Boring Bar Applications – Setting Up Your Tools For Success
The interior diameter and length of a component feature are what set the limitations in boring applications; nevertheless, it is these two features that help in selecting the best bar for a certain application too. The fundamental boring bar guidelines recommend choosing the largest possible bar diameter and the smallest possible overhang. Clamping the bar right, effective chip evacuation, and choosing the insert based on the cutting conditions, are other critical factors to consider.
Clamping the boring bar
So as not to introduce a weak link in the setup, modern high performance boring tools need to be clamped with high stability. In order to properly balance the cutting pressures, it is crucial to clamp onto a minimum of three to four times the diameter of the bar. To ensure the greatest amount of contact between the bar and the holder, split collars and sleeves are strongly advised. Using highquality sleeves and adapters can support tooling optimizations.
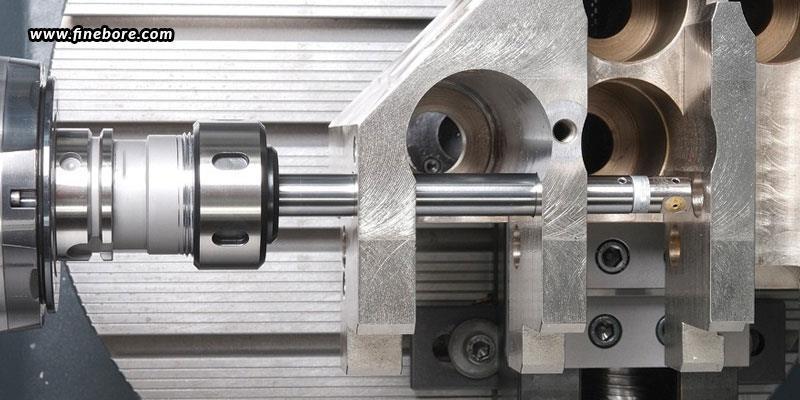
Chip evacuation
In order to prevent damage to the work piece at high stock removal rates, the chips must be evacuated from the hole at a faster rate. High-pressure systems and adequate coolant flow can help with efficient chip evacuation. For some applications, it might be advantageous to bore upside-down to provide chips more room to escape when they are drawn centrifugally to the outside walls of the bore diameter.
Choosing the appropriate insert
The lowest cutting forces will be produced when a positive style insert is used in conjunction with a more positive macro geometry. The most positive geometry with a chip breaker suited for the required cutting data should be chosen, if the application permits. In order to prevent vibrations or poor chip management, a slight compromise between wear resistance and cutting-edge strength may be necessary in some boring applications. A negative type insert should be used in short overhang configurations for semi-finishing and roughing applications. However, it’s crucial to realize that negative style inserts can typically use up to 20% more horsepower, and can generate significantly more cutting forces than positive style inserts, which in turn results in cutting forces being generated at a significantly lower rate.
Recommended overhang for different types of bars
Every boring bar application, as we all know, is uniquely different. A steel bar can be used for overhangs up to four times the bar’s diameter. Though, it is highly recommended to start thinking about a carbide or heavy metal bar as soon as you exceed four to five times the overhang of the bar diameter. Internally damped bars are a powerful productivity booster in applications with long length to diameter ratios exceeding eight times the bar diameter because they significantly improve speed and feed capabilities and lessen vibration tendencies. Damped boring bars with carbide reinforcement can be used for anything over that, and perform well for overhangs of up to 14 times the diameter.
You ought to be in a better position to make the right decision, now that you’re aware of everything that has been said so far. So, take into account every crucial factor and contact FineTech Toolings, the most reliable precision boring bars manufacturers in Bangalore, for assistance in obtaining the most suitable premium quality boring bars.
For more information, visit: https://finebore.com/