achieved in less than 1 year and the happy operator received a licence to operate with a clean bill of health.
The Government Environmental Impact Cost as calculated by the IPCC dropped from £63,000 to just £57.
Both the MCPD and IED regulations are aimed at reducing air pollution and improving air quality in the UK. If you operate a tank storage facility in the UK, it is important to ensure that you are complying with these regulations to avoid penalties and to protect the environment. With this ever-increasing focus on our environment and air quality, tank storage facilities are required
to provide reporting metrics and quantify emission reduction as part of the ESG, Net Zero and ISO 14001 environmental reporting.
Revolutionising breather vent testing is ‘Vent-Less’, the world’s first mobile and automatic test bench which checks functionality, performance and leakage rate.
Developed with artificial intelligence and QR code technology, Vent-Less performs comprehensive test results in a fraction of the time required to test the valve manually. The test report can be produced instantaneously including photographs and QR code technology.
For more information, see below.
www.assentech.co.uk
HARTING has developed new solutions for rail vehicles which focus on the safety and durability of the entire infrastructure.
The Han® HPR (High Pressure Railway) VarioShell is an IP69K housing system which has been specially designed for jumper applications. As the cover is removable, the housing/hood can be installed from both inside and outside the rail vehicle.
The VarioShell can be used as a surface or panel mounted housing and is a robust alternative to distribution boxes for installation on the roof, outer wall or bogie.
PPS launched new fire safe single source wall solution for all applications
Paroc Panel System in collaboration with BTS Facades & Fabrications, has launched Vantage® PPS – a fully certified single source full wall system –an all-in-one solution, which facilitates installation twice as fast as a comparable built-up system.
The Vantage® PPS is a class-leading noncombustible (Euroclass A2-s1,d0) sandwich panel with a structural non-combustible (Euroclass A1) stone wool core, combined with the CWCT tested Vantage® SF Rainscreen front face, tested to the tested to the latest BS84142:2020 standard.
Vantage® PPS system offers a number of benefits: its long-spanning capabilities reduces the need for secondary galvanised steel purlins for significantly faster construction times, reduced material use and potential cost savings. It also offers reduced cold bridging, excellent acoustics and, with panels from 80mm to 300m, a wide choice of thermal insulation options and U Values are available.
Specifically, the collaboration brings the air and water-tight structural support base of Paroc Panel System panels, manufactured using AST® Technology to ensure their high tensile strength, reliable longevity, and fire resistance to the BTS Vantage® SF Rainscreen range, itself CWCT tested and provides the ultimate design flexibility.
The Vantage® PPS system is ideal for a wide range of construction applications, including data centres, retail developments, leisure, and other commercial buildings where a fast, fire-safe, water-tight solution is required to be installed.
For details about the Vantage® PPS system panel visit https://www.parocpanels.com/ en-gb/news/2020/vantage-pps
or contact: Paul Kinsey, UK Representative T +44 (0)7876 563 175
The Han® HPR HPTC (High Performance Transformer Connector) has been developed to meet all the requirements of the rail market. Hoods, housings and cable glands have been optimised for outdoor use, ensuring the connection between pantograph, transformer and train busbar remains stable.
Neither shrinking nor taping are required in the assembly process and the interfaces are quick to prepare; simply crimp the contacts, insert the insulating body with shield contact into the housing and close the cover.
The Han® HPR TrainPowerLine (TPL) replaces existing
solutions such as UIC, power or Y-distributors for train busbars. It is tailored to modern trains running in a network and can reliably supply all the electrical equipment and systems of the train.
The housings are equipped with Han® HC Modular highcurrent contacts that transmit power up to 800 A / 5100 V DC / 3000 V AC.
To learn more about HARTING’s range of rail products and solutions, please visit www.harting.com/UK/ en-gb/markets/transportation or email salesUK@ harting.com.
TYDE is excited to announce the launch of their new range of Dudley ‘Victoria’ Outlet Valves.
Along with an improved version of the Dudley cable operated Victoria Valve, the all-new Mechanical Dual Flush Victoria Outlet Valve is now available to be ordered from TYDE’s production centre located in the heart of the midlands.
The new Victoria Valves are both WRAS approved and can be serviced in under 5 minutes providing installers with a real time saving advantage. Both of these high-quality Outlet Valves are fitted with long life silicone seals and a choice of button mounting options. The new Victoria Valves offer water saving options with full and reduced flush options as standard. For maintenance or replacement, the robust but simple to use bayonet fixing enables the valve body to be quickly and simply removed from the cistern making the Victoria Valve fast and simple to install and maintain.
The new Dudley Victoria Valves are excellent additions to TYDE’s extensive product range offering both quality and reliability and for peace of mind, the new Victoria Valves come with a 3-year warranty and can be ordered for next day dispatch. Order yours today!
The NMBS Exhibition is the UK's leading exhibition for independent building, timber, plumbing and hardware merchants. TYDE will be there in April, on stand 162 keen to show you what they can offer. There will be product demonstrations, exclusive discounts and special rebate offers for members.
The Design in Mental Health Exhibition aims to cover a wide range of topics within the design, build, management and maintenance of facilities for mental health. 2023 marks the 10th edition of the live event and will be held at the Coventry Building Society Arena on 7th and 8th June.
The ASCP Conference is dedicated to safety and compliance in the social housing and facilities management sectors. The event is being held at the Telford International Centre on 14th and 15th June. Last year TYDE scooped the Highly Commended Award for the OSMO F1 concealed cistern. Visit them on stand D60. They will be displaying their British made, water-efficient products and you can talk to their experts about how they can help with your legislation and compliance challenges.
The Installer Show is the UK's largest heating, plumbing and electrical show with around 300 exhibitors, 100 speaker and 10,000 visitors expected. TYDE will be exhibiting at the annual go-to event for thousands of installers from across the UK at the NEC in Birmingham from 27th to 29th June. Pop along and speak to the TYDE team on stand B32.
After the success of Screwfix Live 2022, TYDE will be returning to the biggest trade and DIY show in the UK in September with more deals and giveaways.
The long established PHEX Plumbing & Heating Exhibition brings together the biggest names in plumbing and heating every year. TYDE will once again be exhibiting at the Manchester and Chelsea shows. Visit them at Old Trafford in October and Stamford Bridge in November to get access to exclusive deals and hear about the latest regulations changes.
Alongside the above events, TYDE will be hosting a number of Trade Days at various merchants across the UK, follow them on their social media pages for more information on venues, dates and times!
For more information visit www.thomasdudley.co.uk/tyde or email us info@tyde.co.uk
Iwill be held in Belfast, Northern Ireland from July 30th to August 4th 2023. ICCM is known as the premier international conference in the field of composite materials and was first held in 1975 in Geneva and Boston. Since then, the conference has been held biennially in North American, European, Asian, Oceanic, and African cities.
Over the few days, hundreds of leading researchers and practitioners across the board will come together to discuss and report their findings and ideas on the latest developments in the advancement and exploitation of a wide range of composites materials and structures.
You can expect themed talks and seminars to take place on subjects
Dincluding material development, testing, modelling, manufacturing and design, all of which should provide a comprehensive global snap-shot of the state-of-the-art.
2023 will be the first time that ICCM has been held in Belfast which in itself has a strong and extensive history with its rich pioneering and engineering heritage. As a prominent powerhouse of the Industrial Revolution, Belfast is the ideal choice for ICCM 2023.
Professor Brian G. Falzon will chair the conference, and be joined by other Plenary speakers such as Dr.
Kenichi Yoshioka – Toray, Dr Chantel Fualdes – Airbus, Mr Mark Braniff -Spirit AeroSystems Inc., Prof Pedro Camanho - U. Porto, Prof Michael Hinton – HVMC, Prof Nguyen Dinh Duc – VNU, and Dr
ia-Stron are excited to be exhibiting at the International Conference on Composite Materials (ICCM23) at the ICC Belfast between 30th July and 4th August 2023.
Visit us on stand 6, where our team will be happy to talk about the benefits of single fibre measurements and our unique automation and sample handling solutions. We will also be showcasing two of our instruments: fibra.stress and LEX/IFSS. fibra.stress is a high-precision, automated tensile tester with integrated dimensional capabilities. Dimensional measurements are crucial for normalising tensile data, reducing data variability and helping to discriminate subtle changes in the fibres. fibra.stress also captures in-situ dimensional measurements throughout the tensile test, from which the Poisson’s ratio can be calculated. This instrument supports a wide range of fibre types/ gauge lengths and multiple testing methods.
The LEX/IFSS uses the microbond method to provide interfacial shear data on the debonding force of micro-droplets on single fibres and filaments. The camera and light source enable users to visualise the fibre/droplet during the test and record the mode of failure with video and image capture. The microbond method can be applied to a wide variety of fibres and matrices and presents a strong alternative to pull-out and fragmentation testing.
Phillip J Crothers - The Boeing Company.
Register for ICCM 23 now, or find more information about the conference below.
www.iccm23.org/registration
Contact details:
T +44 (0) 1264 334700 enquiry@diastron.com www.diastron.com
Interface Force Measurement Solutions (Interface) is a UK company specialising in the supply and distribution of high-quality sensors and associated electronics and displays for a wide variety of industries. Working previously with clients such as Airbus, BAE Systems, and Formula One Teams, we spoke with Tony Rokins, Business Development & Pressure Mapping Specialist, who explained some of the companies well known products.
“Our product portfolio is applicable to many industries. For instance, we are well known for our high-quality pressure mapping systems that are used by many of our automotive and motorsport customers. Our sensors deliver highly accurate,
repeatable measurements and many of our load cells are used by calibration houses as calibration reference devices. Our high-quality, yet competitively priced 3 and 6 axis load cells are used for many R&D, renewable energy and robotic applications.”
In terms of recent developments, Tony continued, “Being responsive to our customer’s needs and being able to offer a high-quality product with strong product knowledge at a competitive price with the best possible lead times is our number one priority. Last year we launched our range of G-Series Load Cells. The range comprises of miniature and small sensors for industrial applications, with capacities starting from just 4.5N Newton up to 200kN with metric threads. These are high-performance devices but aimed at more cost-conscious applications. This is a new market for us, but we have already had increasing interest. We also launched our brand-new e-commerce website on the 1st of April for the G-Series that showcases Interface load cells at competitive prices with all the convenience purchasing online offers,” stated Tony.
The new e-commerce website offers G-Series load cells on short lead times with next business day delivery for small quantities. Following its successful launch in 2021, it has become an increasingly popular product range for students, industrial
engineers, OEMs and anyone requiring a small form force sensor offering accuracy, repeatability and Interface quality.
In the future, Interface is keen to continue its growth trajectory for 2022. Tony mentioned, “we are also working on new, wireless force and vibration sensors for remote monitoring in systems such as luggage carousels. One more area we are pushing for growth is with XSensor’s pressure mapping systems, particularly in the Hi-speed systems designed for high-speed impact or crash testing and tire footprint research. These systems are capable of capturing data up to 2,500 frames per second. The tire sensor can be driven over at speeds of up to 140kph. I believe this is a unique capability we can bring to the industry.”
As the company looks to continue strengthening its position with its customers in its more traditional markets of aerospace, automotive, motorsport, Universities and alternative energy research, it will be attending some expos over the next 12 months and be readily on hand to discuss any questions you may have about force, torque, pressure mapping or pressure, level & temperature measurement.
These expos include Instrumentation, Analysis & Testing Exhibition on the 16th of May 2023 at Silverstone Wing, Silverstone Race Circuit Manufacturing & Engineering at the NEC, Birmingham 7th & 8th June, Stand H48
Automotive Test Expo, Messe, Stuttgart, Germany 12th to 15th June and Advanced Engineering 1st & 2nd November 2023 Stand P172 also at the NEC, Birmingham.
T 01344 776666
Fwear should be part of regular maintenance.
Visual inspection can show some obvious signs such as scored surfaces, pitting or material worn away especially to the flight sides on the screw. Accurate digital measurement of screws, barrels and associated parts provide a clear indication of the amount of wear and what action is needed.
At Magog Industries, our engineers conduct Inspections at our workshops or alternatively carry out the Inspection at the customer’s site. A Report on the condition is made available with recommendation for repair, re-design and replacement. In addition, Magog also offer advice regarding surface coatings to extend service life.
Refurbishment and repair is a cost effective method compared to new replacement.
Depending on the condition it is possible to rebuild flights, grind and polish a screw 3-4 times during its lifetime but is not recommended beyond that.
For more information contact Magog Industries:
T 01920 465201 enquiries@magog.co.uk www.magog.co.uk
As
The Belgian fifth-generation family company, founded in 1883, specialising in the import, trading and export of Tropical Hardwood from Africa, Southeast-Asia and South America, Scandinavian and North-American Softwood, North American and European Hardwoods.
Sustainability and reliability are an essential part of Vandecasteele Houtimport’s DNA. The company is determined to achieve the goal of trading only certified timber by 2025. As far as European Softwood and Hardwoods is concerned, we are at 100% certified. The challenge, however, lies with the Tropical hardwood. Today we are at 80% certified!
We’re living in challenging times. With over 140 years of experience and Belgian savoir-faire, we know there’s only one way - forward.
Vandecasteele Houtimport has a clear vision: only certified timber has a future. Substantial investments have been made over the years to be able to realise this future perspective. You cannot achieve this goal overnight. This is a long term aim, in which all partners must be included. If we want to assure our customers that we keep our promise to only trade timber that comes from wellmanaged, certified forests, we need to be sure that all our trading partners share the same strictest certification and sustainability processes as we do.
This has resulted in several actions within the company. External experts assisted with the procedures and protocols. The team at Vandecasteele was reinforced with 2 forest engineers in Brazil. This sends an important signal to our suppliers. They know that doing business with Vandecasteele Houtimport means: complying with a set of procedures which are continuously refined and updated. All timber transport requires our approval. When in doubt the timber is not accepted.
Masters in diversification
Vandecasteele has a long-term commitment to preserving the forests. The family business imports more than 130 different species of timber coming from 40 countries and has over 120,000 cubic meters in stock, mainly certified
hard and softwoods.
We support the “lesser known species program” LKTS of FSC® Denmark with which we want to help promote the use of lesser known species. We keep these lesser-known species in stock, we promote them and offer them as alternatives for the popular, well-known timber species. There are over 15 certified timber species which can be used as alternatives for Siberian Larch. Such as FSC®
Certified Niové, Movingui, Mukulungu, Tali, Padouk, Jutai, Angelim Amargosso, Red Louro, Sucupira Preta, Sucupira Vermelho, Jatoba, Mandioquira, Cumaru, Basrolucus, Guariuba, Tatajuba, European Oak, Muiricatiara, Purpleheart and Louro Preto.
RE:THINK WOOD
Timber is often prescribed from a specific well-known timber specie. From the point of view of responsible forest management, we have to think differently. What
is the purpose of the timber? What durability class, color and structure of the timber is needed for a specific application?
Preservation of the forest
In a well-managed forest, only mature trees are harvested, which amounts to one to three trees per hectare. After that, felling will not take place for at least 25 years. In this way, the forest is preserved for the future.
Rethink everything
Our goal has caught the eye of a more discerning clientele. We notice a positive evolution in consumer purchasing behaviour. Customers are increasingly asking questions about certification and the provenance of the timber. Buyers are becoming more and more aware of the need to use certified timber. Importing tropical wood goes further than just asking for certified timber. There is a continuous evolution, because of new insights, new legislation, etc.
We work together with external experts, we are broadening our internal knowledge and we continually make progress.
We want to see and monitor a stronger application and support for certified timber worldwide. Vandecasteele communicates continuously with the users via the website and campaigns in order to spread that message.
Since the year 2000, Vandecasteele Houtimport has committed itself through the Corporate Durability Charter by signing up to environmental objectives exceeding the applicable legislation.
In October 2022 we obtained the United Nations “SDG Champion Certificate” from CIFAL Flanders.
For more information, see below.
T +32 56 43 33 00
www.vandecasteele.be
One of the UK’s leading drainage and wastewater specialists is promising to
Lanes Group plc has proven it can significantly speed up the previously difficult process of lining both rainwater and
The company has become the first contractor in the UK to line tall building drain stacks using the Brawo Magnavity LED light cured in place pipe (CIPP) system supplied by trenchless technology specialist S1E.
The system makes lining drains in high-rise buildings much easier and more sustainable, just at a time when problems caused by faulty drainage systems are becoming a maintenance priority for social housing landlords.
Mark Scott, Manager of the Lanes Birmingham depot, which is leading the company’s investment in the Brawo Magnavity technology, said: “Stack repair has been a challenging problem in high-rise buildings for years.
“This technology is a game-changer. It means stacks can be lined more quickly, cost-effectively and to a consistently high quality standard. So, landlords can be confident a significant maintenance headache can be resolved effectively for the first time.”
Lanes is lining stacks on high-rise blocks of flats for a main contractor working for a West Midlands council. The results have been so successful that more blocks are being added to the programme.
The process involves inserting a resin-impregnated flexible felt liner, often with a polyurethane or polypropylene coating, into a pipe. The resin then cures to create a tough, waterproof pipe-within-a-pipe, eliminating defects.
The light head has 96 LED lights, with an electric magnet on the front which decouples from a second magnet to carry out the curing run along the pipe. The Brawo Magnavity system uses LED light to cure the resin. Its LED light array is combined with a powerful electric magnet that holds the lights in place as the liner is inverted into the pipe with compressed air.
Once the liner is in place, the light pack, with its 96 UV LED lights, detaches from the magnet and cures the resin at a speed of up to 0.6 meters a minute as it is pulled back through the pipe.
Because the magnet guides the liner so effectively through the pipe, it can negotiate multiple bends, up to 90 degrees, something other CIPP systems fail or struggle to do.
The specialist 3D liners used by Lanes are flexible so accommodate the 70mm to 100mm changes in diameter in the stack pipes being lined.
The system, which can also be used on horizontal pipe systems, also allows liners to be ‘blind shot’ into pipes from a single chamber, rather than between two chambers.
The advanced low-odour resin developed by Brawo is stable until exposed to UV light, giving the Lanes lining team all the time it needs to prepare the liner for curing. By contrast, ambient cure liners must be inserted in a specified time before the resin starts to harden.
Just two Lanes operatives can operate the system which can be quickly set up in a small space to line both
vertical and horizontal small-diameter pipes much more quickly than conventional systems. Lanes is able to install and cure each of the 47-metre-long stack liners for its West Midland client in around two hours.
Mark Scott said: “The same task would be impossible with hot water CIPP due to the weight of the water in the liner, and would be risky with ambient cure CIPP because of the unpredictability of curing times, and the production of toxic vapours during the process.”
For more information, see below. www.lanesfordrains.co.uk
Volatile weather generated by climate change is likely to put more strain on rail drainage systems than ever before. Innovative thinking and technical excellence from Lanes Group plc is delivering solutions.
Whether it is solving challenging flash flooding problems at a London rail terminus, maintaining stations on the UK’s newest railway line, or carrying out drainage investigations for one of the UK’s most important rail upgrades, Lanes has proven capability and capacity to get the job done.
The company is an industry leader for rail drainage investigation, design, repair, rehabilitation, including pipe and culvert lining, and installation.
Importantly, it also has its own inhouse professional services engineering team, so can provide seamless support for design and implementation of drainage renovation and new installation projects.
As the UK’s largest independent drainage and wastewater specialist, with 36 depots and specialist service hubs, Lanes also has unrivalled national reach and technical experience.
Technical expertise and experience
Rail infrastructure owners and their contractors know that behind the work teams from Lanes sits a company with the heft and expertise to support the most complex and challenging drainage projects.
The Lanes Rail Division incorporates the major service operation that supports Transport for London (TfL) in the maintenance of its London Underground and London Overground rail networks.
The division also includes UKDN Waterflow (LG) Ltd, which delivers a range of drainage investigation and project implementation services for Network Rail and its tier one contractors. Both teams also draw on the civil engineering experience and technical support provided by Lanes Professional Services.
The division’s strength is founded on the decades of support Lanes has provided for TfL in the maintenance of London’s rail network, primarily the London Underground. Working on one of the world’s busiest, and oldest, passenger transit systems, has forged in Lanes a combination of technical expertise and experience fused with a can-do spirit that TfL knows it can rely on.
Lanes delivers drainage, seepage, and structure maintenance services across London’s underground network. It also delivers an FM contract for London Underground that includes painting and decorating, lock maintenance, vegetation control and high access maintenance.
Elizabeth Line – ‘robust maintenance systems’
The high performance levels achieved has resulted in Lanes also being awarded a contract to maintain all stations on the new Elizabeth Line, built by Crossrail, from Reading in Berkshire to Shenfield in Essex and Abbey Wood in East London.
The work, carried out on behalf of London Underground and Rail for London Infrastructure, has notable, in its first 12 months, for an intensive process of asset verification, explains Lanes Rail Director Martin Balcombe.
“We are bringing into maintenance many thousands of assets for the first time,” he said. “This is involving asset verification and developing access methodologies, so assets can be maintained safely, efficiently and sustainably.
“This process is going to continue for at least another 12 months and brings with it challenges that Lanes is well placed to manage. For example, the Elizabeth Line is not a light rail system, like the Underground, so has needed new working methodologies.
“We’re also working collaboratively with the many stakeholders inevitably associated with a line that interfaces with other transport networks across different geographies to make sure maintenance systems are robust and sustainable. In my view, only a service provider with Lanes’ experience and record of consistent high quality delivery can do this with confidence.”
Drainage maintenance for Network Rail
Lanes Rail also provided crucial support during the COVID-19 pandemic. Its teams installed more than 65,000 COVID-19 social distancing stickers at every Underground station, other public locations and all rail depots and offices. They also set up more than 2,000 hand sanitisation units across TfL transport premises.
Lanes Rail, which operates from a service depot at Rainham, in Essex, also delivers services for Network Rail. And it supported the development of HS1, the 67-mile line that links London with the Channel Tunnel.
UKDN Waterflow (LG) Ltd is a separate Lanes company that sits within the Lanes rail division. It also delivers a wide range of drainage services for Network Rail and its main contractors.
Holder of a Network Rail Principle Contractor Licence (PCL), it carries out CCTV surveys and inspections, drain unblocking and cleaning, drainage asset mapping, track drainage, repair, renovation and replacement, new track drainage installation and non-drainage infrastructure works.
UKDN Waterflow (LG) can also deliver wider infrastructure services, often associated with catchment management or upgrade schemes, including: piling; reinforced concrete installation; earthwork stabilisation and remodeling; and vegetation clearance, including tree management.
Delivering rail maintenance work to the highest standard in the most challenging conditions has earned UKDN Waterflow (LG) a strong reputation for delivery that it has sustained over many years.
Innovative culvert replacement project
An example was the replacement of a collapsed concrete piped culvert at Cleeve, near Bristol during a 52-hour Christmas period possession. UKDN Waterflow (LG)’s early involvement in the detailed planning of the optimum solution in close conjunction with Network Rail was crucial to the project’s success.
Its delivery and planning team recommended a novel solution to carry out the removal of track panels needed during the project. Instead of utilising the client’s preferred RRV cranes and support RRV plant, two 50t excavators were used that went on to excavate, install, backfill and place track ballast above the newly installed box culvert structure. Critically, this saved time, and it also dramatically reduced the cost of the work.
Faced with continuous, heavy rainfall during the culvert installation, the operational team needed to redesign the over pumping regime just before work started to ensure the complex installation process was not stalled.
The first of several sections that made up the 28m box culvert was in place 31 hours into the possession, the last nine hours later. Thanks to smart planning that accelerated workflow, the culvert trench was fully backfilled just two hours after that.
Track panels were in place in another four hours, allowing the UKDN Waterflow (LG) team to vacate the site three and a half hours ahead of schedule.
Transpennine Route asset investigations
In another project, the company’s engineers have been working with Lanes Professional Services to devise a novel solution to a persistent flooding problem at the entrance to Victoria Station.
With access to the London Underground station just metres away, and tens of thousands of rail passengers using the space every day, devising a viable design and then implementing it were both huge challenges.
UKDN Waterflow (LG)’s solution, approved by Network Rail, was ingenious. It was to divert the surface water pipes vertically down into the basement with main outfall pipework being slung from the existing roof slab beams of the basement roof and then to a new outfall via installation within a bespoke heading structure.
Head of Rail Services Mark Croxford said: “It’s the ability to combine innovative thinking with a determination to achieve safe and sustainable solutions in a highly regulated maintenance and engineering environment that sets UKDN Waterflow (LG) apart, I believe. Where others may falter, we keep going.”
This determination to deliver applies to another major Network Rail project the team’s involved with. UKDN Waterflow (LG) is delivering asset investigations services for the Transpennine Route Upgrade, the project to modernise the line between Liverpool, Leeds and the North East.
Working for the Amey-Bam Nuttall joint venture leading the work to the West of Leeds, its teams have already surveyed and mapped 40 kilometers of drainage lines between Manchester and Dewsbury.
This has involved intensive investigations in more than 100 catchments, with the capture and reporting of 60,000 pages of data, gathered with CCTV surveys, topological surveys and asset condition surveys.
Project Manager Ian Sandford said: “Drainage is critical to service sustainability and reliability. It’s the only infrastructure element that interacts with all other systems. Therefore, Network Rail knows it must gather as much data as possible to ensure it’s correctly installed. This makes our job challenging, but the feedback we’re getting is positive.”
Integral professional services support
Lanes Professional Services is doing all the CAD work associated with the project. Its engineers and technicians also carry out stand-alone investigation and design work for rail clients, including topographical surveys, laser mapping, structural engineering design, and drainage and hydraulic design.
For example, they are helping Network Rail solve longstanding track flooding problems at Clapham Junction, one of the busiest stations in the country and, arguably, the most strategically important one in London.
Investigations involving CCTV, topographic and laser scanning surveys – have led to a solution designed to turn what has been frequent flooding, with subsequent major service disruption, into a system that can cope with once in half a century events.
Andrew McQueen, who heads up Lanes Professional Services, and has more than 25 years’ experience working in the rail environment, said: “Our aim is to create the best and most cost-effective outcomes that extend the life of assets and can be implemented with least disruption to the traveling public.
“That often involves thinking creatively and using remote working technologies that deliver solutions with least impact. The knowledge and experience of our teams delivers the creative thinking, and the financial clout of Lanes gives us the most appropriate technical solutions our clients need.”
For more information, see below. www.lanesfordrains.co.uk
Oliver Valves secured a £320,000 order to supply a range of single isolation needle valves, 2 valve manifolds and “IN” type double block and bleed valves for fitment to Modular Wellsite Packages in Saudi Arabia.
Wellsite packages are integrated skid-based units that house all of the equipment between the Christmas tree and the production header. The skids are expected to be installed near the respective wellheads to control the flow and pressure of oil or gas. They include; wellhead shutdown panels to control the wellhead valves, power distribution system with single phase and 3-phase power distributed to modules across the well site. A huge chemical injection system for flowline protection against corrosion, sampling pots to facilitate fluid sampling, and flow lines fitted with instrumentation valves that measure temperature and pressures.
Oliver Valves are to manufacture over 2,000
custom-made valves constructed from Alloy 625 and stainless-steel material that will see the order fulfilled over the next few weeks.
To find out how Oliver Valves can custommanufacture your valves, contact us by telephone +44 (0)1565 654 089, email: sales@ valves.co.uk or website: www.valves.co.uk
The 2023 Commerical Vehicle Show (CV) is back at the NEC, Birmingham from the 18- 20 April.
As the UK’s leading Expo for the road freight industry: this year’s focus will be on the all-new truck zone, showcasing the latest models from the truck manufacturing industry.
With a dedicated theatre programme on zero emission transitions and technology: showcasing the latest batterypowered electric trucks, hydrogen fuel cell trucks, through to HVO trucks, the shift from fossil fuels to more sustainable fuels is now today’s reality, not tomorrow’s dream.
The Expo is the largest and best attended in the road transport industry, with over 11,100 visitors expected from road freight, distribution and logistics: including renowned companies such as Scottish Power, Royal Mail fleet, RAF, Sainsbury’s and DHL. This is the perfect opportunity to showcase new product lines,
generate leads and sales and network with over 200 exhibitors and a large footfall of visitors.
With over 78% of visitors holding purchasing power responsibility, there is a strong probability of not just securing leads, but sales during the three-day event.
From small fleet operators to large scale corporations like Ford, this is the annual event to promote the latest trucks, vans, trailers, vehicle conversions and storage solutions, telematics, and related accessories, all under one roof.
The 2023 Commercial Vehicle Show (CV) is at the NEC, Birmingham from the 18- 20 April.
www.cvshow.com
Weven after decades in the sun.
Tried and tested in all real applications
For trucks and last-mile vehicles, this is the impact-resistant, robust material High Impact with optional AntiBac surface, the non-slip floor covering AntiSlip for interiors or LAMILUX Super, which protect the underbody from stone chippings. When installed in the side wall and roof, the world’s first LAMILUX Sunsation® reveals the advantages of the innovative gelcoat technology with 20 times better UV resistance than the gelcoats currently available on the market. LAMILUX Composites also enables translucent roofs for daylight intake during loading and unloading.
In the case of buses, LAMILUX demonstrates its flair for design: LAMIfoamtex with its soft-touch surface, Composite Floor, which resembles laminate flooring, and LAMIGraph, for interior cladding, are the proven materials of choice here. The manufacturer also presents a robust and durable material, LAMILUX X-treme, for use on roofs and side walls. LAMILUX AntiSlip non-slip flooring, which is also
Oliver Twinsafe manufactures a 10” x 8”, 900 class valve as a customised solution for the Maersk Gryphon floating production, storage and offloading vessel (FPSO) that’s now owned by Total Energies and is operating 200 miles off the Aberdeen coast.
The vessel is connected to subsea well clusters at a water depth of 112 metres, and equipped with topside production facilities to separate gas, oil, water mixtures and compression of gas for export.
Offshore installations such as an FPSO, give critical consideration to the space and weight of valve design, so compact design is key. Twinsafe manufactured a valve to a Compact Standard Length (CSL), with face-to-face dimensions in accordance with ASME B16.10. The double block and bleed design allows the valve to be installed within the same space as a single isolated ball valve, but with two isolates and a bleed valve positioned in between to maximise safety.
The first isolated ball valve is fitted with a Rotork spring pneumatic actuator that’s fitted with a limit switch for remote and local visual indication of the valve position, and a control panel containing the air filter regulator and solenoid valve.
The second isolated valve is fitted with a manual gearbox.
To find the perfect valve solution for your project, telephone Oliver Valves on +44(0)1565 632 636 or visit their website at www.valves.co.uk
Bott Ltd have invested significantly in a new flexible workspace at their vehicle conversion site in Ashby de la Zouch, Leicestershire. The site extension can now accommodate up to 25 additional vehicles and has a dedicated conversion space for Alternative Fuel and Electric Vehicles. The impressive site has been fitted with over 20 flexible charging points allowing vehicles to be held and delivered with an optimal state of charge.
The vehicle conversion site is also home to an Alternative Fuel and Electric Vehicles training and awareness showroom designed to increase customer knowledge on the transition from ICE to Alternative Fuel and Electric Vehicles. In addition, the investment has seen the arrival of a new drive on weighbridge for accurate axle and payload weight recording.
bott have also adapted their van racking and storage solutions to meet the additional needs of Alternative Fuel and Electric Vehicles. Lightweight van racking and storage options have been developed to harness power and provide maximum performance for the vehicle.
available as a visually attractive LAMILUX Anti Slip Style variant, once again scores points in the luggage compartment.
Focus on lightweight construction, sustainability, robustness, function and hygiene Installed in a wide range of vehicle types, LAMILUX Composites saves a considerable amount of weight while still producing extremely robust superstructures. In sandwich or prefabricated constructions, this composite material sustainably reduces the fuel consumption of the vehicles. High strength and stability create robust constructions that ensure that heavy mechanical stress in daily traffic leaves less traces on the composite materials.
The high damage tolerance also leads to a longer value retention of the vehicle, lower repair costs and easier repair and
At this year’s CV show, held at the NEC, bott will be bringing insight and expertise on Alternative Fuel and Electric Vehicles and how they can support with decision making on vehicle conversion requirements for this ever growing market.
www.bottltd.co.uk
t Sustainable label and sleeve constructions approved by EPBP and following RecyClass Design for Recycling Guidelines
t Solutions for re-use and re-fill bottle schemes that reflect latest legislation in many countries
t Main application are returnable 1 Showcasing printing excellence and premium labels that make products stand out on the sales shelvesLiter PET bottles commonly used in the mineral water market
Germany – CCL Label, the world leader in specialty label and packaging solutions, will be showcasing their latest innovations and best practice examples at the Interpack trade fair that takes place in Duesseldorf, Germany, from May 4 to 10.
Sustainable Solutions: Meet the “Sustainable Label Family”
One of the center pieces of the CCL exhibition will be the “Sustainable Label Family” that shows labels and sleeves that were developed for better recycling of the primary
packaging such as PET bottles, returnable glass bottles and other packaging types like HDPE and PP containers. The labels have special built-in features that support in the sorting and recycling stages by easily detaching, floating or shrinking.
“Many of the solutions of the sustainable label family, such as the low-density polyolefin shrink sleeve EcoFloat®, the Pressure-Sensitive Label for returnable glass bottles, WashOff, and EcoStream® that was developed for PET bottle
recycling, have been endorsed by the European PET Bottle Platform (EPBP) and follow the recommendations of the RecyClass”, explains Marika Knorr, head of Sustainability & Communication. “We are active members of these organizations to make sure, that our label innovations are in line with the official Design for Recycling Guidelines because we want to support the increase in recycling of FMCG goods.”
“Returnable systems for example like we have seen them for beer and water, are on the rise in many countries due to changing legislation and an increased awareness for sustainable solutions”, says Simon Peace, vice president Sales & Marketing Beverage Worldwide. “We are proud to have established WashOff labels in the market for many years now and that have a proven track record with major brands when it comes to the labels excellent performance on the washing and refilling lines”.
CCL Label has partnered with international Food & Beverage brands to develop more recyclable packaging. These best practices will be showcased at Interpack 2023.
Innovations that help save resources
CCL Label will also shine a spotlight on their stretch sleeve solutions. As a premiere, CCL will present the thinnest stretch sleeve in the market that is available at the moment – the EcoStretch sleeve has a thickness of 30 micron. It was especially designed for returnable 1 Liter PET bottles that are typically used in the German mineral water market.
This decoration technology has a very small carbon footprint to start with, because the material is very thin and can be applied to the container without using any heat or energy –the sleeve attaches to the container with its own elasticity.
“This extremely thin stretch sleeve is a very sustainable solution. At 30 micron the sleeve is a lot thinner than the ‘standard’ 45 micron sleeves that are usually used, so a lot less raw material is needed to manufacture this sleeve.
This helps reduce the carbon footprint of the product,” says Danny Freund, business development director for stretch sleeves at the Voelkermarkt site in Austria. “We calculated that beverage brands can save up to 32 tons of plastic material per 100 million sleeves – which is approximately the weight of over 5 adult African elephants.”
Printing Excellence and innovative Technology
“Printing Technology is ever evolving and CCL makes sure to invest in the latest technologies to serve our customers in the best way possible“, says Reinhard Streit, vice president & managing director Food & Beverage at CCL. We have expanded our digital and hybrid capabilities and can combine different technologies. This enables us to go far beyond conventional printing and enables us to deliver outstanding printing results like high-embelished sleeves that have an outstanding effect on the sales shelf!”
CCL is presenting a lot of best printing practices that have been developed together with many brand partners in the last years at the booth.
Where to find us
CCL will be showcasing in Hall 8a / B30
A product’s decoration might only seem a small part, but it plays a crucial role in making the entire packaging impactful and more sustainable. The label or sleeve is essential for the brand experience – it’s what consumers recognise a product by, what they connect with. Additionally the product decoration plays a key role when it comes to recycling, reuse and lowering the carbon footprint too! Join us at our booth at Interpack and learn more about our “Sustainable Product Family” and how you can reduce, reuse or recycle with them.
For more info, appointments and tickets visit www.interpack.ccllabel.com
Aico has recently welcomed the Housing Ombudsman Service to an online event focusing on damp and mould in the housing sector and best practices to keep residents safe.
“A Spotlight on Damp and Mould: It’s not lifestyle” report, published in October 2021 placed the responsibility for resolving poor quality housing in the hands of social landlords. The report provided 26 recommendations for landlords to assess their approach to resolving cases of damp and mould. In February 2023, The Housing Ombudsman published a follow up report to provide insight into landlords’ responses to the 2021 report. This new report included a number of actions that landlords have taken as a result, including improving surveying equipment, the use of sensor technology, resident facing apps and the use of an online dashboard, such as the HomeLINK Connected Solution.
Following the reports, HomeLINK’s Sustainability & Ethics Lead, Sam Collier, welcomed Victoria King, Sector Learning and Development Lead for the Housing Ombudsman Service and Mark England, Head of Innovation, Sustainability and Procurement for Coastline Housing. The panel also welcomed Alan Park, Compliance and Systemic Investigations Manager at the Housing Ombudsman Service for an engaging and thought-provoking Q and A session.
With over 500 attendees, Sam Collier opened the event giving an overview and timeline of the increased efforts to prevent damp and mould cases by the sector as a whole and highlighted the work yet to be done. Victoria King presented on the “It’s not lifestyle” report one year on, highlighting a need for a change in culture and The Housing Ombudsman’s recommendations. Victoria was followed by Mark England, who shared Coastline Housings approach to the report, highlighting the use of data and a proactive approach.
HomeLINK’s Sustainability & Ethics Lead, Sam Collier who hosted the session commented “Aico decided to host the Housing Ombudsman Service (HOS) on this webinar as we believe we all have a part to play in tackling damp and mould in the sector. We know our customers are facing a huge uphill task to improve the condition of their housing stock, and this event provided some excellent insight into what steps they can take to make progress in this area. It's great to see the HOS providing recommendations around innovative tools such as sensors, dashboards and resident apps to enhance the data landlords have about the condition of their properties, so they can make better informed decisions, and improve the health of their homes and the wellbeing of their residents. The example provided by Coastline Housing showed the impact these approaches are already having, and hopefully one other landlords can follow.”
Victoria King, Sector Learning and Development
Lead for the Housing Ombudsman added “In our damp and mould report, we said that landlords need to have a sustained focus on culture and behaviours to ensure issues are not dismissed. This event helps the sector to do that, and we highlighted our recommendations again,
including the need for landlords to develop a damp and mould strategy and for landlords to implement a proactive communications strategy. Whilst we know this is now a priority for many landlords, especially for those attending events such as this, we urge senior leaders to go faster and further in their efforts to do what is right by their residents.”
This event was the first in a miniseries being hosted by the market leader on damp and mould. In the next webinar on May 10th, HomeLINK’s Product Manager, Jordan Toulson, will take an in depth look at a case study surrounding damp and mould, what approach the landlord has taken and how technology can support. To register for the next
event, please visit: https://bit.ly/3TCPcZb
To watch this full webinar on demand, please subscribe to Aico TV here: www.youtube.com/@ aico-tv
www.aico.co.uk