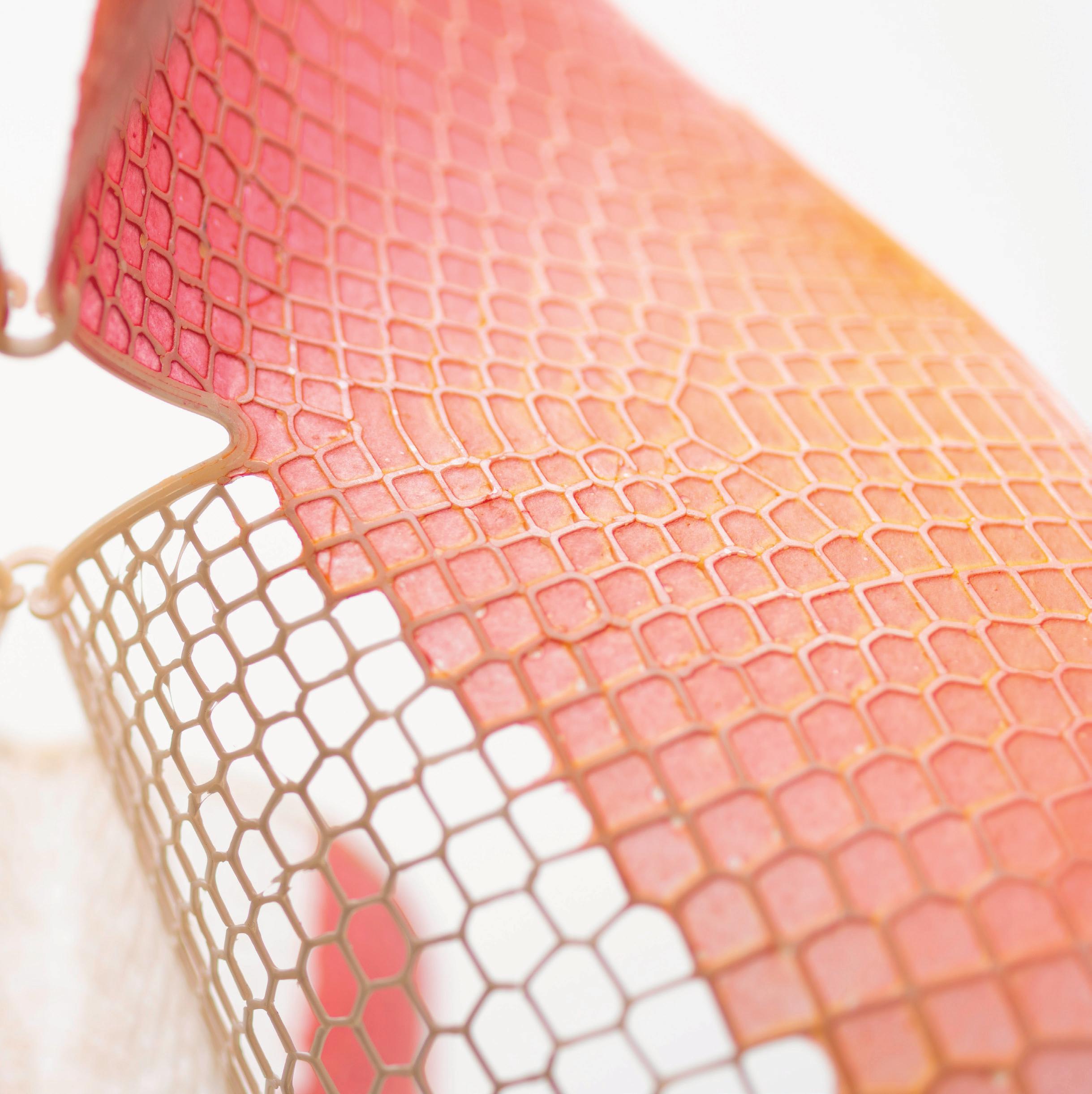
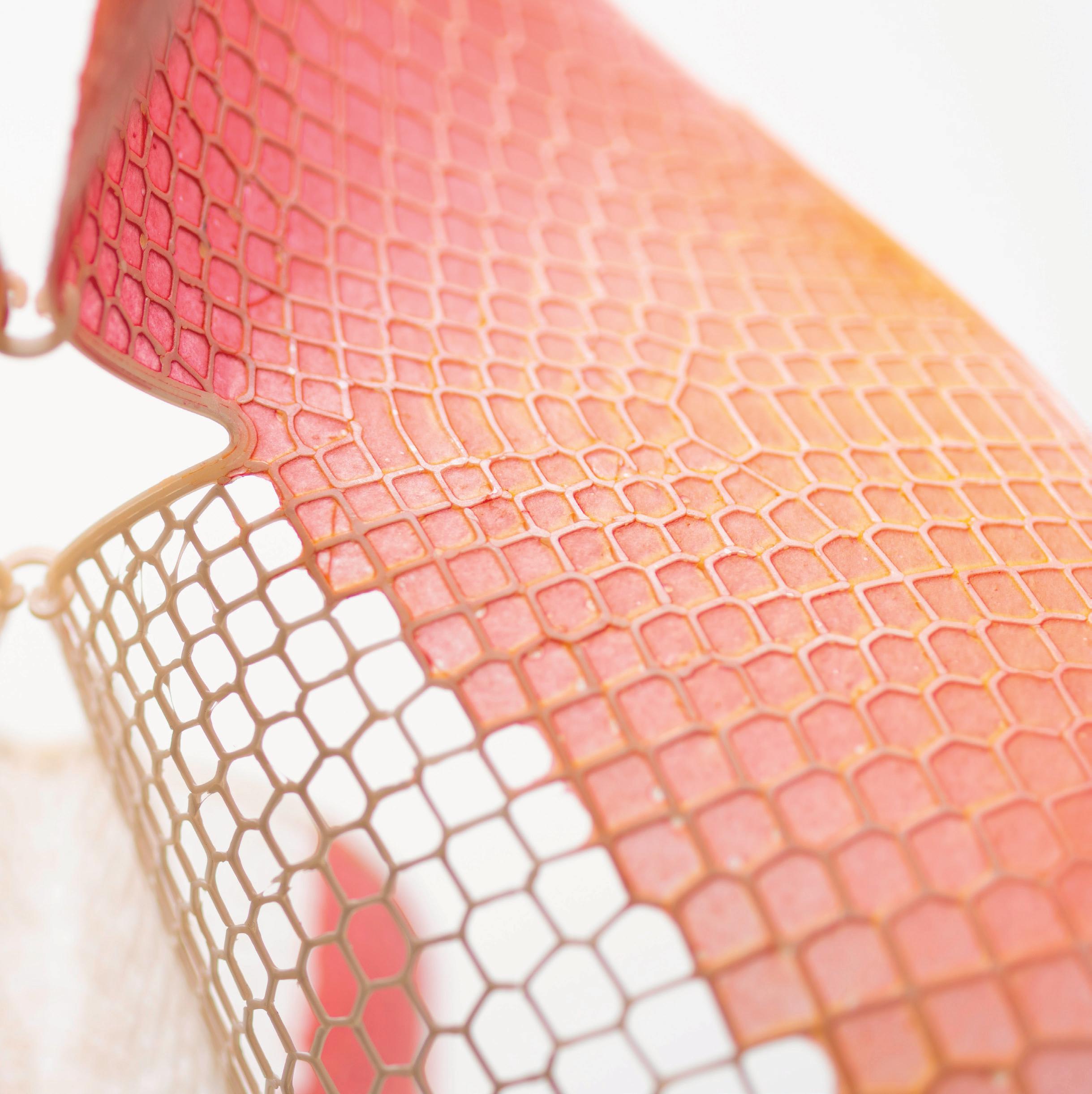
CRAFTING PLASTICS! STUDIO
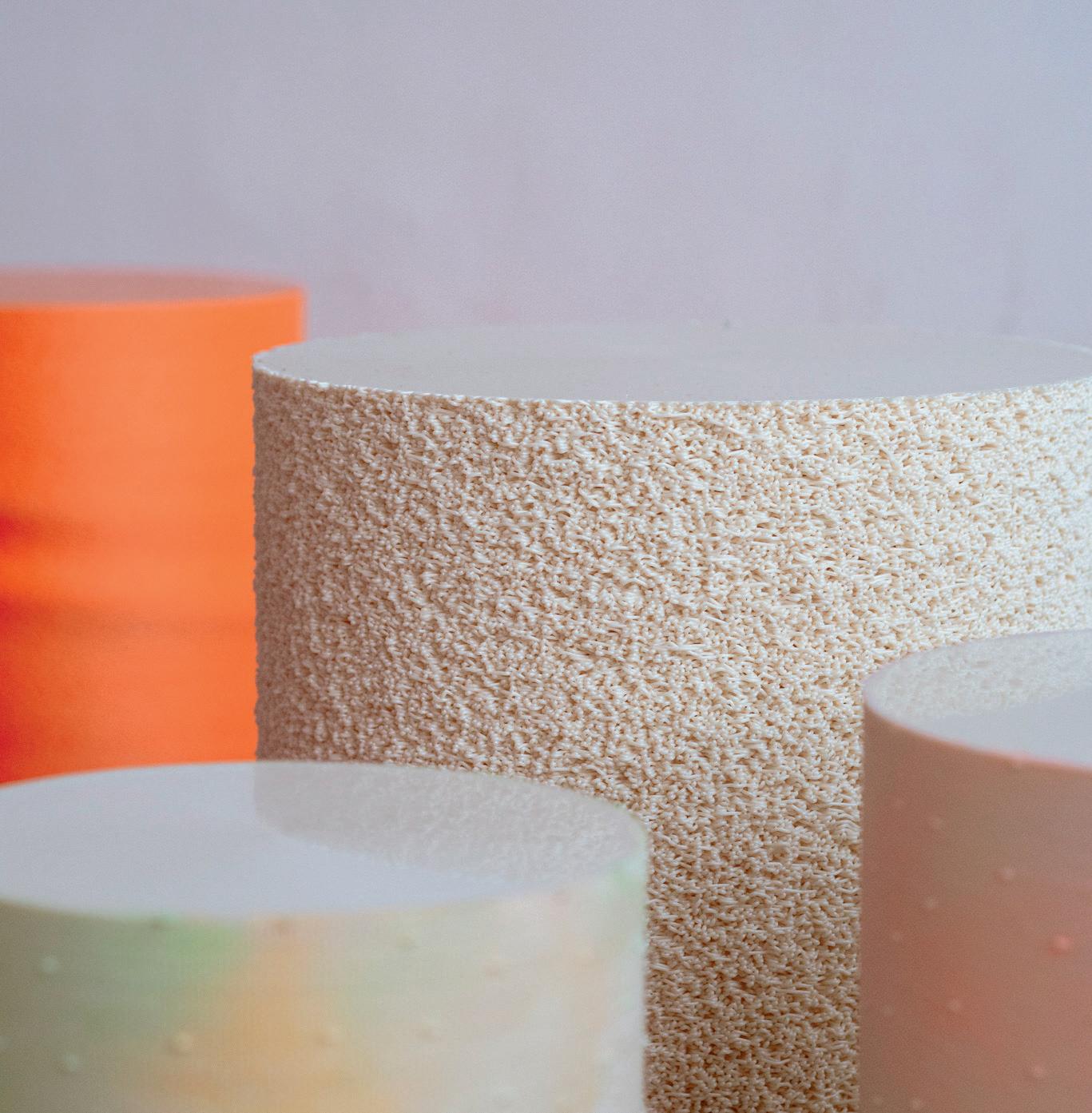
CRAFTING PLASTICS! STUDIO
Cover : Sensbiom 2 by crafting plastics! & Dumolab, Alcova - Milano Design Week 2023 Photo : Adam Sakovy Left side : Collection 13 & Senseables, Alcova - Miami 2023 Photo : Welinnacrafting plastics! studio’s Vlasta Kubušová on the merging of science, design and sensation
renewable sources like corn or sugarcane to lactic acid, which is then polymerized into PLA chains.
So, your studio makes the material, and the products?
On the one hand, we are developing our own biopolymer composites, helping companies implement them in circular products.
Kvasnovska
Could you explain what bio polymers are? In particular your own material, NUATAN?
Biopolymers are valuable and degradable polymers sourced from organic materials derived from biological resources like starch and cellulose.
Unlike plastics derived from fossil fuels, biopolymers offer biocompatibility and they degrade relatively quickly.
We focus on thermoplastic materials which could replace fossil fuel based plastics in durable consumer goods.
NUATAN, our line of trademarked materials, is based on two main biopolymers - PHA and PLA, along with a few other bio-based additives.
PHAs (polyhydroxyalkanoates), biodegradable polymers, are produced by microbial fermentation, converting renewable carbon sources into polymer chains within cells. PLA is produced by fermenting starch from
On the other hand, we are demonstrating the capabilities of biodegradable plastics in our own collections. We are also engaged in material design research projects, ranging from advanced endeavors on environmentally responsive materials to practical investigations into utilizing local resources like cellulose, seaweed, mycelium, and agricultural waste as building blocks for innovative material formulations.
You mentioned circular products there, what does that mean?
Circular design embodies a holistic approach to product creation, focused on sustainability and especially resource efficiency. It centres on the principles of durability, reusability, repairability, and recyclability, aiming to minimise waste and support a circular economy.
Multiple organizations and companies are already trying to introduce circular design tools and products, but the process needs to be accelerated.
NUATAN cup Photo : Patricia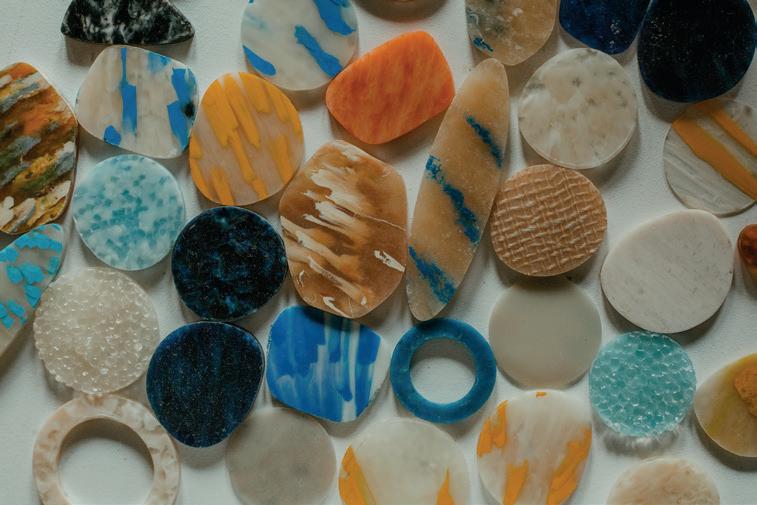
You’re just back from the Alcova design show in Milan, what was that like?
It’s was a great week, but intense. The event was actually a little bit outside of Milan, in an old abandoned villa. But there were more than 90,000 visitors. It’s the best way to connect with people across the design worlds.
We were showing some of the new stools created from our materials. We call the series ‘Collection 13’ and ‘Senseables’. It’s a range of functional biodegradable 3D printed stools and side tables - The Senseable series change colour when exposed to sunlight.
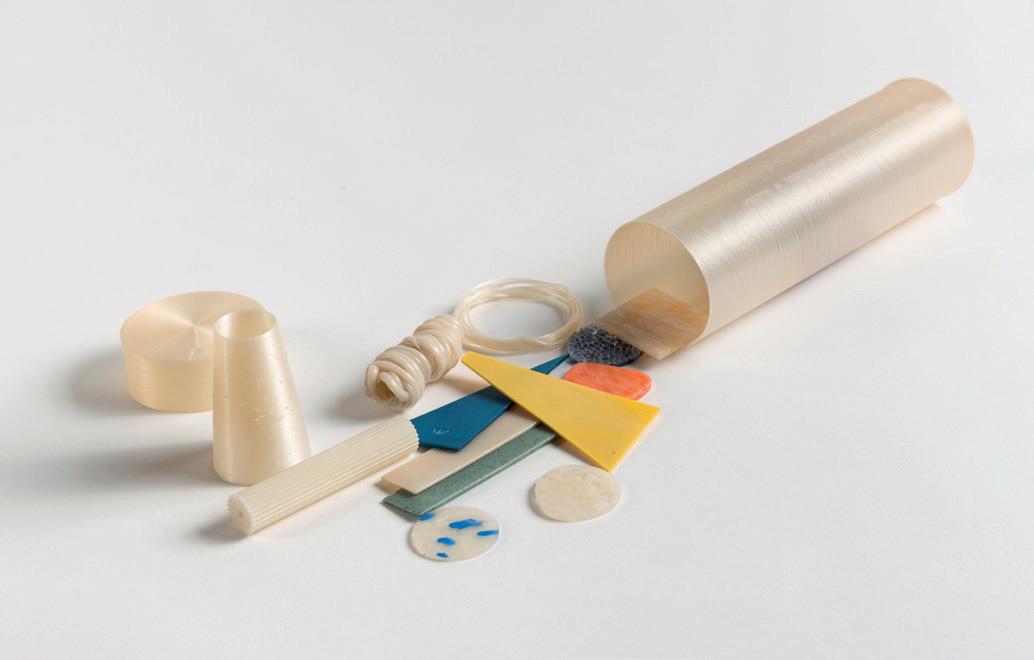
So your materials actually respond to the environment? How did you come up with that idea?
The idea started with a project that we called, ‘Breathe in, breathe out’, a collaboration with Berlin-based Office MMK. That was about giving bioplastics a new identity.
After many exhibitions and tonnes of presentations, we realised that although we are telling people about bioplastic, they have no way to recognise them in the world, there’s no common labelling, and the fossil fuel based plastic industry lacks transparency…
So we’ve been thinking about other properties that these new materials could have. Things that could help people to distinguish between what’s synthetic and what’s natural.
NUATAN sample box Photo : Adam Sakovy NUATAN Materials Photo : Patricia Kvasnovska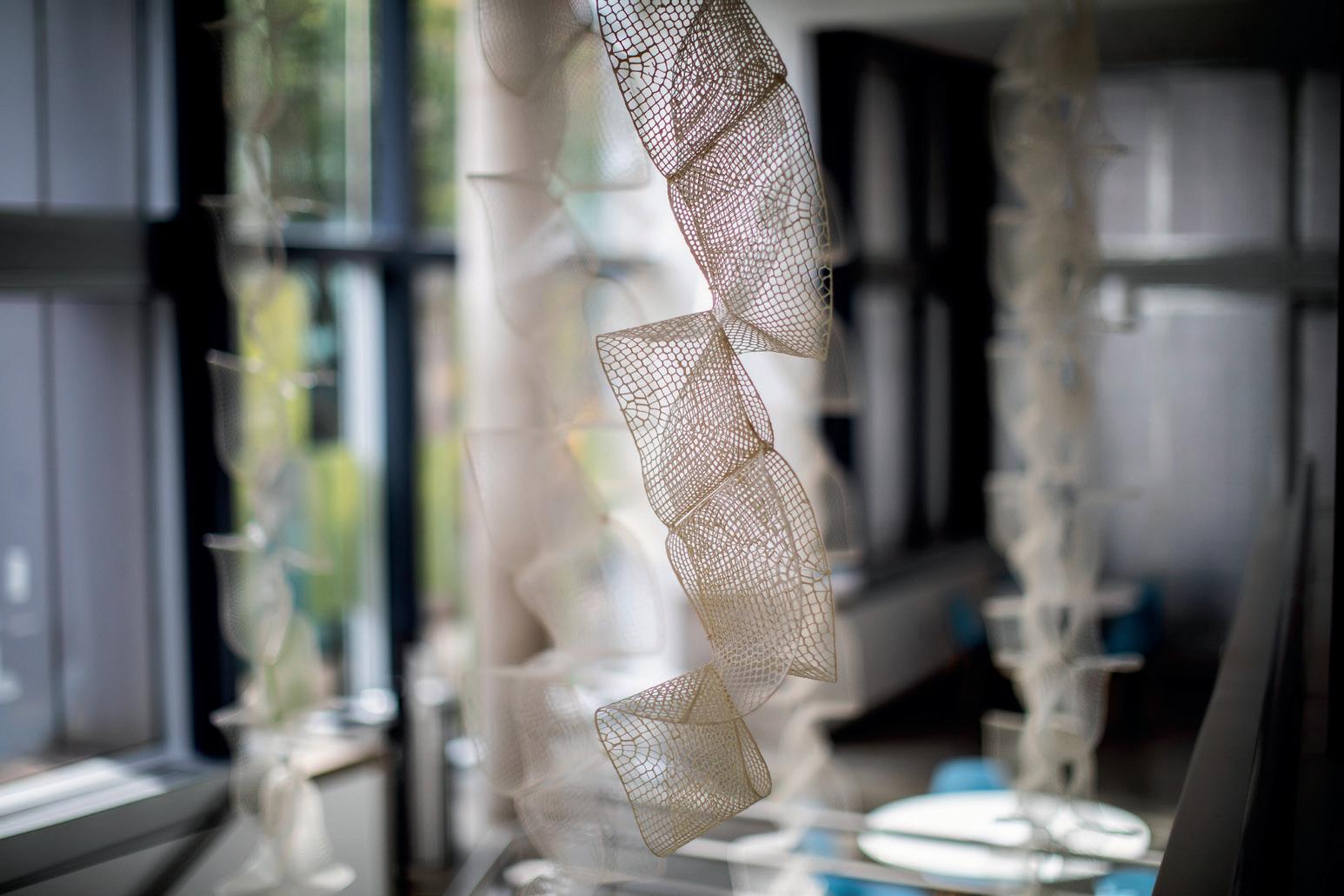
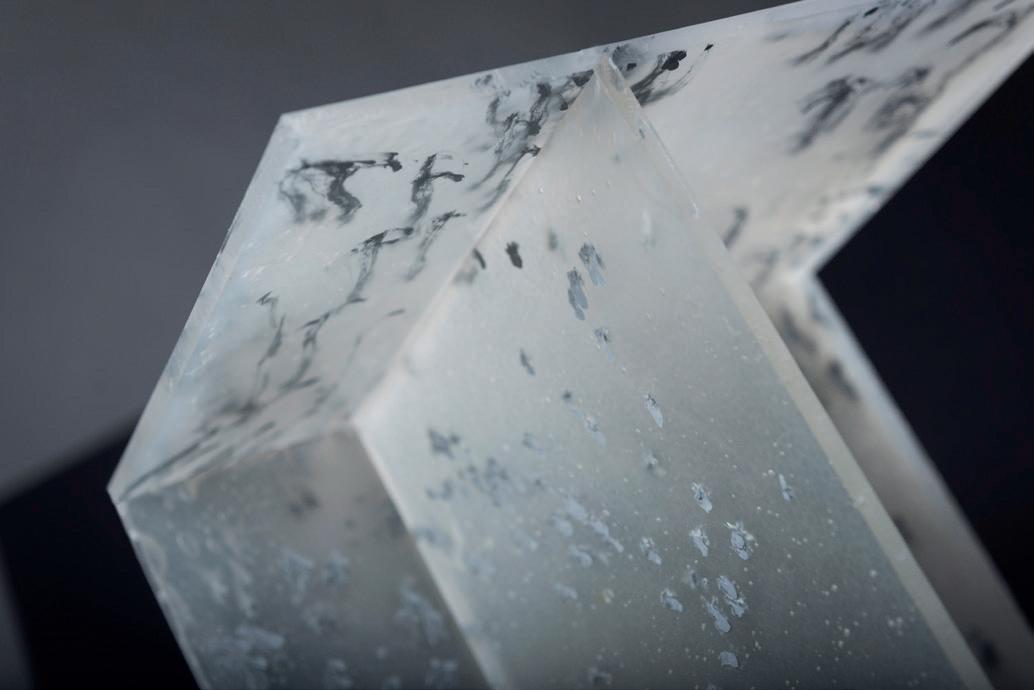
"We are trying to make something that is usable and scalable right now, so the materials can have an impact."Collection 3 Photo : Adam Sakovy Sensbiom 1 by crafting plastics! & Dumolab ICA Philadelphia Photo : SUCAR
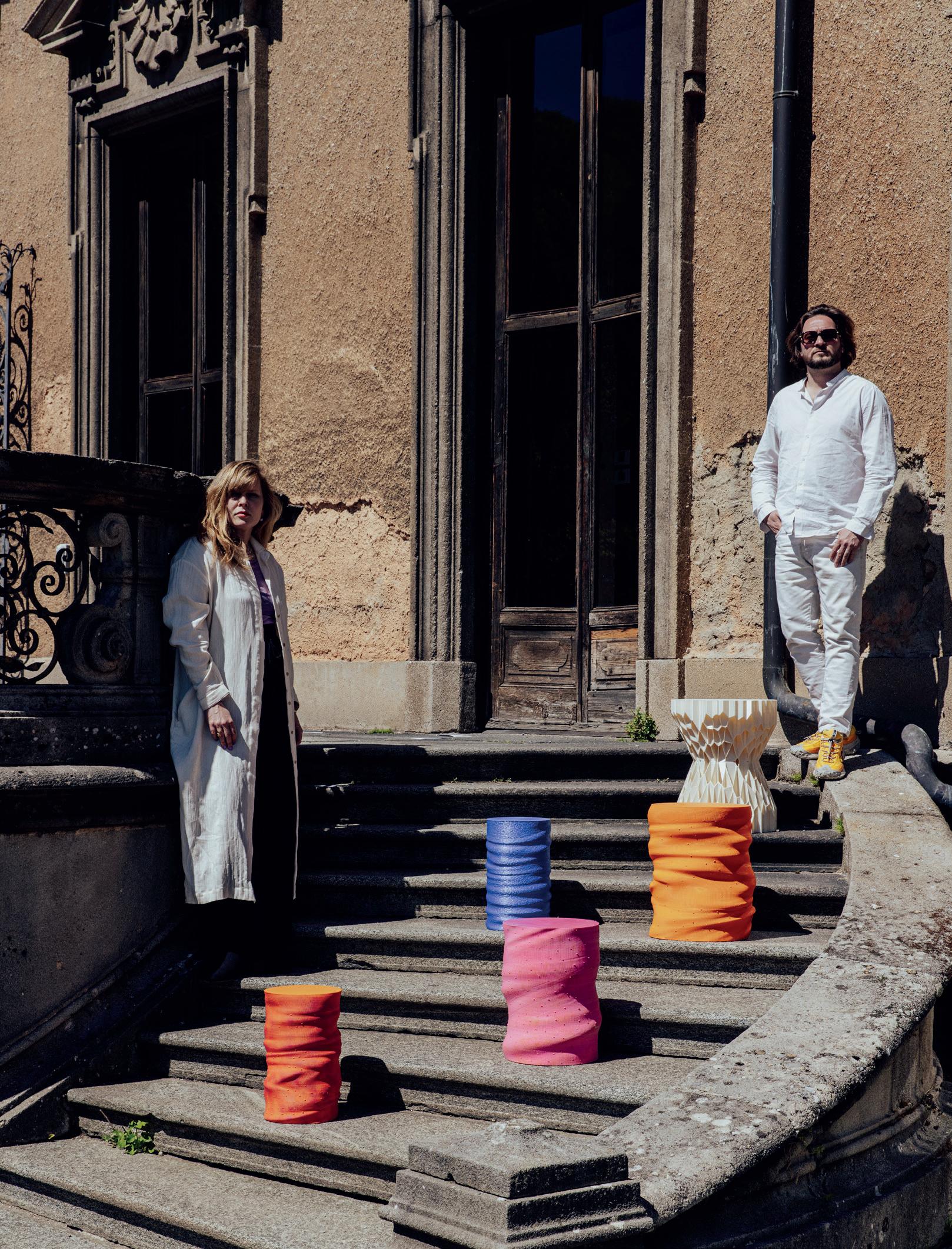
"What if the new materials could be programmed to detect invisible threats you can not see and tell you something about the environment by changing themselves?"
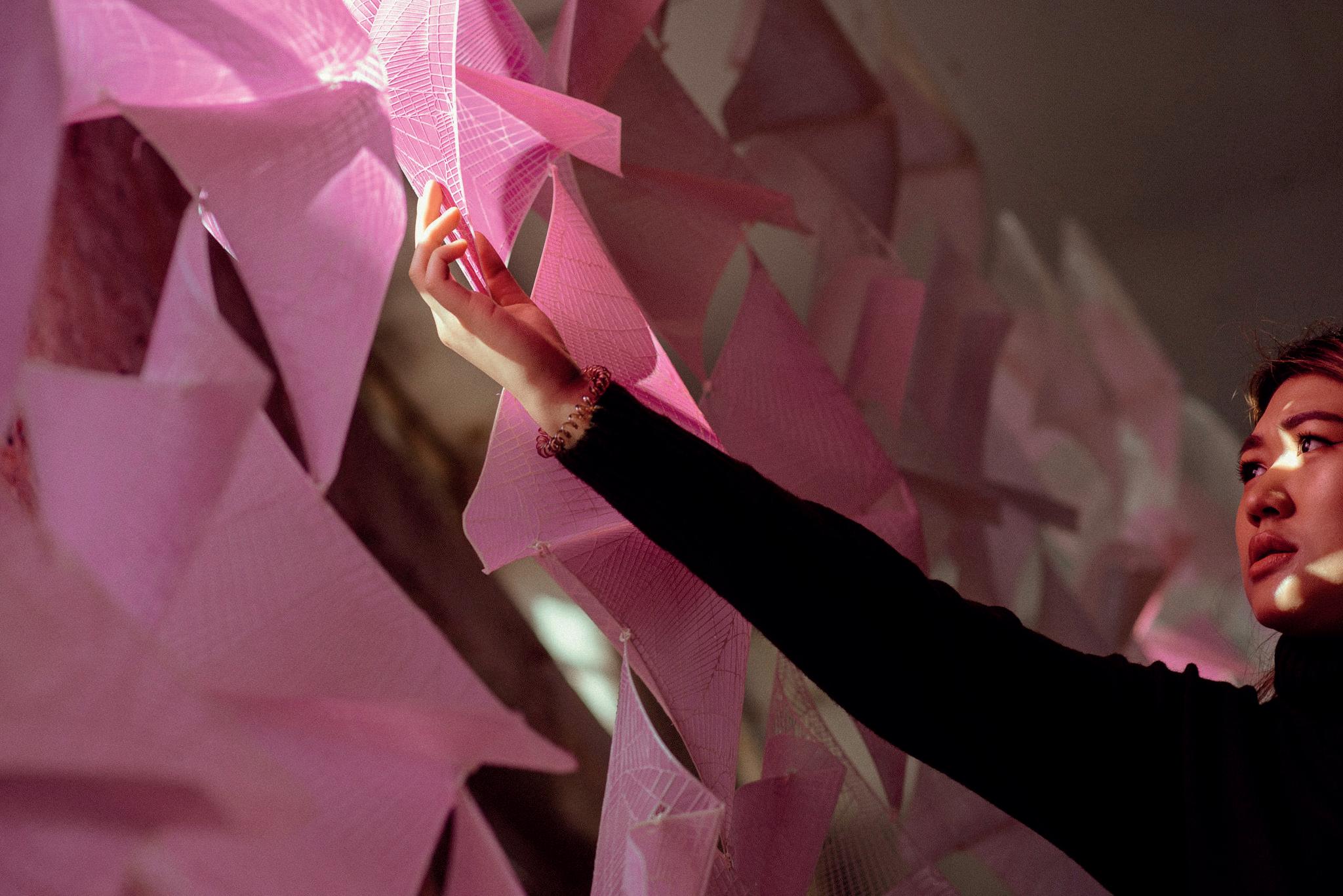
That would be quite an achievement.
Well, when we are working with biopolymers in the laboratory, we always smell the materials, the melting starches and sugars. But once the material is processed, you don’t smell anything, it lacks identity.
We thought it would make an interesting research project, to figure out whether we could make materials that have a specific smell. Working with researchers, we analysed the aroma active substances within the biopolymers. And then we recreated the smell of the origin of the biopolymers and put it in our plastics.
The way people reacted to this material was completely different, they started to ask questions, and perceived the material as something that has its natural origin.
So we decided to push it a little bit further. What if the new materials could become dynamic, almost life-like? Can we program them to detect invisible threats you can not see and tell you something about the environment by changing themselves?
That sounds so futuristic. Did it work?
This was the avenue we explored when I did my Fulbright in the United States, at University of Pennsylvania. With a group of people at Dumolab we started to develop materials that could potentially detect harmful molecules in the environment and signal it by changing colour.
The first iteration explored how we can use synthetic biology methods, (such as cell-free expression systems) to activate biological materials.
For the second version of the project, called SENSBIOM 2 (Senseable Biomaterials for Healthier Habitats), we developed a lattice structure, 3D printed from NUATAN materials that worked as a scaffold. This was cast together with cellulose, chitin and silk fibroin material that reacted to UV exposure.
This version was shown for the first time at Milan Design Week, also, because they have the worst UV exposure of all the European cities. Believe it or not, in April, the UV level reached 8 every day.
Did everyone start applying sun screen?
The interesting thing is, people have this information available already, in their apps.
But suddenly, when it becomes tangible, the whole conversation about climate change comes to life. There is something to see and to touch. It’s happening in front of their eyes. It’s not just another data point on your iPhone.
Collection 6
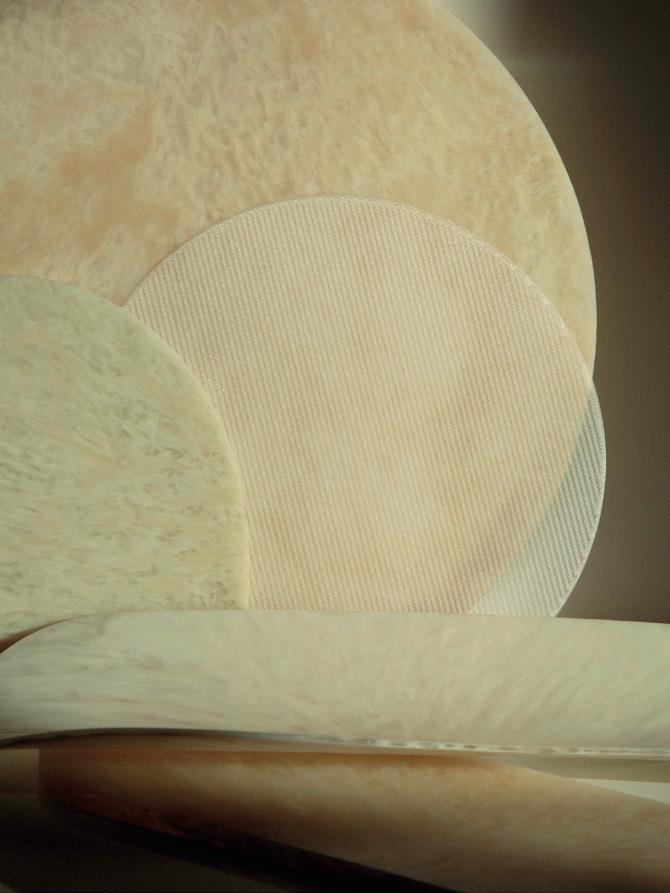
Did you start out in product design?
I did, but also media and art production. I have a master’s degree in film too, which I did at the same time as product design, because I found both of these fields very fascinating.
That’s also how I met my partner and studio cofounder, Miroslav Král. He was studying set design for theatre and film at the Academy of performing arts.
We started to work together on multiple projects. Theatre pieces, films and product design projects were part of it. But also, we organised lots of design events and cultural events in Bratislava, design conferences and multi-culture events including the well-known format Creative Mornings Bratislava.
How did this lead you to get involved with bioplastics?
It was maybe 10 years ago. As we were doing these various projects, we used so many materials (especially plastics) that we do not know anything about). We realised that we needed some better materials to use. I think that was the start.
I tried to look around for alternatives to fossil fuel based plastics. There were already quite a lot of bio plastics, available. Well, there were companies claiming that they have the solutions ready to use, but it was not very transparent.
The more questions we had, the less answers we got! In the end, we just didn’t really know what we were using.
How do you get around that kind of problem?
It was during one of our morning events that we organised here in Bratislava. We invited some scientists and we discovered the world of bioplastics a little bit deeper.
We thought it might be quite an interesting challenge for designers to see how we can change the direction of the development of biomaterials.
Back then, biomaterials were mostly about producing very thin films for packaging and for agricultural purposes. We wanted to look at it a little bit differently.
So like a designer!
We wanted to see if we could really use bioplastics for something durable, but still biodegradable. So we started to collaborate with some of the scientists at various institutions.
They thought we were just playing around, that we would only produce one-off products. Not something serious. They just didn’t believe that these materials, these biopolymers would be suitable for that kind of usage.
But we were fascinated by the spectrum of possibilities this materiality offered. We worked very seriously and eventually came up with different compositions, and they started to work very well.
What kind of market were you thinking of for these new materials?
By then I was doing my second masters at the University of the Arts in Berlin.
The main theme of the master course was ‘Transfecting Design Systems’ and it supported collaborations between product and fashion designers. Together with my colleague Verena Michels we came with the idea of exploring what we can do with biomaterials in the fast fashion industry - one of the most polluting industries.
As a result, we developed several prototypes of fashion items, raincoats and eyewear. After the studies, with Miro, we came up with plans to produce eyewear frames from bioplastics.
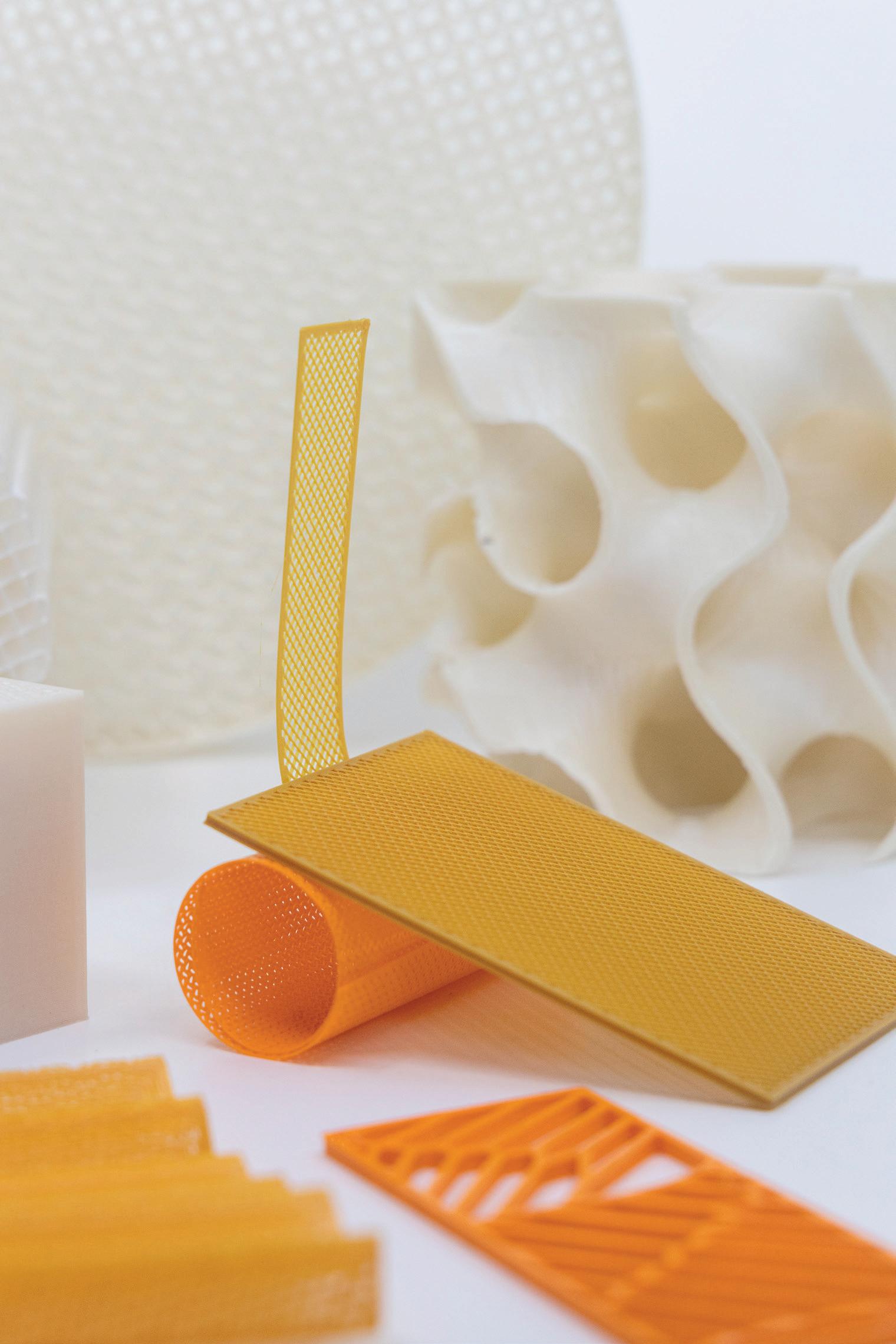
"I have learned that this is important: Do not give up!"
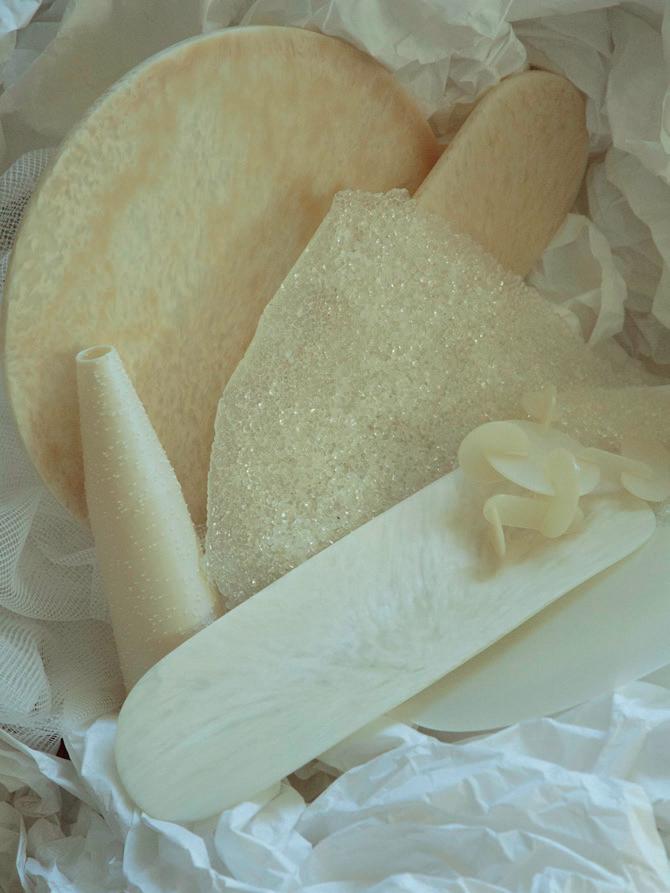
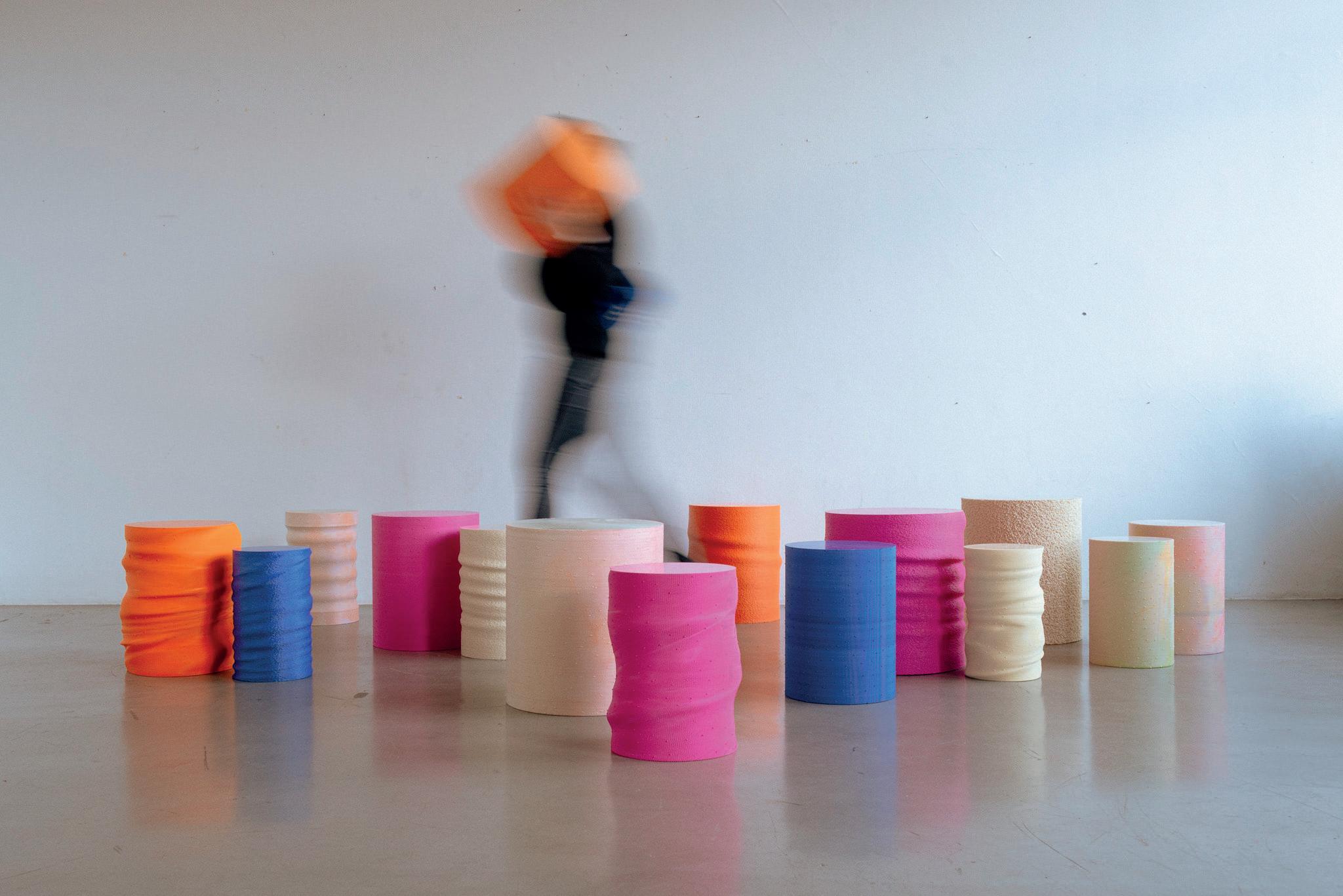
13
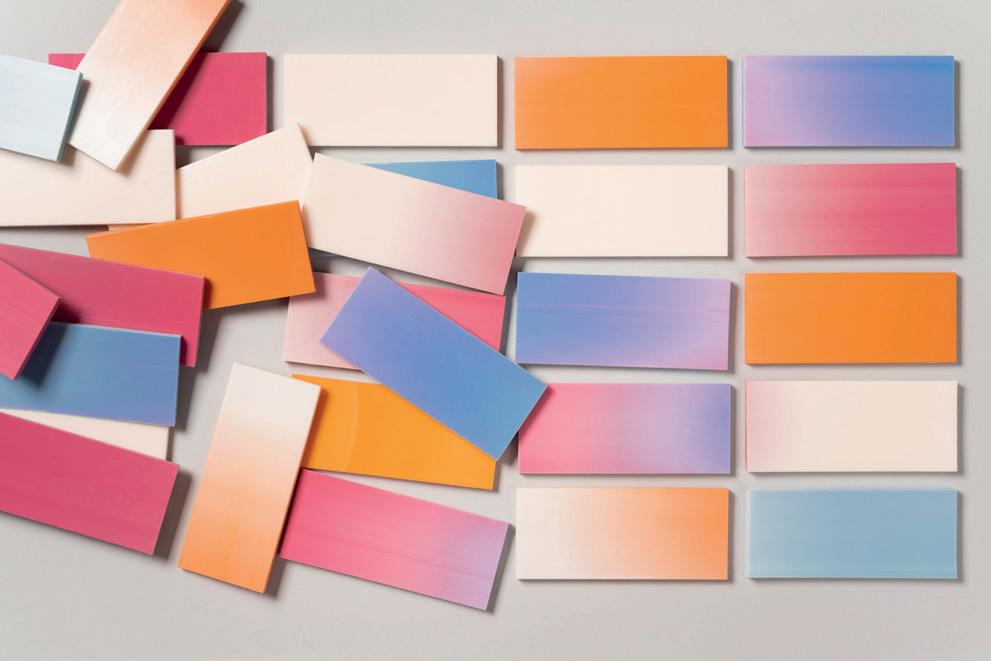
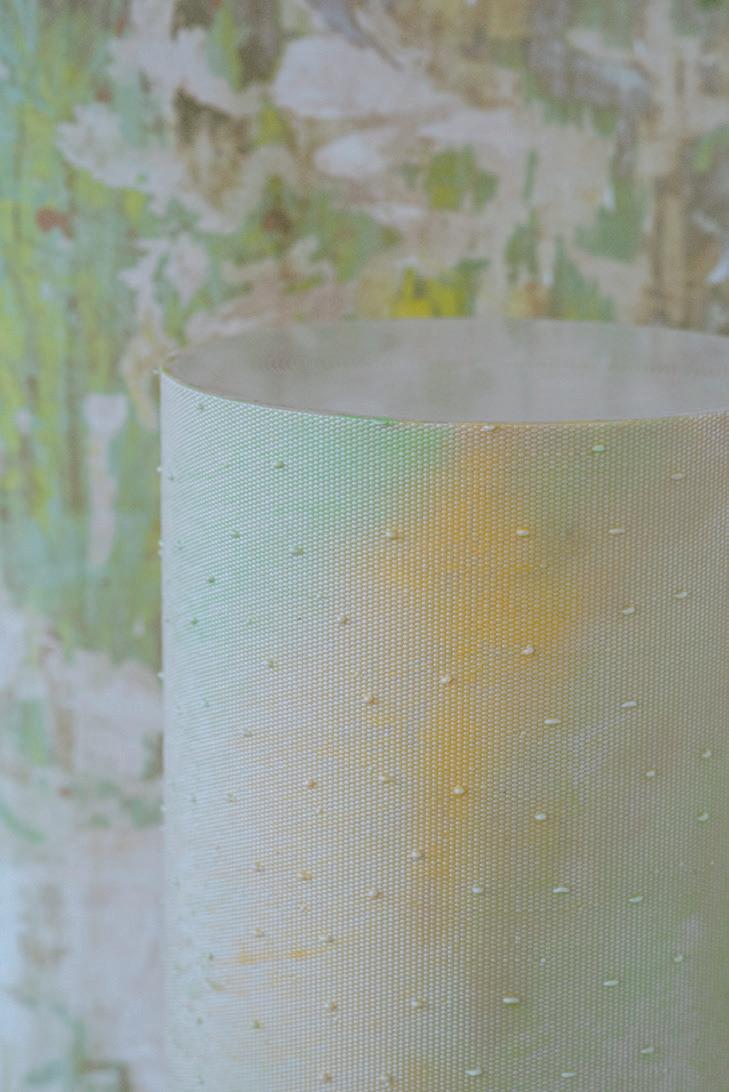
Senseables, Alcova - Miami 2023
"Even if people say they love the idea of biopolymers, if what they are presented with looks greenish brown, and not very aesthetically appealing, they will always choose the sexy looking alternative."
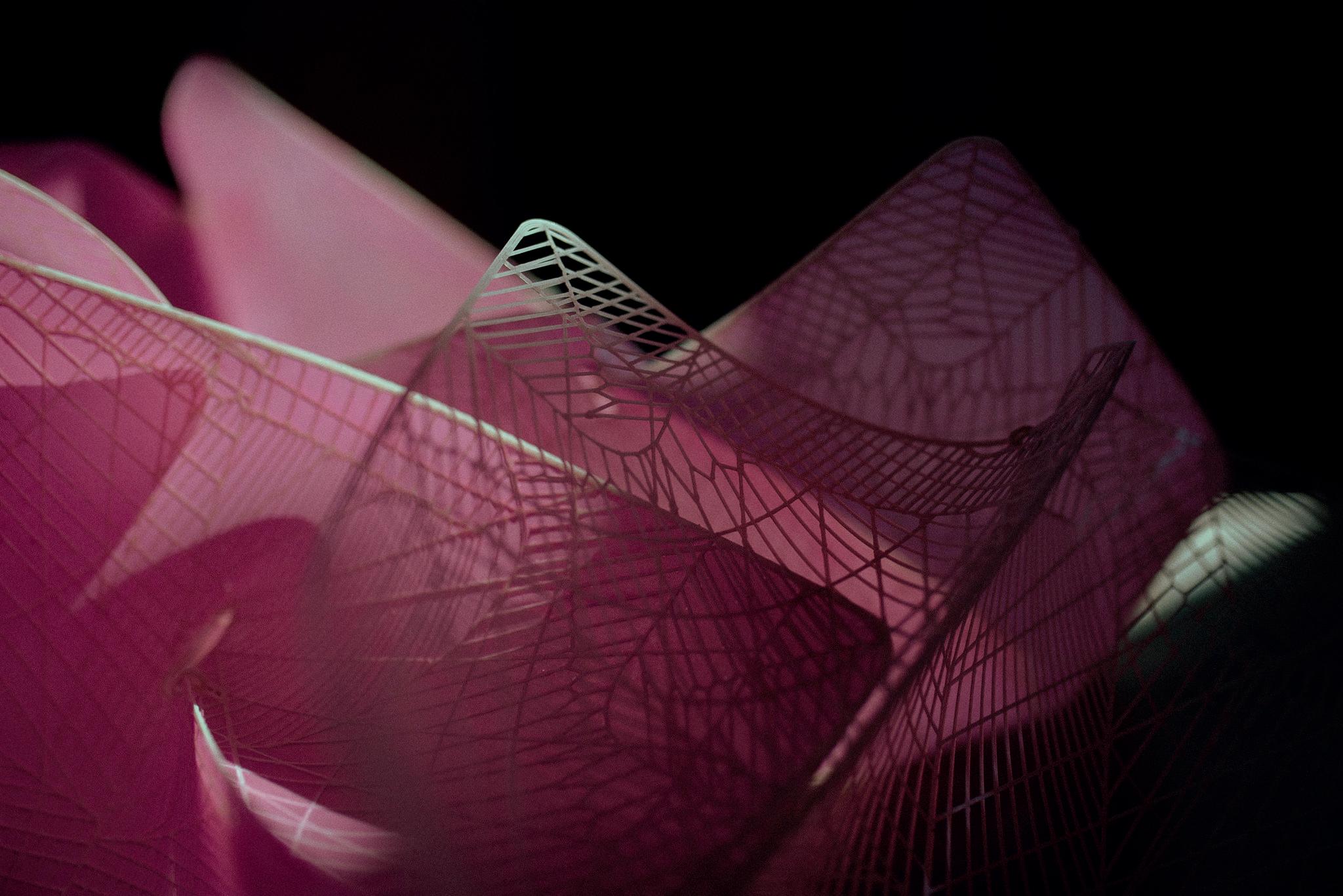
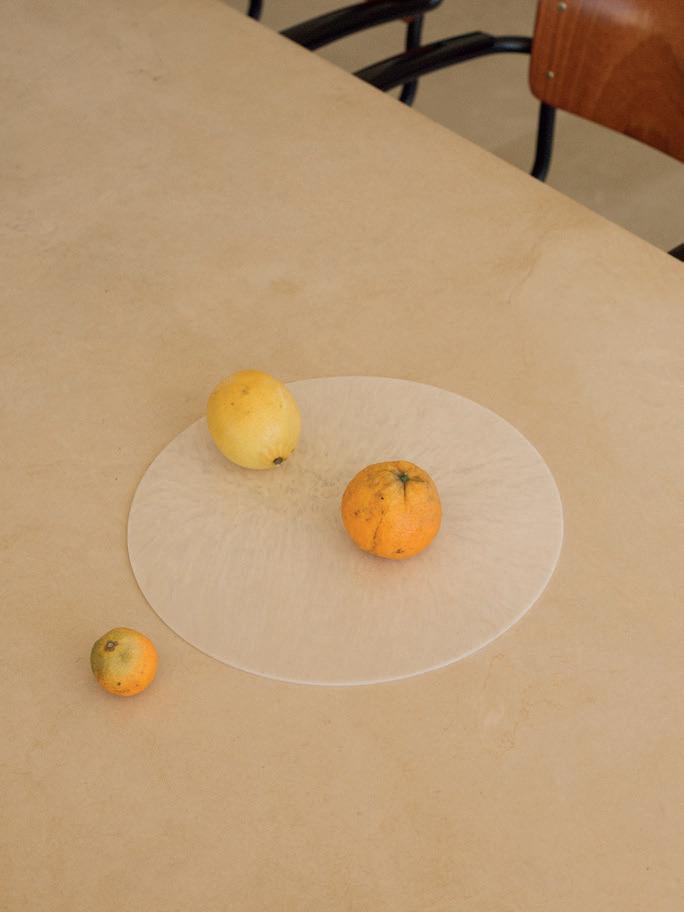
"This is about discovering how you can learn from scientists as designers, and other way around."
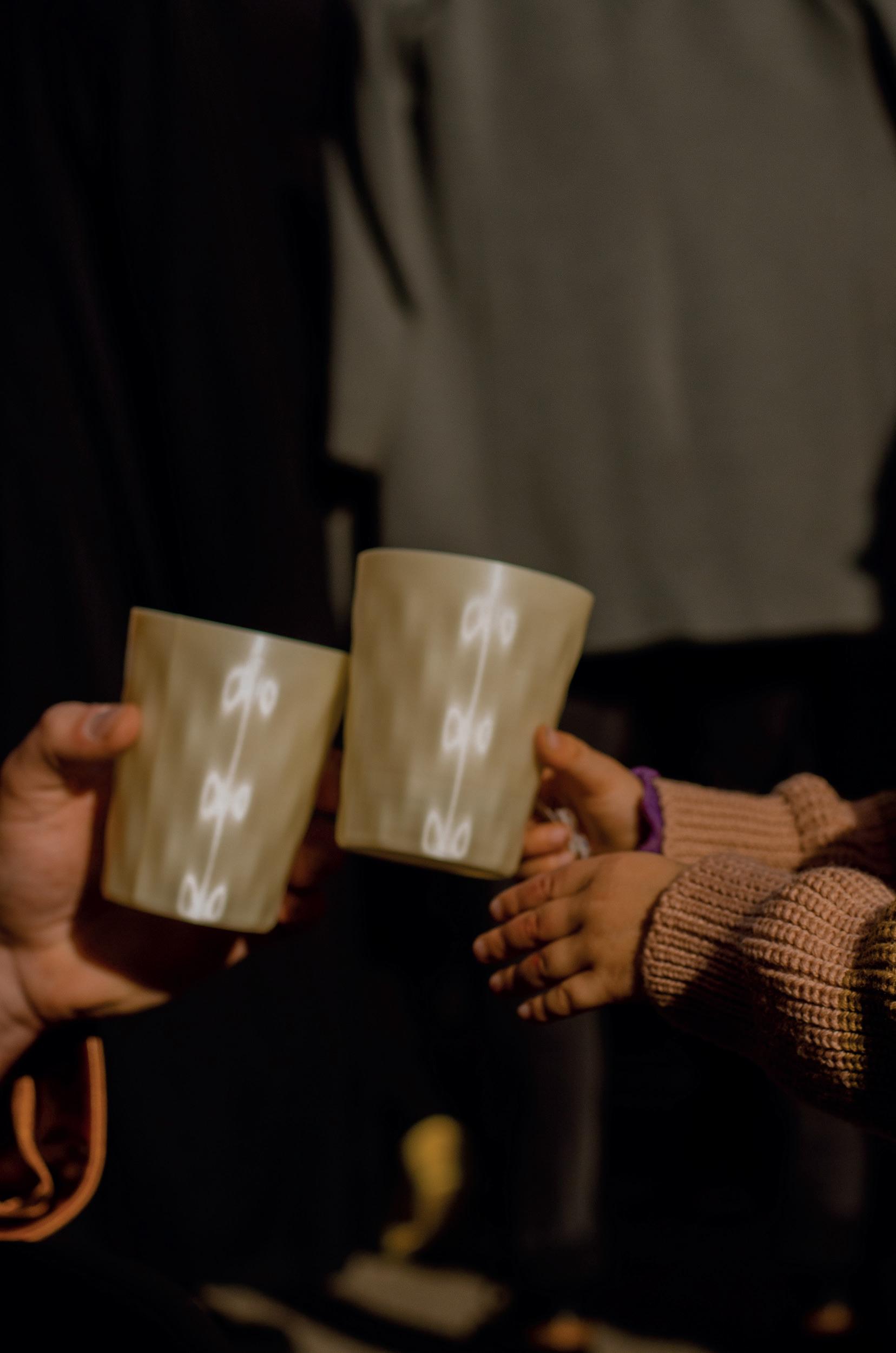
If bioplastics work, why isn’t everyone using them?
That is a question I ask myself every day! If we, as a small, innovative design studio, are able to make it happen, why isn’t industry doing the same?
When we started, we were maybe a bit too early. People had only just started to understand the issues with plastics in general. Then recycling plastics came along. So all the companies and producers started to understand and communicate the value of recycling.
I think bioplastics - plastics that are biodegradable, biobased, or both - are only starting to find their place in the system now.
For big companies, the process to change the material in their supply chain is a big challenge. Many factors and stakeholders have to come together to make it happen. But the infrastructure is still missing. I feel, it is happening, it could happen faster, but these are processes that are hard to force.
Are things moving in the right direction at least?
One important thing is that there are more and more producers of renewable resources now. That means the prices are starting to come down.
Governments are also putting more policies in place. That’s what forces the producers to start using these materials.
When we started out, producers were interested in terms of marketing (it is still happening), but not in the long haul. Implementing a new material can take months, it’s not easy.
Is it still difficult to get biomaterials into production today?
From the very beginning, we were aiming to make it easy for manufacturers to switch to our materials, like NUATAN, even with their standard technologies. But it still requires people who are open to the idea.
You need to win over all the different types of people in these companies to actually make it happen.
What was it that first of all made you think, ‘we need an alternative to plastics?’
We knew that we wanted to have our own studio and we just wanted to do something that made sense. Something that would do good for the planet and for people. Creating healthier materials has been our driving force.
There was also the fact that bioplastics seemed overlooked by industry. We knew they were real, we had them in our hands and they seemed to be working fine. So why weren’t they being used?
At the beginning we were very naive. But in the end, all the effort that we have put in is now paying back. I have learned that this is important: Do not give up!
Circular Gastro System, Dobry Trh 2023
Photo : Katka PsenakovaSo, I think bioplastics will slowly come to be normal, but it needs pressure, both from the government side and from consumers themselves.
Many design-driven innovations start from a great idea that could make a difference. But then these difficulties come along, like finding money, trying to find the right people to help you scale and so on. And that’s where many projects end.
What’s the secret to keeping those projects on track?
One of the good things about our studio, what really helped us to survive, is that we are not just material scientists or material producers and we are not only product designers.
We combine lots of different things together. As designer you learn how to communicate with many types of people, and this role of mediator is very important in innovative projects.
We really like to be multidisciplinary. This gives you a completely new perspective on any project and keeps you questioning what you are doing.
We do lots of research projects that go beyond bioplastics. For example, we are exploring possibilities of how to make interactive biomaterials, and how to grow biomaterials for functional products and intermediates. But we are also trying to make something that is usable and scalable right now, so the materials can have an impact.
Did you just say ‘growing’ the biomaterials?
There are several classes of biomaterials or biological materials.
The NUATAN compounds we have created, they’re mainly produced by fermentation of sugars and starches. The raw biomaterials you can already get in the form of either pellets or powders and the magic happens in the right ratios of biopolymers and additives.
But we are also working with other types of biopolymers. Stuff like cellulose or algae, seaweed, and also agricultural byproducts. So that’s second type of materials, that we are using for our composites.
In another type of our material project we use mycelium. for instance, creating mycelium bricks. That’s where the material is grown.
"I feel like circular design is now starting to be a must at least for the new generation of designers."
Is each type of material suited to a particular use?
We developed NUATAN so that it’s easy to do injection moulding, sheet extrusion, for eyewear and the furniture industry, or as filaments for 3D printing. This is the material we developed as the solution for ‘now’. This is what we’re trying to scale.
You can use NUATAN for multiple categories of products. We are mainly focusing on products that are durable and multiple use. The cups that we developed, they are able to survive at least 500 uses. So they would be ideal at festivals or public markets for instance. Then once they are not needed, you can place them in industrial or electric compost together with food waste.
The materials made from cellulose, algae and silk fibrion, we started to use for interaction. We are trying to find a way to use a different chemical or synthetic biological processes to make them interactive - with the user or the environment.
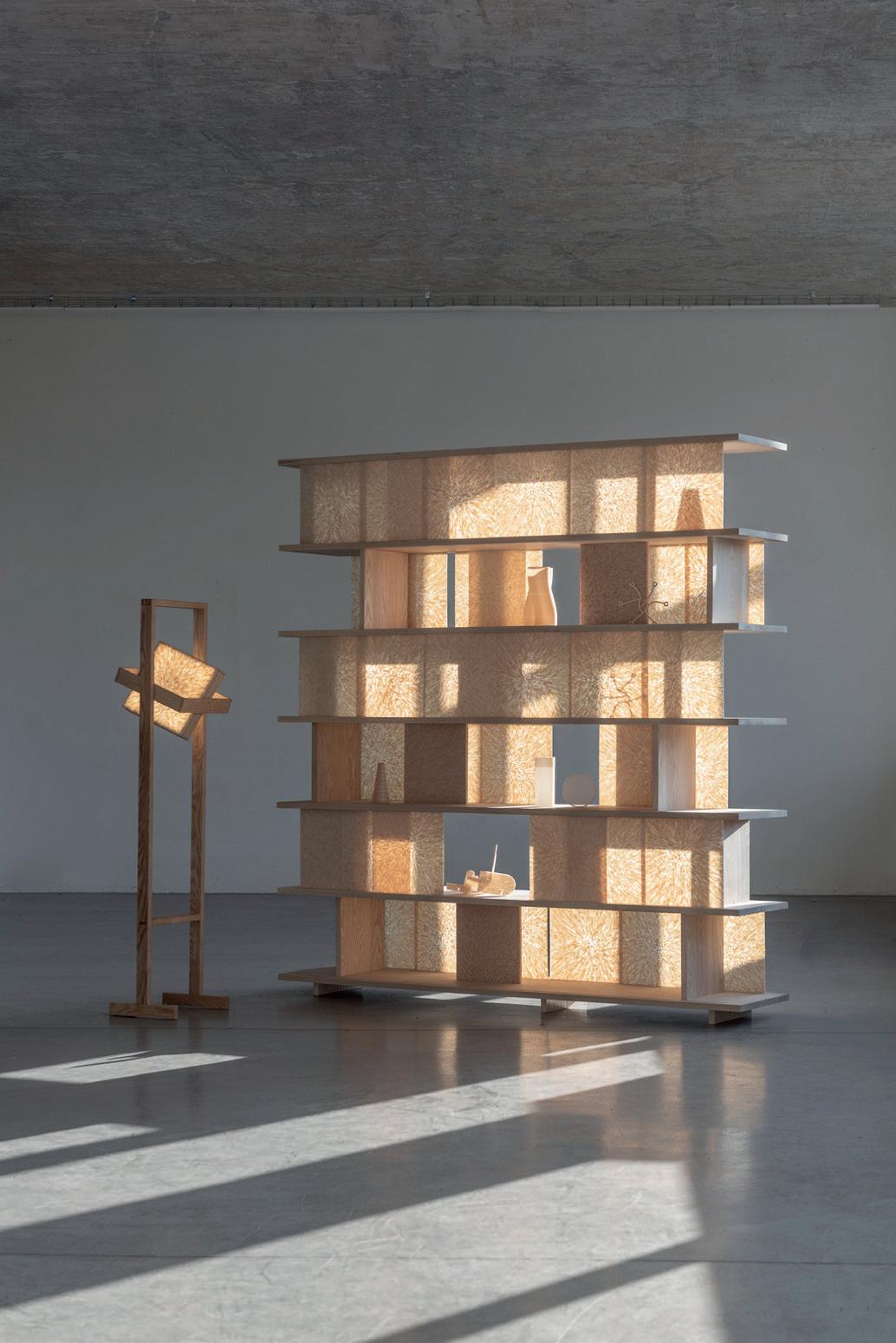
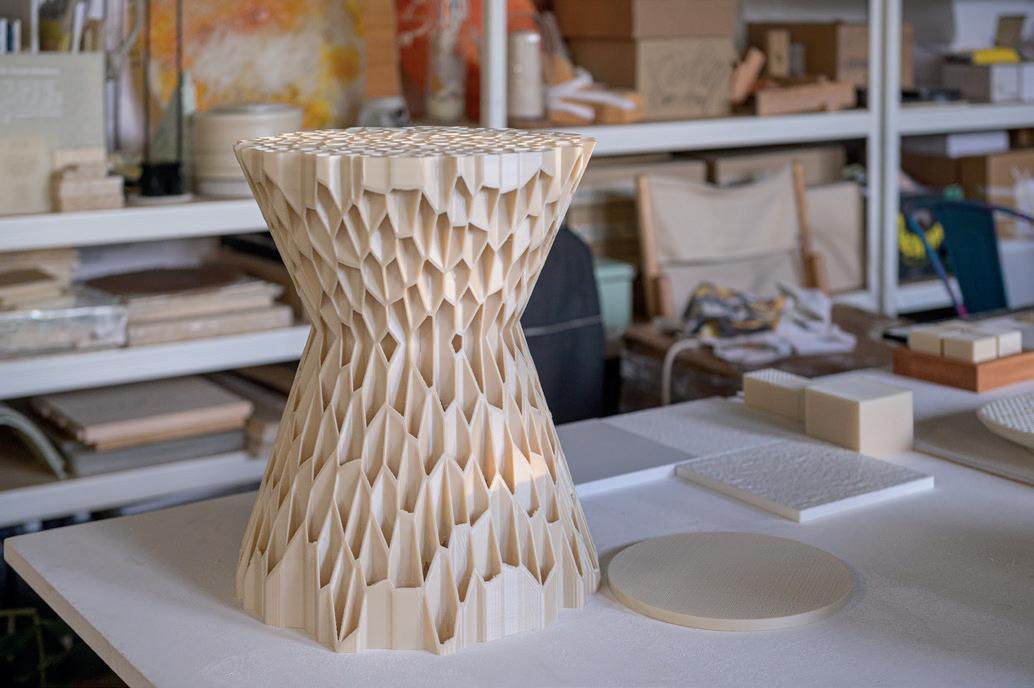
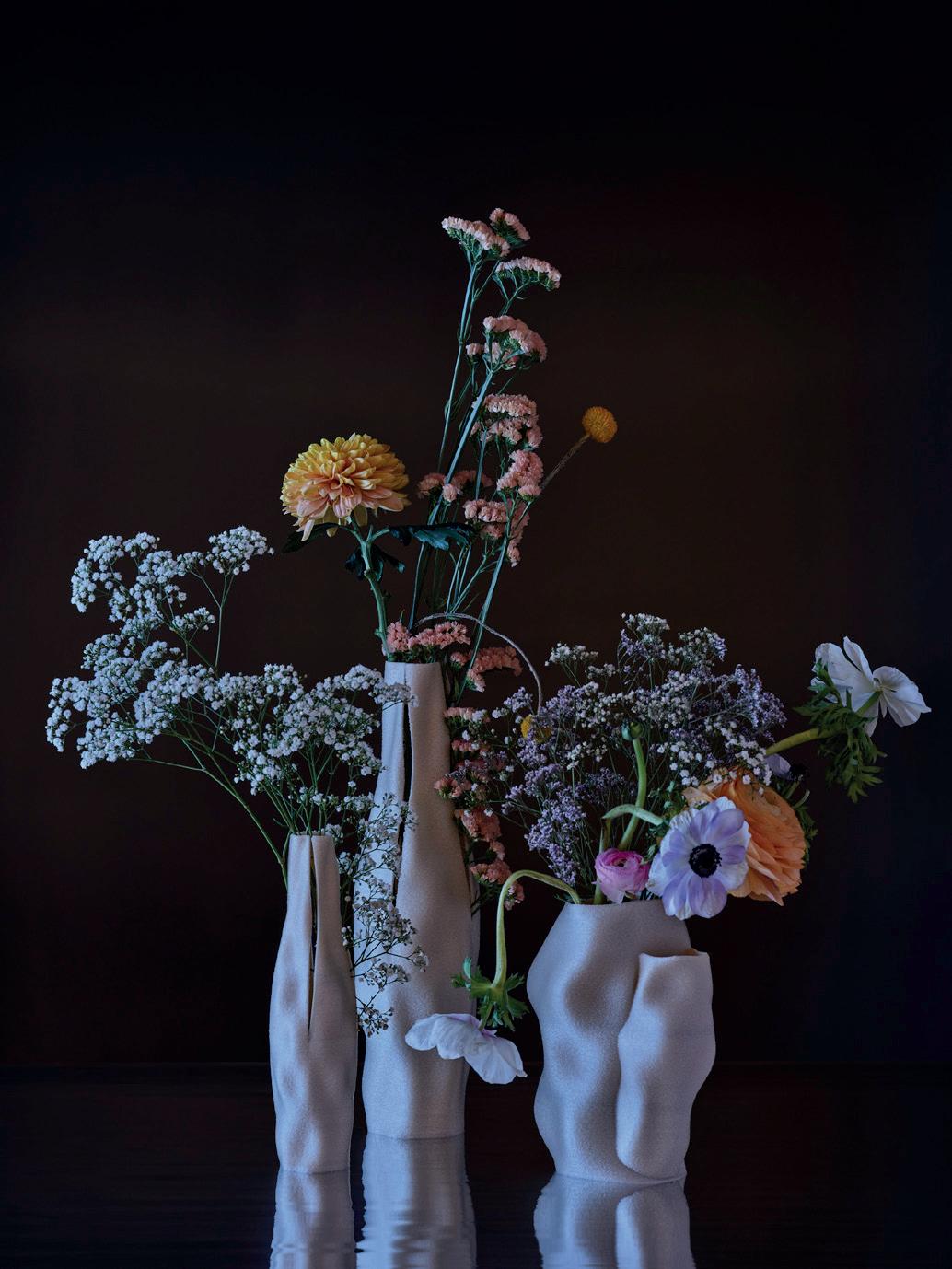
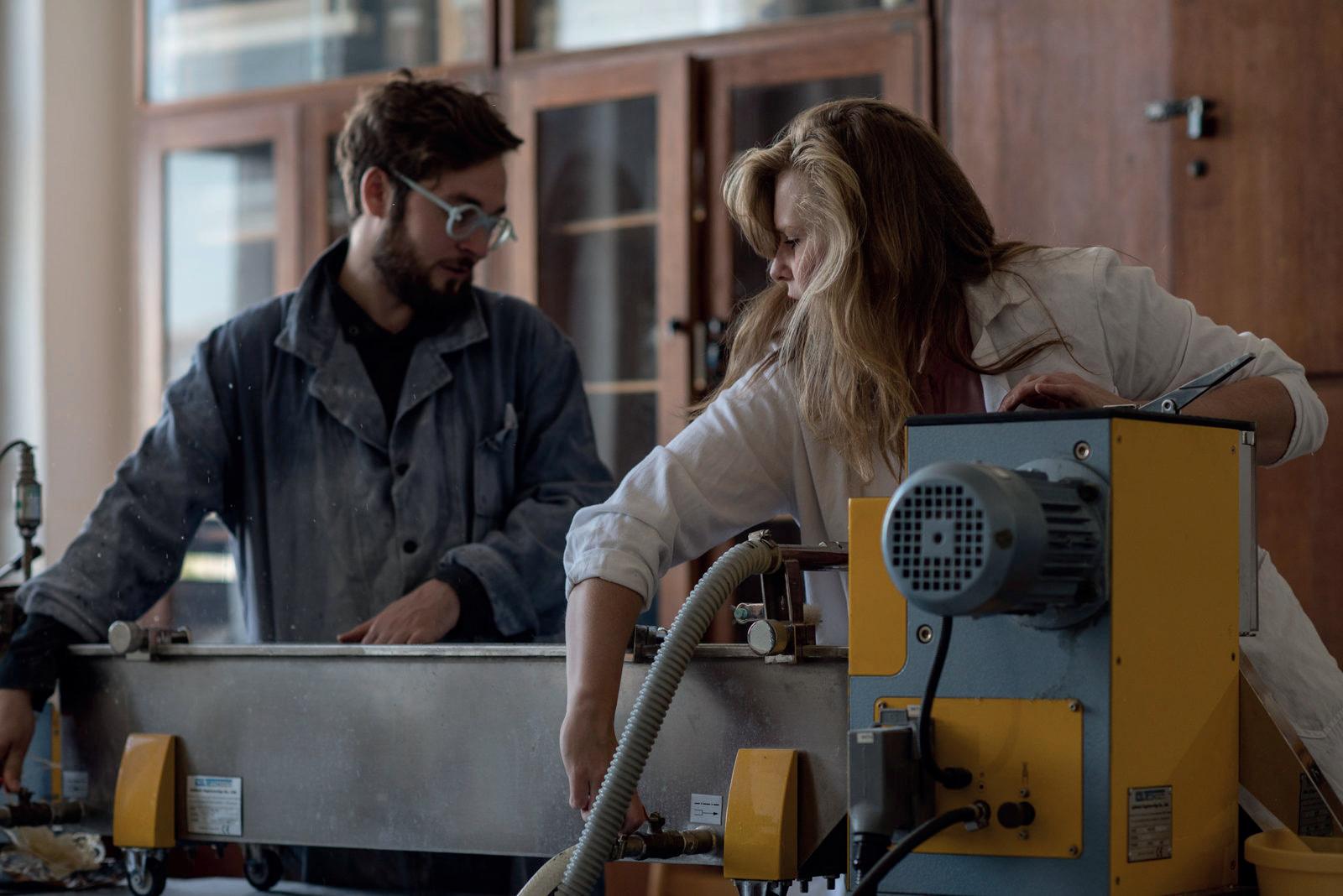
"We really like to be multidisciplinary. This gives you a completely new perspective on any project."
So, for instance, to make them sense and response to help in real time informing about the invisible threats. That’s what this category of materials offers.
And then there’s the mycelium materials. That’s the project I’m involved with at MIT and the Redhouse studio, called Mycohab. It’s about growing mycelium for food, but also, from the waste, you can make bricks to use as a building material for construction.
The mushroom is having a bit of a renaissance, isn’t it?
The interesting thing is, like a lot of very innovative new materials, this mycelium project started as a project proposed for NASA. Scientists are trying to find a way to transport only the smallest amount of material, because it’s very expensive.
The idea is, when you get where you’re going, you expand the material on the ground. And they thought, ‘if it works on Mars, can we just use it here?’
Your NUATAN material, it’s beautiful, like jade. Not at all as you would picture a biopolymer
From the very beginning, our intention was to create something that overcame the prejudice against biomaterials.
Even if people say they love the idea of biopolymers, if what they are presented with looks greenish brown, and not very aesthetically appealing, they will always choose the sexy looking alternative. That’s why we are trying to find new aesthetic narratives for this material.
Is the design world keen to use these new materials?
I can see a huge difference in attitude now, from when we launched NUATAN in 2018, at the London Design Festival.
I feel like circular design is now starting to be a must, at least for the new generation of designers.
You clearly love studying, and it’s a diverse range of subjects you’ve covered.
I definitely love studying. I think it’s something that I will do for the rest of my life. I’m assistant professor at Slovak University of Technology, I do teach sometimes at University of the Arts in Berlin and I’m global teaching assistant for the MIT/ Harvard class ‘How to Grow Almost Anything’.
I much prefer this Renaissance style of learning and being creative. It’s a pity that this isn’t more widely accepted in academia.
In this field of creating new types of design, or even in designing systems, you don’t have to be the best in all fields. You just have to understand them enough to know what the consequences are and understand how they connect in the system. Your projects could have value outside your specific field of study.
"We wanted to have our own studio and we just wanted to do something that made sense. Something that would do good for the planet or for people."
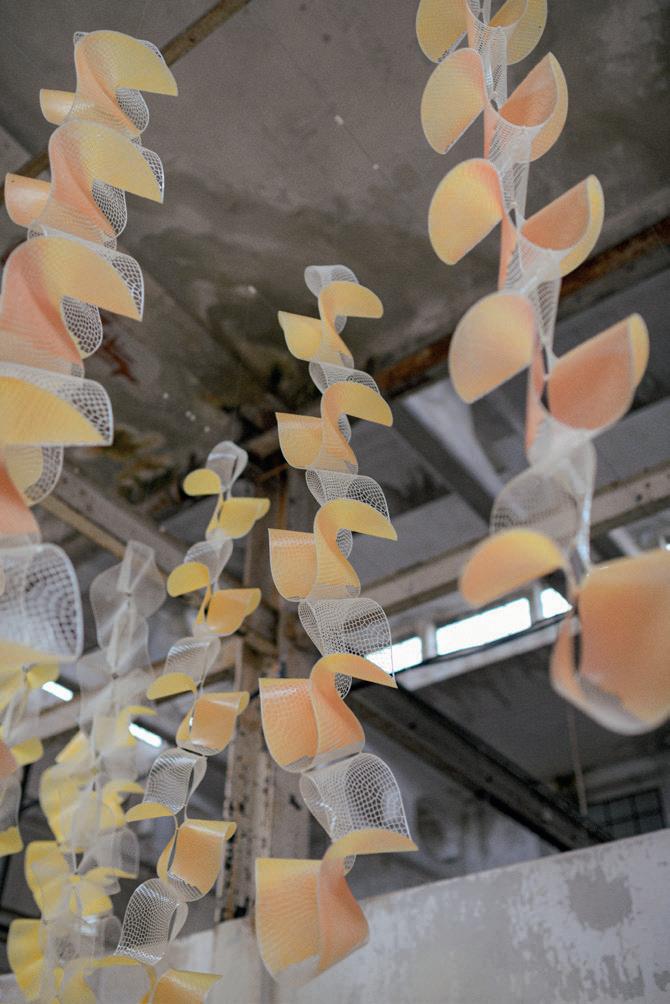
What can we do to help the various disciplines interact?
Actually, with friends we are developing an initial concept for a university ‘design-science’ course. This is about discovering how you can learn from scientists as designers, and other way around.
I enjoy working with scientists, because they think a little bit differently in terms of process, and what a successful solution looks like.
We have done lots of projects, where different types of people with different types of backgrounds are involved. That can cause a lot of struggle, because everyone has different ideas about what the project should bring to them.
So many interesting projects have fallen apart because the communication within the interdisciplinary team was missing. In the next few years, I would like to focus on this a little bit more just to explore what tools can actually help to maintain good collaboration within this type of multidisciplinary, innovative projects.
That could lead to a real explosion of interesting new projects
It would also make life more fun. Once you overcome these problems, you can just learn from the mistakes, right?
In the end, only a project where you didn’t learn anything is truly unsuccessful.
Sensbiom 2 by crafting plastics! & Dumolab, Alcova - Milan Design Week 2024 Photo : Petra Hurai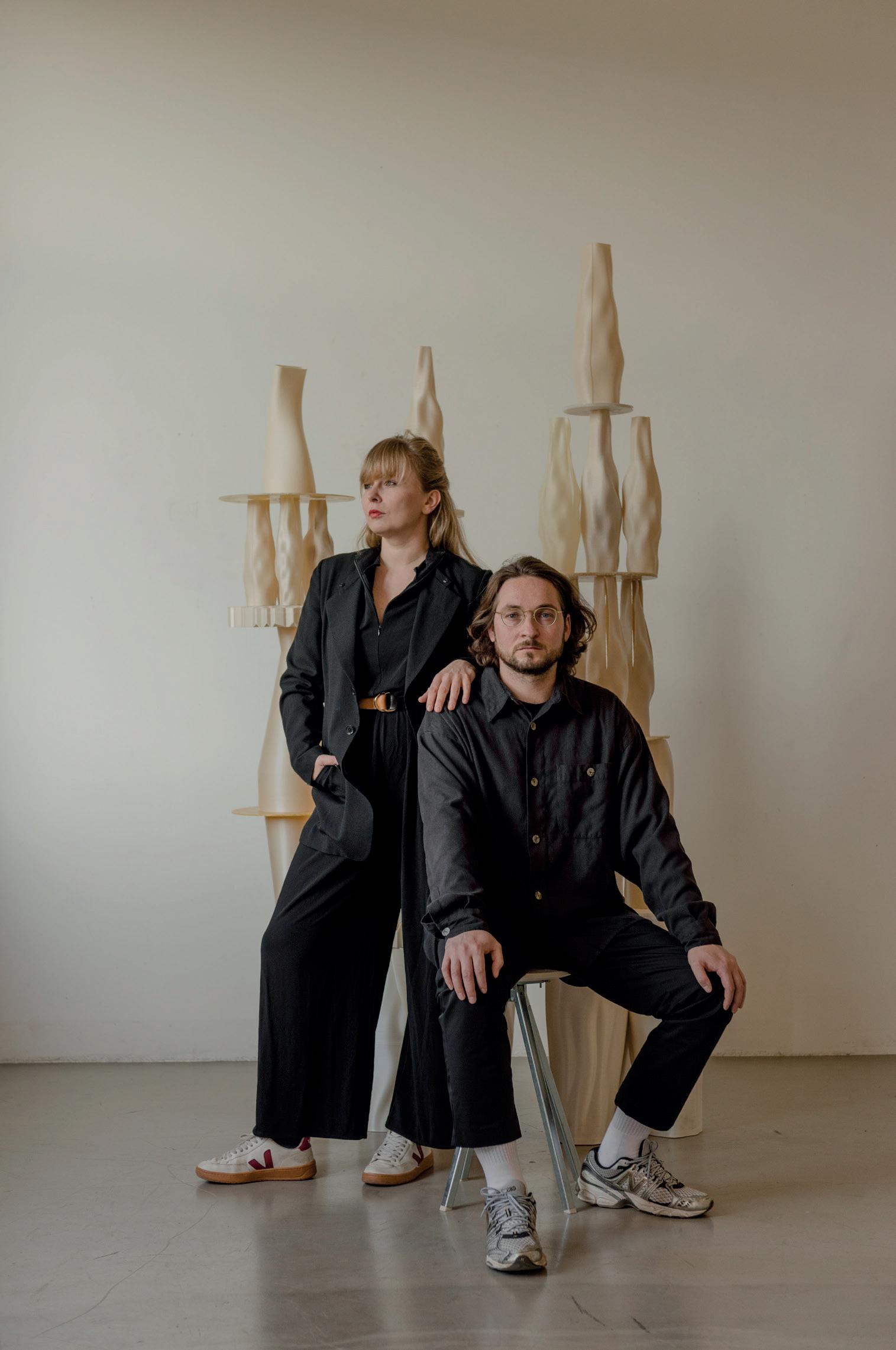
LAURA STRAßER Product Design 2017
PHOENIX DESIGN Industrial Design 2018
43 UWE R. BRÜCKNER Scenography Design 2018
44 BROUSSE & RUDDIGKEIT Design Code 2018
45 ISABELLE CHAPUIS Photography Design 2018
46 PATRICIA URQUIOLA Product Design 2018
47 SARAH-GRACE MANKARIOUS
MARC TAMSCHICK Spatial Media Design 2020
54 TYPEJOCKEYS Type Design 2020
55 MOTH Animation Design 2021
56 JONAS LINDSTRÖM Photography 2021
57 VERONICA FUERTE Graphic Design 2021
58 CHRISTOPHE DE LA FONTAINE Product Design 2021
59 DAVID KAMP Sound Design 2021
60 THOMAS KURPPA Brand Design 2021
61 NEW TENDENCY Product Design 2022
62 MARTHA VON MAYDELL Illustration Design 2022
63 STUDIO KLARENBEEK & DROS Design Research 2022
64 JOUPIN GHAMSARI Photography Design 2022
65 LOTTERMANN AND FUENTES Photography Design 2022
66 SUPER TERRAIN Graphic Design 2022
67 EIKE KÖNIG Art Design 2023
68 CHRISTOPHER NOELLE Light Design 2023
69 DENNIS HINZE Sport Fashion Design 2023
70 KLASIEN VAN DE ZANDSCHULP Interactive Design 2023
71 VALENTIN VODEV Industrial Design 2023
72 GERMANS ERMICS Sculptural Design 2023
73 MADE BY JAMES Type & Logo Design 2024
74 SNASK Branding & Video 2024
Design Friends would like to thank all their members and partners for their support.
Support Design Friends, become a member. More information on www.designfriends.lu
In collaboration with Partners Service Partners
Design Friends is financially supported by COLOPHON
PUBLISHER Design Friends
COORDINATION Dana Popescu
LAYOUT Isabelle Mattern
INTERVIEW Mark Penfold
PRINT Imprimerie Schlimé
PRINT RUN 250 (Limited edition)
ISBN 978-2-919829-02-6
PRICE 5 €
DESIGN FRIENDS
Association sans but lucratif (Luxembourg)
BOARDMEMBERS
Anabel Witry (President)
Guido Kröger (Treasurer)
Heike Fries (Secretary)
Claudia Eustergerling, Reza Kianpour, Dana Popescu, Hyder Razvi (Members)
COUNSELORS
Charline Guille-Burger, Silvano Vidale WWW.DESIGNFRIENDS.LU WWW.CRAFTINGPLASTICS.COM
This catalogue is published for the lecture of CRAFTING PLASTICS! STUDIO “Biomaterials in practice : From lab to reality and beyond” at Mudam Luxembourg on 15th of May, 2024 organised by Design Friends
