Selecting The Most Apt Boring Head
The outcome of a boring operation is influenced by the choice of the boring head, tool deflection, lubrication, cutting edge geometry, cutting parameters, chip evacuation, and temperature. Precision boring would not be possible if any of these parameters were not adequately controlled. There are a variety of boring heads available to choose from, with each type having unique physical characteristics. Every variety of boring head has distinctive qualities and is appropriate for carrying out particular tasks. But, the kind of boring head used highly depends on the kind of boring bar and the setup .
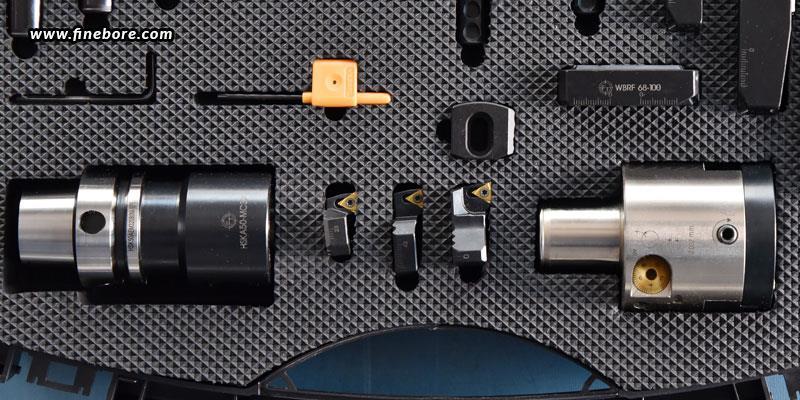
Precision boring depends heavily on how the boring head and machine are set up. The rigidity of the drill bits is the secret to precision boring. It is suggested to utilize a larger diameter boring bar with a shorter clamping length in order to increase rigidity. The precision improves with larger diameters and shorter clamping lengths. It must also be taken into consideration that boring bars do not spin in tandem with the spindle and do not have alignment flats on the shank. The spindle axis is the centre of rotation for the boring bar. Therefore, the boring bar’s orientation is crucial, which is the rake angle of the boring bars in a boring head. It is advised that boring should only be done with a boring head in neutral position.
How can better boring results be guaranteed?
It is advised to start with a cutting speed that is equal to half of the regularly computed value when utilizing the boring head, and then progressively increase it. The explanation is that the cantilevered nature of the boring head and the challenge of maintaining continuous lubrication throughout the process may cause the stiffness to decrease. Do not rotate the boring head faster than 600 rpm due to the potential for rotational imbalance, which poses a safety risk.
In addition to the rotating speed, the cutting depth is also quite important. When installing the boring head, there is a safe minimum depth of cut. The surface of the hole is smeared, resulting in an inconsistent hole size and finish, if the cutting depth is kept less than the minimum depth. Typically, the safe minimum depth ranges from 0.003 inches to 0.005 inches. However, the minimum depth of cut could also be smaller than this range, if the boring bars used are made of tougher materials.
In general, boring heads are used for larger holes, when tolerances are strict and accuracy is essential. The boring head can also improve the surface finish of the hole. Additionally, the boring head can be utilized to process the workpiece by turning an inner diameter hole with the cutting tip pointing inward, in addition to a precise outside diameter hole. This results in improved precision and accuracy.
Where to get your boring heads?
FineTech Toolings is where you can go to when you’re looking for boring heads that can deliver a guaranteed result. Whether the application you’re operating on is concerned with finish boring, rough boring, deep boring, large diameter boring, or any other kind of specialty boring, these precision boring head manufacturers in Bangalore have it all for you.