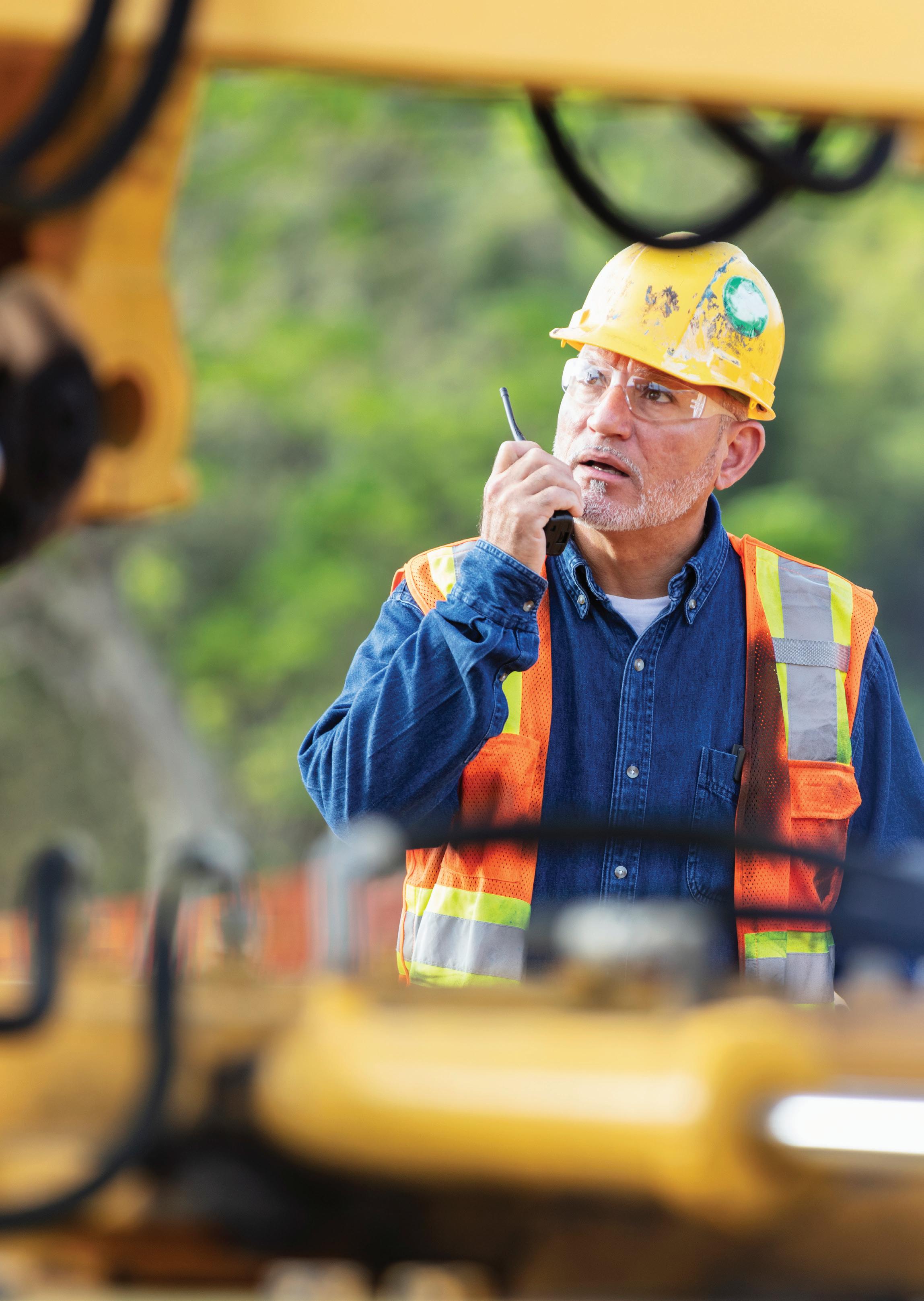
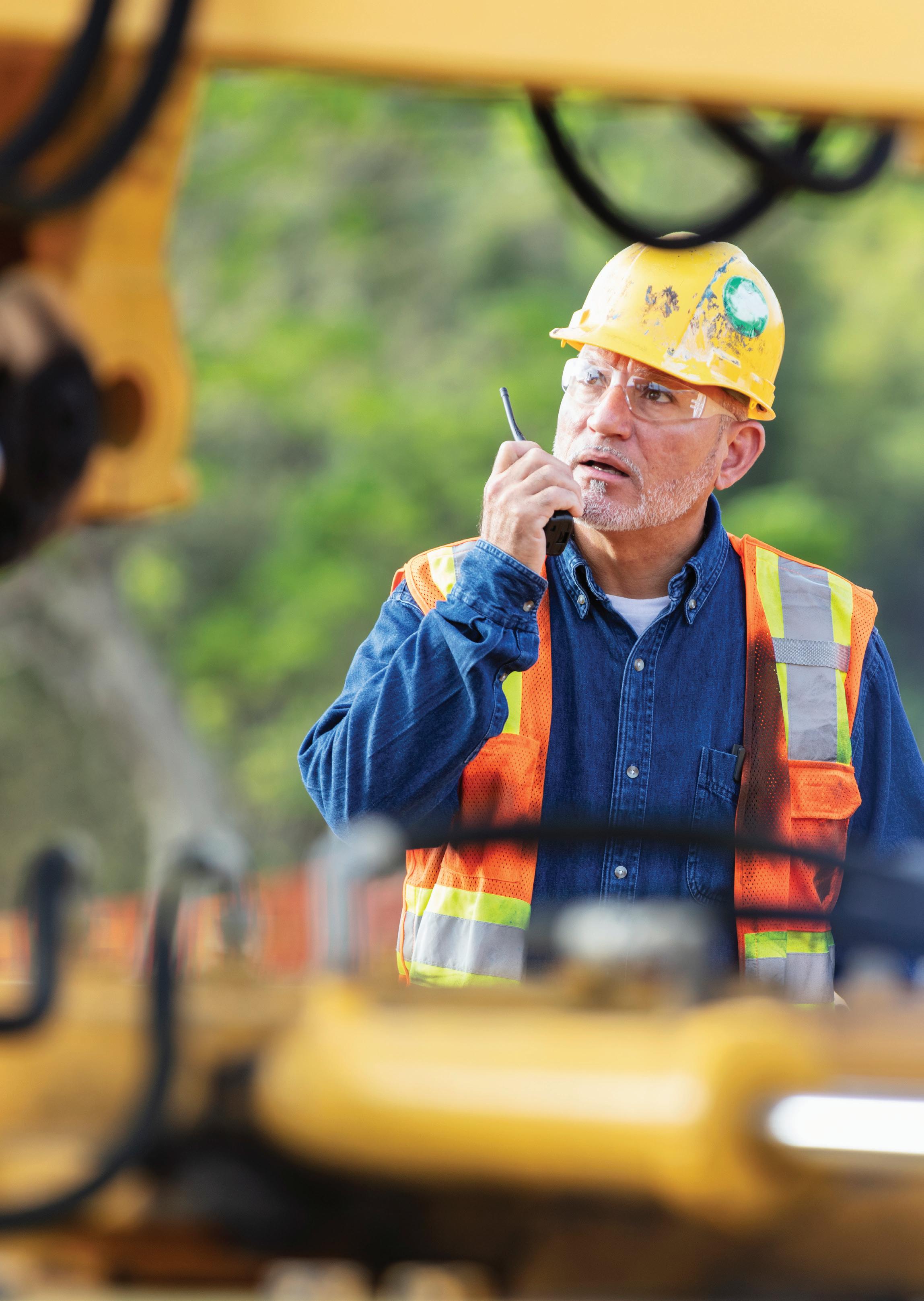
Combating Construction’s Biggest Time-Wasters
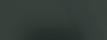
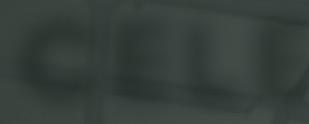
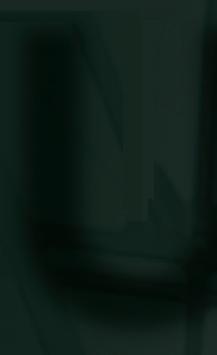

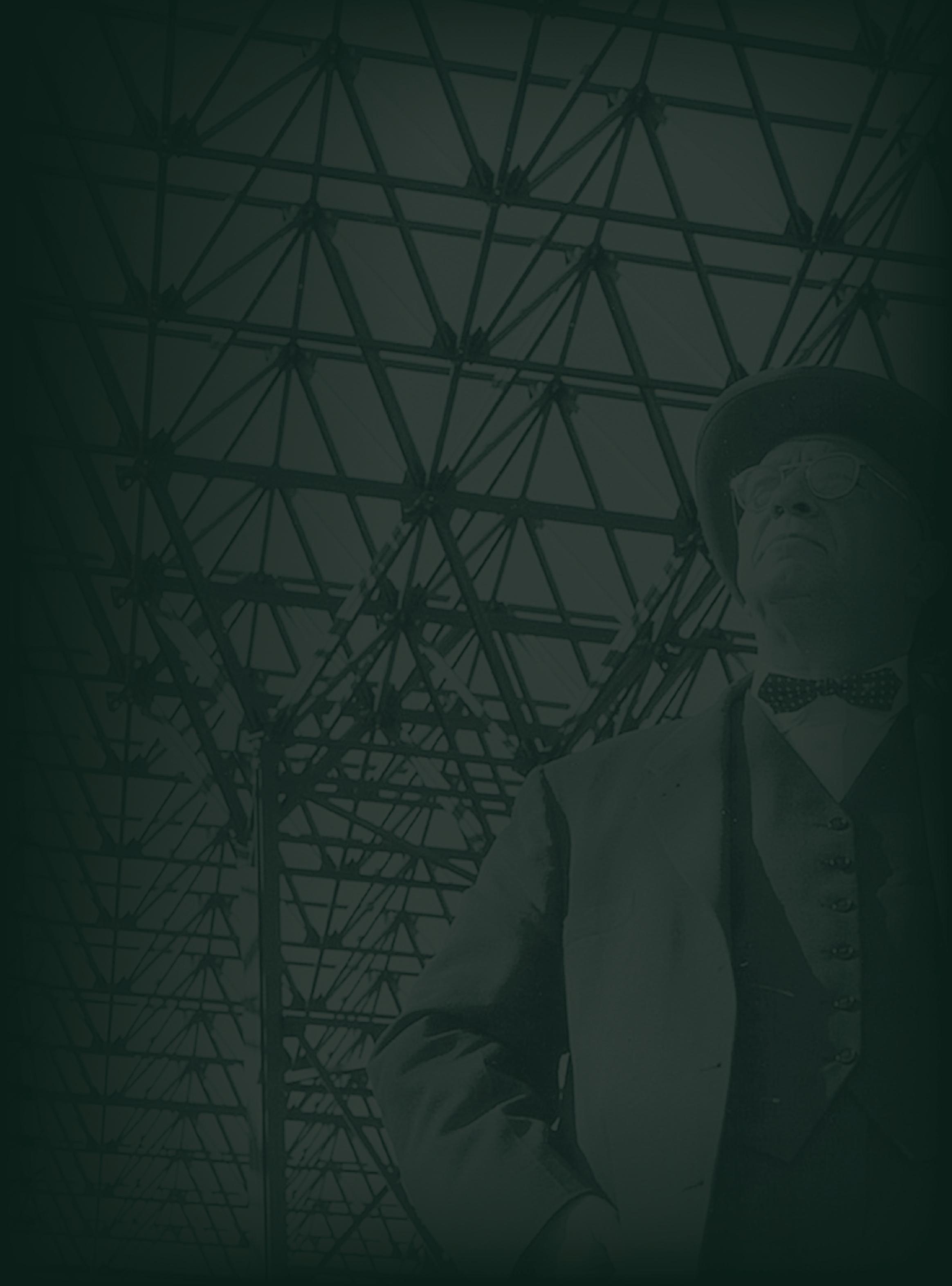
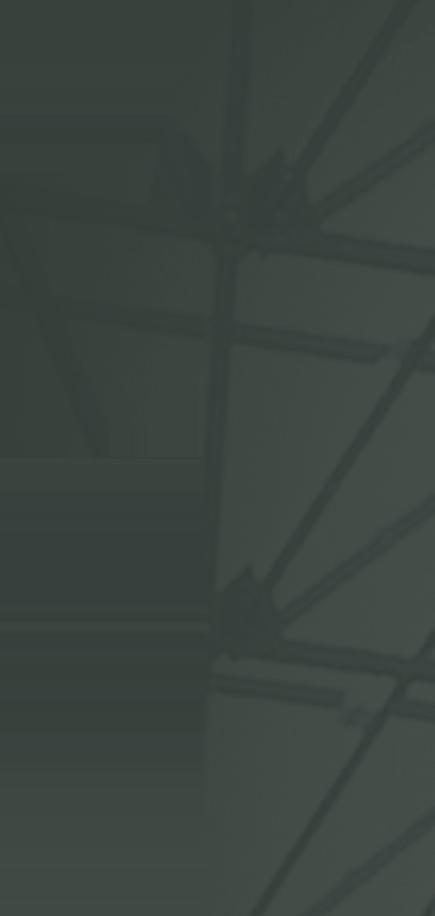
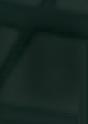
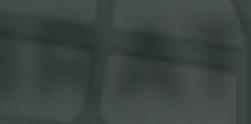
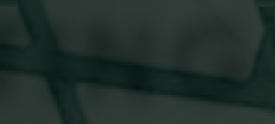
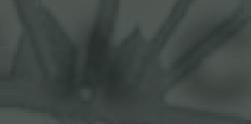
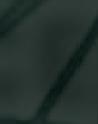
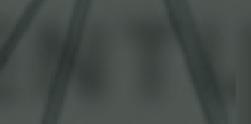
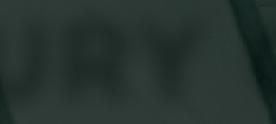
CELEBRATING A CENTURY OF
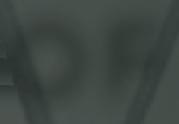
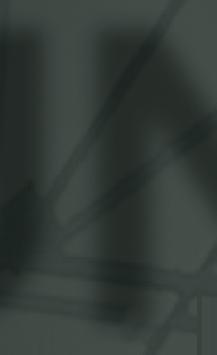
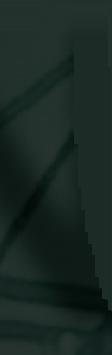

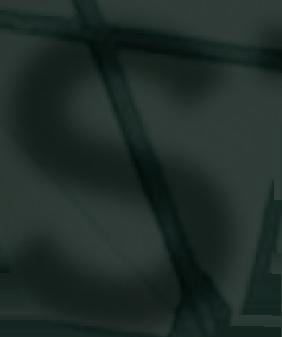
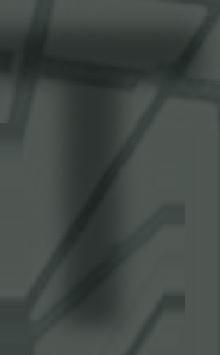
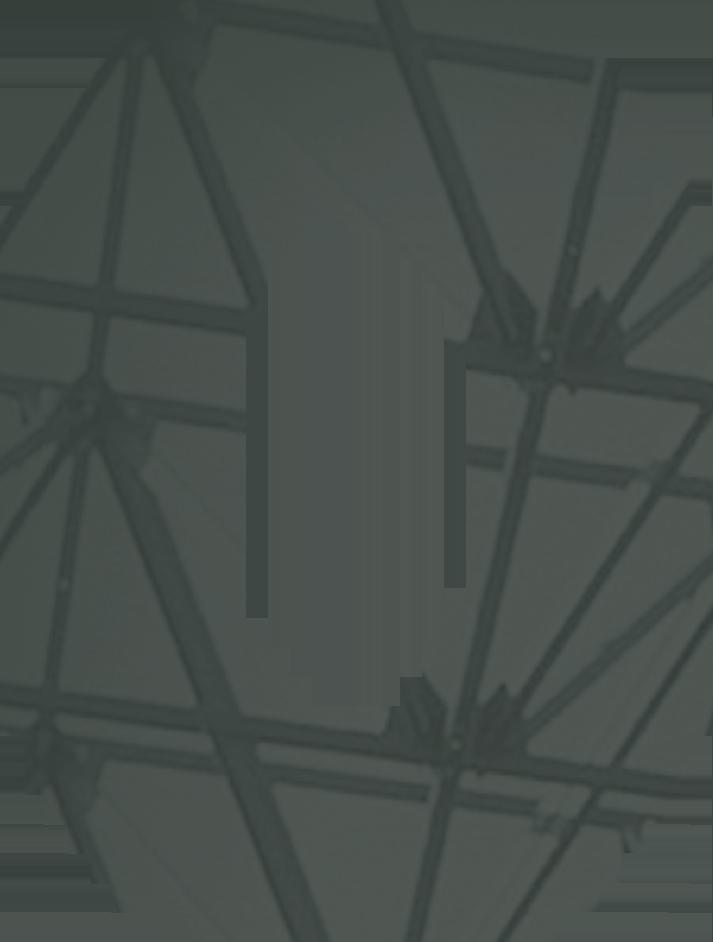
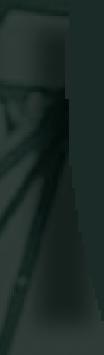
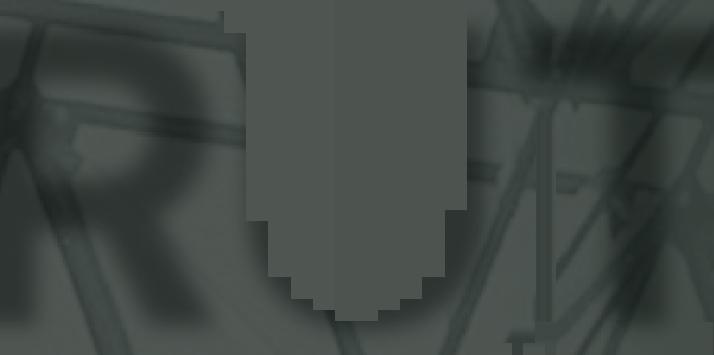
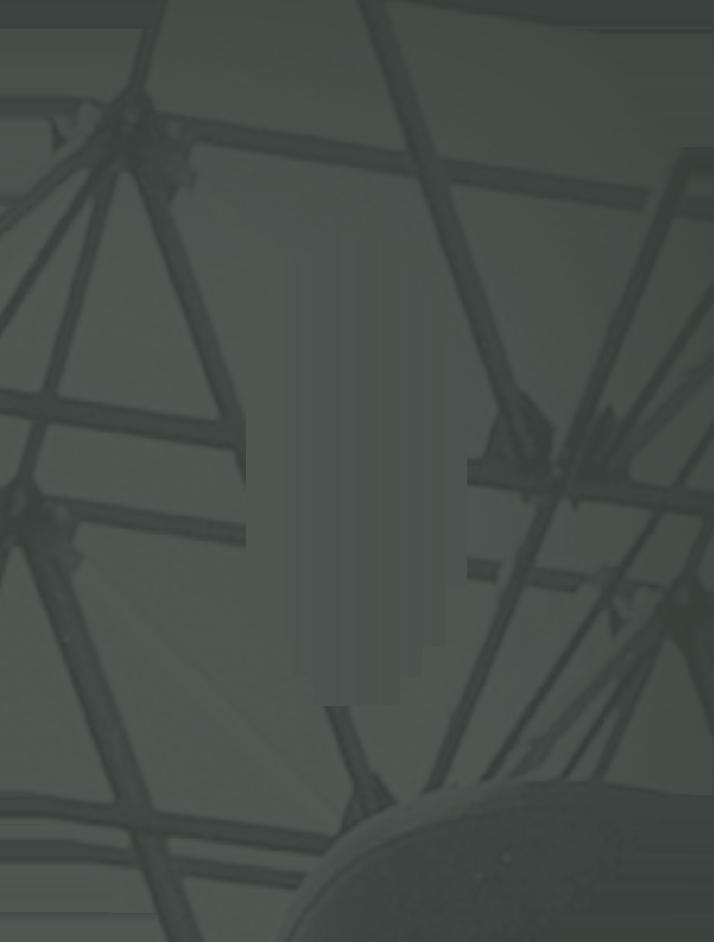
UNISTRUT
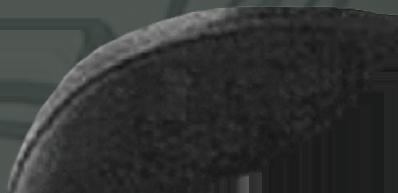
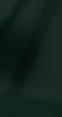
The year is 1924, the first round-the-world telegram is sent, and Charles Attwood forms the company that would become the leader in metal framing,
From our early days as the first adjustable frame system in electrical power stations, to becoming an integral component in global construction projects, Unistrut continues to evolve through innovation.
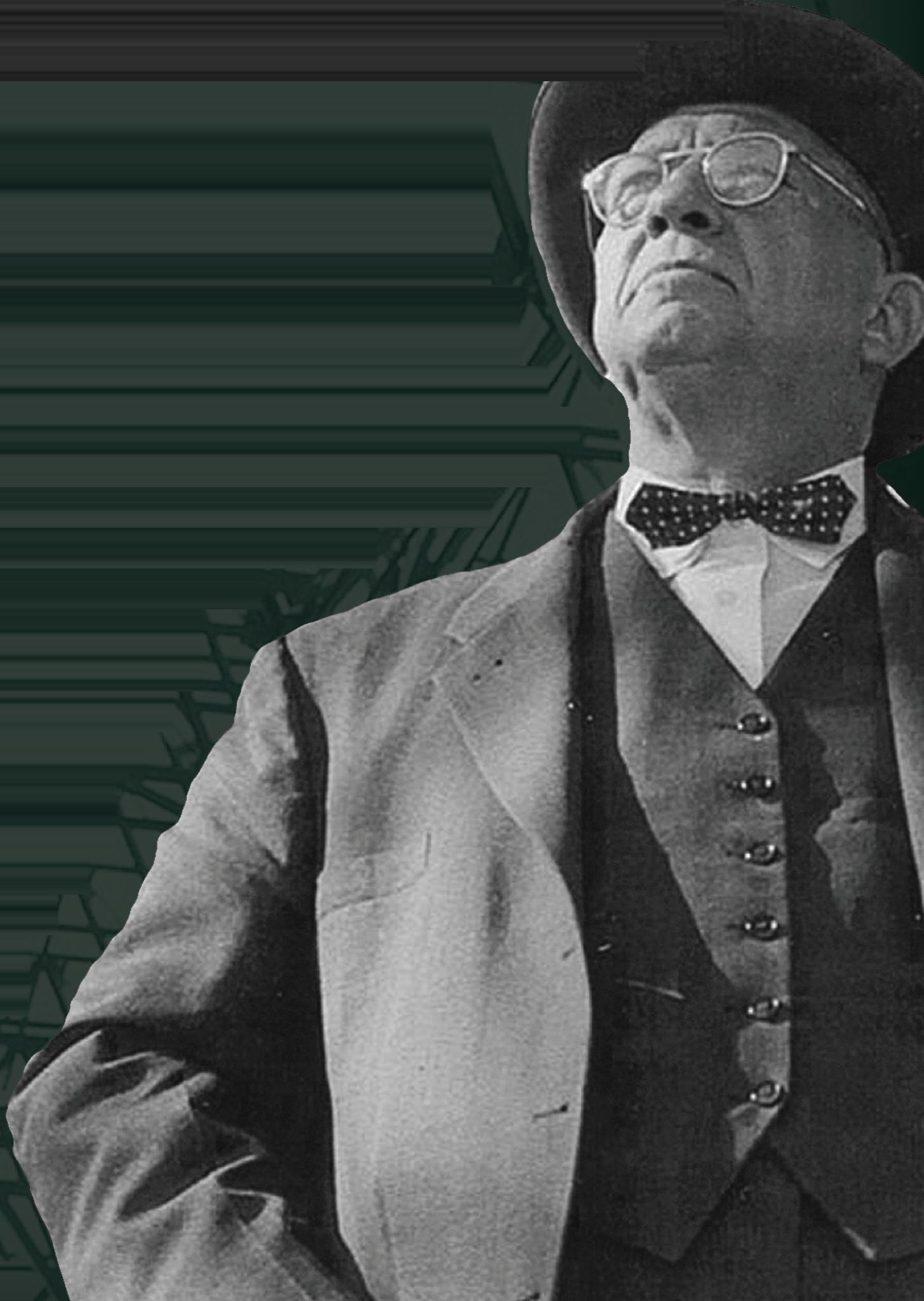

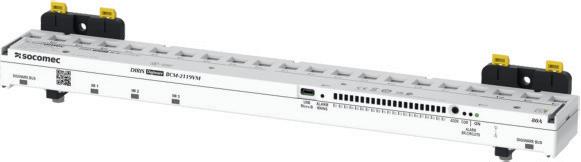

Branch-Circuit Meter Strip With Integrated Current Sensors
The DIRIS Digiware BCM is a branch-circuit meter strip with 21 integrated sensors and allows individual circuit monitoring within any electrical panelboard (Remote Power Panel, lighting panel, power panel, etc.).
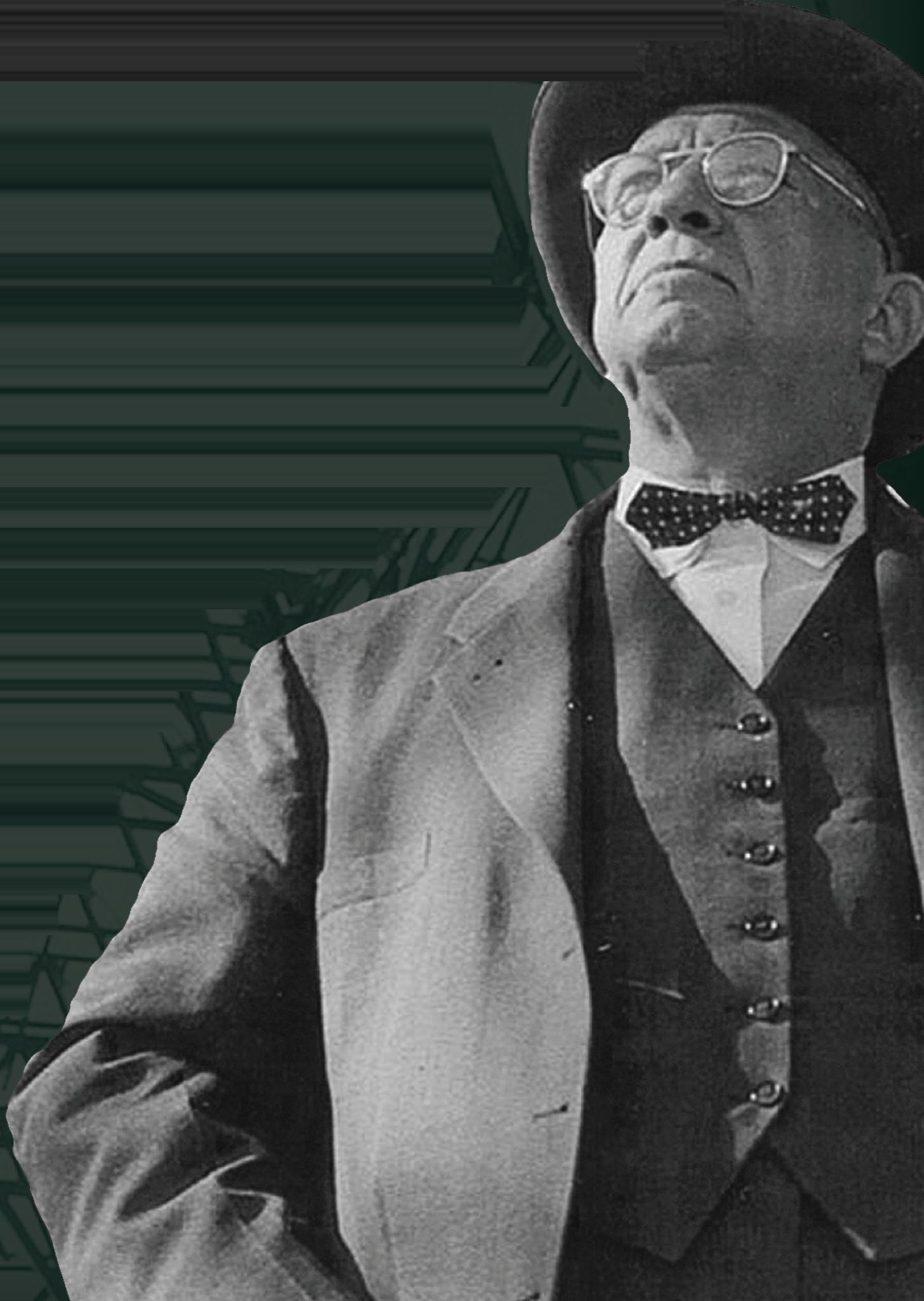
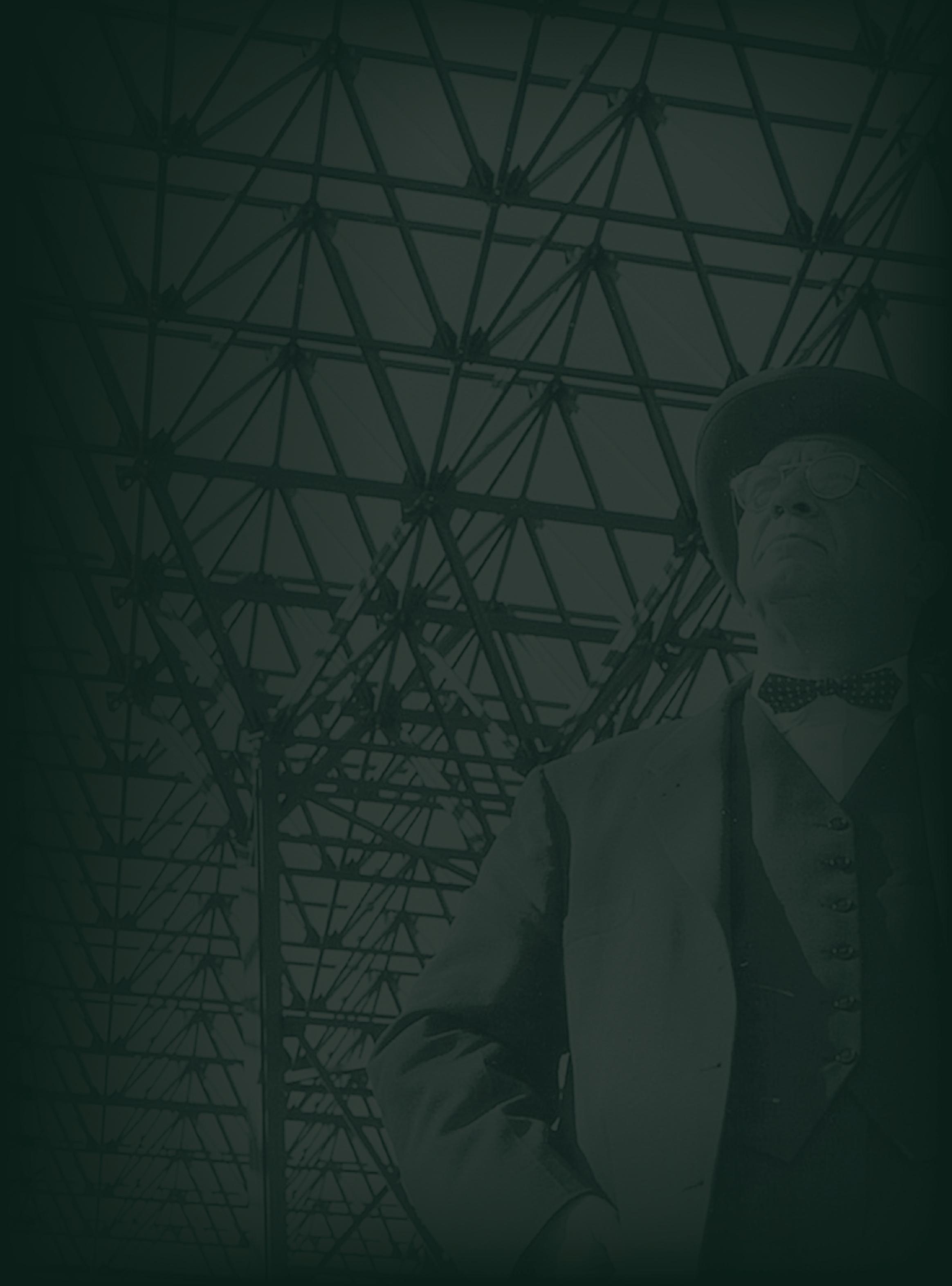
The DIRIS Digiware BCM is equipped with three RJ12 channels which can connect to TE/TR/TF current sensors to monitor the main feed or an extra circuit.
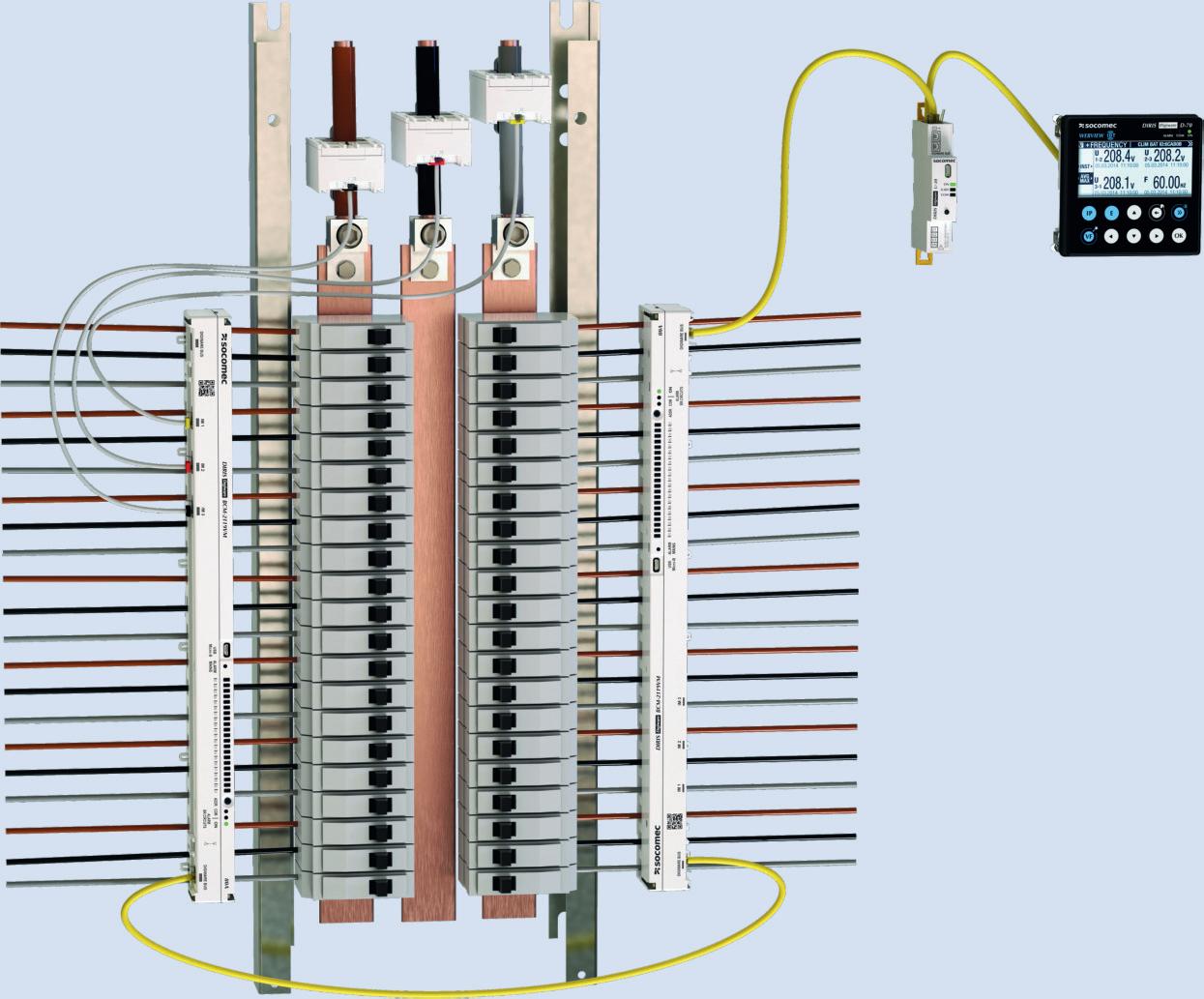
ADVANTAGES
No additional CT leads required.
Monitors 21 circuits plus a main feed. Power metering and earth leakage monitoring.
Robust plastic cover safeguards components.
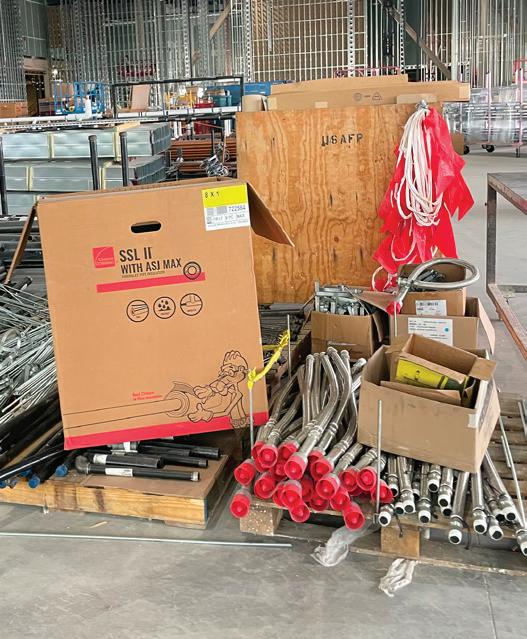
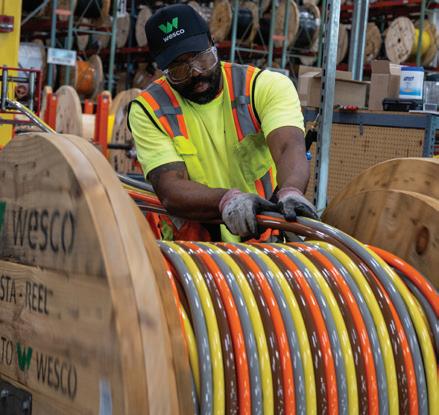


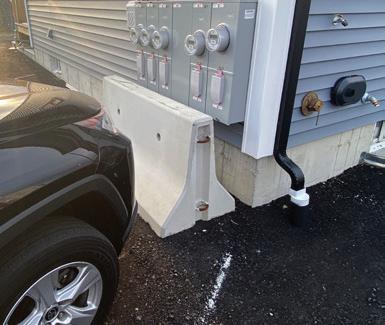
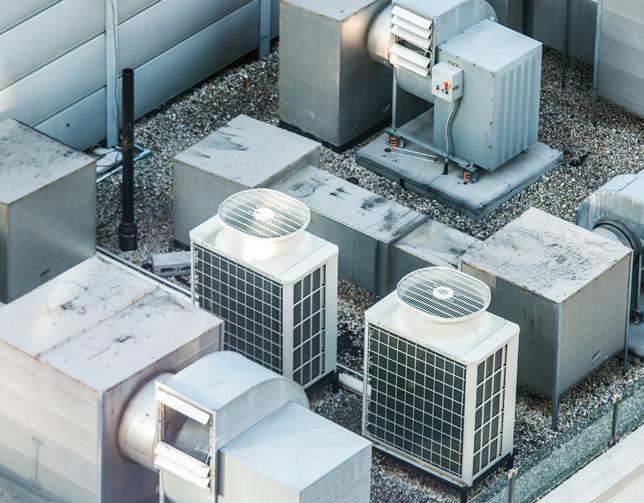
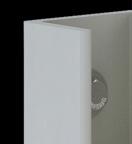
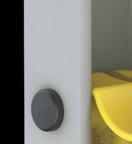
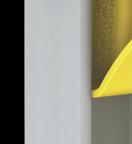


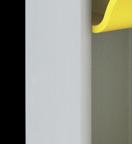
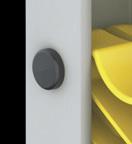
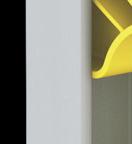
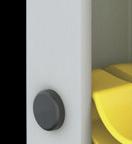
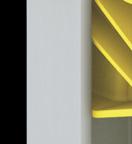

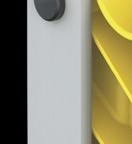

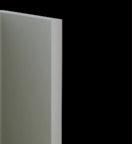
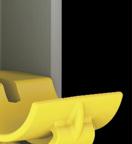
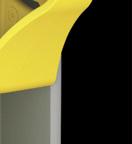
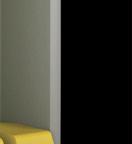

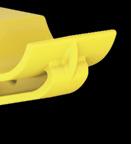


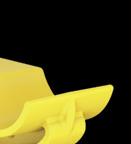
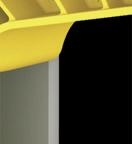
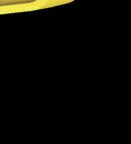
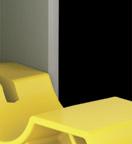
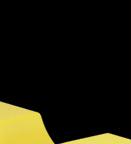


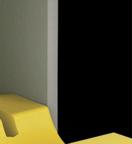
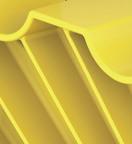
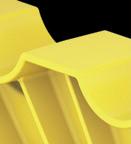
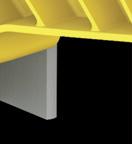
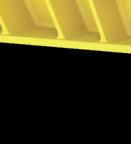
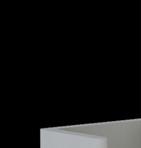
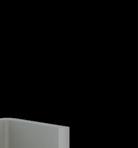
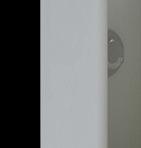
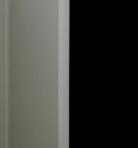


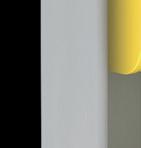
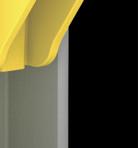
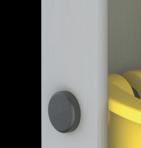
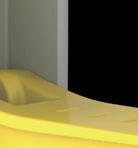

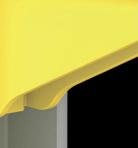
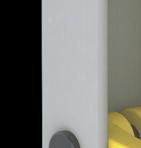
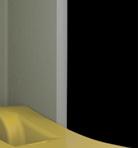

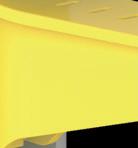

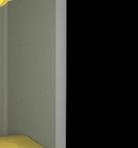

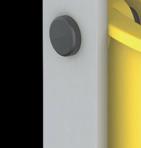
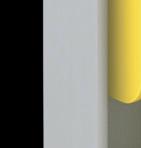

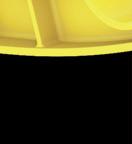
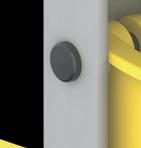
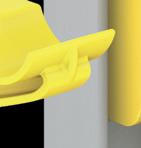


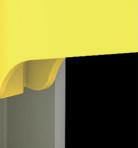

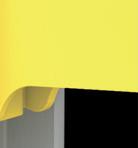
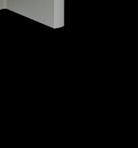

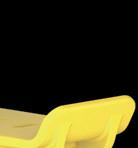
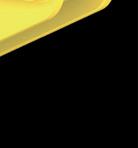
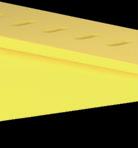
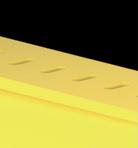
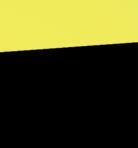

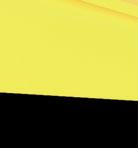
And Vaults
The BNT Nonmetallic Cable Support For Power Manholes
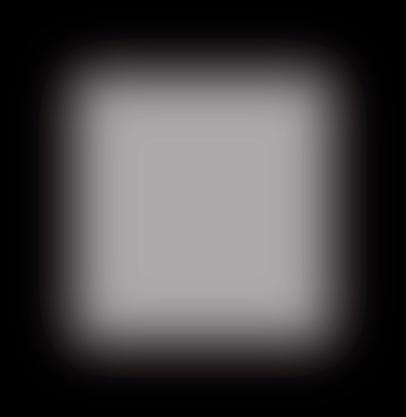
Underground Devices
BNT Nonmetallic Cable Supports:
High Load Capacity
Arms Can be Used With Nonmetallic or Steel Stanchions
Will Not Rust or Corrode
Insulators Not Required
Excellent Dielectric Properties
Multiple Stanchion Lengths Available
Arms Available in Multiple Lengths With Integrated Saddles or a Flat Surface
Molded from UL Listed
Glass Reinforced Polymer
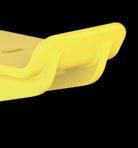

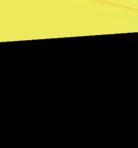
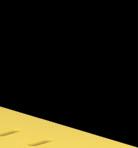




BNT Saddle Arms Installed in a Nonmetallic Stanchion

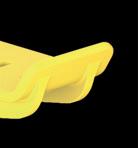

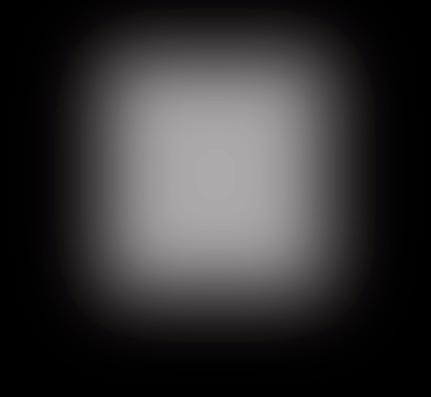
ECMWEB.COM
With its exclusive online content, ecmweb.com is a valuable source of industry insight for electrical professionals. Here’s a sample of what you can find on our site right now:

CODE CONVERSATIONS
PODCAST — SECURING A STRING OF LIGHTS THE RIGHT WAY
Podcast Ellen and Russ talk about general requirements for wiring methods as outlined in Art. 300. ecmweb.com/21282044
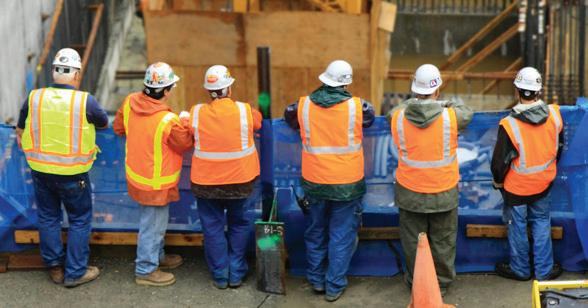
RECENT STUDIES DISSECT CONSTRUCTION LABOR CHALLENGES
Construction Tom Zind examines how supply, quality, and price combine to pressure contractors on productivity measures.
ecmweb.com/21282887
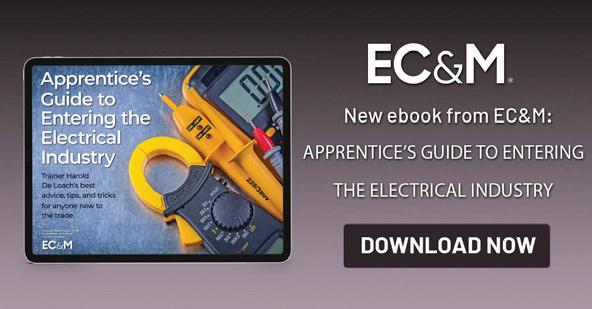
APPRENTICE’S GUIDE TO ENTERING THE ELECTRICAL INDUSTRY
E-Book From the e-books library: Trainer Harold De Loach’s best advice, tips, and tricks for anyone new to the trade.
ecmweb.com/21283455
Editorial
Group Editorial Director - Buildings & Construction: Michael Eby, meby@endeavorb2b.com
Editor-in-Chief: Ellen Parson, eparson@endeavorb2b.com
Managing Editor: Ellie Coggins, ecoggins@endeavorb2b.com
Editor: Michael Morris, mmorris@endeavorb2b.com
Art Director: David Eckhart, deckhart@endeavorb2b.com
Consultants and Contributors
NEC Consultant: Mike Holt, mike@mikeholt.com
NEC Consultant: Russ LeBlanc, russ@russleblanc.net
Sales and Marketing
Vice President: Mike Hellmann, mhellmann@endeavorb2b.com
Regional/Territory Account Manager: David Sevin, dsevin@endeavorb2b.com
Regional/Territory Account Manager: Jay Thompson, jthompson@endeavorb2b.com
Media Account Executive – Classifieds/Inside Sales: Steve Suarez, ssuarez@endeavorb2b.com
Production and Circulation
Production Manager: Brenda Wiley, bwiley@endeavorb2b.com
Ad Services Manager: Deanna O’Byrne, dobyrne@endeavorb2b.com
User Marketing Manager: James Marinaccio, jmarinaccio@endeavorb2b.com
Classified Ad Coordinator: Terry Gann, tgann@endeavorb2b.com
Endeavor Business Media, LLC
CEO: Chris Ferrell President: June Griffin COO: Patrick Rains
CRO: Paul Andrews Chief Digital Officer: Jacquie Niemiec
Chief Administrative and Legal Officer: Tracy Kane
EVP, Group Publisher – Buildings/Lighting/Digital Infrastructure: Lester Craft
Electrical Construction & Maintenance (USPS Permit 499-790 , ISSN 1082-295X print, ISSN 2771-6384 online) is published monthly by Endeavor Business Media, LLC. 201 N. Main St 5th Floor, Fort Atkinson, WI 53538. Periodicals postage paid at Fort Atkinson, WI, and additional mailing offices. POSTMASTER: Send address changes to Electrical Construction & Maintenance, PO Box 3257, Northbrook, IL 60065-3257. SUBSCRIPTIONS: Publisher reserves the right to reject non-qualified subscriptions. Subscription prices: U.S. ($68.75 year); Canada/Mexico ($ 112.50); All other countries ($162.50). All subscriptions are payable in U.S. funds. Send subscription inquiries to Electrical Construction & Maintenance, PO Box 3257, Northbrook, IL 60065-3257. Customer service can be reached toll-free at 877-382-9187 or at electricalconstmaint@omeda.com for magazine subscription assistance or questions.
Printed in the USA. Copyright 2024 Endeavor Business Media, LLC. All rights reserved. No part of this publication may be reproduced or transmitted in any form or by any means, electronic or mechanical, including photocopies, recordings, or any information storage or retrieval system without permission from the publisher. Endeavor Business Media, LLC does not assume and hereby disclaims any liability to any person or company for any loss or damage caused by errors or omissions in the material herein, regardless of whether such errors result from negligence, accident, or any other cause whatsoever. The views and opinions in the articles herein are not to be taken as official expressions of the publishers, unless so stated. The publishers do not warrant either expressly or by implication, the factual accuracy of the articles herein, nor do they so warrant any views or opinions by the authors of said articles.
Reprints: Contact reprints@endeavorb2b.com to purchase custom reprints or e-prints of articles appearing in this publication.
Photocopies: Authorization to photocopy articles for internal corporate, personal, or instructional use may be obtained from the Copyright Clearance Center (CCC) at (978) 750-8400. Obtain further information at www.copyright.com.
Archives and Microform: This magazine is available for research and retrieval of selected archived articles from leading electronic databases and online search services, including Factiva, LexisNexis, and ProQuest.
Privacy Policy: Your privacy is a priority to us. For a detailed policy statement about privacy and information dissemination practices related to Endeavor Business Media products, please visit our website at www.endeavorbusinessmedia.com.
Please Note: The designations “National Electrical Code,” “NE Code,” and “NEC” refer to the National Electrical Code®, which is a registered trademark of the National Fire Protection Association.
Corporate Office: Endeavor Business Media, LLC, 30 Burton Hills Blvd., Ste 185, Nashville, TN 37215 USA, www.endeavorbusinessmedia.com
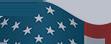
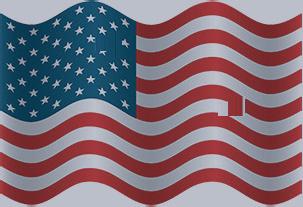

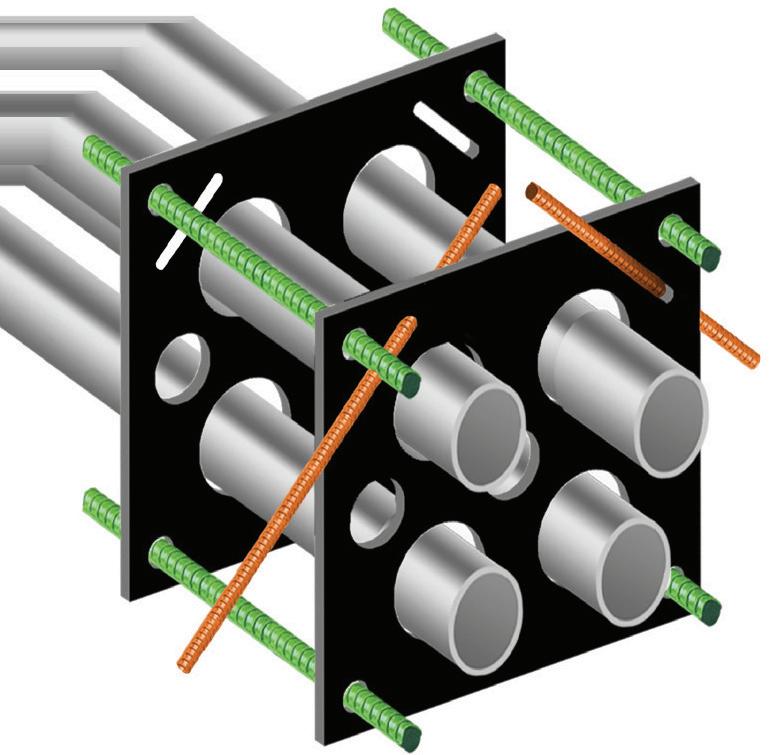


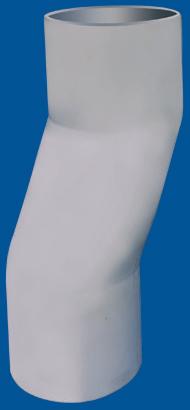
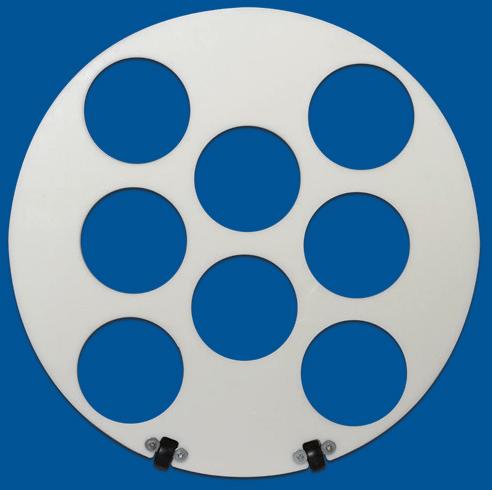
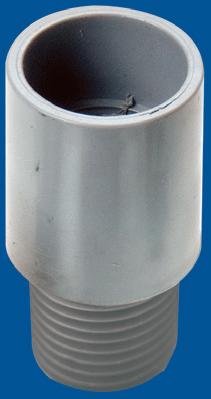



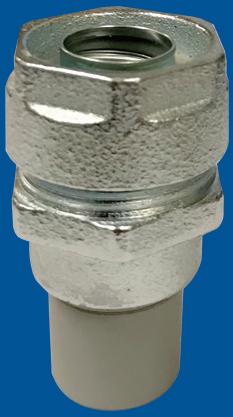

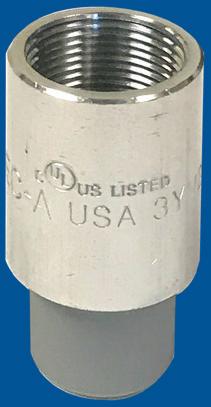
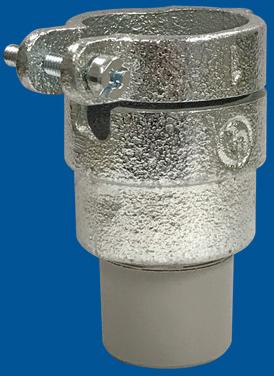
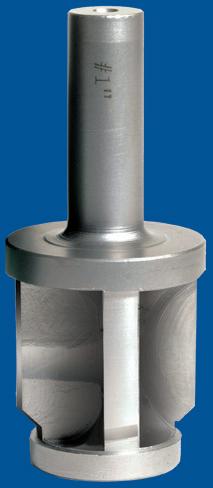
New Solutions to Old Problems
By Ellen Parson, Editor-in-Chief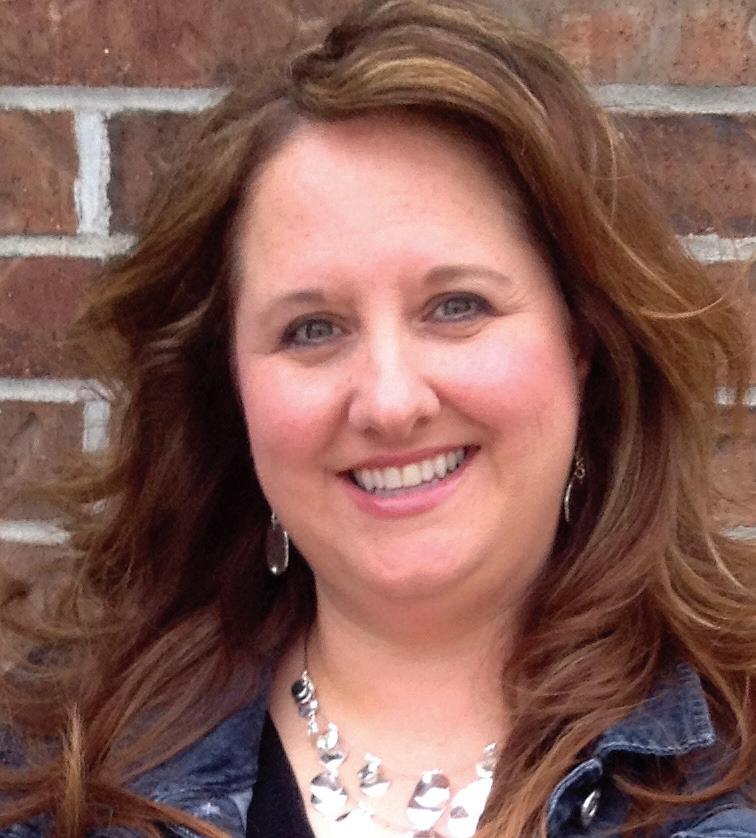
Depending on which source you’re looking at, the country’s skilled labor shortage numbers change slightly — but they’re always staggering, at least in my mind. To offset the ongoing workforce shortage, the construction industry will need to recruit an “estimated 501,000 additional workers on top of the normal pace of hiring in 2024 to meet the demand for labor,” according to a proprietary model developed by Associated Builders and Contractors. In 2025, the organization predicts the industry will need to attract nearly 454,000 new workers to meet demand. Not surprisingly, employment of electricians, a critical component in this shortfall, is projected to grow 6% from 2022 to 2023 — faster than the average for all occupations, according to the Bureau of Labor Statistics. So any way you slice it, what we have is a huge gap — a gap that’s often hard to envision a viable solution for. But if there’s one thing I’ve learned over more than 20 years of covering the electrical construction & maintenance industry, it is that electrical professionals are passionate, creative, and persistent people. As the vacancies get larger and the stakes get higher, industry veterans continue to seek out new solutions to old problems.
Harold De Loach, a master electrician, electrical trainer/instructor, and founder/ director of The Academy of Industrial Arts in Philadelphia, is one of those people. Contributing training articles to EC&M print, online, and our E-Train e-newsletter for the last several years, Harold is on a mission to invigorate the electrical profession, employing creative ways to recruit, train, and retain the next generation of electricians. His content, geared toward electrical apprentices, has been so popular with our audience that we decided to release a series of e-books featuring Harold’s most engaging articles. The first installment — offering tips and best practices for anyone interested in entering the electrical industry — is now available for a free download at ecmweb.com/21283455. Look for more “apprentice’s guide to…” e-books coming this year on electrical calculations, conduit and cable basics, installation and wiring, and interesting niche applications.
Another electrical industry visionary is Mike Greenawalt, Rosendin Electric’s CEO Emeritus. I recently had the privilege of sitting down with Mike on my “EC&M On Air” podcast to discuss the new ground-breaking partnership he’s established between Rosendin and Arizona state educators to create a pre-apprenticeship program for Grand Canyon University (GCU). This is a fascinating discussion in which Mike, who tells his personal story of going from a C student to apprenticeship to running a $3-billion electrical contracting company, joins Edward Cota with Arizona’s Department of Education and chief strategy officer/chairman of the Arizona Education Economic Commission to explain how this innovative partnership took shape, what model the program follows, and why this seemingly unconventional approach is seeing such great success. Catch Part 1 of the podcast at ecmweb.com/21283517, and look for Part 2 next month. This training program is a perfect example of how thinking outside the box leads to innovative solutions that are changing the narrative of how students (and their parents) view the skilled trades. As they emphasize in the podcast, “the hand that rocks the cradle rules the world.” Listen to the full episode for all of the details.
Due to the ongoing challenges surrounding doing more with less in the construction industry, this issue is dedicated to the theme of “workforce management.” Check out the cover story on page 24 by Dr. Heather Moore and Dr. Perry Daneshgari of MCA, Inc. on “Combating Construction’s Biggest Time-Wasters” in which they explain how to define, measure, and improve productivity on electrical job sites. On page 30, Wesco International’s Sean Nacey lays out how prefab solutions boost labor productivity through best practices. Offering insight into construction labor productivity trends, FMI’s latest study, summarized on page 34, offers an inside look at why contractors who establish sound operating processes perform better than their peers. And finally, Kenny Ingram of IFS breaks down why restructuring the construction industry’s productivity problem is beyond a labor issue in his piece on page 42. All of these articles demonstrate fresh perspectives on solving the industry’s productivity puzzle, ultimately making electrical professionals more efficient and profitable.
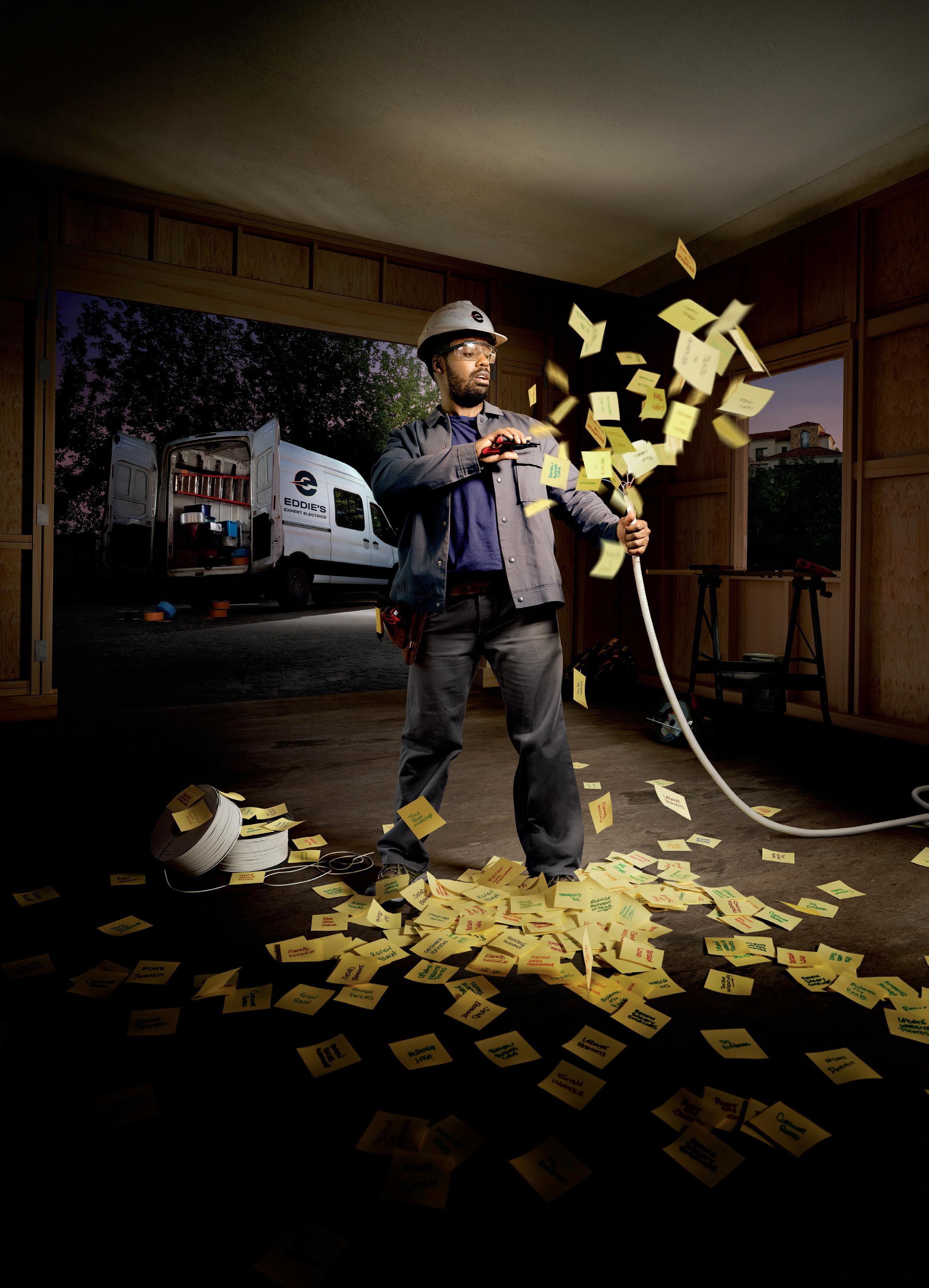
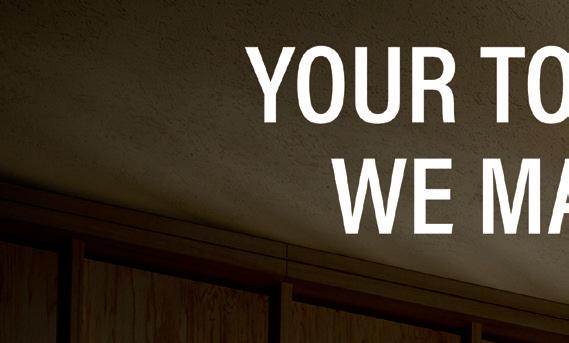
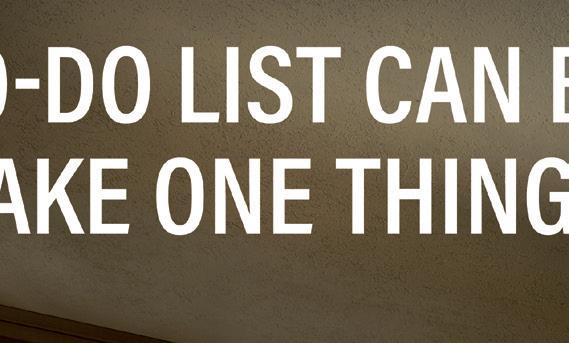
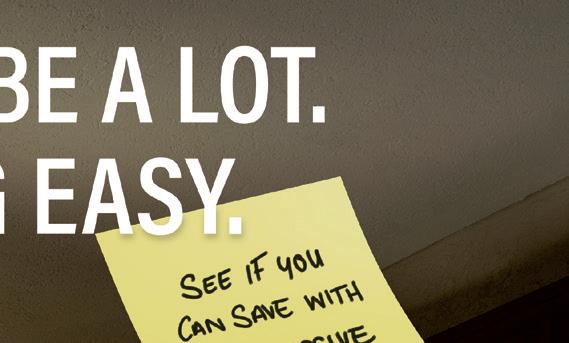
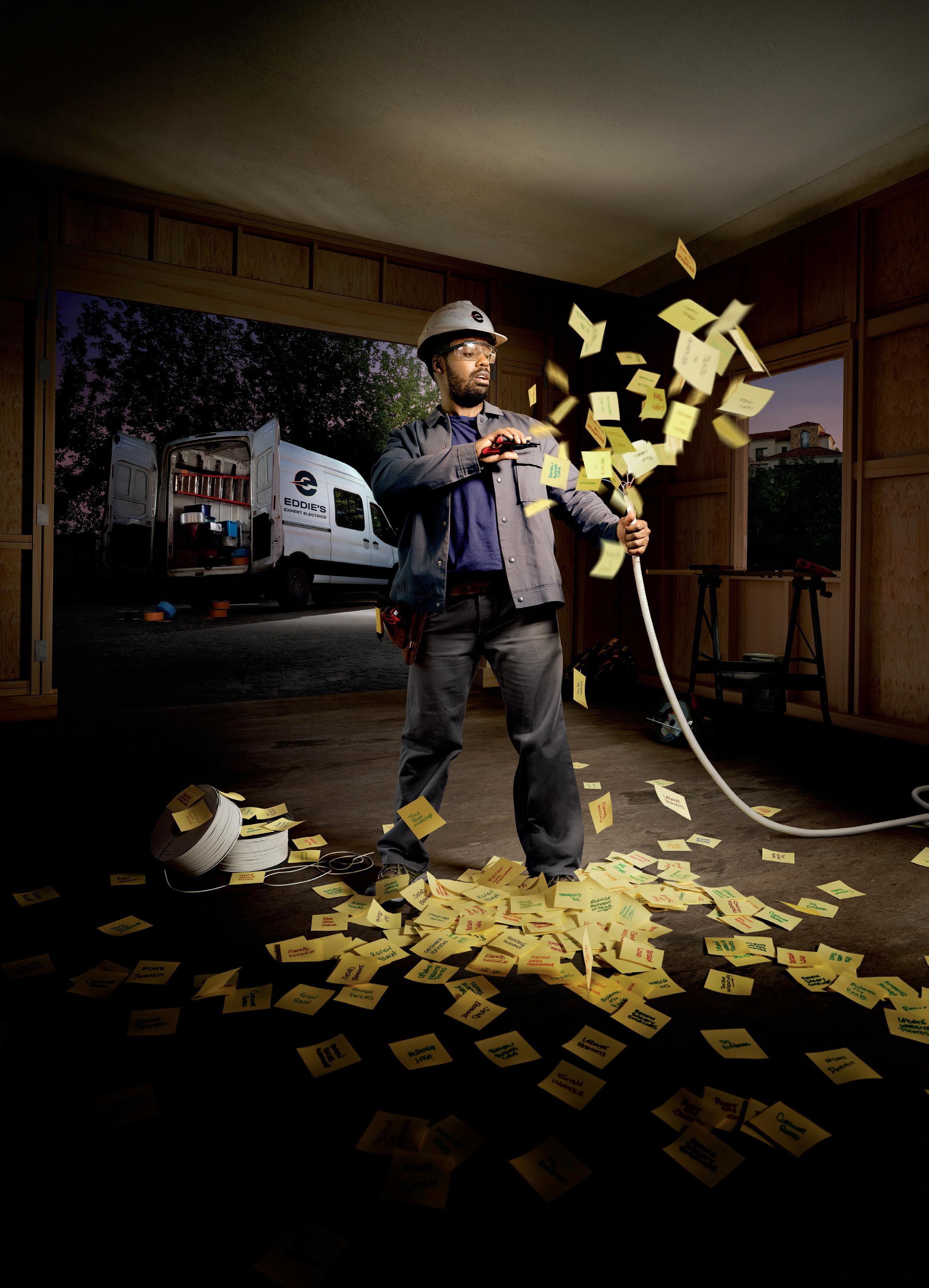
a n d s e r v c e d b y a f fi l i a t e d a n d t h i r dp a r t y i n s u r e r s
P r o g r e s s i v e C a s u a l t y I n s C o C o v e r a g e p r o v d e d
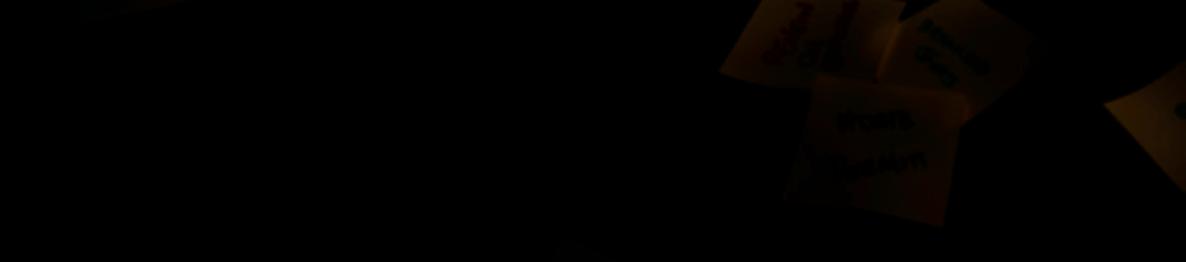
As a small business owner, you can’t escape your to-do list. That’s why Progressive makes it easy to save with a commercial auto quote, so you can take on all your other to-dos. Get a quote in as little as 6 minutes at ProgressiveCommercial.com
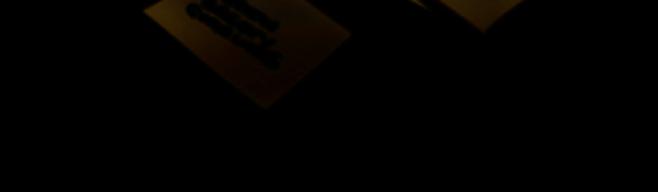
The Largest Construction Projects of 2024
Federally funded trophy jobs will fill the construction pipeline again in early 2024.
By Jim Lucy, Electrical WholesalingDevelopers of projects in the rail/transportation, semiconductor chip, and electric vehicle (EV) construction verticals continue to enjoy federal funding from the Infrastructure Investment and Jobs Act (IIJA) and the Creating Helpful Incentives to Produce Semiconductors (CHIPS) Act.
While updating our construction project database, EC&M’s editors were surprised at the continuing surge of rail, semiconductor, and EV projects breaking ground or on the drawing boards (Table on page 10). The Albany Nanotech research center in upstate New York is expected to eventually attract $10 billion in investment in new manufacturing facilities, research and development labs, and training from a consortium of semiconductor manufacturers, including IBM, Micron, Applied Materials, and Tokyo Electron for construction of the first and only publicly owned High NA Extreme Ultraviolet Lithography Center in North America.
The Port Authority of New York and New Jersey also has big construction plans, with a $3.6-billion capital expense budget to fund several major projects, including the ongoing construction at John. F. Kennedy Airport; the replacement of the Port Authority Bus Terminal; and the development of a new AirTrain system at Newark Airport.
Oklahoma City may one day be home to the tallest tower in the United States if the Matteson Capitol’s plans for the Boardwalk at Bricktown go through (Photo). The developer wants to build a 1,907-ft apartment mixed-used tower. According to a post at www.freepressokc. com and an article in The Oklahoman, the 5-million-sq-ft development, currently estimated at more than $700 million in total contract value, would also include 1,776 residential units in a 134-story apartment tower as well as restaurants and other retail stores.
Other trophy jobs include the Willets Point redevelopment in Queens, N.Y., which will include several hundred units of affordable housing and a $780-million soccer stadium; the $1.9-billion Children’s Hospital inpatient tower in Philadelphia now underway; and the $1.6-billion LG Energy battery plant in Queen Creek, Ariz.
Additional projects of note include the $480-million Project Cosmo data center in Cheyenne, Wyo., now in the planning stage; the $406-million Sherco Solar Farm underway in Becker, N.M.; the $315-million Florida State University Health Hospital, Tallahassee, Fla., now being planned; and the Sherwin Williams headquarters in Cleveland on the drawing boards.
Overall, forecasters with the American Institute of Architects (AIA) and the Dodge Construction Market and are looking for a steady, unspectacular year for the construction market.
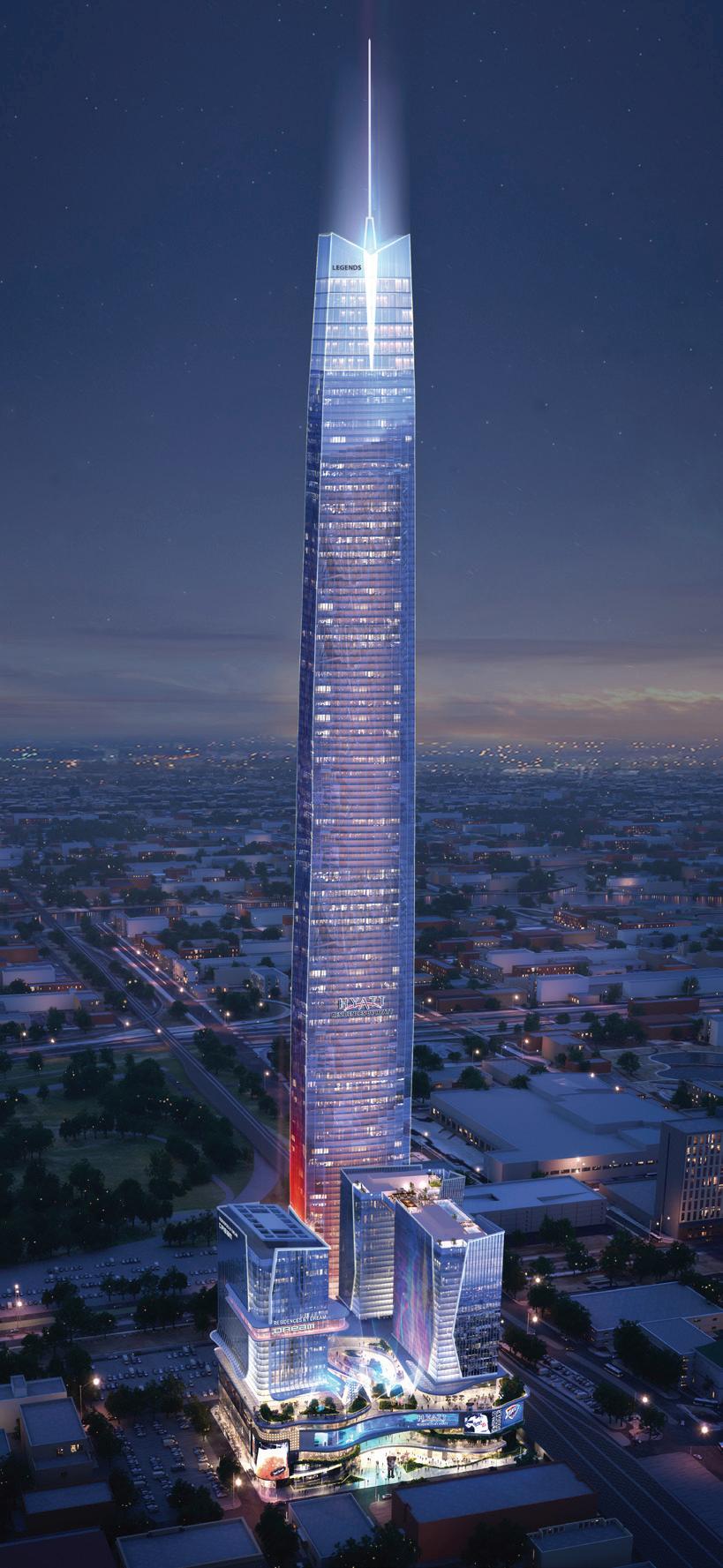
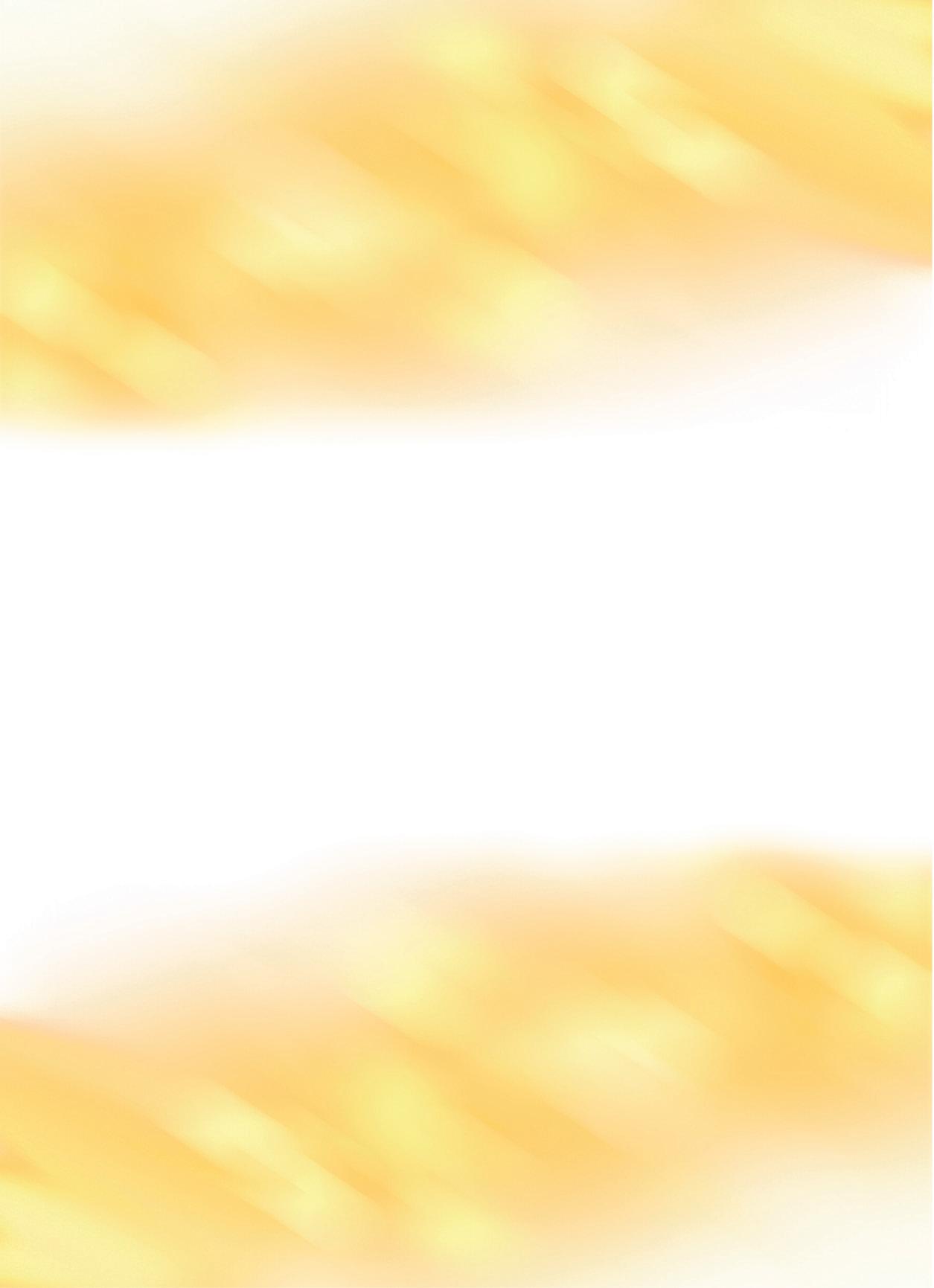
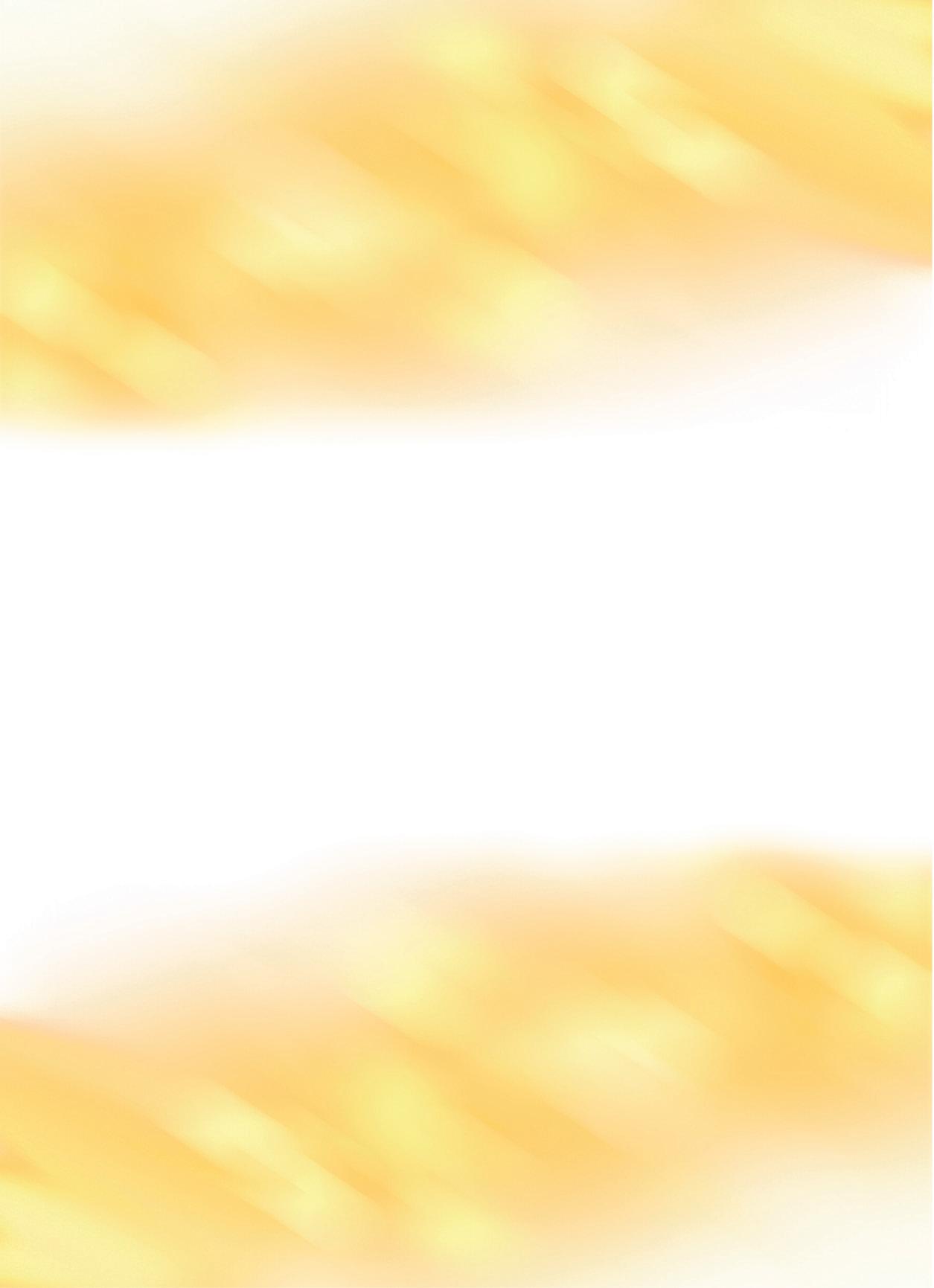
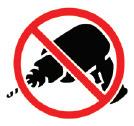
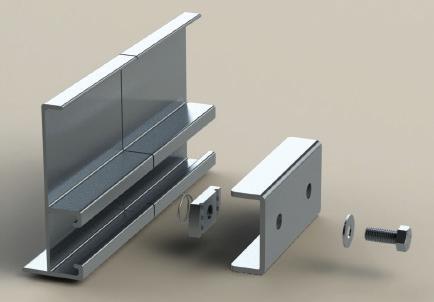

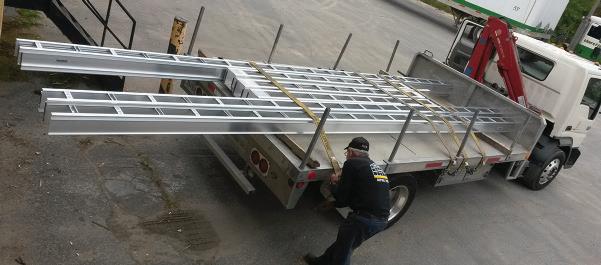
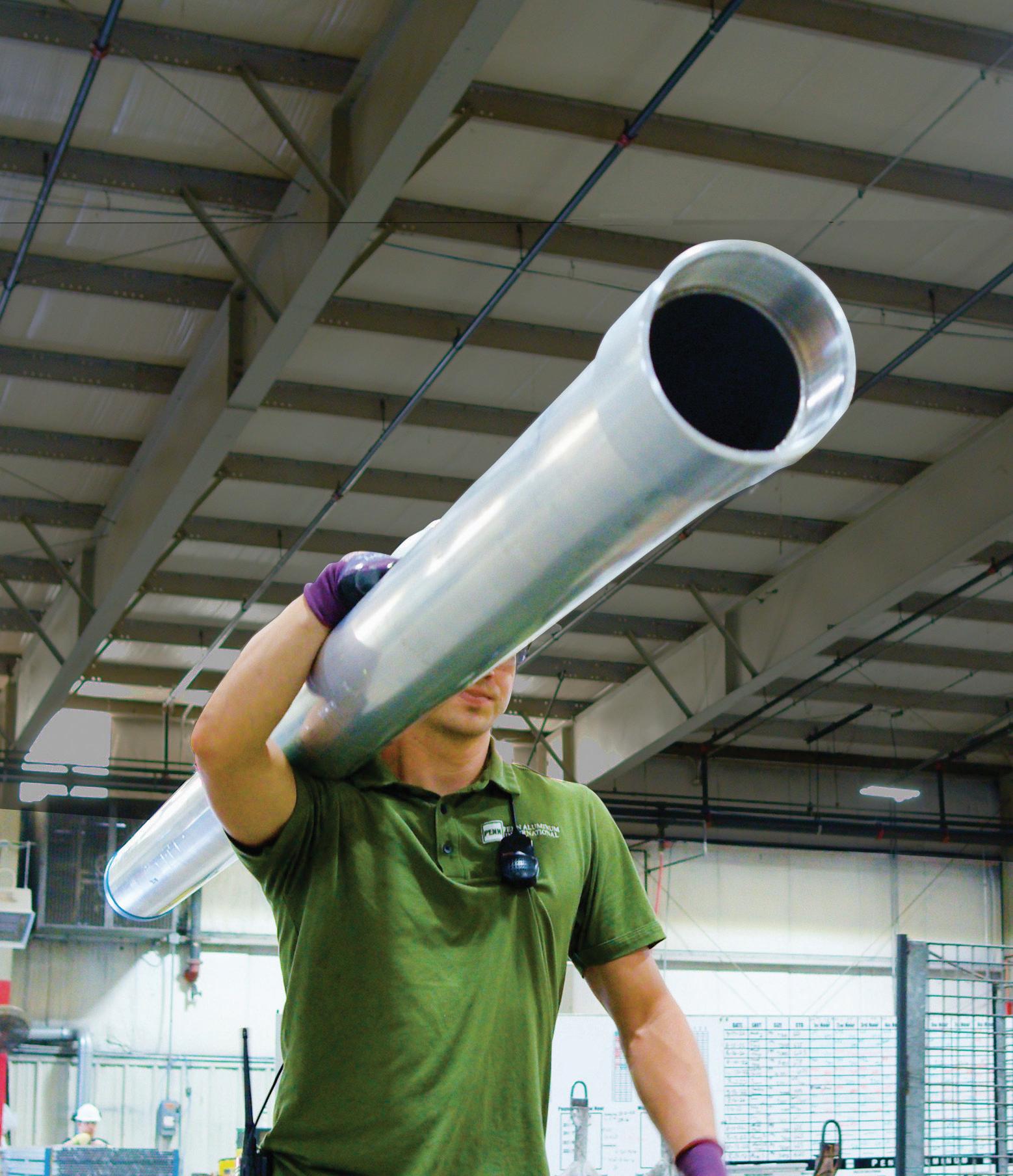
Electrical contractors are discovering the many important advantages of Penn Aluminum Conduit & EMT compared to steel.
• Lower total installed cost
• 1/3 the weight of steel
• Safer to lift/carry
• 100% recyclable
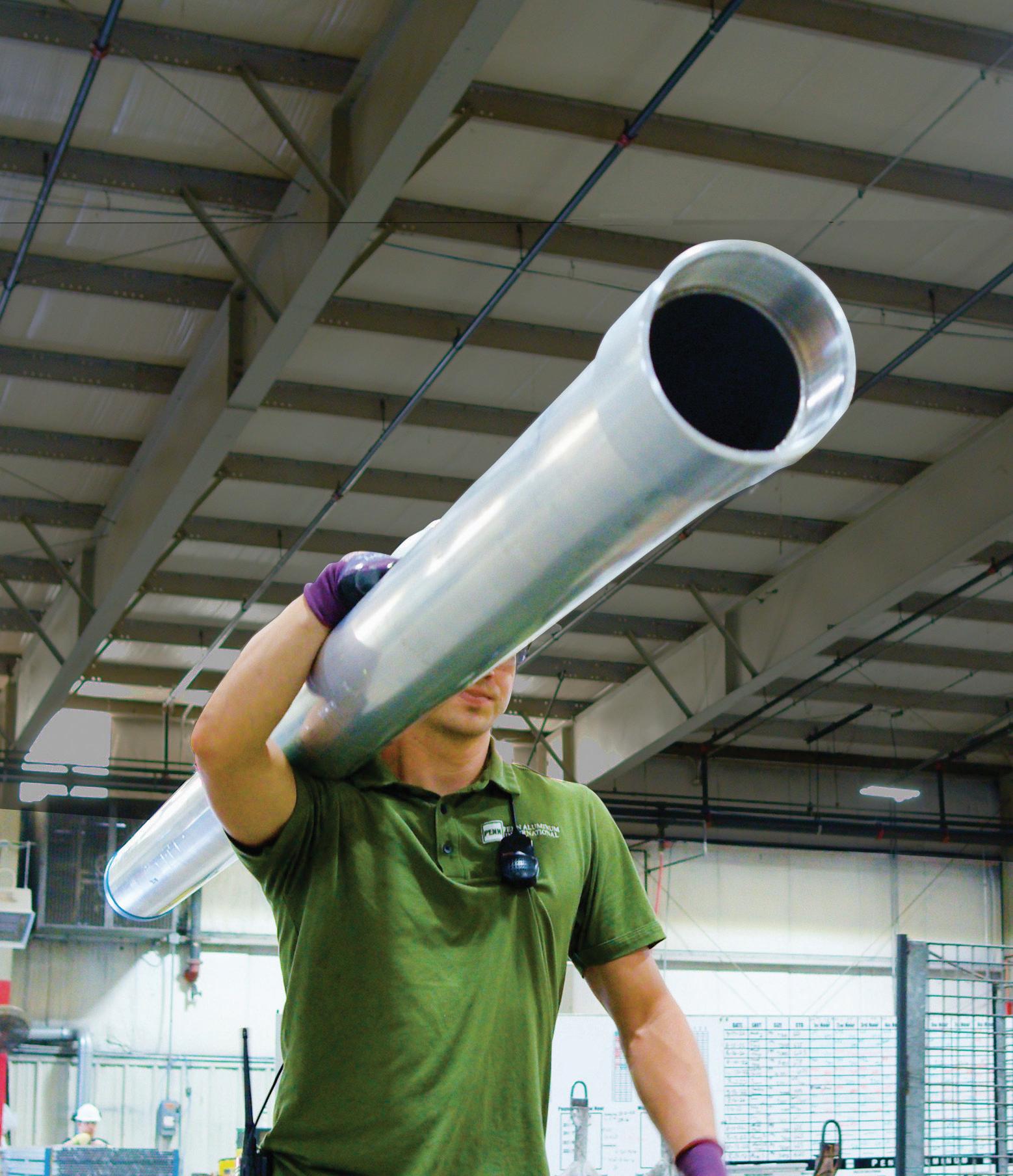

Today’s construction market is more competitive than ever, with electrical contractors needing ways to increase productivity while maintaining jobsite safety. Penn Aluminum Conduit & EMT offers solutions to meet these challenges. Aluminum provides numerous benefits compared to heavy steel conduit products, resulting in total installed cost savings.
That’s why Penn Aluminum Conduit & EMT is The Smart Choice for electrical contractors.
Understanding the Impact of Harmonics
How to mitigate the effects with power quality data
By Jason Axelson, Fluke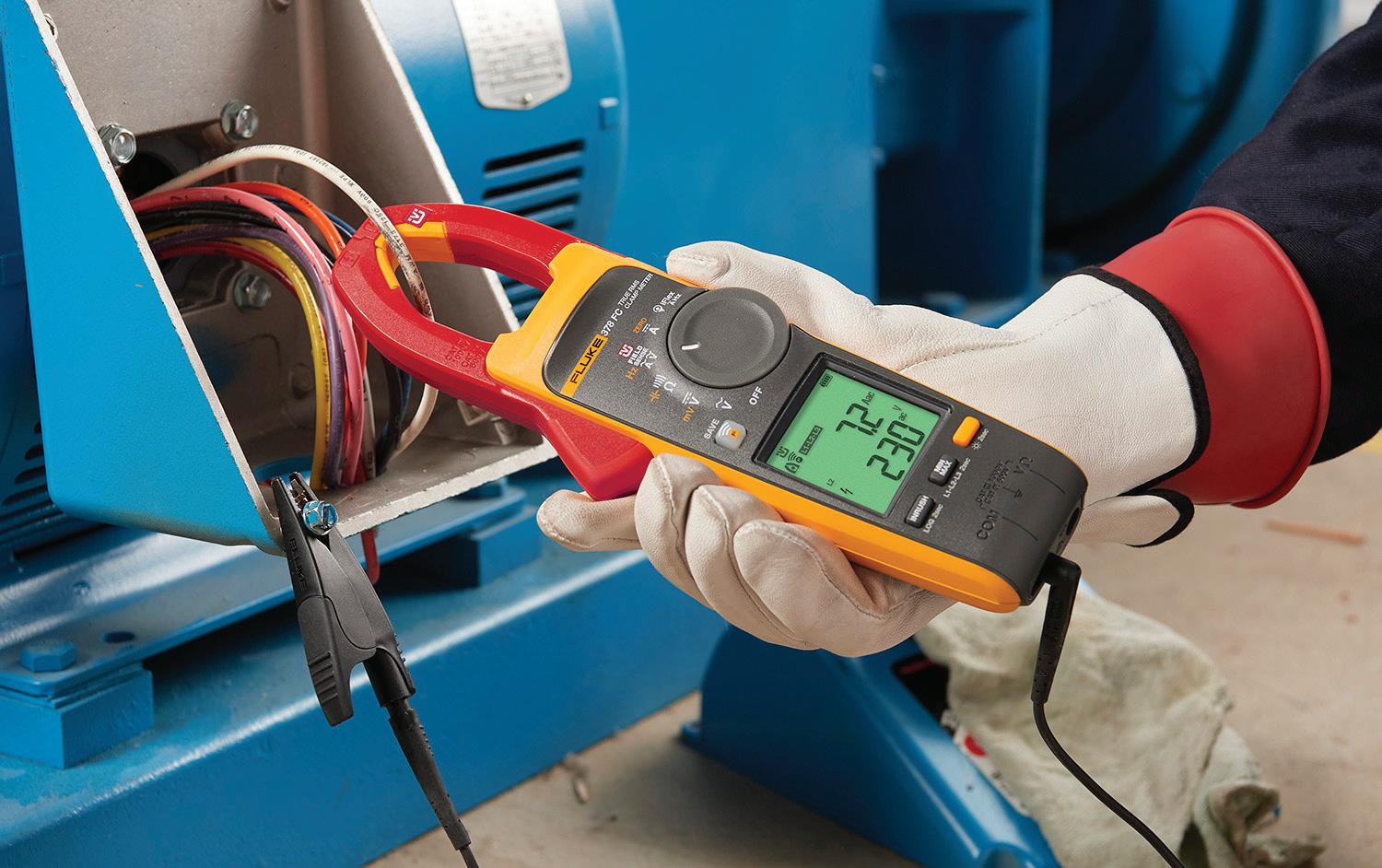
Power quality measurements and data tracking are essential in determining the reliability and efficiency of your power system. Power quality is the measure of the consistency of the electrical supply that is delivered to your equipment and devices that rely on it to run smoothly.
Harmonics, in turn, are a component you want to watch out for while taking power quality measurements. They can have a significant impact on the performance of your system. Harmonics are essentially unwanted electrical frequencies that can distort the waveform of an electrical signal. They are caused by non-linear loads, like variable-frequency drives, computers, or electrical equipment that use switching power supplies. These non-linear loads can produce harmonics that distort the waveform of the electrical signal, which can lead to a wide
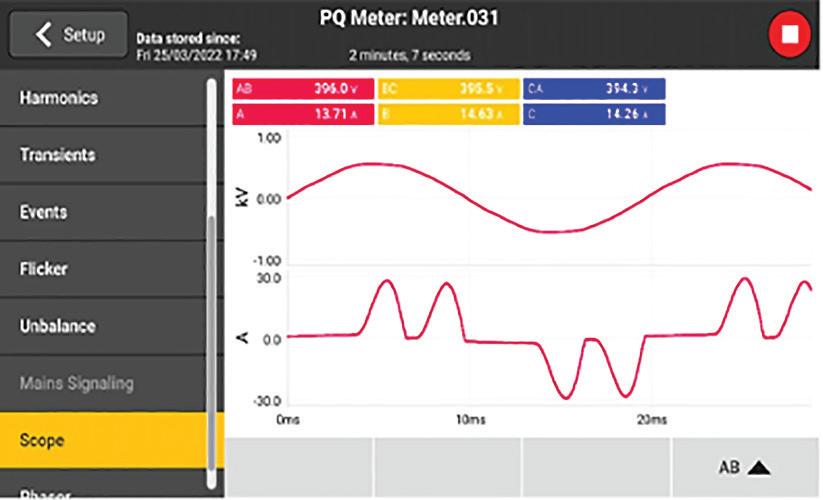
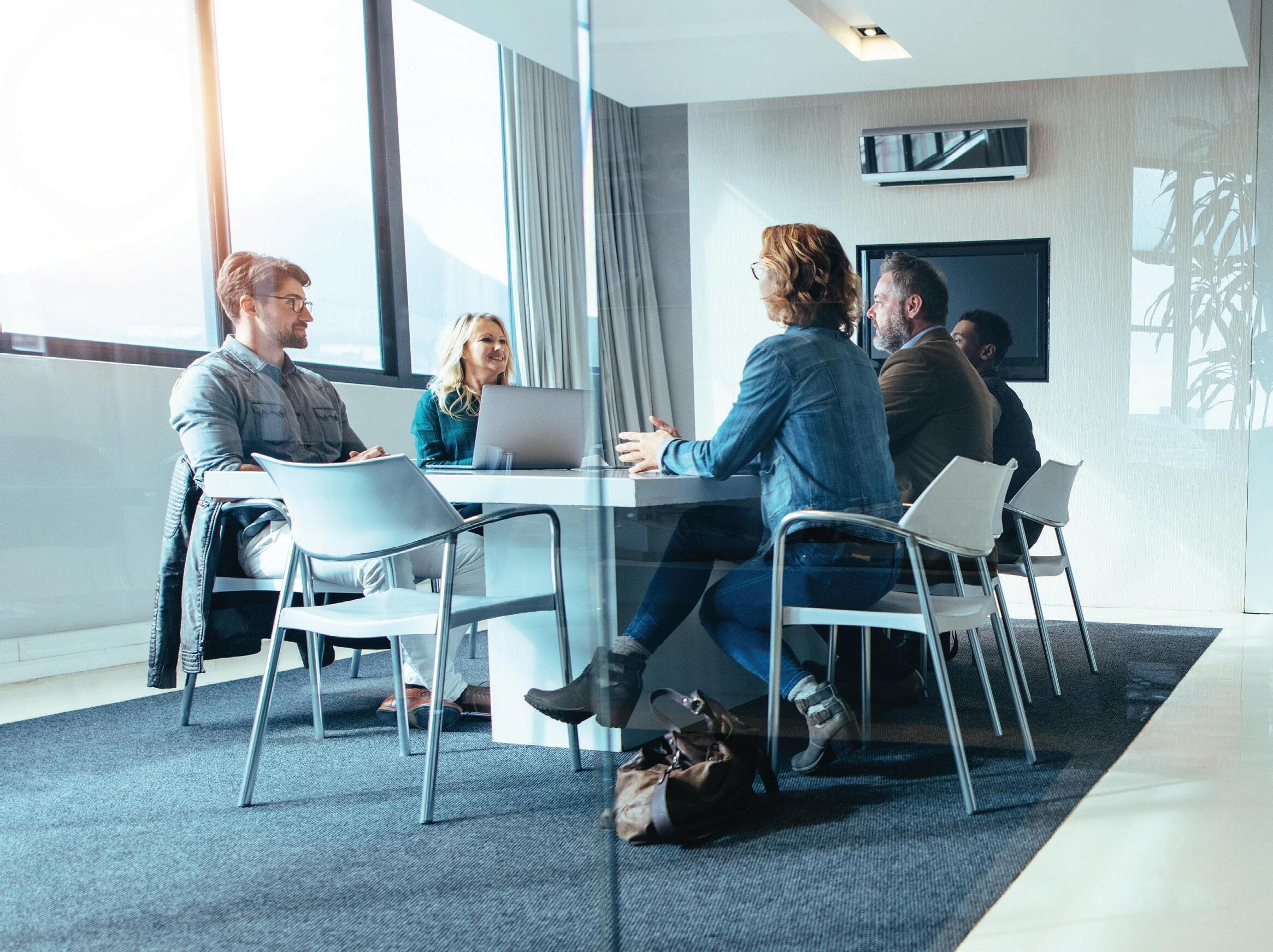
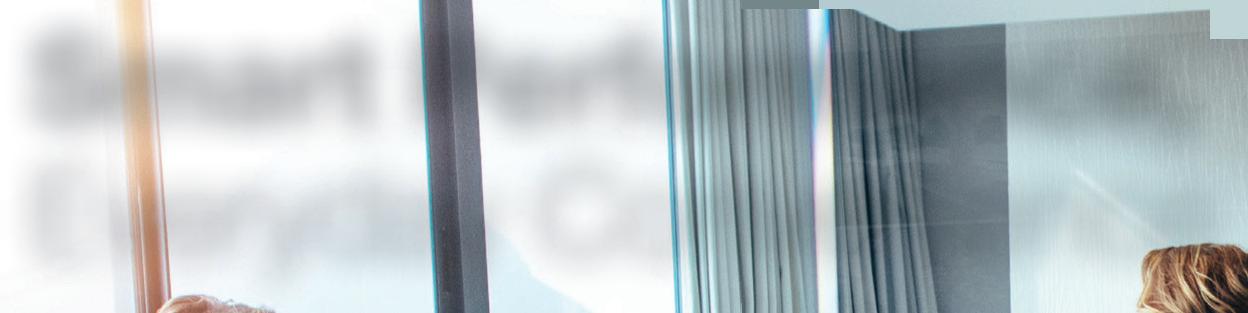
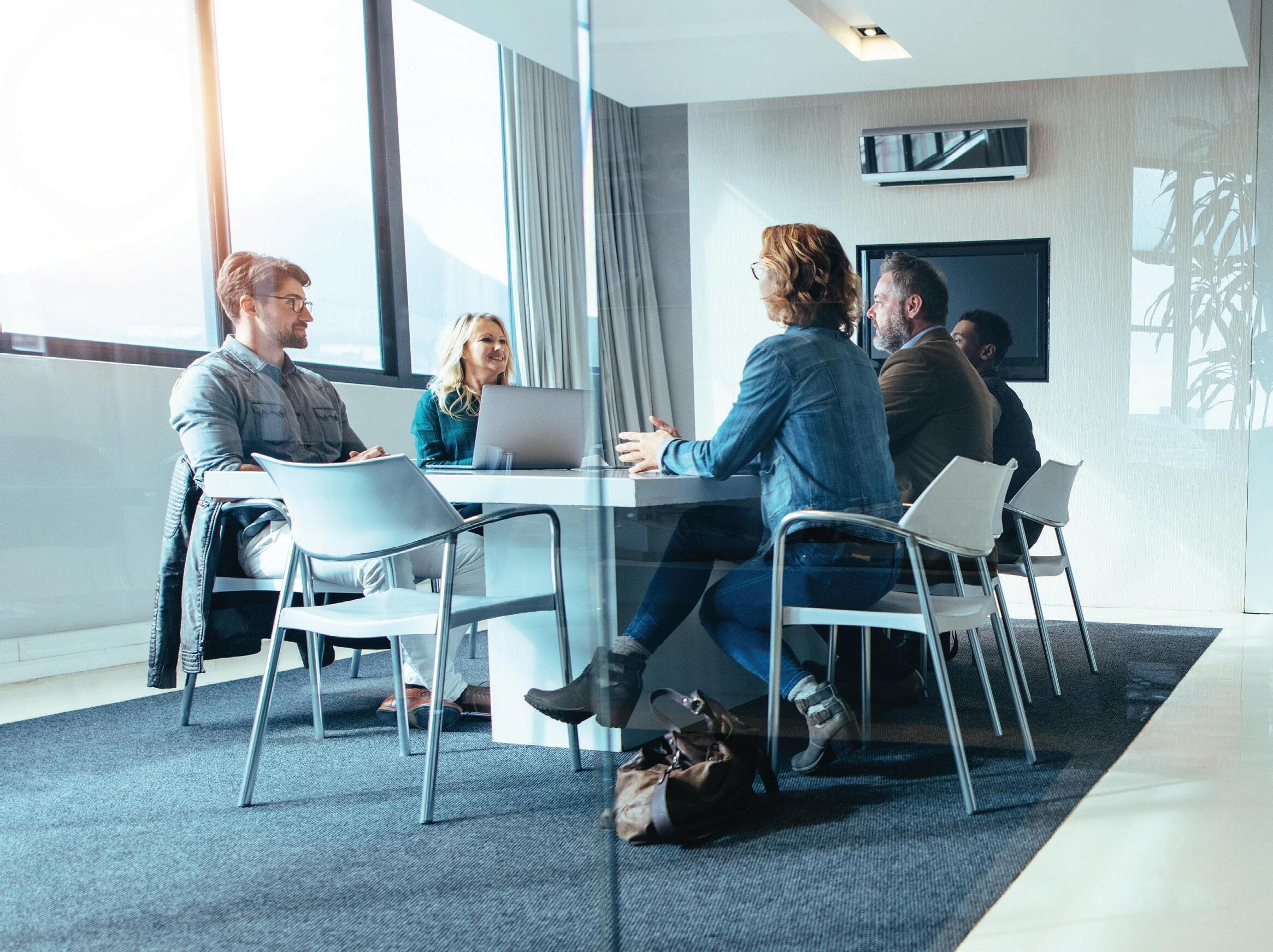
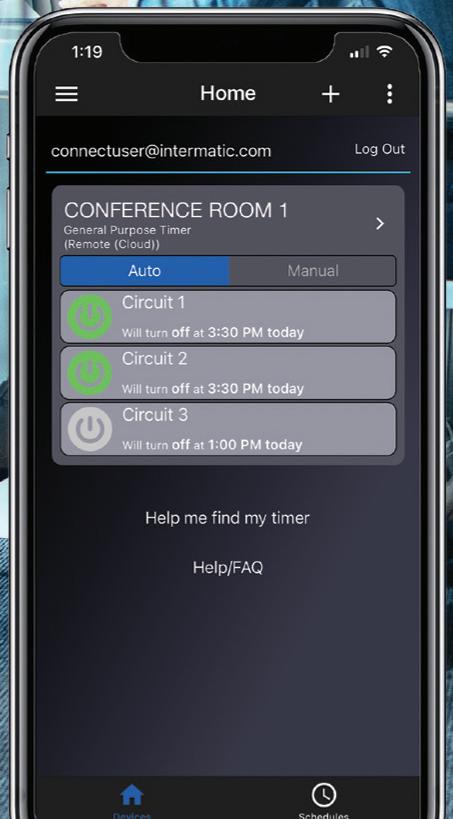
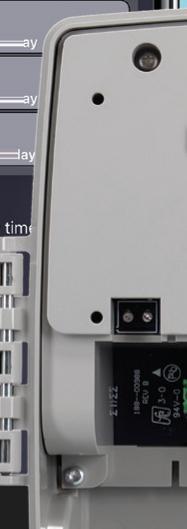
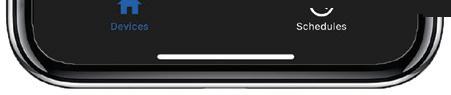
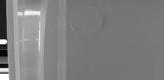

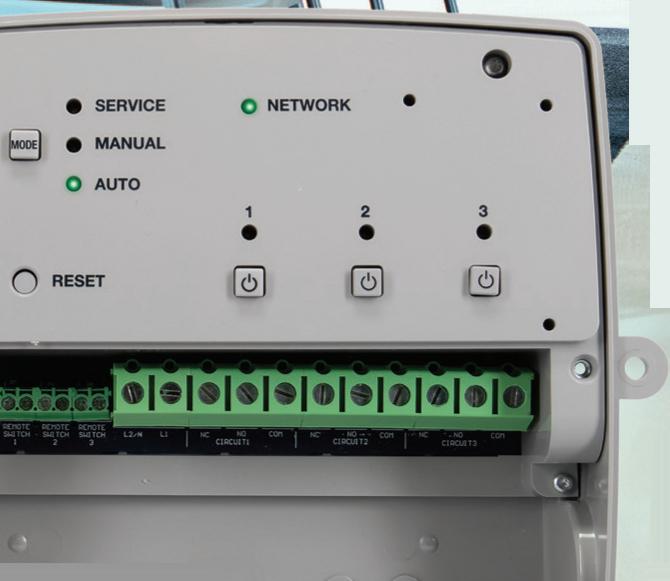
Simplify lighting and load schedules with the ETW Series 365-Day Programmable Wi-Fi Timer. This versatile smart control combines robust scheduling features with everyday convenience, including smart control via the Intermatic Connect app. Available in two or three-circuit models, the ETW Series allows for seamless scheduling of outdoor lighting, indoor lighting, motors, pumps, and more.
•
• Remote Access
• Intuitive Naming
•
• Remote Override
• Visual Cues
•
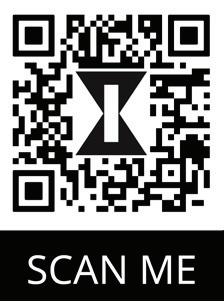
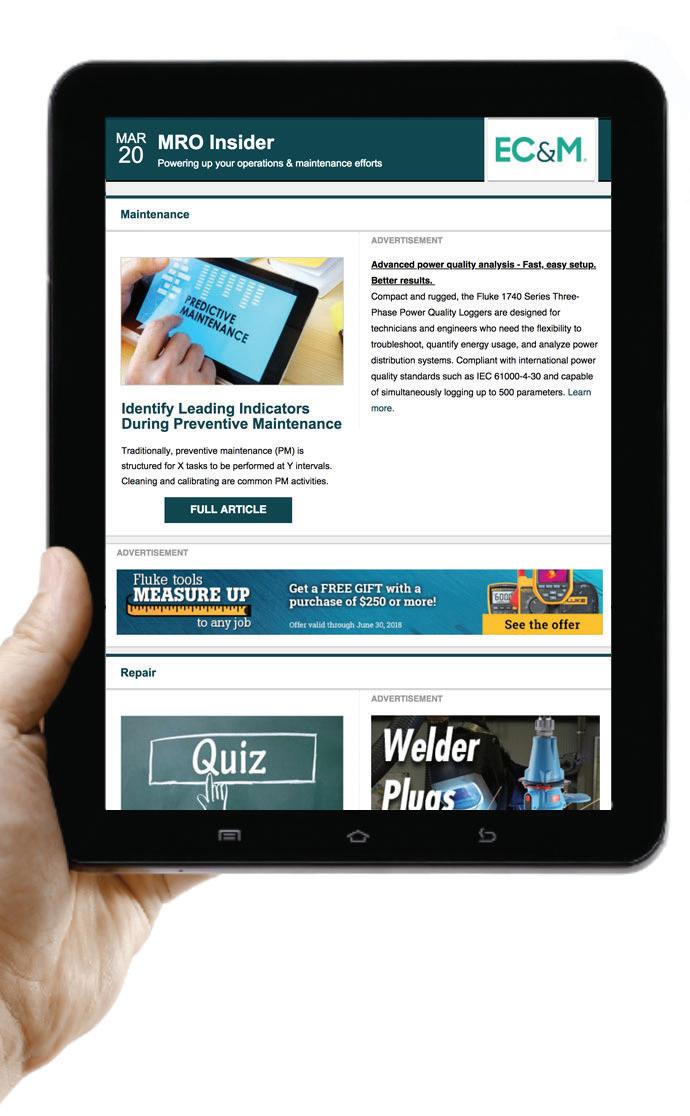
MRO Insider
This e-newsletter, published monthly, is focused on electrical engineers, plant managers, maintenance engineers, facility and energy managers, maintenance supervisors, electricians, and technicians who work in industrial, commercial, and institutional facilities.
Topics covered include:
• Maintenance, repair, and operations
• National Electrical Code on the production floor
• Safety procedures & programs
See all of our EC&M e-newsletters at www.ecmweb.com
range of problems within your system. See the Figure on page 12.
IMPACT OF HARMONICS ON YOUR SYSTEM
One of the most significant issues you may see if harmonics are present is increased heat in electrical equipment. Overheating on transformers, motors, and other electrical devices can lead to reduced efficiency and premature failure. Overheating can also cause insulation breakdown, which can result in short circuits, fires, and other safety hazards.
If you’re seeing a reduced power factor or lower efficiency of the power system, it could be another sign you’re dealing with harmonics. Power factor is essential to ensure that the electrical supply coming into your facility is used efficiently. Harmonics causing that reduction can have a cascading effect leading to increased energy consumption, higher utility bills, and reduced electrical system capacity.
The presence of harmonics can also be seen in smaller ways around your facility. Things like flickering lights or communication system interference. No matter how the issues present themselves, harmonics can have a significant impact on the performance of your power system. It’s best to monitor and mitigate their effects when those issues show up.
MITIGATING THE EFFECTS OF HARMONICS
Start with making sure you have routine preventive maintenance checks of your non-linear loads. That way you can catch and address the problems before they get too large.
Once you have found an issue, you’ll want to start with the issues you’re seeing, properly identifying the root cause of the problem, and isolating the source. Start by measuring with a clamp meter that can indicate power quality issues (Photo 1 on page 12). A tool like this can help indicate total harmonic distortion (THD) and show all harmonics present. THD for voltage should not exceed 5% to 6%, and THD for current will run considerably higher.
Excessive THD for voltage means any number of problems could be occurring,
and you should continue to get to the bottom of them so corrective action can be taken. To further investigate the magnitude and effects of the individual harmonics, you’ll need more detailed information from a more powerful tool, like a power quality analyzer (Photo 2 on page 15).
Once you have found an issue, you’ll want to start with the issues you’re seeing, properly identifying the root cause of the problem, and isolating the source.
A power quality analyzer can record disturbances, like harmonics, in your line power by recording and monitoring the power quality over some time. Your analyzer can pick up all sorts of potential problems like dips and swells, wasted energy and electrical disturbances, or other issues that can cause the malfunction of control circuits.
Harmonics can be a significant problem in a power system, often leading to reduced efficiency, increased energy consumption, and larger safety hazards. It’s important to monitor your power systems to identify the presence of harmonics and mitigate any havoc caused on a system before it creates costly downtime or repair issues. By taking these steps, power system operators can ensure that their systems are reliable, efficient, and safe.
Jason Axelson is a product application specialist for Fluke. He has more than 15 of experience helping customers and partners find solutions for power quality, scope meters, and battery testers.
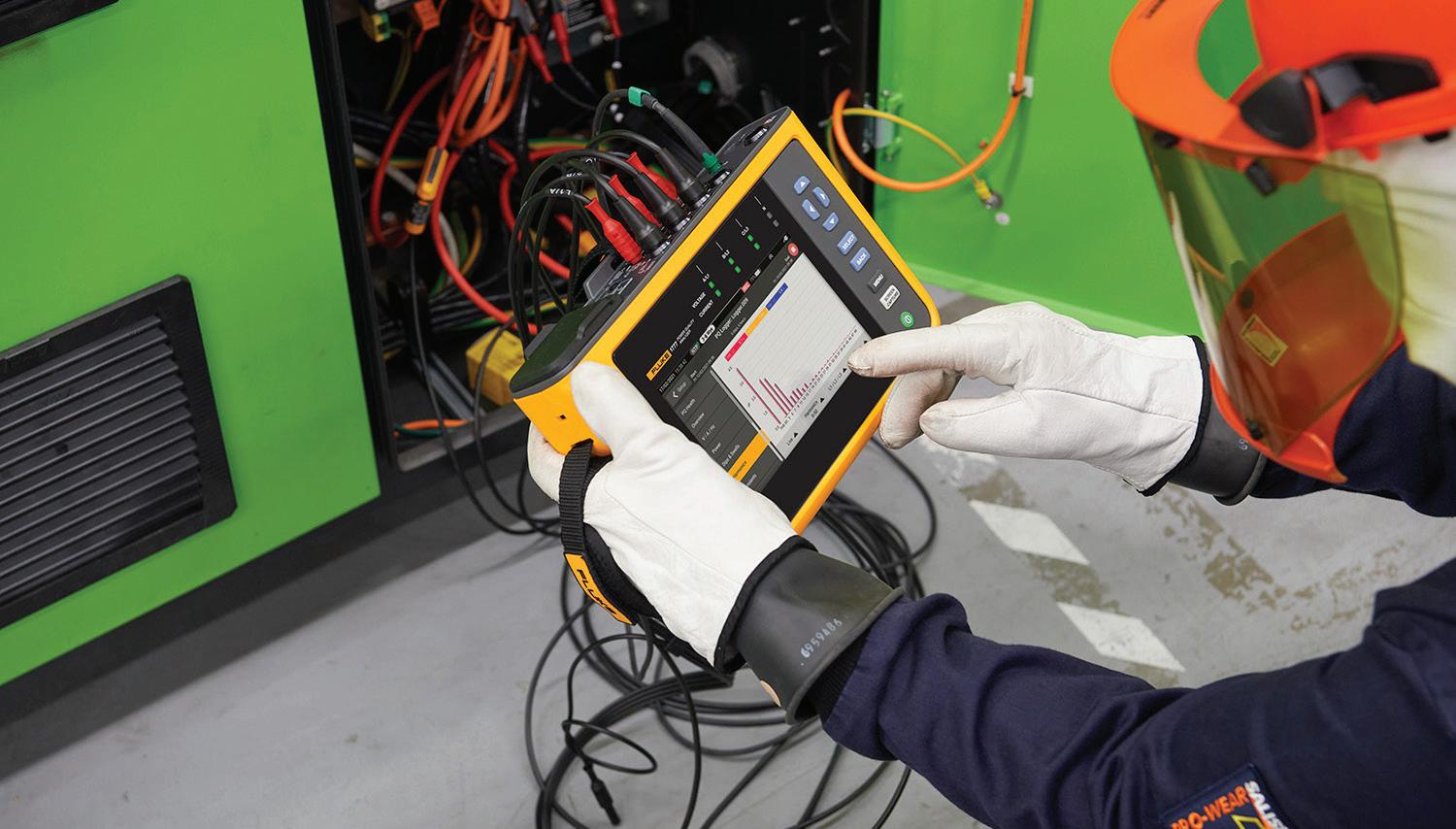
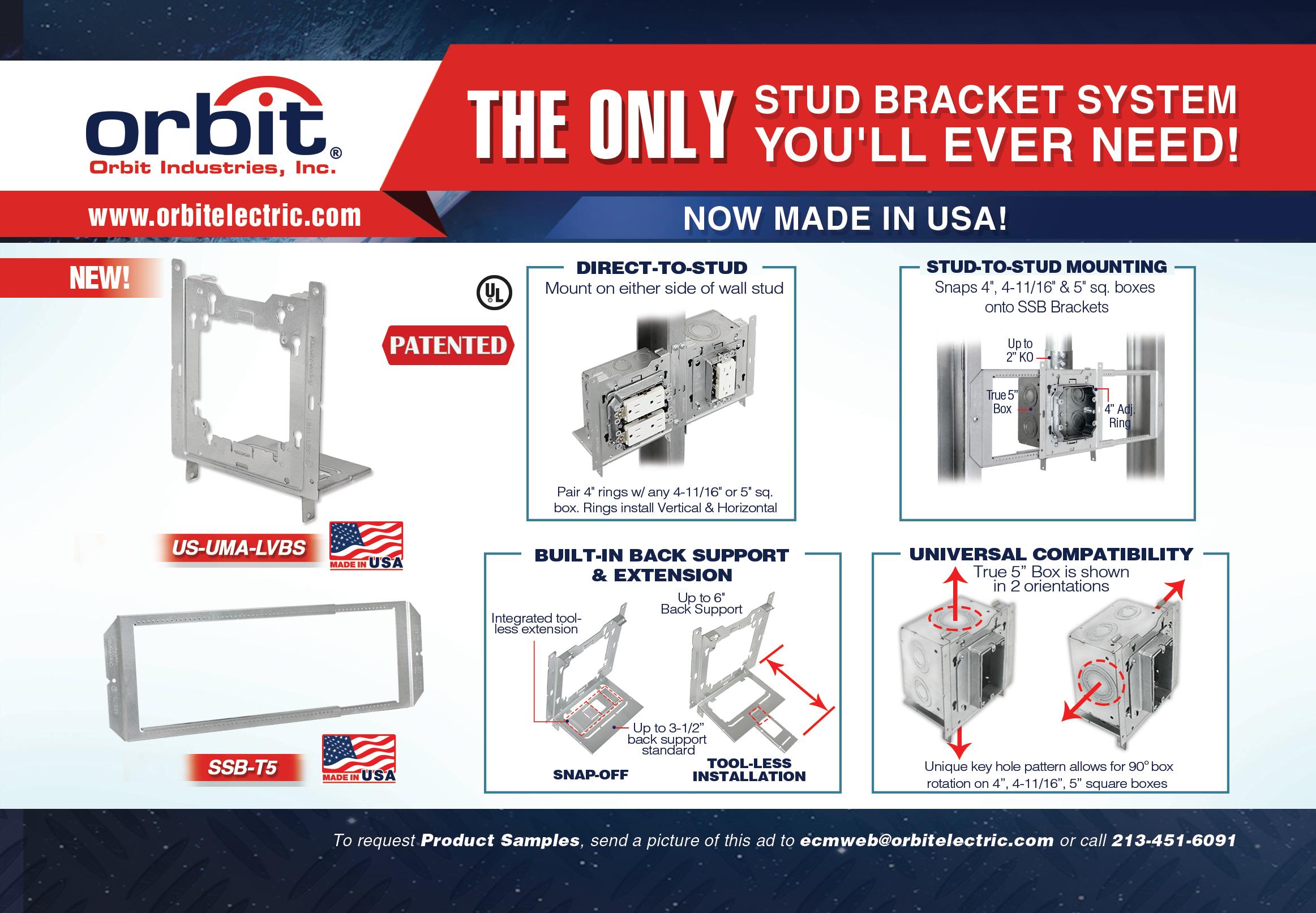
Is Troubleshooting Considered Energized Work?
A guide to NFPA 70E requirements for electrical troubleshooting and repair
By Ron Widup and James White, Shermco IndustriesWhen discussing electrical safety, a question frequently asked by NETA technicians is, “When does troubleshooting end, and when does repair begin?” This question is often paired with, “What does 70E say about troubleshooting and repair?” We hope to make things clear for everyone in the field.
NFPA 70E DEFINITIONS
To begin, look at the definition of “working on” (energized electrical conductors and circuit parts) in Art. 100 of the 2024 edition of NFPA 70E. It says, “Intentionally coming in contact with energized electrical conductors or circuit parts with the hands, feet, or other body parts, with tools, probes, or with test equipment, regardless of the personal protective equipment (PPE) a person is wearing.
“Informational Note: Examples of ‘working on’ can include but are not limited to diagnostic testing (such as taking readings or measurements of electrical equipment, conductors, or circuit parts with approved test equipment that does not require making any physical change
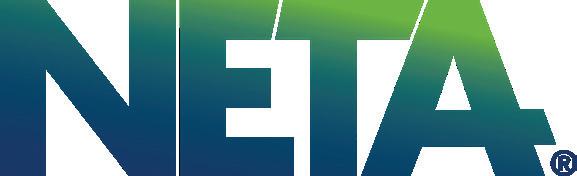
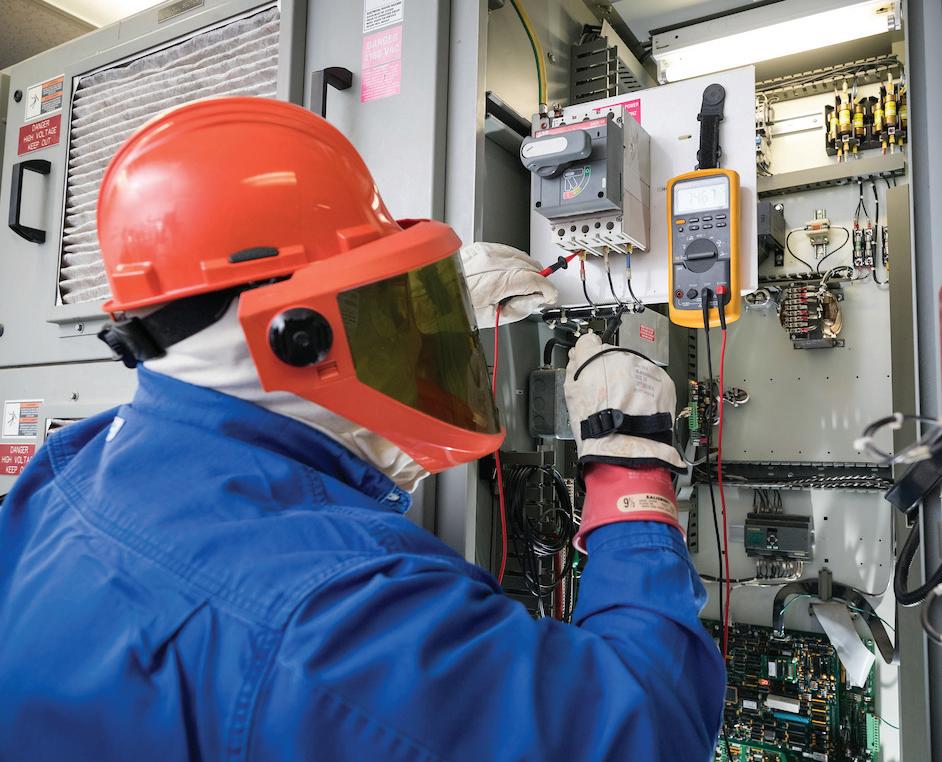
to the electrical equipment, conductors, or circuit parts) and repair or physical alteration of electrical equipment, conductors, or circuit parts (such as making
Electrical Testing Education articles are provided by the InterNational Electrical Testing Association (NETA), www.NETAworld.org.
NETA was formed in 1972 to establish uniform testing procedures for electrical equipment and systems. Today, the association accredits electrical testing companies; certifies electrical testing technicians; publishes the ANSI/NETA Standards for Acceptance Testing, Maintenance Testing, Commissioning, and the Certification of Electrical Test Technicians; and provides training through its annual PowerTest Conference and library of educational resources.
or tightening connections, removing or replacing components, etc.).”
A lot is going on in the above definition. The first sentence begins with “Intentionally coming in contact ….. with the hands, feet, or other body parts ….” So, in this definition, contact is not accidental, but intentional with any part of the body. This separates it from unintentional contact (incident) or any type of equipment failure. That sentence continues “with tools, probes, or with test equipment, regardless of the personal protective equipment (PPE) a person is wearing.” This makes it clear that using voltage testers or any other type of test equipment is included, and PPE doesn’t change this; you’re still working
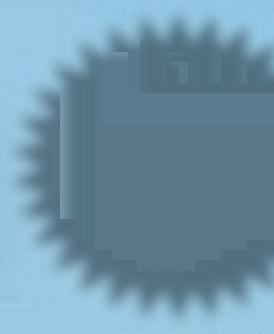
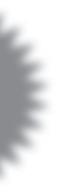

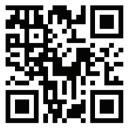
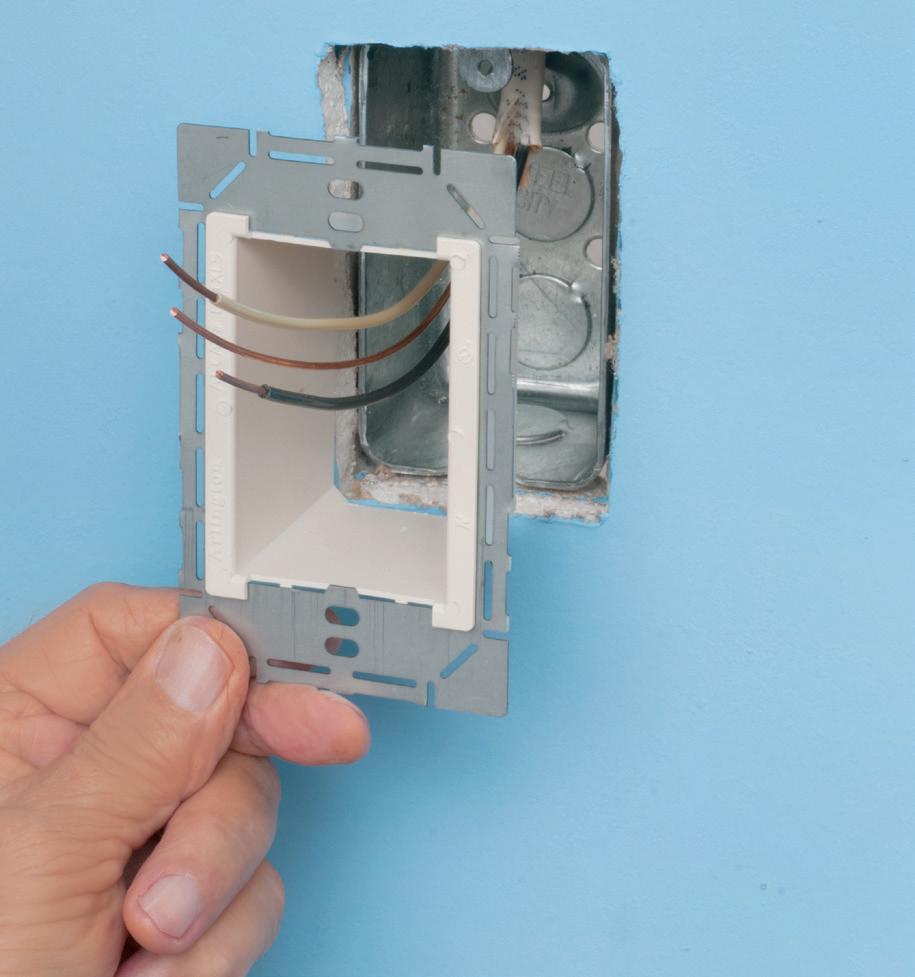

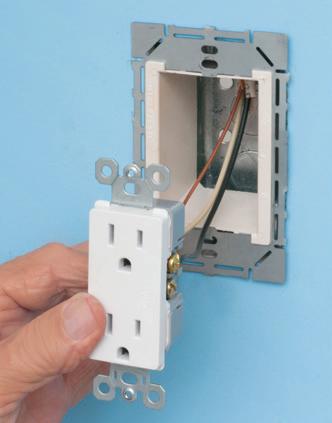
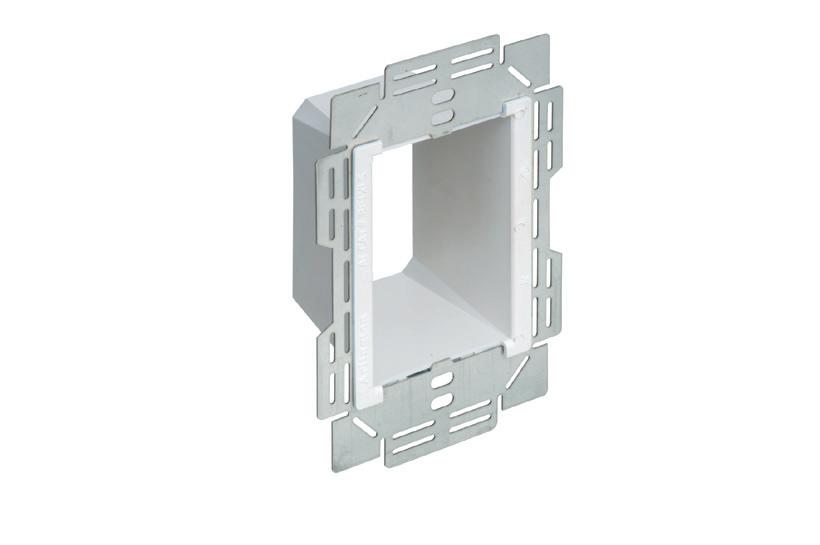



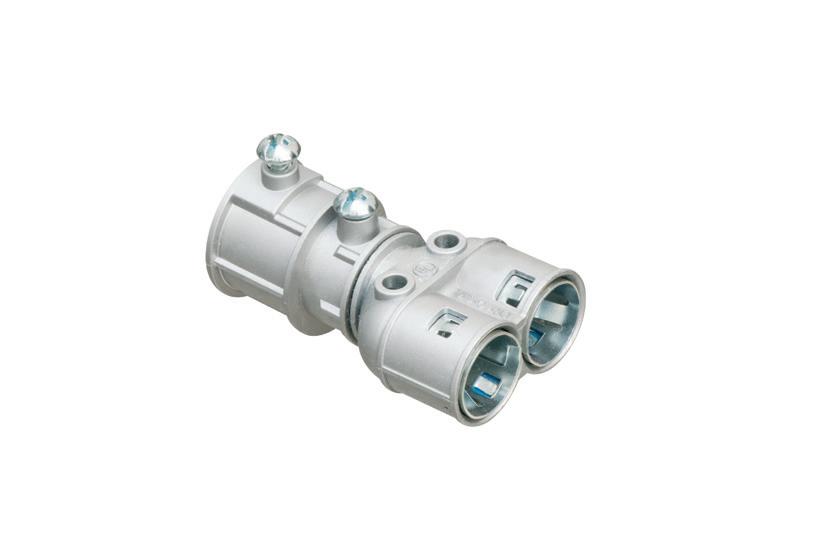
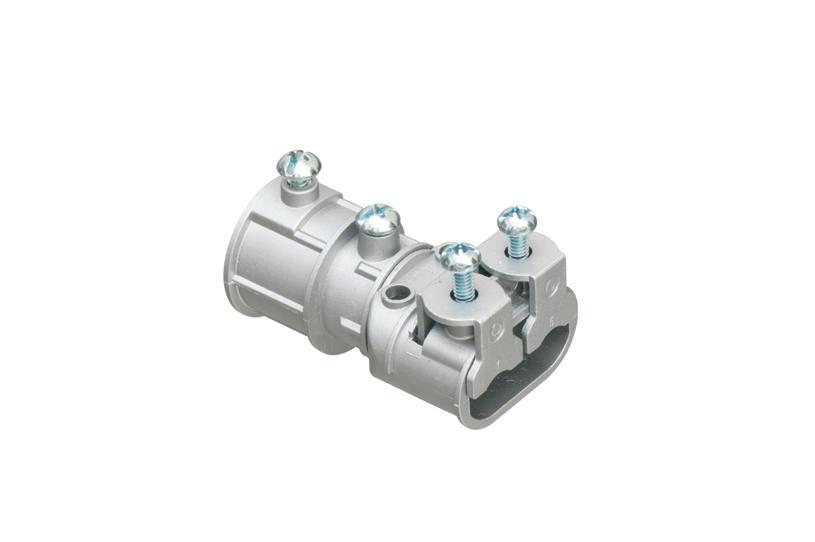
ELECTRICAL TESTING EDUCATION
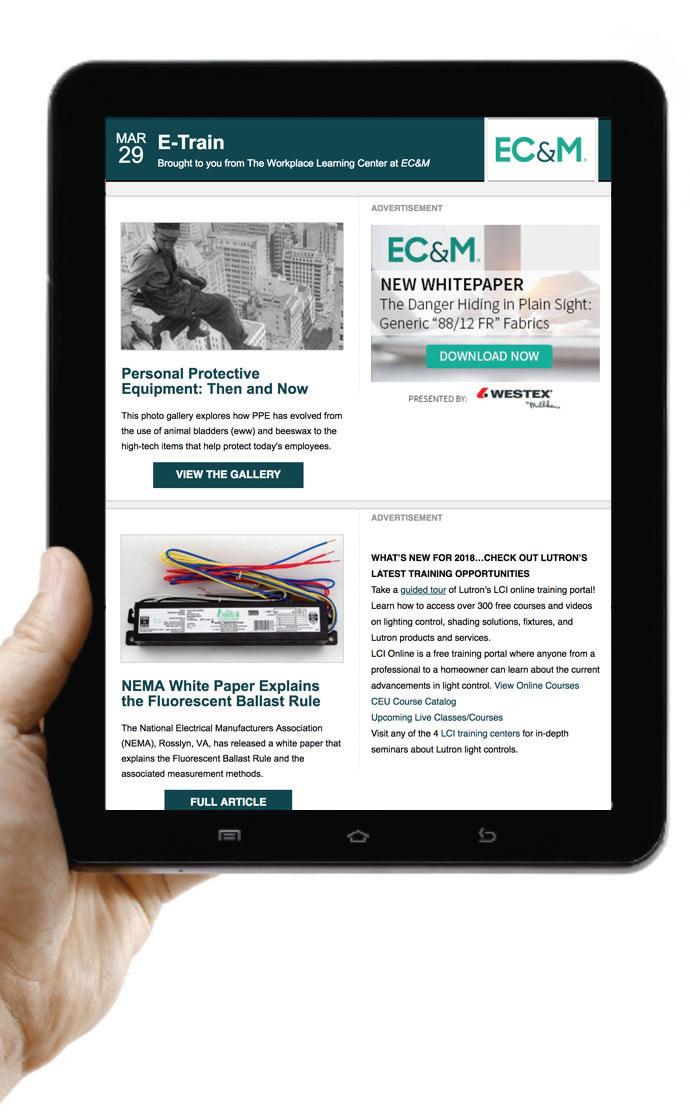
E-Train
This e-newsletter, published monthly, brings you the latest training courses available in the industry. Rely on E-Train for refresher courses or for continuing education.
Topics covered include:
• PLC certification
• Short-circuit current ratings
• Relay testing
• NFPA 70E
• Thermal imaging
• Lighting controls
Subscribe Today
See all of our EC&M e-newsletters at www.ecmweb.com

on energized electrical conductors or circuit parts. Many technicians believe that troubleshooting is not “working on.” Clearly, it is, and appropriate PPE is necessary.
The Informational Note states there are two categories of “working on”: 1) diagnostic testing; and 2) repair. Diagnostic is defined as “taking readings or measurements of electrical equipment, conductors, or circuit parts with approved test equipment that does not require making any physical change to the equipment.” This would include
absence-of-voltage testing, troubleshooting, calibration, or voltage testing.
Again, PPE is mandatory because using voltage-rated probes on energized electrical equipment is not considered safe. There is an exception in Chapter 3 for laboratory work, but it would not apply to NETA-type testing and maintenance work. Article 350 applies to this work where a specifically trained and responsible person known as the Electrical Safety Authority (ESA) can make job-specific requirements that may be different than those found in Chapter 1.

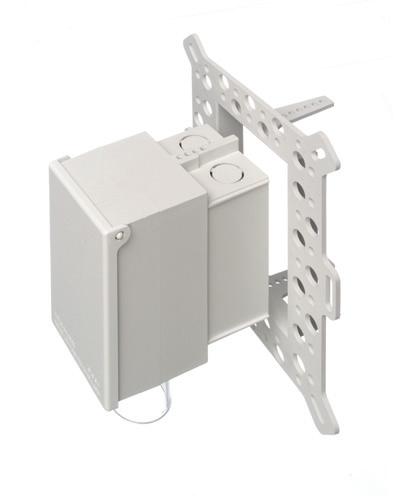
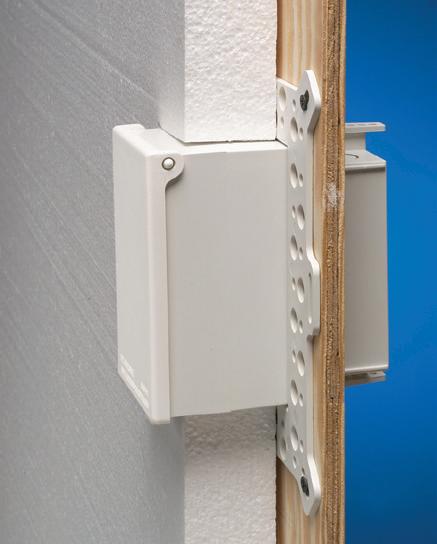
•
•

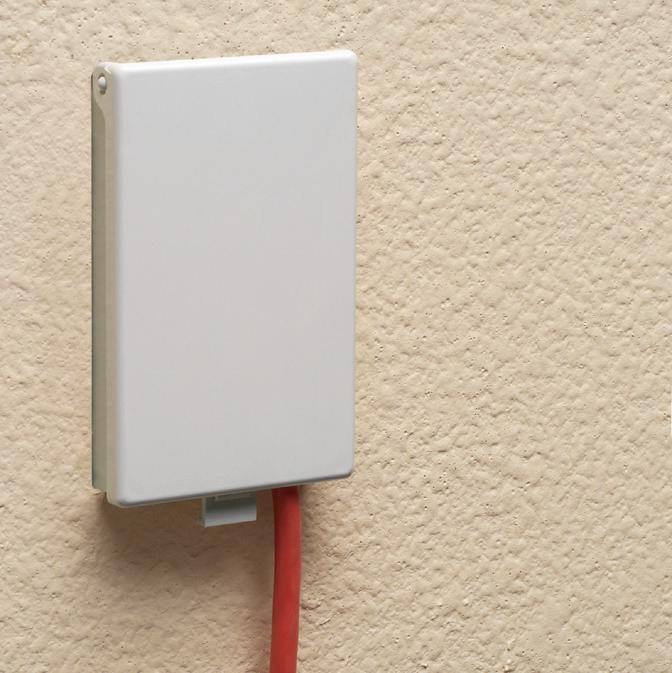
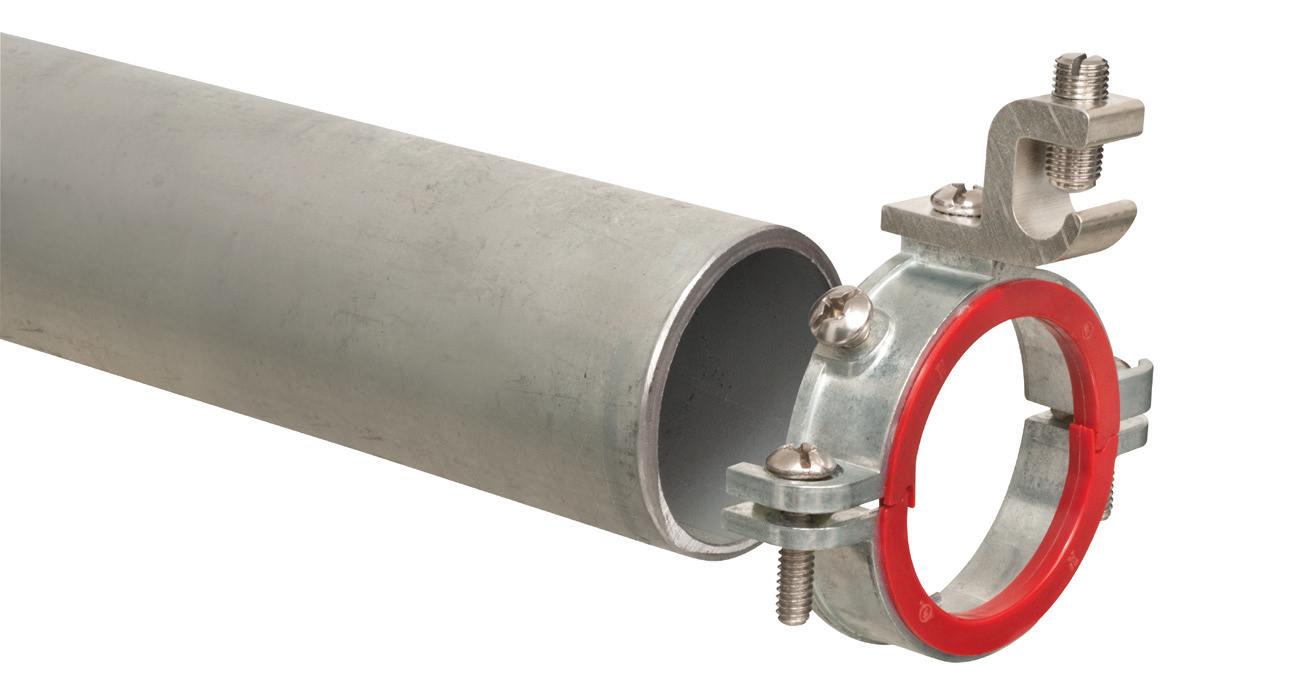
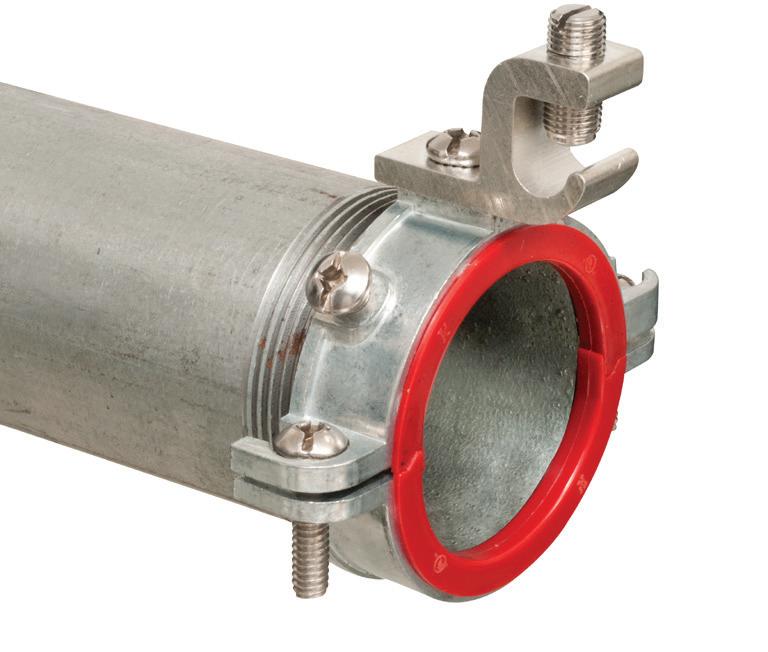
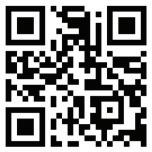
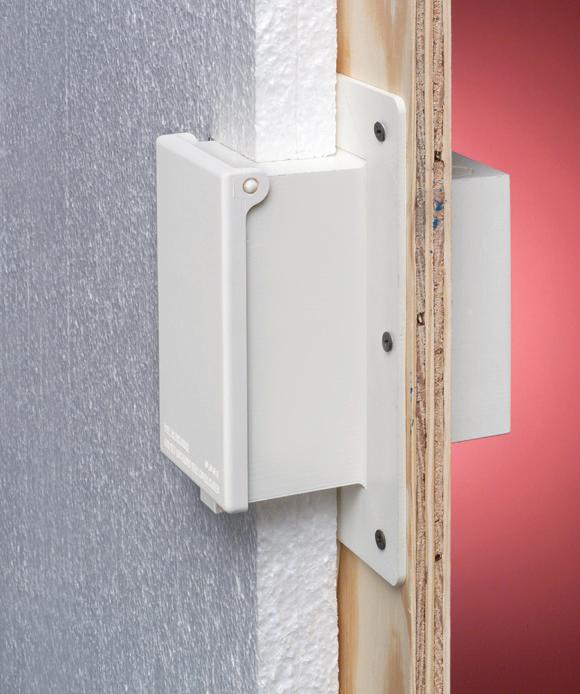

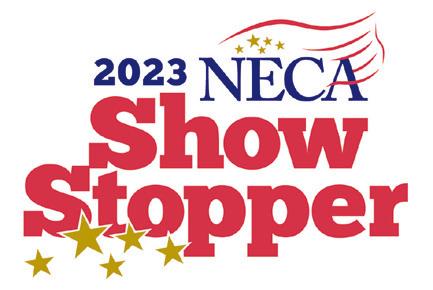
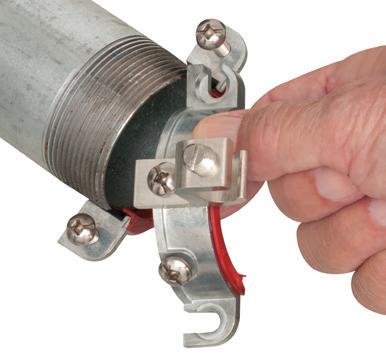
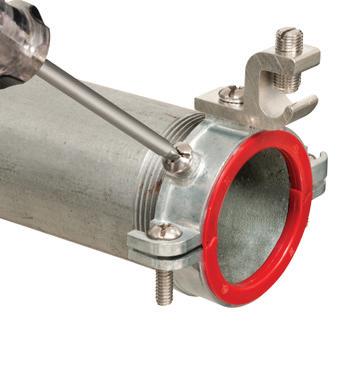
ELECTRICAL TESTING EDUCATION
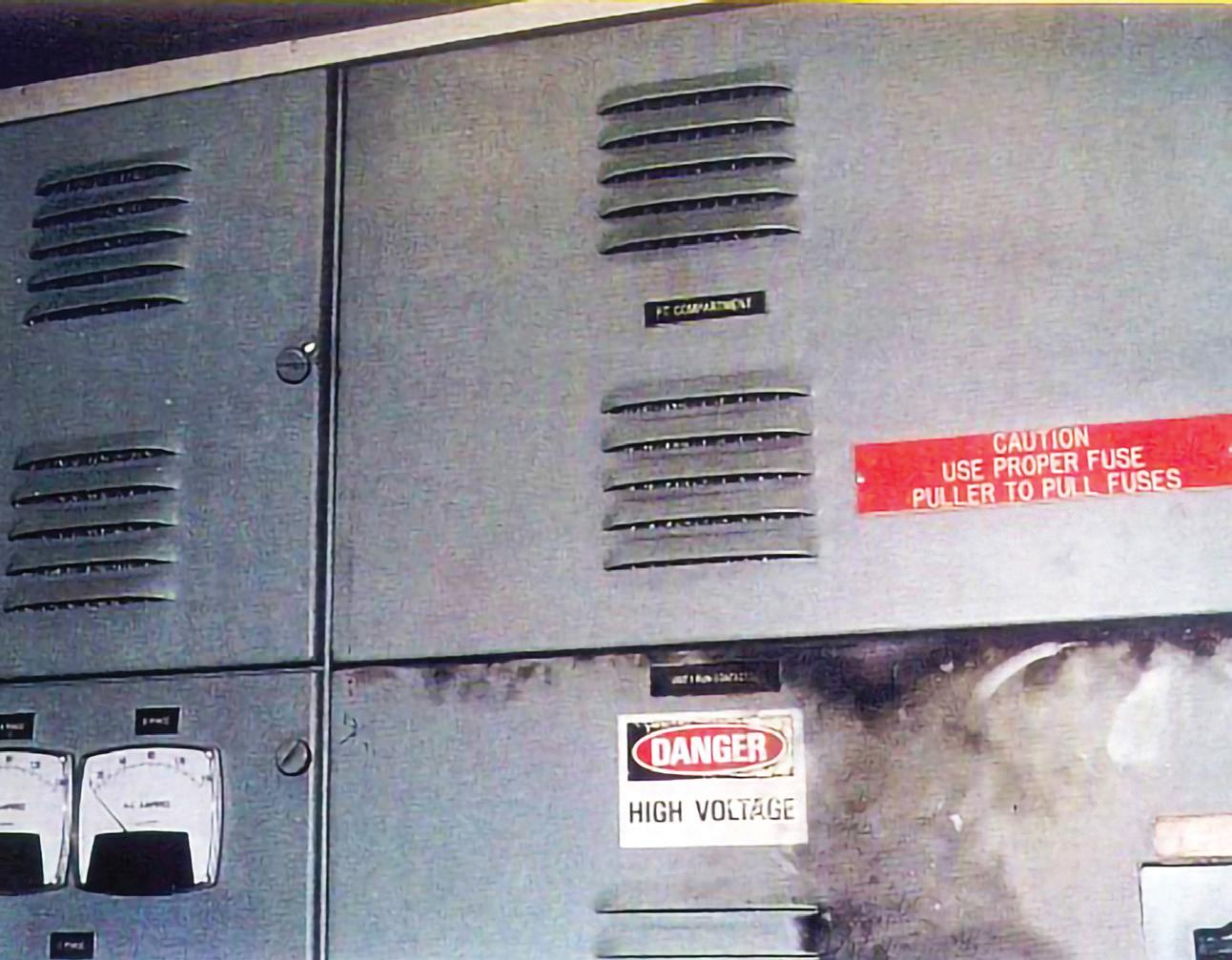
The second category of working on (repair) is defined as “any physical change to the electrical equipment, conductors, or circuit parts (such as making or tightening connections, removing or replacing components, etc.).” We have seen many instances where this is misunderstood or just violated, especially during maintenance-type activities.
A TROUBLESHOOTING CASE STUDY
Here’s a true story. A job leader took an apprentice to a switchgear room where low- and high-voltage equipment was installed. He pointed out areas the apprentice was to avoid, such as the main incoming line compartment. He worked with the apprentice for some time cleaning low-voltage connection strips and the inside of the panels.
When the job leader was called away to another part of the job, he told the apprentice, “Don’t work on anything that looked hot,” and walked away. The apprentice continued to clean, tighten connections, and inspect the lowvoltage control compartments. In each compartment, he used his voltmeter to determine whether the terminals were energized (Photo 1 on page 18).
Then, the apprentice came to a compartment that contained 4,160V
potential transformers. This compartment was marked “PT Compartment,” but it did not have a sign on it warning
of high voltage. The compartment immediately below the PT compartment did have a “Danger High Voltage” sign on the top of its compartment door (Photo 2).
The apprentice opened the door without the warning label and attempted to test the terminals of the 4,160V PTs. There was no indication of danger to the technician (Photo 3).
As soon as the test probes touched the PTs, an arc flash occurred. The apprentice was fortunate, as he survived the incident, but he spent several days in the hospital’s burn unit. He could have very well died, as he was not wearing any PPE.
Photo 4 on page 22 shows the aftermath of the PTs blowing up, while Photo 5 on page 22 shows the low-voltage tester used to test 4,160V PTs — a catastrophic scene for sure.
This case history, “Who’s at Fault — Owner or Contractor?” was presented at an IEEE Electrical Safety Workshop by Joseph Andrews. It shows why the 70E definitions are so critical. What people don’t know, they don’t know. There is a ton of useful information contained in
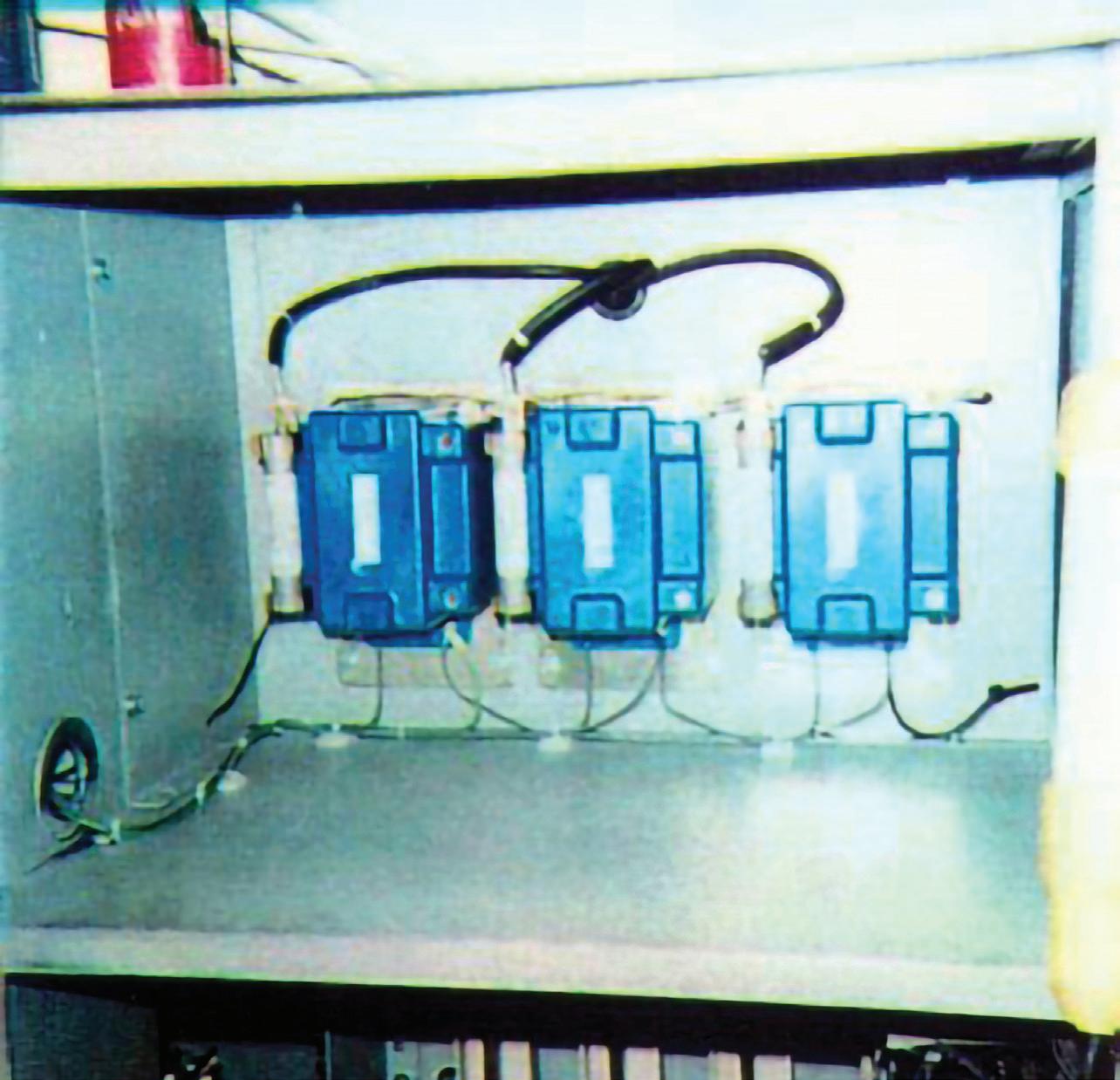
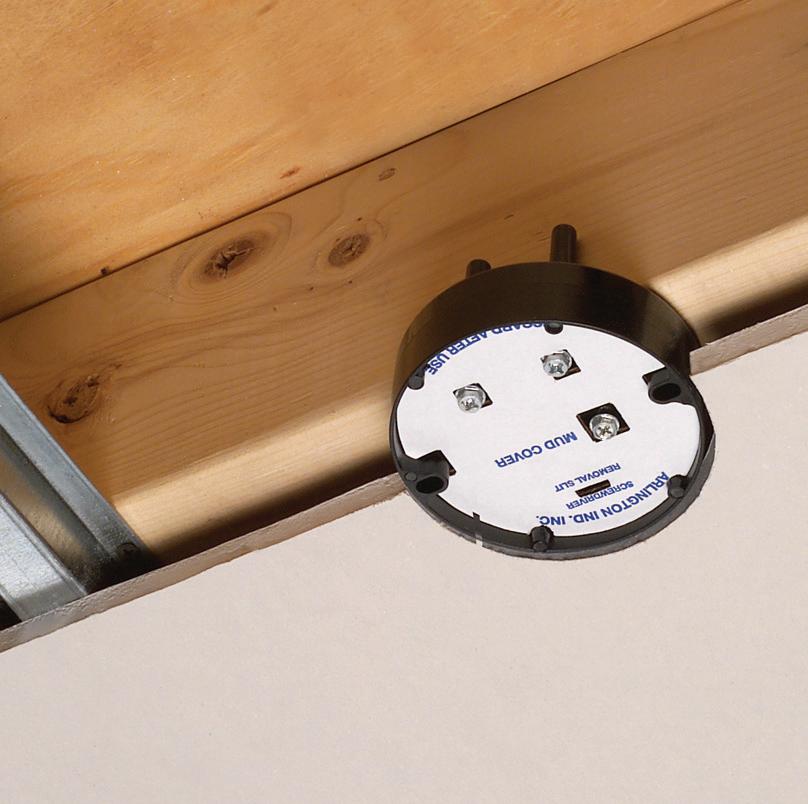
Arlington’s convenient fan/fixture pan box works with 1/2", and single or double 5/8" drywall –on furring strips or hat channel.
• Easy mounting in new work
•Fan bracket installation screws ship captive until ready for use
•Secure joist-mount installation
•14.4 cu. in. UL/CSA Listed
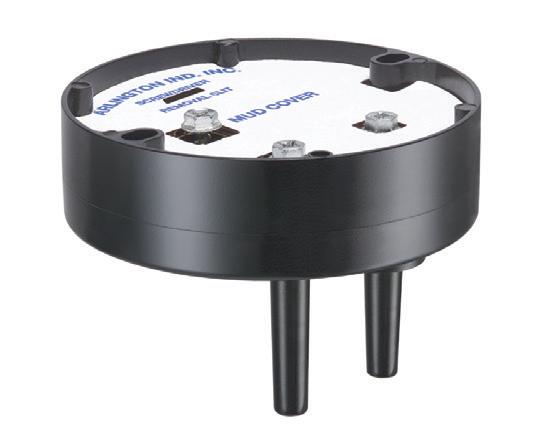
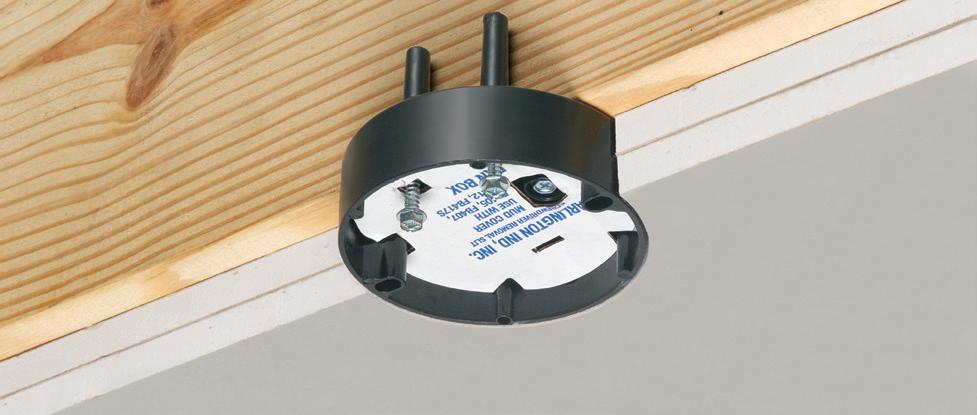
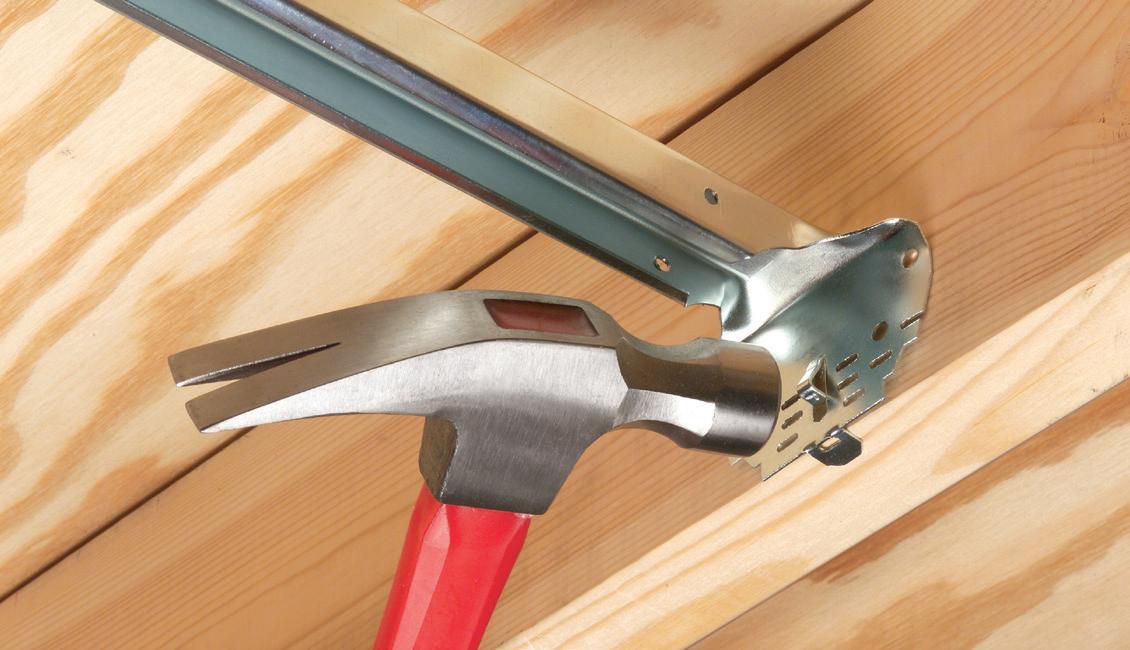
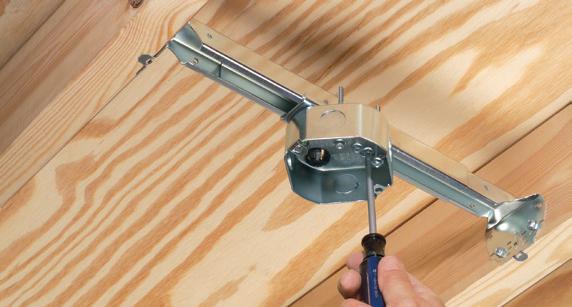
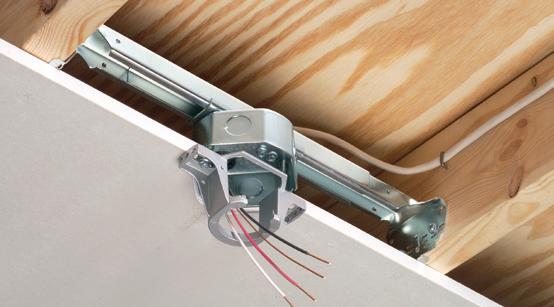


ELECTRICAL TESTING EDUCATION
the Art. 100 definitions. You may feel there is no danger in using an insulated (or uninsulated) screwdriver to tighten connections or in using a voltage tester to perform absence-of-voltage testing. However, there could be danger lurking just around the corner.
Chapter 1, Art. 130, Sec. 130.2(C) provides exemptions to the use of an energized electrical work permit. The entire section is reproduced below:
“(C) Exemptions to Work Permit. Electrical work shall be permitted without an energized electrical work permit if a qualified person is provided with and uses appropriate safe work practices and PPE in accordance with Chapter 1 under any of the following conditions:
(1) Testing, troubleshooting, or voltage measuring
(2) Thermography, ultrasound, or visual inspections if the restricted approach boundary is not crossed
(3) Access to and egress from an area with energized electrical equipment if no electrical work is performed and the restricted approach boundary is not crossed
(4) General housekeeping and miscellaneous non-electrical tasks if the restricted approach boundary is not crossed”
Note that the first sentence says, “Electrical work shall be permitted without an energized electrical work permit if a qualified person is provided with and uses appropriate safe work practices and PPE in accordance with Chapter 1 under any of the following conditions.” The person must be qualified to begin with. Unqualified persons are not permitted to be near energized electrical conductors or circuit parts. Second, that qualified person must be provided with and use appropriate safe work practices and PPE. An unqualified person would not know or be able to determine what is appropriate. The person in the case history above could not determine those two things.
CONCLUSION
Supervisors at any level — whether it’s in their title or not — must not make assumptions about what a person knows or doesn’t know. They must ensure the technician’s safety.

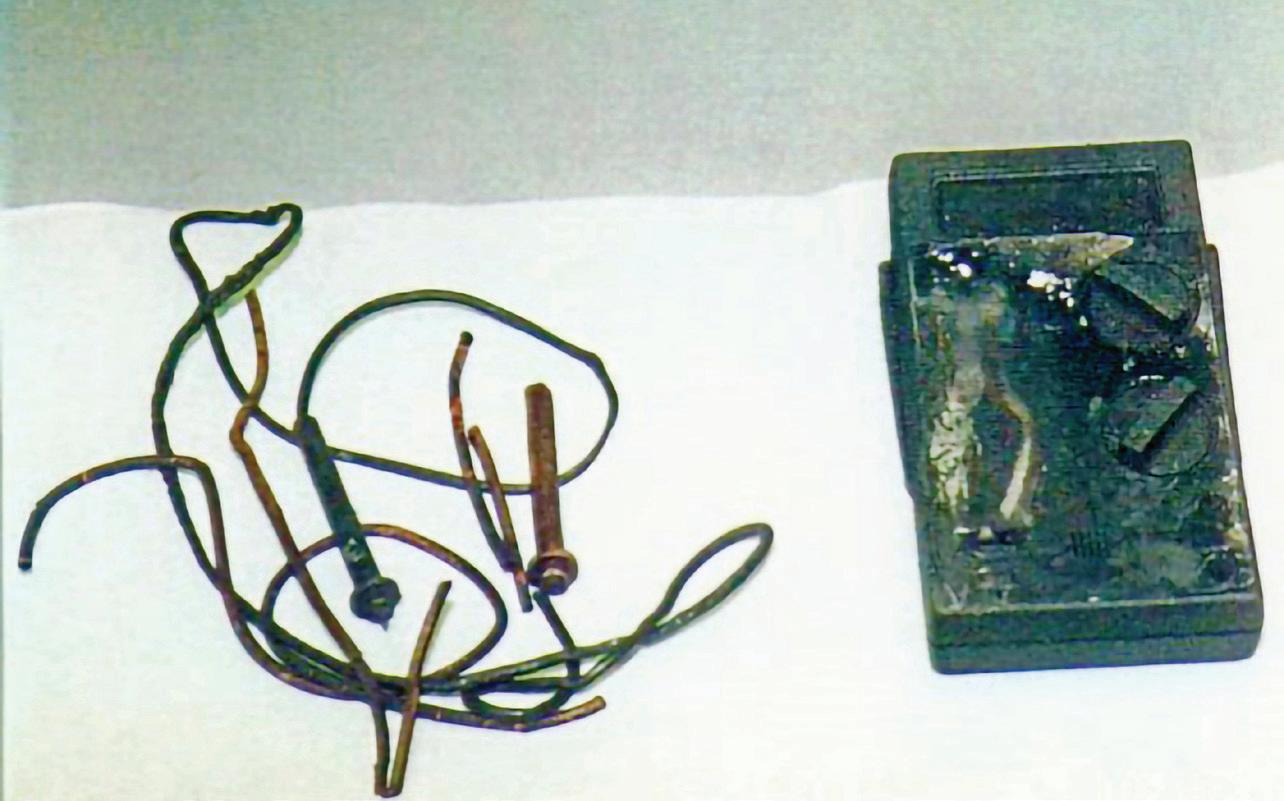
Troubleshooting, testing, and even tightening connections are considered by many to be safe. The previous example shows how wrong that assumption can be — and it is not just apprentices who make that mistake. Troubleshooting the control power transformer on a 4,160V motor starter has caused many incidents. One technician told us how the guts of his Wiggy (he was pretty old) flew across a building, striking 15 feet high on the opposite wall. If that coil had hit him, he would have been severely injured or
killed. With electricity, small mistakes can be painful or fatal.
Author’s Note: This article was originally written by James R. “Jim” White of Shermco Industries. We have taken Jim’s work, updated it, and offered this revision in his honor. Great job, Jimbo!
Ron Widup is the vice chairman, board of directors, and senior advisor of technical services for Shermco Industries and has been with Shermco since 1983. He can be reached at rwidup@shermco.com.

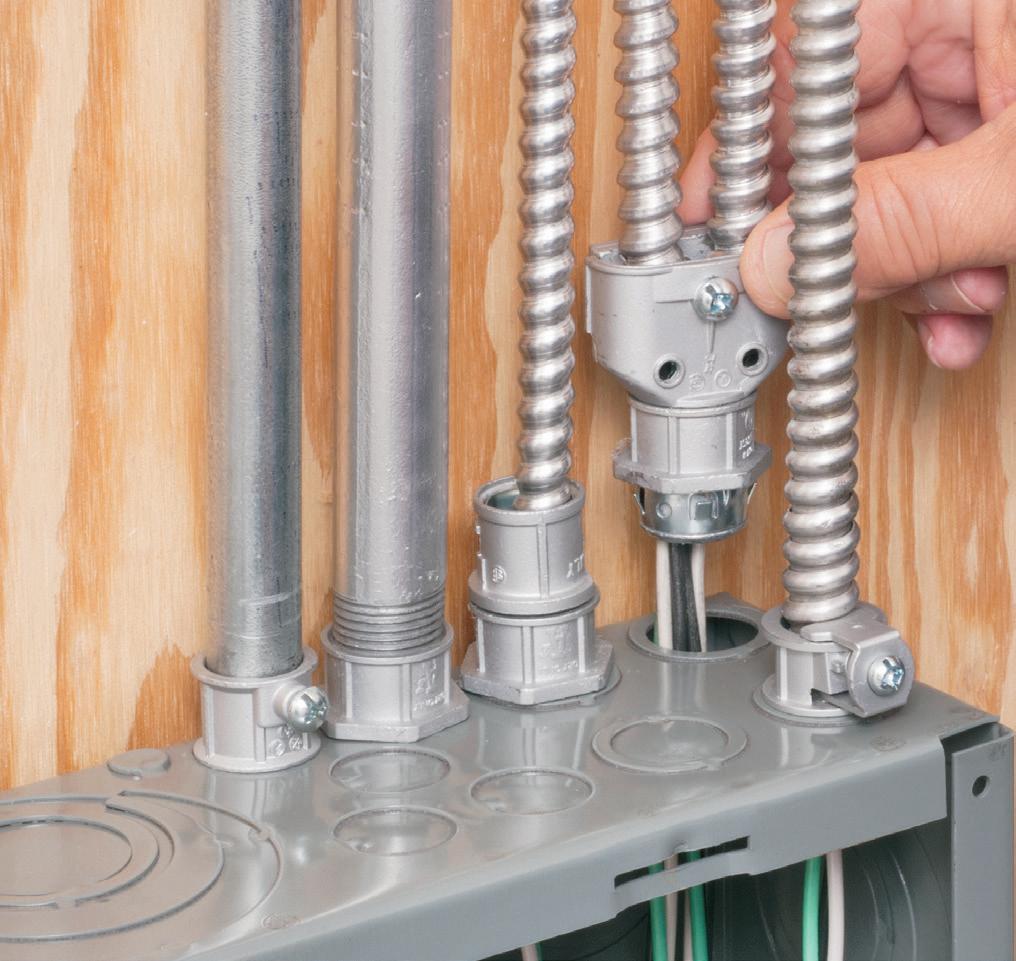
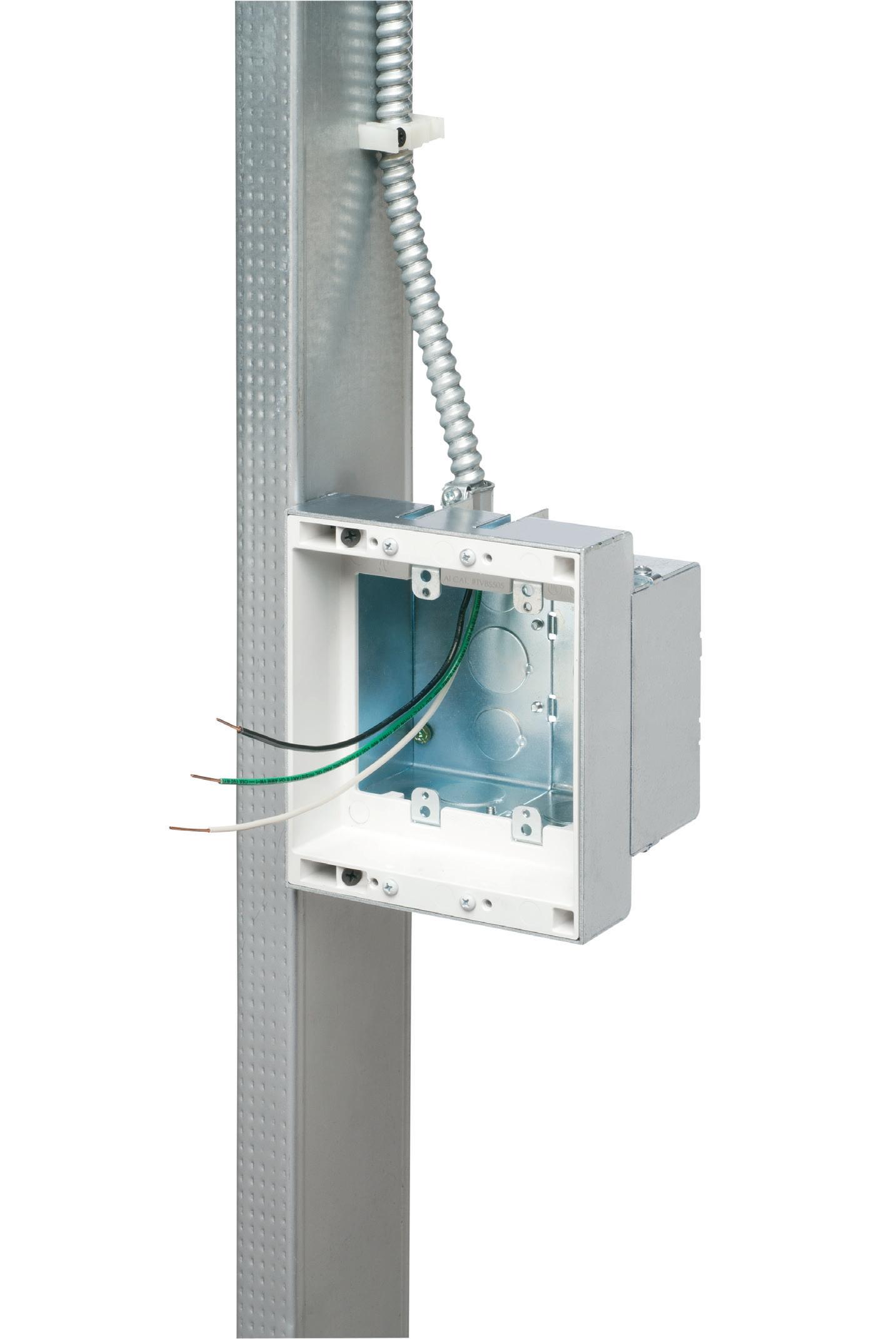
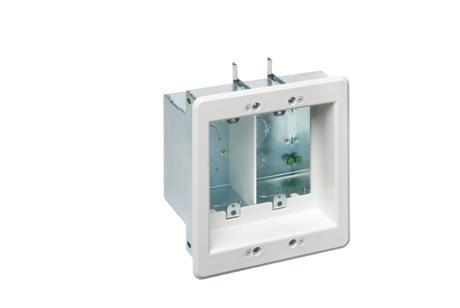
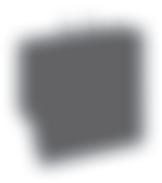
•
•
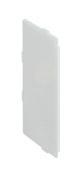
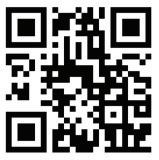


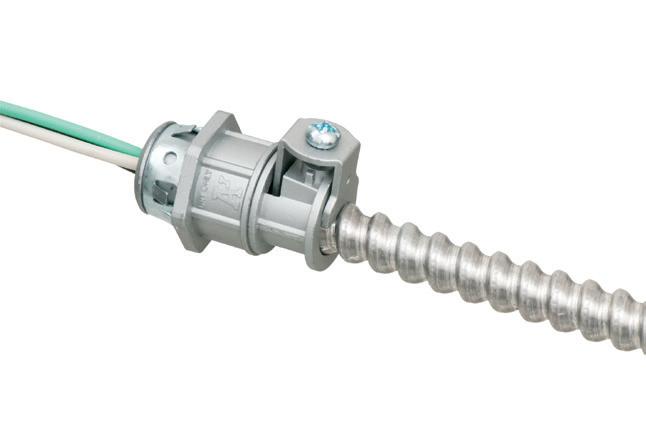
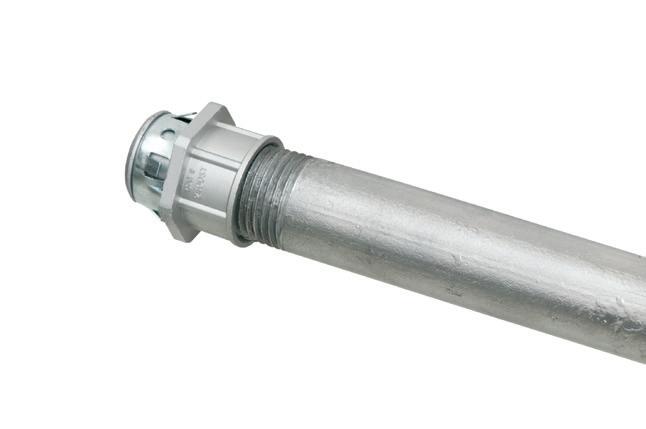
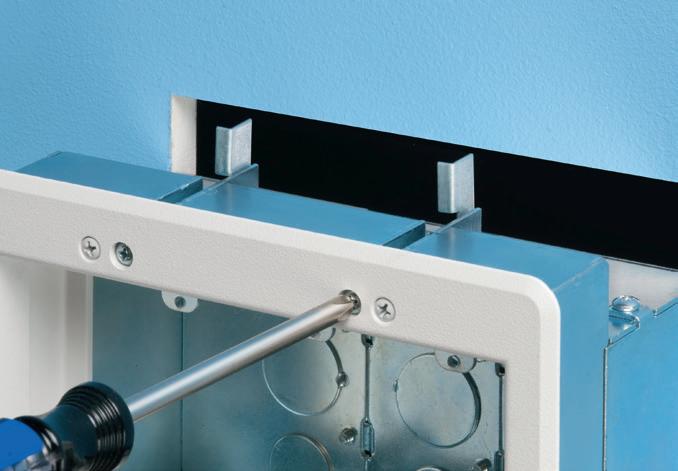

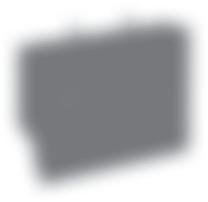
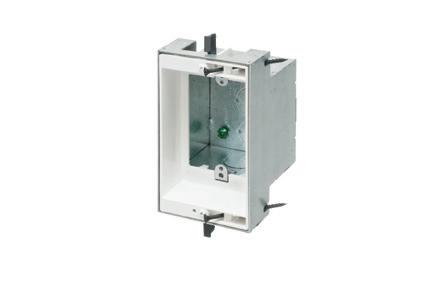
Learn how to define, measure, and improve productivity.
Productivity, like any other word, is very often left to interpretation of the user. Unless it’s clear what it is supposed to represent, it could be a very confusing means of measurement. Definitions of productivity can relate to economic factors or individuals. An inquiry in any search engine will result in something like:
“Productivity, in economics, measures output per unit of input, such as labor, capital, or any other resource. It is often calculated for the economy as a ratio of gross domestic product (GDP) to hours worked.”
Labor productivity may be further broken down by sector to examine trends in labor growth, wage levels, and technological improvement. Corporate
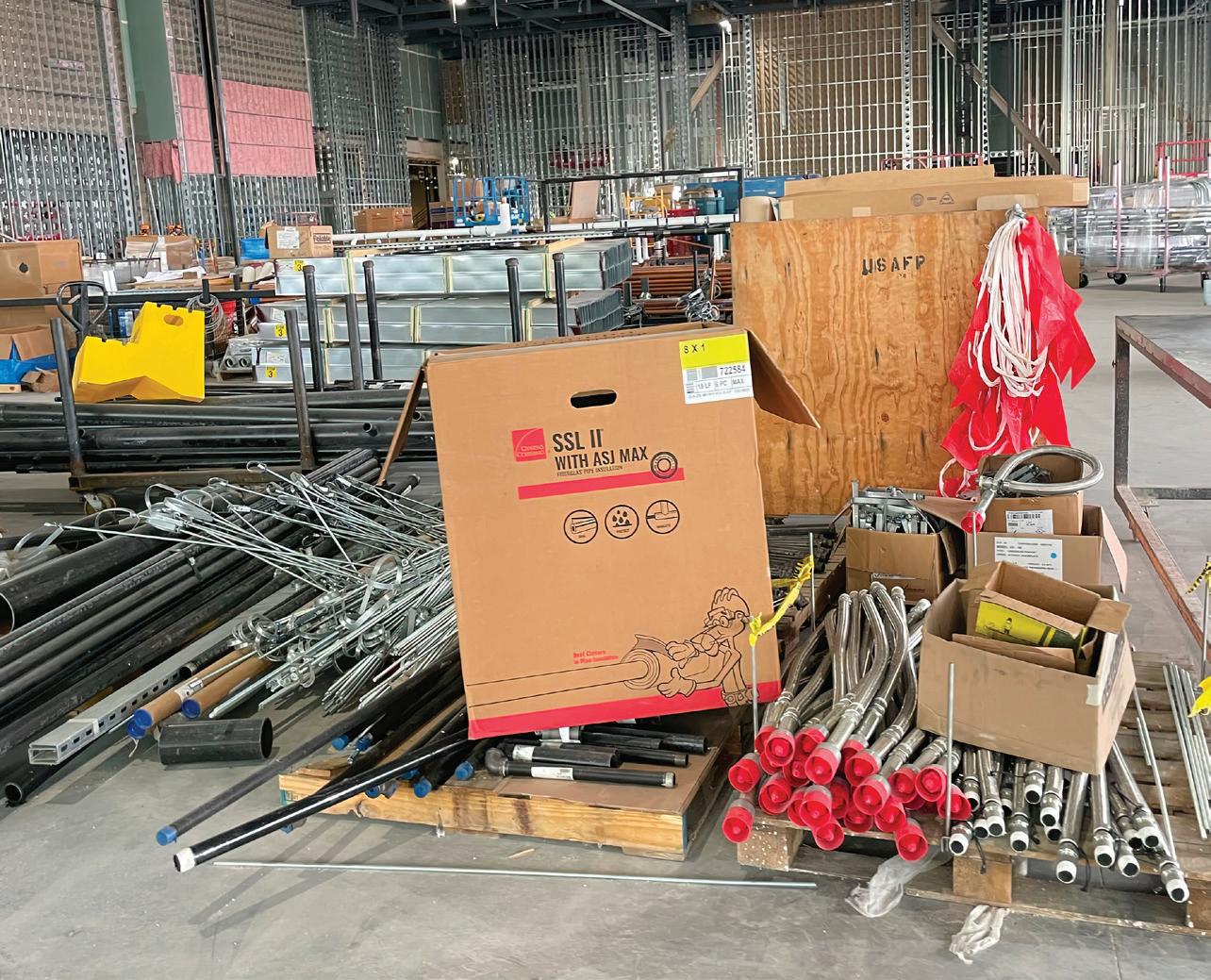
profits and shareholder returns are directly linked to productivity growth.
At the corporate level, productivity is a measure of the efficiency of a company’s production process. It is calculated by measuring the number of units produced relative to employee labor hours or by measuring a company’s net sales relative to employee labor hours. Here’s a quick summary to make sure we’re all on the same page at this point.
• Productivity, in economics, measures output per unit of input.
• When productivity fails to grow significantly, it limits potential gains in wages, corporate profits, and living standards.
• The calculation for productivity is output by a company divided by the units used to generate that output.
• Auto giant Toyota and online marketplace king Amazon are prime examples of businesses with an impressive level of productivity.
• Productivity in the workplace refers simply to how much work is done over a specific period.
Ask ChatGPT the same question, and (depending on what you type into the prompt) you’ll get something like this:
“Productivity generally refers to the measure of efficiency and effectiveness in completing tasks or achieving goals, often in relation to the resources utilized. It is a key concept in various fields, including economics, business,
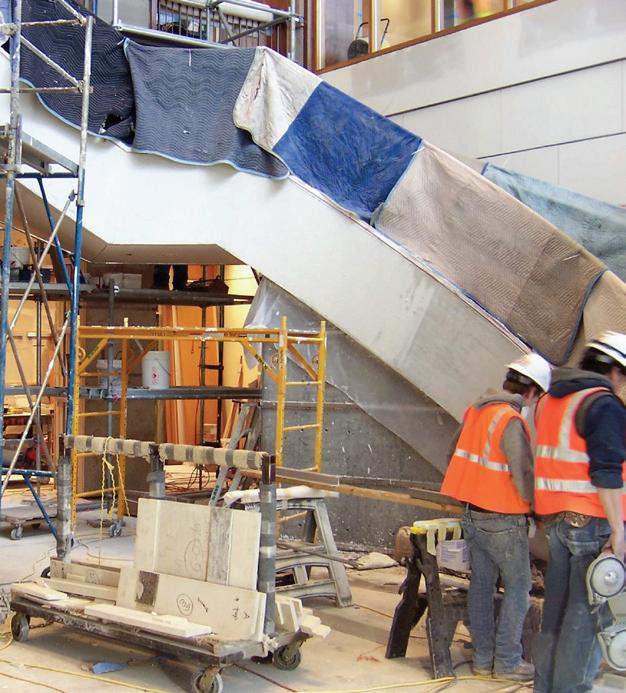
and personal development. Productivity can be assessed at individual, organizational, or societal levels and is typically expressed as the ratio of output to input.”
In the context of work or business, productivity is often associated with the amount of output (goods, services, or work) produced per unit of input (time, labor, capital, etc.). Higher productivity implies that more is accomplished with the same or fewer resources, reflecting efficiency improvements.
These definitions or measurements leave a lot to be desired for the electrical contracting community about how to measure, correct, and improve labor productivity. All the measurements are related to the system’s output and not the outcome, as noted in ASTM E2691-20: Standard Practice for Job Productivity Measurements. They also do not help contractors define the waste to improve productivity.
In construction, the phrase “productive labor” is used to define an individual’s pace of work. Both of these methods (the economic and individual productivity measurements) make one flawed assumption — everything that labor does contributes to productivity. One visit to most jobs will quickly prove that assumption wrong. For example, the job site environment depicted in the Photos shows the realities of activities that have nothing to do with individual pace of work. In fact, you could have the most productive, well-trained, motivated electricians who simply cannot get their work done because other trades’ materials are in the way.
To define the productive activities, you should start by identifying the wasteful activities. The Table on page
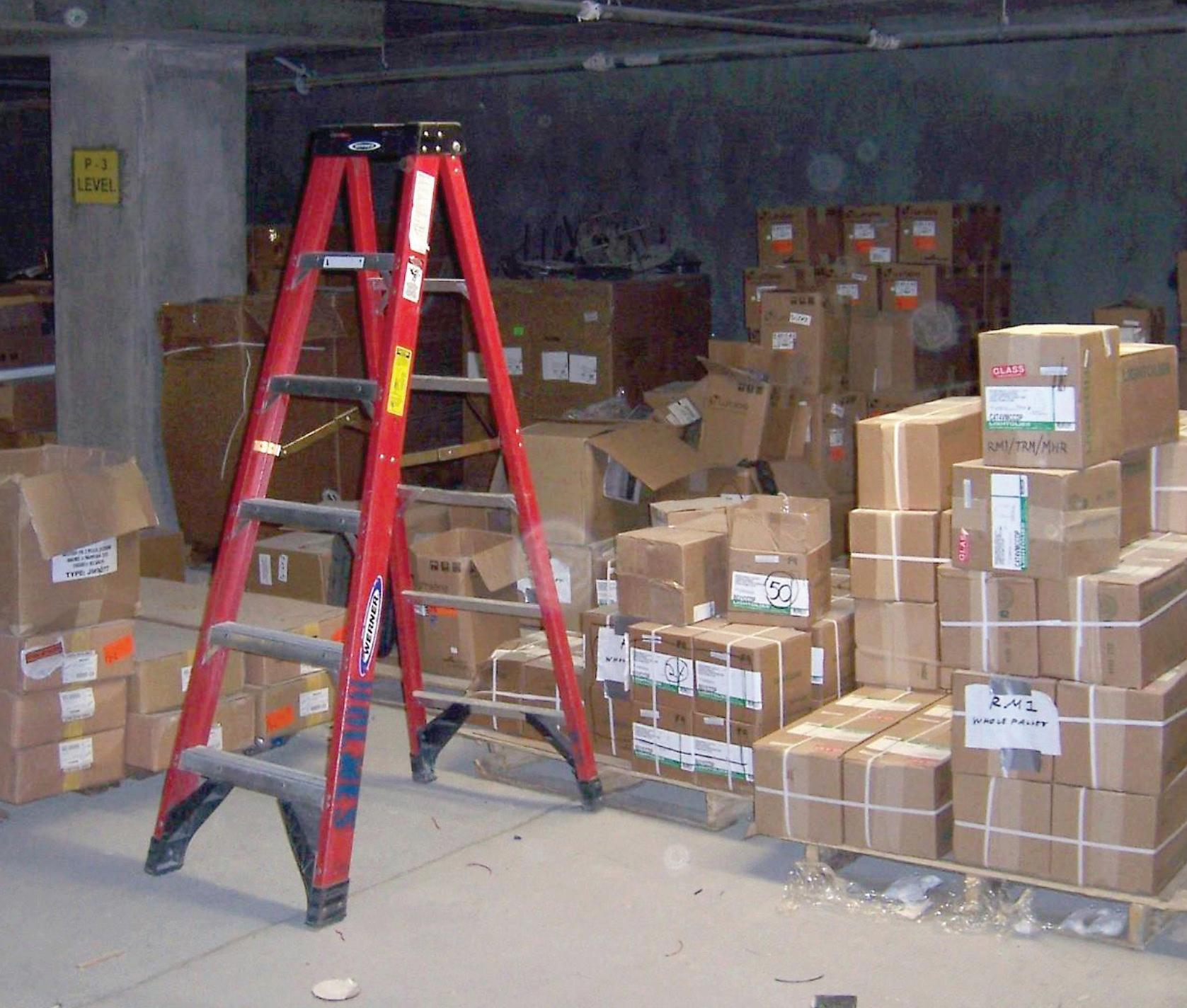
26 shows a list of wasteful activities on a job site. These activities can consume more than half of the labor’s time and kill productivity. Even though the output gets corrected “eventually,” the wasteful activities still drive unnecessary costs and time in construction. The customer may be happy with the final product because they didn’t have to pay as much or wait as long to get it. For example, the role of electrical inspectors is to uphold the National Electrical Code (NEC) requirements; however, when a foreman has to double-check his journeyman’s work to make sure it’s correct before it even gets to final inspection, that is waste — and this doesn’t even take into account the time it will take to correct the work if it’s wrong.
Once the waste is understood, now it needs to be measured. Before you do that, however, let’s take a look at two consecutive days on the same hypothetical job site.
Figure 1 on page 26 depicts the potential differences on a job site with and without interruption. On both of these days, the labor will be considered productive because:
1. They showed up on time.
2. They did everything they were told to do.
3. They got paid in full for a full day of work.
So why would one day be considered more productive than the other?
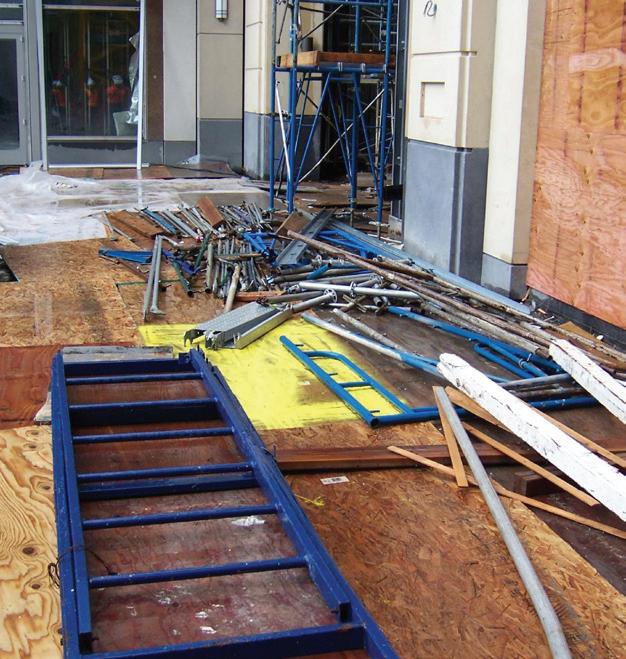
When specialty trades arrive on job sites like the ones shown in these three photos, which are in complete and utter disarray, labor productivity inevitably suffers. Electrical contractors should visit their job sites regularly and unannounced. Although it may seem like a waste of time, doing so could save you a lot of time and money, especially if you come upon these types of scenarios.
Because as willing and productive of labor as you might have on the job site, for the workers to be able to produce an outcome, they need to be able to do the work that they contracted will get paid for as planned and scheduled. Ask yourselves, when are you going to be able to catch up with the lost time when all the days are spoken for?
In Construction, WASTE = Whatever the Labor Does Other Than Final Installation
Type of Waste Examples
Material handling
Ordering, receiving, returning, moving, unpacking, counting, sorting, or checking material
Chasing down missing information Latest drawings, RFIs, POs, schedules
Rework Taking down or pulling out material already installed
Movement around the job site To/from break rooms or restrooms, moving from one area to another for installation Inspection Checking others’ work or own crew’s work Wrong installation Installing the wrong material, installing in the wrong location, etc. Source: Agile
Different Day, Different Results
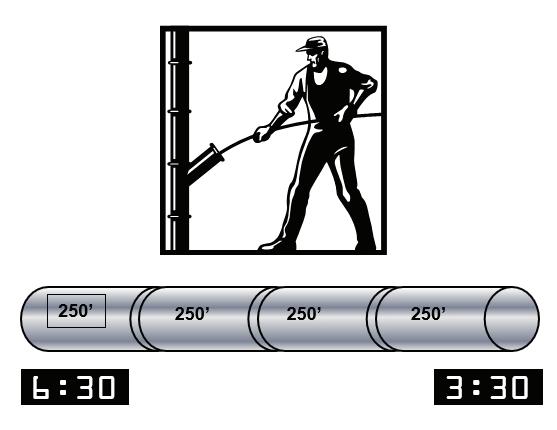
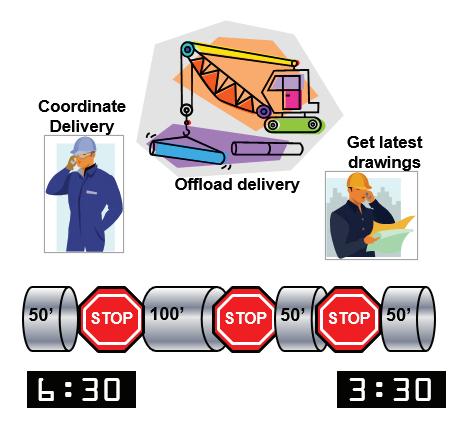
To improve productivity outcomes and reduce the impact of labor force shortage errors, “go-backs,” and waste have to be identified, categorized, and quantified. These issues used to be felt only by the trade contractors, where productivity directly impacted their pocketbooks. However, given the ongoing labor shortage, the issues with on-time and on-budget project deliveries will persist for general contractors too.
To improve this situation, all parties in construction need to focus on the data-driven approach to reduce waste. Our February 2021 Job-Site Intelligence column, “Managing Schedule Changes on the Job Site,” gives how-to guidance on using agile project scheduling (APS) to connect the management of work, effort, and time between all parties on a job site, using data not just “coordination meetings” and “conversations” to raise and resolve problems. Agile construction techniques provide a way to identify trades’ obstacles and work progress, which neither lean nor IPD processes were able to achieve on their own.
The tools to make this change happen have been discussed in many of MCA’s previous articles in EC&M, including:
1. Digitalization of the work to be performed in the format of a work breakdown structure (WBS).
2. Measurement of production rate and its acceleration and deceleration.
3. Daily schedules, which identify, categorize, and quantify the obstacles.
4. Feedback to the company and project manager.
Once you have the activities on the job site categorized, you can then use established methods to measure and reduce the impact of the non-value transfer activities (NVTA) and increase the value transfer activities (VTA). Figure 2 shows one of these measurements as well as the before and after improvements. One of the established tools to measure NVTA is SIS(R), which is part of ASTM E2691 for Common Cause variation management. Figure 3 on page 28 is a sample of the obstacle activities on a job site that contribute to the NVTAs.
To move this viability further upstream, Staff Electric Company in Milwaukee is using a collaborative tool (DCI™) to enable AI application from the time a job is bid to the closure of it. The NVTAs start at the preconstruction phase of any project and continue to its closure and commissioning. Figure 4 on page 28 shows the predictive nature of the DCI.
In conclusion, for five decades the construction industry has continued to stagnate on the labor productivity front ( Fig. 5 on page 28). Now, with fewer labor “inputs,” this equation will certainly result in less construction put-in-place (CPIP). Paying attention to waste and improving the value transferred by construction trades has gone from an electrical contractor’s competitive advantage to an industry requirement.
Any electrical contractor would say they are interested in productivity improvement, but using the correct definition, measurement, and resulting data

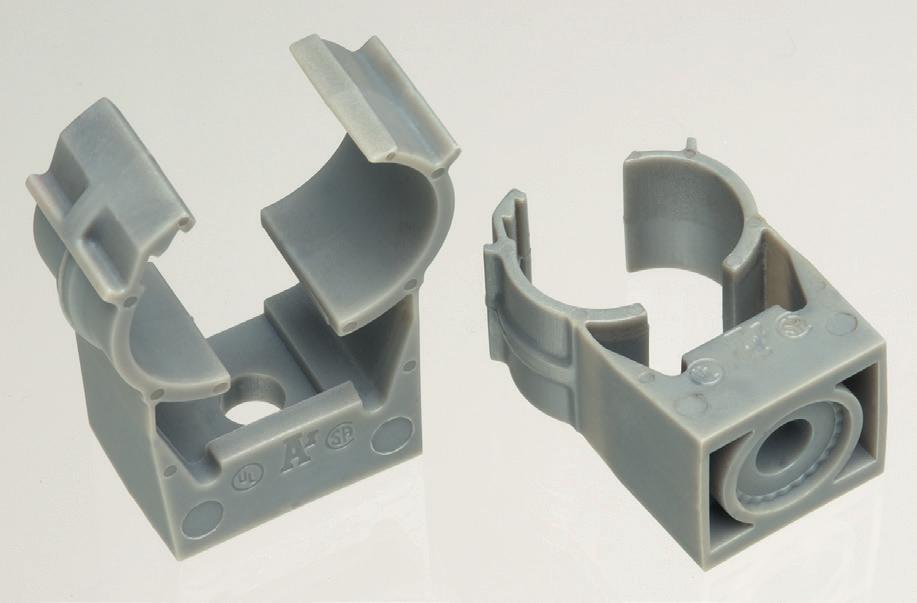
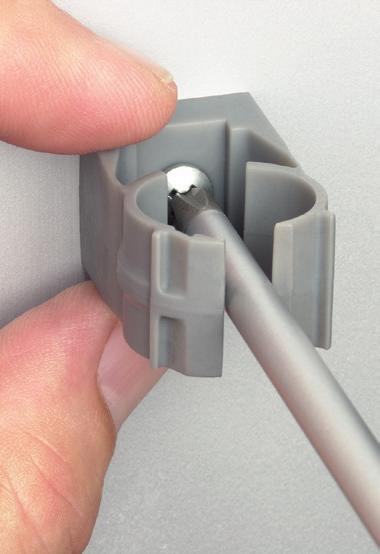
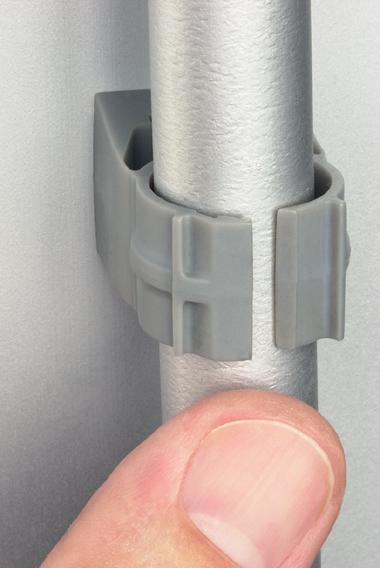
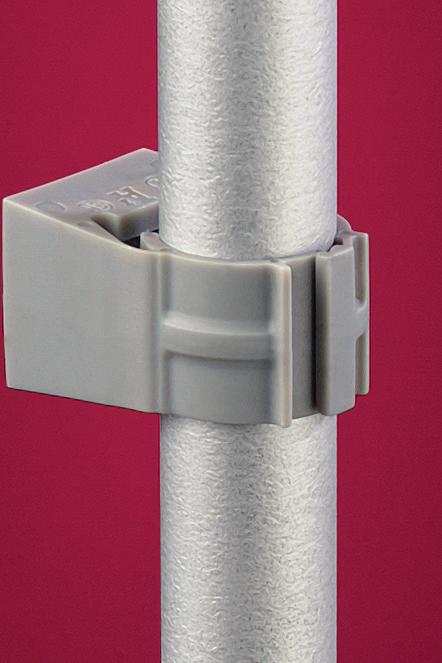


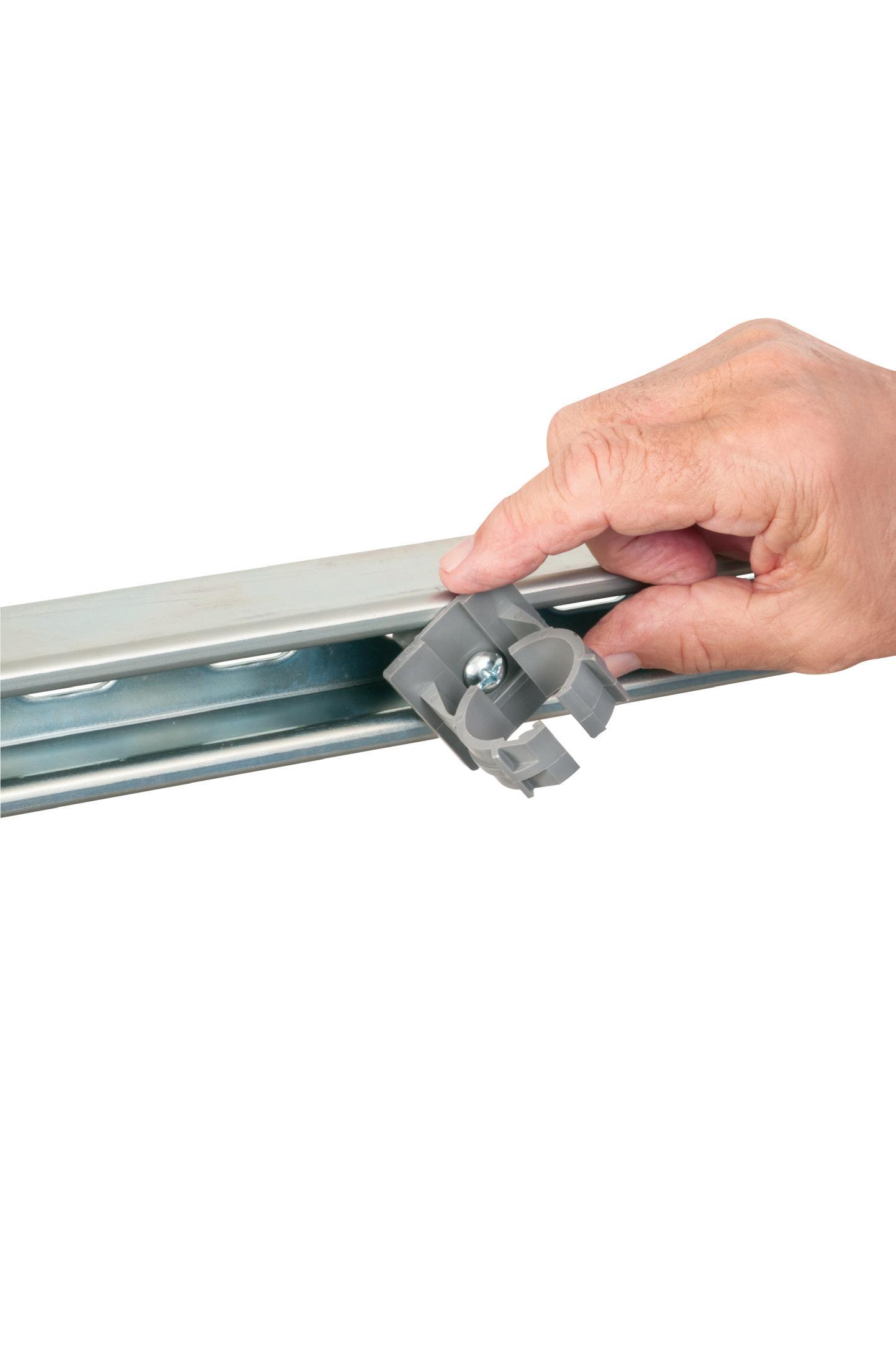
to get there is the key. From the job-site intelligence you can gain in reviewing our regular columns to the application of agile construction principles, reducing waste is not as complicated as it seems. It starts in the work environment — not in spreadsheets or accounting software. There’s a lot of wasted effort, cost, and time on your job sites right now. The best place to start is to get out there and observe, measure, and think systematically of what you can do to make it better. Dr. Perry Daneshgari is president and CEO of MCA, Inc., Grand Blanc, Mich. He can be reached at perry@mca.net. Dr. Heather Moore is vice president of customer care and support. She can be reached at hmoore@mca.net.
NON-METALLIC • VENTED FOR EASIER STACKABILITY
CONCRETE PIPE SLEEVE
THE EASY, ECONOMICAL WAY TO SLEEVE THROUGH CONCRETE POURS!
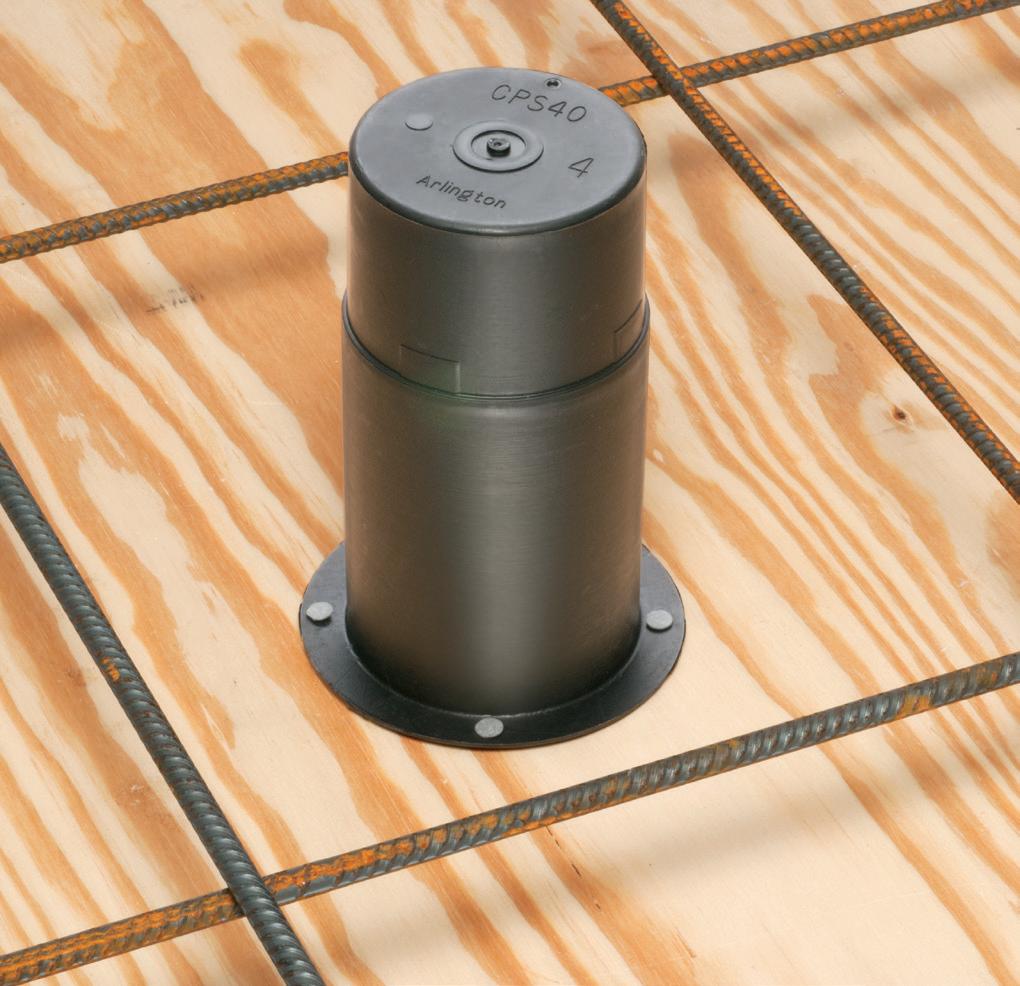
800/233-4717
• www.aifittings.com
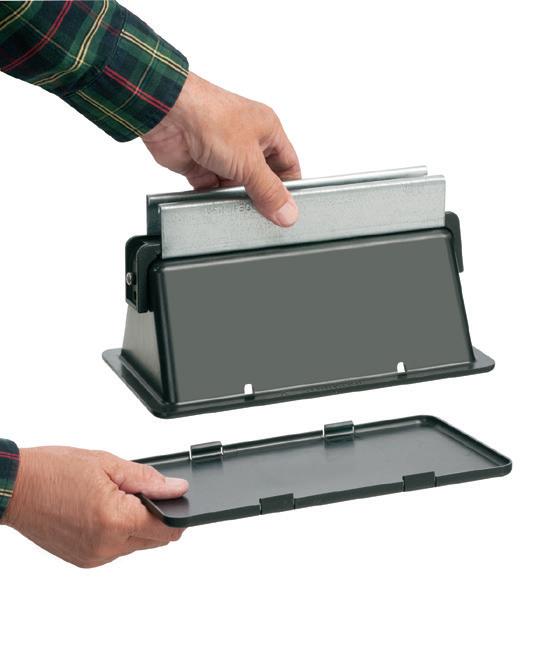
2312ECM_Arlington_866432-1223_21.indd 1
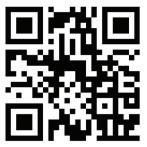

Arlington’s Concrete Pipe Sleeves are the economical way to sleeve through concrete pours in tilt-up construction WALLS – and FLOORS allowing cable and conduit to run easily from one floor to the next.
No costly core drilling – No cutting holes in the form. Plus, you can position the hole prior to pouring the concrete.
• Attaches to form with nails or screws
• Stackable up to 23" h for extra deep pours
• Vents keep wet pipe sleeves from sticking together
• Multiple hole sizes: 1-1/2" • 2" • 3" • 4" • 5" • 6"
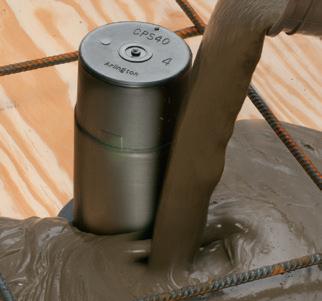
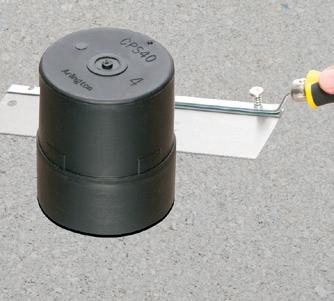
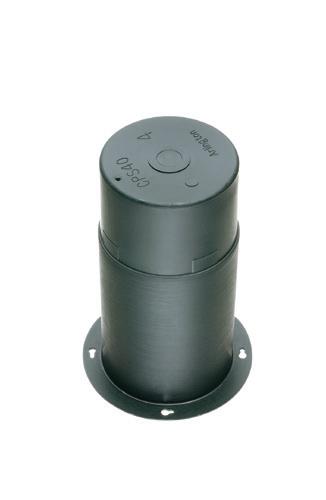
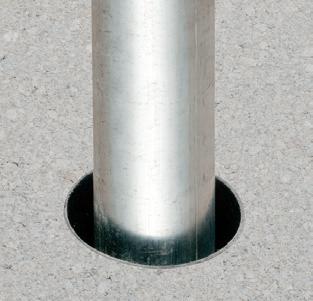
Product info aifittings.com/landing/concrete-pipe-sleeve
11/14/23 1:21 PM
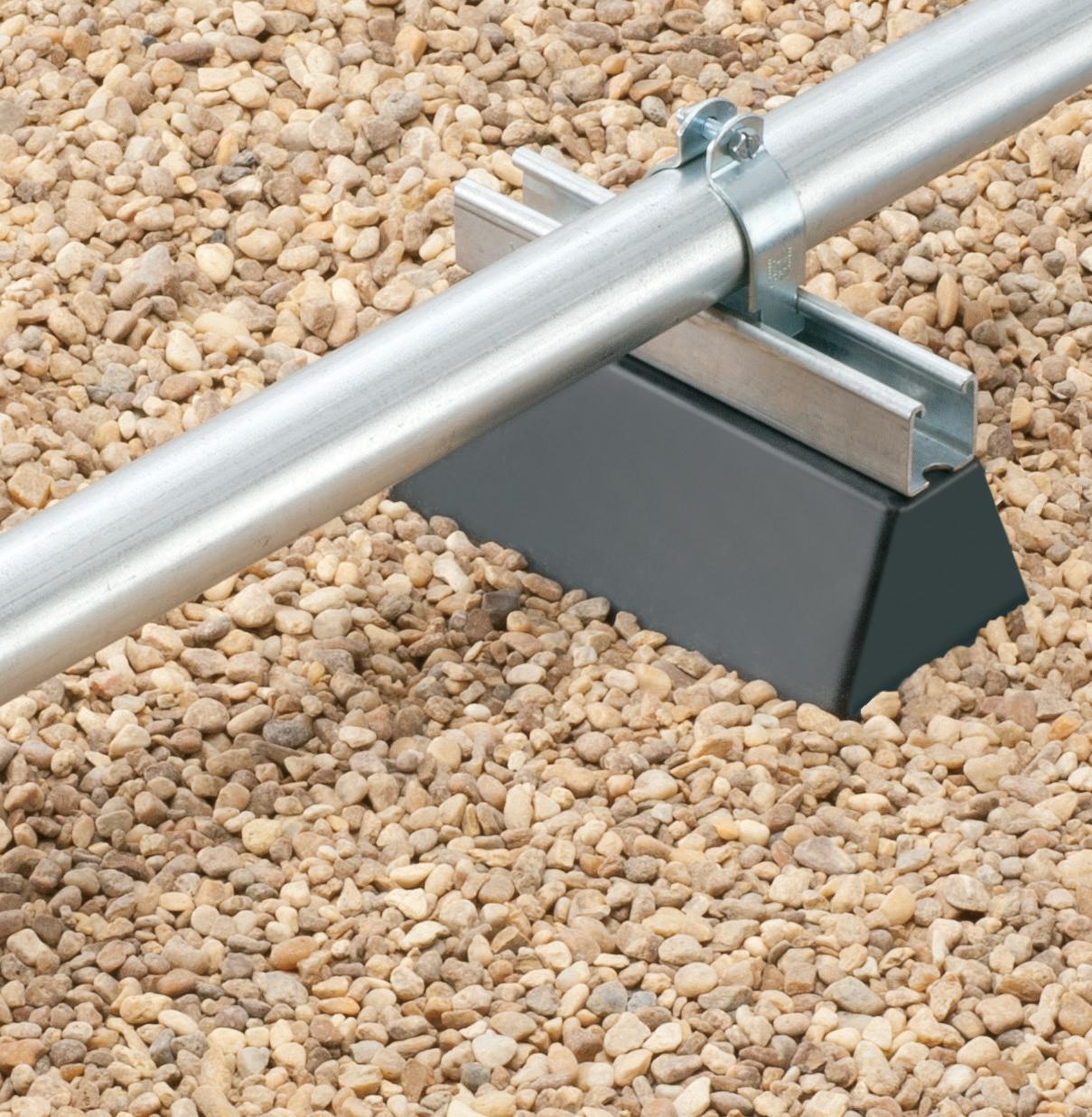
ROOF TOPPER® supports raise conduit/raceway 4" or more off the roof surface, allowing contractors to comply with the 2017 NEC® for temperature adjustment for circular conduit.
The heavy-duty base, made of 100% recycled material, sits on the roof deck. There’s no need to mount ROOF TOPPER to the surface with mechanical fasteners. Offered in a variety of sizes and configurations, ROOF


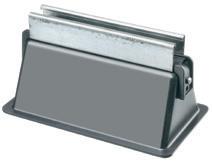
supports up to 2000 lbs, and stands up to extreme rooftop conditions protecting and elevating conduit or raceway above the roof deck.
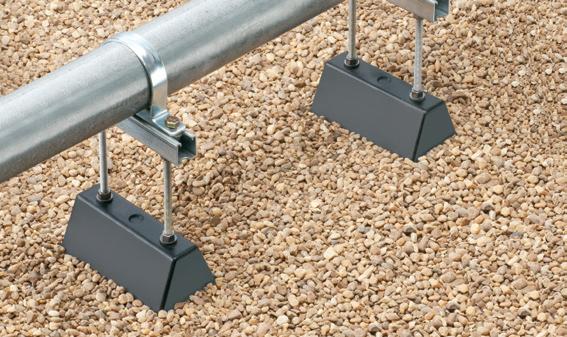
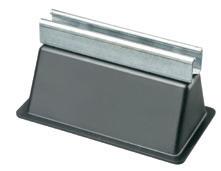



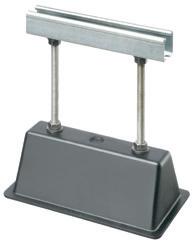

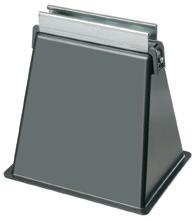
How Prefab Solutions Boost Labor Productivity
A look at use cases and best practices
By Sean Nacey, WescoImagine hiring a five-star chef and expecting them to not only prepare a meal but also create the menu, shop for groceries, purchase all the cooking supplies, and even chop vegetables. You wouldn’t do that, of course, for two main reasons. First, the low-skill prep work could be done long before the chef arrives. Second, you want the highly specialized (and highly paid) chef focused on what they do best: cooking the meal. You don’t want to waste money paying the chef to perform tasks that just about anyone could do. In a construction environment, the same theory applies. You want the highly skilled and specialized workforce to focus on areas that only they are equipped and licensed to perform.
One labor productivity solution that electrical contractors can leverage is prefabricated (or prefab) solutions. This can help contractors get the maximum value out of skilled labor, which also is expensive and in short supply. While using prefab solutions isn’t a new approach, labor shortages and an increasing desire to maximize profitability bring these solutions to the forefront as a mechanism to improve efficiency and effectiveness in today’s tight labor market. But while it can be helpful, prefab solutions don’t apply to every situation. There are certain types of projects where they may be more relevant than others.
HOW THIS APPROACH WORKS
At its core, prefab solutions allow contractors or their distribution partners to leverage lower-skilled/cost labor
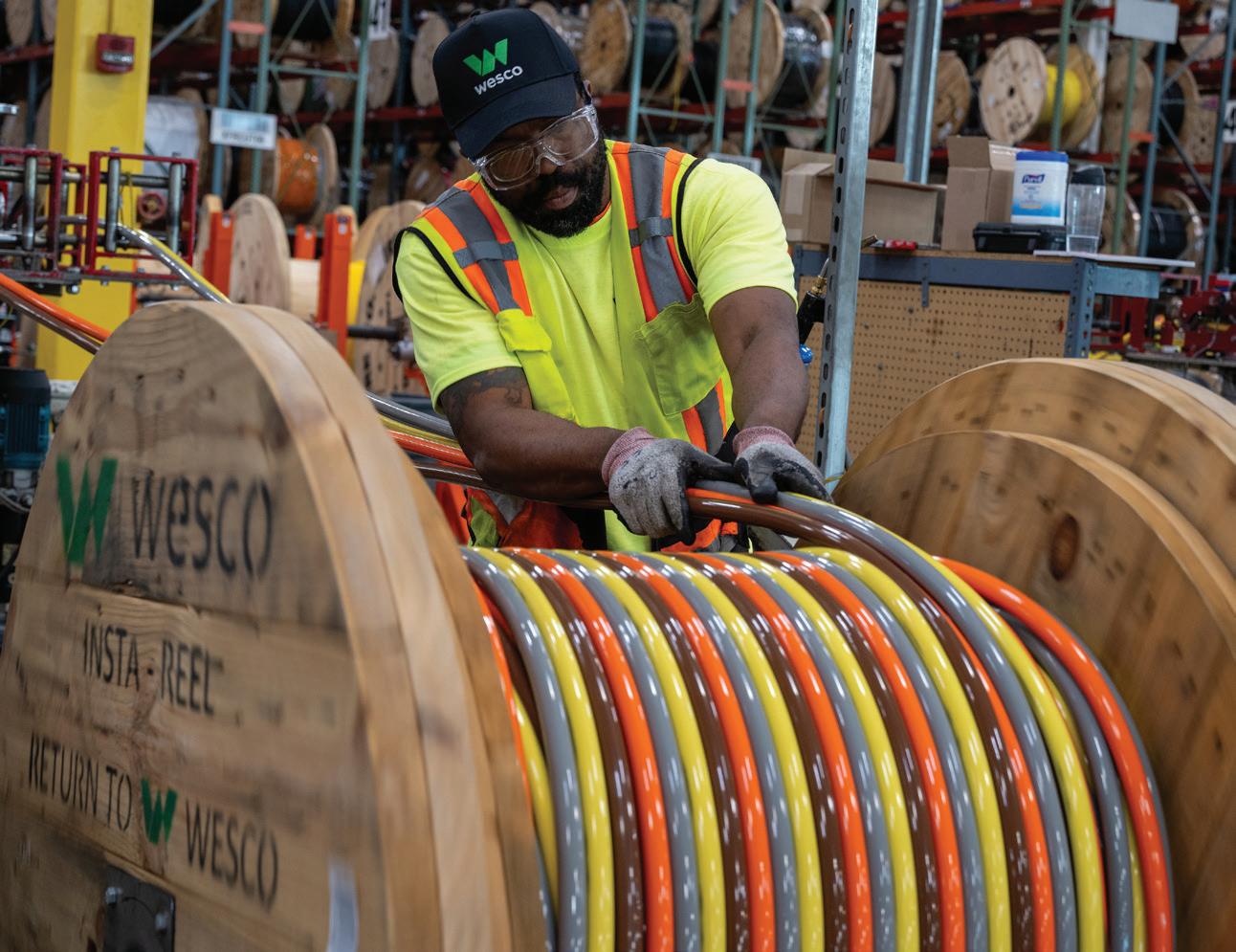
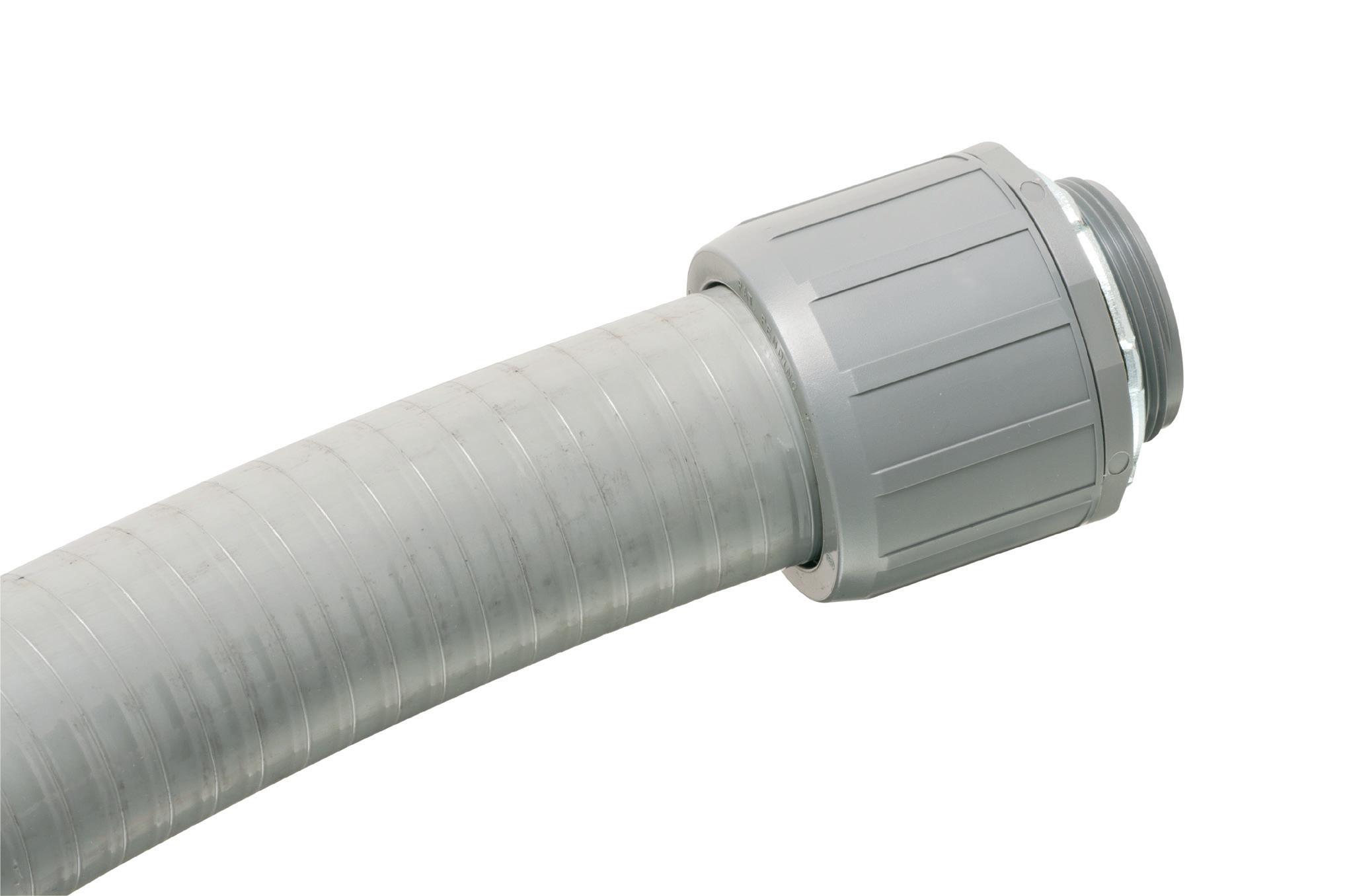
to perform low-skill, often repetitive tasks off site — typically at their place of business instead of at the job site. This can encompass everything from unpacking products to assembling basic components (such as luminaires or electrical box assemblies) and then transporting them to the job site in a state where they can be simply installed by a licensed electrician. By executing these routine tasks off site, contractors can reduce their operating costs, while empowering skilled workers to focus on those tasks that only they are equipped to complete.
WHEN TO USE IT
Generally, prefab solutions are most effective on large-scale projects that have a lot of repetitive elements, such as hotels, multi-family homes, commercial buildings, and manufacturing facilities. In a hotel project, for example, there could be hundreds of similar-sized rooms — all with the same lighting and overall electrical design (e.g., all receptacles in the same spot). In this example, lighting kits can be assembled and pre-wired off site, allowing the electrical contractor to more quickly and efficiently install the equipment upon arrival to the job site.
1.25"• 1.5"• 2" Non-metallic
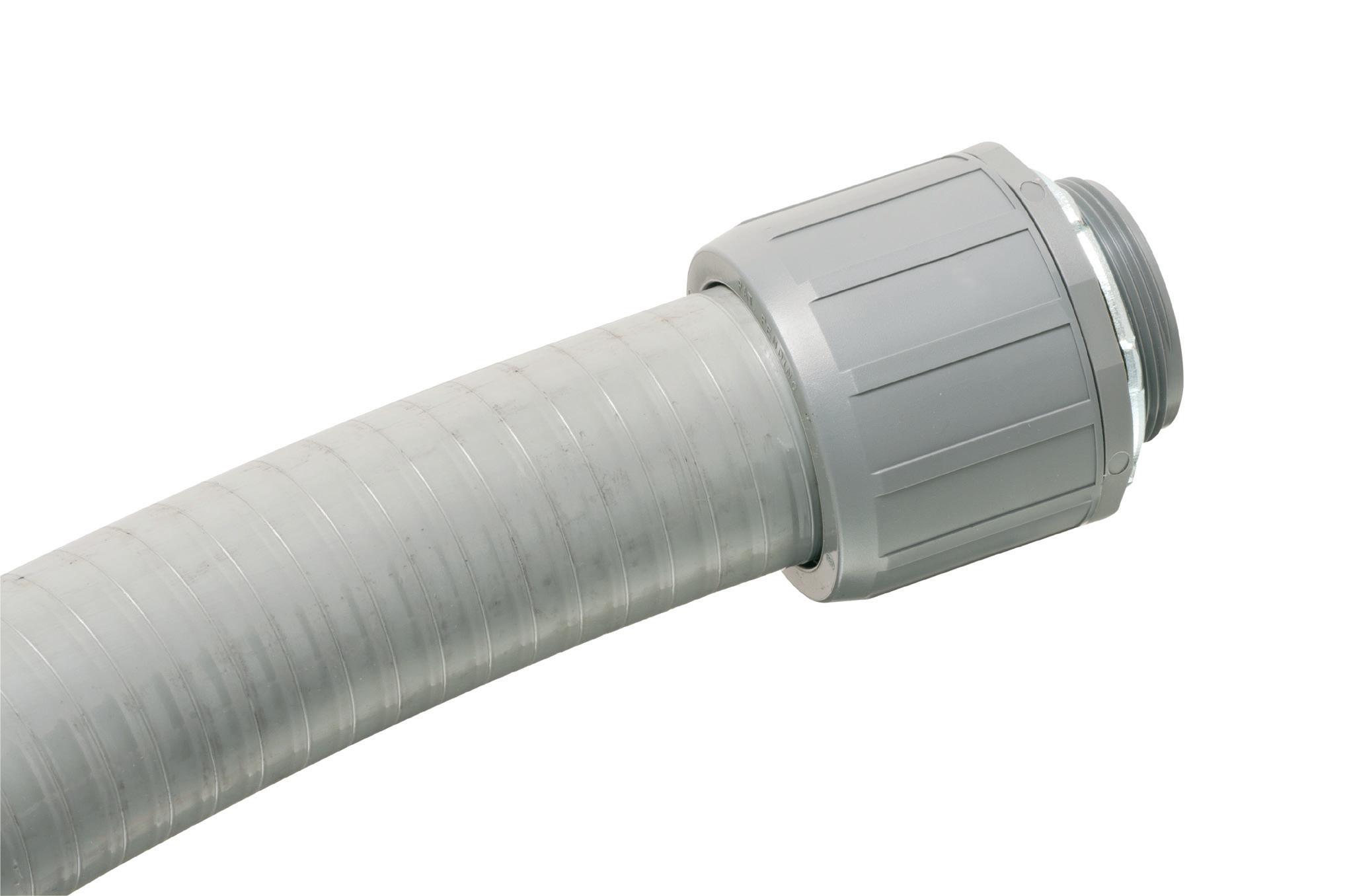
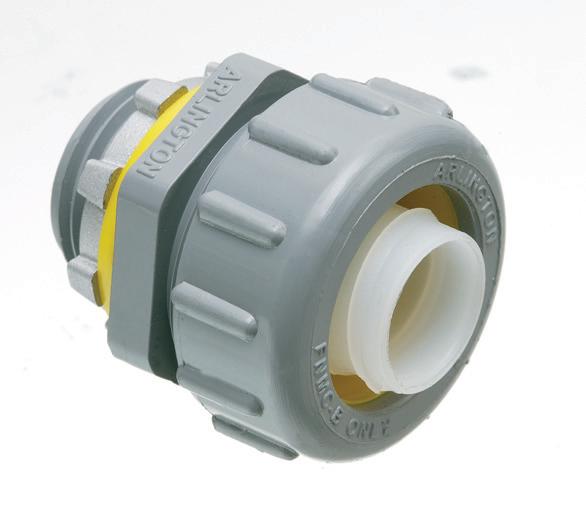
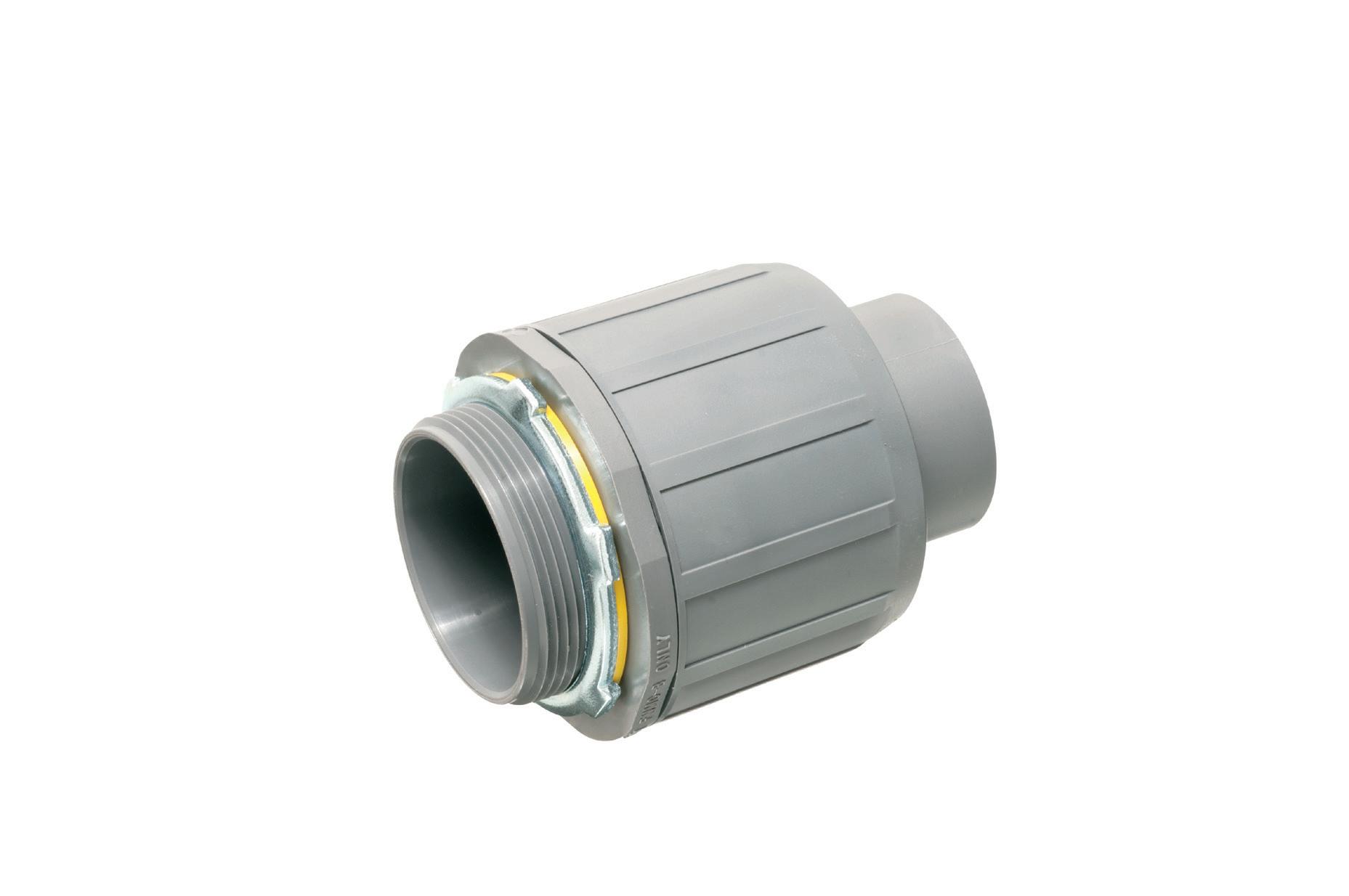
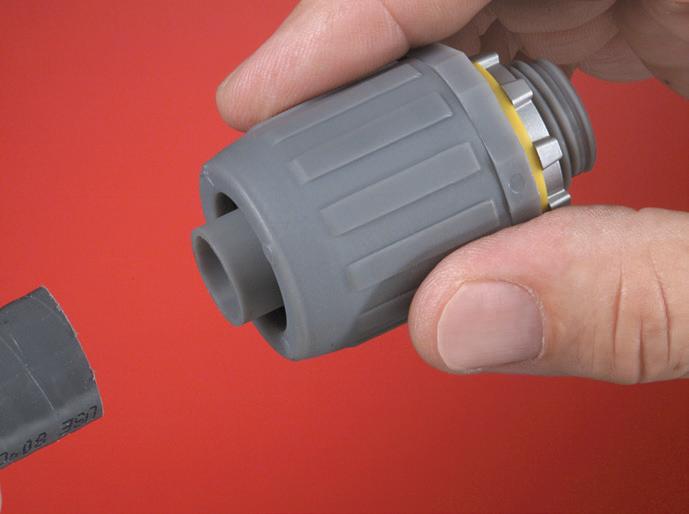
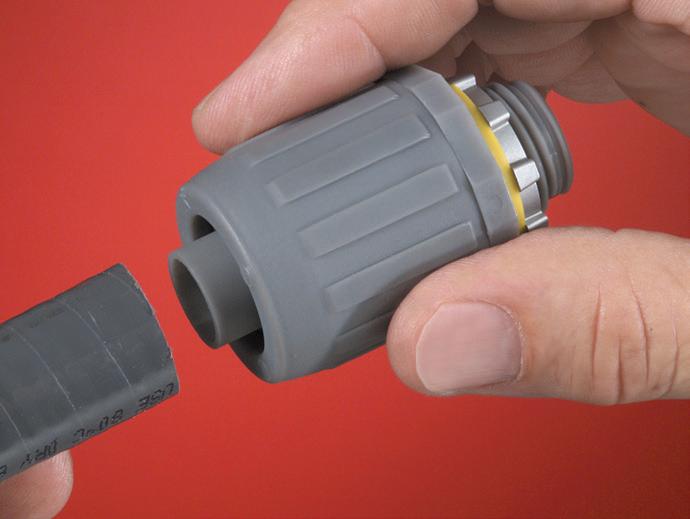

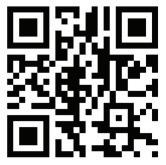
93B
Snap2It® push on connectors. They offer the fastest, easiest installation on non-metallic liquid-tight conduit, type B. FORGET the TOOLS! Simply push the connector on to conduit. That’s it!
You’ll get a super-secure, liquid-tight seal. Plus, they ship fully assembled – No disassembly required. Competitively priced, they’re removable and reusable too.
Straight and 90° 1/2", 3/4" and 1" trade sizes* NEW LARGER Non-metallic sizes
1-1/4", 1-1/2" and 2"
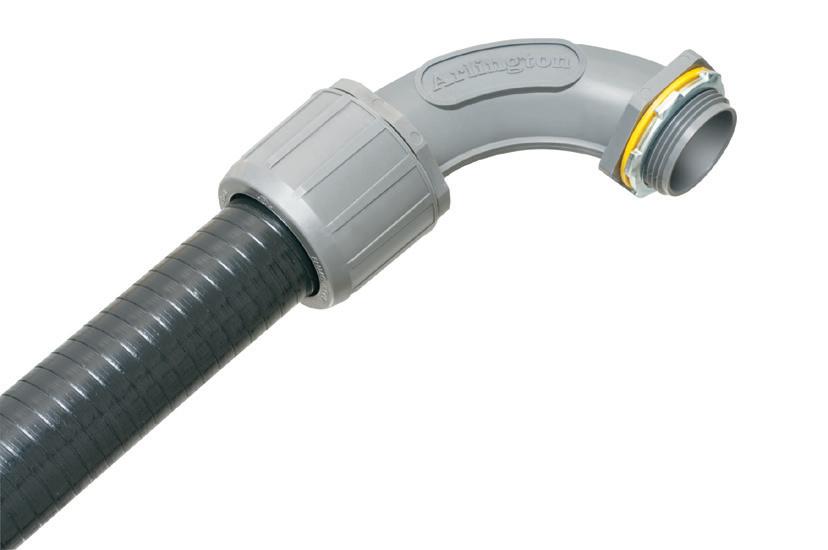
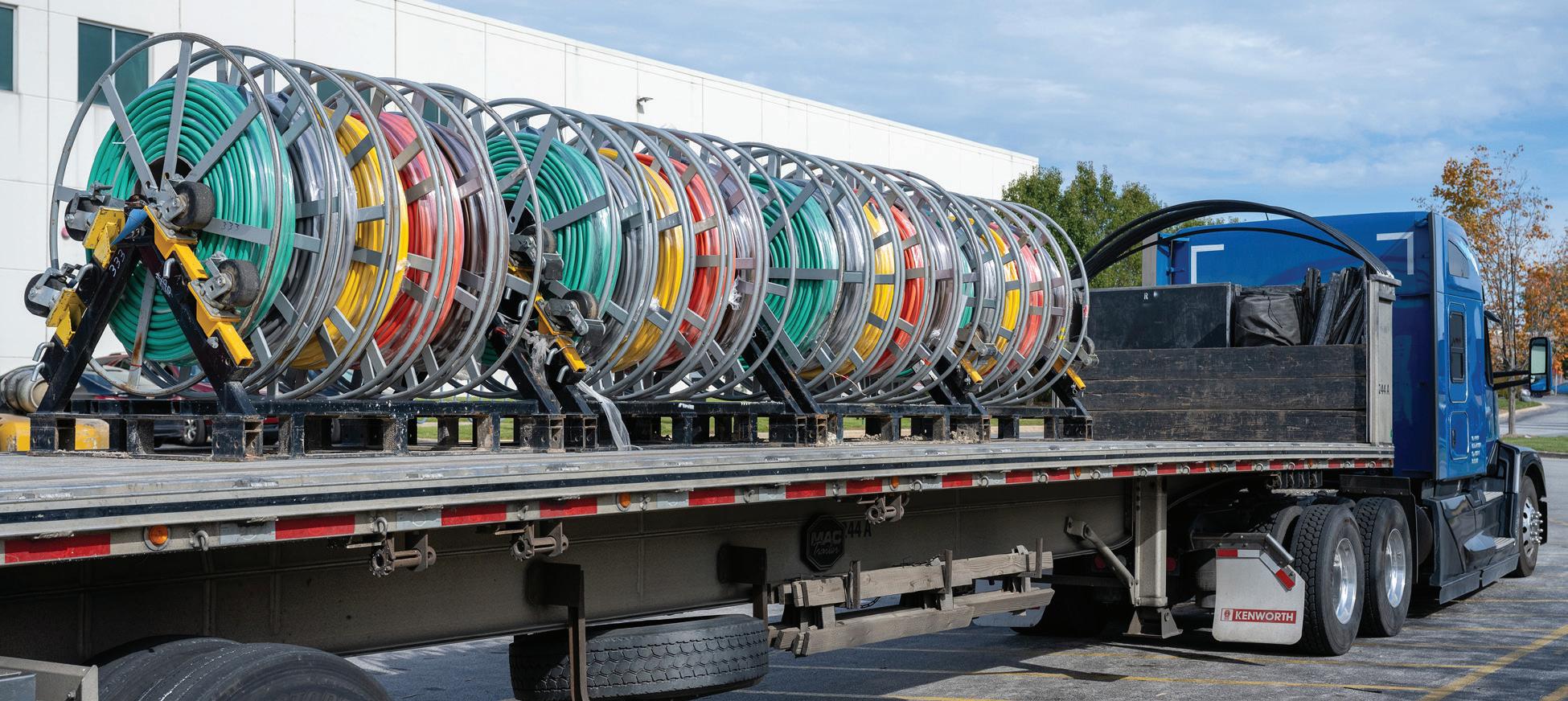
Prefab solutions are also especially helpful on solar projects. Any solar project that uses more than three solar panels will need to incorporate a combiner box, which, as the name implies, combines the electrical output of multiple panels into a single circuit. Combiner boxes simplify the wiring structure and maintenance but take a significant amount of time to assemble. Using prebuilt combiner boxes that arrive ready to install can materially reduce on-site labor and cost. And as the number of solar projects grows (along with their size and complexity), the importance of using solutions that save installation time cannot be understated.
With non-productive labor averaging 31% of a labor unit, a bit of ingenuity could help to optimize labor and ensure that a skilled worker’s time is not wasted on low-skill, repetitive processes. Utilizing prefab solutions can significantly cut down on the cost and scope of work executed at the job site.
There’s also an element of safety and comfort to consider in determining when to use prefab solutions. Contractors don’t always work in ideal conditions. They may have to wire or install service panels in extreme cold or work in a crawl space or attic that’s 110°F on a hot summer day. Utilizing prefab solutions can help cut down on time spent in extreme conditions. It can also allow contractors to leverage large equipment or automation processes that simply aren’t feasible in the field. In a market where labor is at a
premium, helping to ensure comfortable working conditions can be a competitive advantage that attracts much-needed skilled workers.
PREFAB BEST PRACTICES
If going the prefab route makes sense for your project, it’s also important to consider several best practices to ensure you’re maximizing your return on investment (ROI).
Understand when and where to use them: Utilizing prefab solutions offers several benefits, but might not make sense in every application. Does the size or scale of the project justify it? Does the job-site location or geographic footprint make prefab more cost-effective? Would it make your business more competitive in a bid, or create new opportunities?
Understand the volume you need to justify your investment: Prefab operations can encompass anything from a few people to a 100,000-square-foot facility with dozens of employees and large, complex equipment. Regardless of the investment level, you want to ensure workers consistently have projects to work on to justify the cost.
Lean on value-added partners: Partners can be especially helpful when it comes to utilizing prefab solutions effectively. At a minimum, they can help you understand if it makes sense for your project or business. In certain applications, they can even provide the prefab solution(s), such as a solar combiner
box, freeing up worker time. They can also help amplify your team’s expertise and capabilities. For example, a commercial building project might also include installing advanced security cameras that incorporate sensors and analytic capabilities. If that falls outside your organization’s area of expertise, the right partner can provide the products pre-assembled, pre-configured, and ready to install.
DELIVERING ON PROJECT EXECUTION
From supply chain challenges to labor shortages and rising labor costs, contractors are encountering new obstacles that can adversely impact on-time performance and their overall competitiveness and profitability. As projects continue to grow in size, scale, and complexity, these pressures will only intensify.
While prefab solutions have existed for decades, general and specialty trade contractors are increasingly using them to optimize labor performance and cost. They have proven to reduce costs, boost productivity, maximize skilled labor, and help contractors expand into new geographies to grow their business. As prefab capabilities continue to grow, contractors should consider whether these solutions could drive their business forward.
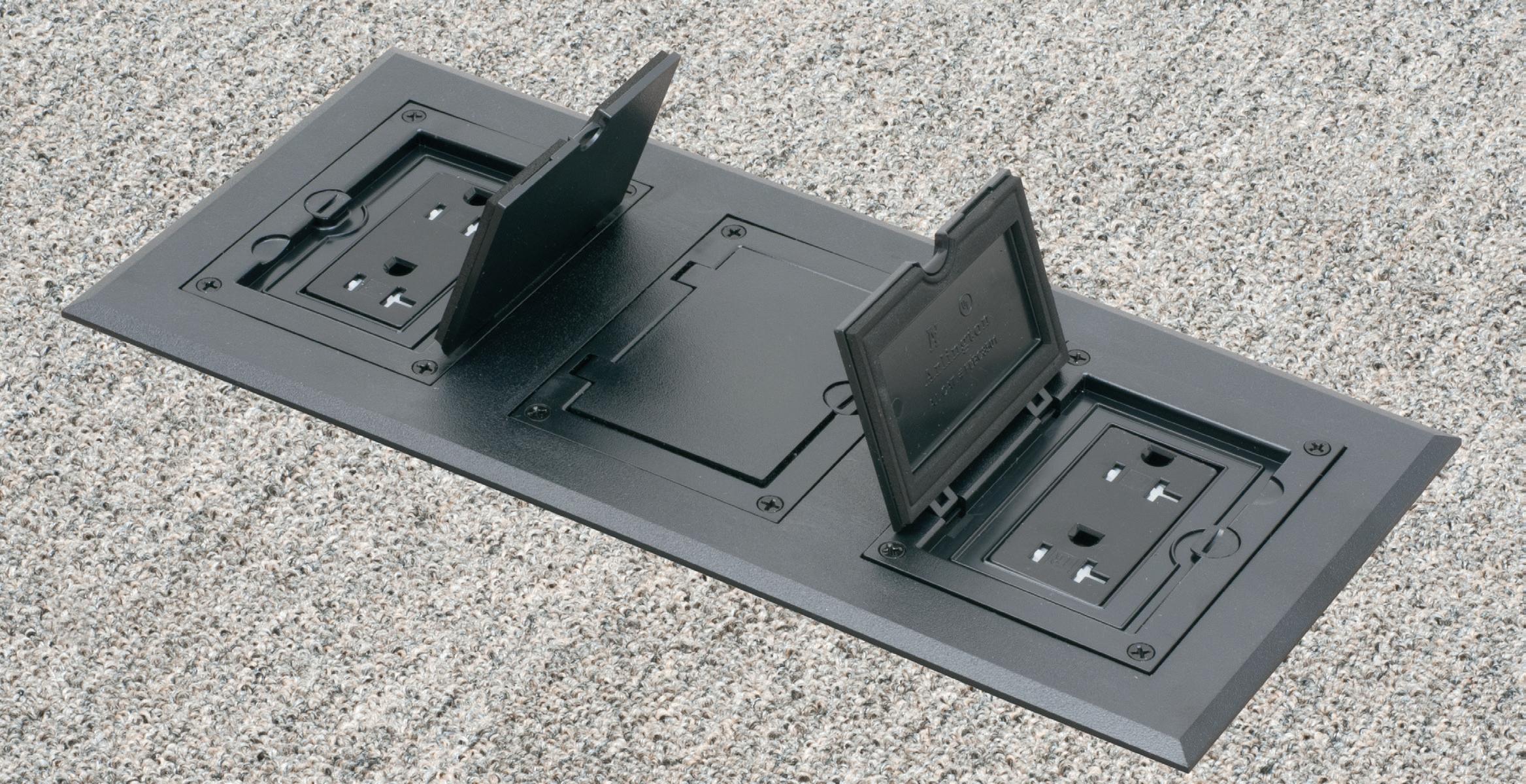
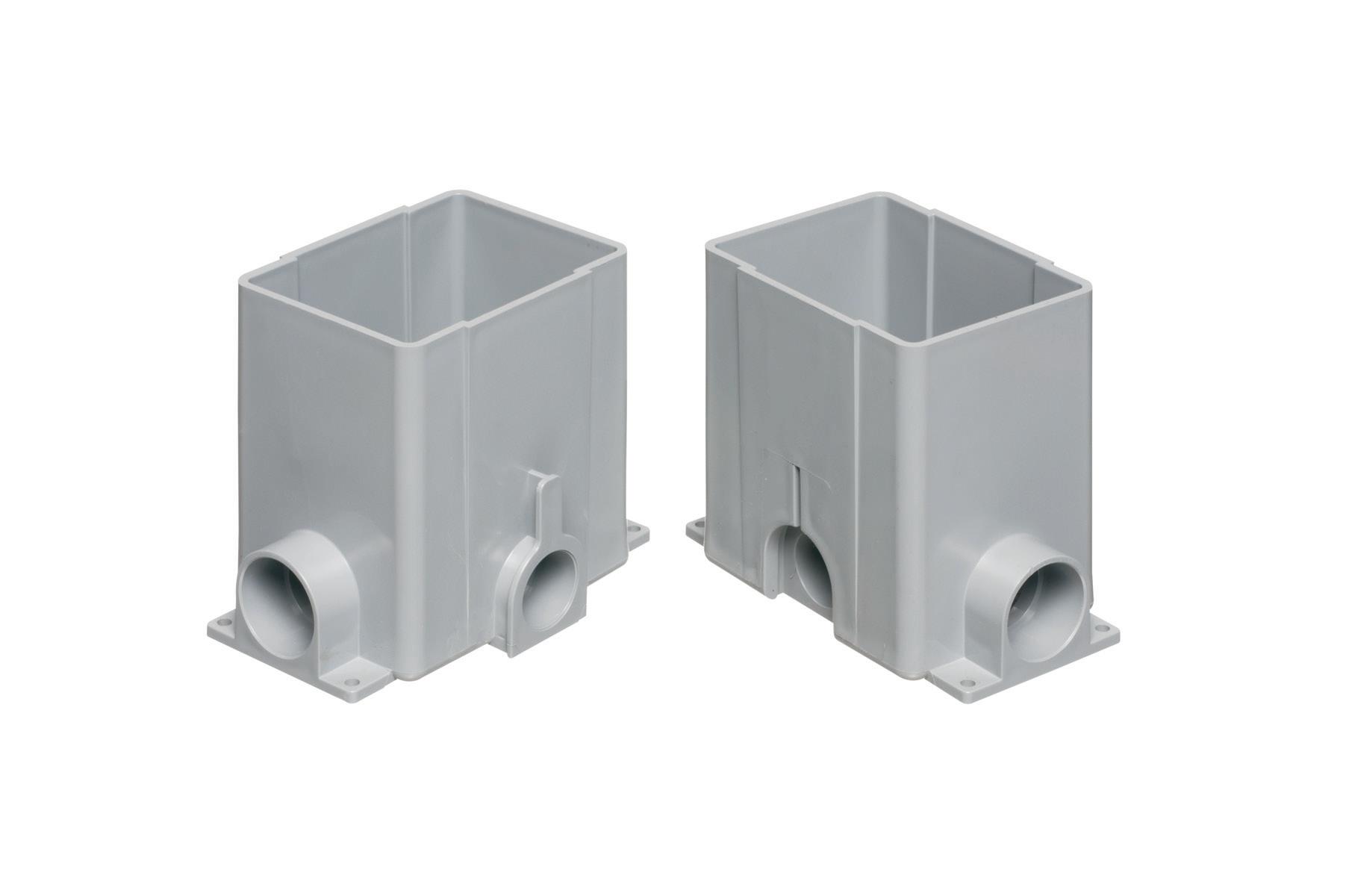
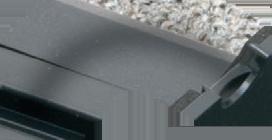

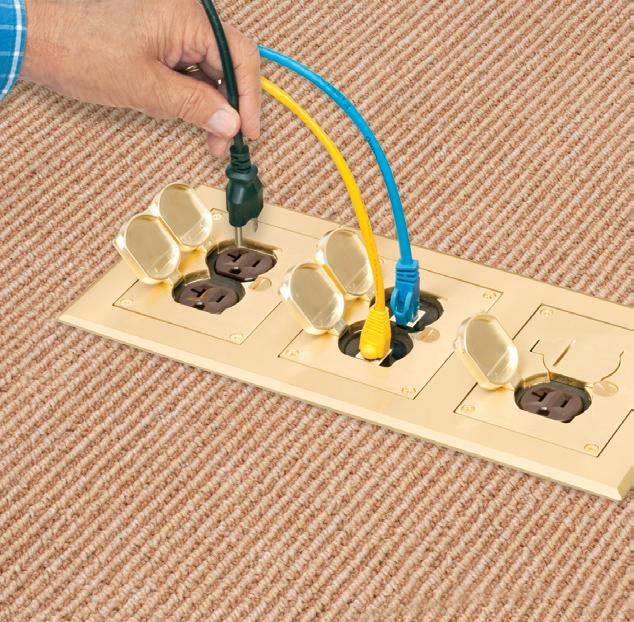
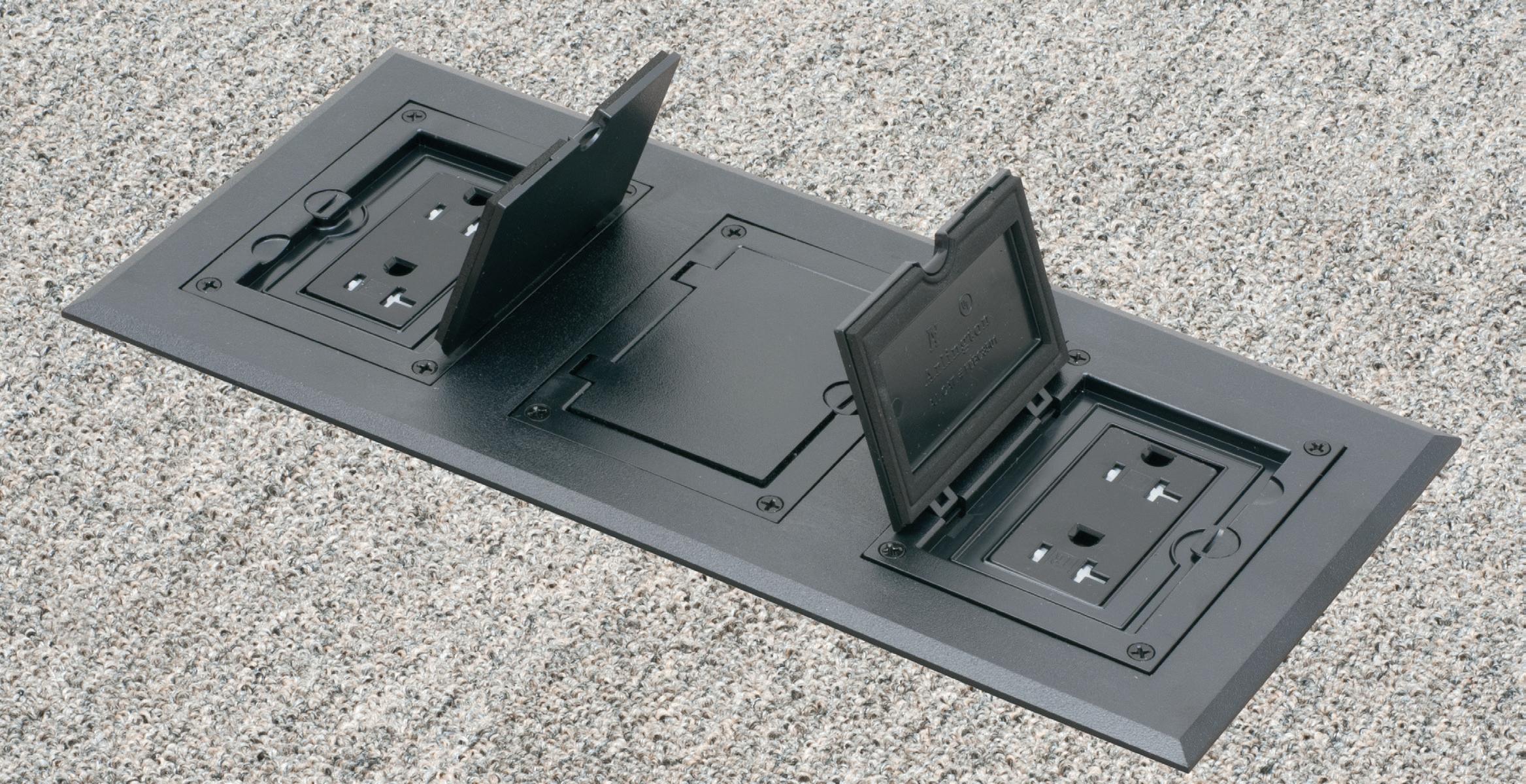
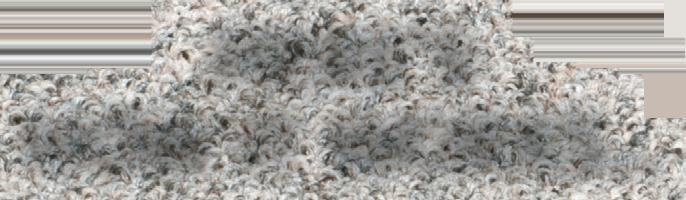
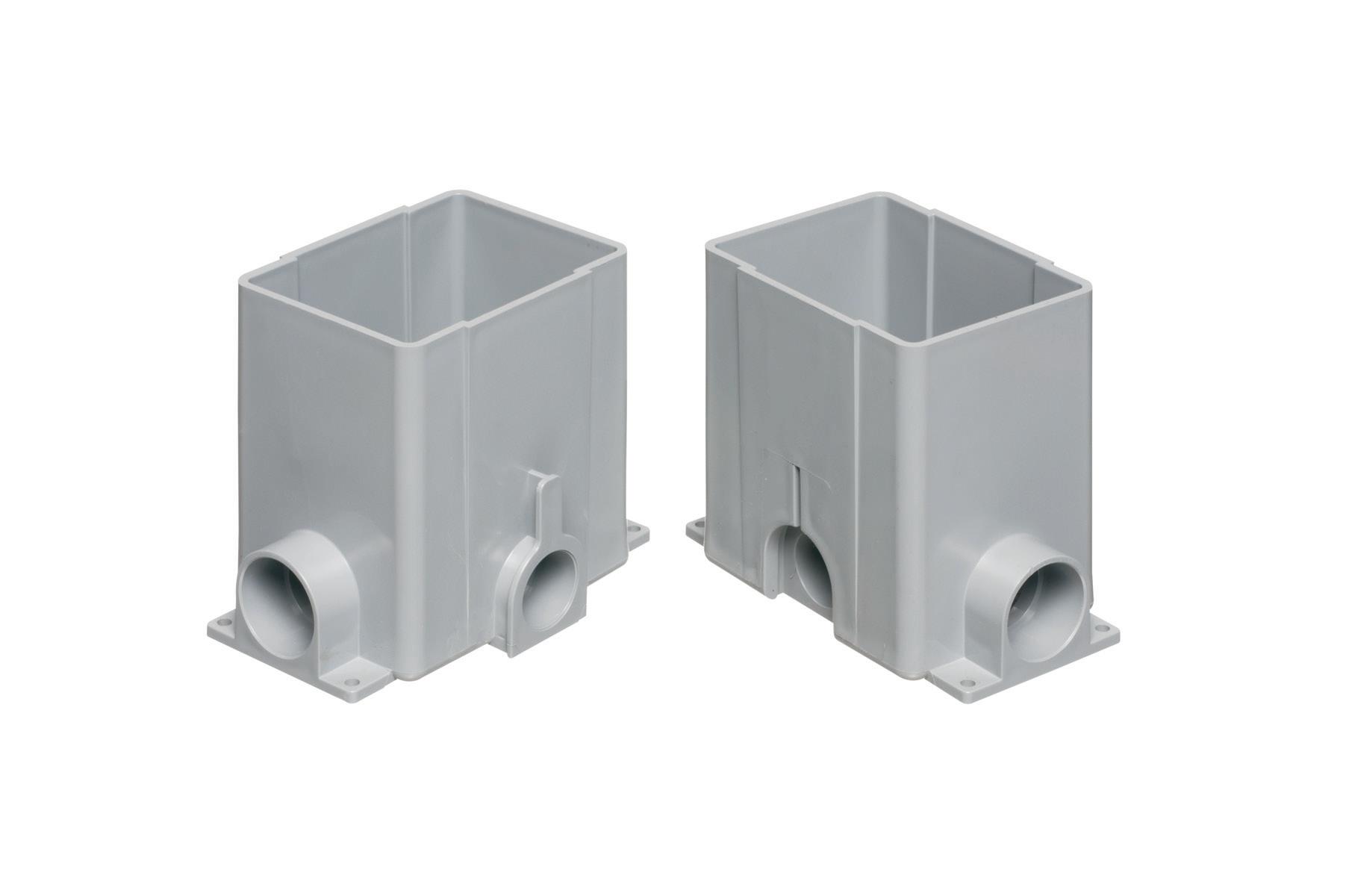
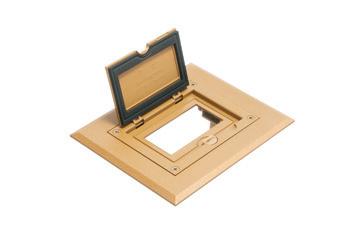
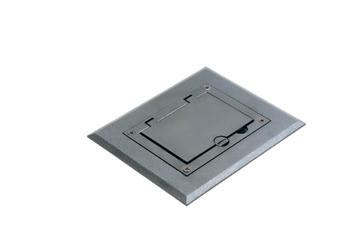
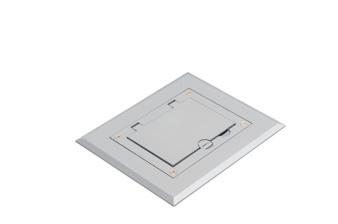
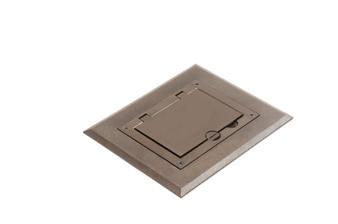
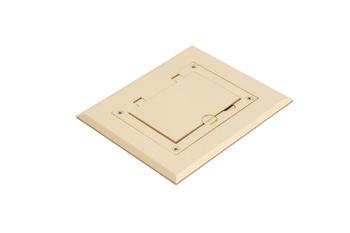

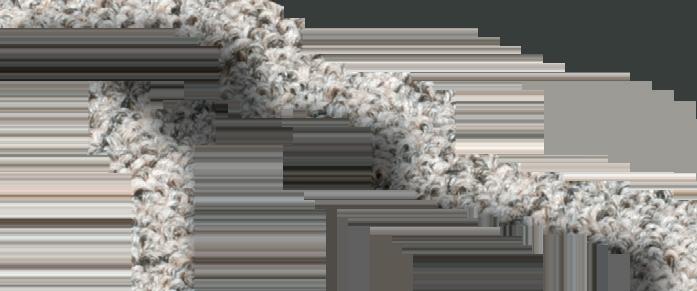
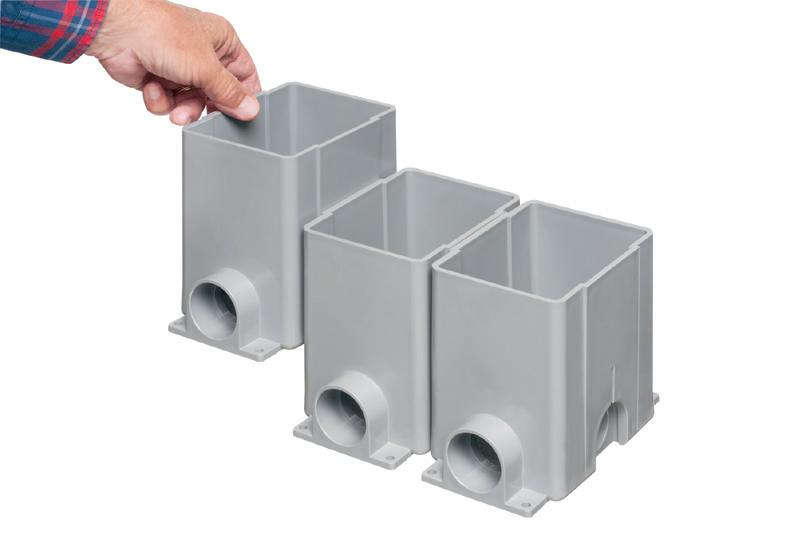
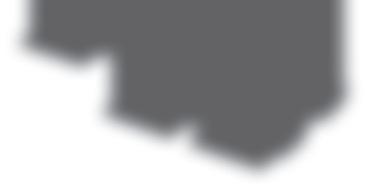


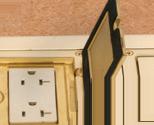
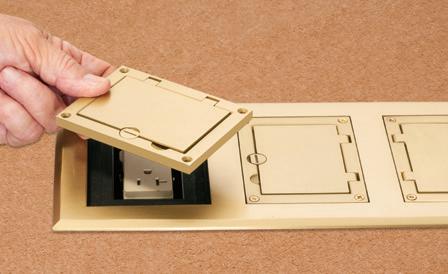

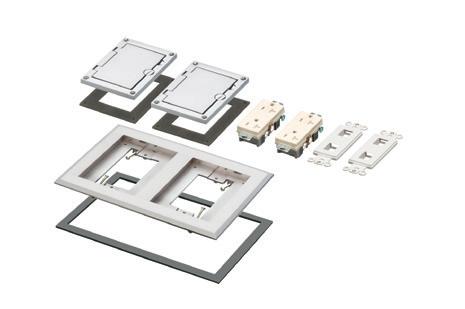
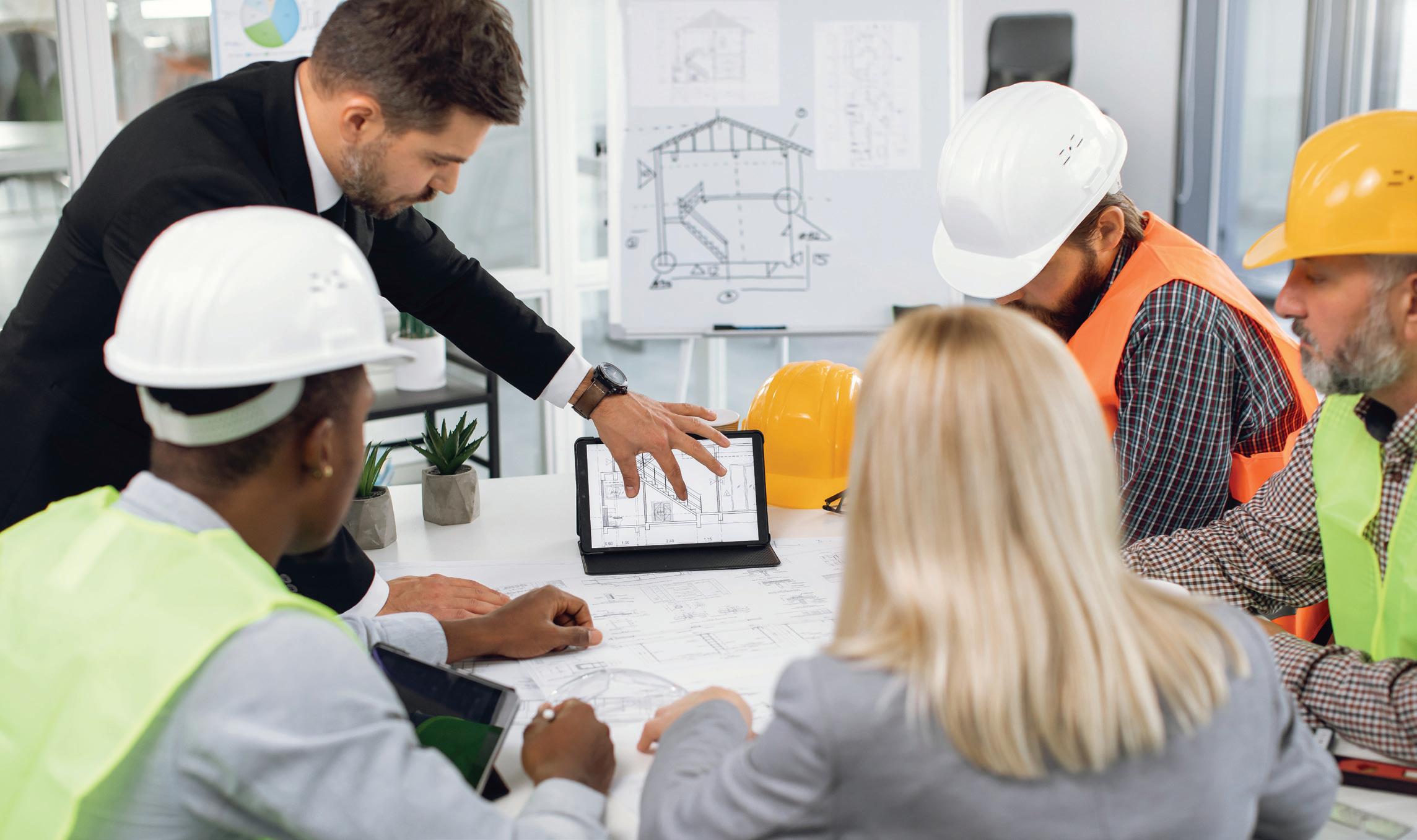
Construction Labor
Productivity: The $20 Billion Opportunity
FMI’s 2023 labor productivity study offers an inside look at why contractors who establish sound operating processes perform better than their peers.By Michael Keller, Tyler Pare, and Jake Howlett, FMI
Construction is a labor-intensive business. Despite tremendous advances in design, coordination, and management technologies, the physical installation of work in the field remains reliant on people. Of the nearly $900 billion in construction put in place by laborintensive contractors in the United States in 2022, FMI research suggests contractors lost approximately $30 billion to $40 billion due to labor inefficiencies. At the individual
contractor level, these labor productivity deficits translate to project and enterprise margin erosion.
Labor productivity is a challenge for the construction industry, and it appears to be getting worse. FMI’s 2023 Labor Productivity Study confirms the well-documented trend of productivity decline, with only 23% of respondents claiming labor productivity improvements over the last 12 to 18 months. Almost half of respondents (45%) saw declining labor productivity, and a third saw stable labor productivity trends in their businesses.
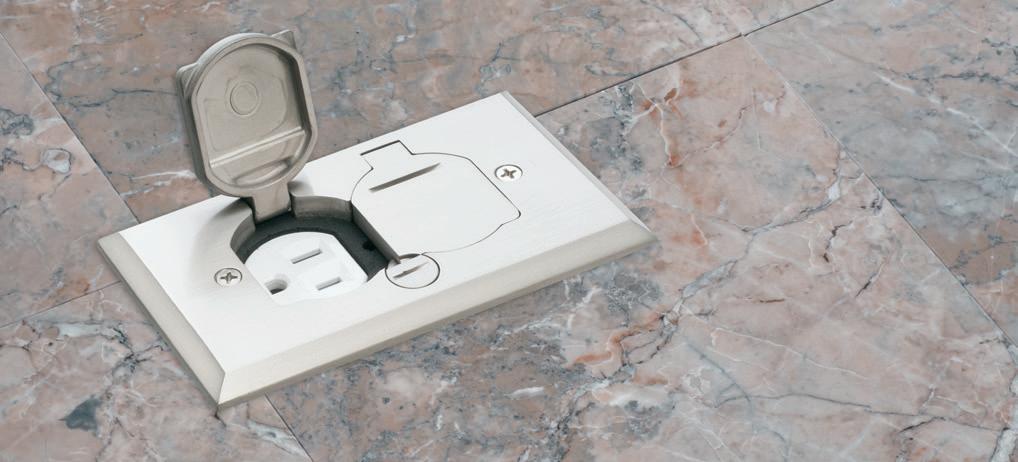
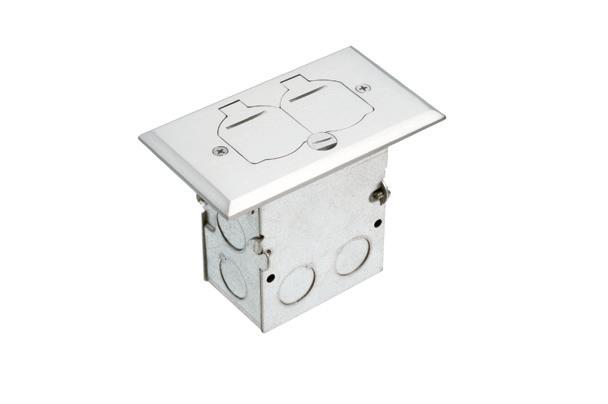
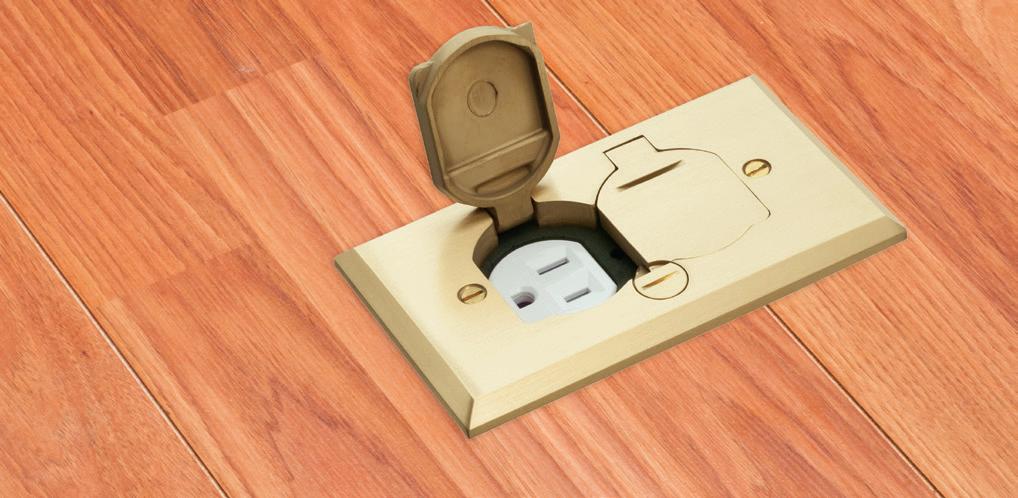


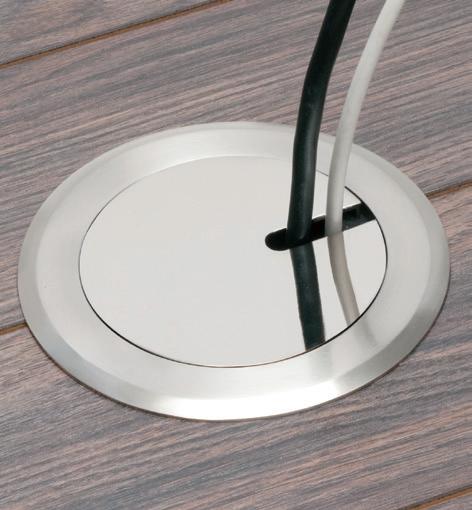
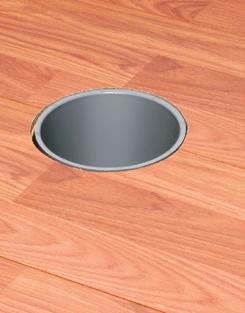

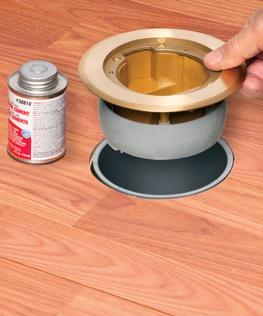

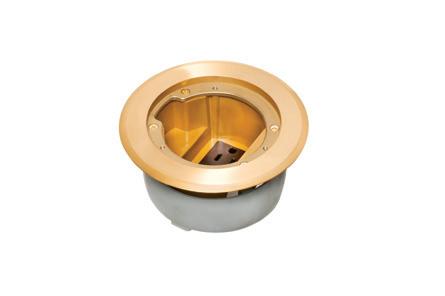
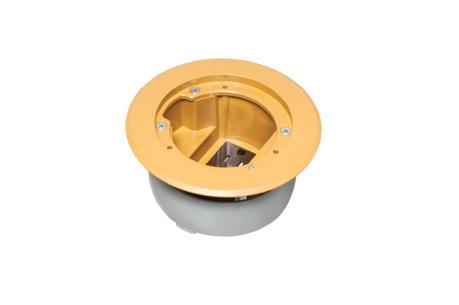
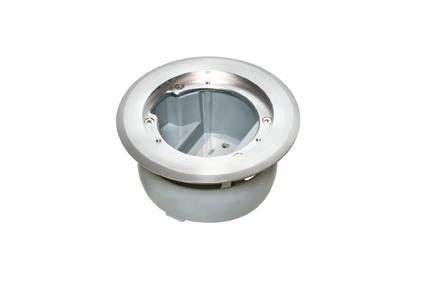

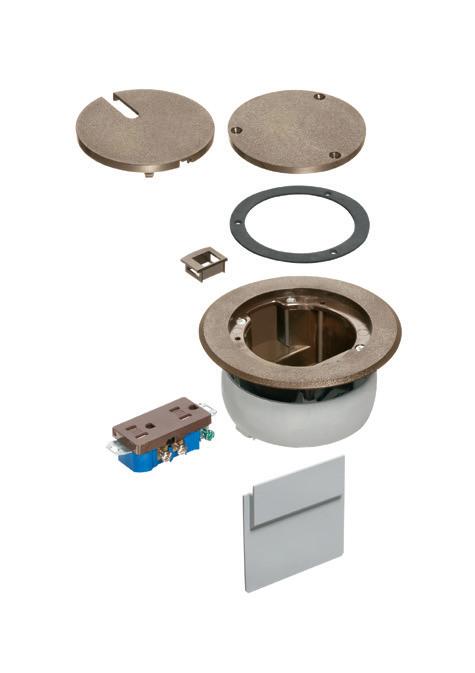
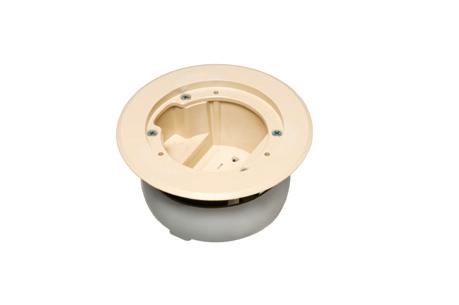
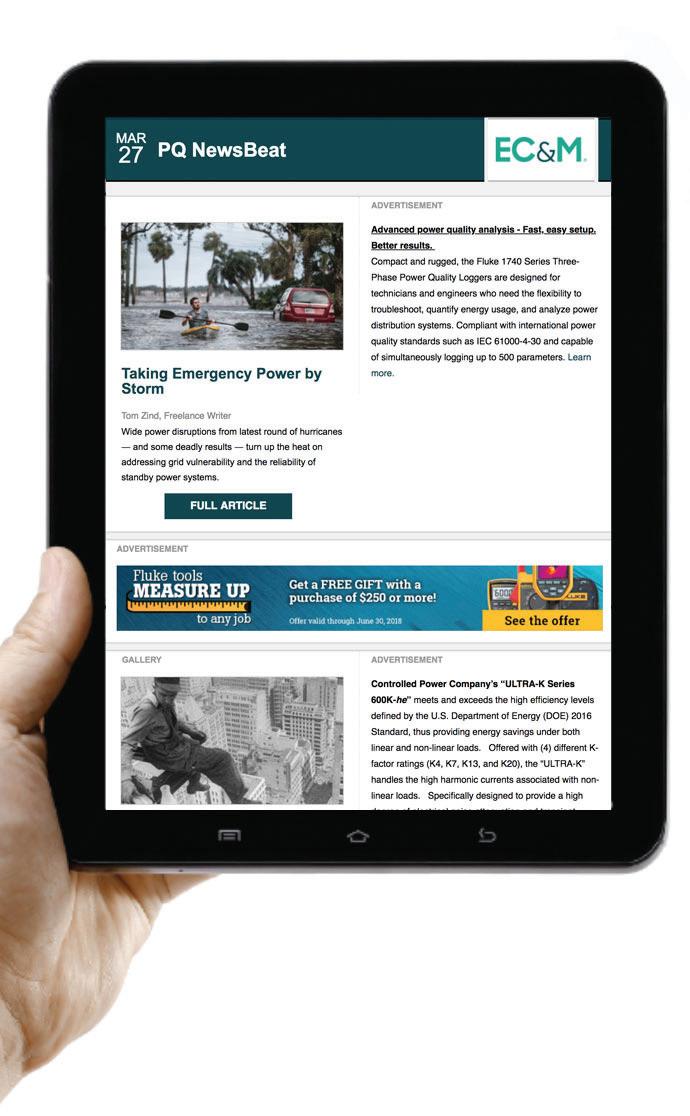
PQ Newsbeat
If you’re an engineer, commercial or industrial facility manager, or electric utility employee concerned about the quality and reliability of power delivery, this e-news-letter (sent out monthly) is for you.
Topics covered include:
•
•
•
What Top-Performing Companies Do Right
1. Pre-job planning: This requires consistent and thorough translation of proj ect information from estimating to operations, followed by in-depth planning by project teams to develop strategies for optimizing labor productivity and project performance.
2. Look-ahead planning: This needs a weekly cadence of field leaders com municating resource needs (labor, equipment, materials, subcontractors, and information) for upcoming activities to be coordinated and supported by proj ect management.
3. Daily goal setting: Field leaders establish and communicate clear, quantifi able production expectations and objectives for crews daily.
4. Labor productivity tracking and feedback: Field leaders and project teams need regular reporting of productivity information in digestible formats so they can discuss project performance and detect labor risk early. This requires well-vetted budgets with hours and quantities before mobilization, accurate reporting of time and quantities by field leaders throughout the project, and reinforcement of the right behaviors.
5. Cost-to-complete forecasting: This critical report is based on a monthly analysis of the costs incurred to date, the percentage of the job that is com pleted, accurate forecasting, and re-estimating the cost to complete the remainder of the scope of work. Accuracy of the cost-to-complete forecast increases with up-to-date direct cost accounting, early buyout and locked-in pricing, field input on the remaining work and accurate productivity tracking that can be utilized to project labor costs.
6. Exit strategy: During this phase, the project team meets to re-energize, focus, and develop a plan to finish a project on time and mitigate the risk of late project margin fade. This would typically occur when the project is near 80% completion.
7. Post-job review: After project closeout, this meeting shares and documents the lessons learned, provides production feedback to estimating, and captures trends for future success and continuous organizational improvement.
The study explores the major challenges that must be addressed to improve productivity for the industry, including both internal and external obstacles that contractors face in their pursuit of performance optimization. Additionally, FMI identifies key management practices and traits of high-performing contractors, including planning behaviors, project controls and support for the field. To produce these findings, FMI surveyed more than 250 senior leaders from laborintensive, self-performing contractors in the summer of 2023 to understand productivity challenges and best practices.
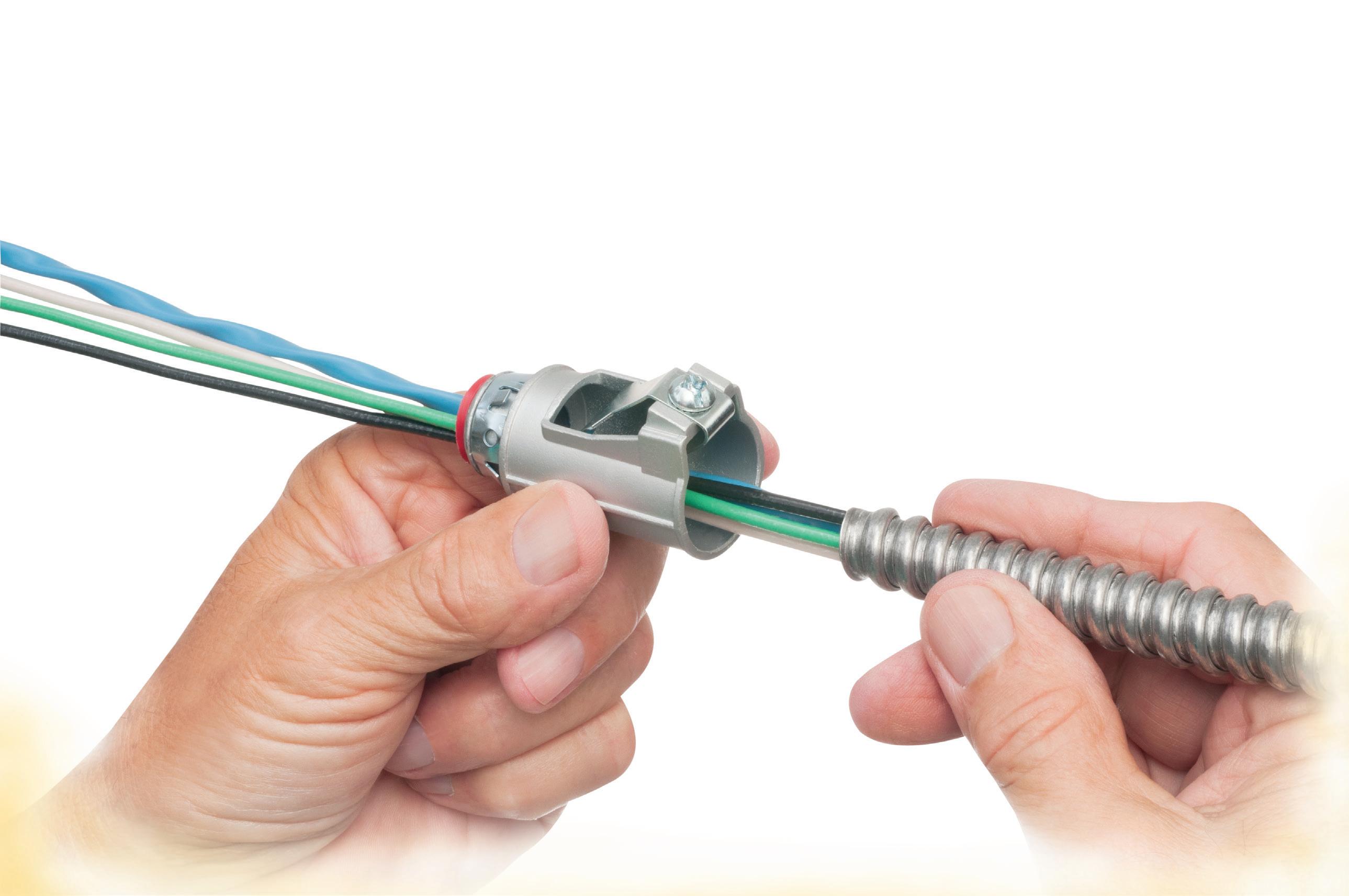
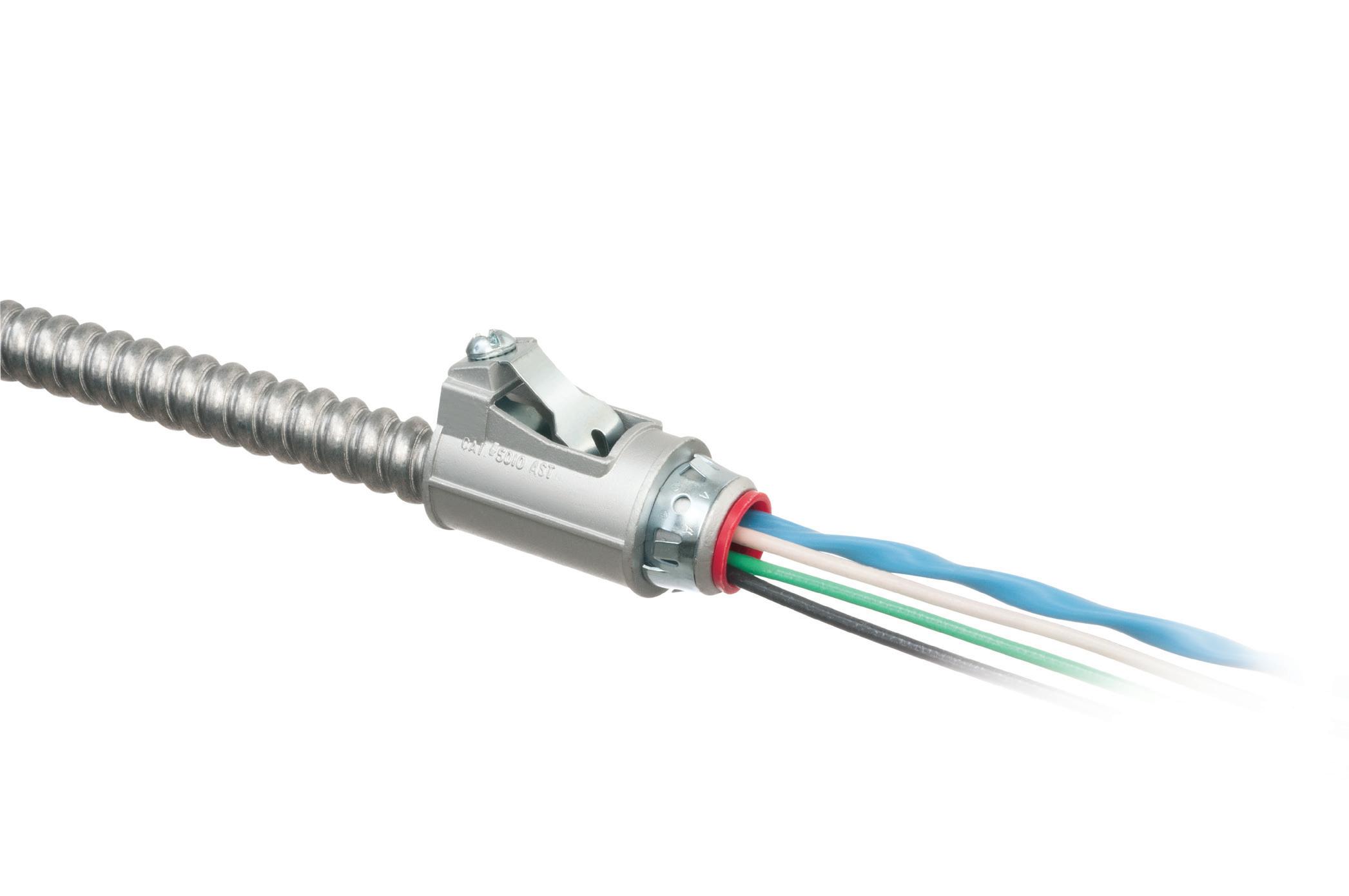

PRODUCTIVITY DRIVES PROFITABILITY
Contractors believe 11% to 15% of field labor costs are wasted or unproductive. Although it is unfair to expect contractors to reduce their waste or unproductive time to zero, respondents conservatively believe that 6% to 10% of labor spending ($15 billion to $25 billion) could be saved through better management practices.
In 2012, 57% of those surveyed by FMI said productivity had slightly or significantly improved. By 2023, that figure fell to 23% (Fig. 1 on page 38). Similarly, in 2012, only 25% said productivity had
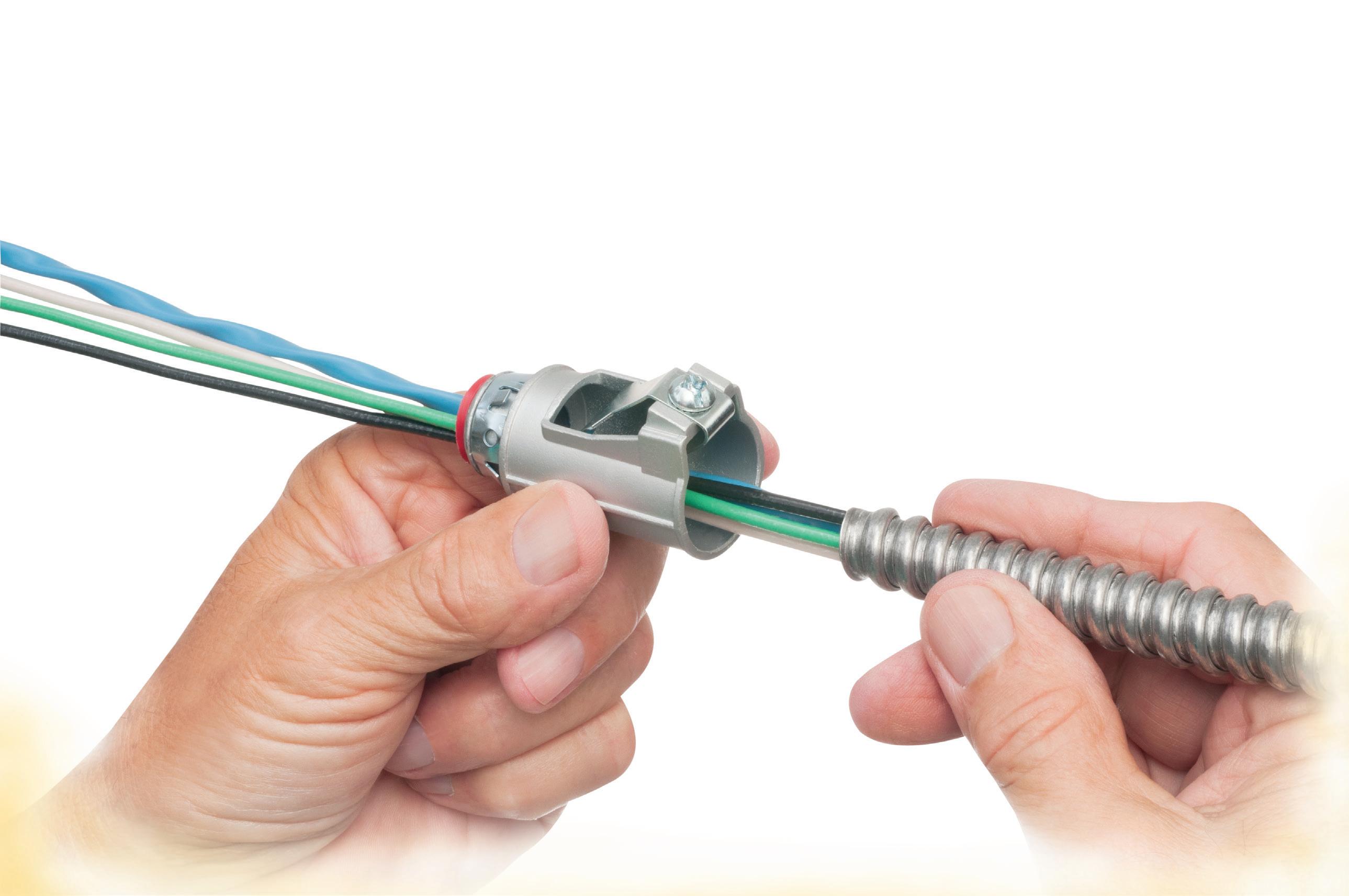
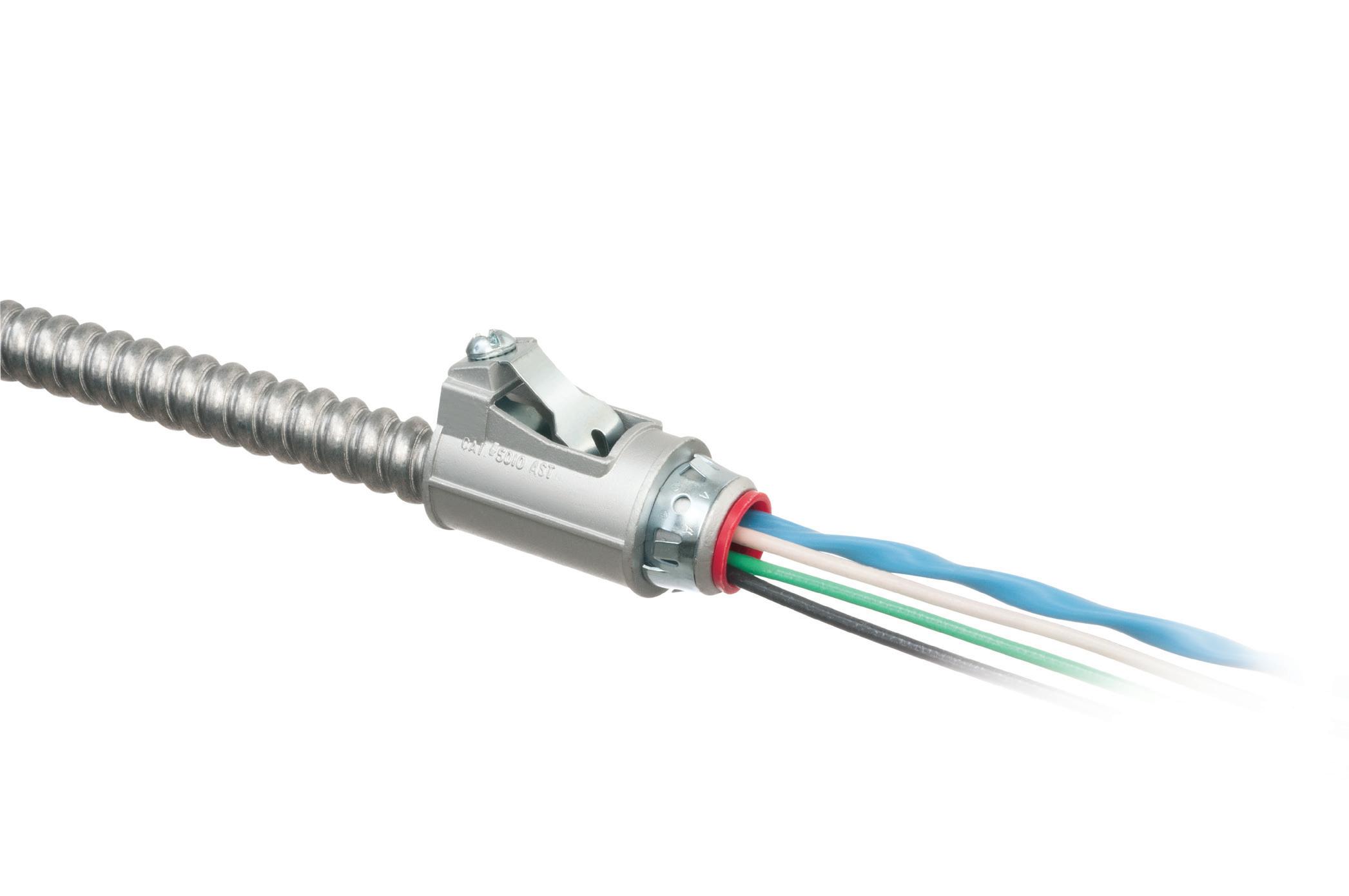
•
Fully assembled, SNAP2IT® fittings handle the widest variety of MC cable AND THE NEW MC-PCS cables.
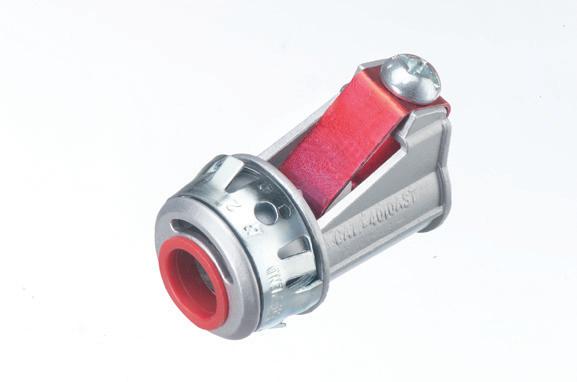

Compared to fittings with a locknut and screw, you can’t beat these snap in connectors for time-savings!
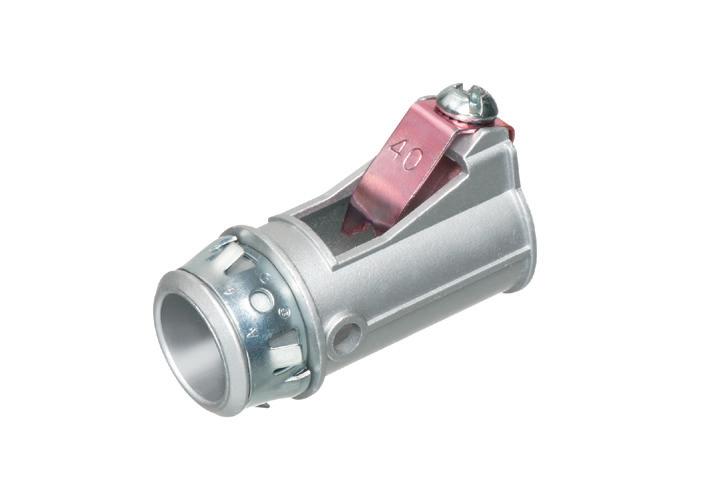
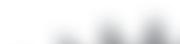
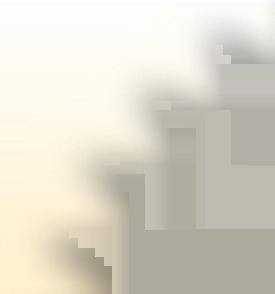




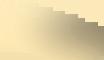

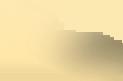






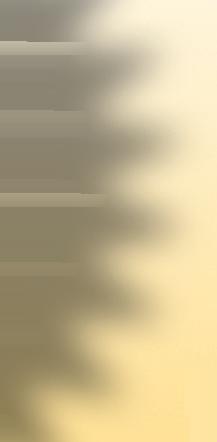

MCI-A cables (steel and aluminum)...including the new MC-PCS cable that combines power and low voltage in the same MC cable
ANY Snap2It Connectors LISTED for MC cable are also LISTED for MC-PCS cable! These products offer the greatest time-savings.
• Fast, secure snap-on installation
• Easy to remove, reusable connector
From cable Loosen screw on top. Remove connector from cable.
From box Slip screwdriver under notch in Snap-Tite® Remove connector.
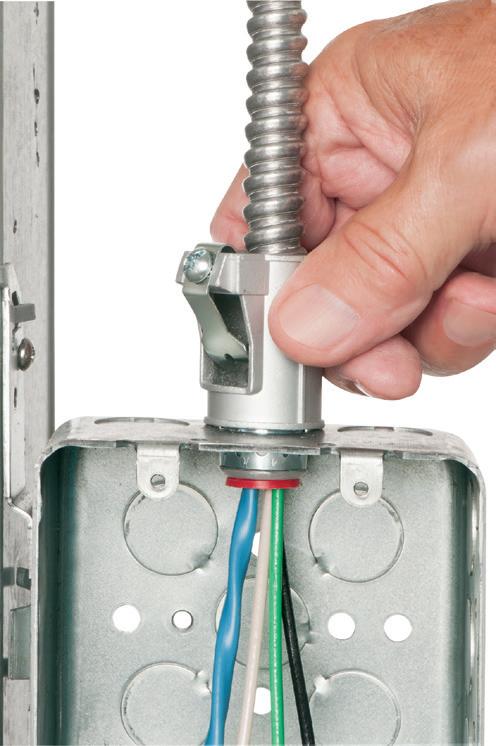
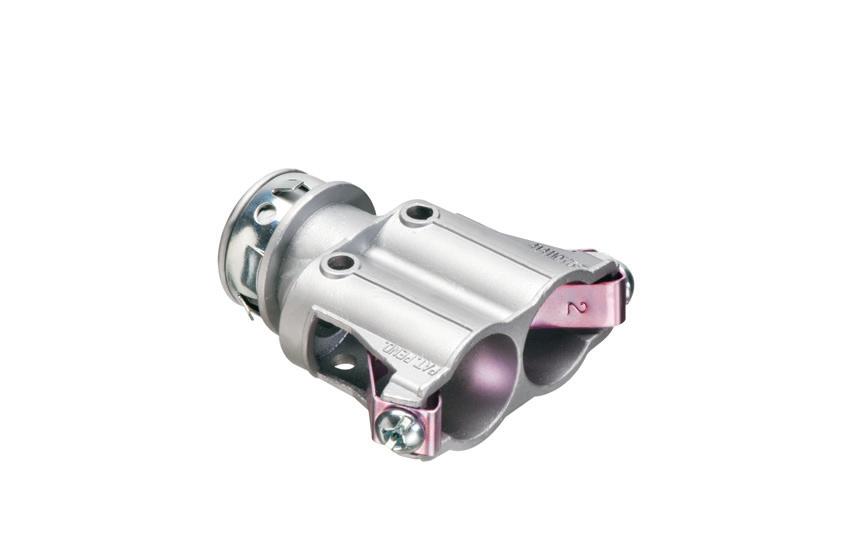
4141107ST
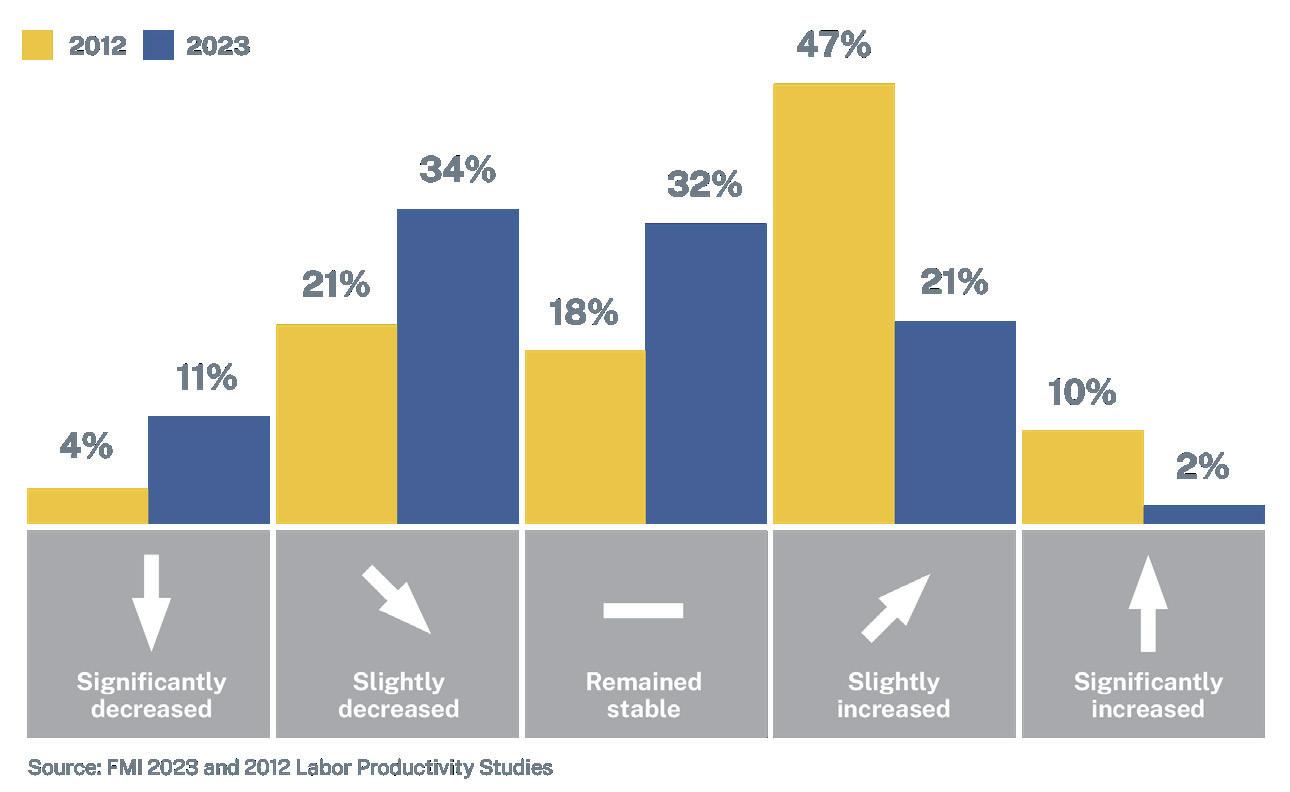
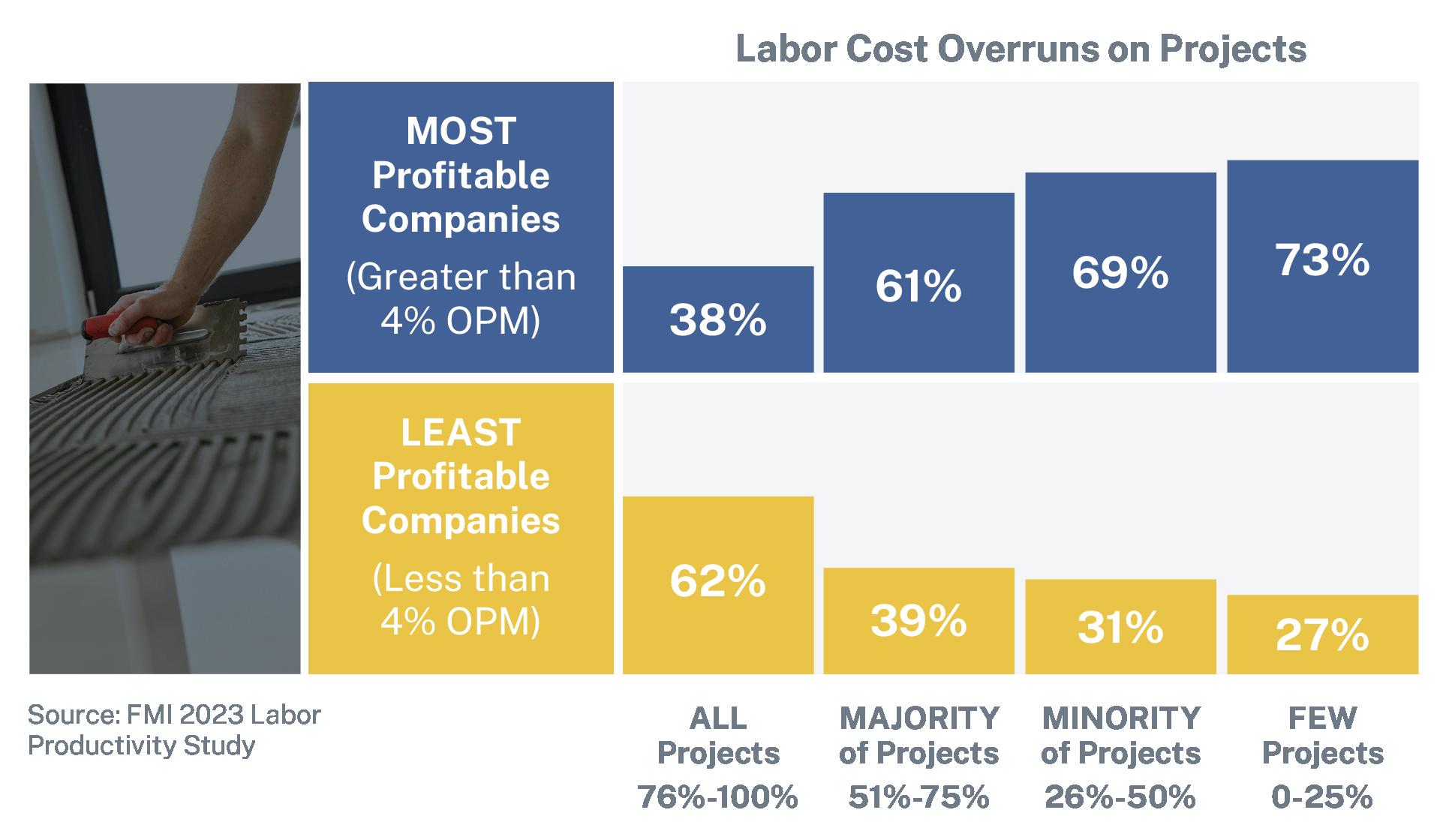

slightly or significantly declined, and by 2023 that figure
Humans are the biggest driver of putting work in place, so it’s no surprise
that many of the top challenges (either internal or external) uncovered in the survey were directly related to people. First and foremost is finding skilled
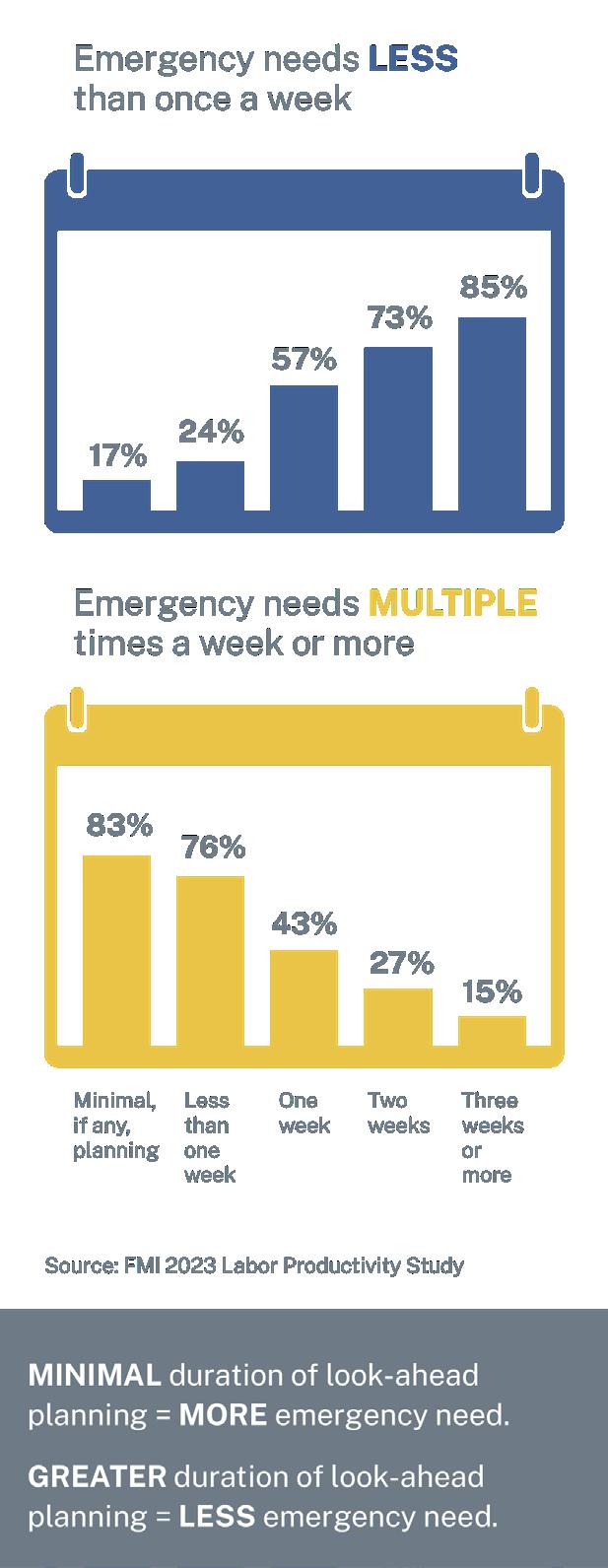
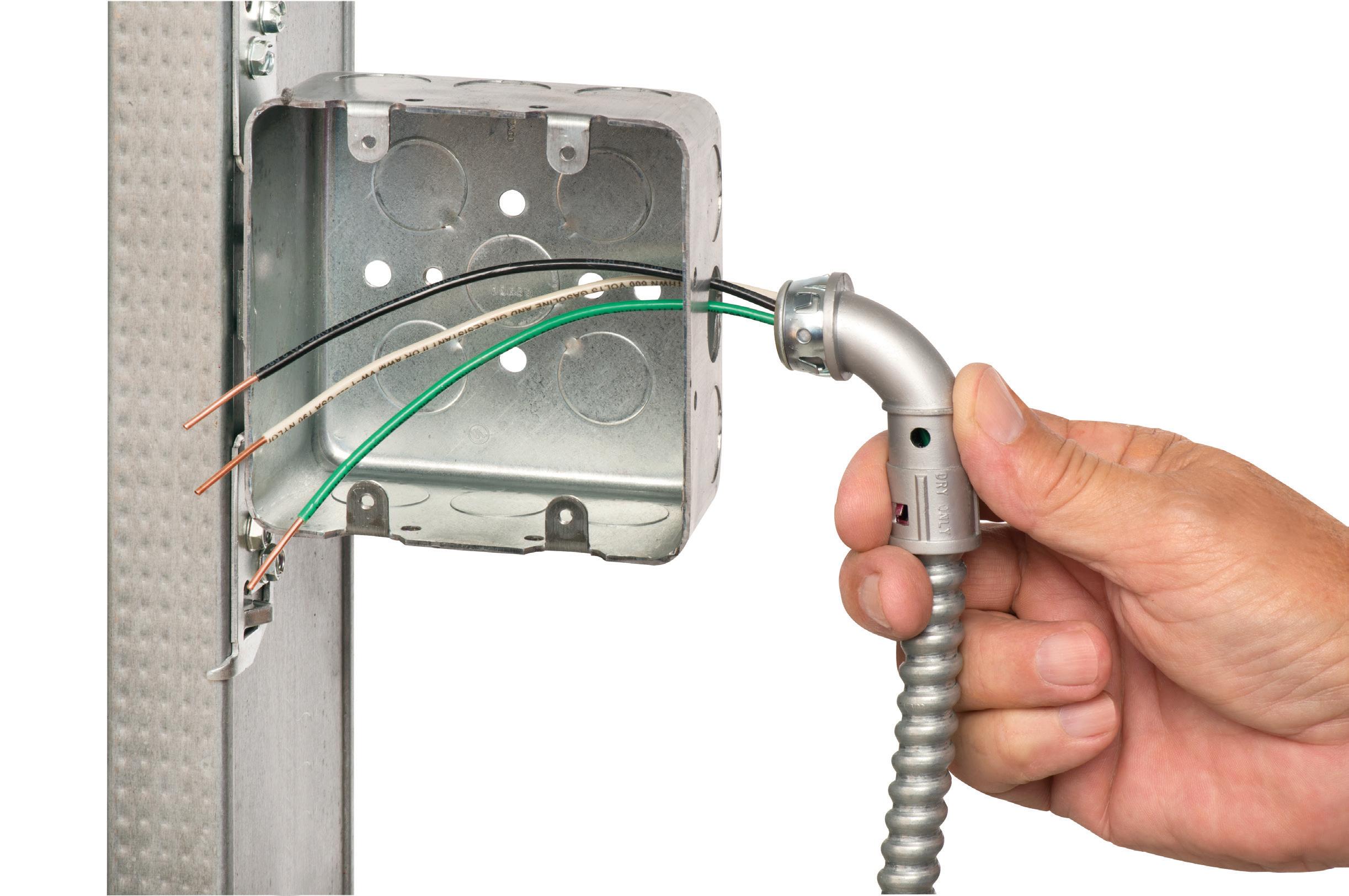
workers, especially in the field. As FMI’s 2023 Talent Study revealed, 93% of firms can’t find the workers they need, with the biggest gap in talent associated with field leadership.
The labor productivity study backs that up with 63% of respondents citing lack of qualified craft labor as the No. 1 internal factor impacting productivity. After a lack of labor, contractors said their top internal struggles were associated with poor planning and communication by field management and project management as well as subpar project team collaboration and site logistics.
HOW TO SOLVE THE LABOR PRODUCTIVITY PROBLEM
Here are a few factors that are within a contractor’s control to influence the outcome with it comes to job-site efficiency.
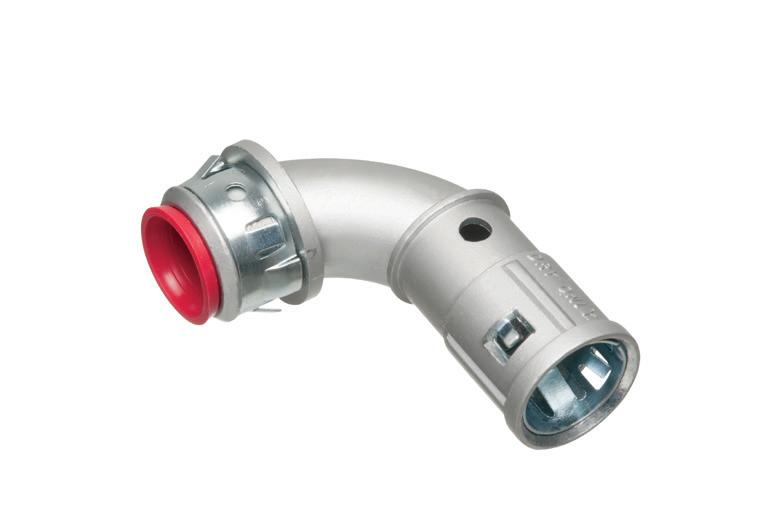

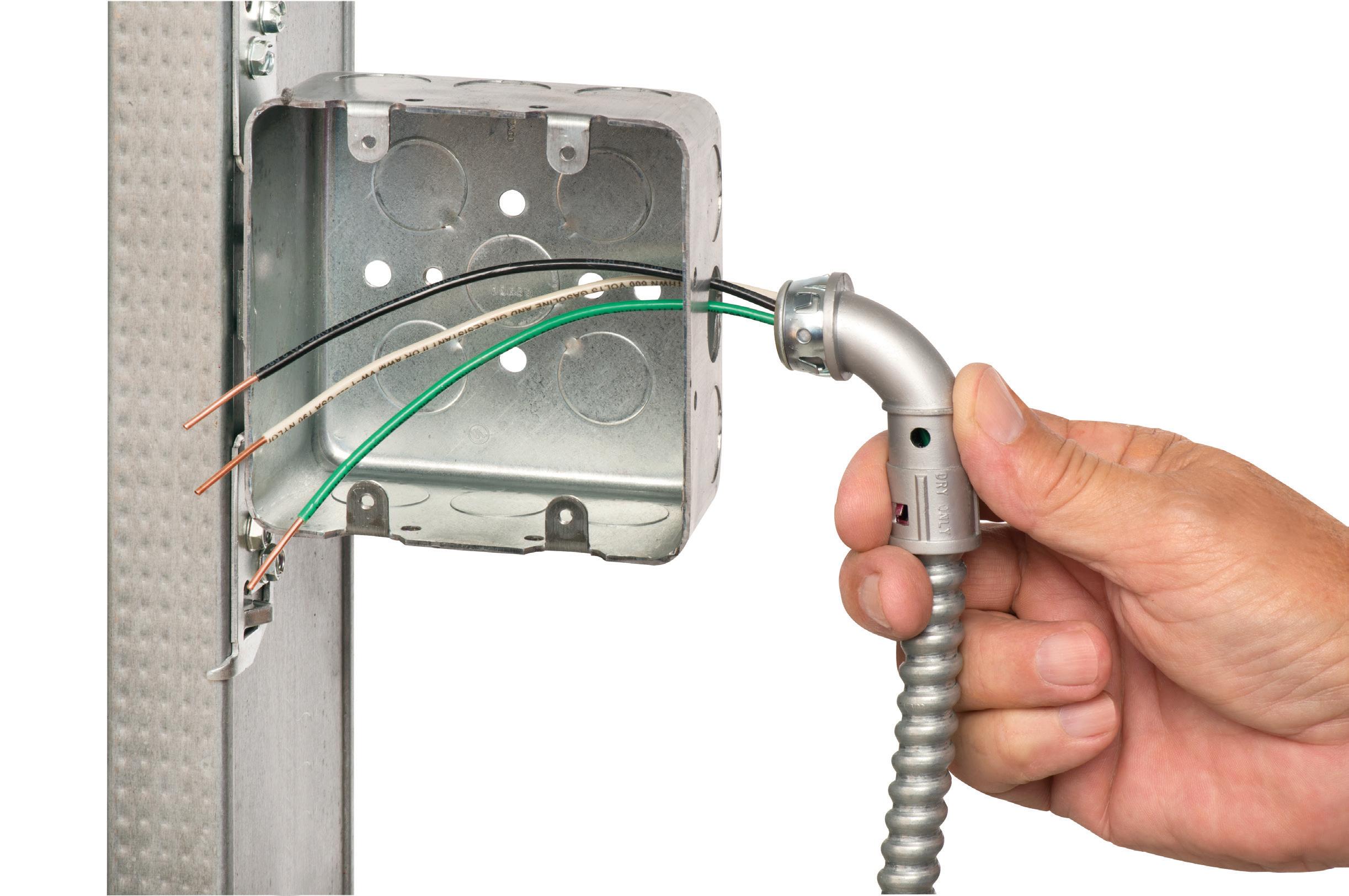
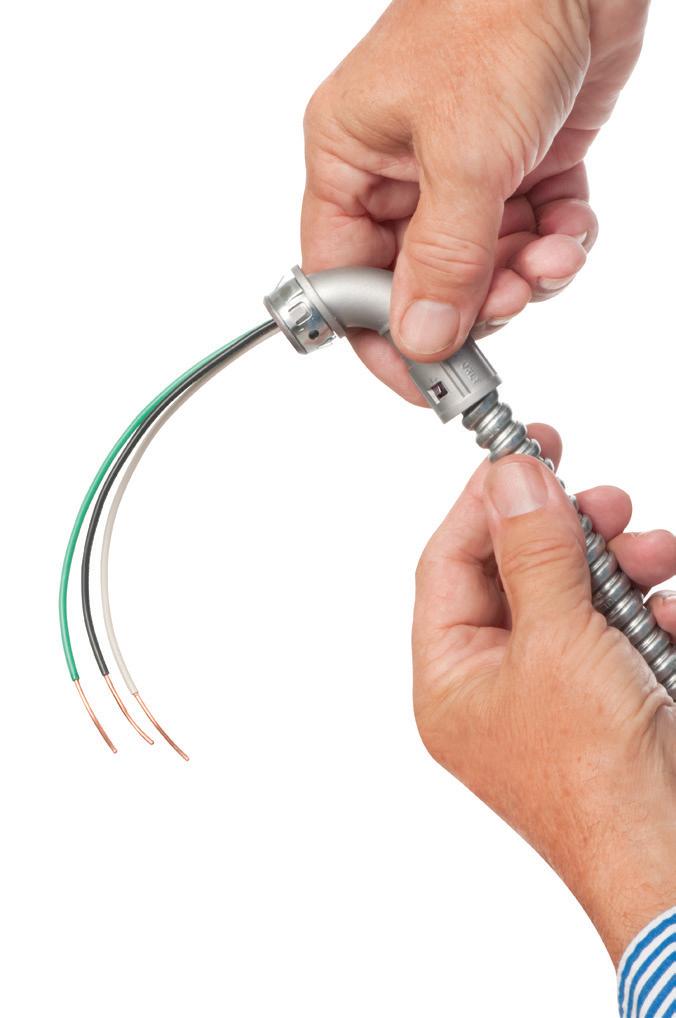
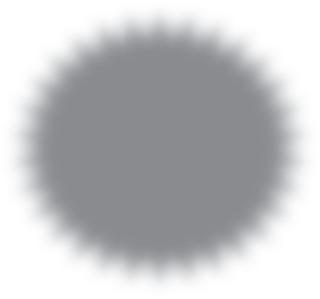
Project labor budget performance
Contractors are in the labor-management business, and understanding labor costs has a clear, direct effect on profitability. One of the ways FMI assesses the overall efficiency of labor-intensive contractors is how regularly they meet or beat estimated labor budgets.
When projects overrun on labor budgets, project margins suffer. If project labor overruns are a common occurrence, enterprise profitability suffers. This obvious connection between labor performance and profitability is confirmed through contractor feedback in the study. Those firms with fewer labor overruns tend to be more profitable.
Avoiding labor overruns on a singular project can be managed by experienced project and field leadership. However, avoiding labor overruns at scale across a large number of projects requires organizational standards for proactive planning and project controls (Fig. 2 on page 38).
Planning is critical
Projects that fall behind early rarely make miraculous recoveries. The discipline of in-depth, collaborative field and office planning before mobilization (pre-job planning) is one of the greatest influences on labor productivity.
FMI’s data shows that the earlier field leaders are involved — and the better prepared they are before mobilization — the higher the profit margins. The percentage of contractors with operating profit margins (OPMs) greater than 4% steadily
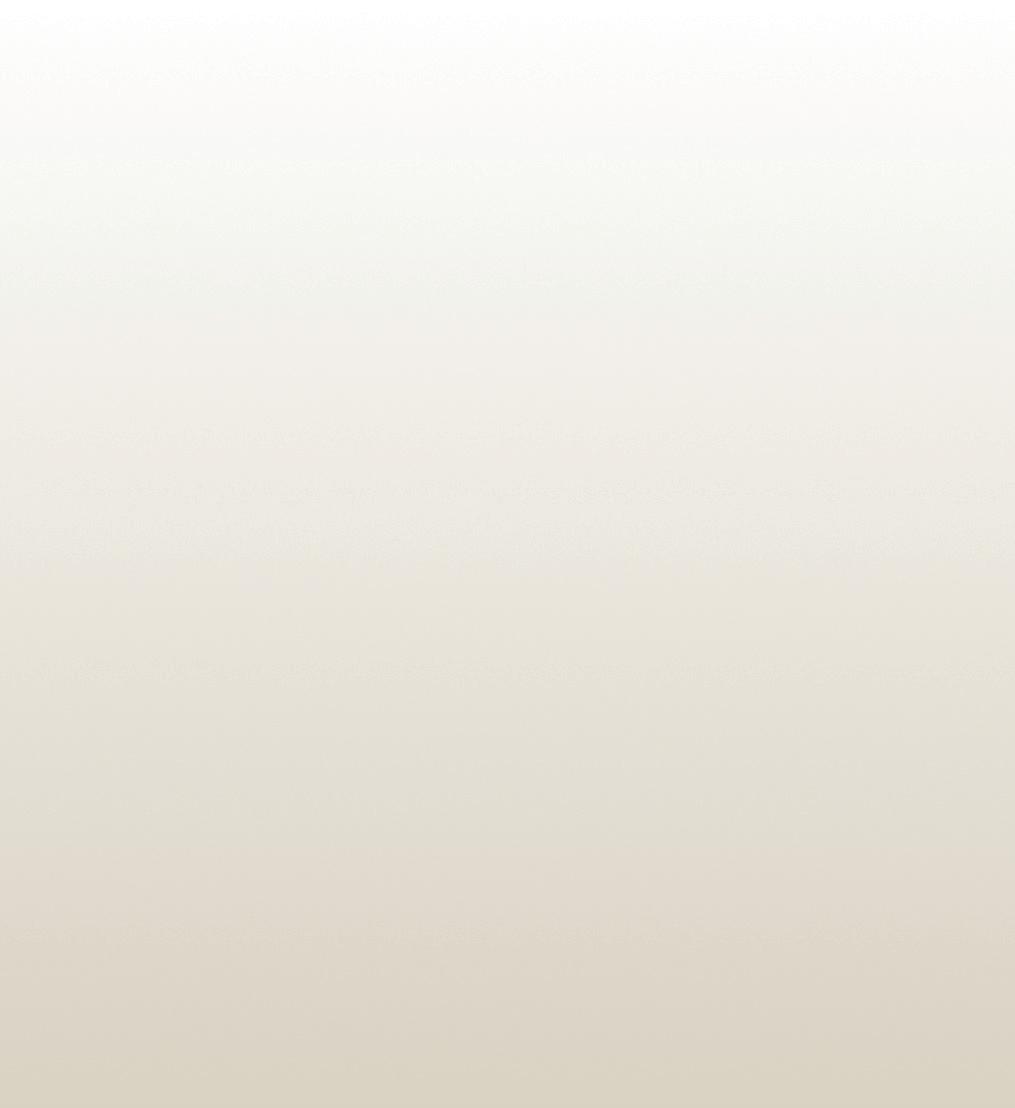
increases along with their field teams’ levels of readiness (Fig. 3 on page 38). However, field managers who shoulder the stress of on-site execution are particularly susceptible to burnout. FMI research found that executives expect 30% turnover for field managers over the next five years, which means that keeping staff engaged and providing the right support will be crucial.
In Fig. 4 on page 38, the study compares the duration of look-ahead planning and how frequently field managers have resource emergencies. Results show that the further out contractors plan, the fewer emergency events they have every week. Of the contractors that do minimal planning, 83% have resource emergencies multiple times a week, while only 15% of contractors that plan for three weeks or beyond have resource emergencies multiple times a week.
Cost-to-complete forecasting
In addition to field leader preparedness and detailed look-ahead planning, the accuracy of cost-to-complete (CTC) forecasting correlates with higher profit margins. Cost forecasting discipline is a key marker of contractor maturity and sophistication. Contractors that can accurately forecast their costs know where their projects stand and what it will take to finish the job.
That level of confidence requires accurate tracking of installed quantities and labor hours from the field, reliable cost reporting, and strong communication between field managers and project managers.
BUILDING A BETTER FUTURE
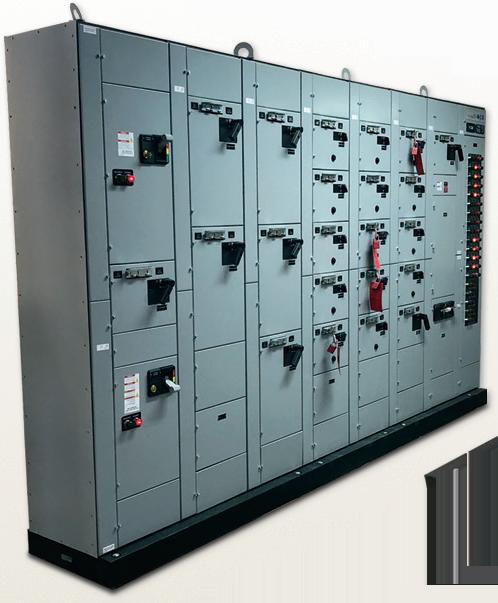
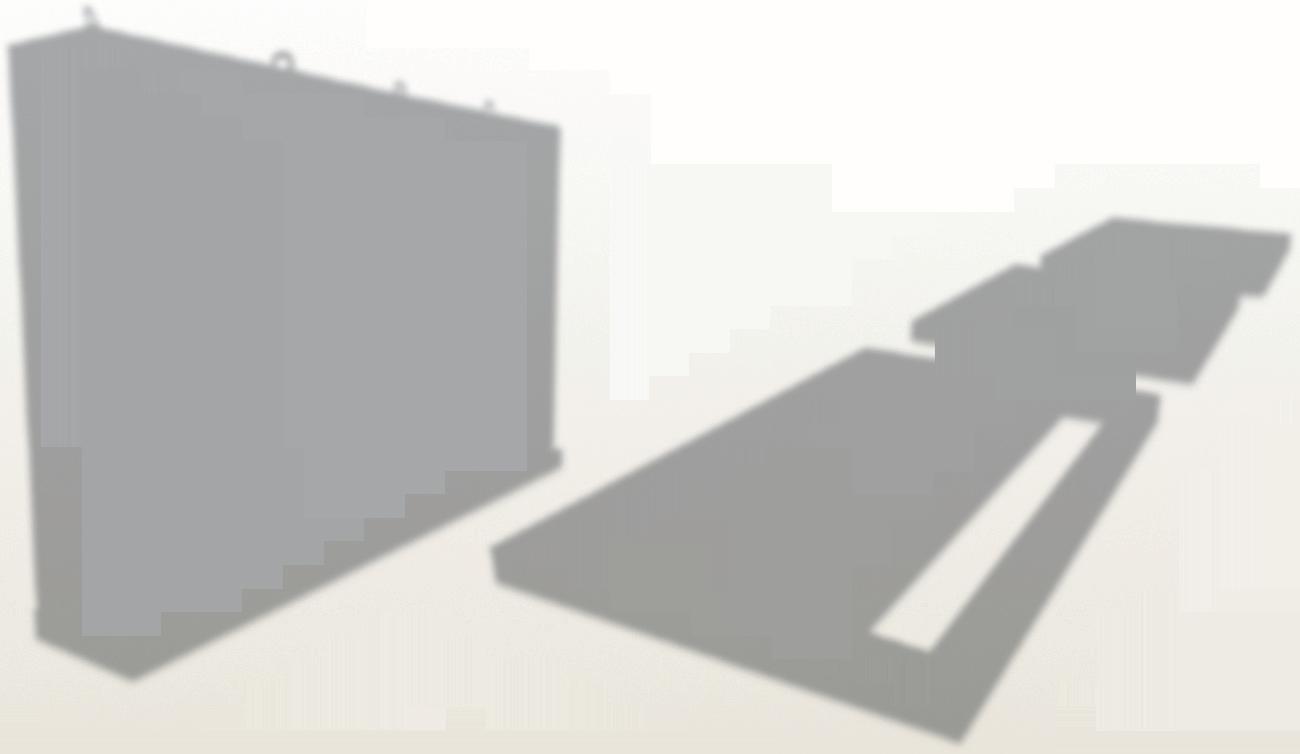
Not surprisingly, 70% of contractors in the study highlighted improving planning and execution practices as their top priority for adjusting operations over the next 18 months. For best practices on what top-performing companies do right, see “What Top-Performing Companies Do Right” on page 36. Additionally, leadership training and development was the second-highest priority listed.
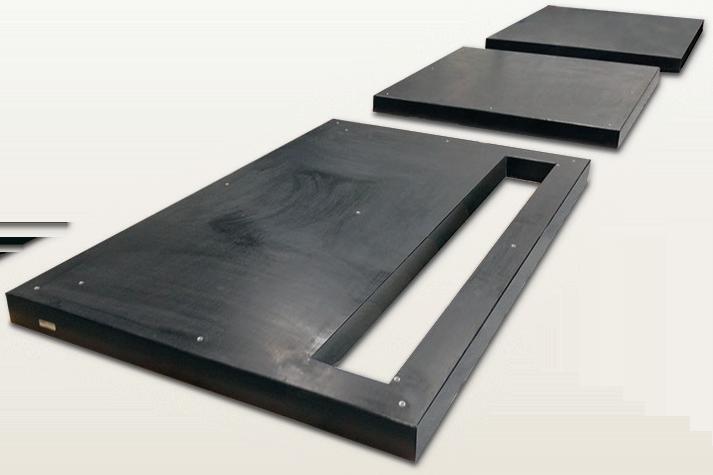
Contractors that establish sound operating processes and train their people to be successful in their systems perform better than their peers. This takes significant time and discipline. If done well, however, it can have a significant impact on the bottom line and improve employee engagement and retention.
By getting a handle on productivity, giving workers the tools needed to be successful and diligently planning for jobs, companies can improve margins and profitability. In an industry where one bad job can make or break a company, harnessing the power of your biggest asset — your people — will ensure you continue to successfully operate and thrive.
Michael Keller focuses on providing expert guidance on strategic planning, productivity, and operational excellence at FMI. He can be reached at michael.keller@fmicorp.com.
Tyler Paré leads FMI’s performance practice, which helps contractors optimize profitability and manage risks. He can be reached at tyler.pare@fmicorp.com.
Jake Howlett is an analyst in FMI’s performance practice where he focuses on facilitating data analytics processes for client deliverables and internal projects. He can be reached at jake. howlett@fmicorp.com.
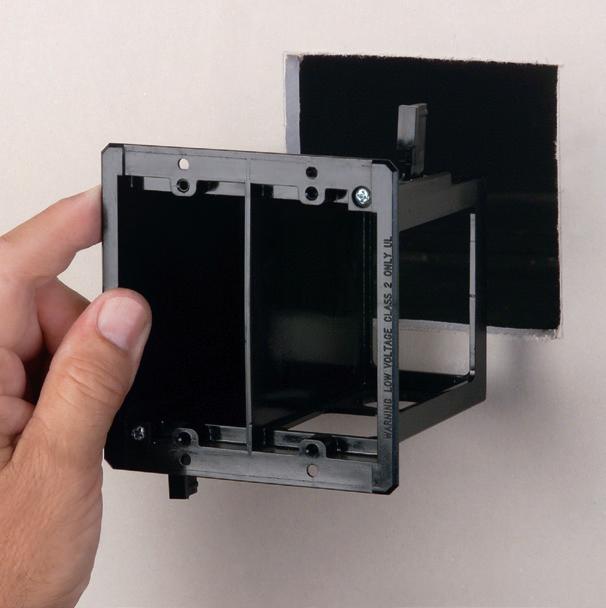
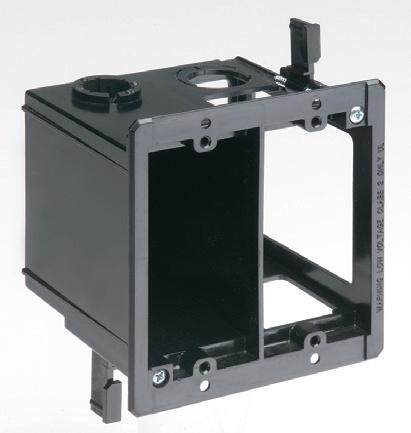
•
•
•
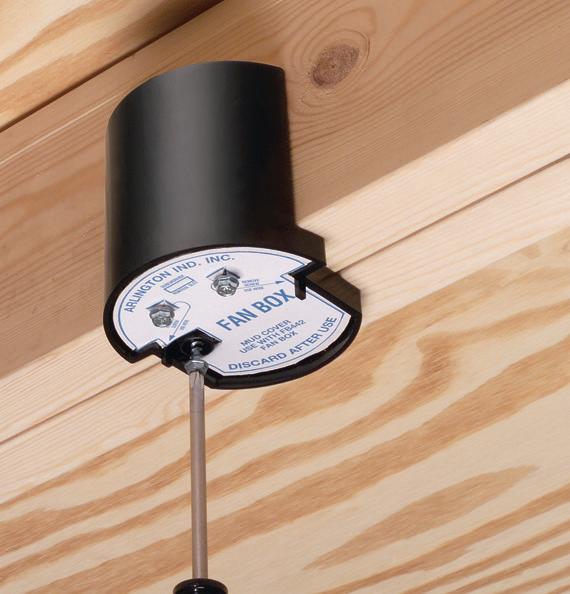
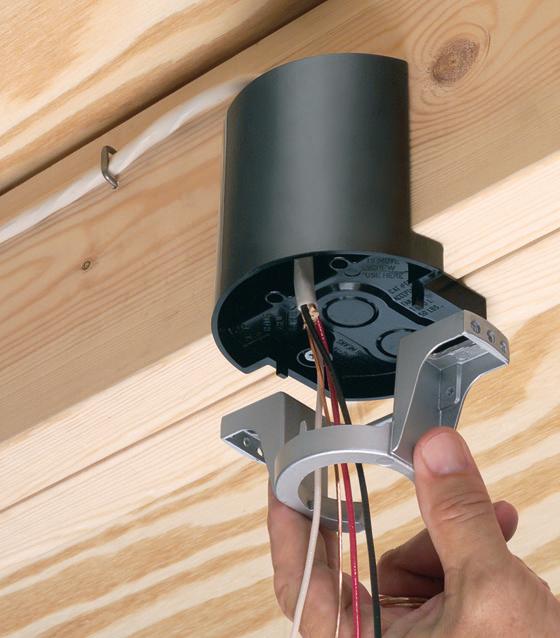
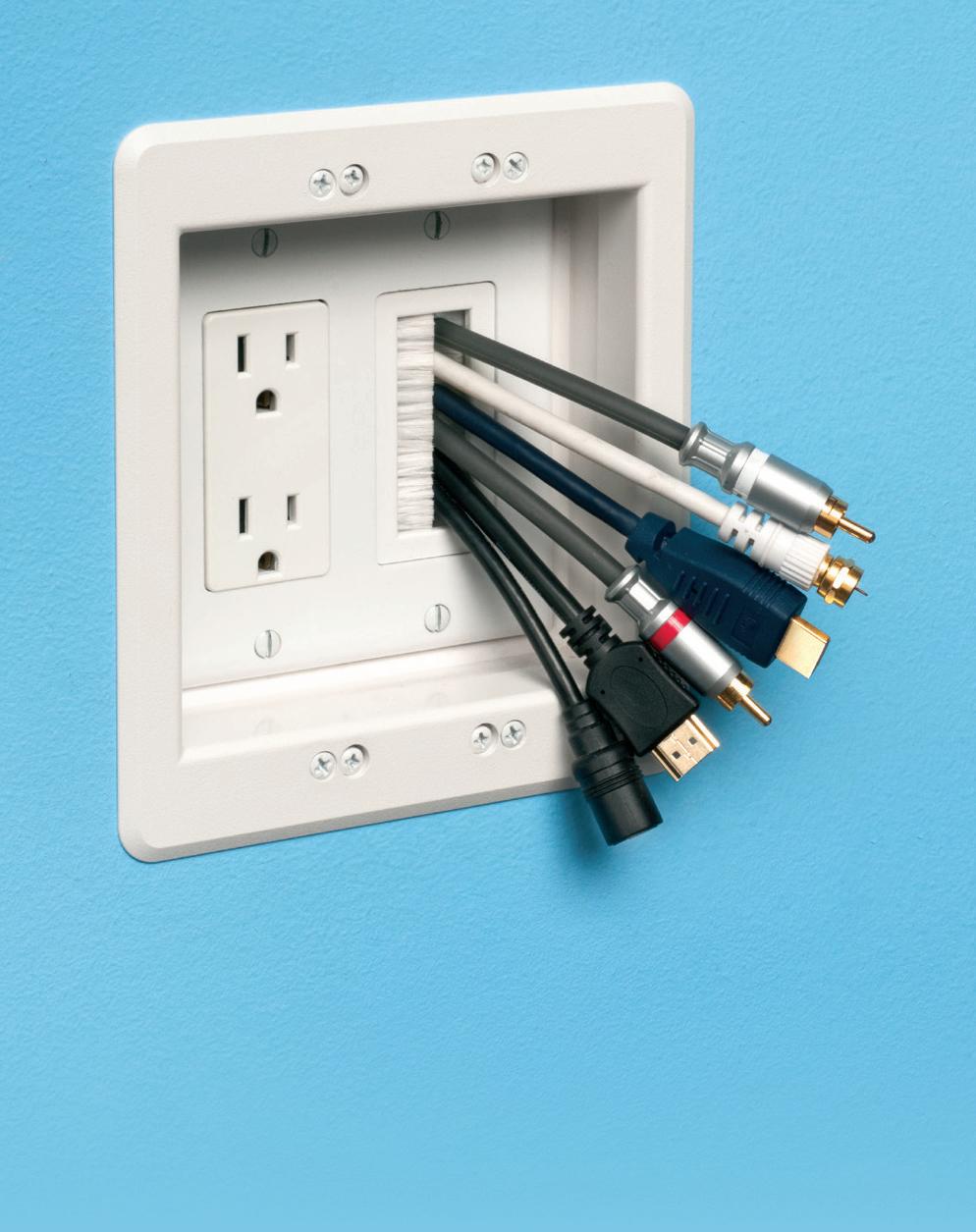

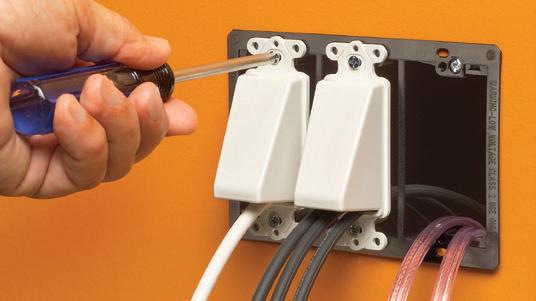
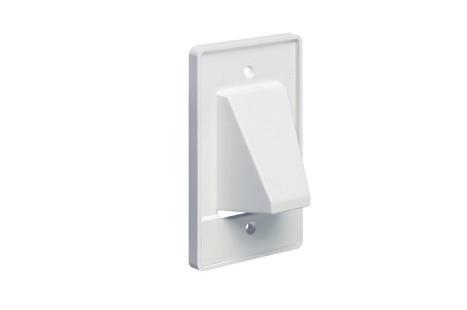
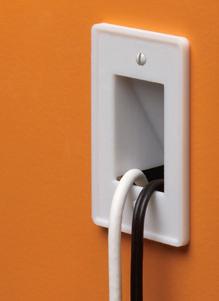




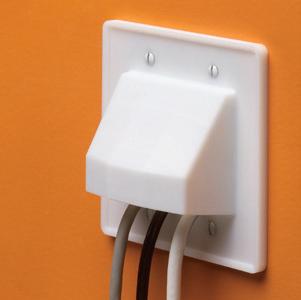
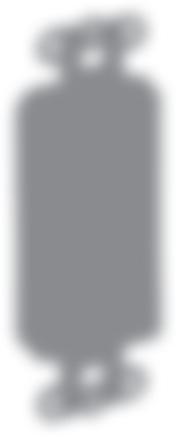
Restructuring Construction Industry Productivity
It’s beyond a labor issue.
High inflation and labor shortages are a major challenge for many industries, and no more so than in the construction and engineering (C&E) sector, where productivity has historically always been low. C&E firms can improve project efficiency by increasing productivity, lowering costs, and reducing waste. And it’s not all just about tackling labor issues — that’s just one interrelated issue.
The construction industry has lagged the manufacturing industry in terms of productivity gains in recent decades. This is due to several factors, including fixed and repeatable processes, the use of automation, and standardized materials that are common in manufacturing but not in construction.
By their very nature, construction projects are often unique and complex, making it difficult to develop standardized processes and automate tasks. The industry is also highly fragmented, with many small- and medium-sized businesses, which can make it difficult to implement industry-wide initiatives to improve productivity. And if that wasn’t enough, two additional issues must be factored in. The construction industry faces a shortage of skilled workers and is often subject to weather delays, which can disrupt schedules and impact productivity.
According to metrics from the Becker Friedman Institute for Economics at the University of Chicago, “The productivity struggle within the construction sector is real, and not a result of measurement error. Given its place in the economy, this productivity decline has real effects: Had construction labor productivity grown over the last five decades at the (relatively modest) rate of 1% per year, annual aggregate
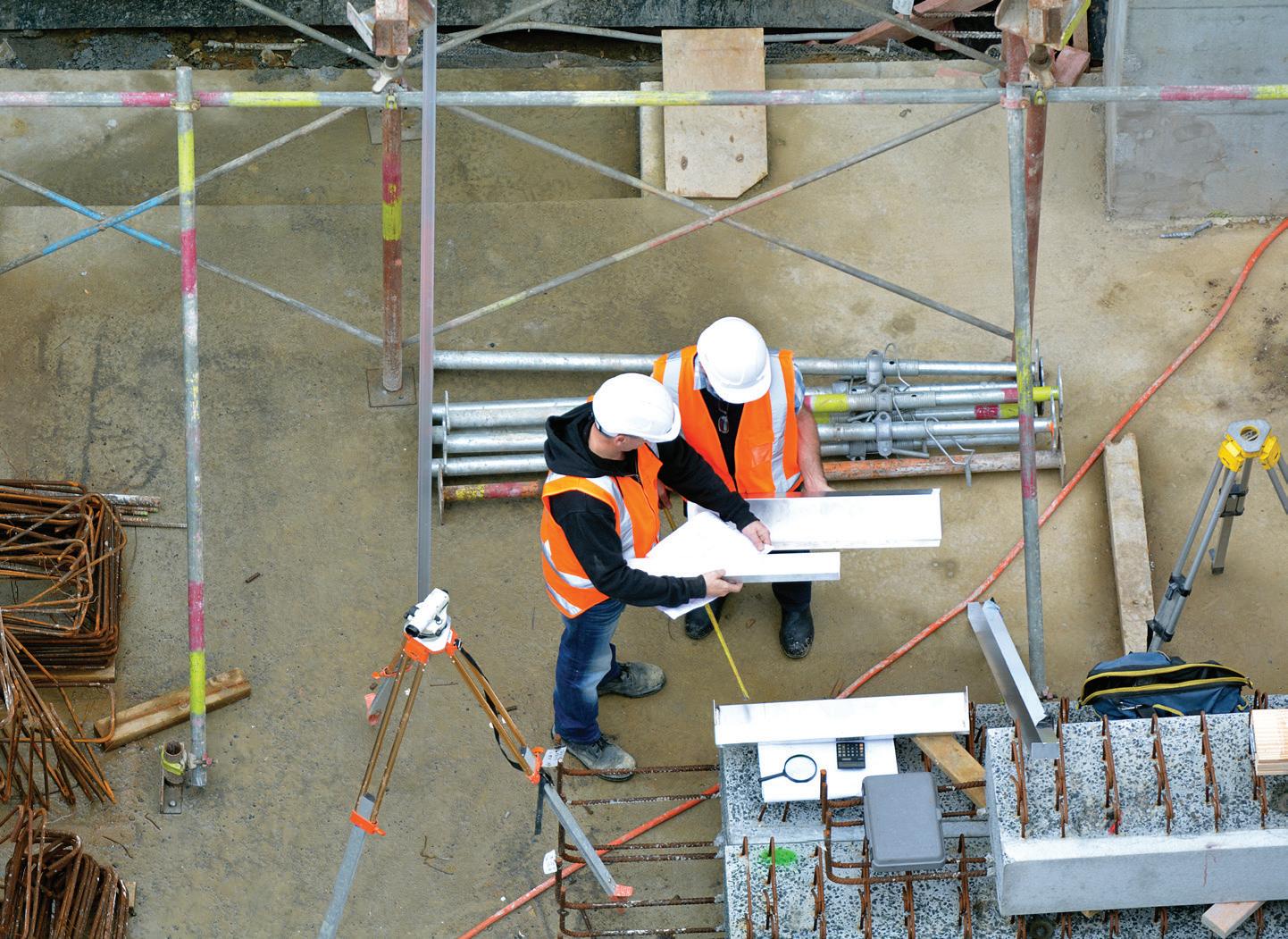
labor productivity growth would have been roughly 0.18% higher, resulting in about 10% higher aggregate labor productivity (and, plausibly, income per capita) today.”
WORKING SMARTER AWAY FROM THE CONSTRUCTION SITE
There are certainly lessons to be learned from the manufacturing industry here. A strong industrialized construction trend in the industry is evidence that electrical contractors and clients see benefits in adopting new ways of working. Modular and prefabrication strategies are certainly increasing, and there is a trend toward doing less work on the construction site and more work off site in production or supply hub locations.
Modular work can be performed more efficiently, at a lower cost, and at a higher quality. Shop environments
let the same number of people perform more work, so as the aging skilled workforce retires, modular will be attractive for human capital management purposes. It’s no wonder more contractors, house builders, and engineering firms are pushing the use of shop-based construction, and more project owners are seeing the value.
BOTTLENECK IS NOT ALWAYS THE LABOR POOL
If you consider where the cost comes from in a construction project, it is typically dominated by four types of costs: labor, material, subcontractor, and equipment, such as cranes, excavators, etc.
There is a tendency to focus on labor productivity, but for some, labor costs can be as little as 10% of the project costs. Therefore, depending on the project, it may not necessarily be the right area to

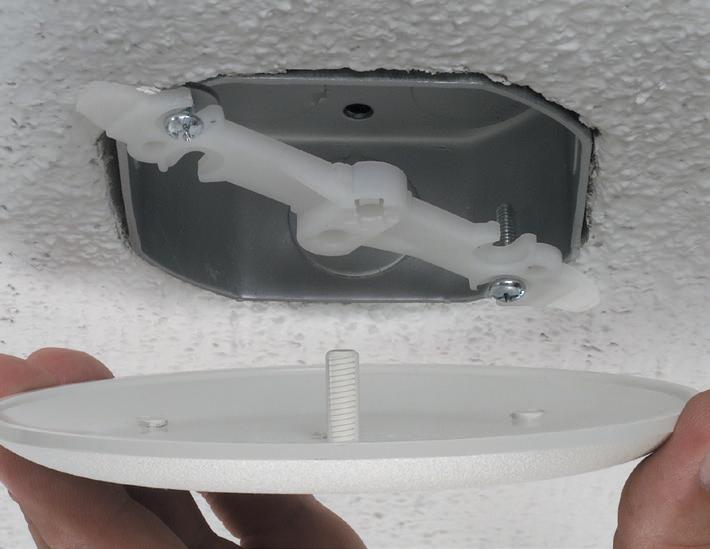
Versatile bracket design with ‘A’ and ‘B’ openings for use on flat or uneven ceilings.
•No
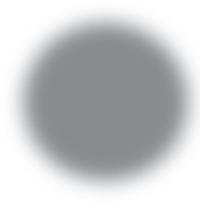
Easy installation. Attach the bracket to the box with #8 or #10 screws. Back the screws out
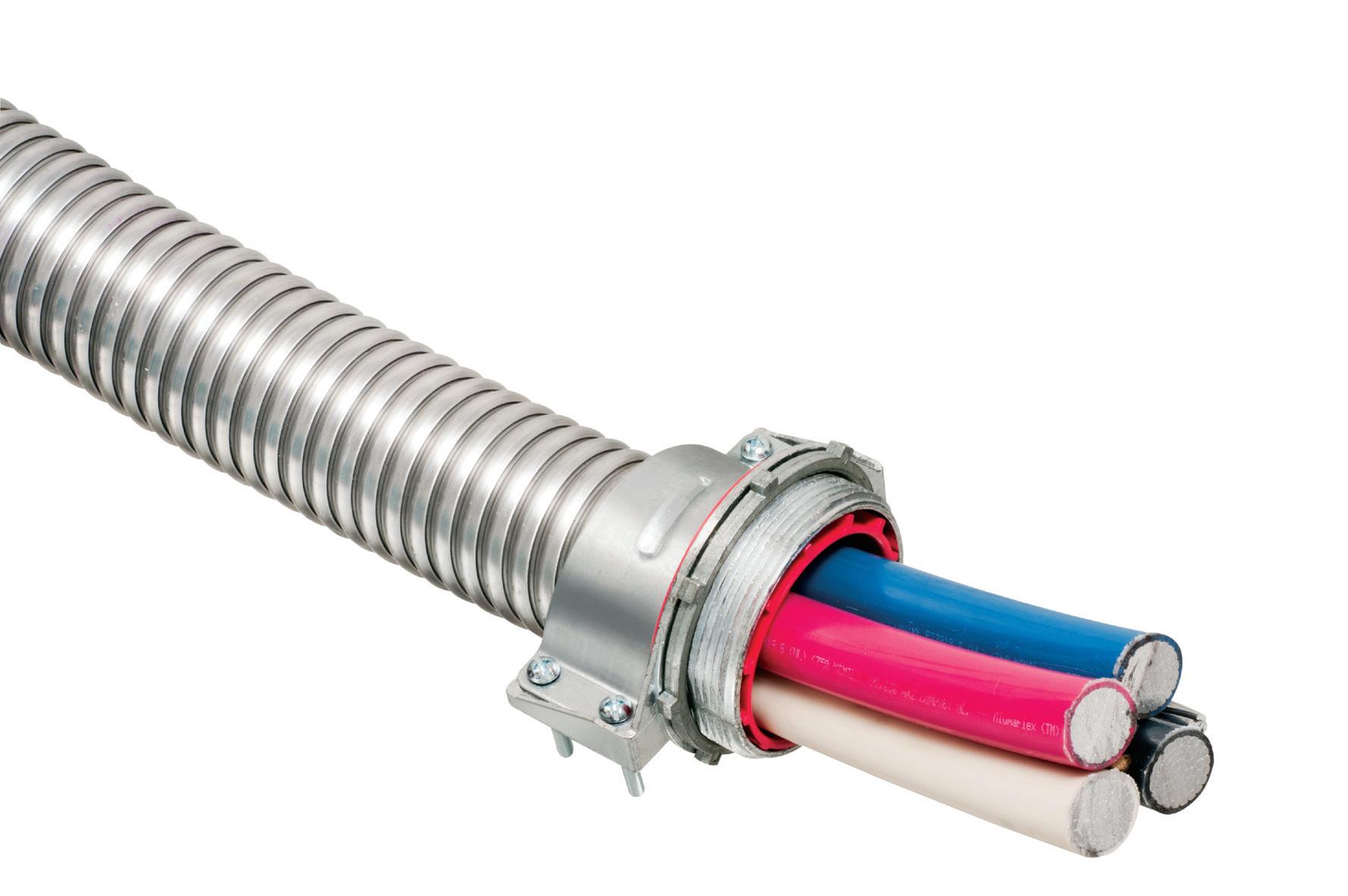
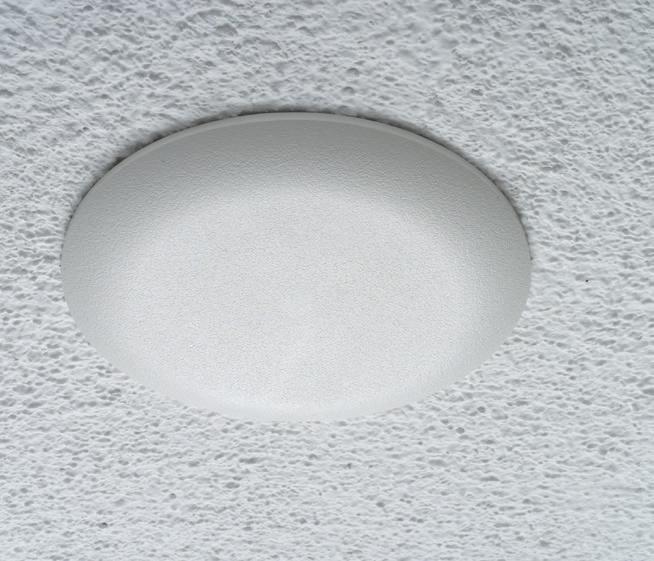

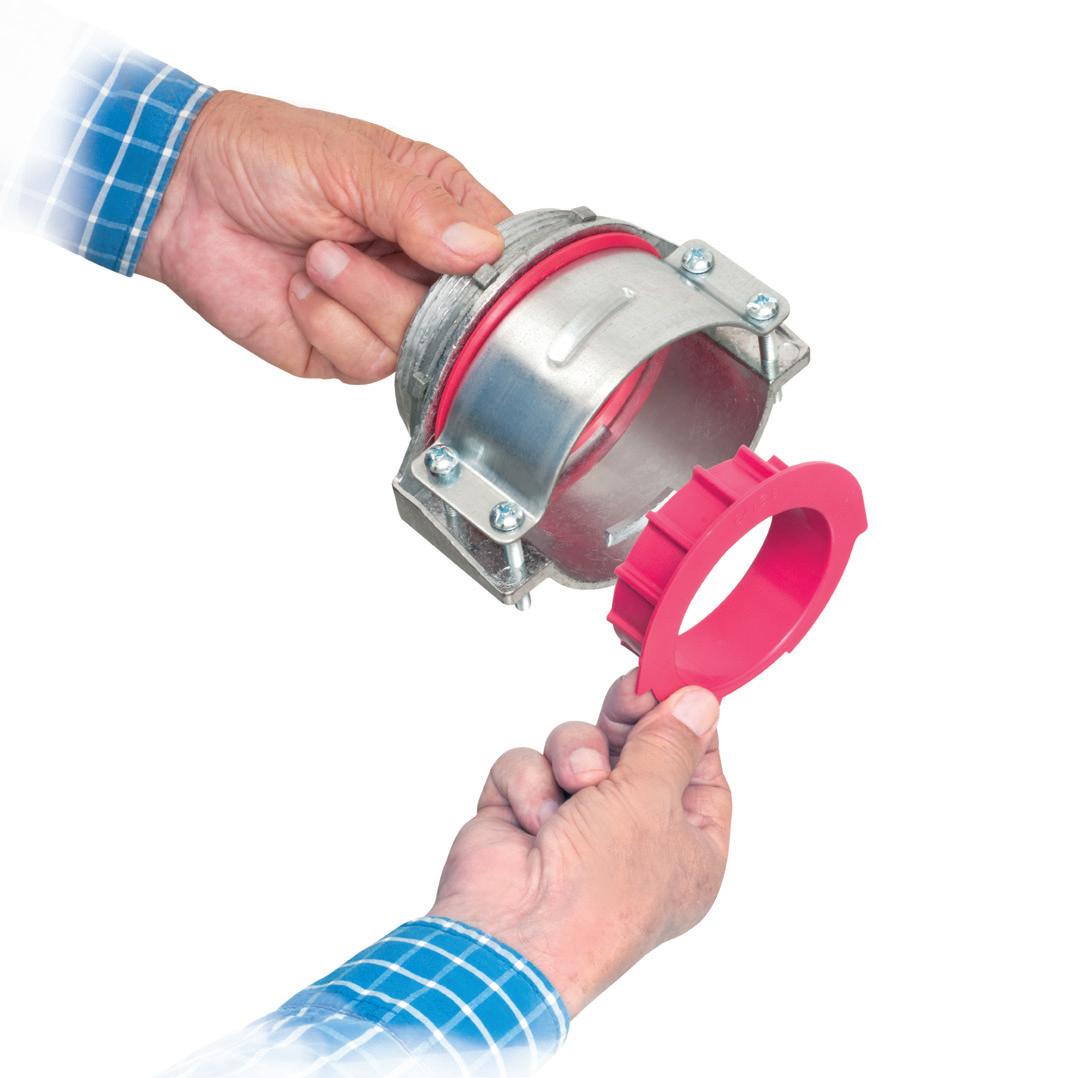
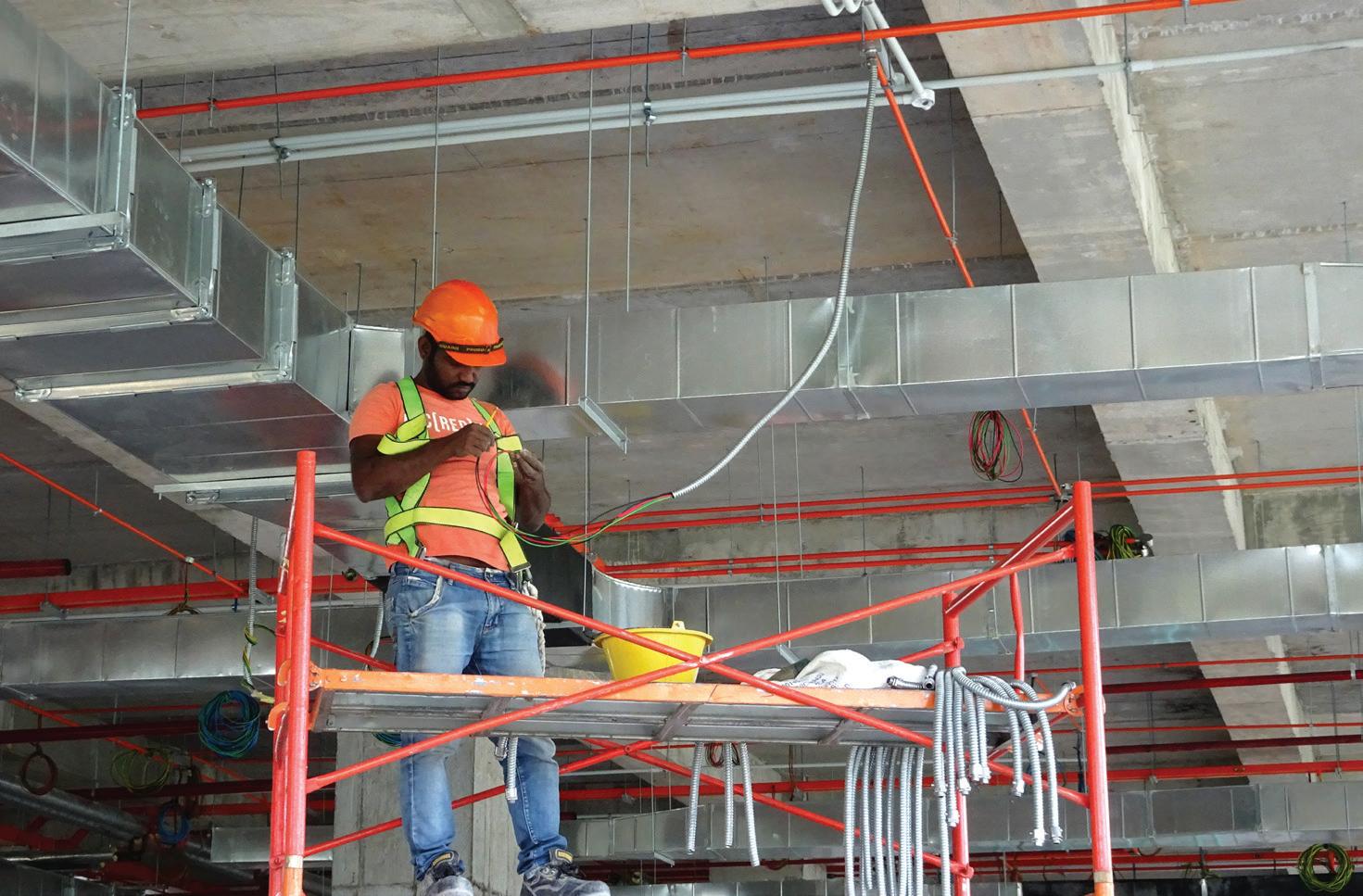
prioritize. Let’s look at the composition of total project costs.
The make-up of the project costs will differ based on factors such as your role — are you a main/general contractor, a specialty contractor, or a material/ equipment supplier? Also, it matters whether you’re following a self-perform or subcontract construction model. This means that the focus on where to reduce costs will vary across different organizations and projects.
LOOKING AT THE BIG PICTURE
Perhaps the real answer lies in not focusing on these four resource types as four independent areas, but instead recognizing that minimizing project costs requires a synchronized approach. There are many reasons for poor productivity — from bad planning and scheduling, too many scope or design changes, inexperienced labor, bad weather, etc. So, there is a huge opportunity to improve and reduce costs here.
For example, when you measure labor productivity and witness workers standing around on a construction site not doing productive work, the obvious question comes up… why? In most cases, it is not their lack of knowledge, skill, or willingness to work hard that is the issue, but the fact that they are stopped because the other resources are not available — such as materials or equipment — or because they are waiting for another work package to finish before they can start or continue their
work. This is possibly the main reason why manufacturing work can be executed at a lower cost and with more reliable completion dates.
If you accept this argument, then the focus for the industry is to have integrated project and resource planning with structured work packages that can be planned and synchronized to eliminate waste and increase total resource productivity. This will also improve project delivery performance and increase project margins.
SUBCONTRACTORS ADD EXTRA LAYER OF COMPLEXITY
Most contractors deliver projects using a mix of self-perform and subcontract models. Subcontract packages must be efficiently managed. Stats from the National Association of Homebuilders show it takes 24 subcontractors (on average) to build a single home. Therefore, it’s critical to have effective business processes in place to ensure that the subcontractors deliver work on time and to a high quality.
Successful management of subcontractors relies on the collaboration of multiple key roles within a project, and the transparency of data, ensuring that the main contractor is working from a single source of truth. Any supporting construction software tool must provide a platform with one source of truth, where the data is real-world, live, accurate, and protected from manipulation — allowing contract and project
managers to evolve away from struggling to handle hundreds of different static Excel spreadsheets at any one time.
EQUIPMENT MANAGEMENT — SWEAT THE ASSETS
Now let’s look at the equipment — another place where project costs can be reduced is by improving their management of assets and equipment. Most construction companies have equipment sitting idle for long periods, which means that the project is incurring unnecessary costs that directly hit the bottom line. Better planning and tracking of equipment can significantly reduce equipment costs.
Many construction and engineering companies operate multiple business units, some of which are not project-centric (e.g., service or facilities management to offer asset operations and maintenance services or an off-site manufacturing plant, or they may own equipment that they rent or hire to internal/external construction contractors).
For these business units, optimizing their resources is just as important to maximize business unit performance. As an example, a maintenance service provider can significantly cut down costs by utilizing intelligent AI-based resource planning and scheduling software to plan and schedule work most efficiently. This smart AI technology can also be implemented in various types of businesses for similar benefits.
RESTRUCTURING CONSTRUCTION PRODUCTIVITY
In all of this, it is key to focus on reducing project costs in a synchronized manner. This means looking at all the factors that contribute to costs. Labor is one, but materials, subcontractors, and equipment are three important pain points. By using integrated project and resource planning, construction companies can identify and eliminate wasted time/resources and improve overall productivity. By adopting new technologies and ways of working, the industry can ultimately become more efficient and profitable.
Kenny Ingram is the vice president of engineering, construction & infrastructure at IFS with specialization in construction, contracting, engineering, infrastructure, and shipbuilding.
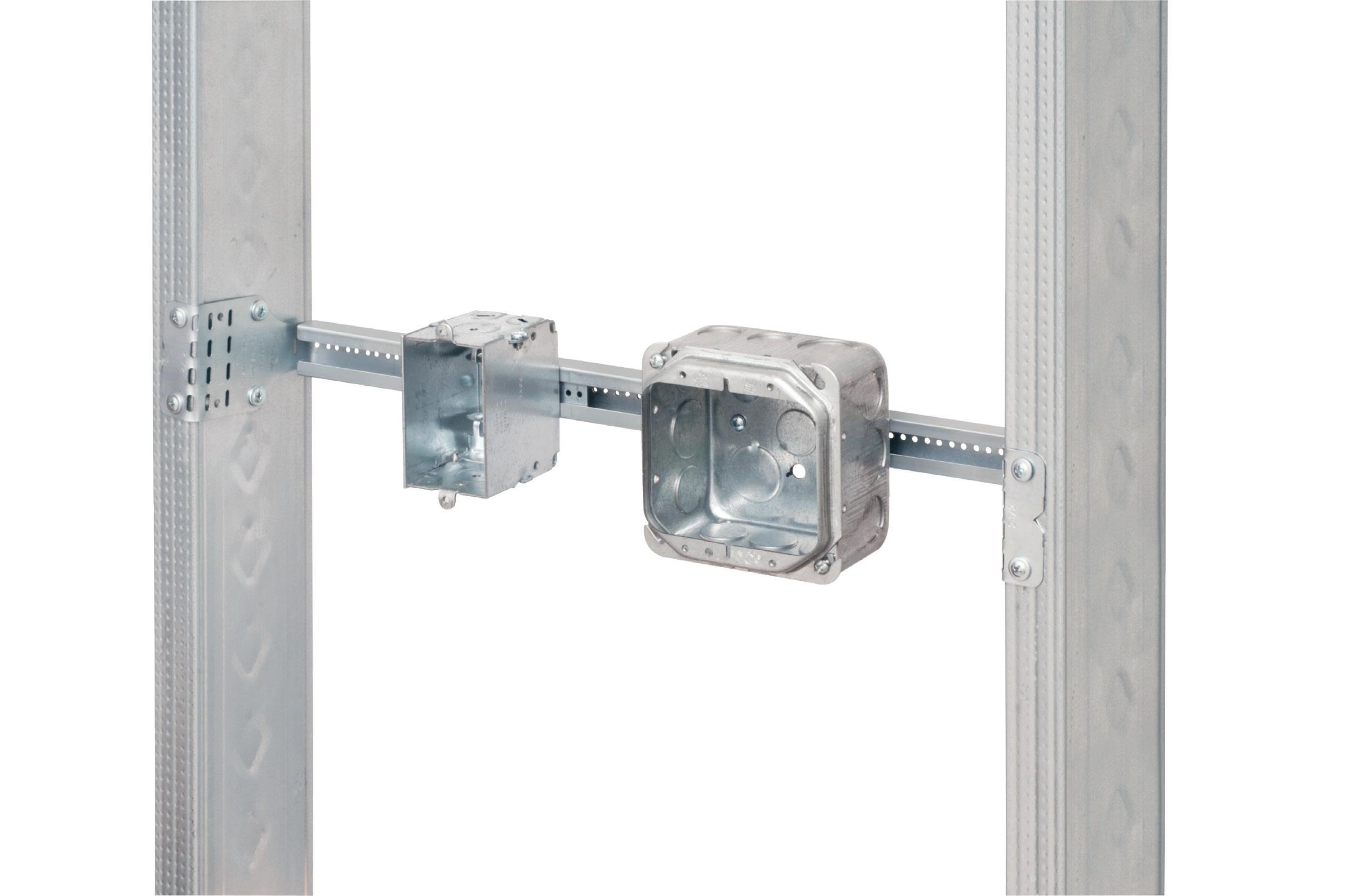

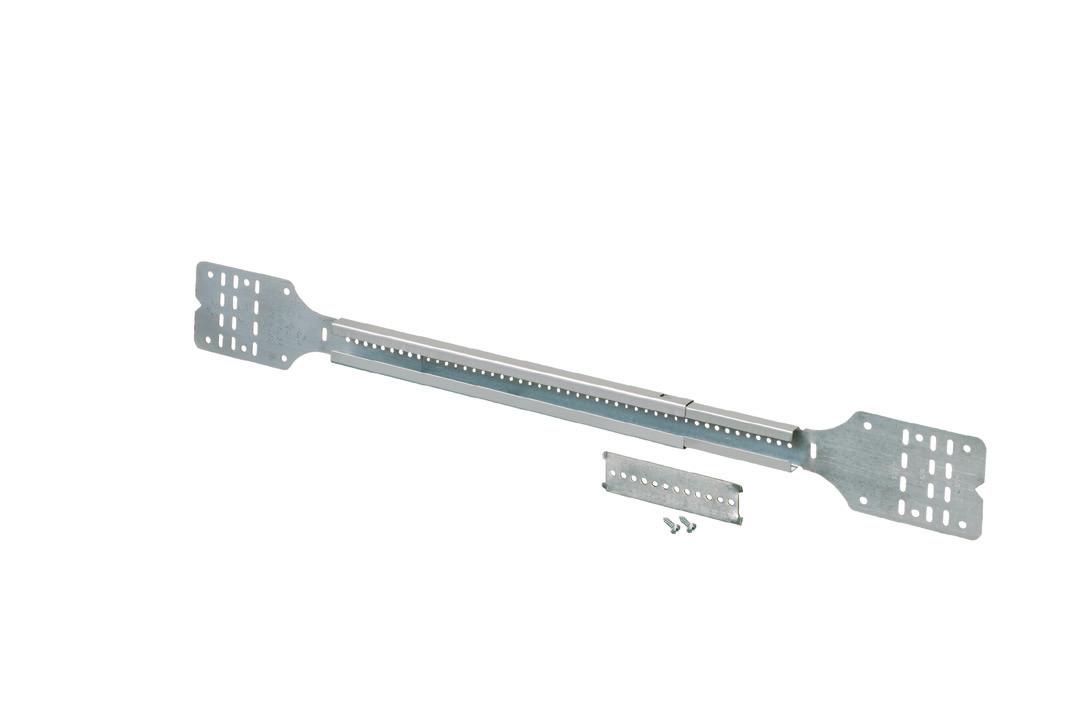
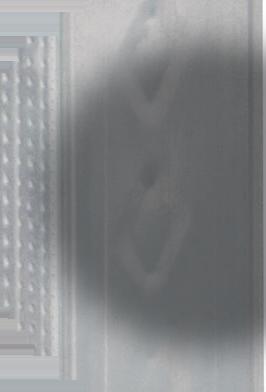

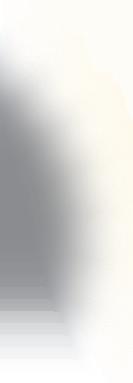

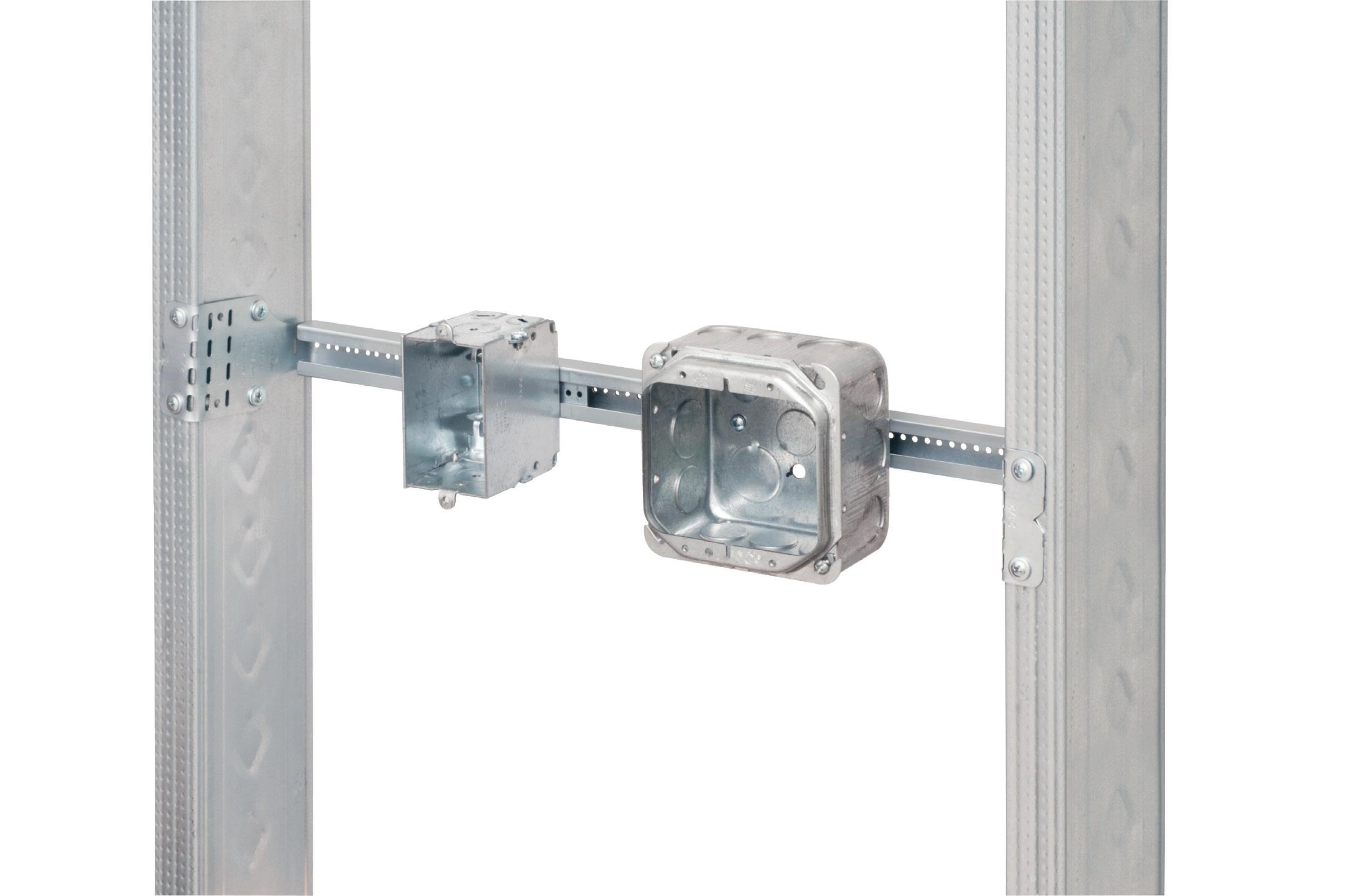

Here’s the easy way to mount single or two-gang wood or metal studs with non-standard stud cavities.
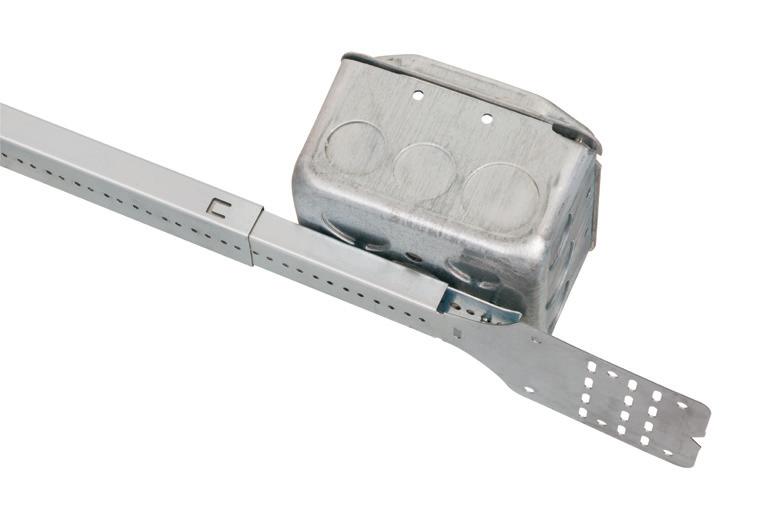
Arlington’s steel SliderBar™ looks great and saves about 20 minutes per box over cutting, nailing and placing extra 2x4s!
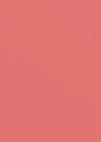
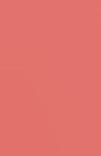
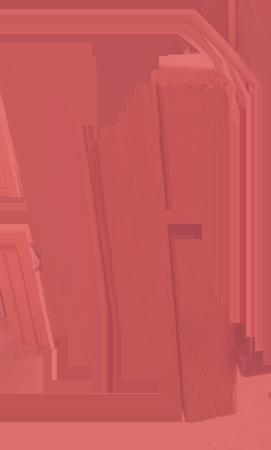
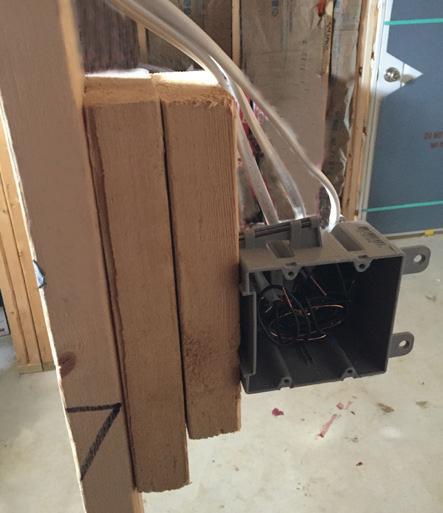
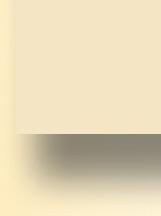


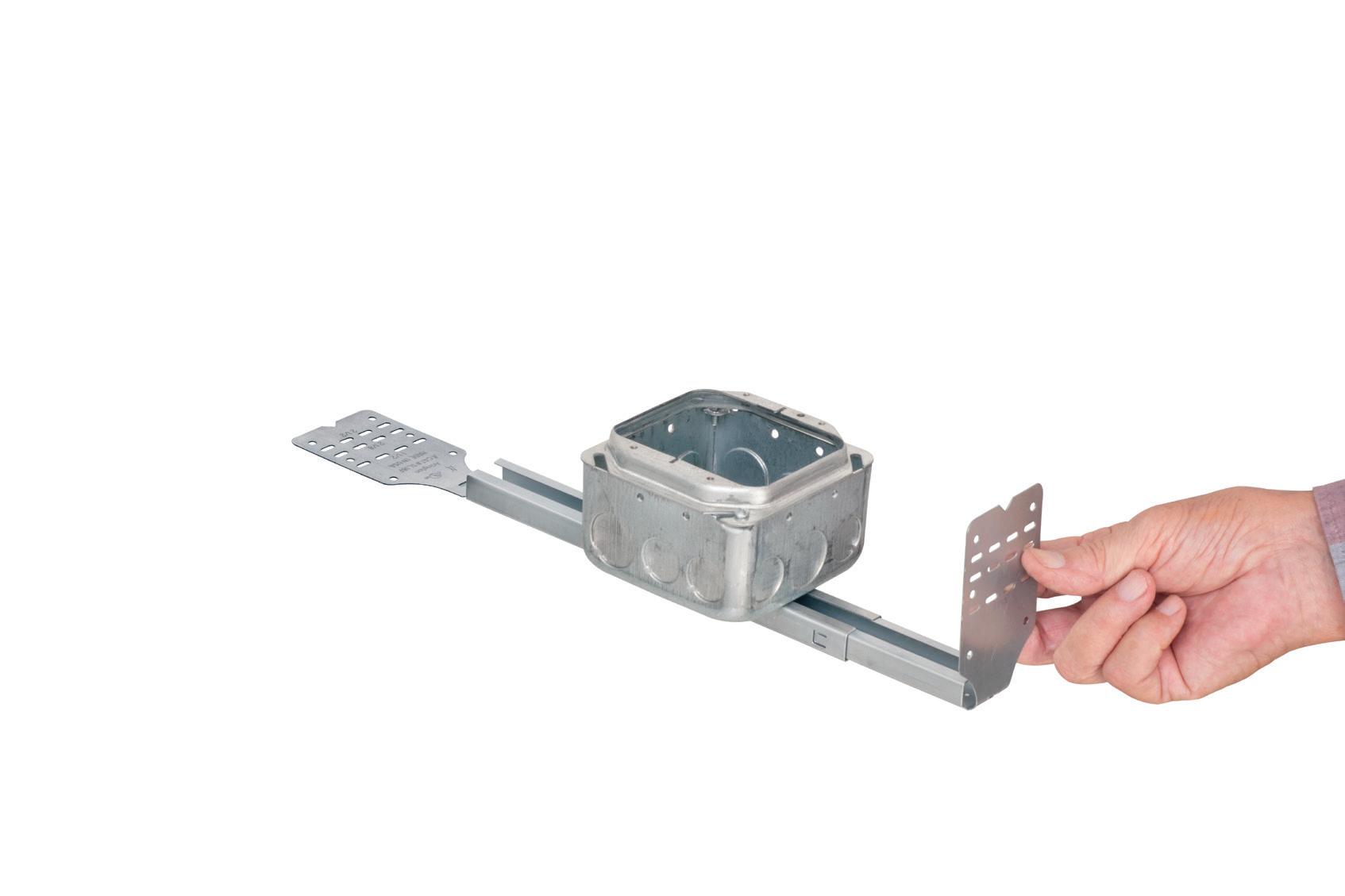
It’s available in two styles – with pre-bent brackets –or FLAT BRACKET ends. And in two adjustable sizes for studs spaced 12 to 18 inches – or 15 to 24 inches apart.
The extra convenient SliderBar with FLAT brackets comes with a steel mounting bracket for installing almost any metal box, and our plastic SLB101 and SLB102 boxes, on the bar anywhere in the stud cavity.
Use the SL18BKT mounting bracket.to add another metal box on FLAT SliderBar.
•
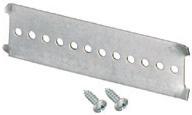
The Electric Tortoise and the Fleet Hare
As rental cars, trucks, buses, and other fleets increasingly go electric, charging infrastructure has emerged as a major roadblock.
Solar, BESS, and load
management offer relief.
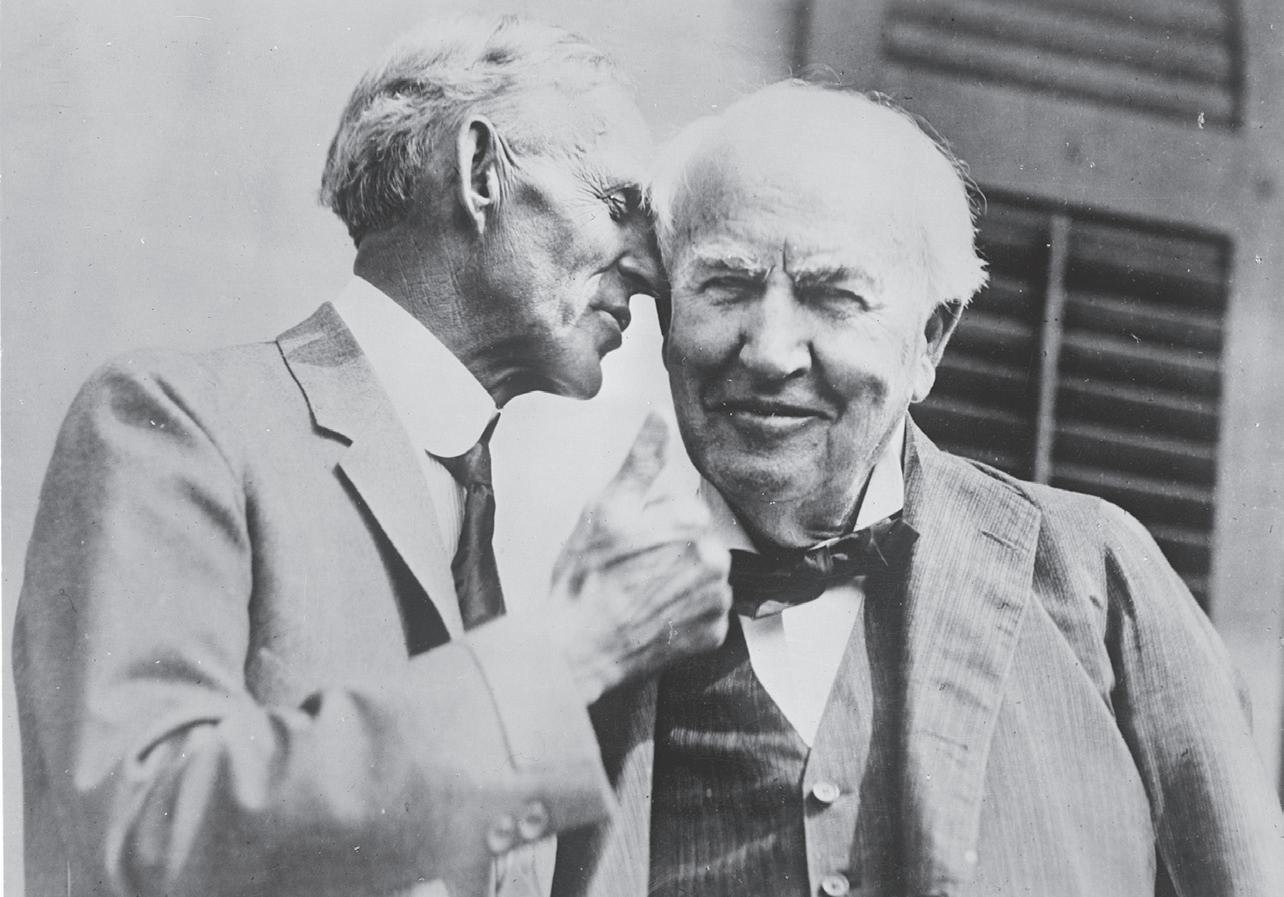
Henry Ford and Thomas Edison were friends for half a century. When he’s making presentations about fleet electrification, Rajiv Singhal includes a slide with a photo of Ford whispering into Edison’s ear. “It’s like he’s saying, ‘Our two industries are going to intersect,’” says Singhal, who leads the zero emissions transportation team at 1898 & Co., Burns & McDonnell’s consultancy subsidiary. “And that’s what’s happening. Transportation never spoke utilities, and utilities never spoke transportation — and now they have to speak those two languages. This picture (Photo 1) is from 1925 (almost exactly 100 years). Who would have thought this was going to happen?”
But these days, fleet electrification projects often feel like they’ll take another century to complete. Although the selection of electric delivery vans, terminal tractors, trailers, buses, rental cars, and trash trucks keeps growing, charging remains a significant roadblock — not just long charging times and the paucity of public chargers, but also the difficulty getting them installed at the business’ own facilities.
“Charging infrastructure may be one of the longest lead time components of our decarbonization plan for last-mile delivery vans,” says one executive, speaking on background, whose company currently has chargers at more than 100 of its depots nationwide.
Electrical contractors and design firms are turning this problem into a business opportunity by identifying ways around some of the roadblocks so projects can move forward rather than being shelved. In addition to helping clients, some firms also are extending this consultancy role to electric utilities for grid planning. In fact, one
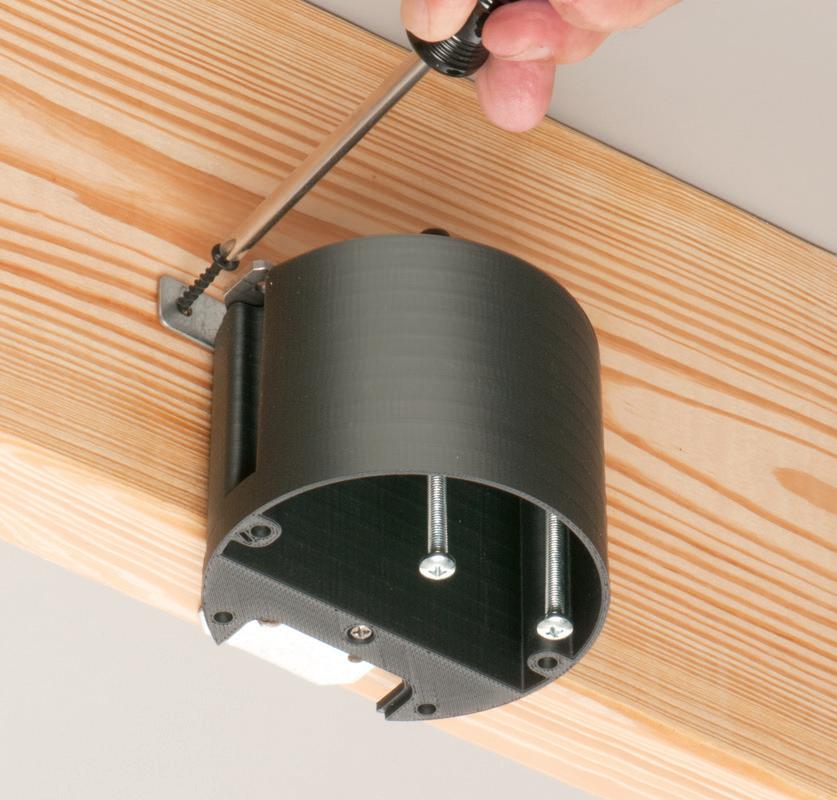
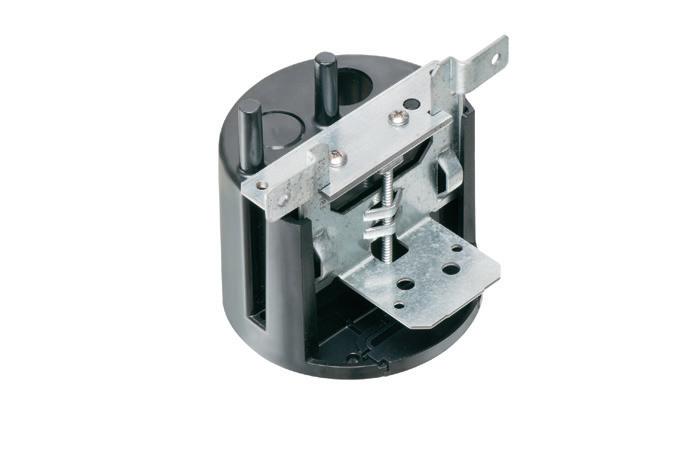
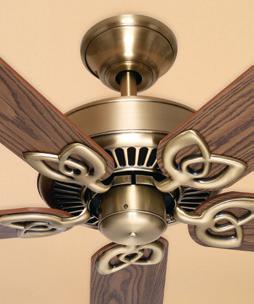
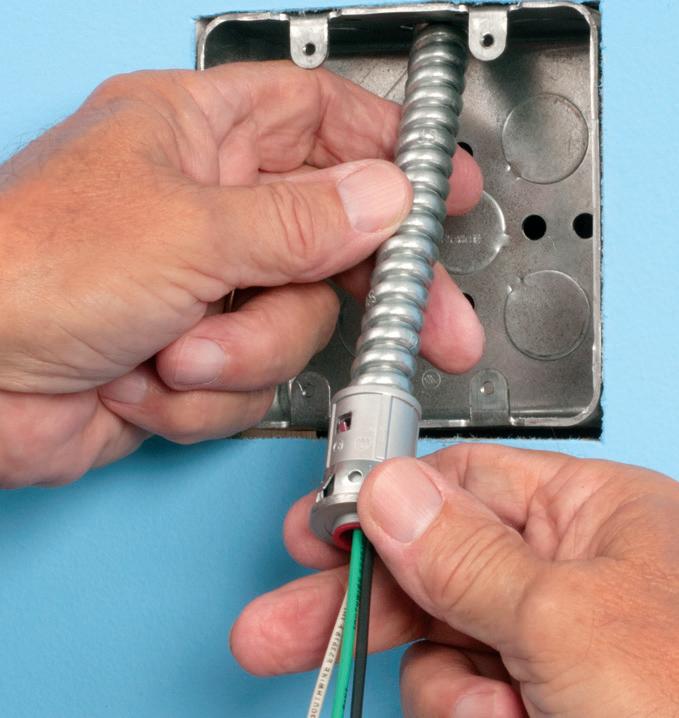
Arlington’s IN/OUT™ fan/fixture boxes adjust up to 1-1/2" to accommodate varying ceiling thicknesses, like single or double FBA426 is Listed for fans up to 70 lbs; fixtures up to 100 lbs.
Pre-set for 1/2" ceiling – depth adjustment screw positions the box flush with the ceiling after it’s in place Complies with 2020 NEC, 314.20 for set back boxes
• (4) screws attach box securely to joist in new work
• 2-Hour Fire Rating
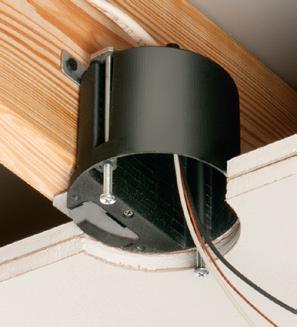
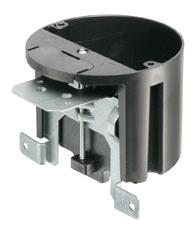
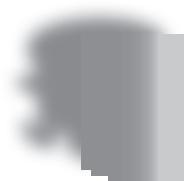
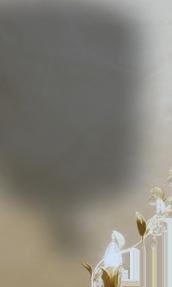
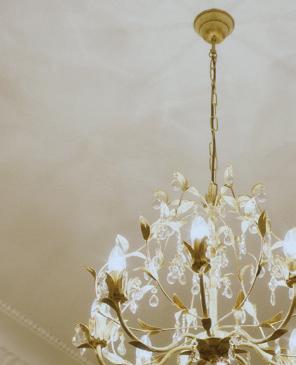
Arlington’s new one-piece RETROFIT
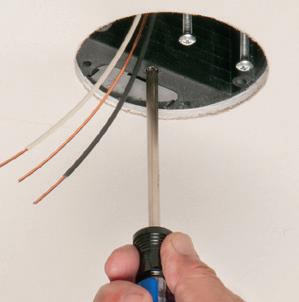
1
2


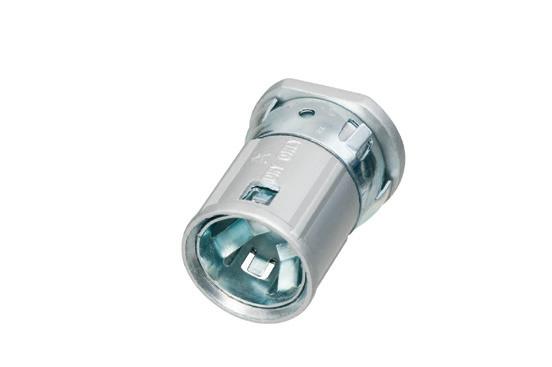
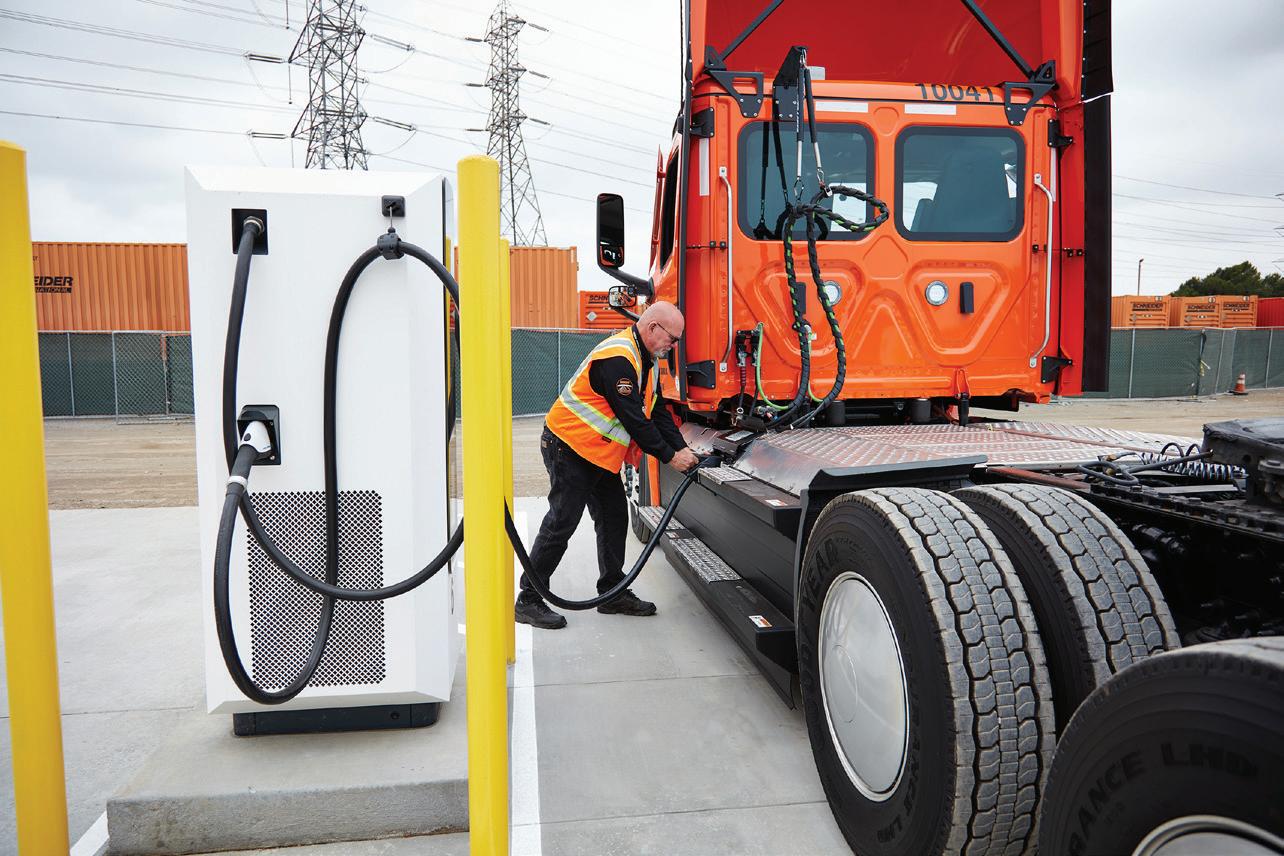
CODE EVOLUTION AFFECTS OPTIONS
The National Electrical Code (NEC) provides guidance about sizing a system.
“It’s a rather straightforward calculation: however many [chargers] you need times the load of the charger, and that’s what the Code is going to make you do,” Orcutt says. “You have to take 125% of that because, in some cases, it’s considered a continuous load — meaning it goes longer than three hours.”
The Code is evolving in ways that affect fleet electrification, but opinions vary about whether those changes help or hurt.
“If anything, the Code has gotten more stringent about EV charging instead of more accommodating,” says EnTech’s Waack. Some changes worth noting include the following:
common hurdle is whether the local electric utility can provide enough power to a site to charge dozens or hundreds of EVs.
“Utility lead times continue to be one of biggest challenges facing this industry,” says Geri Waack, director of eMobility solutions at EnTech Solutions, a division of Faith Technologies Incorporated (FTI). “We’ve seen providers have power available almost immediately, while others have lead times of 18 months or more.”
In some cases, the necessary infrastructure isn’t in place because the client’s facility is in a remote area, such as a sprawling new logistics park on the outskirts of town where land is cheaper. Closer in, the nearby substations and lines often are maxed out.
“I’ve heard places where they’re saying it can be three years before they get a connection,” Singhal says.
ALTERNATIVES TO AN ALTERNATIVE
Electric utility-related challenges, such as grid constraints and demand pricing, have some fleet owners considering workarounds to keep their electrification plans on track (Photo 2). Later, some of these short-term solutions can be expanded and upgraded for the long haul if they make good business sense.
“Alternative energy options, such as solar, battery energy storage, and microgrids, allow clients to offset utility demand and pricing, as well as create grid independence,” Waack says.
Lenexa, Kan.-based Henderson Engineers currently has two projects where the required amount of power is several miles away.
“They’re having to bring in new utility lines that far to supply the load,” says Clif Orcutt, electrical technical manager. “So, we are considering doing some onsite battery storage for other reasons, as well, one of which is to offset the utility peak demand. It’s not enough to totally account for all the EV charging, but the owner can expand on that later if they decide that it’s worth the investment.”
One deciding factor is how many EVs need to be charged.
“Solar does not cut the [utility] bill because, depending on the fleet size at that given site, it may not be enough solar to fulfill that demand,” says 1898 & Co.’s Singhal. “Battery storage is expensive. It’s good for peak shaving. But if you have to run an operation for, say, eight hours, batteries will be very expensive.”
Even for major businesses, a battery energy storage system (BESS) capable of charging dozens of vehicles can be cost prohibitive.
“From what I’ve seen, the installed cost is about $1 million for a megawatt,” Orcutt says. “That is definitely a barrier to entry, and that’s not including the cost of the solar panels to charge those batteries. PV [photovoltaic] has been around for a while, and batteries have too. But specifically in this application, batteries are the newer technology — so it’s tough to get a price on those at this size.”
• Section 625.42: Elaboration on charger management software and engineers’ ability to downsize services and feeders if it is used.
• Section 625.44(B): Expanded allowable amperages for mobile chargers.
• Section 625.49: Allows “island mode” where EV chargers are allowed to export power and operate off-grid.
• Section 625.54: Requiring GFCI protection on receptacles used for EV charging; leads to more expensive but safer installations.
Others say Code changes are providing flexibility that could make some projects viable.
“The latest NEC is starting to build in compliance methods that include a load management system,” Orcutt says. “Basically, a control system says: ‘We’ll never charge more than X.’ If there are too many chargers plugged in at once to do all of that load at 100%, either they stagger some on or off, or they reduce charging on all of them.”
Some systems can provide additional flexibility by managing other electrical devices around a facility rather than just the chargers. For example, if a garage door opener isn’t in use, the allotted amperage load for that device can be redirected to the charging station. When someone needs the garage door to open, the control system will respond by decreasing the power flowing to the charging station.
Sometimes, load management systems can make one location more viable than others (Photo 3 on page 50).
“The client may come to you with six sites they’re considering,” Orcutt

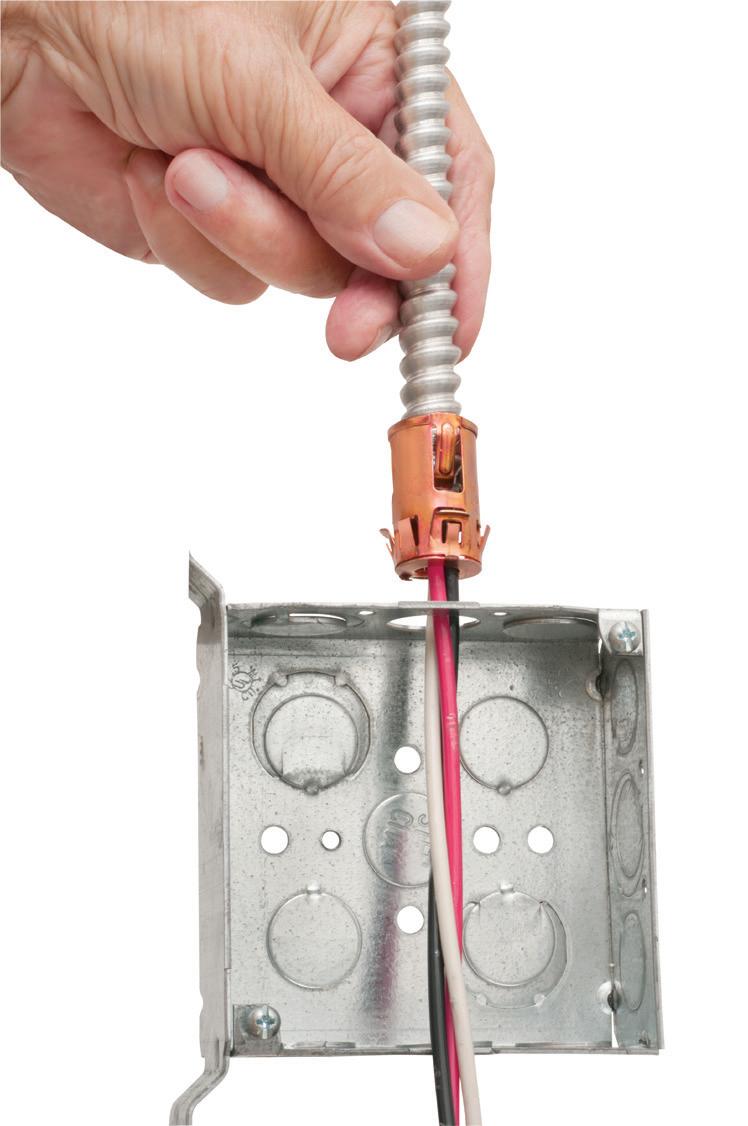
Snap 2it® connectorS

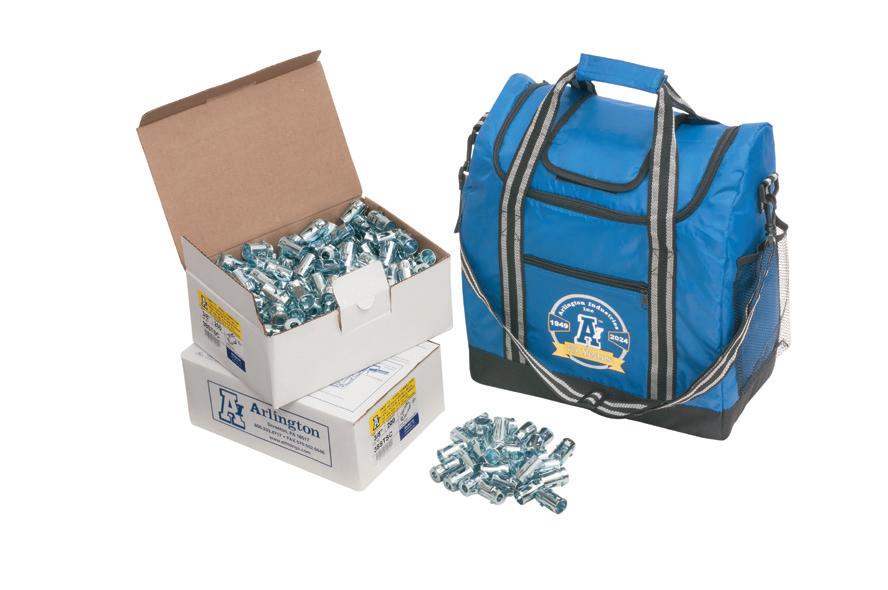
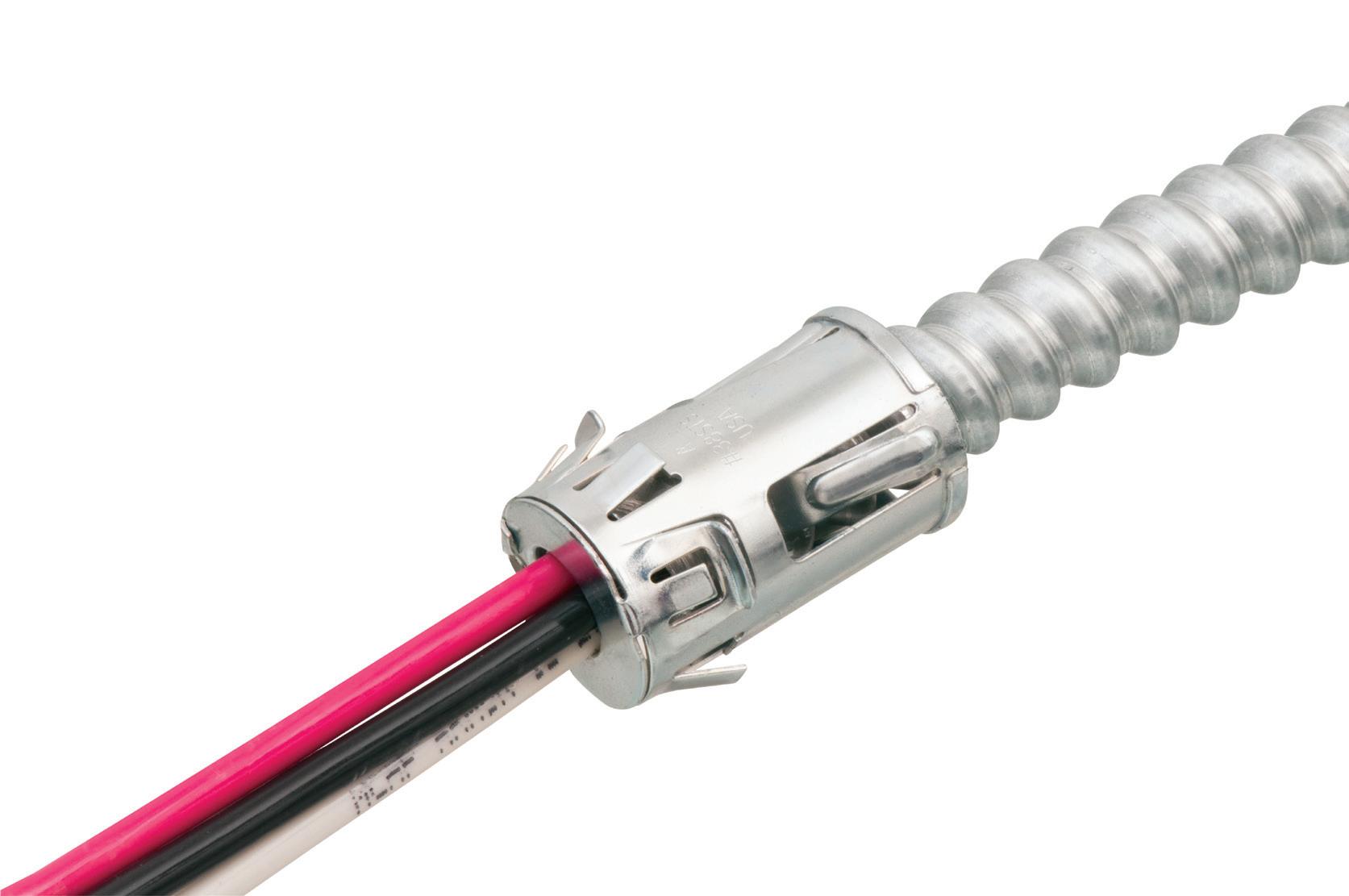
steel connectors offer easy, secure installation. And save time! Just push the cable into the connector and rotate the connector clockwise.
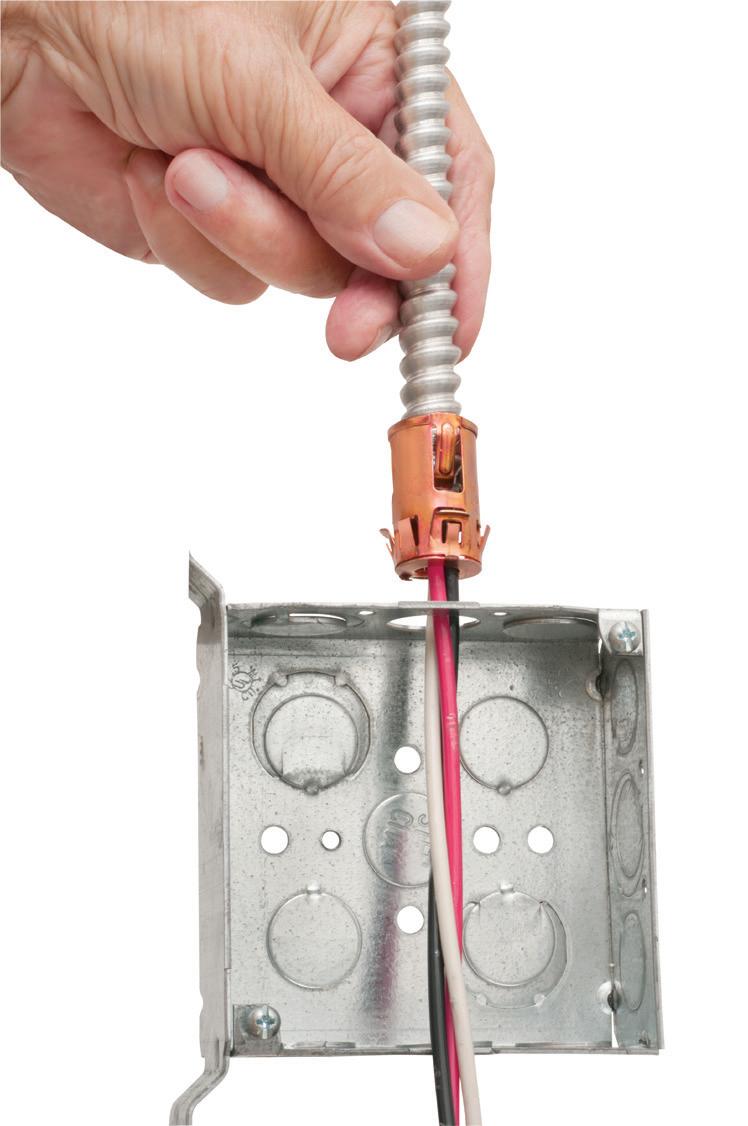

5 YEARS 7
Available in 3/8" trade size, both connectors install into a 1/2" knockout, and are Listed for steel and aluminum AC, HCF, MCI and MCI-A cable.
The tinted 40STS has more room inside for easier cable insertion.

for use with AC90 and ACG90 cable.
• Tested to UL 514B and Listed to meet UL ground fault requirements
• Removable Unscrew the connector counterclockwise to remove it from the cable. Remove the connector from the box using a flat blade screw driver. Release the snap tangs from the inside of the box while pulling the connector out of the knockout.
• Packed in heavy-duty, 200-piece boxes
says. “We do a study to tell them for each, here’s what the utility can handle at this time frame, and here’s how we can bring in load management technology to maybe make this site work in the short term rather than years.”
The larger the load, the more likely the project will require a dry utility consultant, which works to ensure that all the necessary utility infrastructure and capacity are ready to go.
“A dry utility consultant knows the [local] utility requirements in and out,” Orcutt says. “We coordinate through them with the utility. It’s more prevalent on the West Coast from what I’ve seen, mainly because those utilities have a lot more strict requirements. It’s kind of almost a specialty.”
This process can include striking a balance between supply and demand.
“We can have discussions with utilities on how the business plans on charging their vehicles on a schedule, let’s say, and how that interacts then with the other electric loads happening on the grid at that same time,” Orcutt says. “There can be an agreement that gets made there as far as the capacity of equipment and power delivered to the site. Instead of looking at just one block [of time or] peak demand number, you’re looking at more of the energy profile through a day and/or through a year.”
THE RANGE FACTOR
Each type of fleet has its own business drivers for electrification, but some apply across the board.
“From a cost and operational standpoint, fleet operators are motivated by the potential for long-term cost savings on fuel, maintenance, and operational expenses, as well as increased operational efficiency due to their quiet operation, reduced maintenance needs, and improved efficiency in stop-and-go traffic,” says Jeffrey Kinsey, vice president of engineering at EverCharge. “EVs are also becoming more accessible and available, and government incentives, tax credits, and grants for EV adoption are also playing a role in encouraging fleet electrification.”
Some types of vehicles are better candidates for electrification than others because of how and where they’re used. For example, terminal tractors move trailers around a seaport or logistics park but never take them across town or across the county. So a transportation
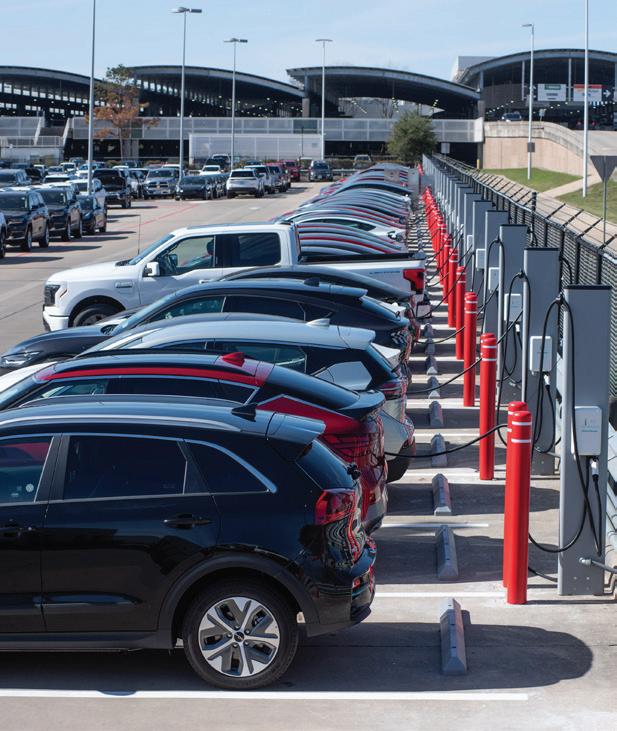
RENTAL RIPPLES INTO RESIDENTIAL
Electrification in the passenger vehicle market is further along in terms of selection, adoption, and public chargers, but it’s still a niche compared to internal combustion engines (ICEs). That could give rental fleets another reason to add even more EVs — and benefit electrical contractors serving the residential market. For example, in November 2021, Hertz ordered 100,000 Teslas to make 20% of its fleet electric. However, in more recent news, Hertz announced it was selling about 20,000 electric vehicles (including Teslas) from its U.S. fleet as EV demand cools.
company might choose to electrify its terminal tractors first because they’ll always have access to chargers on site.
The business case for local delivery vans and long-haul trucks is more challenging. At a November 2023 conference, J.B. Hunt Vice President and Chief Sustainability Officer Craig Harper summarized the pros and cons.
“We have five today, and drivers love them,” he said. “They are quiet and powerful, but there are problems. You don’t have the range; that is one-fifth of what diesel provides. It also weighs more, and it takes longer to charge.”
Harper also cited research showing that 21% of public charging stations are down at any given time — a big barrier to adoption that gets even bigger when you consider that there aren’t that many to begin with. As an October 2023 EC&M story found, major truck stop operators such as Love’s are struggling with many of the same challenges as their customers: getting enough power and demand charging. That’s why some truck stop operators are considering solar and BESSs.
Another barrier to the electrification of long-haul trucks is that truck parking is in chronically short supply. That’s why so many drivers resort to camping out on highway on and off ramps when they reach their federal hours-of-service limit.
“A big portion of today’s truck parking network — about 40,000 spaces — is at rest areas on the interstate where commercial activity isn’t allowed,” says Jeffrey Short, American Transportation Research Institute (ATRI) vice president. “That’s a federal law, so there aren’t going to be chargers at those locations anytime soon.”
“Data from IHS that says that people have a tendency to rent cars to try new technology, so it makes sense that rental cars should be electric,” says Ben Prochazka, executive director at Electrification Coalition, which partnered with Enterprise on a study into the EV rental market.
The rental electrification trend also could spur even more demand for home chargers.
“Rentals tend to be big volume sellers in the used car market,” Prochazka says. “That creates an opportunity for used EVs to be much more available.”
Besides growing consumer interest in renting EVs, another driver is government incentives for fleet owners.
“In the Inflation Reduction Act, there are big incentives for charging infrastructure: up to $100,000 available on a per-unit basis,” Prochazka says. “That’s going to help reduce some of those cost barriers that might exist in the short term. Some states have additional infrastructure incentives or additional vehicle incentives, like in California, where they have an additional tax credit that’s available. Colorado [is another] example.”
Finally, some electrical contractors and design firms are leveraging their fleet electrification experience to help utilities plan grid upgrades that need to accommodate more than home charging.
“Lots of utilities are asking us today: ‘Tell me about this new EV load and how/what can I do to prepare myself. I need to build the rate case plan. I need to put [in] infrastructure for the next five, 10, 15, 20 years,’” says 1898 & Co.’s Singhal.
Kridel is an independent analyst and freelance writer with experience in covering technology, telecommunications, and more. He can be reached at tim@timkridel.com.

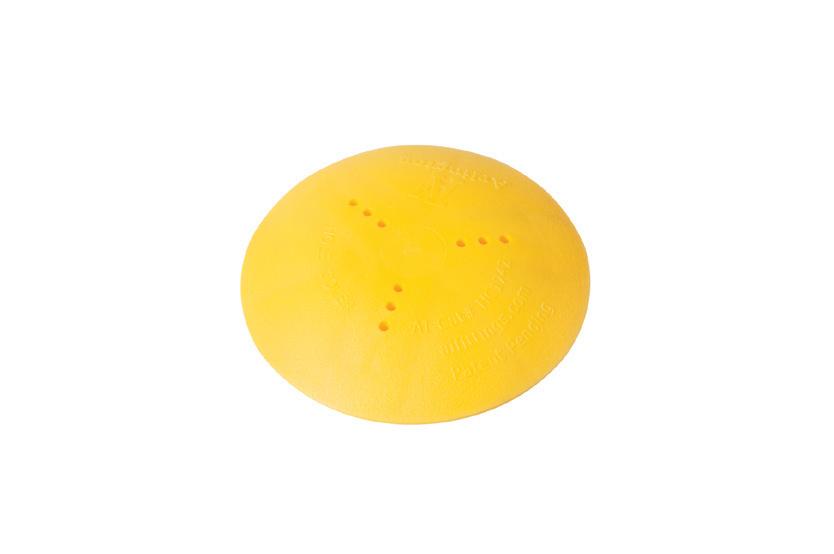
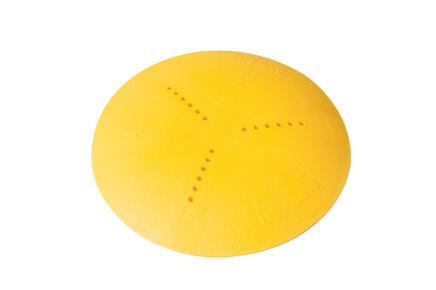
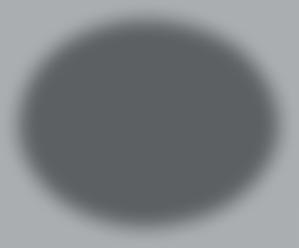

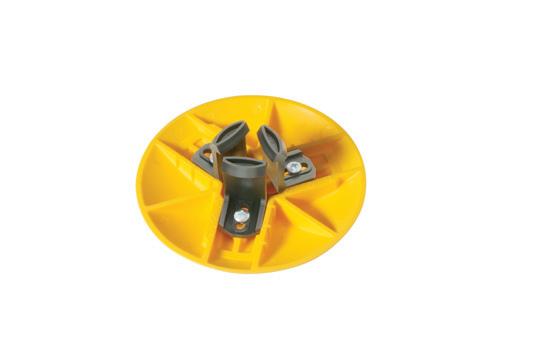

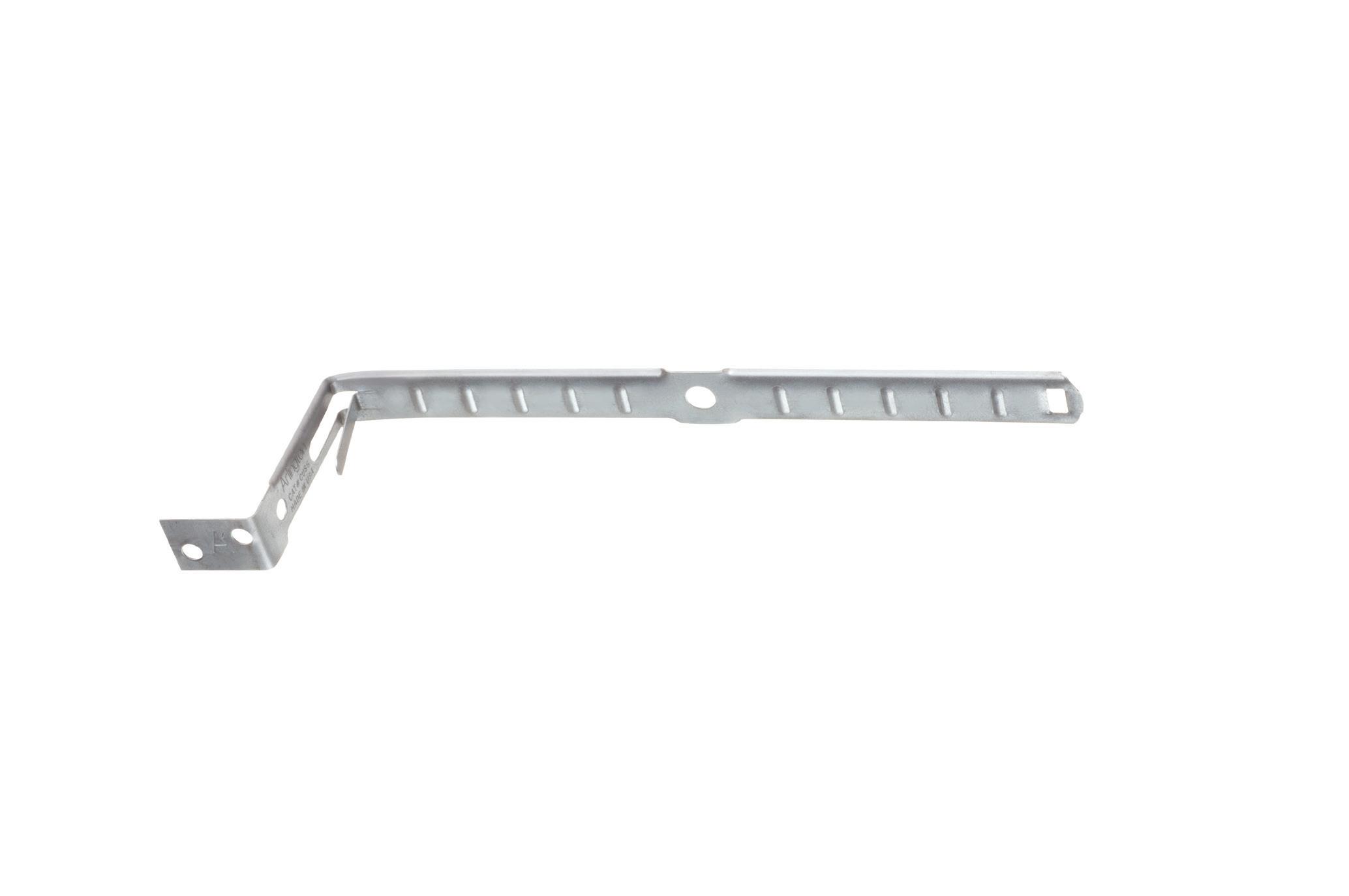
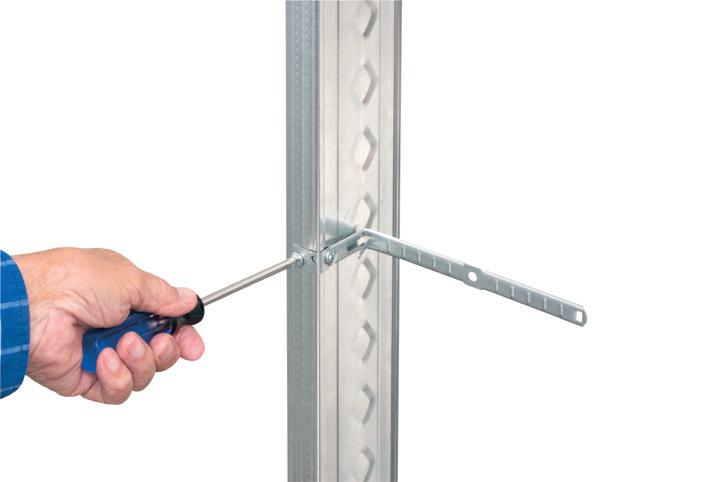

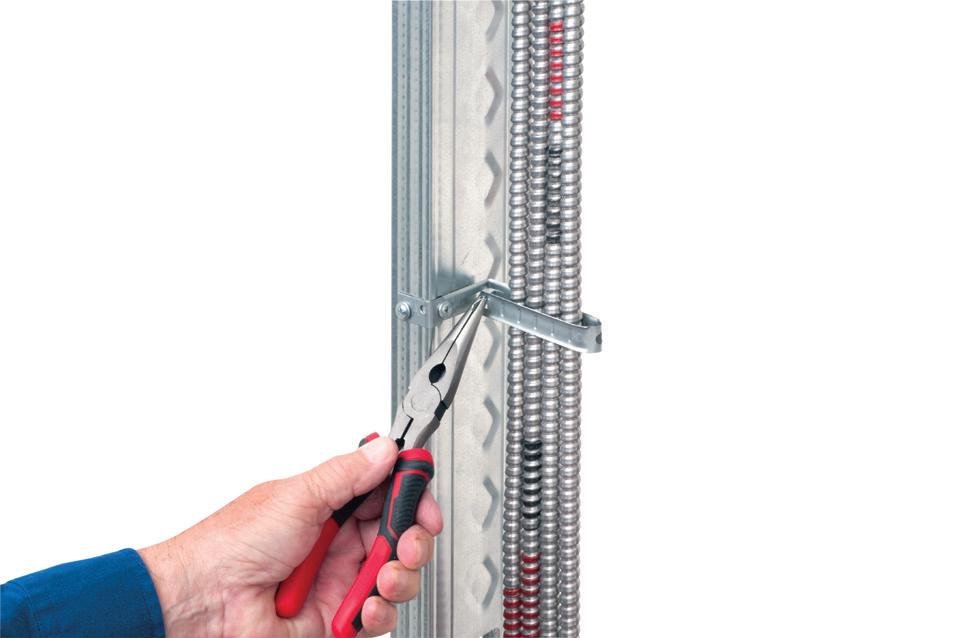

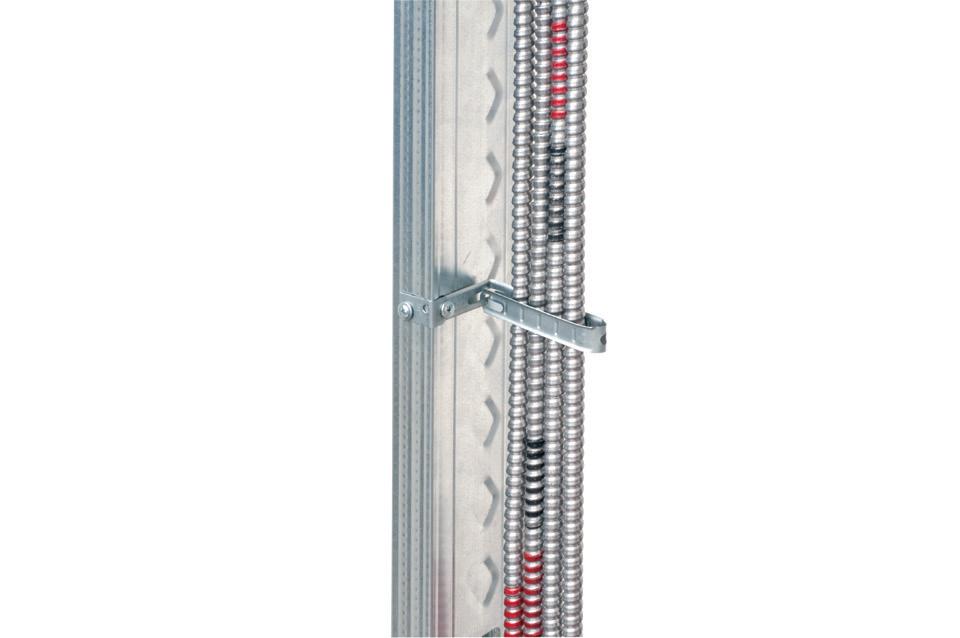
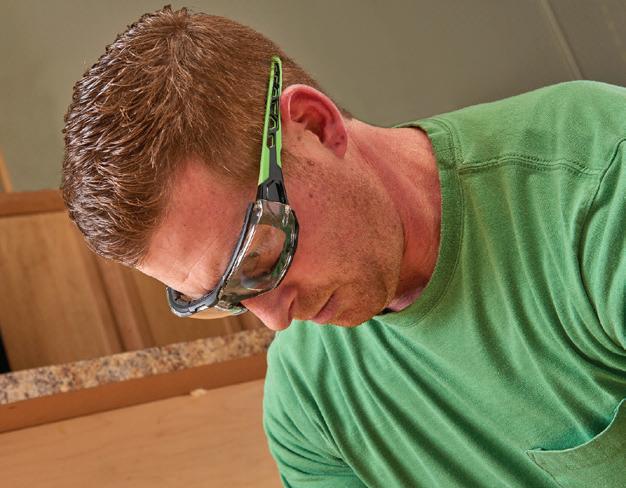
Protective Eyewear
Grasshopper eye protection combines comfort features with a wall of protection against dust, dirt, and fog. A soft EVA foam dust filter with built-in air channels fills the gap between the glasses and the face, keeping dust out. These goggles feature a removable dust gasket to allow for quick conversion into standard protective eyewear. In addition to a clear lens, it is available in a smoke lens option for normal outdoor conditions (18% of light passes through), while indoor/outdoor clear mirror lenses provide all-around tint for protection from the glare of bright artificial lighting and sunlight (50% of light passes through). For extra safety, it is fully dielectric with no metal anywhere in its construction, according to the company.
Brass KnuckleSelf-Retracting
Lifeline
The CR3-Edge personal self-retracting lifeline (SRL) is a robust, 8-ft, Class 2 SRL created for applications where the connective device of the fall protection system has potential to impact the edge of the hazard in the event of a fall. Key features include overhead and foot level tie-off options to optimize usage in a wide range of applications; an extra-large protective shock pack cover; Class 2 fall clearance charts integrated into the shock pack; and a digitally enabled QR code on the housing links to the website product page for instant access to the instruction manual, technical data sheet, compliance documentation, and other important product information. Guardian

Electric Service Tool Kit
The automotive electric service tool kit is a base of insulated tools for use with hybrid and electric vehicles (EVs) as well as troubleshooting and repair to EV charging stations. Stored in a standard toolbox, the tool kit includes the company’s double-insulated diagonal cutting, needle nose, slip joint, crimping, and water pump pliers as well as a variety of doubleinsulated cushion grip screwdrivers. The company’s tools are tested to 10,000VAC, rated for 1,000VAC/1,500VDC when working on energized parts, and marked with the (double-triangle) international safety symbol.
Cementex
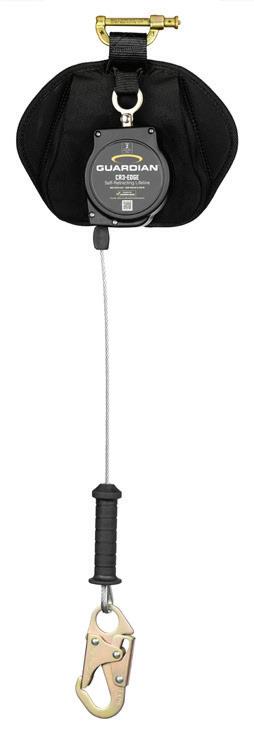

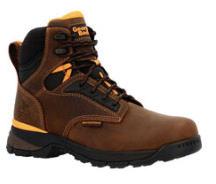
Work Boots
The TBD (Tougher Beyond Dispute) collection features protection and support in a lightweight, flexible boot design. Styles include: a waterproof Chelsea work boot that meets ASTM F2892 electrical hazard standard for soft toe work boots; a midheight lace-up with a soft toe that meets ASTM F2892 electrical hazard standard for soft toe work boots; a mid-height lace-up featuring an ergo-fit safety toe compliant with ASTM F2413 protective toe classification and ASTM F2413 electrical hazard standards; and a waterproof wellington pull-on that meets ASTM F2892 electrical hazard standard for softtoe work boots.
Georgia Boot
Oscillating Blade

The universal fit carbide oscillating blades feature application specific designs that, according to the company, deliver extreme durability and superior cutting life in metals. High-performance carbide teeth deliver up to 50 times longer cutting life versus standard bi-metal blades. An optimized blade and tooth design along with Black I.C.E. (industrial cooling element) keeps the teeth cool and buildup free for fast, clean cuts. The blade has a 1.5-in. cutting depth, and its universal fit, adapter-free design allows it to attach to most tools.
Diablo Tools
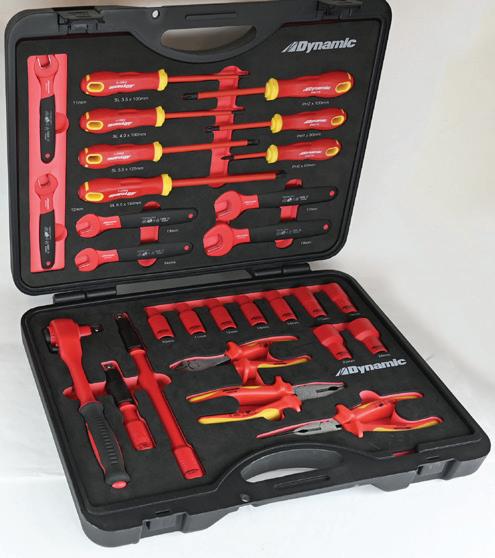
Insulated Tool Set
The company’s 28-piece insulated tool set is designed to meet the needs of commercial and residential electricians, industrial maintenance professionals, mobile/field service technicians, and EV mechanics. Each tool within the set has been tested to 10,000AC and is VDE certified to 1,000VAC in compliance with IEC 60900. The insulated tool set includes a ½-in. drive ratchet with a selection of extensions and six-point metric sockets. It also contains open-ended metric wrenches, slotted screwdrivers, Phillips screwdrivers, side-cutting pliers, lineman’s pliers, and long-nose pliers. For secure storage, the set comes with a lockable case.
Dynamic Tools

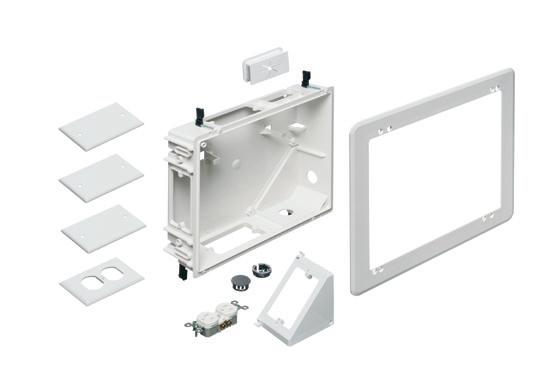
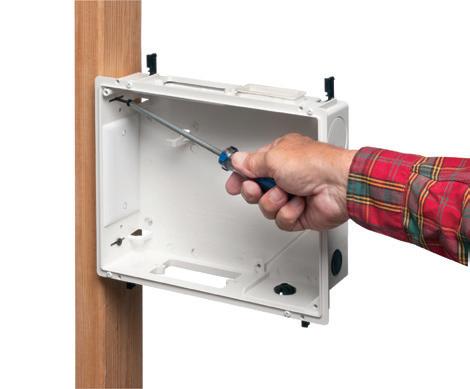
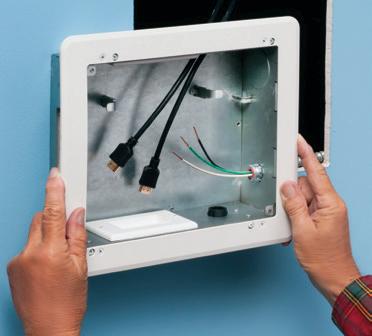




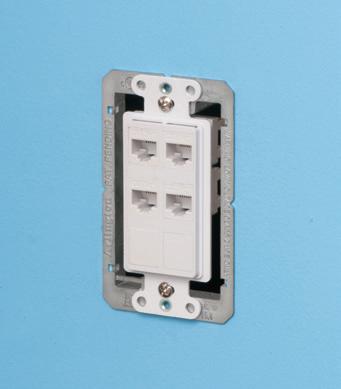

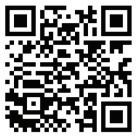
PRODUCT NEWS

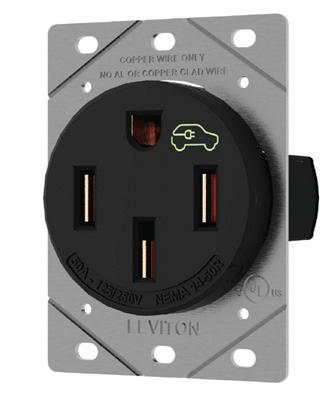
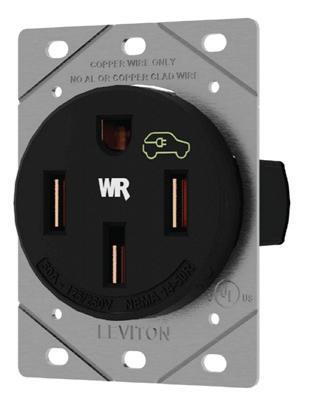
Gas Nailer
The FORCE ONE gas nailer is compact, light, and offers 105 J of power. Able to nail both premium and regular nails from 13 mm to 38 mm in length, the FORCE ONE can fix all of the company’s nailer accessories directly onto materials, including steel beams, concrete, and concrete blocks. According to the company, the FORCE ONE has an improved position of the gas cell, providing enhanced balance to the tool for better stability during usage. Also, the slim and long one-piece nose enables use in narrow spaces. In addition, the gas nailer fixes 2.8 nails per second and can drive 3,000 nails per battery load.
CeloClamp Meter and Thermal Imaging Camera
The FLIR CM276 is a professional clamp meter with infrared imaging, a visual camera, and solar photovoltaic (PV) direct current (DC) built for electrical test and measurement. The CM276 allows electrical professionals to troubleshoot electrical system components with infrared guided measurement technology and radiometric multispectral dynamic imaging (MSX), which overlays visible camera details onto the thermal image, helping users safely execute inspections and identify hazards before contact is made. Built into the CM276 are a 160 × 120 thermal resolution Lepton thermal camera module, a visible camera, and an LED work light for illuminating dark cabinets and spaces. Everything is housed inside a ruggedized casing that is IP40 rated and drop-tested up to 2 m. The clamp meter includes in-device rechargeable lithium polymer batteries for all-day use.
Teledyne Flir

EV Charging Receptacle
The new industrial grade 50A heavy-duty EV charging receptacle is a solution to power today’s plug-in electric vehicle charging stations. The receptacle is designed to sustain the necessary extended charge time and high frequency of insertions required by plug-in EV chargers. A weather-resistant model is available for outdoor use. The receptacle is built of durable high-impact nylon and features heavy-gauge, high-performance copper contacts. Pressure wire terminal connections help to ensure full contact with the conductors, and a high torque value is necessary to ensure proper connection. The device may be used with #4, #6, or #8 AWG copper wire only. Installers may use #10 AWG solid or stranded copper wire for the ground connection.
Leviton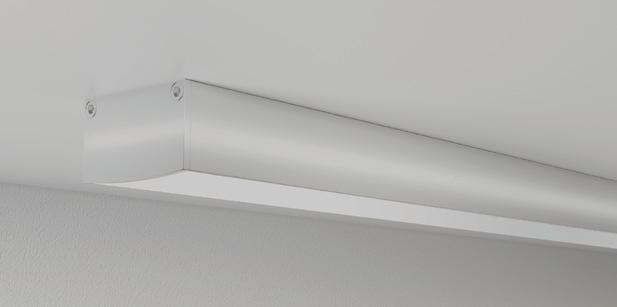
Tape Light Channel
Surfa 8 is a low-profile, surface-mount aluminum channel that provides hot-spot free illumination when paired with nearly all of the company’s tape lights. At 1.14 in. wide and 0.64 in. high, the Surfa 8 channel accommodates 43 of the company’s tape lights, including those for wet locations and RGBW applications. A patented aluminum construction design features countersunk hex hardware, providing a clean, modern look for both indoor and outdoor commercial and residential spaces. The Surfa 8 is shipped in 4-ft and 7-ft kits that include one field-cuttable aluminum channel with a snap-in lens, a two-pair pack of aluminum end caps with screws, mounting clips with screws, and an allen key for complete and easy installation.
Alloy LED
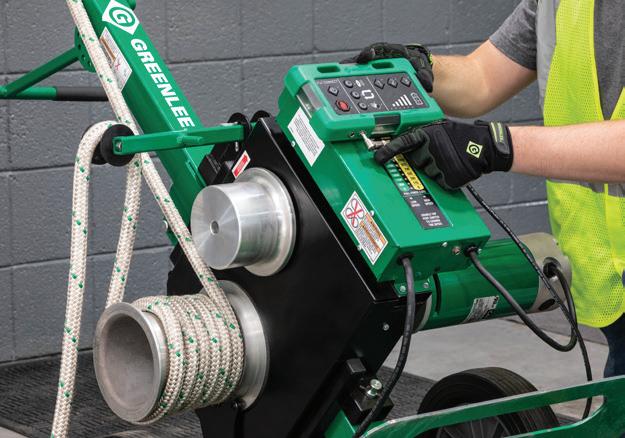
Pulling Accessory
Pull Connect is a pulling accessory that wirelessly synchronizes both sides of a cable pull and allows it to be stopped from either side. According to the company, the easy-to-use design allows cable pulling operators to focus on the pull for enhanced safety and confidence on the job site. The product pairs with the company’s existing pulling equipment and is designed to communicate through walls, floors, and other obstructions for a synchronized pull. Pull Connect units are interchangeable, allowing them to be used in all modes (pull side, feed side, and optional repeater). It is controlled by a foot switch for handsfree operation and provides visual cues to ensure noise is not a factor during pulls. A quick-stop button on the Pull Connect also allows the users further control of the pull.
Greenlee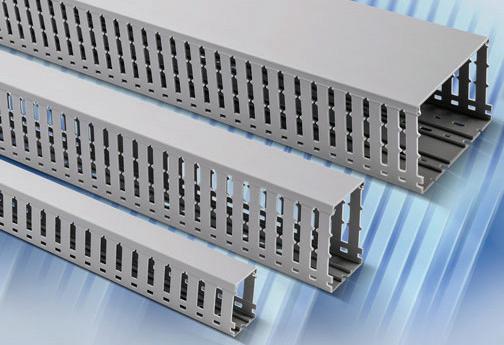
Wire Duct
The company has added the new AchieVe WDW series wire duct that provides more options for easy wire management. This rugged, wide finger, rigid wall wire duct is made of self-extinguishing UL 94 V-0 rated flame-retardant PVC material. AchieVe wire duct features convenient upper and lower score lines to facilitate breaking off individual fingers when extra space is needed for wider cables. The new AchieVe WDW series wide finger wire duct is available in gray, sold in 6.56-ft sections with up to a 6-in. width (cover included).
AutomationDirect
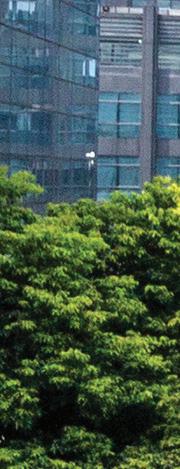

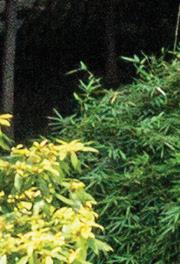
WHERE FACILITY CHALLENGES
FIND SOLUTIONS
CENTRAL VALLEY
March 20-21, 2024
Modesto, CA
NORTHWEST
May 8-9, 2024
Portland, OR
facilitiesexpo. com
SOUTHERN CALIFORNIA
April 17-18, 2024
Anaheim, CA
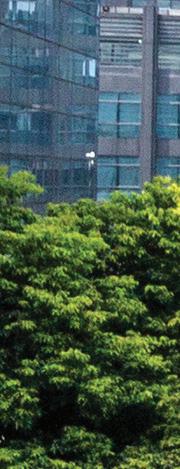

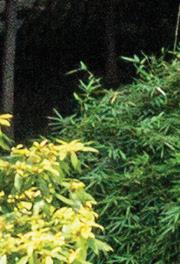
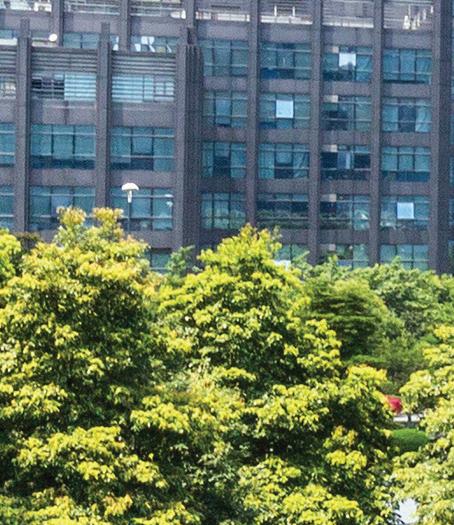
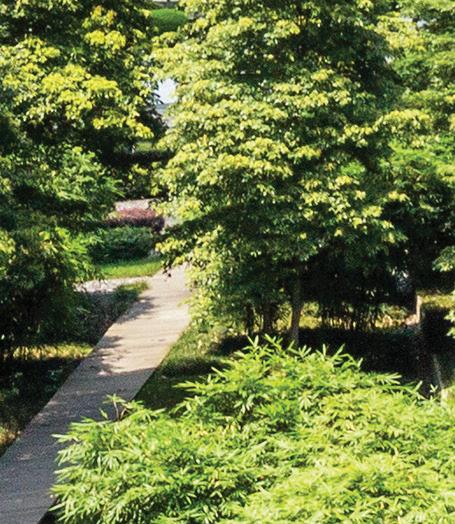
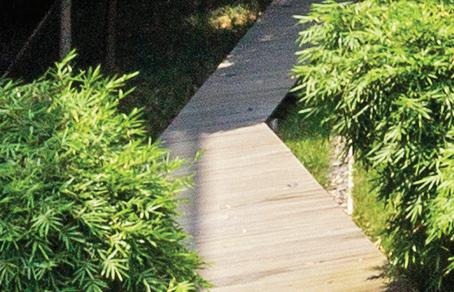
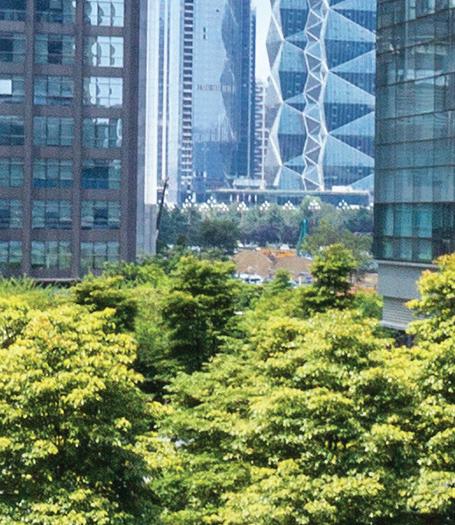
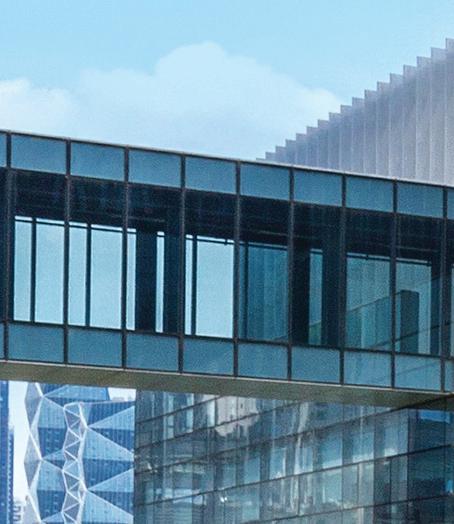
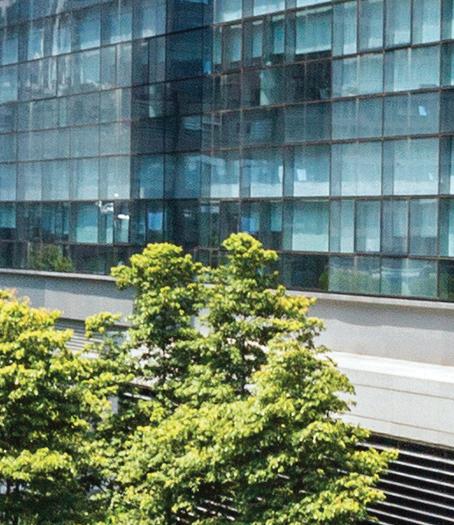
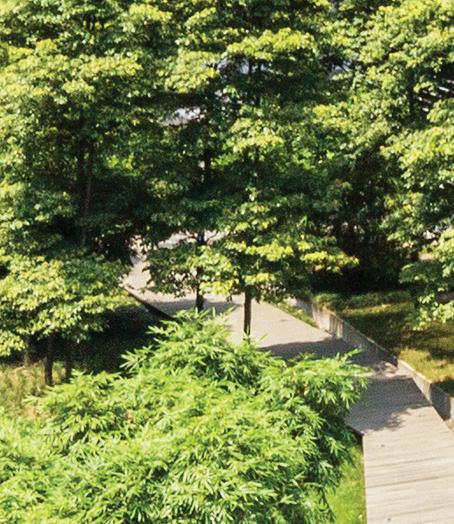
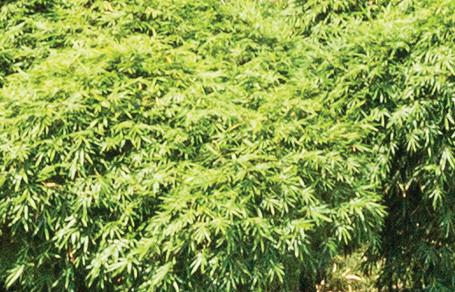
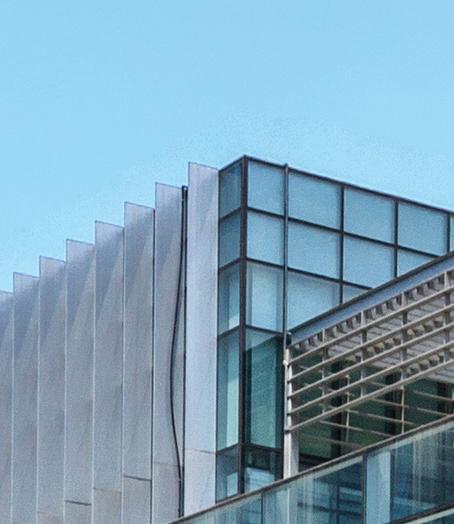
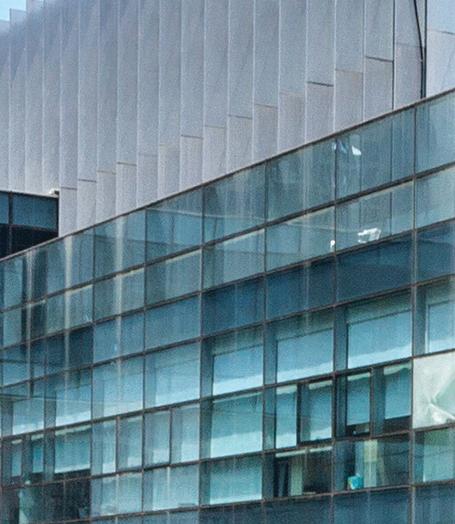

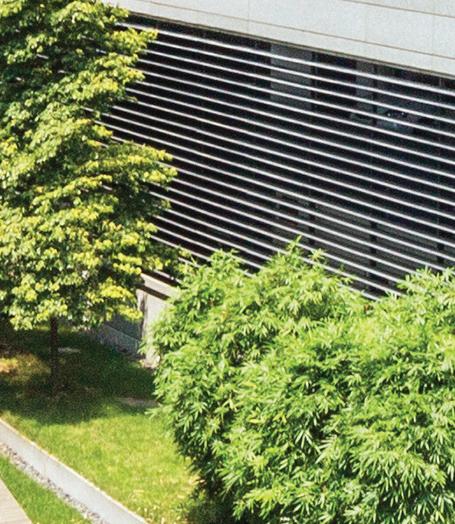
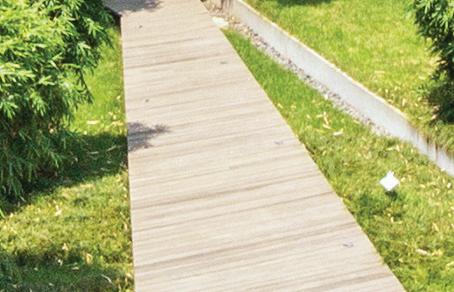
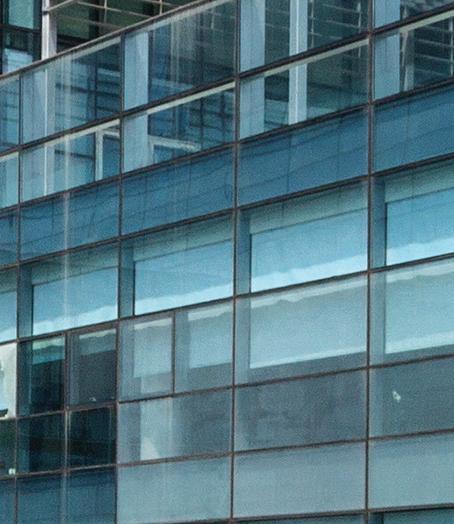
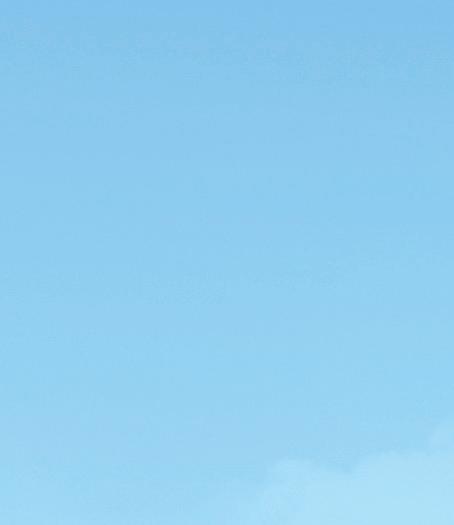

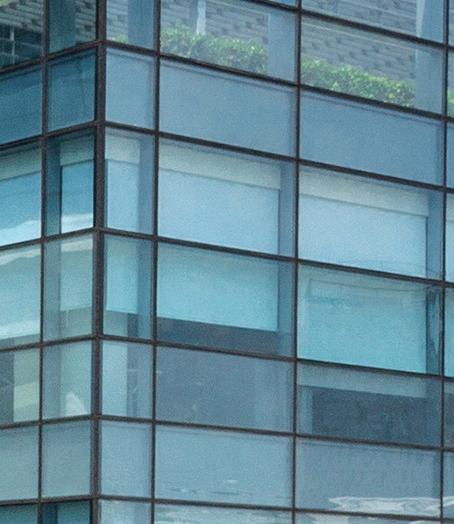
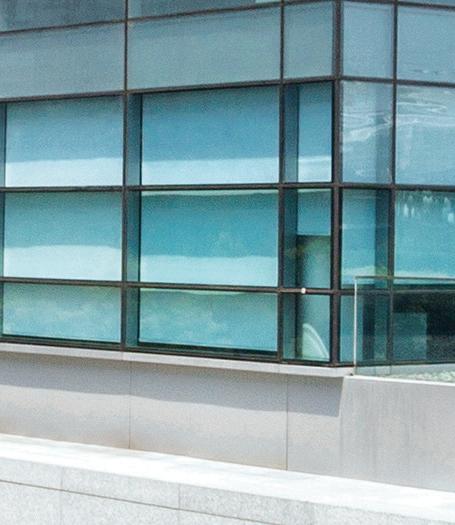
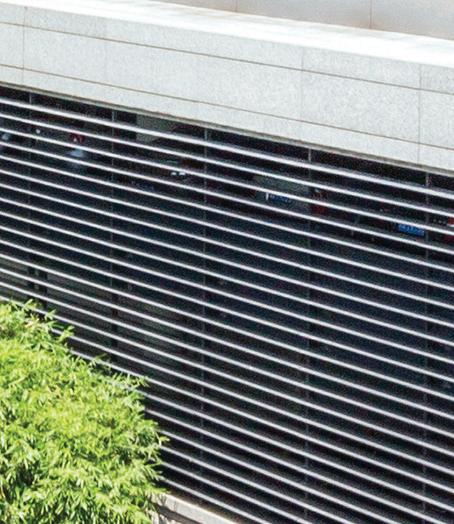
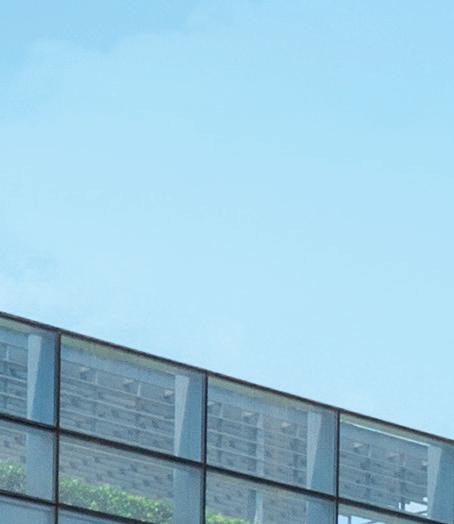
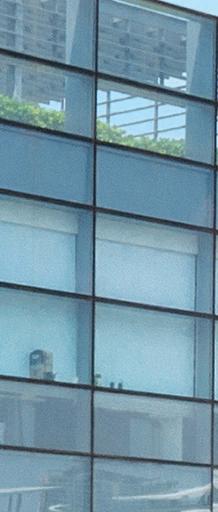

NEC Requirements for Standby Power Systems
Standby power systems “kick in” when the normal power source is interrupted. But which type do you have?
By Mike Holt, NEC Consultant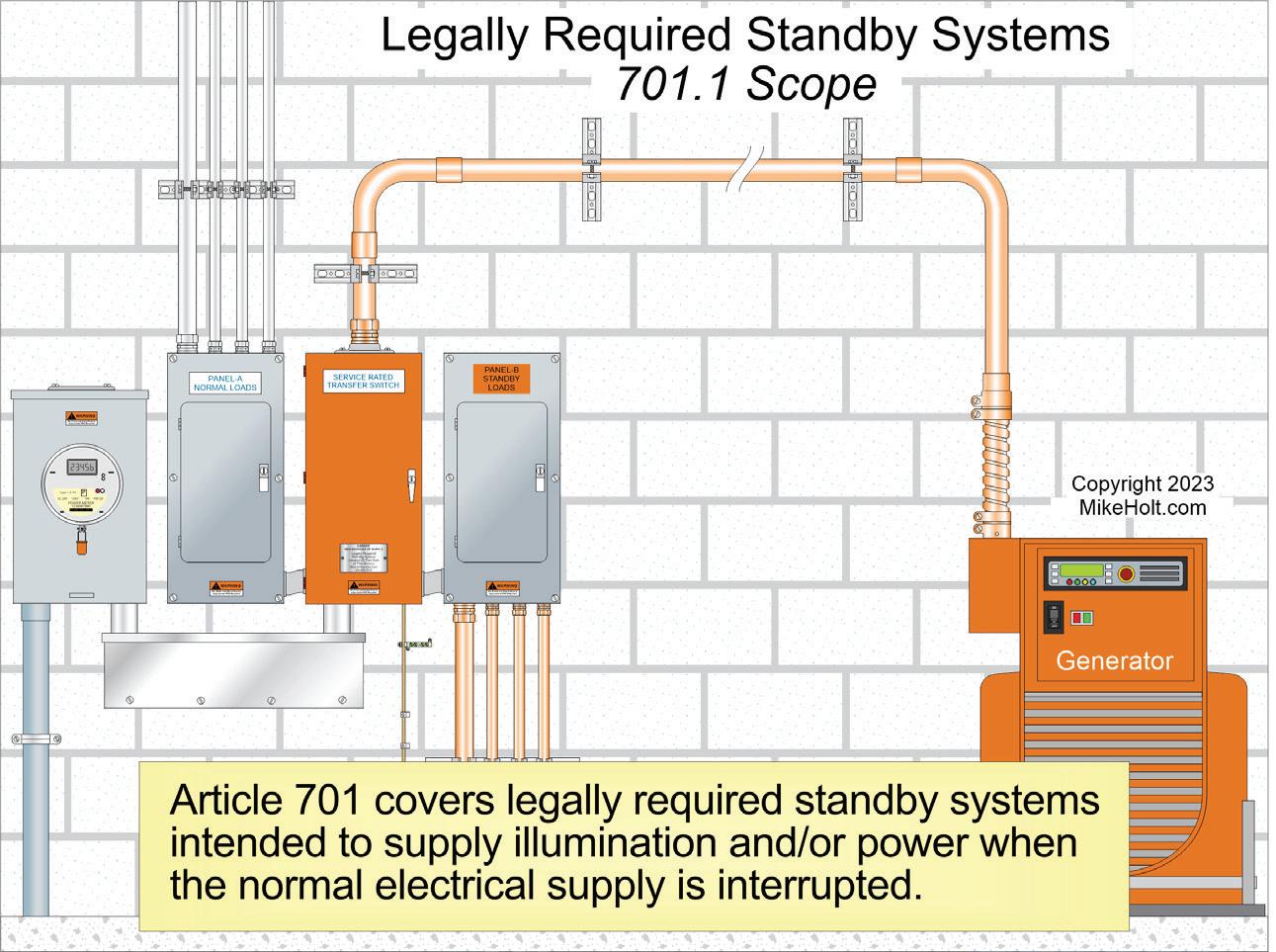
The NEC recognizes three types of standby power systems:
• Emergency systems [Art. 700]. These are generally used to provide power so occupants can safely exit in the event of fire or other disaster. Other uses include providing ventilation essential to maintain life and running fire pumps.
• Legally required [Art. 701]. A government agency requires the facility to have a standby power system, usually due to public safety concerns.
• Optional [Art. 702]. This is a backup the facility owner/operator chooses to have, usually due to financial concerns.
The requirements for each differ, and a single facility could have all three types. Let’s look more closely at legally required systems.
LEGALLY REQUIRED
Article 701 covers the installation, operation, and maintenance of legally required standby systems consisting of circuits and equipment intended to supply illumination or power when the normal electrical supply is interrupted. The goal is to aid in firefighting, rescue operations, control of health hazards, and similar operations (Fig. 1).
Legally required standby systems typically supply loads, such as heating and refrigeration systems, ventilation and smoke removal systems, sewage disposal, lighting systems, and industrial processes that, when stopped, could create hazards or hamper rescue or firefighting operations [Sec. 701.1 Note 4].
COMMISSIONING AND MAINTENANCE
To ensure the legally required standby system meets or exceeds the original installation specifications, the authority having jurisdiction (AHJ) must conduct or witness the commissioning of the legally required standby system upon completion of the installation [Sec. 701.3(A)].
Legally required standby systems must be periodically tested in a manner approved by the AHJ to ensure adequate maintenance has been performed and the systems are in proper operating condition [Sec. 701.3(B)]. Running the legally required standby system under the loads of the facility to make sure power transfers within 60 seconds is often considered an acceptable method of operational testing.
Legally required standby system equipment must be maintained per the manufacturer’s instructions and industry standards [Sec. 701.3(C)]. Part of the NEC-required maintenance is performing overcurrent protective device (OCPD) maintenance (lubrication, testing, etc.) per the applicable standard. This will greatly reduce the chances of malfunction that can result in massive legal and financial liability.
This maintenance must be performed by qualified personnel, which usually means outsourcing the work to a qualified testing firm that has both the personnel and the equipment.
A written record must be kept of all required tests and maintenance [Sec. 701.3(D)]. The NEC does not specify the required record retention period, but it is typical to keep such records in a CMMS where they can reside indefinitely if desired.
CAPACITY AND RATING
Equipment for a legally required standby system must be suitable for the available fault current at its terminals [Sec. 701.4(A)].
The alternate power supply must have adequate capacity per Parts I through IV of Art. 220 or by another approved method. The system capacity must be sufficient for the rapid load changes, and transient power and energy requirements associated with any expected loads [Sec. 701.4(B)].
The legally required standby alternate power supply can supply legally required standby and (also) optional standby system loads if there is adequate capacity (for the extra loads), or where a load management system includes automatic selective load pickup and load shedding; this is to ensure adequate power to the legally required standby system circuits [Sec. 701.4(C)].
TRANSFER SWITCHES
Transfer switches must be automatic, listed, and marked for emergency system or legally required standby system use. Meter-mounted transfer switches are not permitted for legally required standby system use [Sec. 701.5(A)]. Automatic transfer switches must be able to be electrically operated and mechanically held [Sec. 701.5(C)]. The short-circuit current rating of the transfer switch must be field marked on the exterior of the transfer switch [Sec. 701.5(D)]
SIGNALS AND SIGNS
Audible and visual signal devices must be installed where practicable to indicate [Sec. 701.6(A) through (D)]:
• A malfunction of the standby source of power.
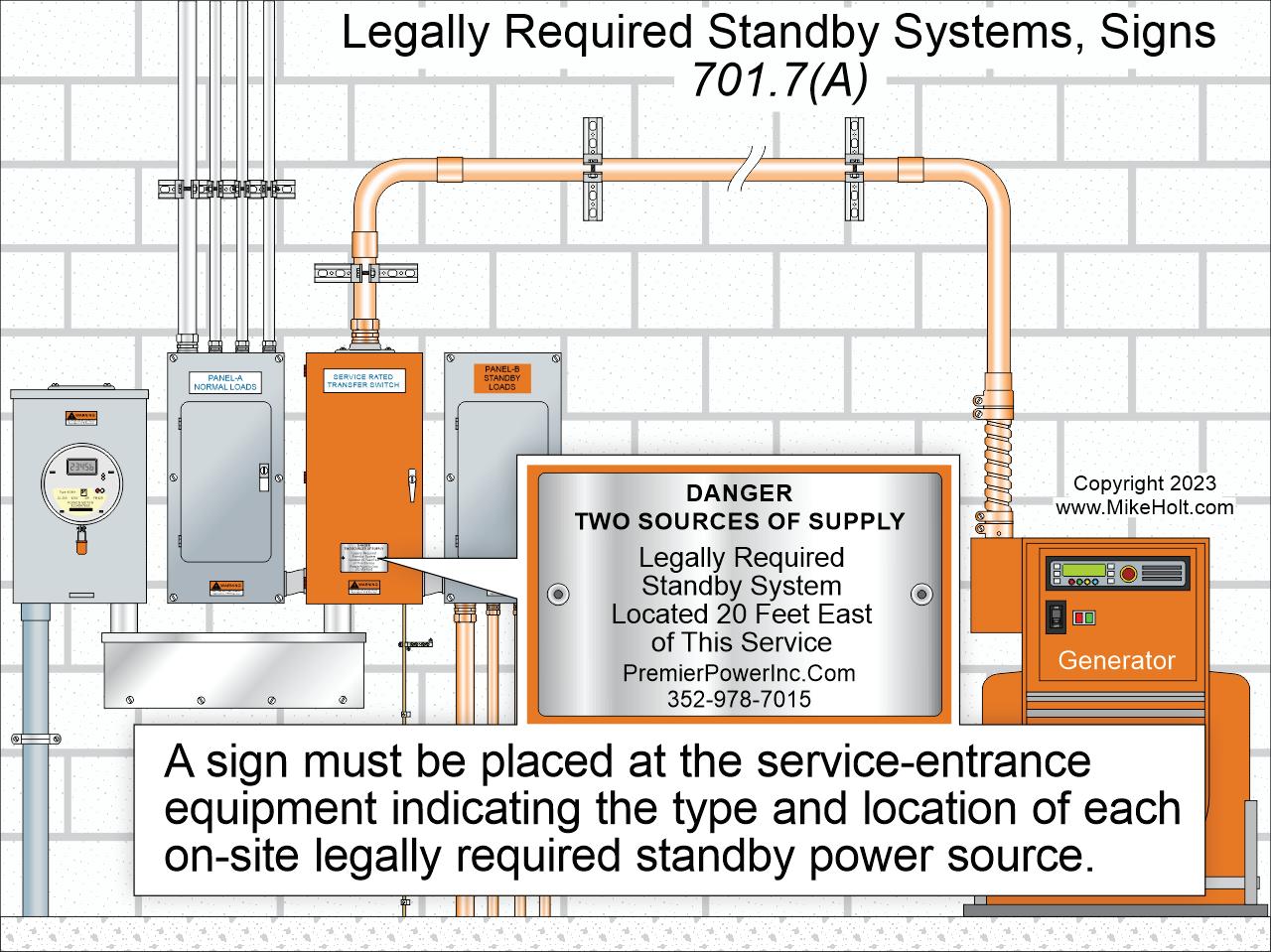
• Whether the standby source is carrying load.
• If the battery charger is not functioning.
• A ground fault in a 4-wire, 3-phase, 277V/480V wye-connected system rated 1,000A or more.
A sign must be placed at the serviceentrance equipment indicating the type and location of on-site legally required standby power systems [Sec. 701.7] (Fig. 2).
CIRCUIT WIRING
Unlike wiring for emergency systems, which must be kept entirely independent of other wiring, the wiring for legally required standby systems may be installed with other (normal) wiring because legally required standby system loads are not essential for life safety [Sec. 701.10].
POWER SOURCES
If the normal supply fails, legally required standby power must be available within 60 seconds [Sec. 701.12]. The supply system for the legally required standby system power supply can be one or more of the types of systems described in Sec. 701.12 (A) through (I)].
(A) Power Source Considerations. In selecting a legally required standby
source of power, consideration must be given to the type of service to be rendered, whether of short-time duration or long duration.
If the normal supply fails, legally required standby power must be available within 60 seconds.
(B) Equipment Design and Location. Consideration must be given to the location or design, or both, of all equipment to minimize the hazards that might cause complete failure due to floods, fires, icing, and vandalism.
Note: For further information, see ANSI/IEEE 493, Recommended Practice for the Design of Reliable Industrial and Commercial Power Systems.
(D) Generator Set.
(1) Prime Mover-Driven. A generator approved by the AHJ and sized per Sec. 701.4 is permitted as the legally required power source if it has the means to automatically start the
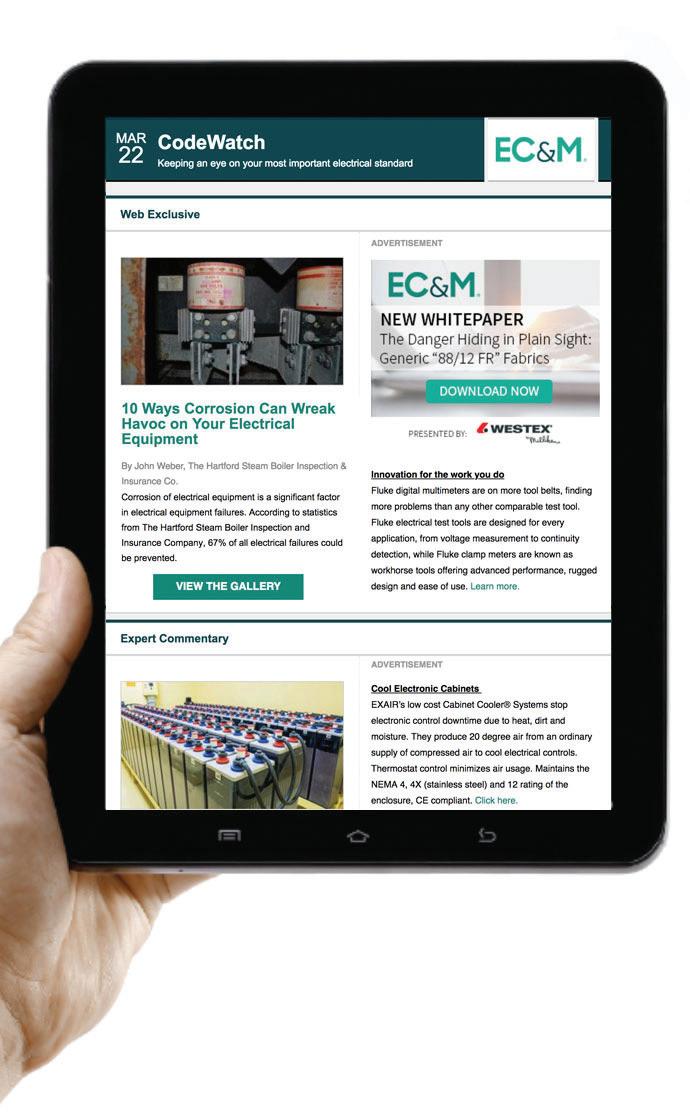
CodeWatch
This e-newsletter, published twice-monthly, is dedicated to coverage of the National Electrical Code. The content items are developed by three well-known Code experts.
CodeWatch promises to:
• Address changes in the Code
• Explain how to properly apply the Code
• Test your knowledge of the Code
• Provide information on upcoming Code-related seminars and shows
See all of our EC&M e-newsletters at www.ecmweb.com
prime mover on failure of the normal power source.
(E) Stored-Energy Power Supply Systems.
(1) Types. Stored-energy power supply systems must consist of one the following types:
(1) Uninterruptible power supply
(2) Fuel cell system
(3) Energy storage system
(4) Storage battery
(5) Other approved equivalent stored energy sources that comply with Sec. 701.12
(F) Separate Service. An additional service is permitted as the legally required power source where approved by the authority having jurisdiction [Sec. 230.2(A)] and the following additional requirements:
(1) Separate service conductors are installed from the electric utility.
(2) The legally required service conductors must be electrically and physically remote from other service conductors to minimize the possibility of simultaneous interruption of supply.
To minimize the possibility of simultaneous interruption, the service disconnect for the legally required power system must be remotely located from the other power system’s service disconnect [Sec. 230.72(B)].
(G) Connection Ahead of Service Disconnecting Means. If approved by the AHJ, connection ahead of (but not within) the same cabinet, enclosure, or vertical switchboard or switchgear section is permitted as the legally required power source. See Sec. 230.82(5) for additional information.
(H) Microgrid Systems. The system shall isolate the legally required standby system from other loads when the normal electric supply is interrupted or it must meet the requirements of Sec. 701.4(C).
(I) Battery-Equipped Emergency Luminaires. If used with legally required standby systems, they must comply with Sec. 701.12(H). This requirement is new with the 2023 revision.
This list in the 2023 revision differs from the one in the 2020 revision. For example, (J) Unit Equipment was dropped from the list. There were also some renumbering and editorial
changes, such as “DC Microgrid Systems” is now “Microgrid Systems.”
OVERCURRENT PROTECTION
The OCPDs for legally required standby circuits must be accessible to authorized persons only [Sec. 701.30]. Some facility managers consider the job done if they put a sign on the door, but accessibility must be restricted by something more substantial such as a lock on the door.
OCPDs for legally required standby systems must be selectively coordinated with all supply-side and load-side OCPDs. The design must be made by an engineer or similarly qualified person and it must be documented and made available to those authorized to design, install, inspect, maintain, and operate the system [Sec. 701.32(A)].
“Selective coordination” means the overcurrent protection scheme confines the interruption to a specific area rather than to the whole system [Art. 100]. For example, if a short circuit or ground fault occurs with selective coordination, the only breaker/fuse that will open is the one protecting just the branch circuit involved. Without selective coordination, an entire floor of a building can go dark.
If legally required standby system OCPDs are replaced, they must be re-evaluated to ensure selective coordination is maintained [Sec. 701.32(B)].
If modifications, additions, or deletions to the legally required standby systems occur, selective coordination is required of the legally required system(s) [Sec. 701.32(C)]. Note: See Figure 701.32(C) for an example of how legally required standby system OCPDs selectively coordinate with all supply-side OCPDs.
AVOIDING PROBLEMS
Be careful to not mix the requirements for the different types of standby power systems. They serve different purposes and thus the NEC requirements differ (which is why we have three standby power system Articles, not just one). However, the NEC provides the minimum requirements [Sec. 90.2] not the optimal requirements. Nothing stops you from using selective coordination in an optional standby system even though that’s required only for emergency and legally required systems.
Test Your Code IQ
How much do you know about the National Electrical Code?
By Mike Holt, NEC Consultant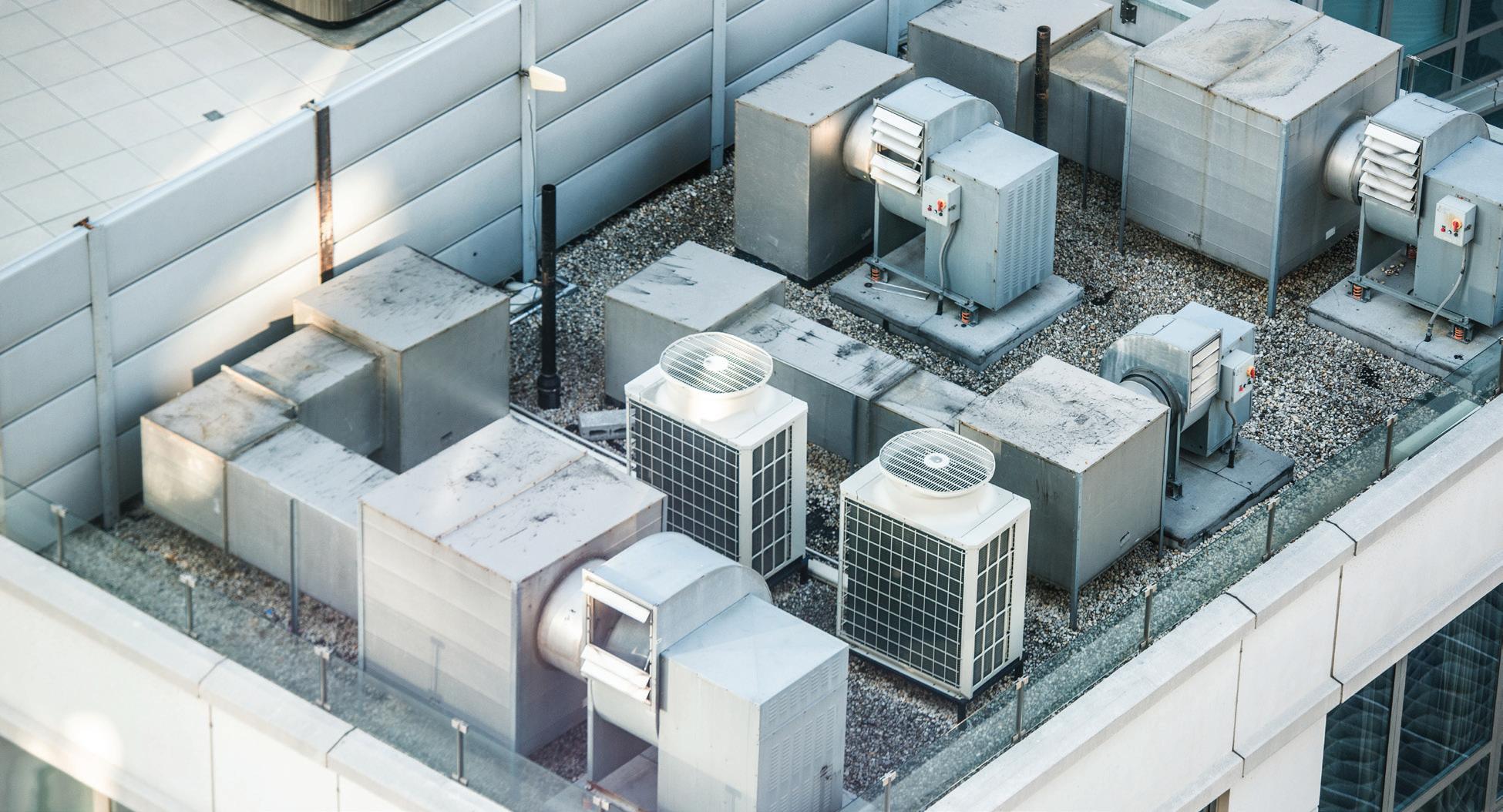
All questions and answers are based on the 2023 NEC.
Q1: Where air-conditioning and refrigeration equipment is installed outdoors on a roof, a(an) _____ conductor of the wire type shall be installed in outdoor portions of metallic raceway systems that use compression-type fittings.
a) equipment grounding
b) grounding
c) equipment bonding
d) bonding
Q2: The grounded conductor brought to service equipment shall be routed with the phase conductors and shall not be smaller than specified in Table _____ when the service-entrance conductors are 1,100kcmil copper and smaller.
a) 250.102(C)(1)
b) 250.122
Q3: Locations in which combustible dust is in the air under normal operating conditions in quantities sufficient to produce explosive or ignitible mixtures are classified as _____.
a) Class I, Division 2
b) Class II, Division 1
c) Class II, Division 2
d) Class III, Division 1
Q4: Each resistance welder shall have an overcurrent device rated or set at not more than _____ of the rated primary current of the welder.
a) 25% c) 125%
b) 80% d) 300%
Q5: Noncombustible surfaces that are broken or incomplete around boxes
employing a flush-type cover shall be repaired so there will be no gaps or open spaces larger than _____ at the edge of the box.
a) 1/16 in.
b) 1/8 in.
c) 1/4 in.
d) 1/2 in.
Q6: Tightening torque values for terminal connections shall be as indicated on equipment or in installation instructions provided by the manufacturer. An approved means shall be used to achieve the_____ torque value.
a) indicated
b) identified
c) maximum
d) minimum
See the answers to these Code questions online at ecmweb.com/21283494.
Illustrated Catastrophes
By Russ LeBlanc, NEC ConsultantAll references are based on the 2023 edition of the NEC.
AWFUL AWNING LIGHTING INSTALLATION
I spotted this hookup underneath an awning installed above the entranceway to a local business. There are many problems to point out here. The lack of support for the box is one big problem. The conductors are literally supporting the box. This does not comply with any of the box support requirements in Sec. 314.23(A)-(H).
Another huge problem with this installation is the lack of an equipment grounding conductor (EGC). The liquidtight flexible nonmetallic conduit (LFNC) only contains a black and white conductor. Section 406.4(B) requires an EGC to be connected to the grounding terminal of the duplex receptacle. This non-weather resistant duplex receptacle does not comply with either Sec. 406.(9)(A) for damp locations or Sec. 406.9(B) for wet locations. The enclosure for the duplex receptacle also does not comply with either of those two Sections.
Finally, the incomplete LFNC raceway does not comply with Sec. 300.12. The exposed THWN conductors are not sunlight resistant as specified in Sec. 310.10(D). Based on all the visible problems I can see here, I tend to doubt any GFCI protection is provided for this duplex receptacle as required by Sec. 210.8(B)(6). All in all, I think this is a pretty scary installation.
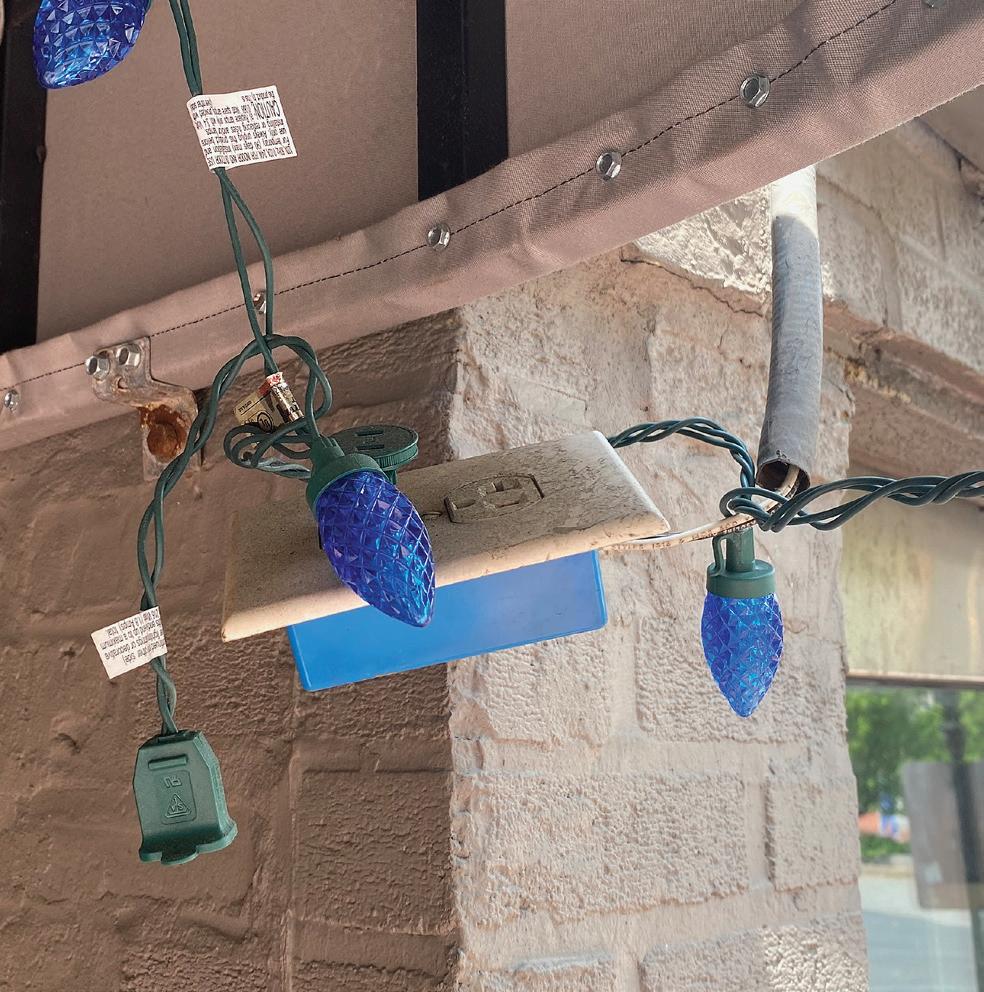
GOOD INTENTIONS, BAD OUTCOME
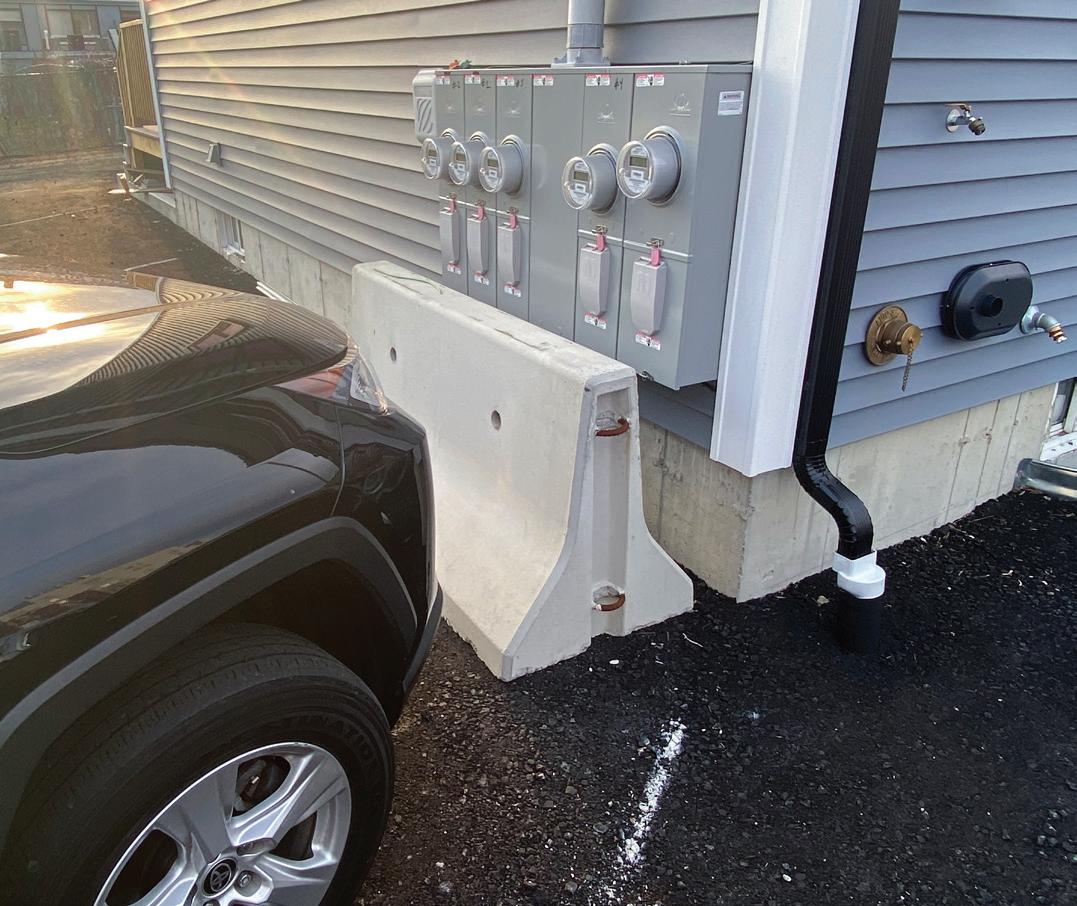
Placing a concrete barrier in front of this brand-new electrical service was a good idea to protect the equipment from being damaged by vehicles parking near this building. It may have been an attempt to protect per Sec. 240.24(C). Unfortunately, the location of the concrete barrier should have been better planned out. Its present location is smack dab in the middle of the working space required by Sec.110.26(A). The location of this barrier is so close to the electrical equipment that it prevents the removable lift-up covers from being easily lifted up and out of the equipment. Thankfully, the flip-up covers for the circuit breakers can be fully opened at least — otherwise, that would have been a nightmare if one of those breakers needed to be turned off in a hurry.
With the present layout, I would not consider these overcurrent devices as being readily accessible as required by Sec. 240.24(A). Sliding that concrete barrier out 3 ft could make for a Code-compliant installation, but, of course, that may cause problems with parking. A better solution needs to be found here.
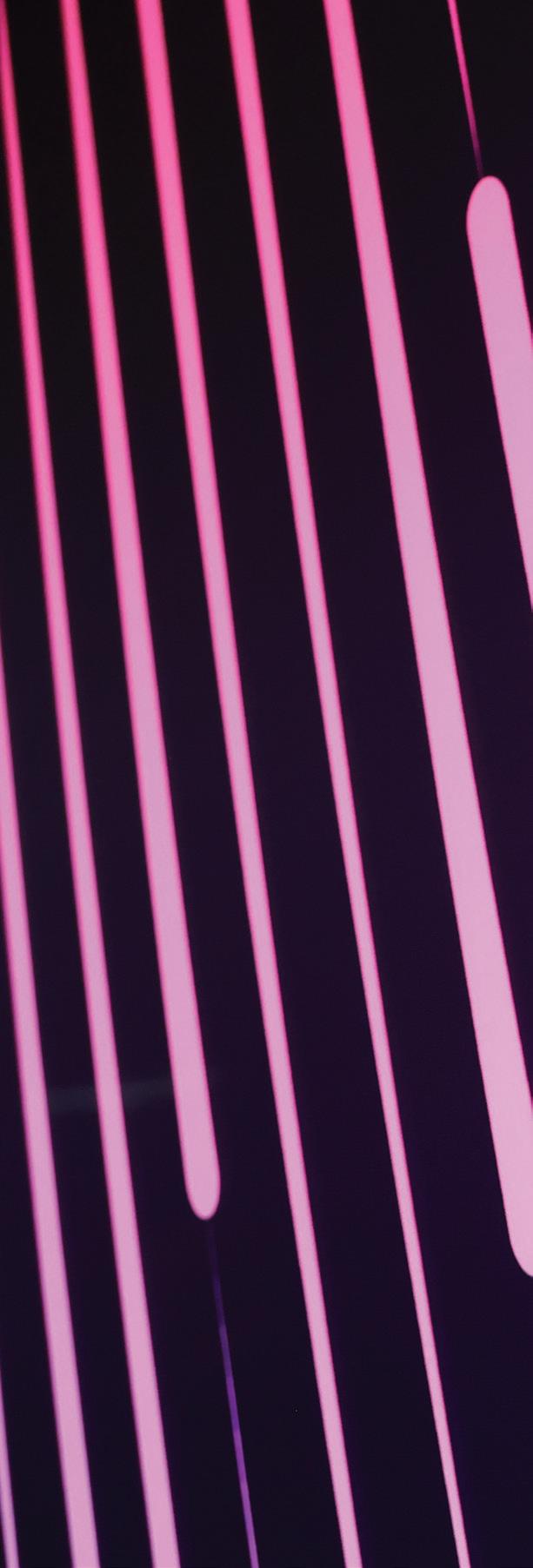
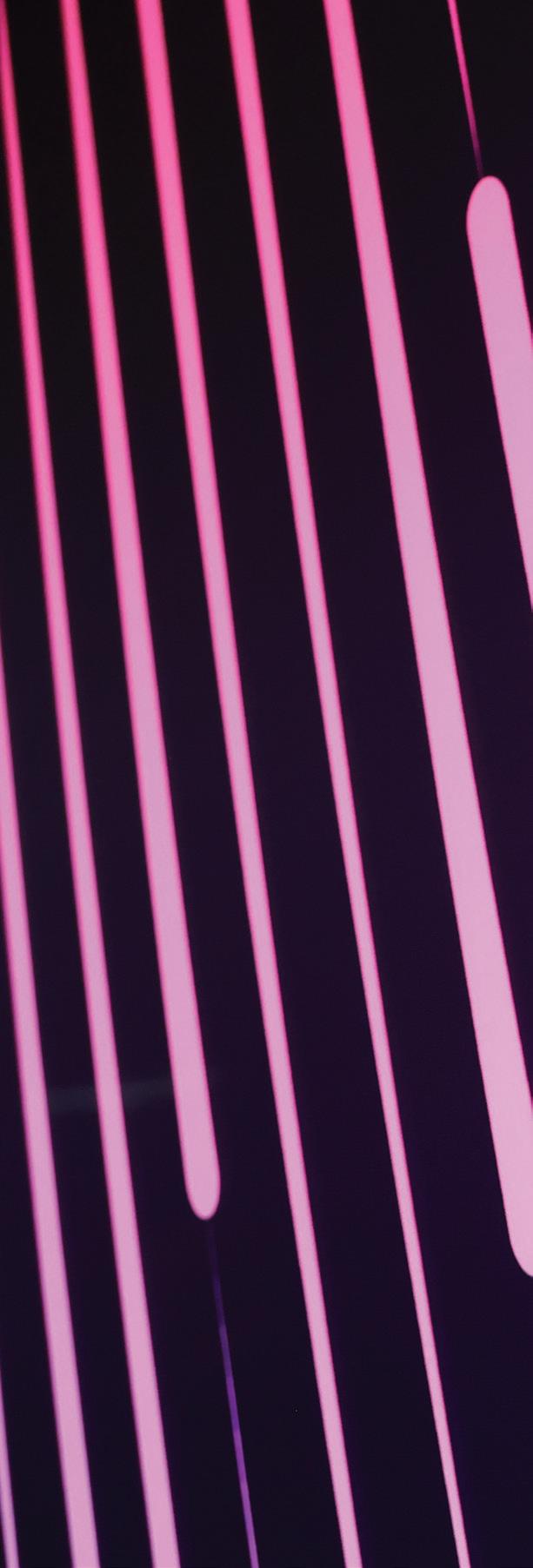
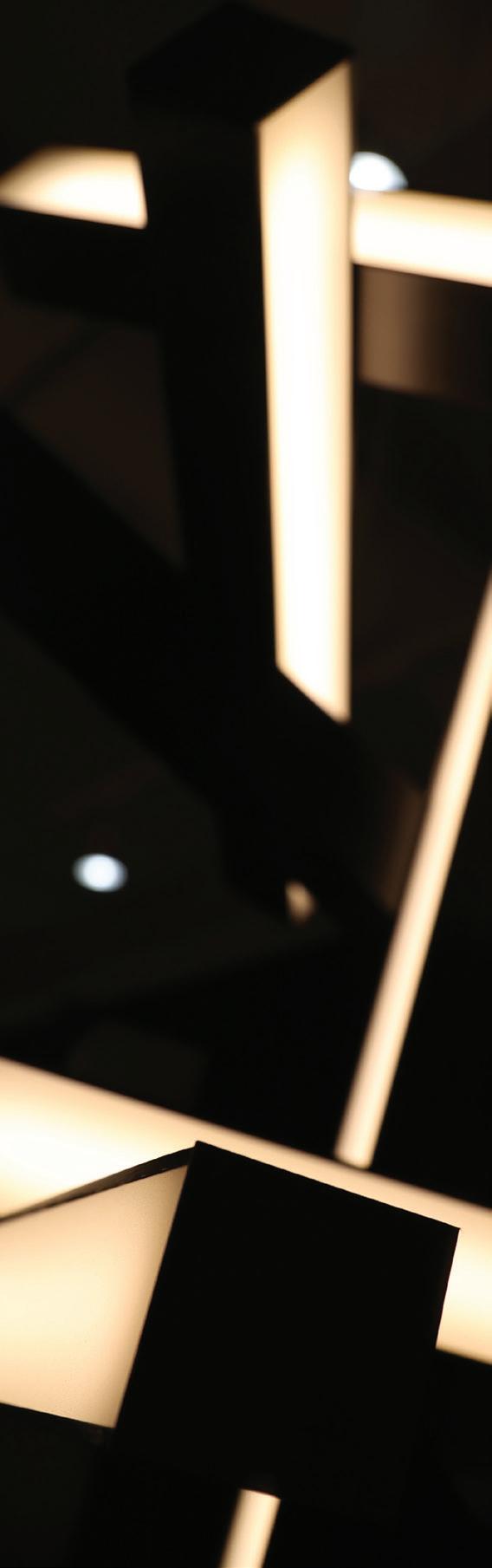


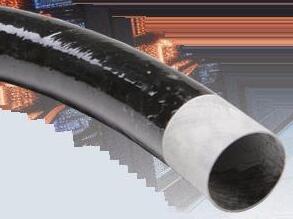
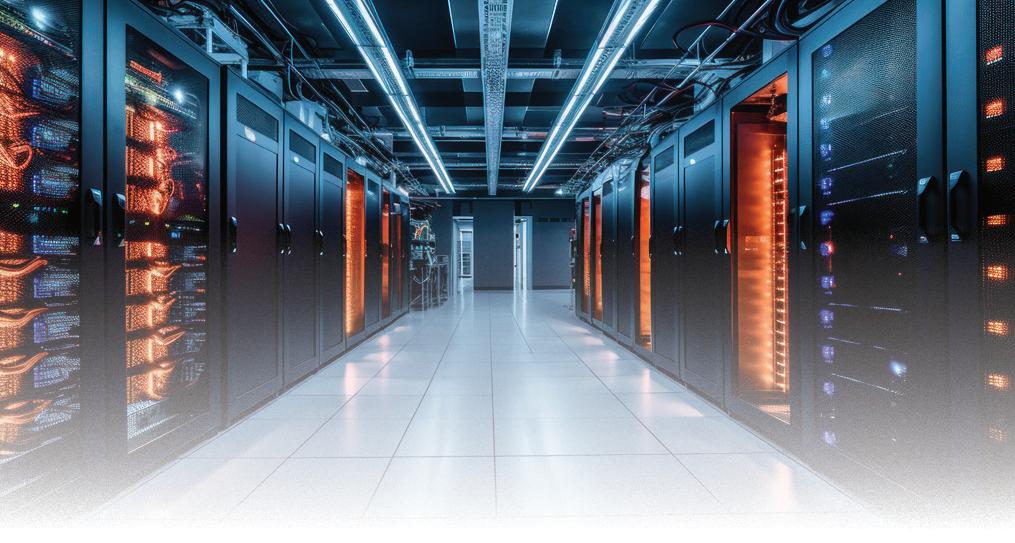

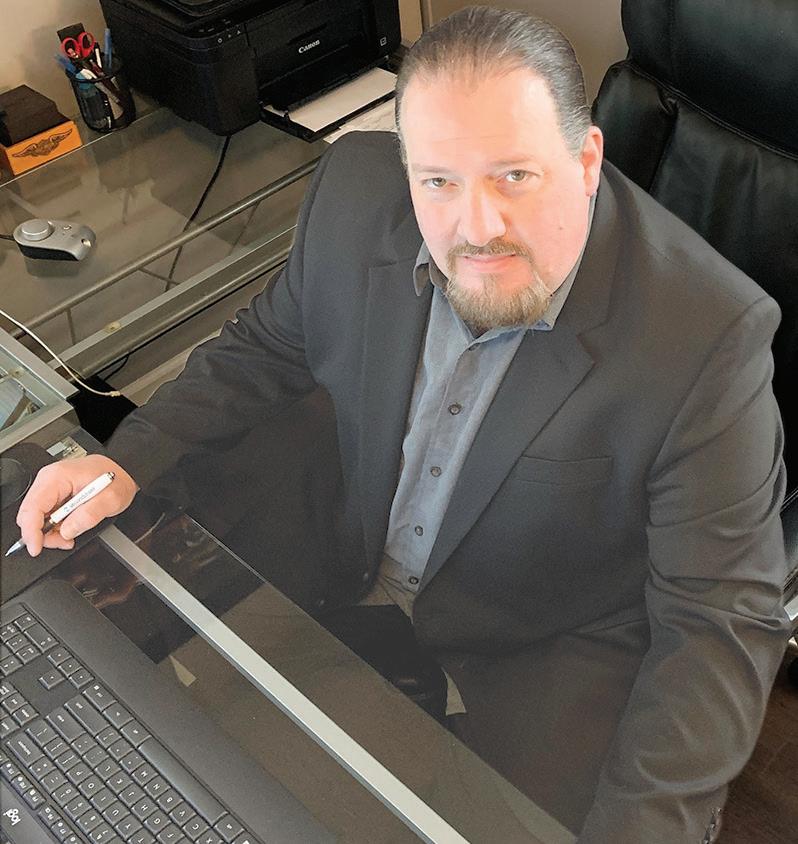
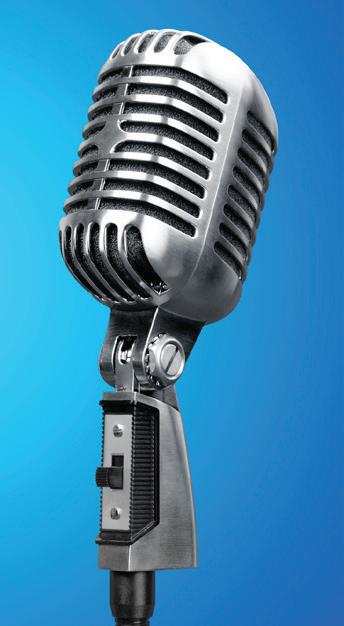

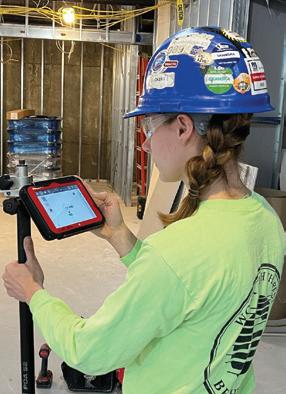
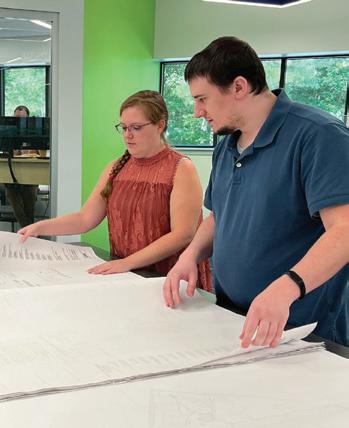
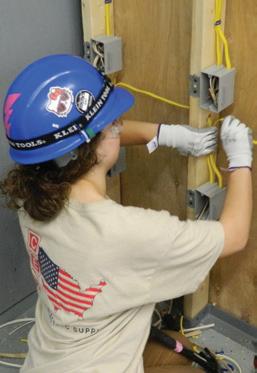
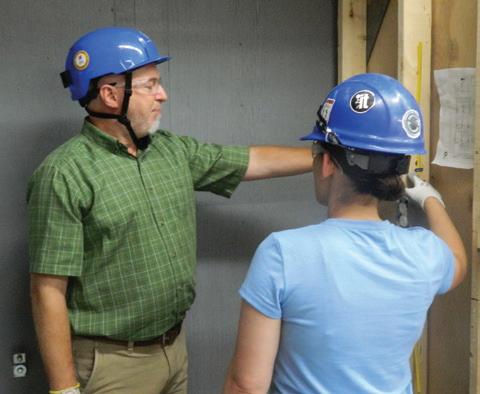

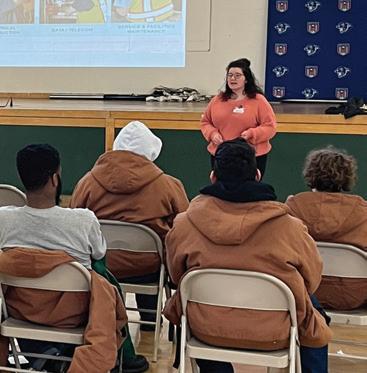
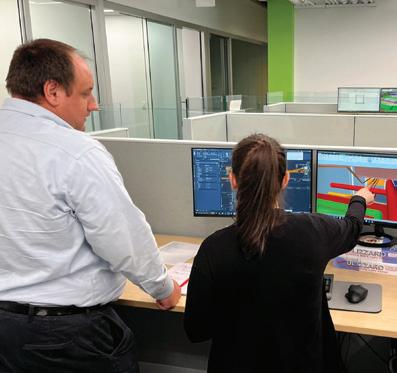
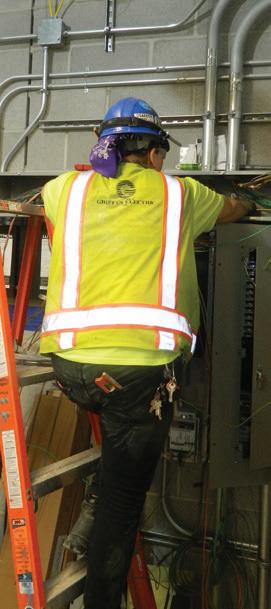

To place a display ad (1/6 page or larger), call the Advertising Sales Representative for your area.
Vice President
Mike Hellmann
Andover, MA
Phone: (978) 289-0098
E-mail: mhellmann@endeavorb2b.com
Western U.S. & Western Canada
Ellyn Fishman
Key Account Manager
(949) 239-6030
Email: efishman@endeavorb2b.com
Northeast U.S. & Eastern Canada
David Sevin
Account Manager
24 Houghton Street
Barrington, RI 02806
Phone: (401) 246-1903
E-mail: dsevin@endeavorb2b.com
Midwest, Southeast,and Southwest
Jay Thompson
Account Manager
7450 W. 130th Street, Suite #210
Overland Park, KS 66213
Phone: (913) 967-7543
E-mail: jthompson@endeavorb2b.com
Marketplace/Inside Sales
Steve Suarez
Media Account Exec
7450 W. 130th Street, Suite #210
Overland Park, KS 66213
Phone: (816) 588-7372
E-mail: ssuarez@endeavorb2b.com
CODE VIOLATIONS
By Russ LeBlanc, NEC ConsultantHow well do you know the Code? Think you can spot violations the original installer either ignored or couldn’t identify? Here’s your chance to moonlight as an electrical inspector and second-guess someone else’s work from the safety of your living room or office. Can you identify the specific Code violation(s) in this photo? Note: Submitted comments must include specific references from the 2023 NEC.
Hint: An alarming identification method
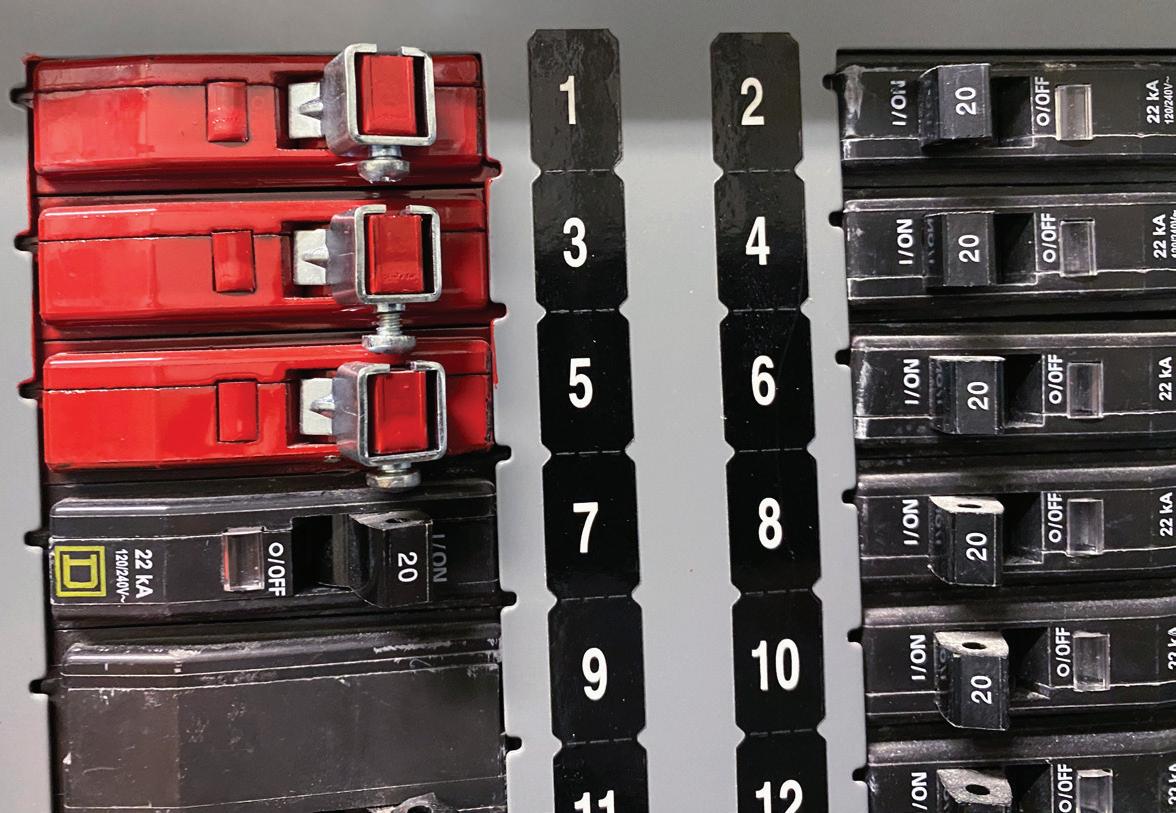
‘TELL THEM WHAT THEY’VE WON...’
Using the 2023 NEC, correctly identify the Code violation(s) in this month’s photo — in 200 words or less — and you could win an Arlington Industries 18-in. Slider Bar and plastic box for mounting between studs with non-standard spacing. E-mail your response, including your name and mailing address, to russ@russleblanc.net, and Russ will select three winners (excluding manufacturers and prior winners) at random from the correct submissions. Note that submissions without an address will not be eligible to win.
JANUARY WINNER


Our winners this month were Mark De Angelis, an EC&M reader from Pembroke, N.H.; Ronnie Morales, a fire systems inspector for the City of Temecula, Calif.; and Cassandra Knapp, a participant from Corinth, Miss. They were able to correctly cite some of the Code violations in this photo.
Section 408.7 requires unused circuit breaker openings to be closed with closures identified for that purpose or some other approved means that could provide protection equivalent to the enclosure walls. Section 110.12(A) also requires unused openings to be closed up. Installing circuit breakers from several different manufacturers may be a violation of Sec. 110.3(B) if the breakers are not listed for use with this particular panelboard.
The lack of descriptors for many of the circuits is a violation of Sec. 408.4(A). Each circuit must be clearly marked to indicate its specific purpose. Even the spare positions containing an overcurrent device are required to be marked to indicate they are spares, per Sec. 408.4(A)(3). Lastly, Sec. 110.27(A) requires live parts to be guarded against accidental contact by approved enclosures.

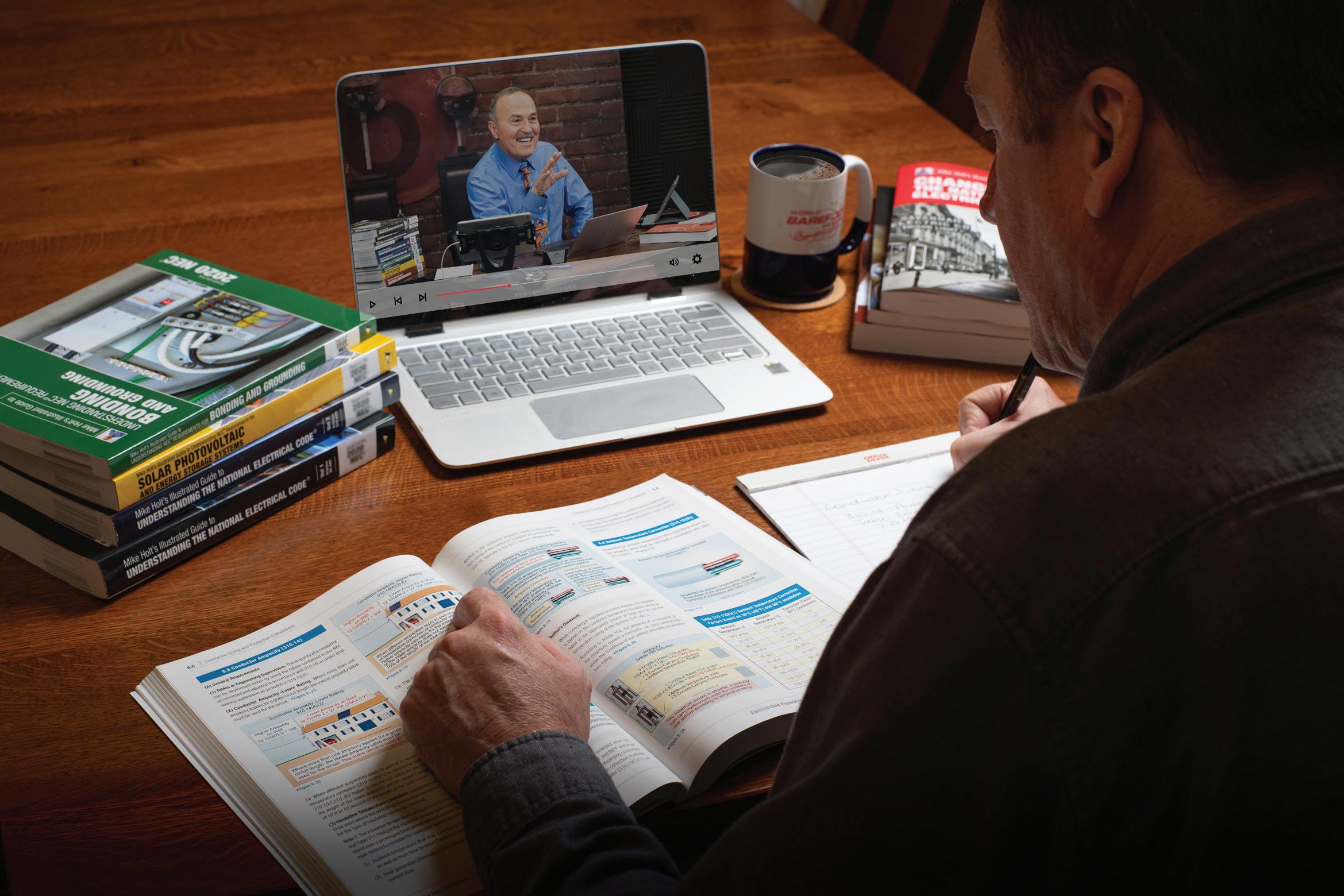
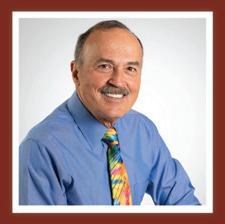
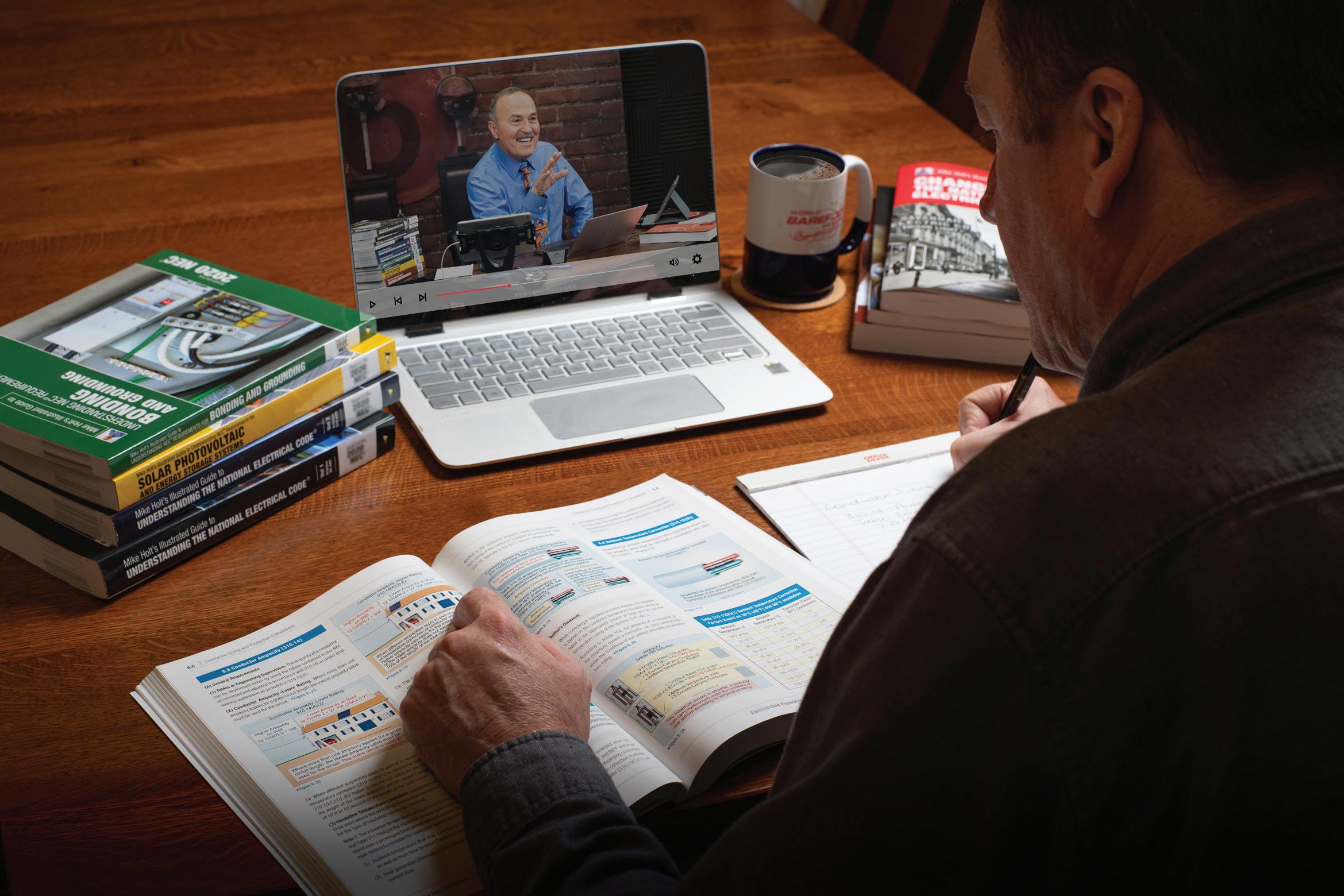
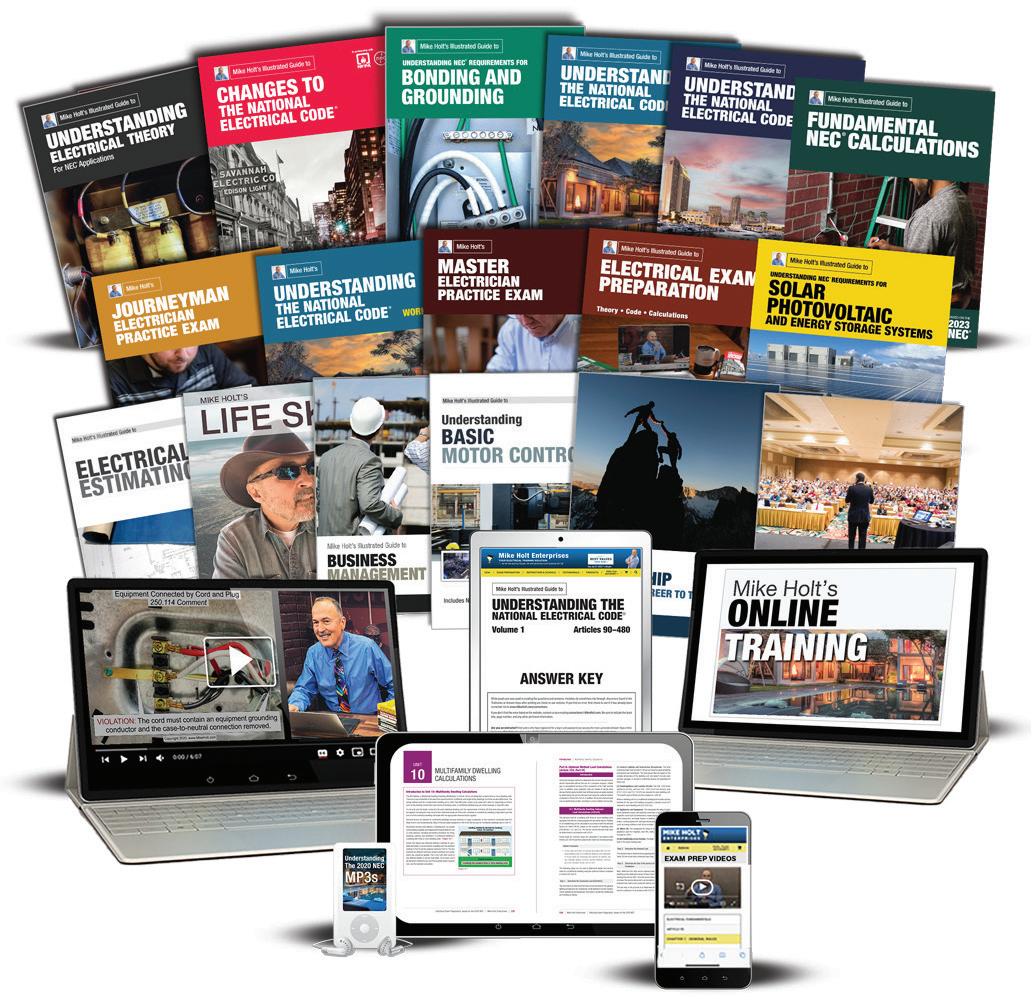
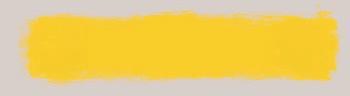
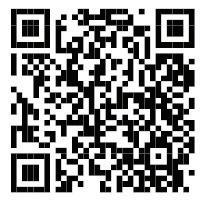
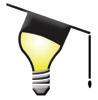

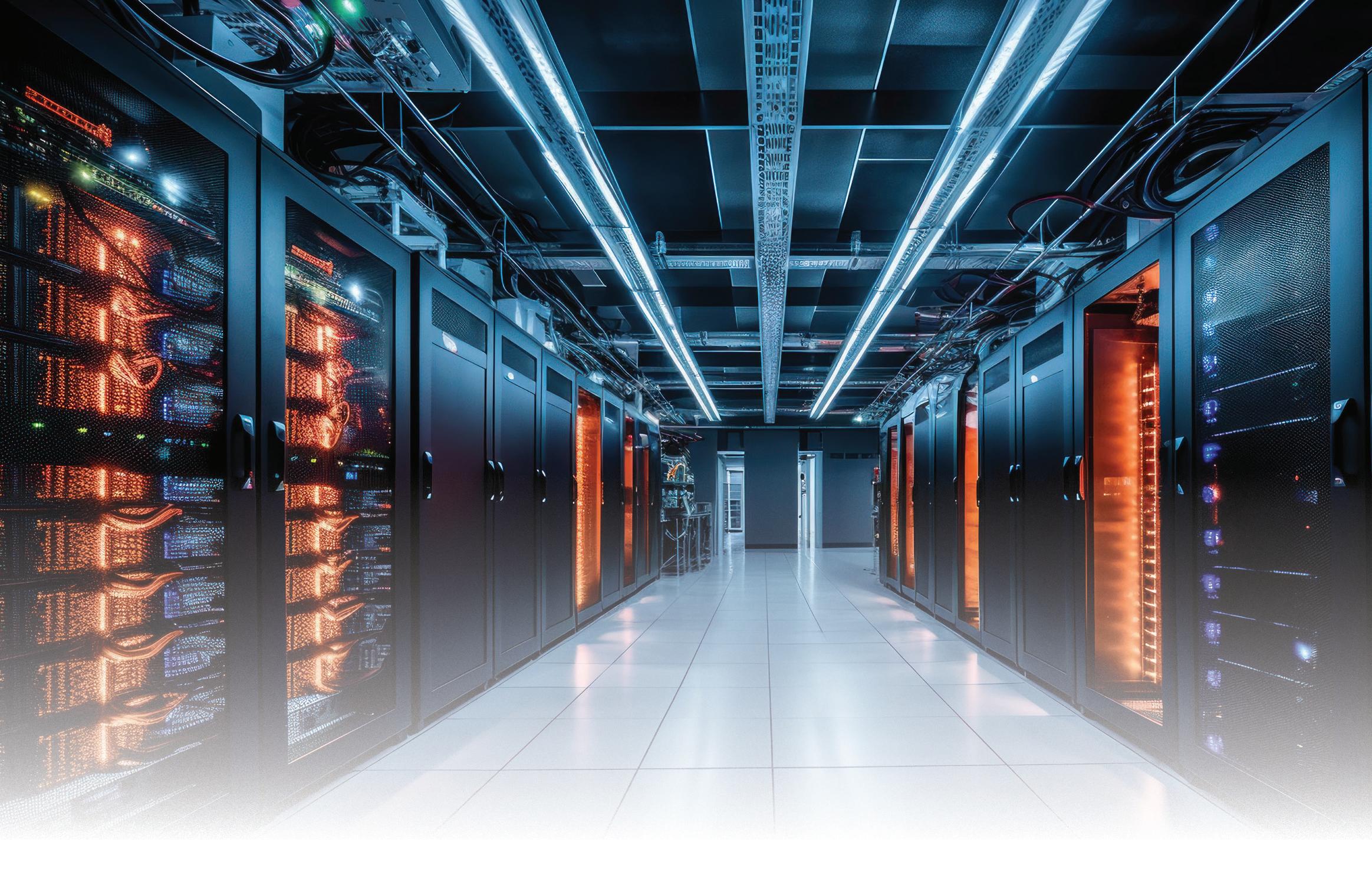
NO BURN-THROUGH CHAMPION DUCT® ELBOWS SOLVE PROJECT CHALLENGES
No burn-through eliminates elbow repairs
Lower materials and installation costs

DOWNLOAD NEW ELBOW EGUIDE
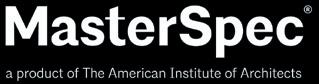
Fault resistance makes repairing cables easy
Durable and corrosion-resistant for project longevity
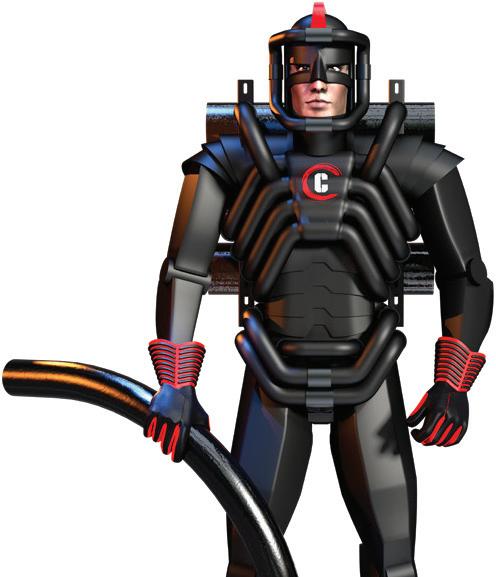