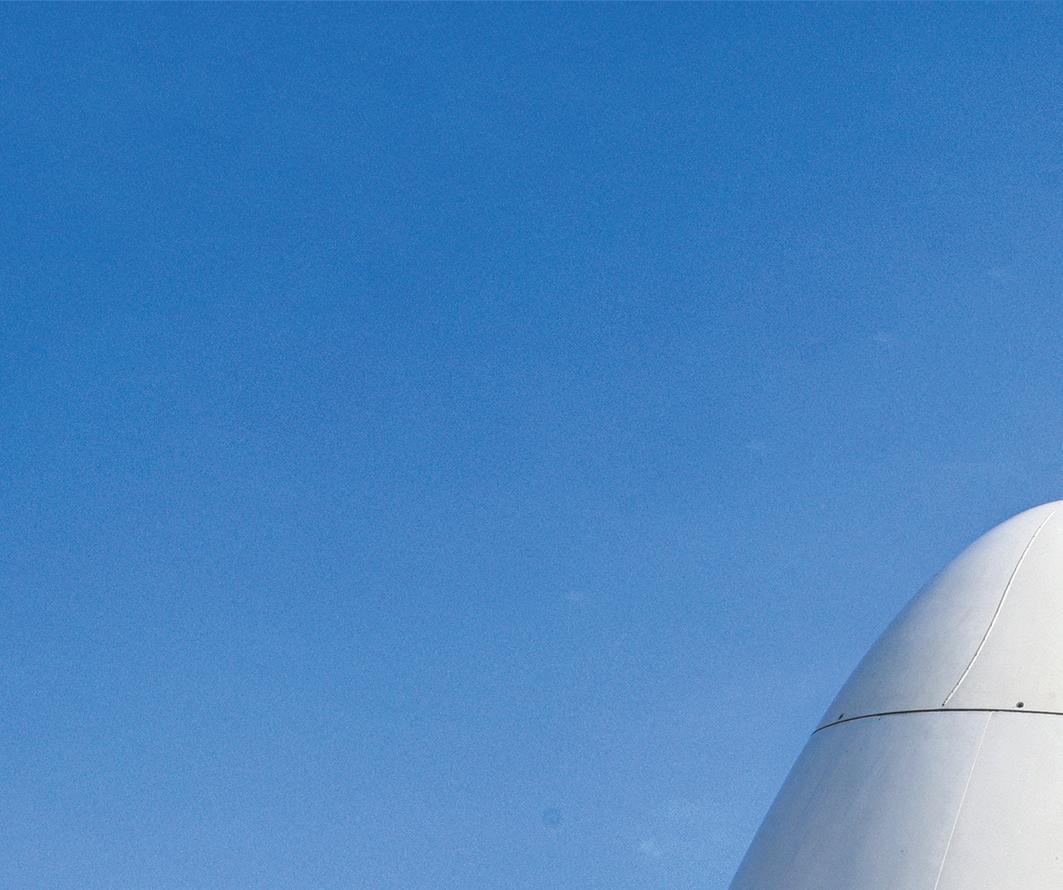
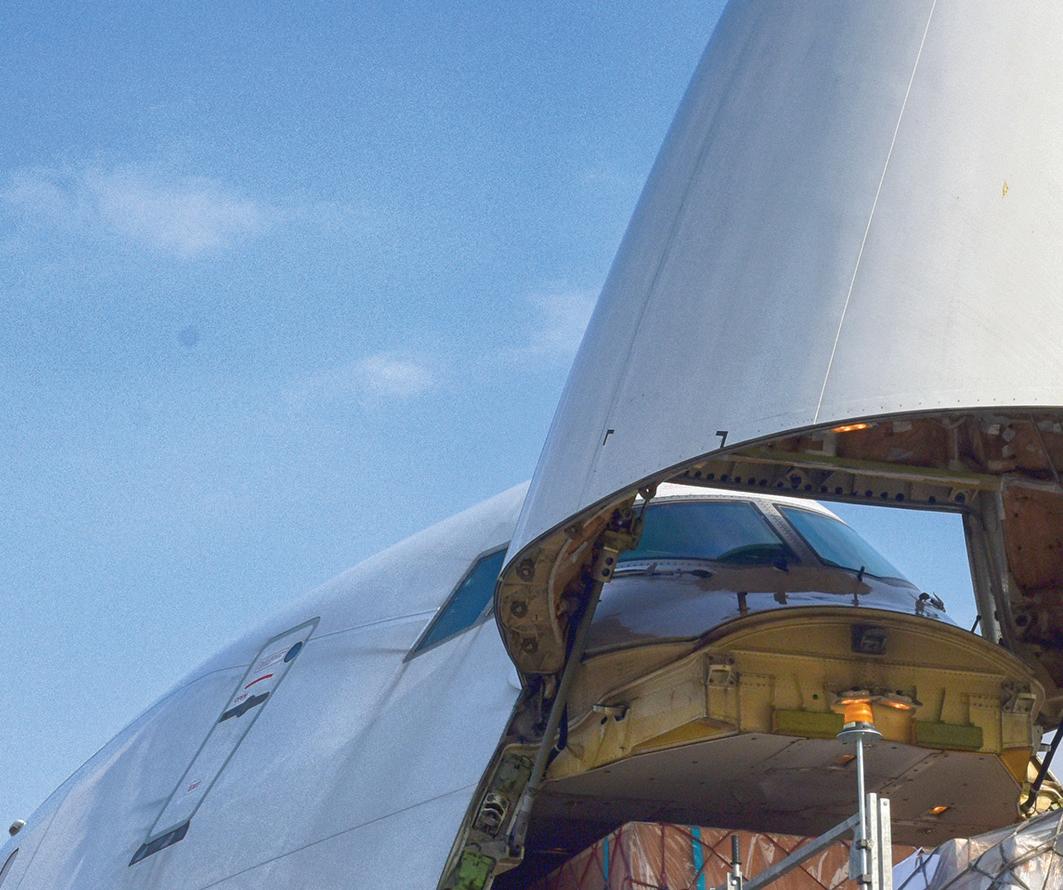
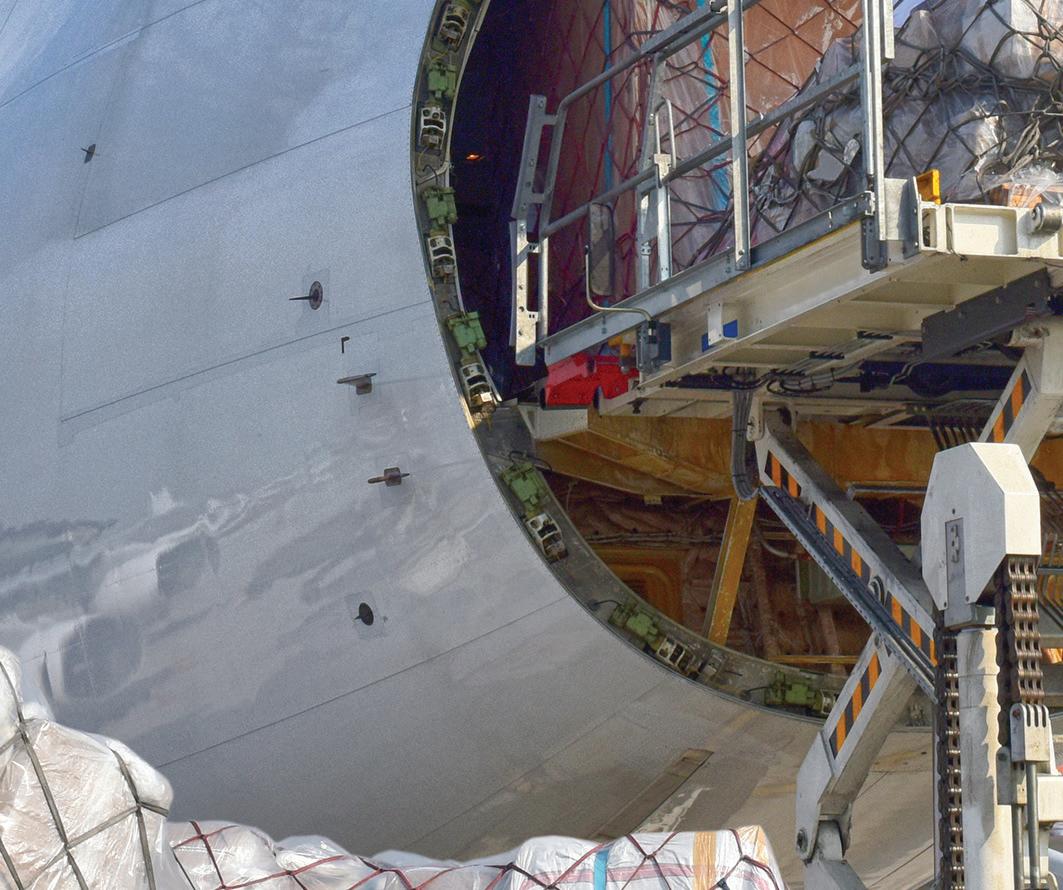
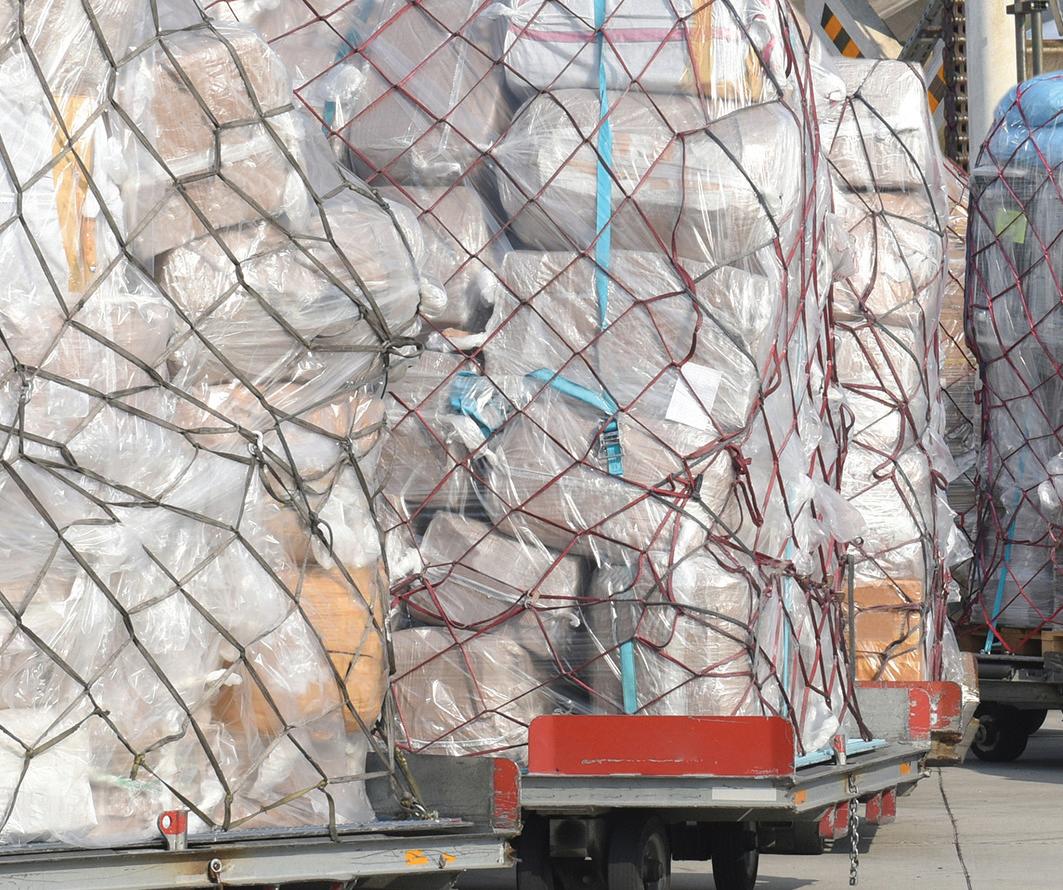

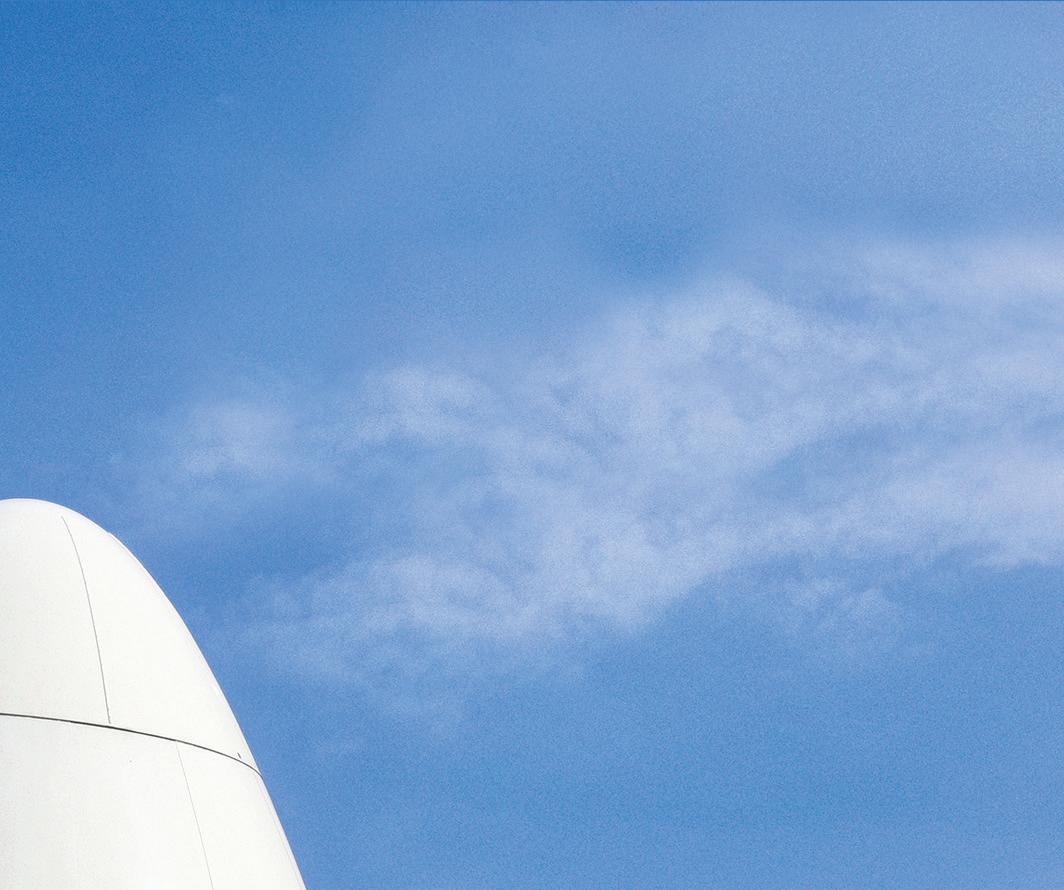
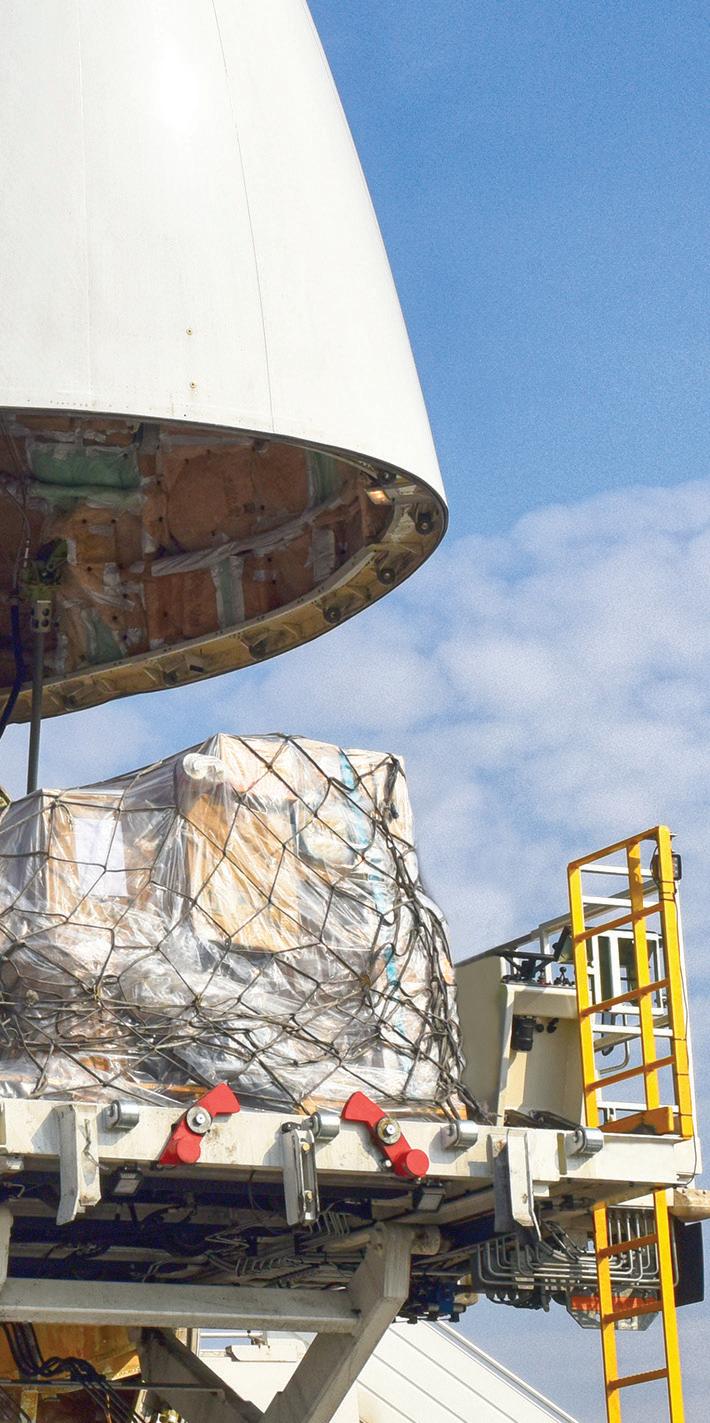
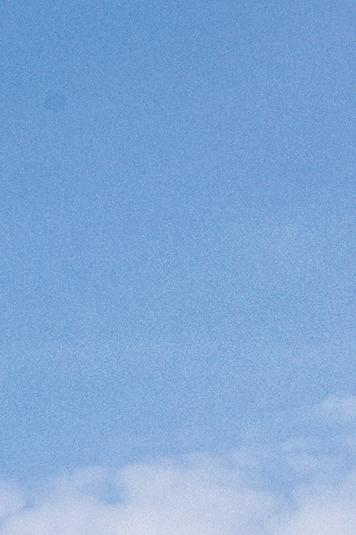
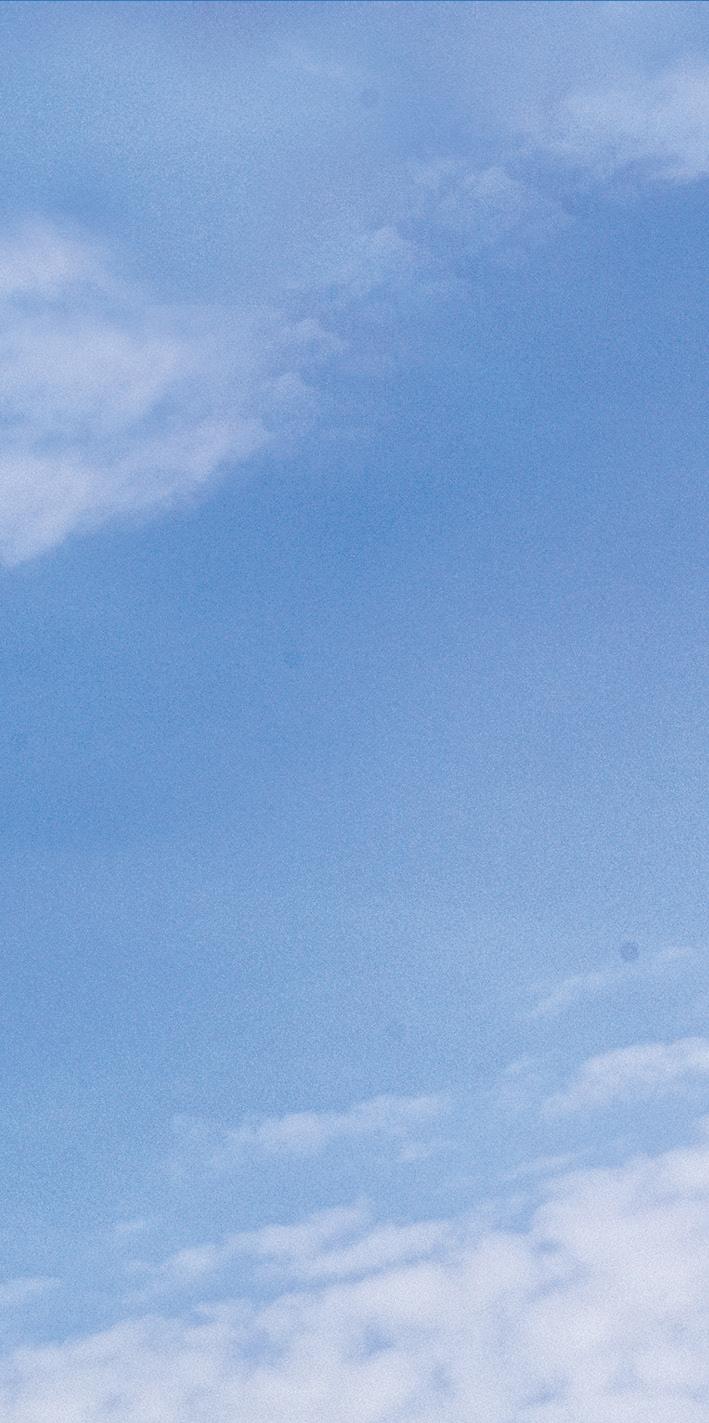

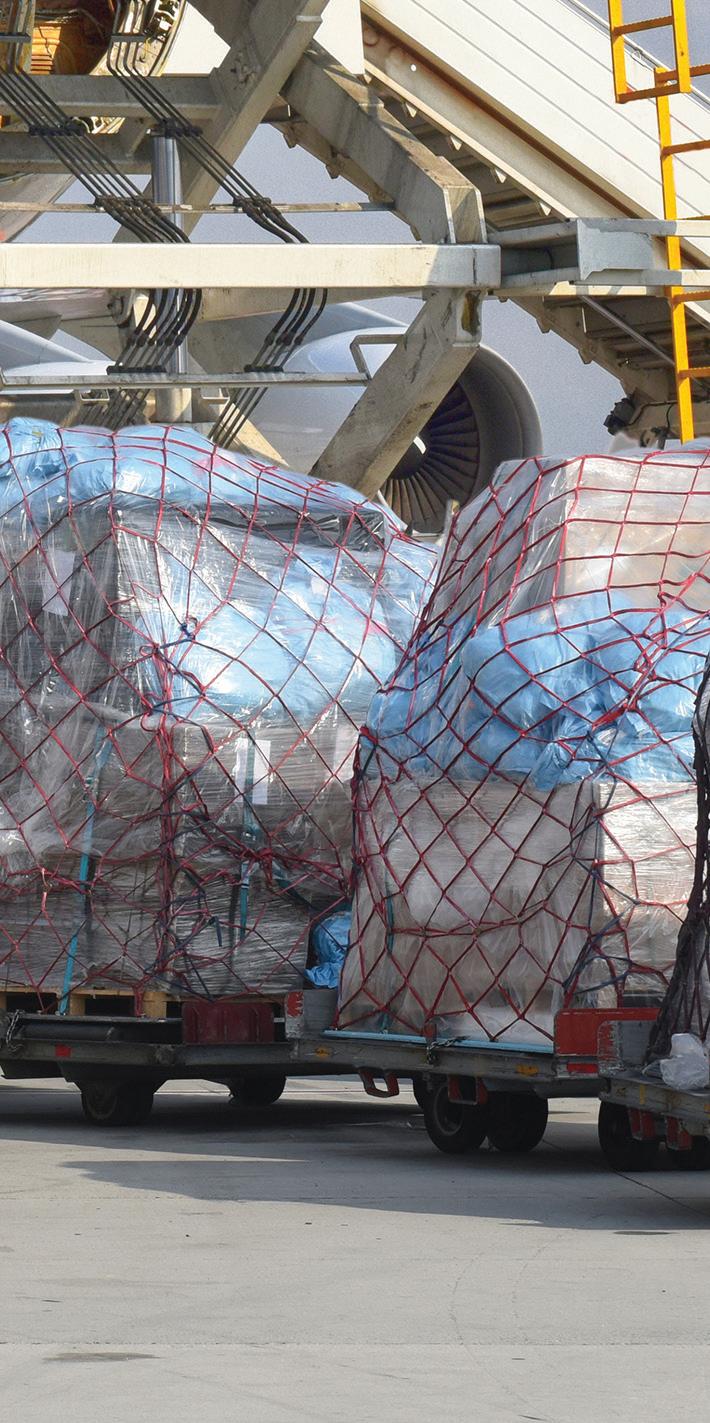
Driving the industry are an urgent need for workforce upskilling, infrastructure modernization, and the integration of sustainable practices
Driving the industry are an urgent need for workforce upskilling, infrastructure modernization, and the integration of sustainable practices to meet evolving e-commerce demands and regulatory standards.
Publication of the new regulations means stakeholders – including ground handling service providers, regulators, and industry groups – will need to prepare to ensure compliance and a smooth transition.
Safety on the ramp depends on consistent adherence to industry best practices and standards... and common sense
There’s nothing like an in-person event when you’re learning a new industry. Seeing people in the esh, hearing them speak of the issues that keep them up at night, getting a sense of the “vibe” in the crowd... they’re all vital parts of understanding what makes a group of professionals tick, and how we, as media, can best deliver a valuable message. After all, we can only get so much from sitting behind a desk, staring at a screen.
As I’m writing this, I’m just two months into my role with Ground Support Worldwide, and fresh from my recent attendance at the Aviation Fuel Handling Training Symposium, hosted by Gammon Technical Products in Irving, Texas, Feb. 18-20. I won’t pretend I understood a lot about what was discussed, but what I did take away from the event were a few clues about the critical issues facing ground handling providers.
For starters, I decided there was no better subject matter to begin my education with than fuel. At the end of the day, nothing much happens without it. To use a somewhat corny phrase, you could even say it’s the “lifeblood of aviation,” feeding the mechanically majestic beasts that take us to the skies. I’m getting carried away, but you get my point.
Speaking of feeding a beast, my favorite presentation at the symposium was “SAF 101” delivered by Amy Carico, director of fuel services and technical standards for Airlines for America (don’t miss our related report on page 33 of this issue). She had me at “101,” since I was craving a back-to-basics message after trying desperately to wrap my head around very technical topics for two days. But her approach to the subject got even more interesting - you might even say enticing - because she centered it all around an analogy between sustainable aviation fuel and synthetic beef. Yes, beef.
Not only did her slides contain mouth-watering images of juicy steaks and burgers, the comparison perfectly illustrated her points about what it means for a fuel to be organic vs synthetic, the advantages and challenging properties of both, their roles in achieving greater sustainability, what happens when you blend them, and ultimately, the importance of keeping the end goal in sight: safe and cost-effective ight.
The primary message I took from Carico’s presentation is that SAF is a complex term that can not only mean more than one thing, but can be easily misunderstood when considering fuel makeup and use. That being said, there’s no mistaking the purpose behind SAF, which is the development of cleaner alternatives to petroleum-based fuels for the health of the planet and all who live on it.
Comparing sustainable aviation fuel to alternative beef products was an engaging and entertaining way to get a complicated point across, and was de nitely food for thought.
JENNY LESCOHIER Editor In Chief jlescohier@endeavorb2b.com
VP / MARKET LEADER INFRASTRUCTURE & AVIATION GROUP
Brandon Williamson 512-739-2102 bwilliamson@endeavorb2b.com
EDITOR IN CHIEF Jenny Lescohier 920-650-1579 jlescohier@endeavorb2b.com
ACCOUNT EXECUTIVE Joe Flores 732-664-5776 jflores@endeavorb2b.com
INTERNATIONAL SALES MANAGER
Stephanie Painter +44 1634 829386 fax +44 1634 281504 stephanie@painter-lowe.com
LIST RENTAL
Michael Costantino 402-836-6266 michael.costantino@infogroup.com
Kevin Collopy 402-836-6265 kevin.collopy@infogroup.com
PRODUCTION & CIRCULATION
Art Director Jennifer Dakas
Production Manager Sheila Ward 603-891-9132 sward@endeavorb2b.com
Ad Services Manager Terry Gann tgann@endeavorb2b.com
Audience Development Manager Debbie Dumke 920-563-1776 ddumke@endeavorb2b.com
INTERNATIONAL GSE EXPO
International GSE Expo Event Director Sue Ralston 847-848-0943 sralston@endeavorb2b.com
ENDEAVOR AVIATION GROUP Penny Hazeltine, Administrative Assistant
Chris Ferrell CEO Patrick Rains COO Paul Andrews CRO Jacquie Niemiec CDO Tracy Kane CALO Amanda Landsaw CMO
Kylie Hirko EVP - Transportation Paul Mattioli EVP Endeavor Business Intelligence
SUBSCRIPTION CUSTOMER SERVICE 877-382-9187; 847-559-7598 CIRC.GROUNDSUPPORTWW@OMEDA.COM PO BOX 3257 NORTHBROOK, IL 60065-3257 Ground Support Worldwide (USPS 0015-386), (ISSN 1934-2861 print; ISSN 2150-4016 online) is published 6 times per year in January/February, March/April, May/June, July/August, September/October and November/December by Endeavor Business Media, LLC. 201 N Main St 5th Floor, Fort Atkinson, WI 53538. Periodicals postage paid at Fort Atkinson, WI 53538 and additional mailing offices. POSTMASTER: Send address changes to Ground Support Worldwide, PO Box 3257, Northbrook, IL 60065-3257. Canada Post PM40612608. Return undeliverable Canadian addresses to: Ground Support Worldwide PO Box 25542, London, ON N6C 6B2.
Subscriptions: Individual print and digital subscriptions are available without charge to qualified subscribers worldwide. Please visit www.aviationpros.com and click on “Subscribe”. Publisher reserves the right to reject non-qualified subscriptions. Subscription prices: U.S. $62.50 per year, $122.50 two year; Canada/Mexico $92.50 per year, $172.50 two year; All other countries $135 per year, $256.25 two year. All subscriptions payable in U.S.
Mallaghan has launched North America’s first-ever fully electric refrigerated catering truck for the aviation industry.
The CT6000E, which is the result of a collaboration between Mallaghan and International Motors, LLC, was unveiled at Logan International Airport, Boston, during a ceremony attended by Governor Maura Healey, State Representative Adrian Madaro, and Boston City Councilor Gabriela Coletta-Zopata.
Its electric powertrain eliminates tailpipe emissions, reduces noise pollution, and boasts operational capabilities, aligning with global efforts to reduce the carbon footprint of airport GSE.
“This launch marks a significant milestone for both Mallaghan and the aviation industry as a whole in North America,” said Joe Griffith, chief commercial officer at Mallaghan.
“The CT6000E not only reinforces our commitment to innovation and sustainability, but also supports our
partners in their pursuit of greener, safer, and more efficient operations.
“We are proud to lead the way with this cutting-edge electric catering truck and excited to see it in action at Logan International Airport.”
As the first of its kind, the CT6000E, which features a number of new technologies aimed at efficiency and safety, including an advanced aircraft-controlled approach system (CAS) to help reduce aircraft damage, 360-degree Birds Eye camera system with onboard hard drive, and on-board telemetry, will serve as a first model for continued production.
“We are thrilled to partner with Mallaghan to introduce the first fully electric aircraft catering truck in North America - a testament to what’s possible through purposeful collaboration centered around helping customers reach their goals. This innovative zero-emissions vehicle highlights our commitment to
April 15-17
World Cargo Symposium
Dubai, UAE
April 29-May 1
NBAA Maintenance Conference
Columbus, OH
May 13-15
IGHC IATA Ground Handling Conference
Nairobi, Kenya
May 13-15
CNS Partnership Conference Miami, FL
May 20-22
EBAA EBACE
Geneva, Switzerland
June 3-5
Ground Handling International Americas Orlando, FL
July 21-27
EAA Oshkosh Oshkosh, WI
Sept. 16-18
GSE Expo
Las Vegas, NV
delivering products and services that meet each customer’s unique needs,” added Debbie Shust, VP of customer insights and experience, International.
Engineered for effective catering services, the CT6000E will be operated by premium airline catering company, DO & CO.
Mallaghan products are currently sold in more than 100 countries across the world with leading aviation clients including American Airlines, dnata, gategourmet, IAG, LSG, Newrest, Southwest Airlines, Qatar Airways, and Servair.
Royal Schiphol Group, in collaboration with KLM, is testing an all-electric, self-driving baggage vehicle from Aurrigo International plc to streamline baggage transport so luggage from passengers with long layovers can be delivered from the aircraft to a temporary, secured storage location.
The first phase of the AutoDollyTug trial began in August last year, testing the route from the temporary baggage storage area to a secured storage location. At the appropriate time, the autonomous vehicle delivers the baggage to the baggage hall, where it can be entered into the system and further processed to the connecting fleet.
During this time, the vehicle maps the platform environment using 3D cameras and then autonomously picks up and drops
off containers, maneuvering through the busy baggage hall.
“Schiphol is committed to creating a more sustainable, emission-free ground operation. We are replacing our entire vehicle fleet with a connected network of autonomous, emission-free vehicles,” commented Jan Zekveld, senior manager innovation at Royal Schiphol Group.
“By doing so we automate all related processes. Even in an autonomous ground operation, employees will continue to play a crucial role, with their work becoming more varied and supervisory.”
for Commercial Air Travel in New York JetBlue, along with its fuel partners, marked the first-ever regular supply of sustainable aviation fuel (SAF) for commercial air travel in the region at New York’s John F. Kennedy International Airport (JFK).
This milestone for SAF availability in the Northeast brings to reality a past announcement from JetBlue, outlining its 12-month agreement with World Fuel Services for at least 1 million gallons of neat SAF to be provided by Valero Marketing and Supply Company, a subsidiary of Valero Energy Corporation.
“JFK has been JetBlue’s home for 25 years, and our operations here should set the standard we envision for our entire network.” said Ursula Hurley,
chief financial officer, JetBlue.
Hurley continued, “Thank you to the many teams and partners who have helped make this possible. Incorporating SAF into our flights is an important lever in decarbonizing the aviation industry and expanding its availability to our Northeast airports is a big step.”
To ensure a consistent supply of SAF, Diamond Green Diesel LLC produces the fuel and Valero then combines it with conventional jet fuel to create blended SAF. The blended SAF is then delivered by World Fuel via existing jet fuel distribution infrastructure, where it is claimed by JetBlue for use in their fleet at JFK Airport.
The importance of ground handling services in ensuring safe flights has been recognized with the European Commission’s publication of the first-ever ground handling safety regulations, bringing this area of aviation operations into the regulatory framework of the European Union Aviation Safety Agency (EASA).
The new rules come in two parts: Commission Delegated Regulation (EU) 2025/20 containing requirements for organizations and Commission Implementing Regulation (EU) 2025/23 with requirements for competent authority oversight of ground handling services and of organizations providing those services.
The existing regulations on Air Operations, Aerodromes, and Cybersecurity have also been amended as part of this regulatory package, thus enabling a smooth integration of the new ground handling requirements as a natural interface between aircraft operations and aerodrome operations.
EASA’s task is to support the industry and competent authorities in implementing the needed changes by 2028.
“For this major area of aviation, EASA will now build further on the mature standards currently used in the industry. With the new authority oversight, ground handlers become formally responsible for the safe provision of services, thus relieving air operators of this obligation when operating from an EU aerodrome in the scope of EASA Regulations,” said Jesper Rasmussen, EASA flight standards director.
Nordisk Aviation has signed an agreement with Emirates to supply up to 10,000 advanced fire-resistant AKE containers designed to reduce the risk of lithium-ion battery fires in baggage and cargo transport.
The provider of unit load devices (ULDs) manufactures AKE containers designed to offer robust fire protection
against Li-ion battery incidents, and the company says their design prioritizes sustainability, with most components being 100% recyclable.
To validate the containers’ fire resistance, Nordisk Aviation collaborated with Emirates on a rigorous testing program. While the aerospace standard (SAE AS8992) primarily addresses Class A paper fires, Nordisk Aviation and Emirates developed a more stringent testing protocol.
According to reports, the test involved 1,000 18650 lithium-ion battery cells among 60 pieces of luggage, along with flammable materials such as clothing, toiletries, and alcohol bottles.
The Nordisk AKE container contained the fire for the entire six-hour test, demonstrating its ability to prevent oxygen inflow while allowing flue gases to escape, thus effectively suppressing fire spread.
This agreement not only provides Emirates with cutting-edge fire protection technology but also establishes a foundation for continued collaboration and innovation in aviation safety.
Air Culinaire Worldwide has launched a new order management portal. The platform delivers an experience akin to popular food delivery apps but is engineered specifically for in-flight catering needs.
“This is the first and only endto-end order management solution for in-flight catering,” said John Lee, CEO of Air Culinaire Worldwide. “The ease of use, customization, and capabilities of this system will transform how flight departments handle their in-flight catering orders. For the first time, users have complete visibility of their catering operations – from order tracking and simplified invoicing to extensive regional menu browsing and
streamlined checkout – all in one intuitive interface.”
Some platform capabilities:
• Order tracking – Know exactly when and where your order is.
• Quick invoice access – Simplified record-keeping for expense tracking.
• Order from over 1,200 locations
– Live menus from our 23 owned
and operated kitchens along with our global network
• Coming Soon* Business aviation software integration – Sync catering with your preferred flight management tools.
“With 23 owned and operated kitchens and the industry’s largest network of vetted third-party caterers, we’ve built unmatched global coverage. This digital platform is the next step in our innovation journey,” said Lee. “We’re already developing integrations with leading flight management systems, expanding our eco-friendly packaging initiatives, and strengthening our farm-to-flight program that brings fresh, local ingredients to every kitchen in our network.”
Global GSA Group announces its subsidiary, Mondial Airline Services GmbH, has been appointed by AEGEAN as the general sales agent for the airline’s cargo operations throughout Germany.
The agreement, signed by AEGEAN and Mondial Airline Services GmbH, became effective on February 19, 2025. Under this new partnership, Mondial Airline Services GmbH will oversee cargo sales across AEGEAN’s extensive network connecting Germany to Greece and beyond.
The agreement covers 80 weekly flights from Germany to Greece, including daily connections to Athens (ATH) and Thessaloniki (SKG) from multiple German cities, with expectations of more flights during the summer season.
In addition to ATH and SKG, customers will gain access to over 80 international destinations, including strategic routes to Yerevan (EVN), Larnaca (LCA), Tbilisi (TBS), Tel Aviv (TLV), Malta (MLA), and
Tirana (TIA), offering a wide range of cargo options. The weekly cargo capacity will accommodate general cargo, spare parts, and machinery components - commodities vital to various industries. The flights will be operated by the modern fleet of AEGEAN, ensuring reliable and efficient service.
Leveraging the extensive global network and advanced digital tools of Global GSA Group, this collaboration will enhance the cargo operations of AEGEAN by optimizing capacity utilization, streamlining bookings, and providing real-time data analytics. It will also give customers access to cutting-edge digital solutions that improve transparency and efficiency in cargo management. These innovations are expected to strengthen AEGEAN’s competitive position in the German market while offering businesses more reliable and flexible cargo solutions.
“AEGEAN is a highly valued partner, and we are thrilled to represent
Jettainer’s next generation of its cloud-based IT solution, JettwareNG implements a new design for real-time overviews of airline loading devices and enables faster development of customer features.
JettwareNG offers information about all ULDs in a network, including ULD history with all movements. Thanks to several new APIs, the software can be integrated into existing IT architectures. There’s also a comprehensive dashboard view with a relevant key process indicator to maintain complete information about loading equipment. The mobile web application, JettApp, is accessible via any browser and no longer requires installation on mobile devices.
“This upgrade represents the next milestone in Jettainer’s digital journey. Driving digitalization is crucial for us to further improve the efficiency of our services and add value for our customers. Therefore, our goal is to become the digital market leader in ULD management. To
them in the German market,” said Zafer Aggunduz, chief commercial officer of Global GSA Group. “With their extensive network and reputation as Greece’s leading airline, we believe this partnership will yield strong results and look forward to developing it further.”
Ismail Durmaz, chairman of Global GSA Group, added: “We are delighted that AEGEAN has chosen Mondial Airline Services GmbH for this important role. With daily flights from key German cities and over 3,500 flights expected during the summer season, this partnership offers great potential. Our team is committed to delivering outstanding results and expanding our cooperation with AEGEAN in the future.”
underline this ambition, we are implementing IATA’s ONE Record target for ULD management,” says Jettainer CEO Dr. Jan-Wilhelm Breithaupt.
“JettwareNG is Jettainer’s next-generation IT platform, designed with the latest technology to ensure seamless, efficient and future-ready ULD management. With faster updates, enhanced functionality, and an intuitive user experience, our customers can streamline operations, reduce complexity, and stay ahead in a digitalized air cargo world,” states Andreas Baumann, head of innovation and IT product development.
3000+
IN LAS VEGAS!
SEPTEMBER 16-18, 2025
• Discover the latest innovations in Ground Support Equipment
• Network with 250+ Exhibiting Companies and 3,000+ Industry Professionals
• Explore 138,000+ Sq. Ft. of Indoor & Outdoor Next-Gen Equipment in Action
• Experience the perfect business trip— from the Exhibit Floor to the Vegas Strip!
Driving the industry are an urgent need for workforce upskilling, infrastructure modernization, and the integration of sustainable practices to meet evolving e-commerce demands and regulatory standards.
BY KALEA TEXEIRA
The air cargo industry stands at a critical juncture in 2025, grappling with unprecedented challenges while embracing transformative innovations. Labor shortages, capacity constraints, geopolitical tensions, and sustainability imperatives are reshaping operational strategies, while technological advancements in automation, arti cial intelligence (AI), and digitalization are rede ning ef ciency and resilience.
This comprehensive analysis synthesizes ndings from industry reports, case studies, and regulatory frameworks to provide actionable insights for stakeholders navigating this complex environment. Key themes include the urgent need for workforce upskilling, infrastructure modernization, and the integration of sustainable practices to meet evolving e-commerce demands and regulatory standards.
Labor shortages remain among the most pressing challenges for air cargo operators in 2025. The scarcity of skilled personnel - exacerbated by immigration restrictions and outdated hiring practices - has led to operational delays, increased overtime costs, and heightened safety risks.
Inadequate staf ng at cargo terminals has extended shipment wait times, directly impacting customer satisfaction and supply chain reliability. Overburdened employees face declining morale, creating a cyclical problem of burnout and attrition that further strains productivity.
Leading organizations are implementing reskilling programs that combine technical training with softskills development to address these gaps. Microlearning
modules and immersive technologies like virtual reality (VR) are being deployed to simulate real-world scenarios, enabling workers to master equipment handling and safety protocols without disrupting operations.
Some airlines have adopted AI-driven predictive analytics to identify skill gaps and tailor training programs, resulting in improvements to operational ef ciency. Partnerships with academic institutions complement these initiatives to create pipelines for talent in logistics management and aviation engineering.
Air cargo terminals worldwide are operating at or near capacity, struggling to accommodate the surge in e-commerce-driven shipment volumes. At some major hubs, legacy infrastructure has led to bottlenecks in cargo processing, with average handling times increasing by more than 20% since 2023, in some cases.
Operators are investing in automated storage and retrieval systems (ASRS) and AI-led sorting technologies. Deployment of caster decking and IoT-enabled smart containers are signi cantly reducing cargo processing times while minimizing human error.
Modernizing infrastructure extends beyond terminal upgrades. Airports increasingly integrate with road and rail networks to create seamless multi-modal logistics corridors. The Port of Oakland’s Phase 2 expansion project, for example, which includes electri ed cargo loaders and automated guided vehicles (AGVs), has enhanced connectivity between air, land, and warehouse operations.
However, such projects require signi cant capital, posing nancial challenges for operators already contending with in ationary pressures.
Geopolitical shifts, particularly U.S.-China trade disputes and regional con icts, have forced air cargo operators to recon gure supply chains. Alterations in global air freight routes due to tariff uncertainties and sanctions have increased average transit times.
Forward-thinking companies are adopting agile logistics models, in some cases leveraging blockchain for real-time shipment tracking and diversifying supplier networks across Southeast Asia and Eastern Europe, reducing geopolitical risk exposure.
New trade policies, such as eliminating duty-free exemptions for low-value shipments, have complicated customs processes. Air cargo operators must now submit
digital manifests 12 hours before departure, necessitating upgrades to compliance management systems.
Collaborative platforms like IATA’s ONE Source have standardized documentation across 150 countries, reducing clearance delays. Mid-sized carriers’ compliance costs remain high, however, averaging $4.3 million annually.
Technological transformation and operational efficiency
AI is revolutionizing air cargo operations through applications in route optimization, predictive maintenance, and demand forecasting, enabling reduced fuel consumption through analysis of real-time weather data and optimized flight paths.
Similarly, predictive maintenance algorithms serve to decrease equipment downtime while extending
the lifespan of critical assets like aircraft tugs and conveyor systems.
The shift from paper-based processes to digital platforms has accelerated, with most cargo handlers now using IoT sensors for real-time tracking. Blockchain technology ensures data transparency across supply chains, enabling stakeholders to monitor environmental conditions (e.g., temperature, humidity) for sensitive shipments like pharmaceuticals.
kam@globalgroundsupport.com
There’s more to your gate than meets the eye…
EcoGate
– your high-efficiency ground support system
More efficiency, more intuition, more savings, more progress. But only if you look deeper than individual GSE units and start capitalizing on the connections between them.
Unleash the hidden value in your gate equipment
Lufthansa Cargo says it’s committed to leveraging AI and automation to enhance operations and deliver superior service.
“We have successfully implemented several promising use cases that highlight the potential of AI and automation to improve efficiency, reduce costs, and drive innovation,” the company said.
The automation of various processes counteracts the agerelated loss of knowledge and simultaneously increases the efficiency and quality of operations. In addition, employees are already being relieved through initial projects, including the first steps in automated rebooking in the event of unforeseen flight changes at the Frankfurt hub or automated written statements in service centers.
This enables Lufthansa Cargo to respond to customer enquiries more quickly and efficiently, especially in irregular situations, which has significantly improved the customer experience, according to the company, which stated around 40% of inquiries are now answered fully automatically, while administrative process steps have been automated for the remaining inquiries in order to shorten the processing time there as well. Further development for additional use cases is already in the planning stage.
A pilot project between Lufthansa Cargo and Fiege Air Cargo Logistics to use automated guided vehicles (AGVs) on Lufthansa Cargo premises has been running since the fall of 2024. Currently, two autonomous tow vehicles transport freight between several buildings in order to gain experience and build up basic expertise within the company. In the future, the use of AGVs will not only increase efficiency and quality at the Frankfurt hub, but also contribute to the company’s
Sustainability imperatives and regulatory pressures
Sustainability has transitioned from a voluntary initiative to a regulatory mandate. The International Air Transport Association (IATA) mandates a 5% SAF blend for all cargo flights by 2025, driving investments in biofuel production facilities.
Major companies are committing to achieving net-zero emissions, deploying electric ground support equipment (eGSE) and solar-powered warehouses at major hubs.
Meanwhile, circular economic principles are gaining traction, particularly in recycling unit load devices (ULDs) and packaging materials.
Simultaneously, fleet modernization initiatives are replacing older aircraft with fuel efficient models, cutting CO2 emissions per ton-mile.
Cybersecurity in a digitally dependent ecosystem Advancements aside, the industry’s reliance on digital
Lufthansa Cargo is actively working to establish an open industry-wide data standard.
resilience in the face of personnel-related bottlenecks due to the increasing shortage of skilled workers and heavy peaks. Looking ahead, Lufthansa Cargo said it plans to continue investing in new AI and automation initiatives.
“Our goal is to systematically identify and implement new use cases that deliver measurable improvements in our operations,” it said. “By embracing cutting-edge technologies, we aim to stay at the forefront of the air cargo industry and provide exceptional value to our customers.”
With its involvement in the IATA ONE Record initiative, Lufthansa Cargo is a pioneer in the digitalization of the air freight industry and is actively working to establish an open industry-wide data standard.
In addition to operating a modern fleet and using sustainable aviation fuel (SAF), the focus is on continuously optimizing flight operations. In 2024, Lufthansa Cargo was able to save almost 5,700 tonnes of kerosene through targeted fuel efficiency measures, which corresponds to a CO2 reduction of around 18,000 tonnes.
systems has exposed vulnerabilities to AI-driven cyberattacks. In 2024, a ransomware attack on a major European cargo handler disrupted 15% of global air freight for 72 hours, highlighting the need for robust defenses. Solutions include zero-trust architectures, which restrict access to critical systems, and AI-powered threat detection platforms which aim to reduce incident response time.
Strict data privacy laws, such as the EU’s General Data Protection Regulation (GDPR), require cargo operators to encrypt sensitive customer information. IATA’s Cybersecurity Certification Program has standardized protocols across 210 airlines, ensuring compliance while maintaining operational flexibility.
Strategic recommendations and future directions
What can be done to move air cargo handling into the next era with greater efficiency and cost effectiveness? The following areas offer ideas for a good start:
• Workforce Development: Expand partnerships with technical schools and offer tuition reimbursement programs to address skill gaps.
• Infrastructure Modernization: Prioritize automated systems and multi-modal hubs to alleviate capacity constraints.
• Sustainability Integration: Accelerate SAF adoption through government subsidies and industry consortia.
• Cybersecurity Resilience: Allocate 5% of IT budgets to AI-driven threat intelligence systems.
Future research should focus on scaling AI applications for small-to-medium airports and optimizing hydrogen fuel cell technologies for ground support equipment. Cross-industry collaborations, such as the Air Cargo Tech Summit, will play a pivotal role in standardizing green technologies and sharing best practices.
The air cargo industry’s ability to thrive in 2025 hinges on its capacity to balance operational challenges with technological innovation. By addressing labor shortages through targeted training, modernizing infrastructure,
and embracing sustainability, stakeholders can build resilient supply chains capable of withstanding geopolitical and economic shocks.
As digital transformation accelerates, proactive investments in cybersecurity and AI will ensure competitiveness in an increasingly dynamic market. The path forward demands collaboration, agility, and a relentless focus on efficiency – qualities that will define the next era of global logistics.
Texeira is a strategic aviation leader and retired U.S. Air Force officer with over two decades of experience in aerospace operations, workforce development, and program optimization. Founder of StratComm Consulting LLC, she has worked as a program analyst at the Federal Aviation Administration and as the director of logistics for the DC Air National Guard. Texeira frequently contributes thought leadership on the future of aircraft maintenance, discussing emerging trends such as digitization, sustainability, and data-driven decision-making to foster meaningful dialogue among aviation professionals.
Publication of the new regulations means stakeholders - including ground handling service providers, regulators, and industry groups - will need to prepare to ensure compliance and a smooth transition.
BY MARIO PIEROBON
The aircraft ground handling sector in Europe is preparing for significant regulatory changes that will shape compliance in the coming years, thanks to the publication of the first-ever ground handling safety regulations from the European Union Aviation Safety Agency (EASA).
Stakeholders - including ground handling service providers (GHSPs), regulators, and industry groups - are working to ensure compliance and a smooth transition, as these regulations aim to create a consistent framework across European Union (EU) jurisdiction, emphasizing safety and industry best practices. In this
article we explore the ongoing efforts of GHSPs and industry associations to align with the proposed regulations.
Preparing for the new regulations
Ryan Abram, chief operating officer at dnata airport operations, explains that the expectation is for ground handling service providers to demonstrate compliance by adhering to industry practices, specifically the IATA manuals for ground operations: the Aircraft Handling Manual (AHM) and the Ground Operations Manual (IGOM).
“GHSPs have worked in collaboration with EASA, IATA, and other
stakeholders to support this route as an acceptable means of compliance (AMC),” he says. “GHSPs should review their existing procedures against the draft regulations, conducting a gap analysis exercise as an important part of the preparation phase. dnata’s Ground Operations Manual (dGOM) closely aligns with the IGOM, so we are confident we will be able to demonstrate compliance across our operations.”
The industry has been actively involved throughout the development of the new ground handling regulations by means of an EASA Ground Handling Expert Group, which includes authorities and
service providers, according to a spokesperson for EASA.
“Since the draft regulations were published, EASA has hosted a webinar for the industry, and there has been continued discussion and dialogue with the entire ground handling community,” says EASA.
Several members of ASA World have been actively involved in the rule-making process for the new EASA regulations from the outset, providing them a solid understanding of the proposed rules. Over the past year, ASA World members have focused on several key activities, according to ASA World’s new director general, Waleed Youssef.
“Our members have disseminated draft rules within their organizations to Conducting ‘mock audits’
Since the draft regulations were published... there has been continued discussion and dialogue with the entire ground handling community.”
—
European Union Aviation Safety Agency (EASA)
with various competent authorities (CA) to test the ‘co-operative oversight’ approach, evaluate links between headquarters and local operations, and identify areas needing further guidance for both GSPs and CAs,” he says.
“Our members have also aligned training programs with industry standards and participating in expert groups working on Rule Making Task
(RMT.0728) to ensure the regulations are practical and future-proof. Finally, they have leveraged their expertise in handling regulatory shifts during the long transition from publication of the regulations to adoption and enforcement.”
ASA World recognizes that the new EASA regulations do not impose a single industry standard but rather allows ground handlers to
determine the most suitable compliance framework for their operations, explains Youssef.
“This could include IATA’s AHM and IGOM standards, ISAGO certification, or SAE standards for de-icing/anti-icing. One key aspect still under discussion is the absence of an EU-wide certification process for GHSPs,” he says. “Unlike flight operations and aerodrome oversight, the new regulations rely on self-declarations rather than prior certification by national authorities. Oversight will be conducted through audits and inspections instead of pre-approval.
“This change places greater legal responsibility on ground handlers to ensure full compliance from the moment they submit their declarations to the authorities. The industry has been actively preparing for this reality, and our members have strengthened their internal compliance structures, safety protocols, and reporting mechanisms to effectively meet these obligations.”
With the publication of the new regulations, EASA’s task now is to support
the industry and competent authorities in implementing the needed changes by 2028.
“If further changes were to occur, GHSPs will need to react accordingly in their operations, which may result in the need for process changes, although we hope and believe this is an unlikely scenario. GHSPs with operations in multiple locations, like us, may find this more burdensome if forced to manage different operating procedures in different jurisdictions,” Abram says. “We have developed and implemented industry best practices across the world, and it is our consistent application of these that ensures safe and efficient ground handling operations.”
European delegated and implementing acts leave very little room for maneuver once they have been sent to the Parliament and the Council for final scrutiny, according to an IATA spokesperson.
“The Parliament and the Council have a certain period, depending on the complexity of the act, to object the draft act as submitted by the Commission. If neither body raises an objection, the act is effectively
adopted. Amendments as such are not possible at this stage,” says IATA.
Youssef also believes the proposed regulations are unlikely to change following the outcome of the extensive consultation process that has taken place.
“However, individual member states may include additional requirements when incorporating the regulations into local law,” he says. “This is not desirable for our members who operate in multiple jurisdictions and strive for commonality of equipment, processes and training, especially as we believe that commonality brings great benefits to safety and efficiency.
According to EASA, competent authorities have been involved in the expert group along with the industry. “To help prepare for future oversight, EASA, national authorities and the industry have participated in mock audits to help with initial preparations,” says EASA. “As the regulation will become applicable in 2028, there will be a program of promotional activities between publication and applicability to help the entire ground handling community prepare for implementation.”
GHSPs and industry expect a practical introduction of the regulatory oversight process, although there may be some questions during the initial implementation, according to Abram.
“As an industry, GHSPs understand the goal of consistently applied procedures, supporting best practice performance and the goal of safety,” he says. “dnata supports the Emphasis a harmonized, collaborative approach to the new regulations offers a promising outlook for a smooth and effective implementation.
regulatory oversight program within the EU and would encourage other aviation authorities around the world to adopt the same approach.”
Regulators are going through a parallel preparation process to ensure they can effectively supervise GHSPs’ compliance under the new framework, illustrates Youssef.
“This includes building a workforce of competent inspectors with specialist knowledge in ground handling operations. In some cases, we believe that competent authorities will work with experienced GHSPs to develop training programs for inspectors, promoting collaboration between regulators and industry stakeholders,” he says. “This knowledge-sharing approach,
successfully implemented in ight operations and airport inspections, will enhance regulatory oversight while ensuring practical and industry-aligned enforcement.
“From an industry perspective, we see collaboration between EU member states as essential to maintaining consistent standards of oversight. We encourage a harmonised approach that ensures fairness and operational clarity for GHSPs operating in multiple European jurisdictions.”
The nal approval of the new ground handling regulations means the aircraft ground handling industry remains focused on maintaining
safety and operational standards while preparing for the upcoming oversight framework. While the regulations may introduce new requirements, particularly regarding self-declaration and regulatory oversight, the emphasis on a harmonized, collaborative approach offers a promising outlook for a smooth and effective implementation.
Dr. Mario Pierobon provides solutions in the areas of documentation, training and consulting to organizations operating in safety-sensitive industries. He has conducted a doctoral research project investigating aircraft ground handling safety. He may be reached at mariopierobon@alphaomega.dev.
→ Towbarless, Remote-Controlled, and Electrically Driven
→ Extremely Compact Design: Optimized for superior maneuverability and efficient gate positioning
→ Unique Oversteering Protection: The system autonomously corrects potential oversteering issues
→ One-Person Operation: Best-in-class visibility ensures maximum safety around the aircraft
→ Online Live Support: Our technicians can access all parameters via the Mototok Cloud, providing real-time assistance to your service staff
→ Unmatched Quality: German-engineered and manufactured for exceptional reliability
→ Efficiency Booster: No waiting for a pushback tug, no driver’s license required, low maintenance requirements
Safety on the ramp depends on consistent adherence to industry best practices and standards...and common sense.
BY REBECCA KANABLE
Safety is for everyone involved in aircraft towing, according to Pete Johnson, director of sales and service, Americas at Aero Specialties. Here he explains important details crucial to safe towing operations.
When it comes to towing procedures, ramp personnel should adhere to industry best practices and standards to ensure safe and ef cient ground handling operations. These include all relevant aviation regulations and guidelines set forth by the International Air Transport Association (IATA) and the International Business Aviation Council (IBAC), as well as by regulatory authorities, including the Federal Aviation Administration (FAA) in the United States and the European Union Aviation Safety Agency (EASA) in Europe.
IATA offers general guidelines for aircraft towing procedures, emphasizing safety, equipment suitability, effective communication, area clearance, towing techniques and emergency procedures. FBOs and ground handling providers adapt these principles into their speci c towing protocols, considering regulatory requirements and operational needs. IBAC’s
Weight
International Standard for Business Aircraft Handling (ISBAH) is another resource speci cally created to enhance the safety and ef ciency of business and general aviation ground handling.
Most ground handlers have established guidelines for towing with comprehensive standard operating procedures (SOPs) that outline proper towing procedures, including a pre-tow check, equipment usage, communication protocols and emergency procedures, says Johnson.
Speci c training and certi cation requirements for
ground handling staff involved in aircraft towing operations at FBOs can vary depending on local regulations, type of aircraft and FBO policies.
“[Ground handling providers] should ensure that their staff receive comprehensive training and certi cation to perform aircraft towing operations safely and ef ciently, contributing to the overall safety and success of operations,” Johnson says.
He points out AERO Specialties assists customers with proper towbar use and maintenance.
Aircraft towing operations face common challenges. Some are daily, others are occasional. Johnson outlines seven strategies to address these common challenges.
1
Limited maneuverability – Aircraft can be challenging to maneuver, especially in congested areas. Ground handling staff should be trained on proper towing techniques, including maneuvering in tight spaces and congested areas. Clear signage and designated pathways on the ramp should facilitate safe and ef cient towing operations. Wing walkers should also be employed when the operation requires additional eyes.
2
Variable weather – Adverse weather conditions can impact towing operations. Ground handling staff should monitor weather forecasts regularly and plan towing operations accordingly. They should also consider rescheduling or adjusting operations during adverse weather conditions.
3
Communication – Ground handling providers should establish and implement clear, standardized communication protocols between ground and ight crews, including using radios, hand signals, or electronic communication devices. In addition, regular training sessions should be conducted to ensure all personnel are familiar with communication procedures and can effectively relay instructions and information during towing operations.
4 Equipment maintenance – It’s necessary to develop a comprehensive maintenance program for towing equipment, including regular inspections, servicing, and repairs as needed, and a system should be implemented for tracking equipment maintenance schedules and ensuring compliance with manufacturer recommendations and warranty requirements.
5 Ramp management – Ground handling providers should collaborate with airport authorities and each other to develop and implement ramp management procedures to minimize congestion and optimize space utilization.
6
Adherence to procedures – Ground handling staff should receive thorough training on towing protocols, including weight and balance considerations, aircraft-speci c procedures and regulatory requirements. Accountability measures, including regular audits and performance evaluations, should be implemented to ensure strict adherence to towing procedures.
7
Safety culture – Ground handling providers should foster a safety culture within the organization by promoting awareness, accountability and continuous improvement in safety practices. This can be done by encouraging open communication and reporting safety concerns or near-misses to identify areas for improvement and implement corrective actions.
Technology can assist towing operations. For instance, by integrating AERO Specialties’ SiPsHitch Linear Force Monitoring System into aircraft pushback tugs and tow tractors, operators gain real-time alerts to potential
ALEXANDERON | SHUTTERSTOCK
7 COMMON AIRCRAFT TOWING MISTAKES TO AVOID
According to Pete Johnson at Aero Specialties, common mistakes to avoid when towing aircraft include:
• Skipping safety checks on towing equipment.
• Ignoring communication protocols.
• Taking shortcuts in maneuvering.
• Overlooking environmental factors.
• Improper use of equipment.
• Lack of training or experience.
• Rushing procedures at the expense of safety.
“Avoiding these shortcuts and mistakes is crucial to ensure safe aircraft towing operations,” Johnson says.
overstress situations, mitigating the risk of costly damage to aircraft, tugs and other equipment.
“It offers additional bene ts such as operator performance improvement, training support and comprehensive data logging capabilities. The system eliminates uncertainty by recording all forces applied to the nose gear, providing invaluable protection for pilots and service providers,” Johnson says.
By implementing these strategies, Johnson notes ground handling providers can effectively mitigate the challenges associated with aircraft towing operations and ensure safe and ef cient ground handling practices.
Rebecca Kanable , a veteran journalist, worked with Endeavor Business Media’s aviation group from 2021 to 2024 as assistant editor of Airport Business, AMT and Ground Support Worldwide. She previously worked for various publications, including trade magazines and newspapers.
• 5000-PSIG rated
• 36 SCFM discharge rate
• Portable
• Single acting, double acting and 2-stage configurations
Air Driven KEEP LOW PRESSURE O2/N2 BOTTLES IN BUSINESS 40% MORE FILLS
HIHPG1 SERIES
OXYGEN NITROGEN& BOOSTERS
Primary use for Charging, Purging, and Reclaiming... Onboard Oxygen Bottles • Struts • Escape Chute
High Altitude Low Opening (HALO) • Life Rafts • Tires
Even if your source gas pressure drops below 300-PSI
Hydrant operators must adopt new procedures to stay compliant and ensure seamless, safe refueling operations.
BY DR. DEREK COUSINS
Jet fuel is supplied to aircraft either by a fueling truck or through an underground network of pipes known as a hydrant system.
Refueling can take many hours depending on the aircraft. Hydrant systems are preferred for their operational efficiency and ease of use, particularly for larger aircraft that require significant amounts of fuel. Hydrant systems minimize the need for transporting fuel via trucks across busy airfields, reducing logistical complexity and ensuring a safer, more streamlined refueling process.
Hydrant systems are essential for efficient aircraft refueling, but they come with operational challenges. In the event of a leak, without a reliable tightness monitoring system, operators may face significant fuel losses, operational delays, and environmental risks before the issue is identified. Tightness monitoring is crucial to identifying leaks early, minimizing downtime, and preventing financial and safety risks, allowing hydrant systems to operate smoothly and meet regulatory requirements.
Hydrant systems are the backbone of efficient aircraft refueling
operations, and their performance depends on strict adherence to industry guidelines. The Energy Institute’s Recommended Practice (RP) EI 1540 outlines the best practices for the design, construction, maintenance and testing of these critical systems.
With the release of the sixth edition, significant updates have been introduced that directly impact the way hydrant operators manage their systems. These changes aim to improve operational reliability, tighten leak detection standards, and reduce downtime. For operators, this means adopting new procedures to
Hydrant systems’ performance depends on strict adherence to industry guidelines.
stay compliant and ensure seamless, safe refueling operations.
Historically, tightness monitoring for airport hydrants was addressed in two separate standards: EI 1540 and EI 1560. However, with the latest update, the key elements of EI 1560, which covered the operation, inspection, maintenance and commissioning of aviation fuel hydrant systems, have now been integrated into EI 1540.
This consolidation streamlines the guidelines, making EI 1540 the single reference point for both hydrant system design and operational best practices.
Sensitivity requirements in the previous specification for EI 1540 were based on the ability to “detect leaks equivalent to 0.04 liters/hour/cubic meter at a reference pressure of 7 barg, require a fuel hydrant shutdown period of about 1 hour and can be used on a regular basis.”1
In the previous specification, the sensitivity of a pressure-based system scales with hydrant volume, so a 4 liter/hour leak in 100 m3 gives approximately the same pressure drop as an 8 liter/hour leak in 200 m3.
The same standard is applicable to hydrant volumes of any size. The reference pressure accounts for the leak rate changing with pressure (a smaller pressure difference between inside and outside the pipe section results in a smaller leakage) and thus the operational pressure of the hydrant network determines the hole size to be detected.
The new standard addresses a concern that it was possible to cover an entire hydrant network as one section of a large volume and have a correspondingly large leak that would then go unnoticed. Under the new standard, optimal volume for each
hydrant section should be under 200 m3. The leak detection sensitivity threshold for hydrant sections operating with this volume should have a leak detection sensitivity threshold of 0.02 l/hr/m3 at a reference pressure of 700 kPag (7 barg). This makes the requirement twice as sensitive as the fifth edition’s specifications.
At a busy airport, finding time for tightness testing or any other maintenance activities is a challenge and most automated tightness monitoring systems can only be activated during quiet periods at the airport, which vary from region to region.
The new EI 1540 standard recommends testing every 24 hours to limit the total leak volume.
Previously, it was possible to treat an entire hydrant network as a single section with a large volume, which allowed for a larger leak to be detected while still remaining compliant with the standards.
To enhance leak detection precision and accuracy, EI 1540 recommends that pipeline sections be isolated using double block and bleed valves (DBBs), dividing the network into smaller, more manageable sections, ideally with volumes less than 200 m3
This ensures that each segment is correctly isolated, preventing issues caused by passing valves, which can interfere with the effectiveness of tightness monitoring systems.
After installing a tightness monitoring system, there is a requirement to validate the system.
Typically, this is accomplished by inducing a leak and confirming that the leak is detected, details of the procedure will be available from
the vendors. It is recommended under EI 1540 that revalidation of the system be completed annually as a minimum.
The new standard tightens the minimum detectable leak size in internal, pressure-based tightness monitoring systems, and increases the testing frequency thereby reducing the risks associated with undetected leaks. To comply with these updated guidelines, operators should focus on performance improvement and optimization of their existing systems.
For hydrant sections with volumes below 200 m 3, the increased sensitivity requirement targets a minimum leak of 0.02 l/hr/m 3 at a reference pressure of 700 kPa. For sections above 200 m 3, such as feeder lines, while the target leak rate is 4 l/hr at the same reference pressure, Atmos aims to achieve 0.02 l/hr/m 3 across all volumes as best practice for optimal performance. Operators are encouraged to work closely with their tightness monitoring vendors to achieve this level of sensitivity.
Meeting the new standard may involve re-commissioning or fine-tuning current systems. Operators can use these updates as an opportunity to improve the overall reliability and efficiency of their systems, ensuring compliance while reducing operational risks.
1 https://publishing.energyinst.org/topics/ aviation/aviation-fuel-handling/ei-1540-designconstruction-operation-and-maintenance-ofaviation-fuelling-facilities
Dr. Derek Cousins is aviation product manager at Atmos International. Since 2000, Atmos has been supplying tightness monitoring systems for jet fuel pipelines and airport hydrant systems around the world.
OshKosh AeroTech builds on its LEKTRO 88 legacy with a more streamlined and advanced model
BY JENNY LESCOHIER
Oshkosh AeroTech advances sustainability, autonomy, connectivity, and intelligent monitoring systems for airports of the future with its LEKTRO 88i towbarless electric tow vehicle.
Designed to be highly maneuverable in hangar and ramp aircraft positioning, the LEKTRO 88i was displayed at CES 2025 in Las Vegas in January. It is a redesign
of the company’s legacy product, the LEKTRO 88.
“At Oshkosh AeroTech, we are dedicated to providing innovative solutions that support the aviation industry’s evolving needs,” Ranjit Nair, president of Oshkosh AeroTech, states. “CES 2025, alongside our parent company Oshkosh Corporation, [offered] an exciting opportunity to showcase how our technologies
are advancing ground support operations, driving efficiency and providing outstanding passenger experiences across airports.”
With a purpose-built chassis, LEKTRO 88 tow tractors are designed to move aircraft with an MTOW up to 120,000 lbs., making them ideal for pushbacks and towing regional jets and turboprop aircraft. They are also able to tow a wide range of
business aircraft and are popular for FBO corporate flight departments worldwide.
Aircraft nose gear is secured using a patented strap and cradle system, which eliminates towbars and reduces wear and tear on landing gear. This helps simplifiy maintenance and reduce the complexity that may come with the capture systems on many towbarless tractors.
Electric LEKTRO 88 models are low maintenance while offering zero-emission operations in all weather, or indoors. Hybrid diesel/ electric onboard charging options are available.
Meanwhile, a tight turning radius helps create a small operational footprint and maximizes hangar utilization, while single-person operation and ease of use aid in simplifying training to alleviate workforce challenges.
LEKTRO 88i advances design and intelligence
In this reboot of the LEKTRO 88, Oshkosh AeroTech’s team of engineers focused on prioritizing quality of design, operational efficiency, and maintenance accessibility. One significant change is the move to more modern PLC logic, which allows for telemetry integration through the company’s iOPS platform.
This means Oshkosh’s advanced connectivity solution will be available to accommodate different aspects of fleet management. Also, through PLC control, features such as enhanced control functionalities, including slowed turns and accelerated winch-out capabilities, have been implemented.
For maintenance and repair purposes, the tractor has been streamlined with accessibility features and storage capacity has been increased by 27%.
Gross vehicle weight - 10,000 lbs.
Maximum tow capacity - 120,000 lbs.
Turning radius -
• Turn radius to outermost point - 191.24 in.
• Maximum turning angle (inner steer wheel) - 70° approx.
• Maximum turning angle (outer steer wheel) - 43° approx.
Operating performance -
• Maximum vehicle speed (forward, unloaded) - 11 mph
• Maximum vehicle speed (forward, loaded tow) - 4 mph
• Maximum vehicle speed (reverse, loaded tow) - 6 mph
Capture and pickup system -
• Universal nose gear cradle with front and side gates with 12,000-lb. lift capacity
• Hydraulic winch with 8,000-lb. pull capacity with nylon belt including automatic cut-off
• Double D-Ring 2- by 29-in. nylon strut strap with protective sleeve
• Double D-Ring 1- by 29-in. nylon strut strap
• Rubber chine protectors
• Single winch and cradle control keypad located on wheel fender
Drive Motor - 30kW SRIPM dual drive motors
Further, the LEKTRO 88i features AC drive motors, full compatibility with Lithium-ion batteries, and an enhanced drive/steering design.
Innovating for the airport of the future
Oshkosh AeroTech says its presence at CES emphasized its role in shaping the future of aviation through advanced ground support and gate equipment technologies, including:
iOPS intelligent monitoring systems - a fleet management solution that provides real-time data on ground support equipment and gate operations. The iOPS technology enables actionable insights, remote
diagnostics, and promotes efficiency, helping address downtime and optimizing operations for smooth passenger flow.
Sustainable ground support solutions - including electrification technologies designed to help control emissions, drive energy efficiency and align with environmental goals.
Operator support enhancements - advanced telematics, geo-fencing and operator monitoring tools to help promote secure, efficient and environmentally responsible operations.
Autonomous vehicles - promoting efficient operations through the use of autonomous, self-driving vehicles and gate equipment.
Tiger Gas can tow up to 60,000 lbs., has a 100-percent steel bodyon frame with bolt-on chassis components and a Kubota ICE powertrain. This familiar design offers capability, operations and serviceability that’s proven in the GSE space. Tiger Gas gives users the option to easily convert their powertrain to lithium-ion if and when they’re ready, on their timeline.
AviationPros.com/53075132
The Trowin FLTT (Bobtail) is based on the Ram 3500 Chassis. The heavy-duty rear body is available for single or dual rear wheels and a variety of couplers.
AviationPros.com/53075375
The TIM80 Aircraft Tow Tractor has a DBP of 80 kN and provides a towing capacity up to 114 tons on wet concrete and a 1% slope. With its compact, robust, durable chassis and high capacity powertrain, the TIM80 offers a sound/vibration insulated cabin with windows on all sides, instrument panel and ergonomic, versatile and comfortable working space for the driver and passenger. The TIM80 provides tight maneuverability capabilities through its 4 Mode Steering System (F2WS-R2WS-4WSCrabSteering) and overall dimensions. A dual independent breaking system is provided for safe braking during towing operations.
AviationPros.com/21283887
The P250 Electric Tow Tractor ensures fast and safe transfer of heavy loads over short and medium distances. This is made possible by powerful electric motors as well as easy-touse hydraulic steering. The turning radius of the P250 is also very short. Hydraulic elements are located between the cabin and the frame.
This design prevents uneven ground from leading to excessive vibrations in the cab. The solid one-piece frame surrounds the entire cart and is designed for the high demands of intensive environments. The P250 pulls a maximum towed load of 25 tonnes and reaches a top speed of 25 km/h. The P250 has three independent braking systems that ensure safety in all driving situations.
AviationPros.com/21277030
The Bobtail is a revolutionary system that enhances the ef ciency and safety of airport towing operations. With the Bobtail, ground support equipment can be moved effortlessly and securely, ensuring smooth and seamless ground handling operations. The Wilcox GSE Bobtail TRUX is manufactured using the nest materials and adheres to the highest industry standards, ensuring durability and longlasting performance.
AviationPros.com/53075184
The Flightcom Wireless Headset Systems provide immediate and hands-free, real-time communication. They do not have any wires or clumsy belt stations – the headsets are completely self-contained. Enjoy range of up to 1,600 feet, automatic superior noise-canceling gates, and a listen-thru feature for enhanced situational awareness and overall safety. Widely deployed for pushback, deicing, aircraft movement, maintenance, cargo loading/unloading, training and more.
AviationPros.com/21159188
The ProMod Ecco Headset is a lightweight and comfortable headset that effectively blocks out interfering noises for clear communication. The headset comes standard with an earcup PTT, and also features a high-quality, noise-canceling microphone on a exible mic boom that swivels for right or left side use.
AviationPros.com/12222697
Made by Safety Wand Corp., this unit offers an enclosed battery compartment with a spring on both ends to help protect the batteries. The circuit board is epoxy-coated industrial grade, and the commercial grade LED is brighter. The industrial mechanical switch is rated for 10,000 uses. Other features include stainless steel internals, an anti-roll base. It’s virtually indestructible.
AviationPros.com/21112614
AIRLINK 2085 establishes a cordless, full-duplex, audio conference for operational teams. Speci cally designed for aeronautic applications, it can be used during maintenance operations or departure procedures in a noisy context. Features include: audio conference for up to four or ve operators, aircraft/ ground communication, full duplex communication, range up to 300 meters, DECT technology, audio wideband 100Hz-7KHz.
AviationPros.com/21110613
The David Clark Company Series 9900 Wireless Headset Communication System is being used by ground crew personnel in hundreds of airports for leading carriers in the United States, Europe and Asia. The system is ideal for pushback operations, aircraft towing, maintenance and deicing/anti-icing operations. The Series 9900 system enhances the safety and situational awareness of ground personnel to protect against potential injury, incidents, and costly aircraft damage.
AviationPros.com/21158250
Ramp Communications sells and repairs David Clark wired and wireless headsets used during pushback, deicing and maintenance operations. The company services more David Clark headsets and related accessories than anyone in the United States, except for the factory. Ramp Communications’ quality, expertise, speed, and price is unmatched and company guarantees satisfaction.
AviationPros.com/12434274
WS LITECOM PRO III HEADSET
3M PELTOR
The analog and digital two-way radio enables clear, hands-free communication in high levels of noise and integrates seamlessly into existing two-way radio systems. With Bluetooth multi-point functionality, workers can be wirelessly connected to two mobile devices. Plus, workers stay protected, aware and able to communicate face to face while never removing their hearing protection through level dependent functionality. All of this technology is combined with the professional-grade durability and all day wearability of the Peltor brand.
AviationPros.com/21144571
The SWATCOM A-KABEL Passive Ground Mechanics Headset (AK-5850H) connects directly to an aircraft. Supplied with or without in-cup PTT (push-to-talk) and ¼” stereo connector for direct connection to aircraft intercom port or into pushback lead or direct to pushback tug.
AviationPros.com/21267105
GBY JENNY LESCOHIER
The use of sustainable aviation fuel is growing, and with it, the understanding of the benefits and challenges of its use.
round Support Worldwide attended the Aviation Fuel Handling Training Symposium, hosted by Gammon Technical Products, Feb. 18-20 in Irving, Texas, where industry experts presented to approximately 300 professionals from around the world.
Among the experts was Amy Carico, director of fuel services and technical standards at Airlines for America (A4A), whose presentation “SAF 101 - Introduction to Alternative Jet Fuels and Their Handling” provided an overview of this growing industry. A4A contributed these responses to GSW questions.
GSW: What does the term “SAF” really mean?
A4A: Sustainable aviation fuel (SAF) is one of the many terms describing liquid aviation fuel that emits less carbon on a lifecycle basis than traditional, petroleum-based aviation fuel, while satisfying other relevant sustainability criteria and still meeting the rigorous specifications required to ensure safety of flight.
SAF can be produced from a variety of feedstocks that are coupled with production pathways that use different fuel-processing technologies. Depending on the feedstocks and production pathway, today’s SAF can reduce lifecycle emissions by around 60-80% when compared to conventional jet fuel, with 100% reduction possible in the future.
Jet fuel has always been a complex mixture of hundreds of unique molecules, and each batch is unique,
Amy Carico, director of fuel services and technical standards at Airlines for America (A4A), spoke at the 2025 Aviation Fuel Handling Training Symposium in February.
based on the crude slate and re nery processing. Sustainable Aviation Fuel meets the same technical and safety standards as conventional jet fuel. To be used in aircraft today, SAF is blended with conventional jet fuel.
GSW: What is SAF made of?
A4A: SAF can be produced from different feedstocks including oils and fats, oil seed crops, woody wastes, municipal solid waste, CO2 and water.
All SAF that is used in aircraft today is a mixture of a synthetic blend component (SBC) and petroleum-based fuel. SBC, often referred to as neat SAF (not yet blended with conventional jet), is the industry-accepted technical term referring to a nished product meeting one of the ASTM D7566 annexes.
Prior to blending, SBC or neat SAF is not yet approved as a nished fuel and cannot be used in aircraft. It must be blended with conventional jet fuel prior to testing/certi cation as ASTM D1655 compliant jet fuel.
A mixture of SBC (or neat SAF) with conventional jet fuel creates Semi-Synthetic Aviation Turbine Fuel (SSATF) or Semi-Synthetic Jet Fuel (SSJF). After the SSJF has received one of several sustainability certi cations, it is then deemed and quali ed as SAF. These are the industry-accepted technical terms.
Only SSATFs or SAFs that are already blended can be approved as nished fuels, and then be used in aircraft just like any other jet fuel.
GSW: Is there such a thing as fully synthetic aviation fuel?
A4A: Fully synthetic aviation turbine fuel (FSATF) is the industry-accepted technical term for a finished fuel that
is made wholly of synthetic components (no conventional jet fuel). These are also commonly referred to as “100% SAF” and have been used on a number of demonstration flights conducted by airlines and OEMs. Because there is not yet an approved ASTM standard for these fuels, they have not yet been used on commercial flights.
FSATFs may contain fuel produced using only a single method of production or may be multiple approved D7566 annexes/production processes blended with each other. FSATFs are molecularly identical to conventional jet fuel and necessarily contain aromatic molecules in order to comply with ASTM D1655.
GSW: What do SAF logistics look like?
A4A: Most SBC or SAF production facilities are not adjacent to standard refining facilities, and SBCs need to be transported to blending facilities before transport to airports.Pipelines are the safest, most efficient, most economical way to transport liquid fuels. Almost all jet fuel moves by pipeline. Today, no pipelines move SBCs or neat SAFs - only blended SAF can go into a pipeline.
To scale the SAF industry, infrastructure investments across the supply chain are needed. For example, the majority of pre-airfield tanks are not equipped to conduct a proper blend. Expanding the locations where SAF is produced and blended can support delivery of this fuel to airports.
EI 1533 is a document, produced through collaboration of the world’s leading subject matter experts, containing quality assurance requirements for semi-synthetic jet fuel and synthetic blending components. It defines handling procedures, testing and controls for various types of transportation and equipment used
Once [SAF] has met D1655 requirements, it is considered the same as conventional fuel.
— Airlines for America (A4A)
for import, export and shipping of SBC or SAFs. It is the global standard for handling of SBCs and SAF.
GSW: How should SAF be handled at airports?
A4A: SAF requires no special handling, with no special checks or equipment modifications. Once the fuel has met D1655 requirements, it is considered the same as conventional jet fuel.
GSW: What is the industry’s goal for adopting SAF usage?
A4A: U.S. carriers transport over 2.6 million passengers and 61,000 tons of cargo per day while contributing just 2 percent of the nation’s greenhouse gas emissions.
U.S. operators are committed to achieving net-zero emissions by 2050. Expanding the availability, affordability, and usage of SAF will be essential to reach that goal. U.S. airlines have pledged to work across the aviation industry and with government leaders to make three billion gallons of cost-competitive sustainable aviation fuel (SAF) available for use in 2030. Reaching these goals will require significantly increased commercial scale production and more affordable SAF.
GSW: What do you foresee for the future of SAF usage?
A4A: The SAF industry is still in its infancy. As such, because of the high cost of SAF and the limited production of this fuel, SAF quotas or mandates are not appropriate. But support for voluntary SAF deployment initiatives
and incentives can help to scale the growing industry.
SAF must meet rigorous certification and environmental criteria, and there are currently very few producers of SAF, so the costs are very high while logistics for feedstocks, production, blending and delivery are still being established. Scaling this industry will require continued policy support and stakeholder engagement to ensure that SAF is both affordable for airlines and profitable for fuel producers.
U.S. airlines are committed to making SAF commercially viable to support our environmental and supply diversification goals and have engaged with fuel suppliers and other stakeholders to support the nascent industry. There is still significant work to do to scale up supply and make SAF cost competitive with conventional jet fuel.
Accordingly, U.S. airlines welcome support for efforts to make SAF fully commercially viable and deploy SAF where it makes sense as we scale up. U.S. airlines are reaching out to policymakers, renewable fuels producers, and increasingly with the agriculture industry to find ways to more rapidly scale up the availability of affordable SAF. If we are collectively successful, in addition to the environmental benefits, there are benefits to be gained for fuel producers, farmers and other feedstock providers, airlines, and the traveling public.
We encourage fuel producers, airports, policymakers, environmental organizations and other stakeholders to work with us in cooperative ways to develop, evaluate and support policies that will, quite literally, get SAF off the ground.