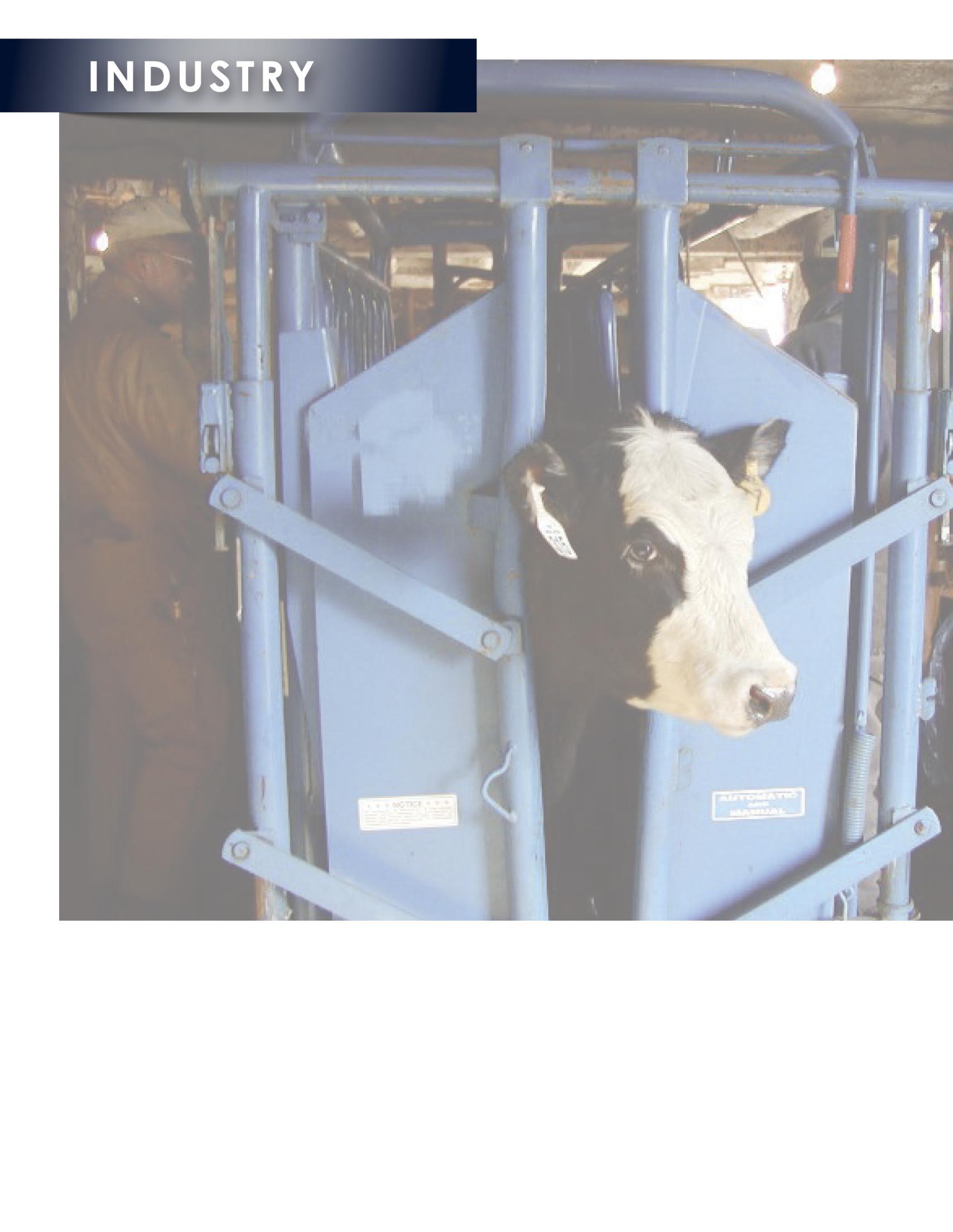
7 minute read
Understanding Squeeze Chute Safety
By Rob Eirich, Director, Nebraska Beef Quality Assurance, and Extension Educator, University of Nebraska-Lincoln
Reprinted with permission from Nebraska
Cattleman
Cattle handling and processing involves a number of working elements, and the safety of people should be a top priority. It is also important to ensure the proper handling and safety of the cattle being processed. Using squeeze chutes for restraint is common practice in all segments of the beef cattle industry. Today, there are many different manual and hy draulic chutes on the market, each with different features for safety and low-stress handling. The following information highlights some safety points for producers to consider.
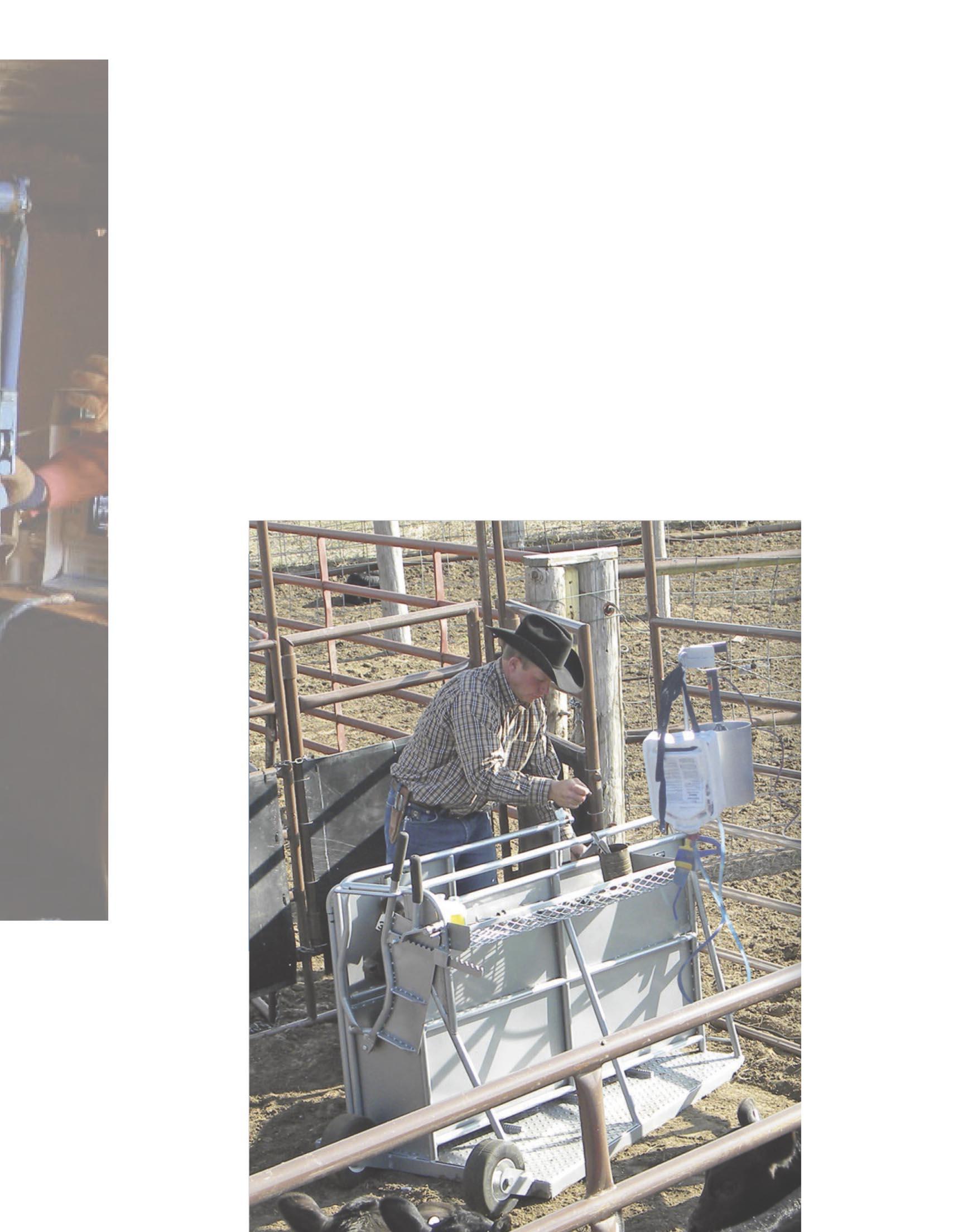
Chutes have many working parts with levers, handles and linkages, all of which can pose safety risks, so proper operation is key. Often, the levers protrude from the chute and are used for operating the headgate and squeeze chute functions; these can be under pressure as animals are being restrained. This pressure can cause injuries to hands, wrists and arms. When operating these levers, it is important to be sure that the locking device on each lever is operating properly to hold the headgate and squeeze in place while processing. If the locking device is worn or not operating, these handles can fly open and potentially injure your crew. With hydraulic chutes, there is less risk with levers, but the hydraulic cylinders and linkage must be checked and well maintained, and have safety shields in place to eliminate the risk of injury. Both designs must be maintained to ensure stops and locking devices are in good working condition.
One of the major injury risks with squeeze chute operation is pinch and pivot points. These are areas where parts come together or can press two parts together. Two main pinch points are the headgate and the sides of the squeeze chute. As animals are processed through the facility, applying the appropriate amount of pressure for restraint is important; with manual operation, the amount of pressure should be adequate to restrain but not cause pain from the pressure. Hydraulic chutes should be maintained to the pressures as directed in the operator’s manual. Operators and crew should keep themselves out of these pinch/pivot point locations while restraint is being applied. Due to the speed and pressure that occurs during chute operation, if someone gets caught in these pinch points, injuries can/do occur.
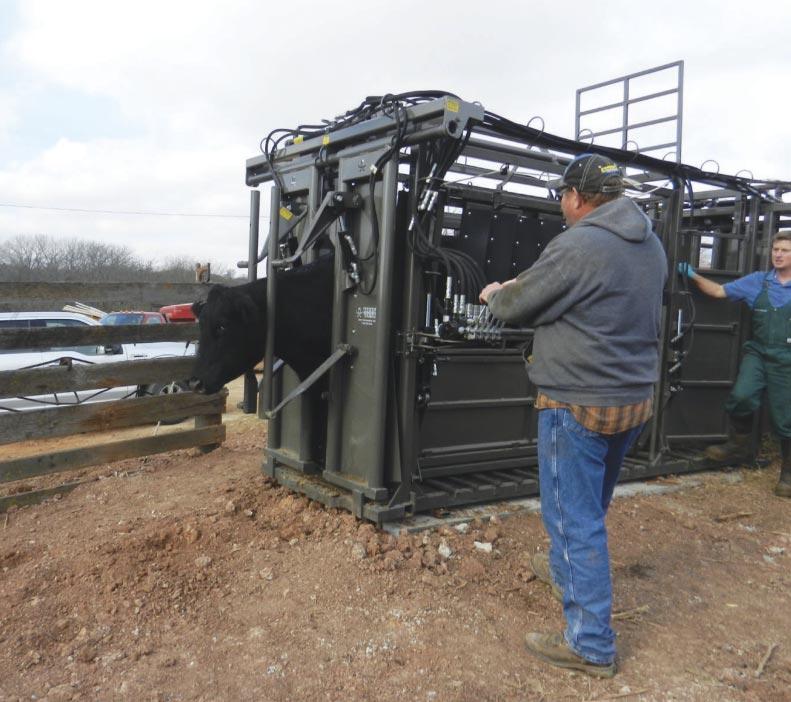
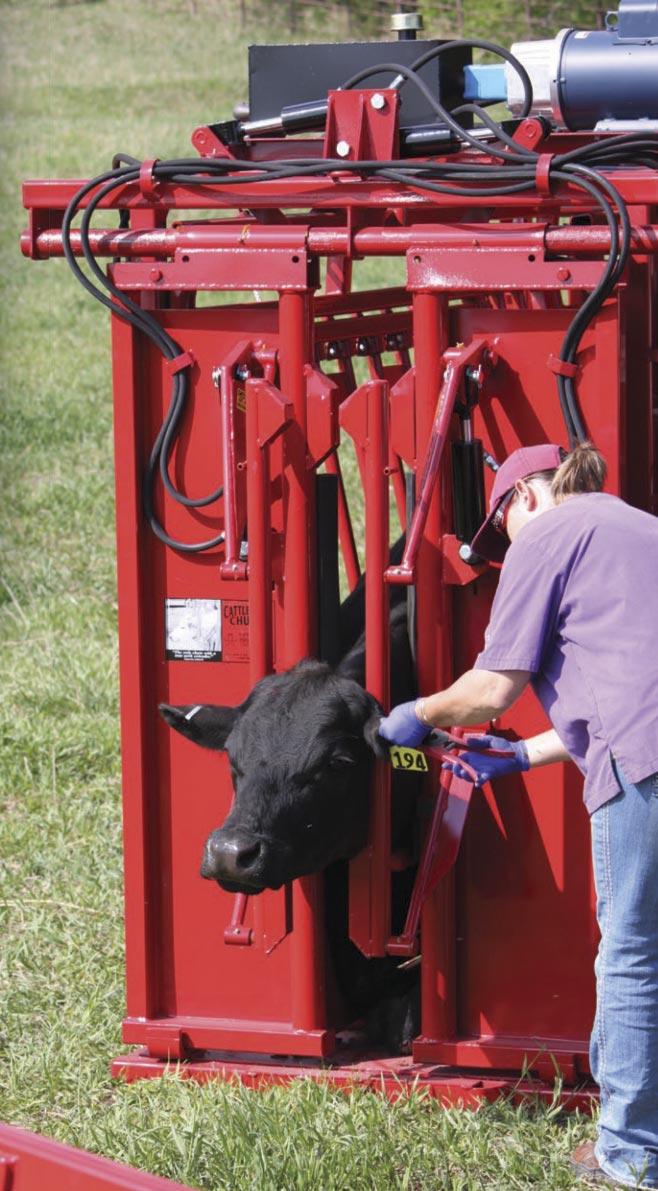

Currently, many chute designs feature neck extenders or additional head restraints. These are safety features to keep an animal’s head or neck from being thrown around during the administration of animal health products. Make sure the linkages and latches work properly on these parts as well. The features can add pinch points to the equipment. These should properly restrain the head and neck without putting additional pressure to the head. Operators and personnel should keep hands and arms out of these moving part for safety.
For proper processing, chutes have a number of access features. The access points could be doors, removable panels, drop-down bars or side gates, and all have latches to secure them in place when restraining an animal. As chutes get used, these latches will wear and should be checked and maintained on a routine basis. If latches are not operating properly, the access points can open unexpectedly, which can cause injury risk to the processing crew members.
Another safety risk can be worn rope or cable that could break during restraint. These linkages might be part of the automatic headgate operation or opening and closing of rear or side gates. Many new chutes use a lever linkage to open and close gates, but they should also be checked for worn parts and latches.
With a number of different manual and hydraulic chutes on the market, it is difficult to list all of the points to check for proper operation and safety of both the animal and crew. Below is a checklist to review before processing begins, to ensure safety:
• Check chute for any broken parts that might have sharp edges sticking out.
• Check linkages for proper operation and worn parts (bearings, bolts, latches and handles).
• Check all latches to ensure proper lock and release function.
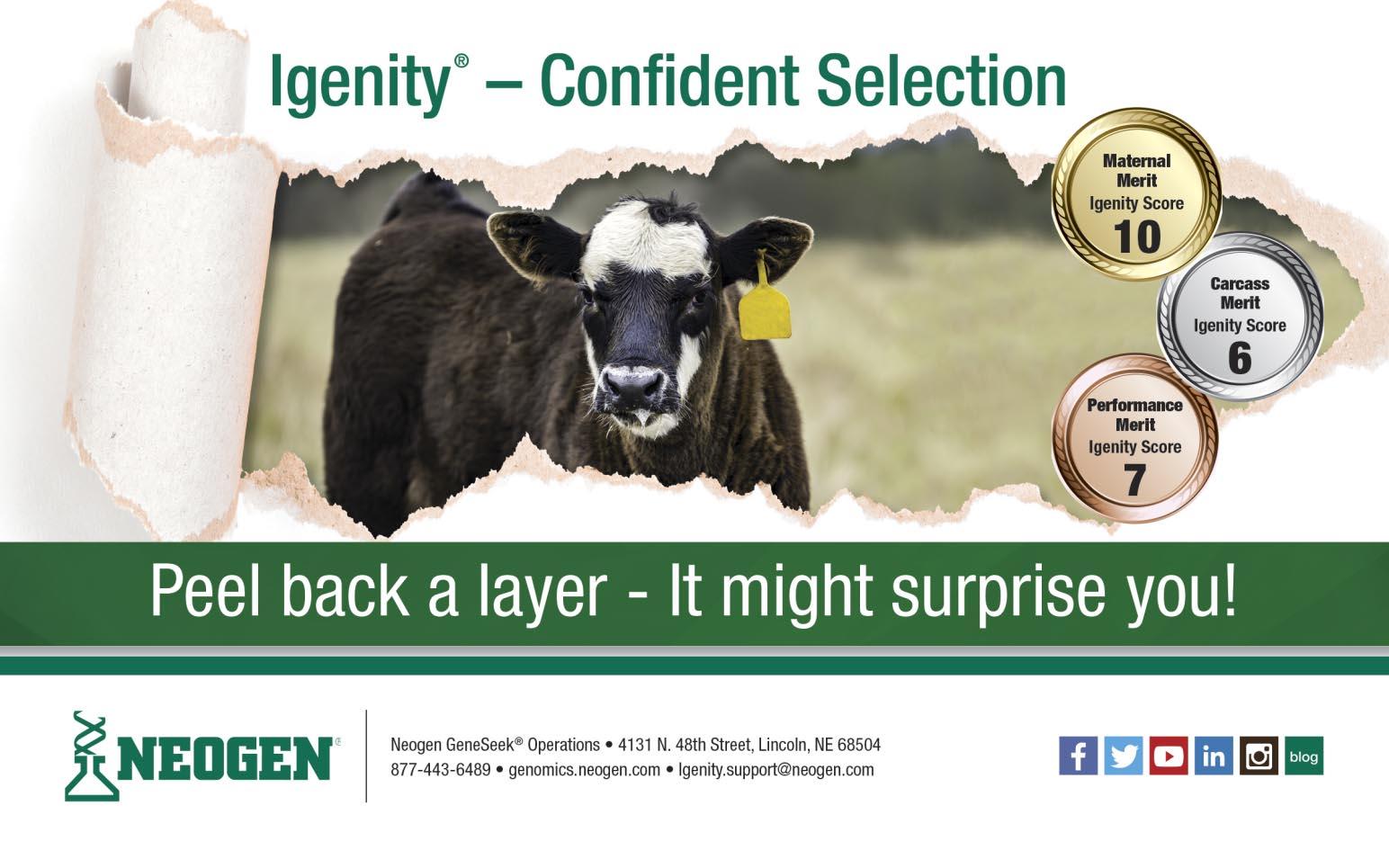
• Lubricate pivot points and linkages as directed in operation manual.
• Check to make sure cables and ropes are in good condition.
• Make adjustments for the size of the animal being restrained.
• Check hydraulic pump, lines, cylinders and connections for worn parts.
• Check hydraulic pump for proper operating pressure (see operation manual).
• Keep chute clean and well-maintained for safe operation.
• Train personnel on proper operation of equipment and handling procedures.
Crew safety should be the top priority during processing, in addition to proper equipment to ensure animal care during restraint. It is always important to check your complete processing facility to ensure it is well maintained to reduce the risk of accidents and injuries. Maintaining corrals, alleys, gates and chutes on a regular basis will improve safety and extend the useful life of the facility.
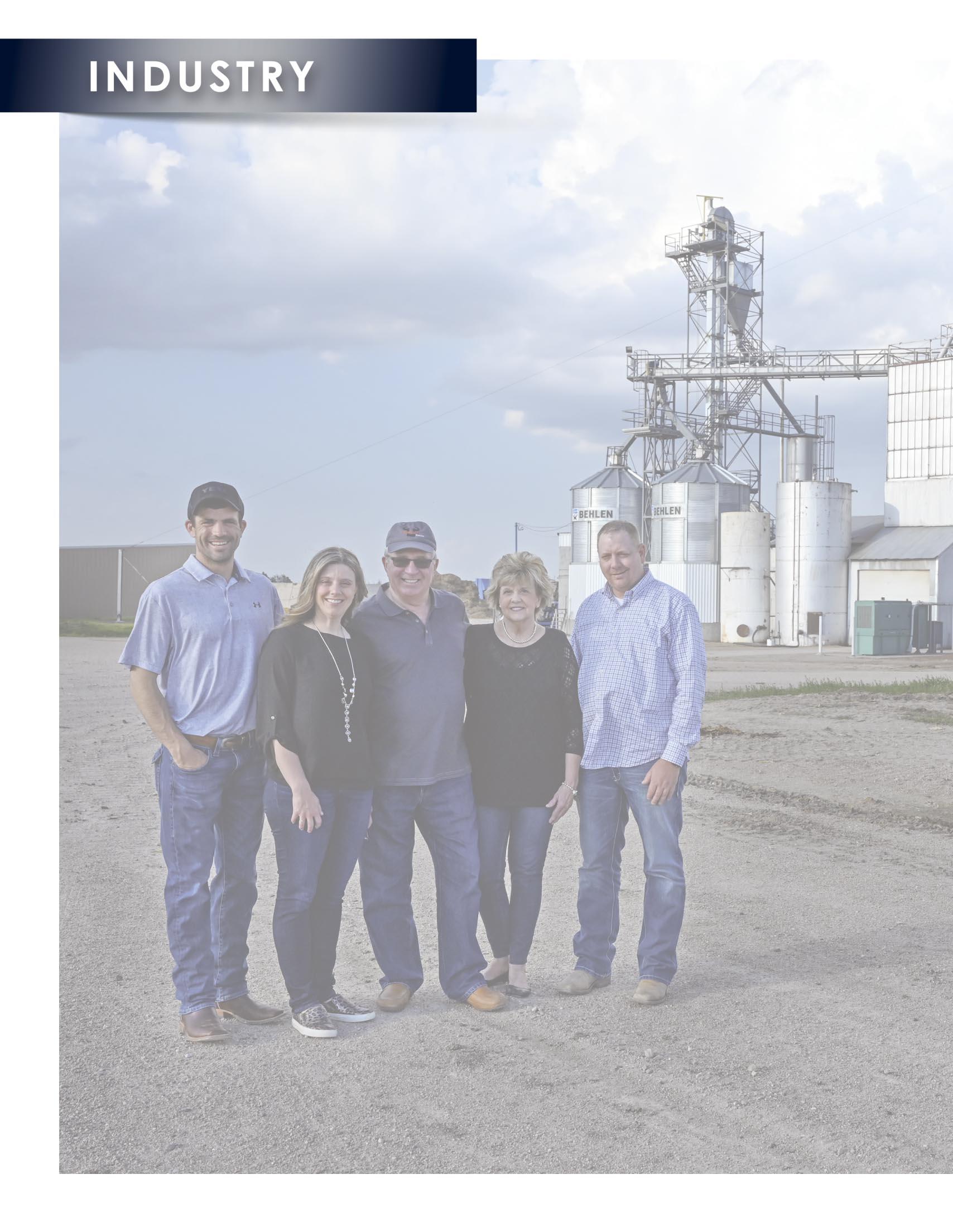
2019 CAB Feedlot Commitment to Excellence

All-in cattle feeding
Timmerman family receives CAB honors
By Miranda Reiman, Certified Angus Beef
They were raising children with diverse skillsets and diverging dreams.
Veteran cattle feeders Norm and Sharon Timmerman, of McCook, Neb., encouraged their children to follow their own passions, and they did. After college, Jason started with Timmerman Feeding near Omaha, while CPA Kristin ran her own accounting firm and Ryan pursued a degree in business management with a sports and recreation option.
Today, they have all returned to the family business that now includes, Jason and Wendy, Kristin and husband Jeff Stagemeyer, and Ryan and wife Nicole.
“It’s nice to be that good of friends with your family members, who like to work together,” Norm says. “It all fell into place.”
The family brings a shared trust and camaraderie to the work they do for the feeding company they jointly own: NA Timmerman Inc. They started in 2012 with yards at Indianola, Neb., and McDonald and Colby, Kan., now also including locations near Holyoke and Sterling, Colo., with a one-time feeding capacity of 80,000 head.
For their dedication to grid marketing, feeding premium cattle and a call to doing the best job every time, the Norm Timmerman family received the 2019 Feedyard Commitment to Excellence Award from the Certified Angus Beef ® (CAB®) brand.

The quality kind
“There are a lot of small feedlots that specialize in the high-quality type, but larger feeders don’t always have the benefit of picking and choosing what cattle they feed. They need to keep the pens full and often feed a wide variety,” says Paul Dykstra, beef cattle specialist for the brand. “They’ve really evolved over the last 20 years or so, under Jason’s vision, to procure cattle that will do well on a grid.”
In 2005, the Timmermans tested grid marketing with sales of 2,100 head on a Cargill formula. Today that number is closer to 150,000 annually. It’s changed their procurement and it’s changed their harvest targets.
“We keep the feedyard full and we manage our risk and we try to maximize our performance to the best of the ability of our cattle,” he says, “versus the old cash system: hurry and sell, or wait and make them too big. When they’re ready, they’re ready, we just keep rolling and just manage the risk on the other side of it.”
Despite a difficult winter and early spring for Great Plains cattle feeding, the Timmerman marketings still hit 38% CAB and Prime for a three-month average into this summer. In recent years with more cooperation from Mother Nature, their branded quality numbers have been significantly higher across the board.
Jason and Jeff have extensively used artificial insem ination on the 700-head cow herd they own together, which shows them the impact of genetics on the final results. Three years of feedyard data on the progeny reveals more than half of make CAB and Prime.
“When we get a pen of high-grading cattle that have a lot of CABs, it directly affects us,” Jason says, “because it’s money in our pocket.”
Partners with PAC
In a quest for continuous improvement, the family has contracted with Production Animal Consultation (PAC) for nearly a decade for health advice and access to benchmark information.
“We use the data to look at how we can get better. Where can we improve?” Jason says.
When Dr. Shane Terrell or bilingual trainer Jose Valles make their rounds, “the benefit is tenfold, because it gets everyone enthused to go out and do a good job,” Jason says.
The number of ranch direct calf-feds that come into the operation is unique for their size, says Terrell, but the family is able to make it work because of their network of backgrounders and their attention to detail.
“A desire to continue to do well,” tops the reasons why Terrell enjoys his monthly stops to each of the yards.
“They’re good people and a good family-run operation,” he says.
Their work ethic is evident.
Extra effort
“Hard work will give you a lot of luck,” Norm says.
Pen maintenance, feed delivery and cattle health monitoring – they all add up.

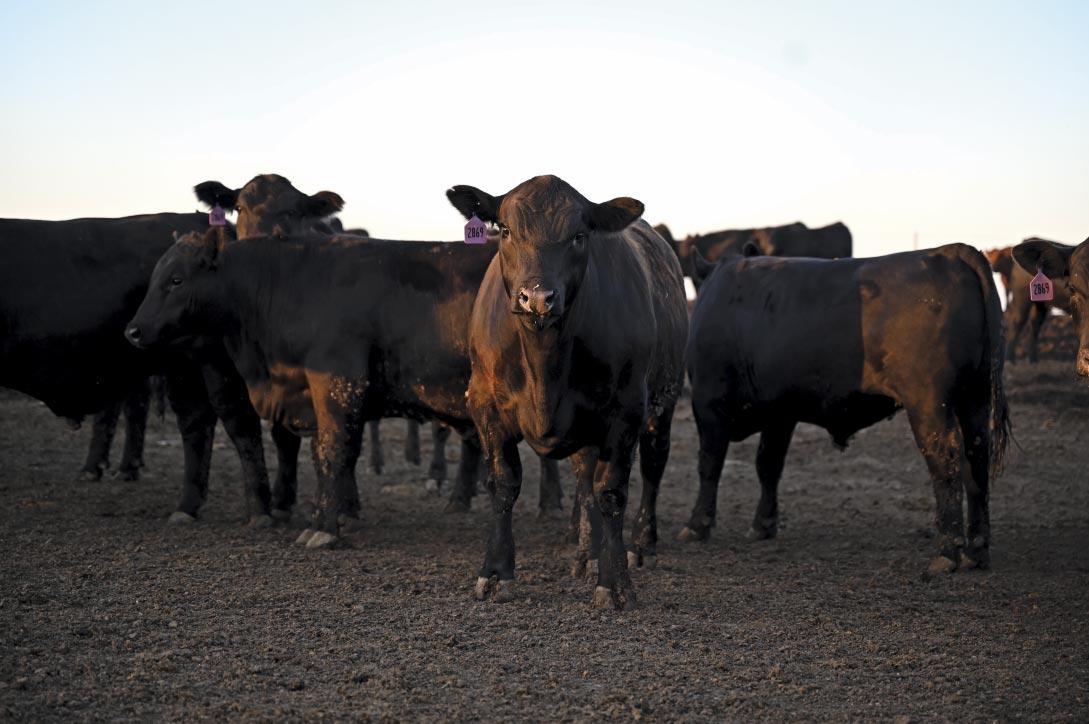

“There is no room for error. It’s a sole responsibility,” Ryan says. “The job we do at the feedlot impacts our customers. There’s a lot of money involved… it’s their livelihood.”
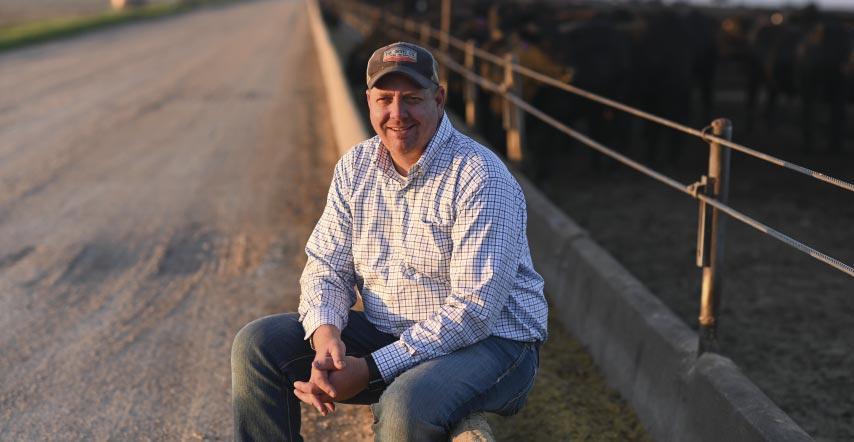
It’s not like a Timmerman to let people down.
“These are the things that are important to the Timmerman family: their faith, being a good family member, working hard at what you’re doing,” Kristin says.
She and Jeff bring a fresh perspective to the finances, giving purchasing advice and making insurance decisions.
“My dad and I knew the outside very well, but needed someone in the back that could complement us – luckily we had family that could do that,” Jason says.
Leo’s legacy
They had a good example of seeing partnership in action. Timmerman Feeding of Springfield, Neb., started by Leo Timmerman, was into the hands of the next generation, brothers Gerald, James, Ronnie and Norm, when they expanded to Indianola, some 250 miles west.
“This was a farm and we built it from scratch. The office started in our trailer house, where we lived,” Norm says, giving credit to Sharon. She kept the books there by day and made it a home by night.
By this decade, with the third generation involved, it was a natural time to let each Timmerman branch individually exercise their entrepreneurial spirit.
They gave their children the opportunity Leo Timmerman gave them.
“It evolved to where I was doing more, more and more,” Jason says, noting the risk management shifted to him through the years. “Then it’s how do you keep it organized? Trial and error. Mistakes, mistakes, mistakes.”
Years like 2014 remind them it’s fun to make money. Years like 2015 keep them humble.
“I don’t think it will ever be easy. You’re in an environment dealing with people, dealing with Mother Nature. You’ve got the element of risk,” Jason says. “It will never be easy, it’s just about how you manage your way through it.”
History says they’ll do it. Being a Timmerman means they’ll do it well.