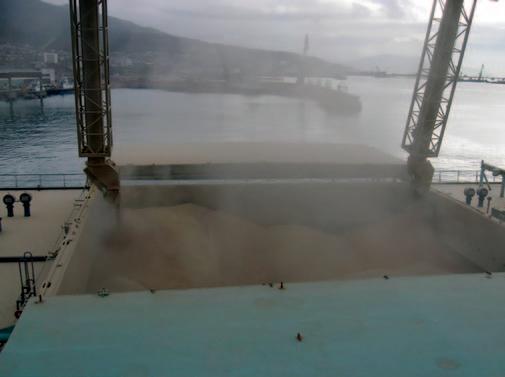
2 minute read
Dust suppression system with mineral oil for silos and grain terminals
Dust is a common issue in grain handling facilities, and it can lead to a range of problems and challenges. Some of the key problems associated with dust in grain handling facilities are:
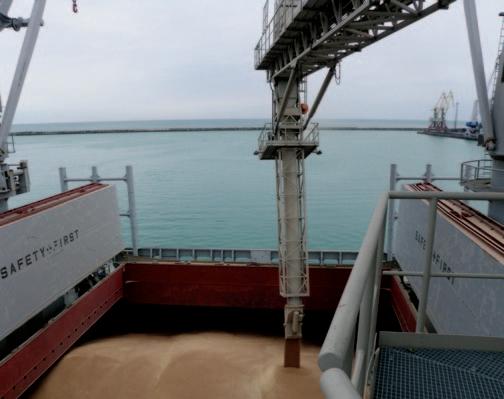
Health hazards: dust can contain v allergens, mold spores, and fine particulate matter. Prolonged exposure to grain dust can lead to respiratory health issues.
Fire and explosion risk: grain dust is v combustible, and can lead to fires and explosions. This presents a significant safety risk to both workers and the facility itself. There is the potential to cause catastrophic damage and loss of life.
Reduced visibility: excessive dust in v the air can reduce visibility within the facility. Increasing the risk of accidents and collisions involving vehicles and equipment.
Premature wear and tear: dust v particles are abrasive and can cause faster deterioration of machinery. This results in higher maintenance and replacement costs.
Operational inefficiencies: dust v accumulation leads to operational inefficiencies. Blockages and reduced equipment performance can disrupt the flow of grain. Thus causing delays and productivity losses.
Product contamination: by v developing contaminants, impurities, and molds, dust can degrade the quality of the grain. This is particularly problematic for the grain intended for human or animal consumption.
Environmental impact: dust v emissions can have environmental consequences on local wildlife and communities. Dust particles have a negative impact on nearby vegetation, air, soil, and water bodies. To address these problems, a dust suppression system must be implemented. This system is essential for creating a safer and more efficient handling system. ICCE has developed a system that uses mineral oil as an agent for dust suppression. The system can reduce the dispersion of dust particles during grain processing and storage operations. Some of the key advantages are:
1. Improved air quality: mineral oil helps reduce airborne dust. Thus improving the air quality and minimizing respiratory health risks.
2. Dust emission reduction: by binding to dust particles, mineral oil reduces dust emissions. Which is crucial for regulatory compliance and environmental responsibility.
3. Equipment protection: minimizing dust extends the lifespan of machinery and equipment.
4. Fire prevention: mineral oil dust suppression can reduce the risk of fires and explosions in grain facilities.
5. Personnel safety: enhanced safety measures result from reduced dust levels. Lowering the risk of accidents and respiratory issues for workers.
6. Environmental responsibility: mineral oils align with environmentally friendly practices.
7. Cost effectiveness: mineral oil dust suppression systems has proven to be more cost-effective compared to the other solutions.
ICCE offers a complete solution. From the design to the supply, start-up, and maintenance of the installed system. The entire solution includes following the specific processes and considerations: Identification of dust generation v points: determine the key areas within the handling facility where the dust is generated. These points can include conveyor belts, chutes, transfer points, and loading/unloading areas.
System design and installation: v ICCE designs a dust suppression system with the corresponding documentation. The design considers the facility layout, airflow patterns, and specific dust areas, thus, ensuring effective dust control.
System supply: ICCE provides and v installs a complete system on a turnkey or supervision basis.
Personnel training: this includes v understanding the system's operation, maintenance procedures, and safety protocols.
Mineral oil application — installation and functioning of the system is as follows:
1. Spray nozzles or misting systems are placed in dust-prone areas. Mineral oil is automatically sprayed onto surfaces where dust is generated. The fine mist of mineral oil particles helps bind with dust particles, making them heavier and less likely to become airborne.
2. Control and monitoring: the system includes a control and management system for managing the operation of the dust suppression system. The system manages the frequency and intensity of mineral oil spray. This is based on dust levels and operational needs.
3. Maintenance and refilling: routine maintenance of the system is essential to ensure effectiveness. This includes cleaning nozzles, checking pipelines for blockages, and refilling mineral oil reservoir.