Answering Some Challenging Questions About Boring Tools
There are numerous ways to create holes, but some methods are superior to others. And, of the lot, boring seems to be one of the most popular options. But, as much as boring is popular, so does it come with some queries and doubts. Here are some such handful intriguing queries that may arise in your mind regarding the same.
How many modular parts can be utilized in a boring setup?
As always, the quickest setup is preferable. This is made possible by modular boring assemblies that use systems that open up a variety of options for reductions, extensions, and dampening. But there are restrictions. A maximum of four or five components, excluding boring head insert holders, should be used in any boring assembly.
When to consider roughing, and when finishing?
There are a variety of factors that can decide on making the right choice, which include hole diameter tolerance, length to diameter ratio, cast parts, and surface finish. For instance, if the hole diameter tolerance is tighter than 0.004 inches, finishing heads ought to be considered, and if anything above that, then roughing heads are the better choice. If the length of the hole is longer, a roughing head should be used to true up such a hole before finishing. A part made from a casting process will typically have hole well undersized, and the holes will also tend to be curved and out of position to some degree. This is where a roughing head should be used to prep up the hole. Finally, a bore with a tight surface finish will always require a finish boring head.
How should a hole be prepared before boring?
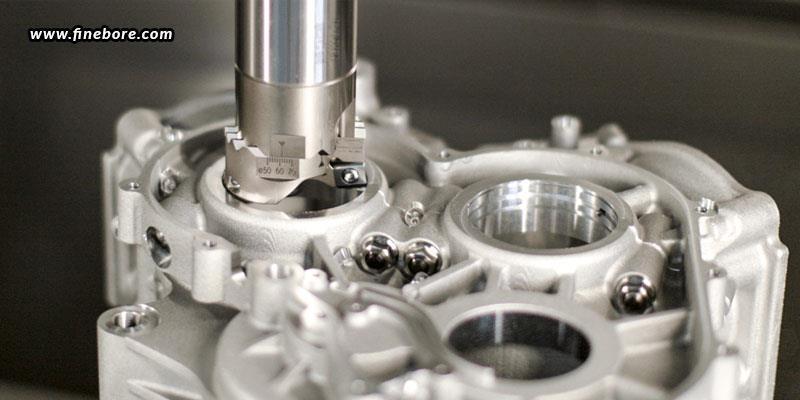
When castings and weldments are present, rough and fine boring is best carried out after the workpiece has been machined to square the hole to the entry surface. When a hole has been chamfered and the rough or semi bore is clear of any chatter or deep scallops made by rough milling, fine boring tools should also be used to enter the hole.
How to be certain about the length of the boring tools to be selected?
Diameter and gauge length are only two factors in right-sized tooling. The reach required to get to the bore and its depth must also be taken into consideration. In other words, you should plan your setup for eight inches of reach if the hole is three inches deep but the tool needs to reach five inches to get to the bore.
How to keep the chips under control during boring?
Optimizing the cutting speed should be the first priority. High cutting speeds typically result in cutting conditions that keep the chip load consistent. Next must be determined the chip load in inches-per-revolutions (IPR) that produces C-shaped chips that are as short as possible. Finally, performing a trial cut to improve chip form is also advisable, as this will be worthwhile in the long run.
These are just five most popularly tricky questions answered. You may have more to clear off in your mind. After all, boring is a challenging process . You can then get in touch with FineTech Toolings to help clear off all such queries, while also providing you with the best possible precision boring tools in Bangalore. For more information, visit: https://finebore.com/