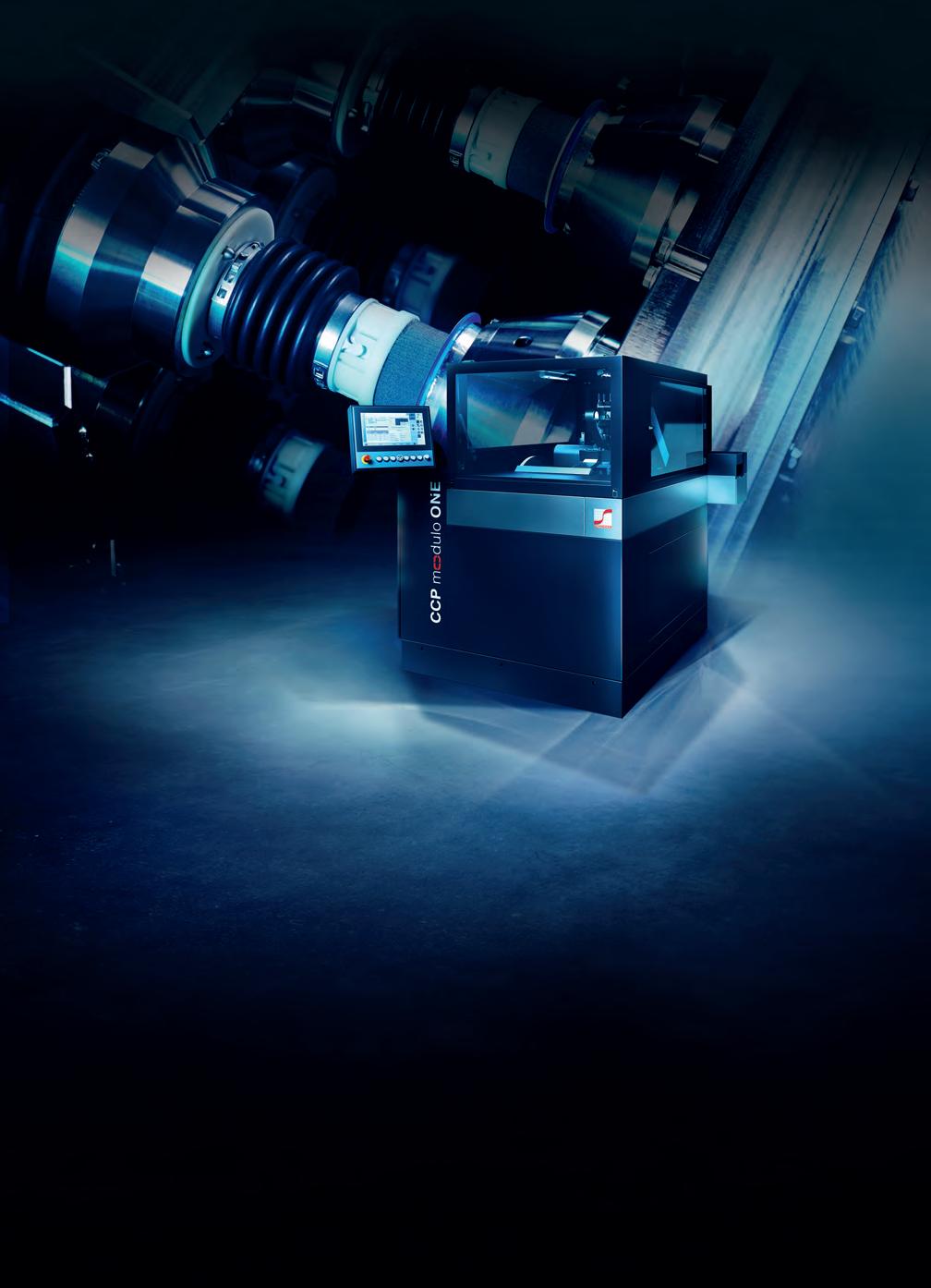
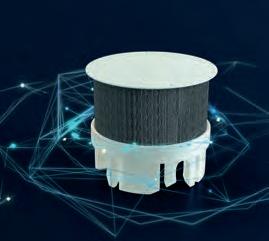
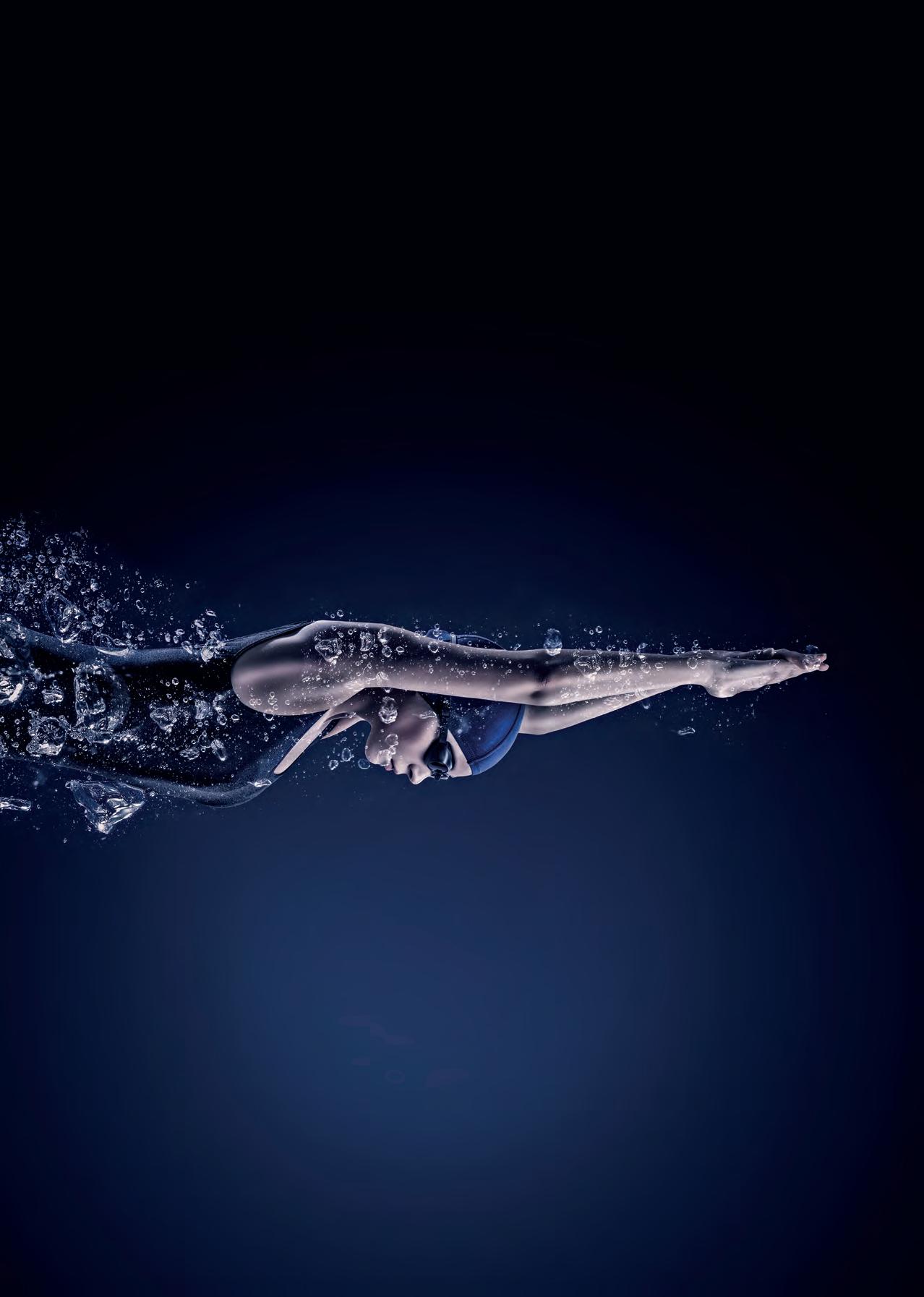


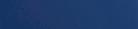


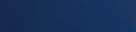
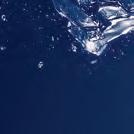
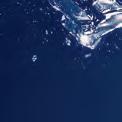




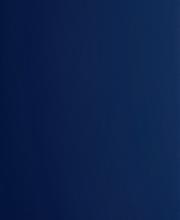
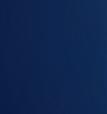
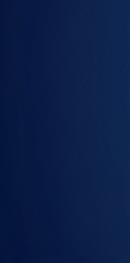


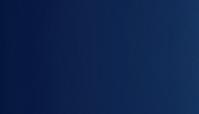
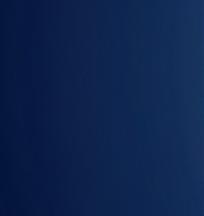
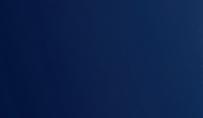
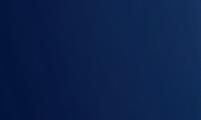

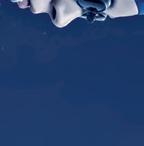

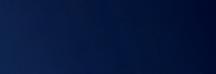
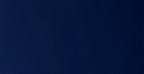



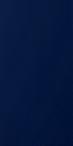

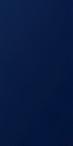
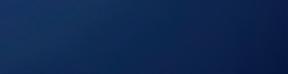
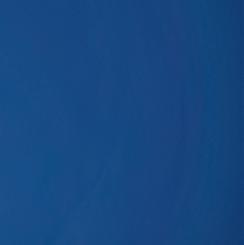
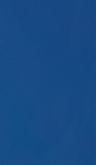













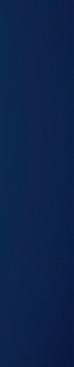



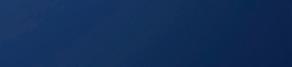
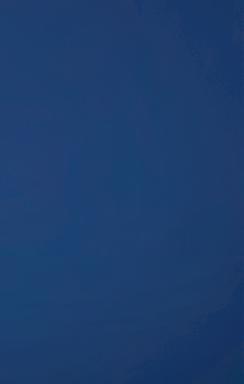
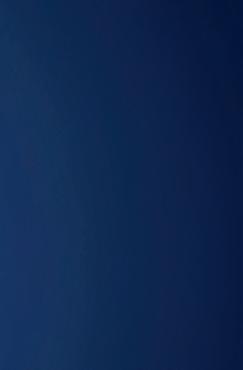


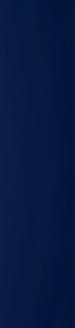



July 28 of this year set a new sad record. It is the so-called Earth Overshoot Day, the day in the year on which mankind – mathematically speaking – has used up all the natural resources that the earth can provide in a year.
In 1970, Earth Overshoot Day was still at the end of December. At that time, humanity's consumption of resources could at least hope to regenerate the Earth. More than 50 years later, we theoretically need more than 1.5 Earths to satisfy our requirement for resources.
Humanity is thus living well beyond its means. Even if some countries evidently consume far more than others. Qatar or Luxembourg, for example, occupy the unwelcome first places, while many developing countries or small island states do not live beyond their means at all.
This is also due to the fact that industry con tributes a significant share, which is why many industrialized countries also score poorly in the comparison. In such countries, the average ecological footprint per person is greater than the global biocapacity per person.
Fortunately, many companies and even entire industries are now beginning to take action. Slowly but surely, they are adapting their production processes. In this issue, we look at how well they are doing under the heading "Sustainable Processes".
The focus is not only on how to minimize the impact on the environment. It is also about creating healthy working conditions and working economically. In other words, creating a sustainable environment that ensures that future generations are not worse off than the present one. To this end, our authors in this issue address a wide variety of challenges in the lab in their articles:
Can spectacle lenses be produced sustainably despite the use of alloy?
Do certain production processes represent a risk to the health of lab employees?
How does meaningful sustainability report ing work?
These are just a few of the questions addressed in detailed articles in this issue. Some of the answers to these questions give us hope, others give us pause for thought – but, either way, they are all worth reading ◆
Horizons Optical in the US
Horizons Optical, an international R&D company placed in Barcelona, Spain, that is focused on the develop ment and distribution of technology for the optical industry, has settled a subsidiary in the US, Horizons Optical of America (HOA).
The opening of the subsidiary goes through the creation of customer service and commercial attention. The recent set up subsidiary placed in Lewisville, Texas, will be providing technology and services all around US and LATAM markets as well as Canada, being closer and supplying Horizons Optical partners with efficient service. A professional reinforced team is leading the new subsidiary on one side with Ulises Pérez, responsible for the technical customer support depart ment and with Albert Pogorschelske, leading the commercial team. Both are experienced professionals in the optical industry and will meet challenges with a multi-disciplinary team and will be supported by advanced equipment in lens design and coating analysis. Santiago Soler, CEO of Horizons Optical, stated: “The opening of a new branch office in the United States is a milestone for Horizons Optical. We are very proud and excited to be able to start operating in this market, which is full of op portunities and growth possibilities for the company."
Santiago Soler.
EssilorLuxottica and Politecnico di Milano have created the first ever joint research center aimed at designing the smart glasses of the future, EssilorLuxottica Smart Eyewear Lab.
The agreement was announced by Vittorio Colao, Minister for Technological Innovation and Digital Transition; Giuseppe Sala, Mayor of Milan; Fabrizio Sala, Lombardy’s regional Minister for Research, Innovation, University, Export and Simplification, and Internationalization; Ferruccio Resta, Rector of Politecnico di Milano, and Francesco Milleri, Chairman and CEO of EssilorLuxottica. It involves an investment worth over 50 million Euro. The project will encompass industrial research and experimental development of devices underlying a new generation of wearables which are capable of autonomous network connection. It is a project that is meant to enable the development of technologies and services by means of a widely used interface such as eyewear.
The EssilorLuxottica Smart Eyewear Lab will initially last five years and will employ when fully operational over 100 researchers and scientists working closely together in a dedicated space within the Innovation District, which the Politecnico di Milano is currently developing in the Parco dei Gasometri, located in the Bovisa area in Milan. The University thus aims to bridge the gap between universities and businesses, develop ing a highly international research environment that fosters synergies a nd transversality. The project’s main challenge will be the development of core hardware, software and application technologies to enable humans to interact with the digital world.
The organizers of Vision Expo, The Vision Council and RX, shared details on The Panorama, a new Show Floor neighborhood planned for Vision Expo West, taking place September 14-17, 2022 in Las Vegas at the Venetian Expo & Convention Center. The Panorama is designed to showcase cutting-edge technology in the vision industry.
“Driven by our commitment to leading the vision industry forward, we are thrilled to announce the debut of The Panorama,” said Mitch Barkley, Vice President of Trade Shows and Events at The Vision Council, co-organizer of Vision Expo. “The addition of The Panorama neighborhood was inspired by the rise of new companies in the tech innovation category. The new neighborhood will make the show floor easier to navigate, allowing attendees to explore these tech-forward companies that are revolutionizing the industry in one, centralized location.”
The Panorama will spotlight the innovative frontier of vision technology, including cutting-edge business solutions, medical advances, software and wearables that are paving the path for what’s to come in the industry. It will include more than 20 exhibiting companies, including Optify; Notal Vision; Roya; Virtual Field; and Visibly, among others. For companies interested in learning more about participation or moving into this neighborhood, please contact Mike Annunziato at michael. annunziato@rxglobal.com.
To sufficiently limit greenhouse gas emissions
At least
million people were affected by hunger in 2021, according to a recent report from the Food and Agriculture Organization of th e United Nations (FAO). That's 46 million more than 2020 and 150 million more than in 2019.
of human societies and natural
the
Source:
to the
climate, the World Resources Institute analyzes that $5 trillion per year will need
be invested between
and
Eyewear is still reliant on store-based retailing, which accounted for 87% of eyewear sales globally in 2021. Within store-based retail,
shops is by far the leading channel for
SCHNEIDER’s Control Center, the brilliant mind inside to the Modulo Line, now comes with real-time cost tracking to monitor the true and unique costs of the job while it is being produced. The new in-depth breakage analysis breaks down all the reasons and causes for breakage and offers a detailed analysis of all parameters involved, providing the basis for active trouble shooting. The intelligently designed management cockpit is now also available for stand-alone or classic lab layouts, even if there is no physical connection between the machines at all. The Modulo Control Center has been tailored specifically to the needs of ophthalmic labs and features an extensive set of features and functionalities that sets it apart from a conventional MES. Visit www.schneider-om.com
A novel generator/polishing geometry configuration NURBS (Non Uniform Rotational BSpline) software runs the surfaces generator including In-Lab progressive optimization. A fast diamond pivot tool avoids vibration common to free form generators. Thus, no process-calibration is needed saving time for production efficiency. True curve consistency gives always power accuracy. Another feature of this robust generator is its ability to produce program exact prisms. This saves alloy and bypasses another time-consuming step and a large source of error. Exact and smooth surfaces translate to a 120’’ 150’’ seconds polishing time; a complete job every 2.5’ minutes. A ZERO SCRAP PROCESS. Visit www.augenopticos.com
MIDO is warming up for the 2023 edition After an edition with results that exceeded all expectations, with 22 thousand visitors in 3 days, MIDO is warming up for the 2023 edition. The appointment for all eyewear professionals is from 4 to 6 February 2023 at Fiera Milano Rho. At MIDO 2022 the more than 670 exhibiting companies from 45 countries met visitors and buyers from over 50 countries, mainly from Europe (especially Germany) but also from the United States, Israel, Brazil, India and the United Arab Emirates. For over 50 years MIDO has been the heart of business and trends in the world of eyewear, where all the players in the supply chain can get together: from manufacturers of frames, lenses and machinery to designers, from large multinationals to small innovative companies, ready to make business. The eyewear sector is in turmoil and is preparing to turn the spotlight on next year. MIDO is active on the online platform www.mido.com and on the official social channels: Instagram (@mido_exhibi tion), Facebook (@MIDOExhibition), Twitter (@MIDOExhibition) and LinkedIn.
MAFO - The Conference 2023
Date: February 03, 2023
Location: Fiera Milano Rho in Milano/Italy
Are you interested in giving a lecture on a new topic in ophthalmic optics? If so, please feel free to contact us! You can submit your ideas matching the special topic “Lab Visions” but also other relevant topics for the ophthalmic industry.
With the theme of MAFO - The Conference 2023, we would like to encourage the industry to share visions for the future based on the current innovations in the industry, its exciting R&D topics and global developments.
Our invitation to give a lecture is free of charge. Therefore, please note that your presentation should not have any commercial or promotional content.
The auditorium consists of physicists, engi neers, technicians and executives from the global ophthalmic optics industry.
You can find topics and impressions of past MAFO conferences here: www.mafo-optics.com/gallery
Please submit your proposal no later than September 15, 2022.
Rebekka Nurkanovic rebekka.nurkanovic@mafo-optics.com Phone: +49-208-306683-18
The technology of photoinitiated polymerization, known since ancient Egypt, is widely used in various industries, and in the 20th century it gained huge importance in the paint industry of Europe: back in 1967, a progressive industrial technology for curing by that time with ultraviolet radiation (UV radiation) of unsaturated polyesters (the most common materials at that time) was proposed. The main advantage of the process then was a significant reduction in the time for obtaining the finished coating. By François Breton
In addition to the time gain, a significant advantage of the process was the reduction of production space due to the compactness of the equipment. In total, the availability on the market of raw materials for the synthesis of unsaturated polyester resins, the development of a technology for the industrial production of photoinitiators (at the initial stage, benzoin esters were used as photoinitiators) and the presence on the market of industrial sources of UV radiation (initially, low-pressure mercury lamps with a power of 0.5–1.0 W/cm; and since 1970 high-pressure mercury lamps with a capacity of 20–30 W/cm) contributed to the rapid introduction of UV-cured materials on an industrial scale throughout Europe by the end of the 1970s.
In the ophthalmic industry, with the growing usage of polycarbonate as a lens material predominantly in North America, there was a need for protecting the lens surface from scratches, hence the need for an abrasion resistant coating. Given the fact that the lenses are surfaced from the concave side, even if the initial lens could have been dip coated or in mold coated, the back side still remained to be coated. It was then obvious, with the shape of the lens and the initial low number of pieces to be coated, that spin coating the back side was the most suitable technology to be used. Of course, UV curing could only be the technology used in order to cope with the need of fast lens delivery at the optical shop. From a chemical viewpoint the main monomers used were methyl acrylates and their derivatives as it was already known that PMMA
(most widely known under its Plexiglas trade name) was more abrasion resistant than polycarbonate while having a good transparency. The first consequence of this type of UV cured hard coatings was that when customers in North America wanted an anti-reflective coating to be applied on their lenses, those premium lens treatments could not fulfil their role. The main issue was that, due to limited adhesion, those coatings were peeling off after a few weeks only. This phenomenon was not so well understood at that time, leading to a bad perception of the AR coating treatments in that part of the world. This is the main reason why the ratio of AR coated lenses is still much lower than in Europe or Asia. Significant improvements have been achieved in the design of UV curable coatings with the introduction of nanofillers and vinyl silane monomers, leading to a much higher abrasion resistance level and a better compatibility with AR coatings. Yet, in order to remain UV curable, monomers still require a high level of double bonds (C=C) to make them susceptible to create a polymer network under UV activation. This organic part makes the UV curable coatings extremely compatible with organic lens materials, either thermosetting (such as CR39 or High Index) or thermoplastic (such as polycarbonate). This is the reason why there is no need for a surface activation prior to the coating ap plication. A simple cleaning/degreasing with isopropanol will allow a good coating adhesion on the lenses. However, unlike the thermally curable coatings that are nearly purely inorganic once cured, they cannot achieve the same level of compatibility with AR coatings that are made of inorganic materials (mostly oxides and fluorides).
First of all, it is a resin system that employs a photoinitiator molecule to absorb ultraviolet radiation and utilize that energy to initiate the polymerization of a set of monomers and/or oligomers. A schematic of a typical UV formulation is given in the image below.
After that quick classification the description of UV-curable resins opens up in many directions, all based on the end use application. Viscosities can range from water-thin at room temperature to that of traditional hot-melts. The resin systems are filled with nano particles such as SiO2 or TiO2 to increase hardness and/or refractive index. Resin functionality can vary from traditional mono-, di- and
The monomers and oligomers are used to tailor the properties in both the uncured and final cured state. Additives such as viscosity modifiers may be added to aid processing. The photoinitiator molecule is the key to understanding the resin system’s capabilities and requirements. UVcurable resins are best classified by photoinitiator’s reaction mechanism with the two most common classes being free-radical and cationic/anionic.
tri-functional monomers to hyper-branched oligomers with func tionalities greater than 18! Given the fact the coating should not be yellowing on ageing, the monomeric and oligomeric backbones can only be of an aliphatic nature and may contain pre-polymerized constituents such as polyesters or polyurethanes to further improve physical performance.
At this point, it might be necessary to refresh our memories and recall the various categories of UV lights:
▶
The UV-A region extends just beyond our visible horizon (315 to 400 nm wavelength) and recent trends in photoinitiator chemistry employ this region more and more. This low frequency region has the highest depth of penetration into materials and the photons in this region as the safest to use (lowest energy).
▶ The UV-B region (280 to 315 nm) generally receives its classification due to its properties as a transition region. While most UV-A radiation does not have significantly damaging biological effects, the higher energy UV-B radiation does; you know this effect as sunburn.
▶ Many of the earliest UV-functional materials employed absorption in the UV-C region (e.g., benzophenone-type initiators). Wavelengths in this region (200 to 280 nm) are often referred to as “germicidal” wavelengths due to disruption of DNA processes at the cellular level. A further distinction of the UV-C region is that these wavelengths are almost completely absorbed by the ozone layer while UV-B radia tion is only partially absorbed (thank you ozone layer!).
Free radicals can only be generated upon absorption of UV radiation and the source of UV radiation is defined and controlled by the process.
Since the most widely used UV curing lamps are based on the mercury (Hg) radiation spectrum, the UV curable lacquers must contain benzophenone as photoinitiator as shown by the absorption spectrum. Benzophenone is nearly transparent to the UV-A and UV-B region and only in the highest frequencies of the UV-B region (~290 nm) does UV radiation begin to excite benzophenone valence electrons.
Once the free-radicals are generated, the polymerization mechanism is no different than any free-radical polymerization process. The chain propagation, termination and transfer steps found in other free-radical processes are consistent in UV polymerization. Mechanistically, it is only the initiation process to generate free radicals that separates UV polymerization apart. It is this initiation process however that gives UV-curable resins, specifically free-radical UV-curable resins, a very unique advantage over traditional free-radical systems and that ad vantage is control.
In the UV polymerization process you have complete control over the number and rate of free-radicals generated at any point in the process. Free radicals can only be generated upon absorption of UV radiation and the source of UV radiation is defined and controlled by the process.
The strongest absorption efficiencies do not occur until well into the UV-C with a peak absorption wavelength of 254 nm. Benzophenone and benzophenone-type photoinitiators are among the shortest wavelength (highest frequency) absorbing photoinitiators for UV curable resins as oxygen begins to absorb electromagnetic radiation below 220 nm. Benzophenone-type photoinitiators require a co-initiator, usually an alcohol or amine, functional groups that can readily have hydrogens abstracted, in addition to the photoinitiator. The absorption of UV light by this type of photoinitiator causes an excited electron state in the photoinitiator that will abstract a hydrogen from the co-initiator, and in the process, splitting a bonding pair of electrons. An example mechanism is shown below.
As we have seen in the previous chapter, once in contact with UV light, the monomers will turn into free radicals. Those free radicals are the main responsible for cancers, especially for skin cancers. Having carried out my PhD experimental work in a laboratory specialized in free radical polymerization, I would like to pay tribute to some of the re searchers who dedicated their life to that chemistry and who all died from cancers related to that chemistry: Prof. Michel Bartholin (19412006), Prof. Jean Guillot (1937-1999), Prof. André Revillon (1943-2010) and Dr. Christian Graillat (1947-2017). The fact that they were based in Lyon (France) where the International Agency for Research on Cancer (IARC) is also located, prompted the latter to organize a seminar entitled ‘Exposure to Artificial UV Radiation and Skin Cancer’. Of course, the main target was about the tanning cabinets that had grown over Europe without any serious control of the possible damages on the human body.
Measurement of ambient solar UV radiation has been performed worldwide for many years. However, UV radiation detectors for research or individual use have been developed only recently. There are two principal types of instruments: steady spectroradiometers, which screen the entirety of the UV spectrum (100–400 nm) within a few minutes, and broad-spectrum dosimeters, which can measure solar irradiance within a few seconds. Individual dosimeters, which can easily be placed at strategic places on individuals, are of the second type. Broad-spectrum instruments often include a weighting factor representative of a given biological spectrum (e.g. skin erythema). The biologically relevant UV radiation dose at a given wavelength corresponds to the measured UV radiation multiplied by a weighting factor specific to the biological endpoint considered (e.g. erythema, pigmentation, carcinogenesis, etc.) at that wavelength. For the overall dose (E eff expressed in watts per
Excess generation of free radicals may overwhelm natural cellular antioxidant defences, leading to oxidation and further cellular functional impairment.Benzophenone
The fully automated CDS 1000 is the most reliable hard coating machine. Producing up to 160 lenses/h, it is a perfect fit for medium and large size labs. It features six cleaning tanks and offers continuous and fast processing without any batching. Varnishing takes place by thermal polymerization. An automatic refill system provides consistent and stable process control - keeping detergent and varnish tanks at the same level and condition. A unique water cascading and filtrating system enables city water savings up to 75%, making the CDS 1000 an environmentally-friendly coater.
square meter (W.m-2)), the weighted components are added for all the wavelengths included in the interval considered. The specifications of the relative erythemal effectiveness are defined by the parameters de scribed in table 1.
The standard erythemal dose (SED) is a measure of UV radiation equivalent to an efficient erythemal exposure of 100 joules per square meter (J.m-2). The clinically observed minimal erythemal dose (MED) is defined as the minimal amount of energy required to produce a qualifying erythemal response, usually after 24h. The erythemal re sponses that qualify can be either just-perceptible reddening or uniform redness with clearly demarcated borders, depending on the criterion adopted by the observer. Since 1997, the Erythemal Efficacy Spectrum of human skin has become an International Organization for Stand ardization/International Commission on Illumination (ISO/CIE) standard that allows, by integration with the emission spectrum of any UV source, calculation of the erythemal output of this source.
The UV index is a tool designed for communication with the general public. The UV index expresses the erythemal power of the sun: UV index = 40 x E eff W.m-2 (see table 2). It has been determined that the maximal daily dose that a worker exposed to UV would be able to receive without acute or long-term effects on the eyes is at 30 J.m-2 (eff), which corresponds to a little less than 1/3 of SED. This value takes into account an average DNA repair capacity in the cells. However, there are still no recommendations for safe doses for human skin.
We all know that the main source of natural UV radiation is our sun. Thanks to our ozone barrier in the stratosphere, at ground level, UV radiation represents about 5% of solar energy, and the radiation spectrum is between 290 and 400 nm.
Artificial sources are the various lamps which have gained impor tance in many industries, including the medical industry. Some treatments do use UV radiations but there is a strict control of the wavelengths and the power of the lamps used for those specific zones of the human body.
Excess generation of free radicals may overwhelm natural cellular antioxidant defences, leading to oxidation and further cellular functional impairment. In reality, the oxidative damage potential is greater, and thus there is a constant small amount of toxic free radical formation, which escapes the defence of the cell. Oxidative stress is proportional to the concentration of free radicals which depends on both processes (formation and quenching). The degree of oxidative stress experienced by a cell will be a function of the activity of free radical generating reac tions on one hand, and the activity of the free radical scavenging system on the other.
UV-induced generation of reactive oxygen species in the skin develops oxidative stress, when their formation exceeds the antioxidant defence ability of the target cell (Katiyar and Mukhtar, 2001). Although the skin possesses an elaborate antioxidant defence system to deal with
In the ophthalmic industry, with the growing usage of polycarbonate as a lens material predominantly in North America, there was a need for protecting the lens surface from scratches, hence the need for an abrasion resistant coating.
UV induced oxidative stress and immunotoxicity, excessive and chronic exposure to UV light can overwhelm the cutaneous antioxidant and immune response capacity, leading to oxidative damage and immu notoxicity, premature skin aging, and skin cancer. Acute exposure to UV irradiation depletes the catalase activity in the skin and increases protein oxidation (Sander et al., 2002).
Damage done to genes in the DNA may result in genes that produce ineffective proteins; some of these proteins are watchkeepers over the DNA integrity.
Some of these mutations may involve genes known as tumor suppressor genes. These genes code for proteins that function to repair damages in DNA or cause cells that are damaged beyond salvage to be removed through a process of apoptosis (programmed cell death).
Most often, it is a series of mutations in tumor suppressor genes and other genes that leads to the formation of a cancer cell.
It may be thought that the stability of the free radicals created from the UV activated monomers is too short to produce effects on the opera tors who are working with them on a daily basis, but given their high amount and their ability to react with oxygen from the ambient at mosphere, they can easily transfer to any receptor, such as the skin or the respiratory tract.
Therefore, it can only be recommended for laboratory workers to wear suitable personal protective equipment, that is of course including gloves and face masks fitted with active carbon cartridges.
Future coatings developments should move away from UV curing to IR curing, as not only this would be much safer for the ophthalmic laboratory operators, but also would lead to much harder lens surfaces with premium quality AR coatings. ◆
Breton graduated with an engineering degree in Chemistry followed by a PhD in Organic Chemistry and a PostDoc in Polymer materials. He started his career in big US companies such as GE and Goodyear before entering the Optical sector back in 1999 with SDC Coatings. He successively worked with NGL and FISA before creating his own company named Chemoptics. This company later became HPMAT (High Performance MATerials) to reflect activities outside the optical sector and a JV was created in Russia under the name of FBOptics but as can be expected, it is now ‘on hold’ until further notice!
Hard and AR coatings are key to producing premium lenses – and having these steps in-house allows labs to control quality and delivery times, as well as generating revenue and profit. However, building and running a coating facility can be a formidable challenge, especially for smaller labs and for those starting a completely new Rx manufacturing facility that includes coating. By Andy Huthoefer
There’s the initial investment for equipment and cleanrooms, the space requirements, and then hiring and training highly skilled operators. Plus – once the coating lab is up and running – the added process time, which can range from three to ten hours depending on which technology is chosen. Until now, that is.
Satisloh, a leading optical manufacturing technology provider, recently introduced a completely different way of coating ophthalmic lenses. One that makes entering the world of coating production much easier: film lamination.
With this new method, an all-in-one, multi-layer film is laminated to the lens in a fast and easy process – completely replacing the conventional coating processes and consumables.
This sophisticated Tech-Film AR is prefabricated at Satisloh and includes the hard coating layer, the AR coating stack and the super-hydrophobic layer on a carrier foil as well as an adhesive that bonds to the lens.
By prefabricating Tech-Film, the manufacturer removes all the capitalintensive and complicated steps of coating production from the lab and replaces it with three simple process steps that are performed on much less expensive and complex equipment.
1. Like any coating process, film lamination requires perfectly clean lenses. This is done with a quick manual pre-cleaning followed by fine cleaning in the Hydra-Film table top wash system. This takes just two minutes per pair.
2. Then lenses go into a small, table top plasma treatment unit for 4–5 minutes per pair. Here they are etched with plasma which activates the lens surface for Tech-Film adhesion.
3. Now the lenses are ready for the actual lamination. This happens in the Film-Pod, a compact machine with two process stations. At station one, the Tech-Film is thermoformed to match the shape of the lens back curve which prevents bubbles and wrinkles from forming during lamination. At station two, the film is bonded to the lens for permanent adhesion. Together both steps take just 4–5 minutes per pair.
The initial investment required for a film lamination line is about one third of that for a conventional coating facility. This makes it an af fordable option for small labs and new entrants. And because all required equipment is simple to operate, staff are confidently coating lenses after just a short training.
Space comes at a premium in every lab and even more so in small and new labs. A traditional entry level hard and AR coating lab typically needs at least 19 m2 / 450 sq. ft. while a film lamination line requires as little as 5 m2 / 54 sq. ft. and no cleanroom is necessary, which contributes to the lower investment cost and gives labs flexibility to place the lamination line anywhere in their facility.
Speed is one of the biggest advantages of film lamination. It takes just 15 minutes per pair compared to the 3–10 hours processing time for conventional hard and AR coating. Because the Film-Pod laminates Tech-Film AR to the back side of lenses, blanks that are pre-AR coated on the front are used. This is the fastest way to coat a pair of lenses and get them out the door. Later this year, a Film-Pod technology extension will be released for labs that want to use uncoated blanks and laminate both back and front. This will take less than 30 minutes per pair, total for both sides. Still a good cycle time for hard and AR coating that also opens up an additional business opportunity for labs: offering express service at a premium.
Beyond the manufacturing advantages, laminated lenses also provide benefits to the end consumer: the film’s stabilizing effect makes lenses up to 18x more impact resistant than FDA standard requirements, allowing labs to grind minus lenses up to 40% thinner (depending on
[…] the film’s stabilizing effect makes lenses up to 18x more impact resistant than FDA standard requirements, allowing labs to grind minus lenses up to 40% thinner (depending on local standards and regu latory requirements), making them lighter as well.Fig. 2: Film lamination equipment at Mido 2022. Picture: Hanna Diewald
local standards and regulatory requirements), making them lighter as well. Furthermore, the optical properties of Tech-Film AR eliminate potential visual imperfections such as interference fringes (Newton rings) that occur with non-index matched hard coatings, creating the perfect coating for lenses of all indexes all the way up to 1.74. Today’s labs care about the environment. With film lamination no hazardous materials are needed in the lab (i.e. no hard coating lacquers).
The power and water consumption in the lab is much lower as well, reducing the lab’s environmental footprint.
With a capacity of 25–30 lenses per hour for backside lamination (200 lenses per 8-hour shift), much faster process times, lower investment, less space required and a smaller environmental footprint plus premium coated lens properties, film lamination is suited for small labs and new optical manufacturing entrants launching a coating lab. It brings the entire value chain in-house while avoiding the challenges that come with conventional coating. In addition, the fast process times make
film lamination an interesting express service production cell for all size labs.
Satisloh is convinced that film lamination shifts the paradigm in optical manufacturing: easy AR processing at a fraction of the invest ment and time, producing a premium lens. And this is just the begin ning: Tech-Films for other coating applications (e.g. polarized, tints, m irrors, etc.) are under development to expand process options using the same equipment. Film lamination will potentially change coating the way freeform technology changed surfacing. The possibilities are endless.
Andy Huthoefer, an optical industry veteran with more than 20 years of experience in North America and Germany, is Head of Marketing and Product Management for Satisloh.
Huthoefer’s previous experience includes Head of Global Aftermarket Operations for Satisloh, Director of Strategic Planning for Carl Zeiss Vision International and VP Marketing at Carl Zeiss Optical in the US. He holds an engineering degree in ophthalmic optics from the University of Applied Sciences in Aalen, Germany and is a licensed optician.
If you want to hear more about film lamina tion, watch the MAFO Talks presentation by Andy Huthoefer, followed by a Q&A session with Prof. Dr. Peter Baumbach.
Deblocking and alloy recovery have long been overlooked as areas of investment in favor of other areas of the lens making process. Yet these processes are rich in opportunity for sustainability, efficiency, and cost savings. Traditional alloy recovery methods are messy and outdated, and often hazardous. Alloy spills in surrounding areas, transfers to surface saver tape and contaminates water waste. If deblocking and alloy recovery become completely waterless, lab expenses decrease, and environmental conditions improve. By Alex Incera
Consider this: a lab processing 2,000 jobs per day produces 4,000 liters of alloy-contaminated water per year and 350 kg of alloy waste per year. The result is $10,000 US per year for disposal of hazardous material like water and tape, and $25,000 US per year to replenish the wasted alloy. This is a serious problem for the environment and a large expense to the lab.
Deblocking and alloy recovery also expose laboratory personnel to a variety of safety hazards:
Direct exposure to heavy metals in alloy including cadmium, indium, and lead
Direct exposure to hot, molten material
Automated deblocking systems allow alloy debris to reach the back/ concave surface resulting in scratches and/or coating defects
Alloy residue/film remains on tape after automated deblocking
These issues result in frequent intervention and troubleshooting, further compounding the variety of safety hazards. It’s costly for the lab, and completely unsustainable for the safety of the lab and the environment where alloy-contaminated water and waste end up.
There are substantial opportunities to address health, safety, and envi ronmental issues while also reducing costs and improving efficiencies.
There is now an innovative, sustainable solution to these problem areas. Surfacing labs can now incorporate a deblocking and alloy recovery system that is simple, clean, automated, and does not utilize water.
Coburn Technologies has developed a fully automated deblocking system that deblocks lenses cleanly without water. The Agility Autodeblocker is fast, deblocking over 200 lenses per hour. Simple mechanical operation without the use of water results in no contaminated water, no melted alloy, and no splatter of alloy, extending the life of alloy and reducing waste. Once a job tray enters the machine, both lenses are automatically removed from a job tray, placed onto the appropriate deblocking rings, and then deblocked simultaneously using a mechanical action. Contrary to deblocking with powerful water jets that displace alloy, cause alloy waste, and produce contaminated water waste, Agility separates the lens from the block, without water, in one clean, swift, mechanical action. The system is gentle to the lens, causing no “shock” that would cause lens breakage. This system is also scalable to be implemented with or without an alloy recovery system.
Job is presented along conveyor
Data is read from LMS
Turntable rotates to appropriate deblocking ring
Deblocking ring rotates to correct axis
Lenses are loaded into deblocking rings
Deblocking function is performed
Lenses are returned to tray in correct orientation
Block with alloy is placed on conveyor or into collection bin
Coburn has also developed the first ever fully automated alloy recovery system, which processes over 200 lenses per hour like the Agility Au todeblocker. The Integrity Alloy Recovery System was announced in 2021. Its simple, waterless operation uses induction heating technology
to separate alloy from blocks. This is done by melting a very thin layer of alloy where it meets the block, causing the alloy puck to be released while fully intact. This method produces no contaminated water, splatters of alloy, or alloy waste. Alloy can then be neatly collected separately from blocks. These steps are all carried out in a matter of seconds.
1. Load block with alloy – blocks with alloy are diverted as lenses pass on to de-taping and cleaning, then the blocks enter the turret and are picked up to be heated.
2. Heat – the block is heated, and a thin layer of alloy is heated, releasing the alloy puck from the block.
3. Drop alloy puck – the alloy puck is dropped into a collection bin.
4. Place block on pins – blocks can be stacked on pins or into a collection bin.
Diagram of alloy recovery steps.
The alloy recovery system is also scalable and can be implemented with or without the Agility Autodeblocker system. Aligning the autodeblocker’s conveyor with the Integrity conveyor creates a complete, hands-free, sustainable system of deblocking and alloy recovery. Sustainability is a worldwide phenomenon, one that has become a necessity in every industry. Coburn sees sustainable deblocking and alloy recovery as the next new frontier in lens processing. ◆
Alex Incera has been the President of Coburn Technologies, Inc. since January 2011 when the management team purchased the company from Gerber Scientific, Inc. Prior to joining Coburn, Incera was President of Gerber Coburn and Vice President of Gerber Scientific, Inc. from September 2008. Incera earned a Master’s degree in Mechanical Engineering with a concentration in Control Theory from the Mas sachusetts Institute of Technology (MIT) in Cambridge, MA, a Bachelor’s degree in Mechanical Engineering from Columbia University in New York, NY, and a Bachelor’s degree in Mathematics and Physics from Providence College in Providence, RI.
The wavelength of blue light is at the short end of the range light that is visible to the human eye. Blue light is more energetic, reaching deeper into the eye and thus endangering the eye more than lowerenergy light. The modern lifestyle means that we are increasingly exposed to it (see MAFO 04/2022, page 15). In this second part of the observations on blue light, the contribution of spectacle lenses to reducing the undesirable effects of blue light is examined. By Fritz Paßmann
Now let's turn to what spectacle lenses have to offer. Light is information. Anti-reflective lenses offer better vision. The transmission of a lens is made up of the reflections on the front and back and the absorption coefficient of the lens.
The transmission factor is thus the ratio of the outgoing light to the incident light. Antireflection coating (for “increased transmission” or “simple camouflage” in the military) reduces the amount of reflection and thus increases transmission. In the diagram on page 26 , the difference between a blue-control layer and a super antireflection
Highest Flexibility at Maximized Performance: With yields and cost per lens coming more into focus than ever, we enhanced the flexibility and raised the performance of this machine to up to 100 lenses/h in mixed mode operation.
Hybrid Polishing Tools: Reduced tool types, longer lifetime and faster polishing at unbeatable surface quality. Fastest tool exchange with magnetic holders.
Image Recognition System: Integrated tool inspection for permanent visual monitoring of the tool condition in the machine without interruption.
Special Lens Production: Due to 3 interpolating CNC-axes, the ASP 80 Twin-A is the perfect tool to polish also special lenses like lenticular, high cylinder and extreme geometries up to radius -25mm, depending on aperture diameter.
Inside: Enhanced data capture and machine monitoring technology. Contact your local sales representative for more information, or meet us in person at VEW in Las Vegas, SILMO in Paris or SIOF in Suzhou.
coating can be clearly seen. While the super antireflection coating, or better broadband antireflection coating, allows almost no reflection over the entire range of the visible spectrum (orange line), the bluecontrol coating (blue line) has a much poorer antireflection in the short-wave range – which is intentional. However, the residual reflection color is now also intensely blue.
The Japanese pharmaceutical company Mitsui Chemical manufactures the polymers in the MR ophthalmic lens range. It is a leader in the production of high-index lens materials, from 1.6 (MR8) to 1.67 (MR10) and 1.74 (MR174). A (relatively) new product is used to protect against excessive blue light. UV+420cut technology is used to produce transparent lenses that block UV wavelengths and cut off the 400–420 nm range of the spectrum in high energy visible light (HEV). This means that it provides better protection against radiation that could damage the eye.
A UV420 lens shifts the transmission curve into the visible range of light. This results in a basic tint to the material. In some cases, an additional color is applied over this “yellowish tint”.
The measurement report clearly demonstrates that this material is in category 0 of filter lenses. Such lenses are suitable for night driving and signaling. The transmittance in the signal colors red, yellow, green and short-wave blue is over 88%, while the long-wave blue component is blocked by 24%. Together, the lens material and the coatings provide increased contrast due to the stronger scattering of the short-wave light being reduced by reflection and absorption. Demonstration tools offered by lens manufacturers are not just gimmicks but impressively illustrate the effectiveness of blue-light protection. In sales talks, they should be used for demonstration purposes in addition to the expert advice provided by the optician.
When talking about blue-light protection, the large majority of cataract patients in the population must not be ignored. Due to hardening and loss of transparency of the crystalline lens – using the slit lamp a brownish/yellowish coloration is clearly visible – the blue part of the light especially is no longer processed. After insertion of a transparent intraocular lens (IOL), this blue component is now over-interpreted, and customers speak of “increased blue vision”.
Therefore, in the past, a lens with a yellowish tint, a blue filter, was fitted. However, this did not turn out to be such a good idea, since in time the perception of colors “returned to normal”. Nowadays, blue-light attenuators are also used in IOLs, which filter only a relatively small amount of the blue light. Often a violet-light filter is also offered, but both incur additional costs (in Germany).
Antireflection coating (for “increased transmission” or “simple camouflage” in the military) reduces the amount of reflection and thus increases transmission.Degree of reflexion
of occasional eyeglass wearers need their glasses for viewing screens.
of the German population over the age of 14 is online every day. That's almost 50.2 million people.
of employees in Germany are affected by digitalization in the workplace. of all private households in Germany own at least one car.
In the last 20 years, the per centage of people suffering from sleep disorders has almost doubled.
of the population surfs on the internet before going to bed.
Source: StratemeyerThe German Ophthalmological Society published a press release in October 2021 on blue-light damage from screen use.
A three-pronged study showed: “There was no difference in terms of sleep quality between the group that had activated the night-shift setting and the group that had not activated this function, nor to the group who had not used an iPhone at all,” Prof. Dr. rer. nat. Michael Bach reports. The Freiburg-based vision researcher's tip is therefore: “Anyone who wants to look at an electronic device before falling asleep should avoid maximum brightness – this recommendation may sound trivial, but it’s true.”
At the end of the report on the myth of blue-light damage, there is a dig at the optometry community: The president of the German Ophthalmological Society (DOG), Professor Dr. med. Hagen Thieme, thinks it is important to bring these findings to a wider audience. “They serve to educate and protect consumers from misleading ad vertising and confusing misreporting in the pursuit of purely commercial interests,” says the director of the University Eye Clinic in Magdeburg.
I do not see offering blue-light attenuating spectacle or contact lenses as a “purely commercial interest”, but as a service and expertise offered by specialists for good vision. The advantages outweigh the disad vantages, and the customer can feel he is doing something for the health of his eyes in the long run. A few more facts and figures can be found above.
Blue-light-attenuating spectacle or contact lenses provide safety in everyday multimedia life with tablets, monitors and cell phones when
of the German population is a driver of motor vehicles. This corresponds to around 36 million drivers.
working online from home, during home-schooling, meetings and webinars; especially when digital media are used intensively.
For people concerned about protecting their health, these filters serve as preventive measures against any long-term damage which might occur.
Although there is as yet not enough scientific evidence, they may also act as a prophylaxis against AMD. Children and adolescents in particular benefit from early protection against high-energy radiation. There is an improvement in contrast, which is particularly beneficial to vision when driving at dusk. Customers experience less vision fatigue, their eyes simply feel more comfortable. ◆
Fritz PaßmannFollowing his training as an optician, Paßmann completed his master's degree. Since 1991 he has worked as a freelance lecturer at various chambers of crafts and technical schools in the areas of theory, workshop and refraction. The lecturer for optometry was head of the optometry department at the HWK Dortmund (Germany) from 20072018. He is interested in modern teaching and learning methods. Paßmann is a co-developer of the PASKAL 3D experience refraction.
During the period from 2007 to 2010 we kept producing different units and versions similar to the first prototype but innovating each time the deblocking function reaching the point when we used the mechanical deblocking (dry process) keeping the detaping process by high pressure water jet. Special mention required to those companies that trusted us and supported our innovation and, by investing in our machines, let us evolve our products.
It was in 2006 when Eugenio Casas and his company Insomec Integra Soluciones S.L. developed the first prototype of the “DL80” machine and it was the starting point of our carrer into ophtalmic industry automation. It was the first automatic machine in the world to deblock alloy by hot water inmersion and water jet and to detape ophtalmic lenses by high pressure water jet.
Having the trust of companies such as Essilor, Signet Armolite, INDO, Indústrias de Óptica
Prats, CODIR and NOVACEL was unvaluable for us.
In 2007 and 2008 patents concerning the procedures used to deblock alloy (by hot water and also dry mechanical deblocking) and to detape ophtalmic lenses (by high pressure water jet) were registered by Insomec Integra Soluciones S.L.
Eugenio Casas Gilberga, founder and CEO at Insomec Optical Technologies First DL80 prototypeDuring years 2008 to 2009 Insomec Integra Soluciones S.L. and Satisloh GmbH agree to collaborate in the development of the first prototypes of automatic machines for their (at that time) new NUCLEO Project, later know by ART (alloy replacement technology) system. Same principles were and are used in these procedures of deblocking and separating the adhesive layer by high pressure water jet (Insomec procedure patent).
It was a pleasant and interesting collaboration but after 3 years
we quit fundamentally because even at that time, we understood that plastic was not a complete
During 2011 the interest shown for our technolgy starts paying off. The German company Team H&K GmbH was working in a complementary technology to ours and, instead of competing, we decided to join and work together to be able to supply our products at an international level. From that moment on, we
replacement for alloy and would end up being another option available in the market. It’s been 14 years since then and we keep thinking the same…
In 2008 Insomec Integra Soluciones S.L. creates its subsidiary Insomec Optical Technologies S.L. The optical division... is born in the middle of the big European economic crisis and there is no doubt it was a tough time for everybody, but after all those years and projects, a huge experience is accumulated in our backs.
divided the production 50% in Barcelona (Spain) and 50% in Frankfurt (Germany).
The fruit of that collaboration were our successful machines DBA2 (alloy deblocker) and TSA2 (detaper), both protected by the procedure patent from Insomec.
In 2013 Insomec agreed with the German leader company Schneider GmbH & Co, to confer a license agreement allowing them to integrate part of our products in its worldwide commercial network but keeping our respective production centres and our independency. This succesful partnership continues to this day.
The help of our market leading partner, Schneider Optical Machines, makes it even easier to reach any part of the world.
An affordable price and a low cost per lens ratio make both machines a great investment.
More than 400 machines around
the world guarantee our success. Transform your batch and manual process into a complete automated task while reducing the man labour cost and the downtime.
Insomec Optical Technologies is proud to celebrate the 10 years of success of our patented process of deblocking and detaping carried on our DBA and TSA machines. Incomparable characteristics and performance still make alloy the best option and our machines help labs all around the world reach their goals with our complete automated process.
Trust DBA. Trust TSA. Trust the originals. Trust Insomec. TSA and DBA (sold by Insomec)
In June, Schneider invited to the DigiCON for the sixth time. With the event, the company wants to offer its customers the opportunity to experience a wide range of technological innovations and at the same time also exchange ideas with each other. In 2022, it took place from June 22 to 25 and marked the culmination of an innovation-filled year for the machine manufacturer with the revelation of their new system for inline coating. By Rebekka Nurkanovic
150participants from 25 countries accepted the invitation to Schneider's home region of Hesse, Germany. A cocktail reception in the Marburg Lokschuppen gave the starting signal for the DigiCON. In balmy summer evening temperatures, the attendees enjoyed drinks and live music as they got in the mood for the coming days and already had the opportunity to discover the conference venue.
The stars of DigiCON were of course the innovations for the ophthalmic industry. In the event hall, the machines of the Modulo ONE series, the new generation of the Modulo line, were presented in the two following
days under the header "The power lab of the next decade". Three large screens ensured that even the last row of seats had a clear view of the speakers and slides. Time and again, live feeds were also provided to the machine hall at Schneider’s headquarters in Fronhausen, so that a vivid impression of the respective machine was created. Simultaneous transla tors were available for the Spanish and Portuguese-speaking visitors.
Gunter Schneider started the conference with a look back at the history of the Modulo line which was conceived in 2008 and launched in 2012 with the vision of creating systems – not machines – in order to solve complex challenges. After continuous extensions of the line over the following decade, the company decided that the next piece of the puzzle would be to fulfill the vision of all-in automation and started the biggest
View into the machine hall at Schneider's headquarters in Fronhausen. Pictures: Schneiderproduct launch campaign in Schneider’s history in 2021: they announced 11 innovations in 11 months and then presented a new machine every month. The goal of the series: complete automation, where almost no manual steps have to be performed anymore. "With Modulo ONE, we have succeeded in completing the existing Modulo system in such a way that, for the first time, we can manufacture fully automatically – from warehousing to surfacing, cleaning, coating and edging. This development represents a very special milestone in the history of eyewear optics and will have a major impact in the future," Gunter Schneider proudly sum marizes the result of the series of innovations.
Each Modulo ONE machine was presented by experts with in-depth knowledge of their product. Among the highlights of the new launches is CSI Modulo ONE, for example, a system for the automatic detection of cosmetic defects. The optical system screens the surface for irregularities, and characterizes and evaluates them with the help of artificial intelligence. It detects any common defects such as scratches, pits, center dots, haze, chatter, cutting marks, spiral and fringes. AWS Modulo is a fully-auto mated warehousing system for efficient and space saving storage and retrieval. The Modulo Control Center is tailored to the needs of ophthalmic labs. It interacts with the interlinked machines, conveyors, and support systems to capture real-time data on every relevant aspect of the lab. The Automated Dome Loader (ADL) is a fully-automated dome loading system for batch coating that loads, unloads and flips the lenses if both sides of a lens need AR coating. The all in one surfacing center Modulo Center ONE features integrated milling, lathe turning, polishing and laser marking technology. After years of development, the inline coating line was presented as a world premiere at DigiCON. Modulo In-line Coating completes Schneider's Modulo vision. It consists of two parts and automates the backside coating process with cleaning, hardcoating and rapid response coating. The company is particularly proud of this development and expects it to have a significant impact on the future of eyewear optics. All eleven innovations can be seen on the dedicated plattform www. modulo-one.com.
Thursday and Friday afternoon, visitors had the opportunity to experi ence the new system in full action. In the large, light-flooded machine hall in Fronhausen, the Modulo ONE machines were in operation. Schneider employees explained and demonstrated all functions in detail and were available to answer questions.
The organizers had also come up with a special gift. In the run-up to the conference, visitors could transmit their refraction values to Schneider and then choose one of three 3D-printed red spectacle frames at the beginning of DigiCON. A specially created app made it possible to track the production and cost progress of each pair of lenses and the red spectacles were subsequently handed out at the lakeside. As a result, the participants are among the first who can now call a pair of lenses from the "power lab of the next decade" their own.
[…] the company decided that the next piece of the puzzle would be to fulfill the vision of all-in automation and started the biggest product launch campaign in Schneider’s history in 2021.
Each day's informative presentations and machine tours were followed by a varied evening program. After the first day of the conference, ad venturous spirits could get behind the wheel of a hot rod and explore the streets of the surrounding area. Afterwards, everyone met on the shores of Lake Niederweimar and enjoyed the sunset (of an unusually hot day for the time of year) with cool drinks and a sumptuous dinner. Friday evening Oktoberfest was on the agenda, with German folk music, entertainment, traditional dishes and of course beer. The last day of DigiCON will be particularly remembered by the participants who came from far away: Saturday was dedicated to the Germany Experience, which included a boat tour on the river Rhine, a wine tasting and a visit to a monastery.
The Marbug Lokschuppen provided a particularly fitting setting for the presentation of Schneider's innovations. Not only because of its appealing ambience, but also because the site itself was a labor of love for company founder and CEO Gunter Schneider. The former locomotive shed was in pitiful condition when Schneider acquired it five years ago. Under strict preservation orders, it has
since been converted into a multi-functional space that was completed just a few weeks before DigiCON and houses a modern event venue, restaurant, bar, and the Innocou Coworking and Founder Hub.
DigiCON 2022 offered extensive presentations of innovations as well as a varied entertainment program and Schneider is accordingly very pleased with its success. "The unveiling of our power lab of the next decade as the grand finale of our 11 innovations in 11 months campaign was a very special moment," says Gunter Schneider. "After this big splash, we presented our technologies one after the other, for example the world premiere of our brand new inline coating system, and could repeatedly feel the enthusiasm of our customers. We have already received several requests from clients to implement our new technologies in their labs." His closing words: "DigiCON 2022 was a mega-experience of which we are very proud. With the development of the power-lab of the next decade, we were able to turn a long-awaited vision into reality and are very excited that we were finally able to present this innovation, developed over years, to our customers."
Rear view of Marburg locomotive shed. Source: Rebekka Nurkanovic Atmospheric end of the day at Lake Niederweimar. Tapping of the barrel at the Oktoberfest. Boat trip with a view.What will the future look like? In a complex world with multi-layered challenges, it is sometimes difficult to see the big picture clearly. In its most recent research, the innovation network Future Meeting Space (FMS) has developed three future scenarios for business events post-COVID that give the future of events a face. By Matthias Schultze
The study titled “Changing Ecosystems – Future Scenarios for Business Events in the Age of Borderless Communica tion” illustrates how events will change due to different influencing factors and enables us to see for each of the three scenarios how change will impact venues, event formats and technologies. Let’s take a look.
In the "tried and trusted – renaissance of the real" scenario we envisage a world where we return to the familiar with in-person meetings remain ing the be-all and end-all. In this environment, central, large event venues dominate, designed to accommodate as many attendees as
possible. Spaces feature classic layouts but also special club-like areas as well as personal work and recreation spaces. Event formats are similarly conventional with a high degree of structure. This means presenting content in classic presentations and interactive formats or creative workshops only used very selectively for specific target groups and topics. Importantly, networking opportunities and meeting others become the focus of events, as personal interaction is the highest priority for attendees.
From a tech perspective, the “tried and trusted” scenario results in events that require less equipment, simply because they are run purely on-site as opposed to digital or hybrid set-ups. Digital tools are only used if they enhance the physical experience and support face-to-face exchange.
Keyvisual globe. Pictures: GCB / Future Meeting SpaceThe “diverse and flexible – the global community" scenario is the exact opposite of the return to the familiar approach. Flexibility regarding time and space rules and events are no longer bound to one place as digital attendance is easily possible. Worldwide co-operations between venues emerge and multi-site events supported by technology become a mass phenomenon. Smaller venues in city centers, which are not necessarily dedicated event spaces, are favored.
When people attend events in person, they make a very deliberate decision to do so. Meeting others face-to-face is their highest priority then as networking and socializing is very limited in the digital space. In general, providing purely informative content at both physical and hybrid events decreases while attendees are enabled to make their own topic-related experiences. New modular workshop formats are developed that can be customized by attendees. As people thus create their own personal event, the degree of participation in the preparation and planning of events is high, which results in innovative concepts.
To enable virtual and in-person attendance, virtual communication platforms and digital tools are integral parts of many events. Hybrid events become standard and to support interaction between physical and virtual attendees, the availability of smart surfaces in venues becomes key. VR/AR technologies are used to support virtual attend ance. As attending events is increasingly linked with private trips in order to make the most of travel and justify the effort involved, apps that support getting to know the given destination are on the rise.
In the “green and aware – the net zero society” scenario sustainability is the guiding principle of all actions. Existing buildings are chosen as venues and utilizing venues to the maximum is key, with large event venues also serving as educational facilities or temporary workspaces.
In general, attendees expect event venues to be authentic and sustainable throughout. To create climate-neutral buildings, both the building technology and other infrastructure elements need to be renewed and designed to meet sustainable standards. “Green events” is the central
While conventional speaker presentations largely disappear, new formats which integrate the natural environment are in demand, includ ing moving events in the open air. The overall guideline for event formats is to reduce things to the essential. Improvisation and developing innovative solutions together with attendees come to the fore. In fact, event organizers increasingly only provide the platform, without stipulating a fixed program.
Investment in new technologies and digital tools rises, with the aim of creating new solutions for sustainable and ecological resource management. Green technologies that enable a more sustainable economy are key. Also, as people pay increasing attention to their mental and physical health, systems for integrated health management play a role when planning and running events. Cognitive environments that can be adapted to specific user needs become a megatrend, and for the purposes of their health and well-being, attendees also accept the use of new technologies such as tracking systems. ◆
Matthias Schultze, Managing Director, GCB German Convention Bureau. Since 2010, Matthias Schultze has been responsible for Germany's national and international positioning and marketing as a leading meetings and conventions destination at the GCB German Convention Bureau with offices in Frankfurt, New York and Beijing. Together with partners from business and science, he has initiated various projects that examine the potential of digitization and provide impetus for the future of business events - including the innovation network "Future Meeting Space" and the hybrid, spatially distributed congress "BOCOM".
In the “green and aware – the net zero society” scenario sustainability is the guiding principle of all actions.“Green and aware – the net zero society” scenario.
Implementing sustainability in a business successfully requires a sustainability strategy, a definition of clear objectives, and the right mindset. Once concrete actions are taken to implement the strategy measuring results is key to evaluating the outcome, highlighting what has been achieved and adapting the strategy. The effective implementation of sustainability measures needs to be made quantifiable: by using the right Key Performance Indicators. By Colin Bien
How can sustainability be quantified and measured? The basic principles are no different from other areas of financial reporting: the prerequisite is a solid ac counting process, based on defined Key Performance Indicators (KPIs), precise collection of data, and the review and evaluation of the data to control and improve on results. That is why sustainability accounting is a vital part of sustainability reporting, but it is not the only reason why it is well worth taking a closer look at sustainability KPIs.
Since 2017 large companies in Europe have been obliged to submit annual reports on their CSR activities. From 2024 onwards, this obliga tion will be extended under the new European "Corporate Sustainability Reporting Directive" (CSRD). The future regulation will also apply to smaller companies, affecting up to 50,000 companies in Germany, for example. They will be obliged to disclose specific sets of data and in formation, according to the so-called ESG (Environment, Social, Governance) indicators. But reporting on sustainability measures is
Sustainability measures bring change to established processes and their effect and effectiveness can be hard to predict. With the help of pre-defined KPIs, a structured and ongoing assessment and amendment is possible. KPIs are therefore a particularly important tool for better decision-making, e.g. if energy consumption goes down slower than planned, the measures can be amplified or additional measures im plemented swiftly. Also, cross- or side-effects of measures taken can be corrected early on, reducing risk, cost and ensuring timely adaptation of strategy, and thereby make planning more reliable and effective. Data collection is a vital part of sustainability management and measurement. To avoid it becoming a time-consuming and potentially costly task, it is advisable to use CSR/ESG management and accounting tools right from the start. There are smart tools available and companies that make an early investment in systems save the time otherwise spent on hand-crafted spreadsheets in which data can get lost or buried.
KPIs must be consistent with strategy
However, the use of KPIs should inform the company’s sustainability strategy, answering the central question: what impact do we want to create and how can it be measured? Here is an overview of indicators for each of the sustainability dimensions:
Social sustainability KPIs
Employee satisfaction
Employment development
Ratio of men to women
Expenditure on training and further education
Labor and social standards at suppliers
Expenditure on social commitment
Employee complaints
Environmental sustainability KPIs
Energy consumption
Water consumption
Amount of minerals and other resources used
Waste production
Water waste
GHG emissions, e.g. CO2 or methane
Energy consumption per product manufactured
Material consumption per product manufactured
Percentage of recycled/recyclable materials
Economic/governance sustainability KPIs
Profit development (in relation to sustainability measure)
development
satisfaction
Development of risks assessment
paid
to regional value chains
KPIs turn the sustainability strategy into a strategic investment in the future Measuring results is as important in sustainability implementation as it is in any other business activity. Sustainability KPIs and controlling help monitor cost, effort, and effectiveness of actions, inform important stakeholders, provide information essential to building the company’s reputation, and inform better decision making. KPIs are key components of any serious and successful implementation of sustainability manage ment – and they help prepare the business for the future. ◆
This article was first published on www.nrole.de
Colin BienDr. Colin Bien is an economist, sustainability expert and entrepreneur. He has been active as a researcher, trainer, and consultant for sustain ability and transformation in business. He is initiator and co-founder of the online academy for sustainability in business, nRole GmbH, and the SaaS provider WeShyft, a provider of integrated sustainability management. He also hosts the sustainability podcast “Masters of Change”. You’ll find him at the nexus of sustainable business models, education, and communication, building momentum around the transition towards a sustainable economy.
[...] cross- or side-effects of measures taken can be corrected early on, reducing risk, cost and ensuring timely adaptation of strategy, and thereby make planning more reliable and effective.
Small labs (< 100 L/shift)
Medium sized labs (100 - 3000 L/shift)
Mass production labs (> 3.000 L/shift)
Lens materials
materials, mineral AR coating including mirror coating
Further special coatings anti-fog
Top coatings (hydrophobic, oleophobic)
Top coatings from separate thermal source
In-chamber tinting full color (absorption coating)
Gradient tinting color
Productivity HMC+ Ø 70 (avg. lenses/h) [both sides coated]
Process time [both sides coated] (minutes)
Dome/segment number of sectorsDome, Flip-over systemDome, Flip-over system3 segments 4 segments Full dome/segment capacity Ø 70 48
96 144
Flip-over capacity segment Ø 70 16
High-vacuum pump system (capacity L/s) Turbo pump. 1450 L/sTurbo pump. 2050 L/s Turbo pump. 2050 L/s Turbo pump Gate valve (in case of turbomolecular pump) /
Roughing pump system (capacity m3/h) single stage 100 m³/h single stage 100 m³/h single stage dual pump 2x100 m³/h single stage 300 m³/h
Cryogenic booster pump with Meissner trap x
(chemical
45
52 1800 x 1900
2100
2000
2650
Weight (kg / lbs) 1200 / 3300 1350 / 3640 2200 / 4850 2800 / 6173 Dimensions (w x d x h) / [mm / inches] (machine without conveyor) 2260 x 1150 x 1310 / 89 x 45 x 52 2260 x 1150 x 1450 / 89
2200
Small labs (< 100 L/shift)
Medium sized labs (100 - 3000 L/shift)
production labs (> 3.000 L/shift)
Lens materials
coating including mirror coating
Further special coatings
Top coatings (hydrophobic, oleophobic)
Top coatings from separate thermal source
In-chamber tinting full color (absorption coating)
Gradient tinting color
Productivity HMC+ Ø 70 (avg. lenses/h) [both sides coated]
Process time [both sides coated] (minutes)
Dome/segment number of sectors
Full dome/segment capacity Ø 70
Flip-over capacity segment Ø 70
High-vacuum pump system (capacity L/s)
Gate valve (in case of turbomolecular pump)
Roughing pump system (capacity m3/h)
Cryogenic booster pump with Meissner trap
Weight (kg / lbs)
Dimensions (w x d x h) / [mm / inches] (machine without conveyor)
Flip-over
(physical vapour deposition)
(chemical vapour deposition)
Second distribution mask
Sputter
Electron beam gun (number of pockets/kW)
source (kW)
source (kW)
of vacuum measurement systems
heater (kW)
by Quartz-crystal/optical
diagnostic
connectivity
information
(800 l / min.)
x 950
31
1950
38
Small labs (< 100 L/shift)
sized
(100 - 3000 L/shift)
production labs (> 3.000 L/shift)
materials
coating including mirror coating
Further special coatings
Top coatings (hydrophobic, oleophobic)
Top coatings from separate thermal source
In-chamber tinting full color (absorption coating)
tinting color
Productivity HMC+ Ø 70 (avg. lenses/h) [both sides coated]
coating
Process time [both sides coated] (minutes) First lens 5 min., 3 min. after
Dome/segment number of sectors single piece flow
Full dome/segment capacity Ø 70
Flip-over capacity segment Ø 70
High-vacuum pump system (capacity L/s)
valve (in case of turbomolecular pump)
Roughing pump system (capacity m3/h)
Protect-Blue, Protect UV,
Complete, Premium Drive,
Infrared, In-chamber tinting
pump
valves
Cryogenic booster pump with Meissner trap not needed
Weight (kg / lbs)
(w
inches] (machine without conveyor)
Flip-over
(physical vapour
(chemical vapour
distribution
by
Will Daniels is the president and CEO of DAC Technologies. His parents wanted him to become a radiologist but Will decided to go into the optical industry. Aged 49, he is now already a 27 year veteran of this field. But he could also imagine loving to work as a hockey coach. In his spare time, Will likes to travel and occasionally play a round of golf.
If you could change one thing in the world, what would that be? I would stop people from using the word “hate”.
In your opinion, which movie/book should everyone have seen/read?
Movie: “A Good Year” by Ridley Scott. Book: “Never Split the Difference” by Chris Voss.
If your life were to be filmed, which actor should play your role? Ralph Macchio.
Which celebrity – past or present – would you most like to meet personally, and why?
Terry Fox, because I still remember seven-year-old me being in awe of him as much as 49-year-old me is still in awe of him.
If you had to do without one of your senses – vision or hearing – which would it be?
Hearing, I could not live without seeing the faces of the people I love.
What is your favorite place in the world? / If you could choose one country to live in, which would it be? My mother’s house in Guelph, Ontario, Canada. If I could choose one country to live in, it would be Canada.
What was the last event that deeply moved you? The outpour of condolences from friends, family and acquaintances when I lost my father.
What does a perfect day at work look like to you?
Under one hundred e-mails and less than three hours of conference calls.
Which profession did your parents have in mind for you? Radiologist.
If you didn´t do your current job, what else would you do? I would love to be a hockey coach.
What is the best thing about your job? The people, customers and co-workers.
When was the last time you were fed up with your job? The time I had a return flight for a business trip from Rio de Janeiro, Brazil to Frankfurt, Germany … in a middle seat.
What does a new customer mean to you? An opportunity to show them they made the right decision.
What has annoyed you today? Made a coffee and left my cup at the coffee maker… it was cold when I remembered. I was annoyed with myself.
In your opinion: which thing is completely overrated? Cable news.
What was the most significant innovation of the last fifty years? The smartphone.
What would you do differently in your next life? Stop and smell the roses more often.
and
the
about other
and the
for
and
Last but not least, you will
the
Adding in-house coating not only grows your bottom line, but also allows you to control delivery time and quality. And coating isn’t intimidating when you partner with us! Our experience is based on developing and manufacturing sophisticated coating systems, processes and consumables for almost 60 years.
Covering the full process chain, we offer a wide range of proven and easy to install AR, mirror and top-coat processes as well as matching coating consumables for all lens materials and coating quality requirements. No matter which process, our expansive knowledge guarantees uniform coating quality within each batch and from batch to batch.
Still wondering if adding in-house AR coating is the right move for your company? OUR EXPERTS ARE READY TO HELP!