DRIVEN TO SOLVE
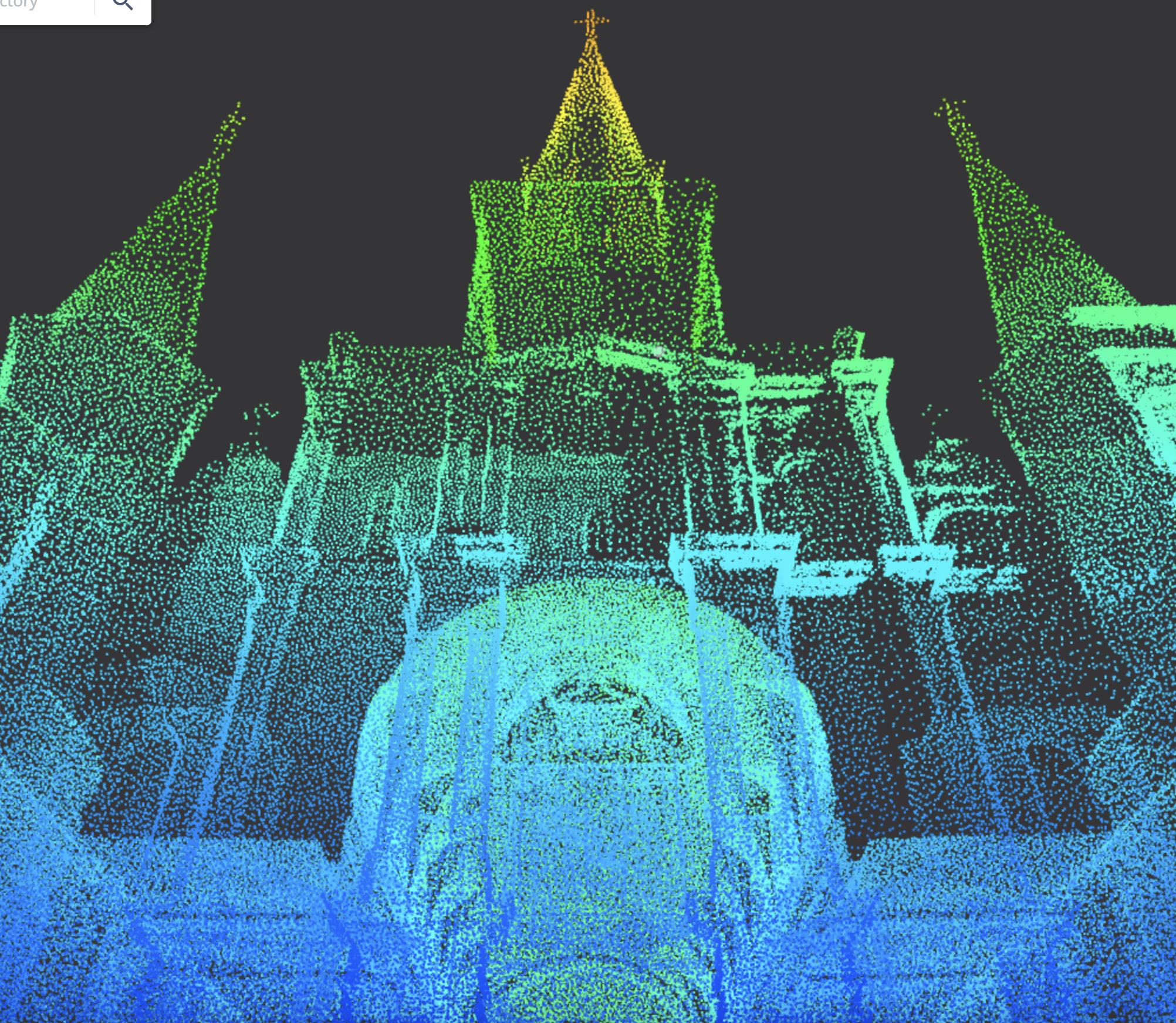
Please join us in welcoming John Tav to the Directors' table.
John Tav has always had his sights set on the future— whether it's the next device, application, or process. He’s never content with the status quo. When he joined EIS in 2012, he was a talented Mechanical Designer with a degree in Information Technology from Tulane University, a role he could have easily continued in. However, after years of hands-on industrial experience, his passion for emerging technologies became undeniable, and his focus shifted.
John quickly began applying his technical expertise to implement innovative solutions to workplace challenges. His initiatives have not only aligned with industry needs but have also helped position EIS as a thought leader. As Chief Technology Officer, John now leads the EIS Technology Division, developing strategies to improve industrial safety, efficiency, and cost savings. Additionally, he oversees the Captura brand, guiding its development of new software and use cases for the architecture, construction, and emerging markets.
Please send us your article ideas, artwork, photography, content suggestions, funny engineer jokes, baby pictures, announcements and anything else you would like to see in the EIS company newsletter. This newsletter is for you so let’s make it GREAT!
To upload video, pictures and content over 2mb please use our media folder at
A special thank you to everyone who volunteered their time to contribute.
We start each journey with our employees by understanding their unique personality profiles. We aren't just searching for great candidates; we're seeking the perfect match.
EIS stands out in the industrial market by valuing both practical experience and innovative technology. We designate Tech Champions to ensure the company remains knowledgeable and ahead of industry trends.
Integrity is at the core of each EIS division. Each person has a diverse set of experineces ensuring projects are done right the first time. Collaboration across divisions brings multiple perspectives to each project.
We believe in organic, strategic growth. Rushed expansion without a longterm plan stifles innovation and leaves employees dissatisfied. Our diverse approach cultivates well equipped employees for better project outcomes.
Congratulations to our team! We are happy to announce that EIS has been named a 2024 Top Workplace by the Times Picayune and The New Orleans Advocate. This is the fourth year in a row that we have received this honor. EIS Marketing Coordinator Lisa Bordlee and HR Associate Tiffany Pfister attended the ceremony at the Higgins Hotel in New Orleans to receive our award.
Kevin Kern
WHAT’S YOUR CURRENT ROLE ON THE TEAM?
As a Business Development Representative of EIS and Captura, my primary focus is on driving growth and establishing client relationships. My role involves identifying new business opportunities, developing strategic partnerships, and ensuring client satisfaction across both entities.
HOW HAVE YOU GROWN PROFESSIONALLY WHILE WORKING AT EIS?
In addition to receiving my drone pilot license, I have grown significantly into my role as a Business Development Representative, learning valuable skills and gaining deeper insights into the industry. Over the years, I have developed strong relationships with clients, leading to long-term partnerships and repeat business. I have learned to work closely with multiple teams across our company to align strategies and deliver solutions.
WHAT HAS BEEN ONE OF YOUR GREATEST ACCOMPLISHMENTS?
One of my greatest accomplishments has been successfully introducing our scanning capabilities to the local Architecture, Engineering, and Construction (AEC) markets. This achievement stands out not only because of its technical and strategic significance but also because of the profound impact it has had on our clients in this sector.
WHAT DO YOU LIKE BEST ABOUT OUR COMPANY CULTURE?
Teamwork! As an athlete I value high level teamwork, which you certainly get here at EIS/Captura.
WHAT’S YOUR CURRENT ROLE ON THE TEAM?
I am currently a Mechanical Designer, but my career at EIS began in 2021 as a Reality Capture Technician. Although I initially applied for a different position, EIS recognized my previous laser scanning experience and offered me a role in reality capture. They also provided me with the opportunity to gain mechanical design experience simultaneously. In 2023, I transitioned to the role of Mechanical Designer, though I still assist with reality capture scans when needed. Each day, I contribute to various design projects and am fortunate to work with a team of highly skilled professionals whom I greatly admire. Overall, it’s been rewarding to see projects come together, knowing that my contributions have played a part in the team’s success.
WHAT ADVICE DO YOU HAVE FOR OTHERS INTERESTED IN THIS FIELD?
Reflecting on my own journey, I would advise starting with patience and staying focused on your goals. Even if you’re not where you want to be today, make the most of your current situation and watch your progress unfold. While my previous roles weren't my ultimate objectives, they provided valuable insights into pipe design, and I believe those experiences have given me a significant advantage.
WHAT DO YOU LIKE BEST ABOUT EIS COMPANY CULTURE?
I appreciate the family-style culture at EIS, which emphasizes work-life balance—a priority for me. I also value the employee events and the opportunity to spend time with colleagues outside the office.
Tyler Andrew
Mechanical Designer
Employees receive an allowance of 20 Nectar Points each month to give away to coworkers and managers.
Points to Give
Allow you to shout out your coworkers for the awesome work they do. These points expire at the end of the month and cannot be carried over.
Points to Redeem
Are when your coworkers shout you out for the awesome work that you do! These points never expire, and they are what you will use to cash in for rewards.
Questions about Nectar HR?
Email Tiffany Pfister at tpfister@eisllc.net .
Nectar HR Login
Q. Who came up with the name Captura?
Joe Brinz, CEO: That's a good question. We actually got some help from a marketing company based in Baton Rouge. The idea was to choose a name that emphasized our goal—capturing the world around us.
John Tav, CTO: One of the suggestions from the marketing company was “Optimus Prime,” but it felt too pretentious. Captura stood out as the clear choice.
Q. Why create a separate brand?
Joe Brinz, CEO: At EIS, we’ve been using LiDAR scanners for a long time, primarily for the petrochemical market. The directors at EIS felt that the technology had potential beyond industrial use. Captura was created to focus on broader applications like schools, commercial buildings, and government structures, also allowing us to focus on software development. We wanted to keep the software development separate from EIS to clearly differentiate our services. This made it easier from both a business standpoint and when pitching to clients.
John Tav, CTO: Another reason was our company’s name. When you go outside the industrial sector, leading with “Engineering and Inspection Services” confuses people. But with “Captura,” we can introduce ourselves as a Digital Transformation company specializing in Reality Capture. This builds trust because we have a solid background in industrial applications, which sets us apart from other newer companies in this field.
Captura opens up opportunities beyond industrial projects, allowing us to explore other markets.
By Anna Rockhold
Joe Brinz, CEO: We've spent a lot of time using technology for our engineering and design work. Captura wasn’t founded just because we saw an opportunity to buy some cool new machines and suddenly position ourselves as leaders in scanning and digital capturing. It was built on solid engineering principles that we use daily.
We realized the technology had advanced to a point where we could capture large areas in a fraction of the time it used to take. That’s when we invested in new LiDAR machines and started perfecting the use of that technology. Suddenly, more markets began opening up to reality capture technology, and that’s how Captura really took off.
Q. What are some of the new areas Captura has ventured into?
John Tav, CTO: We’ve expanded into disaster recovery, offering reality capture services for pre-loss, as-is documentation, and post-disaster insurance claims. We also now provide modeling and simulation services and have started integrating AI and machine learning into our software development efforts.
Q. Kevin, you have been instrumental in business development for the AEC market. Can you tell me what the differences are coming from the Industrial market?
Kevin Kern, Business Development: Well, going from industrial to the AEC world (Architecture/ Engineering/Construction), there's not a whole lot of difference. Both clients need spatial data that's collected for them to manipulate for whatever their purpose is. It's typically going to be for design and remodeling and something to that nature.
The biggest thing, I think, is the commonality of all the different markets that we exist in is the need for efficiency and cost effectiveness that our service really provides. I think the more that we can educate clients on the technology and they try it out then they really start to believe in it, they start to see the time and money saved.
John Tav, CTO: So, 2014 is when we started using laser scanning for industrial purposes at EIS. Back then I was a mechanical designer, so I had been to the field many times with and without scanners.
The typical workflow would be you go out, to understand the scope, then measure everything, sketch it out. What would take us typically two full days in the field, and I'm talking about two full 10 hour days in the field, now it would take us about two hours in the field with the scanners.
And again, you always have that, you know, that I forgot one measurement moment. Do I have to go back out to the site? How do I explain that to my supervisor that, oh, I forgot a measurement, I need to go back, and drive an hour each way, gain access to the site, and now I'm eating into the project budget.
There's always those types of scares in project management that you want to avoid. Laser scanning gets rid of all those. Saves a lot of money on the front end of the capture portion, whether it's sketching and tape measuring to laser scanning. And on the back end of your design work, you don't have to go through each sketch trying to create a 3D map. Now everything is already there and directly placed into CAD or REVIT. It's a great tool because it saves time from a design standpoint.
Q. Do you think the oil and gas industry is dying? Is that why you're moving the business towards technology?
Joe Brinz, CEO: Is the oil industry dying?
Absolutely not. Let me clarify. The question is whether the oil and gas industry is nearing the end of its life, and the answer is definitely no.
We still rely heavily on fossil fuels globally for almost everything. It's going to take a long time before alternative energy sources can even begin to match the amount of energy we need for day-to-day activities, whether it's for transportation, or other uses.
Now, as for why I’m venturing more into technology and not just focusing on the engineering and design side of EIS—it’s because I see technology as a differentiator. In my view, you don’t want to be the second or third company pitching to a client with the same services as everyone else. I like to be the first, offering something unique—something other engineering firms haven’t fully embraced or thought through, especially in terms of how it impacts both our firm and the industry as a whole.
Surprisingly, the industry has adopted digital twin technology and reality capture much faster than I expected. Including technology as part of our service offerings is critical for two reasons. First, it gives us an edge when meeting with clients. We can say that not only will we complete the engineering and design to the highest standard, but we’ll also do it as efficiently as the latest technology allows.
Second, it’s helping us diversify into new markets. Technology is evolving beyond just oil and gas.
continued... We're seeing AI, mechanical integrity assessments, failure rates, and other advancements— much of which starts with reality capture. The truth is, the digital twin concept is going to be used across every industry worldwide.
According to the latest figures from the Reality Capture Network, less than 2% of the world has been digitally captured. The market potential is enormous, with uses ranging from remote training to safety and more. The applications for digital twins are limitless, and we want to be part of that journey.
This is why I’ve focused on technology—because it’sgoing to reshape the way we approach engineering, design, and even inspections. I saw it coming, and I didn’t want to be left behind. I wanted to be ahead of the curve.
Q: Taylor, tell me about your favorite project that you've worked on since you've been at Captura.
Taylor St. Pierre, Reality Capture Specialist: That would have to be the abandoned hospital. We were there for a while, and it felt a lot like urban exploration. We got to wander through all these hallways, and you see things in abandoned places that you really don't expect.
Q: Like what? Ghosts?
John Tav, CTO: For me, some of the industrial projects stand out—especially the refinery in Beaumont. That was one of the most challenging due to its sheer size. We captured 4.5 million square feet in just three months. From a project management standpoint, finding the right people, getting the equipment, and coordinating everything was a massive challenge, but we pulled it off.
Besides that, the work we did after Hurricane Ida hit in 2021 was also memorable. We were deployed just five days after the storm. We never knew what we were walking into, so we approached each building like we would any other. The one that stands out the most for me is the St. Louis Cathedral.
It's such a significant historical landmark in New Orleans, with incredible architecture and so much history behind it. It's one of the coolest buildings in the city. We had the privilege of exploring every part of it—the spires, the roofline, the attic spaces, even the bell tower. Climbing up there and seeing every nook and cranny was an experience not many people get to have. It was definitely a very special project.
We are now part of that history. The footage Taylor created has been featured in the London Clarion Herald and on London Live. It's kind of worldwide now.
Taylor St. Pierre, Reality Capture Specialist: (Laughs) Yeah, you definitely get ghost story vibes walking around. You never really know where the hallways lead. It was shut down after Katrina, so by the time we were there, it had been abandoned for about 15 years. It was completely empty—even animals hadn't settled in. It was just... still.
We actually went back for another job after the initial scan. Seeing the comparison was incredible. At first, it looked almost apocalyptic. But afterward, it had this concrete parking garage vibe—completely different from the original. The transformation was striking. That adventurous vibe, combined with seeing the before-andafter changes, really stuck with me.
Q: John, what is your favorite project?
a. Elevation view of the St. Louis Cathedral
b.
WEARABLE
HANDHELD
AERIAL
PHOTOGRAMMETRY
VIRTUAL REALITY
To ols We Us eI n Digita l Tr ansformatio ns .
ARTIFICIAL INTELLIGENCE
TheEIS Technology Division and Captura use similar toolsfor separate markets. Yet, both areatthe forefront of technology consistently weighing client needs wit hproject budgets, time, and accurac y
TERRESTRIAL
METROLOGY
MACHINE LEARNING
John Tav, CTO: Good question. Digital transformation, in a nutshell, is about making a client’s processes more efficient by using digital tools. Every client is at a different stage of their digital transformation journey. This journey can range from something as simple as This can range from something as simple as converting paper documents to PDFs, to more advanced efforts like capturing entire sites or applying new technological tools to their workflows, such as sensors or IoT integrations. That’s essentially what digital transformation is—though it's a very broad concept.
We can provide one-on-one consultations to understand the client’s specific needs and help them progress through their digital transformation, ideally through multiple stages. But it goes beyond that. We also support them
with instrumentation, electrical, civil, structural, and mechanical engineering. This helps them advance through the next stages of their digital transformation journey, depending on what they need. We have resources within the company, and we can also reach out externally if needed. And even though the process is ongoing—it's never truly finished as technology keeps evolving—some clients are already very advanced. They've reached a point where they’re saving millions per year by using digital tools daily, and they’re seeing a great return on their investment. Or, we can bring in a larger team, leveraging the diverse strengths and expertise across our company, to help them move forward as a whole. Whether it's on the industrial scale for turnarounds, or on the building construction side with other relevant tools, we have the ability to assist at any scale.
Stop Work Authority (SWA) empowers employees, at any level, to halt a job or task when a hazardous situation appears imminent, without fear of retribution.
Stop Work Authority (SWA), also known as Right to Refuse (RTR), is not required by OSHA, but there are many benefits to implementing a procedure that gives employees the right to stop unsafe or unhealthful working conditions. Adding Stop Work Authority to a health and safety program is a good way to strengthen the safety culture at an organization when workers know they can exercise SWA without repercussion.
Because work conditions can change, having a program in place like Stop Work Authority encourages employee involvement in hazard observation and increases the chances that hazards are identified well before they become near misses or tragic incidents.
The Stop Work Authority procedures should cover everyone at a work location or on the job site including employees, contractors, subcontractors, and visitors. Stop Work Authority does not only apply to extremely dangerous work situations or obviously unsafe behavior like explosion hazards or when someone becomes distracted and walks under a heavy load. Depending on the circumstance, correcting hazards after work has been stopped can also include easy fixes like instructing personnel to wear the proper PPE or moving a tripping hazard.
Stop Work Authority provides
� an additional layer of protection for people and property.
� a framework for workers, subcontractors, and management to respect safe work.
� a procedure that protects individuals from negative consequences when they exercise their right to refuse dangerous work.
� the specific steps workers can take to protect themselves and their co-workers from a potentially hazardous situation.
� the organization with empowered, competent workers who have the responsibility, obligation, and right to stop work if they believe it will create a dangerous situation.
� examples of what kinds of work situations may require work to stop
� the obligation and responsibility that workers have to halt work before an incident happens
� assurance that there are to be no negative consequences, from the company, management or co-workers after a worker uses their authority to stop work
� a zero tolerance for bullying or ridicule towards anyone who uses their authority to stop work
� training requirements
There may be obstacles and challenges that employees need to overcome as they begin to actively participate in a Stop Work Authority program. The following excuses are not good reasons for any worker to fail to use their authority to stop work when unsafe actions or a hazardous situation arises at work.
� Fear of alienating a co-worker by calling them out on an unsafe act
� There is a sense of urgency to getting the work done and stopping work would cause a delay
� An unsafe act may be performed by someone with more experience, and you feel like it is not your place to call attention to the risky behavior
� Anxiety that you have misinterpreted the situation
� Peer pressure influencing you not to speak up
� Fear of embarrassment or ridicule
� Unclear understanding of the SWA process or what unsafe acts may be deemed worthy of stopping.
� Worry that stopping work may impact production or the ability to meet a deadline
� Other workers are present and no one else is saying anything
� Assuming you don’t have the authority to stop work if you witness unsafe behavior or a dangerous situation
� Accepting “we’ve always done it this way” as an excuse for performing work in an unsafe manner
� Fear of angering a supervisor or management
Every organization will set up their Stop Work Authority program differently, but the general steps of a SWA procedure are as follows:
� Stop the work. When an unsafe action or situation is observed, the work is immediately halted.
� Notify the affected personnel and supervisor. Provide a clear explanation of the reason why the work was stopped. Take immediate action to make the area safe.
� Investigate the reason why the work was halted. Review and discuss the situation and come to an agreement on the stop work action.
� Correct the unsafe behavior or situation. Hazards should be eliminated before work resumes.
� Resume the work. After corrective actions have been completed all affected personnel should be notified that work can continue.
It is not enough to just declare that Stop Work Authority now exists within an organization. Clear communication of the SWA policies is crucial, including:
� the exact steps an employees should take and how the entire process works from start to finish
� Monitor and follow-up. While immediate corrections may have eliminated the hazard, additional actions may be implemented to prevent future occurrences. Preventative actions may include monitoring activity, root cause analysis, additional training, safety program updates, follow-up inspections, further investigation, targeted safety meetings, or documentation.
By Anna Rockhold
Binh has been with the EIS team since June of 2008. He is one of our most experienced Sr. Mechanical Designers on our design team. Binh has been instrumental in securing and retaining work from several clients, including Chevron Oronite. He has embraced the use of technology in all aspects of design; he was the natural choice for this position. Some of his new responsibilities as the Design Team Technology Champion will include:
Developing a plan to incorporate data referencing in our model reviews with customers.
Developing a process for production of simulations of the models showing demo and installation procedures.
Working closely with the Captura Team to test new software platforms that can provide an improved digital experience for customers.
Providing recommendations to the Design Group regarding the development and testing of new workflows that utilize the most cutting edge technologies (AI/MI) to improve efficiencies within the Design Group.
Todd is a Mechanical Integrity and Onstream Inspection SME. He has a genuine interest in improving the technology offerings of the Inspection Division and works closely with the EIS Technology Division to develop areas where tech can improve the overall inspection process. Todd has been instrumental in securing several long term clients. Some of his new responsibilities as the Inspection Team Technology Champion will include:
Testing of new technologies as they apply to inspection tracking and planning.
Testing of new technologies as they apply to gathering field data for Mechanical Integrity/Analytical Engineering.
Providing support and recommendations for the development of CML software for location and data tracking.
Providing support and recommendations for the development of inspection circuits in Digital Twins.
May - August
By Lisa Bordlee
Valero's Reel United Big Bass Tournament - Benefiting the United Way of Mid & South Jefferson County Beaumont, Texas
Reuters Downstream Galveston, Texas
Expo Pasadena, Texas
San Jacinto College Tech Test Day
Pasadena, Texas
Fish-O-Rama Fishing Tournament
- Supporting the Children's Museum and STEM in Region 5 Schools Lake Sam Rayburn, Texas
Port Arthur Industry Show
Port Arthur, Texas
B R Area United Way
Golf TournamentExxonMobil Baton Rouge, Louisiana
By Lisa Bordlee
Employees with access to the EIS SharePoint now have a new internal communication site named the HUB. Within this central location, you can access company links in one place, make requests, and stay up-to-date on company news and events.
Here's what you can find in the HUB!
• Links to HR benefits and company websites
• Links to EIS and Captura social accounts.
• Calendar of upcoming EIS internal and external events.
• Submit IT Support Ticket.
• Request Office Supplies.
• Links to the EIS Driven to Solve Newsletters.
• Visit the Marketing Department Page.
» View and download brochures, videos, and presentations.
» Request new marketing materials.
» Submit event requests.
» Suggest social media posts.
» Report a website or collateral error/issue.
https://eisllcla.sharepoint.com/sites/theEIShub
.
You’re invited to the Engineering & Inspection Services LSU Tailgate! Join us with your family and friends as we rally behind the Tigers at our tent on the iconic LSU Campus in Baton Rouge. Celebrate with the EIS team in a lively atmosphere filled with delicious food, refreshing drinks, and a whole lot of fun!
Our tent will be located in the Three Olives Tailgate District on South Stadium Drive outside Patrick Taylor Hall on the LSU Campus.
Join us for a ROARING good time at the same location for the following 4 SEC Games:
Patrick Taylor Hall Three Olives Tailgate District
Sat Oct 12 Sat Nov 23 Sat Nov 30 Sat Nov 9
A safety strategy that helps industrial environments is the use of visual controls. The method relies on the idea that visual management techniques work to create an environment where communication can be clear to employees without the help of words and interruptions in a process. This simple idea has the potential to help quickly identify problems, reduce waste, reduce costs, shorten lead times, reduce inventory, and most importantly—give employees a safe working environment.
Some of the visual cues that a facilit y can use include:
Floor tape can be color coded to denote status, hazardous areas, mark where emergency equipment resides, as well as egress routes. Floor shapes, such as footprints and arrows can also be useful
Ando n lights can be trigge re d au tomatically or manually. They work to aler t operat ors, management, and main tenance pe rsonnel of tool malfun ct ion, safet y problems, among other things
Floor and wall signs are used t o show pedestrian pathways and exi ts, iden ti fy hazard s, and marking where things go.
Labe ls for pipe ma rking, equipment, and oth er locations that require empl oyee s to be warned of the hazards that exist around them.
We'd like to give a fond farewell to our amazing summer interns Jonah Barnett, Evan Schwartz and Jonah Anderson. Jonah B. is attending LSU for Electrical Engineering and spent time in our Beaumont, Texas location. Evan and Jonah A. are both studying Mechanical Engineering and spent time at our Metairie, Louisiana location. They each gained valuable and hands-on experience working with our teams. They learned real world industry skills such as basic mechanical theory, ASME/API Code research and application, and engaged in technical discussions with managers and clients.
As EIS continues to grow, we are always in search for talented individuals to join the team. Please spread the word to those you know who may be interested in our open opportunities. A full list is available at the following:
eisllc.bamboohr.com/careers
Source: WeeklySafety.com
By Lisa Bordlee
A Photon checks into a hotel and the receptionists asks if he needs any help with his luggage. "No, thanks," says the Photon "I am traveling light."
Have a joke, crossword or other game you’d like to contribute to our newsletter? Let us know! Send to
May - June - July - August
1 Year
Julian Moore
Trent Martin
Caleb Hardy
Allen Gautreaux
Michael Rios
Will Buquoi
Clyde Diaville
2 Years
Mark Varisco
Steve Waldrop
Ryan Small
Yvette Patton
Mark Terrio
Jordan Guillot
Cody Smith
Julio Morales
3 Years
Taylor St. Pierre
Eddie Pace
Mark Michiels
Therese Holmes
Will Fontenot
Mario Villarreal
Tonya Chauvin 14 Years
Binh Nguyen 16 Years
Mac Troxclair 9 Years
Darren Kling 18 Years
Frank Cuadra 13 Years
Drew Colvin Sr. Civil/Structural Engineer ExxonMobil, Texas
April Carpenter Human Resources Manager Metairie, Louisiana
Lamar James API Refractory Inspector
Syngenta
Anna Gibbens
Electrical and Instrumentation Engineer Metairie, Louisiana
Mark Plaisance Analyzer Technician in Drafting Shell Norco
Logan Adams Reality Capture Technician Metairie, Louisiana
James (Matt) Sherman Project Support Group Drafter Beaumont, Texas
Tammy Brockett Document Control/Admin Specialist Beaumont, Texas
Noah George 3D Laser Scanning and Surveying Technician Beaumont, Texas
Nate Nevala Sr. Project Manager Beaumont, Texas
Richard Yerdon RT/NDE Technician Port Allen, Louisiana
Andrew Wappler Civil/Structural Designer Beaumont, Texas
Caleb Adkins Mechanical Drafter Beaumont, Texas
Connor Casso Supply Chain Analyst Chevron Oronite
Jeff Pelletier
RT/NDE Assistant Port Allen, Louisiana
Eric Ortiz Electrical Engineer Beaumont, Texas
Stan Spooner Instrumentation Designer Beaumont, Texas
Kaiden Adkins
TML Drafter ExxonMobil, Texas
• Treat everyone as a valuable member of the EIS Family.
• Focus on nurturing trust and understanding between one another and clients.
• Commit to personal growth through continuous learning opportunities.
• Take initiative to improve systems and processes.
• Take ownership and deliver on promises.
Engineering & Inspection Services (EIS) is a full-service engineering, design and inspection firm delivering practical solutions for our clients through technical expertise and emerging technologies. We are driven to solve the most complex challenges our clients face. EIS serves the U.S. refining and petrochemical industries while our technology team Captura also serves the AEC, Manufacturing, Disaster Recovery and many new developing markets. Our offices are located in Metairie, Louisiana and Beaumont, Texas, with a dedicated Inspection Division headquartered in Port Allen, Louisiana.
Let’s keep in touch
504-837-3310
info@eisllc.net
www.eisllc.net