Quality and Testing Regulations for Upholstered Furniture
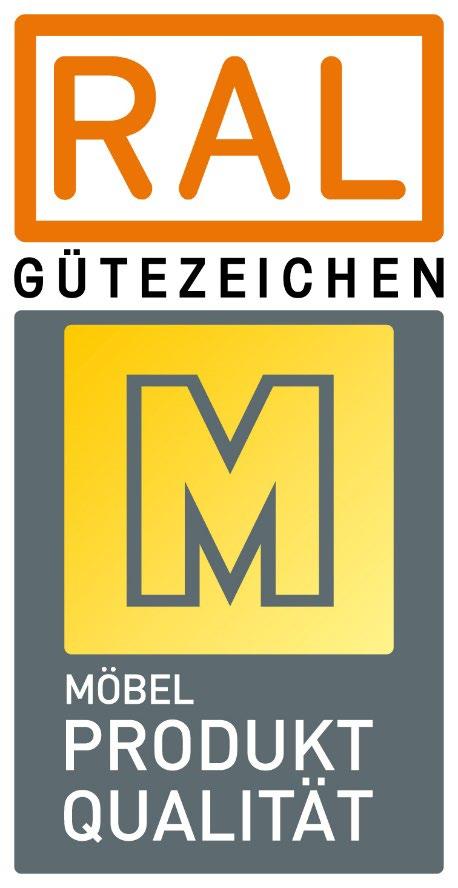
Quality Assurance
RAL-GZ 430/4
Dated: January 2022
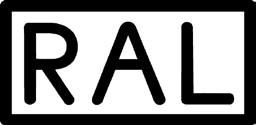
Editor
RAL Deutsches Institut für Gütesicherung und Kennzeichnung e. V.
Fränkische Straße 7
53229 Bonn
Tel.: (+49) 228 68895-0
Fax: (+49) 228 68895-430
E-Mail: RAL-Institut@RAL.de
Internet: www.RAL.de
Reprinting, even in parts or extracts, is not permitted. All rights, including those of translation into other languages, are reserved by RAL.
© 2022, RAL, Bonn
Quality and Testing Regulations for Upholstered Furniture
Quality Assurance
RAL-GZ 430/4
Deutsche Gütegemeinschaft
Möbel e. V.
Friedrichstraße 13 - 15
90762 Fürth
Tel.: +49 911 950 999 80
Fax: +49 911 950 999 850
E-Mail: dgm@dgm-moebel.de
Internet: www.dgm-moebel.de
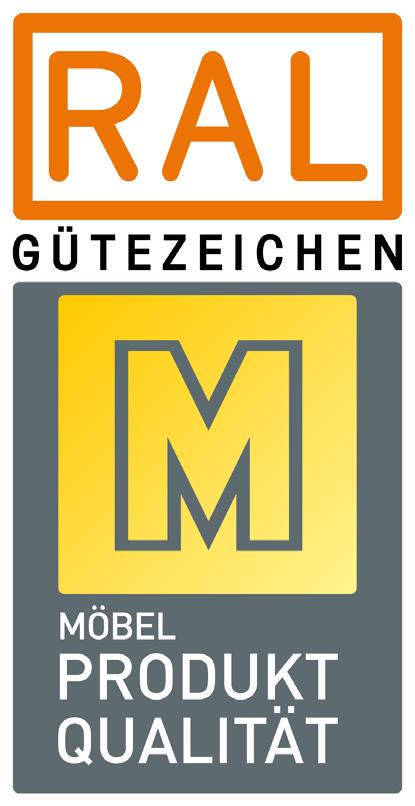
These Quality and Testing Regulations have been established by RAL Deutsches Institut für Gütesicherung und Kennzeichnung e. V. (RAL German Institute for Quality Assurance and Labelling) under the principles for quality labelling in a recognition process together with expert groups and responsible authorities
Bonn, January 2022
RAL Deutsches Institut für Gütesicherung und Kennzeichnung e. V.
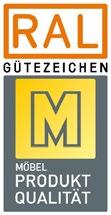
Foreword to the Furniture Quality Assurance RAL-GZ 430
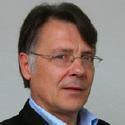
RAL-GZ 430 has been the “gold standard” for good furniture quality for more than half a century. However, its contents require constant adaptation in order to meet the needs of changing consumer requirements on the one hand and technical as well as social developments on the other. Standards, laws, and other recognised rules of technology are constantly changing. They are an essential part of RAL-GZ 430, which in its quality requirements, however, often goes beyond normative basic requirements.
With the claim of a holistic quality standard for furniture, RAL-GZ 430 includes in testable form the topics of processing quality, utility and comfort, product safety, healthy living as well as sustainability in product design and material selection.
The previously proven requirements and test methods have been adopted largely unchanged in this new edition of the RAL. In detail, however, changes, updates and adaptations were necessary, based on the experience in dealing with this set of rules and due to changes in standards which are referenced in this RAL.
As the person responsible for the editorial processing of the results of the DGM working groups, I would like to express my special thanks to the staff of these working groups as well as to the editorial team of the DGM. Without the dedicated cooperation and competent contributions of the voluntary DGM working group participants, further development and updating of RAL-GZ 430 would not have been possible.
Reimund Heym Head of Technology and Standardisation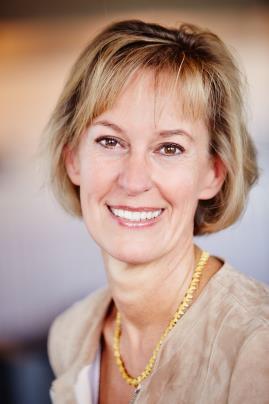
It all started with RAL-GZ 430. It is the basis for the “Golden M” certification, which focused on quality, function, and environmental compatibility early on. It was and still is a matter of consumer protection.
I am all the more pleased that the Deutsche Gütegemeinschaft Möbel e. V. recognised early on that quality, and thus durability, is an essential part of sustainability. Various certification offers in this area followed, whether it was climate neutrality or emission measurements of the products. Then, in 2019, very consistently, the Advisory Board for Sustainability was founded to meet the everincreasing pressure for change, which was also of a legislative nature. Today, sustainability is no longer a trend, nor is it a megatrend, but a must, an imperative. We need to recognise that companies are part of the environment and part of society, that we are all part of a system with interdependencies, no matter what we do or don’t do. Sustainability management is a journey that never ends for companies. With its various certifications, the DGM offers companies goals and intermediate destinations for this journey, and thus also offers the end-consumer reliable information on the subject of sustainability. With this in mind, I am honoured to be able to shape the future with the wonderful people on the Advisory Board and I look forward to continued constructive discussions leading to results for the good of all.
Dr Susanne Steinhauer Chairwoman Advisory Board for Sustainability5.4.
6.1.
6.1.1.
6.1.2.
6.2.
6.3. FRAMES
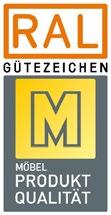
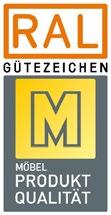
6.3.1. Wooden and wood-based frames
6.3.2. Metal frames ........................................................................................................................
6.3.3. Frames, supporting elements and swing arms
6.3.4. Deflection of the seat frame
6.3.5. Connection of elements .......................................................................................................
6.3.6. Upholstered furniture standing elements
6.3.7. Furniture casters...................................................................................................................
6.4. FITTINGS FOR UPHOLSTERED
6.4.2. Fittings with electric motor drive .........................................................................................
6.5. SURFACES OF UPHOLSTERED FURNITURE
6.5.1. Wood and wooden-based materials ....................................................................................
6.5.2. Varnished surfaces
6.5.3. Melamine
6.5.4.
6.6. SPRINGING
6.6.2. Wood lath springing
6.6.3.
6.6.4.
6.6.6. Upholstery carriers (seat)
6.7.
6.10.
6.11. UPHOLSTERY
6.11.1.
6.12.1.
6.12.2.
6.12.3.
6.12.4.
6.13.
6.13.2.
12.1.
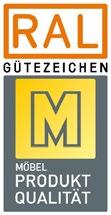
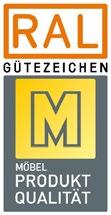
1. Area of Application
These Quality and Testing Regulations apply to the condition of upholstered furniture (also made of rattan, bamboo, willow, etc.), that may be labelled with the RAL quality mark. All legal regulations must be observed as a matter of principle. In addition, quality assured upholstered furniture must meet the requirements as defined below. All standards relating to the scope of these Quality and Testing Regulations shall be consulted as well.
Only the most recent versions of standards or their relevant replacements are valid.
The requirements take into account as standard climate according to DIN 50014 a temperature of 23° C and a relative humidity of 50% and apply to furniture in new condition.
Proper transport and professional assembly of the products are assumed.
2. Quality and Testing Regulations
The basic requirements for quality assured furniture are regulated by the relevant standards and guidelines of the Quality and Testing Regulations, compliance with which is mandatory as a prerequisite for initial testing according to Section 3.1.
Furniture that contains functional and constructional elements not included in RAL-GZ 430 must conform to current technological standards.
3. Monitoring
Monitoring is divided as follows:
• Initial testing
• Internal quality control
• External quality control
• Repeat testing
• Testing and monitoring reports / Approval license
• Testing costs
• Inspectors
3.1.
Initial testing
Passing the initial test is one of the requirements for the award and use of the quality mark of the Quality Association. Initial testing is carried out in the production facilities of the applicant. As part of this assessment, random laboratory test samples are taken from ongoing
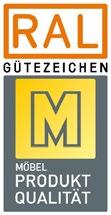
production by the commissioned third-party inspector. If the applicant can provide test certificates for supplied products or materials, the test procedure is reduced. It is, however, important that these documents (test certificates may not be older than 1 year) are based on the current technological standards and the tests were carried out by competent and neutral testing institutes.
3.2. Internal quality control
Ongoing internal quality control, which can be reproduced at any time, is mandatory for all quality mark users. Users must carefully record the results of internal quality controls, keep them for at last 5 years and present them to the appointed inspector for inspection upon request within the scope of external quality control procedures.
For the two most common leather types, emission testing with a test duration of 28 days (with indication of the 3-days-value) must be carried out in a test institute determined by the Quality Community each calendar year. For all other leather types, one short time emission test (duration: 3 days) is to be carried out in each monitoring cycle. The test reports must be sent to the DGM office in a timely manner and presented to the tester in the following monitoring test.
3.3. External quality control
In order to ensure the consistent quality of quality assured products, external quality control is carried out every 2 years on the premises of the quality mark user. Within the first 3 years of awarding the quality mark/membership, external quality control is carried out annually. This test covers the inspection of the results of all quality control measures (e. g. internal quality control, test reports from competent, neutral testing institutes) and the inspection of the proper manufacturing of “quality assured furniture”.
3.4. Repeat testing of external quality control
If deficiencies in the quality assurance are detected during external quality control measures, the Quality Committee can order a repetition of the test, whereby the type, content and scope of this test are determined by the Quality Committee of Deutsche Gütegemeinschaft Möbel e. V. Should the repeat test also conclude with a negative result, the Quality Committee may, in agreement with the Executive Board, take further measures in accordance with Section 11.5 of the Implementing Regulations for the Award and Use of the Quality Mark.
3.5. Test and monitoring report / Approval license
The contracted external inspectors must draw up corresponding test reports on the tests and quality control procedures carried out; the applicant or quality mark user each receive copies of said reports.
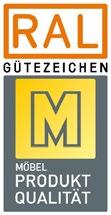
Based on the passed tests, the DGM office issues an approval license for the furniture programs listed therein for a certain term.
3.6. Testing costs
The applicant or quality mark user must bear all arising testing or monitoring costs.
3.7. Inspectors
The Quality Association appoints suitable, expert testing institutes to carry out tests and monitoring measures.
Institutes entrusted with this task must prove their identity to the applicant or quality mark user by submitting a written identification before starting their work.
4. Sustainability
Sustainability is to be understood as a development that is ecologically compatible, socially just and economically efficient.
Important in this context is a long product life, which can only be achieved through high quality, which contributes significantly to saving resources and which is therefore an essential part of sustainable economic activity. Another aspect of sustainability is the consideration of social impacts.
Sustainability as well as the environment and personal health are particularly important to consumers today. In close cooperation with leading testing institutes and taking into account more recent specifications of the Federal Environment Agency, the requirements were revised and adapted to the latest scientific findings.
These requirements apply to furniture as purchasable by consumers in furniture stores.
Manufacturers must ensure that all supplied materials (including those from abroad) comply with the statutory European and German regulations (e. g. Chemicals Act, Banned Chemicals Ordinance and Ordinance on Hazardous Substances, REACH POP) as well as additional DGM requirements.
In case of mandatory normative, legal, safety-relevant as well as contractual specifications regarding the use of materials, substances and requirements, the effects on the requirements according to RAL-GZ 430, especially in the contract sector, are not taken into consideration.
The initial and monitoring tests are to be carried out according to Point 3.
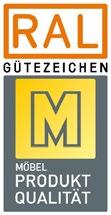
4.1. Protection of health
The preparations (paints, adhesives, stains, coatings, etc.) must not contain substances of the following categories as formulation components:
Substances according to Regulation (EC) No 1272/2008 (CLP Regulation): Categories Carcinogenic 1A and 1B, Mutagenic 1A and 1B, Toxic to reproduction 1A and 1B
a) Sensitising substances according to the Technical Rule for Hazardous Substances (TRGS) 907 and the EC Regulation 1272/2008, Annex VI
b) Substances which are of very high concern for other reasons, and which have been included in the list (so-called candidate list 1)) established in accordance with REACH Article 59(1)
c) Acutely toxic (poisonous) of the category Acute Tox. 1 or Acute Tox. 2
d) Toxic to specific target organs of the category STOT SE 1, STOT SE 2, STOT RE 1, or STOT RE 2
Excluded from these regulations are:
a) Process-related, technically unavoidable impurities that are below the classification limits for mixtures.
b) Monomers or additives that react to form polymers or are chemically bonded (covalently) into the plastic during plastic production if their residual concentrations are below the classification limit for mixtures
4.1.1.
Requirements for test samples
The examinations in test chambers can be carried out both as whole-body tests and as component tests The selection of test samples is to be agreed between the testing institute and the manufacturer and is to be carried out in such a way that all model variants awarded the quality mark are represented by the test.
4.1.2.
Test material
The final products falling within the area of application differ in shape, materials and the number of materials used. Therefore, in each individual case, the test procedure and the selection of test samples must be determined by the testing institute responsible for the surveillance test in consultation with the manufacturer.
1 Link to the candidate list of Regulation (EC) No 1907/2006 on the Registration, Evaluation, Authorisation and Restriction of Chemicals (REACH): https://echa.europa.eu/de/candidate-list-table
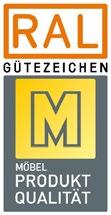
For furniture made of wood and wood-based materials with a three-dimensional surface, there are two ways of testing:
a) Whole-body testing, especially for small furniture, chairs, etc.
b) Component testing, especially for modular furniture and furniture programs with similar components
4.1.2.1.
Whole-body testing
The product to be tested must be taken directly from current production. Supplied parts may not be older than 10 days. A deviation from this specification is permissible if the manufacturer proves that individual supplied parts used in the normal production process are regularly older than 10 days.
Immediately after removal from production, the product must be placed in airtight packaging.
4.1.2.2.
Component testing
In the case of component testing, e. g. for furniture programs, the testing institute selects the components to be tested in consultation with the manufacturer. The different materials used, in particular different coating systems, must be taken into account. The selection must be made in such a way as to ensure compliance with the requirements of the award criteria for the product to be tested. In the case of components with a total area share of no more than 5% of the product, sample analyses and emission testing are not necessary.
The components to be tested are be taken directly from the current production in sufficient quantity. Supplied parts may not be older than 10 days. A deviation from this specification is permissible if the manufacturer proves that individual supplied parts used in the normal production process are regularly older than 10 days. In the case of flat components, at least 3 parts must be taken as a stack, of which only the middle part is used for the emission test.
The testing institute must be consulted about the exact sample quantity, taking into account the size of the component and the emission test chamber to be used. The samples taken from the same components must be immediately packed together in airtight packing. The individual samples should be placed as close to each other as possible to minimise unavoidable emissions during transport to the testing institute
4.1.2.3.
Transport
The packaged sample material must be transported to the testing institute as quickly as possible. No more than 7 days may elapse between packaging and arrival at the testing institute.
4.1.3.
Sample preparation
Until the start of the test, the test sample or sample material must be stored at the testing institute in packaged form.
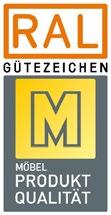
When preparing the test samples for the emission test, only those flat components should be used that are stored on the inside of the stack and not those on the outside.
Components and complete products can be tested in their original condition in a large test chamber. In this case, possible low results for semi-volatile compounds must be taken into account. As a rule, test samples are to be taken from the sample material which can be examined in a test chamber suitable for volatile organic compounds. The test samples should represent the materials used and the different surfaces of a complete piece of furniture. Any narrow surfaces exposed by cutting must be sealed with a suitable sealant.
Self-adhesive, low-emission aluminium foil has proven suitable for this purpose. Any selfemission of the aluminium foil must be determined in preliminary tests.
When calculating the emission area, the surfaces on both sides and the narrow surfaces (without surfaces subsequently sealed as a result of test sample cuts) must be included
After completion of the test samples, they must be immediately placed in the test chambers or stored in packages until the test chamber is loaded.
For the manufacturer's own internal documentation, a sampling protocol (dates of production, packaging, shipping, etc.) must be created for each sample.
The time between packaging of the samples at the manufacturer and loading of the chambers should be as short as possible. According to DIN EN 16516, the test must be started within 8 weeks after sampling, provided that the sample is stored in the laboratory in the specified packaging and under normal indoor conditions. Sampling, sample receipt and test start must be documented in the test report.
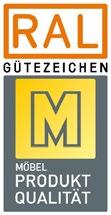
4.1.4. Emission requirements for upholstered furniture and materials
Table 1 – Emission requirements for upholstered furniture, upholstered chairs, and leather/artificial leather
Parameters
Upholstered furniture (Armchair) Textile cover 1)
Upholstered furniture (Armchair) Textile cover 1) Upholstered chairs
Other aldehydes acc. to current list of LCI values 3)
TVOCspec. (C6 – C16) acc. to AgBB 3)
TSVOC (<C16 – C22)
Artificial leather:
CMR substances 4) acc. to EU Cat. 1A and 1B ∑ < 10 µg/m³ per individual value < 1 µg/m³ per individual value < 1 µg/m³ per individual value < 1 µg/m³ per individual value
Odour (see explanations below) < 3.0 < 3.0 < 3.0
VOC without LCI acc. to AgBB 3)
R value5)
1) For leather upholstery see whole-body testing for leather chairs
2) The test can be terminated on the 7th day after loading if the required final values of the 28th day are reached and no increase in concentration of one of the detected substances can be detected compared to the measurement on the 3rd day
3) Sum of all individual substances ≥ 5 µg/m³) at test chamber concentration
4) The substance Dimethylformamide (DMF, CAS 68-12-2) is treated separately during the assessment of CMR properties. For DMF, a limit value (based on the LCI value) of < 15 µg/m³ after 28 days applies. The value after 3 days shall not be included in the total evaluation. For the calculation of the R value, DMF must still be taken into account. This regulation is valid for a transitional period until 31.12.2023. As of 01.01.2024, it will no longer apply.
Formaldehyde and acetaldehyde are excluded from the CMR assessment (classification: Carc. 1B).
5) The R value is based on the current list of LCI values according to AgBB; https://www.umweltbundesamt.de/sites/default/files/medien/4031/dokumente/agbb_bewertungsschema_2021.pdf
Table 2 – Emission requirements for upholstered furniture (2-seater and 3-seater sofa)
Parameters
Upholstered furniture
2-seater sofa
Textile cover 1)
Upholstered furniture 2-seater sofa
Textile cover 1)
Upholstered furniture 3-seater sofa
Textile cover 1)
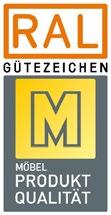
Upholstered furniture 3-seater sofa
Textile cover 1)
Other Aldehydes acc. to current list of LCI values 3)
TVOCspez. (C6 – C16) acc. to AgBB°3) < 450°µg/m³ < 3600°µg/uh < 450°µg/m³ < 5400°µg/uh
TSVOC (<C16 – C22) < 80°µg/m³ < 640°µg/uh < 80°µg/m³ < 960°µg/uh
CMR substances 4) acc. to EU Cat. 1A and 1B ∑ < 10°µg/m³ < 1°µg/m³ per individual value < 1°µg/m³ per individual value
Odour (see explanations below)
< 3.0 < 3.0
VOC without LCI acc. to AgBB 3) < 100°µg/m³ < 800°µg/uh < 100°µg/m³ < 1200°µg/uh
R°value 5) < 1 < 1
1) For leather upholstery see whole-body testing for leather chairs
2) The test can be terminated on the 7th day after loading if the required final values of the 28th day are reached and no increase in concentration of one of the detected substances can be detected compared to the measurement on the 3rd day
3) Sum of all individual substances ≥ 5 µg/m³) at test chamber concentration
4) The substance Dimethylformamide (DMF, CAS 68-12-2) is treated separately during the assessment of CMR properties. For DMF, a limit value (based on the LCI value) of < 15 µg/m³ after 28 days applies. The value after 3 days shall not be included in the total evaluation. For the calculation of the R value, DMF must still be taken into account. This regulation is valid for a transitional period until 31.12.2023. As of 01.01.2024, it will no longer apply.
Formaldehyde and acetaldehyde are excluded from the CMR assessment (classification: Carc. 1BB).
5) The R value is based on the current list of LCI values according to AgBB; https://www.umweltbundesamt.de/sites/default/files/medien/4031/dokumente/agbb_bewertungsschema_2021.pdf
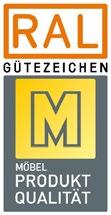
Definitions of TVOCspec and TSVOC
TVOCspec:
Sum of all individual substances found ≥ 5 µg/m³ in the retention range C6–C16 (between nhexane up to and including n-hexadecane). The determination is carried out in accordance with the currently valid AgBB scheme. Data in the AgBB scheme for C substances apply here to CMR substances of category 1A and 1B.
TSVOC:
Sum of all individual substances ≥ 5 µg/m³ in the retention range > C16–C22. In individual cases, LCI values have been derived for SVOC. The SVOCs for which LCI values have been determined are to be included in the R value calculation for the requirements after 28 days and are no longer subject to the sum SVOC value. The sum of the TVOCspec value and the sum of the individual SVOC with LCI value must not exceed the TVOC requirements after 28 days (AgBB procedure)
General information on TVOC and TSVOC:
The basis for measuring the emission of volatile organic compounds and formaldehyde is the BAM test method in the current version. The requirements for the test chamber procedure and the analysis are based on DIN EN 16516 in conjunction with the DIN EN ISO 16000 et. seq. series of standards.
Whole-body testing for leather chairs
If only leather-covered models are offered in an upholstered furniture series, a white upholstery (complete upholstered furniture without leather cover) shall be tested for the whole-body test:
Due to their high emission relevance, leathers are subjected to a separate emission test, whereby the testing institute, in consultation with the upholstered furniture manufacturer and the tannery, selects representative test samples that ensure compliance with the requirements for the corresponding series. Small test chambers (e. g. 20 litres) or emission measuring cells are suitable for the component testing of leather. In test chambers, the leather is tested back to back. It must be ensured that the area-specific flow rate of 1.5 m3/m2h is maintained over the entire test period (28 days).
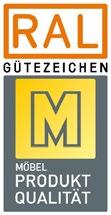
Alternative test certificates for leather and textiles
For upholstery leather, test certificates according to LEATHER STANDARD by OEKO-TEX are also recognised as an alternative for pollutant testing
For upholstery fabrics, test certificates according to STANDARD 100 by OEKO-TEX or according to the IVN NATURTEXTIL label are also accepted as verification.
Exception: Permethrin is not included in the STANDARD 100 by OEKO-TEX and must be tested separately – if it has a wool component.
4.1.4.1. Odour
The odour test shall be performed after a minimum of 3 and a maximum of 28 days of residence time in the test chamber. In case of a previous test according to Point 4.1.5. testing can be carried out after the previous test is completed. In the case of several tests, the result of the last test series (longest period in test chamber) is definitive.
Requirements:
Score to be maintained: Level 3.0
The majority of individual scores must not be above level 3.0.
The average must be ≤ 3.0.
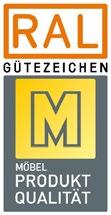
Testing:
Odour neutral room:
Temperature: 23° C ± 1° C
Humidity: 50% rel. humidity. ± 5% rel. humidity
Airflow rate: Depending on the type of test sample
Chamber volume: The chamber volume is based on the specified test chamber size (Table 1)
Room loading: Depending on the type of test sample
At least 7 test persons independently assess the odour intensity according to a 5-point scale:
1 = no odour
2 = weak odour
3 = distinctive, not unpleasant odour
4 = unpleasant odour
5 = unbearable odour
The following should be recorded:
• Age and sex of test persons
• Room size
• Room temperature
• Room humidity (rel. humidity)
• Date of assessment
• Time span between production and odour assessment
• Type of odour
Test persons: The test persons (at least 7 persons, at least 3 of them women) should spend at least 10 minutes in a room with clean air before the odour test. The odour assessment is performed undiluted. The test persons should not have any previous exposure to the odours to be evaluated.
Mean value:
Of all the individual values determined, one highest and one lowest are not to be used for averaging. Only the mean value is given in test reports.
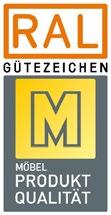
4.1.5. Additional material requirements
4.1.5.1. Leather
Table 3 – Additional material requirements for leather
Testing in the test chamber must last 28 days
PCP, chlorophenols and bromophenols
2-Thiocyanomethylthiobenzothiazol (TCMTB)
Methylene-bis-thiocyanate (MBT)
4-Chlor-3-methylphenol (CMK)
N-octylisothiazolinone (N-OIT)
o-phenylphenol (oPP)
Azo dyes, which release certain amines, are not permitted (in accordance with EU Directive 2002/61/EC)
Carcinogenic, mutagenic, or teratogenic dispersion dyes, potentially irritating dyes and pigments containing cadmium, mercury, lead, or nickel must not be processed
Chrome (VI)
4.1.5.2. Chlorophenols
Threshold value
Method of analysis
each < 1 mg/kg DIN EN ISO 17070
500 mg/kg DIN EN ISO 13365
< 5 mg/kg DIN EN ISO 13365
< 300 mg/kg 1 DIN EN ISO 13365
< 100 mg/kg 2 DIN EN ISO 13365
< 500 mg/kg 3 DIN EN ISO 13365
< 30 mg/kg DIN EN ISO 17234-1 and -2
Not detectable
In accordance with DIN 54 231
≤ 3 mg/kg DIN EN ISO 17075
Pentachlorophenols / Tetrachlorophenols / Trichlorophenols
Test specimen: natural fibres, wood-based materials, latex
Requirements:
Table 4 – Values to be maintained for individual biocides
Natural fibres < 1 mg/kg < 1 mg/kg
Latex < 0 5 mg/kg < 0 5 mg/kg < 1 mg/kg
Wood-based materials < 3 mg/kg < 3 mg/kg
1 Concentrations of 4-Chlor-3-methylphenol (CMK) can total up to 600 mg/kg, so long as the test chamber concentration does not exceed 12 µg/m 3 after 28 days
2 Concentrations of N-Octylisothiazolinone (N-OIT) can total up to 250 mg/kg if concentrations of n-OIT in the test chamber are not provable after 28 days (< 1 µg/m3).
3 Concentrations of o-Phenylphenol (oPP)) can total up to 1000 mg/kg, so long as the test chamber concentration does not exceed 23 µg/m3 after 28 days
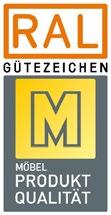
Method of analysis:
The sample is heated with 1 m KOH in a drying oven. An aliquot of the extract is derivatised with acetic anhydride. The derivative is extracted with n-hexane and analysed on capillaryGC by ECD. Other methods are permitted if comparability has been demonstrated
4.1.5.3. Pyrethroids / permethrin
Test specimen: animal wool material
Requirements for wool material treated against wool pests:
An effective protection against moths requires about 35 to 75 mg/kg, and against beetles about 75 to 100 mg/kg.
Concentrations between 3 mg/kg and 35 mg/kg are therefore viewed as contamination without function and are not accepted
For permethrin concentrations between 35 mg/kg and 100 mg/kg, the manufacturer is obliged to include the following sentence in the product information:
“Product contains permethrin for protection against wool pests.”
Concentrations above 100 mg/kg are not accepted.
Requirements for wool material not treated against wool pests:
Permethrin < 3.0 mg/kg.
The concentration of the other pyrethroids detected shall not exceed 1 mg/kg.
If this limit value is observed, the manufacturer is obliged to include the following sentence in the product information: “Not protected against wool pests.”
Method of analysis:
Determination of the absolute content in material samples
Approx. 1 to 5 g of material sample are weighed into an extraction tube and sealed with a suitable g lass wool or filter paper. The extraction tube is extracted with a mixture of nhexane-acetone 1:1 for six hours on the Soxhletextractor.
The extract thus obtained is concentrated on the rotary evaporator and made up to a defined volume (approx. 5 ml) with the extraction agent.
The measurement is carried out on the GC- MS (SIM mode). The method detects permethrin, furmecyclox, piperonyl butoxide, tetramethrin, cyfluthrin, cypermethrin, fenvalerate and deltamethrin.
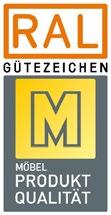
Limits of determination: 0.1 to 1 mg/kg (depending on compound and weight )
4.1.5.4. Other biocides
Test specimen: textiles made of natural fibres and animal wool
For textiles made of natural plant fibres, insecticides/fungicides and herbicides shall be determined.
For animal fibres, only insecticides/fungicides are to be determined.
For synthetic fibres, biocide tests are not required.
Insecticides/fungicides:
Aldrin, Azinophosethyl, Azinophosmethyl, Bromophos-ethyl, Captafol, Carbaryl, Chlordane, Chlordimeform, Chlorofenvinphos, Coumaphos, Cyfluthrin, Cyhalothrin, Cypermethrin, DDD, DDE, DDT, Deltamethrin, Diazinon, Dicrotophos, Dieldrin, Dimethoate, Endosulfan α- and β-), Endrin, Esfenvalerate, Fenvalerate, Heptachlor, Heptachlor epoxide, Hexachlorobenzene, Hexachloro-cyclohexane (α, β- and δ -), Lindane, Malathion, Methamidophos, Methoxychlorine, Mirex, Monocrotophos, Orthophenylphenol, Parathion, Parathion-methyl, Pentachlorophenol, Phosdrin/Mevinphos, Profenophos, Propetamphos, Quinalphos, Tetrachlorophenol, Toxaphene (Camphechlorine);
Herbicides:
2,4,5-T, 2,4-D, DEF, dichlorprop, dinoseb and salts, MCPA, MCPB, mecoprob, trifluralin
Requirements:
The total (sum) content of the biocides detected shall not exceed 1 mg/kg.
Method of analysis:
Different analytical methods are used depending on the substance or substance class (e. g. extraction on the Soxhlet, column chromatographic purification, qualitative and quantitative determination by GC-ECD, GC-MS).
Limits of determination: 0.1 to 1 mg/kg
Proof can also be provided by presenting valid STANDARD 100 by OEKO-TEX certificates.
Exception: Permethrin is not included in STANDARD 100 by OEKO-TEX and must be tested separately if a wool content is present.
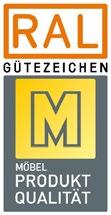
4.1.5.5. Azo dyes
Test specimen: leather, natural fibres, and synthetic fibres
Requirements:
Azo dyes that release certain amines must not be used (according to REACH Regulation (EC) No. 1907/2006). This requirement applies to textiles and materials that come into contact with human skin for more than a short period of time.
Value(s) to be observed:
The amines listed in Regulation (EC) No. 1907/2006 (REACH Regulation) must not be detectable (i. e. < 30 mg/kg).
Testing:
The test procedure is described in the official list of investigative procedures (“Amtliche Sammlung von Untersuchungsverfahren nach §64 – Lebensmittel- und Futtermittelgesetzbuch” [German Food and Feed Code]):
Natural fibres: B 82.02-2 (DIN EN ISO 14362-1)
Polyester fibres: B 82.02-4 (DIN 14362-2)
The following must be stated in the test report if contents per amine component below 30 mg/kg are present:
“According to the scope of testing, azo dyes, the use of which is prohibited under Regulation (EC) No. 1907/2006, were not detected.”
Proof via manufacturer’s declaration possible.
4.1.5.6. Disperse dyes and pigments
Requirements:
• Carcinogenic dyes
• Mutagenic or teratogenic disperse dyes
• Potentially sensitising dyes
• Dyes containing heavy metals are not permissible.
Testing according to DIN 54231
Proof via manufacturer’s declaration possible.
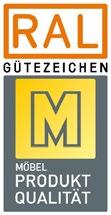
4.1.5.7. Flame retardants in PUR foam
Test specimen: PUR foams
Requirements:
The use of halogen-organic flame retardants and plasticisers is not permitted.
(Exception: furniture in buildings with increased fire protection requirements, such as theatres).
Value(s) to be observed:
Tris(2-chloroethyl)phosphate (TCEP): < 10 mg/kg
Tris(2-chloropropyl)phosphate (TCPP): < 50 mg/kg
Tris(1,2-dichloro-2-propyl)phosphate (TDCP): < 50 mg/kg
Method of analysis:
Extraction and determination by GC-MSD*
*Or equivalent method
4.1.5.8. Heavy metals
The following requirement only applies to furniture for small children:
Test specimen: varnished surfaces and possibly natural fibres and synthetic fibres, e. g. for seat covers, etc.
Values(s) to be observed: see toy standard DIN EN 71 Part 3
4.1.5.9. PAH (Polycyclic aromatic hydrocarbons)
Testing and evaluation according to AfPS GS 2019:01 PAC
GS Specification “Testing and Evaluation of Polycyclic Aromatic Hydrocarbons (PAH) in the Award of the GS Mark” of the Product Safety Committee (AfPS) as of April 2020 or the respective current regulation.
Maximum PAH levels to be observed for materials of relevant contact/grip and actuation surfaces to be categorised based on the results of the risk assessment.
Proof via manufacturer’s declaration possible.
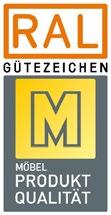
4.2. Protection of the environment and climate
4.2.1. Energy and eco-balance
The efforts of manufacturers to minimise the energy and atmospheric environmental impact associated with the transport of their products and supplier materials must be evident from appropriate documents.
The use of self-generated, renewable energy (e. g. burning waste wood) and the purchase of CO2 neutral energy are to be preferred.
To optimise the use of materials and energy with regard to a sustainable eco-balance, the implementation of a life cycle assessment based on the systematics of the standards DIN EN ISO 14001, DIN EN ISO 14040 and DIN EN ISO 14044 is suitable.
A life cycle assessment or environmental declaration of the products according to DIN EN ISO 14025 (EPD verification) is also recommended).
4.2.2. Human and ecosystem health
In addition to the legal regulations on the handling of chemicals that are harmful to humans and the environment (e. g. REACH Regulation), this Furniture Quality Assurance RAL-GZ 430 contains extensive testing requirements to ensure furniture that has been tested for harmful substances
4.2.2.1. Liquid coating systems
Operators of coating plants must comply with the requirements of the 31st Federal Imission Control Act (BlmSchV). This shall be proven via the manufacturer’s declaration
4.2.3. Use of materials
4.2.3.1. Solid wood and wood-based materials
Solid wood and wood -based materials must comply with EU Regulation 995/2010 and, as far as possible, originate from sustainably and legally managed forestry (FSC/PEFC documentation). When using waste wood in wood-based materials, the Waste Wood Ordinance must be observed. Proof of the pollutant limit values of the Waste Wood Ordinance according to testing in compliance with the EPF standard .
4.2.3.2. Plastic components
Plastic components > 50 g should be labelled according to DIN EN ISO 11469 and should not contain additives of other materials that conflict with recycling.
4.2.3.3. Adhesives
The VOC content of adhesives should not exceed 10% for water-based systems and 30% for solvent - based systems.
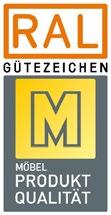
4.2.3.4. CFC
CFC must not be used in production (CFC halogen ban).
Proof via manufacturer’s declaration.
4.2.3.5. PVC
The use of PVC should be limited to furniture parts for which no equivalent other materials are available and for which the special properties of PVC are required.
The use of PVC must be indicated in the product information (PI). Dismountable PVC parts are exempt from this regulation if they are clearly marked as PVC parts.
4.2.4. Circular economy
4.2.4.1. Constructional layout – wear – durability
The principles of recycling-friendly design (VDI 2243) must be observed. The use of recyclable and biodegradable materials is to be preferred.
For wear parts, a functional, compatible replacement is ensured over a period of at least 5 years. As the wear of upholstery cover materials depends on the intensity of use and on regular cleaning and care, this requirement does not apply to upholstery materials (textiles / leather).
The durability of the products shall be ensured by appropriate design. In addition, maintenance care (see annex 12.5 ) contributes to a long life of the product.
4.2.4.2. Packaging
The packaging material must be suitable for reuse or recycling. The packaging must be designed in such a way that any volatile components of the furniture can outgas
4.2.4.3. Reusability / recycling
With regard to reusability and recycling, no material preservatives (fungicides, insecticides, flame retardants) and no halogenated organic compounds may be added to the furniture, or the materials used for its production (wood-based materials, adhesives, coatings, etc.).
This excludes fungicides used solely for in-can preservation in water-based coatings and glues or flame retardants in which inorganic ammonium phosphates (diammonium phosphate, ammonium polyphosphate, etc.), boron compounds (boric acid, borates) or other waterreleasing minerals (aluminium trihydrate or similar) are used for flame retardation.
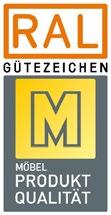
4.3. Social responsibility
With a view to sustainable human resources development and to ensure health, occupational safety and social working conditions, a company should, in accordance with good management practice, define and document responsibilities and procedural rules concerning this matter.
These include in particular:
• Fair hiring practices
• Continuing education of employees
• Social responsibility in company regulations
• Social ethics
Social ethics may also include social measures for the local environment of the operating site (e. g. sponsoring cultural or charitable institutions).
Compliance with the requirements can be achieved through membership of the UN Global Compact (see annex 12.13 . ) or equivalent certificates.
The Deutsche Gütegemeinschaft Möbel supports the UN Global Compact and its 10 principles. These guiding principles for business and human rights are to be implemented by the manufacturers. The implementation is documented during the monitoring audits.
With regard to social responsibility for products of the supply chain over which the company has no direct influence, preference is to be given wherever possible to supplier companies that take social standards into account
4.4.
Advertising statements
Advertising claims must not contain any statements such as “biologically tested” or similar statements that play down hazards as laid out in the EU Directive 67/548/EWG
Article 23 (Designation) Section 4 (e. g. “non-toxic”, “no risk to health”, “free from …”)
5. General Quality Principles
It is a prerequisite for “furniture with the quality mark” that suitable materials and construction elements are used which are appropriate to the product and have been professionally processed. Safety, function, and utility are assessed according to the latest standards of technology at the time of product launch. Environmental and health protection as well as product information are essential quality features.
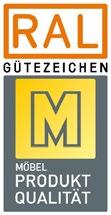
Deviations from the Quality and Testing Regulations
Deviations from the requirements laid out in the Quality and Testing Regulations may be made if an equivalent or higher quality and safety objective is achieved by other means. Suitable proof is required.
Visual inspections
Visual inspections are carried out under the following conditions (unless otherwise specified):
General assessment: At distance of 2 to 3 m
Detailed assessment: At distance of 0.7 ± 0.1 m
Assessment basis: normal vision; diffuse daylight (without direct sunlight or artificial light).
Parts that are not visible in the position of use or subordinate parts as well as irregularities that are only visible in grazing light are excluded from the assessment.
5.1. Product information
The product information for upholstered furniture shall be made available to the retailer for marketing purposes and for passing on to the end customer and contains the following details based on RAL-GZ 430/4:
1. Product name
2. Product label*
3. Materials (frame construction)
4. Cover materials**
5. Model variants
6. Dimensions
7. Weight
8. Type of upholstery
9. Maximum load***
10. Maintenance and use instructions (see annex) 12.5
*Labelling obligations according to the Product Safety Act (ProdSG) and the Textile Labelling Act must be observed
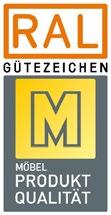
**Upholstery material –Textiles / Microfibres
• Textile designation
• Type of fabric
• Material composition
• Abrasion resistance
• Rubbing fastness
• Light fastness
• Lint formation
**Upholstery material –Leather
• Leather name
• Leather type
• Leather thickness
• Light fastness
• Rubbing fastness (dry)
**Upholstery material –Artificial leather
• Artificial leather name
• Composition of coating materials
• Abrasion resistance
• Rubbing fastness
• Light fastness
*** According to the scope of application, DIN EN 12520 takes into account a user weight of up to 110 kg; DGM recommendation for user weight: armchair 130 kg, 2-seater 200 kg (2 x 100 kg), 3-seater 240 kg (3 x 80 kg); For higher user weights see also DIN 4573; For the load on armrests, especially with functional fittings, a maximum weight of 30 kg is recommended for normal use.
In addition, the following information should be included in the product information, if applicable:
• Information on wear parts and their repair or replacement, repair service if necessary (For wear parts, a functional compatible replacement of at least 5 years is guaranteed).
• Information on the type and origin of the wood predominantly used
• Information on other materials (proportion > 3 weight percentage)
• Information on the assembly of the products and on disassembly for removal and subsequent material recycling. For special product groups, the Ecodesign Directive (2009/125/EC) must also be observed.
• In the case of furniture that falls under the Electrical and Electronic Equipment Act (ElektroG, see annex 12.4.) appropriate labelling must be applied to the furniture and the method of disposal must be indicated in the operating instructions.
• If PVC must be used, this must be stated in the product information.
5.2.
Transport and assembly guidelines
The transport and assembly guidelines for upholstered furniture in accordance with the annex 12.1 must be observed.
5.3.
Maintenance care
In order to maintain the product life as long as possible and thus guarantee the consumer a long period of use, as well as to effectively conserve resources in the sense of the circular economy, maintenance care of the upholstered furniture is required in accordance with the annex 12.5 (see Point 5.1).
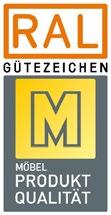
5.4. Dimensioning of upholstered furniture
5.4.1. Definition of “left” and “right”
The position for determining “left” and “right” is standing in front of the upholstered furniture in each case.
Note: For office furniture, the designation left/right is made from the sitting position.
5.4.2. Dimensions (general)
The dimensions (approximate dimensions) are to be given in cm and refer to a level, horizontal standing surface.
Test: Measuring tools
Measuring tools (steel ruler, pocket rule, T-square, tape measure, radius gauge)
Spirit level
Vernier height gauge
Measuring accuracy of the measuring tools ± 1 mm. The padding must not be pressed in when measuring.
Height and depth
Specify external dimensions of height (H) and depth (D)

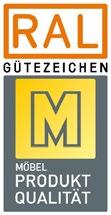
The padding must not be pressed in during the measurement. Measurements are taken at right angles to the wall or floor.
Width
Indicate the largest outer dimension of the width (W), for movable and adjustable arm sections the maximum width.
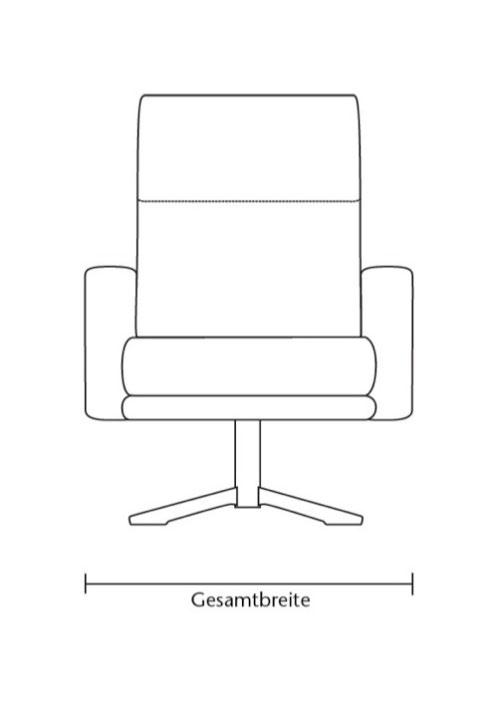
The padding must not be pressed in during the measurement.
Seat height
Highest point of the seat in unloaded new condition.
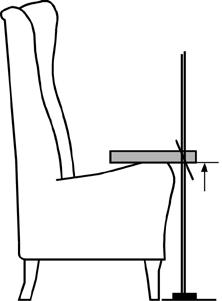

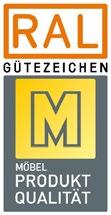
The padding must not be pressed in during the measurement.
Measurements are to be taken from the highest point (in the centre of the seat if the seat is concave) – seat horizontal to the floor.
Tools: spirit level, vernier height gauge
Seat depth
To determine the seat depth, measure the distance from the back to the front edge of the seat

Seat height
Seat depth
The padding must not be pressed in during the measurement. The useful depth is measured The prerequisite for this is that the scale rests on the seat surface, with the angle at the front edge of the seat set to touch.
5.4.3. Tolerances
The harmonious overall impression of upholstered furniture when new must not be disturbed by any dimensional deviations of individual elements.
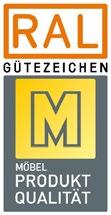
Dimensions of upholstered furniture are to be understood as approximate dimensions. Deviations of individual upholstery elements from each other: Uniform upholstery elements (e. g. seat cushion left to right): ≤ 1 cm.
In the case of corner pieces, add-on pieces and element groups, larger deviations are possible with particularly casual upholstery – taking into account the harmonious overall picture.
In the case of functional upholstered furniture, larger distances are often necessary for functional reasons. Furthermore, optical deviations to firmly upholstered parts of the same series may occur.
Due to the function being exercised, a seam offset can already occur during the first adjustment, which can only be removed again by aligning. The difference may only be measured in the aligned state.
The tolerances in relation to the nominal dimension (e. g. width, depth, height) must not exceed ± 2 cm for nominal dimensions up to 150 cm and ± 2.5 cm for nominal dimensions > 150 cm.
Note: The determination of tolerances refers to horizontally aligned furniture. The requirements also apply to convertible upholstered furniture with lying surfaces.
Verification of nominal dimensions
Tolerance for exposed wooden frames: ± 0.5 cm in height / width and depth
Tolerance for rattan: ± 1.0 cm in height / width and depth
The angle tolerance for tightly-screwed, upholstered corner seats must not exceed ± 0.5 cm per running metre.
Verification of nominal dimensions
6. Construction of upholstered furniture
6.1. Quality of wood and wood-based materials
6.1.1. Solid wood
DIN 68360, T.2*, ID - 5/81 (for frames)
DIN 68360, T.2*, IND - 5/81 (for exposed wooden frames)
*Standard withdrawn (see Pt. 6.1.4)
Testing according to the above-mentioned standards
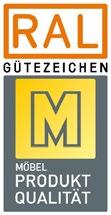
6.1.2. Wood equilibrium moisture content
Wood equilibrium moisture content according to DIN EN 13183-1
Requirements:
Exposed wood/decorative wood: 6 to 10%
Non-visible wood frames: max. 12%
Testing according to the above-mentioned standards
6.1.3. Visible woods
Visible woods may have the characteristics listed in the characteristics overview based on DIN 68360 Part 2 (withdrawn since June 1996 – replaced by DIN EN 942) (see Point 6.1.4 ).
Visual inspection
6.1.4. Solid wood – Assessment criteria
Characteristics overview based on DIN 68 360 Part 2 – 5/81 (standard withdrawn*)
ID: Non-visible parts
IND: Visible parts
Characteristics ID IND
General
Surface
Colour differences
Blue stain
Sapwood
Grain deviation
Longitudinal cracks
The wood must be healthy (free from wood-destroying fungi and insects) and free from pith on the parts visible after assembly.
The surface must be even and sanded.
Saw and plane marks on the parts visible after assembly are inadmissible, unless a specific treatment of the surface, e. g. brushing, sandblasting, or burning, has been agreed.
Permissible
Permissible: blue stain, i. e. low blue stain in the initial stage.
Permissible: natural colour differences
Not permissible: on surfaces that remain visible. Bluing on non-visible surfaces is permissible.
Permissible: e. g. for pine and other wood types with similar properties as sapwood.
Not permissible: for wood types whose heartwood and sapwood differ significantly in properties.
Not permissible: spiral graining and deviations in grain direction exceeding 2 cm per m
Permissible: small cracks and permanently**(see footnote) repaired cracks which run in the direction of the grain, do not pass through, and do not interfere after surface treatment.
Transverse cracks Not permissible
Characteristics ID IND
Resin pockets / resin zones
Bark remnants
Tree edge
Insect damage
Knots
a) Not improved knots
Permissible: resin pockets permanently** (see footnote) repaired down to the base.
Permissible: if they are permanently** (see footnote) repaired.
b) Plugged knots
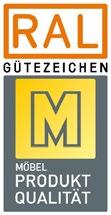
Permissible: resin pockets permanently** (see footnote) repaired down to the base.
Not permissible
Permissible: without bark in places that are no longer visible after assembly
Not permissible: except for isolated feeding tunnels up to 2 mm in diameter made by green wood insects.
Not permissible.
Permissible: only sound, intergrown knots that do not affect the stability of the parts and their usability. Note: Stability and usability may be affected if, for example, the largest knot diameter is greater than 1/3 of the width of an element, as in the case of a frame.
Not permissible: wing knots and dark knots.
Dowel edges must be glued over the entire surface. Gluing depending on the application of the element according to stress group B2 to B4 in compliance with DIN 68 602 (replaced by DIN EN 204).
Permissible: dowels up to 25 mm in diameter and chain dowels up to 3 dowels.
Not permissible
*The national standard has been replaced by DIN EN 942- 6/2007. This DIN, however, does not contain the assessment criteria proven in practice in the same way **Permanently here means repair with wood that is also glued in over the entire surface at the edges.
6.1.5. Wood-based materials
Wood-based materials (chipboard):
DIN EN 312-12
Other wood-based boards:
According to DIN or quality standards
Blockboards, plywood, moulded wood, MDF boards
Testing according to the above-mentioned standards
6.2.
Quality of metal elements
The material shall be dimensioned according to the expected use requirements in accordance with the relevant technical rules.
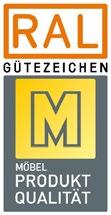
This is deemed to be fulfilled if the durability, strength, and safety tests are met.
6.3. Frames
6.3.1. Wooden and wood-based frames
The durability of frame connections and the attachment of upholstery materials must be guaranteed.
Strength testing see 6.13
6.3.1.1. Frame edges
At all points where threads, fabrics and rubber belts can cut into the frame, the material must be rounded to prevent the abrasive material from cutting into or through the frame.
This requirement may be waived if the construction or the material fulfils the objective of avoiding cutting in another way.
Visual inspection, haptic test, radius template
6.3.1.2. Frame connections
The connections in the frame assembly must be selected so that they meet the strength requirements and are noiseless under normal use. Metal connections must be secured with connecting and clamping screws.
Fits according to DIN 68101 and DIN EN 204, adhesives D 2.
Verification through technical test (see strength testing 6.13); seat test
6.3.2. Metal frames
All metal elements must be designed with regard to their surface in such a way that the visible surfaces are smooth and corrosion-resistant in accordance with the climatic conditions of interior rooms, and corners and edges in the accessible area are rounded and not sharp-edged (edge radius: recommendation ≥ 3 mm).
After the corrosion test, there must be no signs of corrosion on the visible surfaces.
Testing according to DIN EN ISO 6270-2, 2 cycles AHT (condensed water alternating climate with alternation of humidity and temperature)
6.3.3. Frames, supporting elements and swing arms
Requirements see strength testing 6.13
Strength testing 6.13
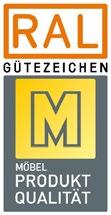
6.3.4. Deflection of the seat frame
Central load on the seat surface: 1,500 N
Permissible deflection (level, smooth floor as standing surface): 1/100 related to the support width (front standing elements)
Dimensional and visual inspection
6.3.5. Connection of elements
The functionality of the connections of row elements must correspond to the expected stresses and be easy to assemble.
Inspection by assembly / disassembly and visual inspection
6.3.6. Upholstered furniture standing elements
The surface pressure caused by standing elements on the floor must not exceed 2 N/mm² in the unloaded state and 4 N/mm² in the loaded state (test weight 75 kg per seat).
Testing by area measurement / weight measurement and calculation
6.3.7. Furniture casters
Furniture casters must comply with DIN EN 12528
6.4. Fittings for upholstered furniture
6.4.1. Functional fittings
Made of metal and/or plastics, wood, and wood-based materials
Function
• Pull out
• Tilt
• Height adjustment
• Depth adjustment
• Rotate
• Swivel
• Angle adjustment
Example
• Shelf
• Adjusting the backrest
• Rise aid
• Seat depth adjustment
• Swivel armchair
• Armrest
• Headrest
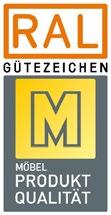
Adjustment fittings must be designed in such a way that there is no risk of injury when they are adjusted and in use. Unintentional adjustment or loosening of a set position must be prevented by design measures.
The fittings must not have any burrs or sharp corners and edges in the access area and must not have any open tube ends. They must be corrosion-resistant in accordance with the climatic conditions of interior rooms.
To avoid the risk of crushing and pinching caused by moving parts that can be touched during intended use, a distance of less than 8 mm or more than 25 mm must be maintained between these parts in any state of movement.
Excluded are functionally unavoidable shearing and crushing points that occur during controlled movement processes during use.
A safety notice should be provided, warning users about dangers due to improper use
6.4.1.1. Durability of functional fittings
Functional after wear test (3,000 cycles under normal operating conditions)
– No abrasion that can cause contamination
– No disturbing noises
A number of cycles (up to 10,000) is required for systems with assumed frequent use (e. g. backrest adjustment function by gravity or motor).
Visual inspection, haptic test, durability testing acc. to DIN EN 13759 with test dummy 100 kg
6.4.2. Fittings with electric motor drive
must comply with the applicable EN standards and CENELEC regulations. Documentation must be available.
Electrical components (e. g. power supply unit) must comply with the safety requirements.
CE marking and the corresponding safety standards according to EN and CENELEC directives in accordance with the Machinery Directive (see also HDH Guideline Application of the EC Machinery Directive to Furniture), Low Voltage Directive and EMC Directive); (see annex 12.4.)
6.5. Surfaces of upholstered furniture
6.5.1. Wood and wooden-based materials
Solid wood (visible surfaces)
Wood must comply with the wood quality characteristics of the table (DIN 68360 Part 2*); (see 6.1.4) *standard withdrawn
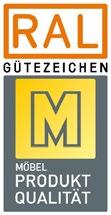
Visual inspection
Glue and adhesive joints
Visible glue and adhesive joints must be properly sealed. They must not show any excess glue at the points visible in the position of use.
Visual inspection
Veneered surfaces
Not permissible on visible surfaces are:
• Glue penetration
• Resin pockets
• Loose, overlapped, and sanded spots and cracks
• Markings after the substrate and glue have dried
• Zigzag showing through
Permissible on visible surfaces are:
• Minor, healthy intergrowths in the veneer, which are natural
Visual inspection
Edges, narrow surfaces
Edges must be free of tears and must be broken or rounded evenly over the entire length. The edges of the standing surfaces must be chamfered or provided with gliders.
Visual and/or dimensional inspection, if necessary haptic test
6.5.2. Varnished surfaces
For exposed wooden frames and storage shelves (integrated functional part):
Chemical stress: 1 C
Testing according to DIN 68861, Part 1
Abrasion stress:
Testing according to DIN 68861, Part 2
2 F (at 25 revolutions)
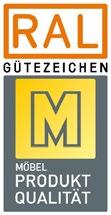
Scratch stress: 4 E (≥ 0.5 N)
Testing according to DIN 68861, Part 4
6.5.3. Melamine resin coated surfaces
Chemical stress: 1 B
Testing according to DIN 68861, Part 1
Abrasion stress: 2 D (50 to 150 revolutions)
Testing according to DIN 68861, Part 2
Scratch stress: 4 C
Testing according to DIN 68861, Part 4
Behaviour in dry heat for storage areas: 7 C (100° C)
Testing according to DIN 68861, Part 7
Behaviour in wet heat for storage areas: 8 B (70° C)
Testing according to DIN 68861, Part 8
6.5.4. Metal surfaces
Galvanised – painted – coated surfaces:
After the corrosion test, there must be no signs of corrosion on the visible surfaces.
Testing according to DIN EN ISO 6270-2, 2 cycles AHT (condensed water alternating climate
6.6. Springing
6.6.1. Wave springs
Tempered spring steel wire according to DIN EN 10218, diameter 3.6 to 4.0 mm, rustprotected or varnished Hinges for fastening the spring made of plastic or metal plastic-coated to avoid noise. Guideline value of 10 cm for the centre distance of the wave springs. A deviation due to the design is possible. If the distance is greater, the wave springs must be connected transversely to prevent buckling.
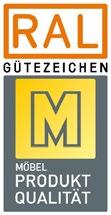
Dimensional and visual inspection, strength testing 6.13
6.6.2. Wood lath springing
At least 5 layers glued together; at least 5 mm thick, 50 mm wide; spacing 100 mm, noiselessly mounted.
Dimensional and visual inspection, strength testing 6.13
6.6.3. Metal spring hinges // metal spring bands
Flat spiral springs; approx. 15 mm wide; individual springs must be connected to each other; spacing approx. 80 mm.
Dimensional and visual inspection, strength testing 6.13
6.6.4. Rubber belts
Seat:
Pretension 40 to 60% at a force of 200 to 250 N
Belt width at least 50 mm; tolerance: nominal width ± 2 mm
Dimensional and visual inspection, strength testing 6.13
Back:
Pretension 70 to 120% at a force of 150 to 200 N
Belt width at least 50 mm; tolerance: nominal width ± 2 mm
Dimensional and visual inspection, strength testing 6.13
6.6.5. Back springing // Back underspringing
Requirements as in 6.6.1, but diameter 2.5 to 3.2 mm
Dimensional and visual inspection, strength testing 6.13
6.6.6. Upholstery carriers (seat) // Upholstered support (seat)
Materials to be carried on flat springs and spring cores
The upholstery carriers/supports must not shift in relation to the spring element and the supported upholstery layer
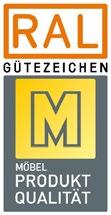
6.7. Foams
Block foam:
Strands of “endless” foam produced in a continuous process. The required parts are cut out of the block, the surface has a pore structure and is rough.
Moulded foam:
Foaming takes place in a mould. The required parts are removed from the mould ready for use. The surface has a skin and is smooth.
See also annex 12.9
Requirements for foams
Table 5 – Requirements for foams
(Net weight is the actual density of the prefabricated foam part in kg/m3) PUR foam (Block/moulded foam)
Volume weight: weight for base cushions, cushions and covers on elastic spring elements;
Testing according to DIN EN ISO 845
Seat: ≥ 33 kg/m3 net
Back: ≥ 24 kg/m3 net
Covers: ≥ 19 kg/m3 net
Physical values
Compression set according to DIN EN ISO 1856 (50%) ≤ 5%
Loss of firmness
Determining degree of softening by using constant impact loading DIN EN ISO 3385 (DIN EN ISO 2439 Procedure A)
Seat:
Back:
Decrease in thickness
20%
30%
Seat: max. 5%
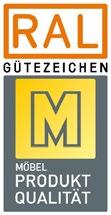
Back: max. 5%
Permissible tolerances
(Except corner pieces and wicker furniture)
Volume weight according to DIN EN ISO 845 ± 5%*
Compressive stress value (compression hardness) DIN EN ISO 3386-1 ± 15%*
Indentation hardness according to DIN EN ISO 2439 Procedure C ± 15%*
Compression hardness and indentation hardness for processed upholstery (new condition) ± 15%*
Odour emission: See 4.1.4.1 and VDA 270 – for incoming goods inspection.
*Minus tolerance: The minus tolerance may only be used when volume weight does not fall below abovestated minimum values; e. g. the volume weight for the seat may not fall short of 33 kg/m3, for the back of 24 kg/m3 and for covers of 19 kg/m3.
6.8. Spring cores
Drawn spring steel wire according to DIN EN 10270; phosphated;
Strength ≥ 1570 N/mm²;
Diameter 2.0 to 2.5 mm;
Spring ring diameter 60 to 90 mm;
Diameter tolerance ± 0.02 mm.
Up to 100 mm height: 4-speed springs; from 100 to 140 mm height: 5-speed springs.
(Above 140 mm, a machine-made spring core [Bonell] should not be used.)
Frame: Frame strip steel rolled and hardened according to DIN EN 10132-4, DIN EN 10140; Strength approx. 1,500 N/mm². The frame is clamped to the springs by means of cold-rolled strip steel 0.70 x 9 mm. Tolerances ± 0.02 mm.
Spiral wire for connecting the individual springs; Ø 1.3 to 1.4 mm. All springs must be connected to each other
Other types of spring cores are also permissible if they meet the quality requirements, e. g. pocket spring cores.
Dimensional inspection; strength testing 6.13
6.9. Covers / non-woven fabrics
Definition: The cover has the task of protecting the back of the upholstery fabric against abrasion. It can additionally supplement the cushioning effect of the comparatively compact base upholstery with a soft elastic cushioning layer.
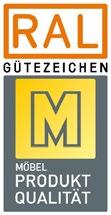
The upholstery elements are to be provided with a cover in the sense of this definition.
The cover must be selected and processed in coordination with the cover fabric in such a way that no fibres can migrate through the cover fabric to the outside.
This requirement is considered to be fulfilled if no fibres are visible from the outside after the strength test 6.13 (see visual inspection).
Binder-bonded non-woven fabrics
a) For side panels and back panels:
Volume weight: > 6.5 kg/m³
b) For covering utility surfaces such as seats and seat backs with textile covers:
Volume weight: > 6.5 kg/m³ min. 100 g/m²
Dimensional and weight test according to DIN EN ISO 3385
Thermally strengthened non-woven fabrics
For covering utility surfaces:
Volume weight: ≥ 10.0 kg/m³
min. 100 g/m2
Height loss: Load change: 80,000 max. 60% in accordance with DIN EN ISO 3385
Dimensional and weight test / Technical test according to DIN EN ISO 3385
Quilted non-woven fabrics with textile covering
For covering utility surfaces:
Volume weight: ≥ 10.0 kg/m³
Height loss: Load change: 80,000, max. 60% in accordance with DIN EN ISO 3385
Dimensional and weight test / Technical test according to DIN EN ISO 3385
6.10. Upholstered cushions with loose filling material (feathers and down)
There is no suitable test method available for upholstered cushions that can simulate a practical load on the finished upholstered cushions. For this reason, no requirements for functionality are specified. As material characteristics and thus as pure material requirements
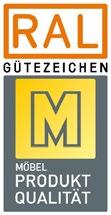
for filling material (feathers and down), DIN EN ISO 3385 is suitable for defining some basic requirements:
Note: If other filling materials are used, proof must be provided that comparable material characteristics are obtained.
Due to the wide variety of filling materials used in upholstered cushions, the empirical values have been compiled from a tried and tested filling material. In principle, it applies to all filling materials that the service properties are fulfilled if they have been proven by strength and durability tests of the original material.
6.10.1. Filling materials
6.10.1.1. PUR foam sticks
Physical characteristics of the PUR foam
Seat cushion ≥ 33 kg/m³ net
Back cushion ≥ 24 kg/m³ net
Armrest ≥ 24 kg/m³ net
Proportion of dimensionally identical sticks (length/volume) at least 90%.
6.10.1.2. Feathers and down
Original feathers and down from geese and/or ducks are used.
In accordance with the quality and labelling regulations for feathers and down DIN EN 12934, the following filling materials are available (all data in weight percentage):
• Original goose and/or duck three-quarter down: Min. 30% down / 70% small feathers
• Original goose and/or duck half down: Min. 15% down / 85% feathers
• Original goose and/or duck feathers, containing down: Min. 9% down (to be introduced after a revision of DIN EN 12934)
• Original goose and/or duck feathers: Down content < 9% (same designation = pluck)
Testing in accordance with DIN EN 12934 and the testing regulations of the International Feather Office: Down content: Tweezer sorting
Poultry species: microscopic determinations due to the different structures
Cleanliness: Haze measurement/turbidity measurement
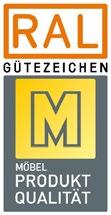
Determination of the oxygen number
6.10.1.3. Feather filling material mixed with other materials
Mixture ≥ 50% small feathers unusable part max. 2%
Definition of “small feathers”:
Small feathers are feathers with a length of max. 10 mm. The proportion of new broken feathers, which is to be allocated to the original goods, is max. 15 % of the feather proportion.
Note: For pure feather mixtures, please see 6.10.1.2
Filling quantity
Functionally correct with sufficient material cohesion; tolerance ± 3% depending on the specified weight
6.10.1.4. Upholstery fabric
6.10.1.5. Testing possibilities
In principle, loose cushions must not significantly change their intended functional properties (starting from new condition) over a longer period of use.
This requires regular maintenance care (smoothing, tapping, fluffing up) depending on the intensity of use.
If there is a deviation from the material specification defined under “Upholstered cushions with loose filling”, proof of comparable usage characteristics must be provided by subsequent testing.
Requirements:
Upholstered cushions must have a sufficient and in continuous use lasting bulking capacity.
The change in volume when testing the resilience (compression set) in accordance with DIN EN ISO 1856 must be < 10%.
Test:
Testing in accordance with DIN EN ISO 1856 on the complete cushion with a surface load of 0.005 N/mm2. The surface is the projection surface of the cushion. The test is carried out in a normal climate (23° C / 50%).
Before measuring the initial height, the cushion must be loaded once for one minute with a surface load of 0.005 N/mm².
In each case 30 minutes after unloading, the initial height and the final height are measured after the 72-hour continuous load under a preload of 2% of the surface load.
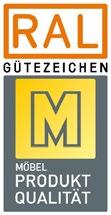
6.10.2. Upholstery fabric
Ticking, smoothly covering the filling
Feather-proof according to Stumpp
Air-permeable according to DIN EN ISO 9237
Pressure diff. 1 mbar
Feather and down denseness according to DIN EN 12132-2, at least 10,000 compressions
Air permeability according to DIN EN ISO 9237
6.11. Upholstery materials
Requirements and test methods
The respective requirements are taken from DIN EN 14465. The requirements take into account a wide range of different qualities.
Note:
Special materials which do not meet the following requirements due to their design-oriented conception and are nevertheless processed may not be associated with the RAL quality mark unless the deviating usage properties are clearly indicated in the product information.
6.11.1. Fabrics for upholstered furniture
6.11.1.1. Tensile strength
This characteristic must be determined for all fabrics except knit and non-woven fabrics.
DGM requirement: At least 350 N
DGM plus, high requirement: At least 400 N
Testing according to DIN EN ISO 13934-1
6.11.1.2. Tear resistance
This characteristic must be determined for all fabrics except knit and non-woven fabrics.
DGM requirement: At least 25 N
DGM plus, high requirement: At least 30 N
Testing according to DIN EN ISO 13937-3
6.11.1.3. Resistance to seam slippage
This characteristic must be determined for all fabrics except knit and non-woven fabrics.
DGM requirement: Max. 5 mm
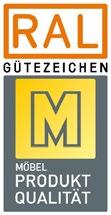
DGM plus, high requirement: Max. 4 mm
Testing according to DIN EN ISO 13936-2
6.11.1.4. Abrasion resistance
“Abraded” or “completely abraded” means significant changes in structure or appearance such as loss of pile loops, loss of fibres in the flock layer, or destruction of three or more pile loops. These should be indicated in the test report, as should the evaluation interval at which they occurred. This information is purely informative.
Colour change (general):
After 3,000 Martindale cycles, a fastness rating of at least 3 must be achieved.
Assessment is carried out using a greyscale in accordance with DIN EN 20105-A02.
Flat woven fabric
Destruction of the test sample is usually achieved when three threads in a flat woven fabric are completely destroyed.
Assessment according to DIN EN 14465
DGM requirement: ≥ 16,000 Martindale cycles
DGM plus, high requirement: ≥ 25,000 Martindale cycles
Testing according to DIN EN ISO 12947-2
Chenille
Destruction of the test sample is usually achieved when three threads in a chenille fabric are completely destroyed or when the chenille layer is completely abraded (whichever occurs first).
Assessment according to DIN EN 14465
DGM requirement: ≥ 12,000 Martindale cycles
DGM plus, high requirement: ≥ 16,000 Martindale cycles
Testing according to DIN EN ISO 12947-2
Knitted fabric
Destruction of the test sample is usually achieved when a hole appears in a knitted fabric (without pile) due to a completely destroyed thread.
Assessment according to DIN EN 14465
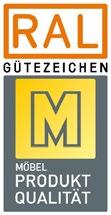
DGM requirement: ≥ 16,000 Martindale cycles
DGM plus, high requirement: ≥ 25,000 Martindale cycles
Testing according to DIN EN ISO 12947-2
Loop pile fabric
Destruction of the test sample is usually achieved when the pile is completely abraded in a loop pile fabric.
Assessment according to DIN EN 14465
DGM requirement: ≥ 20,000 Martindale cycles
DGM plus, high requirement: ≥ 40,000 Martindale cycles
Testing according to DIN EN ISO 12947-2
Pile fabric
Destruction of the test sample is usually achieved when
• in a pile fabric the pile layer is completely abraded without destroying the warp/weft threads
• in a knitted pile fabric, the pile layer of 5 mm2 is completely abraded without destroying the warp/weft threads.
Assessment according to DIN EN 14465
DGM requirement: ≥ 20,000 Martindale cycles
DGM plus, high requirement: ≥ 40,000 Martindale cycles
Testing according to DIN EN ISO 12947-2
Flocking material
Destruction of the test sample is usually achieved when the fibre layer of the flocking material is completely abraded or detached without the carrier fabric being frayed or abraded.
Assessment according to DIN EN 14465
DGM requirement: ≥ 20,000 Martindale cycles
DGM plus, high requirement: ≥ 40,000 Martindale cycles
Testing according to DIN EN ISO 12947-2
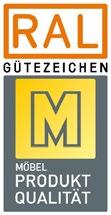
Non-woven fabric
Destruction of the test sample is usually achieved when a hole is observed in a non-woven fabric. A hole means that the top layer is abraded in such a way that a different looking layer or the base fabric is visible.
Assessment according to DIN EN 14465
DGM requirement: ≥ 20,000 Martindale cycles
DGM plus, high requirement: ≥ 40,000 Martindale cycles
Testing according to DIN EN ISO 12947-2
Napped fabric
Destruction of the test sample is usually achieved when the fibre layer of a napped fabric completely abraded.
Assessment according to DIN EN 14465
DGM requirement: ≥ 12,000 Martindale cycles
DGM plus, high requirement: ≥ 18,000 Martindale cycles
Testing according to DIN EN ISO 12947-2
6.11.1.5. Pill formation
Must be determined for flat woven fabrics, knitted fabrics (without pile), loop pile fabrics and non-woven fabrics
A scouring agent fabric made of wool (according to DIN EN ISO 12947-1) must be used and the category must be determined after 2,000 Martindale cycles
DGM requirement: At least grade 3 to 4
DGM plus, high requirement: At least grade 4
Testing according to DIN EN ISO 12945-2
6.11.1.6. Light fastness
For light colours, a tolerance of a fastness rating of 0.5 applies.
DGM requirement: At least fastness rating 4
DGM plus requirement: At least fastness rating 5
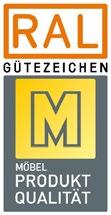
Testing according to DIN EN ISO 105-B02 Procedure 2
(Procedure 3 may be used for quality control purposes.)
Correction of the test procedure referencing was made on 15/05/2024
6.11.1.7. Rubbing fastness dry
DGM requirement: At least fastness rating 4
DGM plus requirement: At least fastness rating > 4
Testing according to DIN EN ISO-105 X12
6.11.1.8. Rubbing fastness wet
DGM requirement: At least fastness rating 3
DGM plus requirement: At least fastness rating 3 to 4
For dark and brilliant colours and blends, for natural and viscose fibres the following applies:
DGM requirement: At least fastness rating 2 to 3
DGM plus requirement: At least fastness rating 3
Testing according to DIN EN ISO-105 X12
6.11.1.9. Colour difference
Permissible colour difference between the supplied material and the sample material according to greyscale (DIN EN 20105- A02)
Upholstery fabrics:
DGM requirement: At least level 4
Micro fibre fabrics:
DGM requirement: At least level 3 to 4
6.11.1.10. Flammability
Cigarette test according to DIN EN 1021-1 must be passed.
Testing according to DIN EN 1021-1
6.11.1.11. Upholstery fabric processing
Seam allowance
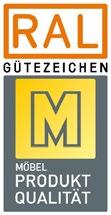
The fabric must be processed with a seam allowance of at least 10 mm. Depending on the fabric type, higher seam allowances may be required. The pattern repeat is subject to the manufacturer's series processing and must be specified in the product information.
Patterned fabrics
Taking into account a harmonious overall impression, care should be taken to ensure a uniform pattern finish.
Exceptions:
• Deviations due to model or cutting
• Diagonally patterned fabrics
• In the case of corner solutions, depending on the incidence of light and the type of cover material, oscillation (colour difference / light/dark effect) may occur due to the production process (characteristic of the product).
Multi-coloured flat woven fabric / chenille
With contrasting colours / stripes, there may be visible colour shading at the seams.
Processing direction
For industrial as well as pattern and model-related reasons, upholstery fabrics can be processed in warp and weft direction.
Velour processing
Care must be taken to ensure a uniform direction of weave:
• Industrial standard: selvedge runs parallel to seat edge
Mohair velour processing
The mohair velour with a laid pile in one direction is processed according to the pile. Care must be taken to ensure that the direction of the strokes is uniform:
• In the back from top to bottom
• In the seat from back to front
Exceptions:
Deviations due to model or cutting.
Thread straightness
Care must be taken to ensure a uniform appearance. Thread straightness is not possible due to the manufacturing conditions.
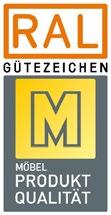
6.11.2. Leather for upholstered furniture
The following test requirements apply to new, unused leather. For used leathers, the tests and test results are only a guide.
Note for incoming goods inspections, see appendix 12.7
Point 3.2 Self-monitoring must be observed as well.
6.11.2.1. Definition leather
Definitions of terms related to leather according to DIN EN 15987, RAL 060 A2 and RAL 061 A1 as well as DIN 68871.
Labelling regulations for products related to leather according to RAL 060 A2, RAL 061 A1, DIN 68871 and DIN EN 16223-1 must be observed.
6.11.2.2. Colour migration
Determination of colour migration fastness to plasticised polymers.
Requirement: grey scale ≥ 4
Testing according to DIN EN ISO 15701
6.11.2.3. Light fastness
For all types of leather, at least light fastness level 3 (light fastness type 3) must be demonstrated – unless listed separately below.
Aniline leather, natural
Aniline leather, refined (optimised for use)
Semi-aniline leather, lightly pigmented
Leather, pigmented
Full grain leather / nubuck
≥ Level 3
≥ Level 3
≥ Level 4
≥ Level 5
≥ Level 3
If particularly high usage properties are advertised, at least level 6 must be demonstrated in each case.
Testing according to DIN EN ISO 105-B02 Exposure method 3
White leathers must not show any yellowing after three days of (dark) storage at 50° C.
Visual assessment according to DIN EN ISO 20105-A02; grey scale at least level 4 to 5
6.11.2.4. Rubbing fastness
Requirements:
a) Suede leather/nubuck; aniline leather, natural
Felt dry
No. of cycles Level
50 3
Felt welt
Felt moistened with alkaline sweat solution
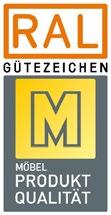
20 3
20 3 (pH value 8)
(Colour black: at least level 2)
Note: For the colour black, no higher value than at least level 2 can be achieved at present according to the state of the art.
b) Aniline leather, refined (optimised for use) No. of cycles Level
Felt dry
Felt welt
Felt moistened with alkaline sweat solution
100 3
40 3
30 3 (pH value 8)
(Colour black: at least level 2)
c) Semi-aniline leather, lightly pigmented
Felt dry
Felt wet
Felt moistened with alkaline sweat solution
No. of cycles Level
500 4
80 3 to 4
50 3 to 4 (pH value 8)
(Colour black: at least level 2)
d) Pigmented leather No. of cycles Level
Felt dry
Felt wet
Felt moistened with alkaline sweat solution
500 4
250 3 to 4
80 3 to 4 (pH value 8)
Note: If particularly high usage properties are advertised, at least level 4 to 5 must be demonstrated for all types of leather.
The colouring of the felt is assessed using the grey scale DIN EN 2015-A03; the damage to the surface is also assessed according to DIN EN ISO 11640.
6.11.2.5. Permanent bending strength
Semi-aniline leathers and pigmented leathers must not show any cracks, grey fracture, or detachment even after 50,000 buckling cycles
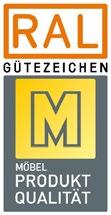
This test is not necessary for suede/nubuck.
Aniline leather and aniline leather, refined (optimised for use) must not show any cracks, grey fracture, or detachment even after 20,000 buckling cycles
Testing according to DIN EN ISO 5402-1
6.11.2.6. Adhesion of the finish
Minimum value for the adhesion of the finish for smooth leather ≥ 2.0 N / 10 mm strip width.
Separation within the finish layer is not permitted, even if the force is greater than 2 N/10 mm.
Testing according to DIN EN ISO 11644 in N/cm; at least 3 samples from different locations
6.11.2.7. Tear propagation force
The tear propagation force must be ≥ 20 N.
Testing according to DIN EN ISO 3377-1
6.11.2.8. Cold fracture resistance of the finish
No fractures of the finish may occur.
Testing according to DIN EN ISO 17233 up to -15° C
6.11.2.9. Water drop fastness
Testing and requirement based on DIN EN ISO 15700
Evaluation of water drop penetration time
Test duration:
Aniline leather, natural
Aniline leather, refined (use-optimised)
Semi-aniline leather, lightly pigmented
Pigmented leather
Suede leather / nubuck
Grey scale at least level 3, no permanent swelling
6.11.2.10. pH value of the leather
According to DIN EN 13336 ≥ 3.5
Testing according to DIN EN ISO 4045
At least 10 min.
At least 10 min.
At least 10 min.
At least 30 min.
At least 10 min
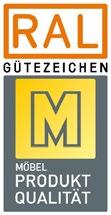
6.11.2.11. Dyeing for leather
Leather must be dyed throughout. Absolutely 100% colour uniformity between surface and inner zone is not possible due to processing reasons. Slight differences in colour are permissible. The colour of the crust (uncoated leather) must match the top layer.
Visual assessment
Colour difference
Permissible colour differences from the delivered material to the sample material as well as within a leather hide and on the processed upholstered furniture according to grey scale
DIN EN 20105-A02.
Requirements:
Leather type:
Aniline leather, natural
Aniline leather, refined (use-optimised)
Semi-aniline leather, lightly pigmented
Pigmented leather
Full grain leather / nubuck
Visual assessment
6.11.2.12. Water vapour permeability
At least level 3
At least level 3
At least level 4
At least level 4
At least level 3
Measured in mg (cm² x h) This test is currently still considered a recommendation
Leather type: Requirement
Aniline leather, natural
Aniline leather, refined (use-optimised)
Semi-aniline leather, lightly pigmented
Full grain leather / nubuck
Testing according to DIN EN ISO 14268 (without pre-treatment)
6.11.2.13. Water vapour uptake
Measured in mg/ (cm² x 8 h)
Test climate 23° / 50% rel. humidity
3
2
2
10
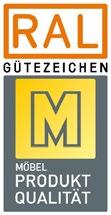
This test is currently still valid as a recommendation.
Leather type: Requirement
Aniline leather, natural 8
Aniline leather, refined (optimised for use) 6
Semi-aniline leather, lightly pigmented 6
Full grain leather / nubuck 10
Testing according to DIN EN 17229
6.11.2.14. Elongation in the tensometer
Measurement of the permanent elongation in the tensometer according to DIN 53323 or JUP 13.
Within 30 ± 10 s bring the pressure up to 5 bar, hold for 10 s, release for 30 s, then read off the permanent elongation at 1 bar.
15 to 20%, nominal value 18
6.11.2.15. Resistance to ageing and temperature
Visual assessment of colour shade and surface. No changes must be detectable after the test, e. g. no cracks, colour changes, strong shrinkage, changed grain.
Evaluation of a colour change with the grey scale according to DIN EN 20105-A02: at least level 4 to 5.
Testing after 3 days at 60°C in a heating cabinet
6.11.2.16. Leather processing
Leather cuts and seam designs may have additional dividing seams for leather processing due to material and processing reasons (product information).
Natural and growth characteristics
Natural and growth characteristics include all fused and closed injuries and features which have occurred on the living animal. These may be processed while maintaining the usual durability and harmonious overall appearance. Open, not overgrown and subsequently developed damage to the skin is considered a defect. This includes tanning and finishing defects as well as storage damage.
Split leather
Split leathers such as split velour and covered split leather as well as leather fibre materials are not permitted for use surfaces (seat, back, armrest inner surfaces, armrest tops).
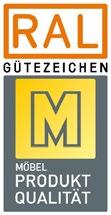
If these leathers are used in the clamping part or carcase area, the upholstered furniture must be clearly labelled with the identification (product information).
6.11.3.
Artificial leather for upholstered furniture
According to DIN 16922, artificial leather is a coated textile. For the purposes of RAL-GZ 430, artificial leather in the narrower sense is understood to be a coated textile with a leather-like surface and/or leather-like characteristics. The composition of the coating materials must be stated, also in the product information (e. g. 95% PVC, 5% PUR).
6.11.3.1. Surface characteristics
Rubbing fastness
Dry Fastness rating > 4.5
Wet Fastness rating > 4.5
Testing according to DIN EN ISO 105-X12
Light fastness
In principle, all artificial leathers must correspond to at least level 5.
If particularly high usage properties are advertised, at least level 6 must be demonstrated.
Testing according to DIN EN ISO 105-B02 Exposure method 3
Light-coloured or white artificial leathers must not show any yellowing after 3 days of (dark) storage at 50° C in a circulating air oven:
Requirement: ∆b ≤ 0.5 according to the CIELAB system against the zero sample.
Storage conditions according to DIN EN 12280-1, Procedure 1
Colour measurement with a suitable colour measuring device according to DIN 5033-7
6.11.3.2. Strengths
Tear resistance
Longitudinal > 25 N
Transverse > 20 N
Testing according to DIN EN ISO 4674-1, Procedure B
Maximum tensile strength
Longitudinal > 380 N/5 cm
Transverse > 280 N/5 cm
Testing according to DIN EN ISO 1421, Procedure 1
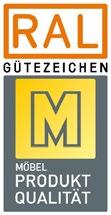
Adhesion strength of the coating to the substrate
Longitudinal > 25 N/5 cm
Transverse > 25 N/5 cm
Testing according to DIN EN ISO 2411
6.11.3.3. Wear characteristics
Rubbing resistance according to Martindale
Martindale 51,200 cycles dry
Martindale 25,600 cycles wet
Level < 2
Level < 2
Testing according to DIN EN ISO 5470-2, Procedure 1 with wool fabric*
*In deviation from the standard DIN EN ISO 5470-2, significant colour changes due to rubbed-off print application must be assessed with level 3 and are therefore not permissible.
Continuous folding behaviour Ballyflex 23° C 50,000 cycles
Longitudinal
Transverse
Testing according to DIN EN ISO 32100
Hydrolysis test (only for PUR artificial leather)
Level ≤ 1
Level ≤ 1
Evaluation of surface condition: no cracks, no detachment, after test 21 d / 70° C / 95 to 98%: no delamination and no stickiness
Continuous folding behaviour Ballyflex 23° C 15,000 cycles
Longitudinal
Transverse
Testing according to DIN EN ISO 32100
6.12. Upholstery
Level < 2
Level < 2
General quality criteria for the properties of various upholstered furniture (see also DIN 68871)
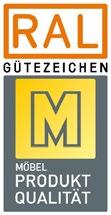
6.12.1. Type of upholstery
6.12.1.1. Firm upholstery
Upholstery construction in which the rippling of the covers is largely prevented by design measures (pre-stretched upholstery). Design- or model-related ripples, e. g. at curves, gathers are design- or construction-related.
Visual inspection, haptic test, wave measurement according to 12.6
6.12.1.2. Casual upholstery
Soft, loose upholstery structure in which a model-related or design-related waviness of the covers as well as seat marks are typical for the product.
Visual inspection, haptic test, wave measurement according to 12.6.
6.12.1.3. Particularly casual upholstery
An “particularly casual upholstery” is characterised by a very comfortable and soft surface on utility surfaces This is achieved, for example, by a ticking with various fillings (e. g. fibres, beads, down, feathers or similar materials). In the upholstery construction, a foam core or foam cushion usually represents the basic upholstery.
The covers can already show a clearly visible wave pattern on the seat, back and armrests when new or after the first use, which is desired due to the design, material and construction and will increase with use. The size of the sewn covers also has a similar influence on sinking and cover stretching.
Conclusion: The softer the upholstery and the larger the seat surface, the greater the sinking in and ultimately the cover stretching.
Visual inspection, haptic test, no wave measurement
6.12.2. Quality criteria
The seat and backrest hardnesses of a set must be largely uniform for upholstered parts of the same size and shape when new. Exception: Upholstered elements that differ in design and shape or deviations intended for design purposes.
Upholstery characteristics must be maintained even with proper, prolonged use.
6.12.3. Functions
Waves and folds may occur or be present due to the function (e. g. seat and back, armrests, side sections, head and foot sections).
Visual inspection, haptic test, seat test
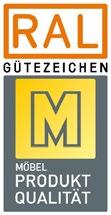
6.12.4. Quilted mats / chamber cushions / cushions with loose fill material
Marking of the chambers, quilting and/or filling materials represents a material and modelrelated property.
Visual inspection, haptic test, no wave measurement
6.13. Functional / strength test of frame and overall upholstery construction
The following requirements refer exclusively to results from laboratory testing and serve to evaluate the construction and the upholstery structure.
The durability of the upholstery is verified by measuring the change in indentation depth, the loss in height and the change in hardness after the threshold load test (strength test point A) in the seat area.
a) Firm upholstery
Indentation depth chance:
Height loss (formation of hollows):
Hardness change:
b) Casual upholstery
Indentation depth change:
Height loss (formation of hollows):
Hardness change:
c) Particularly casual upholstery
Indentation depth change:
Hardness change:
A specification for height loss is not possible.
≤ 10%
< 10 mm
< 20%
≤ 10%
< 15 mm
< 20%
≤ 15%
< 25%
During the strength tests according to Points A, B and C, no fractures may occur on the frame, on the slat base or on fittings.
The upholstered furniture must not cause any untypical, disturbing noises during use.
Notes:
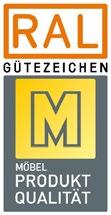
Applying a dynamic load with the drop weight of 75 kg corresponds to a person weight of 120 kg
For persons with a weight > 120 kg, the information in the product information should be taken into account or the manufacturer contacted before concluding the purchase contract with regard to the strength and durability of an upholstered piece of furniture.
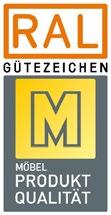
6.13.1. Threshold load of the seat surface with drop weight
Drop weight 75 kg, 300 mm diameter, curved underside R = 400 mm
Free fall of the test stamp, fall height and impact points variable depending on reaction force
Loading (reaction force)
Load change (drop load)
Seat centre Seat edge 1,500 N
N
Determination of the indentation depth change by means of a test stamp at preload 100 N and end load 750 N
Reaction force
1,500 N and 2,000 N
Total load change 30,000
The indentation depth is the difference between the indentation depths before and after the endurance test. The percentage change is calculated from the difference between the indentation depths before and after the endurance test. The percentage value refers to the new condition
The loss of height (formation of hollows) at preload 50 N and the change in hardness at a force of 600 N are determined according to DIN 68888.
Notes:
Pillows with loose fillings are to be fluffed up before measurement. The first determination of the indentation depth is made after 100 drop loads, the second after 30,000.
7.
Additional information for interested parties:
e.g.: Threshold load of the seat surface with drop weight: https://www.youtube.com/watch?v=tD64QxZ5Kec
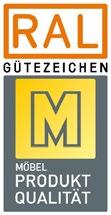
6.13.2. Threshold load of arm supports
Secure furniture against sliding away, both arm supports are simultaneously loaded swelling outwards.
Pressure pieces according to DIN EN 1335.
Force application angle:
For upholstered furniture 15° to the vertical outwards; for couches only one armrest is loaded.
Force application point:
At a distance of 250 mm from the seat edge
Load Load changes
400 N 10,000
850 N 10
In the case of arm supports with functional fittings, the manufacturer's information on load capacity must be observed during the test if necessary (see Point 3).
6.13.3. Threshold load of backrests
Seat surface statically loaded with 75 kg (in the centre).
Threshold load on backrest via pressure piece 250 x 200 mm, front side with horizontal radius R = 400 mm.
Height of force application 450 mm above the loaded seat surface, in the middle of the backrest width.
Minimum distance to upper edge of backrest 150 mm.
Direction of force application perpendicular to the angle of inclination of the loaded backrest.
Load Load changes
350 N 25,000
750 N 10
Notes:
For multi-seat elements, the backrest test shall be performed in the same manner.
When testing multi-seat sofas, each adjacent seat surface is loaded with 75 kg during the threshold load test (based on DIN EN 1728).
For the test in the seat centre and at the seat edge, see the following Figures 1 and 2.
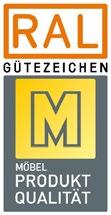
1: Threshold load – Seat centre
7. Safety
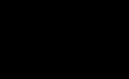
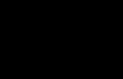
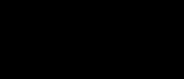

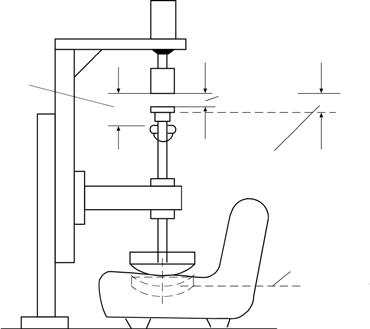
In accordance with the Product Safety Act (ProdSG) the following applies:
A product may only be made available on the market if it does not endanger the safety and health of persons or other legal interests listed in the legal ordinances pursuant to Article 3 when used as intended or in a foreseeable manner.
Upholstered furniture must be stable and sufficiently loadable (DIN EN 12520 [DIN EN 1728]*, DIN EN 1022).
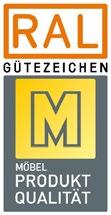
Accessible frame edges must be designed in such a way that there is no risk of injury when the furniture is used as intended. Edge radius taking ergonomic aspects into account: ≥ 3 mm.
*According to the scope of application, the safety standard takes a user weight of up to 110 kg into account. For higher user weights see also DIN 4573.
Dimensional and visual inspection, haptic test
8. Electrical Appliances
Only electrical equipment and components that comply with the current and relevant EU directives or EN standards may be used.
In the case of furniture subject to registration in accordance with the Electrical and Electronic Equipment Act (ElektroG), appropriate labelling must be applied to the furniture and the method of disposal must be indicated in the operating instructions.
Note for electrical safety: see 12.4 “Guideline for electrical equipment/ components in furniture”.
9. Labelling
Furniture that complies with these Quality and Testing Regulations and which has been awarded the quality mark can be labelled with the quality mark shown below:
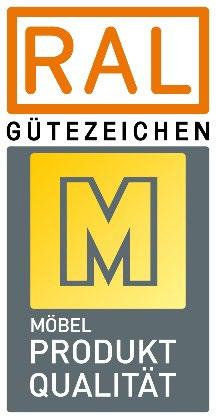
RAL-GZ 430 / 4
The implementation regulations of the Deutsche Gütegemeinschaft Möbel apply exclusively to the use of the quality mark.
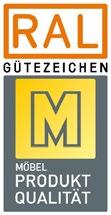
10. Amendments
Amendments to these Quality and Testing Regulations require the prior written consent of RAL to become effective. They come into force after a reasonable period of time after they have been announced by the Executive Board.
11. Implementing Regulations for the Award and Use of the Quality Mark of the Deutsche Gütegemeinschaft Möbel e. V.
11.1. Assessment basis
The assessment basis for the quality mark consists of the Quality and Testing Regulations for Furniture. It is amended and further developed in line with technical progress.
11.2. Awarding the quality mark
11.2.1 The Deutsche Gütegemeinschaft Möbel e. V. awards the right to use the quality mark for furniture to manufacturers of quality furniture upon application.
11.2.2 The application for the award of the quality mark must be submitted in writing to the office of the Deutsche Gütegemeinschaft Möbel e. V., Friedrichstraße 13-15 in 90762 Fürth. The application must be accompanied by a list of the products which the applicant wishes to have approved for quality assurance as well as a legally binding signed certificate of commitment (Sample 1).
11.2.3 This application is reviewed by the Quality Committee. The Quality Association commissions a neutral testing institute to carry out the initial testing. The test result is sent in writing to the Quality Committee, the applicant, and the Executive Board of the Quality Association. In addition, the Quality Committee may arrange for a factory inspection to be carried out by authorised inspectors or inspectors authorised by the testing institute. The applicant shall bear the costs for this as well as the cost for the inspection of the products. The Quality Association may authorise the testing institute to request an advance payment for inspection costs.
11.2.4 If the result of the inspection is positive, the Executive Board of the Quality Association awards the quality mark to the applicant on the recommendation of the Quality Committee. The award is certified (Sample 2). If the result of the inspection is negative, the Quality Committee will defer the application. It must give reasons for the deferral in writing.
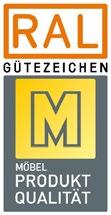
11.3. Use of the quality mark
11.3.1 Users of the mark may only use the quality mark for products that comply with the Quality and Testing Regulations.
11.3.2 The Quality Association has the sole right to have marking materials of the quality mark produced for all purposes (embossing stamps, printing blocks, matrixes, seal stamps, rubber stamps, etc.) and to issue them or have them issued to the users of the quality mark or to grant permission for their production and to specify the type of application in more detail.
11.3.3 The Executive Board may issue special regulations for the use of the quality mark in advertising on brochures, offers, order confirmations and delivery bills, etc., in order to maintain fair competition and prevent misuse of the quality mark.
11.3.4 The right to use the quality mark ends in case of death, opening of insolvency proceedings, liquidation, withdrawal or if the user of the quality mark renounces the right to use the quality mark by legally signed declaration to the Managing Director by registered letter on a date determined by the user.
11.3.5 If the right to use the quality mark has been legally withdrawn, the award certificate and all means of labelling with the quality mark must be returned; there is no entitlement to reimbursement. The same applies if the right to use the quality mark has otherwise expired.
11.4. Quality Control
11.4.1 The Quality Association is entitled and obliged to monitor compliance with the Quality and Testing Regulations as well as the lawful and proper use of the quality mark.
11.4.2 Every user of the quality mark must take the necessary precautions to ensure that the products bearing the quality mark comply with the Quality and Testing Regulations. Careful records must be kept of the required internal quality control procedures. In addition, every user of the quality mark shall subject these products to the monitoring tests arranged by the Quality Association to the extent and frequency in accordance with the requirements of the Quality and Testing Regulations and shall bear the testing and transport costs incurred as a result.
11.4.3 The Quality Committee commissions neutral testing institutes (officially recognised material testing institutes or equivalent testing institutes) to carry out the monitoring tests and makes the necessary agreements with them.
11.4.4 Assessors authorised by the neutral testing institutes may carry out monitoring tests at the company of the quality mark user at any time without prior notification up to twice a year, inspect the records of the company's own inspections and visit the company during operating hours. Products requested by the assessor as test pieces
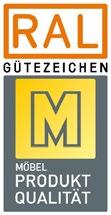
are to be handed over immediately. The assessor is entitled to dismantle finished products during the inspection. If the test is carried out elsewhere, the test pieces must be clearly marked by the assessor immediately upon removal. Products of the quality mark user can also be taken from the trade.
11.4.5 The appointed testing institute determines the test results independently of the bodies of the Quality Association. The testing institute prepares a test report for each test, a copy of which is sent to the Quality Association and to the quality mark user in question. Further dissemination of the test result is prohibited.
11.4.6 In case of a negative test result or in case of complaints about products of the quality mark user, the Quality Committee has the test repeated.
11.4.7 In the case of inspections requested from the Quality Association by third parties, the inspection costs are borne by the complainant in the event of an unjustified complaint, and by the quality mark user in the event of a justified complaint.
11.5. Sanctioning of violations
11.5.1 If the Quality Committee identifies deficiencies in quality assurance, it proposes sanctioning measures to the Executive Board of the Quality Association. Depending on the severity of the violation, the Board may:
11.5.1.1 Issue an instruction and/or a warning against the user of the quality mark,
11.5.1.2 Order an increase in the number of monitoring tests to be carried out for a certain period of time,
11.5.1.3 Impose the payment of a contractual penalty depending on the extent of the breach in question, up to EUR 10,000 in favour of the Quality Association,
11.5.1.4 Withdraw the right to use the quality mark temporarily or permanently.
11.5.2 If deviations from the Quality and Testing Regulations or an infringement of the conditions of use of the quality mark are detected during inspection of the products of the quality mark user, an instruction or warning will be issued. Depending on circumstances, the latter is issued in conjunction with an ordered increase in the number of monitoring tests to be carried out and/or by the imposition of a contractual penalty. The contractual penalty is to be paid to Deutsche Gütegemeinschaft Möbel e. V. within 14 days after the decision has become legally binding.
11.5.3 The right to use the quality mark will be withdrawn temporarily or permanently if the Quality and Testing Regulations or the conditions for use of the quality mark have been repeatedly violated, or if the quality mark has been misused, or if a deliberate violation
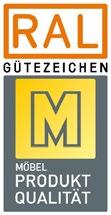
of the Quality and Testing Regulations has been proven, or if the quality mark user otherwise grossly violates the quality assurance through their conduct.
11.5.4 Should a member use the quality mark without authorisation or allow a third party to affix it to their products or permit the third party to use the quality mark in any other way, a contractual penalty of up to EUR 10,000 will be due for each individual case. Any legal action ensuing from such behaviour will not be affected by the issuing of said penalties.
11.5.5 A penalty as laid out under Section 5.1 may also be issued if the quality mark user delays or obstructs immediate monitoring tests as described under Section 4.
11.5.6 The affected party must be heard before any measures are taken. Before the right to use the quality mark is withdrawn from a quality mark user, the affected party must be given the opportunity to make a statement within a period of 4 weeks.
11.5.7 In urgent cases, the Chairman of the Quality Association may provisionally prohibit a quality mark user from using the quality mark with immediate effect. Such an order must be confirmed or rescinded by the Executive Board of the Quality Association within 14 days.
11.5.8 The duty of the Quality Association to intervene against impairment of the use of the quality mark and in the event of misuse of the quality mark also obliges the users of the quality mark under trademark law to notify the Managing Director of the Quality Association without delay of any violations of the conditions of use of the quality mark and any cases of misuse of the quality mark of which they become aware and to submit substantiating documents so that the violation can be prosecuted in an appropriate manner. Failure to do so shall be punished in accordance with Section 5.1.
11.5.9 Measures taken by the Quality Association to protect the quality mark within the meaning of these provisions shall not affect the right of quality mark users to assert any claims for compensation for damage directly incurred by them as a result of infringement under civil law.
11.6. Objection
11.6.1 The quality mark user may lodge an appeal with the Quality Committee against a penalty notice in accordance with Section 5.1 within 4 weeks of notification of the notice. A decision on the appeal must be made within 4 weeks. The appeal has a suspensive effect; however, in the event of an acute risk of misleading the market, the Quality Committee may provisionally confirm a sanctioning measure in accordance with Section 5.1.4 even before deciding on the appeal.
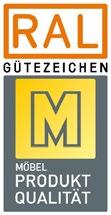
11.6.2 If the objection is rejected, the complainant may take legal action in accordance with Section 11 of the Articles of Association within 4 weeks of being served with the decision rejecting the complaint.
11.7. Reinstatement of usage rights
If the right to use the quality mark has been withdrawn, it may be re-awarded after three months at the earliest. The procedure is determined in accordance with Section 2. However, the Executive Board of the Quality Association may impose additional conditions.
11.8. Amendments
These Implementing Regulations together with samples (declaration of membership, award certificate) are recognised by RAL. Amendments, including those of an editorial nature, require the prior written consent of RAL to become effective. They come into force after being announced by the Executive Board within a reasonable period determined by the Executive Board of the Quality Association.
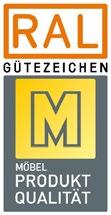
Certificate of Commitment for the Quality Assurance of the Deutsche Gütegemeinschaft Möbel e. V.
1. The undersigned / the undersigned company hereby applies to the Deutsche Gütegemeinschaft Möbel e. V. for
admission as a member*
the award of the right to use the quality mark for furniture in conjunction with the product related addition according to Section 2 of this Certificate of Commitment.
2. The undersigned / the undersigned company confirms that they have read the Quality and Testing Regulations for Furniture in conjunction with the
Quality and Testing Regulations for Cabinet Furniture, RAL-GZ 430/1*
Quality and Testing Regulations for Kitchen and Bathroom Furniture, RAL-GZ 430/2*
Quality and Testing Regulations for Tables, Chairs and Corner Seats, RAL-GZ 430/3*
Quality and Testing Regulations for Upholstered Furniture, RAL-GZ 430/4*
Quality and Testing Regulations for Beds, RAL-GZ 430/5*
Quality and Testing Regulations for Mattresses, RAL-GZ 430/6*
Quality and Testing Regulations for Waterbeds, RAL-GZ 430/7*
Quality and Testing Regulations for Office Furniture, RAL-GZ 430/8*
Quality and Testing Regulations for Children’s Furniture, RAL-GZ 430/9*
Quality and Testing Regulations for School Furniture, RAL-GZ 430/10*
Quality and Testing Regulations for Outdoor Furniture RAL-GZ 430/11*
The Articles of Association of the Deutsche Gütegemeinschaft Möbel e. V.,
The Quality Mark Statutes for the quality mark Furniture,
The Implementing Regulations with Samples 1 and 2 and hereby recognise them without reservation as binding in themselves.
Number of employees: ...............
(Place and date)
*Please mark as appropriate
(Stamp and signature of the applicant)