Classification of Mechanical Seals
FSA Knowledge Series
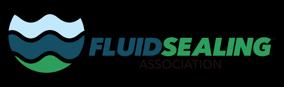
DISCLAIMER
While the FSA makes every reasonable attempt to ensure that the information contained in this document is accurate and current, the FSA, its officers, directors, volunteers, and authorized agents are not responsible for any errors or omissions contained therein nor are they responsible for any results obtained from the use of or reliance upon its content. All information is provided “AS IS,” with no guarantee of completeness, accuracy, timeliness or of the results obtained, and without warranty of any kind, express or implied. In no event shall FSA or its officers, directors, volunteers, or authorized agents be liable to you or anyone else for any decision made or action taken in reliance on the information con tained herein or for any for any consequential, indirect, special, or similar damages, even if advised of the possibility of such damages. The informa tion contained in this document is for informational purposes only and does not constitute professional advice. It also includes references to certa in standards that may change over time and should be interpreted only in light of particular circumstances. It is your sole responsibility to confi rm the current state of any referred to standards. FSA reserves the right to modify or update the document content and to modify this Disclaimer at any t ime, effective upon posting of an updated version of this Disclaimer.
© (April, 2023), Fluid Sealing Association. All Rights Reserved.
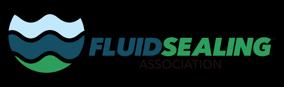
Abstract
This Fluid Sealing Association Knowledge Series training presentation introduces the different configurations of mechanical seals. This section includes seal types:
▪ By arrangement
▪ By design
The wide variety of seal types is due to the diversity of applications: machinery, fluids, and processes Selection of the best type is not always easy and straight forward as there are usually multiple choices. The most effective choice is usually a compromise between economical and technical factors.
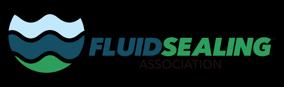
Mechanical Seal Classification
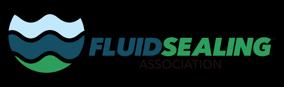
Single Mechanical Seal Arrangements
Inside Mounted
▪ Seal assembly mounted inside the seal chamber
▪ Sealed pressure is on the outside diameter of the seal faces
Stationary Mating Ring and Housing
Outside Mounted
▪ Seal assembly mounted outside the seal chamber
▪ Sealed pressure is on the inside diameter of the seal faces
Stationary Mating Ring and Housing
Fluid Rotating Seal Assembly Rotating Seal Assembly
Inside Mounted is the most common arrangement
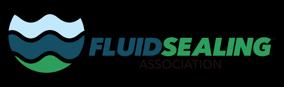
Dual Mechanical Seal Selection
Dual seals are used when one or more of the following criteria cannot be achieved by using a single seal design:
▪ Emission control of process fluid to the environment under normal operating conditions (e.g. EPA emission limits)
▪ Emission of process fluid under upset conditions or failure of the primary seal
▪ Acceptable life (time between repairs) as a result of inadequate lubricating properties of the pumped medium: too many solids, too close to vapor pressure, too low viscosity in combination with pressure and speed, or too high-pressure differential for one set of faces
The choice between a pressurized and un-pressurized seal is not always easy and must be evaluated on a case-by-case basis.
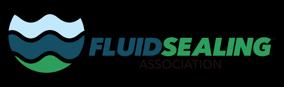
Dual Mechanical Seal Classification
Dual seal can be classified based on the pressure between the two seals within the seal assembly relative to the pressure in the seal chamber.
Pressurized Seals
▪ Pressure is above the seal chamber pressure (typically min. 30 psi/2.4 Bar)
▪ External fluid lubricates both seal face pairs
▪ Leakage to atmosphere is the external fluid
▪ Also called a “Double Seal” as traditionally they are used in a back-to-back arrangement
Unpressurised Seals
▪ Pressure is below the seal chamber pressure (typically atmospheric pressure)
▪ Inner seal faces lubricated by pumped fluid, outer by the external fluid
▪ Leakage to the atmosphere is external fluid, possibly mixed with small amounts of pumped fluid
▪ Also called a “Tandem Seal” as traditionally they are used in a face-to-back arrangement
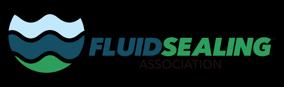
Dual Mechanical Seal Arrangements
Dual mechanical seals can be arranged in 3 different arrangements:
▪ Face-to-Back Can be pressurized or unpressurised
▪ Back-to-Back Commonly pressurized only
▪ Face-to-Face Commonly pressurized only
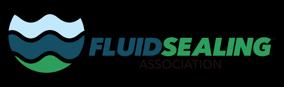
Mechanical
Seal Classification by Design
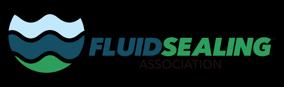
Mechanical
Seal Classification by Design
Pusher versus Bellows
▪ Defined by the secondary seal type: o-ring or polymer wedge versus bellow, rubber or metal
▪ Application fields of each seal type overlap
▪ Most apparent distinction is the pressure limit
▪ Acquisition cost can vary widely
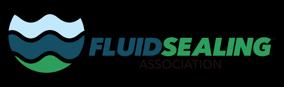
Mechanical Seal Classification by Design
Unbalanced versus Balanced
High closing forces
Low leakage
For pressures up to 14 Barg/200 psig
Not recommended for volatile liquids
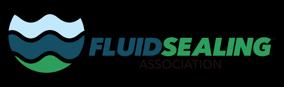
Mechanical Seal Classification by Design
Seal Face Patterns and Texturing
▪ Examples include hydro-grooves, wavy faces, tapered faces
▪ Intended to increase opening forces in order to improve lubrication.
▪ Friction is reduced at the expense of a higher leak rate
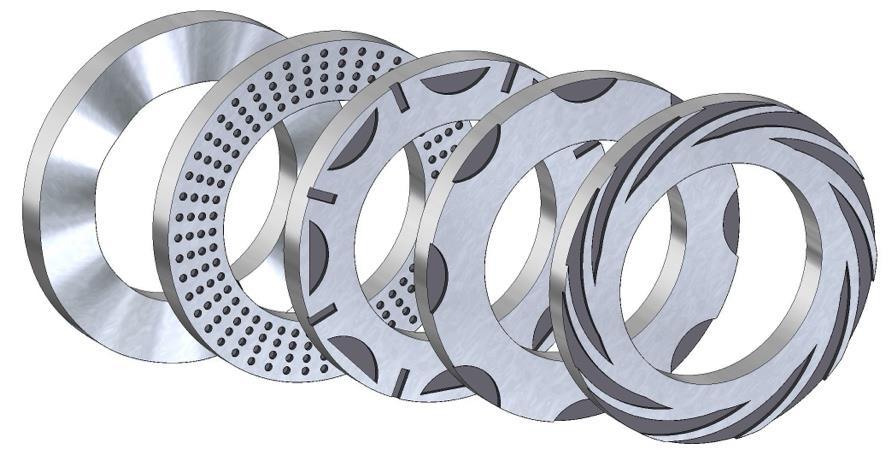
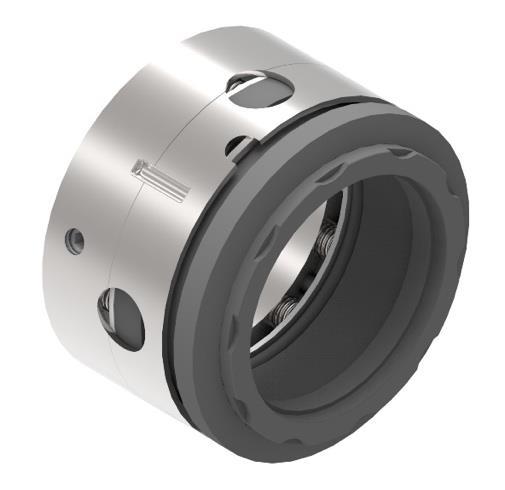
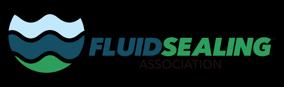
Mechanical
Seal Classification by Design
Rotating versus Stationary Flexible Element
▪ Mechanical seals with stationary flexible elements (bellows or spring) seals are recommended for equipment with high speeds (tangential velocities greater than 25 m/s (5000 ft/min).
▪ Stationary spring seals are also more suitable for machinery with inherently larger tolerances, such a heavy-duty slurry pumps and older pumps which have looser tolerances.
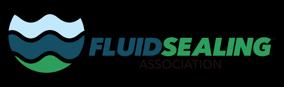
Mechanical
Seal Classification by Design
Cartridge Seals
▪ Seal is pre-assembled with sleeve and flange in one unit
▪ Easy to install
▪ Spring load is preset
▪ No measurements during installation
▪ May be factory tested with air, water or oil
▪ More costly when compared to noncartridge seal
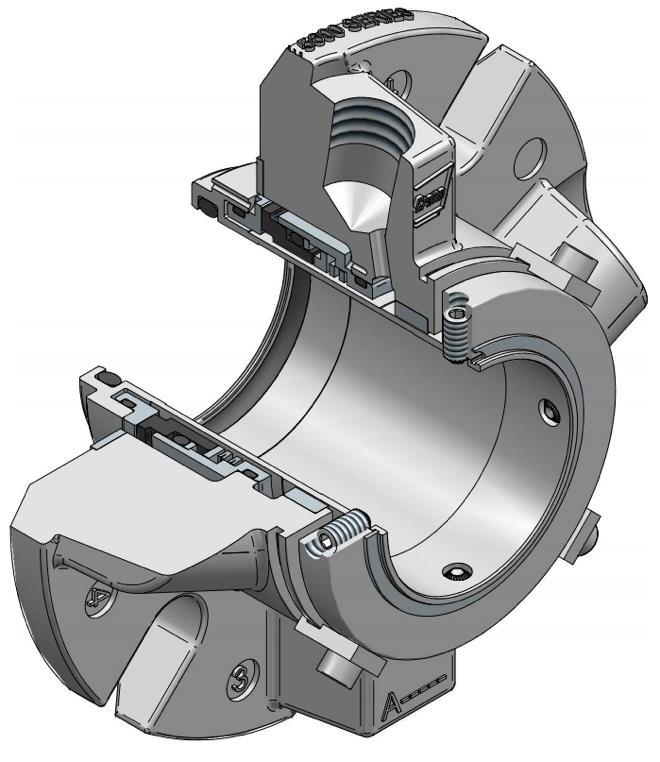
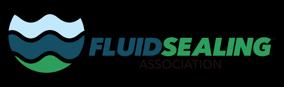
Mechanical Seal Classification by Design
Split Seals
▪ Seal is axially split
▪ Does not require disassembly of the pump to install - reduces down time
▪ Leaks more then a conventional seal
▪ Split seal are more costly compared to conventional seals
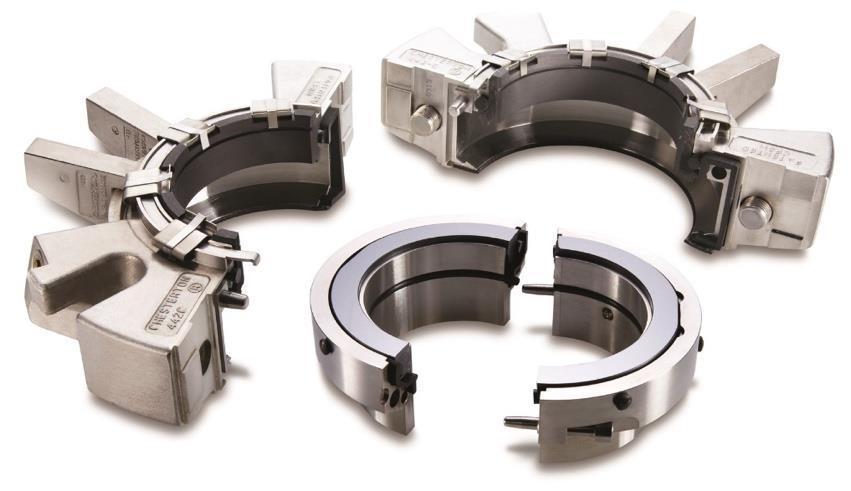
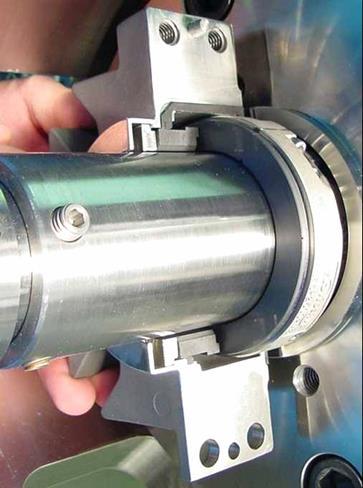
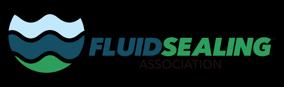
Containment Seal Classification
• Intended to contain the leakage of the primary mechanical seal.
• May provide redundancy if the primary seal fails.
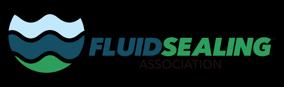

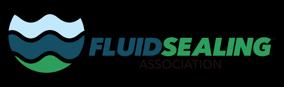