
6 minute read
PURPOSE
Is the importance of inertia in the process of material fragmentation currently understated? The Purpose project seeks to challenge the established framework by which material fragmentation is understood, work which holds important implications for material design and development, as Professor José A. Rodríguez-Martínez explains.
The process of dynamic fragmentation is currently understood largely as a statistical phenomenon, in which defects play a fundamental role in the fracturing of a material and therefore limit its capacity to absorb energy. While this approach to understanding dynamic fragmentation is fairly well established, Professor Jose Rodríguez-Martínez and his colleagues in the Purpose project are now exploring an alternative framework. “We think that the effects of inertia are important. Inertia could reduce the effect of defects – either material or geometric – on the final fragmentation of a structure,” he explains. This suggests that defects could play a secondary role in dynamic fragmentation, with inertia controlling the process to some degree. “There is a kind of competition, but when inertia becomes dominant the role of defects may turn to be secondary,” says Professor Rodríguez-Martínez. “It is inertia, together with other properties, that controls dynamic fragmentation, and therefore the energy absorption capacity of a structure when it is subjected to impact loading.”
Purpose project
This theory is the focus of interest in the Purpose project, with researchers looking to test it on both traditionally manufactured and printed metals supplied by a manufacturer. Professor Rodríguez-Martínez and his team are taking a three-pronged approach to this work, involving numerical calculations, analytical models and experiments. “We are developing numerical calculations, based on computational mechanics, while we are also developing analytical models. These analytical models are simple, but they capture the basic physics behind the fragmentation process,” he outlines. In the experimental work, Professor RodríguezMartínez is essentially investigating four different configurations. “First, we are analysing the fragmentation of expanding rings. We are manufacturing extremely thin rings, with a thickness of let’s say 1 millimetre. In collaboration with a university in the US, we are then performing experiments in which these rings are expanded at very high velocities, at rates of up to 250 metres per second,” he explains.
The rings are placed under great strain by this expansion and eventually they fragment into several pieces, with researchers in the project investigating the mechanisms which control the number of fragments and their size, as well as a variety of other topics. Metallic materials behave in a non-linear manner, so identifying the factors which affect how they fragment is a complex and demanding task. “From an experimental point of view, it’s much more complicated to interpret the data,” says Professor Rodríguez-Martínez. The second type of experiment that is being performed in the project involves expanding thin wall tubes, which Professor Rodriguez-Martinez says is subtly different to the first experiment with the rings. “The stress state in the structure is different, and this changes the fragmentation pattern,” he explains. “We will analyse, by the comparison between the ring expansion experiments and the tube expansion experiments, the effect of the stress state on the fragmentation process.”
A third experimental arrangement involves the axial penetration of thinwall tubes. Instead of expanding the tube
radially, the experiment here centres on penetrating the tubes axially in a certain manner, leading to the formation of what are regularly called petals, a specific type of material fragment. “We are analysing the number of petals that are formed,” outlines Professor Rodríguez-Martínez. The fourth experimental arrangement centres around the dynamic collapse of thick-wall tubes. “In collaboration with a high-tech Israeli company, we are using an electromagnetic field to collapse quite a thick cylinder, in such a way that the cylinder will fragment by the formation and development of multiple shear cracks,” continues
many potential benefits.
Professor Rodríguez-Martínez. “These four different canonical configurations will lead to different fragmentation patterns. We aim to understand the mechanisms which control the fragmentation of these metallic materials, and will obtain results from both printed metals and traditionally manufactured metals.”

Metallic materials
Researchers are studying a number of different metallic materials in the project, one of which is a titanium alloy used extensively in the aerospace industry. Alongside the titanium alloy, researchers are also looking at three other industrially important materials. “We are testing high-strength steel, which for years has been used in the automotive industry, as well as an aluminium alloy, which is also widely used in the automotive industry because of its high strength-to-weight ratio. Then we are also testing Inconel, a superalloy that has been used for manufacturing aircraft engines,” says Professor Rodríguez-Martínez. The aim is to investigate the influence of the mechanical properties of these four materials on their fragmentation behaviour, information which Professor Rodríguez-Martínez says is highly valuable to manufacturers. “We believe that in developing basic science and understanding the basic mechanisms that control fragmentation, we will help to design or tailor structures and materials with an improved energy absorption capacity,” he explains.
The current priority in the project is to investigate the basic mechanisms which control the fragmentation of a material, yet Professor Rodríguez-Martínez is very much aware of the wider commercial relevance of this research. Once the fragmentation of these materials is understood in greater depth, the next step could be to look towards technology transfer. “We could work with manufacturers for example, and help identify which type of materials should be used for applications where energy absorption capacity is particularly important,” outlines Professor Rodríguez-Martínez. The project’s research will yield important results for the commercial sector, believes Professor Rodríguez-Martínez. “We are in close contact with industry, and I think that this work will be very fruitful,” he enthuses. “It will take time of course for the results to filter through, due to the intricacy of the research involved, but certainly we are in touch with industry.”
This will be combined with continued research into the fundamental behaviour of materials. The focus of attention in the project is on the four different metals that have been described, but in future Professor RodríguezMartínez says they could look to analyse even more complex materials. “This is not only on the material basis, but also the structural basis,” he says. The advent of 3-D printed metals is having a dramatic impact on the materials sector, and the project’s research will help to further reduce costs and enable the wider use of the technology. “The ability to manufacture protective structures with additive manufacturing will lead to a drastic reduction in costs for manufacturers, as it will help reduce energy consumption and improve productivity. There are many potential benefits,” says Professor Rodríguez-Martínez.
PURPOSE Opening a new route in solid mechanics: Printed protective structures Project Objectives
The ERC grant PURPOSE is the first attempt to address the fragmentation of printed metallic materials using experimental, analytical and numerical procedures simultaneously. This project aims at providing a definite identification to the mechanisms which control dynamic fragmentation, a fundamental problem in the leading edge of knowledge that has remained unsolved for the last 70 years.
Project Funding
European Research Council (ERC) Starting grant PURPOSE (Grant agreement 758056).
Project Collaborators
• Laboratoire d’Etudes des Microstructures et de Mécanique des Matériaux LEM3, Université de Lorraine • Faculty of Mechanical Engineering, Technion • IMDEA Materials Institute • Rafael Advanced Defense Systems • Department of Materials Science and
Engineering, Texas A&M University • Department of Aerospace Engineering and
Engineering Mechanics, University of Texas at Austin • Departamento de Engenharia Mecanica
Universidade Federal de Santa Maria • Materialise
Contact Details
José A. Rodríguez-Martínez Associate Professor Head of the research group: Nonlinear Solid Mechanics Department of Continuum Mechanics and Structural Analysis University Carlos III of Madrid T: +34 91 624 9904 E: jarmarti@ing.uc3m.es W: https://www.nonsolmecgroup.com/
Professor Rodriguez-Martinez
Dr Rodriguez-Martinez is Associate Professor at the University Carlos III of Madrid and head of the Nonlinear Solid Mechanics research group. His research on the mechanical response of materials and structures subjected to extreme loading conditions has been funded with three European Grants over the last five years: the ERC grant PURPOSE, and the Marie Skłodowska-Curie Actions OUTCOME and QUANTIFY.
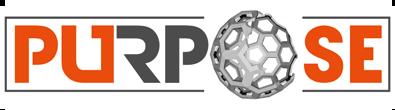