
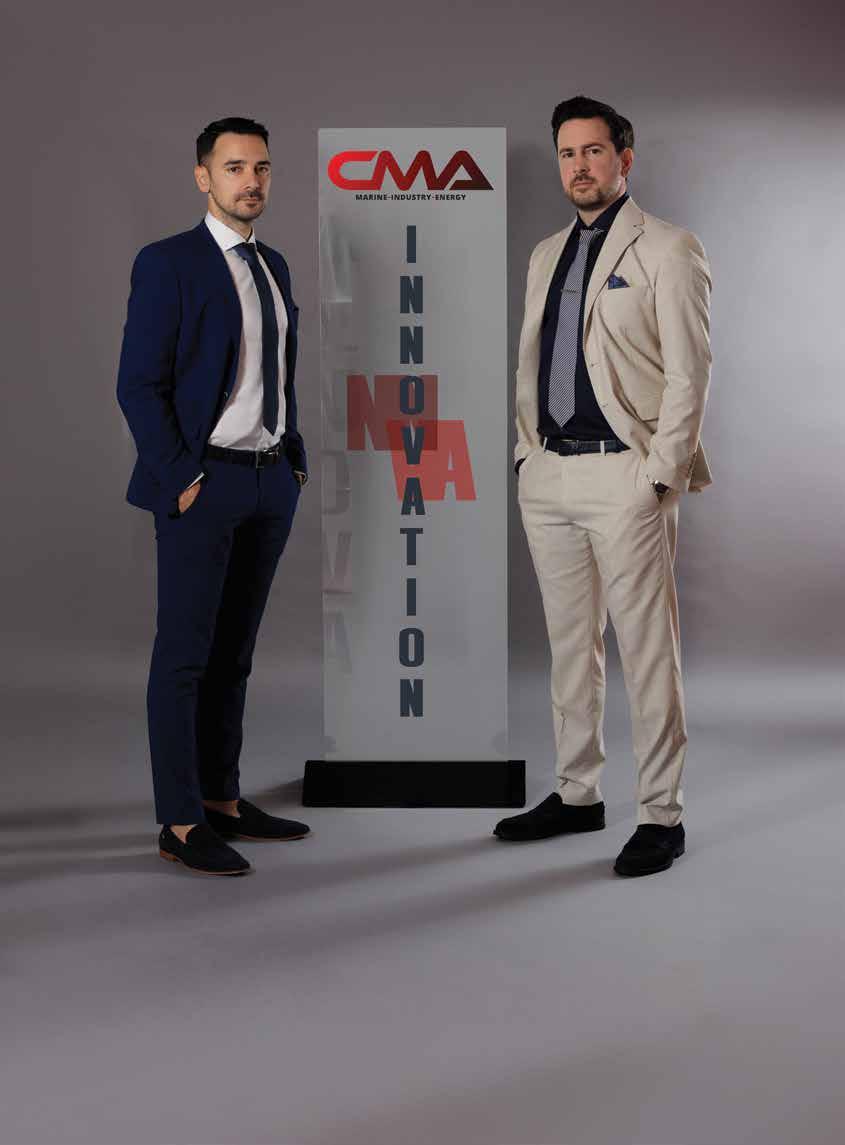

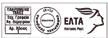
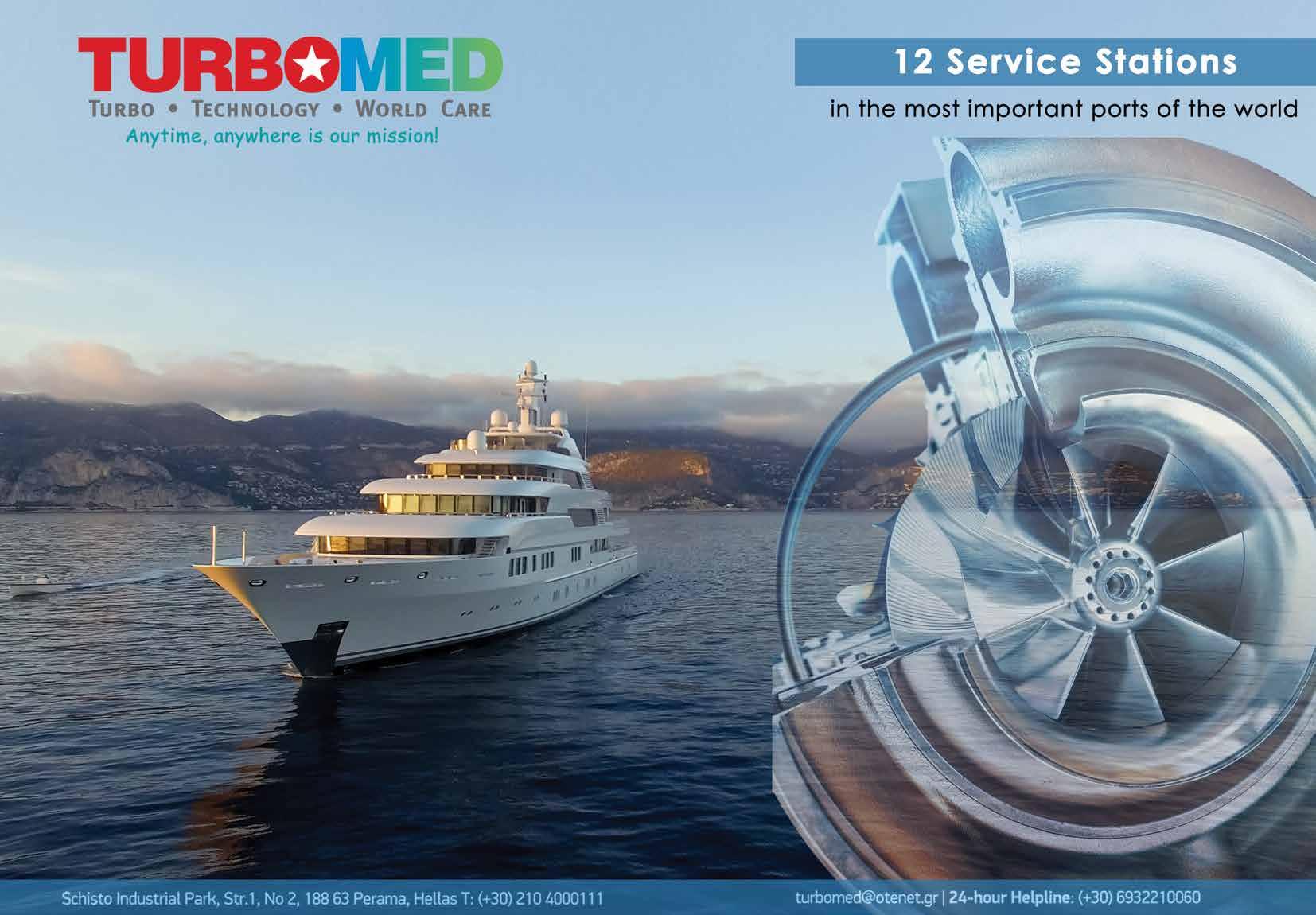
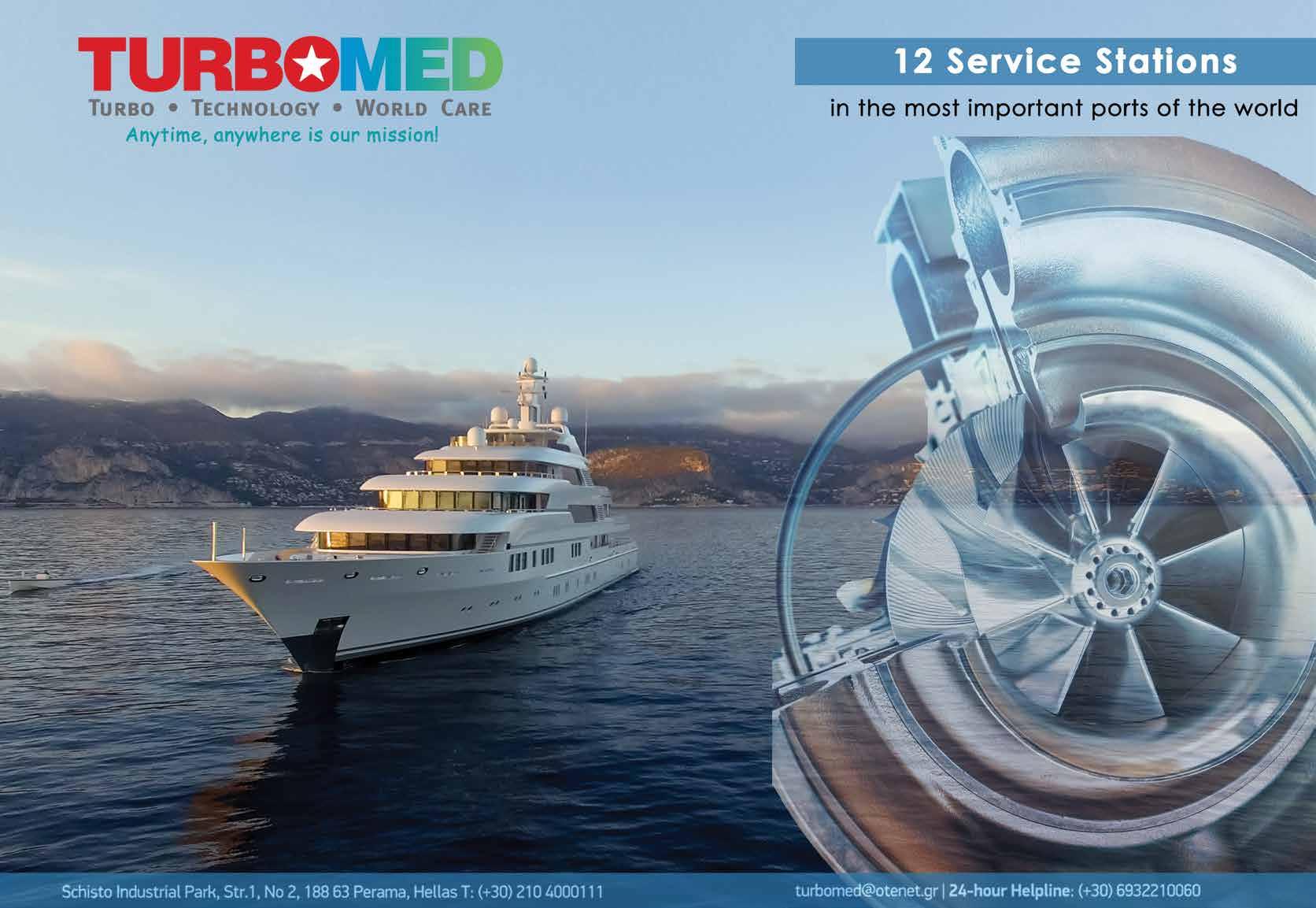

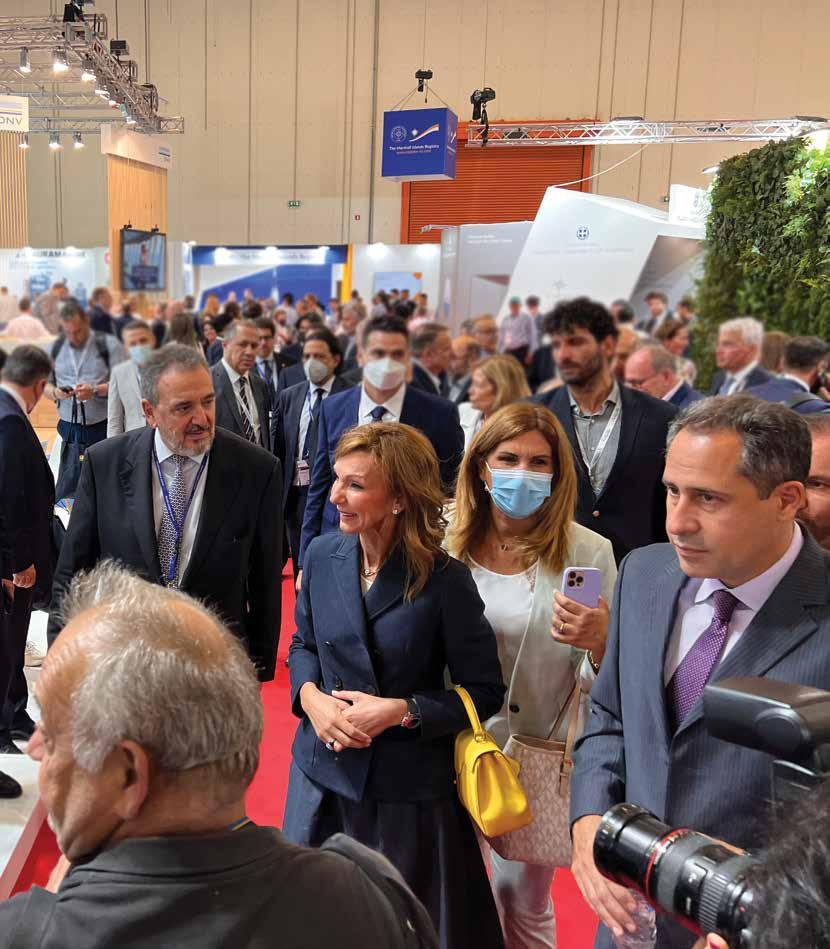
Over 90% of global trade relies on the maritime industry, a vital sector connecting nations, facilitating commerce, and driving economic growth. At the forefront of maritime progress stands Posidonia, one of the world’s most prestigious maritime exhibitions. Held biennially in Greece, Posidonia serves as a crucial platform for industry leaders to converge, collaborate, and chart the course for a sustainable and technologically advanced future of maritime excellence.
From humble beginnings in 1969, Posidonia has transformed into a maritime powerhouse, shaping the industry on a global scale. Over the decades, the exhibition has witnessed phenomenal growth, not just in size (think: a doubling of exhibition space in 1990) but also in its international reach, attracting a record-breaking 28,000 visitors from over 100 countries in 2022. These milestones solidify Posidonia’s status as a beacon for maritime innovation. It’s more than just showcasing the latest products; Posidonia fosters collaboration and sparks groundbreaking ideas, from cutting-edge ship designs to sustainable practices that propel the future of the maritime industry.
Posidonia’s influence transcends the confines of its exhibition halls. It acts as a powerful economic engine, propelling the maritime sector forward. Billions of dollars in business deals, investments, and strategic partnerships are forged at Posidonia, fostering innovation and propelling industry growth. Imagine a bustling marketplace of ideas, where ship owners connect with cutting-edge technology providers, investors identify promising ventures, and collaborations blossom that reshape the future of shipping. This is the dynamic reality that unfolds at Posidonia.
Furthermore, Posidonia serves as a global ambassador for Greek maritime excellence. It’s a platform where Greece proudly displays its rich maritime heritage, dating back millennia. Visitors can explore exhibits showcasing the ingenuity of Greek shipbuilders, from the craftsmanship of traditional vessels to the awe-inspiring designs of tomorrow’s megaships. Posidonia also highlights Greece’s technological prowess, with presentations on groundbreaking innovations in areas like sustainable propulsion systems and digital navigation. By showcasing these achievements, Posidonia cements Greece’s position as a leading force in the global maritime industry
Posidonia is more than just an exhibition; it’s a crucible of innovation where the future of the maritime industry is shaped. Renowned speakers, industry leaders, and exhibitors from across the globe converge to showcase cutting-edge technologies like autonomous vessels and AI-powered navigation systems. Lively conferences delve into the hottest trends, from digitalization and sustainable shipping to the rise of mega ports. But Posidonia isn’t just about presentations; it’s about dynamic networking events where attendees forge partnerships, brainstorm solutions, and turn groundbreaking ideas into reality. This interactive forum allows Posidonia to offer not just a glimpse into the maritime future, but the opportunity to actively shape it.
Posidonia’s allure transcends borders, attracting participants and stakeholders from every corner of the globe. With representation from diverse sectors of the maritime industry, the exhibition serves as a melting pot of ideas, cultures, and perspectives. As Posidonia charts its course for the future, the excitement is palpable. The maritime industry is undergoing a transformative shift, driven by powerful forces like sustainability, digitalization, and decarbonization. Posidonia is poised to be at the forefront of these changes, not just reflecting industry trends but actively shaping them.
Future Posidonia exhibitions can be expected to place a spotlight on emerging solutions that address the industry’s environmental footprint. Imagine exhibits showcasing zero-emission vessels powered by alternative fuels, presentations exploring innovative green port technologies, and conferences tackling the challenge of waste management at sea. Posidonia will serve as a launchpad for these ideas, fostering collaboration between industry leaders, sustainability experts, and government regulators to translate them into reality.
The digital revolution is also transforming the maritime sector, and Posidonia will be a key player in navigating this change. Expect to see demonstrations of cutting-edge technologies like autonomous navigation systems and artificial intelligence for optimized shipping routes. Panel discussions will delve into the potential and challenges of data-driven decision making and the future of the connected ship. Posidonia will act as a platform for knowledge exchange and collaboration, ensuring the maritime industry embraces digitalization for a more efficient and safer future.
Posidonia’s unwavering commitment to adaptation ensures its enduring influence on the global maritime landscape. By anticipating and embracing industry trends, Posidonia will continue to be a catalyst for progress, a platform for groundbreaking ideas, and a meeting point for the brightest minds in the maritime sector. The future of Posidonia is bright, one that promises to propel the maritime industry towards a more sustainable, digital, and prosperous future.
In an era of heightened environmental consciousness, Posidonia remains committed to promoting sustainability and social responsibility within the maritime sector
Posidonia stands as a timeless monument to the enduring legacy and global influence of the maritime industry. From its humble beginnings as a regional gathering, it has transformed into a world-renowned exhibition, navigating the currents of innovation with unwavering resolve. Posidonia isn’t merely a showcase of maritime excellence; it’s a driving force, a compass guiding the industry towards a sustainable and prosperous future. Here, at this global confluence of industry leaders and visionaries, partnerships are forged, not just for commercial gain, but to chart a new course for a more connected and environmentally responsible maritime landscape. Posidonia’s unwavering commitment to progress ensures its enduring role as a beacon, illuminating the path towards a brighter horizon for the maritime industry.
Petrofin Research© presents, for the 23rd year running, an overview and an in-depth analysis of the bank loan portfolios to Greek shipping, as of 31st December 2023. Petrofin wish to thank all participating banks for their steadfast support, without which this research would not have been possible. The portfolios show both the shipping loans outstanding, as well as loans committed but undrawn. The committed but undrawn loans may be viewed as an indication of each bank’s ship lending momentum and / or the extent of its involvement in newbuilding finance. You may find the whole analysis with graphs and tables at nafsgreen.gr
In 2023, the shipping markets were mixed with tankers, offshore, gas and chemical carriers experiencing improved conditions, whilst dry bulk and containers were experiencing soft markets. Overall, the Clarkson’s second hand price index was flat compared to 2022, although tankers showed a 39% average price increase for the whole sector with dry bulk at minus 8% and containers at minus 13% (Clarkson’s Shipping Intelligence). Whilst geographical concerns and high energy prices continued added by the attacks on the Red Sea route by Houthis and the difficulties with the drought creating congestion in the Panama Canal, owners tried to reconcile relatively high vessel prices with correspondingly lower earnings in dry bulk and containers and questions over the longer term sustainability of the tanker market.
An issue facing owners was the high level of interest rates. This rendered cash flows difficult to justify vessel purchases unless owners included a speculative ‘hope’ factor over possible higher rates in the future.
The above ship financing conditions were hardly ideal in 2023 with banks having to restrict LTVs accordingly. Bank deal flow did improve as the year progressed as owners became more confident that future market conditions would improve in 2024 – 2025. Greek owners concluded 226 S&P transactions in 2023 as opposed to 292 in 2022 but the total DWT remained virtually the same at 2.4m DWT. Greek buyer interest increasingly drawn by newbuildings resulting in the remaining newbuilding slots in the Far East to be filled quickly. However, this did not affect bank loans as deliveries would be 2-3 years forward.
By the end of 2023, Greek owners have had amassed considerable liquidity. Some used this to place new orders, whilst many others used it to reduce ‘expensive’ bank loans. Hence banks found that even though loan volume had picked up during 2023, they could not maintain their loan portfolios due to prepayments and amortisations.
Overall, the latest Petrofin Bank Research showed that Greek related loans fell by 2% to $ 50,891m with the Petrofin Index for Greek ship finance falling to 308 in 2023 from 314 in 2022 and 443 at its peak in 2008. The long term fall is mostly due to the exodus of major ship lenders over the years, primarily from Europe, as banks increasingly focused on non asset based lending and lending closer to home. It would appear though that this trend seems to have run its course as over 80% of existing lenders, according to Petrofin Research, seem to have both the appetite and capacity to grow.
A key feature of 2023 was the increased popularity of Sale and Leaseback deals, as well as greater interest in ship lending by funds. Such providers would offer competitive pricing but most of the time a higher LTV and longer maturities which Greek owners found attractive. Admittedly, SLBs were more prevalent among public companies and / or major owners, which sought the opportunity to release capital where appropriate or finance new acquisitions or newbuildings using less of their own capital. Such competition became intense and denied shipping banks the opportunity to conclude more business.
The exception to the rule was the Greek banks which managed to grow despite the SLB competition. Greek banks had an advantage in having long term close relationships with Greek clients, as well as benefits from ancillary services. Additionally, as the credit rating of Greece and of the banks improved, loan margins became more competitive and Greek banks experienced a considerable growth in deposits from shipping clients. Without on the whole increasing their LTVs, Greek banks were able to grow by 12.25% in 2023 and to show the highest level of year end commitments that were yet undrawn by 60.83% year on year.
There has been no change in the top spots with UBS (Credit Suisse) still being the top among all banks and Eurobank top among Greek banks. With the departure of HSBC from having a Greek presence, it is noteworthy that the number of International banks
with a Greek presence declined to 6 from a total of 11 in 2015. With much improved electronic communications, banks interestingly focused on reducing their international presence and costs by bringing it closer to home and this is one reason for the decline. It is arguable in the improved economy of Greece and higher credit rating, as well as excellent performance by shipping that Greek shipping might entice some of the departees to return via representative offices as this invariably assists marketing.
On the other hand, international banks without a local presence have remained at approximately 35-40 since 2015, with marketing taking place remotely or by visits and focused on the existing clientele.
The overall number of banks remained the same y-o-y at 50, although it is reasonable to say that those now lending are more committed to Greek shipping lending than before.
Far East financing experienced good growth especially via SLBs whose value is not known precisely. However, most major Japanese, Chinese and Korean banks are engaged in ship finance bilaterally or via SLBs with an increasing interest in Greek clients.
Newbuilding related bank finance has also increased by 14.2% y.o.y. reflecting the renewed interest by Greek Owners in newbuildings, both with dual fuel design but also the latest IMO III yard eco designs.
It was a challenging year form syndications for most banks with the exception of BNP Paribas showing a 287% y-o-y increase.
Capital market activity in 2023 was subdued across the board with shipping IPOs, follow ons and shipping bonds, all decreasing, especially compared to 2022.
Conditions for raising capital in 2023 were not supportive. However, it is noteworthy that the Scandinavian investment market remained strong with numerous shipping investments and high investor appetite.
Greek owners remain overwhelmingly bullish of the shipping markets. This is evident by the competition for vessels (especially modern eco units) coming up for sale, as well as in seeking newbuilding slots, now stretching up to 2027 – 2028. Despite geopolitical tensions and uncertainty, it is widely believed that the ton/mile increases as a result of these factors will not disappear any time soon. In addition, there is a widespread belief that sooner or later US interest rates will start falling and that cash flows shall improve. It is this belief and the absence of newbuilding slots that has resulted in an average increase of 3% for tanker prices, 8% for dry bulk prices and 12% for container vessel prices, in the first months of 2024. Overall, the Clarksons second hand price index is showing a 10% increase for the first 3 months.
However, for ship lending to increase, the volume of second hand vessel sales must rise and however, due to the limited availability of vessel candidates for sale, S&P activity by Greeks remains similar to 2023. It is possible, therefore, unless vessel sales shortly rise,
that the volume of shipfinance may not rise, despite the increased appetite of many banks. Newbuilding deliveries in 2024 are also not appreciably higher than 2023 and they are only expected to rise from 2025 onwards. Hence, it is difficult to see from where loan growth might arise.
Competition from non-bank sources of lending remains high, especially as both lending is still focused on an approximately maximum 60% LTV, whereas SLB at 70% or over. It is anticipated that once interest rates shall fall, SLB attractiveness might further increase, unless banks decide to offer more competitive terms.
One area where banks have offered more competitive terms has been in loan margins and arrangement fees, where for medium size clients margins have reduced to 2.5% over SOFR or less. Greek banks, in particular, are keen to offer even lower margins, where LTVs are lower. One area, which might produce additional bank loan volumes, might be the financing of takeover and mergers occurring between public companies. The discount of share price over book value of shipping stock has prompted the interest of many buyers e.g. Starbulk, Economou and others. Here, banks might play a pivotal role, especially where the offer is a cash or part cash offer. Where the banks can play an important role is in vessels offering new technology and reduced emissions. Most of such vessels are dual fuel and usually purchased or ordered by public companies or major owners. As banks are interested in financing low emissions, vessels, in line with their ESG policy and the Poseidon principles, this is an area in which the banks could compete effectively.
Banks have been cautious in their lending. Whilst it is not expected that they will become aggressive, as their clients’ financials and liquidity become even more robust. It is expected that they will be able to compete more effectively in the future and offer more attractive terms. Banks have the benefit of enjoying additional non-loan related income from annulling services, which is expected to grow In addition, investment related banking is expected to develop further in 2024.
An area of concern lays with the Basle IV new guidelines, becoming effective in 2025, whereby asset financing, such as shipping, may require more capital allocated for each loan up to 100% of the loan portfolio. This and other regulations coming into effect may well undermine a bank’s ability to offer low loan margins and may give a further advantage to leasing / SLB structures, which are not subject to these regulations.
Public markets are recovering and are expected to be more active in 2024 and the same applies for the Scandinavian market. Syndications and club deals are also expected to mark progress in 2024, for large scale refinancings and newbuilding finance.
Greek bank finance is entering into a new phase, where bank demand for loans and competition will become fiercer, especially for tier clients but where overall volumes may not permit significant growth.
Founded in 1987 by Mr. Dimitrios Argoudelis, CMA D. ARGOUDELIS & CO S.A. has navigated a remarkable trajectory in the realm of marine automation and technology. From its inception, the company set its sights on establishing a solid foundation within the industry, a mission later fortified by the technical expertise and business acumen of Mr. Argoudelis’ sons, Mr. Ioannis Argoudelis and Mr. Nikolaos Argoudelis.
However, the path to success was not without its challenges. Economic crises, fierce competition, and the unprecedented disruptions of the COVID-19 pandemic tested the company’s resolve. Yet, propelled by the dedication and professionalism of its workforce, CMA emerged stronger, establishing itself as a prominent leader in marine automation.
Central to its success has been a steadfast commitment to quality, exemplified by its ISO certifications and rigorous adherence to international standards. Moreover, CMA’s visionary approach to education and training underscores its dedication to fostering talent and promoting innovation within the industry.
Looking ahead, CMA envisions a future defined by technological advancements, sustainability, and digitalization. With a focus on green solutions and cutting-edge automation, the company is poised to drive transformative change within the maritime sector.
As CMA prepares to showcase its latest innovations at Posidonia 2024, the exhibition holds profound significance. It offers a platform to connect with industry peers, explore emerging trends, and showcase its commitment to shaping the future of marine automation.
In this dynamic landscape, CMA D. ARGOUDELIS & CO S.A. remains steadfast in its mission to lead the way in marine automation, forging new paths of innovation and resilience for years to come.
How did your company come into existence, what were its initial stages like, what obstacles did it confront, and what factors propelled it towards success, establishing it as a prominent leader in the realm of marine automation and technology?
Our company was founded in 1987 by Mr. Dimitrios Argoudelis, a visionary with a deep passion for marine automation. The initial stages of our company were marked by a strong focus on establishing a solid foundation in the marine automation industry. This foundation was later expanded and strengthened by his sons, Mr. Argoudelis Ioannis and Mr. Argoudelis Nikolaos, who both brought their technical expertise and business administration skills to the helm.
Throughout our journey, we faced several significant obstacles. The economic crisis posed serious financial challenges, while the highly competitive environment demanded constant innovation and adaptation. Additionally, the COVID-19 pandemic introduced unprecedented global disruptions, affecting supply chains and client operations worldwide.
Despite these challenges, our company’s trajectory towards success was propelled by several key factors. The unwavering dedication and teamwork of our employees, who deeply believed in our vision, played a crucial role. Their commitment, coupled with our commitment to providing high-quality services and products, established us as a prominent leader in the realm of marine automation and technology. Our achievements stem not only from our capacity to surmount challenges but also from our enduring dedication to excellence and innovation across all endeavors.
What has been the most challenging experience you’ve faced in your career, and what do you consider your most significant achievement thus far?
The most challenging experience I have faced in my career has undoubtedly been managing a company that specializes in marine automation. This field requires a constant balance to maintain the high standards necessary for success and a good reputation. A particularly difficult period was when, in a time of very high job demand, we lacked several key senior engineers. This gap posed a significant risk to our quality standards. Managing the transition, ensuring that the quality of our services remained uncompromised while we sought suitable additions, was a substantial challenge. As for my most significant achievement, it would be the total construction and delivery of a new building ship, focusing on the electrical and automation aspects. We completed this project with 100% success, meeting all specifications and client expectations. This achievement not only stands as a testament to our team’s expertise and dedication but also significantly bolstered our position in the industry, enhancing our reputation for quality and reliability in marine automation projects.
What significance do you attribute to the term “quality,” and in what ways do you believe it can steer a company toward achieving exceptional levels of product and service delivery?
“Quality” embodies the essence of excellence, encompassing everything from product design to customer service. It’s the cornerstone of a company’s reputation and directly impacts customer satisfaction and loyalty. Prioritizing quality drives continuous improvement, fostering innovation, efficiency, and trust. By consistently delivering high-quality products and services, a company can differentiate itself in the market, build a loyal customer base, and ultimately achieve sustainable success.
In recent years, your company has demonstrated a notable and tangible commitment to matters concerning education and training. How significant is the realm of training to your organization, particularly concerning cutting-edge technology, and what strategic initiatives do you envision undertaking in this domain moving forward?
Education and training are paramount to our organization’s mission and success, especially in the realm of cutting-edge technology. We recognize that staying ahead in today’s fast-paced world requires continuous learning and upskilling. Moving forward, we envision strategic initiatives that prioritize accessible and innovative training programs, partnerships with educational institutions and industry experts, as well as investments in digital platforms and tools for remote learning. Our goal is to empower individuals with the skills and knowledge needed to thrive in an ever-evolving technological landscape, driving both personal and organizational growth.
What does shipping mean to Greece? Can you envision Greece without its maritime industry? How would things differ without our shipping, which has long been intertwined with Greek life and drives entrepreneurial endeavors with remarkable success?
Shipping holds immense significance for Greece, woven deeply into the fabric of its identity and economy. It’s not just an industry but a cornerstone of Greek life, driving entrepreneurial endeavors with remarkable success. Without its maritime industry, Greece would undergo profound changes, as shipping contributes significantly to the national economy, provides employment opportunities, and sustains a vibrant maritime culture. The absence of shipping would impact not only economic prosperity but also the country’s historical legacy and sense of identity as a maritime nation.
Do you believe that technological advancements in the shipping industry are best achieved through collaborative efforts?
Absolutely, collaborative efforts are essential for driving technological advancements in the shipping industry. By fostering partnerships among industry players, technology providers, research institutions, and regulatory bodies, we can leverage diverse expertise and resources to tackle complex challenges and accelerate innovation. Collaboration enables the sharing of knowledge, resources, and best practices, ultimately leading to more robust and sustainable solutions that benefit the entire maritime ecosystem.
CMA envisions the transformative potential of advanced technology and recognizes its pivotal role in shaping the future of marine operations. Looking ahead, what developments do you anticipate in this realm in the coming years?
At CMA, we foresee significant advancements in the integration of advanced technology within marine operations. This includes further automation to streamline processes and enhance safety, the continued development of sustainable energy solutions to reduce environmental impact, and the widespread adoption of digitalization and IoT for data-driven decision-making. We anticipate innovations in remote monitoring and control systems, as well as advancements in artificial intelligence and predictive analytics to optimize efficiency and performance across the maritime industry.
Recognizing that diversity is not merely a slogan but a potent catalyst for positive change, CMA acknowledges the challenges in cultivating a dynamic, diverse workforce that not only enriches problem-solving capabilities but also fosters superior corporate practices?
CMA as a member of Diversity Charter Greece, recognizes the intrinsic value of diversity as a driving force for positive change within the organization. Understanding that diversity goes beyond a mere slogan, CMA acknowledges the complexities involved in cultivating a truly inclusive workforce that enhances problem-solving capabilities and promotes superior corporate practices. By prioritizing diversity and inclusivity in recruitment, retention, and professional development initiatives, CMA strives to foster a dynamic and inclusive environment where individuals from diverse backgrounds can thrive, contribute their unique perspectives, and collectively drive innovation and excellence.
With the recent introduction of the pioneering automation lab at BCA College’s City Campus, do you anticipate this state-of-the-art facility to revolutionize maritime education and industry practices, presenting a multitude of advantages for both students and shipping companies?
The automation lab at BCA College’s City Campus holds immense potential to not only enrich students’ educational journeys but also catalyze positive transformations within the maritime industry. This cutting-edge facility offers hands-on experience with the latest automation technologies utilized in maritime operations, ensuring that students graduate with the skills necessary to excel in modern workplaces.
Automation plays a pivotal role in enhancing efficiency within maritime operations by streamlining processes, reducing manual labor, and mitigating the risk of human error. Equipped with practical training from the lab, students are poised to contribute to the efficiency and competitiveness of shipping companies upon entering the workforce.
As shipping companies increasingly integrate automation into their operations to remain competitive and comply with regulations, graduates from institutions with automation labs are in high demand. Their adeptness with automation technologies makes them valuable assets for navigating the evolving landscape of maritime industry practices.
Moreover, automation often accompanies advanced safety features that prioritize accident prevention and ensure the safety of crew members and cargo. By educating students on these safety protocols, the automation lab prepares them to uphold safety standards as they embark on their careers in the maritime sector.
In a recent statement, you emphasized the importance of investing in the future of the shipping industry for its growth and sustainability. You also mentioned your dedication to fostering talent and promoting innovation in the sector. Could you elaborate on what this commitment entails?
At CMA, our commitment to the future of the shipping industry involves pioneering new automation systems tailored specifically for maritime needs. We’re dedicated to sustainability, developing energy-efficient solutions to reduce fuel consumption and carbon emissions. Embracing digitalization and IoT, we’re introducing products leveraging data analytics and automation to enhance vessel performance. Additionally, our remote monitoring systems empower ship operators to optimize efficiency and minimize downtime through real-time diagnostics and adjustments.
What are your predictions for the direction of the shipping industry in the next decade? Additionally, what potential obstacles do you foresee that could hinder the green transition? Finally, how does Greece plan to uphold its leadership role in global shipping amidst these changes?
In the next decade, the shipping industry is likely to witness a transformative shift towards sustainability and digitalization. We anticipate increased adoption of green technologies such as alternative fuels, emission reduction measures, and eco-friendly vessel designs to mitigate environmental impact. However, potential obstacles to this green transition include regulatory challenges, high upfront costs, and infrastructure limitations. Greece, as a global maritime leader, plans to uphold its position by leveraging its expertise and investing in sustainable practices and innovation. By embracing green technologies, fostering collaboration, and advocating for regulatory frameworks that incentivize sustainability, Greece aims to remain at the forefront of the shipping industry’s evolution.
In the realm of technological advancements, what transformations do you anticipate in terms of integrating digital technologies, automation, and artificial intelligence to enhance efficiency, safety, and competitiveness within the shipping industry?
The integration of digital technologies, automation, and artificial intelligence (AI) is poised to revolutionize the shipping industry, offering unprecedented opportunities to enhance efficiency, safety, and competitiveness. We anticipate advancements such as autonomous vessels, smart navigation systems leveraging AI for real-time decision-making, predictive maintenance through machine learning algorithms, and comprehensive data analytics for optimized route planning and fuel consumption. These innovations will not only streamline operations but also improve safety by reducing human error and enabling proactive risk management. Ultimately, they will empower shipping companies to achieve greater efficiency and competitiveness in a rapidly evolving global marketplace.
A few years ago, discussions surrounding autonomous vessels, smart navigation technologies, real-time monitoring of ship systems for optimized performance, remote operation control, and data analytics for enhanced decision-making and reduced operational costs may have seemed far-fetched or even akin to science fiction scenarios. With many of these technological advancements now becoming reality, how prepared do you believe the shipping community is to adopt them? Additionally, how prepared is your company for these impending changes?
The shipping community has shown a growing readiness to embrace technological advancements in recent years, driven by the potential for increased efficiency, safety, and cost savings. However, the pace of adoption varies across sectors and regions due to factors like regulatory frameworks, infrastructure, and investment capabilities. As for our company, we have been actively investing in research and development to stay at the forefront of these changes. We have implemented strategies to integrate autonomous vessels, smart navigation technologies, and data analytics into our operations, ensuring that we remain competitive and resilient in the evolving maritime landscape.
What are your objectives for the upcoming years, and which opportunity do you perceive as the most significant for your company to capitalize on?
As an ambitious and rapidly expanding company, CMA D. ARGOUDELIS & CO S.A. is poised for significant growth with our latest premises expansion. This expansion empowers us to further accelerate our advancements in automation engineering, professional services, and customer support.
Our new headquarters will feature state-of-the-art Learning Centers led by Senior Trainers deeply versed in marine automation. With a robust array of training courses, our objective is to empower seafarers to acquire new knowledge, hone essential skills, and cultivate the right mindset. We are dedicated to pioneering innovative training practices, committed to delivering a truly unparalleled learning journey.
In addition to our training facilities, the extra 1500 square feet of space will accommodate new Hydraulics department, a larger warehouse, expanded sales area, and a spacious private conference room for crucial meetings. Embracing an open-plan design for most of our workspace, all employees will be desked together, fostering an environment conducive to innovation, creativity, and enhanced networking opportunities.
In the upcoming years, our primary objectives revolve around introducing new technologies to the marine market with a keen focus on reducing carbon emissions and digitizing shipping. We recognize the critical need for sustainability and efficiency in maritime operations, and we are committed to leading the charge in these areas. To capitalize on these goals, we have established a new Research and Development department. We believe there is a substantial opportunity to invest in and develop innovative solutions for the marine industry. This initiative not only aligns with global trends towards environmental responsibility but also positions us at the forefront of the next wave of technological advancements in marine automation. By leveraging our expertise in this field, we aim to drive significant progress in making shipping more sustainable and efficient, which we see as the most significant opportunity for our company in the near future.
What level of significance does the Posidonia exhibition hold for your company, and what benefits do you anticipate deriving from participating in this year’s event?
For CMA D. ARGOUDELIS & CO S.A., Posidonia 2024 represents a pivotal moment building upon the triumphs of their debut in 2022. As specialists in automation for marine, industry, and energy sectors, our presence at this esteemed global shipping exhibition holds profound significance. Participating in Posidonia 2024 offers invaluable prospects for driving business expansion, forging vital industry connections, and actively contributing to discussions on sustainability and innovation within maritime and energy domains. At the event, CMA will showcase cutting-edge technologies, seize networking opportunities, pursue market expansion, gain insights into industry trends, and elevate brand visibility and reputation.
Island Oil (Holdings) Ltd is a diversified group of companies that primarily deals with the supply and trading of marine fuels. Founded in Limassol in 1992, Island Oil has since expanded and been embraced by the maritime industry as a most reliable partner. Entrusted by blue-chip clients from local and international shipping markets, the group has built a strong reputation through its human-centric values and its culture of conducting business based on trust and mutuality.
Headquartered in Limassol, the group has physical supply stations in Cyprus, Romania, and Israel, along with trading desks in Piraeus, Singapore, London, Hong Kong, Shanghai (through representation of an agent.) and, most recently, Seoul.
Additional services include the international trading of marine spare parts through the subsidiary NavTech Supplies Ltd, the provision of ship-agency services in ports serviced by own vessels, and the supply of fuels for the onshore light industrial and hotels market in Cyprus through subsidiary EJ Papadakis Ltd. The group also has an in-house ship management company, Petronav Ship Management Ltd, a fully owned subsidiary which manages the vessels operated for physical bunkering.
Island Oil (Holdings) owns 12 tanker vessels for the supply of marine fuels, nine of which are operated by Island Petroleum Ltd, the group’s physical supply arm. As mentioned above, Island Petroleum operates physical supply stations in Cyprus, Romania, and Israel, offering VLSFO and MGO. Emphasizing quality and reliability, the company performs own product analyses to safeguard conformity to the specifications ordered by the customer. Additionally, through structured organization and strong operational supervision, Island Petroleum minimizes the customers’ waiting time, from free pratique to barge alongside. Behind the company is a dedicated price risk management team offering tailored advice and fixed forward contracts. With an abundance of trade finance lines and excellent credit rating, Island Petroleum can form a reliable, long-term supplier for your marine fuel needs in the Eastern Mediterranean and Black Sea.
Island Oil Ltd is the group’s arm for global trading of marine fuels, with trading desks operating out of 7 different countries. Over thirty years, Island Oil has built a stellar reputation through a genuine client-oriented approach, strong financial management, controlled
growth, and a highly skilled and trained team of professionals. The company enjoys healthy credit lines from energy majors and first-class physical suppliers. Through thorough vetting of physical suppliers, Island Oil ensures that delays and disputes are avoided for its customers. The company’s excellent credit rating, payment reputation, and plentiful trade finance lines guarantee a reliable partnership.
Island Oil Holdings’ CEO & Founder, Mr. Chrysostomos Papavassiliou, has said in interviews that the group’s business development strategy revolves around sustainable growth. “We mean sustainable both in the sense of how we interact with society and our environment, and how we can guarantee longevity while growing as a company”, he stated.
With the sustained growth of the group has come a maturity that allows it to efficaciously navigate the ever-changing shipping and energy markets. To this effect, the group has developed EU ETS solutions for the marine fuels industry so that customers can rest assured that they will receive practical consultation in this crucial matter. Additionally, the group can help customers optimize carbon credit procurement with budget control tools and allow seamless purchasing of carbon credits alongside fuel purchases. Finally, customers can surrender their EU allowances through auctions in the primary market, trading in the secondary market, or by engaging in future contracts. Additionally, foreseeing increased demand for alternative marine fuels, Island Oil was recently certified by the ISCC as a biofuels trader. Furthermore, the group has established strategic partnerships with accredited startups and research institutions to develop biomethane fuel solutions for onshore and offshore applications in Cyprus.
At the same time, Island Oil Holdings has implemented energy-saving and environmental measures in their own fleet, including pollution prevention technology and ballast water treatment. Three of the group’s vessels are engaged under EMSA contracts specifically for pollution prevention services and are fully equipped for this purpose. These measures have been taken in line with the group’s ESG strategy, which also has its first ESG report on the way. Finally, Island Oil Holdings is close to finalizing a Decarbonization Strategy which will accelerate the group’s path towards a more sustainable future.
Marine Plus S.A. was established by Mr. Dimitris Vranopoulos in London in 1988 and its subsidiary office was set up in Athens in 1990. A+P Appledore (UK) was the first yard the company represented, followed by Unithai (Thailand). During an overseas trip to Shanghai in 1991, Mr. Vranopoulos participated in the Marintec exhibition. With the assistance of a translator sourced through the Greek embassy, standing in a small booth, and handing out business cards in English and Chinese to all exhibitors, the first contacts with Chinese yards were established. The first repair in China was booked in 1992. Cooperation with Turkish shipyards started in the early 90’s as well with Tuzla S/Y which was owned by Kahraman Sadıkoğlu at the time. Since then Marine Plus has managed to be granted the confidence and trust both by the major Shipyards in China and other areas of the world (S/E Asia, Middle East, Europe, Americas) as well as the Greek shipping community, as a provider of high quality maritime services worldwide.
Today, with over 35 years of experience and offices in Athens, Istanbul, Singapore and Houston, Marine Plus can effectively provide almost any technical support required by vessels trading Worldwide, ranging from dry dockings, conversions, new building contracting/supervision, minor voyage or port repairs, BWMS, Scrubber, LNG fuel systems, other machinery equipment, IMO & VGP Sampling Tests and Analysis, supply of spares, supplies and provisions, UW services, FFE, LR/LB inspections, certification, repairs and more. Marine Plus has built up a very close, long-term, and constructive cooperation with the best ship repair yards in the World. This has been a slow process that has taken years of commitment and hard work, a combination of strong interpersonal relationships with the senior management of these yards as well as a concentrated team effort to ensure each repair project undertaken is a success both for their Greek customers as well as the yards’ is representing. Thus, it is conducting over 200 dry dock repairs annually, and has been granted the trust by more than 250 loyal customers from the Greek Shipping Community.
As Mr. Vranopoulos explains “Our real job begins after we receive a firm booking, especially during the vessel’s repair at the yard, where key milestones are monitored as well as overall progress, maintaining agreed schedules, docking dates, sufficient labor for prompt execution of works etc. During this period regular contact with the attending Supt Eng as well as
the head office is maintained. Monitoring and expediting work progress is greatly assisted by our local associates who deal with working-level yard staff, whilst we also keep contact with senior yard management as and when their intervention is required.”
With this mentality and proven professionalism, Marine Plus has managed to gain the trust of the Major S/Y facilities in China (both Government owned and Private) and Turkey as well as to sign exclusive representation agreements with key repair facilities (yards) in other strategic locations Worldwide, such as Dubai Drydocks.
Marine Plus
a. Exclusively represents SunRui Marine Environment Engineering, a subsidiary of CSSC Group, the largest Shipbuilding Conglomerate in the World. SunRui has developed the well known to the International Maritime Community products BalClor BWMS, SOxFree EGCS (Scrubber system), SCR De-NOX system, GasLink LNG FGSS /Methanol LFSS /Ammonia AFSS / Onboard Carbon Capture and Storage System (OCCS) and can organize turn-key retrofitting projects in collaboration
with Chinese Repair Shipyards. Recently the Marine Plus – Sunrui Service and Training Center was established in Athens to cover all the required services for Sunrui equipment as well as the training of the crew / office technical personnel.
b. Also represents Xiamen SunRui Ship Coating : Paint (a subsidiary company of the Unified State-Owned CSSC Group and sister company with SunRui Marine Environment Engineering).
c. Cosco Shipping Heavy Industry Technology (Weihai) : Alternative Maritime Power System (AMPS) / Cold Ironing, (a subsidiary company of the worldwide well-known COSCO Group).
d. Shanghai Donjun Automation Equipment : Valve remote control systems.
e.USR : E mergency GenSets, Marine and Land use Generators ( a high-quality and standards Maker, which has cooperated with reputable Makers such as Honda, Cummins and Kubota.
f. Kexun: Internal Communication Systems and Alarms.
g. Tongzhou (Marine Propeller Systems and Energy Saving Devic-
es).
h. Anhui Sunny (Marine Lighting), and other reputable makers of marine equipment.
Marine Plus is also running 2 sister companies in Greece
i. JNE Marine who is the exclusive agent of Mitsubishi Purifiers in Greece. Also specialized in the supply of spares and specifically engineered components from the Chinese / Korean market.
ii. Marine Plus Safety which provides spare parts and attendance needs for FFE/LSA Equipment.
Also worth mentioning, is the success their NB department has had during the last NB cycle. Only last year, 2 NB projects were secured for Greek interests for Ultramax and MR Tankers, with several other projects at LOI stage. Marine Plus permanent association with Chinese Shipyards has given them a unique advantage to assist and secure off market opportunities. Marine Plus, believes that in the coming decade, China will be the center of world shipbuilding.
METIS with its expertise and technological competence develops innovative solutions that meet the needs of multiple departments, roles and management levels in a shipping company. In this interview we host Mr. Panos Theodossopoulos, CEO of METIS with whom we discuss all the latest developments.
What sets METIS apart from other companies in the industry?
From its inception, METIS positioned itself innovatively in the market, addressing the entire spectrum of what we call digitalization in shipping. It covered the whole range from automated data collection from the vessel all the way to analysis based on market needs, principles of naval architecture, laws of physics, and with the use (when required) of advanced machine learning and artificial intelligence techniques. Recent mergers and acquisitions in the maritime tech market aimed at creating similar groups that cover the whole spectrum of needs required by shipping companies, confirm the validity of our initial strategy.
What needs do the analyses you produce cover, how do they assist a shipping company, and in what roles are your solutions aimed?
In general, our solutions help in analyzing and understanding past vessel performance, monitoring current operational status in real-time, and predicting future behavior for the whole fleet. As for the areas they touch upon, the spectrum is quite broad, but they focus on the key axes of optimizing the operational performance of vessels, reducing fuel consumption and consequently costs, as well as effectively managing environmental footprint and regulatory obligations, especially regarding emissions.
Some indicative examples include:
• Monitoring, analyzing, and predicting consumption during any vessel voyage and under any weather conditions.
• Scheduling hull/propeller cleaning based on actual consumption increase.
• Monitoring and predicting pollutants and carbon footprint based on regulations.
• Monitoring and analyzing charter party performance.
• Scheduling and optimizing voyages based on vessel condition, weather, and carbon footprint.
• Monitoring and analyzing main engine and generator operation.
We address the needs of both technical and performance departments, as well as those of operations, chartering and commercial departments. We also cater to the needs of multiple levels of management, as different information is required by the technical director, fleet manager, superintendent, and obviously, the CEO or the Owner.
I understand that the use of reliable data is paramount for conducting any analysis. How does METIS handle this issue, and what is the importance of data acquisition frequency?
I’ll start by saying that METIS has been pioneering the use of automatic collection of high-frequency signals from ship operations since its inception. This way, we managed to
minimize human error in data collection and recording as well as to reduce the workload for the crew.
Of course, sensors and data transmission can introduce errors as well, so we have developed a very detailed and rigorous process for monitoring the availability of signals in regard to the timely reception and the completeness, as well as the validity and quality of measurements received. Having reliable data is the most important factor for any kind of analytics. The other significant factor is the frequency of the data reception since, as a general rule, the more data points we have available the more detailed and advanced analytics we can provide.
Can you share a recent success story where METIS helped a client achieve their goals?
Certainly, there are many success stories, but if I had to highlight a few recent ones, I would mention the case of a large client of ours, for whom we monitor the entire fleet . Recently, we assisted them in submitting their annual EU MRV and IMO DCS reports (for fuel consumption and emissions) based on automatic data collection and analysis from the METIS platform. This is an example of how we help our customers ensure their regulatory compliance, having full control while reducing time and effort. Another case involves an off-shore ship (SOV) management company serving floating wind farms. There, based on the real-time condition of the vessels and the weather, they optimize the order in which they schedule visits to each wind turbine and are able to offer better services to their clients.
We also often have cases where our clients use data and analysis from our platform for communication purposes with charterers and dispute or resolve cases regarding the compliance of the attained performance of a vessel versus the agreed charterparty terms.
Lately, our clients frequently utilize our platform to assess the performance of Energy Saving Devices and the vessel’s overall performance by comparing conditions before and after their installation.
What do you think about Artificial Intelligence? What have we seen so far in shipping and what should we expect in the future? Is it a panacea or is it a buzzword?
My opinion on Artificial Intelligence is that, especially at the onset of digital technologies entering the shipping industry, the term “artificial intelligence” was overused, perhaps even exhausted. The truth is, it’s neither just a buzzword nor a panacea. It’s another - very powerful - tool we use in leveraging and analyzing the data we collect.
I often say that the optimal conclusion and consequently the value we provide to our clients should follow the triptych: (1) principles of physics and engineering (as we deal with very complex physical phenomena), (2) human knowledge and experience, and finally (3) advanced analysis which also includes the use of machine learning techniques and artificial intelligence. Lastly, I’d like to mention that METIS, from its beginning, experimented with using AI in various domains one of which is as an additional means of interfacing with users. We introduced an industry-first maritime chatbot for user-to-platform communication, which we are currently re-evaluating to leverage new generative AI technologies and large language models.
Is there an opportunity for cooperation with other companies
that offer similar or related services? What is your position on this matter?
While we have great faith in the strength of our team, we recognize that we cannot and do not wish to specialize in all possible fields or cover all the needs of our clients. Therefore, collaborations within the industry are both legitimate and beneficial, and we already engage in various partnerships.
This mentality is also reflected in the architecture of our platform which can act as an intelligent data hub able to receive or share data to any 3rd party service provider through mulpiple interface options.
Initially, collaborations arose upon client request. However, we have now taken a step further and have already developed a range of partnerships offering complementary services. This way, we enrich our own functionality through collaborations and we strengthen the relationship we build with our clients.
For example, we collaborate with weather forecasting companies, with route optimization services and manufacturers of mechanical equipment to monitor and analyze the operation of their machinery, etc.
Can you refer to current METIS research and development initiatives aimed at developing innovative solutions or improving existing services?
The METIS platform is a dynamic entity that is constantly evolving, both in aspects invisible to the client concerning stability, speed, and system security, as well as in functionality and usability.
Recently, we have placed significant emphasis on improving the user experience to increase productivity, as well as ease of understanding and absorbing information. We are completely redesigning the interface environment, and during the Poseidonia event, we will launch it, presenting the new face of METIS to the market. Moreover, we are very active in participating in R&D projects, in cooperation with Academic Institutions, shipping companies and other stakeholders both at the national and European levels, on related subjects.
Looking ahead, what emerging trends or technologies is METIS monitoring and how does it plan to adapt its services to address these changes?
Part of our DNA at METIS is to constantly monitor emerging trends and new technologies that are affecting or are going to affect the maritime sector in the future.
The maritime industry has now entered the phase of decarbonization, and this is a dominant factor in how it will operate from now on. We believe that the use of digital technologies is the “twin” of decarbonization. In this context, and with our goal always being to empower individuals and companies to evolve and work in new, innovative ways in order to achieve their goals, we are commited to be present and supportive in this journey.
New fuels, energy-saving devices, operational optimization are just some of the issues that will concern us and which we are already monitoring.
Additionaly, we believe that the maritime industry is entering a new era characterized by increased transparency needs in its operations, driven by regulatory frameworks, market forces, financial institutions, commercial realities (ESG, etc.), and the technology itself. In this context, with transparency being one of our core corporate values, we strive to help our clients navigate this journey of transparency in the best possible way.
Safe Bulkers champions sustainable shipping through modern fleets and eco-friendly practices, ensuring compliance with stringent environmental regulations while fostering growth and resilience.
Safe Bulkers is an international provider of seaborne transportation services of dry bulk commodities. With a modern fleet of 45 bulk carriers with an aggregate carrying capacity of 4.8 million dwt (5.3 mil dwt including the newbuilds) and an average age of 9.85 years, the Company’s vessels transport a wide range of dry bulk cargoes across the globe, including major bulks as grains, coal and iron ore and other minor bulks as bauxite, alumina and fertilizer. Incorporated in the Marshall Islands, Safe Bulkers has been listed on the NYSE since 2008 with its common stock trading under the symbol “SB”. The Company’s operations are managed by its Cypriot, Greek and Monaco-based management companies, Safe Bulkers Management Ltd, Safety Management Overseas S.A. and Safe Bulkers Management Monaco Inc., which provide full technical, administrative and commercial services to its vessels. With 43 out of 45 of the Company’s vessels flying the quality EU Cyprus flag, Safe Bulkers is currently the largest ship-owner under the Cyprus Registry.
Overall, Safe Bulkers operates a modern, young and energy-efficient fleet of 45 vessels, twelve of which are eco-ships built after 2014, and nine are IMO GHG Phase 3 - NOx Tier III ships built 2022 onwards. The Company’s fleet consists of dry bulk vessels of four sizes, namely 8 Capesize vessels with carrying capacity of about 180,000 dwt; 17 Post Panamax vessels with carrying capacities of between 85,000 dwt and 100,000 dwt; 11 Kamsarmax vessels with carrying capacities of between 80,000 dwt and 83,000 dwt; and 9 Panamax vessels with carrying capacities of between 75,000 and 78,000 dwt.
Being a successor to a company first established in 1958, Safe Bulkers has a proud tradition of more than 65 years of enduring and resilient presence within the drybulk sector, through consistent outperformance and a steadfast commitment to sustainable growth. Over the past decades, Safe Bulkers has formed strong partnerships with key players in the dry bulk market and has been well-recognized for its operational excellence, strong financial profile and transparent corporate governance practices. Each year since 2020, the company issues its annual Sustainability Report published on its website(www.safebulkers.com) in order to better inform its stakeholders on the company’s approach and performance on Environmental, Social and Governance (ESG) matters.
Safe Bulkers is committed to maintaining one of the most efficient fleets in the dry bulk segment. Ahead of the increasingly stringent environmental regulations and the IMO greenhouse gas emissions (GHG) reduction goals, Safe Bulkers has made significant steps in minimizing the environmental footprint of its fleet while enhancing its competitiveness and resilience for the future. In this context,
Safe Bulkers has been implementing a number of strategies, which include: (i) a comprehensive fleet renewal and expansion program by selling older less efficient vessels while selectively acquiring second-hand younger tonnage with improved design characteristics and ordering new modern vessels, and (ii) an ongoing program for fleet monitoring and upgrading with newer eco-efficient technolo-
gies.
Since 2018, Safe Bulkers has allocated north of $550 million in newbuilding vessels and energy saving and environmental upgrades, involving the application of ultra-low friction paints, ducts and PBCF and the installation of Ballast Water Treatment Systems (BWT) and Exhaust Gas Cleaning Systems (EGCS), known as scrubbers. As of today, twenty-one (21) vessels in total have been upgraded. The Company also uses biofuels in certain voyages, targeting a lower CO2 emission factor and lower environmental impact.
Furthermore, the Company has engaged in an extensive investment program focusing on its fleet renewal. As part of its fleet renewal program, the Company signed contracts for the acquisition of two dual-fueled newbuilding Kamsarmax dry-bulk vessels, capable of operating with methanol and fuel. Note that these vessels when powered by green methanol, can produce close to zero GHG emissions based on the life cycle assessment (LCA) methodology well-to-propeller (WTP). As all the Company’s newbuilds, these dual-fueled vessels are designed to meet the future requirements of the IMO regulations and especially those relating to the reduction of greenhouse gas emissions (EEDI - Phase 3), as well as those related to nitrogen oxide emissions (NOx-Tier III).
At the same time, following the recent deliveries of its first nine Phase 3 newbuilds - MV “Vassos”, MV “Climate Respect” MV “Climate Ethics”, MV “Climate Justice”, MV “Pedhoulas Trader”, MV “Morphou”, MV “Rizokarpaso” and the most recent MV “Ammoxostos” and MV “Kerynia” - Safe Bulkers has an outstanding orderbook of 8 newbuild dry bulk vessels with prompt scheduled delivery dates, one in 2024, two in 2025, four in 2026 and one within the first quarter of 2027. All the newbuilding vessels are designed to operate to the highest operational and environmental standards, compliant with the future requirements of IMO regulations and especially those relating to the reduction of greenhouse gas emissions (EEDI - Phase 3), as well as those related to nitrogen oxide emissions (NOx-Tier III). As the first nine newbuilding vessels, all the newbuilds will fly the quality Cyprus flag, enhancing the Cypriot Registry with the most advanced green ships of the global market. All these efforts contribute to the Safe Bulkers’ clear-cut plan to minimize any emission adversities and set goals for 2025, in order for its fleet vessels to be environmentally compliant and adhere to high environmental standards. Preparing for the decades to come, the Company is closely monitoring the transformation regulatory framework around the decarbonization pathways of the shipping industry, constantly reviewing its environmental agenda and looking to find solutions that are right for its fleet and always align with the IMO’s targets and future requirements. In an ever-changing world, there can be no doubt that Safe Bulkers has strong foundations that combine a great team, efficient fleet, world-class partnerships, a clear vision and a solid corporate strategy, on which the Company can build further and evolve, ready not only to address the future challenges but to capitalize on growth opportunities that may arise.
“Nothing is as important as passion and we are passionate about shipping and about growing our footprint in this exciting industry. That is why more and more shipping organizations are choosing to work with KPMG and we are becoming the clear choice in the provision of professional services to the sector.”
Ioannis BravosShipping, ports and logistics entities have been operating in an increasingly challenging economic environment, characterized by volatility, increasing regulation, environmental concerns, piracy and geopolitical risks, among others. All these factors have contributed to a challenging business environment that puts even seasoned executives to the test.
A competent business advisor is the one that identifies, has knowledge on and focuses on the intricacies and complications that the shipping and shipping related industries face.
Our dedicated people have the knowledge, understanding and experience of maritime issues to provide a wide range of services to help our clients reach their objective.
KPMG enjoys a reputable and rapidly expanding presence in the maritime industry and is deeply committed to one of Greece’s most important sectors.
• The role of education and training for the future in shipping is very important. Things are chang-
ing dramatically almost every day. How must the training be transformed in order to make people ready for their future career in the industry?
As shipping moves towards digitalization, there is a great need to be able to onboard seafarers whose skills meet the advanced technical requirements of modern vessels. It seems that there is a need for increased simulation training with even more sophisticated simulators that could be tailored to the specific equipment models used by each company.
• KPMG enjoys a reputable and rapidly expanding presence in the maritime industry and is deeply committed to one of Greece’s most important sectors. What are your future plans in order to protect and increase KPMG’s maritime portfolio?
We want to continue support the industry and expand the range of services we offer to our existing and future clients to help them reach their objectives and overcome the challenges they face. We put quality, as well as client’s needs. at the center of our focus and we will continue investing to deepen our expertise in the sector.
We unite for positive change. Collaborating with purpose, we drive innovation, solutions, and a better future. Join us in this journey of impactful outcomes.
In an era where digital transformation reshapes sector after sector, the maritime industry stands on the cusp of its own digital revolution. As businesses across all domains remain alert and watchful about the potential disruptors that could overturn established norms and power balances, the threat—or opportunity—of a tech-led radical change in maritime operations is great.
Digital disruption changes the fundamental expectations and behaviours in a culture, market, industry, or process and is caused by, or expressed through, digital capabilities, channels, or assets. In the maritime sector, this disruption can be seen in several key areas: automation, data analytics, supply chain optimization, and environmental monitoring, to name just a few.
These technologies offer profound advantages. For example, automation in shipping logistics not only enhances efficiency but also improves safety, reducing human error and optimizing route management, which can result in significant financial benefits. Data analytics allow for real-time decision-making, forecasting, and better management of resources, which are crucial in a field as dynamic as maritime operations. In an era of heightened environmental awareness and technological progression, the maritime industry faces significant challenges. Two of the most pressing issues are compliance with the upcoming European Union Emissions Trading System (EU ETS) regulations and the continuous optimization of vessel performance. This is where Oriani Hellas comes in, being a beacon of digital innovation and expertise in the maritime sector. Oriani Hellas selects and represents some of the most innovative and “value adding” global digital providers to unlock the full potential of shipping enterprises. Oriani Hellas acts as a trusted advisor regarding maritime digital transformation for shipping companies located in Greece and EMEA. It represents solutions that not only address these challenges but also set new standards in operational efficiency and sustainability.
EU ETS “arrived” in the shipping industry in January 2024, and mandates that large ships trading in European waters must monitor, report, and verify their carbon emissions. The aim is to reduce greenhouse gas emissions by making polluters responsible for their emissions through a cap-and-trade system. Adapting to the EU ETS involves setting up systems to accurately monitor, report, and verify emissions data for vessels. This is technically complex and costly, especially for companies that do not have existing frameworks suited to the standards required. Companies need to invest in cleaner technologies, retrofit older vessels, or modify operational practices. As companies adapt at different rates, there’s a risk that those slower to integrate changes could face competitive disadvantages, potentially losing market share to more agile or innovative competitors. Finally, non-compliance could result in hefty fines and a tarnished reputation, urging shipping companies to seek effective strategies to manage their carbon liabilities.
Oriani’s
To assist shipping companies in understanding the complexities of the EU ETS, Oriani represents OceanScore, a comprehensive management platform designed to streamline the tracking and allocation of EU allowances (EUAs). This platform enables companies to efficiently manage EUAs by assigning them to specific charterers, voyages, or
vessels, thus ensuring full compliance. Moreover, OceanScore includes a built-in trading platform, allowing companies to actively manage their carbon credits by buying or selling EUAs as needed, turning regulatory compliance into an opportunity for cost management and strategic trading. Depending on the level of understanding within the company, OceanScore can also offer an advisory service. This will help guide companies on the actions they need to take to ensure compliance, the best internal process for their types of operations and state of their data, and how to setup the necessary accounts.
The optimization of vessel performance is crucial for reducing operational costs, enhancing safety, and minimizing environmental impact. This includes precise fuel management, efficient weather routing, and overall vessel operational efficiency, which are essential for the high competitiveness in today’s market. The drive towards optimization is not just about reducing costs or complying with regulations—it’s also about enhancing competitive advantage in a tight market. Shipping companies that can effectively manage these aspects of vessel performance are better positioned to respond to market demands and regulatory changes quickly and profitably. Therefore, the discussion about optimizing vessel performance is both a technical challenge and a strategic imperative, requiring a balanced approach to innovation, investment, and change management.
Ascenz Marorka, a combination of specialist performance companies now operating together within one platform, is at the forefront of Oriani’s technical solutions for vessel performance analysis and optimization. Ascenz Marorka provides an all-encompassing package of hardware, including sensors and data acquisition units, coupled with advanced software that delivers deep insights into vessel performance and fuel consumption. The software can operate with high-frequency data or with just noon-reports if the sensors aren’t available, covering all levels of digitally enabled ships. This technology supports the operations teams as well by including advanced weather routing and optimization, allowing ships to operate more efficiently and cost-effectively while always focussing on safety.
At Oriani Hellas, we view these challenges not as threats, but as opportunities. As a trusted partner in maritime digital transformation, Oriani Hellas is positioned to lead this shift. Our strategy revolves around integrating new technologies with industry knowledge to deliver solutions that not only meet but exceed the needs of our partners. Collaborations between traditional maritime businesses and tech giants or start-ups can lead to a symbiotic growth environment where innovation thrives, and financial benefits are obtained by all. By partnering with these entities, we facilitate the adoption of advanced technologies and foster an ecosystem of continuous innovation. Oriani Hellas assists shipping companies in Greece and EMEA to unlock their full potential by leveraging the power of digital platforms, for the benefit of all departments. Oriani Hellas represents a number of innovative global digital providers, including: Ascenz Marorka, OceanScore, Maritime-Trainer, Sedna, Bearing AI, ShipNet, Procureship, Captain’s Eye, 3D Cosmos, MedAssist.online, Purple TRAC, The Ship AS, Health4Crew & Guide2Inspections.
In the maritime industry, Oriani Hellas emerges as a pivotal player, bridging the gap between traditional shipping practices and cutting-edge digital solutions, particularly in navigating the complexities of EU ETS compliance and optimizing vessel performance for sustainability and competitiveness.
Philip Uhrskov Nielsen, Co- Founder ORIANIThey say that a port on its own cannot “win the world”. However, Piraeus seems to have done it, “silently” with the stubbornness of its productive ranks. It has earned an important place in the interest of investors who have evaluated its geopolitical potential, but also appreciated the hidden surplus values it has. If we attempt a brief review, we will find that major shipping centres in the world ranking have given way to Piraeus, which, however, falls behind in “Maritime Finance & Law”. I keep on saying that we need to look at the qualitative - and not only - characteristics so that port, city-productive classes and shipping interact.
We need to see the opportunities rising and take advantage of them. The achieved revitalization of the shipbuilding sector is one of these opportunities, as well as the fact that India, following China, “saw” the opportunity to have its products exported faster to the European Union.
The celebration of Poseidonia is an “opportunity” to be the beginning of a new joint effort to consolidate Piraeus in the first place of the world ranking in the category of Shipping, Ports & Logistics, Maritime Finance & Law, as a center of ship ownership, but also as a shipbuilding center which promotes innovation across the entire scope of the shipping business. And this opportunity should not be lost as the optimistic, creative and outgoing spirit of our country emerges at Posidonia. At the same time, the large port shows as a modern business, tourist, shipping and commercial center of international recognition and range.
P.C.C.I. has always been present in every effort to highlight the role of shipping and the importance of business initiatives in international trade and the shipbuilding industry, with a focus on Piraeus. It here where the heart of the strongest shipping beats, the shipping of the Greeks, the most advanced gateway to the east of the EU.
for its import and export trade.
Business activities related to transport, energy, logistics, supply chain, finance, value added services, manufacturing, shipbuilding, assembly, legal, insurance and reinsurance services for shipping have a business horizon in Piraeus. We must take advantage of all those business and operational possibilities that are under the “wrap” of the “blue economy”. I believe that, in the field of blue economy with a focus on innovation, there is a wide scope for the development of synergies, given that Piraeus is a developed and highly specialized productive “cluster” of the maritime economy, with global connections, among the most important shipping powers in the world. We should not forget that maritime innovation is capital and knowledge intensive, while the synergies that can be developed across most maritime activities and sectors will create valuable new jobs.
The development of innovation-focused strategies has proven to act as “magnet” for investment, especially now that global shipping is looking for technological and other solutions that will lead it faster and safely to the “green transition”. At this point, we should mention the importance and role of “Maritime Hellas”, the Greek shipping cluster, which, under the global brand name “Greek Shipping”, supports extroversion, innovation, but also the development of all those fields in which synergies can be developed by promoting the indisputable quality characteristics of the products and services that Piraeus businesses produce and offer.
Piraeus, benefiting from its geopolitical position and reputation as an international shipping center, provides priceless value for a wide range of business activities. And it is up to all of us to develop them together for the benefit, not only of the local, but mainly of the national economy.
“Identifying trends and monitoring maritime safety related incidents should be an integral part of our industry experts in order to ensure safety at sea,” stated Mr. Iasonas Lalizas, Marketing & Communications Director of LALIZAS, lifesaving equipment manufacturer.
Indeed recently, there has been a noticeable increase in the occurrence of fires on ships transporting electric vehicles equipped with lithium batteries (EVs). The occurrence of lithium batteries catching fire unexpectedly during transport has highlighted the urgent necessity to prevent and minimise such incidents.
Therefore, authorities are increasing awareness about onboard fires and implementing new revised standards and regulations to actively prevent them.
The revised EN 469:2020 standard, adapted from the MED Directive, imposes significant changes to the design and performance requirements for firefighting suits.
This new standard becomes effective on August 25 this year, and from that point forward, all firefighting suits onboard EU-flagged vessels must adhere to the updated standard.
For over forty years, LALIZAS has been designing and producing a diverse range of life-saving equipment for the commercial shipping sector.
Moreover, LALIZAS has the necessary resources as well as the professional expertise to properly advise ship owners and management companies to ensure both the safety of the ship and its compliance with international regulations.
This is achieved through the Fire, Safety and Rescue (FSR) services that LALIZAS offers worldwide in all major ports.
Furthermore, as a part of LALIZAS’ continuous efforts to improve safety at sea, the company is consistently working on enhancing and broadening their range of Life Saving Appliances and Fire Fighting Equipment.
Additionally, the manufacturer’s expansive line of FFE products (fire extinguishers, fireman suits, etc.) are carefully engineered to meet and exceed all required regulations and standards pertaining to
maritime and national safety protocols.
Given the present circumstances, when there are increasing numbers of fires caused by EVs, the marine sector is in need of additional safety measures.
LALIZAS, always trying to be one step ahead of times, offers an extensive range of firefighting gear, which includes the latest Fireman Suit called Antipiros.
The Antipiros Fireman Suit meets the new updated EN 469:2020 standard, achieving the rigorous standards of Level 2 performance requirements, while at the same time providing excellent fire protection and durability, as well as freedom of movement!
The Antipiros Fireman Suit has been certified as Level 2, in compliance with the new updated EN469:2020 standard, offering the maximum levels of protection against heat (contact heat - heat transfer), water penetration and water vapour required for roll-on roll-off (RORO) type vessels, the type that most often carries EVs, which run on lithium batteries, a suspected major factor in the recent increase of fires on ships.
Ever since the company’s establishment in 1982, LALIZAS has consistently placed maritime safety at the forefront of its operations. As a leading provider of all-encompassing safety solutions, the company excels in adjusting to changing risk environments and continuously demonstrates its commitment to the motto that Safety is not just a product, it is an ongoing process
LALIZAS will be attending once again the upcoming Posidonia Exhibition, and present their newest products when it comes to safety at sea, including the new Antipiros Fireman Suit, at the LALIZAS Pavilion (no.3.414), drawing a strong presence and significant influence within the international maritime community.
Moreover, the company is actively contributing in this year’s Posidonia Exhibition, organising a Conference with industry experts offering their knowledge and expertise on issues regarding safety at sea. “We are happy to attend this year’s Posidonia Exhibition, to share our knowledge with the international maritime community, promote awareness on safety issues at sea and offer effective solutions,” concluded Mr. Iasonas Lalizas.
“POSIDONIA 2024 coincides with our 60th year anniversary! We could not be more proud to have been associated with the Greek shipping community for such a long time and to have witnessed first-hand the Greek shipping miracle! It all started in 1963, when our Founder, Mr Damianos Constantinou, came from London to Piraeus and opened the first International Accountancy Practice of the country. ‘I was privileged to have been given the opportunity to contribute to the Greek shipping miracle, as well as to have been involved in laying the foundations of Posidonia Exhibitions’ said Mr Damianos Constantinou, Founder of Moore Greece. Over the course of time, Moore services evolved significantly in order to respond to the needs of our clients. Traditional bookkeeping and payroll services gave way to accounting and financial reporting in accordance with international standards. Auditing was also added to our service offering, to further enhance the reliability of financial information to its users. Traditional taxation services also evolved to local and international tax planning at corporate and personal level. Advisory services became more elaborate especially in the areas of business valuation, internal review and business process optimization.
Technology was very soon introduced to our services, as early as the 1970’s, when Moore introduced the first shipping accounting software, the predecessor of Maritime Accounting Software (MAS), our current collaboration with EPICOR ERP for shipping accounting and reporting. Financial and management reporting has always been a focus area for us and we used technology to design financial reporting tools that eliminate the possibility of human error in data accumulation. This is why, we can produce a vast amount of management accounts and financial reports, quickly, consistently, and error-free.
We are also very proud to have been training and developing the skills of generations of shipping accountants, controllers and finance managers. Many of the industry’s top finance executives started their careers as junior auditors and accountants with us and, after years of work and having gained significant experience servicing our clients, they moved on to work in the industry, as our clients. We have recently also partnered up with SQ-Learn to create masterclasses on financial reporting on various challenging areas.
We believe that technology offers a unique opportunity to gain knowledge from tutors who are top professionals in their field, from the comfort of someone’s home and at their own pace. Our audits and the sharing of the knowledge and experiences that we have accumulated over the years form seeing millions of transactions in hundreds of companies, has contributed significantly to the overall enhancement of the quality and reliability of financial information in the Greek shipping industry. As banks became more regulated, audited financial statements became a prerequisite for every new loan and refinancing, a safeguard that banks trusted in order to continue to extend their credit to the shipping sector.
Over the past years regulation has intensified even further in all industries and shipping companies need to adopt to a challenging environment of continuous change, to which, however, they are no strangers. The most tectonic of all changes in the recent history however is a shift in people’s mindset and a pressure from societies for companies to adopt greener, more humane, and more ethical practices. Consumers and investors have grown to care about business conduct almost as much as they care for financial performance. The terms sustainability and ESG came into our lives and – as the industry was formerly in need of reliable financial information – it is now in need for reliable sustainability related information to satisfy the pressure from financiers and charterers. Moore is the ESG in shipping pioneer, proactively shaping the private shipping norms of ESG reporting and helping companies present reliable ESG reports that are tailored to the needs of private shipping. We are thrilled to have worked alongside the Hellenic Chamber of Shipping in developing ESG Guidelines for its members as well as alongside the clients who have already chosen to prepare their ESG report, to be ahead of their competitors.
Posidonia 2024 finds us excited about the prospects that lay ahead of us and our clients: ‘Over the passing of decades we have witnessed what makes a successful shipping company: And that is the ability of the owner to anticipate the changes and position themselves courageously to ride their waves’ said Mr Costas Constantinou, Managing partner of Moore Greece and Global Maritime Leader of the Moore Network”.
An increasingly complex, digitalised maritime industry is challenging designers, shipyards and vendors to deliver the kind of vessels that can safely navigate the transition to a low carbon, high efficiency operating environment. With new technologies enabling innovative approaches to design and performance across all types of vessels, the industry wants to know that class rules are keeping pace with developments.
The emergence of a goal-based approach from the International Maritime Organization (IMO) signaled a sea-change in the way regulators could develop criteria that could be applied to any technical solution, rather than the traditional prescriptive approach. The rate of technology development is challenging to an industry which is often incorrectly labelled as slow and resistant to change. Owners and operators are looking to move quickly to cut emissions and maintain a competitive edge. This necessitates a requirement structure that applies a risk-based approach to class rules, which helps by quickly and efficiently identifying unintended safety consequences of employing new technology onboard their vessels, thereby allowing owners and operators to make fleet-wide decisions with speed and confidence.
In response to growing demands for a framework that can enable innovation, ABS has updated the Marine Vessel Rules and introduced new Rules for Alternative Arrangements, Novel Concepts and New Technologies to provide a process for applying functional requirements, developed in accordance with the guidance in IMO Circular 1394, and risk-based methods to designs that do not have established Rules.
This approach is aligned with the IMO process for alternative arrangements. ABS has received positive feedback from flag Administrations who also face the challenge of evaluating new ideas against regulations that were often written with a specific technical solution in mind.
The new Rules and approach can address any innovative idea that does not have defined requirements. Some examples may be the incorporation of new materials for a lighter vessel, equipment to handle new fuels, or a new vessel type that operates in a manner not seen before.
The updated ABS Rules enable shipowners to integrate new tech-
Updated Marine Vessel Rules include new functional requirements and a risk-based methodology to accommodate the latest technology, writes Ezekiel Davis, Vice President, Regional Business Development, Europe, ABS
nology knowing that they have been through a risk-based process as part of a comprehensive ABS Class review. At the C-suite level, the enhanced rules create an environment to explore the impact of incorporating advanced digitalization capabilities and new decarbonization technology into a fleet.
For shipyards and technical personnel, the Rules provide a series of pre-defined objectives and functional criteria. ABS working with other stakeholders can determine the acceptability of the new technology and identify risks to existing systems. With approval times reduced by as much as half for the adoption of new technology, project managers can make fleet-wide decisions with speed and confidence.
The Rule enhancements are a result of a multi-year collaboration with industry, shipyards, shipowners, equipment manufacturers, designers and regulators. Over 600 ABS clients took time to provide feedback through ABS Technical Committees, questionnaires, and other avenues.
In addition to the request for a framework adaptable to new technology, two other important requests were to provide easier access and to improve the clarity of the existing Rules.
To meet those requests, ABS has also released Rule Manager 2.0, an intuitive application that allows users to quickly search and access content across the suite of ABS Rules and Guides. This follows the 2023 launch of the industry’s only Custom Rule Book application, a powerful tool which allows users to instantly create tailored rules sets for their specific vessel or project. Rule Manager 2.0 will also be available to MyFreedom™ Portal subscribers which will allow more personalization and content.
Commentary and updated text simplify class requirements, reducing interruptions during survey and plan review by clearly describing what is required for compliance. New images and figures have been added to explain complex technical content more easily.
By enhancing ABS Rules with risk-based requirements and strengthening the technical content to account for compatibility with objectives, functional requirements and prescriptive criteria, ABS has created a robust infrastructure to enable the innovation and technology to support our clients and the wider maritime industry’s evolving decarbonization and digital ambitions.
“In an era defined by rapid technological advancements and growing environmental consciousness, the shipping industry finds itself at a critical juncture. With the rise of Artificial Intelligence (AI), the implementation of Environmental, Social, and Governance (ESG) policies, and the advent of sustainable innovations, the maritime sector is undergoing profound transformations. As we navigate these changes, events like the Posidonia exhibition serve as crucial platforms for showcasing progress, fostering collaboration, and shaping the future of shipping.
Our commitment to sustainability is steadfast, as evidenced by our recent investments in green energy solutions. Foremost among these is our implementation of Photovoltaic systems, a move that not only powers our shipyard operations but also extends to the vessels berthed or docked at our premises. The vast expanse of land under our ownership enables us to harness solar energy effectively, significantly reducing our carbon footprint and aligning with stringent legislative measures. By providing clean energy alternatives, we eliminate the need for vessels to rely on their own generators, thereby further mitigating environmental impact. At our Shipyard, we recognize that sustainable practices require more than just infrastructure; they demand a skilled and adaptable workforce. That’s why we have continued to invest in training programs to equip our personnel with the expertise needed to install and maintain green energy systems such as scrubbers and advanced propulsion technologies on vessels. In recent years, we have successfully completed numerous installations of scrubbers, bolstering our reputation as pioneers in sustainable maritime solutions. Our commitment to innovation extends beyond the present, as we continually explore new technologies and methodologies to enhance the efficiency and sustainability of our operations.
As advocates for environmental responsibility, we hold ourselves to the highest standards of sustainability. We are proud to announce that we are currently following the procedures outlined by ISO 14001 and are on track to receive certification. This demonstrates
our commitment to minimizing our environmental impact and also underscores our dedication to providing ship owners and operators with reliable, sustainable solutions.
In response to growing demand and evolving industry needs, we are expanding our repair capacities to accommodate more vessels, including those of greater capacity. Through strategic investments in infrastructure and technology, we aim to streamline the repair process, minimize downtime, and maximize efficiency. Our goal is to provide ship owners and operators with unparalleled service while maintaining our commitment to sustainability.
In the new building sector, we are proud to announce our recent endeavors in the construction of specialized vessels measuring up to 100 meters in length. These vessels represent the pinnacle of innovation, incorporating cutting-edge technologies and design principles to enhance performance, efficiency, and environmental sustainability. By pushing the boundaries of traditional shipbuilding, we aim to set new standards for the industry while reaffirming our commitment to a greener, more sustainable future.
Posidonia serves as a cornerstone event for the maritime community, offering a unique opportunity to showcase advancements, exchange insights, and forge partnerships. At this year’s exhibition, Chalkis Shipyards will unveil its future plans, highlighting its commitment to sustainability, innovation, and customer-centric solutions. Visitors can expect to learn about the shipyard’s ambitious initiatives, green technologies, and strategic vision for navigating the evolving maritime landscape. As stakeholders converge at Posidonia, they play a pivotal role in shaping the industry’s trajectory towards a more sustainable and prosperous future.
In conclusion, as the shipping industry embraces AI, ESG policies, and sustainable innovations, events like Posidonia serve as catalysts for collaboration and progress. By harnessing the power of technology, adhering to sustainable practices, and fostering partnerships, stakeholders can navigate the complexities of an ever-changing landscape and pave the way for a more resilient and environmentally responsible maritime industry”.
As a technology developer, ERMA FIRST is fully committed to helping shipowners meet the targets for decarbonisation they face for 2030, 2040 and 2050 the zero-carbon future.
Our view is that the targets set for carbon reduction by the International Maritime Organization for 2030 (30%) and 2040 (70%) are eminently achievable if all stakeholders act sooner rather than later We also passionately believe that – in advance of alternative fuels – uptake of new technologies will be the key route through which shipping advances along its decarbonisation ‘road map’.
Building on its vast experience as a ballast water treatment system manufacturer, ERMA FIRST has increasingly turned its attentions to the challenges its customer base faces to cut emissions from regulations such as the CII, EEXI and EU ETS.
One strategy has involved evaluating and improving upon solutions which are already accepted for the contribution they make to improving vessel efficiency. For example, an immediate step owners can take to cut fuel use and emissions by 2% to 3% is to fit a boss cap fin (BCF). Installed at the hub of a ship’s propeller a BCF effectively utilizes water swirl, while its fins catch and absorb the rotating water force. Together they reduce energy loss by weakening the propeller hub vortex, boosting thrust and improving propulsion efficiency.
But there are hundreds of different propeller and ship types and sizes, making it prohibitively expensive to design bespoke BCFs for individual vessels and limiting the effectiveness of off-the-shelf models.
The innovative modular design behind the ERMA FIRST FLEXCAP overcomes this issue. At least 22 different models are possible from combining various fins, caps, and flanges. Adjusting the angle of the fins or the selection of the cap based on a specific vessel’s needs effectively gives the owner a bespoke propeller cap at the cost of an off-the-shelf model. The modular design ensures a low cost that means a return on investment is achievable within less than12 months.
ERMA FIRST’s efforts to help owners have also focused on technologies which cut carbon emissions in port and at sea. For example, ERMA FIRST BLUE CONNECT is an alternative
The clock is relentlessly ticking towards net zero for shipping, but the immediate future demands decarbonisation solutions that work with the carbon-based fuels of today.
By ERMA FIRST GROUP Co-Founder & Managing Director, Konstantinos Stampedakis.maritime power system which enables vessels to connect to a port’s electrical grid to run onboard services, systems, and equipment. Meeting all latest international standards for cabling and connections, the solution means a ship can switch off its diesel generators, in order to reduce both emissions and noise while in port.
BLUE CONNECT has received approval in principle (AiP) from leading classification society Bureau Veritas and is also recognized as an Energy Saving Device by DNV. The first installation of BLUE CONNECT will be made this Spring, while ERMA FIRST has received orders for six to eight units to be delivered by the end of the year.
At sea, the focus has been on onboard carbon capture and storage (CCS) as a method of cutting ship emissions, with two versions of the same ERMA FIRST system under development, called the ERMA FIRST CARBON FIT. Under normal operating conditions CCS systems are expected to cut emissions by 15% to 30%.
An Amine Absorption version is aimed at deepsea ships with the system capturing CO2 through well-established technology which absorbs CO2 from the flue gas and stores it in a liquid state. This reduces the volume for long distance voyages. In this case, the technology has secured AiP from Lloyd’s Register and DNV.
A simpler Calcium Hydroxide-based version is aimed at shortsea vessels. In this case, the organic alkali absorbs CO2 from flue gas in a specially designed reactor and dehydrated calcium carbonate slurry is stored onboard until its disposal at authorised facilities.
ERMA FIRST is aiming to install pilot units in August 2024, with commercial sales following from the second half of 2025, with clients indicating intent to place orders.
If supporting more sustainable shipping will demand continuing investment, ERMA FIRST’s commitment is clear, also extending to the ballast water treatment systems that first brought its name to a global maritime audience. In fact, the potential for stricter ballast water regulations ahead require renewed commitment at a time when many competitors are abandoning the market.
Whatever the requirement, ERMA FIRST’s growing portfolio of sustainable solutions has been built through a blend of in-house experience and new expertise that is committed to help owners improve vessel performance and extend the life expectancy of their ships in the decarbonised future.
It is a reality that today’s energy costs and demanding emissions reduction regulations as EEXI & CII indexes, force many ship owners to consider waste heat recovery systems as an option, in order to allow their vessels sail in a more sustainable and competitive way . Plenty of Green technologies have flourished in the last years, from EGCS to Wind sails, from hull modification & coating to ORC. Marine Green technologies manufacturers are always forced to step up to the situation and be able to support ship owner with robust and reliable systems and this fairly new eco-system of “Green” manufacturers is drastically changing the maritime sector into a modern, efficient, innovative and eco-friendly industry.
Psyctotherm’s orientation to innovation keeps producing products and systems that improve vessel efficiency and allow greener operation in modern maritime sector. From idea to concept, from concept to research, from research to trials, from trials to test installation this is the way to end up with marine type approved fully commercialized products with running hours in actual installation and candidates for New building shipyards’ makers’ lists. Through our research branch we are successfully delivering Green systems, focusing on utilization of waste heat produced on board. The technologies of ours that have biggest impact on fuel savings are 1) Organic Rankine Cycle (ORC) 2) High Temperature Heat Pumps (HTHP). Both of technologies’ principle of operation are related to typical thermo-dynamic cycles and change of phases and use engineering principles of refrigeration, which is our main field of occupation. We aim with both technologies to unlock waste heat recovery applications that were not possible in the past and make our systems core items for the ships of the decades to come.
Brief introduction to ORC & HTHP
Organic Rankine Cycle (ORC) systems’ principle of operation is similar to the typical water-steam Rankine Cycle, but instead of
water it is uses refrigerant so can operate at lower temperatures. Refrigerant is evaporated using waste heat source and is routed to expander which rotates and produces electricity. Then it goes back to condenser to return to liquid phase and is pumped to evaporator again to close the cycle. System is type approved by IACS class, has received ESD letter and we have installed it in marine application with very positive results, as system keeps running truly automated and unmanned. ORCs can recover waste heat from M/E’s JW, from excess steam or even from exh. gasses.
High Temperature Heat Pumps (HTHP) are truly a niche technology with limited number manufacturers world wide. Principle of operation is similar to typical Heat Pumps, what changes is the operating temperature range, which can reach temperatures up to 120 °C, meaning that heat pumps now can be used at applications that were not ever covered before.
This way heating on board can become very efficient, steam consumption minimized and flexibility maxed.
Psyctotherm Research branch
Our research team is working in the field of heat recovery, upgrade, and conversion to electricity for more than 15 years. Their main technologies are advanced Organic Rankine Cycle (ORC) and High Temperature Heat Pump (HTHP), for exploiting (waste) heat sources. Such as solutions are perfectly suited for ships integration, which reject huge amounts of heat, mostly at low-medium temperature ranges. These amounts of heat can either be converted to electricity or upgraded and reused in the ship processes. On top of that, all recent regulations bring pressure to the ship owners to enhance energy efficiency of their vessels, reduce CO2 emissions and improve EEDI/EEXI. Psyctotherm research branch fulfills all the above targets with its ORC and HTHP solutions that is the result of long-term intensive research and development.
Psyctotherm has long experience on marine refrigeration services, repairs & compressors replacements, having delivered special customized projects with high standards. With stock options on spare parts and inhouse manufacturing, we can deliver in tight schedules a complete service.
Typical HVAC & Refrigeration services:
❖ Refrigerant conversion to compliant Green ones (e.g. to R407f).
❖ Repairs on Central Air Condition system & Reefer Plant.
❖ Coils replacement.
❖ Repair on Chillers.
❖ Compressors service.
❖ Performance upgrades.
❖ Start up / Commissioning services.
Contact us: sales@psyctotherm.gr
Advanced HVAC & Refrigeration services:
❖ HVAC/R automation conversion
❖ New Condensing Units.
❖ Compressor replacement with different brand.
Psyctotherm is an HVAC / Refrigeration manufacturer, established in 1969 and located in Piraeus, Greece in a total 2.000 m² surface area of facilities . We have an in house R&D dept. involving 6 people, which works on optimizing & developing our products and takes part in European Research programs of 10 mio, from which we have been awarded 3 seals of excellence award.
Multiple levers are available to meet the International Maritime Organization’s goal and keep shipping within its “GHG budget” to 2050. Ship performance to reduce fuel consumption will save emissions and costs now and will anticipate the need to use new green fuels (when they become available) as efficiently as possible. See BV’s Decarbonization Trajectories report.
Shipping’s carbon footprint is significant across global supply chains. As receivers, shippers and traders step up their sustainability reporting, including scope 3 emissions, pressure will only increase on shipping. Requirements of banks and capital markets will be an additional incentive. This is an opportunity for those able to move first and opportunities exist.
Increasingly shipping will have to work with and influence other sectors and decision makers to create shared value to support a better, cleaner, more efficient shipping industry. New green fuels are a critical area for such a collaborative approach, but it will be some time before they are a significant lever.
The development of new approaches to global supply chains for all industries will be vital to for the scale of demand required and resilience in the face of trading practice, energy needs and new geopolitical realities. This will eventually rely heavily on the creation of new value chains, new trades and routes for seaborne energy transportation, carried as hydrogen or ammonia, in a new fleet of ships potentially transforming shipping’s role and image in global supply chains.
Shipping needs action for more efficient ships and longer-term collaborative action for new value and supply chains for green energy. An immediate opportunity is to focus on the existing fleet. Renewing the global fleet with vessels capable of burning new fuels will be a slow process and as well as the need for the fuels of the future, fleet renewal and rates of retrofit will be limited by shipyard availability and capacity. The world’s main shipyards are already fully booked until 2027 or even later. So, if we can’t “newbuild” our way out of the decarbonization challenge yet, we must manage the tens of thousands of vessels that are currently at sea and new ships delivering today will operate into the 2040s and beyond. This calls for a greater focus on solutions that can help keep shipping within its “GHG budget” to 2050, which means improving the energy efficiency of the current fleet.
If we are to achieve the IMOs’ decarbonization goal and regional requirements such as those of the EU, we will have to reduce energy consumption by:
- voyage optimization and weather routing
- energy-saving devices
Bureau Veritas, as a global testing, inspection and certification organization is addressing both
- new energy sources such as wind propulsion and shore power
- operational measures, including reducing speed and waiting times
- use of currently available fuels – methane and biofuels
BV is taking action to help make the energy transition a success by developing new partnerships and a fresh approach that covers entire supply chains. And this is where BV’s Future Shipping Team (FST) comes in. The Future Shipping Team was created to enable the sharing of research and expertise within the BV Group, both upstream and downstream of the maritime sector, including carbon capture, CO2 value chain, biofuels, hydrogen and methanol, for example.
With 240 people from across the BV Group, the FST is leading bringing together expertise from within and outside the maritime sector around 12 workstreams, ranging from new fuels and technologies to life-cycle assessment of renewable energy sources, traceability and evaluation of ESG progress. This has created an enhanced dialogue with new stakeholders such as financial institutions, charterers and energy suppliers.
As a testing, inspection and certification body, BV’s role is also to provide validation that will help build trust between stakeholders along supply chains. For example, playing a key role in fuel certification, using its independent expertise to validate the sustainability credentials of feedstocks and ensure that the fuel, be it biofuel or e-fuel, is safe to use on board and is what it claims to be. The multi-fuel era will bring a greater focus on fuel quality and traceability going forward, and this is where our VeriFuel colleagues are playing a critical role in the FST. The same validation and traceability capabilities are also supporting the development of guidelines and a framework for a “book and claim” system. This will be key to breaking the “chicken and egg” dilemma and sending the right market signals to support the development of new production facilities. With sustainability reporting gaining prominence, BV is also supporting fuel producers in calculating greenhouse gas emissions, and once on board, works with shipowners in measuring the emissions impact of burning new fuels.
BV is also working with banks and investment funds to support their due diligence processes in assessing whether an asset is truly green or not.
These are just some of the areas where BV is focused - harnessing the power of the broader Bureau Veritas organization with 83,000 people, dedicated to being a preferred partner enabling customers to navigate technological and societal change to transform and perform sustainably.
At Bureau Veritas, each and every one of us is by your side to help you navigate your decarbonization journey.
Supporting you with practical advice, tools and technology for you to make the right decisions for your business.
Learn more at marine-offshore. bureauveritas.com
Shaping a better maritime world.
Bureau Veritas was founded in 1828 to address marine risks. Our priority is safety - for our clients and society.
Today we are a multi-sector Testing, Inspection and Certification (TIC) organization with more than 75,000 people world-wide and about 1,400 laboratory and testing facilities.
Bureau Veritas Hellas M.A.E. 23 Etolikou street, 18545 Piraeus Greece
Tel: (+30) 210 406 3000 e-mail: grc_lpr@bureauveritas.com
Proven ship efficiency gains available from shaft generators including permanent magnet technology can now be secured for a payback of under four years, according to ABB.
Shaft generator systems have been installed on small and medium-sized ships since the beginning of the direct current (DC) era, but the recent steps to make the inclusion of permanent magnet technology cost effective has made the option compelling for a far wider audience.
Simply defined as rotational electrical machines that take power from the main propulsion engine to produce electricity, today’s shaft generators are more efficient, lighter and more compact than ever before, with even the largest ships now candidates for installation.
ABB Marine & Ports has secured a leading position across the merchant shipping markets as a supplier of new generation shaft generators including permanent magnet technology. The combination of permanent magnets shaft generators and ABB’s ACS880 drive deliver a system which can achieve efficiency gains of up to 20 percent compared to a traditional diesel generator, the supplier says.
Based on current fuel prices, ABB calculates that drawing Power-Take-Off (PTO) from the main engine to generate electricity instead of powering up the auxiliaries will mean payback can be achieved within four years or less, depending on fuel type used.
“In today’s market, very few owners and operators are likely to disregard a proven technology which offers an efficiency gain of up to 20%,” said Michael Christensen, Global Segment Manager for Cargo, ABB Marine & Ports.
Also critical is the contribution the system makes to reducing ship emissions, added Christensen, in line with the general requirement for a sustainable shipping future and new IMO regulations on emissions (EEDI/EEXI, CII), including CO2. “Our permanent magnet shaft generators offer a flexible, market-ready means of achieving efficiency targets as they are defined in CO2 emissions per capacity mile within the IMO regulatory framework,” he said.
From both designer and user perspectives, however, it is also the inherent simplicity of the new generation of shaft generators which has been winning hearts and minds. The system offers connection via a DC-Link to ABB’s
ACS880 drive system provides intelligent control of energy sources like shaft generator, auxiliary engines, thrusters, batteries and fuel cells, with all of the vessel’s electrical power needs distributed using a single DC bus. Christensen’s assessment of owner enthusiasm for the solution is strongly supported by ABB’s recent references. Following accelerating orders for permanent magnet shaft generators from roll-on, roll-off, bulk carrier and container ship, ABB reached a milestone order from COSCO Shipping covering ten newbuild containerships and has since then become the solution provider for the world’s four leading container lines.
Deliveries also included a landmark deal to equip twelve 210,000dwt bulk carriers owned by Bermuda-based Himalaya Shipping. Built by New Times Shipbuilding in Jiangsu, China, these Capesize vessels also include low voltage drives and transformers from ABB.
Other high-profile orders include installation of systems onboard a pair of 130-meter length CO2 storage vessels operating as part of the Northern Lights carbon capture and storage project (CCS), due delivery by China’s Dalian Shipbuilding Industry Company in 2024.
Alongside the increased flexibility and functionality available to ACS880 drive systems, owners are attracted to the solution by the ease with which it can be installed and maintained, as well as its compact profile, added Christensen. “The PM machine is around 20 percent smaller - and 20 percent lighter - than the equivalent synchronous excitation machine.”
With the permanent magnets providing rotor magnetization, the set-up does away with the need for separate equipment, which reduces the number of components at the installation stage. The absence of the excitation machine also disposes of carbon brushes – which require frequent replacement.
Christensen also pointed out that the efficiency gains brought by the ABB shaft generator system could work their way to fewer genset running hours - reducing maintenance – or even as consideration of lower installed genset power.
In the dynamic landscape of maritime technology, cybersecurity emerges as a paramount concern, echoing the sentiments of the forthcoming Posidonia 2024 exhibition.
Cyber security constitutes a collective responsibility encompassing all ship design and operation stakeholders. In an era dominated by smart ships, cybercriminals persistently seek vulnerabilities in communication and tracking systems to penetrate networks. Consequently, safeguarding against malware, ransomware, and other cyber threats is paramount.
Recognizing the critical importance of cyber security, regulatory bodies such as the EU are explicitly incorporating shipping into their critical infrastructure frameworks. The forthcoming IACS Unified Requirements mandate robust cyber security measures during the vessel design verification process. This entails system suppliers integrating resilient cyber security features into their offerings, while shipyards and designers prioritize cyber security in system procurement and integration.
At Posidonia 2024, where industry leaders will convene to shape the future of shipping, cybersecurity must occupy a central position in discussions surrounding innovation and sustainability. As stakeholders gather to
By Anastasios Mastrangelopoulos, Senior Cybersecurity Consultant, Industrial & OT Cyber Security, DNV Maritimeexchange insights and foster collaborations, DNV emphasizes the pivotal role of cybersecurity in driving technological advancement while safeguarding critical assets and data. DNV also highlights the relationship between cybersecurity and eco-friendly maritime solutions. By safeguarding digital systems, cybersecurity enables the seamless integration of sustainable technologies, facilitating a transition towards greener and more efficient shipping practices.
DNV cyber security expertise is expanding rapidly
DNV’s commitment to cyber security is further evidenced by its recent acquisition (June 2023) of Nixu, a leading cyber security services provider. DNV is integrating Nixu with its own cyber security businesses to form one strong organization with more than 500 cyber security professionals dedicated to providing cyber protection solutions for demanding IT and industrial control system environments in the maritime, energy, telecommunications and financial services industries, among others.
As the industry converges soon in Athens to explore the latest advancements, DNV underscores the significance of fortifying vessels against emerging cyber threats, setting a precedent for resilient and secure maritime operations.
Central to our discourse is the concept of defence-in-depth, which advocates for a multi-layered approach to cybersecurity. By integrating technical, procedural, and organizational measures, ship designers can create a robust framework that mitigates cyber risks and ensures the integrity of onboard systems.
Furthermore, DNV underscores the importance of cultivating a cybersecurity culture
within maritime organizations. Through comprehensive training programs and awareness initiatives, companies can empower their workforce to proactively identify and respond to cyber threats, thereby enhancing the industry’s overall resilience.
DNV’s Cyber Secure class notation serves as a beacon for compliance with the IACS Unified Requirements. By scrutinizing onboard systems, vessel design networks, and operational procedures, it offers guidance and validation of cyber security measures. Notably, the Cyber Secure Essential class notation certifies adherence to IACS UR E27 and E26 standards, underscoring its pivotal role in ensuring cyber resilience. The Cyber Secure notation, grounded in internationally recognized standards such as the IEC 62443 series, offers a comprehensive approach to cyber security across the maritime data value chain. Leveraging existing industry practices enables cost-efficient adoption of cyber security measures, ensuring robust protection against evolving cyber threats.
In conclusion, as digitalization makes great strides in the shipping world, connectivity and system integration expose ships to growing cyber risks. This means that cyber security must be engineered into the design of every new vessel. Suppliers must deliver secure systems, and yards must combine these systems into a secure, painstakingly documented overall concept that provides a strong foundation for cyber-secure operation over the vessel’s lifetime. By prioritizing cyber resilience from inception, stakeholders can mitigate cyber risks, ensure regulatory compliance, and safeguard the integrity of maritime operations.
your language!
Posidonia brings the maritime world together. Gathering in Greece to speak the common language of shipping.
At DNV we want to make sure you always have global expertise and a trusted local partner at your side. We understand your needs and through our experts around the world, we help you solve your challenges.
Join us at Posidonia, stand 4.115 to meet Leonidas Karystios, Global Fleet Technology Director, Gas Carriers, and George Teriakidis, Area Manager and experts from across our global network. www.dnv.com/posidonia
Headway Technology Group (Qingdao) Co., Ltd. brought her largest lineup of products to Posidonia at booth 410 of Hall 2, showing the latest low-carbon solutions for shipping. Those products included Methanol Fuel Supply System, Exhaust Gas Cleaning System, Carbon Capture Utilization and Storage System, and Ballast Water Treatment System.
Headway is established in 2005 as a high-tech enterprise with the purpose of scientific and technological innovation, dedicated into providing low carbon solutions and technical service worldwide. Headway owns independent R&D center and production base in Qingdao, China. Headway’s product portfolio includes 3 segments: Carbon Neutralization, Water Treatment and Smart Shipping, which are all developed under the long adherent R&D ideology of “Be Innovative, Stay Excelsior”. OceanGuard®BWMS received USCG Type Approval in 2018, following the recognition of all major classes and flags, and stood out as a truly worldwide recognized BWMS. Headway announced her 1st order of EGCS and the launch of Alternative Fuel Supply System in 2019, and sailed the course of low carbon solution.
In 2023, Headway redefined her vision as “Innovation for Better Low Carbon Solution”and formed a new ecology of low carbon oriented products including alternative fuel supply system, EGCS, CCUS, methanol synthetic system, etc.
Among the portfolio, Headway would like to call the attention to OceanGuard® Exhaust Gas Cleaning System, which has concluded excellent resource of the whole industry chain to meet the requirement of customers. According to the director of Headway’s EGCS team, Headway is capable of providing both Open Loop and Closed Loop solution to customers. Furthermore, Headway has been providing Open Loop solutions with “Hybrid Ready” design, which ensures the delivered Open Loop system can be upgraded into a Hybrid system without dry-docking. During the coronavirus epidemic, Headway is still able to provide a dependable EGCS solution with the delivery time as fast as 4 months.
OceanGuard® Methanol Fuel Supply System(LFSS), which independently developed by Headway Technology Group, is adaptable for both ocean-going and inland waterway vessels. It integrates several key components, including low-pressure magnetic circulation pump, high-pressure magnetic circulation pump, buffer unit, duplex filter, heat exchanger, mass flow meter, and backflow adjustment valve. This skid-mounted module is designed for installation in hazardous zones. By effectively adjusting the backflow, the module promptly regulates the pressure and flow rate of methanol fuel, ensuring optimal performance and precise control in fuel supply operations. The system has completed the initial prototype tests in the laboratory and is currently on the joint-test verification on an independent
test platform. Furthermore, OceanGuard® LFSS has obtained two orders in 2023 and receive high recognition from customers and more orders are on the way.
Oceanguard® CCUS , which adopts Headway’s self-developed high-efficiency decarbonizer and high-speed centrifugal decarburization technology. It can not only avoid the inconvenience of large size and high energy consumption of traditional decarbonization scrubber, but also achieve a carbon dioxide removal efficiency of more than 80%, and the purity of carbon dioxide after liquefaction of more than 99.6%. It can save 25% of ship fuel costs (joint installation with Exhaust Gas Cleaning System). Furthermore, the captured CO2 can be directly used in the field of industry, through the carbon chain management and trading cloud platform of the Headway Energy Efficiency Management System, At present, the system has been already approved by DNV, RINA,CCS and other major classification societies.
Last but not least, OceanGuard® BWMS, as adopts patented Advanced Electro-catalysis Oxidation Process(AEOP) to treat ballast water which ensures mainstream single treatment of all type ballast water without hydrogen generation corrosion, nor extra layout of small pipelines. The rated treatment capacity of one single BWMS is 5200m³/h, and higher capacity can be achieved by multiple units in parallel. Headway is one of the major manufactures who hold the Independent Intellectual Property of filter. It is developed specially for ballast water treatment and has been proven by independent laboratories and shipowners as a reliable solution even in extreme conditions. Headway has been providing Turn-key solution and performed very well even during Covid-19 because of the complete industrial chain, timely delivery of filters and comprehensive services.
Looking ahead, Headway remains unwavering in its vision of “Innovation for Better Low-Carbon Solutions,” with an approach focusing on marine decarbonization and digitalization. Rooted in research and development, fueled by innovation, and grounded in exceptional service, Headway continues to make strides in enhancing its products, technology, and management practices. Headway, relied on the cooperation with 120 global partners, based on mutual trust and benefit, to embrace the future of green shipping and sustainable development, to pioneer in decarbonization strategy, Zero-Emission Shipping and marine environmental protection.
As the maritime industry charts its course through the unpredictable waters of global trade, Posidonia stands as a beacon of resilience and innovation. Once again, we proudly announce our attendance at this prestigious event, marking our continued commitment to shaping the future of shipping. At Posidonia 2024, we are excited to unveil our further expansion and advancements that will redefine the landscape of maritime services.
As part of our overarching growth and network enhancement strategy, PISR is embarking on a significant expansion. In a concerted effort to meet our client’s diverse needs, we are enhancing our local presence and responsiveness by expanding our network of direct offices. This includes the establishment of new regional hubs in pivotal maritime hubs such as Miami, New York, Hong Kong, and Tokyo. These strategic initiatives are designed to offer tailored services with swift turnaround times, ensuring our clients benefit from unparalleled support regardless of their location.
Our Deputy Registrars Network has grown to 63 worldwide, achieving more expansive coverage and capability to serve clients globally. This expansion underscores our steadfast commitment to maintaining safety and compliance standards at sea. It is a testament to our dedication to fortifying our network and expertise to better address our clients’ evolving needs.
At PISR, we continuously strive to enhance our digital infrastructure to meet the evolving needs of the maritime industry. One significant upgrade we are proud to unveil is enhancing our e-PISR platform. This upgrade includes seamless integration with software solutions for monitoring, sanctions tracking, and other essential functionalities, providing our clients with enhanced efficiency and compliance capabilities.
Our upgraded e-PISR platform is a testament to our commitment to innovation and expertise. It represents the fusion of digital innovation with our professionals’ deep industry knowledge and experience.
At PISR, we understand that the future of shipping lies at the intersection of leveraging cutting-edge technology alongside our team’s insights and expertise. That’s why we continue to invest in digital innovation while upholding the highest standards of professionalism and industry knowledge. We can deliver unparalleled value to our
clients.
In addition to our core offerings, Palau International Ship Registry is proud to provide fast, cost-effective, and efficient Yacht Registration services. Supported by the latest Pleasure and Commercial Yacht Safety Codes updates, our registry offers a comprehensive suite of advantages and value-added services tailored to the yacht sector This commitment to excellence is evidenced by the remarkable growth in our yacht fleet throughout 2023 and 2024.
At PISR, safety and compliance are paramount. We remain steadfast in our commitment to upholding international rules and regulations, working closely with shipowners to tackle the shipping industry’s challenges. We strive to ensure safe transit and trade for all stakeholders through open communication and regular updates on security advisories and best practices. By aligning with organizations such as the International Maritime Organization (IMO) and BIMCO, we demonstrate our ongoing dedication to client safety and regulatory compliance.
As the shipping industry undergoes rapid transformation, we recognize the importance of providing clear guidance and support to our clients. Trends such as nearshoring and regulatory shifts necessitate a proactive approach to navigating the complexities of global shipping. Through our comprehensive digital solutions and value-added services, we empower our clients to thrive in this dynamic environment. With a focus on adaptability and continual improvement, we remain committed to driving positive change in the maritime industry.
“Posidonia 2024 marks a pivotal moment for PISR as we unveil our expanded network, digital innovations, and unwavering commitment to safety and compliance. In our journey through the intricacies of the maritime industry, we remain steadfast in our commitment to sustainability, innovation and client-centricity,” remarked CEO Panos Kirnidis, HCG, BEng, MSc. “As we navigate the complexities ahead, our dedication to collaboration, technological advancement, and nurturing our personnel will drive us toward excellence and growth in the maritime sector. We eagerly anticipate meeting fellow industry leaders and stakeholders, forging new partnerships at Posidonia 2024.”
EUROPE I GREECE I 5 SACHTOURI STR, PIRAEUS - Tel: + 30 210 4293500
USA I TEXAS I THE WOODLANDS I 9595 SIX PINES DRIVE - Tel: + 1 832 631 6061 CYPRUS I LIMASSOL I ZENAS KANTHER 2B I - Tel: +357 25 747638
The marine industry is pushing hard to lower its carbon footprint and meet tough regulations. At RINA, we are working on many fronts to support these goals.
Spyridon Zolotas, South Europe and MEA Senior Director at RINA, addresses the challenges we face in adopting new technologies and meeting regulations: “As we navigate through the complexities of integrating new technologies such as large battery storage and hydrogen fuel systems, it is crucial to also enhance the infrastructure supporting these innovations. The goal is to not only meet but exceed global emissions regulations, thereby securing a sustainable future for the maritime industry.”
Recent projects include a collaboration with a global leader in the engineering and construction for the energy and infrastructure sectors on the use of ammonia: an initiative that encompasses studying the installation of ammonia containment systems and the use of ammonia-fuelled engines and gas turbines. Another ground-breaking project with Eni focuses on the use of HVO (Hydrogenated Vegetable Oil) biofuel produced by Eni, as well as of other energy carriers such as “blue” or “green” hydrogen and ammonia from biogenic, renewable or waste raw materials not competing with the food chain, in the naval sector.
In March 2024, we signed an agreement with Eni and Fincantieri to develop joint initiatives for the energy transition. With this partnership we formalised the commitment to develop joint projects to decarbonise the maritime sector in the medium to long term with the goal of Net Zero by 2050.
RINA is also working with the industry on methanol options. In April, the company awarded an Approval in Principle to the Greek NAP Consulting for their design of a methanol-ready RoPax vessel. Methanol offers a viable alternative as it can reduce the carbon dioxide in emissions generated by marine diesel oil or marine gasoil, especially when bio-methanol is used.
A further project with Aasen Shipping showcases how immediate actions can lead to substantial environmental benefits. It has integrated hybrid propulsion with batteries in its ships, which now set a benchmark in fuel efficiency, significantly reducing annual fuel consumption and, consequently, emissions.
When considering new fuels, shipowners are faced with problems relating to available onshore infrastructure and knowing which fuels will be readily available for bunkering in the future. In the light of this consideration, LNG represents a good interim solution. Together with Maran Dry Management Inc. and SDARI, RINA developed a project for an LNG and hydrogen powered 210,000 DWT bulk carrier. The concept is based on a propulsion arrangement which reduces the running machinery at sea and combines the ship’s fuel (LNG) with steam to produce hydrogen.
RINA recognizes that innovation in ship design and operations plays a critical role in achieving efficiency. For instance, the Greecebased ferry company, Attica, has revolutionized its fleet management through digital transformation, optimizing operations and reducing emissions effectively trough SERTICA.
The role of digitalisation cannot be overstated. RINA’s SERTICA suite has now been implemented on over 2,600 ships, enabling precise monitoring and reporting of fuel consumption and carbon intensity, crucial for meeting regulatory standards and optimizing performance. The integration of enhanced Safety Management Systems (SMS) further ensures compliance with safety standards while streamlining operations, helping the industry’s transition to greener practices. Planned Maintenance System (PMS) technology now also incorporates real-time data analytics that can anticipate when a ship needs maintenance. This means ships can avoid unnecessary breaks in operation and keep critical parts running longer. Predictive analytics will help operators know exactly when to do maintenance, avoiding the extra costs and risks that come with doing it too early or too late.
In the end, the power of data analytics will be crucial for making informed decisions in ship operation. By analysing information such as fuel use and equipment function, shipowners and operators can gain valuable knowledge. This knowledge leads to better decision-making that improves both the cost-effectiveness and environmental sustainability of maritime journeys.
Looking towards 2030, RINA envisions a significant shift towards low-carbon and carbon-neutral fuels including biofuels, synthetic fuels, and LNG, along with a focus on alternatives like green hydrogen and ammonia. Battery technology will evolve, facilitating the broader adoption of electric and hybrid propulsion systems, especially in short-sea shipping. Innovations in battery density and charging infrastructure are expected to enable longer journeys and faster turnarounds for electric vessels. Nuclear power should also not be ignored as a viable option for decarbonisation. Furthermore, the continuous push to reduce emissions will likely drive increasing advancements in ship design, including the use of advanced hull coatings, air lubrication systems, and wind-assisted propulsion technologies. These are set to decrease fuel consumption further and enhance operational efficiency. We also anticipate the emphasis on digital tools and predictive maintenance systems will continue to revolutionise fleet management, making operations more proactive and efficient.
The maritime industry is a dynamic and challenging market with constant changes and volatile conditions. In view of the upcoming environmental regulations, shipping companies face the challenge of decarbonizing their operations while maintaining their bottom line. The goal of Net Zero carbon emissions in shipping presents challenges particular to this industry, in terms not only of technology, but also of logistics and supply chain. Some 11bn tons of goods every year are transported by ships worldwide, therefore besides developing a fuel technology suitable for marine operations, a worldwide infrastructure for the bunkering of ships must also be developed in ports.
The availability of zero carbon fuels is uncertain not only due to the high resources/ energy requirements to produce them, but also because shipping will have to compete with other industries in the future to obtain these fuels. In addition, the cost of any new fuels is expected to be significant.
Therefore, in parallel with the use of low/ zero carbon fuels, the use of other technologies to reduce fuel consumption and to capture carbon onboard, will be key for shipping in the path towards Net Zero emissions.
In Oceanking, we have always been following closely market developments in the maritime sector. We continuously research and evaluate available marine technologies, in order to provide our customers with cutting-edge, sustainable solutions to meet new market trends and upcoming regulations.
Our company is a leading technical and commercial marine company in Piraeus, Greece, providing high-quality services to the Greek and international Shipping community, as well as the Hellenic Defence & Public Sector. Customer support, problem solving and technical expertise is embeded in our DNA and since 1989 we have been supporting our customers, leading shipping companies in Greece and Cyprus, in their development and transition towards a new era in shipping.
In order to assist our customers in their decarbonization journey, we have formed partnerships with leading equipment manufacturers to share knowledge, know-how and skills. Taking a holistic view and evaluating the different options depending on ship type and operating profiles, our aim is to offer innovative, turn-key solutions, including project coordination, installation supervision, pre-commissioning and life cycle support. Based on well proven technology and solid experience we can be a one-stop-shop for the shipping decarbonization needs:
• Electric/ hybrid Propulsion
• Wind Assisted Ship Propulsion
• Onboard Carbon Capture Systems
• Onshore Power Supply & Shaft Generator
• Shaft Power Limitation
• Propeller Efficiency Optimization & Energy Saving Devices
• Equipment and Systems for DF vessels
Besides selecting a suitable and reliable technology, system support and availability of spare parts are key to ensure a smooth and efficient operation of the systems and consequently the seamless operation of the vessels. OCEANKING’s dedicated After Sales Department, in cooperation with our experienced partners and their global service networks, provide 24/7 integrated logistic support service worldwide, including original spare parts supply, system upgrades and retrofits. Supporting vessels during their whole lifetime, we deliver tailor-made solutions, focusing on system reliability and optimization of total life-cycle costs, as well as onboard service and training.
Our subsidiary, OCEANKING ENGINEERING, employs highly-skilled electrical/ electronic and mechanical engineers, and supports customers with dedicated engineering services for equipment we represent, including:
• Commissioning
• Service onboard
• Maintenance
• Annual surveys
• Equipment calibration
• Remote troubleshooting
Given the importance of customer training to ensure the optimal and cost-effective operation of the systems, we provide training services for the systems we supply in cooperation with our partners:
• “Hands-on” training courses for the operation and maintenance of specific equipment
• Specialized training for marine equipment and systems
• Simulation and virtual reality solutions for maritime training
To enhance our operations we are continuously strengthening our team focusing in the development and growth of our people. Our sales & engineering team consists of graduate marine engineers, naval architects and electrical engineers, with solid professional experience, including ship design, shipbuilding, ship operation and support, plan approval and on-site supervision for new-buildings and conversions.
Today, we are a strong team of 35 people with diverse prespectives and complementary skills, sharing a common vision: to excell in supporting our customers with efficient, reliable and sustainable solutions.
κυβέρνησης, διπλωμάτες, εκπροσώπους περιβαλλοντικών και ναυτιλιακών οργανώσεων, μέλη της ελληνικής και διεθνούς ναυτιλιακής κοινότητας και ΜΜΕ που συγκεντρώθηκαν στη δεξίωση του Διεθνούς Νηολογίου του Παλάου (Palau International Ship
As we navigate through an era of rapid technological advancement, C&A Stavros Kassidiaris S.A. has remained at the forefront of innovation and upgraded its services in the field of electrical, electronic, and pneumatic automation systems for both the marine and industrial sectors.
Among the diverse sectors C&A operates in, the marine industry stands out as a cornerstone of its business, with unique challenges and opportunities.
Over the course of 45 years, the company continuously evolves, always managing to meet the demands of customers and the market, playing a leading role in the broader shipbuilding and repair sector in Greece and abroad. It holds a distinguished position in the field of providing automation services for ships, while also representing and distributing in Greece, products from more than 50 manufacturers of electromechanical equipment such as: Hyundai Electric & Energy System Co. Ltd, Schaller Automation GmbH & Co. KG, Fuji Electric SA, Selco APS, Danfoss SRL, Tyco Marine/Johnson & Johnson, PR Electronics A/S, Bosch Rexroth SA, Aventics/ Emerson, Jiangsu Honest Marine Cable Co Ltd etc.
As it continues to grow, engaging in various types of businesses, and advancing in terms of expertise, the company has successfully obtained numerous certifications:
From the Certification Bodie Bureau Veritas
• ISO 9001:2015 for product and service quality management
• ISO 14001:2015 for environmental management
• ISO 45001:2018 for occupational health and safety management
From the Ministry of Economy and Finance
• GR AEOC 004019 154 18 - ΑΕΟ certificate (Authorized Economic Operators)
From the Ministry of Infrastructure and Transportation
• 24352 : Number of “Register of Contracting Companies”, for the undertaking of Public Works
From the Ministry of Citizen Protection
• “Α.Π. 3015/39/60/791-λδ”, for a license to operate a private company providing security services
From the Ministry of National Defense:
• N-CAGE CODE: G2426 certification as a NATO manufacturer
• Νο. 4981 certification for classified projects in the armed forces and NATO installations
These certifications, along with the experience, specialization, trained personnel, the wide range of products, and specialized solutions with custom-made constructions, enable C&A to engage in significant collaborations and gain the trust of major companies for the completion of demanding projects.
Recently, there has been the announcement of a significant collab-
oration between C&A Stavros Kassidiaris S.A. and Naval Group for the construction of electrical power and automation panels. The project involves the under-construction «Belharra» frigates for both the Hellenic and French Navies.
C&A underwent evaluation procedures in accordance with the particularly stringent standards of the Naval Group across all project production processes, including equipment, materials, experience, environmental management, development strategies, corporate governance, certifications, and the potential for after-sales services. As a result of the above assessment, the company achieved an excellent score of 94,3/100.
Additionally, C&A initiated another collaboration with Eltrak SA, a leader company in the heavy equipment sector. The project was about the design and construction of control panels, power management controllers and distribution and starter panels for the auxiliary equipment, for 6 container ships. The C&A team was also responsible for the installation of the electrical equipment.
This collaboration with a major industry player underscores C&A ‘s robust standing, reliability, and effectiveness.
C&A Stavros Kassidiaris S.A. is the head of the C&A Group of companies along with Mantanco S.A. (Representative – Importer – Distributor of Electromechanical Materials) and Selectron S.A. (R&D of Maritime Instruments). «Cool & Active Marine» is the latest incorporation as far as expansion is concerned.
The company’s object is the operation of tourist boats. It is based in Piraeus and the boats are docked in «Flisvos» Marina.
With the growth of the business, the need for more space, to accommodate its personnel and professional activities has emerged. Among the group’s upcoming plans, there is the expansion of the building premises.
Adjacent to the current location of the main offices, a new building will be constructed.
The forthcoming multi-storey building will provide an enhanced capacity for undertaking a greater number of projects, particularly those of heightened complexity. With ample available space, the workflow process will be streamlined, expediting project completion. Furthermore, part of the envisioned developments involves the establishment of an accreditation laboratory specifically designed for calibrating measuring instruments. This facility will be meticulously aligned with the distinct requirements and specifications of various standards, catering specifically to the needs of diverse sectors such as business, maritime, and industrial fields.
C&A Stavros Kassidiaris S.A. has established itself as a leading company in the industry, thanks to its reliability and its ability to expand into new markets and activities. With the aim of pursuing sustainable growth, it adopts practices that align with ESG criteria, shaping its policies and capacity to devise innovative strategies and generate long-term value with a broad horizon.
As the global energy transition takes form, tanker owners are assessing their options. Nikolaos Michas, Lloyd’s Register Global Tanker Segment Director, explains the rational for investment.
Tankers of many different types will be required to transport the world’s energy. Large crude oil tankers will be needed for few more decades. Oil production is not expected to peak before the end of this decade and at least one more generation of crude oil tankers will be needed.
There are currently 750 tankers on order, of which nearly 17.5% of the vessels and 36% of the ordered tonnage are for Greek owners. These numbers may look healthy, but compared to a decade ago numbers are far lower as owners hold back on newbuild investments.
This reticence, whilst understandable, doesn’t match the forecasted outlook and tankers of various types will be required to transport crude oil, refined products, and petrochemicals for many years to come.
Further, as we have seen with product tankers, the shift to new cargoes, as the demand of products increases, will be heavily impacted by the need for global industry decarbonisation. Ammonia and methanol vessels will be required to support the need for these alternative fuels.
We have seen a surge in product tanker contracts over the last year. However, in relative terms, product carriers on order still represent only about 12% of the fleet according to GT (Gross Tonnage) and 9% of the fleet according to number of vessels, significantly below the median level. Moreover, almost 40% of the fleet is more than 15 years old.
There has been a series of VLCC (Very Large Crude Carriers) orders placed in the early weeks of the year. Even so, tankers on order in this class represent only about 6% of the fleet, a long-time low that I don’t believe has been equalled so far this century. And in this sector, more than 250 vessels or about one third of the fleet are older than 15 years.
Tanker demand is set to grow as energy requirements in rapidly growing populous regions, such as India and Africa, underpin new tanker trades, whilst a switch from Russian to Middle East and US crude oil supplies destined for Europe boosts tonnes miles. Meanwhile, more tankers are choosing to re-route away from the Red Sea and instead transit around the Cape of Good Hope, which is currently absorbing a significant volume of tanker capacity. Longer term, a build-up of refining capacity closer to oil producing regions will mean more shipments of long-haul products, driving tonne-mile demand for clean tankers, chemical carriers, and gas
So tanker owners face a unique conundrum. A new vessel ordered today would not be delivered before 2027. It would be nearly mid-century by the time it reached its twilight years. Would the tanker still be needed by then?
ships. The bullish market seen over recent months is set to continue.
The tanker conundrum
Demand may be there today, but the impact of the energy transition and how quickly this could change market fundamentals makes the long-term outlook uncertain.
So tanker owners face a unique conundrum. A new vessel ordered today would not be delivered before 2027. It would be nearly mid-century by the time it reached its twilight years. Would the tanker still be needed by then?
If asked today, definitively yes, but I would be hedging my bets if you asked the same question in ten years’ time.
Meanwhile, many owners are put off by today’s prices, but I believe they are likely to increase as builders capitalise on strong charter markets and their existing robust orderbooks.
LR is seeing increased interested from owners in feasibility studies on options such as life extension or replacement; the installation of energy saving devices; or engine retrofits.
However, the economics are complicated because many older tankers may be only marginal upgrade candidates. This applies to the majority of ships that have passed their third special survey Payback periods for complex retrofits could well be uncertain, or simply too long.
Investing in older vessel upgrades may no longer be a matter of choice. If tankers are to pass charterers’ increasingly rigorous vetting procedures, they must have carbon intensity indicator (CII) ratings of A to C. I expect most tankers older than ten years will almost certainly fall into categories D or E and therefore require remedial action.
Meanwhile, new carbon regulations, such as the EU Emissions Trading System (ETS) and FuelEU Maritime will have an impact. There other strategies to consider. For example, a combination of energy saving devices could make perfect sense for a mid-life products tanker.
Options could include mewis ducts, pods, rudder bulbs, advanced hull coating systems, wind-assisted propulsion systems and wind sail technology to name a few. There has been a slow penetration of these technologies into the tanker sector so far, but more installations are scheduled for later this year and are likely to increase as owners seek to maximise an ageing fleet.
Expert insights into the future of alternative fuels
Discover how we can support your maritime decarbonisation ambitions at Posidonia, Booth 4.201
Book a meeting
In the ever-evolving and challenging seas of the maritime industry, Marasco Marine Ltd distinguishes itself as a dedicated advisor in marine insurance. The company excels in refining standard insurance offerings into specialized policies that resonate with the unique requirements of each client. With a commitment to clarity and precision, Marasco Marine Ltd adeptly simplifies the complexities of marine insurance, ensuring a straightforward and effective service for its clientele.
With a rich history that dates back to 1991, Marasco Marine Ltd has not just been a part of the maritime narrative but has been actively shaping it, fostering a Culture of Risk Prevention that is revered across the shipping community. This article marks the beginning of a series that delves deep into the ethos of Marasco Marine Ltd, unveiling how its culture of risk prevention isn’t just a strategy but a legacy that safeguards and propels maritime ventures towards success and prosperity.
Marasco Marine Ltd’s journey is a testament to unwavering commitment and unparalleled expertise. With 32 years under its belt, Marasco has not just witnessed the maritime industry’s evolution but has been a proactive catalyst in driving change, particularly in the realm of risk prevention. The company’s ethos is deeply rooted in a philosophy that transcends the transactional nature of business, focusing instead on adding enduring value to its clientele and the broader shipping community.
At the core of Marasco’s success is its specialized team of experts and the illustrious Advisory Board. This isn’t just a group of professionals; it’s a cadre of maritime maestros, each a maestro in their respective field, be it naval architecture, marine engineering, or maritime law. This collective expertise forms the backbone of Marasco’s risk prevention strategies, ensuring that every policy is not just a contract but a covenant of safety and stability.
Understanding that each vessel and voyage is unique, Marasco Marine Ltd prides itself on offering tailor-made marine insurance policies i.e H&M/WAR/LOH/K&R/P&I/FDD/MII and MARINE CLAIMS HANDLING SERVICES. This bespoke approach ensures that every aspect of a client’s need is meticulously addressed, echoing Marasco’s commitment to not just meet but exceed expectations. The goal is clear – to minimize, if not eradicate, marine accidents and claims, and to strategically lower the premiums charged by Hull and P&I underwriters.
The risk prevention culture at Marasco Marine Ltd is not a mere aspect of its operations; it’s the very essence of its identity. It’s a culture that’s been meticulously cultivated, deeply ingrained, and passionately upheld. This culture resonates through every advisory session, every policy drafted, and every claim handled, ensuring that risk isn’t just managed; it’s masterfully mitigated.
Aligning with Marasco Marine Ltd is not just a business decision; it’s a strategic move towards ensuring enduring success in the volatile maritime sector. Partnering with Marasco means embracing a culture of foresight, excellence, and unwavering support, a partnership where your success and prosperity are not just goals but guarantees.
In the vast and often unpredictable maritime landscape, Marasco Marine Ltd stands as a lighthouse of guidance and reliability. Its legacy, built on a robust culture of risk prevention and a bespoke approach to maritime insurance, ensures that every client it partners with is not just insured but insured for success.
*Marasco Marine Ltd Is an independent Marine Risks Management Company which has over 30 years of marine insurance expertise in P&I and H&M insurance with an unwavering commitment to client’s success, by introducing specialized strategies in Risk Prevention and Risk Management in its daily modus operandi, with additional services such as: safety audits, and the introduction of safety protocols, which is very crucial for its clientele’s P&I and H&M insurance covers and premium cost control. More about Marasco Marine Ltd, its full list of services, unique structure and its Board of Advisors, can be found at www.marasco-marine.com
• turbochargers
• impellers
• rotor shaft complete
• turbine blades
• oil pumps
• bearings
• bush sealing
• plain / trust bearings
• gas inlet & outlet casing
• nozzle-ring / cover-ring
Since 1980, TURBOTEC PISTOLIS LTD has been one of the trustworthiness firms, in the field of turbochargers and marine technology with great experience.
Company’s overall philosophy lies in providing products of the highest quality, along with specialized services, both to greek and international customers.
Located in its modern, six-story building, with stock, ready to deliver, spare of the highest technology.
TURBOTEC-PISTOLIS LTD has service station in China, Shanghai, for standard overhauling and emergency repairs of the ship. Thus saving its customers valuable time and avoiding unnecessary expense. Guarantee is its professional experience. The company, continues providing certificates of Quality ABS-ISO 9001-2015.
TURBOTEC PISTOLIS LTD has a world-wide network of highly skilled technicians able to access the ship and estimate the damages on T/C wherever it is located, and ensures that the highest standards of quality are met in all work carried out. The team of expertise is available 24/7 basis through direct services lines. The Company’s Customer Service Nerwork has been carefully designed in such a way, so as to be able to provide all necessary assistance to the company’s clientele, both locally and internationally.
This year’s International Day for Women in Maritime will focus on the crucial role of women in ensuring maritime safety worldwide, while highlighting the changing attitudes towards gender in the industry.
Observed globally on 18 May every year, Women in Maritime Day seeks to raise the profile of women in maritime, while promoting their recruitment, retention and sustained employment in the sector
Currently, only 29% of the overall maritime workforce and 20% of the workforce of national maritime authorities are women. Women make up less than 2% of seafarers worldwide.
Speaking at an international event to mark the occasion on Friday, 17 May 2024, the Secretary-General of the International Maritime Organization (IMO), Mr. Arsenio Dominguez stated:
“We must – and will – do more. By investing in women’s education and professional development, we empower women, drive innovation and foster sustainability within the maritime industry, to the benefit of all.”
The rise of digitalization and automation as well as green technology in the sector will require new skills and potentially signal new career opportunities for women.
“Change is both necessary and coming… With increase in trade and the transition towards a greener and more sustainable sector, the opportunities to enhance diversity and inclusion are in front of us. I want you all to look at how you can drive understanding, awareness and change within your own organizations,” said Mr. Dominguez.
He recognized the work carried out under IMO’s long-standing Women in Maritime programme, which takes a three-pronged approach of ‘training-visibility-recognition’ for women.
Initiated in 1988, the programme supports gender equality and the empowerment of women through gender specific fellowships; access to high-level technical training for women; support for career development opportunities in maritime administrations, ports and maritime training institutes; and by facilitating the establishment of professional women in maritime associations, particularly in developing countries.
IMO is strongly committed to helping its Member States achieve the UN 2030 Agenda for Sustainable Development and the 17 Sustainable Development Goals (SDGs), particularly Goal 5 to achieve gender equality and empower all women and girls.
IMO is hosting an international symposium on Friday, 17 May 2024 at IMO Headquarters in London, under the theme ‘Safe Horizons: Women Shaping the Future of Maritime Safety.’
The Symposium features a line-up of distinguished seafarers, maritime professionals and maritime leaders who will speak about reframing maritime safety through a woman’s lens, and how to implement a holistic approach to safety at sea, taking into account gender considerations.
As part of the programme, the first-ever IMO Gender Equality Award will be handed to Ms. Despina Panayiotou Theodosiou of Cyprus, former President of the Women’s International Shipping and Trading Association (WISTA International).
Amidst the evolving landscape of the maritime industry, Cyprus remains steadfast as an admirable example of maritime excellence. With a robust ship registry and a vibrant maritime cluster, Cyprus has firmly established itself as a premier maritime hub.
In the past year, the Shipping Deputy Ministry has spearheaded various strategic initiatives, showcasing a firm dedication to excellence and innovation. Central to Cyprus’s maritime success story is its commitment to providing top-notch services while prioritizing maritime safety and security. Supported by the wealth of expertise within its workforce, Cyprus has earned recognition as one of the most reliable and competitive maritime flags globally.
Over the last six months, Cyprus has seen a notable increase in registered tonnage—a clear sign of continued support from shipowners worldwide and growing interest from new partners. This surge, alongside increasing interest in registering vessels with the Cyprus Ship Registry, points toward a promising future for Cyprus’s maritime sector. With a renewed focus on elevating quality and safety standards, Cyprus is poised to expand its fleet and enhance its global standing further.
The Cyprus Tonnage Tax System remains a cornerstone of growth, attracting a growing number of companies. With 420 companies now benefiting from this system—a 14% increase over the past year—shipping continues to play a crucial role in Cyprus’s economy. The overarching goal remains unwavering: to continually bolster the competitiveness of the Cyprus flag and the maritime sector.
To reinforce its competitiveness, Cyprus has established two advisory committees dedicated to enhancing the quality and competitiveness of its flag and maritime cluster. These committees are set to play a pivotal role in offering consultation and fostering collaboration within the maritime community.
Embracing the transition to sustainability, Cyprus aims to fully digitize the Shipping Deputy Ministry by 2024, increasing efficiency and supporting the shipping industry’s competitiveness. Technology serves as a powerful tool in offering innovative solutions to pressing challenges, and Cyprus has made significant strides in simplifying procedures, reducing bureaucracy, and embracing a paperless Maritime Administration.
The One-Stop Shipping Centre has begun operations, providing services and addressing requests from shipping companies and related entities, streamlining processes across government authorities to support the Shipping Deputy Ministry’s collaborators. This marks the beginning of a comprehensive plan to centralize all shipping-related services from other governmental departments and ministries,
aiming to provide efficient service promptly.
Cyprus also acknowledges the importance of maintaining the quality of its fleet, consistently achieving “White List” status in the Paris and Tokyo MoUs on Port State Control. The nation’s top priority remains maintaining and improving the exceptional quality for which the Cyprus flag is renowned. Cyprus’s rise in the Paris MoU’s White List ranking reflects its steadfast focus on maritime safety and security standards, further reinforced by legislative measures to enhance these standards and protect the marine environment.
Decarbonizing shipping is also one of the most significant challenges faced by the shipping sector. The urgent need to address climate change has placed a spotlight on the maritime industry’s carbon footprint. As a leading advocate for sustainable shipping, Cyprus believes that comprehensive and diverse measures are necessary at both global and regional levels to achieve emissions reduction targets and ensure a sustainable future for the industry Cyprus actively participates in the IMO and EU deliberations to formulate a broad and diverse set of actions to achieve emissions reduction targets. However, it is crucial to incentivize shipowners for their investments in sustainable practices to accelerate widespread adoption.
Thus Cyprus supports the shipping industry to achieve its decarbonization goals and in this respect provides green tax incentives to shipowners and operators, encouraging and supporting ships registered under the Cyprus flag to use alternative fuels. Whilst such incentives were introduced from the fiscal year 2021, these have recently been revised and new incentives have been approved to reward vessels demonstrating effective emission reductions with a 30% reduction in annual tonnage taxes for compliant vessels.
As Cyprus commemorates the 60th anniversary of its Ship Registry, it reflects on a remarkable journey of maritime excellence while charting a course for even greater success in the future. With a clear vision, extensive experience, and unwavering commitment, Cyprus aims to lead its shipping industry toward greater prominence on the global maritime stage.
In conclusion, Cyprus’s maritime achievements and aspirations demonstrate its dedication, innovation, and resilience in navigating evolving challenges and opportunities. As the nation continues its voyage of progress, its commitment to excellence and sustainability ensures a promising journey ahead.
As cruise tourism has surpassed its historical levels, with a significant and ever-increasing contribution to the economy and a leading role in environmental sustainability and responsible tourism, the cruise sector is emerging as a leader in the tourism industry and in the green transition of shipping.
CLIA’s annual State of the Cruise Industry Report for 2024 includes the release of 2023 passenger volume, which reached 31.7 million— surpassing 2019 by 7% – almost two million more passengers than 2019. The report also shows continued demand for cruise holidays, noting intent to cruise at 82%. The forecast for cruise capacity shows an increase of 10% from 2024 through 2028, as cruise lines make ongoing, concrete progress in pursuit of net-zero emissions by 2050.
Cruise continues to be one of the fastest-growing and most resilient sectors of tourism —rebounding faster than international tourist arrivals— and a strong contributor to local and national economies. In 2022, cruise tourism cruise generated 90% of economic impact compared to 2019, despite passenger volumes that year at 70% of 2019 levels. Over the past 50 years, cruise tourism has demonstrated its leadership in managed tourism and is an industry that has plenty of room for continued responsible growth given cruise travel comprises just 2% of overall travel and tourism. The industry also continues to lead the way in environmental sustainability and destination stewardship, with cruise lines making advancements in technology, infrastructure and operations, and in green skills training for crew.
According to the CLIA’s Annual Report, Cruise is Thriving: 2024 is forecast to
see 35.7 cruise passengers sailing, as the Intent to cruise is 6% higher than 2019, with Millennials being the most enthusiastic cruise travelers of the future. The global cruise capacity is forecast to grow from 677K lower berths in 2024 to 745K lower berths in 2028. Each year, the fleet becomes more efficient, as cruise lines invest in propulsion technologies with conversion capabilities for future alternative fuels and utilize a range of technologies and innovations to advance their sustainability initiatives. These impressive facts match with the significant Global Economic Impact of the industry. In 2022, cruise generated $138 billion to the global economy, 1.2 million jobs – up 4% compared to 2019 – and $43 billion in wages. At the same time, 63% of those who have taken a cruise say that they have returned to a destination that they first visited via cruise ship for a longer stay, extending the economic impact. For 2023, the economic impact is forecast to be even greater, given the 50% increase in the number of passengers sailing in 2023 compared to 2022.
CLIA-member cruise lines are sailing to a better future: Reducing emissions at berth and at sea by investing in technologies, infrastructure, and operational efficiencies. CLIA cruise line members are making huge
investments in the green transition of the industry, investing in new ships, new technologies, alternative fuels and innovations for the benefit of everyone. The order book from 2024 to 2028 includes 56 new ships, worth $38 billion.
The cruise industry is investing billions in new ships and engines that allow for fuel flexibility to use low to zero-GHG fuels, once available at scale, with little to no engine modification. These fuels and energy sources include green methanol, bioLNG and synthetic LNG, hydrogen fuel cells, photovoltaic/ solar (in use on five ships today), battery storage, wind (in use on three ships today). In the same direction, our members are working on 32 pilot programs testing sustainable fuels. Today, 4 ships are sailing using renewable fuels.
In addition, CLIA has launched a study with classification societies RINA and DNV which, based on fuel infrastructure, technology and ship routes, will identify the investments required at local level to decarbonise the industry by in 2050.
At the same time, we are pioneers on waste management practices, including repurposing and reducing waste onboard, water conservation practices, food waste minimization solutions, advanced wastewater treatment systems (AWTS) and systems designed to protect marine life.
Focus on people
Cruise is the best vacation value there is, with incredible guest experiences delivered by a talented workforce. To highlight the tremendous employment opportunities that cruise tourism supports around the world, CLIA has published a new skills and workforce publication, An Ocean of Opportunities. With at least 56 new ships coming online between 2024 and 2028, there are vast opportunities for careers in cruise, which boasts an impressive employee retention rate upwards of 80%.
According to this workforce skills report, in 2024 cruise lines will employ a multinational workforce of nearly 300,000 seafarers representing more than 150 countries, as well as tens of thousands of employees on land. What is also worth mentioning is that 94% of women seafarers work in the cruise industry and that women hold around 40% of senior leadership roles at cruise companies.
The situation in Greece
Cruising in Greece is also booming, with 2023 set to be a record year in the industry’s
history with over 7 million cruise passengers in the country and 5,230 arrivals. In 2024, this trend will continue and we are expecting a new record. In total this year, 131 cruise ships will operate in Greece, 70% of which will homeport or partially homeport in Greek ports, more than any other time. Homeporting has multiple economic benefits for the country – due to the revenue from passenger accommodation before and after the cruise and their air transport, but also the need to refuel, maintain and supply the ships, as well as crew changes and their spending in the country.
The economic benefits are already evident: In 2022, cruising in Greece supported more than 14,300 jobs and contributed a total of €1.4 billion to the country’s economy. Cruise’s contribution to the Greek economy came from four main activities: cruise line supplies, shipbuilding activities, shore-based passenger consumption and crew spending in Greece. Passenger consumption contributed €324 million to Greek GDP, representing 53% of the total contribution. In terms of employment, cruise lines (cruise
crew and corporate head office employees) accounted for approximately 2,425 jobs in 2022. In addition, cruise lines created jobs in the wider economy, with a total of 11,915 jobs created through direct, indirect and induced contribution. Most of these jobs (43%) were created by passenger consumption and related activities.
Still, the development of the cruise also requires appropriate management to be sustainable, based on local communities’ needs, and aiming for the passenger experience to be worthy of the high expectations. The contribution of CLIA and its members is important in this area as, with great respect for the communities that support the cruise industry, we collaborate on itineraries, port operations and improved destination management practices to provide sustainable, optimal experiences for communities and visitors.
Whilst cruising in Greece is on the rise, the rest of the Eastern Mediterranean region has been affected negatively by the current security situation in the Red Sea and broader region. Cruise operators place their first priority on the safety of passengers and crew, and are adjusting itineraries as needed in their interest in the Eastern Med and the Red Sea.
While itineraries to Israel are currently on hold, decisions on Cyprus, Egypt and Turkey vary. The reason is that the perception of the passenger is also important. It is not enough for a country to be safe, but it needs to be perceived as safe as well. How long will this last and to what degree will the region be affected from the cruise perspective is largely unknown, and our thoughts are with all who are impacted by the attacks.
In the G7 Transport Ministerial Session on Maritime Connectivity on 13 April 2024, CLIA’s European Chairman Mr Pierfrancesco Vago, expressed the cruise industry’s solidarity with the wider maritime sector on the imperative to ensure seafarer safety, considering current situation. CLIA highlighted how the maritime sector is united in condemning the attacks and is calling upon the international community to adopt the adequate measures to protect seafarers at the next IMO Maritime Safety Committee on 1524 May 2024, and to develop adequate solution to the crisis. In 2023, the Caribbean, Bahamas and Bermuda remained the biggest cruise destination market in the world with 44,2% of cruise visitors, with the second one being the Mediterranean (18,5%).
American Steamship Owners Mutual Protection and Indemnity Association, Inc. (the American Club) was established in New York in 1917 and is the only mutual Protection and Indemnity club domiciled in the Americas. Interestingly, it was created as a matter of national security as a solution to then WWI UK sanctions barring American operators from insuring with UK clubs. The Club insured the US merchant fleet through two world wars before internationalizing. Today it provides P&I cover for ship operators throughout the world.
The Club is a member of the International Group of P&I Clubs, a collective of twelve mutuals which together provide Protection and Indemnity insurance for some 90% of the world’s ocean-going tonnage. Through this unique structure, the member clubs, while remaining individually competitive, share large casualty loss exposures, related extraordinary expertise, and serve as a platform supporting the industry voice of ship operators - a key stakeholder in the global chain of trade. Indeed, the Group - and through it, the American Club - serves to provide peace of mind to all stakeholders in the chain, from people, to communities, to ports, to other operators, countries, and authorities throughout the world, thereby enabling global trade.
The American Club’s principal activity is the providing Protection and Indemnity (P&I) insurance and Freight, Demurrage and Defense (FD&D) cover for risks on behalf of its Members, both owners and charterers. The Club provides insurance cover for liabilities including, but not limited to, damage to cargo, oil pollution, damage to and restoration of the ocean environment, wreck removal, and illness, injury and/or death to people on board such as passengers and seafarers. The Club also provides P&I and FD&D insurance to the operators of smaller vessels through its fixed premium facility, Eagle Ocean Marine (EOM). In addition, through its wholly owned subsidiary American Steamship Owners Marine Insurance Company (Europe) Ltd. (the American Club (Europe)) in Cyprus, the Club participates in the P&I and FD&D sector in Europe.
The American Club is subject to regulation by the New York State Financial Services Department, widely recognized to be the most
demanding licensing authority in the United States. It requires detailed reporting, exceptional transparency, and robust security. In addition to providing quarterly statements to New York State regulators in accordance with their statutory demands, the Club also publishes an annual report in accordance with Generally Accepted Accounting Principles (GAAP) providing for easy comparison with other Group clubs.
In recent years, the Club has successfully built on its US heritage and expanded to all major shipping hubs around the world to become a truly international insurer with a global reach second-tonone in the industry. Day-to-day management is provided by Shipowners Claims Bureau, Inc. (SCB) from its headquarters in New York. Extensive resources are provided by SCB’s satellite offices in London, Piraeus, Hong Kong, Shanghai, Limassol, and Houston. In addition to the resources of the Managers, the Association’s worldwide network of independent claims correspondents is available to Members around the clock.
The American Club appeals to prospective Members through its commitment to personalized service, a “can-do” attitude, and an enthusiasm to achieve the very best results for its Members both large and small. It has consistently maintained an ethos of being the solutions provider by extending maximum effort to understand the membership and to provide the highest level of support within the parameters of the Rules. The Club remains committed to ensuring this remains its highest priority.
The Club represents a significant and important voice in the industry and in the International Group, serving small to medium size operators, many with traditional family heritage. The American Club prides itself on its personal relationships with its Members and sees itself as an extension of the operations of the Members; serving as partners from the liability perspective for this sector of the shipping industry. As a niche Club, it enjoys the privilege of maintaining a real connection to its individual Members around the world through its regional offices and remains committed to that partnership. It has and will continue to ensure the membership has a voice and that it is heard.
CMA D. ARGOUDELIS & CO S.A. is gearing up for the prestigious POSIDONIA Exhibition 2024, set to unfold in Athens from June 3rd to June 7th at the Metropolitan Expo area Positioned at Stand 1.159 in Hall No 1, the company is poised to unveil cutting-edge products and solutions tailored for the Marine Industry POSIDONIA stands as a cornerstone event within the shipping industry’s calendar, attracting a global congregation of shipbuilders, equipment suppliers, and service providers. Anticipate robust engagement from technical and commercial executives representing Greek and international enterprises amidst the bustling exhibition halls.
Leveraging its profound expertise in automation, CMA D. ARGOUDELIS & CO S.A. is excited to announce several initiatives:
•Introduction of new automation systems meticulously crafted for the maritime domain.
•Hydraulics division expertise with certified products and services
•Rollout of innovative, energy-efficient solutions aimed at curbing fuel consumption and mitigating carbon emissions during marine operations, aligning with the industry’s escalating focus on sustainability.
•Presenting pioneering products and services poised at har-
nessing the potential of digitalization and Internet of Things (IoT) technologies within the maritime sector. These offerings are engineered to optimize vessel performance and streamline operations through advanced data analytics, connectivity, and automation.
•Showcase of state-of-the-art remote monitoring and control systems empowering ship operators to remotely oversee equipment performance, diagnose issues in real-time, and enact adjustments to enhance efficiency while minimizing downtime.
•Unveiling a groundbreaking new energy project, designed to revolutionize energy efficiency and sustainability in the marine industry.
In addition to its exhibition presence, the company is thrilled to announce its participation in the POSIDONIA Seminar Room 1B on Wednesday, June 5th, 2024, from 14:45 to 16:30
During this session, the company will deliver a compelling presentation titled “Innovative Energy & Digital Solutions for Shipping,” underscoring its commitment to driving forward the industry’s technological evolution.
CMA D. ARGOUDELIS & CO S.A. is looking forward to welcoming you to its stand and engaging in insightful discussions at this esteemed gathering of maritime professionals.
needs of the shipping industry with our partners’ offerings, ensuring mutual satisfaction through reliability, quality, and competitive pricing. We prioritize long-term partnerships, emphasizing sustainability and shared values to meet our clients’ needs properly & effectively.”
Euploia Drydocks & Services Ltd possess a dedicated business development team tasked with scouting key shipping markets like China, Korea, and Japan, among others, to cultivate strategic partnerships aimed at delivering competitive products and services. This initiative enables us to retain our market share, uphold quality standards, and provide customers with competitive pricing. This effort aligns with our goal of continually enriching our portfolio with new representations, who share our principles and prioritize sustainability, based on long-term partnerships and reliable sources capable of fulfilling any ship’s needs.
Charis Valentakis commented that: “Our dedicated business development team at Euploia Drydocks & Services Ltd is actively cultivating strategic partnerships to enhance our portfolio with sustainable, quality-focused representations. This enables us to retain our market share, uphold quality standards & ensuring competitive offers.” It is our company’s policy to adapt to new regulations, such as those set forth by the International Maritime Organization (IMO) etc., pertaining to ships. We achieve this by forming partnerships with manufacturers whose products comply with regulations. This approach ensures that we meet the needs of our customers by providing them products and services that are complying with these regulations while also aligning with our broader goals of innovation in the marine industry.
Charis Valentakis added that: “I am truly inspired by our relentless commitment to establishing impactful collaborations and partnerships within the marine industry. We, as Euploia, have a proactive approach outlined in adapting to new regulations, emphasizing the importance of forming strategic partnerships with compliant suppliers to meet customer needs timely & effectively.”
Drydocks & Services Ltd stands as a beacon of resilience and innovation. As the maritime sector faces unprecedented challenges and opportunities, our company remains at the forefront, adapting, innovating, and leading the way towards a sustainable and prosperous future. With a legacy of reliability, we’re a trusted partner, actively responding to emerging trends and focusing on sustainability and customer satisfaction.
Euploia Drydocks & Services Ltd has been providing innovative and cutting-edge products and services of the highest standard since 2012. We act as an agent and service provider for prominent equipment manufacturers in the following areas: Marine Equipment & Systems, Spare Parts & Technical Services, Dry-docking Operations, Afloat Repairs & Conversions, Underwater services, Safety products & Services, facilitating the global supply of equipment, spare parts, and services. Our Mission is to meet and exceed our customer’s expectations by providing Products & Services of the highest standards in local and worldwide markets, accompanied with timely deliveries and competitive prices, honoring always our contractual commitments.
As a service provider, Euploia Drydocks and Services’ key to success is to blend the needs of the shipping industry with what our principals/partners can offer, ensuring balance and satisfaction on both ends. Our primary concern is to meticulously examine our client’s needs and strive to promptly meet them with reliability, quality, and competitive pricing.
Charis Valentakis, (Managing Director) stated that: “Our commitment at Euploia Drydocks and Services is to seamlessly blend the
We strive to attend all major maritime events and exhibitions because we believe it’s vital. Participating in these events not only allows us to engage with our existing clientele but also opens doors for forming new collaborations. In addition, our customers have the opportunity to stay updated on our new representations, products, and services as well as to contact makers for questions or clarifications in person. As always, we will be participating with our own booth (Hall 2, Stand no: 2.101) at the largest maritime exhibition in the world, Posidonia Exhibition. Posidonia continues to shine as a prime platform for showcasing the latest advancements, fostering meaningful connections, and driving forward the Greek maritime sector.
Charis Valentakis asserted that: “From cutting-edge technologies to strategic partnerships, the Posidonia exhibition embodies the spirit of progress and collaboration, propelling the Greek shipping industry to new heights. With the planned reopening of the country’s two major shipyards, it will result in the reactivation of regional companies that provide services to the shipyards, thereby boosting our country’s marine industry.”
In the ever-changing maritime landscape, Euploia Drydocks & Services Ltd remains a steadfast pioneer of innovation and sustainability, with a commitment to excellence and customer satisfaction, we navigate the challenges of the industry by creating strategic partnerships, embracing regulatory compliance, by offering innovated products. Taking into consideration all the above, Euploia’s intention is to offer products and services that contribute to the preservation and development of the Greek maritime industry.
This is a double interview with Simone Trevale, Sales Manager / Fluid Global Solutions s.r.l.& Vanessa Fantazia, Key Account Manager | Spare Parts Dept. Armonia Trading & Commercial Applications Limited.
The interview covers various aspects of the maritime industry, including the importance of reliable equipment onboard vessels, fostering collaboration for organizational success, meeting customer preferences, customer-centric strategies, the significance of specialized technicians and tools, the impact of automation on workplace safety, and recognizing contributions from partners like Greek agents. Additionally, it highlights the role of in-house maintenance and service activities in enhancing market competitiveness.
The unforgiving nature of the marine environment demands exceptional reliability from all onboard equipment, especially pumps. To ensure smooth operations and crew safety at sea, what critical factors should be considered when selecting high-quality pumps specifically designed for use in vessels?
We can say the two main points to be considered when selecting new pumps are: the material, which should be compatible with the pumped fluid to ensure the correct lifetime of machinery, the dimensions of the full assembly which must be compatible with the available space on vessel, which sometimes is restricted. We can say the two main points to be considered when selecting new pumps are: the material, which should be compatible with the pumped fluid to ensure the correct lifetime of machinery, the dimensions of the full assembly which must be compatible with the available space on vessel, which sometimes is restricted.
In today’s competitive landscape, how can fostering a collaborative work environment drive improved performance and achieve measurable success for the organization as exemplified by the principle “Working together means winning together”?
In today’s fast-paced business world, collaboration isn’t just helpful—it’s essential for lasting success. At our company, we live by the motto ‘Together, we win,’ shaping our culture and driving our achievements. Collaboration taps into our team’s combined smarts, skills, and experiences, driving us towards shared goals with synergy. Moreover, collaboration isn’t limited to internal teams. As exclusive agent of FLUID GLOBAL SOLUTIONS in the Greek market, our collaborative approach
extends to our external partnerships as well. By working closely with our principal, understanding their objectives, and aligning our strategies, we can deliver exceptional value to our customers while driving mutual growth. In conclusion, cultivating collaboration isn’t just nice—it’s essential. When we adopt the ethos of ‘Teamwork equals triumph,’ we boost performance and foster a culture of shared success, driving our organization ahead in a competitive world.
What strategies can your company employ to effectively meet the preferences of its customers and deliver their favourite products in 2024?
As we look ahead to 2024, meeting the preferences of our customers and delivering their favourite products remains a top priority for our company. To achieve this, we employ a multifaceted approach that encompasses several key strategies. Firstly, we invest in thorough market research and customer analytics to understand evolving preferences. Secondly, we prioritize innovation and product development to stay ahead. We continuously seek feedback from customers and industry experts to identify emerging needs and opportunities. Additionally, we prioritize customer satisfaction by focusing on streamlined ordering and personalized support, ensuring convenience and responsiveness across all operations. Furthermore, we leverage technology to enhance the customer experience and streamline operations. Our principal FGS is offering online platform for easy ordering and tracking, sriving to make the purchasing process seamless and efficient for our customers. We value our customers and prioritize nurturing strong relationships with them. Through proactive communication, engagement efforts, and loyalty programs, we create a sense of community and loyalty. With these strategies, we’re committed to meeting our customers’ preferences and delivering their favorite products well into 2024 and beyond.
To thrive in the dynamic 2024 market, what customer-centric strategies can companies implement to accurately predict and deliver their customers’ most desired products and ensure a seamless experience for acquiring these favourite items?
In our commercial department we chose to carefully select products and customers to match each other, by reading accurate reports with statystics and promote only competitive products or specific ones to key customers
We believe records are central in the optimization of orders, for this reason it is important to have a modern and powerful software where database must be clean and provide connecting links to products/brands/vessels. We do support our customers with our records to build such database from the records in our hands.
In industries demanding pinpoint accuracy and unmatched expertise, how much do a company’s foundation rest upon the pillars of specialized technicians and the right tools for the job?
In the shipping industry in which we specialize, where safety, efficiency, and reliability are paramount, the foundation of a company heavily relies on specialized technicians and having the right tools for the job. Specialized marine technicians, including engineers, navigators, and mechanics, are experts in vessel operations, maintenance, and repair. Their skills ensure smooth sailing, reduce downtime, and prevent accidents at sea. From routine inspections to complex repairs, they play a vital role in maintaining ship integrity
and readiness. Furthermore, having access to the right tools and equipment is essential for maintaining and repairing vessels effectively. This includes for example specialized machinery for engine overhauls, precision instruments for navigational calibration, and safety equipment for emergency situations. Employing advanced technology like predictive maintenance helps shipping companies tackle issues before they worsen, ensuring smooth operations and peak performance. In shipping, skilled technicians and advanced tools are essential. Technicians use tools for accurate diagnostics and precise repairs, while the tools empower technicians to maintain safety standards and comply with regulations.
How impactful are technical-scientific meetings and practical tests in shaping your days, positioning you as key players in the advancements and innovations of tomorrow?
The importance of skilled employs is high and central in our daily work, in order for our company to be always identified as specialized in our product and keep our profile transparent for all our customers. For this reason we plan weekly some hours of specific lessons dedicated to sales and operational teams.
To what extent has automation contributed to the reduction of workplace accidents and product damage, and how might this trend continue to evolve in the future?
Automation, including robotics and AI, has notably curbed workplace accidents and product damage in shipping, fostering safer and more efficient operations across various aspects of the shipping industry. Automation reduces human error by handling routine tasks like cargo handling, loading, unloading, and navigation. This minimizes accidents and product damage while ensuring precision and consistency in operations. The regulatory bodies increasingly emphasize safety standards and environmental sustainability, there will be a growing impetus for shipping companies to invest in automation technologies that not only enhance safety but also reduce emissions and minimize environmental impact. Looking ahead, the trend of automation in the shipping industry is expected to continue evolving so to usher in a new era of efficiency, safety, and sustainability.
Can you quantify the impact of your Greek agents on FGS’s reputation in Greek shipping, and how will you formally recognize their contribution?
As I said above, the relationship with our Greek agent, exclusive ARMONIA, is based on mutual trust and this has increased year after year, leading to a very significant increase in turnover, if you consider that we started 3 years ago. I think that the two companies should thank each other, because it is thanks to the trust they convey to customers that the latter feel protected and confident in having good services, with high quality products, managed by people who love to show their face. THANK YOU ARMONIA
Is in-house maintenance, revamp, and design crucial for your core business, even without traditional production? How do these activities impact your market edge?
Since some years already we introduced maintenance and service activities with a specific team, so we became a reference point for vessels sailing in Italy, where we can provide superfast solving actions for any urgencies and now have daily jobs. By means of some problems solved in the due time required, we acquired some random customers who became customary.
Dr. Michalis Pantazopoulos, Senior Vice President & General Manager of the Liberian International Ship & Corporate Registry’s (LISCR) Piraeus office, managers of the Liberian Registry
The Liberian fleet evolution within Greek shipping is testament to the strong links which have existed between Greek shipping and the Liberian flag, dating back to the day in 1949 when the Stavros Niarchos-owned oil tanker World Peace became the first ship to be registered under the Liberian flag. From that time, until the present day, the Greek shipping community has supported the Liberian Registry, and vice-versa, through good times and challenging times. This relationship has grown stronger still during the economic downturns, the geopolitical unrests and tensions, and the pandemic challenges of recent years, during which shipowners and operators have looked to their ship registries for innovative solutions to help maintain safety, efficiency and profitability.
As Greece remains the undisputed number one shipping nation in the world, Liberia remains the number one flag of choice for Greek shipowners, having contribute to the quality growth of Greek shipping, which is testament to the trust and respect that exists between the Greek shipowners and the Registry.
Today the Liberian Registry, with 5,974 ships, has a total tonnage of 264 million GTONS (average age 13 years), representing 14% of world shipping. Greek shipowners have honored us with 1,652 of their ships (149 million DWT) making the register the first choice in Greek shipping, that is about 25% of our total fleet.
The Liberian Registry was the first flag State to introduce electronic certificates over more than a decade ago and we also operate a dynamic ship detention prevention program, and recently introduced an online Duty Officer video call system to provide 24/7 instant support to Liberia flag ships in service. Liberia has also approved electronic record books for installation onboard Liberian registered ships, has authorized IHM Expert Companies to work with shipowners in maintaining and updating the inventory of hazardous materials (IHM) Part I onboard ships, and has developed an API (Application Program Interface) that allows electronic transfer of fuel oil consumption and carbon intensity indicator data. In addition to the electronic certificates, services and digitization, our online client-interface system, WayPoint, offers shipowners secure, real-time, user-friendly access to their fleet details anytime and anywhere in the world. WayPoint is a centralized, single database compiling all information relating to the performance and registration of Liberian vessels.
The Greek controlled Liberian fleet over the last 20 years has evolved as follows: 2005 - 160 vessels, 2008 - 480 vessels, 201 - 600 vessels, 2014750 vessels, 2017 - 1.050 vessels, 4/2024 - 1,652 vessels. The Liberian Registry is the largest White Listed ship registry,
achieving this success on all MOUs, Paris, Tokyo and USCG Qualship 21. The safety of the ships, seafarers, and environment are our number one priority. The registry has invested a great deal into the expansion of its network of inspectors, auditors, and global staff providing technical and safety related support to the Liberian fleet. Our incentives have been recognized by the Greek shipping industry making the Liberian Flag the preferred flag of Greek shipowners as the recent data from the Greek Shipping Co-operation Committee of London (March 2024).
Our Commitment to Greek Shipping - The Greek Office – 2 Efplias Str., Piraeus
The LISCR Piraeus office was established in 2000 at Efplias 2 in the heart of the port and is one of the Registry’s longest-established office with dedicated and highly professional staff available to assist the shipmanagers and the vessels whenever is needed. The Greek shipping community appreciates the broad spectrum of quality services and support offered locally including corporate, vessel registration and mortgage, plan approvals, seafarers’ certification, and technical, safety, ballast and security services and certification. Our motto “All Services Locally” has received acceptance, recognition, and appreciation by the Greek shipping community, as there is there is not any flag state that have the capability to offer all these services locally in Piraeus or elsewhere.
Our approach to Greek shipping is simple based on hard work, consistency, responsibility, credibility, immediate response and service, any day and hour as shipping works around the clock. Our aim is to find solutions, to support the vessel and the operator.
Shipping
Shipping is an industry of partnership and not a one-way street, and we are committed to share with shipowners our experiences, our networks, our technology, and our global network to ensure their vessels get the support they need to operate in an ever changing and increasingly complicated regulatory environment. Liberia is committed on a continuous improvement effort moving towards systems, procedures and processes that will improve not only shipping but the community at large and this is a commitment more than ever now.
As the Liberian Registry celebrates 75 years of existence in the internationally competitive shipping industry where longevity is a badge of honor that is awarded only to businesses that are in it for the long haul and survive because of the quality services they provide, we feel honored to be part of the Greek Shipping community. For this our gratitude and commitment to the Greek shipping community is the ground we have been founded on since 1948, and continue stronger today.
The two H2-powered vessels will be built in Norway and will operate in the country’s most challenging Arctic waters
Two hydrogen-powered passenger ferries ordered by Norwegian transport company Torghatten Nord are set for Lloyd’s Register (LR) class following Approval in Principle (AiP) awarded in August 2022. Designed by The Norwegian Ship Design Company to operate in the challenging waters of the Vestfjordstrekninga fjord in the Arctic Circle, the two vessels will be built at Norwegian shipyard, Myklebust Verft.
At 117 metres long with a 120-car capacity, the duo will be the world’s largest hydrogen-powered ships, operating on green hydrogen at least 85% of the time. Operating at an average speed of 17 knots in often challenging conditions, the vessels will navigate the 278km-long Vestfjordstrekninga ferry route connecting Bodø, the islands of Røst and Værøy, and Moskenes. A hydrogen storage unit onboard the vessel will feed gas to the fuel cells, creating electricity to propel the vessels and power their auxiliary systems, reducing CO2-emissions on the route by around 26,500 tons each year.
The alternative fuel newbuilds with biodiesel backup, bring together LR as the class society, owner Torghatten Nord, The Norwegian Ship Design Company, Myklebust Verft shipyard, systems integrator SEAM, and hydrogen supplier GreenH. The Norwegian Maritime Authority will flag the two vessels.
The H2-powered ferries join another set of LR-classed vessels currently being built in Norway; two construction support offshore vessels (CSOVs) are being built at Vard Langsten shipyard and will enter service late in 2025 or early 2026.
Nick Brown, CEO, LR, said: “These flagship hydrogen-powered ferries represent a significant milestone for Norway as it furthers its continuing commitment to clean hydrogen infrastructure. We see significant interest in green hydrogen as a maritime fuel especially for short-sea shipping and look forward to working with our Norwegian customers —Torghatten Nord, Myklebust Verft and The Norwegian Ship Design Company — to ensure this innovative project is progressed with safety, reliability and sustainability at its core.”
Marius Hansen, Managing director, Torghatten Nord, said: “We are delighted to be working with Myklebust Verft on this project,
as together with our partners we set the standard for a completely new class of ship that reduces emissions and supports sustainable operations. This project is a significant boost for the Norwegian technology and shipyard environment and we are proud to make it happen in Norway.”
Leiv Sindre Muren, CEO, Myklebust Verft, said, “We are delighted that Myklebust Verft has been selected to build these innovative, large-scale hydrogen-powered ferries, showcasing Norway’s level of expertise and ambition and augmenting its maritime hydrogen power infrastructure. We look forward to developing our relationship with Lloyd’s Register as we partner on these complex newbuilds.”
Alf Tore Sørheim, Acting Director General of Shipping and Navigation, Norwegian Maritime Authority, said: “Signing contracts for zero-emission vessels is a significant milestone. The Norwegian Maritime Authority is pleased to see Norwegian shipping companies taking responsibility and driving forward new technologies for reducing emissions, and that they have competent partners to assist them in this endeavour. We look forward to collaborating with LR, the shipping company, and suppliers towards the certification and commissioning of the vessels.”
Gjermund Johannessen, CEO, The Norwegian Ship Design Company, said: “We are excited to finally start building the two hydrogen ferries for Torghatten Nord and look forward to continuing our good collaboration with Torghatten Nord and Myklebust Verft. These hydrogen ferries are unmatched by any other ferries in the world today, with the largest hydrogen installations in a ship ever by a substantial margin. We have developed a unique hydrogen concept using hydrogen’s physical properties for achieving optimal safety. We believe hydrogen will play an important role for zero-emission short-sea shipping.
Through close and fruitful collaboration with Torghatten Nord and their technical team from tender and during all development stages, the project is now more than ready to welcome the well-respected shipyard Myklebust Verft onto the project.”
What if you could get cleaner oil in your application without having to change it?
With RecondOil Box from SKF, you can use the same oil over and over again. In fact, you can get cleaner oil than ever before. Your machines can perform better, and at the same time, your oil can be transformed from a costly CO footprint into a sustainable asset.
Don’t change oil. Change to circular use of oil.
#circularuseofoil
As the maritime industry navigates the complex waters of environmental sustainability, regulatory compliance, and operational efficiency, the transition to alternative fuels and innovative cargo handling solutions has become a paramount concern. At the forefront of this transformative journey, DESMI’s participation in the Posidonia event in Greece this June underscores its commitment to pioneering solutions that not only meet but exceed the demands of modern maritime operations.
DESMI’s newly launched, high-efficient, and reliable Methanol Pumps are setting new standards in the safe handling of alternative marine fuels. Recognizing methanol as a key player in the quest for greener alternatives to fossil fuels, these pumps are designed with a seal-less, mag-drive configuration, making them ideal for managing environmentally sensitive fuels. The Methanol Pump’s insulated composite canister, designed to eliminate eddy loss and ensure low power consumption, along with a built-in PT100 for temperature monitoring, showcases DESMI’s dedication to innovation and safety. Its compact design offers flexible installation options, especially in confined spaces, making it a game-changer in the industry.
mitment to sustainability and operational efficiency. By optimizing pump and fan speeds according to current conditions, OptiSave™ not only ensures significant fuel savings but also assists in complying with the International Maritime Organization’s (IMO) efficiency regulations. This intelligent power management system exemplifies how DESMI’s innovative solutions contribute to reducing the maritime industry’s environmental footprint.
In the realm of cargo handling, DESMI’s Deepwell Cargo and Booster Pumps for Gas and Chemical Tankers embody the pinnacle of efficiency and safety. These pumps are engineered with an energy-efficient design, superior suction capabilities, and proven technology to facilitate the safe and efficient handling of liquified gases. With the ever-changing nature of global cargoes, DESMI remains at the ready to assess and adapt to new cargo types, ensuring its pumps can withstand the most aggressive chemicals and gases today and in the future.
The OptiSave™ Energy Saving System epitomizes DESMI’s com-
With Carbon Capture and Storage (CCS) becoming increasingly crucial in the fight against climate change, selecting the right pump is vital for achieving low operating costs and minimizing CO2 emissions. DESMI’s expertise in pump technology plays a pivotal role in enhancing the efficiency and effectiveness of CCS applications, further demonstrating its commitment to limiting global temperature increase through innovative solutions.
As the maritime industry stands on the brink of a new era, DESMI’s offerings—from its revolutionary methanol pumps and advanced cargo handling solutions to its energy-saving systems—highlight the company’s dedication to leading the charge toward a more sustainable, efficient, and compliant maritime future. At Posidonia, DESMI not only showcases its current product lineup but also its vision for future developments, signaling a steadfast commitment to innovation, environmental stewardship, and the global maritime community’s evolving needs.
Marine Corrosion Service (MCS) is a company providing Marine Cathodic Protection solutions and services in China. The company has an expert engineering team, who is available for the marine ICCP anti-corrosion system & MGPS anti-fouling system.
MCS is also authorized service stations and spare distributors of the main makers in China.
Based upon its experienced engineers, with the best spare part solutions (it has sufficient inventory of the spares to be stand by for the emergency needs), which enable the company to carry out the complete engineering work on the systems with competitive cost.
MCS’s specialties are:
• Technical service & Spare parts for Impressed Current Cathodic Protection Systems (ICCP)
• Technical service & Spare parts for Marine Growth Prevention Systems (MGPS)
• Technical service & Spare parts for Shaft Earthing Device (S.E.D)
• Spare parts (valves/hoses/lights/electronic components/hatch cover spares/pump/motor, etc...)
• Sacrificial Aluminum and Zinc Anodes
The service area: For yards and ports in China, Singapore, South Korea, Turkey, Dubai, Oman, etc...
Armonia Trading & Commercial Applications Limited stands as a beacon of resilience and innovation in the vast expanse of the maritime domain, where swirling currents of geopolitical tensions, environmental imperatives, escalating costs, and evolving regulations perpetually test the waters.
Amidst unprecedented challenges and opportunities, our company remains at the helm, steering towards a sustainable and thriving future. With a distinguished legacy of reliability and ingenuity, we have established ourselves as a trusted ally in the maritime realm.
Armonia Trading & Commercial Applications Limited has been at the forefront of delivering innovative, cutting-edge products and services of unparalleled quality. Serving as agents and service providers for renowned equipment manufacturers, our expertise spans Marine Equipment & Systems, Spare Parts & Technical Services. Our mission is to surpass customer expectations by delivering products and services of the utmost quality in local and global markets, with punctual deliveries and competitive pricing, all while upholding our contractual obligations.
We endeavor to enrich our portfolio by cultivating new alliances based on enduring partnerships and dependable sources capable of fulfilling every ship’s requisites. Prioritizing quality, affordability, reliability, and credibility, we place great emphasis on ensuring that our sources consistently deliver. Furthermore, we aspire to collaborate with partners who share our ethos and principles, aligning our objectives and values, with sustainability at the forefront.
Ms Vanessa Fantazia, Key Account Manager of Armonia Trading and Commercial Applications Limited asserts, “At our company our commitment is to seamlessly integrate the needs of the shipping industry with our partners’ offerings, ensuring mutual satisfaction through reliability, quality, and competitive pricing.”
Our primary objective is to forge strategic alliances and collaborations with manufacturers and suppliers of spare parts and services in the maritime sector, to enhance our service spectrum, broaden our market outreach, and drive innovation. Additionally, we remain steadfast in our dedication to regulatory compliance and innovation, continuously updating our practices to align with evolving regulations and fostering a culture of innovation through research and development endeavors.
Ms. Vanessa Fantazia affirms, “I am truly inspired by our unwavering commitment to establishing impactful collaborations and partnerships within the marine industry. By prioritizing long-term value, regulatory compliance, and innovation, we not only augment our service offerings but also contribute to the advancement of the maritime sector.”
We endeavor to participate in major maritime events and exhibitions, recognizing their significance as pivotal platforms for engagement. As always, we eagerly anticipate our presence at the largest maritime exhibition, the Posidonia Exhibition, where we will be showcasing our capabilities at booth number 2.101. Posidonia remains an indispensable forum for showcasing the latest innovations, fostering meaningful connections, and propelling the Greek maritime sector forward.
Ms Vanessa Fantazia emphasizes, “From pioneering technologies to strategic partnerships, the Posidonia exhibition epitomizes the spirit of progress and collaboration.”
Amidst the ever-evolving maritime landscape, Armonia Trading & Commercial Applications Limited continues to lead the charge in innovation and sustainability. With an unwavering commitment to excellence and client satisfaction, we navigate industry challenges by forging strategic partnerships, embracing regulatory compliance, and fostering innovation.
In this interview, Dimitris Poulos shares their strategic vision and cutting-edge initiatives in response to the maritime industry’s decarbonization efforts. Discover how they are leveraging advanced technologies, partnerships, and innovative solutions to lead the way towards a more sustainable future.
As the maritime industry runs towards decarbonization and transitions to new fuels, which is the Alfa Laval stand on this direction?
Alfa Laval is looking on that direction with high focus and we want to be pioneer on that journey. We are giving very high focus in the alternative fuel technology, as always we had an expertise in fuel treatment , and also to all technologies that are giving energy efficiency on board and reduces emissions, energy, waste and fuel consumption. Through our own R&D , alliances, acquisitions, joint ventures & minor stake holding in new start ups , we are trying to develop more our know how in new technologies that will lead future decarbonization & energy efficiency equipment. Is not easy exercise and there is very challenging to follow all these different technologies and ideas that are coming globally. Our organization is not enough to cover all the possibilities and new ideas that are coming in the market, we have created a special department for this function, and for this reason we are working mainly with partnerships and not only with other manufacturers but also with shipowners that are sharing same directions with us. Currently we are already in the fourth generation of scrubbers & preparing the new version after the last MEPC guidelines, we have configured our separators to work with biofuels, we have a new Waste Heat Recovery system with great success in the market and new energy storage system the E-Power Pack. Also, already we supply methanol booster systems to methanol vessels, we have more than 100 FSS modules installed or under order, we have ready our methanol burners for our boilers, we have a much more efficient Fresh water Generator, and we have a new joint venture with Wallenious to design & produce wind boost
systems, currently under construction the land installation for real scale tests and measurement. And already we are a company that produces air lubrication systems for fuel oil energy savings and already becomes an ALFA LAVAL product with the name OceanGlide. Already we have tested and sold several systems , we are now on the finetuning stage of this technology and will be our main arrow for improving energy efficiency on the ships. The above are some of the new products & developments , for sure more will come soon, ALFA LAVAL wants to lead the way forward.
How challenging is the journey that you describe? Are the decarbonization targets easy to be achieved?
As we explained before , this is very complicated. Maritime industry really will be challenged a lot on that journey as the targets are very strong and strict from the timeframe point of view where other business areas are less. But targets must be financially viable in order shipowners to adopt. And there are so many stakeholders in the process that have to be aligned. In the end will be a cost for the alignment that this will be transferred to the cost of transportation operations. And as you know ship transportation represents the 90% of the global transportation. How ready are governments to absorb this increase of cost? See what is happening with the energy prices and how much governmental policies are vibrating. In any case, a strong financial help will be needed in order maritime industry to be decarbonized and for sure this has to be done step by step in order to absorption of additional costs to be done smoothly As a conclusion, we, our partners, our customers and others in the marine industry are working to achieve the decarbonization we all know must happen. The private sector can and must work faster, but a global framework of policies, resources and financial incentives is needed to make that feasible.
But expect the challenging future there is also the today. How Alfa Laval anticipated and helped customers in recent strong geopolitical crisis events and how you see the market today?
Recently are coming crisis events very challenging for shipping & all industries. Routes have been redesigned and traditional routes have been abandoned. A lot of technical issues must be solved by relevant distance. Alfa Laval with relevant global footprint & network was able to anticipate & really help our customers as we are present in more 100 ports globally and with three distributor centers and global sourcing facilities we have absorbed the supply chain issues generally much better than other manufacturers. The war added some more challenges especially in supply chain of certain parts but our global establishment really help us to anticipate. Market seems very fruitful for the tankers, bulk carriers are turbulent but in the healthy levels , containers are normal and recently freights jump again and generally as average we are in a good momentum. Shipbuilding is continuing with strong numbers despite increased prices of new ships. This fact make us as a global manufacturer of shipbuilding equipment to see also short term period with high optimism about our operational & financial result.
Air lubrication reduces drag and fuel consumption, and it’s never been easier to implement. Alfa Laval OceanGlide gets proven results with fewer compressors, minimal hull penetrations and no large sea chest. So even existing vessels can achieve fuel savings of up to 12%.
The secret is OceanGlide’s unique combination of air lubrication with fluidic technology. Fast and simple to retrofit, it creates an even, controllable air layer across the entire flat bottom. To see why fluidic air lubrication is your path to savings, visit www.alfalaval.com/oceanglide
RightShip, the leading global ESG focused digital maritime platform, and INTERCARGO, the International Association of Dry Cargo Shipowners, proudly launch the Dry Bulk Centre of Excellence (DBCE), an independent, not-for-profit industry organisation dedicated to the administration of the Dry Bulk Management Standard (DryBMS) framework.
DryBMS was developed by INTERCARGO and RightShip, with input from experts and stakeholders across the sector, as an industry tool to raise standards and best practices across safety, security, environmental performance, and social welfare in the dry shipping sector. INTERCARGO and RightShip have worked closely to establish the DBCE to further evolve and disseminate the DryBMS framework.
An independent, not-for-profit organisation entirely separate from its founding organisations, DBCE will be run by an independent management team and will adopt a governance model convened from ship owners, managers, and charterers. This will foster greater cooperation and collaboration between key stakeholders and achieve the common purpose of improving standards and driving operational excellence via active industry participation.
The DBCE Board of Directors will be chaired alternatively by representatives from the community of ship owners/ ship managers and charterers and will have representation from RightShip, INTERCARGO and other industry stakeholders creating a truly collaborative industry initiative.
The DryBMS framework will continue to be accessible to the industry, and, from May 2024, DBCE will maintain a secure portal where ship owners and managers can complete digital self-assessment against the DryBMS framework. Ship owners and managers will then have the optional ability to share the results of their self-assessments with their charterer customers. In addition, DBCE will
establish an independent self-assessment audit verification process for evaluating and verifying actual performance against self-assessments. DBCE will accredit independent auditors to its defined standard, whom companies may engage to perform audits of their self-assessments in their respective ship management offices.
DBCE will be led by a newly appointed managing director, Ian McLeod, who commented, “I am delighted to be driving this new initiative. The launch of the DBCE is the next step for the industry in going beyond compliance and achieving excellence, with the support of the DryBMS framework. The welfare of crew, protection of the environment, and sustainable operation of assets form the bedrock of this initiative, all of which encourage companies towards better operational practices. This benefits not just ship owners, but all in the industry. We urge ship owners, managers, and other stakeholders across the sector, to use this tool and to join us on this transformative journey to make dry bulk shipping stronger, safer, and more sustainable.”
Steen Lund, RightShip’s CEO, stated “It is exciting to be part of a such an important endeavour in lifting standards across dry bulk shipping. DBCE is more than just an administrator for the DryBMS standard; it is a catalyst for collaboration and proactive engagement across the sector. This launch can’t come at a more crucial time –ship owners and managers must be given the resources they need to achieve excellence and strive for zero harm.”
Dimitris Fafalios, Chairman of INTERCARGO, said “We are collaborating in a scheme that is being developed by the industry and for the industry, which will administer a truly robust standard with the help and expertise of those that the industry relies upon to implement and support it. DBCE’s independence is crucial, ensuring the organisation always works for the benefit of the dry bulk industry as a whole.”
In 2024, Tsavliris celebrates 85 years from the commencement of the first Tsavliris shipping company and 60 years from the foundation of Tsavliris Salvage & Towage
The roots and the background behind the establishment of the Group goes back to the mid 1920’s when the Founder, Alexander G. Tsavliris, arrived in Piraeus from Asia Minor and started to build his own business. Young Alexander bought (together with his brothers and uncle) a small, wooden, coal-burning tug of about 10hp, named “ALECOS” and nicknamed “Bourboulas”. Later he moved to London, where he studied and worked, establishing his first company in 1939.
At the end of Second World War he purchased his first ship, a 1,200-dwt tons collier, whilst his first ocean-going ship soon followed as he set about creating a fleet of dry cargo ships. Alexander returned to Piraeus in 1956 to become one of the expanding shipping community’s leading owners. During the following years, Tsavliris purchased a number of war surplus Liberty ships and other secondhand freighters. In the following years, Alexander G. Tsavliris decisively strengthened his dry cargo fleet so that by 1965 he had a substantial fleet of 17 ships.
However, what was destined to mark his shipping course and also proved to be the main future activity of the Group in the maritime arena, was his decision to become engaged in the sector of tugs and salvage operations. In 1964 he established Tsavliris (Salvage & Towage) Ltd. which acquired 17 tugs and salvage vessels totaling 25,000 hp, within the next 18 months. The new enterprise soon became the largest operator of its kind within the Mediterranean Sea and beyond. It offered reliable services, covering Greece’s
entire waters. By the end of 1969, following the addition of further acquisitions, the Alexander G. Tsavliris’ fleet of tugs totaled 29 units and was internationally appraised as one of the major players in this demanding shipping sector, maintaining salvage stations in crucial parts of the world.
As well as being a significant employer, with over 1,000 (mostly Greek) seamen, Tsavliris had long contributed to supporting the Greek economy and had patronised the development of the country’s ship repair sector by repairing and maintaining his fleet locally. He also maintained a Greek-flag (as well Cyprus and British flags) policy for most of his ships. At the beginning of the1970s, he went further by ordering two dry cargo ships from Hellenic Shipyards Skaramanga (owned by Stavros Niarchos). The vessels remained in the Group’s fleet for more than 15 years.
Having created a major international shipping enterprise, Tsavliris sadly passed away in 1973 at the height of his career, at the relatively young age of 59, leaving a great legacy behind. During his 35-year journey in the shipping industry, he had managed to establish a solid group, which among its activities established the largest salvage & towage enterprise ever in the history of Greek shipping.
In mid-1973, his three sons Nicolas, George and Andreas, took over the business and followed in his footsteps. They continued to invest in the family’s ocean-going fleet until the mid-1990s when they decided to focus entirely on the salvage sector amid intense fluctua-
tions within the international maritime markets.
The Tsavliris brothers decided to expand further their salvage & towage business, operating from offices on the Piraeus waterfront. By fully utilising the wealth of experience gained over decades, and assisted by first-class well-trained crews, they moved ahead dynamically. Their activities and accomplishments have demonstrated professionalism and reliability through their active participation in Greek and international organisations and fora. With an impressive record and immence experience gained in dealing with thousands of marine casualties of all categories worldwide, the Tsavliris Group stands ready to assist the global shipping industry with top-quality professional services including:
• Contingency Planning & Emergency Response
• Marine Salvage & Ocean Rescue
• Deep-Sea Towage
• Wreck Removal & Demolition
• Fire-fighting
• Pollution Abatement
• Ship & Cargo Recovery
• Anchor Handling & Offshore Support
• Sub-sea Works
• Casualty Engineering
• Management & Consultancy
• OPA90 Services in USA
•nSPRO Services in China
The Founder of the Group Alexander G. Tsavliris.
Ιn 2023 the Tsavliris Cultural Foundation proudly announced a full scholarship in maritime studies «In Memory of Alexander G. Tsavliris» to commemorate the 50 years since his passing.
To begin with, could you give us a brief overview of Ecochlor and its mission within the marine industry?
Certainly! Ecochlor has been protecting the marine environment for over two decades, initially by introducing a superior ballast water treatment technology and more recently by delving into other “green” maritime solutions. At its core, our mission is based on a commitment to preserve the world’s waterways through innovative and effective energy-efficient technologies.
Collaboration is key to our vision. By partnering with like-minded technology providers, we’re able to optimize maritime operations for shipowners in an eco-friendly manner. This shared effort goes beyond just adhering to industry regulations—it’s about actively contributing to the industry’s shift towards decarbonization.
To what end you might ask? By bundling energy-efficient technologies, we’re supporting shipowners in their pursuit of decarbonization objectives, contributing both to the wellbeing of marine environments and the viability of the maritime industry.
In your opinion, what constitutes a state-of-the-art ballast
water management system today?
To me, what defines a true, state-of-the-art BWMS is its technological efficacy, ease of operation and adaptability to environmental variables that are all supported by unwavering reliability. Additionally, energy efficiency is an indispensable feature in today’s market. It is very important that BWMSs operate within a minimal carbon footprint to align with the new decarbonization goals.
I also believe that the investment of a high-quality system is justified not only by the operational benefits but in the peace of mind it offers. Although cost considerations are inevitable, the value of reliability and compliance both now and with any future regulations cannot be underestimated.
How does Ecochlor differentiate its ballast water management solutions from competitors in the market?
We set ourselves apart from other Makers as the only one to use chlorine dioxide (ClO2) for treating ballast water ─ a method used in the purification of drinking water for over 80 years. This approach differs fundamentally from the UV treatment or Electrochlorination alternatives offered by most BWMS companies.
Not only is the ClO2 treatment method highly effective against aquatic invasive species, but its efficacy remains consistent across a wide range of water conditions, i.e. salinity turbidity and temperature. It does not need retreatment or neutralization upon discharge. As a result, it allows for gravity ballast and gravity deballast operations ─ something not often seen in other technologies.
A key element of Ecochlor’s system is its very low power consumption, making it an ideal choice for shipowners prioritizing energy efficiency alongside the new MARPOL VI compliance goals.
Beyond mere compliance, Ecochlor delivers a system that is extremely easy for crews to operate and is supported by an extensive global service network.
From your perspective, what are some of the biggest misconceptions about ballast water management and decarbonization in the shipping sector?
First off, one big misconception about ballast water management and decarbonization is that they run on separate tracks. The reality is that these issues are both intertwined; a solution for one can influence the other in a significant way and have a positive impact on the other. For example, utilizing an energy-efficient BWMS can reduce a ship’s carbon emissions.
Cost is another area hidden of misconception. The initial expense for decarbonizing ships or retrofitting a BWMS does pose a significant investment. However, this fails to appreciate the long-term savings
or efficiencies gained that, over a vessel’s lifetime, can often outweigh the initial expenses.
Some people in the industry also believe that taking small actions toward lowering emissions are too minor to make a real difference. This could not be further from the truth! With the pressing climate challenges any steps ─ like route or weather optimization, slow steaming, or investing in an energy efficient BWMS or new technology ─ when combined as one can have a very large impact on a vessel’s operation and meet or even exceed the IMO’s 2030 emission reduction goals.
What is the most significant challenge today in ballast water management, and how is Ecochlor addressing these challenges?
I think that one of the biggest challenges right now facing shipowners is the realization that their initial choice for a BWMS was not the best one for their vessel. There are many reasons for that, the system might not be not performing adequately or the BWMS manufacturer has ceased operations and are not providing necessary equipment servicing. Additionally, owners are finding out that many systems are just too complex for the crew to operate correctly and, therefore, hold a very real risk of non-compliance.
Whilst some shipowners have chosen to endure these less-thanideal circumstances, this mindset can introduce long-term complications with their BWMS compliance. This is especially true in the United States where there is no Experience Building Phase and we are already starting to see a significant rise in financial penalties that failed PSC inspection.
Instead, shipowners should be looking at this problem proactively. Reassessment and investment in an upgraded, energy-efficient BWMS, such as our EcoOne® filterless system, allows shipowners to not only comply with environmental regulations but to simplify operations for crew members and at the same time improve the overall energy efficiency of their ship, thus, lowering their carbon footprint.
Could you share a case study that highlights a recent BWMS replacement with Ecochlor’s technologies?
We recently completed a project on an ATB that required the replacement retrofit of an installed UV BWMS. Its frequent operations in shallow and muddy water conditions presented technical challenges for their existing system.
We addressed these challenges by installing our EcoOne® hybrid BWMS, which offers the option of automatically disengaging the filter when its use is not required, or reengaging the filter when the water condition changes. This feature ensured that the system could adapt to the ship’s trade route with varying water types without compromising performance.
Additionally, given the crew’s large number of responsibilities at port, along with limited expertise in the operation of heavy equipment, it was important that the system was easy to use along with reduced demands in running it.
Would you mind explaining the significance of MARPOL VI and the new CII ratings for our audience? How Ecochlor is helping shipping companies comply with its regulations?
The IMO MARPOL VI objectives, together with the newly introduced Carbon Intensity Indicator (CII) ratings, indicate a significant shift in the maritime industry toward more stringent environmental regulations, propelling shipping companies to employ cleaner operating practices. Whilst aiming to reduce carbon emissions from ships, these regulatory measures will require an investment in greener technologies, such as operational adjustments for energy efficiency and the potential of redesign. Shipping companies must adapt to these standards or face penalties, increased operational costs and competitive disadvantages.
Ecochlor is playing an instrumental role in assisting owners to meet these challenges through its portfolio of energy-efficient technologies. Our trio of products have the potential to cut emissions by over 40%, “future-proofing” our client’s ships for their decarbonization targets set for 2030.
By incorporating cutting-edge solutions like our EcoOne® filterless BWMS, coupled with Armada Technologies’ passive air lubrication system (PALS) and Sinotech’s carbon capture and storage system (CCS) it will have the dual effect of helping shipowners reduce their environmental footprint while concurrently enhancing their ship’s operational efficiency.
What are the biggest challenges your clients face in achieving compliance with decarbonization targets?
Our clients face many obstacles when it comes to meeting their emission reduction objectives. Unfortunately, the root of the problem lies in the fact that most alternative fuels aren’t as readily available as one would hope. This is a key concern because without a diverse supply of these cleaner fuels, meeting regulatory benchmarks will be all that more challenging.
On the other hand, there’s quite a lot of buzz around many of the emerging energy-efficient technologies. Solutions, such as our 2nd generation PALS and the latest Sinotech CCS installations, are showing immense potential to owners. As representatives of these technologies, we are well-versed in how these solutions can help shipowners strike that ever important balance between fulfilling their environmental responsibilities in a way that won’t compromise their business success.
Finally, can you tell us about any upcoming projects or partnerships that Ecochlor is excited about in the context of sustainable maritime solutions?
I’m really excited about what the future looks like for Ecochlor! We’re currently in the middle of finalizing what promises to be a game-changing enterprise that will increase our focus on bringing sustainable maritime solutions even further. Whilst I can’t share all the details just yet, you can expect an alliance that brings together Ecochlor’s innovative green technology with a true leader in the environmental maritime industry.
Three
Panos Smyroglou, Ecochlor, VP of Sales & MarketingMaritime professionals are standing at the crossroad between commercial shipping operations and the integration of green technologies to meet new regulatory requirements. The question that looms large over every shipowner, every port, every maritime practitioner, and every innovator is — will the current pace of reducing greenhouse gas emissions (GHG) take us to our targets before we reach that first deadline in 2030 and which would be the safest path to that date and beyond, particularly for the shipowners and charterers that are required to invest towards the targeted GHG reduction?
Shipowners are confronted with the practicalities involved in the implementation of the MARPOL VI regulations, the complexities of the EU ETS policy as well as adjusting to the Carbon Intensity Indicator (CII) ranking — which in and of itself is a pretty daunting feat. But beyond the complexities of these new regulations, the basic principles of achieving fuel efficiency, crew training, and the integration of green technologies onto these vessels are challenges that deserve your serious consideration.
The stakes are high, but I believe that the rewards are even greater! Energy-efficient technologies not only align with current decarbonization targets but also provide a competitive edge to owners looking to lower fuel consumption.
Innovative technologies once considered unattainable are now available, providing concrete ways to cut emissions without sacrificing shipping economics. Achieving true shipping efficiency requires a collaborative effort involving a few key technologies rather than relying on a single solution.
Ecochlor presents a trio of cutting-edge and energy-efficient equipment designed to enhance vessel operations while achieving a remarkable 40% reduction in CO2 emissions. The bundled package includes the EcoOne® filterless ballast water management system (BWMS), Sinotech carbon capture and storage (CCS), and Armada Technologies’ passive air lubrication system (PALS). These solutions are not just speculative - they are actively being installed on ships, with operational data being collected right now to optimize their performance at sea.
Ecochlor has almost 400 BWMS installed or on order and more than 23 years of experience in operations. In 2021, our company introduced the EcoOne®, which has redefined the ballast water management model by offering a filterless system that is both exceedingly efficient and remarkably simple to operate and has the added advantage of very low power. With our responsive global service support, the EcoOne® provides shipowners not just with a compliance solution but an eco-friendly, economical, and crew-friendly technology that stands out in the BWMS field.
At the helm of efficiency, Armada Technologies’ (Armada) has introduced to the market the world’s first compressor-free, hull air lubrication system offering vessel owners genuine fuel savings.
Armada’s PALS uses the ship’s forward motion to create a precise air: water mixture for lubrication. Unlike traditional methods that rely on high-energy compressors, PALS consumes significantly less power. It has three operating modes depending on the sailing conditions, i.e. either fully passive or active air or active water, the latter by utilizing small capacity water pumps at slow steaming. With its performance control system and machine learning, PALS ensures far better bubble control and delivery vs. 1st generation ALSs.
In early September, Armada plans to install their PALS on a Cool Company Ltd. (CoolCo) vessel, a major LNG carrier company. Armada, along with support from Ecochlor, will handle the design, engineering, procurement, and support for this exciting technology CoolCo will then conduct sea trials and share performance data with Armada following ISO or ITTC guidelines.
Sinotech “raised the game” in marine operations with its adaptable CCS technology. Engineered for versatility, their modular design integrates with both existing fleets and newbuildings. Whether partnered with an existing exhaust cleaning system (scrubber) or stand-
• No filter!
• No minimum pressure required
• 100% flow rate in all ports
• 7kW power consumption no matter what equipment size
• USCG & IMO APPROVED
• Only minor modifications to the ballast piping are needed to retrofit Senza BWMS
Contact us
ing alone for low sulfur fuel-operated vessels, Sinotech’s solution is primed for energy-efficiency. The scrubber has options tailored for open-loop and hybrid systems, which can be tailored to meet your ship’s specific demands. The patented amine solution can be stripped of the absorbed CO2 at 90°C, 25% below the industry standard. Along with the efficient heat recovery design, it results in a very low energy demand per ton of captured CO2. The Sinotech liquefaction process is the most efficient way to store CO2 simplifying onshore disposal logistics.
In January 2024, Sinotech completed, the first installation on a 95k DWT bulk carrier, the Alkimos, owned by Victoria Steamship. In addition, Ecochlor and Sinotech have entered a Letter of Intent (LOI) with the Greek shipowner, Diana Shipping. Under the LOI, plans are underway to equip Diana Shipping’s capesize dry bulk carrier, the MV G.P. Zafirakis, with Sinotech’s scrubber and CCS technology. The system promises to capture and liquefy up to 25% of CO2 emissions!
For this pivotal project, Sinotech has conducted a comprehensive feasibility study and will manage all phases of the implementation-from detailed engineering to providing a complete turnkey solution as well as crew training and ongoing support to achieve type approval certification for the installed system. Additionally, the offloading and responsible disposal of the stored CO2 will be facilitated by Sinotech at a network of expanding facilities in China. At the same time, Sinotech’s close cooperation with the Global Center of Marine Decarbonization (GCMD) in Singapore, will ensure that the risk assessment and all reporting, including the Life Cycle Assessment (LCA) of the offloaded LCO2 are done in a professional manner. In addition, reflecting last month’s MEPC 81 meeting, the very likely local utilization of the CO2 in China, including methanol production, will ensure MAXIMUM carbon credits for the Owners!
Conclusion
My call to action is clear: Don’t stay idle. It’s important that these innovative solutions are used in your charge toward sustainability. The time for action is unquestionably right now.
Technologies like EcoOne®, Armada Technologies, and Sinotech are leading the way, guiding the maritime industry towards a greener footprint where operations are not just ecoconscious but also remarkably efficient and compliant with global environmental regulations.
Decarbonization isn’t just a buzzword; it’s an inevitable future.
Shipping decarbonization will require a broad and resolute commitment to alternative fuels, operational best practises, and energy efficiency enhancements. With zero carbon fuels further out on the horizon, the pursuit and deployment of Energy Efficiency Technologies (EETs) is under the spotlight for the near-term reduction in emissions they deliver. EET’s allow owners to wring every last calorie from the fuels we currently burn, simultaneously creating environmental benefits and commercial savings. Steven Jones, CEO of the Sustainable Shipping Initiative, emphasizes this, stating: “As the maritime industry works to meet ambitious emissions reduction targets, prioritising energy efficiency is a strategic imperative that pays dividends both financially and environmentally. The return on investment for ship owners is clear - lower operating costs, compliance with regulations, and a smaller carbon footprint that appeals to charterers and cargo owners seeking greener supply chain options. Energy efficiency is a rare opportunity where economic and environmental interests are perfectly aligned for the benefit of the entire shipping value chain.”
To realize these opportunities, its vital to consider what is the supply landscape and market dynamics of EET both now and in the coming years. Over the past decade we have witnessed extensive fleet deployment of lower cost, and well proven, flow modifying devices such as propeller boss cap fins and Mewis Ducts. By accepting their technological maturity, it’s safe to say that the industry has embraced the ‘novel’ and it has become ‘normal’. Similarly, advances
and onboard demonstration of wind propulsion technologies have enabled steady uptake. We continue to see substantial time, effort and resource applied to the deployment of wind technology, whether that be at the IMO MEPC, advocacy groups (e.g. IWSA) and direct marketing through the many technology providers. Air Lubrication systems have seen rapid uptake based on strong pay back periods without the need for quite such vocal independent industry advocacy and are now widely deployed across different ship categories and operating profiles. Richard Tyrrell, CEO of CoolCo, comments: “The need to improve the environmental performance of shipping is clear and we have embarked on this journey with a $75 million investment program that is focused on the retrofit of EETs to our LNG fleet. Next generation Air Lubrication systems are an important part of this program with positive results expected from an installation later this year.”
This then begs the question as to why the ratio of sales of wind propulsion technologies to Air Lubrication is 1:4 in favour of Air Lubrication and why the number of flow modifying device orders continue to dwarf that of ALS and wind propulsion technologies orders combined.
The claimed performance of wind propulsion technologies is extremely encouraging and that, as a technology category, wind assisted propulsion must play its part in the makeup of a decarbonized shipping future. That said, the sales figures appear somewhat paradoxical. The underlying drivers for this are nuanced and not simply a result of claimed performance, total cost of ownership and/ or relative ease of operability between the two technology categories. Instead, more subtle drivers predominate, or at least heavily influence decision making.
What is certain is the question should not be whether to install energy efficiency technology or not, but rather a question as to how to fit ALS, flow modifiers and wind assisted technologies in a commercially attractive manner. To set a new course towards clean maritime operations the industry must think bigger and more aggressively, set aside decision making based rigidly on archaic go- or no-go payback period durations and be willing to make environmental decisions built on commercially solid foundations. This isn’t purely the responsibility of the owner, or the technology provider, but instead requires a concerted effort of a much boarder spectrum of stakeholders.
Whilst this may sound a bit “I have a dream”, it is certainly possible. Sustainability issues are interconnected and to drive meaningful change, the industry must take a collaborative systems approach. It is my belief that the missing piece of the puzzle could be as targeted as EET technological performance certainty.
With technological certainty, we develop a self-supporting positive feedback loop that drives EET investment, delivers higher margins and creates step change environmental improvements. Without it we create a considerable set of obstacles, any one of which could derail an investment decision. For instance, if the Maker has high
performance certainty, they can offer reliable and tight tolerance performance guarantees. If the owner has tight tolerance performance guarantees, they can reliably accept more commercially onerous terms in charter party agreements and in doing so offer more competitive vessels to the market. If the charterer has more competitive options, they can safely assign value and share in the benefits of the technology with the owner in the form of higher day rates and/ or extend charter lengths. As a result, the owner can invest in more specialized, higher CAPEX new build projects, safe in the knowledge they will realize a solid return on their investment whilst simultaneously enhancing resale values.
Bolstering this further, if the financier has performance certainty, they can reduce the cost of capital available to owners to fund (potentially multiple) energy efficiency technology installations. As a direct result the EET business case becomes more compelling and, in many cases, a ‘no brainer’. This opens the door to multiple EET installations that together produce savings far greater than the sum of their constituent parts. With zero carbon fuel alternatives so far on the horizon, performance certainty may well be the much needed tool to meaningfully decarbonize shipping in the short term, whilst providing an enabler for the zero carbon fuels of the future.
The question then becomes, how can we deliver performance certainty in our energy efficiency offerings when a lot of the factors influencing performance are external, environmental, and completely out of operational control; to the example of wind propulsion technologies, this would constitute geographically variable wind speed and direction. A nice resolve for this predicament is to ‘accept that which cannot be changed, to change what can be changed and gain the wisdom to know the difference’.
Air lubrication providers in particular could have the most to gain from a relentless focus on what can be controlled. For instance, the
boundary layer of an air lubricated vessel is, in essence, a black box. We can ‘enter inputs’ in pursuit of higher performance, but realistically the behaviour of a bubble in the extremely dynamic boundary layer is, in absolute terms, unpredictable. Even the creation and injection of the bubbles is fraught with uncertainty. Too big and the bubbles break apart, coalesce or are sucked out of the boundary layer, too small and it does not deliver sufficient air to displace sea water and create meaningful frictional resistance reduction. The method of injection is also critical. Supply at too higher pressure and the majority of air is pushed through the boundary layer and wasted to ocean, supply at insufficient pressure and air is trapped within the system, unable to overcome the hydrostatic pressure needed for boundary layer aeration. Low control ALS is fraught with factors that are not within the commercial discretion of the Maker or even owner in certain instances. For instance, vessel speed, vessel utilization, hydrostatics or sea state are all either orders placed on the vessel or are external environmental states. However, what can be adapted are the number, type and set points of the ALS control mechanisms. With the proper management and interpretation of raw performance data we can begin to identify patterns of performance and ultimately optimize the output across speed, draft and environmental operating states. Over time and applied consistently, we can begin to develop technological certainty.
This is the approach Armada Technologies have prioritized and heavily invested in. With discreet control of bubble size, air:water ratios and the momentum balance at point of injection, Armada’s Passive Air Lubrication System (PALSTM) is well placed to deliver verifiable patterns of performance and deliver it on an ongoing basis. Taking a first principals design approach, questioning unsupported yet accepted truths and relentlessly experimenting in the world’s preeminent test facilities, we have applied fresh knowledge that has supported the design and engineering of the ground breaking PALS system.
Imagine your ship’s ballast water management system (BWMS) has become the one piece of equipment that generates the most tension and operations issues every time your ship enters port.
Once a mere afterthought, the system now poses a multitude of challenges, from complex operating requirements that leaves the crew struggling, to non-existent service support causing vessel downtime and potential loss of revenues. And, what about those BWMSs that still require very expensive United States Coast Guard (USCG) Type Approval updates? Or, the systems that were not designed with energy efficiency in mind and now have a costly impact on overhead costs when using ship-to-shore power and which may even impact the vessels’ efficiency rating?
The harsh truth is that many existing BWMS, though compliant when installed, are now unable to meet the strict standards set out in the IMO BWM Convention and the USCG protocols. For shipowners, these issues are not petty annoyances, rather they involve monetary losses, compliance liabilities, and operational inefficiencies ─ a
trifecta of problems threatening to drag down both profit and efforts towards sustainability.
Amidst these various challenges, one question stands out: Rather than continue to try to patch up the old one, is it in fact time to consider a new ballast water management system?
If choosing replacement over expensive modifications, a window of opportunity presents itself to the shipowner — a chance to correct previous choices, a chance to do better.
It would be illogical for shipowners to replace a deficient BWMS technology with an identical one and then to expect different results, such a decision could be considered madness! Learning from the past and anticipating future regulations are essential steps in selecting a long-term viable solution for ballast water management. Today’s choices must account for system effectiveness and flexibility as well as operational simplicity for the crew. In addition, Carbon Intensity Indicator (CII) conformity, and the impending goals of MARPOL Annex VI, necessitate that power efficiency be a top priority.
For those seeking answers, take comfort in knowing there is a reliable, tried-and-tested solution to this problem.
The EcoOne® filterless BWMS from Ecochlor, with its hybrid options, offers a combination of efficiency, reliability, and simplicity in ballast water treatment and stands out for its exceptional energy-saving abilities. It was engineered to have limited impact on shipping operations, and operates on remarkably low energy—just 10 kW for processing 3,500 cubic meters of water per hour (m3/hr.). This performance marks a significant difference in many competitor systems, which can consume upwards of 500 kW under suboptimal conditions. The adjustment in power consumption isn’t just marginal; it’s a radical shift that reduces operational expenses and efficiency to a new level.
The EcoOne® BWMS offers several compelling advantages:
• Simplicity and Reliability: It’s remarkably easy for the crew to operate without the need for frequent adjustments whilst remaining highly effective in all water types.
• Energy Efficiency: There are significant reductions in power requirements, with no need to treat or neutralize when de-ballasting. The system also offers gravity ballasting options which present even more opportunities to minimize energy usage.
• Regulatory Assurance: The system meets the all the IMO and USCG regulatory standards for approved treatment flow rates up to 16,200 m3/hr.
• Unrivaled Support: There is a dedicated global service team that is ready to provide support in three time zones to maximize vessel uptime along with reducing any maintenance headaches. By integrating the EcoOne® Filterless system, a vessel ensures compliance not only with the current BWM regulations but also supports with the
ship’s further-reaching objectives of reducing fuel consumption and carbon emissions for MARPOL VI goals.
Everyone recognizes that the costs associated with upgrading or replacing BWMS can be considerable and include not only the system’s capital costs but also installation, maintenance, and operational overheads. Despite these costs, the long-term benefits justify the investment. Lower maintenance expenses, reduced risks of non-compliance penalties, and the wider operational flexibilities that comes from a more versatile technology solution are just a few of the financial incentives.
Additionally, non-compliance can be a costly gamble to shipowners. Consider the recent crackdown by the U.S. EPA – large financial settlements, expected to increase in the future, serve to remind everyone that non-compliance is nothing short of playing roulette with the company’s operations and industry standing. Compliance is not just about regulatory obedience but about adopting systems, like the EcoOne® filterless BWMS, to avoid these problems in the first place!
With the clock ticking, compliance with Ballast Water Management Systems (BWMS) isn’t just recommended, it’s a critical necessity. The countdown to meeting D2 standards by September 2024 is on, followed by the end of the BWMS “Experience Building Phase.” At this point, inaction, or delay in retrofitting an improved solution for BWM treatment for your ship is a recipe for failure. And, choosing to replace BWMSs with a subpar system, isn’t a viable option; the risks are too great and the losses are too significant.
Unithai Shipyard and Engineering (UTSE) strategically located within the deep sea port Laem Chabang, closed to Bangkok, Ko Si Chang and Map Ta Phut port, which is at the heart of Thailand’s chemical and oil tankers, container, dry bulk, car and offshore trades. Our accomplished team are committed to the highest level of quality with a capacity to repair more than a hundred vessels per year.
Unithai Shipyard and Engineering (UTSE) strategically located within the deep sea port of Laem Chabang, closed to Bangkok, Ko Si Chang and Map Ta Phut port, which is at the heart of Thailand’s chemical and oil tankers, container, dry bulk, car and offshore trades. Our accomplished team are committed to the highest level of quality with a capacity to repair more than a hundred vessels per year.
Land area 688,000 m2
Unithai Shipyard and Engineering (UTSE) strategically located within the deep sea port of Laem Chabang, closed to Bangkok, Ko Si Chang and Map Ta Phut port, which is at the heart of Thailand’s chemical and oil tankers, container, dry bulk, car and offshore trades. Our accomplished team are committed to the highest level of quality with a capacity to repair more than a hundred vessels per year.
Unithai 2 191 x 34.4 m Upto 50,000 DWT
Unithai 3 300 x 49.6 m Upto 180,000 DWT
Quay 380 m, 1 x 45 t crane
Floating Crane, 1 x 100 t
Land area 688,000 m2
Land area 688,000 m2
Unithai 2 191 x 34.4 m Upto 50,000 DWT
Land area 688,000 m2
Unithai 2 191 x 34.4 m Upto 50,000 DWT
Unithai 3 300 x 49.6 m Upto 180,000 DWT
Unithai 3 300 x 49.6 m Upto 180,000 DWT
Unithai 2 191 x 34.4 m Upto 50,000 DWT
Quay 380 m, 1 x 45 t crane
Floating Crane, 1 x 100 t
Quay 380 m, 1 x 45 t crane Floating Crane, 1 x 100 t
Unithai 3 300 x 49.6 m Upto 180,000 DWT
Quay 380 m, 1 x 45 t crane
Floating Crane, 1 x 100 t Moo 3 Tambon Tungsukhla, Sriracha District, Thailand 510 5559 sbd.marketing@unithai.com Web : www.unithai.com
Location: 48 Moo 3 Tambon Tungsukhla, Sriracha District, Chonburi 20230, Thailand
Email: sbd.marketing@unithai.com Web : www.unithai.com
Phone : +66 65 510 5559
Location: 48 Moo 3 Tambon Tungsukhla, Sriracha District, Chonburi 20230, Thailand
Email: sbd.marketing@unithai.com Web : www.unithai.com
Phone : +66 65 510 5559
Faced with the dual conditions of ever-increasing environmental regulations and the practical realities of global trade initiatives, the marine industry stands at a critical period. With many emissions-reducing technologies to choose from, onboard Carbon Capture and Storage (CCS) has emerged as a key player in this transition. Shipowners and operators are now at the forefront of controlling emissions at sea and selecting the right CCS system is essential.
This article will explore the key attributes of an effective Carbon Capture and Storage application for maritime use, showcasing the adaptability, performance, and green credentials of Sinotech’s CCS solutions. We will take an in-depth look at how the Victoria Steamship Company leveraged this technology on their vessel, the ALKIMOS, to meet their environmental and operational goals.
CCS presents a compelling proposition for shipowners, especial-
ly in conjunction with an exhaust gas cleaning system (EGCS or scrubber) ─ with an opportunity to significantly cut carbon intensity on their fleet, thus aligning with both CII mandates and MARPOL VI objectives. Additionally, operators can sustain long-term financial gains stemming from lower fuel oil prices and reduce the cost of emission certificates (e.g. EU ETS).
When it comes to a complex, long-lasting investment in CCS technology, operators must consider two important factors to ensure the most beneficial and seamless integration. The first is directed by functionality, including the extent and efficiency of CO2 capture, amine recycling capabilities, and the design’s compatibility with existing vessel systems along with the length of trade routes. The second is the cost, not only in terms of initial purchase but also in the long-term impact on operational efficiency and logistics.
Sinotech CCS has emerged as a leader in maritime carbon capture technology, benefitting from years of operational experience and innovation of Sinopec’s land-based CCS at power stations throughout China, and now as having the first CCS system installed on a bulk carrier. The installation, aboard Victoria Steamship’s vessel the ALKIMOS, combined with an EGCS, was completed within a threemonth period, showcasing Sinotech’s ability to tackle challenges head-on.
Victoria Steamship recognized the pressing need for drastic emission reductions to meet environmental standards and to better align with MARPOL VI 2030 requirements. Given ALKIMOS’s substantial main and auxiliary engine setup, an innovative CCS solution to cut its carbon output was necessary.
Sinotech addressed these demands with a customized carbon capture solution, involving an energy efficient amine-based absorption process that captures carbon emissions from the ship’s exhaust without the requirement for a stripping tower and CO2 liquefaction setup. The Sinotech CCS technology can capture up to 95% of CO2 emissions, with typical capture rates of 25 - 35%, balancing fuel consumption with on board CO2 storage and length of trading routes.
The ALKIMOS CCS package engineered by Sinotech CCS included:
• An open-loop scrubber to curtail SOx in exhaust gas;
• A CO2 absorption tower for direct exhaust gas carbon removal;
• Two 10 kW rotor sail wind turbines to provide sustainable electricity on board.
The scrubber allows the vessel to benefit from the price gap between HFO and expensive low sulfur fuels and cools down the exhaust gas followed by the CO2 removal. At this stage, a custom-blend amine solution absorbs the carbon dioxide and a clean exhaust gas is released via the funnel whilst the saturated amine solution is stored in converted ballast tanks.
The ALKIMOS installation targeted a capture rate of 15% CO2 emissions, around 0.5 t/hour, and included storage sufficient for a 40-day cruising range.
With the current development of and capital investment in CO2 trading hubs and terminals, global availability of CO2 offloading infrastructure in ports is expected to increase significantly in the next few years. Until then, offloading of captured CO2 from the ALKIMOS will be arranged through Sinotech, using their partner’s land-based amine recycling and CO2 storage facilities operating in specific Chinese ports.
By optimizing storage as a saturated amine solution in modified ballast tanks, Sinotech CCS delivered reduced capital expenditure (CAPEX) and complexity during installation as well as lower onboard power consumption. Its CCS efficacy was proven after commercial vessel operations commenced and with a successful CO2 offloading in China. Through this case study, Sinotech illustrates its dedication to moving the maritime industry toward a sustainable future through Carbon Capture and Storage systems.
Conclusion
Phil Gao, Managing Director of Sinotech said: “The achievement of our CCS system on the ALKIMOS affirms our steadfast commitment to a sustainable maritime industry. It stands as evidence that ecological responsibility can coexist with excellence in shipping operations paving the way for a greener tomorrow in the maritime industry.
By choosing Sinotech CCS, a shipowner can advance their fleet’s efficiency and adaptability as well as highlight the company’s drive for a cleaner, more responsible shipping world.”
In summation, the selection of an appropriate Carbon Capture and Storage system is not just a commitment to environmental stewardship, but also a strategic decision to place your shipping business at the forefront of operational efficiency.
More than a trader, more than a repairer, more than a
TURBO GENERAL provides all types of turbochargers, repair and maintenance services from various manufacturers, including Accelleron (formerly ABB), MAN, PBS, MET, NAPIER, KBB and IHI. With an extensive inventory of new, genuine, reconditioned, alternative and OEM spares of advanced quality, stored in Piraeus, Singapore, Shanghai, Rotterdam, sourced from independent factories across Europe, Greece, South Korea, Japan, Turkey, India, the Czech Republic and China, TURBO GENERAL can supply parts immediately reducing transportation charges. Operating form HQ within 2,000 sqm facilities next to Skaramanga shipyards in Athens Greece, all turbocharger spares are handled on-site.
TURBO GENERAL also offers top-notch turbocharger training seminars via local marine academies, offering in-depth instruction on safe operations, maintenance and service. Its commitment to excellence ensures that participants gain the skills and knowledge needed to optimize turbocharger performance and ensure sustainability.
TURBO GENERAL has also established its own workshop in Shanghai Pudong, serving the nearby islands. Together with her experienced flying team of engineers and the experienced partners around and a tested network in major ports such as Singapore, Istanbul, Rotterdam, Antwerp, Barcelona, Napoli, Cyprus, Dubai, South Africa, Nigeria, Texas, Chile and all the major Australian ports can attend any regular maintenance or damage any time 24/7.
With 50 years of uninterrupted operation and under the same registration number, TURBO GENERAL maintains its commitment to excellence by implementing ISO 9001, 45001, 14001 awarded by LR.
GET STC (General Engineering Technology) is based in four locations Perama, Piraeus, Skaramangas and Tuzla Turkey. It is fully equipped to undertake any machinery work, construction and manufacturing of spare parts according to sample in our workshop facilities.
GET STC has in house engineers and technicians to support any technical challenge and a flying team ready to travel worldwide. Our professional office staff, which includes ex technical managers, runs a dedicated claims department dealing with H&M claims. Technical consultation on complex technical matters and shipyards specification preparation and representation of them is within our scope of business. Our experience sales and trading department is ready to provide solutions for engine room spares for main and aux engines of all the makers, bridge equipment, accommodation and ship supplies.
When or where GET STC engineers cannot travel, there is a network of approved suppliers and workshops worldwide who can undertake underwater surveys, engineering projects in China and the Gulf. Marine EMHI in OMAN is our partner for local ports and projects.
GET STC serves as the exclusive representative of reputable foreign companies including SKF RECONDOIL (ex Europafilter) (a revolutionary oil cleaning product) and SAMOA products such as diaphragm pumps, made in Spain, superior to other similar products and very easy in maintenance with stock available in Piraeus, Germany and Spain. It has also representations of various types of sensors and transmitters by Micro Sensor with stock in Greece and China. Other representations include ICCP Anodes and Earth Grounding Devices, which are highly competitive in all Chinese ports and Istanbul where its principals maintain stock. Via other representations GET STC offers Hydraulic seals by Kintowe, fire protection products by Huoke, hydraulic cylinders by Haite, accommodation systems by Kangbo and laser cutting, and cladding equipment by Senfeng.
GET STC is also taking its first steps in technical management and procurement for companies engaged in the transportation of livestock, as well as bulk carriers.
GREEN MARINE specializes in technologies that are currently applicable for CO2 emission reduction on vessels, representing reputable Chinese, Korean, and European makers for rotor sails, scrubbers, water ballast treatment, air lubrication and more.
GREEN MARINE serves as representative of foreign companies such as Bluesoul and the Norwegian Torgy LNG which are makers of scrubbers and LNG and Hydrogen solutions, Wux¡ Bright Sky Electronics (BKSY) who deal with BMWS VDR and fire extinguishing systems and alarms, Great Honor International Development with clean energy equipment, Clustertech who provides weather intelligence services, Hiconics of Media Group, a producer of VFD and energy storage systems, Lyen Marine who deals with CPP, thrusters and fuel optimization, and Grit Ocean who deals with cables, outfitting and propellers. Finally, our Turkish principals, Bulutlu Marine are producing electrical switchboards and energy saving studies.
VESSEL JOIN is startup company that takes a step beyond to the traditional manning agency. Through its online platform, it directly connects shipping companies with seafarers. The moto is ‘find seamen online’!!
TURBO GENERAL, GET STC (General Engineering Technology), GREEN MARINE and VESSEL JOIN along with their affiliated companies GMSS (General Marine Services and Shipmanagement) and GENERAL CHAMBERS & CONSULTANCY OFFICES operate under the umbrella of A General Group of Companies. Each entity brings its unique expertise and services to the maritime industry, ensuring comprehensive solutions for clients worldwide. We continue the expansion of our Group looking forward to embracing more partners who share the same values and principles.
You can visit the companies of A General Group during Posidonia exhibition at Hall 3, stands 3.167 and 3.325.
What sets BPCO LTD apart is not only its comprehensive range of services but also its unwavering commitment to excellence and customer satisfaction. With a dedicated team of professionals and a personalized approach to client relationships, the company has earned a reputation for reliability, integrity, and innovation in the maritime industry.
As BPCO LTD continues to expand its global footprint and drive innovation in the maritime sector, it remains steadfast in its mission to deliver exceptional value and quality to its clients, setting new benchmarks for excellence and reliability in the shipping industry
BPCO LTD’s commitment to excellence is reflected in its diverse range of services, which encompasses every aspect of the maritime supply chain. From drydock repairs and energy efficiency devices to aftersales services and support, the company offers a holistic suite of solutions designed to enhance vessel performance, optimize operations, and minimize downtime. Among the key services offered by BPCO LTD are:
Green Technology Services
Through our exclusive collaboration with Becker Marine Systems,
we’ve gained access to cutting-edge technologies and expertise, including energy-saving devices, maneuvering systems, and rudder technology. Our focus is on offering clients the latest advancements in energy efficiency and environmental stewardship, empowering shipping companies to achieve their sustainability goals while optimizing operations with new technologies.
Furthermore, in line with our dedication to providing top-tier green technology services, BPCO LTD has recently ventured into the realm of wind propulsion through our partnership with Deal Eng. We’re harnessing the power of Rotor Sails to further enhance sustainability efforts within the shipping industry.
Additionally, we’re excited to announce our new exclusivities with Jungwoo, a renowned provider in the field of green technology. This collaboration covers a wide range of offerings including LNG FGSS (Liquefied Natural Gas Fuel Gas Supply Systems), LH2 FGSS (Liquid Hydrogen Fuel Gas Supply Systems), V.I.P (Vacuum Insulated Pipe), and D.W.P (Double Wall Pipe). These cutting-edge solutions aim to revolutionize fuel storage and transport, ensuring maximum efficiency and safety in energy operations. Moreover, we value our partnership with FURUI Cit Co., Ltd, a trusted name in the industry, specializing in FUEL TANK TYPE-C and CRYO-
GENIC STORAGE solutions. These innovative technologies play a crucial role in facilitating the storage and transportation of fuels and cryogenic substances, aligning perfectly with our mission to provide comprehensive and sustainable solutions to our clients.
Prioritizing Green Solutions, BPCO LTD exclusively represents PANASIA Systems, global leader in eco-friendly and energy-efficient solutions focusing on air quality, water quality, and hydrogen business. Our commitment extends to Carbon Capture, Utilization, and Storage (CCUS), where we utilize carbon dioxide for commercial applications through the PAN-CCUS™ system and the PANAGEN Hydrogen Generation System, both developed by PANASIA for the marine industry. We’ve also incorporated Cold Ironing Systems (AMP), into our offerings. AMP systems allow ships to connect to shore-based electrical power while docked, significantly reducing emissions and noise pollution generated by onboard generators. By enabling vessels to rely on cleaner shore-based electricity instead of burning fuel while in port, AMP systems contribute to a substantial reduction in greenhouse gas emissions and improve air quality in port areas.
Aiming into the green technologies we have agreement and close cooperation with Sea Forrest which represent the pinnacle of sustainable energy production, harnessing renewable sources such as solar, wind, and hydroelectric power to generate electricity without harmful emissions. These innovative systems play a pivotal role in combating climate change and promoting a greener future by providing reliable, low-carbon energy solutions for communities and industries worldwide. Through our European Supplier we aim to provide more and more options for the Greek shipowner.
HYUNDAI LIFEBOATS (HLB), represented exclusively by BPCO LTD since 2018, a leading worldwide supplier for: GRE/GRP Pipes, Lifeboat & Davit, Part Supplies, Inspection & Repair Sox Scrubber Dampers.
HLB has ventured into the production of GRE pipes with the goal of mitigating discharges.
Our services extend beyond new building projects to encompass retrofits, ensuring that existing vessels can also benefit from our green technology offerings.
With a focus on sustainability and efficiency, BPCO LTD supplies cutting-edge fuel additives designed to improve efficiency, reduce emissions, and enhance fuel performance in marine engines. By leveraging the expertise of Power Research Inc, BPCO is able to offer our customers tailored solutions that not only improve engine performance and fuel efficiency, but also align with our commitment to sustainability.
Continuing its commitment to green initiatives, BPCO LTD expands its partnerships by including companies specializing in cutting-edge Green Technology devices. This includes collaborations with providers of advanced batteries and innovative wind assistance rotor sails engineering.
Drydock Repairs: BPCO LTD provides expert drydock repairs to ensure the seaworthiness and operational efficiency of vessels of all sizes. The company takes pride in its partnerships with some of the largest shipyards globally, cementing its position as a leader in maritime repair services. Annually, the company undertakes approximately 120 drydock repairs, showcasing its expertise and commitment to excellence. These operations span across key shipyards in
the Far East, including China, Indonesia, and Malaysia, as well as extending into the East Mediterranean region, Greece and Turkey.
As the exclusive agent in Greece for Cernaval Group Shipyard in Algeciras and MMHE Shipyard in Malaysia, BPCO provides access to world-class facilities and technologies, guaranteeing top-notch quality and efficiency in every repair project.
Underwater Services: With a team of skilled divers and technicians, BPCO LTD specializes in a wide range of underwater operations, including hull inspections, cleaning, and repairs. The company’s commitment to excellence is further underscored by its exclusive collaborations with industry leaders such as Underwater Shipcare, Caribbean Sea Diver, SHIPLUS Marine and Underwater Services Inc. Whether it’s components for Impressed Current Cathodic Protection, Marine Growth Prevention System, or Shaft Earthing System and Rudder Bonding System, clients can rely on BPCO LTD to provide the right parts to keep their vessels operating at peak performance. Our partnership with Oceana Marine Services enhances our ability to meet the diverse needs of our clients, further solidifying our commitment to excellence in underwater services providing ICCP technical service, MGPS and Shaft Earthing System (S.E.S) and Rudder Bonding System.
Afloat repairs: BPCO LTD has developed considerable knowledge and wide experience in the Maritime Sector. We strive to deliver fast, innovative, efficient, and integrated maritime services to our clients. Our network consists of companies fully equipped and manned by experienced personnel that can offer quality services. By representing exclusively SHIPLUS Marine Services and Cromwell S.A, our network consists of companies that are fully equipped with state-of-the-art facilities and manned by seasoned professionals. Whether it’s ship repairs, maintenance, or emergency interventions, we have the resources and capabilities to deliver prompt and reliable solutions.
Supply of Genuine Spare Parts: The company serves as a reliable source for genuine spare parts, ensuring that shipping companies have access to high-quality components and materials to support their maintenance and repair needs. BPCO LTD supplies genuine HSD (ex-Doosan) Engines for marine equipment, ensuring top-notch performance and reliability for maritime operations.
Partnering with Taehwa Kalpa, BPCO LTD is able to offer one of the key products that the company is known for- its compressed non-asbestos joint sheets and gaskets. By offering a comprehensive gasket package, the company caters to a broad spectrum of industries, thereby reinforcing its position as a leading gasket manufacturer in Korea.
After Sales Support and Troubleshooting: BPCO LTD stands firmly committed to ensuring the satisfaction of its customers by offering dedicated after-sales support and troubleshooting services. With a focus on maintaining smooth operations, BPCO LTD’s team of 15 service engineers is readily available to address any issues or concerns that may arise. With the biggest and privately owned Service Centers in Greece and Manila, our experienced team undertakes crew training, equipment troubleshooting and aftersales management for all Panasia Systems. Additionally, BPCO boasts a warehouse stocked with Panasia Spares, ensuring prompt access to replacement parts when needed.
BPCO’s Service Engineers undertake all the MGPS & ICCP technical services in all East Med Shipyards.
Entering the realm of Tradeforce, a company specialising in medium and high speed diesel engine spare parts supply and technical support.
Nestled at Alimos in Greece for more than a quarter century, this is where reliability and care transcend mere words—they are the core values extended to all customers. Open doors and viable solutions await, whether it is for repairs, maintenance, or just sound technical advice.
Tradeforce Navigation SA was established by Alexander Christodoulopoulos in 1978 with the vision of providing unparalleled service to the maritime and industrial world. With a focus on late classic medium and high speed diesel engines, Tradeforce has carved a niche for itself as a trusted provider of spare parts and comprehensive services tailored to meet the diverse needs of a very special client base.
For over four decades, Tradeforce has been proudly serving hundreds of engines installed on all kinds of marine and military vessels and numerous land installations for power production and industrial use, which has cemented the status of a reliable provider of quality diesel engine spare parts and sophisticated services. The global presence touches every corner of the world, serving some of the largest shipowners, fleet managers, military navies, and land applications. Their repeated trust is a testament to their unwavering commitment to excellence, reliability, and care.
Dedication to crafting solutions that not only meet but exceed customers’ expectations, connecting commercial needs with technical excellence, is the core of the business. From engine blocks,crankshafts of short blocks to standard maintenance parts, every effort is made to ensure that the customers’ needs are met to the highest standards.
As maritime challenges grow with each passing day, Tradeforce
stands ready, embracing innovation and creative solutions to meet and surpass industry standards and requirements. Tradeforce scope spans a wide array of engines from esteemed brands like PIELSTICK, DEUTZ MWM, SULZER A/S, NOHAB, and WARTSILA DIESEL, to name a few. The aim? To be a one-stop solution for all diesel engine-related needs.
The pillars of the strategy are a robust stockpile and well-established international cooperations, the capacity to identify technical requirements, and the care to provide the best possible solution to address both routine and unexpected maintenance needs, regardless of their extent. This proactive approach, coupled with engine-specific expertise, guarantees swift and effective service, ensuring minimal downtime and peak operational performance at every step. A team of highly experienced and specialised engineers is ready to manage maintenance, repairs, and investigations with unmatched precision and care, globally.
At Tradeforce, expect nothing less than efficiency, transparency, and a personal touch. Engage and be met by a highly experienced and dedicated team that will support you at every turn.
Looking ahead, the market dynamics continue to evolve, and as diesel engines play a pivotal role, Tradeforce is ready to seize the opportunities and meet the challenges that come with an aging fleet, focusing on engines with extensive installation bases, which are of high value to their operators.
In summary, Tradeforce Navigation SA stands out for its deep knowledge of diesel engines, emerged as a frontrunner in providing the support required. Tradeforce’s dedication to dependability, reliability and ingenuity sets them apart, offering tailored solutions for a wide range of customer requirements. With the motto “Powering Solutions with Care”, showcasting proficiency across esteemed brands, Tradeforce guarantees effectiveness, clarity, and individualized attention on a global scale.
"Experience unparalleled reliability and care with Tradeforce For over four decades, the trusted provider of legacy engine spare parts and technical support worldwide From maritime to military vessels and land installations, the commitment to excellence ensures minimal downtime and peak operational performance Expect efficiency, transparency, and a personal touch by an experienced team. Power your solutions with care, at Tradeforce."
Official agents for; JFE Engineering Corporation
Official distributors for; QuantiParts BV, a Wärtsilä company
In the ever-evolving landscape of the maritime industry, where innovation is not just a choice but a necessity, the focus has shifted significantly toward the well-being of crew members aboard vessels. Beyond mere income, job satisfaction and retention now hinge on comprehensive welfare and lifestyle benefits. In this rapidly changing paradigm, one company stands out for its pioneering approach to enhancing life at sea: Agwa. Agwa’s breakthrough solution is revolutionizing the industry with its innovative onboard vegetable grower. The era of depending solely on sporadic deliveries or limited provisions is over. Agwa introduces an onboard vegetable grower that is not only fully autonomous but also remarkably hassle-free.
At the heart of Agwa’s innovation lies a fusion of cutting-edge technology and insights from user behavior science. The result? A user-friendly device that effortlessly cultivates clean, fresh, and flavorful produce— anytime, anywhere. The Agwa device harnesses the power of three main data branches— Image Analyzer (AI), Sensory Data, and User Behavior— leveraging sophisticated AI machine learning to monitor and collect data in real-time. This data is then fed into our revolutionary AI ‘Virtual Agronomist,’ which formulates a precise growth plan tailored to each plant’s unique needs and status. The device does not require any intervention from you; everything is managed automatically by a virtual agronomist. All you have to do is pick and eat.
The brilliance of this mechanism lies in a seamless integration, ensuring that the Agwa device consistently delivers a bountiful supply of fresh vegetables while requiring minimal intervention from the user. With our intuitive App, crew members have instant access
to the status of their vegetables and the corresponding growth plan, putting the power of fresh produce at their fingertips.
Since its launch, Agwa has earned praise across the maritime industry, with an increasing number of companies adopting our devices to boost the welfare of their crew members. By prioritizing the physical and mental health of seafarers, these companies are not only fostering a more resilient and sustainable maritime workforce, but also securing their position as industry leaders committed to excellence.
The impact of Agwa extends far beyond individual vessels or companies; it represents a fundamental shift towards a more holistic approach to maritime operations. By addressing the fundamental need for fresh, nutritious food at sea, Agwa is not just enhancing the quality of life for crew members but also elevating standards across the entire industry.
For decision-makers and shipping companies, the implications are clear: Agwa presents an unparalleled opportunity to meet and exceed the evolving expectations of modern seafarers. Your interest in Agwa is not just about investing in a product; it is about investing in the future of maritime welfare and sustainability.
To conclude, Agwa’s successful performance at sea is not merely a testament to its innovative technology or cutting-edge solutions; it’s a testament to the power of human-centric design and forward-thinking innovation. As we navigate the complexities of the maritime industry, let Agwa guide you toward a future where the well-being of crew members is not just a priority, but a standard of excellence.
JNE Marine Ltd is a well rooted and established company in Greece & Cyprus, providing a wide range of products and services for more than 25 years.
Mitsubishi Kakoki Kaisha & Samgong
• Exclusive representation in Greece & Cyprus of the Japanese origin centrifugal separators (purifiers)
• Maintenance / Repair Services via our authorized service hub located in Piraeus
Hydra Consult International
• Exclusive representation in Greece & Cyprus
• Company specialized in Framo Systems & hydraulic equipment
Hatchtec Marine Service Ltd
• Authorized distributors of the Chinese expert for Deck machinery, providing high quality spares and services for Hatch covers, Grabs, Cranes, Winches & Windlass
Cygnus Instruments Ltd
• Exclusive representation in Greece & Cyprus of the leading UK company in Ultrasonic thickness gauges measurements and leak detection units for cargo hatch covers
Toei Engineering Co., Ltd
• A leading Japanese company specialized in reconditioning and repairs for 2 stroke and 4 stroke engines
Dealfeng New Energy Technology Ltd.
• Design and Installation of Rotor Sail System
Spare Parts Supply
• Specific engineering parts mainly from the Chinese and Korean market, covering the whole spectrum of engine room located machinery.
• cylinder liners, cylinder covers, piston crowns, piston skirts, for most of the common propulsion main engines, diesel engines, and consumable parts
• spares for compressors and various types of pumps, vacuum, vacuumarator pumps
• panama chocks, bollards, chain stoppers, anchors and anchor chains
JNE Marine Ltd has persistently labored over the years to build customer’s trust and establish an extensive portfolio averaged to 250 ship management and owning companies within 2023, reflected by a retention rate that exceeds 90% in both the Greek and Cypriot market.
Through relentless dedication to innovation and customer-centric solutions, Turbomed has once again raised the bar in the marine turbocharger industry. The Portable Balance Machine represents a culmination of years of research and development, aimed at empowering marine operators with unprecedented capabilities in onboard maintenance.
In a monumental stride towards enhancing the efficiency and reliability of marine turbocharger services, Turbomed has unveiled its groundbreaking innovation: the Portable Balance Machine. This cutting-edge technology not only promises to streamline the process of rotor balancing but also marks a pivotal shift in the paradigm of onboard maintenance for turbochargers in maritime vessels worldwide.
“Through relentless dedication to innovation and customer-centric solutions, Turbomed has once again raised the bar in the marine turbocharger industry,” remarked Mr. Theofanis Lampropoulos, Mechanical Engineer Officer of Turbomed. “Our Portable Balance Machine represents a culmination of years of research and development, aimed at empowering marine operators with unprecedented capabilities in onboard maintenance.”
Turbomed stands as the sole provider worldwide of the “portable onboard” service, setting an industry standard in accessibility and convenience for turbocharger maintenance. With over 50 years of experience in service, maintenance, and repair of all kinds of turbochargers, Turbomed brings a wealth of expertise and proficiency to every project.
“At Turbomed, our commitment to excellence extends beyond innovation to encompass professionalism in every aspect of our operations,” emphasized Mr. Yiannis Paraskevopoulos, CEO of Turbomed. “Our team of highly skilled technicians is available 24/7, 365 days a year, ensuring prompt and reliable support for our clients worldwide.”Traditionally, the task of balancing turbocharger rotors has been a cumbersome and time-intensive affair, often necessitating the removal of components and transportation to facilities for maintenance. However, Turbomed’s Portable Balance Machine offers a transformative solution by enabling rotor balancing to be conducted directly onboard ships, circumventing the need for costly and time-consuming offsite procedures.
“Our Portable Balance Machine is designed to seamlessly integrate into existing onboard maintenance workflows, enabling marine operators to conduct rotor balancing with ease and efficiency,” stated Mrs. Rokana Dora, Marketing and Sales Executive of Turbomed. “Its
compact and portable design ensures minimal disruption to vessel operations while delivering maximum impact in terms of performance and reliability.”
“As maritime regulations become increasingly stringent and operational demands escalate, the need for innovative solutions that enhance efficiency and sustainability has never been greater,” emphasized Mr. Yiannis Paraskevopoulos, CEO of Turbomed. “Our Portable Balance Machine emerges as a beacon of progress in this regard, offering tangible benefits and driving lasting impact in the realm of onboard turbocharger maintenance.”In addition to our pioneering Portable Balance Machine and our unwavering commitment to professional service, Turbomed offers comprehensive support in turbocharger spare parts procurement. Regardless of the brand you rely on, Turbomed stands ready to provide you with the necessary spare parts to keep your turbocharger systems operating at optimal levels.
Our extensive network and industry connections enable us to source parts from various manufacturers, ensuring compatibility and performance. Furthermore, Turbomed proudly holds the esteemed designation of an authorized service station for KBB, a testament to our dedication to meeting and exceeding the highest standards of quality and expertise in turbocharger services. Our technicians undergo rigorous training programs to equip them with the knowledge and skills necessary to carry out their duties with precision and efficiency, guaranteeing that your turbocharger maintenance needs are in capable hands. Whether it’s routine servicing, emergency repairs, or spare parts procurement, Turbomed is your trusted partner for all turbocharger-related requirements.
In conclusion, Turbomed’s introduction of Portable Balance Machine represents a significant milestone in the evolution of onboard turbocharger maintenance, offering unprecedented levels of efficiency, reliability, and convenience. As shipowners and operators strive to optimize the performance, profit and sustainability of their fleets, this innovative technology stands poised to drive transformative change and deliver tangible value in the years to come. Embrace the future of turbocharger maintenance with Turbomed and experience the difference firsthand.
“JNE Marine Ltd is a well rooted and established company in Greece & Cyprus, providing a wide range of products and services for more than 25 years.
Mitsubishi Kakoki Kaisha & Samgong
• Authorized representation in Greece & Cyprus of the Japanese origin centrifugal separators (purifiers)
• Maintenance / Repair Services via our authorized service hub located in Piraeus
Mitsubishi Selfjector Hercules – Series
Over the many years since its initial release in 1942, Mitsubishi Kakoki Kaisha Ltd has continuously served the needs of our customers. By exploiting the technical capabilities, high quality, and advanced service systems we have accumulated over the years, we have achieved sales of more than 100,000 units.
With our new series models, the “Mitsubishi Selfjector Hercules (SJ-H),” we offer a compact unit providing high separation performance and superior purification of marine fuel oil, lubricating oil, and even the mineral oil utilized in a wide range of industry segments.
The Mitsubishi H Series has achieved the highest degree of perfection and excellent stability while integrating new technologies, including high centrifugal force and highly efficient discs.
The latest upgraded model, HIDENS, requires no adjustment of gravity disc replacement, and it enables water separation from fuel oil up to a density of 1,010 kg/m3 (15°C) and lubricating oil.
Features
• Uses a field-proven pressure sensor type of water detection system.
• Substantially reduces sludge discharge volume due to the adoption of a new integral algorithm.
• Simplifies installation work due to detectors incorporated into the main body.
We hope that our Purifiers would contribute to your safe voyage”.
Experience: means the knowledge we acquired from our long duration activity, in connection with the thoughts we made on anything that we saw or happened to us, GOOD or BAD
Fifty years ago, the word “diver” was connected only with the sea sponges, and it was a profession for few. Shipping development and environmental challenges opened new horizons in the underwater technology, and “diving “is not that simple anymore. Working under pressure is not a matter of “a diver”, but it is a matter of a well organised team. Nick Segredakis Diving Ltd. is a Commercial diving company specialising in the underwater services for the last 35 years.
NSD Ltd, quickly does any type of: Underwater hull, sea-chests, grids or, propeller & rudder cleaning, measuring, servicing, and repairing as well as, underwater welding and installation of transducer and anodes.
NSD Ltd, owns an approved method for in-water, temporary & permanent repairs, according to international standards.
In little time from the moment of notice a team of divers can be on site, in any required location of Greece, as well as, to many other places all over the world, ready to offer emergency and routine services.
NSD Ltd., is building up its reputation by being reliable while honouring its commitments so, her customers can enjoy preferential treatment through a mutual profitable relation.
NSD Ltd., shall be happy to be contacted on any inquiry covering its field of activities.
“Navitec is a flexible all round mobile workshop specialized in all afloat repairs and offers a 24 hrs service. Starting at our fully equipped workshop in the heart of the port of Antwerp, our mobile repair teams are geared up to carry out fast and quality repairs in the whole ARA area.
It is Navitec’s mission to assist crew, owners, charterers and technical managers alike in maintaining operability of their vessels in the best possible way.
In order to achieve this, we employ highly skilled labour and Ship Repair Managers with experience at sea and in ship repair. Our solution- oriented approach allows us to face any challenge in afloat repairs and safety items for seagoing vessels.
Founded in the late seventies as a welding shop, Navitec has developed, grown and diversified with a strong focus on emergency ship repairs. Late 2023 we merged with our sister company NaviSafe and added safety services (LSA & FFE) to our activities. We currently employ around 50 people, run a fleet of over 30 vehicles and next to Antwerp, we frequently operate in Rotterdam, Ghent, Zeebrugge, Flushing and Dunkerque. Occasionally work even takes us as far as Hamburg and Le Havre and once every so often we go even beyond that.
As a testimony of how we deploy our knowhow and expertise skilfully to help ships get back on track everyday, we’d like to refer to a recent project involving the removal and refitting a rudder, rudder stock and steering gear afloat doesn’t scare us away. When our customer was faced alignment issues between components, their vessel couldn’t continue her voyage. The whole assembly, steering gear, rudder and rudder stock had to be removed from the vessel for inspection and repair. This usually requires a drydock. To get everything out of the vessel, we had to crop a large hole in the stern shell plate of the ship to create a technical exit. Removing the 5T rudder stock and 27T rudder did not only require a barge, heavy chain blocks and two large mobile cranes, but also
extensive rigging experience and proficiency of our specialists. After removal, the steering gear was sent to the manufacturer in Poland for an overhaul.
After repair of the steering gear and rudder stock, everything had to be put back in place and aligned properly. All new bushings were fabricated as per the original drawings in our own specialised workshop.
While removing a rudder of that size is a big project in itself, refitting is even a lot more challenging. Its own weight combined with its buoyancy, the difficult location under the stem of the vessel, wind and swell, make it quite difficult to align within 10ths of a mm. All the while keeping an eye out not to damage any parts.
A unique job in challenging circumstances, but Navitec delivered, thanks to our team of experienced colleagues on the one hand and thanks to our professional workshop on the other.
Our workshop is located in the heart of the port of Antwerp, and his been for over 40 years. Recently we added a completely new office building, a two stories building on 500 square meters of land. It allows us to welcome customers in a nice, light and professional environment. Above all however, it serves as a comfortable working environment for our staff who spend a lot of time here everyday. We want to ensure they can execute their job with all the necessary resources and that they can enjoy a decent lunch spot, clean showers and locker room. The new building also meets all the latest environmental standards: a roof full of solar panels, excellent ventilation systems, rainwater recovery and so on. It helps us to contribute to a better world.
We are proud to serve almost all major shipping companies as loyal customers. They help us maintain our focus and incite us to continuously improve our organizational efficiency and our services.
Navitec is renowned for its flexibility and quick response times. Our emergency phone line is manned 24/7 and customers value our proactive and solution-oriented approach.
We mean it when we say we’re always there for you”.
For all your afloat ship repairs, 24/7:
• Steel repair
• Pipe fitting
• Winches & cranes
• Engine mechanics
• Pumps & valves
• Refrigeration
• Electricals
• Hydraulics
• Cargo securing
• ...
Despina Panayiotou Theodosiou, Co-Chief Executive Officer of Tototheo Maritime, has been honored with the first-ever IMO Gender Equality Award. Presented by Secretary-General Arsenio Dominguez at the International Maritime Organization Women in Maritime 2024 event, the award acknowledges her significant contributions to gender equality and women’s empowerment, especially during her tenure as President of WISTA International.
Despina Panayiotou Theodosiou voiced gratitude at being selected as recipient of the first ever IMO Gender Equality award, presented by Secretary-General Arsenio Dominguez ahead of the International Maritime Organization Women in Maritime 2024 event. The award recognised Co-Chief Executive Officer of Tototheo Maritime, Ms. Panayiotou Theodosiou’s leading and pivotal role in advancing gender equality and empowering women through her tenure as President of WISTA International.
Ms. Panayiotou Theodosiou said it was a tremendous honour to have been chosen for the award. “Over the last 10 years raising awareness of the incredible work women are undertaking within the maritime industry and the importance of gender diversity, equity and inclusion have been a key focus for me on both a personal and professional level,” she said.
The IMO said Ms. Panayiotou Theodosiou had brought significant attention to WISTA’s mission, shed light on the challenges faced by women in shipping, and raised awareness among industry stakeholders and international policy and decision makers. Her actions had also amplified the voices of women, highlighting their important contributions to the maritime industries.
Ms. Panayiotou Theodosiou was instrumental in gaining consultative status for WISTA International at IMO, and the two organisations have since launched joint initiatives, such as the Women in Maritime Survey 2021 and the Maritime Speakers Bureau. The survey, which will be repeated this year, examined representation and distribution of women working in the maritime sector. The Speakers Bureau is a platform for female experts across a variety of maritime fields which seeks to ensure that conferences and events feature inclusive panels with a range of perspectives.
“During my time as President of WISTA International it was a privilege to be part of the driving force behind many of the initiatives related to advancing gender equality within the industry. When I look at what has been achieved I feel an immense sense of pride for being able to play a part in bringing about change,” Ms. Panayiotou Theodosiou said.
“With that said, we still have a long way to go, and I’d like to take this opportunity to encourage everyone to continue to break down the barriers, acknowledge the need for change and work together to create a more inclusive and diverse maritime industry,” she added.
She extended her gratitude to the President of the Republic of Cyprus, Mr. Nikos Christodoulides and Shipping Deputy Minister, Ms. Marina Hadjimanolis for supporting her nomination.
The IMO Gender Equality Award has been established to recognize individuals, irrespective of their gender, who, either in a personal capacity or as representatives of their institutions, have made significant contributions to advancing gender equality and the empowerment of women in the maritime sector.
Tototheo Maritime specializes in maritime technology solutions focusing on optimizing vessel and fleet performance in the fields of satellite communication, navigation systems, digitalization and end-to-end cyber security services.
Interactive 360 vir tual tours, available on any computer, tablet or phone (Android and iOS)
Online/Offline and VR compatible
Immersive walkthroughs, making the familiarization and learning experience widely accessible and tailor made 360 VR-Tour
Enabling vir tual remote inspections
The highly anticipated ESG Shipping Awards International 2024 took place on the 20th of May, honoring outstanding achievements and innovative initiatives within the global maritime industry. Held at the Grand Hyatt in Athens, the event marked another year of celebrating shipping companies worldwide that demonstrate exceptional best practices in Environment, Social, and Governance (ESG).
The ESG Shipping Awards 2024 International signifies a pioneering Greek initiative, the world’s inaugural event of its kind, established in partnership with the Ministry of Shipping and the Hellenic Chamber of Shipping. Winners hailed from diverse regions and various maritime operations, showcasing the global impact of sustainability efforts across the industry.
“The ESG Shipping Awards is more than an awards ceremony,” remarked Helena Athoussaki and Katerina Stathopoulou. “It is a platform of recognition, collaboration, and knowledge-sharing, driving the maritime industry globally towards a more sustainable and prosperous future.”
In his opening greetings Mr. Manolis Koutoulakis, Secretary General of Maritime Affairs & Insular Policy, stated that the ESG Shipping Awards serve as a crucial stakeholder platform, highlighting key players and initiatives in the Maritime Economy during a critical era marked by global, European, and regional crises, he then added “The ESG Shipping Awards initiative, along with the ESG Confer-
ence and workshops, as a remarkable and successful journey that has increased the visibility of the ESG framework within the shipping industry, positioning it as a leader in sustainability. “
The Chairman of the judging committee, Mr. Jan Fransen, underscored the challenges faced during the evaluation process and highlighted the diverse range of entries reviewed, showcasing the industry’s strong commitment to ESG principles.
The Honorary Recognition Award was presented to Mr. Emanuele Grimaldi Chairman, International Chamber of Shipping, for his significant contribution to promoting sustainability in the maritime industry.
The esteemed Private Philanthropy Recognition Award has been presented to Mr. Panagiotis Angelopoulos & Mr. George Angelopoulos in honor of their remarkable dedication to philanthropic efforts and their unwavering commitment to providing support to those affected by Storm Daniel in the Thessaly region.
“Mr. Panagiotis and Mr. George Angelopoulos have been active philanthropists for many years, supporting various causes and initiatives aimed at improving the well-being of communities in need. Their response to Storm Daniel is just one example of their enduring commitment to humanitarian efforts.” said the organizers when presenting the award. The prestigious Motivation Award, focusing on environmental excellence, was received by the prominent founding members including Lloyd’s Register, Capital Group, Navios Mari-
time Partners, Neda Maritime Agency, Star Bulk Carriers Corp. and Thenamaris. This award recognizes their significant support for Maritime Emissions Reduction Centre (M-ERC), a not-for-profit collaborative initiative based in Athens, which aims to optimize the efficiency of the global fleet and promote solutions for reducing greenhouse gas emissions. The Motivation Award was presented by Mr. Emanuele Grimaldi, who highlighted the collective impact of these founding members in fostering environmental sustainability within the maritime industry. The announcement of the ESG Leader Award marked the conclusion of a memorable evening, characterized by celebration, reflection, and a collective commitment to a more sustainable future in the maritime industry. As the event wrapped up, the organizers expressed their excitement and anticipation for the upcoming ESG Shipping Conference International scheduled to take place in Athens in October 2024.
The winners of the ESG Shipping Awards International 2024 are as follows:
Supply Chain Leader Award:
Gold: Euronav
Silver: Seanergy Maritime Holdings Corp. & Atlantic Bulk Carriers Management Ltd.
Bronze: Laskaridis Shipping Co.
Presented by the organizers
Technology Leader Award
Gold: AIDA Cruises
Silver: Baleària Eurolíneas Marítimas
Bronze: Columbia Group Presented by Enablon
Governance Leader Award
Gold: Navios Maritime Partners
Silver: Pioneer Marine Group of Companies & Genco Shipping & Trading Limited
Bronze: Performance Shipping Presented by EUROBANK
Community Contribution Leader
Gold: Latsco Shipping
Silver: Berge Bulk
Bronze: Wallem Group
Presented by Tallon Commodities Ltd
People Leader Award:
Gold: Tsakos Group of Companies
Silver: Navios Maritime Partners L.P.
Bronze: Seanergy Maritime Holdings Corp.
Presented by WATSON FARLEY & WILLIAMS
Diversity Equity &Inclusion Leader Award:
Gold: Diana Shipping Services S.A.
Silver: Bernhard Schulte Shipmanagement
Bronze: Columbia Group
Presented by The Liberian Registry
Social Leader Award:
Gold: Fleet Management Limited
Silver: Chandris (Hellas) Inc. - Century Bulk Carriers Management
Bronze: Stem Shipping CO. S.A
Presented by Marine Tours
Climate Change Award:
Gold: Carnival Corporation & plc
Silver: Capital Group
Bronze: Odfjell and Höegh Autoliners
Presented by PPG
Environment Leader Award:
Gold: Berge Bulk and Diana Shipping Inc.
Silver: Lemissoler Navigation Co. Ltd
Bronze: Carnival Corporation & plc
Presented by Bureau Veritas
ESG Leader Award:
Gold: Norwegian Cruise Line Holdings Ltd.
Silver: Pacific Basin Shipping
Bronze: Safe Bulkers Inc.
Presented by Deloitte
On Friday, May 10th, at the Faros Hall of the Stavros Niarchos Foundation Cultural Center, the Propeller Club, Port of Piraeus, held its annual Members’ Day event, in the presence of the United States Ambassador to Greece and Honorary President of the Club, George Tsunis, the Chief of the Naval General Staff, Vice-Admiral Dimitrios Kataras, the Commander in Chief of Hellenic Fleet, Vice-Admiral Polychronis Koulouris, the Chief of the Hellenic Coast Guard, Vice-Admiral, Georgios Alexandrakis, the 2nd Deputy Commander of the Hellenic Coast Guard, Vice-Admiral Tryfon Kontizas, as well as a number of distinguished guests.
A special welcome ceremony was conducted before the event, where the President and members of the Board of Governors welcomed the 200 new members by presenting them with their Propeller Club certificate and pin.
The evening opened with a warm welcome from the General Secretary of the Propeller Club, Christos Timagenis.
This was followed by the welcome address of the President, Costis Frangoulis, who commented: “Tonight is a special night as we welcome 200 new members to Propeller Club of Piraeus, but also to the wider family of the International Propeller Club, the largest networking organization in global shipping, with 80 Clubs and over 6,000 active Members.”
While he continued: “We are delighted to welcome you and hope that you take pride in joining this historic organization today, as it approaches its 90th anniversary of serving and contributing to the Greek society and shipping industry.”
The evening continued with the greeting of Ambassador George Tsunis.
During his remarks, U.S. Ambassador to Greece and Honorary President of the International Propeller Club, Port of Piraeus, said: “For a century, the Propeller Club has supported our multifaceted maritime relationships, building bridges between the United States and the global shipping community... With the largest, newest, and most modern fleet in shipping and such a dynamic shipping community, we are excited about the future of the shipping industry in Greece.”
In his capacity as a longstanding and esteemed Lifetime Member, Stamatis Tsantanis, Chairman and CEO of NASDAQ listed companies Seanergy Maritime Holdings Corp and United Maritime Corpo-
ration, extended a warm welcome to the new members and stated the following: “We wish to emphasize our pride in being members of the International Propeller Club, Port of Piraeus, as Seanergy and United Maritime. We are dedicated supporters of this institution, which seeks to enhance Greek-American maritime cooperation while maintaining its longstanding philanthropic reputation.”
The evening’s keynote speaker was Sveinung Støle, Deputy CEO of the Angelicoussis Group, who was introduced by the Club’s General Secretary, Christos Timagenis.
Mr. Støle addressed the topic: “Navigating Through Challenging Times Towards a Sustainable Future”, stating: “We all need to find solutions to decarbonize our industry. Decarbonization is a transition, not a switch, it doesn’t happen overnight. The shipping industry needs to control the process and narrative of the energy transition, in cooperation with other parties, such as regulators, the government, and organizations such as the Union of Greek Shipowners and INTERTANKO. We need to manage our existing fleets in the safest and most efficient way until the end of each vessel’s trading life. We believe that all new vessels must be dual-fuel, which can lead to a 40% reduction in CO2 emissions today. We believe LNG is the best solution; it is proven, safe, competitively priced, and available today. It will be supplemented with bio-LNG and later synthetic LNG, meaning that the LNG solution will take these vessels to net-zero emissions.
Thus, dual-fuel vessels can last until 2050. For other non-carbon fuels, such as ammonia, hydrogen and methanol, these must be green meaning made from renewable energy, and there will be technological developments that will ensure their safe use, but these are not there today”.
Following his speech, a very interesting fireside chat was held between the President of the Club, Costis Frangoulis, and Sveinung Støle.
Costis Frangoulis then formally inducted him into the Propeller family, as an Honorary Member by pinning him with the Club pin, and presenting him with the Certificate of Honorary Membership.
A plaque of recognition was also awarded to the outgoing Economic Counselor of the US Embassy, Erik Holmgren, in appreciation of his contribution during his stay in Athens.
A cocktail reception followed.
Eni, a global energy company, Fincantieri, one of the world’s largest shipbuilding groups, the only one active in all high-tech marine industry sectors, and RINA, a multinational inspection, certification, and engineering consultancy, have signed an agreement to develop joint initiatives for the energy transition. The partnership formalises the commitment to develop joint projects, in line with the partners’ strategies, to decarbonise the maritime sector in the medium to long term with the goal of Net Zero by 2050. Additionally, the establishment of a permanent global observatory regarding future technological, regulatory, and market developments will be evaluated.
The three companies will conduct a comprehensive analysis and evaluation of the most sustainable alternatives to support the maritime decarbonisation pathway. This will also be based on the development of complementary solutions to fuels already available for other hard-to-abate sectors. The partnership’s areas of interest also include an analysis of the reference energy infrastructure and the development of new logistic structures, including the investments that the sector requires.
Giuseppe Ricci, Chief Operating Officer for Energy Evolution at Eni, commented: “The collaboration with Fincantieri and RINA, two major Italian players, is a further step in our journey towards the transition and decarbonisation of maritime transport. To meet the objectives of the UN 2030 Agenda, it is important not only to manage what is immediate but also to act with a medium to long-term perspective, developing partnerships to create more sustainable solutions and products. The ability to network among the partners, with their wealth of skills and technological capabilities, can make a significant contribution to finding more effective solutions for decar-
bonising maritime transport and meeting the needs of shipowners and logistics operators, always leveraging a holistic approach”.
Pierroberto Folgiero, CEO and Managing Director of Fincantieri, said: “We are highly committed to supporting our clients in addressing the industrial challenges of the maritime energy transition, and this initiative is aimed at initially creating a hub of study to harness Italy’s extraordinary expertise in new technologies, novel fuels, and their profound industrial implications for the ship system. We are very pleased to join forces with Eni and RINA in an alliance to materialize existing solutions and to pave the way for the future with a proactive ecosystem approach. Indeed, new technologies must be industrialized on board ships, just as new fuels must be produced and distributed at the dock. Only with a concept of “operationalizing innovation” can we lead our industry and project our shipbuilding leadership into the future”.
Carlo Luzzatto, CEO and General Manager of RINA, said: “We strongly believe in the value of collaboration and the opportunities it brings, particularly when it involves players of international calibre such as Eni and Fincantieri. Together, we have the opportunity to share knowledge and experience and to contribute to more sustainable solutions that support the shipping supply chain. RINA brings to the partnership its engineering and technological skills, developed across various sectors, to support shipping in its journey towards reducing its carbon footprint, without excluding any energy options”.
The understanding may be the subject of subsequent binding agreements that the parties will define in compliance with the applicable legislation, including that relating to transactions between related parties.
Pantheon Tankers Management and Alpha Gas will install RINA’s SERTICA digital logbooks to ensure smarter and more efficient digital logkeeping across their fleets. Digital logbooks mark a significant advancement over their paper predecessors. They not only reduce the burden on the crew of manual entry but also ensure greater accuracy and integrity of data. This transition is crucial in an industry where the accuracy of log entries is fundamental for compliance with international regulations and for operational analysis.
The move of Pantheon Tankers Management and Alpha Gas aligns with the group’s strategy to embrace digitalization. By leveraging an array of digital tools and platforms across operations, the group aims at enhancing operational efficiency while bolstering the support for vessels and departments.
Michalis Kontaratos, Financial Advisor & Corporate Strategy for Pantheon Tankers Management and Alpha Gas said, “The shift towards electronic logbooks was initiated by our proactive internal processes aimed at
enhancing operational efficiencies. SERTICA provides the flexibility to select specific logbooks and ensures seamless onboard integration with an easy installation process. Its user-friendly interface greatly benefits both our crew and office staff.”
Lars Riisberg, RINA Digital Solutions Executive Vice President, commented, “SERTICA Logbook not only mitigates the risks of human error but also enhances the strategic decision-making process through actionable insights derived from data analytics. It is also a versatile tool. SERTICA Oil Record Book (ORB), for example, can adapt to each vessel’s unique characteristics”.
The partnership between Pantheon Tankers Management and Alpha Gas and RINA includes a major focus on training to ensure a seamless integration and an effective use of digital logbooks across the fleet. Kontaratos concluded, “Our goal is to ensure that all team members are proficient and comfortable with the new digital logbook system, enabling us to leverage this technology to its fullest potential.”
Pantheon Tankers Management owns a versatile fleet of 39 crude oil and product tankers, including 9 VLCCs, 9 Suezmaxes, 7 Aframaxes, and 14 MR tankers, demonstrating operational excellence and market adaptability. Alpha Gas, specializing in LNG vessel management, operates a fleet of 8 LNG ships.
RINA, leading certification and engineering company, provides a wide range of services across the Energy, Marine, Certification, Infrastructure & Mobility, Real Estate and Industry sectors. With revenues in 2022 of 725 million euros, 5,300 employees and 200 offices in 70 countries worldwide, RINA is a member of key international organizations and an important contributor to the development of new legislative standards.
IBIA - The International Bunker Industry Association and BIMCO have signed a Memorandum of Understanding (MoU) to collaborate on some of the monumental challenges and opportunities within the areas of bunker, marine energy and maritime sectors and help facilitate shipping’s decarbonisation efforts.
The parties have agreed to leverage their respective expertise and resources to develop innovative solutions and initiatives to facilitate the transition towards cleaner fuels and efficient and sustainable shipping practices. The partnership MOU will focus on addressing the following key areas:
Research and Development: Collaborate on research initiatives, studies, and projects relevant to the bunker/marine energy industry and maritime sector.
Information Sharing: Share relevant information, publications, and data that may be beneficial to the members of both organisations.
Training and Education: Explore opportunities for joint training programs, seminars, and educational initiatives to enhance the knowledge and skills of professionals in the maritime and bunker/marine energy industry.
Influence: Work together on efforts to address common issues and challenges faced by the industry.
Commenting on the MoU, Alexander Prokopakis, Executive Director of IBIA, stated:
“This partnership between IBIA and BIMCO marks an important step towards addressing the pressing challenge of decarbonisa-
tion in the shipping industry. The collaboration underscores the industry’s collective commitment to navigating towards a greener future for maritime operations.”
David Loosley, BIMCO Secretary General & CEO said:
“As we work towards the checkpoints and targets of the updated GHG strategy of the IMO, working across all sectors that influence and support decarbonisation of shipping will be key. Our ships will be relying on many different fuel solutions in the process and working toward the safety and availability of those is crucial.”
IBIA and BIMCO are committed to driving progress towards a more sustainable and environmentally responsible future for the global shipping industry.
Moore Greece is very proud to have assisted the International Association of Dry Cargo Shipowners (INTERCARGO) with their very first ESG Review. The ESG Review highlights how INTERCARGO’S recent activities relate to each of the pillars of ESG: Environmental, Social and Governance. Echoing INTERCARGO’s commitment to quality dry bulk shipping, the Review also suggests how ESG has become an increasingly important topic for all stakeholders in the dry bulk shipping community
The Chairman of INTERCARGO, Dr Dimitrios J. Fafalios, expressed his “sincere gratitude to the dedicated professionals at Moore Greece for their effort and skill in preparing this ESG Review”. He concluded that “with the support of all members, INTERCARGO will successfully transition to a future where day-to-day operations of the dry bulk shipping sector are fully aligned with the principles of sustainable development”.
Costas Constantinou, Managing Partner at Moore Greece and Global Maritime Leader of the Moore Network, pointed out that “Moore Greece has been a trusted partner to the Greek shipping community for the past 60 years, proactively responding to needs of the industry for quality and transparency in reporting to their stakeholders. Moore Greece is excited to have been working alongside INTERCARGO and to have helped shape the INTERCARGO 2024 ESG Review”.
Pinelopi Kassani, Governance, Risk & Compliance Partner Moore Greece, highlighted that ‘INTERCARGO’s ESG Review is an important initiative for the dry bulk sector. INTERCARGO’s global outreach as demonstrated by its 250 members and 3.300 vessels, helps bring the ESG discussion of the sector forward by highlighting many of the sector’s common topics that relate to the environment, the society and corporate governance’.
Moore Greece proudly supported the International Association of Dry Cargo Shipowners (INTERCARGO) in producing their first Environmental, Social, and Governance (ESG) Review. This comprehensive review illustrates how INTERCARGO’s recent activities align with the three pillars of ESG, emphasizing the growing significance of these principles for stakeholders in the dry bulk shipping industry.
NAFTOSOL Ltd specializes in Steel, Piping and Mechanical works in Piraeus. Over the past four decades, the company has grown into a general contractor of large ship repair projects, showcasing a long reference list of satisfied Owners with high retention rates. Building long-lasting relationships based on mutual benefit lies at the core of NAFTOSOL’s way of doing business.
Another area where NAFTOSOL has been proudly rendering its services to the Greek fleet is Afloat Repairs. The ability to send experienced Riding Teams (Greek or Romanian), of all specialties, on short notice, on board vessels to deal with the most severe and urgent cases, has made the company the One-stop Workshop for the most discerning technical departments.
NAFTOSOL’s experienced Greek engineers, who have overhauled countless Main Engines and Diesel Generators, bring the company’s motto to life. The vessel needs to be repaired and maintained efficiently, in order to get as fast as possible back to what she does best, i.e. keep the world turning.
NAFTOSOL’s CEO, Mr Thanasis Pirinis, has also been involved in complete vessel Drydockings, by establishing in 2005, NAVALINK Srl inside Midia Shipyard SA in Romania, where more than 200 Greek vessels have been drydocked. This experience has been brought into NAFTOSOL’s organizational structure, allowing the company to have successfully performed numerous drydockings in Perama / OLP. Long standing cooperations with specialized subcontractors guarantee the best cost and quality for all repair projects, while clients enjoy dealing with one solid counterparty during drydocking.
Lastly, the outgoing nature of NAFTOSOL’s Management has resulted in a global network of collaborations with well-established repair companies in key maritime hubs, allowing the company to provide worldwide quality marine maintenance services locally, with zero travelling costs for Owners.
In short, NAFTOSOL wants to be the solution to most technical matters that arise. From gangway repairs afloat to complete drydockings in Piraeus – you can rely on us.
NAFTOSOL’s services to Greek fleets:
• Steel & Piping Repairs
• D/G & M/G Overhaulings
• Riding Teams
• One - Stop Drydockings in OLP/Perama
• BWTS Turn-key installations
• Worldwide Marine Maintenance
Certification
NAFTOSOL holds the ISO 9001:2015, ISO 14001:2015 and OHSAS 18001:2007 certificates, granted by Bureau Veritas (BV) to always ensure highest quality of the services rendered.
In addition, NAFTOSOL has been granted by BV with our own required documentation of all WPSs (Welding Procedure Specifications) & WPQRs (Welding Procedure Qualification Records), in order for our certified welders to always deliver welding procedures of the highest quality.
www.naftosol.gr
by having Clean & Dry Oiland save money, oil, energy and reduce your CO2 footprint
Clean oil is paramount for optimum vessel operation. 80% of all oil related system or engine breakdowns are caused by contaminated oil. Even new oil is not clean. Oil can be contaminated by particles, water, acidity, and oil degradation products.
Installing an offline oil filter technology, keeps the oil clean on your marine equipment like main- and auxiliary engines, cranes, winches, gears, thrusters, stern tubes, valves, HPU, diesel engines, etc. removing harmful contaminants from engine lube oil, hydraulic oils, gear oils, diesel fuel and even from biodegradable oils (EAL).
General benefits maintaining your oil clean
• Reduced wear and failure of components
• Increased oil and marine component lifetime
• Reduced risk of breakdowns
• Increased availability & reliability
• Fewer oil changes
• Reduced manpower
• Reduced maintenance costs
• Reduced CO2 emissions
CJC® Oil Filters are used on the following systems
• Engine Lube Oil: Diesel Engines
• MGO, MDO Fuels: Diesel Engines
• Gear Oil: Thrusters
• Hydraulic Oils: Cranes, Winches, Cargo Pumps, Steering Gears, HPU’s and other hydraulic systems
The CJC® Engine Lube Oil Filter provides owners, operators, and crews with a simple, cost effective and efficient method for maintaining LO quality, meeting OEM lube oil cleanliness requirements. Can be installed on both 4- and 2-stroke main and auxiliary engines. This technology differs from the traditional centrifugal purifiers on many parameters: CJC® Oil Filters have a very high filtration rating of 3/0.8 micron, removing large amounts of even the smallest and most harmful particles. Furthermore, it absorbs condensate water and removes varnish. Sludge problems are eliminated and as no heating is required, cost savings on energy are obtained. Lube oil consumption and wear on spare parts are reduced. With a very small footprint and a flexible design, the filter is easy to install.
Benefits by replacing the Centrifugal Purifiers with a CJC® Engine Lube Oil Filter
• 97% energy savings
• 97% reduction in CO2 emissions
• Up to 60% less oil consumption
• 99% reduction in lube oil sludge
The CJC® Marine Diesel Filters ensures the day tank is always full of clean and dry diesel, installed between the bunker tank and the day tank. For purification of diesel and gas oil on small and medium consumption engines. With high flow rates and high efficiency for both water and particle removal, the diesel is kept continuously clean and dry, fulfilling the requirements acc. to Common Rail
injection systems, obtaining lower operational costs and reduced maintenance costs. Furthermore, sludge production is eliminated. With a very small footprint and a flexible design, the purifier is easy to install.
Due to new environmental regulations from the US Environmental Protection Agency, you might have to change from mineral oils to biodegradable oils in thruster, stern tubes, rudders etc. With a CJC™ Desorber/Filter Combi Unit you remove water from even emulsified biodegradable oils.
The CJC® Condition Monitoring Unit, offers real life condition monitoring of your equipment & oil, which in turn can help avoid breakdowns, by giving early warnings and detection of abnormal behaviour.
C.C.JENSEN is the global leader and the expert in offline oil filtration and purification - with more than 70 years of experience. Designs and manufactures of CJC® Offline Oil Filters, Marine Diesel & Lube Oil Purifiers and Desorbers for all kinds of oil systems for the marine industry. Located in Denmark with 14 Subsidiaries and over 50 Distributors worldwide.
Coral Piraeus Ship Repairs PC, led by Mr. VASILIS KANAKAKIS since 1990, has established itself as a leader in ship repair services, boasting a successful track record in the Greek and international markets. Committed to high standards, Coral Piraeus employs modern equipment and innovative technologies like the DOCKBOY Hydroblasting System to ensure superior quality, efficiency, and environmental sustainability in its ship repair projects.
CORAL PIRAEUS SHIP REPAIRS PC has been actively participating in Greek and International market since 1990
Under the management of Mr. VASILIS KANAKAKIS the company has charted an upward course and undergone a successful business route, with significant national & international clientele expansion.
Our main fields of expertise focus on the provision of services, such as: Hydroblasting – Gritblasting – Painting – Drydocking – Chemical cleaning –Afloat repairs – Steel & Piping works –Machinery works
Our long experience and deep knowledge, alongside our well qualified staff and partners combined with our modern equipment ensure the: high quality, competitive performance, and minimum duration of undertaken projects.
CORAL PIRAEUS SHIP REPAIRS PC undergone 90 ship-repair projects during the year of 2023 Our target is the Quality without compromise and our effort is to meet our client’s individual needs, ensuring complete fulfillment of all requirements.
In Coral Piraeus Ship Repairs PC, we have been always functioning with respect and sensitivity to the environment and human value. Our corporate functions, are subject to international standards, being certified by ISO 9001:2015 – ISO 14001:2015 - ISO 45001 - 2018 by Bureau Veritas. The corporate headquarters are located in Piraeus. Workshop and Warehouse Facilities are located within the repair zone of Perama.
The latest technology is incorporated in Coral Piraeus philosophy using new innovative Hull Treatment Advanced Technologies.
Alongside the traditional Spider Surface Robots, the new DOCKBOY Hydroblasting System, specialized in Ultra High -Pressure Water Blasting 3000-Bar Surface Preparation. With our Skilled Staff we achieve highly efficient performance and minimum duration of the Treatment Process. Combining This Ultimate Surface Treatment Quality, with the advantages of Hull Silicon Paint Application results in the least Hull Water-Resistance and the best possible Cruising Performance
This type of service constitutes the best choice of ship-owners in Drydocking Industry of 2024
“PSB & CO. S.A. - Papadakis Shipyards Brokers - although started and continues to be one of the leaders in Dry Dock and Repairs business (for more than 35 years now), the last 10 years has expanded its activities into the LNG / Dual Fuel engine maintenance as well as into the Shipping environmental-friendly (green) Industry.
Water Ballast Management Systems(WBMS): As official representatives of “Headway Technologies”, Chinese WBMS manufacturer, we have successfully installed 396 systems for our customers in Greece, but also in USA, for New Buildings and retrofit vessels, and continue to confirm more and more orders for the system itself, but also for the full installation projects of the same.
DeSOx Scrubbers: With the Korean company “Global Echo” as a partner in Greece we have installed up to now 34 Scrubbers for New Buildings and retrofit projects, with the last installation to be performed at Skaramagas Shipyard, for a vessel managed by Thenamaris. Our company has also recently confirmed an order for Scrubbers for additional 18 New Buildings and retrofit vessels to be installed within 2024 and 2025. Global Echo Scrubber System is the only system to be installed without the need of D/D, with completion time 14 days within Korea and 18 days within Greece, China, UAE etc.
Now with the successful installation of Global Echo’s System in Skaramagas, we are confident that we will have additional order confirmations for passenger vessels as well as for other vessels trading in Europe.
Carbon Capture Machineries: This year at Posidonia Exhibition, we will present with our Chinese partners our Carbon Capture equipment and installation. Our partners have already installed their Carbon Capture system at a Panamax size vessel and now we are negotiating for a fleet agreement with a Greek-owning company. In the months to follow, after Posidonia, some seminars and courses will take place in Greece, to present to Owners and managers the technical properties and details of the Carbon Capture Systems, relevant costs, and operation details.
Also, our company is the Exclusive agent of the Korean company “Korea Global Service (KGS)” that consists of ex-Hyundai engi-
Mr. Gregory Papadakis, Managing Director of PSB & Co. S.A., together with Mr. Dimitrios Heliotis, COO of Horizon Tankers and Target Marine Group and the President of Zhoushan Changhong International Shipyard, at the Signing Ceremony for the New Building projects.
neers and electricians who can perform overhauling, troubleshooting, maintenance, and repair for ME and MC-C types, all electrical panels etc. as well as supply of spares parts for that equipment, but also sophisticated full service for DF and X-DF engines.
Apart from their Korean station KGS has also established offices in China, Singapore, and Dubai. Alternatively, their Korean S/Es can attend your vessels while calling any other port abroad. The maintenance that we can cover concerns, main Engine service with spares (ME engine D/D maintenance, Alpha lubricator/Pneumatic system maintenance) full Electric service (Dock maintenance for switchboard(H.V & L.V), Generator maintenance), ME Engine reconditioning (HPS pumps and FIVA valves), Reconditioning & Retrofit service (Turbocharger, HiMAP, Kongsberg, ACONI, Old Hyundai HiAN ACB to HGN Type) and many other Korean makers services.
AFLOAT REPAIRS: PSB & Co S.A has established its exclusive cooperation with local workshops as well as Ship Repair Yards. In particular PSB & CO S.A. represents exclusively “DUNGQUAT S/Y” in Vietnam with a Graving Dock of 280x86 meters, but also with the Vietnamese company “ISHITECH”, that is specialized in all kinds of engineering and mechanical jobs, offering assistance to all kind of vessels for afloat repairs.
At Santo Domingo with exclusive cooperation with the company “Midiraless”, an experienced local workshop able to deal with all kinds of repairs at both anchorage and berth.For day-to-day business, PSB & CO. S.A. is dealing with spare part supply, underwater and safety inspections, provisional supply and in general in all technical matters a fleet could ask for.
Thanks to numerous ship owning/managing companies that we serve, with an aggregate of more than 800 vessels, we have the negotiating and purchasing power to get the best prices for our customers and the apt ability to serve them with local stations and warehouses worldwide, also concentrating in common, but also in most remote and unpopular areas, like West Africa, Latin and South America, Australia etc.To conclude, our vast customer list and our company’s longevity in the demanding shipping market, is our best reference and assurance to our old and new customers that PSB & CO. S.A. can deliver at the highest possible level of performance”
Digitalising processes makes shipping more flexible, efficient and eco-friendly. Artificial Intelligence (AI) is playing role of growing importance in these efforts. At the leading international maritime trade fair in Hamburg, the topic will be covered in depth at the AI CENTER, where innovative start-ups will showcase their solutions.
Under the heading of “Driving the Maritime Transition”, SMM 2024 will not only focus on the maritime energy transition but also on digital transformation. Predictably, future alternative fuels enabling carbon-neutral ship operation will be in short supply and expensive. It is therefore crucial to optimise the energy efficiency of ships steadily, whether they are newbuilds or vessels in service. Dominik Schneiter, CEO of the Swiss ship engine manufacturer WinGD and chairman of the Digitalization Strategy Group of CIMAC, the global non-profit association dedicated to ship propulsion engineering, believes that retrofitting existing ships is one of the industry’s foremost challenges today. Digital tools, Big Data and IoT (Internet of Things) technology can provide a wide range of means to improve the operational efficiency of ships significantly and meet ever stricter regulatory requirements. For example, the technology company Acceleron offers a comprehensive solution called Tekomar XPERT.
AI in
AI is emerging as a main driver of digitalisation in the industry in general, and in the maritime business in particular. “Over the next ten years, Artificial Intelligence will increasingly play a key role in our industry; it can even help us cope with the shortage of skilled labour,” says Rolf Stiefel, Regional Chief Executive for Central Europe of the classification society Bureau Veritas. One typical application is the development of an automated drone-based inspection service to detect corrosion, cracks and deformation inside cargo tanks. Florian Heinemann, Senior Director Data Insights & AI at Germany’s biggest liner operator, says he is “convinced that by 2030 all business processes at Hapag-Lloyd will be AI-based”.
With this in mind, SMM 2024 will put the AI topic centre stage: The AI CENTER in Hall B6 will be entirely dedicated to advanced AI technologies and potential applications in the maritime industry “Early adopters of AI will benefit from competitive advantages,” ex-
plains Ragnar Kruse, co-founder and CEO of AI.HAMBURG and initiator of the AI CENTER. From sales & marketing to customer support, any business process can be optimised using AI, he stresses: “Many start-ups are now integrating AI technologies in software products that any company can afford. They will be featured at the AI CENTER at SMM.” A typical example: the Swedish company Cetasol offers iHelm, a software application that generates digital twins of various operational components on board ships. “Our iHelm solution uses AI, which makes it highly adaptable, enabling our customers to map their processes in a way that is future-proof,” says Cetasol founder and CEO Ethan Faghani. The company says its solution can reduce fuel consumption by 10 to 25 per cent without requiring major component retrofits or conversions.
The leading international maritime trade fair will be a great opportunity for industry visitors to get comprehensive information about current developments and join the highly dynamic AI community.
“Our AI CENTER at SMM 2020 sets a new standard,” says Claus Ulrich Selbach, Business Unit Director – Maritime and Technology Fairs & Exhibitions at Hamburg Messe und Congress. The AI for the Oceans Awards will be another highlight at the trade fair: “This is where SMM, in cooperation with Deutsche Meeresstiftung, Forum Oceano and AI.HAMBURG, will honour start-ups that use AI to protect the oceans,” says Selbach.
The jury for this competition consists of 14 distinguished members, including personalities such as Charles Goddard, Editorial Director of the Economist, and aquanaut Fabian Cousteau, grandson of the legendary oceanographer Jacques Cousteau. Start-ups must submit their proposals by 1 July 2020 at the latest. Award winners will receive a 10,000 euro prize, a campaign on LinkedIn and a presentation to an expert audience in a true win-win competition that benefits both, the environment and committed start-ups.
The findings of the latest Seafarers Happiness Index report by the Mission to Seafarers show a positive start to 2024, with an overall increase in happiness from 6.36 in Q4 2023 to 6.94 out of 10 in Q1 2024.
This was driven by a positive trend across all the aspects of seafarer happiness covered by the survey during this period.
The Seafarers Happiness Index (SHI) is a quarterly survey undertaken by the Mission to Seafarers, delivered in association with Idwal and NorthStandard, and supported by Inmarsat. The survey offers vital insights into the sentiments and experiences of the men and women that serve at sea.
In contrast to the consistent decline observed in 2023, the Q1 2024 SHI report depicts a mixed but cautiously optimistic rise in satisfaction among seafarers, shedding light on the positive and negative aspects of seafaring life.
The positive shift in seafarer wellbeing reflects improvements in several areas. These include enhanced financial security through fair wages and timely payments, fostering job satisfaction and camaraderie through positive crew relationships, as well as improved connectivity facilitating better communication with loved ones.
Additionally, seafarers reported the benefits of supportive company policies and leadership initiatives promoting crew wellbeing through access to recreational facilities, shore leave, high-quality culturally tailored food, and the prioritisation of health and safety concerns. Comprehensive training programmes have further bolstered seafarer competence and professional development.
Conversely, the report also underscores persistent challenges that will require systemic reforms to improve seafarer wellbeing. These challenges include addressing work-life balance issues such as extended contracts and limited shore leave, which contribute to excessive workloads, stress, and fatigue. Substandard living conditions, connectivity issues - though improved – remain an issue, and disparities in access to welfare facilities are significant concerns. Moreover, poor management practices, including inadequate leadership and discrimination, alongside limited career advancement opportunities and predatory recruitment practices, continue to impact seafarer satisfaction.
A pressing issue highlighted in Q1 2024 is the persistent allegations of fraudulent working hours reporting, resulting in inadequate rest periods and compromised safety standards. Seafarers are increasingly expressing unease and scepticism toward reported working hours’ accuracy, with a reluctance to speak out against potential misconduct. The manual nature of the process combined with a lack of contextual factors is perceived as inherently vulnerable to fraudulent activities, raising doubts about data integrity and effectiveness in capturing the nuanced realities of seafaring life.
Andrew Wright, Secretary-General, The Mission to Seafarers, said: “After the depressing slump in seafarer happiness that we witnessed in 2023, it is encouraging to see a brighter start to 2024. We are cautiously optimistic that this points towards a better year ahead for seafarers, but sustained improvement will require meaningful action. Between us, we have the tools at our disposal to make a difference to the lives of those working at sea, and it is up to us to act.
“Despite the challenges they face, seafarers continue to demonstrate remarkable resilience. The Mission to Seafarers remains committed to amplifying seafarers’ voices, advocating for meaningful reforms, and fostering a culture of respect, inclusivity, openness, and integrity within the industry. Together, we strive to build a maritime industry that not only values seafarers’ contributions, but also safeguards their wellbeing and happiness at sea.”
Yves Vandenborn, Head of Loss Prevention Asia-Pacific at NorthStandard, commented: “As an organisation advocating for seafarer wellbeing, NorthStandard finds it heartening that the Index captures rising seafarer happiness levels in the first quarter of 2024, especially given the decline reported in 2023. We are also encouraged that the overall increase from 6.36 / 10 to 6.94 is driven by gains across all 10 markers used, instead of a selective few. NorthStandard will continue to raise awareness of the experiences of seafarers, and we believe it is crucial that we capture more data about all of those working at sea. We therefore also welcome the fact that female participation in the SHI this quarter was at its strongest ever, representing just over 9% of all respondents.”
Thom Herbert, Senior Marine Surveyor and Crew Welfare Advocate at Idwal, added: “The Q1 2024 Seafarers Happiness Index highlights both progress made and areas requiring further improvement. We are encouraged by the positive trends, particularly around financial security, crew relationships, and enhanced training opportunities. However, we must remain vigilant in addressing persistent challenges like work-life balance, substandard accommodations, and any discriminatory practices that undermine seafarer dignity and morale. Idwal remains committed to championing transparency, accountability, and a culture of care that empowers seafarers to thrive both professionally and personally.”
The Mission to Seafarers, in collaboration with industry partners, is actively addressing the ongoing challenges affecting seafarer wellbeing, providing direct support through a global network of seafarers’ centres and ship visits, chaplains, staff and volunteers, and digital solutions like the ‘Happy at Sea’ app for seafarers.
The Mission would also like to express its appreciation to the shipping companies and shore managers who encouraged crew to participate, as well as to the seafarers who took the time to complete the survey. We encourage more seafarers to step forward and share their experiences, as their contributions are fundamental in driving positive changes within the industry.
«Our Ocean 2024»:
«Welcome to my beautiful country. Welcome to the birthplace of the Ocean.
Ο
Ωκεανός: according to the myth, the son of Uranus (the sky) and Gaia (the earth). A Greek Titan indeed, who always flows surrounding the Earth.
Today, as we gather in the cradle of maritime civilization, our task is to chart a course for its sustainable future. We live on a planet, that we call Earth, while it is quite clearly Ocean, as two thirds of it are covered by water.
Sustaining oceans is sustaining life itself. With this realization, we must join forces to save our oceans. For a viable future for us all.
In recognition of this common mission, I congratulate the Greek State on embracing this inspired initiative and hosting “Our Ocean”. Greece’s destiny has been etched by the ebb and flow of the sea. With a coastline that stretches over 20 thousand kilometers and a tapestry of 6 thousand islands… the sea is our identity. We, Greeks, breathe, live, and flourish from the sea. The sea is our bridge to the world.
This legacy has given rise to the largest ocean-going fleet.
Greek shipping is an economic and strategic powerhouse… It boasts a modern and technologically advanced fleet, proof of our commitment to the environment.
We are proud to be leaders in an industry that secures the welfare of humanity. By making global trade possible. By being the most cost-effective mode of transport for essential goods and energy. We maintain the living standards of people worldwide. Shipping is the backbone of the global economy.
The annals of history attest to this instrumental role shipping has played – and is playing - even in the face of unprecedented challenges.
Ladies and Gentlemen,
In shipping, we prioritize safety and environmental stewardship. We operate under the strict global rules of the International Maritime Organization (IMO). We adhere to its conventions, of which 21 are directly environment-related, and we take pride in the effectiveness of these measures. Our industry is rigorously regulated for the prevention of pollution by oil, chemicals, garbage, sewage, and air
emissions.
In facing the climate crisis, our sector’s commitment is unwavering.
It is fair to say that shipping has outperformed most other industrial sectors when it comes to reducing carbon emissions, considering that it is a fossil fuel captive industry.
Shipping is by far the least carbon intensive means of transporting goods.
Despite its expansive reach, the shipping industry’s Green-HouseGas footprint on a per capita basis, compares to that of the lowest emitting countries. Bear in mind that shipping carries around 90% of global trade and emits less than 1/15th of the top emitting country
But even that comparison is misleading.
The essence of shipping transcends the industrial activity of any single country. We serve the needs of 8.1 billion souls. We unite countries, people, the world.
Yet, we are aware of, and we also fully embrace our responsibility. We firmly support the ambitious targets set by our global regulator, IMO for net zero Green-House-Gas emissions by 2050.
We commit to turn targets into action.
However, shipping is interconnected with many other industries and out-of-sector stakeholders, who determine important parameters of its activity. To achieve this goal, we must all go hand in hand.
As we move from the age of hydrocarbons to the dawn of renewable materials, shipping is poised once more to be a cornerstone in this transformative era.
Shipping is responsive, reliable and resilient.
It will power the engine of progress, in the reshaping of the supply chains. And steer us towards a sustainable future.
Ladies and Gentlemen,
For us in shipping, the ocean is our home.
We honor and protect it.
Ocean conservation is our way of thinking and acting.
Greek shipping moves beyond aspirational initiatives.
We are at the forefront of technological developments and innovations.
“Our Ocean Conference” is a great call to showcase our commitments to the environment.
Let us all navigate forward, united with vigilance and vision. Let our industry be a beacon of common sustainable progress. Let our legacy to the future generations be an ocean bursting with life».
Cruise Lines International Association (CLIA), represented by its European Chairman, Mr Pierfrancesco Vago, participated alongside the International Chamber of Shipping (ICS), in the G7 Transport Ministerial Session on Maritime Connectivity on 13 April 2024.
At the meeting, Mr Vago expressed the cruise industry’s solidarity with the wider maritime sector on the imperative to ensure seafarer safety, considering current security threats in the Red Sea and elsewhere. CLIA highlighted how the maritime sector is united in condemning the attacks and is calling upon the international community to adopt the adequate measures to protect seafarers at the next IMO Maritime Safety Committee on 15-24 May 2024, and to develop adequate solutions to the crisis. The cruise industry employs one-third of the world’s seafarers and believes that safety must be integral to any international response to the security situation.
Discussions also focused on what infrastructure investment will be needed to preserve global maritime connectivity in light of international climate change commitments. Adaptability of the global maritime network to reflect the new needs in decarbonised energy sources will be a key factor in maintaining global connectivity, while meeting climate objectives.
Mr Vago said, “This was an important opportunity to raise the vital issue of seafarer safety with G7 Ministers. It was also valuable
to discuss the industry’s transition to a future of low and net-zero carbon fuels and what this means for future maritime connectivity It will be vital to ensure the new types of fuels and the necessary portside infrastructure are available at scale in the locations where they are needed to avoid bottlenecks in maritime routes.”
The cruise industry is leading a step change in the technologies and fuels used in shipping to address the climate challenge. Within the next two decades, starting already today, there will be ships sailing that will use new types of fuels as the industry moves away from fossil fuels towards low and net-zero carbon fuels. The new technologies that the industry is deploying and testing onboard cruise ships will also be critical for wider application across maritime.
To help identify future needs, CLIA recently announced that it has launched a study on global investment needs to expedite the energy transition of our sector. This study will include a mapping on the infrastructure and energy needs at ports served by the cruise sector.
The cruise industry plays a critical role in maintaining and enhancing strategic maritime industrial capacity in Europe. Cruise ships represent 80% of the orderbook value for European shipyards, making our industry critical to maintaining the technical know-how of these countries in complex shipbuilding.
New resource serves as a gateway to crucial information and data about future fuels and technology in shipping.
Access to latest information on zero and near-zero marine fuels and technologies, including pricing information and the latest research, can be found on futurefuels.imo.org.
The website has been developed by the Future Fuels and Technology Project (FFT Project), a partnership project between IMO and the Republic of Korea, supporting the development of new regulation within the possible IMO Net Zero Framework to achieve the targets contained in the 2023 IMO GHG Strategy.
The website includes sections on:
• Latest Information: current data on alternative fuels and supply, up-to-date indicative prices, information on the IMO Data Collection System (DCS).
• Future Insight: insights into the readiness, scalability and sustainability of new marine fuels and technologies, including fuel price forecasts, R&D and demonstration projects, as well as information on relevant initiatives in the shipping and energy industries.
• News and Events: a selection of global news, information resources (including reports and journal papers), and information on IMO events related to GHG emissions reduction in international
shipping.
• Training and Cooperation: training materials and useful tools on alternative fuels, energy efficiency technologies and other GHG reduction measures.
Technological innovation and the global introduction and availability of zero or near-zero GHG emission technologies, fuels and/or energy sources for international shipping are integral to achieving the overall level of ambition identified in the 2023 IMO GHG Strategy
Data providers and collaborators involved on the Future Fuels website to date include Ammonia Energy Association, Argus Media, DNV’s Alternative Fuels Insight, IAPH, Ipieca, Korean Maritime Cooperation Center (KMC), Methanol Institute, OECD, SEA-LNG, SGMF, Zero Emission Shipping Mission and ZESTAs, and the IMO partnership projects GHG-SMART, GreenVoyage 2050 and NextGEN. Current information on the website is sourced from a range of stakeholders and data providers who have joined the initiative in its early stages. Other data providers are invited to join this collaboration.
The FFT project’s website aims to enhance access to information for all stakeholders involved in IMO’s climate change discussions and to facilitate relevant information sharing. Inclusion on the website does not imply endorsement or expression of any opinion on the part of IMO regarding the data or the data sources.
Biofouling greatly impacts fuel consumption, increasing CO2 emissions. Operating with high performing antifouling systems and continuous monitoring of fuel consumption, fouling and speed loss keep track of your vessel’s condition, and can help you reduce fuel cost and carbon emissions.
The proven performance of Jotun Hull Performance Solutions can reduce fuel cost by as much as 14,7%.
Jotun established Hull Performance Solutions (HPS) in 2011 to make it easy for operators to maximise hull performance and thereby reduce both fuel costs and greenhouse gas emissions. The solution consists of Jotun’s advanced antifouling products, combined with a transparent method for measuring the impact of antifouling on vessel energy efficiency.
HPS consist of four key elements which work together to optimise performance:
• High performance antifoulings
• High-end technical service
• Performance analysis
• Performance guarantee
MEGATUGS was established in 1978 and is widely recognised as one of the leading professional towage and salvage companies in the marine industry dedicated to provide safety and support at sea.
MEGATUGS scope of services includes harbour & ocean towage, salvage, wreck removal, oil spill response, commercial diving, offshore support and lifting services
HEAD OFFICE
2, Iroon Polytechniou str., 18863 Neo Ikonio, Greece
Tel. +30 210 45 22 131, Fax. +30 210 4180176
BRANCH OFFICE
42, 26th Octovriou str., 54627 Thessaloniki, Greece
Tel. +30 2310 256380/1, Fax. +30 2310 256382
e-mail: info@megatugs.gr | megatugs.com