Handbook of Adhesion Promoters
George Wypych
Published by ChemTec Publishing 38 Earswick Drive, Toronto, Ontario M1E 1C6, Canada
© ChemTec Publishing, 2018
ISBN 978-1-927885-29-1 (hard cover); ISBN 978-1-927885-30-7 (epub)
Cover design: Anita Wypych
All rights reserved. No part of this publication may be reproduced, stored or transmitted in any form or by any means without written permission of copyright owner. No responsibility is assumed by the Author and the Publisher for any injury or/and damage to persons or properties as a matter of products liability, negligence, use, or operation of any methods, product ideas, or instructions published or suggested in this book.
Library and Archives Canada Cataloguing in Publication
Wypych, George, author Handbook of adhesion promoters / George Wypych.
Includes bibliographical references and index.
Issued in print and electronic formats. ISBN 978-1-927885-29-1 (hardcover).--ISBN 978-1-927885-30-7 (PDF)
1. Adhesives--Handbooks, manuals, etc. 2. Adhesion. I. Title.
TA455.A34W974 2018 620.1'99
C2017-905289-6
C2017-905290-X
Printed in Australia, United Kingdom and United States of America
5
8.28
1.1 DEFINITIONS
Here are some of the most common definitions used in the field:
An adhesion promoter is used as an additive or as a primer to promote adhesion of coatings, inks, or adhesives to the substrate of interest. An adhesion promoter usually has an affinity for the substrate and the applied coating, ink, or adhesive. Without the adhesion promoter, the properties of the applied coating may not be sufficient to meet the performance requirements needed for the end product such as a painted automotive plastic surface. In automotive coatings, the term adhesion promoter refers to the primer, which achieves adhesion of the subsequent paint layer to TPO substrate. This adhesion promoter is usually comprised of chlorinated polyolefin (CPO) as the active adhesion-promoting component, other resins, and pigment(s). [Eastman Chemical]
The objective of adhesion promoters and coupling agents is to create as many stable additional bonds on these phases (presumably substrate and coating). It is not always possible to differentiate the additives from one another. Other terms include also couplers and modifiers. [BYK]
A coupling is defined as the act of bringing or coming together (pairing) or a device that serves to connect the ends of adjacent parts or objects. [Merriam-Webster]
Primer is a substance used as a preparatory coat on wood, metal, or canvas, especially to prevent the absorption of subsequent layers of paint or the development of rust. In cosmetics, a primer is a cosmetic applied to the face before another product, intended to improve the coverage and lasting effect of the second product. [Oxford Dictionary]
With Latin prefix sub-, “below”, the substrate (substratum) refers to a layer under something else. [Merriam-Webster]
With many other definitions adjusted to the needs of particular applications, we may find even more confusing explanations of the meaning of these words because they are used in many technical and non-technical disciplines.
For the purpose of this book, we will use adhesion promoter as a primary single compound which is able to interact (either based on chemical or physical principles) with two layers of materials for which adhesion needs to be improved. The primer will be considered rather as a formulated product (containing usually more than one component) to perform according to a specific process of promoting adhesion (surface immersion, brush coating, spraying, etc.). Under this definition primer should not only have the ability to increase adhesion but also form a uniform sub-layer on the surface of the substrate due to adjustment of its viscosity, wetting properties, drying rate, etc.
1.2 HISTORY
Various simple technological processes of binding were used as early as 10,000 years. In the Neolithic period, a resin from birch trees was used to attach the heads of spears and axes. Later, when Iceman was discovered on Hauslabjoch (lived around 3300 BC), tools and pieces of clothing were found, including an ax made from yew wood whose blade was attached with birch pitch (adhesive) and strips of leather.
Other examples of products used as adhesives include animal blood, protein, various plant resins and asphalt that were used as adhesives in Babylon to build houses and temples. Such applications were used all over the world, even recently (Asia, Africa). It is expected that this technology is known for at least 7,000 years.
Fish and animal glues were known to Egyptians 4,000 years ago. They were obtained by boiling of animal hides, hooves, and connective tissues and used for reinforcement of papyrus scrolls and production of furniture (Tutankhamun casket was glued using this technology). This was the first technology of adhesive production which involved professional people having knowledge of how to make a glue. Glue produced in this way was expensive and, therefore, used only for furniture for noble people. The technology was later transferred to the Greeks and Romans.
Greeks and Romans further developed the technology. The ancient Greeks used adhesives in carpentry. The glues were usually made out of egg whites, blood, bones, milk, cheese, vegetables and grains. Tar and beeswax were implemented later by the Romans. Also, Chinese used ox and stag horns for the production of adhesives at least 3,000 years ago.
In South America, the developments came in this area later or perhaps earlier developments are still unknown. In the mid 14th century, the Aztecs used the adhesive properties of blood for construction work. The structures are still in an excellent condition.
The modern area of adhesives begins in the 19th century with the use of natural rubber as adhesive in 1830. Eleven years later vulcanization of rubber was discovered by Goodyear and used for adhesive purposes, followed by celluloid (1864) and phenolic resin (Bakelite, 1905). The big developments came about during second world war including polybutadiene (1935 and later developments, Buna or earlier in Russia), epoxy resin (1938 and later), cyanoacrylate (1942-1951, Eastman, superglue), and thermoplastic glue (hot melt, Procter & Gamble, 1940).
Bookbinding illustrates how important was the development of adhesives to the book production. Books were produced in various forms (scrolls, tablets, parchment sheets, etc.) for millennia but “pages” could only be held together by threads, ropes, etc. because of lack of durable glue. In 1447, Gutenberg introduced printing press which automatized printing process, but bookbinding was still done by manual work because there was no glue available to match the developments in printing. So book production remained manual process until developments in the 20th century. Perfect binding was invented in 1895 but it was first adapted for book production by Penguin Books (UK) in 1935 using cold glues which were quite rapidly becoming brittle with time. Hot-melt bookbinding1 was developed by DuPont in 1940 which started the modern area of publishing and made books available to anyone who was interested in reading (because their price was not any longer an issue). Polyamide having softening temperature in the range of 45155oC was the first polymer used for bookbinding by hot-melts.
Just before the second world war, polyurethanes were invented by Otto Bayer in 1930 which also opened the door to many applications depending on adhesion.
In the early days of production of adhesives in the 20th century, little scientific studies were done regarding the reasons for adhesion or its lack but it became obvious in the 1940th that the further development of composites containing glass fibers cannot proceed if problems of adhesion between glass fibers and polymer matrix would not be addressed.2 Dow Corning, producer of glass fiber, had vital interest in this field. The first application of the low molecular compounds for enhancement of adhesion was patented for Dow Corning by Joseph Keil in November 1954 when Edwin Plueddemann was still working in Westvaco Chlorine Product Corporation. The proposed adhesion primer was based on titanate. In 1957, Plueddemann moved to Dow Corning and begun his work resulting with a large body of knowledge which we have today on synthesis, compounding, and application of silane products which are extensively used today. His work also resulted in over 100 patents for Dow Corning and fundamental monograph2 which has been republished in extenso by Springer in a soft cover in 2013, suggesting that there is still interest in the book and that the findings are still relevant.
Silane-based adhesion promoters still dominate the field of adhesion promotion but as Chapter 7 will show materials which belong to more than 30 categories of chemical are now involved in the adhesion promotion of many manufactured goods and the field has grown to importance in polymer processing technology worthy of thorough review in the context of new developments and applications.
REFERENCES
1Brown, R G, US2612463, DuPont, Sep. 30, 1952.
2Plueddemann, E P, Silane Coupling Agents, Springer, New York, 1991.
Mechanisms of Adhesion
There many methods which help in adhesion improvement. Technical literature usually contains a discussion of roles of interlocking (mechanical adhesion), diffusion, adsorption, surface reaction (chemical bonding), wetting, and electrostatic forces in the fostering adhesion in various material pairs.1
There are several other important mechanisms in play which are to be considered in order to form the full picture of combinations of principles for the overall adhesion in a given product. In the case of diffusion, the effect of chain entanglement has to be included which emphasized the mechanics of the chain effect on adhesion.
Hydrogen bonding is a mechanism by which adhesion properties can be reversed depending on the physical state of matter. This differs substantially from the surface reaction which is based on covalent bonding (a specific reaction between two substrates).
Properties of polymer blends are known to depend on the state of the interface between the blend components. This in blends is frequently created by the use of compatibilizers, meaning a separate phase which acts by connecting two incompatible phases using an intermediate layer of material which is able to agree with both partners. This mechanism can be used as an example because it also applies to the pairs of materials other than the components of the polymer blends.
Reversible hydrolysis is known to be a part of many adhesives and sealants. It permits them to recover lost adhesion when water is removed from the interface between adhesive and substrate.
Some crystalline properties of materials (especially in the case of various reinforcements) contribute to increased adhesion between materials (e.g., fiber and polymer matrix). Effects of heteroepitaxy and transcrystallinity immediately come to mind as essential influences on adhesion.
There are now many connections between polymers and living organisms which are influenced by adhesion, for instance in colonization of polymeric surfaces by microorganisms leading to their biodeterioration or affecting the durability of implants. Organisms such as barnacles or octopus have uncommon means of adhering to surfaces. Understanding these mechanisms is crucial for the development of various additives included, for example, in paints.
Finally, the difference between, for example, human tissue and polymeric material used for prosthetics and other similar purposes is intentionally blurred by various means in order to make these materials compatible. Here, we arrive at the importance of cellular adhesion which is very important for the application of various man-made materials in medicine and as such it also requires an explanation.
Based on the above short discussion, the mechanisms which are included in this chapter will be presented in the following order:
•mechanical interlocking
•surface condition and shape
•diffusion and entanglement
•adsorption
•acid-base and electrostatic interactions
•surface free energy and wetting
•crystalline properties
•interphase formation
•chemical bonding
•hydrogen bonding
•reversible hydrolysis
•microbiological and biological adhesion
•cellular adhesion
There will be some inevitable similarities of adhesion principles between mechanisms discussed in these groups because nature of things does not have clear borders. Also, the understanding of some mechanisms will be reinforced by the information included in the discussion of other principles of adhesion because they are inter-related. This chapter is probably the most important part of this book because of its focus on practical principles by which adhesion can be improved as opposed to a focus on an explanation of principles of physics and chemistry alone. For this purpose, practical observations and examples will be included in the following discussion.
2.1 MECHANICAL INTERLOCKING
The surface of material, even when it appears smooth and shiny, is full of imperfections such as voids, craters, pits, holes, pores, cracks, scratches, deep valleys, and other structures having many different names. In addition to the existing imperfections, an intentional increase in the surface roughness is produced by a mechanical action (sandblasting or sandpaper abrasion) and various physical (such as plasma treatment, flame, corona discharge, laser, or microwave) or chemical processes (modification, wet etching, dissolution of some components, etc.). These processes are discussed in Chapter 4.
Figure 2.1 shows that the use of increasingly rougher sandpaper results in the increased surface roughness of the aluminum sheets.2 The initial surface roughness of the aluminum sheet was Ra = 0.6 μm (as indicated in the figure caption).2 After using sandpapers with grits of 80, 50, and 36, the surface roughness values changed to 3.75, 5.63, and 8.31 μm, respectively.2 The bond strengths of samples roughened by these sandpapers were increased by 20, 50, and 30%, respectively.2 It can be noted that the surface that was too rough (obtained with sandpaper having a grid of 36) resulted in a poor polymer penetrability, void formation, and stress concentration, all of which led to a lower bond strength increase.2 This means that the interlocking is guided by some principles related to the shape and the size of imperfections on the substrate and most likely by the rheological properties of the material (adhesive) deposited on the surface for bonding.2
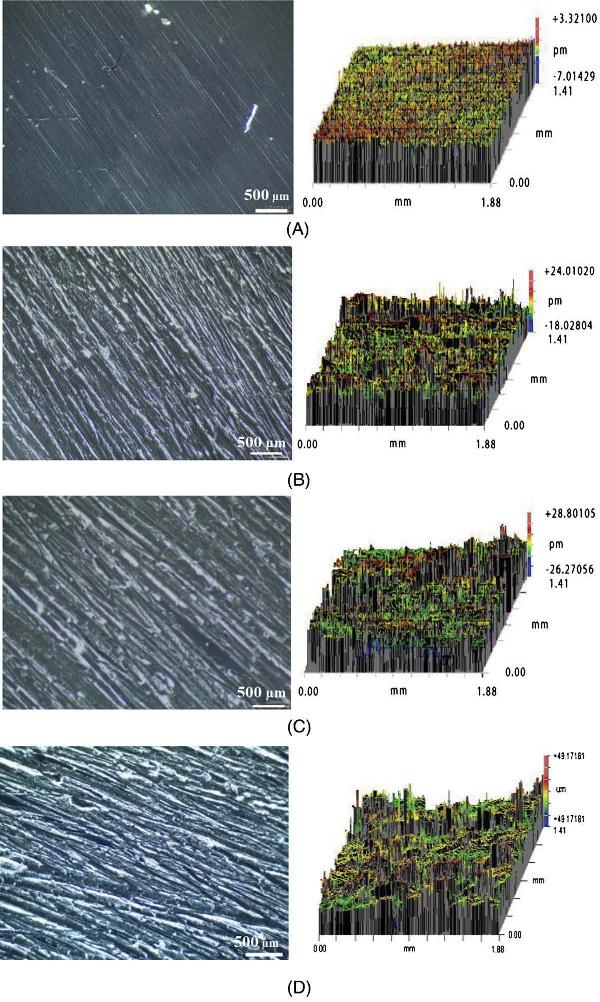
Figure 2.1. Optical microscopic images (left) and the corresponding 3D surface profiles (right) of the aluminum roughened with different sandpaper grit sizes: (A) as-received (Ra= 0.6 μm), (B) grit 80 (Ra= 3.75 μm), (C) grit 50 (Ra= 5.63 μm), and (D) grit 36 (Ra= 8.31 μm). [Adapted, by permission, from Mousa, S; Kim, G-Y, J. Mater. Process Technol., 222, 84-90, 2015.]
Figure 2.2. Schematic illustration of proposed interfacial structure. Absorption of Ag/PPy occurs in the PTFE by penetrating through the nano-sized pores filling the voids. [Adapted, by permission, from Horvath, B; Kawakita, J; Chikyow, T, Appl. Surf. Sci., 384, 492-6, 2016.]
Figure 2.3. Cross-section of copper coated glass fiber reinforced epoxy composite after sandblasting with Al2O3, (a) untreated, (b) after 2 s, (c) after 4 s, and (d) after 6 s. [Adapted, by permission, from Njuhovic, E; Brau, M; Wolff-Fabris, F; Starzynski, K; Altstadt, V, Composites, B66, 443-52, 2014.]
Figure 2.2 shows that even such impenetrable and seemingly uniform material as polytetrafluoroethylene contains pores which can be penetrated by silver/polypyrrole nanocomposite to become the grounds of a strong adhesion between the two.3 Polypyrrole enters into the PTFE substrate in a form of dispersion through the nano-sized pores, along with silver nanoparticles having only up to 12 nm size.3 This is possible due to its rela-
Figure 2.4. Peel strength as a function of roughness depth. [Adapted, by permission, from Njuhovic, E; Brau, M; Wolff-Fabris, F; Starzynski, K; Altstadt, V, Composites, B66, 443-52, 2014.]
tively good wettability of PTFE.3 The nanocomposite is absorbed by PTFE substrate up to 1-2 μm depth.3 The dispersion transforms into a solid form and the mechanical interlocking occurs within the substrate causing the nanocomposite to strongly adhere to PTFE.3
In the high-quality zinc coatings on steel substrates, the adhesion strength depended on surface roughness.4 Mechanical interlocking, created by the polishing process, was the main phenomenon determining the adhesion of the zinc coatings to the steel substrates.4 The optimal value of surface roughness was 0.3 μm above which adhesion was gradually decreased.4
In another development, glass fiber-reinforced epoxy composite was sandblasted for 2-6 seconds in order to increase adhesion of the copper coating to its surface.5 Figure 2.3 shows the cross-section of copper coated surface after sandblasting. Increasingly a rougher substrate surface results from prolonged sandblasting leading to additional undercuts and consequently anchor points.5 Figure 2.4 shows that the peel strength is a function of surface roughness depth which increases with the duration of the treatment.5 Acoustic emission analysis was used in combination with peel testing.5 For the untreated specimen having a very low adhesion, the acoustic emission signals could not be detected.5 Acoustic emission energy released during the peel test was a function of surface roughness.5 A higher roughness depth led to a stronger adhesion force, and consequently also to a larger total cumulative elastic energy release in the form of sound waves.5 This observation directly proves that the mechanical interlocking increases adhesion because no other treatment was performed for these samples.5
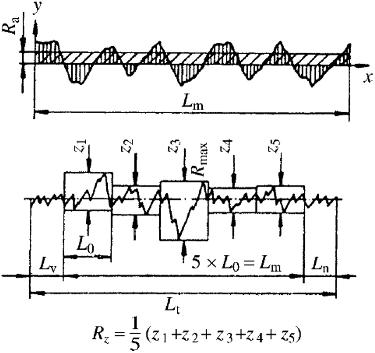
Figure 2.5. Calculation of the average surface roughness, Ra, and the mean peak-to-valley height, Rz, values. [Adapted, by permission, from Sancaktar; E, Gomatam, R, J. Adhes. Sci. Technol., 15 (1), 97–117, 2001.]
In the study of adhesive bonding of carbon fiber epoxy laminates, the relationships were complicated by the mode of testing.6 The lap shear strength increased with the increase in the polar component of the surface free energy and decreased with the surface roughness of the fibers and the surface area available for bonding.6 In the double cantilever beam testing, the mode I adhesive fracture energy proportionally increased with the density of summits and the mean summit curvature.6 Therefore, the main adhesion mechanisms in the single
Figure 2.6. Cross-sections of PP plates after roll imprinting at 130°C with various undercut angles. a 35o, b 30o, c 25o, d 20o, e 10o, f 0o. [Adapted, by permission, from Matsuzaki, R; Tsukamoto, N; Taniguchi, J, Int. J. Adh. Adh., 68, 124-32, 2016.]
lap joints (shear testing) are likely influenced by the chemical composition of the surface (absorption and chemical bonding), whereas the mechanical interlocking predominates in the double cantilever beam joints (mode I testing) which causes delamination of the substrates.6 This experiment shows that the geometry of force application plays an essential role in the mechanism of damage and the range of forces which can be tolerated by the material.6
Surface roughness is characterized by several methods including arithmetic mean roughness, Ra, and maximum individual peak-to-valley height, Rz 7 These values are explained in Figure 2.5.
Mechanical surface treatment such as abrasive action not only affects surface roughness but also removes surface layers which may have different properties then the bulk (and usually do).8 This may change reactivity of the surface, wetting behavior, and surface energy, and open crevices which are covered by skin.8
Figure 2.7. Tensile adhesive strengths of PP plates with various undercut angles. [Adapted, by permission, from Matsuzaki, R; Tsukamoto, N; Taniguchi, J, Int. J. Adh. Adh., 68, 124-32, 2016.]
When polydimethylsiloxane surface was treated with oxygen and argon plasma different behaviors were observed.9 Oxygen plasma treatment resulted in formation of hydroxyl groups and surface roughness whereas only surface roughness was changed in the case of argon plasma treatment.9 Oxygen plasma treatment gave only slightly higher peel strength than was the case of argon plasma treatment.9
In still another study, the surface roughness was induced to polypropylene by roll imprinting process (no removal of original skin).10 The imprinting rolls had different undercut angles (Figure 2.6) and these undercut angles influenced adhesion (Figure 2.7).10 The adhesive strength increased as the undercut angle increased.10 The average strength of the 25° undercut specimen was 1.7 times higher than that of the specimen without the undercut micropattern.10 This points out to the fact that anchoring geometry (more extensive interlocking) increases the adhesive strength.10
2.2 SURFACE CONDITION AND SHAPE
Under this title, we will discuss some less known observations which lead to the change of adhesive properties which can be explained in a fundamental way. This refers to the effect of probe shape, observations in railway traction, and effect of small particles on the substrate surface on adhesive (or traction) properties.
Adhesive forces typically show a monotonic increase up to a maximum when relative humidity increases.11 But in the atomic force microscopy, the decrease in adhesion between a probe tip and surface was reported when relative humidity was increased.11 This was attributed to a blunt tip shape.11 Specifically, the decrease in adhesion was attributed primarily to a transition from a rounded to a blunt tip shape.11 The adhesive force between a probe tip (described by a power law) and a surface consists of capillary forces, composed of Laplace pressure, surface tension forces, and van der Waals forces.11 Calculations indicated that the monotonic decrease in adhesive force occurred for a blunt tip and
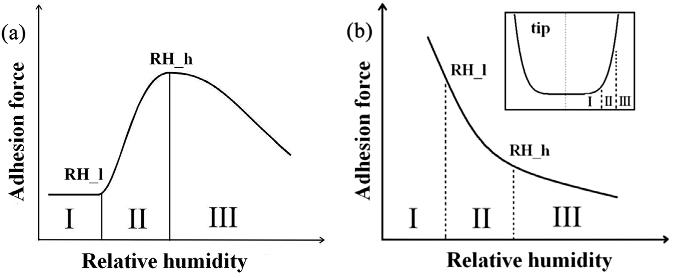
Figure 2.8. (a) Typical schematic of the functional relationship between the adhesive force and the humidity, and (b) anomalous schematic of the counter-intuitive monotonic decrease of the adhesion force with increasing humidity. The inset shows the tip shape. [Adapted, by permission, from Yang, L; Hu, J; Xiao, H; Quan, W, Particuology, in press, 2017.]
a small tip-substrate separation distance (less than 0.3 nm) with an increase in relative humidity (Figure 2.8).11
It is known from practice that in autumn trains occasionally overrun station or pass signals, which are dangerous occurrences.12 Incident analysis showed that the incidents more likely occur in the morning (5:00-10:00) and at night (20:00-24:00).12 This suggested that the dew effect may be important.12 It was found that the wet leaves in the contact area with rails produce very low friction coefficients (below 0.1).12 Wet leaves tend to produce a low friction/traction coefficients of around 0.05.12 The effects of iron oxides, temperature, pressure, and the presence of leaves were identified as the primary reasons for low traction.12
Figure 2.9. Model of weak boundary layer. [Adapted, by permission, from Bikerman, JJ. The Science of Adhesive Joints Academic Press, New York, 1961.]
Figure 2.9 illustrates the reasons for inferior adhesion which were suggested by Bikerman long time ago.13 (Interesting to note that two of these reasons (impurities and reaction between components) were mentioned in the railway case problems.) These inhibitors of adhesion are very common in practice in the form of air pockets, dirt particles, oily surface, and reaction products (corrosion, products of oxidation, products of degradation on wood surface, skin formation, etc.).13
The examples given in this section may seem slightly remote from the main topic of this chapter but they should not be rejected from consideration because they may help to explain some practical observations other than included in this section.
2.3 DIFFUSION AND ENTANGLEMENT
Figure 2.10. Steps involved in fusion bonding of thermoplastic surfaces. [Adapted, by permission, from Asseko, ACA; Cosson, B; Lafranche, E; Schmidt, F; Le Maoult, Y, Composites, B97, 53-61, 2016.]
Figure 2.11. Welded joint interphase. [Adapted, by permission, from Asseko, ACA; Cosson, B; Lafranche, E; Schmidt, F; Le Maoult, Y, Composites, B97, 53-61, 2016.]
There are two important stages in this mechanism, if polymers are involved, namely diffusion and entanglement formation. Diffusion process permits chain of one material (e.g., adhesive) to penetrate the other material (e.g., adherent). In most cases, interdiffusion occurs due to the diffusion products of both materials (adherent and adhesive) to cross the boundary between them (called interface) and to form an intermediate layer which has a composition different than any of the two components and it is called interphase. Figure 2.10 illustrates these two steps leading to the formation of interface.14 From the illustration, it becomes pertinent that temperature is one of the most important variables of the process.14 It is also quite obvious that thermal welding processes are the primary examples of this type of the mechanisms of adhesion.14 Figure 2.11 shows the result of welding of polycarbonate containing glass fiber (top) and polycarbonate containing carbon black (bottom).14 Both glass fiber and carbon black are found in the interphase.14 Macromolecular structures on each side of the welding interphase penetrated to establish an entangled network.14
The effect of temperature can be clearly seen from Fick’s law of diffusion:
where:
xaverage interpenetration depth
Ediffusion activation energy
Rgas constant
Ttemperature
ttime of contact
Considering that Fick’s law of diffusion has limitations in the description of polymer chain movements, reptation theory was later developed and adopted to the description of interdiffusion of amorphous polymers in welding processes. The distance of interpenetration of chain through interface is given by the following equation:15
[2.2]
where:
χ(t)displacement of center of mass during a time t
Rg gyration radius of chain
τrep reptation time
This equation shows that when the time of contact (diffusion time), t, equals the time of reptation, τrep, then the weld will reach cohesion strength of interphase.15,16 In the nonisothermal fusion welding of ethylene polymers, the cohesion strength at interphase nearly reached cohesion strength of bulk of the material (polyethylene) after less than 10 s of contact time under infrared radiation.16 The reptation of the shortest chains contributed to the restoration of the entanglement network of the longest chains within a timescale much shorter than the reptation time of the longer chains.16 This shows that shorter chains diffuse faster than the longer chains and it explains the frequent observation that the weld interphase is somewhat weaker than the bulk because it preferentially contains shorter chains.
The time of reptation can be calculated from the following equation:
[2.3]
where:
ζ friction coefficient of monomeric unit
Naverage length of chain given in number of random links
blength of random link (for example it has an average molar weight of 140 Da for polyethylene chains)
kBoltzmann’s constant
Ttemperature adiameter of reptation tube
This equation shows that the molecular weight of the polymer (chain length) has very strong influence on the time of reptation (the third power of the chain length and the fourth power of the chain link length).
The mechanism of diffusion-controlled adhesion has limited influence on overall adhesion when substrate material is highly crystalline or crosslinked and when contact between the two materials occurs well below their glass transition temperatures.8
Figure 2.12 shows polyolefin surface (bottom) painted with thermoplastic polyurethane/olefin block copolymer paint (top).17 Between the paint and the substrate, there is an interphase layer (top picture) which is expanded at the bottom picture because of formation of extension fibrils during paint delamination.17 The presence of these fibrils means that polyurethane chains from the paint diffused into the blend substrate during painting and the subsequent drying step and entangled with TPU in the blend.17 The entanglement between the paint and the substrate generated a physical link that provided adhesion.17
Raman spectroscopy was used for detection of interdiffusion in two-component injection molded parts.18 The two-component injection molded parts were made out of combinations of five materials chosen from polypropylene, styrene-based thermoplastic elastomer, polycarbonate, polystyrene and polymethylmethacrylate produced at varying melt temperatures.18
Figure 2.13 shows an example of results. TPE is present between -5
Figure 2.12. SEM micrographs of cross-sections of painted TPU/OBC blends. (upper) 25% TPU, (lower) the same blend in extension. [Adapted, by permission, from Song, J; Batra, A; Rego, JM; Macosco, CW, Prog. Org. Coat., 72, 492-7, 2011.]
Figure 2.13. Raman bands of the material combination PP/TPE normalized band integrals along the line scan. [Adapted, by permission, from Bruckmoser, K; Resch, K; Kisslinger, T; Lucyshyn, T, Polym. Testing, 45, 122-33, 2015.]
Figure 2.14. Effect of number of atoms in hydrocarbon chain of silane on the shear strength of PAA/glass adhesion. [Data from Jiang, ZX; Meng, LH; Huang, YD; Liu, L; Lu, C, Appl. Surf. Sci., 253, 4338-43, 2007.]
μm and +2 μm and PP is present between -1 μm and +5 μm (0 is the original interface).18 The results indicate that both materials were simultaneously detectable between -1 μm and +2 μm, meaning that the interdiffusion length was 3 μm for the material combination of PP/TPE at 180oC. For PC/TPE and PS/TPS the interdiffusion lengths were 2 μm and for PC/PMMA less than 1 μm.18 It was also noticeable that the selected temperature had important influence on the interdiffusion length.18
The effect of entanglements was studied using silanes having different lengths of hydrocarbon chain (methyl, propyl, octyl, and dodecyl).19 These silanes were grafted onto silica glass surface and compounded with polyarylacetylene.19 The physical entanglement interaction between the chain of coupling agent and the chain of PAA resin was the main mechanism of the improvement of the interfacial adhesion (Figure 2.14).19
Chain entanglements are very important for obtaining high adhesion. This statement can be verified based on the typical maximum strength which is in the range of 100 N/m for entanglements compared with around 0.04 N/m for adhesive strength caused by van der Waals forces in fully wetted applications.
2.4 ADSORPTION/INTERACTION
The adsorption theory was introduced more than 50 years ago and it is the most accepted theory of adhesion in spite of the fact that it is a combination of actions of many different physical principles.20 The theory states that materials adhere because of action of interatomic and intermolecular forces between adhesive and substrate if they are in the intimate contact. In our discussion, this theory is split into the primary physical principles and discussed under separate sections below, such as acid-base, electrostatic, ionic, coulombic, wetting, and surface energy. The theory of adsorption is also known under the name of the thermodynamic theory.8
2.5 ACID-BASE AND ELECTROSTATIC INTERACTIONS
2.5.1 ACID-BASE
INTERACTIONS
Acid-base interactions are the major factors among short range (<0.2 nm) intermolecular forces which help to keep two molecules in proximity until other mechanisms of adhesion could make this interaction more permanent.
Drago’s equation was proposed to predict exothermic enthalpy of acid-base interaction, as follows
where:
EA, EB susceptibility of components to undergo electrostatic inteaction CA, CB susceptibility of components to undergo covalent bonding A, Bacidic and basic component, respectively
This equation can be used to predict endothermic enthalpy of polymers adsorbed on inorganic substrates.21 More frequently this enthalpy is predicted based on Gutman’s donor and acceptor numbers, as follows21 [2.5]
where:
number (basicity)
number (acidity)
Acid-base interactions and many important scales characterizing interactions of solvents have been broadly discussed elsewhere and the discussion and data can be used in other areas including adhesion of polymers.22
XPS chemical shift and acid-base interaction correlate well and can be used for quantification of polymer susceptibility using standard probes to establish a calibration curve.21 Then, the magnitude of −ΔHAB of the interaction between solvent and polymer for more complex polymeric systems, such as a fully formulated coating or adhesive, can
be interpolated.21 The whole procedure for this method of determination is well described in literature.21
Here are some examples of application of acid-base properties in the development and understanding of the adhesive properties of materials.
Carbon fibers unsized and sized using polyimide and polyurethane were used in the epoxy composites to study their adhesion to the composite matrix.23 Epoxy matrix is basic (basic component of surface energy = 66.8 mJ/m2).23 The unsized and sized fibers are acidic (an acidic component of surface energy = 32.4 (unsized), 20.5 (polyimide-sized), and 15.3 mJ/m2 (polurethane-sized), respectively).23 This shows that sizing decreased the acidic properties of fibers.23 Composites containing unsized, polyimide-sized, and polyurethane-sized had tensile strengths of 3.2, 2.6, 2.6, MPa and interfacial shear strengths of 28, 19.4, 13.5 MPa, respectively.23 This shows that the decrease in acidic component of surfaces energy (decease of acid-base interaction) caused proportional decrease in mechanical performance of composite.23
The effect of acid-base properties on performance of adhesive dental polymers was studied.24 Three resins (polymethylmethacrylate, PMMA, polyhydroxyethylmethacrylate, PHEMA, and bis-GMA/triethyleneglycoldimethacrylate, TGD) used in adhesive interactions with tooth hard tissues were evaluated according to the Fowkes acid-base theory of interfacial interactions.24 Acid-base work of adhesion of these resins was as follows: 5.3 (PMMA), 5.6 (TGD), and 15.3 mJ/m2 (PHEMA). PHEMA was the most basic out of the three.24 The inorganic component of tooth enamel and dentin (hydroxyapatite) is calcium phosphate having acidic properties.24 The strong affinity of PHEMA toward tooth hard tissues is based on the the Lewis acid-base interaction between PHEMA the electron donor and hydroxyapatite the electron acceptor. PHEMA molecules can displace water from the acidic sites of hydroxyapatite, and polymerized PHEMA can establish strong acidbase interactions with the hydroxyapatite surface.24
The correlation between the acid-base properties and the tensile strengths of adhesive joints were evaluated for low-pressure plasma-treated polymer surface.25 A good correlation between the mechanical strength and the acidity parameters were found for surface treated polyetheretherketone and polyacetal bound with epoxy and polyurethane adhesives.25
2.5.2 ELECTROSTATIC INTERACTIONS
Incompatible materials (for example, polymeric and metal surfaces) may form an electrical double layers which are the acting elements of the electrostatic attraction theory (known also as a parallel plate capacitor theory). The mechanism treats an adhesive-substrate system as a plate capacitor having the strength of interface dependent on the charge density.8
Commercially available reverse osmosis membranes are polyamide composite membranes composed of a polyamide rejection layer and polysulfone support membrane.26 The performance of membranes is affected by bacterial growth onto the membrane surface to form biofilms containing extracellular polymeric substances such as proteins and polysaccharides the phenomenon called “biofouling”.26 The adhered matter can be removed by the chemical treatment but it requires additional operation and amide bonds in the polyamide membranes are cleaved by a chlorine treatment, causing membrane performance to deteriorate.26 In the alternative method, the membrane is immersed into an aqueous solu-
tion of phosphorylcholine polymer containing cationic amino groups, poly[2-methacryloyloxyethyl phosphorylcholine (MPC)-co-2-aminoethylmethacrylate].26 The cationic phosphorylcholine polymer adsorbed on the anionic membrane surface prevents bacterial adhesion and solves the problem of reduced performance.26
Microbial adhesion is initiated by passive adsorption via attractive physicochemical interactions (e.g., van der Waals and electrostatic forces).27 At high ionic concentrations, van der Waals interactions are predominant.27 At low ionic concentrations, the adhesive forces are increased with increasing electrostatic attraction.27 The electrostatic interactions contribute to microbial adhesive forces on solid surfaces.27
Chemically crosslinked poly(allylamine hydrochloride)-dextran adhesive films can load negatively charged drugs such as ibuprofen based on the electrostatic interaction between microgel and ibuprofen molecules and release them under some physiological conditions (e.g., change of ionic concentration).28 Adhesive films based on electrostatic interaction can be designed to bond/debond multiple times by an externally applied electric field.28
Figure 2.15. An ideal coexisting situation of three components at later period of in situ suspension copolymerization. [Adapted, by permission, from Wang, X; Wang, L; Su, Q; Zheng, J, Compos. Sci. Technol., 89, 52-60, 2013.]
Unmodified silica nanoparticles were used to prepare a polymer-based nanocomposite with improved interfacial adhesion and dispersion.29 Methyl methacrylate was copolymerized with a small amount of the cationic functional comonomer 2-(methacryloyloxy)ethyltrimethylammonium chloride (MTC).29 The aim was to improve electrostatic interaction between the positively charged copolymer matrix and negatively charged fillers and consequently to achieve improvement of the mechanical properties (Figure 2.15).29 With 10 wt% silica and 1 wt% comonomer, the tensile strength was increased by 20.7% and the flexural strength was improved by as much as 140.7%.29
2.6 SURFACE FREE ENERGY AND WETTING
The thermodynamic adsorption model of adhesion is based on the most obvious principle that all materials are subject to attraction forces between their atoms and molecules. The surface tension is a direct measure of interatomic and intermolecular forces. The general principle of good adhesion requires that interfacial tension has to be minimized between the solid and liquid.
Surface tension property is known from 1855 when Young developed equation describing the surface free energy of liquid on a solid surface: [2.6]
where:
s the surface free energy of a solid substrate
γl the surface free energy of liquid (surface tension of a liquid)
θ wetting angle (popularly known as contact angle) (angle of solid-liquid interphase)
Contact angle can be measured by various types of instruments (goniometers, highresolution cameras) and calculated using the following equation:
where:
hheight of a droplet
rradius of a droplet
The equation [2.6] applies only to one-dimensional spreading and, therefore, it has mostly historical importance (it is not used for calculations or modeling).
The work of adhesion is measured using Dupré’s equation, as follows
but the surface tension of the liquid is taken from one the equations given below.
Considering that the surface tension is a combination of dispersion forces (van der Waals forces) and polar forces (hydrogen bonding), Fowkes proposed the following equation for description of the total surface tension:
where:
dispersion component
polar component
The dispersive component contains all the London forces such as dispersion (London-van der Waals), orientation (Keesom-van der Waals), induction (Debye–van der Waals) and Lifshitz-van der Waals (LW) forces), and the polar component consists of hydrogen bonding (acid/base) component.30 The equation only considers the dispersive interactions of the system and, therefore, it is not reliable in the case of complex systems.30 It can provide useful approximations for simple systems.30
Geometric means theory was developed by Owens and Wendt resulting in the following equation:31
[2.10]
Due to the presence of a polar term, at least two liquids of known surface tension have to be used in the test to calculate solid surface components.31,32 Several other theories are popular among researchers. Their broader account can be found in the review papers.8,30 Currently the surface tension of adhesive components is determined using several (5-10) liquids of different surface tensions and proportions between dispersion and polar components.
The effect of the surface treatment on the surface properties of carbon fiber in the epoxy laminates has been analyzed.33 The shear strength and mode I fracture energy of laminate was correlated to the polar component of the surface free energy.33