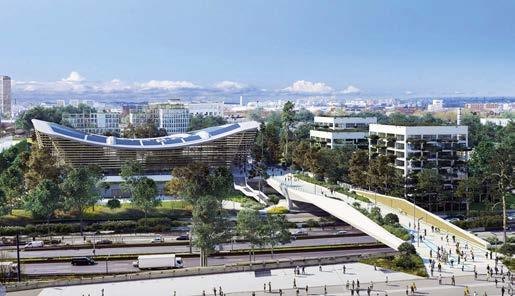
19 minute read
Ein Hängedach aus Holz für das Olympische Wassersportzentrum in Saint-Denis
from Holzbau 2/2022
Das neue Olympische Wassersportzentrum in Saint-Denis wird für die Olympischen Spiele 2024 in Paris erbaut und soll danach als Multifunktionsarena weitergenutzt werden. Die nach unten gewölbte Hängedachkonstruktion reduziert nicht nur das Luftvolumen in der Haupthalle und damit den Energieverbrauch der Arena, sondern minimiert als Holzkonstruktion auch den CO2Fußabdruck des Gebäudes. Die Dachkonstruktion besteht aus bis zu 89 m langen Holzträgern. Nach seiner Fertigstellung gehört das Wassersportzentrum weltweit zu den größten in Holzbauweise ausgeführten Sportstätten und stellt gleichzeitig einen neuen Weltrekord für weitgespannte Holzkonstruktionen auf. Der folgende Beitrag stellt den Gesamtentwurf und die wichtigsten technischen Merkmale sowie Berechnungsmethoden der Konstruktion vor. Auch das Lang- und Kurzzeitverhalten der eingesetzten Materialien (Beton, Stahl, Holz) sowie die nichtlineare Analyse der großen Dachverformungen werden erläutert. Außerdem befasst sich der Beitrag mit der Sensitivität des Dachtragwerks in Hinblick auf Fundamente, Betonsockel und Steifigkeit der Holzverbindungen, die speziell für hohe Torsionslasten und die verschiedenen geometrischen Konfigurationen ausgelegt sind. Darüber hinaus geht der Bericht auf das Montageverfahren und die Steuerung von Fertigungs-/ Montagetoleranzen sowie die Geometrieprüfung vor Ort ein, die für eine solche zugbeanspruchte Struktur unerlässlich sind.
Timber catenary roof of the Olympic Aquatics Center in Saint-Denis
The Saint-Denis Aquatics Center is a multi-sports facility built for the Paris 2024 Olympic Games and for the city of Saint-Denis. Its concave roof reduces the air volume of the main hall and thus its energy consumption; the timber design limits its carbon footprint. The result is a pure timber roof made of catenary elements spanning up to 89 m. When completed in 2024, it will be one of the largest wooden sports complexes and the world record holder in terms of span for tensioned timber structures. The report on the Aquatics Center timber roof presents its global design and its details of the main technical characteristics required for its construction. Also included are the calculation methods combining the materials used (concrete, steel, timber) with their long and short-term performance and a large displacement non-linear analysis. Moreover, the report focuses on the sensitivity of the roof to factors such as foundation, concrete base, and stiffness of the wood connections that are especially designed to withstand the high tension loads and the various geometric configurations. Finally, the installation methodology and the management of the fabrication/ erection tolerances as well as the control of the geometry on site, which are essential for such tensile structure, are presented in the report.
Stichworte Holz; zugbeanspruchte Konstruktion; Leichtbau; Hängedach Keywords timber; tensile structure; lightweight structure; catenary roof
1 Projektbeschreibung
Das Wassersportzentrum SaintDenis ist die größte Sporteinrichtung, die für die Olympischen Spiele 2024 in Paris neu gebaut wird (Bild 1). Der Entwurf der olympischen Spielstätte ist eine Zusammenarbeit der Architekturbüros Atelier 2/3/4 und VenhoevenCS sowie den Tragwerksplanern von schlaich bergermann partner aus Paris. Die Baufirmen Bouygues Construction und Mathis sind mit dem Bau der Holzkonstruktion beauftragt. Im Jahr 2024 werden hier die olympischen Wettkämpfe im Wasserpolo, Synchronschwimmen und Wasserspringen ausgetragen.
Das Gebäude besteht aus einer Haupthalle, die ein 50mSchwimmbecken beherbergt und während der Olympischen Spiele Platz für etwa 6000 Zuschauende bietet. Die Schwimmhalle mit einer Grundfläche von fast 10.000 m2 wird von einer weitgespannten Hängedachkonstruktion aus Holz überdacht. Im folgenden Beitrag sollen das Tragwerkskonzept des Dachs, die statische Berechnung sowie generell die Verwendung des Baustoffs Holz in diesem Projekt näher erläutert werden. Nach den Olympischen Spielen wird die Kapazität des Wassersportzentrums auf 2500 feste Sitzplätze reduziert, um so eine Nachnutzung für andere Events zu ermöglichen. Das Gebäude wird dann um einen Wellness und Fitnessbereich sowie um eine Kletterhalle ergänzt, wobei sich die Hauptnutzung weiterhin auf den Schwimmsport konzentrieren soll. Bei Bedarf kann der ursprüngliche
Bild 1 Gesamtansicht des Wassersportzentrums Overall view of the Aquatics Center
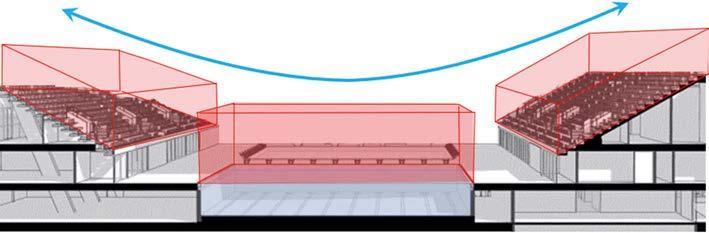
Quelle: schlaich bergermann partner
Bild 2 Regelquerschnitt des Wassersportzentrums mit den einzuhaltenden Lichtraumprofilen über den Sitzreihen und dem Becken Cross-section of the Aquatics Center with clearances above seating area and swimming pool
Zustand wiederhergestellt und die Zahl der Sitzplätze auf 6000 erhöht werden, um wichtige Schwimmwettkämpfe wie Europa oder Weltmeisterschaften auszurichten. Damit wird es im Großraum Paris zum wichtigsten Wassersportzentrum der Region.
1.1 Architektonische und nachhaltige Ziele für das Dach
Im Mittelpunkt der Überlegungen zum Entwurf des Wassersportzentrums stand die Frage, wie das Dach zur Nachhaltigkeit des Projekts beitragen kann. Zwei wesentliche Gestaltungsmerkmale wurden daher erarbeitet: Zum einen ist das Dach als Holzkonstruktion ausgeführt, zum anderen passt sich die Geometrie an die Nutzfläche der Schwimmhalle an und optimiert so das Hallenvolumen auf ein Minimum. Dadurch verringert sich der Energieaufwand für deren Beheizung. Das Dach des Olympischen Wassersportzentrums orientiert sich an den Abmessungen und lichten Höhen, die über den Becken und Tribünen einzuhalten sind, wodurch eine hängende, konkave Geometrie entsteht (Bild 2).
Das Volumen der Schwimmhalle konnte durch die besondere Form des Dachs um fast 30% reduziert werden, was zu einer Energieeinsparung in derselben Größenordnung führt. Außerdem werden durch den Einsatz von Holzträgern sowohl das Gesamtvolumen an benötigtem Baumaterial (das Gewicht des Primärtragwerks beträgt 90 kg/m2 bei einer Spannweite von 89 m) als auch die CO2Emissionen pro kg/Material optimiert. Im Vergleich zu einer einfachen Stahlfachwerkkonstruktion (100 kg/m2) werden so Emissionen von rund 2000 t Kohlenstoff eingespart.
1.2 Tragwerkskonzept und Dachkonstruktion
Das Dach des Wassersportzentrums wird durch eine Serie von parallel angeordneten, hängenden Holzlamellen gehalten (Bild 3). Die Holzlamellen sind in einem regelmäßigen Abstand von 1,05 m angeordnet. Ihre maximale Spannweite beträgt 89 m. Sie werden in drei Abschnitten von 25 m bis 30 m Länge auf die Baustelle geliefert und vor Ort zusammengebaut. Die horizontalen Kräfte des Dachs werden von zwei waagerechten Fachwerkträgern mit einer Breite von 3 m bis 9 m aufgenommen und auf die seitlichen Stützen verteilt, die in einem Raster von 10,5 m stehen. Die konkaven Holzlamellen können in diesem effizienten Tragsystem filigran ausgeführt werden. Die Dachränder dagegen bilden das Rückgrat der Konstruktion und müssen durch ihre konstruktive Durchbildung den hohen horizontalen Lasten standhalten. Die horizontale Steifigkeit wird durch das Dreieck aus Stützen und Zugstangen gewährleistet. Wegen seiner hervorragenden Fähigkeit Druckkräfte aufzunehmen und um gleichzeitig dem architektonischen Gesamtkonzept zu folgen, sind die Stützen im Innenbereich der Schwimmhalle aus Holz. Aufgrund der Witterungseinflüsse, denen die Stützen außerhalb der Halle ausgesetzt sind, sind sie hier aus Stahl.
Das primäre Dachtragwerk wird durch eine obenliegende Dachschalung aus Holz sowie seitlich angeordnete Auskreuzungen vervollständigt (Bild 4). Die Stabilität der Konstruktion in Spannrichtung der Holzlamellen wird durch das Kräftepaar aus Stützen und Abspannung gewährleistet. Die Aussteifung senkrecht zur Trägerachse erfolgt durch zwei mittig angeordnete, vertikale Auskreuzungen aus Stahl.
Hängedächer reagieren empfindlich auf Sog und asymmetrische Windlasten. Die filigranen, weitgespannten
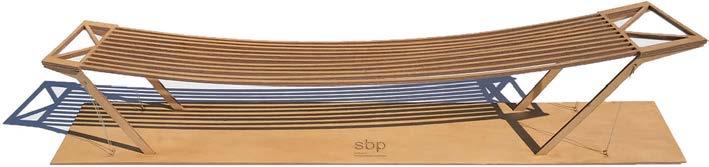
Quelle: schlaich bergermann partner
Bild 3 Modell im Maßstab 1:150 eines Holzträgers für das Dachtragwerk Model in scale 1:150 of a timber girder for the roof structure
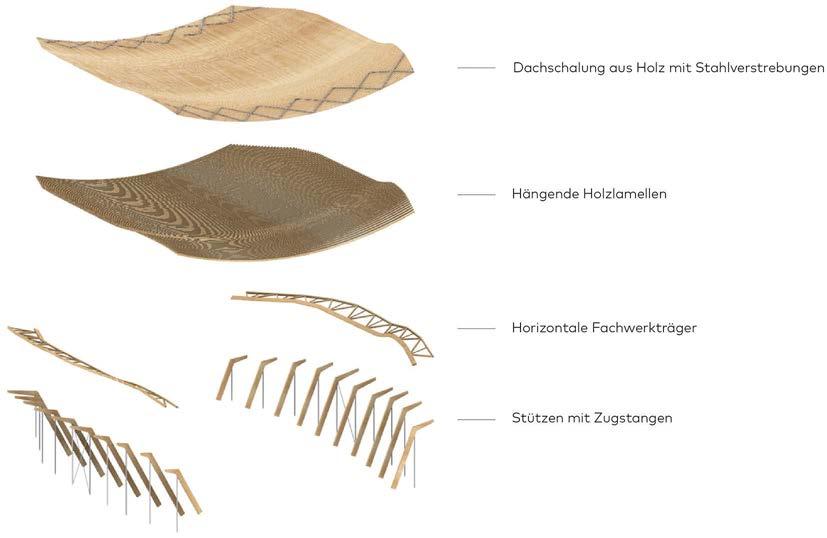
Quelle: schlaich bergermann partner
Bild 4 Explosionszeichnung des Dachtragwerks Elements of roof structure
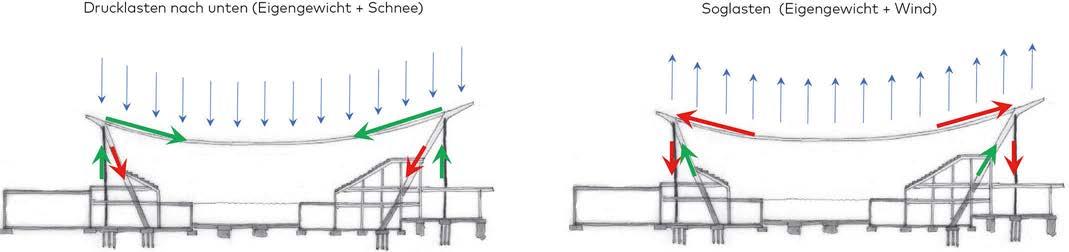
Bild 5 Konstruktionsprinzip des Dachs Roof structure
Holzträger (21 cm × 52 cm, GL24h) tragen die Lasten aber nicht nur auf Zug ab, sondern können auch Druck und sogar Biegung als Träger aufnehmen. Bei Soglasten kehrt sich das statische System um. Die hängende Holzlamelle wird zum Bogen. In diesem Fall werden die Dachränder auf Druck beansprucht, was zum Vorzeichenwechsel in Stützen und vertikalen Elementen führt (Bild 5).
Für das Projekt des Wassersportzentrums wurde ein detailliertes Windgutachten mithilfe einer Windkanalstudie erstellt. Trotz optimierter Windlasten müssen Sogkräfte und zum Teil erhebliche asymmetrische Lasten bei der Dimensionierung des Dachs berücksichtigt werden. Bei einem klassischen Hängedach aus Stahlbändern hätten diese Beanspruchungen zusätzliche stabilisierende Abspannungen oder zusätzlichen Ballast im Dach erfordert. Durch die Verwendung der Holzlamellen ist jedoch nur eine lokale Verstärkung der außenliegenden Holzlamellen notwendig – insbesondere, um die Schnittstelle aus Dach und Glasfassade sauber auszubilden.
1.3 Maße und Geometrie der Konstruktion
Das Besondere an dem hängenden Holzdach des Wassersportzentrums ist seine Größe. Die Grundrissabmessungen ohne Fassaden betragen 95 m in Längsrichtung (Raster 10,5 m) sowie 70–105 m in Querrichtung. In Querrichtung ist das Dach in drei Teile gegliedert: den mittleren, größten Teil, bestehend aus den Holzlamellen, sowie den zu beiden Seiten auskragenden Vordächern (4–9 m), bestehend aus den horizontalen Fachwerkträgern (Bild 6).
Die Variation der Holzquerschnitte im Projekt verdeutlicht die unterschiedliche Beanspruchung der Tragelemente. Die Stützen haben einen Querschnitt von 60 cm × 150 cm. Die Randbalken der horizontalen Fachwerkträger variieren von 40 cm × 70 cm bis 40 cm × 150 cm. Verwendet wurden Brettschichtholzbinder der Qualität GL28h. Dagegen wirken die Holzlamellen mit 21 cm × 52 cm in GL24h filigran und betonen die Leichtigkeit des Dachs.

Quelle: schlaich bergermann partner
Bild 6 Abmessungen eines Dachträgers Dimensions of a roof girder Bild 7 Geometrie des Dachtragwerks Geometry of the roof structure

Neben seiner Größe besteht eine weitere besondere Herausforderung in der variablen Geometrie des Querschnitts. Denn das von den Architekten entworfene Dach folgt dem exakt notwendigen Mindestvolumen und entspricht keiner linearen Form. Die Höhen der Stützen variieren entlang der Längsachse des Gebäudes und orientieren sich in horizontaler wie auch in vertikaler Richtung am Lichtraumprofil der Schwimmhalle (die lichte Höhe im Bereich des Sprungturms ist größer als die über dem Schwimmbecken).
In der Folge unterscheiden sich alle 91 Holzlamellen des Wassersportzentrums in ihrer Form, ihren Anschlusspunkten sowie in ihrer Krümmung voneinander. Angesichts der Fertigung der Balken in drei Segmenten und ihrer geplanten Montage auf der Baustelle hätten so insgesamt 273 große und unterschiedlich gekrümmte Holzelemente hergestellt werden müssen, was einen erheblichen Einfluss auf die Kosten bedeutet hätte. Um diese Mehrkosten zu vermeiden und die Anzahl der modularen Holzelemente zu begrenzen, wurde die Dachgeometrie optimiert. Der höchste Punkt und damit wichtiger Bereich bei der Geometriefindung ist der Bereich der Sprungtürme (in Bild 7 zwischen den gestrichelt angedeuteten Referenzlamellen). Auf beiden Seiten des Turmspringerbereichs werden zwei Referenzlamellen definiert, welche nach außen in Ost und Westrichtung in gleicher Krümmung mit unterschiedlichen Längen geometrisch weiterentwickelt sind.
Die Holzlamellen im Turmspringerbereich werden in ihrer Form einzeln definiert, um sich so weit wie möglich an die geplante Dachform anzupassen. Auf diese Weise kann die Anzahl der Segmente mit unterschiedlicher Krümmung von 273 auf 66 verringert werden.
2 Tragwerksuntersuchungen und Berechnungen
2.1 Berechnungsmethode
Zu den Merkmalen einer gekrümmten, konkaven Geometrie gehört, dass sie nichtlineare Berechnungen zweiter Ordnung erfordert, bei denen große Verschiebungen berücksichtigt werden müssen. Es handelt sich zudem um Konstruktionen, die zwar sehr effizient, aber auch sehr sensitiv auf veränderte Rahmenbedingungen, Kräfteübertragungen und veränderte Steifigkeiten reagieren. Dies führt unter Umständen zu erheblichen Auswirkungen auf die Bemessung.
Für das Wassersportzentrum erhöht sich diese Sensitivität aufgrund mehrerer Faktoren:
– das Bauwerk steht auf einem Betonsockel (zwei bis dreigeschossiges Gebäude), – mögliche Auswirkungen durch die festen Stahltribünen, die zum Teil auf den Stützen des Dachs ruhen, – Fassaden, die ohne Stützen direkt am Dach aufgehängt sind und auf dieses erhebliche Kräfte übertragen, – Veränderung der Steifigkeit der Materialien während ihres Lebenszyklus durch das Kriechverhalten von
Beton und Holz.
Um alle wesentlichen Punkte untersuchen und dimensionieren zu können, wurde bereits im Wettbewerb ein Rechenmodell entwickelt, das alle konstruktiven Teile (Betonsockel, Holztragwerk, Fassade) beinhaltet. Dieses Modell wurde im Laufe der Projektphasen weiter verfeinert und angepasst (Modelle in den Bildern 8a, 8b, 8c).
Bei einem Berechnungsmodell dieser Größe (19.000 Knoten, 38.500 Elemente) ist es so gut wie unmöglich, nichtlineare Berechnungen für alle vorgeschriebenen Lastkombinationen unter allen Bedingungen durchzuführen (d.h. die Berücksichtigung von nichtlinearem Verhalten bei kurz und langfristigen Belastungen mit separaten Kriechkoeffizienten für Holz/Beton/Stahl).

Bild 8 Ansicht der Modelle aus der Studienphase: a) Modell im Maßstab 1:200 für den Windkanaltest, b) globales Rechenmodell (GSA), c) BIM-Modell View of models during the study phase: a) model for wind-tunel testing (scale 1:200), b) global GSA model, c) BIM model

Bild 9 Ergebnisse für die verschiedenen Konfigurationen, die während der Sensitivitätsstudie getestet wurden (maximale Verformung der Holzlamellen) Results achieved considering several configurations tested during the sensitivity study (maximum deformation of the timber girders)
Um dennoch eine präzise Berechnung mit allen Einflüssen und Randbedingungen durchführen zu können, entschied sich das Projektteam für eine lineare Kombination der grundlegenden Lastfälle (ständige Lasten, Schnee, Wind, Temperatur etc.), welche vorab nichtlinear nach zweiter Ordnung berechnet wurden.
Hierbei handelt es sich um einen konservativen Ansatz, da die mit zunehmender Verformung steigende strukturelle Effizienz der Holzlamellen nicht vollständig berücksichtigt wird. Der Ansatz bietet jedoch den Vorteil, dass einerseits die Ergebnisse in Bezug auf Kräfte und Verformungen nicht zu hoch angesetzt sind und andererseits in einer Berechnungszeit umgesetzt werden kann, die mit den Anforderungen des Projekts vereinbar ist.
Zu Beginn der Studie wurde die Gültigkeit dieses Ansatzes in einem Vergleich überprüft, der sich auf repräsentative Kombinationen aus Kurzzeitbelastungen bezog. Die Ergebnisse der zwei Methoden (Projektmethode und Kombination der nichtlinearen Berechnungen) verdeutlichen, dass bei dem gewähltem Rechenmodell sowohl Kräfte als auch Verformungen leicht höhere, also konservativere Werte haben (Kräfte ca. 3–5%, Verformungen ca. 10%).
2.2 Sensitivitätsanalyse
Um die Bedingungen und Faktoren, die das Verhalten der hängenden Holzdachkonstruktion beeinflussen können, zu erfassen, wurde bereits zu Beginn der Entwurfsphase eine Sensitivitätsstudie durchgeführt. Ziel war es, verschiedene Parameter zu testen und ihre Auswirkungen auf die Strukturelemente sowie die kritische Bedeutung für die Berechnungen zu bewerten und zu berücksichtigen. Getestet wurden u.a.:
– Betonsockel (Verlängerung der Stützen/Zugelemente), – Federsteifigkeiten der Verbindungen am Fuß und
Kopfpunkt der Stütze, – Steifigkeit der Pfahlgründungen.
Die Ergebnisse dazu sind in Bild 9 dargestellt. Die größte Auswirkung auf das Holzdachtragwerk hat die Modellierung des Sockels (d.h. Verlängerung der Stützenlänge und Drehung der Stütze/der Zugstangen durch Verformung der Stützen).
Die Federsteifigkeit der Anschlüsse hat geringeren Einfluss und liegt bei 3–5%.
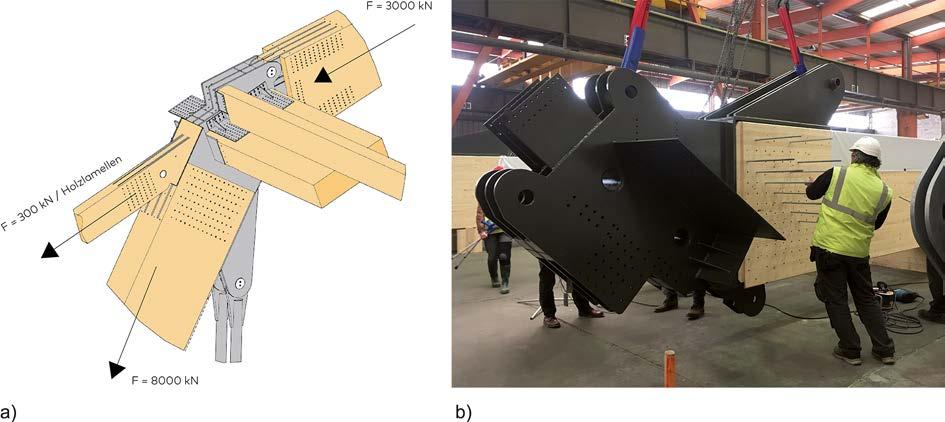
Quelle: schlaich bergermann partner
Bild 10 a) Anschlussdetail zwischen Stütze/Fachwerkträger/Vordach, b) Montage der Beschläge in der Werkstatt a) Connection detail between support/truss/canopy, b) assembly of fittings in the workshop
2.3 Anschlüsse
Die Anschlussdetails der Dachkonstruktion fallen je nach Geometrie und den zu übertragenden Kräften sehr unterschiedlich aus. Gleichwohl folgen sie zwei wesentlichen Vorgaben: Einerseits wurde besonders auf Steifigkeit geachtet, um unerwünschte Verformungen in der Gesamtkonstruktion zu vermeiden, andererseits sollten die Anschlüsse so einfach und reduziert wie möglich gestaltet sein. Die Montage auf der Baustelle musste schnell, sicher und unkompliziert mittels StahlStahlVerbindungen durch Verschraubung oder einfache Bolzenverbindungen möglich sein. Nur so konnte die Montage den strengen Projektzeitplan einhalten.
Der Anschlussknoten am Dachrand (Schnittpunkt Stütze, Holzlamelle, Abspannelement) stellte eine besondere Herausforderung dar (Bild 10a). Dafür wurden große Beschläge mit einem Gewicht von mehr als 4000 kg entwickelt und hergestellt. Mittels des globalen Berechnungsmodells wurden die Anzahl der Schlitzbleche sowie die Dicke der Beschläge berechnet. Der Beschlag wurde in der Werkstatt durch eine Stabdübelverbindung mit der Stütze verbunden (Bild 10b). Der Anschluss zum Vordach und den Zugstangen erfolgt auf der Baustelle (Gabelkopfbolzenverbindungen). Die Untergurte der horizontal verlaufenden Fachwerkträger schließen vertikal mit zwei außenliegenden Blechen an, um den Querschnitt des stark beanspruchten Trägers nicht zu reduzieren.
Eine weitere wichtige Verbindungsstelle findet sich zwischen den drei Segmenten der Holzlamellen. Die hier auftretenden Kräfte sind zwar viel geringer (maximale Axialkraft von 600 kN, Moment von 250 kNm an der Verbindungsstelle), allerdings weisen sie auch einen viel kleineren Querschnitt auf. Für diesen Anschluss musste eine einfache und vor Ort schnell realisierbare Verbindung gefunden werden (insgesamt 364 Anschlüsse), die zudem nicht sichtbar sein sollte. Die dafür entworfene und ausgeführte Verbindung beruht auf der werkseitigen Anbringung von Schlitzblechen in den Holzlamellen. Diese Schlitzbleche werden vor Ort durch Stabdübelgruppen miteinander verbunden, die die Übertragung von Axialkräften und Momenten ermöglichen. Der Zuschnitt der Holzlamellen ist so ausgeführt, dass nach dem Zusammenbau nur die Bohrungen für die Stabdübel sichtbar bleiben. Basierend auf diesem Fügeprinzip konnte ein Großteil der Arbeit in der Werkstatt erfolgen (z.B. Anbringen der Schlitzbleche an den Zugelementen mit mehr als 40.000 Stahlstiften). Das ermöglicht eine schnelle Montage vor Ort (Einhub und Montage eines Holzzugteilsegments in weniger als 20 min).
2.4 Versuchsreihe
Im Rahmen des Projekts wurden mehrere Versuchsreihen durchgeführt. Die meisten betrafen die Dachkonstruktion und die Methode zur Befestigung der PVModule darauf, einige bezogen sich auch indirekt auf das Holzdach.
So wurden v. a. Tests im Originalmaßstab an einem Modell durchgeführt, um die Wechselwirkung zwischen den Holzlamellen und der von ihnen getragenen Last abschätzen zu können.
Ein Grund für diese Versuche war der besondere Aufbau der Dachkonstruktion. Diese besteht u.a. aus einer Schaumglasdämmung (übliche Dämmung für Dächer in Räumen mit hoher Luftfeuchtigkeit), welche auf einer Stahlwanne aufliegt, welche wiederum auf den Holzzugelementen montiert ist. Die Dämmung weist in Verbindung mit der Dachschalung eine gewisse Steifigkeit auf, weshalb eine mögliche Wechselwirkung mit der Steifigkeit der Holzlamellen untersucht wurde.

Quelle: schlaich bergermann partner
Bild 11 Versuchsreihe zur Belastung der Holzzugbänder mit aufgebrachter Dacheindeckung Series of tests regarding the timber girders with roofing
Da diese Wechselwirkung in einem Rechenmodell nahezu unmöglich darzustellen ist, wurde sie an einem maßstabsgetreuen Modell überprüft (Bild 11). Sie wurde sowohl unter zwei Lastsituationen (Biegung und Schwingung eines Holzträgers) als auch im Hinblick auf zwei unterschiedliche Phasen getestet: vor und nach dem Anbringen der Dacheindeckung über der Dachschalung aus Holz.
Die Versuche verdeutlichen, dass das Aufbringen des Dachs die Steifigkeit der Holzlamellen um etwa 10% erhöht. Außerdem wurde die darauf aufgebrachte Kraft auf einen Wert erhöht, der dem dreifachen Wert der zulässigen Spannung, die sich aus dem Berechnungsmodell ergibt, entspricht. Unter dieser Belastung war ein Knistern des Schaumglases zu hören, was auf eine Neuordnung der Struktur der Schaumglasblöcke hindeutet. Sichtbare Schäden oder bleibende Verformungen wurden am Modell jedoch keine beobachtet.
3.1 Fertigung in der Werkstatt
Der Vorfertigungsgrad der Holzelemente in der Werkstatt liegt bei diesem Projekt bei fast 100%. Dort wurden die Brettschichtholzträger sowie die Verbindungsbeschläge hergestellt. Durchgeführt wurden die Arbeiten von der Firma Mathis und ihren Subunternehmen.
Die Fertigung der Holzträger erfolgte weitgehend maschinell und mit Robotern, um exakte Anschlusspunkte von Stützen, Vordach oder Holzlamellen mit den Stahlbeschlägen gewährleisten zu können (Bilder 12a, 12b). Neben der dadurch hohen Präzision ermöglicht diese Fertigungsweise auch eine schnelle Montage vor Ort. Daher waren für die Montage des primären Holztragwerks (einschließlich der Beplankung) auf der Baustelle weniger als sieben Monate erforderlich. Das entspricht einer Dachfläche von etwa 10.000 m2 und einem Volumen von 2200 m3 Holz.
3.2 Montageverfahren
Die Dachmontage verlief in mehreren Phasen, nach einer festgelegten Reihenfolge parallel zu den Materialtests; hauptsächlich, um den zeitlichen Ablauf der Montagephasen zu überprüfen und bei Bedarf spezielle bauliche Maßnahmen berücksichtigen zu können. Der Ablauf sah wie folgt aus:
– Montage von Stützen/Vordach/Zugelementen am
Boden, dann Einhub des Dachsegments mit einem 500tMobilkran – Errichtung der mittleren Segmente (Verstrebungen) mit provisorischen Abspannseilen (Bild 13) – Errichtung der Stützen von der Mitte hin zu den Seiten – Montage der Holzfassaden an den geneigten Stützen
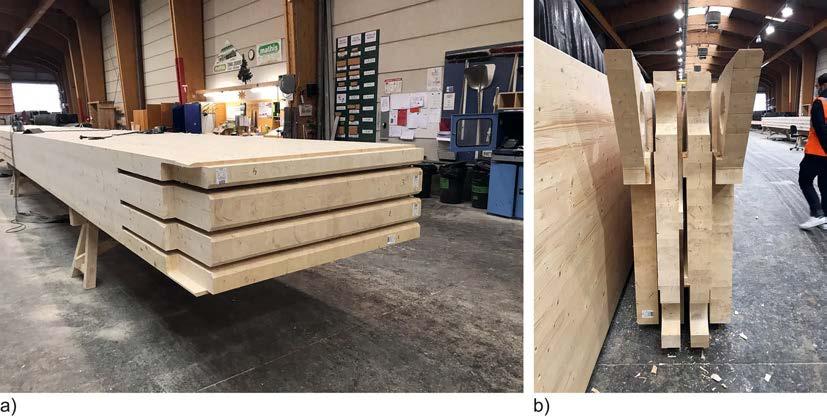
Quelle: schlaich bergermann partner
Bild 12 a, b) Herstellung der Holzrahmen in der Fertigung der Firma Mathis a, b) Manufacturing the timber frames in the workshop of the company Mathis
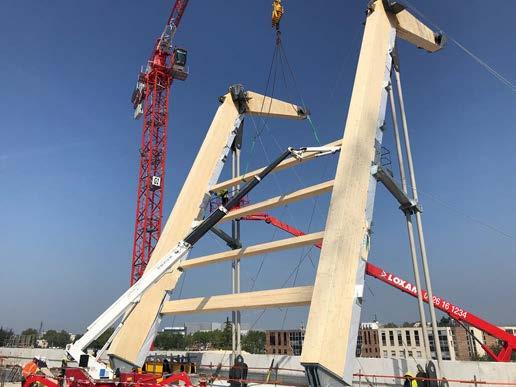
Quelle: schlaich bergermann partner
Bild 13 Montage des ersten Segments auf der Baustelle Assembly of the first segment on site
– Einhub und Montage von Gurten und Diagonalen der
Fachwerkträger für das Vordach – Montage der Holzlamellen mit zwei provisorischen
Stützen in der Mitte der Dachkonstruktion (Bild 14) – Verbindung der Holzlamellen und schrittweise Montage der Holzbeplankung
Nach dem oben beschriebenen Montageprinzip wirken die Kräfte in den Stützen und Zugstangen während der Bauphase und bis zum freien Spannen der Holzlamellen in umgekehrter Richtung. In diesem Zustand werden die schlanken vertikalen Zugstäbe Druckkräften ausgesetzt und müssen daher mit provisorischen Stützstreben stabilisiert werden (Bild 13).
Ein weiterer entscheidender Schritt im Montageablauf ist die Montage der Glasfassaden im Westen und Osten des Gebäudes. In einem früheren Planungsstadium war vorgesehen, die Fassaden sukzessive, eine nach der anderen, zu montieren. Dies hätte jedoch einen für das Dachtragwerk kritischen Montagelastfall generiert, da Wind in die auf einer Seite noch offene Halle eindringen hätte können – wie in eine Art Tasche. Der Winddruck auf die Unterseite der Holzlamellen hätte zusammen mit dem natürlichen Windsog auf dem Dach zu einem Anheben der Dachkonstruktion geführt, das von den Zugbändern nicht hätte aufgenommen werden können. Um dem entgegenzuwirken, wurde der zeitliche Ablauf angepasst und eine simultane Montage der zwei vorgehängten Glasfassaden (West und Ost) während eines Zeitfensters mit stabiler Wetterlage ohne starken Wind geplant.
3.3 Toleranzabweichungen
Bei diesem Projekt mussten, bedingt durch die großen Spannweiten, geringere Toleranzen als im Holzbau üblich eingehalten werden. Zudem war es für die Statik wichtig, den Einfluss einer Geometrieabweichung auf das Tragverhalten des Dachs zu analysieren und zu verstehen.
Selbst unter Berücksichtigung strenger Ausführungstoleranzen (± 1 cm Betonanker am Fuß der Stütze, ± 2 mm für die Länge der Stahlanker, ± 3 mm für die Länge der Holzstützen) kann es im ungünstigsten Fall zu einer bis zu 4 cm großen horizontalen Verschiebung des Verankerungsknotenpunkts der Holzlamellen kommen. Diese seitliche Verschiebung kann wiederum zu einer zusätzlichen vertikalen Verformung der Holzlamellen von bis zu ± 20 cm führen.
Diese geometrischen Abweichungen könnten zu Problemen bei der Dachentwässerung sowie der Montage der vorgehängten Fassaden führen und waren daher zu unterbinden.
Um die Bautoleranzen ausgleichen zu können, wurde auf der Baustelle eine zusätzliche Unterfütterung im Bereich der Fußpunkte der Holzstützen vorgesehen. So konnte während des Einbaus die Position der Stützenfußpunkte in vertikaler Richtung um ± 2 cm verschoben werden. Um

Bild 14 a, b) Montage der ersten Holzzugbänder auf der Baustelle a, b) Assembly of the first timber girders on site
die Blechdicke der Unterfütterung zu bestimmen, wurde die genaue Position der Verankerungen für Stützen und Zugelemente erst auf der Baustelle ermittelt; die exakte Länge der Stützen und Zugelemente wurde bereits im Werk berechnet. Die Daten wurden dann final analysiert, um den Toleranzausgleich genau zu definieren und so die theoretisch errechnete Position der Lamellenverankerung einzuhalten. Mit dieser Vorgehensweise, Segment pro Segment, werden die Bautoleranzen größtenteils ausgeglichen und auf ein Niveau reduziert, das für die Montage und Nutzung des Dachs und der Fassaden akzeptabel und zulässig ist.
Autorinnen und Autoren
Benjamin Touraine (Korrespondenzautor) b.touraine@sbp.de schlaich bergermann partner 25 rue du Général Foy 75008 Paris, Frankreich
Michael Zimmermann m.zimmermann@sbp.de schlaich bergermann partner 25 rue du Général Foy 75008 Paris, Frankreich
Cécilia Gross c.gross@venhoevencs.nl VenhoevenCS Hoogte Kadijk 143 F15 1018 BH Amsterdam, Niederlande Laure Mériaud l.meriaud@a234.de Workshops 2/3/4 234 rue du Faubourg Saint-Antoine 75012 Paris, Frankreich
Zitieren Sie diesen Beitrag
Touraine, B.; Zimmermann, M.; Gross, C.; Mériaud, L. (2022) Ein Hängedach aus Holz für das Olympische Wassersportzentrum in SaintDenis. Bautechnik 99, Sonderheft Holzbau, Ausgabe 2, S. 85–93. https://doi.org/10.1002/bate.202200078
EMPFEHLUNG DER REDAKTION
Mit dem Beitrag des Teams der FH Aachen zum SDE 21/22 wird im Projekt LOCAL+ ein kreislauffähiger Holzmodulbau mit einem innovativen Wohnraumkonzept geplant und umgesetzt. Ziel dieses Konzepts ist die Verringerung des stetig steigenden Wohnflächenbedarfs durch ein RauminRaum Konzept. Gebäudetechnisch wird in dem Projekt nicht nur das Einzelgebäude betrachtet, sondern unter Berücksichtigung des Gebäudebestands wird für das Quartier ein innovatives und nachhaltiges Energiekonzept entwickelt. Ein zentrales Wasserstoffsystem ist für ein Quartier geplant, um den Stromverbrauch aus dem Netz im Winter zu reduzieren. Zentraler Bestandteil des TGAKonzepts ist ein unterirdischer Eisspeicher, eine PVT und eine Wärmepumpe mit intelligenter Regelstrategie. Ein Teil des neuen Gebäudes (Design Challenge DC) wird in Wuppertal als Hausdemonstrationseinheit (HDU) präsentiert. Eine hygrothermische Simulation der HDU wurde mit der WUFISoftware durchgeführt. Da im Innenraum Lehmmodule und platten als Feuchtigkeitspuffer verwendet werden, spielen die Themen Feuchtigkeit, Holzfäule und Schimmelwachstum eine wichtige Rolle.
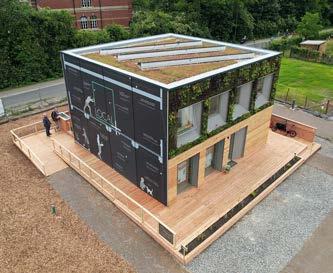
Quelle: SDE 21/22
Haus LOCAL+ FH Aachen Ghinaiya, J.; Lehmann, T.; Göttsche, J. (2022) LOCAL+ – ein kreislauffähiger Holzmodulbau mit nachhaltigem Energie und Wohnraumkonzept. Bauphysik 44, H. 3, S. 136–142. https://doi.org/ 10.1002/bapi.202200010