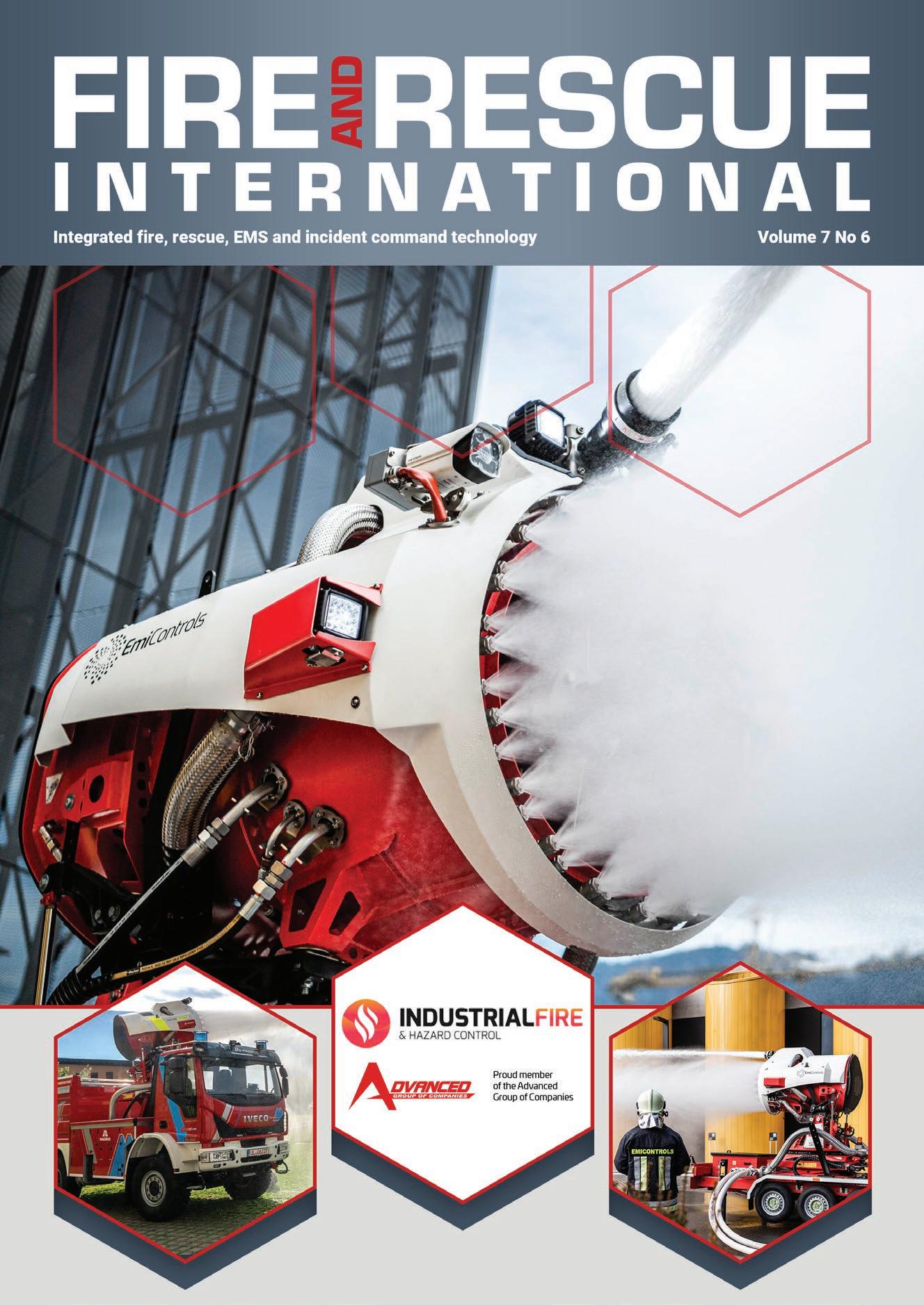
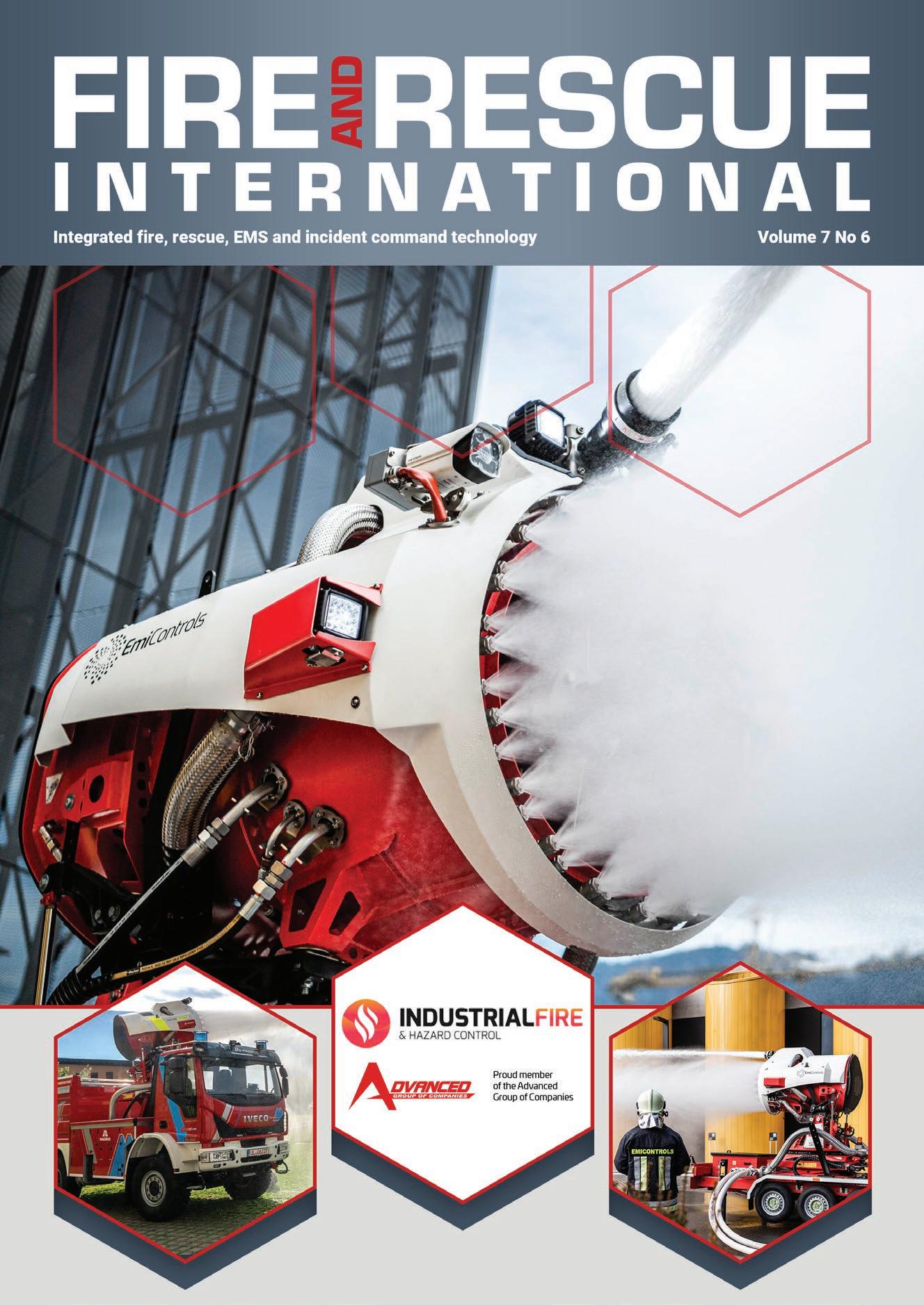
I wish you could see
I wish you could see the sadness of a business man as his livelihood goes up in flames or that family returning home, only to find their house and belongings damaged or lost for good.
I wish you could know what it is like to search a burning bedroom for trapped children, flames rolling above your head, your palms and knees burning as you crawl, the floor sagging under your weight as the kitchen below you burns.
I wish you could comprehend a wife's horror at 3am as I check her husband of 40 years for a pulse and find none. I start CPR anyway, hoping to bring him back, knowing intuitively it is too late. But wanting his wife and family to know everything possible was done to try to save his life.
I wish you knew the unique smell of burning insulation, the taste of soot-filled mucus, the feeling of intense heat through your turnout gear, the sound of flames crackling, the eeriness of being able to see absolutely nothing in dense smoke-sensations that I've become too familiar with.
I wish you could understand how it feels to go to work in the morning after having spent most of the night, hot and soaking wet at a multiple alarm fire.
I wish you could read my mind as I respond to a building fire "Is this a false alarm or a working fire? How is the building constructed? what hazards await me? Is anyone trapped?" Or to an EMS call, "What is wrong with the patient? Is it minor or life-threatening? Is the caller really in distress or is he waiting for us with a 2x4 or a gun?"
I wish you could be in the emergency room as a doctor pronounces dead the beautiful five-year old girl that I have been trying to save during the past 25 minutes. Who will never go on her first date or say the words, "I love you Mommy" again.
I wish you could know the frustration I feel in the cab of the engine or my personal vehicle, the driver with his foot pressing down hard on the pedal, my arm tugging again and again at the air horn chain, as you fail to yield the right-of-way at an intersection or in traffic. When you need us however, your first comment upon our arrival will be, "It took you forever to get here!"
I wish you could know my thoughts as I help extricate a girl of teenage years from the remains of her automobile. "What if this was my sister, my girlfriend or a friend? What were her parents reaction going to be when they opened the door to find a police officer with hat in hand?"
I wish you could know how it feels to walk in the back door and greet my parents and family, not having the heart to tell them that I nearly did not come back from the last call.
I wish you could feel the hurt as people verbally and sometimes physically, abuse us or belittle what I do or as they express their attitudes of "It will never happen to me"
I wish you could realise the physical, emotional and mental drain or missed meals, lost sleep and forgone social activities, in addition to all the tragedy my eyes have seen.
I wish you could know the brotherhood and self-satisfaction of helping save a life or of preserving someone's property or being able to be there in time of crisis or creating order from total chaos.
I wish you could understand what it feels like to have a little boy tugging at your arm and asking, "Is Mommy okay?" Not even being able to look in his eyes without tears from your own and not knowing what to say. Or to have to hold back a long-time friend who watches his buddy having rescue breathing done on him as they take him away in the ambulance. You know all along he did not have his seat belt on. A sensation that I have become too familiar with.
Unless you have lived with this kind of life, you will never truly understand or appreciate who I am, we are or what our job really means to us...I wish you could though.
~ Author unknown Source: Angel Fire
LIMPOPO PROVINCE, HOTEL @ TZANEEN
Fire teams’ exercises
Swift water rescue
High angle rescue
Obstacle and Confine space
Vehicle extrication & Rescue
Individual exercises
Tire tossing
Flacking fire hoses
Lifting foam cans
Climbing tower
Forcible entry
Operating charged hoses
10km marathon

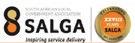
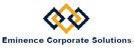
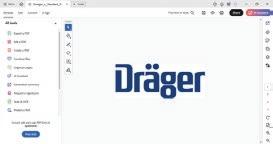


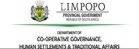






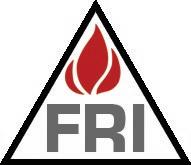
4 Credits and comment Competition
5 FRI Images Cover profile
6 EMI Turbines from Industrial Fire and Hazard Control: Cutting edge firefighting
National Disaster Management Centre
12 2024 National Fire Services Indaba held in George, Western Cape by Dr Bongani Elias Sithole People
17 Retired Chief Fire Officer Danie Wilds receives award for ‘Excellence in Tuition and Module Design’ Lithium-ion battery storage and fires
18 Extinguish lithium-ion battery fires fast with FlameBlock Lithium Black: Advanced fire suppression for lithium-ion battery thermal runaway
21 Fire safety design and planning approach for a Lithium battery storage warehouse by Karel Roodt
24 Firematic fire suppression and detection systems
28 Why traditional fire extinguishers can't tame Lithium-ion battery fires: The unusual chemistry of Lithium-ion battery fires
36 Important considerations for Lithium-ion battery energy storage systems (BESS) in South Africa by Dr Marika du Plessis
Fire testing
31 Ignis Fire Testing: The future of fire testing
Cancer prevention and the role of PPE
38
Raising awareness of firefighter safety and cancer risks: A personal journey and call to action by John Lord
41 The cancer risk for firefighters: A South African perspective by Lenny Naidoo and Jackie de Billot
46 Dräger: Understanding the toxic twins: HCN and CO
52 Navigating PFAS and the shift to NFPA 1970: Key changes for firefighter PPE by Robin Charnaud Inside front cover Poem: I wish you could see by author unknown
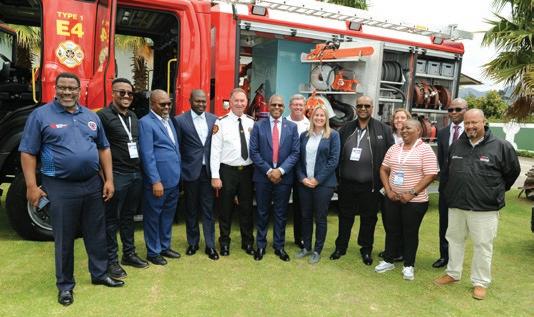
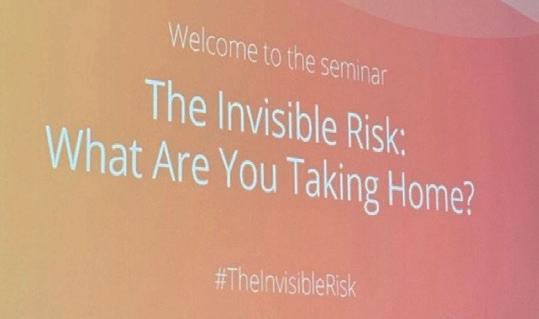
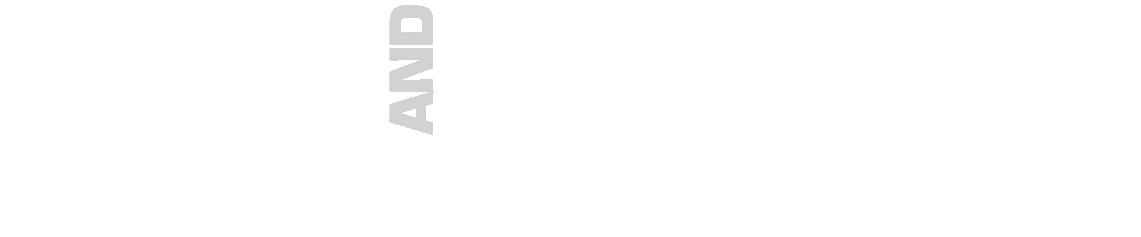
George building collapse
54 Victoria Street building collapse: Fire and rescue when the unimaginable happens by Santa Sternsdorf
62 Western Cape urban search and rescue response to the George building collapse; a provincial perspective by Colin Deiner
68 George structural collapse: Emergency Medical Service response by Richard Botha
72 George building collapse: Challenges, priorities and key observations by Colin Deiner
Wildfires
78 Extinguishing technology in action: fighting wildfires by Tristan Reitz
82 The importance of weather stations’ maintenance by Kelvin Price
84 Veldfire investigations: Sooner or later? by Rob Erasmus
87 Command Corner: Downhill fireline construction with fire below by Chief Tim Murphy
88 14th NMU Fire Management Symposium and field day held in Karkloof, KwaZulu-Natal
Training
102 Rope Rescue Awareness and Operations Training: NFPA 1006 compliance at ETS Emergency Training Solutions
Technical rescue: borehole rescues
106 Young child trapped in borehole rescued: Rescue confront their worst nightmare by Julius A Fleischman
Heritage
116 The history of the hood worn underneath the firefighting helmet

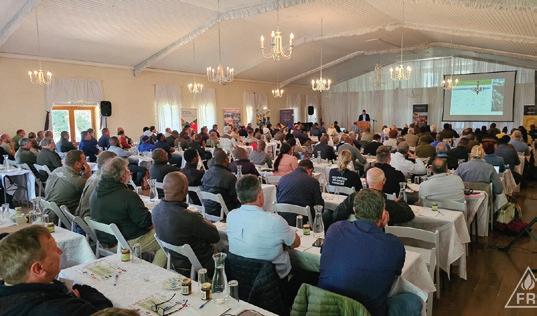
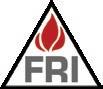
Editor
Lee Raath-Brownie lee@fireandrescue.co
Cell 082 371 0190
Advertising advertising@fireandrescue.co
Design and layout
Marc Raath marc@fireandrescue.co
Digital newsletter
Pierre du Plessis pierre@fireandrescue.co
Accounts and circulation
Kelebogile Chimaliro accounts@fireandrescue.co subs@fireandrescue.co
Secretary Kelebogile Chimaliro pa@fireandrescue.co
Administration Kelebogile Chimaliro
Contributions
Africa
Dr Bongani Elias Sithole
Colin Deiner
Karel Roodt
Dr Marika du Plessis
Lenny Naidoo
Jackie de Billot
Robin Charnaud
Santa Sternsdorf
Richard Botha
Kelvin Price
Rob Erasmus
Julius Fleischman
Europe
Tristan Reitz
UK
John Lord
USA
Tim Murphy
Publisher
Lee Raath-Brownie
FIRE AND RESCUE INTERNATIONAL
Tel 011 452 3135/6 Fax 086 671 6920
Box 8299 Greenstone 1616 www.fireandrescue.co
Subscriptions
Free of charge
Contact: subs@fireandrescue.co
Copyright
All rights reserved
Comment
In our 65th edition of the Fire and Rescue International (FRI) magazine, share indepth technical and research articles, motivational leadership guidance, incident management strategies as well as practical hands-on advice from experienced leaders. Enjoy the read!
Cover profile: Industrial Fire and Hazard Control
Industrial Fire and Hazard Control introduces the EMI Turbines, which uses a high-performance turbine pump to propel water or foam at an elevated velocity to fight fires in industrial and petro-chemical sites, mines, airports (ARFF), wildlands and in the municipal environment.
Disaster Management Centre (NDMC)
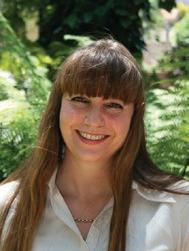
Lee Raath-Brownie
The NDMC shares an overview of the National Fire Services Indaba 2024, which marked a pivotal moment in the transformation of South Africa’s fire services.
People
Retired Chief Fire Officer Danie Wilds receives award for ‘Excellence in Tuition and Module Design’. Well deserved!
Lithium-ion (Li) battery storage and fires
In our special feature on Li battery storage and fires, Karel Roodt, shares insight on the fire safety design and planning approach for a Li battery storage warehouse, while suppliers of suppression equipment such as FlameBlock, Firematic and SafeQuip share their technology for detection and suppression strategies for Li battery fires and its thermal runaway. Dr Marika du Plessis also shares important considerations for Li battery energy storage systems (BESS) and we share a profile on the Ignis Fire Testing facility in Cape Town.
Cancer prevention and the role of PPE
In our ongoing campaign on cancer prevention, John Lord writes about raising awareness of firefighter safety and cancer risks: A personal journey and call to action, in which he shares his personal experience. Lenny Naidoo and Jackie de Billot of Vanguard Fire and Safety look at the South African experience and prevention. Dräger shares an insight into the toxic twins: HCN and CO and Robin Charnaud details the key changes for fighter PPE with the shift to NFPA 1970.
George structural collapse
Santa Sternsdorf of George Fire and Rescue Department, together with Richard Botha of the Western Cape EMS-Rescue share their experience, challenges and lessons learnt from the rather extraordinary rescue operations during the building collapse in George.
Colin Deiner’s article in this edition also features the George building collapse, providing insight into the Western Cape’s urban search and rescue response from a provincial perspective. In a separate article, Deiner unpacks the challenges, priorities and key observations from this memorable and very noteworthy incident.
Wildland fires
FireDos’ Tristan Reitz shares their extinguishing technology for fighting wildfires, while Kelvin Price provides insight into the importance of weather stations’ maintenance. Rob Erasmus discussed wildfire investigations and Chief Tim Murphy unpacks downhill fireline construction with fire below.
We share an indepth overview of the 14th NMU Fire Management Symposium and field day, which was held in Karkloof, KwaZulu-Natal.
Training
ETS Emergency Training Solutions shares their Rope Rescue Awareness and Operations Training in compliance with NFPA 1006.
Technical rescue
In this edition, Julius Fleischman unpacks the strategies and technicalities of the recent rescue of a young child, who was trapped in borehole.
Thank you to all our local and international contributors, advertisers and readers for their continued support! Fire and Rescue International is your magazine. Read it, use it and share it!
Lee Raath-Brownie
Publisher
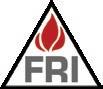
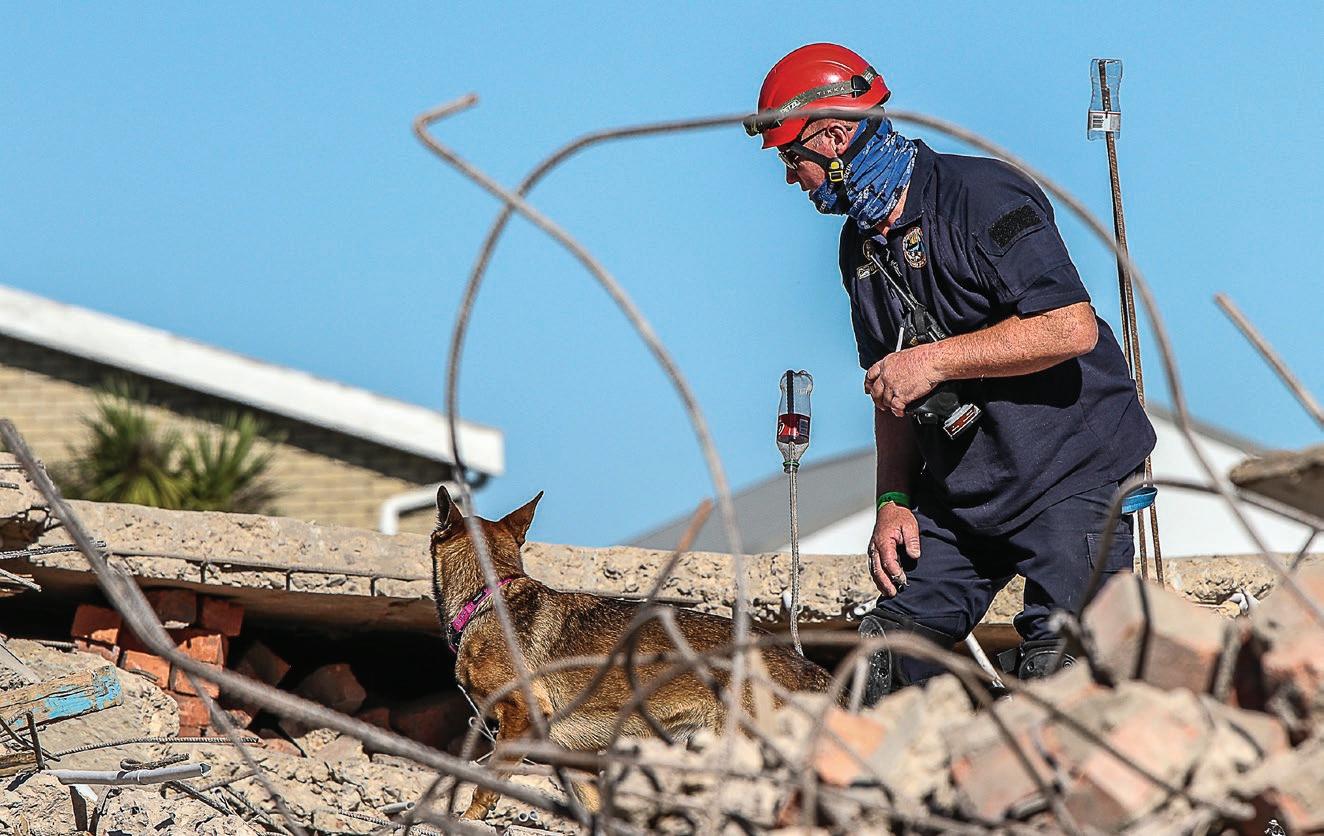
Congratulations
To Deirdré Cloete for her photograph ‘George building collapsed on 6 May 2024, which left 34 people dead’, taken with a Canon EOS 77D with a 70/200 lens. Camera settings: f/5.6 1/1000sec, ISO 200 EXP0, no flash.
Well done!
Deirdré Cloete wins this months prize money of R2 000!
Photo description:
"Desperation fills the air as fire and rescue teams dig through the rubble of a collapsed building, searching for any signs of life. Search dogs, exhausted and covered in dust, mirror the urgency and fatigue of their handlers in this heart-wrenching scene."
Fire and Rescue International’s (FRI) bi monthly photographic competition is open to all its readers and offers you the opportunity of submitting your digital images of fires, fire fighters, disasters, incidents, emergencies and rescues.
Rules
• All photographs submitted must be high resolution (minimum 1meg) in jpeg format
• Allowed: cropping, curves, levels, colour saturation, contrast, brightness, sharpening but the faithful representation of a natural form, behaviour or phenomenon must be maintained
• Not allowed: cloning, merging/photo stitching, layering of two photos into one final frame, special effects digital filters
Fire and Rescue International (FRI) reserves the right to publish (printed or digitally) submitted photographs with acknowledgement to the photographer
• Winners will be chosen on the merit of their photograph
• The judge’s decision is final and no correspondence will be entered into afterwards
Entries must include:
Name of photographer
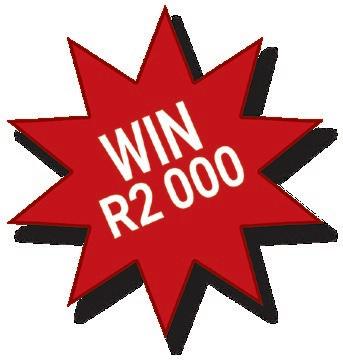
Contact details (not for publishing)
Email (not for publishing)
Name of photograph
Brief description of photograph including type of incident
Camera, lens and settings used
All entries must be emailed to: lee@fireandrescue.co
EMI Turbines from Industrial Fire and Hazard Control: Cutting edge firefighting
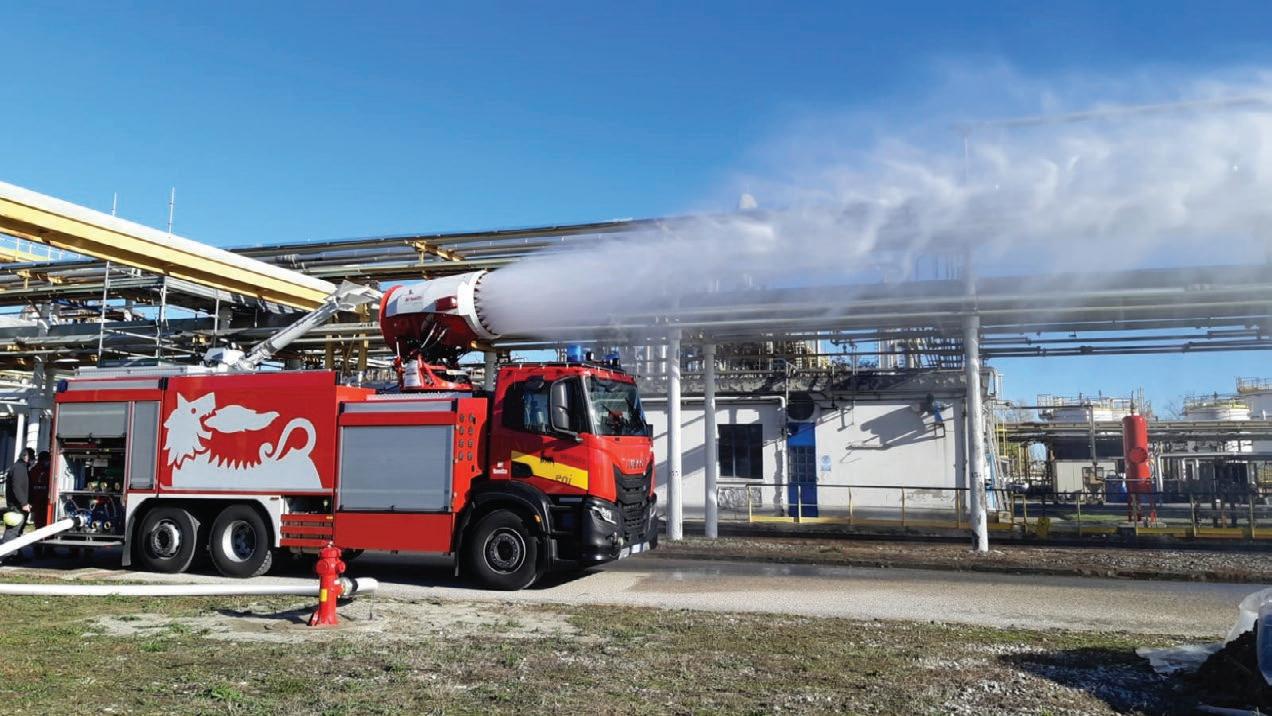
Industrial Fire and Hazard Control is constantly investigating cutting edge firefighting techniques that combine water efficiency with powerful firefighting capability. Our focus is on maximum fire mitigation with the minimum water application. Consider that the World Resource Institute ranks South Africa within the top 30 driest countries globally…..we owe it to our clients to provide the most effective firefighting technology using the least amount of water.
It is for this reason that Industrial Fire and Hazard Control focuses so intensely on
microlising of water delivery at a fire incident. Our systems are based on breaking down water into extremely fine droplets or mist, using specialised pump and delivery devices.
We are proud to add the EMI Turbines to our product range to complete the full offering.
The EMI Turbine is a gamechanger that significantly improves water efficiency and reduces firefighter risk; the primary aim of all fire departments.
The EMI Turbine uses a highperformance turbine pump
to propel water or foam at an elevated velocity to fight fires in industrial and petro-chemical sites, mines, airports (ARFF), wildlands and in the municipal environment.
The EMI Turbine delivers a water mist, with droplets up to 500 microns in size, aimed at optimising the cooling effect of water while using it as efficiently as possible.
By atomising water, the system can cover larger areas up to 600m2 with less than one litre of water, making it possible to extinguish fires that would otherwise require vast amounts of resources.
One of the standout features of the EMI Turbine-based systems is the ability to reach areas that would otherwise be inaccessible. Whether fighting fires in multi-storey buildings, airports (ARFF) dense forest or wildland areas or industrial and petro-chemical sites as well as in mines, this systems can project water or foam over long distances and high elevations. This extended reach is particularly critical in underground mine fires, wildfires or tall-building fires, where fire crews might need to operate from a distance to ensure safety.
With the growing concern over our water conservation, the EMI Turbine firefighting system stands out for its efficiency.
This system delivers more water in a shorter time with less waste, ensuring that valuable resources are not overused during critical operations. The efficiency also translates into better control over the fire, allowing crews to suppress fires with precision and minimal water runoff.
Ventilation is another critical function of the EMI Turbine, particularly in scenarios where smoke, heat or toxic gasses need to be cleared from an area to allow for safe operations or evacuations.
The turbine generates a powerful airflow that can be used to push smoke and gasses out of enclosed spaces such as tunnels, large industrial facilities or urban buildings.
In fire scenarios, smoke can quickly fill an area, reducing visibility and making it difficult for people to escape.
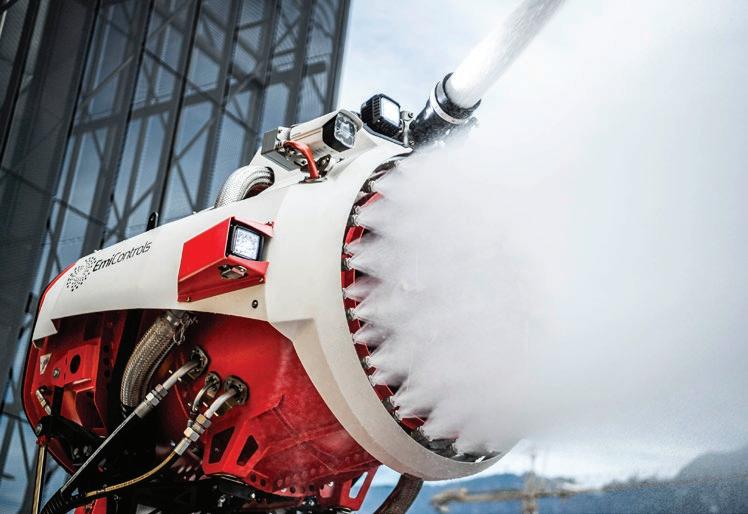

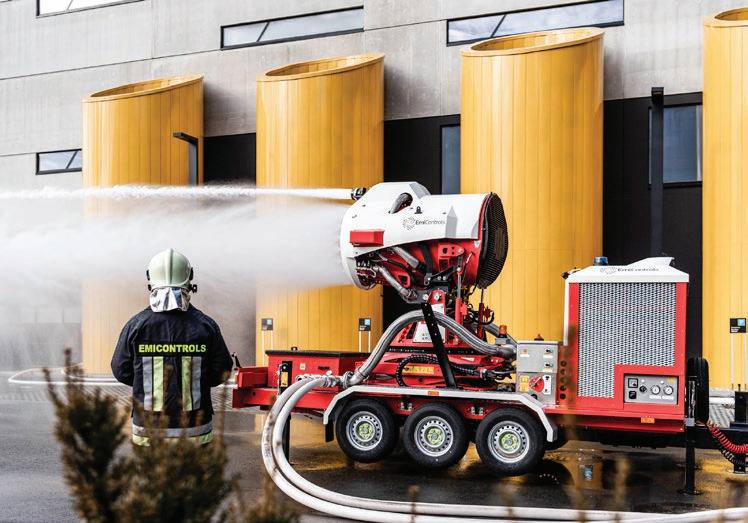
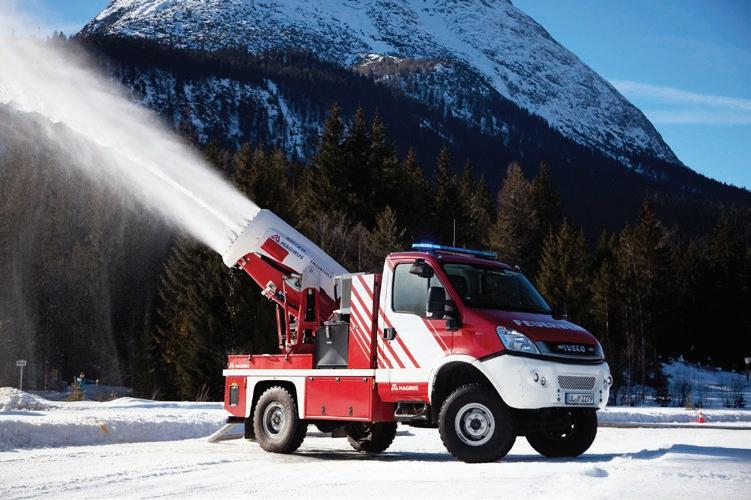

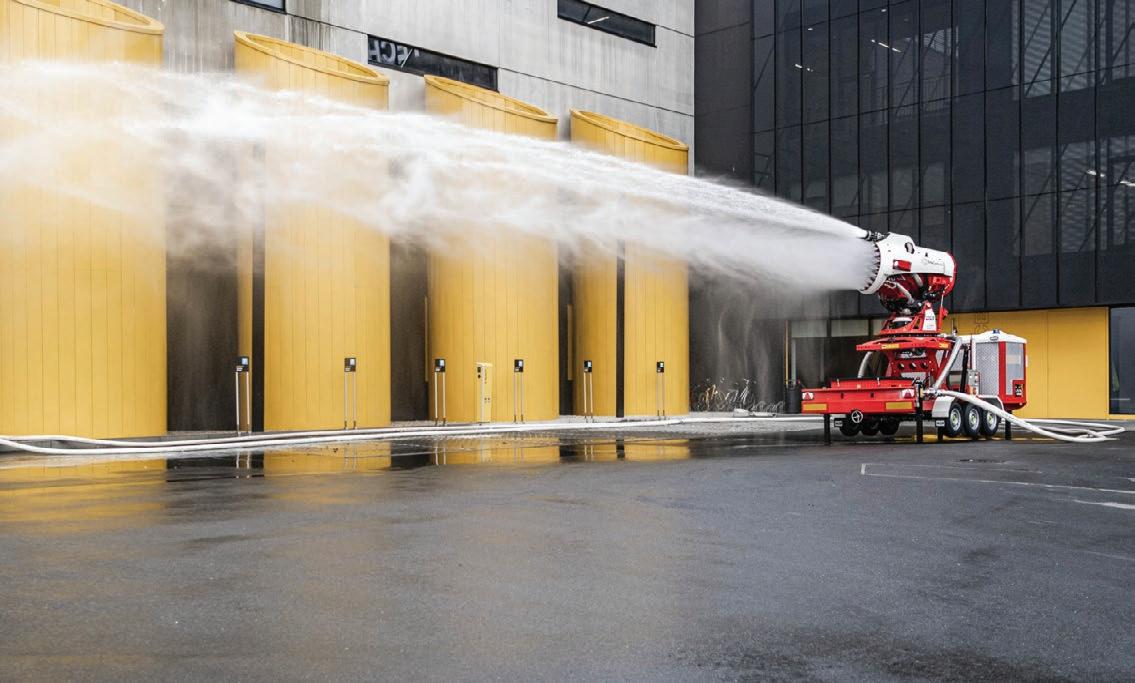
The EMI Turbine can be used to create positive pressure in stairwells or other escape routes, ensuring that these paths remain clear and allowing for safe evacuation.
This capability is especially important in high-rise buildings or other large structures, where smoke can render escape routes impassable within minutes.
The turbine’s ventilation function is, however, not limited to emergency situations as it can also be used in industrial and mine settings to maintain air quality by preventing the build-up of hazardous gasses or fumes.
The EMI Turbine can be equipped with different nozzle heads, allowing it to be adapted for specific tasks. For example, in
situations where high expansion foam is needed, the EMI Turbine can be fitted with a nozzle that optimises the distribution of foam over a large area. This flexibility makes it possible to tailor the EMI Turbine to the unique requirements of each incident.
The FT60h
The FT60h offers the following key advantages and benefits:

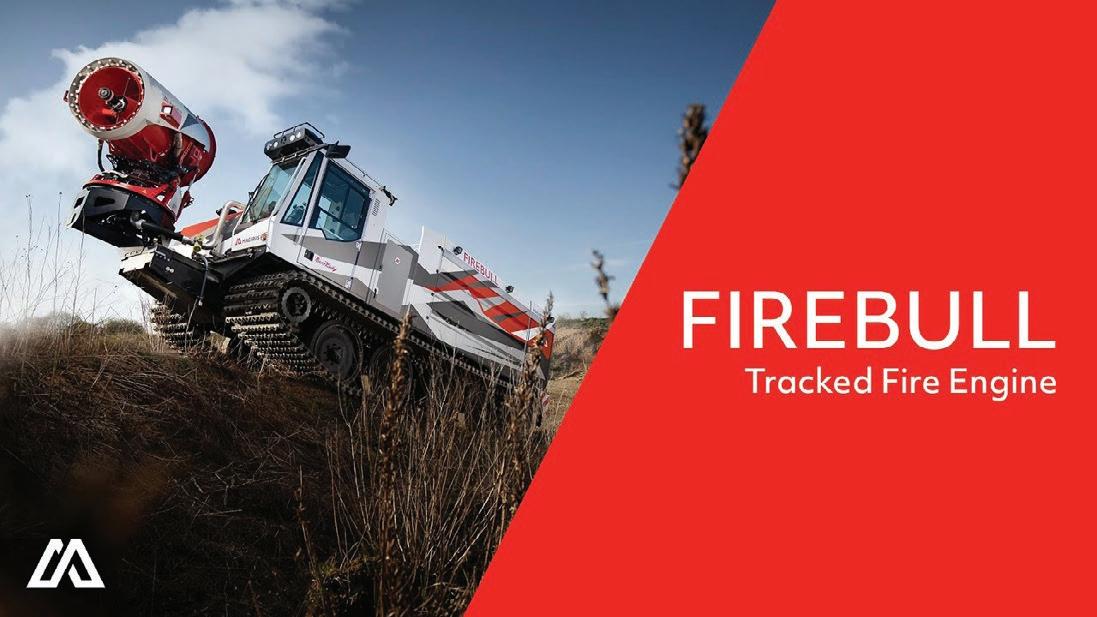
• Flow rate of up to 7 000l/min with two independent water circuits
• Superior throw distance of up to 85 m
• High flexibility in generating different water spray patterns (remotely adjustable)
• Precipitation of hazardous materials
• Ventilation and air-only operation
• Low and high expansion foam compatibility, suitable also for retarder and gel additives
FT60hx
The FT60hX offers all the advantages of the FT60h but has an additional head monitor attached to the turbine that can be swivelled sideways. The head monitor can be controlled separately from the turbine and thereby increases the extinguishing area many times over. The head monitor is ideal, for ensuring targeted firefighting, while the turbine is cooling the area or creating escape paths.
The ability to combine firefighting, hazmat mitigation and ventilation in a single unit, makes the EMI Turbine an asset for any organisation involved in emergency response or industrial safety.
Incorporating an EMI Turbine firefighting system into your department’s toolbox, is not just about having the latest technology, it is about making fires safer and more manageable. By offering increased water pressure,
extended reach, enhanced efficiency and reduced firefighter exposure, the EMI Turbine system will become indispensable for tackling fires across different settings. As firefighting challenges evolve, so too should the tools we use to combat them.
Adding the EMI Turbine firefighting system to your operations is not just an upgrade; it is a commitment to smarter, more effective fire suppression.

For more information on the EMI Turbine, please reach out to us:
Trevor Fiford mobile: 082 651 2580, email: trevor@industrialfire.co.za
Zarto Williams mobile: 061 158 6941, email: zarto@industrialfire.co.za
Lee Marques mobile: 061 225 2710, email: lee@industrialfire.co.za
Kevin Naidoo mobile: 081 732 1480, email: kevin@industrialfire.co.za
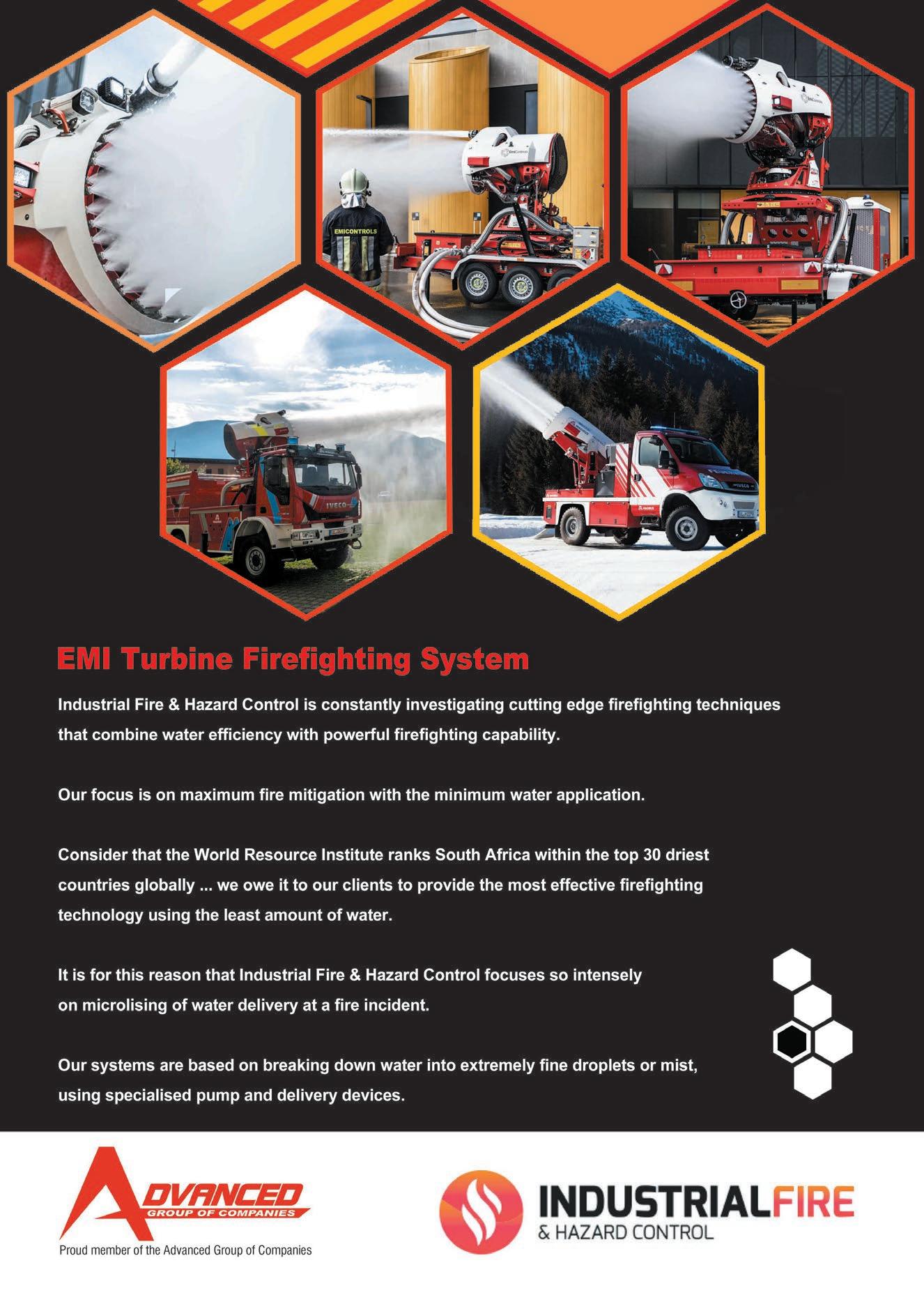
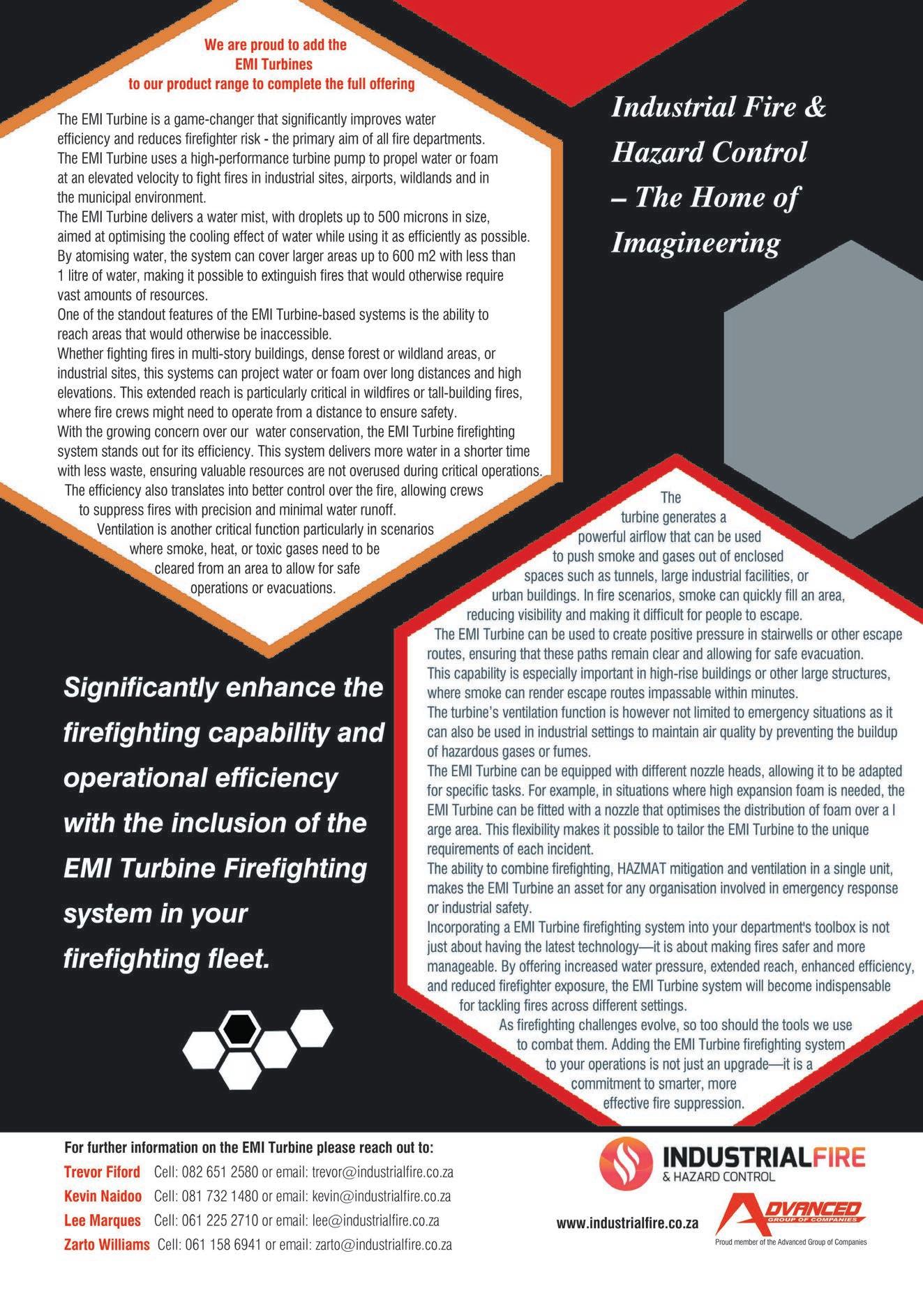

2024 National Fire Services Indaba held in George, Western Cape
By Dr Bongani Elias Sithole, Deputy Director General: Head - National Disaster Management Centre

The National Fire Services
Indaba 2024, hosted by the Minister of CoGTA, the Honourable Velenkosini Hlabisa (MP), took place at the King George Protea Hotel in George, Western Cape, under the theme Repositioning Fire Services in South Africa. This crucial gathering brought together policymakers, fire service professionals and stakeholders to
address the evolving challenges and strategic direction of fire services in the country. The Indaba underscored the importance of strengthening fire service capabilities, modernising frameworks, and fostering intergovernmental collaboration to ensure effective emergency response and resilience.
Background
Fire services in South Africa play an essential role in safeguarding lives, property and the environment. However, the sector faces pressing challenges, including limited resources, outdated infrastructure and increasing fire risks due to climate change and urban expansion. Recognising these challenges, the government has committed to repositioning fire services through legislative
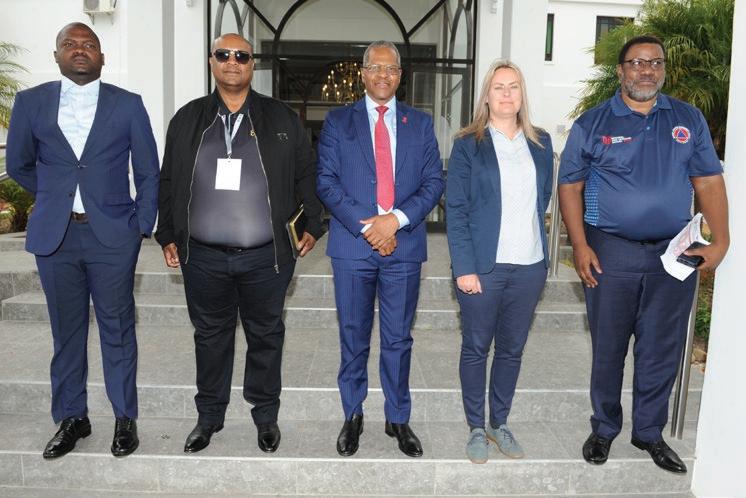
reforms, enhanced funding mechanisms and alignment with national development frameworks such as the District Development Model (DDM).
The Minister’s role in the National Fire Services Indaba Minister Velenkosini Hlabisa played a pivotal role in setting the strategic direction of the National Fire Services Indaba, emphasising the need to reposition fire services as a core pillar of South Africa’s disaster management and community safety framework. In his keynote address, the Minister highlighted the importance of modernising fire services, integrating them into the District Development Model (DDM) and ensuring that they are adequately resourced to respond to the increasing risks posed by climate change, urbanisation and economic disparities. He underscored the government’s commitment to strengthening legislative reforms, particularly through the Draft Fire Services Bill and advancing the 2030 Fire Services Strategic Roadmap, which seeks to create a more resilient, well-funded and technologically advanced firefighting system.
He also acknowledged the challenges faced by municipal fire services, including funding constraints, inadequate training, and aging infrastructure and assured delegates that the
Dr Elias Sithole, Head of the NDMC
National Disaster Management Centre (NDMC) is working closely with provinces and municipalities to reposition and strengthen fire services in the country.
His announcement that South Africa would host the Africa, Europe and Middle East (AEME) Earthquake Response Exercise (ERE) during November 2025 was met with enthusiasm, as it signalled the government’s commitment to benchmarking against global best practices in fire and disaster management.
The Minister also played a key role in recognising the contributions and sacrifices of firefighters and emergency responders. He led the presentation of certificates of recognition to first responders involved in the George, Victoria Street Building Collapse and reinforced the Government’s commitment to ensuring that firefighters receive proper training, protective equipment and financial support.
Additionally, he stressed the need for stronger collaboration between government, private sector stakeholders and

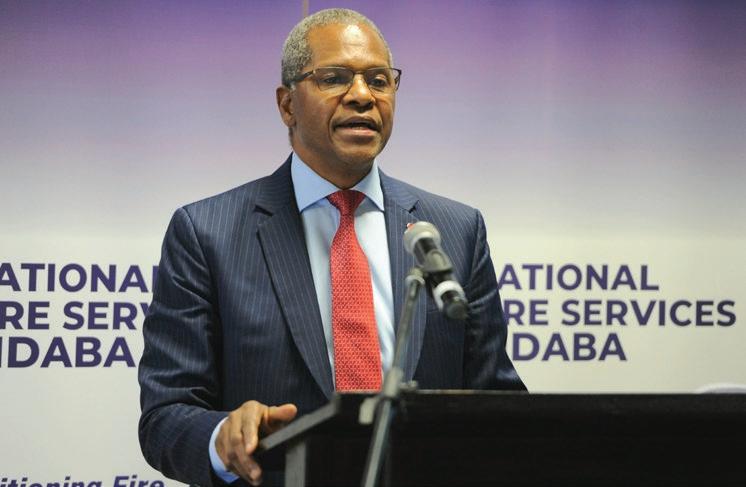
community organisations, urging all delegates to work collectively to turn the Indaba resolutions into tangible action.
His leadership and vision provided a clear roadmap for repositioning fire services in South Africa, setting the tone for actionable change in the sector.
The Indaba served as a platform to assess progress, exchange insights and define a clear roadmap for the future.
Over the past year, significant strides have been made, including:
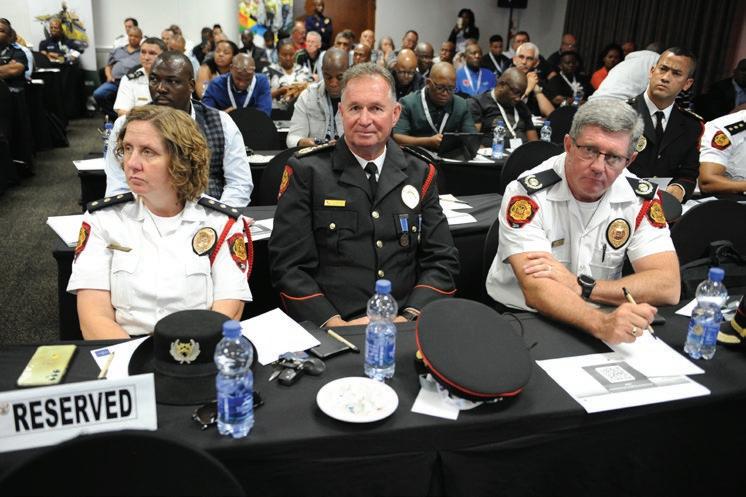
• The approval of a 2030 Strategic Roadmap for Fire Services, providing a clear strategy for modernisation and improved coordination.
• The development and implementation of a National Urban Search and Rescue (USAR) Governance Framework, aligning with international standards to strengthen South Africa’s emergency response.
• The revival of the Fire Brigade Services Board, which had been inactive since 2008, ensuring more effective governance and accountability in fire services.
• Progress on legislative reforms, particularly the Draft Fire Services Bill, which seeks to modernise fire service laws and ensure equitable access to firefighting resources.
Indaba objectives
The primary objectives of the Indaba were to:
• Strengthen fire services governance and coordination
Address gaps in the legislative framework, including finalising the Draft Fire Services Bill and improving regulation of private fire services.
Minister of Cooperative Governance and Traditional Affairs, Minister Velenkosini Hlabisa

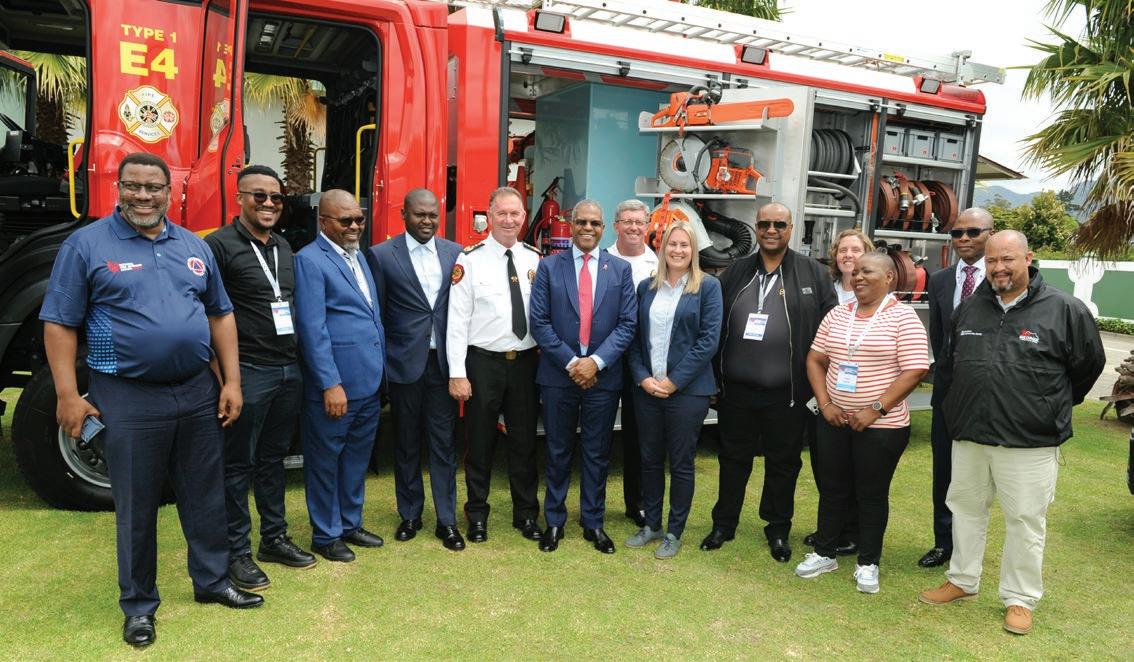
• Improve fire service funding
Implement a sustainable funding model to address resource disparities, particularly in under-resourced rural and peri-urban areas.
• Enhance intergovernmental collaboration
Integrate fire services into the DDM for more coordinated service delivery across national, provincial, and municipal levels.
• Modernise firefighting capabilities
Leverage new technologies, including Artificial Intelligence (AI), to improve fire prevention and response strategies.
• Capacity building and training
Expand training programmes to equip fire personnel with advanced skills and ensure operational readiness.
• Community engagement and fire prevention awareness
Strengthen partnerships with
traditional leaders, community organisations and fire protection associations to promote fire safety awareness.
Indaba outcomes and resolutions
The Indaba resulted in a set of strategic resolutions that will guide the future of fire services in South Africa:
1. Legislative and policy reforms
• Fast-tracking the Draft Fire Services Bill to address regulatory gaps and provide legal clarity for private fire services.
• Strengthening oversight mechanisms through the revived Fire Brigade Services Board, ensuring national standards and equitable service delivery.
2. Implementing the 2030 Fire Services Strategic Plan
• Operationalising the funding model for fire services, prioritising under-resourced areas.
• Positioning the National Fire Services Advisory Committee support the Fire Brigade Board to monitor and evaluate progress on strategic goals.
3. Strengthening intergovernmental coordination
• Embedding fire services into the District Development Model (DDM) for improved integration with municipal planning and resource allocation.
• Enhancing partnerships between national, provincial, and municipal fire services, along with traditional leaders and community organisations.
4. Capacity building and technological advancements
• Expanding fire training programs, with a focus on advanced firefighting techniques and the integration of artificial intelligence (AI) in firefighting and prevention.
• Securing additional funding for fire stations, personal protective equipment (PPE)
and firefighting vehicles, including repurposed Working on Fire Programme resources.
• Hosting the Africa, Europe and Middle East (AEME) Earthquake Response Exercise (ERE) in 2025, a major international training opportunity for South African fire services.
5. Addressing emerging fire risks
• Developing comprehensive strategies to mitigate wildfire risks, particularly on traditional lands.
• Enhancing Urban Search and Rescue (USAR) capabilities through improved coordination, compliance with international standards and increased training.
6. Community engagement and awareness
• Continuing the roll-out of the National Fire Safety and Prevention Strategy in

municipalities, strengthening fire safety awareness campaigns targeting vulnerable communities, particularly in rural and informal settlements.
• Strengthening collaborations with fire protection associations (FPAs) and community-based organisations to improve public education and risk reduction efforts.
7. Recognition and acknowledgment
• Establishing an award programme to recognise outstanding contributions within the fire services sector.
Conclusion
The National Fire Services Indaba 2024 marked a pivotal moment in the transformation of South Africa’s fire services. With a clear roadmap and strategic
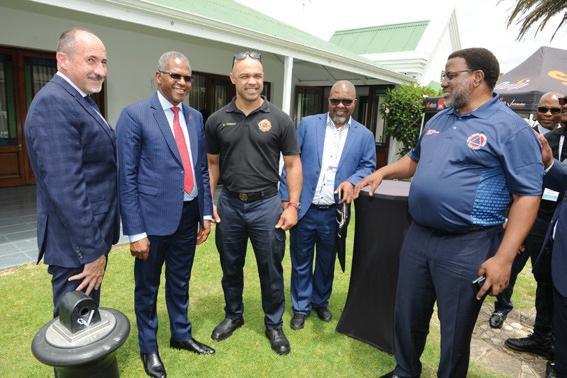
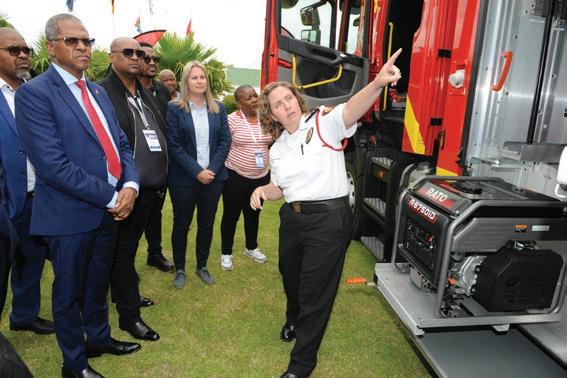
commitments in place, the sector is poised to become more robust, responsive and resilient. The collaboration between government, private sector and civil society will be instrumental in translating these resolutions into tangible progress. As South Africa moves towards 2030, the repositioning of fire services will not only enhance emergency response capabilities but also contribute significantly to community safety and sustainable development.
The dedication of fire service personnel, policymakers and all stakeholders ensures that South Africa’s fire services remain a cornerstone of national resilience. The resolutions of this Indaba set the stage for a future where fire services are not just reactive responders but proactive enablers of public safety and disaster preparedness.
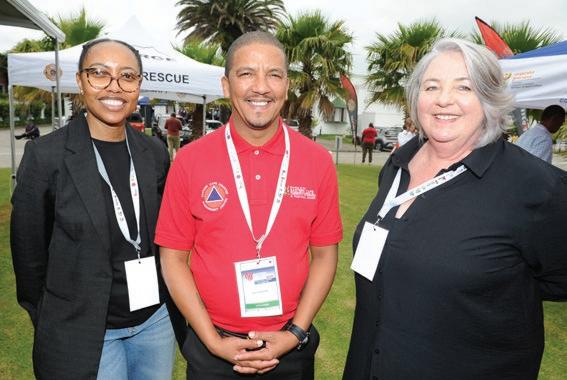

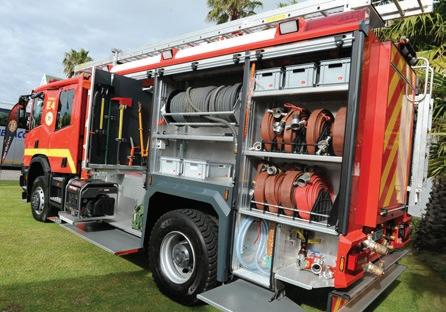
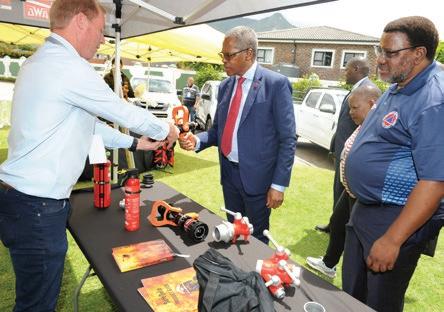
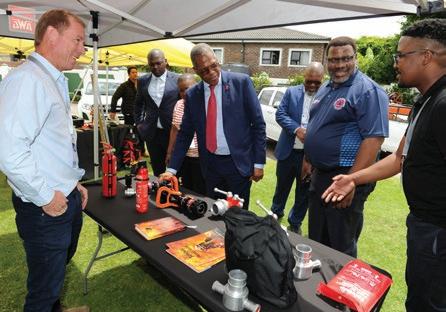
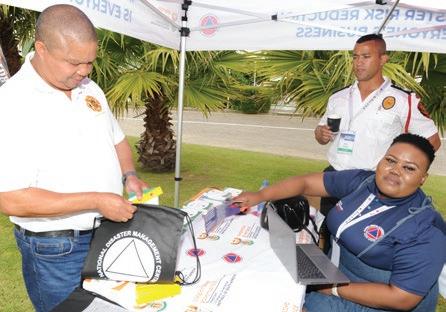
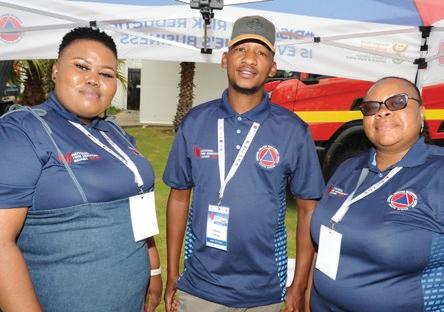
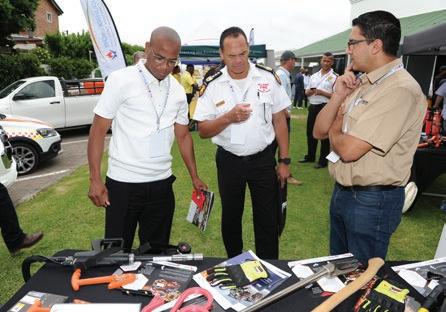
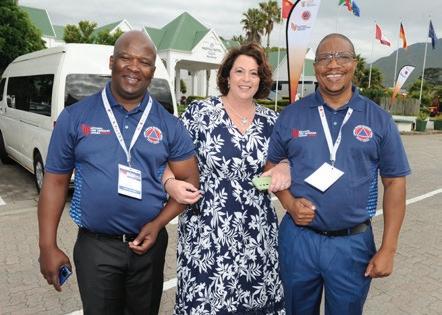
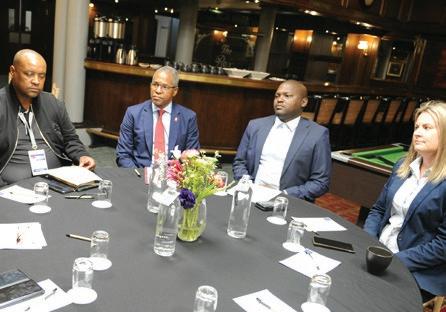
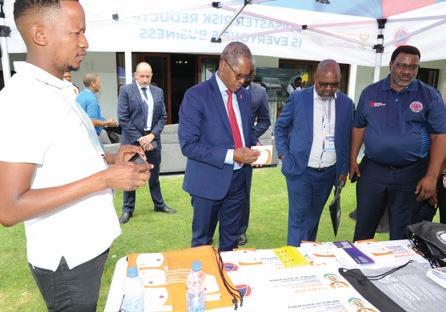
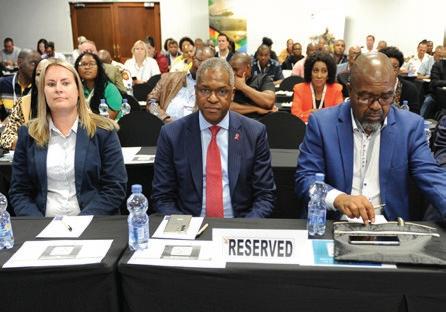
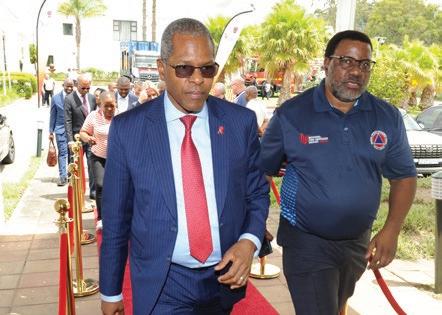
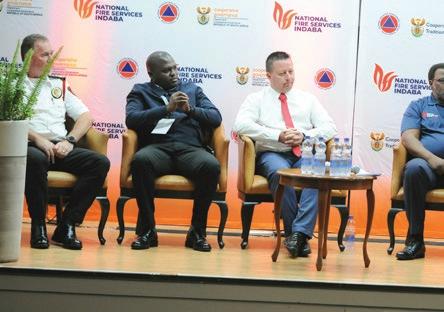
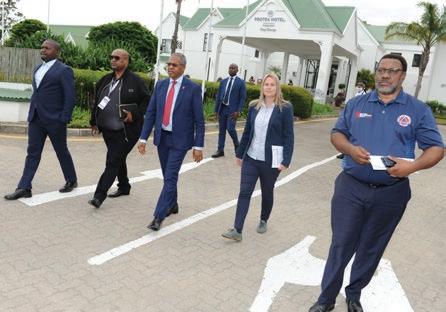
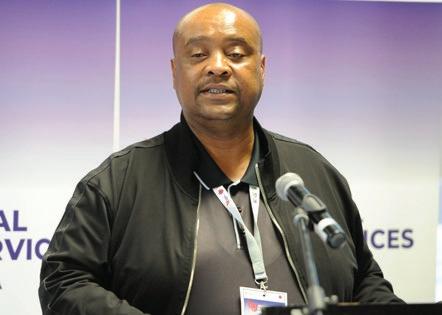
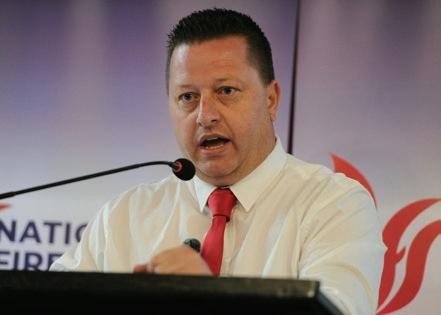
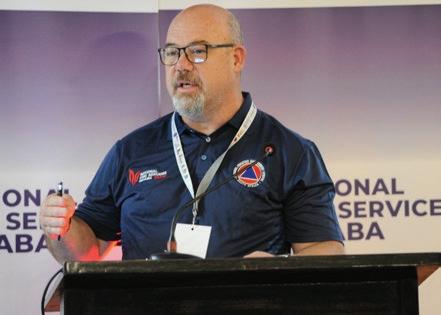
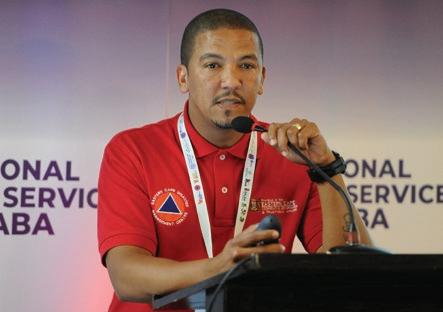

Retired Chief Fire Officer Danie Wilds receives award for "Excellence in Tuition and Module Design"
Retired Chief Fire Officer Danie Wilds, who is now involved with Stadio Higher Education as a lecturer and in the development of study materials, recently received the award for "Excellence in Tuition and Module Design."
"I am very grateful, proud and feel extremely privileged to receive this award," were Danie's humble words.
Stadio's offering of Fire Service qualifications originated from a request by the Southern African Emergency Services Institute (SAESI) and an agreement made at that time to develop Fire Service qualifications to replace the qualifications offered by SAESI for nearly sixty years with SAQAaccredited qualifications.
With a 45-year career culminating in the role of Chief Fire Officer Danie Wilds brings a wealth of experience and knowledge to fire service education. His expertise is reflected in numerous authored, compiled and edited study manuals, including the renowned STADIO fire-related study guides.
Additionally, his contributions extend to published magazine articles and a 33-year involvement with the examinations and activities of the SAESI Education Committee, culminating in a welldeserved life membership.
His passion lies in nurturing the next generation of fire service leaders. As a lecturer, he is committed to enhancing students' knowledge of Fire Technology, Fire Safety and Fire Science Management, inspiring them to become competent and effective officers.
His ultimate goal is to equip students with the skills and understanding necessary to excel
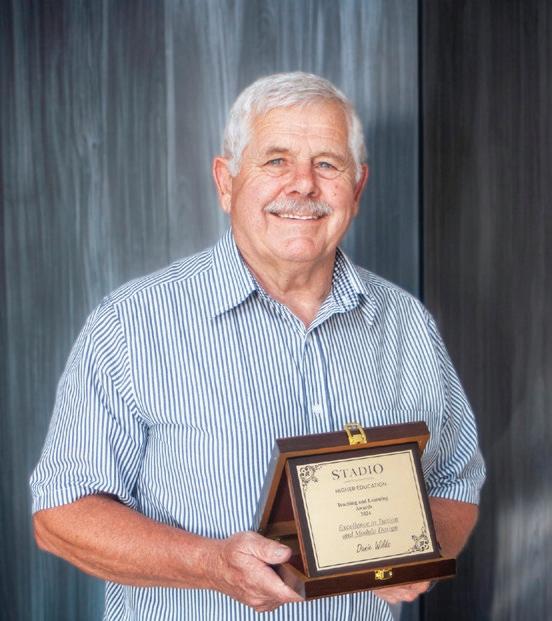
in their careers and elevate the standard of community service.
Danie makes it very clear that being involved in the development and training of firefighters is a great pleasure and a privilege.
He enjoys it immensely, although he hopes that the younger generation will soon take over from him and be equally passionate about developing our firefighters and officers.
He will always remember the highly skilled members in the fire services and their sense of professional purpose and commitment to a common goal.

Retired Chief Fire Officer Danie Wilds
Extinguish lithium-ion battery fires fast with FlameBlock Lithium Black: Advanced fire suppression
for lithium-ion battery thermal runaway
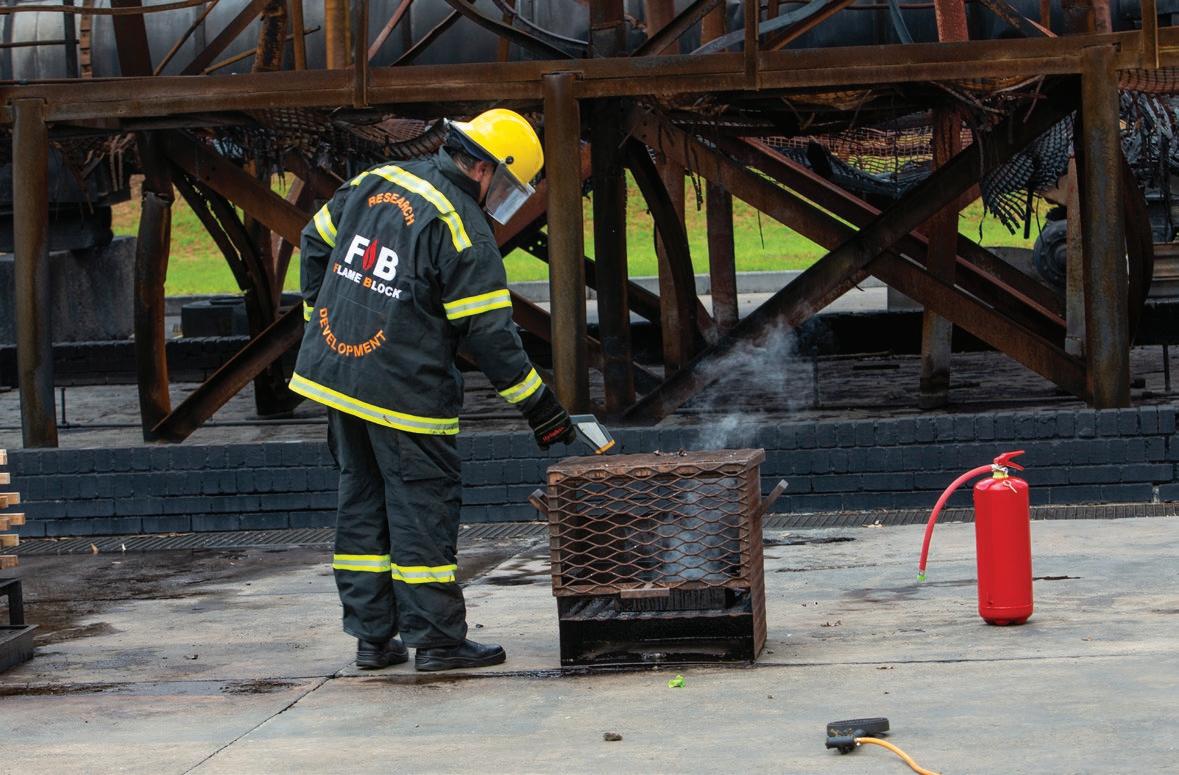
Lithium-ion battery fires present a significant hazard due to their high energy density and the risk of thermal runaway, a self-sustaining reaction that traditional fire suppression agents struggle to contain.
Conventional extinguishers, including water, CO2 and dry chemical agents, fail to sufficiently cool the battery or prevent reignition, making them inadequate for lithium battery fire scenarios.
FlameBlock Lithium Black is an advanced suppression agent
engineered specifically to mitigate lithium-ion battery fire hazards.
Developed in South Africa, this proprietary formulation incorporates mineral-based and salt-based compounds that actively interrupt the thermal and chemical processes driving battery fires. More than a simple extinguishing medium, it actively absorbs heat, suppresses oxygen radical formation and stabilises volatile gases to prevent re-ignition.
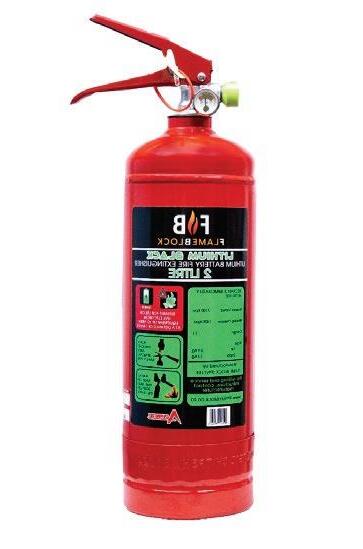
Key mechanisms of action
1. Rapid fire suppression
• Forms a thermally insulating barrier that isolates the fire source from ambient oxygen.
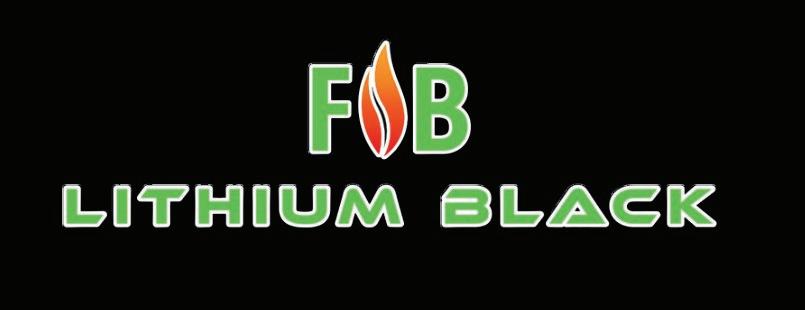
Lithium Battery Fire Extinguisher
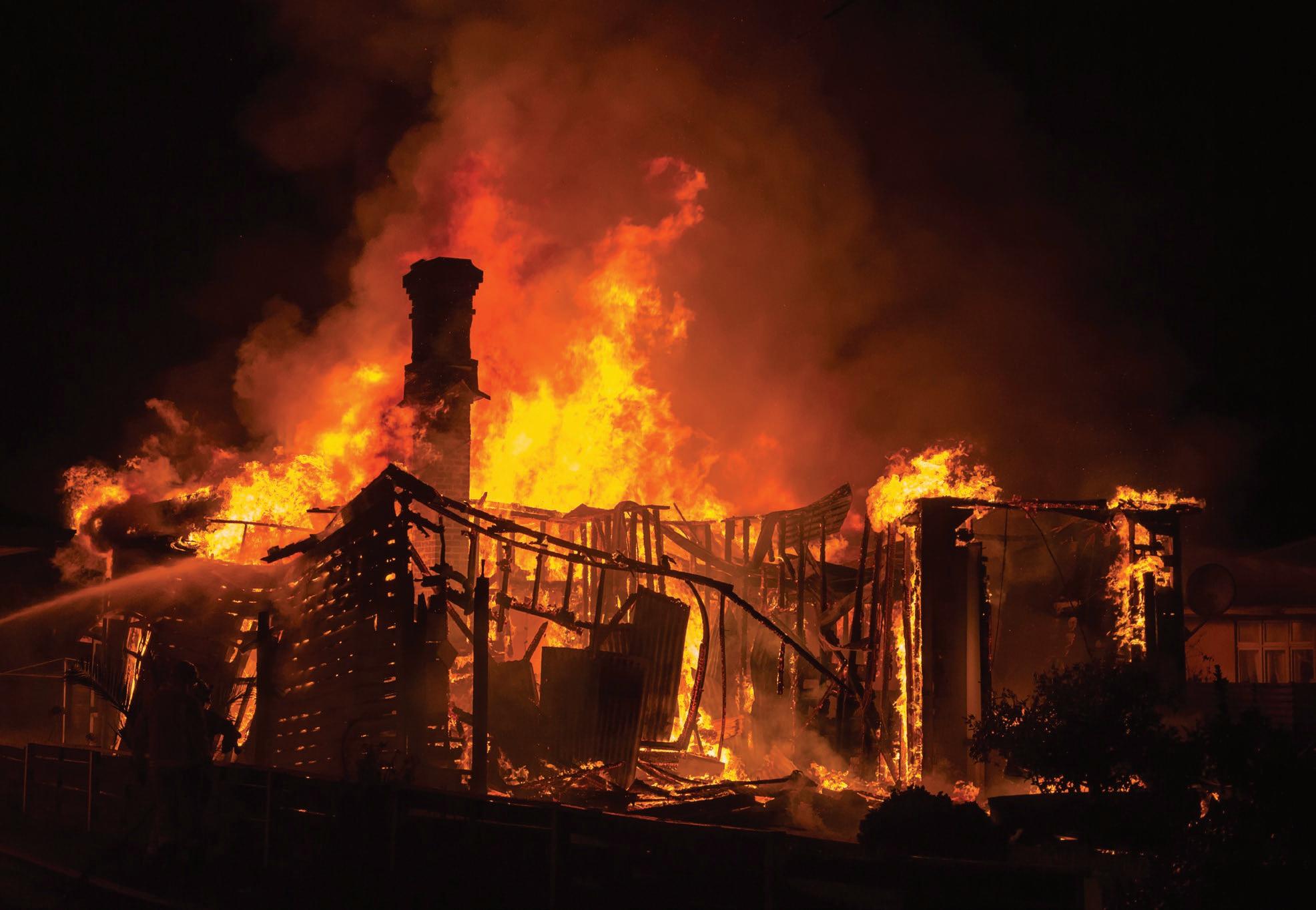
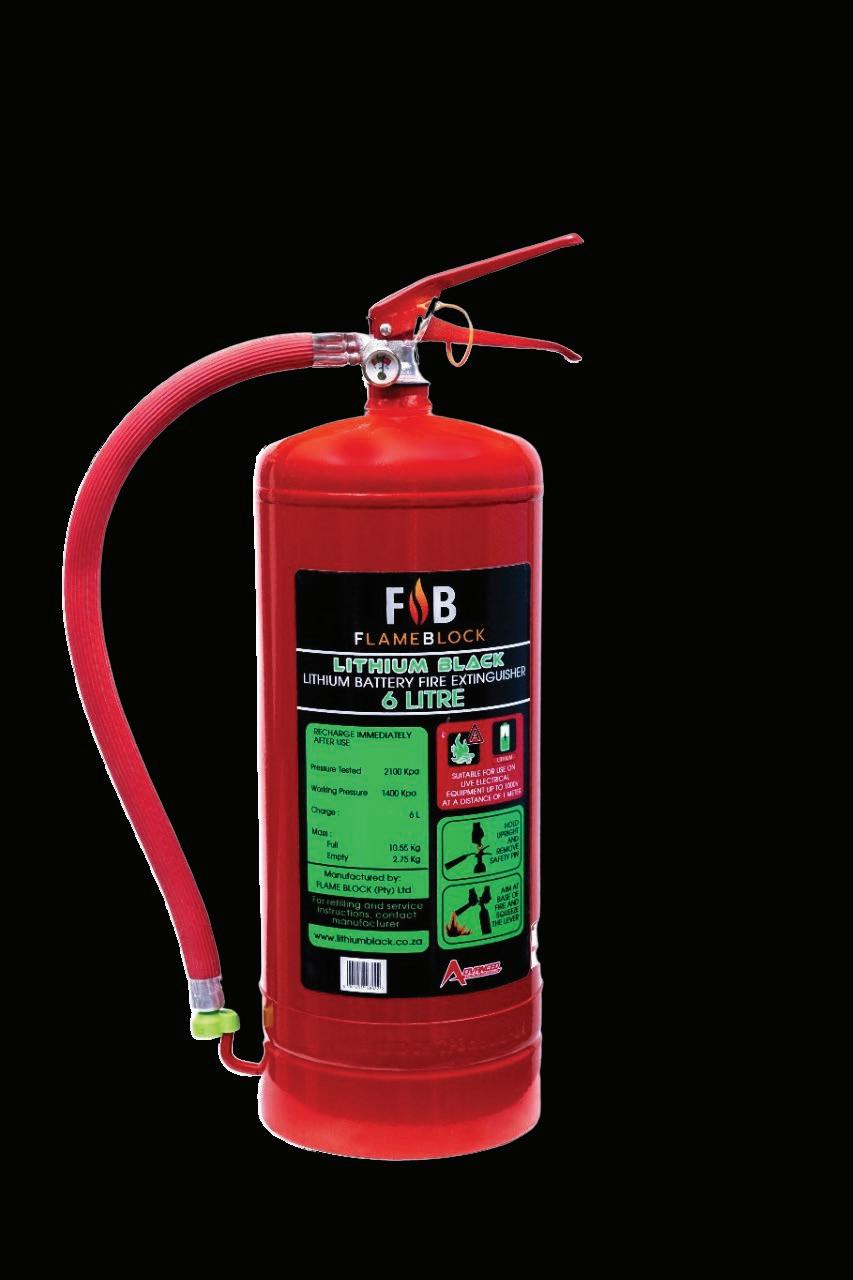
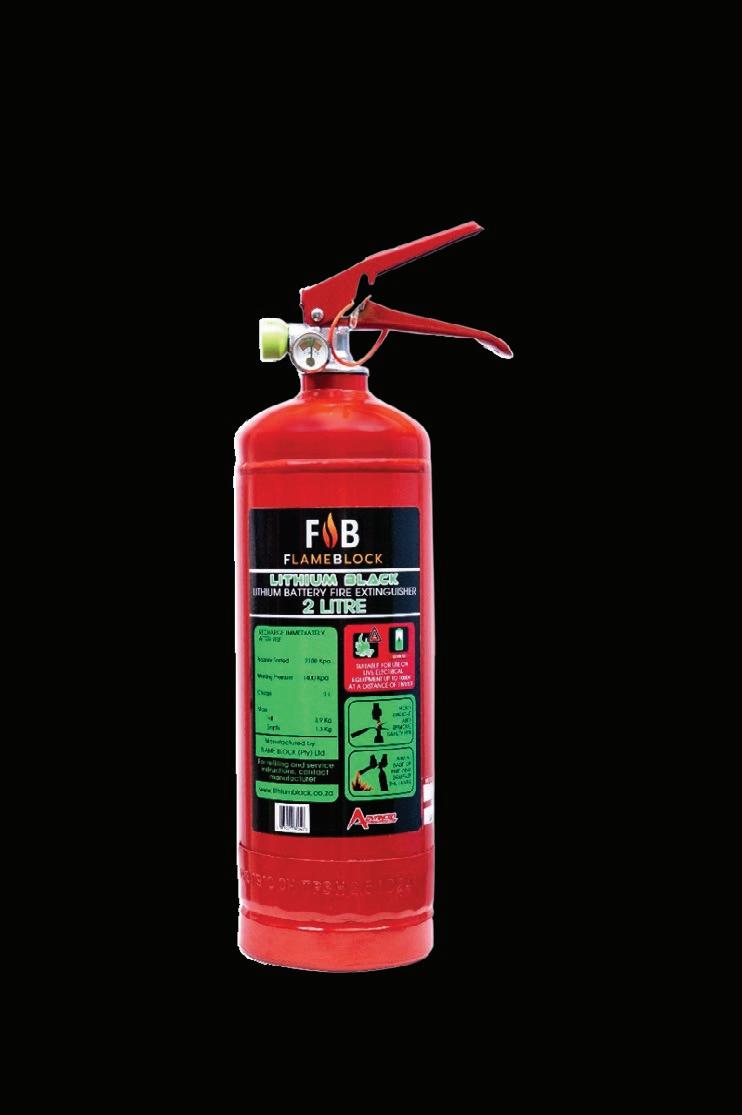
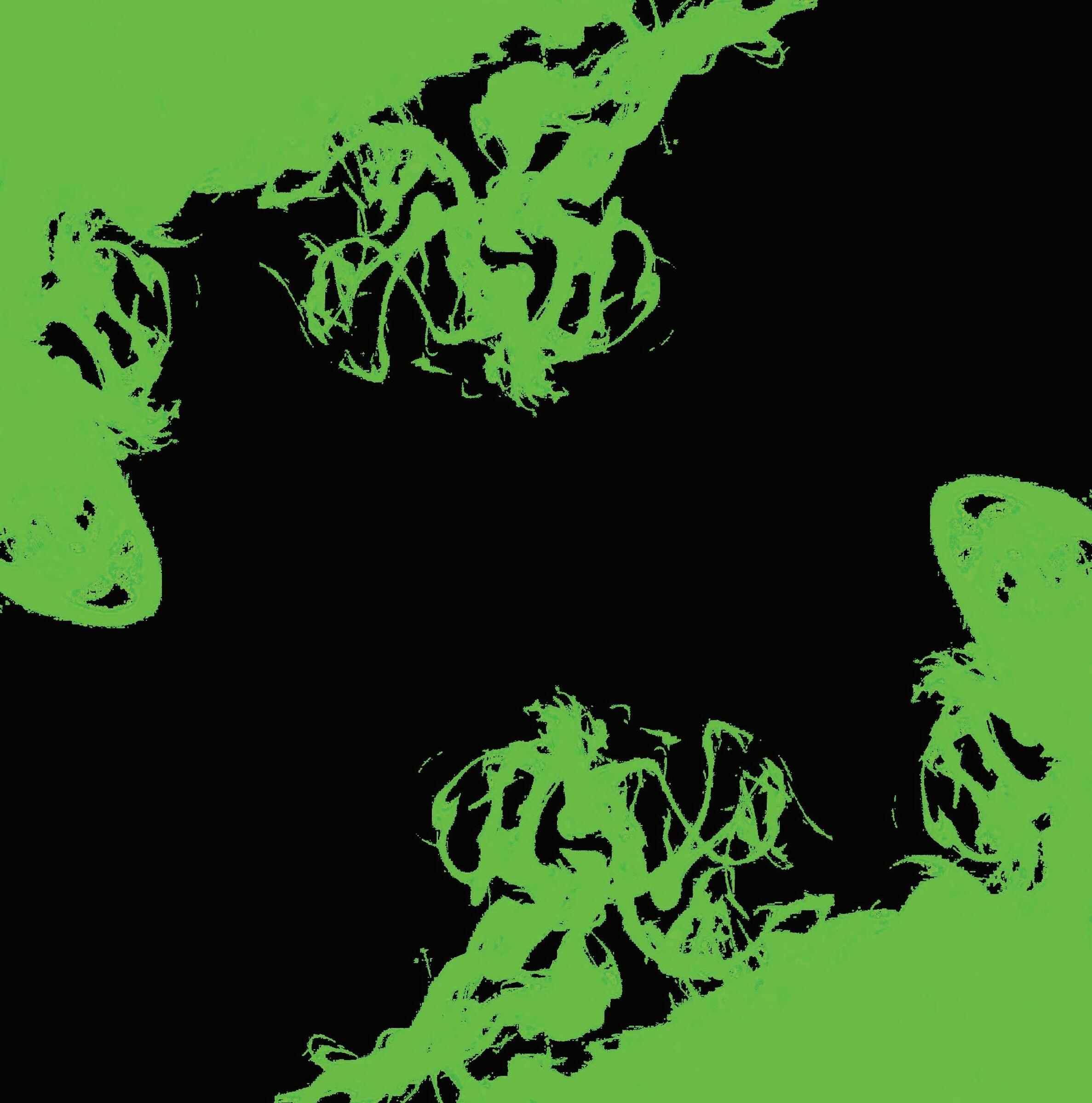
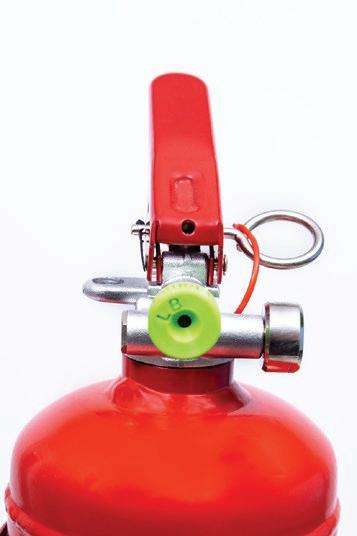
• Disrupts the combustion process by chemically neutralising oxygen radicals released during battery decomposition.
2. Advanced cooling capability
• Actively extracts heat from the burning cell, reducing temperatures to below 80 degrees Celsius, preventing thermal propagation.
• Effectively slows down exothermic reactions that sustain thermal runaway.
3. Gas containment and re-ignition prevention
• Creates a protective layer that encapsulates the battery, minimizing the escape of flammable electrolytic gases.
• Suppresses the release of hydrogen and other volatile combustion byproducts, reducing explosion risk.
4. Battery discharge mechanism
• Neutralises charge accumulation in affected cells, reducing stored electrical energy that could reignite the fire.
• Ensures that damaged battery modules remain in a deactivated state postsuppression.
Validated performance and industry applications
FlameBlock Lithium Black has undergone rigorous independent testing at the University of Stellenbosch and Ignis Fire Labs, confirming its effectiveness in mitigating lithium-ion battery fire hazards across multiple applications. It is a critical safety solution for industries reliant on lithium-ion technology, including:
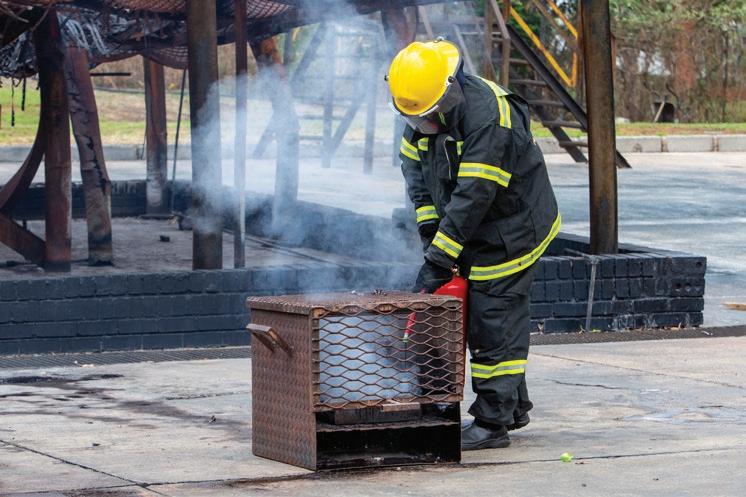
• Electric vehicles (EVs): Suppressing battery pack fires in passenger and commercial transport.
• Energy storage systems (ESS): Protecting grid-scale and residential battery storage solutions.
• Aerospace and marine: Ensuring safe lithium battery transport and storage.
• Industrial and commercial settings: Providing essential fire suppression for robotics, power tools and critical backup systems.
Why choose FlameBlock Lithium Black?
• Designed specifically for lithium-ion battery fire suppression
• Rapid temperature reduction prevents further thermal runaway
• Chemically neutralises reactive oxygen species (ROS)
• Forms an isolating barrier to contain flammable gas release
• Electrically neutralising properties reduce re-ignition risk
• Extensively tested and validated in real-world applications
Secure your safety with proven fire suppression technology
As the use of lithium-ion batteries continues to grow, so does the need for reliable, cutting-edge fire suppression solutions.
FlameBlock Lithium Black is the trusted choice for professionals and organisations requiring advanced fire safety measures.
For detailed technical specifications, safety data sheets or to place an order, visit: www.flameblock.co.za or contact us at sales@flameblock.co.za.

Fire safety design and planning approach for a Lithium battery storage warehouse
By Karel Roodt, managing director, The Fire Engineer
With the rise of renewable energy and electric mobility, Lithium-ion battery storage warehouses are becoming increasingly common in South Africa. However, these facilities present unique fire safety challenges due to the flammable nature of Lithium-ion batteries and the potential for thermal runaway.
As a fire engineer, a comprehensive fire safety design and planning approach should be adopted to mitigate these risks, ensuring compliance with South African National Building Regulations (NBR), SANS codes and international best practices.
This article outlines a conceptual fire safety strategy for a Lithium battery storage warehouse, considering local and international codes, decisionmaking in fire code selection and the importance of hazardous chemical containment and fire water runoff management.
Understanding fire risks in Lithium-ion battery storage
1. Thermal runaway and fire hazards
Lithium-ion batteries can selfignite under fault conditions, overheating or mechanical damage. Once ignited, the fire spreads rapidly due to:
• Exothermic reactions within the cells
• Production of flammable gases such as Hydrogen and Methane
• Challenges in extinguishing, as the fire can reignite even after suppression
2. Toxic and corrosive byproducts
Fires in Lithium-ion storage facilities release toxic gases such as Hydrogenfluoride (HF) and can cause severe environmental contamination if fire water runoff is not managed properly.

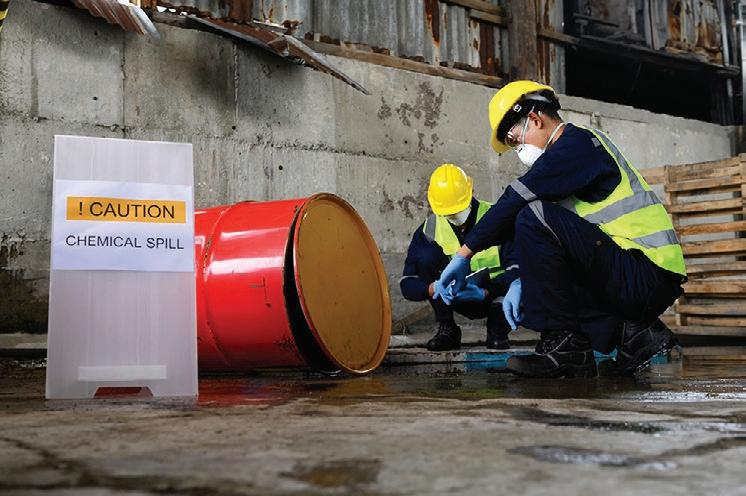
Step 1: Regulatory and fire code selection
The selection of fire safety codes and guidelines depends on factors such as storage method, warehouse classification and operational risks. A comparison of the relevant fire codes are shown in the table on the previous page.
The fire engineer approach should typically integrate SANS 10400-T and SANS 10263, with elements of NFPA 855 and FM Global Data Sheet 5-33 for a hybrid best-practice approach.
Step 2: Fire protection strategies
1. Active fire suppression
Considering the challenges of extinguishing Lithium battery fires, a combination of fire suppression technologies is required:
√ Water mist suppression (SANS 10287, NFPA 750): Effective at cooling and preventing fire spread
√ Gaseous suppression (FM200, Novec 1230) (NFPA 2001, SANS 14520): Suitable for enclosed battery rooms
√ Dry chemical suppression (NFPA 17, ISO 7202): Immediate fire knockdown in isolated battery racks
√ High-expansion foam suppression (NFPA 11, SANS 10287): Used in large open storage areas
[ Avoid standard sprinkler systems: Water alone is ineffective on Lithium-ion battery fires and can lead to electrical hazards. Currently we are aware of only one supplier with a listed deluge sprinkler system.
2. Passive fire protection
√ Fire-rated battery storage compartments (EN 14470, SANS 1253)
√ Fire barriers and fire-resistant doors (SANS 10400-T, NFPA 221)
√ Smoke ventilation and gas extraction (SANS 10400-O, NFPA 92)
√ Explosion venting in case of gas release (NFPA 68, ATEX Directives)
Step 3: Warehousing of dangerous goods and containment
Why dangerous goods classification matters
Lithium-ion batteries are classified as Dangerous Goods (DG) Class 9 under SANS 10263 and UN 3480/3481, requiring special segregation, containment and environmental protection measures.
Key warehouse safety considerations
√ Primary containment: Battery storage compartments with firerated separation
√ Secondary containment: Spill trays, bunded areas for electrolyte leaks
√ Tertiary containment: Drainage design for hazardous fire water runoff
An example of a warehouse fire safety layout
Why fire water runoff containment is critical During a fire event, contaminated runoff containing heavy metals and toxic electrolytes can infiltrate stormwater systems, causing severe environmental damage.
Solutions
• Polluted water holding tanks (SANS 10263)
• Oil-Water separators and chemical treatment systems (ISO 14001, NFPA 30)
• Spill response procedures and absorbent deployment
Conclusion
The design of a Lithium battery storage warehouse demands a multi-layered approach to fire safety, integrating:
√ Code-driven decision making: Balancing SANS 10400-T, NFPA 855 and FM data sheets
√ Advanced fire suppression technologies: Water mist, gas suppression and foam systems
√ Passive fire containment: fire-rated compartments and explosion venting
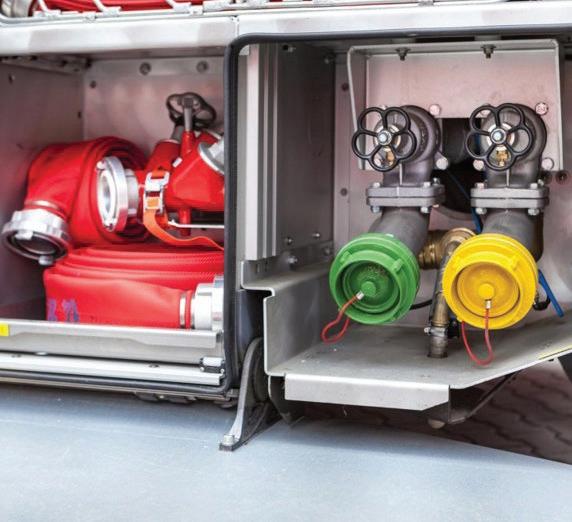
The design of a Lithium battery storage warehouse demands a multi-layered approach to fire safety
√ Dangerous goods handling and fire water runoff management: Preventing environmental contamination
By applying Fire Engineer’s structured fire safety approach, warehouse operators can mitigate risks, protect assets
and ensure compliance with both local and international safety standards.
Need expert guidance on Lithium battery storage fire safety? Contact an experienced fire engineer for a customised fire safety strategy.

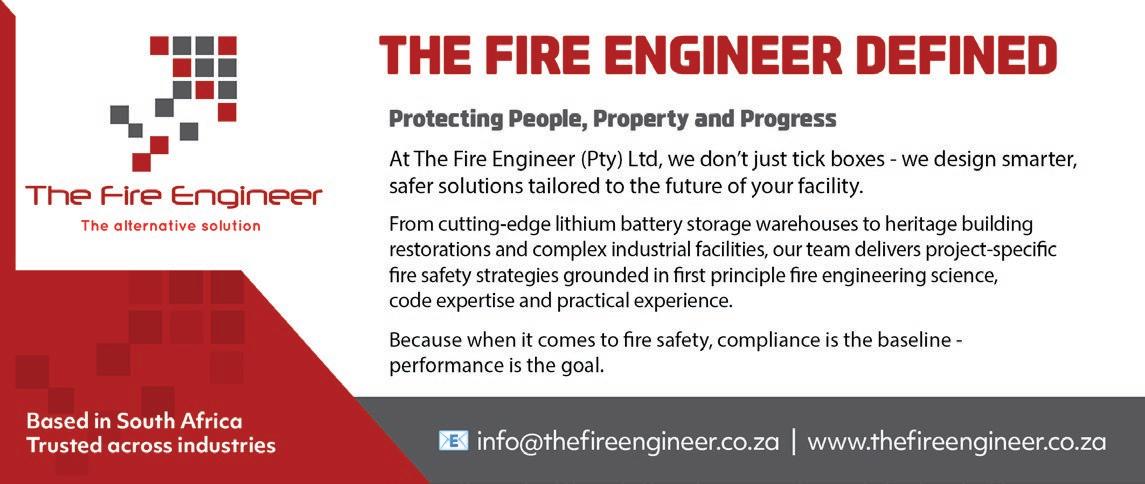
Firematic fire suppression and detection systems
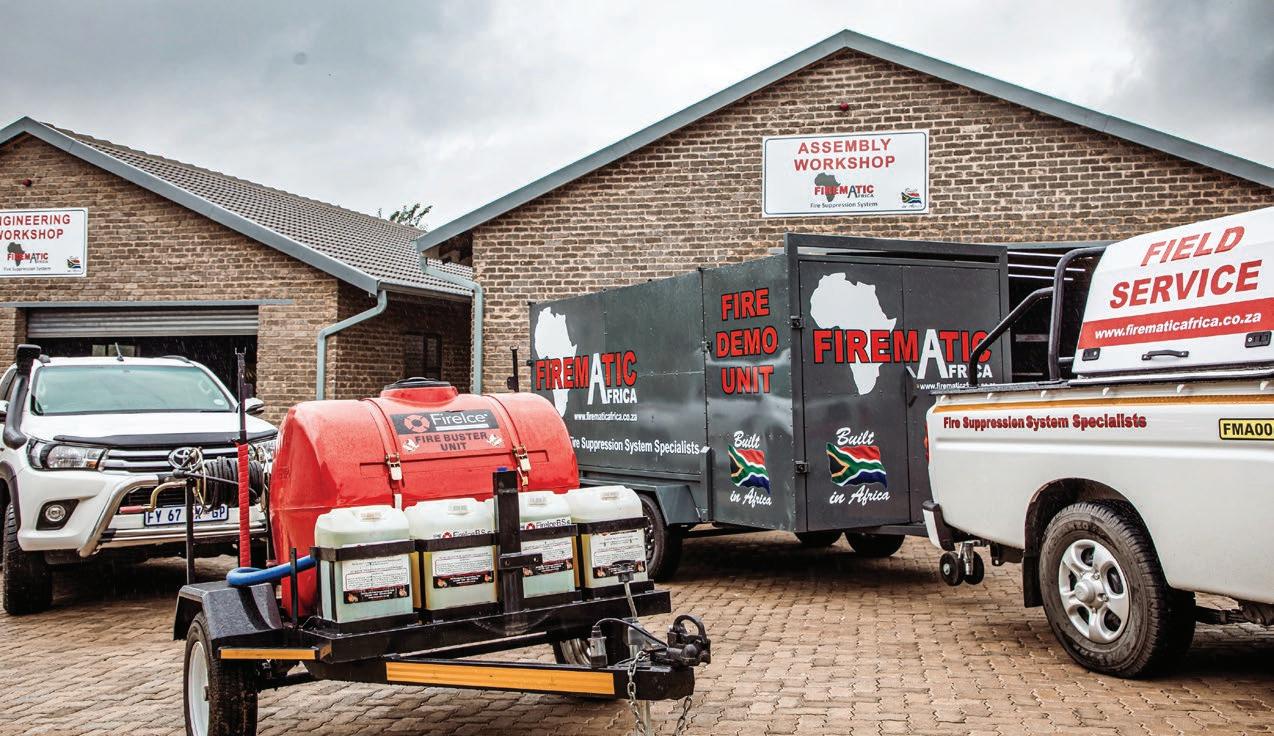
Firematic Africa (PTY) Ltd is the original equipment manufacturer (OEM) of the Automatic Firematic Africa Fire Detection and Suppression Systems, which was established more than two decades ago by Mr John O’Reilly, a graduate of the South African Fire Service Institute (SAFSI) and the Institute of Fire Engineers (IFE).
"Designs are done by our professional (Pr) engineer and comply with all statutory regulations."
Firematic has since grown to an established company with newly built offices, workshops, training centre, various agencies and a footprint that stretches over seven countries.
Firematic Africa will design, manufacture, supply, service, maintain, repair and install fire detection and suppression system that will suit your needs and environment.
Our product is unique, effective and manufactured locally with local employment, local procurement and a level 2 B-BBEE status. Our team of engineers, professional technicians, quality control and management stand ready to
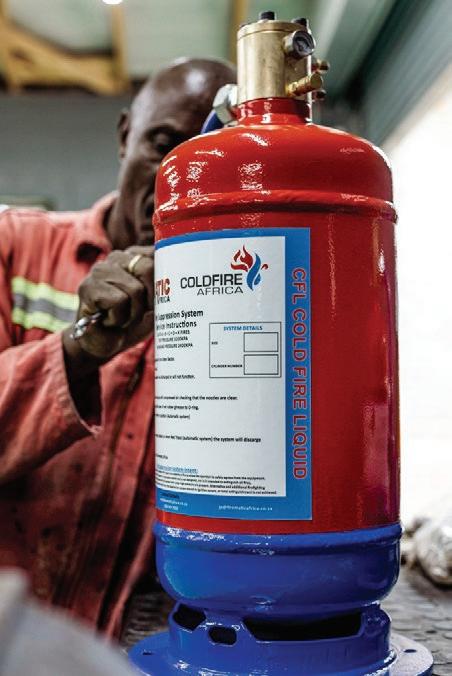
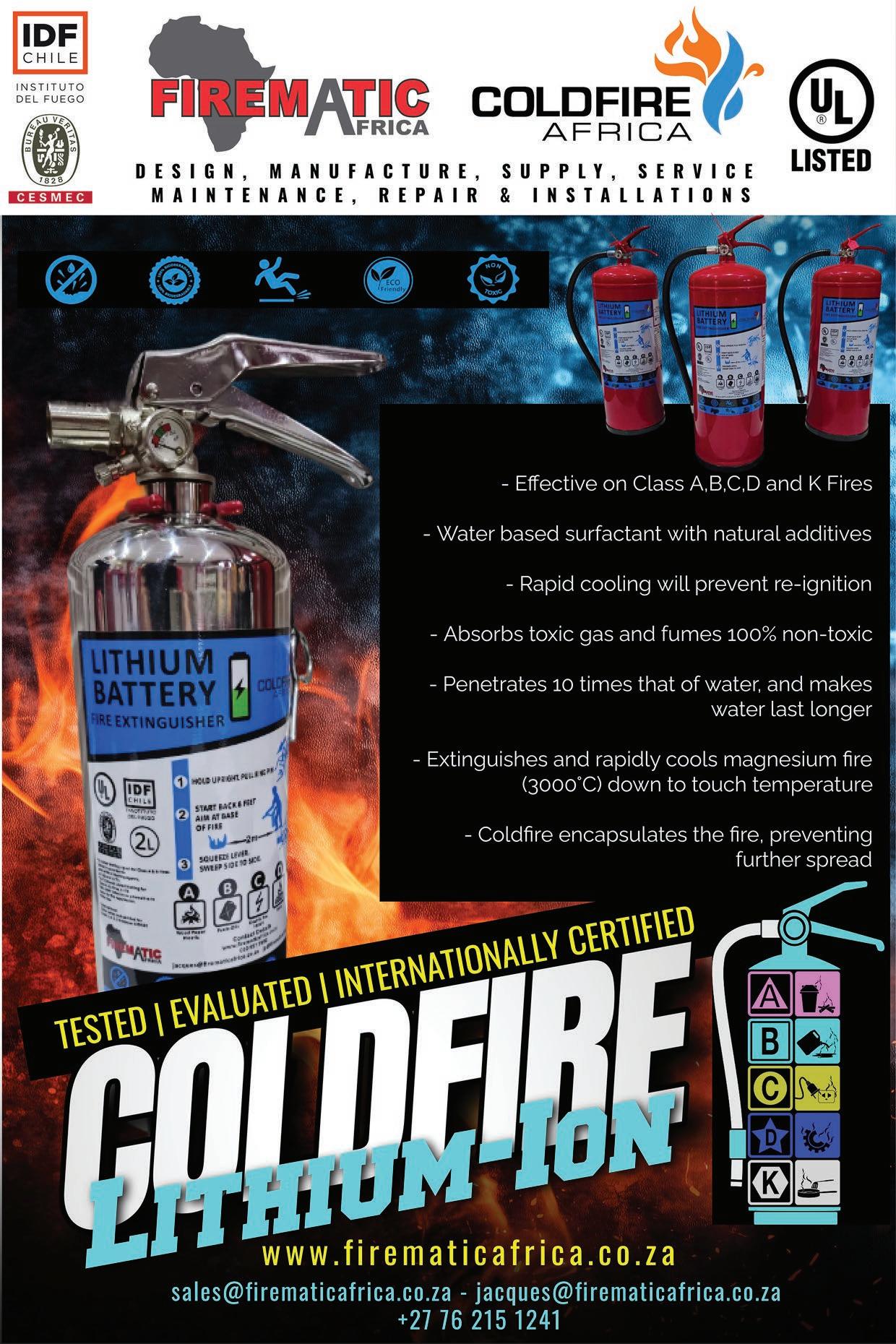
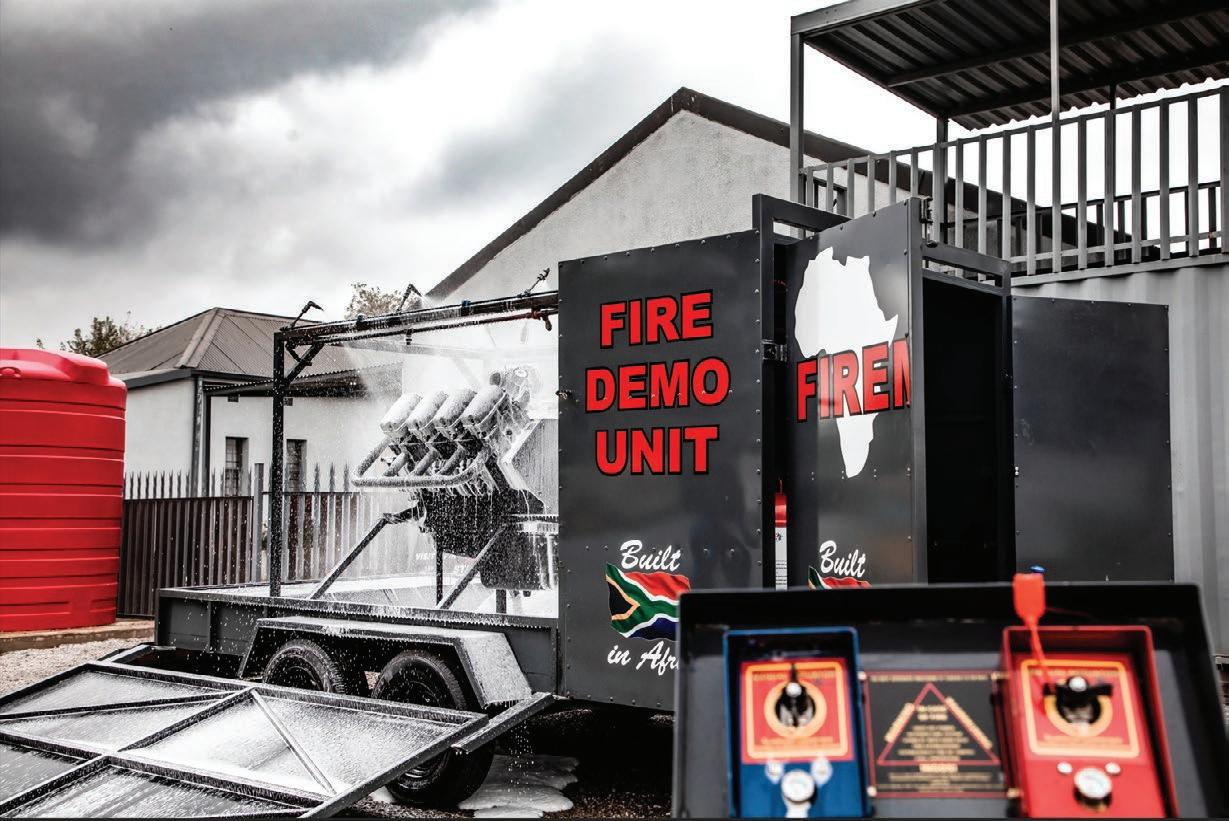
assist your company in your need for a quality fire detection and suppression system.
A reliable and robust yet uncomplicated and automatic
system, perfectly designed for any surface, underground and factory conditions. No matter how remote your location, our system needs no power source to operate effectively and is not
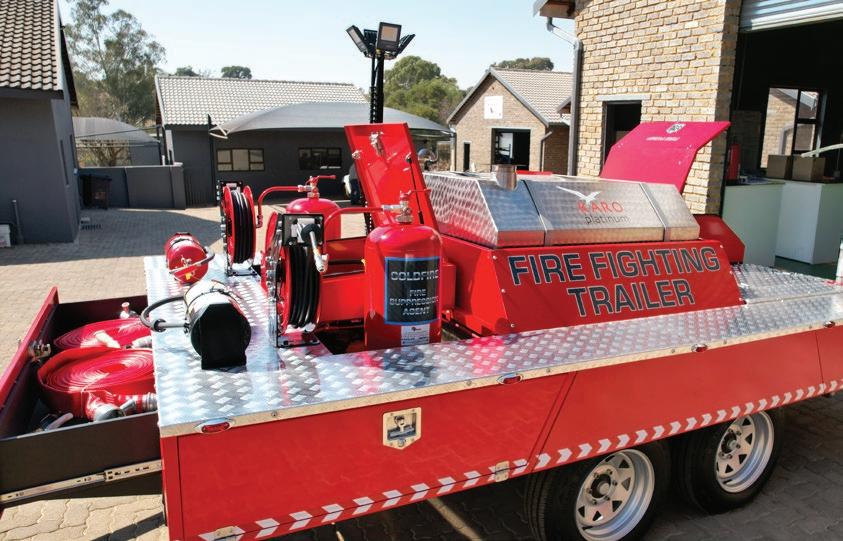
influenced by any power source negatively. It is a fail-safe system that is easy to maintain and very affordable. Regardless of the location, terrain and conditions our system remains reliable and is constantly in automatic mode.
The Firematic Africa dry chemical powder (DPC) system is a versatile fire suppression system for Class A, B, C, D and K fires.
Types of applications include but are not limited to: All trackless mobile machinery (TMM) such as dump trucks, load, haul, dump loaders (LHDs), drill rigs, cranes and excavators.
Also all earthmoving/yellow machines such as graders, dozers and backhoe loaders (TLBs), busses and coaches,
airport tugs, haulage trucks, telescopic handlers, people carriers, forestry machines and mining equipment.
Depending on your risk assessment, we will design a system custom made for your needs and environment, to suppress a fire.
You have the options between dry chemical powder (DCP), Coldfire Liquid or a combo system. Our systems are perfect for transformers, diesel bays, conveyor belts, battery bays, pump rooms etc, whether surface or underground, in a factory or remote where there is no electricity or power source.
Designs are done by our professional (Pr) engineer and comply with all statutory regulations. Our product range include TMM, earth moving and vehicle fire detection and suppression systems, conveyor fire detection and suppression systems, stationary fire detection and suppression, Coldfire Liquid/ Lithium-ion and the Firematic Africa Fire Buster Unit.

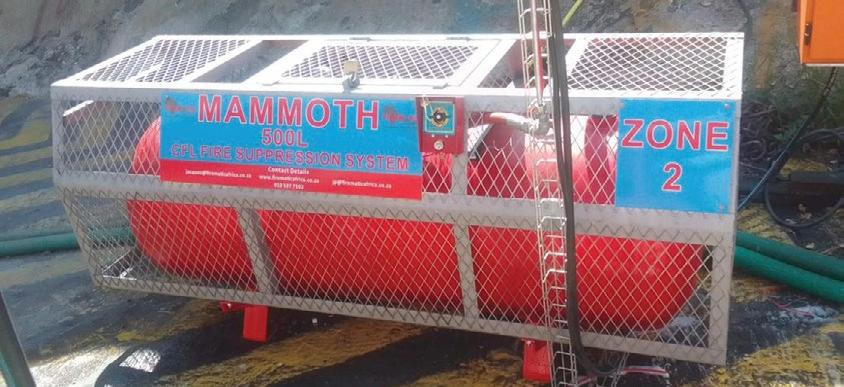
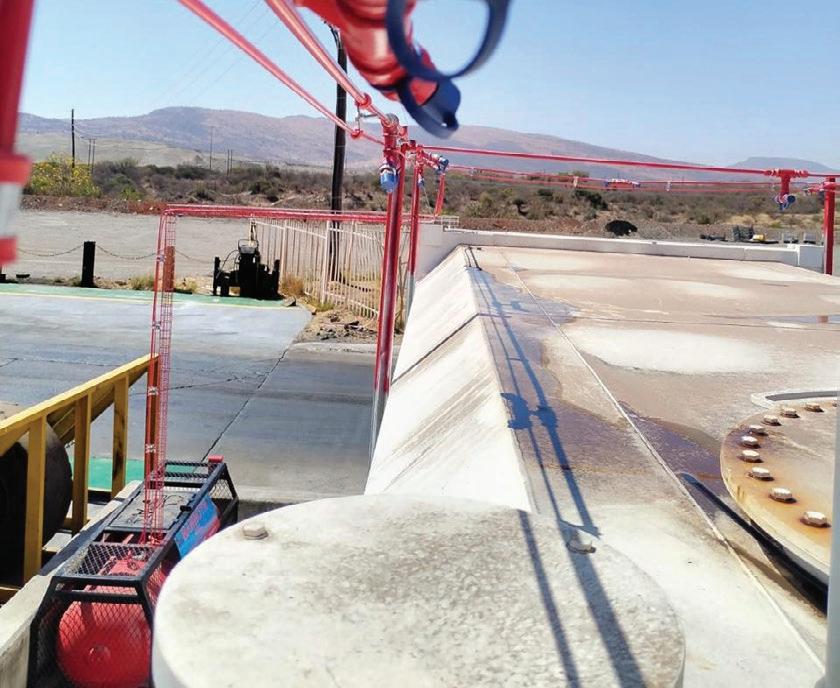
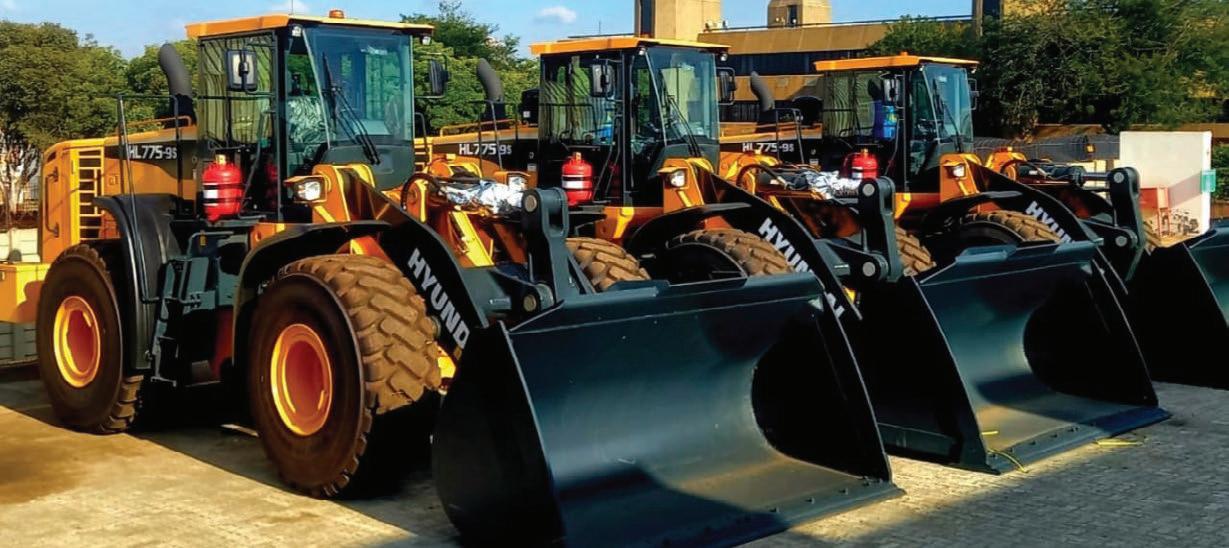
Lithium-ion
Why traditional fire extinguishers can't tame Lithium-ion battery fires: The unusual chemistry of Lithium-ion battery fires
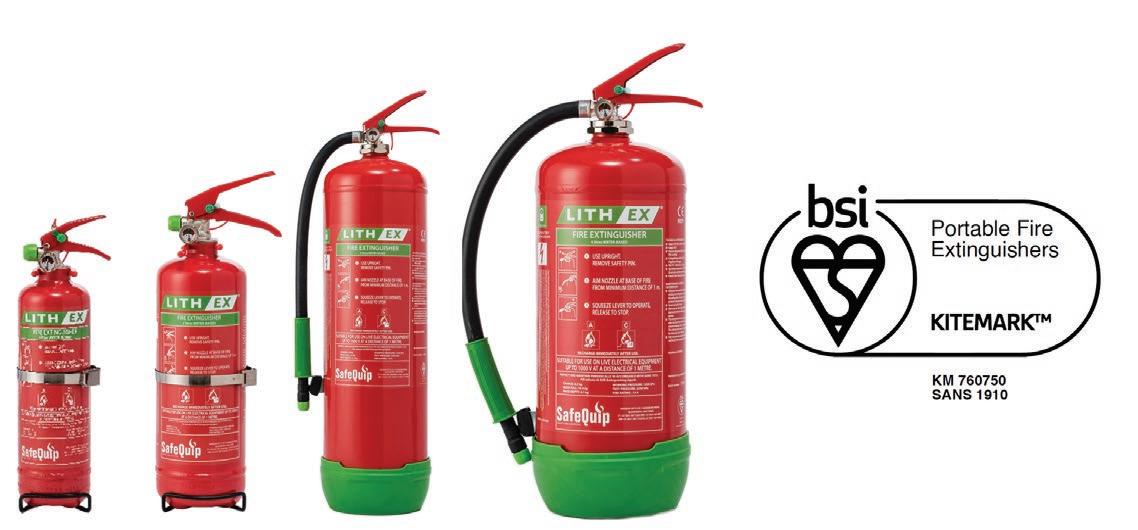
You might wonder why a regular fire extinguisher, the kind you might have in your home or workplace, can't handle
Lithium-ion battery fires. SafeQuip, a leading distributor of fire-related equipment, explore why Lithiumion battery fires can be intense and tricky, unpredictable and can occur often with any warning.
Understanding Lithium-ion battery fires
Lithium-ion batteries, while highly energy-dense and efficient, can occasionally malfunction or become damaged. When this happens, a chain reaction called thermal runaway can occur, leading to a fire.
Here's a simplified explanation of how thermal runaway unfolds:
1. Trigger event: Something goes wrong with the battery, such as physical damage, overcharging, or a manufacturing defect.
2. Release of hot gasses: The affected cells inside the battery swell and release hot, flammable gasses.
3. Fire ignition: These gases ignite at high temperatures and can quickly spread the fire to neighbouring cells or flammable materials.
The limitations of traditional fire extinguishers
Traditional fire extinguishers are designed to combat fires by removing one or more elements of the fire triangle: heat, oxygen and fuel. They work well for typical fires involving materials like wood, paper or flammable
liquids, where the fire triangle principles apply. However, Lithium-ion battery fires are a different beast altogether and here's why regular extinguishers can't quench them effectively:
1. Lack of appropriate agents: Traditional fire extinguishers use agents like water, foam or dry chemicals. These agents may not be suitable for Lithium-ion battery fires because they don't address the unique challenges posed by the high-energy density of these batteries.
2. Inadequate cooling: In a Lithium-ion battery fire, simply cooling the flames with water isn't enough. While water can lower the temperature temporarily, the fire can reignite because it
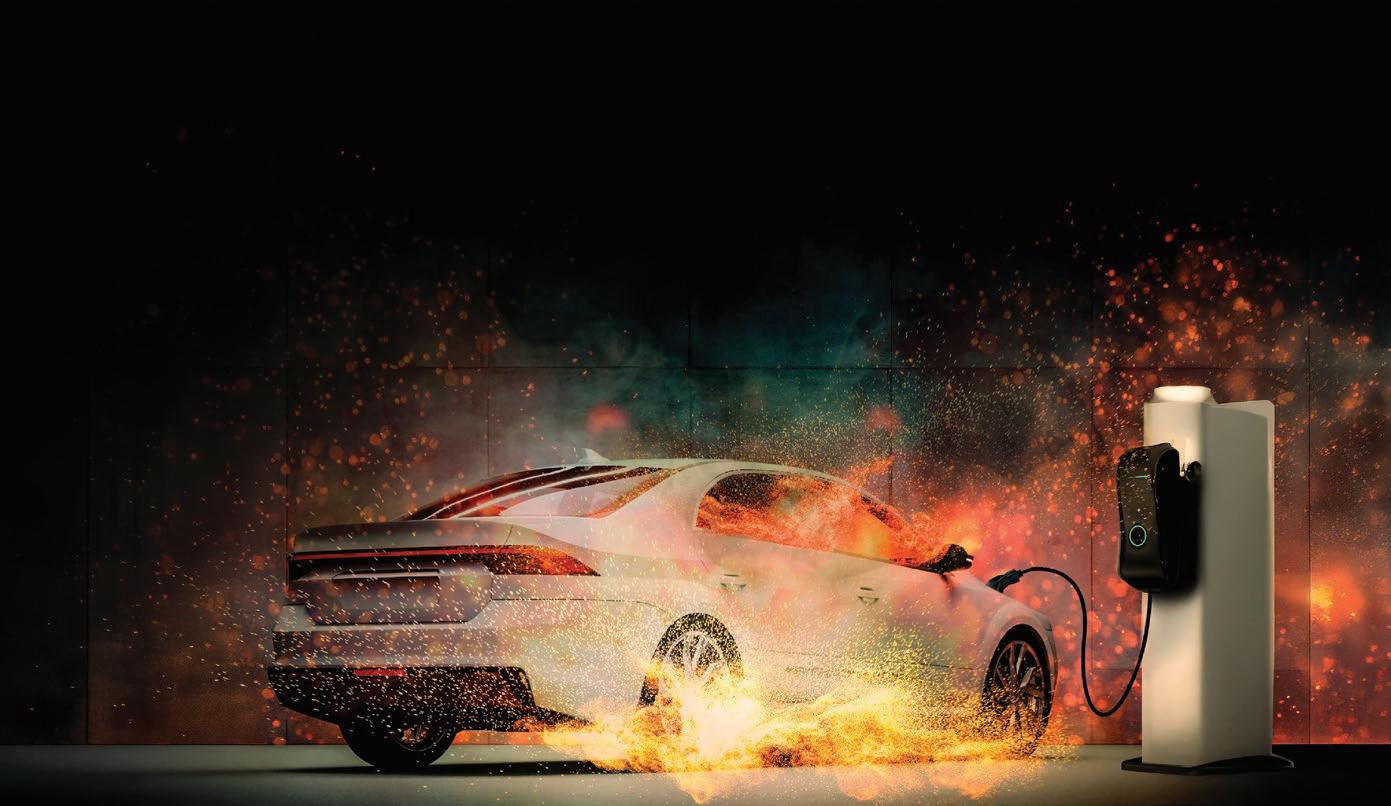
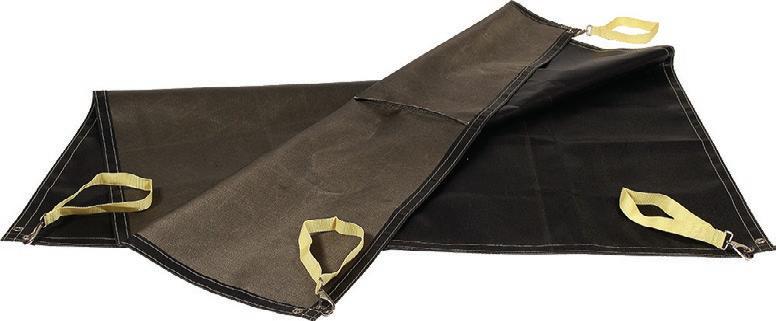
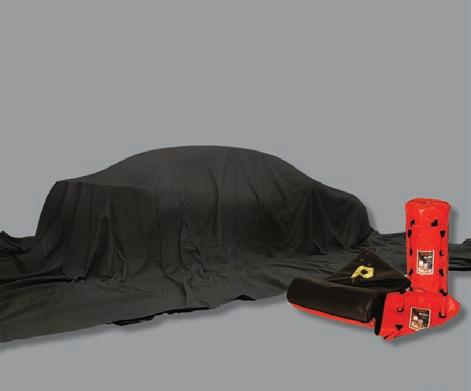
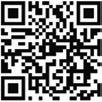
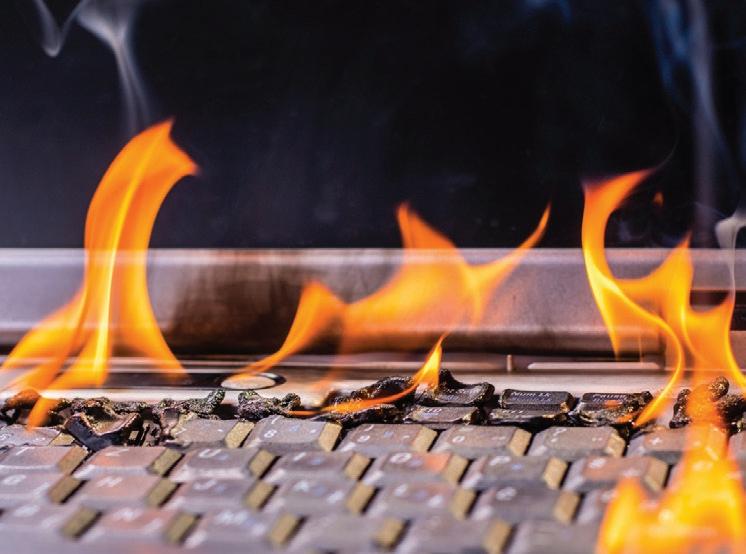
doesn't address the root cause, the internal reactions within the battery that sustain the fire.
3. Re-ignition risk: Even if you manage to temporarily extinguish the flames with a traditional extinguisher, there's a significant risk of re-ignition. If the battery is still compromised and the thermal runaway isn't stopped, the fire can flare up again once the extinguishing agent dissipates.
4. Electrical conductivity: Many traditional extinguishing agents are conductive, which means they can cause short circuits in electronic devices like Lithium-ion batteries. This could potentially worsen the situation and make it more hazardous.
The Solution: Aqueous Vermiculite Dispersion (AVD)
So, if traditional fire extinguishers aren't suitable for Lithium-ion battery fires, what's the solution? Enter Lith-Ex Fire Extinguishers containing aqueous Vermiculite dispersion (AVD). AVD is a cutting-edge fire extinguishing agent designed specifically to combat the unique challenges
posed by Lithium-ion battery fires. AVD – an agent specifically designed for Lithium-ion battery fires. AVD is made from the naturally occurring mineral vermiculite combined with water. It is a very effective agent that cools, encapsulates, prevents propagation and extinguishes Lithium battery fires.
How to use Lith-Ex fire extinguishers
Lith-Ex fire extinguishers are your trusty allies when it comes to Lithium-ion battery fire safety. Here's a quick guide on how to use them effectively:
1. Stay calm: In the heat of the moment, keeping your cool is paramount. Take a deep breath and assess the situation.
2. Grab Your Lith-Ex: Ensure you have a Lith-Ex fire extinguisher on hand. These are specially designed to combat Lithium-ion battery fires.
3. Pull the pin: Hold the extinguisher upright and pull the safety pin to unlock it.
4. Aim low: Always aim the nozzle at the base of the fire where the Lithium-ion battery is
burning. This is where you'll have the most impact.
5. Squeeze and cover: The aim is to cover the entire battery as quickly as possible. This can be achieved by moving around the burning battery and making sure the complete battery surface is covered. The sweeping motion will allow AVD to form layers covering the battery. These layers will encapsulate the fire. Do not just aim at one spot but make sure to cover the total battery fire. Squeeze the handle to release the extinguishing agent and sweep it from side to side, covering the entire fire. Keep a safe distance and stay clear of any splashing.
6. Watch and wait: After the fire is out, keep an eye on it to ensure it doesn't reignite. Stay safe and ready.
The SANS 1910-2022 approved, Lith-Ex fire extinguisher range, from SafeQuip, carries NTA 8133:2021 (KIWA/POOO55865) test approval, which proves its Lithium-ion battery fire extinguishing capability.
SafeQuip's Lith-Ex fire extinguishers are available in various sizes to suit different needs and environments and can be purchased from select retailers, as well as through SAQCC approved servicing agents. To find out more about the availability of the Lith-Ex fire extinguisher range, email info@ safequip.co.za.
To learn more about how SafeQuip is pioneering improvements in fire safety, visit www.safequip.co.za. You can join the conversation and stay updated on new advancements by following SafeQuip on Facebook and LinkedIn.

Ignis Fire Testing: The future of fire testing
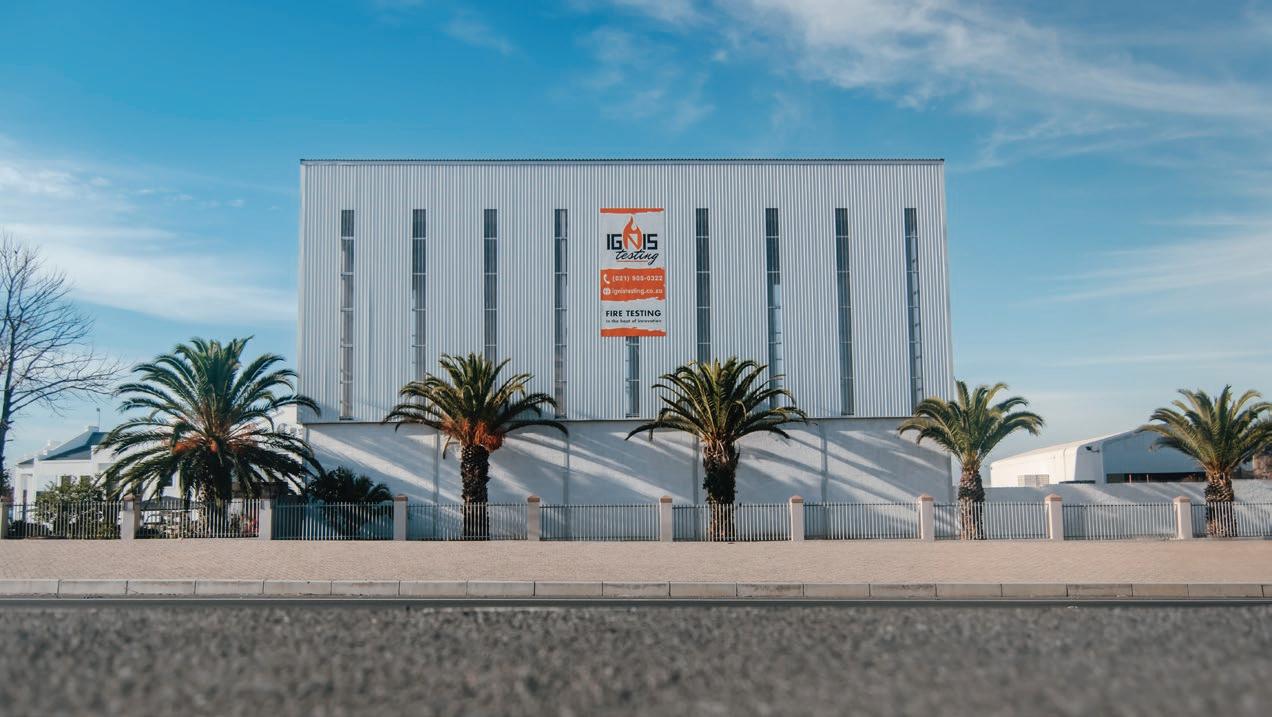
Ignis Fire Testing proudly announced the launch of its augmented testing laboratory, setting a new benchmark in fire safety testing.
With its central location near Cape Town and Stellenbosch, this facility is designed to meet the burgeoning global demand for fire safety services and a crucial local need.
With a mission to enhance fire safety compliance worldwide, Ignis Fire Testing’s new premises allow for a broader range of tests and increased capacity. They showcase South African engineering excellence while meeting the stringent international standards.
The Ignis Fire Testing’s expanded laboratory and workshop was officially launched on 19 August 2024, in Blackheath, Cape Town. This multi-million Rand investment is the largest known privately-owned fire testing facility in Africa and boasts collaboration with Stellenbosch University’s Fire Engineering Research Unit (FireSUN). To limit costly imports and boost innovation, all their equipment, software and control systems are created in-house.
Dirk Streicher, civil engineer and owner of the new 1 500-squaremetre facility, featuring an 18-metre-high roof, says fire testing is a neglected field in South Africa. “We saw the gap in
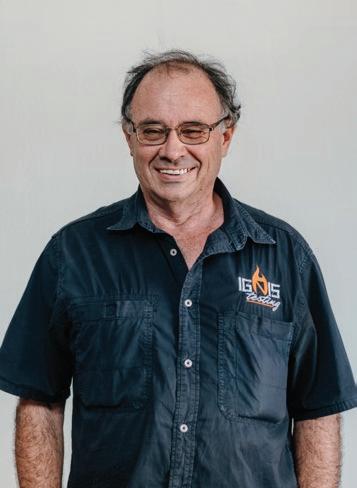
Dirk Streicher, civil engineer and owner and founder of Ignis Fire Testing
the market for local fire testing,” said Streicher.
Streicher is the owner, founder, mastermind and chief engineer behind Ignis Fire Testing. He has a master’s degree in Civil Engineering and 45 years of experience in road construction, specialised
Ignis Fire Testing’s facility in Blackheath, Cape Town

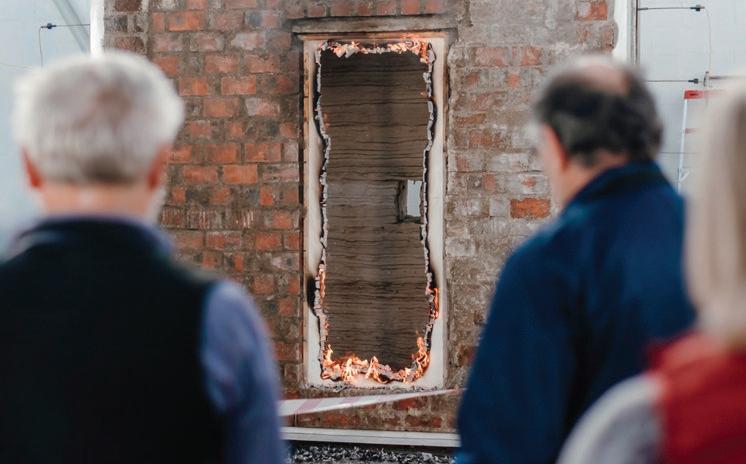
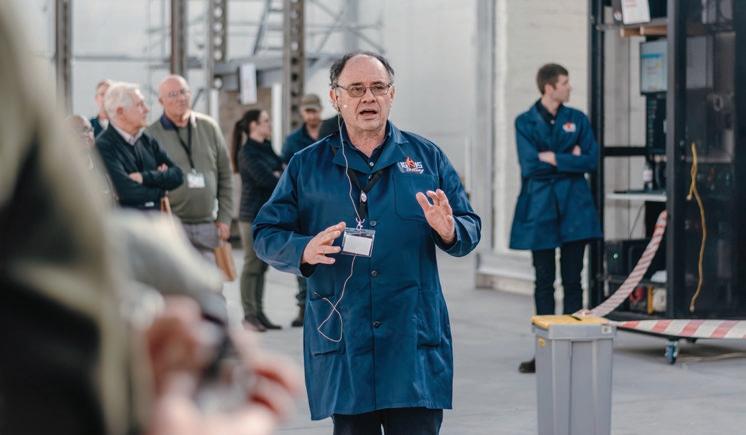
joinery manufacturing for large construction projects and property development.
His involvement in the construction industry made him aware of the need for fire testing in South Africa and around the globe, ultimately leading to the establishment of Ignis Fire Testing as his “retirement project”.
“Fire testing is at the heart of a fire-safe environment; yet minimal modern testing facilities exist in Africa to meet this demand. This is the reason behind the launch of the privately owned Ignis Fire Testing in Cape Town,” said Streicher.
Streicher is also an extraordinary faculty member at Stellenbosch University’s Fire Engineering Research Unit (FireSUN), where he supports many postgraduate students in their studies, coauthors research papers and occasionally lectures.
Research and development
Ignis Fire Testing collaborated with Stellenbosch University’s Fire Engineering Research Unit (FireSUN), led by Prof Richard Walls. They work closely with students and staff, granting access to their testing facilities for research purposes, supporting postgraduate degrees and co-authoring papers that push the boundaries of fire safety engineering.
Prof Walls said at the opening, “Today is a very exciting day for fire engineering in the industry. Moving forward, testing is critical in our industry but we also see how much there is to do. So this is the first step.”
He emphasised the importance of fire testing and fire
Attendees at Ignis Fire Testing’s launch watching a fire resistance test demonstration
Attendees at Ignis Fire Testing’s launch watching a fire resistance test demonstration
Dirk Streicher, owner of Ignis Fire Testing, explaining to attendees at the launch how a fire resistance test is done

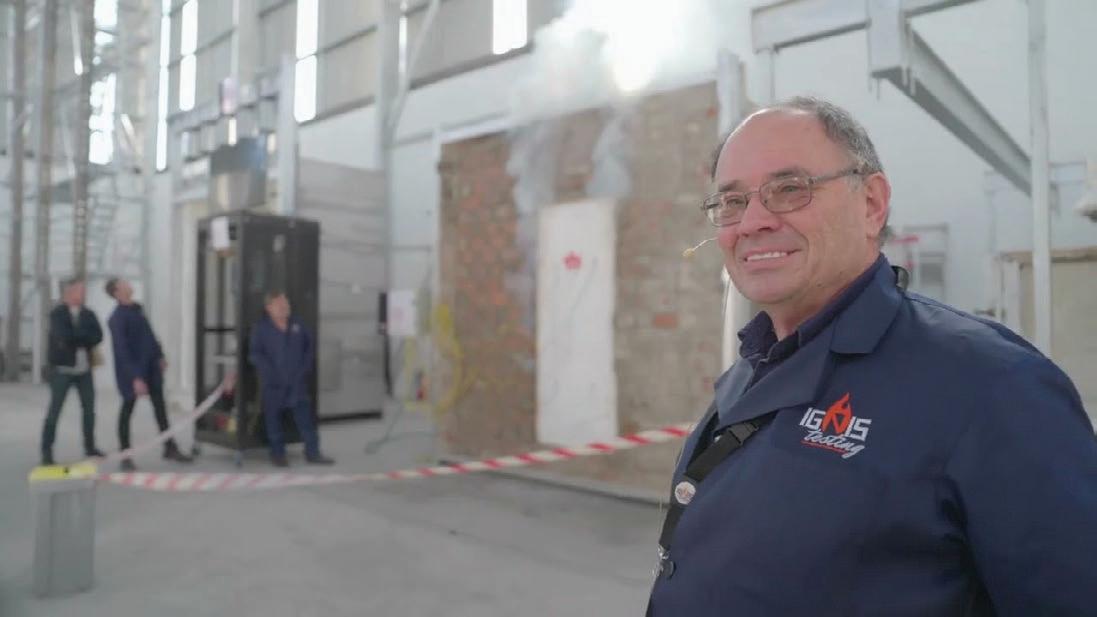
engineering. “Fire testing will be fundamental to promote sustainability; hence there will be a growing emphasis in the coming years. Major new challenges will arise in green energy, growing populations, poverty, taller buildings, bigger warehouses, ageing infrastructure and ageing populations. Fire Engineering will be called to address the needs. Test lab capacity in South Africa needs to at least double in the next ten years,” said Prof Walls.
He added, “With the Stellenbosch University now producing students in Fire Engineering, it would not surprise me if we see the Cape become the centre of excellence. We have a base here to serve the African continent.”
International commendations
Dr Brian Meacham, who is the director at Risk and Regulatory Consulting of Crux Consulting LLC in Shrewsbury in the USA, was one of the guest speakers
at the official opening. Dr Meacham is regarded as a global expert in Fire Engineering, having worked for the World Bank and the Asian Development Bank in policy development.
Dr Meacham highlighted the importance of Ignis Fire Testing’s laboratory to a firesafe environment. “It is really interesting for me to be here and look at the fire test lab and celebrate the launch because fire testing and fire data is the core of everything we do. You cannot build a safe building, safe automobile, safe aircraft, safe mine, safe anything without considering the materials’ fire safety performance. It is at the core of every design,” he said.
Laboratories like Ignis Fire Testing provide data for engineering analyses, said Dr Meacham. “Everything starts with the data. We can’t run engineering models without good data. If we’re running engineering
models without good data, it’s not good engineering.”
“I applaud the work that is being done and I really applaud the relationship with Stellenbosch University because it is a way to really bring things together and make a super important contribution to the future,” said Dr Meacham.
He concluded in saying, “I’m just really happy to be here and see what I consider a significant advancement globally for more fire testing. And to have it here, in this region in South Africa and to have it as a resource across the continent is great.”
Available fire tests
Ignis Fire Testing offers an extensive range of fire safety tests, adhering to South African and international standards, including ISO codes. The facility includes several custom-built furnaces ie fire resistance tests, a set of reaction-to-
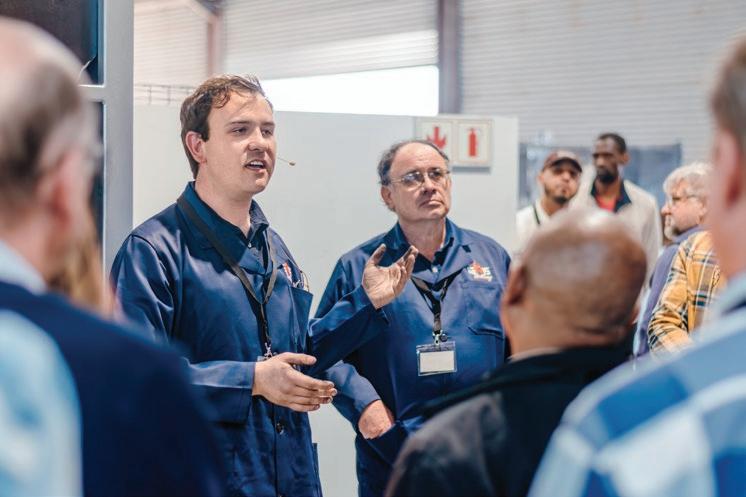
fire classification tests, cone calorimetry confirmation testing, room corner and gas suppression tests, façade tests and supplementary and auxiliary fire equipment, such as sprinklers, tests. These were all designed and built by Ignis Fire Testing’s team.
The facility is equipped to assess various products such as lithium-ion batteries and solar panels and can adapt to special requirements beyond standard procedures.
Ignis Fire Testing also tests fire doors to determine the time it takes for a fire to destroy them; the burn time and behaviour of insulation material when it faces a fire; as well as the fire-resistance, if any, of for example tent material.
Furthermore, it also incorporates sustainability measures such as rainwater harvesting, solar power and advanced air filtering systems.
Streicher said, “We saw the gap in the market for local and international fire testing.
Where do you go if you have to test products or materials to adhere to fire safety standards? There are few local options. Even internationally, the testing demand is bigger than the supply, leading to major backlogs. It is also very expensive for South Africans to test abroad.”
“Our biggest clients are manufacturers and suppliers of fire-related installations and
items,” says Streicher. “And the facility has the capacity to expand as demand grows.”
Accreditation
There is no legal accreditation requirement for a (fire) test laboratory in South Africa.
Regarding the SANS 10177 series of fire test standards; Fire testing of materials, components and elements used in buildings, there is no reference made about the level of expertise or qualification of the operators of a fire test laboratory.
SANS 10400 covers the requirements and validity of a test report in the application of the National Building Regulations.
Please note that a testing laboratory issues a test report and not a certificate. It is a testing authority and not a certification body. The test report is a summary of measurements, results and observations done in a controlled manner according to prescribed codes and standards valid for the sample submitted
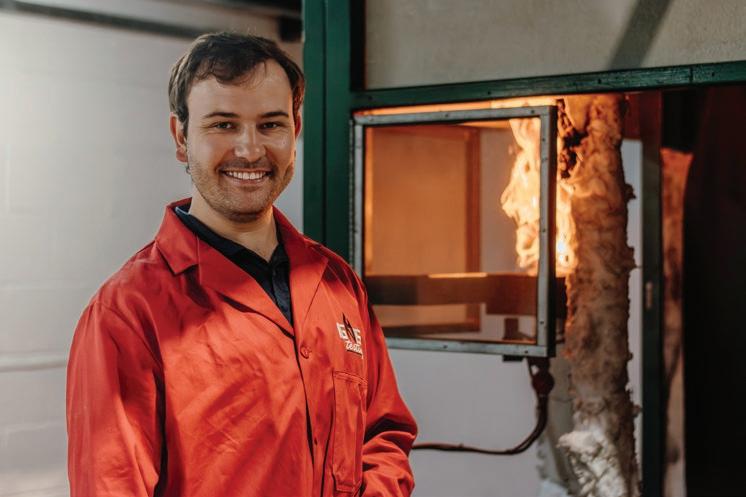
Carlo Kuhn, chemical engineer, demonstrating to the attendees at Ignis Fire Testing’s launch how a single burning item test is conducted
Carlo Kuhn conducting a single burning item test, which forms part of a suite of reaction-to-fire tests
by a sponsor. The professional conduct, integrity and competence of the laboratory personnel determine the quality and correctness of the test.
In terms of Fire Engineering, SANS 10400 Part A General Principles and Requirements and SANS 10400 Part T Fire Protection, is of importance. Clause 3.7 of Part A defines a competent person in short as a person who is qualified by virtue of his education, training, experience and contextual knowledge.
The definition of a fire engineering competent person is a person registered in terms of the Engineering Profession Act, 2000 (Act No. 46 of 2000), as either a Professional Engineer or a Professional Engineering Technologist and is generally recognised as having the necessary experience and training to undertake rational assessments or rational designs in the field of fire engineering, according to SANS 10400 Part T Fire Protection.
In SANS 10400 Part A, Annex B Commentary on the National Building Regulations, clause B.6 covers Test reports and certificates. This section still refers to Council for Scientific and Industrial Research (CSIR) and South African Bureau of Standards (SABS). The building fire research division of CSIR closed a few years ago, so reference to CSIR fire testing is now irrelevant. The support of the SABS waned dramatically during the past few years. As a result, this leaves Agrément as a default certifier. Ignis Testing was approached by Agrément to perform fire resistance
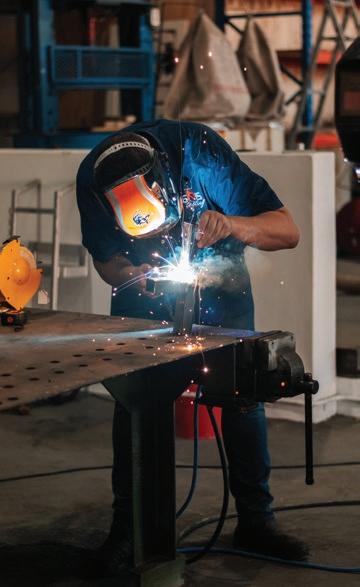

testing for their clients. The clause further states that a local authority can consider test reports from independent laboratories such as universities or private enterprises.
Ignis Testing also work in close relation with the Stellenbosch University and Thermal Insulation Products and Systems Association South Africa (TIPSASA) in research, development and quality reviews. Furthermore, Ignis Testing is also appointed to do fire testing on behalf of SABS. In terms of a quality management system, it must be noted that Ignis Testing is ISO 17025, Testing and Calibration Laboratories, compliant.
To complete the circle, a test report issued by Ignis Testing will have the same standing and validity as an A19 certificate (Appointment of Persons Responsible for Design, Inspection and Assessment
Duties) issued by a registered Professional Engineer and will thus form part of the supporting documentation submitted by the appointed competent fire engineer under clause A19 of SANS 10400 Part A and form AZ4 in Annexure D of SANS 10400 Part A.
Because Ignis Testing is operated by Professional Engineers, Ignis Testing is bound by the Code of Conduct for Registered Persons: Engineering Profession Act (Act No 46 of 2000). A copy of the code of conduct is available here. The only reasons a test report issued by Ignis Testing should be repudiated is when the ECSA Code of Conduct for Registered Persons is contravened or gross negligence can be proven. The only other reason is when a different test was specified by the sponsor than the one required by the appointed competent person.

Dirk Streicher at work in the laboratory
All Ignis Fire Testing’s equipment is built in-house
Important considerations for Lithium-ion battery energy storage systems (BESS) in South Africa

impressive. Undoubtedly, loadshedding and the increase in cost of electricity have been important factors that added to the need and willingness for South-Africans to adopt this technology. Many households are the envy of their neighbours with their shining lights in the dark hours of power cuts.
This technology has many benefits and is truly helpful for its users but the fire risks associated with these battery energy storage systems (BESS) are often overlooked to the detriment of emergency personnel, insurance companies, businesses and, most importantly, the public at large. In a white paper released in 2024
in the number of installations world-wide. The main reason cited for this decrease in failure rate is “lessons learned from early failure incidents that have been incorporated into new designs and best-practices”.
Unfortunately, due to poor regulation, testing and reliability of quality of system components, South-Africans largely do not enjoy the benefits of the “lessons learned” globally, and we can still expect a much higher failure rate, injuries and losses locally. That is the bad news. Fortunately, the good news is that this situation can be remedied by implementing and mandating some wellestablished guidelines for BESS
systems that are now available internationally. Furthermore, to implement some basic and minimum fire safety requirements for BESS installations would be quite easy in South-Africa, and it will be a start in the right direction.
Most people have watched spectacular fires from Lithiumion battery products online, so the concept of thermal runaway, the ejection of flammable and toxic gasses, and the almost instantaneous large jet flames are firmly established in our minds. The potential deflagration risk when these gases are accumulated in an enclosed space is less well-known however, and most users of BESS systems are totally unaware of this risk. There have already been a few large residential (and industrial) explosions internationally, caused by larger groupings of Lithium-ion cells typically found in electric vehicles (EVs) and home BESS systems.
Locally, a BESS deflagration occurred in Vanderbijlpark, South-Africa, in January 2025, where the occupants of the house sustained injuries ranging from mild to serious burns. The owners of the property described the incident “like a bomb went off in their house” and that even the roof lifted. Due to the large energy density in Lithium-ion batteries and their inherent fire and explosion risk, Lithium-ion
batteries have been classified in South-Africa as Dangerous Goods, Class 9, in SANS 10228 at least since 2010. Most Municipalities specify a maximum limit in weight that should not be installed without a dangerous goods certificate. Although, most home installations do not reach this limit, businesses are often close to or over this threshold. Depending on the manufacturer, a 30-kWh energy capacity BESS system might already require a dangerous goods certificate. Since this legislation is already in place, the Fire Service can easily start regulating the larger installations and thereby improve their own emergency responder safety and that of the public at large.
The current best practice guideline available for BESS installations of any size is NFPA 855 (free to view at nfpa.org if you register on the website). This standard gives simple and clear guidance on location requirements for BESS installations, maximum allowed stored energy based on a certain location, and critical size and separation requirements to limit fire spread. Just enforcing these sections of NFPA 855, as part of issuing a dangerous goods permit, will already unlock at least some minimum fire safety benefit from lessons learned internationally. NFPA 855 also gives easy to apply guidelines on the same topics for one- and two-family dwellings and townhouse units that, if applied, will reduce the life safety risks associated with home BESS systems significantly.
Ideally, every BESS installation in South-Africa should be required to comply to the complete NFPA 855 standard. That being said, there are especially two requirements in this standard
that makes compliance of current installations in SouthAfrica challenging. The first is the requirement of NFPA 855 that only UL 9540 listed equipment may be installed and the second is that explosion control is required, in general, for installations exceeding 80 kWh. (A typical home installation may be in the range of 5 to 20 kWh.)
UL 9540 is the primary compliance standard available for BESS systems as a whole. This standard ensures complete compliance and compatibility of all the components used in a BESS system. Some suppliers in South-Africa already sell products compliant to this standard, and mandating compliance for products sold in our market should be considered. If we look at the majority of products available in our market, however, they do not comply to any fire safety standard at all, not at cell level, module level or systems level. So, while aiming for system level compliance is preferred, we should at least require cell level compliance as a minimum. Most countries require basic cell level fire compliance to either UL 1642 or IEC 62619 for BESS systems as a minimum for products sold in their market. If South-Africa does not implement at least a requirement for this basic cell level fire compliance, we cannot expect the same level of fire safety that most other countries enjoy in the foreseeable future.
In South-Africa there are numerous installations where local shipping containers are re-purposed for BESS containers which do not have any explosion control. Emergency responders should, therefore, always rely on work procedures to safeguard them against possible
deflagrations. A clean agent or any type of gaseous suppression system installed in containerised BESS systems, including aerosol type suppression systems, may in some circumstances increase the risk of a deflagration. Emergency procedures should therefore always consider this possibility. Best practice currently for firefighters is to set-up at a distance away from a burning/off gassing BESS container system, evacuate the public if applicable, and just let the unit burn itself out. Water should only be used to cool surrounding areas to limit fire spread and should preferably not be sprayed on the flames of the BESS system. This philosophy would not be possible in every situation, but if it can be followed it may reduce the impact of the incident to a minimum and eliminates further incidents and possibly injury as much as possible.
Businesses, the public and emergency workers cannot count on proper fire engineering design of BESS products in the South-African market yet. As we work towards better fire safety compliance requirements, however, we can implement immediate steps to increase the life safety of users. Enforcing the NFPA 855 requirements on the location, maximum allowed stored energy, critical size and separation for BESS systems on as many installations as possible would be a valuable first step. Also, educating installers and users to look for compliance to UL 1642 or IEC 62619 (cell fire safety standards) as a minimum for home installations and UL 1973 (module fire safety standard) and/ or UL 9540 for larger installations, will support those suppliers and manufacturers that takes the lives and property of their clients in terms of fire safety seriously.

Raising awareness of firefighter safety and cancer risks: A personal journey and call to action
By John Lord, managing director, SimTrainer UK and founder of the Invisible Risk Foundation

Iam honoured to write this article in support of Lee Raath-Browne and the fire and rescue community, with the aim of fostering a broader understanding of the global risks to firefighter safety, particularly in relation to cancer awareness among responders.
My name is John Lord and I am the managing director of SimTrainer UK, a specialist training company focused on incident command.
It was established following my retirement from Lancashire Fire and Rescue Service in 2011, after a career spanning 32 years, starting in 1979 with Lancashire County fire brigade as it was known then.
I served in a variety of operational roles throughout my tenure, ultimately retiring as the lead for incident command in the training department. This brings my total service to the fire and rescue community through ops and training to nearly 46 years.
Over the years, I have had the privilege of working with 62 airport fire services across the UK, the Crown Dependencies and internationally, including in Dubai, the Seychelles and Gibraltar. Additionally, we have provided training services to five major oil refineries, onboard our tutor team we now have an associate tutor with over 20 years of experience in the oil and gas industry.
This extensive background has provided me with a deep understanding of response and specialist operations.
Why
I began the journey into cancer awareness
The impetus for my involvement in cancer awareness and the current campaign is deeply personal. Both my wife and I are cancer survivors and our experiences with the disease have cast a long shadow over our lives for the past 13 years.
We remain positive and grateful for the opportunity to continue
our lives and it is this gratitude that fuels my passion to help others. There is no political agenda, nor any intention to sell products; simply a desire to assist those who may be struggling to understand the risks or cope with a cancer diagnosis.
I was diagnosed with prostate cancer, a disease that is both underappreciated and widely misunderstood, particularly as it pertains to male firefighters. In addition to this, I have endured ongoing pain from five benign tumours in my left thumb, which continue to affect me daily and will in the end need further treatment, in total 10 surgeries in the last 10 years.
The genesis of the seminars
During the COVID-19 pandemic, I organised several webinars for the UK’s Rescue Firefighting Service (RFFS) community to facilitate communication during lockdown. One of these sessions focused on the risks of contamination, with esteemed guests such as Abby Hannah, Jo Taylor of De Wipe and Dr Dave Megson from Manchester Metropolitan University.
Through my research, I became aware of the important work being done by the Fire Brigades Union (FBU), particularly through
John Lord, managing director, SimTrainer UK and founder of the Invisible Risk Foundation
Professor Anna Stec. However, I also recognised that retired firefighters, as well as those in aviation and industrial sectors, were not being adequately included in these discussions, despite their exposure to the same hazards.
I was concerned that the true extent of the problem was being under-reported and the picture was not entirely accurate.
With the support of my friend and advocate Alisdair Couper, managing director of Terberg DTS, we realised the need to scale up our efforts. This led to the first conference at Cranfield University in November 2022, where the 'Invisible Risk' was brought to light for the first time.
One of the most poignant moments of that conference was when retired fire officer Martin Green, a true champion in the fight against firefighter cancer, spoke about his personal journey. Sadly, Martin passed away in 2024 but his contributions to this cause will never be forgotten.
This year’s Manchester conference, in March 2024, which was a resounding success, was attended by over 140 organisations and 235 delegates, making it the largest event of its kind. Once again, Professor Anna Stec was a keynote speaker, alongside Dr Emily Watkins, both of whom continue to lead in the fields of toxicology and firefighter health.
I am deeply grateful for the generosity, financial support and passion of Alisdair Couper, without whom these events would not have been possible.
A change in practice
The impact of our efforts has been tangible. UK airport fire services have made significant strides in tackling contaminants, with leading institutions such as Biggin Hill Airport and Leonardo Helicopters setting an example.
In local authority circles Surrey FRS and Hampshire Isle of Wight FRS have done great work and all airports have made notable improvements in ensuring the safety and well-being of their staff.
When we began this journey, only three sites were routinely screening staff for prostate cancer from the age of 40. Today, that number has risen to twelve, with some sites also screening female colleagues for breast cancer, aligning with practices in the United States.
Unfortunately, the UK’s National Health Service (NHS) has yet to fully recognise the enhanced risks faced by responders, which remains a significant barrier to further progress.
Some argue against screening, citing concerns about false positives. However, it is important to note that a PSA test is merely a screening tool, not a diagnosis.
The full diagnostic process involves much more, as I know from personal experience. Early detection, both for prostate cancer and other forms of cancer, can save lives and reduce costs by enabling quicker returns to work and offering better mental health support for employees during treatment.
The need for global collaboration
My concern, however, is that large organisations continue

to work in silos, failing to collaborate effectively across sectors. While the aviation industry has been proactive in sharing best practices, industrial and local authority fire and rescue services remain largely disconnected. It is crucial that we bridge this gap, so that all responders, regardless of their sector, have the same level of awareness and understanding.
Through organisations like JOIFF and other key bodies, I am seeing a commitment now thus ensuring that responders on high-hazard sites are as well-informed as their counterparts in aviation and local authority fire services.
The invitation to collaborate is open to all and we are eager to share knowledge through seminars, conferences and virtual talks worldwide.
A measure of success
On a deeply personal level, I take great pride in the fact that I have been able to offer counsel to
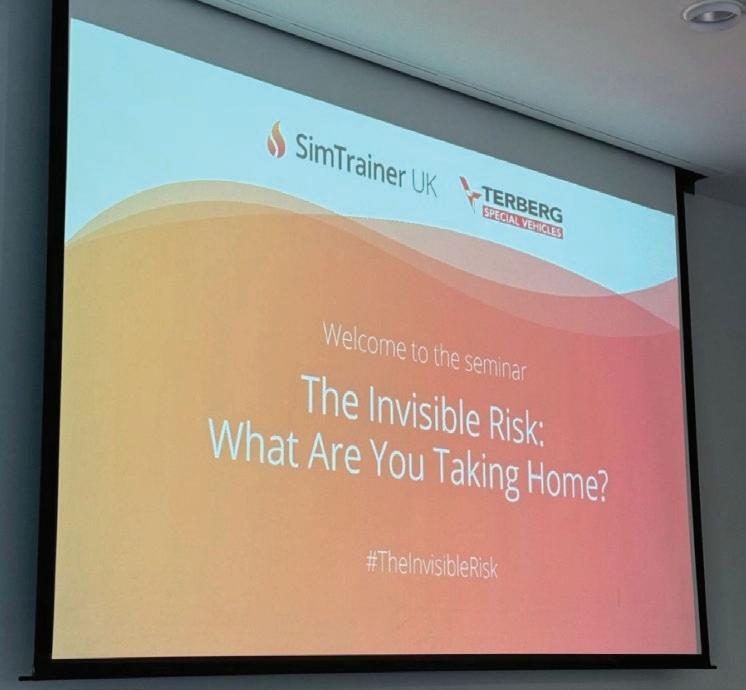
eight fire officers across the UK, whose cancer diagnoses were detected and treated following our seminars and discussions. Their gratitude for the support I provided reaffirms the value of our work. This is the motivation that drives me: to save the lives of my fellow responders.
The changes we have witnessed in operational practices, with a focus on safer working environments and greater awareness, are truly heartening. These efforts help to ensure that not only are staff kept safer, but their families are also better protected.
Our work continues to gain traction internationally, with colleagues in the United States and Scandinavia sharing valuable insights and experiences in the fight against firefighter cancer, but we have no room for complacency, the job is not done.
To that end, credit to my own champions alongside Alisdair Couper people who have made huge contributions on awareness Robbie Burns, a serving Firefighter, cancer survivor, Andy Slater PGI Safety, Jo Taylor De Wipe, not forgetting the esteemed academics doing so much already mentioned.
A wish list for the future
Looking ahead, my wish is to see an end to silo working and a greater spirit of collaboration across the globe. This is not about scoring points or seeking individual accolades but about working together to protect all agencies, regardless of their size or scope.
We must do more to protect our female colleagues, gather better data on the specific risks they face and ensure that retired firefighters and responders receive better support when diagnosed with cancer.
Screening needs to become universally adopted, allowing us to identify health issues early and take action that saves lives and reduces costs.
In the UK, many are working hard to ensure the NHS to implement SNOMED codes that specifically cover firefighters and others exposed to occupational toxins. This process should be adopted worldwide to ensure that those who protect us are properly protected in turn.
Furthermore, we must acknowledge that a cancer diagnosis is not just an individual issue; it is a family issue. The mental health challenges associated with a diagnosis must not be overlooked and it is crucial that we offer comprehensive support to families as well as to the responders themselves.
Finally, the message must reach all emergency responders such as police, medical staff and others because cancer respects no uniform, no role and no location.
For me personally, the next step is to establish the Invisible Risk Foundation, which will continue to raise awareness, train champions in firefighter safety and provide support to those facing a cancer diagnosis.
Together, we can make a difference. Through collaboration, awareness and proactive action, we can reduce the risks faced by firefighters and responders worldwide. The fight is far from over but with the support of all involved, we can continue to protect those who risk their lives to protect others, anywhere in the world needs to be the aim.

The cancer risk for firefighters: A South African perspective
By Lenny Naidoo and Jackie de Billot, Vanguard Fire and Safety
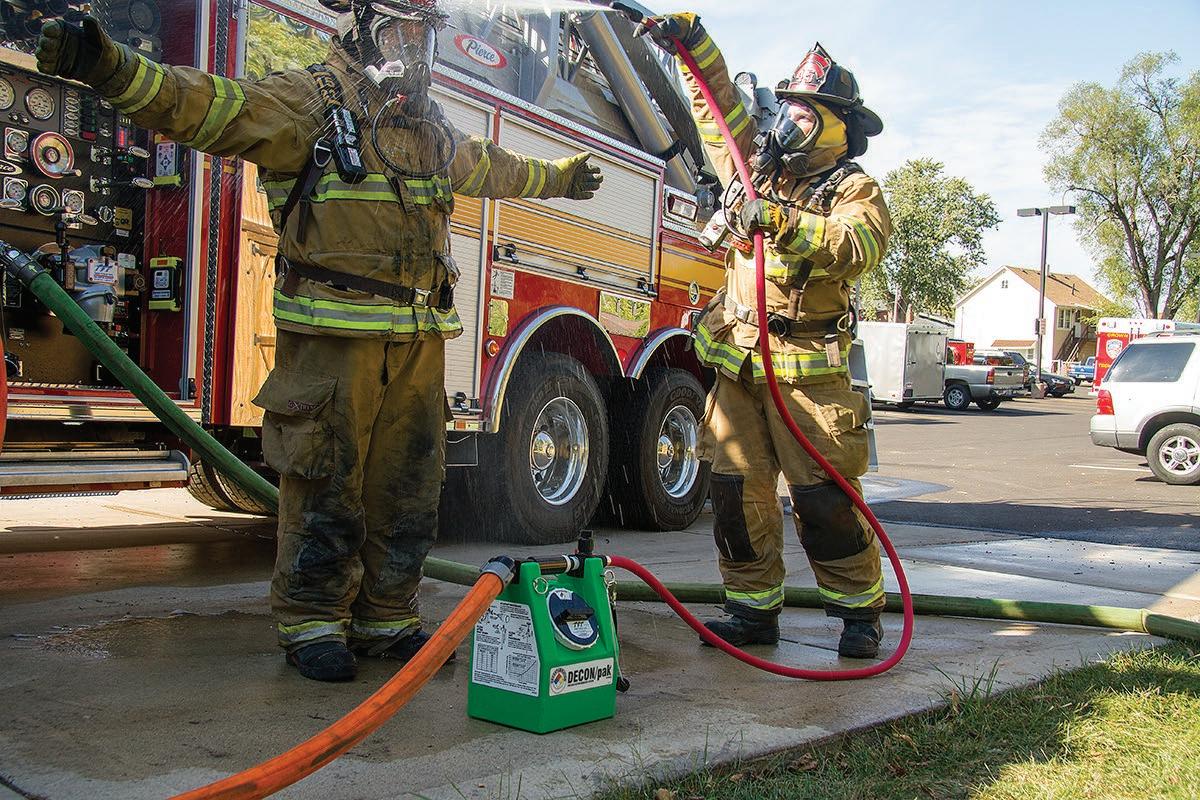
Firefighters around the world face unique occupational hazards, one of the most alarming being their increased risk of developing cancer. Research from the Centre for Disease Control and Prevention (CDC) and the National Institute for Occupational Safety and Health (NIOSH) indicates that firefighters have a nine percent higher risk of being diagnosed with cancer and a 14 percent higher risk of dying from cancer than the general population. Given these troubling statistics,
it begs the question: What would the percentage be for South African firefighters and could it be even higher?
The firefighting environment: a cancerous cocktail Modern homes, vehicles and commercial buildings are constructed using an array of synthetic and plastic materials. When these materials burn, they release harmful chemicals, including carcinogens like polycyclic aromatic hydrocarbons (PAHs), a group
of over 100 chemicals known to cause cancer. South African firefighters face the same exposure to these toxins, which can be inhaled or absorbed through the skin. As buildings burn, the situation becomes even more hazardous when materials such as asbestos and diesel exhaust are introduced into the environment.
Wearing proper personal protective equipment (PPE), including self-contained breathing apparatuses (SCBA), is
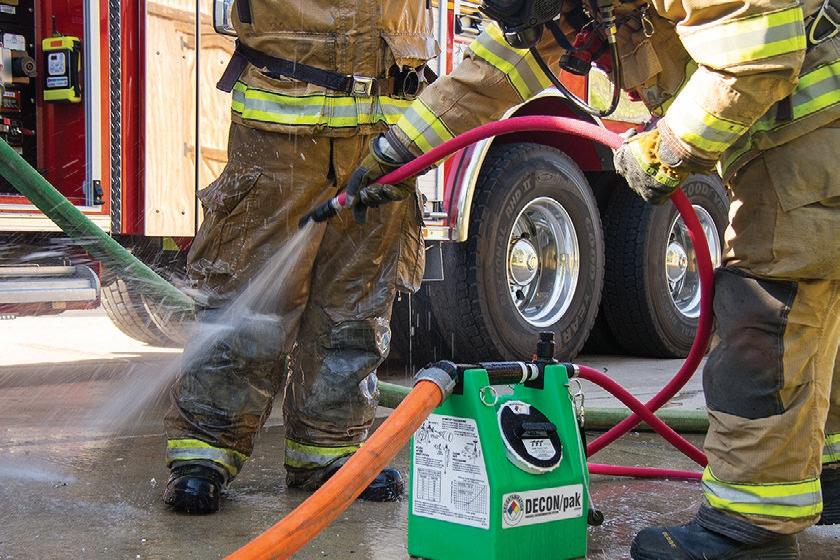
crucial for firefighters to reduce exposure to these dangerous chemicals. However, even with PPE, toxic substances can still penetrate turnout gear, exposing firefighters to carcinogenic risks.
The global risk: a global phenomenon Studies conducted on first responders to catastrophic events like the World Trade Centre (WTC) attacks on 11 September 2001, revealed heightened levels of clonal haematopoiesis among firefighters. Clonal haematopoiesis occurs when a blood stem cell makes cells with the same genetic mutation, leading to blood cancers. This condition underscores the potential for devastating longterm health consequences faced by first responders and more alarmingly, it could be a growing issue for South African firefighters too.
The National Firefighter Registry: a step toward prevention In 2018, the US Congress established the National Firefighter Registry (NFR), which tracks firefighters’ health and
exposure data to study the links between workplace exposures and cancer. While this initiative is still in its early stages, it offers hope for identifying and mitigating cancer risks. South Africa does not yet have a comprehensive national registry but it is clear that the country could benefit from similar tracking mechanisms.
The current state in South Africa: Gaps in standards and legislation South African firefighters are subject to the Occupational Health and Safety Act (OHSA), which mandates that employers ensure a safe work environment. Yet, firefighting is inherently risky and the environment is often uncontrollable. While South Africa’s fire services adhere to international safety standards, there is still a lack of robust national protocols to document exposure during every turnout or specialised medical screening after hazardous material exposure. Furthermore, there are no comprehensive national standards for entrylevel firefighter medical or physical assessments.
Research and development in firefighter health rely heavily on international reports, which fail to fully address local conditions or specific risks faced by South African firefighters.
Reducing cancer risk: What can South African firefighters do?
Despite the heightened risks, there are proactive steps that South African firefighters can take to reduce their exposure to carcinogens and improve their health outcomes.
1. Reduce exposure to diesel exhaust:
• Maintain and use diesel exhaust containment or removal systems in fire stations.
• Ensure apparatus engines are not idling inside stations.
• Keep bay doors open before starting fire engines and until engines are off after returning to the station.
2. Proper PPE and SCBA maintenance
• Follow NFPA 1851 and manufacturer’s instructions for cleaning and maintaining PPE after every fire.
• Test and maintain SCBA daily to ensure proper function.
• Use SCBA and remain on air through the end of overhaul operations and during any smoke exposure.
• Ensure decontamination of gear on the scene before returning to the station.
3. Clean yourself after every fire
• Wash exposed face, hands and neck as soon as possible with wet wipes or soap and water at the fireground.
• Shower as soon as possible after returning to the station and cleaning equipment.

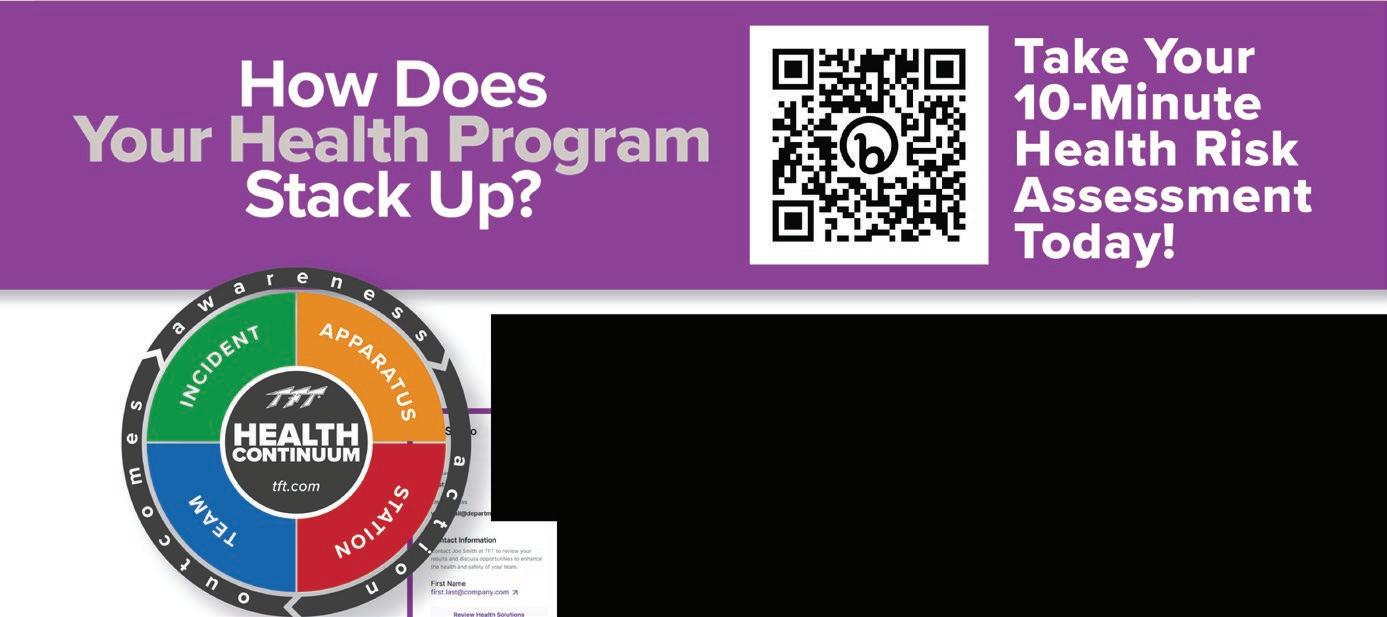
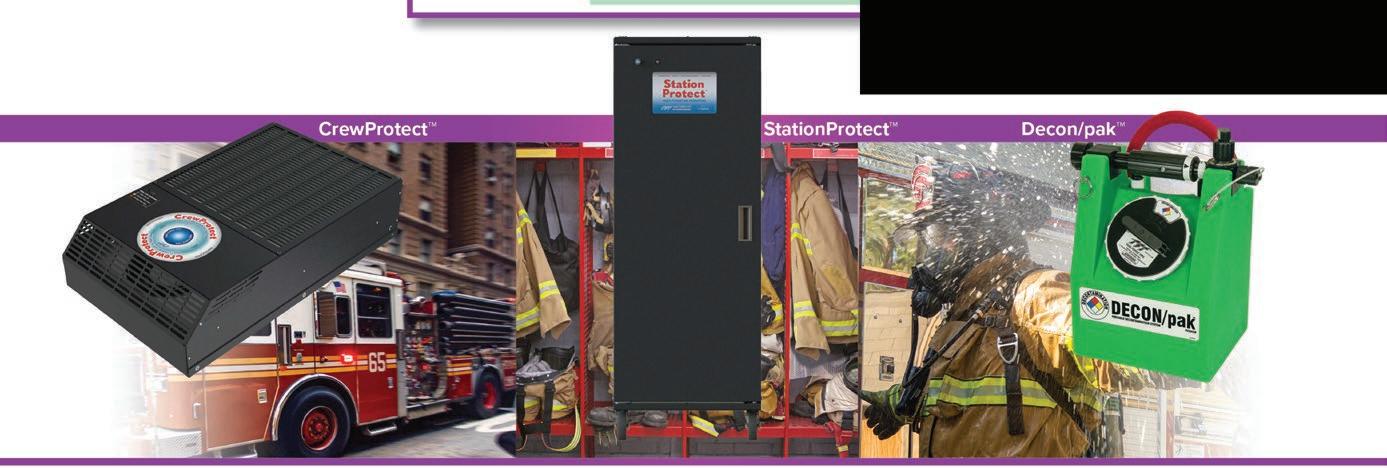

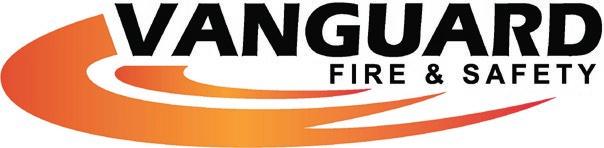
Awareness to Drive Action and Achieve Your Goals
The Health Continuum captures four points of exposure and potential health concerns for your department. These categories encompass the places a firefighter might experience a health risk on duty: station, apparatus, incident, team.

The goal is to provide a framework for you to evaluate and discuss health programs at your department and make it easier to address these concerns while building a comprehensive plan to minimize health risks.
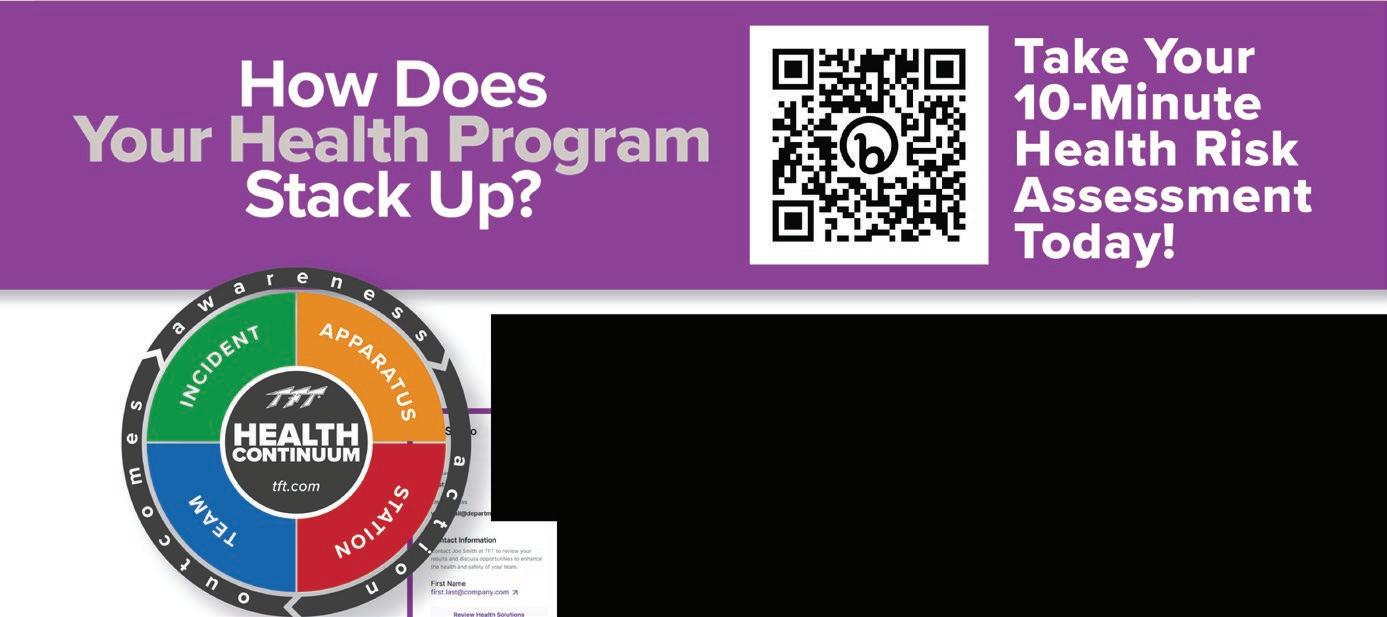
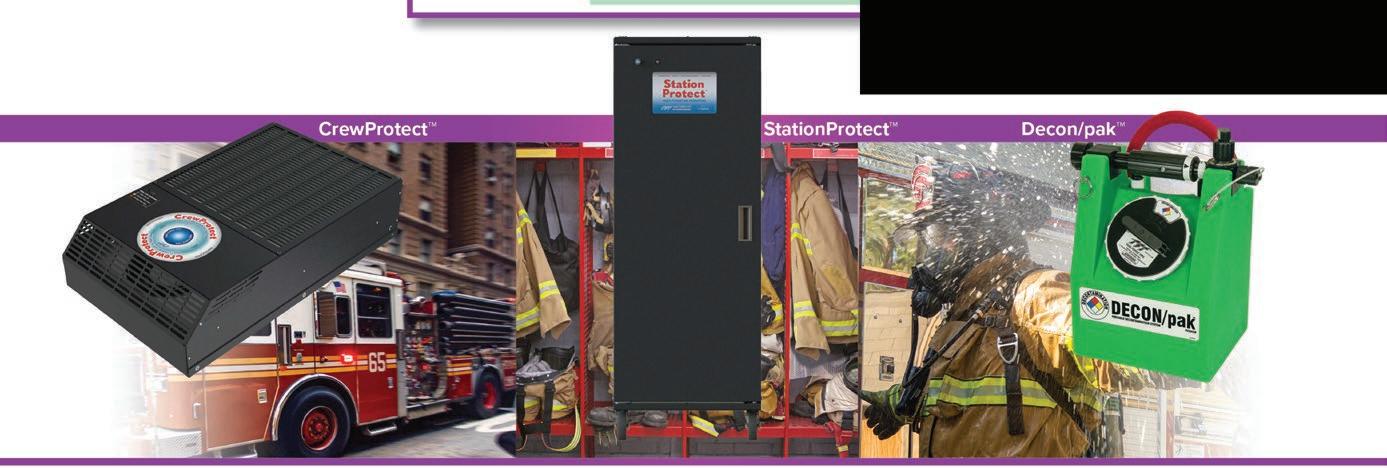


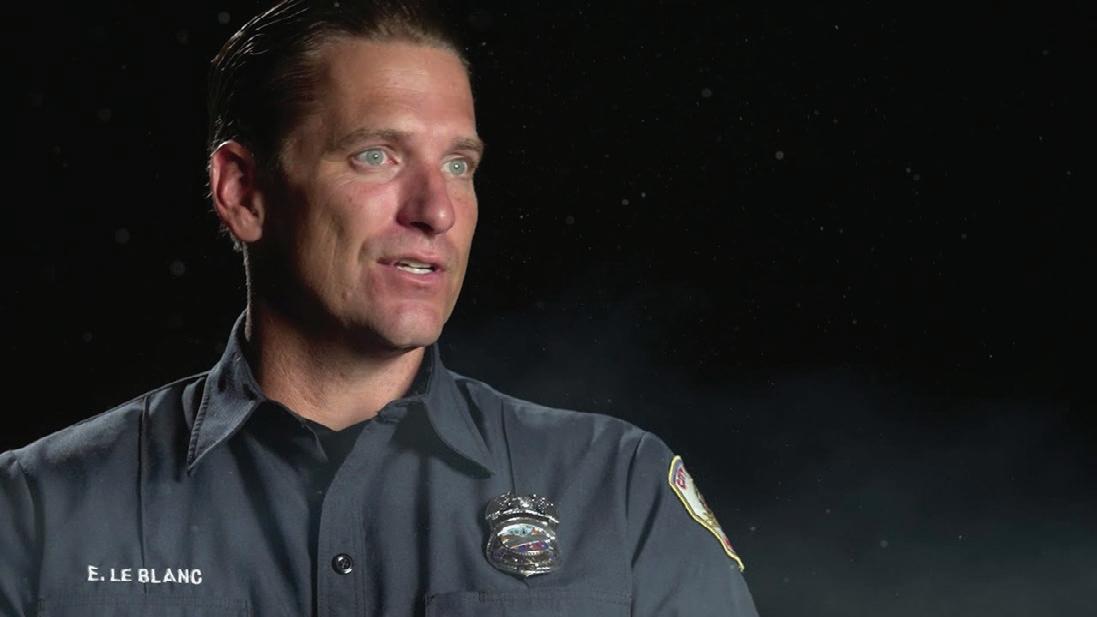
• Change into clean clothes after showering.
4. PPE storage and handling
• Store contaminated PPE in airtight containers to prevent cross-contamination in fire stations.
• Only store gear in designated areas, away from living and sleeping quarters.
5. Always wear PPE and SCBA
• Do not rely solely on gas detectors to decide when to wear PPE. Contaminated particles linger even after a fire is out.
• Wear full PPE and SCBA during overhaul, as well as at car fires or trash fires.
6. Talk to your doctor
• It’s vital for firefighters to discuss their occupational history with healthcare providers. Inform your doctor about your work exposure, even if you’re retired or changing providers.
• Discuss cancer screening,
including early age screening and more frequent check-ups, to monitor any changes.
7. Track your exposure
• The International Association of Firefighters (IAFF) recommends that firefighters keep a personal record of exposures and incident responses. This documentation could be crucial for identifying long-term health effects.
Task Force Tips: A solution for decon
Recognizing the growing concern about cancer rates among firefighters, Task Force Tips has developed innovative solutions aimed at improving firefighter safety through enhanced decontamination (decon) processes. Decon is vital in reducing the lingering effects of harmful chemicals that firefighters are exposed to during and after firefighting operations. Task Force Tips’ decontamination solutions include:
• Decon Pack: This is an effective tool designed for the immediate decontamination of firefighters right at the fire scene. The Decon Pack provides a quick, efficient way to begin the decontamination process, reducing the exposure time to hazardous materials before the firefighter even leaves the scene.
• Crew Protect: This device is installed in the cab of the fire truck during the return to the station. It works by cleaning the air within the cab, helping to eliminate toxins and particulates that can linger after a fire. This ensures that firefighters and their crews are not breathing in harmful chemicals on their way back to the station, providing an additional layer of protection.
• Station Protect: Designed for use in the storage area where PPE is kept, Station Protect helps to clean the air and reduce emissions of volatile organic compounds (VOCs)
and particulates. This product is especially beneficial in areas where firefighter gear is stored, preventing the contamination of the firehouse environment and minimising exposure to harmful substances.
These solutions are part of a growing push to prioritise decontamination as a standard practice in fire services. The ability to start the decontamination process at the fireground, in transit and in the fire, station is essential to reducing the long-term health risks faced by firefighters.
The importance of healthy lifestyle choices
Adopting a healthy lifestyle can further reduce the risk of cancer and other diseases. Maintaining good nutrition, engaging in regular physical activity and avoiding tobacco and alcohol are key strategies for mitigating the longterm health impacts of firefighting.
Conclusion: The need for change
The risks of cancer faced by South African firefighters
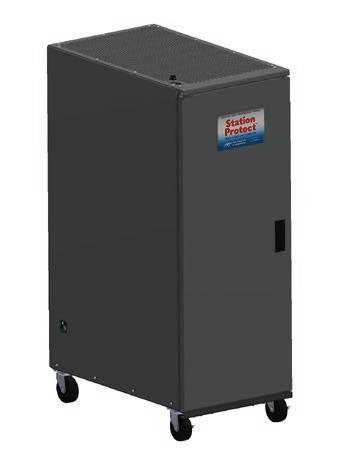
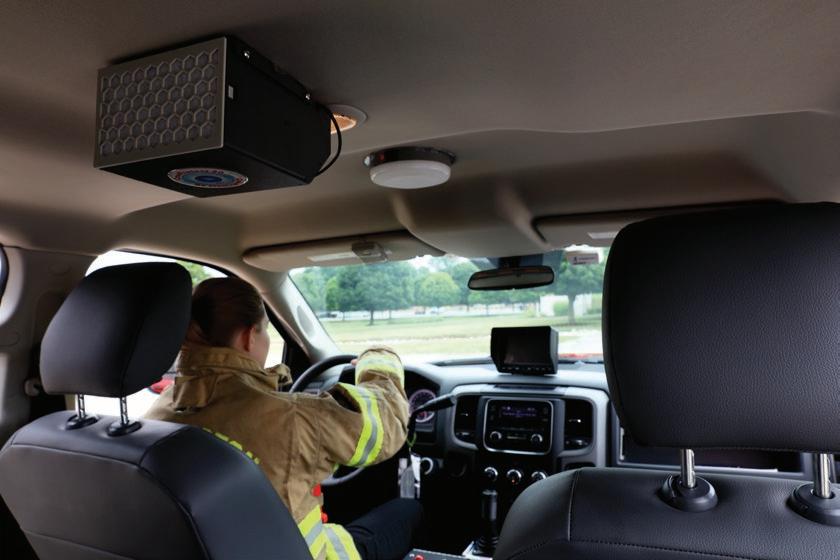
are undeniable but there are tangible steps that can be taken to mitigate these risks. Increased awareness, stronger national standards, improved PPE protocols and regular health check-ups are essential for safeguarding the well-being of those who serve and protect the nation.
Firefighters’ health should be prioritised, ensuring that they are
not only equipped to save others but also empowered to protect their own futures.
As we continue to honour the brave men and women of South Africa’s fire services, it’s imperative to support efforts to improve safety protocols, enhance health surveillance and mitigate the long-term risks associated with their noble work.
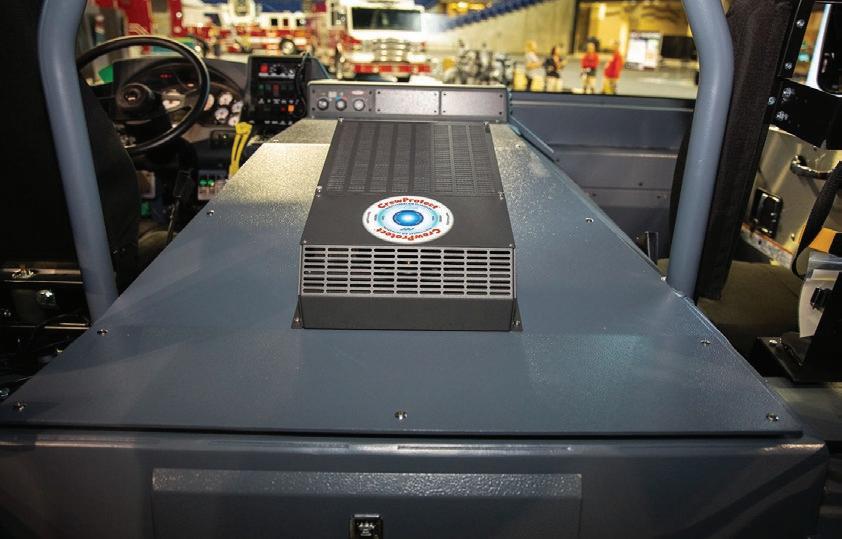
Dräger: twins:
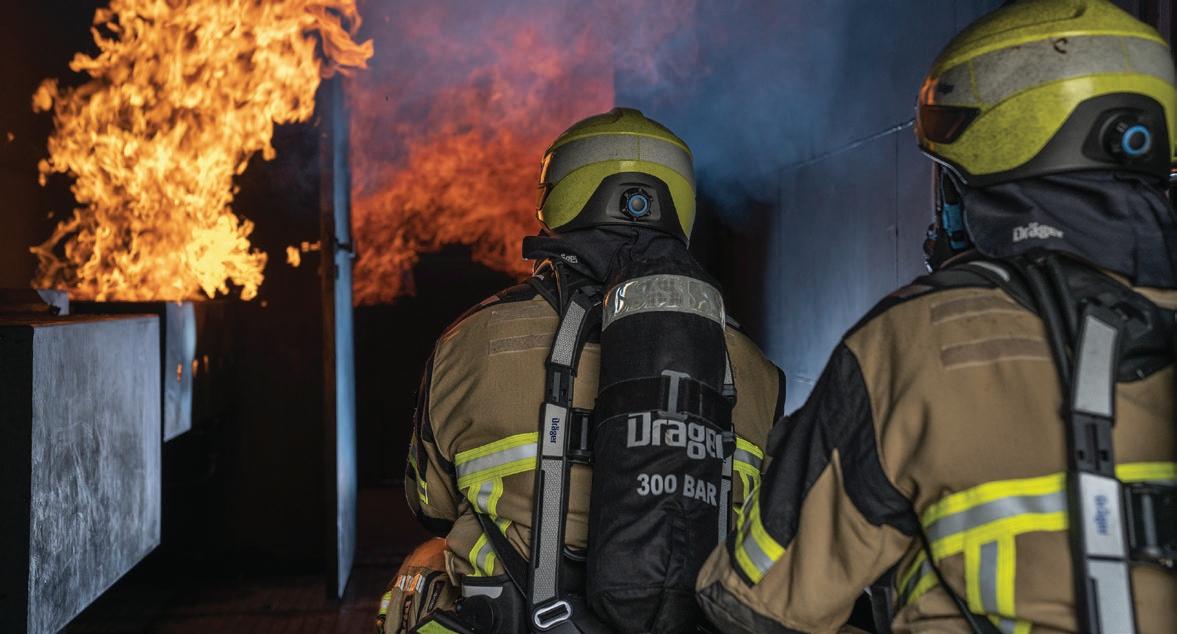
Sfirefighters at risk, including carbon monoxide (CO) and hydrogen cyanide (HCN). Dangerous individually, significantly more harmful together: What you should know about the “toxic twins”.
Together, CO and HCN, known in the fire industry as the “toxic twins”, create a deadly chemical asphyxiant that can put the firefighter or fire victim into cardiac arrest at the time of the fire.
Because the combination of CO and HCN is exponentially more harmful than exposure to these agents individually, measuring each gas against its single alarm threshold is insufficient for overhaul operations.
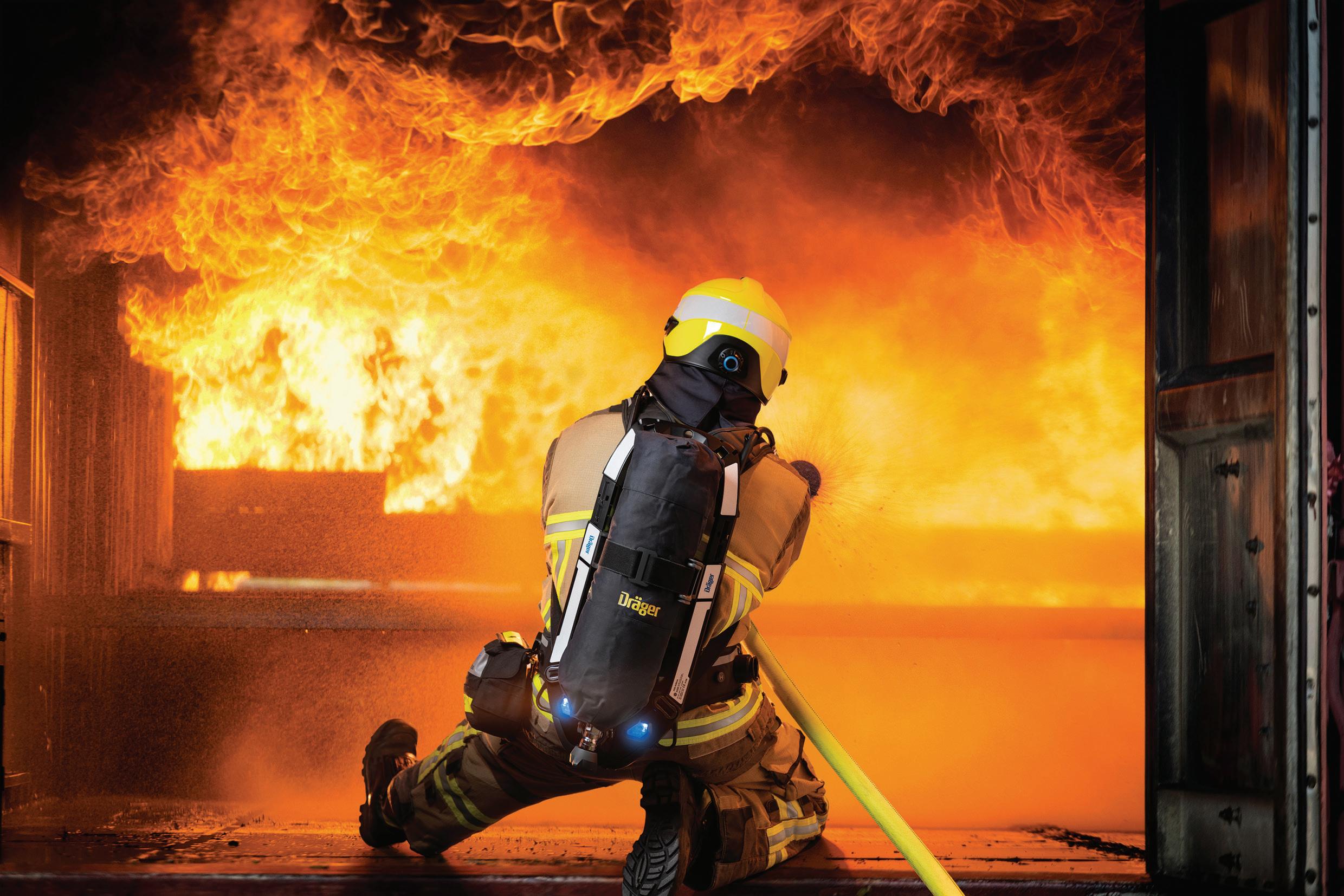
Smoke from structural fires produces many toxic gasses that put firefighters at risk, including carbon monoxide (CO) and hydrogen cyanide (HCN).
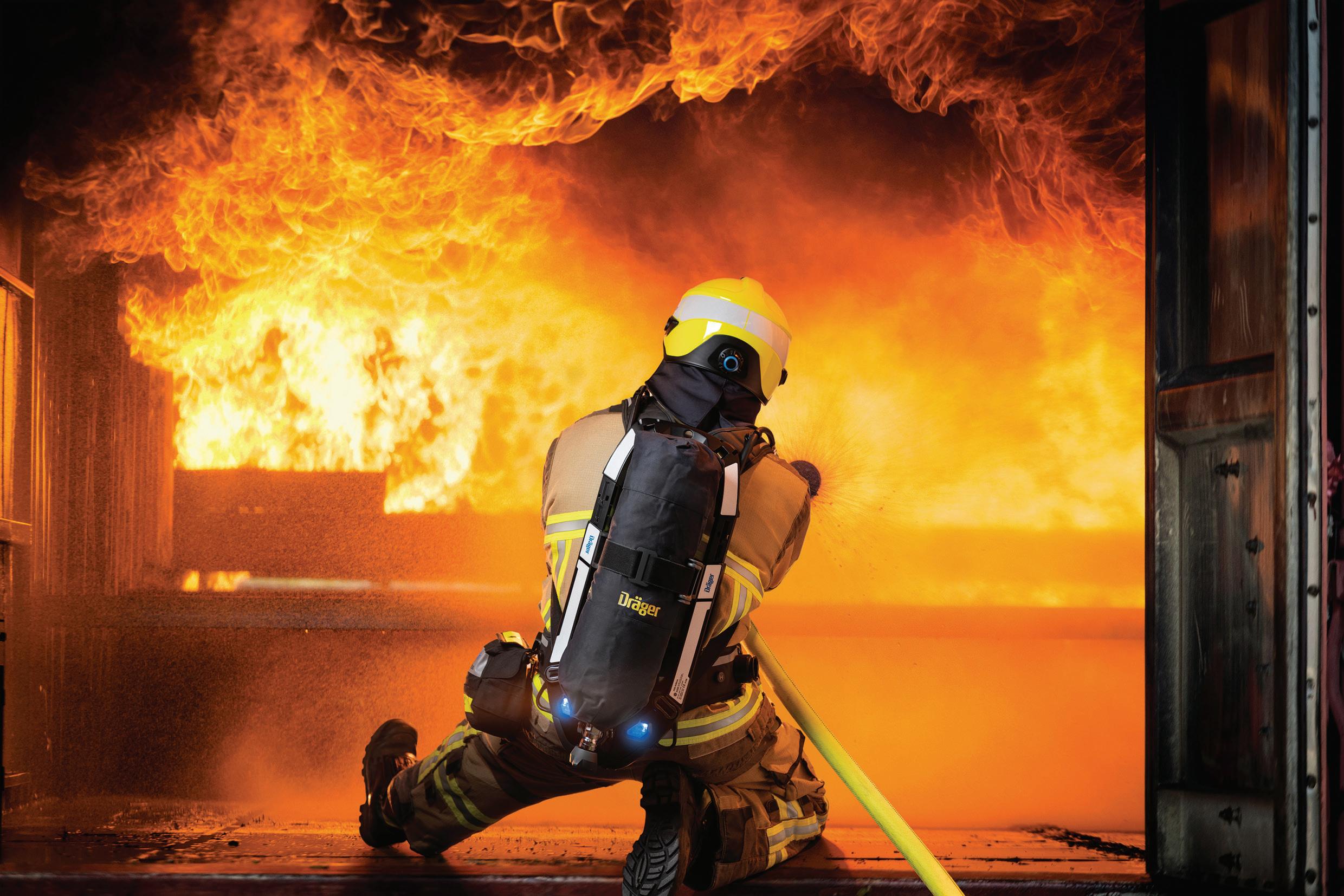
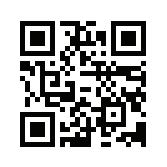
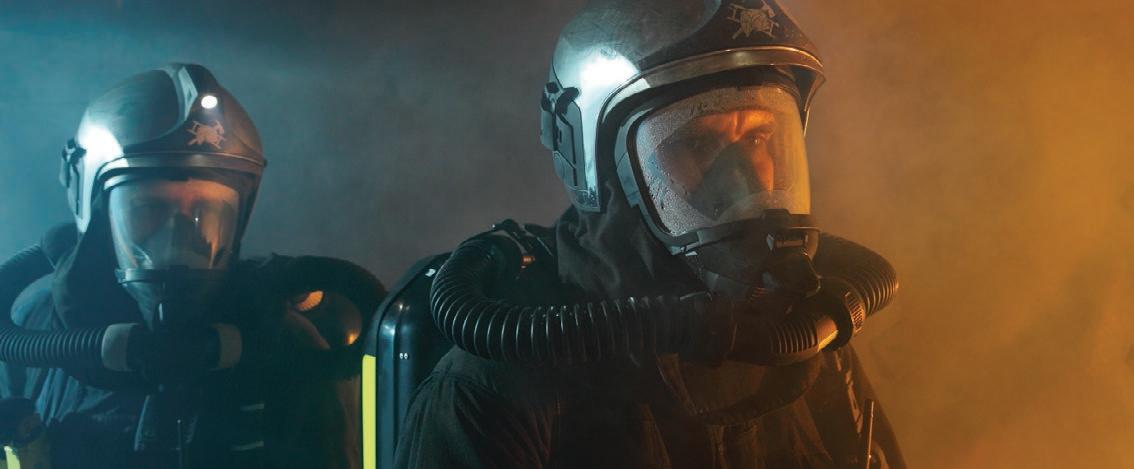
Together, CO and HCN, known in the fire industry as the “toxic twins” create a deadly chemical asphyxiant that can put the firefighter or fire victim into cardiac arrest at the time of the fire
of quantitative decomposition occurred in 2003 at the Station Nightclub in West Warwick, Rhode Island. Two pyrotechnic devices were set off during a band performance, creating an exothermic reaction that threw sparks over a distance of 15 feet for about 15 seconds.
These sparks ignited a substandard sound suppression foam board that was wrapped around the stage to project sound into the audience. As temperatures soared from the initial flames, thermal decomposition of the foam board began to produce high quantities of smoke filled with HCN.
Subsequent investigations and a simulation of this event by NIST concluded that with an inadequate sprinkler system in the building, the performance area was uninhabitable within 90 seconds. Many of the 462 people in the room were overcome by the HCN/CO in the smoke before they could get out of the structure. 100 people lost their lives and more than 200 were severely burned or injured as a result of this event.
Where there is smoke, there are toxic gasses in residential fires today, the leading cause of death is from smoke inhalation, not burn injuries. A 2011 study by the NFPA shows an 8-to-1 ratio of smoke inhalation to burns for deaths in home fires.
During a fire, oxygen levels decrease and the environment is likely to contain high levels of carbon monoxide and many other toxins.
Moreover, smoke produces toxins regardless of its thickness, colour or movement. It is impossible to tell from looking at smoke how much toxic gas is coming out of the structure. It’s pretty obvious that there are toxins in heavy, turbulent smoke but they can also be present in light coloured smoke or even haze.
While firefighters are exposed to harmful substances both through their lungs and their skin, lungs are 300 times as efficient in getting toxins into the body.
HCN: the silent killer
While the threat of CO has been
known for years, firefighters are trained to watch for symptoms of carbon monoxide poisoning, including headaches, nausea and drowsiness.
Exposure to high levels of carbon monoxide can be fatal but what is often overlooked is the presence of cyanide. While many associate cyanide with chemical weapons and hazardous material (hazmat) scenarios, research has shown that cyanide is a significant contributor to the thousands of fire-related deaths each year.
Studies have shown that in fire smoke, hydrogen cyanide can be up to 35 times more toxic than carbon monoxide.
The NIOSH short-term exposure limit (TLV-STEL) for HCN is 4.7, above which concentration a worker should not be exposed (averaged over 15 minutes). Exposures cannot be repeated more than 4 times per day. The American Conference of Governmental Industrial Hygienists (ACGIH) has assigned 4.7ppm as a worker ceiling limit (TLV-C), above which concentration a worker should never be exposed.
Studies showed HCN levels of 200ppm common in normal structural fires: That is lethal in 30 to 60 minutes.
and bizarre actions, causing the firefighter or victim to make life threatening decisions.
Where there is smoke, there are toxic gases
In residential fires today, the leading cause of death is from smoke inhalation – not burn injuries. A 2011 study by the NFPA shows an 8-to-1 ratio of smoke inhalation to burns for deaths in home fires. During a fire, oxygen levels decrease and the environment is likely to contain high levels of carbon monoxide and many other toxins.
The prevailing thought had been that if you get a person out of the smoke and into fresh air, the toxins will be replaced by the fresh air. It is now known that the toxins are stored in the body and can be difficult to displace.
Facts about HCN
• HCN is 35 times more toxic than CO
• HCN can enter the body by absorption, inhalation or ingestion and targets the heart and brain
Moreover, smoke produces toxins regardless of its thickness, color or movement. It is impossible to tell from looking at smoke how much toxic gas is coming out of the structure. It’s pretty obvious that there are toxins in heavy, turbulent smoke – but they can also be present in light colored smoke or even haze.
Exposure to high levels of carbon monoxide can be fatal, but what is often overlooked is the presence of cyanide. While many associate cyanide with chemical weapons and hazardous material (hazmat) scenarios, research has shown that cyanide is a significant contributor to the thousands of fire-related deaths each year.
Studies have shown that in fire smoke, hydrogen cyanide can be up to 35 times more toxic than carbon monoxide.
• HCN can cause heart attacks and cardiac arrest, then hamper resuscitation
respiration, the body provides nutrients to key enzymes that allow our bodies to function properly. However, when HCN is inhaled, it has a high affinity for a key enzyme called cytochrome C oxidase, which basically shuts down the aerobic respiratory path. The result is anaerobic respirations, resulting in lactic acidosis and other toxic substances that are created in the tissues and organs.
While firefighters are exposed to harmful substances both through their lungs and their skin, lungs are 300 times as efficient in getting toxins into the body.
HCN: the silent killer
Because of the extreme toxicity of HCN, firefighters who experience dizziness, weakness and rapid heart rate after a fire may actually be feeling the effects of HCN. It is theorised that many firefighter heart attacks and cardiac arrest during or following fire operation may be HCN-related.
• HCN can cause bizarre and irrational behaviour, hamper ability to perform role or to self-rescue and can hinder or prevent rescue by others
• HCN can incapacitate a victim within a short time
While the threat of CO has been known for years, Firefighters are trained to watch for symptoms of carbon monoxide poisoning – including headaches, nausea, and drowsiness.
HCN also has a narcotic-like effect and can result in irrational
800 ppm
1,600 ppm
The NIOSH short-term exposure limit (TLV-STEL) for HCN is 4.7, above which concentration a worker should not be exposed (averaged over 15 minutes). Exposures cannot be repeated more than 4 times per day. The American Conference of Governmental Industrial Hygienists (ACGIH) has assigned 4.7 ppm as a worker ceiling limit (TLV-C), above which concentration a worker should never be exposed.
Studies showed HCN levels of 200 ppm common in normal structural fires: That is lethal in 30 to 60 minutes.
How HCN affects the body
HCN is a cellular asphyxiant that interferes with aerobic respirations. During normal
Individuals inhaling hydrogen cyanide associated with smoke often experience cognitive dysfunction and drowsiness that can impair their ability to escape or to perform rescue operations. Exposure to low concentrations (or initial exposure to higher concentrations) may result in stupor, confusion, flushing, anxiety, perspiration, headache, drowsiness and rapid breathing.
–
Headache in the forehead within 2 – 3 hours, extending to the entire head within 2.5 – 3.5 hours
Dizziness, nausea and limb twitching within 45 minutes, coma within 2 hours
Dizziness, nausea and limb twitching within 20 minutes, death within 2 hours 3,200 ppm
Dizziness, nausea and limb twitching within 5 – 10 minutes, death within 30 minutes 6,400 ppm
Dizziness, nausea and limb twitching within 1 – 2 minutes, death within 10 – 15 minutes
Death within 1 – 3 minutes
2 – 4 ppm
4.7 ppm
Max workplace concentration for 8-hour work – Europe
Perception threshold
NIOSH REL: STEL 10 ppm
20 – 40 ppm 0.004
45 – 54 ppm 0.0054
100 – 200 ppm
OSHA PEL: TWA
Slight symptoms after several hours
Immediate and subsequent damage within one hour
Deadly after 30 – 60 minutes
Immediate death
Drägerwerk AG & Co. KGaA
Exposure to higher concentrations of HCN result in prostration, tremors, cardiac arrhythmia, which can be delayed two to three weeks after the fire exposure, coma, respiratory depression, respiratory arrest and cardiovascular collapse.
Unfortunately, there is no quick test that be administered to individuals at the site of a fi re to check for HCN toxicity. As a result, all firefighters need to be on the alert for HCN poisoning in fellow firefighters, both at the fire scene and afterward at the station.
If a firefighter or victim shows significant signs of HCN toxicity, HCN antidotes can be administered to help speed the person’s recovery.
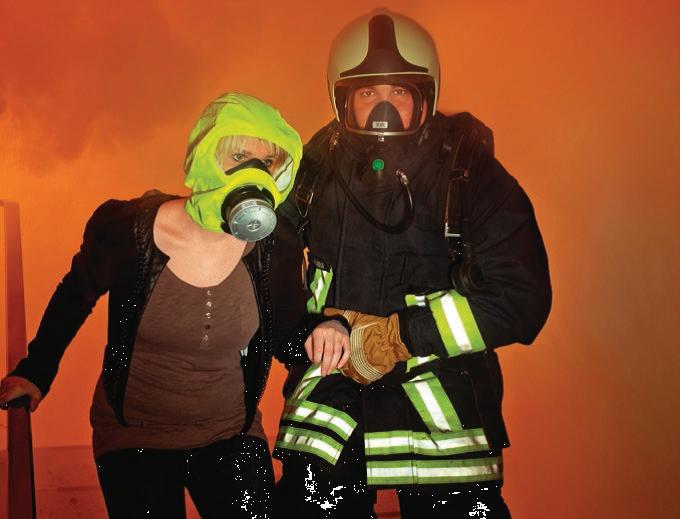
If a firefighter or victim shows significant signs of HCN toxicity, HCN antidotes can be administered to help speed the person’s recovery
possible cyanide poisoning is critical for saving lives.
If a fi refi ghter or victim shows signifi cant signs of HCN toxicity, HCN antidotes can be administered to help speed the person’s recovery.
Treatment of a possible HCN patient
Because cyanide gas in fi re smoke can quickly become lethal, early attention to
Symptoms of HCN Poisoning
The prehospital treatment of acute cyanide poisoning entails removing the person from the source of cyanide, administering 100 percent oxygen and providing cardiopulmonary resuscitation, if necessary.
• Coughing up carbonaceous sputum
• Soot or burns around the mouth and nose
• Shortness of breath, chest tightening, headache
• Smell of almond extract on the breath (anecdotal)
• Cardiac issues
• Disorientation, possibly bizarre behavior
• Drowsiness
• Possibly bright red skin discoloration (for prolonged exposure)
• Lethargy
• Weakness
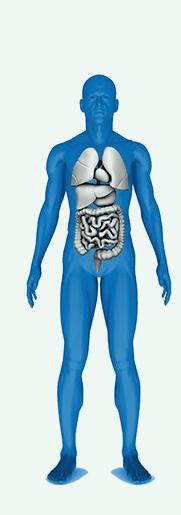
A new antidote called hydroxocobalamin has been effectively used in France for the past 10 years. It is designed specifically for use on-scene or at the hospital for acute HCN poisoning from any source. Hydroxocobalamin neutralises cyanide by fixing it to form cyanocobalamin (vitamin B12), which is excreted in the urine. It does not reduce the blood’s capacity to carry oxygen.
Beware of secondary HCN exposure
Firefighters also need to realise that because soft body tissue acts like a sponge, fi re victims absorb a lot of the combustion byproducts. When a victim is removed from a contaminated environment and brought out into clear air, their body tissue begins to outgas some of the contaminants. Therefore, emergency responders working on the victim become exposed to the same contaminants, including HCN and many other chemicals.
After the victim has been delivered to the hospital and
the firefighters go back to their station, the rescuers may start to experience headaches, nausea, vomiting and things of that nature. While these symptoms may be a result of work stress, it’s just as likely caused by exposure to contaminants such as HCN and CO.
How can firefighters protect themselves?
While firefighters cannot avoid exposure to toxic substances such as HCN and CO in the line of duty, they can protect themselves by adhering to the following guidelines:
• Wear PPE: This requires energy and an ongoing commitment on the part of the firefighter
• Monitor toxic gasses: Make gas monitoring a standard procedure
• Use SCBA: Keep SCBA on until it has been determined that air is safe to breathe and make SCBA available for drivers/ operators
• Shower in an hour: By showering within an hour, firefighters can reduce exposure to toxins by 90 percent. If they wait until they go home that night, they have received 100 percent exposure.
• Decon: Decontaminate PPE according to Fire and Emergency Training Institute (FETI) guidelines
• Watch out for each other: Be alert to symptoms in fellow firefighters, both at the fi re scene and back at the station
• Education and training: Institute a training programme that focuses on making firefighters aware of the hazards of hydrogen cyanide.
New technology provides early warning of toxic twin
danger Research shows that the combination of CO and HCN is actually more harmful than exposure to either one individually.
If both gasses are inhaled together, they have a toxic mutually reinforced effect: CO prevents oxygen from reaching vital organs, HCN attacks the central nervous system and the cardiovascular system, causing people to become disoriented and confused. Thus measuring each single gas against its single alarm threshold is not ideal for overhaul operations.
Dräger, a leading provider of high quality safety equipment to firefighters worldwide for more than 125 years, has introduced new “toxic twin” signal processing technology that provides protection against the combination of CO and HCN.
The standard settings for the alarm threshold are for CO 30 to 35ppm (A1) and 50 to 60ppm (A2); for HCN 1.9 to 2.5ppm (A1) and 3.8 to 4.5ppm (A2).
The previous state of the art was to treat and measure CO and HCN separately; no adjustment was made for the presence of both gasses. Each alarm threshold was analysed separately and not enough attention was paid to the toxic mutually reinforced effect.
With the toxic twins signal processing, the gas values are measured together and are added. An alarm is triggered by scaling the concentration of both substances.
Dräger has incorporated “toxic twins” function into the Dräger X-am® 5000 and 5600 gas monitors with firmware 7.0 or later as well as into the Dräger X-am® 5800 and Dräger X-am® 8000.
Summary
This new gas monitoring innovation increases firefighter safety during overhaul based on scientific research conducted in the US. With this new technology, Dräger provides the best possible safety against the toxic mutually reinforced effect of hydrogen cyanide and carbon monoxide.

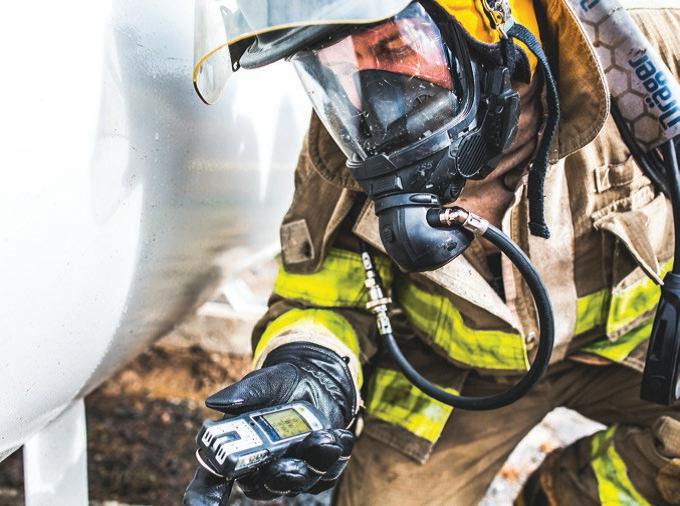
Beware of secondary HCN exposure
Navigating PFAS and the shift to NFPA 1970: Key changes for firefighter PPE
By Robin Charnaud, Charnaud and Co (Pty) Ltd
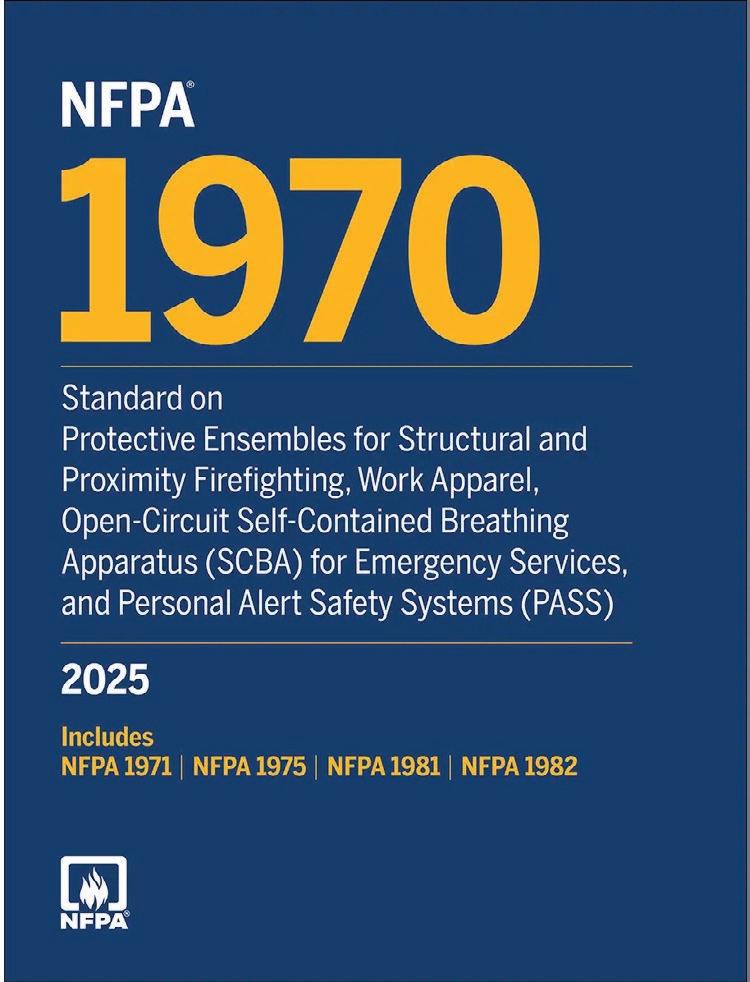
The landscape of firefighter personal protective equipment (PPE) is undergoing significant transformation with the upcoming release of NFPA 1970, a consolidated standard replacing NFPA 1971, 1975, 1981 and 1982.
Among the most critical changes are those addressing Per- and Polyfluoroalkyl substances (PFAS) and the broader push for safer, more effective firefighter gear.
The consolidation and its impact NFPA 1970 aims to streamline fire
service standards, consolidating four key documents into a single, more manageable framework. This consolidation, expected no earlier than August 2025, will impact purchasing decisions as manufacturers’ transition to certifying products under the new standard.
PFAS and restricted substances: A core focus
A major driving force behind the NFPA 1970 revisions is the increasing concern over PFAS exposure. The standard introduces stringent requirements to limit these harmful substances in firefighter clothing. Key changes include:
‘PFAS-Free’ claims and restricted substance limits
• NFPA 1970 will mandate the use of acceptable test methods to measure total fluorine, establishing a basis for ‘PFAS-free’ claims.
• Specific restricted substances, including various PFAS, will be identified and manufacturers will be required to test materials to ensure compliance with strict limits.
• Independent, certified testing will be mandatory.
• The basis of these restricted substance limits are being modelled after the international OEKOTEX 100 standard along with the

criteria from PPE Supplement, which chooses the most rigorous requirements for hazardous substances found in global regulations.
Chemical runoff testing
• A proposed test, previously utilised in Europe, will assess the ability of garment outer shells to repel, absorb or allow penetration of liquids like diesel fuel.
• Data relating to PFAS based finishes, and how they react to washing will be recorded and reported.
Enhanced protection and performance
Beyond PFAS, NFPA 1970 introduces several key changes aimed at improving overall firefighter safety:
• Mandated particulate-blocking hoods: Structural firefighting hoods will be required to meet particulate-blocking
capabilities, with stricter criteria for coverage, seam testing and preconditioning.
• Durability and service life: New criteria will ensure turnout gear maintains performance properties over its expected service life, with enhanced preconditioning protocols involving repeated washing, heat, UV and flexing.
• Contaminant removal and cleaning: A "cleaning index" will be introduced to measure the effectiveness of contaminant removal from clothing materials, promoting better decontamination practices. Measurement of semi-volatile organic chemicals and heavy metals from garment and hood materials.
• Improved breathability: An evaporative resistance test (Ret) will be added to assess garment breathability, complementing total heat loss (THL) measurements and helping mitigate heat stress.
• Full ensemble performance: A new annex will provide optional criteria for measuring the "systems" performance of complete firefighter ensembles, including thermal protection, heat stress impact and gear interoperability.
• SCBA updates: NFPA 1970 will also update intrinsic safety criteria for SCBA, addressing the increasing use of electronic components.
The
importance of staying informed
Fire departments must familiarise themselves with NFPA 1970 once it is issued. The standard's implementation will significantly impact PPE purchasing and maintenance. The focus on PFAS reduction, enhanced protection and improved performance highlights the ongoing commitment to firefighter safety.

Victoria Street building collapse: Fire and rescue when the unimaginable happens
By Santa Sternsdorf, station commander, George Fire and Rescue Department
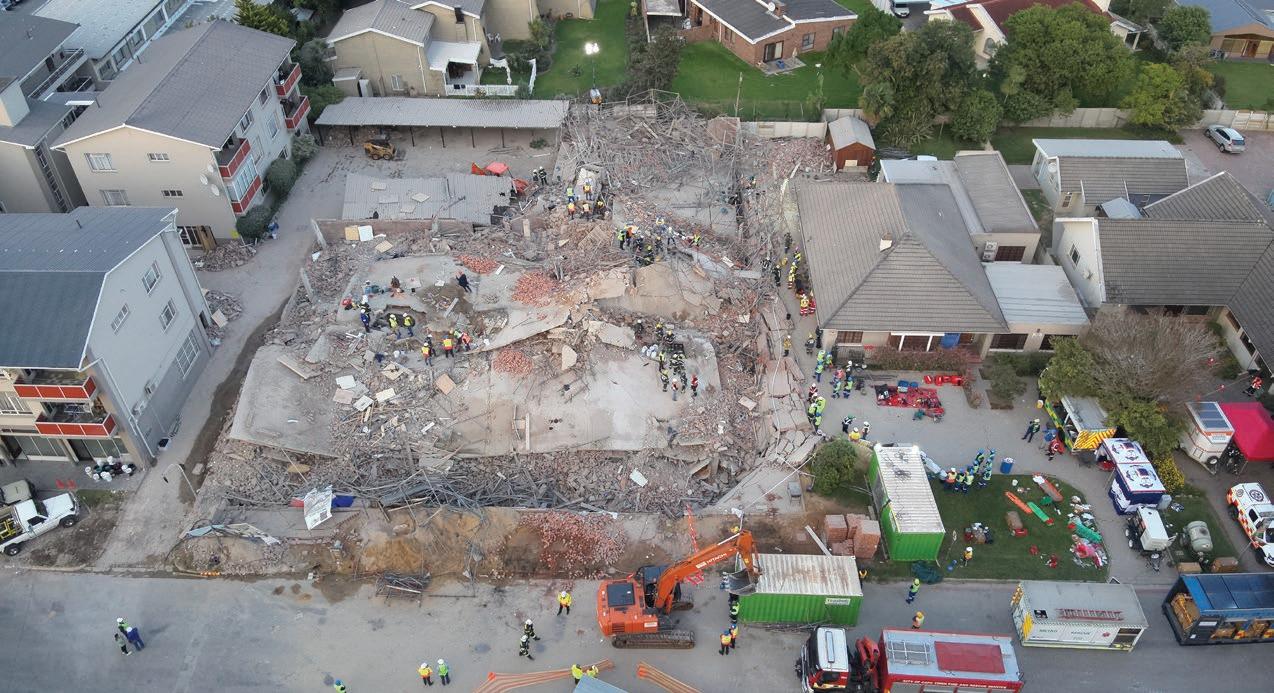
No textbook in the world can prepare you for the unknown when disaster strikes. Rescue workers experienced this truth first-hand when a five-storey building under construction collapsed in the city centre of George, South Africa, on Monday, 6 May 2024, killing 39 people and injuring 28 others.
The incident, which became known as the Victoria Street Building Collapse, attracted worldwide media attention and redefined emergency services’ approach to search and rescue of collapsed buildings in urban environments.
It also set a new standard for interdepartmental cooperation within a municipality as well as for collaboration between municipalities and other emergency response and humanitarian services.
George Fire and Rescue Chief Fire Officer Neels Barnard, who was the incident commander for the building collapse, said complete implosion of a multistorey building with multiple deaths, was exceptionally rare in South Africa and responders would seldom be exposed to the full implications of such an incident. “Victoria Street
demanded every grain of skill, experience and initiative to address the wide range of unique challenges. We were privileged to be supported by experienced rescuers from across the country, some of whom had worked on rescue and recovery following natural disasters in other parts of the world,” said Chief Barnard.
The incident scene
The structure, once completed, was going to be a five-storey, 42-apartment building including an underground basement for parking vehicles, which stood on pillars in the basement supported by weight bearing walls.
An aerial view of the incident site and SAR operations
The building collapsed in pancake fashion with very little debris beyond the two-metre perimeter. The adjacent buildings, an apartment building on the eastern side and a residence on the western side, were nearly unaffected with only a cracked window and three broken roof tiles.
There were two asbestos-roofed parking structures, at the back of the collapsed building’s property, being used by occupants of the neighbouring apartments. A section of the asbestos roof had been damaged in the collapse and immediately raised hazardous material concerns.
The George Municipality’s main building is situated directly across the road from the collapsed building site.
Situated in the centre of town, the collapsed building site is less than a block from the city’s main road, known as York Street.
Initial reports indicated about 82 people were working construction-related jobs on the site at the time of the collapse. Demographics of workers included students from a local trade school, male and female and foreigners from countries
such as Mozambique, Zimbabwe, Botswana and Lesotho.
Initial response
The first report was made within seconds from the collapse at 14h09, by a civilian, directly to the mobile phone of the George Municipality Fire Chief, Neels Barnard.
The George Fire Department responded with its full on-duty operational staff complement and four senior officers. All other relevant emergency and municipal services were informed and dispatched immediately thereafter. Every emergency worker will confirm that when a call is received regarding a building collapse, the image in one’s mind is mostly that of partial collapse, section of floor or wall, a roof segment or support. No one could have imagined the scale of the collapse and people involved. Even engineers, who witnessed the aftermath, stated that buildings are meant to be designed to fail in section or parts, not all at once.
Upon arrival, initial objectives were to take control of the scene, close it off, triage patients and distinguish people on the scene between bystanders, workers and
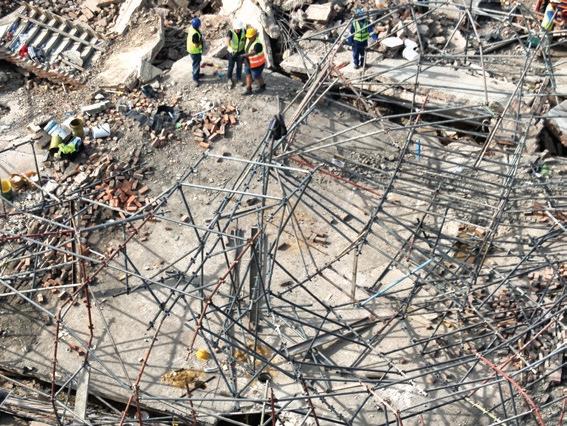
patients. Fire and rescue services also assessed the general stability of the scene, the building rubble pile and surroundings. Finding direction in the chaos to implement some structure was a very big and difficult task. There were a thousand things to consider and arrange, to give all a sense of direction to know what to do.
George Municipality Fire and Rescue took incident command (IC) with triage being set up by private ambulance services until the state’s Metro EMS ambulance service arrived and took over the management thereof.
22 patients, mostly tagged green/ walking wounded and two patients tagged blue/deceased, were rescued and recovered within the first four hours of the collapse.
Construction supervisors initially estimated 59 or 62 people on site but a figure of 82 had come from the Multi Agency Centre (MAC).
Responders quickly realised that the scale of the incident required specialised equipment and more assistance and contacted the Western Cape Disaster Management Centre (WCDMC) at 14h30 to request provincial rescue support.
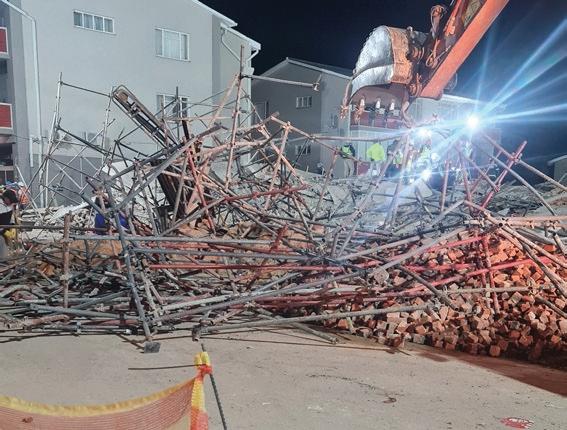
Scaffolding on site posing risk to rescue workers
The following resources were dispatched or activated in response to the request:
• Western Cape Department of Health and Wellness
• Search and Rescue capabilities from Cape Town including:
• Western Cape Provincial Search and Rescue cache
• Breede Valley Municipality Search and Rescue
• City of Cape Town Fire and Rescue team together with heavy-duty equipment
• SARZA Search and Rescue (highly specialised and trained volunteers owning 4x4 vehicles)
• South African Police Search and Rescue including K9 search dogs
Initially, all bystanders and workers were called off the rubble to allow for the site to be assessed and teams to be organised. Rescue teams were then formed by combining fire service, ambulance rescue technicians, other rescuers and volunteers.
Safety officers were appointed for each rescue team that went into the rubble. Later, the area
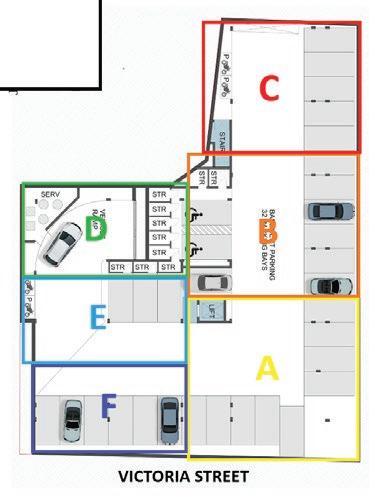
was divided into six sectors, with a safety officer overseeing three sectors each.
Initial challenges on the scene included determining the location of live victims and determining which types of resources were required to rescue them. Scaffolding was hanging precariously over the front (north) and western side of the collapsed building, which was considered dangerous.
The action plan for the first 24 hours was:
Establishing the incident command, site sectorisation (6 sectors were demarcated from Alpha to Foxtrot), structural stabilisation, access victims whose position was known, patient removal and emergency care (live victims were prioritised), identification of possible voids and further void exploration and using intelligence plans to identify location of possible victims
With operations going into darkness on Day 1, the George Municipality Electrotechnical Department set up spotlights around the scene to ensure 360-degree illumination. The block on which the site was situated, had lost electricity when the building collapsed. The electrical source to the site was isolated and the rest of the block’s power restored.
George Municipality’s Civil Engineering Department provided yellow plant and tipper trucks for the removal of debris for ease of movement around the site.
Ongoing operations
Twelve hours into operations, with most of the rescue teams having arrived on site, the scope
of the extended operation was estimated to be about 14 to 28 days’ work.
Shift systems were implemented to manage human resources, tool staging areas were established and an area was created for rescue workers’ care.
The senior management team of the George Municipality under the leadership of the municipal manager, gave the chief fire officer full authority to execute the operations. Their presence during the incident assisted in quick and decisive consultation and decision making to ensure optimal resources were available to the rescue teams’ disposal.
Rescue mode
Considering the first 72 hours as the most likely to find live victims, the operation remained in ‘rescue mode’ with the main objectives being:
• Location, access and releasing from the rubble victims whose positions were known
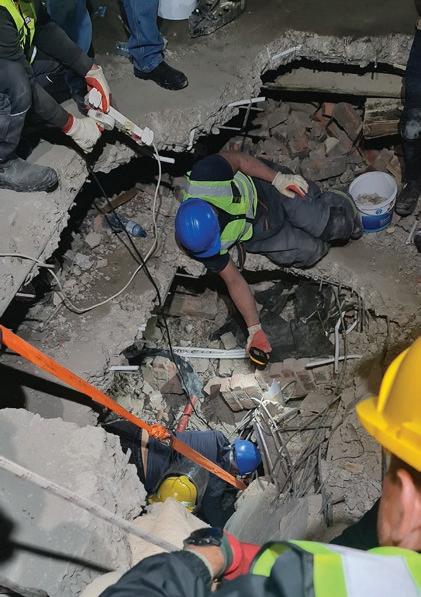
• Marking areas where victims known to be deceased were located
• Identifying two large voids inside Sectors Bravo and Echo
• Securing access points, first with rebar and later using wooden T-spot shores
• Confined space search operations
• Removal of destroyed scaffolding and moving all debris off-site.
Department of Labour (DoL)
Officials of the National Department of Labour arrived on Day 2 and insisted on access and jurisdiction based on the accident site’s status as a worksite on which people were employed, injured and killed. However, since it was still an active rescue site, legal jurisdiction remained with local rescue authority: George Fire and Rescue, supported by Western Cape Province Disaster Management.
Labour officials were given access to the site to observe. The department also insisted that building rubble that had been removed from the imploded site had to remain on the property until the necessary structural tests and investigations could be undertaken. The site’s location and size, as well as health and safety concerns, did not allow for it.
The George Municipality Solid Waste Department made an emergency decision to transport all incident rubble to a dedicated space on its refuse site, where it could be guarded by municipal law enforcement and a private security company, until the Labour Department’s investigation was complete. The trucks transporting the rubble were escorted by the George Traffic Department to prevent in-transit tampering.

Asbestos risk
The asbestos roof of the parking structure was damaged during the collapse, creating a potential health and safety risk to everyone on site. Incident commander, Fire Chief Neels Barnard, arranged for an accredited service provider to remove all asbestos from Delta Sector before work could recommence.
Extended rescue mode
While the possibility of survival was diminishing, the team remained in extended rescue mode, treating the site with care in expectation of more live rescues. This approach paid off when a worker was found alive on Day 6 relatively unharmed.
Nonetheless, the removal of deceased victims’ bodies from under the rubble was becoming priority because of health risks associated with decomposing bodies.
At the same time, information was being collected regarding the collapsed building’s construction, layout, collapse patterns, risks and material behaviour of the rubble.
Structural delayering was becoming urgent for rescuers to reach deeper where victims may be trapped but efforts were being hampered by substandard building materials that were not responding as was expected.
Transition to heavy demolition assistance
A specialised demolition company was brought in to assist with the breakup and removal of building material. The company arrived on Day 5 and started delayering from Charlie Sector.
Void backfilling (stability)
Engineers were becoming concerned that the retaining wall for the basement was becoming unstable due to the pressures from the sides, as well as the failure of the ground floor that was supposed to counterweight from the sides. The cement slabs, which formed the ‘floors’ of the building, were laying on top of uneven rubble, causing it to start losing integrity.
The area against Victoria Street was suitable for backfilling with rubble from other sectors to help stabilise the retaining wall but
Damaged asbestos roof in Delta Sector
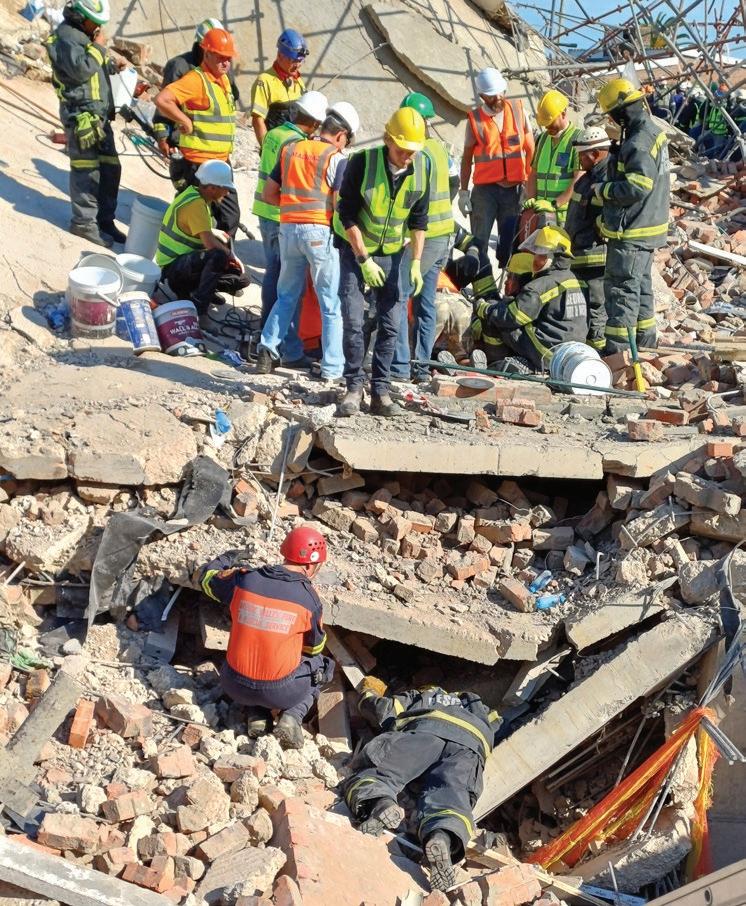
was searched and cleared twice by K9 dogs to confirm that there weren’t any people in the space, before backfilling started.
Rescue and recovery
Rescue operations were a combined rescue and recovery process but priority was given to locations of known living patients.
Operations were complicated by the poor quality of building materials which did not behave in the manner rescue workers were accustomed, such as concrete that would turn into powder instead of breaking into manageable pieces, causing concrete slabs to unexpectedly shift. These factors were of great concern to the safety of emergency personnel.
The rescue and recovery rate ran as follows over the eleven days of the incident, bearing in mind the original estimated number of people missing, according to the Multi Agency Centre (MAC), was 82.
First four hours: 22 rescued, two deceased (24)
Day 2; 7 May 2024: 8 rescued, 3 DOA* (35)
Day 3; 8 May 2024: 1 rescued, 1 DOA (37)
Day 4; 9 May 2024: None (37)
Day 5; 10 May 2024: 3 DOA (40)
Day 6; 11 May 2024: 1 rescued, 2 DOA (43)
Day 7; 12 May 2024: 7 DOA (50)
Day 8; 13 May 2024: 11 DOA (61)
Day 9; 14 May 2024: 1 DOA (62)
Day 10; 15 May2024: None
Day 11; 16 May 2024: None. Site handed over to SAPS/DOL.
* DOA = Dead upon rescuers reaching the victim
The final count of people rescued was 34 and 28 bodies recovered; totalling 62. Five of the rescued people succumbed to injuries in hospital, raising the final death count to 39.
The remaining persons unaccounted for were later verified by the South African Police Service (SAPS) as not having been present at the time of the collapse.
The pinnacle of the rescue operations was when Mr Gabriel Guambe was discovered alive on Day 6. With morale low and hope dwindling, the initial thought was that the sounds the rescuers were hearing under the rubble could not possible be that of a survivor. It was too good to be true. Verifying every indication from the K9s to the camera and acoustics’, the discovery of a survivor gave renewed vigour into all on site. His survival after 118 hours under the rubble was the miracle everybody prayed for. It was the embodiment of why we became rescuers.
Hospitals
Local hospitals activated mass casualty protocol with the George Hospital (state) and Mediclinic (private) excellently, providing the required emergency care to victims. Patients were sent to emergency care centres based on the triage process and capacities of each hospital as the only selection factors.
Rescue equipment
Rescuers made use of a wide range of equipment, including power and hand tools, across a diverse rescue site.
Rescue operations prioritising live victims
Battery operated tools worked best and small power tools, such as angle grinders, were essential in breaking up rubble, cutting reinforcement rods and for working in confined spaces.
Some private companies sponsored hard-wearing parts such as drill bits and blades, which required administration functions to ensure that all sponsored and paid services were correctly processed before items were used.
Dedicated personnel were assigned to handle tool maintenance exclusively such as cleaning, sharpening and battery charging, which was very effective. Tools were readily available at a moment’s notice.
Non-emergency support and logistics
The George community has handled its share of disasters, including the 2017 Knysna Fires and the 2018 Outeniqua Mountain Fires and local NGOs and communitybased organisations were familiar with emergency services workers’ needs. Well-connected networks of resources were very quickly activated and a full catering facility was set up on site. By Day 3, they were able to provide nearly three hot meals a day.
The George Fire Department implemented a colour tag system to identify authorised people on site. Emergency workers carried green, volunteers for search and rescue as well as outside construction workers were labelled orange and volunteers working the food, rest and recovery area wore pink labels. The system was not perfect and small adjustments were made throughout the incident as required. According to sign-in sheets, approximately
1 000 people volunteered on site on Tuesday (Day 2).
Construction volunteers were reduced after Day 3 and completely stopped on Day 4.
A major logistical challenge was the personal protective equipment (PPE) required for volunteers as they were not allowed onto the rubble pile without a helmet, safety shoes, gloves and a reflective bib. It was also difficult to ensure the safety of volunteers. Donations from companies and NPOs helped tremendously to address this challenge.
The logistics of food and water became an operation almost on its own. Small shipping containers were donated to help with storage. The Garden Route Health Department monitored food preparations and storage as well as health and hygiene on site. Wash basins and sanitising stations were set up with a very strict individual, ensuring everybody washed their hands before entering the food area.
K9 response (trained dogs)
The K9 response consisted of K9
Search and Rescue Organisation (volunteers organisation), the SAPS K9 unit and, later, joined by dogs from the Gift of the Givers humanitarian organisation. Five dogs and their handlers worked the incident with the assistance of another two when required.
The dogs initially helped finding live patients. Each positive indication from a dog was verified by a second dog before efforts at a specific place would commence. Later, the dogs were used to find possible deceased patients (cadaver search).
Interpretation of the dogs’ finds and information provided by their handlers, informed decisions that Incident Command made about action plans.
As mentioned before, dogs were used to confirm that there were no people in an area where backfilling was required to stabilise a retaining wall.
The extended period of operations took its toll on the dogs and lessons learnt included the establishment of shifts and ‘off duty’-dogs to be taken off
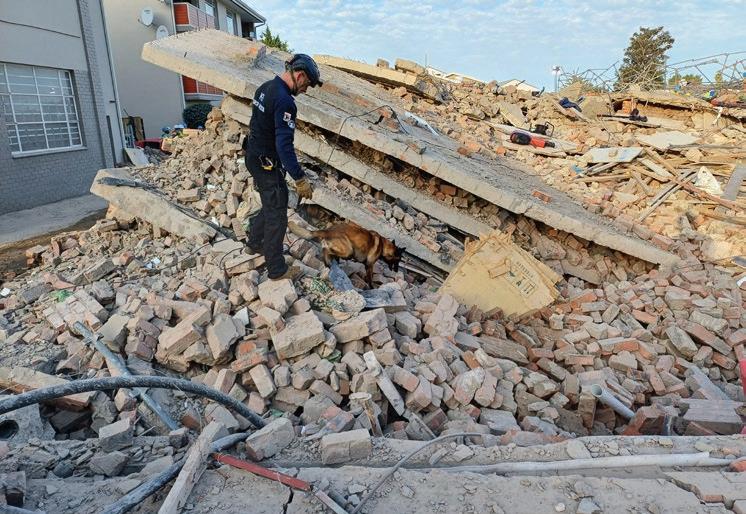
Dog hander and K9 conducting a search
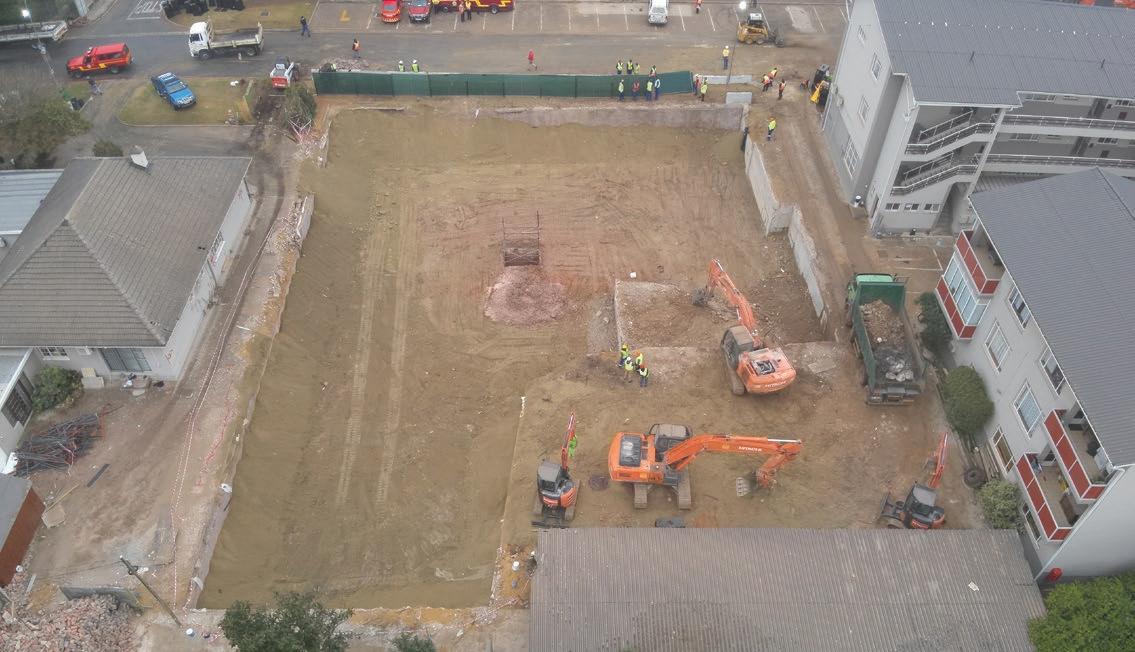
site completely to reduce noise stress and overstimulation.
People working on site were asked to refrain from eating on the site and rubble pile where dogs were required to work, as the food scents could interfere with the smells required to locate people under the rubble. The site had to be kept as ‘sterile’ as possible in order to give the dogs the best opportunity to give accurate indications.
As with other rescue data sources, it was realised that information provided by dogs could sometimes be limited or wrongly interpreted and should therefore not be interpreted as the sole indicator for rescue action.
Humanitarian assistance
Families of the victims arrived at the scene within hours and were initially accommodated at the edge of the site. By the next morning it was clear that a structure was required where families could wait for news, out of the elements yet close enough to be updated and
cared for and they were relocated to the nearby Town Hall.
Their needs became a challenge to resolve and the National Department of Social Development (DSD) was slow to assist and not really equipped to deal with the situation. The George Municipality Social Services section provided some assistance supported by NGOs and NPOs.
To try and address basic needs of family members, only spouses, parents and children were allowed inside the hall. However, it was difficult to confirm familial connections, which some opportunistic bystanders abused to try and obtain donations under false pretences.
Since many of the victims on the site were from foreign African countries, recording connections to victims was a great challenge due to language barriers and the search for suitable interpreters took time. Some of the victims
were known by more than one name. This made it difficult to match the list of names received from the Multi-Agency Centre to the names given by the families.
The families were eventually helped with mattresses and blankets to sleep in the hall while waiting for news, with food and food parcels also provided.
It was later realised that the proximities of families near the site was not ideal. Every time an ‘all quiet’-signal was called by blowing an air horn, the families would interpret it as someone having been found, setting of an emotional response to try and find out if family members were found dead or alive.
Media
Media coverage on the building collapse was almost unprecedented. Managing the media became a balancing act between safe and fair access and protecting the privacy and dignity of victims and their families.
Site cleared before handing over to SAPS
The media was initially kept on the periphery of the incident as part of safety measures but by Day 3, Wednesday, 8 May 2024, they were allowed to move to designated safe areas around the site. This concession was made to allow media better coverage but also to control their movements.
The George Municipality Communications Department reported 2 302 news clips for the month of May 2024, information derived from contracted news clip services. About 2,4 billion views of media material linked to the George Municipality and the Victoria Street Building Collapse, were reported. The equivalent advertising value for this media coverage would have cost R48,7 million.
Pathology and SAPS investigations
Pathology services became part of the rescue teams as their staff are trained in most of the rescue principles but also to provide the necessary guidance when a victim was found deceased.
The SAPS dive unit officers were also included for legal proceedings of inquest documentation as they had to provide the statements for legal proceedings for the deceased.
On Day 3 (Wednesday) the undamaged part of the parking structure at the back of the site was converted into a temporary holding area where Pathology Services could complete the required processing before a victim was transported off site and to the mortuary.
The SAPS investigation continued throughout the rescue and recovery process. At times, operations had to be adjusted to allow core
samples to be taken from cement slabs. Engineers and investigators were assigned a safety officer to escort them on site while rescue operations continued.
Incident statistics
• The live rescue success rate was 54 percent of victims found alive on site
• More than 140 rescue workers and more than 1 200 civilian volunteers were a part of the incident
• George Municipality spent more than R8 million on the incident
• The total cost of the incident, including expenses of other organisations but excluding hospital costs, is over R12 million
• An estimated 6 000 tons of rubble and building material was removed from the site in 11 days and one hour
Western Cape Chief Director
Disaster Management and Fire and Rescue Services, Colin Deiner, substituted incident commander duties with George
Fire and Rescue Services Chief Neels Barnard.
Deiner said the Victoria Building Collapse incident would be unforgettable for many reasons. “It was profoundly sad and shocking but is also testimony to the brave rescuers, committed workers and a compassionate community. In the face of many challenges, a multi-agency team overcame differences and obstacles and managed to work together for the greater good. When it mattered, the experience and character of the people, and deep-seated relationships sustained us through eleven intense days,” said Deiner.
References and appreciation
• Manager Fire and Disaster Management George Municipality CJJ (Neels) Barnard
• Western Cape Chief Director Disaster Management and Fire and Rescue Services, Colin Deiner
• George Fire and Rescue Staff, DC Johan Brand and SO Johan Crouse
• Athane Scholtz, Editing

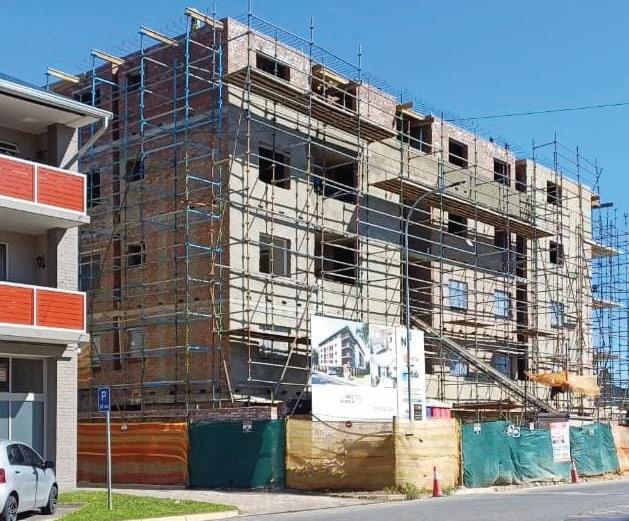
The building prior to the collapse
Western Cape urban search and rescue response to the George building collapse; a provincial perspective
By Colin Deiner, chief director, Disaster Management and Fire Brigade Services, Western Cape Government
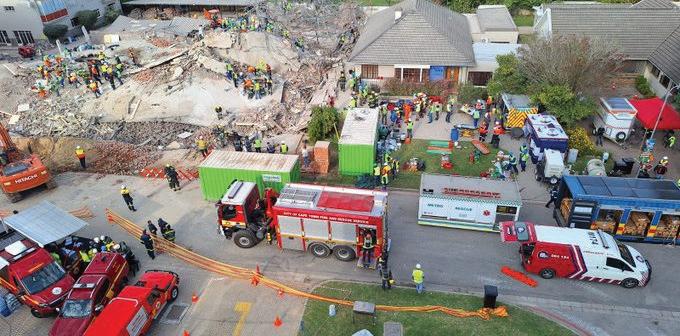
Monday, 6 May 2024, will be remembered by many people as a day that changed their careers and, in many cases, their lives, forever. In this article I will provide my own observations of the operations and touch on the history of technical rescue in the Western Cape and how we were able to respond to this incident and manage it to its successful conclusion. I hope I will do the responders and the pioneers of this discipline justice. They thoroughly deserve it.
On that Monday, I was meeting with our provincial Disaster Operations Director in my office just after 14h00, when I received an urgent phone call from the
George Fire Department Chief Fire Officer, CFO Neels Barnard, who informed me that a fivestorey residential building, which was in the final stages of its construction, had collapsed and that several construction workers were missing. My immediate reaction was to activate the full capacity of the Western Cape Emergency Response System and get them to George as soon as possible. The first decision was to activate the Provincial Disaster Management Centre from where we could collectively determine what was needed and how we would respond our resources. It was agreed that a core group would try to get to George as soon as possible to determine
the conditions at ground zero and report back to Cape Town on the most critical needs.
After a faster than normal road trip, we arrived in George around 21h00 and was met by Chief Barnard, who proceeded to brief us on the situation and the immediate needs. Several first responders from the George Fire Department and Provincial Emergency Medical Rescue Services were already on the scene and had, at that stage, rescued approximately 20 construction workers. The George Municipality had acted very quickly and ensured that sufficient lighting had been installed to ensure that
operations could proceed through the hours of darkness.
By the time of our arrival, the Provincial Urban Search and Rescue (USAR) Unit had already responded with a team of rescue technicians from its base in the Breede Valley. The Provincial Department of Health and Wellness had responded with additional rescue technicians from various bases and their Heavy Rescue Unit from Cape Town. We had also requested the City of Cape Town Fire and Rescue Services to respond with one of their Heavy Rescue Units together with a team of rescue technicians. The bulk of the team from Cape Town was made up of experienced rescue technicians who, just a year earlier, had responded to the major flooding disaster that had struck the KwaZulu-Natal coast and cost the lives of more than 140 people.
When the sun rose on the morning of Tuesday, 7 May 2024, most of the resources that were needed had arrived and were being deployed to the six sectors identified by Incident Command (IC). What followed over the next 10 days was a herculean effort by more than 200 rescuers and approximately 400 support personnel that led to 28 people rescued and 39 bodies recovered. The incident grabbed the imagination of the nation and many people sat glued to the various television and online news channels to stay updated on the events as they unfolded. Senior media reporters from all the mainstream media outlets in the country converged onto the town and literally camped out on the space provided to them from where they reported on all aspects of the operation,
ranging from the actual rescue to the humanitarian efforts and the family members of the victims. As the actual events that transpired are well covered by other contributors in this publication, I will focus on the response by the various provincial services and their activities.
Provincial capacity
The Western Cape Province has a rich history in the development of technical rescue dating back to the 80s when the legendary Dr Alan McMahon recognised the need for a specialized rescue capability which focused, among others, on the operation of cranes for rescue purposes and management of victims trapped underneath heavy loads. The formation of the Metro Rescue System was further developed by Dr Cleeve Robertson and Dr Wayne Smith, who were instrumental in creating a world-class rescue service. The introduction of structural collapse by the rescue manager, Neville van Rensburg, established Metro Rescue as the leading rescue service in the country. The Western Cape Chief Fire Officers Committee, which is representative of the municipal and designated fire services in the province, also identified the need for a dedicated USAR system in the province and established the Western Cape USAR working group who played a leading role in the programme as it currently exists.
A large amount of work was done prior to the 2010 FIFA World Cup to develop an integrated system, which included the acquisition of a broad range of equipment and an ongoing training programme to ensure a good number of rescue technicians available for any major technical rescue incidents. The province currently maintains
a register of approximately 130 rescue technicians who are employed as rescuers, firefighters and emergency medical personnel in their normal day but can be made available when needed.
Another important component of this endeavor is the Western Cape Incident Command System (ICS), which has been developed over several years and is utilised during the summer seasons when the province is affected by frequent large wildfires. The ICS is specifically designed to manage all aspects of a major incident in which large numbers of responders are involved. All services are required to implement this system during major emergencies and annual refresher training is provided to ensure that they are kept current and brought up to speed on any new developments in the system.
A further vital cog in the system is the network of NGOs and volunteer organisations that give of their time to work beside the formal services in the various rescue operations across the province.
With its long coastlines and outdoor environment, which is conducive to outdoor activities, the South African Police Services Divers and Rescue Team are valuable partners as are NGOs such as SARZA, who not only provide their specialised offroad rescue skills but also their impressive command and control application, which they are able to deploy for a wide range of eventualities.
In a previous article I discussed the Western Cape Fire Services Mutual Aid Agreement and the benefits it holds for, particularly, wildfire response in the summer season.
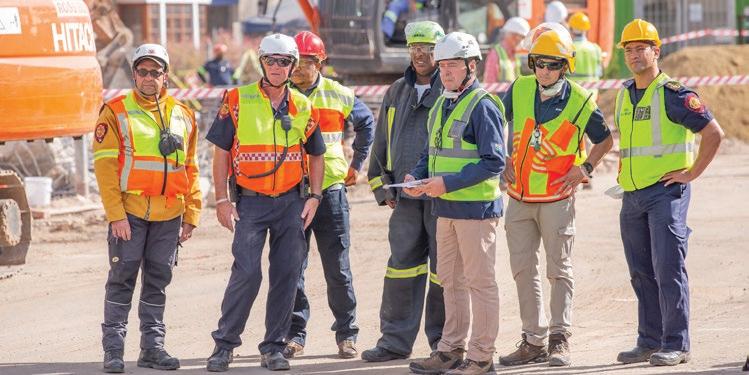
The agreement was instrumental in the province being able to deploy 1 108 firefighters within two days to the Knysna wildfire disaster in 2017. The agreement was invoked several times during one of the busiest wildfire seasons in the province’s history between December and April this year and set the trend for a large, combined response to George in May 2024.
Deployment in George
The deployment of the Provincial Disaster Management Centre staff to George was the fifth major incident that they had managed following the large wildfires in January and February 2024, a 10day regional electricity black-out in the Central Karoo district in March 2024 and widespread flooding in April 2024. The ever increasing volume of major incidents that they are confronted with has had the advantage of building a solid base of operational experience. I must stress that the Western Cape disaster management system doesn’t only consist of the full time staff employed in the centre but includes a wide range of disciplines ranging across the disaster management spectrum including rescue, infrastructure, health, humanitarian and security services. Most of these people have been involved in disaster response in some form since the 2017 “Day Zero” drought disaster
and have dealt with many diverse incidents since then.
No report back on this disaster will be complete if we don’t mention the community of the town who arrived on the first day and provided meals and sustenance to the many people working on the scene. They were there from the first day until the final hours and, in that time, provided thousands of meals and drinks at all hours. I was personally inspired by the display of support by this remarkable group of people. They also had to endure the trauma of the teams who inevitably migrated to the rest area for a coffee or a meal after recovering a victim dead or alive. They took it in their stride and (just like the rescuers) put the pain and trauma behind them and continued with their task.
Decisions
The first objective of the Incident Command Team was to ensure the safety of the rescue and support teams, which would enable the saving of lives. It was important to manage the expectations of the public, media and the rescue teams who were encouraged by the frequent shouts by people still trapped beneath floor slabs.
Management of fatigue became an important added priority and soon a system was introduced
where teams were rotated off the site and forced to rest before returning for the next “shift”.
Continuous arrangements needed to be made for prolonged work in the darkness and, at one point, a threat of rain also required us to plan for that eventuality.
Encouraged by the signs of life in several places, the decision was made to stay in ‘Rescue Mode’ for as long as possible and to adapt our tactics to support this strategy. Rescuers were for the first time exposed to entirely foreign conditions such as one trapped victim who was able to communicate with his family using his cellphone. The victim was advised that, to save battery life, to only turn his phone on at certain times. He was rescued on the Tuesday evening.
After the rescue of four survivors on day three it was decided to continue in rescue mode for as long as there was a possibility of finding a live victim. Many of the decisions were dictated by the instability of the structure. On day three, it became necessary to find a way to delayer the five floors that had formed a “pancake” collapse over most of the structure. The size of the slabs was huge and this necessitated cutting them into manageable sizes, which could be removed by crane. This decision resulted in a considerable slowing down of activities, which created a fair amount of confusion and anguish among the bystanders and families of the victims who thought that the rescue operation was ending. A hurried media briefing was called and, with the expert help of Prof Richard Walls of Stellenbosch University, we were able to explain the reasons for our decision. Prof Walls had
contacted us on the morning after the collapse and offered his services, which we immediately accepted. After rearranging his schedule and getting replacements for his lecturing duties at the engineering faculty, he made his way to George where he provided critically important advice on the stabilisation and removal of the slabs.
Another important decision that was made was to contract the services of a specialist demolition company to assist in the delayering process. We were fortunate to have access to the services of a company with an excellent track record in focused demolition work and operating in limited spaces. Ross Demolition arrived late on day four and, after a short planning session, deployed their equipment in support of the operations. The risk of damage to entrapped victims is high when heavy demolition equipment is deployed and this necessitated the placement of additional look-outs at strategic points around the machinery. This proved to be a good decision as it accelerated the effort and allowed the teams to quickly access more victims and remove them with more ease.
The Miracle on Victoria Street
Even though the last live victims had been recovered late on the third day, it was decided to stay in rescue mode and not to move over to recovery mode. The reasons for this decision were that we were able to access more voids with the demolition equipment and that the rotation of our rescue teams was ensuring a high working tempo. On Saturday, 11 May 2024, late morning, rescue dogs detected a victim after a layer had been removed in a sector designated close to the lift
shaft. A second dog verification and subsequent seismic and acoustic search indicated that the victim was still alive. Communication was established with him soon after and then followed a careful process, which entailed core drilling at identified points to determine the extent of entrapment and explore the options for releasing him. After a careful and focussed operation, Gabriel Guambe was rescued after being trapped for 118 hours.
For many of the people involved, this single event represented the combined success of all the days and hours of dedicated effort by so many people. The Premier of the Western Cape, Alan Winde, who was passing Mossel Bay on his way back to Cape Town when he was informed of the live rescue, immediately had his driver turn his vehicle around to George where he was among the first to congratulate the teams.
Final observations
There have been several reports and presentations made about this incident and many positive (and some negative) observations have been made by various people. Some of my own observations are the following:
• Capacity: In 2012 the Western Cape Government took the decision to improve the capacity of fire and rescue services in the province and what followed was a capacity building programme, which ensured that every fire and rescue service in the province receiving new vehicles and equipment over the next 12 years. This did not only improve the local capability but also, together with the capacity of the Western Cape Emergency Medical Services capacity, greatly strengthened the
combined provincial response to major incidents.
• Early response is crucial: The fact that a response was initiated on this scale immediately after the call for assistance, ensured that specialist skills and equipment could be deployed within a few hours of incident and ultimately the significant number of lives saved.
• Support: The unconditional support provided by the Premier of the Western Cape Province and the relevant cabinet minister and department heads, meant that whatever equipment was needed, was made available without delay. The Minister responsible for Disaster Management in the province, Minister Anton Bredell, arrived on the Monday evening and was present throughout the rescue phase of the operation to ensure that any assistance was provided.
• Plan together: The importance of planning and practicing together can’t be overstated. Emergency services in Western Cape spend many hours planning for the risks identified as part of our risk assessment process. That was evident when many of these groups were called upon to carry out this mission.
In closing
The commitment I observed over the 11 days and one hour that passed from the moment of the collapse to when the site was handed back to the relevant authorities, has left me with an enormous sense of gratitude. I was privileged to have played a small part in this mission. For that I will forever be thankful.
Photos courtesy of Deirdré Cloete, Deds Photography

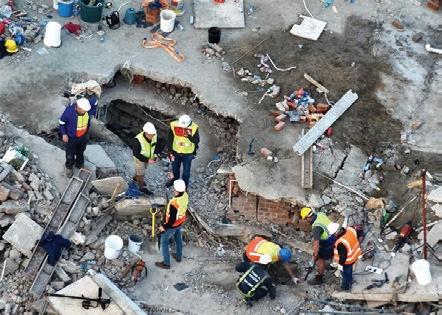

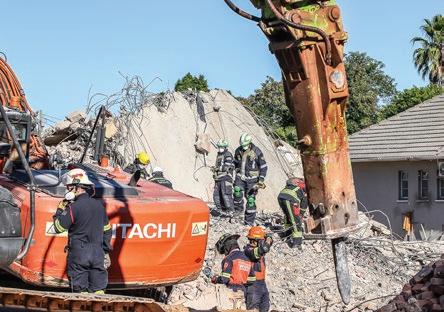
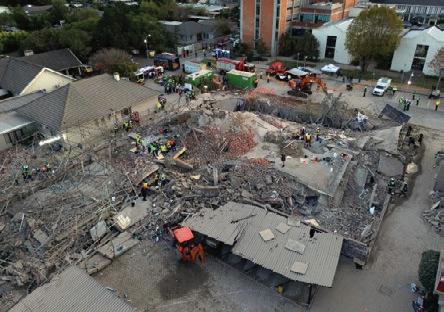
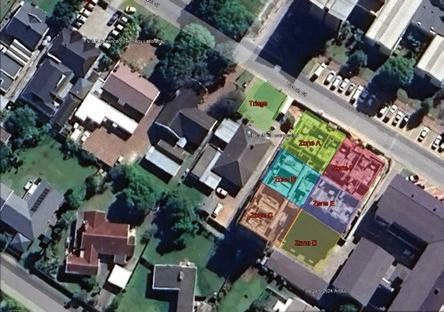
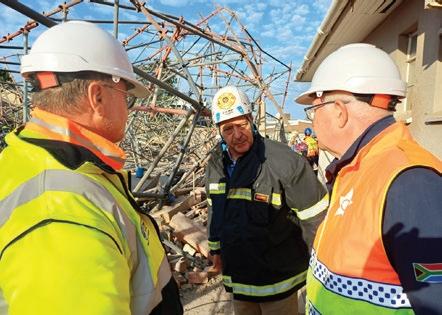
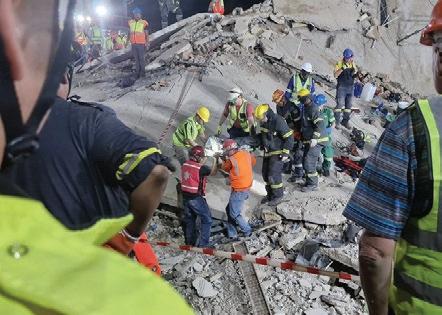
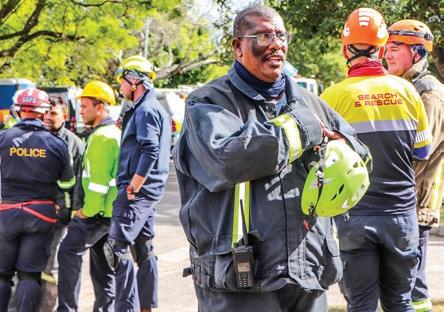
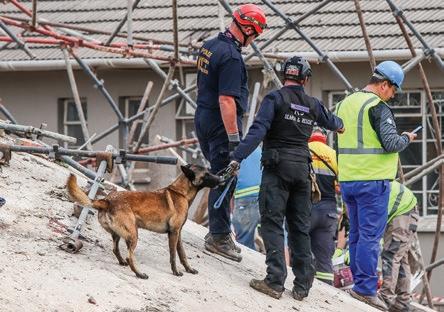
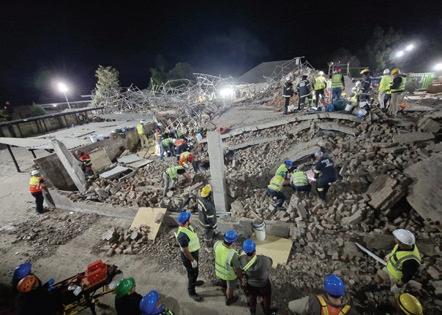
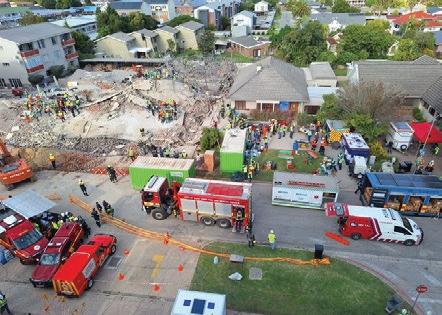
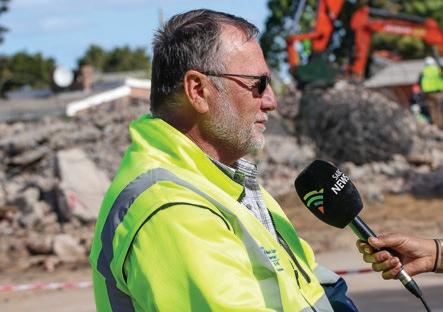
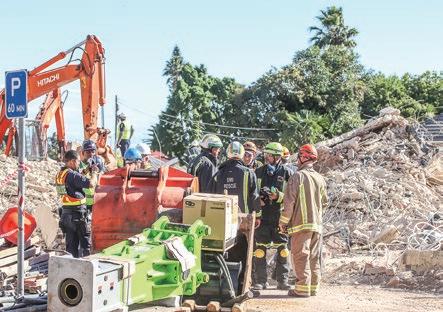

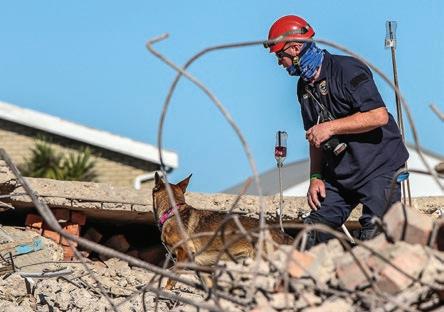

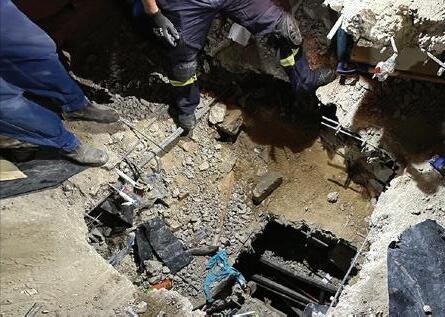
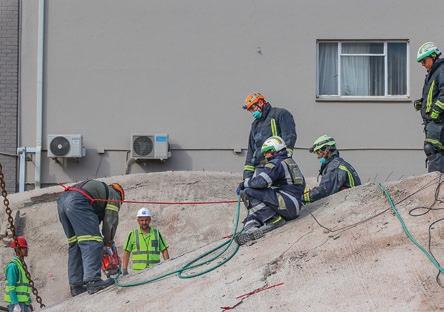
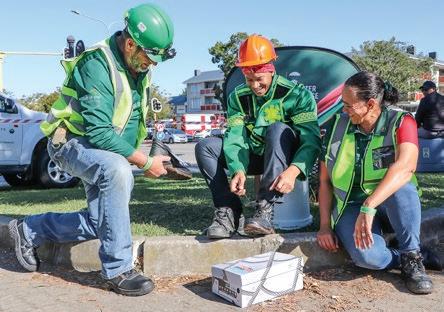


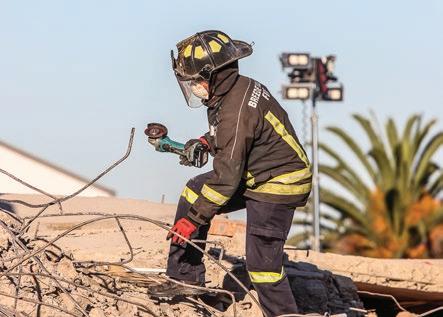
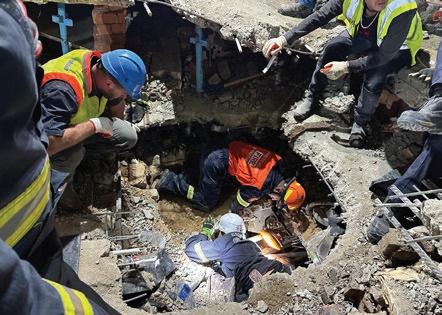
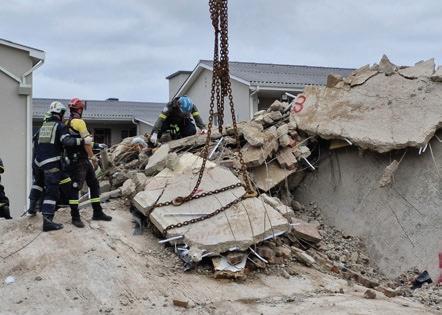


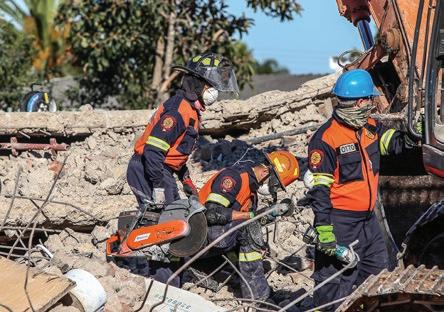
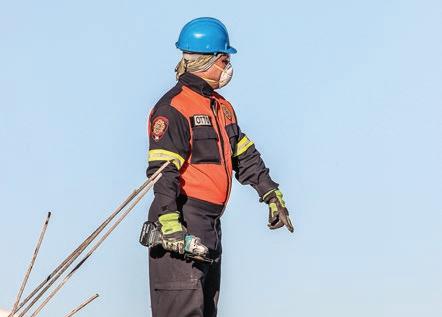
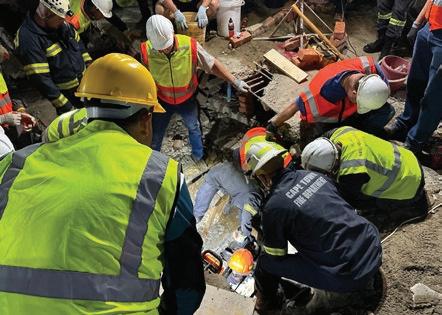
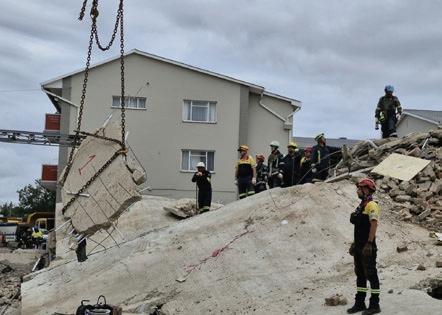
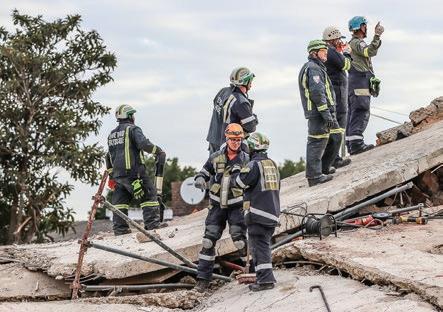
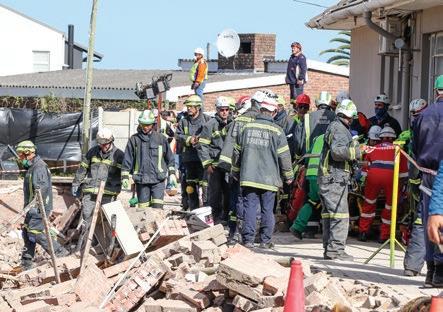
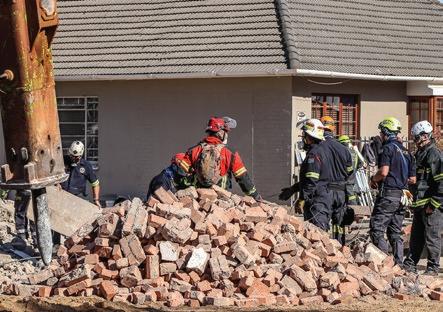

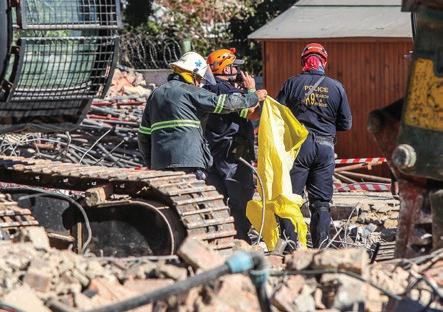
George structural collapse: Emergency Medical Service response
By Richard Botha, EMS-Rescue, Western Cape Government Department of Health and Wellness
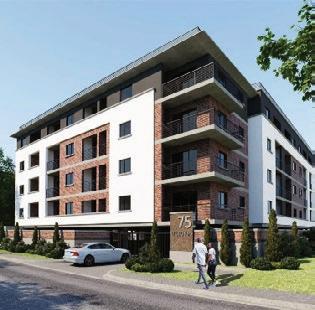
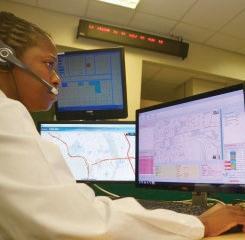

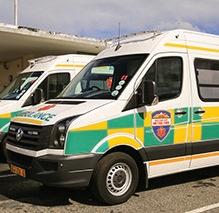
Monday, 6 May 2024, was an unforgettable day for us in the Garden Route and Provincial EMS. Our service team embodies the motto: “A health-focused EMS system delivered by skilled, efficient and motivated personnel, equipped with the necessary resources that can be rapidly accessed and responds promptly to ensure patients receive appropriate care in the shortest possible time, leading to the best patient outcomes.”
At 14:14, our Garden Route EMS Call Centre received a call regarding a building collapse on Victoria Street, across from the George Municipality building, with reports of people trapped inside. All EMS units, including Ambulance, Rescue, Planned


Patient Transport, and the Management Structure, were dispatched.
Upon arrival at the scene at 14h24, we assessed the situation and immediately implemented the Major Incident Medical Management and Support Plan (MIMMS). This plan is invoked when the number, severity or type of casualties or the location of the incident, requires extraordinary resources. We reported to Chief Fire Officer Neels Barnard, the incident commander of the George Fire Department, providing a scene report detailing the building collapse and the fact that workers were trapped under debris. Additionally, a methane report was relayed back to our call centre.
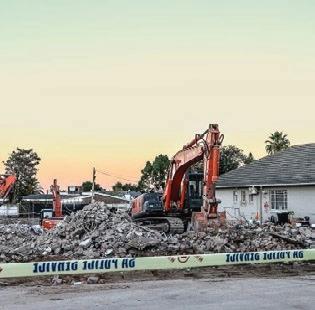
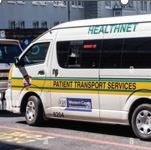
Major incident: Declared a major incident
Exact location: Incident on Victoria Street opposite the George Municipality building
Type of incident: Multiple-storey structural collapse
Hazards: Unstable structure, building material like scaffolding Access and egress route: From York Street into Victoria Street Number and severity of casualties: 70 plus trapped under the building material
Emergency Services: EMS –Ambulance and Rescue, Fire Service, Police, Traffic, additional resources were requested from District and Provincial The Control, Safety, Communication, Assessment, Triage Treatment, Transport (CSCATTT) principles were
followed in conjunction with ICS Operational Section Chief layout.
Command “Bronze, Silver, Gold” and Control, Safety, Communication, Assessment, Triage Treatment, Transport
Our EMS Rescue Team, led by Richard Botha, collaborated with the multi-sectoral rescue teams, to facilitate the rescue of individuals trapped under the building structure. The highly trained and designated rescue technicians specialised in structural collapses worked seamlessly together, utilising all available rescue equipment from local, district and provincial levels at the scene.
Our medical teams ensured a high level of performance in triage, treatment and transportation, working alongside
local and provincial medical doctors under the leadership of our Provincial Disaster Medicine Doctor, Dr Wayne Smith. In total, we rescued 14 patients classified as red, seven as yellow, seven as green and 34 as blue from the collapse site. The rescue operation was successfully concluded on 17 May 2024.
Lots of rescues was done and people lives were saved, but there is one rescue that was giving hope for more lives that might be saves. That was the rescue of Gabriel on day 6 when the K9 Search and rescue dogs, our EMS Search and Rescue Camera team gives us the positives that there is a patient that is still alive under collapse concrete floors. The rescue teams has started the drilling and breaking of the

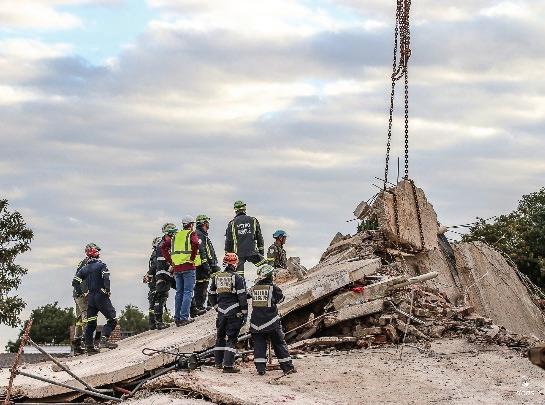
concrete finally a light in the end of darkness for Gabriel as he was medically stabilized and packaging for removal from the rubble by the rescue team for a full examination by our medical team and transportation with the ambulance to the hospital.
Successes
• Collaboration of the multidisciplinary rescue teams
• The success rate of medical and rescue staff in collaborating as a cohesive unit to save and transport lives
• The efficiency of rescue workers functioning inside a unified command structure/ system
• Positive and functioning command controlled system
• The success of the rescue operation and the survival rate
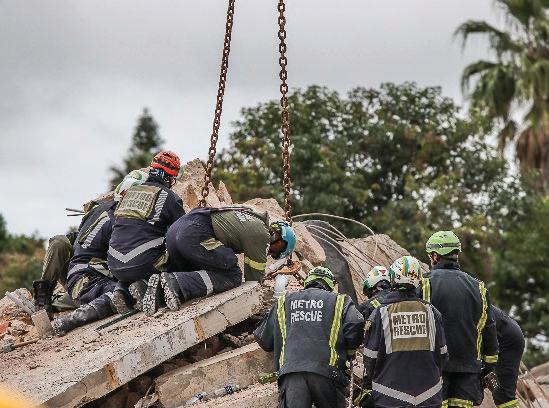
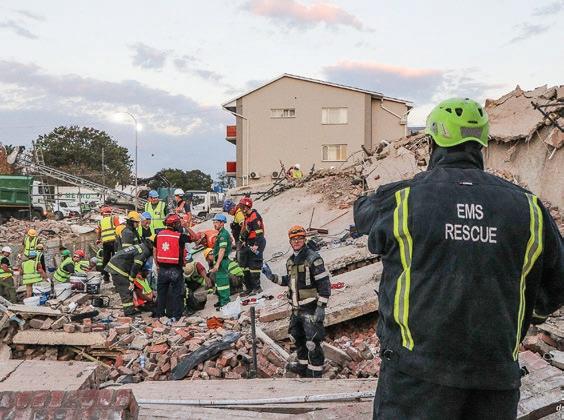
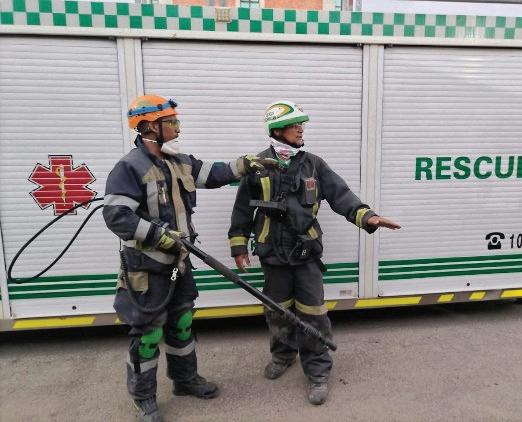
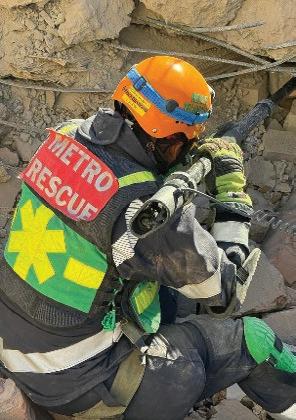
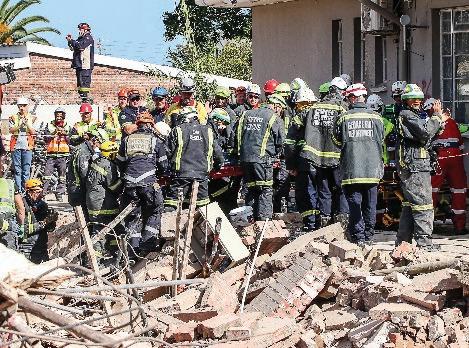
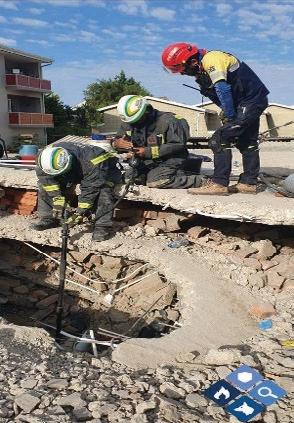

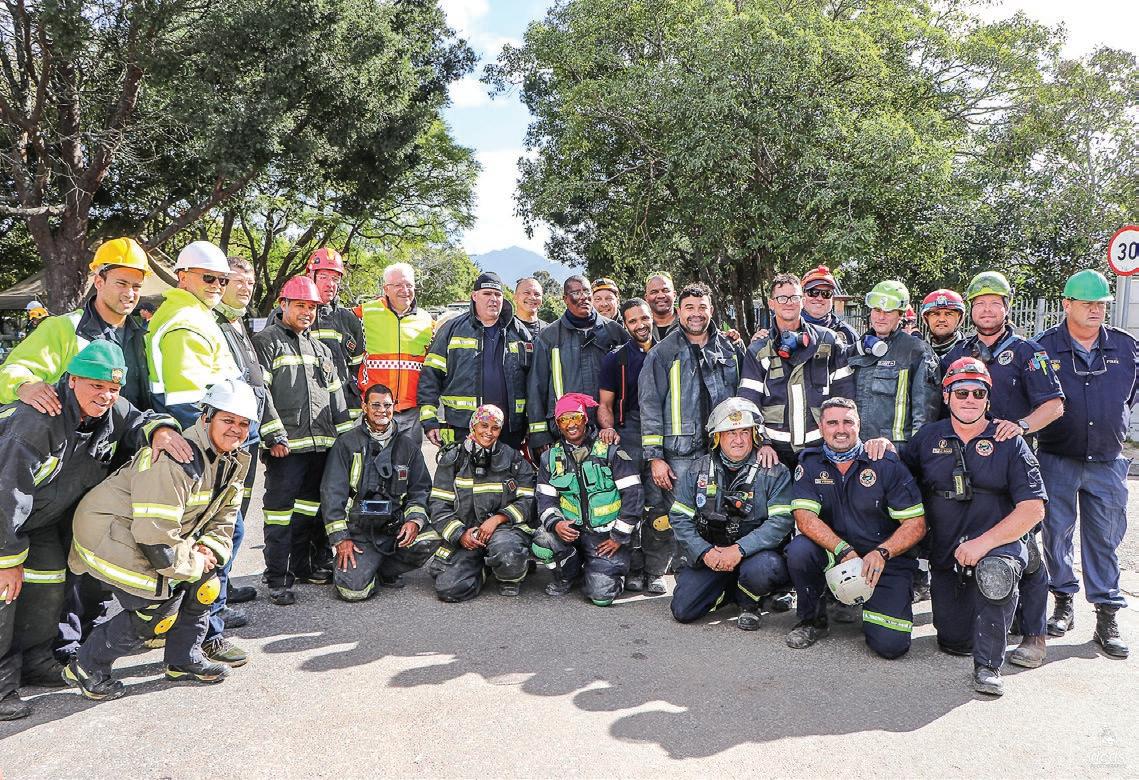
• Metro Rescue structural collapse training provided rescuers with a platform from which to work
• A support George community, kitchen and refreshment team
• Excellent assistance from Government on national, provincial and local level, the community and nongovernmental organisations
• The South African President extends wishes and compliments all rescues for their diligent efforts and achievements.
Lessons learned for improvement
• Imperative requirement: a motion sonar scanner is crucial for accurately determining the location and orientation of patients currently restricted
• Comprehensive volunteer management system – skills and support
• Skills training programmes with
the aim of capacity building
• Dog handler’s involvement training focuses on the role of a Disaster Management system
We would like to acknowledge and express our gratitude
for the efforts, diligence and commitment of the EMS personnel, rescuers, SAPS, Fire and Disaster Management personnel and all volunteers whose support was instrumental in executing the rescue operation.

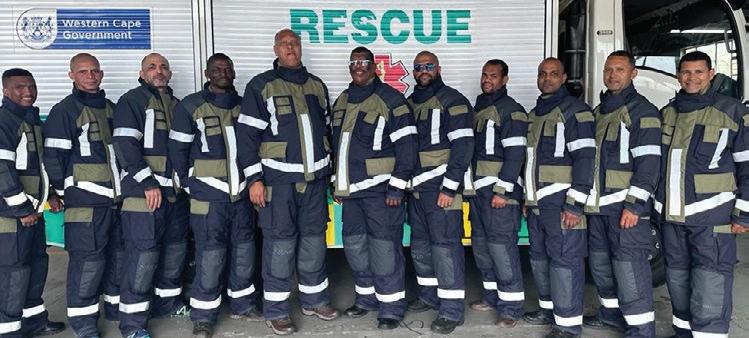
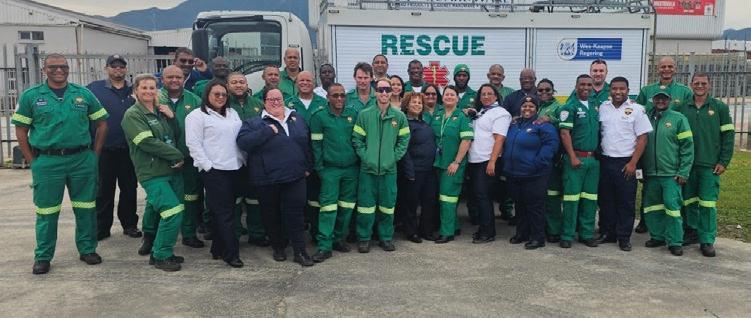
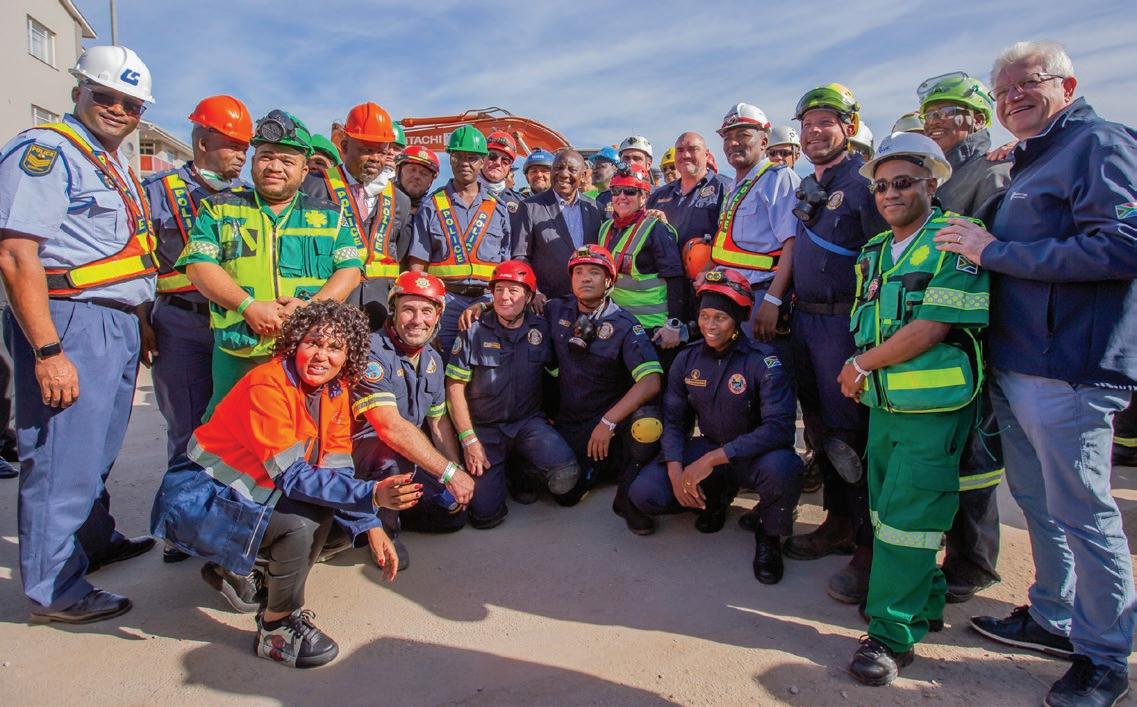
George building collapse: Challenges, priorities and key observations
By Colin Deiner, chief director, Disaster Management and Fire Brigade Services, Western Cape Government
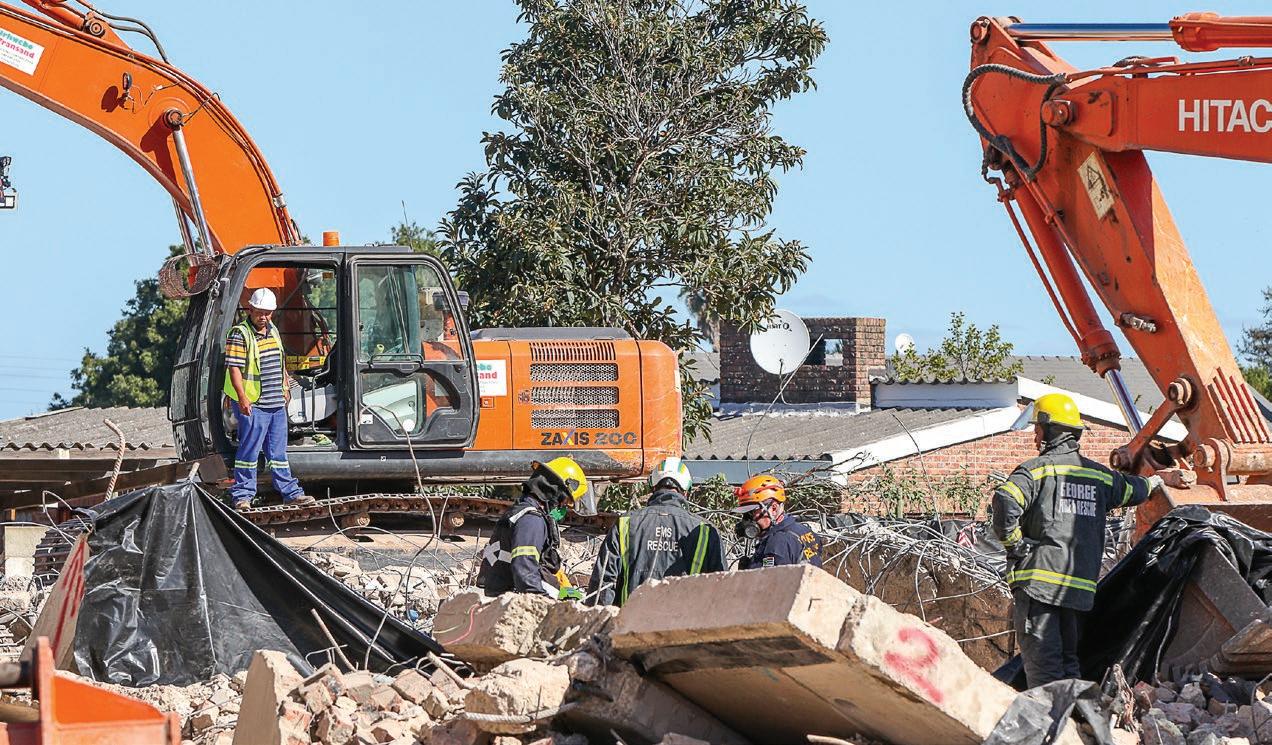
The structural collapse incident, which occurred at 75 Victoria Street in George, Western Cape, on 6 May 2024, drew wide attention from across South Africa and even in other parts of the world. Large numbers of people followed the incident on live television news channels, the internet and social media, waiting to see if more people were being rescued as the rescue operation progressed over eleven days that it took to finally hand the site over to the responsible authorities. The structure, initially planned as a five-storey building with forty-two
apartments and an underground basement for parking vehicles, suffered a catastrophic collapse during its construction phase. The building was supported by pillars in the basement and weight-bearing walls.
The location of the site is particularly notable, situated in the heart of George's town centre, less than a block away from York Street, the city's main thoroughfare. Across the road from the collapsed building site stands the George Municipality main building, highlighting the centrality and urban context of the area.
While the contractors were applying the final changes to the building just after 14h00 on that Monday afternoon a sudden and catastrophic collapse of the entire structure occurred leaving a large number of construction workers injured and trapped on the surface or at different points in the structure. The first official responders to the incident were the George Fire Department and the local base of the Western Cape Emergency Medical Services. Upon arrival they found a chaotic scene with a large number of injured victims inside a stifling cloud of concrete dust and
mangled scaffolding surrounding the layers of collapsed floors.
For any fire department in the world this would have been a daunting prospect however the initial actions taken by the first in commanders and managers of the fire department and medical rescue services paved the way for a smooth escalation of operations into a major rescue operation involving several hundreds of rescuers from across the province. The George Fire Chief, Mr Neels Barnard and the regional Emergency Medical Rescue head, Mr Richard Botha made the early call to escalate the incident to the provincial authorities. The Provincial Disaster Management Centre (PDMC) immediately convened an emergency meeting where it was decided to activate the Provincial Urban Search and Rescue unit, which is station at the Breede Valley Fire and Rescue Service, the Provincial EMS heavy rescue unit and the City of Cape Town’s technical rescue unit. An offer was also accepted from the South African Police Rescue Unit, who also responded upon the approval of that request.
Understanding that most of the above units would take upwards of five hours to reach George from Cape Town arrangements were being put in place to remove the visible and reachable patients and to prepare for a protracted operation that would have to be performed during the hours of darkness. The also prepared to ensure that the teams arriving from Cape Town would be able to hit the ground running by setting up briefings when they arrived.
The first arriving units were briefed on the initial priorities, which was to locate the known victims
and release them. Establishing command over several responding agencies was one of the initial challenges however the presence of a large number of experienced rescuers who had cooperated on many previous emergency operations resulted in this being addressed and by early morning a solid command system had been established which ensured a safe and effective operation with clear goals and objectives.
The initial command priorities were set as follows:
• Site sectorisation
• Structural stabilisation
• Access known victims
• Patient removal and emergency care (live victims prioritised)
• Identification of possible voids
• Further void exploration
• Using intelligence plans to identify location of possible victims
• Scaffolding removal
• Debris removal to off-site location
Two serious challenges facing incident command was the substantial number of unstable scaffoldings, which has collapsed alongside the building and causing stability and access problems for the rescuers and the volumes of debris that was being removed from the site. On Tuesday (Day two) morning, it was decided to remove all the scaffolding as well as two storage containers that were located on the street (front) side of the collapsed structure. This allowed a safer and unimpeded access to the site.
The removal of debris to an off-site location was a crucial decision for several reasons. The first being that the site was surrounded by a street and other (residential and business
structures which provided limited open space. Secondly, in many structural collapse incidents in the past, where there was no debris management plan, rescue teams had, in their haste to recover victims, tended to remove debris of one part of the structure and place it right next to where they were working, often right on top of trapped victims. It would then seriously delay accessing these previously undetected victims. In this incident a site was identified near the George airport several kilometres away. Although this required more heavy trucks it ensured a tidy area which resulted in the incident being concluded in a brief time.
Victim location
After the removal of the surface victims in the first few hours of the operation the initial location of trapped victims became the priority. Victims had been heard tapping and shouting at four separate teams and teams then had to determine the exact location of these victims. The first action was to try and contact the victims and, in that way, try to determine their position and condition. Thereafter, one search and rescue canine would be deployed to search the area followed by a second canine. The practice on a second dog verification is used as it has been experienced that canines might generate a false positive scent if they get exhausted from having worked for an extended period. In a structural collapse scenario, canines might only respond positively at the opening of a void where the victim is trapped and, not necessarily, right at the victim. This is because the concrete structures density would impede the flow of the victim’s scent.
In this case the search team should analyse the structural components and try to form a picture of where the collapsed voids might be. Drilling a series of core holes in that area might provide a better indication of the victim’s location.
The decision to extend the rescue phase of the operation for as long as possible necessitated the extended use of seismic and acoustic listening devices which detected movement and, where teams were able to communicate with victims they were encouraged to tap with bricks or similar items at short intervals to assist the teams to locate them. A remarkable story that unfolded during the first two days was when trapped victim was able to send text messages to this parent indicating he was alive and giving an approximate indication of his position. His father then made his way to the
site and showed the messages to the rescuers. Contact was made with him, and he was advised to turn off his phone and only turn it on periodically to save battery life. Through this form of communication he was successfully rescued on the evening of Tuesday, 10 May 2024.
The victim location process involves a scientific method where evaluating the event that led to the collapse and the subsequent condition of the collapsed structure plays a key role. There are six questions that must be answered which should then provide a guide for incident command to plan the search operation:
• Time of day? – In this case (14;09) workers were on site and just resuming work after their lunch break. Some had not yet returned from lunch.
• Time of year? – May in the Southern Cape is at the onset
of winter which could result in colder temperatures at night, and this could impact any trapped survivors.
• For what was the building used? – A five-storey residential complex in the final stages on construction: expect building materials, new concrete and similar features. Victims will be mostly construction workers.
• What did the building look like? - Building plans were accessed early which gave a good indication of the building features.
• How did the structure collapse? - Pancake collapse with little void formation
• How and when was the building constructed? – New building.
Site sectorisation
To streamline the incident command process and to better coordinate the considerable
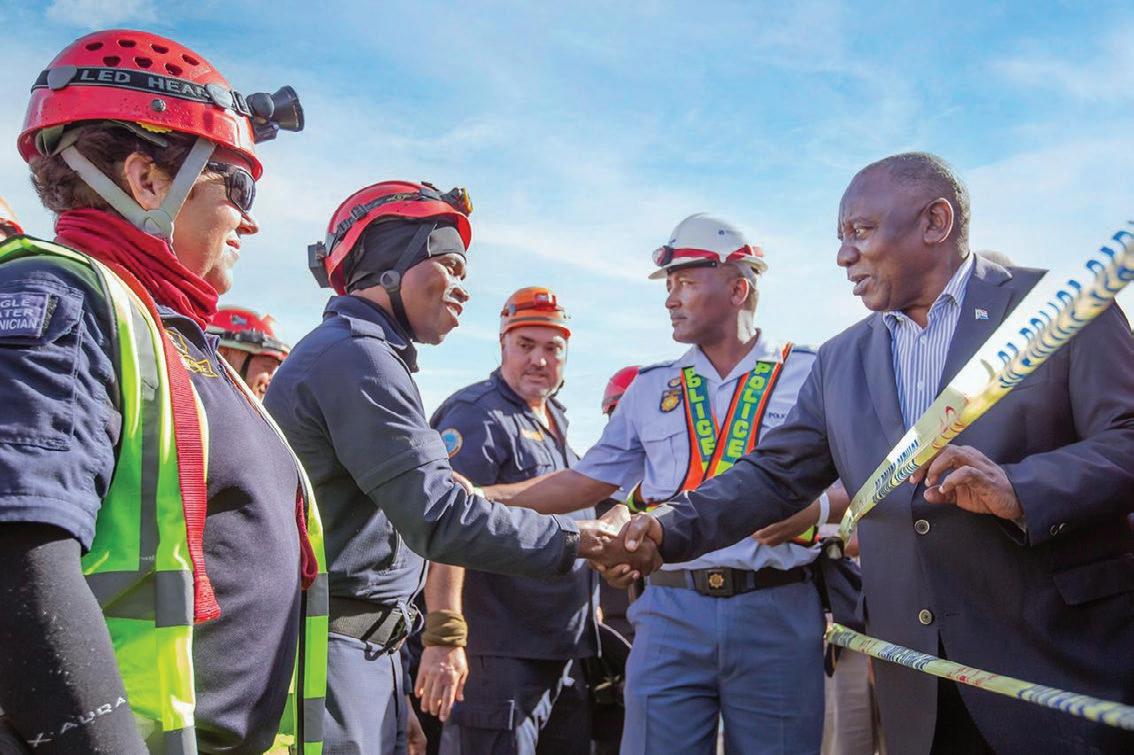
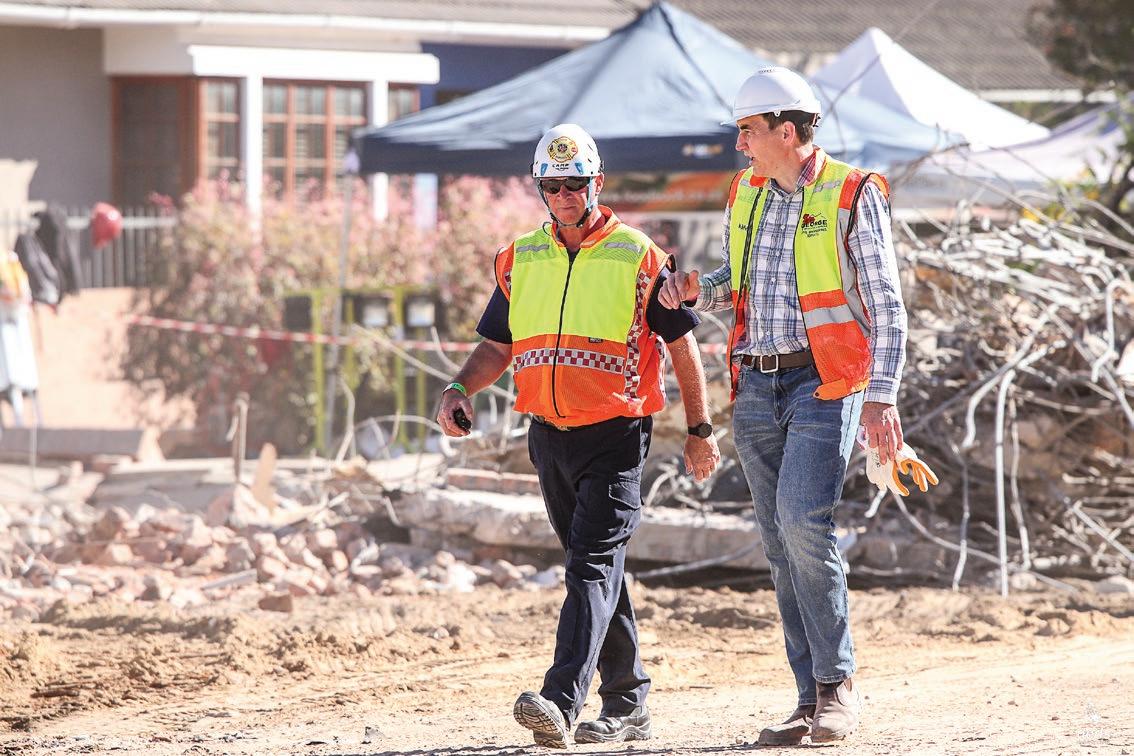
number of rescuers that were arriving over the following days the site was divided up into six sectors with each sector designated a commander for a particular work period. This allowed for the allocation of resources to be prioritised and ensured that everyone was made aware of the location of access and egress paths, safe areas (in the event of an evacuation), heavy vehicle movement routes and equipment staging areas. The INSARAG structure marking system was also implemented and proved to be an important indicator of the location of seriously trapped, deceased victims.
Engineering challenges
Already in the initial stages of the operation it became clear that the expertise of structural engineers would be a critical factor. To this end the George municipality
deployed its head of engineering and his staff to the site. A number of private structural engineers also volunteered their help and were deployed to the various sectors to advise on structural stability and safe debris removal. Early on day two of the incident a call was made to Professor Richard Walls of Stellenbosch University to make his way to George to advise on the delayering of the large concrete floors and the stability of the structure, particularly the lift shaft which was supporting a number of collapsed floors and was causing serious stability challenges. An additional team of engineers was also appointed by the Western Cape Premier with the specific purpose of investigating the cause of the collapse. An agreement was reached with this group that they would be allowed to investigate the scene and collect evidence alongside the rescue operation but
that the removal of trapped victims would be the priority.
Some of the challenges confronting the engineers included the quantity of rubble and thickness of slabs, large flat slabs stacked on top of each other making access difficult, rebar fracture, the partially collapsed scaffolding, which was removed on day two and a parking garage roof next to the structure which consisted of asbestos sheeting which had to be removed before access could be achieved from the rear of the building.
Two particularly difficult problems were the unstable retaining wall which surrounded the structure and the continuous movement of the floors as work was being done on and around them. After a thorough search of the trench that had formed around the retaining
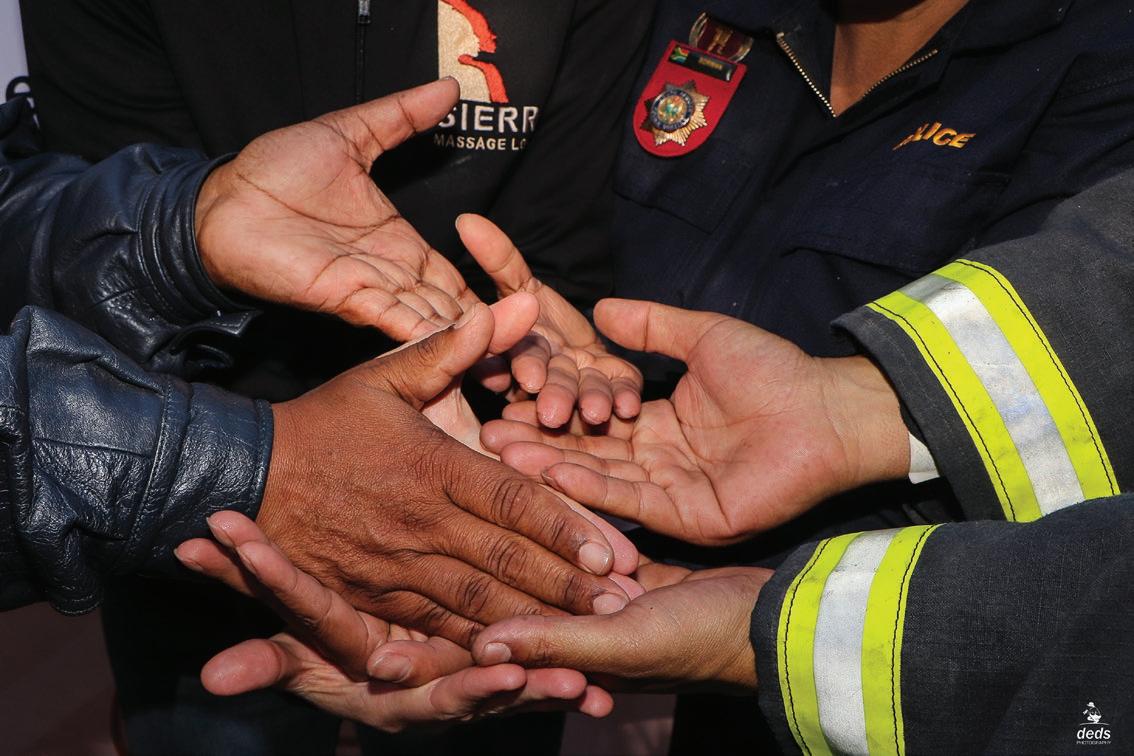
wall it was decided to fil it up with building rubble, which had the advantage of stabilising wall and creating a platform for heavy machinery to move over.
A series of cracks that had formed at various times during the early operation were marked with spray paint which enabled the engineers to detect any unwanted movement.
Fatality management
The Forensic Pathology Services of the Western Cape Health Department were among the first responders on the scene and immediately prepared to receive and process a large number of fatalities. This incident command team had determined that there was a good chance that several people could still be alive and for this reason it was decided to prioritize live victims. Compounded entrapments of
deceased victims would only be done when an area was cleared of live victims. When a deceased victim was located and it was found that the removal would take up several hours that area was marked and secured and returned to later.
Although the collapsed structure was primarily a rescue site it was also considered a crime scene where the police were needing to collect and record evidence with a good chance of crucial evidence being destroyed by rescue crews. It was here where the deployment of the SAPS rescue team and divers by the provincial headquarters was of immense value. These members are trained in the protection of evidence and work with municipal and provincial rescue services often. They functioned as the link between the police forensic investigators and the
rescue teams to ensure that both could achieve their objectives.
As the incident progressed past 24-hours a temporary victim area was constructed out of view of the media and public where recovered bodies could be taken for processing before, they were transported to the government mortuary facility.
Ongoing operations
The initial decision to stay in “rescue mode” for the first 72-hours ensured that eleven victims were rescued from compound entrapment situations on day one and two and with the arrival of a specialised demolition team from Cape Town late on day three it was decided to extend rescue mode for a longer period. This proved to be the correct decision and proved to be so when the last live victim was rescued after 166 hours on Saturday, 11 May 2025.
The identification of two large voids on the back and left side of the building on day three allowed rescue teams to enter the basement where they progressed slowly, shoring the roof with temporary shores as they moved forward. This was a particularly hazardous mission, and additional precautions had to be taken by the teams to deal with the possible lack of oxygen in the voids. Unfortunately, no victims were found in these voids and the mission was aborted when a team encountered a wall in the basement, which impeded their progress.
The transition to heavy demolition equipment was carefully planned and steps were taken to ensure that any paths cleared for the movement of the demolition vehicles had already been signed off as clear of any victims. A team of lookouts were also delegated to each vehicle to ensure that no bodies would accidentally come into contact with equipment and suffer damage as a result. The working procedure that was decided on commenced with the sector commander determining the path of movement for the heavy machinery, consisting of a tractor loader backhoe or digger (TLB) and tipper trucks, which would then move into position under the supervision of the lookout team leader. The TLB would then carefully work through its designated area and clear debris until the next floor had been reached. Search teams would then move into position and core drill a number of index holes after which the canines would be sent over the area. In the event of a positive indication by the canine, the technical search team would move in with their seismic and acoustic device and attempt to isolate the sound and contact the victim. This
process continued throughout the operation and resulted in all victims being successfully located and removed.
Key observations
Due to the high media profile this incident generated both during and after its completion a lot of comment and opinions were offered in the formal media and the various social media platforms. There have naturally also been a fair number of debriefs which has resulted in a range of recommendations on how the response to structural collapse incidents of this scale can be improved. I wish to conclude with some of those recommendations.
Capacity is the key to rapid and successful disaster response Over the last 15 years the Western Cape emergency services (Provincial Disaster Management, Department of Health EMS and city of Cape Town) have invested heavily in training and equipment to deal with large scale sudden onset disasters. The system has often been tested by the devastating seasonal flooding experienced every winter. Having this capability available on 6 May 2024 was the biggest contributor to the success of the operation.
Rapid response is invaluable
The response by the emergency services in George as well as the rapid activation of provincial resources from as far afield as Cape Town and Breede Valley ensured that many surface and partially entrapped victims were saved early on which contributed to their recovery.
Clear Incident Command must be established early
The Provincial Government
implemented an incident command system (ICS) which has been used to manage many large scale wildfire operations in recent years and was also used to management the COVID-19 pandemic and the 2017 “Day Zero” drought. This system is designed to provide clear guidance and objectives to incident commanders and can provide scalability when an incident scope is expanded to the level where large numbers of responders are involved.
Staff/equipment management must be ongoing
The reason for the tempo of the operations being maintained over such an extended period was due to the rotation of rescue crews for the duration of the incident. Teams would work for a pre-determined work period and was then required to leave the site completely where they would rest and be fully prepared to return for their next shift. An equipment maintenance area was also provided for where immediate field repairs and maintenance was done by experienced rescuers.
Constant safety and strategy re-evaluation
Constant safety and strategy re-evaluation as the structure is dismantled; as the structural members are removed and concrete/steel is cut and breeched, the building will tend to become unstable in certain areas. Constant monitoring and reevaluation are required to ensure that any changes in stability are addressed immediately.
And…Safety is always top priority.
Photos: Deirdré Cloete

Extinguishing technology in action: fighting wildfires
By Tristan Reitz, Dipl.-Ing. (FH), market manager Fire Service and Mobile Fire Protection at FireDos
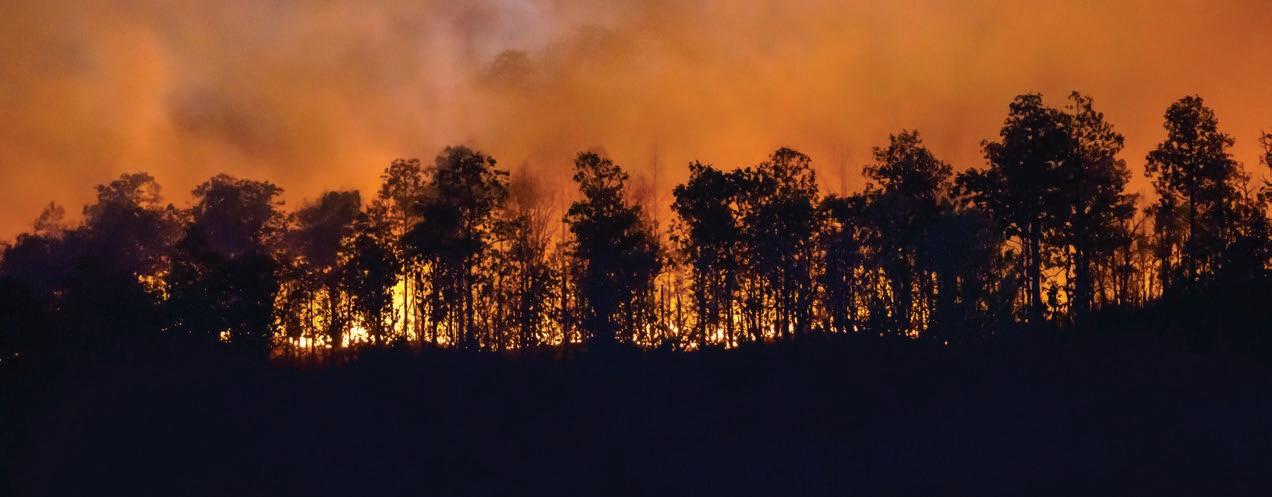
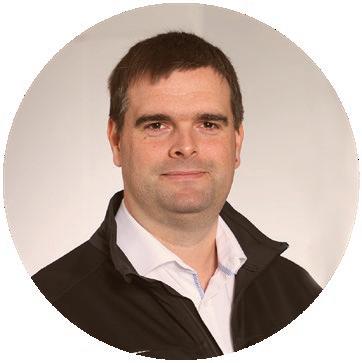
Thanks to preventive fire protection, typical residential fires are declining, while at the same time, climate change is exacerbating prolonged droughts in the natural environment. As a result, the danger of forest and vegetation fires increases more and more. These types of fires have always existed, of course and in certain regions of the world, annual “fire seasons” are nothing unusual.
However, it can be observed that the forest fire season is
getting longer from year to year and the fires are getting more and more intensive.
The global impact of these wildfires is substantial. Beyond the destruction of forests, air quality deteriorates significantly and large quantities of carbon emissions are released, further exacerbating climate change. This phenomenon, known as the ‘fireclimate feedback loop’, intensifies the cycle of climate change.
Preventive measures are crucial in managing vegetation fires. This involves ensuring that forest fires do not start in the first place or do not escalate into large wildfires. Key strategies include removing easily combustible, dry undergrowth, thinning out dense forests and creating firebreaks.
Technology plays a critical role in the early detection and control of forest fires:
• Early detection systems: Using drones, satellites and specialised sensors to monitor and detect fires at an early stage helps in localising and containing them swiftly.
• Firefighting technologies: Improving firefighting equipment and methods is essential. Effective extinguishing techniques aim to fight vegetation fires quickly with as little water as possible in order to minimise the impact on the environment.
Requirements of mobile firefighting technology for wildfires
In many cases, the technology and tactics are mainly designed for fighting fires in urban areas.
The rising number of forest and vegetation fires demands increasingly effective extinguishing methods
Tristan Reitz, FireDos
The flame front of forest and vegetation fires, however, usually does not run along well-prepared roads including water mains and hydrant networks but off-road on field, forest and farm tracks with a wide variety of topography.
A forest or vegetation fire that extends over several hectares brings its own rules with regard to spreading speed, temperature, wind strength and direction. Fighting and containing such fires requires a high degree of mobility.
Mobility is a crucial factor in firefighting. Emergency vehicles must be robust and equipped with the right technology to combat fires effectively. The use of extinguishing robots equipped with fire monitors, such as the M2 from FireDos (Extinguishing robot Magirus Wolf R1), protects and relieves the burden on emergency personnel.
In forest and vegetation fires away from urban infrastructure, water is a valuable good resource that must be used in a targeted and economical way. In this case, economical means a maximum water delivery of between 25 to 50l/min, delivered in bursts. This amount of water
corresponds to approx. two D-size hollow jet pipes. Using a so-called ‘wetting agent’ instead of pure water can increase extinguishing efficiency by up to 100%. To precisely and reliably maintain the low proportioning rate of the biodegradable foam concentrate, suitable proportioning systems are required. Portable systems like the DZ1000 or the new DZ1000 light from FireDos are designed for this purpose.
Use of wetting agent for more effective use of water as an extinguishing agent
An increase in the effectiveness of extinguishing is possible with the use of wetting agent added to the water, and in some cases it is also indicated, in particular when burning into the ground is taking place or a lot of dead wood is present. Wetting agent added to the extinguishing water reduces the surface tension and soaks much deeper into the substance on fire or the ash layer.
The foam agent industry has provided suitable foam agents for the field of forest and vegetation firefighting. According to the manufacturers’ own statements, these foam agents are harmless
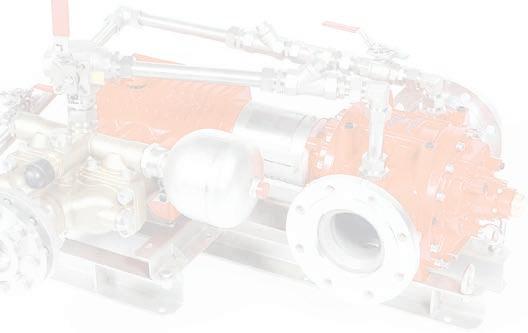
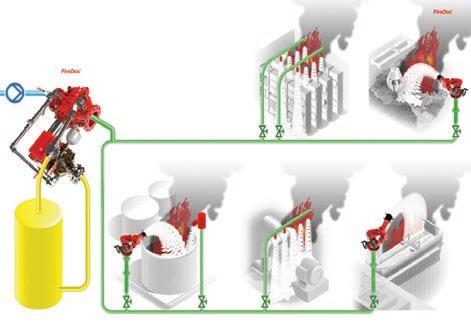
to the environment when used as intended and they are 100% biodegradable. In addition to generating wetting agent for vegetation fires, they are also suitable for fighting Class A and B fires with wetting agent and/ or foam. The proportioning rates vary greatly and these in turn have a significant impact on logistics and effectiveness at lower proportioning rates.
Electronic pressure proportioning systems
Today, there is a large number of pressure proportioning systems on the market, which are permanently installed in fire trucks and are driven by the 24V on-board voltage of the vehicles. These systems have become established in the vehicles, also because of the DIN 14430 pressure proportioning systems. These electronic proportioning systems are now comparatively inexpensive to purchase. However, a look at the technical data and the corresponding working diagrams reveals that the proportioning and working range is limited. The generation of foam with a foam pipe of 400 l/min flow and a 1% or 3% proportioning rate is no problem for all pressure proportioning systems. +27

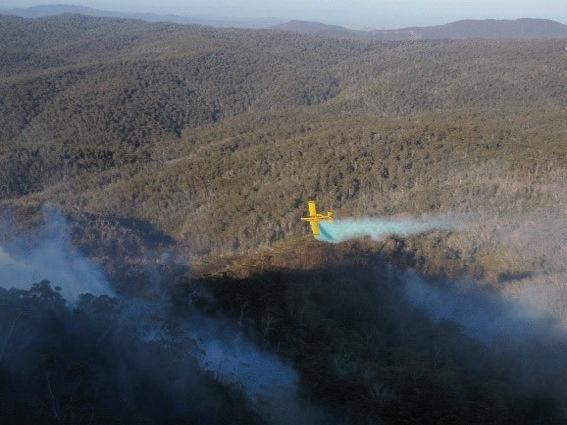
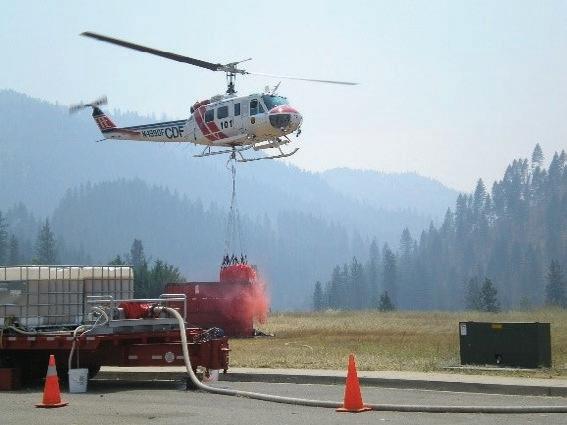
The situation is different for the generation of wetting agent with only a low extinguishing agent output. A guaranteed and constant proportioning of foam concentrate for the generation of wetting agent in the range of 0,1% to 0,3% can only be ensured by most electronic proportioning pumps from a water delivery of at least 100 l/min and more. In the case of interval extinguishing by repeatedly opening and closing the jet pipes, deviations in proportioning can occur, which then leads to “overdosing” of the mixture. The electronic systems are adjusted to the water flow by a measuring section, inductive measurement of the flow rate. Due to the fluctuating delivery of extinguishing water, the dosage is not exact and for a certain period of time no wetting agent is produced but foam.
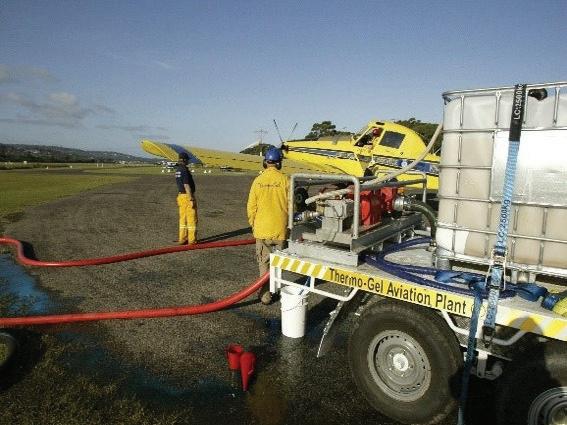
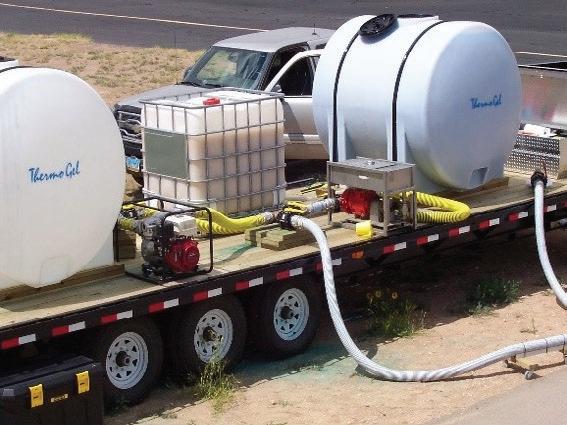
Mechanical pressure proportioning systems
Purely mechanical systems represent an alternative to electronic pressure proportioners. The foam pump is not driven by a 24V electric drive, but by the discharged extinguishing water. This water flows through a closed water motor with a turbine wheel, the principle is similar to the mill wheel in a water mill. This turbine wheel in turn drives the foam pump, eg, in the form of a piston pump. The system (drive turbine and foam pump) is thus purely mechanical and the proportioning of wetting agent is always automatically controlled as a direct function of the volumetric flow rate.
The foam agent is thus added in exact proportion to the water flow. This means that the turbine
wheel in the water motor turns faster or slower depending on how large or small the water flow rate is. Accordingly, more or less foam agent is added by the foam agent/proportioning pump. Overdosing is not possible.
This results in the following operational advantages for the application in vegetation firefighting:
• Purely mechanically driven pressure proportioning systems do not require any external power.
• Thus, they are not only suitable for vehicles but can also be used independently, eg, on a roll-off container, trailer or mobile in connection with a portable fire pump.
• Depending on the size, the unit can be comfortably carried to
Using a so-called ‘wetting agent’ instead of pure water can increase extinguishing efficiency by up to 100%
the scene by firefighters.
• Large hose distances can be overcome without the water/ foam premix segregating.
• Loading on carts, roll-off containers or even trailers is possible without any problems.
A useful field of application for mobile systems is the filling of external fire-fighting water tanks for helicopters. In some cases, these tanks are partially filled by ground personnel if the approach to the next suitable water intake point is too far. Here, too, it makes sense to add wetting agent or gel to the water to achieve a better extinguishing result. If necessary, a dye can also be added to mark drop zones. This task is much more complicated or even impossible with conventional pressure proportioning systems. Incidentally, the turbine proportioning systems described above were developed for the chemical industry, where very precise proportioning, sometimes of several media at the same time, is very important.
Portable pressure proportioner for the production of wetting agent
The DZ1000 portable pressure proportioner and the new DZ1000 light were specially developed for varying extinguishing scenarios
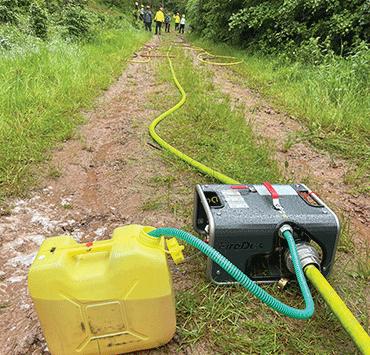
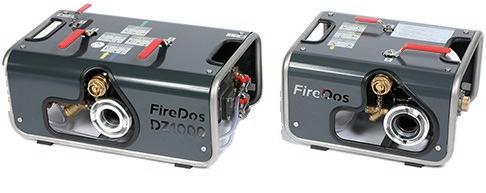
and offer maximum flexibility in mobile use. Both proportioning systems are of purely mechanical design and guarantee precise proportioning of the foam agent over the entire operating range from 140l/min to 1 000l/min. The proportioning rates of 3%, 1% and 0,3% (DZ1000) and 1% and 0,1% (DZ1000 light) can be easily switched during operation. Wetting agent is already generated from a flow rate of 90l/ min, with the new DZ1000 light even starting at 70l/min.
For all types of jet pipes, regardless of their height difference, eg, when used on turntable ladders
• Ideal for the pulsating/ intermittent extinguishing method
• Suitable for extinguishing foam and wetting agent
• The DZ1000 light also impresses with its low weight:
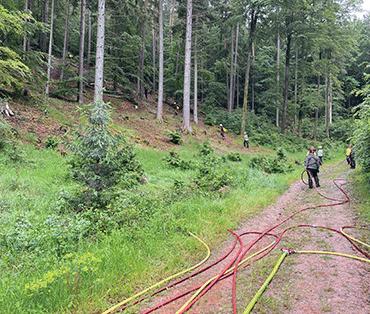
at just under 25kg, it can even be carried by a single person.
Conclusion
The rising number of forest and vegetation fires demands increasingly effective extinguishing methods. Fighting forest fires effectively depends on the right technology. By using wetting agent, water can be used more economically and effectively as an extinguishing agent in many cases. Compared to electrically driven pressure proportioners, mechanical systems offer some advantages not only for this application.
FireDos is available through DoseTech Fire. For more information, contact Michael Feldon at DoseTech Fire on Mobile: +27(0) 83 251 9346 Tel: +27(0)86 111 1544 Email: mgf@dosetech.co.za. Visit www.dosetech.co.za

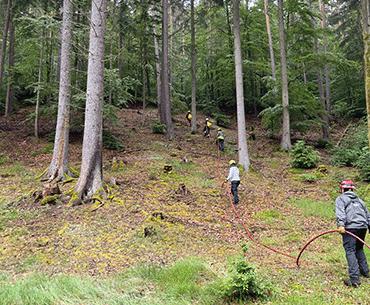
Forest fire exercise 2024 with the DZ1000 Light: The DZ1000 Light proportioning system demonstrated its effectiveness with an 80-metre height difference, handling a 100l/min output at the nozzle while being connected to a 200-metre D-line
The portable foam proportioning systems DZ1000 and DZ1000 light
The importance of weather stations’ maintenance
By Kelvin Price, managing director, CW Price and Co
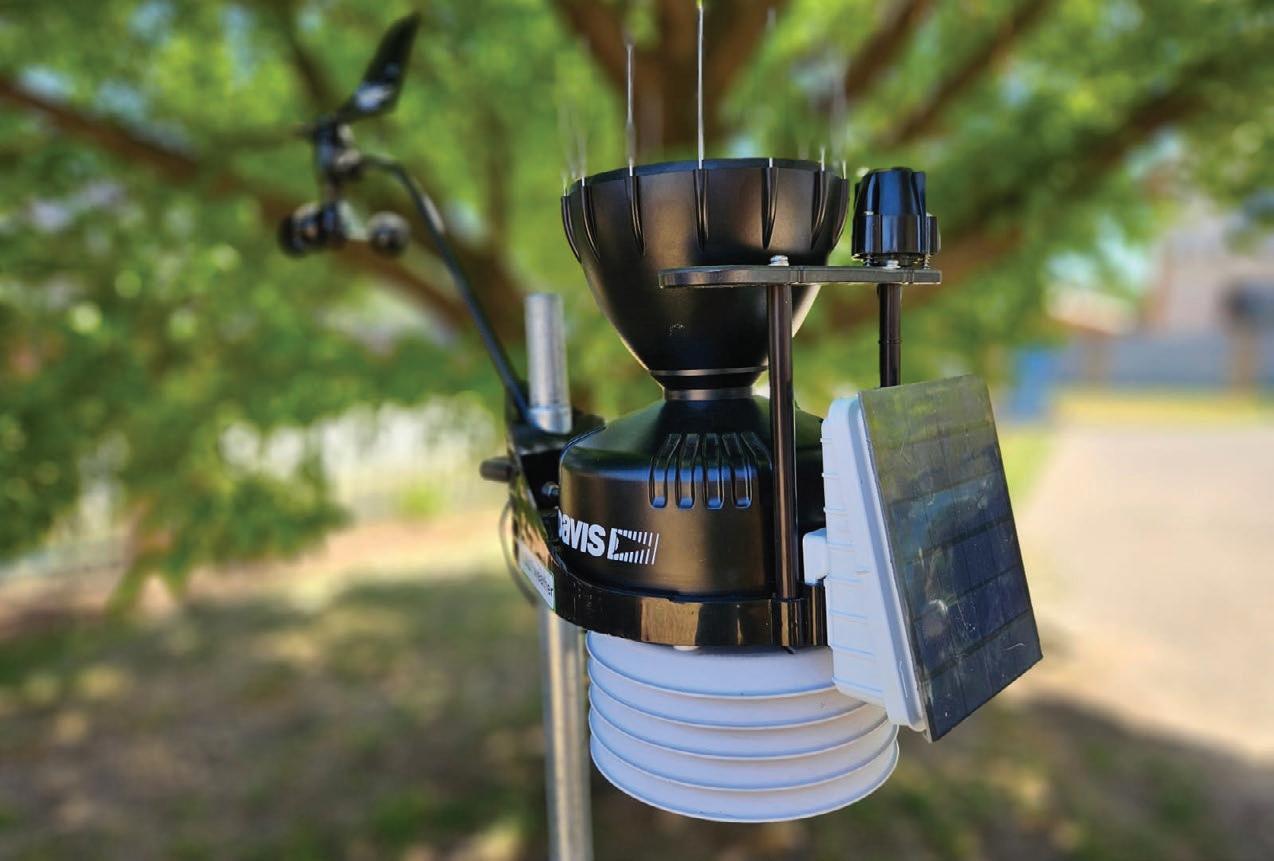
Maintaining a weather station is crucial for ensuring accurate data and prolonging the life of your equipment.
A single unmaintained sensor can skew the whole data set. Imagine overlooking the service of your weather station’s rain gauge. The tipping bucket could accumulate unwanted debris over time that may block the rain gauge and intrude on the measuring system.
Such interference might then provide inaccurate rainfall and most importantly Fire Danger Index (FDI) data.
Here are some key steps to keep your weather station in top shape:
• Regular cleaning: Clean the sensors, such as the anemometer, wind vane, temperature/humidity sensor and rain gauge, to remove any debris or buildup. This helps maintain accurate readings.
• Battery and power check: Ensure the power supply is functioning correctly. Replace batteries as needed, especially in colder months when battery performance can decline.
• Sensor verification: Regularly check and calibrate all sensors to ensure they are providing accurate data.
• Inspect mounting hardware: Check the stability of mounting brackets, cables and poles. Ensure they are secure and free from corrosion.
Regular maintenance is akin to taking your weather station for a health check-up
• Protect from environmental factors: Depending on your location, protect your weather station from extreme weather conditions, dust and debris. For example, clear solar panels of dust and debris to maintain efficiency.
• Seasonal maintenance: Perform maintenance at least once at the beginning of each fire season, with extra attention during summer and winter when weather conditions can be harsh. Depending on weather conditions and the surrounding environment, some may need to perform maintenance as frequently as every month
By following these steps, you can ensure your weather station
continues to provide reliable and accurate weather data. For your Davis/VitalWeather stations, there might be additional maintenance tips available in the user manual or from the station provider.
Remember, regular maintenance is akin to taking your weather station for a health check-up. It’s all about ensuring that each sensor, be it the rain gauge, wind vane, temperature/humidity sensor or anemometer, functions correctly to provide accurate data. So, please pay attention to the importance of regular weather station maintenance. It is a small task that significantly protects your investment and ensures accurate ambient weather data at your fingertips.

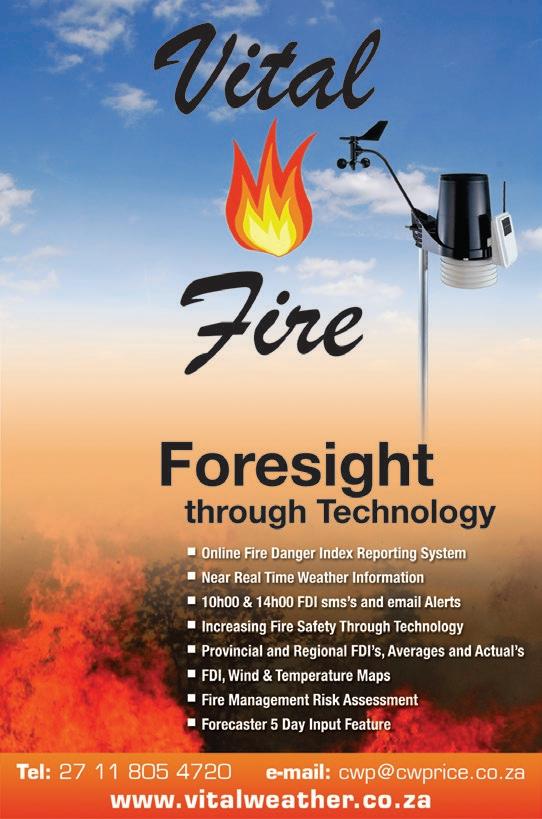
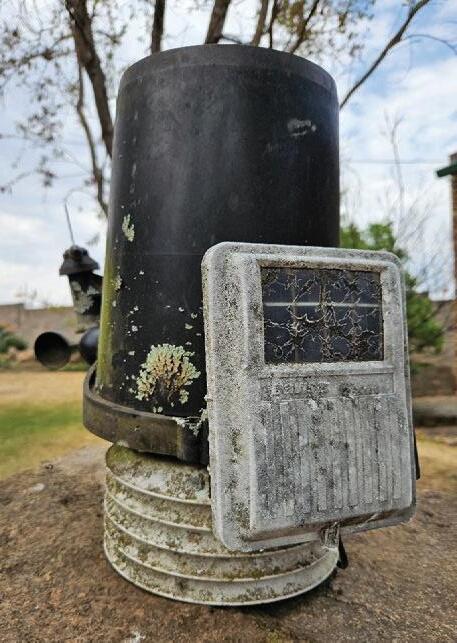
Do you really expect this to operate correctly?
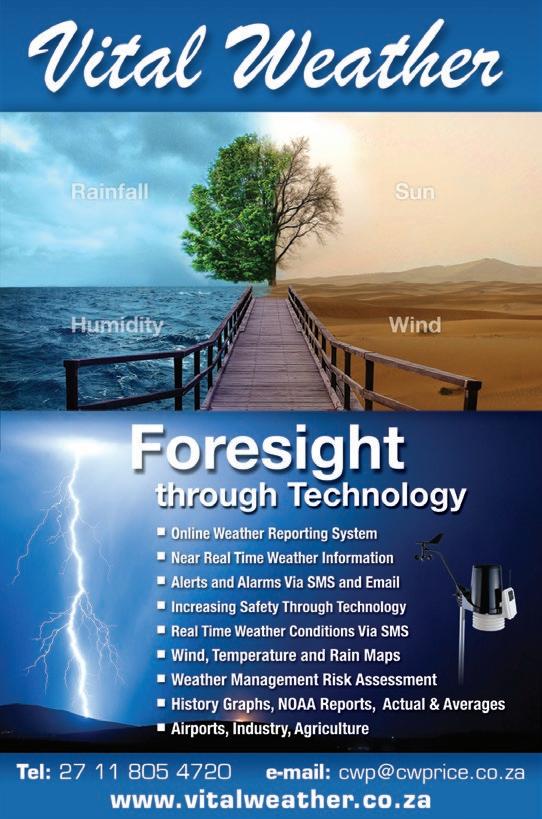
Veldfire investigations: Sooner or later?
By Rob Erasmus, director, Enviro Wildfire Consultancy (Pty) Ltd
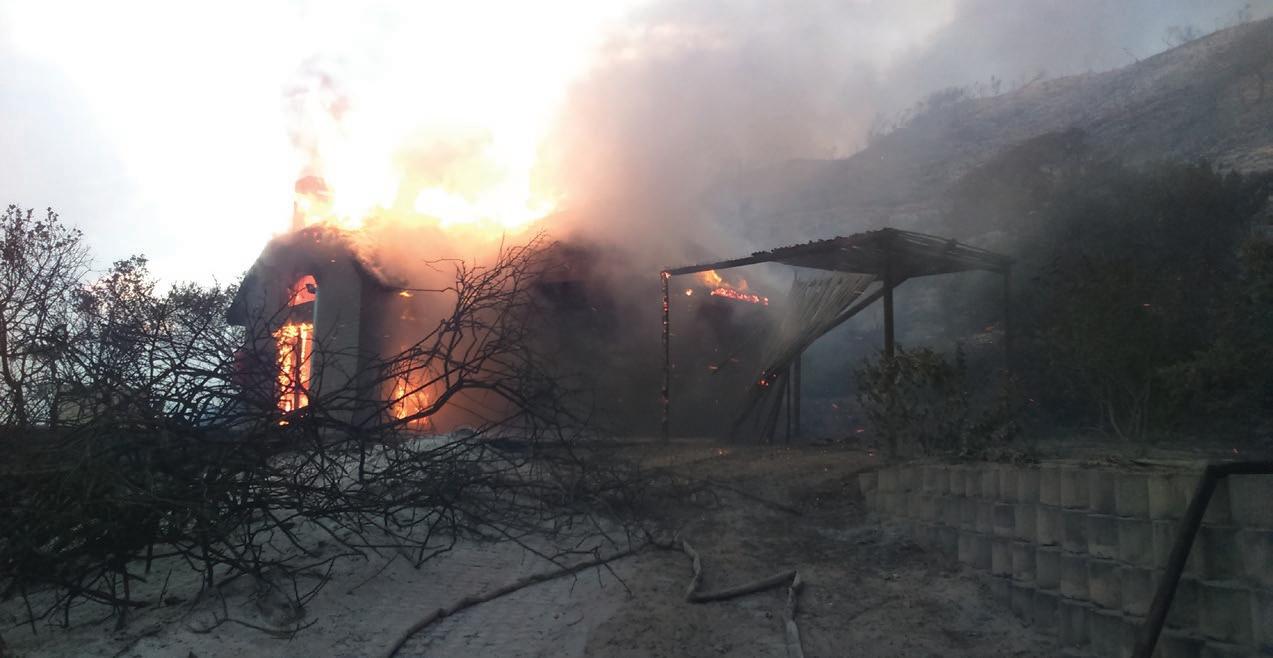
With the growing number of veldfires occurring across South Africa that are causing loss to be suffered, the need for validated information and sound evidence is becoming ever more important in litigation matters. It is common sense that the sooner an investigation is undertaken the more accurate the information and evidence will be, equating to an increase in the likelihood of success during civil claim matters.
Fire investigations are normally undertaken to obtain information so as to be able to make informed decisions ie whether to prepare for criminal prosecution or civil proceedings, alternatively that the findings can be used
by insurers and/or attorneys to either seek damages for loss suffered or alternatively to prepare for defending a client in litigation matters.
The general benefits of having a fire investigation conducted early, even if only a preliminary undertaking, include:
• Eye witness accounts are more reliable and of greater accuracy
• The origin of the fire is less likely to be contaminated and thus a greater likelihood of the origin and cause being accurately determined
• Evidence to document and determine fire spread is more reliable
• The time and effort required
to conduct the investigation is significantly reduced, which equates financially to a lower cost
It is safe to state that in most cases a landowner will know early during a wildfire situation if there are going to be costs for fire that starts or spreads from their property, alternatively that spreads onto their property. Such costs can include:
• Own losses (infrastructure, crops, firefighting, loss of income, etc): Such losses may or may not be covered by insurance.
• Third party losses by the neighbours and/or guests.
• Fire suppression costs from the local fire department (including aerial support) and neighbours.
When one considers the potential overall costs (which can easily amount to over R1m) when compared to the almost insignificant amount for an investigation, the value of such an early undertaking resulting in an accurate report is self-explanatory.
It is a fact that the majority of wildfire litigation matters hinge on the fire investigation report. A good accurate reliable fire investigation report can be the difference between a case being won or lost.
The steps for a landowner who has reason to believe that they are going to need to recover losses or when they believe that they have caused loss to be suffered to a third party, should be:
• Contact their insurer if they have one and advise them
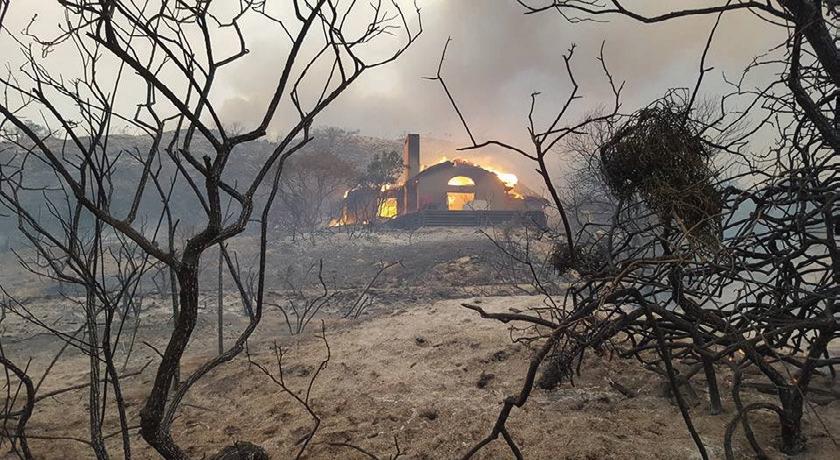
of the situation, adding that they recommend that a fire investigation be conducted to document the origin, cause and spread of the fire. This information can become the cornerstone or foundation of the claim or defence. In many cases the insurance company will authorise and actually cover the costs of the investigation.
• If the landowner does not have insurance, they should contact their attorney to advise them of the situation and similarly suggest that the fire be documented in preparation for litigation.
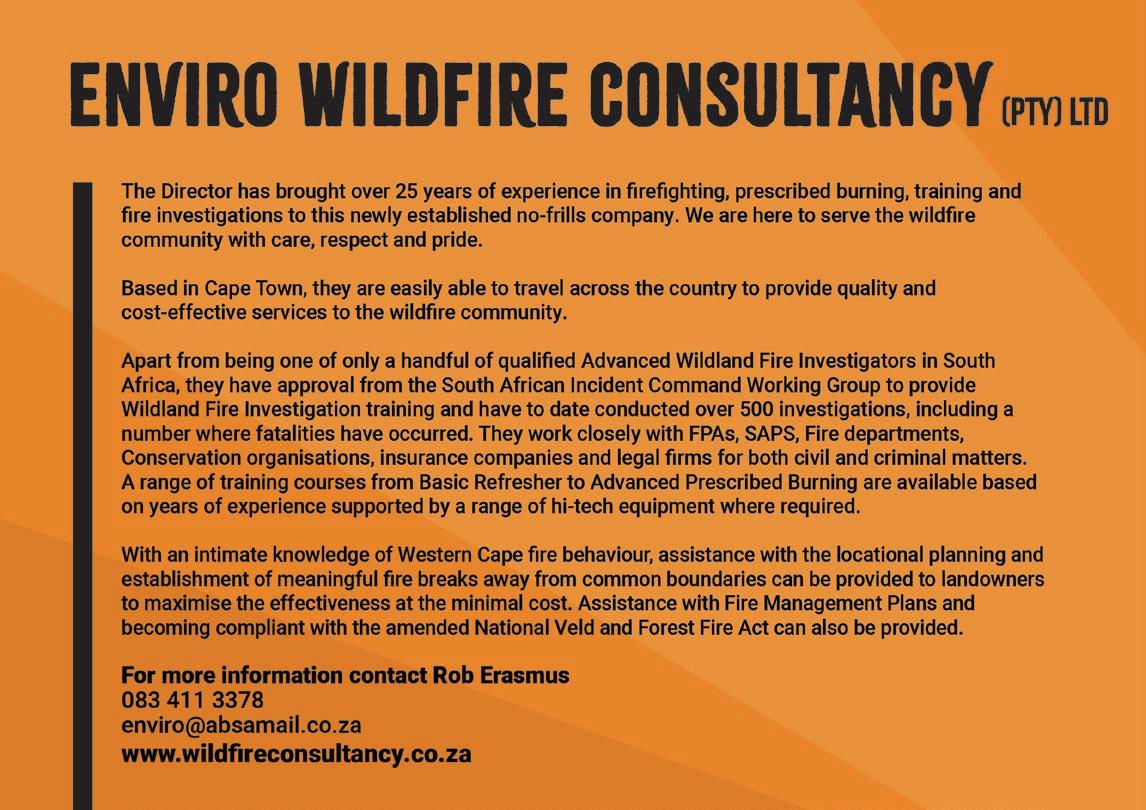
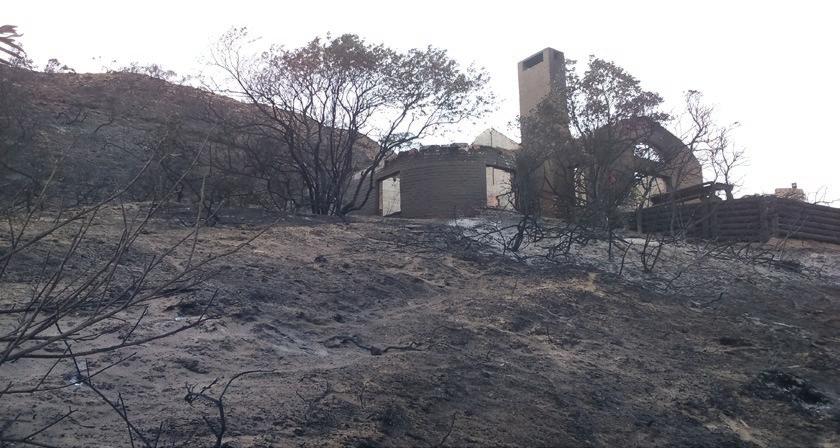
The benefit of a fire investigator being appointed by a legal representative is that the report is privileged and is drafted in contemplation of litigation. Thus even if there is information that suggests that the client was negligent, such information remains privileged.
In general the mandate for a veldfire investigation where loss has been suffered consists of:
• Determining the origin of the fire using the scientific method and eye witness accounts
• Determining the cause of the fire using evidence
• Determining the spread of the fire and the conditions present when the fire crossed the property boundary
• Determining if the landowner where the fire originated was compliant with the requirements of the National Veld and Forest Fire Act (NVFFA) and if they were a member of the local Fire Protection Association on the day of the fire
• Determining if the party that suffered loss was compliant with the requirements of the National Veld and Forest Fire Act (NVFFA) and if they contributed to their own loss.
In order to determine the origin and cause of a veldfire, permission needs to be obtained from the landowner where the fire originated. If such person is not willing to provide the required permission, it is then necessary for attorneys to submit a formal letter request. In the majority of such cases permission with terms and conditions is then granted. An experienced wildfire investigator will quickly be able to determine if the origin of the fire has been purposefully disturbed/ contaminated and such findings would be included in the report which could suggest that the landowner has wilfully made an effort to conceal the cause of the fire.
The cost to conduct a general fire investigation consists of:
• Preparations for the investigation (determining the mandate, travel and accommodation arrangements, access permission, maps of the area, names of witnesses and appointments made to interview them, etc.)
• Travel, accommodation and meal costs where applicable
• Site visit and interviews
• Purchase of South African
Weather Services (SAWS) data where necessary
• Purchase of thermal hotspot satellite data where necessary
• Report writing
• Post report submission consultation
It must be stressed at this point that the longer the time lapse between the fire and the investigation, the more effort is required when conducting the site visit and interviews. The cost can literally treble between conducting the fire within a week of it occurring and three months later.
While it might appear at first that a fire investigation report is a costly outlay, without a good and accurate investigation report that would substantially increase the chances of a successful litigation seeking to recover losses that could amount to hundreds of thousands of Rand, alternatively to provide a defence for a respondent, the initial cost (depending on the investigator) is insignificant.
Rob Erasmus of Enviro Wildfire Consultancy (Pty) Ltd is a qualified Advanced Wildland Fire Investigator with 18 years of experience and has conducted over 500 investigations that include civil, criminal and fatal veldfires. He has provided expert witness in a number of courtroom matters and has a healthy knowledge of litigation requirements and procedures. Approved ‘Wildland Origin and Cause Determination Fire Investigation’ training can also be provided.
Contact Rob Erasmus on mobile: 083 411 3378, email: enviro@ absamail.co.za or visit: www.wildfireconsultancy.co.za

Command Corner: Downhill fireline construction with fire below
By Chief Tim Murphy, US Forest Service Africa Disaster Management Technical Advisor
As a general rule, construct line moving uphill. Many firefighters have lost their lives attacking wildland fires from above.
If there is no practical alternative to constructing line downhill, proceed only after weighing the following considerations:
• Has the area been scouted for fire perimeter and behaviour? Discuss what you need to know about the fire perimeter and fire behaviour before building fireline downhill with fire below.
• Will wind direction be at your back? Will it stay at your back? Talk about how winds can change when you are on a slope eg time of day, upslope and down slope breezes, etc.
• Is the area free of chimneys and gullies? How would you negotiate your line location if there were chimneys and gullies below where you needed to be working?
• Are there adequate safety zones and escape routes as you progress downhill? How
do you maintain adequate safety zones and escape routes as you progress downhill?
• Can you carry your burnout downhill as you go to provide an anchor point and safety zones? Discuss how you decide when to carry the burnout with you or wait until you have tied in down below.
• Have lookouts been posted? What do the lookouts need to be on the watch for?
• Do you have good communications, especially with lookouts and crews working towards you? What are some of the dangers of not communicating with lookouts and crews working towards you? What are the benefits of maintaining good communications?
• Can the line be completed and burned out before the fire reaches the line? Discuss how this would affect where you locate the line.
• Do you have adequate resources to complete the assignment? What additional

Chief Tim Murphy
resources might you need to safely take on an assignment that includes building fireline downhill with fire below?
• Is aerial support available if needed? What benefits can aerial resources provide? What might be an added danger from aerial resources in this type of situation? (common denominators).
• Has everyone been briefed on the assignment, fire behaviour, weather, communications, escape routes and safety zones, hazards and tactics? Discuss who might provide this briefing and where and when it might occur.

14th NMU Fire Management Symposium and field day held in Karkloof, KwaZulu-Natal
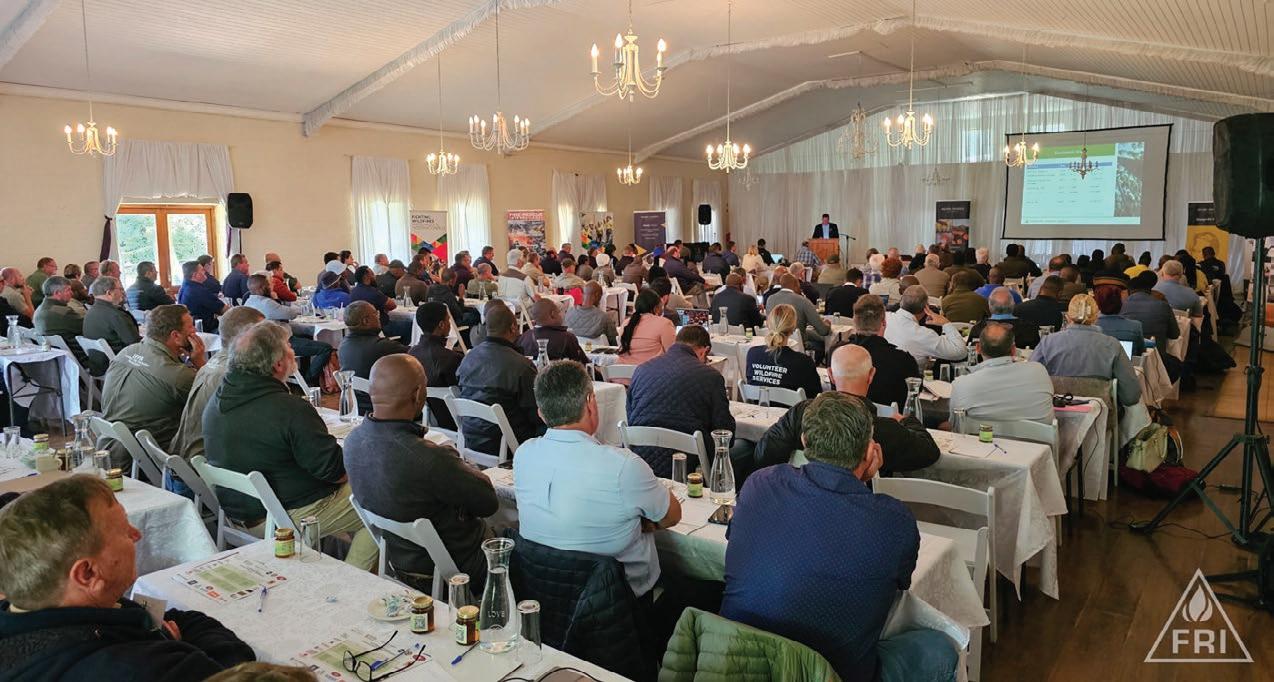
The Forestry Department (George Campus) of the Nelson Mandela University (NMU) held its 14th Fire Management Symposium from 6 to 8 November 2024 at the Halliwell Country Inn in Karkloof, KwaZulu-Natal, South Africa. The symposium was hosted in partnership with industry stakeholders. The theme of the symposium was "Educating and training for effective wildfire management".
The symposium brought together fire managers, stakeholders and wildland fire management agencies from various sectors, including
nature conservation, agriculture, fire services, fire protections associations, disaster management and forestry.
Tiaan Pool, the Head of Department: Forestry Department at NMU, welcomed all and shared the usual formalities.
Dr Ronald Heath: ‘Educating the nation’ Keynote speaker, Dr Ronald Heath, director: Research and Protection at Forestry South Africa (FSA), discussed ‘Educating the nation: The effect of sound fire management on the lives of South Africans’. He detailed the economic, social
and environmental impact of wildfires, highlighting the fact of the shortcomings in quantifying economic loss such as the lack of data and that it excludes the cost of suppression, the impact on associated value chains, business disruption and associated impacts such as tourism.
Dr Heath shared the statistics of the impact on the displacement of communities and the impact on settlements, adding the financial and health impact on humans due to fatalities and injuries due to burnovers, smoke inhalation causing lung disease and heart failure, mental health including PTSD, depression,
anxiety and substance use and aircraft and vehicle accidents.
The environmental impact includes vegetation loss, habitat destruction, soil degradation water contamination, erosion, climate change, impact on precipitation and air quality.
He said that we need to acknowledge that sound fire management has significant positive effects on the lives of South Africans. Dr Heath added that proper fire management strategies are crucial in reducing the risk and severity of uncontrolled wildfires and are key to environmental management. He added that to counter the expected increase in wildfires, we need accurate climate data at regional and local level. The use of technological advancements to fight the fires and enhanced rapid response will ensure increased capabilities. He also highlighted the importance of training, education and fire awareness programmes and said that collaboration between stakeholders needs to be improved to build a sound fire management strategy.
International: Bryan Yockers, ‘Prairie Project - Agents of change’
International presenter, Bryan Yockers, the education and outreach facilitator with the Prairie Project in the USA, shared his presentation on ‘Agents of change: Enhancing student understanding of fire, herbivory and rangeland ecosystem services’. The project targets the youth to teach values that will enable them to be agents for change when they grow up. He said that data shows that the interventions do make a difference, through empowering educators.
The
problems
Woody plant encroachment
Land use change
More extreme climate
Increasing wildfire
Yockers said that 260 hectare of prairie is lost per day per state in the great plains area through tree encroachment. The biome collapse leads to major consequences at the biome level. There is a disconnect between the people and the reality of where their food is coming from (urbanisation).
Prairie Project Educator Cohorts focus on developing rangeland literacy thorough various projects, classes and case studies. Yockers also shared the preliminary results of the project, which showed that there was an increase in understanding and practice.
Rob Thompson: ‘Three key elements: surprise, anxiety and disturbance’
The second day keynote address was by Rob Thompson of NCT Forestry Agricultural Cooperative Limited, who discussed the ‘Three key elements: surprise, anxiety and disturbance’, providing an overview of the recent NCT chip mill fire in Richard’s Bay. The fire was spread by the melting conveyor on 30 September 2023.
Using the triangle form from the fire triangle, Thompson shared some practical recommendations to prepare for the increasing risks of unintended fire incidents. Some strategies suggested included to be prepared through training using simulations, competency tests, drills and procedures prior to incidents.
The solutions
Multi-species grazing/browsing
Prescribed burning
Patch-burn grazing
He added that it is important that risk appreciation includes the awareness of the weather, capacity and ground conditions. Readiness means being capable, equipped and on site and the accuracy of decisions is based upon competency, caution and experience/intuition. He furthermore detailed the triangle for control ie command, supervise, strategise and response included reach/access, rate/volume and refill/replace. Thompson said that to sustain as the fight goes on, rations, rest and remedial formed the triangle and to understand, you need to monitor, report and record.
“Own it! Predict, protect and warn the neighbours”, said Thompson and after the incident you need to strengthen your position by reflecting, repairing and regrouping leading to the prevention triangle of prevention, which includes mitigation, reengineering and sharing the lessons learnt in order to defer future incidents.
Eric Stoch: ‘From the Tribal Council to the fireline’
Eric Stoch, chairman of the North West Umbrella Fire Protection Association (NWUFPA), discussed, ‘From the Tribal Council to the fireline: A revolutionary model for tribal and Khoi-San integration in fire safety’, amongst various other pertinent fire management issues. Stoch shared the details of the NWUFPA management committee and its local and district FPAs,

highlighting the importance of protection in rural communities. He added that representatives of the local tribal councils serve on their executive committee and act as brand ambassadors for the FPAs He said that NWUFPA through their NWUFPA College has trained their own instructors, 38 facilitators and 33 assessors, with some doing the US FEMA courses.
He said that NWUFPA is representative of 56 traditional leadership areas, which has made a difference. They are also spreading the message through partners to the community including the disabled.
Stoch said that invaluable role of Working on Fire needs to be acknowledged. “Strategic firebreaks have now been implemented, with 1 500kms of roads covered. We need to face the reality of fatalities and need collaboration between stakeholders. Let’s find solutions that work and train accordingly. However, we need appropriate
budgets”, said Stoch. “More training is needed and we need to build partnerships in order to create capacity.”
Johan ‘Savage’ Breytenbach: ‘Training and education in commercial farming communities
Savage Breytenbach, manager of the Free State Umbrella Fire Protection Association (FSUFPA), presented on ‘Training and education in commercial farming communities’. He highlighted the importance of increasing the wildfire resilience of rural agricultural communities and shared the lessons learnt during the past 10 years of training these communities.
Breytenbach said we need a reality check relating to the lack of personal capacity and capability within communities as well as organisational and institutional capacity, adding that comprehensive and holistic capacity building is needed at all levels. He shared the
challenges such as time for training due to the agricultural rhythm, the misconceptions of risk, response versus risk management, biases, systemic failures, cost etc and the Dunning - Kruger effect, where a person’s lack of knowledge and skill in a certain area causes them to overestimate their own competence aka “you don’t know that you don’t know”.
Highlighting the key lessons learnt, Breytenbach noted that the standalone training of firefighting is ineffective. He added that we need to acknowledge and accommodate the fact that there is a local knowledge base and provide for extended support and further development.
“Training must provide the individual with principals and concepts that enable adapting knowledge to local conditions and experiences”, said Breytenbach. “We need to allow for practical experience and enable local communities to develop
organisational capacity. To sustainably implement integrated fire management in rural agricultural communities, we need to implement strategic training in order to build organisational capability. This must be done on three levels ie individual, organisational and systemic”
Roger Johnston: ‘Gaps and training/education needs of contractors in the forestry industry’
The CEO of the South African Forestry Contractors Association (SAFCA), Roger Johnston, discussed the ‘Gaps and training/education needs of contractors in the forestry industry’. He provided an overview of SAFCA and its collaborations and member distribution per province.
“Contractors play varying roles in fire suppression etc depending on the relationships with clients”, said Johnston. He said that when it comes to training, not one scenario fits all as some grower companies are totally
outsourced to contractors while others are a mixture of own operations and contractors. Also, some teams very well trained whilst others are lacking.”
Sharing some photos of recent wildfires, he highlighted the importance of firebreaks.
“Communication between grower companies and contractors is vital especially the level of involvement, responsibilities and training. Training needs to be provided for management and on the ground fire personnel, with an understanding by all the chains of command and responsibilities, especially in a big fire when replacement teams are needed.” He added that core training must include the integrated fire management and Incident Command System/ operational command.
“Holistic fit-for-purpose training is needed on actual equipment and environment with a focus on the basics with relevant
refresher training. Foresters and contractors must learn to work together. Train as a team and not in isolation. We need to train them that people come first, dwellings and equipment second and plantations third,” said Johnston. He also highlighted training in escape routes and safety zones and the importance of physical fitness of firefighters.
Stephen Devine: ‘An international view on future needs of veldfire training and education’
FireScape’s Stephen Devine shared, ‘An international view on future needs of veldfire training and education’. He said, “Improving operational effectiveness in wildland fire management begins with rethinking training structures to make them as realistic as possible. By integrating scenariobased learning and simulations that mimic complex, real-world conditions, firefighters are better prepared for unpredictable situations. Expanding scenariobased training allows individuals
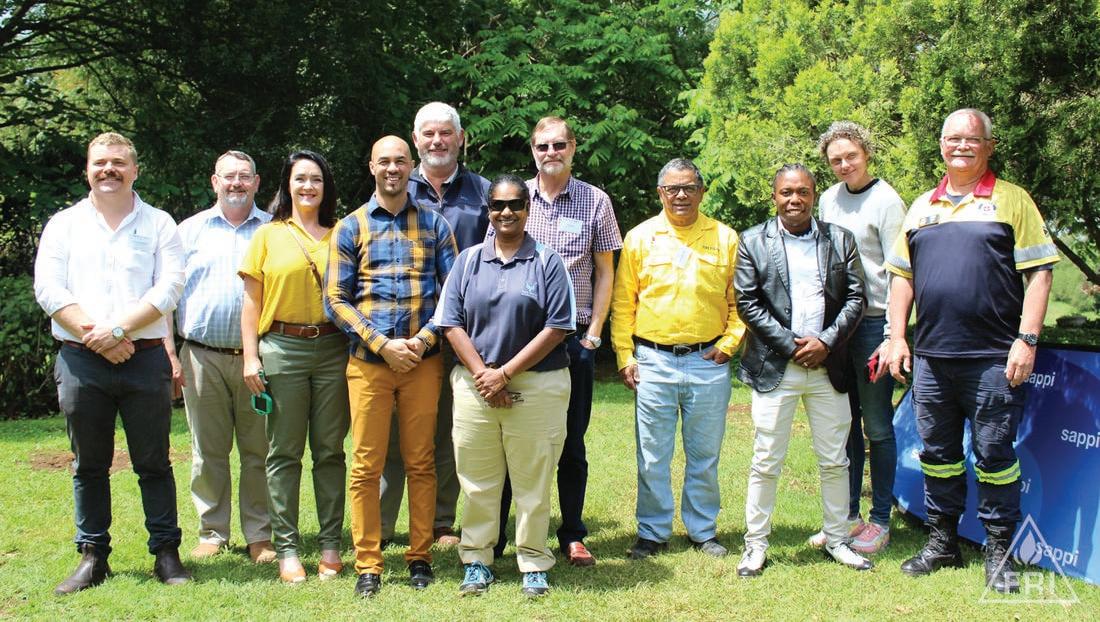
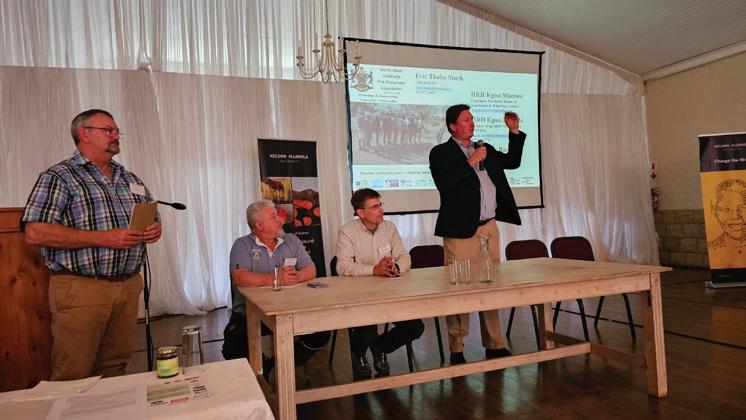
and teams to practice under high-pressure conditions, building essential decisionmaking and response skills.”
Devine also highlighted the importance of benchmarking against global standards adding that ICS needs to be standardised. “We need SOPs and standardised training as well as competent leaders. We also need to invest in predictive fire modelling and its implementation”, said Devine.
Frank Smook: ‘Flight operations: Training the guardians of the sky’ Kishugu Aviation’s Frank Smook, shared a very insightful presentation on ‘Flight operations: Training the guardians of the sky, in which he detailed aerial firefighting techniques. He shared an overview of Kishugu Aviation, which has been operating since mid-1980. He also elaborated on Kishugu Aviation Training Organisation (ATO), who’s instructors are experienced pilots, pilot trainers and certified trainers with over 10 000 hours of training experience.
Smook mentioned the various careers in aerial firefighting ie command and control pilot,
single engine air tanker (SEAT) pilot, helicopter (UH-1H) pilot, aviation support vehicle (ASV) driver, helicopter personal assistant (HPA), heli-tack, bomber loader and aerial dispatcher, detailing the purpose, functional capability and requirements for each.
He also discussed the future of aerial firefighting sharing insight into night-time aerial firefighting. Smook also elaborated on aerial firefighting methods saying, “Aircraft don’t put fires out; we cool them down and ground crews put the fires out.”
Thobi Mkhize: ‘The importance of community engagement and fire awareness’ Mondi’s head of stakeholder
management, Thobi Mkhize, discussed the ‘The importance of community engagement and fire awareness to offset unwanted fires in commercial plantations’. She said that Mondi has 245 communities surrounding their plantations of which about 70 reside on the land with 56 schools that have a direct impact on fires. She shared the economic, environmental and social impact of fires. “The best defence against fire is a community working together”, she said.
“The vital role communities play in fire prevention and the practical steps that can be taken to engage them effectively, emphasising shared responsibility, awareness and preparedness. Community engagement and fire awareness are essential in preventing unwanted fires in commercial plantations. When local communities are informed, trained and involved, the risk of catastrophic fires can be significantly reduced. Protecting our plantations requires an integrated approach through engaging with our stakeholders”, said Mkhize.
“We need to encourage active community participation in fire prevention and invest in
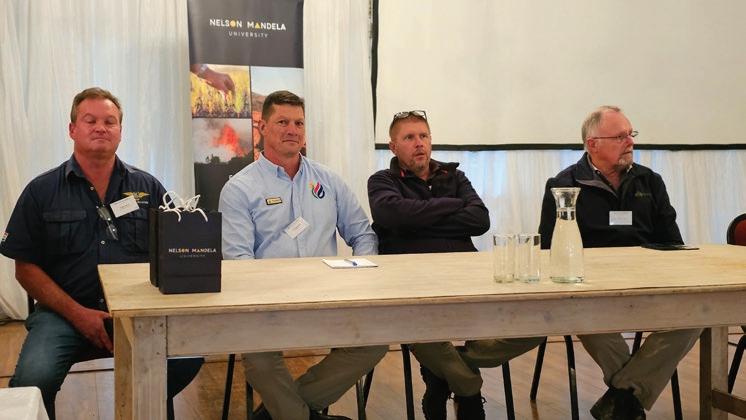
continuous fire awareness education and sustainable fire management practices”, concluded Mkhize.
Marius Atterbury: ‘Bridging the education and training gaps within local authorities regarding veldfires’
The Fire Protection Association of Southern Africa’s (FPASA’s) Marius Atterbury presented on ‘Bridging the education and training gaps within local authorities regarding veldfires’. He shared the background and history to FPASA saying that long time ago there was fire, which led to fire safety standards and that 40 years ago, you became a fireman by listening to and observing firemen. “In South Africa, the establishment of legislation to directly address veldfires are similarly birthed from tragic loss of lives as a result of veldfires”, said Atterbury.
He detailed the Organisational Framework for Occupancies (OFO), the South African Qualifications Authority (SAQA) and Quality Council For Trades and Occupations (QCTO), related to wildland firefighting training, saying that it is a sad losing the NMU Advanced Diploma in Forestry qualification but looking forward to the ‘new package’. “Training is a business; to get the training, we need to show the business that there is a customer”, said Atterbury. “The way forward is to engage with all spheres and stakeholders in order to forge ahead with a forestry-based qualification.”
Jeanette Relling: ‘Future training and education needs for veldfire management’
The Kishugu Training Academy’s Jeanette Relling discussed the
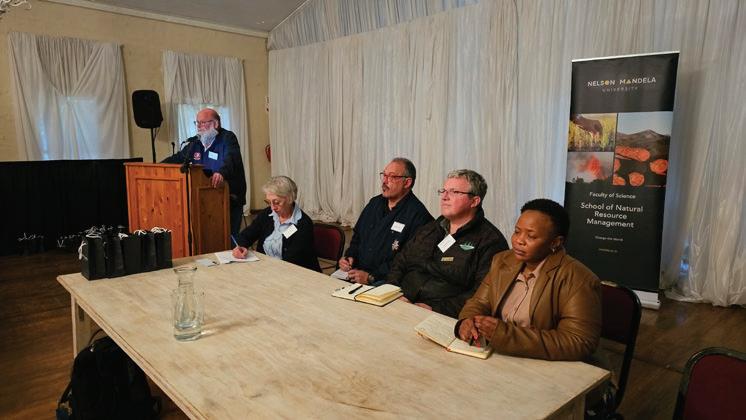
‘Future training and education needs for veldfire management’. She said that the Kishugu Training Academy formed part of the Kishugu Group and has been operating since 2003, providing the training component of the WoF Programme in the WoF –Kishugu Joint Venture.
“Increased fatalities and injuries underscore the urgency for specialised training. It’s not about to train or not to train but to train and what to train”, said Relling. She added that the QCTO) is slow to respond to requests and is not aligned with the industry’s needs. She highlighted the need for professionalisation, especially wildland firefighting as a standalone, specialised occupation. “A structured curriculum, certification and clear career paths, are important as well as specialised roles such as incident commanders, fire behaviour analysts etc.”
Relling also discussed the importance of including technology in training and operations and the ‘Train-thetrainer’ approach for knowledge dissemination and the benefits of Geographic Information Systems (GIS), drones and remote sensing, virtual reality (VR) and
simulation-based fire scenario training. Then there are the community-based programmes to reduce dependence on formal firefighting teams. “The school-based fire awareness programmes instil fire safety and prevention awareness in younger generations. We also need to learn from countries with extensive wildland fire experience such as Australia, Canada and the USA”, said Relling.
James Ballantyne: ‘In the blink of an eye, everything can change’ James Ballantyne of Kwamahlati Training Services shared in his presentation on ‘In the blink of an eye, everything can change; your legal rights and responsibilities and practical implementation of the requirements and regulations as per the OHS Act and lessons learned from recent incidents’. He said that through the OHS Act legislation, you need to prove your innocence, they do not need to prove your guilt. Ballantyne shared information of the OHS Act highlighting the definitions and Regulations as well as the general duties of employers to employees and the offences, penalties and special orders of court and what the Act requires.
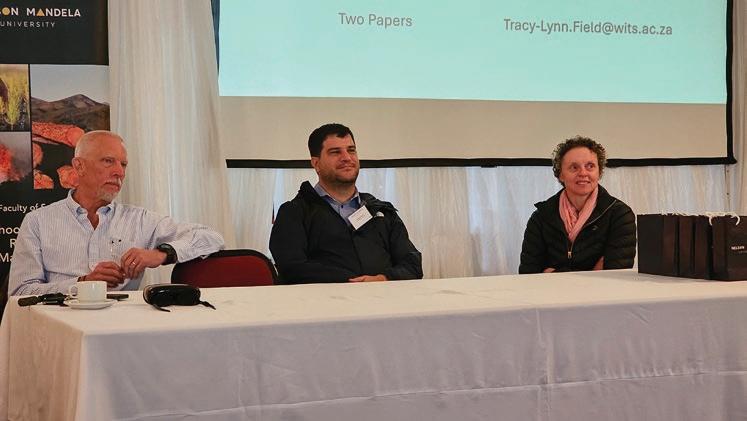
“Make sure everything that you can control is under control”, said Ballantyne. He added that managers should set an example and the importance of risk assessments, induction and practical training.
Hannes van Zyl: ‘Problem based learning: A new teaching and learning strategy’ Programme coordinator BSc Hons Forestry at NMU, Hannes van Zyl, looked at ‘Problem based learning (PBL): A new teaching and learning strategy’, which is the approach adopted by the EU-sponsored Forest21 programme. Van zyle described the difference between PBL and tradition teaching, saying, “PNL is a student-centred approach to learning that involves groups of students working to solve a real-world problem. Through PBL, students not only strengthen their teamwork, communication and research skills but they also sharpen their critical thinking and problem-solving abilities essential for life-long learning.”
He added that research has shown that new knowledge is retained better when you try to determine what you already know about the subject before you start learning. “It is this activation of prior knowledge
that prepares your brain for the storage of new information”, said Van Zyl. The seven steps of PBL are seven steps of PBL are: clarifying unfamiliar terms, defining the problem, brainstorming, analysing the problem, formulating learning objectives and goals, self-study and synthesising findings/reporting.
Prof Tracy-Lynn Field: ‘Give me a (fire)break Field professor of Environmental and Sustainability Law at the University of the Witwatersrand, Prof Tracy-Lynn, discussed ‘Give me a (fire)break: Exploring apportionment of liability in South Africa’s recent veldfire jurisprudence’. She explained how South African courts interpret the National Veld and Forest Act 101 of 1998 and the law of delict to determine liability for damages resulting from uncontrolled veldfires.
Prof Field also discussed the need for courts to adapt to climateinduced risks to ensure that legal systems can address emerging environmental challenges effectively such as veldfires.
Advocate Glenwin Sefela: ‘Setting the veldfire scene’ NMU lecturer in Law Faculty/ Natural Resource Management
legislation, Advocate Glenwin Sefela, discussed, ‘Setting the veldfire scene: A reflective overview of the National Veld and Forest Fire Amendment Act and the National Veldfire Act’. Advocate Glenwin Sefela shared the additions incorporated in the National Veld and Forest Fire Amendment Act 13 of 2023 saying the changes include the name change, definitions, formation of an FPA, joining of owners to an FPA, ministerial exemption, ministerial delegation, extension of “Enforcement powers” and appeals.
Advocate Sefela said it highlights the necessity of an integrated approach to veldfire management and that it is aimed to integrate management strategies with the emphasis on a coordinated approach.
Laura Coetzee: ‘Transforming fire detection strategy with ultra-early fire detection’ Director at Boabab Sentinel t/a Dryad Africa’s Laura Coetzee shared the results of an ongoing project on ‘Transforming fire detection strategy with ultra-early fire detection’. She discussed the impact of wildfires saying that wildfires affect around 100 000 hectares in South Africa each year, with 80 percent of them being caused by humans. She also mentioned the importance for commercial forestry for South Africa and that wildfires not only destroy trees but also harm soil quality, reduce biodiversity and incur millions in revenue losses.
She described the limitations of traditional detection and detailed the ultra-early detection pilot project currently at PG Bison’ where they deployed 77 sensors across 115 hectares
to test early detection under real conditions adding that the solar-powered sensors detect critical gasses, like CO and NO2, before smoke appears. “The sensors form an interconnected network, monitoring changes minute-by-minute and sending real-time alerts. This system shifts fire management from reactive to proactive, enabling earlier interventions”, said Coetzee. “The system is adaptable, meaning it can be scaled for different forest types and risk levels.”
Hannes Vosloo: ‘Sappi fire management strategies and tactics in the Lowveld region’ Sappi Mpumalanga fire manager, Hannes Vosloo, shared ‘Sappi fire management strategies and tactics in the Lowveld region’ saying that most of the work is done pre-fire season, detailing their nine-month preparation for the fire season, which includes servicing and upgrading fire suppression equipment and infrastructure such as roads, water re-supply and aerial support, conducting community engagement and awareness campaigns, preparing firebreaks and access roads and selecting and training personnel for fire management roles.
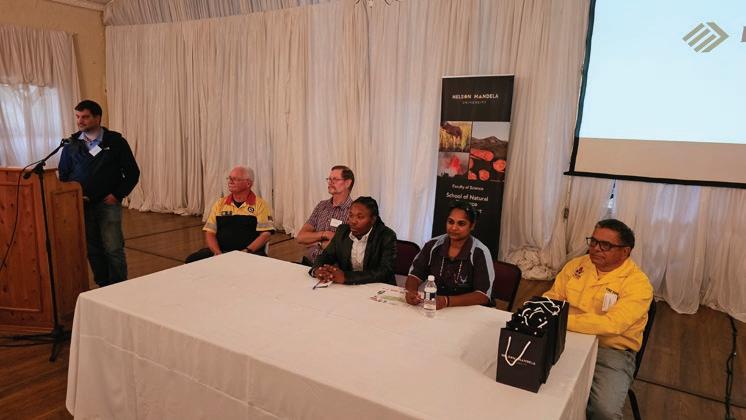
He also detailed their focus during the fire season, which includes detection and reporting, initial response, personnel, vehicles, aerial support, extended response and post fire reviews. Vosloo highlighted the importance early detection and rapid response, saying, “We try to get to fires early while they are still warm. We overreact; it is cheaper to turn aerial support back when not needed than not having it early when needed most.”
Matthew Danckwerts: ‘Reliability of fire pattern indicators used in wildfire investigations’ Wildfire forensic investigator/ fire ecologist at MJ Danckwerts Consulting (Pty) Ltd, Matthew Danckwerts, discussed the ‘Reliability of fire pattern
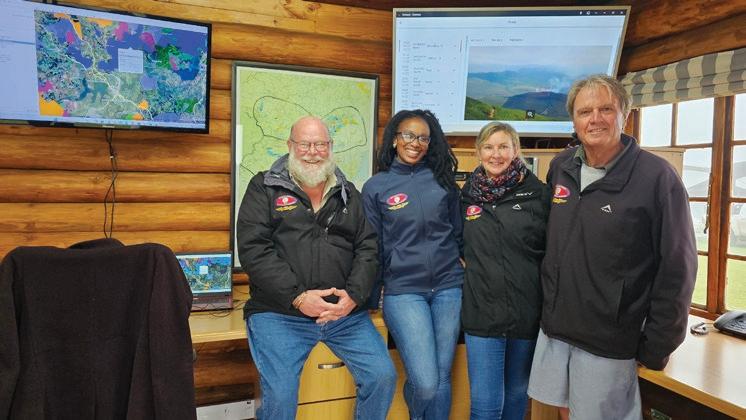
indicators used in wildfire investigations’, following a series of landscape fire experiments conducted in the Eastern Cape. He said that fire pattern indicators are not as reliable as previously believed and that using indicators in conjunction with each other can lead to more accurate conclusions about fire patterns and spread.
Danckwerts said, “Leeside charring on pole type fuels, unburnt plant litter and undercutting of grass stems are reliable indicators of wind direction and fire intensity. A good understanding of fire behaviour is required to interpret indicators reliably and accurately.”
Angel Goldsmith: ‘Mobilising social capital for fire risk reduction at South Africa’s wildland-urban interface’ PhD candidate at Kings College London Faculty of Social Science and Public Policy, Angel Goldsmith, discussed ‘Mobilising social capital for fire risk reduction at South Africa’s wildland-urban interface’, detailing the study objectives, which focusses on leveraging the relationships and networks within and between communities to enhance fire risk management
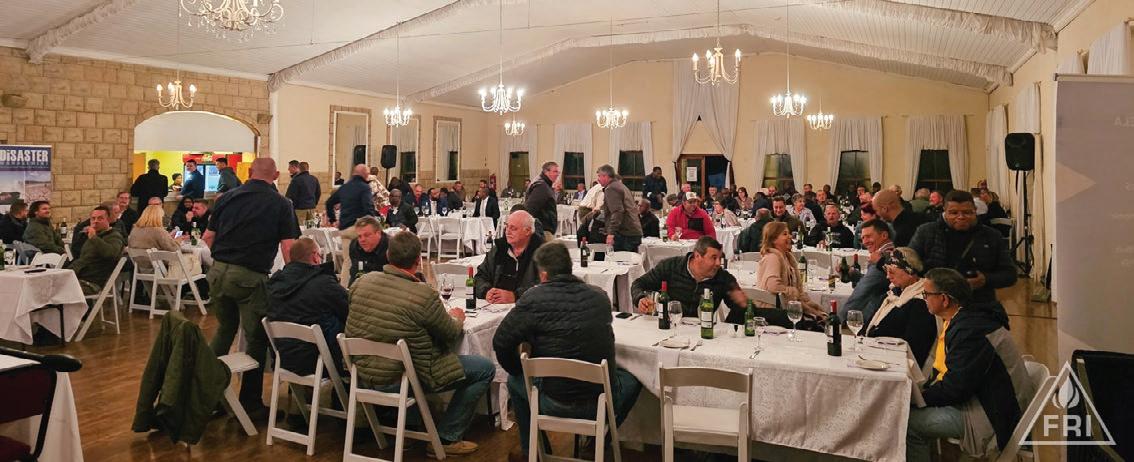
and education in WUI. Goldsmith also detailed the case study sites and methods and the results.
The study compared the various types of settlements ie informal settlements, township settlements and formal settlements, identifying the diverse types of social capital, delving into bonding social capital (within community), bridging social capital (collaboration between communities) and linking social capital (relationships with external entities). Goldsmith said, “Communities have different levels of social support and resources, known as social capital. This difference makes it harder for fire risk education and awareness programs to work equally well for everyone, as some communities may lack the support networks or resources needed to fully benefit from these programmes.”
Kelvin Price: ‘The latest developments in weather monitoring’
Managing director of CW Price and Co, Kelvin Price, shared ‘The latest developments in weather monitoring’, highlighting the importance of weather station maintenance and cleaning. Price provided background information on the history of
VitalWeather and its products. “We developed our own solution that eliminates housing, backup battery and a charger therefore dramatically reducing system price. This development is now 4G/LTE compatible with huge improvement in uptime, plus Wi-Fi connectivity and vastly improved memory for cell tower outages”, said Price.
He added, “Remember VitalWeather and VitalFireWeather is not only for FDI predictions but is also extremely useful for research purposes, nurseries, insurance claims and post fire analysis and investigations.”
Navashni Govender: ‘Char height as a robust and affordable postfire proxy for fire intensity’ Senior manager for conservation at Kruger National Park Skukuza, Navashni Govender, looked at ‘Char height as a robust and affordable post-fire proxy for fire intensity’. “Fire intensity plays a crucial role in fire management, influencing both immediate firefighting strategies and longterm ecological outcomes ie reducing hazardous fuelloads, maintaining ecosystem health,
firefighting strategies and protecting human life and property. However, the direct determination and measuring of fire intensity is very difficult and therefore post fire indices allows the fire manager to measure fire intensity and therefore understand its effects”, said Govender.
She shared the details of the studies in the Kruger National Park, saying that fires and megaherbivores are ecosystem drivers. “The use of post-fire indicators, specifically scorch and char height, are proxies for fire intensity, offering detailed insights into the intensity and ecological impact of fires. By leveraging these indices, fire managers can make informed decisions about rehabilitation, risk mitigation and future fire management practices, ultimately contributing to healthier and more resilient ecosystems.”, said Govender.
Col Ivor Rimmer: ‘SARZA, a volunteer search and rescue partner’
Honorary president of Search and Rescue South Africa (SARZA), Col Ivor Rimmer, shared an overview of ‘SARZA, a volunteer search

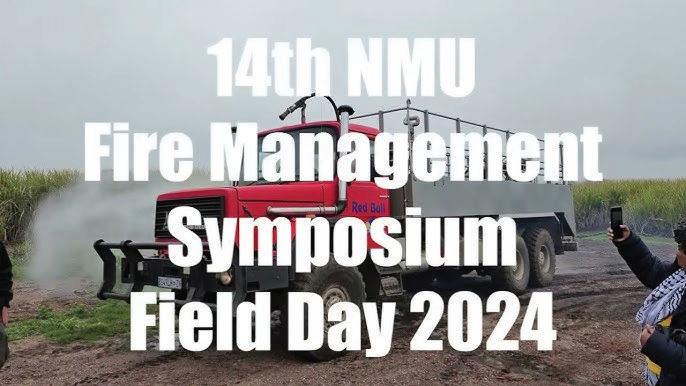
and rescue partner’. He said that SARZA’s mission and objective is “To provide a competent, efficient volunteer search and rescue service, dedicated to saving human life, that’s able to operate in rough and difficult terrain in support of other services in times of civil disaster or other emergencies.” Col Rimmer said that its first operations were in 1990 and he shared details of their local rescue operations such as the unrest in 2021, the KwaZulu-Natal floods, the Jagersfontein slime dam collapse, the Boksburg tanker explosion etc.
Their international rescue operations included the 2010 Haiti Earthquake, the Japan tsunami in 2011, the Philippines typhoon in 2013, the floods in Malawi in 2015, the Mozambique Cyclone Idia in 2019 and the Turkiye earthquake in 2023.
Col Rimmer also emphasised the importance of continuous training and skill development
among its members to effectively handle diverse rescue missions.
Trevor Abrahams: Wildland Fire Canada Conference 2024 Working on Fire’s managing director, Trevor Abrahams, shared some insights on the recently held Wildland Fire Canada Conference 2024 and provided a snapshot of its take home messages:
• Scientific methodologies and social engagement need changing
• Community engagements and awareness
• Evacuation successes in threatened communities
• Enhance prevention and preparedness
• Allow credible collaboration
• Research engagement
• Physical and mental health of those exposed.
Field day
The event included a field day where participants visited a sugar cane farm in New Hanover where
several demonstrations were conducted by various suppliers. These included the Red Bull Magirus Deutz fire engine and Trident Africa’s Suleiman Dhliway, who demonstrated the new Trident foam.
André Scheepers of Anco Manufacturing demonstrated their latest compressed air foam system (CAFS), the Anco CAFS 800 firefighting unit.
Jackie de Billot of Vanguard Fire and Safety demonstrated the Pro Pack and several nozzles for foam and water.
This was followed by a visit to the KwaZulu-Natal Fire Protection Association’s airstrip and base in Shafton, where delegates could visit several industry exhibits.
Fire and Rescue International was its official media partner. View our online photo gallery: NMU Fire Symposium 2024
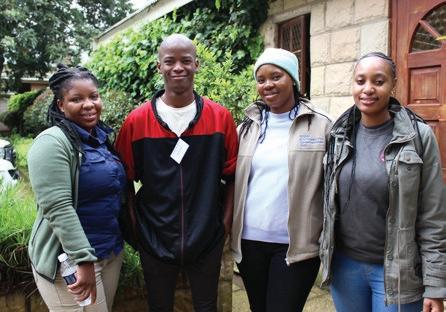
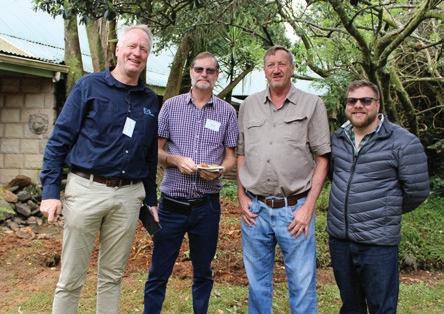
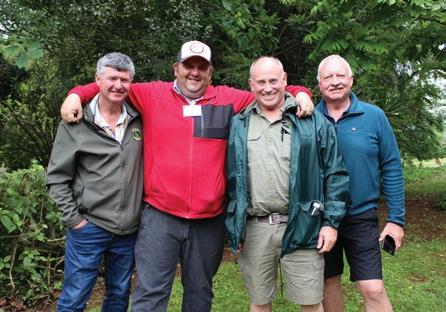
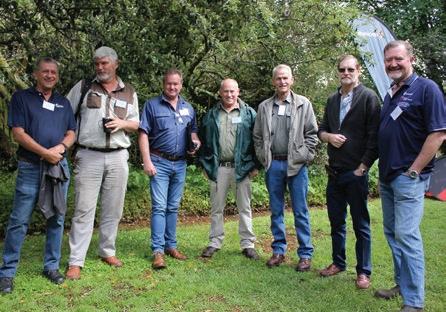
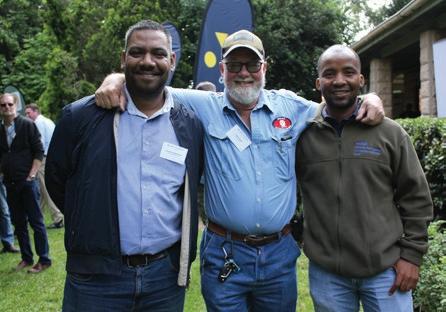

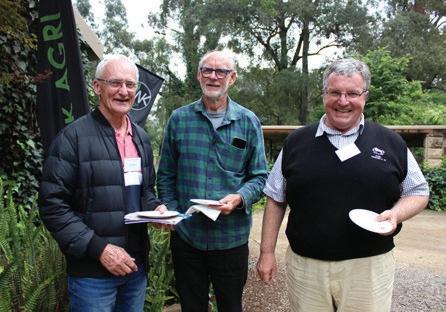
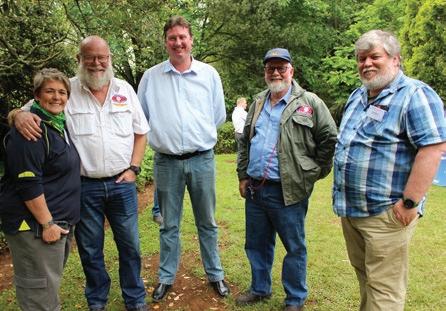
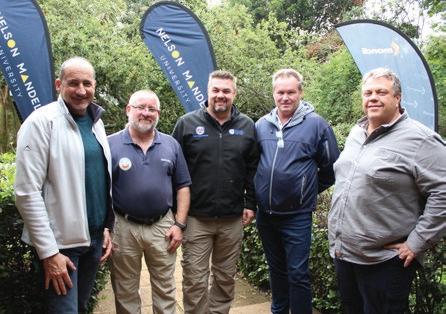
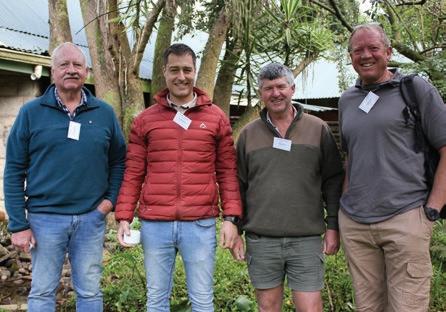
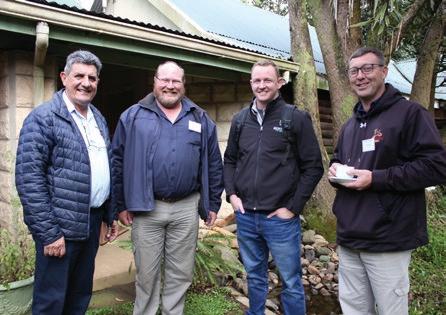
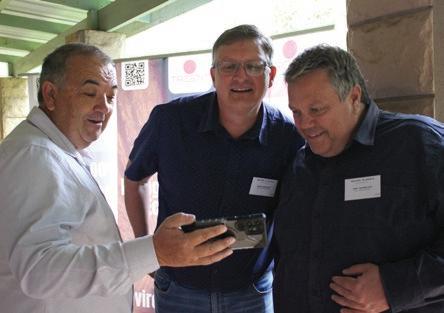
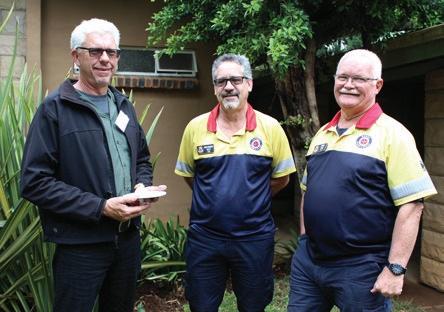
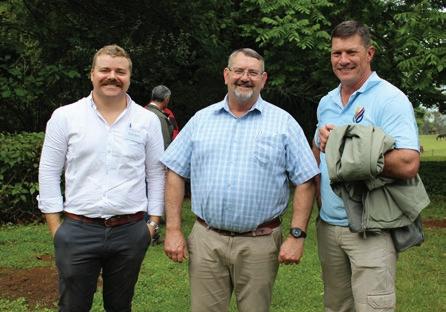
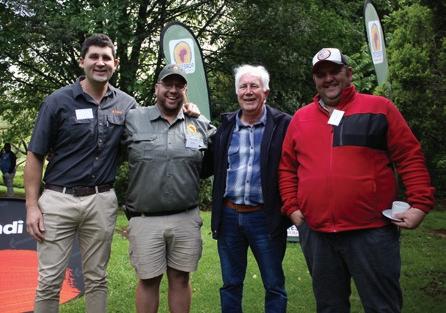
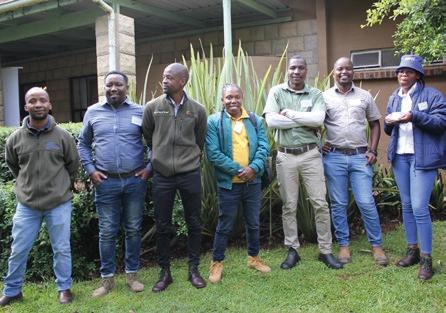
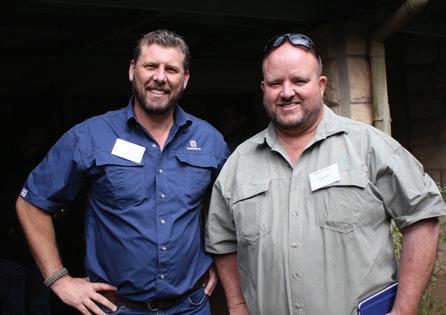
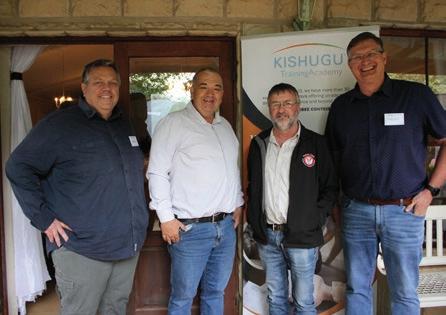
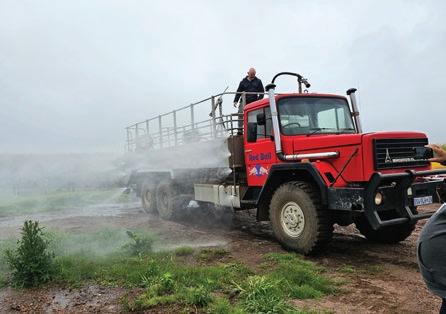

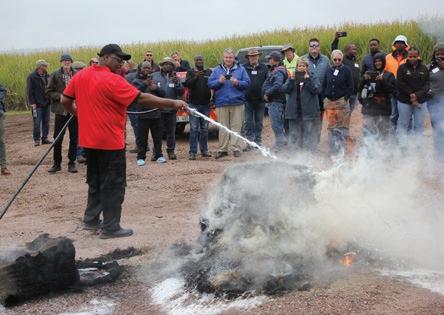
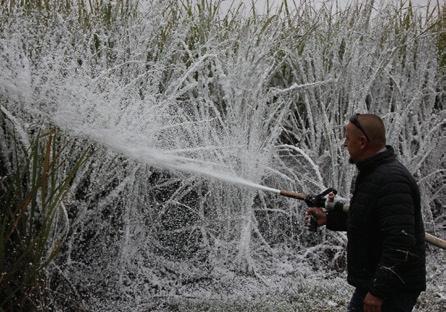
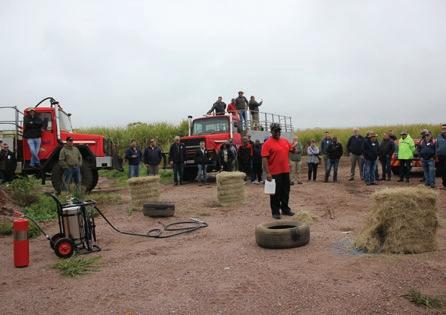
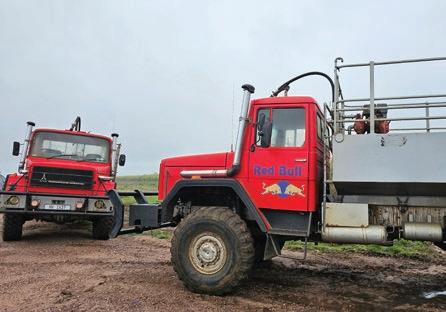
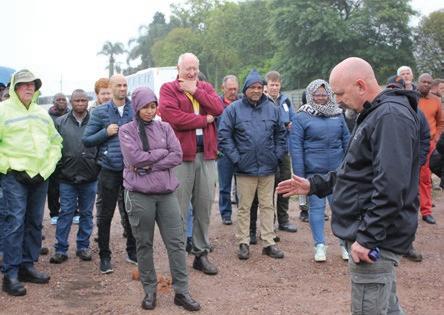
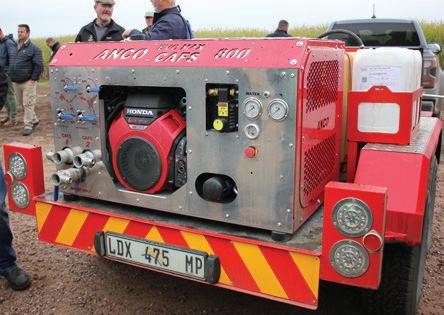
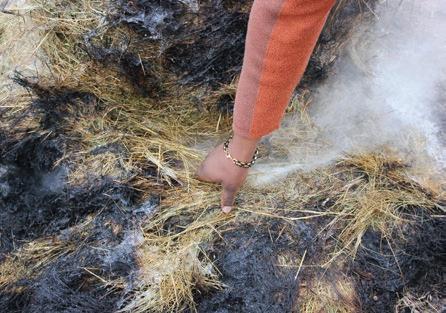
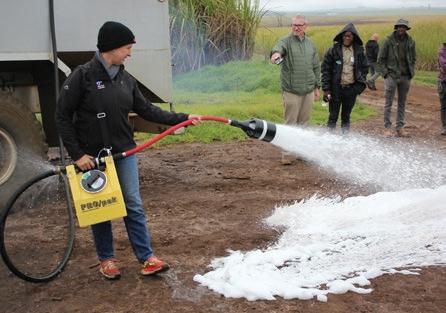
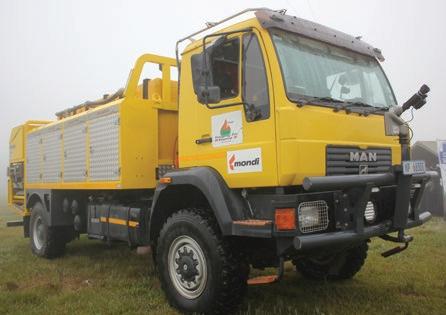
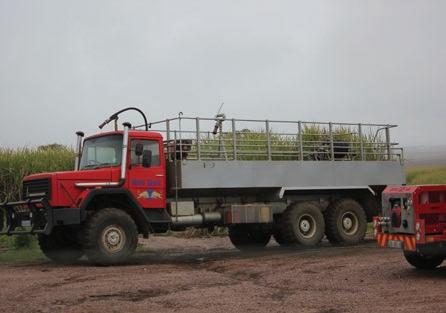
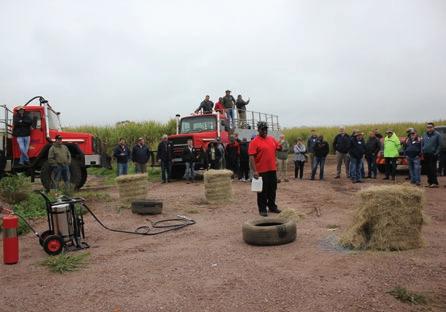
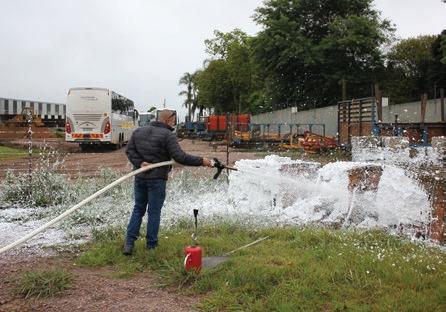
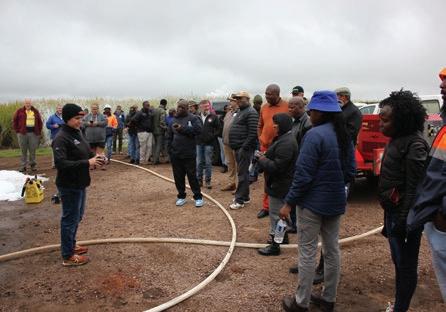
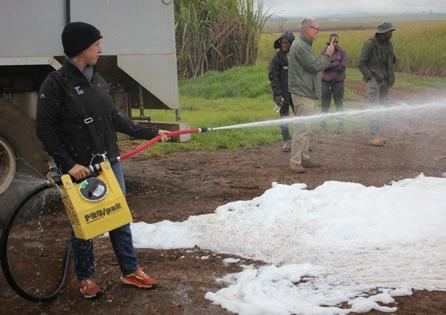

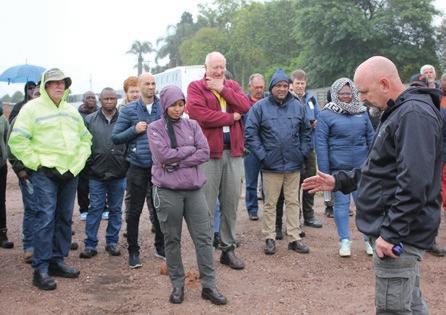

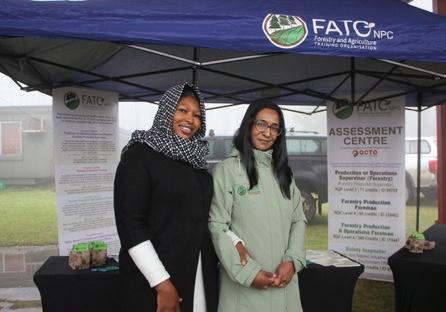
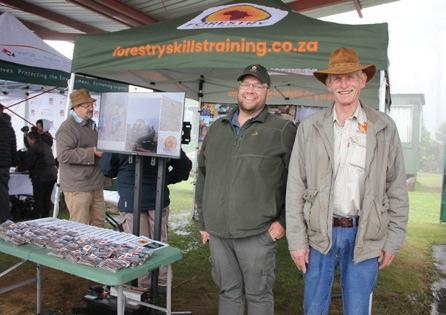

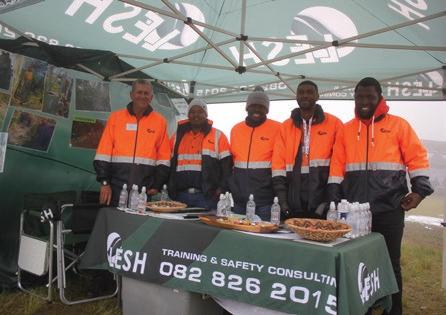
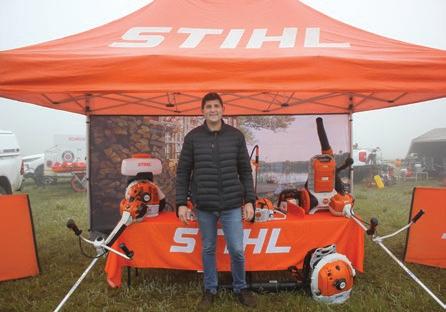
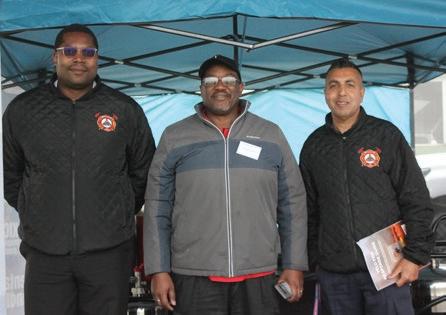
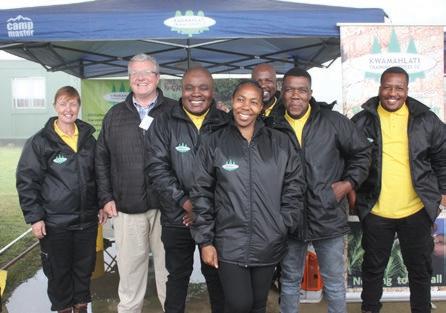
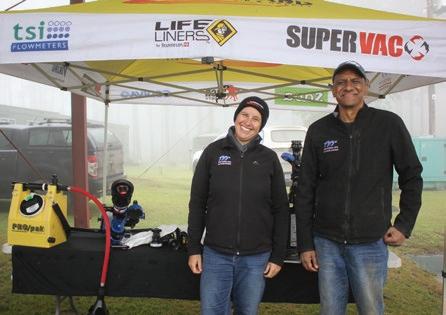
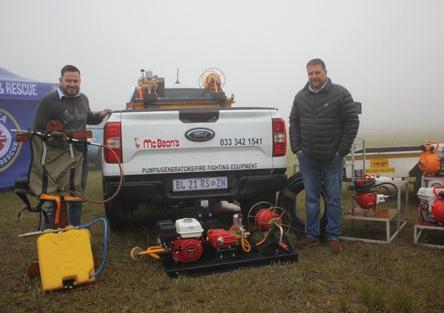
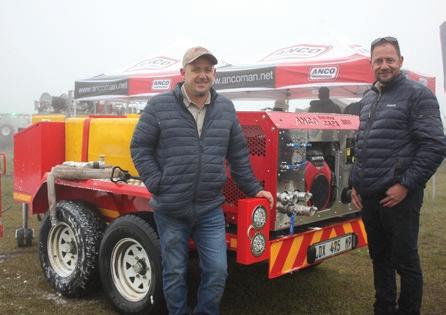
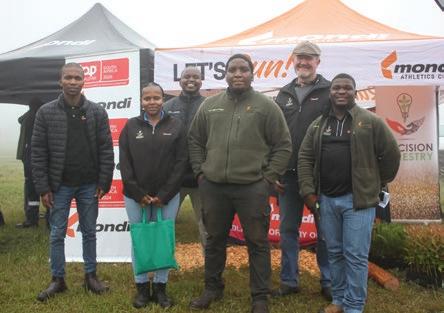
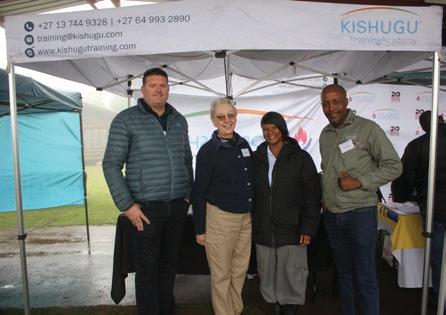
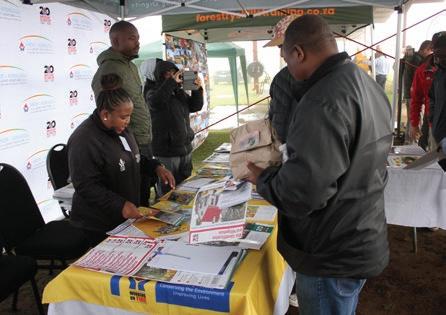
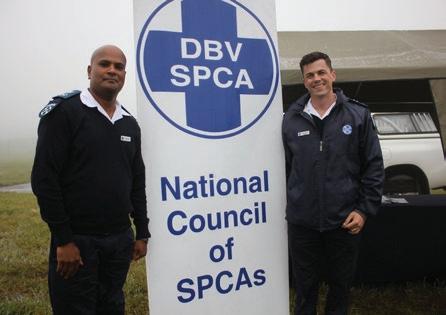
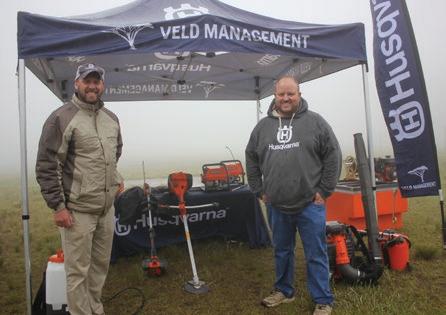
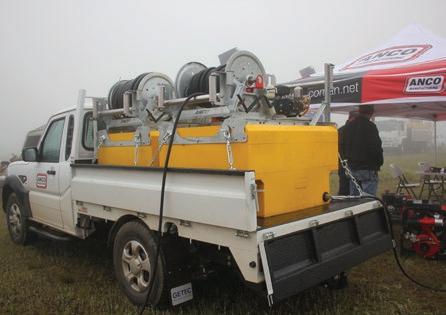
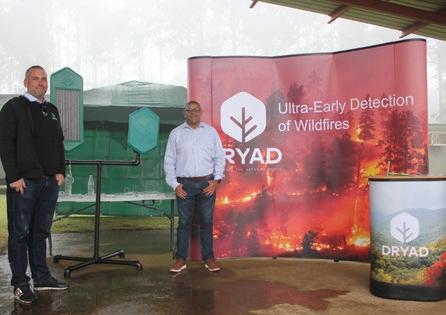

Rope Rescue Awareness and Operations Training: NFPA 1006 compliance at ETS Emergency Training Solutions
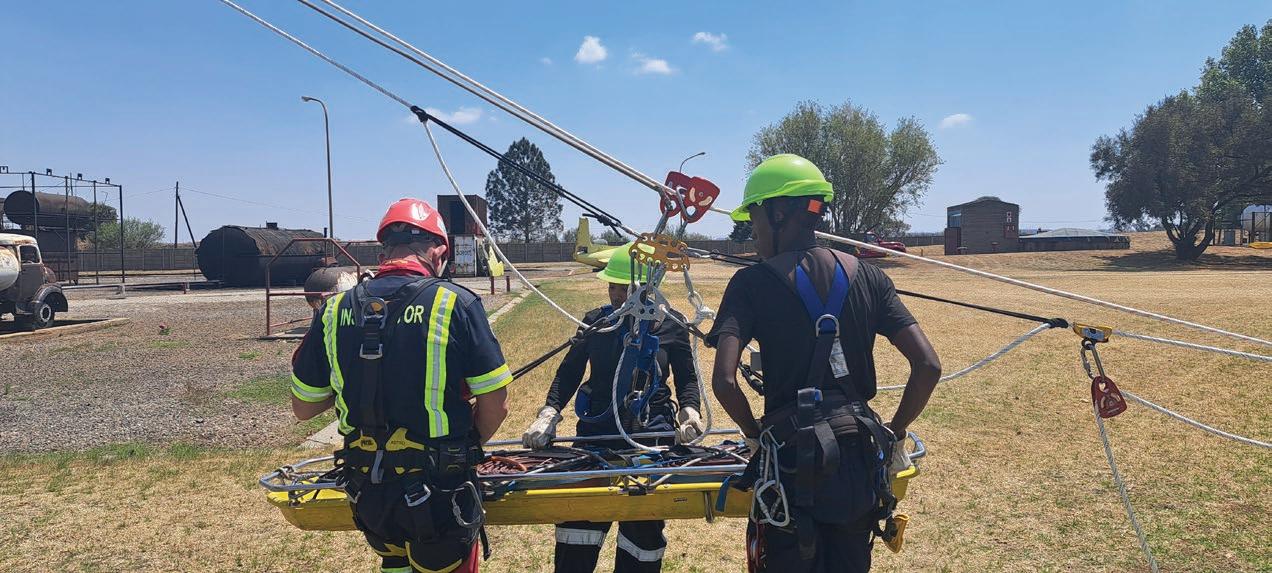
Rope rescue operations are critical in emergency response situations where individuals must be safely extracted from heights, confined spaces or difficult terrains. The NFPA 1006: Standard for Technical Rescue Personnel Professional Qualifications outlines the competencies required for technical rescue professionals, ensuring they have the skills, knowledge and expertise for safe and effective rescues.
This guide covers rope rescue awareness and operations training based on NFPA 1006 standards and how ETS Emergency Training Solutions provides high-quality training to meet these requirements.
Why choose ETS for rope rescue training?
At ETS Emergency Training Solutions, we are committed to delivering world-class rescue training aligned with NFPA 1006 standards. Our expert instructors have extensive real-world experience, ensuring trainees gain hands-on, practical knowledge. Our courses equip personnel with the necessary skills to respond effectively to emergency situations while prioritising safety and compliance.
Understanding NFPA 1006
The National Fire Protection Association (NFPA) 1006 standard categorizes training into three levels:
• Awareness Level: Basic understanding and support role
• Operations Level: Hands-on participation under supervision
• Technician Level: Advanced technical expertise and leadership in rescues
ETS offers Rope Rescue Awareness and Operations training, ensuring your team is fully prepared for high-risk rescue scenarios.
Rope rescue awareness level
The awareness level is the foundational training phase for personnel who may be required to support rope rescue operations. While they do not actively conduct rescues, they play a crucial support role.

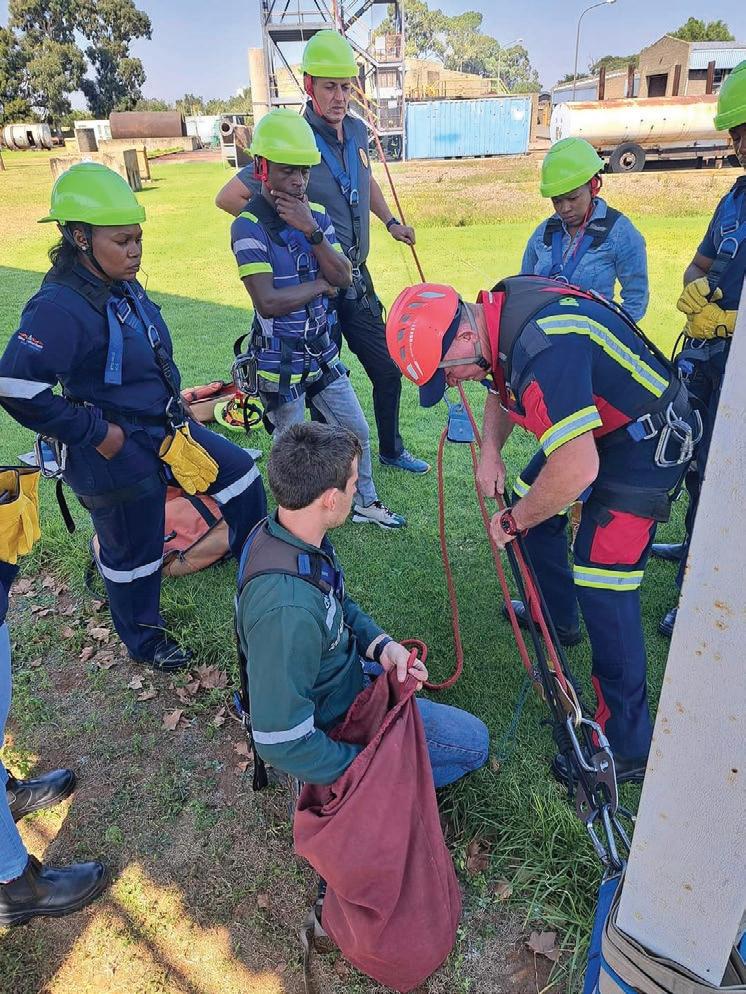
Key competencies
• Recognising situations that require rope rescue
• Identifying hazards associated with rope rescue incidents
• Familiarising themselves with essential rope rescue equipment and its applications
• Supporting operational personnel by securing the scene and providing assistance
• Communicating effectively with the rescue team
Rope rescue operations level
The operations level builds upon the awareness level, equipping personnel with hands-on skills to actively participate in rope rescue
scenarios under the supervision of a technician. This level involves practical training and specialized equipment use.
Key competencies
• Establishing and managing anchor systems: Securing ropes to stable points to support rescues
• Knot tying and rope handling: Using essential knots such as figure-eight, bowline and Prusik knots
• Setting up and operating mechanical advantage systems: Utilising pulleys and belay systems to facilitate rescues
• Performing essential rescue manoeuvres: Safely lowering and raising rescuers and victims
• Implementing patient packaging and transport techniques: Utilising litters, harnesses and other equipment for victim extraction
• Executing self-rescue techniques: Ensuring rescuers can extricate themselves when necessary
Equipment used in rope rescue
ETS provides training on various industry-standard tools and equipment, including:
• Ropes (static and dynamic): Designed for strength, durability and flexibility in diverse rescue scenarios
• Carabiners and connectors: Used for attaching equipment and ensuring secure connections
• Harnesses and helmets: Critical protective gear for both rescuers and victims
• Pulleys and ascenders/ descenders: Assist in controlled movement during rescues
• Belay devices: Used to manage rope tension and prevent uncontrolled descents
Importance of NFPA 1006 Compliance
Compliance with NFPA 1006 ensures that rescue personnel meet industry best practices and safety standards. Training at the awareness and operations levels enhances:
• Rescue efficiency: Enhancing response effectiveness and improving victim survival and recovery outcomes
• Safety for rescuers and victims: Minimising risks associated with high-angle rescues
• Interoperability among agencies: Enabling seamless coordination between fire
departments, emergency services and specialised rescue teams
Why train with ETS?
• Accredited training programmes: Courses aligned with NFPA 1006 standards and industry requirements
• Experienced instructors: Learn from experts with real-world emergency response experience
• Hands-on practical learning: Focused on realistic rescue
scenarios beyond theoretical knowledge
• Customisable training options: Tailored courses to meet the specific needs of your organisation
Enrol today!
Equip your team with the expertise needed for highangle rescues through ETS Emergency Training Solutions’ Rope Rescue Awareness and Operations Training.
Contact ETS today to learn more about course schedules, enrolment options and customised training solutions.
Mobile: +27 72 980 2046 Tel: +27 16 363 0254/3, Email: pinkie@etsafrica.co.za Visit: www.etsafrica.co.za
Ensure your team is trained, compliant and ready with ETS Emergency Training Solutions.

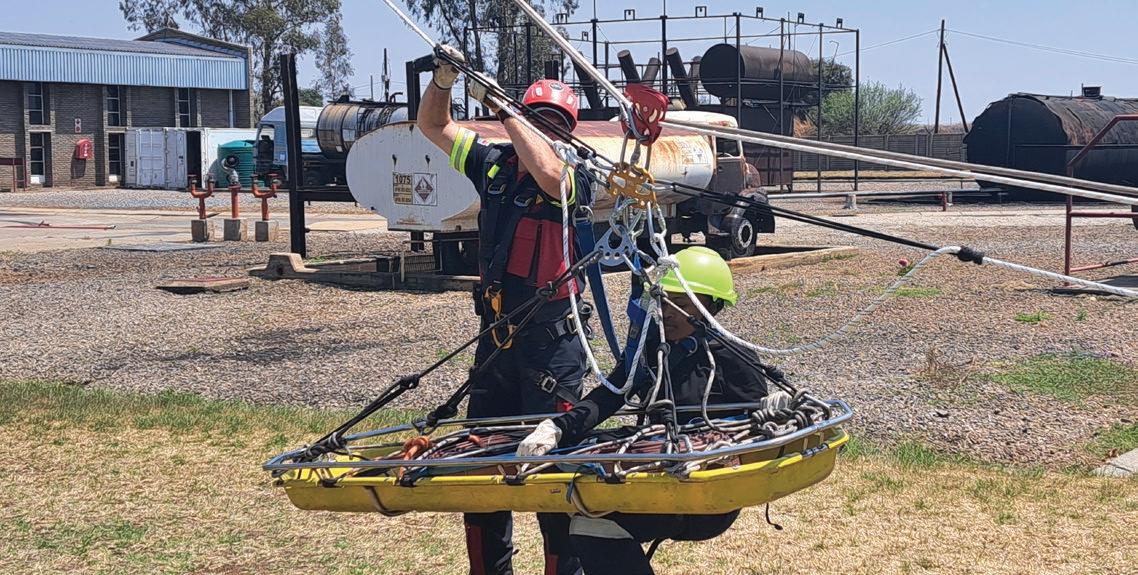
Young child trapped in borehole rescued: Rescue confront their worst nightmare
By JA Fleischman, Free State College of Emergency Care (FSCoEC)
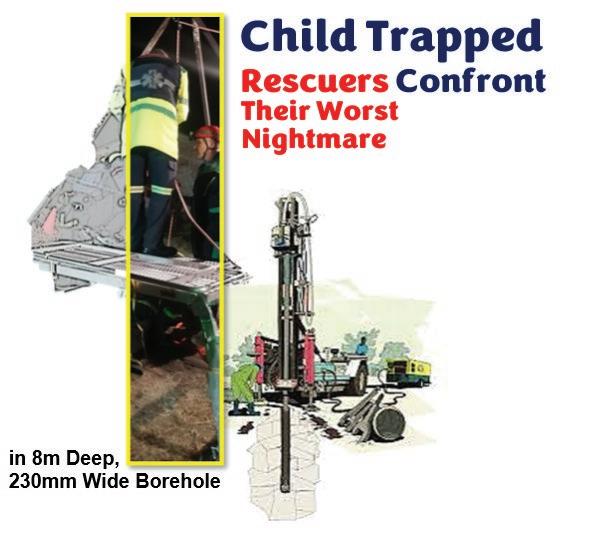
On Friday, 13 December 2024, a three-year-old boy went missing around 13h00. His distressed parents initiated a search and ultimately located him at approximately 19h00 in an unused borehole situated about 30 kilometres northwest of Bloemfontein in the Free State, South Africa.
A large-scale rescue operation was launched involving Mangaung Fire and Rescue Service, the Emergency Medical Services (EMS), ALS and Rescue Free State College of Emergency Care (FSCoEC), Search and Rescue South Africa (SARZA)
Free State and various other emergency services.
The child had accidentally fallen approximately eight metres deep into a narrow borehole, prompting an urgent response.
The borehole presented significant challenges to the rescue operation due to its confined space, narrow diameter of approximately 230 millimetres and precarious structural condition. Upon arrival, the SARZA Free State established a mobile command post.
First responders assessed the borehole’s structure and
determined the child’s position below the surface. Firefighters, paramedics and specialised rescue teams immediately began evaluating and preparing the scene for extraction.
Thank goodness, the three-yearold boy was responsive and audible during the assessment. The area surrounding the borehole was secured to prevent further accidents or collapses. Equipment such as confined space communication devices, rope technical gear, excavation tools and machinery were brought to the site by local farmers, community members and businesses to assist in the rescue efforts.
After working throughout the night, the three-year-old was successfully rescued at approximately 05h35 on the 14 December 2024. Immediate medical evaluation was conducted by paramedics on-scene, followed by transportation to the hospital for further observation and care. The well was sealed immediately after the rescue to prevent future accidents.
The successful rescue of the threeyear-old boy was a testament to the prompt coordination and expertise of all the emergency response teams and members of the public and local businesses.
Let us delve deeper into the miracle of the borehole and explore what we know and what we have learned. Borehole rescue operations have gained attention due to the increasing number of children falling into uncovered boreholes/ wells, particularly in rural areas. Various innovative approaches and technologies have been developed to enhance the efficiency and safety of these rescue missions.
Challenges in borehole/well rescues
Borehole/well rescues, particularly involving children, present numerous challenges that significantly impact the success rates of these operations. Despite advancements in techniques and equipment, the statistics reveal a concerning trend. The complexities of these rescues arise from various factors, including environmental conditions, operational limitations, and the nature of the incidents.
Depth and structure of bore wells
Bore wells can reach depths of up to 1 500 feet, creating significant difficulties for rescuers. The depth often complicates access and increases the time required for rescue operations.
The diameter of boreholes/ wells typically ranges from 6 to 12 inches, making it difficult to manoeuvre equipment and rescuers effectively.
Environmental conditions
Unknown levels of humidity, temperature and oxygen at the depths of bore wells pose serious risks to trapped children and complicate rescue efforts. High humidity can lead to

hyperthermia, while low oxygen levels cause suffocation.
Rescuers often face challenges related to soil conditions (rocky, sandy or soft), which can affect digging operations and the stability of the surrounding area.
Time sensitivity
The urgency of these rescues is critical; a delay can be fatal. The average time taken for successful rescues is often extended due to the need for careful planning and execution.
Each moment counts as prolonged entrapment can lead to severe injuries or death due to environmental factors or trauma from falling debris during digging operations.
Resource limitations
Effective rescue operations require substantial resources, including heavy machinery, medical teams and trained personnel. Often, these resources are not readily available in remote locations where many accidents occur.
The lack of supportive infrastructure in rural areas exacerbates these challenges, making it difficult to mobilize necessary equipment quickly.
Psychological factors
The emotional distress experienced by both the victims and their families can complicate rescue efforts. Maintaining communication with trapped individuals is crucial but
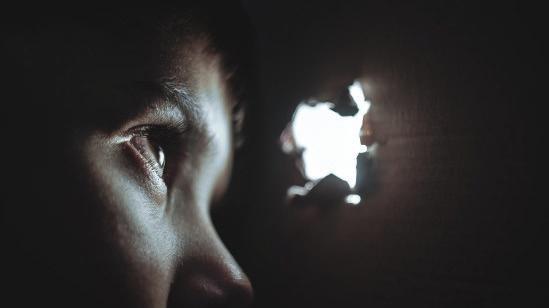
challenging due to the depth and narrowness of bore wells.
Safety concerns
Traditional methods often pose risks both to the trapped individual and rescuers, making robotic and automated solutions preferable.
Children trapped in boreholes face several critical risks that can jeopardise their safety and survival.
Oxygen deprivation
One of the most immediate dangers is the lack of oxygen in the confined space of a borehole. As time passes, oxygen levels can drop significantly, leading to hypoxia, which can cause unconsciousness or death if not addressed quickly.
Hyperthermia
The temperature inside a borehole can rise rapidly, especially in warmer climates. Increased temperatures combined with humidity can lead to hyperthermia, which poses a serious health risk and can be lifethreatening if the child remains trapped for an extended period.
Physical injuries
The process of falling into a borehole can cause physical injuries to the child, such as fractures or trauma from hitting the sides of the hole. Additionally, during rescue attempts, there is a risk of exacerbating these injuries if not handled carefully.
Psychological trauma
Being trapped in a dark, confined space can lead to severe psychological stress and trauma for children. This can manifest as panic attacks, anxiety or longterm psychological effects even after rescue.
Dehydration and malnutrition
If a child is trapped for an extended period without food or water, they may suffer from dehydration and malnutrition, which can further complicate their condition and reduce their chances of survival.
Infection risks
Depending on the conditions within the borehole and how long the child is trapped, there may be risks associated with infection from dirt or contaminants present in the borehole environment.
Rescue delays
The complexity and timeconsuming nature of rescue operations can lead to significant delays in reaching the child. This time factor is crucial, as any delay increases the severity of all risks
Most common causes of borehole/well accidents
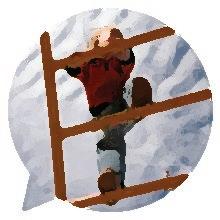
Borehole/well accidents, particularly involving children, are a tragic reality in many regions, all over the world. The most common causes identified in borehole/well incidents are:
Children falling while playing
A significant number of accidents occur when children fall into bore wells while playing
nearby. This is often due to a lack of supervision and awareness about the dangers of open boreholes/wells.
Unclosed or abandoned boreholes/wells
Many bore wells remain uncovered or improperly sealed after they are no longer in use. This creates hazardous conditions, as children can easily fall into these deep holes.
Temporary or flimsy covers
In some cases, bore wells are covered with inadequate materials that can easily be displaced. These temporary covers do not provide sufficient protection against accidental falls.
Lack of warning signboards
The absence of clear warning signs near bore well sites contributes to the risks, as potential dangers are not communicated effectively to the public.
Blocking visibility
In some instances, vegetation or other obstructions can block visibility around holes/wells, making it difficult for parents and guardians to supervise children effectively.
Delayed response to incidents
When accidents occur, a lack of immediate response can exacerbate the situation. Delays in rescue operations can lead to tragic outcomes, as time is critical in such emergencies.
Public awareness and inspection failures
By addressing the causes of bore well accidents through improved public awareness, stricter regulations and prompt action on unused wells, communities can significantly reduce the risk of these tragic
incidents. A proactive approach involving education, regulation and community engagement is essential to safeguard vulnerable populations, particularly children, from the dangers posed by open boreholes/wells.
Miracle in the borehole:
Rescuers race against time to save trapped child
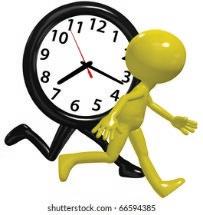
The complexity of these rescues is compounded by various technical challenges and the urgent need for effective solutions.
Rescue teams are engaged in a frantic operation to save a child trapped in a borehole, highlighting the urgency and challenges faced during such critical situations. The child, who has been stuck for several hours, is alive but in need of immediate assistance.
Rescuers are thinking of employing heavy machinery and specialised techniques to remove soil if needed without risking further collapse, as they battle against time and the elements. As the situation unfolds, the hope remains that the child will be safely rescued from this harrowing ordeal.
The rescue team faced several emotional challenges during
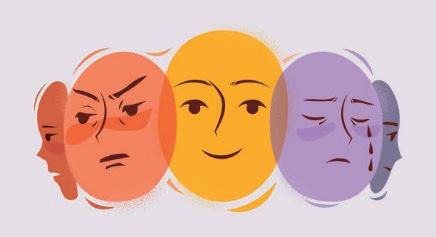
the operation to save a child trapped in a borehole 8m below with the possibility of injuries and less oxygen.
Emotional distress
Rescue workers often experience high levels of psychological distress, the pressure of potentially failing to save a life can exacerbate these feelings, leading to significant emotional strain.
Anticipation and anxiety
During the rescue operation, the team likely felt a mix of anticipation and anxiety as they awaited updates on the child’s condition. The uncertainty surrounding the situation can create a tense atmosphere, heightening emotional stress for the rescuers as they grapple with fears of the worst outcomes.
Burden of responsibility
Rescue workers bear the heavy burden of responsibility for the lives they strive to save. This profound sense of duty can lead to feelings of guilt or inadequacy, especially if they perceive any delays or obstacles in the rescue efforts, which can further impact their mental well-being.
These emotional challenges underscore the complex
psychological landscape that rescue teams navigate while performing their critical roles in life-threatening situations.
Considering this, we took a moment as a team to pause and ask God for help in coping, planning, and leading us with the emotional stress associated with our demanding work.
Team support and structure
A strong sense of teamwork provides emotional support among team members. Wellcoordinated efforts and solidarity helped reduce feelings of isolation and strain during highstress situations. Experienced personnel supported less experienced colleagues, creating an environment where mutual support was emphasised.
These strategies collectively aimed to enhance the mental wellbeing of rescue workers, enabling them to perform their critical roles while minimising the emotional toll of their challenging work.
The danger of a borehole rescue is significant due to various factors that complicate the process and increase risks for both the trapped individual and the rescuers.
Challenges in borehole rescue operations
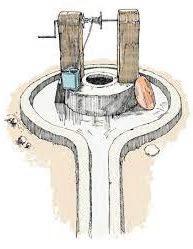
Time sensitivity
Rescues often take an extended period, sometimes exceeding 30 hours, which can be critical as trapped individuals may face lifethreatening conditions such as suffocation or dehydration. The longer the delay, the higher the risk of fatality.
Physical risks
Traditional methods involve digging a parallel hole to reach the trapped individual. This approach poses several hazards:
• Cave-ins: The excavation can lead to collapses, endangering both rescuers and the trapped person.
• Injury during rescue: Tools and machinery used in digging can inadvertently harm the trapped individual, especially if they are not carefully managed.
• Resource limitations: Effective rescue requires significant resources, including heavy machinery and skilled personnel. In many cases, these resources are not readily available, leading to delays and ineffective rescue efforts.
• Environmental hazards: Boreholes may contain harmful gasses or contaminants that can pose additional risks during rescue operations. For instance, oxygen levels can drop significantly in confined spaces, complicating efforts to provide adequate breathing support.
• Psychological impact: The stress of being trapped can lead to panic and psychological trauma for the individual involved, complicating their physical condition and response to rescue efforts.
The environment inside a borehole significantly impacts the rescue process, introducing various challenges that can complicate and prolong efforts to retrieve a trapped individual.
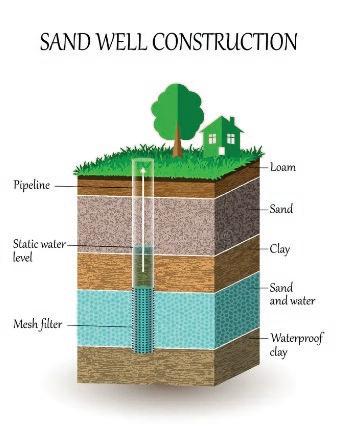
Atmospheric conditions
• Oxygen levels: The air quality within a borehole can deteriorate quickly, leading to low oxygen levels. This poses a serious risk to the trapped individual and complicates rescue efforts, as rescuers must ensure adequate ventilation or oxygen supply during the operation.
• Temperature variations: Boreholes can experience extreme temperature changes, which can affect the physical condition of the trapped person and the equipment used in the rescue.
Structural stability
• Risk of collapse: The walls of a borehole may be unstable, especially if they are not properly cased or if the surrounding soil is loose. This instability can lead to cave-ins during rescue operations, putting both the trapped individual and rescuers at risk.
• Water accumulation: If a borehole collects water or slurry, it can create additional hazards such as drowning risks or complicating access to rescue equipment.
Contamination risks
Pollutants and hazards: Boreholes may be susceptible to contamination from nearby sources, such as septic tanks or industrial waste. This contamination can pose health risks to both the trapped individual and rescuers, necessitating precautions to avoid exposure to harmful substances.
Accessibility challenges
• Narrow space: The confined space within a borehole limits movement and makes it difficult for rescuers to manoeuvre tools and equipment effectively. This constraint can slow down the rescue process significantly.
• Equipment limitations: Specialised equipment may be required to navigate the unique conditions of a borehole, which may not always be readily available or easy to deploy.
Psychological factors
Panic and stress: The environment inside a borehole can induce panic in the trapped individual due to darkness, confinement and uncertainty about their fate. This psychological state can complicate communication with rescuers and hinder effective rescue strategies.
Several safety measures are implemented to prevent borehole collapse during a rescue operation. These measures are crucial for ensuring the safety of both the trapped individual and the rescuers.
Protective systems
• Shoring: This involves installing support structures to stabilise the walls of the borehole and prevent cave-ins. Shoring systems must be designed by a professional engineer if the borehole is deeper than 20 feet.
• Sloping and benching: Creating sloped walls or benches can help reduce the risk of collapse by distributing the weight of the surrounding soil more evenly.
Atmospheric testing
Conducting atmospheric testing is essential, especially in deeper boreholes, to check for hazardous gases and oxygen levels. If unsafe conditions are detected, appropriate emergency equipment must be provided to ensure safety during rescue efforts.
Gas detection
Rescue teams utilise gas detection technology to monitor air quality within the borehole. This ensures that rescuers are aware of any hazardous gases present, allowing them to take appropriate precautions before entering or conducting operations in the confined space.
Cameras and lighting
High-resolution cameras and LED lighting systems are deployed inside boreholes to provide visibility of the trapped individual. This technology aids in assessing the situation and planning the safest approach for extraction without compromising space or safety.
Safety
protocols
Rescue plans: Comprehensive rescue plans are developed that outline specific procedures for dealing with confined spaces, including safety measures for rescuers, equipment needed and communication strategies during the operation.
Controlled excavation techniques
Directional boring: This method minimises surface disruption and reduces risks associated with traditional trenching techniques. It allows for safer access to the trapped individual without extensive excavation that could destabilise the borehole.
Safe access and egress
Providing safe access points, such as ladders or ramps, ensures that rescuers can enter and exit the borehole safely without compromising its structural integrity.
Monitoring during drilling
During drilling operations, monitoring material return and maintaining clear annulus around drill rods help prevent uncontrolled soil movements and pressure build-up that could lead to collapse.
Expert involvement
Engaging experienced professionals in borehole drilling and rescue operations ensures
adherence to best practices and safety protocols, reducing risks associated with structural failures.
Borehole collapse during rescue operations can occur due to various factors, each contributing to the instability of the borehole structure.
Geological factors
• Soil composition:
Boreholes drilled in loose or unconsolidated soils, such as clay or sand, are more prone to collapse. These soil types may not provide adequate support for the borehole walls, especially if proper casing is not installed.
• Rock formations: The type of rock encountered during drilling can affect stability. Soft or fractured rocks may require additional support to prevent collapse.
• Water table fluctuations
• Changes in groundwater levels can exert varying pressures on borehole walls, increasing the risk of collapse. Seasonal rains, droughts or over-extraction of water can lead to significant fluctuations that destabilise the surrounding soil structure.
Environmental factors
• Natural events: Heavy rainfall, earthquakes or flooding can destabilise boreholes by causing soil erosion or shifting the geological structure around the borehole.
• Vibrations from nearby construction: Activities such as construction work nearby can create vibrations that weaken the borehole walls, leading to potential collapse.
Rescue teams undergo extensive training to prepare for a variety of challenging emergencies.
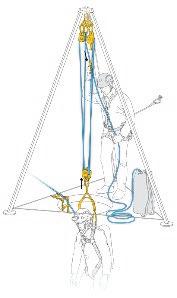

Their training equips them with the necessary skills and knowledge to respond effectively and safely. These specialised training are essential for ensuring the safety of both rescuers and victims.
• Rope rescue systems
• Patient care and movement
• Incident command system (ICS)
• Safety protocols
• Scenario-based training
• Specialised equipment
• And much more……
The role of the Incident Command System (ICS) in borehole/well rescues
The Incident Command System (ICS) is pivotal in managing borehole/well rescue operations effectively. It
provides a standardised, allhazard approach that enhances coordination among various agencies during incidents.
Structured leadership and decision-making
ICS establishes a clear hierarchy with defined roles, enabling quick and informed decision-making. This structure ensures that each team member understands their responsibilities, which is vital during high-pressure situations where timely decisions can save lives.
Enhanced coordination among agencies
ICS promotes collaboration among multiple agencies by providing a common language
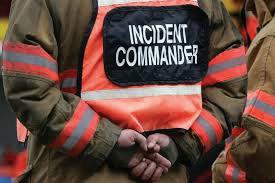
and standardised procedures. This unified approach allows various responders to work seamlessly together, reducing confusion and improving operational efficiency during complex incidents like natural disasters or large-scale emergencies.
Scalability and flexibility
The ICS framework is designed to adapt to incidents of varying sizes and complexities. It can expand or contract based on the needs of the situation, allowing for the efficient allocation of resources and personnel as the incident evolves. This flexibility is essential for managing emergencies effectively without overwhelming the system.
Improved communication
ICS training emphasises clear communication protocols, which are critical for sharing information among responders and with external stakeholders. This clarity helps prevent misunderstandings and ensures that all parties are aligned on objectives and strategies during the response effort.
Objective-driven management
ICS focuses on setting clear, measurable objectives that guide operations. Regular reviews of these objectives ensure that the response remains aligned with the evolving needs of the incident, allowing teams to adjust their strategies as necessary.
Resource management
Training in ICS equips responders with skills to manage resources efficiently. This includes logistical support for securing necessary personnel, equipment and supplies, which is vital for maintaining operational effectiveness throughout an incident.
Safety and accountability
The structured nature of ICS enhances safety by promoting a proper span of control and accountability among team members. Each role within the system is designed to ensure that personnel are monitored and supported throughout the incident, reducing risks associated with emergency operations.
Conclusion
As we successfully conclude our borehole rescue operation on Friday, 13 and 14 December 2024 of the three-year-old boy, expressing our sincere gratitude to everyone involved, is essential. We extend our heartfelt gratitude to all the dedicated individuals and teams who played a vital role in this borehole rescue operation. Your unwavering commitment, expertise and quick response
made a significant difference in a critical situation.
To the rescue personnel who worked tirelessly under challenging conditions, your bravery and determination did not go unnoticed. We appreciate the long hours you spent coordinating efforts, ensuring safety and providing care.
To the medical teams who were ready to assist, your preparedness and compassion were crucial in supporting those affected. Your skills in emergency care have undoubtedly saved lives.
We also want to thank the community members and volunteers who rallied together to provide support and resources during this time. Your solidarity
and willingness to help exemplify the strength of our community.
This rescue was not just a testament to your professional capabilities but also to your genuine humanity. Thank you for being there when it mattered most.
We have not only achieved our immediate goals but have also gained valuable insights that will enhance our future efforts. Let us carry forward the lessons learned and remain committed to our mission of safety and excellence in all our efforts. Thank you for your hard work and professionalism.
This successful rescue not only highlights our capabilities but also reinforces our commitment to safety and excellence in all our operations.
A graphic illustration of the borehole rescue
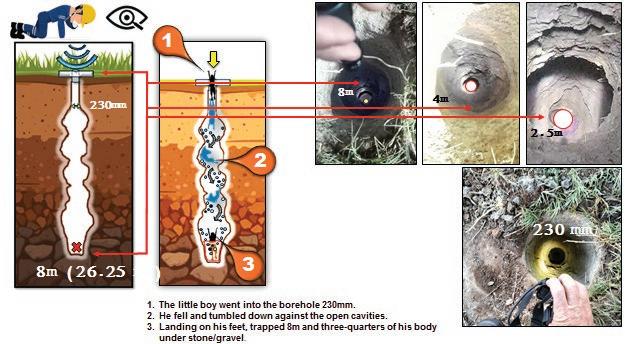
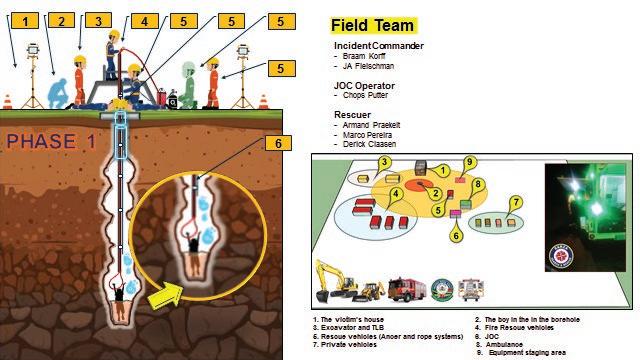
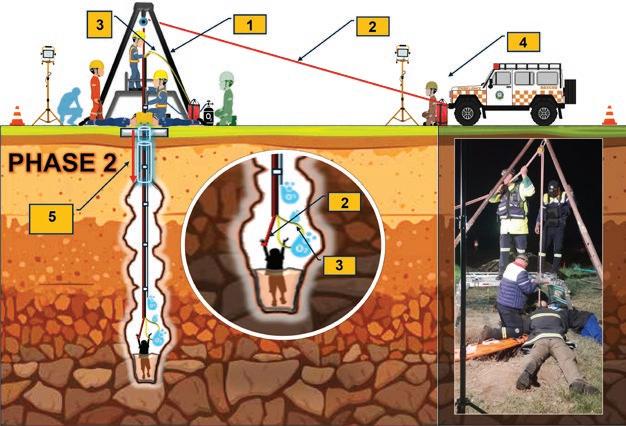
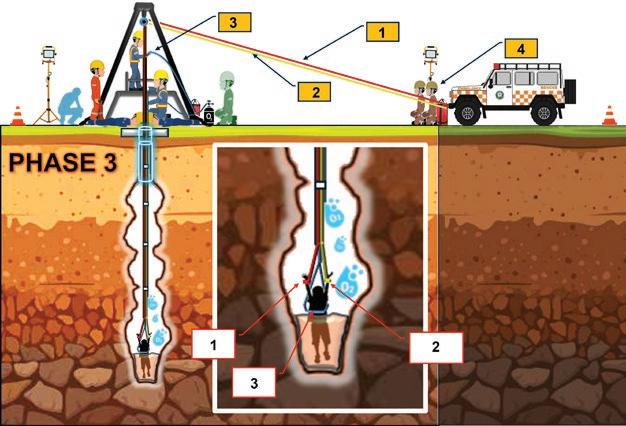
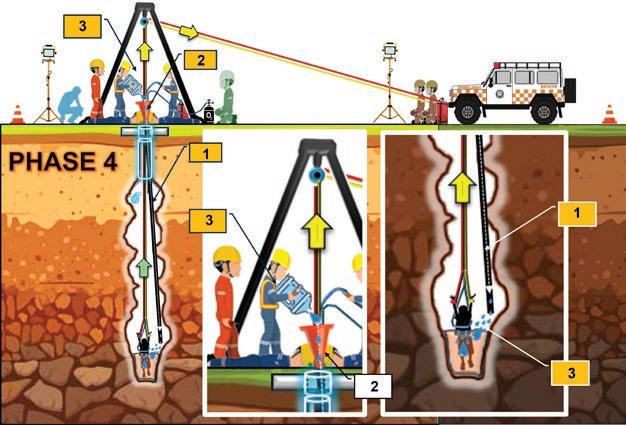
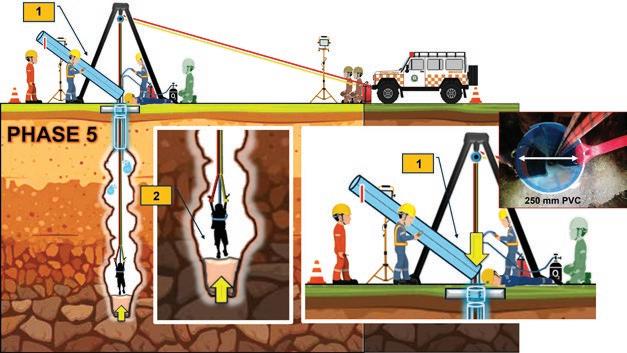
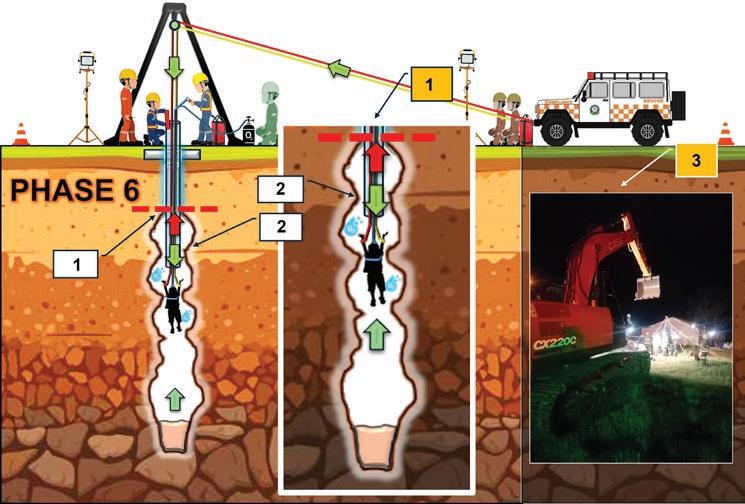
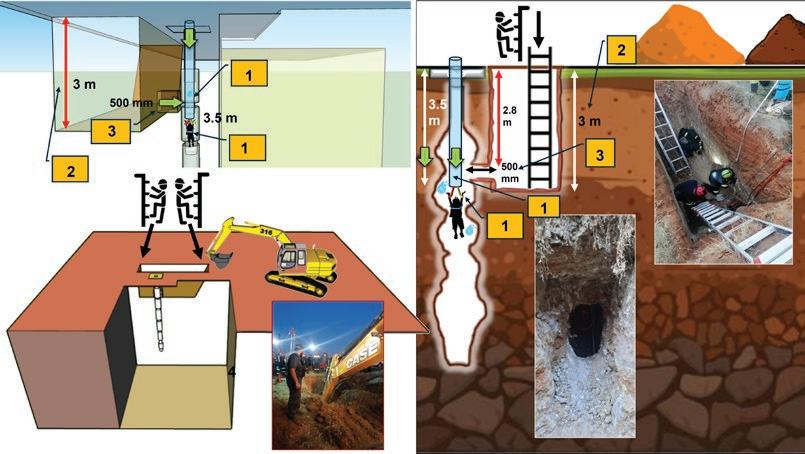

The history of the hood worn underneath the firefighting helmet
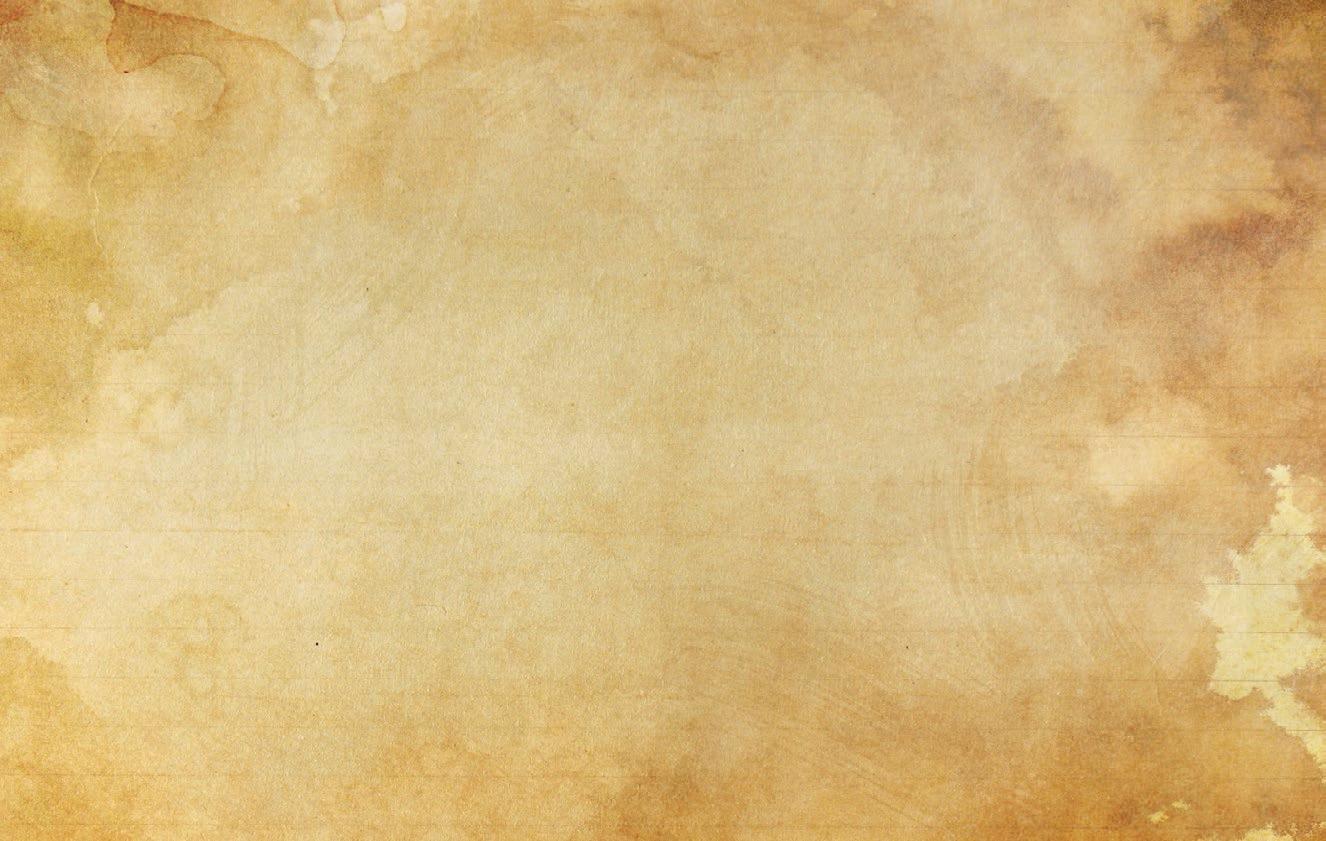
A Circa 1891 Vajen
Bader fire protection helmet/hood

The firefighting uniform is a critical piece of equipment for anyone working in dangerous fire environments. While most people are familiar with the bulky protective gear worn by firefighters, few realise the importance of the hood worn beneath the firefighting helmet.
This simple yet vital garment has an interesting history and plays a key role in ensuring the safety of firefighters during hazardous operations. The evolution of the firefighter's hood tells a compelling story of both technological advancement and an increasing understanding of the dangers associated with firefighting.
Early firefighting gear
In the early days of firefighting, protective clothing was minimal and often consisted of simple garments like wool or leather coats and trousers. Firefighters wore helmets primarily for head protection but there was little
thought given to how to protect the rest of the body, especially the neck, ears and face.
As firefighting practices evolved and fires became more intense due to urbanisation, the need for more comprehensive protection grew. Firefighting helmets, which began as simple leather or metal structures, were designed to shield firefighters from falling debris but they left other areas of the body vulnerable to heat, smoke and fire exposure.
The development of the firefighting hood
The first true "hood" worn under a firefighter's helmet emerged in the mid-20th Century, although similar items had been used in some capacity before. The early hoods were made from simple cotton or wool fabrics. They were designed to protect the neck and ears from heat and flying debris. These early designs were far from the highly specialised hoods worn
by modern firefighters but they served an important function at the time by providing some level of heat resistance and coverage to the exposed skin.
The hoods were often worn with basic helmets and could be fastened under the chin or pulled over the head as a protective layer. However, they didn't provide significant protection from the more dangerous elements of fire such as intense heat, thermal radiation or toxic gases. As such, the initial designs of firefighting hoods were more about comfort and basic coverage rather than advanced protection.
Advancements in materials: the rise of the fire-resistant hood By the 1970s and 1980s, technological advances in material science led to significant improvements in firefighter protective gear. The development of heat-resistant and flameretardant fabrics revolutionised firefighting gear, including hoods.
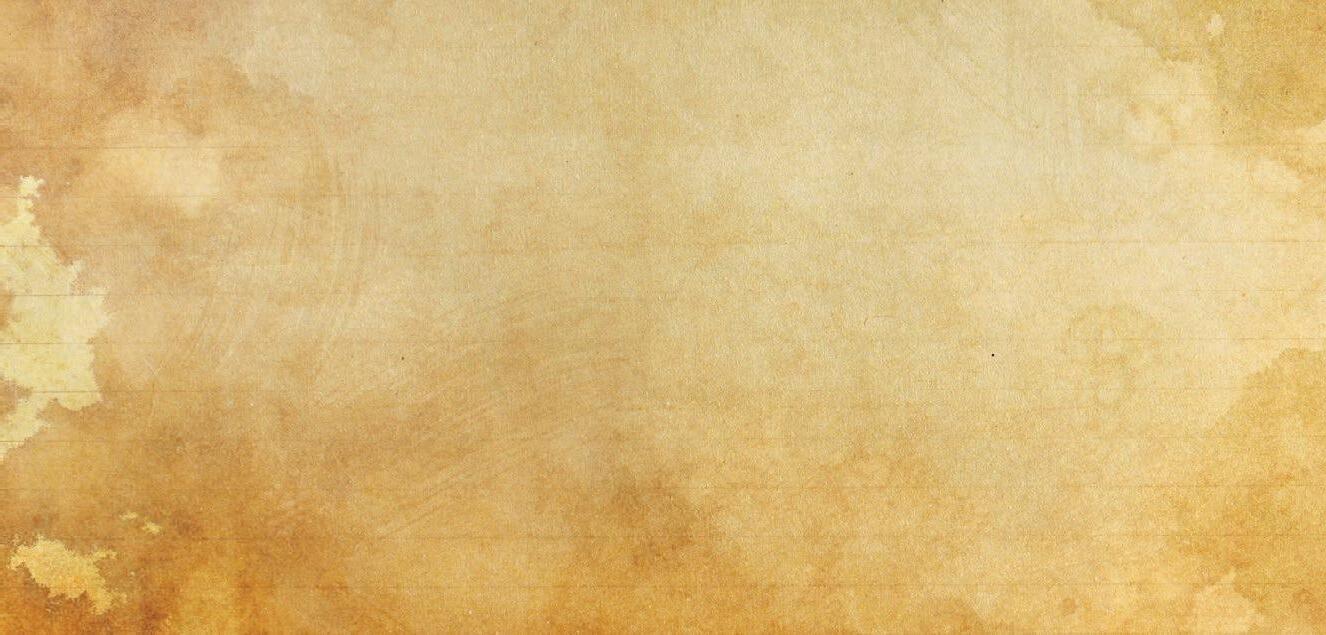
Materials such as Nomex and Kevlar became widely used due to their ability to withstand high temperatures without degrading. These fabrics are known for their flame resistance, durability and strength, making them ideal for use in environments where firefighters encounter extreme conditions.
Hoods began to be made from these advanced materials, offering firefighters better
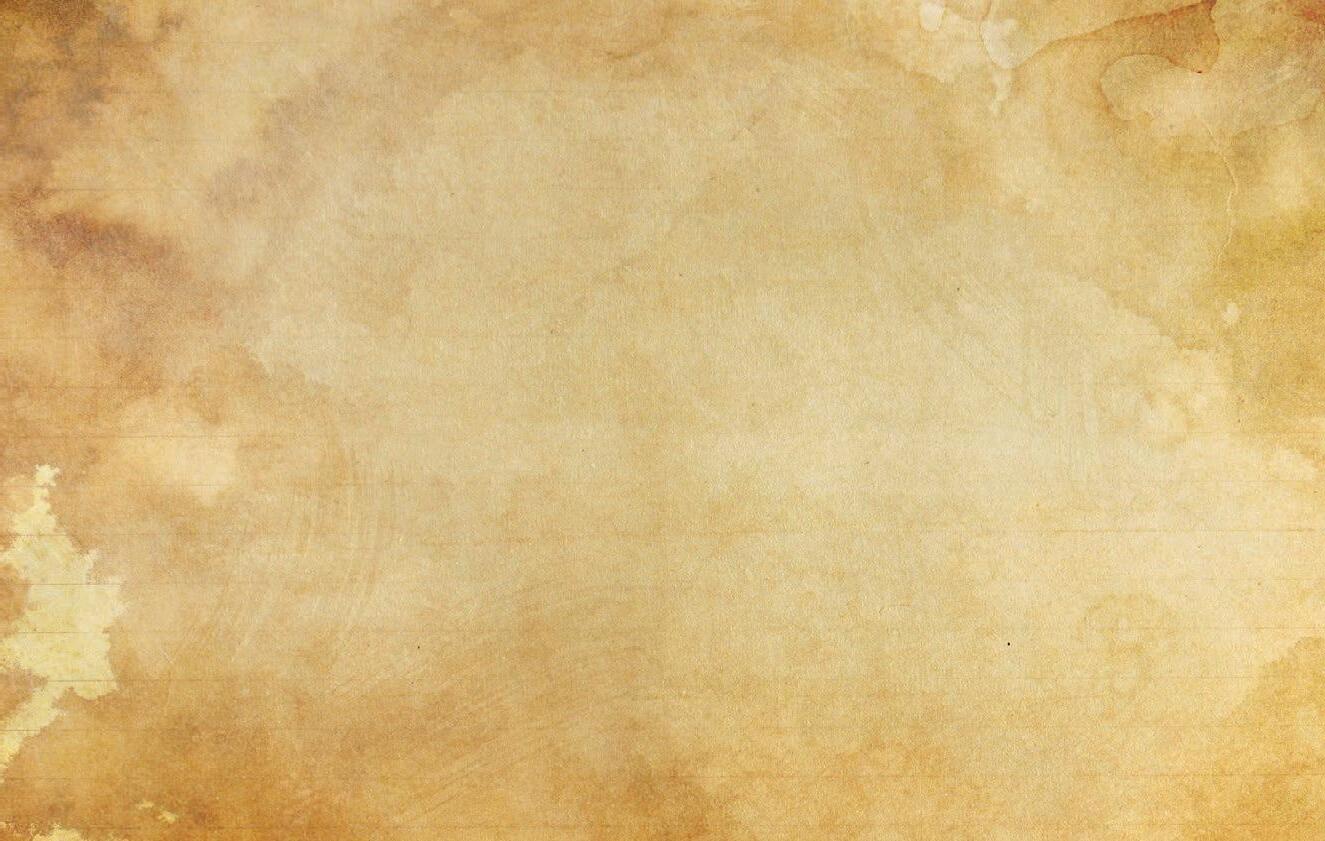
protection than ever before. They were designed to fit snugly under the helmet, covering the neck, ears and face to reduce the risk of burns and heatrelated injuries. These materials allowed for greater flexibility and comfort, while also improving protection against radiant heat and toxic gases, both of which pose serious dangers during firefighting operations.
The use of flame-retardant materials in the hood coincided with improvements in firefighting suits as a whole. Fire-resistant turnout gear, which consists of jackets and trousers, was paired with these advanced hoods to create an integrated safety system. The combination of these elements drastically improved firefighter safety, allowing them to operate in more dangerous conditions for longer periods of time.
The modern firefighting hood: functionality and design
Today, the modern firefighting hood is a highly specialized piece of protective gear. Typically, it is made from a blend of fireresistant materials such as Nomex, Polybenzimidazole (PBI) and Kevlar, which provide excellent protection against heat, flames and electrical hazards. These hoods are also designed to be lightweight, breathable and comfortable to wear for extended periods.
A contemporary firefighter's hood fits snugly around the neck, ears and lower face, offering protection from both direct flames and thermal radiation. The hood is often made with an extended neck that tucks securely into the turnout coat, ensuring that no gaps are left in the protective
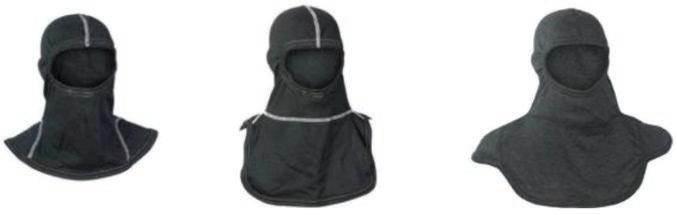
layers. The material is designed to wick away moisture, preventing the buildup of sweat and helping to regulate body temperature. In addition, modern hoods are designed to be flame-resistant while still allowing for maximum mobility and flexibility.
Some advanced hoods also come with additional features, such as an integrated mask for respiratory protection, which helps to filter out toxic smoke and gases. This addition has become increasingly important as firefighters are exposed to a wider range of hazardous substances, including carcinogenic chemicals that are released during a fire.
The role of the hood in firefighter safety
The primary function of the firefighting hood is to provide crucial protection to the most vulnerable parts of a firefighter's body. The head, neck and face are areas that are particularly susceptible to burns and the risk is exacerbated by high temperatures, radiant heat and the presence of harmful gases during a fire. Without the hood, a firefighter could face severe burns or even life-threatening injuries.
The hood helps to prevent burns from direct flame contact but it also reduces the effects of thermal radiation. When
fighting fires, firefighters are often exposed to intense heat, even from a distance. The hood shields the firefighter’s neck and face from this heat, offering an additional layer of protection against long-term damage. In some cases, the hood can even prevent respiratory injuries by providing a layer of material that filters out some of the toxins and smoke inhaled during firefighting.
From its humble beginnings as a simple cotton or wool garment to its current design as a sophisticated piece of protective equipment, the firefighting hood has undergone significant evolution. Today, it serves as a vital component of a firefighter's protective gear, safeguarding their neck, face and ears from the hazards of extreme heat and toxic environments. Thanks to advancements in materials and technology, firefighters are better equipped than ever to face the dangers of their profession.
The hood, once a simple afterthought, has become an indispensable part of a firefighter’s arsenal, contributing greatly to both their safety and effectiveness on the job. As the field of firefighting continues to evolve, it’s certain that the humble hood will continue to play a crucial role in protecting those who risk their lives to save others.
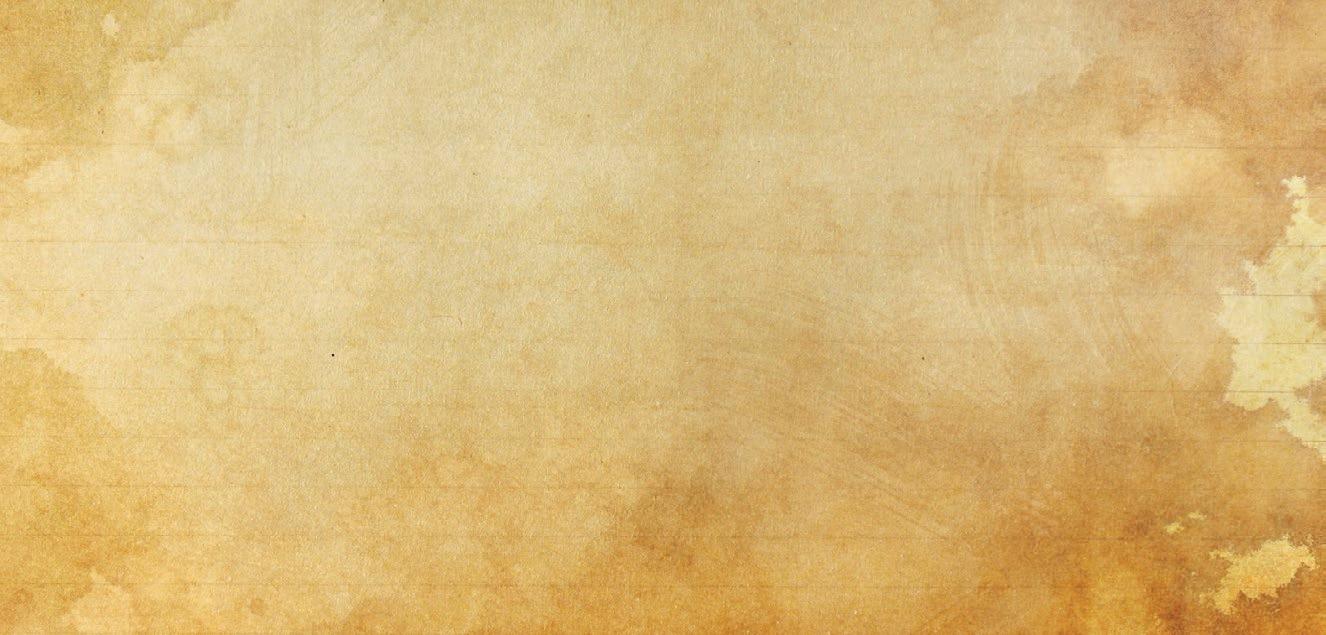

Different styles of modern hoods in terms of length and coverage
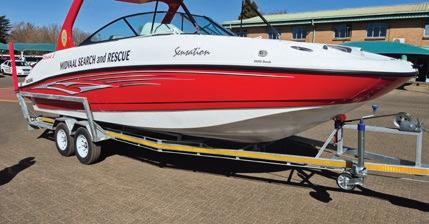
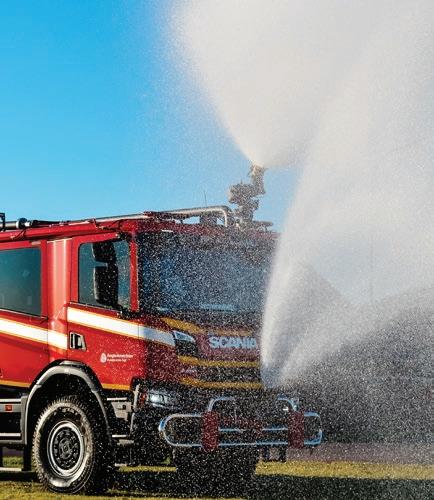
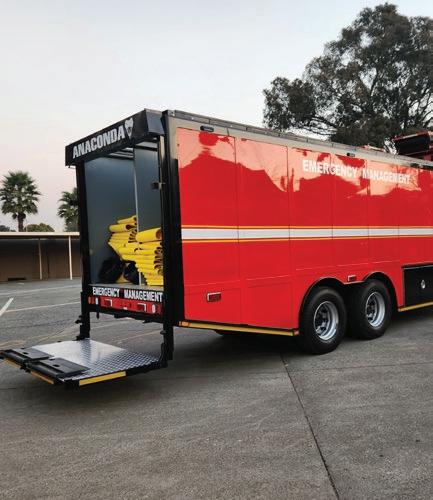
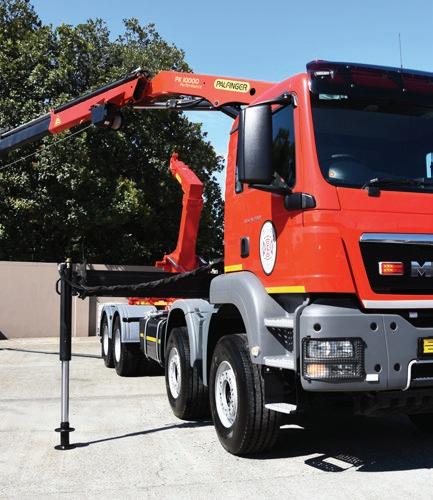
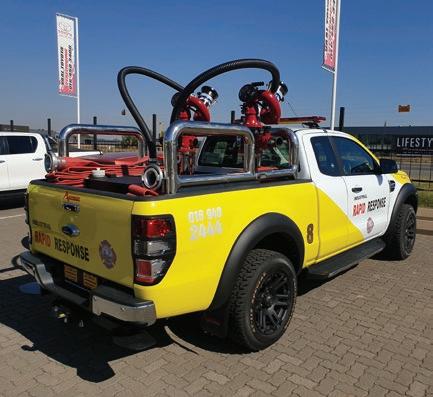
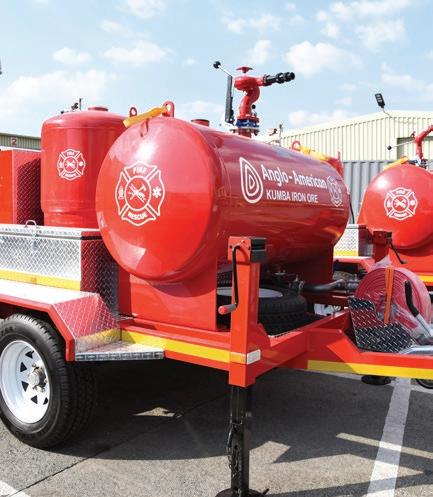
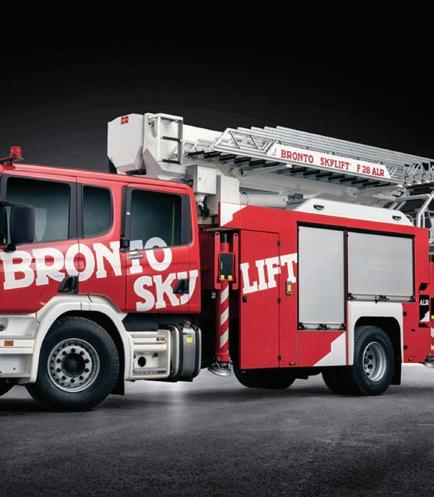
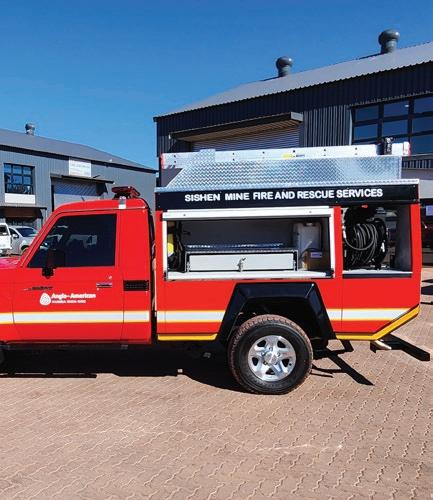
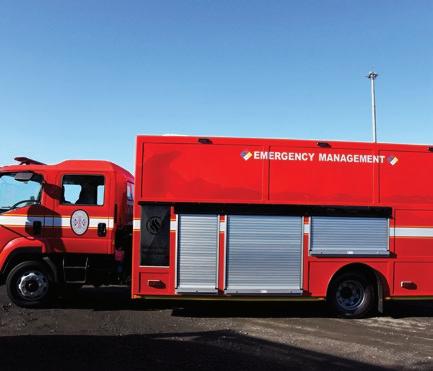
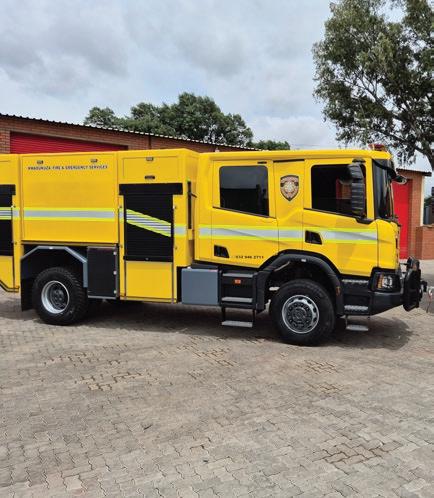
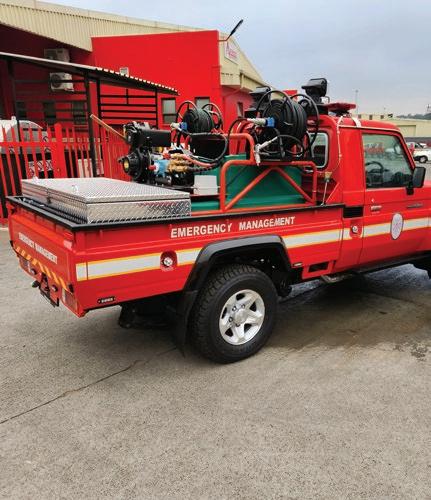

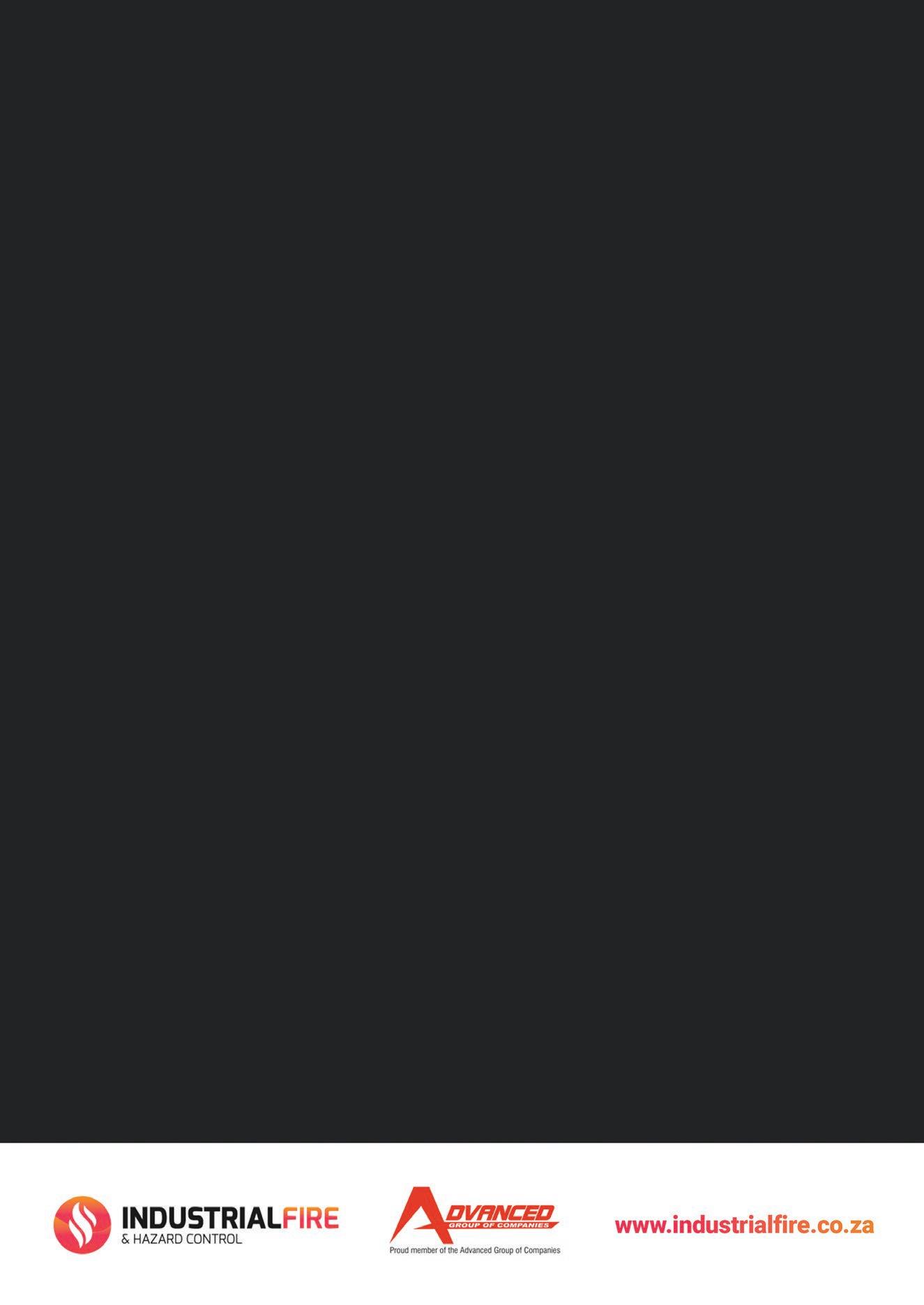