Visit to download the full and correct content document: https://ebookmass.com/product/agitator-design-for-gas-liquid-fermenters-and-bioreact ors-gregory-t-benz/
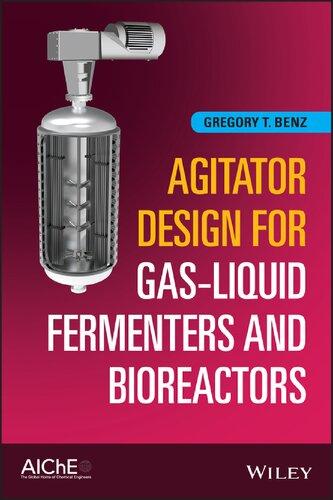
More products digital (pdf, epub, mobi) instant download maybe you interests ...
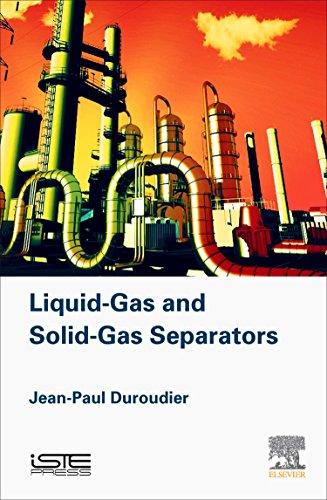
Liquid-Gas and Solid-Gas Separators 1st Edition JeanPaul Duroudier
https://ebookmass.com/product/liquid-gas-and-solid-gasseparators-1st-edition-jean-paul-duroudier/
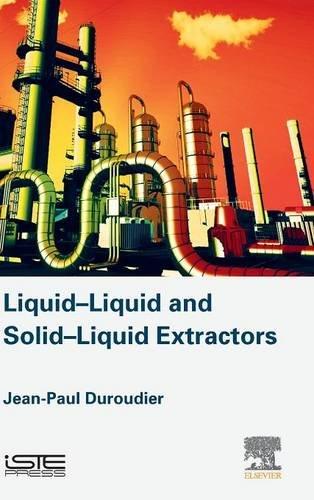
Liquid-Liquid and Solid-Liquid Extractors 1st Edition
Jean-Paul Duroudier
https://ebookmass.com/product/liquid-liquid-and-solid-liquidextractors-1st-edition-jean-paul-duroudier/
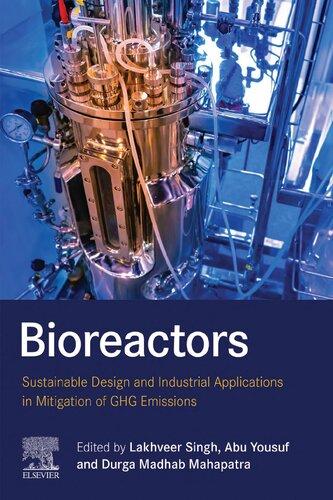
Bioreactors: Sustainable Design and Industrial Applications in Mitigation of Ghg Emissions 1st Edition
Lakhveer Singh (Editor)
https://ebookmass.com/product/bioreactors-sustainable-design-andindustrial-applications-in-mitigation-of-ghg-emissions-1stedition-lakhveer-singh-editor/
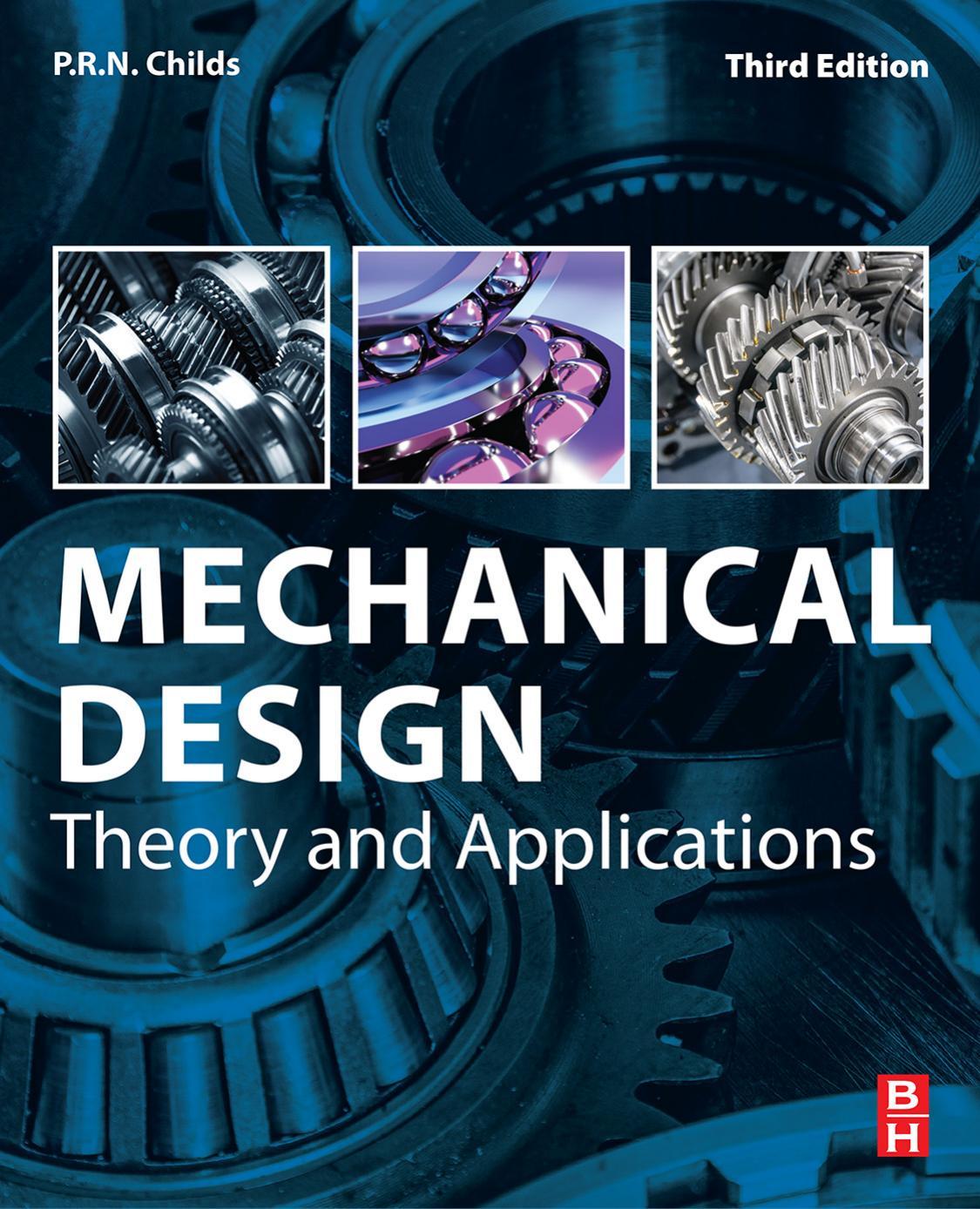
Mechanical Design: Theory and Applications T. H. C.
Childs
https://ebookmass.com/product/mechanical-design-theory-andapplications-t-h-c-childs/
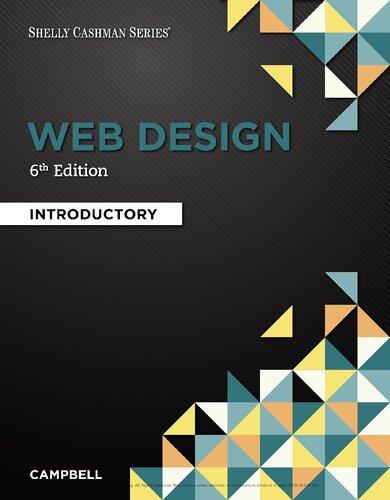
Web design introductory. Sixth Edition / Jennifer T. Campbell
https://ebookmass.com/product/web-design-introductory-sixthedition-jennifer-t-campbell/
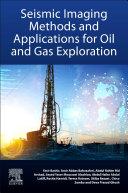
Seismic Imaging Methods and Applications for Oil and Gas Exploration Yasir Bashir
https://ebookmass.com/product/seismic-imaging-methods-andapplications-for-oil-and-gas-exploration-yasir-bashir/
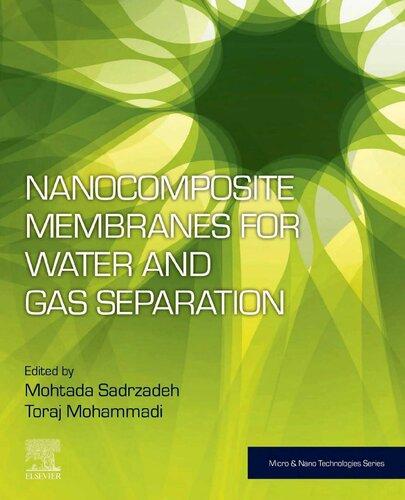
Nanocomposite Membranes for Water and Gas Separation Mohtada Sadrzadeh (Editor)
https://ebookmass.com/product/nanocomposite-membranes-for-waterand-gas-separation-mohtada-sadrzadeh-editor/
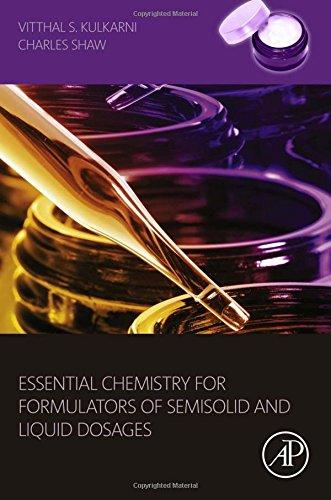
Essential Chemistry for Formulators of Semisolid and Liquid Dosages 1st Edition Vitthal S. Kulkarni Phd
https://ebookmass.com/product/essential-chemistry-forformulators-of-semisolid-and-liquid-dosages-1st-edition-vitthals-kulkarni-phd/
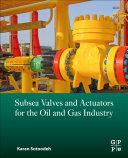
Subsea Valves and Actuators for the Oil and Gas Industry Karan Sotoodeh
https://ebookmass.com/product/subsea-valves-and-actuators-forthe-oil-and-gas-industry-karan-sotoodeh/

Agitator Design for Gas–Liquid Fermenters and Bioreactors
Agitator Design for Gas–Liquid Fermenters and Bioreactors
Gregory T. Benz
Benz Technology International, Inc., Clarksville, OH, USA
Copyright © 2021 by the American Institute of Chemical Engineers, Inc. All rights reserved.
A
Joint
Publication
of the American Institute of Chemical Engineers and John Wiley & Sons, Inc.
Published by John Wiley & Sons, Inc., Hoboken, New Jersey.
Published simultaneously in Canada.
All rights reserved. No part of this publication may be reproduced, stored in a retrieval system, or transmitted, in any form or by any means, electronic, mechanical, photocopying, recording or otherwise, except as permitted by law. Advice on how to obtain permission to reuse material from this title is available at http://www.wiley.com/go/permissions.
The right of Gregory T. Benz to be identified as the author of this work has been asserted in accordance with law.
Registered Office
John Wiley & Sons, Inc., 111 River Street, Hoboken, NJ 07030, USA
Editorial Office
John Wiley & Sons, Inc., 111 River Street, Hoboken, NJ 07030, USA
For details of our global editorial offices, customer services, and more information about Wiley products visit us at www.wiley.com.
Wiley also publishes its books in a variety of electronic formats and by print-on-demand. Some content that appears in standard print versions of this book may not be available in other formats.
Limit of Liability/Disclaimer of Warranty
In view of ongoing research, equipment modifications, changes in governmental regulations, and the constant flow of information relating to the use of experimental reagents, equipment, and devices, the reader is urged to review and evaluate the information provided in the package insert or instructions for each chemical, piece of equipment, reagent, or device for, among other things, any changes in the instructions or indication of usage and for added warnings and precautions. While the publisher and authors have used their best efforts in preparing this work, they make no representations or warranties with respect to the accuracy or completeness of the contents of this work and specifically disclaim all warranties, including without limitation any implied warranties of merchantability or fitness for a particular purpose. No warranty may be created or extended by sales representatives, written sales materials, or promotional statements for this work. The fact that an organization, website, or product is referred to in this work as a citation and/or potential source of further information does not mean that the publisher and authors endorse the information or services the organization, website, or product may provide or recommendations it may make. This work is sold with the understanding that the publisher is not engaged in rendering professional services. The advice and strategies contained herein may not be suitable for your situation. You should consult with a specialist where appropriate. Further, readers should be aware that websites listed in this work may have changed or disappeared between when this work was written and when it is read. Neither the publisher nor authors shall be liable for any loss of profit or any other commercial damages, including but not limited to special, incidental, consequential, or other damages.
Library of Congress Cataloging-in-Publication Data
Names: Benz, Gregory T., author.
Title: Agitator design for gas–liquid fermenters and bioreactors / Gregory T. Benz, Benz Technology International, Inc., Ohio, US.
Description: First edition. | Hoboken, NJ, USA : Wiley, 2021. | Includes bibliographical references and index.
Identifiers: LCCN 2020051152 (print) | LCCN 2020051153 (ebook) | ISBN 9781119650492 (hardback) | ISBN 9781119650508 (adobe pdf) | ISBN 9781119650539 (epub)
Subjects: LCSH: Bioreactors–Equipment and supplies. | Fermentation–Equipment and supplies. | Mixing machinery–Design and construction. | Gas-liquid interfaces.
Classification: LCC TP248.25.B55 B46 2021 (print) | LCC TP248.25.B55 (ebook) | DDC 660/.28449–dc23
LC record available at https://lccn.loc.gov/2020051152
LC ebook record available at https://lccn.loc.gov/2020051153
Cover Design: Wiley
Cover Image: © Courtesy Gregory T. Benz
Set in 9.5/12.5pt STIXTwoText by SPi Global, Pondicherry, India
I dedicate this book to my late father-in-law, Richard Durchholz, for inspiring me as an engineer and a person; to Wayne Ramsey, for mentoring me and giving me the opportunity to design the largest fermenters built by Chemineer up to that point; to Ms. Jian Li, my colleague and friend, for helping me to succeed in managing the China office and understanding Chinese culture, and my wife, Kim Benz, for encouraging me and supporting me in the massive undertaking of writing this book.
Contents
Preface xix
Foreword xxi
Foreword for Greg Benz xxiii
1 Purpose of Agitator Design 1
References 2
2 Major Steps in Successful Agitator Design 3
Define Process Results 3
Define Process Conditions 5
Choose Tank Geometry 6
Calculate Equivalent Power/Airflow Combinations for Equal
Mass Transfer Rate 7
Choose Minimum Combined Power 7
Choose Shaft Speed; Size Impeller System to Draw Required
Gassed Power 7
Decision Point: D/T and Gassing Factors OK? 8
Mechanical Design 8
Decision Point: Is the Mechanical Design Feasible? 8
Repeat to Find Lowest Cost 8
Repeat for Different Aspect Ratios 9
Repeat for Different Process Conditions 9
Finish 9
Summary of Chapter 10
List of Symbols 10
References 10
3 Agitator Fundamentals 11
Agitated Tank Terminology 11
Prime Mover 11
Reducer 13
Shaft Seal 13
Wetted Parts 13
Tank Dimensions 14
How Agitation Parameters Are Calculated 14
Reynolds Number 15
Power Number 16
Pumping Number 17
Dimensionless Blend Time 17
Aeration Number 18
Gassing Factor 18
Nusselt Number 18
Froude Number 19
Prandtl Number 19
Geometric Ratios 20
Baffle Number 20
Dimensionless Hydraulic Force 20
Thrust Number 21
Typical Dimensionless Number Curves 21
A Primer on Rheology 25
Newtonian Model 26
Pseudoplastic or Shear Thinning, Model (Aka Power Law Fluid) 27
Bingham Plastic 27
Herschel–Bulkley 27
Impeller Apparent Viscosity 29
A Bit of Impeller Physics 29
Summary of Chapter 31
List of Symbols 31
Greek Letters 32
References 32
4 Agitator Behavior under Gassed Conditions 35
Flooding 35
kla Method 35
Power Draw Method 36
Visual Flow Pattern Method 37
Effect on Power Draw 38
Holdup 39
Example of Holdup Calculation 40
Holdup “War Story” 40
Variable Gas Flow Operation 40
Mechanical Effects 42
Summary of Chapter 42
List of Symbols 42
References 43
5 Impeller Types Used in Fermenters 45
Impeller Flow Patterns 45
Axial Flow 46
Radial Flow 47
Mixed Flow 47
Chaos Flow 48
Examples of Axial Flow Impellers 49
Low Solidity 49
High Solidity 52
Up-pumping vs. Down Pumping 55
Examples of Radial Flow Impellers 56
Straight Blade Impeller 56
Disc, aka Rushton, Turbines 57
Smith Turbines 62
CD-6 Turbine by Chemineer; aka Smith Turbine by Many Manufacturers 62
Deeply Concave Turbines 66
Deep Asymmetric Concave Turbine with Overhang (BT-6) 68
Examples of Mixed Flow Impellers 73
Examples of Chaos Impellers 74
Shear Effects 76
Specialty Impellers 78
Summary of Chapter 80
List of Symbols 80
References 81
6 Impeller Systems 83
Why Do We Need a System? 83
Reaction Engineering 83
Fermenter History 84
Steps to Impeller System Design 85
Choose Number of Impellers 86
Choose Placement of Impellers 86
Contents x
Choose Type(s) of Impellers 87
Choose Power Split or Distribution Among Impellers 93
Choose D/T and/or Shaft Speed 93
D/T Effects with Variable Gas Flowrates 96
Conclusions on D/T Ratio 98
Design to Minimize Shear Damage 99
Sparger Design 100
Ring Sparger 100
Pre-dispersion 103
Fine Bubble Diffuser 104
Summary of Chapter 105
List of Symbols 106
References 106
7 Piloting for Mass Transfer 109
Why Pilot for Mass Transfer 109
Methods for Determining kla 112
Sulfite Method 112
Dynamic Method; aka Dynamic Gassing/Degassing Method 112
Steady-State Method; aka Mass Balance Method 113
Combined Dynamic and Steady-State Method 114
Equipment Needed for Scalable Data 114
Data Gathering Needs 120
Experimental Protocol 121
Summary of Chapter 128
List of Symbols 128
References 129
8 Power and Gas Flow Design and Optimization 131
What This Chapter Is about 131
Where We Are in Terms of Design 131
Design with no Data 131
Design with Limited Pilot Data 133
Design with Full Data 135
Choose Minimum Combined Power 136
State of Design Completion 141
Additional Considerations 142
Summary of Chapter 142
List of Symbols 142
References 142
9 Optimizing Operation for Minimum Energy Consumption per Batch 145
Purpose of This Chapter 145
Prerequisite 145
Conceptual Overview 145
Detailed Procedure 146
Minimizing Total Energy Usage 150
Practical Design 150
Additional Considerations 150
Summary of Chapter 152
List of Symbols 152
References 153
10 Heat Transfer Surfaces and Calculations 155
Purpose of This Chapter 155
Design Philosophy 155
Overview of the Problem 156
Heat Sources 156
Cooling Sources 157
Heat Exchange Surface Overview 158
Principle of Heat Transfer Calculation 164
Calculations By Type of Surface 166
Vessel Jacket, Agitated Side 166
Simple Unbaffled Jacket, Jacket Side 167
Dimple Jacket, Jacket Side 167
Half-Pipe Coil, Jacket Side 169
Helical Coil, Inside 171
Helical Coil, Process Side 171
Vertical Tube Bundle, Inside 173
Vertical Tube Bundle, Process Side 174
Plate Coil, Inside 175
Plate Coil, Process Side 176
Example Problem: Vertical Tube Bundle 176
Problem Statement 176
Problem Solution 177
Additional Consideration: Effect on Power Draw 182
Additional Consideration: Forces on Heat Exchange Surfaces Used as Baffles 183
Additional Consideration: Wall Viscosity 184
Additional Consideration: Effect of Gas 185
External Heat Exchange Loops 186
Summary of Chapter 187
List of Symbols 187
References 189
Further Readings 189
11 Gasses Other Than Air and Liquids Other Than Water 191
General Principle 191
Comments on Some Specific Gasses 191
Ammonia 191
Carbon Dioxide 192
Carbon Monoxide 192
Hydrogen 192
Methane 192
Oxygen 192
Economic Factors 192
Disposal Factors 193
Effects of Different Gasses on kla 193
Effects of Different Gasses on Driving Force 195
Operating Condition Effects 195
Constraints on Outlet Concentration 196
Safety 196
Liquids Other Than Water 198
Summary of Chapter 198
List of Symbols 198
References 199
12 Viscous Fermentation 201
General Background 201
Sources of Viscosity 201
Viscosity Models for Broths 202
Effect of Viscosity on Power Draw 203
Example Problem 204
Example Problem Answer 204
Effect of Viscosity on kla 205
Effect of Viscosity on Holdup 207
Effect of Viscosity on Blend Time 207
Effect of Viscosity on Flooding 209
Caverns 209
Estimating Cavern Size 211
Xanthan and Gellan Gums 212
Viscosity Models for Gums 213
Installation Survey 214
Effect of D/T and No. and Type of Impellers on Results in Xanthan Gum 217
Production Curve 218
Heat Transfer 218
All-Axial Impeller Design 218
Invisible Draft Tube vs. Axial/Radial Combination 222
Mycelial Broths 223
Typical Viscosity Model 224
Morphology Effects 224
Recommendations 225
Summary of Chapter 227
List of Symbols 227
References 228
13 Three Phase Fermentation 231
General Problem 231
Effect on Mass Transfer 231
Effect on Foam 233
Emulsion vs. Suspension 233
Complexity: How to Optimize Operation 233
Summary of Chapter 234
List of Symbols 234
References 234
14 Use of CFD in Fermenter Design 237
Purpose of This Chapter 237
Basic Theory 237
Methods of Presenting Data 239
Velocity Distribution 240
Cavern Formation 240
Blending Progress 242
Flow Around Coils 245
Bubble Size, kla, Holdup 247
DO Distribution 248
Summary of Chapter 250
List of Symbols 250
References 250
15 Agitator Seal Design Considerations 251
Introduction 251
Terminology 251
Main Functions of Fermenter Shaft Seals 252
Common Types of Shaft Seals 254
Material Considerations 265
Methods of Lubricating Seals 267
Seal Environmental Control and Seal Support System 267
Seal Life Expectations 272
Special Process Considerations 272
Summary of Chapter 275
Reference 275
16 Fermenter Agitator Mounting Methods 277
Introduction 277
Top Entering Methods 277
Direct Nozzle Mount 278
Beam Gear Drive Mount with Auxiliary Packing or Lip Seal; Beams Tied into Vessel Sidewall 281
Beam Gear Drive Mount with Auxiliary Mechanical Seal; Beams Tied into Vessel Sidewall 283
Beam Gear Drive Mount with Auxiliary Mechanical Seal; Beams Tied into Building Structure 284
Complete Drive and Seal Mount to Beams Tied into Vessel Sidewall, with Bellows Connector 285
Complete Drive and Seal Mount to Beams Tied into Building Structure, with Bellows Connector 287
Bottom Entering Methods 287
Direct Nozzle Mount 288
Floor Gear Drive Mount with Auxiliary Packing or Lip Seal 288
Floor Gear Drive Mount with Auxiliary Mechanical Seal 289
Floor Integrated Drive and Seal Mount with Bellows Connector 291
Summary of Chapter 292
References 292
17 Mechanical Design of Fermenter Agitators 293
Introduction 293
Impeller Design Philosophy 294
Discussion on Hydraulic Force 295
Shaft Design Philosophy 297
Shaft Design Based on Stress 298
Simple Example Problem 302
Sample Problem with Steady Bearing 304
Shaft Design Based On Critical Speed 304
Cantilevered Designs 306
Example Problem 308
Units with Steady Bearings 311
Solid Shaft vs. Hollow Shaft 315
Role of FEA in Overall Shaft Design-Simplified Discussion 319
Agitator Gear Drive Selection Concepts 319
Early History 320
Loads Imposed 320
Handle or Isolate Loads? 323
Handle Loads Option 1: Oversized Commercial Gear Drive 323
Handle Loads Option 2: Purpose-Built Agitator Drive 324
Isolate Loads Option 1: Hollow Quill Integrated Drive with Flexibly
Coupled Extension Shaft 325
Isolate Loads Option 2: Outboard Support Bearing Module 328
Bearing Life Considerations 329
Noise Considerations 330
Torsional Natural Frequency 332
Important or Useful Mechanical Design Features 332
Summary of Chapter 333
List of Symbols 333
Greek Letters 334
References 334
18 Sanitary Design 335
Introduction 335
Definitions 336
Construction Principles 336
Wetted Parts Construction Methods 336
Welded Construction 336
In-Tank Couplings 338
Mounting Flange Area 341
Axial Impellers 344
Radial Impellers 345
Bolts and Nuts 347
Steady Bearings 348
Use of Castings, 3-D Printing 349
Polishing Methods and Measures1: Polishing vs. Burnishing 350
Polishing Methods and Measures2: Lay 351
Polishing Methods and Measures3: Roughness Average 353
Electropolish 355
Passivating 357
Effect on Mechanical Design 357
Summary of Chapter 357
Additional Sources of Information 358
List of Symbols 358
References 358
19 Aspect Ratio 359
Acknowledgment 359
Definition and Illustration of Aspect Ratio 359
What Is the Optimum Aspect Ratio? 360
Effects of Z/T on Cost and Performance at a Given Working Volume 361
Vessel Cost 361
Agitator Shaft Design Difficulty 361
Power Required for Mass Transfer 361
Agitator Cost 362
Airflow Requirements 362
Compressor Power 362
DO Uniformity 362
Heat Transfer Capability 363
Real Estate/Land Usage Issues 363
Building Codes; Noise 363
Illustrative Problem Number 1 363
Vessel Dimensions 364
Airflow and Power 366
Heat Transfer Data and Assumptions 367
Heat Transfer Results 369
Blend Time, DO Uniformity 371
Capital Cost (Agitator Plus Vessel Only) 372
Other Operating Costs 372
So What Is the Optimum Aspect Ratio for This Problem? 373
Illustrative Problem Number 2 373
Illustrative Problem Number 3 376
Summary of Chapter 380
List of Symbols 381
References 381
20 Vendor Evaluation 383
Product Considerations 383
Gear Drive Ruggedness 384
Design Technology 384
Impeller Selection 384
Shaft Design 385
Company Considerations 385
Reputation with Customers 385
Company Size 386
Years in Business 386
Years Under New Ownership 386
Employee Turnover 387
Vertical Integration 387
R&D Program and Publications 388
Depth of Application Engineering 389
Testing Laboratory 389
ISO Certification (Necessary vs Sufficient) 391
Quality Control Program (Not Lot Sample; 100%) 391
Rep vs Direct Sales (a Good Rep Annoys the Manufacturer) 392
Service Capability 393
Typical Delivery Times and Performance 393
Parts Availability 394
Price (Least Important) 395
Willingness to Work with Consultants 395
Vendor Audit Checklist 396
Use of an Outside Consultant 397
Summary of Chapter 399
List of Symbols 399
References 400
A. Appendix to Chapter 20 400
21 International Practices 401
Introduction 401
North America 401
Vendors 401
Design Practices 402
Selling/Buying Practices 402
Degree of Vertical Integration 403
Role of Design Firms 403
R&D 404
Culture 404
EU 405
Vendors 405
Design Practices 405
Selling/Buying Practices 405
Degree of Vertical Integration 406
Role of Design Firms 406
R&D 406
Culture 407
Japan 407
Vendors 407
Design Practices 407
Selling/Buying Practices 407
Degree of Vertical Integration 408
Role of Design Firms 408
R&D 408
Culture 408
China 409
Vendors 409
Design Practices 409
Selling/Buying Practices 411
Degree of Vertical Integration 412
Role of Design Firms 412
R&D 412
Culture 413
Summary of Chapter 413
Cultural Resources 413
Afterword 415
Index 417
Preface
This is a book about fluid agitation, as applied to gas–liquid systems such as fermenters or bioreactors (We will use those terms interchangeably in this text.). The specific focus is on mechanically agitated systems, consisting of a closed vessel with a rotating shaft and impellers, as this is the most common and versatile way to achieve process objectives in a gas–liquid system. Though airlift and bubble columns have also been used, they will not be discussed in any detail here, as that is not the focus of this book.
Many books have been written about fluid agitation. Many books have also been written about fermentation. Much, though not all, of the material in this book has been covered in such books. However, all such books cover much more than agitator design for bioreactors. For example, typical books on agitation cover topics such as solids suspension (almost never an issue in fermentation), highly viscous systems (>50 000 cP), specialized impellers such as helical ribbons, anchors, augers, and others that have no use in fermenters, mixing in high-yield stress fluids such as paper stock, etc. Likewise, books on fermenter design usually cover some topics on agitator design but also cover feeding strategies, reaction kinetics, cell metabolism, sensitivity to concentration and temperature changes, product recovery, and a whole host of other topics. Little has been published in such books about how to acquire the proper pilot data for agitator design, or how to minimize energy consumption.
The main purpose of this book is to be a single-source reference on all the major issues related to agitator design for bioreactors. It is intended to save the reader time by avoiding the need to consult multiple references or sift through many pages of text to find what is needed specifically for fermenter agitator design. This book will also cover important related topics such as heat transfer, power cost, basic agitator mechanical design, and vendor bid evaluation.
Though some introductory fundamental theory is included, the main focus is on practical application of theory to real-world agitator design. This book is more of a how-to book than an academic treatise. The relative brevity of the book is
intentional. It is hoped that the brevity will encourage people to actually read the entire book, not just skim an occasional page or chapter.
This book is intended to be useful for a variety of people. Since it is primarily a technical document, most readers will have a science or engineering degree. Many will be Chemical Engineers. Some will be chemists or microbiologists tasked with operating facilities in a way that can produce scalable data. Academic degrees among readers will vary from Bachelor up through Post-Doc. Most readers will be employed by companies using bioprocessing to make valuable products as well as many making commodity products. Some will work for agitator manufacturers. If used as a course supplement, some will be college students or professors. Toplevel managers may want to skim the contents to make sure their teams are properly staffed and have a high-level view of what their team should be doing. They will find the overview and flow chart described in Chapter 2 especially useful. Chapters on energy use optimization will also be of interest to business unit managers. Information on bid evaluation should be of interest to procurement professionals. Although written primarily for users of agitation equipment and operators of fermentation facilities, engineers employed by agitator manufacturers will likely find it of interest as it provides a deeper window into the details of these applications than they are accustomed to, as well as how their bids may be viewed in a competitive environment.
A note about symbols: rather than make the reader refer to a list of symbols in the appendix, each chapter has the symbols used in that chapter at the end. That should save the reader some time. Also, it lets the author use the same symbol for different purposes in different contexts, reducing the number of symbols needed. For example, C means off bottom impeller clearance in most cases, but in the context of mass transfer correlations, it is used as an exponent, and it can also mean dissolved gas concentration.
Most of the book is focused on gas–liquid agitation, as that is the controlling parameter for most bioreactors. By that I mean the agitator is primarily designed to disperse gasses into liquids. This does not mean evolving gas from solution, which is a separate case. The fundamentals presented are applicable to other processes as well, such as miscible liquid blending, but design procedures for these problem categories are not presented here.
Gregory T. Benz Benz Technology International, Inc
Foreword
Genetic modification, microbiome, green technology, renewable fuels and chemicals, bio-degradable plastic, pandemic recovery, prebiotics, probiotics, agricultural biologics, world food shortage, meatless meat, animal free dairy, human and animal health. What do these important concepts have in common? They all rely on the use of bioreactors to realize the ultimate benefit to current and future generations.
The most powerful of these products utilized in human and animal health can generate the world supply in quantities measured in pounds. Vaccines, antibiotics, probiotics, prebiotics, and others have a large portion of their cost included in research and development, clinical trials, and regulatory approval processes that bring challenge to this business space. In these cases, the bioreactors capital and operational cost impact to the cost of goods sold is small compared to the margins and returns of a successful product launch. These applications historically required a focus on agitation and reactor design with a focus on functionality versus a minimization of operating cost. These products are apportioned in quantities measured in microgram to gram quantities with price measured in millions of dollars per pound in some cases.
On the other end of the spectrum are commodity products utilized every day in quantities measured in tens to hundreds of millions of tons per year. Fuel, polymers, industrial chemicals, animal feed ingredients, and the like. These products’ sales prices are measured in pennies to dollars per pound and operate on tight margins. Making these products in bioreactors is more challenging as a result requiring a focus on things such as reactor design, power optimization between the agitator and air compressor can be a competitive advantage or define the success or failure of a venture.
The teams I worked with directly had the pleasure of working with Greg Benz for the past 15 years on commodity products. From development to commercialization, the details of reactor design mattered significantly in these projects. The information provided in this book allowed the proper questions to be asked during
process design. Bench, pilot, and demonstration trials were designed to be commercially applicable as a result. This allowed for realistic process design, rate, titer, and yield demonstrations to be applied to financial and process modeling early in the process. It also prevented mistakes that saved hundreds of thousands of dollars through effective understanding prior to spending significant development dollars.
Our team worked with the smallest start-ups to the largest most established biotech companies in the world as a contract research and manufacturing operation. Each time agitation questions are asked, Greg is the go-to expert that everyone already knows and has positive experiences with. Greg’s knowledge and experience in this area is of significant importance to realizing the benefit of modern biological technology. I am happy to see that he has decided to put his knowledge and experience in a more detailed writing as I have referenced his course materials hundreds of times in the past 15 years. Thank you to Greg, the biotechnology industries favorite “Professional Agitator.”
Jeremy Javers PhD St. Joseph, MO 1 September 2020